TEIGNBRIDGE
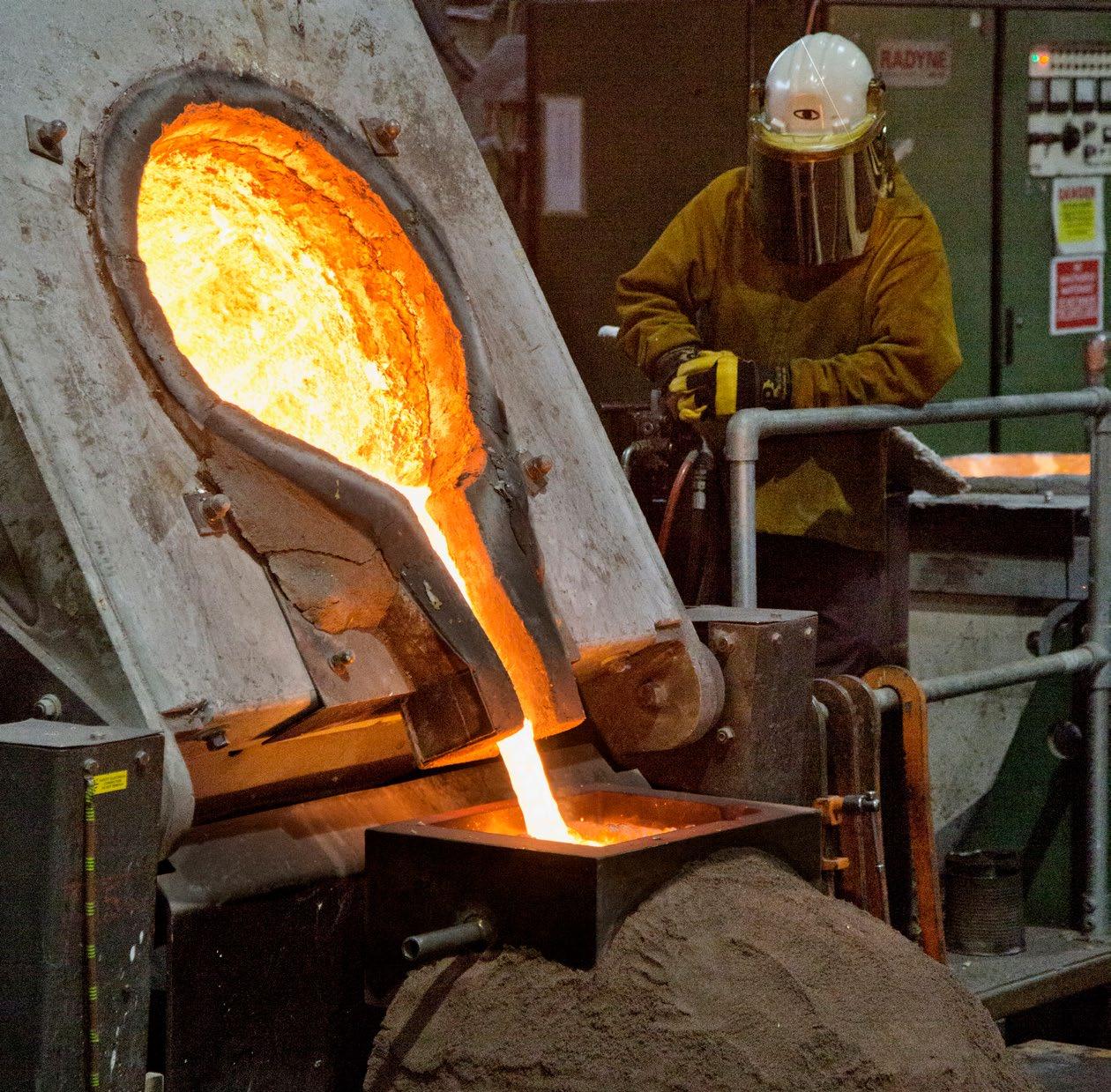
The technical magazine for those involved in the design, construction and refit of superyachts
Supplier
Quick, the Italian maker of
18 CEO in Conversation: Ned Wood of Bowmaster Anchor deployment manufacturer Bowmaster is making strides in its sector, despite a remote location in New Zealand.
20 Build Report: Making Maverick
The second in Cantiere delle Marche’s Flexplorer series, 44-metre Maverick has been designed and built expressly for a round-the-world tour.
32 Concept in Focus: Design Without Constraint
Luiz de Basto’s 92-metre Project Med takes inspiration from an open architectural concept proposed by Lateral Naval Architects.
40 Build Report: Lessons Learned
Aquarius II, a modern classic ketch in-build at Royal Huisman, is the beneficiary of hundreds of tweaks to enhance operations and performance.
52 Build Report: Team Toro
Project Toro is the first in a new engineering platform from Turquoise Yachts offering faster delivery and ample opportunity for customisation.
64 OEM: Stern Stuff
A visit to Teignbridge Propellers in the UK reveals the science behind propeller design and how they are made.
76 Inside Angle: James Hutchinson
Project management experience in production boatbuilding has given Hutchinson Yacht
Consulting a unique perspective in the superyacht world.
80 Hulls & Appendages: Flight Club
The latest foiling technology has overcome many of the shortfalls of older systems, but are foiling superyachts feasible?
91 Ops & Maintenance: Rust Never Sleeps
All ferrous metals are prone to corrosion, but Pulsed Eddy Current Array can help mitigate the damaging effects of rust.
98 Sustainability: Green Your Shipyard
Shipyards are gradually switching on to the need to implement more sustainability into their operations, business practices and infrastructures.
106 Industry Opinion: Now is the Time
Feargus Bryan of the Superyacht Technology Steering Council explains why the time is ripe for collective action.
110 Refit & Repair: Sailing on an Uneven Keel
Mark Small, Technical Director at Rob Doyle Design, describes a mighty repair job when the largest sloop in the world lost its keel tip.
118 Ask the Experts: Composites
Choosing the right composites for the right application is not always straightforward. A panel of leading experts offers words of wisdom.
Welcome to the first of this year’s three editions of How to Build It
At the close of last year, SYT iQ reported that 2023 had seen a 51 percent decline in the total sales of 24-metre plus sailing yachts – the lowest point in the past six years. This rather sombre statistic provided the perfect excuse to visit one of my favourite shipyards. In-build at Royal Huisman for repeat clients, 65-metre Aquarius II is a modern classic cruising ketch and the kind of project the Dutch brand excels at. She is also the beneficiary of more than 700 design tweaks collated by her captain and crew during five years of operating the owners’ previous Huisman.
Talking of new builds, for this issue we also travelled to Italy to catch up with 44-metre explorer Maverick during her fitting out at Cantiere delle Marche, one of the most consistent shipyards building over 40 metres, and to Turkey, now ranked second behind Italy in terms of numbers of units in build, to take a peek at 79-metre Project Toro under construction at Turquoise Yachts.
In keeping with the international flavour of this issue, our concept analysis comes courtesy of Miami-based designer Luis de Basto and those clever people at Lateral Naval Architects in the UK. Project Med takes inspiration from a study by Lateral that reduces the need for watertight bulkheads, the main engineering limitation when defining an interior arrangement. De Basto’s open architectural concept is the result of looking at the rules “in a slightly different way.”
Amidst all the talk of alternative fuels and greenhouse gases, the carbon footprint of the facilities building the yachts has usually taken a back seat. Not anymore. We look at how shipyards are switching on to the need to implement more comprehensive sustainability solutions in their business practices – and the operational and financial benefits that can be enjoyed as a result. But for me the most rewarding assignment was a trip to Teignbridge Propellers in deepest Devon. I thought I knew something about stern gear, but quickly realised I was almost entirely ignorant of how propellers are designed and manufactured. After being introduced to a fascinating process that combines the latest CNC technology with old-fashioned human labour, I learned why propellers sometimes ‘sing’, what ‘fettling’ is, and why the moulds for casting are made one blade at a time using ‘patterns’. I hope you learn something too.
Justin Ratcliffe - Editor
At West Istanbul Marina, we're passionate about what we do. With decades of experience, our team is dedicated to providing a customized plan for yacht maintenance & repair, because we believe that every yacht is as unique as its owner.
We treat each yacht with utmost care, no matter the size. As part of our services, we offer a progress report so that our clients rest assured that their yacht is in good hands and will be delivered within the agreed time-frame. With our 700 Ton Travel-lift, 14 yacht sheds and 600 berths, we’re able to accommodate yachts up to 90m long.
EDITORIAL
EDITOR IN CHIEF
EDITOR | HOW TO BUILD IT
EDITORIAL CONTRIBUTOR
NEWS WRITER
FEATURES WRITER
WRITER
SOCIAL MEDIA MANAGER
CONTEN CREATOR
Francesca Webster
Justin Ratcliffe
Charlotte Thomas
Sophie Spicknell
Enrico Chhibber
Amy Larsen
Marina Vargas
Nick Smits
DESIGN PRODUCTION
CREATIVE DIRECTOR
GRAPHIC DESIGNER
UI/UX DESIGNER
Ivo Nupoort
Beatriz Ramos
Claudia Sabbadin
INTELLIGENCE
HEAD OF INTELLIGENCE
RESEARCH ANALYST
DATABASE MANAGER
DATABASE MANAGER
YACHT HISTORIAN
Ralph Dazert
Adil Zaman
Syrine Mellakh
Darwin Manguiat
Malcolm Wood
SALES & ADVERTISING
HEAD OF SALES
SALES MANAGER
SALES MANAGER
CLIENT SERVICE MANAGER
SALES ITALY
Marieke de Vries
Justus Papenkordt
Daniel Van Dongen
Johanna Borreli
info@admarex.com
CORPORATE
FOUNDER & DIRECTOR
TECHNOLOGY DIRECTOR
FINANCE DIRECTOR
Merijn de Waard
Fabian Tollenaar
Laura Weber
The Port Authority in Livorno, Italy, home to Benetti’s superyacht shipyard, has issued tenders for the concession of four areas, totalling approximately 53,000 square metres, between the Calafati Docks and Pisato, to establish a new facility for the construction of superyachts.
The plan presented by RINA Consulting recommends technical adjustments and administrative procedures, as well as demolishing or renovating certain structures and making improvements to the docks. These investments would fall under the responsibility of future concessionaires.
The driving force behind the plan is the substantial demand within the luxury yacht industry for more dedicated spaces for building vessels to address the order backlog.
After successful first-stage testing, Williams Jet Tenders has approved HVO100 fuel (Hydrotreated Vegetable Oil) for all its Yanmar 4JH engine-powered tenders, including the DieselJet 415, 445, and 505, and SOLAS 505. HVO fuels bring environmental benefits such as reduced greenhouse gases, fewer particulates, and lower SOx and NOx emissions.
“We are committed to finding innovative sustainable solutions that reduce the direct emissions impact from our factory and our vehicles,” says Sarah Moore, sustainability specialist at Williams Jet Tenders “By using UCO HVO, a renewable fuel made from waste cooking oil, we will accelerate our efforts to decarbonise.
Williams was recently awarded a grant by Innovate UK Edge to test alternative and more sustainable composite materials and complete Life Cycle Analysis (LCA) for its TurboJet 325 and DieselJet 415 to calculate their carbon footprint.
Sanlorenzo and Nautor Swan have announced the muchanticipated signing of a Memorandum of Understanding signalling the initiation of an exclusivity period to evaluate the potential joint strategic opportunities between the Nautor Swan Group and Sanlorenzo.
“The combination of these brands within the same group would create a unique Maison of motor and sail yachts at the top-end of the nautical competitive landscape,” says Massimo
Perotti, chairman and CEO of Sanlorenzo, who is eager to add luxury sailboats to the Sanlorenzo line-up.
“A strategic partnership with Sanlorenzo Group would offer several opportunities to move forward on this virtuous path with joint investments in innovative technologies, in sustainability, and in a more extensive service network for our customers globally,” adds Leonardo Ferragamo, chairman of Nautor Swan.
Maritime security eLearning platform VIRSEC has launched a course on lithiumion battery safety awareness to help yacht crews, officers, captains and yacht managers recognise and implement measures to prevent L-ion fires and respond to battery-related emergencies.
Gulf Craft has announced it is exploring hydrogen tech with the aim of developing a zero-emission Majesty yacht that could be powered by an innovative LOHC (Liquid Organic, Hydrogen Carrier) energy system. The research programme is being conducted in partnership with H2-Enterprises, a company that has been working on hydrogen technology for the last 13 years.
“CO2 emissions need to be reduced rapidly and radically to achieve the climate change goals. Our LOHC technology is suitable for replacing the current carbon-based, pollutant-contaminated CO2 and NOx based energy system,” says Michael Stusch, executive chairman and CEO of H2-Enterprises.
Gulf Craft chairman Mohammed Hussein Alshaali maintains that the collaboration will allow the company “to lead in a new era of emissions-free luxury, where opulence and sustainability intertwine seamlessly.”
Navico Group, a division of the Brunswick Corporation, has announced a partnership with Oyster Yachts. Under the agreement, B&G, CZone and Mastervolt will be the preferred electronics and power suppliers across Oyster’s fleet of 50 to 90-foot sailing yachts.
“With our wide range of industry-leading brands, Navico Group is uniquely positioned to offer premium integrated systems and technology that will provide an enhanced experience on the water for Oyster’s customers,”says Ton de Winter, EMEA president, Navico Group.
Navico is also expanding its Michigan facility to create two Centres of Excellence, one in metal fabrication and the other in electrification. The multi-million-dollar investment will increase quality and efficiency while improving manufacturing capabilities.
In its recent MGN 681, the UK’s MCA introduced the requirement that competent persons undertake battery charging operations. ISM Code 6.3 further mandates yacht managers to establish procedures for personnel, especially regarding safety and environmental roles. The online course comprises eight short lessons that provide an in-depth study of the electrochemistry and hazards associated with Li-ion batteries in order to keep onboard personnel updated regarding safety protocols. More information is available on the VIRSEC website.
Derecktor Fort Pierce, Florida, has been designated as a Foreign Trade Zone (FTZ. The designation brings with it substantial benefits for the marine industry by alleviating duty and taxes on imported boat parts and foreign-built yachts within the zone. Foreign-built yachts can be brought into Derecktor Ft. Pierce without incurring the typical 1.5 percent import duty. This opens up opportunities for prospective US buyers to explore vessels that were previously restricted. Moreover, major refit projects conducted within the FTZ benefit from deferred duties until the project’s completion. Upon completion, vessels can leave the U.S. without the obligation to pay duties or taxes. The FTZ designation also facilitates operational flexibility, allowing vessels to enter and exit the zone during owners’ trips and yacht charters.
Quantum’s new F45 Hybrid Hyraulic/Electric Integrated Power System for the 50 metre-plus market was unveiled in November. Testing has demonstrated that the system is highly efficient, offering a smooth power source and requiring 50 percent less power than a traditional hydraulic system. Unlike traditional systems, the F45 only consumes energy as required, when required, partially due to the elimination of control valves in exchange for a servo motor. Quantum has also developed two new methods of storing and recovering power for future use, to overcome the power fluctuation challenge. This new solution is called MESS—Mass Energy Storage System.
OutSail has developed its first retractable wing sail for the yachting sector, the OutSail 60 prototype, that can offer 30% fuel savings in average wind conditions. The wings automatically adjust to wind strength and direction and can be fitted with solar panels to offer power up to 30kw of solar power under way or at anchor. The wing has been designed by Arpan Rau, Robotics Engineer and OutSail has recently moved to a large facility for the construction of its 20 metre-plus wings.
Swiss Ocean Tech has launched its Anchor Guardian to reduce the risk of anchor dragging and to provide prediction and immediate alarms. The system consists of an anchor module on the chain, a boat module attached to the hull and a user interface at the helm station, with the modules feeding realtime information back to the user interface to alert the captain of changes to the anchor positioning. During anchor deployment, the user interface simultaneously reports boat, chain and anchor movements, and once settled, the captain receives a continuous stream of intel around the anchor and chain, including sediment type, force and current. This allows the Guardian to predict the anchor hold and alert the crew of potential issues, before they take place.
Helicopter Visual Landing Aid specialist Optonaval has launched its GPI light beams that enable pilots to locate helidecks from c.5 nautical miles, and guide helicopters to position above the landing area. A high-resolution camera with motorised zoom facing towards the approaching helicopter will assist visual surveillance of helideck landing operations. When not used as GPI, the camera can be integrated in the CCTV system and act as pan / tilt camera for additional observations.
The Push/Pull Captive Reel Winch moves horizontal and vertical underwater foils, sail controls, or retractable superyacht recreation spaces such as extendable stern platforms in two directions (in and out, side-to-side, up or down). This single winch solution saves at least 400 kg and approximately 50 cubic centimetres of interior space below the cabin floor. Proof of concept is installed in a 43 metre monohull. It has a 20-tonne capacity. Its design replaces the need for two winches and their accompanying space and power requirement. It also assists the marine industry’s move towards electrification of control gear in preference to hydraulics.
New projects in early stages of construction that present opportunities for OEMs, suppliers and subcontractors.
The 68m ketch is an evolution of several highly successful sailing yachts including the 54.6-metre Adele, the 54.64-metre Marie, the 52.5-metre Anne and the 49.7-metre Meraki, all of which were a result of this design and build partnership. American designer Bunny Williams is responsible for her interior decoration. Van Ineveld & Co will also work as the owner’s representative during her build. The 68m ketch has been commissioned by a highly experienced repeat client, who wanted increased accommodation and the ability to cross the Panama Canal.
LENGTH: 67.93-metres BUILDER: Vitters COUNTRY OF BUILD: Netherlands DELIVERY YEAR: 2026
NAVAL ARCHITECTURE: Hoek Design EXTERIOR DESIGNER: Hoek Design INTERIOR DESIGNER: Bunny Williams
Started on speculation in June 2023 and sold in November, the first hull of the new Bilgin series offers a different design to her sistership the Bilgin 164, with a larger and more traditional bow shape, to create an overall sleeker appearance. The Bilgin 170 features an elongated bridge deck aft, extending by 1.5-metres to amplify her living space and offer a spacious and shaded area for guests to unwind. Her beach club on the lower deck ensures plenty of natural light with expansive windows when all three doors are closed.
LENGTH: 52-metres BUILDER: Bilgin Yachts COUNTRY OF BUILD: Turkey DELIVERY YEAR: 2025
NAVAL ARCHITECTURE: Unique Yacht Design EXTERIOR DESIGNER: Unique Yacht Design INTERIOR DESIGNER: Hot Lab
Construction began on the Columbus Crossover 42 yacht on speculation at the Columbus Yachts Savona shipyard in Italy in May 2022. She features exterior design by Hydro Tec, in collaboration with Francesco Guida, with interior design by awardwinning designers Hot Lab. The model was first introduced in April 2022, with the first hull sold in November 2023.
LENGTH: 42-metres BUILDER: Columbus Yachts COUNTRY OF BUILD: Italy DELIVERY YEAR: 2025
NAVAL ARCHITECTURE: Columbus Yachts EXTERIOR DESIGNER: Hydro Tec INTERIOR DESIGNER: Hot Lab
Announced in June 2023, the 44-metre superyacht, designed by long-time partner Francesco Paszkowski, takes inspiration from the shipyard’s traditional fast aluminium boats. The superyacht features a traditional layout, with the master cabin located forward on the main deck, where a conversation area and the dining area can also be found. Two fold-down balconies at the stern offer a generous sunbathing area and a pool.
LENGTH: 44-metres BUILDER: Baglietto COUNTRY OF BUILD: Italy DELIVERY YEAR: 2025 NAVAL ARCHITECTURE: Baglietto EXTERIOR DESIGNER: Francesco Paszkowski INTERIOR DESIGNER: Margherita Casprini and Francesco Paszkowski
Sold in September 2023, the full custom YN256 is under construction at the shipyard in Monnickendam. The 45.2-metre motor yacht will have an eco-conscious design and will be equipped to meet the needs of all guests onboard. Project YN256 is characterised by her glass superstructure and round bilge displacement hull. Her distinct exterior styling includes a slightly flared bow and metallic bronze-painted features, as well as a cleverly designed funnel that acts as additional storage, and minimises the size of her radio masts.
LENGTH: 45-metres BUILDER: Royal Hakvoort COUNTRY OF BUILD: Netherlands DELIVERY YEAR: 2026
NAVAL ARCHITECTURE: Hoek Design EXTERIOR DESIGNER: Hoek Design INTERIOR DESIGNER: Hoek Design
BY FRANCESCA WEBSTER
Quick Spa originally specialised in the sales, installation and after-sales management of marine electronics, refrigeration, air conditioning, heating and electrical systems. But the company has developed beyond recognition since it was set up over 40 years ago in Ravenna.
Founded in 1982 by Michele Marzucco and Alfonso Peduto, the Italian nautical product manufacturer Quick Spa has evolved over the decades, expanding into its neighbouring sectors with a series of major acquisitions. At the 2023 METSTRADE, Quick announced the acquisition of Nemo Industrie, yacht components manufacturer, only weeks after closing on yacht control systems manufacturer Xenta Systems.
We join Lorenzo Cesari, long term Quick employee and Sanguineti CEO, to discuss the company’s continued expansion.
In 2022, Fondo Italiano d’Investimento SGR and Armònia SGR acquired a majority stake in Quick Spa, with the ambition to undertake a series of acquisitions to broaden the Group’s portfolio. Having taken over Catt, the group’s flagship company that specialises in the mechanical processing of aluminium and steel parts as well as plastic manufacturing, in the early 2000s, the search was on for a manufacture of deck equipment and products. Reviewing a number of potential brands, Quick honed in on Sanguineti, another historic Italian company, that specialises in the design and manufacture of products such as gangways, boarding ladders, winches and handrails for super motor and sailing yachts.
Quick completed the acquisition of Sanguineti in 2023, appointing Cesari, who has worked at the Group for over 20 years, and charging him with an ambitious three year growth plan. “The goal we aimed for is to achieve significant growth with an ambitious three-year outlook: in 2023 turnover increased by 36% and we foresee a further growth of 33% in 2024, in order to reach a turnover doubling by 2026, thanks also to investments of €3.5 million by the Group. The relocation of the company’s headquarters to Casarza Ligure (GE) will allow the company to expand its space by about 6,000 square metres total, including about 3,500 square metres of covered space, making it possible to absorb the orderbook and increase production capacity, including a 35% increase in the workforce.”
Both Nemo and Xenta have been 100% acquired by the group, with Nemo providing the production of components for sail and motor yachts, specifically hatches, portholes, furlers and gangways. With the goal to provide products for the entire yachting segment, Nemo will focus on the sub-30 metre segment. “Sanguineti and Xenta solidifies the group’s position in a
Last year, Quick Spa completed the extensive refit of a 1996 Falcon 80 motoryacht, Project Maverick, to serve as a comprehensive demo boat and ongoing R&D vessel for its growing portfolio of products. The main Quick systems include the MC2 Seacentric System, the electric stabilisation system comprising Viator carbon fire fins and Intercepta trim tabs; Quick Nautical Network, a device allowing the integration of Quick systems with third-party navigation protocols; the new XR6 vertical windlass; new synchronous BTAC 300S thruster propellers; and a Proportional Control System (PCS) for precise and perfect feedback from thrusters, fins and windlass when under way or manoeuvring.
growing market,” explains Cesari, “and are part of the broader strategy to focus on the growing 40-70 metre sector. Historically Quick has provided for the sub-30 metre segment but the recent acquisitions will bolster the production capacity and reputation of Quick in the superyacht sector.”
One of the main strategies of the group has always been the centralisation of product production at the headquarters in Ravenna. This allows the company to closely oversee the quality control of all components within its 50,000 square metre facility, centralising the research and development and design of all products within the group. Despite this centralisation, each of the acquired companies retain their unique identity, something that Cesari explains is at the heart of Quick’s acquisition ethos. With an impressive annual production exceeding 640,000 products, Quick Spa exports its products worldwide, through a network of more than 110 distributors. With a clear growth strategy centred on new technologies, acquisitions, and market expansion, Quick Spa is set to achieve its goal of surpassing €100 million in revenue by 2026.
Facing page: From left Lorenzo
Founded in Auckland in 2008, anchor deployment manufacturer Bowmaster has taken a lead in its sector despite a remote location in New Zealand. The company was originally the deployment system department of anchor manufacturer Manson Anchors set up by Kiwi offshore sailor Kerry Mair. The decision to create a stand-alone business to design and build modular and bespoke anchoring systems led to the foundation of Bowmaster. Recent projects to carry its systems include Abeking and Rasmussen’s Liva O, Lurssen’s latest Kismet, and the Echo Marine catamaran Charley 2. We sat down with Ned Wood (pictured left), Technical Sales Director, to find out more.
BY FRANCESCA WEBSTER
What is the scope of Bowmaster’s portfolio?
From small tenders to 200 metre-plus vessels, we have a range of approximately 40 different systems for integrating 15 different anchors into a vessel. The systems – chain, anchor and windlass – are customised depending on the size of the vessel and the hull material, and from a material perspective we design and build systems in aluminium, carbon steel, duplex and ordinary stainless, as well as titanium. Today we produce 40-60 systems per year for the luxury marine industry.
How have anchor systems evolved in terms of design and materials used?
Manson Anchors have launched 10 new Class-approved anchors in the last 10 years. The use of higher strength materials means that the anchor is getting material where it’s structurally needed and ensures greater holding power. This has resulted in the most recent anchors achieving Super High Holding Power certification and a much more robust construction. We continue to use more exotic materials such as titanium to ensure an optimised anchor combined with weight saving.
What are the most critical fail points for anchoring systems?
One fail point is potentially where you have competing systems (eg. hydraulic/pneumatic) that fight against the windlass. Anchor systems can also be vulnerable to bumps during deployment, by a boat or pier for example, which can cause them to fail and not retract. In our systems everything is designed and built to fail above chain break load, so in essence the chain will snap before the system fails. A 100-metre yacht, for example, might use a 42mm diameter chain, which has a break-load of 1280kN or 128 tonnes.
It’s worth mentioning that anchor systems are required by Class to be able to be deployed immediately by pressing ‘go’ on the winch or releasing a brake, so if you lose power you can still stop the boat in an emergency. We like to keep things as simple as possible, so we generally use gravity to deploy the system, and the windlass to lift the anchor back up and stow it.
Tell us about your testing procedures?
We test everything on site before installation. It’s much easier to solve potential issues while the system is still in our factory than when aboard the vessel. This saves time in the build and lowers the risk of problems when the vessel is in use. Within the facility we undergo testing that simulates the anchor deployment and the potential loads. We are essentially a mini shipyard and are inspected and tested by the same regulatory bodies, be that Lloyds or ABS, who check and test all welds throughout the build process. When we’re building a new, bespoke system, we often build a steel mock-up of the hull, with the anchor pocket and deployment system to validate the design and make any necessary tweaks.
What about your submarine anchors – what advantages or disadvantages do they offer?
Space is always finite on a boat, so ensuring that it’s used in the most efficient way is a priority. We can do that by changing around the anchor type and anchoring arrangement. People are sometimes nervous about submarine systems because you can’t see the anchor chain, but you would normally use underwater cameras to look at chain direction in a standard system and use your GPS to drop a pin where you drop the anchor, so you know the chain direction from where the anchor lies and your current recovery position. Moreover, due to the flair in the topsides of a yacht it is very hard to actually see the anchor chain, which is why some yachts have viewing hatches in the hull at deck level. Once captains are familiar with using a submarine system they are usually happy with the performance. And from a crew point of view, polished anchors and anchor pockets are not required and there is no ‘bleed’ from a rusty galvanised anchor that can leave unsightly marks on the hull.
Are there any challenges associated with manufacturing in New Zealand?
We have a very low dollar compared to the US dollar or Euro, but a highly skilled workforce. Freighting to Europe is normally just one percent of the contract value, so it really doesn’t affect us, beyond the perception of being in the Southern Hemisphere, which can sometimes be negative. From a positive perspective, we can design during the night European time, so clients see updates first thing in the morning and we can receive their feedback during our working day. We also try to design anchoring systems that require low ongoing maintenance and we only use quality components that can be sourced globally, so ongoing supply is not an issue.
Maverick, the second in Cantiere delle Marche’s Flexplorer series, is fast approaching completion at the shipyard in Ancona.
Owned by Tom Schröder, Top Gun aficionado and now principal shareholder in the shipyard, the 44-metre explorer yacht has been designed and built expressly for a round-the-world tour.
Facing
When Tom Schröder was first introduced to Cantiere delle Marche in 2019 at the Cannes Yachting Festival, he was particularly struck by the onboard technical spaces. “I could see how well everything had been put together and that impressed me,” says the German-born entrepreneur. “I thought that sooner or later I wanted to own a CdM.” A year later he attended the launch of Aurelia, the first Flexplorer, and a few months after that he signed the contract for Maverick in the midst of the pandemic. Little did he know at the time that he would end up investing in the company.
“Maverick had been in construction for a year and I had built up a very good relationship with the management – always the most important factor in an investment decision,” he says. “When the main shareholder decided to sell his stake in the company, Vasco [Buonpensiere, then sales & marketing director, latterly CEO and co-owner] told me about the management buy-out and investment opportunity. Naturally I checked out the numbers and everything, but I’d already decided I wanted to step in because I trusted the management.”
Like her predecessor Aurelia, Maverick embodies all the key elements of a true explorer vessel – robustness, long range, ample storage, seaworthiness in all weathers, and so on – but the flexibility and functionality that defines the Flexplorer concept has been ratcheted up a notch.
The trademark A-frame crane, for example, has undergone important upgrades. Custom-built in carbon fibre by Advanced Mechanical Solutions (AMS), the lifting capacity has been bumped up to 4,000kg and its dimensions increased to improve the functionality of the aft deck. Aurelia’s crane is not full beam and the recesses that house the structure and close flush with the deck when not use (the teak planks are cut at 45 degrees to further disguise the join) reduce head height in the lazarette that houses a gym. Maverick’s crane is wider and its recesses are further outboard, so they intrude less on the beach club, laundry and technical spaces below. Moreover, the crane has a mobile snatch block that can be positioned directly above the tenders and toys instead of moving them around the deck on cradles during lifting operations. A portable, carbon-fibre davit crane by Atlas is used to handle smaller loads with sockets located around the deck perimeter. The mooring system in the stern has also been revised. Aurelia has her winches mounted on the main deck with hawseholes in the stern quarters, which limited the length of the collapsible bulwarks. By moving the mooring winches and fairleads to the swim platform, the side platforms now extend all the way aft on main deck to create an open garage-come-beach area of 135 square-metres. The heated 3,300-litre capacity pool in the centre of the aft deck is another new addition, although in explorer mode it is more likely to be used for storage than swimming.
The aft deck will carry several tenders, including a 9.55-metre custom chase boat designed by Valerio Rivellini. With an aluminium hull, carbon fibre topsides and powered by a 370-hp inboard Yanmar engine, it will be able to carry a jet RIB tender on its aft deck for rapid transfers (called Iceman and Goose respectively after other Top Gun characters, towing one support craft is also easier than towing two). The custom tender is being assembled offsite, although the shipyard built the aluminium hull and plan is to offer the design to CdM clients as a standalone product.
“Maverick represents the maximum evolution of the Flexplorer concept within the 500GT threshold.”
Maximising the loading capacity of the main deck aft meant concentrating the living areas forward and adding a fourth deck to house the wheelhouse and captain’s cabin.
The upper deck is now dedicated to the owner’s use, with a VIP suite on the main deck forward and four guest cabins on the lower deck. Additionally, there is a ‘crow’s nest’ or observation deck under the radar mast (the winglets are a styling feature that recall the tail fins of the F-14 fighter jets in Top Gun).
The extra deck brings with it added volume and the yacht is rated at 499GT – appreciably more than average for her length overall. Despite the higher superstructure, however, her profile looks balanced on the water.
“Maverick represents the maximum evolution of the Flexplorer concept within the 500GT threshold,” says Sergio Cutolo of Hydro Tec, responsible for the naval architecture and exterior design. “Because of the increase in volume at the top of the vessel and extra weight towards the bow, we had to keep the construction and outfitting materials as light as possible and reevaluate the hull form, which has a different distribution of immersed volumes to compensate for the longitudinal weight distribution.”
The owner’s previous yacht was a 74-foot Sunreef sailing catamaran (also called Maverick), which he sold in 2018. The idea of building an explorer yacht and a world tour came during the Covid lockdown while holed up at home. Due to start after this year’s Monaco Yacht Show, the seven-year, globetrotting expedition will take in high latitudes as well as the Northwest Passage. To this end, Maverick is partially winterised with preheating for lubricants and the hull has an ‘Ice Belt’ around the waterline. Ice strengthening usually involves doubling the number of frames where reinforcement is needed to make the whole hull structure several times stiffer, along with thicker plating for extra strength to prevent buckling caused by floating ice, but CdM already builds to higher specs than normal.
“The transversal hull structures we design for CdM offer a simple and reliable solution that combine strength and efficiency while minimising impact on the living spaces inside the hull,” explains Cutolo. “Whereas in a similar vessel you may have a shell thickness of 5-6 mm around the waterline, Maverick has a longitudinal strip of 12mm plating, at least double what you would usually expect to find. This transversal structure offers optimal support for the thicker shell plating around the waterline without the addition of longitudinal stringers.”
Sales of explorer yachts have boomed in recent years, thanks in part to younger, adventurous owners who are less interested in cruising the usual hotspots. The explorer category often favours styling over substance, with the result that most so-called ‘explorer’ yachts are no more designed for long distance passage-making than your average SUV is for serious off-roading. CdM is different and since launching its hardy Darwin Class of steel-hulled explorers in 2010, the brand has carved out a niche for itself in the market for ocean-going, pocket explorers under 500GT. As Vasco Buonpensiere points out: “We believe it should be you that sets the limits of what you want to do with the boat. Not the boat.”
With 16 projects under contract and seven deliveries, including Maverick, scheduled for this year alone, CdM has seen production turnover increase from 37 to 80 million and its staff double in the last three years. Due to lack of space, its steel hulls are currently built up the coast in Trieste and Porto Marghera near Venice, but a new onsite construction shed will bring all the steelworks inhouse by the end of the year.
According to Buonpensiere, the entry of Tom Schröder as majority shareholder will not affect day-to-day operations: “Tom wants to stay small, stay family, stay high quality, because that’s what attracted him to the brand in the first place,” he says. “The most important thing is that his is not a speculative investment.”
Although technically a series builder, CdM has always offered a high level of customisation. However, the brand is also developing new models of around 100 feet/200GT, a size range in which clients are accustomed to more standardised products.
“Clients upsizing from 70 or 80 feet are often nervous about customisation and prefer less choice, not more,” says Vasco Buonpensiere. “I’m a big believer in the smaller boats because they are the foundation of this company. We have quite a few Australian owners, for example, where most of the market is for boats under 35 metres. Especially in boom times you see yards start to build bigger, but nearly all our clients start at 100 feet.”
The layout of Maverick’s main and lower decks is similar to Aurelia’s. The asymmetrical arrangement of the main saloon, which is widebody to starboard, remains, but the galley is designed to be more family-friendly and communicates directly with the saloon with no intervening pantry. In line with the yacht’s explorer vocation, there is a large walk-in cold room inside the galley with more cold/dry storage space on the tank deck, and in the full-height tunnel that runs between the engine room and the crew quarters –one of the features that the owner first liked about the brand.
Maverick is powered by conventional Caterpillar C32 ACERT diesel engines for a range well above 5,000 nm at 10 knots. The fact that CdM has no current plans to build a yacht with hybrid propulsion – although it is researching PTO/PTI solutions and salt batteries – may seem retrogressive at a time when sustainability is a hot topic, but the strategy is a logical consequence of its practical approach to yacht building as well as the type and size of vessel it specialises in.
“We had the hybrid conversation with Tom, as we do with all our clients, but the more you look into it the less it makes sense for us and our owners,” says Buonpensiere. “Firstly, an explorer has to be reliable, so simplicity is the top priority. Secondly, Maverick burns around 70 litres of fuel an hour at 10 knots, so any additional savings a hybrid system may provide will never outweigh the extra cost. Thirdly, alternative fuels require more storage and technical space on board, which is a problem on the size of yachts we build.”
Instead, CdM has opted for something far simpler and more sustainable: wind power. Maverick will carry a wing kite (see sidebar) supplied by Wingit in Germany, which during long transfers can tow the yacht at low speed assisted by the engines (having the props turning at idle speed reduces drag). It is a solution that appeals to the owner’s sailing background and Wingit is working with CdM to develop a kite system specifically tailored to the requirements of its explorer fleet.
Dresden-based Wingit was set up in 2010 by kite surfing enthusiast Stephan Schröder (no relation to Maverick’s owner). The company began with wing kites for smaller sports boats and nearly 40 have been installed to date, but later started receiving requests for automated systems on larger yachts. It is currently developing a special system for CdM able to handle much higher loads based on a feasibility study for kites of 20, 25 and 30 square metres on a steel-hulled vessel like the Flexplorer displacing 440 tonnes. The results show that they will be able to tow the yacht at over 8 knots on wind power alone, or more when engine assisted. The size of the kite does not dramatically affect performance, but the smaller the surface area the greater the angle it can sail to the wind.
No mast is required to fly the kite, just a deck-mounted coupling above the height of the railing in the bow for attaching the three control lines –one to take all the forces and the other two for steering. After inflating, the kite is released and launched it into the air by pulling the lines. When the kite reaches the optimal height, it begins to trace a figure of 8 in the sky on an automatically controlled flight path. To bring the kite down the auto pilot moves it to a position directly above the boat where it exerts the least force. It can then be winched down and collapsed for stowage.
“The advantage of a kite over a conventional sail system is that it does not need a tall mast, flies higher in the sky where there’s more wind, and generates up to 10 times more power than a traditional sail per square metre,” says Schröder. The main thing is not the size of the kite but the speed at which it performs the figure of 8 in the sky – ideally you want constant flight speed to maintain constant power.”
How can engineering free us from the evolutionary constraints in superyacht design? This was a question asked by Lateral Naval Architects when they unveiled a concept in collaboration with Michael Leach Design at the 2022 Monaco Yacht Show. Coined Free From Bulkheads (FFB), the proposal stripped down the technical backbone of a conventional yacht by removing restrictive watertight bulkheads. Luiz de Basto’s Project Med, presented at last year’s show, takes inspiration from this open architectural concept.
BY FRANCESCA WEBSTER
Seeing the FFB was a lightbulb moment for Luiz de Basto, who has been experimenting with ‘floating’ decks since the 1990s and saw the FFB as the technical solution. Starting with a 60-foot, planing speed boat, the original concept evolved into the 45-metre Yara first published in 2000, which featured an enclosed flybridge floating over an open foredeck.
Yara was never built, but the idea of an openplan deck with a floating superstructure stayed with de Basto and over the years he sketched variations of the concept. The latest is 92-metre Project Med, which features an almost entirely open-air, open-plan main deck dedicated exclusively to convivial entertainment.
“The concept draws inspiration from the traditional towns across the Italian, French and Spanish coastlines, where piazzas are the centre of life,” says de Basto. “I wanted to create an environment for guests to relax together out in the open, and provide a variety of locations for dining, entertainment and socialising.”
A single open deck with a floating, reflective glass superstructure, the concept presented a number of challenges from an engineering perspective, notably the superstructure with its four structural pillars and a central stairwell. The overhanging structure had to be light, but also have a high level of structural integrity to withstand the dynamic loads of a seagoing vessel. It also needed to be able to support the huge glass surface that wraps around the superstructure. As in the design of bridges and buildings, de Basto incorporated lattice-truss engineering into the superstructure design.
“I considered buildings like Heathrow Airport with its huge lattice structure,” he explains. “The glass is floating above the frame, but it is quiet inside the building, despite planes roaring overhead. I imagined adapting this for the marine world and realised that the structure itself could become an interesting architectural motif of its own.”
Andy Douglas, chief structural engineer at Lateral, took up the proposal and began researching potential avenues to incorporate such a structure into a yacht.
Opening spread: The 92-metre Project Med.
Left: Luiz de Basto’s 45-metre Yara
Below: The CAD model of the lattice frames supporting the yacht’s glass superstructure.
“We began by looking at existing examples of architecture and bridges and came up with the solution of having transverse frames with diagonals across it alongside some longitudinal supports.”
“We began by looking at existing examples of architecture and bridges and came up with the solution of having transverse frames with diagonals across it alongside some longitudinal supports,” says Andy. “De Basto liked the solution, so we created an initial CAD model of the superstructure, before creating an FEA model for analysing the strength and stiffness of the structure and proving it would be able to withstand the loads at sea.”
By reducing the large foredeck overhang and adding additional supports to prevent potential drooping, Lateral was able to demonstrate that the overall concept was viable and the resulting steel lattice-truss arrangement provided the necessary strength, as well as maximising the space between the lattice framework providing large unobstructed windows.
Below: Project Med within a shipyard, with
Bulkheads have always been the main engineering limitation for defining a superyacht’s interior configuration. Lateral’s FFB platform limits the bulkheads to the decks at waterline level, thereby creating a new, unconstrained deck adjacent to the waterline, which opened up the potential for more layout innovations and, ultimately, an elevated user experience. It also allowed de Basto to create his open-plan main deck and to utilise the whole of the lower deck for guest accommodations. Unlike traditional yacht designs and drawing again on the architecture of Mediterranean coastal towns and villages, the resulting corridors are angular and irregular.
Project Med validates the FFB platform by demonstrating that there is demand for a new approach to general arrangements on yachts, but also that a seemingly radical concept can be structurally feasible.
“We’ve had a lot of clients interested in something different,” says Lateral’s chief mechanical engineer, Simon Brealey. “These are clients who question the status quo and want to live without constraints near the water. We’re also constantly having to redesign and redevelop platforms to suit different designers’ ideas. Sometimes this process of aligning designers and owners to technical requirements can create friction and delay projects so the FFB process removes many of these problems.
“ We played with the parameters of the beam and freeboard to see at which point you can remove the watertight bulkheads from the lower deck, but still be compliant with the stability requirements.”
In developing the FFB platform Lateral first analysed the existing fleet. The majority of yachts had the same double-deck engine room, crew cabins forward, a beach club or garage to aft, and guest accommodations in the middle. Taking an 85-metre yacht of 2,500GT as its baseline, Lateral’s goal was to create a new design that opened up these spaces, offering designers more creative potential and more fluid environments for guests to enjoy.
Adrien Thoumazeau, Principal naval architect and research & development coordinator at Lateral, was the main driver behind the concept. His initial concept, dubbed the Lateral Skateboard, was a reimagining of the desired result – a clean and empty deck unhindered by technical mechanisms. To execute this goal, Adrien created a parametric model to test the platform with different engineering arrangements.
“We played with the parameters of the beam and freeboard to see at which point you can remove the watertight bulkheads from the lower deck, but still be compliant with the stability requirements,” he explains. “We quickly realised that increasing the yacht’s beam was not the way forward, but that increasing the freeboard and raising the deck height was the way we could solve the problem and still be compliant.”
Typically a yacht’s lower deck is 0.5 metres above the waterline, whereas the FFB platform has the lower deck at 1.5 metres, at which point the watertight bulkheads can be limited to the technical deck, leaving the lower deck almost entirely free. “The beauty of that,” continues Thoumazeau, “is that in combination with an e-hybrid propulsion system, we’re able to put the engine room fully below the lower deck as well, creating a 70-metre unrestricted lower deck.”
An additional advantage of the increased freeboard is that shell door platforms can be opened on the lower deck in the beachclub or alongside guest staterooms, and because they are higher above the waterline they are no longer susceptible to wave-slapping.
To remain within the 2,500GT envelope, however, the additional deck height had to be taken from elsewhere and so the superstructure has been reduced, which is the compromise when working with the FFB platform. The result is a more streamlined profile, which is not necessarily a bad thing: “You’re shifting the living and luxury onto the lower deck, allowing the focus of the main and upper deck to be purely for guest experience,” says Brealey. “It’s not a sacrifice, just a different approach, with all guest areas closer to the waterline.”
Lateral have identified a sweet spot of 75 to 85 metres as the ideal length before running into potential damage stability issues. Naturally, such a dramatic adjustment comes with regulatory challenges, but these are not insurmountable. “Bending the rules in the superyacht world is very difficult, and we’ve definitely faced questions about how the FFB will increase costs and whether it poses extra risks, but we see no potential issues when it comes to regulatory approval,” says Brealey. ““We’ve done nothing radical. We’ve worked within the letter of the rules, only looking at them in a slightly different way.”
In-build at Royal Huisman and scheduled for delivery later this year, 65-metre Aquarius II is so similar in style and spirit to her smaller predecessor that you might think you’re seeing double. But under her modern classic exterior, the custom cruising ketch benefits from literally hundreds of tweaks to enhance operations and improve performance.
BY JUSTIN RATCLIFFE
Launched in 2018, 56-metre Aquarius redefined the modern classic genre. Graceful and understated yet powerful and exciting to sail, she came first in class at her racing debut in the St. Barths Bucket. Aquarius II may be a full nine metres longer, but the ideology behind her design has not changed. “She’s basically the same boat on steroids,” says her captain.
Aquarius II reunites the Dutch shipyard with Dykstra Naval Architects, interior designer Mark Whiteley, owner’s rep Godfrey ‘Goddy’ Cray, and yacht captain James Turner. The latter came to the project armed with a checklist of 728 ‘improvements’ meticulously compiled during five years of sailing the previous yacht. That’s not to say there was anything wrong with Aquarius Indeed, she was “close to perfect” for her owners and their decision to build bigger was dictated by a growing family and the
desire for a fourth guest cabin, more crew accommodation, a larger gym, and generally more space for onboard services such as the laundry and galley.
The checklist deals mostly with technicalities affecting the everyday operation of the vessel, such as the orientation of HVAC drip trays, the position of the fuel tank vents and relocating a hydraulic cooling pump. In other words, the kind of things you can only figure out when the yacht has been sailed a lot. Rather than a catalogue of errors, it was an invaluable inventory outlining how operations, maintenance and comfort could be enhanced.
“All shipyards have their preferred way of doing things, but input like this is beneficial for both parties because we get a better boat at the end of the day and they can incorporate the lessons learnt into subsequent projects,” says the captain.
Facing
from
Exhilarating performance was a priority from the start as the owners aim to repeat St Barths Bucket victories in 2019 and 2022 with the new boat. The issue, however, is that bigger doesn’t necessarily mean better in terms of sailing performance.
“The design issue with sloops approaching 50 metres and ketches over 60 metres is that you struggle for sufficient keel draft and sail area,” explains Cray, working on his third Royal Huisman project after Ngoni and Aquarius. “Maintaining the right balance between the two is essential and If either is compromised then performance will be limited, which is why the naval architecture always comes first on sailing boats.”
Unlike her smaller sibling, Aquarius II has a lifting keel with a variable draft from 4.8 to 7.6 metres for access to most anchorages and marinas as well as stability and performance when powered up. The keel trunk, milled from solid aluminium, penetrates the area between the galley and crew mess with only a small impact on interior volume.
More complicated was the sail area and mast height. On world cruisers these are restricted by the Bridge of the Americas over the Panama Canal that has a ‘Panamax’ air draft limit of around 62.5 metres. However, it did not escape Cray’s notice when Unfurled, a Vitters sloop with a 65-metre mast, was able to pass under the bridge heeled over by using water bags attached to her rig. With this in mind and taking into account the owners’ request for more interior volume, the design team came up with a proposal for a 61-metre yacht with a 64-metre main mast, plumb bow, bowsprit and submarine anchors.
“We thought we’d ticked all the right boxes, but just to be sure I did a final check with the port authority in Panama,” says Cray. “It turned out they were no longer entertaining a heeled-state transit under the bridge. Oops!”
Rudder feedback is the grail of a highperformance steering system and the compelling advantage of mechanical steering systems. While hydraulic steering provides power, it does so at the cost of eliminating feedback to the helm. However, the high loads of sailing superyachts require mechanical systems to use high gear ratios to make steering loads manageable, commonly resulting in 8-10 turns of the wheel from hardover to hard-over. This means small course adjustments require a lot of wheel movement.
This was the conundrum Edson Marine was looking to resolve with its new powerassisted steering system, displayed at METSTRADE last year and being fitted for the first time on Aquarius II. After looking at electric power-assisted steering systems in the automotive industry, the US-based company designed its own solution with a software package developed specifically for large sailboats whose steering systems are loaded up in one direction for much longer periods compared to cars.
“The system basically comprises an electric motor with a gearbox that is driven by a torque sensor between the wheel and the rudder,” explains Edson’s president, Chip Johns. “That sensor measures how much torque the helmsman is putting on the wheel and the data is sent to the control software, which decides whether to add or subtract load. It’s a variable system with five levels of assist.”
With just one torque tube instead of two, the Edson system already reduces weight and friction, providing an incremental improvement to the mechanical steering on Aquarius II. The power-assist function is a separate module engineered to add 140 Nm (Newton Metres) or about 103.25 ft-lb of torque. In practical terms, if 20 kg of rim load are required to turn the wheel, the system is able to reduce the loading to around 5 kg and make a 4-turn lockto-lock manoeuvre as easy as 10 turns using conventional mechanical assistance, all without losing the feel of the rudder.
“It’s not just about racing in the St Barths Bucket, because the system will make it easier for owners - as well as their friends and children - to enjoy cruising on a prolonged reach, for example,” says Johns. “Whatever we can do to make the sailing experience more enjoyable is good for the owner and good for the industry.”
At this point the owners reiterated their commitment to sailing performance, even if it meant going beyond the Panamax limit. They also voiced their preference for a classic spoon bow like Aquarius as opposed to a plumb bow configuration with a bowsprit. No longer constrained by air draft the main mast height was pushed up to 67.5 metres and the hull extended to 65 metres overall.
The extra length means that Aquarius II has nearly 45 percent more interior volume than her predecessor, more than enough to accommodate the extra cabins, guest space and service areas. To better illustrate what this increase in volume signifies in practical terms, Cray produced a table for the owners comparing the main areas aboard both boats. The figures show that the owner’s areas range from 21 to 55 percent larger, the gym nearly 39 percent, the galley 67 percent, and the laundry a whopping three times bigger.
Although less weight means more performance, combining aluminium construction with carbon composite elements as Royal Huisman had done on 60-metre Sarissa would have produced only incremental gains at significant extra cost. Instead, the structural weight was reduced by using FEM analysis to study local loads and
vary the size and spacing of the hull frames according to where reinforcement is needed. Combined with Rondal’s fully integrated carbon rig and sailing system (see sidebar), carbon elliptical rigging from Carbo-Link and Doyle’s structured luff sail technology, the result will be an elegant bluewater cruising yacht with a muscular turn of speed for the occasional superyacht regatta.
“The slender hull shape, lifting keel and extra mast height means the yacht will be quick around the race course, but also responsive in the light airs typical of the Med,” says Erik Wassen of Dykstra. “With a 400-tonne boat flying more than 2,000 square metres of canvas and sailing with over 16 knots of boat speed, the loads on the rudder are tremendous. It’s a very fine line between having a good feel on the wheel and struggling at the helm, so we put a lot of effort into optimising the rudder shape and balance.”
To further enhance steering responsiveness, US-based Edson Marine was brought in to develop a torque-assisted system that reduces the number of turns of the wheel from lock to lock while maintaining the hands-on ‘feel’ of the mechanical cable and wire steering (see sidebar).
Throughout the design and specification process, Cray was attentive to technological developments that might be considered of limited value. Innovations can add function and enjoyment, but they may also come with downsides in terms of time, cost and reliability.
“Our goal with Aquarius had been to keep it as simple as possible within the bounds of a luxury yacht,” says Cray. “Given the nature of superyachts that’s a bit of an oxymoron, but it was important to steer away from risky innovations and the same mantra applies for Aquarius II. That said, we have incorporated some current but tested developments.”
One such is the semi-hybrid technology for power generation and management. The hybrid system comprises a 900kW MTU diesel engine for propulsion with a 70kW alternator/shaft generator mounted on the gearbox that can run the hotel loads when the yacht is motoring, and two fixed-speed diesel generators coupled to a 125kW battery bank for peak shaving. Instead of the second generator cutting in during peaks
in demand, the batteries can absorb the excess. The system brings efficiency and flexibility benefits as the generators are sized according to energy usage over 24 hours, not the total energy demand at any one time.
The MG Energy batteries are housed in a A60-rated watertight and floodable compartment low down in the hull amidships. In the remote case of thermal runaway, a network of fireproofed pipes help to dissipate the heat outboard. The battery pack can also supply electrical power to the shaft generator to feed power into the grid. All Royal Huisman yachts have a small electric power pack for minor hydraulic functions that is powered in port via the shore converter. The system on Aquarius II offers enhanced flexibility. So when in harbour, for example, the captain doesn’t need to start up the engine or generator to operate the passarelle. Further, the hydraulic system is load sensing and can adjust pressure and flow rate to reflect the requirements of one or more consumers for smoother and quieter operations.
“New-builds like this are all about maintaining momentum.”
The high-modulus carbon rig and integrated sail handling by Rondal is another area that has benefitted from close consultation with the crew and the lessons learned from operating the previous boat. More than a scaled-up version of the rig on Aquarius, the state-ofthe-art system introduces additional refinements for pushing the yacht hard under racing conditions with a crew of 30 while also being able to cruise safely with minimal numbers of permanent crew.
“The primary design variable is mast stability, which is driven by local and global buckling,” says Edoardo Volpe, Rondal’s project lead engineer. “Mast stability is optimised by engineering the mast tube section size, shape and by controlling the stiffness properties of the laminate, including fibre type and direction, to keep the weight low while complying with classification. The secondary variable is mast tuning or trimability.”
Aquarius has checkstays and runners for modify mast bend controlling the shape of the mainsail, but Aquarius II makes use of deflectors to control mast bend and stability. More effective than checkstays as they pull back laterally instead of downward, deflectors also reduce drag to enhance racing performance. While in cruising mode deflectors are locked at a certain position, like checkstays, to make rig handling easier with a short-handed crew, also in reefed conditions.
Another improvement is the continuous carbon elliptical rigging from Carbo-Link. Structurally, this is exactly the same as Carbo-Link’s round-section cables and just as strong, but the elliptical shape provides better aerodynamics and less windage when sailing or at anchor, which means less vibration. Carbon rigging is susceptible to resonance that can be surprisingly noisy – an important consideration when the mizzen mast passes through the
Many of the 700-plus items on the checklist of improvements involved the onboard systems. Overseen by Royal Huisman project manager Dimitri van Zwieten, it fell to systems manager Sjoerd Schrichte and lead engineer Richard Daenen to integrate them into the schematics of Aquarius II in consultation with the crew. As part of the shipyard’s custom build approach, it was then routed into its proprietary construction management software that logs all the system components according to type, function, location and ‘skid’ number (the system racks that are pre-assembled for subsequent plug-and-play installation). The result is a complete guide to how the onboard systems have been designed and executed in case of repair or replacement in the future. The data is also routed into Navisworks, a 3D modelling program that can track seamlessly through exterior and interior
owner’s suite and the mizzen forestay is the longest and skinniest exposed stay on the boat.
The higher mast meant that the masthead could be designed with better separation between the forestay and Code 0/A3 sails for easier handling when racing. Cruising superyachts tend to leave the Code 0 up as crews are getting smaller and handling big free-flying sails (ie. sails attached to the rig only through their corners) can be a messy and sometimes dangerous business. Sensors measuring mast compression and loads on runners, deflectors, forestays and main sheets provide real-time feedback.
Additionally, Rondal shares its software with Doyle Sails so they can run both the sails and the rig through the same program to see how the spars and rigging behave.
“Loads are getting higher and captains are more reluctant to fully trust their own sailing experience,” says Volpe. “Part of our job is to give them as much information as possible so they know how best to handle the rig.”
net spaces and is used across all departments to review the project in build.
In addition, Royal Huisman has long embraced product development and management methodologies such as Concurrent Engineering and Stage-Gating to ensure complex projects don’t get bogged down by the sheer number of decisions that have to be made and solutions found. Involving multiple disciplines simultaneously rather than consecutively, and breaking projects into a series of stages with decision ‘gates’ helps to keep the ball rolling.
“New-builds like this are all about maintaining momentum,” concludes Cray. “Planning is important because you need to keep it flowing, and Royal Huisman are very good at doing the groundwork upfront. Otherwise the risks in terms of budget, build time and reliability just keep mounting up.”
Project Toro is the first in a series from Turquoise Yachts based on an in-house engineering platform that offers clients faster delivery times combined with ample opportunity for customisation. Now in the outfitting stage, we travelled to the shipyard in Istanbul to visit the project before her launch later this year.
Project Toro began in classic fashion with a charter client looking for a pre-owned yacht to buy. His long-term broker, Simon Ting of SuperYachtsMonaco, marked a potential 60-metre candidate and designers Harrison Eidsgaard were brought in to assess the interior for refit. After discussions with the client, however, it was felt the yacht wasn’t ticking the right boxes and the focus changed to a new build. Armed with a preliminary exterior and interior design by Harrison Eidsgaard, Ting began the search for a suitable shipyard.
“We initially focused on northern Europe, but this was during Covid, slots were scarce and prices were going crazy,” recalls Ting. “I’m one of those brokers who likes finding deals that represent good value for money, so my search quickly shifted worldwide. Turquoise in Turkey had a hull they had started on spec but was still in the very early stages that fitted my client’s needs, so we jumped on it.”
Project Toro (NB65), as it is now known, is a 79-metre vessel of 2,050GT that can accommodate up to 14 guests in seven staterooms. Her technical platform is shared with others in build at Turquoise Yachts, including Project Vento (NB74), Project Arrow (NB75) and Project Bravo (NB76), which vary in length overall but have the same 13.2-metre maximum beam. Toro is powered by conventional Caterpillar diesel engines, but the platform has been engineered to offer the option of an mtubased hybrid propulsion package.
“There are variations within that common structural envelope that allow us to create a variety of solutions for our respective clients with different interior layouts and exterior styling,” says Turquoise executive director, Burak Akgul. “The shared technical platform means we can cut short the upfront engineering time of each project, a saving that is then passed on to the client.”
Facing
Ting interviewed a number of technical consultants, but chose to partner with Monaco-based ACP Surveyors headed up by Andrea Carlevaris, because they have worked together in the past and because ACP had been part of the owner’s team on Roe (NB66) launched by Turquoise in 2021. With Project Toro the relationship is somewhat unusual insofar as ACP is the owner’s technical rep, while all commercial considerations and direct relations with the owner are handled by Ting.
“In the case of a change order, for example, our job is make sure Simon has what he needs to have that informed conversation with the owner and advise him on the best outcome,” says Carlevaris. “It’s a relationship based on trust that also suits the shipyard as the project managers generally prefer to deal with technical people. It seems to work well as we haven’t had a single change order that has been refused by the client.”
Harrison Eidsgaard’s superstructure and interior design are completely bespoke, but as part of a series with a common technical platform there were limits to what engineering changes could be made. Nevertheless, by working closely with the shipyard’s in-house technical department, the owner’s team has been able to introduce significant features that set Project Toro apart. Arguably the most demanding of these features is the Neptune Lounge.
Facing
BCE Glass in Istanbul was founded in 1970 and its first yacht project was 66-metre Aglaia (now Ahimsa) launched by Vitters in 2011. Today it has a branch office in the Netherlands and is a leading supplier of turnkey glazing solutions in the marine sector, offering full-scope support from design consultancy to engineering services. As this issue of How To Build It was going to print, BCE Glass was completing the process of obtaining Lloyd’s approval for the hull windows in Project Toro’s Neptune Lounge. This has involved extensive destructive testing, including the setting up of a 40-metre water column to test the glass at a pressure of 4 bars, as well as tests to evaluate the strength of the window frames and mullions.
The windows themselves are made of laminated double glazing with an air gap to reduce condensation issues and provide a barrier against waterborne noise from the propellers and underwater exhaust. Interlayers of varying elasticity add strength and dampen different sound frequencies (the stiffer the material the higher the wavelength it absorbs). Each of the six windows has a total thickness of 116mm, which is based on FEM calculations to simulate loading in different sea conditions and impact scenarios.
“The glass is bonded to the window frames, but because they’re installed at a negative angle and above the water, Lloyds also required mechanical fastening,” says Ahmet Ozcan, head of BCE’s specialty glazing division. “We developed a proprietary retainer system comprising a flange imbedded inside the glass with no penetrations or external fixtures, so if the bonding should fail for any reason the glass remains in place.”
BCE also produced the mirrored glass for superstructure windows on the main, owner’s and bridge decks. Glass on large yachts is nearly always chemically toughened and BCE is investing in a 3,000-square-metre extension to its factory to house a new chemical toughening plant, but the process of submerging the glass in a bath of molten potassium salts at 450°C rules out applying any coatings, including the aluminium oxide used to produce a mirror effect.
BCE has developed its own closely guarded method for producing chemically toughened glass that is also mirrored. Moreover, as the coating is imbedded in the glass it is not susceptible to moisture that can break down the bond between the glass and the silvered backing, causing it to come away and leave unsightly black spots.
Underwater viewing ports are rare on superyachts. Although the mechanical properties of glass are well understood and submarine windows appear on yachts such as Feadship’s Savannah and Abeking & Rasmussen’s Elandess, Class societies are still conservative when glass appears below the waterline. The complexity and cost of meeting the required criteria can be enough to dampen initial enthusiasm, but the owner of Project Toro decided to push ahead regardless.
The windows are supplied by BCE Glass in Turkey (see sidebar). Comprised of six large panes of double-glazed laminated glass, each 120mm thick and weighing 800kg, three are positioned above the waterline and three below in a space that makes up part of the spa on the lower deck aft. Access is via a watertight door and the room extends down into the tank deck.
The glass, however, wasn’t the main challenge. Turquoise Yachts routinely mounts its engines on springs rather than rubber bushes to dampen noise and vibration, but as the Neptune Lounge is positioned between the engine room and the props, structure-borne sound were always going to be a concern.
“Because the lounge is on two levels inside the hull with a wall of glass, we especially wanted to avoid low-frequency resonance from the engines and underwater exhaust,” says ACP’s project manager, Simone Curti. “This low-frequency noise is something you’re more likely to feel as vibrations than hear. The normal limit of human hearing is around 20Hz or cycles per second, but we can pick up mechanical oscillations in frequencies well below 1 Hz, so our sensitivity to vibration is much broader than the range of human hearing.”
Acoustic consultants Van Cappellen Sound Solutions were brought in to recommend further damping measures, including the redesign of the drive shaft brackets. As a result noise levels are expected to be up to 30 percent lower in the Neptune Lounge than the contractual 53dB in harbour mode.
Unusually, the full-height windows on the upper decks from amidships aft are of mirrored glass. External doors are clad in the same mirrored glass, which meant they had to be engineered and built to precise tolerances so when closed they are perfectly flush with the surrounding glazing. An additional issue is that during washdowns the calcium carbonate found in ‘hard’ water leaves behind chalky deposits as limescale, which is particularly noticeable on mirrored glass if not dried immediately. For this reason, Project Toro has two filtering systems that work in tandem: a water softener and a reverse osmosis purifier to remove unwanted impurities and sediments.
While the superstructure was still under construction at Turquoise Yachts’ metalworking shipyard in Kocaeli across the bay from its outfitting facility in Istanbul, it was realised that navigational visibility from the bridge and wing stations could be improved.
“We had to find a remedy that required only minimal modifications to the existing structure and didn’t adversely affect the exterior lines by Harrison Eidsgaard,” says İlker Dorkip, Turquoise’s project manager.
“Initially we thought of having fold-out platforms but the final solution, completely engineered in-house, was to have hydraulic wing stations that pop out 1.2 metres from the sides to maximise visibility fore and aft.”
Most superyacht shipyards would outsource engineering works like this. The fact that Turquoise can rely on its own technical office makes life easier for the owner’s reps. Unforeseen issues can be resolved on the spot in a meeting without having to involve outside contractors. Moreover, the knowledge and experience accumulated over time stays in-house and can be applied to subsequent projects.
Turquoise is receiving more requests for large pools on the upper decks, which offer more privacy than the usual location on the main deck aft. The pool on Toro’s bridge deck actually spans two levels with an RGB waterfall feature cascading down from the sundeck and a skylight at the top. Measuring 8.5 metres in length and three metres wide with underwater audio speakers, its 15 tonnes of water can be dumped into a heated recovery tank three decks below in minutes and pumped back up again when at anchor in 20.
“Turquoise in Turkey had a hull they had started on spec but was still in the very early stages and fitted my client’s needs, so we jumped on it.”
The fold-down side bulwarks in the stern increase the usable deck area, but created another conundrum as to where to place fairleads and cleats when moored stern to in a marina. ACP and the shipyard’s team came up with a smart system that from the mooring winches on main deck has the lines feed into a stainless tube and exit between the staircases folding bulwarks on the swim platform. They then then run at deck level through a fairlead to the bollards on shore. By keeping tensioned mooring lines under cover and low to the deck the system is safer but also looks clean and tidy. Additionally, an electric roller for the shore cable means crew don’t have to manhandle heavy power cables back and forth.
Turquoise began testing AkzoNobel’s sprayable fairing compound on 53-metre Jewels, but it was limited to parts of the superstructure such as the mast and shell doors in the hull. It is now used for all Turquoise projects and on Project Toro the epoxy surfacer has been used everywhere above the waterline.
“It’s more expensive but is much quicker because it comes ready mixed and you can apply it wet on wet to bigger sections without having to wait for it to dry,” says Taylan Salgur, Operations Director at Turquoise. “We had to retrain our painters but the fairing time has been cut by 25-30 percent.”
On area where new build projects can easily run over budget are the IT systems and Project Toro’s, on special request of the owner, is particularly advanced and complex. Combining multiple solutions for fail-safe redundancy, from standard VSAT and Starlink to One Web and Poynting Wavehunter, the system is based on MBX technology that can combine the bandwidth of different cellular links into an unbreakable, high-speed Ethernet connection. An integrated filter also means any hardware connected to MBX complies with Lloyd’s Register Marine Type Approval standards for electromagnetic (EMC) compatibility. Videoworks, a longterm partner of Turquoise with an office in Istanbul, is the systems integrator.
“Turquoise is receiving more requests for large pools on the upper decks, which offer more privacy than the usual location on the main deck aft.”
“I’ve never seen such a focus on the IT system,” says Carlevaris. “We were briefed in one of the first meetings with the owner’s IT team, but the challenge has been tracking all the industry developments while building the yacht at the same time. When we started, for example, Starlink still wasn’t available and we will be one of the first to have the new OneWeb antenna.”
Not so long ago Turkey was viewed simply as a cheaper alternative to building in Europe. That view is fading fast. The premier Turkish yards can now compete with – and sometimes outshine – their counterparts in Italy and northern Europe in terms of quality as well as price, which is why Ting chose to build with Turquoise Yachts in the first place. In this context, Project Toro is an example of the kind of creative engineering, skilled execution and flexible attitude that has seen Turkey creep up the league table of yachtbuilding nations.
Teignbridge Propellers has been designing and manufacturing propellers and stern gear since 1974. With subsidiaries in India, Dubai and Malaysia, we visited its UK headquarters to discover more about the science behind propeller design and how they are made.
BY JUSTIN RATCLIFFE
“Some clients are specifically interested in fuel economy for longer range, or low noise and vibration.”
It is entirely fitting that Teignbridge Propellers near the seaside town of Torquay is housed in a historic building built by Isambard Kingdom Brunel, the great civil and mechanical engineer. Among his many achievements, Brunel designed the SS Great Britain, the first iron-hulled, propeller-driven ship to cross the Atlantic Ocean in 1845. Nowadays marine propellers come in multiple shapes and sizes, but they all convert rotational motion into thrust by producing a pressure difference in the surrounding water. Until quite recently, their design was driven by trial-and-error and was viewed as something of a dark art, but modern computing power allows engineers to predict propeller performance before they even get wet. Teignbridge Propellers has been at the forefront of these developments. The largest producer of custom propellers and stern gear in Europe, Teignbridge is one of very few companies that can execute the whole design and manufacturing process
in-house. Able to react quickly to relatively simple requests for commercial ships and workboats, it increasingly operates at a higher level to meet the more specific needs of military vessels and large yachts. Bold and the restored classic Haida are just two superyachts equipped with its propellers, while repeat clients include Mengi Yay, Bilgin Yachts and leading production boat builders.
“Some clients are specifically interested in fuel economy for longer range, or low noise and vibration,” says Mark Phare, Group Managing Director. “At the moment, for example, we’re designing propellers for electrically driven foiling tenders, but also for autonomous minesweeping vessels that need to have both a low magnetic signature and a low noise signature. So we’ve been doing all sorts of research into how to minimise propeller noise, which includes special coatings as well as the actual propeller geometry, which is know-how we can transfer to superyachts.”
Propeller performance revolves around mechanical strength, hydrodynamic efficiency, noise and vibration, and cavitation [the formation of vapour cavities in water induced by low pressure]. These four criteria often pull in opposing directions, so the challenge is to find the best balance according to the specific requirements of each customer.
“We’ve probably reached the top of the efficiency curve in propeller design as we know it and most of what we do today is navigating the design space to find the optimum compromise based on use,” says Dr Saeed Javdani, head of the Innovation & Technology Department. “If you want low noise and vibration, for example, you may have to sacrifice some efficiency, because to have a quieter propeller you need a bigger blade area ratio, which increases frictional drag across its surface and reduces efficiency, and so on.”
Noise is a key consideration for superyachts, which is why they usually have propellers with highly skewed blades to avoid propellertip vortex, the dynamic behaviour that can create wave-like disturbances, resulting in unwanted cavitation and high-pitched ‘singing’. Highly skewed blades mean the vortices shoot off into the water rather than hitting the hub (the issue can also be remedied by introducing a chamfer to the trailing edge of blades).
Shafts, bearings, seals, brackets and rudders also affect the noise signature of vessels. Teignbridge designs and produces all these components and was an early manufacturer of velocity aligned rudders and brackets. The first such rudder was patented three decades ago by the U.S. Navy to delay cavitation erosion damage on its vessels. A revolving propeller causes the angle of water flow to vary along the span and chord of a straight rudder, which can result in cavitation that reduces performance, increases erosion and produces undesirable noise. A velocity aligned rudder is ‘twisted’ in the direction of the attacking propeller stream that follows the rudder surface, reducing pressure peaks and cavitation, while deflecting the water flow to increase efficiency (in sea trials of its velocity aligned rudder, Teignbridge recorded an average increase in speed of one knot at maximum engine speed).
Propeller geometry is based on parametric definitions of pitch, skew, rake, blade section, and much more. Driving performance in a particular direction whilst operating in the complex wake of a ship or boat is a complex process. Teignbridge utilises powerful simulation tools, including state-of-theart Star CCM+ CFD and Siemens HEEDS software, to understand the interaction between propellers and other appendages and the fluid flowing around their surfaces. This suite of advanced design tools allows for automated, AI-driven optimisation by coupling performance feedback to changes in the geometry parameters. The cycles are then repeated to hunt for improvements and up to 500 designs for a particular application
can be produced over a 48-hour period. These numerical simulations are proving particularly useful with the arrival of hybrid and electric propulsion systems, which deliver power to the propeller in a different way than conventional diesel drive.
“Electric motors and shaft generators have a big influence on the way the propeller is designed to avoid overloading and how the blades are optimised to absorb the higher torque and efficiently convert it into directional thrust across the complete motor speed range,” says Dr Javdani.
“These developments in power supply and their control systems affect every component in the drive train from the gearbox to the propeller.”
“We’ve probably reached the top of the efficiency curve in propeller design as we know it.”
The industrial process of manufacturing marine propellers, from the making of the moulds to the casting and final finishing, has remained virtually unchanged over the decades. As with their design, however, digital technology is increasingly prevalent.
Teignbridge has over a dozen CNC machines, including 5-axis mills for machining blades, CNC lathes for turning shafts, rudders and brackets, and 3D printers for making smaller propellers out of plastic filament. These machines can work to tolerances within the thickness of a hair, but much of the process is still carried out by hand.
The most common technique is sand casting using aluminium bronze for its high fatigue and corrosion resistance. The mould cavities are formed by individual spindle patterns, basically wooden replicas of the final propeller blades, which are made by hand in various shapes and sizes. Teignbridge has a storeroom containing hundreds of these patterns that can provide over 16,000 different design combinations by varying the number of blades and their pitch.
The patterns are a bit larger than the final article to allow for contraction as the metal solidifies inside the mould. The mould itself is built up into a propeller shape one blade at a time for reasons of flexibility, time and cost. Shaping the pattern is time consuming and costly, so full patterns – usually made of aluminium – are more expensive than individual ones, but the moulding time is shorter and they are very durable.
Teignbridge also makes patterns quickly and cheaply from machined polystyrene, but these are less sturdy and more suitable for urgent one-offs. A few years ago, for example, the company was asked to replace a damaged propeller on Va Bene, Eric Clapton’s yacht. The boat was chartering in the Balearics and needed a quick turnaround, so the prop was unshipped in Barcelona and transported by road to the factory, where it was scanned and reversed engineered to make the polystyrene pattern. The new propeller was delivered within five days.
“When we get a project, we have to decide what kind of pattern to use based on final usage and the projected production run,” says Phare. “For up to three or four propellers we use a spindle pattern; over that we would probably use a full pattern; and if it’s a one-off a polystyrene pattern is ideal.”
Below: Teignbridge also designs and produces shafts, seals, bearings and brackets. Bottom: Wooden patterns for making the moulds.
The industrial production work in the foundry has changed little over the decades and still relies almost entirely on human hands. The sand used to make the moulds is sourced from a single quarry in Cheshire because it has just the right pH and varied grain size (if the grains are too uniform and tightly packed the gases cannot escape from the mould). In order to shape the sand, it is mixed with a binder resin which is activated by catalyst just before use. The mould maker then has to work quickly to ensure the binder doesn’t set too early. However, Teignbridge recently invested in a new robot – nicknamed ‘Dudley’ after the foundry’s longest serving employee – that will be able to take over some moulding tasks.
“The ingots of AB2 aluminium bronze begin to melt at around 1100°C, but we heat them to a higher temperature to ensure the metal remains molten throughout the casting process,” explains metallurgist Ryan Leese, Foundry Manager at Teignbridge.
“The metal has a long way to travel through the runner and filter system before entering the bottom of the mould – that
takes time and all the while it’s losing heat. The worst that can happen is that it starts to solidify and stops moving, so we heat it up a bit more to give it the ‘legs’ to make sure it reaches the tips of the blades. How much we heat it depends on the size of the propeller and is based on experience.”
As the metal turns from liquid to solid it shrinks by 4 per cent in volume, so a reservoir on top of the mould is capped with a ‘feeder head’ containing exothermic powder that generates its own heat. This cap is changed up to a dozen times to keep feeding the casting with liquid metal and avoid deformation through shrinkage.
After the casting has been removed from the mould, the finishing process starts with ‘fettling’ with a grinder to remove any unwanted metal and rough patches. The final polishing is done by hand to create the trademark patterns that every propeller manufacturer adds to its products. However, Teignbridge recently invested in a new robot – nicknamed ‘Dudley’ after the foundry’s longestserving employee – which will be able to take over some moulding tasks.
Ongoing investment in technologies and processes has resulted in Teignbridge Propellers launching a number of innovations onto the marine market. In response to pitting in propeller shafts due to corrosion, for instance, in the late ‘80s it developed Temet 25, a high strength duplex stainless steel alloy with outstanding corrosion resistance in seawater. Temet 25 is now the yachting industry standard material instead of Monel K500 and Aquamet 22 or 17.
Another innovation is the 5-blade C-Foil propeller, which has a special wedgesection near the blade root that helps reduce cavitation and improve efficiency. Independent computer modelling and comparative sea trials have shown it generates approximately 5 per cent more thrust than standard propeller designs. In 2019, the company received a special mention at the DAME Awards for its Clamp on Blade (CoB) propeller, the result of a research project into high-efficiency propulsion systems in partnership with the Energy Technologies Institute in the UK. Thanks to a unique blade attachment method and propeller to hub diameter ratio, the detachable blade system is the most efficient of its kind. It also means yachts can more easily carry spare blades to replace damaged ones without having to use a slip or dry dock.
“The industrial production work in the foundry has changed little over the decades and still relies almost entirely on human hands.”
Previous spread: Pouring molten aluminium bronze into a large propeller mould.
Left: The trademark markings on the blades are added during final polishing by hand. Every propeller manufacturer has its own pattern.
This year Teignbridge celebrates its 50th anniversary and will build 5,500 square metres of new production space next door to the current facility. Over the decades it has produced propellers for almost every kind of craft imaginable from tankers, bulk carriers and warships to leisure boats, foiling tenders and superyachts, but more recently it has responded to a gradual change in mentality whereby shipyards and naval architects are involving its engineers earlier in the design process than was the case as little as five ago.
“People are more aware of the interaction between propeller, rudder, hull shape, brackets, wake field, and so on,” says Dr Javdani. “We’re getting more requests to look into what’s going on at the back end of the vessel, which is why we now prefer to focus on design for stern gear rather than just propellers. We’re an engineering and manufacturing company, but we don’t just supply products anymore – we supply solutions.”
James Hutchinson spent 15 years as a senior project manager with Sunseeker International and Princess Yachts before setting up Hutchinson Yacht Consulting (HYC) in 2013. That experience gave him a unique perspective as an owner’s representative in the superyacht world. In 2016 he was joined by Guy Roberts, who had also worked for Princess Yachts in a senior project management role. Over the past decade HYC has been involved in over a dozen new-builds at Feadship, Lurssen, Amels, Heesen and Benetti, some of which are ongoing. Our discussion started with how James began his first custom superyacht project.
“The more I’m involved in this business the more I realise we need to step back and think, because everything that we do has to be done for good reason.”
James: That was 44-metre Moon Sand with Feadship that launched in 2015 and was the reason I decided to leave Princess and set up on my own. I already knew the client because he had owned several Sunseekers and I had provided technical support from the shipyard side. One day he called me out of the blue and said he was considering building a custom yacht with Feadship and would appreciate my advice. And it all evolved from there, starting with a meeting at De Vries in Aalsmeer where for the first time in my career I was sat on the other side of the table representing the owner. It was during the build of Moon Sand that Feadship started talking with the same client about building a limited series, which became the 34-metre Lagoon Cruiser. I thoroughly enjoyed the whole process and began to realise that my former experience with Sunseeker and Princess was actually standing me in good stead.
In what way was it useful?
James: I worked closely with Feadship and the owners to facilitate making the Lagoon Cruiser more of a custom superyacht, even though it was a productionbased, semi-custom series. We needed to put together a common technical specification and it raised questions about what a 34-metre yacht needs in order to still be a Feadship. The shipyard realised that the smaller the boat, the more valuable volume becomes and you have to make good use of every square centimetre. There was also a client requirement for them to be very quiet at a time when Feadship were also building Como and Kiss and investing a lot in noise and vibration. And, incredibly, the Lagoon Cruisers are among the quietest yachts we’ve ever been involved with to this day.
How do you share the workload as a two-man team?
Guy: Early on I had a supporting role because I too had made the move from the production boat world and it was my first time on the other side of the table. Now both try and stay appraised of all our projects, although one of us needs to have that deep knowledge of the details. We work with other technical advisors and our approach is very much that of knowing our limitations. We bring expertise as and when needed, but you can’t be an expert in every domain, especially when technology is moving forward so quickly, so we call upon other expert opinion and the two of us appraise that opinion and determine what the best solution is for the client.
James: You need wise counsel within your own organisation, so we will spend most days pinging ideas and thoughts off each other. The more I’m involved in this business the more I realise we need to step back and think, because everything that we do has to be done for good reason. That’s really important. And I think it’s good that we share those decisions, because you’re stronger doing in that way – two heads are definitely better than one.
The other thing is that we don’t take on more than two or three projects at a time, and they are typically at different stages of development. Usually one of us will take the lead on a particular project, but that doesn’t mean the other one isn’t involved. As Guy said, it’s all about the minutiae and those need to be handled by a single person, but the other is not too far behind. We often ask ourselves whether we should grow or not – it’s a difficult question because we love what we do and if we grow the team we can take on more projects, but end up doing less of the work.
Guy: We’ve actually declined a few projects over the past 18 months, which is hard to do when you’re selfemployed, but we don’t want to stretch ourselves too thinly. We’re only as good as our last project and all our work comes through recommendations. We’ve been fortunate in that we’ve had a lot of client referrals and we want to keep it that way.
You’re both relatively young – is that an advantage at a time when yacht owners are getting younger?
Guy: I think it plays into our hand to some extent, yes. You know, we can relate to younger clients, but we’ve had our fair share of boats for older owners as well. Certainly we’re working on a few pre-contract projects at the moment with much younger owners looking to build the sort of family yacht that both James and I can relate to very well.
James: And I think younger owners are setting the direction of the industry. The ones we’re dealing with are far more conscious and aware of what they want to build, so I think they will help provide a positive direction for the industry moving forward.
You mentioned future direction – does that mean younger owners are also more eco-minded?
Guy: I can’t comment on everyone, but the ones we’re dealing with are realistic and realise there’s a journey to get to a more sustainable future in yachting. There are paths you can take to make it better and there is an appetite for intelligent energy architecture among some of the owners we’re talking to.
James: I think we all know it’s going to be a stepby-step process and that the boats that are being designed now for delivery in the latter part of this decade need to have that approach. At the moment it’s about navigating a course between combustion engines, fuel cells and batteries and if you don’t get the pioneers making those first steps, you’re not going to get to the end game. So I think we have to be open-minded, realistic and understand that these are incremental steps in the right direction.
HYC PROJECTS DELIVERED TO DATE
Moon Sand – 44m Feadship (2015)
Avatar – 34m Feadship (2016)
Kamino – 34m Feadship (2016)
Moon Sand Too – 34m Feadship (2016)
Letani – 34m Feaedship (2017)
Promise – 51m Feadship (2018)
Galvas – 56m Heesen (2019)
Stella M – 60m Amels (2021)
Moon Sand – 55m Lurssen (2021)
Maverick – 40m Benetti (2023)
HYC PROJECTS IN BUILD
65m Feadship (2024)
37m Benetti (2025)
50m Benetti (2026)
awlgrip.com
Having come and gone more than once over the past 150 years, hydrofoils are all the rage again and here to stay this time. The latest technology has overcome many of the shortfalls of older systems, but are foiling superyachts feasible?
BY CHARLOTTE THOMAS
Over the past two decades foiling has taken off, literally and figuratively. It started with the innovative boards designed by surfers, followed by the specialist one-man classes like the foiling International Moths. Then came the highperformance sailing projects such as the 60-foot foiling trimaran l’Hydroptère, which broke the 50-knot barrier in 2008 and hinted at an exciting if highly specialised future for foils. But the idea of foils on mainstream leisure boats and superyachts has always seemed somewhat remote.
More recently, the advent of electric propulsion in tandem with the rising interest in foils, thanks largely to their adoption by the SailGP and America’s Cup sail racing programmes, has again brought foiling to the fore because they resolve a very basic problem. For boats with electric propulsion, or experimental hydrogen fuel cells in the case of the new America’s Cup chase boats,
hydrodynamic drag means that displacement hulls and (to a lesser extent) planing boats struggle to attain a practical range for the given powercarrying capacity between charging. It is here that foils offer a clear advantage: if you can get your boat to emerge from the water and ‘fly’, you don’t need to worry so much about drag and the given power you are carrying in your battery banks can take you that much further.
“Our strategy is go faster to go further,” says Michael Jost, former Chief Strategy Officer at the VW Group who oversaw the start of the Group’s long-term transition away from fossil fuels. It’s a game plan Jost is employing with his new venture, eD-TEC, which has developed the all-electric eD-QDrive system. SilentYachts is coupling the system with a foiling 28-foot HYSUCAT multihull design to create a 40-knot electric boat that the catamaran builder claims still offers a range of 70 nautical miles.
Opening spread: The 40-knot Enata Foiler.
Facing page: The protoype Valo Alpha Hyperfoil has an active stability system and flight control software.
Below: Attaching the immense foils on Baltic’s radical Raven
Next spread: Raven powered up.
When the Baltic Yachts 111 Raven hit the water for sail trials in the summer of 2023, all eyes turned to this sleek, foil-assisted superyacht. As the team gradually edged the yacht towards its performance limits, the yacht started hitting consistent speeds in the high 20-knots range, and the sailing world was abuzz. However, this style of yacht will probably remain an outlier and while great for exhilarating performance on the water, it is not ideal for coastal cruising with the family. The leeward foil is designed to carry up to 60 percent of the yacht’s displacement at speed, but the engineering that has gone into creating a structure capable of handling the extreme loads has been immense.
“The fitting which is bolted to the hull-deck joint of the foil arm is one metre long and
made of machined titanium, for example,” says Kenneth Nyfelt, Sales Director at Baltic Yachts. “The tolerances on all those fittings are incredible fine; you cannot allow any rattling or any vibration from it because then you are dead.”
Henry Hawkins believes it will take time for most owners to gain confidence in the technology: “Look at how long it took us to get carbon rigging and canting keels onto boats; they’re still the unknown, and what people have taken from the racing scene is that the foils are always breaking,” he says. “So there’s a hump to get over, but I think there is a realisation that there is something to be offered by foiling technology, and it’s a question of how long it will take to find its way into the mainstream.”
“There’s a hump to get over, but I think there is a realisation that there is something to be offered by foiling technology.”
Across the spectrum, the combination of foils and electric drive systems is taking hold. Small boat builders such as Swedish brand Candela, Enata in the Middle East, Navier in the US and Edorado in the Netherlands, among others, are already building foiling leisure, passenger, water taxi and workboat vessels. The water toy world is alive with eFoil boards and the personal watercraft segment is also getting wise with projects such as the Valo Hyperfoil that adds retractable active foils to electric-drive jet skis. However, things get a little more complicated when it comes to larger craft. The advent of high-speed hydrofoil passenger vessels in the latter part of the 20th century was followed by a marked decline as the limitations of larger foilers became apparent – notably, the need for flat hulls with limited viability in bigger seas, and the potential for striking waterborne objects that could damage or destroy foils made from materials that were not as advanced as they are now.
Considerable progress has been made in sailing with vessels such as the F50 used on the SailGP circuit, the new AC40 and AC75 yachts for the America’s Cup, along with the Ultime trimarans and IMOCA 60s. All these boats show how consistent 40- to 50-knotplus performance is possible through the extreme application of surface-piercing foil technologies. Indeed, there has even been a crossover with sailing yacht projects like King Marine’s FlyingNikka mini maxi and sailing superyacht Raven 111 from Baltic Yachts that use foils to mitigate some of the displacement rather than making the hull fully fly. At the same time, however, they have also highlighted some of the limits to mainstream adoption. The foil wing tips are one. Even when the arms are folded under the hull for docking, they project more than two metres either side the yacht. Then there is the complex (and expensive) structural engineering needed to build and mount the arms into the topsides. Finally, there’s the sailing aspect, which requires precision and experience when powered up in foil-assisted flight.
For Seattle-based naval architect Paul Bieker, one of the world’s foremost experts on hydrofoiling, sailing foilers will always be limited by these constraints: “I would be surprised if fully foiling configurations find a significant place in mainstream, non-professional sailing yachts,” he says. “They require a lot of sailing skill and focus, high maintenance, expensive equipment, and they have a significant potential for personal injury.”
Retractable foiling systems like the Dynamic Stability System (DSS) developed by Hugh Welbourn, Gordon Kay and Will Brooks, offer advantages such as improved righting moment, reduced heel and better motion in a seaway, plus more stability for big-boat, big-sea sailing.
“Raven is not a yacht you could imagine relaxing in – it’s a balls-to-the-wall affair,” says Henry Hawkins, Executive Vice-President at Baltic Yachts. “But we used the DSS on the Baltic 142 Canova and it’s a completely different kettle of fish. There was a wish for a performance increase, but it wasn’t the driving factor behind the owner’s decision to install it.”
The design demands of creating a full-flight vessel are, for the most part, incompatible with larger luxury yachts.
Weight is a critical issue, for one, and while that can be overcome by adding larger foils, which in turn offer a greater aspect ratio and therefore greater lift, but there is an upper limit to the practical design of hydrofoils.
“In general, the weight of a vessel scales with the length squared and the amount of lift that you can get off a foil scales with length squared – this reality means that there is a point where hydrofoiling gets more difficult
with increased size,” says Bieker. “That said, the control of active hydrofoils tends to get easier with size because the actuators do not have to move as fast as they do in a smaller boats with smaller foils.”
Bieker thinks there is more potential for moderatesized foiling motoryachts: “The operating parameters for motoryachts are better defined and there is great potential for improving fuel consumption and comfort,” he says. “That said, they will still be significantly more expensive than non-foiling vessels.”
Romain Ingouf is Technical Director at Artemis Technologies, a maritime engineering firm that emerged out of the Artemis Racing team that competed in the America’s Cup. The Belfast-based company has partnered with Condor Ferries to develop the 24-metre Artemis EF-24, a commuter ferry equipped with electric eFoiler propulsion able to carry 150 passengers at a top speed of 36 knots with a range of 95 nautical miles. Ingouf suggests that 24 metres in length overall with a displacement of around 75 tons is the sweet spot for a foiling monohull powerboat design.
“You don’t want to have a boat that has foils sticking out at the sides because you need to get alongside docks and manoeuvre around marinas, and so forth,” he says.
“You can certainly go bigger, to as much as 36 metres most likely, but then very rapidly you need a very beamy boat to have the aspect ratio on your foil so you are more efficient at creating lift without adding too much drag. Is foiling the solution to everything? Very likely not, although it’s fantastic in some applications.”
“Foiling technology is set to grow, particularly as the superyacht industry enters its own energy transition.”
Smaller foiling boats and RIBs, whether using full-flight foils or foil-assist solutions, offer plenty of potential as standalone leisure boats, chase boats or tenders, particularly as alternative drive systems come on stream. Among many pioneers in this field is Gordon van Hardenbroek, an industrial designer and co-founder in 2015 of foiling boat company Edorado.
“We started with a basic design premise of taking a planing hull, taking out the combustion engine and putting batteries in,” he says. “There weren’t many people doing it at the time, but we found as soon as you start going fast the range plummets. And I don’t believe that battery tech will improve enough to solve that problem. We realised that adding foils – in our case an active system made possible thanks to advances in sensors and computation – could double our range. Finally we realised that market demand was for retractable foils.”
In addition to creating their own 8.35-metre 8S model, Edorado is also planning to release a preengineering platform that targets the superyacht sector. “The 8S is very much about flying,” he says. “It’s not about getting you from A to B, but rather the goal is the flying itself.”
The future for foils beyond smaller vessels may be limited when it comes to full-flight solutions, but that doesn’t exclude potential for foils in large yacht design. Indeed, appendages that can improve efficiency and comfort – particularly when combined with stabilisation systems to offer multi-axis motion control – have been available for more than a decade. The Hull Vane, a fixed foil or wing designed and patented by Van Oossanen Naval Architects that was first fitted on the 42.4-metre Heesen yacht Alive in 2012, has proven itself on more than 65 yachts as well as commercial and military vessels.
“The Hull Vane is derived from a device we developed for the French America’s Cup campaign in 2002,” says Perry van Oossanen, the studio’s
Managing Director. “It’s not really intended to make a boat a foiling vessel as it’s designed for displacement hulls; we’ve taken a different approach by taking the vessel as it is and trying to enhance performance where we can.”
The effect is less radical, but so is the technology involved. The location of the Hull Vane under the transom is important relative to the centre of gravity and works best if there’s a steep upcoming flow, which means quite steeply angled buttocks to the transom, but it can be retrofitted on any type of displacement hull.
“It works well for a Froude number [the resistance of a partially submerged object moving through water] of 0.2 and upwards,” says van Oossanen.
“For a 50-metre boat you’re there at five or six knots, and for an 80-metre boat you’re there at around 13 to 14 knots. We’ve installed it on a 100-metre patrol boat, but essentially the bigger the yacht the faster it needs to go to gain maximum benefit of the Hull Vane.”
Hull Vane BV has also developed Foil-Assist, a partial foiling solution mounted amidships on fast planing vessels that applies the same concept to fast hulls and was first used two years ago on a Wajer runabout. It should be noted that both the Foil-Assist and Hull Vane increase not only efficiency but also onboard comfort – an important consideration for any yacht owner.
“However, although applications for foils are definitely increasing, there are a lot of owners out there who are not really interested in the foiling stuff,” warns van Oossanen. “They want to have volume, space and luxury and they don’t necessarily want to cruise at 30 knots.”
While that may be true, foiling technology is set to grow, particularly as the superyacht industry enters its own energy transition. Even if methanol in reformers for fuel cells or multifuel engines becomes the energy carrier of choice, its energy density is considerably lower for a given volume compared to conventional diesel. So while the fuel may be cleaner, yachts will need to burn less of it for a given volume of tankage to avoid losing too much practical range, while adding more tanks means taking volume away from guest areas. In this scenario, non-flight hybrid foiling solutions could find their niche in mainstream yacht production and there may be a place for more extreme solutions for owners who want a more engaged boating experience.
“There is potential for hydrofoil-assisted, nonflying boats, but there is no substitute for flying,” says Bieker. “Once you feel the acceleration that occurs when that last bit of hull leaves the water it is hard to stomach partial foiling solutions.”
When it comes to technology, rely on us
All ferrous metals are prone to rust, even stainless steel, especially in a marine environment. It can be delayed but not denied completely. If identified promptly and precisely, however, the cost of repairing the damage caused by corrosion can be mitigated.
BY JUSTIN RATCLIFFE
Galvanic, stray current, oxidation, windborne rust – there are various types of corrosion that afflict metal yachts. Some are easy to spot; others can remain hidden until the vessel undergoes a major refit or special survey. They all cost time and money to remedy. And it’s not just a question of getting rid of unsightly but superficial iron oxide: extensive corrosion, pitting or grooving of load-bearing components can lead to buckling, cracking and other structural defects.
The traditional method for identifying corrosion is with the naked eye, which usually involves dismantling equipment and stripping off surface treatments to reveal the bare metal underneath. Finding out how deep the corrosion has penetrated then involves bashing away at the steel with a hammer. Ultrasonic corrosion monitoring with high-frequency sound waves is a nondestructive screening method, but metal thickness is measured only at the point where the sensor is placed and surface treatments still have to be removed.
Pulsed Eddy Current Array is a nondestructive electromagnetic inspection technology used for measuring metal thickness and detecting corrosion in ferrous materials typically hidden under coatings like teak, fairing compound and fire insulation. The technology allows large areas of metal substrates to be rapidly scanned with multiple probes that can penetrate up to 300mm to provide high-resolution imaging. Using dedicated software, the results are compiled as a plotted corrosion map onto a plan-view of the vessel.
“PECA allows large areas of metal substrates to be rapidly scanned for corrosion through coatings like teak, fairing compound and fire insulation. The results are plotted on a corrosion map.”
With a history stretching back over a century, Brookes Bell is a go-to firm for incident investigation, forensic analysis, technical dispute resolution and expert witness work in the maritime and energy industries. Working closely with the naval and commercial shipping sectors, its PECA analysis process is the only one of its kind formally approved by Lloyd’s Register. Assisting the company in bringing the same service to the superyacht world is consultant Patrick Yeoward, an MCA 3000t master mariner with over 20 years’ experience of building, refitting and operating large yachts.
“A lot of our focus is on the dispute resolution and forensics side and probably 80 percent of the business is commercial shipping,” he says. “But there’s a big tie-in with services for superyachts and something we’ve been looking at over the last few years is how to become more proactive and less reactive by helping to stop things happening, rather than putting a hand up after it happens and say ‘Oh, you shouldn’t have done it like that’.”
Asset integrity inspection is a time-sensitive activity: owners and their captains need to balance private or commercial use of the yacht with downtime for appropriate repair and maintenance. Because PECA works through insulation and cladding, the scope and frequency of inspections can be ramped up without increasing downtime. Corroded areas can also be identified before a yard period, which allows shipyards to prepare work schedules and order materials in advance. Moreover, knowing the location of generalised corrosion beforehand improves the efficiency of complimentary methods such as radiography and ultrasonic testing that can specifically target these areas. It offers a further advantage when surveying yachts for sale:
“Two of my colleagues were just in the south of France to scan a yacht that was being sold,” says Arron Jackaman, principal inspection engineer at Brookes Bell. “Potential buyers want to understand the state of materials and so we performed an inspection and found minor patches of corrosion. We’ve done other inspections where corrosion was suspected, but it transpired the steelwork was in good condition. Either way, it means buyers have a better understanding of the condition of the asset.”
Pulsed eddy current equipment has been successfully applied for the detection and sizing of corrosion under insulation (CUI) for several years. A pulsed eddy current technique uses a stepped or pulsed input signal for greater penetration depth and relative insensibility to variations in coating thickness, or what is termed ‘lift-off’. Unlike ultrasonic thickness testing, no direct surface contact between the probe and the object is necessary.
PECA employs multiple elements in a sensory array for much faster scanning times. Intended for the rapid inspection of simple geometries in horizontal and vertical planes such as steel hull, deck and bulkhead plating, it is also suitable for steel pipework that may be encapsulated in fireproofing. Even complex shapes like bends in pipes can be inspected and it can be used in conjunction with other screening techniques if required.
The rules prescribing corrosion margins and deviations from the design values vary depending on the type of vessel and the Class Society, but the degree of “allowable material diminution” due to corrosion is generally between 10-30 percent (corrosion rates are expressed in terms of mm per year of surface wastage and are used to provide a corrosion allowance in the original thickness of the material).
• The areas to be analysed are mapped out into scan zones, either by individual plate sections or broken down into specific zones to tackle the various geometries aboard a vessel.
• PECA probes scan the assigned sections or zone. The resulting data is integrated into a 3D file as a mesh layer to produce a model or digital twin called a CMAP and create a visual representation of the scan, highlighting areas of concern.
• Each plate or zone is also given its own report sheet for further analysis. This provides a clear overview of the condition of each plate or zone, identifying areas that need to be repaired, replaced or carefully monitored.
• The final stage of the CMAP service involves the creation of a tabular report of each plate or zone. This sets out the physical characteristics of each location, illustrating the average remaining wall thickness, material loss and maximum wall loss values.
“Lloyds were very clear that our accreditation is not solely based on the PECA technology, but also on how our CMAP software makes the data easily legible for clients.”
In the recent case of a 50-metre motoryacht scanned during a pre-sale inspection, Brookes Bell analysed the side decks and main deck fore and aft, equating to some 110 square metres, at a cost of around €15,000. Some patches of corrosion were found and 0.6 square metres of steel structure were earmarked for replacement.
“When I first spoke with the captain he was very worried because they’d already had to replace steel about a year-and-a-half ago and were starting to see signs of water ingress,” says Patrick Yeoward. “They were talking about ripping all the teak decking up and starting over again, which would have been massively more expensive in comparison.”
The small area of steel and corresponding teak were eventually replaced by Cantiere Rossini in Pesaro, Italy, at a cost of less than €10,000 – a figure that doesn’t compare with the cost of replacing all 110 square metres of teak decking estimated at upwards of €220,000.
“Critically, PECA allowed us to limit the scope of work to the deck areas that really needed attention without having to first remove the teak to assess the condition of the steel,” says Alfonso Postorino, shipyard director at Cantiere Rossini. “In these cases the precision of the measurement is of the utmost importance - just a few millimetres can make all the difference.”
Brookes Bell has a contract with the Royal Navy to inspect its Type 23 Frigates to create a baseline or snapshot of material state year on year in areas known to be prone to corrosion. Using its own powerful analytical reporting and modelling software tool called CMAP Marine, the resulting data can be overlaid one on top of the other to create models of how the corrosion progresses over time.
“Predictive rather than reactive maintenance is key,” continues Jackaman. “But the complex electromagnetic data gathered from a PECA analysis is only useful or valuable if it can be correctly interpreted. It would certainly be difficult to relate the raw data to the actual vessel without the right visualisation tools. In fact, Lloyds were very clear that our accreditation is not solely based on the PECA technology, but also on how our CMAP software makes the data easily legible for clients.”
Modelled on Brookes Bell’s 3D data visualisation software, CMAP basically
highlights the condition of the remaining steel thickness and material loss in percentage terms. For ease of reference, a colour bar displays sound metal as dark blue and increasing material wastage is indicated as the colours progress through the spectrum to bright red. This provides an intuitive overview of the areas that may require renewal or ongoing monitoring. It doesn’t take any special training to understand that red is an issue, but by providing understandable data in a legible format, CMAP allows yacht owners and operators to make better, quicker and more informed decisions.
“We’ve spent a number of years honing our own analysis,” adds Jackaman, “because there are several things that can cause signals that look like corrosion but aren’t necessarily. Seam welds, internal structures, cable trunking, aluminium scuppers, and many other features, can appear as corrosion. We routinely recognise false positives, which is just as important as identifying corrosion.”
Investment by shipyards in sustainable solutions and best practice not only helps protect the environment, it can also bring significant operational and financial benefits.
BY CHARLOTTE THOMAS
While it may be true that the shipyard phase currently accounts for just one to three percent of a vessel’s carbon footprint, that will change with the advent of fossil-free fuels. Amidst the energy transition, shipyards are gradually switching on to the need to implement more comprehensive sustainability solutions in their operations, business practices and yard infrastructures.
There have been some high-profile developments in recent months. Fincantieri has announced a plan to install solar panels across five of its sites in Italy, generating a total of 10 megawatts to reduce energy draw on the national grid by 11GWh annually. Palumbo has installed solar panels at its Malta yard, a wind turbine at its Naples facility and aims to achieve full sustainability across its seven shipyards by 2030. Feadship in the Netherlands, Monaco Marine in France, and Gold Coast City Marina & Shipyard in Australia are all assessing eco solutions from rainwater collection to wastewater treatment. However, harvesting renewable energy or paying more attention to recycling is only a fraction of what’s involved in greening a shipyard.
With a workforce of over 3,000 employees across five sites, Princess Yachts has a significant economic and industrial impact on the city of Plymouth in the UK. The company is taking its commitment to sustainability very seriously by re-assessing every facet of its operations with the aim of increasing efficiency and reducing costs, which makes for a compelling business case. Overseeing this sustainability drive is Laura Parry, who joined Princess Yachts in 2020 as Environmental & Compliance Manager. Since then she has seen her role grow exponentially.
“I started off as the sole person within the company with this focus, assisting the health & safety department,” she says. “I now have an intern from the city’s university and two environmental sustainability business partners who work across all five sites.”
That extra help is needed: the policies that Princess is investing in and that Parry is overseeing are extensive, and potentially transformative for the business. It starts with ISO compliance, in particular standards 9001 (quality), 14001 (environmental management system) and 45001 (health & safety). Standard 14001, especially, is about continual improvement, which is monitored internally but also audited annually by Lloyd’s Register. Coupled to this has been an investment by KPS Capital Partners, the American private equity company that became the new owners of Princess Yachts in February 2023.
“The new shareholders are very keen on environmental sustainability and we have a good plan of action for 2024,” says Parry. “There is a clear focus on sustainability from the top, which really helps our cause.”
In addition, a university PhD student is making a complete lifecycle assessment of one model line, literally deconstructing it to analyse every aspect of the construction from the nuts and bolts to energy waste.
“Without that we could put our finger in the air and say we think our biggest impact is waste management, but the truth is we don’t know,” admits Parry. “What this LCA will do is point us in the right direction with qualitative and quantitative data. It’s already led us to tweak and change our operations.”
The end goal is to move the shipyard from a linear to a circular economy and address end-of-life issues, particularly as the yard builds in GRP, by working with its
procurement team to go back to the roots of the supply chain.
“That’s not only for our own good; it’s also supporting other people to be on that journey, because that’s how you inspire people, by taking them on the journey with you,” says Parry. “Working with your suppliers is really where it all starts.”
There is another element of policy at Princess Yachts that delivers financial benefits and links to energy efficiency. The voluntary Climate Change Agreement (CCA) scheme, established in 2001 as part of the UK’s overall commitment to reducing CO2, aims to make energy and carbon savings through energy efficiency targets whilst also helping maintain competitiveness by reducing energy costs in eligible industrial sectors. “Businesses pay a climate change levy, but there are potentially huge financial savings to be had by applying and committing to those agreements,” Parry explains.
There is a list of eligible activities that a company can review, and if a site represents 70 percent of that activity it can apply to for an agreement. In Princess Yachts’ case, it was surface engineering due to the laying up of the hulls and decks. They surveyed the sites and determined the relevant facts and figures, which were signed off by the Surface Engineering Association and then the Environment Agency, and the result is a reduction in tax. The financial impact can be considerable – well into six figures for businesses the size of Princess Yachts.
Tangibles that can be quickly addressed include reducing waste-to-landfill, shifting waste-to-energy partners from 50 kilometres away to a local plant, increasing recycling, sourcing eco-material alternatives and looking at how to reduce waste by using material off-cuts for other purposes. Princess Yachts runs a digital waste dashboard that allows Parry to monitor positive or negative change in waste management and reduction.
“For any company, it’s about working in collaboration with different departments,” she advises. “I might have the technical expertise, but without the support from the rest of the business we would not have seen the progress made so far.”
These studies have led to some unexpected changes in best practice. The yard uses Crestomer structural adhesive extensively, for example, but then has to handle the responsible disposal of the packaging.
“When we looked into the disposal compliance, because it’s hazardous waste, we discovered that the liners weren’t being properly squeezed out, which meant a considerable amount of wasted product,” Parry points out. “So by improving compliance we actually made financial savings. Those savings for a large boatbuilder can easily equal tens of thousands of euros just through recovered product.”
Similar gains can be made in other areas. The company has undertaken remedial works to remove air leaks, which will deliver significant annual cost savings, and completion of the transition to LED lighting in all the production areas is expected to deliver a six-figure saving. “We’re also looking at a centralised compressor plant at one of our biggest sites to improve running and efficiency,” adds Parry. “It’s quite an investment in infrastructure, but it improves efficiency and will mean we become smarter in how we operate. We’re also adding photovoltaics to the sheds, and biomass heating was commissioned in 2022.”
Like at Princess Yachts, Txema Rubio believes it is important to have someone within the company who is focused solely on the sustainability aspect and can support all departments. “That’s a real game-changer,” he says, “because it helps to have small initiatives at every single level of the company.”
It extends beyond the obvious measures like increasing recycling to more advanced strategies for a circular economy. The yard’s procurement department together with a sustainability coordinator is checking what the industry can offer in terms of new interior materials, and it is inviting sub-contractors to find and promote new ideas and facilitate conversations.
It is also manifested in initiatives such as the group’s Refit for the Future service launched in April 2023, which aims to assist owners looking to reduce the environmental impacts of their yachts through the application of the latest tech to drive sustainability.
“We explain to crews and owners more the concept of transition and that the sustainability path is not a one or a zero – there will never be the perfect final solution for an asset built 15 years ago,” Rubio says. “But that doesn’t mean you can’t improve things.”
Operating as a refit shipyard presents its own set of challenges, because you’re not working on vessels from raw material to finished product, or at least not with the same degree of control over the process that a new-build yard has. However, refit offers other opportunities to reshape the sustainability landscape across the industry. “Shipyards can do two things – one is what you are doing as a business, and the other is what you’re implementing on the assets you are working on,” says Txema Rubio, Commercial Director at MB92. “A new-build yard can choose the type of propulsion, the materials, et cetera. In refit it’s a completely different story, but we have an important role to play, because at the end of the day we’re receiving an asset and we’re being asked to improve it.”
MB92 was an early adopter of sustainability and has been proactive in sourcing solutions. For the yard element, installing solar panels on the shed roofs has been one aspect, but equally important is where the rest of their power comes from. Its Barcelona shipyard, for example, has an agreement with the energy provider that all its electricity comes from renewables, which ties in with new yard policies that all yachts in the yard must use shore power – running diesel generators is no longer allowed.
Similarly, yachts can only be painted on hardstanding, not afloat. Hardstanding is a much higher cost per day than berthing and that means telling clients that if they want to have a paint job at MB92 they will have to pay at the hardstand rate, not the berthing rate.
“We lost a lot of clients in the beginning, but now clients understand why we have that policy,” says Rubio. “It means the yard has much more control over
everything, from water treatment to prevention of leaks and spills, and it ties in to other yard infrastructure and machinery investments that contribute to reducing the environmental impact of every aspect of the yard and its operations.”
These measures include water treatment plants that treat everything, even rainwater, before it gets discharged, and Sea Bins that skim plastics and other debris from the harbour water before they can reach the open sea- When the new shiplift was built at MB92 La Ciotat, they received permission to use HVO in all the machinery, which means a 90 percent reduction in carbon emissions. When it comes to the business side, Rubio says there is a more fundamental driver than simply return on investment.
“There’s no choice, we cannot not do it, so doing it quicker gives you an advantage and you are a leader,” he maintains. “Plus if we don’t take care of our playground, the sea, then we have nothing to sell to our clients.
The amount of investment, the percentage of your revenue you apply to that, I think is different in each case. We’re investing a lot and we’re making business decisions because we truly believe it’s the future. And finally, as an industry, we need to get away from greenwashing.”
Moreover, Laura Parry from Princess Yachts believes it is important to look outwards as well as working from within the company.
“I think it’s essential to work with as many groups and organisations as we can, because at the end of the day I want to be transparent – and if I can make savings within our organisation, why wouldn’t I want to share that with other organisations?” she asks. “Environmental sustainability shouldn’t be competitive; it should be about sharing ideas and best practice.”
The Superyacht Technology Steering Council is a forum for industry professionals to discuss new and emerging technologies, as well as how best to develop sustainable legislation and lay the foundations for continued growth. Founder Feargus Bryan explains why the time is ripe for collective action.
BY FEARGUS BRYAN
Ihave been lucky enough to have been involved in the yachting industry for the better part of 40 years, first as a young captain and then as a designer and technical manager overseeing the construction and operation of some of the most iconic vessels in the superyacht fleet. Looking back over the decades, I see an industry that has grown exponentially from the adventurous and laid-back yachting lifestyle of the ‘80s into a truly international industry that has a significant impact – environmentally, socially and economically – on many regions around the globe.
However, the industry’s image is threatened by a sharp increase in public interest in the UHNWIs who build and own superyachts. By association, the industry is coming under increasing scrutiny from a legal, financial and regulatory perspective, as well as from mainstream media. Many see this scrutiny as a negative development; I see it as an opportunity to provide much needed structure and guidance to the industry. I truly believe that the superyacht sector can be a sustainable industry, but it must be underpinned by solid foundations so it can weather aggressive scrutiny and continue to thrive.
The question is, how do we rebuild the foundations of a structure that is already in place? I have spent five years talking to colleagues, both in and outside the industry, and have settled on a collaborative approach to solving some of the challenges we face. The Superyacht Technology Steering Council is a body of like-minded stakeholders in the superyacht community who are using their collective experience to help put those foundations in place. After a period of consultation, we have started working on initial mandates with the goal of providing a network of support and a collective voice for the industry.
One self-criticism is that we tend to innovate and develop in isolation, which is not a sustainable way of doing business. In doing so, we deprive ourselves of the collaborative power that comes from working together with other industry stakeholders. The Council is playing an active role in fostering more dialogue between mainstream tech companies and the superyachting sector, for example, but also between players within the industry.
When I was working as a fleet technical manager I saw yacht crews ‘crowd sourcing’ solutions to technical and operational problems on a daily basis. They frequently called colleagues on other yachts to discuss problems and solutions. This approach is proven to be effective, but most of the solutions found are not being shared with the OEMs and the designers further upstream, stymying the innovation process. Yacht crews
play a vital role in maintaining the value of the yacht and providing that all-important positive experience for owners, so we aim to support them and nurture their problemsolving activities.
One of the biggest industry challenges currently is human resources. Every company I have spoken to has voiced the same concerns over finding qualified personnel and the problem is only going to get worse as the fleet expands. There are training courses for crew, technical colleges for marine engineers, and apprenticeship schemes for yacht builders, but the problem again is that they operate in relative isolation. At the Council we are helping to develop programmes as well as assist graduates with first job placements, but we also have to reach out beyond the industry to better explain the opportunities available for young professionals in yachting.
“One self-criticism is that we tend to innovate and develop in isolation, which is not a sustainable way of doing business.”
When I started in this industry the yachting sector was relatively nascent and there was little or no framework of regulation governing the design, construction and operation of large yachts. Class and Flag authorities were not quite sure how to apply rules created for merchant shipping. Times have changed, but historically the industry has not been proactive in implementing legislation, which is sometimes hastily applied at the last minute. As a result there is still some confusion surrounding IMO and MARPOL regulations and Flag-based directives. We believe this is primarily a communication problem and that we can help by educating the yachting community on the role of the different regulatory bodies and the effect their strategic goals can have on legislation. In this way, owners, captains and shipyards can make more informed decisions and absorb rule changes with minimal impact.
Last but not least is the challenge posed by the increasing pressure to comply with ESG (Environmental, Social, Governance) protocols. In more mainstream sectors, ESG accreditation is a standard part of demonstrating to the public that a company or organisation has completed key sustainability initiatives and has become a sustainable business. The lack of ESG accreditation in the yachting sector is becoming an impediment for outside companies to do business with us and is already impacting its ability to fund and insure projects. We are starting to take concrete measures to reduce our environmental impact, but we also need to react to the social governance aspects. We want to help the industry, both on and off the water, to prepare for ESG accreditation.
These are all significant challenges and none of them are going to be resolved overnight. But the first step in building the foundations for sustainability and prosperity is to harness the smarts of as many stakeholders in the superyacht industry as we can.
You can apply for membership of the Superyacht Technology Steering Council on superyachtcouncil.com
When Rob Doyle Design in Kinsale, Ireland, received a call from the largest sloop in the world saying the yacht had lost the tip of its keel off the coast of Peru, the team had to set in motion a repair job from the other side of the world.
Mark Small, Technical Director at Rob Doyle Design, recounts how it was done.
BY JUSTIN RATCLIFFE
On 12 May 2022, we received a call from the captain of 77.6-metre M5 saying they had collided with a submerged object while sailing off the coast of Peru. The yacht had slowed significantly, but the impact was nothing like hitting a container. The crew concluded it was probably a freak encounter with a whale.
They undertook a full internal inspection around the keel box, hydraulic locking rams and locking shims. There was no apparent damage to any part of the structure or fittings, so M5 continued sailing into Lima and arrived the following day. On arrival the captain decided to inspect the outside of the hull with a diver to make sure they hadn’t lost any anodes in the collision. It was only at this stage that it became apparent that the lower third of the keel was missing. No other
damage was visible.
The keel of M5 was originally designed at 150 tonnes with a vertical lifting fin and large bulb. During a later refit it was decided to install carbon rigging and change the keel configuration from a fin and bulb to a straight fin, removing 50 tonnes of ballast in the process. To comply with grounding loads the sacrificial lower third of the fin, which weighs 33 tonnes, is connected to the main fin with a series of bolts that shear off if the designed grounding load is exceeded. In the collision M5’s keel performed as designed with the sacrificial tip parting from the keel, which is why the yacht had no structural damage. Interestingly, she continued to sail after the accident with no perceptible change in her sailing characteristics. We will return to this later.
When the full extent of the damage became clear the first priority was to move the vessel to a place where the repairs could be carried out. At Rob Doyle Design we undertook an extensive review of the damage and produced a stability assessment with the keel tip missing. The vessel is DNV/Red Ensign classed and following the assessment we found that she still fully complied with the Motor Yacht Stability requirements. Unsurprisingly, however, the yacht failed the Sailing Yacht requirements. Specifically, the Range of Positive Stability was now 73 degrees (90 degrees required) and the Angle of Equilibrium was 8 degrees (15 degrees required). On submission of our stability assessment, it was agreed with Class that the vessel could be moved, but could not set sail. The next items on the list were to find someone to build a replacement 33-tonne keel tip, and a yard where the repair work could be carried out. Initially, we didn’t think this would be too much of an issue as we had the whole west coast of the USA to work with. We were wrong.
We scoured the entire USA and Canada and contacted multiple manufactures but failed to find a single company that could supply a new keel tip to the specifications required. In the end, we had to return to Irons Brothers, the original manufacturers in the UK. Now all we had to do was transport 35 tonnes of keel and cradle across the Atlantic and the USA – in itself not a straightforward task as it was an off-gauge load.
While looking for a keel manufacturer, we were also searching for a shipyard capable of taking in M5 and removing the keel so the new tip could be attached. This process had been done twice before in 2016 and 2018 and we have a precise and approved process to safely undertake the task in a dry dock, on the hard, or in an enclosed basin. To cut a long story short, after months of work we resigned ourselves to the fact that the work to replace the keel couldn’t be done in the USA. Now what?
It quickly transpired that replacing the keel was going to take a long time. The keel tip would not be ready until September or October, we were struggling to find a shipyard, and now the owner’s summer cruising season was in jeopardy. The owner rightly pointed out that when they lost the keel nobody really noticed any difference in the sailing characteristics, so could we not ask Class to allow the yacht to sail for the summer with some restrictions? As Technical Director for Rob Doyle Design and knowing we were dealing with the biggest sloop in the world that had lost a portion of its keel and ballast, I was very sceptical that this would be allowed. However, the owner requested that we explore all options with Class so he could rescue the cruising season.
Following a detailed conversation with Class
and the captain of M5, we agreed that we would undertake a VPP analysis of the yacht both with and without the keel. Comparing this to the known data already on file, we were able to establish the real-world effect of different sailing scenarios and how the missing keel tip affected the stability of the vessel. We decided to limit the assessment to sailing with a maximum sail area of one reef in the mainsail and the J2 set with maximum heel angle of 15 degrees. What really surprised us all was that losing the keel tip really made only about a 1.2-degree difference in sailing heel angle with the reefed main and J2, which correlates with the yacht’s behaviour under sail after the collision. We submitted a 150-page Sailing Stability Report to Class and it was approved very quickly and in time to rescue the sailing season.
“Nothing like that has ever been done on a superyacht of this size, let alone the biggest sloop in the world!”
Fast forward to March 2023. Still unable to find a suitable yard to undertake the repair work in the USA, by now we were looking to return to Europe as the only option. Then we got a call from co-captain Ryan Bergman: “How about putting the keel tip back on using divers?”, he asked.
The idea had come from Roger Woolsley, a good friend of the owner’s who works in the aviation business. They were on M5 together but couldn’t sail without the keel tip, so Roger discussed the problem with his military contacts and other knowledgeable
friends. They suggested using divers to replace the keel tip.
My first reaction was: “Nothing like that has ever been done on a superyacht of this size, let alone the biggest sloop in the world!”
However, we agreed to have a video meeting with the proposed dive team. It is very rare that you meet with a group of people with limited experience of superyachts that immediately inspire trust, but that is was what happened in our first meeting with Subsea Global. We spent a few hours talking through potential snags and solutions
and by the end of the meeting we were all convinced that the operation was feasible, and why hadn’t we thought of it earlier?
The plan of action was as follows. The keel tip and cradle, now fitted with a base plate to stop it sinking into the mud, would be craned onto the sea bed; M5 would be positioned immediately above and the keel and cradle lifted into position using air hoists; the slots and bolt galleries would then be aligned, the plates adjusted where needed, and the bolts fitted at the correct torque; finally, the cradle would be dropped back onto the seabed and M5 could sail away. Every stage of the process would be carried out underwater with a Class surveyor on board the yacht to oversee the operation from start to finish. What could possibly go wrong?
As it turned out and bar the usual hiccups, nothing of any major significance went awry. In close cooperation with Class, the dive team and SD De Kock, the other cocaptain of M5, we developed a procedural document for the works, which were carried out at a commercial dock in San Diego. The keel arrived at the dock early on Tuesday 9 May 2023, almost a year after the initial collision. The divers entered the water the same afternoon, working largely by touch in conditions of very poor visibility. After 48 hours of working continuously with three dive teams in eight-hour shifts, they exited the water in the afternoon on the Thursday with the job completed.
Fitting the bolts to the correct torque had been complicated by the presence of the cradle, but with the agreement of the Class surveyor this was completed a week later in Seattle. The whole project was a master class in what is possible when you have a good team working together for a common cause.
Own
yachteye.com
Composites combine the advantages of different materials, such as high strength, low weight and corrosion resistance. Choosing the right composites for the right application is not always straightforward. There are various factors to consider, including the design criteria, loading conditions and cost-effectiveness. Moreover, advances in materials and processes mean the choice is not getting any easier. Henry Lloyd Williams, head of design at Atlas Carbon Products, Coen Meerbach, business unit manager at Solico and Paul Buyse of Carboncraft share their insights.
Beyond hulls and superstructures, how have the applications/uses of advanced composites in yacht building expanded in recent years?
Henry Lloyd Williams: The yacht building industry has been experiencing the steadily increasing adoption of composite-based manufacturing for many years. No longer just used for hulls and masts, these materials are now being used for all sorts of other components. Almost all parts can be produced from composites and in many applications can offer a lighter or stronger solution. Composites also offer the ability to manufacture more complex shapes that would be much more difficult to machine. The incorporation of composites isn’t just a technical upgrade; it’s a fundamental change in how yacht components are conceived and constructed, reflecting the industry’s adaptability to new materials and methods.
Coen Meerbach: Aside from optically good and efficient surfaces, we see an increase towards more complex structures, where composites are used as a solution for their mechanical performance. For example, we developed carbon fibre superyacht winches together with Rondal, capable of handling loads of up to 24 tonnes. Carbon fibre composites were also used to resolve natural frequency issues in large cantilevering decks of a recently delivered superyacht, where aluminium and steel simply couldn’t deliver the required results.
Paul Buyse: The application of composites in the marine sector has grown in all directions, both in structural and nonstructural parts. This can indeed be seen on the main components of that yacht but also in the accessories. Lightweight solutions can help keep the weight down and contribute to the structural integrity whilst contributing to the stability of the yacht. This applies to structural features such as a mast or superstructure, but also for interior elements. The common factor is enhancing the guest’s experience on-board whilst by combining comfort, safety and ease of operations for the crew. This applies for example to sun-awning systems, swimming pools/Jacuzzis, swim ladders and platforms, but also navigation light masts, flagpoles, tender fenders and booms, gangways, boarding passerelles and deck railings.
The use of prepreg composites combined with vacuum bagging or autoclave moulding generally produce superior results, but are there cases where a wet lay-up by hand is still preferable?
Henry Lloyd Williams: Wet lay-up proves ideal for handling intricate small parts that might pose challenges with prepreg. The material’s user-friendly nature simplifies the lay-up process, making it more accessible for various applications. Additionally, wet lay-up presents a notable advantage for those without access to an autoclave. Autoclaves are complex and expensive pieces of machinery and prove inaccessible for lots of small businesses, the use of wet lay-up and other manufacturing techniques gives those smaller manufacturing firms the opportunity to compete in the marketplace.
Coen Meerbach: The Southern European market often builds large yachts utilising gelcoat and polyester or vinylester resins, and we believe they are very successful. The Northern European market focuses more on steel or aluminium hulls, with composite components. Those components are in turn more often made with prepregs. Though prepreg provides superior results, it is typically also more costly, and often not always necessary. Essentially, every method and materials have advantages and disadvantages and we believe you cannot have one method or material for all purposes.
Paul Buyse: Indeed, more advanced technologies enable better and more reliable results to the lamination process when applied correctly. This includes surface finish and fibre-to-resin ratio, which influence the mechanical properties and weight of the part. The selection for one or the other production method can be based on a series of factors, such as the mechanical properties, target weight, production volume, tooling strategy, available equipment or experience, and ultimately target cost. Wet lay-up could still be a good option in a custom but non-structural part that is not so weight critical. We also see wet lay-up being used for repairs or off-site operations, where resources are limited. In most cases a wet lay-up procedure and bonding of structural parts can be vacuum consolidated to reduce risks and improve results.
When the highest strength and rigidity combined with the lowest weight is required, the obvious answer is carbon fibre composite. But is that always the case?
Henry Lloyd Williams: While carbon fibre boasts exceptional strength, its vulnerability to impacts and scrapes makes it unsuitable for applications that demand toughness. In scenarios where a component must endure knocks or harsh conditions, opting for metal could prove more appropriate. However, carbon fibre offers exceptional strength to weight characteristics that other materials cannot compete with. For example, here at Atlas all our davits (cranes) are produced from 100% carbon fibre. This makes the davits lightweight and therefore easily portable while still being able to lift incredibly high loads of 500kg (up to 1000kg in some designs). This level of performance just would not be possible with any other material choices. A typical steel structure crane of this safe working load would weigh in the region of half a ton, whereas our Atlas Standard Davit weighs about 60kg making it extremely light weight, portable and therefore easy to operate.
Coen Meerbach: Most often, carbon is superior, due to its mechanical properties. However, most structures are designed to meet specific stiffness requirements. On such occasions, traditional metallic structures are very efficient, but carbon has the low-weight advantage, making it an interesting material solution. Note that carbon’s strengths are in its in-fibre directional strength and its density. For (local) stiffness requirements, we will often adopt sandwich structures if possible, making light and stiff structures.
Paul Buyse: We agree that carbon fibre has an exceptional combination of mechanical properties, especially when the part is weight and stiffness critical. But there are other factors such as geometry and structural design that can make a big difference. This makes it possible to consider other materials and still offer a low-weight solution at a lower cost and carbon footprint. A hybrid between glass and carbon fibres can be an interesting choice. Either in the same laminate or in different components. For example, the product shell could be e-glass and only some features of the internal structure are carbon fibre to add the strength and stiffness where most needed. A popular application of this hybrid solution can be seen on structural beams. Where the tapes and capping are carbon while the shear web and main body is e-glass.
With sustainability in mind, how do bio-resins and natural fibre composites (NFCs) like flax compare with more conventional epoxies and materials, and is this a field you’re exploring?
Henry Lloyd Williams: Currently, bio-resins and NFCs may not match the outstanding properties of conventional materials like epoxies. However, the need for maximum strength isn’t always paramount. We are actively delving into this domain, considering the use of more sustainable materials, especially for less critical components. Given the rapid advancements in this field, it is anticipated that sustainable choices will soon emerge as viable contenders against traditional material options.
Coen Meerbach: We believe that the most interesting aspect from an environmental perspective, is the resin. We see that there are interesting materials being developed for the construction industry. There, the up-and-coming standard is a fully biobased and fire retardant resin. With regards to the fibres, we see some
interesting advantages with flax, but also see other fibre materials arising, with interesting performance and price.
Paul Buyse: On structural components we see that natural fibres have a hard time to compete with more traditional materials. The weight penalty on the parts to achieve similar properties is significant. This is also influenced by limited experience and validation on long term behaviour in regards to durability and reliability. Nonetheless, it is feasible to apply them on non-structural components with lower loads and less exposure to water. Bio based resins on the other hand have a much lower threshold to adopt aside of the higher cost. I think the crucial element is to look at the total bill of CO2 equivalent for the product. This includes the impact of the material choice considering the raw material and processing until cured parts. In that sense, we often consider recycled PET core materials. This also raises the question of the end-of-life and circularity of composites.
What new composite materials and/ or moulding processes are emerging of relevance to yacht builders?
Henry Lloyd Williams: A notable development is the rapid growth of the use of 3D printed moulds, marking a significant stride in sustainability. The ability to melt down and recycle obsolete moulds suddenly allows an eco-friendly solution to a once ‘disposable’ problem. With heavy use, moulds can quickly need to be renewed and updated, to ensure precision and consistency.
Coen Meerbach: Together with PD Composites and Curveworks, we are proud to be part of the development of a 46 foot sailing yacht that was built using a ‘panel assembly’ method. This method uses thermoformed foam core panels that are positioned in an assembly jig, sealed and then over-laminated to form the inner skin. This joined panel assembly can then be removed from the jig and the outer skin can be added. Also, we have recently supported a client with the development of complex shaped carbon fibre frames. These were made with Ex-Core’s expanding core material, removing the risk of carbon fabric bridging and delivering parts while making bridging of the fabric a thing of the past.
Lastly, we see that large yachts are more-andmore often raising questions regarding the maintenance of their hull doors. In a worst case scenario, we have seen corrosion issues leading to missed charter income. Yachts (up to 12 pax) can have their door built whilst the yacht is in service, and during a docking have the door replaced for a maintenance free composite version. An added benefit is the lightweight design, which will also reduce stress on the mechanical and operating components.
Paul Buyse: There are a few on-going developments including core kitting and recycled carbon fibres. The last one has limited application as most structural parts require a continuity in the fibres, but it certainly has its place. Two more recent breakthroughs are additive technologies (3D printing) and thermoplastics. These have advanced a lot in recent years allowing builders to rethink their production methods. A good example is the 3D printing of moulds and tooling which can be very efficient to build but also reduce waste by reusing the mould materials to print new ones. The same applies to thermoplastics where the material from an older product can be reused to build a new one.
SuperYacht Times B.V. Silodam 256, 1013 AS, Amsterdam, The Netherlands
31 (0) 20 773 28 64 info@superyachttimes.com www.superyachttimes.com
Cover Images
Teignbridge by Justin Ratcliffe Enata by Guillame Plisson Project Toro by Turquoise Yachts
How to Build It is published by SuperYacht Times B.V., a company registered at the Chamber of Commerce in Amsterdam, The Netherlands with registration number 52966461. The magazine was printed in February 2024.
When your skills become a seamless unit with your equipment and materials, you are on the way to a perfect paint job.
With our yacht coatings, you can achieve outstanding durability, maximum gloss and longevity from the first to the final layer. Enjoy the creation of easy, efficient and high-performing finishes.
Scan the QR Code to explore our product range →
Celebrating 20 Years of Excellence
instagram.com/alexsealpaint linkedin.com/company/alexseal-yacht-coatings