
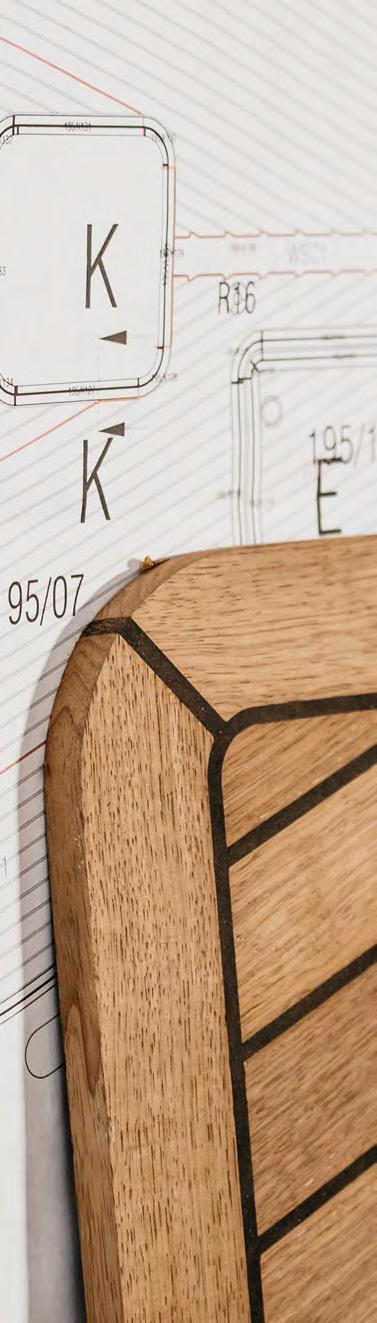
TAINTED TEAK: The end of an affair?
TAINTED TEAK: The end of an affair?
The technical magazine for those involved in the design, construction and refit of superyachts
ROSSINAVI’S AKULA: Keeping it simple
43
Concept in Focus: The Return of the Nautilus Inspired by a 150-year-old novel, will the Nautilus ever be buildable? U-Boat Worx believes it can.
49 Tech Talk: Staying Connected
Kris Cardona of YOT Ltd offers his take on how new tech is transforming IT and comms on board.
54 Build Report: Keeping it Simple
A sneak peak of 59-metre Akula as Rossinavi’s first explorer yacht approaches completion.
70 Build Report: Pump Down the Volume
Exclusive access to Feadship’s 103-metre Project 1011 in the company of project manager Leo Boonstra and owner’s rep Erik Spek of Azure.
82 Manufacturers: Clear as Crystal
A visit to Tilse GmbH in Germany to find out how the rules and regs are keeping pace with technical developments in glass manufacturing.
94 Sponsored Content: Smarter Anchoring
The team at Swiss Ocean Tech on how high-tech AnchorGuardian can keep your vessel safe.
95 Sponsored Content: Full Custom Craftsmanship
Custom Tenders founder Richard Faulkner on customisation in the tender sector.
96 Inside Angle: Occam’s Razor
Superyacht consultancy Occam Marine is named after a philosophical concept that recommends problem solving by searching for the simplest solutions.
100 Sustainability: Tainted Teak
The search for wood alternatives that can replicate the looks and performance of old-growth teak is fully under way.
110 Sponsored Content: The Perfect Partner
From building viaducts and offshore platforms, Dutch aluminium specialist Bayards has developed into a leading manufacturer of superyacht hulls and superstructures.
112 Case Study: The End of Filler?
Coating experts Wrede Consulting in Hamburg are building a full-size yacht to test new methodologies for fairing hulls and cladding superstructures.
119
New Tech: Rise of the Robots
Is the custom nature of a superyacht a definitive barrier to adopting robotic automation in the build process? Read on.
128
Refit & Conversion: Master of the Seas
A look behind the scenes of 70-metre conversion Project Master at Icon Yachts as the future explorer yacht enters the detailed engineering phase.
140 Refit & Conversion: Flight of the Falcon
When new owners decided to refit 88-metre Maltese Falcon, they assembled as many of the original contractors as possible.
150 Alternative Fuels: We Have the Technology
Lateral Naval Architects and PA Consulting look into the feasibility of developing a hydrogen fuel manufacturing and bunkering infrastructure.
157 Ask the Experts: Light Up Your Life
With more yachts opting for extravagant light portfolios, we speak to a panel of experts in the field to find out how the sector is continuing to evolve.
EDITORIAL
EDITOR IN CHIEF
EDITOR | HOW TO BUILD IT
EDITORIAL CONTRIBUTOR
DIGITAL EDITOR
NEWS WRITER
TRAVEL WRITER
WRITER
WRITER
VIDEOGRAPHER
Francesca Webster
Justin Ratcliffe
Charlotte Thomas
Emma Becque
Sophie Spicknell
Jessamie Rattray
Enrico Chhibber
Amy Larsen
Muaz Abourched
DESIGN PRODUCTION
CREATIVE DIRECTOR
GRAPHIC DESIGNER
UI/UX DESIGNER
Ivo Nupoort
Beatriz Ramos
Claudia Sabbadin
INTELLIGENCE
HEAD OF INTELLIGENCE
RESEARCH ANALYST
DATABASE MANAGER
DATABASE MANAGER
YACHT HISTORIAN
Ralph Dazert
Adil Zaman
Syrine Mellakh
Léandre Loyseau
Malcolm Wood
SALES & ADVERTISING
SENIOR SALES MANAGER
SALES MANAGER
SALES MANAGER
CLIENT SERVICE MANAGER
SALES ITALY
Marieke de Vries
Justus Papenkordt
Daniel Van Dongen
Johanna Borreli
info@admarex.com
CORPORATE
FOUNDER & DIRECTOR
TECHNOLOGY DIRECTOR
FINANCE DIRECTOR
Merijn de Waard
Fabian Tollenaar
Laura Weber
Welcome to this bumper issue of How to Build It to kick-start the boat show season. You’ll notice how this third edition is a good deal fatter compared to when we launched the magazine exactly a year ago, a sign of just how well the publication has been received by marine suppliers, contractors and manufacturers. So well received, in fact, we’ve had to cap the number of ad pages to maintain our editorial focus!
We look far and wide to come up with content you won’t find anywhere else and in this issue that includes two exclusive in-build reports. First we visit Rossinavi for an exclusive look at their very first explorer yacht. It’s hard to miss the bright red hull of 59-metre Akula, whose owner was so closely involved in the design process that he taught himself to use CAD software. We also investigate the engineering and technical challenges associated with Feadship’s secretive Project 1011 when her owner asked for a 100-metre-plus yacht with the volume and guest space of a vessel almost twice the size.
I remember writing about the potencial of robots in yacht building years ago. At the time it seemed they were poised to take over messy manual jobs like fairing, sanding and painting, even welding. But that hasn’t happened to any significant extent. We ask if the custom nature of a superyacht is simply not conducive to automation, or whether there are other factors at play?
And talking of filling and fairing, have you ever wondered why we are still adding tons of filler compound to our yachts solely for aesthetic purposes? Coating experts Wrede Consulting in Hamburg believe they have a lighter, faster and more efficient solution – and they’re building a full-size yacht to their theories to the test.
Still in Germany, in addition to doing amazing things with glass on yachts, Tilse GmbH has been instrumental in defining the approval and classification criteria for onboard glazing. We travelled to the company headquarters near Berlin to learn more first-hand.
The industry-wide focus on sustainability and the first prosecutions for the illegal importation of teak from Myanmar mean yacht builders can no longer turn a blind eye to teak of doubtful origin. We look into the most promising wood-based alternatives and investigate which, if any, come close to simulating the prized properties of old-growth teak.
Add in-depth reports on the refit of Maltese Falcon in Italy and the conversion of Project Master in the Netherlands, as well as our regular columns and commentaries from industry experts, and I think you’ll agree this issue of How to Build It is the most stimulating and varied yet. Enjoy!
Justin Ratcliffe - Editor
For generations, we have been realizing the most extraordinary living spaces with dedication and expertise. On water and on land. As a leading international partner in interior+ outfitting, we turn visions for living into reality – for both indoor and outdoor areas.
We are crafting visions.
Following up on our article about 3D printing in issue 2 of How To Build It, the Dutch shipbuilding company Royal Van der Leun has been commissioned with the electrical installation, engineering and automation of a 3D ferry to be used as a passenger vessel during the 2024 Paris Olympics.
In addition to being the largest 3D-printed ferry ever, the vessel will be fully electric, with power for charging the batteries supplied by a hydrogen-powered generator on shore, as well as automatic mooring and contactless charging. Lidar, cameras and RTK-GPS are used for position and course determination, making a captain unnecessary and enabling autonomous operation. The ferry is being constructed by Holland Shipyards Group, with autonomous navigation developed by Roboat for service in France.
Aqua superPower, the British company providing electrically marine superyacht chargers, has continued to expand its portfolio of charging hubs across Europe and the United States. Founded in 2021, the company has now secured £3.2 million in funding from the UK government to deliver a marine charging infrastructure to the UK’s south coast for boats under 24 metres. The company plans to have installed an additional 150 charging stations
globally this year as the demand for charging stations continues to steadily increase. The company is currently ‘partway through building networked charging corridors’, and provides the upfront capital and funds the grid and charging provision to lower the barrier to entry for market players. Aqua superPower is also making headway in continental Europe with chargers installed at the Cala del Forte marina in Ventimiglia owned by Monaco Ports.
A new photovoltaic system has been installed at Amico & Co that will supply renewable energy to cover 53 percent of the refit shipyard’s annual needs and Waterfront Marina production activities.
The on-site system occupies an area of over 4,300 sqm with an array of 1,782 solar panels developing a maximum power of about 1 MegaWatt peak (1MWp). This new investment made by Amico & Co represents another important step towards clean manufacturing and fuller integration of the superyacht
activities with the city of Genoa.
“With some pride we can say that since the very start of our activities, with greater intensity since the early 2000s, we have made investments that have gone in the direction of what we now call sustainability,” says Alberto Amico, President of Amico & Co Spa. “Our strategy was and is the implementation of work process efficiency, particularly through covered and permanent warehouses and other facility technologies, which guarantee 73 percent consumption savings when compared to any temporary facility.”
Azimut-Benetti has signed a deal with Eni Sustainable Mobility to supply renewably sourced HVO biofuel to its fleet. HVOlution, a biofuel made of 100 percent HVO (Hydrogenated Vegetable Oil), is produced in Eni Sustainable Mobility’s Venice and Gela biorefineries from waste raw materials and vegetable residues or from oils generated from crops in a circular economy model. Factoring in the entire logistics and production chain, HVOlution can deliver emissions reductions of up to 90 percent compared to the benchmark fossil blend, depending on the raw materials used for its production. The use of HVO will begin in Summer 2023 for the technical testing of new yachts, sea trials and prototype model handling and owners will be able to take delivery of yachts with HVOlution biofuel already in the tank.
Presented as the next evolution in fully integrated helmto-propeller solutions, Volvo Penta claims its Volvo Penta IPS 40 drive offers outstanding comfort, performance, and sustainability. Building on the efficiency of the Volvo Penta IPS, the new platform is a powerful and flexible solution for superyachts from 25 to 55+ metres with top speeds between 12-40 knots.
“A new star is emerging in our range, where we are looking forward to delivering our trademark helm-topropeller experience to a whole new class of vessels,” says Johan Inden, president of Volvo Penta’s marine business.
Instead of having a bigger engine, the Volvo Penta IPS 40 drive will be powered by two existing D13 engines that are paired with a compact after-treatment system to comply with the latest IMO Tier III standards. But the platform is already prepared for a mix of power sources, from combustion engines running on renewable fuels to fully electric or hybrid solutions. The dual power input design offers flexibility and modularity on the journey towards increased sustainability and can be installed in a twin, triple or quad set-up, meaning each vessel will have from 4 to 8 power sources.
Volvo Penta is carrying out in-house development and in-water testing using its own passenger high-speed ferry test boat, strategically located near its marine test facility in Gothenburg, Sweden. Rigorous testing is in progress to ensure the durability and performance of the propulsion package with field tests in an offshore-energy crew transfer vessel serving as the subsequent phase leading up to the anticipated 2025 delivery.
HamiltonJet has launched a new range of high-efficiency waterjets called the LTX Series. Optimally designed for medium- and low-speed operation, the company has claimed that this is the first waterjet to rival the energy efficiency and bollard pull of the best propeller-based systems between zero and 30 knots.
With its large nozzle, lower input energy, lower jet velocity and lightweight structure the LTX waterjet is lean and low-speed efficient. The absence of hull appendages plus an optimised pump geometry have allowed HamiltonJet customers to save fuel for over a generation, not everyone wants to go fast: “Our customers’ needs are changing and so is our environment,” says HamiltonJet CEO Ben Reed. “We understand that operators not only want to reduce their impact on the environment and lower their energy costs, but also maximise efficiency.”
OneWeb, the global low Earth orbit (LEO) communications network, has launched a Try Before You Buy service and will now take bookings from maritime users who want to benefit from OneWeb’s 100 mbps+ enterprise grade flexible connectivity packages at sea. With 634 OneWeb operational satellites now in orbit, the OneWeb constellation is complete and fully operational down to 35 degrees latitude. OneWeb will have the final ground stations completed and operational requirements in place, ensuring the Company remains on track to deliver full global maritime services by the end of the year.
Now OneWeb will start selling services to the maritime industry, via its specialist maritime distribution partners. OneWeb and its partners have also developed a range of hardware terminal products which are available from trusted maritime communications providers Intellian and Kymeta. Offering hardware terminal products from two established providers with different form factors enables greater choice for customers.
By Georgia Tindale
Beginning a new-build superyacht project is one of the world’s most exciting and challenging undertakings. With a plethora of different factors to take into account – including timescales, costs, competing priorities and so on – it is a remarkable achievement every time a superyacht touches water and the celebratory champagne is poured.
One company which has been diligently working to streamline the build process for all individuals involved is Pinpoint Works. Based in London, Pinpoint Works was founded by superyacht captain, James Stockdale, after he was frustrated with the inefficiency of the workflow and communication found within new build projects.
Fast forward to today, and Pinpoint Works offers a dynamic, affordable and customisable interactive worklist management platform which has already saved countless hours on board vessels across the industry. It has been used to manage ongoing work lists for hundreds of superyacht projects to date, including 200 new builds and over 100 projects which are currently under construction.
Bolstered by the added backing of the financial management experts at Voly Group – whose accounting software has the accolade of being found on board 15% of the industry’s yachts – and who acquired the company in February this year, Pinpoint Works is in the ideal position to help you save time on your superyacht project, whatever your role within the industry. It is a web-based system and is also available for convenient use as a mobile app for iOS and Android.
With its foundations firmly rooted in yachting, Pinpoint Works has been created, tested and approved by a broad range of parties including shipyard project managers, independent contractors, paint surveyors and yacht crew. Just some of the wide ranging pain points addressed by the tool include tracking build progress in real time and managing costs, the reporting of interior and exterior defects, logging unplanned engineering maintenance, improving interdepartmental communication – and the list goes on, with yachts in-build, yachts undergoing refits and survey all able to reap the benefits. Here, we dive into just a few examples of how those working at the heart of yachting have made the most of Pinpoint Works.
Acting as the shipyard’s representative to the client and the day-to-day contact for the owner’s teams, the shipyard project manager or supervisor typically manages one new build project at a time.
For these extremely busy individuals, the pros of using Pinpoint Works include speeding up and streamlining all communications, quick logging and locating of defects on
board, fast and efficient creation of reports to pass on to contractors and other stakeholders, viewing works on a timeline, setting reminders for task follow up, and many more. Indeed, one project supervisor for a 50-metre new build project recently commented on his experience of using the platform. “We use Pinpoint Works frequently. New activities can easily be monitored on all the projects thanks to the daily digest in the mailbox.” Quick tracking of all activities can also be found directly within the system itself through a dashboard for those keen to reduce their email load.
He continued: “The ease and flexibility of the platform for inserting comments make it a powerful and versatile tool which third parties of the project can also use. Reports can be used for official purposes as an attachment to the PODA [Preliminary Operation and Delivery Acceptance] during a new build process or to officially close a report of a warranty period after two years.”
Managing all elements of the project on behalf of the owner, this team functions as the day-to-day link between the shipyard and owner. The benefits of using Pinpoint Works for this team are numerous and include super-fast and efficient communication, the ability to quickly generate reports for daily/weekly meetings, defects and non-conformity, paint inspections, room acceptance, FAT/HAT/SATs and much more.
Finally, it is worth noting that Pinpoint Works has also made waves further afield, with a project manager for the technology integration specialists HMC – responsible for installing AV systems on yachts and cruise ships – commenting on his recent experience of using Pinpoint Works. “We have successfully used Pinpoint Works during installation, commissioning, and handover for new build and refit projects on yachts and cruise liners at the largest scale. Pinpoint Works adds value to our company by providing a truly collaborative and coordinated software solution.”
With service locations in West Palm Beach, Fort Lauderdale, Istanbul, La Spezia, Antibes, La Ciotat, Barcelona and Mallorca, Heinen & Hopman will be at your disposal around the clock. From installation to 24/7 service, Heinen & Hopman’s skilled engineers are aware of the divergent problems that can be encountered onboard.
Meet us at the
Winner of the Queen’s Award for Enterprise: Innovation 2022, Compass is a cloud-based programme accessible by multiple users across various platforms and devices. It runs efficiently on iOS or Windows and can be used on laptops, tablets, and desktop computers. Clients have access to a range of services to support regulations & compliance and, most importantly, navigation of the seas. The platform offers digital chart corrections, passage planning, map overlays with weather, warnings and MARPOL, weather reports, integrated Imray cruising guides and licence and regulation compliance management. The platform can also be supported by a digital yacht manager to support the yacht in all of its activities.
Viareggio-based Inoxstyle has launched its latest product, the hand-crafted Nautical Shower. Made from either Marine Grade AISI316L stainless steel or carbon fibre with an array of finish options, the Nautical Shower has been designed to align with any yacht design and is protected from even the most severe weather conditions. Assembled without the use of tools, the shower is quick to assemble and the water connections are invisible. The Nautical Shower is lightweight and is custom made to measure for each superyacht project and the new carbon fibre option can be combined with stainless steel appliances for a unique and stylish finish.
Besenzoni has developed a new range of ladders/platforms called Oceano: currently including 3 models (LP100 Plus, LP200 e LP300), which differ in size and finish, but it is always evolving and expanding. The installation of these multifunctional ladders/platforms, totally tailor-made according to the yacht’s characteristics, allows to benefit from an additional space at the stern that can be exploited in many ways, offering a pleasant bathing experience, allowing the guests on board to fully enjoy the sea and the contact with the water.
Their main function is as a bathing ladder or from boarding/ disembarking but they are not limited to this since they can be used both as an extension of the beach area and as a convenient tender lift platform.Among the features of this multifunctional ladder is the ability to lift loads of up to 400 kg safely with the simple use of the hand control that manages its handling in a very smooth and intuitive manner.
Multiplex integrates “Tulip” lights into its awning system which means that the top seller from the Bremenbased carbon specialist can also be used in the dark. Multiplex developed the so-called “Tulip”, a very elegantly designed, non-dazzling lamp that shines in red, green, blue and white and which can also be dimmed. The highlight of the “Tulip”, is that it serves as an uplight that can be used to illuminate the awning or - turned by 180° with a flick of the wrist - to shine downwards and illuminate the floor. The milled aluminium body in which the LEDs are cast is waterproof to protection class IP 67. The “Tulip” draws energy from a rechargeable battery that only needs to be recharged after 16 hours.
Mounting or dismounting the lamps is done in seconds. In addition to easy handling, the innovative multiplex product is characterised above all by a very long service life - the LEDs are designed for an operating time of 50,000 hours.
Luxury Carpet has just launched its new Ocean Collection, inspired by waves, atolls, shells, mother of pearl and jellyfish. Taking cues from marine life, the new collection has been designed for use as both flooring and as decorative items suitable for any area of a yacht’s interior. Elisabetta Santoro, who has worked with Luxury Carpet on a number of previous collections, has designed this new sartorial collection specifically for the luxury yachting industry. After a preliminary search of images and a selection of the best for shapes and colors, the marine subjects have been adapted and the shells’ streaks, nacres’ shades and jellyfishes’ tentacles become textures of rugs and carpets produced by Luxury Carpet Studio. This aspect has been developed using an embossing technique, a particular hand work that requires a lot of careful craftsmanship.
The 55 inch HD series X multi vision display from Hatteland technology. This cutting edge 4K widescreen chart table uses ultra-high definition back lit LED technology, is optically bonded and comes with several mounting options. Having recently completed a project on the 89m Amels Here Comes The Sun’, the feedback from Captain Colin Boyle has been extremely positive - “The new touch screen chart table has been a welcome addition to the bridge. We’ve already incorporated the screen into a number of daily tasks, while passage planning, we can for example, simply place a weather overlay over charts, lay waypoints at the push of a finger or simply zoom in or out on points of interest.
On top of that we can view radar, CCTV, GA drawings, share itinerary with the owner and a whole host of other tasks and with it being fully adjustable at the touch of a button, it’s proving user friendly and very adaptable.
FMD (Fundamental Marine Developments) was founded on operational experience in the naval, superyacht and cruise ship sectors. The FMD Glass Crusher has a 20-litre bin that can contain around 60 wine bottles or 160 small beer bottles. Built in stainless steel it can crush a Champagne magnum into sand in less than 10 seconds, reducing its volume by 90 percent. The German company takes an environmentally responsible and creative approach to solving enduring problems encountered when treating waste streams on board vessels while conforming to the requirements of
MARPOL Annex IV &
V.
Italian manufacturer Bonomi won a DAME award for its electric Joy cleats. Available with a 12V or 24V motor with working loads from 80-500kg, the range made from polished 316 stainless steel offers a safe and effortless way to secure the correct tension on mooring lines without the need of additional locking device. The self-tailing Joy system integrates a freely rotating roller to take up the mooring tension with a motorised, toothed sheave like a winch. By bringing together in a single piece of hardware all the functions needed during docking procedures, the Joy range does away with winch-assisted cleats often found on large yachts.
MarQuip maintains its Exhaust Heat Exchanger is the most compact in the world. Most heat recovery systems are bulky and installed in parallel with the exhaust to ensure liquids don’t boil and damage the system when heat from the exchanger is not being used. These exchangers have their own hot valves to re-route exhaust gases through the bypass. Developed with partners Kelvion GmbH and Seable&Co, MarQuip’s Exhaust Heat Exchanger has no bypass or hot valves. The design guarantees cooling over the exchanger without the need for warm water thanks to the combination of a cooling back-up system and wet exhaust.
Named after the Japanese cherry blossom, the 71.75-metre motor yacht represents a noble new generation of Feadship yachts that combines uncompromised luxury, technology, engineering and propulsion. Sakura was started on speculation, Sakura’s interior draws on the ‘Japandi’ style with its combination of Scandinavian warmth and Japanese minimalism. She features clean exterior lines with light colours and bright spaces inside. Sakura will be equipped with twin MTU engines, providing her with a top speed of 14.5 knots, a cruising speed of 12 knots and a range of 4,500 nautical miles.
LENGTH: 71.76-metres BUILDER: Feadship COUNTRY OF BUILD: Netherlands DELIVERY YEAR: 2025
NAVAL ARCHITECTURE: Azure Yacht Design EXTERIOR DESIGNER: Studio De Voogt INTERIOR DESIGNER: FM Architettura
Project Spyder will span five decks with a beam of 13.8-metres. Some of her core features include a 100 square-metre beach club, complete with four opening balconies for terrace use, a beauty massage room, a bar and a spa. She’ll also have a 10.3-metre swimming pool, a helipad and a wellness suite on the sundeck. The Italian Sea Group collaborated with brokerage Kitson Yachts for the contract of the yacht, which is due for delivery in 2027.
LENGTH: 88-metres BUILDER: Admiral COUNTRY OF BUILD: Italy DELIVERY YEAR: 2027
NAVAL ARCHITECTURE: Admiral EXTERIOR DESIGNER: Espen Øino International INTERIOR DESIGNER: FM Architettura
Unveiled at the Monaco Yacht Show 2022, the Swan 128 is the latest addition to the Swan Maxi range. As the second largest model to be released by Nautor Swan since the Swan 131 (launched back in 2006), the full-carbon Swan 128 superyacht is a brand new model which completes the upper segment of the builder’s Maxi range and will be fully RINA classed upon completion.
LENGTH: 38.9-metres BUILDER: Nautor Swan COUNTRY OF BUILD: Finland DELIVERY YEAR: 2025 NAVAL ARCHITECTURE: German Frers EXTERIOR DESIGNER: Micheletti + Partners INTERIOR DESIGNER: Loro Piana Interiors (Misa Poggi)
Sold to a Mexican owner, the Panorama 53 builds on the Panorama 50 platform unveiled in 2022. The Panorama 53M is designed with an innovative hybrid e-MOTION propulsion system composed of twin MAN diesel engines, four variable speed generators, two permanent magnet electric engines, and a generous pack of lithium polymer batteries. She can accommodate up to 12 guests in her five spacious staterooms at the bow on the lower deck. Her owner’s suite is situated on the main deck and includes a small private external terrace.
LENGTH: 53-metres BUILDER: Admiral COUNTRY OF BUILD: Italy DELIVERY YEAR: 2025
NAVAL ARCHITECTURE: The Italian Sea Group EXTERIOR DESIGNER: Piredda & Partners INTERIOR DESIGNER: Unknown
The yacht was sold in March 2023 to a European customer and features a steel hull and aluminium superstructure. Her design will be characterised by a dynamic profile with the typical ISA hallmark of the three arches connecting the decks. Additionally, the beach club will have the ability to be an open platform to transform the aft deck lower-level space into an expansive living area equipped with a gym, lounge, and spa meeting all the needs of those onboard.
LENGTH: 66-metres BUILDER: ISA COUNTRY OF BUILD: Italy DELIVERY YEAR: 2025
NAVAL ARCHITECTURE: Palumbo Superyachts EXTERIOR DESIGNER: Studio Vallicelli Design INTERIOR DESIGNER: Alberto Pinto
The model was first announced in December of 2022 and the first renderings of her interior spaces revealed a chic contemporary design, with bold, organic shapes and patterns throughout. The yacht provides accommodation for up to ten guests across five sumptuous staterooms. The sale was facilitated by David Legrand and Alain Auvare of Fraser Yachts representing the seller at Palm Beach international Boat Show 2023.
LENGTH: 52.6-metres BUILDER: Mengi Yay COUNTRY OF BUILD: Turkey DELIVERY YEAR: 2025
NAVAL ARCHITECTURE: Mengi Yay Yachts EXTERIOR DESIGNER: VYD Studio INTERIOR DESIGNER: VYD Studio
Project Tempest features a sprawling saloon with expansive windows, and the main deck features a full-beam owner’s suite complete with a private desk/vanity area and his and her bathrooms. On the lower deck, two twin staterooms and two double suites offer flexible arrangements. Riza Tansu has meticulously crafted the interior design, reflecting his signature laid back beach house style. Combining wooden flooring, light surfaces, minimalist lines, and contemporary aesthetics exudes tranquillity. Performancewise, she is powered by twin MAN engines giving her a cruising speed of 13 knots and a top speed of 16 knots.
LENGTH: 37.3-metres BUILDER: Aegean Yachts COUNTRY OF BUILD: Greece DELIVERY YEAR: 2025
NAVAL ARCHITECTURE: Endaze Marine Engineering EXTERIOR DESIGNER: Riza Tansu INTERIOR DESIGNER: Riza Tansu
Developed around the Tankoa T450 concept by Giorgio Cassetta, the TX450 is a new version based on the same 45-metre design, but developed into a full-custom project. The TX450 features a four deck arrangement with all guests staterooms situated on the main deck – an unusual feature for a yacht in her size category. There is a generous master stateroom and the yacht’s social areas are focused around the upper and bridge decks. The interior also offers a gym, spa area and a convertible room, which brings the number of the guest cabins up to six if required.
LENGTH: 45-metres BUILDER: Tankoa COUNTRY OF BUILD: Italy DELIVERY YEAR: 2025
NAVAL ARCHITECTURE: Tankoa EXTERIOR DESIGNER: Cassetta Yacht Designers INTERIOR DESIGNER: Cassetta Yacht Designers
Announced in the Summer of 2022, Project Bullseye will feature a five deck configuration designed exclusively by London studio Winch. Liz Cox who heads the Cecil Wright build team will be working with Winch Design who have previously worked on builds such as Slipstream. Nobiskrug’s in-house will work to ensure the hull is perfectly optimised in terms of seakeeping and propulsion efficiency.
LENGTH: 77.2-metres BUILDER: Nobiskrug COUNTRY OF BUILD: Germany DELIVERY YEAR: 2025
NAVAL ARCHITECTURE: Nobiskrug EXTERIOR DESIGNER: Winch Design INTERIOR DESIGNER: Winch Design
Originally signed with Brodosplit shipyard for a Swiss client, the build yard for Vela has recently changed, with the owner opting for the Brodotrogir shipyard as an alternative. Croatian press reported that the contract for Vela was signed for nearly €17 million for the construction of the steel hull and aluminium superstructure. According to sources within the yard, the entire project is expected to exceed €100 million.
LENGTH: 128-metres BUILDER: Brodotrogir COUNTRY OF BUILD: Croatia DELIVERY YEAR: 2026
NAVAL ARCHITECTURE: Unknown EXTERIOR DESIGNER: Unknown INTERIOR DESIGNER: Unknown
HP Watermakers emerged in 1995 as a branch of the Zucco family’s manufacturing company specialising in the production of high-pressure parts for watermakers. With a production facility on the outskirts of Milan, everything from the design to the final factory testing takes place in-house.
BY FRANCESCA WEBSTER
One of HP Watermakers’ most recent innovations, the HP Part-Net interface, has transformed the way desalination plants are utilised on board yachts. Even before the introduction of Part-NET, its RP TRONIC pressure regulation system had propelled HP Watermakers ahead in terms of user-friendliness. But watermakers were still hidden away inside technical spaces or engine rooms. Part-NET shattered this norm by bringing the watermaker onto the multifunction display (MFD), allowing captains to access all functionalities directly on any chartplotter or domotic system.
HP Watermakers carries out its own research and development to stay at the cutting-edge of technological developments. As a small, nimble family company, it has the agility to swiftly respond to new challenges and ideas. With a technical team with decades of experience in the field, it can turn an idea into a final product within days by employing advanced machinery such as CNC laser-cutting machines, 5-axis turning and milling machines. By producing 85 percent of the components in-house, HP Watermakers maintains a steady control over the manufacturing process to guarantee high quality.
“While the industry faces numerous challenges today, we’ve proactively tackled supply chain distribution by maintaining a substantial stock of materials for the production of hundreds of units,” says Gianna Zucco, co-founder of HP Watermakers.
“The small-scale manufacturing setup requires a high level of stock to facilitate fast deliveries and prevent material shortages that could disrupt production and cash flow. To build a solid foundation for the company, our management has consistently reinvested its profits into securing a stable and sustainable supply chain.”
Approximately 95 percent of production is destined for the yacht and superyacht industry, amounting to around 400 units per year and the company is among the few watermaker companies worldwide that manufacture a significant portion of their own components. Moreover, since 2019 it has helped pioneer the production of the only MFD-interfaced watermaker available on the market, garnering acclaim from end-users in the process. Recently, a new addition to its product lineup was revealed: the most compact 500 lt/h unit on the market. Built on the frame of a 120 lt/h unit, it consumes just 3KW/h.
Looking ahead, the company anticipates significant developments in the sector as people spend longer stretches of time aboard their yachts, necessitating the autonomous generation of energy and water as basic necessities. “In this scenario, our strategic positioning as a supplier becomes crucial as we
Producing more than 300 units per year, HP Watermakers had a turnover in 2022 of €3 million, with a prediction for 2023 to exceed this turnover. The company supplies 80 percent of its products to businesses outside of the Italian industry and 95 percent of the turnover comes from the luxury yacht market.
Principal yachting customers are; Dutch yards Wajer, Steeler and Vanquish, Italian yards Azimut, Sanlorenzo and Absolute and the Spanish yacht builder Sasga and the company’s top model is the SCA Model launched to the market in 2021.
strive to guarantee the always-on production of fresh water on board,” says Zucco.
Digitalisation has emerged as a vital component of the company’s operations. In 2017, it introduced its BiBi® system, enabling remote control of the unit via the internet. Over 200 yachts currently utilise this service, allowing HP service technicians to identify and prevent issues by remotely accessing the units. By diagnosing problems and dispatching the appropriate parts before the issue escalates, BiBi® has proven to be a powerful asset in ensuring problem-free cruising. Moreover, installing BiBi® comes with a four-year warranty.
To ensure comprehensive service and support for the global fleet of yachts, the company operates four offices and stores worldwide, located in Fort Lauderdale, Dubai, Cape Town and Male. It has also established a sales and service network spanning 53 countries, which allows the team to swiftly address the needs of clientele across the globe.
“As HP Watermakers continues to pioneer advancements in the water desalination sector, we are focused on pushing the boundaries of innovation,” concludes Zucco. “By leveraging cutting-edge technology, expanding our global presence and prioritising customer satisfaction, we are poised to shape the future of watermakers for the yachting industry.”
In 2020, the family-run engineering firm Iacomelli changed hands for the first time in its 60-year history when American businessman Chris Bizzio took over the helm. Based in Pistoia, Tuscany, Iacomelli is a key supplier of steel carpentry and engineering to the yachting industry. We caught up with Chris to find out how he has navigated taking over a wellrespected Italian firm, tripled the company’s turnover and reinvigorated production workflow
BY FRANCESCA WEBSTER
What motivated you to take over Iacomelli in 2020 in your first experience of the superyacht sector?
I worked for over 25 years in both the consulting and fashion business, but always as a director or CEO. Other than having been on a yacht, I knew very little about the superyacht sector. At around 50 years old I told myself I should try the entrepreneurial side of working as both my grandparents were entrepreneurs and my father had his own business. A lawyer friend of mine told me that Iacomell was looking to sell. Iacomelli had a generational issue as the children already had their own career paths and none of them wanted to work in the company, so it was destined to be shut down. Fortunately, I was able to step in. I found a company rich in craftsmanship, knowhow, and much goodwill in the industry. I was able to use my experience acquired in areas such as supply chain and business development. Since I joined the company our sales have grown three-fold.
How have you navigated the changing landscape in the sector, particularly with Italian shipyards buying up key suppliers?
Our strategy is to focus more towards handmade custom products. The expertise we have in matching metal carpentry with electronics or hydraulics and giving the customer a turnkey solution is almost unmatched in the industry. We strive to develop unique solutions that best answer our customers’ needs. I see that shipyards are taking over key suppliers, but after a while these suppliers stop innovating because they are absorbed by the “system”. We are free to explore different aspects of our business and to find out-of-the-box solutions. Some may think the share of the pie is getting smaller, but when you’re able to find bespoke solutions for your customers, you have a new market open to you.
How have you adapted to the cultural and business differences as an American owner taking over an Italian company?
Well, let’s say it’s like “rigour meets creativity”. Obviously, my background brings to the table rigour, processes, budgets, P&L, cost controls etc. but then I must match this with Italian design, creativity, craftsmanship, unstoppable searching for solutions, and the ability to develop different paths to the same result. As an American I view things as the glass being “half full”, while some Italians often take the “glass half empty” perspective. I try to navigate between these two assessments. It’s not always easy and certainly challenging. To change a company culture like that of Iacomelli, which has been around for over 60 years, is not something you do overnight, in fact my approach is to demonstrate with facts that sometimes there are better ways of doing things. Italians are not afraid to express their emotions, even at work. And meetings
can sometimes appear to turn into heated debates. It’s important to consider this as constructive conflict that will help everyone work more effectively and build stronger relationships of trust.
Are there any specific strategies you want to implement to ensure the company’s survival and growth?
I think for us the path is to give the customer custom turnkey solutions. Our products are made by hand unlike our competitors, most of whom use machines. This way of working adds to production times, but the result is a higher quality and higher functioning products. Today’s shipyards are pushing the development and innovation to their suppliers, and we need to meet that challenge. In Iacomelli since I took over, we have invested over €900,000 in innovation, but we also have to offer shipyards new or pioneering products that can involve a mix of materials to solve, for instance, an issue of weight. My plan is to grow – in sales, in efficiency and in the goodwill our customers have towards us.
Are there any steps you have taken to strengthen and secure the supply chain for Iacomeli’s operations?
One area we are working on is to give our suppliers access to immediate payments, so by working with us we can address immediately the issue of giving the supplier the necessary working capital to fulfill our orders. In essence we work as a bank for our suppliers. Another area is visibility. We try to give our suppliers visibility in the mid-term, the so-called “demand forecasting”, so that they see and understand what is ahead for them in the future. The third area is lifetime value. If you are a supplier and work with us, over time your lifetime value will grow as our relationship continues as we like to build on our relationships over a long period.
Are there any plans to diversify Iacomeli’s client base or expand into new markets?
I would love to grow internationally, especially in northern Europe, but unfortunately Italian companies don’t have a great reputation in an international field. Sure, there are some great Italian companies, and our design and creativity are outstanding, but if you dig a little deeper, issues such as reliability, deliveries, willingness to serve the customer, language, all come into play, so I get a lot of push-back from international customers as they are reluctant to partner with us. It’s difficult to change this mindset but I won’t give up trying. Regarding our expansion strategy I would love to branch out in the superyacht sector. Today we develop doors, pantograph doors, sliding doors, mooring doors, tender garage doors, stern platform doors, etc. I need to see where I can diversify, but always within our sphere of legitimacy.
devices with sound
That spread by Belcanto, our audio system, perfectly integrated with our controls and sockets collections: emotion to listen and beauty to admire. In the picture, the Il Contralto speaker, integrated in a control plate from the PLH Mono series.
Showroom - Via Voghera, 4a - Milano | info@plhitalia.com | plhitalia.com
Heesen Yachts has gone from strength to strength since Frans Heesen acquired Striker Boats in 1978. According to our own market intelligence, over the last 10 years the shipyard has delivered an average of three to four yachts per year with an annual turnover of around €200 million.
BY RALPH DAZERT & JUSTIN RATCLIFFE
Asmall industrial town in the southern Netherlands about 90 minutes by car from Amsterdam’s Schiphol Airport and far from the sea, is not the most likely place to find one of the world’s top superyacht shipyards. Nevertheless, the municipality of Oss is home to Heesen Yachts, one of the area’s biggest employers with approximately 500 staff on its payroll and up to 500 more engaged as external contractors.
Following the war in Ukraine and the sanctioning of one of its UBOs, last year Heesen announced that the company ownership “is once again 100 percent Dutch” and controlled by a Dutch foundation presided over by Heesen CEO Arthur Brouwer and Chairman of the Supervisory Board, Anjo Joldersma. Coming in the wake of the Covid crisis, the shipyard handled a tricky situation speedily and transparently with no effect on production or sales.
“The transition to a Dutch foundation has not impacted Heesen’s day-to-day operations,” says Mark Cavendish, Heesen’s CCO, who returned as a board member after Friso Visser stepped down from the role earlier this year. “The change in ownership structure was primarily aimed at ensuring long-term stability. And yes, we do expect this structure to remain in place in the foreseeable future.”
While the yard’s original shed is still in operation and currently houses the 50-metre full-aluminium, semi-displacement Project Jade, there are no fewer than seven other construction halls, of which six contain covered drydocks. During our visit, there were nine new-build projects in various stages of construction at the shipyard. Another four projects were in earlier stages of construction elsewhere in the Netherlands and two further yachts were undergoing sea trials.
While Heesen outsources the construction of its steel hulls in the north of the country, it builds its aluminium hulls in-house in Oss (the aluminium superstructures are made close to the yard by a local subcontractor). In 2000 the shipyard established its own furniture factory, Heesen Yachts Interiors, when it acquired the Oortgiese company close to the Dutch-German border, but it also works with external contractors for the interiors.
“The change in ownership structure was primarily aimed at ensuring long-term stability. And yes, we do expect this structure to remain in place in the foreseeable future.”
Heesen Yachts is a leading exponent of building superyachts on speculation, but the practice requires deep pockets and brings inherent risks. Heesen CCO Mark Cavendish explains:
“The decision-making process for starting a new spec build involves many factors, such as – but not limited to – the level of inquiries for certain yacht models or sizes, the availability of capacity in our sheds, financial considerations, the capacity of our workforce – you name it. Our management team will make the final decision, but all departments give their input in order to have full buyin when we make the choice for a new speculation yacht to start. However, in the end, the choice always remains somewhat of a calculated risk. At Heesen, we’re well prepared to take this risk, as we have shown over and over across several decades that we are very good at selling yachts.”
The fact that even its series yachts have custom interiors by established international designers would seem to add an extra dimension to speculation projects in terms of costing. Series yachts are sold at fixed prices, but presumably some designers cost more than others?
“The choice of a certain designer over another for a new speculation project does not really have a significant impact on the price of a yacht,” continues Cavendish. “We set a budget for the designer and some parameters for them to work with. However, if the designer has a particularly good idea, but it would stretch the budget, then we can be flexible if we think it will make for a more attractive yacht commercially.”
“The current business model is centred on three distinct product lines: Series, Smart Custom, and Full Custom, which offer varying degrees of personalisation and speed of delivery.”
Over the years, Heesen’s product strategy has evolved to suit market needs but has generally aimed at combining series, semicustom and full custom production. The current business model is centred on three distinct product lines: Series, Smart Custom, and Full Custom, which offer varying degrees of personalisation and speed of delivery. At first glance, this is confirmation of the way the company was already operating, but the difference lies in the messaging: “The aim was to bring more clarity to our product offering by refining our terminology,” explains Cavendish. “In a competitive market, a clear proposition is vital for success.”
There is a lot of fudging when it comes to defining what terms like ‘series’, ‘semi-‘ and ‘full-custom’ actually mean in the superyacht world and the lack of clarity can sometimes be misleading. Heesen likes to keep the record straight, not least as an aid to managing its own clients’ expectations.
“For instance, if a client arrives late in the build cycle and wants all kinds of changes, we have to gently explain what we can and cannot do,” says CEO Arthur Brouwer. “We have to be very careful that these instances don’t start a snowball effect in our production that takes up too many resources. If there is a significant delay in the build cycle of one project, it can affect others and that can be very risky for the shipyard. We have managed significant changes without issues,
but there have been others where we felt we couldn’t accommodate all the changes requested and had to let the customer go.”
Series production has traditionally been Heesen’s bread and butter, accounting for up to half of its production. It is important to note, however, that the interiors are always customised and only six to 12 units in each series are built. Moreover, as in the automotive world, a life-cycle change is introduced after every fourth to sixth hull (the latest in these periodic changes is the new 50-metre Steel series designed by Harrison Eidsgaard announced at FLIBS last year). This allows products to be adapted to the market and technological developments, while avoiding over-supply of the same yachts down the line when they enter the pre-owned market.
Heesen has the in-house engineering capacity for one or two full-custom project like Project Skyfall and Project Sparta per year. Any more and it has to start in-sourcing some expertise as the lead times for the engineering are that much longer. Alongside that it can handle a Smart Custom project and two or three series yachts.
“We can adapt our workflow, but the stretch starts when we have two Smart Custom projects that begin close together, for example, because we have to scramble all our resources at the pre-production stage,” says Brouwer.
Ever since Frans Heesen agreed to build Octopussy that broke the 50-knot barrier and was the fastest yacht in the world when delivered in 1988, technical innovation has figured strongly in Heesen’s makeup. Nowadays that innovation is focused less on raw speed and more on combining performance with fuel economy. In 2013 it launched 65-metre Galactica Star, the first yacht with a Fast Displacment Hull Form (FDHF) devised by Van Oossanen Naval Architects, which offers resistance values that are typically 20 percent lower than a well-designed hard chine hull form at semidisplacement speeds. In 2014 it was the turn of 42-metre Alive, the first yacht with a Hull Vane, a patented foil also by Van Oossanen that is fitted below the transom to reduce water resistance and pitching motions. Model tests at the towing tank of Wolfson Unit in Southampton showed fuel savings of 20 percent at 12 knots and up to 23 percent at 14.5 knots. In 2017 the yard delivered 50-metre Home, the first hybrid-powered Fast Displacement yacht (the entire Heesen range is now offered with hybrid propulsion). Last but not least, 80-metre all-aluminium Galactica, its largest yacht to date, features a patented ‘Backbone’ structure for additional rigidity with zero weight penalty.
Heesen has sold 37 yachts in total since 1 January 2013 for an average of 3.7 sales per year. These comprise 10 projects started for the client (Full Custom or Smart Custom) and 27 on speculation. 20 of the total number of sales were for yachts between 40 and 50 metres, 12 between 50 and 60 metres, and five over 60 metres LOA. At the time of writing, the company had 14 projects in-build.
2023:
` 80m Full Custom, full-aluminium GENESIS (sold)
` 67m Full Custom, steel SPARTA (sold and for resale by owner)
` 60m Full Custom, full-aluminium ULTRA G (sold)
` 55m Series on spec, steel fast displacement RELIANCE (sold and for resale by owner)
` 55m Series on spec, steel fast displacement APOLLO (sold)
2024:
` 56.7m Series on spec, full-aluminium fast displacement AKIRA (sold)
` 55m Series on spec, steel fast displacement SERENA (sold)
` 50m Series on spec, aluminium semidisplacement JADE (available)
` 50m Smart Custom, based on the 50m steel displacement OSLO 24 (sold)
2025:
` 55m Series on spec, steel fast displacement VENUS + 20950 + 21050 (all available)
` 50m Series on spec, full-aluminium fast displacement ORION (available)
Within its three product lines, Heesen builds fast displacement and semi-displacement motor yachts in steel or aluminium between 49 metres (up from 37 metres not so long ago) and 80 metres, with a sweet spot somewhere in the middle. But the business strategy that Heesen excels at is building yachts on speculation, a potentially risky practice that it has honed to perfection (see sidebar). These are the projects that the shipyard finances and starts building itself with the aim of selling them at a later point during construction (half of the projects currently in-build were started on spec). The advantage is that owners don’t have to wait for so long for delivery and means the yard can guarantee availability to the market in the future. This proved especially true in the immediate aftermath of the Covid pandemic when demand exceeded supply. “Yacht building has changed insofar as you used to be able to plan a year or two in advance,” Brouwer notes. “Now you have to look four or five years ahead.”
Key to the success of Heesen’s on-spec build program is the close relationship it enjoys with the brokerage community. The annual Heesen Ski Cup in the Italian Dolomites, for example, is a coveted trip among brokers. The event is all about having fun, but has a serious side too as a ‘thank you’ to their hard work during the course of the year. Heesen has good reason to be thankful as the vast majority of sales, whether new-builds or pre-owned yachts, are concluded through brokerage houses.
The current facilities in Oss, as well as the surrounding bridges and waterways, mean the shipyard cannot build much over 80 metres, but this is not seen as a drawback. The market for 90-metre plus superyachts is smaller and driven by a handful of yards like Lürssen, Feadship and Oceanco. Attempting to break into a new category would also risk impacting the yard’s margins: “We are content with our current facilities in Oss and have no plans for a second facility,” says Cavendish. “We are committed to optimising our operations and delivering exceptional yachts from our existing premises.”
Although no longer a family company, Heesen retains a familiar design DNA and a strong brand identity. This may be one reason why it has avoided joining the trend for building catamaran and explorer yachts. Its XV67 concept, for example, began life as the Xventure, a 57-metre expedition yacht, but has been restyled as a bluewater voyager that will inspire owners to venture into new terrain in 7-star comfort.
“The XV67 designed by Winch Design is not a rugged explorer with a utilitarian look as we’ve come to expect from explorer yachts,” says Cavendish. “On the contrary, it’s a concept design that belongs to our Full Custom yacht proposition, and is a refined luxury yacht with exploring capabilities.”
It is well known that superyacht sales are hard-wired into the global economy. With an ongoing war in Europe, shifting inflation and widespread recession on the cards, the economic outlook is far from rosy and SYT iQ registered a drop in new motor yacht sales over 40 metres of about 40 percent during the first quarter of 2023 compared to the same period in 2022. Heesen’s CCO, however, is confident that the company is better prepared than most to weather these market fluctuations and is not unduly perturbed by the uncertainty.
“While it is too early to draw definitive conclusions, it is worth noting that the first quarter is typically the slowest in terms of sales,” offers Cavendish. “Let’s see what the rest of the year brings.”
Everything you love about Awlcraft 2000, including tried and trusted application characteristics and repairability, but now enhanced with our next generation color platform.
Awlcraft 3000 gives you deeper, more vibrant colors and a long lasting, high gloss finish to turn heads.
Our 26-berth marina facility and 4,000 ton ShipLift, operational since 2019, represent the latest components in our extensive and technically advanced refit facility. But it is the skill of our workforce, our operational partnership and our rapport with our clients that makes a refit complete. It’s why Amico & Co and Genoa are together redefining what a refit and superyacht hub can be.
U-Boat Worx unveiled its Nautilus yacht-submarine concept at last year’s Monaco Yacht Show. The Netherlands-based company followed up earlier this year with new interior renders in partnership with Officina Armare and the project has since grown from 37.5 to 42 metres in length. But can a vessel inspired by Jules Verne’s fictional novel Twenty Thousand Leagues Under the Sea ever be a feasible proposition?
BY JUSTIN RATCLIFFE
U-Boat Worx knows what it’s talking about when it comes to manned personal submarines. Its model range – all designed and engineered entirely in-house using leading-edge 3D and FEM software tools – can accommodate from one to 11 people and operate at depths from 100 metres up to 3,000 metres. The company has a perfect safety record after many thousands of dive hours all over the world and its Cruise Sub 7 model carried on expedition-style cruise ships recently completed more than 1,000 Antarctic dives in a single season.
“Our expertise for the past 15 years has been underwater vessels; now we have to start thinking like yacht designers as well,” says Lex van Rijswijk, who heads up the Nautilus design team at U-Boat Worx. “Naturally, we started with a feasibility study to determine whether it was buildable at all, but we’re well past that stage and it’s definitely feasible.”
The 1,610-tonne vessel will have a depth rating of 150 metres, but it has to also work as a yacht on top of the water, which is why U-Boat Worx has partnered with leading Dutch shipyards and marine research centres to assist with some of the technical parameters such as strength, weight, propulsion, speed and range when operating on the water’s surface. The pressurised hull will be built of stainless steel, whereas the deck structures will be a mix of stainless steel and GRP. The four circular viewing ports on each side of the hull, which are close to four metres in diameter, will be of acrylic as on all U-Boat Worx submersibles (the windows bear an uncanny resemblance to an engraving in the first 1871 edition of Twenty Thousand Leagues Under the Sea that shows Captain Nemo at the helm of of the Nautilus behind the “bi-convex” window of the pilothouse).
Top: What the seascape might look like through the yacht-submarine’s viewing ports.
Facing page: The hardtop folds away and the tender is launched for underwater operations.
A specific area of research for the project partners has been the propulsion package. Diesel-electric systems on yachts are not designed to operate at a depth of 150 metres, while U-Boat Worx is more accustomed to working with much smaller propulsion systems. The most likely solution is a hybrid diesel-electric drive with batteries and the design team is in contact with propulsion suppliers to see who can the deliver the optimal outcome.
“Nautilus is an evolution of our Under Water Entertainment Platform [UWEP] that we presented in 2021,” says Roy Heijdra, head of marketing at U-Boat Worx. “It’s about the same length but the main difference is that the UWEP platform is fully electric, because we envisioned it to be a shorebased operation where people go out in the morning, have lunch on the water, maybe do another dive in the afternoon, and then return to base. Nautilus, on the other hand, is conceived as both a submarine and a fully functioning yacht that needs more range, hence the hybrid diesel-electric propulsion.”
The idea is that Nautilus will engage dieselelectric drive on the surface and full electric battery power below the water. U-Boat Worx predicts it will be able to remain submerged for six hours at four knots, while in DE mode on the surface it will have a range of around 3,200 nautical miles at 8-9 knots.
“One of the first practical considerations that came to my mind is the sundeck equipment,” says Heijdra. “Do you have to stow everything below deck when you submerge? We asked our design partners to look into this and they came up with a pretty unique deck set-up whereby most items can remain on deck. The bar fridge, for example, is housed in a watertight housing. Another thing we had to take into account were the hydrodynamics in submerged mode, so features like the hottub and louvred hardtop can be retracted for less resistance and better speed and range underwater.”
Clearly, a 42-metre yacht requires a tender of some sort and there is dedicated docking slot in the stern platform. But what happens to the tender in submarine mode? In fact, the tender always remains on the surface because an important safety precaution for all manned submarine operations is that communications with the surface must be maintained at all times, which effectively means having an officer on standby in a waiting tender. Clearly there are safety factors that affect submersibles much more than yachts, not least the immense pressure at 150 metres underwater (pressure increases in relation to the surface by 1 bar for every 10-metre increase in depth, not accounting for atmospheric pressure), and U-Boat Worx is liaising closely with the classification society DNV. The principal design philosophy underlying DNV rules for submersibles is that redundancy is provided for all the essential systems, so that in the unlikely event of a failure they all remain functional and safe surfacing is guaranteed.
“The pressure hull and all pressurised components are required to undergo tests that significantly exceed the design diving pressure,” says DNV submersible expert Jonathan Struwe. “All the systems are tested during the various manufacturing stages, then again under controlled diving conditions, and finally at design diving depth. The role of the class society in all this is to ensure an independent critical review of the design by considering any foreseeable failure modes and load cases, reconfirmed and proven by load and functional tests.”
“The pressure hull and all pressurised components are required to undergo tests that significantly exceed the design diving pressure.”
Surface stabilisation systems, either fins or gyros, are the subject of ongoing research, but the low-rise, hydrodynamic superstructure brings with it the advantage of in-built stability: “We have much more hull structure below the water than ‘superstructure’ above centre of gravity means the vessel has a very low centre of and a higher centre of buoyancy [the centre of the volume of water displaced by the hull],” explains van Rijswijk. “This is the opposite of what you find on a conventional yacht, and so Nautilus is already much more stable and may not require further stabilisation. And if the conditions get too rough, you can just submerge!”
The General Arrangement has also to be finalised. Currently the proposed layout includes a master stateroom and four guest cabins, an observation lounge and gym, as well as accommodation for up to six crew. Because of the need for redundancy,
the technical spaces will likely occupy a higher portion of the hull volume than a yacht of comparable size. What has been fixed are the positions of the deck hatch and the elevator in the back of the vessel (provisioning a yacht or submarine of this size by the stairs alone was not deemed feasible). The rest is still open for discussion and layouts can be customised according to client preference.
Despite the engineering and classification challenges that lie ahead, Roy Heijdra is optimistic they are all surmountable and that a modern version of the Nautilus will see the light of day more than 150 years after Jules Verne first floated the idea.
“We’re talking with actual clients and we’re going to build this thing,” he concludes. “If I had to put money on it, I would say that in the next two to three years we will build a Nautilus.”
A reliable and constantly available internet service on board depends on a well-designed and managed IT infrastructure. In this occasional series of dispatches from industry contributors, YOT Ltd technical director Kris Cardona offers his views on how new tech is transforming the maritime industry.
BY KRIS CARDONA
“As yachting has evolved, so has the need for shoreside IT support with remote service providers and remote monitoring solutions.”
The recent technology shift has been facilitated by the emergence of new Low Earth Orbit (LEO) satellite-based technologies, such as Starlink and OneWeb, each offering their own advantages. The vast increase in bandwidth capabilities in the maritime industry parallels the shift in the early 2000s in the traditional home/ office setting, where slower ADSL lines and server rooms were eventually replaced by faster fibre broadband connections and cloud-based services, maximising continuous server power. This transformation is paving the way for a new era of connectivity in the maritime industry, allowing for more efficient operations and improved communication between vessels and the shore.
In recent times, IT and comms have undergone rapid evolution, transforming the maritime industry by offering more than just basic email and fax services onboard. Thanks to the introduction of LEO technologies, vessels now feature advanced systems that provide always-on, high-speed internet similar to that of a well-equipped office. As a result, this has unlocked a world of opportunities, such as the emergence of automated navigational functions and even unmanned autonomous vessels that were once deemed impossible.
The increasing demand for high-speed internet at sea has brought added pressure to improve onboard bandwidth, manage the QoS and improve SD-WAN capabilities. However, rather than simply flooding the network with bandwidth, we’re exploring using SD-WAN technologies to enhance the efficiency of these connectivity sources, particularly by leveraging cloud solutions in a secure manner. Better to focus on embracing the future of IT and developing a hybrid onboard/cloud-based service that integrates seamlessly and securely to enjoy the benefits of the cloud without entirely relying upon it.
Almost every intelligent system onboard now needs to talk to the IT network. These smart systems are increasingly complex and designed for office/home-based environments that simply connect to the cloud services. Work areas on modern yachts now resemble floating offices, with systems and servers integrated into a network that allows for the broadcast of AV streams and the interaction of various devices. In the past, network engineers had to ensure that all systems would continue functioning even if the internet connection was down. However, the current onboard IT systems are much more advanced and require cloud-based services and even more bandwidth to function efficiently.
As the maritime industry continues to embrace cloud-based services like Microsoft 365, onboard email servers are becoming less common, with users opting to access their messages from anywhere in the world with an internet connection. This shift to cloud-based services is not limited to email. Other onboard services, such as the AV systems, are also transitioning now that they have stable WAN infrastructures, which before LEO technologies were considered unreliable. Nowadays, multiple high-speed internet connections are available and it doesn’t have to come at a high cost, especially compared to traditional systems.
The evolution of technology in the maritime industry has led to the development of more intelligent onboard solutions, including high-quality 4K video streaming and cloudbased services. However, this new landscape brings with it the heightened threat of cyber-crime. As IT networks become more complex, it is vital to ensure these solutions are implemented securely, with backups in the cloud and the appropriate technology to encompass all cloud bubbles into a single, secure environment.
This requires carefully managing the expansion of the IT perimeter from a single onboard ‘shell’ or network to multiple online services in the cloud to prevent cybercrimes. If skilled hackers are determined to damage your IT infrastructure, they can. For every service you sign up for, from Microsoft 365 to Netflix, a piece of information is shared with the service provider, whether large or small. Every service is a way in or out – a doorway that a hacker or virus can penetrate. And a yacht can have hundreds of user accounts with brands like Cisco, HP, DELL, Kerio, Sophos, Acronis, Veeam, Zinwave, Peplink, Poynting, QNAP, Axis, and many more. By adding security layers to your IT infrastructure, you put in place more obstacles that need to be overcome, but also give yourself more time to react and mitigate any damage as much as possible.
There are many IT problems to juggle on board, and now in the cloud, in order to keep the vessel, crew, guests and owner safe from any threat. As yachting has evolved, so has the need for shoreside IT support with remote service providers and remote monitoring solutions. These providers have the resources to help owners, captains, crew and guests resolve any hardware or software problems that may arise quickly and with minimal interruption. What might have taken ETOs and AV/IT officers weeks to sort out a few years ago, can now be resolved in just a few hours by an experienced shoreside integrator and service company.
Akula , Rossinavi’s first explorer yacht, is what it says on the tin: a robust, unfussy, steel-hulled passagemaker custom designed and built for adventurous round-the-world cruising.
BY JUSTIN RATCLIFFE
Akula is Ukrainian for ‘shark’ and at almost 60 metres in length and 1,240GT 240GT represents a huge step up for her Swiss owner. His previous motor yacht after switching from sailing boats was the first 24.5-metre Naumachos 82, the pocket explorer of just 180GT launched by Cantiere Navale di Pesaro in 2007. Despite the massive difference in scale, however, the two yachts have more in common than the bright red paintwork of their hulls.
“We’re either cruising or at anchor and covered 6,000 nautical miles or more each year with the Naumachos” says the owner during lunch in Pisa close to where the yacht was undergoing final preparations prior to her launch.“I started thinking of a larger boat because we spend several months on board at a time and needed more space, and because we also planned to do a world cruise I wanted to be able to remain at sea for up to 30 days without reprovisioning or refueling.”
“I started thinking of a larger boat because we spend several months on board at a time and needed more space, and because we also planned to do a world cruise I wanted to be able to remain at sea for up to 30 days without reprovisioning or refueling.”
The owner turned to Andrea Carlevaris, founder and senior surveyor of ACP Surveyors in Viareggio, with whom he had struck up a friendship when buying the pre-owned Naumachos. The original idea of finding a suitable donor vessel for refitting was dropped when nothing was available that suited his specific wish list. So attention turned to building a custom yacht, originally under 50 metres and 500GT, although to paraphrase a line from a famous film about another shark, it quickly became clear he was going to need a bigger boat.
With bold exterior lines by Gian Paolo Nari and interior design by FM Architettura, the owner was deeply involved in defining the yacht’s layout and technical details. He even learned to use CAD software and
knew in advance what domestic appliances he wanted for the galley (Electrolux).
With an initial spec list in hand, the pair approached several leading European shipyards, but the focus kept revolving back to Rossinavi as the most capable and accommodating. A build contract was signed off at the end of 2020.
“Building new is always challenging, but if you then go full-custom the choice of yards is drastically reduced,” says Carlevaris. “Rossinavi were willing to build within the tight timeframe and during the Covid lockdown, which was quite a risk for them. We had an able shipyard and an owner who knew what he wanted; my job has been to help both parties build the best possible product – oiling the wheels, if you like.”
The owner’s wish list explains many of Akula’s aesthetic and technical attributes. He was adamant from the start that the hull should be unfaired with a commercial finish. Carlevaris wasn’t convinced because of the impact it might have resale value, but the owner was wholly unconcerned, arguing that adding tons of filler for purely aesthetic reasons makes no sense on an explorer yacht (he refers to Akula as a ship) designed to carry a container on deck if necessary.
“If you look at building a custom boat from an economic point of view, you wouldn’t build it all,” says the owner. “Besides, I wanted a yacht for my own use, not for some potential owner in the future.”
Another unusual choice was synthetic decking instead of teak throughout the yacht. This was driven by a determination to use sustainable materials where possible, a desire that informs the whole project, but also because it requires virtually zero maintenance. The eventual choice was heavy-duty Bolidt more commonly found on cruise ships, instead of its sister company Esthec whose products target the yachting industry.
The owner further wanted diesel-electric propulsion with azimuthing pods. Akula’s electrical energy comes from four variable frequency Caterpillar (C32 and C9.3) generators driving twin Veth L-drive thrusters with counter-rotating propellers. Offering quiet and efficient propulsion with DP capability, the full integrated 2,600kW package will provide a predicted top speed of 14 knots and a range of 5,500-plus nautical miles at a cruising speed of 12 knots.
“We developed our experience of dieselelectric propulsion with projects like Endeavour II, Polestar [ex-Polaris] and Alchemy,” says Federico Rossi, chief operating officer at the family-owned shipyard. “With full-custom yachts, especially when the build time is quite restricted, it makes sense to use systems and solutions that you’ve already worked with and can guarantee will provide the required performance.”
Like Polestar, Akula also meets the requirements of Class II of the FinnishSwedish Ice Class Rules (FSICR). For steelhulled vessels with no ice strengthening, Ice Class II means the yacht is able to operate independently in very light ice conditions. Akula has some local hull reinforcements and heated sea chests, but will still require a pilot and accompanying vessel when summer cruising in high Arctic waters.
Essential for spending long periods on board was the complete separation of the crew and guest circulation flows, as well as a private study area for both the owner (on the bridge deck overlooking the open aft deck) and his wife (adjacent to the master stateroom on the main deck forward) where they could work uninterrupted. The yacht is Starlinkready, but in addition to VSAT the owner specified a Poynting Wavehunter 5G antenna dome with the highest throughput cellular internet connection available on the market for fast and seamless connectivity.
The real estate dedicated to these work spaces, which on other yachts might serve as a media room, sky lounge or more guest accommodation, is a clear indication of the owner’s priorities. In fact, Akula has just three guest cabins, all on main deck, plus a convertible lounge next to the master stateroom, for a maximum of 10 guests including the owners, although most of the time she will carry less than half that number. Despite her diminutive size, the Naumachos 82 was able to carry more passengers.
The lower deck is devoted to the crew accommodation and hotel services with an enormous pro-spec galley, walk-in fridge and freezer, dry store, large laundry, and a goodsized crew mess. A service hatch in the side of the hull allows crew in a tender to load/ offload provisions when at anchor. Further, galley has an adjacent scullery, an additional working area used for cleaning dishes and storing utensils that houses a glass crusher and refrigerated waste storage unit: “I bet you won’t find another superyacht in-build today with a scullery,” says Carlevaris proudly.
Aft of the switchboard and engine rooms is a garage for storing bikes, paddle board and other toys, as well as the pod compartments and two workshops – one for the engineer and one for the owner. “I like to tinker,” says the owner by way of explanation.
In addition to the separate guest and crew staircases, a service lift runs from the technical space on the under-lower deck
“Building new is always challenging, but if you then go full-custom the choice of yards is drastically reduced.”
up the bridge deck. Used by both guests and crew, the landing doors open on both sides into their respective areas to respect guest privacy (the entire yacht is designed to be disability-friendly so the lift, passarelle and passageways are wide enough for a wheelchair to pass). The pantries on each deck are more like small galleys.
Rossinavi is accustomed to resolving the daily technical challenges of building custom superyachts, but Akula is unlike anything they’ve done before – and not just because she is the shipyard’s first explorer yacht.
“The most critical thing is to be on the same page as the owner’s team in order to manage expectations,” says Federico Rossi. “So you start with the overview of the project and then whittle it down to the details. That’s the most delicate and maybe the most difficult phase of the entire development process.”
Take the lack of fairing, for example. Having no filler removes a dirty and time-consuming phase of the construction, but it throws up its own set of problems for a yard more used to delivering superyachts with a perfect sparkling finish. By way of example, Rossi points out the bulwark handrails on the open aft decks. Metalwork that has been filled and faired presents a flat, uniform surface for fitting railings and the like. Due to distortion after welding, each unfaired metal plate is fractionally different to its neighbour and so allowances have to be made. To cancel out these differences, the handrails aboard Akula are mounted on rubber collars of varying thicknesses. Although the height may differ by only a couple millimetres, without them the handrails would look wonky.
Unlike conversions from working boats where technical and storage spaces are built into the donor vessel, the functionality of new-build explorer yachts can sometimes be compromised by the demands of modern living afloat. Thanks mainly to the owner’s insistence, this did not happen on Akula
“All parties worked hard to keep that functionality intact,” says Rossi. “This is an issue we came across when building Taransay, a 39-metre modern replica of a yacht built in 1930. Back in those days much more interior space was devoted to the technical spaces and operational aspects of the vessel. It’s something we tend to overlook nowadays.”
In true explorer fashion the custom tenders, a 9-metre Tideman and an 8.5-metre X-Craft, are stowed in an semiopen garage on the main deck aft. Both are hardy vessels but the Tideman is especially rugged and made from High Density Polyethylene (HDPE) that can be recycled and made into composite wood or plastic lumber. The bulwarks fold out for launching on both sides by two 4-tonne capacity, custom beam cranes. A small lobby or reception areamud room on the main deck aft is fitted with hanging wardrobes so guests can remove dirty or wet garments before proceeding directly to their cabins.
“The hull lines were studied precisely for the Veth pods to achieve the top speed of 14 knots and cruise speed of 12 knots, as well as a huge range at economical speed –ambitious targets considering this is a 1,200plus GT vessel displacing over 1,250 tons,” says Giuseppe Arrabito, founder of Arrabito Naval Architects.
“We already had experience of diesel-electric drive trains with azimuthing pods from previous Rossinavi projects such as 70-metre Polestar, so we started the project well aware of how best to optimise the hull lines for this kind of propulsion. The Veth pods are equipped with electric motors delivering 1000kw to each pair of counter-rotating propellers by Rolla to deliver optimal efficiency in combination with low noise and vibration, as well as excellent manoeuvrabilty.
“Like the 50-metre Rossinavi No Stress just launched, we did not tank test the hull. CFD calculations are so accurate nowadays that tank testing, which is costly and timeconsuming, usually only serves to confirm the CFD data. This is quite a recent phenomenon and I still remember our first CFD calculations back in 2006, which were not nearly as reliable as tank tests back in the day.
“Since 2010 we have designed and developed no fewer than 18 hulls with Rossinavi from 38 to 70 metres in both steel and aluminium, all one-off projects with full-custom naval platforms started from a blank sheet of paper. Each one has presented its own set of challenges and we’ve just been contracted for three more full-custom projects: a 44-metre in aluminium, a 53-metre in aluminium, and a 63-metre in steel.”
Veth Propulsion developed the Veth Integrated L-drive in collaboration with Visedo with a flattened permanent magnet (PM) motor and counter-rotating propellers to increase efficiency while reducing installation space and noise reduction. The result is a very compact, lightweight thruster offering 360-degree thrust for outstanding maneuverability. Unlike Azipods, the design enables as few electrical components as possible to be fitted underwater where they are vulnerable to damage and create more hydrodynamic resistance. Diesel-electric propulsion is already quiet, but having no gear transmission in the vessel, water-cooled PM motors (versus air-cooled asynchronous motors) and electrical rather than hydraulic controls, means the Veth L-drive reduces noise even further. Because the L-drive has only one gear transmission, it is also more efficient, less ‘lossy’ and it can be mounted flexibly. The patented ‘Shark Tail’ housing developed in collaboration with Promarin has been optimised using CFD calculations and the asymmetric shape ensures an optimal flow of water toward the second propeller.
The main saloon and dining room are on the upper deck aft. Inside is a gym and spa with massage table and sauna, the obligatory pantry, and dedicated server room for the AV and navigation equipment. Forward is the observation lounge, a highlight of Akula’s design. The first part is enclosed, but two bright yellow doors open onto the ‘sky’ section in the forepeak – a kind of loggia open to the elements above with cut-outs in the steel hull plating (the hope is that a polished stainless-steel spray rail on the bow will keep the area reasonably dry in a seaway). Below the sky observation lounge is a covered mooring deck, which although completely hidden from sight provides an example of Rossinavi’s ingenuity at devising bespoke solutions. The regulations regarding mooring hardware on deck refer to specific distances above the waterline. Akula’s mooring deck is slightly below the minimum distance, so the shipyard mounted the bollards and winches on a raised platform while maintaining a full-height walkway all around so the crew can easily access the equipment. The solution has since been applied to a 44-metre project in-build. Another highlight is undoubtedly the wheelhouse. The wrap-around design with enclosed wing stations mirrors the layout of
commercial ships and working boats, much like that of Olivia O or Project Master (the 70-metre conversion under way at Icon Yachts also reviewed in this issue) that are both based on supply vessel platforms. The largest pane of glass is over seven square metres that offers outstanding visibility fore and aft.
“Simplicity is the ultimate sophistication,” Leonardo da Vinci is credited with saying and the Furuono bridge is not integrated, which reflects the owner’s preference for thoroughly reliable, low-tech solutions. Domotic controls have been eschewed in favour of manual operation and simple on/off functionality. He was even against televisions on board – and the hottub on the bridge deck – until his family convinced him otherwise. It’s worth noting also that he felt no need for a helipad either.
Following her delivery in the autumn, Akula will remain in the Mediterranean, perhaps venturing as far as the Red Sea where her owner is considering an expedition with Yachts for Science, a non-profit organisation that brings together yacht owners and marine scientists, to survey underwater tombs off the Egyptian coast. But once the warranty period has passed and any snags resolved he fully intends embarking on a round-the-world cruise: “The only question is, do we turn right or left?”
HEMP PATTERNS
NEW INDOOR & OUTDOOR HEMP COLLECTION
MADE OF 75% HEMP YARNS
Erik Spek and Onne Logger, owners of Azure Yacht Design & Naval Architecture in the Netherlands, are accustomed to combining the studio’s technical expertise and creative flair when engineering one-off superyachts. But 102.8-metre Project 1011 in-build at Feadship’s De Vries facility has proved more challenging than most.
BY CHARLOTTE THOMAS
When the experienced owner of the Amels yacht Here Comes The Sun – for whom Azure had worked on the yacht’s refit – came to Erik Spek and Onne Logger with an idea for a new-build project, they leapt at the chance. As the owner’s brief unfolded, however, the began to realise the complexity of what they had taken on. Not only did the owner want the 100-metre-plus yacht rated at a fraction under 3,000GT to offer the volume and guest space of a much bigger vessel, the delivery schedule was dangerously tight. Nonetheless, the project got off to a flying start.
“We started at Easter time in 2020 and from April to September we created the layout,” says Spek, who was also taken on as the owner’s representative. “We went out to tender in August and signed the contract with Feadship at the end of October. So the contract process went very quickly – just four weeks from first pricing to signing.”
A key element of Project 1011 is her single deck engine room that minimises the impact of the technical spaces and therefore maximises the guest spaces. “Under normal circumstances it would have been impossible,” says Spek. ”But because of the collaboration between Feadship and Azure, ‘we said, ‘let’s see if we can make this work’. And we did make it work.”
The owner opted for conventional shaft propulsion with MTU diesels after choosing diesel-electric drive with Azipods on a previous yacht, which had proved difficult to pack all the equipment in. The engine room is located a long way forward to benefit from the maximum depth of the hull, but the single-height deck and limitations associated with getting the right shaft line angles posed another engineering challenge.
The answer was to place the engines facing the wrong way with the gearboxes forward and the drive shafts effectively doing a U-turn to run aft outboard of the engines and through the hull in the stern. This means the shaft lines are some 37 metres long – the
longest the shipyard has ever installed. Space – or rather the lack of it – also proved an obstacle when it came to the exhaust treatment systems and the fact that the engine room is under the waterline. Outboard on each side of the hull is a small technical space on the deck above inside which the SCR and particulate filter units are housed. The solution also creates an elbow above the waterline – good practice for preventing water backfill (an idea Azure came up with during the concept development of 75-metre Kensho). Finally, proposed by the shipyard, the seawater inlet and pump are mounted in the double bottom of the yacht, thereby using the space in between for the cooling system. According to Spek, this has never been done before on a yacht.
The idea of a single-deck engine room has caught on thanks to Project 1011. “It gives you so much more real estate to use,” says Spek. “Now there’s only a small technical area on the lower deck and the rest is all cinema and tender garage. It was a no-brainer for the owner and was also one of the key points to start the project.”
The decision to stay below the 3,000GT threshold was partly the result of the owner’s previous experience of larger yachts that were unable to access many harbours, often required a pilot, and were manned by more commercial-minded crew. He did not, however, want to forego the amenities and space associated with his larger yachts –and that’s where the fun and games lay for the Azure team.
The engineering and technical challenges extended to all aspects of the build. For example, the main deck guest cabins enjoy six-metre swathes of glass; the aft tender garage includes a 15 metrelong shell door (the largest De Vries has ever built) to allow for a 13 metre tender; there is extensive use of fully retracting glass doors; a state-of-the-art bridge on the wheelhouse deck; and a structurally complex glass staircase and elevator in the central atrium. Further, the requested build schedule was very demanding.
“Three years and three months is an aggressive schedule for a very complex yacht of 3,000GT and almost 103 metres,” says Leo Boonstra, project manager at Feadship De Vries. “We really searched the boundaries spatially and engineering-wise, not only on the volume side but also because the number of sliding doors, the amount of glass and the central atrium made the project quite challenging.”
Then there was the single-level engine room on the lower deck that had not been done before in this size category. Even the air conditioning system was unusual, employing the mandatory vertical fire zone amidships to run trunking from lower-deck fan rooms throughout the yacht – a solution that saved space and mitigated noise in the guest areas. Further, the owner made several major changes during the build that “made it quite interesting,” quips Boonstra.
To keep to the tight schedule, Boonstra worked backwards from delivery time, through the minimum fit-out time, and the hull and superstructure period, to calculate the time left for engineering. From that they developed a plan, together with the hull and superstructure builder, to do a lot of things in parallel to try to win back more time for the engineering process. Then there was the
timeline for finalising the exterior and interior design by Sinot Yacht Architecture & Design.
“Luckily, it was my third project with Zlatko Imamovic (Sinot’s senior designer and project manager), Boonstra points out. “Many designers would have said it couldn’t be done, but Sinot really performed. The intense collaboration between Sinot, Feadship and Azure has been key to the success of the project.”
The owner’s previous yacht was 6,000GT and his request to create the yacht under the 3,000GT threshold (2,999.8 gross tons to be exact) but with much the same amenities proved the biggest challenge for the Azure and De Vries teams, and required some smart thinking when it came to space design and rule exploration together with Lloyd’s Register. Some GT wins, such as creating recesses for the central atrium that could be deducted, were relatively straightforward. Others required more investigation and some smart interpretation.
“The yacht has a covered mooring deck forward, but we found that if you make one-third of the height open, then you can deduct all the volume inside,” says Spek, “So together with Sinot we created a feature with horizontal bars in the topsides and calculated the space between to make sure it was just over that one-third rule.”
The winter garden on the main deck aft features sliding glass panels to open the entire area up. Other elements such as the rescue boat and life-raft recesses have also been designed to be excluded. In effect, this means the owner is getting a much bigger boat than other yachts of the same gross tonnage.
In fact, Spek and Logger estimate that Project 1011 is equivalent to a yacht of around 3,700GT.
The engineering went as far as shaving millimetres off the height of the overhead technical spaces above the deckheads. Spek roughly calculates that by reducing the height from 600mm to 550mm they saved at least 40GT throughout yacht. The flipside was that it posed a problem for the installation of equipment like drop-down televisions. “It certainly makes it harder for the shipyard fitters and it definitely requires more engineering time and flexibility from the yard,” says Spek. “I would say if you did this with an inexperienced shipyard it would be a nightmare.”
“The decision to stay below the 3,000GT threshold was partly the result of the owner’s previous experience of larger yachts that were unable to access many harbours, often required a pilot, and were manned by more commercial-minded crew.”
While Onne Logger represented Azure as the project naval architects, Spek was retained as the owner’s representative. The project team was deliberately kept very small, essentially comprising Spek, Logger, Imamovic, Boonstra and, in the latter stages of the project, chief engineer Christian Dunn. Invaluable also was the contribution of fleet manager Jake Jacobson, who has worked with the owner for 15 years and was able to help Spek understand how the client uses his yachts on a daily basis.
“I know from recent projects that you sit down to discuss things and before you know if there are 30 people round the table,” says Boonstra. “We agreed from the start to limit the size of the team for Project 1011, so there are only a few decision-makers. We decided to keep it only to the people who could say yes or no.”
The fact that business partners Spek and Logger had potentially conflicting roles required a period of adjustment within the team. “It’s different and it’s new, and it took some time to get my organisation in the spirit of the project,” says Boonstra. “You need to win trust, and if we didn’t all have trust in each other then this project would have been impossible. And it was fun to see Onne and Erik arguing over things because Erik was defending the owner!”
For Logger, there were several advantages to the pair taking contrasting roles. “I think it brings a lot of efficiency,” he says. “And for sure we had some funny situations in the weekly meetings when Erik and I were fighting about some solutions and items, and the shipyard was like, ‘What’s happening here?’ But we always came up with a solution during the same meeting and not by doing all sorts of investigations that would take months and months.”
The fact that Project 1011 is successfully on schedule despite all the engineering and timing demands placed upon the team by the owner, who has remained involved in every detail and pushed yard and designers on all aspects of the build, is testament to what can be achieved when naval architect and owner’s
representative hail from the same core team.
“If a client wants to create his own masterpiece, his own dream, I think we have the in-house skills to create something that’s really unique but also feasible,” says Spek. “This was the starting point for Project 1011 We began with a clean sheet of paper and the owner saying ‘This is what I need’. And because I was involved in the development from the start, I knew every centimetre of the project.”
Sam, Electrical
1 OF 500 SKILLED CRAFTSPEOPLE
Whether refit, restoration or build, every Pendennis project is a true team effort. Our time-served tradespeople are experts in their field, crafting precise and perfect work at every step of the way.
The demand for ever larger glass elements on yachts has presented designers and manufacturers with opportunities – and challenges. Tilse GmbH in Germany, a pioneer of glazing solutions on superyachts, has also been instrumental in establishing the rules and standards to keep pace with developments in design. We visited the company headquarters near Berlin to find out more.
BY JUSTIN RATCLIFFE
It has been said that best superyacht interior design is the exterior scenery. Helped by advances in glass manufacturing techniques, designers have been quick to follow the lead of land-based architecture firms likes Eckersley O’Callaghan, which advised Feadship on the extensive glazing aboard 78-metre Venus, to create seethrough worlds that break down the barriers between inside and outside. The result is yachts with bigger windows made of glass offering greater strength, safety, clarity, and protection against heat loss and gain. But the marine environment is very different from dry land and yachts are not the same as
buildings. For a start, the glass on a yacht is subject to constant flexing and accelerations and has more to do with the watertightness of the vessel than its structural integrity. The design pressures of marine glass are higher because it has to be able to resist green water and gale-force winds. Additionally, owners expect the glass on their yachts to be of better quality than in their homes, while clarity and scope of vision in the wheelhouse are safety factors stipulated in Class regulations. And it’s not just about windows in the hull and superstructure any more: pools, bulwarks, skylights, floors and even underwater windows made of glass are now commonplace on large yachts.
“Before we were obliged to use the toughening services of other companies, who in some cases were also our competitors”
The rural village of Nennhausen not far from Berlin in what used to be East Germany seems an unlikely location for a trailblazing company like Tilse. Surrounded by green fields, its orderly group of industrial buildings is nestled among neat grass verges and firewater ponds. After setting up the company in 1974, founder Hans-Joachim Tilse moved operations there from Berlin after the unification of Germany. The facility has gradually expanded over the years and the latest additions have effectively doubled Tilse’s production capacity with new bending ovens, CNC cutting and grinding machines, and a state-of-the-art chemical toughening plant.
“Before we were obliged to use the toughening services of other companies, who in some cases were also our competitors,” says Henning von der Thüsen, managing director of Tilse and the founder’s son-in-law.
“At a certain stage of production we had to send the glass to subcontractors as far apart as Italy, Switzerland and Belgium, but some of it was getting damaged during transport. That gets very expensive with double-curved glass of two or more plies, because if one breaks we have to reproduce all of them.”
The sheets of glass are made at the glass mill using the float method by which the molten ingredients are ‘floated’ over a layer of liquid tin to create perfectly flat glass. But all the subsequent processing is done in-house by Tilse, from the initial 3D measurements on board the yacht and subsequent design of the glass elements, to the bending, toughening, lamination and final installation. Its Formglas Spezial, developed specifically for marine use, has type approval from Lloyds Register.
“Our turnkey approach to projects is what differentiates us from other suppliers in the market,” says von der Thüsen. “That means the client comes to us with a series of openings in the hull and superstructure of his yacht and by time we’ve finished we’ve filled those holes with glass. It’s a one-stop shop and we take responsibility for the entire process from start to finish.”
Sitting on the table in Tilse’s conference room is a sample of the thickest laminated glass
it has produced to date. Designed for an underwater Nemo lounge on a superyacht and comprising 13 layers of chemically toughened glass plus an insulating layer, the actual curved glass window measures 3.8 metres by 1.8 metres and weighs 2.5 tonnes. Black borders on each glass ply disguise the many layers for better aesthetics, but also protect the adhesive used to bond the window in place from UV light. Underwater windows are generally required to be double the thickness of the hull structure and because they are subject to constant water pressure, the long-term strength properties of the glass and stiffness of the interlayer need to be taken into account during their design. The largest window Tilse has delivered in terms of surface area is 5.8 metres by 1.8 metres and weighs 2 tonnes. Installing these outsize windows presents its own set of challenges. They are usually moved into position with a suction unit suspended from a crane, but locations underneath the hull or an overhang cannot be reached using this method. In these instances, Tilse uses a custom-made machine of its own design nicknamed ‘the Monster’ equipped with a counter-weighted telescopic arm.
Tilse has drawn on its 40-plus years of experience in the marine sector to help define the rules and regulations governing the use of glass on superyachts. In 2007, the company set up an ISO working group with other industry players to define the design and approval criteria for glass on yachts. There were existing rules for opening and non-opening windows on ships, but Class surveyors tended to interpret the regulations differently with the result that suppliers like Tilse were often required to carry out costly destructive testing of its glass to prove it was safe in different situations. Furthermore, rules like BS MA 25:1973 were established when the main type of glass allowed on yachts was thermally not chemically toughened.
“These different interpretations created uncertainty and unpredictability, both for us and the shipyards,” says von der Thüsen. “We needed to find a common approach and so based on our knowledge of the behaviour of glass, its known bending strength for instance, we established a formula for calculating the required thickness of glass to meet varying design pressures depending on the size and location of the aperture.”
The standardisation process took five years and resulted in ISO 11336-1:2012, which is today the reference for Classification Societies and Flag States in all standard glass applications on yachts over 24 metres in length under 3000 GT carrying up to 12 passengers. ISO 11336-1:2012 effectively changed the mindset of the yacht industry and provided the necessary tools to better understand and explore the potential of glass for new onboard applications. ISO 11336 was also the first attempt to provide standards for bonded glass windows, which previously were usually fixed mechanically. Bonding with polyurethane (PU) or Silyl Modified Polymers (SMP) allows a degree of elasticity or ‘swimming’ to compensate for the hogging, sagging and torsion due to the vessel’s movement (silicon-based adhesives are not permitted in marine applications because of the risk of silicon contamination of metal surfaces from lubricants on manufacturing tools that can lead to de-wetting and adhesive failure). The main disadvantage of PU and SMP adhesives is that they are not UV and temperature stable – hence the black borders mentioned earlier. Deformations and accelerations of the vessel, temperature and wind suction
Top: When the glass arrives from the foundry it is first washed and inspected for defects against powerful backlighting before processing.
loads, are all factors that determine the bond thickness and the adhesive’s ‘bite.’
ISO standards are not static and are generally revised every five years to take into account the latest developments in science and technology (ISO 11336 is due for revision this year). In special cases, physical testing is also necessary. Hull windows and portholes close to the waterline are required to have deadlights fitted on the inside to protect against floating objects such us shipping containers. This is not practical on larger windows – including Tilse’s Nemo window that is under the waterline – so sacrificial layers of glass provide additional protection. Finite Element Analysis can help determine the number of additional plies required, but the results may still have to be confirmed by impact testing in the lab.
“If a client comes to us wanting an underwater window or another special glass application, then we need to design it together with the shipyard,” says von der Thüsen. “Because the Classification Society is not only looking at the glass, but also the surrounding structure.”
A critical component of laminated glass that contributes to both the strength and longevity of laminated glass is the interlayer, the material sandwiched between two or more glass plies that sticks them together. A high adhesion level helps to reduce the risk of delamination, but the trade-off is lower impact resistance and safety performance. The most commonly used interlayer is PVB foil (polyvinyl butyral), but it is sensitive to humidity which in open-edge applications on yachts can lead to delamination as the interlayer degrades. For this reason, Tilse has developed its own adhesive resin interlayers that are 100 percent moisture resistant and filter out almost completely harmful UV rays that also are responsible for the fading of interior furnishings.
The visual quality of glass is slightly harder to define. Hadamar Guidelines used to assess the visual quality of glass in buildings are not considered sufficient for superyachts. The most common solution is a specification agreement between the client, designer, shipyard and glass contractor that stipulates the number, type and size of defects per square metre. However, such is Tilse’s reputation for high quality that its regular customers rarely carry out factory assessment tests before installation.
Chemically toughened glass that has had its atomic structure reconfigured by submerging it in a bath of molten potassium salts at 450°C, is more expensive than thermally treated glass but superior in several ways. The composition of the chemical bath can also be modified and tailored to enhance certain properties based on the required specifications or intended application (Tilse’s in-house recipes are a closely guarded secret), which has opened the way for using glass on yachts beyond its classic function in windows or doors.
Heat-treated glass can be heat strengthened or tempered, but both are produced in a very similar way. Basically, the glass is heated to approximately 650°C and then force cooled to create surface compression in the glass.
Controlling the rate of cooling determines whether the glass is heat strengthened or tempered. For tempered glass the cooling is much more rapid, which results in higher surface and edge compression.
Chemically toughened glass has little or no optical distortion and a higher degree of resistance to abrasion, bending, impact and temperature fluctuations than heat strengthened glass, which is prone to surface deformations and anisotropy, the stress or strain patterns in the glass that appear as iridescence (especially when wearing polarised sunglasses) caused by uneven heating or cooling in the furnace.
The curved windows aboard 70-metre Eco (now Zeus) designed by Martin Francis were revolutionary when Blohm&Voss launched the yacht in 1991. Francis had developed a knowledge of glass while working with architect Norman Foster in the 1970s and later with I.M. Pei on the famous glass Pyramid in front of the Louvre in Paris. In fact, Eco’s windows were inspired by the curved windshields of Parisian buses.
“Our turnkey approach to projects is what differentiates us from other suppliers in the market.”
A company ironically called Flat Glass, a German subsidiary of Pilkington, was contracted to make the curved panes using heat toughened glass. The costly tooling to create the curves passed the heated glass panes between two matching moulds to bend them into the desired shape (faint stretch marks in the corners of the windows show where clamps were applied to lift the glass). These moulds were made of wood with screw jacks to adjust them like the staves of a barrel. When they were pulled apart, air jets had to follow the exact same curvature to cool the glass uniformly.
The next challenge was to prove to the Lloyd’s surveyors that they were strong enough for the job as storm shutters could not be fitted to the rounded windows. “We did a calculation based on a worst case scenario of asymmetric loading if a wave went over the foredeck and wedged itself under the bottom of the glass”, says Francis. “Lloyd’s accepted our calculation, but required additional storm mullions that could be fitted in place from the inside. These have never been used. Because of her low freeboard in the bow, we also designed a foredeck locker that acts as a buffer to redirect green water into the centre of the curved glass at its strongest point.”
Eco’s windows were effectively a massive experiment and it is highly unlikely her windows would meet today’s more stringent safety and quality standards. But the gamble paid off: “I calculated that we needed at least one spare piece of glass for each pane because they were going to destroy the moulds,” says Francis. “To this day –touch wood – none of the spares have been used.”
More recently, Francis worked with Eckersley O’Callaghan to design the SkyDome on the P&O cruise ship Iona. The massive glass roof measuring 41 metres by 29 metres can move independently from its support structure to compensate for the deformations of the ship due to the wave loads and vibrations from the engines.
In building construction it is the measure for the insulation of a
With the increasing size of windows on yachts one of the most important – and overlooked –performance measurements of glass is the solar factor expressed as the g-value. This is the ratio between the thermal energy coming from the sun entering the interior and the energy arriving on the external surface of the glass. A portion of solar energy absorbed by glass is emitted both inwards and outwards, but the solar factor indicates the amount of incoming solar energy. The higher the g-value, the more heat the glass will allow through.
Adding more layers of glass or an air gap has little effect on the solar factor. Tinted glass is an effective way to lower the g-value and Tilse installed particularly dark grey glass on 90-metre Dar built by Oceanco. Adequate shading is another important consideration. The way we perceive the solar factor can be described as the difference between walking out onto the aft deck into direct sunlight on a hot summer day, and coming out into the shade of a canopy. Interestingly, the temperature in both cases is the same, only the level of solar radiation is different. Von der Thüsen believes shading solutions should also be a part of window design on yachts if large areas of glass are to be combined with energy efficiency.
“The designers have their own ideas and unfortunately we are rarely consulted on this issue,” he says. “It is especially apparent in
motor yacht designs with raked, automotivestyle windshields in the wheelhouse with no overhang to provide shade. The regulations don’t allow tinted glass or special coatings on the bridge, so the air-conditioning is always full on during the day. This cools the glass down on the inside, which leads to condensation on the outside and then you might see a superyacht with its wipers on in beautiful sunny weather!”
Thermal transmittance – the rate of heat flow through the glass due to the difference between indoor and outdoor temperatures expressed as the Ug-value – is more important on yachts designed to cruise between hot and cold regions. This is because the Ug-value is basically an expression of how well a glass window will hold in heated or cooled air. In this case, adding an air gap does improve the insulation properties.
“The size of windows on yachts may be getting bigger, but there is a limit to how big they can get,” concludes von der Thüsen. “The largest standard flat glass in production is 6 metres by 3.21 metres and although longer and wider sheets can be produced for special applications, that’s the upper limit of our focus. It’s not question of technology but practicality, because these glass pieces still have to be transported by road and then installed on board. When they get too big and heavy, the logistics start to outweigh the advantages.”
By Georgia Tindale
From whichever angle it is viewed, the role of the superyacht captain in 2023 is a highly complex and challenging one. Whether it’s addressing the needs of the owner, crew, or the not-so-simple task of navigating the vessel across the seas from A to B, these individuals have a huge amount to manage day to day.
One element of the captain’s role which often flies under the radar is the act of anchoring the vessel. Although superficially this may seem a simple enough task, the safety issue of avoiding dangerous anchor drag, as well as the potentially devastating consequences to marine environments of unsafe anchoring practices quickly serve to complicate this view.
Step in: AnchorGuardian. Developed by a crack team of six marine experts from Swiss Ocean Tech and ready to make its debut at the METSTRADE show in Amsterdam this year, AnchorGuardian was born out of the realisation that the technology to help captains and crew anchor safely and securely, wherever they were based in the world, simply did not exist in this form.
In a nutshell, AnchorGuardian functions by acting as the captain’s eyes under the water, monitoring the movement and positioning of a ship’s anchor and delivering intelligent data back to the crew throughout the entire anchoring procedure (from laying to lifting) to inform them of any risk of anchor drag and any other issues. In this way, AnchorGuardian offers an enhanced dimension of underwater safety by providing predictions and triggering immediate alarms with sub-meter accuracy.
Harnessing AnchorGuardian’s proprietary and state-of-the-art sensors, this patented technology operates independently of GPS and any movement from the ship, meaning that it feeds back the most accurate data possible, free of any distractions. As NMEA2000 compatible software, AnchorGuardian can be seamlessly integrated into the existing communications system on board, with the user interface accessible on the ECDIS, via tablet, or via the AnchorGuardian app on any mobile device.
Vitally, the high-tech AnchorGuardian solution exists to intellectualise, rather than to automate, anchoring for captains and crew, moving the act of anchoring from a reactive to a proactive process.
Company Founder Thomas Frizlen explains more: “The focus of our efforts is safe anchoring. For that to succeed, the anchoring process has to become transparent. We give captains the information and control they need to set the anchor in the best possible way and to monitor it in real time while anchoring.``
He continues: “We take the principle of anchor watch to the next level by combining AnchorGuardian’s intelligence with big data to warn captain and crew before the anchor starts to drag. Since we collect the data directly at anchor, we are also independent of any movements of the ship itself. False alarms caused by wind, current or swell are thus excluded. Our mission is to bring safety to anchoring, for sailor, ship and sea.”
Alongside the safety concerns of anchor drag, if it is not monitored correctly, anchoring can have a majorly negative impact on the natural marine environment. The larger the boats, the heavier the anchors and the higher the impact on the marine seabed. These anchors can leave large scars in Posidonia meadows which can take more than a century to heal.
Thanks to the data provided by AnchorGuardian, captains and crew can avoid anchoring in particularly sensitive areas, minimising the vessel’s impact on the fragile marine environment.
Finally, as winners of the 14th INNOVATION WORLD CUP (2023) and finalists in both the Smart Yacht Innovation Awards (2023) and the Ocean Innovation Awards (2022), AnchorGuardian is already being recognised both within yachting and further afield for the sustainable environmental impact of its innovative technology, as a recent testimonial highlights.
“As one of the leading shipping companies worldwide, Eastern Pacific Shipping (EPS) understands the need to minimise anchor dragging, both for the safety of our seafarers onboard and for environmental preservation. Swiss Ocean Tech brings their revolutionary technology to address this concern,” comments Gil Ofer, EPS Special Advisor for Innovation.
To find out more about AnchorGuardian, visit anchorguardian. com or come and meet the team behind the solution at its official debut at METSTRADE 2023 (15-17th November).
A limited supply of systems are now available for 2024, which can be pre-ordered via info@swissoceantech.com.
By Georgia Tindale
Custom tender builder, Compass Tenders, was founded by Richard Faulkner almost twenty years ago. The yard, which is based on the Hamble River in Hampshire, UK, has delivered more than 65 superyacht tenders to date and now has at least six tenders in-build at any one time. Francesca Webster sat down with Richard to find out more about the value of customisation in the tender sector.
Founded on the principle of designing and constructing premium, customised superyacht tenders, Compass Tenders specialises in taking design cues from the motherships and incorporating them into the tenders themselves.
“We have an incredible in-house team, and two individuals who work almost exclusively on client proposals.” Richard explains, “The first thing we ask for is the exterior design of the mothership and the garage information. Taking design cues from the parent superyacht, be that the bow shape, superstructure lines and hull form, or specific elements of the detailing, we replicate the aesthetic and ensure a continuity of style and quality.”
The next discussion is about usage requirements and operational intention. “Yes, the tender has to look the part, but it has to be a perfect match in terms of both form and function, too,” adds Richard. “With such an experienced team, we don’t necessarily need to involve the superyacht’s designer for defining the tender’s look but we always welcome collaboration.”
A great example of the superior levels of customisation achieved by Compass, is the tender for the 2021-launched support yacht Nebula, a 68m built by Astilleros Armon and designed by Schwalgien Yacht Design. Working closely with the design team, Compass designed and built a striking 12.3m catamaran tender, which is stowed on the yacht’s aft deck and echoes the lines of the mothership with eye-catching accuracy.
More recently, Compass Tenders delivered an 11.1m limousine and 10.1m open tender to Oceanco’s 105m H3 This duo were designed in conjunction with Reymond Langton and the interior of the limousine, with its teak floor in intersecting geometric shapes and leather panelling is a beautiful example of how design attributes can be replicated and carried through to the tender.
Whilst a proven platform suits some customers, and is an option offered by Compass with their Latitude range, others embark on a completely custom project. Of the 12
boats Compass Tenders currently has on order, six are full-custom commissions.
As Richard explains, some owners are concerned about the performance or capabilities of a full custom tender, and prefer to adapt an existing platform to their liking. At Compass Tenders, however, the team builds its tenders on a series of tried and tested hull forms, allowing them to ensure the boat’s stability and capabilities.
“Our hulls are built from composite and the entire construction is completed here on site. In the build oven we can precisely measure the resin ratio so that we can monitor the overall weight distribution and material quality, we have dedicated paint booths and woodwork studios, and we find this better enables us to achieve the consistently high standards required by our clients,“ says Richard.
While the hull is still in the mould, the structure, including bulk heads and engine mounts, is assembled and bonded in, so that the entire structure is cooked together. Following a post cure, the hull is broken out of the mould and is already a highly stable structure when it is released, avoiding any change in form or shape, helping the team to guarantee the stability of the moulded hull.
With 100 skilled personnel, many of whom have been with the company for 10 years or more, the experience within the team means Compass Tenders can deliver custom builds in as little as 18 months. For Richard, this talented workforce is a key element of the company’s success, ensuring consistently exceptional standards from start to finish, and through to aftersales, with the same individuals working with owners and project teams from the moment the contract is signed.
Compass Tenders is a master in its field, dedicated to delivering bespoke tenders to the world’s most iconic superyachts.
To find out more, or to reach out to the team:
Website: www.compasstenders.com
Email: info@compasstenders.com
Phone: +44 (0) 2380 457 844
Superyacht captains and close friends Lee Stevenson and Giles Frankal set up bespoke superyacht consultancy Occam Marine in 2021. The company name is derived from Occam’s Razor, a philosophical concept that recommends problem solving by searching for the smallest possible number of explanations or the simplest solutions.
BY JUSTIN RATCLIFFE
As owner’s representatives or responsible for the technical oversight of projects – sometimes both at the same time – Occam Marine has quickly garnered industry recognition and currently has four major new-builds on their books. These include the 110-metre Project Shackleton at Lürssen and the 80-metre Project 826 at Royal Van Lent Feadship. We began our conversation by asking about the reference to Occam’s Razor in the company name.
Giles: There’s a tendency to overcomplicate things in our industry, whereas our frame of mind is more ‘Let’s find workable solutions after analysing the issues and employing the Occam’s Razor ethos.’ We know from working in shipyards around the world that things can get overly complex. It’s a case of recognising the intricacies involved and introducing flexibility at either end of the process from the designer to the shipyard. At some stage there’s always going to be a disconnect, and so what we do is really act as a buffer or intermediary and propose workable solutions and an agenda that satisfies all parties. Of course, it’s not always going to run like that, but a little flexibility is important.
Lee: I think that one of our strongest elements as a company is understanding how to form relationships in order to achieve the best possible outcomes. I’ve been involved in new builds at yards where the adjacent project has struggled due to competing interests between stakeholders. On Project NB826 at Feadship I’m responsible for the technical oversight, but I work closely with the owner’s rep. For this relationship to succeed, we both fully understand and respect each other’s role within the process. I’ve done a couple of new builds as captain with Feadship in the past, so I understand how the yard likes to work and how to create the best experience for the owner and crew. We understand that all stakeholders involved have slightly different priorities; that the principal seeks value, that the shipyard has got to make a profit and, in fact, all stakeholders have to balance their books. Therefore, everyone has their reason for being in the shipyard and having a full understanding of how that meshes in the right way is very important. Another important relationship to consider is the one we have with the family office – if you don’t have that relationship and trust in place, it won’t derail the project necessarily, but it can slow things down, so it’s something we try to
establish very early on in the project.
Lee: The reason we set up the business together is because we offer something different to other project management or technical supervisory companies. Every member of our team has operational experience, having worked on new builds and as sea-going officers. We feel that this gives us particular insight into how yachts should be built from an operational perspective –something which is quite often overlooked. There are very few companies that can take a project from the germ of an idea in a client’s head to a fully operational yacht.
Giles: It can sometimes be the case that when a crew arrives too early on a project, it creates complexity and increases costs. And these days, of course, with Brexit, British crews have to be on rotation at European shipyards and that also means additional costs. We actually did a cost matrix of how much we can save doing it our way for a fairly standard 70-metre new-build, and we found that the savings were upwards of 2 million euros. What that really means is that we’re capable of delivering the boat so that a crew can come in three or four months before the end and have everything ready for them.
Giles: Project Shackleton at Lürssen presented a rather different scenario. In this case I am the owner’s rep, as well as providing technical and project management services. The idea with this particular project was to take a completed yacht without a luxury interior and then put it through a complete redesign and rebuild at a different shipyard, so it will be delivered as a new boat. As you can appreciate, the complexities around this project have been considerable. The yacht had to complete a technical sea trial before arriving in its new location, therefore we recognised in this case it was appropriate to employ the officers that would eventually sail with the boat. If you’re starting a standard new build and creating a contractual specification, you probably wouldn’t need such a big team. But when taking over such a large, complex project and then changing it, I think you need to have a good team on the ground straightaway to field the sheer volume of questions and queries coming our way. In the case of Project Shackleton, this worked well because we have full control over the sea going crew and our own technical team. Ultimately, we know what works. And, crucially, what doesn’t.
Previous
Yachting has an enduring love affair with teak, but for how much longer?
Shrinking stocks of wild forest teak, an industrywide sustainability drive and the first criminal convictions for the illegal importation of Myanmar teak, are pushing shipyards to seek out wood alternatives.
BY JUSTIN RATCLIFFE
DISCLAIMER: Although synthetic or composite decking materials are widely available, due to space limitations this article focuses on natural or treated woods that aim to replicate the aesthetic and technical properties of old-growth teak, still the preferred choice on superyachts.
Any talk about teak is inextricably mixed up with the environmental, political and humanitarian situation in Myanmar. Although not exclusive to the country formerly known as Burma, about half the wild teak left on the planet grows in Myanmar, which has long been the de facto exporter of the prized hardwood. However, since June 2021 when the state-owned Myanmar Timber Enterprise (MTE) was sanctioned by the EU, any imports of teak from the country constitute a breach of those sanctions.
Earlier this year the District Court of Amsterdam confirmed the criminal convictions of one company and two individuals for importing teak from Myanmar into the Netherlands via the Czech Republic in breach of due diligence provisions defined in the EU Timber Regulation (EUTR). No one is going to prison and the fines imposed represent little more than a slap on the wrist, but these first prosecutions represent a step towards keeping illicit teak out of the EU and came as a wake-up call for timber merchants and yacht builders alike. Shipyards are not legally responsible for the sourcing of the teak used on their yachts unless they are directly importing the wood themselves. It usually passes through many hands and only the first importers are required to prove it is legally sourced. But traceability and due diligence can be very difficult to establish, which is why some yards use independent verification providers like Double Helix Tracking Tecnologies, a Singapore-based company that relies on a DNA-based system to verify where the teak originated.
In the past yacht builders have tended to turn a blind eye, but they are well aware of what is at stake. Most have stockpiled supplies of old Myanmar teak, but these are rapidly running out. One decking specialist told us that the top north European shipyards have sufficient supplies for up to eight more new-build projects, depending on size. Understandably, the price of old-growth teak has gone through the roof. Another decking contractor we talked to was recently quoted €50,000 per cubic metre for a batch of stockpiled Myanmar teak, three times the going rate for plantation teak (including wastage, at least 10 cubic metres of teak are required to deck a 70-metre motor yacht).
There are good reasons why teak has been used by boat builders for at least 2,000 years. It has a high oil content, high tensile strength and an exceedingly tight grain, which make it tremendously weatherproof. It is resistant to rot, cracking, fungi and mildew with a low shrinkage ratio, so fluctuations in moisture content do little to change the size or shape of the battens. It also contains silica, which is what lends the wood its non-slip qualities – and blunts cutting tools.
Plantation teak is ready to harvest after 20-25 years, but shipyards much prefer teak that grows slowly in the wild and may be four times older. Young teak trees in the forest have to compete with established trees, so only the strongest grow to maturity. Because of the dense forest canopy they reach for the sunlight without sprouting low branches, resulting in a straight grain with no knots or ‘moisture traps’ that weakens the lumber. Widely spaced plantation trees cultivated in direct sun do grow lower branches, which are pruned off but leave pin knots and moisture traps. Grown quickly to maximise return on investment, they have wider growth rings and a looser grain, which means the wood is less dense.
The Janka Wood Hardness Scale measures the force needed to embed a 11.28mm steel ball into a piece of wood. That force is recorded in pounds-force (lbf) in the US, or kilograms-force (kgf) or newtons (N) in other parts of the world. Teak appears on this scale with a rating of 4,740 N, Cumaru is 14,800 N, and Ipé is 15,620 N.
But hardness is not the only consideration for boat builders, nor the most important. Teak is very dimensionally stable, an important factor when laying decks. Its shrinkage coefficient is 5.3% (Ipé is 7.2% and Cumaru is 7.7%). Heat-treated woods are favoured because although they lose a small amount of density, their dimensional stability is improved substantially.
Other factors are Modulus of Rupture (MOR), sometimes referred to as ‘bending strength’, which is used to determine a wood’s overall strength, and Modulus Elasticity (MOE) that measures a wood’s deflection but not its ultimate strength (some species of wood will bow under stress, but not easily break).
German decking specialists Wolz Nautic has been using FSC-certified plantation teak for series yacht production for over a decade, processing up to 100 cubic metres of timber per year with results that are “absolutely comparable with previous Myanmar quality…” However, the quality of plantation teak depends on the plantation, slow growth and care of the trees.
“We’ve carried out tests with renowned wood institutes which prove that the plantation teak tested from Latin America shows almost the same performance, properties and durability as, for example, teak from Myanmar – the difference is very small,” says managing partner Michael Wolz.
Laminated teak (sometimes and misleadingly called ‘green teak’) is plantation wood glued together in 1.2mm layers. The lamination process improves durability and also lends the deck a tighter ‘grain’ that simulates oldgrowth teak, but the seams are susceptible to weathering and the strongest adhesives are far from eco-friendly.
“We began looking into alternatives to Myanmar teak more than 10 years ago and there’s some really good plantation teak out there,” agrees Richard Strauss, CEO of Florida-based Teakdecking Systems that has a base in Barcelona and has installed teak decks on superyachts such as Oceanco’s 109-metre Seven Seas and 127-metre Koru.
“Let’s not forget that teak is grown in many places around the world – Costa Rica, Thailand, India, Tanzania, Bolivia. We have four people in our acquisitions team and they travel the globe to ensure not only the quality, but also legality of the teak we buy.”
But performance is not the only consideration. The tight grain of old-growth teak is widely considered more aesthetically pleasing. Although good planation teak may be comparable to Myanmar teak from a technical standpoint, “Visually, some compromises may have to be accepted,” admits Wolz. This is especially true when it comes to superyachts, where the tendency has been to seek out the finest – and often rarest – materials.
Above: Lürssen launched a research project back in 2008 to find an alternative to natural teak. The result is Tesumo made from treated
In 2008, Lürssen launched a research project in collaboration with the University of Göttingen to investigate different treatments that improve the properties of wood species and make them more teak-like. The result is Tesumo, a treated Limba wood grown in tropical West Africa that its creators claim offers the strength, beauty and warmth associated with teak, and more.
“We had already tested alternative natural decking materials, but the results were disappointing because all the other timber species failed in one way or another”, says Dr Bernhard Urban, Head of Development & Innovation at Lürssen. “So we focused on thermal modification and impregnation. Each of these processes led to specific improvements of the tested timber, but neither met our defined requirements for high-quality yacht decking. Finally, we started to test a combination of the twostage modification processes that led to the desired results.”
Lürssen has been working with Wolz Nautic
The European Timber Regulation (EUTR) came into force in 2013 to make it much harder for illegally harvested wood to be sold in the EU. The regulation required operators to exercise ‘due diligence’ with verified documentation, although the provisions were often side-stepped. In the wake of the 2021 military coup in Mynamar, several nations – including the US, Canada, Australia, the UK, as well as the EU – imposed economic sanctions that also targeted the Myanmar Timber Enterprise (MTE). Nonetheless, a subsequent report by the London-based Environmental Investigation Agency (EIA) documented how Myanmar teak was still being trafficked through Italy to the rest of Europe. In March 2023, the Forest Stewardship Council (FSC) launched an initiative to focus attention on the ongoing impact of the yachting industry on the world’s forests, and last May the EIA named 12 American timber firms that have imported teak from Myanmar since the start of the 2021 military coup, including several yacht decking companies.
on Tesumo. Using weight- and noisereducing cork as a levelling material, the system has been tested on smaller yachts for more than six years with positive results. Custom projects include 183-metre REV Ocean, set to become the largest explorer yacht in the world. Tesumo was also chosen for 26-metre Project Ocean, the all-aluminium explorer yacht approaching completion at UK-based Arksen.
“As teak is still the expected finish on a yacht, we wanted to find an option with the same look, feel and performance as teak without the same sustainability issues,” says Ewan Hind, COO at Arksen. “While there are some synthetic options for decking, our requirement to find a timber deck with similar properties to teak and an improved end-of-life strategy meant we had a small pool of options. From reviewing the alternative timber options against a range of points, including aesthetics, price point and ease of installation, Tesumo came out as the top choice for our application.”
The Hill Robinson Group is committed to delivering extraordinary service every day. With a deep-rooted passion for providing exceptional experiences, we take great care in managing every aspect of a yacht's operation with meticulous attention, utmost discretion, and unwavering dedication. Our international team consistently achieves remarkable feats, ensuring that our clients receive nothing short of excellence.
We invite you to explore and witness the remarkable day-to-day accomplishments that define our organisation.
Marine Maple is a treated wood that has been thermally modified, an age-old process that dates back to the Vikings who cured the wood for their ships with fire. Only heat and steam are used to trigger physical and chemical reactions in the wood at a cellular level. In addition to improved dimensional stability, thermal modification adds other desirable properties such as better resistance to mildew and mould.
“Our entire business is based on teak, but we could see the writing on the wall and first started experimenting with alternatives about 15 years ago,” says Jon Winstanley, managing director of Modesty Yacht Carpentry in Palma de Mallorca and creator of Marine Maple. “At the very least we had to be able to offer our customers an alternative.”
Winstanley originally focused on thermally modified ash with good results, until the Emerald Ash Borer beetle destroyed tens of millions of ash trees in 30 states across the US. He then switched his attention to hard maple, which is grown in sustainably managed North American forests. Marine Maple’s key features are its strength (harder than teak on the Janka scale – see sidebar), colour and grain straightness, as well as good adhesion qualities to glues and caulking compounds. Heat-treated wood tends to be more brittle and requires care when cutting and bending, but once in place behaves in the same way as teak and requires similar care.
First installed on the swim platform of a busy charter boat in Ibiza and having proved a durable substitute for teak, at the time of writing a Marine Maple deck was being installed on a 35-metre new-build motor yacht. Southern Wind Shipyard is also offering Marine Maple as a decking option on its new 100-foot line of ‘Smart Custom’ sailing yachts.
“Among the options available in the market, we have identified Canadian maple as the most interesting choice for our yachts and their intended use,” says Andrea Micheli, CCO at Southern Wind, which recently completed the first Life Cycle Assessment of a SW105 calculated over a 30-year period. “At least for the time being, we prefer maple over cork, reconstructed teak, reconstructed wood, and other synthetic materials, due to its better aesthetic and overall technical characteristics.”
Oceanco commissioned an independent
study of Marine Maple, along with other treated wood alternatives, to compare its properties to teak. The principle tests measured the uptake of salt water and the effect on the equilibrium moisture content (EMC), dimensional stability, and cleavage strength as a measure of the tendency to splinter. Marine Maple did not perform quite so well as teak in its reaction to the salt water treatment, but has a cleavage strength that is superior to teak.
You would think that other hardwood species could easily stand in for teak, but it’s not that simple. Cumaru, for example, sometimes called ‘Brazilian teak’, is among the hardest and most durable woods on the planet. Ipé is another tough South American variety known as ‘ironwood’ that has the same fire rating as concrete or steel. Ipé is so dense it sinks in water, which could be problematic on a yacht but also makes working it very difficult. The issue with both these species, however, is that illegal logging and clearcutting (the logging method in which resilient natural forests are harvested and replaced with man-made tree plantations) have a high ecological impact.
Iroko or ‘Africa teak’ is a very durable wood that silvers over time like teak and is much less expensive. According to the IUCN Red List, a database of the conservation status of the world’s biodiversity, Iroko is classified as ‘Lower Risk’, a classification below ‘Vulnerable’. But that assessment was made in 1998 and documenting the journey of the lumber with a chain-of-custody paper trail to prove the wood was legally sourced from a certified rainforest in West Africa is not straightforward.
Meranti or shorea wood is a tropical hardwood from Southeast Asia that has many of the same properties as teak. Unlike tropical hardwoods that have become endangered due to illegal harvesting, the bulk of Meranti wood is supposedly sourced from sustainably managed forests. Nonetheless, it is listed as endangered on the IUCN’s Red List due to excessive logging, habitat loss, insufficient regeneration and a slow recovery rate.
Accoya is the brand name for a sustainably sourced soft wood produced in The Netherlands with a low total lifetime carbon cost that has undergone a non-toxic modification process using acetic acid. This basically amounts to pickling the wood in really strong vinegar that interacts with the molecules to make them resistant to binding with water. The result is real wood that doesn’t rot, warp, swell or shrink.
Cork is a bark rather than a wood that is harvested without harming the tree. It is naturally water-, rot- and stain-proof, pleasant to walk on, doesn’t heat up underfoot, acts as an acoustic and thermal insulator, and requires minimal maintenance. Combined with manufacturing processes to increase its consistency, MarineCork is marketed by Italy-based SACE Components as “the ideal solution for those looking for quality alternatives to teak and imitation teak.” MarineCork has been adopted by Azimut Yachts for its new Sea Deck range and during Milan Design Week 2023 the builder displayed a floating installation made from recycled cork. Arksen is also offering cork as a decking option.
Feadship is also actively looking into natural, treated and composite alternatives to teak. Its research ranges from simply exposing test panels to the elements on the roof of the shipyard (with periodic cleaning as per manufacturer protocols) to more specific analyses to measure hardness, water absorption, shrinkage and elasticity. One test measures thermal effusivity, the ability of a material to exchange heat with its immediate surroundings (ie. our bare feet), which translates into how cool or warm a material ‘feels.’ Surprisingly, natural teak has quite high effusivity and feels hotter underfoot in relation to some composite alternatives like Flexiteek or Esthec.
“An unforessen difficulty we came up against was getting hold of product samples to test,” says Giedo Loeff, Head of R&D at Feadship. “This was due to reasons such as limited supply and ongoing development, or because the product was simply no longer available.”
One such product to have fallen by the wayside is Lignia. Its manufacturers claimed the resin-infused softwood made from FSC-certified pine had aesthetic and tactile properties very similar to teak, and was even longer lasting. Spirit Yachts in the UK decked its 50CR sailing yacht with it, yet despite winning a DAME award in 2019 Lignia went into administration two years later.
Below: There is no doubting the physical and aesthetic properties of old-growth teak, but its continued use is hard to justify from a sustainability perspective.
Wild forest teak is not necessarily gone forever. Myanmar Timber Enterprise continues to harvest and stockpile teak and if democratic government should return to the country, or the military junta improve its human rights record and forestry practices, sanctions could be lifted and a ready supply of old-growth teak come back online.
But that possibility overlooks the ethical and environmental arguments. Wild teak may be desirable, but cutting down century-old wild trees to make decks that might last 20 years is clearly irresponsible from an environmental perspective. Once felled, the wastage is mind-boggling and the yield for decking purposes from a good teak log may be as little as 12 percent. Moreover, because the logs are first quarter sawn and then
cut across the growth rings, which is what lends teak deck battens their straight grain and structural stability, fewer boards can be made from each log.
Our obsession with old-growth teak looks increasingly anachronistic when feasible and sustainable wood alternatives are available. They may not have exactly the same technical or aesthetic properties as Mynamar teak, but not using them is hard to justify in an industry aiming to improve its green credentials.
But the biggest barrier to more widespread adoption of alternatives to teak is likely ongoing reticence among the owners themselves: “It’s always hard to break traditions, but we bring it up for discussion every single time,” says Lürssen’s Dr Urban. “Clients are aware of the sustainability issues, but not all are really willing to be a guinea pig.”
By Francesca Webster
Founded in 1963, the Dutch aluminium specialist Bayards is a worldrenowned superyacht hull and superstructure manufacturer. Bayards has built a reputation for excellence and partners with some of the world’s most acclaimed superyacht builders. Huib Slings, managing director, and Dirk Poot, marketing manager, explain more.
An example of the aluminium superstructures that Bayards specialises in.
Bayards entered the superyacht sector in the 1990s, at a time when the Dutch yachting industry was beginning to take shape. The move was even motivated by requests from a local yacht builder and the company has therefore developed alongside the superyacht industry, learning from its requirements and adapting its capabilities. Today the company specialises in the construction of yachts of 50 metres and above, working on hundreds of projects since it first entered the sector more than three decades ago.
The largest of its three facilities is in Nieuw-Lekkerland near Rotterdam on the river Lek. Located on one of the area’s largest rivers, the facility is ideally situated to serve the shipyards of both the Netherlands and Germany.
Bayards is an experienced co-engineering partner, working closely with the designers, naval architects and engineers. Huib Slings explains, “Many of our team members have been with Bayards Group for decades, and the level of in-house aluminium engineering expertise complements and extends that of the shipyards themselves. We use that knowledge to help shipyards and designers realise complex engineering concepts, to predict and overcome challenges before they arrive, therefore improving the owner’s experience and streamlining the build process.”
T: +31 (0)184 683 000
The expert knowledge of the sector is complemented by a state-of-the-art machine park. “Working across five industries means that we have our finger on the pulse of technological developments.” explains Dirk Poot. “Today we have one of the largest milling machines in Europe, a size rarely seen in a shipyard, as well as a cutting edge Friction Stir Welding machine.
Co-engineering projects alongside the yards also means that the interface between engineering and production is very efficient and modifications during the building process can be actioned quickly. Not only does outsourcing construction to Bayards mean uncompromising quality, it also reduces the risk of ‘hot works’ being conducted at the shipyard itself. Bayards is also committed to employing sustainable approaches in its work, and utilises low-carbon footprint aluminium throughout the complete building process.
With 60 years of experience under its belt, Bayards has become a household name as a manufacturer of complex aluminium structures and is the ideal partner for the superyacht construction industry. To find out more about the company and its capabilities, reach out to the team now;
E: sales@bayards.com
L: linkedin.com/company/bayards-yacht-structures/
W: www.yachtstructures.com
27•30 SEPTEMBER 2023
The AZ Project is aimed at researching new methodologies for fairing hulls and cladding superstructures. The brainchild of KayJohannes Wrede, coating expert and founder of Wrede Consulting in Hamburg, his theories are being put into practice on a 30-metre motor yacht in-build in Bremerhaven.
BY JUSTIN RATCLIFFE
Beyond the fried fish outlets that line the seafront in Bremerhaven, a half-built yacht sits in a modest construction shed next to Dörries Yachts. The classic two-decker with a canoe stern designed by De Vries Lentsch is effectively a floating laboratory initiated by International Maritime Research (IMR), a sister company of Wrede Consulting, and funded in part by the German government. The yacht’s deckhouse is still a network of steel frames and carbon modules, but the hull is complete and has been faired, although the two sides use visibly different coatings – for reasons that will become apparent.
The AZ Project was started three years ago by a consortium of international companies under the guidance of IMR and Wrede Consulting in a supervisory role as a full-scale R&D project comprising two areas of research: to test new methodologies for filling and fairing, and to develop a modular process for cladding the steel structure of a superstructure with composite sandwich panels.
Traditional production of the final surfaces on metal yachts requires several labourintensive steps. Correcting pronounced defects such as welding distortions or the connection with functional elements like doors, windows and hatches with filler compound is time-consuming, heavy and costly. Part of the research program was to resolve these issues with a composite fairing solution for hulls.
“Fairing the metal hulls of superyachts requires a lot of filler, many tons in some cases,” says Kay-Johannes Wrede, founder of Wrede Consulting. “The thicker the filler the more sensitive it is to temperature fluctuations and flexing, leading to cracking and flaking, We wanted to save weight, reduce the time-consuming filler work, and achieve better thermal insulation of the hull to save energy costs. Our proposal is to use a foam core laminated with GRP in a modular, industrialised manufacturing process.”
Like many good ideas, the concept is not new. Going back over 20 years, Fagerdala Marine Systems, a division of Fagerdala World Foams in Sweden, developed a coating system based on the application of a foam composite structure on the aluminium hull of a yacht (see sidebar). The system proposed by Wrede, however, benefits from advances in engineering and technology over the past two decades to increase manufacturing accuracy and efficiency.
After laser scanning the bare hull to create a 3D model, a new surface is CNC milled from foam panels that are pre-laminated with fibreglass on the outside. These panels are then glued onto the existing structure like a giant jigsaw puzzle to create a robust and very stiff ‘skin’. The 3D model exactly measures every deflection, imperfection and weld seam in the hull so the foam panels fit flush with the metal plates to provide a ready-made faired finish. Only a minimal amount of fine filler is required on top to provide a perfect exterior finish.
“This sandwich construction offers several advantages,” says Enno Herrmann of Innovative Composite Solutions (ICS, a joint venture company set up to market the developed products), who is also a qualified composite boatbuilder and technical project manager on the AZ Project. “The foam is much lighter and can be engineered to reinforce parts of the hull where traditional filler is susceptible to cracking. It also provides better insulation, which means the steel or aluminium doesn’t heat up so much, so there is less expansion. That’s a good thing especially on dark-painted hulls because expansion creates stress between the metal hull and the filler, which is liable to break off.”
Whereas filler serves only an aesthetic purpose, composite fairing also has a practical function. Different grades of foam can also be used for different parts of the hulls according
Previous spread: Kay-Johannes Wrede inside the steel structure of the deckhouse. Note the corner with prototype cladding attached.
Left: Wrede and marketing manager Christopher Rothe at the Wrede Consulting headquarters in Hamburg. Facing page, top: The
to the pressure loads. The stiff skins provide high bending stiffness, while the foam core supports the shear and compressive stresses and stabilises the skins, preventing global and local instabilities. The weight reduction results in fuel-savings, lower inertia, as well as increased stability and buoyancy.
Other probable advantages include reduced risk of galvanic corrosion since the hull is covered by closed-cell foam; and no condensation as the insulating effect of the foam on the outside means the inside shell temperature remains above the dew point. In addition, damaged panels can be easily replicated from the 3D files and replaced (in fact, nowadays structural and/or filler problems are usually repaired using the sandwich system).
However, the research program does not stop there. In order to compare performance with conventional fillers over time, the portside of the hull has been covered with the composite fairing solution while the starboard side has been treated in the traditional manner using different types of filler in collaboration with Pinmar and AkzoNobel. Standard 830 two-ingredient epoxy filler has been used in the bow area and Awlfair SF hot spray filler system elsewhere on the hull. Sensors imbedded in the coating materials will measure relative temperature, expansion rates and wave pressure loads.
In the late 1980s, Swedish inventor Sven Jönsson decided to refit his all-aluminium motor yacht. The sleek, 100-foot vessel was launched as Edi in 1939 for the industrialist Torsten Kreuger, but her hull was a badly buckled and the deckhouse was in a very poor state of repair. Supported by the Royal Institute of Technology in Stockholm, Jönsson drew on his knowledge of teak-decking systems and adhesives to develep an elastic, waterproof glue to withstand the forces between a rigid closed-cell foam sheet and the twisting and flexing metal hull. A new superstructure was also created out of 3mm aluminium. Vacuumglued sheets of closed-cell foam were added and the foam surface was then planed to shape, laminated and painted.
In 2005, after 14 years of service in the Mediterranean and the North Sea, some areas were opened up to see how well the concept had worked in practice. In a bottom section below the engine room, a small area of foam had separated from the metal. The cause was a broken rivet that had allowed oily bilge water to penetrate the hull plating and dissolve the aluminium primer. All the other surfaces were like new.
Fagerdala Marine Systems AB later became the owner of the prototype vessel M/Y United Spirit and patented the Fagerdala Hull System (the patent has since expired). For reasons unknown, the thoroughly tested and proven coating technique never took off.
The second phase of the AZ Project is to research a method of gluing laminated foam panels to existing metal structures to create perfectly shaped superstructures. Welding superstructures out of steel or aluminium is challenging when it comes to creating complex shapes and the end result still has to be fully faired. Further, care has to be taken with aluminium superstructures that twist and flex in a seaway, which again can lead to unsightly cracks in the filler.
“Like the composite fairing system, the basic idea behind the composite cladding for the deckhouse is to make the the yachts lighter and the whole build process faster and more efficient,” says Wrede. “So we’ve developed three prototype sandwich panels that can be glued directly onto the steel framework of the superstructure to replace the metal plating.”
Again, composite superstructures on superyachts are not new. Lürssen, Nobiskrug and Abeking & Rasmussen have built yachts with at least partial composite superstructures. Notably, when Paris-based Pierrejean Design Studio created the sleek, modern design for the Swift 141, the former Dutch frigate that became 141-metre Yas, the company’s engineers determined that the steel superstructure should be replaced with a composite construction throughout. Even the helicopter landing pad is made of sandwiched panels of Divinycell foam and eight plies of carbon fabric. These were all hugely expensive one-off projects, however. Wrede’s composite system, on the other hand, is conceived with pre-fabrication and ease of assembly in mind.
from top: The pre-laminated foam panels are glued onto the hull and require only minimal filler for a perfectly smooth finish; a render of what the 30-metre yacht will look like when finished.
Arguably the biggest single challenge for Wrede Consulting and the Centre of Maritime Technologies, a body that conducts its own technical research in strategic maritime areas, is gaining Class approval in a conservative industry where steel and aluminium are still the de facto building materials for ships and large yachts. In case of fire, they are required to prove that everything is equivalent to steel construction.
“The issue with composite materials is that the resin used in the manufacture does not like heat, so part of our research was to come up with sufficient insulation to get Class approval for a system that we can always use for coating the steel superstructure frame,” says Wrede. “We were able to improve the fire rating with insulation on the inside and now have Class approval ‘in principle’ for the process.”
There are other drawbacks. Tooling design and development increases the lead times as well as cost, and cut-off wastage is also a factor. Reconfigurable tools or adaptive moulds to make the laminated thermoformed panels helps reduce the cost, delivery time and waste. Complex double-curved shapes from 3D files can be shaped in minutes with a high surface quality and one mould can make many unique mould surfaces.
Having invested around €2.5 million in the project to date, Wrede is looking to sell his floating laboratory and construction is paused while waiting for an owner to come forward. Her Caterpillar C18 main engines are already on site and the shafts and rudders have been ordered. There is also a complete interior design concept by Schnasse Interior Design.
“Ideally, we would like to see it used as a charter boat in different climates and conditions to have as much data feedback from the imbedded sensors as possible, “says Christopher Rothe, head of marketing at Wrede Consulting. ”Clearly it will take a client who buys into the research part of the project, but the advantage is that he or she could take delivery of a high-quality, Dutchdesigned yacht in less than a year.”
27•30 SEPTEMBER 2023
Is the custom nature of a superyacht a definitive barrier to adopting robotic automation in the build process? As Industry 4.0 reshapes manufacturing processes across the board and robot technologies evolve, the answer might not be as straightforward as you think.
BY CHARLOTTE THOMAS
Something big is happening in manufacturing. It has been labelled Industry 4.0, otherwise known as the Fourth Industrial Revolution, and it’s all about bringing further automation to manufacturing processes. We know of the rise of the machines in the automotive sector (who can forget Fiat’s classic ‘Hand Built By Robots’ TV ad campaign in the late Seventies?), but since the 1980s commercial shipbuilders have also been adopting these new technologies. Programmable welding robots, for example, were a natural progression from automotive applications centred on rinse-and-repeat actions for the mass production of standardised parts. Most large-scale leisure yacht builders today use some form of automation, whether it is multi-axis CNC machines for the preparation of moulds or
components, table cutters for producing build components from sheet materials, or automated spray booths for interior fit-out and furniture components. Groupe Beneteau has started to adopt robots to apply gelcoat, while others such as Cranchi use overhead Kawasaki robots for cutting and spraying fibreglass and top coat on yachts up to 24 metres.
Robotic automation and assembly has become an obvious path for companies making repeatable, high-volume products, from engine manufacturers to jet-ski companies. Genmar took it a step further (before eroded sales sent them into bankruptcy in 2009) with its Virtually Engineered Composites (VEC) hulls that promised a hull in an hour and the capacity to produce 20,000 small boats a year on an automated production line.
Robotic automation and assembly has become an obvious path for companies making repeatable, high-volume products, from engine manufacturers to jet-ski companies.
Automating the filling, fairing and painting process for superyachts presents a series of challenges, not just because of the size and complexity of a yacht’s hull, but also with regard to the quality of finish. In the commercial sector several companies are developing automated painting robots that can crawl the hull, removing old paint and adding new, with the added advantage of handling overspray. Palfinger’s Hull Treatment Carrier is one example, and AkzoNobel recently invested in Dutch start-up Qlayers that is building hull and topside crawler paintbots for the commercial sector (perfect for working vessels but unlikely to pass muster for superyachts).
Robosurf’s solution starts with a complete 3D hull scan to calculate how much filler is needed at any given point to produce an even skin. The robot applies filler to precisely the right thickness, meaning minimum filler is used in the application process. It is also capable of fairing the filler, although that requires some clever software engineering to compensate for the vibration of the robot. It can also apply paint and the company produces robotic painters for the construction industry, but getting the superyacht industry to adopt that tech will likely prove more challenging.
But pundits argue that superyachts are very different. They are not consistent like small series boats or the block assembly of large ships, so the processes cannot be automated, and robot welders cannot access spaces like fuel tanks that humans can.
“Shipyards are very much behind in digitisation and automation when it comes to production – they are very late adopters, which I can understand because it’s such a sensitive topic,” says Patrick MacHill, partner and co-founder of Robosurf, which has developed automation technology for surface finishing and paint application in the yachting segment. “On the other hand, there’s never been a better time because the technology is there, it’s proven and there are so many benefits.”
Benefits include improved efficiency and sustainability. In filling and fairing, for example, the robotic process is more precise, uses less material and has less wastage than conventional filling and fairing by hand. Moreover, it can cover up to 10 squaremetres per minute, which represents a huge time saving over conventional methods. Robosurf brought its solution to market in 2019, the same year that AkzoNobel brought out its Awlfair SF spray filler. It was perfect timing. Robosurf took an industrial robot and combined it with a steel frame on which the robot arm could move up and down to cover up to 17 metres vertically. They have since combined this with a second robot that adds mobility to the unit for horizontal freedom of movement. Using a 3D map of the hull, the operator can instruct the robot where to apply filler. Robosurf says the scanning of a 70-metre superyacht hull it undertook in Ancona early in 2023 took less than a day. Once the robot has been primed with the surface map information, it can cover up to 10 square-metres a minute – a significant time advantage for what typically can be a very long and labour-intensive filling process. One of the limiting factors is the cost of the equipment – €1 million or more In the case of the Robosurf solution. It is a big number for a yacht builder with relatively small output, but MacHill is convinced that it can offer a very quick return on investment when the numbers are crunched and refers to the 70-metre hull by way of example.
“The complete filling and fairing could take a year or longer, with 20 to 25 man hours per metre,” he says. “But if it costs between €800,000 and €1.5 million to complete that process, depending on where you are, that still means a RoI [Return on Investment] within a build, or maybe two.”
The efficiencies in terms of material used and time saved are considerable. Further, for some yards it might make sense to rent the robots rather than buy them outright, and Robosurf plans to offer leasing from a few days up to 36 months. There are also plans to offer upgrades via what Robosurf calls app kits, which combine hardware components (the sanding tool, for example) with the software needed for the robot to use it.
“Shipyards are very much behind in digitisation and automation when it comes to production.”
With medical and military applications the key drivers for development, exoskeletons are a relatively new entry to the industrial sphere. But when Daewoo Shipbuilding and Marine Engineering unveiled its trials with full robotic exoskeletons in 2014, the potential was plain to see as the powered exoskeletons enabled yard workers to perform superhuman feats, such as carrying 100-kilogram pieces of metal with ease. Fast forward nine years and the technology has become commonplace with companies such as Ekso Bionics and Ottobock offering solutions for a variety of industries.
Exoskeletons typically come in two varieties – actuated and passive. The former feature some form of power assistance, whereas passive solutions typically offer positional support or mechanical assistance to reduce fatigue when, say, working with your arms overhead for long periods. The tech has already made its way into superyacht construction. Heesen Yachts has introduced exoskeletons for some of its workforce after trialling equipment from Rotterdam-based manufacturer SkelEx. Royal Huisman has also adopted exoskeletons for its workforce, using Ottobock’s Paexo Shoulder.
“Our employees have to perform lengthy and difficult overhead tasks such as welding, electrical wiring and painting,” says Erik Slomp, Royal Huisman’s yard manager. “They’re delighted, because using the Paexo Shoulder not only gives them the necessary support to continue performing these strenuous tasks throughout the day, but is also very comfortable to wear.”
Cobots – or collaborative robots – are a new type of robot that are starting to offer manufacturing opportunities. They are small, light robot arms that have been designed specifically to work alongside humans rather than separate from us. They can be programmed and controlled through smartphone apps and can be taught routines intuitively, meaning you do not have to have an army of programmers to use the tech. With multiple interchangeable tool heads they could be used for everything from sanding wood components in the cabinetry workshop to picking parts and assisting with component building. They also require much less investment than the large industrial robots, typically running to the low- to midtens of thousands of euros.
“I think this is only the beginning,” says MacHill. “At the moment we are mainly focusing on the hull because it’s a big area that consumes a lot of time, energy and resources. But there is scope for the scanning and digitisation of the superstructure and technical areas which adds value and creates a more complete set of documentation. Then we can think about smaller robots for the smaller areas. This is something that could be developed because the technology is the same – it doesn’t matter if it’s big or small, it’s the quality of the application that counts.”
There is also potential for gantry-style robot stations for the platform or series builders operating in the 30 to 50-metre aluminium- and steel-hulled segment, where hulls and superstructures are more consistent and where robotic solutions could speed up production processes for hull treatment prep and finishing. Moreover, installing automatic storage and retrieval systems (ASRS) could help a shipyard streamline its components and parts
cataloguing, particularly pertinent given recent supply chain issues.
MacHill emphasises that robots do not represent a threat to human workers, although their jobs may well change. Robots still need to be programmed, and often the people who were doing the job of the robot before are retained in supervisory and quality control capacities. Robots may also provide an answer to another problem that shipbuilding in general faces: the shortage of skilled workers in key trades.
“We need open-minded players in all aspects and all fields to come together and work together,” MacHill concludes. “It needs a mental shift, but what they offer and the savings they deliver are amazing – who wouldn’t want this?”
“Robots may also provide an answer to another problem that shipbuilding in general faces: the shortage of skilled workers in key trades.”
Robots have started to appear in our homes and gardens as little autonomous helpers for vacuum cleaning and lawn-mowing. Similar technologies are now being applied for ship hull cleaning in-water and antifouling applications in dry dock. They mitigate the need for humans to get involved with harmful coatings and offer the possibility to rethink how we tackle fouling. Robots, for example, were used to remove the original Chromium 6-laden paintwork using water jets from the Project Master conversion project at Icon Yachts, formerly a supply and rescue vessel. CleanROV, Mini-Pamper, HullWiper ROV and the wonderfully named Robotic Hull Bioinspired Underwater Grooming tool (HullBUG) are all variations on a theme: automated hull crawlers that use vortices or magnets to cling to the hull and gently brush to remove fouling. The use case is potentially strong for yachts, which typically spend long periods at rest when fouling becomes an issue.
Leading paint manufacturer Jotun has also joined the hullbot revolution, launching Jotun Hull Skating Solutions in 2020, and with it the HullSkater robotic cleaning device. Designed to be carried aboard and deployed regularly, Jotun also offers HullSkater as a service rather than an outright purchase. The HullSkater was developed in collaboration with technology specialists including Kongsberg, Semcon, DNV-GL, Telenor and key shipping companies, and Jotun claims that if all ships converted to the tech it would have the potential to reduce CO2 emissions by at least 40 million tonnes per year.
“Moving away from traditional, reactive methods of managing fouling to a proactive approach will ensure that vessels are always operating efficiently and sustainably, and also conserve the ocean environment,” says Alfie Ong, global sales director at Jotun.
Conversions are always inspiring but rarely straightforward. We visited Project Master at Icon Yachts in Harlingen as the stripped-down donor vessel was entering the detailed engineering phase of its transformation into a 70-metre explorer yacht.
BY JUSTIN RATCLIFFE
“It’s vital to select the right donor vessel for the needs of the client,” says Sikke Jan Wynia, Chief Operating Officer at Icon Yachts. “Does he want an old platform where you remove more, or a newer one that you can upgrade? We basically filter the knowledge we have of the market against the client’s set of the requirements and then advise based on a detailed feasibility study. It can be a selection process over multiple vessels and many discussions before a decision is reached.”
In the case of Project Master the shipyard opted for Ocean Ness, a 66-metre offshore rescue and supply vessel built in 2001 by Kleven Werft (the same yard that delivered the explorer yachts 107-metre Andromeda and 116-metre Ulysses) as Havila Tigris for Havila Shipping in Norway. Tough and seaworthy, offshore supply vessels (OSVs) make ideal candidates for conversion into explorer yachts as they are usually between 40 and 80 metres in length and generally available for a fraction of their original build value. Some OSVs are ice-classed, as in the case of Sanaborg that was converted into the 68-metre explorer yacht Ragnar and relaunched by Icon in 2020. Ocean Ness, however, was built to operate in the North Sea between Norway and the UK, which is inhospitable but not ice-strewn.
Only after the donor platform had been identified and a preliminary general arrangement developed in-house was Espen Oeino contracted to create a new exterior profile for his first conversion project and what Icon calls a ‘luxury expedition vessel’. The shipyard prefers not to bring in designers earlier as they are sometimes tempted to redesign more than is strictly necessary, which can prove both wasteful in terms of time and cost.
“A magic moment is always when the owner sees the donor vessel for the first time,” says Marek Hasenkopf from Icon’s Project Development team. “It’s always a very special moment because it’s the first opportunity to get an idea of the scale of the vessel. That’s when the project really come to life and becomes tangible with the client’s enthusiasm clear to see.”
At the time of our visit, Project Master had been stripped down to bare metal and received a coat of protective primer. During the feasibility study it was discovered that the original green paintwork of Havila Tigris before she was repainted red contained Haxavalent chromium or chromium 6, which was once added to coatings for corrosion protection but poses health risks when removed by abrasive blasting. Icon solved the issue by removing the old paint with robotic waterjets. A square patch of the hull in the bow has been finished with light grey top coat to have an idea of what the final colour will look like, although it has not yet been decided whether the yacht will have a commercial finish or be partially faired.
“The vessel spent many years in the North Sea and had clearly taken a few beatings,” says Sikke Jan Wynia. “We’ve fixed some of the bigger dents, but there’s no point in adding tons of filler to an explorer yacht like this just
Below:
to make it look nice. Practically is key and the decking will be synthetic, for example.”
The crew, service and technical spaces were all originally in the forward half of the vessel where the rather complex splitlevel layout and original bulkheads remain largely intact, but the functionality is being thoroughly repurposed. For example, as a rescue vessel Ocean Ness was able to accommodate up to 200 survivors in a space below the foredeck, which was used for helicopter winching operations. This area has been completely stripped out and will turned into a wellness deck with gym, massage room, sauna and steam room, along with a medical treatment room.
The open main aft deck, on the other hand, is due to be completely transformed by adding a new steel superstructure comprising five large guest suites on main deck and an owner’s deck with a 135-square-metre master stateroom and fully certified helideck for a twin-engined helicopter on top. Further, an eight-metre section of the hull is being rebuilt by nearby Talsma Shipyards to include a four-metre swim platform. Besides increasing the overall length to 70 metres, these various additions will raise the interior volume from 1950GT to around 2800GT.
To ensure stability would not be an issue, the yard carried out an inclining test to determine the lightship weight and centre of gravity of the donor vessel as a final part of the feasibility study. Freshwater ballast can be added to the double bottom sections (as opposed to dischargeable seawater ballast and all the extra management rules that entails) in case additions to the envisaged design become desirable later.
Initially the idea was to also keep the original main engines, shafts and thrusters, but it soon became clear that a more fuel efficient and eco-friendly package would futureproof the vessel. Ocean Ness was powered by two enormous, air-started, nine-cylinder Bergen diesel engines producing over 5,000 horsepower each for powering through the roughest seas. These were connected via 26-metre long drive shafts – sources of considerable noise and vibration – to Kongsberg azimuthing pods. An explorer yacht requires only a fraction of that kind of installed power and, apart from anything else, very few yacht crews today are trained to operate such engines.
“The vessel was due for her fourth special survey and we started thinking it was smarter to do something completely different,” says Rob Pijper, says Rob Pijper, operational director with JMS Yachting and owner’s rep on Project Master. “The biggest challenge with these conversions is that you’re changing the ship type and that means you have to comply with current statutory rules. Instead of running inefficiently on those massive engines from anchorage to anchorage, why not have an IMO Tier-III compliant, hybrid diesel-electric system with battery banks for quiet, zero-emission manoeuvres so you can always run the generators at peak efficiency?”
At the same time as Pijper and the Icon team were making their deliberations, Voith Schneider came out with an all-electric version of its established L-Drive thruster (see sidebar). The great thing about the Voith propellers is that they offer excellent manoeuvrability as well as integrated hull stabilisation. This meant conventional fins were not needed and, ultimately, less maintenance is required because the two functions are combined in a single system (the new stern section has been reconfigured to account for the new thrusters).
Project Master’s diesel-electric system will comprise five gensets of 500kW each for a top speed of 14 knots and can draw on hybrid energy from up to 2MW of Li-ion battery banks. The batteries are housed low down on the tank deck in what was previously the pump room and a dispersion tank containing emulsifiers for dispersing oil spills.
“My advice to the client is that the yacht should be future-proofed for the next 20
years,” says Pijper.” So I’d like her to be able to drive into Monaco on batteries, recharge overnight, and sail out again under batteries the next day. That’s my yardstick. There are ongoing discussions about making her future fuel-ready as we have such big tanks.”
Ocean Ness was designed to refuel platforms and other vessels and could carry a massive 800 cubic metres of fuel. That capacity has been reduced to around 600 cubic metres by repurposing some of the tanks, but the finished yacht will still have a huge range in excess of 20,000 nautical miles. The working vessel also had two bow thrusters, a retractable unit and a controllable pitch tunnel thruster, required for Dynamic Positioning redundancy in all sea conditions. Both have been removed with a view to reconditioning and the tunnel thruster will be replaced with a quieter, fixed-pitch electric model.
Above, right: The cavernous engine room has been stripped of all the old machinery to make way for a new diesel-electric propulsion system.
“The biggest challenge with these conversions is that you’re changing the ship type, and that means you have to comply with current statutory rules.”
VOITH SCHNEIDER
At the working end of Project Master’s diesel-electric propulsion are two electric Voith Schneider Propellers (eVSPs). The cycloidal propellers combine propulsion and steering in a single unit and, like many seemingly new solutions, were originally developed 90 years ago by Austrian engineer Ernst Schneider for a hydroelectric turbine. The first eVSP units with an integrated electric motor were delivered in 2021 and Project Master is the first time they have been used on a superyacht.
The propulsion units consist of a circular metal disc 2.10 metres in diameter, which is fitted with six movable and controllable 1.75-metre long blades installed at 90 degree angles to the disc’s perimeter. Each blade can rotate around its vertical axis and change the angle of attack in sync with the rotation of the plate, so that each blade can provide thrust in any direction. The magnitude of thrust is determined by the rotational speed of the disc, while the blade angle determines the direction of thrust. Both under Dynamic Positioning and when travelling at full speed, they can also counteract up to 90 percent of the rolling motion of a ship. Delivering high torque, fast response and precise manoeuvring without any gears even in adverse conditions, the 1100 kW electric PM motors ensure a more direct and almost loss-free conversion of the electrical drive power into thrust and keep noise emissions to a minimum. Due to the low maintenance requirements, operational costs are appreciably reduced.
Voith has also developed the rcVSP, which stands for ‘remotecontrolled Voith Schneider Propeller’, a technology enabling ship assistance and manoeuvres to be carried out remotely.
From the start of Project Master , every effort has been made reuse, recondition or recycle as much of the original equipment aboard the donor vessel as possible.
The anchor windlass, bollards and cleats will remain, for example, and although the Bergen engines were removed they have already been serviced and sold to a shipping firm in Hamburg.
The original 12-metre ‘daughter’ boats, the fast support boats carried aboard rescue and supply vessels, are being refitted as yacht tenders by Jachthaven Bouwmeester in Amsterdam. Stowed on both sides of the upper deck amidships and designed to align with Project Master’s interior design concept, one will be enclosed and the other open. New engines and control systems have been ordered, while their old engines are being reconditioned with a view to resale. At the time of writing, one of the hulls had been sandblasted and coated.
The MacGregor davits for launching and retrieving the daughter boats will also be reused, although their engineering will be simplified. Designed for long-term operation in severe conditions of up to sea-state 6 and SOLAS approved, the MacGregor davits are self-contained units with incorporated emergency back-up power systems for guaranteed operation even during deadship conditions.
“We believe that this commitment to sustainability ensures that the conversion of Project Master not only enhances its functionality but also contributes to a more responsible yachting industry,” says Icon COO Sikke Jan Wynia.
The walk-around wheelhouse with enclosed wing stations and views aft as well as forward is typical of OSVs. Only 88-metre Olivia O built by Ulstein Verft and 59-metre Akula recently launched by Rossinavi and reviewed in this issue of How to Build It, have anything like it. Designed for cold and stormy conditions, all the bridge windows will be replaced with modern glazing to provide solar protection in hot climates as well. Under the bridge is a technical space for walk-in maintenance access to the fully integrated electronics. An exterior gangway will be widened slightly to make movement for crew on watch more comfortable given the outward leaning windows.
Converting an existing and aging vessel necessarily requires a lot of reverse engineering, but this is all in a day’s work for Icon Yachts. Placed somewhere between a commercial shipyard and superyacht builder, they have solid experience of pinpointing owners’ requirements and matching donor vessels to their needs. Following on from Legend and Ragnar, Project Master is their most ambitious adventure to date. It also promises to be the most spectacular.
Say hello to better onboard connectivity with OneWeb's global satellite network and streamlined, superyacht user terminal.
Connect now go.oneweb.net/superyacht
Whether enjoying a leisurely cruise or some serious sailing, a good night’s rest is as essential on water as on dry land.
Head Office and Production: Graanmarkt 4, Zwaagdijk-Oost, the Netherlands, T +31 228 562 045, info@neptune.nl
Sales & Advice Balearic Islands, Palma de Mallorca: M +34 646 897 378 +34 627 844 229, mallorca@neptune.nl
Sales & Advice Spain, Alicante: T +31 228 562 045, info@neptune.nl
When new owners acquired Maltese Falcon early in 2022, they channelled their vision into a technical refit at Lusben in Livorno. The best way to bring the iconic yacht up to date and protect her legacy well into the future was to assemble as many of the contractors involved in the original project as possible.
BY CHARLOTTE THOMAS
When Perini Navi launched the mighty Maltese Falcon in 2006, she represented not only the culmination of extraordinary ingenuity and vision on the part of her pioneering owner, the late Tom Perkins, but also a long list of subcontractors and suppliers. Her groundbreaking Dynarig had been pulled from design theory and engineered into existence on what would quickly become one of the most-photographed yachts in the world. But the development of her rig and sail plan introduced other technical challenges, from the unstayed rotating masts to the unique furlers and associated monitoring systems. Her place in the limelight is well deserved, but with that comes a certain pressure to maintain her iconic status.
Fast forward to 7th April 2022, when new owners took possession of the 88-metre yacht in the eastern Mediterranean. Neither they
nor their captain, Pierfrancesco Cafaro, were strangers to Perini Navi, having owned and sailed the 52-metre Perini La Luna around the world. But Maltese Falcon is a very different animal. It took 12 years for someone to build a second Dynarig yacht, and by the time Black Pearl was taking shape many of the technologies had evolved. This presented Maltese Falcon’s new owners with a dilemma.
“The previous owner had essentially left much of the yacht as she was in 2006,” says Captain Cafaro. “In September 2022 we decided to come to the Lusben yard in Livorno, which had a suitable dry dock available, and we set out a huge plan to refit her – although we reduced that a little in order to save the summer 2023 season. Why Lusben? Because it looks easy but it’s very specialist work and a mistake can stop the boat. I wanted it done by a big shipyard like Azimut-Benetti who can give us a warranty.”
The nature of Maltese Falcon means that most of her core equipment and control systems are completely custom, and refitting her in Italy rather than in her homeports of Malta or Palma meant that all the expertise that went into the original build was on the doorstep. Most of the contractors had heavy work schedules, but by staying local the team maximised the chances for the works to be completed in time for the 2023 Med season. The process started with the decision to strip the hull back to bare metal. “It wasn’t anything that the previous owners had done wrong, it’s just that the paint was 15 years old and the yacht has done a lot of sailing,” says Cafaro. “Also at close to 90 metres, there is some movement in the hull and that had clearly taken its toll on the filler.” It was also a chance to change the colour of the hull; gone is the Falcon’s original black paint scheme and in its place is Perini blue.
On deck, there have been alterations and additions to the guest areas. The addition of a fixed bimini, for example, now offers weather protection and shade for the aft deck dining table. Made by Massimo Forti of F.M. Srl and stretching from the superstructure to the mizzen mast, it creates an area that when the saloon doors are fully open offers 50 metres of protected indoor/outdoor living (F.M. was also responsible for the class-certified welding and hotworks for the new exhaust system where it meets the hull).
There have been some changes inside too, with much of the dark gloss and stainless steel décor replaced with warmer hues and softer touches, all under the watchful eye of Roman studio Emanuela Esposito. The artwork has been changed to reflect a Japanese influence, and the guest areas, cabins, VIP and master have all been overhauled. The guest bathrooms have been gutted and refitted with pale marble and less masculine palettes, and the deckheads have been replaced with new leather.
The crew quarters have also received a makeover with a new wooden floor, new Miele appliances for the laundry, and new lower crew and upper guest pantries, as well as a completely new main galley installed by commercial specialists CS Refrigeration. All the tanks have been de-rusted and painted, the bilges painted and the sensors replaced.
Cacini & C was involved in the original Maltese Falcon project for implementing the sailing control and monitoring system. The company was responsible for designing the software, building the hardware, installed and commissioning it on-site in Tuzla, Turkey. Cacini’s main task was to design, build and install a new ship automation and monitoring system. The project comprises eight new automation panels, the integration of three new diesel generators, and the replacement of all sensors throughout the yacht.
“One of the hardest challenges was to install the new wiring,” says Angelo Cacini, the company’s chairman. “This required laying more than 15 kilometres of cables, basically across the whole boat.”
A second team worked to refit and, on occasion, to redesign some of the yacht’s core services ranging from the compressed air system to 24 volt distribution, the urea system and the rebuilding of lighting in several technical zones including the engine room.
“This refit is a big upgrade for the whole boat,” says Cacini. “A lot of the elements have been replaced with up-to-date systems in an overall modernisation of the yacht with significant improvements in terms of increased features and reliability.”
The real focus and biggest challenge of the refit, however, has been a multi-millioneuro technical overhaul. Due to the extent of the works and the complexities of the systems needed to control, drive and monitor the Dynarig which presented the biggest challenges for the team, the choice of Lusben and the decision to use the contractors involved in the original build proved a wise decision.
Ascheo was brought in to service all the motors and hydraulics that control the rotation of the masts (see sidebar). The owner’s team considered switching to electric drives as on Black Pearl, but electric motors were too big for the existing space so they had no choice but to work with
the original system. Fabbri Fiore was also brought back to overhaul and update the unique Dynarig furlers, winches and deck hardware, while Cacini & C – another of the original build contractors – returned to update the sail control system and the yacht’s monitoring system (see sidebar).
“Since the very beginning, the Maltese Falcon project has been an amazing challenge for all suppliers that has exerted a magic charm on all the companies participating in her construction,” says Angelo Cacini. “The opportunity to work again on this vessel rekindled these feelings, and the captain – working side by side, day by day with the workers onboard – transferred the new owners’ intention to make the Maltese Falcon greater than ever.”
Part of the original plan for the winter 2022-23 refit was the addition of a swimming pool on the bridge deck aft in the area that serves as a terrace for the VIP cabin. The 10,000-litre capacity pool, presented a challenge for the design and engineering teams, as well as for the schedule of the refit works as in order to be signed off, it would have to to be emptied within three minutes. This would normally mean installing a large pump in the engine room, which is fine on a new-build, but problematic for a refit. The solution that was agreed upon was that the pool could drain to the main deck below.
“Procedure means all the documents and designs have to be approved by ABS, but they were taking too much time and without that authorisation you can’t start building,” says Cafaro. “They told us they should be able to give authorisation by January 2023, but we didn’t trust that timeline so we decided to postpone those works.”
The paperwork has now been completed, and the plan is for Lusben to begin construction of the pool module ready for installation in a brief followup refit period between the end of September and early November 2023.
“They are all contractors that I know well, but they are all so full of work that it can be hard for them to give a firm completion date,” says Cafaro. “If they tell us the pool needs more time, we won’t do it this Autumn because we have to be in the Caribbean at the end of the year. But if they can do it, then we can start the Caribbean season with another big new feature.”
For the mechanical upgrades the team turned to 2gtech, yet another of the original build team, to replace the three generators with modern, more efficient and more appropriately sized LindenbergAnlagen 270kW gensets based on MAN engines, and to overhaul the original Deutz-MWM main engines. A urea tank and SCR exhaust treatment system has been added alongside a new exhaust system and silencers. Meanwhile Manrico Francesconi Srl in Viareggio , who was also involved in the original project, replaced all the fan coils in the air-con system and made some improvements to the compressors.
Similarly, all the bridge PLCs and navigation electronics have been updated or replaced by Caim and the entire yacht rewired to replace the old halogen lights with warm-Kelvin LEDs – a huge upgrade that will have a positive impact on power draw and heat generation.
After flirting with Kymeta flat panels for satcomms a few years ago, these have been removed and Maltese Falcon has gone full Starlink, even removing the traditional TV antennas. The yacht also has a new firesuppression system.
As with most refits, the team frequently came across more than they bargained for when digging deep into systems: “Sometimes we decided to do some works and we opened things up and found the situation was critical because it hadn’t been looked at for many years,” Cafaro says. “For example, when we were overhauling the mechanical and shaft elements, we realised the Rolls-Royce systems that usually have to be serviced every five years hadn’t been done for 10 years. It not only added to the budget, but facing these kinds of problems – which we found in more than one department – has taken up a lot of time and energy.”
The result is a refreshed Maltese Falcon that will stay relevant into the future as environmental responsibility takes centre stage. “We could have spent half of what we
did, but sustainability was a very important consideration for the owners – the boat had to be updated for the next 10 years,” says Cafaro. “Can you imagine using the gensets from the original build in 2032? You would be arrested as soon as you turned them on! And even if you weren’t, you would be out of the charter market because people are increasingly mindful of what’s going on. That goes for the crew too. So the focus was on safe sailing first, then doing it without damaging the environment.”
What is clear from the love and attention (and money) that has been invested in the refit of Maltese Falcon, is that the sailing yacht is still able to capture the imagination and stir the emotions 15 years after her launch. Just as important, the experience and expertise that went into building her is as valuable today as it was then.
The overhauling of the Dynarig was left to Ascheo, who developed and installed the original system. The team was tasked with servicing the rescue crane and helm wing stations, and the hydraulic mast rotation units (indeed, Ascheo’s team now includes the original designer of the MRU system). Aside from replacing worn-out components, the team was also able to update the MRU hydraulic supply system, leading to a 50 percent reduction in noise.
It wasn’t all plain sailing, however: “We faced the challenge of insufficient information about previous troubles and maintenance coupled with limited time and space on board, also due to other refit work that was happening on the yacht,” says Ascheo president Guglielmo Lorenzoni. “All three systems had never been built before, and coming back on board meant we could observe and evaluate their condition after 18 years of operation. Maltese Falcon is certainly one of the most prestigious constructions in yachting and the refit keeps her abreast of the times, as well as improving the liveability on board with the noise reduction.”
Lorenzoni’s advice for such a complex technical refit is simple: “Proactively coordinate so all agencies are informed and ready to service the boat before it docks,” he asserts. “Remember that new technologies could offer opportunities for energy saving. Using the original suppliers could bring some advantages, and keep in mind the availability of spare parts, obsolescence, and long delivery times.”
This presentation summarises the results of a thought-provoking study by Lateral Naval Architects and PA Consulting into the feasibility of developing a net zero fuel manufacturing and bunkering infrastructure to support a superyacht powered completely by hydrogen technology.
BY LATERAL NAVAL ARCHITECTS & PA CONSULTING
We are frequently asked what the best fuel choice will be in the future. The only reponse is, “There is no single answer.”
The net zero future will be an eco-system, and as such no one solution will prevail. No one can operate in isolation, because as an eco-system there has to be interdependence. Many fuel types, technologies and solutions will be leveraged to serve various industries. Collaboration is therefore key at regional, national and international level.
The decarbonisation of the wider marine industry has already begun with numerous alternative fuel projects underway. Many are technology demonstrators on a modest scale, but the challenge lies in the scalability and speed of bringing solutions to market in a practical, operational manner. This is a slow process and the transition away from a fossil fuel-based infrastructure will take a significant amount of time.
In the context of superyachts, and the wider marine industry, the issue is not one of technology. We have the technology available today to deliver net zero solutions, whichever chemistry of alternative fuel is pursued. The laissez-faire approach will be to wait for the commercial marine industry to coalesce and then leverage the solutions adopted. However, it is unrealistic to expect that the specific needs of the superyacht industry will be considered with the result that we are left on the back foot and forced to use ship-side solutions that are ultimately a compromise.
Could we, for example, build our own fuel production and distribution network specific to our needs? If we had decentralised alternative fuel production facilities, say one in the Mediterranean and one in the Caribbean, could we create a green corridor with sufficient footprint to cover the majority of the superyacht milk-run? It is not difficult to imagine how with time and investment that network might expand to cover a greater geographical area. This is not a silver bullet solution. It would require us to start small and think big, take a long-term view and lead by example.
Consider this: of our industry’s existing client base, six out of 10 of the wealthiest people in the world already own a superyacht. We have already sold them our products; how can we make it compelling for them to invest in the future of alternative fuelled superyachts?
To answer this, we first set about investigating smaller questions. What would be involved, and what is the scale of investment needed? As a starting point, we have used the Aqua project, a 110-metre liquified hydrogen concept design from 2019. As noted in our opening narrative, liquefied hydrogen will not be the only answer to the net zero future, so the metrics and outcomes may differ for other fuel types, but the feasibility of the proposition still holds.
To determine the building blocks of the required production and bunkering demand, an operational profile was assumed. This profile is typical of the majority of superyachts in seasonal use in the Mediterranean and Caribbean. Using the Aqua design and operational profile, we defined the monthby-month bunkering demand, assuming two facilities as previously described.
It should be clarified that the study of infrastructure is based on the production of green hydrogen, which refers to hydrogen produced by electrolysis. Electrolysers are relatively embryonic in technology, but are undergoing rapid improvements in capability. Energy used to produce the hydrogen is from low carbon and renewable sources such as wind, hydro and photovoltaics.
The production of green hydrogen via electrolysis demands a significant supply of water, generally between 40-45 litres for every kilogram of hydrogen produced. This water demand would typically be met by desalination. Lastly, the gaseous hydrogen output from the electrolyser, undergoes cryogenic liquefaction to improve the volumetric energy density of the final product. Liquefaction, whilst essential from an energy density perspective, is in itself a very energy intensive process. The gaseous hydrogen must be converted at approximately 30 bar and stored at -253°C. This requires approximately 10kWh for every kilogram of hydrogen, which is about one-third of the energy contained within the hydrogen itself.
Approximately 90 million tonnes of hydrogen is used across three principle industry sectors: refining, fertiliser and chemical production. This is mainly black or grey hydrogen derived using energy from fossil fuels. Decarbonisation of this hydrogen footprint is a huge challenge for industry. To put it into context, if all of the available renewable electricity derived from hydro, nuclear, wind and photovoltaics was employed in this task, around 50 percent of that energy would be required to decarbonise the current demand from these three primary markets. This highlights how far there is to go before the availability of green hydrogen would reach wider scale availability. Globally, however, there is significant investment in hydrogen infrastructure. Around 17 governments have announced hydrogen policies and strategies with approximately 500 green hydrogen infrastructure projects underway around the world. These are mainly clustered around coastal locations to support local industry and maritime infrastructure.
Our study examines two scenarios to determine, firstly, the overall technical feasibility and, secondly, the economics of the proposition. The first scenario draws directly on the worldwide development of green hydrogen infrastructure and examines how a hydrogen bunkering facility might be strategically located, but with the fuel procured from a hydrogen production hub. The second scenario examines the creation of a truly independent network incorporating onsite production and bunkering at a local decentralised facility. Within this presentation, only results relating to scenario two are presented (the outcome of scenario 1 can be found in the full text of the public domain technical paper supporting this work).
The study of bunkering requirements established an average output of approximately 30 tonnes per month would be required. To supply this demand, the various components of the decentralised facility have been determined and the level of renewable energy needed to power the process calculated at approximately 4MW. Considering equipment sizing for the capacity demand, access and safety distances, the total footprint of the facility would be approximately 20,000 square-metres. To give a sense of scale, if the same energy was to be provided by a solar array then approximately 50-80,000 square-metres would be needed. This is a utility scale facility and highlights any notion of onboard solar energy production as wholly unfeasible.
“Around 17 governments have announced hydrogen policies and strategies with approximately 500 green hydrogen infrastructure projects underway around the world.”
The headline CapEx (capital expenditure) to establish two bunker facilities, would be US$84 million with an annual OpEx (operational expenditure) of US$5.7 million dollars. With the CapEx amortised over 15 years, there is an average annualised cost of US$11-12 million. Based on comparison with the operational fuel costs of an equivalent diesel-powered yacht, the cost of achieving net zero via this approach would be approximately US$7-10 million per annum. How could the economics be improved? This study is based on an idealised scenario of building two bespoke production and bunkering facilities, serving a single yacht with seasonal operation. Not surprisingly, the levelised cost per kilogram of hydrogen derived by this approach is extremely high. If the CapEx could be leveraged across a greater number of yachts, then costs rapidly begin to fall. Additionally, non-seasonal production would in practice be sold to other industries, thereby further increasing plant utilisation and reducing the cost per kilogram further. By way of comparison, there are large hydrogen projects currently under development that will produce gaseous hydrogen for under $10 per kilogram. Whilst that cost excludes liquefaction, it gives an indication of just how far costs could be reduced to make the proposition more economically compelling.
Is it a plausible and feasible proposition for the superyacht industry to invest in their own net zero fuel production and distribution infrastructure? We believe our study illustrates that it is both technically possible and that the economics could be made compelling.
The size of the production and bunkering plant required is relatively small, but the geographical footprint of the renewable energy to power it is large. This is an interesting reflection point for our industry to understand the scale of renewable energy required to achieve net zero. A 4MW power plant in fossil fuel terms is relatively easy to understand, but a solar farm of 50-80,000 square-metres puts our energy use into stark context.
The cost on a single yacht basis is clearly very high, possibly as high as a quarter of the procurement cost of the yacht itself. And as a first-in-class example a fully liquified hydrogen design represents a significant investment and technology risk. However, the potential to reduce costs on a multi-yacht investment basis is plausible, and the technology to implement both the landbased and ship-side technical solutions are commercially available. In our view, a purely hydrogen powered superyacht is also feasible within the next generation cycle of superyacht development, at acceptable technology readiness levels and within a properly strategized project. Other alternative fuels, such as methanol, can further leverage the proposition of an industry-led approach to net
zero production and bunkering. The technical solutions to our net zero future already exist. We need to inspire those who have the means to enact them to take action. If you are reading this as a stakeholder in our industry, then you can help make it happen.
With more yachts opting for extravagant LED light portfolios and designers manipulating light in new and previously unconsidered ways, we speak to a panel of experts in the field to find out how the sector is continuing to evolve. Julie Clark (managing director, Savage Lighting); Stefan Wiendecke (Yachtlite); Dr Toby Robertson (head of engineering, OceanLED); Alessandro Palagi (owner Palagi); and Michele Orlandi (Luce5 Yachting) share their insights.
BY FRANCESCA WEBSTER
What are the most recent developments in LED technology and driver systems?
Stefan Wiendecke: We have been using digital LEDs for a while now, where each individual LED can be controlled individually. This makes it possible to create special effects - especially in our custom-made products such as lettering or helicopter landing decks. Professional programming and controls allow undreamt-of possibilities for spectacular lighting scenes.
Dr Toby Robertson: In its infancy, LED lighting technology moved on rapidly with large jumps in performance seen yearly. However, in more recent years these improvements have slowed due to LED and driver technology reaching their limits in performance. What has changed though, is the advent of underwater light optics. With the use of optics specifically engineered for underwater use it is possible to significantly enhance the lighting effect. Lights fitted with optics can illuminate larger areas, and minimise light loss, thanks to the more focused beam of light produced.
Alessandro Palagi: The trend we see in the market today is the use of LEDs to provide new features to lighting. The use of compact multi-chip light sources allows for mixing different CCCT of white. This is going to be available also for compact downlight solutions like DimToWarm or Turnable White, where we have the freedom to change the colour of the white light between cool and warm light and change the lighting scenario of the same environment.
“The quality is determined by colour trueness and a stable luminous intensity. For this purpose, the appropriate selection of LEDs is mandatory.”
How is the ‘quality’ of LED light determined?
Stefan Wiendecke: The quality is determined by colour trueness and a stable luminous intensity. For this purpose, the appropriate selection of LEDs is mandatory. When we include new LEDs in our program, high quantities of the selected LEDs are purchased by us or blocked for us directly after the successful completion of appropriate test procedures. This allows us to maintain a consistent quality for several years before another, new LED is used as a replacement.
Dr Toby Robertson: The CRI (Colour Rendering Index) is how we measure LED quality. This applies to ‘white’ light sources and defines the ability of that light source to show the true colour of objects. It is defined on a scale with 100 (the sun) defined as the best light quality, and values below this being poorer quality.
For underwater lighting however, the CRI is less important as the much more dominant impact on the colour rendering is due to the water quality. What is more important is the ‘binning’ of the LEDs; when LEDs are produced, there is variance in their performance in terms of colour and brightness (flux). During production, LEDs are ‘binned’ – this involves the manufacturer measuring the colour and flux of each LED, and segregating them into a ‘bin’ of similar performing LEDs. Lower-cost LEDs tend to come from manufacturers who employ larger bins, resulting in more variance between colour and brightness between LEDs. So, the end product would also suffer from this issue.
Michele Orlandi: The quality of light strictly depends on the quality of the LED used. Therefore, only through correct LED selection, technically known as LED binning, is it possible to achieve high levels of quality represented by high efficiency values, low CCT tolerances and high CRI values. Luce5 produces all the LED chips used in our products in-house, choosing and purchasing not only the electronic components but also the LEDs, always preferring selections with 2 or at most 3 MacAdam steps [also known as SDCM (Standard Deviation of Color Matching), MacAdam steps for measuring colour differences in the appearance of LED light]. This selection also makes it possible to track the production of the diode, ensuring the ‘repeatability’ of the LED, which means being able to provide products with the same lighting characteristics over time.
Alessandro Palagi: The main parameters are the colour rendering index CRI and colour targeting. Those parameters have been well defined many years ago and now we see that more and more people start to be familiar with them. Instead the difference between High Power LED and Midpower ones is still difficult to explain. The first ones have longer lifetime and less colour shifting over the time, they can provide stable light and colour for over 15 years, while with the Midpower LED, the lifespan can be much shorter.
What are the most common lighting mistakes made when appropriate expertise is not applied?
Stefan Wiendecke: Different light colours in various luminaires in the same area! Such as downlights, step lighting or furniture lighting. Therefore, when our products are used together with other products, we recommend our Dual-White LEDs, where you can adjust the colour temperature, or match them to the other lighting temperatures. Alternatively, you can also match the colour temperatures with RGBW-LEDs. This is then only a question of the controls.
Dr Toby Robertson: Spacing and the achievable effect in the water, as well as what is a realistic budget for a system. The biggest mistake though, is how the client thinks about lights. The old way of thinking is that more lumens equals a ‘brighter light’, but that isn’t true. The lumens figure is usually misinterpreted and potentially used to mislead people. Historically, the solution to having a more powerful lighting effect was to increase the lumen capacity of the light and pump more energy through it. The flaws with this solution are two-fold, first, the lights can only maintain a huge lumen output for so long (a few minutes), before they need to ‘throttle back’ so they don’t overheat. The second flaw is you haven’t really solved the core problem of ‘light dispersal’. Everyone approaching underwater lights should look for sustainable solutions that don’t compromise on quality, reliability and performance. Underwater optics supercharge a light’s performance, well beyond the point of simply adding more lumens.
Michele Orlandi: The most common mistake is to think in terms of the quantity of light. Little importance is given to the illumination of vertical surfaces (which make the space appear larger) and a ‘symmetrical’ distribution of luminaires is often used. The essence of light design is instead based on where, how and why. Light not only illuminates but also creates darkness: by creating a light accent on a detail, it emphasises it precisely because it contrasts with the ‘darkness’ that surrounds it.
What are the main considerations when choosing underwater lights in terms of number, colour, beam length/angle, etc?
Stefan Wiendecke: To create a perfect light effect around the ship, the spacing of the UWL must be adjusted to the light emission angle. If we are talking about weld-in lamps, we recommend the Louvre series from Lumishore. In this system, the LEDs are not placed deeply in a welded-in tunnel but are close to the outer hull of the vessel. A restriction by a welded tunnel does not exist then at all.
How is the Water Ingress Protection (IP Rating) calculated and what level of protection does it provide ?
Julie Clark: The rating is measured by how resistant a product is against solids and water, IPP66 is always recommended on the exterior. This means IP (Ingress Protection) is equal to t dust 6 (completely Dust-Tight) for the first 6, and liquids 6 (protected against powerful jets of water against the enclosure with no harmful effects) for the second 6.
Stefan Wiendecke: There are different levels of IP protection, which are always specified by the luminaire manufacturer. If the IP protection is sufficient for the intended use and the installation has also been carried out correctly, there should be no problem with the tightness.
Dr Toby Robertson: The IP rating is not ‘calculated’ as such, it is a standard as defined by IEC 60529, and ISO 20653. The first digit of the IP rating relates to the ingress of solid objects e.g. dust, and the second digit is the ingress of liquids.
Alessandro Palagi: There are specific tests according to the kind of rating.
The IP65-66-67 of our exterior products are the most challenging ones because we need to always have the maximum output of lumens, heat dissipation and watertightness.
Research has shown that electric light can impact circadian rhythm and affect our health, alertness, productivity and more. Can you implement a circadian lighting system on yachts?
Julie Clark: Savage have recently launched the smart DMX-C Lighting range, in conjunction with Crestron Electronics, with this partnership circadian lighting can be perfectly implemented onboard. In addition each fixture is individually addressable, dismissing the need for complex circuits.
Stefan Wiendecke: In principle, this is possible. The luminaires must of course be capable of ‘full colour’ and the control system, including networking, must be programmed accordingly. This is no longer a problem with today’s state of the art.
Dr Toby Robertson: Potentially, yes this could be implemented on our colour change underwater lights, as intensity and colour could be dynamically adjusted to the time of day. However, such a system would be more beneficial being used on interior lighting rather than the exterior underwater lights.
Michele Orlandi: Our R&D and Software Development departments are able to give maximum support to the design and implementation of circadian lighting. We are able to develop, create and provide all the necessary tools for these types of projects, from the development of hardware, software / programming and, of course, lighting fixtures.
SuperYacht Times B.V. Silodam 256, 1013 AS, Amsterdam, The Netherlands
31 (0) 20 773 28 64 info@superyachttimes.com www.superyachttimes.com
Cover Images
Ribelle by Tilse Teak image by Arksen Akula by Rossinavi
How to Build It is published by SuperYacht Times B.V., a company registered at the Chamber of Commerce in Amsterdam, The Netherlands with registration number 52966461. The magazine was printed in August 2023.
Always a perfect match
The finish of your yacht should reflect your expectations of durability, longevity, color, and gloss. ALEXSEAL® offers outstanding finish performance with different systems: The polyurethane Premium Topcoat 501, the acrylic Topcoat X, and the polyurethane High Solid BaseCoat/ClearCoat.
instagram.com/alexsealpaint fb.com/AlexsealYachtCoatings WWW.ALEXSEAL.COM
Three possibilities with one target: Giving you a choice to find the right solution for your application parameters and finish characteristics.
Scan the code and learn more about our Topcoat solutions →