PRINTING: Mindset over matter?
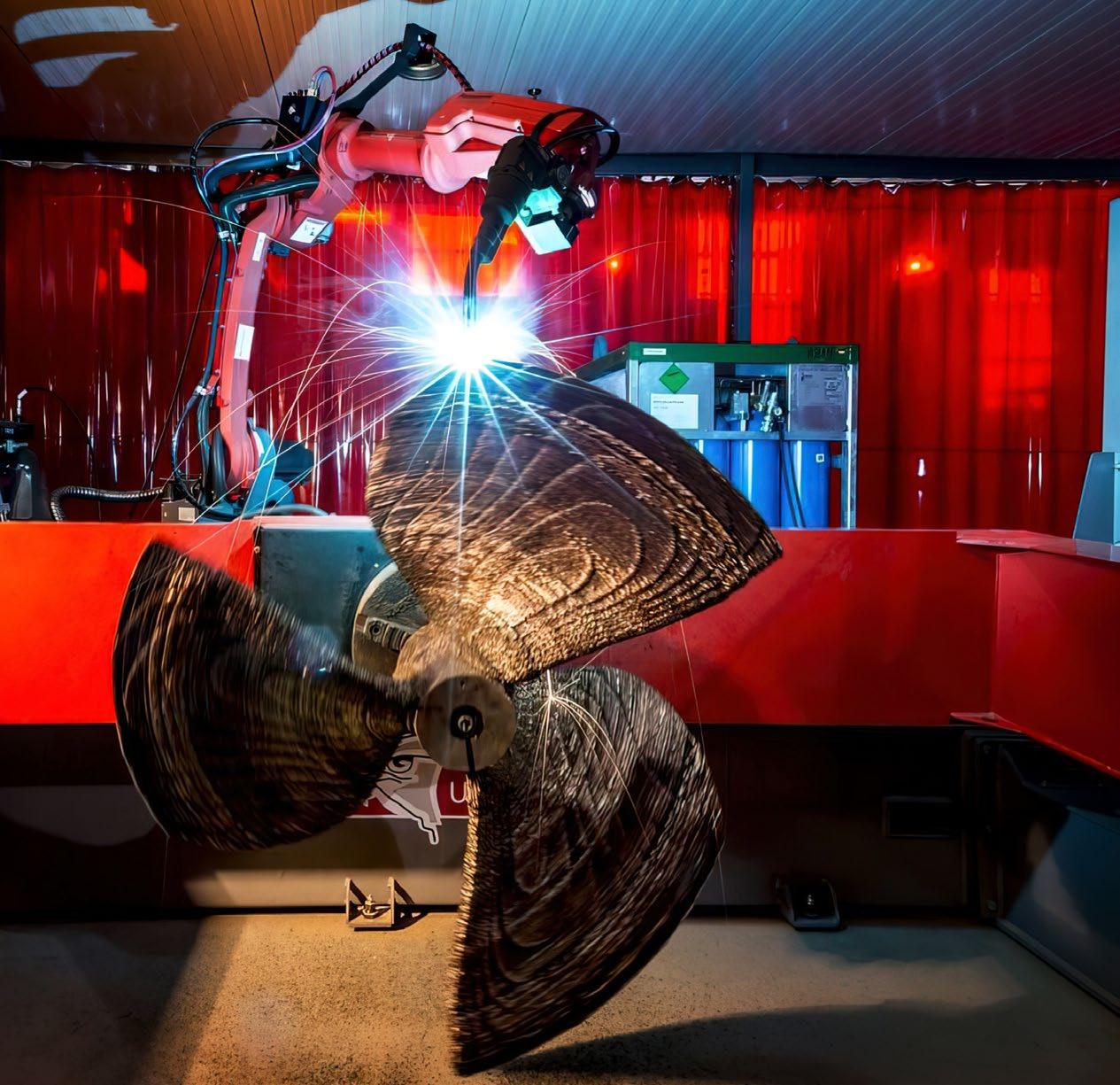

MARIN: The human factor
PRINTING: Mindset over matter?
MARIN: The human factor
The technical magazine for those involved in the design, construction and refit of superyachts
20 Supplier Spotlight: Oldenburger
A look into the German outfitting company’s plans to increase
and streamline
22 CEO in Conversation: Carol Driessen of Vyva Fabrics
A chat about the business of supplying high-quality fabrics to the yachting industry.
25 Business Talk: Soaring High
Restructuring and reappraisal of its market offering has rewarded Baglietto with a healthy order book and record-breaking revenues.
35 Concept in Focus: Just Wing It
A super-sized sailing yacht with wing masts, is Royal Huisman’s Wing 100 concept the ideal crossover between sail and power?
42 Build Report: One of a Kind
We go behind the scenes of FB283, Benetti’s only full-custom yacht in build and currently approaching completion in Livorno.
54 Build Report: Practically Unprecedented
A closer look at Oceanco’s Project H, the radical rebuild that challenges the industry to reconsider the potential of an existing superyacht to take on a new identity.
67 Operation & Maintenance: Oiling the Works
A visit to Spectro Jet-Care in the UK to find out high-precision fluid analysis can also spot potential problems and failures before they occur.
74 Inside Angle: Building with Burgess
Ed Beckett and Peter Brown have refreshed Burgess’ approach to new-build sales, we found out more.
78 Dockside: Energy Conundrum
Propulsion is only half the story in the battle for energy efficiency when the hotel load is the biggest consumer on superyachts.
86 Case Study: The Human Factor
Think MARIN, and you think tank tests. But the Maritime Research Institute Netherlands is pursuing a much wider scope of maritime research.
94
Safety & Security: No Smoke without Fire
The industry is reassessing its fire prevention regulations following a spate of onboard fires. But are lithium-ion batteries really the culprits?
102 Guest Space: Going Up
A visit to Lift Emotion in the Netherlands, a key player in the highly specialised and competitive market for custom elevators on superyachts.
112 New Tech: Print Your Parts
Is 3D printing the miracle solution that will allow us to print entire boats in a matter of days?
118 Refit & Conversion: Grand in Green
A visit aboard a classic Feadship approaching the end of an in-depth refit at the family-run Balk Shipyard near Amsterdam.
129 Ask the Experts: Is a Perfect Paint Job Possible?
We pose this and other coating questions to a panel of industry professionals.
EDITORIAL
EDITOR IN CHIEF
EDITOR | HOW TO BUILD IT
EDITORIAL CONTRIBUTOR
EDITORIAL CONTRIBUTOR
FEATURES WRITER
DIGITAL EDITOR
NEWS WRITER
TRAVEL WRITER
CONTENT CREATOR
VIDEOGRAPHER
Francesca Webster
Justin Ratcliffe
Charlotte Thomas
Phil Draper
Alexander Griffiths
Emma Becque
Sophie Spicknell
Jessamie Rattray
Ruben Griffioen
Muaz Abourched
DESIGN PRODUCTION
CREATIVE DIRECTOR
GRAPHIC DESIGNER
UI/UX DESIGNER
Ivo Nupoort
Beatriz Ramos
Claudia Sabbadin
INTELLIGENCE
HEAD OF INTELLIGENCE
RESEARCH ANALYST
DATABASE MANAGER
DATABASE MANAGER
YACHT HISTORIAN
Ralph Dazert
Adil Zaman
Vicky Linardou
Léandre Loyseau
Malcolm Wood
SALES & ADVERTISING
SENIOR SALES MANAGER
SALES MANAGER
SALES MANAGER
CLIENT SERVICE MANAGER
SALES & MARKETING SUPPORT
Marieke de Vries
Justus Papenkordt
Daniel Van Dongen
Johanna Borreli
Jochem Eenkhoorn
CORPORATE
FOUNDER & DIRECTOR
TECHNOLOGY DIRECTOR
FINANCE DIRECTOR
Merijn de Waard
Fabian Tollenaar
Laura Weber
In my last Editor’s Letter I compared the first issue of this magazine to a custom prototype, adding that we fully intended tweaking the design and optimising the specs in subsequent issues to establish a proven platform for the industry. Six months later, welcome to the ‘new and improved’ second edition of How to Build it.
The sharp-eyed among you will notice that the graphic design has evolved. It is still clean and contemporary, but now a touch crisper and more current. What hasn’t changed is the content, which remains as varied, engaging, relevant and up-to-date as before. The subjects may be technical, but the language and layout is always lucid and concise.
Our cover stories provide an indication of the diversity of subject matter in this issue. Earlier this year I was lucky enough to attend the unveiling of Project H, for example, and have never seen anything quite like it. It certainly piqued my curiosity about the challenges and perceived advantages of rebuilding a superyacht as opposed to refitting or building new.
Likewise, a visit to the famous Maritime Research Institute Netherlands, or MARIN for short, proved an eye-opener. The technicians working there spend a lot of time messing about with yellow models in towing tanks. But they also do much more, such as training crews using kinematic motion machines that can be programmed to simulate virtually any kind of sea conditions and navigation scenarios. Or testing emerging fuels and power systems in a prototype engine room of the future to find the ideal balance between sustainability and efficiency.
And then there’s additive manufacturing. Since becoming more readily available and affordable 3D printing captures fewer headlines, but it’s swiftly being integrated into everyday industrial workflows – including the yachting sector – and it’s safe to say we will see much more of it in the future. Just don’t expect to see a 3D-printed superyacht any time soon. Whatever your sphere of specialisation, I’m certain you’ll find something of interest to read in the pages that follow. Enjoy!
Justin Ratcliffe - Editor
A+T Instruments, UK-based manufacturer of high-end yacht instruments, has appointed Nils Jolliffe as Chief Operating Officer. Responsible for general management and scaling operational processes to support company growth reported to be running at 40 percent year on year, Jolliffe brings with him experience from previous senior positions at Auxitrol Weston, DDC Electronics Ltd, Bowman Power Ltd, Eaton Aerospace and Raymarine.
Last November A+T unveiled its new 520 series of masthead-motion wind sensors, said to be the first production unit sensors that can directly measure wind acceleration/ velocity at the masthead then transmit this to the instrument processor for masthead motion compensation.
“I’ve been amazed by the range of high quality, innovative products A+T have developed in a short space of time and list of customers switching to A+T in the superyacht and race boat market is impressive,” says Jolliffe. “The customercentric, fast paced, can-do attitude of the team is something that really appealed to me and I’m excited to be part of helping the company continue its development and growth. There’s plenty more innovation to come and our customers will love the focus we’re putting on their needs coming first.”
In Issue 1 of How to Build It, we published an extensive article (Fuelling Change) on the challenges of switching from fossil fuel to biofuel. We have since learnt that the crew of 44-metre Lammouch, a popular Med charter yacht managed by Burgess, has embraced sustainable change by switching to biofuel.
In November last year the yacht took delivery of 15,000 litres of second-generation biofuel, the culmination of a long preparation process that included included six months of discussions with the engine manufacturer Caterpillar, Class approval and agreement from the owning and management companies.
The new fuel, Cristal Power XTL 100 marketed by Fioul 83, is an HVO (Hydrotreated Vegetable Oil) product derived from the recycling of used cooking oil, treated
with hydrogen and mixed with fresh cooking oil. With no engine modifications required, this biodegradable, renewable fuel reduces CO2 emissions by 50-90 percent and toxic particulates by 80 percent. The fact it is odourless and reduces noise also makes a positive difference in terms of onboard comfort.
Cristal Power XTL 100 is more expensive than conventional diesel for the moment, largely because the used cooking oil collection network has not yet reached an economy of scale.
However, the yacht’s owning company was willing to accept the small additional cost because of the reduction in ecological impact it offers.
“I am very proud to manage a yacht whose owner has taken such a positive, progressive decision,” said Burgess charter manager, Caroline Boisson.
The first version of the Yacht Environmental Transparency Index (YETI), which scores and compares yachts based on their environmental credentials, was launched at METSTRADE 2022 and shared with members of the industry. The tool is designed to “emphasise the operational efficiency of a yacht’s lifecycle to reduce ecological impact by benchmarking vessels against an average operational profile.”
YETI 1.0 works by expressing the calculated emissions in ‘EcoPoints’, which are divided by the yacht’s gross tonnage to determine a relative score that is comparable within its class. The defined classes for YETI 1.0 are <500, 500-3000GT, and >3000GT.
To use YETI 1.0, data about a vessel’s general parameters (speed-power, load determination, generators, battery bank, and heat distribution system) must be submitted on the input sheet. When joining the fleet review, yachts are provided with a feedback report that includes a YETI 1.0 score, an explanation of how this score was determined, comparison to the rest of the assessed fleet within a given class, and suggestions for potential areas of improvement.
“The groundwork has been done, it is now time for the industry and owners to utilise this reliable reference to know where a yacht stands and what opportunities there are to improve its environmental credentials,” says Robert van Tol, executive director of Water Revolution Foundation, the non-profit organisation that is a driving force behind YETI.
Italy-based Videoworks has responded to requests from shipowners and shipyards by setting up a Connectivity & Communication Solutions Business Unit dedicated to developing cutting-edge solutions in the field of on-board connectivity. It is the latest step in an evolutionary process that was announced last year at the Monaco Yacht Show together with ONE Web, a latest generation Internet experience that provides streaming and IP TV services with a fast connection very similar to 5G, in order to offer on the water what people are used to having on dry land.
“It was important to seize this particular moment because we are witnessing an authentic revolution in the world of connectivity, with systems evolving very rapidly: new technologies, new players with LEO (Low Earth Orbit) satellite systems, such as Starlink and ONE Web, with which we are cooperating closely,” says Paolo Tagliapietra, who is coordinating the new Connectivity & Communication Solutions B. “The stated goal is to have a bandwidth capacity similar to the one we are used to on the mainland. Today’s yacht owners want to be able to access platforms such as Netflix with the same speed and image quality they are used to having in their living room at home. Videoworks guarantees the technology to do so.”
EST-Floattech, Dutch specialists in the development and installation of maritime battery systems, has signed a long-term framework contract with Rolls-Royce Power Systems for its DNV-certified Green Orca 1050 lithium-polymer battery module aboard 10 new-build vessels.
The first order of the new partnership is for nine hybrid fast ferries equipped with MTU hybrid propulsion to be operated by Liberty Lines in Italy between Sicily and Croatia. Each of the modules has a capacity of 10.5 kWh. The sister passenger vessels of identical design will be built at Astilleros Armon in Spain. Of more interest to our readers, however, is a second order for the hybrid propulsion system of Project Arrow, a 76-metre superyacht in build at Turquoise Yachts in Istanbul. Delivery of the 1,512 kWh battery pack is planned for 2023 and the yacht designed by Enrico Gobbi of Team for Design is slated for delivery in 2025. In both cases, the battery systems can be used for cruising speeds of up to 8 knots and in all-electric mode when entering and leaving port, anchoring and manoeuvering for zero emissions and minimal noise.
Australian specialist pump designer and manufacturer Davies Craig has introduced a new range of marine, DC-powered, electric water pumps, the culmination of more than five decades of design and production experience in the field of fluid dynamics. The EWP pumps are unique in that they employ a flat, printed-circuit electric ‘pancake’ motor coupled to an impeller for compact size combined with high-flow circulation capability and low current draw.
Targeting the rapidly growing demand for cooling circulation pumps to maintain thermal stability in lithium-ion battery packs, the pumps can be managed by a patented digital controller which modulates flow rates in response to selected temperatures. The algorithm takes into account not just the actual temperature but the rate of change so that in the case of a rapid increase in coolant temperature, for example, the pump will accelerate to prevent overshooting the selected value.
The EWP is available in 12 and 24 volts and produced in five capacities with the largest delivering a maximum of 9,000 lt/hr. Besides applications in electric and hybrid power systems, they can also serve as circulation pumps in closed-circuit condenser cooling and chiller A/C units.
“Our markets have largely been industrial and automotive, but we know that many of our EWP pumps have found their way into marine applications,” says engineer and company co-founder Daryl Davies. “Now with the rapid evolution of electric and hybrid power plants, we foresee a significant demand for this product and so we established a marine division to develop it further. There are tens of thousands currently in service in automotive applications with a zero-failure rate.”
Hundested Propeller, the manufacturer of controllable pitch propellers, controllable pitch gearboxes, thrusters and control units, has announced a new hydro-electric pitch control unit. The compact Hundested FR-ELH is designed for shaft line setups and direct electric drive, or installation aft of a standard reduction gearbox without pitch control. All the pitch control units have high-quality thrust bearing design, long stroke for feathering propellers and can be delivered with semi-flexible foundations. The lightweight FR-ELH weighs around 100kg and incorporates many of the solutions from the hydraulic FR-HP model that has been proven to perform very well, but features new developments for additional benefits. Although specially developed for electric propulsion, it can also be used in conventional drive lines; improved mounting points make it simple to dismount for servicing without losing the alignment of the propulsion line; and easy installation means the only connections are 24V and three wires for feedback signals with no constantly running hydraulic pumps or motors required. Additionally, it can hold propeller pitch without consuming power.
The first Hundested FR-ELH hydro-electric pitch control unit was delivered in December 2022 for installation aboard a new 88-foot sailing yacht with direct electric drive and power
The Expert Power Control 87 Series is a new type of IP Power Distribution Unit from Gude Systems that offers 30 switchable load outputs, which is the perfect control and monitoring centre for 19-inch racks. The Series offers flexibility, with switchable IP power solutions that make it possible to switch certain devices or areas onboard on and off without interrupting the power to all other devices. This makes it possible to optimise power consumption and save energy.
Smart PDUs provide an extra layer of protection against overvoltage and overheating by being able to cut off power
to specific devices when problems occur. The system also includes Intelligent power strips that are monitoring systems that allow ETOs to monitor and control the power consumption and performance of specific devices. In addition, plug-and-play sensors for the PDUs allow monitoring of ambient temperature and humidity. System-critical conditions on the yacht are thus detected at an early stage.
Switchable IP strips allow you to shut down specific devises for maintenance and repair and Smart PDUs from GUDE can be easily integrated into leading AV control systems.
Italy-based i-Carbon was set up by four friends who combined their experience in project management, engineering and innovation technology with a love of sailing to develop innovative deck gear crafted from metal alloys and carbon fibre. The company’s most recent products include a new range of deck filler caps, stanchions and pop-up cleat.
The i-Carbon fully retractable cleat is mounted recessed into the deck to be perfectly flush with the teak decking. The refined, functional design requires no drainage and they can be fitted without necessarily having to access the deck’s underside.
The new deck fillers are made of marine-grade aluminium or polished AISI316L stainless steel and have an asymmetric handle that gives them a more technical and racier ‘automotive’ look. They can also be custom engraved on request.
Made of pre-preg, autoclaved carbon-fibre tubes with a AISI316L stainless steel base, the i-Carbon stanchion system comprises three types: fixed stanchions that are permanently installed on board; removable stanchions with quick-connect fittings for the base and male plug that carries the carbon tube; and removable stanchions with a deck socket and bayonet coupling device that engages with a 90° rotation. The stanchions are available in three sizes with tube diameters of 33mm, 45mm or 66mm depending on size and Class of vessel.
Having seen how a billiard table on a cruise ship is useless in even moderate waves, a passenger challenged his engineer friends to design a billiard table for use at sea. Cybernetic specialist Svend Heier took up on the challenge and in 2000 a stabilised billiard table was tested on a ferry running between Norway and Germany. During the test trip one of the engineers working on board became seasick. A clever head suggested that he should have a rest on the stable billiard table. It worked, and the idea of a stabilised bed was born along with Stable company in Arendal, Norway.
Billiard and pool tables are not uncommon on superyachts, which led to an unusual partnership between the French company Billards Toulet and Stable to develop a stabilised table aimed at the yacht market. Uniquely, the gyroscopic system is housed inside the table itself to eliminate accelerations due to roll and pitch and neutralise the lateral forces. Sensors pick up the vessel’s movements and the table is automatically adjusted by computercontrolled electrical actuators.
“The reaction time is fast,” says Svend Heier. “We sample the accelerations at 100 Hertz and the system can react to roll periods of down to 1.5 seconds, but on a standard 7-8 second roll period we can eliminate 98 percent of the movements. That is more than enough to play a normal game of pool as the beize cloth provides an element of friction as well.”
Stable is also able to stabilise ping-pong and foosball tables, art and sculptures, wine cellars, gaming zones and workout areas, drone and telescope platforms, antennas and radars, and even bowling alleys.
The Swedish company SKF has developed the first electric, zero-speed fin stabilizer. Under construction for a new-build superyacht in Germany, the electric stabilizer will offer low noise and vibration with the electric motor only turning when the fin is moving. The fin uses only electric parts with no moving parts within the control cabinet. In addition, the stabilizer offers low installation costs due to fewer components and virtually no layout restrictions when compared to traditional counterparts.
Available between 5-9 metres, with larger sizes in development, the first electric fin has been developed as part of SKF’s path to net zero by 2050. The new stabiliser over zero-speed stabilsation and is fully retractable.
devices with soul
plhitalia.com
What for everybody are just command plates, switches or keypads, for us are “devices with soul”, high tech products with an artisanal soul, designed and made in Italy.
The original and elegant Slim collection, with only 4 mm of thickness, confers to the environment a refined, elegant and understated touch. Here, in the brushed brass protected version, with one button.
The second Amels 80 was sold in December 2022, only three months after the first hull. The model was first announced in an online event earlier in the year, and is the first series to have been designed for Amels by Espen Øino. Her owners are keen divers and the yacht will be equipped to accommodate their various passions. She has a 2,175 GT and will have a top speed of 16.5 knots, powered by twin Caterpillar engines.
LENGTH: 79.8-metres BUILDER: Amels COUNTRY OF BUILD: Netherlands DELIVERY YEAR: 2026
NAVAL ARCHITECTURE: Damen Yachting EXTERIOR DESIGNER: Espen Øino INTERIOR DESIGNER: Jonathan Quinn Barnett
In September 2022, Sanlorenzo signed the contract for its new flagship, the 1,950 GT 73 Steel. A larger sister of the 72 Steel, also currently in-build at the shipyard, the yacht features a diesel-electric propulsion system aimed at minimising emissions and her interior configuration has been designed in close collaboration with her owners. The yacht has a steel hull and aluminium superstructure.
LENGTH: 73-metres BUILDER: Sanlorenzo COUNTRY OF BUILD: Italy DELIVERY YEAR: 2026
NAVAL ARCHITECTURE: Sanlorenzo EXTERIOR DESIGNER: Zuccon International Project INTERIOR DESIGNER: Unknown
Sold in September 2022 to an American client, the Sportiva 66 has a steel hull and aluminium superstructure. The yacht has a sporty profile with reverse bow design and she is under construction at the Ancona shipyard with Ian Kerr of Kerr Maritime overseeing the technical specifications and construction. The yacht has a top speed of 18.5 knots.
LENGTH: 66.4-metres BUILDER: ISA COUNTRY OF BUILD: Italy DELIVERY YEAR: 2025
NAVAL ARCHITECTURE: Palumbo Superyachts EXTERIOR DESIGNER: Nuvolari Lenard INTERIOR DESIGNER: Unknown
The new Baglietto flagship was first announced as a speculation construction in October 2022 and the announcement was swiftly followed by her sale in December. The T60 is the largest in the T-Line series and is the big sister of the 52-metre model, of which eight have already been sold. She features a steel hull and aluminium superstructure, has a 1,000 GT and is powered by twin Caterpillar engines to top speeds of 16 knots.
LENGTH: 60-metres BUILDER: Baglietto COUNTRY OF BUILD: Italy DELIVERY YEAR: 2026
NAVAL ARCHITECTURE: Baglietto EXTERIOR DESIGNER: Francesca Paszkowski INTERIOR DESIGNER: Unknown
Sold in December 2022 to repeat Heesen clients, Setteesettanta, Hull YN 20857, has a lightweight aluminium construction and will be fitted with two compact and fuel-efficient MTU 16V2000M72 (1,440 kW) diesel engines that will offer top speeds of 18 knots. She will accommodate up to 12 guests between a six stateroom configuration.
LENGTH: 57-metres BUILDER: Heesen COUNTRY OF BUILD: Netherlands DELIVERY YEAR: 2026 NAVAL ARCHITECTURE: Van Oossanen Naval Architects EXTERIOR DESIGNER: Omega Architects INTERIOR DESIGNER: Cristiano Gatto Design
Enzo was first announced in October by the partner companies SIMAN and Axis Group Yacht Design. She has a six stateroom configuration for up to 12 guests including a full-beam master suite to the fore of the main deck that features large windows offering panoramic views. There is also a VIP stateroom on the upper deck which can be converted when not in use to a gym, home office or playroom. She is powered by twin Caterpillar engines and will have a top speed of 15 knots.
LENGTH: 50-metres BUILDER: SIMAN Srl. COUNTRY OF BUILD: Italy DELIVERY YEAR: 2025
NAVAL ARCHITECTURE: Axis Group Yacht Design EXTERIOR DESIGNER: Horacio Bozzo Design INTERIOR DESIGNER: Unknown
The Sunreef 43M Eco sailing catamaran has been designed for all-year exploration and incorporated solar panels in her hull, her mast and boom that generates “green energy for unlimited, emission-free cruising”. The customisable yacht will be tailored to her new owners’ tastes and host a plethora of amenities including a spa, bar and fitness area. She is equipped with composite-integrated solar panels, a hydrogeneration propulsion system, electric engines and performance sails. She is also constructed from ethically sourced and sustainable materials, accentuating her eco offering.
LENGTH: 42.7-metres BUILDER: Sunreef COUNTRY OF BUILD: Poland DELIVERY YEAR: 2025
NAVAL ARCHITECTURE: Sunreef EXTERIOR DESIGNER: Sunreef INTERIOR DESIGNER: Sunreef
This is the first motor yacht under construction from StellarPM, a relatively new name on the yacht construction scene. The company is based in the US, with construction taking place in Asia, and the first ONE 108 has been sold to a North American client. The yacht belongs to the recently launched StellarONE series, and there is also a 40-metre model, the StellarONE 130. She is powered by twin Caterpillar engines to a top speed of 14 knots.
LENGTH: 33-metres BUILDER: StellarPM COUNTRY OF BUILD: Vietnam DELIVERY YEAR: 2024 NAVAL ARCHITECTURE: Ginton Naval Architects EXTERIOR DESIGNER: StellarPM INTERIOR DESIGNER: Unzile Acar
Enhance your Superyacht with smart Power Distribution Units
More power safety
Less service deployments
Higher energy efficiency
No more AV downtimes
The German manufacturer Oldenburger has been outfitting yachts for more than 70 years. Today, the company continues to expand with new factory spaces under construction and more than 250 permanent employees working at the facilities in Dinklage, Germany, and an additional 110 situated in Shanghai serving the Australasian and American markets. Despite its broad portfolio of products, including the aeronautical and residential sectors, the yachting industry accounts for 85 percent of the company’s turnover.
BY FRANCESCA WEBSTER
On average Oldenburger works on three new-build and around 30 refit projects per year, of which the major share are full custom. Joining the conversation from the very earliest stages allows the company to implement clauses that protect it and its clients from protracted build schedules. However, offering turnkey solutions means that amendments to design can cause major disruptions to schedules and over the last two years the company has had to navigate through difficult waters, made more complex by supply chain issues.
The current expansion is one of the ways that the company is looking to mitigate increasing costs. Unifying the two Germany-based build facilities on the Dinklage site, the expansion sees the construction of two new build sheds that should improve production flow.
“Four years ago, Oldenburger had three companies, respectively for aircraft, retail and the superyacht market, but we needed to streamline our production processes so that we could focus our efforts on the superyacht industry as main business. While all the markets are still operational, they now operate under one company, situated at the original factory site. Yachting is our primary focus and over the past two years we have been looking to improve our workflow, not only for us but also for our clients, so that we could continue to offer competitive rates and deliver our products on time. However, we were still building between two separate facilities and that cost us in terms of time and money, with a huge amount of travel needed and the team split between two locations. The new facility will unify all of our plus-100 carpenters and joiners under one roof, meaning better teamwork and in the end, better products.”
The expansion will also allow the company to accept more new-build orders over the coming years. Many of its superyacht projects are 80 metres or above and demand for its expertise is increasing every year. While many shipyards have in-house joinery departments, very few are able to keep up with the increased demand for custom projects over recent years.
“When it comes to these very large scale projects, there are very few shipyards that have the expertise, or capacity that we offer,” says Carsten Loge. “This industry demands a high level of skill, you are talking about creating joinery down to the tenths of a millimetre and even small mistakes can cost a large amount of money.”
Oldenburger uses some of the most accurate machinery in the world. Automation is becoming far more prevalent, believing that superyacht quality can only be ensured with all the developed and highly complex machinery. Nesting machines, CNC machines and milling machines are all employed on a daily basis in order to manufacture as efficiently as possible.
Reliance on machinery also helps to reduce energy consumption, something the company has focused on by implementing energy-saving insulation and heat recovery technology. However, while the company is committed to sustainability, it has been very difficult to implement alternatives within the yachting industry, though they do suggest eco-friendly solutions to both designers and shipyards.
One of the biggest challenges facing the outfitting industry is to remain aligned with class regulations, particularly when it comes to fire-proofing interiors. Benjamin Bäker, head of sales and marketing, explains: “The regulations are strongly related to the design of the interior. In a REG-B certified project, everything must be at least flame retardant, while in a REGA project many of these issues can be avoided. So for each project, in terms of classification, we have to make sure that some of the materials can be bent that way. Here we have to certify the materials through a variety of ways.”
Unsurprisingly, R&D is important and Oldenburger has an expansive department dedicated to research. In recent years it has launched patents for a number of products, including ceiling drop guards and teak floor guards, and its R&D team are constantly testing new lacquers and adhesives.
Vyva Fabrics’ brutalist concrete studio, in part designed by company founder and CEO Carol Driessen herself, is quite a landmark in the north Amsterdam boatbuilding enclave near to Damen Shipyard. We paid the studio a visit to talk about the business of supplying fabrics to the yachting industry.
BY ALEXANDER GRIFFITHS
Carol Driessen, founder and CEO of Vyva Fabrics, was supporting her father’s marina business when a job offer from a client led to her working as a European sales rep for an American faux leather manufacturer. She had the knack and found her niche. Vyva Fabrics began from a small harbour warehouse in Amsterdam in 1990 supplying upholstery materials for boats and yachts. Today, it is a successful wholesaler of high-quality fabrics and vinyls.
Vyva Fabrics has grown into a major business. Tell us more about the journey.
It was originally just me and a single line of material, an outdoor material: Sunbrella acrylic. I shipped it from the States in 150-metre rolls – too much for my clients. Rather than waste the material, I created a sample book from the leftovers and went door-to-door to outfitters, designers and shipyards. And that’s how Vyva was founded; I really started from nothing. As my portfolio grew, so did my team. I was initially only interested in the marine industry, but I began taking jobs in hospitality, healthcare and many other sectors. Most of our clients are no longer maritime, but at a conservative estimate, I’d say 70 percent of the yachts built and refitted here in the Netherlands feature our fabrics.
How does Vyva Fabrics fit within the design funnel, and who do you typically liaise with on yacht projects?
It all depends on the project. Many designers that know us and our product portfolio build a complete package for their projects themselves, but others seek advice. There are many things to consider with material choice: durability, quality, sustainability, fire retardancy, costs, and so on. Typically, we liaise with designers and architects that we meet with, but it’s not uncommon for shipbuilders and outfitters to be here in our studio, especially for smaller projects.
How fierce is the fabric segment and is the competition primarily from large well-established firms, or smaller boutique sellers?
There are many suppliers competing with us on price, and quite often they are cheaper than us. Sourcing from regions like China, they can slash costs but they also compromise on quality. This is okay for a lot of buyers, but when you’re in the business of supplying fabrics and materials for superyachts, quality is everything.
Attitudes to sustainability and ethically sourced materials have accelerated dramatically. Do you think non-recyclable materials will be phased out anytime soon?
We do think recyclable or sustainable fabrics will increase a lot and we’re all for it, launching sustainable collections such as Hemp, REVYVA, Dinamica and Econic. We’ve offered sustainable solutions for a decade now, and nobody was interested initially.
Annual turnover: €12.5 million
Number of employees: 20
Number of current yacht projects: 12
Number of materials in portfolio: 30 each in 30 colours
Completed yachts: approx. 70 percent of Dutch fleet
But now if it’s not 70 percent recycled or more, many clients aren’t interested. People are now willing to pay the premium. The challenge nowadays is to produce sustainable fabrics and vinyls without diminishing the quality. We still like working with our PVC vinyls as they’re extremely robust and last for decades, so you could argue that is more sustainable than using a 100 percent pure linen, which needs to be replaced after a couple of years. Due to the high fireretardant specs of vinyls, it’s still work in process and some will never be replaced with sustainable substitutes.
Are there fire retardant materials that are also eco-friendly?
Two years ago we launched our REVYVA collection made from post-consumer PET bottles that is 100 percent recyclable after use with extremely high fire specs. The collection has sold very well and we decided to add a Bouclé or looped yarn version as well.
Besides the fabric collection, in May we’re also launching our first ECONIC vinyl collection. This durable, high-quality artificial leather looks like natural linen and feels pleasant to the touch, but is completely phthalate-free and contains 75 percent recycled, bio-based and renewable ingredients. We also use bio-graded PVC resins from agricultural biomass and forestry, and bio-based plasticisers from soybean oil, which contain no chemical flame-retardant additives but still meet European fire standard EN 1021. The collection has the eco-label OEKO-TEX® Standard 100, which guarantees that the synthetic leather does not contain any substances that could be harmful to people or the environment.
Is the supply chain still problematic? How do you ensure you deliver on time, every time?
Before 2019 it wasn’t uncommon for outfitters to place orders a month ahead of time, but now they’re used to long delivery times so they plan further ahead. When the pandemic broke out we knew we had to change our approach. We have a huge warehouse with plenty of space, so we filled it up and from January to June of 2020 we were just filling our inventory – and it really paid off. Orders from the marine sector slowed down, but demand for outdoor and garden fabrics spiked, bringing sales up by around 30 percent compared with previous years. Many people during the lockdown were investing in their own properties, doing up the interior and exterior spaces. We were crazy busy. And now with the marine business booming, with order books signed until 2025, 2026 even, the supply chain challenges have all but passed. We also have a slightly different mentality and orders are now being placed well ahead of time.
Founded nearly 170 years ago, Baglietto is one of the oldest yacht brands in the world. The company has seen some highs and lows, but recent restructuring and a reappraisal of its market offering has been rewarded with a healthy order book.
BY PHIL DRAPER
Italian semi-custom and full-custom superyacht builder Baglietto had a lot to celebrate as 2022 came to a close. A turnover of around €110 million for the year 2021-22 to the end of August broke all records and, according to CEO Diego Michele Deprati, the year ahead is looking better still with a burgeoning order book as the brand consolidates its position in the competitive sub-500GT sector. The Baglietto management team secured contracts for no fewer than nine new-builds between 40-60 metres last year, an incredible tally by any standard and one that takes the brand with the Soaring Seagull logo to new heights. Overall the brand’s order book now includes 17 projects to a value of almost €370 million. And with four more yachts ‘scheduled but still available’, it has a total of 21 yachts to build over the next three-and-a-half years with an average length of 47 metres – that’s over three kilometres of superyachts.
Roughly 80 percent of Baglietto’s turnover comes from just three semi-custom models: the all-aluminium DOM133, and the steel and aluminium T52 and T60 models. The remaining 20 percent is from fullcustom projects, which in theory at least can be built in any material, including composites. Virtually all the present order book was generated with yacht broker assistance, although it has an office in Fort Lauderdale to support sales and service operations throughout the Americas. It also recently established independent brand representatives in Australia and Brazil, and is actively seeking similar partners elsewhere in the world.
Present client demographics is Americasfocused with some 60 percent of current projects in progress for owners based on that side of the Atlantic. Of the remainder, 30 percent is European and 10 percent ROW. But the intention is to spread the net further afield and spread the risks of any market downturn.
“Our ultimate aim is to grow the business to the point where we can deliver six or seven big boats a year,” says Diego Deprati. “Anything more would start to diminish the levels of service that we pride ourselves on. Our ability to listen and tailor solutions accordingly is what sets us apart and, beyond the attractiveness of our various models, that is really what underpins our recent sales successes.”
Last year, Baglietto delivered one semi-custom model and two full-custom projects. These handovers included Attitude, the second of its DOM133s (although strictly speaking she is the first, as the earlier Run Away delivered in 2020 was slightly shorter, had less volume and was originally billed as a DOM123), the full-custom 38-metre Enterprise (C10235), and the Superfast 42 Rush (C10236).
This year will see five more projects concluded: the third and fourth DOM133s (C10243 and C10244) and the first two Baglietto T52s (C10238 and C10240), plus the full-custom 41-metre Francesca II (C10242).
An increasingly demanding schedule in 2024 should see five handovers: two DOM133s and three T52s. And in 2025 a further three DOM133s and three T52s will be delivered, plus a possible Fast 43 (C10226) that is currently on hold. Further out, there were several 2026 delivery slots at the time of going to press. The only firm delivery that year, however, is the first allnew, 60-metre T60 flagship (C10260), which was sold at the end of last year only three days after the sale of the eighth T52.
“Our ultimate aim is to grow the business to the point where we can deliver six or seven big boats a year.”
Baglietto has two main facilities roughly halfway between Genoa and Pisa. The biggest is in the historic naval port of La Spezia, the second largest city in Liguria after Genoa. The other is in the Tuscan city of Carrara, which lies to the south-east of La Spezia and is famous for its marble quarries. In typical Italian fashion Baglietto employs just 90 people directly, but around 750 people will be working at any one time at its two shipyards.
Since 2015, the Gavio Group has also owned Bertram, the famous North American sportsfisher brand. Now based at a yard in Tampa on Florida’s Gulf Coast, its activities are overseen by Diego Deprati from Italy. Baglietto’s Carrara facility has just started building a Bertram 35 and a Bertram 39 as part of a brand relaunch in Europe planned for this summer. Based on an industrial estate a few minutes’ drive from the sea, the Carrara yard occupies around 10,000 sqm and originally belonged to Cantieri Navali Cerri (CCN), which built fast series yachts in composite until around five years ago. The Gavio Group acquired CCN in 2011 before it saved Baglietto from the wreckage of the Camuzzi Group, which ran the business from 2004 through to its collapse in 2010 following the global financial crisis. CCN had already completed a handful of one-off metal projects up to 50 metres when in 2020 it was merged with Baglietto in a strategic move to optimise synergy between the two shipyards, but also simplify and strengthen Baglietto’s brand identity in a busy market. Today, Carrara focuses its resources on the semi-custom, all-aluminium DOM133s, all of which are then moved to La Spezia for final finishing.
The La Spezia site occupies a 35,000sqm site that was once Cantieri Ferrari. It was acquired in the mid 1990s by the Camuzzi Group when Baglietto was still headquartered in Varazze, the coastal town to the west of Genoa where it all started back in 1854.
There are three main construction sheds in La Spezia with six construction bays – all of them busy – plus the company’s administrative offices, where it builds
the steel/aluminium models and custom projects. Deep-water quays can take yachts up to around 70 metres in length and most disciplines are handled in house, but fabrication work is sometimes outsourced as and when space is needed.
Investment in capacity has been significant in recent years. From the start of its involvement, the Gavio Group has allocated around €60 million to renovating the facilities, with €13 million across the two sites over the past year alone. In La Spezia work will soon start to fill in one dock and extending two others to accommodate what is claimed to be the largest travelhoist in Europe – a gigantic Cimolai machine with a 1,120-tonne capacity capable of moving yachts of around 70 metres. The hoist arrived last summer and clearly demonstrates the management’s ultimate ambitions for the site.
Eight of the all-aluminium sub-400GT Vafiadis-designed DOM133s have been sold to date, all with twin Caterpillar C32 main engines, although two are hybrid versions with twin CAT generators and Siemens control systems. Top speeds are around 17 knots depending on load, but hybrid versions will be about a knot slower and have slightly different GAs. The big selling points are proximity to the sea aft and the high-volume interior. Six of the eight are expected to charter, but all are built to MCA regs. Interior design is open to owner choice.
Baglietto’s steel and aluminium T52 is an evolution of its earlier 46-metre and 48-metre models. Francesco Paszkowski handled the overall design and worked with Margherita Casprini on the interiors of five units. The fourth’s interior will be by Studio Vafiadis, the fifth by Team4Design and the sixth by Alberto Mancini. Of the eight T52s signed to date, most have the standard CAT C32 engines, but the first and sixth are hybrids. The first hybrid is powered by MTU engines with Siemens controls. The sixth will have a CAT/Siemens hybrid installation, and the seventh is a ‘mild hybrid’ comprising auxiliary solar panels and a battery bank for hotel loads during the day, but no electric propulsion.
Designed by Francesco Paszkowski, the steel and aluminium 1,000GT T60 will have double the volume of the T52, despite still being a trideck. The hull design is presently being tank-tested. Key features include a 60-sqm beach lounge with pool and a walkaround upper deck that can be configured as a private owner’s deck, which leaves room for four guest cabins forward on the main deck and the option of a fifth on the lower deck. The standard powertrain includes twin 3512 Caterpillars, which should deliver a maximum 16 knots and transatlantic range at a 12-knot cruise speed.
Baglietto admits to having the same supply-chain issues as everyone else in a post-Covid world. For instance, whereas orders for engines pre-pandemic where placed six months in advance, now that lead time is between 12-14 months.
“Plus, of course, prices have shot up by anything from 10-40 percent,” says technical manager Andrea Lavagnino.
“That means on average bought-in materials and equipment are now around 15-20 percent more expensive.”
Despite supply-chain pressures, Baglietto is still quoting 30-month build windows for the DOM133 and T52 models from cutting metal to final delivery, and a T60 should only take a couple of months more. The tenth DOM133 and ninth T52, for example, which are the next available as of January 2023, come with early 2026 delivery slots and fabrication will start this summer with or without clients. Baglietto is lucky to have the Gavio Group’s financial muscle behind it should it need to fund speculatively, but given the current health of the order book that eventuality seems unlikely for the foreseeable future.
One of five Bagliettos launching this year, the 41-metre, all-aluminium, 300GT Francesca II is a custom project for American owners. Their previous yacht was a Cerri Flying Sport 102 built at the old CCN operation and their new sports fly two-decker, based on a Bacigalupo planing hull, has a reduced draft for the Bahamas. Francesco Paszkowski oversaw the design and again worked with interior specialist Margherita Casprini on the interior. The first unit is referred to as a ‘Superfast 42’ with triple 1,920hp (1,432kW) MTUs coupled to KaMeWa waterjets for a top speed of 33 knots. Handover is in spring 2023.
Beyond having two DOM133s and two T52s on its schedules with hybrid propulsion, plus a mild hybrid project, like other yacht builders these days Baglietto is keen to be seen to be doing as much as possible on the sustainability front.
One initiative is billed as Bzero, an unusual hydrogen fuel cell solution that harnesses solar energy to extract hydrogen from seawater – essentially taking the H out of salty H2O using AEM-type electrolysers. The solar energy required will come from photovoltaic panels located on hardtops and spare areas of superstructure. The hydrogen produced will be stored in solid form at room temperature and at relatively low pressure of just 10 bar. As this process is virtually continuous there is no need to store large quantities of the fuel and smaller tanks mean more space on board for guest amenities. The solution is deemed more sustainable than more mainstream solar power solutions because it reduces the reliance on lithium-ion batteries. Using a small generator overnight could see hydrogen harvested 24/7, which is much better for the environment than
running big generators inefficiently.
This spring should see a test rig installed in shipping containers in La Spezia, but as with other fuel cell solutions, the concept is only suitable for hotel loads (RINA looking at certification for a 55kW system) and cannot realistically be scaled to include powertrain requirements.
“The main downside to this technology today is cost,” says CCO Fabio Ermetto, the joined the Baglietto management team in 2021 bringing with him invaluable experience from his time with Camper & Nicholson, Fraser Yachts, Heesen and Benetti. “At the moment it looks like being more than double the hybrid premium. Plus finding the space needed for the associated hardware inside and out is problematic. For instance, it would be much harder to find the necessary room aboard our DOM133, which would probably need to forfeit a guest cabin or possibly even two for it, but it would be much easier to accommodate aboard a T52 or T60 without obviously compromising guest real estate. Despite these drawbacks, I’m confident Baglietto will be building boats with such systems on board very soon.”
Th ree years ago Baglietto hadn’t launched a yacht not designed by Francesco Paszkowski for over a decade. The Florentine designer has done more than any other to define the brand’s signature aesthetic and continues to do so, but other designers are being welcomed with a view to expanding its market offering. Argentinian designer Horacio Bozzo, for example, penned the exteriors of 40-metre Club M (C10232) and 54-metre C (10231), full-custom projects with interior design by Achille Salvagni and Hot Lab respectively. The DOM 133 is designed by Stefano Vafiadis, who is being primed to take over the family studio from his father Giorgio, while Alberto Mancini and Enrico Gobbi are also busy on projects. It’s safe to assume that there
will be collaborations with other designers in the future.
Such has been the success of the DOM133 that Baglietto is already working on what comes next. Look out for a smaller 35-metre or 300GT-ish DOM model from early spring this year with the first scheduled to launch in 2025, and there are also plans for a slightly bigger version. Although both these will be DOMs in terms of philosophy and designation (the name comes from the Latin word ‘domus’ meaning home) they will be quite different in terms of specification, although expect both to still be available with either conventional or hybrid propulsion.
The 100-metre Wing 100 sailing yacht concept was first unveiled by Royal Huisman in September 2022 and claims to redefine the performance, handling and energy efficiency of large sailing yachts by harnessing wing mast technology. But does such a rig make sense for a super-sized yacht?
SOPHIE SPICKNELL
Wing masts have been gaining momentum as an efficient and sustainable solution for both the commercial and superyacht sectors in recent years.
The rotating airfoil-shaped wing mast makes a smooth transition from mast to sail on the leeward side. This provides cleaner airflow around the mast, thus less drag and more power driving the vessel (the shipyard calculates the yacht will be capable of 24 knots under sail). The wing mast dimensions and structure can also take greater compressive loads without buckling, so can be self-supporting.
Moreover, conventional sailing rigs require time and crew effort to set, manage and take down, meaning that shorter passages are often made under power. The rig system of the Wing 100 is based on a proven concept and the mainsails and staysails of the combination wing mast/soft sail rig can be set in a matter of minutes.
“The Wing 100 is designed as a sailing yacht with a very efficient sail plan aimed at minimising crew requirements whilst maximising sailing capability,” says Erik Wassen, senior designer at Dykstra Naval Architects in Amsterdam, which worked with Royal Huisman on the concept (the interior design is by Mark Whiteley). “The Wing 100 has the ability to feather the main sails for unfurling, furling or reefing, even when sailing deep courses. The rig ensures a fast and efficient performance, but can be comfortably managed by remote control, and if the wind strength increases, the sails can be rapidly de-powered to ensure a modest angle of heel.”
“The Wing 100 is designed as a sailing yacht with a very efficient sail plan aimed at minimising crew requirements whilst maximising sailing capability.”
Can a wing mast rig be built on such a scale? Not a problem for Royal Huisman, which can draw on the expertise of its sister company Rondal, a leader in the manufacture of very large composite masts and integrated sail management systems. In fact, the Wing 100 concept has two 73-metre, free-standing wing masts with airfoil profiles, and each mast is complemented with a single in-boom furling mainsail and furling jib.
“The masts are able to rotate 250 degrees, or 125 degrees each side, to allow changes to the sail set without changing course,” says Wassen. “The free-standing wing masts have no standing rigging or associated deck clutter and the masts are rotated relative to the boom by hydraulic rams. By changing the mast rotation angle the shape of the airfoil can be adjusted to maximise or reduce the power generated by the rigs.”
Dykstra Naval Architects was instrumental in the development of the Dynarig and sail-assisted cargo ships, although Royal Huisman is at pains to point out that the Wing 100 is a true sailing yacht and not a heavy sail-assisted motoryacht. Like the Dynarig, however, the concept is designed to appeal not only to die-hard sailors, but also motoryacht owners looking to reduce their environmental footprint.
“Sustainability is crucially important for all of us and for future generations,” says Royal Huisman CEO, Jan Timmerman.
“The emergence of sailing yachts on this scale, with the level of energy efficiency and eco-responsibility offered by the Wing 100, would have been unthinkable just a decade ago”
“Yacht owners and the yachting industry obviously want to contribute by reducing environmental impact and by limiting the use of valuable natural resources.”
The Wing 100 will have an electric propulsion system that can be adapted to alternative power sources as new fuels or hydrogen fuel cells become available. A hydro generator powers the onboard systems and charges the battery bank. While under sail up to 200 kilowatts of energy can be harvested in this fashion, which Royal Huisman claims is equivalent to a fuel saving of over 40,000
litres during the course of a year. The renewable energy systems further include 480 square metres of solar panels integrated into both her masts, which can generate 250 kilowatts of energy or another 20,000 litres of fuel saved in a year.
“The addition of the vertical solar panels on the masts allows the Wing 100 to generate more energy without the need for a motor,” says Timmerman. “In total, the Wing 100 is calculated to save over 225,000 litres of fuel per year compared with similar sized, conventional engine-powered superyachts.“
Although alternative energy technologies are evolving all the time, they are not always new. Royal Huisman built the world’s first truly hybrid sailing yacht in 2009, the ketch-rigged sailing yacht Ethereal , noted for her pioneering hybrid propulsion system and 500kWh of stored energy in a Li-ion battery bank. From that moment on, energy efficiency and hybrid propulsion have been at the forefront of the shipyard’s R&D.
Moreover, solar cells have already been integrated into wing masts, although on a smaller scale. The 24-metre polar expedition sailing yacht NanuQ launched in 2019 by KM Yachtbuilders to a design by Dykstra Naval Architects, has two freestanding, rotating wings masts by Hall Spars with a soft sail combination. Each wing mast is covered with 20 solar panels per side for a total of 40 square metres of panels. The main sails are handled by closed-front OceanFurl booms with hydraulic furling motors and can be reefed at virtually any angle of sail.
Like NanuQ , the Wing 100 concept is designed to be built in full aluminium rather than steel to benefit from the lighter weight with no significant loss in structural stiffness. Less weight combined with the hull’s shallow-draft canoe body means less hydrodynamic resistance.
“Typically for a 100-metre yacht to go upwind you would want a deep, high-aspect ratio keel, but the draft may be limited to five or six metres for practical reasons,” says Wassen. But because the Wing 100 is so big, a deep keel is not needed for stability, but is required for the side-force production. So a centreboard is one possible option to increase sailing performance”.
The raised foredeck allows the structural beam to be full-height and increase the structural stiffness, while the free-standing rig reduces both local and global loads on the structure.
“If you have a ketch or a sloop, for example, a rig of this size induces massive rigging loads and mast compression, increasing the longitudinal bending moments on the vessel,” explains Wassen. “But with a freestanding mast you don’t have this issue. The absence of shrouds and spreaders also emphasise her minimalist aesthetic.”
“The team at Royal Huisman is incredibly excited to be at the forefront of this conceptual revolution,” concludes Timmerman. “The emergence of sailing yachts on this scale, with the level of energy efficiency and eco-responsibility offered by the Wing 100, would have been unthinkable just a decade ago.”
As Benetti focuses resources on its series superyachts, the only full-custom project currently in build is FB283. Launched in January and approaching completion, we visited the 62-metre steel and aluminium yacht in the company of designer Giorgio Cassetta, owner’s representative Nicola Nicolai and the Benetti production team, to find out what makes her one of a kind.
BY JUSTIN RATCLIFFE
The story of FB283 began with a meeting during the 2019 Monaco Yacht Show when a client approached Benetti for a fullcustom yacht in the 60-metre size bracket. Matters moved quickly and Giorgio Cassetta was taken on by the client to define exterior and interior design and layout. By the end of the year Nicolai Yacht Consulting & Project Management had been engaged to represent the owner and finalise both the contract and technical specs. A build contract was signed in February, 2020. Less than three weeks later Italy was the first European country to impose a lockdown in response to the worsening Covid-19 pandemic.
“There was a period of intense discussion and planning before the contract,” says Benetti project manager Elisabetta Maria Di Noto. “The owner wanted to be able to cruise comfortably at 20 knots – fast for a steel-hulled displacement yacht – with very low noise and vibration levels. This already presented a technical challenge, but he was also adamant that he didn’t want any surprises during construction in terms of added costs. So we went into a lot of detail to be absolutely certain that everything was spot on before cutting metal.”
“The final owner’s meeting took place at the beginning of February when we coordinated all the involved parties to finalise the contract details,” adds owner’s rep Nicola Nicolai. “Agreeing on all the revisions and finalising the design and specifications of a 60-metre, full-custom yacht typically takes many months – we did it in two,”
The total external glazed area aboard FB283 covers 223 sqm and weighs approximately 8,500kg. The very large single panes of curved glass were supplied by Viraver, which has manufactured glass for multiple Benetti projects, including 107-metre Luminosity, as well as other Italian shipyards. The Padua-based company has invested in some of the most advanced technologies for glass processing. These include gravity glass bending systems able to produce large curved surfaces of up to 6.5m x 3.10m without flaws or undulations, a state-of-the-art chemical toughening plant, a gigantic autoclave (9m x 3.5m) and various ‘clean’ rooms for assembly in a controlled environment.
Gravity bending is a process by which the glass sheets are loaded onto a bending die that supports only the edges of the sheets to avoid distortion, then subjected to heat treatment in a gravity bending furnace. When heated to the viscoelastic phase at 580–640°C, the glass literally sags into the desired shape by the action of gravity under its own weight. The process combines digital accuracy with human expertise as the furnace operator determines how much heat is applied and where to facilitate bending. Domenico Miceli, Viraver Sales Director, calls it “industrialised craftsmanship.” The technology to bend glass on such a large scale was relatively new when FB283 was being designed and Cassetta was quick to take advantage.
The biggest single panes on the yacht are those in the upper salon. Measuring 5.9mx1.8m they comprise three layers of laminated glass plus two interlayers to produce a stronger yet thinner installation. Given the sheer size of the windows, IR filters inserted between the layers significantly reduce the transmission of solar heat and thus power demands on the air-conditioning system.
“Combined with chemical toughening, the ‘structural‘ interlayers means less material can be used to achieve better mechanical performance,” says Miceli. “In fact, the panes on FB283 are just 33mm thick, which is over 40 percent less compared to ISO 3254:1989 requirements using thermal hardening techniques and normal PVB interlayers. That means less weight, higher strength and better optical quality.”
The arrival of Covid piled on more pressure. Nicolai worked for Benetti as director of project management for over ten years before setting up his own consultancy firm, and Cassetta has long experience of collaborating with the shipyard on production models and full-custom projects. Both know the company inside out and hand-picked the project team headed up by Di Noto.
“Because the groundwork had already been done before signing the contract we didn’t have a lot of wriggle room, but Covid meant we had to completely change our way of working,” says the Benetti project manager. “We set up weekly online meetings with Giorgio and Nicola to flag up and settle problems. We also enabled the client to make a decision or state his preference in a timely manner and, in some cases, even ahead of schedule. During the pandemic he even learned Italian!”
Although no sister ship was available, the owner had chartered various Benetti yachts and referenced Spectre , the 69-metre full-custom yacht with exterior design and layout by Cassetta and project management by Nicolai that has a top speed of 21 knots. Van Oossanen Naval Architects were tasked with designing a Fast Displacement Hull Form that was then tank tested at MARIN in the Netherlands (see sidebar p.51). The build team was unable to attend these tests because of travel restrictions, but they were patched in by live video feed together with the owner.
Beyond the need for speed, the owner also specified ceiling heights of 2.3 metres throughout and an oversized tender. In fact, the forward garage houses a customised 10-metre Novamarine BS100 – enormous for a 62-metre yacht – and to get her in and out the portside shell door is 11 metres in length. The big garage and high ceilings presented challenges for both designer and shipyard.
“Contractually, ceilings heights usually refer to the interiors, but in this case the exterior decks and the staircases were included,” says Nicolai. “Even the technical spaces on the tank deck have full-height ceilings. That took a lot of fine-tuning and we were working to tolerances measured in millimetres.”
To aid precision and streamline the production process, it was decided from the start that the entire yacht, from net
space drawings to fitted furniture, would be designed in 3D for optimal accuracy between departments. Combined with the coordination done at the planning and design stages, 3D design meant the shipyard could fast-track construction despite the complications caused by Covid. Because they were unable to meet in person, Cassetta provided the owner with 3D googles and a web-based stereo VR tour for viewing ‘walkthrough’ renders of the exterior and interior that were constantly updated as the project evolved. When the hull and superstructure arrived in Livorno in November 2021, outfitting started immediately and double painting shifts were set up to keep the project on track. Within 15 months the yacht was ready for launch.
Facing page:
Following spread:
Although the general arrangement is broadly conventional, closer inspection reveals elements created to serve an informal family lifestyle aboard an exclusively private yacht. Cassetta reappraised the conventional main salon and dining room, for example, by eschewing the formality of a space that occupies prime real estate but is rarely used. Instead he designed a widebody, open-plan living and dining area, and a six-metre-wide flush connection with the open aft deck through sliding glass doors that open completely. Combined with very large, one-piece windows supplied by glass specialists Viraver (see sidebar), the whole area – inside and out – is designed to be a bright, airy and relaxing hub for all the family at any time day or night.
“Life on superyachts mostly take place on the upper decks and the main deck is often dead space,” says Nicolai. “In Giorgio’s layout the main saloon and aft deck are designed to create a social area over 20 metres long and bring life back to this overlooked part of the boat.”
The classic beach club set-up in the transom, which does not always make the smartest use of available space, was also reassessed to create a combined entertainment and storage area. So in addition to a hammam and massage room, there are racks for bikes and paddle boards, stowage for fishing gear, a dive room with compressor, hanging space for drying wetsuits and extra washing machines.
“The basic idea is that although this not a huge yacht, the onboard spaces and layout have been
designed to suit a very specific purpose and usage,” says Cassetta. “We challenged most of the commonly accepted ergonomic criteria, such as the risers of the exterior staircases that we made less steep and hence much more comfortable than usual.”
The passarelle in the stern is designed to rotate 45 degrees so it can be used when the yacht is moored alongside in the marina, avoiding the need for a side-boarding ladder. In fact, the widebody design prompted discussions with Cayman Registry about fire boundaries and escape routes from the lower deck accommodation. The solution was to use the main staircase as a secure conduit to the upper deck pantry that exits onto the side deck – arguably a safer muster point than the main deck in a badly listing vessel.
The exterior profile is crisp and uncluttered with a subtle reverse sheer in the bow that adds a muscular touch to the graceful lines. Hidden from view in the forepeak is a cosy nook that Cassetta calls the ‘love seat” (the mooring station is on a technical deck below) and the glazed structure on the sundeck houses gym equipment. Exterior detailing is minimal and wherever possible integrated into the functional design, as in the case of the louvred bulwarks on the upper deck that serve as freeing ports for green water to drain overboard.
The interior design, also by Cassetta, reflects the purity of the exterior styling. Based on oak, leather and brushed travertino, the effect is sober and classic yet clean and contemporary.
The acoustic design of FB283 was entrusted to Cergol Engineering in Trieste, specialists in noise and vibration numerical analysis with over 30 years of experience.
“This project was particularly challenging because of the yacht’s high displacement speeds,” says company founder Valter Cergol. “Generally speaking the faster the boat, the higher the frequencies and the louder the noise, but to meet the contractual parameters you can’t just throw more weight at the damping treatments and insulation materials because that may affect the yacht’s performance.”
Besides floating floors throughout that nowadays are standard on large luxury
yachts, this meant prescribing a range of materials of varying thicknesses depending on the location on board, from rock wool and ceramic fibre to sandwich panels in rubber, cork and calcium silicate.
Cergol Engineering was also responsible for the vibration analysis to mimimise resonance between the hull structure and the main potential sources of vibration like engines, generators and propellers, even at high cruising speeds. One of the most effective solutions for damping torsional vibration excitations in this respect is the drive train with Smart-Link flexible couplings by Rubber Design between the propeller shaft with a separate thrust bearing, and the gearbox.
As the name suggests, the patented Fast Displacement Hull Form (FDHF) by Van Oossanen Naval Architects combines the efficiency of a full-displacement hull at low speed with the top-speed performance of a semi-displacement yacht. As a comparison, the FDHF’s resistance values are typically 20 percent lower than a well-designed hard chine hull form at semi-displacement speeds. More commonly associated with aluminium hulls, the challenge was that FB283 was a steel-hulled yacht with a high speed requirement.
“The owner was very well informed and was aware of the compromise required when choosing between speed and comfort in terms of motions,” says Managing Director Perry van Oossanen. “He was concerned about sacrificing too much comfort to reach the desired speed? So we really had to push to keep the comfort levels as high as possible despite the speed requirement.”
Typically, when a hull is optimised for high speed you get a ‘stiff’ boat with a high GM (metacentric height) and an uncomfortable, jerky rolling motion. Thanks in part to relatively flat surfaces on the after part of the hull that generate some lift as the yacht moves through the water (FB283 is also fitted with an interceptor to further reduce drag), the FDHF can exceed theoretical hull speed but still provide the kind of soft and stable ride in waves that a displacement hull is famous for. “You have to be very attentive to how to balance both factors,” says van Oossanen. “It’s more a question of finding the sweet spot than doing something radically different.”
MARIN was able to assist the project team in this respect. At the time of the tank testing, Enrico Della Valentina of MARIN’s yacht division was leading an ISO working group to establish a comparative scale of motion-related comfort aboard large
yachts. Now in effect as ISO 22834:2022, it compares designs and layouts, identifies the most comfortable positions on board and evaluates the impact of stabilisation systems.
It works by selecting a minimum of five zones (typically a crew cabin, the wheelhouse, the master suite, the main saloon/dining room and the beach club) and appoints each area a maximum of five points whereby the higher the number the higher the onboard comfort. Of course, you need to make it all visible and understandable so MARIN has an app that allows clients to select multiple onboard areas and compare motions in various sea states, headings and speeds.
“The owner was very intrigued by this discussion,” says Della Valentina. “Clients can choose as many onboard areas as they like, but they need to be distributed along the length of the yacht to fully appreciate the difference in motions. I also say they shouldn’t to be scared about simulating the most demanding conditions, because it’s a kind of a crash test. This is not a case of showing how bad a vessel is, but how good it is.”
Benetti’s last full-custom launch was 107-metre in 2020 at the end of its so-called ‘Giga Season’. Of the 55 yachts currently in build averaging over 44 metres in length, there are no other one-off designs. This makes FB283 all the more unique, especially as despite a demanding brief and global pandemic the project progressed in record time for a Benetti custom build.
“That wouldn’t have been possible without all the advance planning and close collaboration between the owner’s and builder’s teams,” says Nicolai. “Shipyards don’t like changing their standard work practices, but in this case everyone was driven by the desire to find what was best for the project.”
“A revolutionary yacht that has undergone a complete transformation which is practically unprecedented in its scale and nature” is how Oceanco describes Project H . We talk to her owner’s representative and the shipyard’s project engineering manager about one of the most ambitious rebuilds ever undertaken.
BY JUSTIN RATCLIFFE
At what point does a refit become a rebuild? There is no hard and fast rule, but a safe bet is that when you start removing superstructure and replacing major systems, you’re talking rebuild. In the case of Project H , there is virtually nothing left of the original yacht except her hull, and even that has been extended and modified. This is a rebuild that challenges the entire industry to reconsider the potential of an existing superyacht to evolve and take on new shapes. The original yacht was launched by Oceanco as Al Mirqab in 2000. Designed by Richard Hein, one of the shipyard’s original investors, at 95 metres she was the largest Oceanco until 110-metre Jubilee (now Kaos ) came along 17 years later. Powered by triple, military-spec MTU 20V 1163 TB93 diesel engines for a massive 30,000 combined horsepower, she hit 30 knots during sea trails. When the yacht became available in 2018 and was acquired by her current owners, the stage was set for Hein, founder and CEO of The A Group in Monaco, to be reunited with both the yacht and the shipyard that built her.
“We wanted to do something different and so we sat down to show that you could take a very high-tech yacht from 20 years ago and make her IMO Tier III compliant under today’s regulations.”
Rebuilding was not originally envisaged. However, an initial survey revealed that the engines and generators were showing their age, the result of many hours on the clock, and would need to be replaced. That led to a discussion about bringing the yacht into IMO Tier III compliance – the first hint that something more than a major refit was being considered. The second was when UK-based studio Reymond Langton Design was engaged to create new concepts for the exterior as well as the interior design.
“When it comes to refits, people in the beginning have a certain intent and that is modified as the project develops,” says Hein, as the outfitting of Project H continues at Oceanco following her floodlit presentation last January. “We wanted to do something different and so we sat down to show that you could take a very high-tech yacht from 20 years ago and make her IMO Tier III compliant under today’s regulations. We also wanted to give her a completely new look; not just a cosmetic facelift and a new lick of paint. Once that decision had been taken, things started moving very quickly. The yacht was completely re-engineered and redesigned to Oceanco standards, as with any new construction, and she now carries a full 2023 certificate.”
Various new-build shipyards in northern Europe were approached, but were dissuaded as the scale of the redesign became apparent and the extent of the likely disruption to their production schedules emerged. Their reaction was unsurprising. Attempts are made to keep so-called ‘emergent work’ to a minimum during refits. But like the proverbial onion, the extent of work only becomes apparent as the layers are peeled away and the danger is that the expanding work list will eat away at the icing on the yard’s cake in terms of profit.
Rebuilding removes a lot of that uncertainty, but not the risk. Processes such as cutting away old superstructure and stripping out machinery are not part and parcel of building new yachts. Even starting with an existing hull requires a lot of reverse engineering to fit new machinery into existing spaces.
“I’ve worked at Oceanco since 2007 and only ever done new-builds,” says Marco Kal, Oceanco’s project engineering manager.
“Starting with something already, even if it’s just a hull, requires a very different approach in terms of engineering and construction, organisation and project management. All your drawings are 20 years old and they did things a lot differently back then. That was the biggest challenge for me in the beginning and, to be honest, it follows you all the way through the rebuild programme. We had to start from scratch.”
“About the only piece of heavy equipment that remained in place is the 300kW ZF electric bowthruster, but that was completely overhauled, so is effectively new.”
“The turning point came when I was flying back to Monaco and one of the Oceanco directors was travelling on the same plane,” recalls Hein. “We got talking and fixed an appointment at the shipyard the following week to talk. During that meeting, it became clear that Oceanco had the capacity and, just as important, the will to do this. There was common interest between all parties concerned to see what we could do with it. So nearly 17 years after I’d sold my shares in Oceanco, I found myself back there and felt at home very quickly.”
By mid-September 2019 the yacht was in the newly acquired Zwijndrecht construction facility and metal cutting began in early October. Eight metres were added to the steel hull in stern and two metres to the forward deck line. Several new transom shapes were tank tested in the water basin at MARIN. Despite the increase in displacement and changes in weight distribution, the hull is now more efficient with a cruising range of 6,000 nautical miles at 14 knots, which jumps up to 7,500nm at 12 knots.
“The naval architecture and engineering were intense,” says Kal. “Life was made easier by the fact that she was already a high-volume
vessel for her length and we had room to play with. We can also build a bit lighter these days but, even so, we removed 110 tonnes of steel and added 198 tonnes during the hull extension. In the process, the gross tonnage increased from 3,045GT to 3,521GT.”
When the work was at its peak, as many as 500 people were working on the project, 300 of them on board. All the cabling and wiring, piping and ducting, HVAC and fire-fighting systems were stripped out, as well as the main machinery and propulsion gear. The 10,000hp MTUs were replaced with Tier III compliant MTU 16V4000M73L (2,832kW) units. Four Scania DI 16-74M (511bkW at 50Hz) gensets were installed, double the original capacity to service today’s hotel loads, and a fourth 78kW unit as a harbour genset enclosed inside a sound shield. Gearboxes and shafts were taken out, propellers replaced with 2.5-metre diameter Sip Marine 5-blade props, watercooled frequency drives added, and all the tanks sandblasted and treated. There were no zero-speed stabilisers in 2000, so the old fixed fins were replaced with Quantum XT fin stabilisers. About the only piece of heavy equipment that remaind in place is the 300kW ZF electric bowthruster, but that was completely overhauled, so is effectively new.
Previous spread: Emerging from the shed in Zwijndrecht for the first time, Project H is revealed during a light show.
Right from top: 100 tonnes of aluminium were removed from the superstructure, and another 107 tonnes added, to make way for Reymond Langton’s new exterior and interior design.
In terms of the exterior restyling, the question was always what to keep and what to renew. In the end, 100 tonnes of aluminium were cut away, but 107 tonnes were added to create the new superstructure design by Reymond Langton Design that has utterly transformed the look of the yacht with its long, lean lines and 392 square metres of strip glazing. Although details are not yet available, the interior with accommodation for 20 guests in 10 suites has been completely refurbished and the general arrangement heavily modified.
Aside from her physical transformation, the work undertaken brings the yacht up to today’s standards in terms of technology, safety, capability and sustainability. In addition to IMO Tier III compliance and technical upgrades, upcycling an existing superyacht makes powerful sense at a time when the industry is working to reduce its environmental impact on the planet.
“To build a new yacht of this size you would normally spend up to a year in the design, planning and engineering phase,” says Hein. “In this case, the yacht arrived at the shipyard one week and the next we
started cutting metal. The most difficult part is having the vision of where you want to finish up and managing all the expectations. That takes teamwork and I don’t think we could have done this with anyone else than Oceanco.”
Oceanco believes that the owners saved up to a year by starting with an existing hull –and that is without factoring in engineering lead times or lack of new-build slots over the next few years. Time saved usually outweighs cost savings when you consider that building a new hull and superstructure is roughly 20 percent or less of the total
build cost. What is less measurable, but arguably just as rewarding, is the sense of satisfaction associated with preserving and repurposing an existing vessel.
“With the achievements from Project H’s transformation, we are positive to be breaking new ground,” says Oceanco CEO, Marcel Onkenhout. “It might not be a fit for every owner, but then again Oceanco does have a tendency to colour outside the lines of yachting norms. It has been a very rewarding project to work on, particularly for myself, having been involved in her original construction over two decades ago.”
Heritage boats are refitted and returned to their former glory and commercial vessels are converted into superyachts, but Project H is neither of those. Conversions differ from even the most extensive refit insofar as they change the purpose of the original vessel. Like a conversion, a rebuild depends on the suitability of the donor vessel, but its purpose does not change. Rebuilding is closer to what we now call ‘creative reuse’ or ‘upcycling’; the process of transforming waste materials or unwanted products into something new of greater perceived value and quality. Or as Hein puts it: “It’s about seeing the potential for all vessels, rather than starting from a blank sheet of paper each time.”
So would Hein do it all over again? “Definitely. At the time we weren’t certain how far we could take it, but in the event we proved to the world that we can take a vessel that was built in a different era with all the technological constraints that implies, and give her a new lease of life – recycle her, if you like – in terms of appearance and in total compliance with the highest standards and regulations. Project H began as a yacht of yesterday; now she’s a yacht of tomorrow.”
With service locations in West Palm Beach, Fort Lauderdale, Istanbul, La Spezia, Antibes, La Ciotat, Barcelona and Mallorca, Heinen & Hopman will be at your disposal around the clock. From installation to 24/7 service, Heinen & Hopman’s skilled engineers are aware of the divergent problems that can be encountered onboard.
Meet us at the
From tankers and superyachts to tugboats and tenders, all vessels rely on fluids for propulsion, lubrication, cooling and hydraulic systems. Maintaining oil and fuel in optimal condition ensures peak performance and safe operation while also reducing wear and tear. That much is well known, but fluid analysis can also spot potential problems and failures before they occur.
BY JUSTIN RATCLIFFE
At first glance, the Spectro Jet-Care headquarters in Odiham, a quaint village in rural Hampshire, doesn’t look like a state-of-the-art laboratory. Housed in a Grade II listed complex, hidden behind the exposed brickwork and wooden beams are some of the most advanced instruments available for analysing oil, fuel, hydraulic fluid, filter debris and water used in firesuppression fogging systems. Founded in 1976, the private company started out offering oil analysis services to the aviation industry. Then came Gas Path Analysis, a state-of-health diagnostic method that measures gas turbine parameters and compares them with expected values. The resulting trend data provide early indications of potential issues, reducing maintenance costs and preserving performance. Today, Spectro Jet-Care has laboratories in the UK, USA and Switzerland and all three operate under the highest certification levels.
“We’re not just a standard processing lab – our goal is to find something.”
“We’re not just a standard processing lab – our goal is to find something,” says Larry Rumbol, Marine Development Manager.
“We’re talking parts per million of 18 or more different elements that point to a specific problem such as worn bearings or fuel oxidation. Think of it like a blood test when your doctor is looking for early warning signs that something isn’t quite right.”
Left and Bottom:
Some of the most advanced instruments available for analysing oil, fuel, hydraulic fluid, filter debris and water are housed in Spectro Jet-Care’s Grade II listed headquarters in Odiham, UK.
It wasn’t long before a private jet owner approached the company to provide the same laboratory services for his superyacht. There are other companies offering similar testing procedures for the marine sector, but Spectro was the first to specialise in superyachts and now has more than 1,300 yachts over 25 metres in length on its books. Unlike commercial ships, large yachts tend to be used infrequently, but are required to function at optimal efficiency and at top speed. But it is not just a question of performance: guest comfort is also of utmost importance. If the AC goes down on a working vessel because of contaminated fuel in a generator it is not such a big deal, but the same could spell disaster for a charter yacht. In other words, prevention is better than cure.
Spectro Jet-Care used to draw its first oil samples during sea trials, but the process now starts when the yacht is still in build following a strategic partnership with IDEA Data Solutions, the German software firm that provides a full suite of planned maintenance systems for superyachts.
IDEA works with captains, engineers and shipyards during the design phase to populate the database for the planned maintenance systems (PMS) that is part of Class certification.
“Ninety-five per cent of marine breakdowns in the first year are due to poor installation of components,” Rumbol points out. “We can spot that early on when the systems are running in, so now our data goes straight into IDEA’s planned maintenance software. When something needs to be sampled, or rectified as a result of the lab report, it will pop up on the dashboard as a task that has to be done.”
Spectro Jet-Care’s marine analysis program does not only cover oil and fuel. Degraded grease, or even the wrong kind of grease, can lead to winch failure; dirty hydraulic fluid can mean passarelles or stabiliser fins may not work; contaminated water can lead to a malfunctioning fogging system; and debris in filters or on magnetic detectors can be studied under a Scanning Electronic Microscope (SEM) to draw conclusions about the likely source.
“Without data you’re just another person with an opinion,” said W. Edwards Deming, the American engineer, statistician and father of data management. He meant that without insight from data we tend to draw conclusions based on instinct, speculation or theory, whereas conclusions based on data analysis are logical, transparent and provide stronger evidence to support determinations.
Conversely, without an opinion you are just another person with data. In other words, data might have
all the answers, but you still need to ask the right questions to unlock those answers. In fact, much of Spectro’s work is about solving problems by connecting all the pieces of the puzzle, like detectives at a crime scene.
“Debris usually collects because something went ‘bang’, but did it break through fatigue, was it consequential damage from something else breaking, was it misuse, or was it a latent defect?” asks Rumbol. “Take metallic debris in a filter, for example. It could be part of a valve guide or piston ring, but we think it’s a piece off the tip of a fuel injection nozzle. We then ask ourselves why that might happen, so we go back and discover there is water in the fuel that causes cavitation in the nozzle tip, which eventually breaks off.”
The trend graphs provide decisive evidence in this forensic process, but other variables can creep into the equation. For example, the same type of oil from the same manufacturer can
contain different additives depending on where it is produced in the world. One additive, zinc dialkyl dithiophosphate (ZDDP), can cause ‘shedding’ of copper in the oil cooler pipes, for example. This shows up as a spike in the trend graph and might initially indicate bearing wear, but should disappear after 150 hours or so of running in.
Spectro Jet-Care supplies its clients with prepaid sample kits for the different analyses. For redundancy purposes at least two instruments are used for each test and the results are ready in just two working days after delivery of the samples by courier, or 24 hours in critical cases.
“A fast turnaround is important,” says Rumbol, “because if a yacht has a serious problem there’s no point letting the chief engineer know about it two weeks later.”
Each diagnosis is colour-coded green (normal), yellow (early warning) or red (advance warning) and all the report data is available for download online via the dedicated webECHO portal. The company even has a switchboard operator available 24/7 to receive calls for urgent help.
The company also has a tamper-proof verification kit for testing bunker fuel for microbial contamination, low flash point, high sulphur content that results in corrosive sulphuric acid forming after combustion, and high FAME (biofuel) content when the fuel is liable to start absorbing water. Off-spec fuel is sufficiently common to warrant a whole field of maritime law specialising in bunker claims and disputes.
“Planned maintenance of a superyacht is rather like owning a farm when previously you owned a house,” says Rumbol. “Everything becomes much more complex and requires dedicated software to manage all the data.”
PMS on superyachts works in conjunction with Continuous Machine Surveys (CMS) and Condition Based Maintenance (CBM) and is mandatory according to the International Safety Management Code (ISM). It helps meet not only safety and environmental objectives laid out in the Code, but is also an investment in the protection of the asset and the optimisation of its management.
A PMS basically allows owners and operators to plan, perform and document vessel maintenance to comply with Class and equipment manufacturer requirements.
A systematic approach to maintenance is based on risk assessment and begins with the establishment of a complete database of machinery, equipment and fittings, including all spares, specifications, manufacturer and vendor contact details, and other information derived mainly from the manufacturer data.
Planned maintenance is increasingly predictive thanks to machine learning and the kind of operational data analytics and preventative asset health monitoring able to reduce the reliability risks.
High-precision testing is not just about avoiding equipment failure; it is also about reducing downtime and preventing excessive wear. Once accelerated wear starts the route to failure is a very steep curve and is rarely evident in time for rectification to be effective. The result is what the insurance industry calls “catastrophic failure” when a component fails beyond repair and causes collateral damage. A further benefit of sample analysis is the graphical trend analysis that provides instant awareness of a problem resolved or on-going. History of this nature increases the value of the superyacht, especially one where there is a choice of similar spec yachts available, and Rumbol is working with brokerage houses to instil a mindset
of taking fluid samples as soon as they take a used yacht onto their books, rather than an owner’s representative finding fault at a later stage and risk losing a sale or paying an inflated price for repairs.
The next challenge for Spectro Jet-Care is monitoring the emergence of alternative energy systems such as fuel cells and what maintenance and operational issues they may present in the future. Liquid methanol, for example, can be corrosive for some engine tubings and casings, and hydrogen gas raises issues of lubricity. “We’re constantly in touch with the engine and oil manufacturers and looking into these questions,” says Rumbol. “We’re not there yet, but we’re certainly at the front of the queue.”
Above: All the report data is colour-coded according to urgency and available for download online via the dedicated webECHO portal.
Like Spectro Jet-Care Oil, SailADV in Italy offers fluid analysis, but its laboratory tests support a wider range of services designed to quantify actual performance over time in relation to the original design data.
The company was founded by Giovanni Palama, a naval engineer and former professional sailor specialising in navigation and tactical evaluations under team managers such as Torben Grael, Tommaso Chieffi, Vasco Vascotto and Mauro Pelaschier. He imported this experience of performance measurement into his own consultancy firm to respond to a specific need of the yachting industry, namely how to measure performance and seaworthiness in a scientific and repeatable manner. Today, SailADV has offices in Ancona, Pisa and La Spezia and works with all the top Italian shipyards.
“We measure performance parameters throughout the entire yacht and especially the health status of the onboard systems,” says Palama. “So oil, fuel and grease analysis is only part of the overall equation; we also look at vibration, power management systems, thermographic analysis, 3D scanning, strain gauge for measuring loads, and more.”
The company draws on new technologies such as Motion Amplification, whereby special video and image processing is able to detect minute vibrations invisible to the naked eye in order to understand the causes creating the motion that can lead to reduced efficiency or failure of components. And in response to the increasing complexity of diesel-electric and hybrid drivetrains, it uses high-frequency data sampling to analyse problems that may arise with the electrical systems on board.
“With our numbers we can support the technical office and production team by checking how all the different systems work together,” says Palama. “It’s important also from a warranty perspective to have a clear picture of the yacht at the beginning of its working life as a benchmark to check if the
performance drops off in two, three or six months’ time.”
Palama believes a preventative approach to maintenance is not sufficient for superyachts.
Unlike commercial ships that are in continuous use, every superyacht has a different operational profile, which makes it difficult to establish common patterns of wear and tear. Instead, constant monitoring of real-time performance provides a more accurate tool for condition-based maintenance.
To this end, SailADV has developed its own proprietary monitoring systems based on a Linux real time architecture for both shortterm data acquisition during sea trails and permanent installation on board to measure long-term trending. H-LOG, for example, is a logging device installed on the yacht for the whole of its life cycle designed for systematic, coordinated and synchronous recording of data variables over a long period. H-BOX, on the other hand, is a portable device certified by Lloyd’s Register for data acquisition during sea trails.
SailADV collaborated closely with Benetti to log and analyse 5,000 variables 10 times per second during the sea trials of all its 100m+ superyacht projects. It also has a three-year contract with Sanlorenzo to measure and optimise the performance parameters of its superyacht range built in La Spezia, including Massimo Perotti’s own 34-metre SX112 Almax and a performance analysis of the solar panels and the Lithium-ion batteries aboard the new SP110 during its first season.
Burgess recently refreshed its business strategy by setting up a dedicated new-build sales team under the guidance of Ed Beckett (below left), naval architect and partner, and Peter Brown, senior partner and sales broker. We sat down with them at the Monaco Yacht Show to find out more and began by asking why they had felt the need to take a new approach.
BY JUSTIN RATCLIFFE
Peter Brown: We’ve been involved – both by good fortune and design – in big and exciting new builds like Dilbar, Azzam, Lady S and Bravo, from a technical project management viewpoint, but also during the commercial discussions about build price, choosing a designer and the shipyard, and so on. Over the years it’s become increasingly obvious to us that the commercial and the technical side have to go hand in hand and that any technical decision you make almost always has an effect on the commercial side, and vice-versa. During Covid we had the opportunity to sit down and review our processes and we made the conscious decision to funnel all new-build enquiries through a dedicated sales team. It might seem an intangible shift, but for us it’s seismic. Increasingly our clients want us to guide them from cradle to grave, and this is just part of that journey.
Can you give me a specific example of how that might make a difference?
PB: We’re currently involved in a very big project now where the variations to the contract regarding the luxury interior are huge. I mean, were talking numbers that are the same as building a 70-metre, and that’s just the interior. That is a whole new negotiation in itself and the discussions about materials, suppliers and installation are so closely bound together that the technical and commercial decisions have to be made together.
So you’re basically talking about a team that provides a closer connection between the sales and technical departments?
Ed Beckett: Yes, it’s about working more effectively and collaboratively as a unit from the start to plot the best route through to contract. However good our engineers and technicians, they are not necessarily the best people to plan that route, or manage client expectations. And although we have some terrific brokers who know their clients inside out, they don’t know the technical details, or nuances of certain shipyards or designersso well.
PB: I think the industry had opened itself up for criticism because there has been a perception that for a commission a broker will take a client to a shipyard and they might know the market, the operational costs, the charter revenue or the importance of resale value, but they have less understanding of the intricacies of the build process, the decisions that have to be made and the additional costs on top of the contract price: the risks, basically. We have all that knowledge in-house and we have to make it work better for our clients and for us. As a company we need to be more adept at putting our best foot forward in every single new construction enquiry.
We hear about the projects that go through but not about those that fall by the wayside. What is the most common reason why a new-build project does not proceed?
EB: There are plenty of reasons, some of them quite intangible. Success might be a question of having the right people in the room at the right time having the right conversation, but you’re trying to change it from luck and good fortune to skill and knowledge. It’s a very specialist thing to build a superyacht and there’s no substitute for experience and expertise.
PB: Mismanagement of expectations probably, and the level of risk – commercial and technical. At the end of the day, our job is to mitigate those risks and make sure the client is paying the right price for the right product, and that it does what he or she wants it to do.
EB: And provide opportunity. Because we hear about a boat that might be coming to the market mid-build, or a new-build slot might suddenly become available. And as soon as that happens we can move on that information, whereas before our focus was less targeted and calculated.
PB: For example, I had a client last year who loved the Benetti Oasis, but wasn’t prepared to wait three or four years for it. I happened to know there was one in construction for sale and he took delivery last July. Ed and his team took over and tweaked the specs to suit the client; it was a perfect example of how the team can work together.
Does this mean the pair of you are now only focused on new-build sales?
EB: I’m looking to pull out of the day-to-day running of new builds that may take 3-4 years in order to follow new projects from the initial enquiry and developing the concept up to the point of contract, then while providing a degree of support to contracts post contract predominantly circling round and starting again. During that pre-contract phase the Burgess project manager will become more and more integrated.so he can then carry it through to completion. The pre-contract phase is critical, because if you get the fundamentals wrong the project is not going to work.
PB: I wear two hats because I have to keep my knowledge of the market up to date. Clients invariably want to know what their options are, which also means considering how the asset might depreciate and what it will be worth in five years. So I’m driving new-build sales together with the rest of the team – Ed, Sean Bianchi and Eleonora Pitasso – but I like to keep a foot in the pre-owned yacht market as well.
Some builders offer brokerage houses Central Agency rights for new builds. Would you consider that?
PB: I think with new-build CAs there’s a danger of being seen as more of a dealer and we want to preserve our independence. Strong relationships with a yard is one thing; an exclusive agreement is another and that doesn’t reflect our ethos. It can become a slippery slope because other shipyards are then much more reticent about giving out information you might need to service your clients. I think if the industry is open to criticism it’s where commissions are being paid and value not being added, and that’s what we want to avoid. Everyone has to be clear about their responsibilities and our loyalty is to the success of the project.
www.reintjes-gears.com
Alternative fuels and propulsion are all the rage when it comes to more sustainable yachting, but the hotel load is a far bigger consumer than most people realise. We explore the challenges and solutions to improving energy efficiency.
BY CHARLOTTE THOMAS
Talk about alternative fuels and the opportunity to reduce emissions is a sure way to get the superyacht industry animated. It is exciting stuff, but superyachts simply don’t sail like commercial ships that are at sea for most of the year cruising at a constant speed with propulsion the biggest energy consumer. For yachts, propulsion is only half the story and there is another revolution quietly getting under way that has been made possible by more advanced and more ubiquitous data sensors.
“Within the last five years there has been much more data available and we’ve been able to track it,” says Lennart Pundt, head of yacht project development at Lürssen. “For example, with the yachts we’ve built, on average the yacht is at top speed just one percent of the time, at cruising speed 15 percent of the time and, depending on whether it is a charter or private yacht, between 60 and 80 percent of the time the yacht is at anchor or in harbour.”
The non-profit Water Revolution Foundation (WRF) has been working with shipyards and individual yachts over the past three years to gather similar data with the aim of creating more detailed operational profiles for yachts.
“Our data shows that, on average, energy consumption – and therefore fuel consumption – is split 50/50 between propulsion and hotel load,” says WRF executive director Robert van Tol. “Of course, for the existing fleet it is quite hard to change the propulsion part or the underwater hull shape, but there are certainly a lot of actions you can take on hotel loads.”
In many cases the energy split is even more hotelweighted: “On one of our 140-metre yachts, the actual hotel load is perhaps 1,500kW but the propulsion is 15,000kW,” says Pundt. “However, despite being one tenth of the power of the propulsion system, the hotel load actually accounts for 75 percent of the fuel consumption.”
According to Hanna Dabrowska, formerly a senior naval architect at Feadship who now works for Water Revolution Foundation, one problem is that many yachts are overpowered for redundancy purposes. She also highlights the issue of load balancing with the actual operational profile of yachts often a long way from the calculations made when the power systems were being designed and installed.
When combined with the huge energy demands that heating, ventilation and air conditioning (HVAC) place on the yacht systems, the hotel load becomes a serious energy consumer. This is a sustainability issue, particularly at a time when large yachts are in the firing line, rightly or wrongly, in the mainstream media.
While some aspects of the hotel load have become more efficient over the years as new technologies replace old (LED versus incandescent or halogen lighting, for example), the fact remains that the HVAC system is by far the biggest consumer of electrical power on yachts.
Developments in this field are now starting to make a difference (see sidebar), although the downside may be increased system complexity and demands on technical space, which in turn impact serviceability and interior layout.
“There is more willingness on the client side now to accept that if we want to be more energy efficient then some systems have to be more complicated,” says Pundt. “And we’re seeing that we have to install additional technologies that might increase maintenance and downtime.”
As the biggest hotel load consumer on most yachts, the HVAC system also presents one of the greatest challenges in improving efficiency, but a handful of pioneering HVAC system manufacturers are tackling the problem head on.
MAR-IX in the Netherlands , for example, which supplies and works with Silent-Yachts, has developed its proprietary Hyper Thermal Process (Hyper TP) technology that it claims offers the highest reductions on hotel load currently available. The system essentially views everything on board, from the AC to the pool, as connected parts of the same whole, and uses smart system design and intelligent monitoring and control to take heat generated by one process – from, for example, the HVAC chillers – and use it for another process such as heating the pool water. The company claims Hyper TP can result in energy savings of up to 80 per cent.
The Yacht Environmental Transparency Index (YETI) is a joint industry project managed by Water Revolution Foundation that aims to create a system whereby a yacht’s environmental profile can be compared to a benchmark operational profile. The benchmark operational profile was developed by analysing fleet AIS data, which showed that on average yachts spend 10 per cent of the year cruising, 30 per cent at anchor and 60 per cent in port. YETI gathers various data points from propulsion and hotel loads, among others, and assigns a yacht a score that can be used to calculate its environmental impact and, perhaps more importantly, identify areas for improvement. YETI 1.0, the first phase of the tool, was officially launched at METSTRADE in November 2022.
“YETI is not designed to judge but to give a baseline assessment which then allows for more informed and knowledgeable decisions,” says executive director Robert van Tol. “If you replace diesel with an alternative fuel like methanol, consumption still needs to come down – it doesn’t mean that you can just switch and be cleaner.”
“In our case, we don’t want to use the generator, and we need to save power because otherwise the batteries would quickly be depleted.”
Conventional HVAC systems often use a chiller unit to produce cold air and then individual reheaters to regulate the temperature of the air in each room or cabin. One first step to better efficiency is obvious: put a hot water circuit next to the cold water circuit and use waste heat instead of a reheater. But that requires more piping and larger equipment, as does using waste heat from the generators to produce cold water for the AC system with absorption chillers.
“That’s a very big piece of equipment,” Pundt points out. “If we had more space, we would use it much more – it’s quite common on cruise ships, but it’s just coming on yachts.”
For Michael Köhler, founder and CEO of SilentYachts that builds solar-powered motor catamarans up to 37 metres, an energy-efficient hotel system is not a nice-to-have but a must-have.
“Aside from having opening windows that encourage natural airflow, which can reduce the demand on air-conditioning, our aeration system is totally different compared to most other boats,” he says.
The Silent-Yachts system employs heat and cold recuperation, with the existing cold air not pumped out but used to pre-cool incoming hot air, and heat from various system elements recycled for water heating or other requirements.
“The whole system is optimised,” says Köhler.
“On conventional boats they do not really care because when they turn on the AC they need to start the generator anyway. In our case, we don’t want to use the generator, and we need to save power because otherwise the batteries would quickly be depleted.”
The problem with many of these solutions is that they run counter to the way owners and guests
like to use their yachts, which suggests that tech advances have to be accompanied by a change in user behaviour if we are to see significant gains in efficiency. The preference is generally to have cooled interior spaces, but doors are often left open for ready access to the outside decks, which means the AC is working in overdrive. Moreover, smart zone tech that switches a light on when you enter a room, for example, can work in some environments, but on a superyacht it may need to come on before the door is opened because that is the level of of service expected.
Pundt makes the point that energy efficiency is about holistic systems design: “It doesn’t work to just say ‘OK, we exchanged this piece of equipment and everything’s good’. It’s many bits and pieces, everything does its bit, and if you go all the way you could reduce the electric load by 50 percent.”
Tracking technology that enables smart zoning of homes and yachts, which uses machine learning and AI to learn client patterns and preferences, is the latest technology to move beyond switching entertainment from room to room in a follow-me mode. Italian company Videoworks, for example, recently launched its Next Gen Room Automation system that aims to improve hotel load efficiency.
Mainly designed for new-builds, the system combines existing subsystem sensors with presence sensors and external sunlight sensors, and has been developed as a marine-specific solution to take account of HVAC architecture, yacht movement and navigation.
“The three actions in order of impact are machine support in controlling the HVAC system, regulating and managing the lights, and using AV-IT efficient devices,” explains Maurizio Minossi, CEO of Videoworks.
“With all ship sub-systems on the same network, we have several software solutions to achieve savings. Across HVAC, AV-IT, lighting and other systems we can target around a 15-20 per cent improvement in efficiency.”
The extensive use of glass has become an owner-driven trend in modern yacht design, but it creates further problems when it comes to efficient energy consumption.
“In Dubai the sun delivers about 1,000 watts per square metre, which means a huge amount of heat energy over a large area of glazing,” says Köhler. “Even if you have a shading system, you still need an incredible amount of power just to get rid of that heat.”
Pundt agrees that large glazed surfaces are more in demand than ever, but designers are now more willing to compromise in an effort keep heat out of the boat: “They want the glass, but now they say ‘I hear you, let’s make the overhang a little bit bigger’.”
Other techs from land-based applications are starting to find their way into yachting: “We are using doors from a new supplier from the residential market, which seal better and therefore help reduce the air conditioning load,” says Giovanna Vitelli, vice president of Azimut-Benetti. “What we have already done in Benetti and are now taking down to even the 55-foot Azimut, is re-using the heat generated by the engine for the hot water on board.”
The advent of alternative fuels, and especially fuel cells, raises the question of whether all this striving for efficiency is really necessarily. After all, if the energy is green, why worry about using less of it?
But clean energy is not a panacea that cures all, at least not in its current evolutionary form.
“It’s so complicated to put a fuel cell on board a vessel that it’s worth doing everything else to lower the energy requirement so you can put less fuel cells on board in the first place,” says Pundt, “This actually goes hand in hand with the big leap in systems that we’re designing.”
The fact is that there is no readily available, off-the-shelf Net Zero technology that is easy to install, has a small footprint and is low maintenance. The diesel engine is very compact and fossil fuel has a high energy density, which alternative fuels cannot match yet. “Using energy on board will become more painful,” Pundt predicts. All the more reason why we should be getting excited not just about propulsion tech, but hotel load efficiency as well.
The Maritime Research Institute Netherlands, better known by the acronym MARIN, is globally recognised for its tank testing facilities. But a recent visit to its headquarters in Wageningen revealed a much wider scope of research and investment aimed at ensuring a smarter, safer and more sustainable maritime sector.
BY JUSTIN RATCLIFFE
We’ve all seen photos and videos of bright yellow hull models bobbing about in MARIN’s water basins. Despite the rise of Computational Fluid Dynamics (CFD), tank testing remains a demonstrably objective way to quantify the behaviour and performance of vessels in realistic conditions. But the institute’s track record in maritime research and concept development would not be possible without other tools and facilities.
“We don’t just play around with scale models in big swimming pools all day,” says Enrico Della Valentina, team leader of MARIN’s yacht division. “We want to bridge the gap between design and operation. So we have the software tools, simulators and measurement techniques to reliably predict not only performance in the design phases, but also to optimise the subsequent operation of the ship or structure,
including the human factor.”
He shows me the latest example of this mission as he guides me through the sprawling MARIN complex. Nestled in a space between two existing buildings and viewable from the company canteen are the foundations and curved steel ribs of what will eventually be the Seven Oceans Simulator Centre (SOSC).
Due for completion in 2024 at a cost of around €17 million, the SOSC will contain moving simulators, a VR/AR experience room and human-factor monitoring equipment that simulate complex maritime operations. The spherical simulators will be unique because advanced visualisation environments can be projected 360-degrees around the users, but also upwards and downwards for a full-immersion experience.
“Every aspect of the simulation – from throttle response and turning circle to roll angle and motion behaviour in waves from different directions – is true to life.”
simulating the kind of conditions they might come across.”
The FSSS was designed to train military personnel in high-speed boat handling and navigation by providing dynamic feedback from imposed forces that simulate slamming, broaching and surfing. It comprises a control console that is an exact replica of those used by the Royal Netherlands Navy and springloaded seats mounted on top of a hexapod, a kinematic motion device typically used for racing car simulations. The hexapod motions can be precisely programmed to simulate degrees of pitch, roll and yaw (a tugboat setup can also be lowered into place through a soft patch in the roof) while specific locations or environments are projected onto a 200-degree screen in front of the console.
Although the SOSC will be housed in a new structure, much of the hardware is already in use at MARIN’s existing simulators that include Full Mission Bridge facilities, Compact Manoeuvring Simulators and a Fast Small Ship Simulator (FSSS). I was invited to try out the FSSS, which was originally set up to resolve a specific problem faced by Dutch Special Forces using high-speed craft (HSC).
“These boats need to reach their target as quickly as possible in all sea conditions and the onboard teams have to arrive in one piece,” says Marta Ibarrondo, Project Manager Maritime Operations at MARIN.
“The problem was that they were getting thrown around and injured because of the very high accelerations and G forces. Our job was to reduce the likelihood of injury by
My scenario required steering a RIB through a moderate but increasing sea into the open transom of a waiting mothership and accelerate up a docking ramp. I failed repeatedly, feeling the impact each time the boat hit the sides of the ship (Special Forces are trained to carry out the manoeuvre at night in heavy seas when the mothership is underway). Fortunately, the FSSS is also used to simulate less extreme situations.
“Take stabilisers, for example.,” says Della Valentina. “Various factors come into play when deciding which system to install on a yacht, but comfort is high on the list. The concept of comfort is notoriously subjective, however, and quantitative methods for motion criteria give no insight into how we experience those motions, or how they might affect the operation of the vessel.
By taking the data from CFD, model tests and sea trials and feeding it into the FSSS, we can simulate what different systems actually feel like in various sea conditions.”
The software can also simulate different
Above: Rendering of a command bridge atop a hexapod able to simulate ocean-going vessels in any sea condition or scenario.
Dynamic Positioning systems, hull shapes and metacentric heights (GM). A higher GM provides better stability and seakeeping, but a lower GM generally means more onboard comfort. MARIN has identified an ideal GM of between 1.2 and 1.5 metres when the motions are still soft but the yacht is safe and stable. Clients can experience what that feels like in the simulator before a yacht is built. What’s more, the system can be programmed so they experience it from the beach club, main saloon or owner’s stateroom.
Whatever the scenario, MARIN is careful to validate the numerical models not only through model tests but also via feedback from experienced operators and instructors, so that every aspect of the simulation – from throttle response and turning circle to roll angle and motion behaviour in waves from different directions – is true to life.
Another important element that is still being researched is the notion of cybersickness, the feeling of dizziness or nausea that Virtual Reality can induce. It is different from motion sickness insofar as VR can produce a sense of disorientation, whereas simulations may result in oculomotor disturbances or mismatches between what we see and how we move – factors that have to be understood and accounted for when fine-tuning the numerical models.
“The human factor is usually decisive in high-risk situations and is an important research area for us.”
These simulators will be gathered under one roof in the SOSC and by linking them together they can be used to recreate complex or critical multivessel operations. MARIN is routinely consulted during investigations into maritime accidents. Much of this work is covered by NDAs, but MARIN itself uses the example of an incident in January 2022 when a bulk carrier called the Jiulietta D broke anchor and ran adrift in a part of the North Sea where a wind farm was under construction. The ship collided with a chemical tanker, hit a transformer platform and wind turbine foundation, and narrowly missed a gas production platform.
During a complex rescue operation, the crew were airlifted to safety and tugs managed to tow the ship away before it ran aground, but the outcome could have been much worse. To learn how things might have been done differently, the SOSC will be able to simulate the Force 9 winds and six-metre high waves, as well as the relative positions of the wind turbines, from the different perspectives of
the Jiulietta D and the smaller rescue vessels, as well as relative to each other.
The crews on the simulators receive feedback from instructors who are following the entire operation and the simulation can be stopped or reversed to explore alternative responses to the emergency. In the simulated coordination centre the captain is able to call the Coast Guard to request evacuation and search and rescue helicopters can be dispatched.
“Meanwhile we have specialists and psychologists to analyse the stress factor and participants are wired up to measure brain activity, eye tracking, blood oxygenation, and so on,” says Della Valentina. “The human factor is usually decisive in high-risk situations and is an important research area for us.”
The airlift procedure can also be simulated. Winching operations at sea are always risky, but especially during a storm. In the SOSC’s
Maritime Experience Lab, a crew member standing on a hexapod can experience the motion of the vessel and what it’s like trying to grab hold of a helicopter lifeline from a stricken ship (MARIN is also researching haptic technologies to recreate the sensation of touch and make the experience even more realistic).
What do superyachts have to do with bulk carriers in the North Sea? Well, yachts also break anchor, run aground and collide with other vessels (when 63-metre Utopia IV collided with the tanker Tropic Breeze in 2021 in the Bahamas, ‘catastrophic force’ pierced the tanker’s stern causing the ship to sink). Crowded marinas and busy cruising grounds offer plenty of potentially hazardous situations. By analysing the interaction between the sea, people and vessels regardless of type, the SOSC aims to make all maritime operations safer and more efficient.
The energy transition and decarbonisation of the maritime sector is well underway. Initially prompted by IMO regulations and other legislation, shipyards are now acting on their own initiative to develop carbon neutral – and ultimately zero emission –power and propulsion systems. This creates opportunities, but also uncertainties: what will be the fuels of the next decade; which power system will prove the most reliable; how will energy be stored, distributed and managed? To investigate these questions and more, MARIN is completing a prototype engine room of the future as part of its Zero Emission Lab (ZEL) with the aim of finding the ideal balance between zero emission and efficiency. The ZEL is basically an extension of MARIN’s old cavitation tunnel used to study the interaction between propeller hydrodynamics and power systems. Once completed, it will be possible to test various propulsion set-ups: an electric motor powered by batteries, a supercapacitor, a hydrogen fuel cell, or a methanol (dual-fuel) generator set, or combinations of these systems. The cavitation tunnel means solutions can be tested in real-life manoeuvring or crash stop conditions, for example, and the modular architecture allows for emerging solutions to be integrated in the future.
As a Joint Industry Project comprising stakeholders in different maritime sectors from tugboats and transport vessels to cruise ships and superyachts, Bureau Veritas, Damen, MTU Rolls-Royce, Wärtsilä, Sanlorenzo and Oceanco are just some of the partners that have signed up to the project. Using simulation, monitoring and Big Data technology, a ‘digital twin’ of the ZEL has also been developed to allow vessels to be built and operated in virtual reality.
“Each ZEL partner is looking into the best options available for a specific operational profile, which creates an environment for
accelerating the learning curve through combined research,” says Della Valentina.
“The beauty is that it also removes the risk factor of going at it alone, because if you invest in the wrong technology you can still profit from the findings of the other partners.”
Initial evaluations were made using a special tool to investigate and compare different energy carriers and power conversion systems. The tool basically lists the main characteristics of the selected solutions to derive required volume and weight, typical investment price, efficiency (power output) and emission levels. Combining this data with the expected range and required power provides a quick scan of viable solutions that can be evaluated according to user-defined criteria.
Last November MARIN published a Specification and Exploration report outlining new propulsion, power and energy (PPE) systems for eight different vessel types (Use Cases), the first in a 5-stage process that will end with the testing and validation of the lab models.
“We realised that the challenges faced by the yachting industry in developing more efficient and sustainable powertrains are just too many to be managed by individual shipyards or research teams,” says Paolo Bertetti, vice-president of product design and innovation at Sanlorenzo, which in 2024 expects to launch a prototype 50-metre yacht equipped with fuel cells that generate electricity from reformed methanol. “By joining forces with MARIN, industry suppliers and other shipyards, we can be faster in defining the most promising propulsion solutions and then compare the pros and cons with state-ofthe-art simulation tools. For Sanlorenzo, and the yachting industry at large, it means we can shorten the time to market of more sustainable propulsion solutions.”
MARIN currently operates 7 real-time simulators, which can be used separately or combined for research, consultancy and training purposes. As an add-on to traditional design services, it enables design and operational feedback before starting new-build projects.
Full Mission Bridge I (FMBI): Especially suitable for simulating large oceangoing vessels.
Full Mission Bridge II (FMBII): A flexible facility capable of simulating a wide range of vessels.
4 Compact Manoeuvring Simulators (CMS): Smaller simulators that can be used to simulate tugs and other vessels.
Fast Small Ship Simulator (FSSS): Used for highspeed craft such as RIBs or planing yachts. It can also be converted to a tug setup.
A spate of yacht fires in recent months has prompted the industry to reassess its fire prevention regulations, particularly with regard to the smaller vessels in the fleet. But what form will these regulations take, and are lithium-ion batteries really to blame for the flames?
BY CHARLOTTE THOMAS
In a year of dramatic headlines, the word ‘fire’ seemed to crop up a lot in 2022, although the incidents of fire aboard yachts over 24 metres has been fairly constant in recent years (see graph P.97). The proliferation of lithium-ion batteries is often blamed, but in many cases the jury is still out. While classification societies handle structure, machinery, electrical and control engineering, regulations covering fire suppression and prevention lie in the hands of Flag States, and therefore are dictated by the various yacht codes. It is here that an interesting fact emerges:
“An initial look at the list of accidents makes it clear that most of the fires last year were on smaller yachts,” says Lorenzo Pollicardo, Technical and Environmental Director at the Superyacht Builders Association (SYBAss).
“This means they fall outside compliance with International Maritime Organisation [IMO] requirements in terms of safety, and some of those yachts are built to comply with the Recreational Craft Directive rather than yacht codes.”
This has led to industry discussions on how to adapt existing regulations, or implement new ones, that will cover more of the fleet, and where to draw the boundary for regulatory compliance.
“We have drafted the REG Yacht Code as an equivalence to SOLAS, the Load Line Convention and the Maritime Labour Convention, and we have notified IMO accordingly,” says Julian Smith, Principal Surveyor, Global Safety and Compliance at Cayman Island Registry. “So effectively we have used the underlying conventions that are published by the IMO, mindful also of the fact that yachts have their own unique sets of challenges in design and operation that makes them markedly different to merchant shipping.”
One of the challenges, Smith points out, is the rate of technological change: “We’ve got a great deal coming through both in terms of electro-mechanical systems on the one hand, and alternative fuels on the other, and then there are electrically driven tenders and toys. And traditionally, maritime regulation hasn’t been known for its agility.”
From Seabobs to electric tenders with power outputs ranging from 1kWh units to 60kWh liquidcooled battery banks, the proliferation of e-toys and tenders poses a challenge in terms of garage design and fire safety.
“We get a lot of enquiries from crew now about advice for battery toys and about fireproof covers,” says Roxane Ducruet, managing director of Superyacht Tenders & Toys MC. “Our advice is not always to fully charge products on a fast charger, and to consider fireproof battery cases. We work with companies supplying fireproof cases that match the shape of their batteries, and some Flag States are now requesting these. We are also starting to see big superyachts in build that have dedicated battery rooms.”
It is advisable not to be on the bleeding edge with new toys that may not been tested extensively, and to be careful of where you source them. “There are a lot of cheap products coming from China or other markets that may not have as stringent safety requirements as we do in Europe,” says Rory Boyle, Burgess project manager. “Things like the CE mark are useful to gauge safety – and that applies not only to toys, but also to other equipment such as interior gadgets and even torches.”
Another issue is that toys are often designed to be as light as possible, and that may mean critical structure has been removed to keep a battery safe from damage or water ingress. Seabobs have been around for years, and their heavy battery banks are well-proven. “But when you look at foil-boards or anything designed to go above the water, maybe alarm bells should start ringing if they don’t come from a known brand or source,” warns Boyle.
“I think the sub-500GT market is one area we need to look at improving on and we are currently consulting with the industry on how best to do that”
For yachts above 500 gross tons there is a significant difference in regulatory requirements compared to those below 500 gross tons. Above 500GT there are A-class boundaries for the tender garage, mandatory requirements for a fixed extinguishing system and a fully addressable fire detection system. This goes some way to explaining why there is an apparent weighting of fires and smoke-related damage at the smaller end of the fleet (notwithstanding the greater statistical likelihood of fire aboard the much higher number of smaller yachts). The question then becomes, what do shipyards, designers and project managers need to be aware of with regard to new potential
regulations, and what else can be done to mitigate risk on smaller yachts? “I think the sub-500GT market is one area we need to look at improving on and we are currently consulting with the industry on how best to do that,” confirms Smith.
Discussions include introducing new regulations for yachts between 300GT and 500GT, while the Maritime & Coastguard Agency (MCA) currently has a marine guidance note in draft form that specifically addresses recent fires and the storage of small electrically powered craft on yachts. It cites an estimation of 16 total losses due to fire between August 2021 and August 2022, and proposes guidance for lithium-ion batteries on board.
While the cause of many recent fires has not been conclusively established, it seems likely some were started by lithium-ion batteries. Malta’s Marine Safety Investigation Unit’s (MSIU) report into the 2021 fire aboard M/Y Siempre while it was moored in Olbia, Italy, could not exclude that lithium-ion batteries were either the cause of the fire, or a contributing factor in its intensity and spread. The yacht had numerous batterypowered toys on board and the fire broke out on the open aft deck where the majority of them were stored.
Battery fires are almost impossible to put out. Li-ion battery chemistry means they produce their own flammable off-gases and the fire becomes self-sustaining in a process known as ‘thermal runaway’. At that point gaseous fire agents and waterbased suppression systems are simply ineffective. The advice – and current proposed regulation – is to include fireretardant boxes that can at least contain a fire, plus ventilation systems that extract off-gases from the top and the bottom of a compartment or battery store. There is also a growing number of commercially available detection systems that monitor battery storage compartments for the off-gases or
The fire risk associated with Li-ion batterypowered tenders and toys on superyachts has raised awareness of how best to monitor their storage on board. The AX8 Thermal Monitoring Camera from Teledyne FLIR, for example, combines thermal imaging with a camera that can alert the crew to the early warning signs of battery failure. Compact and easy to install with a temperature range of -10 to 150 degrees Celsius and a thermal sensitivity of 100mK, temperature variations of as little as 0.1 degrees Celsius can be flagged up on screen. A change in temperature will sound the alarm long before any smoke appears, which means valuable extra minutes to ensure the safety of those on board and possibly extinguish or at least isolate the problem.
“We know that thermal imaging cannot solve the issue, but it goes a long way to mitigate the risk,” says Hans Groenenboom, Sales Director at FLIR Systems in the Netherlands. “The technology and risks are unlikely to be improved in the very near future, so it’s important for yacht owners to consider as many preventative measures as possible if the opportunity is there.”
temperature changes that show early signs of cell failure (see sidebar).
Ed Beckett, a naval architect in Burgess’s New Construction team, suggests that as electric tenders grow in popularity the onus is not just on the shipyard, Flag or Class. “It’s important to engage with the tender builder in the design of their battery system and how it will interact with the yacht, not only to ensure it’s safe when out on the water but also equally about how it is stored and charged,” he says. “It is more involved than for a diesel tender, where an owner might just pick the one he wants that fits in the garage space.”
Size comes into play here too. Rory Boyle, naval architect and project manager on the Burgess Technical Services team, says that typically with clients for yachts over 500GT, and for custom projects with custom tenders, it is very easy to have the conversation about safety and suitability. Problems arise at the smaller end of the market where production superyachts are built to tight volumetric tolerances with garages that are designed for specific production tenders, with little room to spare for additional systems or insulation. “There’s a lot of talk about fire safety, and rightly so, but what we’re trying to ensure is we don’t have the fire in the first place,” says Smith. ”That comes down to battery design and construction, battery storage, charging and battery monitoring. Thermal runaway can be initiated by a number of different failure modes including an internal or external short circuit, excessive storage
temperature, or poor battery management practices. It is also interesting to note that we’ve had two cases in the last 18 months of thermal runaway with batteries that were neither on charge nor under load. One was for an e-Foil and the other an e-scooter.”
Even in cases where such toys are stowed in the open, a yacht still presents a combustible environment. Teak decks contain teak oil, fairing compounds are flammable, composite boats burn quickly, while aluminium will melt if not insulated properly and starts to lose its mechanical properties at just 200 degrees Celsius. Investigators into the case of M/Y Siempre reported that once the fire had taken hold on the open aft deck “it did not take long for the various flammable fittings, fabrics, wood panels, etc, to contribute to the fire spread through most of the yacht and before the fire could be brought under control.”
It is important also to recognise that not all fires are caused by batteries, and not all battery fires are caused by defective equipment, but the human factor and crew training play a significant role in both. A fire that broke out aboard M/Y Kanga when anchored off Croatia in 2018 was caused “in all probability” by the lithium batteries of an electric surfboard. It took less than 25 minutes for the fire to spread from the lower deck to the sun deck, accompanied by explosions. However, crew members were not aware of how dangerous lithium batteries can be, even after some batteries were found to be leaking.
The fact remains, however, that not all yachts are built to a commercial code particularly if their intended use is purely private. It can be costly and technically onerous to meet all the requirements of code, particularly for elements that are surplus to the intended operational profile. Furthermore, the smaller the yacht, the more difficult it is to include fire systems and fire-damping materials in the structure of the vessel. In this regard, the advice is four-fold.
First, consider building to code equivalence where possible when it comes to fire systems and monitoring, even if the yacht is going to be used privately.
“It is not uncommon for commercial compliance to be on the options list for smaller yachts,” says Beckett. “Much of that compliance relates to safety and security, and when you put it to owners I think a lot of them will say that, actually, they want to protect their asset and their family.”
Second, establish in advance what sorts of tenders and toys the client might want aboard, and to design with those in mind.
“All too often you get to the end of a build and somebody turns up with all sorts of toys that they want to store between the jet skis which are full of petrol,” warns Beckett. “The earlier we have those conversations, the more we can look at dedicated battery charging boxes, or the provision of fire extinguishing equipment.”
Third, ensure good technical oversight during the build by a knowledgeable team who will be questioning the cabling, chafe points, electrical anomalies and other factors that can play a
critical part in preventing the causes of fire throughout the vessel, not just in the garage area.
“Part of that oversight role is ensuring the boat being built matches the way it is going to be operated,” says Beckett. “There’s nothing worse than designing for storing things in one area, then the owner turning up with a bunch of bikes and things that have to be stored somewhere less suitable.”
And fourth, liaise with the insurance underwriters in order to understand what they require, and what they will or will not cover. This has become more pertinent over recent months as many of the biggest yacht insurers start to rethink their cover of certain types of toys, or at least impose battery handling and storage requirements. Some, especially those insuring vessels over 300GT, insist on vessels being built and maintained to IACS class, pointing out that classification societies are updating their requirements for charging, storage and emergency response regarding potential incidents with Li-ion batteries.
“All too often you get to the end of a build and somebody turns up with all sorts of toys that they want to store between the jet skis which are full of petrol.”
Smith emphasises the importance of taking a measured view of any regulatory changes, which in turn take into account the findings of ongoing investigations into incidents of fire without responding in a knee-jerk fashion.
“There’s a lot to think about when we’re introducing new regulations, and that’s where we are at the moment,” he says. “We are getting a great deal of feedback from the industry and it will be interesting to see the final draft – I am confident it will be measured, technically and commercially feasible, and it will set the appropriate level of additional fire safety measures based on what we understand to be the increased risk.”
While the details are still being worked on and have yet to be finalised, consultations with the industry on elements such as the installation of fixed extinguishing systems suggest that 300GT
would be the lower limit for such requirements in terms of what is technically feasible. Smith further points out that Cayman already has experience of fitting fixed extinguisher systems on yachts between 300GT and 500GT and strongly encourages designers, engineering teams and project managers to factor these systems into designs that fall into that bracket. Furthermore, he emphasises that guidance notes will remain as such rather than becoming a shipping notice, at least for now.
“Once it has been published and people have used that guidance for a while, we will be able to establish whether or not it is wholly or partially suitable, at which point we will be able to finalise the technical content and incorporate it within the REG Yacht Code,” he says.
The consultation period for MGN 681 (M) was due to end at the start of February. Watch this space.
Custom elevators on superyachts are more than a means of vertical transport: they are complex feats of engineering often designed as mobile masterpieces. We spent a morning at Lift Emotion in the Netherlands to find out more about a highly specialised and competitive market with room for only a handful of key players.
BY JUSTIN RATCLIFFE
“Starting up an elevator company specialising in yachts would be almost impossible today,” says Mike Brandt, who founded Lift Emotion with business partner Eef Kwakkel in 2007. The financial crisis struck less than a year later. Bad timing, you might think, but in fact Lift Emotion was the result of a lucky break. At the time Brandt was working as a mechanical engineer for another lift supplier on 75.75-metre Ocean Victory (now Ebony Shine) at Feadship. When the company ran into financial difficulties, the shipyard asked him to help out.
“Ocean Victory was our springboard into the business, because after that Feadship signed us up for Musashi and her sistership Fountainhead,” continues Brandt. “Around the same time we finished the lift installations on Amevi and Alfa Nero at Oceanco, followed by orders from Delta, Trinity and Derektor in the US, and what was then Proteskan Turquoise in Turkey. You could say we started with a bang.”
Bigger yachts with more deck levels have raised client expectations and suppliers like Lift Emotion, Holland Marine Lifts (HML), Lutz in Germany and Bertazzoni in Italy have had to step up to the plate in terms of technical
and aesthetic innovation. In 2007 the lift aboard Ocean Victory was a fairly discreet rectangular design, but just two years later Musashi’s all-glass lift enveloped by a stainless steel and glass staircase had become a focal point of the Japanese-inspired interior design. Nowadays, elevators that combine custom engineering with specially commissioned artwork or lighting installations are more the rule than the exception.
Innovation is often driven by developments outside the yachting sector. Lift Emotion, for example, has built a lift inside an armoured bus for a Middle Eastern client with mobility issues, and devised the ‘twisting’ lift for the Steve Jobs Theatre at Apple headquarters in Cupertino, California, which is fitted with seismic dampers in case of earthquake. But at least 80 percent of its turnover comes from tailor-made solutions for superyachts and during our visit the company was working on 22 elevator projects for yachts of up 125 metres in length.
“Our strength since day one has been that we offer tailor-made products and every lift that leaves our facility is one-of-kind,” says Brandt. “The best marine elevators are never standard – they set the standard. This is both an advantage and a challenge.”
The regulations governing “Lifts on ships” for passengers and crew vary slightly between classification socities and flag states, but all are based on ISO 8383 or EN81 codes of practice. Importantly, these codes only set out guidelines for marine elevator settings and how to perform inspections.
EN 81-20 defines the technical requirements for the construction of elevators and for the testing of lift components.
EN 81-80 stipulates rules for the improvement of the safety of existing passenger and goods elevators.
EN-13015 deals with “maintenance for lifts and escalators”.
ISO 8383 lays down statutory requirements for the design, installation and inspection. It is worth pointing out that there is no such thing as an ISO or Class approved marine elevator supplier. Additionally, classification societies only refer to the ISO 8383 code and do not add further instructions or guidelines. An exception is RINA, which stipulates it is the owner that needs to authorise the marine elevator service company. Different flag states can have their own additional rulings.
Whatever the size of yacht, the perennial challenge for any marine lift contractor is lack of space – what Brand wistfully calls “the story of our life.” Most lifts on yachts rely on hydraulic systems. To go up, a pump pushes fluid into the cylinder that drives the lift car up. To go down, the valve opens and oil is allowed to flow back into the reservoir and the car returns down using gravitational force. For technical and safety reasons elevators require space at the top of the trunk as well as at the bottom in the pit (and possibly a separate machinery room) to house the telescopic cylinder.
It follows that the more deck levels and the bigger the lift car, the larger the cylinders, pumps, and so on. Lift Emotion’s spectacular glass lift that connects five decks aboard Benetti’s 107-metre Luminosity has two, three-stage hydraulic cylinders protruding deep into the fire-rated machinery space on the under-lower deck.
Hydraulic systems have the advantage that the mechanics are familiar to yacht crews who can carry out routine servicing themselves. On the other hand, ship systems rely on high-pressure, low-volume hydraulics, whereas elevators use low-pressure, highvolume systems. These require a stand-alone pump unit, usually fitted with a variablefrequency drive to avoid more fluid being pumped than is effectively used, which is bad for energy efficiency and heats up the fluid unnecessarily.
In certain cases other mechanisms may be more appropriate. Electric traction elevators have rolling steel cables over pulleys or sheaves and the weight of the car is balanced by a counterweight (although having a counterweight that can easily weigh over 1000kg on a moving yacht brings its own challenges). Drum drives raise and lower the car using an electric motor to wind two cables or wire ropes directly onto drum winches. Lift Emotion installed a lift of this type at the top of the lift shaft aboard Nobiskrug’s 80-metre Artefact because
there was insufficient room underneath for a hydraulic system.
An early request for the lift car on Luminosity was to have a three-metre high ceiling and correspondingly tall glass doors, although only the main deck had landing doors of the same height. Lift doors and landing doors obviously need to open and close simultaneously. This is done by a clutch mechanism that engages with and opens or closes the landing door at the same time as the lift door. An electric impulse from the elevator controller – the brain of the elevator – sets the process in motion when the car is safely at the proper floor, but Luminosity’s irregular deck heights presented a technical challenge because the opening mechanism is usually housed on top of the lift car, which doesn’t always correspond with the height of the landing door. The issue was resolved by mounting the electric door mechanism under the car.
In fact, the doors are the hardest working part of an elevator and the cause of most breakdowns. “When the equipment is adjusted correctly, both sets of doors open and close in a smooth mechanical movement, but even a small misalignment can result in a very noticeable malfunction,” says Brandt. “This usually happens not because something fails, but when somebody forces the door or blocks it with their foot.”
Marine lifts had an inauspicious start. The first ship to have one was the Royal yacht Victoria and Albert III in 1900. The elevator was made by London-based Waygood & Co. and functioned perfectly, but the yacht tipped over when her dry dock was flooded causing major damage. The same company later installed the electric lifts aboard the ill-omened Titanic.
Waygood & Co. merged with Otis, today the world’s leading elevator and escalator company, which claims to move two billion people every day. Founded by the American industrialist Elisha Otis, in 1854 he demonstrated his safety elevator in dramatic fashion by stepping inside and cutting the hoist ropes: the lift fell just a few inches before being arrested by a saw-toothed ratchet bar.
Modern elevators have two basic sets of safety components: electrical and mechanical. The electrical components include the controller, sensors and software systems whereby the sensors monitor functions like the speed and position of the car and door-lock state, and send the data back to the controller. The mechanical components include the machine brake, overspeed governor, safety brakes and, finally, buffers at the bottom of the trunk. With advances in programmable electronic systems, the control systems are able to identify which link in the safety chain is open and tailor the response based on the situation.
Because the crew are expected to rescue themselves in rare cases of breakdown, service elevators on yachts require further precautions such as a ladder inside the car, another inside the shaft, and an escape hatch at the top. In reality, such lifts are also used by staff, perhaps nannies with children, so Lift Emotion prefers to class them as passenger elevators.
There are multiple safety procedures for when entering the pit below the car, or the trunk top above it, for maintenance purposes. These should
offer fail-safe guarantees, but accidents do happen, usually due to human error (there have been several lift-related injuries on yachts and at least one fatality).
Safety is also a factor when considering pop-up lifts that emerge on the sundeck. For the 60-metre Benetti Diamonds Are Forever, owner John Staluppi requested a lift that appeared from under a table so there was no trace of it when not in use.
Bertazzoni’s marine division, which supplies most of the Italian shipyards, duly obliged. Lift Emotion has installed several pop-up lifts, but Brandt makes a point of explaining to designers and owners that they can restrict the use of the top deck, especially during charters.
“The thing to remember is that you have moving machinery coming out of the deck where there are people and perhaps children,” he explains.
“That means the area has to be closed off and the lift has to slow down to allow the deck hatch time to unlock and open. Technically, you should have a crew member on deck pushing a button to bring the lift up, but no one wants that. Owners often decide against it once they understand the limitations and potential hazards.”
“It’s not just the lift car that can be made of carbon fibre; it’s also the shaft structure. That could mean an additional 200kg saved on each deck level.”
Holland Marine Lifts (HML) is a family business set up by Emile van der Starre in 2002 at a time when the superyacht industry was peaking.
Today it has a predominantly Dutch client list that includes Feadship, Oceanco and Heesen.
During METSTRADE last year it unveiled a carbon-fibre lift car in collaboration with Opulent Designs International.
“Opulent was looking at new applications of carbon fibre and reasoned that if weight is sometimes a critical factor on yachts, then a lightweight carbon-fibre lift would make sense,” says van der Starre. “We started a collaboration about a year ago and at METS we displayed the first prototype.”
Constructed for Opulent by specialists Supernatural-X in the UK, the weight of the ultralight carbon-fibre frame alone is just 48kg, whereas a steel cabin would be as much as 400kg. A fully functional carbon fibre lift system is being further developed at the HML facility near Rotterdam and testing is due begin in March 2023. The car will likely be too light for a hydraulic drive system, which requires a certain weight or pressure to force fluid back into the reservoir so the car can descend, and HML is looking at an electric belt-drive system.
“It’s not just the lift car that can be made of carbon fibre; it’s also the shaft structure,” van der Starre points out. “That could mean an additional 200kg saved on each deck level, which on high-performance yachts can make a significant difference.”
Less weight means smaller power packs and lower energy consumption. Other advantages of carbon fibre construction is that it allows designers to create more adventurous shapes, while the high strength of carbon composites means less material is required, which also saves space.
“We’re always looking at ways to improve the design and technology, but yacht builders are quite conservative and change comes slowly,” says van der Starre. “I believe the market is ready for a carbon-fibre lift and judging from the enthusiastic reactions to our protype it looks like the industry thinks so too.”
Roll and pitch can have a detrimental effect on lift operations. Marine lifts should be able to perform reliably in heavy seas (up to ±10º rolling for a period of 10 seconds, or up to ±5º pitching for a period of 7 seconds) and Lift Emotion has developed its own algorithm for calculating the potential loads and prevent deflection of the lift trunk. Most guest lifts are in the main lobby amidships where vertical accelerations are lowest, but service lifts and dumb waiters are often further forward or aft where the forces are higher.
Comfort is also a question of speed. The maximum speed for comfortable travel between two floors is usually reckoned to be around 0.58 m/sec, allowing time for the car to accelerate and decelerate. Over longer distances it can be faster (Luminosity’s lift car travels at 1m/sec) because there is a greater interval between the speeding up and slowing down phases. The comfort factor is not so much top speed as acceleration and jerk, or rate of change of acceleration.
The final challenge for lift manufacturers is the installation. This usually happens in the busiest part of the yacht when the interior outfitting has already started. Assembling the elevator on site is far too disruptive, so companies like Lift Emotion pre-assemble as much as possible of the shaft and cabin
in the factory, including any glasswork. The whole thing is then transported by truck to the shipyard and hoisted in through the top deck in two or three sections. The 15-person elevator on Project X – the biggest of its kind on an 80-metre yacht with a 1,125-kg payload –was up and running in a matter of days. Elevators are so familiar that we rarely consider how they work – or break down. The basics of lift mechanics have changed little since the 1800s, but modern technology offers infinitely better safety and comfort. Mechanical valves have been replaced with electrical ones; electromechanical limiter switches are giving way to digital encoders and magnetic strip readers for measuring the distance between stops; the latest inverter pumps provide more precise control of the hydraulic fluid flowrate and pressure for smoother operation; rubber belts are replacing cables and chains; and lift cars are being built of lightweight aluminium instead of steel. These developments mean lighter systems can be installed on ever smaller yachts and last year Lift Emotion fitted a three-deck guest elevator aboard Van der Valk’s 34-metre Lady Lene, its most compact yacht project to date.
From class-approved propellers to fully printed hulls, 3D printing is making headlines. We take a look at the opportunities for yachtbuilders and ask whether the industry is more confined by mindset than technology.
BY CHARLOTTE THOMAS
From model-making to printing food and even using biogel to print replacement organs, it seems there is nothing 3D printing cannot do. The use of additive manufacturing, as it is also known, for the production of plastic, metal and ceramic elements is already viable across a range of industries, but is it the miracle solution that will enable us to print entire boats in a matter of days?
“When we started out, we looked at how we could introduce this technology in a field where everything is strictly artisanal,” says Paolo Nazzaro, co-founder and MD of Superfici, an Italian additive manufacturer based in La Spezia. “The shipyards reacted like it was arcane magic, and it took time to prove to them that we could use new technology to improve design and functionality.”
With clients ranging from SACS, Heinen & Hopman and Raymarine to Sanlorenzo, Amer, Tankoa, Perini and even Lamborghini, the message is starting to get through, although the challenge now is convincing shipyards to change the way they approach design. Nazzaro points to a tender helm console Superfici designed and printed for SACS, which was an exercise to show that when you change the way you build parts you also change the way you design them.
“Now they understand,” he says. “We design not only the exterior but also the internal parts because we print everything as one; it means parts are becoming more complex even though they are actually easier to build, and shipyards are starting to change the way they conceive projects.”
“It’s a different mindset,” agrees Adam Wheeler, Design Office Manager at Sunseeker International. “Rather than just designing for manufacture, we can design for form now. The beauty of 3D printing is it lends itself to free thinking. There are no limitations.”
Sunseeker has started using 3D printing across its range and has set up an internal programme known as RAMP (Research into Additive Manufacturing Processes). Currently its 60-strong design office uses 3D printing primarily for components in nonvisible areas, but the tech allows the team to create complex pieces that are not possible to manufacture by conventional injection moulding, such as parts for plumbing or air-conditioning ducts that can maximise
available volume, or elements like plenum boxes and manifolds that by printing them whole mitigates the risk of leaks through human error.
“We can develop and realise organic shapes that subtractive manufacturing doesn’t allow us to do,” Wheeler confirms. “It’s definitely the future and we’ve got high aspirations as to how we utilise additive manufacturing going forward, although the print resolution isn’t quite there yet to print a major moulding without having to revisit it with paint or other finishing.”
For Will Penfold, Senior Project Manager at 3D printing company AMufacture in the UK, designers and shipyards are still playing catch-up with the technology. “A lot of the time parts come to us that have been designed for injection moulding or machining and are not designed with 3D printers in mind,” he says. “We then advise how they can tweak the design and add value or features, because we can print parts that can’t be made in any other way.”
AMufacture prints custom components for high-end race boats, and low-volume production parts for sailboats, motoryachts and luxury tenders. A supplier to companies like Sunseeker and Harken, it announced at the start of 2023 that it was the new 3D printing technical partner for SailGP.
“Over the past six months we’ve had a lot of conversations with a lot of different marine companies, not only in the UK but also in Europe,” Penfold says. “It suggests that the technology is on the verge of becoming mainstream in the marine sector.”
There are a bewildering number of 3D printing technologies. Not all are suitable for finished parts or the marine environment, and others may be promising for future adoption but right now are very expensive. The key methods currently include:
Fused deposition modelling (FDM): A method of material extrusion, this is perhaps the best-known 3D printing technology in which a print head lays down extruded layers of melted plastic filament, concrete or other materials. It is used in most hobbyist 3D printers.
Vat polymerisation: In this method, light is used to selectively cure a photopolymer resin in a vat to create a complex solid shape. Stereolithography (SLA) is perhaps the best-known process, but there are many variants based on differing light sources and proprietary processes.
Powder bed fusion : In a way, this is a more advanced version of FDM whereby a thermal energy source is used to fuse powder particles (thermoplastic, metals or ceramics) to build a solid object layer by layer. Selective laser sintering (SLS) and multi-jet fusion (MJF) are two example technologies. Parts produced using these methods tend to have excellent mechanical properties and can have complex geometries.
Material jetting: Material jetting works in a similar way to a standard inkjet printer, but instead of ink uses photopolymers which are sprayed in layers and then cured with UV light.
Binder jetting: This process is similar to SLS but uses binder droplets rather than heat to fuse power particles. It is a low-cost process for functional metal parts, although mechanical properties do not match those of powder bed fusion parts.
Direct energy deposition (DED): An electron beam, laser or plasma is used to feed and fuse material simultaneously when it is deposited. Wire arc additive manufacturing (WAAM) used to create the RAMLAB/Damen propeller is a form of DED. The tech is expensive and parts require surface finishing, but it can be used for high-end components in automotive, aerospace etc, making it one to watch for superyachts in the future.
While the possibilities for 3D printing are immense, there are still some barriers to its widespread adoption in yacht construction. The WAAMpeller project by RAMLAB in Rotterdam showed the potential of additive manufacturing when it successfully printed a ship propeller in nickel alloy, aluminium and bronze that was subsequently class-approved by Bureau Veritas. However, the propeller required additional finishing, and the cost of such printing technologies is still prohibitively high for smallscale production.
There is also the problem of size with most printers currently offering print scales of up to around one cubic metre, and the rapidly changing nature of the technology means it is a hard call for a yard to invest in a serious printer – one reason why third-party print companies will likely continue to provide off-site parts manufacture even as the technology matures.
“The interesting thing is in metal 3D printing, which is still a bit boutique and expensive,” says Penfold. “But as new technologies come online, that’s getting cheaper and there are a lot of fabricated parts that suddenly you’re going to be able to print.”
The result is more design freedom, which promises to provide savings in both cost and weight – advances that are probably only two to three years away. Similarly, the issue of size is being overcome not by larger print beds, but by designing in junctions that allow for component elements to be bonded together.
“In FDM printing you can build bigger with print beds up to 12 metres long, but the quality is not great,” says Penfold. “The print technology that we use, which is MJF (see sidebar), can create parts that are 100 percent homogenous and equally strong in every axis. As the technology matures and metal printing gets cheaper, I think that will be a big thing for the marine industry.”
It is not just ease of manufacturing that 3D printing offers; it also opens up opportunities for spare parts on demand or, in the case of older models or obsolete parts, one-off replacements via laser scanning, modelling and printing.
The idea of a yacht carrying its own 3D printer and printing off plastic and metal parts on demand is also tantalising, and this prospect was further bolstered in 2017 when Rotterdam-based RAMLAB partnered with Damen, Promarin, Autodesk and Bureau Veritas to 3D print a class-approved, 1.35-metre diameter ship propeller. The reality, however, is that such steps are likely many years away not least because of cost, space and the need for parts to be finished post-printing.
“I don’t think we’re all going to have 3D printers on our yachts,” says Will Penfold, “but I think instead of having ten parts on a shelf somewhere gathering dust, companies will have a design on a server and when someone needs a part it will just be printed off and three days later it will be on board, rather than having to go through the longer process of conventional fabrication. We’re already in discussions along those lines.”
Despite the challenges, 3D printing allows for complex geometries, custom designs and limited production runs, all of which are pertinent to the low-volume, high-quality nature of yacht building. Another relevant advantage is that the materials used are fully recyclable and reusable, which means an end-of-life solution for parts and tooling, waste reduction for prototyping, and the evolution of parts on the fly without having to create new moulds.
So does this mean that we will soon be cruising in printed yachts that have come off a production line in a matter of days? This prospect was mooted in 2019 when the University of Maine printed a 7.62-metre open boat that broke three world records in 3D printing. But while you can now 3D-print houses, and 3D-printed boats are being made in the Netherlands for use on calm canals, it is unlikely we will get to this point in mainstream yachting.
“The way the University of Maine boat is printed means it can float, but it would crack if you tried to navigate with it in waves,” says Nazzaro. “The other problem is weight (it came in at 2.2 tons).”
Instead, Nazzaro believes the future is more likely in 3D printing moulds, which can then be used to build boats. AMufacture’s CEO and co-founder Craig Pyser agrees that printing tooling will become more widespread, but in tandem with CNC machines. Clearly, we are on the verge of more widespread adoption of 3D print tech in yacht construction, and that opens up some delicious prospects in terms of design and efficiency.
“Someone said to me in my early days in this field that with 3D printing, complexity is free,” says Pyser. “When I fully understood what that meant it was an incredible moment, because it means clients are only limited by their imagination. And what excites me isn’t so much the advancements in technology, where you’ll probably gain on speed and the range of materials you can utilise, but about the increased understanding and adoption of 3D printing across various industries, including marine.”
Below:
Additive-manufactured consoles by Superfici for SACS (top) and Amer showing the modelling, 3D printed and finished stages.
Balk Shipyard began building wooden boats back in 1798. Today, the family-run business with a rare royal warrant of approval has evolved into a specialist refit yard able to take on technically demanding projects. A case in point is Emerald , a 50.4-metre classic Feadship approaching the end of a 15-month refit at the yard near Amsterdam.
BY JUSTIN RATCLIFFE
The Emerald story begins in 1990 when she was launched as Alfa Alfa, a 45.55-metre Feadship with the new ‘hardedged’ exterior lines fashionable in the mid’80s, a trend borrowed from the car design world. She changed hands and names several times before ending up in Malta as Legacy V By the time the current owners came across her, she was looking a little tired and in need of a facelift to bring her up to modern standards. That process is now approaching completion at Balk Shipyard.
Although Emerald is the first experience of ownership for her new owners, they have chartered extensively and had particularly enjoyed family time aboard 53-metre Mirage, another Feadship with the more classic lines of a decade earlier. She has an awardwinning refitted interior by Design Unlimited and the UK-based studio was tasked with coming up with proposals to refresh their new acquisition inside and out.
“The owners wanted to combine the best features of yachts they had chartered, then wrap them within the signature Feadship
exterior,” says Marcus Raynor, lead designer at Design Unlimited. “They had a precise, family-oriented vision for the boat and extensive changes were proposed to modernise and improve the interior spaces for both guests and crew, and the exterior design went through an equally extensive process of styling evolution rather than revolution.”
The next step was to find a yard to carry out the refit work and the tender went out to various companies. As the yacht was in Malta, the most obvious choice was somewhere in Italy or Turkey, but because the yacht had been built in in the Netherlands her owners eventually decided she should be refitted in her country of birth at Balk Shipyard.
“She arrived here with all the guest spaces completely stripped out and just a few loose wires and smoke detectors hanging down from the ceilings,” recalls Peter Lassche, Balk project manager. “But before starting on the interior we had some major metalwork to do.”
The hotworks involved cutting off and lengthening the stern to make way for more comfortable stairs connecting the main deck and swim platform. The original steps on either side of the transom door into the now enlarged lazarette had been straight, narrow and somewhat steep; the new ones are wider and gently curved with shallower risers for more comfort and under the portside stairs is a telescopic passarelle. In addition, the extended cockpit provides more al fresco relaxation and dining space on main deck. Mulder Design was contracted to redraw the underwater lines in the stern.
At some stage in the yacht’s history an Opacmare Transformer had been added by attaching it on top of the swim platform, an inelegant solution that hampered use
of the deck space. The new stern meant it could be integrated flush into the platform for a much more attractive and practical result. The brow over the bridge windscreen was extended to offer more shade and the imposing radar mast was restyled to lend the yacht a sleeker profile.
Also known as the boat deck because the guest tender is stored there, the upper deck was originally served by two cranes, which have been replaced by a single custom unit with a capacity of 3.5-tonnes. Built by LCW Lagendijk, a company more accustomed to supplying ships and offshore platforms vessels, it can extend 6.5 metres to facilitate tender operations on both sides of the yacht (an MOB tender and jet skis are stowed in the bow on main deck).
“To maintain the yacht’s balanced lines and provide a shady overhang on the deck below, the sundeck was also extended aft.”
A new addition is a spiral staircase on the starboard to the main deck aft. This much improves circulation for both guests and crew as the only prior outside access was from side-deck stairs amidships.
The sky lounge on the upper deck was extended aft in line with the foot of the exterior stairs to the sundeck, and the traditional hinged doors onto the open aft deck were replaced with a modern, sliding glass doors that open up the room to the exterior. A new dining table for a full compliment of guests and sofa seating was added in the stern. Once the tender is in the water, the boat deck is likely to be the hub of family life on board.
To maintain the yacht’s balanced lines and provide a shady overhang on the deck below, the sundeck was also extended aft. Here again the arrangement was completely modernised to make way for a custom-built, 6,500-litre capacity Aquademi hottub flanked by sunpads on a raised level overlooking the foredeck, as well as a wet bar and new sofa seating. The rest of the metalwork was more a question of taking away material than adding it. The window mullions in the master suite on the main deck forward, for example, are now slimmer to make way for larger windows and the fashion plates were reduced in size to allow more light into the main salon and better views outboard.
To improve comfort at anchor, the old hydraulic stabilisers were replaced with electric Quantum XT extendable fins to increase the effective fin area and improve zero-speed stabilisation. The naval architects at Mulder Design advised on the positioning and installing of the three-metre long fins– much larger than the originals – that are required by Class to have a separate watertight box or cofferdam and thicker steel plating surrounding the entry points into the hull.
“That meant cutting two huge holes in the hull and building reinforcements into the engine room and the fuel tanks under the guest cabins,” says Lassche. “These are very tight spaces because the engine room is full of machinery that you have to try and work around.”
Apart from removing a couple of opening portholes in the hull (which shouldn’t have been there under Flag rules) and adding new AC chiller units, no major work was done in the engine room, where the original twin 770-hp GM Detroit diesels were overhauled but remain in place.
It was not just the interior décor and furniture that were redesigned and rebuilt; the layout also underwent a dramatic transformation, which meant ripping out and replacing wiring, piping, AC ducting, and much more. “We basically took her back to a bare shell and started again,” says Lassche.
The new materials and colour palette based on dark wenge veneer, light-toned soft furnishings and natural stone varieties resulted from a visit by the Design Unlimited team to the owners’ residence in London to align their interior concept with the family’s feel for finishes and style.
“We combined face-to-face collaboration and physical sample testing with the latest CAD and visualisation software to finalise the interior design package, says Raynor. “The result is a stylish mix of sophisticated opulence and serene informality that will also appeal to a wide charter market.”
Apart from the new décor and bathroom fittings, adding vanity desks and increasing storage, the guest accommodation on the lower deck aft of the engine room (two double and two twin single cabins with sliding beds) is one of few guest areas that remained more or less intact. Elsewhere the owners requested a VIP cabin in addition to the master stateroom on the main deck forward – quite a challenge on a yacht the size of Emerald built at a time when optimising space was not the priority it is today.
The first step was to do away with the existing VIP cabin on the lower deck forward of the engine room. This had the advantage of increasing the size of the crew quarters by about 30 percent, allowing for a larger crew mess, a dedicated laundry room, a chief engineer’s cabin, and additional refrigerated storage. The crew accomodation was in good condition, so the décor was refurbished rather than replaced and the new additions finished in the same style.
Relocating the VIP to the main deck was more complex. The old yacht had no fewer than four staircases for guest and crew use arranged around the galley amidships. This was clearly inefficient. Design Unlimited cleverly reduced the number of staircases to two, improving circulation flow in the process while maintaining privacy for guests, but also creating a modern and user-friendly galley with a large pantry that did not exist before. It also freed up floor space, which in addition to shifting the forward bulkhead in the master stateroom 800mm forward and repositioning the ensuite bathroom, provided just enough room for a comfortable VIP cabin.
“The rearrangement is a win-win on a number of levels,” says Raynor. “It does away with the rather poky VIP on the lower deck, increases crew comfort, reduces the number of staircases, improves the galley layout, and introduces two nicely proportioned suites on main deck where before there was only one.”
The new staircase arrangement means a stairs emerges from under the observation sofa directly into the wheelhouse. The navigation and communication electronics on the bridge were completely upgraded and a new Böning control and monitoring system installed by integrators Royal Van der Leun, along with new wing stations.
“The challenge here was fitting a lot of new hardware and cabling into a console designed for the much simpler systems of 30 years ago, while still maintaining the access space for someone to be able to crawl inside if something needs fixing,” says Lassche.
The captain’s cabin was flipped to the starboard side with direct access from the wheelhouse. This created space on the port side for a ship’s office/ radio room and a servery area dressed as a guest space where guests can help themselves to a cool drink, or it can be manned by crew if required.
In the main saloon the staircase to the lower deck cabins was rotated 90 degrees anticlockwise so the entrance was from the starboard side rather than the middle of the room. This increased the available floor space in the lounge for freestanding furniture. Feature partitions introduced between the saloon and the forward dining room provide a degree of separation and easily accessible storage for tableware.
Thanks to the sympathetic touch of the designers and specialist experience of the shipyard, Emerald is a better looking Feadship than when she first hit the water more than 30 years ago – by no means a foregone conclusion when refitting classic yachts. Her new interior, built and installed by Metalika in Slovenia, is fresh and contemporary yet in keeping with the timeless exterior styling, and her layout is vastly more conducive to modern family life afloat and the expectations of eventual charter clients. Add a glossy Jotun topcoat in Orion Green and Emerald is a picture postcard example of how an extensive yet sensitive refit can give an old yacht a new lease of life.
With its partners and in combination with their own FPP and CPP systems, Piening Propeller can realize Hybrid solutions for any kind of demand, with:
• Multi Mode, Electric Drive Mode, Boost Mode, Generator Mode or Recuperation Mode.
• Hydraulic pitch control of the CPP, using ordinary water
Design and Manufacturing of complete Propulsion Systems with Fixed-Pitch Propeller or PCP > 800 mm Ø info@piening-propeller.de
Coatings and paint have come under increasing scrutiny in recent years with technologies evolving and the field becoming more competitive. We ask a panel of experts – Richard Jennings (global technical manager at AkzoNobel), Eduardo Diaz Pereira, (yachting technical sales support, Gruppo Boero), Remy Millott, (Group CEO, Pinmar) and Thomas Schultz (sales director, Alexseal Yacht Coatings) – about the challenges and technologies within the sector.
Which quality criteria can be measured and standardised?
Richard Jennings: There are a myriad of outside factors that contribute to the overall appearance of the coatings once they are applied. These can include the preparations, how clean the spray area is, and the present atmospheric conditions when applying the product. The coating can be measured in terms of quality, gloss, and colour. Beyond that, the coatings manufacturer will work with the applicators to inform them of the best practices in order to achieve the best
finish possible for their application. Additionally, there are a number of groups that are working on creating quality standards for the market, including ICOMIA and ISO. These quality standards are being developed by a cross-functional team of coatings professionals from across the industry. They help inform customers of what to expect from their paint systems, the measurements on colour, gloss levels, distinction of Image (DOI), etc.
Eduardo Diaz Pereira: Some quality criteria can be measured by specific tests carried out by standardised devices. Acceptance criteria are usually defined by each site and approved at the contract stage. From a practical point of view, the part that is receiving more and more attention is the enamel, as it is the visible part where colour, gloss, DOI, orange peel, etc. are measured, and where the acceptance standards are even higher than those for classic car refinishing, even though the surfaces involved are huge.
Remy Millott: It’s important to establish that observing a paint finish can be a subjective
process; everybody sees things slightly differently and environmental conditions can also play a factor. However, in our opinion there are a core set of parameters that can be reliably measured and referenced as part of the final finish. These core parameters are colour shade, gloss, distinctness of image (DOI), paint film thickness, dust inclusions and surface fairness.
The Pinmar Standard is our proprietary quality standard built around these fundamental parameters, the measurement processes, and the target values to be used in specifying, measuring and accepting exterior paintwork on our new build and refit projects. Introduced in 2011 as the industry’s first comprehensive statement of how a client’s expected paint finish should be measured and agreed, measurable paint acceptance criteria are now written into all major paint contracts by the shipyards and industry surveyors and consultants.
Thomas Shultz: From the technical side, the layer thickness, which should be between 50 - 100 µ for the topcoat, depending on the colour shade, is an important criterion. The same applies to the adhesion of the various layers of the coating. This is evaluated with the pull-off test for primer and filler and with the cross-cut test for the topcoat.
Richard Jennings: This is usually determined prior to application where the applicator and the owner / owner representative spray out large panels to agree on the correct colour, gloss level, DOI, and the overall finish. The panel that is selected will serve as the criteria or standard for the full application on the vessel.
Dust inclusion would be one of the prevalent reasons for a rejected paint job. The reason being that a superyacht has a large amount of surface that likely had its previous coating either heavily sanded or completely removed, so some of the sanding residue may be still present in the area. Additionally, if there are quite a few people coming in and out of the application area, the presence of dust can increase. One of the major tasks prior to the application is to ensure that the overall area is “clean” for the paint to be applied.
Thomas Shultz: Craters are also a common
complaint. They can be caused by parallel work on the yacht, which also contaminates the air. For example, wood particles get into the air during teak work, and the atmosphere is also contaminated by anti-fouling coatings applied at the same time. But critical temperatures below 15 or above 30 degrees Celsius or very low (<30%), or very high (>80%) humidity are also factors that can have a negative effect on the coating, resulting in orange peel on the surface.
How long on average does a topcoat last and what does it depend on?
Richard Jennings: This is a challenging question, as the answer is “it depends.” So many different factors influence this such as the coating itself, location, and maintenance schedules. On the type of coatings, some have very good UV protection and colour retention. Another important factor is where the yacht will spend most of its time; in areas with high exposure to UV such as the tropics or areas with more seasonal weather. How well is the yacht maintained and whether correct maintenance products are being
used will also have influence.
These factors all play a part in the lifespan of a coating on superyachts, where we see the average lifetime ranges from 3-5 years. However, under correct care, this lifetime could be greatly extended.
Eduardo Diaz Pereira: On average, the performance and quality of the topcoat is guaranteed for 24 months, sometimes 48 months. After this period the colour and gloss can change drastically. Of course, the durability of the topcoat is closely linked to the maintenance and care carried out by the crew.
More specifically, since topcoats are two-
component polyurethanes, their resistance to ageing, chemical attack, etc. is extremely high. Durability depends mainly on maintenance and care. The use of inappropriate detergents, abrasives, etc. can cause premature deterioration of the material.
Remy Millott: This will depend very much on the specification and type of topcoats used, a traditional Polyurethane topcoat will perform well for 3 to 4 years. Some of our clients favour a shorter refit cycle to maintain the pristine look of their yacht, while others, especially those involved in yacht charter, prioritise the earning potential of the vessel and will arrange refit
periods based around their compulsory 5-year engineering surveys and maintenance schedule.
Do different paint colours require different maintenance procedures?
Richard Jennings: Certain paint systems can offer greater protection such as a base coat and clear system compared to a traditional solid colour or single stage coating. The reason that this makes a lot of sense is that you are asking one product (single stage) to offer the colour, aesthetic and protection in one coating. Whereas a base (colour) and clear coat application
focus the product attributes, where the base is providing the colour and possibly an effect (e.g., metallic) and the clear coat provides the gloss and the UV protection. Regardless of colour, the maintenance care is essentially the same with proper and regular washing of the surface, with a PH neutral soap and a polymer polish to protect and help extend the life of the coating.
Eduardo Diaz Pereira: There are certainly colours that are more critical from a maintenance point of view because they make defects, scratches and abrasions stand out more. For example, the same defect will look different on a white paint than on a dark blue or black paint. In some cases, it is preferable to finish the paint with a clear coat to make maintenance easier. The use of polishing processes to a greater or lesser extent causes abrasion, albeit controlled, to the topcoat, reducing performance and long term expectations.
Remy Millott: In short, no, the same maintenance programme should be applied by yacht crew regardless of the paint colour. Some considerations need to be taken when it comes to washing and cleaning darker colours , as over cleaning a darker coloured paint system will leave more noticeable results than on a lighter colour. It is a fact that certain colours (typically darker) will not last as long as a traditional white topcoat due to heat penetration and direct sunlight which breaks down the paint system more quickly.
Can the paint application process be made faster, more reliable and less costly?
Richard Jennings: If you want high quality and a fast turnaround, you will not achieve it at a low cost. That being said, there are ways to improve the throughput of the coatings process to make it more efficient and provide the finish the applicator and owner will be proud of. Labour is the largest item cost when it comes to the cost of the coating, and coating a yacht is typically a very manual process. At AkzoNobel, we have developed Awlgrip products and systems that do speed up the coatings process for example our Awlfair SF (Spray Filler), which can improve the application of filler to the hull by up to 3 times as compared to traditional hand application with a reduction of voids and
rework. This saves on labour and time with a step improvement of the finish.
Eduardo Diaz Pereira: One of the themes of research and development is to make the application cycle simpler, leaner, cheaper and more environment-friendly. In this sense, the increase in the volume solids of primers and fillers and the ease of sanding the fillers contribute to reducing the time needed for the painting cycle. A lean and simple cycle also reduces possible errors (incorrect curing times, incorrect mixing ratios for two-component systems, etc.).
Rationalising and standardising the products to be used also means that less material has to be kept in stock, with the consequent advantages in terms of safety (the products are usually solvent-based and flammable) and shelf-life, avoiding the use of products that are too old.
Remy Millott: That is the holy grail for paint applicators, and we are constantly striving to achieve this, however unfortunately, faster and less costly are rarely applicable together! The easiest way to shorten the paint schedule is to add extra manpower, split shifts and overtime to the project through an acceleration package. Even then there are built-in latencies that must be respected in terms of product curing times and how quickly you can apply the next phase
of the paint system.
Electrostatic application offers considerable advantages over conventional paint spraying. The improved transfer efficiency massively reduces the amount of overspray during applications, providing better working conditions during large applications for the workforce, less emissions, less dust, and a higher quality finish overall. It has been proven that a greater dry film thickness (DFT) can be achieved using this technique, which benefits the owners with better operational and cosmetic performance of the coatings.
During a refit period the benefits of the electrostatic performance allow larger areas of a yacht to be painted at once, in turn reducing the number of individual paint shoots required. The technology allows Pinmar to reduce and de-risk delivery and refit schedules, providing long term benefits to both shipyards and yacht owners.
Thomas Schultz: Regular training and further education of the paint crews are essential for efficient work. A thorough understanding of the adjustment possibilities of the material ensures the most significant possible safety during the actual application. This is also the reason why Alexseal regularly offers Paint Schools for Applicators.
Are biocide-free antifoulants as effective and what are the latest developments?
Richard Jennings: These new technologies have a learning curve that operators need to adjust to as they are different from traditional fouling control products that they have applied for decades. These first generation biocide-free products are typically silicone-based and require special handling when lifting and blocking the boat, and they also require several steps to apply the coating . Additionally, in water maintenance may be required, as these new biocide-free coatings have moved from an active coating to a semi-active coating. Traditional antifoulings work by using an active ingredient or biocide to keep fouling from attaching to the vessel. With application of these new coatings, you are likely to experience fouling on the boat, but the coatings themselves are typically very slick. This makes it hard for the fouling to adhere and either through usage or cleaning, the fouling is removed.
The first antifouling that was applied as a paint was developed 160 years ago and since then, these coatings have gone through technological advances to deliver the performance owners have come to expect. Alsot, the industry has developed its system of processes over 160 years using traditional antifouling paints. It is going to
be hard to adapt to new technologies and ways of working. These first generation of biocidefree products are a good start and provide the performance that is required, but they just do it in a different way that requires a different way of thinking about hull maintenance. This development is a necessary first step towards moving to a biocide-free fouling control solution for the industry.
Eduardo Diaz Pereira: Currently not, due to the performance required in the superyacht sector. Often a customer will ask for a product with a 2 or 3 year performance (service life), but the sailing factor is very low, so if you don’t have a high performance product, the fouling will easily adhere to the hull. Biocide-free antifoulings have found applications in the marine industry where boats are in motion for the vast majority of their service life (>85%). In the yachting world, boats remain stationary for a very long time (low sailing factor) and experience to date shows that this prevents an antifouling based on physical principles from working properly.
Today, antifoulings, even those containing biocides, are tested according to the strictest European regulations (BPR), which ensure that they are as safe for people and the environment and are compatible with their effectiveness.
SuperYacht Times B.V. Singel 260, 1016 AB, Amsterdam, The Netherlands
31 (0) 20 773 28 64 info@superyachttimes.com www.superyachttimes.com
Cover Images
Project H photo by Guillaume Plisson
3D Printing photo by RAMLAB MARIN photo by MARIN
How to Build It is published by SuperYacht Times B.V., a company registered at the Chamber of Commerce in Amsterdam, The Netherlands with registration number 52966461. The magazine was printed in March 2023.
It takes all kinds of crafts when building a vessel – some are crucial for performance, some for functionality. But, for beauty, the coating process is the most critical factor for a brilliant appearance.
Stay true to your high standards – ask for ALEXSEAL® Yacht Coatings and leave an outstanding, long-lasting impression.
instagram.com/alexsealpaint fb.com/AlexsealYachtCoatings