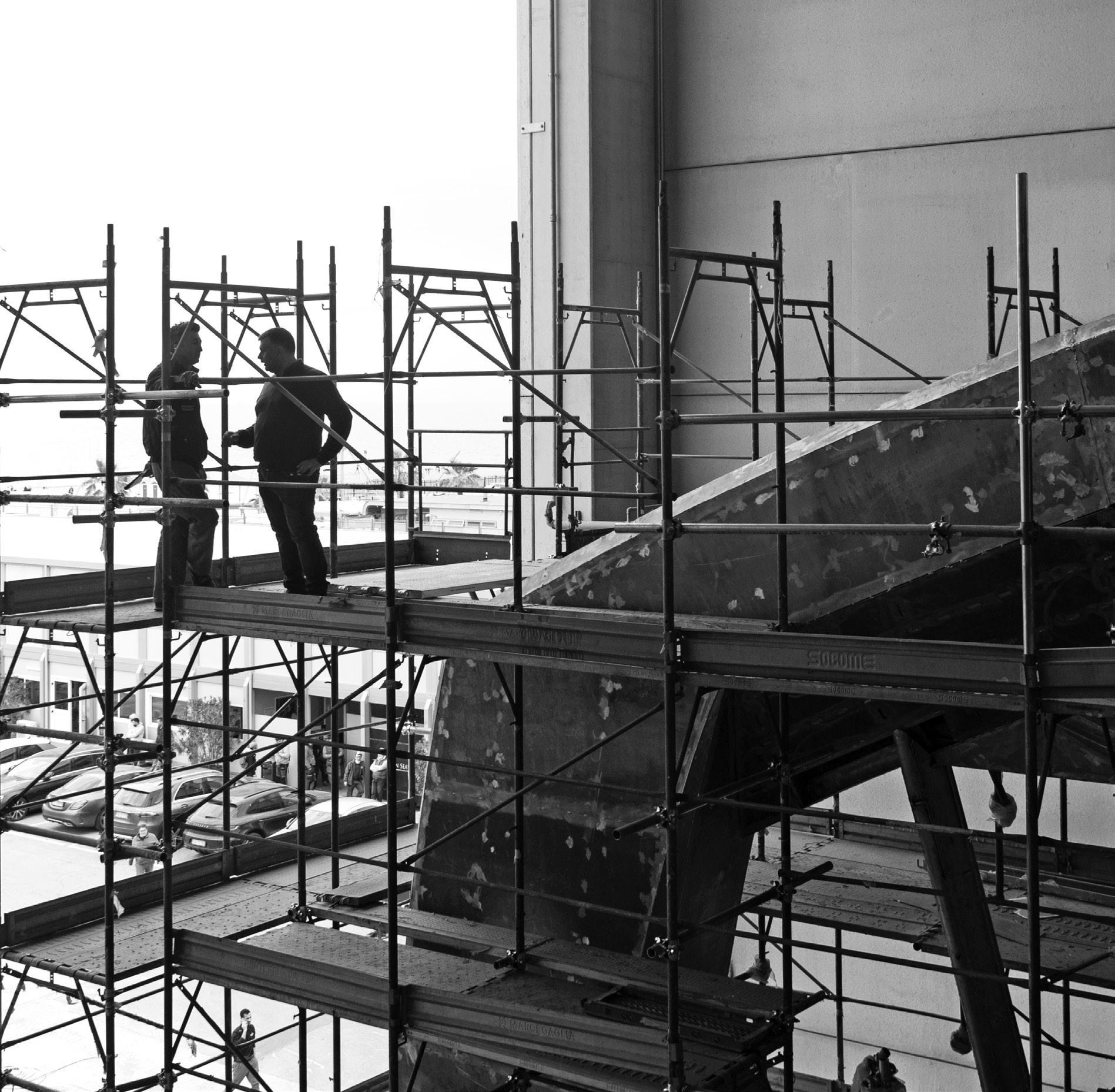
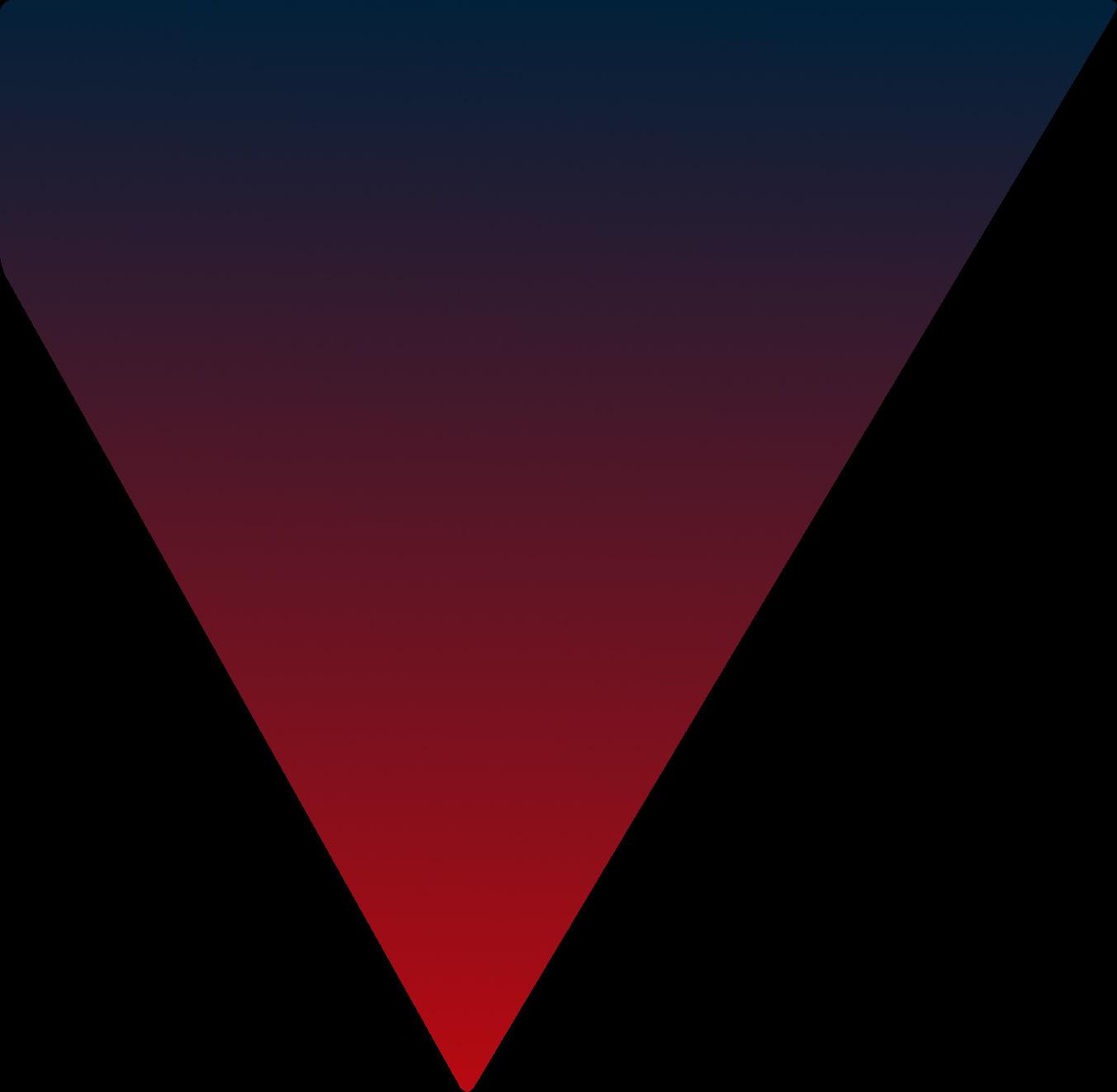

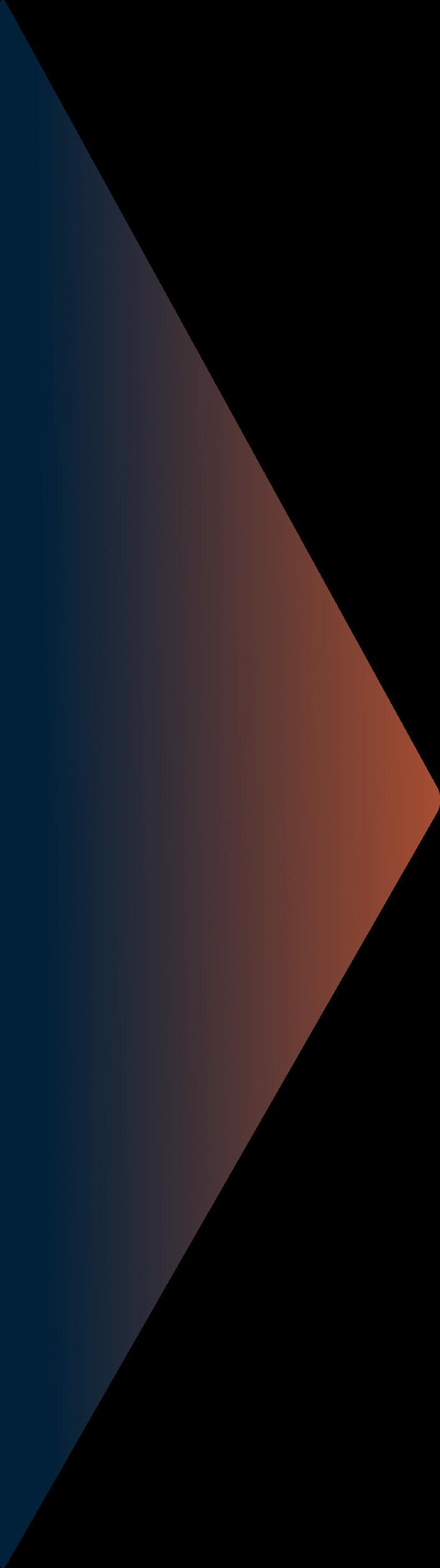
The Domus trimaran concept is certainly impressive. But does it make sense?
Fourteen years after building started in Chile, 85-metre Project X is completed in Greece.
We
Transforming
An in-depth study of how the new Amels 80 evolved from initial idea to the final design.
Sustainability: Fuelling Change
Do renewable fuels offer the most immediate sustainability solution for the superyacht fleet reliant on diesel?
Supply Chain: Lean Times
A word with Matthew Francis, supply-chain director at Sunseeker.
A panel of industry experts determine whether a 100-metre sloop is
or even desirable.
For generations, we have been realizing the most extraordinary living spaces with dedication and expertise. On water and on land. As a leading international partner in interior+ outfitting, we turn visions for living into reality – for both indoor and outdoor areas.
We are crafting visions.
I’ve always been fascinated by the hugely complex business of building a superyacht and how the inkling of an idea in someone’s head is transformed into a finished vessel on the water. In fact, I much prefer investigating that creative and industrial process than writing formulaic descriptions of the completed yachts, and I’m happiest when at the shipyards talking to the naval architects, project managers and production teams.
So you could say the role of Editor of How to Build It is the perfect job for me!
It takes weeks instead of years, but launching a new magazine is not unlike building a yacht on speculation. You have to establish a brief based on your target audience; define the contents and gather a team able to provide that contents (and believe me, there are very few technical journalists writing about superyachts); create a graphic design and layout; and finally put it all into production and deliver the product on schedule. It is an exciting and sometimes exhausting process with plenty of challenges along the way that require patience and compromise to resolve: interviewees are unreachable, hi-res images are unavailable, deadlines have to be stretched, top stories shelved and replacements found at short notice, and so on. But teamwork and a little midnight oil get you there in the end in a scenario that will be familiar to anyone who has working experience of the last 24 hours on a new-build before delivery.
I hope you enjoy reading this first issue of How to Build It and learn something useful from its contents, which is the whole point of the exercise. This is the custom prototype, if you like. Drawing on your comments and feedback, in subsequent issues we fully intend to tweak the design and optimise the specs to establish a proven platform for the industry.
Justin Ratcliffe - Editor
IT IS MORE THAN JUST GLASS.
EDITOR IN CHIEF
EDITOR | HOW TO BUILD IT
EDITORIAL CONTRIBUTOR
EDITORIAL CONTRIBUTOR
EDITORIAL CONTRIBUTOR
FEATURES WRITER
JUNIOR WRITER
TRAVEL WRITER
CONTENT CREATOR
VIDEOGRAPHER
SOCIAL MEDIA MANAGER
Francesca Webster
Justin Ratcliffe
Charlotte Thomas
Phil Draper
Georgia Tindale
Alexander Griffiths
Sophie Spicknell
Jessamie Rattray
Ruben Griffioen
Muaz Abourched
Mieke Koen
DESIGN PRODUCTION
CREATIVE DIRECTOR
GRAPHIC DESIGNER
UI/UX DESIGNER
DESIGN INTERN
Ivo Nupoort
Sean Otto
Claudia Sabbadin
Raja Khilnani
HEAD OF INTELLIGENCE
RESEARCH ANALYST
DATABASE MANAGER
DATABASE MANAGER
YACHT HISTORIAN
Ralph Dazert
Adil Zaman
Vicky Linardou
Léandre Loyseau
Malcolm Wood
SALES & ADVERTISING
SENIOR SALES MANAGER
SALES MANAGER
SALES MANAGER
CLIENT SERVICES MANAGER
SALES & MARKETING SUPPORT
Marieke de Vries
Justus Papenkordt
Molly Eve
Johanna Borreli
Jochem Eenkhoorn
FOUNDER & DIRECTOR
TECHNOLOGY DIRECTOR
FINANCE DIRECTOR
Merijn de Waard
Fabian Tollenaar
Laura Webber
SuperYacht Times B.V.
Singel 260, 1016 AB, Amsterdam, The Netherlands
31 (0) 20 773 28 64 info@superyachttimes.com www.superyachttimes.com
Sales Italy: info@admarex.com
Cover Images
Project Illusion photo by Justin Ratcliffe
Project X by Studio Reskos
Technical drawing by MB92
How to Build It is published by SuperYacht Times B.V., a company registered at the Chamber of Commerce in Amsterdam, The Netherlands with registration number 52966461. The magazine was printed in September 2022.
SpaceX, the spacecraft engineering company founded by Elon Musk, has entered the superyacht sector with a satellite internet service.
The venture is being spearheaded by the subsidiary Starlink Maritime and the objective is to improve internet speeds onboard yachts around the world. SpaceX claims that the service will allow yachts “to connect from some of the most remote waters in the world, just like you would in the office or at home,” with super-fast download speeds of up to 350 Mbps. Coverage is currently patchy and limited to the Mediterranean and the coast of the Americas and Australia, but this will soon change. Starlink Maritime has a roadmap in place for world-wide coverage, across all bodies of water, by 2023.
Starlink Maritime hardware bears a small footprint, demands minimal above deck space, and comes with an easy-to-install mount,” says SpaceX.
The Esaom Cesa shipyard and marina in the city of Portoferraio on the Mediterranean island of Elba has a new, fully adjustable 880-tonne travel lift for the maintenance, repair and refitting works of visiting yachts. The travel lift was designed to have a slipway width of 14 metres and allows the hauling out of large sailing yachts without dismasting and the transportation of superyachts around seven hardstanding spaces.
The facility currently specialises in the storage, refit and repair of yachts up to 40 metres, but the installation of the new travel lift is the beginning of a phase of major restructuring for the historic Portoferraio shipyard.
“The travel lift represents a great leap in the quality of the services we can offer as we aim to be competitive in a market most requested by yacht owners,” says Umberto Buzzoni, chairman and CEO of Esaom Cesa. “Elba and its related industries will also benefit from our investment with the presence of captains and crews, who will be able to visit and get to know our beautiful island.”
Jennifer Rumsey, president and COO of Cummins has been appointed as CEO of the US-based powertrain manufacturing company. Tom Linebarger ended his term on 1 August as CEO and remains on the leadership board as executive chairman.
Rumsey is the seventh CEO of the 103-year-old powertrain company and the first female to hold the position. According to Bloomberg, “Rumsey’s promotion will bring the number of women leading S&P 500 companies to 34, adding back to the ranks after female leaders at First Republic Bank and Match Group Inc. departed earlier this year.”
Sizing Networks for Bandwidth & Enhanced Performance, Including 5G & Future-Proof LEO Satellite Broadband Solutions
• New Player – New Approach – New Performance
• Fastest Internet Speed – No Throttle – Global Coverage
H2Boat has created the first self-producing hydrogen system that can be used aboard sailing and motor yachts. By bringing electrolysers on board, H2Boat has overcome a major issue: how to source hydrogen and opened new possibilities for how hydrogen fuel cells can be used on yachts.
“Yacht owners can find themselves in many different situations, many different countries where refuelling hydrogen is a problem,” says Thomas Lamberti, CEO of H2Boat. “ There currently aren’t any international regulations surrounding refuelling, so it becomes arbitrary with port authorities defining their own systems.
According to H2Boat, the best way to overcome the
issue is by bringing your own electrolysers on board, which can separate the hydrogen from oxygen in water, using a closed system: “The system requires water and electricity, both of which can be sourced everywhere,” he says. “With both of these elements, you can produce and re-charge your hydrogen system in a safe way on board your yacht.”.
H2Boat has overcome the challenges of low pressure through introducing methyl hydrates, which are able to keep hydrogen at a high-volume density under a lower bar storage system. This practical aspect is a core reason why Baglietto has opted for this system with its forthcoming B-Zero project.
Rolls-Royce business unit Power Systems is entering the hydrogen production market. Innovative technology from German electrolysis stack specialist Hoeller Electrolyzer, in which Rolls-Royce has acquired a 54 percent stake, will form the basis of a new range of MTU-branded electrolysers.
The move is part of the company’s transition from engine manufacturer to provider of integrated sustainable solutions and could play an important role in its efforts to make the shipping industry greener with climate-neutral MTU power generation and propulsion solutions.
“Hydrogen is a key power source for the global green energy transition,” says Armin Fürderer, Director Hydrogen Solutions at RollsRoyce Power Systems. “It can be used in fuel cells, hydrogen engines and in the production of climate-friendly sustainable fuels. With our high-performance MTU electrolysers we’ll contribute to making the necessary hydrogen infrastructure a reality, enabling climate-neutral hydrogen-based operations in all applications.”
Development work on the first MTU electrolyser using a polymer electrolyte membrane (PEM) stack from Hoeller is already under way.
The UK Hydrographic Office (UKHO) has said it will stop its paper chart production by late 2026 to increase focus on digital navigation products and services. Plans to withdraw the UKHO’s portfolio of Admiralty Standard Nautical Charts (SNCs) and thematic charts are in response to more marine, naval and leisure users primarily using digital products and services for navigation. “The decision to commence the process of withdrawing from paper chart production will allow us to increase our focus on advanced digital services that meet the needs of today’s seafarers,” says Peter Sparkes, chief executive of the UKHO.
The move to digital navigation solutions has been accompanied by a rapid decline in demand for paper charts, driven by the SOLAS-mandated transition to ECDIS and the wider benefits of digital solutions, including the next generation of navigation services. UKHO stated in its release that “Admiralty Maritime Data Solutions digital navigation portfolio can be updated in near real-time, greatly enhancing safety of life at sea (SOLAS).”
Shipyard Supply Co., sister company of Superyacht Tenders and Toys, released its Compressed Air Hover Chocks that allow for full 360-degree movement without the need for heavy lifting.
Space is at a premium on most yachts and when you have a large number of tenders and toys, your storage area can quickly become crowded, making manoeuvring items problematic for crew.
With the air pressure engaged, the chocks hover at 5mm above deck, allowing movement of the tender or jet ski by hand. When you want to stop hovering, an air shut-off valve can be operated, lowering the chocks safely back onto the deck, dispelling the need for complex locking wheels and tie-down points.
The hover chocks make manoeuvering heavy tenders and toys effortless and only two people are required to operate the chock system.
The Italian company Besenzoni is showcasing a wide range products at the Cannes Yachting Festival, including the multifunctional LP 100 plus ladder/boarding platform.
The LP100 PLUS ladder/boarding platform a product designed to help guests make the most of the area. Its principle function is that of a bathing or boarding ladder, but it can also be used as an extension to a sunbathing platform, and a tender lift. Its operation incorporates a hi-lo movement with a retractable hydraulic platform to extend the last step, for easy quayside access. The new product can be seen in action on the new Nerea NY40 Cosmo.
Also on display are LaPasserella and the SalpaAncora in Besenzoni’s BeElectric range, the new series of electrically powered components featuring new styling and more eco-friendly electric technology.
Sealence, that designed and engineered the innovative outboard jet propulsion DeepSpeed, has launched an all-new hotel system, which guarantees at least 12 hours of silent green energy with only 20 minutes recharge to power all hotel services of yachts of 24-30s.
The Sealence Hotel System (SHS) is offered in three size iterations – 80, 160 and 320 kWh – and promises zero vibrations, noise or pollution from its fuel cell system. “Our plug-and-play system replaces onboard generators, which need to run continuously, with a more efficient unit that can deliver the same amount of energy but only requires 20 minutes of charging time,” says Giorgio Caviglia, Engagement Manager and Special Projects at Sealence.
With saftey in mind, its power banks are fireproof, RINA/DNV-GL certified and can be easily retrofitted and integrated.
“Sealence wants to take part in the energy transition process, and to the electric mobility marine scenario, by proposing the first complete turnkey full electric-hybrid powertrain, based on its revolutionary electric jet propulsion technology,” says Caviglia. “Water should be the only footprint you leave behind.”
HP Watermakers
HP Watermakers will present two key products at the Cannes Yachting Festival 2022: Part-NET 2.0 and MWT Basic. Part-NET 2.0, which allows you to comfortably manage the watermaker from the onboard plotter, retains all the innovations of the previous model, but adds more flexibility and functionality thanks to the customisation possibilities and a very intuitive graphic interface.
Milan-based HP Watermakers was the first company on the market to develop its own interface, Part-NET, which is fully compatible with the on-board electronic systems of leading brands such as Raymarine, Garmin, Furuno, Simrad, B&G and Lowrance. Part-NET allows the user to control the entire desalination system, including pressure and all other operating parameters, without any manual intervention required.
“Boats spend up to 85 per cent of their time in a marina taking water from the quay, which often contains a high quantity of calcium and magnesium that can lead to the build-up of limescale,” explains company founder Gianni Zucco. “That’s not just a problem when it comes to cleaning the boats, but also because it can clog pipes and pumps, shower and toilet systems, tanks and the limestone. The added cost and downtime for maintenance can be significant.”
With a prototype under development and a patent pending, Quantum is introducing a new state-of-the-art, hydraulic/ electric power system, the F45 Hybrid, that uses the best attributes of both power sources. It is efficient, quiet and does not generate heat and it offers smooth power and requires 60% less power than a standard system. The F45 Hybrid boasts up to 60% greater efficiencies, only consuming the energy as required, when required. This efficiency is partially due to the elimination of control valves in exchange for a servo motor.
Electric fin stabilizers on larger vessels (60m+), become cost prohibitive due to the prices associated with gear boxes and servo motors. Electric fins with gear boxes must be designed to handle slamming loads which is easier for hydraulic systems to handle with the relief valves. The new F45 Hybrid uses a high dynamic servo motor coupled to a low inertia hydraulic pump, that directly moves the hydraulic fluid in a closed loop to sweep the fin. This greatly simplifies the overall system and removes all the components that make the hydraulics inefficient.
This new technology is a major game charger for the marine industry. The F45 Hybrid - hydraulic/electric solution meets both the long-term energy efficiency requirements and the peak transient energy needs of the closed marine electrical system. The system will be available in June 2023.
The UK-based furniture-maker is renowned for its custom-designed and meticulously built interior pieces. At Monaco Yacht Show the company is showcasing a brand new collection of outdoor furniture created from progressive materials. The collection comprises seven innovative finishes, and the Maze Coral Rise & Fall Table – the first piece from Silverlining’s Sea + Shore range of dedicated outdoor furniture, the result of 18 months of R&D. “Challenging our team to test the limits of contemporary furniture-making, we have developed new concepts for harsh, outdoor environments” says Jim Birch, Silverlining’s head of design. “Throughout we have incorporated sustainability into one-of-a-kind craftsmanship. In developing this collection, we have re-invented techniques, synthesising cutting-edge technology with traditional materials.”
The five tabletop designs, inspired by marine life’s patterns and textures, come in various shape, base and height configurations. The dining and coffee table designs have a telescopic base for easy transitions from daytime dining to evening entertaining. They are available in a total of 210 combinations, including finishes such as hand-shaded wood marquetry and lacquer ombré patterns, intricate two-tone lacquer work, ‘intaglio’ etched stainless steel, and sand-carved polished cast art-glass.
A selection of significant new-build projects at early stages of construction that present opportunities for OEMs, suppliers and subcontractors.
LENGTH: 51.5-metres
BUILDER: Tankoa
COUNTRY OF BUILD: Italy
DELIVERY YEAR: 2025
NAVAL ARCHITECTURE: Vitruvius
EXTERIOR DESIGNER: Vitruvius
INTERIOR DESIGNER: FM Architettura
Vitruvius Yachts signed the contract for the Vitruvius 10 in April 2022 with Phillipe Briand, head of Vitruvius Yachts, at the helm of the project. The owners requested a large sundeck and plenty of interior space. She will sleep up to 10 guests across six staterooms and be equipped with a hybrid propulsion system. The project will be managed by Albert McIlroy of Optimus Navis.
LENGTH: 47-metres
BUILDER: ProMarine Yachts
COUNTRY OF BUILD: Greece
DELIVERY YEAR: 2026
NAVAL ARCHITECTURE: Alpha Marine
EXTERIOR DESIGNER: Alpha Marine
INTERIOR DESIGNER: Alpha Marine
In April 2022, Alpha Marine Ltd - Yacht Designers & Naval Architects announced they would be starting construction on a diesel-electric superyacht under the new firm ProMarine Yachts. The semi-custom yacht has the option for different interior layouts with either a five or six stateroom configuration.
LENGTH: 65-metres
BUILDER: RMK
COUNTRY OF BUILD: Turkey
DELIVERY YEAR: 2025
NAVAL ARCHITECTURE: RMK Marine and ER Yacht Design
EXTERIOR DESIGNER: ER Yacht Design
INTERIOR DESIGNER: ER Yacht Design
RMK Marine was awarded construction of the go-anywhere explorer in April 2022. The flagship polar explorer has accommodation for up to 12 guests and 20 crew members. She has a library, sauna, gym, beach club, massage room and a medical centre. She will also be one of the few yachts to be classed Polar Code Category B – Ice Class PC 6.
LENGTH: 72-metres
BUILDER: Wider
COUNTRY OF BUILD: Italy
DELIVERY YEAR: 2025
NAVAL ARCHITECTURE: Nauta Design
EXTERIOR DESIGNER: Nauta Design
INTERIOR DESIGNER: Unknown
Nauta and Wider announced the sale and start of the construction of a steel and aluminium superyacht in May 2022. The yacht will be equipped with the Wider hybrid propulsion system comprising two variable-speed generators of 1,860 kilowatts each and a sodium nickel battery bank of approximately 1MW.
LENGTH: 33-metres
BUILDER: Tactical Custom Boats
COUNTRY OF BUILD: Canada
DELIVERY YEAR: 2025
NAVAL ARCHITECTURE: Gregory Marshall
EXTERIOR DESIGNER: Gregory Marshall
INTERIOR DESIGNER: Unknown
The NFT of the Tactical 110 was minted on Opensea on March 10, 2022, and is believed to be the first verified NFT yacht sale transaction on the Ethereum Blockchain. The build of the 33-metre yacht is now underway and is expected to take around 36 months and cost around $12 million USD.
LENGTH: 70-metres
BUILDER: Permare
COUNTRY OF BUILD: Italy
DELIVERY YEAR: 2026
NAVAL ARCHITECTURE: Permare
EXTERIOR DESIGNER: Optima Design
INTERIOR DESIGNER: Luxury Projects
The first Amer 70 Steel superyacht began construction in Tuscany, Italy, in June 2022. The fully-custom design is for a European client and will see Giulio Riva contribute his thirty years of experience in the steel industry to the project as the Director of Works and Quality Control.
LENGTH: 84.9-metres
BUILDER: Royal Huisman
COUNTRY OF BUILD: The Netherlands
DELIVERY YEAR: 2026
NAVAL ARCHITECTURE: Frers Design
EXTERIOR DESIGNER: Frers Design
INTERIOR DESIGNER: Wetzels Brown
The Dutch shipyard announced the sale of the ‘world’s largest sloop’ in March 2022 at the St Barths Bucket Regatta. Being built for an experienced owner, her massive carbon mast, boom and sail system will be designed and produced by Royal Huisman’s sister company, Rondal.
LENGTH: 52.5-metres
BUILDER: Alia Yachts
COUNTRY OF BUILD: Turkey
DELIVERY YEAR: 2023
NAVAL ARCHITECTURE: Azure
EXTERIOR DESIGNER: Azure
INTERIOR DESIGNER: Unknown
On 12th July 2022, Alia announced that the Alia Sea Club had been sold. The yacht will carry an array of tenders and toys, as well as feature a fully certified helipad on her aft deck. She will also accommodate as many as 10 guests and a crew of 12.
Meet us at Monaco Yacht Show, booth DS | Darse Sud Fort Lauderdale Intl. Boat Show, German Pavilion Metstrade, booth . | SuperYacht Pavilion
The revolutionary, fully electric stabilizers by SKF.
The future is electric – and so are our marine stabilizers. Profit from less installation costs, less noise, less vibration, more space and much more fun! Become % electrified now, no compromises!
TEAM Italia has been a leader in the integration and optimization of navigation, telecommunications, security and data transmission for over 20 years. The company has delivered over 500 bridge designs, more than half of which are custom integrated I-Bridge® systems. We visit their new showroom in Livorno to take a closer look at the latest integration.
BY FRANCESCA WEBSTER
The conversation of automation is not new, often facing opposition from captains and owners who raise concerns about the safety and security of digitalising navigation. Over the course of the past decade, however, TEAM Italia has been quietly developing software to improve safety and usability. Its fully integrated i-Bridge integrated touch bridge series both looks good and simplifies vessel control by centralising automation within one system.
During the Monaco Yacht Show 2021, the company unveiled its latest I-Bridge® integration, the Dharma Next EVO and 3D, the result of an updated R&D version of its award-winning series that features a brand new Human-Machine Interface (HMI).
This year, 26 yachts with TEAM Italia consoles will be delivered, including the first Custom Line 140, flagship of the Ferretti Group series, equipped with the Onyx Marine (AMS) monitoring system, fully integrated into the I-Bridge®, as well as Navette 33, 37 and 42. In addition, TEAM Italia was entrusted by the Ferretti Group for two full custom projects for CRN, respectively 52 and 65 metres.
The Italian company is also collaborating with the prestigious Sanlorenzo Shipyard, helping to define and develop new and cutting-edge concepts for four yachts with LOAs between 40 and 70 metres.
TEAM Italia is also onboard the innovative “Tecnomar For Lamborghini 63” projects. Which have extremely sophisticated technological solutions specially developed for
this exclusive fleet announced in a limited edition, as well as on board the major TISG projects between 50 and 75 metres.
Like a standard bridge, the i-Bridge system is centralised at the helm station and operates the steering, propulsion and navigation of the vessel. However, TEAM Italia has integrated these functions with almost all other digitally operated systems aboard the yacht. For example, the i-Bridge is able to monitor and run diagnostic reports, offering the captain 3D diagrams of the systems that identify not only the issue, but also make recommendations for the solution.
“Unlike a fixed bridge, the i-Bridge offers unified controls from any desired sector of the vessel, which means that the controls can be accessed from wherever they are needed,” says Massimo Minellla, CEO of TEAM Italia. “Once a system has been integrated onto the control hub, the captain and crew can make a decision about where to view and control that system.”
While many vessels feature a fixed glass or foil bridge configuration, they have a number of limitations. The mechanical integration of the yacht’s control panel is often chosen during the construction of a vessel and therefore is specifically tailored to the original captain, owner or shipyard’s wishes.
Should the vessel’s management be changed, the modification of a mechanical integration requires the complete reconfiguration of the control panels, which can be
We are able to continually update the software remotely, which is more cost effective than having to manually replace systems.
a hugely costly and timely process. TEAM Italia’s automated and touch screen i-Bridge allows for remote reconfiguration and the fully integrated nature of the bridge means that all systems can be operated from each panel, rather than a fixed order of controls, as with a mechanical integration.
The concept of digitally controlled mechanics has raised concerns in the industry over safety in case of faults and software issues that may lead to damages. While the system is digitally controlled, should issues occur with the control of the vessel the i-Bridge can be mechanically overridden. In the case of software related issues, the TEAM Italia engineers are able to run remote diagnostics and, if necessary, access the system and solve the problem without having to board the vessel.
The obvious fears around the possible breach of privacy have also been assuaged. In order for a TI engineer to access the system they must follow a strict protocol and be admitted by the captain of the vessel. The digital system of the vessel is protected by a strong firewall, which prevents accessing any data unless explicitly permitted.
“The advantage is that we’re able to continually update the software remotely, which is more cost effective than having to manually replace systems as with a fixed glass or foil bridge,” says Minella. “Moreover, should there be a specific fault, the onboard engineer can replace the part and we can remotely programme it.”
The i-Bridge system is entirely customisable. During the production process, TEAM Italia works alongside the yacht designers, shipyard and owner’s team to identify and make recommendations for the best solutions for each vessel, offering up-to four separate stations, which can be arranged as per the desires of the owner’s team.
Once the specifications of the bridge have been determined, the system is pre-assembled at the testing facility in Livorno and the captain and owner is invited to test and trial the ergonomics of the setup. This allows for configuration development, both within the software and the stations themselves.
Already turning its mind to the potential of augmented reality, TEAM Italia is currently developing an AR system to aid in the operation of the technical spaces aboard vessels. This will allow its engineers to assist the onboard technical team in the location and repair of faults quickly and cost efficiently.
Superyachts aren’t just about size. They are as much about comfort, convenience and customisation as they are about scale. Even on the very largest vessels, perfection is a marriage of space-saving design with flawless sophistication. Much like moving into a new house, furnishing a yacht for optimal living is an ongoing process. No degree of personalisation in build can ever result in an entirely future-proofed yacht. And at any expense, why would you want it to?
Whether widening, heightening, extending, or optimising, the scope for enhancing a yacht is almost infinite. From transom fenders and custom-fit furniture to innovative storage solutions, tender whips, boarding options, tennis courts, football pitches, and bespoke awnings – if you’ve got the questions, we’ve got the answers.
Since 2018, our specialist team at Shipyard Supply Co. have been designing, manufacturing and fitting made-to-measure solutions for the finest superyachts worldwide. A dedicated design studio with the advantage of in-house manufacturing, Shipyard Supply Co. has built an enviable reputation as the industry’s leading producer of custom deck equipment.
Whether your starting point is an initial concept or a build-ready component, the team will walk you through every stage of consideration. Be it technical drawings, 3D renders, or photorealistic imagery, our designers will ensure your vision is seamlessly portrayed on screen or in print before advancing to manufacture.
Benefiting from a purpose-built facility, our design studio and production team work in complete unison. Employing the finest crafts-
manship in fibreglass, carbon fibre, stainless steel, marine-grade aluminium, hardwoods and more, we have unparalleled control of our processes from start to finish.
Achieving perfection in an environment at the mercy of the ocean presents complex challenges. Far beyond simply mitigating the impact of saltwater or inclement weather, our experienced team are pushing the boundaries of custom deck equipment, pioneering radical solutions to almost implausible scenarios.
Unperturbed by the structural limitations of a yacht, we excel not just in solving problems but in adding honest and tangible value. From effortlessly manoeuvring a 3-tonne tender in a low-ceiling garage to quickly and easily stowing and stacking jet skis, we strive to seamlessly marry usability with practicality.
With an office and secure storage in Monaco, we have feet on the ground just a stone’s throw from Port Hercule. Identifying exemplary customer service as the trademark of our offering from day one, both our UK and Monaco teams always go the extra mile (nautical, naturally) in their pursuit of perfection. Shipyard Supply Co. has no affiliations with any materials suppliers and are solely committed to finding the most appropriate solution to any request. Able to cater for every project from individual components to large-scale assembly, the team is ready to bring your ideas to life.
Seable&Co is a new company that gathers together four other businesses with more than 80 years of combined experience in the specialist outfitting of superyachts. We catch up with CEO Willem-Jan Kuipers to discover more.
Willem-Jan Kuipers set up 4SeasonsSpa with business partner Rob Lauwen in 2005 to provide innovative and professional spa solutions for luxury hotels, spa centres and residential spaces. The firm pivoted into the superyacht world when it supplied two Jacuzzi systems aboard Feadship’s 78-metre Venus that launched in 2012. Since then it has worked with all the main Dutch and German shipyards.
Stone Natural Class, a specialist in the production and installation of luxury stone products, was acquired in 2018. Bloemen de Maas, the supplier of bespoke exterior furniture, caprails and teak decking, joined the group a year later. Last but not, DTG is the group’s in-house innovations team that combines expertise from multiple disciplines with input from the sister companies.
Dennis Boerman, CFO; Jeremy Elschot, MD SeableStone and group commercial director; Pieter Piers, MD SeableWood and group operations director.
Under Seable&Co, these four original companies have been rebranded as SeableSpa, SeableStone, SeableWood and SeableStudio.
Why is now the right time to rebrand as Seable&Co?
It’s the last stage in a process that we’ve been building since the acquisition of Stone Natural Class and Bloemen de Maas. Together these companies share the same vision of craftmanship, innovation and collaboration, and we’re working on projects together more and more. It is now time to also evoke this shared vision and approach to our clients and the market and see our craftsmen operate as a true team.
Your first superyacht project was little more than a decade ago, but you now have around 50 projects under way. How do you account for this rapid expansion?
After we started with Jacuzzis onboard yachts, shipyards started asking if we were willing to take on a wider scope of responsibilities, including the stone, marble and mosaic work for both the exterior pools and interior spa areas. That led us to acquiring Stone Natural Class, which has worked with Heesen Yachts, Royal Huisman and Moonen
€20 MIL approx. Annual turnover
120 Group employees
50+ Current projects
200+ Completed yachts
for many years. Our conversations with shipyards continued on a strategic level and as the exterior areas became more important and more complex, they asked us if we would take on a full exterior outfit. And that led to the acquisition of Bloemen de Maas, which has been working with top Dutch shipyards for the past 40 years.
Where does DTG – now SeableStudio – fit into the equation?
It was formed as an internal start-up to further boost our in-house innovation. We saw there were quite a few innovations within our companies that were not really taking off, so the idea was to nurture those innovations to the point where they would be able to enter the market successfully and then bring them back to the operating company. A good example is a product we’re developing as an alternative for natural teak. It’s based on 60 percent teak dust from the production of furniture made from plantation teak, which is then mixed with recycled resins and other additives. We also decided to add a UV stabiliser so the product keeps its colour rather than fading like natural teak, because that’s the main reason crews sand the decks. The end result is a material that is 90 percent natural or recycled, requires less maintenance, lasts longer and is applied with the same skill as teak planking. The whole development and testing process was much more manageable in a separate business unit.
What proportion of your work comes through the shipyards or owners’ teams?
I would say 90 percent of our work is directly with the shipyards. But our exterior scope is
high on the agenda for owners, to the extent that for some it might even the main reason they buy a yacht in the first place. In this context, we usually talk to the owner’s team at a very early stage together with the shipyard. Some owners’ teams even contact us before selecting the yard, but nine times out of ten the shipyard is our client. I spoke of collaboration earlier and I see a lot of potential for improvements in these relationships in terms of creating efficiencies. Seable&Co was initiated by listening to clients and bringing together our different areas of expertise, whether it’s exterior or spa spaces. Each of the group companies takes about 50 percent of their work from projects that require two or more of our core disciplines. The other 50 per cent is still on an individual basis. I believe this is a healthy way of approaching the market that keeps every business unit very client focused.
How do you see the outfitting sector evolving, and Seable&Co. along with it?
We are experiencing quite rapid developments with bigger and more complex projects, but if you look at the industry a lot of the subcontractors in the industry have remained the same. You could argue that is a good thing and a sign they are competitive and in good health, but I’m not sure whether all of them can keep up with that complexity. Some companies are perhaps ahead of the curve, but there are far more smaller companies that are likely to have difficulty dealing with more complex projects in terms of contracts, project management, HR, the legal and financial side, and so on, which are all part of the industry growing and becoming more professional. This is the logic behind Seable&Co. By dealing with finance, HR and commercial strategy on a group level, we are basically providing a platform that helps deal with the complexity of projects on an operational level.
As for the development of the market, we see designers, owners and shipyards continue to ask for new features and finishes on board. Recent examples include outdoor firepits, a custom DJ-booth, an outdoor cinema and an artwall waterfall feature. The job of Seable&Co is to work across mediums to translate imagination into reality.
When it comes to helping an owner feel at home and comfortable on board his or her yacht, there are few that wouldn’t argue that the choice of interior and exterior furnishings is a key part of creating the desired onboard ambience. We speak to the experts at the German outfitting company Vedder to answer our burning questions about superyacht outfitting in 2022.
What are the main things you need to consider when designing, creating and installing furniture for yachts?
Moritz Schmidinger (head of project development): At Vedder, as we only focus on custom yachts, this means that every yacht is its own prototype. It is always an exciting challenge to realise and bring the design to life because you start from scratch with every project you do – we harness technology such as 3D engineering to help us assess how best to realise a project.
Another factor is the need to integrate so many different systems – audio, AC, sprinkler, electric and so on – and make them invisible. This is a complex process which needs to simultaneously fulfil all design requirements, safety aspects and also be functional for crew handling.
How much of your work is carried out in-house?
Nicolas Held (managing director): We offer a complete turn-key, in-house process, from the provision of samples, mock-ups and 3D engineering through to production, delivery and installation. We have our own assembly team and internal site managers, as well as experienced external fitters with whom we have worked for a long time. Excitingly, since 2022, we also now have our own metal branch, so we will be increasing manufacturing in-house here as well! At Vedder, we are characterised by a very high degree of prefabrication. This helps us reduce assembly efforts and, most importantly, enables us to carry out projects smoothly, execute them to the deadline and to the highest possible quality.
How do you decide which materials to use?
Christian Menz (head of exterior): As a company which is proud to have outfitted more than 5 percent of the 100 largest 60-metre-plus superyachts since we completed our first project in 1970. We profit from this long-term experience to help us select suitable materials that meet all design and customer expectations but also guarantee longevity. We achieve this by carrying out rigorous tests. Importantly too, since we cover both interiors and exteriors at Vedder, we are able to transfer our indoor flair to the outdoors – only the materials differ, for example, you might need to use waterproof materials like GRP or carbon fibre for the exterior.
How do you keep on top of changing client requirements?
Nicolas Held (managing director): We have a dedicated R&D department and we know how materials work, thanks to the wide experience which we have acquired over the years. Paired with leading innovations, this knowledge enables us to create unparalleled latitudes for designs that resist sun, wind and salt water. As just one example, we use environmental simulation tests in a time-lapse sequence to rapidly determine the effects of UV radiation and salt water, allowing us to optimise the materials we use and continually improve our end product.
Business has never been better for Omer Malaz, founder of Numarine. The Turkish brand celebrates its 20th anniversary this year having repositioned itself as a builder of highquality, value-for-money trawler-explorers.
BY PHIL DRAPER
“Ten years or so ago the average size boat we were building was less than 20 metres and all our models were mainstream – composite planing designs, a mix of hardtops and flys,” says Omer Malaz, owner and CEO of Numarine near Istanbul.
“Although we were a relatively small boutique brand, our principal competitors back then were always the big players like Azimut, Princess and Sunseeker.”
Today, the shipyard’s average delivery is more like 27 metres and it is series building nothing but trawler-explorers in composite and steel. Its competitors now include the likes of Horizon and OA in Taiwan, Sirena in Turkey and Cantiere delle Marche in Italy.
“It’s a strong, growing corner of the market and we’ve been very lucky to be in the right place at the right time,” says Malaz rather modestly.
Malaz is clearly enjoying himself, which is important. He started Numarine because he loved boats and grew up boating with his family. The passion drives the man and the business and for the past two decades his own yachts have been literally of his own making. Few yard owners spend as much time afloat as Malaz and fewer know their products as well.
The way Malaz’s own boating tastes have changed over the past decade serves as an appropriate metaphor for his business. Malaz says he used to speed along at 35 knots screaming at the family to sit down. The horizon was the destination. Time aboard was fun, but the passages could be fraught. These days it’s just as much about the journey.
Today, Malaz is Numarine’s sole shareholder. Over a decade ago he decided to step back, reduce his original 100 percent stake to just 30 percent, and virtually live aboard his own boats with his young family. He timed that
exit well. Just a few days before the global financial crisis kicked off in 2008, he sold the controlling interest to the Dubai-based private-equity firm Abraaj Capital, part of the then €8 billion Abraaj Group.
By 2012, things were less rosy for Numarine and for its majority shareholder, which ended up dissolving under a cloud. In May of that year, Malaz stepped up and reacquired 100 percent control of Numarine. For the next five years he ran the business on its original track. He knew something fun-
Capacity 500,000 man-hours
With an overall length of 32.84 metres, the 32XP was Numarine’s first model to sport a steel hull, although the superstructure is mouldedin-house like the smaller models. Displacing 270 tonnes fully loaded, the first 32XP launched back in 2017 and three more of
this 299 GT model were delivered between 2018 and 2020.
During 2019, a client pushing for more space prompted what has since become the 350 GT 37XP, which has the same beam and hull shape, but an extra 4.51 metres in length overall, an extra half knot of top-end speed
with the same engines, another 40 tonnes of fully loaded displacment, and an extra 51 GT.
The first four 32XPs and the two 37XPs have already delivered and six more are on order. With the run rate heading for little more than two per year, deliveries now stretch into late 2024. The success of the 37XP, which displaces 310 tonnes fully loaded, has rather pushed the 32XP into the shadows. No others have been ordered since the first 37XP splashed, principally because potential 32XP clients have deemed the 37XP premium worth paying. The basic price of a 32XP is €10.5m with a typical delivery ending up around just over the €11.5m mark. The 37XP’s basic price is presently €12.5m.
damental needed to change, but without straying from Numarine’s core strengths: financial solidity and industrial expertise.
That solution eventually became a trawler-explorer focus. Indeed, Numarine hasn’t delivered one of its old planing hardtop or flybridge models for five years and all the old tooling has been destroyed.
That change of focus proved a winner and Numarine was recently the first yacht builder in the country to be accepted into Turquality, the Turkish government’s brand accreditation and grant support initiative. Only the most efficiently managed businesses are accepted into this programme, which requires rigorous vetting by independent auditors.
Currently, Numarine employs 250 people directly, but it would normally have nearer 330 people employed locally, and its model portfolio includes four chunky XP trawler-explorer models. The design credits are the same as they have always been since the very beginning with exterior and interior design by Can Yalman and naval architecture by Umberto Tagliavini. There are at least 25 Numarine trawler-explorers out there already and another 18 or so swelling an order book that extends well into 2024.
The 22XP and 26XP, the smaller two models in the series, are both composite, respectively CE Cat B and Cat A designs. The larger two, the 32XP and 37XP, are steel/composite designs built to Class with RINA. The next new model will be a bigger composite design, but as we go to press the precise designation is being kept under wraps. Numarine’s proposed new flagship is the 45XP, a steel and aluminium trideck with a 9.25-metre beam. With a ball-park base price of €19.5m, this 498 GT
The first composite model was the four-year-old 26XP, which weighs in at 78 tonnes dry. Still a best-seller, the first hull was delivered in 2018 and was conceived from the outset to be flexible for either displacement or planing roles. Its hulls are moulded in halves and are finished with or without an extra moulded-keel insert used to create the necessary profile. A planing version uses a flatter central keel section and separately moulded spray rails bonded to the exterior of the hull after demoulding.
Of the 17 26XPs delivered to date, five are semi-displacement/planing versions, powered either by a pair of 1,550hp MANs for a top speed of around 27 knots or twin 1,200hp MANs that top out just below 20 knots. The owner of 26XP#21 has opted for twin MAN V12-1800s, which should mean a 30 knot top speed.
Five of the remaining dozen were fast-displacement versions, driven by twin 800-hp MANs at 14.5 knots, or 13.5 knots by twin 560hp MANs. Prices begin at €4.54m for a slow displacement version and nearer
€5m for a planing version, but a finished yacht will usually include up to 10 percent more in terms of extras.
The 22XP, the smallest model that weighs in dry from 53 tonnes, is also the newest and is similarly versatile as regards displacement and planing performances. Both versions are priced competitively. In displacement guise, which represent most sales to date, the 22XP has a basic price of €3.58m, but again the usual set of extras account for around 10 per cent more.
At €3.93m, the basic price of a 22XP, reflects the fact that it will have a 25 knot planing specification and triple the horsepower with twin MAN 1200s instead of a pair of 425hp Cummins diesels that top the model out at just under 13 knots.
The first 22XP launched in early 2022 and two more have since splashed. The fourth will be another planing version and should be delivered before the end of the year. The present production schedule has three more completing during 2023 and probably six more in 2024.
yacht is still a long way away from reality. Despite a couple of existing 32XP and 37XP clients being close to taking their next step up with the builder, the stars are not quite aligned.
Building a boat of that size would be a step too far at Numarine’s present facility in Gebze, which is perched on a hill in an industrial estate some 20 minutes inland. The biggest current models already prove a logistical challenge every time one needs to be transported down the hill to either Tuzla Marina or the nearby RMK Marine, where Numarine does its pre-delivery commissioning.
“The current 35,000sqm site has served us well,” says Malaz, “but the next step up will need to be taken from new waterside premises.”
To that end Malaz has already acquired 30,000 sqm of land for a new factory, and has an option on another 30,000 sqm next door. The location is Yalova to the southwest and the other side of Osman Gazi Bridge, roughly half an hour’s drive from the present site in Gebze, but just 20 minutes further out from the centre of Istanbul.
The first phase involves an investment of €20m over the next 2.5 years. Malaz expects to break ground there by the end of year and that the first boats will start on that site within 18 months. Given the build time for a first new 45-metre yacht is likely to be around 24 months, don’t expect to see a new flagship splash for perhaps at least another four years. Eventually, Malaz suspects the whole Numarine operation may well relocate to the coast.
“There are no plans for us to build smaller than the 22XP,” he says. “Our facilities are no longer geared for the sort of volumes that are required to build smaller models cost-effectively.”
Having a large, loyal customer base out there is a big help and repeat business is an important component for the brand. One Turkish client is presently on his fifth Numarine and is negotiating for his sixth.
Overall exports account for around 70 percent of Numarine sales. Since it started Numarine has built and delivered 160 boats, of which just 40 were sold new to Turkish buyers. Sales to the US have been strongest by far in recent years. Happily, the present crisis in Ukraine has not impacted Numarine in terms of owners. Since the beginning it has only had four Russian new-build clients.
Up until three years ago Numarine had a dealer network. Various distributors around the world included the brand in their portfolios
and the network approach was largely responsible for the success of the brand during its first decade when the product range spanned 52-105 feet. However, three years ago it was decided to change the distribution strategy and end all exclusive agreements as well as the dealer margins that went with those agreements, which had been as high as 25 percent for some models.
What that means in theory is that Numarine now sells direct, but in practice many of its deals are concluded with the help of yacht brokers and one broker has engaged with the brand more than any other to earn ‘preferred broker’ status.
“Alex G Clarke at Denison is a great example of what we can achieve,” says Ali Tanir, Numarine’s international sales manager. “He has been responsible for no fewer than six sales over the past year alone. And we hope a recent deal with Patrick Coote at Northrop & Johnson in Monaco will yield similar results for us in Europe.”
Last year, Numarine delivered five boats in total: four 26XPs and one 37XP. However, owing to the continued success of the 26XP and given the ramping up of the new 22XP range, it is now back firmly in growth mode and has 12 deliveries scheduled for this year: four 22XPs, six 26XPs and two 37XPs, which should see turnover exceed €50m, a new record. 2023 is looking similarly solid. The order book presently includes four 22XPs, three 22XPs and three 37XPs.
Numarine is always prepared to start hulls on speculation to shorten delivery times and to maintain an efficient flow of production through its facilities. Given the reputation for self-sufficiency they trade on, explorer specifications tend to be higher than more mainstream yachts, which means add-on costs are relatively low, rarely adding more than around 10% (excluding engine choices) to the final price.
Although the metal hull fabrication is carried out by a nearby subcontractor in Tuzla, the company is virtually self-sufficient in terms of construction disciplines and usually produces all its own composite tooling. It is still the only builder in Turkey with its own five-axis CNC machining centre, one of the biggest of its kind in Europe. Moulding techniques vary, but all are closed process. Hulls and superstructures are vacuum-infused and bulkheads are vacuum bagged and cut using templates. Smaller parts make use of RTM (resin transfer moulding) techniques.
Gurit is its composites engineering partner and Scott Bader is the principal supplier of polyester and vinylester resins and gelcoats, while composite reinforcements mostly come from Turkish local manufacturer Metyx. The composite boats are available with a choice of three gelcoats – white, off-white and light grey – whereas the metal yachts are painted with Awlgrip systems.
Other key partners include ZF for gearboxes; Teignbridge for shafts and props; Kohler or Cummins-Onan for generators (although supply chain issues make these items particularly difficult to source at the moment); Raymarine for bridge displays (although Garmin or Furuno instrumentation are options for US-bound boats); Sleipner for thrusters and CMC for electric fin-stabilisers; Dometic for HVAC systems; Besenzoni in Italy or Data and Bofa in Turkey for mechanical deck systems; and Van Cappellen for the sound and vibration mitigation.
Productivity is essential for any series builder and from the start Numarine has had an industrial approach to boatbuilding, always trying to improve quality and margins. For the past dozen years production has been overseen by technical director Malcolm Hutchison, who previously spent seven years, with Pearl Yachts as COO (Numarine was once a contract builder for the UK-based brand, which is how he got to know the company).
The cost of labour is, of course, one of Turkish industry’s biggest advantages. Wages are probably a quarter or even a fifth of what western Europe is paying. The first 26XP used to take 50,000 man-hours to build, whereas they are currently talking fewer than 40,000. The first 32XP took over 120,000 man-hours, but now a 32XP requires under 90,000 man-hours and the bigger 37XP sister takes 100,000 man-hours (the latter omitting the labour required to fabricate the steel hulls).
Numarine has delivered more than 160 boats over the past 20 years, an average of eight boats a year. Today, it’s delivering a dozen yachts per annum and soon that annual tally will be nearer 15 once its new waterside facility is up and running properly, but it will still be small enough for Numarine to have a personal relationship with each customer.
“And I want to know them all,” concludes Malaz.
The 40-metre Domus concept by Rob Doyle Design and Van Geest Design grabs our attention because we are unaccustomed to seeing multihull yachts on this scale. But is it buildable and are the zero-emission technologies it proposes realistic?
BY JUSTIN RATCLIFFE
“Project Domus grew out of a request from a client for a 40 metre catamaran, and we dived right into it,” says naval architect Rob Doyle, founder of the eponymous studio. “But the more we looked at it, the more we realised the catamaran configuration was too limiting. I’m a keen cat sailor and they work great within quite a specific set of criteria, but when you take them out of a certain size zone you start to see problems arising. After battling with these issues we decided to take a different approach and go a little crazy.”
More space, better performance, less draft and significantly lower heel angles under
way than comparable monhulls. These are just some of the reasons why over the last few years there has been increased interest in large catamarans. However, once you get over 40 metres these advantages may be outweighed by higher build costs, the complexity of distributing systems across two hulls, and the structural challenges resulting from the immense racking forces as they move through the water.
When Rob Doyle Design decided to reassess the catamaran brief from a different angle they took as a reference point 63-metre
Project Fury, a monohull sailing yacht concept created with Van Geest Design in 2021. Fury revised the relationship between gross tonnage or interior volume and its relation to overall length and displacement. A conventional 63 metre sailing yacht would ordinarily have a volume of around 500GT; Project Fury pushed this to over 700GT, a remarkable increase of 40 percent. What would happen if they expanded that concept and applied it to a trimaran?
“We decided to simplify matters and basically build a monohull with outriggers or armas, which meant all the systems and engineering could be centralised in the main hull,” says Doyle. “Everything just fell into place from there.”
Trimarans are usually beamier than catamarans, which equates to more interior volume and deck space. With three hulls in the water there is also better damping effect on a trimaran at anchor than a catamaran, and vastly reduced motions compared to a monohull. Domus is designed to heel at angles of around two degrees to allow the weather hull to come out of the water for less drag and higher performance, but also more comfort under way. These factors make a trimaran an attractive proposition for motor yacht owners interested in making the transition to sail.
The moment of inertia is an important parameter in civil engineering and naval architecture when sizing or selecting a beam structure. It is basically a calculation of the stress caused by a moment on the beam and can be defined as the resistance offered by a cross-sectional area to deflection primarily by bending.
A beam is a structural element that primarily resists loads applied laterally to the beam’s axis (an element designed to carry primarily axial load would be a strut or column). The loads applied to the beam result in reaction forces at the beam’s support points. The total effect of all the forces acting on the beam is to produce shear forces and bending moments within the beams, which in turn induce internal stresses, strains and deflections.
Another plus is that the rigging forces are taken by the main hull, so the crossbeam structures can be simpler and lighter than a catamaran.
“The structural challenges are not as bad as you might first think,” says Mark Small of Rob Doyle Design. “In a standard multihull you have a single beam taking all the loads and into the armas. But because of the nature of Pieter van Geest’s single deck design we actually have an upper and lower beam that together create an incredibly strong closed loop. We’re dealing with the same moments of inertia, but they’re now separated by nearly three metres from top to bottom.”
The result is effectively a huge floating bungalow supported on three hulls with an interior area-versus-length ratio that is off the charts in comparison with monohull sailing and motor yachts, but also sailing catamarans. Domus has almost 800 square-metres of usable interior area, which is not far short of 88-metre Maltese Falcon. The largest private sailing catamaran
afloat, 44.2-metre Hemisphere, has around 350 square-metres of internal space.
“At the beginning it was strange to work with three hulls, but as soon as we decided to have everything on one level it became much more straightforward,” says Pieter van Geest. “It meant we could come up with a villa-like layout with no stairs and airy, semiopen areas. Family life in a way is about protection, so we wanted to build around that idea with secure access to the sea but no need for complicated opening systems.”
It was important that the mast was Panamax for transiting the Panama Canal. To keep the mast height in check a double luffed mainsail was chosen to achieve some of the efficiency of a wing but using a hoistable soft sail. Rob Doyle calculates that it provides between 15-20 percent more drive than a conventional sail plan of the same size.
Like those used by the America’s Cup foiling monohulls, the double skinned sail comes off both sides of the mast instead of the centreline and both skins are joined
at the leech to give a true wing shape, but the soft material means it can be reefed and dropped and stored on the boom. The wing shape is adjusted by rotating the mast, which shortens one side of the wing and lengthens the other. This allows for more lift, less drag, and to increase the angle of attack without losing the air flow.
“Oddly, the rig is probably the most challenging aspect of the whole design,” says Doyle. “That’s because the trimaran configuration has a massive righting moment and just stops heeling at two degrees, unlike a monohull that goes on absorbing forces by continuing to heel. That means the rig has to be designed and built like it’s set in concrete and you need reliable systems that can ease the sheets automatically at peak loads.”
The outer hulls are also fitted with forward daggerboards set at a slight inward angle, not for foiling purposes but to provide some positive lift and prevent the tendency of all multihulls to bury their bows.
Another advantage of the 35 metre beam is that it offers more surface area for the solar cells that are a key part of the power generation systems aboard Domus, which also draw on hydro regeneration, hydrogen fuel cells and battery storage for fully silent operation with zero emissions while at anchor. Again, a lot of the power generation solutions came off the back of creating the Fury concept, a high-performance sailing yacht that provided an opportunity to explore energy recovery from the propulsion system, which in turn influenced the energy storage and generator system capacity.
“We added hydrogen fuel cells into the mix as a direct replacement of the generators,” says Small. “There is still work to be done in that area, but the technology is commercially available and in use. Then we thought ‘Wouldn’t it be great if we could make our own hydrogen through electrolysis’. That technology is also commercially available and we can do that if the boat keeps on sailing, but as we all know superyachts spend 80 percent of their time at the dock.”
Despite the enormous surface area the trimaran offers, solar energy for when the yacht is stationary is also limited because the deck space is also used for other purposes. The key is balancing the various power generation technologies. Based on normal operations in the Mediterranean and Caribbean the designers expect to be able to run all the hotel loads from the solar panels over any 24-hour period with excess energy stored in the batteries for peak shaving.
In fact, when sailing, the yacht can generate about 170 percent of the total energy required on board and that excess energy can be used to create hydrogen. The other advantage is that electrolysis splits water to produce hydrogen and pure water, which is used to produce more hydrogen but also means less reliance on watermakers, a significant power drain on large yachts.
“It’s important to stress that we’re using standardised technology here, nothing especially new or fancy,” adds Small. “The only questionable thing we have at the moment is getting approval from Class for the electrolyser system, which is not there yet.”
Yacht concepts explore new solutions and untried possibilities, but that is not to say they shouldn’t also be feasible. Beyond encouraging potential clients to question conventional solutions, the designers of Domus went out of the way to research all avenues and the result is eminently buildable. The concept can easily be stretched to 80 metres and remain emission free (beyond that size and the amount of renewable energy required to run the onboard loads becomes prohibitive) and could conceivably be shrunk below 500GT.
“We see concepts coming out with every permutation of not thinking stuff properly in the early stages,” says Doyle. “Some of them get a lot of attention and you know there’s going to be a very disappointed owner when he gets into reality of the design. After extensive design research and analysis, we strongly believe if you want all the benefits of multihulls at 40 metres or more in size the only practical solution is a trimaran.”
What are the considerations that owners should bear in mind when looking to refresh the look of their vessel with a new paint job? We caught up with Mark Bournas, Sales and Project Manager at superyacht paint consultancy company CCS, and Dean Smith, director of superyacht consultancy company, Hampshire Marine.
First off, you might be asking yourself the question: “Why would I need a paint consultant for my yacht anyway? Surely it can’t be that complicated.” As with many aspects of yachting, however, the past decade has seen a shift toward professionalisation that renders the services of a specialist consultancy company like CCS invaluable.
“In the past, when someone was interested in building a yacht, they would visit the shipyard, often with their families, and be heavily involved during the build and development process – this created a basis of trust between the yard, contractors and clients,” says Bournas. “As a result, any disputes would often be sorted out between all of these parties and risks were lower
In recent years, the industry has professionalised, meaning that a potential owner will look around for the best commercial contract instead of going to the yard where he feels most comfortable. This increases competition between yards/contractors and means that contracts are leading instead of a relation between the yard and owner.
“This increased professionalisation is a positive thing but it means that you need to have specialists involved in every stage of a build/ refit, alongside strong and dedicated project management from a company like Hampshire Marine,” continues Bournas. “This ensures that the contract is lived up to, and vitally, that owners’ expectations are managed throughout the project.”
Indeed, informed by his 25-plus years of experience representing the owner’s side, Smith highlights the importance of harnessing the technical know-how of a company like CCS.
“The question from the owner is always going to be about appearance: how to achieve an extremely high-quality finish, even in bright sunlight, and how to ensure the performance
and durability of the paint job over time. This is such a key area for any yacht project, and so you need a specialist to oversee this. It’s not just about the paint going on: it’s also the process of how you prepare the surfaces. For example, with a refit project, it could take between 6-8 months and the preparation time can take as much time as the actual painting.”
Once you’ve decided to take the plunge and paint your superyacht it would be natural to ask: “how do I ensure that the paint contract covers my interests, as well as simultaneously including all of the relevant technical and aesthetic criteria and meeting warranty conditions?”
“Having a proper paint contract in place is obviously vital, but it must not be forgotten that painting a superyacht, just like building one, will also involve real craftsmanship,” responds Bournas. “The goal should be that all of the specialists involved will contribute to the finished product and should not just be there just to make their own involvement look better by setting unrealistic criteria. At CCS, we help you navigate the small print to ensure that you don’t run into any issues down the line, and keep your superyacht looking beautiful for as long as possible.”
The 14-year odyssey of Project X began at the Marco Yachts yard in South America in 2008. Relocated for finishing to the Golden Yachts shipyard in Athens, we visited the yacht as she was finally nearing completion.
BY CHARLOTTE THOMAS
Building or refitting an 85-metre yacht is a serious undertaking for any yard, but when an owner approached Golden Yachts in Greece to discuss the completion of a previously stalled project, the team took it all in their stride. After all, they had recently launched their largest new-build yacht to date, 95-metre O’Pari, and already built a fleet of charter superyachts that the yard also owns and manages. Add company founder Captain Paris Dragnis’ experience of owning multiple yachts and commercial ships and it seemed the project was well within the team’s capabilities.
By the time we visited the project in Pireaus, Athens, it had been three years of hard graft, but Project X was on schedule for completion despite the many changes required both through necessity and to meet her owner’s new requirements.
Project X began life as a Ken Freivokh-designed 85-metre yacht with a distinctive glass tower amidships. Her keel was laid in October 2008 at the Marco Yachts yard in Chile, but the project was put on hold. In 2011 the hull was moved to the Delta Yachts yard in Seattle where she lay dormant in a car park. Fast forward eight years, and she was
spotted leaving Seattle in 2019 on a transporter bound for Greece. What followed has not been straightforward.
“I spent almost a week in Seattle three-anda-half years ago surveying the vessel,” begins George Chairakakis, Projects Director at Golden Yachts. “My first impression was that it was a very demanding project, full of hidden problems to be resolved. When something has been ‘abandoned’ for so long it is a big challenge for the shipyard to undertake the completion and to deliver it.”
It wasn’t just the project itself that was demanding there were the requests of designer
When something has been ‘abandoned’ for so long it is a big challenge for the shipyard to undertake the completion and to deliver it.
Ken Freivokh, who retained an active role in the project, and the interior architects Massari Design in Italy. The team also had to modify the hull to accommodate a 3 metre extension; make sure that the system schematics were brought up to date; and bring the yacht into modern commercial compliance.
“We had to uprate a boat that was initially designed as a private vessel, and to consider how to modify the general arrangement to comply both with commercial coding and with new regulations,” says Chairakakis. “The boat is now fully compliant with Malta Commercial Yacht Code 2020, which was one of the most difficult parts of the project.”
The changes from the original design have been significant. First and most obviously there is the stern extension, which allows for a beach club with glass-sided pool, and which takes the overall length to 88 metres. Then a touch-and-go helideck was added to the bow area. Two garage doors and a 9-metre balcony were added aft, along with redesigned garage space to accommodate an owner-supplied Pedrazzini tender, as well as a hammam and sauna in the beach club.
For the interior a major tweak was the area around the central atrium, where two decks have been cut away on the starboard side to create an imposing entrance hall rising 9 metres high and dominated by the three large ‘X-windows’. Trademark Freivokh glass ‘spokes’ surround the elevator column, which
runs from the lower deck, five stops up to the sundeck. The elevator itself, built and supplied by Lift Emotion in the Netherlands, has the largest diameter of any glass lift installed on a yacht of this size. In addition to the changes to the GA, naval architecture and general engineering, there was the challenge of breathing new life into a vessel that had been lying dormant for close to a decade.
“It was a steel hull with a partially completed aluminium superstructure,” says Chairakakis. “It had a partial piping network which we largely disassembled, scrapped and rebuilt from scratch, and there was no cabling, no cable trays even, no machinery, nor even the bases for the engines. There was nothing on board.”
It fell to the Golden Yachts engineering and projects teams to hone the modified design and bring it up to the latest standards. This inclued re-specifying all the machinery and systems and bringing the yacht within modern expectations for emissions and environmental performance.
A central feature of the original design was a large glass lift rising five decks through the yacht, surrounded by glass floor spokes and deckhead panels which are something of a Ken Freivokh trademark. Engineering and building the elevator fell to Dutch specialists Lift Emotion.
“The project started in 2009 and we were involved in the pre-design stages with Ken Freivokh,” says Mike
Brandt, CEO of Lift Emotion. “Then during 2020 we received the order from Golden Yachts to materialise the design for this special elevator.”
The five-stop lift measures 2.5 metres in diameter – the largest trunk installed on an 80 metre yacht to date – and the internal diameter is 1.8 metres. This allows for a lift cabin with a 1,125-kg payload and 15-person capacity. The drive system is hydraulic with an inverter drive and is set in a tandem 11 suspension, meaning two telescopic jacks that pick up the cabin.
“Installing glass lifts is a time-consuming and difficult task, and also means a lot of people in the central staircase – not only elevator people but also other companies working in that area of the boat,” says Brandt. “This is not nice for the yard, nor for all the people involved.”
For this reason, Lift Emotion likes to pre-assemble as much of the shaft and cabin as possible. In the case of Project X, the pre-glazed lift trunk
was delivered to the yard and the whole five-stop, six-deck elevator and cabin installed in a few days.
Project X had the machinery space under the lowest lift stop to integrate the machine room into the lift structure, so the pre-wired pump unit with controls was already installed when the system arrived at the Golden Yachts yard. “In the second week of our installation visit the lift was already running up and down,” says Brandt.
The inside of the trunk also has to look nice, and Lift Emotion created two pillars with integrated guiding and cylinders for the jacks, and these are covered in decorative materials to match the staircase and general design theme. The cabin essentially floats between the two pillars. The final touch is a cabin roof to match the sundeck glass roof and distinctive spoked round ceiling of the yacht.
“We started with the modifications the owner requested, such as the bow helideck area, and the naval architecture for the stern extension,” says project manager Panagiota Mandragou. “We also had to alter the main engines, generators, systems and piping as rules and regulations change over the years, and the trends now are different to when the project was started.”
The team overhauled the engines and generators, then upgraded the technical package by adding diesel particulate filters and other
elements to reduce emissions. Elements of the structure were re-engineered to allow for the cutaways when creating the guest atrium, for example, and major modifications made to steel structures and partitions inside the yacht to comply with regulations.
Moreover, while Golden Yachts was completing the superstructure in the first year of the project, Freivokh and the owner made a lot of alterations, including more crew cabins, the bow modification and helideck, adding or changing storage areas, the garage, the SO-
LAS crane and pantries, and fully modifying the tank-top deck. The project team resubmitted all the drawings to Bureau Veritas for review, including the original drawings from 12 years ago.
“There were the drawings of Freivokh from the start of the project, but the completion of these structures, the installation of the glass elevator, and the whole reinforcing of the boat and the modifications were all Golden Yachts design and construction,” says Chairakakis.
“It was challenging for our plan approval engineers to get approval a second time for the jobs done by another shipyard.”
Coordinating such a complex build and doing it inside a strict delivery schedule comes down to considerable project planning and manpower resources. During the last year of construction as many as 350 people were working on board at any one time. Many of
Project X’s interior design draws on a huge palette of materials and fixtures and fittings from a long list of suppliers and subcontractors. Those materials range from exotic leathers, snake and fish skins – all perfectly matched to a repeating pattern – to varieties of marble with stainless steel inserts and decorative panels made using resin and molten metal.
“A contemporary aesthetic remains throughout the guest areas with natural colours, white tones, soft tactile finishes and leather and fabrics all over, even in the deckheads,” says Dimitra Agapitou.
All the guest and VIP cabins, which are located on the main and upper decks, have personalised colour themes and in total around 150 different materials were used in the interior.
“I think this project has the most materials we’ve used so far, which has definitely made it one of the most challenging,” says Agapitou. “It’s also different working with an external client, but we have previous experience fulfilling special requests and we’re a team of young, hard workers and experienced people who are all ready to collaborate to complete such a project.”
those were carpenters working on the interior, for which the guest areas were mostly handled by teams from northern Italy and Greece. The exquisite stainless steel work such as the curved exterior staircases is by a Greek supplier who works solely for Golden Yachts. Indeed, most of the contractors are long-standing collaborators and it is the yard’s investment in relationships that paid dividends during recent issues with the supply chain.
“It would have been really difficult in the past two or three years without our longstanding contractor relationships,” says Dimitra Agapitou, Interior Design manager at Golden Yachts. “Having established these collaborations over many years has meant that problems can be resolved via email and with photos, as well as affording the opportunity to get ahead of the supply chain issues.”
In spite of these difficulties and the wider challenges, Project X falls seamlessly into
the pantheon of Golden greats, reinforcing that this sometimes overlooked shipyard is capable of taking on projects that few others would dare consider. Captain Paris Dragnis is still a leading presence in the shipyard, even at 78 years of age, and his steadying hand also helps smooth the waters with external clients. “I am happy and, more importantly, the owner is very happy. Because the customer needs to be happy,” he says with a wry smile.
It is testament to the skill of the shipyard that this balance has been maintained and the demands of all parties satisfied even while building was under way. “Golden Yachts is one of the few shipyards in the world that can complete a discontinued project in so short a time and to such high standards,” concludes Chairakakis.
Project X is currently slated for display at the Monaco Yacht Show in September where she can finally make her mark.
SPEED (MAX/CRUISE) 18/16 knots
BUILDER Golden Yachts
NAVAL ARCHITECTURE Golden Yachts
EXTERIOR DESIGN Ken Freivokh
INTERIOR STYLING Massari Design
CLASSIFICATION Bureau Veritas FLAG
Golden Yachts is able to draw on its experience and knowledge of different areas of the maritime industry, all of which came in useful on Project X. The commercial shipping side of the family business, for example, provides insight into the mechanical and systems engineering, while the superyacht business assists with quality assurance and sign off both at the yard and at suppliers’ facilities. In addition, with more than 200 superyacht crew on its books through its fleet of charter yachts up to 95 metres in length, the company receives constant feedback that can impact yacht operations both for private and charter use.
“The feedback and all the information given by those people, as well as the experience that comes through charters all over the world, is an important factor that we take into consideration in all our concept design work, and during construction,” says Chairakakis.
The custom superyacht market has tended to disregard power catamarans, but there are signs this is about to change. Project Illusion, a secretive 43.5-metre power cat in build at The Italian Sea Group, promises to usher in a new age of multihull design that will transform perceptions.
BY JUSTIN RATCLIFFE
Catamaran design and construction is old enough to be well understood, but young enough to still hold some mystique. Large custom catamarans, sail or power, are a rare breed that make up only a tiny proportion of the superyacht fleet, a niche within a niche. This is surprising given they are usually perceived as offering inherent stability, more living space, more efficiency and less draft than comparable monohulls –all characteristics that are usually top priorities for superyacht owners.
Boxy, utilitarian design has not done the genre any favours. Take two quite recent power cat projects: 66-metre Hodor (Astilleros Armon) and 46-metre Charley (Echo Yachts). In these cases, the twin-hull configuration was chosen because it suited their function as support vessels for carrying tenders and toys. The aesthetics were less important. Even 44-metre Hemisphere (Pendennis), the largest privately owned sailing catamaran in the world, turns heads for her sheer size rather than her exterior design.
Project Illusion is completely different and the exterior design was a priority from the start. Admiral is understandably reluctant to reveal too much about its all-aluminium power cat before her launch next year, but radical styling, an asymmetric layout and huge glass windows promise to confound our expectations of what a catamaran should look like.
“The owner was largely unsatisfied with the lack of innovation found in new-build yachts and yachting today,” says Michel Chryssicopoulos, global managing partner at IYC, acting as the owner’s representative. “His vision was to create something unique and groundbreaking from every point of view. We spoke to various designers, but in his eyes nothing was daring enough. As luck would have it, before abandoning the search all together, we were presented with a ‘crazy’ catamaran design by The Italian Sea Group, to which the owner got up from his seat and exclaimed ‘That’s it!’ without hesitation.”
Not surprisingly, the innovative design presented significant technical challenges.
Rated at 700-plus gross tonnes, the project was developed completely in-house by The Italian Sea Group, but Lateral Naval Architects in the UK were brought in to optimise the structural engineering and naval architecture.
“This was a demanding project in a number of ways,” says James Roy, managing director at Lateral Naval Architects. “We have a lot of useful experience with commercial multihulls, but you’re never going to be able to take a commercial catamaran design and apply it to superyacht, even with some tweaks. For a start, the hulls on a fast ferry are much slimmer because they have no
to the superyacht industry. Beyond its core competencies, it focuses on meaningful innovation to enable superyachts to meet the demands
of today’s owners and those of the future. Projects like 106-metre Black Pearl, 110-metre Jubilee and 109-metre Bravo Eugenia (Oceanco) presented demanding specifications requiring specialist knowledge and innovative solutions. BMT Nigel Gee also designed Chief Flying Sun (now Disco Volante GT), a 36-metre power catamaran with a top speed of 42 knots that was built by T-Craft in South Africa and delivered in 1992. “We certainly like a challenge,” says senior naval architect Michael Barakis.
“In the case of Project Illusion it was sticking as close to the original concept as possible in order to make something that everybody was happy with. We had to optimise at every turn to ensure we could achieve this and be spot on first time round because there was no time for reworking.”
The challenge was not just the glass, but also the beautiful yet complex shape of the aluminium superstructure.
accommodation requirement. The process of hydrodynamic refinement might be the same, but you’re dealing with two fundamentally different vessels.”
The team had very little wriggle room to play with because Project Illusion had been sold based on a specific design and specification, as well as a redline speed of 20-plus knots. In each of its hulls the yacht will have a 2000 M96 series MTU engine and a 150kW CAT generator. Both engines and generators are IMO Tier III compliant, which created another challenge for the shipyard when it came to fitting the bulky SCR systems into the relatively narrow hulls.
Weight was a critical factor from the start, especially given the amount of glass. A catamaran’s long, skinny shape hulls mean that as the weight increases they tend to sink proportionally lower in the water than broad-beamed monohulls. The Displacement Designed Waterline (the volume allotted to the submerged part of the hulls) is used in calculations for the superstructure, stability and compliance with various Class societies.
Underestimating the displacement results in a disproportionate increase in wetted surface area, which in turn increases resistance. It can also lead to lower than intended clearance between the underside of the crossdeck and the waterline. Keeping the weight down not only improves speed potential and hydrodynamics, but also reduces overall loads so the hull and crossdeck structures can be built lighter using less material.
“The biggest challenge has undoubtedly been controlling the weight,” says Primiano Protano, technical tesign and R&D teneral tirector at The Italian Sea Group. “Even a small variation in the designed displacement can dramatically affect the drag, trim and speed of the hulls, as well as reduce the height of the cross-deck clearance and increase the risk of wave slapping.”
To simulate physical phenomena and evaluate the structural and fluid dynamics, Project Illusion has been totally designed using Finite Element Analysis (FEA). Simply put, FEA is a numerical method for predicting how a part or assembly behaves under given conditions. As the basis for modern simulation software, it helps engineers identify areas of stress or strain in a design. The numerical results can then be used to optimise shape, geometry or other parameters and reduce the need for physical prototypes. When used in conjunction with CFD, FEA is a sophisticated tool in the design of large yachts for overcoming the tendency of naval architects to err on the conservative side when it comes to displacement.
“Structurally speaking, the challenge was not just the glass, but also the beautiful yet complex shape of the aluminium superstructure,” says Andy Douglas, principal structural engineer at Lateral. “Our experience told us that we had to do full FEA of the whole structure, not only the hulls and cross-deck. This wasn’t just for verification purposes – it was integral to the design to make sure it all worked.”
Most commercial catamarans are approved for restricted service and limited by distance from a safe haven or weather conditions, but Project Illusion is certified by RINA for unrestricted navigation. Lateral drew on its previous experience and compared its findings with different sets of Class rules to ensure the structural engineering complied with regulations. In some cases, it discovered that the Class rules didn’t cover all the loads they were expecting.
“When you combine malleable aluminium with large areas of glass, which doesn’t like flexing, it’s more about the structure’s
deflection than its strength,” adds Michael Benakis, Senior Naval Architect at Lateral. “We couldn’t just throw more material at it because the overall weight was so critical. Yachts normally grow, which means more weight and volume. Here everything had to be contained.”
A defining design characteristic of Project Illusion is the 600 square metres of curved glass and the sheer size of the individual
OMS specialises in the custom design and manufacture of electric and hydraulic marine thrusters and subsea instrument deployment systems. Superyachts with OMC equipment installed include some of the biggest sailing superyachts in the world, including 106-metre Black Pearl (Oceanco), 93-metre Eos (Lurssen) and 85-metre Bold (Silver Yachts). They also built the titanium and carbon fibre bow thruster on Skorpios, the recording-breaking 43-metre maxi racer from Nauta Swan.
“The only reason why we can make electric retracting and swing thrusters is because of the evolution in compact but power dense permanent magnet motors,” says Mark Barwelll of OMS. “They are a quarter the size and weight of a traditional motor and that means we can also move it up and down on top of the thruster instead of having it bolted to the hull structure as used to be case. The development of permanent magnet technology over the last few years has been the driving force behind the push to save weight and increase efficiency.”
panes. Supplied by Sunglass Industry in Italy, the largest pieces are 14 square metres and the total weight of glass is around 23 tonnes.
The laminated glass was chemically toughened rather than heat tempered as it requires less material for the same strength and resistance (the thickest panes aboard Project Illusion are just 400mm, but strong enough not to require storm shutters). The chemical process toughens glass through a sodium and potassium ion-exchange process in a salt bath. It imparts not only higher strength and MOR (Modulus of Rupture or resistance to breaking in bending), but also higher surface quality for superior optics. Special plastic interlayers between the laminates adds further strength and protect against overheating in critical areas. All the windows will be bonded in place using adhesives.
Sunglass usually uses photogrammetry, the science and technology of obtaining accurate dimensions from photographic images, but because of the size of some of the glass panes, in this case the structure was measured using a 3D laser scanner to ensure the panes precisely match the spaces provided.
As in large sailboats, big thruster holes in the bows would have increased drag and adversely affected the catamaran’s performance, so Project Illusion has retractable electric bow thrusters supplied by Ocean Marine Systems (OMS) that rely on compact but powerful permanent magnet motors. The design is especially suited to the catamaran’s deep-V hulls because the thruster can be fitted higher with a longer deployment stroke to clear the hull.
“Powerboats normally overcome the efficiencies of an open thruster tunnel with more horsepower, but the shipyard was chasing efficiency and wanted to achieve a certain speed with a defined number of kilowatts,” says Mark Barwell, sales director at OMS.
“When the thruster is retracted the base plate closes the hole, and because it’s been faired to match the hull shape you basically don’t know it’s there.”
The hull forms were tank tested at the Model Basin in Vienna, but additionally MARIN in the the Netherlands was asked to carry out a numerical seakeeping assessment – an interesting collaboration between two organisations that are usually are competitors. Key to the research was ensuring the correct weight distribution, which is harder to achieve in a catamaran because the centre of gravity is not necessarily where the weight is placed and unbalanced loading negatively affects trim and perfor-
mance. Once you have the weight distribution and you know where the loads are, then you can see how the model reacts in water and calculate the ship motions or damping.
The tank tests in Vienna verified the hull separation to minimise the incidence of wave reflection between the two hulls that can result in increased resistance. Top speed was optimised with the addition of hydraulic interceptors mounted inside each propeller tunnel, which resulted in a 3% gain in powering performance.
After careful consideration it was decided that the inherent stability of the catamaran configuration precluded the need for stabilisers. Catamarans generally have a high GM or metacentric height, which makes
Part of the group that includes German glass specialist Sedak GmbH, Sunglass Industry Srl is a leading glass manufacturer based near Padua, Italy, and specialised in the hot bending of glass. It has one of the largest machines in the world for the chemical tempering of glass and over the years it has supplied curved glass panes for cutting-edge architectural requiring maximum transparency, including Hamburg’s Elbe Philharmonic Hall and the Louis Vuitton Foundation in Paris. It is also a key supplier to the superyacht industry and made all the glass windows for the 75-metre Admiral Kenshò
“The main challenge with Project Illusion was not so much the curved shapes, but the size of the panes,” says Lorenzo Neri from the nautical division of Sunglass Industry. “We’re used to working with compound curves, but we had to make the panes both very large and light. The advantage of having lighter, thinner glass is that it is also more flexible, more than you might imagine, which combined with elastic adhesives means it can flex to some extent with the aluminium structure.”
them very stiff with a low natural roll period. In fact, roll is mostly eradicated by virtue of their width. Attaching fins or foils to the hulls to further enhance ride control is possible, but they would need to have a very large surface area to be effective, which would mean more weight and hence drag.
Related to the stabilisation issue was resonance, or the tendency of a vessel to oscillate with greater amplitude at certain wave frequencies. Wave periods in the Mediterranean are generally 6-7 seconds and 7-8 seconds in the Caribbean. A vessel with a natural roll period within that range could result in more excitation due to resonance. In fact, most monohulls do fall within that range, but a lot can be done with stabilisation systems because they have low GM and low damping. Not so with catamarans.
“We asked where in the world the catamaran would be sailing, because then we can say whether the weight distribution and hull geometry is suitable for a specific area or not,” says Enrico della Valentina, yachts team leader at MARIN. “Admiral was very interested in exploring the stabilisation options, but as the roll period is slightly outside the critical range we advised against it. Another factor is that roll is associated with beam seas, but at anchor you usually have bow or quarterly waves and catamarans respond much better at anchor in these conditions than most monohullls.”
Project Illusion is not the only large catamaran project in build at The Italian Sea Group: work has also started on a 46.5-metre sailing catamaran. In addition to other multihull projects by other brands, they point to something of a renaissiance of the catamaran configuration in a market dominated by monohull superyachts that all too often fall back on estab-
lished technical platforms and unadventurous design solutions.
“This is one of the most exciting new build projects we’ve been involved with to date,” concludes Michel Chryssicopoulos of IYC. “It’s the perfect blend of an audacious owner with a thrilling vision and a shipyard that was up for the challenge.”
J. Ratcliffe
LENGTH OVERALL
MAX. BEAM
DRAFT
GROSS TONNAGE
MAIN ENGINES
BUILDER
NAVAL ARCHITECT
EXTERIOR DESIGNER
INTERIOR DESIGNER
OWNER’S REPRESENTATIVE
DELIVERY
43.9m 14.78m
2.25m
approx. 750 GT
2 x MTU 16V2000 M96L (1939kW @ 2450 rpm)
The Italian Sea Group Tecnomar / Lateral Naval Architects Tecnomar Tecnomar
Michel Chryssicopoulos (IYC) 2023
BOUCLE - FROM PLASTIC TO FABRIC
REVYVA IS SUITABLE FOR IN- AND OUTDOOR USE
REVYVA IS MADE FROM POST-CONSUMER PLASTIC BOTTLES
REVYVA IS 100% RECYCLED & RECYCLABLE
A single-prop fishing trawler is not an obvious choice for conversion into a superyacht, but for the owner of Scintilla Maris it was the only one. We travelled to the Damen Maaskant shipyard near Rotterdam to find out more.
BY JUSTIN RATCLIFFE
Entrepreneur Erik Vonk grew up fascinated by tug boats and trawlers. A part of his family are fishermen from the island of Texel in northern Holland and as a young boy he would spend time sketching the workboats he saw there. At college he borrowed money from relatives to convert an old tugboat and lived on board for some years. In 1979 he emigrated to the US, set up three successful businesses and is now the proprietor of Richland Rum in Georgia. But his old love affair with trawlers never left him.
“In the 1980s and into the ‘90s these steelhulled boats represented the epitome of Dutch shipbuilding,” says Vonk. “They were very sturdily built, almost over-engineered, to deal with conditions in the North Sea. I’d been following the Dutch beam trawlers for years and when one became available as part of a decommissioning scheme in 2006 I decided to buy her, basically with a virtual handshake over the phone.”
The boat in question was Scintilla Maris , a 45.6-metre beam trawler launched in 1988. Beam trawlers are so called because they fish with a net on each side of the hull that is attached to a steel beam to hold them open. It is a method used for catching bottom-dwelling fish, including sole, plaice, turbot and monkfish, and their design owes much to the mainly Dutch shipyards that pioneered them.
Scintilla Maris was the first of eight sisterships built by the Maaskant Shipyard near Rotterdam, now part of the Damen Group, which has over 70 years’ experience of building trawlers. Vonk returned to the same yard to carry out an initial refit to remove all the fishing gear and upgrade some of the onboard systems. The project then ground to a halt for almost a decade as her owner was determined to come up with a work list and specs himself, mainly by spending time on other yachts, while juggling his business interests.
Work resumed in 2019 when the shipyard began a full conversion by stripping back the hull to bare metal and removing the interior, decking and propulsion. After additional modifications to the hull and superstructure, all the metal surfaces were sandblasted, primed and sealed.
“Basically what we’re looking at is a newbuild yacht in an existing shell,” says Vonk. “My reason for doing that is the exceptional quality of the hull, not only in terms of seaworthy design but also engineering and construction.”
By way of example Vonk points to the stainless-steel piping instead of galvanised metal or PVC, the 40mm of West African iroko decking, and the steel hull plates that are 10mm above the waterline and 15mm below (although not Ice Class, the hull is more robust than most explorer yachts).
The extra-thick plates also mean there is no ‘washboard’ effect when the positions of the
frames are visible as is often the case with thinner plating, especially when combined with poor heat management during welding. As the hull was stripped completely on the inside, the yard took the opportunity to remove any dents, an inevitable consequence of the vessel’s former life as a beam trawler (the ‘run rails’ welded to the hull served as protection from the heavy steel beams when deploying and retrieving the nets).
All modifications had to be approved by RINA in order to bring the vessel into Class. The original trawler was rated at 570GT and an early priority was to bring the volume
below the 500GT threshold, principally by creating more semi-open areas. Another major modification was cutting out sections of the hull and bulwarks amidships on both sides with steps leading down to water level, which actually increased hull stiffness as there is a steel box reinforcement under each staircase.
The interior design by Vripack is utilitarian, but also comfortable and not in any way sparse. In keeping with the vessel’s original design, extra windows or portholes are limited in size and framed in brass. High Pressure Laminate (HPL) panelling provides enhanced durability and impact resistance. Floating interior floors and low-frequency insulation serve to minimise noise and vibration.
Maaskant Managing Director Eric Moerkerk showed us around a brand-new fishing vessel the yard had outfitted to give us an idea of what Scintilla Maris will look like when finished. Although below Dutch superyacht standards in terms of luxury materials, the high-quality finish was several steps above what you would expect to find on a working vessel.
“We’re used to working with demanding commercial clients who require a high degree of flexibility,” says Moerkerk. “Owners and their reps are always here in the yard during construction requesting changes and we’re able to react to their needs. This is the nature of the fishing business today and that flexibility means we’re well prepared to handle conversion projects like Scintilla Maris.”
“A
By far the biggest upgrade is the hybrid diesel-electric propulsion system. Stricter emission regulations meant the initial intention to keep the original 4,400-hp Deutz MWM
diesel engine, which was in excellent condition, had to be abandoned. Wabtech EPA T4/IMO Tier III engines, among the most technologically advanced and fuel-efficient medium-duty diesels, were also considered before settling on a hybrid DE system.
Driving the single 3.4-metre Van Voorden propeller is a 2,000-horsepower electric motor (1300kW @ 1000rpm) supplied by Marelli in Italy that Vonk refers to as a “super-silent, vibration-less beast.” The motor is custom-designed with two windings that effectively provide two motors of 650kW
each wound on one stator, which can be energised individually or together for virtually any combination of normal motor speeds.
The electric motor is coupled to a ZF Marine reduction box and three Volvo D16 IMO III gensets (586kW @ 1800rpm). The EST-Floatech Lithium-ion battery bank (2 MW) provides a further level of redundancy and is mainly used to run a full hotel load overnight without generators and for peak shaving, but they can also power the 110kW Marelli bow and stern thrusters for silent, emission-free, electronic anchoring.
Maritiem Elektro Zeeland (MEZ), a tried and trusted local partner of Damen Maaskant, is the engineering firm responsible for integrating all the electrical installations, including the propulsion, power management, automation, navigation, communication, entertainment and lighting systems. The hybrid system based on an AC and DC (back-up) grid can be monitored remotely and basically provides four sailing modes battery mode with limited power and hybrid mode with one, two or three diesel generators that are always running at constant loads. A Dynapilot system from Alphatron Marine and based on DP technology provides full navigational control in all modes via a single joystick.
Unlike modern yachts, two-thirds of the hull is below the waterline and the vessel has a 40-tonne keel. During the conversion weight has been added (including over 20 tonnes of batteries) in order to maintain the design draft. All this translates into a stiff rolling moment, which precludes the need for stabilising mechanisms beyond the original bilge keels.
The general arrangement is still in the last stages of refinement, but when finished the yacht will be able to accommodate ten guests on the lower deck in four double cabins and a full-beam owner’s suite amidships underneath the original hatch into the fish hold (the former hold also provides immense space for storage and a good-size laundry). The main deck features multiple interior, exterior and semi-open areas for relaxation. On the bridge deck the open wheelhouse is enormous for the size of vessel and the owner has reserved
the aft section as a private office. The main tender will be stowed on the sun deck aft and there is a viewing lounge forward overlooking the foredeck.
“Scintilla Maris has been thoughtfully designed as a home away from home,” says Vonk. “The purposing of spaces, the flow between them and the designation between the private and crew areas reflects that. I want to feel at home instantly and when stepping on board and specifically don’t want to feel like a guest in a hotel when on my own boat.”
Erik Vonk is well aware that Scintilla Maris is a highly personal conversion project that is probably more suited to long-range voyages in northern waters than cruising the Côte d’Azur. But his business instincts also tell him that expert advice can make all the difference if he wants to commercialise his investment through chartering and eventual resale.
So we were not the only ones visiting Scintilla Maris. Vonk had also invited William Molloy, head of charter at Moravia Yachting; Roy Posthuma, charter and sales broker also with Moravia Yachting; and Pino Di Mora, senior project manager with Hill Robinson. What followed was a lively and productive discussion about how the onboard amenities, especially the crew accommodation and services, could be optimised without incurring drastic changes to the existing layout.
Some 16 years after her owner acquired her, the transformation of Scintilla Maris from beam trawler into luxury yacht is on track to be completed by spring 2023, which must be something of a record for a conversion project.
“This has been such a long project primarily because taking everything I learned, both the good and the bad, and translating that into something approaching a spec list for the shipyard took an enormous amount of time,” says Vonk. “But it’s been an unusual privilege to be able to do this at the yard where the boat was actually built, where there are still a number of people that built Scintilla Maris. To have that intimate connection with the boat and these guys who have so much pride in their work has been an amazing experience.”
LENGTH OVERALL 45.60m
MAX. BEAM 9.00m
DRAFT 3.90m
GROSS TONNAGE 499GT
MAIN ENGINES 1 x Marelli electric (1300kW @ 1000rpm)
GENERATORS 3 x Volvo D16 IMO III (586kW @ 1800rpm)
BATTERIES EST-Floatech (924 kWh)
FUEL 150,000 litres
WATER 40,570 litres
SPEED (max/cruise/economical) 14/11/9 knots
BUILDER Damen Maaskant
NAVAL ARCHITECTURE Damen Maaskant
EXTERIOR DESIGN Damen Maaskant
INTERIOR DESIGN Vripack
CLASSIFICATION: RINA Y Pleasure Vessel, Unrestricted Green Plus AUT-UMS
FLAG US Marshall Islands DELIVERY 2023
Peter Wilson is co-founder of MCM, one of the industry’s leading yacht construction and management firms. Originally from the UK, he settled in Newport, USA, in the late 1980s and set up MCM with business partner Nigel Ingram. Both have extensive sailing experience –racing and bluewater cruising – but they have also represented owners on numerous motoryacht projects, including 58-metre Najiba (Feadship), 49.8-metre Toute Sweet (ex-Erica, Heesen) and 67-metre Calex (Benetti). Outside of work, Peter enjoys cycling, sailing, motorbiking, photography and tending to his beehives.
How did you and Nigel meet and what sparked your decision to set up a company together?
PW: We met in Antigua in the ‘70s and became fast friends. In 1988 I was wrapping up an America’s Cup challenge and Nigel was finishing the build of a new yacht. We started chatting about what was next. As yachts were getting larger and more complicated, we felt clients needed an advocate to represent their best interests. We also believed there should be more discipline in terms of fiscal and time-related control imposed on the build process. And after 35 years it appears there was indeed a need!
You’re a sailor and in the past MCM was best known for its sailing yacht projects, but you’re now taking on more motor yachts with brands like Feadship and Benetti. Was this a straightforward transition and how does your role change between sail and power?
PW: When one considers today’s sailing superyachts and their relative systems, they have more complications than the equivalent motoryachts. For example, both types of vessels have engines, generators, HVAC, AV/ IT systems, cooking and domestic appliances, desalination and sewage treatment plants, and so on. But on a sailing yacht there are also masts, rigging, captive winches, booms, hydraulic furling and tensioning systems and appendages like lifting keels – all in a hull that is usually less voluminous than a motoryacht. So the transition from a technical standpoint is quite straightforward, although it should be noted that we have been doing motoryacht projects for many years and so they are not new territory for us.
In terms of role differences, in the sailing yacht world there is more focus on the nuances of sailing performance, whereas on motoryachts the performance is well defined and based on engine kilowatts, propeller designs and, of course, the hull shape. The interiors, outfitting, finish and quality are equally important on every superyacht.
What kind of decisions can you make on your own and which require the owner’s approval?
PW: This depends largely on the involvement and experience of the client. In many cases, we have clients that are knowledgeable and have had a string of yachts before. In those cases, the client is often closely involved and brings that experience to bear, and it can be a very collaborative affair. Where a client is per-
haps building for the first time, they may need more guidance. In either case, we present them with the options available in a clear and concise manner when a decision is required and recommend the one we feel is the right choice. This gives the client the benefit of our experience and the requisite information on which to base an informed decision.
Do ‘involved’ owners make your job easier or more difficult?
PW: Having a client closely participate in the project typically makes it more memorable for them as they are really creating their vision. In turn, this makes it more enjoyable for the entire team. Designing and building a yacht is a terrific endeavour and may be a once-in-alifetime opportunity, so we strive
to make it a rewarding experience for the client. We have developed great friendships with many of our clients that outlast the build process.
MCM offers yacht construction and management services. Does it make more sense if the same agency does both?
PW: When we started MCM in 1988, we didn’t have a yacht management division. However, once we had a few yachts ‘under our belts’ it became abundantly clear that there was a requirement for post-construction support the and formalising that support in the form of a yacht management division was a service that yacht owners needed. As the vessel progresses from the build phase to the operational phase, having one company providing both services makes for a seamless transition. Not least because by that stage we have a long-standing relationship with the client, we know the vessel inside and out, we have all the data, drawings and manuals, and we know which design decisions were made and why.
The rules and regulations surrounding vessel navigation and operation have also increased exponentially and the burden is such that captains and crew require shore-based support. Furthermore, the client benefits from the continuity MCM offers; crew inevitably come and go, but we are the common thread and institutional knowledge about the yacht and the programme.
Do you bring in your own preferred suppliers and/or subcontractors for new-build projects, or is that always up to the shipyard?
PW: To ensure there is no perceived conflict of interest, we remain fiercely independent. However, over many years of operation we’ve developed strong relationships with quality suppliers, manufacturers and vendors and can recommend those to the shipyard. We also have real-world experience as to how the equipment performs at sea. However, it is the shipyard that has overall responsibility for the construction process and provides the warranty, so they ultimately decide which suppliers and subcontractors are the best fit and those they prefer to work with.
What would you change about the way we work in the superyacht industry?
PW: The elapsed time from the first conversation to the yacht being handed over can be many years. As an industry, we are always seeking ways to be more efficient and shorten the time required to build one of these masterpieces while maintaining the high quality standards expected. The other challenge is how to build yachts that can operate in an environmentally friendly way. Emissions are being lowered. We need to continue that trend to protect the marine environment we all so enjoy.
Beyond the technical qualifications, what are the personal attributes needed to be a successful owner’s rep?
PW: On the personal side, attributes such as honesty, integrity, patience and respect. Being a good listener is also profoundly important. Other key qualities include staying focused, open-minded, nimble and the ability to adapt. Managing expectations is the most challenging aspect of the job. As these projects become larger and costlier, there are many facets to consider and with sometimes differing agendas, so the ability to develop a team with members sharing a common goal, is fundamental. Lastly, the experience of having been to sea in a multitude of yachts in wide-ranging conditions is enormously helpful. Knowing what happens on the blackest of nights when the wind is fierce enough to blow the oysters off the rocks and the seas become mountains, is a great help when discussing the design and construction of our projects.
From concept to completion, the new 4,300-tonne shiplift at MB92 La Ciotat was four years in the making at a cost of at least €70 million. The project brought together contractors from half a dozen countries to resolve the many logistical, engineering and environmental challenges. We take a closer look at how it was done.
BY JUSTIN RATCLIFFE
Facing page: The
It is difficult to appreciate the sheer scale of the new shiplift in La Ciotat unless you’re standing on top of it. The platform itself is 100 metres long, 20 metres wide, 2.7 metres deep and weighs 1,100 tonnes. It is now open for business, but the total redeveloped area covers 40,000 square-metres and construction work continues on the peripheral infrastructures.
The design and construction of a shiplift is composed of four principal activities: civil works, lift and transfer systems, platform fabrication, and installation followed by commissioning. The most cost-effective approach is for the shipyard to act as the general contractor and issue separate contracts for each of the activities.
MB92 Group divided the cost of the shiplift with La Ciotat Shipyards, the public company that manages the port area, but has spent an additional €13 million on adjacent facilities. The total stake represents a formidable asset for the refit shipyard, which can now host up to six more 100-metre plus superyacht on the hard, adding to an infrastructure that already includes a 2,000-tonne yacht lift, 600-tonne crane, 300-travel lift and 200-metre dry dock.
Installing a shiplift in La Ciotat had been envisaged by MB92 ever since it acquired a majority stake in Compositeworks in 2017. Work got under way the following year
with preliminary simulations in compliance with French regulations and safety codes to determine the optimal size of the shiplift based on the land area available.
“Every increase in lifting capacity is accompanied by an exponential increase in cost, so the final 4,300-tonne capacity represents the best balance between cost, commercial opportunities and the space we had to work with,” says Joe Degabriele, senior business development manager at MB92 La Ciotat tasked with commercialising the shiplift.
Bardex Corporation, a US-based specialist in heavy load handling and positioning equipment, was contracted to oversee the design of the shiplift and transfer systems. In order to better understand the local business culture and practices, Bardex chose to partner with Matière SAS, a French engineering and construction company.
“The design process starts by understanding the client’s needs and objectives for the facility,” says Robert Taylor, senior structural engineer at Bardex. “We also investigate the site setting, access to and from the facility, the yard arrangement and the geological conditions. All of these inform us about the types of foundation system, yacht transfer arrangement and implementation plan that is most appropriate for the project.”
Shiplifts are all about speed and efficiency. In La Ciotat the entire process of lifting and positioning a yacht on the hard takes less than three hours, whereas the same procedure in a traditional graving dock requires the best part of a day. A shiplift can serve multiple parking places, but a dry dock usually hosts just one vessel at a time.
The shiplift relies on very different technology from classic winches and cables. The Chain Jack Lift system is widely used in military shipyards for lifting warships and nuclear submarines. Powered by hydraulic rams, a chain jack hoists by engaging and pulling in a short length of chain, engaging a stop pin, retracting and repeating the process.
The system offers more precise movement of the platform than wire ropes or cables, which are prone to stretching (Lloyd’s requires 20 percent of wire ropes to be removed and destructively tested each year
Cost of platform infrastructure and MB92
Total cost of the shiplift and transfer system (of which €32M from MB92 Group).
and all wire ropes to be replaced every 5-10 years). La Ciotat has 20 chain jack units, 10 on each side of the pit, and each has two closedloop chains for 100 percent redundancy.
The lifting procedure is complex because it involves coordinating the motion of 20 devices connected to the same platform. The system moves one pitch, or two links of chain, each cycle for all 40 chains (factory tests show that the movement of the chain jacks can be coordinated to within one millimetre
€45MIL
Total investment for MB92 Group.
A Waste Action Plan was initiated before demolition and construction work started with the objective of recovering existing materials and reducing their embodied energy consumption by recycling them for the new structures.
• To protect local ecosystems a barrier was installed around the work site to prevent sediment from dredging escaping into open water.
• A submarine ‘bubble’ curtain was rigged to reduce acoustic levels that might disturb cetaceans like whales and dolphins.
• 98 percent of waste materials were recycled. Polluted sand and silt removed from the harbour, for example, was treated and reused for making concrete.
• Recycling on site meant dramatically fewer trucks for transporting waste, which in turn reduced dust and carbon emissions.
• The hydraulic lift system is designed to operate with biodegradable synthetic fluids, not petroleum-based hydraulic fluid.
• A reception tank for grey and black water is connected directly with the town’s sewage system. This avoids the risk of accidental discharge and removes the need to transport waste offsite for treatment.
• The outer wall of the shiplift is lined with a biomimicry system that reproduces the natural habitat of local marine species to encourage reproduction. The 600 sqm of synthetic Posidonia grass is the world’s largest artificial, harbour-based fish nursery.
of each other). The entire lift system resets every cycle, which prevents the accumulation of differential elevation. To ensure all the units are working in perfect synchronisation, remote sensors relay the parameters in real-time to the central command system.
“Hydraulic cylinders are ideally suited to shiplift operations because their movement is consistently precise,” says Taylor. “Bardex has further improved the synchronisation by equipping the lift stations and control system with hydraulic feedback motion control. This technology is widely used in heavy industrial robotic automation applications that require high precision motion control, such as special-purpose arc welding robots.”
To guarantee an uninterrupted supply of electricity, the lifting system has its own dedicated substation with transformers supplied by the French division of the German company Schneider Electric. MB92 invested in a further three substations for the supply of reliable shore power to the yachts and for refit work.
Built by Metallic Bridges Belgium (MBB), the actual platform had to be delivered by special transport. When a yacht enters the lifting pit and the chain jacks are activated, it comes to rest on a modular cradle that can be adjusted to suit the size of the vessel (MB92 ordered four such cradles from Schwartz Hautmont in Spain). As in a graving dock, divers assess that the ‘mating’ between hull and cradle is a snug and secure fit.
Once the platform has been locked at ground level, the next phase is to transfer the yacht sideways off the platform and then longitudinally to a hard-standing space. Four-wheel bogies or trolleys constructed by Bardex Industries in South Korea are aligned under the cradle. The bogies, which have a passive hydraulic suspension system to raise the yacht and its cradle over the top of the chain jack units, run along 6.5km of intersecting rails built by Bemo Rails in The Netherlands and can change direction by lifting themselves off the tracks and turning their wheels 90 degrees.
The two axes of motion meant the rails and intersections had to be installed to a tolerance of +/- 5mm to ensure smooth transfers. Maintaining stability is obviously essential
throughout the operation, especially when moving the yacht off the platform.
“Transferring yachts laterally off the platform required careful coordination of the civil works, structural system and lift station elevations to ensure adequate clearance for the yacht and static supports to pass over the lift stations,” says Taylor. “This type of transfer operation also imposes unbalanced loads on the structural systems. Detailed engineering analysis and the use of hydraulically actuated pin supports were required to ensure the structure remains stable under this loading condition.”
There are five hard-standing places to the side of the platform and one in front of it (a sixth is a common area that can be used for short-term projects such as pre-purchase inspections). Once in position, the cradle is lowered to the ground, the bogies removed and the yacht hooked up to the shore power, fresh water and waste management systems. Anchoring points in the concrete are used for bracing scaffolding and tenting when the yachts need to covered.
At the time of writing, the shiplift and transfer systems were approaching completion before final testing and certification by Lloyds Register (shiplifts come under Lloyds’ Code for Lifting Appliances in a Marine Environment, excluding the civil engineering works). Despite the many technical and logistical challenges, the shiplift was on schedule for its official inauguration in September.
“The most difficult thing has been organising all the different companies around the world and up to 200 personnel working on site each day, especially during the Covid pandemic,” says Mathieu Bauden, the man responsible for coordinating the works as Facilities & Storage Manager at MB92 La Ciotat. “But it’s a great source of satisfaction that when we signed this project four years ago, we decided to open the platform on 15 September 2022. And that is still the opening date.”
9 & 10 November 2022
Dubai, United Arab Emirates
For 100 years the family-owned Dutch shipyard Amels has been at the forefront of superyacht construction. For 17 years the Amels shipyard has pioneered semi-custom superyacht construction with its Limited Editions series. Designed on spec and engineered in-house, the Amels 80 is the shipyard’s latest flagship and breaks new ground for a speculation series. We report from the facility in Vlissingen to find out how the project evolved from first concept to final design.
BY FRANCESCA WEBSTER
Previous spread: Rose Damen and Espen Øino present the Amels 80. Right: A render of the new flagship in the Limited Edition series.
Family owned and operated, Amels, part of Damen Yachting, has held a unique position in the yachting industry for more than 100 years. The Amels Limited Editions concept first took root in 2005 with the aim of creating a series of vessels that not only appealed to a broad scope of owners, but also applied a thoroughly tested platform and an abundance of feedback to create a commercially successful yacht series.
But when designing a new model, who spearheads the project and acts as the ‘owner’ and how does that party bring an impartial view to the project?
“When you’re designing a Limited Editions it’s not like a custom yacht design where you have a very specific and actual client in front of you,” says Rose Damen, managing director of the shipyard. “You have to create that client; they are integral to the design. For the Amels 80 we used my sister Annelies, and in fact the whole Damen family. All of them playing the client, asking the critical questions and then actually challenging everyone involved all the time.”
The 65 and 74-metre Limited Editions yachts were constructed on versions of the same platform, extending the life of the original engineering to nearly 12 years, but clients and brokers were also pushing the shipyard to come up with something new. Initially the team considered employing the same triedand-tested platform, but the Damen family recognised that the market has changed since the platform was conceived. Today, the impetus for yacht owners is about exterior living and the relationship between interior and exterior spaces, something that the previous platform was not designed to do.
“The Amels 80, much like the Amels 60, was born out of a drive and desire to push forward a new generation of Amels Limited Editions,” explains Rose Damen. “The designs evolve as do client needs, and this in turn pushes us to create the platform that we believe will best meet the demands of today and tomorrow.”
While the Damen family may play the owner, client and captain feedback was pivotal during the pre-design stage, particularly those of the Amels 242 series. Eight Amels 242s have now been built, and each owner
offers unique feedback, which is collected and analysed as part of the research process.
“The Limited Editions models are designed without one client in mind and when we succeed with a series we have a spread of clients from different walks of life, who use their yachts in different ways,” says Adriaan Roose, project manager of the Limited Editions range since its conception .
Utilising the experience gained over four generations, both as yacht and shipyard owners, the Damen family distilled the feedback and aligned their own expectations with it, refining the brief to 10 key points.
“The final result is a sum of many wishes, when analysing the feedback interviews you look for those points which correlate between each,” says Rose Damen. “For example, many of the sessions mentioned a long sundeck and that in turn led to a conversation around
The first Amels Limited Editions, the 52.35-metre Amels 171 – the yacht that sparked the long-term relationship with British designer Tim Heywood – was launched in 2007. After the 180 came the 65.5-metre Amels 212, which then evolved into the 220. In 2016 Plvs Ultra, the first 74-metre Amels 242 was launched, and in 2021 came the 60-metre Amels 200, which evolved from the Amels 188 Volpini 2, the world’s first tier III compliant yacht. The final model in the range by Heywood, the third of which is currently under construction.
“We have been hugely successful with Tim Heywood, a legendary designer who has a close relationship with us and has designed more than 40 boats,” says Adriaan Roose. “But for the new Limited Editions we were looking for a fresh approach, in both the design and the platform”
access, which is where the central elevator and staircase joining the sundeck and beach club originated.”
That central elevator came to define the heart of the yacht and was paramount to the design brief shared in the original pitch, demonstrating how important the initial research is to the final concept.
“The starting point was that it needed to be an innovative concept but in line with the characteristics of the Amels Brand: long and elongated, elegant and classic,” Rose Damen continues. “Then we focused on the use and distribution of interior and exterior spaces to align with current client expectations received during our feedback sessions. We felt that the connection between the decks and the interior volumes was a key factor, but to make this work as a Limited Editions concept we included a brief for features and possible changes that were adaptable to individual taste within the platform’s constraints. Finally another of the key 10 points was resale value, because we recognise that the client base is getting younger and that owners may want to move to a larger vessel in the coming years.”
Three design studios were approached for the initial exterior, but it was the design of Espen Øino that was unanimously chosen. It wasn’t actually until the design was selected that the decision to create an 80-metre series was finalised, with Espen suggesting that for the depth of functionality the ‘owner’s’ team had requested, the yacht needed to be that much larger. And so the Amels 80 was conceived.
“When we started out with the Limited Editions range I never would have imagined that we would be able to build such large volumes on speculation, but as time progressed we saw that there was a market demand for larger speculation builds,” says Adrinaan Roose. “It wasn’t only the design brief itself that needed to be taken into consideration, however. Yachts over 80 metres now require a pilot to enter many of the most popular bays and Øino explained that this was also a factor in determining the final size of the vessel.
Like resale potential, from the perspective of Amels, commercial viability is a major consideration when designing a Limited Edi-
tions, as despite a history of success, large scale speculation vessels are a major gamble for any shipyard. This was also one of the reasons that Espen Øino was chosen as the exterior designer.
“He took everything into consideration, including the practical elements and ensured that no part of the design rendered the vessel unsellable,” says Rose Damen. “His ability stems from actual onboard experience, he approached the design not just aesthetically, but from a user and operational perspective.”
The design is critical to creating a commercially viable product; it has to be both unique and innovative enough to catch the eye of owners, while not being so extreme that it becomes quickly outdated. It also has to compare favourably to other yards in terms of price point, and it is here that the discussion of materials becomes all the more important, particularly at a time when supply chains are pinched and vital materials are hard to come by.
Engineering the technical platform in-house majorly reduces cost, because it allows the yard to offer a competitive price, but also provides long-term benefits when it comes to costs of parts and appliances from third parties.
“We thoroughly engineer the platform of our Limited Editions right up to the nuts and bolts, but we are able to distribute the substantial cost of this across a number of yachts, meaning the work is a long-term investment,” explains Adriaan Roose.
In terms of cost-benefit, Roose actually believes that whether or not more than one hull is sold, the project will have been commercially successful due to the process of design and construction. Retaining these skills in-house and having the entire workforce trained in each platform has financial advantages for the future of the yard.
“A costly design will actually work against you in the long term and spending money wisely is vital,” adds Espen Øino, “but that has to be balanced by not cutting corners and creating a yacht that is thoroughly future-proofed.”
The Amels 80 exterior plays with themes from some of the earlier Limited Editions with her contemporary styling, expansive decks and minimalist lines. These elements that make her a distinctly Amels yacht are what Espen
calls ‘design languages’. For example, she has the same near vertical bow as the 60, but with more flowing lines from fore to aft and a gentler, more refined geometry.
“The idea was to create an optimised layout within an optimised framework that was both contemporary and yet also distinctly Amels,” says Espen Øino. “We weren’t looking to create a complicated design –complexity also drives up costs – but it had to have a universal appeal with the form following the function.”
That functionality was essential when it came to defining the exteriors and interiors,
In March, Amels unveiled the Amels 80 in a theatre in Amsterdam, a major diversion from the industry’s traditional approach of announcing new models. Thomas Weiringa, marketing director of the shipyard, felt it was important to diversify the approach to marketing the model and to create a sense of momentum around the concept of the Limited Editions. The team coined the phrase ‘Evolution is our Nature’ during the release, which encapsulates the ethos of the company and its yachts. During the event the shipyard held a private ‘behind the scenes’ moment where current end potential clients had the opportunity to ask questions to Rose, Espen and Paul in an open and intimate setting.
which are the work of Dutch studio Sinot Yacht Architecture and Design. Annelies Damen had created a fairly refined brief for the interior spaces, noting that there needed to be a large owner’s deck, spacious beach club and that the staterooms would all be located on the main or upper decks.
Most importantly, the yacht had to be adaptable and the design flexible so that a spectrum of owners could customise it to their needs, without the need to make major changes to the engineering. This gave Øino and his team a foundation to work with, which was then built upon by Paul Costerus and the team from Sinot who focused their interior designs on the adaptability of spaces.
Nature has been a theme of Sinot’s work in recent years and with the intertwining of the relationship between the yacht and her environment being a key element of Damen family’s concept of the yacht, the studio was a clear choice. The team was briefed to create a warm environment with sustainable materials and to let these materials speak for themselves, without embellishment.
“The materials needed to be made to last, to be rigid and have a lifespan that will protect the interiors for years to come,” says Paul Costerus. “That all plays into the commercial viability of these yachts as well. Amels wants to protect the investment that its clients make by building vessels which have a future.”
More than 40 Limited Editions superyachts have been delivered since 2007, a credit to the success of the concept which began with the Amels 171 – a design which evolved into the 55-metre Amels 180 and of which 25 yachts were sold. With the concept of semi-custom becoming increasingly diluted in the industry, and as a result somewhat disregarded, Amels has worked hard to remain true to the term. The indepth research and transparent approach to its process has resulted in a reputation for the gold standard of semi-custom yacht construction. In the new year the shipyard will begin the second hull of the series, regardless of whether the first has yet found an owner – a further testament to the confidence the shipyard and the management team has in the concept of the Amels Limited Editions.
New and emerging technologies will have a dramatic effect on the way yachts will be engineered and operated in the near future. With the help of Kongsberg Marine, we take a look at how the industry is moving towards smarter and safer navigation by harnessing the power of Artificial Intelligence, Machine Learning and Augmented Reality.
BY JUSTIN RATCLIFFE
As in the automotive sector with driverless cars, marine technology companies are starting to implement automated navigation on ships in a technological transition not seen since the shift from sails to engines. But although Maritime Autonomous Surface Ships (MASS) might make sense in some commercial applications, the operational profile of a yacht is less suited to automating the functions carried out by the crew. However, the same technology still has relevance for large yacht operations.
“When talking about automated navigation it’s important to distinguish between autonomous and unmanned vessels,” says Roger Trinterud, Sales Director at Kongsberg Maritime. “They are not the same thing, so you can have autonomous unmanned vessels and autonomous manned vessels. In the case of superyachts we’re more interested in the latter and how some degree of automation can help crew when it comes to improving safety, predictability and efficiency.”
As a leading supplier of bridge systems for a wide range of vessels, including superyachts, Kongsberg is investing heavily in ‘Full Picture’ technology: smart, automated solutions based on precise sensor data to detect and classify other vessels, objects in the water, the shoreline, and so on, which can then be fused in real time to improve situational awareness, motion prediction and automated manoeuvring. Kongsberg already has such systems up and running for commercial applications in Norwegian coastal waters (see sidebar).
Situational awareness is a key element of the decision making process during navigation, especially in congested waters or at night. Human situational awareness describes our perception of and response to our surroundings and the ability to draw on a range of interconnected experiences to make decisions based on the whole scenario. Artificial Intelligence (AI) basically mimics the structural connectivity of our brains by using sensors, sensor fusion and highend processing to create a similar system of perception and response.
The right synergy between AI and human intelligence exploits the strengths of AI, while enabling the crew to enhance their situational awareness and maintain control. Essentially, it gives the captain a higher understanding of the ship’s surroundings. In turn, interaction with the bridge personnel can make machines more ‘intelligent’ and allows the crew to focus their attention and energy on guest-related tasks.
“The system fuses sensor data from radar and cameras, together with ECDIS charts, GNSS and AIS to create a 3D geo-located model that segments the sky, land and sea and all static and moving objects inside the coverage area,” explains Trinterud. “Objects are classified and tracked and the results are ‘stacked’ in a single representation using Augmented Reality (AR), or you can export the data to view in conventional bridge systems. If the
Three vessels equipped with Kongsberg smart navigation systems represent important steps towards the integration of autonomous technology into everyday shipping operations. The Yara Birkland, an 80-metre autonomous container ship, and the Asko Autobarge, a 67-metre autonomous barge, both operate with reduced crews along the Norwegian coast and will be become fully unmanned from 2024.
The Bastø Fosen VI is a 139-metre car and passenger ferry that has had automatic docking functionality since 2020, but is still manned. The solution is also known as ‘adaptive transit’ by which all docking and crossing functions are au -
tomated, but the bridge is fully staffed and the crew remain in charge. If another vessel or objects are detected on a collision course, for example, an alarm will sound and the captain will take control.
A coastal express cruise vessel operating in Norwegian waters has also been fitted with a smart sensor system for safely navigating a narrow canal that is only 70 centimetres wider than the maximum beam of the hull. International regulatory bodies are still in the early stages of developing legislation to accommodate automatic marine operations and Kongsberg worked closely on all the projects with the Norwegian Maritime Authority .
system comes across a strange object, a kayak for example, it will alert the personnel on the bridge, ask for their input, and ‘remember’ the object the next time through a process of human-assisted machine learning.”
What does this technology provide that a crew cannot do on their own using traditional navigational systems alone? By detecting the fixed shoreline, for example, it can create a virtual navigational centreline so a yacht can stick exactly to the middle of a narrow channel, or when berthing in a tight gap between two other yachts.
Another advantage is that the system can measure what Trinterud refers to as the ‘steel-to-steel’ distance between two vessels, or a vessel and a fixed landmark. Distances are usually measured as the space between the GPS antennas on the masthead, but how useful is that information for two superyachts manoeuvring in a tight anchorage at different angles to each other? More relevant is knowing the closest point between your own bow or stern and the other yacht. Because the camera feed captures the whole outline, the data can be extrapolated to calculate the closest distance between the two vessels, not the distance between their two centre points.
“With radar you may have an accuracy of plus or minus 10 metres, but with the camera data we can get down to one metre or even
The Warsash Maritime Autonomous Surface Ships (MASS) Research Centre, part of Solent University in Southampton, is involved in researching maritime autonomy as well as the human element of working with smart systems. The Centre is headed up by Captain Zakirul Bhuiyan, who has over 30 years’ commercial maritime experience.
“Advancements in technology will make the human-machine interface even more critical for the safe and efficient operation of MASS,” says captain Zakirul Bhuiyan, founding director of the Centre who has over 30 years’ commercial maritime experience.
“Although significant advances have taken place to develop MASS technologies, very little research has been carried out in analysing the human element, the human-machine interface and seafarer training needs for working with smart ships, smart ports and MASS.”
Bhuiyan believes increased automation will impact superyacht operations in three main ways: the reduction of incidents due to human error (the most common cause of accidents); less environmental impact through the optimisation of yacht operations; and lower operational costs for owners because there will be fewer seafarers on board.
The Warsash Superyacht Academy is the largest institution in the UK providing training for superyacht crews. The UK Government’s Maritime 2050 Technology and Innovation Route recognises the valuable experience of existing seafarers and seeks to develop education models to provide the skills required in the face of advancing technologies.
To ensure the regulatory framework for Maritime Autonomous Surface Ships (MASS) keeps pace with technological developments, the International Maritime Organisation (IMO) has completed a scoping exercise to assess existing IMO instruments and how they might apply to vessels with varying degrees of automation. In April 2022 the Maritime Safety Committee (MSC) of the IMO commenced work on the development of a goal-based road map regulating the operation of MASS in the form of a non-mandatory Code,
with a view to adoption in the second half of 2024 as the first stage. The degrees of autonomy identified for the purpose of the scoping exercise were:
Degree one: Ship with automated processes and decision support: seafarers are on board to operate and control shipboard systems and functions. Some operations may be automated and at times be unsupervised but with seafarers on board ready to take control.
Degree two: Remotely controlled
ship with seafarers on board: the ship is controlled and operated from another location. Seafarers are available on board to take control and to operate the shipboard systems and functions.
Degree three: Remotely controlled ship without seafarers on board: the ship is controlled and operated from another location. There are no seafarers on board.
Degree four: Fully autonomous ship: the operating system of the ship is able to make decisions and determine actions by itself.
less,” adds Trinterud. “Moreover, the accuracy of the camera is based on the number of pixels in the image, so accuracy improves the closer you get to the object or objects being monitored.”
The development of autonomous vehicles (AVs) in the automative sector depends on inertial navigation systems that use accelerometers and gyroscopes to accurately track and measure where a vehicle is, how it’s oriented and how it’s moving in every axis. In a marine context, data from a gyro compass fitted with accelerometers and integrated with GNSS can be fed into a computer to produce instant feedback as an ECDIS presentation of a vessel’s current position, speed vectors and estimated future positions.
“You now have a visual prediction or where you will be in 10, 20 or 30 seconds’ time with your current setpoints of propulsion and steering,” says Trinterud. “In automated modes, the predictions also takes future actions into account. Furthermore, because the system calculates the entire length and breadth of the vessel you can see the probable area of water covered during the manoeuvre. If the water in the shaded area is too shallow, for example, the captain on the bridge knows he should intervene and manoeuvre differently.”
Motion prediction can be used simply as a useful visual aid, but as an automated function during manual operations it provides an extra level of safety to the navigator’s formal training or gut instinct and the critical question, “Am I doing the thing?”
Even with the use of CCTV cameras, it is often difficult for a helmsman to judge distances between the hull and the quay, hence bridge wings on vessels for visual confirmation. Elements of both situational awareness and motion prediction come together during docking operations when it is vital to know where the vessel is, and how it is positioned with regards to the quayside and obstacles.
Last June, the self-driving ‘new’ Mayflower arrived in Halifax, Nova Scotia, Canada, having successfully completed a 40-day voyage across the Atlantic from Plymouth, UK. Some 400 years after the original Mayflower sailed the same course, the 15-metre solar-powered trimaran is the first automous vessel to make the ocean crossing. Originally headed for Washington, D.C., the prototype vessel diverted to Canada so the team could fix a faulty starter on the back-up generator.
The initiative was led by Plymouth-based M Subs, which specialises in the design, manufacture and operation of manned and unmanned vehicles for military and commercial markets. A global consortium of partners include Marine AI whose Guardian system uses Artificial Intelligence to enhance the safety and control of both manned and unmanned vessels.
The Guardian system aboard the Mayflower is based on IBM’s powerful ODM (Operational Decision Manager) software – the same software relied on for mission and business decision making. As well as increasing situational awareness, fuel efficiency and safety at sea, the regulatory compliant system combines real-time weather, current and AIS data with local sensors, computer vision and complex modelling to make course, speed and direction decisions. Marine AI uses the term ‘Explainable AI’ insofar as every decision is transparent, auditable and can be interrogated on-the-fly.
Data fusion is also key to Kongsberg’s all-speed autopilot system that combines traditional autopilot and trackpilot functions with joystick and Dynamic Positioning (DP) into a single, common control logic, working from high-speed transit down to zero speed electronic anchoring or station keeping.
Electronic anchoring works on a similar principle to Dynamic Positioning, whereby the effect of wind, waves and current as well as a vessel’s own propulsion system are measured by the position-reference systems, gyrocompass and vertical reference sensors to calculate the forces required from the thrusters to control the vessel’s surge, sway and yaw in the horizontal plane.
“But instead of specifying a DP centre point, electronic anchoring mode allows you to create a circle of any size and the thrusters will not be activated anywhere inside the circumference of that circle,” explains Trinterud. “But when you get close to the perimeter the DP system will enegage the thrusters and gently move you to the other side of the circle and left you drift again.”
Dynamic Positioning will normally try to keep the mother ship on station, but the Kongsberg systems allows a reference point outside the perimeter of the vessel to be specified, say to the centre of a fold-down landing platform. This can be useful during tender operations when safety depends on zero speed difference between the tender and the point of embarkation or disembarkation.
“The technology is ready and could be included in a technical specification tomorrow,” says Trinterud when asked when we might see some or all of these automated functions on a superyacht. “There’s no doubt intelligent data fusion makes for safer and more effective navigation and yacht operations, but of course there is a cost involved and ultimately it’s a decision for individual captains and owners.”
Feadship is looking into how data fusion and AI might affect the design of superyachts and their interior arrangements in the future. Their 81.75-metre Pure concept, for example, does not have a bridge deck – it doesn’t need one as the yacht is controlled from a concealed command centre from where everything is simulated and displayed on
screens, leaving the space formerly occupied by the wheelhouse for guest use.
The information required to drive Pure would come from combined sources such as radar, AIS, maps, depth sounders and cameras strategically placed around the yacht and presented using AR visualisation. Data integration would offer further
assistance to the captain and crew with regards to situational awareness, motion prediction, routing, on-board comfort and finding the most fuel-efficient way to cruise between locations. In later iterations Feadship placed the command centre on the lower deck, which turns the whole bridge deck into prime estate for the owner.
“Most of these technologies are already available and ready to be implemented on superyachts,” says Giedo Loeff, Head of Research and Development at Feadship. “More problematic is the legislative side and whether diverting crew from operational duties still constitutes safe manning, for example. What we’re focusing on now at Feadship is our Polestar Remote Monitoring system that uses data optimisation and AI to provide after-sales services such as diagnostics and predictive maintenance. We’re not there yet and it’s going to take time, but it’s the logical next step.”
A high-tech graphene producer may not seem the most obvious investment for a yacht brokerage house, but for Jamie Edmiston it was a chance to acquire a business that may outline a possible future direction for yachting.
BY CHARLOTTE THOMAS
When Jamie Edmiston, CEO of Edmiston, suffered a flat car battery one autumn morning in 2020, little could he have known it would lead to a company acquisition, a foray into the cutting edge of materials science and a vehicle that could play a part in yachting’s gradual move toward net zero. It was a helpful neighbour who helped get Edmiston’s car going and engineered a meeting between Edmiston and a scientist friend. And so it was that Jamie Edmiston and Alex Holden, Strategy Director at Edmiston, found themselves heading to Cranfield University in Bedfordshire, UK.
The company they were going to see was Cambridge Nanosystems, initially founded in 2012 as a Cambridge University spin-out focused on graphene production and application development. The brain behind much of the tech was company co-founder Professor Krzystof Koziol, Cranfield Professor of Composites Engineering and head of the enhanced Composites and Structures Centre.
“My plan was to go to the meeting, be polite and leave, but we were introduced to Krzystof,” Edmiston begins. “He explained to us what graphene was, and how they had found this incredible technology to create graphene out of methane.”
Long touted as a miracle material, graphene was first postulated in 1947, but it wasn’t until Andre Geim and Konstantin Novoselov at the University of Manchester managed to isolate it in 2004 that its true potential became known. Their work earned them a Nobel Prize and their publication, along with the method they used to isolate a single layer of graphene – using sticky tape – sparked a graphene gold rush.
The Graphene Council describes graphene as a single layer (monolayer) of carbon atoms tightly bound in a hexagonal honeycomb lattice; it is an allotrope of carbon in the form of a plane of sp2-bonded atoms with a molecular bond length of 0.142 nanometres. This basically means that pure graphene is not only the thinnest material known to man (so thin it is considered a 2D material) but also that it has exceptional properties, including being the best conductor of both heat and electricity and almost completely transparent. It is also the strongest material yet discovered (some 100-300 times stronger than steel), as highlighted by the Nobel announcement which offered that a one-square-metre graphene hammock could support a 4kg cat but would only weigh as much as one of the cat’s whiskers.
By stripping the carbon out of the methane, we reduce the amount of CO2 emissions potential when the resulting hydrogen-rich gas blend is burned.
found a new CEO in John Hartley, a Cambridge graduate in climate change and environmental economics; and third, he rebranded the company Levidian Nanosystems. Progress since then has been swift. By focusing on three verticals of graphene, hydrogen and decarbonisation, the business has started to show signs of success with considerable further potential.
Central to Levidian is LOOP, a technology that takes methane – an extremely potent climate change gas that produces CO2 when combusted – and breaks it down into carbon and hydrogen by bombarding it with microwaves which ionise it into plasma.
“This is the point in the process when methane (CH4) is cracked into its constituent atoms,” says Ian Hopkins, chief production officer at Levidian. “By stripping the carbon out of the methane, we reduce the amount of CO2 emissions potential when the resulting hydrogen-rich gas blend is burned.”
Having been “blown away” by their visit, by the time Edmiston and Holden had got back to London, Edmiston had made a decision to invest in the company.
“There were some other shareholders who had totally lost interest and wanted out –they didn’t understand it and it wasn’t their core business,” Edmiston explains. “So on 23 December, 2020, Alex and I signed the papers and I woke up in January as a shareholder in a graphene business.”
Edmiston’s background in branding immediately came into effect. His first step was to rehire some of the key scientists who had worked at the company previously; second, he
The process also locks methane’s carbon into very high quality graphene, collected as a powder, and in addition it can produce pure hydrogen (via a hydrogen separator) that can be used instead of fossil fuels. The LOOP process differs to other methods in that it doesn’t require any added heat or catalysts to crack the methane.
Levidian’s LOOP primarily allows industrial operations that use natural gas as part of their heat and power train to reduce the amount of CO2 emissions they produce. It’s not hard to see how this could apply directly to the superyacht industry, and not just because Levidian can offer a form of carbon offsetting. “LOOP can be deployed to a shipyard to decarbonise any natural gas usage,” says Hopkins.
Moreover, the ability to produce pure hydrogen could prove extremely interesting given
the developments currently underway in alternative power systems on board yachts. “There are a number of hydrogen yacht projects going on as we speak and I’m actually involved in quite a big one,” says Edmiston.
It’s not just reducing CO2 and producing hydrogen that makes LOOP interesting for a shipyard; there is also the high quality graphene that is likely to see increased demand as technological breakthroughs make more graphene products viable, and that could offer a form of cost-offsetting.
“The Graphene Council estimates that the 2019 market for graphene reached US$78.7 million, up from US$10.9 million in 2013,” says Zeitlin. “It is challenging to predict just how enormous the market will be in 10 years, but we can say with confidence that it will grow very rapidly.”
That growing market will likely mean a surge of graphene applications that are particularly pertinent to the yacht industry. “Graphene has a number of applications in coatings that could reduce maintenance and improve antifouling,” suggests Hopkins. Further, development of high-density, fast-charging graphene batteries – perhaps coupled with efficient and flexible graphene solar cells – could dramatically alter the operational effectiveness of all-electric powertrains or hybrid silent running systems.
Levidian announced in late Spring 2022 that it had signed a deal with UAE-based Zero Carbon Ventures for 500 LOOPs which will remove half a million tonnes of CO2, according to Zeitlin. It is perhaps this aspect most of all that is most exciting for Edmiston from a pure business point of view, but also in terms of taking measurable action and spreading awareness of the need to move toward net zero.
“The interest I have in engaging Edmiston and Levidian is not just commercial,” he offers.
“It’s also that we have a strong brand in the yacht business and we have a platform on which we can stand – and some people might listen to what we say. I think if companies like ours take small steps to mitigate what we’re doing, then hopefully we can get somewhere. I’m not claiming to be an eco-warrior and I’m not saying we’ve got the answer, but it keeps the conversation moving forward.”
Ever since Geim and Novoselov made their leap in 2004, the race has been on to develop products that draw on the wonder properties of graphene. While at first it seemed to be a miracle material in search of a purpose, research and improved flows of high quality graphene are finally bearing fruit.
Graphene’s conductivity and transparency make it a great alternative to indium tin oxide (ITO) which is the most commonly used, but expensive and brittle, material for touchscreen tech and graphene touchscreens are already on the market.
The addition of graphene to concrete has also been realised and adding just 0.1 percent graphene to concrete increases its strength and reduces material requirement by up to 30 percent. This is important: if the concrete and cement industry were a country it would be the third largest contributor to global CO2 emissions behind China and the US. Like concrete, adding graphene to rubber also makes a big difference and could extend tyre life by 40 percent.
Graphene batteries are getting nearer to commercial reality and offer super-fast charging along with five times the energy density of lithium-ion batteries. Research teams have also recently made gains in using graphene in PEM (proton exchange membrane) fuel cells. Graphene aerogel is one of the world’s lightest materials and could offer absorption rates several hundred times that of currently available materials for oil and environmental clean-up. Graphene could also prove central to developing far more durable paints and coatings, and its properties also make it a key material for next-generation solar cells or even solar power-producing coatings.
The superyacht fleet has a problem: while fuel cells and multifuel engines may be the future for power on board, what of the 6,000 vessels still reliant on fossil diesel? Second-generation renewable fuels may offer an immediate solution – albeit at a price.
BY CHARLOTTE THOMAS
“Yachts live forever,” says Giedo Loeff, Head of Research and Development at Feadship. “We have a huge, 6,000-strong fleet and we will keep on refitting them. They will survive though to the 2050 Net Zero targets, and in order to decarbonise we need to have all these vessels sail on non-fossil fuel, and they can only run on diesel today. Converting all these yachts to run something else is not impossible, but it’s not viable.”
This is an eye-opening perspective, particularly when everyone seems to be touting hydrogen, methanol and fuel cells as our environmental saviours. With such a large existing fleet, 70 percent of which are below 50 metres in length, and with the technological and design challenges of future fuels still a huge hurdle to overcome, what does that mean for owners now and in the near future?
It turns out there is a solution that enables the current fleet to decarbonise without making any modifications to their vessels. It is often referred to as ‘biodiesel’, although more accurately we should be calling it renewable diesel or synthetic fuel. Biodiesel has been around for some time and is used as an additive to conventional fossil diesel, but it also has a reputation for causing problems in tanks and engines, and for the sometimes non-sustainable feedstocks used to make it.
But things are changing. “First, I think it is important to distinguish between the different types of sustainable diesel replacement fuels,” begins Bart Hellings, COO/CTO of GoodFuels, a Dutch company committed to facilitating the energy transition away from fossil fuels that has supplied a handful of superyachts with renewable diesel. “With biodiesel, many people refer to a product called FAME (fatty acid methyl-ester) that has been around for 20 years or so, but it is way trickier from a technical perspective than conventional fossil diesel. There is also a second-generation product called HVO (hydrotreated vegetable oil) that is a sustainable drop-in replacement for diesel, which has properties that are similar or superior to conventional fossil diesel. This is the fuel that we think could play a very important role in the superyacht sector going forward.”
HVO has been commercially available for around five years and is promoted as an alternative to diesel for transportation, in particular for fleets of trucks and for large commercial ships, as well as for aviation. Indeed, there is a growing list of refineries scaling up production of HVO. Finnish company Neste – one of the world’s largest producers of renewable diesel with refineries in Finland, The Netherlands and Singapore – claims that global renewable fuel production could reach over 1,000 megatons of oil equivalent by 2040, which it says would be enough to replace all fossil fuels used in aviation and maritime transport, as well as a substantial part of road transport. But what of the now?
“This fuel is readily available now – it has been developed for road use and is therefore
The term biodiesel is typically associated with FAME (fatty acid methyl-ester), a first-generation biofuel created through a process of transesterification of feedstock vegetable oils where a glyceride reacts with an alcohol in the presence of a catalyst. It’s a relatively simple process from a technical perspective and that allows for localised production. FAME is rarely used as a straight diesel replacement but is often added to fossil diesel, typically in quantities up to a maximum of 7 per cent in Europe under the EN590 diesel standard.
100 percent suitable for the engines that power superyachts,” says Hellings. “The fuel we supply to the yachting segment is more or less comparable to fossil diesel – it has slightly more energy per kilogram, slight less per litre, but overall you don’t really notice a difference on board. You don’t need to recalibrate the engine or change any equipment.”
This last point is key, because it opens the door for superyacht owners, captains and managers to make the decision to switch to renewable diesel. “Our experience is that you need the whole ecosystem to change,” says Hellings.
The first person you have to convince is the one who pays the bill. To do it in a responsible way, you also need approval from the engine manufacturer, from the Class society, from the insurer, and from the manufacturers of all the other connected components.
All the main engine manufacturers have now updated their guidance to say that renewable diesel that complies with quality standard EN15940 can be run in their engines. Caterpillar, for instance, notes that no engine conversion process is needed, that renewable fuels are compatible with aftertreatment technologies such as SCR, that they are compatible with typical filters and engine oils, and that they can be stored in the same tanks as diesel fuel.
Rolls-Royce, parent to MTU, is taking a proactive approach with a pledge to reduce the emissions of its product portfolio by 35
It’s fair to say that FAME has generated controversy over the past few years. It has a relatively short storage life (making it particularly unsuitable for superyachts where a tank of fuel might well last a season or longer), has poor cold temperature properties, is prone to diesel bug, has a higher water content, has increased chance of injector and filter clogging, and offers less energy density that means a higher fuel consumption.
By contrast, HVO (hydrotreated vegetable oil) is produced by the hydrogenation of waste vegetable oils and animal fats at high temperatures and pressures using hydrogen and catalysts. This produces a colourless and odourless fuel that has an identical chemical composition with fossil diesel.
When produced to EN15940 standards, this second-generation fuel can be used as a straight fossil diesel replacement with no modifications to engines or associated systems, or can be mixed with conventional diesel in any ratio which means it offers the ultimate in flexibility for superyachts: if you fill up with HVO in The Netherlands but can’t easily get HVO at your destination, no problem, just top up with conventional diesel.
Feedstock is the collective term for the source materials from which biodiesel and renewable fuels are derived. Traditionally these would be agriculturally produced oils such
as vegetable oil, rape seed oil, palm oil and the like. Second-generation fuels such as HVO draw on waste products like used cooking oil and animal fat from the food industry,
fish fat from fish processing waste, and technical corn oil that is a residue from ethanol production. However, there is still a limit to these feedstocks, which creates a problem for the increase in production of HVO to meet future demand.
Alternative feedstocks are now being explored by companies like Neste and GoodFuels, including the use of algae, which acts as a carbon sink in its growth phase, and other industry organic by-products such as sawdust and wood chips, which can be converted to liquid fuels through a process called pyrolysis. Further research is being done to explore renewable materials from municipal solid waste streams and to develop processes that will mean waste plastic can be used as a feedstock.
percent by 2030, and part of that will be simply moving away from fossil fuels in its combustion engines. Renewable diesel (a paraffinic fuel oil with a cetane number that is actually higher than fossil diesel) is perfect for that, as it reduces CO2 emissions by up to 90 percent and also benefits from reduced NOx, zero SOx and less particulate matter than fossil diesel.
In spite of this, the uptake of renewable diesel by the superyacht fleet has been minimal. Loeff thinks this comes down to three reasons: understanding, reputation, and cost.
“First it’s about well-to-wake,” he explains. “If you comprehend that, you understand why HVO is something totally different from regular fossil diesel, because it is about running yachts on non-fossil energy. I don’t think everyone understands that truly.”
Second, there is nervousness within the market about biodiesel and FAME having nasty effects on high-spec engines.
Left: Neste uses proprietary NEXBTL technology to turn a wide variety of renewable fats and oils into renewable products, such as fuels and feedstock.
“But HVO is different,” says Loeff, “it’s a synthetic fuel that has no contamination, and engine emissions are also reduced because the fuel has very high purity.”
His third point is that it’s much more expensive than regular diesel, and it has to come typically from much further away when you bunker, so that’s an additional cost in the supply chain.
Hellings agrees, but points out that the cost of renewable diesel also varies significantly, because some countries offer subsidies or incentives for renewable fuels. The Netherlands is a prime example.
“We have a quite substantial incentive scheme for fuel supply to shipping, and that means if we supply HVO out of The Netherlands we would be looking at a price that is between 50 percent and 100 per cent higher than fossil diesel,” he says. “But if we were to supply it out of the Caribbean, we would likely be looking at double or triple the price of conventional diesel.”
The same is true for more localised delivery: there are no subsidies in France, for instance, meaning bunkering would be more expensive on the Côte d’Azur than in Rotterdam.
As HVO production scales up and more feedstocks become viable, does that mean the HVO will become more widely available and, at the same time, more cost effective? Moreover, has the rising price of fossil fuels following the events unfolding in eastern Europe meant that the price gap has closed?
Unfortunately, it seems that the answer to both these questions is ‘no’. In the first instance, a combination of rigorous emissions goals and a drive for transport companies in all sectors to show they are taking positive action on climate change will likely drive demand up in line with that increase in production. On the second point, Loeff suggests that the energy market is uniform and linked whether referring to conventional fossil or renewable fuels.
There is also the question of traceability. “It’s the elephant in the room with these fuels,” says Loeff. “It’s all about transparency, because the products which aren’t traceable or which don’t have the correct certification don’t have value, because you can produce a similar fuel to HVO from natural gas which is a fossil feedstock. The same is true, incidentally, for hydrogen.”
The bigger hurdle, however, is uptake. As Loeff points out, he sees recreational craft using HVO locally in The Netherlands, but use on superyachts so far has been limited:
“I haven’t heard about a yacht bunkering, or at least not for 100% HVO, and certainly not from our fleet yet,” he says. “But I think there will be some owners who understand it and are willing to pay the premium because in terms of the operational budget it’s still manageable. But I do wonder how the budget issue is resolved; I think that only happens when non-fossil is subsidised, like it is in The Netherlands.”
There’s another driver that may dictate the transition away from fossil fuels: legislation. It is already taking shape in the IMO relating to greenhouse gas standards, something that SYBAss is monitoring closely, but more importantly the EU is taking big steps of its own.
“The EU has announced that ships over 5,000 GT will need to report their fuel use, both the amount of fuel and the fuel’s specification,” says Loeff. At the end of the day it will be about global warming potential (GWP) – a means of reporting warming-equivalent emissions – and the adding of that to the Emissions Trading Scheme, which represents the cost that somebody has to pay. “With non-fossil fuels like HVO there’s pretty much no GWP, but with fossil fuels there’s a lot,” Loeff adds.
With the regulations applying to commercial shipping over 5,000GT there is potential for it to include superyachts at the larger end of the scale, although there is debate as to whether yachts will slip under the radar. Either
way, it speaks to a growing shift in the marine environment and it’s not hard to imagine such emissions reporting being extended downwards in the future, which would likely snare considerably more of the superyacht fleet.
Arguably the most critical factor, however, is the collective conscience of the superyacht fleet and their owners. With HVO completely interchangeable with fossil diesel, even owners who baulk at the cost can take small steps toward decarbonisation by moving to 10 per cent or 20 per cent HVO in their tanks.
“There is no real excuse to wait anymore,” Hellings urges. “We understand that it feels uncomfortable to suddenly change to 100 per cent alternative fuel, but that should not be the reason not to do it. We have been supplying the same HVO fuel to the same type of engines for five years already, without any issues; it’s better than the conventional diesel you buy. It’s important to get people on board with this journey as soon as we can, and to get those early adopters who can inspire the next tier.”
The METSTRADE Show is the happening meeting place in Amsterdam where the international leisure marine community gathers. In a hospitable and safe environment, we make you feel at home to meet and mingle with the entire industry. Feel connected and charge yourself to optimise your business.
We talk to Matthew Francis, supply-chain director at Sunseeker, about a tough job made even more challenging by recent global events.
BY PHIL DRAPER
In supply-chain terms it doesn’t really matter whether a yard is building series, semi-custom or full-custom yachts. Handled properly, the procurement process is the same. It is about ensuring the right materials and equipment get to the right point of assembly at the right time, and at the best possible price.
Up until recently efficiency meant carrying minimal stocks of raw materials and components. The idea was to get what you needed delivered by suppliers at the last-minute – the essence of just-in-time and lean manufacturing practices – ideally on ‘terms’, meaning deferred payment. These are lean times,
however. Certain materials and equipment are hard to source, prices are rising, and delivery dates are far from certain.
Like all boatbuilders, Sunseeker has had to adapt to these unusual times and the man charged with keeping things moving is supply-chain director Matthew Francis, who has spent all but two of the past 32 years of his career at Sunseeker. Prior to taking his current job, he was mostly in operational management roles. The two years out were spent as head of group operations at British sailing yacht builder Oyster.
When he started at Sunseeker it employed around 250 people, had a portfolio between
27-47 feet, and was building a little over 400 boats a year with an average ex-works value of little more than £70,000. The boats were much smaller and simpler then. Today, Sunseeker employs 1,800 people, the model range spans 34-131 feet, and the business is presently building nearly 150 boats a year with the average ex-works values more like £2.5m. Some 140 Sunseekers over 24 metres have been delivered since the first Predator 80 was handed over in 1997.
“The supply-chain function does not happen remotely,” says Francis. “The supply chain
function is casting, wardrobe, make-up and scenery. Production is choreography. Operations director Steve Timms and I talk constantly. When I’m discussing issues with Steve, we both get it. It means there’s more focus on the solution rather than being distracted by misunderstandings. For instance, we both know the generators need to go in before the soft hatches, and then the cockpit furniture can’t go in until after the patio doors have been installed.”
Happily the order book is very healthy, which helps procurement visibility. Sunseeker is largely sold out now through until the end of 2023, so its supply-chain team knows what boats need what parts a long way in advance.
When Francis rejoined Sunseeker from Oyster two years ago, he had a team of 10. He has 16 working with him now and needs to push that up to around 20 in the medium term. More staff are needed because the company is in the middle of an aggressive new development programme that will see the product range extended to 22 models over the next couple of years, one of several strategic moves instigated by CEO Andrea Frabetti. The Sunseeker model range included just a dozen models three years ago when Frabetti arrived.
Detailed financial foresight has enabled a much closer management of supplier payments, providing smooth financial controls. Currency issues are always something to watch. Sunseeker does what most businesses do to mitigate against unfavourable currency shifts. “Plus we have currency fluctuation agreements with some suppliers, which shares the risks when exchange rates stray beyond certain limits,” says Francis.
Sunseeker has thousands of vendors on its purchasing system. However, despite more models and big ‘bills of materials’ for every single one of them, just 800 or so are deemed ‘active’, meaning they have supplied products or services over the past two years.
Suppliers are ranked in tiers and appropriately scored. The best a supplier can do is get a high OTIF, which means ‘on time, in full’. The ‘Tier Ones’ are the preferred suppliers, the companies with the closest relationships. There are fewer of those than you might
think, probably under 100 across the whole business. Virtually all are well-known industry names: the big-name engine builders, the main electronics majors, the key thruster and stabiliser manufacturers, the largest deck hardware makers, the obvious composite materials providers, and so on.
The names in the tiers are changing all the time and the ranking system reflects the suppliers’ track record in terms of meeting delivery schedules and warranty claims, and so on, although current market conditions are presenting some very different challenges.
“The best suppliers are often the ones that can best manage the bumps in the road and limit their impact on their customers the least,” says Francis. “The Tier Ones are the heroes, but it’s not all about ticking boxes on a form. Normally we would work hard to decrease our costs. Right now we are more often managing increases.”
Personalities can make a big difference and communication is more important today than ever. Solutions are often compromises, so it
is best for everyone that those compromises are fully understood: “Products don’t solve problems, people do,” says Francis.
“Every supplier is in business at the end of the day,” says Francis, “so we have to be robust in our negotiations, which sometimes ends in ‘no’ from one side or the other. Occasionally personalities do collide and then some can become your ‘Tier Zeros’. However, a change of attitude by a supplier can make all the difference and relationships can be reset.”
Sometimes with all the best wills in the world, supply lines do fail: “Very occasionally we will order what we need twice from two different suppliers knowing full well one is likely to let us down,” continues Francis. “That way we stand a much better chance of getting what we want. And, if we do end up getting both orders fulfilled, that will help us next time.”
Generators are a good example of the issues out there. Boom times in the construc-
tion industry have led to unprecedented demand: “There are just two or three real brand options out there to service our whole model line-up,” says Francis. “And quoted lead times can be 12 months out.”
Engine builders also have had their own delivery problems, usually caused by knockon effects of sub-component supply. Electrical harnesses recently have been an issue, because they previously came from Ukraine.
“Instead of suppliers pushing what we need to us, we are now pulling in what we need from them,” says Francis. “We have now taken responsibility for order collection across virtually the whole business. It’s a more flexible approach and puts us far more in control, leaving our suppliers to concentrate on what they do best. It means less cost, less complexity for both parties. DHL is our logistics partner and when we hear an order is ready to be fulfilled, we essentially instruct them to go get it for us.”
There are several advantages to this approach of controlling what comes in. Prices are negotiated with suppliers that exclude delivery costs, which leaves Sunseeker able to drive a much more attractive deal with DHL, because it is essentially getting a bulk buyer discount rather than paying for one move at a time. A global logistics specialist like DHL is ultra-efficient at moving freight from one place to another and provides a full trackand-trace service.
Francis’s team also keeps an eye on markers that pre-warn of problems to come, such as commodity prices. For instance, hikes in oil prices will always eventually impact the cost of derivatives such as resins. Electronics pricing has gone crazy over the past five months, because microchip costs have soared: “At one point and virtually overnight they went from 70 cents a chip to 70 dollars a chip,” recalls Francis.
Similarly, nickel prices in March of this year were peaking so high that the London Metal Exchange ended up suspending trading. For Francis and his team that run on nickel was an early heads-up that stainless steel prices would soon be rising too and subsequently stainless steel components have virtually doubled in price. A lot of that price volatility was a direct result of the war in Ukraine and Russian sanctions as Russia is the world’s third largest nickel producer. Beyond the iron ore base, 316/316L marine grade stainless steel includes 10-14 per cent nickel.
Aluminium and stainless steel prices have a direct impact on yacht specifications. If the price of, say, metal floor girders gets too high, a spec switch to composites needs to be considered, or vice versa, which in turn can impact overall weight and have knock-on implications as regards the performance of various systems. All these issues get flagged at weekly Executive Team meetings that include the heads of all departments across the business.
The supply chain function is casting, wardrobe, make-up and scenery. Production is choreography.
Evolving market expectations can present their own challenges. For example, yacht windows are getting larger. As those sizes increase, the number of potential suppliers decrease. Less choice of supply ultimately pushes up the risk of being let down. The windscreen of the new Predator 65/65 Sport Yacht is a case in point. Itw is the biggest single pane of glass ever installed aboard any Sunseeker and there are few glassmakers that can supply to such specifications.
Decking also has its issues. Sunseeker is presently transitioning to sustainable alternatives. Over 50 percent of all Sunseekers presently leave with synthetic decks and the remainder with sustainable Forest Stewardship Council-approved teak alternatives. But Francis says that synthetics will be 90 percent by the end of 2023 and probably 100 percent by the end of 2025, although he stresses ultimately the decision comes from the customer. Sunseeker presently has three or four synthetic deck suppliers.
“We’re not wedded to existing marine industry names,” concludes Francis. “We are always looking for new companies beyond the usual suspects. We now have a dedicated member of staff on my team whose job is to look for new potential partners, new materials and new methods. But quality has to underpin everything we do. Ultimately, our job is to source luxury efficiently.”
Is a 100-metre sloop feasible or even desirable? We ask a panel of designers and a spar manufacturer.
The demand for very large sailing yachts is nothing like that for large motor yachts, but over the last few years there has been increased interest in very large sailing yachts. Some projects have been delivered, some are under construction and others are on the drawing board.
We ask a panel of experts – Bart van der Meer (engineering sailing systems at Rondal), Rudy Jurg (sales manager at Rondal), Rob Doyle (Rob Doyle Design), Thys Nikkels (Dykstra Naval Architects) about the challenges of designing, building and operating a 100-metre sloop.
Is it possible to create the mast and rigging for a 100-metre sloop that is both safe and Class approved?
Bart van der Meer: Yes, it is certainly possible to create a complete rig and sailing system for a yacht of this size. It does, of course, present some interesting challenges, but Rondal has built its reputation on resolving challenges.
Rob Doyle: For a 100-metre sloop in terms of length overall, no, it is not possible. For a 100-metre spar height, yes, that is possible. If someone says ’yes’ to a 100-metre LOA yacht they are out of their depth and have not fully researched all the options involved. At RDD we have done a huge amount of research on this question and we are one of the few naval
architects and design studios that have an understanding of the complexibility of such a big rig. Class approval would be difficult, but they will lean hard on the naval architect’s calculations, research and experience.
Thys Nikkels: When we are pushing boundaries with any aspect of a design the answer is always ‘Do your homework!’ If you do not have experience with a certain size or configuration you have to do the necessary research and development to prove the design is feasible. Feasible in concept, safe in construction and safe in operation, only then can you tell a client that it is possible, and to do that you have to work with a team of researchers, material specialists, builders to find the required solutions for the challenges.
Are there any suppliers who would take the risk of building such a yacht?
Bart van der Meer: We have already built three impressive 70-metre-plus rigs and are currently planning a large rig for an 85-metre sloop, which will become one of the world’s largest.
Rob Doyle: There are two really only two manufacturers that can build big rigs. Rigging would be another significant difficulty, along with winches, systems, furling, hull structures, regulations and more.
Even if you could build it, would it be safe to operate for the crew?
Bart van der Meer: Given the exceptional loads, risk factors for the crew are already an important factor in planning sailing systems for today’s largest sailing yachts, especially when racing. These loads and the sheer length and weight of running rigging do increase exponentially when looking at a rig for a 100-metre sloop. But we should keep in mind that, at this end of the superyacht fleet, only the most highly qualified and experienced crew would manage and trim the sail plan. They would do so with access to very sophisticated load sensors and safety triggers to ensure loads and risks remain within the design boundaries. There is also the possibility that these big rigs could be operated fully automatically. Especially as the cost related to fully automating a sailing system becomes smaller in comparison to the overall cost. However, this route could present new challenges of its own until fully proven.
Rob Doyle: We will always design rigs with safe operation in mind, the numbers involved are huge and operation of a sail plan of this size would be very difficult, if not impossible. The size of the systems to control such a rig are significant and very detailed research is required,
the sparmakers can build very big rigs – the limit is the yacht not the spar tube.
Thys Nikkels: In the end, a large sloop will only work for the client if it can be safely and relatively easily operated by the crew. Otherwise the rig will never, or only sporadically, be used.
Have you had any requests for such a large project and do you expect that one day a client will decide to build one?
Rudy Jurg: We have already been introduced to enquiries and concepts of this size that for one reason or another have yet to progress. I have little doubt that 100-metre-plus rigs will be built in the future. The first one will be commissioned by a very ambitious and visionary individual with deep pockets. Once this client’s project is afloat, others are more likely to follow.
Rob Doyle: Yes, we have had requests for such yachts a number of times. What we explain first is that the jump from 78-metre M5 to a sloop with a spar length of 100 metres is enormous. If you have not designed and built big rigs before, then a client is very exposed. At RDD we have designed more big rigs, both sloop and ketches, than many other naval architects, but the numbers are staggering when you present the research and the real build numbers.
What are the cost implications of building a 100-metre sloop compared with a schooner of similar size?
Bart van der Meer: One of the biggest cost implications is that most of the hardware needs to be designed from scratch for the sloop. Nothing on this scale is readily available on the market: no furlers, no toggles, no winches. And it needs to be designed not just bigger, but exponentially bigger. Take a runner winch, for example. From a 30-metre sloop to a 60-metre sloop, the retrieving length will double and the pull force goes from roughly 10 to 30 tonnes. If you want to be able to retrieve the runners at the same time, you’ll need four times more winch power to double the speed and more than double the force.
When you recall it was considered doubtful if you could fly a spinnaker from the mast of a 100-foot sloop 30 years ago, we can see that the evolution of marine design technology has always innovated to address such issues. The expertise is there to make the rig of a 100-metre sloop happen, as long as it is accepted that substantial system development costs as well as the hardware manufacturing costs will bear heavily on the first project. For these reasons, it will certainly cost more than the rig of a 100-metre schooner or ketch.
If someone says ’yes’ to a 100-metre LOA yacht they are out of their depth and have not fully researched all the options involved.
Rob Doyle: Hard questions because if you want to be the tip of the sword, a visionary owner that wants to reach for the stars and build the biggest sloop. But you may need to ask yourself: is the ketch a better option at the 100-metre LOA size?
Given all the factors above and from your own experience, what is the ideal size for a super-sloop?
Rudy Jurg: It is difficult to say there is an ideal size, though we do know that the ‘ideal’ size keeps on growing as larger yachts prove their reliability and their capacity to deliver exceptional lifestyle experiences and amenities to owners and their guests. Ultimately the ‘ideal’ will always be related to owners’ plans, their financial resources, their vision and ambition.
Rob Doyle: I believe an 85-metre LOA sloop would be the limit, but there are different factors at play that have to be understood and it’s more about the length/beam ratio than LOA, which would be a more suitable metric to start with. On the limit of tube lengths, you need to ask the spar maker for that number, but we are comfortable with the tube lengths we have spoken to clients and sparmakers about.
New yacht sales are at record levels and there are more than 600 yachts over 30 metres under construction. These yachts represent a value of billions of euros and the construction of these projects provides employment to tens of thousands of people.
On SuperYachtTimes.com and through our intelligence platform SYT iQ we cover the fleet, market and business side of yachting in great detail. Occasionally, we had in-depth features on technology, sustainability, products in-build projects and other technical areas, but it was not our main focus.
Having bought a software company in 2020 (YachtEye) we also became a supplier to new construction projects. As a supplier to some very large projects, I learned a lot more about the complexity of building superyachts and also realised how little information is actually available on how these yachts are built and what the latest technologies are.
It is not only the shipyards that benefit from more than 600 yachts under construction; walking around the METSTRADE in 2021 I also realised how many suppliers are actually active in this industry.
Around this time I started thinking about a specific publication that focuses on the design, construction and refit of superyachts and all the companies involved. While it is not a very big audience in terms of the number of people, it is composed of people who need to make critical decisions that have a big impact on the future of our industry.
Having pondered for a while, I picked up the project in the period between Christmas and New Year. The two key questions that needed to be answered were: are there enough people interested in reading a technical yacht magazine, and is it possible to generate revenue?
Pitching the idea to a few people, I got a lot of positive feedback and decided to take the gamble and produce the magazine. In the first months, the focus was only on the content and when we started selling ads towards the end of June, the responses from clients did not disappoint. Within weeks we had sold out all the ads.
I am very proud of what the team has put together and the support we have received from our clients. But the big question is, what do you, our reader, think of this new magazine?
I look forward to hearing your feedback on the first issue of How to Build It
Merijn de Waard - Director
It
Stay true to your high standards – ask for ALEXSEAL® Yacht Coatings and leave an outstanding, long-lasting impression.