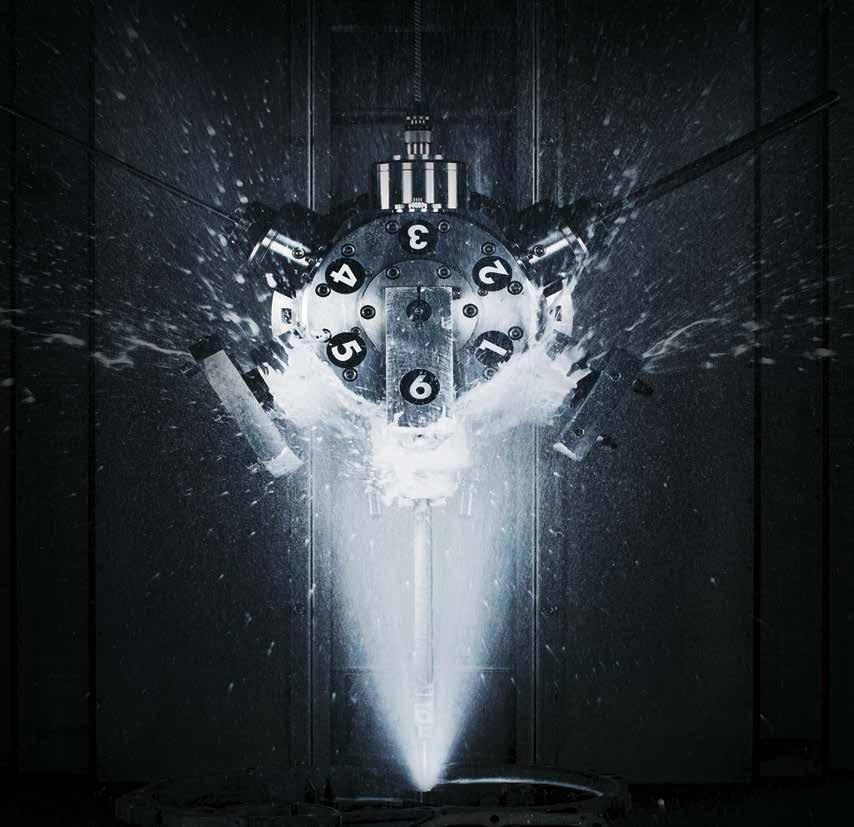
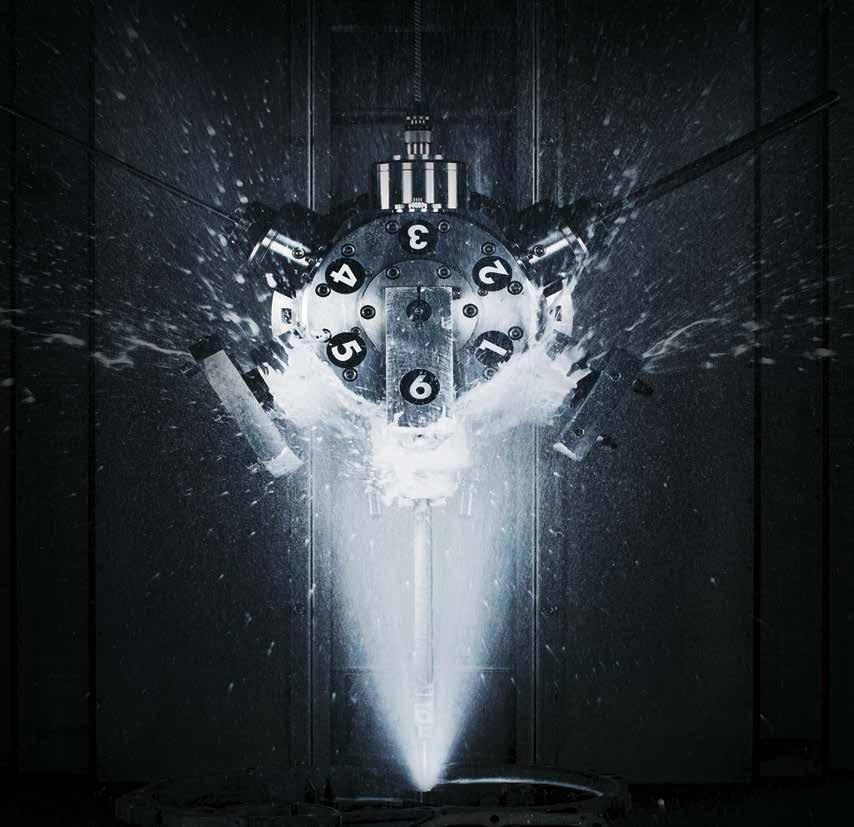
JCC SERIES
Jet Clean Center
DNA | SUGINO’S ongoing beliefs.
Honesty. Innovation. Super Technology.
We have humble and hardworking roots that trace back to Japan in 1938, and now span the globe with locations in 40 countries. Our exhaustive research and development has fueled many innovations throughout our 80 years as a professional engineering company. These innovations are the result of collaborating with our customers and helping them solve the toughest problems manufacturers face today. We believe that listening to our customers and being transparent with them is the foundation for the many strong relationships we have built.
The commitment behind our brand icon.
Sugino’s logo is based on the “!” symbol, and stands for the surprise and delight customers feel when they experience our Super Technology Solutions. Sugino stands for exceeding expectations, and being an innovative partner to our customers around the world.
Cleaning technology that contributes to a carbon-free society.

Explore the JCC (Jet Clean Center) series for the deburring and cleaning of all parts with high pressure water up to 245MPa. Since the JCC’s inception in 1998, it has been highly regarded both in Japan and overseas.
To date, we have delivered more than 6,000 JCC machines in more than 30 countries around the world.
The cleaning and deburring method developed by Sugino is an energy-saving technology that reliably and accurately removes foreign substances such as chips with a minimum of energy. In addition, our original energy-saving package — JCC-eSmart — is installed asstandard, and effectively reduces CO2 by 50% or more compared to the conventional model.
As a leading supplier of deburring and parts-washing machines, we solve customers’ problems in all aspects of quality, safety and environment.
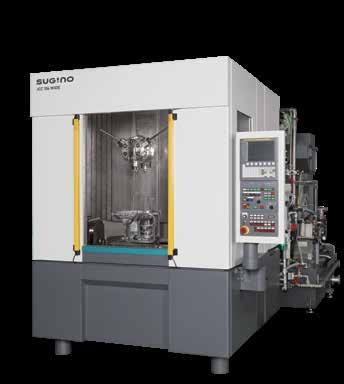
Complete solutions for deburring and cleaning parts.
In addition to our best-selling Open Air and Submerged systems, Sugino offers complete solutions including parts dryers, cleaning liquid purification units, and more. A total solution for your production challenges.
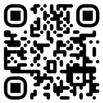



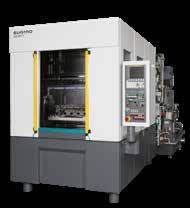
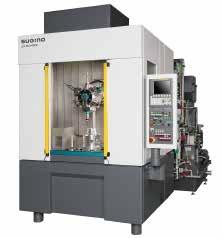

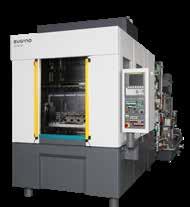
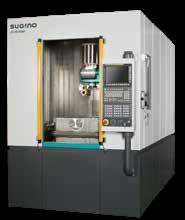
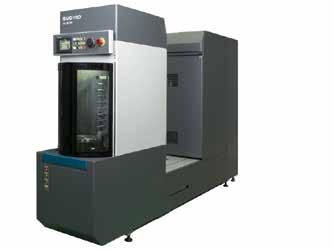
OPEN AIR DEBURRING AND CLEANING
CNC Turret-Type High-Pressure Water Parts Washer
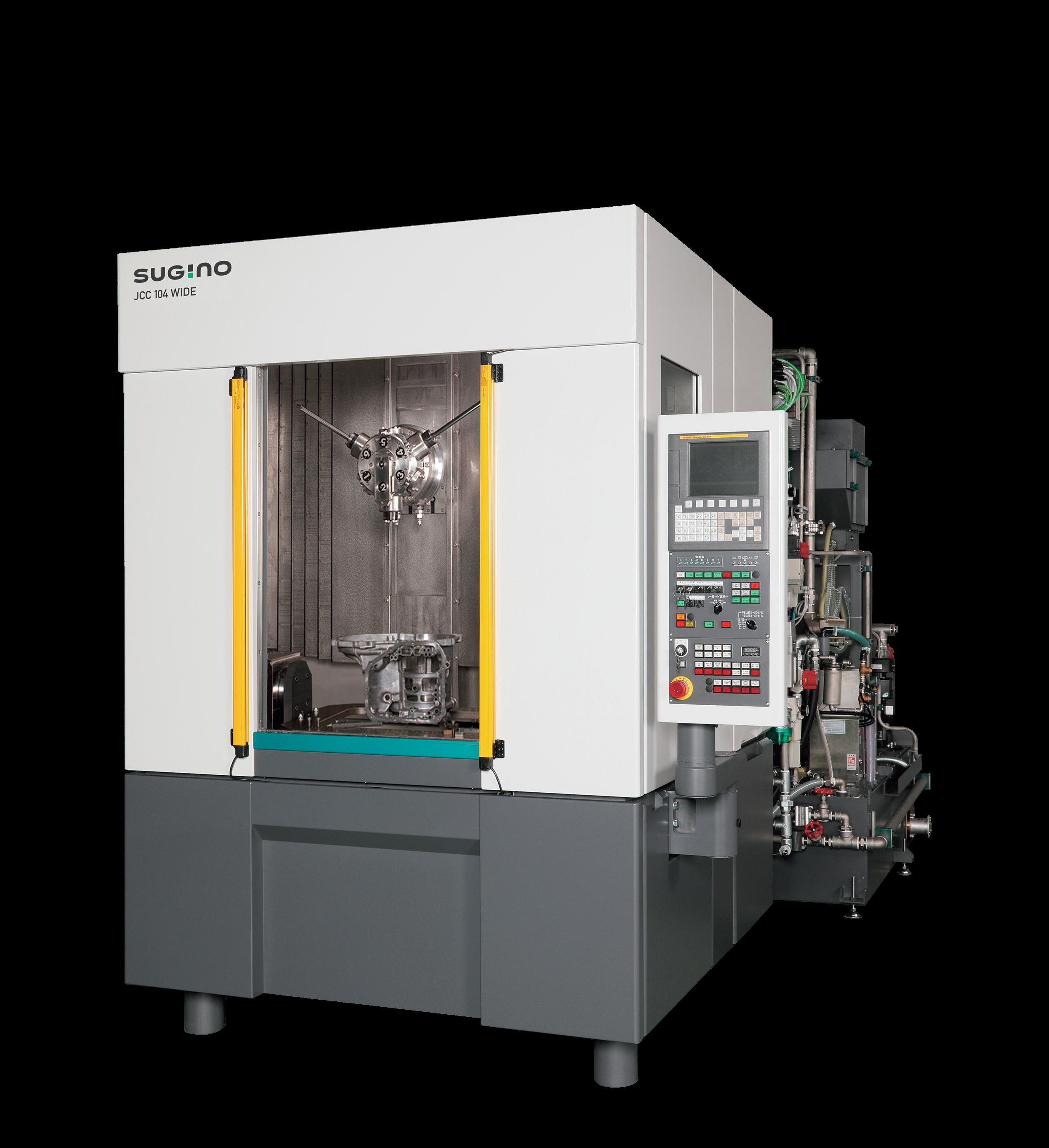
JCC 303 TT

Single Station Equipped with Turn Table, 2 Stations
A deburring washer that removes chips and burrs remaining inside the workpiece with high-pressure water of up to 50 MPa. High-pressure water cleans while deburring, consolidating the deburring and cleaning processes.
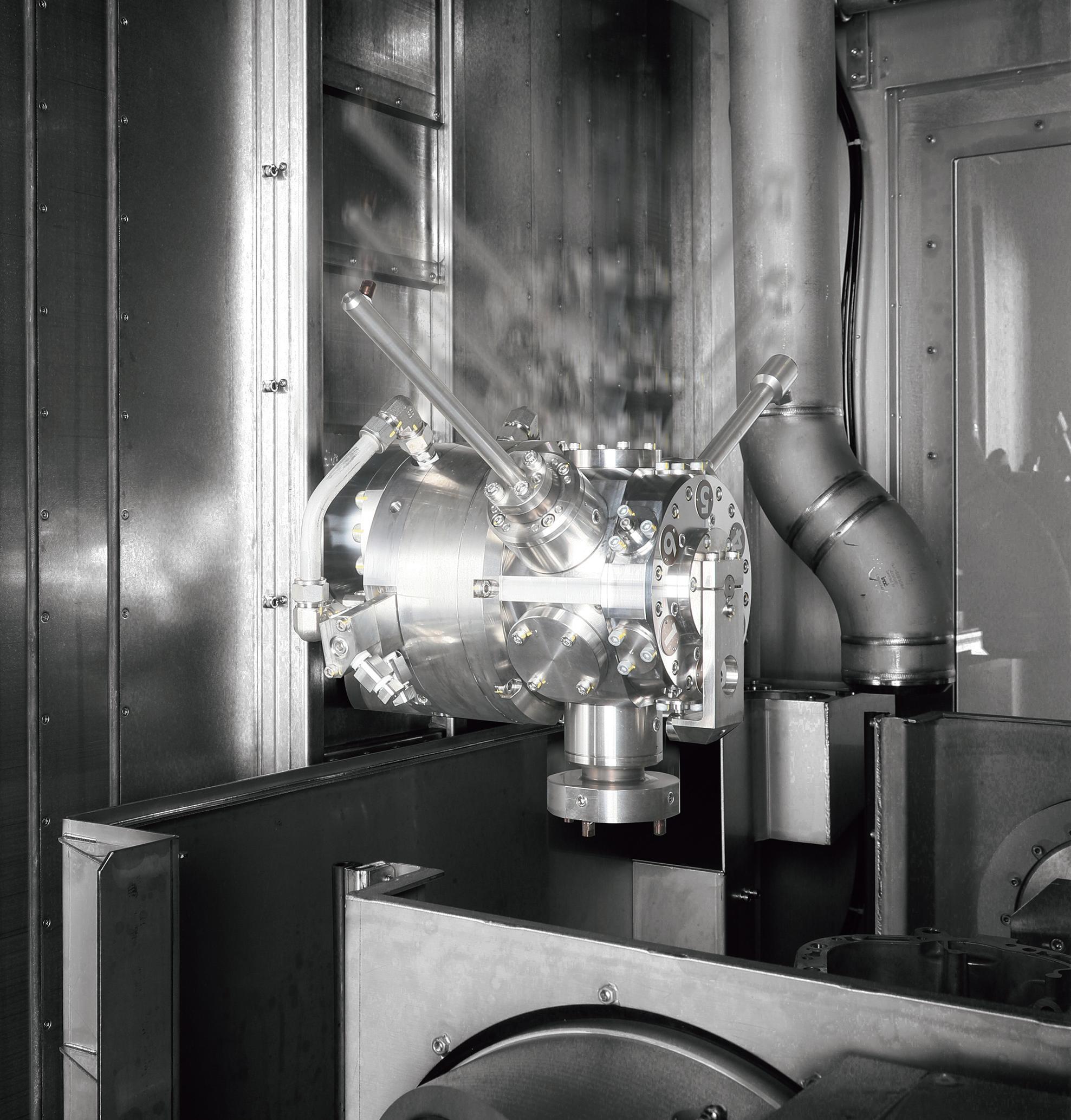
Dramatically Reduce Cycle Time
Upgraded servo-controlled X, Y, Z & A axes reduce rapid time, allowing for shorter cycles compared to conventional models..
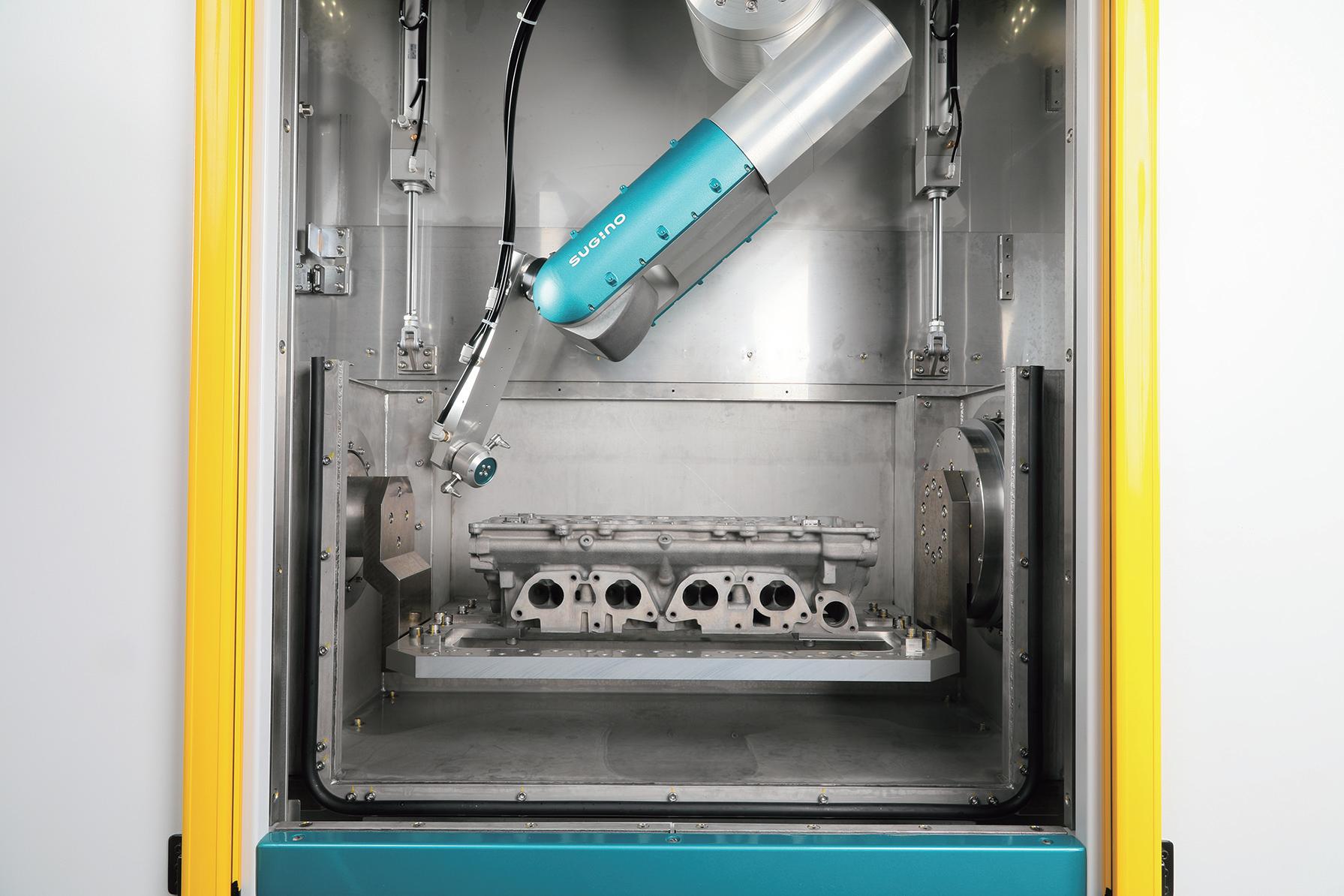
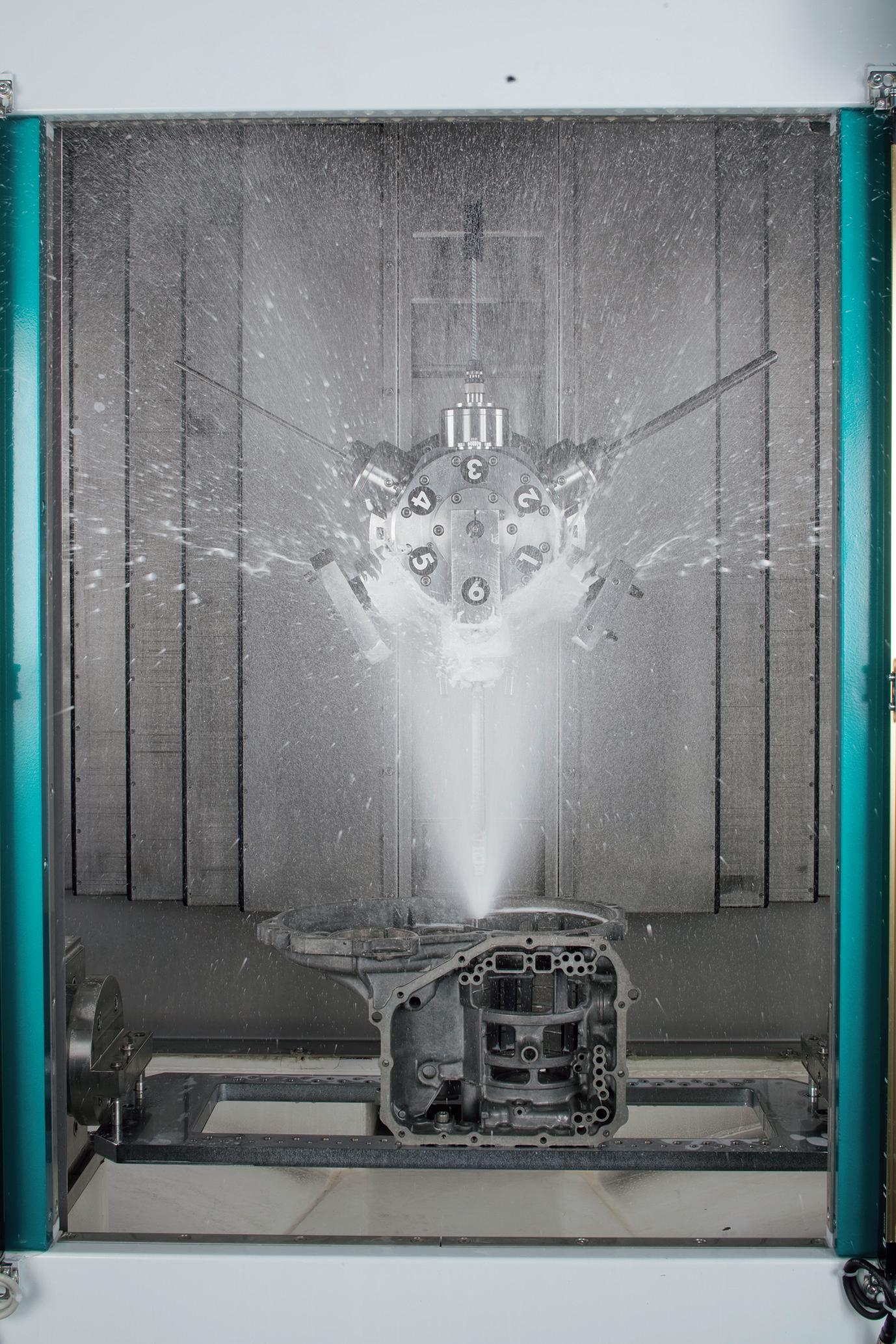
Compared to Conventional Model
Advanced Air Blow Off Option
A robot with an air nozzle moves around the workpiece freely to achieve high-precision, targeted drying. It is more efficient than the conventional nozzle block method and saves energy.
Deburring Cross Holes
APPLICATIONS
Transmission parts, e-axle parts, ABS housing brake caliper, etc.
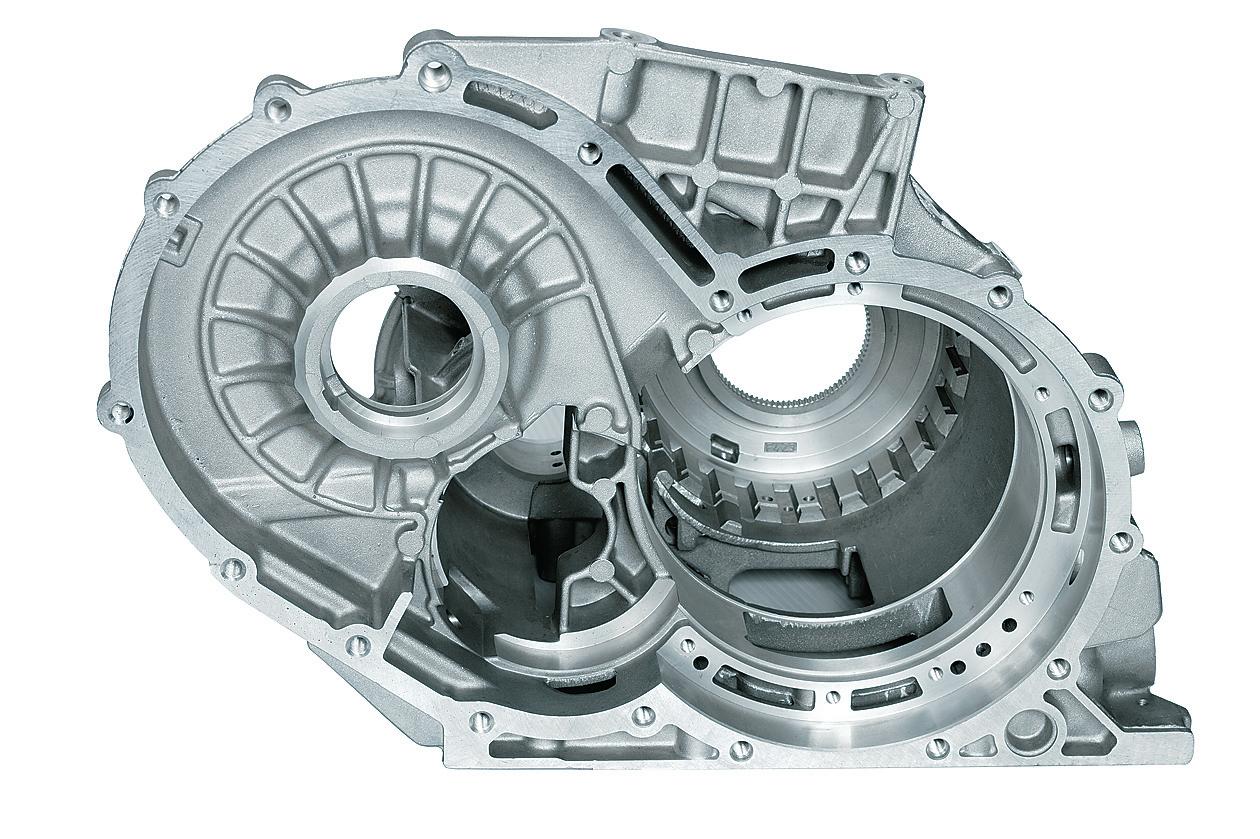
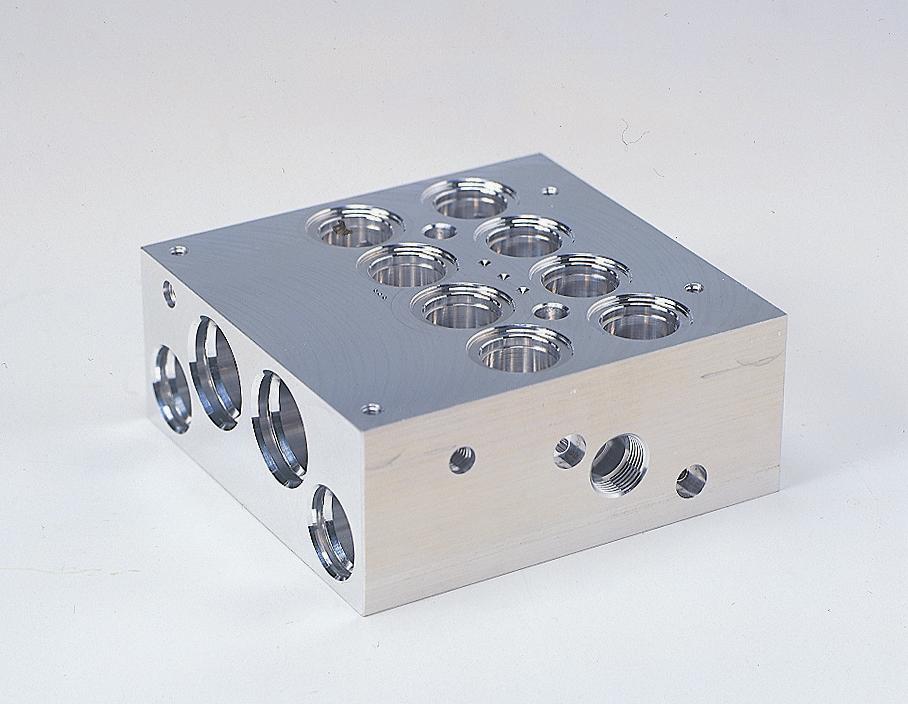

Work material: SCR415 Pressure: 50MPa
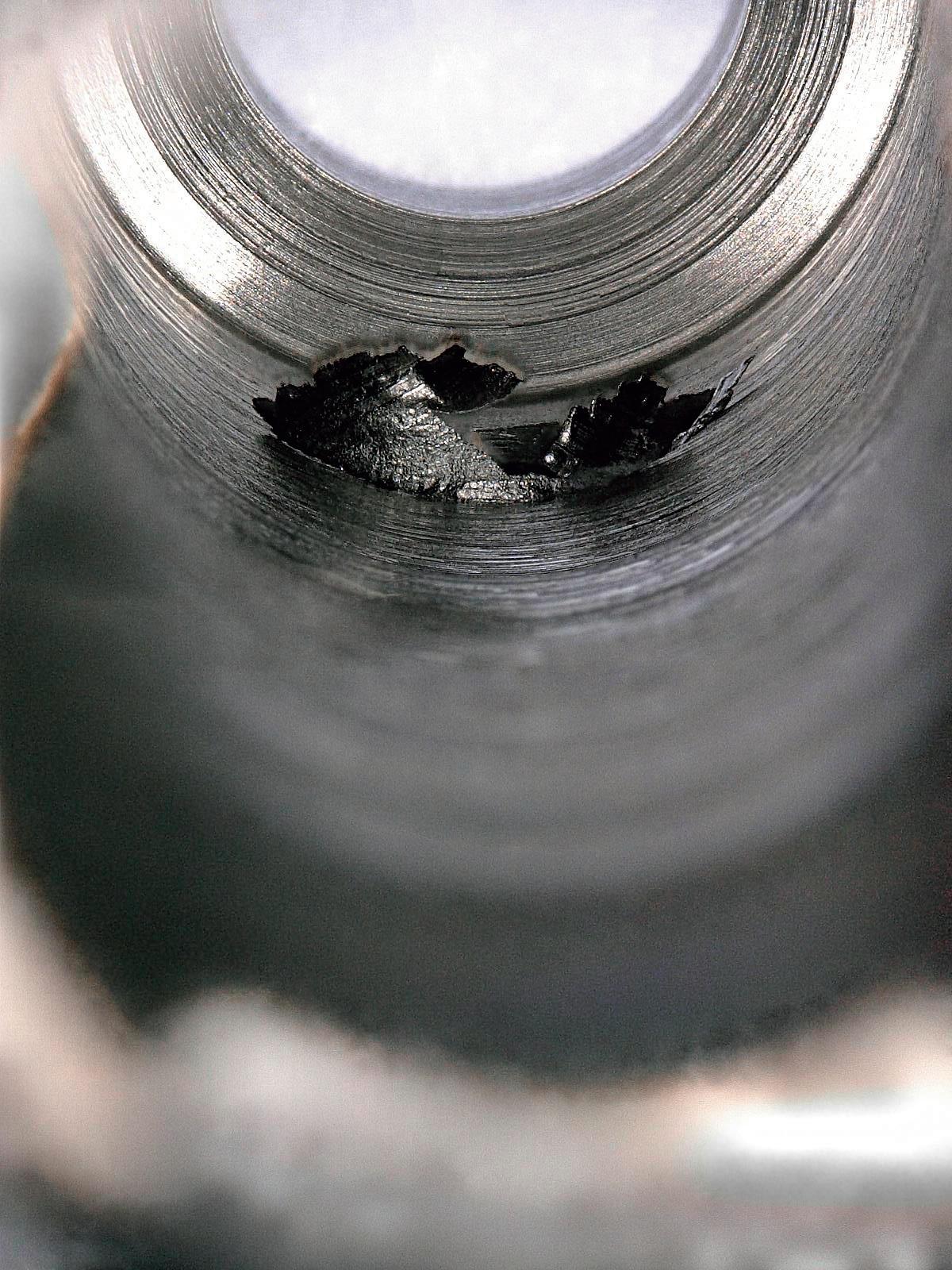
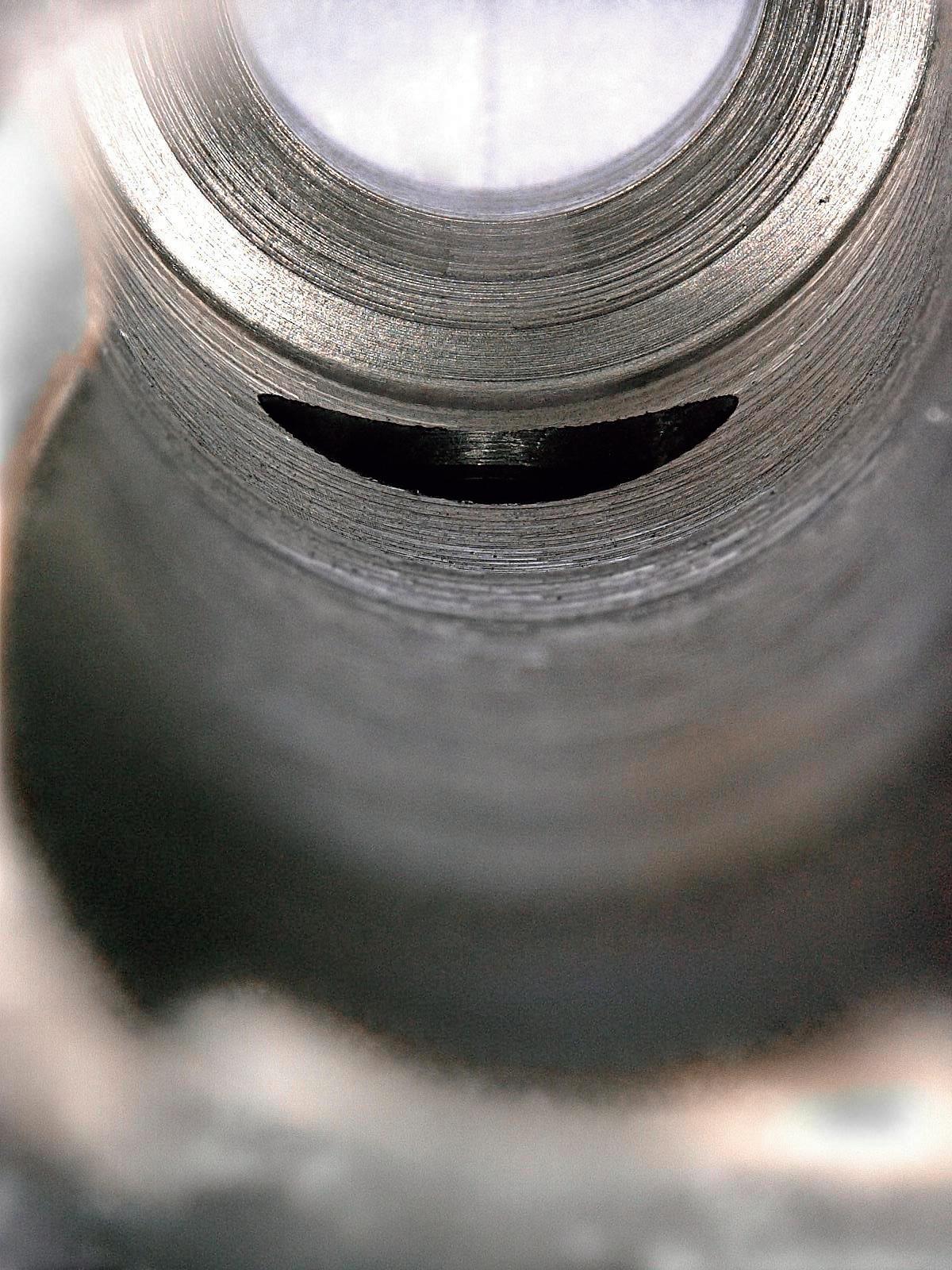
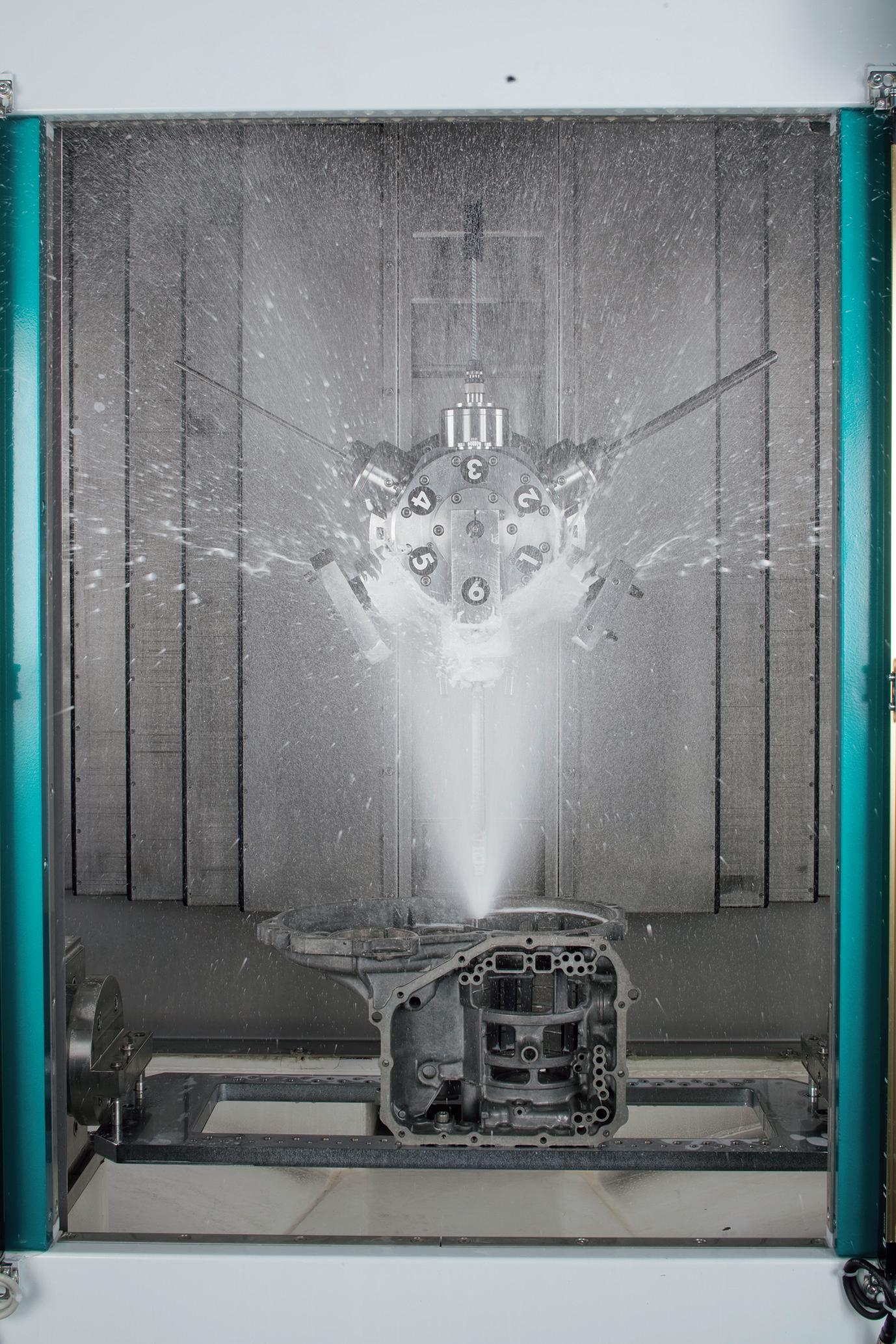
SUBMERGED CLEANING
CNC Turret-Type Submerged Parts Washer
JCC 403 U-JET
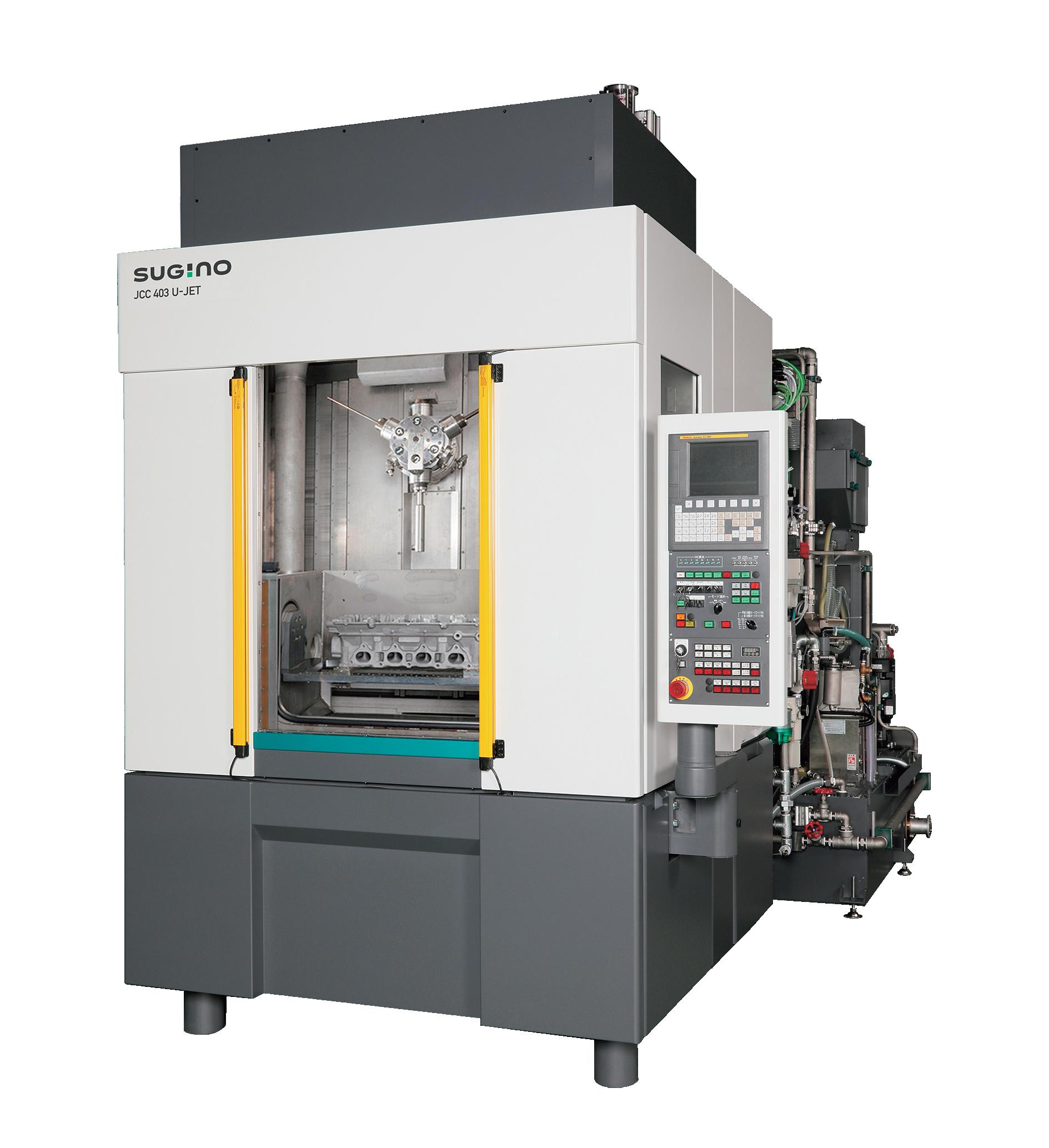
Single Station
JCC 421 UT

Equipped with Turn Table, 2 Stations
APPLICATIONS
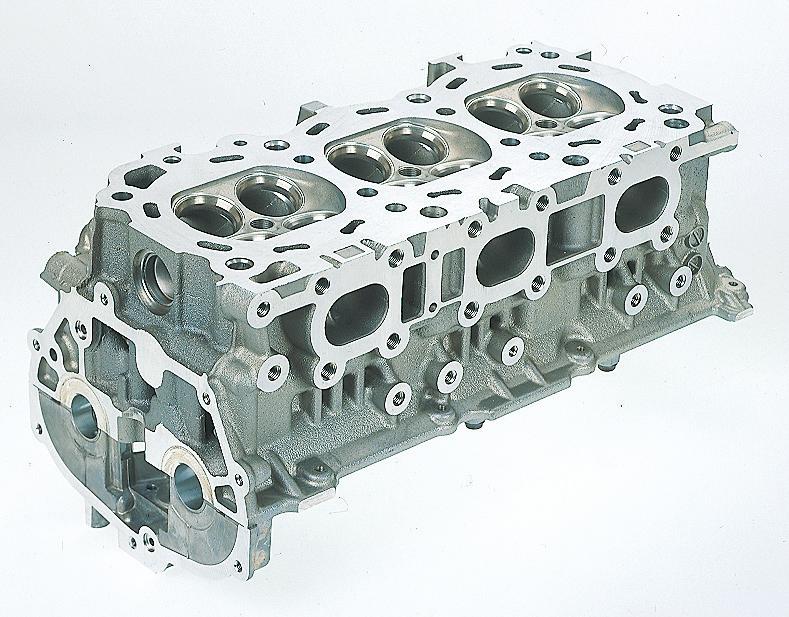
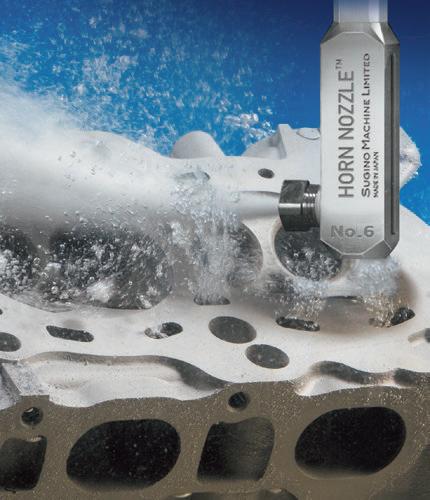
Underwater washing removes chips via the combination of high-pressure water and cavitation. Ideal for workpieces with many holes and taps.
Ideal for Workpieces with Complex Shapes
The synergistic effect of vortex flow due to cleaning pressure and minute vibration due to cavitation generation completely removes chips inside workpieces with complicated shapes such as water jackets.
Supports Submerged and Open Air Cleaning
These models are capable of both submerged and open air parts cleaning. The optimal method can be selected based on the part geometry and workpiece specifications.
Horn Nozzle for Submerged Cleaning
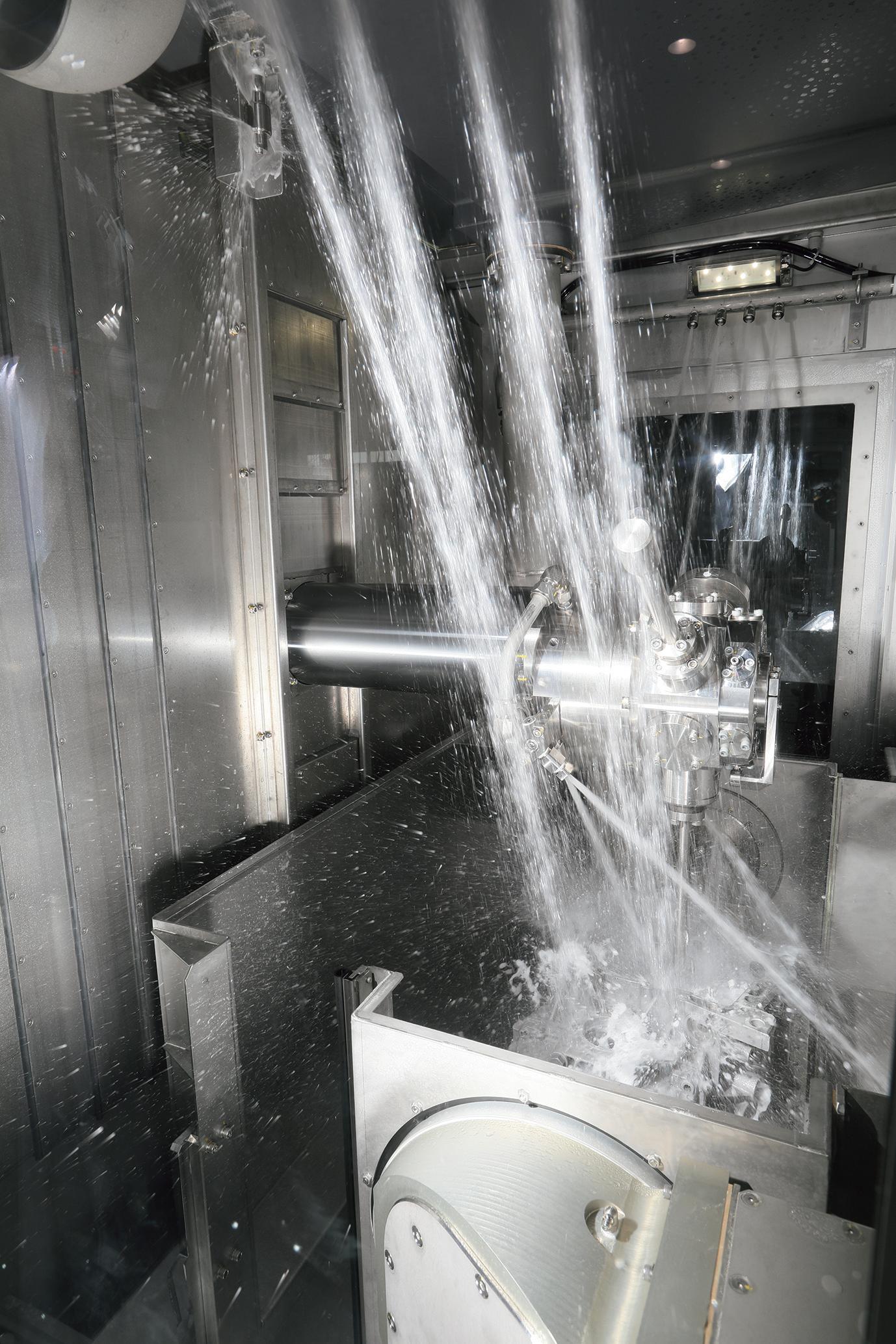
Cylinder head, cylinder block, hydraulic manifold, etc. State
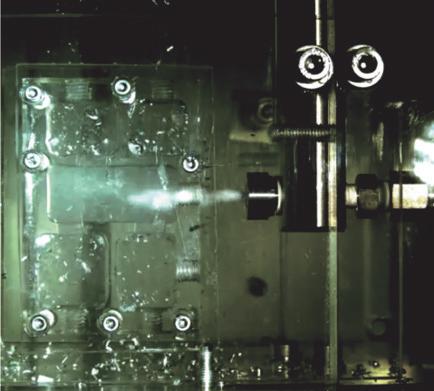
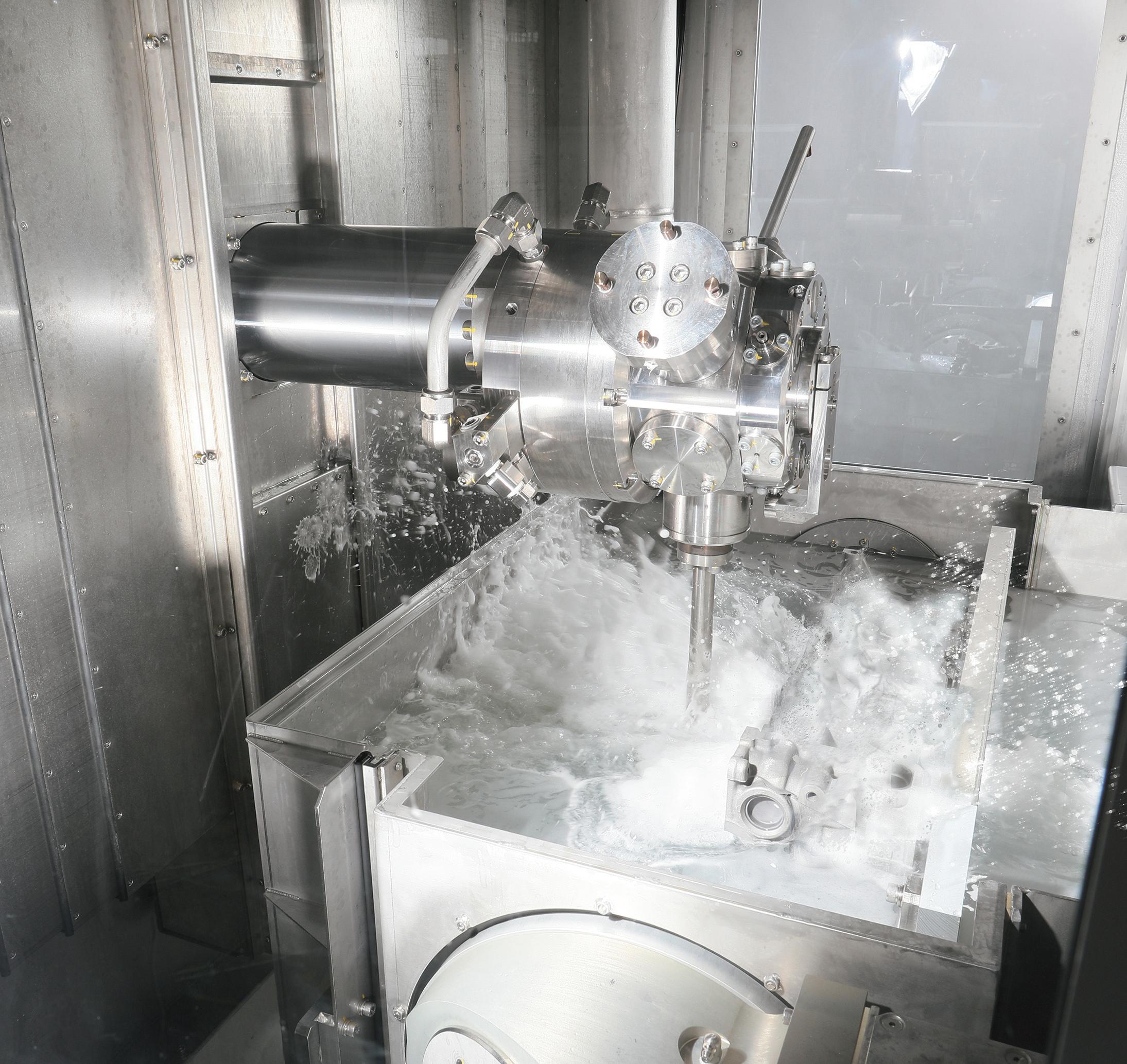
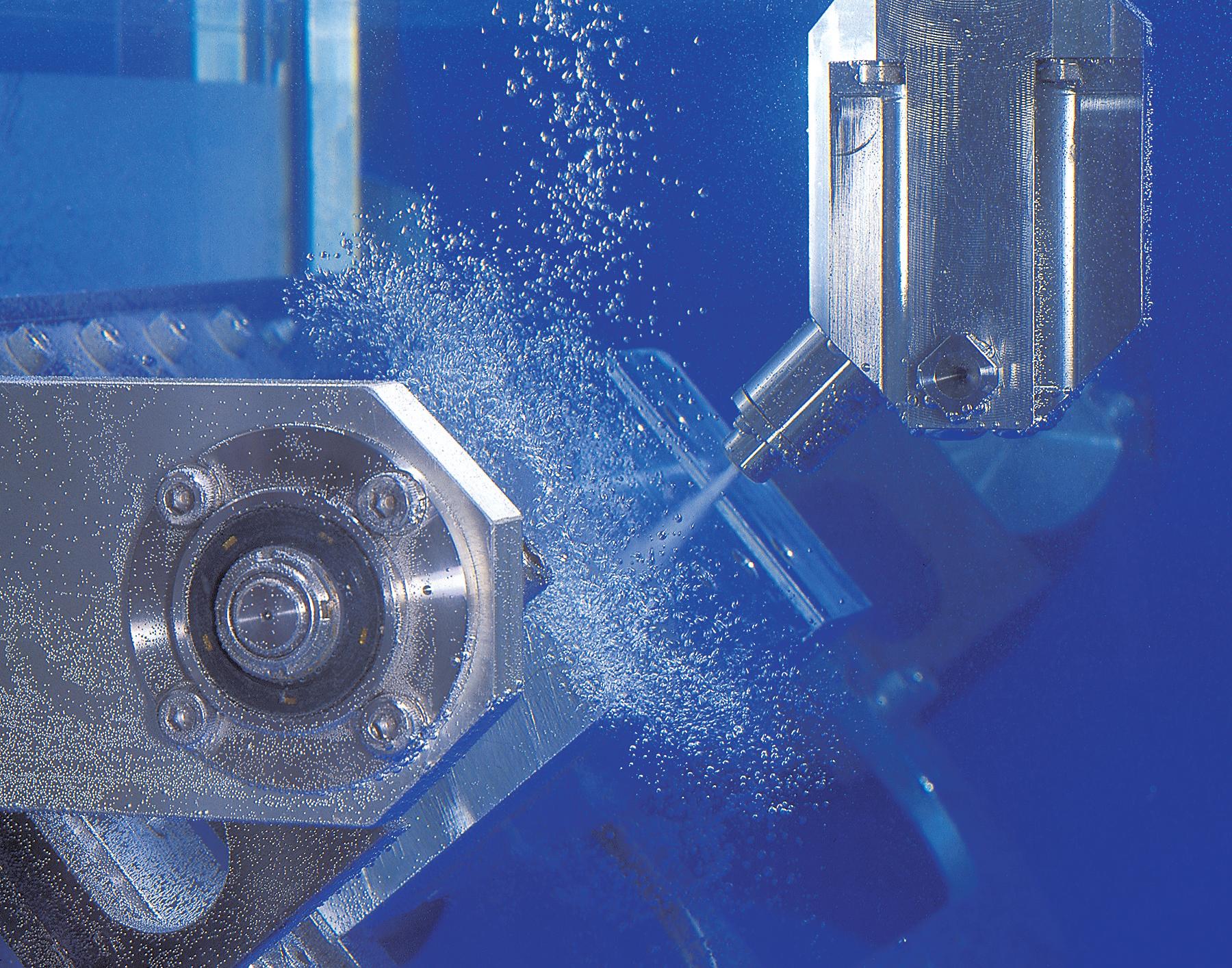
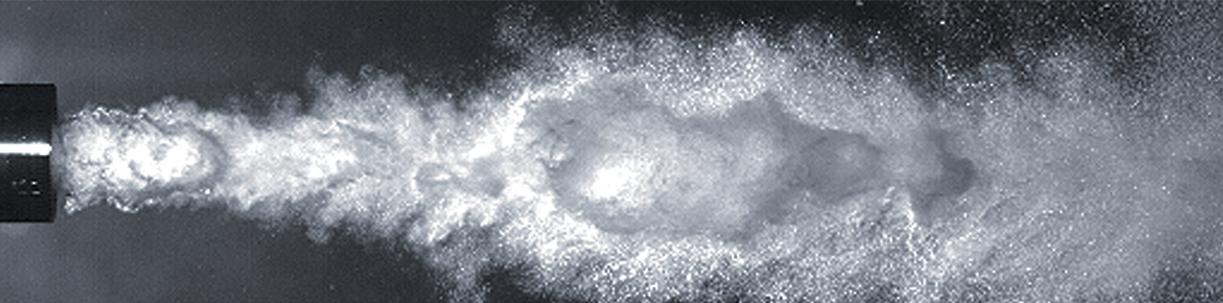
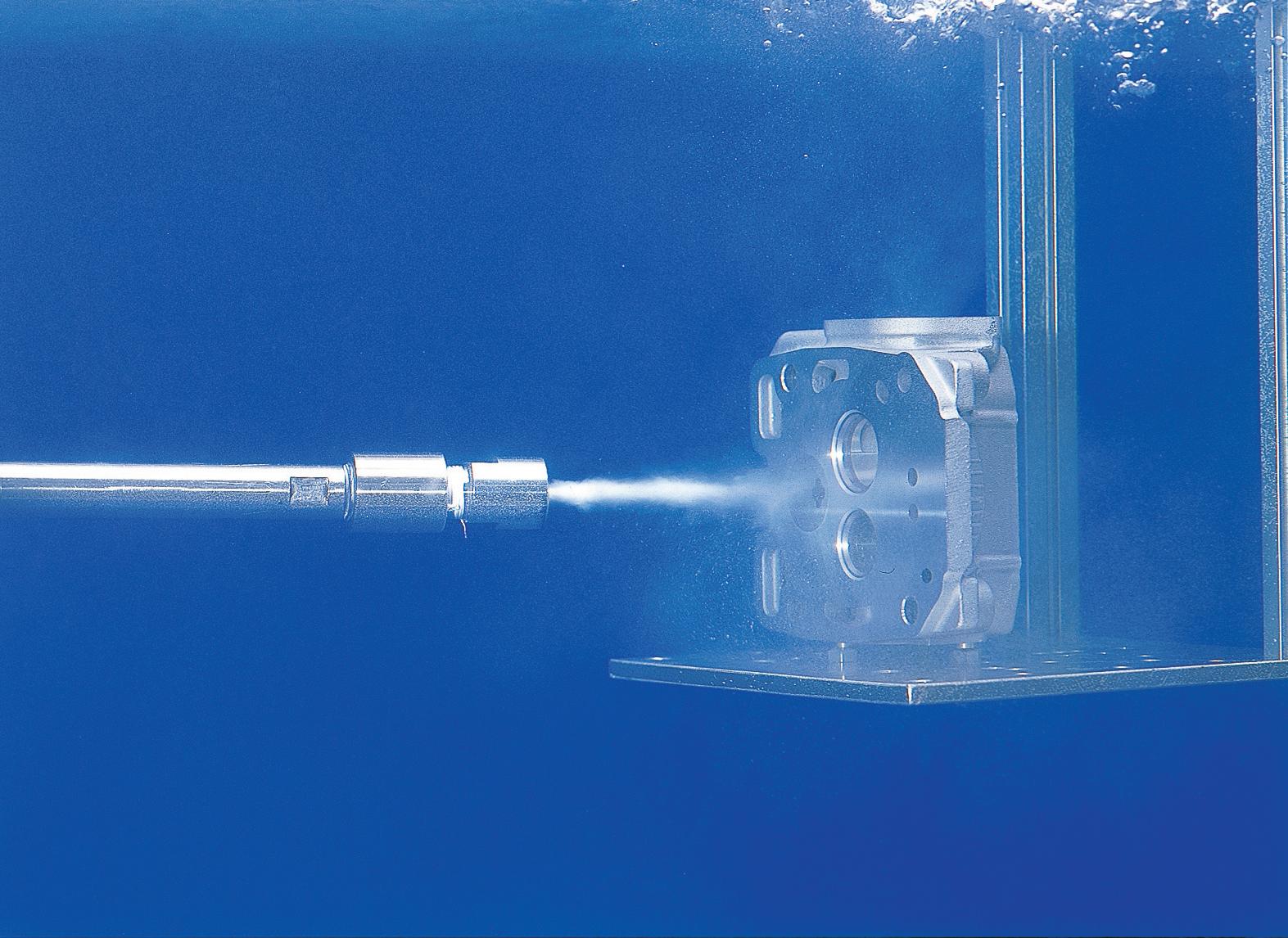
Sugino’s original Horn Nozzle design creates cavitation for high performance submerged washing.
Cleaning Samples/Cylinder Headwork
Material: ADC Pressure: 5MPa
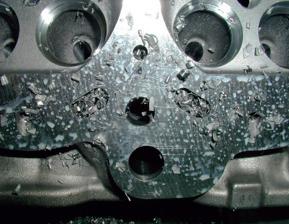
Before Cleaning
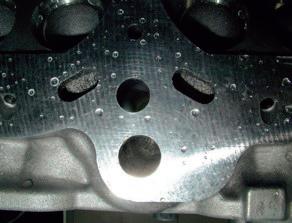
After Cleaning
4 + 1 DEBURRING AND CLEANING
Reach, deburr, and clean all six sides of your workpiece.
JCC 104 4+1
It's our most powerful deburring and cleaning solution yet. The 104 combines indexing 4+1 control and high-pressure water jet deburring to handle hard-to-reach places where burrs hide. With a newly developed hollow 2-axis tilting rotary table with an open bottom, all 6 surfaces can be free of chips and burrs, clean, and ready to go. All packed into an energy-efficient, streamlined solution.
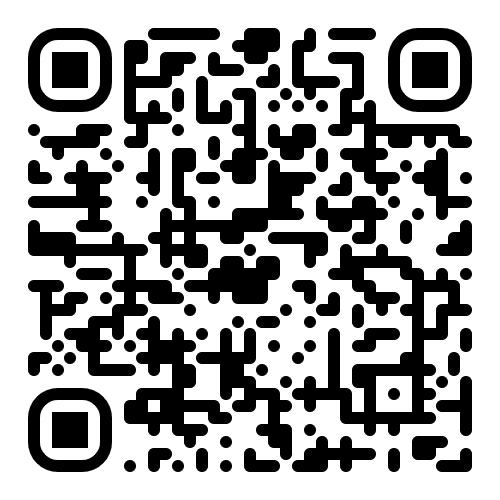
VIDEO
Watch the 4+1 in action.
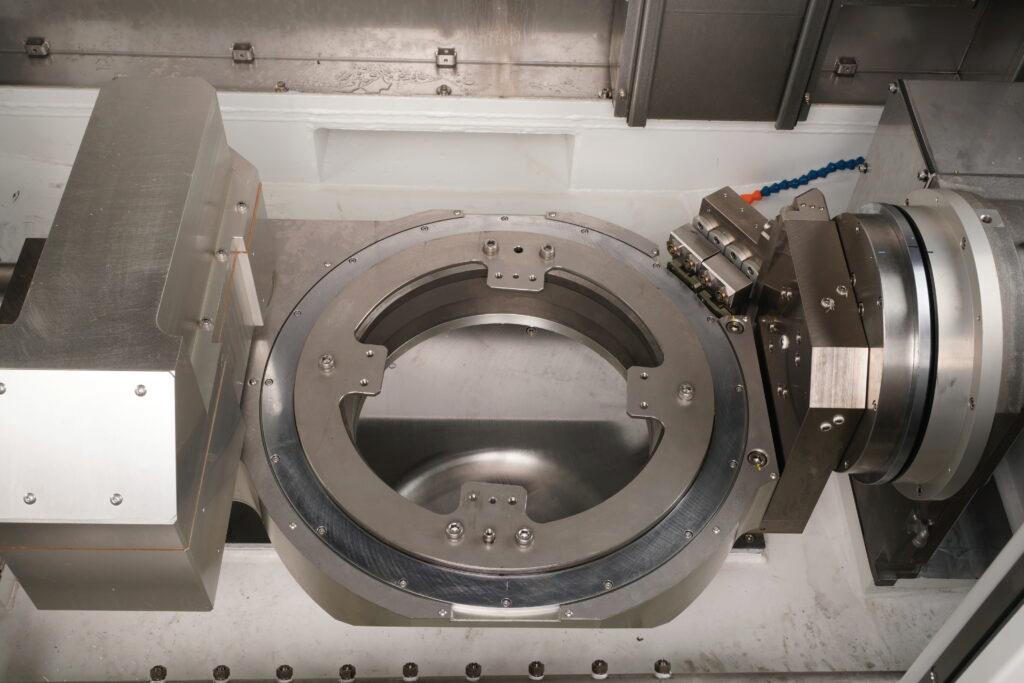
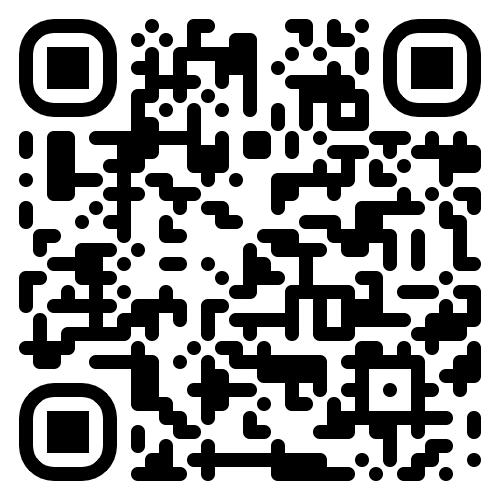
VIRTUAL TOUR
See a Machine Tour & Features
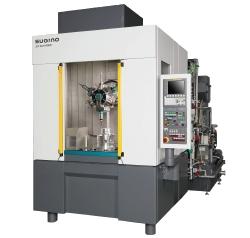
Access All Surfaces of the Workpiece
Equipped with a newly developed hollow 2-axis tilting rotary table with an open bottom for deburring and cleaning all surfaces. The 5-axis indexing control allows deburring on all surfaces of the workpiece, including the mounting surface.
Deburr and Clean with High-Pressure Water
High-pressure water of up to 50MPa can deburr areas where tools cannot reach, such as cross holes, deep holes, and stepped areas. In addition, deburring with high-pressure water also cleans at the same time, allowing the processes to be consolidated.
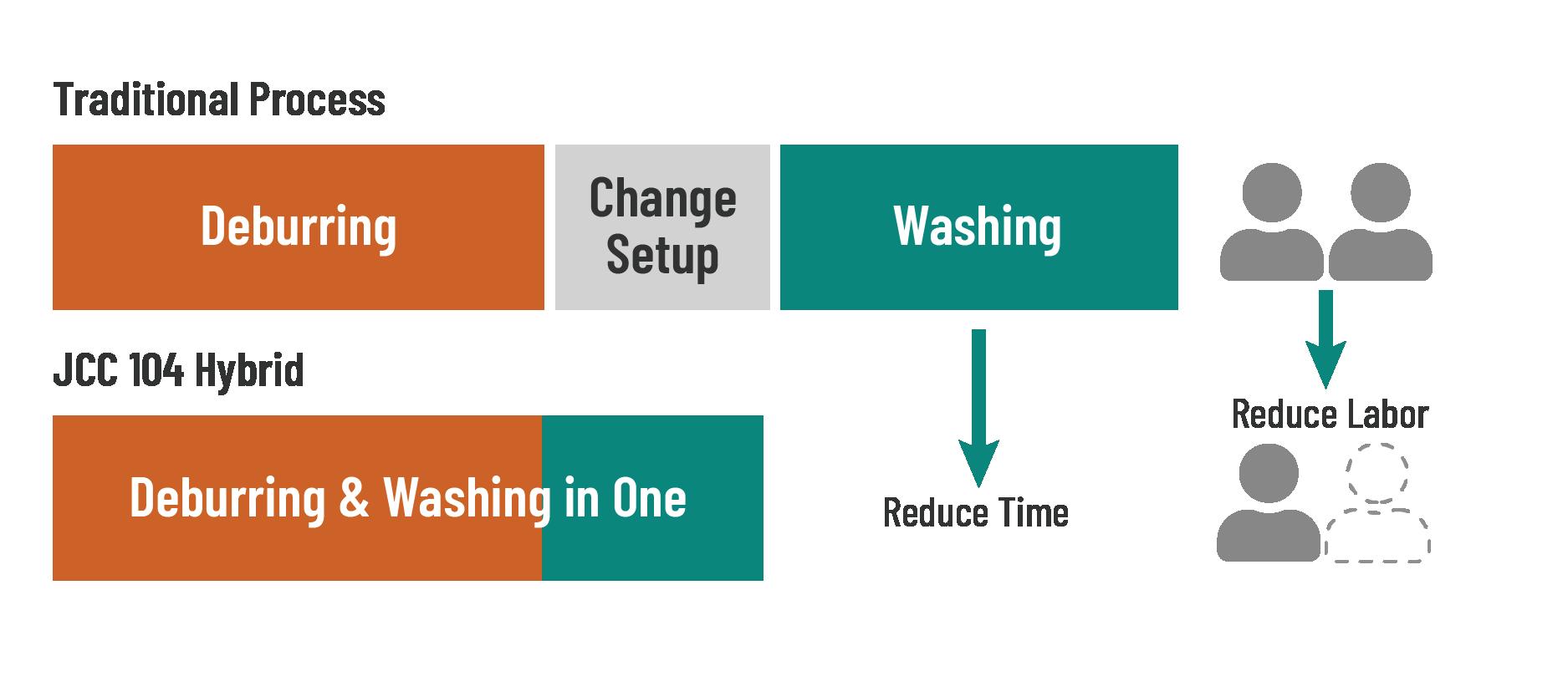
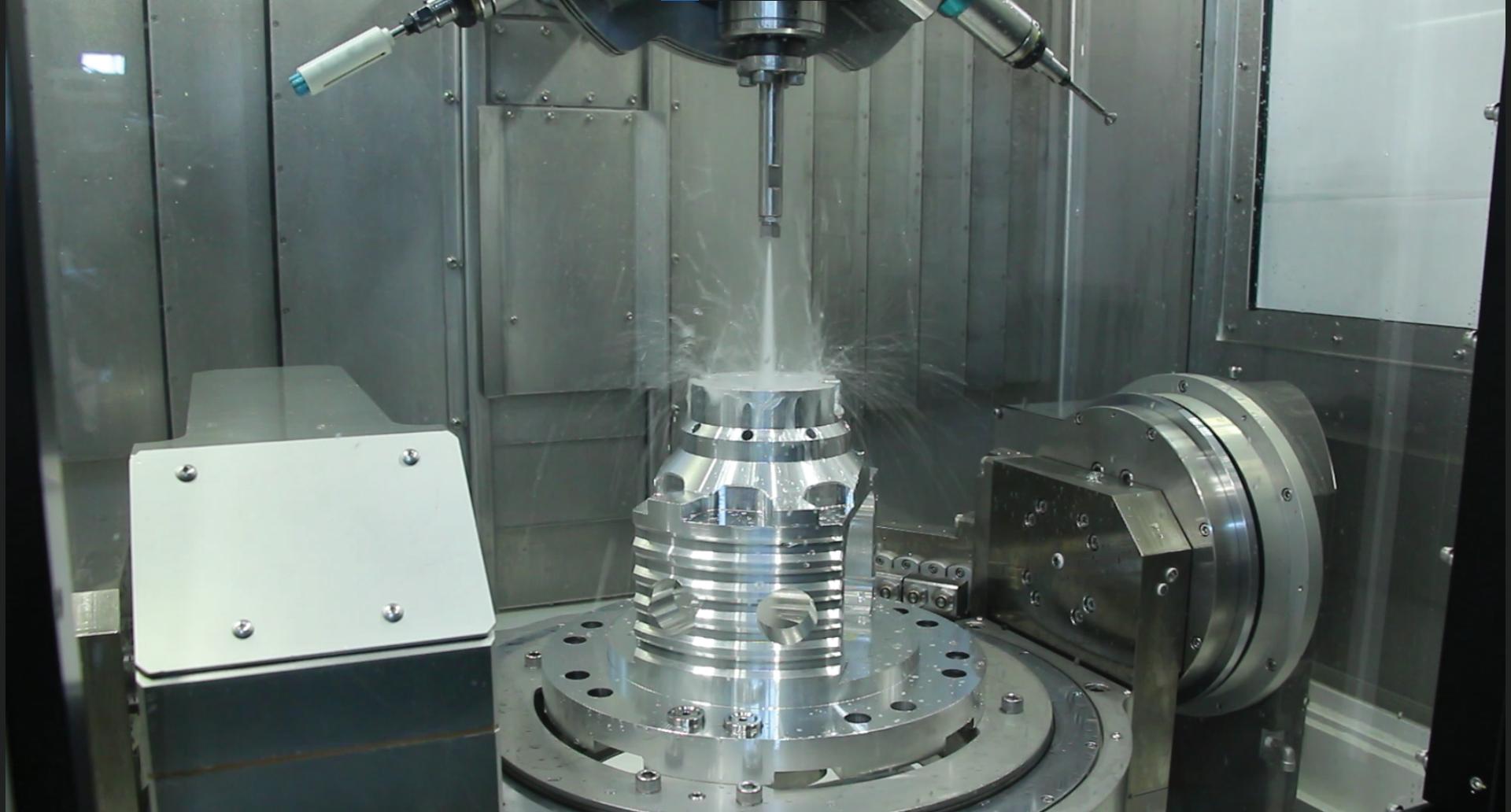
Consolidates cleaning and deburring processes for improved productivity.
The deburring process is often done manually and requires a lot of time and cost. The 104 4+1 can perform highly accurate deburring and cleaning all at once, contributing to automation and labor savings, and improving productivity.
Parts testing can show you exactly how JCC can benefit your production process. Testing takes place at our Wixom Technology Center. And our results report is second to none. To discuss your project or testing, get in touch.
ULTRA HIGH PRESSURE CLEANING
CNC Robot Hand Type Ultra High-Pressure Water Parts Washer
JCC 603 ROBO
A highly efficient and precise washing machine that is capable of transferring, washing, and drying — all within a single machine. The use of a highly rigid robotic hand helps to reduce cycle time and decrease installation space. The world’s first MAX 245 MPa ultra high-pressure water jet enables deburring of steel materials that had previously been difficult to clean up.
APPLICATIONS
Common rails, brake parts, engine parts, mission parts, hydraulic manifold and other parts that are difficult to deburr
Process Consolidation
Saves energy by combining the processes in which the equipment was previously separated for deburring and cleaning into one process - shortening of cycle time.

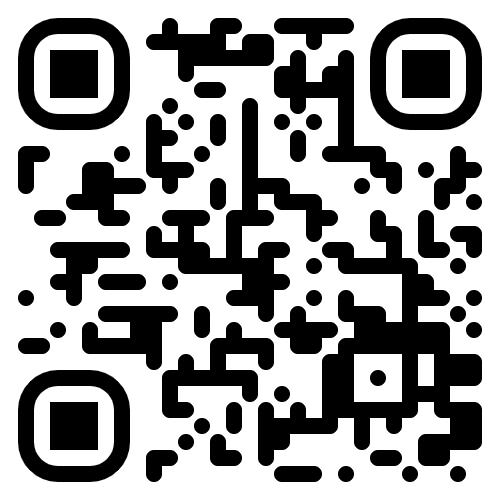
Watch the 603 Robo in action.
Deburring process + Cleaning process
Deburring cleaning process
Deburring with 245 MPa ultra high-pressure water jet
Deburring around cross-holes in cast iron and stainless steel parts, removal of tough edge burrs due to milling, and removal of oxidation scale after hardening.
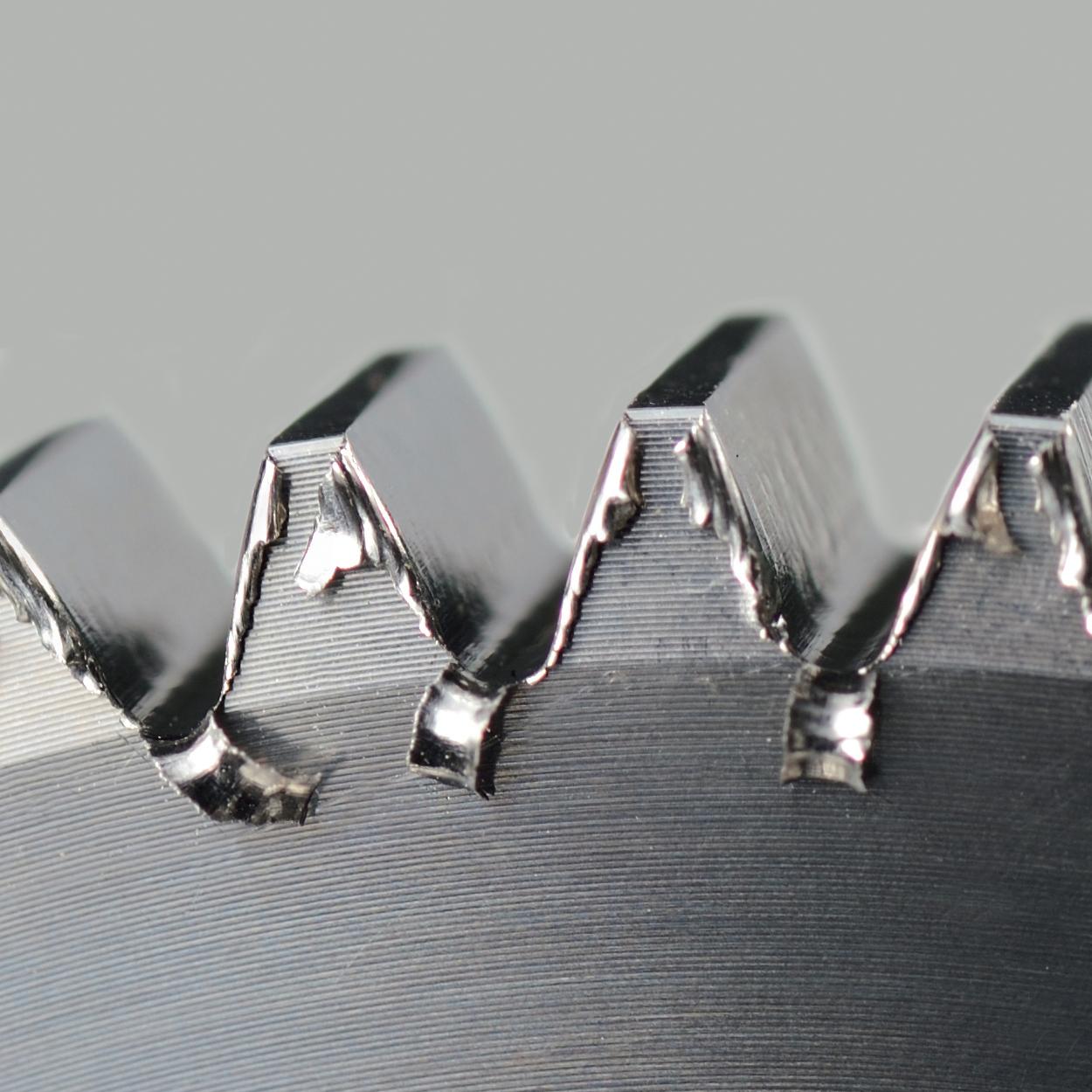

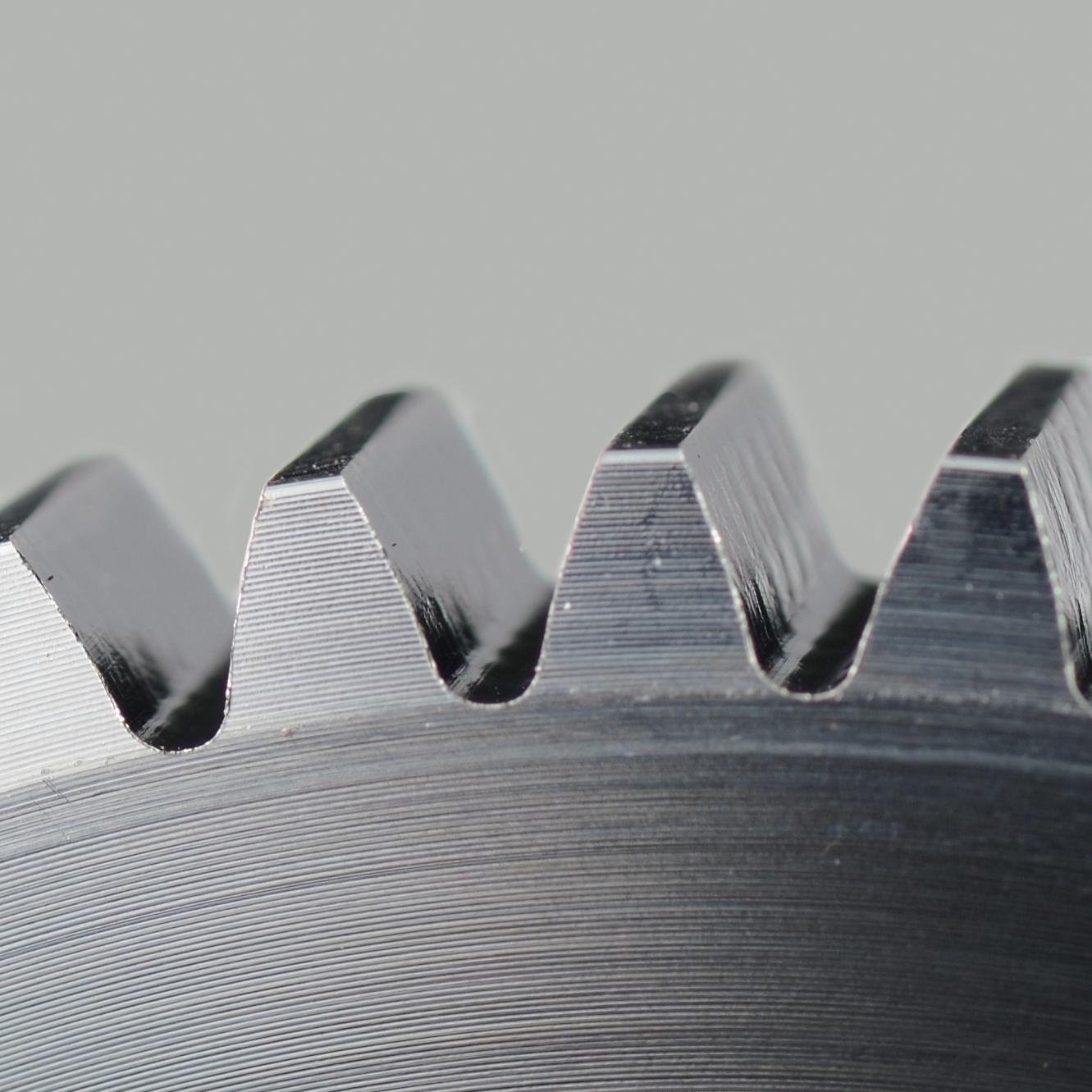
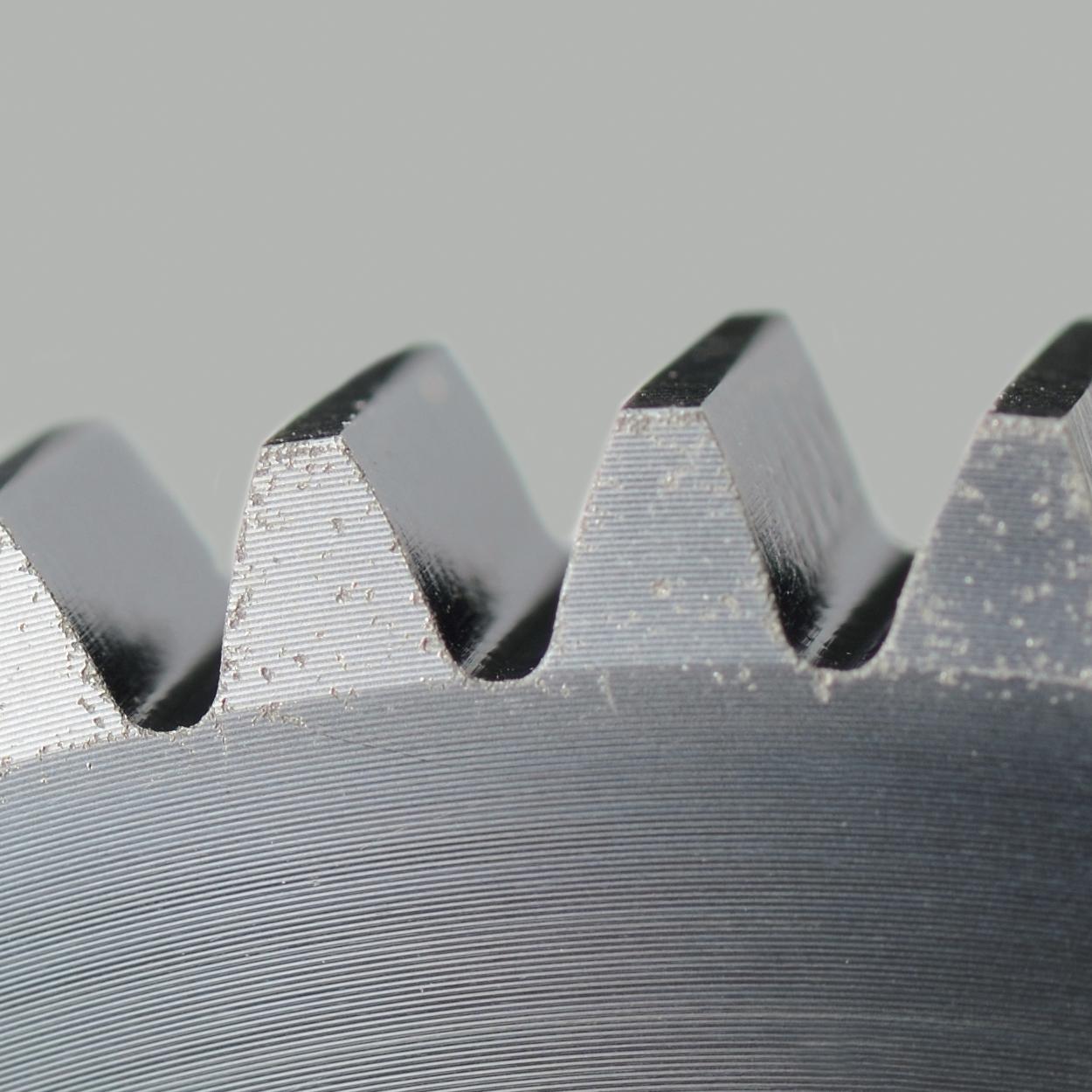
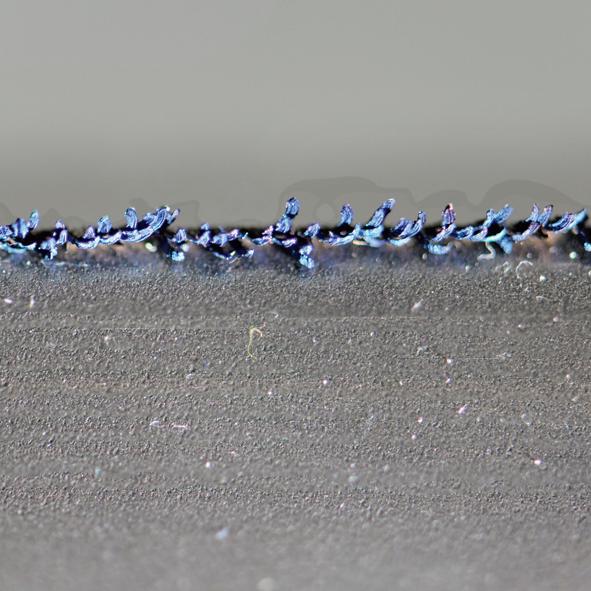
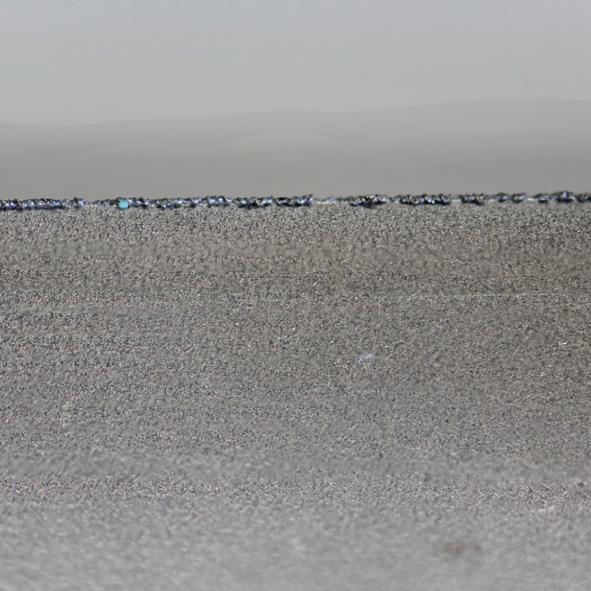
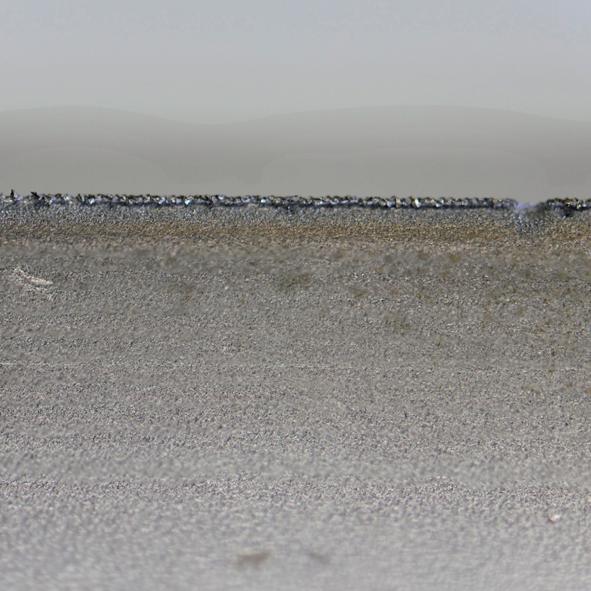
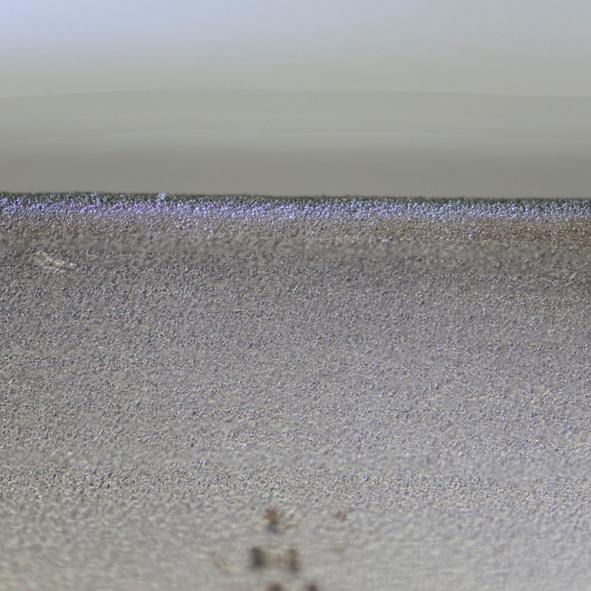

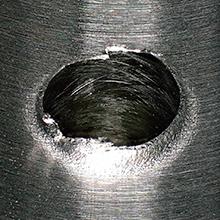


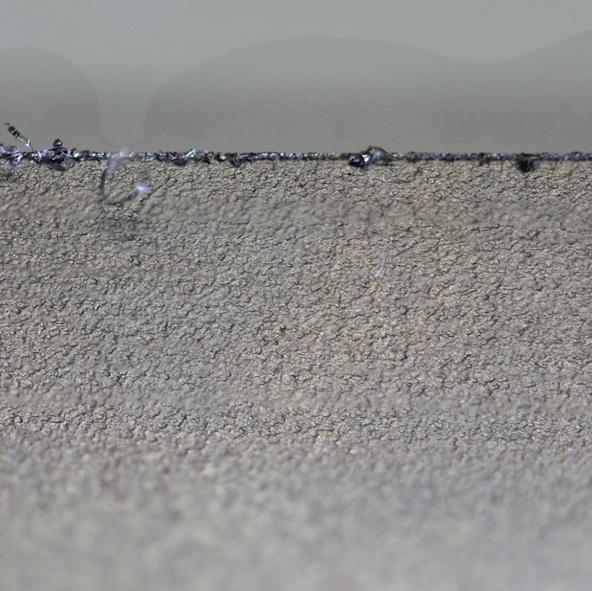
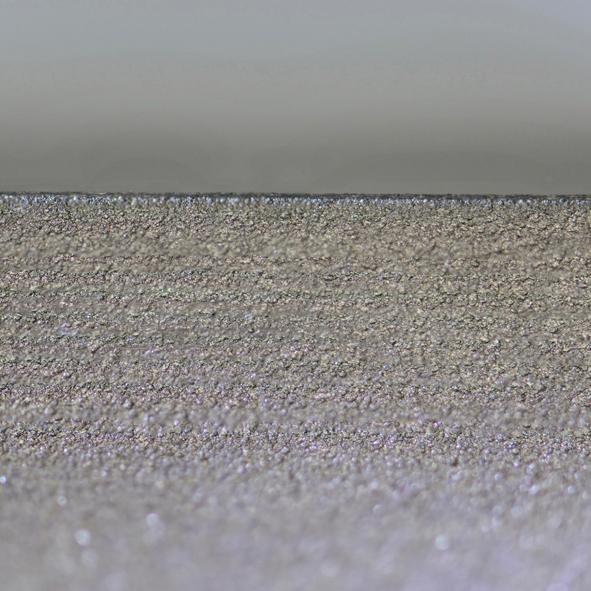

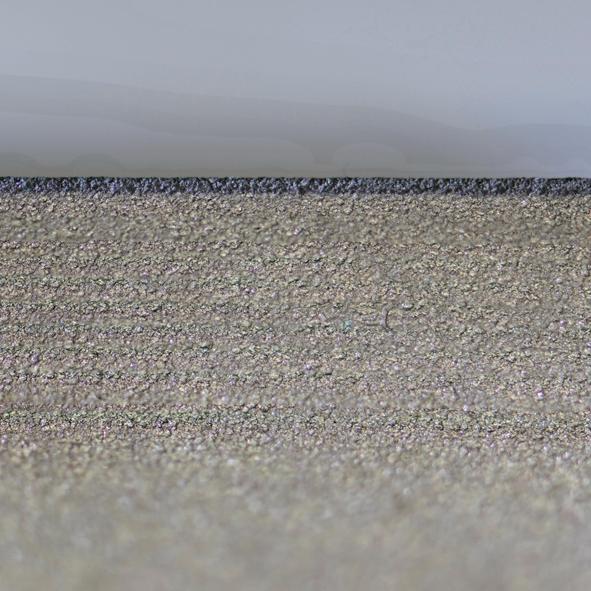
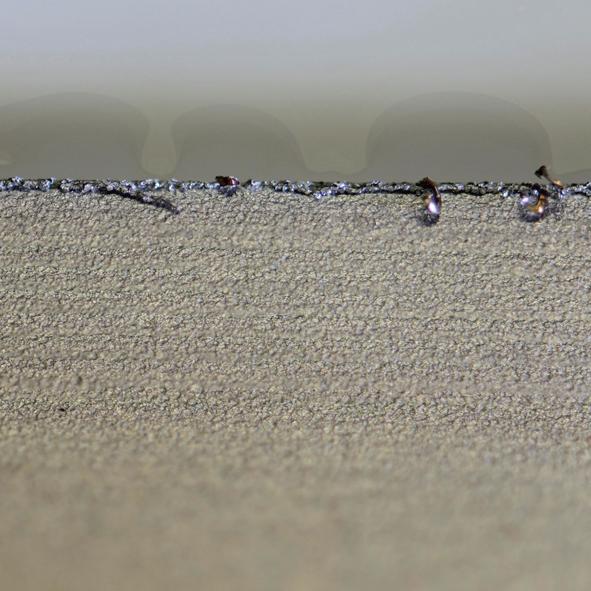

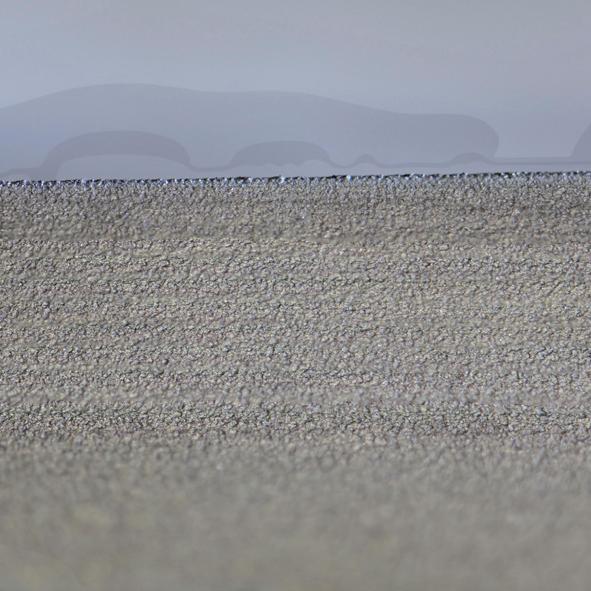
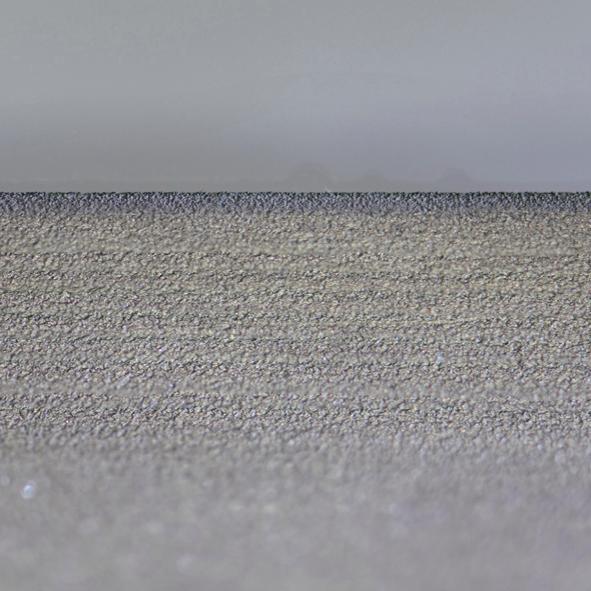
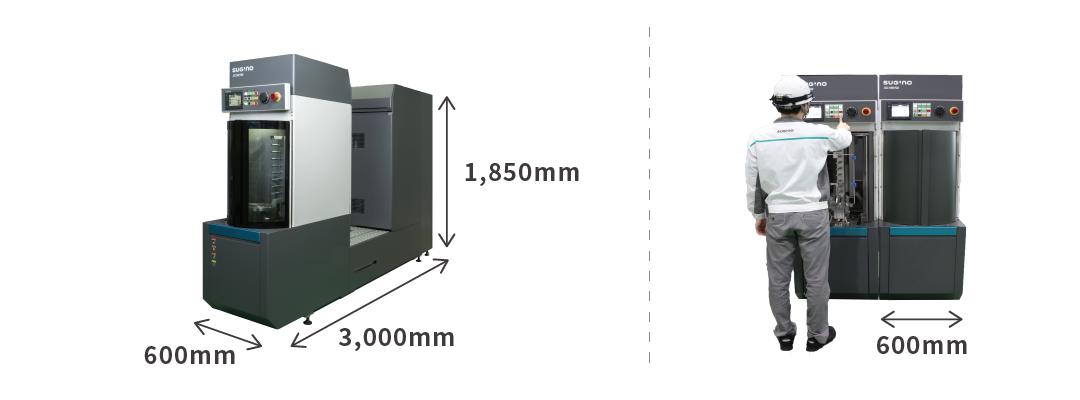
VIDEO
COMPACT TARGETED PARTS WASHING
Effective chip removal for tapped holes and blind holes
JCC MODULE
Low-pressure washers don’t have the power to remove chips and residue from tapped or blind holes. Shower washers don’t provide precision aim, so chips are left behind. Higher pressure systems come with a higher initial cost and increased cost of operation. Sugino’s JCC Module combines a Swing-Arm Targeted Cleaning method with the right pressure to solve these common problems.
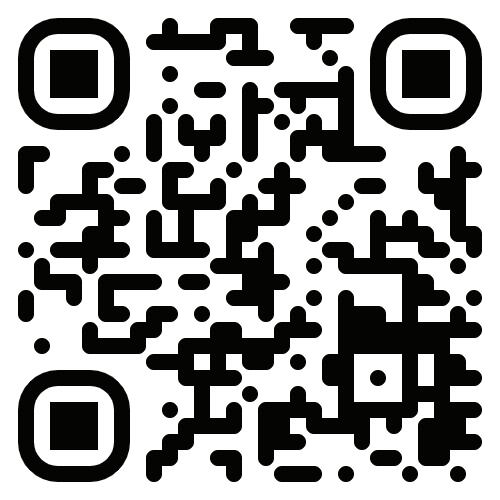
VIDEO
Watch to learn more about JCC Module
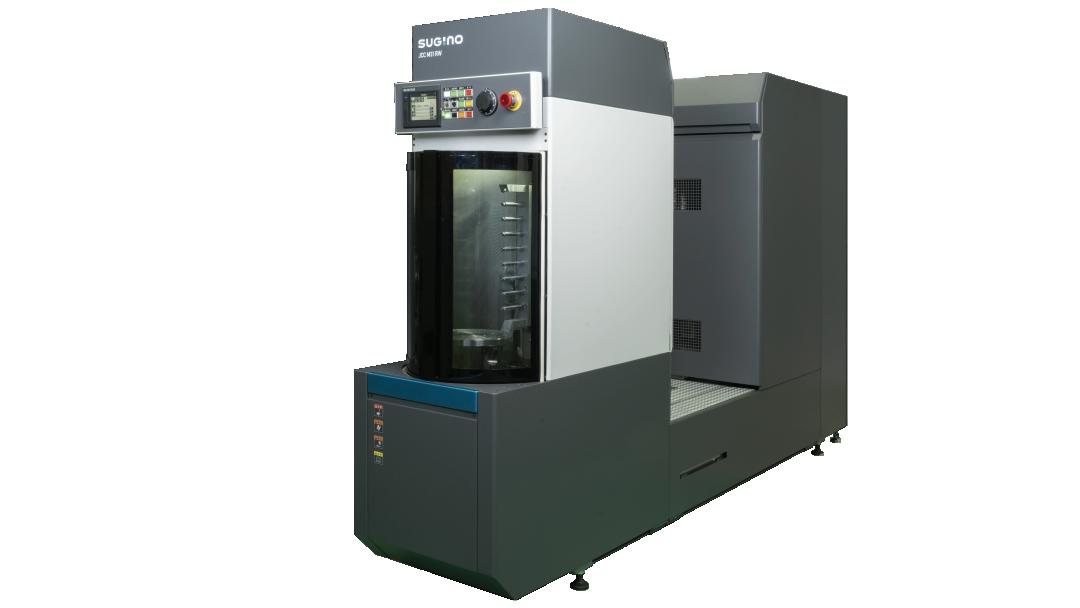

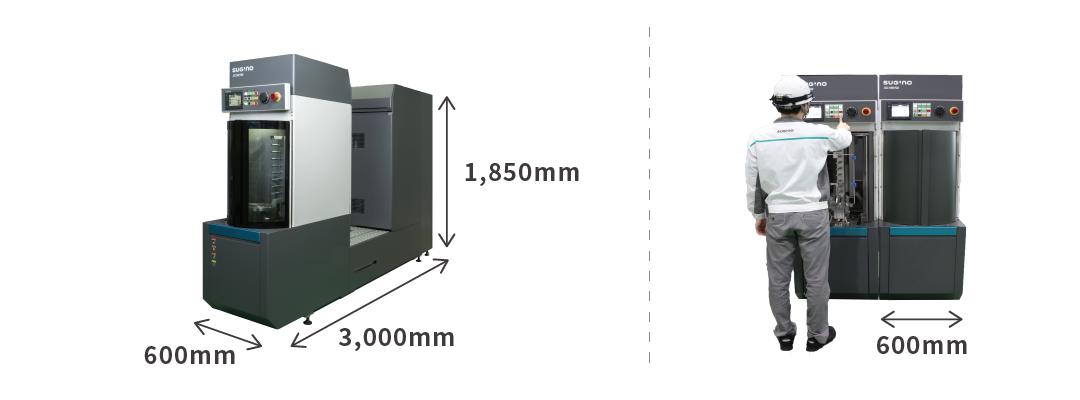
Compact footprint of only 600mm wide
The JCC Module has a very small footprint, just 600mm wide, and is ergonomically friendly. Winner of the 2021 Good Design Award, its compact and modular composition with separate functions makes it easy to introduce into any factory. The height at which the system is placed allows users to handle the workflow, operation, and maintenance intuitively.
Remove chips and oil with Swing-Arm Targeted Cleaning
The secret to high-speed, high-precision cleaning is our patented Swing-Arm Targeted Cleaning. The workpiece's rotation axis and the nozzle's three servo axes move in sync constantly targeting the holes while spraying, in "Swing Targeted Cleaning." High-precision cleaning accurately targets tapped and blind holes. High-speed positioning using multiple axes and high-flow jets from multiple nozzles cleans the entire workpiece quickly and completely.
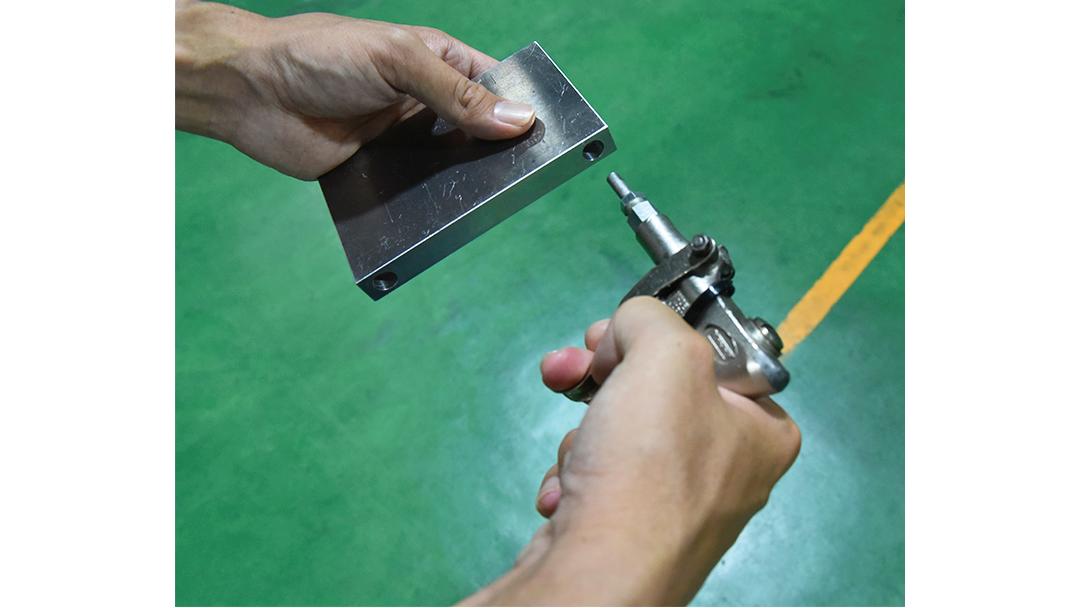
The benefit of automating the process
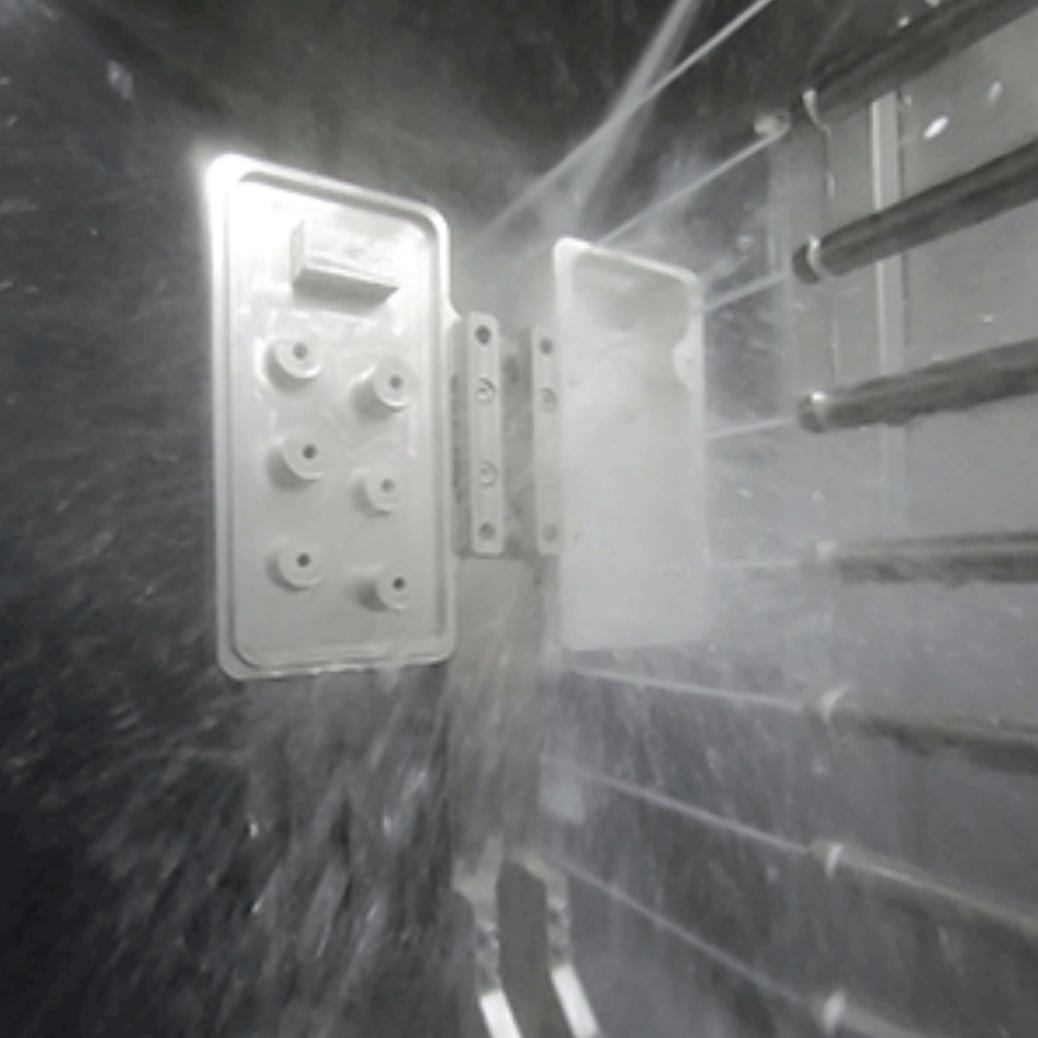
Chip removal is often done by hand, using air blow, a coolant gun, or picking them out piece by piece. These loud and dangerous processes don’t always do the job effectively and performance varies from worker to worker. The JCC Module is a cleaning machine specialized for removing chips from blind holes and tapped holes by spraying water perpendicular to tapped holes and blind holes, completely removing chips every cycle, every time.
High Pressure Targeted Cleaning
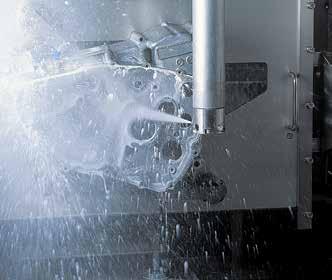
Water is pressurized to a maximum of 245 MPa and utilizes CNC control for focused positioning. The impact force of the high-pressure water jet reliably removes burrs and chips generated on various parts using only water.
High pressure water has a high flow velocity, so chips are reliably removed in an instant.
The combination of the right nozzles and targeted positioning saves time, energy and cost.
The cleaning conditions can be freely changed through CNC programming, allowing for quick response to changes.

Submerged Cleaning
Submerged cleaning is critical for the internal passages of a workpiece. The synergistic effect of the high pressure jets and cavitation creates a vortex, completely removing residual chips from hard to reach places within a part. Even workpieces with complex geometry can be effectively cleaned.
Features of underwater cleaning with U-Jet
When high-pressure water is sprayed underwater, cavitation (fine bubbles) is generated. When these bubbles collapse, an impact pressure of several GPa is generated, and the power is used for cleaning.
Line Up
1 and 2 station setups allow for muliple processes for faster cycle times - and give you options that are designed to fit your deburring, parts cleaning, and drying needs.
Turnkey Compatible
We offer consistent proposals from cleaning / drying to transportation. Machining center, drilling / screwing unit, etc. for our products. We also have a lineup of transfer robots, and it is possible to configure the line with all Sugino equipment. We will propose the most suitable transportation method and system for your production plan.
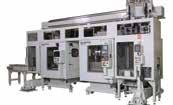
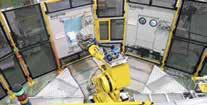
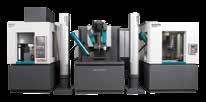
Combination of Washer and Dryer with Gantry Loader


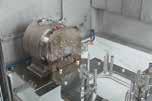
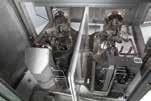
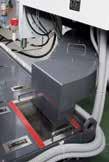

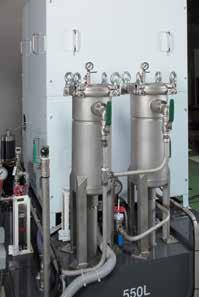
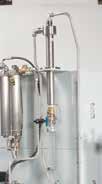
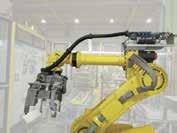
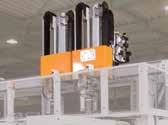
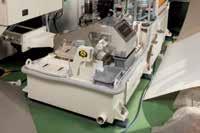
JCC-HM Exclusive Optional Floating Oil Recovery Unit
Fluid Cleaner and Oil Separator
JCC-HM
A portable fluid cleaning unit that removes foreign matter and oil in the liquid with the power of microbubbles. The only power required is air, and the unit can be widely used on a variety of substances from cleaning liquids to cutting oils.
Effectively removes foreign matter and oil in fluid
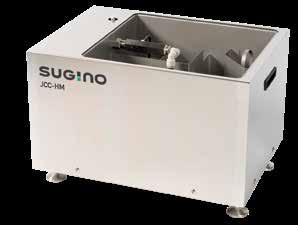
The optional floating oil recovery unit allows you to add even more functionality - simply connect it to the water supply of JCC-HM. If you are already using the HM, it can be retrofitted to recover oil from both the top of the liquid level, and within the liquid itself.


How it works
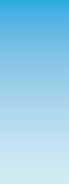
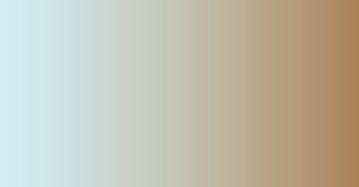
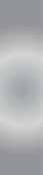


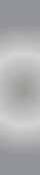
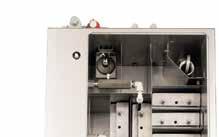



Microbubbles clean and recycle cleaning liquid and cutting fluid, no filter required.
Dirt (foreign matter, oil, etc.) in the liquid adheres to the microbubbles and floats to the surface to purify the fluid.
JCC-HM’s unique internal structure allows quick and clean separation of debris.
Foreign matter and oil adhere to the coalescer and is quickly separated. The unique flow path separates contaminants, prevents re-contamination, and reduces liquid waste. Also, the internal structure isremovable for easy cleaning.
Requires only shop air to operate!
Requires only air power for easy installation and immediate operation. All you have to do is connect two hoses (dirty water IN/purified water OUT) and air.

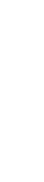




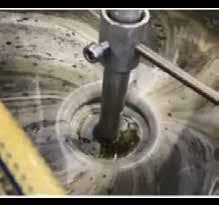




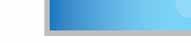

Typical Methods With the JCC-HM Optional Floating Unit

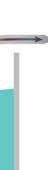
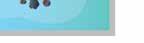

Designed to retrofit to your existing JCC-HM, or added when ever you need it. The bellows portion can stretch up to a max. of 100 mm, automatically follows the fluctuating level of the liquid.
Specifications
*Both processing capacity and air consumption are values at supply air pressure of 0.15 MPa.
Dimensions
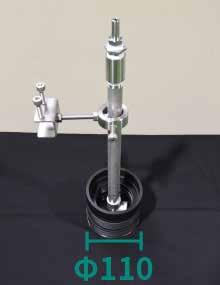
Vacuum drying reduces power consumption.
Compressed air is responsible for high power consumption in factories. The most common use of compressed air is air blow off for drying parts. By replacing air blow off with vacuum drying - where applicable - power consumption is significantly reduced. For JCC turntable models, a vacuum drying unit can be mounted on the front station (as an option). The vacuum dryer is also sold as a standalone unit.

Replacing air blow off means less energy used.
Replacing air blow off with vacuum drying reduces power consumption substantially and requires less manual labor.
Comparison of annual cost and C02 emissions:
Automating with vacuum drying requires less manual labor.


When the air pressure drops, water boils at temperatures below 100° C. By using this principle and lowering the air pressure inside the machine to a vacuum, even the moisture remaining in deep areas of the part are thoroughly evaporated and dry. This also evaporates water droplets that collect in the back of tap holes and inside parts with complex internal geometry.
Our new standard JCC eSmart energy-saving package reduces CO2 emissions 50% or more compared to previous models. Optimized cleaning conditions and stop/start technology employ less water, and require less energy for cleaning and deburring. This energy-saving package (Patent No. 6285880) is now standard on all JCC models. The high-pressure water generation pump typically consumes the most power - with eSmart, pressure is changed programmatically with a new control method, which optimizes power and reduces energy consumption significantly.
Pressure specifications can be set in the CNC program, along with nozzle choice within the turret With eSmart the pressure can be programmed for each part of the workpiece. By optimizing cleaning conditions based on the required cleanliness and deburring specs, energy use is minimized. With stop/start technology, the pump can be stopped during non-cleaning activity such as part transfer, eliminating unnecessary energy consumption.
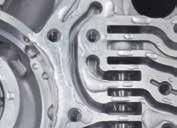


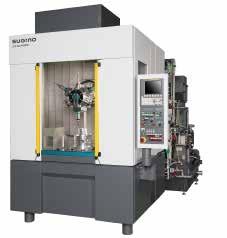
ULTRA HIGH PRESSURE CLEANING
OPEN AIR DEBURRING AND CLEANING
S
Posi
SUBMERGED CLEANING
JC C 603 ROBO
Max. washing water p ressure Max. 245MPa x 4L/min
Rinse wash ing pres sure 0. 8MPa x 100 L/min
Stroke s X- axis 650mm , Y- axis 500mm , Z-axis 500mm , A-axis ±90°, C-axis 360°
Po sition ing Accu racy 0. 08mm
Mach ine Dim en sion s Wid th 1, 600 x Depth 2, 660 x Heigh t 2, 250mm
We ight 4, 000kg
Control Ty pe 3 linear axes + 2 jo in t axes CNC con trol
Wate rproof Spe cification
Comp letely waterpr oo f (electrica l co mp on ents are com pl etely isol ated fr om water spl ashi ng env iron ment)
4 + 1 DEBURRING AND CLEANING
Ma x Wa sh ing Wa ter pres su re Ma x. 50MPa
Flow R at e Ma x. 29L/min
Ma x. S pindle R otat ion Sp eed Ma x. 20,000mi n-1
St roke X-ax is: 750mm, Y- ax is: 500mm, Z- ax is: 500mm
Rapid Travers e Sp eed (X , Y, Z a xi s) 60m/min
Numb ers of T ools 6
Co ntrol Eq uipm ent FANUC 0i-M F Plu s
Ma chine Dime ns ions Width 1,600 x Dep th 2,700 x Hei gh t 2,500mm
We ight (M ain Body) 4,300kg
COMPACT CHIP REMOVAL AND CLEANING
Wash ing Sp ec ificatio n 1. 0MPa x 100L/min or 7.0
We ight 1, 600kg
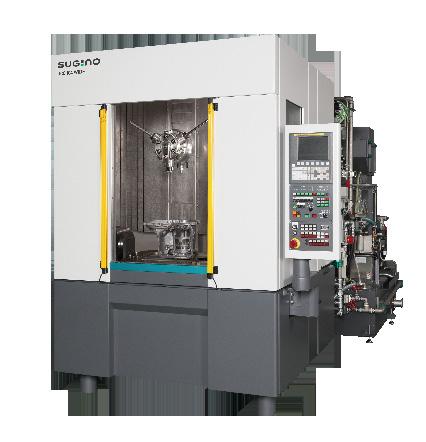
The layout of the pump station can be changed according to the customer’s installation environment. Please contact a sales representative for details. It can also be changed for JCC 303 TT, JCC 403 U-JET, and JCC 421 UT.
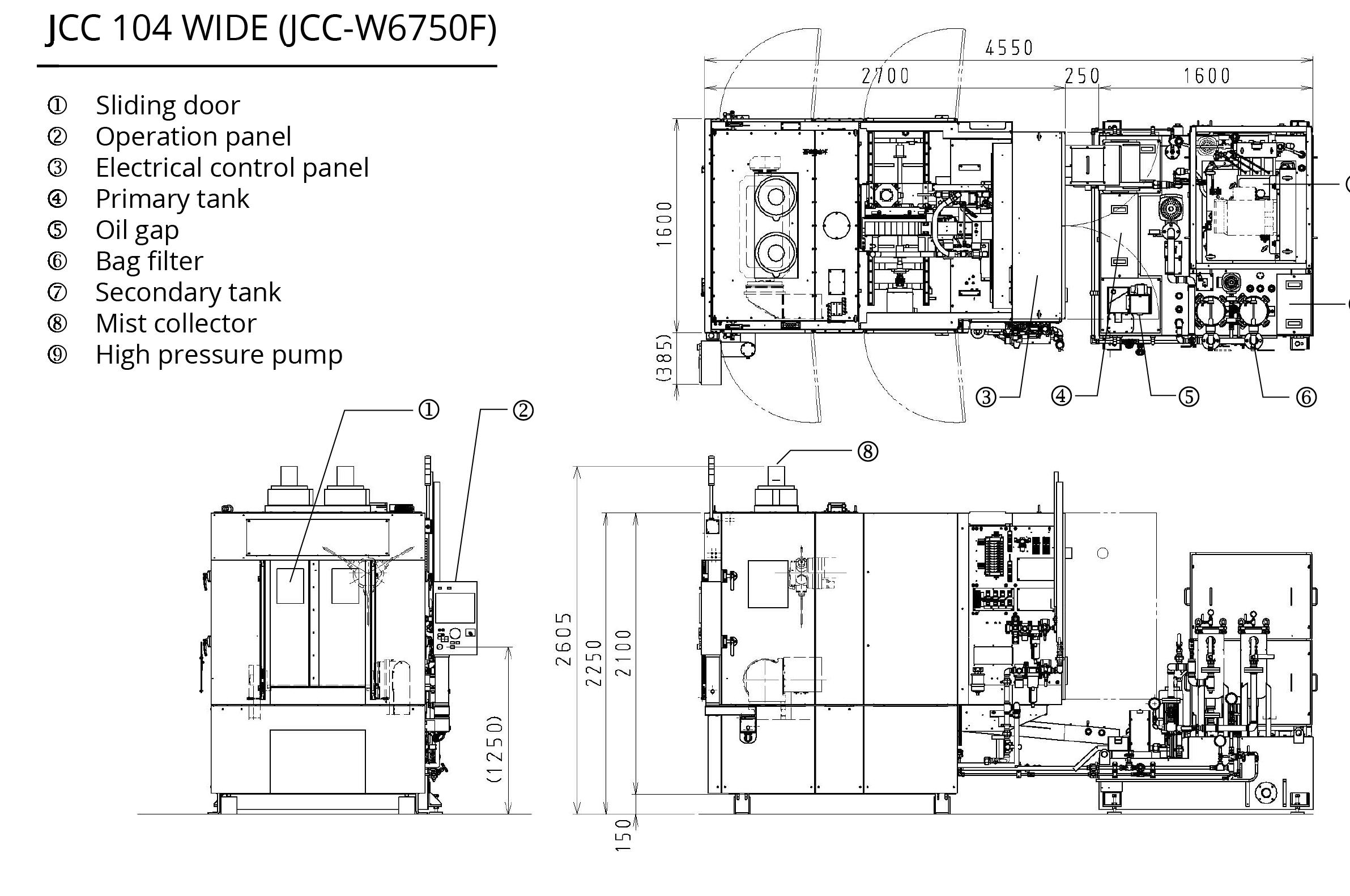
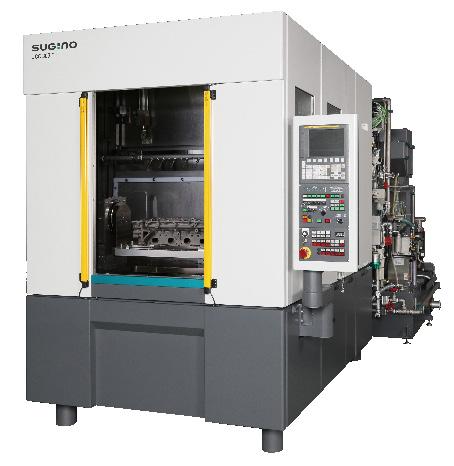
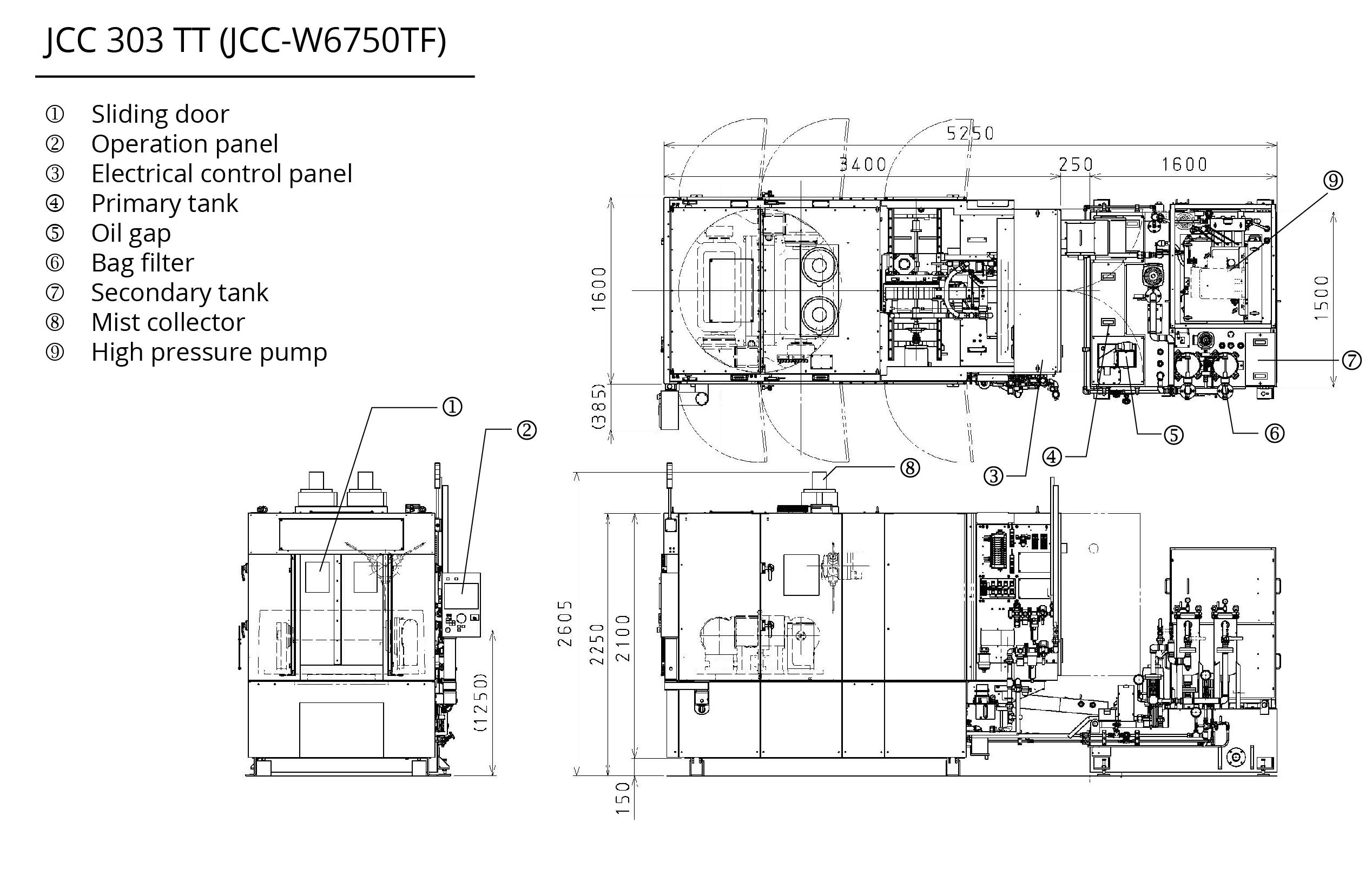
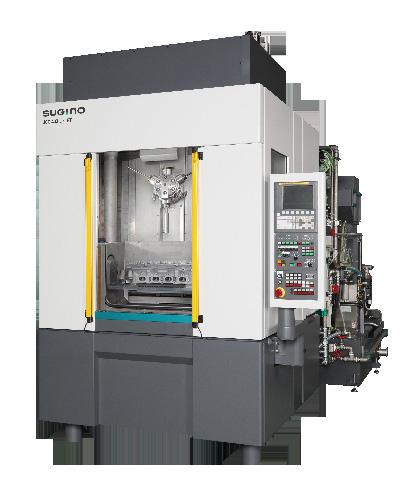
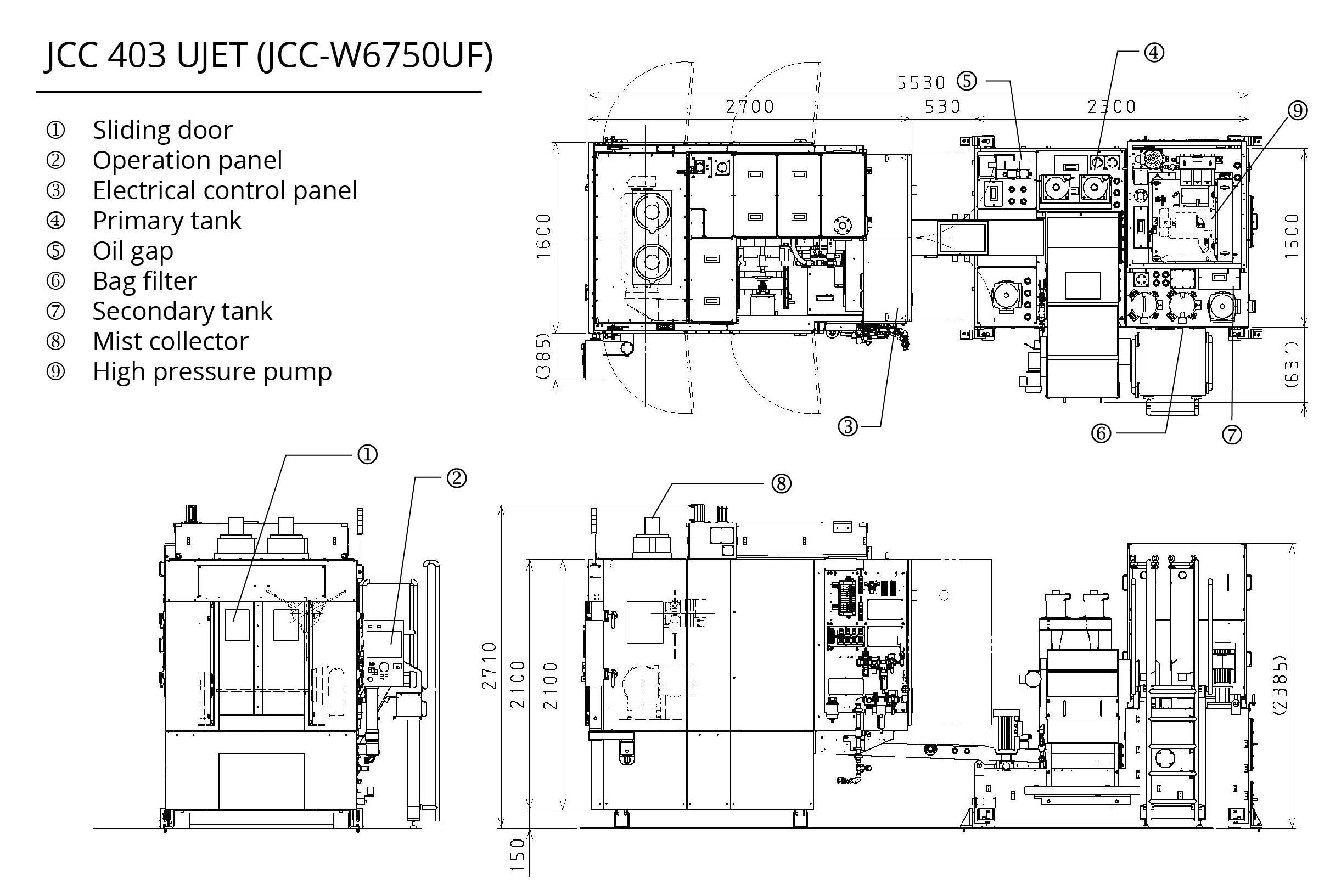
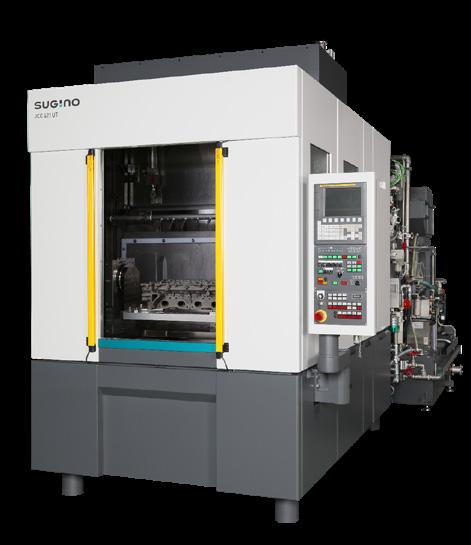
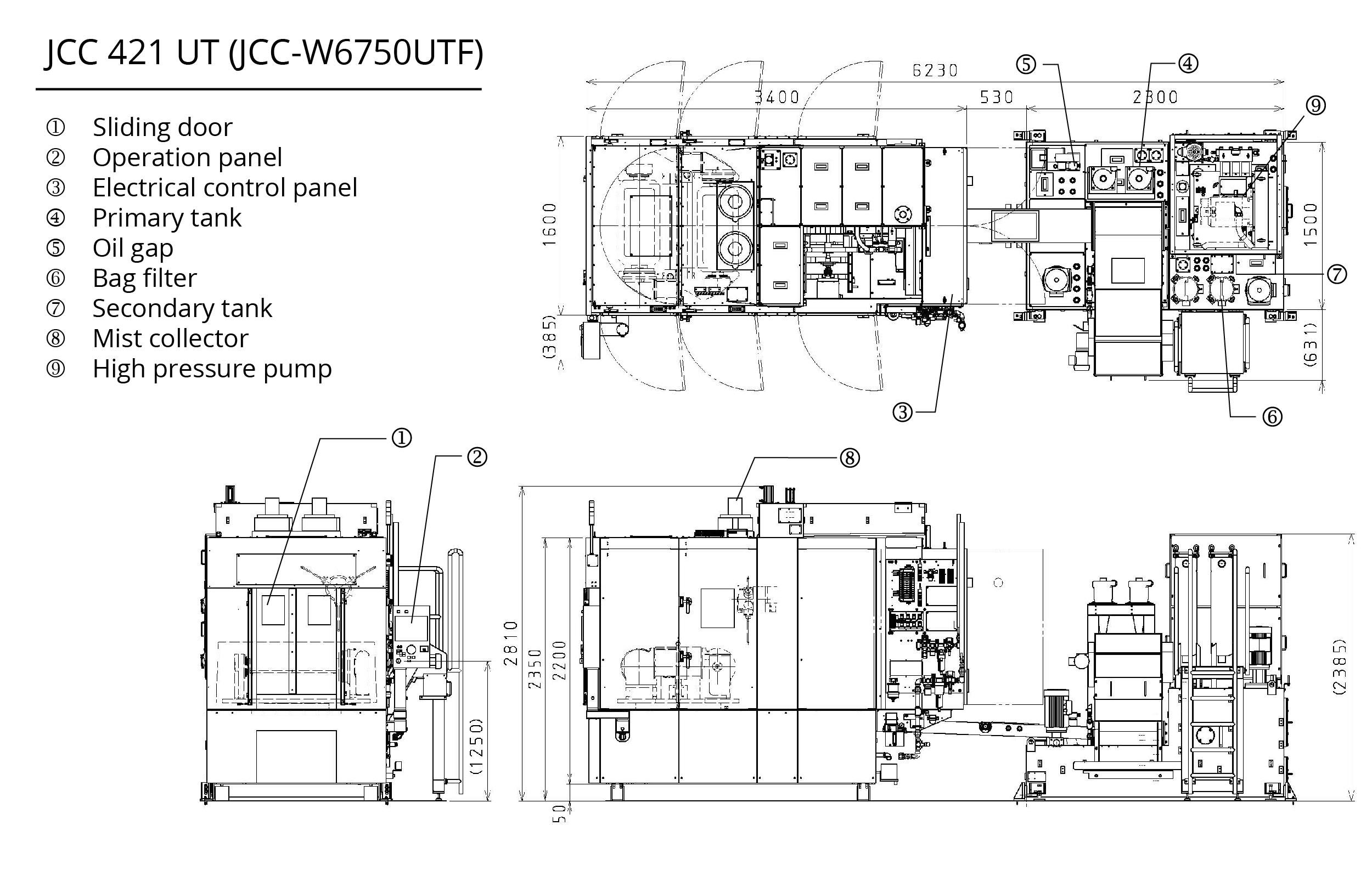
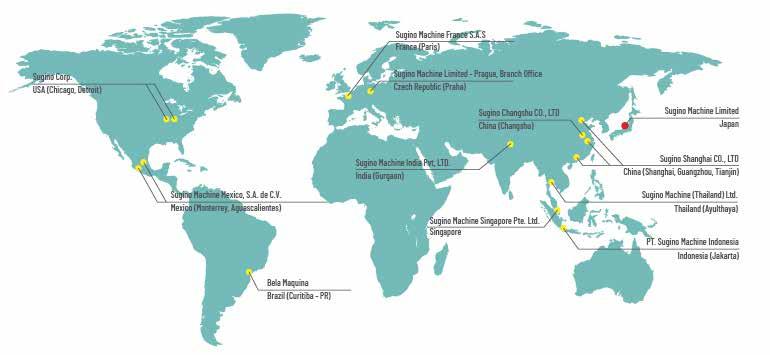
Locations Worldwide
Sugino Corp.
U.S.A. sales@suginocorp.com www.suginocorp.com
Chicago TEL +1-630-250-8585 / 888-SUGINO1 FAX +1-630-250-8665
Detroit TEL +1-248-956-8320
Mexico
Sugino Machine Mexico, S.A. De C.V. ventas@sugino.com.mx Monterrey TEL +52-81-1100-0108 Aguascalientes TEL +52-449-140-7495
Brazil
Bela Maquina contat@belamaquina.com.br Curatiba - PR www.belamaquina.com.br
Czech Republic
Sugino Machine Ltd. - Prague info@sugino.cz Praha TEL +420-257-950-228 FAX +420-257-950-044
France
Sugino Machine France S.A.S contact@sugino.eu
Paris TEL +33-1-84-17-49-87 FAX +33-1-84-17-58-86
Indonesia
PT. Sugino Machine Indonesia
Jakarta
Thailand
Sugino Machine (Thailand), Ltd. Ayulthaya
Singapore
Sugino Machine Singapore Pte., Ltd. Midview City
Sugino Machine Limited
Japan Headquarters: Uozo City, Toyama Pref. TEL +81-765-24-5111 FAX +81-765-24-5051 export@sugino.com www.sugino.com
Sales Offices:
Tokyo Osaka Toyama - Hayatsuki
Toyama - Namerikawa Fukuoka Nagoya Hamamatsu Mito Hiroshima
China
Sugino Shanghai Co., Ltd. Shanghai Guangzhou Tianjin
India Sugino Machine India Pvt., Ltd. Gugaon
Manufacturing Plants
Toyama - Hayatsuki, Japan
Toyama - Namerikawa, Japan
Kakegawa City, Japan
Utsunomiya City, Japan (Kyoritsu Seiki Co., Ltd)
Ota City, Japan (Nihon Jig Co., Ltd)
Kitanagoya City, Japan (M-Tec Co., Inc.)
Changshu, Jiangsu, China
Neutraubling, Germany (Sugino/Zippel GmbH)
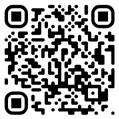
For more details on our Global Locations, please scan the code for our up-to-date locations page.
S ugino Corp. USA 1380 Hamilton Parkway Itasca, IL 60143 TEL 888.784.4661 FAX 630.250.8665 suginocorp.com ✉ sales@suginocorp.com
• Specifications are subject to change without notice for product improvement.
• When exporting this product overseas, based on Japan’s Foreign Exchange and Foreign Trade Law, Please carry out export control procedures.
• , and are trademarks of our company in Japan and abroad.
• The information provided is as of October 2021.
• All rights reserved.