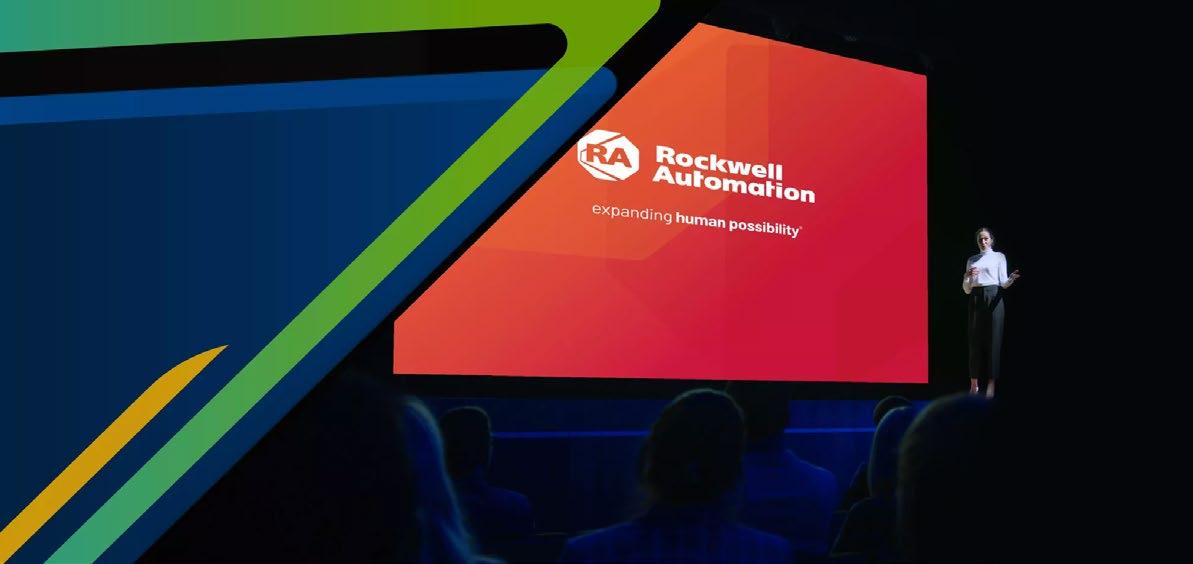
12 minute read
Sustainability is good for buisness
from SPN Sep 2021
by spnews.com
Why Sustainability is good for your business
At a recent virtual conference event, Allie Schwertner, Sustainability leader at Rockwell Automation, made a strong case as to why Sustainability is good for your business
Advertisement
“Leaders should look at efficiency and sustainability as mutually beneficial goals,” said Allie Schwertner, sustainability and energy leader at Rockwell Automation. “Improving the efficiency of operations will reduce waste, which improves the sustainability of processes. This introduces cost benefits, which can then be reinvested in future projects.”
Schwertner spoke as moderator for a keynote session on “Sustainability: From Vision to Impact,” at the ROKLive 2021 virtual event. The session visited with Rockwell Automation partners that have made sustainability a priority and have committed to a positive feedback loop to continuously make processes more efficient and more sustainable.
“In order to help customers meet sustainability goals, it’s important that we hold ourselves to a high standard,” Schwertner continued. “Everything needs to be managed to maintain high sustainability standards in areas such as energy consumption, operational efficiency, waste and recycling.” She welcomed three projects and organizations that are focused on sustainability for waste, energy and water.
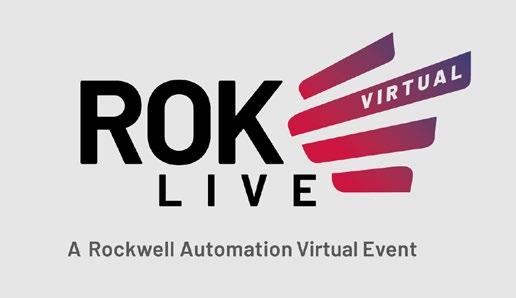
Chemical recycling feeds a circular economy
At packaging company, Sealed Air, the makers of Cryovac food packaging and Bubble Wrap protective packaging, “We have a very high sense of purpose—to leave the world better than we found it,” said Sergio Pupkin, growth and strategy officer at Sealed Air. The company has made a pledge that by 2025 100% of its packaging will be recyclable or renewable.
We want to recycle more in order to drive that circular economy, but the recycling stream for many of our products are still under development,” Pupkin said. So Sealed Air is driving some of that development with its customers, who share a similar recycling journey. “We have the same problems that they have,” Pupkin said. The transformation into smart factories and beyond would not be possible without automation technology and the partnership with Rockwell Automation, Pupkin added. Ron Cotterman, vice president of innovation and sustainability at Sealed Air, took attendees on a tour of the company’s innovation center at its Charlotte campus. The tour focused on three areas: one of its automated packaging lines and two of the labs where the company makes new types of packaging material and recycles plastic back into new materials.
At the food packaging lab, a Cryovac auto loader automatically inserts blocks of cheese into the package and seals them, “with a labor- and energy-efficient process,” Cotterman said. “Before that equipment was available, you would have seen a lot more people manually packaging that cheese into those plastic bags, but because of that automated equipment, it happens in a fraction of a second,” he added.
“We go through a series of process steps to melt it down and to make new plastic material that performs as if it was brand-new, virgin material.. The lab is where Sealed Air does its experiments and the essential R&D work for material innovation at a small scale, before it’s practiced at the large-scale facilities. “This capability is brand-new within our industry,” Cotterman said. The final stop on the Sealed Air tour was the chemistry lab, what Cotterman called the “future of recycling,” where the chemistry is done to make plastic recyclable. “Plastic, whether in the form of a tray or film or bag, can be recycled into raw materials, such as this oil here, that can then be used to make a new plastic. We call that advanced recycling or chemical recycling and we do it because it’s not only good for the planet, but it’s also good for business,”
Reducing the compressed air carbon footprint
Compressed air systems are crucial to many production processes, but they often represent a plant’s largest energy consumer. Case Controls, which provides control solutions for the compressed air industry, has long been working to help companies reduce their carbon footprint with automation. “We were always about energy reduction from a cost standpoint. When the green movement started, we were already doing that. We were already working with our customers to help them reduce energy, save costs and have a good return on investment,” said Lou York, director of Case Controls. The company also has solutions already built to help customers reduce energy consumption, without reinventing the wheel.
Case can also retrofit old systems with its suite of products. “The retrofits are designed to replace and establish the same footprint as what the compressor OEM control system takes up inside the panel,” Sullivan explained. “We design and engineer a retrofit that is literally plug-and-play.”
From reclamation to revenue
Where Dr. Paul Ziemkiewicz, director of the West Virginia Water Research Institute at West Virginia University, grew up in western Pennsylvania, all the big rivers and the small streams were dead from acidic mine drainage. Today, his work at West Virginia University is cleaning up the environment and those waters from the legacy mines that continue to leach contamination. Acid mine drainage typically happens when pyrite in coal is exposed to oxygen in the air and water, reacting to form sulfuric acid, Ziemkiewicz said. In 2015, the U.S. Dept. of Energy showed an interest in identifying sources of critical minerals and rare earth elements. “I talked to people in the industry. I accessed some old data sets and turns out there were a lot of rare earths in acid mine drainage that no one had ever looked at before,” Ziemkiewicz added.
Over a period of about four-and-a-half years, the university developed a process for extracting the rare earth metals. “In order to make this into a commercial product, you have to be able to put feedstock in, hit some buttons and have good stuff come back out the end of it,” Ziemkiewicz said. “We couldn’t do this without Rockwell providing that automation, the sensors and control technology that make the process work.”
Finally, at “Site number 834,” a unit is being built to do both reclamation work on the contaminated waters and extract the rare earth elements for profit. “It is strictly treating the water coming off the #834 site that was previously contaminating the headwaters of the Potomac River,” Ziemkiewicz commented, “The number 834 site is the first integrated demonstration of our technology.” Most importantly, the process is doing reclamation work, and the treatment process itself creates a revenue stream to support the work.
The full ROKLive presentation, “Sustainability: From Vision to Impact,” remains available on demand until October 2021.
Capitalising on data-driven insights
David Harding-Brown ecoveritas’ CEO believes that where there is accurate and reliable data, there is hope of achieving a truly circular economy. SPN asked Harding-Brown to expand on this theory for the benefit of our readers.
Harding-Brown told SPN News. “Where there is accurate and reliable data, there is hope for a truly circular economy. According to the 2021 Circularity Gap Report, only 8.6% of our world is considered circular1. Of the 59.1 billion tonnes of greenhouse gases (GHGs) emitted in 2019, 70% of those GHGs emitted are directly linked to material handling and use, while 80% of all emissions are associated with housing, mobility and nutrition. For consumables, which includes packaging production, approximately 5.6 billion tonnes of emissions are emitted per year. Without these data-driven insights, we would not know where it is best to apply circular strategies, who should bear the responsibility and how they should be executed. This isn’t about achieving a quick win; it’s about planning for the future of our planet, economy and people.
With the Plastic Tax and Extended Producer Responsibility (EPR) reform coming into force very soon, there is now a major data wave on the horizon. Packaging brands and manufacturers must understand how imminent changes in legislation will affect their bottom line, where their supply chain is most vulnerable, and how gathering the right data can impact their circularity model for the better.
For example, the 2021 State of Plastic Recycling report found that consumer goods companies, plastic packaging manufacturers, government bodies and consumers should all be primarily responsible for providing effective plastic recycling resources and solutions. The survey, which was conducted by YouGov with more than 5,000 adults across the US, Mexico, Spain and the UK, indicated that these groups should have a shared responsibility to expand knowledge and influence behaviour to achieve a circular economy. This means that packaging brands, retailers and manufacturers are not alone. If collaboration between key stakeholders is the driving force behind a circular strategy, data-driven insight is the glue tying everything together. At ecoveritas, we have more than 100 years of combined experience in providing business intelligence to packaging manufacturers, retailers and brand owners. Our expertise in data collection means we can use lifecycle assessments, footprint analysis and cost impact assessments to extrapolate meaningful figures that will support a company’s commercialisation strategy, while substantiating a circular economic plan.
For brands that are looking to design out waste early in the production cycle, we can also help by using key data points to minimise the environmental impact of packaging.
A circular economy is not yet out of reach. Data has the power to change our future, so let’s use it while we still can”.
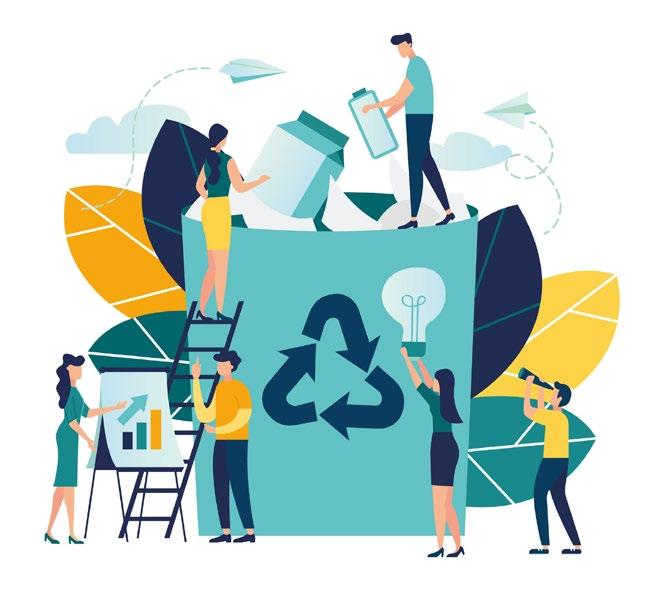
Pushing the boundaries to close the plastic loop
Dow continues to push boundaries to close the loop for plastic packaging and enable a circular economy.
Through collaborative partnerships Dow is accelerating its sustainability commitments with major goals including incorporating 100,000 tons of waste plastic into products by 2025 and enabling 100% of these sold into packaging applications to be reusable or recyclable by 2035.
Two recent collaborations stand out as examples of what is now possible.
It all starts by designing packaging for recyclability from the outset. A recently delivered polyethylene (PE)-based pouch-to-pouch concept saw value chain partners produce and recycle a PE pouch back into raw material, successfully de-inking it in the process. This was then used to create a new pouch, containing 30% recycled materials from the first pouch and designed for recyclability.
Another ambitious collaboration used existing production lines to deliver an easy-to-recycle high barrier flexible stand up pouch. Thanks to the use of mono-material concepts, both pouches are suitable for recycling in existing PE streams.
By combining Dow’s material science with partner knowhow and Dow’s Pack Studios industry-scale capabilities we continue to push boundaries to close the loop for plastic packaging.
Let us show you what’s possible: Dow.com/contact
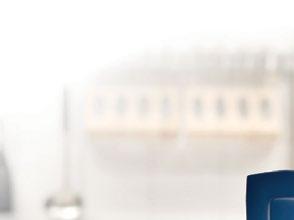
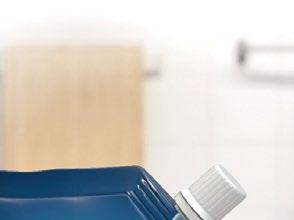
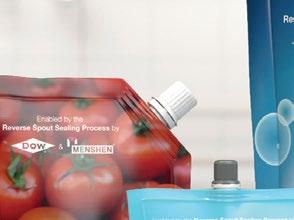
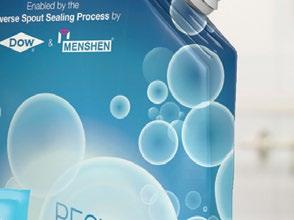

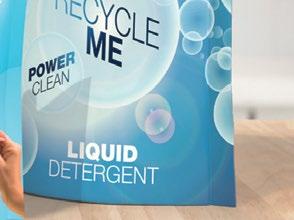
Can we redesign plastics for circularity?
We believe it is time to radically redesign how we make plastic.
Let’s be honest, the plastic waste issue is contributing to environmental degradation. Our industry must accelerate the circular economy for plastics. At Dow, we are leading the charge on making this a reality. We know it’s possible to go further, faster. It all starts by designing plastic for recyclability, harnessing renewable feedstocks, and creating mono-material and recyclable packaging solutions. Increasing circularity for plastics is not easy and no one company can achieve it alone.
The time to act is now. Will you join us? Dow.com/packaging
Optimising 4R’s
Southgate Packaging, one of Europe’s leading packaging suppliers, is a committed member of the industrial movement known as the ‘Circular Carbon Economy’ that aims to create a more sustainable way of working and living. To achieve this, Southgate ensures that every one of its new products meets at least one of the 4R’s: Reuse; Recycle; Reduce and Remove – and are considered the pillars of a successful circular economy.
As part of its mission to be a leader in this field, Southgate invested in a specialist team focusing on new product development as part of its ongoing, pioneering activity to lead the industry in developing sustainable packaging products. In the last 12 months Southgate has launched several new sustainable products including another Paper Tape Dispenser and Void Fill, with more innovations to come.
Southgate, which has more than 60 employees, is committed to developing a line of alternative products to expand its current range and significantly reduce packaging waste and plastic content. The company is determined to play a pioneering and meaningful part in persuading the packaging industry to reduce its impact on the environment and climate change.
Craig Turner, Managing Director of Southgate Packaging, said: “With the increase in demand for packaging supplies having a knock-on effect on the supply chain, we are already starting to see industry restrictions on items such as corrugated boxes. In addition, there is also a need for warehouse space and fulfilling daily order quotas. To meet these changes we are taking responsibility by giving our customers sustainable packaging solutions, reducing waste and plastic content, whilst feeding into the consumer shift for more eco-friendly packaging products. Our mission is to have a suite of ecofriendly options available for every product.”
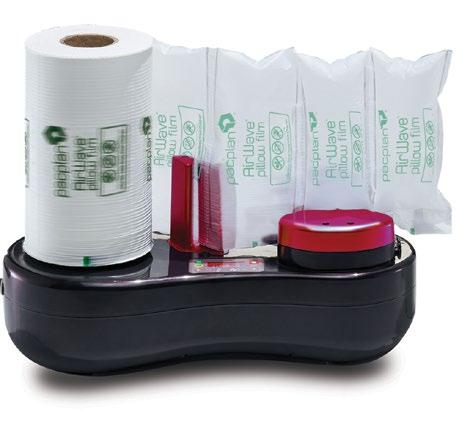
Southgate recently developed the PWN4 air pillow system, which is its fastest small pillow system yet. Its compact size means that it is both mobile and flexible and can be moved around easily to suit customers’ requirements.
The PWN4 is the fastest machine on the market. The four speed modes of 4/6/8/10m per minute offer unbeatable speed without compromising on quality. Additionally, there is no heat-up phase, thus saving time and increasing efficiency.

Craig added: “Our latest product launch is part of our mission to continually focus on product innovation and the development of new, eco-friendly packaging alternatives. We firmly believe that it is a must-have sustainable alternative for those using void fill and will help us and our clients contribute to the circular economy.”
Southgate’s focus for 2021 and beyond will be to develop and promote the idea of a circular economy – inspiring businesses on an international scale to embrace a global solution to sustainability and eliminating waste. New product development is a major part of achieving this goal.
Craig Turner
Managing Director of Southgate Packaging