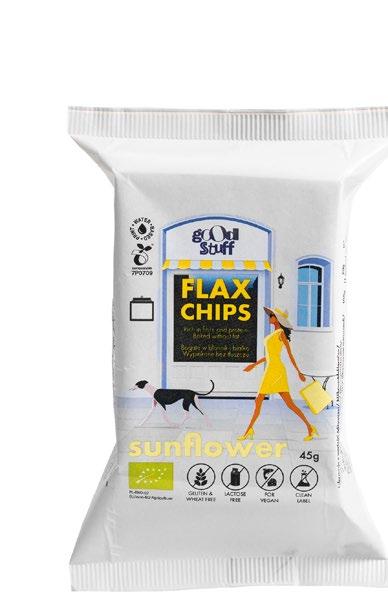
11 minute read
Crunch time for crisps
from SPN Sep 2021
by spnews.com
An innovative packaging company in Poland has recorded a first when it comes to the packaging and content of organic crisps. We take a closer look at the 100% natural, compostable and biodegradable product that appears to beat all others!
Silbo is a dynamic Polish packaging company that was recently given the assignment to devlop new bio-degradable packaging for a eco-friendly range of organic crisps. Flax is a new bio-snack, and its main ingredient is linseed! Its composition is simple, natural and, most importantly, healthy. This ‘healthier diet’ product had to be packed in an environmentally friendly way that was both compostable and biodegradable..
Advertisement
Martyna Smolenska, the commercial director of the crisp manufacturer: ”The Good Stuff” told SPN, ”When we started this project, we were concerned about the ecological values of the packaging, we were looking for a biodegradable material that would meet our high organic and aesthetic expectations. We wanted something original that would be different from what could already be found on the market”.
The answer to this challenge was met by Silbo a leading food packaging company that developed special biodegradable packaging entirely from compostable materials. These decompose in appropriate industrial conditions and change into valuable organic matter in a neutral, harmless way for the planet. After use, such packaging can be discarded into a Bio container. The laminate made by Silbo (a multilayer compostable material) is not only about environmentally friendly raw materials, but also about high-quality printing with water-based inks. These do not release harmful substances into the soil and do not emit poisonous compounds into the atmosphere (as is currently the case with solvent-based printing).
Silbo has been using this type of water-based printing for six years now and was the first in Europe to produce fully compostable flexible packaging.
We have been told that there is still a general belief that compostable materials in packaging do not provide adequate barrier properties. According to Silbo this is a myth. They say that such bio-barrier materials are already available and combinations of renewable raw materials have been developed that meet all specific barrier requirements. In addition, they have excellent resistance to moisture, which as a result, offers secure barriers to gases and aromas. Interestingly, they are also resistant to oils. Thanks to this, the chips can remain pleasantly crunchy and tasty, whist the packaging remains hygienic and functional.
Silbo tells SPN that similar bio-packaging solutions are not only ideal for all kinds of snacks, but also for coffee, convenience dishes, instant products and even dietary supplements.
Smolenska of ‘Good Stuff’ foods commented, ”We like the approach that Silbo has developed towards its customers. We got to know the owner,and the company’s portfolio is impressive. We also appreciate the knowledge that was passed on to us during our on-going discussions. We are not aware of any other food packaging manufacturer that offers such solutions with such pro-ecological properties”
Altogether this sounds like a recipe for environmental success. We endorse the innovative approach to the production of compostable and biodegradable packaging and anticipate that Silbo will be kept very busy by eco-aware food packaging companies throughout Europe!
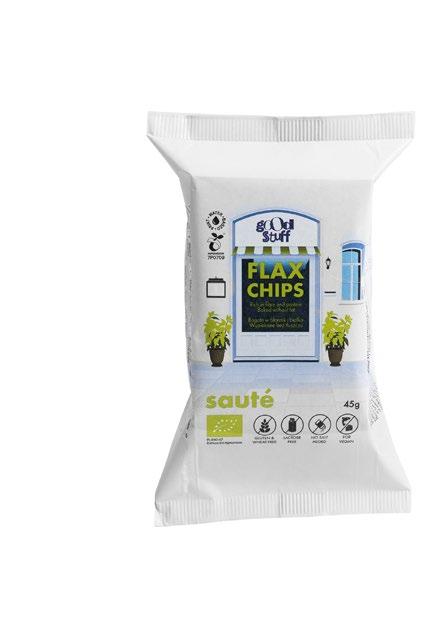

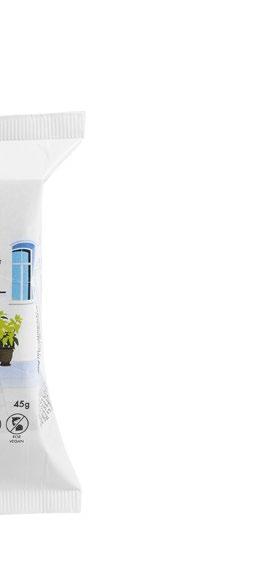
Bio-Packaging under the microscope
Exploring advances in environmentally friendly polymers for food packaging is something that is gaining momentum throughout the industry. Plastics have received much criticism in recent years, however, finding a like-for-like alternative is incredibly challenging. So how viable are these new greener plastics? Ben Smye, head of growth at materials search engine Matmatch, takes a closer look.
The food industry is one of the sectors that has benefited most from the developments in plastics in the past century. Just as refrigeration revolutionised preservation of food for consumers, plastic packaging reshaped product possibilities and food distribution. Plastics provided an effective, massproducible means of extending the shelf life of products by protecting them from oxidation, microbial growth and some damage during transportation.
To this day, thermoplastics are widely used for the majority of food and beverage packaging. This is due to their flexibility, impact resistance, lower molecular weight and, crucially, their ability to be recycled. However, being recyclable is not enough on its own. Since it has become apparent that plastic is often not being disposed of properly or the infrastructure is not in place to support recycling of all plastics, the need has arisen for other environmentally friendly alternatives.
Several materials such as paper, glass and aluminium have grown in popularity for food packaging in recent years. But as any design engineer knows, simply substituting one material for another is not straightforward — the properties of the original material and its replacement need to be taken into consideration. This has led many food packaging companies to consider biodegradable and compostable polymers, which can exhibit comparable properties to conventional plastics.
Defining Degradation
The degradation process that a polymer goes through helps to define whether it is biodegradable or compostable. In the case of the former, the polymer decomposes into carbon dioxide, water, inorganic compounds and biomasses in certain controlled environments, such as under high temperatures or when exposed to certain chemicals. Compostable polymers, on the other hand, are defined much more closely. European standard EN13432 requires that any plastic that’s marked as ‘compostable’ needs to break down under industrial conditions — in temperatures of up to 60 degrees Celsius — in under twelve weeks.
Within these definitions, there are many biodegradable polymers that are proving themselves to be valuable in food packaging. Natural polymers such as cellulose can be used as films and fresh produce packaging; non-natural polymers like polyglycolide (PGA) can function as the protective layer in multi-layer packaging; and synthetic polymers, notably Polyhydroxyalkanoates (PHA), can be used in bottles and containers.
Where biodegradable and bio-based polymers have historically faced limitations, however, is in scalability and compatibility with existing processing methods. But the increased drive in green polymer innovation in recent years is helping to overcome these hurdles. Polylactic acid (PLA), for example, is receiving a lot of interest in food and beverage packaging. This interest has arisen due to its thermal and mechanical properties, as well as its compatibility with processing methods such as injection moulding, film extrusion and thermoforming. These properties have led to it being researched and used in areas like food trays, disposable straws and lids.
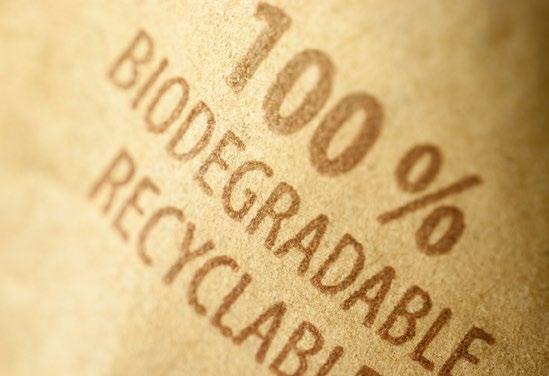
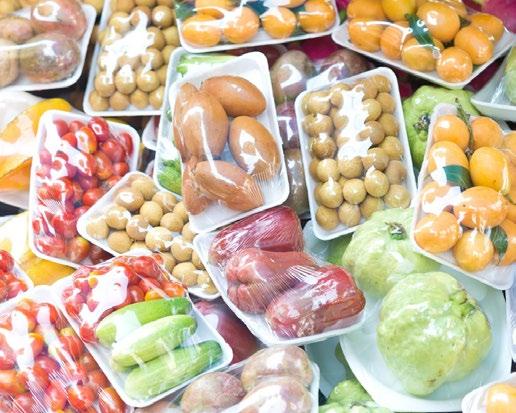
Progress via Partnership
Matmatch works in close partnership with many materials suppliers globally, several of which have ongoing developments in the field of more environmentally friendly packaging substances. One such company is Total Corbion PLA, a leading producer of PLA, a biobased and biodegradable polymer that can be used in packaging applications. Made from renewable sources, PLA offers a reduced carbon footprint when compared with traditional plastics. A number of PLA materials have been food contactapproved, and as development continues on their Luminy portfolio, Total Corbion PLA is providing innovative and biobased solutions to packaging problems.
Another company is Stora Enso, who focuses on bio-based materials. ‘Bio-based’ means the materials are produced from renewable feedstock rather than oil-based sources. Stora Enso is a leading global provider of renewable solutions for packaging. The company’s goal is to move away from fossil-based materials and, as such, their products offer a lower carbon footprint than traditional plastics and often have superior recycling properties.
With so much research and development in the pipeline, the future of environmentally friendly food packaging looks to be full of ground-breaking ideas. And with companies like Matmatch connecting design engineers with materials suppliers that can fulfil their requirements, it seems that there’s a revolution in food packaging just on the horizon.
Orbis Bio-packaging goes orbital

In recent years Orbis has invested heavily in order to make the Circular Economy a reality. Today it looks as if Orbis has made considerable progress towards achieving their goal. SPN takes a closer look at the latest developments at Orbis, by sending them some pretty searching questions. The results are published here.
How ‘sustainability-aware’ would you say your company is and what recent measures have you taken to improve your overall contribution to the circular economy?
“As a manufacturer of plastic transport packaging for many decades, ORBIS’ key principles are Innovation, Durability & Sustainability. Today, sustainability is implemented in the entire product life cycle, from inbound processes and production to recycling. ORBIS goes even further to find new ways of contributing to the circular economy”.
In relation to sustainability, what would you say have been your most important milestones?
“Making transport packaging solutions as sustainable as possible has always been a priority at ORBIS. That is why we use recycled materials wherever possible in production, design our products to have a significantly longer lifetime and recycle 100% of the raw materials”.
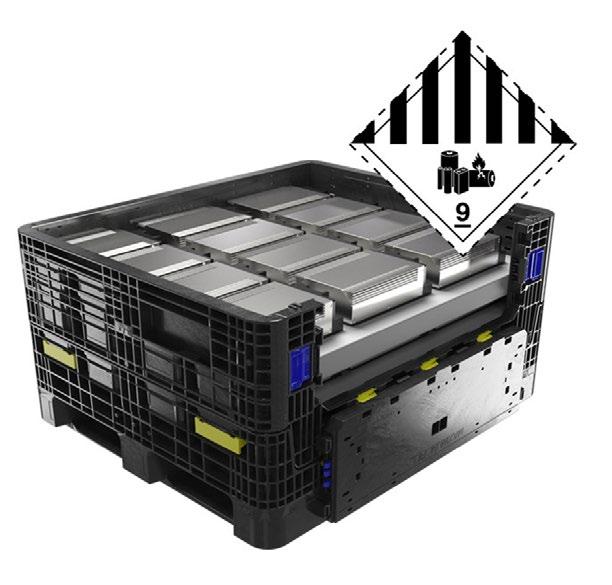
In your opinion what have been the most significant developments in terms of recycling and bio-degradable packaging?
“Using recycled materials for packaging production can be a challenge. ORBIS designed products to be extremely robust and durable – while using recycled materials. In the US, ORBIS recently launched its Ocean in Mind packaging initiative, which focuses on recovering and repurposing single-use plastic waste found on coastlines and using it in supply chain packaging”.
What do you consider to be the most promising market opportunities for your company at this time?
“With rising sustainability targets, ORBIS is looking to address new vertical markets with reusable & recyclable transport packaging to replace one-way packaging”.
ORBIS Lithium Ion Battery Transport box
What are the key drivers for change in your industry sector and how much is the on-going pressure for greater sustainability and recycling affecting your productivity?
“The replacement of metal glitterboxes & corrugated packaging is driving more efficiency and sustainability in industrial supply chains. Also, ORBIS Europe pioneers in developing customer-specific packaging solutions for dangerous goods (e.g. li-ion batteries). As sustainability is a key pillar of our strategy since many years, ORBIS is well prepared for the challenges regarding sustainability and addresses these globally with a wide range of sustainable products and manufacturing processes!
As we are keen to understand more about the latest trends shaping the packaging industry in your sector, what do you consider to be the most significant recent developments?
“In the industrial sector, the development of complete packaging solutions (including dunnages) and UNcertification, if necessary, combined with a wide product range of different sizes is key. In RSC, ORBIS is going to launch different kinds of innovations to replace one-way packaging within the next years and make FMCG supply chains more sustainable”.
Can you describe your product portfolio and its sustainability credentials?
“ORBIS’ product range consist of a wide range of FLC bulk containers, pallets and totes. Each of these product lines has their own credentials when it comes to sustainability.
• Usage of used water & green energy in our plants • CO2 reduction in production process • Significantly longer lifetime of products • Buyback & 100% recycling • See sustainability infographic for additional input on pallets & totes*
Are you planning the launch of any new products in the foreseeable future that you can tell us about?
“ORBIS will be launching a sustainable and efficient plastic alternative corrugated / one-way packaging in Nov 2021 (@Sustainability in Packaging Europe & Deutscher LogistikKongress). The boxes have identical features as cardboard boxes. So, they are ideal for applications with closed supply chain loops (e.g. inbound packaging, finished goods) and compatible with existing automated and manual processes. The reusability (70+) and recyclability bring significant added value to customers’ supply chains:
• Long-term cost-savings • Significant source reduction • Improvements in operations
Our sustainability journey continues. With a new product concept, we have set another milestone in making FMCG supply chains more sustainable”.
How has the Covid 19 pandemic affected your production and manufacturing capabilities?
“Not at the beginning. There is always a need for transport packaging to keep supply chains running. Of course, like every company operating in global markets, ORBIS is affected by the current price increases in logistics and raw materials”.
Why use reusable over single-use packaging? less system downtime faster load/unload times lower labor costs
Equal to 38,000 2-liter bottles Small footprint. Big savings.
REUSABLE TOTES 1 REUSABLE PALLETS 2
31%
Reduce energy usage
71%
Reduce energy usage
79.5%
Reduce solid waste
72%
Reduce solid waste
38.3%
Reduce greenhouse gas emissions
3.2%
Reduce greenhouse gas emissions
Enough to run a refrigerator in 120 U.S. homes for 1 year
Reusables help companies build a more
SUSTAINABLE BRAND
90%
of consumers want companies to do more than turn a profit
75%
of consumers expect businesses to support efforts to stop climate change3 reusable pallets last 18 times longer than wood pallets.4
REUSABLE Up to cycles200
WOOD cycles11
Supply chain optimization with
reusable packaging products + packaging management services =
Long-term cost savings Rapid ROI
Lower environmental impact
Better operational efficiency
Our circular economy
Continuous flow of product for a sustainable supply chain
REDUCE
Reusables are designed to lessen waste, greenhouse gas emissions and energy use.5
REUSE
Sustainable for many trips over a number of years.
RECYCLE
Manufactured, used, reused and reprocessed with zero impact to the solid waste stream.
Our commitment to sustainability
97%
products are recyclable at end of service life
99%
water used in manufacturing operations is reused
100%
products eliminate the need for single-use packaging reusable packaging products are designed for sustainability