
8 minute read
Safety in numbers
from SPN Sep 2021
by spnews.com
Two companies at the top of their game have joined forces to launch the world’s most advanced barrier coating machines. They are offering sustainable water barriers that can be heat-sealed. This is a first for the packaging industry and this new US/EU jointventure adds up to numbers that will make the deal unmissable. In fact, the fast and generous ROI alone makes this a most attractive proposition.
Lennart Group B.V & EcoSafe Barrier Inc have launched their unique EcoSafe Barrier Coating Machines this month. Ecosafe Barrier Inc, is a US producer of paper coating machinery with many patents already under its belt. Now the company has joined forces with the Lennart Group B.V of the Netherlands, to create an EcoSafe barrier coating machine that offers recyclable, sustainable coatings for packaging markets worldwide. The aim of the partnership is to eliminate plastic materials throughout the industry.
Advertisement
This ground-breaking project was launched last month following the success of the company’s water barrier coatings which were tested specifically with recycling and sustainability in mind. From today, all machine models will be built and shipped from the USA by Ecosafe Barrier Inc. The coating systems are specially made for water barrier/ heat seal/ultrasonic seal coatings for optimal performance. For example, the Eco2sheet is a double coating line for sheets measuring 50cm X 70 cm and 77 X 108 cm. The Eco2web machine is a double coating line for sheet sizes 52cm and 77cm widths. These sizes will also be upgraded in the near future.
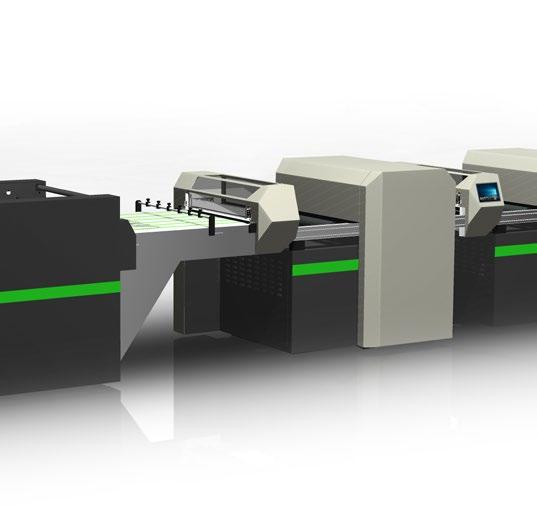
The Eco2sheet is a double coating line for sheets measuring 50cm X 70 cm and 77 X 108 cm
The water-based coatings are made in the EU by our existing partners with each coating being specially made for our machines. There will also be a number of new developments to come soon for both coatings and machinery.
I.Cem Yaray, Co-Founder of Lennart Group B.V, said; ‘’We have been working on the project for the last 18 months and have achieved many goals. EcoSafe Barrier Inc has in-depth knowledge of advanced coating machines. Our coating producer partner has also worked closely with us to create the best possible sustainable coatings for our machines. We all know that plastic is very harmful to nature and to our environment. This is something that we are committed to changing.
Furthermore, we believe that companies should work closely together to reach zero-plastic levels as soon as possible. To this end, we will be supplying our environmentally-friendly machinery and coatings in tandem for our customers”
Yaray added, “Our target is to develop production flexibility for packaging companies whist helping to achieve zeroplastic content in all packaging. Companies do not need to buy different types of cartons in stock. Depending on order types, they will be coating their cartons on Eco2 machines with our eco-friendly, sustainable coatings, whether this is for high volume runs or simply short-run sampling.
The order amount is not important to our system, as the coating costs are so low. R.O.I of the machine is fast and generous. Right now, companies are struggling because of their raw material costs and other variables. Lennart Group B.V. is always looking for cost-reduction possibilities for its clients. In addition, if we are helping the world to reduce global warming, we will also be the happiest people in the world‘’.
Here are a few of the sectors that Eco-Safe told SPN will be the first to benefit:
• Fast Food packaging • Bakery Packaging • Flexible Packaging • Aluminum/Film Lids • Paper Cups/bowls • Pouches • Medical Packaging • Hygiene Packaging • Lamination film replacement in packaging & printing
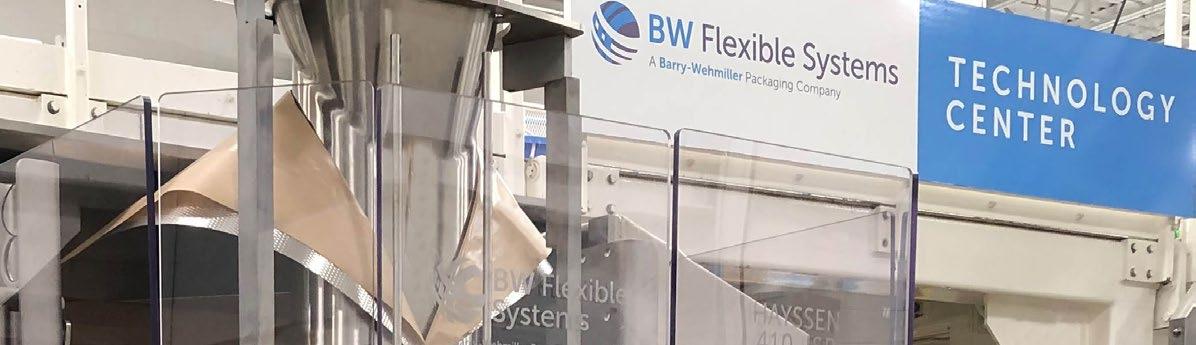
The Growing Pains of Sustainability in Packaged Foods
Michael Dann, BW Flexible Systems’ Global Product Line Leader for Horizontal Form Fill Seal, asks: “How can we as an industry satisfy consumer demand for ‘sustainable packaging’ when the term is still being defined?”
The answer is, of course, complicated. BW Flexible System’s approach to sustainability recognizes that the pathway to truly sustainable manufacturing and packaging needs to be flexible and will require addressing not only the material being used to package products, but the packaging machines and even the manufacturing facility, itself. To accomplish this, the flexible packaging company is setting some ambitious targets and investing in research and development with the intention of leading the way to a cleaner, “greener” packaging future.
Research and Development
One of the major targets in a sustainable packaging strategy is to facilitate the use of recyclable and compostable film structures. In the current market, that means packaging machines need to be able to form, fill, and seal paper, polypropylene (PP), polyethylene (PE) and other widely recyclable films. Further, using thinner films helps to reduce both waste and bulk, but also has the effect of ratcheting up the complexity of creating quality seals.
Recently, BW Flexible Systems partnered with a major film producer in Vienna to develop performance recyclable films for use in horizontal flow wrappers. This partnership not only resulted in film structure development, but advanced BW Flexible Systems’ technology for forming and sealing recyclable and downgauged film structures without compromising seal quality. Paper presents other challenges. Requiring gentler handling than plastic, paper material must still run at the same line speeds as plastic materials. To address this, BWFS studied, tested and answered a handful of underlying technical challenges while developing solutions for its existing Vertical Form Fill Seal machinery.
Compared to plastics, running paper makes it more difficult to create a quality seal, particularly while the film is running continuously. To solve this, BWFS again partnered with innovative sealant manufacturers and made modifications to the forming tube assembly (FTA), specifically accounting for the time and temperature required to properly seal bags from a customer’s chosen material.
The flexible packaging manufacturer also developed a cold punch system to punch peg holes, that is now used across other BWFS packaging systems that handle paper.
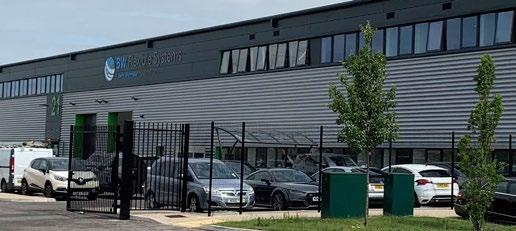
Paper bag samples for Golia Italia lozenge brand

Thinking beyond paper and plastic
Of course, there’s more to developing sustainable, environmentally conscious packaging solutions than film structures alone and BW Flexible Systems has spent considerable time and effort to bring innovative solutions to market that help customers reduce film and product waste, eliminate unexpected downtime, and reduce operator error to help produce more good output per shift.
BWFS has begun rolling out a powerful new, intuitive HMI that helps machine operators more efficiently set-up and run their packaging equipment. Partnered with features like the company’s several film alignment features across both vertical and horizontal platforms, these innovations help reduce wasted material.
This focus on reducing waste has two effects: it creates a more sustainable packaging environment for customers and improves their yearly EBITDA. In effect, by delivering the lowest cost per pack for the customer through ecoconscious improvements, BW Flexible Systems is also helping the environment.
Partnering to meet specific requirements
Of course, sustainable packaging will never be a “one size fits all” endeavor. The differing nature of products to be packaged, varying regional and local requirements, and the demands of different markets means that a certain amount of flexibility will always be required of a packaging solutions provider like BW Flexible Systems. This is why partnering with producers, who intimately understand these issues and their products, is an essential component to delivering truly sustainable packaging solutions.
The newly opened Center for Technological Excellence in Nottingham, UK, BW Flexible Systems’ new state-of-the-art facility, is intended to provide customers the opportunity to collaborate on packaging solutions by gaining hands-on experience and testing machinery using their product and film types before installation. This will include an intentional focus on developing sustainable solutions. “We understand the increasing need of our customers to meet sustainability commitments. At the same time, we recognize the current challenges with labor shortages and the demand our customers have for automation. These challenges, together with increased competition among brand owners, are creating a profound transformation in the packaging industry,” says Michele Allamprese, Vice President of Europe for BWFS said. “The opening of the Technical Center will allow us to fully support our customers through that transformation.”
BW Flexible Systems has also been busy opening new regional sales and service facilities in areas such as South Africa and Russia, providing local sales and support to better meet the challenges in those markets while also reducing corporate travel.

Sustainable manufacturing practices
Finally, manufacturing these solutions should also be as sustainable as the flexible packaging machinery itself. To this end, BW Flexible Systems is charting a path that will see the packaging solutions provider begin seriously tracking and reducing its carbon footprint. Planned future projects include utilizing solar power with a goal of eventually reaching 100% renewable energy usage in the near future, updating plant heating systems from gas to heat pump, and replacing doors and windows with triple glazing in order to boost energy efficiency. The company also plans to update its corporate car fleet with a mix of plug-in hybrid and allelectric vehicles and will add charging stations at its plants.
The road to more sustainable packaging will involve collaboration, innovation, and flexibility across a broad range issues and solutions. BW Flexible Systems’ focus on research and development, collaboration with customers and partners, and development of sustainable manufacturing processes shows the company is poised to build a more sustainable packaging future.
A sample paper bag displaying seal integrity and punched hanging display hole