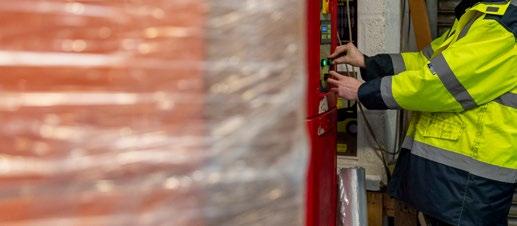
2 minute read
Downgauging without compromise
from SPN Sep 2021
by spnews.com
Packaging companies throughout the UK are seeking ways to avoid the heavy tax shortly to be levied on all those who do not include 30% recyclable material in their products. Wrap-film is one important area where this can be easily and quickly overcome. SPN asked Rick Sellars, Head of Sales at Linden Packaging, what he considers to be the best way forward for those who are still seeking the quickest and most cost effective options.
Sellars told SPN, “In less than a years’ time the Government will begin taxing UK businesses at the rate of £200 per tonne of plastic that does not contain 30% recycled material. In order to avoid this new burden of increased costs, you may be considering switching your current pallet wrap film for one with 30% recycled content. Firstly, think about ways you can reduce the amount of plastic you’re responsible for by looking at high performance films. If you have been using the same stretch film for the last few years, it’s definitely worth evaluating possible alternatives.
Advertisement
Optimised pallet-wrapping
“Many businesses are saving money, reducing plastic content and improving pallet stability by using high performance stretch films which have been correctly optimised on their pallet wrappers. High performance multilayer nano materials can stretch up to 50% further without compromising strength or puncture resistance. In any event, the switch is usually a simple matter of making a minor adjustment to existing machinery. As a transit packaging material, unseen by the consumer, the environmental impact of pallet-wrap isn’t often mentioned, but with stretch film usage in the UK estimated at 140,000 tonnes annually, the environmental impact of downgauging is considerable.
However, selecting the correct stretch film depends on its application and it is also important to assess all stages of the pallet’s journey before choosing a thinner film. In addition, it is worth considering the type of product it will wrap, the distribution process and the wrapping machinery, all of which can influence the outcome.
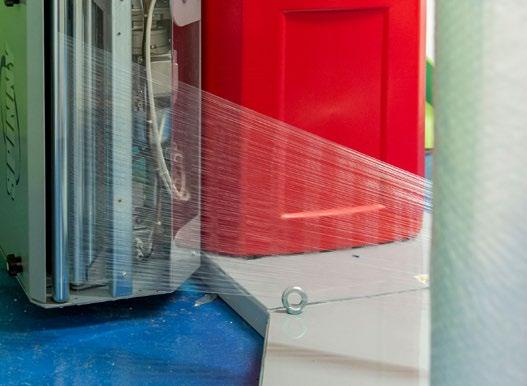
A key tool
“This is where optimisation and pallet stability testing is critical. Rather than simply choosing a thinner film, optimisation is vital to ensure that the right film is being used within your specific packaging lines and operations. Testing offers even more advantages as many pallets are damaged in transit and returned, thereby causing reworking and additional plastic in order to resolve the problem. Testing is not only a key tool for optimisation, but is also an important tool to reduce product damage. Furthermore, it can help to define the best film possible for your operation, whilst using the minimum amount of plastic.
So when it comes to downgauging, rather than thinking about how light you can go, you should aim to downgauge as far as possible without compromise, whilst still ensuring that the wrap provides optimal product protection. This approach will not only help you reach sustainability targets, but save you time and money too.” concluded Sellars.
This rational view of how to quickly and effectively to resolve the impending plastic content tax, makes a lot of sense to us. Especially for those who are wrestling with the many challenges that confront our industry today. This is one solution that can readily tick all the right boxes.
Close-up of water jet machine cleaning