
5 minute read
Cutting down carbon emissions
from SPN Sep 2021
by spnews.com
Carbon footprint cut down to size
News just in to SPN confirms that 3T has wrapped up a significant new contract with the UK’s PFF Packaging Group. This to install its new, advanced transport management system designed to streamline its customer’s deliveries and reduce its own Carbon footprint. The PFF Group is a major supplier of packaging products to supermarkets and food manufacturers throughout the UK, as well as being a leading producer of disposable aprons for the NHS.
Advertisement
3T Logistics and Technology Group has recently been selected by one of the UK’s leading food packaging manufacturers to streamline their customer deliveries and help reduce the company’s carbon footprint. Food packaging manufacturer PFF Group has recently invested in a new transport management system to supply packaging products to supermarkets and food manufacturers across the UK. With increasing changes to their logistics needs due to the continuing pandemic, PFF Group selected 3T as the ideal partner to help them fulfil their growing supply chain requirements.
PFF Group currently also manufactures disposable PPE aprons which are despatched from the company’s Washington site to Department of Health and Social Care depots and distributed for use by NHS frontline health and social care workers. This will be an important element of the new transport management system which utilises 3T Logistics and Technology Group’s cloud-based software. 3T has a proven track record and enviable reputation in the logistics sector for its supply chain and transport management solutions. PFF Group will benefit from this expertise through the platform’s capability to consolidate loads and optimise vehicle usage, thereby reducing journeys and lowering carbon emissions.
Lee Wilkinson, the PFF Group’s supply chain manager, said: “We work with a pool of hauliers and the software enables us to select the best carriers for locations where we can do multiple drop deliveries. By making sure we have filled the vehicles, we are reducing costs and the environmental impact as the amount of carbon per pallet delivered is reduced. The new system also tracks delivery lorries to ensure they arrive on time and manages proof of delivery. This means we are improving service to customers who are increasingly seeking suppliers with reduced carbon usage.”
Rob Hutton, sales and marketing director at 3T Logistics and Technology Group, believes the new partnership with PFF Group will see a reduction not only in costs for PFF Group but also in its environmental impact. “We see the introduction of our TMS solution as a critical step in PFF’s digital transformation. PFF has a vision of reducing carbon footprint and with our transport management system, we will automate and optimise PFF’s transport operations, giving the firm full control of its transport management and bringing greater levels of transparency and visibility.
“The collaboration between 3T and PFF showcases two fast-growing British businesses with a global outlook that are using technology to drive efficiency and innovation. We look forward to working with PFF and providing the logistics solutions it needs to scale their business and further accelerate growth.”
Today 3T is working with a number of high-profile companies across industry verticals, which value a logistics partner that can help them achieve their service, cost and environmental targets whilst digitising their supply chain.
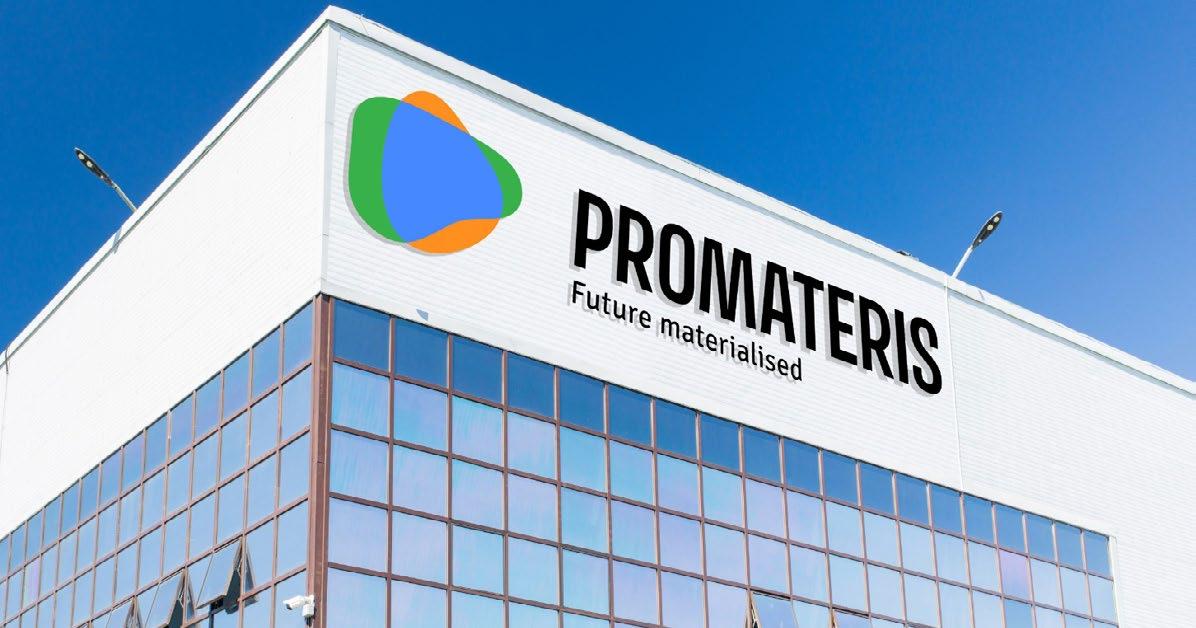
Promateris Packaging
Thanks to a continuous programme of investment and innovative R&D, the leading sustainable packaging company Promateris is extending its bio-packaging operations throughout the CEE region.
Following its continuous strategic investments in stateof-the-art technology, R&D and IT infrastructure systems, Promateris has significantly extended its operations in order to distribute its products to multiple CEE countries. These include Greece, Poland, Moldova, Bulgaria, Hungary among many others. This move is part of the Promateris’ strategic expansion plans in the region for its bio-based and compostable packaging products.
This fast-paced expansion programme is the result of a series of major investments that exceeded more than EUR 10 million over the last 3 years. Much of these funds went to further developing its facility near Bucharest, Romania, which is dedicated to processing bioplastics derived from renewable resources. Following these investments, the company plans to consolidate its leading position in the CEE region, whilst continuing to enhance its current, on-going investment policy.
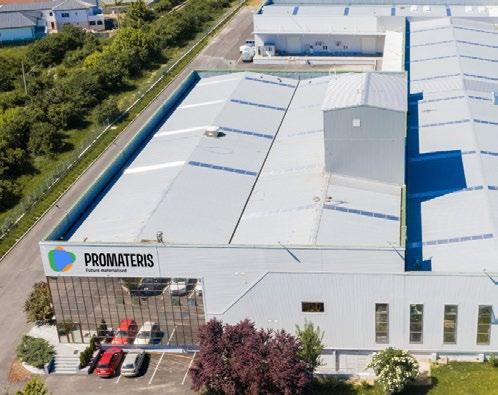
Promateris R&D team, we are able to manufacture products with a reduced environmental footprint. Our strategy includes the manufacturing of products that respect the principles of circular economy”, declares Tudor Georgescu, CEO of Promateris’.
Digital transformation is a priority for the Promateris’ management team. Celebrating more than 60 years since its foundation, the company has undergone major transformation in order to implement up-to-date business processes and manufacturing operations. In 2021, together with their German partner, Theurer, Promateris will implement an ERP/MIS specialized in manufacturing, thus enabling real-time information & insights, as well as advanced automation and production cost optimization.
Furthermore, Promateris is extending its European sales network, as well as its product portfolio.
Tudor Georgescu, CEO of Promateris: “We consider this to be perfect timing for the expansion of our product portfolio, thereby addressing more of our clients’ needs. We will also develop new products bearing in mind two important things: the circular economy principles, and the modern, sustainable retail shelf. We are determined to offer a new generation of packaging, whilst setting an example of best sustainability practices for other companies.”
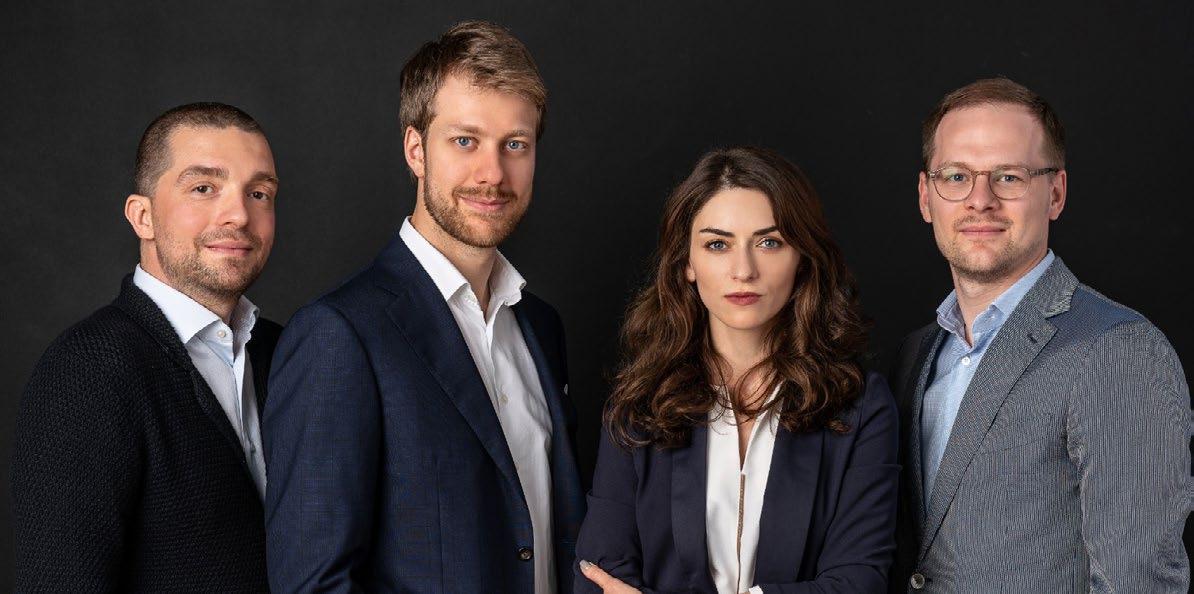
In the future, the Promateris Group aims to develop three new divisions to strengthen its presence in the new markets in which it has recently started operating. 1. Biomaterials - strengthening regional leadership and investing in the production of value-added, flexible bio-compostable packaging for the food industry. 2. Recycling - reducing the volume of virgin plastics used in the production of packaging and replacing them with recycled materials, respecting the principles of the circular economy. 3. Paper - development and production of sustainable solutions, based on paper and biomass, taking into account the biodegradability, regenerability and recyclability of new materials.
Promateris is a leading European manufacturer of sustainable products and solutions for the circular economy. With a history of more than 60 years in packaging manufacturing, Promateris has gained regional leadership and top manufacturing expertise in chemical engineering.
The Promateris Group invests in developing sustainable packaging products and solutions for the circular economy, R&D and end-of-life solutions. The company also operates a plant dedicated to manufacturing specialty compounding for technical applications. Active in Bucharest, Valencia and Warsaw through commercial offices and through distributors in more than 20 countries and 3 continents worldwide.
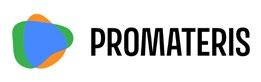
For more information visit: www.promateris.com