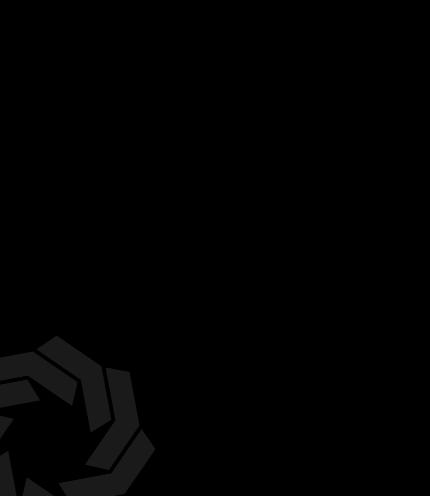

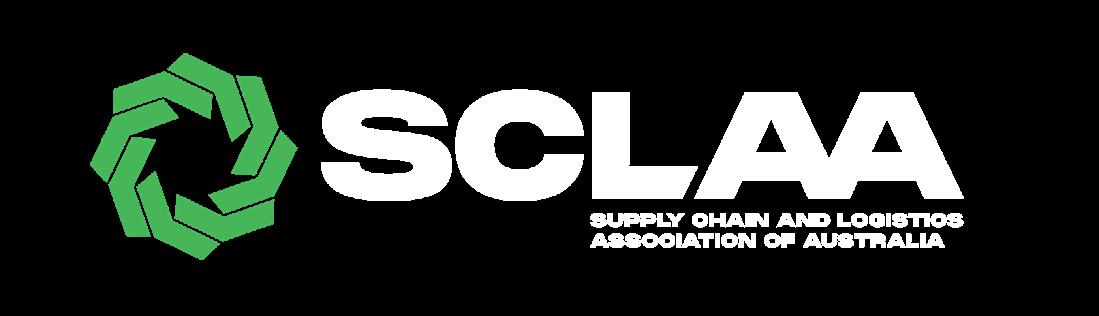



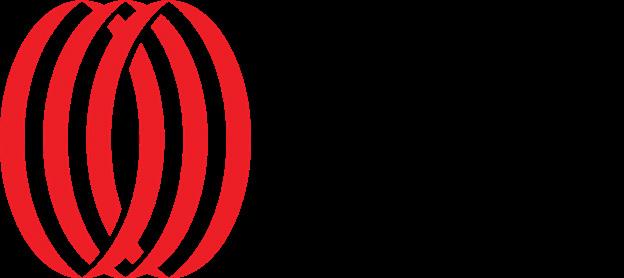
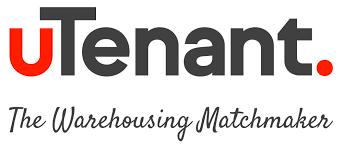

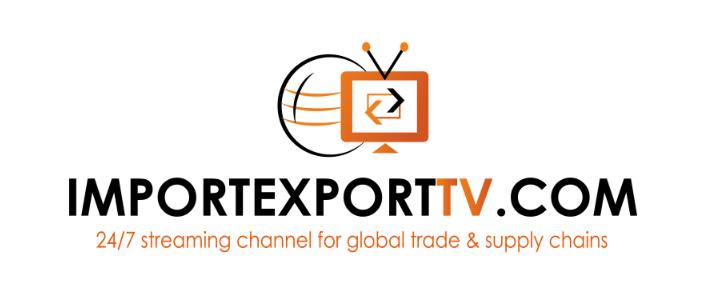
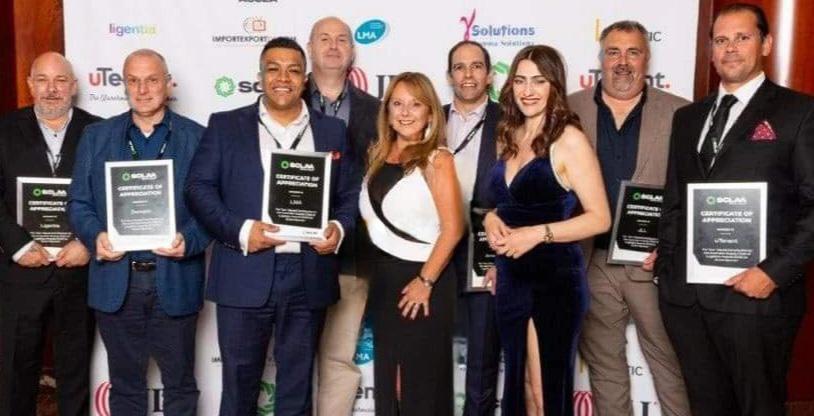
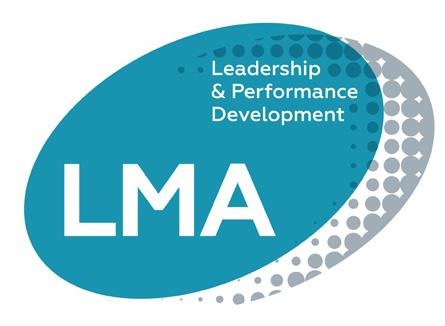

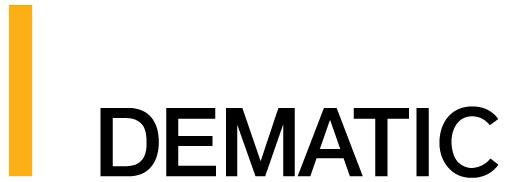

Managing Director, Chain Consulting Services, based in Sydney.
On behalf of the SCLAA, WELCOME!! to the Australian Supply Chain & Logistics Awards (ASCLAs).
We are delighted that you are all here to celebrate and acknowledge the highest of achievements and the changemakers in the industry.
Milestone 60th ASCLAS in March, the turnout was a record breaker, until tonight. There are 450 in the room, (and that’s only because its max capacity at this venue) making this event one of the most important occasions, and officially the largest Awards event in the the Supply Chain & Logistics Industry.
We are going to need a bigger boat next year…. I have had the honour and pleasure of being Chair of this Association over the past year, after serving as Treasurer and Vice Chair in prior years, and in March, in my opening address, I spoke about the 3 C’s :
Connection - Our industry thrives and relies on connectionsYou all understand the interconnectedness between industry sectors. Every single sector relies on every other sector. Inefficiency or crisis in one will naturally have repercussions up and downstream of the chain, a ripple effect at varying levels.
Think congestion of vessels offshore-and the impacts on landside operations and product on shelves. Think container shortage-importers struggling to get products, just in time goes out the window, then struggling to dehire, exporters struggling to get the right container grade at the right time to capitalise on bumper agri seasons.
SCLAA is an association that is committed to providing the platforms and opportunities for industry and its professionals to gather, network and exchange ideas. Networking is just one of the opportunities our association
provides to foster connection. Being part of our association, fills the basic need to be a part of something more, a tribe of like minded individuals, working to make change and how great is it when we can make far reaching improvements for industry overall?
Having worked in the industry for a while now, and been witness to the frustrations of various sectors in how to solve supply chain issues, I know and you all know, the best way is to get key stakeholders in a room to work together towards solutions. SCLAA is just a bigger room.
The whole industry has been working under crisis conditions with peak period congestion landside and quayside, and warehouse crisis as shippers move from JIT to JIC.
And the ongoing crisis within industry-the people shortage….
So as an Association -what do we do?
The SCLAA is Australia’s largest cross sector association in the industry- we are different to the rest because we are truly neutral- like Switzerland, and here tonight, we have the largest cross sector gathering in the industry.
Being part of our association, fills the basic need to be a part of something more, a tribe of like-minded individuals.
Our TRIBE includes those that work directly in supply chain & logistics- shipping, ports, transport, warehousing, importers, exporters, freight forwarders, retailers.
And those that support the work of the industry-IT and software providers, automation specialists, Education and training institutions, legal, financial, industrial property and infrastructure specialists…. we connect the those who have cutting edge technology to solve industry issues or create the solutions needed where none exist as yet.
We remain committed to providing the platforms and opportunities for industry and its professionals to gather, network and exchange ideas-essentially Connect and Collaborate!
We do this via intimate Executive Round table workshops and conferences, Thought leadership and local networking events all to large scale events such as these Awards and National Industry conferences. During the last year SCLAA held over 43 local and National events with over 1700 attendees.
We must be doing something right as our Partnerships have grown by over 67% this year alone. So to the future….for industry and our own SCLAA focus…. I’ll talk about 3 P’s:
A very wise person said -look after your people and your business will take care of itself. I’ve said it before and I ‘ll say it again that People are a company’s biggest off balance asset.
We all need to invest in this biggest of assets. Attraction and retention should be the key focus for the industry -ensure we attract the talent required and continuing development of skills of professionals working in the industry.
Supply Chain & Logistics should be a career choice. Most, myself included, still enter it by chance.
Our focus, along with some of our key partners in the Training, Education and Career development sectors, will continue promote the hell out of the industry.
SCLAA has a had a number of initiatives in play for some time like our Mentoring program.
Now who doesn’t need a mentor? Succession planning at its best…Our Herstories programme promoting female diversity at all levels of Operations, Management and Executive leadership. I am also very pleased to announce a number of exciting new education partnerships: SCLAA has been working with ITLS Sydney University https:// www.sydney.edu.au/business/our-research/institute-oftransport-and-logistics-studies.html on an essential program designed for managers and business owners who want to broaden their understanding of logistics and supply chain management, and acquire knowledge of the latest trends and technological developments in the field.
I am very pleased to announce that we have been successful in our joint submission for government funding, ($300k) which is an achievement in itself. The program will be designed and delivered by supply chain experts and will result in a micro credential for participants.
We have also partnered with WiseTech Academy, https:// wisetechacademy.com/ an initiative from WiseTech Global.
This partnership, due to launch early in the new year, offers -leading online education programs in supply chain logistics and corporate compliance, as well as allow the SCLAA to tailor bespoke e-learning bundles to accelerate professional development for members within the industry sector of their choice.
The courses are quick for the time poor and range from entry level (for newcomers to the industry, allowing for quick assimilation of the basics of Supply Chain knowledge) to complex and specific regulatory knowledge.
SCLAA has also been in discussions with Tafe NSW, https:// www.tafensw.edu.au/ who have recently become a Platinum National Partner and we will jointly promote the Supply Chain industry as a career of choice and connect SME’s in industry, with educational programs.
Look out next year for our careers forum, and many other initiatives SCLAA will be offering in 2023.
Every being and every institution needs to have a purpose.
• Supply chain’s purpose is to make stuff and move it from a to b. Sounds pretty simple, right?
• The industry is facing upheaval-not only are we expected to move goods from a to b in the most efficient and cheapest way possible, now we need to also consider the greenest. Environmental Sustainability and Decarbonization are at the forefront of company strategy overseas. Australia is lagging behind in its consideration and future strategy incorporating reduction of carbon emission.
Companies that haven’t considered these in their future strategy and part of their company vision, will be at a monumental disadvantage.
You may have seen reference to Environmental policy, initiatives and decarbonisation targets in sections on all company tenders- and these sections in RFQ’s are getting bigger.
If you want to crystal ball the future-Check in with your kids, how are they shopping, what’s important to them. The young consumer is doing more research and choosing more carefully where there money is spent.
There is also a subtle shift occurring in consumerism culture. Waste, disposable goods is also a affecting and will continue affect consumer sentiment. Deloittes access economics -$2.5 billion worth of unsold consumer goods in Australia are wasted and sent to landfill-not including food.
We all need to touch the earth lightly and do different, do what’s right - As an industry intimately involved with the manufacture and movement of these goods, we need to plan for this change of sentiment now.
• The Australian Productivity commission estimates that less than 10% of businesses here are using data analytics to make decisions about supply chains. By 2030 -35 the gap will close.
Large scale retailers are already using AI decision engines to work out what their customers want, when they want it and this will have flow on effects to their supply chain providers.
Supply Chains must get much smarter as infrastructure is not infinite resource, - as we have found out with the warehouse crisis this year.
We have all faced Disruptions in recent times, I personally like a bit of disruption-it can be a positive catalyst for change.
The industry, now more than ever is looking for software and tech solutions. I am really excited at the innovation that is around and emerging and even more excited that the industry on the whole is more open to embracing it! So… on to celebrating the most innovative achievers in industry this year…
A record number of Awards submissions was received across all our categories.
Choosing Finalists from such a high calibre of Nominations, was truly challenging and I would like to once again, thank NSW State Director Cathy Anne Jones and the Judging committee, in choosing the worthy recipients.
Of course, such an event would not be possible without the support and hard work of many. I would like to thank our ASCLA Awards sponsors, JLL & Utenant, Gamma Solutions Dematic, Ligentia, Americold, LMA and our Media Sponsor Import export TV.
Also to our Platinum National Partners, Whispir who has provided their technology allowing networking and connections amongst attendees here this evening.
We have 20 of National Partners in attendance here tonight so if your company needs cutting edge tech solutions to gain a competitive advantage, -they are your people and are providing amazing solutions to industry.
There are other special people involved in tonight’s celebration- our Partnerships Manager, Megan White, Secretariat and Stephen Lakey-State Director for Victoria and Chair of the ASCLA Events Committee whose leadership of the Victorian Committee has resulted in bringing to fruition this stellar evening.
On behalf of the SCLAA Board and Committees, I would like to congratulate the Finalists and Award winners, and trust you will enjoy in celebrating their achievements and the evening ahead.
A big thank you to our keynote speaker The Honourable Michael Gallacher, CEO of Ports Australia. https://www. portsaustralia.com.au/
And all the staff at Park Hyatt Melbourne for their assistance with the planning and execution of this event.
SCLAA Directors in attendence (left to right)
Front row: Brian Lynn (WA Director), Megan White (Partnership Manager), Kyle Rogers (Independent), Cam Tran (Independent), Stephen Lakey (VIC/TAS Director).
Middle row: Cathy Anne Jones (NSW Director), Sue Tomic (Chair), Samantha Martin-Williams (Vice Chair).
Back row: Martin Bishop (ACT Director), Don Nardella (Independent), Ben Fahimnia (Independent)
Opex Coca-Cola Europacific Partners Australia Pty Ltd (Connected Coolers Project)
Bulk Group
TMX Global - Munro Project
Geek Plus International Company Limited Officeworks
Starshipit Leopard Systems
Ron Finemore Transport
Modernising Officeworks’ Victorian fulfilment network
At Officeworks, we are focused on driving productivity and efficiency across our business and, with customer expectations around delivery continuing to change, we are modernising and upgrading our supply chain, with increased use and investment in technology.
This is in response to our surging online sales sparked by COVID-19, the work-fromhome ‘movement’ (accelerated by COVID-19) and customer expectation for ever-faster delivery times.
The initial supply chain modernisation program includes:
• Our new customer fulfilment centre in Victoria, which was fully operational from October last year.
• Our new Victorian International DC is scheduled to open later this year, and construction for our WA CFC is about to commence. We will implement process improvements to increase efficiency and reduce costs in our NSW and QLD warehouses, as we review our future capacity requirements in these locations.
Training for our team across industry leading practices to ensure we’re building even greater skills amongst our team so they are fit for the supply chain of the future
This program will improve our overall capacity, productivity and flexibility of our supply chain network, and ensure we can continue to service our customers in the most efficient way.
This award nomination focuses on the investment in our new customer fulfilment centre in Victoria but thought it was helpful to understand our broader strategy when it comes to Officeworks‘ supply chain modernisation and helping make bigger things happen for our customers and team.
In 2020, we identified that our Victorian customer fulfilment centre had exceeded its storage and capacity, exacerbated by the significant uplift in orders we experienced due to COVID-19.
The SCLAA is pleased to congratulate the below finalists and winners (in no particular order)
In mid-2020 an opportunity became available to transition our customer fulfilment centre from Laverton to a brownfield facility in Derrimut.
Working closely with our preferred solution providers Körber and Safer Storage Systems (SSS), we formulated a flexible and agile solution, which included:
• New Warehouse Management System – HighJump Warehouse Advantage (by Körber) P500 Autonomous Mobile Robots (AMR) – 106 Picking Robots (by Körber & Geek+)
• S20C Autonomous Mobile Robots (AMR) – 30 Sortation Robots (by Körber & Geek+)
• Goods-to-Person (GTP) Station with Put-To-Light technology – 9 Station (by Körber & Geek+) Robot Control and Inventory Management Systems – Supporting AMR’s & GTP Stations
• New mobility including voice picking technology and handheld devices – By Körber & Honeywell Access to the new facility was attained at the end of January 2021, allowing for the installation and commissioning of our new solution. Receiving go-live commenced in May 2021 and first order out in July 2021.
Some of the outcomes achieved since the Derrimut site became operational: The facility has brought additional capacity at a far lower cost per pick
• It has the capacity to process 100% more than the previous facility at Laverton At its peak, we expect it to be processing 30,000 lines and 10,000 orders per day
• It allows us to better support our stores by processing customer Click & Collect orders, a growing business
• The facility is solar-powered, helping to deliver Officeworks’ net-zero ambition to use 100 per cent renewable electricity by 2025 as part of our roadmap for net-zero emissions by 2030.
When NPFulfilment needed speed to support spikes in ecommerce, they turned to OPEX Sure Sort® to help meet same day shipping guarantee while boosting profits.
NPFulfilment, a third-party logistics provider (3PL) offering outsourced logistics services across Australia and New Zealand, needed to find a more efficient and less labor-intensive way to consolidate its growing orders and to improve how they sorted individual orders to be more easily assembled and disassembled.
The OPEX Sure Sort’s iBOT® robotic delivery technology caught NPFulfilment’s eye while attending a retail trade event. The system was installed at NPFulfilment in 2018 and it quickly allowed the company to consolidate orders with only one person inducting those orders. The small footprint of the machine offered the flexibility to move the equipment as required to accommodate more client goods. The batch pick and order consolidation process that previously took eight employees now only needed three.
After implementing, NPFulfilment reduced the staff needed to pick and consolidate orders by 50%. The biggest test came in 2020, when on Black Friday their orders surged from 12k to 40k - five times the daily average! With the help of their new automated solution, NPFulfilment met their same day shipping guarantee without having to add expensive labor.
Now, NPFulfilment is working with a much-improved system that utilizes the world’s smartest technology to guarantee orders are picked, packed and ready to ship within two hours of receipt. Sure Sort has allowed the company to scale without adding labor, something that is both attractive to new clients as well as NPFulfilment’s bottom line.
1Fleet has revolutionised how Bulk Group’s Operations department is run and how they manage their sub-contractor fleet. The resultant enhanced visibility over load consolidation opportunities and planning run efficiencies means real-time insights into delivery through GPS tracking, instant driver comms, runsheets, sign-ons and PODs.
Bulk Group will continue to innovate and add additional capabilities that are likely to realise opportunities for application in other supply chain businesses.
Hermandra Maharaj - Metcash Trading Ltd
Scott Barbour - Americold Logistics Ltd
Kyra Dagostino
Mangala Siriwardhane - B dynamic Logistics
Jacqui McCombie - Globelink International Pty Ltd
Revolutionising the supply-chain industry - Mangala Siriwardhane Since co-founding the B dynamic Logistics business in 2016, Mangala Siriwardhane has been revolutionising the supply-chain industry by delivering much needed agility, innovation, and affordability in a very tough business climate where the supply-chain industry is challenged significantly.
With over 16 years experience working in a multinational supply-chain business, Mangala realised the opportunity to do things differently. He knew the best way of solving supply-chain challenges and contributing to customer success was through flexibility and innovation.
Since launching B dynamic logistics, Mangala has led his team to deliver solutions to many customers, transforming their business challenges into opportunities. B dynamic logistics is also creating a name in the industry in a shorter period of time for their flexible service and ‘can do’ attitude, becoming a go-to logistic company when a business requires flexibility and swift action.
With the leadership and guidance of Mangala, the B dynamic Logistic business created its competitive advantage by focusing on 4 key areas (the B dynamic 4 Ps): PURPOSE, PROCESS & PLATFORMS, PEOPLE and POINT OF DIFFERENCE.
Purpose - Solving supply-chain challenges – contributing to our customer’s business success. This purpose is communicated throughout the organisation and demonstrated in everything that B dynamic does.
PROCESS & PLATFORMS – B dynamic has devoted significant effort and investment to improve business processes, as well as developing platforms to improve efficiencies.
PEOPLE – B dynamic has been recruiting experienced people and investing in developing their existing team members to take up challenges. The B dynamic organisational culture creates a positive working environment for team members to shine with 3 core values:
1. Our attitude to be Positive in every situation
2. Our agility to be Innovative creates every opportunity for success
3. Our ability to achieve Excellence in everything we do B dynamic was also recognised as one of the best places to work in Australia and New Zealand by the Australian Financial Review in 2022.
The above three areas (Purpose, Process & People) have helped B dynamic to achieve B dynamic’s AAA point of difference to create a truly remarkable business with a great foundation to become a leading supply-chain business nationally and beyond.
• Ability – Deliver end to end solutions for our customer challenges.
Agility – We do it your way – deliver what our customers need to grow their business.
• Attitude – Anything is possible - can do attitude
Mangala has been a great ambassador of the supply-chain industry with the philosophy of complementing instead of competing with industry contributors. Many large supply-chain companies are reaching out to Mangala and the B dynamic team to assist with projects requiring flexibility.
The Australian Quick Serve Restaurant “QSR”/Fast Food industry in Australia is worth an estimated $21B, fuelled by rapid growth during the COVID pandemic. Since 1996, Americold has been providing customer specific wholesale operations for this segment of the market, with purchasing and inventory ownership warehousing and store order assembly for chiller, freezer and dry products. In addition, providing delivery services to retail stores, all managed by a dedicated Americold QSR customer service team.
Scott Barbour, Americold General Manager of QSR, has been a leader in the QSR cold storage business, growing the Americold business to what is now a significant part of the business and winning prestigious accolades and awards from our customers.
In the past five years, Scott has worked tirelessly to double the Americold’s QSR business and has expanded our service nationally, now with a presence in five Australian states, servicing many well-known fast food brand names. The QSR business segment at Americold now accounts for 16% of the overall APAC revenue and has resulted in the employment of 100+ full time workers.
Scott’s commitment to the industry and his customers has seen him win a number of prestigious awards from prominent Fast Food names such as Domino’s Pizza, Pizza Hut and from the YUM Group who represent KFC and Taco Bell. Scott said “Building trust has been a key element in my success. I care for the brands and products like they are my own and work closely with them all to ensure they have constant supply and can feed their customers.”
Reimagined integration - The possible benefits of adding process costs to waste and bi-products Wespine internally produces Gluts are strategically positioned then strapped to the bottom of all finished packs of timber, a gluts sole purpose is to enable safe storage and forklift access to every pack.
Wespine produces their own gluts from interdependent resource which is collected from Greenmill production runs – collection is restricted to when dependent product is required due to the requirement of enabling full-log utilisation to ensure maximum value is achieved.
Initial process involved collecting glut feedstock from the Greenmill over multiple production runs of mid-range length logs. Length was constrained due the Weinig processing centre which restricted the use of long length resource due to being deemed unsafe due to the nature of gluts, when gluts are produced
through splitting a 125x50 product into 2 pieces of 60x50 the product warps and the longer the product is, the more difficult it is to stack which affects the run rate.
With exponential growth of importing timber with significant volume transferred to Wespine for value-add processing, the glut volume required would increase significantly, this not only affects the feedstock volume, but additionally processing time required.
After consideration, I calculated that by selecting the optimum resource based on overall optimised product mix from the Greenmill optimum glut resource was 6m lengths, but required cost adding to the feedstock collected, first, through Yard stacker- an alternate processing centre, which reconfigures feedstock from rack to pack form, secondly through hobsaw which cuts the pack from 6m to 2x 3m and then finally process the 3m through the Weinig line which machines a groove in the bottom of the product.
The shorter feedstock has resulted in reduction of warping and enabled faster ability to stack and has significantly increased run rates. Throughput increase averages 240% per shift, this means a reduction of run frequency as we are now able to meet increased stock holding whilst using less production time.
This has in turn meant additional availability of Weinig line production time which has now been utilised to divert slow run-rate products from the Yard stacker, so as to increase the yard stacker ability to output higher volumes – additional to the packing of glut resource, due to faster run rates.
The impact of this change has allowed Wespine to increase production of both manufactured Wespine product and additionally imported value added product, without this change, the increased demand for gluts would not have been able to be met, not only for the inability to source gluts externally of the volume and specifications required for our fixed plant but also due to the inability to employ additional staff so as to be able to increase the production hours, as all departments have been running with less than optimum staff due to ongoing recruitment issues.
Adding cost and assigning operational running time against other work centres prior to the processing of an internal use product initially may look like an unattractive suggestion, the benefits though of a truly integrated supply chain speak for themselves.
Whispir - George Weston Foods
Bulk Group
B dynamic Logistics
Ligentia
Dematic - Leader Computers
Leopard Systems - Leopard Cube Swisslog Australia & New Zealand - SKUTOPIA
Globelink International Complexica Pty Ltd
Prological Consulting
Leader Computers “walk the talk” by using smart technology to increase business efficiency, accuracy, and productivity. Leader Computers is a manufacturer and distributor of high-quality Information Communications Technology (ICT) products. Leader is the largest Australian-owned PC manufacturer, with warehousing and sales offices located in Adelaide, Sydney, Melbourne, Brisbane, and Perth. Leader supplies exclusively to IT resellers, with a large client base across the country.
In response to increased demand and as a leading technology company, Leader Computers upgraded its Lidcombe warehouse – which houses approximately 8,500 different products – with an AutoStore™ automated storage, goods-to-person (GTP) picking and fulfilment solution, provided by Dematic. The system at Lidcombe comprises nine AutoStore robots, three GTP ports, and stores 6,662 product bins.
Often referred to as the “Space Saver”, AutoStore provides ultra-high-density storage and buffering for products stored in bins, reducing the footprint required to as little as one-quarter that of traditional manual shelving. The bins are stacked up to 16 high in an aluminium grid and are accessed by energy-efficient robots which run on tracks at the top. When required for an order, an AutoStore robot lifts a product bin out of the grid and delivers it to a GTP port. Here, the operator is instructed to retrieve the required number of items for the order, before the bin is then returned by the robots to the storage grid.
Leader Computers’ requirements for the project were to save labour, save footprint, and to make business improvements with smart technology. With the AutoStore solution, Leader’s operators are now able to pick orders up to ten times faster in some cases, whilst the space required has reduced significantly, freeing up other parts of the facility for different activities and handling large items.
Other business benefits of the AutoStore solution include better security for high-value items, continuous cycle-counting with improved data and reporting, improved ergonomics for Leader’s operators, streamlined replenishment and returns, and better flexibility to meet periods of high demand. In addition, AutoStore uses power regeneration technology with its robots to make AutoStore one of the lowest energy-consuming automation technologies in warehousing.
The new technology-enables Leader to better serve its customers. Before the AutoStore solution was implemented, a large order of a few different types of hard drives could take a few hours to pick. With the new AutoStore system, Leader can pick a similar type of order in just 30 minutes. Overall, Leader’s adoption of the AutoStore solution has enabled them to make intelligent use of their available space, and streamline picking, packing, and replenishment operations, while also allowing room for future growth.
B dynamic delivering End-to-end Supply-chain solutions
B dynamic is one of the leading businesses in end-to-end eCommerce solution delivery for both Direct to market (D2C) and Business to business (B2B) across multiple industries. We have achieved this position by delivering flexible and innovative eCommerce solutions.
Consumer expectations are changing rapidly, and businesses are being challenged by customer demands. Consequently, distribution strategy needs to have the flexibility to change and adapt in order to provide customer satisfaction.
The B dynamic business has grown over the years by solving customer challenges that many of our competitors were not interested in or believed were too hard to solve. We see our customer’s challenges as an opportunity for us to grow. This thinking drives us to go out of our way to transform challenges into opportunities. It has also helped us create our own unique space in the supply-chain industry and create our point of difference.
We focus on delivering end-to-end supply-chain solutions for our customers to make their life easier, allowing them to focus on what they are good at and maintain their customer relationship. Having our in-house technology development and support team, as well as packaging and merchandising sourcing capabilities, enabled us to expand our services beyond traditional warehousing and logistics.
Over the past 18 months we have delivered many end-to-end supply-chain solutions to many customers. We successfully delivered an end-to-end eCommerce solution for ALDI special buys program including design and development of the ALDI shop (customised eCommerce platform), payment management, warehousing and fulfilment, last mile delivery, return management and customer support.
B dynamic has been delivering end-to-end Point of Sales display units to many FMCG companies over the years. This includes designing and manufacturing of the Point-of-Sale display unit, warehousing and inventory management, distributing nationally to merchandisers, in-store execution and management reporting. We also developed a technology platform to manage this process seamlessly and improve efficiency.
B dynamic will continue to look at customer supply-chain challenges and deliver end-to-end solutions to transform these challenges into opportunities.
Winning Group
B dynamics Logistics
TT Logistics (Australasia) Pty Ltd
Penguin Random House Australia
TAFE NSW Electric Vehicle Micro Skills Team
Adiona Tech
LUP Global
Environmental Excellence in 3PL contract logistics
TT Logistics (Australasia) Pty Ltd is proud and committed to environmental excellence to contribute to our corporate and government initiatives towards a carbon neutral future. Our continuous improvement approach and supplying People, Processes and Culture to our clients is an ideal setting that encourages Kaizen in all areas of the business including the environment.
Our parent company Toyota Tsusho has been pursuing social and environment sustainability for almost 75 years and these essentials are strongly embedded in our fundamental corporate philosophy which says:
Living and prospering together with people, society, and the globe, we aim to be a value-generating corporation that contributes to creation of a prosperous society.
We will strive for open and fair corporate activities, be socially responsible and strive for conservation of the environment. We will be creative and strive to provide added value and respect people to create an engaging workplace.
These fundamentals are on top of the corporate pillar basically making them the most important global deliverables of the company.
With the establishment of TT logistics in October 2008 as a 100% subsidiary of Toyota Tsusho Australasia these fundamentals were immediately transferred to TTL.
Operationally Anzen (safety) is obviously our first priority followed by quality, flexibility, visibility and last but not least innovation and these five important elements also represent our mission.
Each of these elements impact our operation and consequently all 3PL contract logistics activities we perform for our business partners. In other words we are required to be sustainable and consider the environment whatever we do.
This is why TTL provides People, Processes and Culture as this 100% captures the essence of what we do and how we do it.
In the last 12 months, Winning Group business entities including; Winning Appliances, Appliances Online, Andoo, Rogerseller and Spence & Lyda have implemented a packaging collection and recycling program for the waste that comes with the supplied packaging of the products we sell. This captures cardboard packaging, expanded polystyrene (EPS) and soft plastics. The program is free for customers and is particularly impactful as it tackles the problematic EPS which is associated with white-goods and prevents this from going into landfill. There is currently no solution for the general public to recycle EPS waste at the kerbside, meaning most EPS goes into landfill.
Our drivers from Winning Services unbox items upon delivery at the customers site, presort the packaging waste and return it to the respective distribution centres (DCs) across the country. At our DCs we now have dedicated packaging sorting areas and teams who sort the waste into four main streams - soft plastic, EPS, cardboard and residual general waste. The cardboard and soft plastic gets compressed, the EPS melted (NSW) or compressed (VIC, ACT, QLD & WA).
After checking and palletizing the cardboard, plastic and EPS, we work with licensed recycling exporters. The EPS is sent to China, where it is used as a raw material for the production of new items such as picture frames and skirting boards
With this initiative we are demonstrating voluntary packaging stewardship. For our largest operation in NSW we invested into the High Throughput Semi-Automatic EPS Densifier equipment (GreenMax M-C200 Automatic cutter/cooling/ loading). This machine is very innovative as it melts the EPS into nuggets and eliminates the problem of EPS breaking in the handling process and littering the environment.
Penguin Random House (PRH) Australia is the result of a merger between the world’s two largest publishing houses in 2013. The company has significant operations in Australia and New Zealand in the form of United Book Distributors and is a premium provider of distribution services to publishers shipping in excess of 30 million units per year to wholesalers, bookshops, retailers and education booklist providers across the two countries.
Penguin Random House global operations extend across 20 countries on six continents and is a cultural institution with a strong moral compass which has always strived to shape a more equitable, diverse, and sustainable world. So, when tasked with contracting a carbon footprint audit and inventory in early 2021, the PRH team viewed it not simply as a compliance exercise that met the parent company’s commitment to reduce gross emissions and achieve carbon neutrality, but an opportunity to establish lasting protocols with local impact.
When the audit report dispelled suspicions that road transport was the company’s biggest carbon contributor, the team used the reports’ findings to challenge established patterns of behaviour. Not only has convincing the affiliate companies overseas to allow more print production in Australia negated the need for almost all costly, emissions-intensive
Leopard Systems - Leopard Cube Project44
Navia Pty Ltd - Navia Connect B dynamic Logistics
Whispir - George Weston Foods Winner Project44
Using the world’s best ocean shipping data to untangle the biggest knot in the supply chain: port congestion. Global supply chains were built on assumptions of stability in ocean shipping. However, the aftershocks of the COVID-19 pandemic have seen ocean shipping descend into disarray. The maritime industry is beset by disruptions and the impacts of disturbingly regular ‘black swan’ events. Central to the problem is the state of ocean ports which have become the largest bottleneck in global supply chains.
The events of recent years have seen container dwell times at some of the world’s most significant ports soar, stranding vessels and shipments for days to weeks at a time, with downstream effects that quickly snowball from merely inconvenient to catastrophic.
More than ever, what global supply chain managers need today is accurate, real-time ocean intelligence to mitigate disruptions and take corrective action when problems arise. Most shippers and third-party logistic companies still depend on unreliable maritime data sources: ocean carriers’ websites, electronic data interchange (EDI) or, satellite-provided vessel location, alone.
In other cases, commentary provided by ‘experts’ or other stakeholders, is often fragmentary or anecdotal in nature. While this makes for good headlines, it does nothing to enable shippers, third-party logistics providers and freight forwarders to manage customer expectations, quantify the impact of congestion, identify opportunities to circumvent it or make better planning decisions upstream.
With a mission to make supply chains work, project44 set out to build Port Intel, a trustworthy single source of truth providing:
Unprecedented visibility over global port traffic and congestion via industry-best data means all options can be evaluated and decisions can be made with confidence. These decisions, which have major downstream implications are among the most important decisions a company can make, which means that the need for trustworthy and comprehensive data is critical.
Port Intel enables customers to bridge the gap between supply chain teams and other stakeholders through easy-tounderstand visualizations of port congestion and communicate trends and needs to stakeholders across the business.
Having such trustworthy, comprehensive data opens new doors for mitigating or avoiding the impacts of port congestion. Through Port Intel, customers can evaluate and execute the most important supply chain decisions with the highest possible degree of confidence, allowing them to overcome delays and disruptions.
Secure. Trusted. Trade. Navia Connect. When it comes to creating new contracts and orders, there is an enormous disconnect between suppliers and customers in the supply chain. Businesses need to buy and sell goods all over the world, but there’s very little transparency, and often not enough security, throughout the contracting process.
Navia is more than a freight forwarder. We pride ourselves on innovative technologies that deliver tangible benefits to our customers and drive the industry forward. With our proprietary software, Navia Hub, we manage the relationship between our clients and our business, providing detailed information and tools around the movement of goods. This year, we’ve got something new. Our team are just about ready to release Navia Connect: A tool that looks to extend the reach of our data and software to benefit the logistics industry as a whole. How? By removing ourselves from the equation entirely. Navia Connect focuses on the relationship between buyers and sellers, delivering transparency, security and simplicity for Procurement Managers around the world.
Yakeen Sagety in partnership with Shell Australia Inbound Technologies Pty Ltd Shipeezi ty Ltd
Ofload - digital end-to-end road freight solution
Trucking is one of the oldest and most manually driven industries in Australia and when it comes to the environment, it is the third-largest carbon emissions contributor. Every day in road freight, 30% of km are driven empty and 1 in 2 trucks stand still. Additionally, the industry is highly fragmented. Over 80% of trucking companies own less than ten trucks, and these small owner-operators find competing with larger transport companies challenging. The Australian freight industry is worth $65BN with 38,000 smallmedium-sized Carriers.
We couldn’t sit back and do nothing. That is why Ofload was created. Our focus is to eliminate waste in transport through technology to support the resilience of small-medium sized transport companies while reducing carbon emissions.
We provide customers a digital cloud-based platform and an end-to-end road freight management solution. The platform manages road freight shipments by matching freight requirements to suitable transport companies, eliminating unnecessary waste by ensuring trucks travel full. It allows simplicity for a Shipper to have many transport companies managing their freight movements with just one touchpoint to book a shipment, track and trace, verify and collect proof of deliveries and invoices.
Transport companies can leverage technology to find more work and manage road freight activities on one platform. Our platform optimises loads to ensure trucks are full and have no empty space, which means more revenue for Carriers and better for the environment. For Shippers, they no longer need to work with hundreds of transport companies to ship their goods. Ofload partners with 1600+ vetted transport companies and through technology, we streamline the booking process enabling them to have one point of contact.
From H1CY’21 to H1CY’22, platform sign-up increased by 276%, demonstrating the benefits Carriers gain from being in a connected supply chain ecosystem. Within this comparative period, we doubled the number of active platform users on a recurring basis. Our impact on Carriers in H1CY’22 is astronomical, completing 6.3M kms representing 420 laps around Australia. Ofload is providing the technology tools and connectivity needed to keep Carrier’s moving. Before partnering with Ofload, the Shipper, Noumi worked with 65 transport Carriers. They’ve now reduced their network to one point of contact and saved a total of ~10% on domestic freight spend.
With over 14,000 removalists in Australia as part of the $2b removals industry, finding a removalist has never really been a problem. But... finding one that’s available, on the day you want, for the price you want that can transport the items you want, is what creates all the stress. Enter Muval.com.au - Australia’s booking & logistics platform for moving house.
Inbound has built technology that is fundamentally changing the way freight moves through the supply chain with its community based vehicle booking and visibility platform.
Founded in 2019, Inbound is a web-based technology platform that connects logistics communities in a way that has not been possible before. It was built to provide practical solutions for some of the most fundamental problems that exist in supply chain and logistics today. These problems add very significant costs, compromise safety and make regulatory compliance virtually impossible.
Inbound has created a ‘community’ of logistics facilities around Australia who use its truck appointment system and mobile apps to improve the service they offer to arriving vehicles. Inbound connects, for the first time, logistics facilities to their transport company users across the supply chain to enable better information and visibility for any truck arrival, at any facility, for any freight, at any time. The Inbound community in Australia is currently made up of over 2500 companies and over 10,000 users and is growing quickly.
Inbound solves the following longstanding problems for logistics facilities with its digital solutions –
• Random Truck Arrivals – with Inbound a facility knows who is coming, when and for what, and can be prepared – this slashes vehicle time on site and eliminates futile trips.
• Reactive Planning – with Inbound, facilities can proactively plan labour and equipment with confidence - no more guesswork.
Paperwork and Manual Process – Inbound at last eliminates physical paperwork from the logistics process and automates the gate process for arriving trucks.
• Visibility - with Inbound, all parties have information available to make better operational and commercial decisions – this information was previously non-existent or required emails and phone calls to track down. For example, clients now use the ‘Inbound client portal’ to follow the movement of their freight at logistics facilities, and the industry has access to the Inbound National LCL availability search function – something that has never been available before.
• Safety – Inbound improves safety outcomes by eliminating queuing and congestion, reducing time on site for drivers, and removing physical contact between driver, staff and forklift operators which improves COVID protocols.
•
• Compliance – Inbound enables much improved compliance with CoR and ABF regulations via its fully integrated, world-class Inbound drivers licence scanners.
* Payments – Inbound enables secure, cargo-level payments, and transforms the way that facilities and the industry handle operational charges such as storage, saving enormous frustration, error and delay.
* Inbound has a had a transformative effect on the parts of the supply chain in which it has operated so far – these include CFS/FAK seafreight bonded warehouses, bulk and general stevedoring ports, 3PL/contract warehouses and intermodal hubs. All of these share the common problems outlined above, and those using Inbound are now lower cost, more efficient, safer and more compliant than they have ever been.
Future sectors that we expect to use Inbound include airfreight facilities, supermarket DC’s, pallet depots, grain packing facilities, rail freight hubs and quarantine facilities, amongst others. We also expect Inbound to expand overseas shortly.
The technology base that Inbound has developed provides excellence in design and enables the industry to expect fastmoving and responsive software that moves as dynamically as the industry does. This is one of the hallmarks of Inbound.
The broader supply chain has been looking for a simple solution to these problems for many years, and Inbound has delivered this using world-class technology and an operational partnership with its clients and the broader industry.
Americold Leadership Academy
Vative Institute of Transport and Logistics Studies
Qube Bulk
Ferry Jie - Edith Cowan UniversityCouriersPlease
Growth and Development Framework - National Training Plan
The National Training Plan facilitates the development of Winning Services (Winning Group business entity) employees through a growth and development framework. Created and run by Winning Academy, our in-house training and development team, this was established to improve the opportunities for learning, growth and development for all team members. With a clear focus on providing employees with clear achievable pathways to enhance skills and improve career advancement possibilities. Winning Academy’s training and development initiatives are focused on three pillars: to build, improve and scale everything we do.
The National Training Plan for Winning Services encompasses: Pre-employment services such as english speaking classes
• Thorough onboarding of new members
• Pathway programs for new starters into leadership and business Opportunity to gain qualification during work hours
• Mentoring and learning circles
• Hackathons for idea creation and employee involvement Ongoing technical toolboxes
• Upskilling using web based quizzing tools to assess team member knowledge (technical, safety and soft skills)
Through our ongoing interactive quizzing platform, we achieved participation results of 87%, a performance rate of 85% and an improvement rate of 6% for knowledge improvement (90% pre campaign to 96% post campaign).
“Leadership and learning are indispensable to one another” John F Kennedy John F Kennedy’s words resonate and guide us at Americold. Our belief that leaders cannot lead without knowledge and a desire to continually learn led our USA team to develop the Americold Leadership Academy (ALA) series of training. Sara Vallee Soti and her trusted HR team customised the training with local content that today aims to educate existing and aspiring leaders and equip them with the everevolving skills needed to be a successful leader.
The key differential in our ALA training is that it was developed in house and focusses on case studies that are relevant to our industry, business and people and therefore is more engaging and beneficial than training from external partners. We
understand that our people are key to our success and that we need to provide opportunities for them to grow within the company.
ALA allows time for our current and aspiring leaders to temporarily step away from their everyday responsibilities and invest time in their development so that they become even better versions of their professional selves. Participants learn key skills in areas such as goal setting, communication and collaboration techniques and how to undertake difficult conversations. They work as part of a team with employees of similar seniority from other work functions across different sites in Australian and New Zealand to share experiences, ideas and work together to solve real company issues. This creates a network of contacts for participants and a greater understanding of how different business functions approach problem solving. Presentation skills are developed and teams have the freedom to creatively deliver their solutions to members of the Senior Leadership Team. “Knowing is not enough; we must apply. Willing is not enough; we must do” Leonardo da Vinci
Americold strongly believes that unless you apply and do, learning is worthless. Each ALA session ends with employees taking time to think about and making a commitment to how they will implement the learning and their new skills into their role. Feedback on the ALA, garnered via post attendance surveys show that 100% of attendees felt that the content, relevance, delivery, and ease of learning allows for the easy application of the skills and techniques into their roles. Check-ins after the training show an increase in personal confidence, increase in productivity, a new level of sophistication when setting goals and an improvement in employee engagement.
In 2022, 439 of our employees have attended the ALA across both Australia and New Zealand and this has resulted in the internal promotion of 12 employees to date. In addition, it has inspired others to stretch their leadership capabilities within the supply chain industry, such as Kyle Hill from our Kewdale site in Western Australia who was selected as a finalist for the Frank Vale award this year.
‘When you cease to learn, you cease to grow’ Albert Einstein.
Developing the next generation of supply chain experts via collaborative futurefocused, contemporary education and development initiatives
The Institute of Transport and Logistics Studies (ITLS) within the University of Sydney Business School is an internationally recognised centre of excellence in logistics, transport and supply chain education and research, with strong linkages to industry and government. We are a diverse team of leading educators and researchers in transportation, logistics and supply chain management. The Institute is a guiding light in attracting leading scholars and innovators in the transport, logistics and supply chain fields. Professor Michael Bell (Imperial College London), Professor Ben Fahimnia (Honda Manufacturing & University of South Australia), and Professor Rico Merkert (Cranfield) have all been drawn by the impactful teaching and research being undertaken at ITLS which has resulted in the creation of the most highlyranked transport and logistics group in Australia and one of the best in the world (appearing amongst the top 10 in multiple world university ranking systems) and an Institute which delivers significantly in all relevant areas of engagement, impact, and performance.
A major priority of ITLS is an ongoing commitment to supporting collaboration/ partnership with industry and government that translate to pioneering education opportunities in a variety of forms. Through a constantly evolving portfolio of offerings, we ensure that ITLS remains at the forefront of innovative training that has a transformative impact in the tertiary education space and beyond. ITLS is particularly focused on developing the next generation of industry leaders both within Australia and globally, with initiatives to increase access to study for members of the industry living in rural and regional Australia and from emerging markets in South-East and South Asia. For this application we will focus on the following recent collaborative initiatives:
• Practice-oriented education through project-based capstone units (industry placement) Micro-credentials in partnership with SCLAA and GS1
• Executive programs in the form of short training courses
A unique Master of Logistics and Supply Management Degree focused on real-world projects with industry partners
• Funded chair position
• Other forms of collaboration
CouriersPlease is one of Australia’s largest franchises and a leading courier service for retailers. Our Australia-wide network of 1600 people across corporate, freight handling and Franchise Partners are responsible for efficiently and safely delivering tens of millions of parcels annually on behalf of 26,000 retail customers. Our activities are freight handling and last mile delivery, and we have 900-plus vehicles on the road.
As the safety and productivity of our people are in their best interests and drive business success, we have continually delivered training and development in these areas. We devised and implemented a range of initiatives to train and educate our people on various hazards and risks, including burnout and fatigue, distractions, general driving conditions and hygiene. Programs such as these were tied to many innovations and process changes, all underpinned by reducing accidents and keeping people safe across our depots and on the roads, while delivering parcels more efficiently.
Our entry in the ASCLA Training, Education & Development Award details the success of CouriersPlease’s two main training and development initiatives: our Chain of Responsibility (CoR) training and our ‘Get Home Safe’ digital driver safety program.
Our Safety Leadership Program is a people-centric program developed by our internal HomeSafe Steering Committee and HomeSafe Leadership Team that strengthens and upskills frontline supervisors and line managers’ leadership capabilities in identifying risks, engaging with staff and embedding the safety management system. With national risk management consulting firm Gallagher, we customised Chain of Responsibility (CoR) training as part of the program. CoR is a nationally legislated program under the Heavy Vehicle National Law (HVNL), aiming to improve safety and reduce incidents across the road transport industry. We created several modules to train our team around CoR’s key elements and codesigned training materials to accurately capture operational procedures and messaging.
All 150 of our management, staff and team members involved in consigning, packing, loading, driving, operating and receiving heavy vehicles participated in the 40-minute e-learning module and passed the 20-question competency test, receiving a certificate on completion.
We identified the need for a driver safety program to reduce immediate critical risks such as fatigue and COVID for our drivers – and build in necessary refresher training to prevent incidents.
Our ‘Get Home Safe’ digital driver safety program – conceptualised, driven and overseen by our HomeSafe Steering Committee and a HomeSafe Leadership Team – has educated over 800 CouriersPlease drivers on hazards and risks, including burnout and fatigue, distractions, general driving conditions and hygiene.
Delivered as nine highly interactive and self-paced learning modules delivered on handheld driver scanner devices – created with the assistance of a specialist employee experience consultancy – the program has taught drivers that health and incident-risk mitigation should be personally prioritised and would also help their own small businesses continue thriving.
Achieved record highest number of manufactured CNC Machines while dealing with post pandemic supply chain issues. ANCA CNC Machines is the manufacturer of high precision tool grinding CNC machines. ANCA is based in Bayswater Victoria, and exports 99% of it’s production to the world. Tool grinding machines have roughly 5 to 6 thousands components, including mechanical, electrical , automation, pneumatics, hydraulics and sheet metals. Many of these components have semiconductors, magnets , rare electronics which were in a very high demand post pandemic. Many automobile manufacturers, CNC machine manufacturers , and automation solution providers had to limit their production outputs , or even shut down the factories due to the shortages in the last 12-24 month.
ANCA CNC Machines, despite all these challenges, could build the record highest number of machines in the last financial year. To achieve this, ANCA Global supply chain reviewed and revised the global supply chain strategy, invested in new partners, and worked closely with engineering, sales and marketing and other stakeholders to overcome challenges. Also, due to the V-Shape economy recovery the industry experienced in 2021, the time to react to the market change was very limited and short. ANCA CNC machines managed to double production output in a very short time and could manage to increase the market share significantly. This required ramping up inventory buffers , increasing team sizes, upskilling and preparing new hires, investing in new tooling and rigs , and last but not least, revise the existing workflows to react to the disruptions fast enough to keep the production line running. ANCA’s global supply chain strategy during and before pandemic was lean focused and didn’t have much focus on other aspects of the global supply chain management. Last year, we’ve redefined our global supply chain strategy with a balanced focus on 4 main areas : Lean, Agile , Resilience and sustainability. We have started increasing our resilience and agility by kicking of different projects and initiatives in these areas such as : Dual sourcing activities , system improvements , nearshoring , localizing , revisiting our logistical arrangements , etc…
Another challenge we’ve faced during this time was lack of skilled labour in the market. ANCA Supply Chain team started number of programs with different universities to bring in IBL students and fresh graduates to fill the talent gap. We’ve also trained and promoted internal resources to lead our supply chain more effectively globally.
Working closely with sales and marketing team helped us to have a better sensitivity to the market and simply make right decision much faster than before. This wasn’t possible without implementation of right tools such as Forecasting system, CRM , forecast accuracy measurement , etc… We also introduced an inventory scenario planning tool to manage our inventory impact caused by the forecast errors.
And finally, close collaboration with Engineering and Manufacturing engineering team could avoid major production stoppages and reduced capacities. Our internal record shows that we’ve had more than 70 major supply issues in the 12-month period and for 50% of these cases our engineering team had to make changes to the design to use available alternatives. This is a great achievement for both operations and engineering team and wasn’t possible without the great work and effort of all the team members.
The Judges were impressed by the number of adaptations and supply chain improvements across this international supply chain achieved during the difficult Covid period.
With Spirits Platform ongoing success and growth, they are proudly able to make regular donations to Mercy Ships. This organisation is an international development organisation that deploys hospital ships and volunteers to developing nations.
Working with its brand partners, Spirits Platform is striving to promote low - and non-alcoholic beverages to respond to a broad range of consumer interests and occasions.
A number of other projects rolled out across their entire supply chain and partners:
Raising Awareness of Responsible Consumption Among Consumers
• Sustainable Packaging
• Sustainability is an essential dynamic to Spirits Platform: A reduced carbon footprint
• More storage and more space with green packaging
Using eco-friendly packaging that is free of toxins and allergens
• Most of Spirits Platforms packaging is biodegradable and is non-toxic and allergy-free.
• Chain of Responsibility enforcement across their Supply Chain R U OK? Events
• Healthy Heads in Trucks & Sheds membership
• Workplace partnership with TAFE NSW
Kyra Dagostino accepted the Judge’s Choice award on behalf of Ferry Jie. Celebrating Ferry’s outstanding dedication and contribution to the alignment of Industry and Education across many years, and his active involvement in promoting and developing Outstanding Supply Chain and Logistics Management Education.
Celebrating strong leaders in industry and last year’s Women in Shipping & Maritime award winner; Managing Director of Globelink for 25 years; industry stalwart, and supporter to many including the SCLAA Mentor program and numerous other selfless contributions to industry.
For Nives’ dedication to her career, her role, professional development and industry involvement. Demonstrated through her public speaking classes, women’s mentorship programs and networking groups particularly geared towards AU-NZ women in business and local and global level. Currently the Commercial Manager for DSV Solutions.
For Doreen’s commitment and impact to the industry hrough developing new procedures, attending and running many seminars and work network gatherings, locally and globally. Very strongly supported nomination and a reputation of excellent customer service that precedes her. Currently Sales & Customer Service Manager at Globelink international.
In recognition of Irene’s incredible journey so far in supply chain roles across Asia, Europe and Australia and her commitment to excellence through education, continuous improvement and giving back. Actively involved in mentoring and research and currently in the KPMG Supply Chain Advisory team.
Following an intensive and varied 16 year career as a Police Officer, Mike Gallacher was appointed to the NSW Legislative Council in 1996.
He has performed the Shadow Ministerial role across a variety of port folios including Ports, Industrial Relations, Transport and Police.
Winning government in 2011, Mike was appointed Minister for Police and Emergency Services, Minister for the Hunter and later the further role of Minister for Industrial Relations.
Mike is widely recognised for his robust approach to policy develop ment and his preparedness to strongly advocate the need for reform. As Minister he led on behalf of Government the public debate on is sues such as measures to reduce alcohol related violence, rampant gang/gun related crime and introduced initiatives to change driver behavior.
Since 2017 he has been the CEO of Ports Australia, the peak industry body for the Ports industry. Mike has been instrumental in lifting the awareness of the Port sector and the important role it plays in Austra lia’s future.
Mike delivered an inspiring key note speech, reflecting on the effects of the pandemic on the industry over the past two years. The standout considerations for the SUpply Chain Industry arising from the disrup tion is Digitization and Decarbonization. Both are high on the Governments agenda.
industry bodies such as the SCLAA. Mike stated businesses can only
Associations.
The SCLAA would like to extend a heartfelt thank you to Mike for his insights and we look forward
Australia for the benefit of our Supply Chain & Logisitics Community.
Kyle presented the journey f Utenant, from Start-up to the present time and reiterated that disruption will be a continuing factor affecting the Industry.
Utenant is a software platform disrupting the warehouse and industrial Real Estate industry by providing an online solution to those with excess warehouse capacity and those businesses in need of a solution.
Kyle also stated that people and life are both a bit like technology. It’s a double edged sword. Life can be up one day and down the next. But you’ve got to experience the lows to enjoy the highs.
People can cause so much destruction, like to our planet/environment yet we’re the only ones that can put it right and sus tain it. Technology is a window to the world but be careful you don’t fall out of it. Yet, make sure you have people around you that will pick you up if you do.
Kyle spoke about Connecting with your vision, purpose and mission, both personally and professionally. To do this we must have difficult conversations with ourselves, partners, investors, customers and suppliers. The best outcomes are birthed from the most difficult conversations. On the subject of people versus technology-Technology can do nothing without people and teams driving it.
“Life is a journey, not a destination. We all share the same destination but we all have different destinies. We all have a story but yet there are two sides to every one. Don’t believe everything you hear, believe what you see and feel!”
“Live, laugh. learn and love and make your journey one that’s remembered. Be kind and leave a positive lasting legacy to all those whom cross your path!”
“Your health is your wealth and life is over in a click, bink or flash. Connect the dots, follow the signs and live in the presentsilante.” SCLAA would like to thank Utenant and JLL for their continued support in sponsoring the ASCL Awards!
What an amazing turnout for The 61st Annual Australian Supply Chain & Logistics Awards! This year saw the return of the awards to its regular November timeslot and was a sellout shortly after early bird pricing ended, making it the most successful to date. The event was held at the fabulous Park Hyatt Melbourne which provided a luxurious marble pillared setting and was hosted by former Logies host, actor & come dian Shane Bourne. The awards attracted the who’s who of Australian Supply Chain with keynote provide by the honour able Michael Gallacher who looked at the past & future chal lenges in Supply Chain and the importance of government working with the industry.
An important aspect of the awards and a key pillar for SCLAA is to provide events that facilitate networking, collaboration & the sharing of ideas. This year we partnered with Whispir to provide an innovative platform where guests could locate companies and people to network with during meal breaks. A simple but important addition that helped bring people together on the night.
The ASCLA’s are now a key event on the Supply Chain cal endar and offers recognition and encouragement for those in the industry that over the past 2 years and even now are under incredible pressure. These challenges also provide op portunity, as the spotlight is increasingly on the industry and awareness of Supply Chain’s contribution to the economy at an all-time high. Certainly, something to celebrate.
Innovation, hard work & excellence are now more important than ever and it was a pleasure to recognise those who have achieved much over the past year. Congratulations to all the ASCLA winners, High Commendation recipients & final ists for your amazing efforts and contribution. Look out for the awards photos & interviews of all ASCLA winners on the SCLAA Social Media pages over the coming weeks - hosted by our valued media partner, Import Export TV.
I am very much encouraged by the leadership team at SCLAA who volunteer their time tirelessly and enthusiastically. Their passion and commitment to the industry that they are a part of is an inspiration to me. My heartfelt thanks goes to the ASCLA inner circle Chief Judge Cathy-Anne Jones, VIC TAS Division President Rakesh Bandipelli & Partnership manag er Megan White. Thanks to SCLAA Chair Sue Tomic for her exceptional leadership and courage to change the associa tion to what it is today. Thanks to the ASCLA committee for your hard work in making these awards so memorable. To the VIC TAS division committee who were the feet on the ground at the event - thanks for your passion and drive on the night. You certainly lived up to our creed - to be humble on the outside, confident on the inside & to support & work with each other as a team to achieve our goals. If this sounds like something that you would like to be involved in for 2023, please reach out to myself – I would love to welcome you as part of the SCLAA family.
Once again we had great support from industry and my appreciation goes to the event sponsors this year, Plati num sponsors JLL & uTenant, Silver sponsors Gamma Solu tions and Import Export TV & supporting partners Ligentia, Dematic, LMA & Americold.
What is next for the ASCLA’s? The massive support from in dustry this year and the popularity of the event will mean that we look at ASCLA 2023 through new eyes with a vision to take next year’s event to a new level. Stay tuned!
The SCLAA welcomes our newest National Partners - Ofload and Logistics Safety Solutions (LSS). As a not for profit Industry Association, run by members for members, our ability to support the SCLAA infrastructure and to expand is highly dependent on our National Partners. We ask all our members to support our valued National Partners where they can.
Ofload is more than a digital freight provider. They are an end-to-end technology supply chain partner for domestic freight movements providing tailored and innovative solutions for hundreds of customers, including companies like Nestle, Metcash, Asahi, Simplot and Maersk.
Every day in road freight, 30% of km are driven empty and 1 in 2 trucks stand still. Additionally, the industry is highly fragmented. Over 80% of trucking companies own less than ten trucks, and these small owner-operators find it challenging to compete with larger transport companies.
That is the vision behind Ofload, to eliminate waste in transport and empower the long tail of small-medium sized carriers through technology.
can
your business in achieving an efficient, flexible and sustainable supply chain?
• By removing the burden of multiple layers of sub-contractors managing your shipments - Ofload manages it all for you.
No more emails and phone calls - digitally book, track and manage your shipments in one single location.
• Know your freight spend and performance - Ofload aggregates your supply chain performance in an easy-to-view dashboard.
Eliminate waste and reduce costs - Ofload prioritises backloading to improve truck utilisation.
• Ofload works collaboratively with its customers and will work with you to find solutions for supply chain improvements. Get in touch with the team today and start shipping with Ofload!
Visit the webiste
Logistics Safety Solutions (LSS) is an Australian owned company that assists its clients and their respective supply chain partners in Australia and New Zealand, manage truck safety and their obligations under their Chain of Responsibility (CoR) via the CoRsafe platform.
Founded in 2012, LSS provides support to some of Australia’s largest consignor businesses and supply chains in manag ing their CoR obligations by:
• Review and development of processes, guides, and manuals relating to the Chain of Responsibility
• Delivery of awareness and role based training to employees via online or in person Monitoring of supply chain parties through online self-assessments and external audits
• Solutions to support clients in both load and driver inspections as well as incident management
Most importantly, CoRsafe is an end-to-end CoR management solution that is verified by Holding Redlich lawyers as fully aligned with the CoR Master Code of Practice.
In August 2021, National Transport Insurance (NTI) acquired LSS.
NTI is Australia’s leading specialist insurer supporting the nation’s transport and logistics industries.
This acquisition brings scale and product development opportunities to the LSS business that will see the CoR-Safe plat form continue to deliver value and expertise to those who engage. Visit the webiste