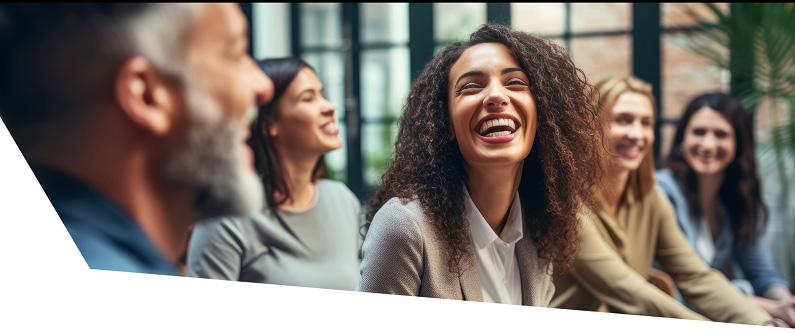
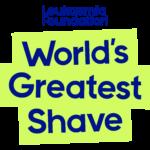
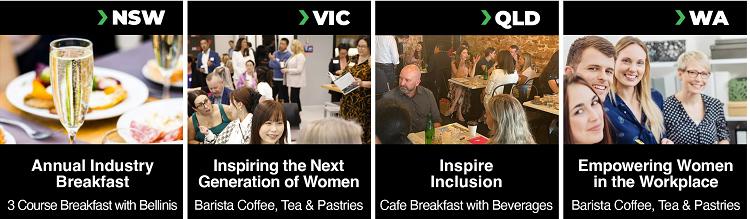

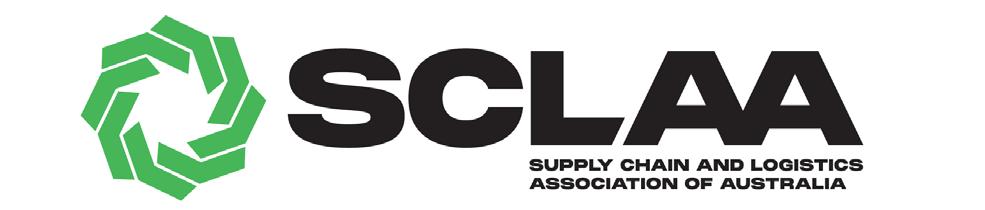
Chair’s Report
New Platinum Partner – ARUP
SCLAA International Women’s Day Events
SCLAA supporting World’s Greatest Shave
IWD Event Sponsors
Landmark Case - A Warning to Transport Bosses
Success Story - Black Bear Fulfillment
Women in Transport and Logistics Eligible for Leadership Development Scholarships
New National Partner - Netstock
Optimising Markdowns
New National Partner – Quantiful
Quantiful partners with Jaycar to power up its demand planning
What to expect from supply chains in 2024 and beyond
Reshoring, software, and expanded AI: key warehouse automation trends for 2024
Zebra Study: Nearly Six in 10 Warehouse Leaders Plan to Deploy RFID by 2028
What is the Chain of Responsibility and who is a party
Navigating 2024’s Supply Chain Challenges
SCLAA Membership – be part of the future
Divisional Reports
Model Code of Practice: Sexual and gender-based harassment.
New AS 4084 Standard for Warehouse Racking in Australia: Ensuring Safety and Quality
Upcoming Events
The start of the year has all of us pondering what is in store for 2024. With a shaky end to 2023 economically, global instability to cargo flows through the Red Sea, and local impacts at our Ports as a result of industrial action and increasing landside fees, many of us hoping that the new year will be a turning point for smoother sailing.
One thing is for certain is that change is inevitable. Within the SCLAA itself, the end of any year brings with it changes in the composition of our Board and Committees and a reset of priorities.
Since our AGM last November, we have bid a fond farewell to our Vic/Tas President Theo Pappas and welcome new State President, Archival Garcia. We have also farewelled long standing member, Director and all round SCLAA and industry champion, Kyle Rogers.
Kyle has been with the Association for over 10 years, during which time his passion for the SCLAA and industry has been instrumental and infectious. So much so that the Vic/Tas has been rebuilt under his State Presidency as one of the strongest and most active committees. His transition to a Directorship has resulted in numerous conference partner alliances, National Partner collaboration and his contribution to canvassing sponsorships for our Awards events over the years has been monumental.
We will miss his passion and zest around the Board room table and wish him all the best for his future endeavours.Kyle’s most recent role as Queensland State Director has now been assumed by Natalie Wallace, and with her extensive stakeholder management skills, we are excited to see her build on the strong legacy in the QLD Division.
Our first Board meeting for the year also focused on changes required within the Association to deliver even greater benefits to our members and Partners.
The Special Purpose Committees and Divisional Committees have started the year with ambitious plans and we kick off with our annual series of breakfast events on 8th March (International Womens Day) across 4 states.
We have partnered with Leukaemia Foundation to promote The World’s Greatest Shave fundraising campaign.
How can the Supply Chain & Logistics sectors get involved?
1. Make a donation online via the SCLAA fundraising page - 100% of donations go to the World’s Greatest Shave.
https://fundraise.leukaemia.org.au/s/1236/998/e
2. Attend the Annual Industry Breakfast and join in the fun of a Live Auction at the NSW event!
If you are attending the NSW Annual Industry Breakfast, we will be holding an Auction of fabulous prizes, including a Professional Corporate Video package, weekends away, accommodation and dinner vouchers, headsets, hampers and more! 100% of all Auction funds donated to Leukaemia Foundation!
Registrations close Monday 4th March so BOOK
NOW at https://www.sclaa.com.au/events/
Set up your own individual or company fundraising page and organise your World’s Greatest Shave event – the bigger the better. Let others know your ‘why’. And then share your page far and wide. https:// worldsgreatestshave.com/
We encourage all our Members, our Corporate Partners and the industry to get shaving or colouring and support the critical services the Leukaemia Foundation provides to Australians facing blood cancer!
SCLAA welcomes our newest Platinum National Partner, Arup.
As a not for profit Industry Association, run by members for members, our ability to support the SCLAA infrastructure and to expand is highly dependent on our National Partners. We ask all our members to support our valued National Partners where they can.
Dedicated to sustainable development, Arup is a collective of designers, consultants and experts working globally. Founded to be humane and excellent, we collaborate with our clients and partners using imagination, technology, and rigour to shape a better world.
As an independent firm, with a trust structure, Arup has no external investors. The Australasia Region encompasses Australia, New Zealand, Singapore, Indonesia, and Malaysia, with a 3000-strong team providing consultancy services to government, corporate and community-based clients.
We design logistics and freight strategies that ensure resilience.
Every economy depends on efficient, data-driven and carefully planned movement of goods and materials. As the last few years have shown, global events can have sudden and significant implications for the local supply of goods and services. Arup helps clients to define and design logistics and freight strategies that ensure resilience across assets and operations.
Our service begins by defining an organisation’s needs to developing their supply chain and logistics strategies. We then move through to business case development and the planning and design of required interventions, how they will be delivered and plans for day-to-day operations. Our approach is collaborative – we work closely with clients to ensure we deliver the right solution first time to achieve our clients’ objectives.
We recognise that the freight and logistics sector is facing transformational change. That means decarbonising the way goods and materials are moved around. It means taking advantage of automation, predictive machine learning and other emerging digital technology. There are ever more complex urban planning requirements and constraints shaping where and how sites operate. And there’s a growing need to run a resilient operation in an era of extreme weather. We help clients to identify the specific risks they face and plan ahead.
SCLAA is encouraging its Members, Partners and the broader Supply Chain & Logistics Industry to support the Leukaemia’s Foundation’s World’s Greatest Shave.
– Blood cancer is Australia’s hidden cancer crisis.
– Every day, 53 Australians hear the words ‘you have blood cancer.’
– Australia loses 16 people to blood cancer every day.
That’s 16 mothers, fathers, sons, daughters, siblings and grandparents. 16 families that lose a loved one.
And those numbers are set to nearly double by 2035. Unless we do something about it.
Family. It’s what really counts. There’s 135,000 of them, just like yours, that are facing blood cancer right now.
And every year, blood cancer rates continue to rise. But together, we can stop blood cancer in its tracks.
The Leukaemia Foundation is committed to improving the life of every Australian currently facing blood cancer.
The Leukaemia Foundation’s World’s Greatest Shave helps improve the lives of every person in Australia facing blood cancer.
Signing up and raising funds will give them the support, care and information they need to not just survive, but thrive.
To fund game-changing research, campaign for change for those affected and to achieve zero lives lost to blood cancer by 2035.
Every strand of hair you change makes living with blood cancer less lonely, daunting and stressful.
When you Shave, Cut or Colour your hair, you’re not just changing your hairstyle, you’re changing the lives of Australians affected by blood cancer. And that’s bloody beautiful.
You can donate via the SCLAA fundraising page via the QR code:
Or alternatively sign up your own company here
https://worldsgreatestshave.com/
GOLD SPONSOR
SILVER SPONSORS
BRONZE SPONSORS
NSW Auction Prizes generously donated by
The recent sentencing of a transport boss under Heavy Vehicle National Law is being described as “groundbreaking” by transport experts who warn it sends a strong message to executives across the country.
The following article is supplied by CoRsafe, an endto-end online management system supporting the Australian supply chain industry to better manage their Chain of Responsibility compliance, as part of the commitment to creating a safer and more sustainable future. Visit www.logss.com.au.
On 23 January 2024, the National Operations Manager of a transport company was sentenced to three years’ jail time, $100,000+ in penalties and costs, and a 12-month prohibition from acting in similar transport roles. It was in relation to a 2020 crash on Melbourne’s Eastern Freeway which saw four police officers killed by a heavy vehicle being driven by an impaired driver.
This case is the first time in Australia that an employee of a company has been found guilty and sentenced of a category one offence, the most serious under Heavy Vehicle National Law.
Supply Chain Technical Manager at supply chain compliance specialist CoRsafe, Aaron Louws, said whilst transport and logistics is highly regulated with a high standard help across the industry, this case is a reminder to individuals that the National Heavy Vehicle Regulator may bring charges against them personally, as opposed to only prosecuting their employer.
“The sentence sends a clear message to parties within the supply chain - the law will be enforced,” Mr Louws said.
“What also makes this case ground-breaking is that the defendant was convicted as an ‘operator’ of a heavy vehicle for their failure to fulfil their primary duty.”
An ‘operator’ is a person who is ‘responsible for controlling or directing the use of a heavy vehicle’but the Court held that this could also include the immediate manager or supervisor of drivers, and senior management who have responsibilities for the use and control of a heavy vehicle.
Throughout the legal proceedings, it was noted the company’s policies and systems were not enforced or adequately implemented or adapted. The transport company and two of its executives have also been convicted over the incident.
“There were multiple examples of non-compliance with many aspects of the policies in the areas of recruitment,
screening, the training of new workers, drug testing, recording work/rest time and adhering to work/ rest requirements. The actual implementation and enforcement of company processes never happened, and if they had, it’s possible this incident may not have occurred,” Mr Louws said.
“We can all learn from this situation. It’s important to demonstrate our standards are in place, and as an industry we work together to ensure that our actions/inactions do everything so far as is reasonably practicable, to ensure this couldn’t happen again.”
Mr Louws sat down with logistics legal expert Nathan Cecil, Partner at law firm Holding Redlich, to break down the details of the case and what it means for businesses and their staff. You can watch the full interview here. Logistics Safety Solutions Pty Ltd (LSS) ABN 25 134 417 379. This article contains general information only and is not advice.
Black Bear Fulfillment have a simple mission: To provide the high levels of fulfillment service to Australian customers, which they experienced as a former eCommerce seller in the US and UK. An eCommerce 3PL specialising in smaller consumer items, such as clothing and cosmetics, Black Bear Fulfillment are 100% Australian owned and operated. They are based in Melbourne and employ more than 40 people after launching just three years ago.
Unlike most 3PL’s they aren’t just focused on the logistics and warehousing side of the business, but also, importantly, the customer. Fulfillment is about people as much as it is logistics, and they needed a software solution to help bring this customer-centric vision to life. I the word of owner/operator Mack Blunsom, “We simply couldn’t do business without Mintsoft”
Watch the video:
https://www.youtube.com/ watch?v=vP4Z-jRo8yo&t=5s
Partial scholarships for women in Transport and Logistics ranging from $1,000 to $5,000 per person, for one of four leadership and workplace skill development programs.
These scholarships are aimed at encouraging more women to increase their impact at work, progress their career, and step into leadership roles.
Registrations of interest close on 22nd March 2024. Visit: https://www.wla.edu.au/industry/transport/
SCLAA welcomes our newest National Partner, Netstock. As a not for profit Industry Association, run by members for members, our ability to support the SCLAA infrastructure and to expand is highly dependent on our National Partners. We ask all our members to support our valued National Partners where they can.
Netstock is a leading inventory and demand planning software trusted by over 2,200 customers to optimise their demand and supply planning.
Netstock has accelerated the growth of organisations worldwide for the last 15 years and has built regional presences in ANZ, North America, and EMEA, gaining deep insights into supply chain planning challenges in each market.
The Netstock difference:
Netstock seamlessly integrates with over 60 leading ERP systems, transforming raw data into predictive insights for confident decision-making. With immediate ROI, Netstock unlocks working capital, enabling adaptability and ensuring exceptional customer service. Customers enjoy tailored onboarding and 24/6 support, along with premier learning resources from the Netstock Learning Academy, backed by decades of industry expertise. Netstock is also ISO 27001 certified, offering its customers data integrity.
Netstock continually innovates its solutions with smarter predictive engines, leveraging AI and machine learning to help customers thrive. With Netstock, customers can:
– Improve fill rate by up to 15%, reducing stock-outs and increasing sales
– Increase forecast accuracy by up to 50% with tournament-based forecast algorithms
– Reduce inventory holding by 35%, unlocking cash tied up in excess inventory
– Reduce time spent on planning, forecasting, and ordering by up to 70%
Netstock solutions
Netstock offers two product solutions that cover both sides of the inventory challenge; supply and demand. The solutions encompass:
– Inventory optimisation
– Demand planning
– Inventory forecasting
– Inventory ordering
– Supplier performance
– Manufacturing & capacity planning
– Sales & operations planning
Real-word transformations:
Netstock is helping businesses in ANZ achieve remarkable results. One such transformation is Adventure Operations who achieved a 30% reduction in inventory in under 12 months. Leveraging Netstock’s tools, Adventure Operations shifted from managing inventory and forecasting in spreadsheets to a proactive, predictive forecasting model. The result? They maintained a robust 95% fill rate, and the key to this turnaround was data visibility, leading to forecast accuracy, streamlined operations, and strategic sales initiatives.
We’re excited to be part of SCLAA and to offer our assistance to members in quickly overcoming supply chain challenges with the help of Netstock.
Getting markdowns right is critical for retailers today. With the ever-growing costs of working capital, no one can afford to sacrifice margin on inventory. At the same time, customers are more price-conscious than ever. Many customers are waiting to purchase during the markdown season, making setting markdown prices fraught for retailers. Markdown promotions are a must, but they have to be perfectly calibrated to meet customer expectations and clear end-of-season merchandise without over-discounting.
Yet markdowns rarely perform as hoped. 40% of retail markdowns fail to clear expected inventory, leading to inventory write-offs and unsustainable levels of waste— all while eating away at revenues and margin. (1) It’s enough to make any merchandiser want to pull their hair out.
The problem with traditional markdown strategies
A majority of markdowns are still done at least semi-manually. Maybe retailers apply rules through a tool, cascading the discounts out across price lists according to clusters or categories. Often these cluster-based markdowns are based on good calculations, using historical performance, merchandiser intuition, and price elasticity as a guide. Unfortunately, these good baselines still often underperform. Why?
Despite your best efforts, no human—or even predictive software— can account for the many factors that affect markdown performance. There are simply too many
items to calculate individual price elasticities. Even if you did so, you’d still be failing to account for changing customer preferences and cannibalisation. It’s no surprise that markdowns so often fail.
Optimising markdowns with AI for higher inventory profitability
That’s where AI makes all the difference. Humans may not have the ability to calculate every individual item’s demand elasticity, as well as the impact all of those discounts will have on each other, but a well-designed algorithm can. It can use sophisticated demand sensing to adjust those calculations to even the smallest signal that demand is changing. When there are gaps in the data, the model can use product similarity to assess a reasonable forecast. It can simultaneously analyse the overall impact of pricing strategy to provide a simple recommendation for each SKU that optimises profitability from each markdown.
Instead of being constrained to overly simplified clusters and categories, retailers can use AI markdown optimisation to ensure that each markdown delivers positive financial impact—all while carefully following your business rules. If you are ready to turn markdown season from a nightmare to a profit engine, it’s time to turn to optimisation.
(1) Per McKinsey research - https://www.mckinsey.com/industries/retail/our-insights/hitting-the-mark-why-markdowns-
SCLAA welcomes our newest National Partner, Quantiful. As a not for profit Industry Association, run by members for members, our ability to support the SCLAA infrastructure and to expand is highly dependent on our National Partners. We ask all our members to support our valued National Partners where they can.
Quantiful is the global leader in AI-powered demand planning software for large-scale retailers.
It uses purpose-built AI to forecast consumer demand over a range of horizons, from short-term Fulfilment Planning through Demand and Supply balancing to long-term Portfolio Planning.
By removing the dependency on spreadsheets and working with a single source of truth, retailers can significantly improve the accuracy of their forecasts, which allows replenishment to be automated and for organisations to unlock significant productivity gains inside planning and operational departments.
To deliver better forecasts, Quantiful merges historical sales and inventory data with external data on consumers’ buying intent generated from over 90 different data sources, including all of the major social and search platforms. With more accurate forecasts retailers can minimise lost sales and reduce their dependency on working capital by as much as 30%
Getting the necessary data into and out of Quantiful is easy, helping retailers to reduce the time-to-value to the absolute minimum. Quantiful works closely with all major ERP providers to ensure data flows smoothly in both directions. With the right inputs Quantiful can deliver useful forecasts in a few weeks.
The company is based in ANZ and is committed to servicing the local market with experienced people on the ground to help retailers get the most out of their technology.
Quantiful is different to other demand planning systems available today because:
1. It allows retailers to pinpoint the precise drivers of demand
To generate forecasts, Quantiful ingests thousands of sales-related data points per product including attributes such as colour, size, cost, discount, etc. Proprietary sales data can also be combined with external data to identify demand signals that can be trended and understood throughout a product’s lifecycle.
2. It can leverage the power of external data sources
Quantiful supports the ability to bring external data sets such as economic, market, social and search into its planning algorithms to improve the quality of its forecasts at every stage in the planning horizon. By combining internal and external data the quality of the insights are significantly enhanced.
3. Multi-time-series forecasting
Quantiful is built on a multi-time series forecasting foundation, unlike many other demand planning solutions. This is ground-breaking as Quantiful takes a ‘whole of portfolio’ approach. This means it can forecast the interdependencies of an entire product set, such as cannibalisation and substitution.
4. Forecasting at scale
It’s all well and good being able to create highly accurate forecasts for a small set of products at a single store. However, problems arise when you try to forecast hundreds of thousands, if not millions, of product locations. Quantiful is proven to deliver highly accurate daily replenishment forecasts for millions of SKU locations.
Quantiful’s clients include Farmers (part of the James Pascoe Group of companies), Pascoes and Jaycar Australia.
Quantiful, the leader in AI-powered demand planning software for retailers, has partnered with leading Australian electronics retailer Jaycar to deliver daily AI-powered demand forecasts for nearly 10 million SKU locations.
Jaycar is a thriving electronics retailer bucking many negative trends affecting high-street retailers today. Thanks to its loyal customer base and progressive approach to portfolio management, Jaycar is experiencing strong growth across its 135+ store network across Australia and New Zealand.
One of the challenges that comes with success in any retail category is stock management. Jaycar approached Quantiful to help improve stock planning for its nearly 10 million SKU locations to reduce stock-outs and maximise sales.
Like many retailers, historically, Jaycar has relied on traditional planning processes using historical data and aggregated store categorisations to forecast demand. Jaycar’s continued growth combined with the volatility in demand today, has meant that this process can often struggle to deliver the customer experience Jaycar is famous for while allowing tight management of inventory costs.
By partnering with Quantiful, Jaycar is transforming its replenishment tools and processes. Powered by its proprietary AI engine, Quantiful will deliver DAILY demand plans for all of Jaycar’s SKU locations, allowing the retailer to set min/max stocking levels across all its stores and, in so doing, maximise sales and optimise working capital usage.
Thanks to its cloud-based architecture, Quantiful can easily integrate into Jaycar’s legacy architecture, minimising the time to value and the cost associated with
onboarding a new enterprise system. Jaycar can also focus its skilled people resources on higher-value activities such as portfolio planning by automating low-value, time-consuming jobs.
Jamie Cormack, Founder and Chief Revenue Officer at Quantiful, said, “Quantiful software is perfectly matched to the challenges presented by Jaycar. We provide millions of accurate daily forecasts to automatically set in-store stock levels, minimising lost sales and making more efficient use of working capital.”
Looking forward, Jaycar plans to use Quantiful’s Gen AI engine to help Jaycar construct a better view of the new products they should be selling at each of their 135+ locations by lending sales data with a range of external data sources provided by Quantiful.
With accurate replenishment planning, better mid-term demand and supply balancing combined with insightful portfolio planning, Jaycar is well-prepared to navigate the more volatile trading conditions that retailers worldwide expect.
Quantiful is the leader in AI-powered demand planning software for retailers. By combining historical sales and inventory data with external data sources Quantiful is able to generate highly accurate sales forecasts that are used by retailers for replenishment planning, demand and supply balancing and portfolio planning. More accurate forecasts allow retailers to sell more, reduce the amount of stock they hold and better meet the needs of their customers.
Quantiful is based in Auckland, New Zealand and is focused on meeting the needs of retailers in the ANZ region.
Geopolitical tensions, extreme weather events and ongoing economic frailties in 2023 put supply chains to the test, underscoring the importance of handling adversary.
As we head into 2024, leaders’ confidence in supply chains is starting to gain momentum again, however, embracing data-driven decisions and contingency plans is crucial.
As consumer dynamics evolve alongside socioeconomic volatility, businesses are being asked to sense demand shifts and orchestrate responsive fulfillment quickly. This is and will remain a huge challenge, but technologies enabling greater agility, transparency and predictivity are easing the burden and leading to many success stories.
Warehouse automation is accelerating dramatically as facilities embrace robotics and smart systems to unlock new efficiency frontiers. Autonomous mobile robots (AMRs) can dynamically shuttle inventory for optimised workflows, and automated storage and retrieval liberates floor space while enabling rapid order processing via optimised SKU locations. Cognitive automation through robotic process automation (RPA) and conversational AI is taking on repetitive administrative tasks for businesses as well.
According to McKinsey, automated warehouses can reduce operating costs by up to 30% with throughput velocity gains over 25%, while research by MIT finds every $1 spent on control towers yields $3-$10 in cost savings. On top of this, data from IBM shows that organisations that use security AI and automation extensively save USD 1.76 million compared to those that don’t. The global average cost of a data breach in 2023 was USD 4.45 million, a figure which is on the rise every year.
To leverage advanced technologies like cloud computing, predictive analytics and artificial intelligence, companies should first establish integrated digital foundations spanning their end-to-end supply chains. Collating the right type of customer, sales and product data is the key to driving enhanced data-driven decision making, real-time visibility, and streamlined flows. Businesses are learning to prioritise data, foregoing a one-size-fits all approach to learn the numbers that matter to their business. The transition from analog or semi-digital processes poses adoption challenges, especially around quantifying return on investment, but there is an understanding now that digitalisation is synonymous with business survival.
Well-designed and optimised supply chains confer many advantages, including meeting customer fulfillment expectations, improving network efficiency, strengthening reliability and resilience, enabling what-if scenario modelling, and maintaining balanced inventory strategies. However, over-dependency on specific partners and inadequate agility to address unforeseen situations can prevent supply chains from achieving their full potential.
In 2024, businesses will look to diversify their supply networks and partners, giving extra flexibility to dynamically shift sourcing, production or distribution based on changing cost economics, lead times or demand.
While automation and analytics unlock supply chain advancements, engaged talent remains indispensable. Labour shortages have hit Australia hard, and a lack of available workers is a persistent problem, which is why we need to create engaging and fulfilling roles alongside automation. Cobots are designed to work alongside humans to complete daily tasks more effectively and productively, automating repetitive tasks to provide better employee safety and wellbeing. For instance, Körber research estimates that a warehouse operator completing a picking workflow will walk around 10 to 15 kilometres a day. As the technology handles execution, employees can shift more towards value added tasks and strategic decision-making.
This concept demands workforce readiness through change management, continuous skills development, and cultural alignment. By empowering people to work alongside intelligent systems, businesses will reap the full rewards of technology and innovation.
Omnichannel fulfilment remains pivotal
The pandemic has shone a light on the importance of a businesses’ every channel – ecommerce, directto-consumer, retail and distributors. If one channel is disrupted or underperforming, profits don’t immediately dip because demand is consolidated in every channel. Developing supply chains which facilitate this is easier said than done, however, and requires sophisticated data management tools.
Order Management System (OMS) will be vital for retailers in 2024, improving fulfillment and profitability to enhanced customer satisfaction. In the era of online returns and same-day delivery, retaining customer
loyalty is crucial – by increasing inventory visibility, businesses can avoid lost sales and stockouts.
What does the future supply chain look like?
In the near future, highly automated supply chains where sensors, vast data, artificial intelligence, cloud platforms and robots enable smart decision automation and precise control of logistics flows will be the standard.
In 2024, the culmination of this technology is being utilised by smart businesses around the world, and it’s a matter of time before the competition is forced to catch up.
A lack of capital availability might be slowing the adoption of fixed, traditional warehouse technology, but there’s no doubt that automation, software and artificial intelligence hold the future of supply chains. Flexible automation gives companies of different sizes the opportunity to explore the benefits of innovative technology without enterprise level capital investment.
The core issues facing supply chains in 2023 – labour availability, capacity, space availability and resiliency –aren’t going away in 2024. But how supply chain leaders address these challenges continues to evolve.
Moving into the new year, we are seeing organisations finding new ways around barriers to automation, increasing their investments in established technologies, and seeking new levels of efficiency and productivity through orchestration and artificial intelligence. Here’s a more detailed look at some of the trends we expect to see this year.
Smaller and emerging organisations face the same labour, efficiency, and speed challenges as their larger competitors. Yet, they often lack the resources to address these challenges through capital-intensive automation projects, putting them at a competitive disadvantage.
In 2024, flexible infrastructure technologies such as mobile robotics and AGVs (Automatic Guided Vehicles) will play a larger role in leveling the playing field. Swisslog’s CarryPick system, for example, is ideal for small-to-medium enterprises (SMEs) because it is fast and cost-effective to implement, delivering significant labour savings, and making easy to scale. For larger companies requiring higher throughputs, Swisslog’s shuttle and grid-based goods-to-person systems come with a potentially larger investment, but can deliver greater returns on a greater scale.
For these organisations that are seeking higher throughputs, standardised configurations of the popular AutoStore system – for which Swisslog is the number one global integrator – will reduce engineering
and software customisation costs while delivering the robust functionality that meets the requirements of most applications.
After years of industry focus on automating each picking to support growing e-commerce and omni-channel distribution, pallet handling systems will recapture their share of the spotlight in 2024.
That’s partly due to the continued momentum around re-shoring, in which Australian and New Zealand based businesses are re-centring their supply chains to improve resiliency. This is driving development of highbay warehouses that support distribution of palletised products and that will result in increased investment in pallet handling technologies, particularly crane-based and shuttle-based ASRS (Automated Storage and Retrieval Systems).
Solutions based on technologies like the Swisslog Vectura crane and PowerStore maximise space utilisation in high-bay warehouses and deliver proven reliability over decades of service. Supply chains already dependent on pallet ASRS will extend the value of these solutions by investing in lifecycle services that ensure reliability and enable adaptability allowing companies to get more out of what they already have.
Machine learning, a form of AI, has been instrumental over the past several years in enabling technologies such as robotic item picking to advance to their current state. Now the incredible advances in generative AI that occurred in 2023 are creating new opportunities for AI in the supply chain.
Initially, we’re likely to see automation vendors apply generative AI to their training libraries to streamline the development of custom training for their customers. Even higher value will be realised as AI works with warehouse software systems to derive insights from the data-rich warehouse environment. Forecasting, slotting, and sequencing processes all stand to benefit. Software to intelligently control warehouse automation, such as Swisslog’s SynQ software, is a key enabler of process optimisation and successful automation
Software takes centre stage
As operators increasingly seek to orchestrate people, processes, and technology within the warehouse, they’ll find their ability to execute on this strategy dependent on the software that controls their automation systems. WMS platforms simply aren’t well positioned to address orchestration challenges as they lack the machinelevel view of operations required. That puts the onus on automation integrators to deliver software solutions capable of capturing data at the machine level while providing a holistic view of warehouse operations. Software platforms that provide real-time visibility into the logical and operational level will become even more valuable as AI enables more accurate forecasts and resources can be aligned to execute on those forecasts with the highest efficiency.
Swisslog’s SynQ software, which stands for synchronised intelligence, synchronises people, process, and machines for efficient operations. In addition to being a WMS, it can perform the task of a WCS (Warehouse Control System), or MFS (Material Flow System), and can seamlessly interact with ERP (Enterprise Resource Planning) and e-shop systems.
SynQ optimises the storage of goods, placing fast moving goods near the point of dispatch, and slower moving goods towards the back of the storage. What further sets SynQ apart from other software is its ability to ‘click and solve’ directly from the 3D visualisation.
Software like SynQ, more than hardware, then becomes the key enabler of successful automation and operators will increasingly seek out solutions with WCS, WMS and MFS functionality integrated in a common modular platform with a common toolset.
Sean Ledbury has more than 30 years of experience in logistics automation, and has engineering qualifications as well as an MBA. As Head of Sales and Consulting for Swisslog ANZ, he leads a market-driven and customer-focused team that aims to deliver optimum warehouse automation solutions to the local market.
A Sydney local, Sean began his career as a design estimator, and has held various business leadership, sales, and integrated systems roles, in areas such as automated and semi-automated picking and conveyor based solutions, sorting, postal and parcel, airport logistics, ASRS, both unit and bulk, as well as right-sized on-demand packaging solutions across multiple regions
Today’s warehouse leaders face ever-increasing demands for speed and accuracy while contending with tighter labor markets, rising costs and economic uncertainty. As a result, decision-makers are accelerating their investments in technology to increase efficiency across the supply chain and future-proof their operations.
Zebra Technologies recently released the findings of its 2023 Global Warehousing Study, which confirmed 58% of warehouse decision-makers plan to deploy radio frequency identification (RFID) technology by 2028 to help increase inventory visibility and reduce out-of-stocks.
Over the next five years, the majority of warehouse decision-makers plan to deploy fixed, passive or handheld RFID readers and fixed industrial scanning solutions that can better track assets, workers and goods throughout the warehouse environment. This year actually marks the 50th anniversary of the invention of RFID, which has become an invaluable problem-solving tool for frontline workers in warehouses and other industries.
The survey also showed 73% of warehouse decision-makers have or will be accelerating their modernisation project timelines, striving for increased productivity in a shorter time frame. This rush makes sense, when you consider that returns management climbed to the top operational challenge cited by nearly half of warehouse decision-makers surveyed—an increase of 10 percentage points year-over-year.
“The significant growth of returns aligns with e-fulfillment growth over the last several years, and it is a mandate for change across every part of the supply chain,” said Andre Luecht, Global Strategy Lead for Transportation, Logistics and Warehouse, Zebra Technologies. “This means warehouse leaders must modernise their operations with technology solutions to handle returns and increase agility, inventory visibility and demand forecasting in order to improve efficiency and make better decisions in real time.”
The majority of warehouse decision-makers (76%) say they are under pressure to improve performance while adjusting to shifting consumer e-commerce demands. Inaccurate inventory and out-of-stocks continue to significantly challenge productivity according to nearly 80% of warehouse employees and decision-makers. In fact, both groups—82% of employees and 76% of decision-makers—acknowledge they need better inventory management tools to achieve better accuracy and determine stock availability. And a significant 91% of decision-makers are addressing this need, citing plans to invest in technology to increase visibility across the supply chain by 2028.
Decision-makers are also automating their warehouses to ultimately optimise their operations and increase their inventory visibility. According to a recent study by Interact Analysis, despite a recent slowdown in demand for automation projects (in part due to a reduction in warehousing construction), this demand is expected to return to growth in 2024.
The Zebra study found that 69% of warehouse decision-makers already have or are planning to automate workflows by 2024 to support warehouse employees and shift them toward more customer-centric, high-value tasks. Over half of warehouse decision-makers believe automation increases worker efficiency and productivity by reducing manual picking, order errors and cycle time. Meanwhile, eight in ten warehouse employees agree that using more technology and automation helps them meet or exceed productivity goals.
Complementing the rise in productivity, eight in ten warehouse employees surveyed also feel more valued when their employers provide them with technology and automation tools to help them work. Similarly, 88% of warehouse decision-makers say adding warehouse technologies, including devices and robotics, attract and retain employees which is extremely important during labour shortages. More than half of the surveyed decision-makers plan to implement machine learning (52%) and predictive analytics (59%) software solutions in their facilities by 2028.
Warehouse decision-makers are choosing solutions based on their ability to help them build sustainable operations, driven largely by regulations, energy costs or shortages along with customer, worker and investor expectations. For example, 77% of warehouse decision-makers are focused on reducing emissions and waste while eight in ten warehouse decision-makers say it’s important that their warehouse technology solutions maximise battery life.
Other sustainable elements decision-makers prioritise today include ensuring accurate mobile device swapout time, connecting to energy monitoring software to maximise efficiency, offering buy-back and certified refurbishment/circular economy programs, and the use of reusable and recyclable materials. Beyond their own operations, 81% of warehouse decision-makers also say it’s
important that technology vendors have sustainability measures in place for running their businesses.
Building Tomorrow’s Connected Warehouse – Today’s headwinds have prompted warehouse leaders to adopt innovative strategies, which will help them address critical challenges and prepare to offset any emerging or unexpected events. Despite global uncertainty, warehouse leaders continue to
invest in data-powered environments that efficiently balance automation and optimised human labour across the supply chain. Going forward, warehouse decision-makers must continue to implement agile strategies to avoid inefficiencies, preserve resources, and provide employees with a performance edge.
To read Zebra’s Warehousing Vision Study, click here
The Chain of Responsibility (CoR) is a concept in road transport legislation that defines who is responsible for ensuring safety across all parts of the heavy vehicle journey. The HVNL identifies 10 functions within the supply chain and attaches a duty to each party that performs one of those functions. That duty is called the primary duty.
Regulatory advice – The primary duty
New regulatory advice about the primary duty is available.
This guidance informs parties in the Chain of Responsibility about the primary duty established under the Heavy Vehicle National Law (HVNL) section 26C and the applying principles.
The primary duty creates different legal obligations compared to prescriptive requirements under the HVNL.
Learn more about the primary duty.
Bastian’s one-question survey has unveiled a vivid tapestry of challenges that await the supply chain sector in 2024. The insights, drawn from the voices of influential executives, paint a comprehensive picture encompassing geopolitical conflicts, economic uncertainties, and technological advancements. As we dissect these challenges, one critical theme emerges — the intensifying war for talent.
The landscape ahead is laden with isolated events, from geopolitical uncertainties to climate-related disruptions, demanding unparalleled resilience. Executives emphasize that navigating these complexities necessitates not just innovation and a customer-centric approach, but a commitment to building a unified and seamless flow of data across the supply chain.
Global conflicts, high interest rates, and inflation pose significant threats, making effective inventory management a major hurdle. Successful navigation requires meticulous planning for demand and supply forecasts, underscoring the importance of collaboration among stakeholders. Yet, it’s the availability of skilled professionals that is crucial for enduring these turbulent times.
Costs:
Addressing challenges in input cost variability and reducing carbon footprints is intricately tied to the scarcity of talent. The war for talent, especially in rural locations, is a recurring theme. Businesses grapple with finding strategic and agile sourcing teams, a task made more challenging by a shrinking pool of qualified talent.
Acknowledging cost-of-living pressures and the difficulty of passing costs onto customers, executives stress the need for innovation. However, innovation itself is tied to the talent pool, as attracting, and retaining skilled professionals becomes central to implementing transformative technologies.
Increased volatility in shipping lead times and rates, coupled with challenges in emission management and electrification, underscore the need for digitisation and transformation. This requires professionals who not only understand these challenges but can also drive sustainable change.
Successful adoption of AI requires dynamic operational changes, often reliant on managing big data faster and embracing AI for risk management. Here, the demand for skilled professionals capable of understanding and implementing AI becomes evident.
The persistent labour shortage, exacerbated by shifts in perception towards manual work, is a pressing issue. Automation is viewed as a solution, but its adoption is hindered by challenges such as investment requirements and accurate growth projections. Talent demand for higher salaries further complicates the situation.
As the supply chain sector ventures into 2024, it’s evident that the war for talent is not just a component but the linchpin of success. Resilience, adaptability, innovation, and sustainability are undoubtedly crucial. However, these elements are intricately linked to the calibre of professionals managing these complexities. The strategic and holistic approach demanded in 2024 is not just about technologies and processes; it’s about attracting, developing, and retaining the talent that will drive the industry forward. Talent is not merely a component of success — it is the very essence of it.
Read our most recent report here and discover what supply chain leaders are forecasting as key challenges for 2024.
The Supply Chain & Logistics Association of Australia combines decades of experience with industry-leading professional development and education programs, networking events, corporate partnerships, and support for its members and partners.
Our strategic purpose is to connect today’s supply chain professionals and partners to tomorrow’s growth opportunites and to support the advancement of our industry by championing collaboration, innovation, and success.
6,000 MEMBERS & INDUSTRY CONTACTS
Expand your horizons with thousands of professional members and industry contacts.
SOCIAL MEDIA FOLLOWING 40.000+
Building enduring industry relationships with individuals and businesses alike.
STRATEGIC REACH OF 50,000+
Via printed and digital media across out network of practitioners and professionals.
EXPLORE OUR RANGE OF MEMBERSHIP + NATIONAL PARTNERSHIP OPTIONS
We have a range of Membership Options suited for every stage of your career, from Students just starting out, to Corporate Bundles and National Partnership opportunities for organisations wanting to partner with SCLAA and be part of the future of our growing industry.
Cheers to a successful start! Last Friday, February 23rd, 2024, the SCLAA QLD division held its first networking event of the year at Ballistic Beer Co., with the generous sponsorship of Falcon Autotech. The event brought together a diverse mix of supply chain and logistics professionals for an evening of lively discussion, relaxed networking, and delicious craft beverages.
During the event, Falcon Autotech, the event sponsor, presented a 5-minute briefing to the attendees. The presentation focused on the innovative and technological solutions they offer in the warehouse automation space. Falcon Autotech highlighted how their offerings compare to their competitors in terms of:
– Overall return on the automation investment – Tech integration requirements
This informative presentation provided valuable insights to the audience and sparked further discussions among attendees.
The atmosphere at Ballistic Beer Co. buzzed with energy as attendees mingled and exchanged ideas. The venue provided a perfect backdrop for fostering connections, with its spacious indoor-outdoor layout and inviting
atmosphere. Whether discussing industry trends, exploring potential collaborations, or simply catching up with colleagues, the night was filled with valuable interactions.
We extend our sincere gratitude to Falcon Autotech for their invaluable sponsorship of this event. Their support played a significant role in making the evening a success, and their commitment to the SCLAA QLD community is truly appreciated.
The first networking event of the year set the bar high, and we look forward to hosting many more engaging and informative events throughout 2024 The next event which celebrates International Women’s Day will be held at Arti & Mai at Albion from 9am – 11am and promises to be event greater with fantastic speakers organised.
Join the Conversation:
Whether you attended the Ballistic Beer Co event or are interested in getting involved with SCLAA QLD, we encourage you to connect with us! Visit our website at www.sclaa.com.au or follow us on social media for updates on upcoming events, membership opportunities, and industry news.
Together, let’s make 2024 a thriving year for the supply chain and logistics community in Queensland!
Natalie Wallace is a seasoned executive boasting over three decades of expertise in the realms of International Freight Forwarding, Contract Logistics, Transportation, Warehousing, and 3PL Logistics. Her extensive background extends to providing comprehensive Supply Chain Solutions across diverse sectors such as Manufacturing, Consumer Goods, Finance, Technology, Retail, FMCG, and E-Commerce Fulfilment.With a wealth of domestic and international experience.
Natalie has collaborated closely with prominent Blue Chip organizations, assuming various Senior Leadership positions. In these roles, she has adeptly delivered consultancy services focusing on Global Supply Chain transformation, E-Commerce Fulfilment optimization, operational streamlining, and strategies aimed at enhancing cost-effectiveness and profitability.
Supply Chain considerations and trends prove to be interesting in 2024 as companies, leaders, services providers and customers are split in terms of what are the critical challenges and solutions must we cater for in the immediate future.
Fulfilment automation remains a subject of interest as evidenced by great attendance to the recent Priority Integrated Solutions site visit. There were over 40 attendees across the 2 sessions and topics of note included labour shortage, end to end consultation and required assistance on return on investment. It’s still a relatively new technology for some people but as it becomes more widespread, no doubt this will be easier and better received.
I would however, advice against a one size fits all solution. AMRs depend a lot on order profiles, accurate forecasts, SKU dimensions and data integrity. Get any of this wrong and you’re looking at a huge investment without a way to recover. More specifically, a lot of
thought should consider the business disruptions that will affect your business in deploying this solution, especially on a brownfield site.
Several attendees noted this solution as a way to address the current labour shortage. It is certainly a challenge today and I believe will be so in the next few years as it becomes increasingly difficult to attract people to blue collar work.
Be sure to register for next week’s webinar (Feb 15th): Disability is Diversity and Diversity is a Superpower to hear about how one company is providing a solution for this across the region whilst also providing a positive impact on people with disability – a hugely overlooked AND underestimated talent pool.
Speaking of underestimated, more women need to be in charge, especially in the supply chain. Period. Join us as we host a great panel of leaders on March 8 to celebrate International Women’s Day. Marie Varrasso (Chief Operating Officer, uTenant), Meaghan Siemensma (Senior Implementation and Sustainability Manager, Bestrane Group), Carly Cummings (GM - Procurement, Planning & Logistics, Vitasoy Australia) and Tessa Boyle (General Manager Customer Supply Chain, CUB) head up a superstar line up for Victoria, hosted by our own Tabitha West. I definitely can’t wait for this one!
One critical issue that cannot be discounted is supply chain disruption. It is a critical strategic topic for all supply chain participants in the ecosystem and it is certainly the new normal.
During February, industry leaders were invited to attend a roundtable discussion on the Importance of Uninterrupted Operations at the Port of Melbourne. The event was hosted by the Victorian leader of the Opposition John Pesutto, MP and Shadow Minister for Ports, Roma Britnell MP, at the Victorian Parliament House. Esteemed colleagues Stephen Lakey & Rakesh Bandipelli represented the SCLAA as Directors and participated in discussions that centred on the effects of port disruption and solutions to mitigate the uninterrupted flow of trade into Victoria.
Items discussed were security requirements, community awareness of the importance of supply chain, economic impact of disruptions to the community and critical transport infrastructure demands.
Carbon emissions is another topic that is always raised as sustainability should be at the forefront of all our minds. In most cases, it is brought up just because someone has to, then it is ticked off and put aside for another day.
From my personal point of view, what’s important for participants is to set aside their political biases and approach these topics with a sense of collaboration. It
is easy for such discussions to devolve in positioning rather than problem solving.
What may be good to consider is who you are solving these issues for? Is it for you? Your company? Or your kids?
Consider that in the future, for them, there might not be another day.
Archival Garcia is the newly elected President of VIC & TAS SCLAA:
An executive leader with almost 20 years’ experience in Supply Chain Management Technology solutions for warehousing and transportation, he has consulted on a wide range of solutions such as WMS, TMS, OMS, Inventory Optimisation, Demand Forecasting and Advanced Transportation Visibility to a wide variety of Tier 1 to Tier 3 businesses including Retailers, Manufacturers, Distributors and Logistics Service Providers.
Archie is currently the Founder and CEO of Ensemble Solutions.
The following is an abridgement of an article originally published on the Safe Work Australia website.
Safe Work Australia has published a model Code of Practice: Sexual and gender-based harassment. The model Code provides practical guidance for persons conducting a business or undertaking (PCBUs) on how to eliminate or minimise the risk of sexual and gender-based harassment at work. It will help you meet your WHS duties.
PCBUs must take a proactive, consultative and preventative approach to sexual and gender-based harassment, whether it comes from colleagues, customers or the public, and whether it’s online or in person. You must identify and assess the risks, eliminate or minimise them so far as is reasonably practicable, and review your control measures to make sure they’re working as planned. Managing the risks may mean changing the layout of your workplace, redesigning the work or the way you do it – training and policies alone are not effective or reliable controls.
You must consult your workers on the risks of sexual and gender-based harassment as well as other psychosocial hazards.
The model Code should be read and applied alongside the model Code of Practice: Managing psychosocial hazards at work. Sexual and gender-based harassment often occurs with other psychosocial hazards and PCBUs must consider the interaction between these hazards when managing risks to the health and safety of workers and others.
Download the model Code of Practice: Sexual and gender-based harassment
Dematic designs, engineers, and manufactures Colby Storage Solutions including ColbyRACK at its Australian headquarters in Belrose, NSW. For more information, visit www.dematic.com or www.colby.com.au
Each year in Australia, warehouse employees are injured because of accidents involving forklifts and warehouse racking.
With steel storage racking systems forming the backbone of warehouse operations, it is essential to ensure racking safety, quality, and structural integrity over the long term.
Following recent developments globally and calls from local industry, the racking Standard in Australia has undergone a significant update with revisions aimed at enhancing structural design, safety measures and operational procedures.
Evolution of the Standard: The new vs. the old
The Standard for selective racking in Australia has recently been updated, with the previous AS 4084:2012 being superseded by:
– AS 4084.1:2023 Steel storage racking. Part 1: Design
– AS 4084.2:2023 Steel storage racking. Part 2: Operation and maintenance
The subdivision of the Standard reflects a more comprehensive approach addressing both design and operational aspects. Expanded and improved guidance is provided to end users and those carrying out inspections of racking systems, particularly in relation to damage assessment and methods of repair.
The major changes
At a high level, the changes in the Standard cover:
Modification of existing racking systems: While the new Standard does not apply retrospectively to existing racking installations, if those systems are reconfigured, modified, or extended then they should be upgraded to the current Standard.
Clarification of seismic design: Previously, designing racking systems with seismic considerations wasn’t common in Australia. The new Standard however mandates the seismic design of selective racks, ensuring all racking systems can withstand earthquake-induced forces, aligning with global best practice. The updated Standard provides clear-cut inputs for seismic design, ensuring consistent adherence across suppliers.
Operational and maintenance focus: The inclusion of operation and maintenance as a separate part to the Standard addresses the industry’s requests specifically supporting and guiding damage assessment and repair
methodologies.
Testing methods: Enhanced methods for testing racking components, ensuring they provide reliable data for safe design of racking.
Structural analysis: Advanced methods of structural analysis, providing a more accurate and reliable evaluation of racking systems.
Direct strength method: Introduction of the direct strength method for designing perforated cold-formed steel racking uprights, aligning with Australian and North American best practices for cold-formed steel design.
Splicing: Splices in upright frames should be avoided.
The new Standard brings changes that will influence the design of new racking systems and upgrades to existing systems. Warehouse owners need to be vigilant and ensure that their racking solutions comply with the updated Australian Standard.
In addition to meeting the new Standard by installing properly designed warehouse racking, it’s also essential for every warehouse to install safety signs and conduct yearly audits and safety inspections. The new Standard requires rack load signs to contain additional information, in particular the ‘tolerance grade’ of the racking system and the name of the firm responsible for the structural design.
The new Standard for warehouse racking in Australia marks a significant step forward in improving the safety and efficiency of storage solutions across the industry.
If you are looking to install a new racking system, modify an existing system, or would just like to learn more about this change in the Australian Standard, visit www.colby. com.au
1300 364 160
secretary@sclaa.com.au
sclaa.com.au