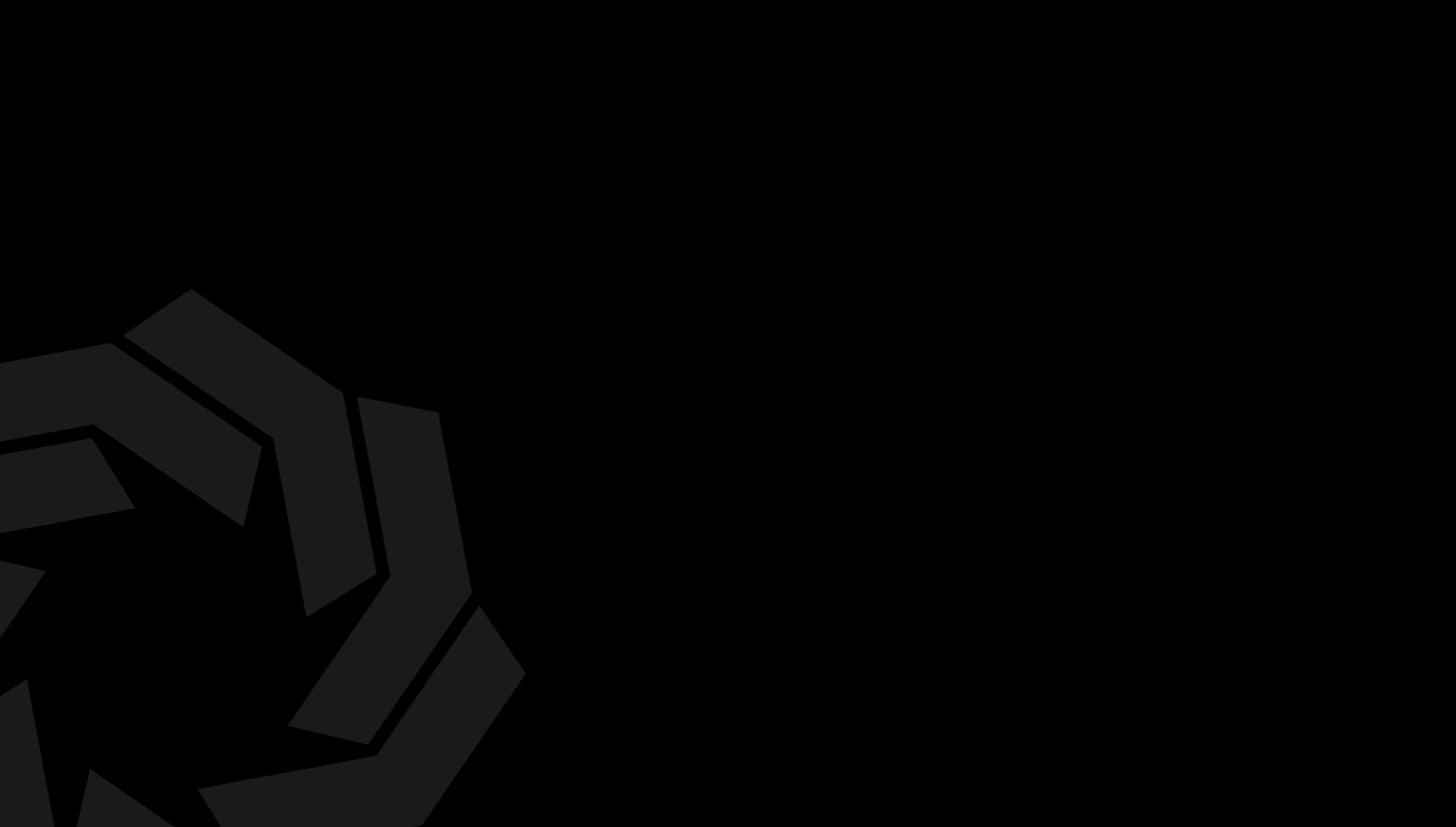
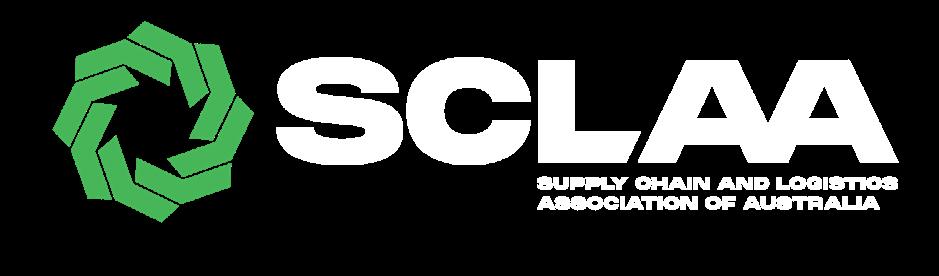
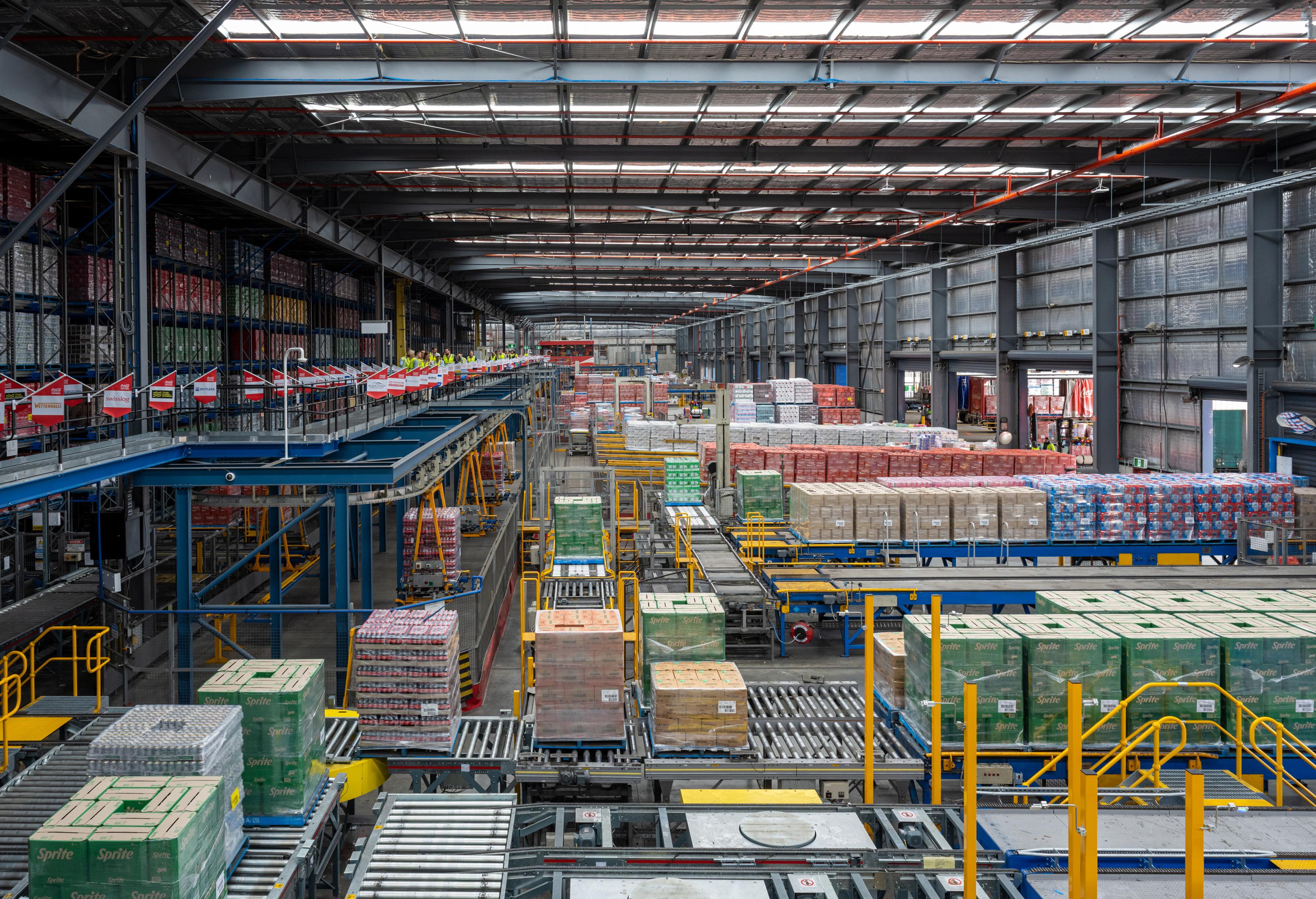
03 05 06 06 07 09 12 13 14 14 15 17 18 19 25 26 27 28 30 33 34
Message from SCLAA Chair
New Platinum National Partner – Bastian
New National Partner – The BUSY Group
New Corporate Members
Straight Talk from David Doherty OAM
Top 10 Lithium-ion Myths
ASCL Awards 2023 – Call for Submissions
ASCL Awards Gala Dinner / Sponsorship Opportunities
Toll Group Selects Dematic as Automation Partner
Körber’s Elevate APAC 2023 Ends on High Note
Adelaide Airport - Air Traffic Control for the Loading Docks
Avoiding Costly Mistakes: The Importance of Accurate Parcel Dimensioning
Divisional Reports
Supply Chain Week - A Recap
Coca-Cola Europacific Partners Expands Mentone DC with Swisslog Automation to add 12,000 New Pallet Spaces
Introducing First-to-Last-Mile Optimization. Envision a More Synchronized Future with Blue Yonder
Embracing the Future of Supply Chain & Logistics
Careers Forum
Warehouse Safety Guide
Upcoming Events
The logistics industry in Australia plays a pivotal role in facilitating domestic and international trade. With its vast geographical expanse and thriving economy, Australia heavily relies on efficient logistics operations to ensure the smooth flow of goods. However, like any other industry, logistics in Australia faces its fair share of challenges. Conversations with SCLAA Partners and members and amongst my Associates continues to revolve around the following
Supply chain disruptions remains the prominent concern in Boardrooms and across Operations. Factors such as natural disasters, global pandemics, trade disputes, and changing government regulations continue to be front of mind with their potential to disrupt the smooth flow of goods across the country. For instance, the COVID-19 pandemic led to significant disruptions in global supply chains, causing delays, shortages, and increased transportation costs. Disruptions highlighted the need for resilience and adaptability in logistics operations.
To address this issue, many logistics companies in Australia are now implementing robust risk management strategies. This includes diversifying suppliers, developing contingency plans, adopting advanced technologies for enhanced visibility, and establishing closer collaboration with stakeholders to ensure effective communication and quick response during crises.
The logistics industry in Australia continues to face a shortage of skilled workers, which poses a considerable challenge for companies. The aging workforce, coupled with a lack of skilled entrants, has created a talent gap that hampers the industry’s growth. This issue is further exacerbated by the rapid advancements in technology, requiring logistics professionals to possess digital skills and adapt to automated processes. SCLAA, in conjunction with ITLS, have initiated a Micro-credential course aimed at Executives/Business owners to pro-
vide understanding if emerging technology and its impacts on the supply chain. https://www.sydney.edu.au/ business/our-research/institute-of-transport-and-logistics-studies/courses/foundations-of-intelligent-supply-chain-management.html
To address the talent shortage, industry stakeholders, educational institutions, and government bodies are working together to promote logistics as an attractive career choice. Initiatives such as vocational training programs, internships, and partnerships between educational institutions and logistics companies aim to bridge the skill gap and encourage more individuals to pursue careers in this field. SCLAA have partnered with both ITLS and Tafe NSW to assist with the alignment of training and education with industry needs. Additionally, companies are investing in upskilling and reskilling their existing workforce to meet the changing demands of the industry.
Australia’s vast geographic size and dispersed population pose significant challenges in terms of infrastructure development. Insufficient transportation networks, outdated facilities, and congestion at ports and airports impact the efficiency and competitiveness of the logistics sector.
To address these infrastructure constraints, the Australian government has initiated several large-scale projects aimed at improving transport networks. For example, the ongoing investment in road and rail infrastructure, such as the Inland Rail project, aims to enhance connectivity and reduce transportation times across the country. Additionally, advancements in technology, such as the utilization of smart systems and automation, are being explored to optimize existing infrastructure and improve operational efficiency.
Sustainable practices and environmental concerns have gained prominence in the logistics industry worldwide, and Australia is no exception. The sector’s carbon emissions, reliance on fossil fuels, and inefficient transportation contribute to environmental degradation.
To tackle this issue, the Australian logistics industry is gradually transitioning towards greener practices. This includes investing in fuel-efficient vehicles, adopting alternative energy sources, optimizing route planning to minimize fuel consumption, and implementing waste reduction strategies. Furthermore, collaborations between industry stakeholders and government bodies are promoting the development of sustainable logistics initiatives, such as eco-friendly packaging, recycling programs, and emissions reduction targets.
The logistics industry in Australia faces a multitude of challenges, ranging from supply chain disruptions
and talent shortages to infrastructure constraints and environmental sustainability. However, the industry is actively adapting and finding innovative solutions to overcome these obstacles. By embracing technology, fostering collaboration, investing in talent development, and prioritizing sustainability, Australia’s logistics sector is striving to enhance efficiency, resilience, and environmental stewardship. As the industry continues to evolve, addressing these trending logistics issues will be crucial to ensure Australia’s future economic and trade growth.
As Australia’s premier Professional association, SCLAA continues to facilitate and assist the industry and its members with respect to these ongoing challenges.
We advocate for the industry and voice industry issues and member concerns through representation on many government and industry Committees. Have your say through various Polls and RFI’s distributed to members.
In June, I chaired at Supply Chain Week https://supplychainweek.com.au/ and was so pleased to see many of our Committee members and National Partners present at the Conference.
I also had the pleasure of attending the Womens Resilience Annual Fundraiser, which is a charity we supported at the SCLAA NSW IWD lunch. Fabulous keynote speakers including Christine Holgate, CEO Toll Global Express, Karen Gunn, NSW Police Commissioner and the ever passionate Simone Allan, Founder of the Womens Resilience Centre. Much needed funds were raised and SCLAA were pleased to support and host a table with our National Partners and Sponsors.
During July SCLAA will once again be providing engaging and informative seminars in conjunction with the CeMat Conference. I am privileged to be Chairing first day of the Conference 25th July https://www.cemat.com.au/ and look forward to seeing many of you at our breakout event on 26th July -all about Embracing the Future of Supply Chain and Logistics https:// www.sclaa.com.au/wa-event/embracing-the-future-of-supply-chain-logistics-cemat-australia-2023/ Both the broader CeMat seminars and SCLAA seminars on 26th July cover a lot of the issues mentioned above and provide key insights in risk mitigation.
I am also very excited to have brought to fruition the initiative of an Industry focused Careers Forum on 27th July. This has been borne from much feedback and support from members and industry alike on the importance of development and attraction of personnel to Supply Chain and Logistics.
This day will provide key insights into Professional development, personal branding and career pathways through training and tertiary qualifications. Full details
and to register - https://www.sclaa.com.au/wa-event/ careers-forum-cemat-australia2023/
And for something a little different, visit the SCLAA stand C11 to meet the SCLAA Committee and executive as well as the opportunity to update your Professional Headshot!
SCLAA continues to deliver benefits to its members by providing the above seminars free of charge to members plus free and automatic registration into the CeMat exhibitions.
Look forward to seeing you there!
Sue Tomic SCLAA National ChairThe SCLAA welcomes our newest Platinum National Partner, Bastian. As a not-for-profit Industry Association, run by members for members, our ability to support the SCLAA infrastructure and to expand is highly dependent on our National Partners. We ask all our members to support our valued National Partners where they can.
Bastian is now a Platinum Partner at SCLAA.
Bastian Consulting is a boutique search practice servicing clients across the Asia Pacific. With over forty years of combined experience spanning across 11 different countries in the Region, Bastian provides customer-focused strategies that deliver results.
Bastian has spent a lot of time curating relationships with business leaders in the Supply Chain and Technology sectors; we have a contact database of over 50,000 professionals and have successfully serviced clients across 14 different countries.
We give our clients a competitive edge because when it comes to attracting talent –we’re proficient in finding candidates not only on the market, but in the market.
Our clients choose us because we:
– Have experience attracting niche and “hard to find” talent
– Know how to turn around bad recruitment processes
– Professionally & effectively promote our client’s employer brand
Provide clients with real-time data accessed through our highly customised database
Use a great recruitment methodology that’s designed to get you results
Bastian offer clients a range of services, including but not limited to:
– Retained Search
Interim Management & Contracting
Market Mapping
In addition to our suite of services, Bastian also has the capability to build customised solutions, tailored to your specific business needs. If you’re looking to hire for growth in the next 12 months, contact stephanie@ bconsult.io to find out how a 12-month retainer model has saved some of our client’s tens of thousands.
The SCLAA welcomes our newest National Partner, The Busy Group. As a not-for-profit Industry Association, run by members for members, our ability to support the SCLAA infrastructure and to expand is highly dependent on our National Partners. We ask all our members to support our valued National Partners where they can.
The BUSY Group is an innovative not-for-profit organisation, leading the way in apprenticeship, employment, and training solutions. We provide employers with customised solutions for their current and future workforce needs and help people realise their potential.
We’re a home-grown, Queensland business that now offers a range of services and programs
nationally. BUSY is committed to our mission of having more people in jobs, more people learning new skills and more communities exposed to positive change, in partnership with employers and industry.
David Doherty OAM is a past President and Life Member of the SCLAA and a highly regarded logistican. Send your Straight Talk feedback and comments to davidoh1@optusnet.com.au
Will things ever be the same again after the Pandemic, and its associated economic and supply chain upheavals?
More importantly, do we want things to go back to “normal” again, as they were pre-Pandemic?
Maybe it is time for new thinking, new initiatives, courageous action, and entrepreneurial spirit. Downturns and difficulties can be a breeding ground for breakthroughs. Did we learn from the disruptions caused by the COVID nightmare?
Real Leaders are needed. Authentic Leaders with consistently applied principles regardless of the difficulties. Legitimate principles must be on show every minute, every day, every week, every month, every year.
Groucho Marx offered, ”Those are my principles. If you don’t like them, then I have some others”.
How are you personally placed regarding consistent valuable principles and authentic behavior? Is there an opportunity for you to reinvent yourself to meet the new post pandemic circumstances?
Barrack Obama said, ”Change will not come if we wait for some other person or some other time. We are the ones we have been waiting for. We are the change we seek.”
Flexibility is a key in Supply Chain performance but it should not come at the expense of principles and ethical conduct.
Value generating Supply Chains depend on diligent honest collaboration and shared benefits. I doubt that is the situation in many Supply Chains.
Trailblazers have produced enormous improvements in business and personal benefit over many years. Are there any trailblazer warriors out there ready and willing to lead us to new endeavors and standards?
Some years back the noted Guru John Gattorna wrote a book; ”The Supply Chain Missing Link-People”. After all the hype and technological developments Gattorna concluded that people were the basis of effective value generating Supply Chains.
I am obsessive now about the necessity to develop young people to meet future challenges. Their personal advancement, and our collective growth, are our pathways to the future.
The upcoming ASCL Awards recognise many elements of performance in our industries/profession. The Future Leaders Award is of particular importance. The Award is named after the legendary SCLAA Life Member, Vince Aisthorpe. Vince was head of the team (along with Nerida Kelton and many others) in SCLAA Queensland
that created and delivered unique annual conferences predicated on low-cost entry, focused learning aimed at translation into immediate use in the workplace, and most importantly, fun, entertainment and enjoyment. The conference also proudly boasted a greater good objective (fundraising for charities including Christmas hampers for those in need). Vince was an outstanding Supply Chain Professional, a true SCLAA Trailblazer, who saw the need to champion young people with dreams of a career in Supply Chain and Logistics.
When the Future Leaders Award is presented at the Awards night in November please reflect on the legacy of Vince. He would be satisfied if we all determined to contribute in some way to the enhancement of opportunities for emerging professionals and practitioners.
Mentoring programs are important, by the way Mentors and Mentees learn and develop through that process.
I am distressed by the political and business leadership malaise effecting all of us. Our National and State Parliaments don’t seem to understand what the suffering communities everywhere need. I don’t want time to be wasted on political weaponising and adversarial grossly negative debate. For goodness’ sake! People are hurting! Focus on facilitating ways to allow people and all communities to pursue better lives.
Democracy is being threatened in many parts of the world. We must not let that threat progress here.
So, I am digressing. Give me a minute to get back to my point.
It is easy to fall into the practice of reacting to issues. Supply Chain disruptions tend to make us think in reactive terms. Real growth comes from creating and implementing. Nurturing young dreamers is a rewarding activity. If you are not a mentor, go and be one. If you haven’t got a mentor, go and get one (regardless of your age or experience level).
Perhaps we should initiate a Mentor and Mentee of the Year Award.
“I want my children to have all the things I could not afford. Then I want to move in with them” (Phyllis Diller)
It is never too late. Decide today to be a part of the future in Supply Chain and Logistics.
“Life isn’t about finding yourself. Life is about creating yourself” (George Bernard Shaw)
Namaste
David Doherty OAM (davdoh1@optusnet.com.au)2. You can simply swap a lead-acid battery for a lithiumion battery to reap all the benefits
Sure, aftermarket lithium-ion batteries are a massive improvement on their lead-acid equivalents, but to enjoy the real benefits, you should consider factoryfitted OEM lithium-ion batteries which have inherent advantages. For example, integrated batteries feature CANbus connectivity, meaning the truck’s factory Battery Charge Indicator (BDI) still works accurately, and the Original Equipment Manufacturer (OEM) technicians can connect to the battery and diagnose any issues via the truck software, eliminating the need to call in a 3rd party provider.
There is growing interest in – and uptake of – lithium-ion batteries in industrial trucks. This newer technology has many advantages, most notably its fast charging and the ability to charge ‘on the go’ rather than having to ‘charge until full’ in one go.
However, there is still widespread confusion and misunderstanding about the battery technology and its suitability for materials handling applications.
Linde Material Handling’s technical experts look at some of the myths:
1. We do a lot of heavy lifting and battery electric machines just won’t cut it
Lifting capacity is not an issue with modern batterypowered equipment. If the capacity plate ratings are the same as the equivalent internal combustion engine (ICE) model, so is the ability to lift heavier loads.
Linde motors and control electronics have the highest performance capabilities, ensuring minimal power loss and maximum energy efficiency.
Our new X-series trucks, for example, are designed to match Linde Hydrostatic IC-powered truck performance.
Also, remember that although lifting consumes a lot of energy, electric units are more energy-efficient than IC units, so the only real potential pitfall is the machine’s ability to store and use that energy. This means endusers must consider whether there are sufficient opportunities to charge batteries throughout the working day.
This video provides insights on how lithium-ion technology works and how Linde chose the right variation of the technology, based on the truck it needed to power.
In addition, the latest generation of forklifts “designed around lithium-ion batteries” can be more compact than lead-acid forklifts.
When considering a swap solution (lead-acid for equivalent lithium-ion battery), users must consider if their applications allow for sufficient opportunities for charging the batteries. In addition, they need to consider additional energy infrastructure costs such as cables and sockets capable of handling higher power draws as well as the installation of new power points closer to the working area or break rooms to avoid unnecessary travel distance to the existing lead-acid charging rooms.
3. Lithium-ion batteries are prohibitively expensive
It is important to take a long-term view of costs. Although the initial purchase price of lithium-ion batteries is higher than lead-acid batteries, they have a lower cost per cycle due to their increased lifetime, making them the most cost-effective solution in the long run.
Linde’s lithium-ion batteries, in particular, have extremely low inner resistance and the most efficient technology, which means less grid energy is wasted, resulting in 30% savings (charging and CO2 emissions) when compared to lead-acid.
So, in the long run, lithium-ion batteries can be significantly more economical.
4. We would need to replace our whole lead-acid fleet with lithium-ion machines
Certainly, it often makes sense to replace the entire fleet so that operators don’t have to switch between different charging regimes and operating procedures.
It also makes sense with an ageing fleet, where there is a decision to retire all existing machines and “start again”.
Replacement is also advisable when there’s a corporate motivation for the switch, such as a commitment to reduce overall CO2 emissions or an operational wish to remove dangerous battery changes or reduce ongoing maintenance requirements.
But a blended fleet is possible if some trucks are not utilised enough to warrant the investment in lithiumion batteries.
Linde has many customers who have staged rollouts.
However, if you do choose to run a blended fleet, you need to be aware that different chargers are generally needed for lead-acid and lithium-ion batteries, so there might need to be clearly marked charging areas and instructions to staff.
5. Our power supply would have to be upgraded to cope with the charging needs of lithium-ion machines
Yes, chargers for lithium-ion batteries have a higher output, which means they require a higher input current compared to lead-acid chargers. However, Linde has various battery/ charger combinations available depending on the utilisation, application intensity, and available charging windows.
A small or medium-sized charger may be used with existing power points, which means peak power draws may be only marginally above that of existing lead-acid chargers.
The Linde lithium-ion range has the option of a “normalsized charger” that may use a similar-sized outlet and current rate to charge the battery in half the time compared to the lead-acid charger it replaces.
Another ‘trick’ is to sequence charge trucks at any time throughout the day. Lithium-ion batteries do not necessarily need one charger per truck, unlike lead-acid batteries that need to be charged at the end of a shift –all at the same time.
Staggering the charging can limit the peak power draw to less than lead-acid chargers. However, where larger chargers are required, or if a business wants to add power points closer to the working area or break rooms, this might require some investment in power supply.
6. Our drivers would have to be retrained and change their work habits to accommodate the charging patterns of lithium-ion machines
Agreed, there will be a need for retraining, as standard AS2359:2 operations dictate that each user should have policies for safe systems of work with supervised practice, on-the-job training, and ongoing regular fresher training. So, there are requirements for records of ongoing training to be maintained by the user in all cases.
However, lithium-ion batteries are easy to use:
o The battery management system talks to the charger to prevent overcharging.
o It manages power delivery to prevent over-discharge.
o It requires no watering or equalise charging.
o Operator must simply know how to plug it into the charger when not in use.
Our customers have found that work habits need to be changed, but this is for the better. Ongoing battery maintenance tasks are all but eliminated, as are dangerous battery changes and the risk of damaging batteries through charging misuse. Unlike lead-acid batteries, lithium-ion batteries thrive on opportunity charging, meaning operators can charge their forklifts during breaks. And the charging process will be quicker and easier since the bonnet no longer needs to be opened to connect the charger to the truck.
7. Lithium-ion batteries are not as stable as lead-acid and represent a safety threat
This is a common myth, but in reality, lithium-ion batteries are much safer than conventional lead-acid batteries. Even though they have a higher energy density than lead-acid batteries, Linde lithium-ion batteries have a multi-level safety system at cell, module, and housing levels, alongside a battery management system (BMS) with comprehensive protective functions. The BMS protects against overload, overcharge, deep discharge, excess current and short circuits.
Linde lithium-ion batteries are developed in-house, which means the trucks have intelligent vehicle control and battery management that are perfectly integrated and aligned.
The CANbus interface enables the battery, charger, and truck to communicate as one system, ensuring optimal performance and prolonging the battery life.
Furthermore, the truck and battery are tested as one system in the development stage – something not always done with lead-acid systems.
This short video shows the rigorous testing Linde does to ensure the safety of our batteries.
8. Lithium-ion batteries don’t last as long as lead-acid batteries
Lithium-ion batteries have a longer cycle life, allowing them to be used effectively in applications with sufficient charging opportunities.
Because lithium-ion electrochemistry has higher energy density and voltage stability, and less inner resistance, it leads to higher power output, increased efficiency, and fast charging capabilities.
Lithium-ion batteries are expected to last around 4,000 full cycles - in contrast to lead-acid’s 1,500 cycles.
9. Lithium-ion batteries are not suited to harsh environments
Again, not true! Through extensive testing, we’ve found that lithium-ion batteries tend to outperform lead-acid batteries in rough surface environments, high-usage environments, low temperatures, and most other environments where lead-acid batteries would have struggled or not performed at all.
There are different types of lithium-ion batteries available depending on the application and utilisation.
Because permissible operating and charging temperatures depend on each specific lithiumion battery group, Linde supplies datasheets and user manuals for each type, which specify the exact operating conditions.
As an idea of the maximum permissible operating environment, the Performance Plus group of Linde lithium-ion batteries can generally operate as follows:
(Note: “harsh environments” is a loose term and can be applied to a multitude of different applications. A Linde MH expert can advise on options out of the scope of the operating environments above.)
10. Lithium-ion batteries pose a serious environmental threat at the end of their life
Despite their long service life, even lithium-ion batteries reach the end of their performance at some point, which is why lithium-ion battery recycling centres are popping up across the globe. This means that batteries can be returned to Linde network service partners. They are then sent to a certified recycling company, with which Linde has set up a comprehensive recycling process for its lithium-ion batteries.
KION has formed a strategic partnership with Li-Cycle which means that up to 95% of the mass of a lithiumion battery can be reused and returned to the material cycle.
The good news is that unlike lead-acid batteries, lithium-ion batteries don’t degrade with use, so a battery made using recycled lithium-ion is just as good as a “fresh” lithium-ion battery. So, lithium-ion is actually a “greener” option.
Curious about the benefits of Lithium-ion for your business? Visit our website to read more on our lithium-ion solution and discover if it’s the perfect fit for your business needs.
Nominations are now open for the Australian Supply Chain & Logistics Awards. The annual ASCL Awards recognise the outstanding achievements of supply chain & logistics professionals and organisations across Australia, celebrating industry excellence and championing collaboration, innovation, and success.
The ASCLA are the industry’s longest running and most prestigious awards. The SCLAA is proud to have been hosting these awards for the last 20 years and recognising and cheering on individuals and companies that have contributed to the advancement of the Supply Chain and Logistics industry in Australia.
Submissions opened: 2nd May 2023
Ticket registrations open: Early Bird open 1st July 2023
Submissions close: 1st September 2023
Finalists to be announced: 27th September 2023
ASCLA Gala Dinner Awards Night: 10th November 2023
We are inviting companies and organisations to become part of these prestigious national awards on the 2023 Awards night. Showcase your organisation, strengthen brand awareness to industry leaders and be the Ambassador of Excellence by recognising its highest achievers.
Annual
Chain &
Awards Gala Dinner to be held at the Grand Ballroom, Fullerton Hotel Sydney.
Date: Friday, 10th November 2023
Time: 6pm start for pre-dinner drinks and canapes
Venue: Grand Ballroom, The Fullerton, Sydney
Dress: Ladies – Cocktail
Gentlemen – Lounge Suit
These prestigious National Awards, hosted by the SCLAA, have been running for over 60 years making them the most sought after, recognised and influential awards across the Supply Chain, Logistics and Transport industries.
AWARDS MC (https://bit.ly/42sCxLb)
Sam McCool – Sam McCool is a world-class MC, comedian, keynote speaker and speaking coach and has completed several International Tours.
Experience a new level of sponsorship in 2023 with an exciting addition to our lineup. Introducing the captivating Sponsor an Award category, where you can leave an indelible mark by sponsoring a prestigious accolade. Beyond the traditional Platinum, Gold, Silver, and Bronze tiers, this opportunity allows you to align your brand with excellence and become an integral part of celebrating the outstanding achievements in the supply chain and logistics industry.
For a deeper dive into the exclusive sponsorship opportunities at this year ASCL Awards Gala Dinner, simply scan the QR code or visit www. ascla.com.au. Should you have any immediate inquiries, please reach out to our National Secretariat at 1300 364 160 or via email at secretary@sclaa.com.au.
www.ascla.com.au
Toll Group Selects Dematic as Automation Partner for its Latest Australian Warehouse Facility Site in Western Sydney.
Dematic has announced that Toll Group, one of the Asia-Pacific region’s largest providers of supply chain transport and logistics, is investing in a Dematic goodsto-person (GTP) order fulfilment solution as part of the development of its new Western Sydney retail distribution and fulfillment facility.
The new site will be located at Kemps Creek, near to Western Sydney International Airport, due to be fully operational in 2025, and complements Toll’s existing Sydney retail distribution and fulfilment facility in Prestons.
Toll Group President, Retail and Consumer, Nick Vrckovski says, “Toll has a long and proud history in Australia. For over 130 years, our curiosity and passion for innovation has propelled us forward to become one of Asia Pacific region’s leading integrated logistics providers.”
“We are excited to work with Dematic to bring the very best in automation technology to our Kemps Creek facility, which will help our customers deliver their goods faster and more efficiently,” adds Vrckovski.
In the Dematic GTP order fulfilment solution, workers will build orders in ergonomically designed high-rate workstations that improve productivity, efficiency, and safety. The orders and items required to fulfil the orders arrive at the workstation precisely when they are needed from a Dematic Multishuttle® storage system. The solution for Toll Group will include 16 high-rate GTP workstations, supplied by a multishuttle system that will also buffer and consolidate orders, plus an additional multishuttle system for despatch.
“The high-density Dematic Multishuttle system feeding items into the GTP workstations will allow Toll to max-
imise space efficiency and inventory storage within its latest supply chain facility in Australia. We’ve designed the solution with additional room for volume expansion in line with Toll’s projected future growth,” explains Terry Jamieson, Business Development Manager at Dematic. “Additionally, the fast-moving pick zones integrated within the GTP order fulfilment solution will provide Toll with a significant improvement in picking productivity as well as with flexibility in responding to e-commerce demands, including fulfilling orders during promotional periods or when particular SKUs are in high demand.” Another advantage will be the ability to customise e-commerce order cartons to be the smallest necessary size, which will reduce transportation costs for Toll’s customers as well as significantly reduce waste.
Dematic will also install its locally manufactured Colby Very Narrow Aisle (VNA) pallet storage racking at the Toll facility.
Toll Group’s Kemps Creek facility is due for completion in 2025.
Dematic designs, builds, and supports intelligent automated solutions empowering and sustaining the future of commerce for its customers in manufacturing, warehousing, and distribution. With research and development engineering centres, manufacturing facilities, and service centres located in more than 35 countries, the Dematic global network of over 11,000 employees has helped achieve successful customer installations for some of the world’s leading brands. Headquartered in Atlanta, Dematic is a member of KION Group, one of the world’s leading suppliers of industrial trucks and supply chain solutions. https://www.dematic.com
Having been hosted in the Americas for over 10 years, Körber’s unmissable Elevate event came Down Under! With attendees joining the team at the region’s first in-person Elevate at Melbourne’s Sofitel. The agenda was packed with Körber customer stories, product information, opportunities to network with peers, and meet with Körber partners and employees.
Elevate APAC 2023 kicked off with a Welcome to Country and introductory remarks by Körber Supply Chain Software’s Anthony Beavis, Managing Director ANZ and Bill Ryan, EVP APAC. Bill opened with a speech on ‘Optimising the Rhythm of your supply chain’ – the key theme for the conference this year – by noting some of the challenges the industry has encountered over the past few years. “When the global pandemic started, the music stopped,” Bill said, also noting “supply and labour challenges that are causing [businesses] to lose your rhythm.” To this end, Bill said the answer was digitisation and technology, as survey results indicated that one in three warehouse operations were still relying on manual labour.
With robotics use in the logistics market projected to grow by 77 per cent in the 2021-24 period, Körber is leaning into tech and digital to solve customer pain points with a 71 per cent R&D spend increase in the 2021-23 period. To meet the challenges of the era, Bill said, Körber Supply Chain Software brought on globally renowned investment firm KKR as a partner, allowing Körber Supply Chain Software to operate as a joint venture with the investment power to flex, adapt, and expand to meet market demands. This partnership, in combination with a portfolio of exciting new solutions and developments at Körber Supply Chain Software, mean the company is – in Bill’s words – “Building the Global Supply Champion”.
Joe Couto, Executive Vice President Global Robotics & 3PL at Körber Supply Chain Software also unveiled the new Robot as a Service (RaaS) program. This solution is a flexible automation technology designed to empower users by increasing efficiencies and stabilising an organisation’s operations. It provides simple access to a global network of robotics service partners for every business size and industry, emphasising the value Körber puts on collaboration and dedication to meeting its customers’ needs. Buyers of this product can reduce their business’s operational costs and time to deployment and invest any remaining capital in other parts of their enterprise by allowing them to purchase robots ‘as-a-service’ rather than in one large upfront payment.
Joe highlighted that “most systems integrators don’t offer a RaaS program and that’s why our solution provides customers with a competitive advantage. We offer contracts with a fixed fleet, but customers can also choose a flex fleet of BoTs for peak periods. We can combine conveyors, pick to light and other accompanying solutions with the RaaS program, and combine SaaS and RaaS into one monthly payment.”
Managing Director at Accenture, Sari Mackay started the second and final day of the conference with an in-depth analysis of the global supply chain, including the need for businesses to reinvent their networks, and invest in regionalised supply chains all while preparing for both just in case and just in time deliveries. “The future of supply chain is data analytics and AI,” Sari says. “Resilient networks are needed to deal with disruptions and drive cost optimisation. Transparency is the most important resource. Businesses need to innovate, challenge themselves, develop new ways of thinking, adopt digital capabilities and data – these things will make or break them.”
Patrick Fountain, General Manager of Super Retail Group also explained how automation combined with data science has transformed the company’s supply chain network and enabled it to optimise its operations and increase productivity. Other presentations included Sarah Owens, Enterprise Sales Manager ANZ at Honeywell on consolidating devices in a supply chain business. As well as Brett Newstead Sales Director, Zebra Technologies Australia, on Supply Chain 4.0, where digitalisation and technology are necessary elements to transform traditional supply chains to the next stage of operating excellence.
Yiau Hwei Chan, Director of Engineering at Körber facilitated the first panel discussion called Driving Positive Change: How Sustainability & Diversity are transforming supply chains. Dr Elise Hoo, SCLAA committee member, Laurel O’Donnell, Lineage Logistics General Manager, Dr George Panas, University of Melbourne Supply Chain Lecturer, Maree Varrasso, CIO at uTenant, and Nicole Katsoulis, Head of People & Culture at Körber spoke about the importance of partnerships, adopting a global perspective, focusing on women in leadership, cooperating with leading industry associations, and incorporating ESG in brownfield and greenfield sites.
“According to a 2021 report from McKinsey & Company, only 41 per cent of the supply chain labour force consisted of female workers,” Laurel explains. “Employers need to check their unconscious bias when they’re hiring women, and women need to stop second guessing their abilities, and apply for promotions and aspire to become industry leaders.”
The final panel discussion was Building agility and resilience to deliver exceptional end-customer experience. Frank de Sa, CIO at The Just Group along with Lian Yu, CIO at Toys ‘R’ Us, Karl Neubauer, CIO at GLOBAL Retail Brands, and CEVA Logistics’ Allan Maki spoke about in-
novation in retail, the need for data collection, autonomous mobile robots, Körber cloud, 3PL and automation, as well as investing in scalable solutions with Körber’s Director of Solution Delivery, Darren O’Connor.
In the main room, attendees networked, visited stalls, and tried Körber’s virtual reality headset, giving them an opportunity to see how the supply chain software company can automate and modify a new or existing warehouse. The event finished with Nicholas Bochner discovering the synergies between conducting an orchestra to orchestrating a supply chain; plus helping the audience to find their rhythm with a spectacular performance from the Melbourne Symphony Orchestra.
Learn more about what was discussed at Elevate APAC here:
• Ticker News Article
• Retail World Magazine
• Asia Food Journal
Adelaide Airport enhances operational efficiency, reduces congestion, and improves security by implementing Mobiledock for scheduling deliveries and providing visibility to tenants.
Adelaide Airport is the main aviation hub for South Australia, connecting over 8 million passengers annually to destinations both domestically and internationally.
The Airport has recently completed a major terminal expansion significantly increasing the number of retail offerings throughout the precinct. Retail and aviation growth has created a necessity for Adelaide Airport to seek a solution to provide operational efficiency across its loading docks.
Inbound deliveries to the Airport are subject to a number of security measures.
These include the screening of all inbound products, and the need to have products collected immediately post screening by those tenants receiving the goods. With the new terminal featuring a number of new retail, food and beverage outlets the volume of inbound deliveries has also increased placing additional pressure on their loading docks.
The effectiveness of the Airports loading docks is in part dependent on the efficiency of the screening processes and in the communication to the tenants of when their deliveries are due.
Unscheduled deliveries can quickly lead to congestion and delays through the screening process, and the risk that the tenants staff are unable to collect the products which leads to deliveries needing to be rescheduled. Congestion around the loading docks also impacts the overall amenity of airport and can lead to increased safety and security concerns.
The Airport was seeking a solution to manage these operational challenges.
Adelaide Airport selected Mobiledock to enable the effective scheduling of deliveries into their two loading docks and to provide visibility and notifications to the tenants of when their deliveries were expected.
They use Mobiledock’s rules engine to ensure that deliveries are made to the dock that is closest to the tenant – saving tenants time and further improving their experience.
Authorised suppliers, carriers and drivers select available times for their deliveries using the Mobiledock booking wizard.
They receive a booking confirmation (or boarding pass) which contains a PIN and QR code and other relevant details for their bookings.
Tenants are also notified automatically of their planned deliveries by Mobiledock notification capability.
When Drivers arrive on site, they present their ‘boarding pass’ which is scanned by the loading dock staff. This confirmation also triggers a further notification to the tenants advising them that their deliveries have arrived.
Since implementing Mobiledock, Adelaide Airport has made significant enhancements to their operational efficiency.
They now schedule deliveries progressively throughout the day which has reduced site congestion and increased safety around the loading docks.
The visibility of expected deliveries allows the Airport to manage loading dock resourcing levels to suit the planned demand, leading to reduced operational costs. The authorisation of the carriers and drivers has also improved security.
Adelaide Airport’s tenants have gained direct visibility of when their deliveries are expected – providing them with the ability to better manage their own resources and costs.
“With the use of Mobiledock, there is a lot of opportunity for us to evolve as we continue to grow and get busier. Mobiledock gives us a platform which we can build on while continuously meeting our business’ needs.”
Lachlan McKenzie, Terminal Operations Manager at Adelaide Airport, expressed his excitement about the potential for growth and improvement with the implementation of Mobiledock. “With the use of Mobiledock, there is a lot of opportunity for us to evolve as we continue to grow and get busier. Mobiledock gives us a platform which we can build on while continuously meeting our business’ needs.”
Adelaide Airport
Your revenue is directly tied to parcel dimensions. Accurate parcel dimensions during inbound operations also directly affect overhead costs and profitability. Yet, chances are accurate dimensions aren’t captured until parcels reach the central hub — where it is often too expensive to recapture small billing inaccuracies, and too late to reduce costs through improved utilisation of warehouse space and vehicles. The result? Millions of dollars in lost revenue and substantial increases in overhead costs, reducing profitability.
Have you ever found yourself having to run additional trucks because parcel volume was not calculated properly? Or perhaps you incorrectly charged a customer for a package and had to spend time and money correcting it? Have you ever had to return a package due to insufficient postage, or made the tough decision to just ‘eat the loss’ because someone miscalculated size and therefore shipping? If you answered yes to any of the above, you’ll appreciate Zebra Dimensioning Mobile Solutions’ Certified Mobile Parcel.
Zebra Dimensioning’s Certified Mobile Parcel is an industry first from Zebra — an internationally certified, fully integrated handheld mobile dimensioning solution. You can get an accurate parcel or package measurement in a split second, no matter where items are picked up or dropped off. This innovative technology streamlines the shipping and logistics process, ensuring you can confidently ship packages and avoid unnecessary expenses. Built for Zebra mobile computers, Certified Mobile Parcel is international weights and measures pre-certified by NTEP (US), OIML (EU/EFTA), MC (Canada), NMI (Australia) and MBIE (New Zealand).
These valuable certifications enable mobile dimensioning that is certified as legal for trade, enabling accurate calculation of shipping charges at the point of parcel pickup and beyond — from homes and businesses to parcel shops, satellite pick-up points and more.
This solution offers advanced features that put it in a class of its own. Its fast measurements can capture dimensions in less than five seconds. Full integration means there are no snap-on accessories to impact ergonomics, ease of use, durability, calibration or reliability. And since it’s a fully mobile solution, dimensions can be captured wherever it will benefit your business — from doorstep collection in homes and businesses to parcel drop-off locations, warehouses, depots and hubs. Integration is fast and easy — this complete solution has everything you need to get up and running: the integrated Time of Flight sensor, pre-installed and sealed Zebra Dimensioning Service and application software; and a Zebra Mobile Dimensioning Application Programming Interface (API) that makes integrating the capture of parcel dimensions into enterprise backend systems as easy as the capture of barcodes. Capture a wide range of box sizes and types in practically any lighting condition and background. Boxes can be plain, wrapped or printed with graphics. With flexible aiming, you can just point the red aiming dot on the top surface of the parcel for first-time, every-time capture of accurate dimensions — even if there are other parcels visible in the camera window. And since you can aim straight down or at an angle, parcels can be on the floor or a counter.
Now, the same Zebra mobile computers that streamline everyday processes for drivers, employees in parcel shops, warehouse workers and more can also capture accurate parcel dimensioning in seconds. The result is increased workforce productivity and efficiency, better customer service, increased revenue, and reduced disputes and damage claims. By leveraging this technology, you can better utilise your warehouse and delivery vehicle fleet, ultimately extracting more value from the Zebra mobile devices that power your operations.
Find out more about Zebra Certified Mobile Parcel here.
We are thrilled to provide you with an exciting update on the activities and events hosted by the SCLAA QLD Division during the first half of the year. It has been an eventful period filled with knowledge-sharing, networking, and industry engagement.
Welcome to the New Year Networking Event: We kicked off the year with a warm networking event at Brewdogs in Murrarie, providing an excellent opportunity for professionals to connect, exchange ideas, and strengthen relationships within our industry. It was a fantastic evening filled with fruitful discussions and exciting possibilities for collaboration.
Chain of Responsibility Webinar: Our Chain of Responsibility webinar held by CORsafe set a remarkable record with the highest registration ever received nationally. The webinar explored critical aspects of the chain of responsibility legislation, offering valuable insights and practical guidance to ensure compliance and enhance safety across the supply chain. We were delighted to see such tremendous interest and engagement from members and non members.
Brunch for International Women’s Day: Sponsored by Sidekicker to commemorate International Women’s Day, we organised a memorable brunch at Artie & Mai in Albion that celebrated the achievements and contributions of women in the supply chain and logistics sector. The event featured inspiring speakers who shared their insights and experiences, empowering attendees with valuable knowledge and perspectives.
Site Tour at Lindsay Transport: In collaboration with Lindsay Transport, we organised an exclusive site tour that provided participants with a behind-the-scenes look at their state-of-the-art facilities. Attendees gained first-hand knowledge of the company’s operations, innovative technologies, and sustainable practices, further deepening their understanding of logistics excellence.
Visiting the Queensland Truck Show with National Partner NTI: We had the pleasure of attending the renowned Queensland Truck Show alongside our national partner, NTI. The event showcased the latest advancements in the transport industry focusing on sustainability and offered a platform for networking and fostering industry connections. We were delighted to engage with fellow professionals and witness the exciting innovations driving our sector forward.
We would like to express our sincere gratitude to all our speakers, partners, and attendees who made these events successful and meaningful. Your support and active participation have contributed to the growth and vibrancy of the Queensland supply chain and logistics community.
As we look ahead, we are excited to bring you more insightful events, webinars, and networking opportunities throughout the rest of the year.
As we strive to stay ahead in the ever-evolving supply chain and logistics industry, it is essential to stay informed about the latest trends and developments. With this in mind, we are delighted to announce our upcoming events for July.
Mark your calendars for the Toowoomba Smart Logistics 2023: Future of Freight Symposium. This high-profile event will bring together industry experts, thought leaders, and key stakeholders to discuss the future of freight logistics. Gain valuable knowledge, engage in
stimulating discussions, and explore innovative solutions shaping the logistics landscape. The symposium promises to be a transformative experience for all participants.
We are pleased to partner with Sidekicker, a leading platform connecting businesses with skilled on-demand workers, to present a webinar on employment trends in the supply chain industry. Join us to gain insights into the changing landscape of employment, recruitment strategies, and emerging job roles. This webinar will equip you with the knowledge to adapt and thrive in the current job market.
Join us for an exclusive site tour of the Coffee Commune, a renowned logistics hub in our region. This tour will provide you with a unique opportunity to witness the intricate supply chain operations behind one of the most beloved beverages. From sourcing the finest beans to distribution, you will gain valuable insights into the logistics processes that keep our coffee cups full. Don’t miss this chance to explore the Coffee Commune and network with industry professionals.
These events are just a glimpse of the exciting opportunities that await you in the coming months. We encourage you to stay connected with the SCLAA Queensland Division through our newsletters and social media channels to receive updates on future events, industry insights, and networking opportunities.
If you want to know more about becoming a member or joining the QLD committee, please reach out to us
on LinkedIn on via the SCLAA website, we would love to have a chat about our passion for the industry and how you can get involved.
We look forward to your active participation as we navigate the dynamic world of supply chain and logistics together. Thank you once again for your continued support, and we look forward to seeing you at our future events.
Papillion Gordon QLD State PresidentPapillion.Gordon@sclaa.com.au
Mobiledockistheleadingglobalsolutionfor managingloadingdocksandscheduling dockappointments
WithMobiledock,youcanrevolutioniseyourdock appointmentbookingandschedulingprocessbyutilising advancedautomationtools,accessiblefromanyinternetconnecteddevice.Saygoodbyetomanualprocessesand gaingreatervisibilityandcontroloverresourceplanning, suppliermanagement,andsecurity,whilereducing congestionatthesametime.
•CarrierCommunication 150AlbertRd SouthMelbourne3205
+61390011565
www.mobiledock.com
In May, the SCLAA VIC/TAS division gathered four exceptional leaders dedicated to driving the transition to net-zero logistics emissions titled “Accelerating to Net Zero”. Stephen Lakey, Director of SCLAA, proudly hosted a thought leadership and networking event that was generously sponsored by Bestrane, a renowned industry leader in supply chain technology solutions. The event featured a lineup of esteemed panellists and had a specific focus on sustainable initiatives fostering in-
sightful discussions and networking opportunities.The panel discussion commenced with Annie Sim, the Go Green Lead at DHL Supply Chain. Annie’s extensive experience in the sustainability industry shone through as she shared DHL’s ambitious goal of achieving net-zero logistics-related emissions by 2050. She unveiled DHL’s roadmap to accomplish this objective and highlighted the remarkable initiatives being undertaken. One such initiative was the DHL Warehouse in Sydney, which boasts Australia’s first dynamic urban solar power station.
Aidan Mullan, the Sustainability Manager at Interface Australia and New Zealand, took the stage next. Aidan’s focus on Interface’s Climate Take Back initiative captivated the audience. He showcased the remarkable journey of Interface towards becoming a carbon negative company by 2040, inspiring others to follow suit. Aidan emphasized the significance of sustainability in fostering innovation and growth, urging stakeholders in the built environment to embrace sustainable practices.
Glen Walker, the Vice President of Asia Pacific at SEA Electric, concluded the panel discussion with an exploration of electric fleet adoption. Drawing from his practical experience in the transport industry, Glen highlighted the cost-effectiveness and environmental benefits of switching to electric vehicles (EVs) in the commercial sector.
The “Accelerating to Net Zero” event served as a catalyst for inspiring change and fostering collaboration within the supply chain sector. It offered a unique platform for thought leaders, professionals, and stakeholders to come together, exchange knowledge, and explore innovative strategies towards achieving a sustainable future. SCLAA is grateful to all who contributed to the success of this exceptional event providing a platform and voice to accelerate the transition to net-zero logistics emissions and shape a greener, more resilient supply chain sector.
The VIC/TAS committee of SCLAA has been receiving numerous inquiries from industry professionals who are eager to contribute to purposeful initiatives within the supply chain and logistics sector. We firmly believe that the strength of our supply chain community lies in the hands of those who are willing to give back. Our committee consists of 21 passionate volunteers from diverse backgrounds who go above and beyond to achieve two clear strategic disciplines: education and connection.
To provide supply chain professionals with the opportunity to learn and connect with others, we are excited to open our doors to those interested in joining our purpose-driven committee. Every second month, we host an “Open Committee Networking Meeting” where members of the local community can learn about our committee’s work, socialize, and connect with like-minded individuals who share a passion for the industry.
In recent meetings, we welcomed Corey Bristow from Safer Storage Systems, this committee meeting also featured Devraj Singh, Supply Chain Graduate at La Marzocco and our VIC/TAS Secretary, who shared his inspiring background of migrating to Australia and beginning his supply chain career as a Master’s graduate. Additionally, we discovered Devraj’s impressive freestyle football skills, leaving our team in amazement.
If you’re interested in becoming part of a close-knit community of supply chain professionals, please reach out to me or any of our team to join us at our upcoming “Open Committee Networking Meeting.”
If you haven’t already signed up for it, do so quickly!
This month we have our next Melbourne based event, a transformative networking and thought leadership event, “Pathways to Progress: Uniting Supply Chain Professionals for Career Growth and Connections,”. This event is designed to engage and empower supply chain leaders, HR professionals, graduate and job seekers, industry thought leaders, educators, and academic professionals, this event offers a unique platform to foster connections, gain valuable insights, and explore new pathways to success.
In today’s dynamic supply chain landscape, it is crucial for professionals to stay ahead of the curve, adapt to emerging trends, and leverage opportunities for career growth. “Pathways to Progress” has been meticulously crafted to meet these needs, bringing together a diverse cohort of passionate individuals from the supply chain and logistics community. This event serves as a catalyst for personal and professional development, fostering a vibrant atmosphere where industry experts and aspiring professionals can connect, collaborate, and learn from each other.
We hope to see you there.
Theo Pappas VIC/TAS State President theo.pappas@sclaa.com.auCongratulations to Michael Farragher, winner of NSW Training Awards 2023 for the best VET Trainer/ Teacher of the year, award for the Central and Northern Sydney Region. Special thanks and appreciation to the following sponsors Training Services NSW and NSW Department of Education.
This is a well-deserved achievement considering his extensive industry experience of over 20 years and his dedication to teaching and inspiring students ever since.
As a Subject Matter Expert, Michael has made significant contributions to the field by redesigning and improving qualification courses for TAFE NSW students at a state level. His commitment to enhancing the educational experience for students entering the supply chain industry is truly commendable.
The partnership between SCLAA and TAFE NSW is vital in ensuring that educators and students have access to the latest trends and industry needs in the supply chain sector. This collaboration enables TAFE NSW to stay up to date with industry advancements and deliver relevant and high-quality education to its students.
The initiatives provided by SCLAA, and TAFE continue to support the invaluable connection for upcoming students and new employees in the industry which would not be possible without the dedication of the people involved to drive and continue to serve for the future.
Michael’s involvement as a passionate and valued committee member of SCLAA NSW further highlights his dedication to serving the industry and is actively involved in the TED (Training, Education and Development) committee, Mentoring Program and Industry liaison at State and National levels.
Michael has attended a coaching session presented with zoo tickets and a cash prize to help prepare him for the State award finals for the NSW Training Awards held in Townhall Sydney in September 2023.
Once again, congratulations to Michael Farragher on this well-deserved recognition for his outstanding contributions as a VET Trainer/Teacher in the field of Supply Chain & Logistics. His expertise and passion have undoubtedly made a positive impact on the industry and the students he has mentored and taught.
Mary Soliman NSW SecretarySupply Chain Week 2023, organized by Akolade, proved to be a remarkable conference that united industry experts, thought leaders, and professionals from many Supply Chain companies with big brands. The International Conference Centre at Sydney’s vibrant Darling Harbour precinct provided an exceptional platform for knowledge sharing, networking, and collaboration.
Supported by the SCLAA, the event spanned over three days, during which participants had the opportunity to attend informative sessions, interactive workshops and engage in insightful panel discussions. Our own Sue Tomic (Chairperson) and Rakesh Bandipelli (Director) helped to chair sessions over the two days.
The Supply Chain Week 2023 showcased real-world case studies and success stories from organisations that have leveraged innovative practices to overcome challenges and drive sustainable growth. It was great to see organisations from both ends of the spectrum, multi-billion dollars to start-ups, presenting how they navigated the past few years, through the turbulent times.
One thing that stood out was when normal business protocols and processes couldn’t be followed, out-ofthe-box solutions were created through constrained thinking. Some went back to basics, some created new protocols and others sought technological solutionsto get through, get by or accelerate the businesses.
Overall, the Supply Chain Week 2023 proved to be a highly informative and engaging event. Attendees left with a renewed confidence, increased knowledge and a widened network. As the industry continues to grow, events like this serve as catalysts for progress, helping professionals stay ahead of the curve and drive positive change in their respective organisations.
One comforting factor that we all learnt over Covid-19 period was that no matter what, supply chains kept running, customer demands were met, orders delivered and, we all managed to get enough toilet paper at the end!
Ishan Galapathy NSW Committee Memberto further optimise production,” said Colin Macdonald, CCEP’s Director of Operational Excellence Supply Chain – Asia Pacific.
Warehousing logistics and automation leader, Swisslog Australia, has extended its automation solution for Coca-Cola Europacific Partners (CCEP) in Mentone, about 20km South-East of Melbourne’s CBD.
In an extended $17.4 million Automated Storage and Retrieval System (ASRS) pallet solution, Swisslog has installed additional Vectura cranes at the distribution centre (DC), which will eliminate the need for CCEP to utilise off-site storage during peak months. The solution will enhance operational efficiency, further improve customer responsiveness, and allow for both software and mechanical upgrades with minimal impact to the DC’s performance.
Swisslog’s data-driven, robotic solution will enable CCEP to optimise operations to fulfil customer requirements more efficiently, including in peak periods. The addition of more infrastructure in Pallet Flow Lane (PFL) dispatch lanes and additional Roll On Roll Off (RORO) docks will enable more efficient turnaround times for trucks inbound from CCEP’s production facility at nearby Moorabbin and outbound from Mentone. Additionally, the extra wrapper and manual infeed positions will allow for greater flexibility in operation of the warehouse.
Swisslog Managing Director, Australia and New Zealand, Dan Ulmamei, said it was rewarding to see an existing customer seeing the value in an extension. “CCEP is clearly committed to improving its operational efficiency, and it saw that further automation could help take it to the next level. Swisslog was delighted to be able to assist as CCEP’s automation partner,” he said.
The new ASRS is joined to the existing ASRS at crossover positions allowing the entire system to be operated as a whole. The solution is a mix of a 3-pallet deep channel on one side and an 8/9-pallet deep channel on the other side, creating an ideal mix of shallow and deep channel storage, with more than 12,000 total storage locations. Overlapping row carrier functionality has been provided as an option to improve effective storage utilisation.
CCEP is one of the largest bottlers of non-alcoholic ready-to-drink beverages in the Asia-Pacific region, and it has partnered with Swisslog to enhance production capacities and deliver efficiencies through automation technology across multiple sites.
“Swisslog has shown great aptitude in understanding the needs of our business and demonstrated a willingness to adapt the application to meet our requirements. The expanded automation solution enhances safety, eliminates off-site storage, and increases our customer responsiveness, which are all important as we look
“The extended automation solution at CCEP Mentone has been designed to allow the flexibility to upgrade any component in the future. The additional three cranes provide further redundancy for the Mentone DC,” explains Ulmamei.
The new solution can be operated as a standalone ASRS or as a part of an integrated solution with the existing ASRS. Most importantly, with the new ASRS capable of functioning as a standalone system, this means the existing ASRS can be taken offline for upgrades to critical components of the ASRS. This reduces the impact on operations for CCEP out of their Mentone DC, should the team need to make upgrade to other existing systems.
The six advanced technologies outlined in this eBook work together to create a truly digital supply chain. They make logistics networks as seamless as possible, increase collaboration across organizations, and enable both inbound and outbound visibility and control. Logistics teams that aren’t actively investing in these capabilities are already falling behind — and they risk losing even more ground as business conditions become even more challenging.
• Introducing First-to-Last-Mile Optimization. Envision a more syschronized future with Blue Yonder
The digital transformations being undertaken by many retail and manufacturing organizations are driving the need for faster, more agile and resilient logistics services. This in turn represents an opportunity and a challenge for third party logistics providers (3PLs), both in terms of delivering these new requirements, capturing these services and accurately billing their clients. It is therefore more important than ever, that a 3PL has a flexible, scalable, and integrated solution to efficiently bill its clients for the services provided.
Category Manager’s Guide
As historic inflation changes how people shop, retailers like yours need to adapt to their customers’ buying habits. In the guide below, you’ll learn about three emerging trends as well as how your category managers meet the changing demands of today’s shoppers – while increasing profits.
• Luminate Billing - a complete, flexible, and powerful logistics solution powering profitability for 3PL Providers
The digital transformations being undertaken by many retail and manufacturing organizations are driving the need for faster, more agile and resilient logistics services. This in turn represents an opportunity and a challenge for third party logistics providers (3PLs), both in terms of delivering these new requirements, capturing these services and accurately billing their clients. It is therefore more important than ever, that a 3PL has a flexible, scalable, and integrated solution to efficiently bill its clients for the services provided.
Insights, inspiration and practical take-away solutions to challenges facing decision makers and front-line professionals in the logistics and warehousing industry.
Come and meet us at Stand C11 where we will have a Professional Headshot photographer - a perfect opportunity to update your personal brand and profile!
9.00am9.15am Opening Welcome
Opening remarks from Sue Tomic, Chair of SCLAA, as she shares her inspiring words and insights, setting the tone for a day of knowledge sharing, connections and industry deep dives.
9.15am9.45am ESG
Why it matters and why you should care.
10.00am10.45am
De-carbonisation Emission, Alternative Energies and Industry Initiatives in Sustainability (Panel discussion)
10.45am11.15am
Warehouse Innovation that Goes Beyond Just the Four Walls (Panel discussion)
We have brought together leaders from across automation, software, operations and supply chain strategy to openly discuss the role technology plays in driving warehouse operations and to discuss how this innovation is going beyond the four walls of the warehouse.
11.30am12.00 pm
Optimising your Supply Chain Network for Maximum Efficiency
Utilising real-time data to improve forecasting accuracy and demand planning.
12.00pm12.45pm
The Importance of Logistics Infrastructure
Understand market fundamentals that shape Australia’s industrial real estate, incl. key trends in rents, vacancies, supply/demand dynamics and impact of e-commerce. Explore ideas and opportunities on developing innovative and flexible supply chain networks and facility design.
1.00pm Break for Lunch
2.00pm3.00pm
Big Data – Bigger than Ever
Data and Analytics for Supply Chain Visibility.
Data isn’t valuable until you use it meaningfully. How should organisations leverage their data assets as they move beyond predictive analytics?
3.00pm3.30pm
The Smart Warehouse
In this session we will look at the latest technology and methods to improve your inventory visibility in the warehouse & e-commerce operations - increasing productivity, reducing errors and improving your bottom line.
3.30pm4.00pm
Technology – Today’s Actions for Tomorrow’s Success (Interactive session)
Map out your current business maturity level and explore practical next steps to get more from your business/team than you thought. Identify your next steps for growth
4.00pm4.10pm Closing Remarks
Followed by drinks and networking
27 July 2023
The Dome Theatrette The Dome Sydney Olympic Park Venue Map
INDUSTRY PATHWAYS FOR YOUR PROFESSIONAL DEVELOPMENT!
9.15am10.00am
Personal Branding - How to Showcase Yourself.
Personal branding highlights an individual, their achievements, ambitions, goals and more. In this engaging session, learn how to unlock a marketing superpower that generates demand for you so you can get your message across, spread your ideas and be valued for your contributions.
10.00am10.45am
Professional Speaking - How to Speak with Confidence and Authority.
Learn how to speak with confidence and authority. Whether you are on stage or off, these skills will help land your dream job, the promotion you deserve or pitch that great idea.
11.00am11.30am
Supply Chain and Logistics Careers Forum - Why SCL is the Hottest Career Right Now.
Getting into a Supply Chain Career-what you need to know. Ideal for students looking to enter a supply chain or logistics career or professionals transitioning cross sectors.
11.30am12.00 pm To be advised
12.00pm12.30pm The Pursuit for Perfection – Continuous Improvement for Personal and Professional Development.
Striving for perfection is not about achieving a flawless outcome, but rather about continuously learning and improving.
12.30pm1.00pm
The Vital Link Between Vocational Education and the Supply Chain Industry.
Learn from an Industry Innovation Specialist with over 20 years of experience in the VET sector who has worked to identify needs and develop future-focused solutions to meet workforce requirements.
1.00pm1.30pm Break for Lunch
1.30pm2.30pm
Open Careers Forum - “Speed Dating” for your Next Career Step Change. What you can do now to get where you want to be tomorrow.
An ideal opportunity to speak one on one with Education Providers, Training Institutions and Industry Professionals on career development.
Australia’s Leading Trade Show for Intralogistics, Robotics, Automation, Warehousing , Supply Chain Management and Materials Handling
Transform. Scale. Sustain.
Attend CeMAT Australia and access:
Free to attend programme, featuring case studies and panel discussions
Networking sessions with peers and vendors
Product demonstrations
25 – 27
July 2023
The Dome, Sydney Olympic Park
Find out more at cemat.com.au
3 Day Event
40+ Content Sessions 100+ Exhibitors
The purpose of this Guide is to draw attention to significant Workplace Health and Safety (WHS) hazards and risks that are commonly found in the Warehouse and Logistics Industry. Its main objective is to provide practical safety tips that can effectively manage risks and prevent unnecessary illnesses and injuries among workers and visitors.
It is important to note that the information presented in this Guide is intended to complement your existing WHS resources and should not be regarded as a standalone replacement or alternative to proper WHS training, induction, or supervision. It is crucial to ensure the establishment and adherence to safe work procedures through comprehensive WHS training, induction programs, and ongoing supervision.
Click here to view a pdf copy of the Warehouse Safety Guide.
1300 364 160 secretary@sclaa.com.au sclaa.com.au