
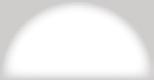
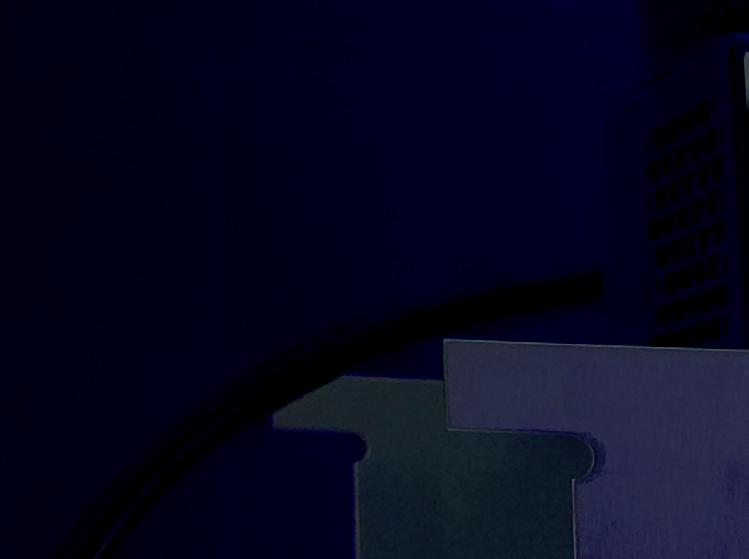


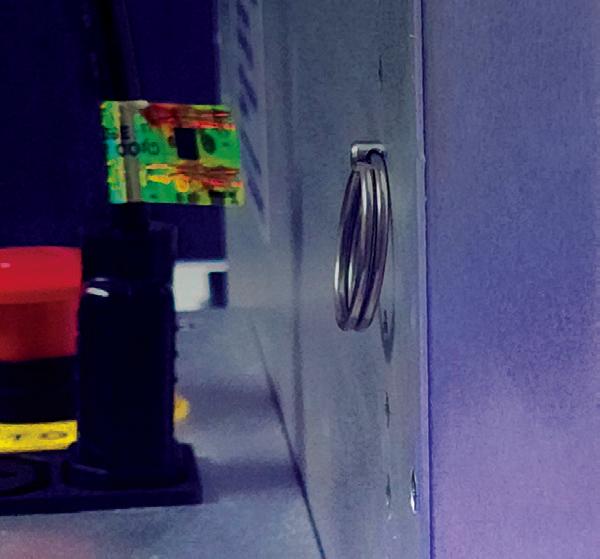
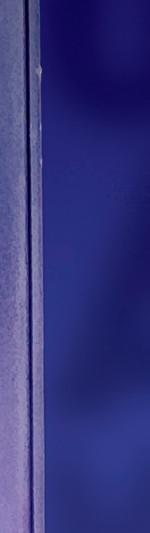
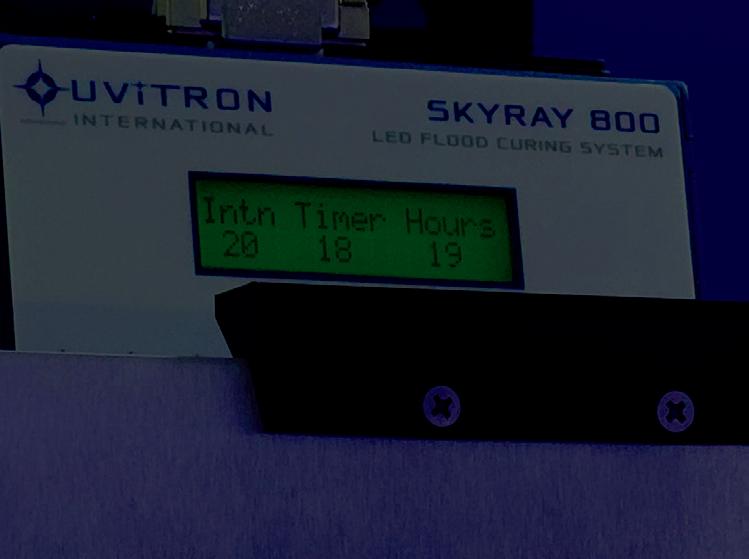
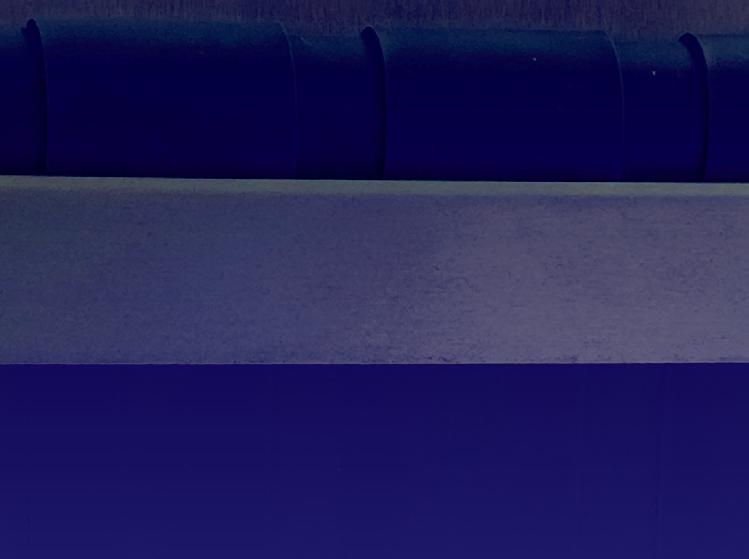
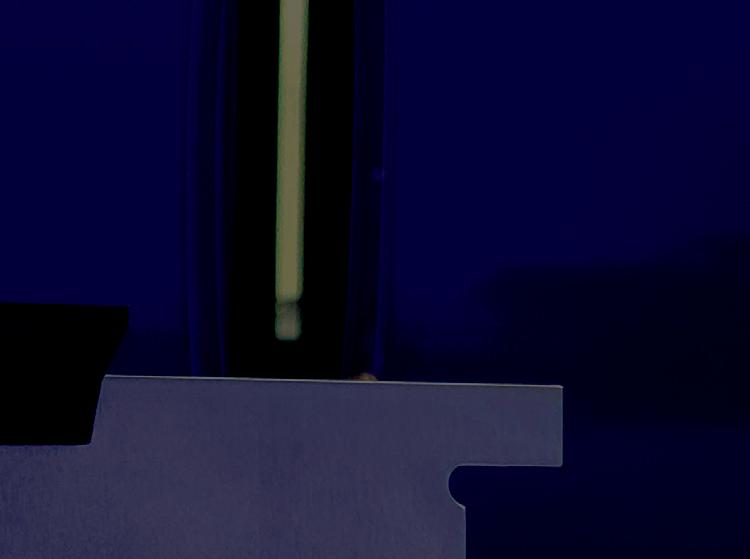
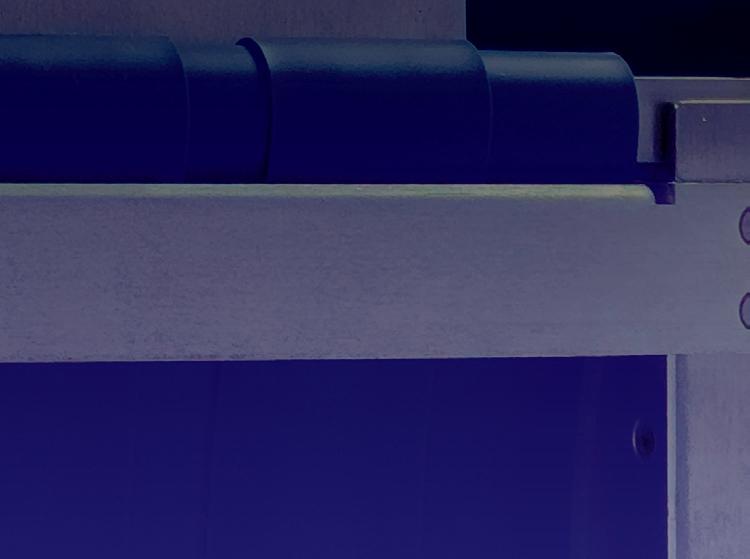


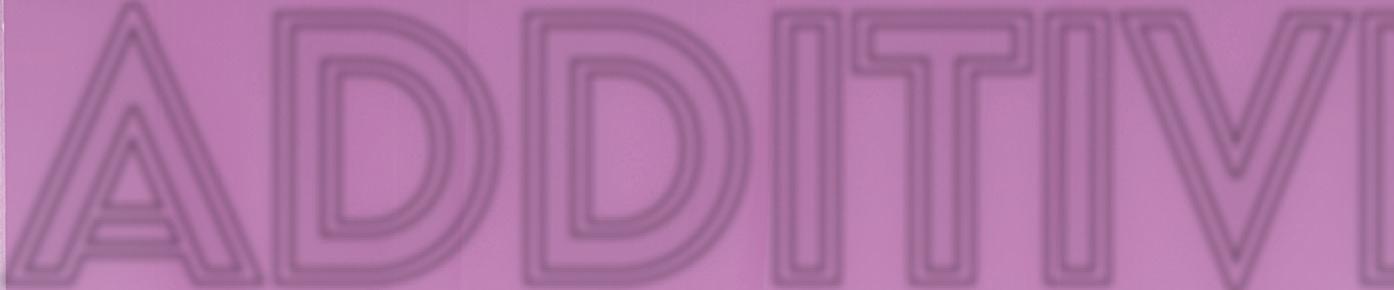
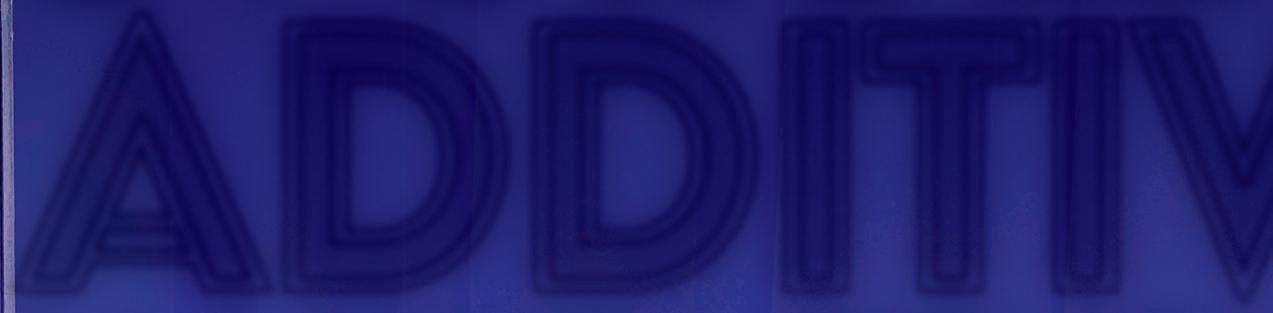
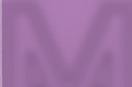



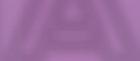
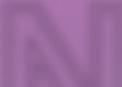
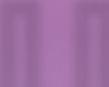
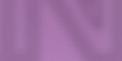
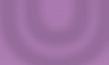



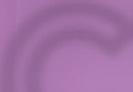
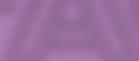
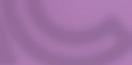

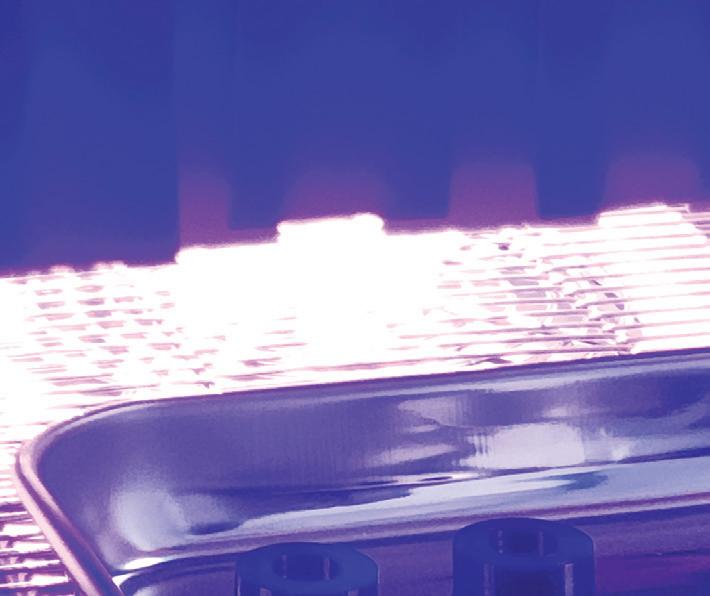


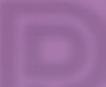


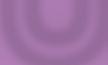


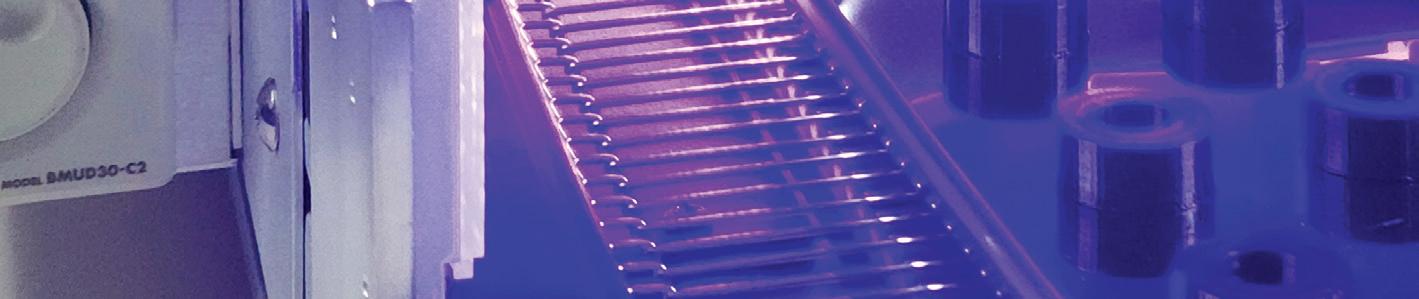

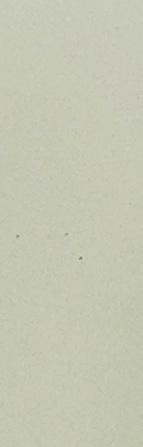
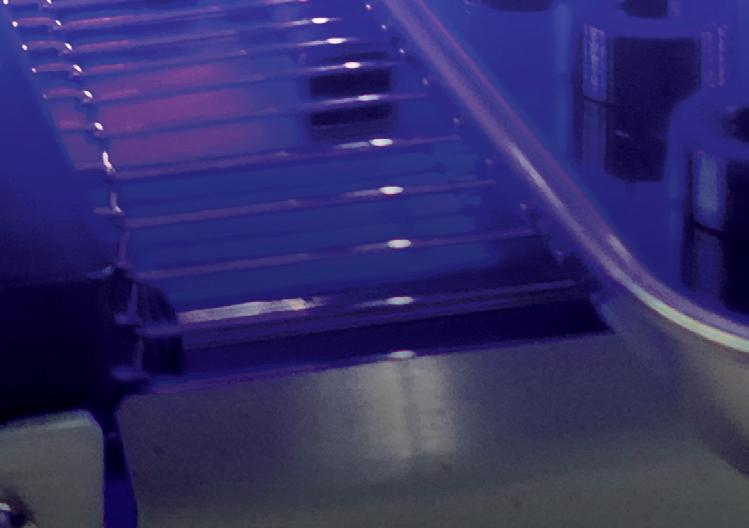
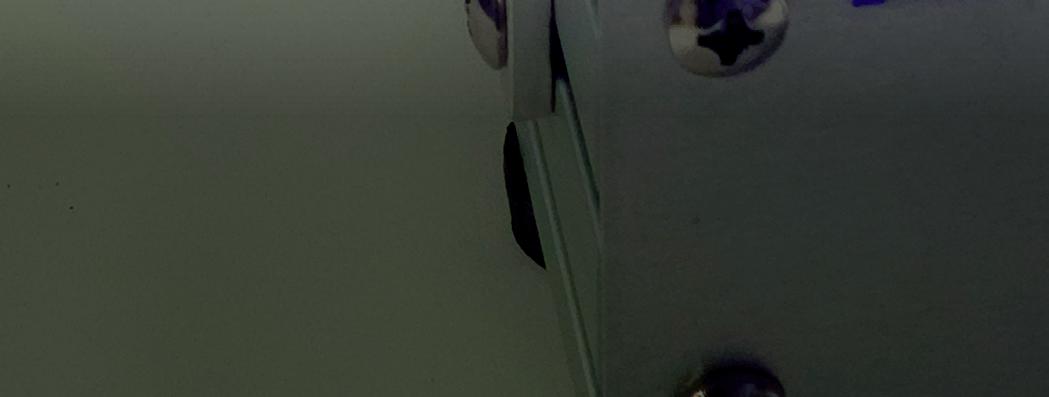
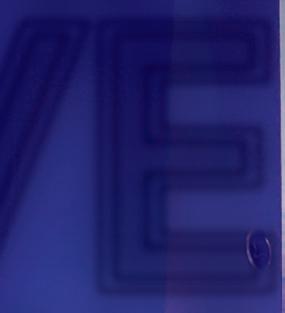
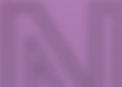
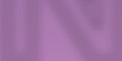

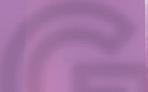
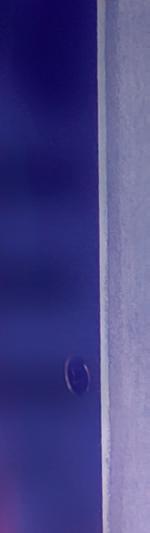
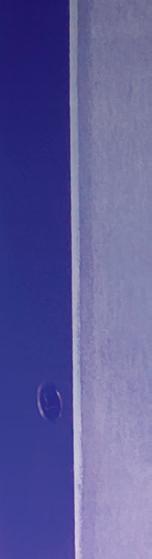
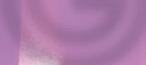
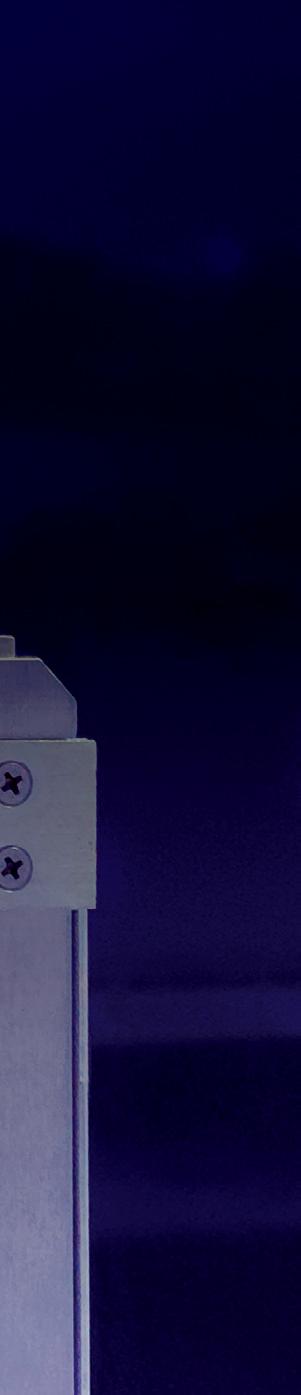
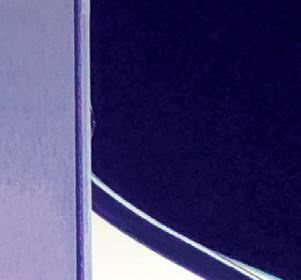
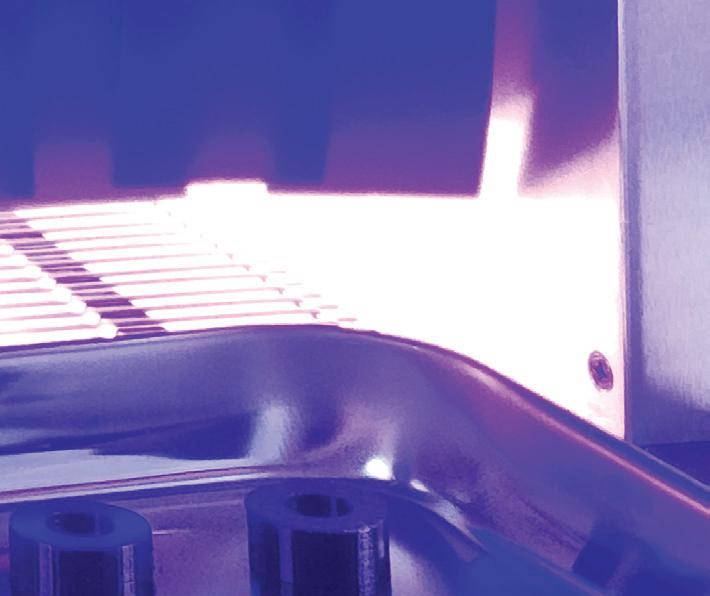
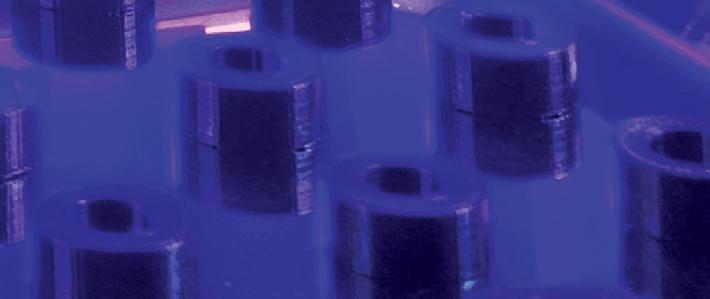
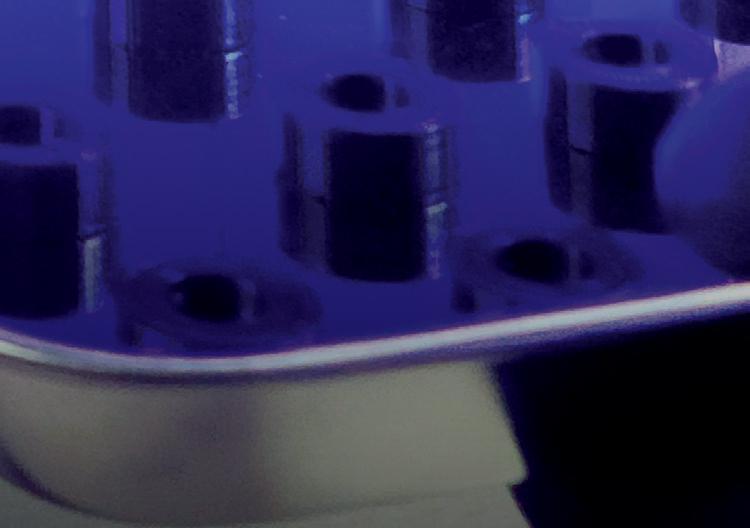
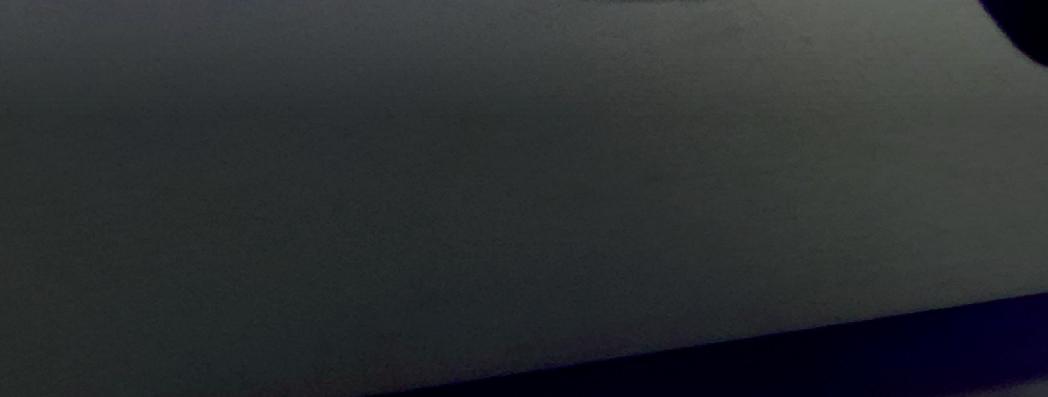
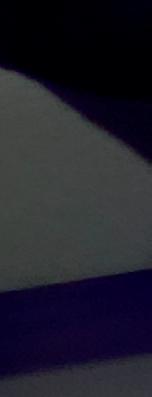
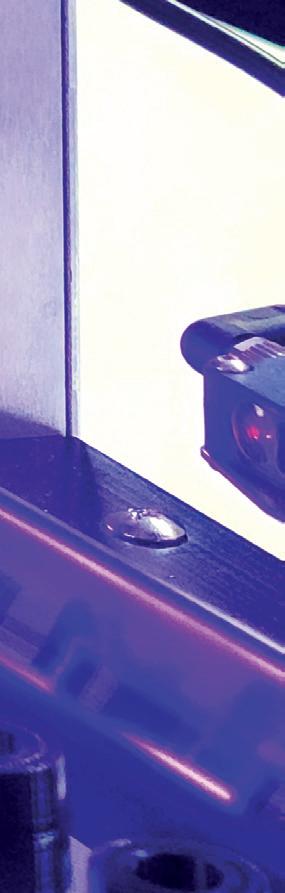


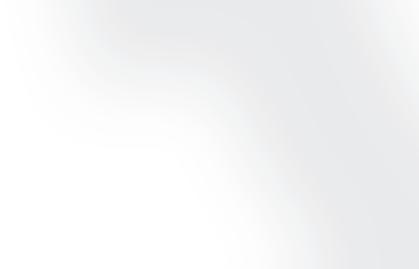
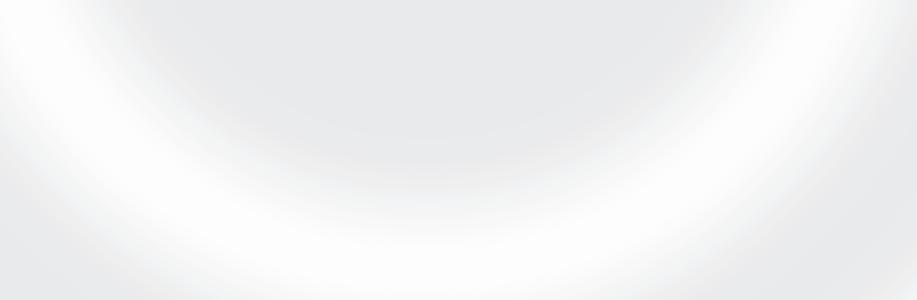
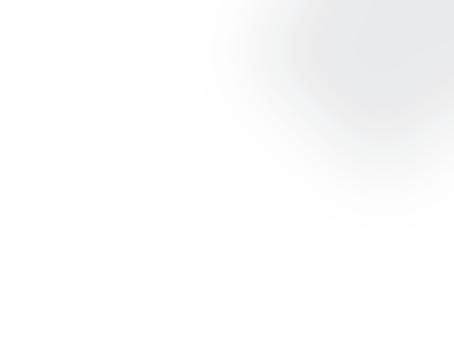

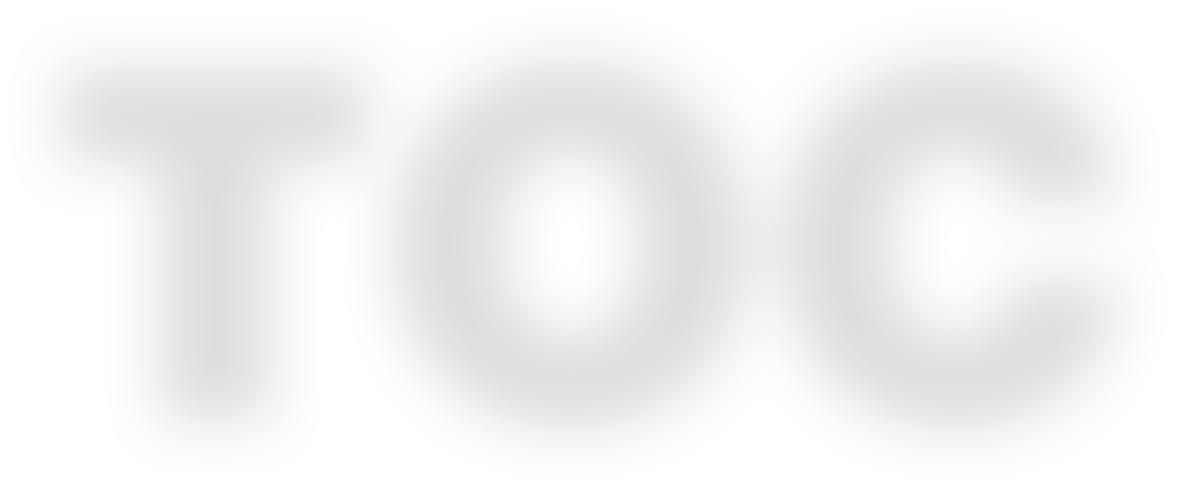
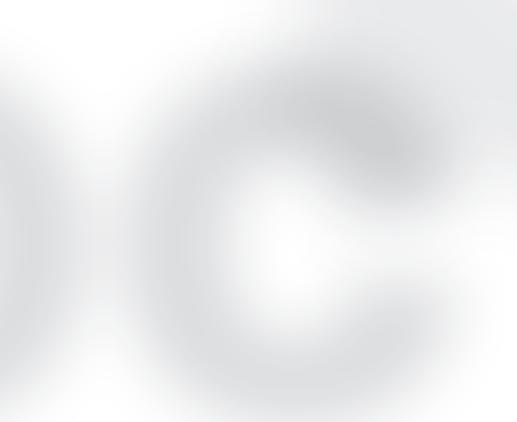
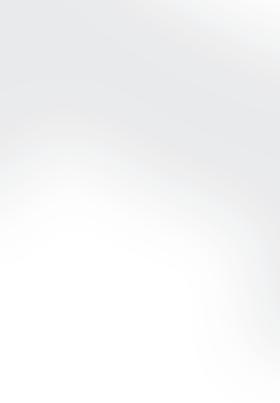
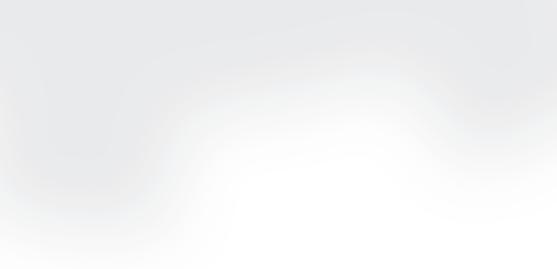



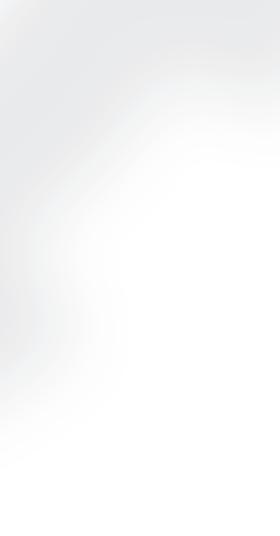
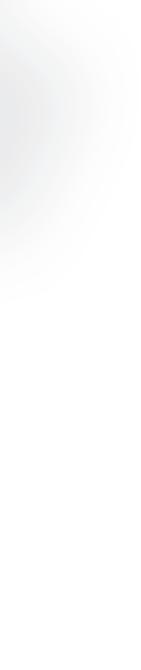
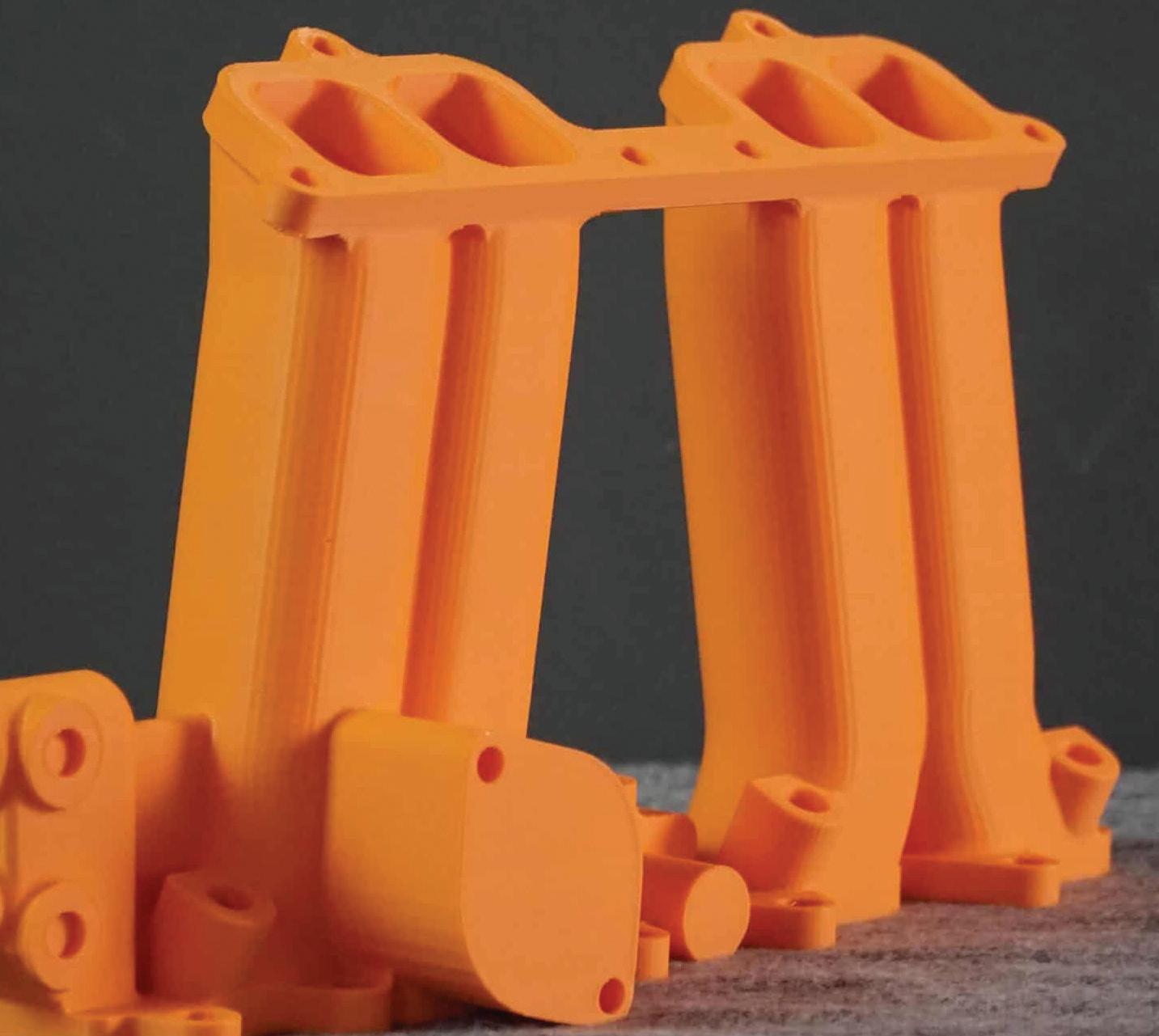
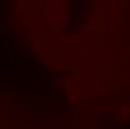
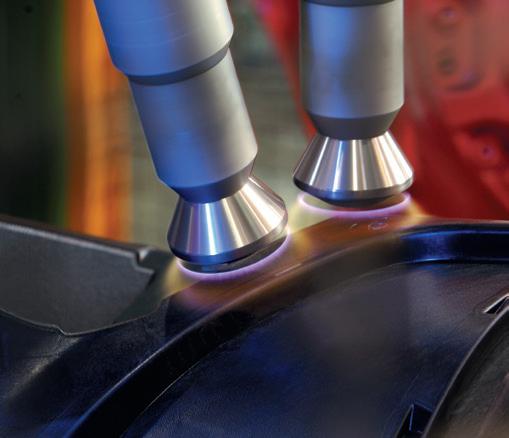

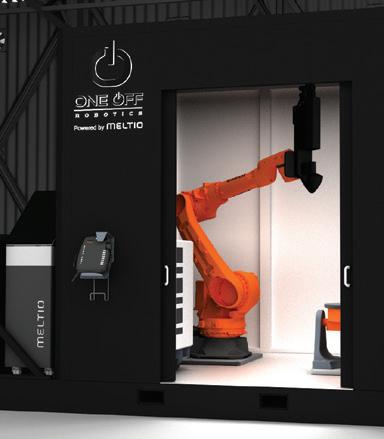

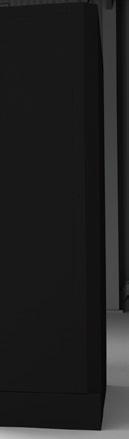


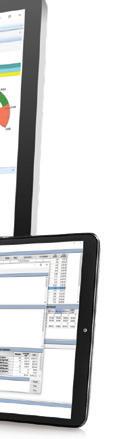
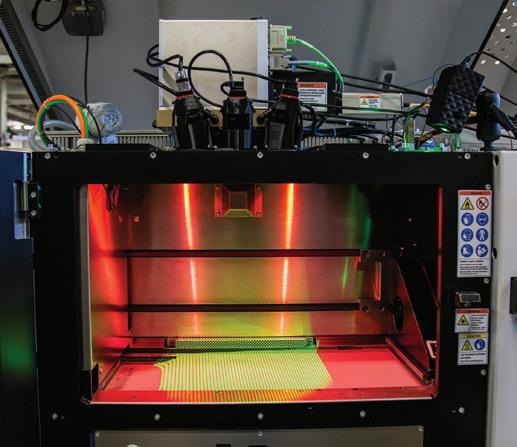
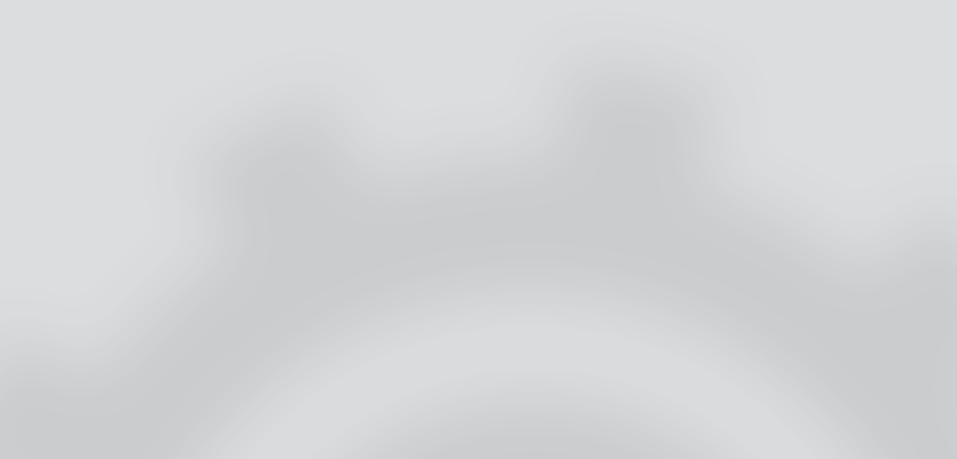

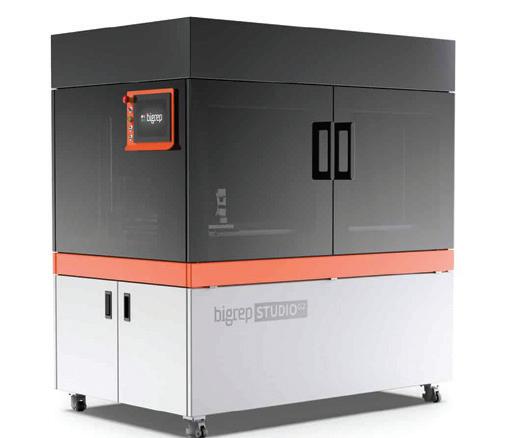



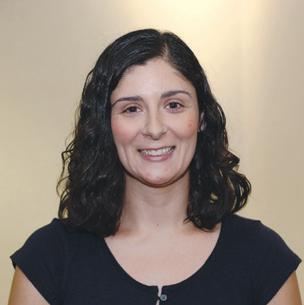
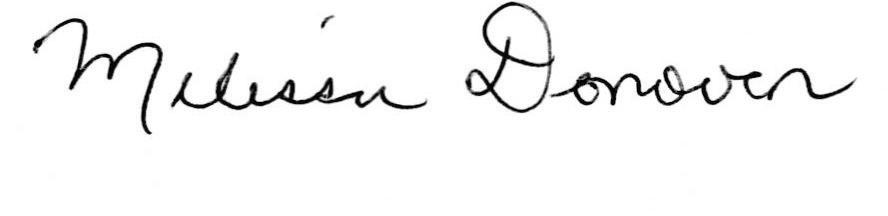



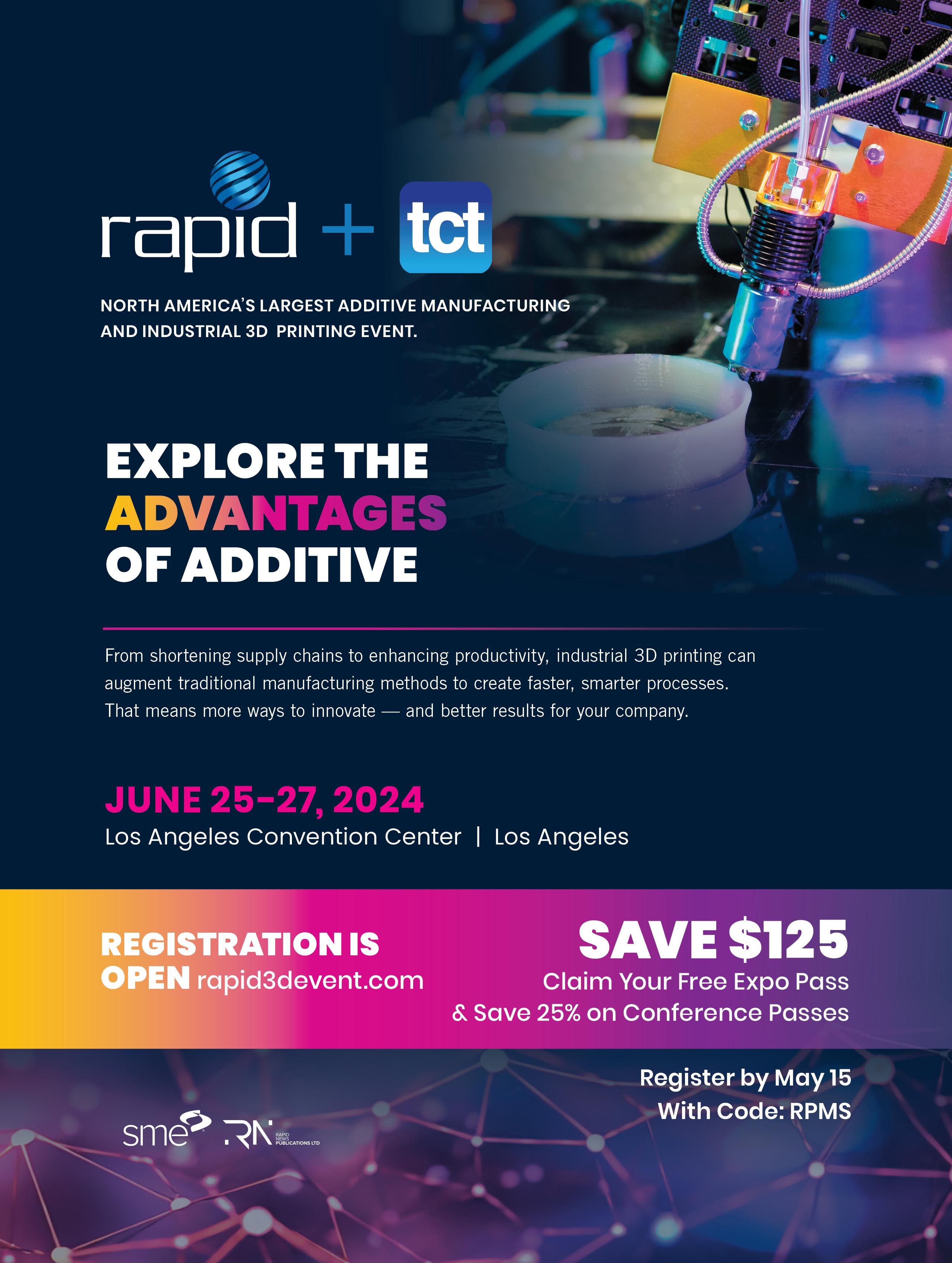
Head to Orlando, FL May 6 to 10, 2024 for NPE2024 The Plastics Show. Every three years the Plastics Industry Association holds this event with the goal of promoting plastics, innovation, and sustainability. Over 2,000 exhibiting companies plan to showcase their latest products and services in more than one million square feet of exhibit space.
Held at the Orange County Convention Center, this year’s show debuts keynote speakers. Opening day includes a presentation from Michael Heinz, chair/CEO, BASF Corporation. Heinz touches on the challenges the industry is facing, the importance of collaboration along the value chain, and provides inspiration for the future.
Here, vendors in the digital print space share their plans for the show.
3DT LLC, booth W1167, promotes its newest product, the HeliDyne corona treatment system. It was developed to produce strong bonding on specialized surfaces like wide, thick, porous, hollow, and over-size materials. HeliDyne’s numerous pin electrodes produce a wide band of corona discharge raising the surface tension and functionality on many materials that are difficult to treat, including foam stock, honeycomb boards, and polymer panels. INFO# 180
C-500 Cylindrical Part Printer is on display, it delivers seamless decoration of cylindrical parts. INFO# 182
Ampacet Corporation, booth S22097, is a global producer of colors, additives, and artificial intelligence (AI) automation technologies. LIAD Smart AI automation is on display. Live demonstrations of inline color measurement and correction technologies utilizing fiber optic sensors and Spectro 4.0 color measurement systems are also shown. Adjusting color on demand due to PCR variations during plastic processing is introduced at NPE2024. INFO# 181
Apex-Desco, booth W2151, encourages attendees to check out how to revolutionize their product package. It showcases the DCP-3 3-Color Closure Printer, which delivers vibrant, high-resolution designs on closures in three colors. Also, the
ARBURG, booth W3743, exemplifies the advanced capabilities of multi-component injection molding through its ALLROUNDER CUBE 2900. This machinery showcases efficiency and precision, incorporating a fully integrated FOBOHA Cube mold with swift and accurate electric cube rotation, thereby reducing dry cycle time by ten percent. Notably, it achieves a 25 percent reduction in energy consumption compared to hydraulic cube machines. The innovation extends to enhanced cooling and cycle time reduction, employing independent hydraulic core pull
1. Plasmatreat, booth W7479, presents a safe, efficient, and environmentally friendly alternative to conventional surface treatments for plastics with its Openair-Plasma technology.
movements on each cube face, optimizing cooling time and slashing production cycle time by up to 30 percent. INFO# 183
Cabot Corporation, booth S11005, is a leading global specialty chemicals and performance materials company headquartered in Boston, MA. Its purpose is creating materials that improve daily life and enable a more sustainable future. This year it presents a broad portfolio of specialty carbons, conductive additives,
black masterbatch, and conductive compounds, suitable for a range of plastics applications from infrastructure and automotive to packaging as well as agriculture. INFO# 184
Enercon, booth W6643, exhibits one of the industry’s most comprehensive platforms of plasma, flame, and corona surface treating technologies. See plasma treaters in operation and how they improve surface adhesion on all types of
plastics, composites, glass, and metals. Learn how the automotive, aerospace, consumer goods, construction, electrical, flexible packaging, medical, window, and door industries use Enercon treaters for adhesive assembly, printing, coating, decorating, potting, and bonding. Discover how Enercon’s Blown-ion 500 plasma treater is breaking barriers for surface treatment effectiveness and throughput. Find out why Enercon’s Flame Pro surface treater is a go-to flame solution. And, see how corona treaters handle all of your film extrusion, solventless laminating, coating, and printing needs. INFO# 185
GTI, booth S30192, highlights its updated portfolio of D65 LED color matching systems. Featured products include the CMB-2540/LED/FS, the MiniMatcher 4e/LED, the MiniMatcher 2e/LED, and PDV-2e/M/LED. The CMB-2540/ LED and MiniMatcher-4e/LED both feature five LED light sources—daylight (D50 or D65 LED), 2700K LED, 3000K LED, 4000K LED, and a 315–400nm Black Light Blue LED. Alternate sources are available. The MiniMatcher 2e/ LED and PDV-2e/M/LED include three LED sources—daylight (D50 or D65 LED), 2700K LED, and 4000K LED. The D65 LED source is compliant with ASTM D1729, ISO 3668, AATCC Procedure #9, and SAE J361 viewing standards. The 2700K, 3000K, and 4000K LED sources are for reviewing color in an end-use environment and testing for metamerism. The Black Light Blue LED source is used to detect fluorescents and optical brighteners. INFO# 186
Inkcups, booth S22065, exhibits its high-speed digital cylindrical printer, the Revolution. This printer offers full-color
2. Koenig & Bauer Kammann, booth S21083, specializes in providing cutting-edge decorating equipment tailored for direct printing on three-dimensional glass, plastic, or metal containers. 3. Discover how Enercon’s Blown-ion 500 plasma treater is breaking barriers for surface treatment effectiveness and throughput in booth W6643. 4. GTI, booth S30192, highlights its updated portfolio of D65 LED color matching systems.
360° graphics, exceptional print quality, and speed. At the event, the Revolution demonstrates decorating 12 oz. stadium cups with its automatic loading and unloading capabilities. Additionally, the Revolution features integrated pretreatment, as well as remarkable speed, printing up to 600 parts per hour. Additional machines on display in the Inkcups booth include the benchtop cylindrical inkjet printer the Helix ONE, as well as the X5-T UV flatbed printer. INFO# 187
Innovative Digital Systems (IDS), booth S18201, encourages attendees to print more, which is the main theme of its booth at the NPE show. A new UV rotary printer developed for the rapid and fullcolor decoration of plastic tubes and other small plastic vessels will be launched at the show. Plus, IDS unveils a new automatic load/unload system, designed to maximize the output of its UV rotary printers. As always, versatility is also on full display as a complete range of UV rotary and UV flatbed printer options are stationed in the booth. INFO# 188
shapes, including articles with handles that have been decorated using digital technology. INFO# 190
KEYENCE Corporation, booths S11151 and S34129, is a worldwide developer and producer of factory automation and quality inspection equipment that includes—automation sensors, vision systems, laser markers, digital microscopes, and metrology systems. The innovative products meet customer requirements in every manufacturing and research industry. INFO# 189
Koenig & Bauer Kammann, booth S21083, specializes in providing cutting-edge decorating equipment tailored for direct printing on threedimensional glass, plastic, or metal containers. Offerings include both traditional screenprinting products as well as innovative digital inkjet capabilities. At NPE it displays articles both screen and digitally decorated using various techniques. It features plastic articles that have been digitally decorated using a unique embossing process with multiple designs. It also has articles of all
Leister Technologies, LLC, booth 12038, showcases the FUSION 1 extrusion welder. It offers a compact and slim design. A double-sided rod intake offers increased flexibility, and an attachable handle ensures increased agility in the welding process. An integrated LED light illuminates the welding zone. The FUSION 1 is ideal for plastic repairs and in pipe, tank, and container construction. INFO# 191
LogoJET, booth S27206, is a UV direct-to-substrate printer manufacturer that provides five-star customer service experiences to businesses that want to print in house. Specializing in high-quality printing on all substrates including plastics, products range from small and mid-size to the new Strata Series large format printers, all including a three year warranty. INFO# 192
Mantle, booth S27055, designs and produces a metal three-dimensional (3D) printer built specifically for precision tooling. Mantle’s printer accelerates product development by automating how precision tool components are made. The metal 3D printing technology delivers the accuracy, surface finish, and tool steel properties required for demanding tooling applications. Tools made with
Mantle’s technology have produced millions of parts while reducing tooling lead times and costs and helping manufacturers solve labor shortages. INFO# 193
Plasmatreat, booth W7479, focuses on pioneering advancements and forward-thinking initiatives in plastics manufacturing. With its Openair-Plasma technology, it presents a safe, efficient, and environmentally friendly alternative to conventional surface treatments for plastics. Trade show visitors can experience a demonstration of treatment and printing on polypropylene, which is a material with a low surface energy making it challenging for inks to adhere properly. Plasmatreat demonstrates how its technology can enhance the surface tension to greatly improve printability. In addition, watch real-time demonstrations of various plastic materials and learn how to test and measure surface readiness. INFO# 194
In May
NPE2024 promises to be worthwhile event. We look forward to reporting on all the product announcements as well as interesting conversation occurring at the show. And if you can’t make this year’s expo, plan ahead—the next one takes place in 2027! IPM
Three-dimensional (3D) printing is a complex process that often involves many parts. If one step in the procedure goes wrong the entire build is jeopardized. Real-time monitoring and issue detection software are important tools to prevent this from occurring. Their use minimizes waste, saves time, and ultimately helps create an efficient method of manufacturing.
Real-time monitoring and issue detection software gather data during the 3D printing process. “The number of data sources is very broad, ranging from printing parameters, oxygen level sensors, and laser paths to more complex data sets like meltpool data, optical tomography, in-situ nondestructive testing, and layer images,” says Jan Van Espen, data intelligence manager, Materialise.
“Software uses a live camera feed to detect 3D printing failures in real time, and a connection to a printer through an external board, like a raspberry pi, to act when a failure occurs. This provides users with the security of running their printers without having to physically monitor them,” shares Peter Lebiedzinski, founder/ CEO, printpal.io.
Real-time monitoring acts as a first defense. “It typically focuses on keeping an eye on whether machine parameters are
within preset tolerances and raise alerts if not,” according to Van Espen.
On the off chance real-time monitoring fails, “issue detection software dives into a deeper level by identifying root causes,” adds Van Espen.
Most manufacturers print parts and do not know the quality of the part for one to 12 months after the print is complete. With in-situ monitoring, the user can know in real time the quality of the part.
— Dr. Niall O’Dowd, founder/CEO, Phase3D
According to Mirco Schöpf, senior software manager, EOS, realtime monitoring and issue detection software is “typically a combination of hardware sensors of different wavelength measuring meltpool emissions and a software performing data acquisition, analysis, and visualization.”
Growth is driven by demand for AM in industries such as automotive, healthcare, aerospace, and defense. Fueling demand is the development of innovative, stronger, lighter, and safer components and parts with reduced lead times and parts, according to the Markets and Markets’ report.
In general, the industrial 3D printing segment has experienced large amounts of growth over the past five to ten years.
“This is due to onshoring, current supply chain issues, cost of small batch production, and cost of labor,” says Matthew Stark, 3D segment manager, Mimaki USA, Inc. And this growth is set to continue, as Stark points out that “many companies/industries have not yet fully adopted 3D printing into their workflows.”
More specifically in regards to plastics, Nirup Nagabandi, Ph.D., VP of materials engineering, Nexa3D, believes 2024 is a pivotal year for 3D printing. “With a better understanding of the technology, more grades of new polymers come into the picture each quarter from various innovations, unlocking more applications. This
enables the growth of polymer printing.”
The continuous introduction of new products is exactly why growth continues, agrees Michael Eggerdinger, business manager – 3D printing materials, BigRep GmbH. “There is a huge variety of printable materials that appear on the market almost every month. Parts can now be printed to fulfill a range of technical requirements, from strength and toughness to chemical resistance. There are plastics available that are flame retardant, others have specific ESD properties, or combine strength and elasticity. More industries see that there is a 3D printing material out there, tailored to their exact needs.”
While opportunity abounds, Francois Minec, global head of 3D polymers, HP Personalization and 3D Printing, believes it must be met cautiously. “The world has seen what can be achieved when we pursue innovation in design with powerful 3D printing technology. The demand is there, but it must be met in a way that is scalable and attainable for even more manufacturers across industries. Fortunately, 3D hardware, firmware, and software capabilities are enhancing thanks to increased integration of advanced data and KPI analytics, artificial intelligence, automation, and other emerging technologies.”
“Not only does this improve predictability, optimization, and consistency in application development all the way through to manufacturing for maximum yield rates, it achieves this all while keeping costs low. The benefit of reliability and repeatability across an entire fleet is a major industry improvement, making production scalable so that even more breakthrough polymer applications are brought to market easier
and faster as business continues to grow into existing and new industry verticals,” continues Minec.
Realizing the full benefit of AM is a process in itself, according to Dr. Victor Roman, managing director, ARBURGadditive GmbH + Co KG. “The actual added value of AM only comes fully into its own when integrated functions, innovative applications, and completely new business models can be realized additively. It is always important to focus on the optimum materials and the ideal component design.”
healthcare, aerospace, and defense industries lead the charge when it comes to adopting 3D technologies, and plastic-based AM is no exception.
“There are growth opportunities in any company that manufactures, no matter the scale. 3D printing can be used to batch manufacture, assist in manufacturing—specialized jigs/tooling, or within the manufacturing workflow—prototyping, fit, and function. Industries that have adopted 3D printing—aerospace, automotive, heavy machinery—have extended their use of 3D printing dramatically over the last five to ten years and that momentum is not slowing,” shares Stark.
Minec believes industries offering mass-personalized goods receive the most value in regards to 3D printing plastics. Healthcare is one example, “where patient-specific parts such as prosthetics and orthotics can improve treatment and care.”
Agreeing with Minec, Nagabandi also sees substantial growth in healthcare. “We foresee growth in nanoscale 3D printing, particularly in microelectronics and biomedical applications like nanomedicine and drug delivery. Additionally, liquid metal printing, known for its speed and environmental friendliness, may gain prominence. These advancements open doors for personalized medicine and sustainable manufacturing.”
“One vision, for example, is to manufacture functional components on demand—decentrally and exactly where and when they are needed. I am thinking here, for example, of personalized implants that are 3D printed in the hospital at the same time as the operation. However, operating equipment and robotic grippers can also be additively manufactured very quickly, individually, and economically,” adds Roman.
Eggerdinger sees opportunity in “highly controlled” industries. “Industries that are highly controlled, and in which certifications are required for materials and production processes, like medical technology, transportation, food industry etc., are often reluctant to adopt new manufacturing technologies due to the high effort that this certification brings about. Aiding those industries
to overcome these challenges, either by providing new and certified materials, or assisting in the relevant processes will help to address these markets.”
Minec also cites everyday consumer products that “can leverage highly personalized manufacturing methods to improve performance and experience for a range of customers. Companies like Brooks Running and Smith Optics deploy HP’s Multi Jet Fusion platform to ensure custom shoe fits while on running trails or mountain slopes.”
For the purposes of this article, we look at five main plastic categories—photopolymers, ABS/ASA, polyamide/nylon, PLA, and other. Each category is used by certain industries, for specific applications, and printed with various technologies.
Also, of note here is the form of the plastic. Markets and Markets classifies form by powder, filament, and liquid. The January 2024 report notes that the powder segment is expected to lead the market during the 2023 to 2028 forecast period in terms of value and volume.
The 3D Printing Plastics Market report states that the photopolymer segment had the largest market share in 2022, in terms of value and volume. “Photopolymers are a type of 3D printing plastic that are transparent and used in liquid form in stereolithography (SLA). They are utilized for prototyping of static models in various end use industries,” notes the study.
“Photopolymers are mainly used when the surface finish plays a central role. Thanks to their low layer thicknesses,
parts made from photopolymers generally require no post-processing. These materials have established themselves in the dental sector in particular and are also used to produce many design samples,” shares Roman.
SLA, as aforementioned, is a popular 3D printing process for photopolymers as it “can utilize a single photopolymer and produce low-cost, high-resolution parts with low material strength,” notes Stark.
Other 3D printing methods that use photopolymers include digital light processing (DLP) and continuous DLP, with each having its own benefits and disadvantages, adds Stark.
ABS/ASA
It is common to favor ABS/ASA for its ease of use and affordability.
“ABS is widely used due to its versatile properties, great aesthetics, ease of printing, and affordability at a business
level,” shares Nagabandi. “Manufacturing aids such as jigs and fixtures; end use applications in consumer products, prosthetics, and housing/covers; prototyping; and low- and high-pressure tooling use a diverse range of plastics.”
A variety of manufacturers, colors, and variants are at a user’s disposal, notes Roman. “ABS/ASA is used in almost every industrial sector due to its range of materials and is probably the most frequently processed material group. Functional prototypes and end products are manufactured in the industrial environment. The material is also widely used in the maker scene.”
“ABS and ASA to a certain degree is a widely used material, particularly in the automotive industry. This popularity stems from its resilience against harsh environmental conditions, including extreme temperatures, and its ability to withstand impacts. These qualities make it a long-standing material choice for injection-molded parts across car interiors and exteriors,” notes Eggerdinger.
Roman thinks ABS’ popularity may change in the future, however. “The rapid industrialization of the 3D printing market will lead to increased processing of more technical and high-performance plastics. I would like to emphasize the group of biocompatible materials here, as 3D printing is perfectly suited to meeting individual requirements in the medical environment.”
Polyamide/nylon is known for its strength.
Citing the mechanical properties of polyamides/nylon as superior to those of ABS/ASA, Roman says plastics are further improved with additives like glass or carbon fibers. As such, he finds that this group of materials is of particular interest to the automotive industry.
“We are experiencing high demand for additively manufactured components made from soft materials and short-fiber reinforced thermoplastics. Flexible connecting hoses and glass fiber-reinforced polyamides for the automotive industry are typical examples,” adds Roman.
Prototyping applications polyamides are used in include jigs, fixtures, and molds. “As a material that can withstand high levels of stress, engineers and designers can thoroughly test and refine designs with polyamides before moving to final production. For final part production, automotive, healthcare, consumer goods, and other industries leverage polyamides and 3D printing processes to manufacture precise and reliable end use parts, fulfilling the need for complex geometries to be brought to life,” says Minec.
A common printing method is powder bed fusion (PBF), this is due to the unique material properties. “Known for being an overall strong, tough, and durable material, polyamides are favored for a range of PBF applications, from automotive and medical to consumer goods, enabling enhanced productivity and reduced costs with advanced 3D printing technology,” shares Minec.
PLA
Due to PLA’s mechanical properties, Roman says it is used by makers and not so much in industrial environments.
“However, with evolving needs, we anticipate higher adoption of advanced
2. ARBURG Plastic Freeforming with an ARBURG freeformer printer processes a range of certified original plastic granules, including fiber-reinforced and multi-material combinations.
materials like PEEK, carbon fiber reinforced materials, and PEKK, especially in end use applications, driven by their enhanced performance and suitability for various industries, such as aerospace and defense. High-performance materials like PEEK find applications in demanding environments due to their superior properties,” adds Nagabandi.
Other
Minec says thermoplastic elastomers and polypropylene are increasingly used. “They offer advantages for applications that require more flexibility, rebound resilience, or chemical resistance. With growing availability of material choices for plastic production, we can expect manufacturers and developers to more closely examine the material characteristics that specific applications require, tailoring selection to meet diverse manufacturing requirements effectively.”
“The processing of liquid silicone also warrants a mention. We see a high demand for the processing of Ultem, particularly in aircraft construction and medical technology,” adds Roman.
Caster seeds, palm oil, and starches are natural sources from which 3D printing plastics—PA11, PA12, and PLA—are made. There is a rising demand for biobased grades of materials due to awareness surrounding sustainability.
Minec says sustainability is shifting from consumers preferring eco-friendly products to demanding them. “This trend prompts more manufacturers to prioritize sustainability throughout their production processes, from research and development to final production, and especially regarding the materials they use.”
“Customized plastic parts made from innovative materials, including bio-based and recycled plastics, are an interesting development. In recent years, the demand for plastics made from renewable raw materials has risen noticeably. This trend
is due to both increased environmental awareness and increased efforts and regulations to reduce the environmental impact of plastics,” explains Roman.
One of ARBURG’s customers uses a freeformer printer, for example, to process granules made from corn starch into customized forks that can be easily returned to the natural cycle after use.
“In addition to the already established renewable raw materials, there are also promising approaches for the production of new bio-based plastics. One example of this is research into the use of algae as a starting material. Developments in this area are increasingly important for 3D printing and we are keeping a close eye on them,” admits Roman.
To reduce the content of crude oilbased chemicals in their compounds, suppliers are creating some unusual materials, according to Eggerdinger. “This includes materials made from wood fibers, for example, while others are created using bacteria supported fermentation. These materials are not only fully bio-based but are also fully bio-degradable. Such considerations will surely play an increasing role in the future.”
Recycling and buyback programs are also being addressed. They allow customers to sell used PA11 and PA12 powders and printed parts, rather than dispose of them. “With these programs, these inherently eco-friendly materials contribute to a circular economy, enhancing their recyclability and availability while centralizing production. The synergy between 3D printing and bio-based materials fosters increased adoption and availability of both resources, highlighting each other’s capabilities and driving innovation in manufacturing,” shares Minec.
As 3D printing technologies evolve, users of the technology are forced to adapt. This means branching out and attempting to try something new, like plastics. Or perhaps fulfill sustainable manufacturing goals and turn to natural resources from which plastics are made. In either case, 3D printing of plastics continues to grow. Users from automotive, healthcare, aerospace, and defense industries are prime candidates. Learn more in our webinar, available online at industrialprintmagazine.com. IPM
Get more information from vendors appearing in this issue! Visit IPMagdirect.com. With just a few clicks, order FREE information from dozens of companies covered in this issue.