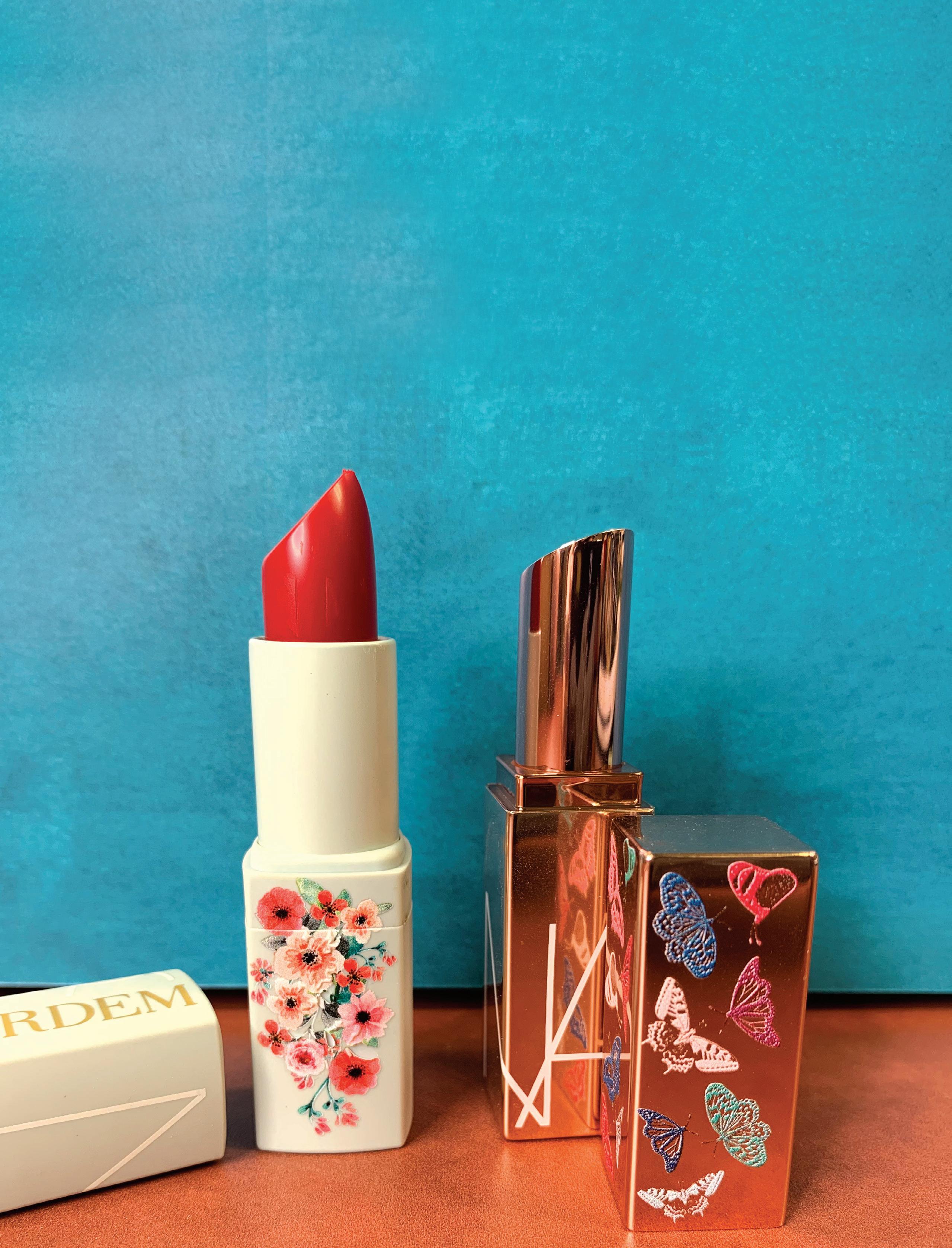
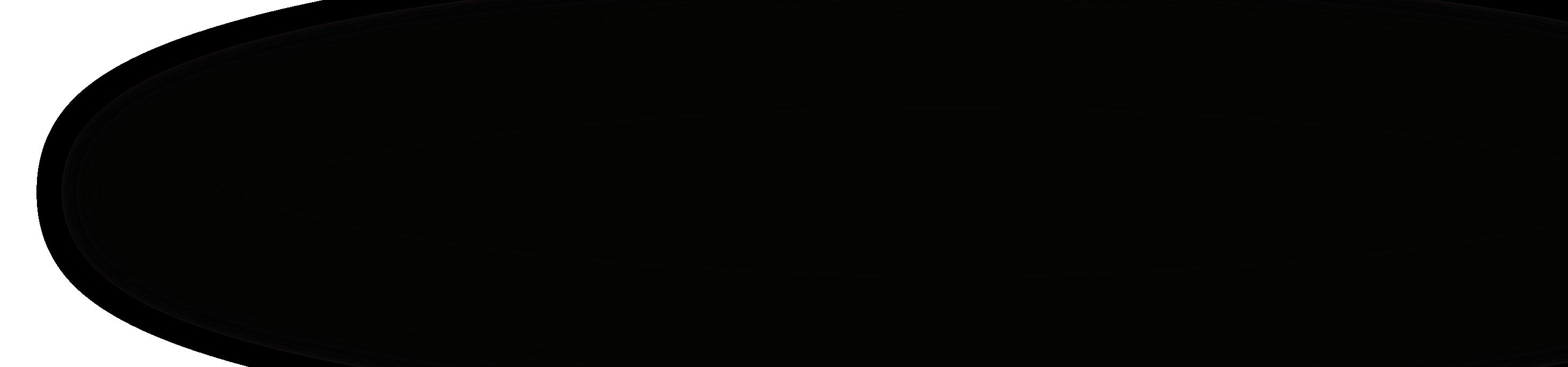
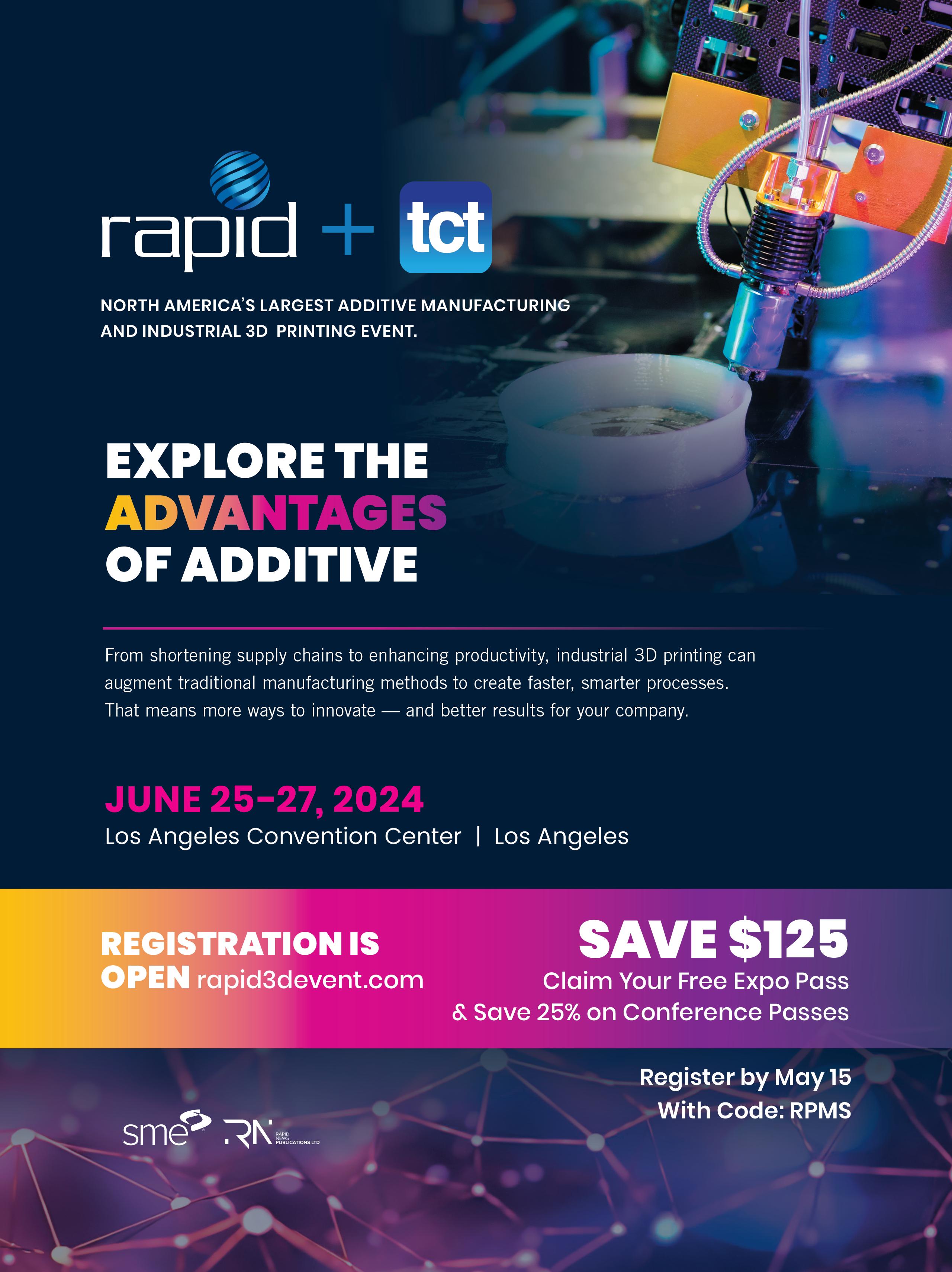
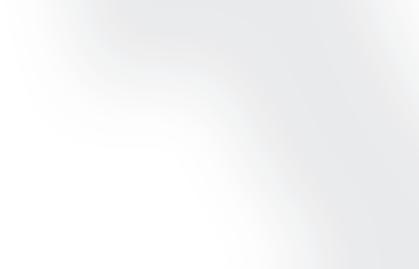
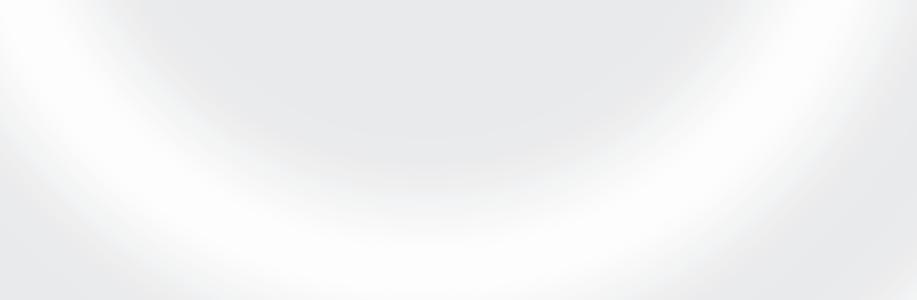
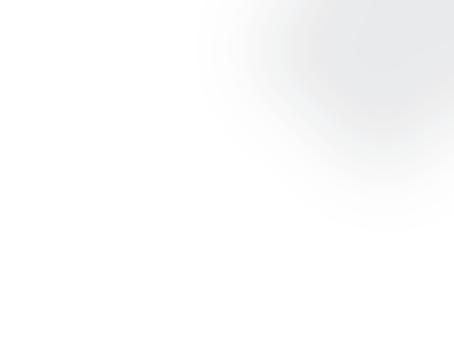
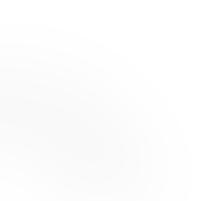

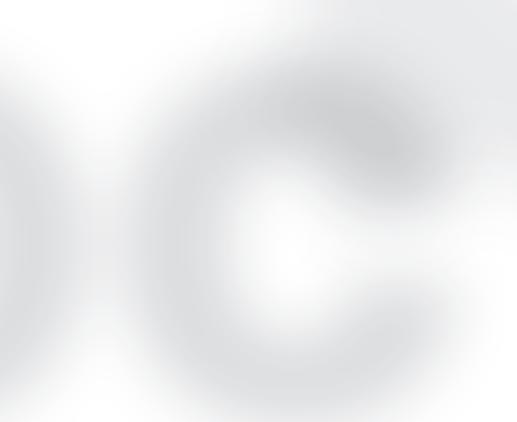
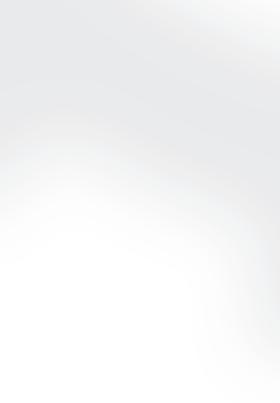
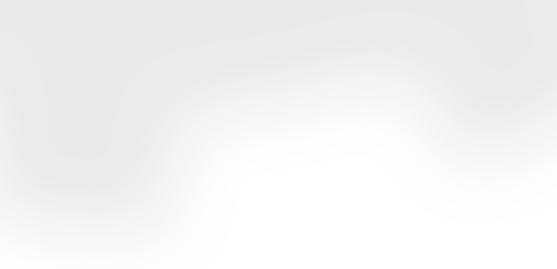



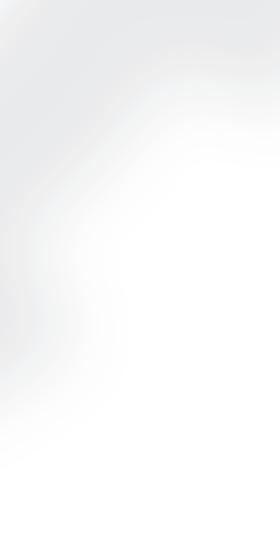
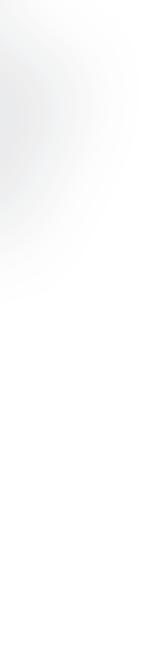
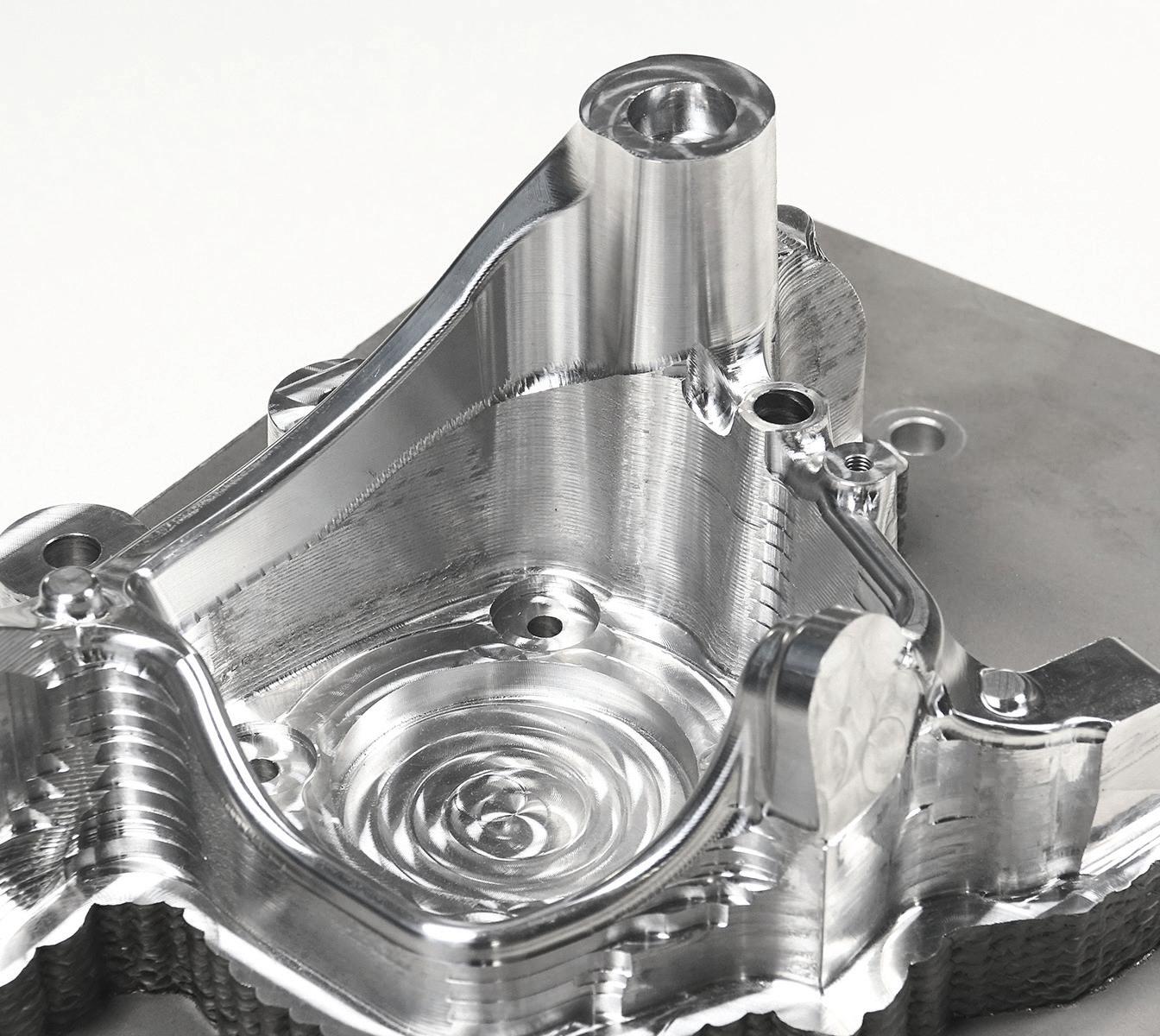
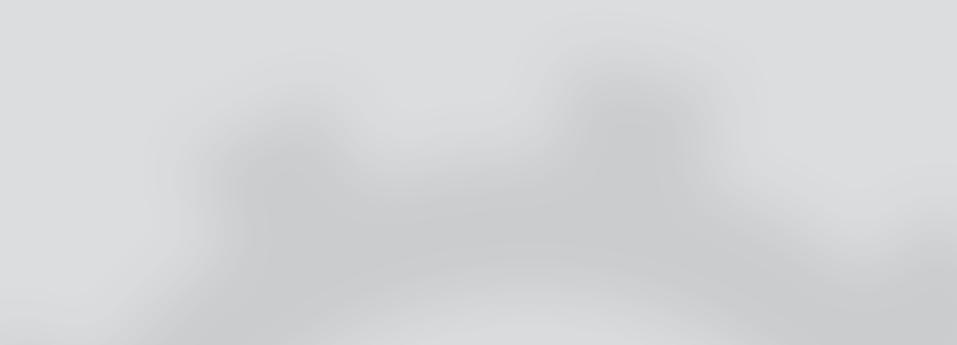
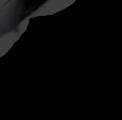

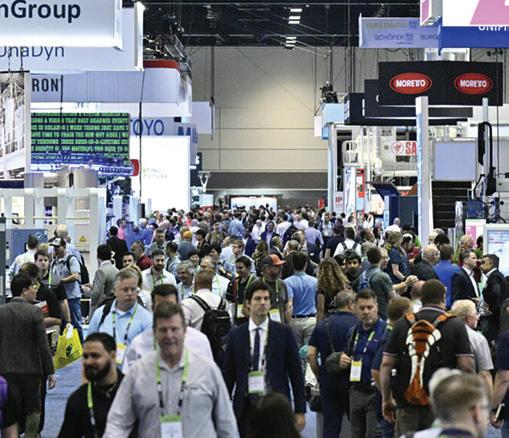

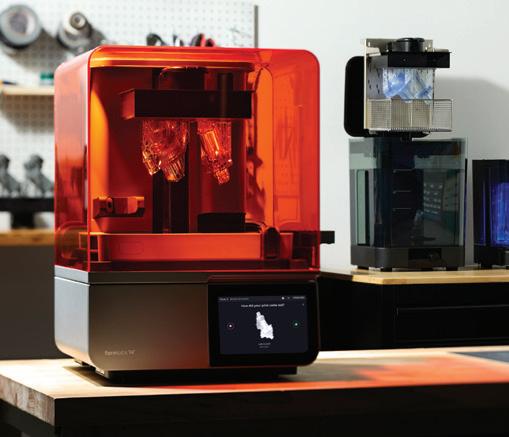

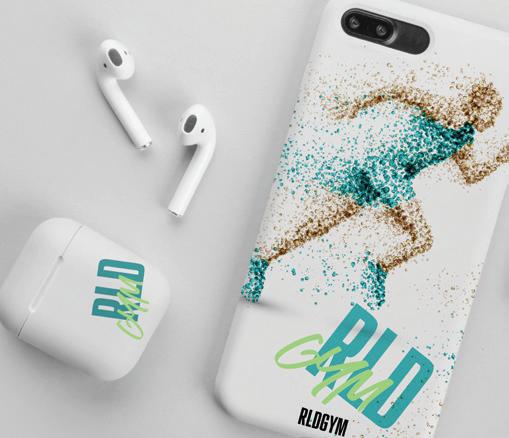

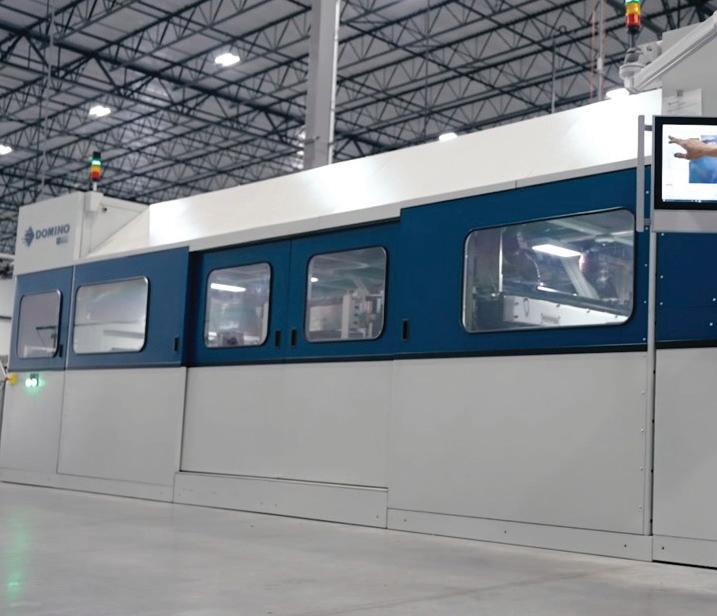
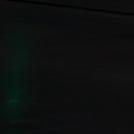
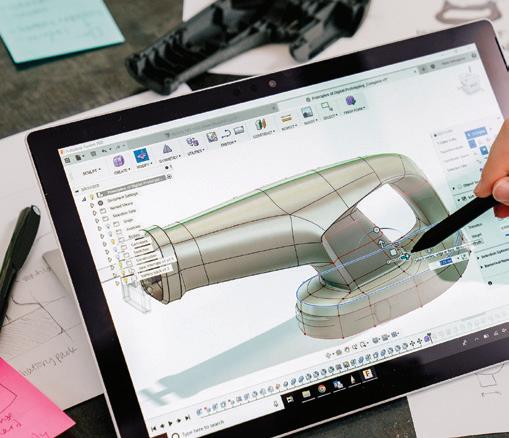

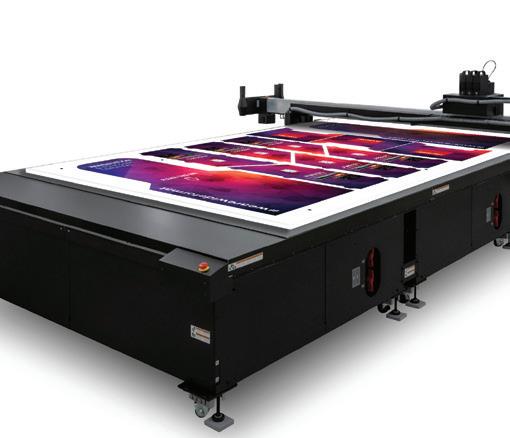

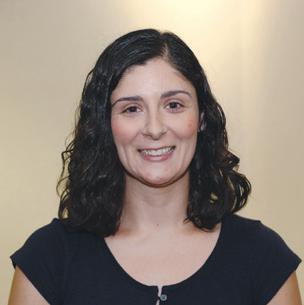
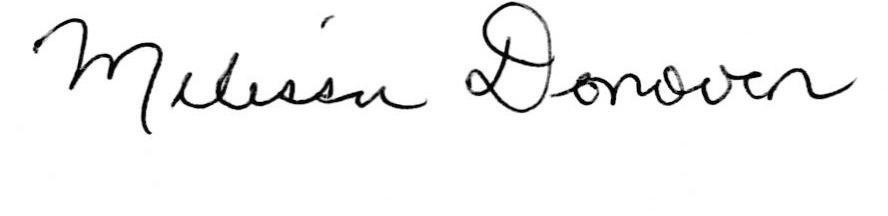



NPE2024 Review
NPE2024: The Plastics Show took place from May 6 to 10, 2024 in Orlando, FL at the Orange County Convention Center. This was the first NPE since 2018, and it was met with excitement from exhibitors and attendees alike. Over 2,200 exhibitors took up more than 1.1 million net square feet of exhibit space. On the show’s second day, the Plastics Industry Association (PLASTICS) announced that it exceeded over 50,000 registrants.
“The energy and excitement at NPE2024 are truly palpable,” says Matt Seaholm, CEO, PLASTICS. “From established industry giants to groundbreaking startups, this show is a testament to the unwavering spirit and ingenuity of the plastics community. We can’t wait to see how this next generation of the plastics workforce will use these resources and connections to foster the future of the industry.”
Michael Heinz, chair/CEO, BASF Corporation, also headlined a keynote. He touched on the challenges the industry is facing and the importance of collaboration along the value chain.
According to data from PLASTICS, 63 percent of the attendees experienced the event for the very first time. 30 percent of the attendees were under the age of 40.
The event served multiple industries including automotive, medical, packaging, building and construction, and consumer products. This was the first year it included keynote speakers. Attendees received insight from Michael Cicco, president/CEO, FANUC America Corporation. Cicco discussed robotics and automation advancements revolutionizing the plastics industry.
This was seen first hand on the show floor. For example, in Innovative Digital Systems’ booth, the company exhibited a robotic arm and conveyor as part of its high-speed rotary UV LED printing process. The part was specifically designed to streamline cylindrical print production.
1. NPE2024 was held in Orlando, FL in May and exceeded over 50,000 registrants.
Part of meeting the challenge head on is accepting and embracing emerging technologies for parts production, like three-dimensional (3D) printing. As such, one of the on-site workshops focused on 3D printing. The multi-hour event included several mini sessions. The first provided a platform for Greg Paulsen, director, applications engineering and marketing, Xometry, to educate attendees on when and why to employ plastic 3D printing or injection molding.
Later in the day, attendees learned how to automate toolmaking with metal 3D printing. Ted Sorom, CEO/co-founder, Mantle, headlined this session. He discussed how he started Mantle to address the specific challenges faced by the tooling industry.
At press time we were awaiting feedback on the 2024 show, but we look forward to reporting on more in the weeks ahead. And keep an eye out for the next iteration, NPE2027, which takes place May 3 to 7, 2027 in Orlando, FL. IPM
demonstrate how HP’s customers in the medical, industrial, and consumer sectors are pushing the boundaries of innovation and accelerating their growth in AM. INFO# 159
JEOL, booth 2421, displays many sample industrial parts made from Ti64, nickel alloy 718, and pure copper, and debuts its newest material offering—3D Printed Pure Tungsten. JEOL’s Electron Beam Powder Bed Fusion technology offers its users unprecedented capabilities in AM—fast build rates, fewer required manufacturing operations equals better business cases. INFO# 160
JuggerBot 3D, booth 2827, features large format composite tools serving defense, aerospace, and rail. All parts are printed with functionality from the JuggerBot 3D, a digital product that leverages vital material and process data to bridge skill-gaps, streamline production, and improve reliability when operating pellet-fed 3D printers. Live printing demonstrations are performed throughout the course of the show on JuggerBot’s large format pellet-fed system, the Tradesman Series P3-44. INFO# 161
Markforged, booth 1813, showcases its next-generation industrial 3D printer—the FX10. Designed to be the most versatile tool for the factory floor, the FX10 features a modular architecture that prints strong, accurate parts every time. The printer features an advanced material chamber with automatic material changeover, a larger print bed with faster print speeds, and advanced sensors to ensure in-print dimensional accuracy. Markforged also showcases the PX100 metal jet binder printer and its new Digital Source platform that enables distributed manufacturing with built-in IP security for part owners. INFO# 162
Materialise, booth 2821, announces the next version of Magics, a leading data and build preparation software for AM. Focused on achieving firsttime-right prints every time, this update introduces enhancements for both
polymer and metal users. By handling complex data with beam lattices, users can optimize their designs and reduce the weight of their parts. Additionally, the upgraded 3D Nester and Support Generation modules help ensure superior build quality. Considering users’ needs and requests for every release, Magics now offers unprecedented speed and includes a dark theme option. INFO# 163
Meltio, booth 2327, exhibits the new Meltio M600 metal 3D printer, which has the capacity to manufacture aluminum and copper parts as well as many other materials such as steels, titanium, inconel, and nickel. Also on display is Force Automation’s robotic integration Made in the U.S. and powered by Meltio and the Meltio wire laser metal 3D printing head integrated in a CNC machine. INFO# 164 PostProcess, booth 2213, showcases three cutting-edge solutions. Unveiled in February, the DEMI X 520 introduces Axial Flow Technology to the Submersed Vortex Cavitation family, revolutionizing automated resin removal. Also featured is the BASE system, automating support removal for fused deposition modeling (FDM) printing. Completing the trio is the DEMI 830, acclaimed for its effectiveness in post-processing across polyjet, FDM, and resin printing methods. INFO# 165
Printpal showcases in partner booths its latest and most advanced artificial intelligence (AI) model that detects various failure types including spaghetti, warping, blobbing, and layer shifting. It does so by using either an externally mounted camera or the camera that comes built into the printer.
Multiple partners, some OEMs, and a cloud management software company showcase this AI capability on their machines and platforms. INFO# 166 Roboze, booth 2127, presents its comprehensive approach to the production lifecycle, from design through to delivery. Discover how its expert consultancy in Design for Additive transforms concepts into functional prototypes swiftly and efficiently, paving the way for robust production with industrial-grade printers such as the ARGO 1000 HYPERMELT and ARGO 500 HYPERSPEED. These printers utilize super polymers and composites to deliver high-quality parts at scale. Roboze not only supplies premier 3D printers but also provides the essential materials and expert knowledge required for every production phase, including advanced post-processing and digital warehousing solutions. INFO# 167
The RAPID + TCT 2024 event promises to be filled with innovation in the AM field. Visit us online at industrialprintmagazine.com to keep up with new announcements at the show and a recap of the event. IPM
Build Preparation Software
by Melissa DonovanThree-dimensional (3D) printed pieces are often complex builds that require software to help in managing the design. This software needs to be able to handle both large volumes of data as well as build sizes. Converting or transferring that data is also a required feature. Build preparation software is an efficient tool for executing complicated 3D builds.
In additive manufacturing (AM), build preparation software is a necessity. When used correctly it creates efficiencies across production, which leads to reduced spending.
“Build preparation software for 3D printing enables more efficient workflows, allowing users to streamline and automate processes, minimize printing time, and accurately plan resource allocation,” notes a representative from Formlabs.
Shawn Hopwood, CMO and head of relations, Dyndrite Corporation, attests that it serves a crucial role in the AM process. “Build preparation software translates CAD into instructions that 3D printers can execute. These software packages are indispensable tools for users across various industries and expertise levels, enabling efficient slicing of models into layer, support generation, optimal orientation, and customizable print settings.”
The three purposes of build preparation software, according to Egwin Bovyn, product line manager Magics 3D Print Suite, Materialise, is to control part quality, optimize machine output, and avoid build failure.
“Build preparation software arranges multiple parts with placement and orientation tools to help find
an optimal build strategy and ensure part quality. This minimizes time spent on manual placement and reduces printing time by optimizing the build volume usage. Good build software also helps with the profitability of your business by optimizing the total usage of the machine and reducing the number of failed builds,” continues Bovyn.
Alexander Oster, director of AM, Autodesk, says the main goal of build preparation software “is to help designers and engineers turn 3D models, ideas, and pixels into matter.” To achieve this “elegantly requires delivering well in several domains,” such as opening a file in another CAD tool, revising the design or modifying it, simulating a model prior to print, and executing inspection tools successfully.
Build preparation software arranges multiple parts with placement and orientation tools to help find an optimal build strategy and ensure part quality.
— Egwin Bovyn, product line manager Magics 3D Print Suite, Materialise
Today’s software solutions are increasingly advanced to keep pace. For example, Dyndrite’s GPU accelerated processing and Python APIs enable
An advantage to standalone, “it offers focused functionality tailored specifically for tasks like build preparation, providing users with specialized tools optimized for their needs. This focus can lead to more robust solutions and flexible usage options,” shares Hopwood.
Integrated software can be a true end-to-end solution, which takes the entire printing process and specific requirements into account. Allowing users to “design, optimize, and place a build to achieve the highest quality and fastest print speeds,” states Bovyn.
“Integrating build preparation software parametrically within CAD and CAM solutions is so empowering to the user that today’s dominant standalone software market will likely contract drastically in the years to come,” admits Oster.
The representative from Formlabs notes that while integrated solutions offer many advantages, there are also disadvantages. “Users don’t need to learn different software and can use a single screen to manage end-to-end workflows. However, these solutions are generally expensive and offer features that many customers don’t require.”
Challenges related to implementing a standalone solution include missing out on the benefits of an integrated solution. “Standalone software may lack seamless integration with other tools, potentially causing workflow inefficiencies and compatibility issues. Additionally, users might miss out on the benefits of a comprehensive software ecosystem, potentially requiring extra effort and increasing support and maintenance costs,” notes Hopwood.
“A standalone solution enables build preparation for one specific technology and for one specific machine. This is very limiting when a company wants to scale its operations. While this software is often created and provided by a machine builder, software development is often not these providers’ core goal, and their solutions often lack advanced performance and algorithms. This can make it difficult to achieve operational excellence with the machines,” shares Bovyn.
Build preparation software helps achieve efficiency as well as predictability during a 3D build. The tools in these solutions focus on data and the right combination of features to yield an optimal final part. IPM
Three-dimensional (3D) printing plays an increasing role in automobile manufacturing. Metal additive manufacturing (AM) is often utilized for this segment and technology continues to evolve.
Early adoption of metal 3D printing was primarily focused on prototyping and fixtures. With this technology, car manufacturers quickly produce prototypes of parts and components, allowing for rapid iteration and design improvement without the need for expensive tooling, shares Mark Norfolk, president, Fabrisonic LLC.
Sebastian Recke, senior key account manager, GEFERTEC GmbH, agrees, adding that car manufacturers utilize the advantages of AM/wire arc AM (WAAM) for items such as sheet metal forming tools.
in Metal AM Printing 1
“Metal printing also allows for rapid production and design iterations for jigs, fixtures, and other tooling equipment used in the manufacturing process. These custom tools help streamline production, improve accuracy, and reduce costs compared to traditional machining methods,” says Norfolk.
As technology evolves, metal printing moves into highly bespoke items for limited run specialty additions. 3D printing enables customization of automotive parts according to specific requirements or individual preferences. This includes
We see 3D printing as paving the way for a transformative future in automobile manufacturing by offering solutions to mitigate supply chain volatility and improve environmental impact.
—
interior features, exterior aesthetics, and even functional components tailored to a particular vehicle or customer, explains Norfolk. Along the same lines, printing has allowed innovation in racing. “In motorsports, where performance and weight are crucial, 3D printing is extensively used to produce lightweight and aerodynamic components. Teams can quickly design and fabricate custom parts to gain a competitive edge on the track,” says Norfolk.
Alexandre Tartas, global head of 3D metals go-to-market, HP Personalization and 3D Printing
In the motorsports sector, Andrew Hawkins, product marketing manager, Additive Industries,
shares that technology is used for production race car parts both structural and non-structural, as well as in the wind tunnel testing environment.
Recke suggests that 3D metal printing is still not primarily used for components installed in the car itself, but instead for tools required by car manufacturers. “Here, series production involves very large quantities at low unit costs. At best, the occasional use of 3D printed metal components can be observed in the luxury segment.”
While mainly leveraged by car manufacturers, the role of 3D printing for functional parts is not out of reach. Alexandre Tartas, global head of 3D metals go-to-market, HP Personalization and 3D Printing, argues that the use of 3D printing technology by automobile manufacturers and tier one and two suppliers has significantly evolved from its initial application in prototyping to its current role in producing engineering-grade, functional parts. “This shift was facilitated by not only significant advancements in 3D printing technologies, which now offer enhanced quality and repeatability in processes that are essential for automotive manufacturing, but also growing acceptance and accessibility to AM solutions for production in recent years.”
By integrating 3D printing capabilities in house, manufacturers gain the ability to rapidly respond to supply chain challenges, enhance performance by design, and transition to electrification in a costdriven industry without the lead times associated with traditional manufacturing methods. “With on demand manufacturing capabilities, OEMs and automotive suppliers can reduce their reliance on external suppliers, ensuring smoother production flows and enhancing overall operational resilience,” offers Tartas.
AM provides manufacturers with more flexibility, stresses Recke. “They manufacture tools and equipment for production quickly and easily. When developing new tools, changes to the component are made without great effort.”
Hawkins believes a key benefit for automotive customers’ production facilities is in reduced lead times compared to conventional production routes, particularly for small series production parts or development parts and jigs and fixtures.
“Also, for small series production parts and complex tooling significant functional performance improvements can be made as well as cost savings.”
To facilitate the widespread adoption of metal 3D printing in automotive manufacturing, Norfolk says several material qualifications issues must be addressed.
“Crucial among these are ensuring consistent material properties across batches, establishing standardized certification processes, testing to validate mechanical properties, implementing process control and quality assurance measures, and ensuring compatibility with post-processing techniques. Additionally, addressing cost considerations is vital to competitiveness with traditional manufacturing methods.”
In general, integrating 3D printing has transformed production facilities by significantly enhancing production flexibility, efficiency, and sustainability. Tartas admits that a common pitfall of traditional machinery utilized for part production is that it is designed to create one specific product, requiring the shipping of various parts, a largely energyintensive and costly process. In contrast, 3D printers optimize production facilities by enabling part production to take place exactly when and where specific parts are needed, eliminating the constraints of fixed tooling and reducing the time, cost, and CO2 footprint associated with part production and logistics.
“We see 3D printing as paving the way for a transformative future in automobile manufacturing by offering solutions to mitigate supply chain volatility and improve environmental impact. While AM currently serves as a strategic, adaptable solution, it holds the potential to uproot and grow the industry by enabling OEMs to rapidly adapt to changing market demands and reduce dependencies on complex, global supply chains, thereby optimizing production resilience and sustainability. Automotive electrification in particular—one of
the key challenges of the automotive industry—will benefit from the great value of metal AM to develop innovative solutions that drive faster transition to electric vehicles,” notes Tartas.
In recent years Norfolk notes progress in understanding the best uses of metal 3D printing within various industries. “With more real-world examples emerging, engineers are increasingly adept at recognizing where 3D printing’s distinct strengths are effectively applied.”
The increasing number of competitors on the market creates a clear dynamic and spurs providers to further develop systems. “In recent years, the quality of the system and sensor technology has continued to improve with experience. The machines score points for their high degree of industrialization, reliability, and robustness, while production speed has increased at the same
time. With the current level of automation, unmanned production is possible 24/7. With over 200 completed component projects, we have mastered the process, which remains one of the biggest challenges in 3D metal printing,” offers Recke.
After adopting polymer-based 3D printing technologies for many years, Hawkins says the automotive industry is able to use more metal 3D printing in its business due to vast improvements in hardware, enabling higher productivity, reduced part cost, and increased material options. “Companies like Additive Industries provide many opportunities to realize serial production, tooling, and prototyping applications by providing flexible, modular, and automated manufacturing systems, which enable automotive manufacturers to produce parts with high throughput in a range of alloys.”
AM is improving thanks to the introduction of engineering-grade materials as well as more stable and predictable
processes. “These advancements make AM much more efficient and cost effective than when the technology was first introduced, which is what is needed from an automotive manufacturing standpoint for the technology to be commercially viable,” comments Tartas.
HP’s journey from prototyping with OEMs to becoming a regular parts supplier for several big-name brands over the years has steered the company towards improving the reliability of its commercial 3D printers. “This experience and direct access to OEMs has also shown us what it takes for AM to be the disruptive production option we know it to be,” according to Tartas.
Norfolk says currently, automotive manufacturers use 3D printing to support manufacturing, versus manufacturing parts using 3D printing. “For example, makers print fixtures, jigs, and custom tooling to enable manufacturing. Automotive companies also use 3D printing for protoytyping—allowing them to quickly go from design to physical model. Some companies are printing spare parts when those parts are no longer in production. Other common applications include brackets that optimize design but would be difficult to manufacture traditionally.”
Many parts are produced in the vehicle prototyping phase, used in place of parts that typically have long lead times such as castings or forgings to enable more time and scope in the design cycle. “For low-volume production of high-specification vehicles, some of these parts are then introduced as the final production solution. Further, 3D printing is used to produce mold tool inserts with conformal cooling for die cast parts, which are enabling higher throughput and tool life due to the design flexibility to create highly optimized cooling channels,” says Hawkins.
The WAAM process is currently used primarily for tools and sheet metal forming tools. “If we look at the reasons for this, we see various advantages for manufacturers. Firstly, AM makes you independent of supply chains. In view of the current global upheavals, we are repeatedly seeing cases in which manufacturers are faced with the problem of procuring the parts they need in good time. Many of our customers therefore rely on local production with raw materials (wire) that are reliably available. Secondly, additional functions can be incorporated into the production process with WAAM, which would be difficult or impossible to achieve using conventional methods, for example by combining different materials or structures. Thirdly, 3D metal printing offers faster production times as well as cost and material
savings compared to conventional manufacturing processes such as milling or casting. Components or spare parts can be produced in a fraction of the usual time. This is particularly interesting for spare parts that are not needed regularly but can still be critical for the performance of a system,” explains Recke.
Compared to milling, metal printing saves up to 95 percent of material, depending on the component, as it utilizes most of the material used, according to Recke. This makes the process particularly interesting for high-quality materials or materials that are difficult to machine.
Tartas points out that OEMs use 3D printed parts on their vehicles every day, many of which are entirely new, highly complex, and sustainable designs made possible only by building additively. These could be engine components that
withstand high-temperature and highpressure environments, high-performance braking systems, and even lightweight auto body parts that improve a vehicle’s efficiency.
AM has the ability to handle many different configurations in comparison to the limitations faced with traditional manufacturing processes. “At the end of the day, it all boils down to part function and design for AM principles—we have to focus on the right parts that would benefit most from being 3D printed,” shares Tartas.
3D metal AM is regularly utilized by car manufacturers for tooling parts. However, as technology advances it is making headway into actual parts production in the automotive space. IPM
on plastic can be more cost effective than traditional methods. “This is because it eliminates the need for additional materials, like adhesives or labels. Additionally, the durability of the plastic can reduce the need for reprints due to damage.”
Plastics are everywhere and often require decoration, notes Larsen.
Hawkes adds that short-run production for a variety of industries provides many opportunities for DTO printing onto plastics. “Manufacturers can brand and differentiate the production of such items to reach additional markets affordably and effectively.”
“Countless DTO printing applications can be produced using plastics as a substrate, but two application types that stand out are personalization and promotional branding,” shares Gonzalez. One example is a print service provider (PSP) that prints its customers’ photographs onto acrylic puzzles, personalized awards, and
2. Modern printing technologies like offset and Apex’s patented, FlexApex, produce high-quality prints directly on plastic. These methods offer vibrant colors, sharp details, and smooth finishes, making printed graphics visually appealing and impactful. 3. LogoJET provides UV printers specialized for direct printing on plastics, catering to a broad spectrum of material types.
even personalized signage. Other PSPs dedicate their work to producing promotional branding. “They can quickly print on trays of plastic items such as pens, badges, cellphone covers, water bottles, and cups.”
The promotional products sector dominates the customization and logo market, leveraging plastics for items like keychains, pens, and various accessories.
“These products provide excellent surfaces for applying vibrant, full-color UV prints directly, making them ideal for brand promotion,” says Cox.
Award and promotion shops are another avenue. “ADA braille printers and industrial manufacturers are all using a variety of plastics,” says Litardo. “The profit margin on ADA braille signs is huge. The profit from ADA braille can easily pay for a printer in a short period of time.”
The demand for premium architectural signage is also on the rise, with a particular interest in utilizing acrylic and other plastics that can be laser engraved or routed. “This technique is widely adopted for creating sophisticated indoor signage for offices, walls, and other spaces. The incorporation of UV printing on these materials allows for the addition of vibrant colors and intricate designs, further elevating the aesthetic and functional appeal of architectural environments. These advancements offer architects and designers new opportunities to integrate branding and directional signage seamlessly into their projects, merging functionality with high-end design aesthetics,” offers Cox.
In consumer products, Larsen sees two areas where digital inkjet decoration helps. “One is for products like cosmetics, with a multitude of color variations on the same label. The second is for mass produced products where the inline capabilities of digital inkjet can save considerable
money in the logistics of procuring, managing, storing, and applying labels.”
“Food, beverage, cosmetic, and medical market players are placing more value on branding of containers and DTO can be a promising method for them,” notes Juan Kim, CEO, Valloy Incorporated.
Consumer electronics is another industry with potential. It frequently uses plastics such as ABS and polycarbonate for casings, panels, and accessories. “These materials are particularly suited for UV inks due to their inherent surface energy, facilitating strong adhesion and lasting prints,” agrees Cox.
Gonzalez agrees that this space is growing for DTO for plastics due to increasing demand for personalized electronic accessories such as phone cases and laptop covers.
Moving into more industrial applications, Larsen points out that high-volume industrial containers like paint buckets and caulk tubes can be short runs or custom colors where the benefits of digital inkjet production is important.
Kim sees industrial substrate decoration on rigid or flexible material as a huge market. “Ceramic tile or artificial marbles are often produced by DTO now.”
The automotive industry utilizes DTO printing on plastics for customizing interiors, such as dashboard panels, trim pieces, and gauge dials. “The opacity lends itself to selectively covering LED panels,” shares Gonzalez.
Cox sees a noticeable shift in the automotive industry from traditional silk screening to digital direct printing for component and part labeling. “This transition allows for more dynamic color options and intricate designs, enhancing the aesthetic appeal and functionality of automotive parts.”
There is also a place for this technology in healthcare and medical devices. “DTO printing on plastics has generated some interest in items that require regular sanitation such as hospital signage and some medical instruments,” notes Gonzalez.
And of course, we can’t forget packaging. “The packaging sector is increasingly opting for direct printing on containers and closures over traditional labels or decals. DTO printing offers a perceived higher value and aesthetic appeal, allowing brands to stand out on the shelves by integrating intricate designs and vibrant colors directly onto their packaging,” says Cox.
Kim agrees, adding that brand owners look for enhanced levels of brand presentation by in-house process. “In-house label printing and cutting can be an option but it needs a separate process line and there are more regulations to limit label size, substrate type, and removability, due to environment and recycling issues. Direct printing covers less coverage on the plastic containers and it is suitable to put in the middle of a production line.”
As a maturing technology, there are still many challenges to direct printing on plastics. Surface preparation is essential to improving adhesion properties on certain plastics.
Properly preparing the plastic surface for printing is crucial. This involves several steps, including ensuring the surface is clean of fingerprints and dust, reducing static electricity that can attract dust, and applying treatments to enhance adhesion. “Removing protective liners from materials like acrylic can also introduce static, complicating the preparation process,” shares Cox.
Adhesion—and the resulting quality—is a top limitation for some plastics. “Not all plastics will provide the necessary adhesion to produce sellable output. There are also plastics that will not handle well during the curing process,” comments Litardo.
Adhesion promoters are designed to significantly improve the ink’s ability to adhere to a variety of plastics.
Employing methods like corona and plasma treatments enhance the plastic’s
surface energy, promoting better ink adhesion. These treatments are crucial for preparing plastics, especially those known for challenging ink adherence,” notes Cox.
“Achieving strong ink adhesion on certain plastics remains a significant hurdle,” admits Cox. Materials like polyethylene, polypropylene, and nylon, known for their flexibility and cost effectiveness, present challenges for UV printing without extensive pretreatment. “These plastics often require additional processes such as plasma treatment, the use of adhesion promoters, or flame treatments to prepare the surface for printing. This necessity adds steps to the production process, potentially increasing costs and complexity.”
Gonzalez agrees, noting that a primary limitation is the surface dyne level of certain plastics, which may require additional priming or surface treatment processes to ensure proper adhesion. “Some plastics are specifically designed to resist degradation or to be stain resistant—these properties usually reduce the surface tension, which reduces the adhesion properties. Another common challenge to DTO is that the print surface isn’t always flat. Most printers have tight tolerances on the
ability to print clearly on uneven surfaces, so prints can end up having different ranges of print quality.”
James Bullington, CTO, LSINC, adds that flexible plastics may require a flexible ink. “Squeeze bottles and flexible cups suffer from cracking and flaking if the layer thickness for a semi-rigid ink is too thick.”
Care must be taken with the jetting distance and static on the surface of the media. “Stadium cups often have a lip that increases the jetting distance from the head to the surface; as a result, they are more susceptible to image defects caused by static on the surface of the media. Plastics often carry a surface charge that will pull overspray onto the surface outside the target print area. Neutralizing the charge becomes essential,” says Bullington.
Cox points out that the diversity in plastic materials means that not all are compatible with DTO inkjet printing techniques. “The surface energy and texture of the plastic play critical roles in how well the ink adheres and the quality of the final print. Plastics with low surface energy or highly textured surfaces may not hold ink as well, leading to issues with print durability and fidelity. This limitation necessitates a careful selection of materials based
is fed onto the machine for processing. Even seemingly basic features, such as the material hold down, play an important role in maintaining the stability of
the substrate and ensuring clean, precise cuts,” adds Drury.
Single face as well as single/double/triple wall are used in corrugated for packaging. In this regard, finishing devices must be equipped to handle media properly.
“All kinds of corrugated materials are being used, depending on the application, from the lighter single face to heavier triple wall,” admits Gallucci.
Drury says single- and double-wall corrugated are more common in most packaging environments, however Zünd can offer individually tailored cutting solutions for every type of packaging application, including for processing related materials such as protective foams.
Corrugated finishing techniques vary. Die or dieless digital cutting both have advantages. We look forward to witnessing what’s next in corrugated finishing at SuperCorrExpo in September 2024.
Dedicated to the corrugated packaging industry, SuperCorrExpo brings together professionals, suppliers, manufacturers, and experts worldwide to showcase the latest technologies and equipment; exchange knowledge and resources; and foster new business partnerships. It takes place every four years and is organized by TAPPI and AICC. We will have more information on SuperCorrExpo in our September issue.