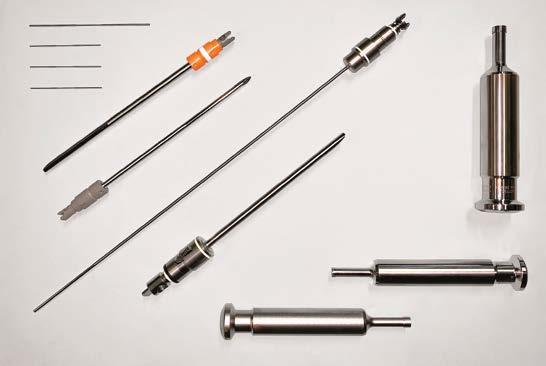
11 minute read
Ghiringhelli, quasi un secolo di
STORIA di copertina
GHIRINGHELLI
RICONOSCIUTA SUL MERCATO MONDIALE COME “PROBLEM SOLVER”, LA STRATEGIA VINCENTE DELL’AZIENDA È QUELLA DI DIVERSIFICARE LE APPLICAZIONI DI RETTIFICA IN TUTTI I CAMPI IN CUI LA PRECISIONE È D’OBBLIGO Patrizia Ricci
GHIRINGHELLI,
QUASI UN SECOLO DI
SOLUZIONI DI RETTIFICA Giunta ormai a pochi mesi dal centenario della fondazione, la Rettificatrici Ghiringhelli spa, azienda leader per la costruzione di rettificatrici senza centri a controllo numerico, è apprezzata in tutto il mondo non solo per la qualità delle sue rettificatrici ma anche per la capacità di soddisfare ogni tipo di richiesta e di offrire un’ampia gamma personalizzata di accessori. Le macchine prodotte dall’azienda di Luino (VA), precise, affidabili ed altamente G Inutile nascondere che i dati dell’automobile siano oggi disarmanti, dato il calo della produzione e della domanda di veicoli registrato quest’anno. È ovvio quindi che l’avere diversificato i settori merceologici applicativi delle nostre rettificatrici senza centri ci permette di affrontare la crisi in atto con prospettive diverse. Tra questi il settore del medicale che, pur con dimensioni inferiori rispetto all’automotive, non solo ha buone prospettive di dell’ago nella cute, diminuisce il dolore dell’iniezione. Negli anni successivi sono diverse le applicazioni realizzate in questo settore con aziende italiane e internazionali. Tra queste, la fornitura di macchine per la rettifica di punzoni speciali impiegati nella produzione di compresse. “Il nostro approccio al settore medicale – spiega Marco Barzaghi, Responsabile Commerciale dell’azienda - è analogo a quello degli tecnologiche, trovano applicazione non solo crescita avendo manifestato negli ultimi anni altri settori, ovvero partiamo sempre dalla nei settori più congeniali della rettifica quali un trend costante, ma richiedendo dal nostro specifica richiesta del cliente per realizzare l’automotive, l’industria dei cuscinetti, l’inpunto di vista, precisioni, tolleranze e caratsoluzioni customizzate. Tra le tante soluzioni dustria dei motori elettrici e l’utensileria, teristiche di impianti del tutto simili a quelle realizzate possiamo citare, a titolo di esempio, ma anche nell’industria tessile, l’idraulica e dell’automotive, consente di realizzare applila fornitura di una nostra rettificatrice senza il medicale, ovvero in tutti i campi in cui la cazioni parimenti interessanti”. centri all’interno di una linea di produzione di precisione è d’obbligo. “Questa strategia azienclip da aneurisma al fine di aumentare la prodale, da diversi anni incentrata sulla diversifiIl settore medicale duttività e l’affidabilità del processo, ed ottecazione dei settori applicativi, si è dimostrata L’esperienza maturata dalla Ghiringhelli nere un prodotto di maggiore qualità. Il ciclo vincente per una piccola realtà come la nostra nel settore del medicale risale agli inizi degli completo comprendeva 23 diverse operazioni particolarmente sensibile all’aspetto dei conanni 80, con la partecipazione allo sviluppo ed era fondamentale garantire l’affidabilità al sumi – afferma Patrizia Ghiringhelli, Ammidella tecnologia alla base dell’ago PIC, risul100% di ogni singolo passaggio per evitare nistratore Delegato dell’omonima società -; il tato dell’“indolor experience” (tecnologia fermi o cali di produzioni dovuti a pezzi non fatto di non essere legati esclusivamente al setindolore). La tecnologia che a partire dalla conformi. La macchina fornita, una M100 tore dell’automotive rappresenta, oggi più che cannula, grazie alla triplice affilatura studiata CNC6A, era stata pertanto dotata di un mai, con l’emergenza epidemiologica in corso, per aumentare la penetrabilità dell’ago ridusistema di carico e scarico dei pezzi compleuno dei punti di forza della nostra azienda. cendo la forza necessaria per la penetrazione tamente automatico e profilo della mola ope-
ratrice eseguito tramite due assi controllati e utensile diamantato in rotazione e traslazione.
Per un altro cliente invece, un’azienda leader nella produzione di protesi ossee e frese speciali utilizzate in chirurgia ortopedica, abbiamo realizzato una soluzione alquanto flessibile che ha permesso non solo di garantire la produzione standard, ma anche di assicurare lo sviluppo di prototipi studiati dal reparto Ricerca Sviluppo. La nostra rettificatrice senza centri APG-S CNC7A è stata equipaggiata con 7 assi a controllo numerico che permettono la profilatura sia della mola operatrice che della mola conduttrice, oltre che il ciclo di lavoro automatico con la possibilità di variare e impostare profili dai più semplici ai più complessi. L’impianto è interfacciato con un sistema di carico e scarico dei pezzi rettificati completamente automatici che prevedeva l’utilizzo di un caricatore a portale a 3 assi a controllo numerico.
Infine, vale la pena citare anche l’ultimo impianto fornito ad un’importante azienda tedesca per la rettifica di cannule e dispositivi per l’esecuzione di interventi in laparoscopia. Sino a quel momento il cliente affidava la fase di rettifica a fornitori esterni, ma la necessità di avere un controllo totale su tutto il ciclo di produzione di questi particolari l’ha indotto alla decisione di introdurre in azienda anche questa lavorazione. Era quindi alla ricerca di un costruttore che gli potesse fornire non solo una soluzione tecnicamente adeguata, ma che lo supportasse soprattutto nella fase di implementazione e di formazione degli operatori dedicati alla gestione dell’impianto. Grazie alla nostra consolidata esperienza e alla nostra riconosciuta capacità di soddisfare le specifiche richieste degli utilizzatori finali delle nostre rettificatrici senza centri, siamo riusciti a conquistare la fiducia anche di questo cliente e ad assicurarci la fornitura. In particolare, proprio per unire ai concetti di affidabilità e alta precisione della macchina anche la massima flessibilità del processo, la scelta è stata per una M100 CNC6A atta alla lavorazione di particolari sia con ciclo a tuffo che in infilata. La macchina è stata corredata di un unico sistema di carico studiato per poter asservire entrambe le operazioni. La rettifica completamente automatica è infatti dotata di 6 assi a controllo numerico per la gestione dei carri di lavoro, della diamantatura mola operatrice e diamantatura mola conduttrice. Dato l’importante quanto delicato utilizzo dei dispositivi prodotti dall’azienda, il cliente richiedeva una soluzione che gli permettesse di ottenere particolari perfettamente conformi alle specifiche e con un certo orgoglio possiamo dire di essere riusciti a garantirgli un processo sicuro al 100% e di averlo pienamente soddisfatto”.
Una produzione su commessa
La caratteristica distintiva della Ghiringhelli è quella di risolvere problemi, ovvero costruire macchine su commessa. A partire dagli anni 80, l’azienda abbandona la produzione standard e si specializza sul mercato mondiale come “problem solver”, rapportandosi con grandi aziende strutturate e importanti gruppi internazionali con notevoli aspettative sulla qualità del prodotto. Nell’ultimo ventennio l’azienda di Luino indirizza tutti gli sforzi di rinnovamento nella conferma di questa politica aziendale per far fronte alle
richieste di tempestività del mercato e al contempo alle esigenze produttive dell’utilizzatore con una soluzione customizzata e realizzata ad hoc. “La scelta di proporci come problem solver ha garantito all’azienda una leadership di mercato, ma ha inevitabilmente portato ad una complessa organizzazione interna. Fino agli anni 90 – precisa Patrizia Ghiringhelli – si attendeva infatti l’acquisizione dell’ordine e la configurazione definitiva della rettificatrice senza centri per avviare le attività interne di costruzione e di sviluppo della commessa. Ne conseguiva un dilatarsi delle tempistiche e un appesantimento dell’intero flusso aziendale. In tempi più moderni i tempi di decisione si sono notevolmente ridotti: il tempo di passaggio tra la conferma dell’ordine del cliente e la consegna dell’impianto risulta decisamente più contratto. Occorreva quindi snellire la nostra organizzazione interna per cercare di essere più tempestivi sul mercato, ma fermo restando la volontà di preservare la connotazione di problem solver che il mercato ci riconosce. Abbiamo così intrapreso un importante quanto strategico processo di riorganizzazione interna che ci ha consentito appunto di mantenere la nostra peculiarità, la capacità cioè di fornire soluzioni personalizzate, e di aumentare l’efficienza interna, scegliendo di costruire le nostre macchine con un approccio modulare. In particolare, ad oggi attraverso una pianificazione puntuale vengono lanciati preventivamente i modelli delle nostre rettificatrici senza centri al centro della richiesta di mercato e viene lasciata la personalizzazione della soluzione solo nelle ultime fasi”. Quello che caratterizza l’azienda più di ogni altra cosa, è che, sebbene la macchina rappresenti il prodotto principale, questa sia solo una parte della soluzione proposta. “Il punto di forza della Ghiringhelli – specifica Barzaghi – è nella vendita di soluzioni di rettifica, il cui punto di partenza è lo studio di fattibilità con il cliente. È da questo co-engineering tra l’esperienza del cliente del particolare da lavorare e la nostra competenza nel processo di rettifica che viene ottimizzato il processo. La soluzione fornita è infatti studiata non solo in funzione della dimensione, geometria, forma e dei volumi dei componenti del cliente da produrre, ma con un’analisi tecnica e commerciale del processo di rettifica richiesto analizzando le possibilità di miglioramento e proponendo la soluzione ad hoc completa di automazione, asservimenti, manipolazione, controllo e misurazione”.
Una organizzazione snella
Il lancio in produzione dei modelli richiede necessariamente che tutta la filiera, a monte e a valle, sia organizzata per il miglioramento del flusso produttivo, dall’approvvigionamento alla realizzazione della commessa. “Accanto alle lavorazioni dei particolari più strategici effettuate all’interno della nostra azienda – spiega Patrizia Ghiringhelli – la realizzazione di numerosi pezzi meccanici è invece affidata a fornitori esterni, costantemente selezionati, che siamo più correttamente soliti definire partner. Tuttavia, questo richiede un grande impegno nella gestione degli ordini e nel controllo delle scadenze per un flusso costante di approvvigionamento. Noi siamo riusciti ad ottimizzare la nostra supply chain e soprattutto ad aumentare l’efficienza in termini di consegna da parte dei nostri fornitori grazie al processo di riorganizzazione interna. In particolare, l’introduzione in azienda dei principi base della Lean Production e il passaggio da una produzione a lotti a una produzione a flussi ci ha permesso di migliorare il flusso dall’approvvigionamento alla realizzazione della commessa stessa. Abbiamo dapprima definito la cadenza di produzione (il c.d. Takt time) e tutti i passaggi interni sono stati pen-
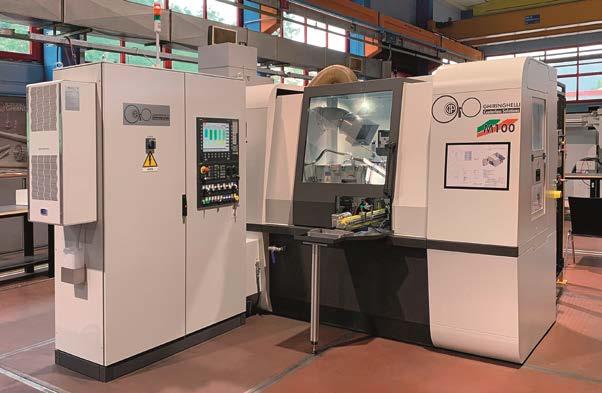
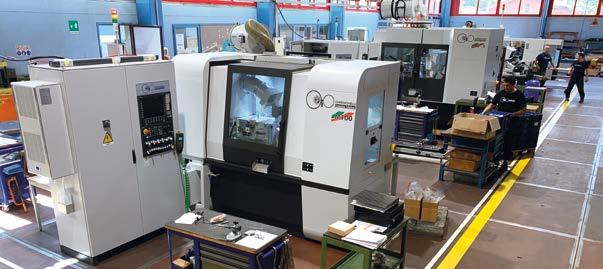
sati in funzione di questa cadenza, abbiamo poi introdotto la logica pull che ha permesso di rendere fluido il processo, in quanto le fasi precedenti sono ora tirate da quelle successive, e di garantire il rispetto dei termini di consegna. Tutti sono coinvolti e devono inserirsi in questo processo, anche i fornitori esterni. La riorganizzazione infatti non è stata applicata solo alle aree aziendali, ma è stata estesa anche alla rete dei nostri partner. Abbiamo a questo proposito stipulato con i nostri fornitori un accordo di fornitura per garantire il rispetto dei
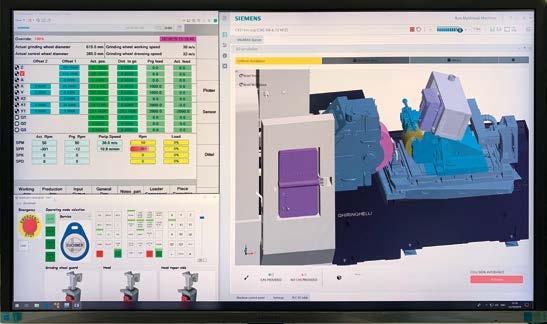
termini di consegna e la conformità delle forniture, e al nostro interno rivisto il layout dei reparti produttivi adottato la c.d. segnaletica orizzontale che ci garantisce ordine e corretto posizionamento di materiali ed attrezzature. Pur essendo una piccola realtà aziendale –
continua Patrizia Ghiringhelli - riusciamo ad affrontare un mercato globale con una indiscussa leadership internazionale e una forte propensione all’export (circa l’80/90% degli impianti sono infatti destinati a Germania/ Cina/Europa dell’est/ Sud America). Risultati questi possibili solo con un’organizzazione efficiente e snella che oggi possiamo vantare anche grazie, come detto, all’adozione dei principi base della Lean Production e all’implementazione di tecniche di visual management che, rendendo appunto immediatamente visibile lo stato di avanzamento delle commesse in produzione, ci permette di migliorare la nostra efficienza e il nostro lead time. Il tutto mantenendo la vocazione di soluzioni customizzate. Il grande sforzo è stato proprio quello di adattare concetti propri e tipici di prodotti standard a un’azienda come la nostra, che è nota sul mercato per costruire una macchina attorno alle esigenze del cliente”. Il processo di ottimizzazione della gestione delle commesse non è ancora completato. “Uno dei prossimi obiettivi – spiega Marco Barzaghi – sarà di ridurre al minino le scorte, anche se una “scorta zero” sarà impossibile da raggiungere per tutti gli articoli che gestiamo, soprattutto per alcuni materiali con lead time lungo di approvvigionamento, ma strategici soprattutto per il servizio post vendita che offriamo in tutto il mondo sulle nostre macchine, attraverso il

personale interno o quello presente nei centri di assistenza esteri, periodicamente formato dalla nostra azienda”.
Il gemello digitale
Diventare più flessibili, riducendo il time to market, i costi e le manutenzioni, migliorando la qualità e aumentando la produttività a tutti i livelli dell’organizzazione di un’azienda è una esigenza del mercato che può essere soddisfatta anche grazie all’introduzione di processi produttivi dotati di gemelli digitali. La creazione di un DT (Digital Twin) del prodotto, processo e automazione impiegati, consente l’interazione in un unico sistema che unisce il mondo reale e virtuale, implementando il concetto di digitalizzazione che caratterizza il paradigma Industria 4.0. “L’automazione – spiega Patrizia Ghiringhelli - ha da sempre caratterizzato le nostre macchine: siamo stati tra i primi costruttori al mondo di rettifiche senza centri a dotare le nostre macchine di un controllo numerico, passando da una versione idraulica ad una gestione elettronica. Fin dall’inizio, abbiamo individuato in Siemens un partner di riferimento per l’automazione delle nostre macchine instaurando una fattiva collaborazione che ha portato la multinazionale tedesca a scegliere, tra un numero limitato di aziende trendsetter in tutto il mondo provenienti da realtà manifatturiere eterogenee, la Ghiringhelli, quale unico costruttore italiano di rettificatrici senza centri, per lo sviluppo del primo CNC “nativo digitale”. Questo ci ha consentito di presentare lo scorso anno alla fiera EMO 2019 di Hannover una rettificatrice senza centri APG-S progettata, realizzata e gestita totalmente impiegando e integrando questo nuovo controllo Siemens denominato SINUMERIK ONE”. Avere una copia digitale della macchina consente al costruttore di ottimizzare la soluzione finale, anticipandone la messa in servizio per l’individuazione di eventuali anomalie in fase di progettazione, e all’utilizzatore di effettuare una serie di test, prove e modifiche, senza intervenire fisicamente sulla macchina. “Questa novità – continua Ghiringhelli - offre all’utilizzatore quella flessibilità che gli consente di testare ed estendere la macchina alla produzione di altre serie di famiglie di pezzi che nel tempo può avere necessità di produrre, rispetto alla famiglia originaria per la quale la macchina è stata realizzata. L’ottimizzazione del processo gli consentirà inoltre di entrare in produzione in tempi molto più rapidi e con una maggiore efficienza. Il gemello digitale rappresenta indubbiamente un plus per i nostri clienti e rappresenta un elemento distintivo a conferma della capacità della nostra azienda di fornire soluzioni su misura del cliente e tecnologicamente avanzate, anticipandone le esigenze e traducendole in prodotti”.
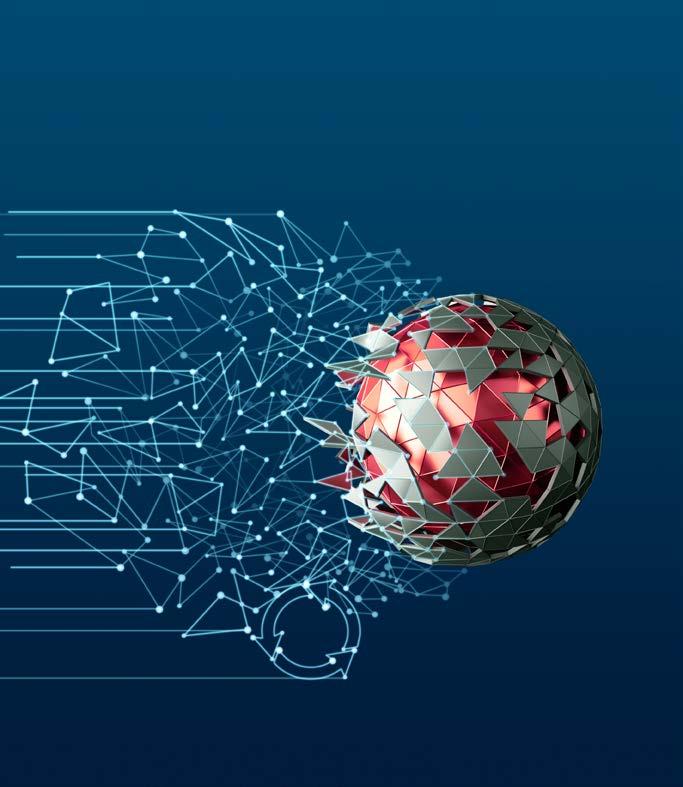
DOSSIER
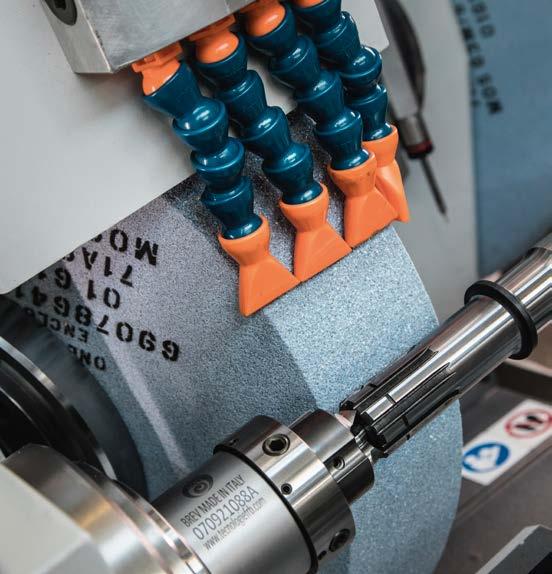