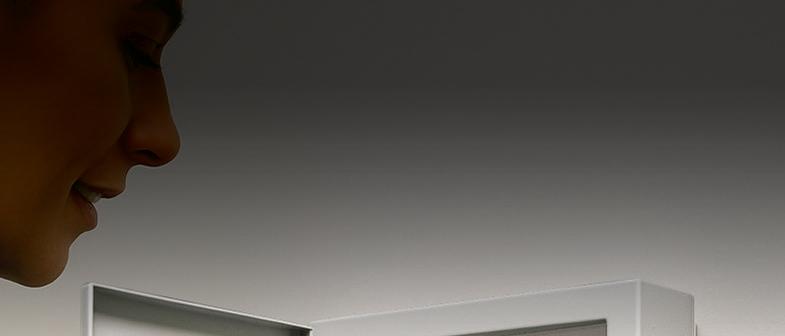
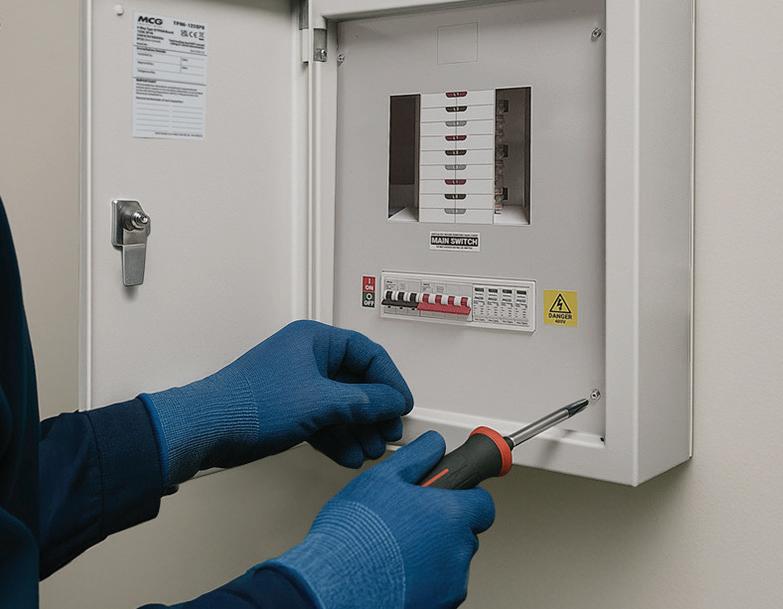

The latest addition to the technologically advanced 30 0 0 Series, the Ei3030 combines individual Optical, Heat and CO sensors for the ultimate fire and CO response, while maintaining the simplicity that Installers love.
Smart, connected and future-proof.
Scan here to learn more about the Ei3030
Add the Ei3000MRF for wireless interconnection and data extraction via the Ei1000G Gateway
SMART HOMES
14 Sponsor Q&A: LUCKINSlive
Corner
18 IR35 update: What the changes could mean for contracting 19 Hit the ground running this Autumn
& MEASUREMENT 24 Safety first, because it matters
Innovation, accuracy, and unrivalled support for professionals
with solar
38 Smart appliances in grid-interactive homes and buildings
40 Digitalisation and the future of low-carbon housing
41 The future’s smart: how IoT is transforming home energy
10 Think you know Greenbrook... think again!
42 Tool up for solar
48 PowerPro:
In June, Chancellor Rachael Reeves unveiled the Spending Review 2025, featuring a significant initiative to lower home energy costs through the Warm Homes Plan.
Commenting on the announcement, Tamsin Lishman, CEO of Kensa, said: “Today’s confirmation of a significant £13 billion budget for the Warm Homes Plan is a hugely positive step towards improving the efficiency of our homes, cutting energy bills and ending our reliance on imported fossil fuels. With home grown renewable energy increasingly the cheapest option available, it no longer makes sense to warm our homes by burning gas extracted thousands of miles away, transported here in tankers, heating the planet in the process.
“The commitment to adequately fund the Warm Homes Plan is a firm acknowledgement of the challenges we face in upgrading our homes, but also of the government’s determination to tackle these head on. For too long heat policy suffered from uncertainty and indecision, delaying action and dampening investor confidence. But today’s Warm Homes commitment, and last week’s confirmation that the Future Homes Standard will soon end boiler installations in new homes, demonstrates the leadership needed to kickstart a clean heat revolution.“
Lisa Peake, EDITOR, lisa.peake@purplems.com
haydon.rainsford@purplems.com
Scolmore Group is pleased to announce the appointment of Charlotte Clarkson as Area Sales Manager for the Hereford, Worcester, Warwickshire, and Staffordshire regions.
Having started her career at the age of 19 as an apprentice with an electrical accessories manufacturer, Charlotte brings a wealth of expertise to her new role. Throughout her career, Charlotte has successfully worked within a diverse range of sectors, including electrical wholesalers, contractors, plumbing and heating merchants, education, and the NHS.
Lucy Electric welcomes Mark England as Digital Solutions Director, as the company looks to expand its new digital solutions offering.
Mark brings over 30 years of industry experience to the role. He most recently served as a global VP of Technology at Xylem, a worldwide leader in advanced water and energy solutions. Prior to that Mark was CEO of Sentec, where he played a leading role in scaling the company from a startup to a global technology consultancy with a specialist focus on developing Smart Grid and Smart Metering technologies.
Mourya Ghosh has joined Enspec Power as its new Head of Engineering. He boasts 15 years of leadership experience in electrical design, product development and cross-functional innovation.
Abount Mourya, Enspec majority shareholder and Chief Technical Officer Tim Rastall said: “His talent for blending insight with real-world engineering solutions makes him the perfect fit for shaping and delivering the next generation of new-to-market technologies. We’re excited to see where his leadership will take us.”
Leeds-based electrical engineering specialist, Meson, has announced a significant business expansion with the launch of a dedicated Commercial Solar division and the appointment of a new business leader.
Dean Betteridge, who brings over 13 years of experience in continuous development, joins Meson from Fera Science, where he successfully managed high-impact projects, including the delivery of £3 million worth of new property and assets.
ABB ELDS responds to Iberia blackout findings “True resilience is about a system that can adapt”
Following last month’s publication of Spain’s official investigation into the April 28 blackout, Adrian Guggisberg, Division President, Electrical Distribution Solutions at ABB Electrification, has warned that grid resilience must now be treated as an economic imperative, not just a technical upgrade. Guggisberg commented: “Today’s critical infrastructure needs a reliable, stable energy supply – yet grids are being pushed to their limits. The rise of decentralised energy sources, electrification of industry and transport, and digitalisation of everything from buildings to mobility are placing unprecedented demands on ageing electrical systems. Managing this variability while maintaining reliability and protection is a major engineering challenge of our time.
“Meeting these challenges takes more than upgrades. It requires a smarter, more connected approach to electrical infrastructure. This includes everything from substations and feeders to automation systems, protection devices, and yes, medium-voltage switchgear – which plays a key role in controlling power flows and isolating faults.
“True grid resilience isn’t about one technology. It’s about a system that can adapt, isolate faults quickly, recover autonomously, and support real-time decision-making. Upgrading the grid is not just a technical challenge; it’s an economic imperative.”
The full report cites inadequate reactive power reserves and a lack of fast-acting fault isolation as key technical shortcomings in the incident.
Alfa Laval calls for ‘big picture thinking’ on heat network zoning rollout
Ahead of the rollout of the Department for Energy Security and Net Zero’s (DESNZ) heat network zones, Alfa Laval is calling for the long-term implementation to go beyond that of just district heating, with a view to creating a nationwide district energy infrastructure.
The initial rollout of DESNZ’s zoning programme began with the identification of 28 pilot locations where heat networks are likely to grow or be built out in the future. Following this, six areas across the UK – Bristol, Leeds, Plymouth, Sheffield, Stockport, and two London sites – are set to be the beneficiaries of £5.8 million in shared government funding in order to help establish the zoning model, with construction set to commence in 2026.
As part of the scheme, it is expected that district heating will be the lowest cost of energy within each zone, with the wider goal of growing total demand from 3 per cent in 2024 to 20 per cent by 2050.
However, with the current rollout only legislating for district heating at present,
Neil Parry, Alfa Laval’s Global Head of District Energy, is highlighting the necessity for district cooling. He said: “The UK is experiencing increasing temperatures due to climate change. By 2050, we will have just as much need for district cooling as we do for district heating, which is why it would be a critical misstep if the ongoing rollout was only limited to the latter.
“Beyond this, the integration of both technologies together is also fundamental to the concept of district energy, which will be critical to tapping into the nation’s waste energy potential and forging a credible path to Net Zero.”
CU Phosco is proud to announce the promotion of Stuart Murray to the role of Contracts Director Designate.
Stuart has been with CU Phosco for over 17 years, having joined the company on a sandwich placement from Northumbria University in 2006. Over the years, he has played a pivotal role in the growth and success of the Services Division.
His dedication to client satisfaction, hands-on approach to project management, and ability to build and lead effective teams have helped CU Phosco deliver high-profile floodlighting and high mast installations across the UK and Ireland.
Ariston, the global expert in sustainable water heating and thermal comfort, has appointed Hans Juergen Bahnsen as its new UK and Ireland Senior Sales Manager.
After spending 15 years in various roles at Bosch, Hans brings a wealth of valuable industry experience, with his most recent role being Head of Industrial Sales for the UK & Ireland. With his strong technical background, proven sales expertise, and effective people management skills, Hans will lead Ariston’s area sales and pre-sales teams, driving increased sales turnover and improved profitability.
Schneider Electric has appointed Jacqui Whitaker as its new Vice President of Finance, UK and Ireland (UKI). Jacqui will lead the UKI finance team, focusing on maximising investment returns, supporting growth opportunities, and driving forward Schneider Electric’s broader sustainability goals.
She steps into the role with nearly a decade of international experience with Schneider Electric, having led the international business finance function across 100+ countries in South America, the Pacific, the Middle East, and Africa.
Toolstation has appointed Sam MacGregor as its new Retail Director. Sam joins the business from Homebase, where she held the role of Retail and People Director, and for two years before that held the position of Head of Marketing. She has held senior roles at some of the best-known retailers in the UK including HEMA, BHS, Asda, B&Q , Somerfield and M&S.
VIVID’s Victory Quay development in Portsmouth welcomes Homes England
Homes England visited VIVID’s landmark Victory Quay development in Portsmouth, recognising the project’s role in delivering not just new homes, but a thriving, inclusive community on the city’s historic waterfront.
Funding from Homes England is playing a vital role in making Victory Quay possible, this support is unlocking the potential of a long-unused brownfield site, allowing VIVID and its partners to focus on delivering 835 high-quality homes, many of which will be affordable.
Tristan Samuels, Group Development and New Business Director of VIVID, said: “Victory Quay is more than just bricks and mortar — it’s about creating a place where people feel connected, supported, and proud to live. Working with our partners is crucial in creating a well-connected, sustainable neighbourhood that will serve the people of Portsmouth for years to come.”
Pauline Schaffer – Director of Infrastructure Funding of Homes England, commented: “Funding from the Brownfield, Infrastructure and Land Fund is enabling the development of around 835 new homes at Tipner East in Portsmouth.
The Victory Quay development is an excellent example of how we are supporting partners like VIVID and Portsmouth City Council to create new homes and thriving places that people can be proud of.”
Segen has announced a strategic partnership with BNP Paribas Leasing Solutions to provide tailored end-to-end financing solutions under the Segen Finance brand.
The new offering will allow commercial and industrial (C&I) end-customers to install solar and energy storage systems with no upfront costs, enabling them to immediately benefit from reduced energy costs and carbon emissions.
Segen Finance will be available exclusively through Segen’s extensive network of approved C&I installers across the UK and Germany initially, with planned expansion across Europe. Installers will be able to offer tailored lease quotes alongside their technical solutions, delivering a seamless experience for end customers.
“This partnership addresses one of the key barriers to clean energy adoption—initial
investment costs,” says Pascale Favre, Head of Technology Lifecycle Solutions at BNP Paribas Leasing Solutions.
“By combining our financial expertise with Segen’s technical knowledge and distribution capabilities, we’re making sustainable energy solutions accessible to more businesses while supporting their cash flow management.”
Nicolas Niedhart, Group Chief Financial Officer at Segen Global, comments: “Our installer network has been asking for integrated financing solutions that make the transition to renewable energy more affordable for their customers. Segen Finance transforms our installers into total solution providers, while allowing their customers to preserve capital for other strategic investments. This partnership represents a significant advancement in accelerating the clean energy transition.”
Our Stainless Steel Grommet is an elegant, premium quality floor-access solution that allows you to connect seamlessly with your underfloor power distribution system.
The Stainless Steel Grommet is designed for use in high-end commercial environments and is suitable for raised floor applications. It can be installed in a range of flexible and efficient configurations that permit safe and easy of access to power and data services within the under-floor void.
carpet installations.
AEI Cables is seeing positive feedback to its guidance for closer working to meet the requirements of the Building Safety Act 2022. The Act makes new stringent requirements for higher-risk buildings which are those deemed to be of at least 18 metres in height or at least seven storeys containing at least two residential units.
Stuart Dover, general manager of AEI Cables, said: “We believe in early collaboration on our own projects and the feedback we are receiving suggests that close working between all parties in the supply chain is helping to meet the requirements of this new legislation.”
The Building Safety Act 2022 identifies a common Golden Thread which requires a comprehensive record to be kept of all safetyrelated information throughout the lifecycle of a building, emphasising the need for clear communication between all parties.
Under the Act, the Building Safety Regulator will oversee the safety and performance of all buildings, as well as having a special focus on high-rise buildings. It will promote competence and organisational capability within the sector including building control professionals and tradespeople.
AEI Cables has also been highlighting the importance of collaboration to help meet the demand for Category 3 Control fire performance cables which are identified under the revised British Standard BS8519: 2020 Code of Practice. These cables reduce harmful smoke, toxic gases and flame spread in the event of a real fire.
The systems powered by these cables –including smoke and heat extraction systems – assist fire services in firefighting and a safe evacuation in the case of life safety.
According to EU diplomats, the European Commission is set to propose a new blocwide climate target to cut net greenhouse gas emissions by 90 per cent from 1990 levels, while allowing flexibility for domestic industries and use of international carbon credits. This shift mirrors recent findings from Aggreko’s surveying of CEOs across Europe, which revealed that high energy costs are prompting many businesses to reassess their decarbonisation timelines to ensure a commercially viable transition.
The company’s recent report, Rebalancing the Energy Transition, based on a survey of 400 CEOs across the UK, Germany, France, and Italy, found that 95 per cent of large businesses have already adjusted their net zero strategies in response to energy supply and pricing pressures. These findings suggest the EU’s proposed shift reflects what is
already happening on the ground in energy-intensive sectors subject to rising costs and grid issues.
According to Aggreko’s research, while 12 per cent of CEOs currently rank the speed of decarbonisation as their top priority, the vast majority remain committed to climate action. Approximately 80 per cent plan to increase investment in energy transition initiatives over the next year.
With this in mind. Aggreko is urging businesses to look beyond timelines and focus on practical, scalable solutions that can reduce emissions while improving energy resilience. Central to this is the role of decentralised energy systems and supply chain collaboration, which Rebalancing the Energy Transition identifies as key to reducing energy costs and accelerating progress toward net zero.
National Gas has secured £500,000 from Ofgem to develop an innovative new type of underground hydrogen storage – which could see a pilot project built in 2026. The system, known as H2FlexiStore, has been developed by Edinburgh energy storage specialists Gravitricity, and is designed to hold up to 100 tonnes of green hydrogen in purpose-built underground lined shafts. The technology can be located where required – for example as part of the National Gas network or next to large industrial users.
The Ofgem funding will enable a consortium – which also includes Southern Gas Networks, Guidehouse, Edinburgh University, Energy Reform and Premtech – to design and model a working system over the next six months, ahead of a potential demonstration phase next year.
The funding comes from Ofgem’s Strategic Innovation Fund and follows the successful completion of a National Gas led feasibility study in 2024, which identified H2FlexiStore as the preferred technology to provide locationally flexible hydrogen storage.
The initial study concluded that underground nodal storage would compensate for the loss of ‘linepack’ (the amount of energy that can be stored in a pipe network) when transitioning to green hydrogen as a fuel. In other words, strategically located nodal storage can improve the resilience and operational efficiency of a hydrogen gas network, with a view to ensuring security of supply to customers.
Once the design project is successfully completed, a third and final project phase could be secured, which would see the delivery of a technical demonstration project, supported by multi-million-pound funding from the Strategic Innovation Fund.
Ratcliffe, Managing Director of GreenBrook, discusses
As many of you know, for many years GreenBrook has been a partner of choice within the electrical industry. Since our humble beginnings over 70 years ago, our product offering has evolved from manufacturing simple mechanical relays to designing the first socket RCD (which has now evolved into the market leading PowerBreaker circuit protection range).
GreenBrook has always sought to provide the very best quality products and services to our loyal contractors and wholesalers and as a result of this we repeatedly added new products to our range (and acquired other respected brands such as MK Sentry and Tillex) to be able to offer a selection of different products that we knew would be of interest to our client base.
This enormous product offering led us to notice over the years that our customers have not been sure where to place GreenBrook as a supplier as we are a “Jack of all trades” - able to supply a plethora of products but not specialising in one particular area. Although we are known for PowerBreaker, the Norslo cable management range, Timers, Door Chimes and Lighting and Fixings - we had such a wide range of products that we needed to streamline our product offering to be able to offer our customers a clearer product identity.
So, we have taken it upon ourselves to do a complete product shake up and re-branding exercise to help us identify as a more modern supplier with a clear message for our customers.
Firstly – we have decided to exit the lighting sector as the market is saturated with specialists that offer such a wide selection that we could not compete with their range depth. This has given us space to hold further stock of the products that we know our customers need.
Of course, we know that all customers value their time, so it’s important that they find the very best products as efficiently as possible.
Acknowledging the sheer amount of choice that wholesalers and contractors have, we’ve taken the opportunity to completely redefine our product solutions by presenting our simplified PRO Series and CORE Series.
The PRO Series contains all our “intelligent and wired-in” products, such as the Circuit Protection ranges, Timers, Occupancy Detectors, Heating solutions, wiring accessories etc
The CORE Series contains all the commodity ranges that are not electrified – such as the cable management products, dry lining boxes, connectors, conduit fittings, ladders etc.
Whether it’s our Pro Series or Core Series, both ranges have a selection of well-known ‘flagship brands’, such as Powerbreaker, MK Sentry, Inchronox Timers, Safetysure and Orion Occupancy Detectors.
Hopefully you agree that our striking new brand identity and eye-catching styling not only makes a statement about how far we have come, but moreover, it announces our mission to positively transform the perception of GreenBrook in our industry.
Peter Ratcliffe, Managing Director of GreenBrook said: “Our new look Green Brook identity is a real departure from our old styling, and every part of our new brand has been reimagined to convey a more dynamic and modern design. In an industry where competition is so high, our new brand will better reflect our intention to offer an unparalleled customer experience to make us stand out from the crowd”
Our mission is to become a leading name for electrical product solutions to Contractors, Wholesalers and Property Developers/ specifiers not only from our product offering but for the service and information we bring to the market.
Forming partnerships is part of our ongoing promise to deliver an exceptional service to customers and the industry as a whole. Whether it be Wholesalers, Contractors or Building Developers & Specifiers, we believe the real value is the investment in working jointly with all stakeholders to help push our industry forward. Our Synergy Cycle beautifully acknowledges our 3 core audiences, and importantly, we also recognise how each of our audiences affect and influence each other.
We are working closely with eminent bodies and strategic partners within our industry to bring useful information to the industry.
By way of our new PODCAST series, The Perfect Contact, we will bring conversations with strategic partners, such as BEAMA and the EDA to discuss issues that are currently affecting our market that will be useful to us all. This will include legislation, government issues, environmental discussions and a general understanding of undertakings in our industry from all the people involved.
Ultimately, our aim is to positively impact the industry by not only manufacturing and supplying quality products, but to also provide innovative resources that enable our customers to be better informed, more sustainable and above all, continually profitable.
Today not only marks one of the most important milestones in the history of Green Brook, it’s also our opportunity to share with you the next exciting phase of our onward journey.
Green Brook - The Professionals’ Choice
As the UK electrical industry continues to evolve under the pressure of rising energy demands, smarter infrastructure, and tighter safety regulations, the need for innovation in power distribution has never been greater. In response, MCG Industrial is proud to announce the launch of its next-generation three phase distribution board. This launch marks more than just the introduction of a new product. It represents a forward-thinking approach to power distribution, built from the ground up to address the real-world challenges faced by electrical engineers, contractors, and commercial clients in today’s rapidly shifting landscape.
MCG Industrial consulted electricians during the design phase to understand their pain points and practical needs. The result? A board that avoids the all-too-common frustrations of cramped internals and awkward component access. Instead, it delivers a robust, spacious, and logical layout that supports rapid installation and long-term durability.
The range
Consists of 4, 6, 8, 12 and 16 way three phase distribution boards, all complete with 125A isolator switch, prewired T2 SPD and protective MCB to comply with the latest 18th Edition wiring regulations.
Key features
• Prewired SPD / MCB configuration – offering optimum device space.
• Quick release reversible door – providing freedom and flexibility.
• Lockable door – preventing access from unauthorised personel.
• Latching front cover – enabling an easier installation.
• Rivet style screw holder – for rapid screw alignment.
• Quick release top and bottom gland plates – saving time negating screw removal.
• Pre-punched drill points and centre mark on gland plates for ease and convenience.
• Raised keyhole mounting points –improving airflow.
• Triangular centre point – for an easy one-person installation.
• Removeable pan assembly – creating
The feedback at CEF Live on the new board was fantastic, contractors had the opportunity to get hands on with the product and could see firsthand how quick and easy the product was to install. Many of these customers vowing to use on their next project.
space for ease of cable dressing and reduces weight for fixing.
• Frameless design – offering quick and easy installation.
• Multiple earth and neutral bars –maximising space for ease of cable dressing.
• Covered neutral bars and incoming devices – reducing live touch points.
• Cable box – allowing more space for cable installation.
• Extension box (c/w din rail) – for flexible system configuration.
• Connector block – providing an electrical connection from the main board to the extension box.
• Single phase conversion kit –enabling a quick and easy three phase to single phase adaption.
Manufactured to BS EN 61439-3 standards and fully compliant with the latest 18th Edition wiring regulations (BS 7671), our board is ready to meet the stringent demands of commercial, industrial and large domestic installations.
The new three-phase distribution board was launched at the UK’s biggest electrical event #CEFLIVE2025 at the NEC in Birmingham on the June 5 and 6. This event which had over 12,000 customer attendees provided a great platform for contractors to interact with this new board.
Martin Berriman, Divisional Manager from MCG Industrial said: “The feedback at CEF Live on the new board was fantastic, contractors had the opportunity to get hands on with the product and could see firsthand how quick and easy the product was to install. Many of these customers vowing to use on their next project.” Available now, for any further information please contact MCG Industrial on 01302 342 642 or alternatively e-mail on info@mcg.co.uk.
Designed for, and in collaboration with, electrical installers
Quick-release pan assembly
Scan the QR Code to view the product video Quick release
The industry is undergoing rapid transformation, driven by technological advancements, sustainability demands, and increasing connectivity. In this landscape, events like The Electrical Industry Awards play a crucial role in recognising excellence and highlighting the innovations shaping the future. We asked Kevin Gutteridge why these events matter and which trends are currently influencing electrical pricing and product information
How do you think sponsoring The Electrical Industry Awards fits with what LUCKINSlive stands for and where the company is heading?
At Trimble Luckins, doing the right thing for the electrical industry is paramount. We celebrate best practice and want to promote innovations that are going to move the industry forward. It seemed like a natural opportunity for LUCKINSlive to collaborate with the Electrical Times and spend some time recognising those in the industry with a similar mission.
We’re doing some really exciting things this year, particularly with LUCKINSlive.com, with the aim of allowing easy connectivity across the electrical supply chain from manufacturers to wholesalers and contractors.
Why do events like The Electrical Industry Awards matter when it comes to encouraging excellence and collaboration?
THE ELECTRICAL INDUSTRY AWARDS 2025 IS SPONSORED BY:
Sharing expertise and experience is so valuable for everyone in the electrical industry - these forums for recognising achievement help to raise the bar and keep the industry pushing boundaries - plus an element of competition is always fun.
Which key trends do you see shaping the industry in 2025?
1. Data-Driven Operations
Real-time data feeds and cloud-based integrations are replacing static catalogues, offering pricing and enriched product information live to wholesalers and contractors. This shift ensures transparency, speed, and operational effi ciency. Access to up-to-date pricing, technical specifi cations, and datasheets enables informed decision-making and streamlined workfl ows.
2. Rising Price Volatility
Particularly in the electrical industry, price fl uctuations are intensifying and manufacturers
can publish changes instantly. There is certainly no need to wait until a new January price list gets printed. To add context, the Luckins’ team of data experts processed 286,114 data changes in 2024 alone. ERP systems integrated with realtime manufacturer data allow live updates so that businesses can generate accurate quotes quickly, improving responsiveness and maintaining competitiveness in a fast-paced market.
At Luckins, we’re certainly seeing demand for renewable energy products like solar panels and EV chargers continue to surge. The Luckins database has grown enormously in this area, as contractors are increasingly tasked with environmental targets to hit. Access to detailed sustainability data helps businesses comply with regulations and lead in green innovation, turning environmental concerns into opportunities and a competitive edge.
4. Multi-Disciplinary Expertise
Modern products often require cross-disciplinary expertise. Contractors and wholesalers are expanding their skill sets to manage these
complex demands and the divide between electrical and mechanical wholesalers has also certainly narrowed in recent years. Centralised, enriched data simplifi es the management of multi-disciplinary projects while ensuring accuracy and compliance.
5. Increased Connectivity
Integrated solutions are reducing manual intervention and fostering collaboration across platforms like procurement and estimating software. Having the information you need at your fi ngertips speeds up workfl ows, improves accuracy, and strengthens relationships across the whole supply chain.
Increased competition from discount retailers with fl exible hours, online ordering, and fast delivery is reshaping expectations. Enhanced e-commerce capabilities with enriched product data help traditional wholesalers provide detailed, user-friendly online experiences to attract and retain customers.
For more information on how to manage product information for the future, visit LUCKINSlive today.
The industry’s largest and most respected event, the Electrical Industry Awards is back.
Brought to you by Electrical Times, the Awardscelebrating its 33rd year - recognise outstanding product innovation as well as individual talents. The winner of each category receives a coveted Electrical Industry Award.
So if you, or your company have something to shout about, these awards will get you noticed.
Gain independent industry recognition for the excellent work delivered by you, highlighted across the range of categories.
Promote your excellence, demonstrate a competitive edge and position your company alongside the best in the business.
A winners reception in central London with food, drinks, entertainment and completely free of charge!
Being a finalist is proof of excellence in your business and proves to clients new and existing you are in industry innovator.
Commercial Product of the Year
Industrial Product of the Year
Residential/Domestic Product of the Year
Lighting Product of the Year
Trade Tool of the Year (Inc. Test & Measurement)
Training Resource/Provider of the Year
Electrical Wholesaler of the Year
Contractor of the Year (Under £2m)
Contractor of the Year (£2-£5m)
Contractor of the Year (Over £5m)
Contractor of the Year – Community involvement
Contractor of the Year – Staff development (inc. apprenticeships)
SUSTAINABILITY: PROJECTS AND INSTALLATIONS
Renewable Installation of the Year
EV Charging Installation of the Year
Electrical Project of the Year
MAIN SPONSOR: SECTION SPONSOR: CATEGORY SPONSORS:
In April, new company size thresholds were introduced by the UK Government, which saw the definition of micro, small and medium-sized businesses change. Rob Rees, Divisional Director at Markel Direct, sheds light on the changes
The contracting sector has experienced a significant amount of change over the last five years – most recently with the introduction of IR35 offset in April 2024 – and the updates to company size thresholds have the potential to impact both contractors and end clients.
What has changed with IR35?
Company size thresholds raised
The main change that has come into force is the rise in company size threshold. Under the current IR35/Off-Payroll Working (OPW) rules (Chapter 10, ITEPA 2003), medium and large companies are responsible for determining the employment status of contractors who work through a Personal Service Company (PSC). If the contractor is deemed an employee for tax purposes, the company must deduct Income Tax and NICs. Small companies on the other hand are exempt from OPW rules, and instead the tax responsibility stays with the contractor’s PSC under Chapter 8, ITEPA 2003 (the original IR35 rules).
The new change sees the threshold of what is considered a small and medium business raised, which will now classify some medium businesses as considered small - meaning that they will now be exempt from the OPW rules. So, what are the new thresholds?
Who will it impact and when?
The new size thresholds mean that some companies that were previously classed as small will now be micro entities and those that were classed as medium will now qualify as small. In fact, government estimates suggest that approximately 113,000 companies and Limited Liability Partnerships will move from small to micro-entity status, and around 14,000 will move from medium-sized to small. Generally speaking, this is positive news for the contracting sector. Since the update to off-payroll legislation in April 2021, which saw the requirement for assessing an engagement (and thus the associated tax liability for the engagement) move to the fee-payer, many end clients have been reluctant to offer outside IR35 roles to contractors for fear of HMRC classifying the engagement as being ‘inside’ IR35. This has led to fewer contracting roles being available.
The reclassification of company sizes is likely to widen the pool of opportunities for contractors, as there is more of an incentive for businesses newly classified as small to work with contractors, as the IR35 engagement determination will lie with the contractor. This means the small businesses would no longer be liable for the additional costs of operating under the OPW rules, which include tax and NICs responsibilities.
However, it is important to note that these changes do not have an immediate practical effect from an off payroll working perspective.
In the HMRC Agent Update, a company must meet the new thresholds for two consecutive financial years to be considered exempt from the previous off payroll working rules.
Due to transitional provisions, companies can assume that the new thresholds applied in the previous financial year; therefore, the earliest that these changes can have a practical impact on IR35/OPW responsibilities is 6 April 2026.
How can those that will be affected prepare for the change?
While there is not a lot to physically do to prepare for this change, companies should speak to their accountants for specific advice on how it will impact them and who they conduct business with.
Contractors should speak to their existing clients to establish if they are/will be affected by the new threshold changes, and consider the impact this will have on their engagement with the client. If the responsibility for determining the engagement will fall to the contractor in the future, the contractor should consider having an IR35 contract review to ensure they do not fall foul of the off payroll legislation, and consider what changes they may need to make to their day rate (if they had previously been working on-payroll or through an umbrella company).
On the impact of the changes, Danny Batey, Senior Tax Consultant at our specialist tax consultancy business Markel Tax, says: “It is hoped that the new changes to the company size thresholds will have a positive effect on the contractor market, although the impact will not be immediate, by allowing contractors that engage with the increased number of small companies, due to the threshold changes, to decide their own IR35 status.
“For contractors that find themselves in this position, it is essential that they seek specialist advice with regards to their contractual terms and conditions and working practices, so they do not leave themselves exposed to a future HMRC IR35 challenge.”
For more information, visit www.markeluk. com/business-insurance/public-liability-insurance
Summer can bring a bit of breathing space in your business, but as autumn approaches and customers return from holidays, jobs that were put off over the holiday season start to move again, so it’s worth getting organised now. From getting a grip on your schedule to cutting down on material waste, there are some simple improvements that can make a big difference when the work starts to pile up again.
Cut down on admin
More than half (56 per cent) of small business owners have experienced poor mental health in the past year, and 73 per cent take fewer than 20 days of annual leave – well below the national entitlement of 28 days. It’s not hard to see why. When you’re running a business, the admin often takes over, leaving less time on site getting work done. Quoting, invoicing, scheduling and chasing payments can eat into your day before you’ve even picked up a tool.
Job management software can help take the pressure off by slashing the time spent on admin. You can group materials and labour into pre-set favourites to create fast, repeatable quotes. With just one click you can turn a quote into a job card and a job card into an invoice. You can even automate reminders for late payments to save more time and keep cash flow steady.
Take control of your schedule
If you’re still relying on a wall planner or trying to juggle jobs and team availability through text messages, things are bound to slip. Double bookings, wasted days between jobs, team members unclear on what they’re meant to be doing – a messy schedule can cause a lot of stress and affect your bottom line.
Job management software makes organising your workload simple. A centralised dashboard gives you a live view of every job in progress. Visual calendars show you what’s booked, what jobs still need to be scheduled and who’s available to take on work. Real-time updates make it easy to track progress and spot if you’re going over budget so you can step in quickly if anything starts to fall behind. It’s easier to plan ahead too – because you can easily see what work is coming up, you can order materials and sort out your team in advance.
Accurate pricing is key to running a profitable business but it’s not always easy. Underestimating labour or forgetting to charge properly for materials can quickly eat into your margin. To price jobs confidently, you need two things: a clear idea of your labour costs and up-to-date material prices. You want to charge enough to make a profit but not so much that
By
you lose out to a competitor. Job management software can help by letting you set standard hourly rates and test different pricing scenarios to see how they impact your bottom line. Some platforms also include price book integration so you can upload your latest supplier prices directly into your quoting system. That means no more guesswork or quoting based on outdated costs.
Don’t forget, it’s also worth adjusting your rates throughout the year. When demand is high, consider charging a premium. During quieter spells, a well-timed discount or promotion might help bring in more work.
Keep an eye on materials
Lost or forgotten materials can quietly chip away at your profits. A few rolls of cable that don’t make it onto an invoice or fittings ordered twice might not seem like much but over time, small mistakes add up.
Adopting a Just-in-Time approach to stock control can help. That means ordering exactly what you need for each job, no more, no less. Stick to what was included in the quote and avoid overbuying. If you do end up with extra, return it for a credit before it ends up buried in the back of a van or worse, handed to a customer and never billed.
Job management software gives you more control. You can link materials directly to individual jobs and clients, making it easy to track what’s been ordered, what’s been used and what still needs to be invoiced. That
visibility helps prevent waste and ensures every item is accounted for.
Get your online presence sorted
If you haven’t updated your website in a while or don’t have one at all, now is a great time to get it sorted. A website acts as your shop window, helping customers find you, learn what you do and get in touch quickly. Platforms like Wix or Squarespace make it easy to build a decent-looking website without needing to hire a developer. You can even add booking forms so people can request a job while you’re out on site. Fergus, for example, has an enquiry management feature that generates a branded contact form for your website. When someone fills it in, the enquiry drops straight into your system, is logged, trackable and can be sorted into categories like ‘To Do’, ‘Contacted’ or ‘Job Created’. You can add manual entries for anything that comes in via call or text so no matter how the lead comes in, it’s logged in one place and visible to the whole team. Getting your business in shape doesn’t mean overhauling everything at once, but a few smart changes over the summer can save you a lot of stress come Autumn. Whether it’s better scheduling, tighter pricing or just making sure your website’s up to scratch, each step makes your business more resilient. So before the calls start coming in thick and fast again, give your systems a once-over.
For more details and to book a demo visit: https://fergus.com
Hampton Beach, a newly developed community in Peterborough by Barratt Redrow (including Barratt and David Wilson Homes), is designed to balance modern convenience with sustainability. Situated around Teardrop Lake, the development provides residents with scenic views, expansive green spaces, and easy access to essential amenities. With Barratt Redrow’s strong commitment to achieving net zero carbon emissions by 2040, sustainability was a key factor in shaping the infrastructure of Hampton Beach.
To support these environmental goals while ensuring safe, well-lit communal spaces, Acrospire, in partnership with GM Briton, was chosen to provide an energy-efficient street lighting solution. The project aimed to install low-carbon, off-grid lighting that would enhance visibility, improve safety, and align with Barratt Redrow’s sustainable ambitions. Acrospire supplied and installed Defender solar luminaires, an all-in-one solar street lighting solution. Specifically designed for the UK market, Defender was selected for its superior performance, delivering up to 10,285 lumens and offering up to five nights of autonomy on a single charge. With a large-capacity battery and an expansive solar panel footprint, Defender ensures uninterrupted lighting, even during prolonged periods of low sunlight.
The solar lighting solution significantly reduces Hampton Beach’s carbon footprint while providing bright, evenly distributed illumination across footpaths and communal areas. By operating independently of the power grid, these luminaires help lower long-term energy costs, eliminate the need for trenching and cabling, and reduce ongoing maintenance.
James Brooker, Area Sales Manager at Acrospire, commented: “With today’s astronomical electricity costs, solar lighting solutions like the Defender make perfect sense for new build developments. By removing the need for trenching and wiring, they pay for themselves quickly — offering a long-term, environmentally friendly investment with no ongoing energy costs. The ability to deliver high-quality lighting without relying on the grid is a game-changer for housebuilders looking to meet their sustainability targets while keeping operational expenses low.”
For further information please visit: https://acrospire.co/ranges/solar/
The recently transformed Overbury office, located on the 13th floor of Chancery Place, Manchester, offers a vibrant and sustainable workspace with a strong focus on collaboration and innovation. SpaceInvader and Light Forms collaborated to create an inspiring, high-performance environment that reflects Overbury’s design vision and its connection with nature. The brief centred around a future-forward and functional office that meets the diverse needs of the team while also implementing organic features.
A standout feature of the new design is the sculptural ceiling, inspired by Overbury’s nautilus shell brand identity. This bold element not only enhances the office’s aesthetic appeal but also serves an acoustic function, improving sound quality throughout the space.
The bespoke lighting for the unique nautilus shell design was developed by the Light Forms team, who crafted a custom, made-to-measure solution using their Lightplane and Serpentine
Trojan Lighting has supplied a major lighting upgrade at Kellanova’s prestigious UK HQ in Landsec owned, MediaCity, aimto reduce energy use, meet updated compliance standards, and introduce smart building controls, without disrupting day-to-day operations.
On this project Trojan Lighting worked with longterm partners, Altec Facilities Management, who were contracted by CBRE to lead the installation and project delivery. Trojan provided 427 Lando recessed modular luminaires to support both open-plan and enclosed working areas with even, reliable and high-efficiency illumination. Trojan also supplied custom brackets to adapt its standard Lando fittings, removing the need for major ceiling alterations
As part of the emergency lighting strategy, Trojan supplied 10 Heathgate Surface Emergency Exit Signs, with all fittings installed in accordance with BS 52661. The overall lighting design followed CIBSE SLL Lighting Guides (LG07) to ensure performance across the workspace.
A Mymesh wireless lighting network, including an Ethernet Gateway, PIR sensors, and access to the Lumitel dashboard was commissioned, giving the facilities team full control over lighting zones, realtime data, and the ability to make changes without needing to access fittings, helping them manage energy and lighting across the floors more efficiently From receiving the order to final installation, the full process was extremely quick, taking under two months. The upgrade also contributes to Kellanova’s wider sustainability targets by cutting carbon and introducing smart infrastructure aligned with modern workplace standards..
luminaires. A series of shorter lengths were used to form the spokes radiating from the centre, allowing each segment to fit seamlessly into the curvature of the ceiling.
In the meeting rooms, it was essential that the lighting profiles were made to the millimeter so that they ran exactly from one wall to the other. In the main corridors, the Serpentine fixture was made to measure and custom-curved to follow the natural flow of the space.
Sustainability was a key consideration throughout the project, reflected in the use of organic shapes and biophilic elements, low-carbon materials, recycled finishes, and a variety of energy-efficient lighting solutions.
The carefully considered design enhances staff well-being and comfort, fostering a collaborative atmosphere while promoting creativity and productivity. The result is a seamless blend of creative technology and natural forms.
Paul Shoosmith, Director at Light Forms, said: “This project was a unique and exciting challenge to work on, and has proven that creating custom lighting doesn’t need to be expensive. We are proud to offer affordable made to measure solutions which can fit the unique needs of any project. Overbury’s new Manchester office design has benefitted staff, clients and the brand by providing an environment that embodies the company’s ethos of unbeatable quality and innovation.”
Thorn Lighting’s advanced Thor lanterns and bespoke gobo projectors have been selected to help revitalise Spennymoor Market Place and Consett Middle Street, aiming to draw more visitors, support local businesses, and promote community pride.
In line with its county-wide improvement efforts, Durham County Council has delivered projects to transform the town centres of Spennymoor and Consett. Thorn Lighting’s solutions have been instrumental in achieving this vision, offering an engaging and adaptable lighting scheme that supports events throughout the year.
Thor lanterns, combined with gobo projectors mounted on bespoke columns, provide the perfect blend of aesthetic appeal and functionality, allowing for tailored lighting themes that change with the seasons and significant events. The adaptive lighting
has helped to create welcoming hubs in Spennymoor Market Place and Consett Middle Street, where people can gather for local events like Christmas festivities and Remembrance Sunday commemorations.
Thorn’s Thor lanterns offer high performance and versatility. These LED smart urban lanterns offer comfortable lighting quality and
spectacular city
Glamox is providing its LED lighting to help cut energy costs and enhance the indoor environment of the historic 16th-century Town Hall in the Swedish city of Malmö. The historical town hall in Malmö was built in 1544–1547, at a time when Malmö was one of the largest cities in Scandinavia. In the 16th century, the town hall was the largest of its kind to be built. The retrofit and upgrade concern the City Hall building, the former District Court in Malmö for the City Office, and Malmö City’s political management – in total, an area encompassing 12,000 m2. The town hall is a “K-marked building”, which means that the building is protected for its cultural and historical value.
Glamox will deliver around 500 LED luminaires for the project, which will illuminate entrances, storage rooms, corridors, meeting rooms, conference rooms, lounge rooms, staff rooms, and light the staircase. Glamox also supplied i60 Correlated colour temperature (CCT) luminaires for use in a room with limited natural daylight. These luminaires, installed at a height of 4.5 meters, add a sense of natural daylight.
Customers who switch from fluorescent lighting to energy-efficient LED lighting can typically reduce the electricity they use for lighting by 40-50 per cent.
“It has been fascinating to help solve challenges related to the retrofit of such a historic building. Since the building is so old, our team had limited drawings to support them in siting the lights. To solve this puzzle, we used a GoPro camera to film the entire premises, to get an overview of the lighting needs in the building, says Anders Olsson Regional Manager Southern Sweden for Glamox.
The town hall is an iconic building, featuring vaulted cellars reminiscent of the Middle Ages and a central hall inspired by the Hall of Mirrors at the Palace of Versailles. It also features the exclusive “Bernadotte room,” which is reserved for royal visits and diplomatic guests.
Glamox’s contract is with the Swedish installer Caanel Elteknik i Malmö AB. Skåne Bygg AB is undertaking the electrical installation for the renovation, with Vinnergi, a Swedish technology consulting firm specialising in property technology solutions, serving as the electrical consultant. Ebba Palmquist was the lighting designer for the project.
“This has been a fascinating project to work on with Glamox. Together, we’ve found creative and tailored solutions to light this historic building, which will continue its long tradition of lighting up Malmö”, says Lars–Göran Andersson at Caanel elteknik i Malmö AB.
The retrofit project commenced in April 2004 and is scheduled for completion by November 2025.
compatibility with any existing management control systems via ZHAGA sockets. Mounted on bespoke columns with illuminated heads, the Thor lanterns seamlessly integrate into both Spennymoor and Consett’s streetscapes, creating an appealing ambiance. Additionally, gobo projectors allow for customisable, eventspecific lighting.
he adaptable gobo projections have helped transform the town centres into dynamic spaces that reflect seasonal changes and important community events, helping residents and visitors connect with these revitalised areas. The Thor lanterns also contribute to a welcoming, well-lit environment, enhancing safety and encouraging more foot traffic in these regenerated town centres.
For more information on Thorn Lightings Thor luminaire please visit: https://www. thornlighting.co.uk
CU Phosco
CU Phosco is proud to announce its exclusive UK partnership with Heper, a renowned family-run lighting manufacturer based in Turkey. This strategic collaboration brings together two companies with deeprooted legacies and a shared passion for engineering excellence, sustainability, and lighting that enhances people’s lives.
With over 130 years of combined experience - CU Phosco celebrating over 100 years of innovation last year, and Heper with more than three decades of expertise - together, CU Phosco and Heper offer a more complete portfolio of lighting solutions for UK specifiers - from road and pathway illumination to specialist tunnel and amenity lighting.
Commenting on the partnership, Heper’s Can Gurel, International Sales development Specialist, said: “We’re proud to be partnering with CU Phosco, a company whose values and engineering-led approach closely align with our own. As two family-run businesses with a strong commitment to responsible manufacturing and high-performance lighting, we saw clear synergies from the outset. We’re already collaborating on exciting projects, including Blackpool Tunnel and Alloa Glassworks, and we look forward to bringing our complementary expertise together to deliver more sustainable, future-ready lighting solutions across the UK.”
With this partnership, CU Phosco reinforces its commitment to offering holistic, high-quality lighting solutions that meet the evolving demands of specifiers and city planners across the UK.
CU Phosco delivers a high mast lighting solution for Farnborough Airport, as part of Domus III
CU Phosco, in collaboration with ATG Airports, has successfully installed a state-of-the-art high mast lighting system at Farnborough Airport. This project, part of Farnborough Airport’s commitment to maintaining world-class operational standards and sustainability, involved the installation of 13 high masts equipped with advanced FL800D luminaires. The new lighting system ensures exceptional visibility on the new apron, supporting the Airport’s sustainability milestones.
The Domus III project was overseen by McLaughlin and Harvey as the Principal Contractor.
CU Phosco, acting as a sub-contractor, was responsible for designing and delivering a comprehensive high mast lighting solution that met the specified standards. As a preferred supplier for Farnborough Airport, CU Phosco has been involved in various projects at the Airport for several years.
The project was pivotal in supporting Farnborough Airport’s environmental goals, minimising energy consumption while using more energy efficient lighting. In 2024, Farnborough Airport was awarded Level 4+carbon accreditation status by the Airport Carbon Accreditation (ACA) scheme, one of only five UK airports and the only business aviation airport to achieve such recognition. Also last year, Farnborough Airport completed one of the largest light-weight solar installations in the South East, enabling the Airport to generate 25 per cent of its own power. In 2022, for a two-week trial period in the lead up to the Farnborough International Airshow, Farnborough Airport became the first airport in the world to offer SAF at the same price as standard Jet A1 fuel, after it took a major step in driving the adoption of SAF by offering it to all customers the year prior. Also in 2022, Farnborough Airport made a commitment to be Net Zero by 2030 or sooner.
CU Phosco collaborated with ATG Airports to provide a turnkey solution that optimised lighting across the Airport’s new apron. A total of 13 high masts, manufactured at CU Phosco’s Bradford facility, were equipped with 50 FL800D luminaires. The luminaires, designed for superior thermal management and high lumen output, ensure exceptional visibility while minimising energy consumption.
Each high mast features the CU Phosco Raise and Lower System, enabling safe and efficient maintenance without the need to close large areas of the apron. This innovative system lowers the luminaire carriage to ground level in one smooth operation, reducing disruption to airport operations and enhancing safety.
The FL800D luminaires, equipped with Samsung CSP LEDs and the AeroFlow® Cooling System, deliver consistent performance and longevity. This combination of advanced optics and robust construction ensures the lighting system meets the stringent requirements set by the Civil Aviation Authority (CAA) and Farnborough Airport.
Zumtobel Group present £42k to Cancer Research UK
Thorn and Zumtobel UK & Ireland presented a cheque for over £42,000 to Cancer Research UK at their annual sales conference on May 23, 2025. Football legend Kevin Keegan, special guest at the conference, joined Managing Director Paul Kilburn in presenting the cheque.
Over the last financial year, employees organised a range of initiatives, including “duvet days”, festive cake sales, and a Christmas jumper day in exchange for donations. In the spring, around 30 Thorn and Zumtobel employees participated in the London Race for Life. A company contribution further boosted the total funds raised to £42,828.40.
Paul Kilburn, Managing Director, Thorn and Zumtobel Lighting UK & Ireland commented: “We’re incredibly proud of our teams for their enthusiasm and commitment. Every duvet day taken and every mile run in London has directly contributed to this significant donation. Presenting the cheque at our conference is a highlight, and we’re excited to see the impact these funds will have on vital research.”
“We’re immensely grateful to Thorn and Zumtobel for their incredible support. Donations like these help us push forward with life-saving research and bring us closer to our vision that people can live longer, better lives, free from the fear of cancer,” adds Jan Leafe, Relationship Manager, Cancer Research UK.
Recent developments to the Building Safety Act 2022, alongside the introduction of the Leasehold and Freehold Reform Act 2024, have outlined significant changes to the UK’s approach to building safety and accountability. These changes have introduced a more stringent framework for ensuring that buildings, particularly those deemed high-risk, undergo appropriate and often overlooked due to funding, remediation. The introduction of remediation orders and a sharper focus on interim fire safety measures ensures that residents are protected while longer-term works are undertaken.
This renewed scrutiny is driving a wave of remediation activity across the country, particularly in residential blocks with already identified safety deficiencies. Since terrible tragedies such as the Grenfell Tower fire,
attention has been placed on cladding and structural issues, alongside fire safety measures, such as emergency lighting. In the event of a fire or power outage, emergency lighting plays a primary role in supporting both evacuation and emergency response.
The updated legislation makes it clear that building owners and accountable persons must take full responsibility for the safety systems in place. For contractors, consultants and facilities managers, this presents a growing opportunity to bring existing systems up to standard and deliver new solutions that align with the legal and safety requirements.
The changes in legislation now place clear legal duties on the ‘responsible person’(often building owners or managing agents) to identify, fund, and carry out necessary remedial work to address risks to life in
buildings. Specifically, the Building Safety Act introduced Remediation Orders and Remediation Contribution Orders, giving the Building Safety Regulator and the Firsttier Tribunal (FTT) the power to enforce remediation of fire safety defects, including inadequate emergency lighting, faulty alarm systems, and other critical safety failings.
For faster, simpler and safer testing.
Kewtech’s complete EV testing solutions
KT66DL
The 12-in-1 complete MFT with EV test capability
KEWEVA
The markets simpli ed EV adapter
Scan to view our EV range
KT64DL
The UK’s smallest MFT with EV test capability
PAT testing is an important part of workplace safety – but it’s only effective when the right tools are used. For contractors and end users, the priority is keeping people and equipment safe, so both your kit and procedures need to be up to the test, says Steve Dunning, managing director at Martindale
PAT testing, sometimes referred to as electrical equipment testing is a critical element of electrical safety in the workplace. And, for good reason – the Health and Safety Executive (HSE) reports that a quarter of all reportable electrical accidents involve portable appliances. That figure alone underlines why proper inspection and testing shouldn’t be optional.
While PAT testing is not compulsory, under the Electricity at Work Regulations (1989), employers are required to ensure that any electrical equipment that could cause injury is kept in a safe condition. While prior visual inspections are always important, looking at equipment alone will not pick up all faults. If, for instance, the insulation in an appliance has been damaged or the earth bond has become disconnected, a visual inspection alone will not be enough. These faults would, however, be discovered by a PAT tester, highlighting the vital role they play in verifying appliances are safe to use.
Portable appliances, as defined in PAT regulations, cover a broad range of tools and devices – essentially anything with a plug that connects to a socket or generator. This includes everything from hand tools on site to kettles and hairdryers in hotel rooms, including those that are hard wired into the wall. If it’s likely to be moved or used while connected to a power supply, it falls within the scope of PAT testing.
The fifth edition of the IET Code of Practice stresses that PAT testing must be carried out by a competent person – someone with enough technical knowledge or experience to carry out the tests correctly, interpret the results and take appropriate action. But that competence is only effective if the right equipment is in place.
A good PAT tester should also be light, compact and easily portable, making it easy to carry and use in all sorts of environments – under desks, cramped plant rooms, behind monitors and on busy commercial sites. Many users won’t be testing all day, every day so the tester needs to offer intuitive operation without requiring extensive training.
A handheld design with clear results that show pass/fail is ideal for quick on-the-go testing, particularly where multiple items need to be checked in a short space of time. Straightforward menus and inbuilt auto-test sequences are also particularly useful, especially for those new to PAT testing.
A rugged casing with a reliable build is essential too, especially for those working on commercial sites or industrial premises where drops and knocks are likely. Battery life is another important factor – no one wants to lose battery power when testing on site. The latest PAT testers are fully rechargeable making them ultra reliable.
Factor in as well that someone carrying out occasional testing might only need a basic pass/fail tester, while a contractor working across multiple client sites might benefit from a tester with onboard data storage and logging capabilities.
Among the trusted options on the market, products from brands like Martindale Electric offer a good reference point. The new HPAT Series of handheld PAT testers are designed for both new and experienced users offering a quick, no-fuss solution for automatic testing for Class I, II and IEC power leads. Compact and lightweight, these testers have straightforward, one-button automatic testing, a sharp colour
display that stays readable in all lighting conditions and a simple pass/fail indication with measured values.
The USB-C charging port means, once fully charged, they can carry out many tests without a recharge. The HPAT650 model can also store results for up to 100 appliance tests with on-screen recall from memory, substitute leakage testing, adjustable test limits for long leads, and a single test execution mode to aid troubleshooting.
A large number of incidents and injuries could be prevented with proper electrical checks, inspections and safety tests. However, both contractors and competent in-house personnel – increasingly on the move – must be able to verify all types of appliances quickly and safely.
From both a reputational and liability perspective, it pays to implement and maintain an efficient and fit-for-purpose PAT schedule to keep all users safe and reduce potential hazards.
For more information visit www.martindaleelectric.co.uk/
Engineered for precision, built for professionals—the new Di-LOG ALVA Series Multifunction Testers redefine electrical testing with advanced diagnostics, intuitive ALVA UI, and EV-ready features. Fully compliant with the 18th Edition, the ALVA Series sets a new benchmark for safety, efficiency, and long-term value
Electrical professionals demand tools that deliver precision, reliability, and efficiency. Enter the new Di-LOG ALVA Series Multifunction Tester, built to exceed those expectations with next-generation testing technology, intuitive usability, and the industry’s first comprehensive support package. Designed to comply with the 18th Edition, the ALVA MFT, ALVA MFT Pro, and ALVA MFT Pro EV raise the bar for electrical safety, EV charge point verification, and site testing.
Next-generation testing with ALVA Intelligence
The ALVA Series boasts a full-colour TFT display and intuitive ALVA UI, making results crystal clear and guiding users through testing procedures with ease. Its extensive RCD compatibility includes types AC, A, EV, B, B+, F, and Selective, ensuring it meets modern installation requirements.
The ALVA Series streamlines testing with intelligent features like Auto Start Loop Testing and Auto Start 200mA Earth Continuity, which automatically identify 2- and 3-wire connections to initiate sequences without manual input. To minimise disruption, a NiMH rechargeable battery system with integrated charging is standard across the range. For the standard ALVA MFT, an additional battery and charger pack are required to enable this in-built charging capability.
EVSE testing is standard across the range, complete with 6mA RDC-MD/PD verification, safeguarding compliance on every EV installation.
functionality
Engineered for professionals who need deeper insight, the ALVA MFT Pro delivers advanced diagnostics and verification: Rmax (R1/R1+R2) highlights high-resistance points, aiding in detecting your maximum continuity measurement and verifying conductor integrity. Zmax (Zs) measures maximum earth fault loop impedance, confirming disconnection times and ensuring protective devices respond correctly. Imax (PSC) identifies the maximum prospective
short-circuit current on a 3-phase supply, which is vital for selecting appropriately rated circuit protection. Ideal for fault-finding and compliance checking, this model also introduces USB connectivity and onboard memory for storing test data—perfect for certification and record-keeping.
Its standout feature? EV Auto EVSE verification, combining Non-Trip Earth Loop, 6mA RDC-MD/PD, and 30mA AC tests into a single, fast, and reliable process, completely verifying the safety features designed within the EV charger. The optional Earth Resistance testing via 3 or 4-pole kits makes it ideal for full site assessments where earth resistance or earth resistivity measurement is required.
ALVA MFT Pro EV – Ultimate EV testing solution
As EV charging infrastructure expands, the ALVA MFT Pro EV is a key player. Building on the Pro model, it includes automated EVSE verification for efficient charger testing—all enhanced by the exclusive DLEV1 EVSE Adaptor included in the kit.
This one-stop solution combines every critical test needed to meet compliance and safety standards in one sequence, making it essential for modern EV installations.
Industry-first ALVA support package
Di-LOG introduces the optional ALVA Support Package—a service plan offering up to five years of calibration, warranty, and accidental damage cover. It’s the only solution of its kind, delivering long-term confidence and cost control. Optional Support package benefits:
ALVA CALIBRATION: Annual five-year calibration with service and firmware updates, returned within 72 hours.
ALVA WARRANTY: Five-year parts and labour protection for component failure.
ALVA TEST LEADS – Auto-shipped replacement test leads in years two and four.
ALVA ACCIDENT – Accidental damage is covered for a fixed fee of £175 + VAT.
Flexible payment plans ensure affordability—no hidden costs, just peace of mind.
Why choose the Di-LOG ALVA Series MFT?
• Full-colour TFT display with ALVA UI for intuitive, guided testing
• Auto Start features for rapid continuity and loop testing
• Wide RCD compatibility across all models
• Rechargeable NiMH battery with in-built charging (optional accessory on ALVA MFT)
• EVSE verification standard, including 6mA RDC-MD/PD testing (requires DLEV Accessory)
• USB and memory functions in the Pro model
• Advanced EV Auto verification with DLEV1 in the Pro EV
• Earth Resistance testing (optional accessory)
• Exclusive five-year ALVA Support Package
• Fully compliant with BS EN 61557
• With precision engineering, EV readiness, and unmatched aftercare, the ALVA Series MFT doesn’t just meet professional expectations—it redefines them.
Discover more at: www.dilog.co.uk/ALVA
By Sim Sharphouse, Operations Manager at Salko UK
In the UK, there were an estimated 50,600 electrical engineers working as of the fourth quarter of 20241. It’s an ever-evolving industry, and increasingly equipment and systems are becoming more complex thanks to the development of Artificial Intelligence, Internet of Things (IoT) and advanced power electronics. This has the knock-on effect of ensuring that precision, reliability and efficiency are even more critical, requiring the sector to be adaptive to new technologies to deliver innovative solutions and maintain high operational standards.
Sim Sharphouse, Operations Manager at Mechanical and Electrical engineering specialist firm, Salko UK, explores the importance of high-quality test equipment to ensure quality installation and management of electrical environments.
Electrical systems
Modern electrical systems form the backbone of operations across a wide range of industries. Across the electrical sector, even a minor fault left undetected can quickly escalate into significant downtime, expensive repairs, or a complete system outage.
Proactive monitoring, maintenance, and fault diagnostics are critical to ensure a project runs smoothly. The value of precision testing equipment is unparalleled. The process allows for the verification of system integrity during and after installation and is also key in ongoing maintenance strategies. Regular diagnostics with calibrated instruments enable teams to detect wear, deterioration or irregularities before they develop into significant failures.
As technologies evolve, the industry faces increasing challenges to innovate and maintain more complex electrical systems. Skilled electrical engineers and advanced testing methodologies are essential to meet these demands, ensuring safety and efficiency across all applications.
Located near Whitby in North Yorkshire, the Woodsmith Project is one of the most ambitious mining developments currently underway in the
UK. The project aims to extract a unique, highgrade polyhalite fertilizer from deep beneath the North York Moors National Park.
When completed, it will feature a 37 km underground conveyor tunnel to transport the mineral to a processing facility on Teesside, making it one of the most advanced and sustainable mining operations in Europe.
The Woodsmith mine is home to two of the deepest commercial mineshafts in Europe. Salko UK has completed the electrical installation which highlighted the critical role of precision equipment in delivering safe and reliable performance under extreme conditions.
Salko UK’s role in the project included the complete management of supply and installation of the electrical distribution system within both the production shaft, reaching 1,594 meters and the service shaft, reaching 1,565 meters. The scope of work spanned equipment logistics and change management, central to this infrastructure is the Transformer 1813-TX-001, which supplies the system at 400V from an 11kV source.
To guarantee the optimal performance of this critical installation, Salko UK implemented a comprehensive testing protocol. This involved the use of advanced instruments to verify the capacity, integrity and continuity of the electrical distribution network. Equipment included low resistance ohmmeters, insulation resistance testers, multifunction testers, proving units and approved voltage indicators - all of which are calibrated annually to ensure the accuracy and validity of test results.
Testing at this level not only confirms the quality of the initial installation but also establishes a standard for future maintenance, helping to ensure the system remains in peak operating condition throughout its lifecycle. By identifying and resolving potential issues early, this proactive approach has played a key role in maintaining project momentum, avoiding costly delays, and ensuring alignment with both schedule and budget.
Implementing a robust testing system at initial stages within electrical projects is hugely important - the continuity of operation is vital to ensure success. Unplanned downtime and unexpected outages can be extremely costly and are often far more complex to resolve after they occur.
Across the electrical industry, these practices must become standard. Investing in tools and test equipment equals faster fault resolution, safer work environments and more streamlined maintenance schedules. Reliable test equipment enables electrical professionals to ensure smooth operations, anticipate potential issues, and maintain consistent performancewhether this be across new installations or the monitoring of an existing system.
Additionally, robust testing systems play a critical role in ensuring the safety of workers by identifying potential electrical hazards before they escalate. The integration of advanced digital testing tools and real-time monitoring technologies, enables electrical professionals to predict and address faults more proactively than ever.
To find out more, visit: salko.co.uk/case-studies
Proactive monitoring, maintenance, and fault diagnostics are critical to ensure a project runs smoothly. The value of precision testing equipment is unparalleled. The process allows for the verification of system integrity during and after installation and is also key in ongoing maintenance strategies. Regular diagnostics with calibrated instruments enable teams to detect wear, deterioration or irregularities before they develop into significant failures.
1500V Open Circuit Test
40Amp Short Circuit Test
1500V DC Insulation Test
GFL (Ground Fault Locator Test) to identify faulty Solar PV Modules
Downloadable Results with Supplied Software Will Test Bi-facial Solar Pv Modules (2 Extra HT305 Reference Cells Needed)
Solar-03 Bluetooth Solar Irradiance Meter Supplied
HT305 Reference Cell Supplied
With the rise of air source heat pumps (ASHPs), the electrical industry faces new safety and compliance challenges. Engineered to meet these demands, Mark Kimberley, UK Market Manager at Hager, explains how it’s innovative Type B HP RCD sets a new benchmark for safety, reliability, and regulatory alignment in modern heat pump installations
The electrical industry is experiencing rapid technological advancements and growing regulatory complexities, especially with the push towards renewable energy solutions such as air source heat pumps (ASHPs). With the increasing adoption of these systems, ensuring safety and compliance in electrical installations has never been more critical. At the forefront of addressing these challenges is Hager’s innovative Type B HP RCD (RCCB), a device designed to meet the unique demands of heat pump applications.
The necessity of Type B RCDs in heat pump installations
Air source heat pumps operate differently from traditional electrical systems. These devices often utilise inverter driven compressors to convert AC power into DC and back again, generating high frequency currents during the AC-DC switching process. These currents can include smooth DC and highfrequency residual currents that exceed the capabilities of standard RCDs.
Type B RCDs are uniquely suited to handle this complexity, as they detect and protect against AC, pulsating DC, and smooth DC residual currents. For heat pump installations, this capability is crucial. Without appropriate protection, RCDs can become magnetised in the presence of DC components, compromising their functionality. This phenomenon, known as RCD blinding, leaves the system unable to detect earth faults, significantly increasing the risk of electric shock.
Hager’s Type B HP RCDs go beyond the standard Type B capabilities. These devices are specifically engineered to function at frequencies greater than 20 kHz, ensuring a minimum tripping threshold of 150 mA for frequencies above 1 kHz. This precision is critical for addressing the unique safety challenges posed by modern heat pump installations.
High-frequency protection: A step above standard Type B devices
Not all Type B RCDs are created equal. While many are tested to handle frequency residual
Heat pumps, with their complex electrical characteristics, highlight the need for advanced protective devices like Hager’s Type B HP RCDs. These devices not only ensure compliance with evolving regulations but also address the unique safety risks associated with modern installations.
currents up to 1 kHz, heat pumps often generate high-frequency currents far beyond this range. Standard Type B devices may trip unnecessarily at these frequencies, leading to potential system downtime.
Hager’s Type B HP RCDs are designed to operate effectively at high frequencies, providing robust protection against residual currents at frequencies greater than 20 kHz. This ensures reliable operation even under the demanding conditions of heat pump systems, eliminating the risk of unnecessary disruptions (see Fig 1).
Misconceptions around RCD types
There is often confusion among installers regarding the suitability of different RCD types for heat pump applications. While Types AC, A, F and B serve specific purposes, they fall short in handling the unique challenges posed by heat
pumps. The advanced capabilities of Hager’s Type B HP RCDs set them apart, offering enhanced protection at higher frequencies that are critical for heat pump applications (see Fig 2).
Ensuring compliance with BS 7671
Regulations play a pivotal role in ensuring the safety and reliability of electrical systems. BS 7671 Regulation 531.3.3 emphasises the need to select RCDs based on their behaviour in the presence of DC components. This ensures that the chosen protective device can tolerate DC currents without becoming magnetised and compromising its functionality.
Hager’s Type B HP RCDs align perfectly with these requirements. Designed to detect and protect against smooth DC faults, they operate effectively at frequencies far beyond the capabilities of standard Type B devices. This compliance ensures that installations meet regulatory standards while providing robust protection against electrical faults.
Additionally, Regulation 134.1.1 requires that electrical installations use proper materials and adhere to manufacturer’s instructions. By choosing Hager’s Type B HP RCDs, installers can confidently meet this requirement, ensuring the safety and reliability of their heat pump installations.
Addressing common misconceptions: Type B+ vs. BS 7671
Some installers mistakenly believe that Type B+ devices, a VDE standard, are suitable for heat pump applications. However, it is essential to note that Type B+ is not recognised under BS 7671. This misunderstanding underscores the importance of selecting devices specifically designed and tested for compliance with UK standards. Hager’s Type B HP RCDs meet these stringent requirements, providing peace of mind for installers and end-users alike.
As the adoption of renewable energy technologies continues to grow, the electrical industry must adapt to new challenges. Heat pumps, with their complex electrical characteristics, highlight the need for advanced protective devices like Hager’s Type B HP RCDs. These devices not only ensure compliance with evolving regulations but also address the unique safety risks associated with modern installations. By offering high-frequency protection and robust performance in demanding conditions, Hager’s Type B HP RCDs set a new standard for safety and reliability in the electrical industry. For installers and specifiers, the choice is clear: when it comes to heat pump applications, Hager’s Type B HP RCDs are a reliable solution. For more information, visit: hager.com/uk
Ensure you are up to date with BS 7671
Have you got your brown book yet?
Every day we see more and more new and emerging technologies in our industry and we need to keep abreast of these changes. To keep you and your customers safe and to keep on top of recent changes, make sure you have the very latest edition of the IET Wiring Regulations.
Use our handy timeline to quickly and easily check that you’re up-to-date at theiet.org/regs-checker-ET
Buy your copies of the book and expert guidance publications, also available as digital subscription packages from the IET Bookshop today at theiet.org/brown-book-ET.
New industry analysis estimates that the combined flexibility potential of all thermal storage systems available could be 10 GW by 2030, more than double the capacity forecast by NESO in their Clean Power 2030 pathway (4GW). Unlocking this potential is essential for meeting the Climate Change Committee’s 7th carbon budget, which projects that the flexibility requirement from all thermal energy storage systems has to be at least 9.3GW by 2030.
Doubled network flexibility capacity will have tangible, real world benefits for UK energy consumers, helping to drive down the cost of energy by accelerating the connection of low carbon generation low carbon generation with less need to construct expensive and time-consuming new network infrastructure. Put simply, flexibility enables the UK to squeeze more capacity out of the existing grid. Enhanced network flexibility is essential to delivering the UK Government’s Clean Power 2030 and Economic Growth missions.
BEAMA – the trade association representing manufacturers of electrical products spearheading the drive to electrification and a sector valued at £14bn – has launched a new report What Should I Do?, which examines the role of heat electrification technologies and how to encourage customers to choose low carbon heating options. BEAMA’s new research indicates that current Government targets risk neglecting the potential of alternative clean heat solutions. These technologies are essential to successfully decarbonising UK heating, tackling fuel poverty – which National Energy Action estimate affects 6.1 million households – and driving UK economic growth.
It’s not a one size fits all approach –customer choice is critical
Currently, just under a tenth of UK homes – 2.6 million in total – have electric heating. While heat pumps offer tangible advantages that could reduce energy costs for many, around 20 per cent of households are unable to accommodate them. Clean Power 2030 must rely on a broad range of heating technologies – including heat pumps, alongside thermal batteries, hot water cylinders, and solar heating solutions – to be successfully delivered within five years and at minimal cost.
BEAMA’s analysis shows that offering a suitable choice of low carbon heating solutions is central to persuading consumers to go
electric. Industry is calling on the Government’s upcoming Clean Heat Strategy to prioritise support of a broad range of technologies and solutions to reflect the wide variation in homes, workplaces and buildings, reassuring customers that they have a choice of low carbon options.
Alternative electric heating technologies that need to be considered from the perspective of flexible storage include:
• Air to air heat pumps
• Domestic hot water heat pumps
• Modern high heat retention storage heating systems
• Phase-change heat batteries
• Smart heat batteries
• Smart hot water cylinders
Further to the above storage options, we must not forget customers living in very low heat and hot water demand dwellings who would typically use panel heaters, electric radiators, electric underfloor heating and instantaneous hot water appliances.
Supporting flexible storage technologies will also help to unlock investment to create local green jobs and drive UK economic growth.
Government must do more BEAMA has called on the Government to create an inclusive fiscal and regulatory policy framework of Domestic Energy Support Schemes that currently fail to adequately promote alternative electric heating solutions include, such as the Warm Homes Plan.
Further support should be provided by extending the current VAT exemption on heat pump installations to the full range of electric heating technologies and incorporating into the Boiler Scheme a grant which subsidises the cost of installing flexible energy stores in households.
Kelly Butler, Strategy Director at BEAMA, commented: “Our new analysis gets straight to the heart of one of the key challenges for electrification - engaging the end user.
“One thing is certain, consumers need a clearer view of the suite of technologies that can provide flexible electric heat and hot water systems. This will allow them to identify the right solutions for their current circumstances which can offer immediate bill savings and future financial benefits associated with new flexibility driven time of use tariffs.
“The Government has committed to reduce bills whilst delivering an energy transition by 2030, meaning this issue needs to be tackled now before it’s too late.”
Yselkla Farmer, CEO of BEAMA, commented: “We are at a defining moment for the electrification of heat and hot water, and our research shows that the opportunity from flexible thermal storage is being underestimated and dramatically underutilised.
“Current incentives, Government, and media messaging can create a confusing picture, leaving many consumers to wonder ‘What should I do?’ We have a responsibility to ensure all households have all of the available options so they can find their own pathway to accelerate their electrification journey.”
Hager Type B HP RCCB – The RCD designed specifically for Heat Pump systems.
• Overcomes the limitations of standard Type B RCDs
• RCD functions at frequencies greater than 20kHz
• Critical high level DC leak protection
• Correct circuit protection for the complete system
• Ensures safety and reliability for the homeowner Scan Here! To watch our video!
The choice is clear.
CDB525HP - 25A Type B HP - RCCB
CDB540HP - 40A Type B HP - RCCB
CDB563HP - 63A Type B HP - RCCB
Hager provides the proven solution to protect heat pumps, ensuring seamless, uninterrupted performance.
By Hope Denton, Acoustic Solutions Specialist at Jacksons Fencing
As the UK works towards its net-zero target by 2050, air source heat pumps (ASHPs) are emerging as a key technology in reducing carbon emissions. These energy-efficient systems extract heat from the outside air to warm homes and businesses, offering an environmentally friendly alternative to traditional heating methods. Predictions indicate that ASHPs will meet 20 per cent of global heating needs by 2030, with the UK aiming to install 600,000 units annually by 2028 as part of its decarbonisation strategy.
However, despite their environmental benefits, the widespread adoption of ASHPs faces challenges - primarily due to noise concerns. They can be disruptive, particularly in residential or densely populated areas. With over 100,000 customers on waiting lists for installation, addressing these noise issues is vital to reduce buyer remorse.
Jacksons Fencing is at the forefront of helping manage noise concerns associated with ASHP installations; addressing noise from the outset of the planning process is key. Involving a noise consultant or acoustician early in the design phase ensures that heat pumps are installed in optimal locations, and that noise reduction strategies are incorporated into the project design. One such strategy is the use of acoustic enclosures.
While ASHPs are a suitable heating solution, the operational noise can create friction between users and neighbours. External units produce a low-frequency hum or whooshing sound, which can be disruptive in noise sensitive areas. Although modern ASHPs are quieter than older models, noise levels can still be problematic, especially when installed close to residential properties. As the demand for ASHPs continues to expand, these concerns must be addressed to avoid resistance from local communities that could slow the technology’s adoption.
Effective noise management begins with strategic planning. Collaborating with a noise consultant or acoustician helps assess site conditions and determine the best locations for heat pump units. This careful planning can ensure noise levels remain manageable and avoid negative impacts on neighbours.
Acoustic enclosures are one of the most effective noise reduction solutions. These structures are designed to reduce sound
transmission, ensuring quieter operation. Acoustic enclosures are made from a variety of materials, such as timber, and can be tailored to meet the specific needs of each installation. They not only reduce noise but also offer additional benefits that can improve the overall quality of life for businesses and homeowners.
What is an acoustic enclosure?
An acoustic enclosure is a structure built around a noise source to ‘trap’ the noise it produces. Typically, these enclosures feature walls made of noise-absorbing materials and a gate for access. In some cases, one side of the enclosure may be left open to prevent the creation of an echo chamber, which could amplify noise. This open side also ensures proper airflow to the heat pump, which is crucial for efficient operation. Some enclosures are designed with louvre features to allow for airflow while still reducing noise, though this may be more challenging and expensive with materials other than timber. Jacksons Fencing supplies acoustic enclosures in kit form, which allows for an airtight fit on-site and provides a cost-effective solution compared to modular systems.
The benefits of acoustic enclosures
Beyond noise reduction, acoustic enclosures offer several additional advantages. In terms of aesthetics, these enclosures can be designed to blend seamlessly with the surrounding environment, reducing the visual impact of the ASHP units. Enclosures can be designed in various shapes - square, rectangular, or even slightly curved - to suit the specific requirements of the installation site.
Beyond their noise-reducing capabilities, acoustic enclosures also provide increased security. Given the high cost of ASHPs, protecting these units from potential vandalism or tampering is essential. Durable enclosures, made from robust materials such as timber, can help deter vandalism and protect the long-term functionality of the system.
The noise reduction achieved by acoustic enclosures can be significant. For example, Jacksons Fencing’s Jakoustic Absorptive barrier can reduce noise by up to 32dB. This reduction is more than enough to halve the sound generated by an average heat pump, which typically produces around 60dB. The difference is particularly noticeable in colder weather when ASHPs work harder to extract heat, often resulting in increased noise levels. Even a 10dB reduction in noise is perceived as halving the sound, making acoustic enclosures a highly effective solution for managing ASHP noise.
As the demand for air source heat pumps continues to grow, addressing noise concerns will be crucial to ensuring their successful adoption. By incorporating noise management strategies early in the design process and using solutions like acoustic enclosures, it’s possible to balance the environmental benefits of ASHPs with the need for quiet and harmonious living spaces. This approach will help pave the way for widespread use of this sustainable technology, contributing to the UK’s ambitious net-zero goals.
Learn more about how acoustic enclosures by visiting: https://www.jacksons-security.co.uk/ blog/acoustic-enclosures-air-source-heat-pumps.
by Alan Siggins, managing director of Airflow
The air quality within buildings plays a crucial role in health, productivity and overall wellbeing. Air pollution represents one of the largest environmental risks to public health globally, carrying substantial environmental and economic consequences that affect both individuals and businesses. Long-term exposure to polluted air is also linked to serious cardiovascular and respiratory diseases, creating significant health challenges.
While outdoor air quality often dominates headlines and conversations, it’s important to note that we spend the vast majority of our time indoors—approximately 90 per cent. For many employees, a considerable portion of this time is spent in office environments. Unfortunately, air quality in offices can be significantly compromised without proper management and ventilation systems. As businesses increasingly recognise the importance of indoor air quality and the associated challenges, there has been a shift in focus towards solutions that can effectively monitor and manage workplace environments. The integration of smart technology and ventilation offers a promising approach to addressing these air quality challenges while also supporting sustainability goals.
With the rapid evolution of technology, smart devices have become a regular feature in many buildings, including offices. As new systems and devices flood the market, it’s easy to integrate them into commercial properties, but harder to identify solutions that will have a meaningful impact on energy efficiency and indoor air quality. When used effectively, smart ventilation and data capture can help facility managers and building operators significantly improve the air quality and working conditions in office spaces.
What is smart technology and smart ventilation?
Smart ventilation uses sensors and automation to improve airflow in buildings, ensuring a healthy and comfortable indoor environment. It adjusts ventilation based on factors like air quality and temperature, reducing energy waste while improving air circulation. In commercial development projects, smart ventilation can be integrated into new buildings or retrofitted into existing structures to enhance energy efficiency and indoor air quality. It is part of a broader trend of smart energy systems, which also include smart lighting, heating, and cooling
As new systems and devices flood the market, it’s easy to integrate them into commercial properties, but harder to identify solutions that will have a meaningful impact on energy efficiency and indoor air quality
systems. These technologies help buildings operate more efficiently, reducing their energy consumption and environmental impact, whilst simultaneously creating a healthier, more productive work environment.
How does smart ventilation impact energy efficiency?
Smart technology improves energy efficiency by adjusting energy usage in real time, based on actual occupancy and needs. This reduces waste and lowers overall consumption during times when the office isn’t fully occupied, such as after hours or on quiet days. Mechanical ventilation with heat recovery (MVHR) systems optimise airflow while capturing and reusing heat from outgoing air. This process helps maintain indoor comfort, reduces heating costs, and boosts overall energy efficiency.
Another key component of smart ventilation systems that contributes to improved energy efficiency is Variable Air Volume (VAV) systems. These involve sensors and dampers that adjust airflow based on the specific needs of different areas or rooms within a building. For example, if a room is empty, the supply of air would be reduced, and if another room is full of people, the system would increase the volume of conditioned air to this area. By integrating these systems into office buildings, the energy waste associated with over-ventilating unoccupied or low-demand spaces is reduced and overall energy use is minimised, reducing
the environmental impact. VAV has the added benefit of reducing operating costs, as well as providing more precise temperature control across the building.
Smart ventilation systems and data capture
As more developers and property managers invest in smart technology to improve the energy efficiency of their properties, it’s important to understand how these systems work. Smart ventilation systems capture data through sensors that monitor indoor air quality, temperature, and humidity. This data is processed to adjust ventilation in real time. By continuously tracking and analysing these factors, these systems can fine-tune operations for maximum efficiency, reducing unnecessary heating or cooling in underutilised spaces. The data collected can also highlight areas of inefficiency so that facility managers and building operators can make further adjustments and improvements. This ultimately leads to lower energy costs and more sustainable, comfortable environments.
Smart ventilation systems offer several benefits that enhance both efficiency and sustainability in office environments. These include:
Real-time monitoring: Smart systems continuously track air quality, temperature, and occupancy, ensuring optimal airflow.
Remote management: Remotely controlled, smart ventilation systems allow for easy adjustments from any location. With smart technology, facilities teams can control systems from one centralised place, making it easier to manage across an entire office building or other large commercial setting.
Energy savings: By automatically adjusting ventilation based on current conditions, smart systems reduce unnecessary energy consumption, leading to significant savings.
Reduced CO2: Smart ventilation systems lower CO2 levels by ensuring proper ventilation while minimising energy waste.
Enhanced productivity: The improved air quality brought about by smart ventilation can lead to higher cognitive function, fewer sick days, and better overall employee performance. This combination of real-time data, remote control, and automatic adjustments results in healthier, more energy-efficient office environments, reducing costs while supporting employee wellbeing and performance.
By Christophe Williams, CEO and Founder of Naked Energy
The public sector is decarbonising at an ever-increasing pace, and this is particularly noticeable in schools, who are using clean energy not only to cut emissions but also to reduce energy costs. Natural gas prices are forecast to increase in 2025 and 2026, and the lack of progress in ceasefire negotiations between Russia and Ukraine means that the price volatility of the past four years will not cease. The only way for schools to increase their resilience to price rises is to switch to renewables. These save money and provide more certainty for budgets, while freeing up resources which can be redirected to students and teachers.
GB Energy’s recent announcement to invest £80 million in solar panels for schools marks a major milestone here. Schools require large amounts of electricity and usually have a high demand for hot water too. Typical photovoltaic (PV) solar installations are the obvious choice to decarbonise the electricity demand, but they miss the biggest part of the larger net zero equation: heat.
Heating accounts for a staggering 37 per cent of the UK’s total carbon emissions, of which the majority comes from space heating and hot water (21 per cent). This is particularly notable for schools, where heating hot water can take up 40 per cent of their gas consumption.
The solution so far has often been to install heat pumps, which work well, but the technology isn’t the ideal fit for every project. The grid connections needed to power heat pumps take a long time to set up, and the National Grid will need more upgrades to accommodate the extra electricity demand.
In a recent survey of hundreds of consultant engineers and M&E contractors who regularly install school heating systems in schools, 36 per cent of those surveyed identified additional electricity capacity for low carbon heating as a barrier to decarbonisation.
This problem isn’t going anywhere. There’s a well-documented back-log of renewable energy projects waiting to get online stretching back years. We desperately need solutions that don’t use electricity, because schools need to reduce their gas usage now.
This is where solar thermal comes into play. This tried and tested technology harnesses the sun’s energy to provide heat directly at the point of use. Solar thermal collectors absorb solar radiation and transfer the heat to a fluidusually a water glycol mixture. It runs in a closed loop and transfers the heat to a heat exchanger, from which it can then be used directly or kept in a storage tank for later use.It works even in cloudier conditions and can be integrated with other heating technology, such as existing boiler systems or heat pumps, to reduce gas consumption and electrical demand.
The advantages are obvious. Firstly, solar thermal systems lead to substantial financial savings and increase the efficiency of other heating technologies. Secondly, it operates at the ‘grid-edge’, which means it doesn’t rely on the grid. This frees up much-needed capacity for electrification projects in other sectors. Thirdly, it saves the public sector a huge amount of money. The £80m of funding for schools from GB Energy is an excellent start but it won’t be enough to decarbonise all schools. However, public sector institutions can take advantage of Heat-as-a-Service arrangements which allows them to install solar thermal with no upfront costs, while providing a fixed cost per kWh of heat that’s on par with, or even smaller than, their current cost of gas per kWh.
Schools can save a significant amounts of money by not paying for the installation and the fixed energy cost also shields them from volatile energy markets, creating savings and security. Finally, it also provides more insulation from geopolitics than other renewable forms of energy, particularly solar PV. 95 per cent of the European solar PV market is supplied by China, which explains why it had an overall trade balance of -€5 billion as of 2023.
On the other hand, solar thermal is a net European exporter, with a trade balance of +€550 million. If there’s anything we’ve learned in the last five years it’s that Europe desperately needs to become more self-sufficient, and solar thermal can help with this.
Of course, achieving net zero is a challenge, but we mustn’t lose sight of the opportunity it’s creating. Investing in the decarbonisation of heat as well as electricity can transform schools into models of sustainability, while insulating them from geopolitical pressures. Solar thermal collectors are crucial in this transformation. It’s a proven, scalable, low-maintenance and low-cost route to reducing emissions while taking pressure off the National Grid.
It’s time to alleviate the pressure on the grid and allow schools to decarbonise their heat right now - we need to use grid-edge technology to help them do it.
Natural gas prices are forecast to increase in 2025 and 2026, and the lack of progress in ceasefire negotiations between Russia and Ukraine means that the price volatility of the past four years will not cease. The only way for schools to increase their resilience to price rises is to switch to renewables. These save money and provide more certainty for budgets, while freeing up resources which can be redirected to students and teachers.
By Don Dulchinos, Director at OpenADR Alliance
Grid-interactive buildings use smart technologies and connected systems to help optimise energy use and interact with the grid. This new generation of smart buildings is helping to transform energy management, delivering greater flexibility and efficiency for users – and cost savings. Importantly however, they are playing an active role in helping balance the supply and demand of energy and reduce strain on the grid.
These intelligent buildings, both residential and commercial, can adapt energy use dynamically, so rather than playing a passive role in just drawing down energy, they reduce demand when the grid is under stress.
By storing and drawing power from a range of distributed energy resources (DER), like solar panels, battery storage, heat pumps and even electric vehicles (EVs), they can treat these electric appliances and systems as potential grid resources. DERs can be aggregated by Home Energy Management Systems or Building Energy Management Systems in commercial buildings.
Smart homes and technologies are not new of course. However, major advances in grid connectivity and communications, and, more recently, with the integration of AI for smarter automation, the industry is taking off. We are seeing more use cases, with grid-interactive buildings, campuses and homes already enabling the localisation, generation and consumption of energy, and working around the bottlenecks in the distribution network.
As an industry alliance, representing many manufacturers of heating, ventilation, air conditioning and refrigeration products and systems, the OpenADR Alliance is seeing real innovation in action, with the adoption of new technologies and solutions.
Standards play a role
Standards are crucial for driving this innovation, particularly in enabling efficient demand response within energy management systems. By mandating standards, governments and regulatory bodies support the role of compliance.
In the US, for example, the CTA-2045 specification – the certified version is also known as EcoPort – enables smart appliances and devices to connect directly to energy management systems (commercial or residential) through a universal port. This interoperability promotes flexibility and adaptive energy consumption across appliances, playing a critical role in encouraging consumers to be greener.
Any EcoPort-certified control module, when plugged into an appliance or energy management system, can reliably establish communications that meet the requirements of the CTA-2045 standard.
The UK has followed suit, with two standards published by BSI in 2021 – PAS 1878 and PAS 1879 – setting out the requirements for energy smart appliances (ESA). The Department for Energy Security and Net Zero (DESNZ) led the development of PAS 1878, incorporating OpenADR as one of the criteria that an electrical appliance needs to meet in order to perform and be classified as an ESA. PAS 1879, meanwhile, addresses the demand side response operation of these appliances.
DESNZ has spoken about how innovation and smart technologies can contribute to the UK’s
ambition to reach net zero by 2050, and the role standards will play in driving this change.
The government’s Flexibility Innovation Program is also playing a role in this as it looks to support innovative solutions, including the development of ESA for the delivery of interoperable demand side response as part of its IDSR program.
Early implementations are largely confined to water heaters, a major source of load response across households. But EcoPort provides a standard interface for energy management signals and messages to many other devices, including energy management hubs, residential gateways, sensors and household appliances, from pool pumps to EV chargers.
A real-world example is in Oregon, where utilities have implemented OpenADR programs that leverage certified, CTA-2045 equipped devices. Local utilities have focused on compliant smart water heaters and HVAC systems, which temporarily reduced energy consumption during periods of high demand. The result has been a significant reduction in peak demand by over 15 per cent during hot summer days, alleviating pressure on the grid and ensuring customers maintained a comfortable environment.
The success of programs like these demonstrates the huge potential for other initiatives. Using technology and fostering greater collaboration between government, energy providers, manufacturers and consumers, can help create a positive energy future. With the growing range of products and systems now available, grid-interactive buildings and homes are set to be a major contributor to this.
The UK housing sector is at the forefront of a digital transformation, as the nation pushes towards a sustainable, net zero future.
Digitalisation is reshaping the way homes are built, managed, and lived in, playing a pivotal role in reducing carbon emissions and enhancing energy efficiency.
By leveraging smart technologies, digitalisation enables seamless integration between lowcarbon heating systems, the electricity grid, and user interfaces, making sustainable living both practical and accessible.
The role of digitalisation in decarbonising UK housing
Digitalisation is transforming the UK housing sector by enabling data-driven insights, automation, and connectivity between systems. This shift plays a significant role in decarbonising homes, aligning with the Future Homes Standard, which mandates new homes to achieve high energy efficiency and low-carbon emissions. With the help of digital technologies, energy-efficient heating systems can now operate in harmony with the electricity grid, balancing energy demand and supply while giving users greater control over their consumption.
Heating, which traditionally depended on carbon-intensive sources, has become a critical area of focus in this digital transformation. Lowcarbon heating systems like networked ground source heat pumps and community heat hubs, when coupled with smart technologies like a Passiv Smart Thermostat, create sophisticated ecosystems where data is used to optimise energy use, enhance comfort, and support grid stability. Through this digital integration, homes can achieve high efficiency without placing undue strain on the grid, making electrification sustainable at scale.
A digital-ready, low-carbon solution
Networked ground source heat pumps, when installed as part of a smart bundled solution, can meet the demands of modern, digitalised homes. They work by extracting thermal energy stored in the ground, which is then amplified by a heat pump to provide consistent, efficient heating. As an electrically driven system, networked ground source heat pumps represent an essential component of electrification efforts, but their digital capabilities are what truly enhance their value.
When integrated with smart thermostat technology, Networked Ground Source Heat Pumps enable residents to set their comfort
By Tom Brough, GTC Sales and Marketing Director
levels. The device then optimises the homes energy use in real-time, making informed adjustments. This removes the need for manual adjustment, creating a seamless, easy-to-use home energy management system.
This smart technology also contributes to grid stability by allowing homes to respond to demand-side incentives. For example, users can be incentivised to reduce their heating demand during peak times, reducing pressure on the grid and lowering overall energy costs. This level of digital flexibility makes homes futureproofed, supporting not only today’s energy needs but also those of a rapidly evolving, decarbonised energy landscape.
Centralised, digitalised heating for larger developments
Community heat hubs bring low-carbon heating to multi-unit developments and urban communities, where individual heat pumps may not be feasible. Community heat hubs use a shared heat network to distribute renewable heat to multiple homes, centralising energy use and creating efficiencies that align well with grid demands. Through digitalisation, community heat hubs offer even greater benefits, with smart systems that allow for heat demand to be controlled, monitored, and balanced across the development.
By integrating Community Heat Hubs with Passiv’s digital energy management platform, a cohesive, adaptable system is created that operates efficiently at scale. The digital energy management platform provides real-time data on energy consumption across the Hub, enabling responsive heat distribution that
matches both user demand and grid capacity. This digital integration also offers housebuilders a scalable, future-ready solution that supports both cost efficiency and compliance with sustainability standards, making it easier to create smart, low-carbon communities.
A digital ecosystem for low-carbon living
Combining networked ground source heat pumps and community heat hubs with smart thermostat technology creates a digital ecosystem that benefits housebuilders, residents, and the grid alike:
For housebuilders: Digitalised heating solutions provide a direct path to compliance with the Future Homes Standard, reducing the complexity of regulatory requirements while delivering enhanced value to prospective buyers. networked ground source heat pumps and community heat hubs, coupled with smart controls, make new homes attractive to modern buyers seeking environmentally friendly, techenabled features.
For residents: Digitalisation offers unprecedented control and transparency, enabling residents to interact with their heating system in meaningful ways. Smart thermostats allow users to set heating preferences, track consumption, and make data-driven adjustments, creating a balance of comfort and cost-efficiency. By taking charge of their energy use, residents can significantly reduce their environmental impact while enjoying a high standard of living.
For the grid: The ability to manage energy demand digitally is invaluable for maintaining grid stability. networked ground source heat pumps and community heat hubs, enhanced by intelligent energy management, allow for demand to be spread across off-peak times, reducing load during peak hours. This digitalised demand management helps balance supply and demand, making the grid more resilient and adaptable as it supports the transition to renewable energy sources.
By embracing digitalisation, the UK housing sector can accelerate its journey to net-zero, creating homes that are not only energyefficient but also intelligent, adaptable, and ready for the future. Through innovation and forward thinking we are helping to build a resilient, low-carbon housing market that benefits everyone—from developers and residents to the energy grid that powers the UK.
Lee Sutton, co-founder and chief innovation officer of myenergi, explores the latest advancements in home energy technologies and explains how ‘eco-smart’ solutions are quickly becoming the preferred next-gen choice for both consumers and electrical professionals alike
Amajor technological trend that’s emerged over the past few years is the boom in domestic energy generation and efficiency technologies, such as solar PV and heat pumps. According to data from the Microgeneration Certification Scheme (MCS), 2024 was a record-breaking year for smallscale renewables, seeing more than 260,000 installations in UK homes and small businesses (a 7 per cent increase from 2023, which was itself a record year), bringing total installations past the 2 million mark.
Of these figures, more than 180,000 were solar PV installations, while nearly 20,000 were battery storage. Perhaps the most striking figure is that of heat pumps, with the number of installations seeing a staggering 43 per cent increase on the previous year to nearly 60,000 units. But why are we seeing such rapid adoption of this sort of tech? Well, the answer is actually quite simple… interconnectivity. On their own, self-generation technologies like solar PV, heat pumps and batteries can help homeowners to use energy more efficiently. Combined, these devices make up part of a fully-connected smart home ecosystems, allowing users to more effectively harness the power of self-generated energy to alleviate the need to draw electricity from the grid.
Is ‘eco-smart’ the future?
In a word, yes! While solar panels, heat pumps and energy storage solutions are becoming increasingly popular, technologies that further increase efficiency and accelerate return on investment are becoming more mainstream.
An ‘eco-smart’ device is one that facilitates interconnectivity between multiple technologies through the internet. For example, a conscious homeowner may want to monitor and adjust the amount of self-generated electricity that’s used to heat their water tank, versus how much charges their electric vehicle. They may opt to prioritise fully charging their EV in preparation for a long journey, for example, or alternatively decide to up their water temperature ahead of a chilly evening. They may even want to take best advantage of agile energy tariffs by only drawing power from the grid during off-peak times, only using their stored and self-generated electricity when prices rise.
Eco-smart technology gives homeowners a tighter grip of how much energy they use, how they use it, and when… it literally puts the power in the hands of the consumer. By greatly increasing the efficiency of self-generation, users can save more energy, reduce their carbon footprint and, crucially, slash their utility costs.
At myenergi, we’re renowned for our innovative range of eco-smart home tech, which has been specifically designed to maximise the value of self-generated renewable energy and help users become more energy independent.
We’re perhaps best known for introducing the first eco-smart EV charging device to market - zappi - a future-proofed solution that’s both mains-connected and integrates seamlessly with renewable energy generation. This type of interconnectivity allows users to leverage the full potential of smart devices, enabling them to maximise their self-generated energy by charging their EVs with cheaper, greener electricity.
We also manufacture a wide range of other devices, like eddi, the UK’s number one solar power diverter, which diverts surplus renewable energy to heating systems; and harvi, our energy monitoring wireless sensor, which allows zappi and eddi to be installed without wiring a direct CT clamp. There’s also libbi, our modular battery storage system, which provides users
with a simple way to capture surplus green energy and access it immediately when they need it most.
Importantly, all these devices can integrate as part of a wider energy ecosystem – all seamlessly managed through the myenergi app. Interconnectivity is the name of the game, and we expect the popularity of IoT-connected technologies to continue rising as savvy homeowners increasingly seek new ways to save money and reduce their carbon footprint
What’s next for smart homes?
Investing in IoT-connected technology is a growing trend among the new age of homeowners who are more eco-conscious and tech-savvy than ever. By harnessing the power of interconnected eco-smart technology, they can effectively hedge against the peaks and troughs of renewable energy generation, maximise their self-consumption and reduce reliance on energy from the grid.
For electrical installers navigating the rapidlyevolving technological landscape, looking towards the latest eco-smart innovations should a clear priority. Not only will it allow installers to add greater value to their existing service offerings, but will help attract a new segment of customers who are more and more looking to reduce their impact on the environment and save on energy costs.
With demand for PV installs surging, David Barnes Marketing Manager at KNIPEX, highlights two new tools designed to meet the specific needs of electricians working in the solar sector
Electricians are taking on more solar work than ever as PV systems become a regular feature on domestic and commercial projects. Recent figures suggest that around 40 per cent of new homes in England are now built with solar panels, reinforcing the growing need for tools designed specifically for photovoltaic installs. That’s why KNIPEX has introduced two new additions to its range, purpose-built for the realities of solar installation. The ErgoStrip PV and MultiCrimp PV are designed to speed up prep, reduce strain and guarantee accurate results on site.
The ErgoStrip PV
The KNIPEX ErgoStrip PV (16 95 03 SB) is a compact, PV-specific version of the popular ErgoStrip, redesigned to deal with common solar cable types. It handles 4 and 6 mm² PV cables like H1Z2Z2-K with ease, as well as round and damp-proof installation cables including NYM types (3 x 1.5 mm² to 5 x 2.5 mm²).
A key feature is its adjustable length stop (6 to 18 mm), making it perfect for preparing cables for MC4 and MC4 EVO 2 connectors. It also includes a notch for PVC single cores (0.2 to 4 mm²). Conical tips improve access in tight spaces and the soft-grip pistol handle and spring-loaded action reduce fatigue during long shifts.
It’s also available as part of the KNIPEX PV Installation Set (00 31 31 V01) which includes the PreciForce PV crimping pliers, making a solid, reliable pairing for fast solar terminations
The MultiCrimp PV
The MultiCrimp PV (97 33 03) is a flexible crimping tool with three interchangeable dies as standard: for MC4/MC4 EVO 2 connectors, wire ferrules and uninsulated connectors. Dies swap out quickly without tools and more options are available to customise it for wider use.
A ratchet lock ensures high crimp quality every time and can be released manually if needed.
The ergonomic, multi-component handles offer all-day comfort and a belt clip means it’s always within reach on site.
As PV becomes a staple in electrical work, KNIPEX’s new range delivers the precision and reliability solar installers need on site.
For more information on the New KNIPEX PV range for 2025 visit https://www.knipex.com/ en-uk/products/new-products
Pliers’ expert KNIPEX has become an Associate Supporter of Band of Builders, the national construction charity that carries out practical projects to help tradespeople facing life-changing or limiting circumstances. Band of Builders brings together skilled volunteers from across the UK construction industry to complete projects that make a lasting difference to the lives of tradespeople and their families. From installing accessible bathrooms and building home extensions, to creating fully adapted outdoor spaces and delivering wellbeing support, the charity harnesses the skills and generosity of the trade to help those in need. As an Associate Supporter, KNIPEX will contribute to the success of these projects through a variety of fundraising activities, raising awareness across its UK customer base.
Founded in 2016, Band of Builders has delivered more than 35 projects across the UK, with a growing community of volunteers and supporters drawn from every corner of the industry. Each project is tailored to the specific needs of the beneficiary – often a tradesperson who has suffered injury, illness or bereavement –and delivered at no cost to the recipient.
The charity recently launched its Supporter Programme to provide structured ways for individuals and businesses to get behind its mission. Associate Supporters like KNIPEX play a key role in helping fund and facilitate the practical work that sits at the heart of Band of Builders’ impact.
“We know that being a tradesperson is about more than just the job – it’s a way of life, and one that comes with its share of risks and challenges. That’s why we believe in supporting organisations like Band of Builders, who are there for the trade when it needs it most.
Together, we can make a real difference,” says David Barnes, Sales and Marketing Manager for KNIPEX UK.
For more about Band of Builders and how to get involved, visit bandofbuilders.org
The customizable crimping pliers for MC4®, MC4® Evo 2 and many other connectors
Universal, high-performance crimping pliers of professional quality for photovoltaic systems
Just one tool with three crimping dies for MC4® / MC4® Evo 2, uninsulated cable connectors and wire ferrules
Quick and easy change of crimping dies without additional tools
Fast and precise cable skinning and stripping for photovoltaic professionals
For fast and precise stripping of solar cables with 4 and 6 mm² (e. g. H1Z2Z2-K) and all common round and damp-proof installation cables (e.g. NYM cable 3 x 1.5 mm² up to 5 x 2.5 mm²)
Length stop for PV cables: adjustable from 6 – 18 mm for repetitive stripping lengths, suitable for all standard solar connectors
Innovative, ergonomic pistol grip design for easy cutting, stripping and longitudinal cut of the sheath Further information on
In May, Tom Jennings was appointed managing director of adi Electrical, a division of multidisciplinary engineering firm adi Group. His journey to the position is incredibly unique, having first joined the company as an apprentice 19 years ago. Here, he speaks to Electrical Times about his progression with the firm, the importance of apprenticeships and more...
A: Q: Q:
How did you decide to go into an electrical apprenticeship?
Originally, I was doing a sports BTEC after I left school, but I hit a brick wall with being back in a classroom. I just couldn’t sit in a room anymore: I wanted to be active, out on site and earning a living. So, when I saw the opportunity to try an electrical engineering apprenticeship and was successful, I never looked back.
What are the key moments from your apprenticeship?
A:
I’ve been quite lucky with my apprenticeship – I’ve never really been static or based at just one site. Thanks to adi, I’ve travelled across the whole country and even into Europe. It was an incredibly diverse apprenticeship and, honestly, it’s been a lot of fun along the way.
I wouldn’t be where I am without the people who supported me throughout, and that all started with my apprenticeship. When you begin an apprenticeship, you’re usually still quite young, but you’re in an adult environment. If you’re lucky enough to have good mentors, people who take you under their wing and build your confidence, it really helps you grow.
By my second year, I was already out on site supporting the wider team. Even though I wasn’t a site supervisor, I was leading on certain tasks, which really built my confidence. The biggest step came toward the end of my apprenticeship. I was thinking about doing a foundation degree, the equivalent to an HND in electrical engineering. adi supported me straight away.
If it wasn’t for people standing up for me, encouraging me and helping me, I wouldn’t have had that opportunity. That’s
Combined with energy storage (of all types – battery/hydro/thermal) we’re set to see the UK getting ever closer to energy independence - something that has been flagged as essential in light of recent turmoil on foreign soils.
what I try to do now for my apprentices - give them a voice.
Q:
A:
How did you find the transition from being hands-on to taking on leadership responsibilities?
Because of the apprenticeship route, and because people gave me opportunities throughout, the transition felt gradual and natural. For example, leading a small crew on-site helps you build the skills to talk to and manage people. It’s all incremental steps. Looking back now, I can see how that early development shaped where I am today. If you flipped it and asked, “Could an apprentice ever get to this position?” it might seem impossible. But it happens through experience, support and consistent growth. I really appreciate what those people
did for me; it’s had a huge impact on my development. And that’s what I try to do for my team now.
Q:
You mentioned working closely with apprentices. Do you see apprentice development as an important part of your role?
A:
We’ve got a total of 48 apprentices, and 15 are in Electrical, though we’re looking to take on another six this year. Apprenticeship development is hugely important within adi as a whole, and we’re proud to say that we’ve achieved the Platinum Membership with The 5 per cent Club, which reflects our commitment to having over 5 per cent of our workforce in earn-and-learn positions, and currently we have over 10 per cent.
The trade is certainly not dying, but there is a skills gap because people are retiring. We’re trying to bridge that gap and get people interested in apprenticeships. There’s so much opportunity, and I certainly see myself continuing to take an active role in growing this side of the business.
The issue is, when it comes to recruitment everyone seems to be chasing quick wins. But what about development? Where are you going to progress to? That’s where we need to work with the younger generation: show them that starting small can lead to something big.
I can use myself as an example, but there are so many success stories out there, and I’ve got some special talent coming through right now. One of my team members started off through adi’s award-winning preapprenticeship scheme, which our business pioneered, and so started in the business at 14. Now, I see him becoming one of our main project engineers in a few years. There are
another two from the pre-apprentice academy on similar journeys within the team.
Is there anything you think adi is doing particularly well when it comes to changing the mindset around trades, and inspiring that long-term passion?
It’s the culture. adi isn’t a corporate company, it’s very family-orientated. People genuinely care and want to help each other develop. It’s not just about following process after process. For some people, structure is important, and that’s fine. But for me, I like being fluid, I like knowing I can go to the boundary to support someone and help them progress.
Alan Lusty, our founder, has always supported that. If you feel like something needs to be done, you can get it done, within reason of course. But it’s all in the name of growing the business and helping people grow with it. That mindset really shapes the culture here.
What’s the vision for the future of adi Electrical? Where do you see the business in the next five years?
That’s why investing in people who share the same values and showing them that there’s a career path for them at adi is key.
: A: A:
For me, it comes back to the apprenticeship scheme - creating a legacy by bringing through the next generation of engineers. Of course, the main focus is continuing to grow the business, but developing future engineers is what drives me. As we grow towards becoming a £24–25 million business, which is a significant part of the Group’s Vision 2030 plan to reaching turnover £200m, finding the right people gets harder and harder.
If you had to give a message to someone considering a career in engineering but who may be feeling unsure, especially a young person, what would you say?
I’d say if you’re bored with what you’re doing, or with studying, and want a challenge, apprenticeships are the best route. The world’s your oyster. Even if you start as an electrician, it doesn’t mean you’ll stay in that exact role. You can move into maintenance, engineering, automation; there are so many directions, and with there being over 23 specialist divisions within adi, apprentices are really spoilt for choice.
But that core foundation, being on the tools, understanding how things work, and learning how to communicate, is invaluable. One of the biggest things for me has been learning how to talk to people.
At university, you’re surrounded by peers your own age. As an apprentice at 16, you might be managing or working alongside someone who’s 40, so you have to learn how to communicate across generations and experiences. It teaches you respect. Also, don’t worry about making mistakes - we all do. But you learn, and it makes you better.
Working with many different people from different backgrounds has impacted my personal life too - it’s made me a better parent and a more thoughtful person. And now, I try to take something from everyone I work with. That’s how you keep improving: not just professionally, but as a person.
What inspired R&B Switchgear Group to implement T Level industry placements as part of your strategy to tackle the engineering skills gap?
As a provider of specialist electrical switchgear and power solutions to complex sectors like oil, gas, and renewable energy, we rely on a highly skilled workforce to deliver bespoke, safety-critical systems. With a large proportion of our experienced engineers approaching retirement, it became clear we needed a long-term, sustainable strategy to build talent from within.
T Level industry placements offered a practical solution. Students arrive with a solid technical foundation so they can get stuck in from the get-go, but it also means we can shape their development early on, ensure they gain relevant hands-on experience, and ultimately start building the next generation of engineers tailored to our business needs.
How did you design the industry placement to ensure that students receive hands-on experience in various areas of the business?
Bringing in T Level students has created valuable opportunities for knowledge transfer between our experienced staff and the next generation of talent. It’s also driven our team to reflect on their own processes and share their expertise more openly. A: Q: A:
We created an in-house training programme that enables students to spend time across every part of the business – from engineering design and planning in the office, to hands-on work in the manufacturing workshop. This exposure helps T Level students build a well-rounded skill set, understand how the business operates as a whole, and apply their knowledge in real-world contexts.
How has hosting 12 T Level students had an impacted in terms of skills development and knowledge transfer?
Q: A: Q: Q: A:
Bringing in T Level students has created valuable opportunities for knowledge transfer between our experienced staff and the next generation of talent. It’s also driven our team to reflect on
their own processes and share their expertise more openly. We’ve seen a clear boost in productivity and energy, with students contributing meaningfully to real work while picking up critical skills.
What has been the key to the success of transitioning T Level students into full-time apprentices at the company?
T Level placements have become an integral part of our early talent pipeline. Our current model is designed to support students through meaningful industry experience, with a view to offering full-time roles that lead to a range of career pathways across the business, including apprenticeships.
Because T Level students are embedded in the business from the outset, they’re already familiar with our systems, culture and technical expectations. As a result, those who join us via T Levels tend to be more prepared and engaged when they progress into permanent positions.
By the time they complete their placements, they’re not just work-ready; they’ve become part of the team. That makes the step into an
apprenticeship feel like a natural progression, for both the student and the business.
We’ve seen first-hand that T Levels provide the students with a solid technical foundation, giving students the confidence and capability to contribute meaningfully to real projects. While exact numbers vary year-on-year, we typically aim to transition around 30–50% of our T Level placement students into formal full-time roles. This approach allows us to assess suitability before committing to longer-term training – helping us grow our own talent in a structured, sustainable way, while saving time and ensuring greater consistency across the business.
Q:
What challenges did you faced while integrating T Level placements and how did you overcome them?
A:
As with any new initiative, there were initial questions around how T Level placements would fit into day-to-day operations. But we found that with careful planning and communication between departments, we were able to integrate students smoothly. Their technical ability and willingness to learn made it an easy fit and our local college was a great support, right through the placement.
The time commitment and onboarding process were comparable to bringing on a new junior member of staff or apprentice –but as we’ve hosted more students, this has become even more streamlined. The value T Level students add more than justifies the initial setup.
Q:
A:
How have T Level students contributed to your company’s overall growth?
Our T Level students have made a real, hands-on contribution across the business. They’re bright, enthusiastic, and quick to learn – taking on real tasks that support live projects and help keep operations running smoothly. Their presence has strengthened the team, boosted productivity, and brought fresh energy to the workplace. They also bring a new perspective and aren’t afraid to ask questions or challenge
established ways of working. In a few cases, that’s led to small but meaningful improvements and greater efficiency. While they’re still learning, they’ve shown they can add value from day one.
How have your existing employees responded to the addition of T Level students and how has it impacted company culture?
The response at R&B Switchgear has been overwhelmingly positive. Our team has enjoyed mentoring the students, and it’s brought palpable new energy into the business. It’s also encouraged more collaboration and a sense of pride in passing on knowledge, which has had a great impact on morale.
How can companies ensure they retain talent developed through T Level industry placements and apprenticeships?
: A: Q: A: Q:
Retention starts with making students feel valued and integrated from day one. Giving them meaningful work, development opportunities, and, when appropriate or possible, a clear pathway into apprenticeships
or full-time roles. This builds loyalty – when people feel invested in, they want to stay and grow with you.
We’re immensely proud that all five of the T Level students we offered apprenticeships to have accepted our offers. We’re thrilled to have them in team for the long term.
Looking ahead, what’s next for R&B Switchgear Group in terms of talent development?
We’re committed to expanding our involvement in T Level placements – each and every placement we’ve hosted has been an incredibly positive experience. T Levels are now a core part of our talent strategy.
We’re immensely proud that all five of the T Level students we offered apprenticeships to have accepted our offers. We’re thrilled to have them in team for the long term.
Find out more about R&B Switchgear Group at: https://www.rbswitchgeargroup.com/
SEND YOUR LATEST PRODUCTS TO lorna.reekie@purplems.com
ESP is raising the bar in home safety with its Espire Dual CO and Heat Alarms –developed specifically for spaces where the risks of both fire and carbon monoxide are present. Ideal for kitchens, utility rooms, and garages, this multi-sensor unit simplifies protection with advanced, dualthreat detection in one compact device.
The Espire CO and Heat Alarms incorporate independent sensors for carbon monoxide and heat detection, allowing each threat to be monitored and managed separately. Certified to BS EN 50291-1 and BS 5446-2, the alarms are third-party approved and backed by a five-year warranty.
The Espire dual CO and Heat Alarms are to be installed in accordance with0 BS EN 50292. Installers can choose from two power options to suit varying project requirements:
• Powered by mains with a sealed tamper-proof 10-year lithium battery.
• Powered by a sealed tamper-proof 10-year lithium battery.
Both models feature ESP’s signature lock-in base, hush function, auto sensor self-test, and 24-hour alarm memory. Installers can also benefit from optional RF-Link modules alarms for enhanced coverage.
Supplied in ESP’s recyclable, eco-friendly packaging and built to last, the Espire CO and Heat Alarms delivers on reliability, versatility, and sustainability – making it the ideal solution for today’s homes. www.espireuk.com
Unicrimp, part of the Scolmore Group, has expanded its comprehensive Q-Fire range of fire-rated products with the introduction of new sizes of its popular stainless steel metal cable ties. This enhancement provides installers with greater flexibility and choice when working in demanding, safety-critical environments.
Stainless steel cable ties are widely used as a secure and versatile fastening solution for bundling and supporting cables, wires, and components — particularly in settings where high strength, durability, and fire resistance are essential. These ties help maintain cable support during a fire, ensuring safety for both emergency services and the public by preventing premature cable collapse.
Already part of the Q-Fire product offering, the stainless steel cable ties have now been made available in additional sizes - 200mm x 4.6mm, 300mm x 4.6mm and 360mm x 4.6mm. With these additions, the Q-Fire range now includes metal cable ties in sizes from 150mm x 4.6mm up to 840mm x 7.9mm, offering greater flexibility for diverse installation requirements. All sizes comply with BS7671 IET Wiring Regulations, ensuring full regulatory alignment for professional electrical installations
The expanded cable tie range complements the full suite of Q-Fire fire-rated products, which includes all round banding, LSF coated saddle clips and p clips, fire safe metal cable clips, stainless steel mounts, and fire resistant sealants and foams. www.unicrimp.com
In the competitive realm of professional trades, having the right tools at your disposal can be the difference between success and failure. Welcome to PowerPro – your go-to source for high-performance power tools engineered specifically for professionals. With an unwavering commitment to quality and performance, PowerPro brings together the most trusted names in the industry, including Milwaukee, DeWALT, and Makita, ensuring that you have access to tools that excel on the job site. It’s not just about having options; it’s about having the tools you need, precisely when you need them.
The PowerPro promise
At PowerPro, we understand that your days are demanding and that time is money. That’s why we’ve built our reputation on providing trade-ready tools designed to withstand the rigours of the job. With over 3,000 meticulously selected products, we cater to every possible need, from essential everyday gear to specialised kits. Our extensive range of tools is chosen with professional use in mind, ensuring that you can tackle any challenge that comes your way. However, choice alone isn’t enough. We know that real job sites demand dependable performance, which is why we only stock power tools from brands professionals trust. Milwaukee, DeWALT, and Makita are not just names; they represent a legacy of unwavering performance and durability you can rely on, job after job.
Speed and availability: your tools, when you need them
In an industry where delays can lead to costly downtime, PowerPro understands the importance of speed and flexibility. Our robust delivery system ensures that you have your tools in hand as quickly as possible. With next-day delivery available (Geographical restrictions may apply) and access to over 400 CEF branches across the
UK and Ireland, we make it easy for you to get exactly what you need, when you need it. Whether it’s an urgent replacement drill or a full suite of tools for a new project, our dedicated team is ready to assist you in finding the right equipment. We are not just suppliers; we are your partners in productivity, and our knowledgeable staff is always on hand to provide expert advice and assistance.
More than just tools
PowerPro’s commitment to the professional trades goes beyond merely supplying tools. We recognise that staying competitive in today’s market requires insight and knowledge, which is why we offer a wealth of trade-focused content designed to keep you ahead of the game. From comprehensive product reviews to time-saving tool pairings, our resource centre is filled with valuable information that can help you make informed decisions.
Understanding industry trends, embracing new technologies, and finding efficient ways to work are essential to maintaining a competitive edge. At PowerPro, we bring you the latest insights and efficiency tips that empower you to work smarter, not harder. Our dedication to providing expert advice is a testament to our commitment to the trade — we aim to equip you with not just tools, but the knowledge to use them effectively.
When you choose PowerPro, you’re not just purchasing power tools; you’re investing in a relationship built on trust, reliability, and expertise. Our team is made up of individuals who understand your needs and the demands of the trade. Whether you are outfitting a construction crew or simply upgrading your personal toolkit, we are here to ensure you find the perfect fit the first time.
Our commitment to excellence doesn’t stop with our products; it extends to our customer service. We strive to ensure that every interaction with PowerPro leaves our customers feeling valued and informed. We recognise that the success of your projects rests on the tools in your hands, and we work hard to provide you with nothing but the best.
Whatever the job, whatever the challenge, PowerPro is designed to keep you equipped, efficient, and one step ahead in your field. We stand by our motto — engineered for power, built for pros. If you’re ready to elevate your work with tools that deliver performance and durability, look no further than PowerPro. Get to work with PowerPro today, and experience the difference that comes with having the right tools and support by your side. Whether you’re cutting, drilling, grinding, or fixing, we’ll help you stay productive and prepared for anything that comes your way.
Luceco recently worked with Senate Group at Peoples Ford in Speke on a two phase project. Refurbishing the new OMODA/JAECOO showroom in phase one before moving on to its existing Ford Car and Transit Centre in phase two.
Beginning with a complete strip out of the existing fittings and fixtures, Luceco designed and supplied a lighting plan that complimented the space and aesthetics of the showroom.
The Platinum and Platinum Mini downlights feature a die-cast aluminium body designed to provide thermal control. A recessed mounted, swing tab design enables easy installation in any ceiling. The Platinum Surface downlight uses the same thermal control design as the rest of the Platinum range, with the flexibility to be surface, suspension or BESA mounted.
Another downlight used was Luceco’s Carbon downlight – a stylish commercial LED solution which has been designed to replace PL type downlights and maximise energy savings. It offers up to 100Lm/W whilst providing less glare and providing a more comfortable ambiance. Also with a recessed mounted design, the downlight is suitable for plasterboard or suspended ceiling systems.
For additional lighting, the Luceco Litera was chosen for its versatility. Available in surface and suspended installation models, it offers high-performance linear lighting with low power consumption, delivering optimal illumination for any commercial environment with efficacy up to 125 Llm/cW.
All lights were installed with emergency features, allowing safe evacuation in case of mains failure with three hours’ worth of back-up power that meets all standards and regulations, and hard wired controls. www.luceco.com/uk/
The Radiator Company has introduced even more options for their Ancona Electric radiator, widening their selection of design-led radiators. The Ancona Electric combines the classic Ancona design with the flexibility of a newly designed, fully controllable electric element, offering more choice when specifying heat emitters for a space.
Made from steel, this multi-column radiator is available in a wider range of dimensions, with three heights - 399mm, 653mm, and 1,853mm. Both the 653mm and 1,853mm options are available in a range of widths, providing even more options for decorating and heating a space.
Another new feature is the option to colour match the element to the radiator to ensure a seamless finish. Available in 188 RAL colours and 36 special finishes. Whether looking for a neutral shade to blend into a space, or a bright and fun colour to coordinate with the interior design.
The element included is eco compliant, offering eight function modes. With the option to operate 24/7, daily, or with three pre-set programmes, the Ancona Electric makes heating a space simple and convenient. In addition, the Open Window function detects an open door or window and turns the radiator off to prevent heat wastage, saving energy and money.
Richard Lister stated: “We are delighted about the new design and added features to the Ancona Electric as customers now have even more options for radiator size with the convenience of electric. Electric radiators are easy and quick to install as they don’t require additional plumbing so can be installed anywhere in a space near an electric wired socket, making them cost-friendly and give customers even more choice.”
Part of the IRSAP Group, The Radiator Company offers unique and innovative radiators in a vast array of finishes, colours, sizes, and formats. With thousands of combinations, it offers the largest selection of designer radiators in the UK. www.theradiatorcompany.co.uk
Part of Click Scolmore’s growing Elucian consumer unit and protective devices range is the AFDD+MCB Combination Unit which is designed to deliver superior protection against electrical fires, overloads and short circuits in one compact, efficient device.
AFDDs (Arc Fault Detection Device) detect and interrupt dangerous arc faults that could lead to electrical fires, providing essential protection in residential, commercial, and public buildings. MCBs (Miniature Circuit Breaker) offer standard protection against overcurrent and short circuits with high reliability and quick response. The range comprises:
• 1 Pole True 10kA B Curve 10A AFDD & MCB
• 1 Pole True 10kA B Curve 16A AFDD & MCB
• 1 Pole True 10kA B Curve 20A AFDD & MCB
• 1 Pole True 10kA B Curve 32A AFDD & MCB
• 1 Pole True 10kA B Curve 40A AFDD & MCB
• 1 Pole True 10kA B Curve 6A AFDD & MCB
• 1 Pole True 6kA B Curve 32A AFDD & MCB
Ideal for applications where residual current protection is already managed, the AFDD+MCB range ensures safety and compliance with the latest standards. It offers overcurrent protection, series arc fault protection and Parallel Arc fault protection
Combining cutting-edge arc fault detection with trusted overcurrent protection, this product significantly enhances electrical safety with minimal installation complexity. www.scolmore.com
BG Electrical, part of the Luceco Group, has launched its latest DC Isolator Switches, designed to meet the growing demand for safe, reliable, and future-ready solutions in photovoltaic (PV) installations. With compliance to IEC 609473 and 18th Edition BS7671 standards, these isolators ensure high performance, safety, and ease of installation.
The BG DC Isolator Switches are available in two variants (25A and 32A), covering installations requiring 16A, 25A, and 32A. This streamlined product range reduces stocking complexity for wholesalers and provides contractors with a universal solution for both 1 and 2 string PV applications.
Fully certified to IEC 60947-3, the BG DC Isolator Switch ensures safe and compliant operation, with a padlockable OFF position for added security. The IP66-rated enclosure offers superior dust and water protection, making it suitable for both indoor and outdoor installations in demanding environments.
With jumper links included as standard, the BG DC Isolator supports both 2-Pole and 4-Pole configurations in a single device, allowing greater flexibility and fewer SKUs. The innovative switch body design allows for easy removal from the DIN rail, reducing installation time and minimising the risk of lost components.
Built to withstand harsh conditions, IP66 rated, with an operating range of -25°C to +85°C, the BG DC Isolator Switch is backed by a 10-year guarantee, ensuring long-term reliability for contractors and wholesalers.
BG Electrical provides future-proof solutions that align with the latest wiring regulations and industry needs. Whether for new PV installations or upgrading existing systems, the BG DC Isolator delivers performance, safety, and ease of use in one compact, durable design. Find out more about our expanding solar ranges and view our wide selection of products here. www.bgelectrical.uk
Chaz Andrews, Technical Manager at Doepke UK asks “should we follow safety recommendations made in product standards?”
am old enough to remember traveling in cars without seatbelts. Yes – people did argue that seatbelts did not make cars safer and they were an unnecessary additional cost! So, what is the problem with clear, simple, and safe guidance being given to the UK electrical industry on the “Type” and use of RCDs with Heat Pumps (HP)?
The Heat Pump Association published its guidance in March 2025. The 1st recommendation (see Q&A 6) highlights the requirements of BS7671 134.1.1 / 510.3, i.e., to follow manufacturers’ recommendations. That is, if the HP manufacturer recommends the use of RCDs with their equipment, you are ill-advised to go against their recommendations, because that is what the HP safety standard is advising as well. So, does that mean that if the HP manufacturer’s documentation does not make specific recommendations about RCDs, you can do what you like? No – BS7671 531.3.3 specifically states RCDs must be selected considering the presence of DC components and frequencies.
We are aware that some manufacturers’ installation instructions may contain issues, either due to ignorance, a genuine error, deliberate omission, or unclear instructions, which could be used to gain a commercial advantage, such as failing to highlight the requirement to use Type B RCDs. Considering the current market knowledge, we must request that HP manufacturers clarify the RCD requirements for their equipment.
RCD Type vis-à-vis HP efficiency
As we explained in 2022, *reference to technical article 23, Inverter (semiconductor control system) controlled equipment, permanently connected to the supply, requires either the manufacturer of the equipment to specify the Type of RCD clearly in their installation instructions or the installer has no option but to use Type B*.
In a nutshell, lower-efficiency HPs, which do not use inverters, may be suitable for use with Type A RCDs (refer to the manufacturer’s installation instructions). However, it should be noted that transients associated with compressor capacitive starting characteristics could result in unwanted RCD tripping during switch-on. Be highly cautious of claims that equipment is suitable for use with Type A RCDs, as it may lead to future problems on-site.
Higher efficiency HPs utilise semiconductor control systems to provide soft start feature, i.e., reduced voltage starting, for compressors. Additionally, the semiconductor control system enables the speed of the compressor and fan to be adjusted based on heating and cooling demands. The characteristics of the control system determine the Type of RCD – see below.
Annex H of BS ENIEC 62477 provides valuable guidance on the suitability and selection of RCDs for use with semiconductor control systems (PECS for short). Whilst this standard is primarily for technical committees producing product standards, Annex H provides a means of reaching reasoned and structured decisions relating to RCD selection associated with HPs. It gives examples of basic circuit diagrams, associated fault currents, and the appropriate Type of RCD: Type F RCDs are designed for use with single-phase supplied inverters, having very specific characteristics – *reference to technical article 23: For example, Type F can be used with inverter switching frequencies up to 1 kHz, provided the smooth DC content does not exceed specified values. To achieve improved efficiency performance, HP manufacturers are now employing inverters with switching frequencies above 1 kHz, which are outside of the performance range of Type F and some manufacturers’ Type B RCDs –* reference to technical article 34.
To simplify selection owing to the limits of the current BSEN Type B product standard and issues with Type B RCDs that only work effectively < 1 kHz, Doepke introduced the Type B HP RCD in 2023, clearly indicating its suitability for use with HPs. Other manufacturers are now replicating this. High demand has led to a decrease in manufacturing costs and market prices.
Installing HPs with increased efficiency performance (modern inverter control) that requires the use of Type B RCD, as opposed to lower-performance HPs associated with Type A RCDs, is a no-brainer when considering the total lifetime running cost for the homeowner.
RCD or not to RCD?
Standards Committees have a duty of care to the users of the standards and those who may be harmed through the associated designs and practices. Standards reflect best practice at the time the standard is written. Consequently, there is always inertia within the market to
adopt new installation practices to support new product technology.
Companies applying standards in product design or installation practice, must decide whether to prioritise safety implications (such as death or injury to a person) over the cost of the safety feature. Note; The Sentencing Council specifically lists “cost-cutting at the expense of safety” as a factor that can be used to increase the severity of a sentence.
The latest safety standard covering domestic ASHPs (BSENIEC 60335-2-40:2024) states in short “installation instructions for appliances intended to be permanently connected to fixed wiring, having a leakage current < 10 mA, shall state that the installation of a residual current device (RCD) not exceeding 30 mA is advisable.” The term shall, in a standard, indicates a mandatory requirement, i.e., you must do it to meet the standard. The term advisable (all standards are advisory) is taken as reasonable or proper under the circumstances.
Consequently, ASHP manufacturers who do not include the above requirement in their documentation do not meet the ASHP product standard. BS7671 clause 134.1.1 states that “the installation of electrical equipment shall take account of manufacturers’ instructions”. See BS 7671 clause 642 as well. The IET is unlikely to issue guidance that contradicts a published safety standard and or manufacturers’ instructions, unless a specific safety issue has been identified.
Does an RCD add significantly to the lifetime costs of HP Installation?
Generally, when we think of domestic fixed equipment, it is typically mounted inside a clean, well-organised environment. Externally ground-mounted chunks of metal connected to a 240V supply are a relatively new consideration for the UK – less than 1 per cent of properties have HPs to date.
Ultimately, under UK law, the responsibility lies with the HP Manufacturer, the company or person responsible for specifying the electrical installation, and those who sign the installation certificate. We cannot argue that an RCD significantly adds to the lifetime costs of HP installations, particularly when choosing highefficiency HPs with solid-state control.
*Technical articles can be found on the Doepke website: https://www.doepke.co.uk/ Downloads-technical-publications.php
Leading power tool manufacturer Makita UK is enhancing its standard factory warranty policy on batteries from one to two years. Since the 1st April 2025, any genuine Makita battery purchased will automatically qualify for a two-year standard warranty without requiring any product registration, and this applies to XGT, LXT and CXT battery platforms.
Makita offers an extensive collection of power tools, cleaning machines, landscaping equipment, and more. Developed using market leading battery technology, the Makita range provides professionals with the ability to work flexibly, and for long periods of time. The increase in the standard factory warranty offers further confidence to users in the quality and reliability of Makita batteries.
“Makita batteries are developed using the latest technology to ensure products are powerful and built for tough, long-term professional use,” commented Tony Coleman, Technical Services Manager at Makita UK. “The new warranty applies to all genuine Makita batteries purchased in the UK from 1st April 2025 onwards and these batteries will automatically qualify without the need to register them. This is a clear indication of our confidence in the technology that underpins all of our products, as well as our commitment to supporting tradespeople across the UK.”
For more information about the warranty terms and conditions, or to explore Makita’s extensive range of products, visit: www.makitauk.com or speak to your local Makita merchant. www.makitauk.com
Doepke UK’s switchgear is built for performance in demanding environments. With ratings up to 630A, it's ideal for commercial and industrial applications – from large machinery to complex TT and PV systems.
Available in 3P+N (unswitched neutral) and 4P (switched neutral) versions, it meets the needs of traditional and modern installations alike.
Assembled in the UK, every unit offers quality, reliability, and fast availability. Based in Daventry, Northamptonshire, Doepke provides next-day delivery through wholesalers or direct collection.
With German engineering and local support, Doepke switchgear combines global quality with the speed and service UK installers trust.
Follow Doepke UK on Instagram or LinkedIn for the latest technical information, or call 01628 829 133, email sales@doepke.co.uk, or visit their website. www.doepke.co.uk
Ovia, part of the Scolmore Group of companies, has expanded its popular Inceptor Milli domestic downlights range with the addition of new Converter Plates. Designed to offer a simple and stylish retrofit solution, these plates make it easier to fit the Inceptor Milli Standard Fitting into ceilings with pre-existing larger holes.
The new Inceptor Milli Converter Plates allow the standard Milli fitting (which requires a Ø64-75mm cut-out) to be retrofitted into ceiling cut-outs up to a maximum size of Ø120mm. This makes them an ideal solution for upgrading or replacing lighting in spaces where ceiling holes are larger than the original fitting's specifications.
The new Converter Plates are available in five distinctive finishes: white, matt black, chrome, satin chrome and antique brass.
Inceptor Milli is a range of 4W and 6.4W dimmable fire-rated LED downlights, available in both standard and baffle designs. They feature pre-wired Flow™ Connectors for quick and easy installation and they are TM66 approved.
A brochure featuring the full Inceptor Milli range can be viewed on the Ovia website –www.oviauk.com – and the Scolmore Group app. It is also available in the new Issue 5 Ovia Catalogue. www.oviauk.com
The New Consumer Unit Range by Axiom (with a twist)
July 2025 will see the CED Group launch a new complete, safe and secure Consumer Unit range by Axiom. This new VAULT collection features both Standard and Surge Protection Consumer Units presented in attractive sleek enclosures.
Starting with Standard Boards, there are eight sizes from 4 way up to 18 way, each fitted with a 100A 2P main switch whilst the four Surge Protection Units consisting of 10, 14, 16 and 18 way, have a main switch plus SPD T2 40KA single module.
VAULT Units have a solid metal construction and are built with a whole range of key features designed for both ease of fitting and use. These include being double clamped, with aligned 32mm entry points, avoiding the need to bend cables, having full MCB blanks and a Terminal Cover with no direct busbar access.
In addition, there are New Main Switches with double terminals for stronger cable grip and a Door with both a curved lid for easy opening and a magnet for holding the door open during installation.
BS EN61439-3 UK/CA CE RoHS
The twist: Every VAULT Unit comes with a Gold Ticket and a unique code - and every ticket is a winner, Crack the VAULT open and submit the unique code to reveal prizes from tools to £500. Further information call 0208 503 8500 or visit the website. www.cedelectrical.co.uk
Click Scolmore is further enhancing its New Media range with the launch of new CAT-6A modules, delivering high-speed data connectivity for today’s increasingly demanding media and network installations.
The new CAT-6A modules are engineered for ultra-fast performance, supporting data speeds of up to 10 Gbps over cable lengths of up to 100 metres. With a high-frequency operation at 500 MHz, they are designed to ensure dependable, high-speed data transfer, even across extended distances.
Ideal for both residential and commercial projects, these modules offer installers a flexible and efficient solution for integrating data, audio, and visual connections. A single New Media faceplate can be configured with multiple interchangeable modules to suit various media requirements. The clip-fit design allows quick, tool-free installation into blank mounting plates.
The new CAT-6A modules are offered in three colour options — black, white, and grey. www.scolmore.com
Customisable
High-quality, robust materials for industrial use
Kompaktes Aluminium-Funktionsgehäuse mit elektrischer Schaltfunktion
(illuminable) push buttons and emergency stop
Werkstoff und Oberfläche:
Variants with pushbuttons, emergency stop function, LED lighting, membrane keypad
aus Aluminium AlMgSi 0,5; gleitgeund naturfarben oder schwarz eloxiert.
Befestigungsarten:
frontseitige Befestigung
rückseitige Befestigung
Rohre mit Durchmesser 30 oder 40 mm
Funktionselemente ab Werk:
Drucktaster mit grüner LED (Schließer)
Drucktaster mit roter LED (Schließer)
Drucktaster mit LED (Schließer)
Anschluss:
Anschlussleitung 5 m aus dem Funktionsgehäuse
herausgeführt
Schutzart:
Anfrage:
Längen, Ausführungen und Beschriftung