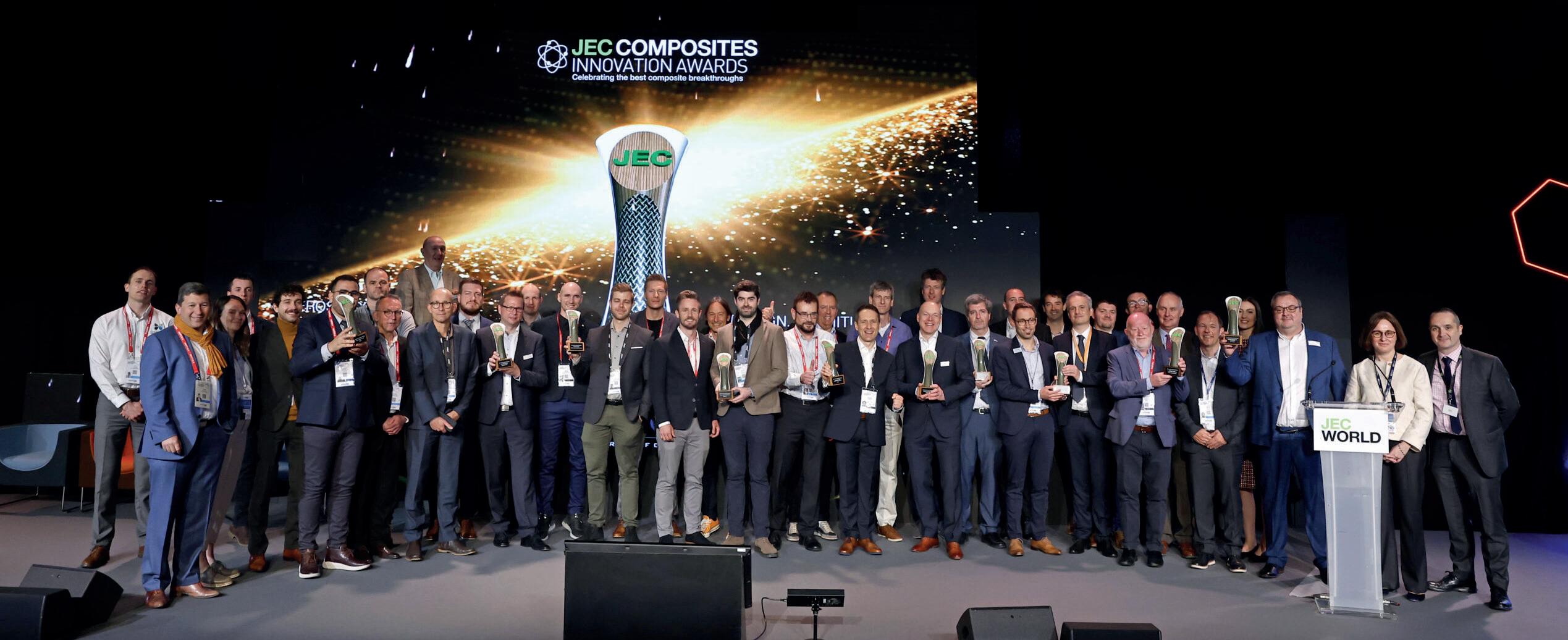
7 minute read
Notiziario dei Compositi - Progetti premiati nel mondo dei compositi
NOTIZIARIO DEI COMPOSITI
JEC Composites Innovation Awards 2022 - Parte 1 Progetti premiati nel mondo dei compositi
A CURA DI RICCARDO AMPOLLINI
Nel corso dei tre giorni della fiera parigina JEC World 2022, dal 3 al 5 maggio, sono stati esposti in un’area dedicata i dieci migliori progetti presentati al concorso JEC Innovation Awards, che riflettevano quest’anno il dinamismo e la resilienza del settore
Ogni anno, fin dalla loro creazione oltre vent’anni fa, gli JEC Composites Innovation Awards ricompensano i progetti più innovativi e la cooperazione tra gli attori dell’industria dei compositi. Più in dettaglio, il concorso ha messo in luce finora 198 aziende e 475 partner, premiandoli per l’eccellenza delle loro innovazioni nel campo dei compositi. La cerimonia di premiazione si è tenuta quest’anno a Parigi il 26 aprile, esattamente sette giorni prima della fiera JEC World, dando così un segnale positivo del desiderio dell’industria di ritrovarsi e di garantire il futuro dell’innovazione nel settore dei compositi. Più che una semplice cerimonia di premiazione, gli JEC Innovation Awards rappresentano un’opportunità per promuovere l’ispirazione e la collaborazione tra gli attori dell’intera filiera, per mettere in mostra su un palcoscenico globale alcuni progetti eccellenti non ancora divulgati e per stimolare l’entusiasmo di un pubblico di esperti sempre desideroso di scoprire nuovi orizzonti e di creare opportunità commerciali La giuria internazionale, rappresentativa dell’intera industria dei compositi, comprendeva quest’anno: Michel Cognet, presidente del consiglio d’amministrazione del Gruppo JEC; Christophe Binetruy, professore d’Ingegneria meccanica, EC Nantes; Kiyoshi Uzawa, professore e direttore, Centro Compositi Innovativi, Istituto di Tecnologia di Kanazawa; Sung Kyu Ha, professore, Università di Hanyang; Brian Krull, direttore globale dell’innovazione, Magna Exteriors; Karl-Heinz Fuller, manager Future Outside & Materials, Mercedes Benz; Deniz Korkmaz, CTO, Kordsa Teknik Tekstil; Henry Shin, capo del centro K-Carbon; Véronique Michaud, professore associato e direttore dell’EPFL (Laboratorio per
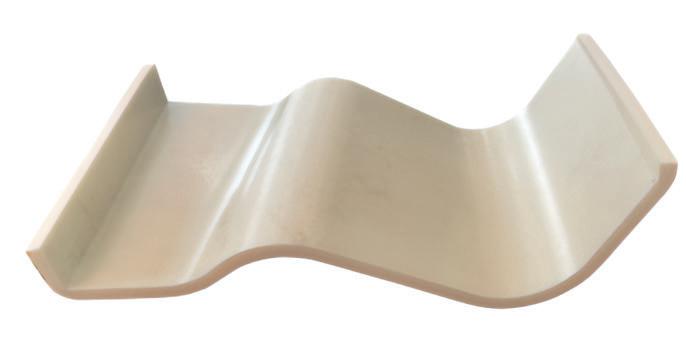
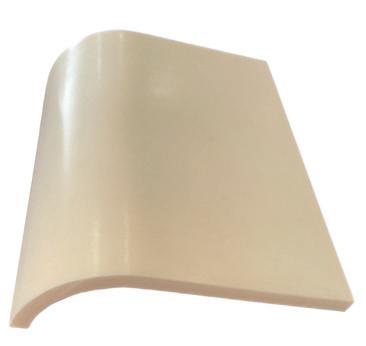
Il primo premio nella categoria “Aerospaziale - Applicazioni” è stato assegnato all’azienda svedese Diab per questi pannelli per interni cabina realizzati al 100% in materiale termoplastico (espanso e non) e quindi completamente riciclabili
la lavorazione dei compositi avanzati); Alan Banks, responsabile delle innovazioni leggere, Ford Motor Company; Enzo Crescenti, tecnico ed esperto di compositi, Airbus. Ed ecco, in sintesi, i progetti premiati per ciascuna delle dieci categorie del concorso.
Aerospaziale - Applicazioni
È stato premiato in questa categoria un pannello sandwich per interni di cabine aerospaziali realizzato al 100% in termoplastico (TP) dall’azienda svedese Diab, insieme ai partner Rescoll, Roctool (Francia) e AkzoNobel (Paesi Bassi). Il pannello è interamente riciclabile e quindi in grado di rispondere alle sfide attuali relative a: sostenibilità, conformità Reach (non sono presenti fenoli), aumento della produttività e ridotti tempi di ciclo (il processo di produzione avviene in un singolo step), risparmio di peso e di costi totali. È composto da rivestimenti in termoplastico e da un’anima in espanso termoplastico Diab Divinycell. I rivestimenti in TP possono essere saldati direttamente sull’anima espansa senza l’uso di pellicole adesive. Tutti i materiali utilizzati in questo progetto sono stati già qualificati presso vari OEM aerospaziali e vengono utilizzati oggi nella produzione in serie. Siamo quindi di fronte a una soluzione concreta e già operativa per gli interni delle cabine aerospaziali.
Aerospaziale - Processi
Il primo premio in questa categoria è stato assegnato alla società spagnola MTorres Diseños Industriales per l’implementazione e il collaudo di un innovativo sistema per la produzione di celle aerospaziali per il partner Airbus Defense and Space. L’obiettivo principale del progetto, denominato IIAMS (Innovative Infusion Airframe Manufacturing System) Cleansky 2, era lo sviluppo di un sistema pilota innovativo, portatile e completamente automatizzato, per la fabbricazione di una struttura composita integrata di cassone alare (compresi rivestimento, correntini, longheroni e irrigiditori in un unico pezzo). Airbus ha progettato il componente. MTorres è stata responsabile della progettazione e della fabbricazione dell’attrezzatura e della dimostrazione. Il cassone alare è stato fabbricato mediante infusione “one-shot” OOA, evitando così successivi processi di assemblaggio e dispositivi di fissaggio. Gli elementi strutturali usano MTorres AFP per fibra secca sottile. Il layup 3D è stato usato per il rivestimento, mentre il layup 2D e l’hotforming sono stati utilizzati per produrre il resto degli elementi. Tra i principali vantaggi che hanno convinto la giuria ad assegnare questo premio vi sono: integrazione delle parti senza elementi di fissaggio; portabilità, basso costo; risparmio energetico, leggerezza.
Tucana è uno strumento abilitante per futuri veicoli elettrici a batteria (BEV), fondato sulla riprogettazione dell’intera struttura posteriore della carrozzeria di una Jaguar I-Pace. Tale strumento ha permesso di posizionarsi al primo posto degli JEC Innovation Awards alla stessa società inglese Jaguar Land Rover e ai partner britannici: Broetje Automation, CCP Gransden, CFMS, Expert Tooling & Automation, Toray International e Università di Warwick. A differenza della produzione tradizionale, che si basa sulla tecnologia RTM (Resin Transfer Moulding) o sul processo in autoclave, non proponibili per volumi elevati (più di 40 mila unità all’anno) né dal punto di vista del business case, Tucana si è concentrata sull’ottimizzazione dell’uso del materiale e sulla massimizzazione della resistenza in MPa/kg. Per raggiungere quest’obiettivo, l’ottimizzazione topologica ha contribuito a definire il percorso di carico principale, creando così lo scheletro della struttura sulla quale sono state posate le fibre di carbonio o di vetro UD (unidirezionali) per la polimerizzazione rapida. Per “dare polpa” allo scheletro e collegare le UD, sono state utilizzate matrici polimeriche a base sia di SMC (Sheet Moulding Compound) rinforzati con fibre di carbonio sia di SMC rinforzati con fibre di vetro, per il loro basso costo, il tempo di ciclo ridotto e l’elevata libertà di progettazione, che permette di produrre forme tridimensionali complesse e caratteristiche progettuali difficilmente ottenibili con i materiali tradizionali. Materiali su misura, parametri di stampaggio specifici e un metodo di modellazione esclusivo sono stati la chiave del successo di questo progetto, insieme ai
Questo sistema di produzione a infusione per celle aerospaziali ha consentito alla società MTorres Diseños Industriales di vincere nella categoria “Aerospaziale - Processi”
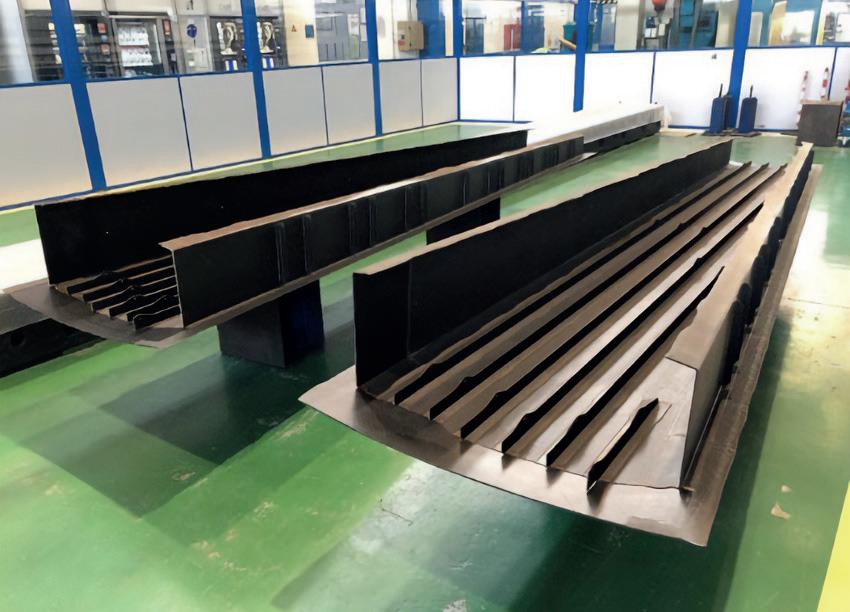
Tucana è uno strumento abilitante per futuri veicoli elettrici a batteria, fondato sulla riprogettazione dell’intera struttura posteriore della carrozzeria di una Jaguar I-Pace
Quest’innovazione messa a punto da Audi si basa sull’integrazione di film solari flessibili non incapsulati, di Apollo Power (Israele), in componenti di plastica fibrorinforzata, utilizzando il processo HP-RTM di Mubea Carbo Tech (Austria)
Riuso strutturale dei compositi termoindurenti in edilizia e ingegneria civile seguenti criteri definiti dalla giuria del concorso: struttura più leggera, riduzione delle emissioni di CO2 come strumento per favorire l’adozione dei veicoli elettrici a batteria; struttura più rigida per rispondere ai requisiti strutturali dei BEV; riduzione del numero di pezzi: meno energia, spazio, logistica (cioè meno autocarri per il trasporto); facilità d’adozione, conformità al processo di produzione automobilistica e all’infrastruttura.
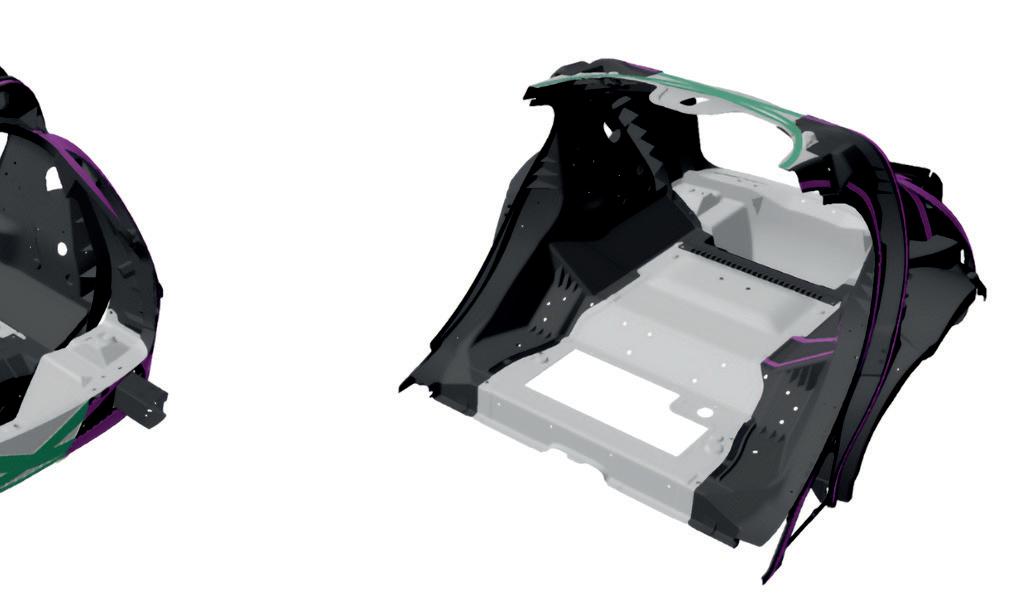
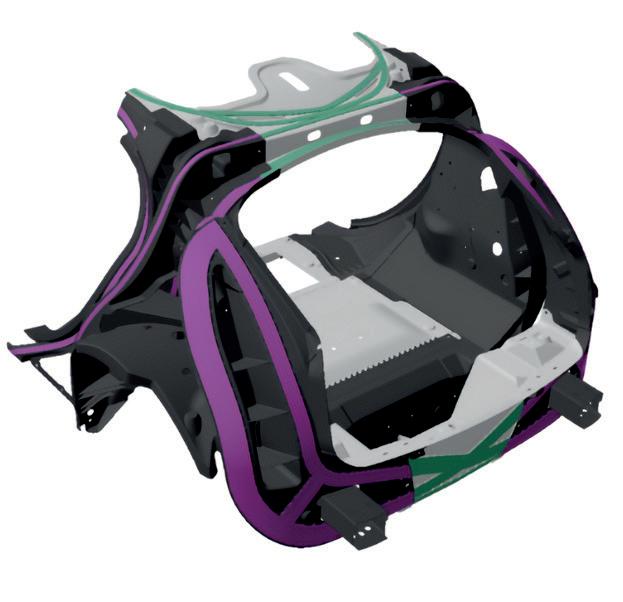

Automotive e trasporto su strada - Superfici
Insieme ai partner Mubea Carbo Tech (Austria) e Apollo Power (Israele), la casa automobilistica Audi è riuscita a ottenere l’integrazione diretta di un pannello solare a film flessibile in componenti auto (tetto, cofano ecc.) realizzati in plastica fibrorinforzata (FRP), utilizzando un processo di stampaggio a trasferimento di resina ad alta pressione (HP-RTM). Il prodotto finale mostra risultati eccellenti, tra cui: la migliore efficienza solare (>200Wp), un design leggero (come minimo, con un peso inferiore del 50% rispetto a un tetto in “vetro solare” standard) e la conformità agli standard di qualità automobilistica (superficie di classe A, con alta estetica e libertà di design). Nell’assegnare a questo progetto il primo premio nella categoria “Automotive e trasporto su strada -Superfici”, la giuria è stata inoltre positivamente colpita dalla possibilità di combinare il film solare flessibile con biopolimeri e fibre naturali, come il lino. In definitiva, le parti realizzate con questi materiali sostenibili possono ridurre enormemente l’impronta di carbonio. La resina a polimerizzazione rapida consente poi una produzione a ciclo elevato, inferiore ai 20 minuti per ciascun componente. Infine, possono essere realizzate forme 3D complesse con un grado più elevato di drappeggio e, quindi, la tecnologia può essere trasferita ad altri componenti e industrie (ad esempio, ferroviaria o aerospaziale).
Edilizia e ingegneria civile
Premiata in questa categoria, l’impresa olandese Windesheim ha messo a punto un’innovativa metodologia di riuso strutturale dei compositi termoindurenti, che permette di riutilizzarli a fine vita per realizzare nuovi prodotti. Si tratta di una delle prime soluzioni circolari per questo genere di materiali, che consiste innanzitutto nel ridurre in piccole parti, come strisce o scaglie, i componenti in composito termoindurente giunti a fine vita. Queste parti più piccole serviranno poi come elementi di rinforzo per nuovi prodotti. Nonostante sia necessario aggiungere una minima quantità di resina vergine e di fibre di rinforzo, il nuovo prodotto è costituito quasi per intero di compositi termoindurenti recuperati e può essere riutilizzato con lo stesso metodo quando, a sua volta, avrà terminato la propria vita in esercizio. A detta della giuria degli JEC Innovation Awards, questa metodologia rappresenta quindi un’ottima soluzione circolare per i compositi termoindurenti usati, per esempio, nelle pale eoliche o negli scafi delle imbarcazioni, rendendoli così prodotti sostenibili.
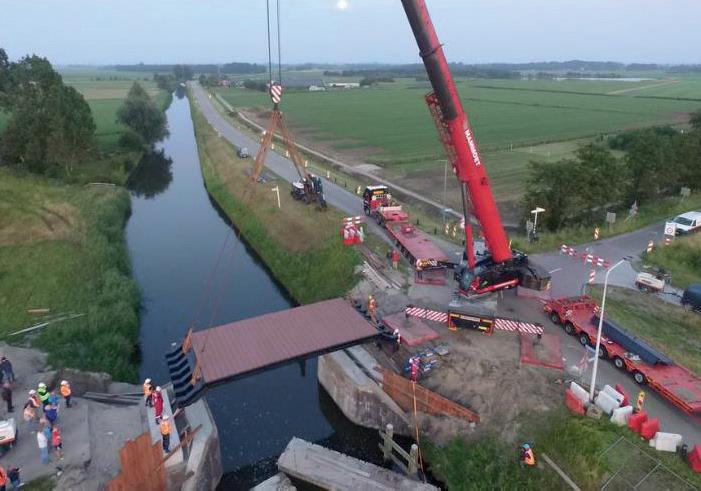
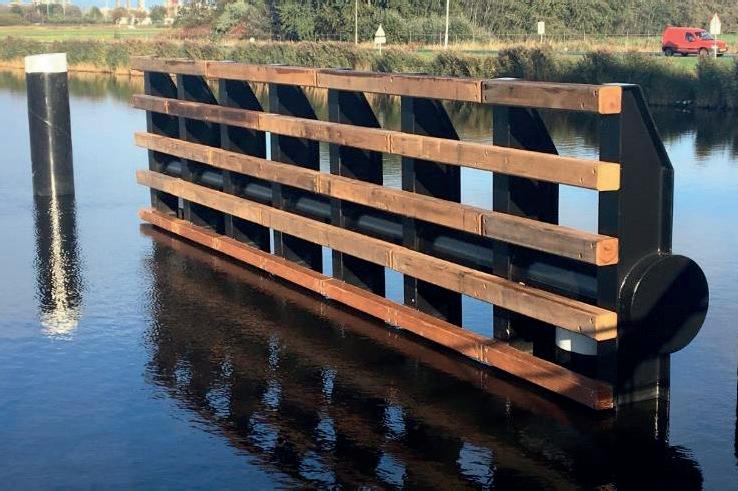