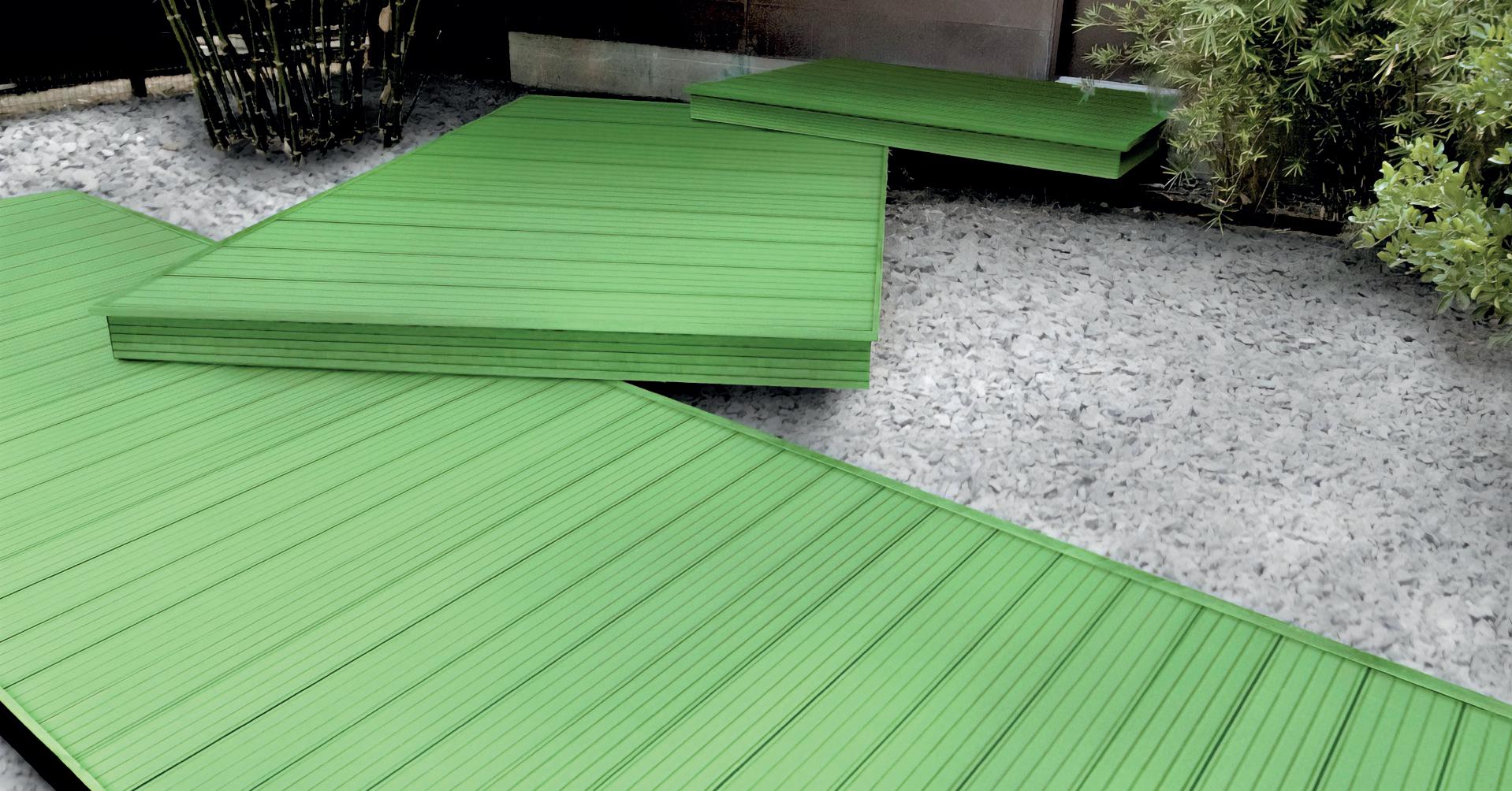
9 minute read
Additividioriginerinnovabile:“unavitadamediano”
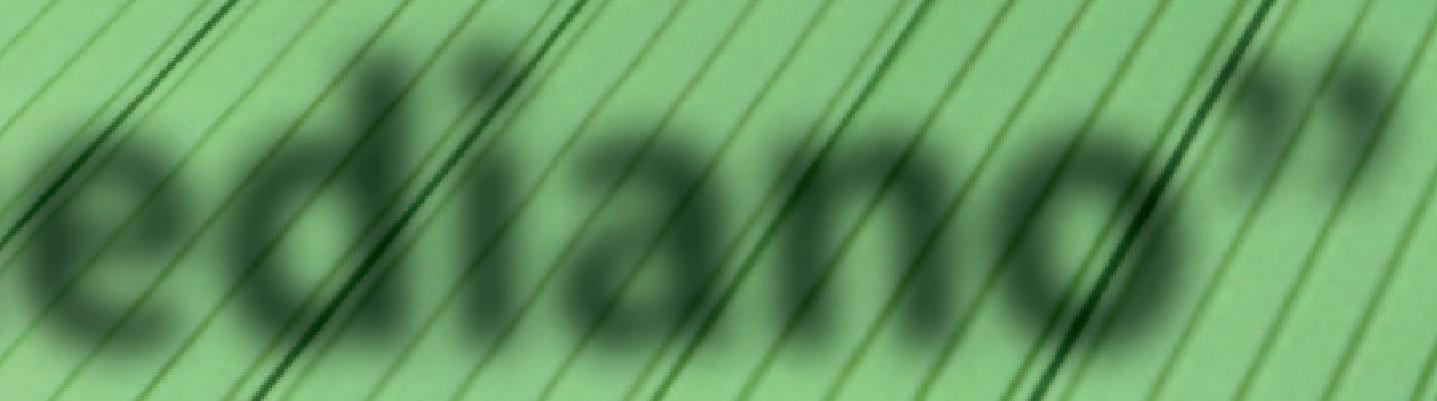

Partendo da una metafora calcistica e da una nota canzone di Ligabue, con questo articolo Bertacchi ci porta alla scoperta di quei compound in cui determinati additivi e riempitivi d’origine vegetale, la cui importanza viene spesso dimenticata (un po’ come accade per il ruolo del mediano in una squadra di calcio), vengono miscelati con i più noti polimeri per creare biocompositi innovativi
DI STEFANO BERTACCHI*
Ogni squadra, si sa, ha le proprie star: quelle che attirano l’attenzione del pubblico e di cui poi ci si ricorda nel tempo. Tuttavia, in molti sport, dal calcio alla Formula 1, è la somma di tutti i membri del team che fa la differenza… anche dei componenti di cui non si ha memoria del nome. Nel mondo delle plastiche e della gomma esiste una situazione simile, in quanto i polimeri principali si prendono la scena, lasciando in disparte altre molecole, la cui importanza è spesso dimenticata. Ecco che, infatti, oltre al PET, al PP o all’SBR, veri VIP di questo mondo, vi sono sostanze additive come i plastificanti e i riempitivi (filler) che rendono compound e miscele finali prodotti dalle caratteristiche uniche. Come veri mediani calcistici, queste molecole hanno il compito, per esempio, di rendere più morbido il materiale, nonostante il loro ruolo non sia sufficientemente sottolineato… anche perché costituiscono una piccola percentuale del materiale totale: una caratteristica che li rende ancor più importanti, perché, pure con poco, sono in grado di fare tanto. Il mondo della bioeconomia entra “in campo” anche in questo caso, poiché alcuni additivi derivanti da biomasse rinnovabili sono ormai diffusi per cercare di fare coppia con le plastiche convenzionali, al fine sia di ridurre l’impatto ambientale della filiera sia di cercare prodotti con caratteristiche sempre nuove. Andiamo quindi alla scoperta di compound in cui determinati materiali, soprattutto di origine vegetale, vengono miscelati con i polimeri a cui siamo abituati, creando prodotti in parte bioplastici e per questo chiamati biocompositi. Proprio una vita da mediano…
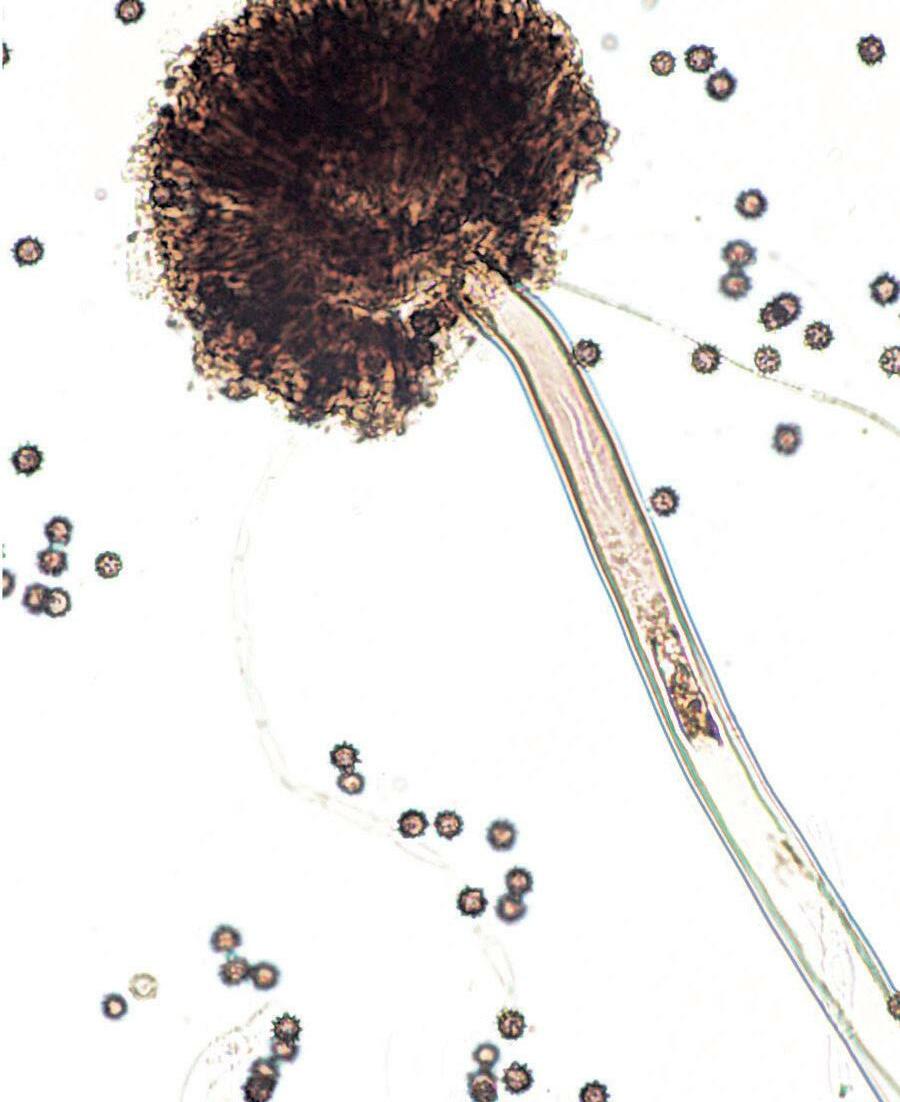
“Con dei compiti precisi. A coprire certe zone”
I plastificanti sono additivi funzionali, che vengono utilizzati per migliorare la flessibilità, la plasticità, la lavorabilità e l’allungamento dei polimeri. Non a caso sono tra gli additivi più importanti richiesti per la lavorazione dei materiali polimerici, e in particolare del PVC, la cui morbidezza è una caratteristica chiave nella produzione di determinati articoli finali: sacchette e piccoli tubi per il medicale, giocattoli, rivestimenti per pavimenti ecc. A livello globale, i tradizionali plastificanti a base di ftalati d’origine petrolchimica sono i più utilizzati, rappresentando tuttora un’ampia fetta della produzione e delle vendite totali di plastificanti. Tuttavia, preoccupazioni riguardanti l’impatto di queste molecole sulla salute umana e sull’ambiente hanno portato a norme rigorose in materia di protezione e sicurezza. Per questo motivo, lo sviluppo di bioplastificanti (ovvero di origine rinnovabile), meglio ancora se biodegradabili, come alternativa agli ftalati, è stato un elemento cardine della ricerca negli ultimi anni. Esempi comprendono: esteri dell’acido citrico, fosfati, poliesteri, alcani alogenati e plastificanti epossidici. Questi ultimi sono formati dall’epossidazione di un doppio legame olefinico a una struttura ossiranica, ovvero il famoso “triangolo” che caratterizza queste molecole. Tali plastificanti epossidici vengono usati per migliorare la stabilità al calore nella
WPC per esterni
Foto al microscopio della muffa , impiegata per la produzione di acido citrico
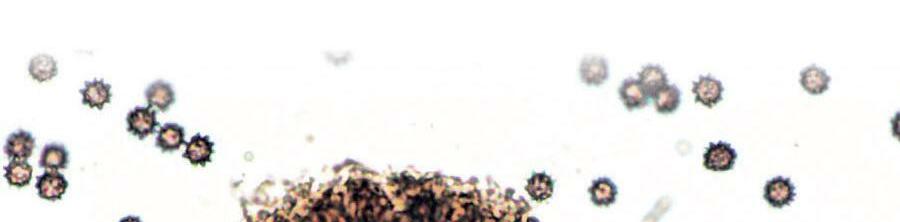
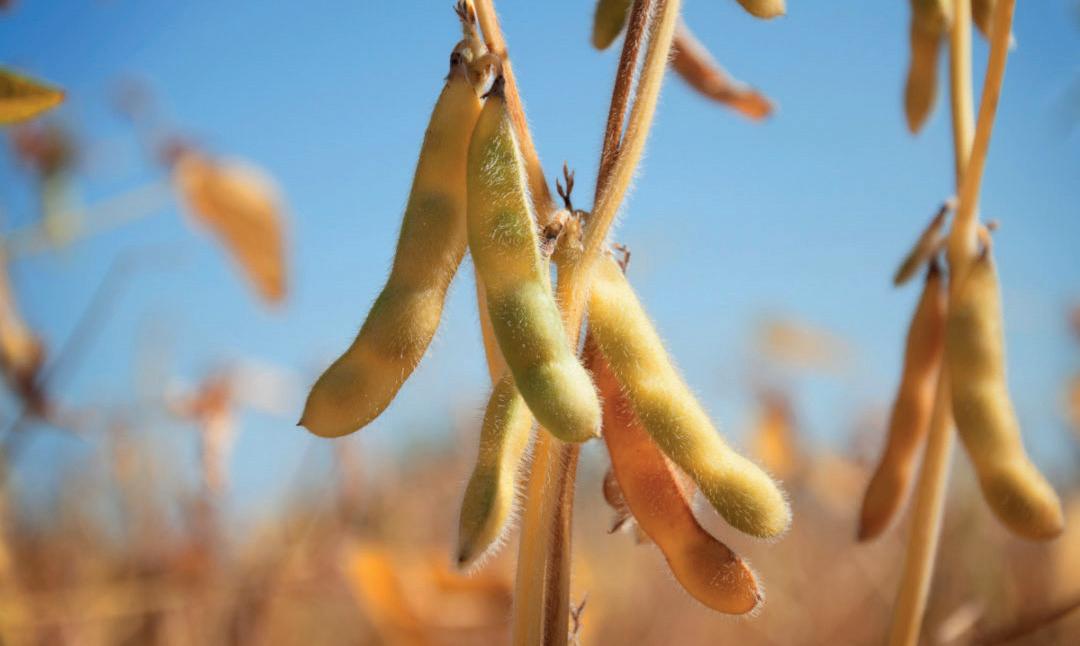
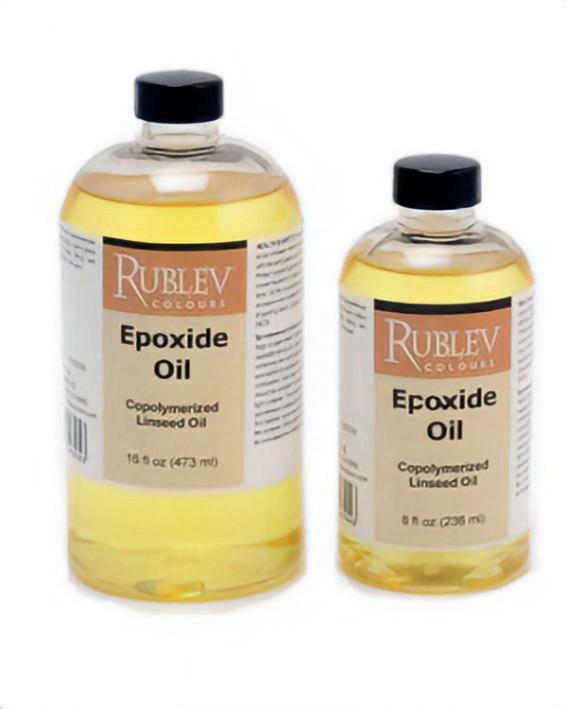
Soia per la produzione di olio come agente epossidato nelle miscele
produzione di articoli in PVC realizzati con tecniche quali: estrusione, calandratura, stampaggio a iniezione, stampaggio rotazionale e spalmatura. Sono utilizzati anche in gomme, resine epossidiche, vernici e rivestimenti. Inoltre, il gruppo epossidico può assorbire e neutralizzare il cloruro rilasciato dal PVC durante la propria degradazione, ritardandone la decomposizione. A questo punto, per ottenere biocompositi, occorre trovare un gruppo alchenico d’origine rinnovabile in grado di fornire il doppio legame richiesto. La natura ci dà una grossa mano in questo campo e la soluzione è molto più vicina di quanto si possa pensare. Gli oli vegetali, infatti, sono ricchi di acidi grassi insaturi, che si differenziano da quelli saturi d’origine animale proprio per la presenza di doppi legami. I famosi acidi grassi omega-3 e omega-6 sono tali proprio per la presenza del doppio legame C=C sul terzo o sul sesto atomo di carbonio, contando dal fondo della catena dell’acido grasso, il cui ultimo atomo è appunto definito carbonio ω (omega, ultima lettera dell’alfabeto greco). Si può quindi ottenere l’olio di semi di soia epossidato (ESO), oppure l’olio di semi di lino epossidato (ELO). L’aggiunta di ESO, in particolare, è in grado di migliorare la stabilità termica del PVC, di ridurre la temperatura di transizione vetrosa delle resine epossidiche e di migliorare l’allungamento a rottura del PBS1. In questo caso, quindi, si unisce un bioplastificante a una bioplastica, per ora biodegradabile, e presto anche completamente di origine rinnovabile. In tale contesto, alcune debolezze del PLA possono essere compensate con l’aggiunta di olio di palma o di girasole epossidati. Ovviamente, l’uso di queste biomasse è da intendersi all’interno di una filiera in cui esse non vadano a interferire con il settore alimentare; cosa che creerebbe problemi in termini di sostenibilità economica, ambientale e sociale. A partire da questi bioepossidi è possibile ottenere anche fosfati, usati come ritardanti di fiamma sempre nel PVC e in altre materie plastiche. I plastificanti derivanti dagli esteri dell’acido citrico sono stati approvati negli Stati Uniti e in Europa per l’uso nel packaging alimentare, per i giocattoli e per i prodotti medicali (codice additivo: E472c)2. La sintesi industriale su larga scala di acido citrico si ottiene, più comunemente, attraverso la fermentazione micologica di fonti grezze di zucchero (come la melassa), usando tipicamente la muffa Aspergillus niger, mediante un processo biotecnologico.
Se è vero che gli opposti si attraggono, alcuni materiali ne sono un esempio perfetto. Infatti, che cosa c’è di più diverso della plastica e del legno? Eppure, questi due materiali possono costituire una vera e propria “strana coppia”, che si manifesta nei cosiddetti compositi legno-plastica (WPC, Wood-Plastic Composite)3 . I processi per la produzione di articoli in WPC includono l’estrusione, lo stampaggio a iniezione o a compressione e la termoformatura4. Li troviamo spesso sotto forma di travi utilizzabili in applicazioni quali: pavimenti, ringhiere, recinzioni, panchine, mobili, rivestimenti per portiere auto, telai di porte e finestre. Il legno è considerato un re tra le fibre organiche, grazie alla sua struttura resistente e alle ottime proprietà meccaniche, rispetto ad altre alternative che vanno dal riso al lino. Queste ultime piante presentano pure il problema della stagionalità, che può rendere difficile il mantenimento della filiera produttiva. Inoltre, il WPC ha l’aspetto “naturale” del legno pur richiedendo molta meno manutenzione, con una maggiore resistenza nel tempo. La sua temperatura di lavorazione non deve però superare i 200°C, per proteggere il legno dalla disintegrazione delle catene di cellulosa. I polimeri che soddisfano questi requisiti sono PVC, HDPE, LDPE, PP, ABS e PS, che quindi sono i primari partner del legno all’interno dei WPC. Sono state effettuate anche numerose indagini sperimentali atte a verificare la possibilità d’utilizzare sia la plastica che il legno di scarto. Ma l’uso dei materiali di scarto nel settore del WPC non si limita ai rifiuti di plastica o di legno: altri materiali di scarto possono essere usati come filler, come nel caso dell’olio motore esausto, utilizzato come agente d’accoppiamento nella produzione di WPC a base di LDPE e segatura.
www.world-grain.com
“Nato senza i piedi buoni. Lavorare sui polmoni”
Si è quindi visto che anche una materia prima considerata “giocatore di serie B” può aiutare a vincere la partita della sostenibilità. L’uso di scarti provenienti da alcuni settori può diventare la fortuna del mondo della plastica, grazie all’unione con i polimeri più noti. Non è quindi un caso che, durante la recente fiera Greenplast di Milano, uno dei temi cardine rilanciato da diversi espositori fosse proprio l’uso di biomasse come additivi della plastica, per l’ottenimento di materiali dalle proprietà innovative. Molte brochure recuperate in fiera approfondiscono proprio questo aspetto e, a scopo meramente esemplificativo e non esaustivo, si riportano di seguito alcune “fonti” di tali brochure. L’azienda veneta Mixcycling miscela plastiche vergini, riciclate, biodegradabili o compostabili, con materiale organico di diverso tipo, creando biocompositi su misura per diverse esigenze. Tra le biomasse a portfolio vi sono: sughero, lolla di riso, legno e vinaccia, con applicazioni che vanno dal packaging ai giocattoli per animali. La gamma Green Spear della start-up toscana Arianna Fibers, a base di fibra lunga di bambù, lino e canapa, apporta ai mate-
riali proprietà di rinforzo e di controllo dell’umidità, rendendoli compatibili con i tradizionali dosatori impiegati negli impianti di processo. La gamma Kern della medesima azienda, a base di gusci di frutta secca macinati e funzionalizzati, consente di aumentare la sostenibilità dei materiali e di conferire ai manufatti una finitura simil-legno. Il Gruppo Maip propone invece Biocoffee, un biocomposito in cui vengono aggiunti scarti di caffè alla miscela brevettata IamNature, a base di PHA (polimero bio-based e biodegradabile). Parliamo quindi di materie prime umili, che però possono fare una certa differenza se poste in squadra con i grandi protagonisti del mondo della plastica. I quali, senza questi partner apparentemente di minor rilievo, rischierebbero di perdere le sfide del futuro. “Anni di fatica e botte e… vinci casomai i mondiali”.
*Biotecnologo industriale e ricercatore presso l’Università degli Studi di Milano Bicocca; scrittore e divulgatore scientifico

[1] Jia, Puyou, et al. “Plasticizers derived from biomass resources: a short review”. Polymers 10.12 (2018): 1303. [2] EFSA Panel on Food Additives and Flavourings (FAF) “Re-evaluation of acetic acid, lactic acid, citric acid, tartaric acid, mono-and diacetyltartaric acid, mixed acetic and tartaric acid esters of mono-and diglycerides of fatty acids (E 472a-f) as food additives”. EFSA Journal 18.3 (2020): e06032. [3] Elsheikh, Ammar H., et al. “Recent progresses in wood-plastic composites: Pre-processing treatments, manufacturing techniques, recyclability and ecofriendly assessment”. Cleaner Engineering and Technology (2022): 100450. [4] Gardner, Douglas J., Yousoo Han, and Lu Wang. “Wood–plastic composite technology”. Current Forestry Reports 1.3 (2015): 139-150. Cassette per ortofrutta prodotte con i materiali ecosostenibili della start-up toscana Arianna Fibers
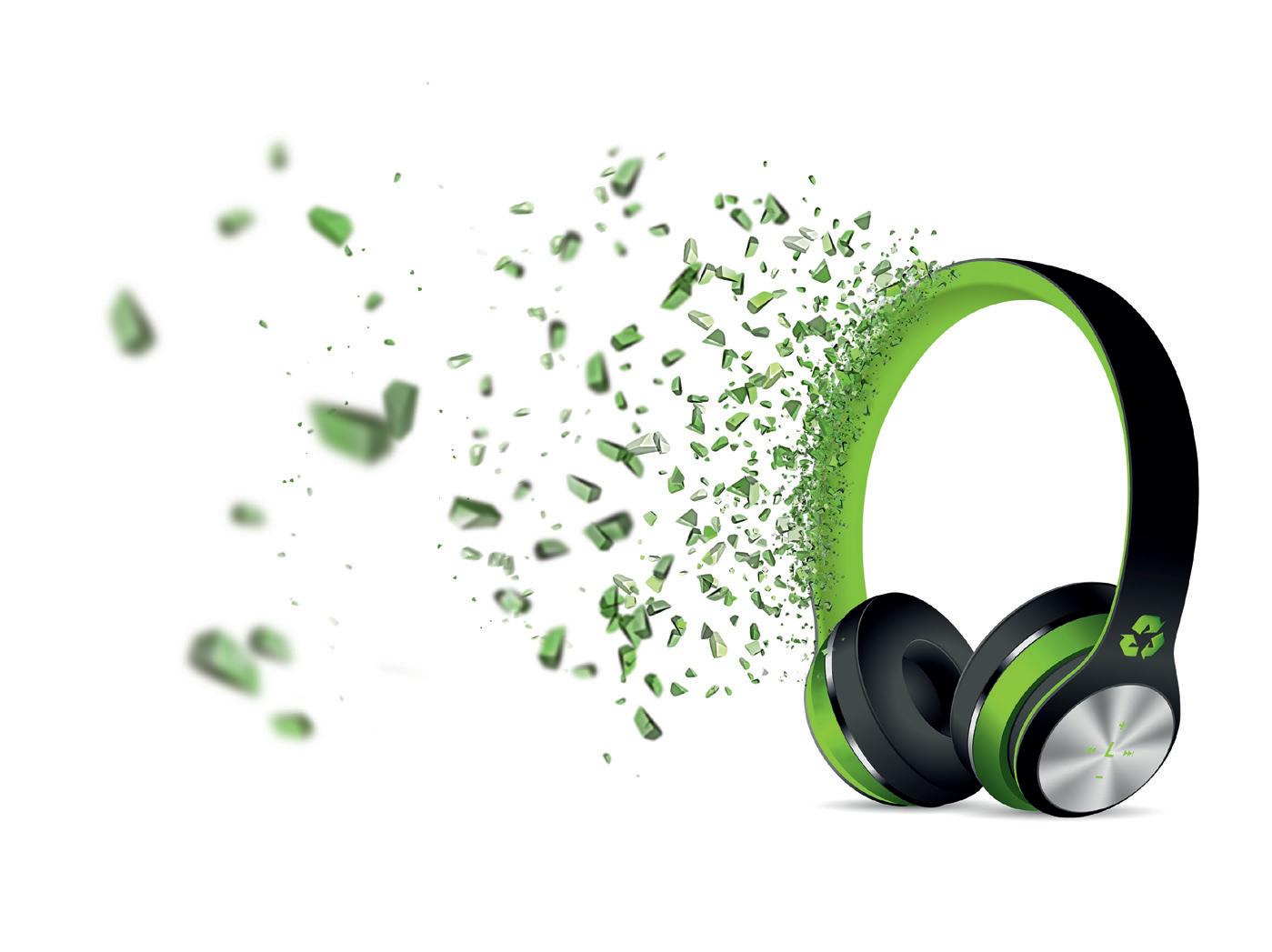
ReFresher
Optimised recycled pellet odour Odour-optimised premium pellets – the result of combining the INTAREMA® TVEplus® and ReFresher opens up a new dimension in quality in recycling and completely new opportunities in the market as a result. So postconsumer plastic can become safe cosmetic packaging or trendy high-end headphones.
K22 MAIN BOOTH: Hall 9 / Booth C09 OUTDOOR AREA: FG-CE03
erema-group.com