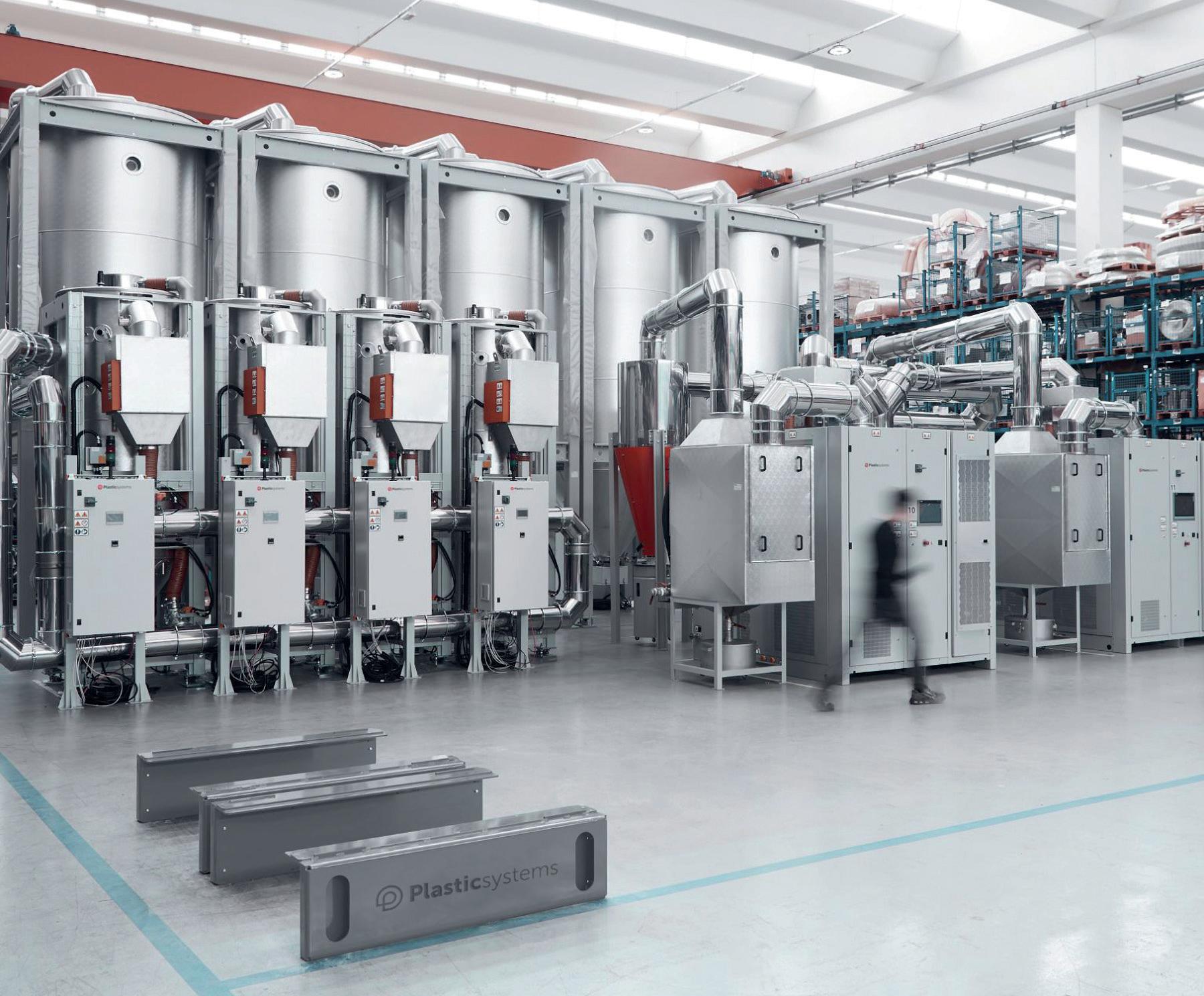
4 minute read
Aognunoilsuodeumidificatore
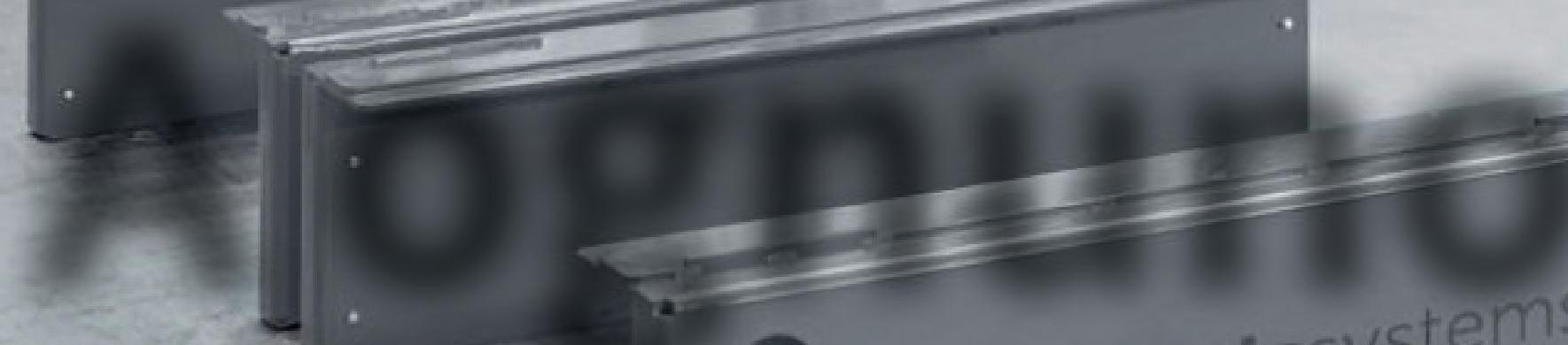
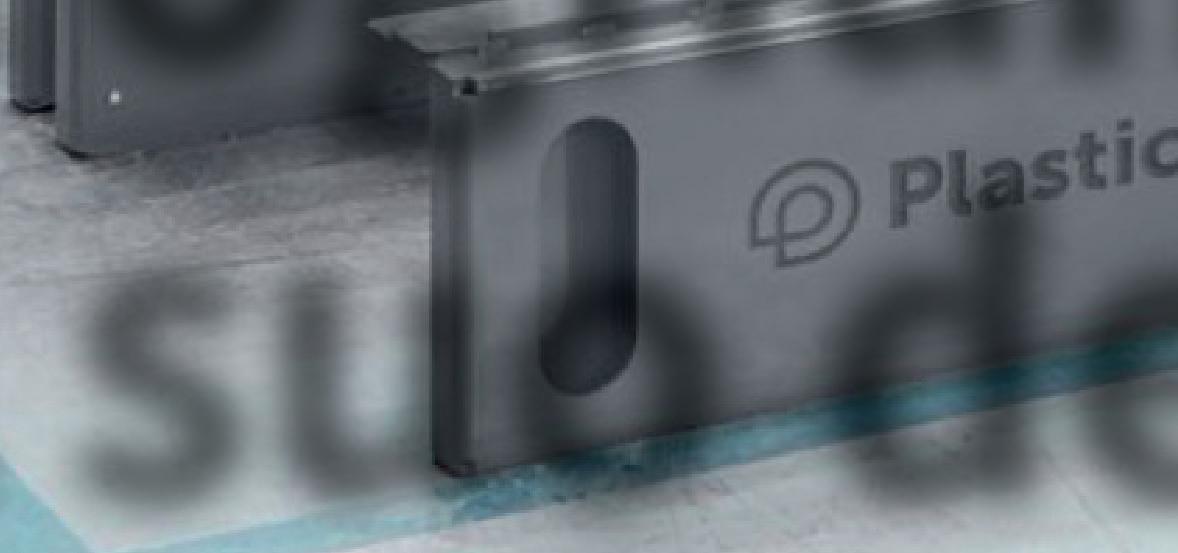


L’azienda veneta ha messo a punto un’ampia gamma di sistemi di deumidificazione, con i quali è in grado di rispondere praticamente a tutte le esigenze della trasformazione di materie plastiche e di assecondare gli standard dell’Industria 4.0
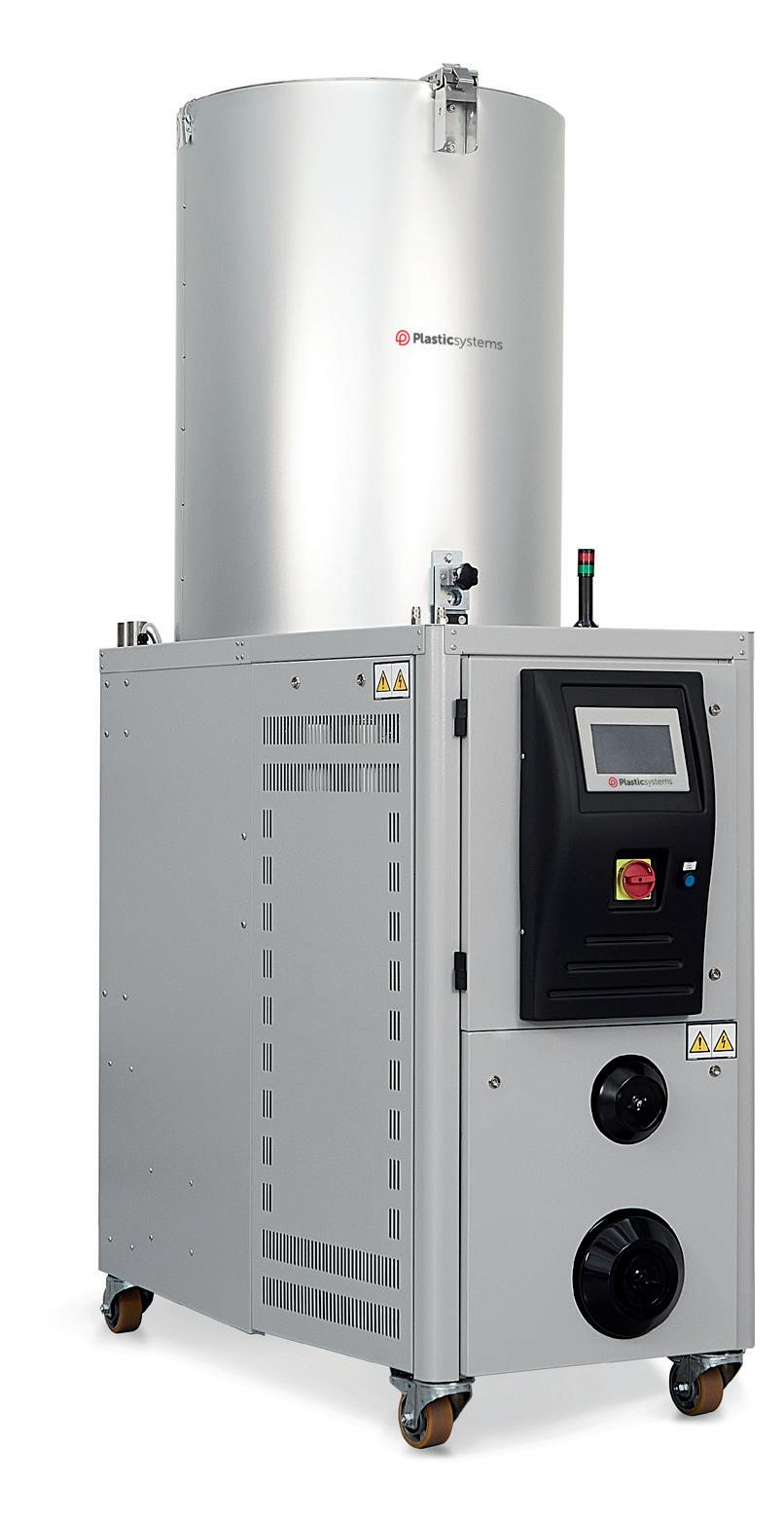
Deumidificatore modello 500 della serie DWC, a rotore e compatta Eff icienza, consumo energetico ridotto e logica da Industria 4.0 distinguono i deumidificatori sviluppati da Plastic Systems, azienda parte del Gruppo Pegaso, disponibili in quattro diff erenti versioni e proposti in funzione della produzione oraria richiesta e del settore d’applicazione.
La versione DAC a doppia torre con fluido, in abbinamento a tramogge da 2 a 100 litri, è indicata per produzioni da uno a 20 kg all’ora. A sua volta configurabile in sette diversi modelli, trova impiego su macchine per lo stampaggio a iniezione di piccolo tonnellaggio. Per produzioni da 5 a 500 kg/h viene proposta la versione DW a rotore, che, in abbinamento con tramogge da 15 a 2000 litri, è disponibile in 10 modelli che trovano utilizzo su macchine per lo stampaggio a iniezione e linee per l’estrusione di medie e grandi dimensioni. La versione DWC a rotore e compatta, dotata di sistema di pesatura e d’ali-

mentazione integrato, si addice, in abbinamento a tramogge da 75 a 750 litri, a produzioni da 5 a 300 kg/h. I sei modelli disponibili vengono impiegati su macchine a iniezione e su linee per l’estrusione di medie dimensioni. Infine, la versione D, a torri e setacci molecolari, è indicata per produzioni da 10 a 5000 kg/h, in abbinamento a tramogge da 50 a 2000 litri. I modelli più grandi, in particolare, vengono installati su macchine per lo stampaggio a iniezione e su linee per l’estrusione di elevate dimensioni. Tutti i modelli offrono prestazioni elevate con dew point superiori a -40°C e sono dotati di sistema di modulazione dell’aria con valvole modulanti/inverter. Il sistema a microprocessore/PLC con touchscreen permette il facile interfacciamento con l’utente, mentre la comunicazione può avvenire in base ai protocolli ModBus, Profinet, Ethernet e OPC-UA. L’utilizzo delle macchine e la loro interazione con gli operatori sono facilitati anche grazie all’adozione di microprocessori con prestazioni sempre più avanzate, sviluppati dalla stessa Plastic Systems, i quali consentono di impostare e gestire con estrema precisione i parametri di processo, quali: dew point, quantità d’aria, tempo di residenza ecc. Il concetto alla base del funzionamento è quello di fornire alla resina trattata la corretta quantità d’aria della migliore qualità e di calcolare il giusto tempo di permanenza in tramoggia, allo scopo di non essiccare più del dovuto per non incorrere in degradazioni causate appunto da una sovraessiccazione. A fronte dei costi energetici particolarmente elevati, soprattutto negli ultimi mesi, i sistemi di Plastic Systems garantiscono consumi che, a seconda del tipo di resina trattato, variano da 15 a 40 Wh/ kg. Ai benefici fiscali legati alla conformità dei macchinari con i principi dell’Industria 4.0, le soluzioni proposte dal costruttore veneto assommano, oltre al ridotto consumo energetico, anche brevi tempi di ammortamento.
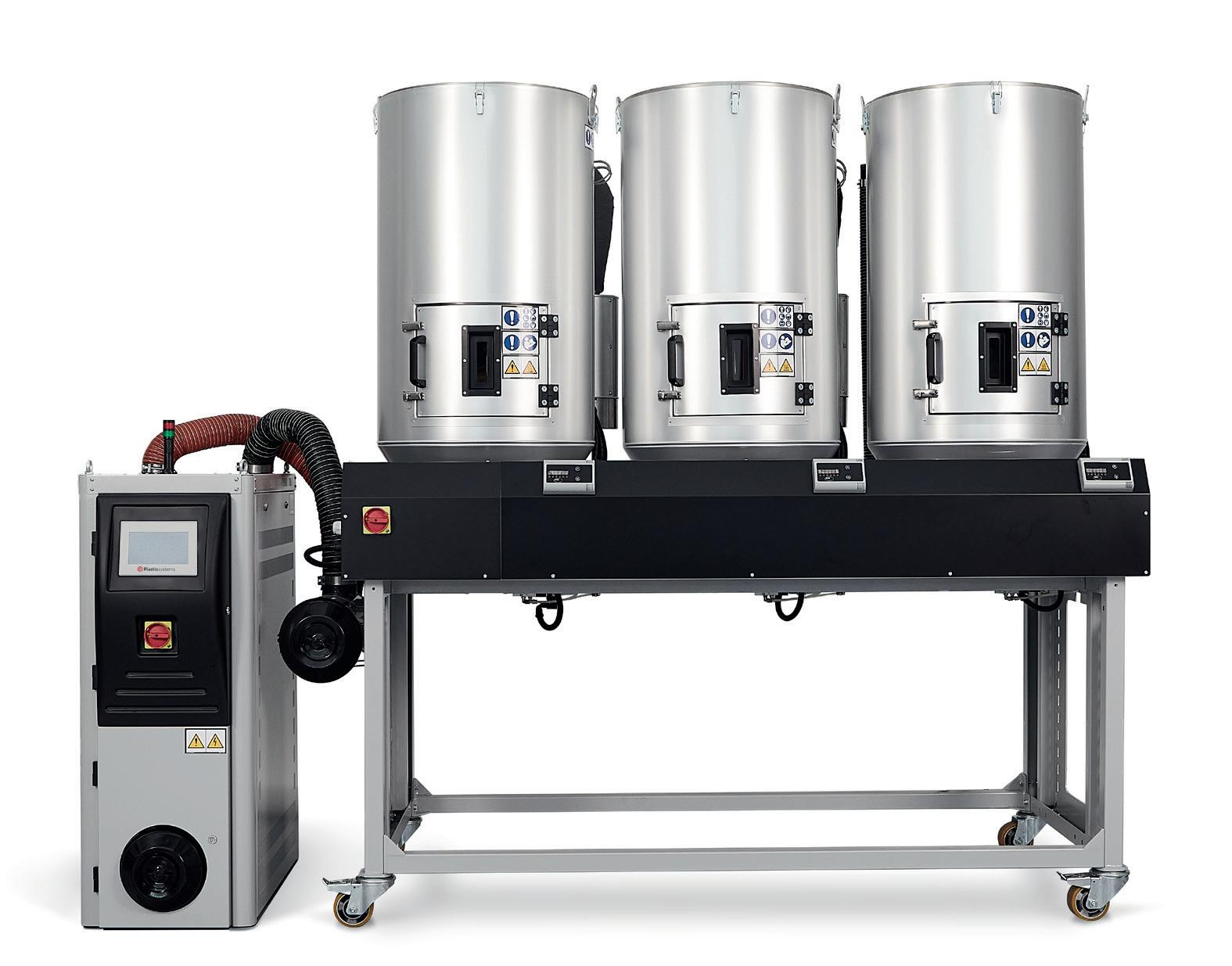
Impianto customizzato
Nel 2021 le macchine di Plastic Systems sono state impegnate in diverse applicazioni con materiali riciclati, in particolare rPET. Tra queste rientra un impianto customizzato di ultimissima generazione per la deumidificazione centralizzata di PET vergine ed rPET, per applicazioni nel campo dell’estrusione, nato dalla consolidata collaborazione tra l’azienda veneta e un importante produttore di isolanti flessibili tecnici.
Prestazioni e flessibilità Progettato mediante software di rendering 3D per adattarsi al meglio, fin da subito, alla realtà produttiva dell’utilizzatore, l’impianto è in grado di processare fino a 2500 kg/h di granuli in rPET ottenuti dal riciclo di bottiglie post consumo e destinati alla produzione di espansi al 100% in materiale riciclato. Questa soluzione risulta ideale per le esigenze del committente in termini di prestazioni ed efficienza, così come in chiave di Industria 4.0. Grazie all’utilizzo della tecnologia a setacci molecolari ad altissima efficienza e all’innovativo design del dryer, l’impianto genera oltre 5000 metri cubi all’ora di aria secca e fornisce un dew point di -50°C. Un doppio sistema di filtrazione e di disoleazione garantisce un tempo di vita maggiore delle parti interne del dryer, setacci molecolari inclusi.
Controllo di processo Il sistema, dotato di otto tramogge, è in grado di calcolare la reale portata dei granuli processati da ogni tramoggia di deumidificazione e di regolare autonomamente la portata d’aria. Un dispositivo per il controllo elettronico dei parametri di processo, di tipo PID “feedback”, misura la reale portata dell’aria inviata a ogni tramoggia e la modula in funzione della portata del materiale trattato, il tutto attraverso interfacce operatore intuitive e studiate ad hoc per consentire la massima comprensione del sistema e facilitarne l’utilizzo. Il controllo del processo è affidato a un PLC e i protocolli di comunicazione soddisfano i requisiti dell’Industria 4.0, garantendo quindi lo scambio di informazioni con il sistema ERP e quello di supervisione del trasformatore.
Deumidificatore modello 200 della serie DW a rotore
Deumidificatore modello 804 della serie D, a torri e con setacci molecolari