
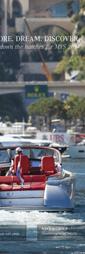
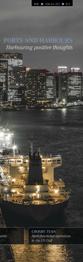
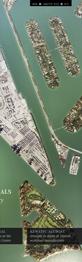
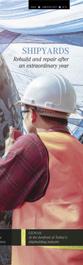
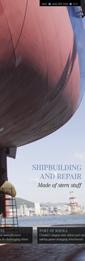
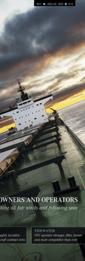
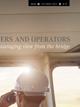
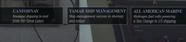
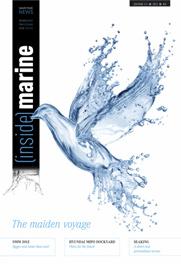
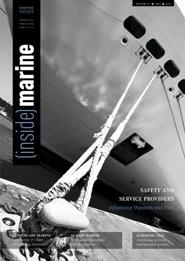
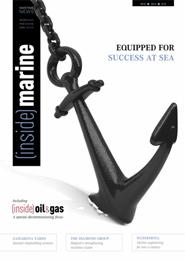
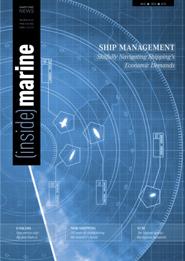
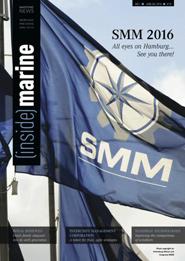
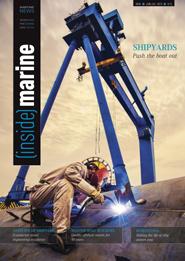
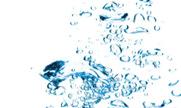
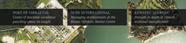
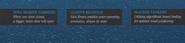
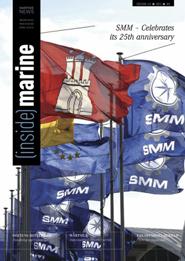
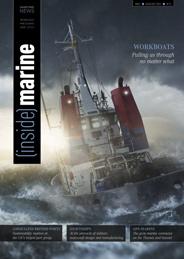
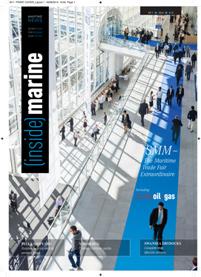
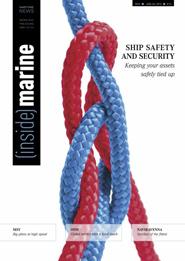
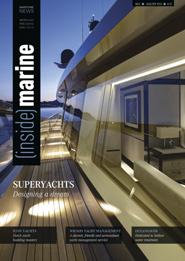
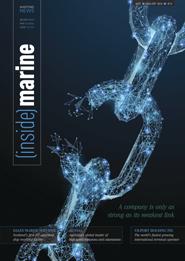
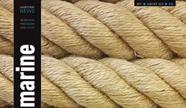

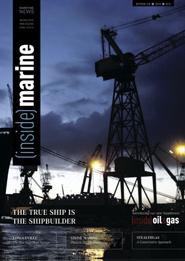
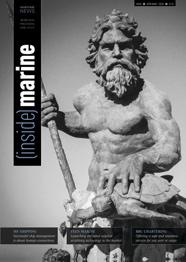
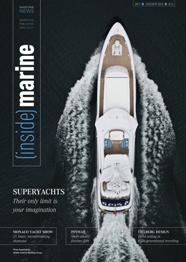
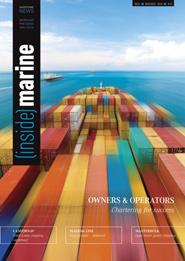
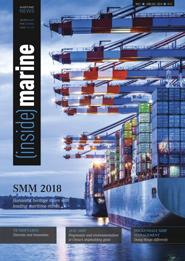
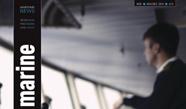
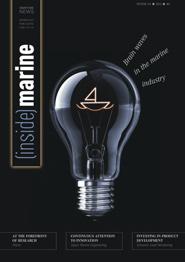
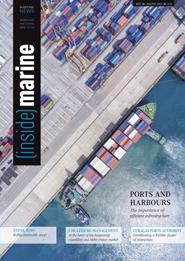
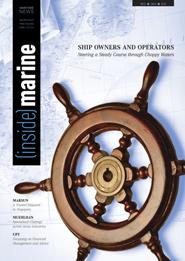
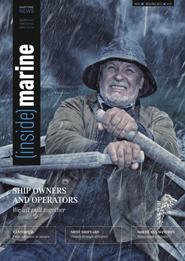
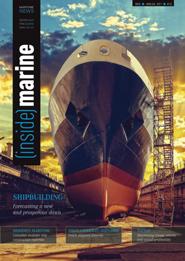
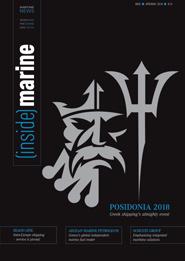
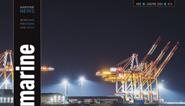
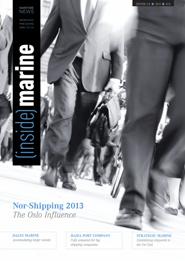
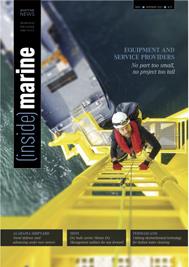
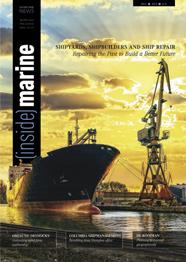
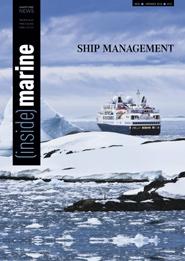
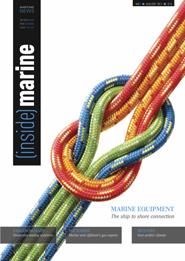
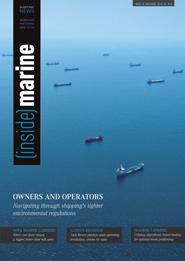
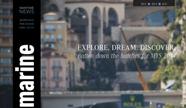
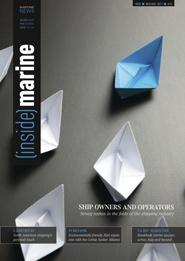
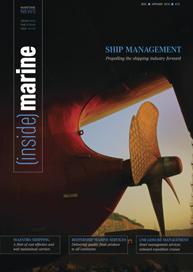
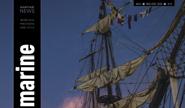
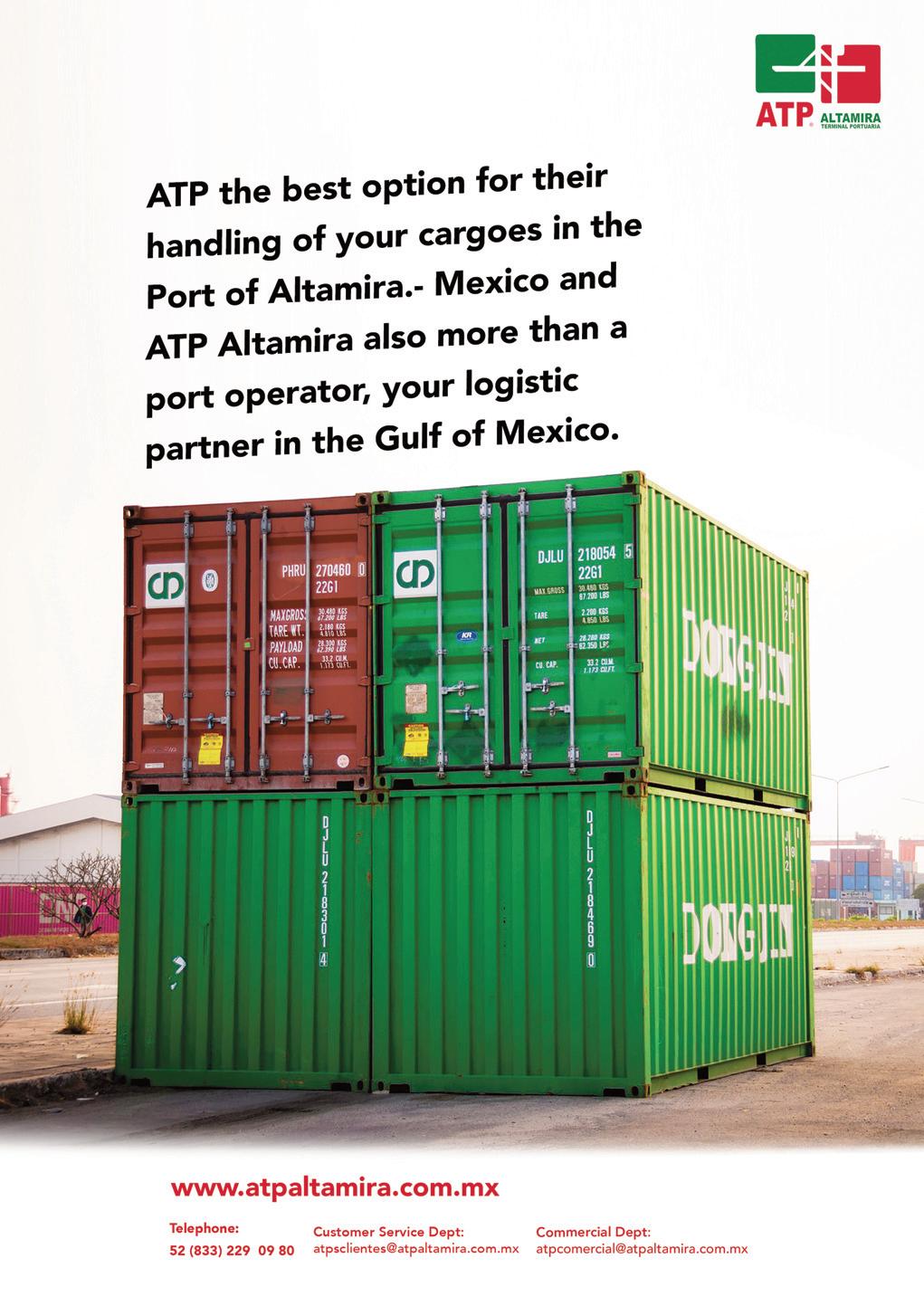
John White Managing Director
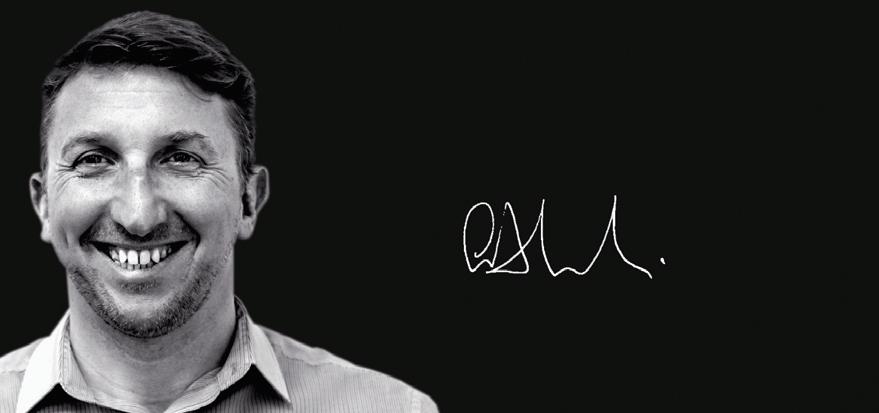
John White Managing Director
Managing Director John White invites you onboard the good ship Nostalgia.
Welcome dear reader to your latest edition of Inside Marine and what a special edition it is for us. I am pleased to announce that the bunting is out in the office as we celebrate our 50th edition of Inside Marine! With some of the turbulent waters that my crew and I have had to navigate whilst at the wheel of this publication, it feels like a tremendous achievement.
What a journey we have been on in over ten years of this edition and how proud I am to report that many of you have been there alongside us, appearing within, or at the very least, reading every edition since we first set sail.
This packed edition is testament to the popularity of Inside Marine amongst you, our maritime readers. It is also a popular magazine to work on within the company and although, like the parent of many children, I of course do not have a favourite amongst our various publications, Inside Marine does hold a special place in my heart being the exmariner that I am. Why is it so popular then? Well, we report on and present news, advertisements, events, company profiles and updates on almost all aspects of the maritime industry and you clearly find this beneficial to help grow your customer and supply chains. Or, at the very least, to grow your knowledge and understanding of what others are up to within the many varied sectors that make up this fantastic industry.
How did we get here? I do not recall exactly the way the conversation went, however, a little over a decade ago, a keen young salesman and editorial researcher working for me, asked for a meeting, during which he presented his case to me about how well the
marine sectors were going within our flagship publication Inside Industry. (Inside Industry, as many of you doubtless know, was our very first publication back in 2009 and covers multiple industry sectors. It is still running smoothly today and long may it continue to do so).
At the time, we were quite content to have our single publication (we now have five!) as it generated more than enough work for us and kept many of you very happy. However, it was fair to say that the marine sector was beginning to dominate other industry groups within the magazine (due in part to the efforts and energy of this keen young crew member), so clearly it had outgrown its first home and was now big enough to leave and stand on its own.
After some time, the keen young man was also able to move up a gear as he became my sales and marketing director! A man whom many of you will know very well in the marine world, Richard Brightmore. Well done that man!
From almost the first edition, it was quite clear that this was a good move as Inside Marine went from strength to strength. Ten years on and it is regularly the busiest and fullest of our publications.
What other milestones have we achieved over the years? Well, there are many, and as always, I am conscious (sometimes) of waffling on, therefore, I’ll mention but a few key markers I think worthy of note that we have enjoyed along our journey.
Firstly, Events! Back when we began, terribly busy as we were, we seldom found the time to attend shows, fairs, exhibitions, and events. With a general industry magazine,
it was of course almost impossible to attend events covering each of the sectors we represented and reported on. Being a specialised magazine, this all changed with Inside Marine. We were able to build some superb media partnerships with many international marine events and indeed attended as many of them as we could in person. What better way to meet many of you face-to-face and enjoy a chat and a drink with you both during and after the event. I am happy to say that after the lockdown events sabbatical for us all, you will be seeing us again soon at the likes of Posidonia and SMM to name but two.
Secondly, Charities! Again, with a general industry magazine, we did not really think about what sort of charities would represent multiple industries. However, along came Inside Marine and with it a scope to cover many marine related charities that serve and support all those who work within this often dangerous and demanding environment.
I am pleased to say that each of our publications now has regular focuses on many global charities are tremendously proud to be able to do our little bit to help promote them. We have Inside Marine to thank for this. As the first of our four specialist publications, it became and remains the benchmark for the others to follow.
I’ll sign off now by simply saying that we could not have done it without you and your input, and I could not have turned all of that input and content into the sort of publication that you clearly love without the genuine hard work, passion and commitment of all my crew members who work aboard this wonderful vessel. I thank you all and here’s to the next nautical marker and the next 50 editions! n
Greek shipping community eager to host a worldwide audience once more
computing in the
industry
maritime industry’s first future-proof digitalisation platform for critical ship systems
in brief
news from the marine industry
68 Dry cargo specialiat banks on cautious approach
INTRESCO
74 Swiss shipping excellence
ABC Maritime
78 Quality, experience and knowledge in shipping
Admare Ship Management
83 Overseeing dry-bulk shipping from the principality
C Transport Maritime
92 Respect to the seas and its people
Augustea Group
96 Boutique service for big ships
Uniteam Marine
102 Sailing bravely where others fear to tread
Universal Africa Lines
109 Oil tankers fuelled by growth
Seven Islands Shipping
114 Bringing a fresh look to ship management
Viridian Maritime
118 Building bridges with multimodal options
Suardiaz Group
122 In tune with sustainable fishing
Echebastar
126 Teamwork makes a couple’s dream work
Nautical Marine Management Services
Equipment & services
132 Innovative thinking gives you wings
Jifmar Offshore Services
138 Raising the bar offshore
AXTech
143 In services of the UK’s maritime sector
The SMS Group
148 Making reliable connections at sea Azimuth Radio Technologies
152 Propelling the marine industry through thick and thin Fundilusa
156 Providing protection in the toughest spots
CORROSION
Environmental technologies
162 Sustainable solutions to submarine cable conundrums
Subsea Environmental Services
168 First every time in global water protection
ERMA FIRST
176 Achieving sustainability by design
Green Maritime Technology
180 Paving the way for a clean tomorrow
Hug Engineering
185 Power on the high seas
KraftPowercon
Ports, harbours & terminals
192 Mexican port set for new highs
Altamira Terminal Portuaria
198 Poti New Sea Port officially opens
Pace Group
202 Rock ‘n’ role Port of Gibraltar
Ship & boat yards
208 Spanish experience, innovation and added value
Aresa Shipyard
214 Reaping ship repairer excellence in the Gulf of Mexico
International Ship Repair
220 Boat company hits full throttle
North River Boats
228 Developing intelligent dredger solutions
ROHR-IDRECO Dredge Systems
236 Dutch marine engineering excellence
VOSTA LMG
Safety & security
242 High stakes on the high seas
Neptune P2P Group
248 Protecting life at sea
BC Service
Superyacht industry
254 Superyacht refits
with a French touch
Atlantic Refit Centre
258 Limitless horizons
Royale Oceanic
Posidonia has long been established as one of the major calendar events of the shipping industry. Posidonia 2018 attracted numerous influential personalities from the Greek and international shipping community and major companies and organisations active in all sectors of the shipping industry. Posidonia 2018 was the largest event in the exhibitions’ 50-year history, welcoming 2,009 exhibiting companies from 92 countries and territories and attended by 23,527 visitors from 104 countries. In total the exhibition was attended by 39,485 participants including exhibitors, visitors and media representatives. www.posidonia-events.com
TOC Europe is part of a global portfolio of events that bring together stakeholders of the container supply chain. Technology and service providers come together to showcase cutting edge solutions to their clients, the terminal operators and ports. The high-level Container Supply Chain Conference, co-located with each TOC event, is aimed at C-Suite strategic personnel including shippers, carriers and 3pl’s as well as the global operators and port authorities. In 2022 many of the conversations within the conference will focus on digitalisation and disruption from the viewpoint of the key stakeholders within the container supply chain. www.tocevents-europe.com
Seawork is Europe’s leading commercial marine and workboat exhibition, providing businesses the opportunity to showcase their products and services to an international audience. The threeday exhibition and conference offers a fantastic range of exhibitor options for businesses to showcase their products and services. This includes pontoon space, open and shell booth space, quayside space, dive tank spaces and sponsorship opportunities. The event hosts high quality exhibitors, speakers and a conference format that focuses on innovation, trends and industry insight, offering an ideal platform for building business connections and signing deals at the event. www.seawork.com
Digital transformation, as well as climate change and the maritime energy transition all take centre stage at the 30th SMM. With an expanded spectrum of key areas and additional presentation formats, the leading international trade fair for the maritime industry accompanies the change at close quarters. Maritime industry professionals from all parts of the world will get the complete overview of innovations from all sectors, and of course they will finally enjoy again the opportunity for live encounters on the exhibition ground as well as in the high-profile trade conferences. www.smm-hamburg.com
Breakbulk Americas is the event for all those involved in the project cargo and breakbulk industry. Focused on companies and projects from Canada down to the tip of Argentina and the Caribbean, this is the place to expand your operations in one of the most promising regions of the world. In addition to meeting more than 200 exhibitors, you’ll find a full conference agenda featuring industry leaders, including shippers, global project forwarders, leading carriers, and more. You will hear perspectives and lessons learned from major project participants, information that you won’t find anywhere else. www.americas.breakbulk.com
The Monaco Yacht Show is world-renowned for the exceptional quality of its superyachts and their impressive length: among the +100 units on display, +40 new models are unveiled as world premieres each year. The fleet has an average length of 50m and mega yachts exceeding 100m. The show has become an emblematic event for private visitors who come to discover an outstanding concentration of superyachts available for purchase or charter and to meet the industry experts in the festive and glamorous atmosphere of the Principality of Monaco. www.monacoyachtshow.com
HoloShip facility will be an engine for technology innovation as Seaspan and Canadian marine sector evolve to digital ship environment throughout vessel lifecycle.
Seaspan Shipyards has launched its new HoloShip facility, an immersive visualisation system that enables Seaspan and the Canadian marine industry community to access a virtual reality environment to develop, integrate, test and demonstrate new digital twin capabilities and transform how ships are built, constructed and maintained.
Modern shipbuilding and through-life support are rapidly evolving with integrated use of digital technology and digital twins. Effective use of digital information is critical for shipbuilders and ship owner s /operators and forms the foundation for connected products and services that can result in more efficient, safer and sustainable fleets.
Seaspan’s HoloShip enables designers, engineers, production teams, and customers to virtually experience, on a 5.6-metre-wide display wall, a fully detailed, three-dimensional and highly accurate digital model of the vessel. Using 3D and virtual reality headsets, participants are transported onto the ship, able to move about to view and interact with the space, as well as with the equipment, components, systems and subsystems. Participants can also access the HoloShip via a networked system at a remote location.
The HoloShip platform enables engineering and design teams to assess and evaluate a wide range of uses and scenarios across all stages of a vessel’s lifecycle, from design and construction through to delivery, operations,
maintenance and training. Integrating advanced visualisation systems allows teams to optimise models and collaborate effectively with customers to increase productivity, efficiency and quality. Emerging digital twin technologies can be leveraged to aid vessel owners and operators to reduce down-time for repair, more effectively maintain, sustain and enhance fleets and lower vessel cost of ownership.
The HoloShip will immediately benefit the non-combat vessels that Seaspan is constructing for the Canadian Coast Guard and Royal Canadian Navy under the National Shipbuilding Strategy (NSS), including the Polar Icebreaker and Multi-Purpose Vessels that are currently in the design phase. It also presents an opportunity to nurture growth across the supply chain, enabling companies to sustain and grow over the long term and better position Canadian technology in the export market.
The HoloShip platform is part of Seaspan Shipyards, value proposition commitments under Canada’s NSS objectives, which are to develop a sustainable, competitive marine industry and to renew the federal fleet with ships built in Canada by Canadians.
The Honourable François-Philippe Champagne, Minister of Innovation, Science and Industry, said: “Seaspan’s investment in its new immersive visualisation HoloShip facility is a critical step for Canada’s marine industry. The HoloShip facility will help enhance the Canadian shipbuilding industry’s ability to seize the opportunities of the digital economy, help to ensure
Canada has the modern ships needed, and create good jobs for Canadians.”
Dave Hargreaves, Senior Vice President, Strategy and Business Development, Seaspan Shipyards, added: “Investment in advanced digital technologies such as our new HoloShip platform contributes to the continued development of Seaspan as one of the most modern shipyards in North America.
“Collaborating with the marine industry community to develop a vertically integrated cluster of Canadian companies that provide both independent and integrated solutions to the global market will also help position and enhance Canada’s reputation as a leader in technology, shipbuilding and ship repair.”
Seaspan Shipyards, a division of Seaspan ULC, is a leader in Canada’s shipbuilding and ship repair industry. With modern facilities and a dedicated workforce of approximately 2,700 in North Vancouver and Victoria, the company has proven itself to be a trusted and strategic partner on a range of complex projects for both government and the private sector.
Through its NSS-related work, Seaspan Shipyards is creating thousands of jobs, generating significant economic benefits, and rebuilding Canada’s shipbuilding and marine industries, contributing more than $2.6 billion to Canada’s GDP and directing more than $1.8 billion in NSS-related contracts to more than 660 suppliers from coast to coast. n
Britain’s leading aluminium shipbuilder, Wight Shipyard Co has secured the new build of two passenger catamarans for operation on the ever-growing Thames commuting and sightseeing line for Uber Boat by Thames Clippers.
Building on the shipyard’s proven technology and sustainability credentials and employing some of the highestskilled personnel in modern shipbuilding based at the iconic Wight Shipyard in East Cowes, the new contract is a significant coup for both the business and the Isle of Wight.
Speaking about the contract, Peter Morton, CEO of Wight Shipyard Co commented: “We are delighted that Uber by Thames Clippers has awarded us the contract to build the next generation of Clipper-class vessels utilising the very latest battery-power technology and re-charging options.
“The Wight Shipyard Co has built a reputation for meeting and exceeding the demands of a global client base, especially in terms of sustainability where our concentration on weight reduction, build quality, hydro-dynamics and efficiency yields real, tangible results and savings. With the fusion of modern drive technology, we have a highly compelling proposition today.”
The hybrid design will allow the new Uber Boat by Thames Clippers vessels to operate solely on battery power to transport both commuters and sightseers along the Thames throughout the Capital’s central zone between the Tower Bridge and Battersea Power Station piers, and recharge while using bio-fuel power outside of Central London.
The technology is not reliant on shorebased charging with the new boats using excess power from the bio-fuel engines to re-charge their batteries for the Central London stretch.
Furthermore, the vessels built by The Wight Shipyard Co. will be some of the quietest ever seen in the passenger boat industry and will stand as future-proofed examples of environmental excellence.
Sean Collins, Founder and CEO of Uber Boat by Thames Clippers recently commented: “For over 20 years we have been at the forefront of innovation for the river marine sector. We are committed to supporting the sustainable growth, infrastructure and economic development on and around the river to endorse the river’s importance to London as a form of transport.
“As a business, we are continuing to embrace the emerging technological advances that will see us continue to develop our fleet and infrastructure, thereby supporting a sustainable future in our industry.”
Wight Shipyard Co has been a trusted builder of Thames Clipper vessels since 2017 when the shipyard received its first commission. Since then, three of the innovative, high-spec and highly durable Thames Clippers have been built and are a muchloved part of London’s waterway as well as
being a vital and eventually net zero carbon commuting option.
And it’s a partnership that is determined to achieve environmental targets, as Sean Collins continued: “Uber Boat by Thames Clippers is committed to achieving net zero with all new builds by 2025 and for its wider fleet, infrastructure and environmental footprint by 2040.
“We’re looking ahead with this hybrid design, ensuring easy conversion to green hydrogen or another renewable energy source – something we’re also focusing heavily on with the new projects we’re undertaking thanks to recent DfT funding. It is the next step in our strategy to net zero and, ultimately, tailpipe zero.”
Peter Morton is unequivocal in his support for the approach: “At Wight Shipyard Co we are firmly on the side of those forwardthinking owners and operators that are revolutionising the industry. Our employees have true global expertise in delivering on the net zero challenge for shipbuilding and we are very proud of what is being achieved, as well as receiving awards such as the Queen’s Award for Enterprise, that are the rubberstamp on our innovative and cost-effective approach to modern shipbuilding.
“We thank Sean and his team at Thames Clippers for not only recognising that the Wight Shipyard Co is at the forefront of the aluminium shipbuilding industry but for trusting us to deliver their future .” n
The technology group Wärtsilä will supply main and auxiliary engines, fuel storage tanks, gas handling equipment and electrical systems for a new RoRo being built for Australian operator SeaRoad Shipping. The orders with Wärtsilä were placed in Q1 2022.
The 210 metre-long vessel is under construction at the Flensburger Schiffbau-Gesellschaft (FSG) shipyard in Germany. The vessel will operate primarily on LNG fuel. Wärtsilä’s depth of experience and in-house know-how on LNG systems was a major consideration in the award of the contract.
The vessel will be powered by two Wärtsilä 46DF dual-fuel main engines and three Wärtsilä 20DF dual-fuel auxiliary engines. The Fuel Gas Handling System and LNG tanks are designed with the Gas Valve Units (GVUs) integrated into the tank connection space. This solution is unique to Wärtsilä and reduces the amount of piping needed, facilitating easier installation.
Wärtsilä will deliver almost every electrical system on board. This includes bridge consoles with integrated navigation, redundant dual-gyro compass systems, nautical sensors, external communication systems, power take-in and take-out (PTI/PTO) shaft alternators with multi-drive technology, monitoring and control systems, switchboards, internal communication, and safety systems as well as lighting.
Wärtsilä will design and integrate the entire electrical package, as well as delivering the cable network. The integration project continues a successful partnership between FSG and Wärtsilä in this area lasting more than 25 years.
“We recognise Wärtsilä’s strong capabilities in LNG-related technologies, as well
as their capabilities in electrical systems, and these solutions are an excellent fit for this vessel,” said Philip Maracke, CEO, FSG. “We thank Wärtsilä for its excellent support and cooperation during the various phases of this project.”
Matthias Becker, General Manager Sales, Wärtsilä Marine Power, added:
“We have enjoyed a very positive relationship with both the yard and the owners throughout this project. SeaRoad is committed to sustainable practices, and this very much aligns with our own commitment to the decarbonisation of shipping operations. The solutions selected for this vessel promote these ambitions.”
Electrical installation will commence this year, whilst the bulk of Wärtsilä’s equipment is scheduled for delivery to the yard during the first half of 2023. The vessel will have 3,987 lane metres for various freight units and is expected to be completed by the end of 2023. It will join Searoad Mersey II and replace charter vessel MV Liekut to operate on Bass Strait between Melbourne, Victoria and Devonport on the Australian island state of Tasmania.
Executive Chairman of SeaRoad, Chas Kelly, said the company is continuously evolving to be the premium freight provider across Bass Strait.
“We’re constantly looking for ways to enhance our logistics solutions for customers and with our investment in this new vessel, the team at SeaRoad is confident in the future of transport between Tasmania and the mainland,” he said.
“At over 40,000 tonnes gross, this will be the largest freight vessel in SeaRoad’s history, continuing to grow our capacity, and providing more options for local agriculture, aquaculture and manufacturing industries.
“We’ve been very pleased with how our two current FSG-built vessels have performed from both an efficiency and an operational perspective. We look forward to continuing our successful relationship with the German shipyard and their expe rienced staff.”
SeaRoad is a privately-owned, Australian integrated shipping and logistics business specialising in Bass Strait. The company provides a customer-focused service through purpose-built RoRo vessels servicing the route between Melbourne (Victoria) and Devonport (Tasmania).
SeaRoad’s current two ships operate a dedicated cargo shipping service six days per week. MV Searoad Mersey II, built in 2016, is the first coastal ship in Australia to use LNG fuel and power technology. The modern MV Liekut joined the SeaRoad fleet in April 2021 under a three-year charter agreement. Liekut will be replaced by SeaRoad’s newbuild vessel at the end of 2023.
In addition to its two Bass Strait shipping vessels, SeaRoad owns and operates a large road transport and container fleet as well as cargo-handling equipment, which the business utilises at its various terminals and depots.
Reporting on the latest developments from the New Zealand maritime sector
The southern hemisphere’s first fully electric, carbon fibre commuter ferry has successfully completed its inaugural round trip with a Thordon seawater lubricated propeller shaft arrangement supplied by New Zealand’s Henley Engineering.
Rere, Mãori for flying fish, joined the East by West Ferries fleet in December 2021 operating the company’s Wellington to Eastbourne route.
Commenting on the ferry’s first trip, between West Queen’s Wharf and Days Bay, Henley Engineering Managing Director, Mark Power, said: “Ika Rere runs like a Tesla Model S! It’s fast, efficient, smooth and quiet. It is a truly inspiring vessel. We hope to be involved in more projects like this.”
Constructed by the Wellington Electric Boat Building Company, the 19-metre Ika Rere is powered by Meridian Energy for Metlink public transport services and owned and operated by East by West Ferries.
It’s wonderful to have a homegrown, sustainable public transport option alongside our electric buses. Ika Rere is driving Wellington’s journey to carbon neutrality “ “
East by West Managing Director Jeremy Ward said the ferry had energised his com pany’s vision of Wellington as a sustainable, smart city.
“Complementing our goal of using Wellington’s harbour-based geography to reduce transport emissions, Ika Rere will also deliver a comfortable and reliable service for passengers.
“Her electric power unit is quieter and smoother with fewer moving parts than a diesel engine. That means less maintenance and less disruption to the sailing schedule.”
Made from carbon fibre, the light yet durable catamaran can transport up to 132 passengers at a speed of 20 knots. East by West’s existing diesel-powered vessels are slower and carry a third fewer passengers.
Auckland based Henley Group – Thordon’s authorised distributor for New Zealand –designed and supplied the vessel’s driveshafts aft of twin 325kW battery-powered electric motors.
The scope of supply included a pair of Thordon SXL seawater lubricated propeller s haft bearings installed in Easiflow GRP sterntubes; shaft seals with Thordon XL oil/grease-free guide bushes; shaft lines and propeller; couplings, mounts, thrust bearings and brakes.
East by West Managing Director Jeremy Ward said: “While the quiet hum of an electric boat is a much more pleasurable experience for passengers, this project was driven by our desire to take climate action. A Thordon Bearings’ zero pollution package was the perfect fit for this eco vessel. A smooth, quiet and water lubricated driveline was an essential environmental requirement.”
The 19m (62ft) long, 132 passenger-carrying fast cat is also the first vessel delivered by the Wellington Electric Boat Building Company (WEBBCo), a joint venture between
the ferry operator and established boatbuilder Fraser Foote.
WEBBCo Managing Director Fraser Foote said: “The ferry is very quiet at 19 knots and silent at 10 knots. It is faster and uses less energy than we anticipated. Ika Rere is a hugely successful project for us. We are the first in the southern hemisphere to have taken a vessel of this kind off the drawing board and onto the water.”
Greater Wellington chair Daran Ponter said Ika Rere would empower customers to choose a renewable method of commuting between Eastbourne and Wellington.
“It’s wonderful to have a homegrown, sustainable public transport option alongside our electric buses. Ika Rere is driving Wellington’s journey to carbon neutrality.”
Meridian Chief Customer Officer Lisa Hannifin said her company was proud to be propelling the maritime innovation.
“As a generator of 100% renewable energy, Meridian is delighted to be supporting the first fully electric passenger ferry. It proves the potential for the electrification of transport to disrupt the status quo while reducing the impact of climate change.
“Our partnership also allows East by West to support 100% renewable energy generation through our Certified Renewable Energy product, enabling them to report their Scope 2 electricity emissions as zero.”
Charity Focus
Sea-Eye – the charity that has saved over 16,000 migrant lives at sea.
“Human rights and the laws of the sea. They’re there for a very, very good reason. But sometimes we can forget why that is. I want to remind everyone that all these concepts are only worth more than the paper they’re written on if we actually put our words into action. And if we don’t, it costs human lives. Every sailor knows, one does not simply leave people behind at sea.”
These were the words spoken by Sophie Weidenhiller, Spokesperson for Sea-Eye, a non-profit and civil sea rescue organisation founded in Germany in 2015. Set up in response to what its founders deemed as the failed migration policies of the European Union, Sea-Eye undertakes search and rescue operations in international waters to save desperate people trying to flee via one of the world’s deadliest escape routes in modern times, in unseaworthy vessels. To date the organisation has completed over 70 missions, where they have saved over 16,000 individual human lives.
Weidenhiller –Spokeswoman
Michael Buschheuer was an ordinary working man who one day decided that he could no longer stand idly while migrants continued to drown day after day in the Mediterranean Sea. So, with a small group of family and friends he set up Sea-Eye in 2015 to do their bit to help during this crisis.
Sophie Weidenhiller, Spokesperson for Sea-Eye said: “He decided to gather some money, and he started this NGO. From then it just kept growing and more people got excited about this and started joining.”
Although Michael is no longer part of Sea-Eye, the charity continues his original mission and has grown since. The charity is able to go on more missions and have bigger ships. In the early days of the charity, the volunteers of Sea-Eye were only able to provide relief by offering supplies and lifejackets as the small ships the charity utilised simply did not have the space to offer much more. So in the intervening years, the charity has worked with larger vessels to assist them.
But the organisation had to grow because the crisis kept on worsening.
Sophie explained what caused her to volunteer with Sea-Eye in 2018: “As a child, I’d love to sail with my dad and we always sailed in the Mediterranean Sea. So that whole area is near and dear to my heart, and to watch it become a mass grave, was just unbearable to me.”
The first ship the organisation used on its missions back in 2015 was an ex-fishing cutter. Built in 1958 and known as the original Sea-Eye, the 26.5m long ship was converted by volunteers to a rescue ship before being transferred to Sicily. It completed more than 20 rescue operations, saving the lives of over 10,000 people before ceasing missions.
After seeing just how dire the situation was the organisation later purchased Seefuchs in 2017 to reach even more of those in need. The former research vessel was almost identical to the SEA-EYE in construction and its crew were actively engaged in multiple rescue missions in the Mediterranean until 2018.
In 2018, Sea-Eye procured it’s third ship, this was a 38m research vessel, formerly the Professor Albrecht Penck, its name was changed to commemorate one of the most poignant tragedies reported during the crisis. This was the Kurdi family, Abdullah Kurdi, his wife Rehanna Kurdi and his two sons Ghalib and Alan fled Turkey in 2015.
Tragically the boat the family were sailing on sank, resulting in all but the father losing their lives at sea. This was symbolic of m any a fate of those who attempted to cross the Mediterranean. On 10th February 2019, Abdullah Kurdi christened the ship after his youngest son, Alan Kurdi. This vessel saved nearly 1,000 people from the sea in just 12 months but has since left Sea-Eye, leaving behind heavy hearts.
Currently the only ship that Sea-Eye operates is its newest, the Sea-Eye 4. This former offshore supply vessel was converted for rescue operations with the support of United4Rescue. The ship by design is well suited to sea rescue as it has greater space for first aid and the onboard infirmary complies with modern standards. The vessel is also equipped with two RHIBs that can reach those in distress as quickly as possible.
Sophie commented: “We also work with a German NGO called German Doctors who sponsored the whole steel container that we call the hospital. She was a supply vessel so there was lots of stuff that we didn’t need that we removed to make room for all the essential search and rescue equipment we need.”
While official number of those who have lost their lives is hard to ascertain, it is estimated to be in the tens of thousands. However, the true scale is much higher.
Sea-Eye – the charity that has saved over 16,000 migrant lives at sea.
After starting out as a small close-knit group of volunteers in the beginning, Sea-Eye now has a pool of over 1,000 voluntary crew members and 800 association members.
“Whenever we go on our rescue missions, the crew on board the Sea-Eye 4 is made up of 25 people. Over half professional seafarers, whilst the volunteers pay for their travel costs out of their own pockets. I think that’s pretty commendable,” Sophie acknowledged.
The Covid-19 pandemic complicated matters for Sea-Eye, who continued operations as stopping was never an option.
Sophie said: “There are still people dying out there, so we can’t not go out. It’s not an option for us. But we do lose time due to quarantines at anchor for the crew after we bring the rescued people to shore and other complications due to the pandemic, such as delays in deliveries and the like.”
The pandemic also saw a dip in donations as the world tightened its purse strings due to financial insecurity. But Sophie explained
the charity was able to come through due to a large stratum of German society who support the charity’s ideals. This support was also found from religious institutions, with both the protestant and catholic church donating. A substantial amount of funding also came from an alliance of over 600 companies and organisations called United4Rescue.
Sophie also mentioned how there have been instances, during the pandemic, when commercial ships have rescued refugees, and encountered huge, and costly delays as a result of these lifesaving endeavours.
“Take the Maersk Etienne as an example,” she said. “They rescued 27 people, but then they weren’t allowed into a port for 38 days. It’s insane.
“For the commercial shipping industry, it’s detrimental if you’re blocked for 30 days, there’s no profit. I’ve even heard reports about ships avoiding certain routes on purpose to not get into this dilemma.”
On a typical mission the Sea-Eye 4 will also have a medical team consisting of two paramedics and a doctor onboard. The search and rescue zone the ship operates in is the central Mediterranean, in international waters. This is where they search for vessels or some form of distress call, and once a vessel has been located the RHIBs are launched as first responders who will assess the situation. They then distribute supplies and radio back. If any people are in critical condition, they are transferred back to the ship to undergo emergency treatment. The large vessel can accommodate hundreds of people if need be.
Sophie said: “If we discover more vessels in distress, we go straight to the next case. If the ship is full, so to speak, then we of course request to be assigned a port of safety. Then usually we must wait because the authorities, especially these days, take longer to prepare everything. I’d say we’re at sea with the people for at least four or even five days, sometimes as long as a week or more until we finally get a port.”
While she admitted that it was sometimes hard to remain positive considering the worsening crisis, she did highlight that the lives saved make it all worth it. In fact, she’s still in contact with a number of those who were saved and seeing them down the line, from sick and malnourished to happy and healthy is a feeling money cant buy.
“We’ve always said from the beginning, even if we can just go out to save a single person, it will still be worth it,” she closed. n
Excitement builds for Posidonia 2022
2022 is gearing up to be the year in which international trade shows return with a vengeance. And what better place to visit your first event in over two years than Posidonia 2022, hosted on the outskirts of Athens during the beautiful Greek summer time. Event Managing Director Theodore Vokos was asked by Daniel Barnes to put into words exactly what it means to the Greek shipping community to finally (we all hope!) welcome again the world’s finest maritime companies to Greek shores.
After a difficult couple of years for everyone, it’s great to be looking forward to Posidonia once more. How appreciative are you, as organisers, to the understanding exhibitors and visitors have offered you during these challenging times?
I see an optimism in the market and by June I believe things will be even more back to normal within the new Covid times we live in. As for exhibitors, we have been extremely lucky and thank them for their support and trust. I have to stress that 70% of our exhibitors from the postponed 2020 event have transferred their participation to 2022 –without any questions. But there are always new obstacles on the way and as you can understand the recent war in Ukraine will have some effect on Posidonia, which remains to be seen. So it has not been been smooth sailing so far for 2022.
We are seeing a lot of interest. 87% of the space is booked at the moment; this is 10% up compared to this time before Posidonia 2018, which was the biggest exhibition in our history.
How will the event differ from previous (pre-Covid) events?
Posidonia 2022 will be a big exhibition no matter what and business will be done on the exhibition floor. It is a good time for the shipping market and one cannot risk missing out on Posidonia. But of course Covid will still be around, in one form or another, and this will affect how people engage with each other, so perhaps we might see fewer social events and more focused business meetings.
Covid may mean that some companies will not send 10 people to cover their 30 sqm stand – they may only send five instead.
But the companies will still be very strongly represented.
Covid will impact participation from China, as quarantine rules for people returning back to China are expected to remain very stringent. However, the big Chinese exhibitors will be here, as they have local offices. It will be the smaller Chinese suppliers who will be having second thoughts. But in general, Posidonia 2022 will retain our very strong Asian participation. Japan, Korea and Singapore are all committed to national pavilions, and local Greek agents will also have the chance to represent Asian manufacturers who may not be able to commit in person.
We are now carefully watching developments in the Ukraine, as we also have exhibitors from the region, and are in touch with them regarding their participation. They want to attend Posidonia, but of course if the war drags on this might not be possible. Let’s hope for the best and that the war will end as soon as possible. But the war high-
lights that nowadays we are living in a very volatile environment and a business must be on guard to face new, unexpected, challenges.
From an administrative perspective for yourself and your team of organisers Theo, how much extra work has it taken to just get to this stage of organising an event compared to previous editions?
Look, it has been a tough job for the team here because not only are they tasked with filling our exhibition space, they have so many more questions to answer than in pre-Covid times. ‘What are your safety protocols?’ ‘If I sneeze, where can I get checked?’ ‘What happens if I’m positive while in Greece?’
All these issues have to be addressed – and you have to be honest about it. We’ve realised that being completely honest with people and telling them what the situation in Greece is, and what we are doing to the best of our abilities in order to deal with any possible scenario, is gaining people’s trust and confidence to attend Posidonia 2022.
The starting point is they want to come and they really want, or need, to attend.
I think we’ve reached the point where virtual events have come to a saturation point. You don’t get the same return anymore from virtual events, people feel it. They want to meet the person. And this is shipping – it is a people industry. It’s an industry where you need to see or discuss the product. So there’s an urgency for the industry to come together.
With companies arguably opting for a more cautious approach to the number of events they attend in the short term, what do you attribute Posidonia’s promising exhibitor figures down to?
The first argument is a no brainer: it’s the Greek shipping industry. It’s still the biggest fleet in the world, it’s the most modern fleet in the world, and it’s a fleet which keeps constantly investing in new products and new ships. The Greek shipping industry is always in the front line of new developments.
On top of that, we are very lucky that we are riding the wave of a boom market. And you know, shipping freights at the moment are skyrocketing, especially in the container and the dry bulk markets. This generates a lot of cash for the Greek shipping community, which is mostly reinvested in ships. Whilst shipbuilding has been rather down in the last couple of years, the prices are still good and shipping companies do have the cash – and want to invest in building new ships or retrofitting existing ones.
Environmental challenges are a very hot topic at the moment and one that will be discussed in length at Posidonia 2022. The simple fact is you can’t keep operating a ship the same way you did just a few years ago. The industry needs to invest in scrubbers, ballast water treatment systems, monitoring systems etc.
Plus the digital revolution is here. There are many products which can make a shipping business more profitable – be it optimum data analytics on how to best choose the route for your ship, how to most efficiently load and unload it – so they have to keep investing, and they’re ready to invest and they have the money at the moment.So, if you’re selling anything shipping related, you have to be at Posidonia as this is where the market is.
The second aspect is that Posidonia is one of the exhibitions which is most engaging. The shipping community comes together and shipowners reach out to exhibitors they meet face to face. There are a lot of social aspects to the exhibition, sporting events,
the Posidonia Games, which one way or the other will take place in accordance with all safety regulations in force at the time of the event.
And last but not least, after having missed so many events, even foreign shipowners will come to Posidonia to meet the industry, because the biggest part of the market will be here. So it looks as good as can be expected right now.
Speaking from experience, it does seem that Posidonia enjoys a more relaxed tone at the event, when compared to other shows. Is it the sunshine, Greek hospitality, or something you put in the water!?
Each international exhibition also reflects cultural traits of the nation which hosts it, so Greek hospitality plays a role for sure –and the weather certainly helps!
Greek shipping is built on long lasting relationships. You will find new products at the exhibition, but you also go to the exhibition to meet long standing partners and reinforce the relationship. So everyone starts from a positive attitude.
For example, Greeks have been building ships in Japan since the 1950s – it’s a relationship valued both ways by both parties. And we look forward to meeting each other again. These feelings are felt across the entire exhibition floor. And you know, shipping is supposed to generate business and profit for everyone.
How is Posidonia 2022’s conference and seminar programme shaping up?
I’m very happy to say that we already have a good number of seminars already confirmed and the requests still keep coming in.
People believe that, yes, in June, we will be able, again, to meet in a conference hall, perhaps with a little bit of a limited capacity, perhaps wearing masks. But we can get into the conference hall. We can talk to each other, and we can debate the issues, because there’s a lot of issues to be debated.
The problem hosting such conferences virtually, as proven over the last few years, is it lacks engagement. Whatever features have been tried, they don’t have the same networking effect, and people don’t have the same attention span either. In virtual events, we have seen people logging in and logging out every 15 minutes. But with a physical programme, people will be fully engaged – and also benefit from that all important networking aspect – once more.
Traditionally, we always start the conference programme with the TradeWinds Shipowners Forum, and this year will be no different as we carry on our long lasting partnership with TradeWinds. Seatrade is coming back after many years and they’re doing a major conference on Thursday, titled the Global Maritime Club Summit. Capital Link, which deals with financial aspects of the shipping community, is also hosting its traditional Monday conference, and HELMEPA (Hellenic Marine Environment Protection Association), which is supported by the Greek shipping community, will also play a key role.
We also have content arranged by the Union of Greek Shipowners, classification societies, and a number of seminars are being organised by national pavilions including the Japanese, Korean, and the Polish participations.
As a family business, Theo, Posidonia seemingly runs in your veins. How long have you been part of the event now?
I’ve been part of Posidonia since 2003. When you compare me to my counterparts at the likes of SMM and Nor-Shipping, I’m certainly considered an old-timer in the shipping exhibitions industry.
But of course, it’s also a family business, like most things in Greek shipping. Posidonia was founded by my grandfather and my uncle in the 1960s. Our track record over the years proves that we manage to deliver and always strive to provide our exhibitors and the international shipping community the best possible event. If you’ve been around for a while, and keep on delivering, the industry will reward you with its trust.
On a personal level, what are you most looking forward to about this year’s upcoming event?
Getting back to basics, first of all; I’m looking forward to Posidonia simply taking place. I’m still waiting for the moment when we cut the ribbon and just welcome everyone through the doors. The second thing I’m looking forward to is happy people. Many people genuinely enjoy attending Posidonia – and Posidonia taking place in Greece, in the summer, of course helps.
I would really like to see Posidonia become one of the first major events which brings the shipping community from all around the world back together, after two years of separation.
But the bottom line is that business needs to keep going. We need to see the industry tackle the challenges it is facing. And, of course, Posidonia can help in this regard, and stimulate discussions and act a little bit as the catalyst which will take the shipping industry further. This always helps. This will mean that we have achieved our goal.
If it’s possible to think mid- to long-term at this moment in time, how do you envisage the Posidonia brand developing in the years ahead?
Brands have to always grow. And this is why 10 years ago we launched a second event, the Posidonia Sea Tourism Forum, which focuses mainly on cruising, yachting and passenger shipping.
This was the only virtual event we held and it had huge attendance in May 2021.
We are always looking at other ways to utilise our brand, but for us, it is crucial to protect the Greek aspect of it – we won’t extend the event to other international locations, which is something other trade show organisers have attempted in the past with limited success.
After all, the name Posidonia itself is derived from the Greek God Poseidon. It is a great brand, we value that, we protect it and I think the market respects our decision.
And finally, what is your overarching message to those amongst the Inside Marine readership that are still undecided about attending Posidonia 2022?
First of all, evaluate the situation both in Greece and your home country to see how safe it is to travel. It looks like the Covid situation will be more or less under control this summer and safety regulations are relaxing a bit around the world. Many of us will be able to travel as safely as possible within the new environment we live in.
In my opinion, the shipping community needs to travel and to meet again. In shipping, if you do not keep up with developments, you’re left behind. That’s unfortunately true. The market changes, products change, services change, technology changes. The only way to really keep up with all the changes is to go to exhibitions. Meet the suppliers. Meet the people who drive the change. Meet the Greek shipping community who looks forward to welcoming everyone who forms part of the global supply chain.
The world depends on shipping to keep the world going. Even during the toughest times of this pandemic when everything was closed, shipping kept going despite all the obstacles – and I don’t think shipping has gotten enough credit for it. The fact that whatever you ordered online – from your office or your home – got delivered to your door, proved that shipping was there. And to safeguard this credibility of the shipping industry, the industry needs to come together to take it further. n
The maritime industry’s first future-proof digitalisation platform for critical ship systems
Dutch based electrical and automation integrator Alewijnse has developed the maritime industry’s first future-proof digitalisation platform for critical ship systems and reduced computing footprint by 75%. In an Inside Marine exclusive, we look at how this has been achieved and how it could benefit your company.
With a 130 year history, Netherlands-based Alewijnse is a global leader in marine technology for critical ship systems for yachts, naval and governmental, and dredging, offshore & transport. The company designs, delivers, and integrates on-board electrical systems, automation systems, and advanced marine electronics.
Using Stratus Edge Computing, the company introduced AlViVi, the maritime industry’s first future-proof digitalisation platform for bridge control of critical vessel systems. The platform relies on application virtualisation to drastically reduce IT requirements and enables ship-wide visualisation of information. Overall, AlViVi reduces onboard computing footprint by 75% and reduces customers’ IT maintenance costs by 50%.
Innovating the AlViVi digitalisation platform
To innovate for customers, Alewijnse sought to solve one of the largest challenges for the maritime industry – simplifying the IT architecture required to operate multiple, critical ship systems in a constrained space. Rather than deploy and manage individual IT architectures spread across the vessel for each control system for propulsion, energy, navigation, communications, electrical, security, and others, Alewijnse turned to Stratus Edge Computing to con -
solidate computing and software, and centralise computing for automa tion and control.
The company developed AlViVi (Alewijnse Virtualisation and Visualisation), a breakthrough digitalisation platform that uses Stratus ftServer to consolidate process-related systems. The innovative AlViVi platform – and first of its kind in the maritime industry –acts as a central hub to integrate and control ship systems, and uses Rockwell Automation’s ThinManager® to distribute information to networked screens for visualisation anywhere on the ship.
With applications virtualised on the Stratus Edge Computing platform, AlViVi is software agnostic, able to run any application whether it be on dredging control, weather monitoring, propulsion, or power and utilities.
For critical ship systems, it was essential that the Stratus platform delivered the highest level of application availability and reliability, and the team incorporated computing redundancy for more than 99.999% availability.
“We chose Stratus because of the technology, especially, the redundancy in the hardware. We use the Stratus ftServer® 4900 which is a fully integrated platform which is simple to deploy, simple to manage and simple to service without the need for IT skills. Additionally, it is more cost effective than multiple servers. The core is organised with Stratus,” said Johan van Rikxoort, Product Manager, Alewijnse Dredging & Offshore.
“Now, we are also retrieving more data from the system itself and visualising it on the SCADA. For example, what is the fault count of the different processors? How is the health status of the server? Our customers now have one view of all critical systems that they can share anywhere on the ship. That visibility and access to information enables quicker response and better decision making for ship operations.”
With its AlViVi platform, Alewijnse consolidated multiple ship systems on a single Stratus ftServer 4900 to perform as the vessel’s server. The result was consolidation of 20 individual
PCs to a single computer platform, which freed up valuable physical space.
According Mr Rikxoort: “In the systems we replaced, there were previously multiple computers and servers performing different functions that were spread out across the vessel. With Stratus, the hardware is all in one place. Our new Stratus-based solution takes up 75% less space, phasing out computer hardware, displays, keyboards, and all of the backend.
“The significant reduction on space used is highly important for our customers. In addition, consolidating on Stratus Edge Computing translates into less hardware and software cost and less maintenance.”
Using Stratus Edge Computing platform, Alewijnse was able to modernise vessel-wide IT architecture for OT control systems, and enable easy management by non-IT staff. With computing redundancy, Stratus removes a single point of failure and eliminates unplanned downtime. Any failed components are automatically taken offline with zero performance impact, and subsystems are hot swappable by OT teams. The new customer replaceable units are automatically detected, and data is resynchronised, avoiding any additional programming or provisioning.
By consolidating management of 20 systems into a single unit with redundant computing, Alewijnse was able to double the lifespan of IT systems from three or four years up to seven or eight years.
Mr Rikxoort explained: “The hardware on vessels faces harsh conditions – salty air, dust from the dredging – and due to that, we have to replace all the hardware every five years. With traditional com-
puters, the operating system is obsolete within five years. The SCADA soft ware for graphic facilitations is also obsolete. You have to then replace computers for not only the dredging control and monitoring but also computers for the survey, data loading, office purposes, and other ship functions.
“With the Stratus platform, at the end of the eight-year lifecycle, we can easily manage, modify, and install a replacement in one location. With ‘loose’ computers, you do it every four years.”
Mr Rikxoort continued: “The AlViVi platform on Stratus is fast, userfriendly and extremely reliable, resulting in maximum uptime and optimal operational safety. By bringing together multiple systems in one environment, the maintenance and management becomes much easier and efficient. Updates are better and faster to test or roll back. This is transformational for how we architect critical systems.”
With the efficiency of the AlViVi platform, Alewijnse can incorporate additional ship systems previously not possible due to IT limitations. It is now feasible to integrate IP-based camera systems on-board and stream to mobile devices. Communication and sonar navigation equipment is embedded into the platform and can be displayed on screen at any location across the ship that operators want.
With Stratus Edge Computing, Alewijnse is offering customers a breakthrough platform to manage critical on-board systems that saves time, money, and space. Backed by the continuous availability of Stratus Edge Computing, Alewijnse has created a platform to innovate for customers and lead technology transformation in the maritime industry.
Smart network company Marlink is partnering with MSC, the world’s largest container shipping line, to support the shipping company’s ambitious digitalisation goals, using Marlink’s hybrid network solutions and advanced, secure IT management.
Marlink deploys a fully managed hybrid network solution, bundling its VSAT connectivity with L-band backup and global 4G connectivity on 127 vessels, providing MSC with seamless, secure connectivity to run its critical business and crew applications. This hybrid network solution is fully secured by Marlink’s Cyber Detection Service which scans real-time outbound and inbound network traffic for targeted cyber threats and takes immediate countermeasures to remediate incidents. In this way the shipping giant can keep its remote vessels securely connected.
The next phase of MSC’s digitalisation strategy sees the roll-out of Marlink’s ITLink management solution across the fleet. MSC
has moved decisively to increase the standardisation of its onboard IT systems and to meet 2021 IMO requirements, enabling fleet managers to monitor operating IT systems and software from shore. ITLink enables MSC fleet managers to remotely access their onboard IT networks for monitoring and troubleshooting in a secure environment and allows software updates and patches to be applied fleetwide – a major efficiency gain for container shipping’s leader.
“Marlink understands the critical requirements that drive container lines; operating a global service with high attention to asset availability, service reliability and security that demand a global approach,” said Nicolas Furgé, President, Digital, Marlink. “Our partnership with MSC will enable them to build a digital ecosystem that supports efficient vessel operations and compliance, powered by world-class connectivity.”
Class society Bureau Veritas has announced it is supporting the classification and construction at Hyundai Mipo Dockyard (HMD) in the Republic of Korea of two 40,000 cbm LPG carriers that will be ‘ammonia prepared’. The HMD hull numbers are 8350 and 8351 and the first delivery will be in June 2023.
“It’s great to confirm this project for the first ships that will receive our Ammonia Prepared notation,” said Ulrik Dan Frorup, Chief Commercial Director, Bureau Veritas M&O. “BV was among the first class societies to develop such classification rules for future installation/conversion of ammonia propulsion. The expertise that we have developed in risk methodology and our track record in LNG as
a marine fuel has supported our ability to develop these rules for new low carbon fuels like ammonia.”
He added: “Ammonia presents specific safety issues related to its toxicity that have to be addressed. The industry leadership we have shown in multi-stakeholder hazard identification (HAZID) and hazard operations (HAZOP) projects has supported the development of our rules and notations for ammonia as fuel.”
The new Ammonia-Prepared notation is applicable to newbuildings, and was developed to support ship owners, designers, shipyards and charterers. Ammonia-Prepared certifies that a ship has been designed and constructed to be converted at a later date to use ammonia as fuel. The notation targets the spaces and structural components that will accommodate future ammonia fuel tanks, fuel handling equipment and ammonia vapor treatment installations. Ammonia Prepared also covers specific requirements for the conversion of engines and boilers from using fuel oil, LNG or multiple fuels to ammonia.
Mark Etcheberry, General Director at Geogas, said: “LPG carriers are frequently used to carry ammonia. From a technical point of view this makes the design suitable to be prepared to burn ammonia as a fuel. At Geogas we are committed in our ESG objectives to promote greener propulsion technologies that are technically feasible. LPG, LNG and ammonia gas fuels support these objectives.”
Bureau Veritas has also developed new rules for ammonia fuelled ships designed to be applied to newbuildings that will use ammonia as a fuel from delivery. BV Rule Note NR 671 for ammonia as fuel addresses the safety aspects of managing ammonia in storage tanks, fuel-piping systems and during bunkering. NR 671 was published in its earliest form on July 1st, 2021 along with the requirements for the Ammonia Prepared notation.
TotalEnergies
Marine Fuels has carried out its first marine bio-
VLSFO (Very Low Sulfur Fuel Oil) bunker delivery in Singapore’s port waters, as part of a biofuel trial recently completed by NYK Line and Anglo American.
During the operation, a B10 biofuel blend that composed of VLSFO blended with 10% second-generation, waste-based and ISCC-certified UCOME (Used Cooking Oil Methyl Ester) was supplied via ship-to-ship transfer to MT Friendship, a bulk carrier owned by Seanergy Maritime Holdings and chartered by NYK Line to transport cargo provided by Anglo American. The biofuel was consumed during her two-way voyage between Singapore and Saldanha Bay, South Africa.
The UCOME bio-component, sourced from the circular economy, can achieve more than 80% reduction of GHG (Greenhouse Gas) emissions compared with heavy fuel oil from a well-to-wake analysis. Consequently, the delivered B10 biofuel blend provides a reduction of up to 10% in GHG emissions. The trial also showed that the biofuel can be safely used in relevant marine applications without any modifications.
According to TotalEnergies Marine Fuel, these results, coupled with the vessel’s smooth operational performance throughout the trial, demonstrate the potential of biofuels in assisting ship owners to meet the IMO’s carbon emissions reduction targets.
TotalEnergies Marine Fuel’s successful biofuel delivery also underlines its pioneering efforts in setting up a local biofuel supply chain for this trial, including land storage, blending and the eventual bunkering operation. The local operation was made possible with support from the Maritime and Port Authority of Singapore (MPA) and the involvement of local partners, including Singapore bunker barging company V-Bunkers and tank storage company Vopak Terminals Singapore at Penjuru.
This biofuel delivery forms part of TotalEnergies Marine Fuels’ drive to develop a range of fuel solutions to help the shipping industry’s move towards decarbonisation.
“We are delighted to partner with NYK Line and Anglo American for our first marine biofuel delivery in Singapore. This trial has allowed us to initiate the structuring of a supply chain with local expertise to create a sustainable, cost-efficient and low-carbon biofuel offer for the shipping sector in the region,” said Laura Ong, General Manager of Trading and Operations for Asia Pacific, TotalEnergies Marine Fuels, based in Singapore. “We will continue to conduct more bespoke trials with our customers and to ultimately provide a scalable solution of this lower-carbon marine fuel.”
TotalEnergies Marine Fuels is TotalEnergies’ dedicated business unit in charge of worldwide bunkering activities, serving more than 200 shipping customers across over 120 ports in Europe, Asia Pacific and Africa.
Six companies have formed a strategic alliance aimed at reducing environmental impact through the development of methanol-fuelled domestic tanker.
Mitsui OSK Lines, MOL Coastal Shipping, Tabuchi Kaiun, Niihama Kaiun, Murakami Hide Shipbuilding, and The Hanshin Diesel Works will collaborate to build the new tanker, which the companies claim will be the first of its kind in Japan.
The vessel development project, which targets delivery of the ship in 2024, was also selected to receive public funding through the Japanese Ministry of Economy, Trade and Industry (METI) and a Ministry of Land, Infrastructure, Transport and Tourism (MLIT) subsidy.
Methanol can reduce emissions of sulphur oxide (SOx) by up to 99%, particulate matter (PM) by up to 95%, nitrogen oxide (NOx) by up to 80%, and carbon dioxide (CO2) by up to 15%, compared to vessels using conventional fuel oil, which is currently
the main fuel for marine vessels. Methanol has outstanding properties for use as a fuel, as it is liquid at normal temperatures and normal air pressure.
Methanol fuel has been more widely introduced on ocean-going vessels as an environmentally friendly fuel, including four MOL Group-operated ships, but this will be the first methanol-fuelled domestic ship. In addition, methanol can be produced with CO2 and hydrogen as raw material, so in the future, it can be produced by utilising the CO2 capture and transport business to synthesise hydrogen, which uses electricity derived from renewable resources such as offshore wind power and wave power.
If this methanol can be used as fuel, it can establish an environmental circulation type business model, enabling a reduction in net CO2 emissions. The six alliance partners will each orchestrate their advantages in technology, expertise, and networks aiming to realise a decarbonised society.
Shipbuilding group VARD has awarded Norwegian Greentech a contract to deliver the ballast water treatment systems (BWTS) to six marine robotic vessels that will be built at Vard Vung Tau in Vietnam for an undisclosed shipowner.
VARD has designed a unique multi-purpose platform that allows for onshore remote control, light crewed or uncrewed operations. The vessels are of VARD 9 60 design. VARD has designed the vessels for an ultra-low carbon footprint, and they are among the first vessels to be prepared for green ammonia and fuel cell and battery technology.
Norwegian Greentech will deliver its energy efficient BWTS to each of the six newbuild marine robotic vessels. The company has developed a method of utilising UV and filters. The chemical-free system has a highly compact design, which , according to Norwegian Greentech, is ideal for difficult-to-fit engine or pump rooms.
“VARD is constantly challenging the supplier industry to provide solutions and products that lower energy consumption, CO2 emissions, operating expenditure and the overall environ -
mental footprint. We are very pleased about this development as it contributes towards creating even better awareness of the various BWTS features that are available in the market,” said Jon Olav Kopperstad, Senior Sales Manager at Norwegian Greentech.
In December 2021, Norwegian Greentech announced that it had secured a contract to deliver the BWTS to eight marine robotic vessels that VARD is building at Vard Vung Tau.
“First eight vessels and now another six. Our deliveries to the first batch of vessels are well advanced, and the next six BWTS systems will be identical to the first eight, contributing towards streamlining and de-risking the entire shipbuilding process,” added Mr Kopperstad.
Norwegian Greentech will manufacture the ballast water treatment systems at its headquarters in Fosnavåg, Norway, and deliver them to VARD’s shipyard Vard Vung Tau in Vietnam. Norwegian Greentech has not disclosed the value of the contract.
Norwegian Greentech is a subsidiary of HAV Group ASA, which is listed on Euronext Growth in Oslo, Norway.
Fuels has opened a new office in Westport, Connecticut, USA, as part of its commitment to global customers seeking ways to decarbonise in American ports and beyond. The office will be manned by LNG, biofuel, LSFO
and MGO experts Maurice Lara and John Lindquist, and will be carbon neutral given GAC Bunker Fuels’ blue carbon projects around the GAC world.
Beyond aligning with the United Nation’s Sustainable Development Goals, GAC Bunker Fuels has pledged zero oil-based bunker sales by 1st January 2030. On 1st September 2020, it stemmed the first marine LNG for a foreign-flagged vessel in the United States and is working with US-based energy utility company Puget Sound Energy to establish LNG bunkering along the US West Coast.
Maurice Lara, GAC Bunker Fuels Trading Manager for the Americas, said: “We want to help our customers decarbonise by offering alternative fuel and are uniquely positioned to do so due to our many established customer and supplier relationships. We are looking for biofuel specialists to join our expanding team to meet their growing needs.”
Joining the new Westport office are members from GAC North America’s team, who in partnership with GAC Bunker Fuels, are promoting their range of shipping services to customers in the Tri-State area with a specific focus on servicing the growing offshore wind sector along the Eastern Seaboard of the US.
GAC is a global provider of integrated shipping, logistics and marine services. Established since 1956, the privatelyowned group employs around 8,000 people in more than 300 offices worldwide.
The world’s smallest ship measures only 1/1000th of an inch. Built by a Dutch team of scientists, it propelled itself via chemical reaction.
The largest tanker ever built was the Seawise Giant. Completed in Japan in 1979, the ship weighed more than 564,000 tonnes and measured 458.45m in length. She was bombed and sank in 1988, but was recovered from the seabed a year later and repaired, before finally being scrapped in 2010.
The Blue Marlin and Black Marlin are ships that ship ships. These semisubmersible heavy-lift ships can carry an eyewatering 75,000 tonnes of cargo… or a whole oil rig.
The world’s deepest shipwreck is thought to be that of the USS Johnston, a World War Two Fletcherclass destroyer. It lies at a depth of 21,180 feet beneath in the Philippine Sea.
Every problem is a gift we would not grow without problems “ “
– Anthony Robbins –
According to Boat International’s 2022 Global Order Book, a record of 1,024 superyachts are on order in 2022 – a rise of 24.7 % from last year’s 821.
The largest ship ever built (although technically not a ship) is the Prelude, a floating liquified natural gas platform, it is 488m long and has a displacement of 600,000 tonnes. This is more than five times the size of a Nimitz class aircraft carrier.
The Panama Canal was completed 107 years ago and when taking into account the cost of inflation, its construction costs of $375 million would today be approximately $8 billion.
The Suez Canal blockage caused by the Evergiven is estimated to have cost the world’s economy around $9.6 billion a day in trade.
Iona, one of P&O Cruises’ newest cruise ships, is the first ship in the world to have an onboard distillery. This oneof-a-kind feature has a custom built 450-litre copper still.
From simple ideas to engineering feats
ABB power conversion technology is ensuring a stable power supply for the fast-charging units serving five new electric ferries on the round-the-clock services crossing Amsterdam’s North Sea Canal. The new ferries have been ordered by the city’s public transport company, Gemeentelijk Vervoerbedrijf (GVB), and are seen as an important step in its strategy to become a sustainable, emissionfree transportation company. GVB will deploy the electric ferries on three busy North Sea Canal routes that transport more than 350,000 cars a year. The ferries will operate constantly, day and night, with only three minutes allowed for battery charging after each 20-minute round trip, making fast charging a critical factor in maintaining a reliable service.
Seahaven, a novel lifeboat system that offers Helical slide-based mass evacuation from large passenger vessels, has passed the rigorous HWST programme. This is a huge step forward in the critical development of Seahaven which brings this game-changing cruise evacuation system one step closer to full market introduction. The two craft system has a total capacity of 1,060 persons and can travel independently at six knots for 24 hours. Survitec has begun working with its customers on the introduction of this game-changing solution to their operations.
Deltamarin has completed the conceptual designs of the ships for Höegh Autoliners. The Aurora class ships will be the world’s largest and most environmentally friendly car carriers ever built. The ships will be powered by MGO and LNG and prepared with readiness for operation on zero carbon fuels such as ammonia or methanol once these become more widely available. Several other features are also included in the design to minimise the environmental footprint of the ships. Combining economy of scale with optimised and future-proofed ship concepts results in the lowest greenhouse gas footprint per transported car in the industry, and a clear path to zero-emission operation.
Britain’s leading aluminium shipbuilder, Wight Shipyard Co, has secured the new build of two passenger catamarans for operation on the ever-growing Thames commuting and sightseeing line for Uber Boat by Thames Clippers. The hybrid design will allow the new Uber Boats to operate solely on battery power to transport both commuters and sightseers along the Thames, and recharge while using bio-fuel power outside of Central London. The technology is not reliant on shore-based charging, with the new boats using excess power from the bio-fuel engines to re- charge their batteries for the Central London stretch.
Harvey Gulf International Marine has begun to operate one of its Tri-Fuel vessels exclusively on battery power and Renewable Liquefied Natural Gas (RLNG), with diesel fuel as back up, moving one step closer to becoming the world’s first ESG certified oil and gas vessel operator. The Carbon Natural RLNG being consumed onboard is a blend of low carbon intensity (CI) sourced biomethane from the swine and bovine industries. The natural methane produced from the waste/by-product of the pork and dairy sectors is recovered via digesters. The processing of the waste and extracting of the methane results in negative CI scored renewable gas. Through blending at an LNG fuelling terminal (the only one in America) it can achieve net zero carbon emissions when RLNG is blended with locally available LNG.
FASTAR® is a self-polishing antifouling paint that incorporates a unique nano-domain resin structure designed to minimise the effect that seawater temperatures, vessel speeds and other external factors have on coating performance. Nippon Paint Marine’s fourth generation antifouling system is available in two main versions: FASTAR® I and FASTAR® XI, with the latter incorporating the company’s patented hydrogel technology. COSCO Shipping has indicated it will coat its entire fleet of VLCCs with Nippon Paint Marine’s new antifouling system FASTAR® once initial applications have been evaluated.
Send us your innovation
We welcome all your latest innovations and product releases. If you wish for us to share these with our readers please send them to us today. Send your innovation to:
seven seas, five oceans, one voice
matrix ship management cool carriers swire bulk sea partners navigation intresco abc maritime admare ship management c transport maritime augustea group uniteam marine universal africa lines seven islands shipping viridian maritime suardiaz group echebastar nautical marine management
Matrix Ship Management is a close-knit marine powerhouse. Based in the long-standing shipping hub of Cyprus, it offers a bespoke range of services to cater to the needs of its customers. “2021 marked our 10th year of operation. We are very pleased that most of our staff have been around for the majority of those 10 years,” said Commercial Director Mike Dobson.
Going strong for a decade, Matrix Ship Management works as a third-party operator, which not only offers the inherent benefits of third-party ship management but also its own excellent in-house style of solutions to clients’ problems. The company initially cut its teeth in the extremely demanding Northwest European ferry sector, before gradually expanding its reach and client base.
“We basically doubled the fleet in the last year, which is fairly impressive,” announced Mike Dobson, Commercial Director of Matrix Ship Management. “From our point of view, we’ve increased our existing business, we’ve taken on three other passenger ferries based out in the Caribbean, and we’ve taken on three extra car carriers across two different clients. We’ve increased our client base and our vessels quite significantly in this last period.”
Based in Limassol, Cyprus, the company is in a large shipping hub with strong community bonds.
“It’s a great place to work, and it’s a great place to live,” said Mr Dobson. “Cyprus has
been a ship management, and to some degree a ship owning hub, for a long time. There’s a huge amount of experience here, with a large British community heavily involved in the shipping industry. So, whilst we might all work for different companies, we’re all friends; we like to work together and discuss challenges outside of work.”
The company offers a wide array of services ranging from full vessel management, technical management, crew management, audits and inspections, and new build supervision. Other services include hotel services management, survey and consultancy, with training also playing a big part of the services provided.
Matrix is also a member of the Cyprus Shipping Chamber, a trade association whose mission is to enhance the reputation of the Cyprus Flag while simultaneously promoting the interests of the Cyprus shipping industry. The association was established in 1989 with just 17 founding members, a number that has since grown to over 200.
“The Cyprus Shipping Chamber has helped with seafarer and vaccination issues for
vessels calling in Cyprus ports,” said Mr Dobson. “They have helped quite considerably to coordinate vaccinations for those vessels or for Cypriot based seafarers. The Cyprus Shipping Chamber, is also a helpful organisation for lobbying government for different legislation changes or whatever might benefit the Cypriot ship managers and ship owners.”
The company was started in 2011 by Managing Director, Mark Crawford and former Managing Director Peter Jordan. It was set up due to the lack of third-party ship management companies aimed at the ferry sector. Not long after being set-up, the company secured a major ship owner who is still with Matrix today.
Mike Dobson was with Matrix when the company was founded and as such, is in a strong position to comment on why the company has enjoyed such success.
“I was here at the start before leaving for a few years on a different project, during which I still did some consultancy work for Matrix,” he clarified. “Matrix is a great company to work for, our staff retention is excellent – the only people who have left have done so to retire, so we’re certainly doing something right.”
Matrix is at its heart an innovative, new generation of ship management and marine
services company, offering bespoke services to its clients. The team has a wealth of knowledge in the maritime sector where demanding safety, quality and environmental factors are ever present.
“We give solutions where people maybe can’t find them elsewhere,” said Mr Dobson. “We are flexible enough, and resilient and dynamic enough to take on a challenge that other ship managers, large and small, might be scared of accepting or unable to generate an acceptable profit margin with.
“We understand that an owner will have built their brand brick by brick and placing it in someone else’s hands is a major commitment and risk. So, we go the extra mile, working closely with the owners, to ensure that through our on-board procedures and customer services, we reflect the brand as the owner would wish.”
The company currently employs over 30 shore-based staff across its offices and approximately 800 crew members under the company’s management. With such a number of seafarers under Matrix’s umbrella, difficulties emerged during the Covid-19 pandemic that brought the historic treatment of seafarers into the public eye.
“In our opinion, seafarers are still treated poorly and are still not getting the easy travel and safe access out of their home countries, so for us moving our seafarers to our clients is most important,” said Mr Dobson. “When Covid first hit we, as with every other crew operator, were having significant challenges moving even EU crew members around within the EU because the rules were just changing continuously.
“Now traveling has opened up a lot more within Europe and the UK for the benefit of our European ship owners, so we can move our European seafarers fairly easily currently.”
Matrix predominantly operates on a short-term contract basis; two-month voyages at the most. As a result, the business has been able to manage any short term travel disruptions more easily than those who have longer contracts.
“It’s fairly easy to manage and fairly acceptable to the crew because they haven’t been away for so long. Obviously we really do feel the pain of the seafarers out there who are on long term contracts and haven’t been home in an awfully long time. Then they are told they can’t get home either until rules or regulations change. Thankfully for us, and our seafarers, we’re not in that boat,” said Mr Dobson.
When speaking about the key challenges facing the sector, Mr Dobson highlighted one of the main areas of concern as being crew shortages.
“There is an ever-decreasing crew pool at the moment in Europe. A lot of people who worked away at sea and haven’t for quite some time now because of Covid find themselves more comfortable to continue working at home or working in their home country.”
This can be attributed to the fact that many crew management companies would historically recruit from the Far East, but due to differing restrictions between countries they would now all have to recruit from the European crew pool. This has seen greater competition between companies, including Matrix, as the pool the company previously had access to is being sourced by additional companies.
Despite the challenges, Mr Dobson was keen to highlight why Matrix remains a standout choice in ship management throughout these difficulties.
“We are keen on training and we do our best in connection with the ship owners to offer the best possible market rates. It’s also about convincing the ship owners to choose the right crew because when you get the right crew and you treat them well, everybody benefits.” n
In our opinion, seafarers are still treated poorly and are still not getting the easy travel and safe access out of their home countries, so for us moving our seafarers to our clients is most important
The world’s largest operator of specialised reefers, Cool Carriers has played an influential role during the pandemic in maintaining the sea transportation trade of fruits and other perishables. Equipped with the biggest reefer vessels ever built, the E-class, and more on the way by 2023, the company is handily placed to continue dominating its sector for years to come. Profile by Andy Probert.
Cool Carriers is a company very much in demand. With its 50-strong fleet of reefers dotted around the globe, it can proudly label itself as one of the key leaders in the logistics chain, ensuring the ocean delivery of fresh fruit and other perishables irrespective of pandemic lockdowns and limitations.
Spearheading this dynamic flotilla are three of the biggest specialised reefers ever built – the E-class series. Cool Express, Cool Explorer and Cool Eagle are presently attached to the leading global banana company, Chiquita, to cover service provision between Central America and North Europe.
With options for another three reefers of a similar build, set to be delivered in 202324, Cool Carriers is more than primed to maximise its global trading and dominate the world’s reefer logistics sector.
“We keep focusing on what we do best: remaining as the leading specialised reefer shipping company in the world and being the specialist’s specialist,” declared Glenn Selling, the company’s Chief Operating Officer.
Following the closing of Swedish shipping company Salénrederierna in the 1980s, it s reefer division was bought out, and Cool Carriers was established in 1984. Since then, the company has changed owners a few times but maintained its leading position in the specialised reefer industry.
Its last iteration, Swedish-based refrigerated shipping specialist NYKCool, along with its reefer fleet, was acquired in 2014 by Baltic Reefers. The company’s original name was restored – Cool Carriers AB.
Cool Carriers has retained its headquarters in Sweden, and has representations in Chile, Cyprus, South Africa, and the USA. It is also supported by a worldwide agency network.
“We are fast, flexible and deliver direct transportation on a global scale. We offer tailor-made services that add enormous value to our customers, such as producers, exporters and importers, while acting as strong links in their logistics chains,” Mr Selling explained.
At any given moment, Cool Carriers’ fleet could be shipping deciduous produce from Chile to the US; citrus fruits from South Africa to North Europe and Japan, or from Argentina and Uruguay to the Western Mediterranean and Northern Europe; bananas from South America worldwide a and kiwifruit from New Zealand to the Med.
The fleet also transports clementines and oranges from Morocco; vegetables from Europe to West Africa; fish from Alaska, Asia and North Atlantic; and specialist transportation cargo from the Baltic to Latin America and Africa.
While the fleet consists of 50 ships and are operated in all major reefer trades, the three newest additions – brought on stream in 2018, 2019 and 2021 – are considered Cool Carriers’ added muscle.
The newest, Cool Eagle, is one of six, all being built by Japan’s Shikoku Dockyard.
The 190m long Panama-flagged vessel comes in at 21,900 DWT, has a container capacity of 340 FEUs and a temperaturecontrolled capacity of 905,950 cubic feet, making it the world’s largest-ever reefer.
It can carry about 6,800 high-cube pallets of citrus in 340 reefer containers on deck and 7,400 high-cube-pallets below deck. This equates to 760,000 cartons of bananas, and the vessel can accommodate 60% more fruit than older reefers.
Her maiden voyage in 2021 saw her loaded with 8,300 tonnes of kiwifruit in New Zealand for delivery to the UK and Europe. She has since called in to meet capacity demands of South Africa’s increasing citrus exports, which are expected to reach a record-breaking 163 million cartons.
Mr Selling confirmed: “We are anticipating the additional three E-class reefers in 2023 to 2025 while looking to continue to expand with smaller vessels, whether they be second-hand or new builds.”
Clients increasingly value the transport solutions offered by Cool Carriers, helping them to maintain product quality, increase efficiency and reduce costs.
“We strongly believe in understanding our customers’ needs to consistently meet their requirements. We consider ourselves a partner rather than a supplier,” Mr Selling added, noting it was a proud service provider to kiwifruit supplier Zespri.
Backing up these commitments, Cool Carriers is a founder member of the 360
Quality Association, a set of voluntary standards for specialised reefer shipping lines and service providers.
The 360 Quality Code not only brings transparency to the supply chain of perishables but aims to meet customers’ needs by promoting the highest quality and cargo care standards on reefers, in port terminals, liner trades and container depots.
Mr Selling reflected that when the pandemic began, “our vessels were probably the safest spots on this planet.” He added: “For various local reasons and regulations, crews remained on board and stevedores did their job and never met the crew.
“ The result was that most countries could maintain necessary export/import even during the most severe Covid-19 periods. It was, however, extremely exhausting for crews having to remain onboard for periods far beyond normal because countries did not permit crew changes.”
He said the company had witnessed continued business growth even through the pandemic as a shortage of container vessels had seen more people turning to the reefer market for their transportation solutions.
Challenges such as spiralling bunker costs and finding terminals to accommodate the company’s growing fleet of specialised reefer vessels remained areas of concern. He explained: “Terminals have
become so containerised; they don’t have the staff or equipment to handle our reefer cargoes. The West Coast of America being an example.”
Cool Carriers follows international rules and regulations to minimise its carbon footprint. “That means we equip vessels with scrubbers, and we otherwise run vessels on low sulphur bunkers. Specialised reefers do have less carbon footprint per transported carton, compared to the container lines.”
Set to flourish further
Still, the company has maintained an excellent customer care record, developing close business relationships, having quick decisions lines, and understanding each client’s core business.
“Cool Carriers has a record of delivering what has been agreed,” underlined Mr Selling. “In addition to being the leading operator, we focus on the larger segment of specialised reefers.
He observed: “The industry for specialised reefers will remain, with ups and downs created by competition from container lines, climate changes and political conflicts. But the pandemic has taught countries to single exporters, the value of the flexibility of specialised reefers. A fact that will be remembered for some time.”
In conclusion, Mr Selling commented: “Remaining fast, direct and dedicated, Cool Carriers will certainly remain, and support the industry for many years to come.” n
With over 200 years of heritage and the infrastructural backing of its robust parent organisation, Swire Bulk is making waves as one of the world’s leading specialist shipping companies. Its fleet of over 150 Handysize and Supramax class vessels are equipped to trade anywhere and carry almost anything. Amidst the ongoing disruption in the global container shipping industry, the company is welcoming a steady stream of new clients seeking innovative freight alternatives to improve their supply chain lead times. Commercial Director Rob Aarvold pulled back the curtain for Richard Hagan and revealed the behind-the-scenes action at the company.
IN2022, Singapore’s Swire Bulk will celebrate the 150th anniversary of its organisational parent: The China Navigation Company. This puts the deep-sea shipping arm of the Swire Group in good company with the likes of Hamburg-Sud, which recently also celebrated the same milestone.
While Swire Bulk is a relatively young enterprise by comparison, having been established in 2012, it benefits from the rich maritime heritage and organisational excellence by which the Swire family’s companies are recognised.
Those business interests range from its ownership of more well-known brands like Cathay Pacific, Swire Properties and Swire Coca-Cola, to the less public entities
such as Finlays Tea and Argent Energy. Altogether, the group employs around 135,000 people globally.
According to Swire Bulk’s Commercial Director Rob Aarvold, whilst his firm has only recently become an independent entity, as a brand it is embedded within the John Swire & Sons business portfolio.
“There are multiple layers and legacies to the company, which deliver the depth and context of the Swire Bulk brand,” he noted.
A modern fleet for modern needs
Swire Bulk, based in Singapore, is a global dry bulk shipping company specialising in the geared sector between Handymax and Supramax size vessels. It is both
a vessel owner and operator, with control of between 150 and 170 vessels at any given time, with the majority of those being within the geared sector (i.e. they have their own cranes on deck).
The fleet is extremely modern, confirmed Mr Aarvold: “We are very proud to have the most modern and fuel-efficient Handysize fleet in existence. The average age of our fleet is 4.8 years on the ships we own, while our long-term chartered fleet is slightly younger at an average of 4.3 years old. We’ve tended to focus our core, long-term charter fleet on much more modern, large deadweight, fuel-efficient ships.”
The company’s fleet is flexible by design, which provides an opportunity to create defined trade triangulations through the carriage of niche cargo; in short, the fleet can trade anywhere and carry almost anything within robust safety limits.
“As a geared operator, we are theworkhorse of the ocean in terms of tramping,” Mr Aarvold underlined. “The reason we trade in this sector is that it’s
a lot less commoditised, and as a more fragmented market you can develop unique cargo combinations: this com mercial agility and solution-based approach suits our style of doing business.
“We’re able to innovate in terms of the cargoes we carry, and we will regularly use the ships’ deck in addition to whatever is loaded inside the hold to load project cargoes.”
By loading more cargo onto the ship and optimising the space available, the commercial team can materially reduce the CO2 emissions per tonne of cargo. In a world in which emissions are now being actively measured, this approach is vitally important to continue to proactively mitigate the carbon footprint of the trading fleet.
The company’s ethos is centred on the Swire family’s Latin motto, ‘Esse Quam Videri’ which translates as ‘To be, rather than to be seen to be’.
“Our ethos is about walking the walk and making sure that as a business we conduct
ourselves in a safe and professional manner at all times,” Mr Aarvold explained.
At Swire Bulk, doing the right thing in terms of reducing emissions is extremely important. One simple measure the business is taking to reduce its emissions involves active monitoring of the fuel efficiency of its fleet. After each voyage, the company produces an Emissions Voyage Completion Report which is provided to the client for mutual review.
This four-page report displays the ship’s actual performance on her respective voyage, highlighting operational issues such as weather or port delays to allow both the client and Swire Bulk to evaluate trade-specific initiatives to improve future voyages and ensure that the fleet is deployed as efficiently as possible.
Since its inception in 2012, the company has tracked every single voyage that every ship in its fleet has completed. The
voyage data is distributed within the company every month, with a particular view to identifying inefficiencies such as extended ballast legs or fixtures with low vessel utilisation.
“Through these simple measures and positive engagement with our charterers, we have managed to consistently reduce our EEOI (Energy Efficiency Operational Indicator) rating over the last six years,” said Mr Aarvold.
The world is experiencing a major container shipping capacity crisis. Rates are transacting at all-time highs, long delays are inevitable, and adding to the problem are issues around crew changes, quarantine periods and ongoing geopolitical trade wars.
The issue came to a very large and very public head in 2021 when the enormous Ever Given
container ship became wedged across the Suez Canal, blocking maritime traffic on both sides of her 199,629 DWT hull for almost an entire week whilst authorities worked to free the big ship.
This saga has resulted in continued supply chain issues and combined with the other logistical challenges referenced, has forced retailers around the world to urgently seek alternative shipping solutions for their products. One of those, according to Mr Aarvold, is the adoption of a decontainerisation strategy, or as a simpler description, the evaluation of loading unitised cargoes on dry bulk vessels.
“The supply chain frustration has resulted in a lot of retail companies looking for new ‘outside of the box’ freight solutions and we have seen a huge influx of enquiries for non-bulk cargoes to be shipped on conventional tonnage,” he remarked.
“Procurement departments continue to evaluate the intermodal options to transport products that would historically load into a container now moving as part cargoes on geared vessels direct to the destination port. As an example, products like coffee packed in one-ton bags, bagged cement, PET resin or even
dry dog food, are now being shipped on handy size tonnage.”
Consequently, according to Swire Bulk, in 2021 the Handysize vessel market performed well above its deadweight with the full year Index on a par with the Panamax market.
Crew welfare and Covid
Swire Bulk’s seafarers are an extremely high priority for the company, and like all of its peers, crew changes in the Covid era have become a major and ongoing challenge. Quarantine periods, border closures and even political and social unrest have conspired to create difficult problems that need to be resolved daily.
In total, 85% of Swire Bulk’s vessels are crewed through its sister company Swire Shipping Fleet Management. Together, the two firms ensure seafarers are well taken care of, aided by the group’s extensive onshore resources and commitment to maintain a positive working experience for the seafarers.
“I’ve been impressed by how well our fleet management has handled the situation despite the huge number of challenges,” Mr Aarvold remarked. “We’ve ensured that crew are proactively vaccinated, and we have regularly chartered flights to ensure that the crew don’t overstay their contracts and can get home to see their families. It has been a huge coordinated effort that should not be underestimated.”
The company shows its appreciation to its crew every June on ‘Day of our Seafarer’, during which the company conducts lucky draws for great prizes, as well as hosting a photography competition for its crews. Winning photographic entries are featured in the company’s calendars that are printed and issued to customers, employees, and to the ships themselves. Vessel masters are invited to host BBQs and themed parties on board.
Meanwhile, crews are invited to join a regular video hook up for global townhall events in which the company discusses its recent news, corporate updates, finan -
cial results and any other significant events within the organisation. In this way, the seafarers are able to stay in touch with the global business activities.
Mr Aarvold said he was optimistic about both the industry and company’s outlook.
“In 2021 we reached a point of almost full utilisation of available tonnage in the geared sector. Global demand remains well supported and on the supply-side, the stress scenarios from Covid and congestion mean we have experienced a more balanced trading situation that has not been seen for the past ten years.
“Layered on top of this S&D environment, we anticipate incremental cargo flows from the implementation of multi-trillion dollar
worldwide infrastructure projects; the majority of which will come with a huge shipping requirement for commodities like c ement and steel; commodities usually serviced by handy size ships.
“We expect that global infrastructure projects will continue to underpin the demand paradigm, whilst the current energy revolution also brings renewable cargo flows to the sector.”
He concluded: “With the current energy prices, we believe, as a business, that there is a competitive advantage for companies who operate a modern, fuel-efficient and flexible fleet and therefore, we retain a positive outlook for the Swire Bulk business over the medium term against the backdrop of a firm fragmented freight market,” he concluded. n
Sea Partners Navigation, based in Cyprus, is a pioneering pool of first-class ship owners established to offer high-quality in-house management services. CEO Vangelis Tsangarides told Andy Probert how the company is driven by a passion for perfection, transparency and advancing outstanding ship management globally.
Located in Limassol, Cyprus, the selfdeclared “European metropolis for ship owners and managers” according to CEO of Sea Partners Navigation (SPN), Vangelis Tsangarides, his company has been busily building a ship-management pool that offers high-quality in-house services to the maritime sector.
“SPN is a pioneering ship management pool model that we strongly believe ship owners need in today’s world,” said Mr Tsangarides, who, since 1996, has worked in ship owning companies in Greece and Cyprus.
“Based on that philosophy, all our shipowner members enjoy the many benefits a pool operates. The aim is to enable them to join forces under one umbrella so that they will enjoy the dividends without the liabilities.”
SPN has created a financial formula based on KPIs to evaluate the return of each shipowner with vessels under its management. The company’s external auditors are engaged in reporting results annually with performance returns in complete transparency.
The benefits are not limited to the pool’s financial benefits, but continue through all levels, from the operational status of
the vessel to detailed budgets and onto high standard CRM, ERP and PMS systems, enabling owners to enjoy full access and fast 24/7 reporting.
Created in mid-2019, SPN’s current focus is managing several LPG carriers for a number of companies. One of its partners is Intergaz, one of the longestserving family businesses specialising in LPG operations.
“Managing LPG vessels of the size of our existing fleet is a demanding process,” said Mr Tsangarides. “Today we manage ships that perform up to 60 round trips annually, and we cannot forget that this performance has occurred during the Covid-19 era, with any zero off-hire periods.
“That is a result of strong dedication and professional services from a small and vibrant team of experts, with an exceptionally professional crew.”
From the beginning, the company invested in a vessel- and office-integrated software system which covers the entire vessel operation, including financial aspects. Office monitoring and reporting are accessible, allowing partners a complete picture of their assets in the blink of an eye.
In 2021, it signed an agreement with BIMCO, to install a vessel digital online performance monitoring platform for pool members by the end of 2021.
“This tool will better monitor our fleet through key performance indicators and industry-leading benchmarks in a continuous effort to excel,” commented Mr Tsangarides.
Within the first half of 2021, one of its partners sold an LPG vessel and acquired a six-year-old LPG Japanese-built vessel. This helped reduce the age of the fleet while offering the latest technology onboard.
Looking ahead, Mr Tsangarides said: “Planning is essential. Before the end of 2021, we were in the process of obtaining the documents of compliance for other types of ships to operate beyond just LPG tankers.
SPN plans to evolve its digitalised ship performance monitoring software for both vessel and office, to offer a safer and more professional management model and create a better advantage in a highly challenging and competitive environment.
“The pandemic was not easy, but we succeeded in managing the vessels without any significant problems,” Mr Tsangarides reported. “Crew changes remain a challenging operation, but we have learned how to overcome the restrictions with good coordination and planning.
“However, travelling and logistic operations costs have increased tremendously. It is more important than ever to coordinate and plan perfectly to avoid further increasing management costs and trouble for crew repatriation. Efficiency and costeffectiveness come with the knowledge of the market.”
He added: “Nevertheless, since inception, we have operated as a full cloud company, where we can operate and monitor ships remotely through digital means. We are also positive that as vaccinations continue, we will manage to have safer crew changes and port calls, and things will slowly return to normal.”
Mr Tsangarides pinpointed what differentiates SPN from competitors in its sector:
“The personal touch that we have with our partners gives us a competitive edge, and for us, every single partner is essential whether they have one or 100 vessels,” he revealed.
“As a young enterprise, we have invested in people, which is another solid strength for our pool. We feel that with the expertise we have at SPN, we offer high-quality standard services. Training and continuous improve -
ment are our top priorities along with the use of cutting-edge technology in management.”
He said: “We can see huge potential in ship management, and Cyprus is one of the main hubs for this specialised, demanding, and professional service.”
Traditional values of good and open cooperation, respect, flexibility and quality services help drive the long-term relationships SPN has with its clients and suppliers.
Unapologetically, Mr Tsangarides added: “Today, the market needs the SPN pool partnership more than ever. We see tremendous changes in different types of vessels, time charter rates, spot market rates, vessel sizes, new rules and regulations for decarbonisation and CO2 emis -
sions, and increasing crew and transportation costs.
“Our vision and goals are to continue excelling for our clients and making SPN a focal point in the industry. As a group, we have more than 20 years of experience in the shipping industry and more than 45 years in the energy sector, LPG market specifically.
He concluded: “With knowledge and experience, combined traditional values and pool arrangements at its core, our company is looking to offer a new era on the dual-axis of ship owning and ship management.
“With these key strengths, we are sure that very soon Sea Partners Navigation will welcome more shipowners with the same values.”
Dry bulk and general cargo transport specialist INTRESCO LIMITED has continued to quietly get on with the job of timely delivery of its country’s key exports despite the growing uncertain geopolitical backdrop. Co-founder and director Maksym Khaulin, speaking to Andy Probert, asserted that having ridden the up and downs of the marine industry for 25 years, the company’s resilience continues to shine on while maintaining the highest shipping standards.
INTRESCO is a fighter, having survived the shipping industry’s deepest depressions of recent years. Now operating a fleet of 12 vessels and managing three others, it’s no wonder the company opts for a considered approach to business.
“INTRESCO is neither a family-owned company nor, as back in the day, tied to the state. It is a three-partner backed venture which has stood the test of time,” said co-founder and Director Maksym Khaulin. Achievement enough that he is still standing in its 25th year.
His first step on the rollercoaster of the marine industry was to walk away from a potential degree in banking and finance at Odessa Economical University.
“I was not the captain, the sailor or studying shipping in university. In the second year of study, and like many students at that time, I didn’t have enough money,” he recalled. “So I asked my father to find a job, any job, that I can work after the university. This was in 1994, and the only advantage I had was that I was fluent in English. At that time in Ukraine, it was a good and essential skill to have.”
Mr Khaulin joined a local tanker shipping company where he was taught different aspects of the industry.
“They didn’t have a dry cargo department, and I was invited to make a go of it. I started to liaise with charterers – with Greek, Turkish and Europeans – and having gained that experience in nine months, I opened my own company in 1995.”
Two years on, he met his two future business partners and together, they opened the International Repair and Shipping Company (INTRESCO). The company’s specialisation was ship repair and modernisation of vessels, followed by their commercial management.
By 1998, Intresco’s London office was opened to coordinate its shipping and ship repair business. Additionally, its first ship management contract was signed, and to support its general cargo transportation activities between the Black, Azov and Mediterranean seas, the company bought its first general cargo vessel, Sagitta, in 1999.
A branch office in Odessa, Ukraine, opened a year later to reflect its growth in technical management services.
“Our idea was that we obtained the funds, organised the ship repair for clients and then found commercial employment of the vessel,” Mr Khaulin succinctly explained. “This supported local owners and helped extend the life of their fleet.”
Despite economic crises in many countries, INTRESCO thrived and adopted many innovation projects.
“We changed fuel systems on vessels, moving from marine gas oil to heavy-duty fuel, which cost two or three times less,” he added.
Having specialised in Handysize vessels between 3,000 and 15,000 DWT, the company decided to diversify: operating smaller and bigger class vessels. This led to it buying the 45,000 DWT Handymax Selecta bulk carrier in 2001 and in June 2006 its first Supramax-bulk carrier, Santana.
Four months before the 2008 global financial crash, INTRESCO switched from
ship repair to traditional ship management services. It was operating around 20 vessels, including 10 Handymax and Supramax bulk carriers, and had on order seven vessels worth $150 million.
Mr Khaulin admitted: “INTRESCO suffered a lot during that crisis. Eight years on, and despite battling to keep our bulk carrier division, we sold our last bulk carrier. The financial crisis had taught us many things.
“We reactivated INTRESCO in 2016 but this time around, we would focus on smaller Handysize vessels to enable us to find our niche and become a player in the market.”
Today, its 12-strong fleet, with an average age of ten years, ranges between 10,000 and 20,000 DWT, and trades on the spot market. Vessels transport bulk and general dry cargo, such as grain, grain
products, steel, fertilisers, petroleum coke, and other commodities along worldwide shipping routes. It also has three Handysize vessels under ship management.
He said: “Ukraine is a big exporter, so we decided to specialise in the transportat ion of these cargoes. Most of our trade, around 70%, is connected between the Azov, Black and Mediterranean markets. The other 30% is shipped from the Black Sea to the Baltic Sea and EU continent. We mainly deliver to Turkey, North Africa, Italy, Spain and the UK.
“We focus on running our vessels, which have less than normal fuel consumption and engine output. Our logistics are not based on fast delivery, but economical delivery of the cargo, meaning low carbon emissions.”
The company, which has been a member of the Baltic International Maritime Council since 2003, retains offices in Valletta,
Malta, and Odessa, Ukraine, which oversees ship management of bulk carriers and chartering of dry cargo vessels up to 20,000 DWT.
Its fully-integrated ship management services comprise vessel performance, focusing on safe and environmentally sound operations, high-quality maintenance programs and achieving customer goals. That includes everything from chartering, operation, repairs and dry docking, upgrading, technical maintenance and safety.
Commenting in general on the state of the marine industry, Mr Khaulin said: “Despite the new requirements in terms of carbon emissions and other issues, there is still not enough control and fulfilment of the control for the management of the older fleet.
“Unfortunately, we are still faced with a lot of corruption that supports the trading of these old vessels. This is a challenge for the safety of navigation and for us: when the market is going down, these vessels can still trade. These vessels operate without insurance, are poorly maintained and seafarers on them are being paid peanuts.”
In 2007, the company opened its own separate crewing services and maintains a pool of Ukrainian seafarers for its fleet. “One of the biggest challenges we face is
the lack of crew and their experience,” he commented.
“Ukraine seafarers are in big demand because they are highly experienced, trained, versatile, and speak excellent English.” Another major challenge today is the region’s geopolitical climate.
He said: “INTRESCO has a reputation for providing excellent and expert technical services, our staff are highly trained and dedicated, and we have the experience necessary – the number one priority in the marine industry today.
“During the pandemic, our staff were very loyal to the company, and we never closed our offices. They were concerned about the management of the vessels and wanted to keep coming to the office to help out daily.”
Looking forward, Mr Khaulin said the company would like to see further expansion with a focus on modern Handysize vessels while retaining business in the dry cargo sector.
“Since 1997, we have maintained longterm relations with charterers, and this will help drive us on into the future. They know they can rely on us to deliver their cargoes without any problems,” he concluded. n
Celebrating 40 years’ in the maritime industry in 2022 with centuries of accumulated experience through its dedicated team, Switzerland’s ABC Maritime AG is a veteran of the ship management game. Since its founding in 1982, the company has taken over 160 ships of every description under its management care. But rather than just focusing solely on the care of ships, the company is also invested in a holistic management approach that includes investment in people; either working on board or working ashore. Daniel Tanner, CEO of ABC Maritime, discussed the company’s management philosophy with Richard Hagan.
Whilst the Covid pandemic rages on and shows no sign of slowing down, countries around the world are confronted on an almost weekly basis with excruciating decisions involving curtailing movement, limiting freedoms and shutting international borders.
For most of us, these limitations have become nothing much more than an extended annoyance and a subject of strongly-worded social media rants. But it’s easy to forget that the fundamentals which allow us to cope with lockdowns are only made possible by a vast army of essential workers battling long hours, intense safety protocols and relentless deadlines to bring us the goods and materials that we rely upon on a daily basis.
The shipping industry is, of course, one of those essential services which transports 90% of all the goods and materials around the world. And for ABC Maritime, the welfare of the onboard team members (seafarers) under its management as well as its shore based team members, is a top priority. Seafarers, in particular, face many additional challenges due to ongoing ad-hoc Covid-related border clo sures affecting their ability to return home or even to their ships.
Caring for the people it employs is a foundational principle of ABC Maritime, one of which it is rightfully proud, confirmed Daniel Tanner, CEO.
“We’ve heavily invested in our human capital, because our people generate the energy for the business to operate on a 24-hour basis, year-round,” he said. “We care about our seafarers and colleagues as though they were family.”
ABC Maritime staff and seafarers are supported by psychology professionals and technology which together monitors and supports their wellbeing. Meanwhile, the company plans to further add to its already commendable holistic crew and staff care through its internal ‘Ethics, Sustainability & Governance’ program which is currently underway.
Whilst the company places immense value on human assets, the ships in its care certainly don’t play second fiddle.
There’s an old proverb that states, ‘You can’t build a reputation on what you’re planning to do’. According to Mr Tanner, ABC Maritime’s reputation in the industry is built upon its actual performance in the decades since it was established.
“The key factor in our history is our long-standing reputation for being a top-tier, total vessel manager.” With the company preparing
to celebrate its 40th anniversary in 2022, it does indeed have a long history in the business.
The company was established in 1982 in Nyon (just north of Geneva), Switzerland, by Mr Tanner’s father Hans Tanner. Its headquarters has remained in Nyon but today it also has offices in Ukraine and the Philippines in order to best serve the majority of its crews that are based nearby while at the same time planning to expand in more strategically placed locations.
That being said, the company boasts a management history of nearly 200 vessels of every kind having passed through its care over the years. It is therefore experienced, equipped and prepared to provide its one-stop-shop services to any client.
Mr Tanner clarified: “Our clients are from and operate in diverse geographical locations, are from different backgrounds and industry profiles. We’re confident that we can become the shipping industry’s number one preferred vessel manager. With our comprehensive services including technical, crew training and supply, chartering, operations management, victualling, spares and supply chain management, and accounting management, there’s no vessel owner’s need that we cannot meet.”
A particular highlight of the company’s technical services is its Technical and Quality, Health, Safety & Environment teams. Most of these members are ex-seagoing engineers and deck officers and they bring all of that experience with them to the company’s services.
“They are in the best position to understand, react to and manage complex and very demanding scenarios,” confirmed Mr Tanner. “Over 80% of all of our superintendent positions are filled either by ex-seafarers of ours or staff who have been with the company for decades.”
ABC Maritime has developed its own specialised ship portfolio in two main market spaces: bitumen carriers, and offshore vessels. The company’s fleet currently consists of three bitumen carriers and seven offshore vessels including barges.
Its managed fleet includes 17 product or chemical carriers as well as several other vessels for which the company provides crew management services.
Mr Tanner was keen to highlight the company’s size and flexibility, both of which help contribute to improved financial returns for its customers.
“We are consistently able to impress vessels owners with our high-quality management and the cost-efficiencies that we can provide thanks to our company structure. We also pride ourselves on customising our service offering to match our clients’ profiles and particular requirements whilst ensuring that we always go the extra mile to satisfy their needs.”
One way in which ABC Maritime offers value-added service is through its cloud-based management software.
Our seafarers care for our management fleet as if those vessels were their own, in close collaboration with our shore staff, who feel exactly the same “ “
“We possess innovative technology that allows us to carry out remote monitoring of vessels even in difficult geographic regions and under challenging conditions,” explained Mr Tanner. “Our clients’ vessels are fitted with always-on broadband connections that allow them to be constantly accessible on-demand by clients or our staff.”
ABC Maritime is particularly proud of the various prestigious international certifications that it has achieved. The company holds a 35plus year Document of Compliance and Safety Management System certified by Det Norske Veritas and Bureau Veritas. The company is also certified with ISO 9001 and 14001 by Det Norske Veritas.
Whilst the majority of the ships in its portfolio are owned by others, ABC Maritime offers the kind of service for those ships that you would expect from someone who actually does own them.
“Our seafarers care for our management fleet as if those vessels were their own, in close collaboration with our shore staff, who feel exactly the same,” Mr Tanner emphasised.
The close working relationship between seafarers and shore support crew enjoyed by ABC Maritime staff is reflected in the company’s unusually strong staff retention record.
“Many of our staff have been with us for over 15 years, with an average employment term of 14 years for ship Masters, and 16 years for Chief Engineers,” Mr Tanner explained.
The company is furthermore regularly audited and vetted by the major oil companies it serves, including Total, Shell, ENI, ExxonMobil and others.
Decarbonisation and emissions reduction in shipping have moved from being trendy buzzwords to action points that all ship owners must confront as a matter of urgency. It’s an issue that Mr Tanner said he and his staff are tackling head-on and hands-on.
“My objective and remit as CEO is to steer us towards a sustainable future based on the various regulations that we must meet. These include those from the International Maritime Organisation as well as other bodies such as the European Union, with all of the goals that the industry must meet by 2030 and 2050.”
ABC Maritime has already begun formulating its decarbonisation and zero-emissions strategies for its future operations, as well as investigating the use of future fuels.
In the meantime, Mr Tanner is proud of everything the company has achieved and is achieving, while being optimistic about the future of ABC Maritime.
“I assumed the honour and privilege of being at the helm of ABC Maritime after my appointment as CEO in 2019. I’m extremely proud of the strength, loyalty and team spirit that every single member of the ABC Maritime family has exhibited, as well as their commitment and resilience. People are the driving force behind our success and they shall always command my respect,” he concluded. n
Admare Ship Management, based in Gothenburg, Sweden, delivers a highly adaptable and flexible vessel management service. This relatively young company sports a diverse but high-end fleet of cargo and RoRo car carriers and their crews within its portfolio. Fleet Manager Tommy Pettersson chatted to Richard Hagan about the company’s history, the unusual flags in its fleet, its focus on sustainability, and its plans for the future.
Admare Ship Management (ASM), is technically still fairly young, having been established in 2017. But that’s not its whole story. The company came about as a result of a merger between two smaller companies also located in Gothenburg. Both had been operational for some time until deciding to join forces and create a new management company, combining their skills and human resources.
However, since summer 2021 the company is again fully owned by the Leomar Group (also known as Ellingsen). Based in Stockholm, the company boasts long experience in the shipping field.
Via its team of nine skilled professionals ashore, it manages an impressive and diverse fleet of modern RoRo carriers and bulk cargo ships as well as their crews.
The company takes full technical and crewing responsibility for all of its ships, providing its ship owners with a comprehensive level of service that punches far above its weight in human resources.
According to Tommy Pettersson, Fleet Manager at ASM, its size is an intentional part of the value that the company delivers to its clients.
“Our focus is on providing a cost-effective, transparent and flexible solution to all of our clients,” he said. “We’re small enough to be flexible and open, but big and robust enough to provide comprehensive support, knowledge and experience to various clients. Whether our clients
have big or small vessels, we adapt to their needs.”
The company’s only office is its headquarters in Gothenburg, where most of Sweden’s shipping-related service companies are located. With its relatively compact – for this industry at least – team, the staff at ASM can’t afford to be rigid in their approach to their workflows.
“We’re a small, tight group, which means that it requires some flexibility from our staff,” Mr Pettersson explained. “We can’t just focus on doing one single job; everyone must be flexible. In practice, that means that no day is like the other. Things can –and do – change quickly, meaning the plans you had for the day can wait for another day!”
O ne aspect of ASM’s fleet that immediately jumps out to the observer is the fact that all of the vessels are flagged in either the United Kingdom or Sweden, instead of the usual, more ‘convenient’ flags such as some of those linked to Caribbean islands or African countries. Whilst decisions about flag registrations are the exclusive domain of each vessel owner, Mr Pettersson highlighted the fact that the owners’ choice of UK and Swedish registrations sends a particular message to the market.
“All of our clients are currently based in either the UK or Sweden and from their point of view, they are serious actors.
For that reason, they take pride in flying the red ensign or the Swedish flag. Flags of convenience have never even been a consideration for them.”
The fleet’s high-end flags are a boon for ASM’s credibility as well. “As a company, I’d say that the flags on our fleet are a warning sign for new (or even existing) clients wanting to bring vessels to our company
bearing low-performance flags,” Mr Pettersson remarked. “It’s a risk that could affect the rest of our fleet.”
Going into more detail on that point, Mr Pettersson discussed the specific threats that more convenient flags pose to ASM’s credibility.
“It doesn’t automatically mean that if you’re flying a flag of convenience, that the vessel is in poor shape with many problems, but it could be. Port inspections involve risk calculations for our whole company. If we’re a high-performance flag company, there is less risk from the flag and port state in terms of inspections. But if we have even one vessel with poor stats or performance, it’ll drag down the rest of the fleet with it. That’s a risk and we try to avoid it. We have clients with very high standards and we don’t want to do anything to risk their reputation.”
Of course, flying a high-performance flag is about much more than just credi -
bility and inspections. There are real benefits that both ASM and its seafarers enjoy, Mr Pettersson confirmed.
“We get the best support and service from these serious, high-performance flags,” he noted. “We have a good relationship with both the UK and Sweden and in case of problems, we can expect that they’ll give us first-class service. In terms of the crew, they have strong unions to support them and good market-related wages. So while it’s a bit more expensive for the owner, in totality, it’s worth it.”
Sustainability is a major theme throughout the shipping industry, particularly given major upcoming European emissions regulations.
“The regulations coming into force in 2023 are massive, it’ll be a major change for many shipowners,” Mr Pettersson
remarked. “A lot of vessels will end up needing to be either recycled, scrapped, or receive heavy investments in order to survive. It’s a big change.”
ASM is collaborating intensively with its ship owners to ensure that its fleet is fully compliant when the first of the regulations begin to take effect in 2023.
“We’re working with our owners and planning emissions reduction measures on a ship by ship basis,” confirmed Mr Pettersson. “The easiest way to reduce emissions is, of course, to reduce fuel consumption and there are a lot of technical solutions for achieving that. But many of those measures can be huge investments. Nonetheless, we’re looking at all options. This is the last year that
we can test things out before the regulations come into force.”
One of the options that ASM is exploring is the use of rotor sails, sometimes known as Flettner rotors after their inventor. They are massive spinning cylinders mounted vertically on a ship’s deck and can be 10 storeys tall. Rotors are able to reduce a ship’s fuel consumption by exploiting a physics phenomenon called the Magnus effect. When air passes over the spinning rotor, the Magnus effect produces a force that pushes the object on which the rotor is mounted – in our case, a ship.
“You can save a lot of fuel through the use of rotors,” said Mr Pettersson.
“It’s a very interesting option that we’re looking into right now. We also have a plan to replace all onboard lights with LED lights, and we have already installed exhaust scrubbers to remove sulphur from the exhaust fumes. Basically, we’re looking into a lot of different decarbonization measures right now, that will be presented to our clients.
That’s an overview of both smaller and larger measures that ASM and its shipowners are exploring, but some of its owners are going straight for the most expensive option.
“Some owners are looking at replacement, next-generation RoRo vessels in order to be competitive,” Mr Pettersson revealed. “The competition for them will be even tougher in the future and fuel efficiency will become a factor, to an extent that it hasn’t ever been the case before.”
One plan, one future, one team
Mr Pettersson concluded with a look into his team’s perspective on the company’s future.
“The merger between two companies is now history and now we are back to having one owner, one philosophy, and a unified plan for the future,” he asserted.
“We’re extremely optimistic and we only see opportunities in our future. Right now, we’re not rushing to find more vessels for our fleet; instead, we’re focusing on maintaining the clients and ships that we already have and providing the best service to them.
“ Word about our service will ultimately spread and it’ll bring us more contracts and more vessels, so while we are happy to grow, we won’t do it at the expense of maintaining our existing service levels. After all, our clients’ success is our success.” n
Monaco based C Transport Maritime (CTM) is a dedicated and highly qualified vessel management company with nearly two decades of experience. With strong roots in the Greek and Italian shipping industry, the company has its own unique insights into overcoming the trials and tribulations of the Covid19 pandemic. “The last year-and-a-half has actually been quite positive from a business perspective, and adding to this we also helped our shipowner clients have a more resilient approach during these tough times,” said Carlos Pena, Chief Commercial Officer for CTM.
Formed in 2004 when DryLog acquired
Coeclerici Group’s bulk carrier pools and management activity, C Transport Maritime (CTM) today manages a hugely impressive fleet of Capesize, Panamax, Supramax and Handysize vessels. Following the acquisition, the company relocated to the Principality of Monaco, from its previous location in Genoa in Italy, taking the majority of the team with it.
Today, CTM is owned by Carras Ltd after the Radziwill family brought the company under the Carras umbrella; this was in 2013 and CTM has continued to thrive ever since.
Currently employing 90 employees in the beautiful surroundings of Monaco, CTM has continued to grow over the years and is now managing around 200 ships at
any one time between core client companies and Revenue Sharing Agreements (RSAs).
Currently managing vessels for five core companies (Carras Ltd, CBC, CTM Ltd, GoodBulk and Stone Shipping), CTM’s stewardship has seen the fleets of these clients grow in size and continue to deliver outstanding results.
Over 2021, CTM managed vessels on behalf of 35 clients including traditional shipowners, family offices, publicly listed companies, commodity traders and financial investment platforms.
During last year, ships under management carried approximately 70 million tonnes of cargo, were fixed for over 40,000 days with around 230 separate, carefully vetted counterparties and called at over
2,100 ports. CTM concluded over 620 fixtures indicating its strong presence in the spot market.
Carlos Pena, Chief Commercial Officer for CTM said: “We are a management company that can deliver this exemplary service at very competitive market rates.”
In order to ensure optimum service to its clients, all of CTM’s many operations and services are coordinated out of its centralised office in Monaco. These services span four major areas: commercial, operations, technical and logistics.
The commercial arm of the company’s services have over 100 years’ experience combined and offer chartering, forward
freight agreements, sale and purchase and tanker management. Within the umbrella of commercial services, CTM also operates RSAs for Supramax, Panamax and Capesize vessels; the latter of which are automatically entered into Capesize Chartering Ltd.
Mr Pena stated: “With an average of 68 vessels over 2021, the CTM Supramax Revenue Sharing Agreement once again proved itself to its members and to the market, delivering outstanding results with an average monthly outperformance of +5% over the second half of the year and a strong +15% in the fourth quarter vis a vis the Baltic Supramax Index.
“The Supramax RSA sold $600 million worth of freight in 2021, 2.6 times more
year-on-year and we achieved a 97% utilisation despite the challenges associated with congestion, quarantines or delays.”
The company also has a team dedicated to managing all aspects of insurance and claims management: not limited to this they are also knowledgeable about bunker markets and hedging.
The highly trained Technical Management team is hands-on with all vessels and their work encompasses newbuilding support, conversion and modifications, sale and purchase inspections, safety and maintenance, and compliance and performance.
Logistics is also at the heart of what CTM has to offer. This department pro -
In recent years, Leth has evolved from being transit specialists into complete service providers in some of the busiest ports and maritime hubs.
We are proud to assist a high-quality company such as C Transport Maritime at the locations for which we offer our services. Through local offices as well as offices in Norway, Denmark, and Singapore, we are always available to assist, whether it is in Egypt, Panama, Denmark, Turkey, Singapore, or Gibraltar/Algeciras.
Regardless of location, personal made-to-measure services are an essential part of the Leth DNA. A flat-structured organisation makes it possible to adapt quickly to our clients’ individual needs and through a vast network of partners worldwide, we save fortunes in terms of time and money on behalf of our principals. Going forward, we endeavour to maintain our position as technological frontrunners and look forward to assisting C Transport Maritime and other first-class companies in maritime hotspots.
vides innovative, reliable and cost-effective solutions to whatever problems may present themselves. A case study that showcases the effectiveness of this team is how they were involved in the design of a multi-purpose coastal vessel (MCV) for a foreign consortium requiring coal transhipment services from larger bulkers to supply a coal-fired power plant.
CTM’s newest business venture is the chartering vehicle Stone Shipping Ltd, incorporated in Bermuda. This company was formed in 2019 to charter-in Supramax and Ultramax vessels on behalf of investors. According to CTM, this novel innovation within the sector is a breath of fresh air for many as it opens up a historically closed market to new investors, where normally this is reserved for those with pre-existing knowledge on the sector and long-standing reputation with strong financial footing.
Talking about this new venture, Mr Pena summarised: “With Stone Shipping, we are bringing our chartering abilities to individuals. If you cannot access all of the capital required to invest alongside us, we raise money from different investors and we then charter ships on behalf of clients.”
Taking market expectations into account, the chartered-in vessels are either chartered out on a fixed rate or employed in CTM’s Supramax Revenue Sharing Agreement (RSA). Investors are able to gain access to CTM’s extensive expertise in the market and commercial capabilities.
Since its inception, Stone Shipping has successfully raised $15 million over two years for three privately invested funds. So far results have been in line and above targets, and Mr Pena confirmed capital raising for a fourth fund will start in April 2022.
CTM is also embracing technology, by building a proprietary trading algorithm and creating a mobile/desktop CTM App for its members. This has really set CTM even further out from the crowd, in how
they are modernising a sector that may be c onsidered entrenched in its ways by some.
“Technology is coming onto the ships more and more,” underlined Mr Pena. “We have developed an app, for example where our clients can see where their ships are and where we have positioned our fleet. We also have some new databases and algorithms that assist us with our trading activities.”
The coronavirus pandemic has affected nearly all sectors of industry, and shipping has been no different. Delays at ports, crew changes, outbreaks and differing restrictions from country to country have been just a handful of the obstacles over the past couple of years.
However, CTM and its affiliated companies have reported positive news. GoodBulk, for example, which is a publicly listed company, has given $131 million in dividends during the pandemic which is equivalent to $4.38 per share. CBC also grew its fleet by
about 60% during this period and CTM took several ships on long term charters.
Mr Pena stated: “Our fleet is employed predominantly on the spot market and 2021 was one of the best years to be in the spot market with a huge divergence between period and spot rates after the first quarter.”
Mr Pena was quick to highlight one of the most pressing factors that the pandemic has impacted – the ships’ crews. Isolation is something that many of us will have faced during this trying time and seafarers may know this feeling better than anyone. Managing this isolation and loneliness was CTM’s top priority – no mean feat when you manage over 1,000 seafarers. By providing more training, 24/7 internet on board, extra entertainment and crew changes to name but a few of the actions the company has taken, CTM has continued to prioritise the wellbeing of its crews.
Speaking on this Mr Pena said: “We have helped our clients perform several crew changes over this difficult period as well as arranged and assisted drydocks and special surveys. With good timing, practicing good hygiene and utilising all the necessary protections (and using local representatives where necessary), we have achieved this.”
Speaking of human connections, 2022 looks set to finally welcome the return of global trade shows and events. Looking ahead to Posidonia 2022 in Athens this summer, Mr Pena said getting back to faceto-face meetings in what is such a personable industry will be hugely positive for everyone in shipping.
“Due to the pandemic, we have not been able to travel too much, so meeting our friends and colleagues is so very important, as is keeping that human side of the industry that other industries might not consider as important as we do in shipping,” closed Mr Pena. n
Following two years of a global pandemic that has pushed companies to look for internal improvements, Augustea Group, a major player in the shipping industry, has used the time wisely to look to the future. “We have invested in new fleet management systems and have reviewed the business, in order to be ready for the new market conditions,” outlined Francesco Amenta, Augustea’s Technical Manager. Article by Romana Moares.
Augustea has not stood still over the last two years – the company has opened a new branch in Athens to be closer to one of its major customers, and invested in digitisation to improve vessel management. Preparations to meet new environmental regulations coming into force in 2023 are also in full swing.
“Ship owners are getting ready to implement the upgrade to meet the regulation and we are proceeding with a mix of solutions now available on the market. We will start with the onboard installation of new devices in our dry docks this year, so that the vessels are emissions compliant by 2023,” said Francesco Amenta, Augustea’s Technical Manager.
In terms of internal business improvements, the company has invested in a new RPS monitoring system to provide better and more efficient fleet management, and has acquired new software to improve vessel navigation and reporting in line with the new regulations.
“We will put all of our vessels onto this new platform with the objective of securing route optimisation,” said Mr Amenta. “The software enables us to track a vessel exactly and optimise
its route depending on weather and other factors. This will result in fuel consumption savings and also ease the work load of crews, as the reporting system is fully automated.”
He added: “Another change is that, given market developments during the Covid years, we have started to explore the possibility of employing crews of different nationalities, specifically Bulgarian.”
Augustea is a company with an impressive history. Established in 1955 by Salvatore Cafiero in Naples, Italy, it has developed into a provider of sea transportation services, primarily dry bulk shipping, deep sea towing services, and transportation with oceanic barges.
Under the control of the Cafiero-Zagari families, Augustea Group has grown to become a leading and reputable player in the shipping industry, with offices and operating branches in Naples and Augusta in Italy, in addition to London, Singapore, Malta, Buenos Aires, the Philippines and Colombia.
The technical and management expertise accumulated over the years has allowed
Augustea to diversify into related markets. The fully-owned subsidiary Augustea Tecnoservice Srl offers a wide array of services for the shipping industry, providing assistance and technical advice, maintenance and repair services to both the market and the operating division within the Augustea Group.
In 2013, Augustea moved into another segment, when it opened a manning agency in the Philippines. Augustea Ship Manning Philippines Inc. incorporated in Manila, provides both ship manning and crew management services, such as the recruitment, selection and deployment of Filipino crew members as well as continuous crew training.
Several years ago, Augustea moved its assets to Malta, which has become an important business base. In 2018, the company entered into an agreement with several other shipping companies there to establish an entity running approximately 30 vessels, thus combining its dry bulk owned fleets under the Star Bulk company name, F ollowing the move, Augustea became a major industrial shareholder of Star Bulk together with the Pappas family, the main shareholder.
Francesco Amenta admitted that the last two years have brought challenges but also opportunities.
“It is no secret that as freight rates increased substantially as a result of Covid restrictions, our financial performance has improved significantly. As a trusted partner, we have sought to provide the same reliable service as before.
“However, Covid-19 did give us a very hard time, in terms of both cost and personnel. Bearing in mind that lube oil consumption accounts for 20% of the daily cost of running a vessel, the greater than 20% price increase has been a major issue.”
However, the primary concern has been the crew. “At the moment, 95% of our crew is Filipino. The Philippines has been one of the countries with strict Covid rules, but has a low vaccination rate due to limited vaccine availability. The country has been amongst the last ones to provide vaccines for seafarers. The fact that it is very difficult to get vaccinated in Manila, with the country’s strict rules in terms of tests and quarantines, means that the impact on the business has been huge.”
Mr Amenta pointed out the vaccination rate on board Augustea’s vessels is now in excess of 60%, thanks to the United States which provides free vaccination to crews on ships calling at its shores. This has been greatly appreciated, as many ports do not accept vessels without a crew’s vaccination: China and the United Arab Emirates are reportedly among countries that have started to require ships to be manned by vaccinated seafarers before entering their countries.
The issue was further compounded by the ongoing crewing crisis, with hundreds of thousands of seafarers stranded at sea due to travel restrictions across the globe.
“This has really been an unprecedented situation and the IMO did very little to help The states of the world were not able to find a common rule, and the lack of care for crew, specifically in some countries, has been quite simply unacceptable,” commented Mr Amenta.
Speaking about the current market conditions, he remains realistic:
“Although there seem to be some signs of better times, the improvement will be slow and is unlikely to happen in the near future. We need to stay firm and focus on consolidating our activities. While pre-Covid you would think twice, now you would think ten times before making any investment.”
Looking further ahead, he revealed there are some new lines of business the company is contemplating, such as offshore wind farms, for which some entities are already building sophisticated vessels.
“ This will be the next potential business for everybody. The market will evolve towards environmentally friendly technology, with energy-saving devices and more efficient, greener vessels being designed and built.”
Mr Amenta concluded: “But for the time being, Augustea is set to consolidate its business, to ensure we are in a better position for the new future.” n
In the vast and often corporate world of ship management, Uniteam Marine in Cyprus stands out for its personal approach to its relationships with clients. Via Uniteam Marine’s own offices around the world, the company offers a comprehensive range of management services to ship owners. John Hadjiparaskevas, Managing Director at Uniteam Marine, returned to update us on the company’s latest news.
Richard Hagan reports.
Uniteam Marine provides a comprehensive bouquet of ship management services, from full management over crew management (including payroll and outsourced HR services), to technical services (including financial accounting and quality management).
Whilst it has traditionally focused on dry cargo vessels, the company has recently added the first tanker to its portfolio. Supplying crew to the cruise vessel segment is also a relatively new but successful venture for Uniteam Marine with over 500 crew currently serving onboard its clients’ cruise vessel fleets. More will be embarking over the next months, now that the cruise industry recovers, adding to Uniteam Marine’s core crewing activities.
Several well-known offshore vessel operators have also entrusted the crewing of their vessels to Uniteam Marine, and with the signing of a crewing agreement for two LNG tankers, this segment will soon be added to the portfolio.
Since Uniteam Marine’s founding in 1986, its footprint has gradually expanded. Complementing its head office in Cyprus,
the company boasts offices in Germany, Myanmar, Singapore, Ukraine and the Philippines. An office in the Middle East is expected to follow soon.
Via its sister company, Uniteam Training, Uniteam Marine provides cutting-edge crew training services to the market. Its state-ofthe-art facility in Yangon comprises bridge simulators, ECDIS stations, an engine room simulator suited for simulating LNG fuel operations, STCW and finally, practical workshop training courses.
According to Managing Director John Hadjiparaskevas, the company’s size makes it more flexible and highly adaptable.
“We are sized in a way that still allows us to deliver a very personal boutique-style service to our clients, but at the same time we are able to pass on economies of scale to our clients’ benefit. Added to our over 35 years of ship management experience, we can quickly respond to individual client needs as well as to adapt our processes and procedures to meet client requirements.
“Our longstanding business relationships with our clients is the best proof of our successful focus on client satisfaction and on delivering a service that meets and exceeds their expectations.”
In November 2021, Uniteam Marine celebrated the opening of its office in Manila, the Philippines, which is already responsible for managing over 500 seafarers. The new presence focuses heavily on recruitin g junior officers, petty officers and ratings from the Philippines region.
“The reaction from seafarers in the Philippines has been very positive; they welcomed Uniteam Marine wholeheartedly,” Mr Hadjiparaskevas commented.
“Our goals for the next five years include career growth of our staff there, as well as more deployment of Filipino seafarers and
ultimately, becoming one of the top-performing local seafarer recruitment agencies in Manila.”
The company’s Myanmar office services a labour market that is largely untapped in the maritime industry.
Mr Hadjiparaskevas continued: “Myanmar is not as explored as other, traditional recruitment markets such as the Philippines. Through our various recruitment offices and a network of associated agencies, we’re able to offer our clients a choice of crew nationalities.”
Uniteam Marine has a people-first approach to managing its seafarers, Mr Hadjiparaskevas confirmed, stating that the company’s focus on crew wellbeing and ongoing training has delivered long-term employee commitment.
“Our people have always been and will continue to be our most important asset. The business cannot survive without them and therefore we put extra effort into really caring for them. In 2021, a number of our seafarers and office personnel celebrated 10, 20, and 25 years seniority with us. We’re like a big family that stays together.”
The company recently launched its ‘We Care’ logo as a representation of the various programmes it is running in connection with crew wellbeing.
“These include our ‘5 paths to wellbeing’, our onboard Mental Fitness Gym, our AntiCorruption and Anti-Bribery Policies, our commitment to the Modern Slavery Act, and our ‘TH!NK LSR (Life Saving Rules) safety campaign,” Mr Hadjiparaskevas explained. “They all form an integral part of who we are as a company and are the reason why we are formalising these commitments into our new Environmental Social Governance Policy.”
Globally, there is a major push towards emissions-free transportation and the maritime industry, with its high emissions, has been a focus of various emissions-related regulatory efforts. Uniteam Marine is taking a proactive stance in dealing with emissions challenges via the various internal programs it’s put in place to prioritise environmental issues.
“For over a decade, we’ve focused on emissions reduction and today we boast
a zero environmental deficiency record,” remarked Mr Hadjiparaskevas. “These efforts also form the basis from which we implement our ‘Ship Energy Efficiency Management Programmes’.”
The company’s Environmental Social Governance Policy is a formal document that will guide policymaking for everything it does, going forward.
“In order to care for humanity, we must care for nature; we must think about what we buy and use, we must adopt sustainable habits and we must commit to a green and resilient future. Therefore, we believe that high standards of corporate responsibility will make good business sense and will enhance and protect our business,” Mr Hadjiparaskevas commented.
The Covid pandemic and its many lockdowns, regulations and border closures are a headache for crews trying to return home or return to work. It’s a constantly moving goalpost, Mr Hadjiparaskevas noted.
“Travel information that is valid today can become obsolete tomorrow, which makes reliable long-term planning impossible and it means crew changes must be handled on an ad-hoc basis,” he said. “Added to that, there’s been a spike in travel costs combined with already costly Covid testing and mandatory isolation periods. It’s a major challenge.
“Our crewing team has done a great job keeping our seafarers constantly updated of the situation and the travel challenges we’re facing. In co-operation with owners and occasionally even charterers, we have always managed to find ways to make the impossible possible.”
Mr Hadjiparaskevas echoed comments heard throughout the industry relating to the plight of seafarers. These are personnel who perform an essential service, but which is still not formally recognised in terms of international travel restrictions
“A global recognition – not just lip service – that recognises maritime workers as essential personnel is what we need. They need to be given preferential treatment when joining a vessel or signing off from one. It was such a shame to see how seafarers were repeatedly denied medical attention in port on the basis that Covid restrictions would not allow shore leave. Practices like that are contrary to basic MLC rights for seafarers worldwide.”
In closing, Mr Hadjiparaskevas revealed his thoughts on the challenges that would affect the maritime industry over the next couple of years. The pandemic featured prominently.
“Restrictions imposed by the pandemic will accompany us throughout 2022 and will continue to have an impact on both the
operational and cost aspects of crew changes. Our top priority is keeping our seafarers motivated and engaged, whilst carefully looking after their mental health and well-being.”
“It remains to be seen how long the positive charter rates currently paid for container vessels and dry bulk ships continue to be achievable. At least for the time being, these help to balance the increased costs that both ship owners and we, as ship managers, are incurring due to the pandemic.”
With the opening of its new office, comprehensive and progressive internal programmes, and its ability to quickly adapt to changing client needs, Uniteam Marine is positioned to enjoy a strong 2022 and beyond. n
John Hadjiparaskevas, Managing Director
Africa, as it is sometimes said, is not for the weak. It is a place full of unique challenges and hard-working people, but it also offers vast opportunities for those who are sufficiently brave and determined. Universal Africa Lines has established itself as a specialist, niche provider of shipping services to the especially challenging West Africa region. Dennis Malkoc, Business Development Head, spoke to Richard Hagan about what it takes to master the African seas.
There’s no getting around it: Doing business in Africa is far from easy. Generally speaking, the continent lacks basic infrastructure and government services that are commonplace in more developed nations. The political landscape is awash with instability and many economies are undeveloped.
But despite it all, Africa’s people are hardworking, tenacious, and they want a better future for themselves and their families, just like anyone else. They are entrepreneurs and visionaries and they are ready to work for a better life. It is truly a vast, often untapped pool of optimism and hope.
When Roger Jungblut came to West Africa in the early 1970s, it was to see the circumstances there for himself and to quantify the challenges faced by the region. He witnessed the lack of infrastructure first hand, but he also saw the opportunity presented by the area’s growing oil and gas industry and the fact that Nigeria did not have a sea link
with Houston, where much of the local industry’s equipment would need to come from.
And so, in 1973 he set up Universal Africa Lines (UAL) to create that missing sea link.
Today, UAL is a specialist cargo carrier focused on hauling oil and gas industry cargo, and project freight, from Europe and the US to West Africa. The company has recently also added a shipping lane from the Mediterranean to West Africa.
From its headquarters in Rotterdam, its contingent of 40 specialist staff ensures that its vessels are kept busy, safe, and on schedule at all times.
In addition to its Rotterdam facility, UAL has sister companies in Houston, Aberdeen and Denmark who are each in charge of the specific shipping lanes that depart from those regions. The Denmark-based office is the newest addition to the UAL, family and is responsible for chartering opera -
tions in general, and more specifically for the company’s new Mediterranean route.
UAL’s two most important destinations are Nigeria and Angola. UAL is the only direct Multi-Purpose Vessel (MPV) liner service connecting the US and Europe with West-Africa.
“99% of the time when your cargo is shipped with UAL, it will remain on board until we reach the final destination as per the clients wishes,” explained UAL’s Head of Business Development, Dennis Malkoc.
“No transhipments are made unless the final destination has certain restrictions such as low draft. For that we use our very own UAL – owned K5 terminal located on the island of Bioko in Equatorial Guinea, which is a free zone and has been part of the UAL family since 2000. A prime example is our service to Malongo port in Angola with our own UAL Lobito from Malabo.”
Conducting business operations on a continent without the political continuity and infrastructural stability of more
developed nations, calls for extreme levels of flexibility and an ability to make decisions on the fly. According to Mr Malkoc, the company’s philosophy revolves around its flexibility.
“We are the only MPV liner service with direct routes from the US Gulf and Europe to West Africa. Because of that we have quick and reliable transit times.”
The company’s impressive fleet of eight ships has been carefully developed to ensure that it can deliver maximum value for its clients at all times and on all routes.
First up is M/V UAL Lobito. This breakbulk cargo ship is specifically designed for the West-African feeder business. Built in 2003 with a very shallow draft, she is the perfect vessel to reach those hard to reach ports/places. Her two cranes have an individual capacity of 36 tonnes and a combined lifting capacity of 70, serving her cargo capacity of 6,258 cbm.
Next we have the 2011 built M/V UAL Africa. This breakbulk vessel, with a 10,774 cbm cargo capacity and two cranes, (each able to hoist 60 metric tonnes or 120 metric tonnes combined), is the sister ship to the company’s MV UAL Bodewes – built in 2012 and boasting the same capabilities. UAL Africa, Bodewes and Houston all feature ultra-modern, wave-piercing X-Bow type hull designs.
Seeing the success of Africa and Bodewes, the company added the aforementioned MV UAL Houston, built in 2012. Her 11,970 cbm in bale grain capacity is facilitated by two cranes on her port side. Individually the cranes can hoist 60 metric tonnes, and 120 when combined. It is the sister ship to the company’s MV UAL Cologne and MV UAL Texas, built in 2014, although Cologne and Texas have two cranes with 80 metric tonnes capacity. And just like UAL Africa and Bodewes, they feature X-Bow hulls.
These vessels are categorised as green vessels, due to them lowering UAL’s
carbon footprint and offering fuel savings of 30% compared to industry standards. UAL was one of the first to implement this revolutionary design within the MPV market.
“Over the last couple of years, UAL has seen a growing need in heavy lifts so we decided to invest in the massive cargo ship M/V UAL Fortitude, built in 2008, designed to take on some of the bigger shipments,” said Mr Malkoc. “With a 15,952 cbm bale/ grain capacity and her two cranes offering a combined hoisting capacity of 360 metric tonnes, she is equipped for every challenge.”
And finally, in January, UAL welcomed an eighth vessel to its fleet: the 138m long M/V UAL Manitoba was built in 2007 at Jiangdong Shipyard in China and boasts a cargo hold capacity of 15,953 cbm. Her two massive cranes offer 120 metric tonnes of lifting capability each, for a combined 240 metric tonnes.
“In addition to our own fleet, we always look at the long-term charter market to add additional tonnage in support of our fleet,” remarked Mr Malkoc. “Currently we have four chartered vessels added to our fleet.
According to Mr Malkoc, UAL’s business model benefits from a widely-held perception that doing business in Africa is difficult and problematic.
“For a lot of our European and US clients , Africa equals problems and a lot of risk. They’re afraid of the risks of doing business there,” he said. “We’ve been working in Africa for so long that it now gives us a special edge in terms of what we can offer our clients versus our competitors. We go to ports that our competitors don’t and won’t go to.”
In its almost 50 year history of working in West Africa, UAL has developed relationships with local agents. It’s critical to the company’s success in the region.
“We have a strong network of local agents who we choose carefully and with whom we’ve worked for a long time,” Mr Malkoc confirmed.
This network is particularly instrumental in the company’s efforts to secure its ships , its seafarers and its cargo against the biggest ongoing regional challenge facing its assets: piracy.
“The Gulf of Guinea has a lot of piracy problems; it’s the main problem we face,” noted Mr Malkoc. “We’ve had our share in the past. It’s a fact of doing business in the area and we have to prepare the best that we can.
“There are three important measures we adopt. First off, we have a strong and reliable agent in each country; next, we follow the local government and security company rules and regulations to the letter; and finally, we don’t take unneces -
sary risks. If, for example, you know that you’re nearing a piracy hot zone, then avoid it. Absorb the extra miles. Don’t be a ‘cowboy’,” Mr Malkoc stressed.
Local and international navies provide ongoing anti-piracy patrols in the region as well as convoy escorts to protect commercial vessels transiting the area. UAL also retains the services of maritime risk control service provider Praesidium International to review, implement and assess security measures onboard UAL ships as well as to
train its seafarers. Where necessary, armed guards and security escort vessels are employed to safeguard its vessels as well.
On the back of a buoyant global maritime freight trade, UAL had a highly successfu l 2021 and is looking forward to an equally positive 2022.
“There is high demand for our services in our shipping lanes, so we urge our clients to plan ahead and contact us well in advance to avoid possible delays on their projects,” Mr Malkoc concluded. n
Chairman and Manging Director Captain Thomas Pinto
Mumbai-based Seven Islands Shipping Limited (SISL) has been operating ocean-going tankers for almost 20 years. India’s secondlargest private tanker shipping company has continued to capitalise on a recent $72 million capital injection, with the DWT capacity of SISL’s fleet now surpassing one million metric tonnes. Report by Jack Salter.
The name Seven Islands Shipping Limited (SISL) is inspired by the seven islands of Mumbai, India’s financial centre and largest city, where the company is located.
Under the leadership of Chairman and Managing Director, Captain Thomas Pinto, SISL has filled a sizeable deficit in India’s imported oil capacity with a flush arrival of newly acquired second-hand ships.
As India is the world’s third largest consumer of crude oil and was the third largest crude oil importer in the world in 2019,
the expansion of SISL’s fleet is timely in addressing the country’s growing oil import requirements, mainly from the Persian Gulf.
SISL owns an expanded fleet of 22 vessels, consisting of two gas carriers, three crude oil tankers and 17 product carriers, the latter of which transport various refined oil products to the points of consumption.
It comes following $72 million of private equity funding from FIH Mauritius Investments – an arm of Fairfax Financial Holdings, one of the largest investment companies in Canada – who secured a 41.4%
share in SISL in 2019. The investment was completed through a direct subscription and secondary acquisition of SISL shares. Currently catering to domestic oil majors as well as international oil companies, SISL’s clients include the likes of Indian Oil, Hindustan Petroleum, Bharat Petroleum and Reliance Industries.
Backed by FIH Mauritius Investments, the expansion of SISL’s ocean-going fleet has progressed at a rapid rate of knots with
the acquisition of additional vessels via the second-hand market and for general corporate purposes.
Nine vessels were acquired in 2020 alone, such as MT Sparkle, MT Gallant and MT Pelican, taking the DWT capacity of SISL’s fleet beyond one million metric tonnes, with a further six vessels acquired throughout 2021 including MT Blossom, MT Lourdes and MT Concord.
Having surpassed a DWT capacity of one million tonnes, SISL is taking advantage of the right of first refusal in crude oil and cabotage for oil products.
In ship charter tenders issued by stateowned oil firms, Indian ships have a right of first refusal to match the lowest rate quoted by foreign-flag ships and take the contract. Moreover, state-run oil firms transporting oil products for local use along the Indian coast have to prioritise Indian flagged ships, according to India’s cabotage law.
Despite recent moves to relax the cabotage laws, thus opening up the intra-India export/import container transportation segment to foreign-flag ocean carriers, SISL remains upbeat and continues to invest in new vessels.
By acquiring more vessels, SISL has been able to increase its market share whilst maintaining a high-quality, safety-first approach. The company maintains an optimal mix of vessels on time and voyage charters in response to market conditions, transporting crude oil, petroleum products, lube oil and palm oils globally.
2019 proved to be a critical year of progress for the company, as it was crowned The Indian Shipping Company with the Highest Growth of Indian Flag Vessels at the 55th National Maritime Day celebrations. FIH Mauritius Investments’ significant finan -
cial backing has evidently enabled SISL to expand its operations and grow the business, and this award is a reflection of that.
Now bolstering an impressive track record of acquiring vessels and earning attractive returns throughout the life of the vessel, SISL intends to become one of the leading shipping companies in India.
In doing so, SISL will continue to try and meet the growing needs and demands of the oil and gas market. However, the company is also weighing up entry into the gas carrier, container ship and chemical vessel markets should the right opportunities present themselves.
Prem Watsa, Chairman of Fairfax India Holdings Corporation, the parent organisation of FIH Mauritius Investments, wrote to shareholders in March 2021 outlining SISL’s fleet diversification plans.
Based on current ship prices and charter rates, he noted SISL’s potential for growth
within the gas carrier and container ship segments. A sharp focus on growth opportunities is enshrined in SISL’s corporate culture, meaning that new business activities are targeted if they give the company an opportunity to grow.
Geopolitical uncertainties, staying afloat financially in contrast to the state of the global oil and gas sector, and the IMO’s 2020 regulations have been testing for SISL.
However, what differentiates SISL from other shipping companies facing the same challenges is that SISL has been operating, owning and managing its own vessels under one roof for many years.
The company also has strong overhead costs and financial monitoring systems, enabling it to remain highly competitive.
Today, SISL has a master mariner at the helm who understands the pressures of operating at sea and ashore, complemented by a highly professional and well-qualified in-house team when it comes to technical and operational management. It’s in-house level of experience and expertise stands it apart from other big shipping names in India.
SISL has built a reputation for safe, ontime port-to-port deliveries as a result, generating client trust and loyalty in the process. The company strives to gain a deep understanding of customer needs and works to provide clients with a comprehensive logistics solution, complete with the timely loading and delivery of cargo as well as regular shipment updates.
By maintaining a close focus on a select group of customers, the opportunity for mutual growth in line with SISL’s mission and vision is created. The company is in relentless pursuit of excellence in order to become a top service provider for its customers, conducting business based on its ability to provide best-in-class service.
All the while, SISL has recognised its responsibilities when it comes to the safely of life at sea and ensuring a cleaner environment. As well as being ISO 9001:2015 certified, SISL is registered under the Government of India’s Directorate General of Shipping (DGS), which deals with the implementation of shipping policy and legislation.
Having signed an MoU with the DGS in 2021 for a commitment of INR 1500 crores towards fleet expansion, as well as setting up a world-class maritime training institute in India and sponsoring two graduates for education at the World Maritime University, the future looks bright for SISL and the Indian shipping industry. n
In the global ship management industry, Viridian Maritime is taking strides to deliver its services backed up by forward-thinking strategies that help exceed the expectations of vessel managers and operators. Founder and Managing Director Arvind Mohan gave Andy Probert an insight into the company’s business model, which also empowers seafarers to fulfil their potential.
Ship management is as old as the maritime industry itself. But the team at Viridian Maritime is bringing a fresh, modern and analytic approach to the sector.
Established in 2017, the Singapore-based company is a niche provider of integrated marine services and solutions. Vessel operations involve technical, crew and marine HSE management, project management, and services related to new building, conversions and lay-up. Asset management extends from tankers, bulk and containers
to more complex and diversified offshore OSV, subsea, jack-up and lift boats.
Viridian’s team currently has several vessels of diversified portfolio under management, and every ‘business win’ not only reconfirms the company’s dynamic approach but also the fact that it is on the right track for growth.
“When we established Viridian, our entire ethos was to change how ship management historically operated,” asserted its Founder, Arvind Mohan. “There was certainly a need for a breath of fresh air as to how assets are managed, how operational teams delivered on their promises to owners and the agreed operating budgets.
“We wanted to change the equation between owner and ship manager and go
beyond a purely transactional service to being partners in the real sense. We aim to act as managers but think like owners.”
He elaborated: “Transparency and trust are words that need to have real meaning behind them. Not just on paper or spoken about, let alone rarely delivered. Having worked with several established organisations, they were evidently lacking. We needed to change this outlook, with more tangible and measurable benefits.”
This extended to the validity of each team member’s experience, what they brought to the table, how cash flow was prudently managed, how KPIs were agreed, how forward-looking monthly management reports worked, and the snapshots given to stakeholders.
“This has made a difference and, with us being a niche service provider, we can exceed asset managers’ expectations. Changing that dynamic between owner and ship manager has enabled us to achieve well-defined objectives, made relationships stronger and growing more organically.”
Mr Mohan certainly accumulated a wealth of experience before Viridian. He has about 30 years’ experience at sea and ashore, extensive international exposure working with owners and managers, and extensive maritime knowledge on a global scale.
After several years of discussions, Viridian Maritime worked further to establish rapport and credibility with its Japanese owners and founded a joint venture to manage their vessels.
“It was a significant achievement for the team and assisted our foray into the Japanese markets,” said Mr Mohan. “We continually work to deliver and exceed expectations in the true sense of what a partnership was meant to be.”
When pressed on what makes Viridian Maritime different from other ship management companies in the industry, Mr Mohan was brutally frank.
“Ship management market, in our view, is a ‘zero-sum balance’ service business. This means a ship manager with 500 managed vessels that faces an exit of ten vessels from its management effectively loses 2% of their fleet. The same number exiting a mid-sized manager with 20 managed vessels faces a wipe-out of 50% of its business. The differences and impacts are stark.”
He said: “The point is that a mid-size manager, like us, will go the extra mile to ensure vessels do not leave their management. The focus, effort, energy and time spent to manage 20 vessels makes an entire difference.”
Viridian’s team seeks to pre-empt what clients require and what they think, helping to underpin and maintain good relations.
“We take prompt action, maintaining collaboration between the client and vessel staff, and thereby causing minimal disruption to business.”
Looking ahead, Mr Mohan indicated that Viridian’s plans are geared towards expansion, specifically in Europe and regionally.
“We have come to believe that thinking locally needs to be strengthened while providing global coverage of operational capabilities with due diligence. Additionally, with ESG at the forefront of shipping and building new vessels, we are keenly studying this to be able to assist owners and operators alike to ensure operational delivery and meeting agreed sustainability goals.”
Given Viridian’s agile business approach, it is no surprise it has adapted faster to change than most during the pandemic. It has ensured inspections, takeovers, and audits have been undertaken to safeguard the assets while extending the necessary care and support to ensure the positive mental well-being of its seafarers.
Indeed, it’s the seafarers’ welfare that remains central to Mr Mohan’s thoughts while trying to keep Viridian Maritime on the right track. He observed: “Seafarers and seafaring continue to change and evolve, and with the current pandemic, we should not be
surprised that prospective young entrants further shun entry to the industry.
“Why would they, when they cannot get home on time, are endlessly quarantined in countries when they travel to embark a vessel, and with so much talk but little action to recognise them as essential workers? All these will have a cascading effect for years to come.”
He added: “Our approach has been to keep communication channels open with our seafarers and be patient to their concerns. Their emotional well-being is what ultimately affects their performance on board. With most of the team ashore having sailed on vessels, this understanding is essential, and we can bridge the gap better.”
When viewing the industry and its challenges, Mr Mohan focuses on what appears to be industry-wide issues; attracting and retaining talent, digitisation and the need for change.
“Concerning talent, look at the oil and gas industry which, over the last eight years, has suffered a ‘brain drain’ with many being made redundant and others moving away from the industry,” he said. “There remains a continued lack of talent across the sector.”
While the industry is moving in the right direction towards digitised ecofriendly assets, he believes there “remains a disconnect between the larger industry players and owners against the smaller to mid-sized owners.”
He explained: “Within a very short time span, there has been so much talk, information and movement within this space that everyone is playing catch up. Many are unclear among this myriad of information, papers and discussions. We suddenly see new building orders being placed, but there remains a clear gap within the industry towards its understanding and adoption.”
He added: “One thing that holds true is that only change is constant, and
these changes do not seem to end. One of our industry’s challenges is to break away from the tried and tested business models to a more agile and nimble model.”
Of Viridian Maritime, he said: “We emphasise empowering our seafarers to increase their potential and their mentoring capabilities. This is also because many new designs and emission technologies are not being designed with seafarers in mind or the inputs from shore-based ship managers. Yet it will be managers like us who will have to adapt to operate these vessels safely and meet all expectations of industry stakeholders. Consultation is essential in working on planning ahead rather than preparation in the last stages.”
Mr Mohan continued: “The phrase ‘business-as-usual’ is obsolete. There is nothing ‘as-usual’ any longer. Viridian’s team continues to be adaptive and responsive to the requirements of our business, our clients and the industry.
“Equally, the old model that ‘we can do cheaper than you’ is changing towards a more agile, driven organisation; exceeding owners’ expectations while accepting that the regimen, landscape and expectations from operators and charterers to meet their minimum criteria has moved on.
He concluded: “With this, a shift in mindsets of service-oriented companies needs to change. Not just in promises made to bring a ship under management, but in demonstrating the delivery of those promises with tangible results. This is what Viridian Maritime is all about.” n
BUILDING BRIDGES WITH MULTIMODAL
Spain’s Suardiaz Group is a multimodal transport and global logistics specialist, operating RoRo car carriers and a bunker fleet across Europe and the Mediterranean region. In response to rising demand for its services, the group is adopting ambitious plans, including a new service between Spain and Morocco. Profile by Andy Probert.
Established in 1945, Suardiaz Group began as a shipping operator before embarking into other transportation sectors, such as forwarding, and transitioning into a logistics specialist, with a global reach that covers rail, terminals, warehouses and air freight.
Today, Suardiaz, headquartered in Madrid, is a truly multimodal transport and global logistics service, with offices and representatives in France, Morocco, Algeria, Mexico, and Peru.
Its main business focus is operating a fleet of RoRo car carriers across Europe and the Mediterranean region and offering bunkering services.
The family-owned group also maintains a fleet of road haulage for door-to-door services and manages railway terminals at Barcelona Port, Granollers, Tarragona, Sagunto, Leon and Sevilla (La Negrilla).
“Having such a diverse range of activities and synergies across the group, we can offer our clients comprehensive logistics based on many multimodal options,” commented Group Commercial Director Marcos Duato.
Suardiaz Shipping Lines, the division that oversees maritime transport services, was a pioneer in the RoRo sector in Spain when it first began operating in the 1970s. Today its seven RoRos cargoes are mainly finished vehicles and trailers, containing components, and combined these with high and heavy loads, such as wind turbines and diversified machineries.
The RoRos, some of which are equipped with hoistable decks for large loads, operate in the West Med and Atlantic corridor of Europe, from Belgium in the north to Morocco in the south.
“The main home ports for our RoRos are Vigo, Tangiers and Barcelona from which most of our business flows,” outlined Mr Duato. “Automotive accounts for 80% of the shipping division’s business, but we also offer services to the textile and agri-food industries.”
Main clients include leading global automakers such as Stellantis Group, Renault, Volkswagen Group, Toyota and Hyundai/Kia. He explained: “The majority of cargo is outbound, so we take finished vehicles from the factories in Spain and Morocco into the north of Europe.
“From the north of Europe we load a mix of vehicles and H&H (high and heavy) cargo and we bring that back into Spain, Portugal, Canary Islands and Morocco.”
RoRo capacities vary depending on the vessels used. Some can carry 1,200 cars and 100 trailers for short, high-frequency routes, while the company’s larger vessels can carry upwards of 3,200 units.
Mr Duato explained the ages of the vessels range between ten to 20 years and reflect the group’s ongoing considerations in the face of uncertainty within the global shipping industry over emissions , fuel and environmental restrictions.
“As a medium-sized group, we have to be very careful with our investments on fleet. A vessel can last a long time, and if you make the incorrect choice, you may have the wrong vessel for the next 25 years,” he cautioned.
“At this moment, we are postponing our decisions on new generation vessels because we’re unsure on the right vessel propulsion. We will await until the regulations are implemented and then make a decision; one that will have a higher probability of being right on the type of vessels we require.”
The company operates Suardiaz Atlántica, a regular high-frequency maritime line between Vigo and Nantes / St Nazaire ports. Operated by RoRos at least three times a week, it is cofinanced by the Marco Polo Programme of the European Commission, and France and Spain.
In recent times, Suardiaz Group launched a new twice-weekly RoRo service connecting Tangier, in Morocco, with Barcelona, with the ability to transport all types of cargo, such as textile, fruit and vegetables, distribution, retail, spare parts for the automotive industry and finished vehicles.
The company has also anchored its presence in the provision of three oil barges to provide fuel to bigger vessels in port. One vessel has been adapted to offer traditional fuels and LNG.
Suardiaz Group also has another mar itime-linked division related to special cargo projects and which continues to grow significantly as it is being called on to provide additional services. All services are underpinned by a 700-strong workforce, including in-house crew management.
While most non-essential services came to a halt during the pandemic, Mr Duato said the company reacted quickly by releasing part of the chartered vessels and selling off smaller tonnage with a view to emerging stronger and leaner.
“There are still some hangovers from the pandemic, not least the supply of microchips to the automotive sector. This has had a knock-on effect on the supply of vehicles, and to logistics specialists like ourselves with low traffic volumes,” he said.
With greater synergy between the multimodal options across the Group, the company sees more flow between sea, rail and road. “We are doing more land-based transport for car manufacturers, and we are moving into the inbound logistics with door to door solutions, with supplies to factories.
“We are focusing on where the factories are located close to the sea and only on the flows suitable for a multimodal solution involving the sea. This includes growing our rail transportation options, linked to movement in and out of the ports.
Mr Duato continued: “Maritime solutions remain at the heart of our operations, but now feature as part of a number of transportation options. It is a complete one-stop solution for the logistics supply chain.”
Indeed, Slisa, a Suardiaz subsidiary dedicated to managing railway terminals, saw a 36% increase in intermodal traffic management in its terminals.
The biggest challenges currently being faced by the group, revealed Mr Duato, include the ongoing volatility in the industry, the ever-evolving regulations for shipping, and the shortage of capacity in the global market.
On the sustainability front, Suardiaz Group is reviewing how it can reduce emissions in ports by optimising vessel routes and speed.
L’ Audace, a Suardiaz ship, also undertook its first pilot test in the port of Santa Cruz de Tenerife and Vigo, supplying electric energy to the vessel from LNG. The actions took place within the Core LNGas Hive project, a decarbonisation initiative co-financed by the European Commission. The project has 42 members, of which Suardiaz is one, to develop and improve the adequate logistic supply of LNG to the maritime sector.
“We are now negotiating with the ports of Vigo and Nantes-St Nazaire in regards to installing power points so our vessels can be plugged into electricity rather than burn fuel while in port,” Mr Duato revealed.
“We are fully committed to the green agenda, and we want to achieve that in the best way possible for the environment and our clients,” affirmed Mr Duato. “Suardiaz comes to the sector with a diversified business model compared to other shipping competitors. We try to be as close as possible to our clients and offer greater flexibility to adapt to their demands.”
He concluded: “Suardiaz Group sees itself as a small but necessary niche player in the market. We have open and long-lasting relations with clients. We focus in providing excellent services, fulfil our promises and ensure they enjoy a value-added experience every time.” n
Spain’s Echebastar is a fishing company that takes sustainability seriously. It is a shining beacon in the tuna industry, often beset by ethical issues and the drive for profit. As the only one in its sector to hold the internationally-recognised MSC benchmark, Echebastar is keen to see others follow in its path – and ensure the long-term viability of the species. Report by Andy Probert.
BYits very nature, the Basque Country’s Echebastar likes to ride its own wave. Doing the right thing has made it a touchpoint in the tuna industry in setting standards for responsible fishing.
While industry critics fret over its ethical, human and fish exploitation records, Echebastar stands alone in an increasingly crowded marketplace that puts its actions firmly where its mouth is.
For 55 years, the company has been catching tuna in the Western Indian Ocean. Its six vessel-strong fleet catches around 50,000 tonnes a year, as permitted by quotas set by the Indian Ocean Tuna Commission to protect fish stocks.
Of this catch, 93% is frozen in brine and goes to canneries located in Indian Ocean countries, such as Seychelles and Mauritius, to help support local economies and the environment rather than shipping it frozen halfway around the world.
The remaining catch is deep frozen to -60°C onboard, which preserves the fish in a pristine state, and this is then processed and sold predominantly to supermarkets for tuna steaks and sushi. This fish makes a higher price, but the production capacity is limited in the current fleet.
But this business model is not what makes Echebastar unique: the company’s commitment to environmental and sustainability practices gives consumers confidence that what they buy aligns with sustainable fishing practices.
Since 2018, Echebastar has held the MSC Certification to fish skipjack tuna in the Indian Ocean. MSC is the leading independent organisation that certifies sustainable and well-managed fisheries worldwide and guarantees to the consumer that the
tuna catch and production accord with the highest principles of responsible fishing.
While still the only commercial tuna fishing company, catching tuna in all purse seine fishing methods, to hold this international benchmark, Echebastar is assessed in several critical areas annually. As of late-2021, the company has completed two and is ahead of target on five other conditions.
“The certification of our fishery against the MSC standard is recognition of the success we have achieved in our efforts to promote sustainable fishing for tuna,” commented José Iriarte, the company’s Environmental and Resource Responsibilities Director.
“But we continue working towards sustainability and a well-managed fishery for Echebastar. We are committed to further improvements.”
He added that Echebastar was keen to see other fishing companies follow in their footsteps and achieve the MSC certification. “We serve as an excellent example to others that we can all fish sustainably while guaranteeing the health of tuna stocks for future generations.”
The company has also developed an innovative catch management system to return by-catch species back to the sea alive. It has independent observers aboard each vessel to ensure that regulations and best practice methods are followed. It pays all its staff at high European rates with regular, lengthy on-shore periods.
Between 2003 and 2015, Echebastar voluntarily reduced its vessels capacity by 25% . It has also reduced the use of FADS, typi cally buoys or floats tethered to the ocean floor with concrete
blocks that attract fish, and uses new FAD models which prevent shark and turtle entanglements.
It has recently signed up to the Sustuntech project, which helps fleets identify where the fish are, which saves fuel and reduces emissions, and is also heavily involved in the SARETU initiative, which collects discarded nets and other abandoned fishing equipment (known as ghost gear) and then reconditions it for recycling.
In 2020, Echebastar, in collaboration with AZTI, implemented the Silky Shark Tagging Project. The main objective was to measure the post-release survival of silky sharks taken as incidental catch in their purse seine tuna fishery and evaluate the impact of their Good Fishing Practices in reducing species mortality. It would also identify the potential for additional mitigation measures to further reduce that impact.
This information will allow detailed analysis of the horizontal and vertical migrations of silky sharks and provide additional data for habitat models, emphasised Mr Iriarte.
“This new project again confirms our commitment to safeguarding the habitats and ecosystem of the Indian Ocean,” he added. “All these policies and developments ensure that we remain at the forefront of sustainable and responsible fishing practices. But we need to be relentless in our pursuit for a better industry.”
As much as the company is seeking to redefine future industry through its own actions, it is down to the end consumer to be engaged and educated.
He reflected that while labelling on a can of tuna does offer data, more needs to be done in helping consumers identify what
best practice is and then seek supermarkets only stocking fish from suitable suppliers.
“Only then will the rest of the industry be forced to adopt best practice methods,” added Mr Iriarte. “Transparency and truth will out in the end.”
He was also quick to emphasise the company’s responsibility in the working environment for its crews, which can be multinational and multi-lingual.
“With upwards of 300 people working on the fleet, we are very sensitive to the crews’ working conditions. We want to demonstrate to stakeholders and consumers that we take our seafarers’ welfare very seriously and seek to obtain certification on this matter.”
Reflecting on the pandemic impact, he commented: “Our seafarers have been immense during this challenging period, and the company is deeply grateful to their commitment.”
Mr Iriarte concluded: “As the seas have supported Echebastar for more than half a century, so it is down to us collectively to protect and nurture it in any way we can. We believe that the industry has a good future, but one that is wholly supported by sustainable and responsible practices.” n
Nautical Marine Management Services is quietly changing the face of India’s shipping management industry. With a successful track record of delivering a variety of services to the famously competitive shipping industry, this family-owned company is a study in patience, persistence and carefully considered decision-making. Managing Director Aishwarya Pilankar spoke to Richard Hagan about what it takes to build one of India’s most successful marine management firms.
Aishwarya Pilankar and her husband, Nandakishor Pilankar, established a small maritime business offering technical repairs on offshore projects and assisting those clients with their crew requirements.
The arrangement was that Mrs Pilankar would be responsible for the administrative, crewing, logistical and financial side of the business, while Mr Pilankar would handle the technical, maintenance and engineering aspects of the vessels under its care. This proved to be a great decision.
Having the two partners each operating in the areas within which they were most skilled is a strategy that helped to launch and maintain the company’s successful trajectory.
Nautical Marine Management Services’ next evolution would come when the company purchased vessels involved with oil exploration. This marked the start of its interests in the oil business, leading to the company first managing tankers on behalf of other owners, and then buying its own tankers several years later, in 2016.
Surprisingly, just before Covid hit, the company made a strategic decision to sell a few of its remaining vessels. The fortunate timing of this reduction in risk and overhead right before the worst of the pandemic arrived, helped the company successfully weather the effects of lockdowns and the other financial impacts of Covid on the business.
Today, Nautical Marine Management Services manages more than 60 vessels on behalf of other owners. It offers a range of ser vices including crew management and training, logistics, maintenance, drydock project management, and importantly, ship chartering and brokering.
“The business has grown, but we still want to grow a lot. We’ve got a long way still to go,” said Ms Pilankar. “We plan to own vessels again but we’ll wait until after the worst of Covid is over. Perhaps sometime in late 2022.”
Ms Pilankar said that in the short-term, she has reservations regarding capital
investments, as she, her husband, and the rest of the Nautical Marine Management Services remain concerned about the current state of the Indian shipping market.
“The price bubble we’re seeing in shipping isn’t sustainable and the industry itself isn’t stable. While there might be a boom in shipping in other parts of the world, I don’t see one in India. There’s not as much capital flowing now. People and even the banks here are reluctant to invest capital; they’re risk-averse. Investors aren’t looking for the high-risk investments involved in shipping.”
This measured, conservative approach to decision-making within the company has ensured that today, Nautical Marine Management Services is a successful and vibrant global company, with a steady base of highly motivated, committed staff.
“Our head office is in Mumbai and we’ve got an associate office about nine hours’ drive from Mumbai. That’s my husband’s home town; there’s a new build yard there for smaller offshore vessels. We operate in collaboration with that yard to work on those vessels. We also have an associate office in Singapore and a chartering and brokering office in Lagos.”
Altogether, the company employs close to 40 highly-trained staff ready to meet any client’s shipping needs, no matter where they or their ships are in the world. It also plans to employ additional staff in 2022. Impressively, many of its staff members have been with the company for very long periods of time.
“The most important thing that I’ve made sure of is that the people who have joined me are there for 15 or 20 years. They don’t want to leave me. That’s the culture here. All of them want to stay with me. None of them wanted to leave, even during Covid.”
As per any other company, Nautical Marine Management Services had to manage some serious financial – and personal – challenges during the Covid-19 pandemic. Thanks to its constructive relationship with its staff, the business was able to weather the storm.
“During the initial stages of Covid, we kept pay levels the same despite business being quiet,” disclosed Mrs Pilankar. “But when that became unsustainable a few months later, we had a big staff meeting and everybody agreed to reduced pay for the next eight months to help see the company through that period. We resumed normal salaries as soon as we could and didn’t lose any staff. Everybody wanted to stay, so they were all happy with that arrangement.”
Ms Pilankar credits the staff’s commitment to the company, to her consistent and fair management style, and constant training.
“The staff feel like family. I don’t push them hard. Instead, I give them deadlines to finish a task and I tell them that they can go home whenever they want, as long as they finish the job. They can finish it in two hours and go home; it’s up to them as to when they finish it. It incentivises them.”
The company is certainly flexible and accommodating, but its staff aren’t able to sit on their laurels – they’re expected to get stuck in wherever needed.
“I’m not someone who wants lots of people around me, so I prefer to give the staff more multi-tasking jobs,” revealed Ms Pilankar. “Staff training is very important to me and as a result, my office staff are now all multi-skilled. I’ve trained them differently compared to our competitors.”
Ms Pilankar’s commitment to her staff is only equalled by her commitment to her relationships with her suppliers.
It’s clear that Nautical Marine Management’s suppliers are a key component to the company’s ability to deliver on its commitments to its customers. According to Ms Pilankar, the onset of Covid has only accelerated those demands.
“With Covid, it’s really difficult; We find ourselves having to arrange ten things to be delivered at one place at one time. But I think we’re succeeding and I hope we continue to do so.”
The current situation has made supplier relationships all the more important as the company continues to impress its customers.
“Our relationships with our suppliers are extremely important. The most important thing for us is to understand each supplier’s culture and how they want to work. We look at things like their return policies and their payment terms. Those issues have to work for us. I’ve retained many of our suppliers for some time now because even though we’re getting new ships and equipment in, the long-term processes and relationship building remain the same,” she said.
Family and business don’t always mix successfully and as we’ve all seen in organisations around the world, it can be either a blessing or a curse. But for Nautical Marine Management Services, it’s been the company’s secret sauce for success. Mrs Pilankar has a uniquely philosophical view on the family dynamic involved in the way she runs her business, her expectations for it and on her personal life.
“I run the business, but I’m okay with not making a huge amount of money for myself because I like doing what I’m doing. And even after 25 years of this, I’m still not 100% done with what I want to achieve. I want to go on learning more and doing more. To do that, I need my people around me and for that, they need to be paid well.
“You may feel that I’m not a typical business person but that’s okay. That’s who I am. I’ve also made my husband okay with it. He has to be okay with it!” she said, laughing. “That’s the advantage of a family business. I couldn’t do that with anybody else running the business with me!” n
seven seas, five oceans, one voice
jifmar offshore services axtech the sms group azimuth radio technologies fundilusa corrosion
Jifmar Offshore Services has never shied away from delivering ground-breaking integrated maritime solutions. It is one of the leading partners in developing the Canopée, the firstever sailing cargo vessel. Sales Director Tanguy Dennielou told Andy Probert more about the innovation and how Jifmar’s decision to diversify has reaped significant growth.
French marine contractor Jifmar Offshore Services has enjoyed a fair wind in its business growth in recent years, with acquisitions, fleet expansion, effective diversification and a vessel named Canopée.
Jifmar, founded in 2005 by visionaries Foad Zahedi and JeanMichel Berud, is a marine contractor operating a 44-strong fleet of modern, versatile and multi-cat DP vessels, barges and ROVs.
Having handled the maintenance, repair and operations of oil terminals in France, it landed a contract with BP and other similar companies. These helped it fuel stratospheric growth, and diversify clientele from Europe to Asia.
But it is Jifmar’s latest project that has caught the attention of the marine world, with its involvement in Canopée as a result of winning a contract from the Ariane Group for a new transport concept.
Once delivered, the ship will load the Ariane 6 launcher components in Bremen, Rotterdam, Le Havre, Bordeaux and Livourne, and be transferred to the Kourou launch site in French Guyana.
The Ariane 6 is the sixth generation of European rocket launchers, which have launched satellites for decades.
The 121m vessel, to be operated by Alizés, a joint venture between Jifmar and Zephyr et Borée, will be equipped with four 30m high Oceanwings. These sail panels will positively affect fuel consumption of the diesel direct mechanical propulsion systems.
Controllable pitch propellers can be put in feather mode when the Oceanwing wind system delivers sufficient power for the vessel under speed. This will shut down both or one of the two Wärtsilä main engines, saving around 35% on fuel consumption.
The vessel, which will have a capacity of 1,500 tonnes, is being built between the Netherlands and Poland, where the Neptune shipyards are located. It has been designed as an open-top vessel with high sides to protect the cargo.
The ship’s name derives from the canopy above the ‘Belly of Paris’, an open underground urban space on the site where Les
Halles de Paris once stood. Alizes will take delivery of the vessel in late 2022.
“Neptune shipyard has a strong track record in building cargo vessels that meet the highest industry standards,” observed Mr Berud. “At Jifmar, we have trusted them for many years to build our innovative and versatile vessels. We look forward to operating this vessel and showing the full potential of wind propulsion.”
Sales Director Tanguy Dennielou said Jifmar’s recent evolution to this point had included three acquisitions between 2017 and 2019. These included VDC Offshore in France, North West Marine in Scotland and Shetland-based Delta Marine. These takeovers had complemented Jifmar’s overall fleet, and include nine DP multi-cat operator vessels, the world’s biggest contingent in one fleet.
Diversified and resilient
Its latest addition was JIF MAIRI, for North West Marine. The 24m vessel was redesigned to meet the needs of customers in the aquaculture sector. It will also be capable of carrying out missions in ports, towing, diving support, ROV support, and wreck removal.
Still going strong is Multicat Roxane Z, Jifmar’s biggest vessel, brought on stream six years ago. The 34m vessel, fitted out for firefighting, anchor handling, ROV support, dive support and cable laying, is capable of working in shallow waters or for deep-sea operations.
Headquartered in Aix-en-Provence, near Marseille, Jifmar today employs 315 people and has 12 subsidiaries, including locations in Houston, Texas, and others in Africa, such as Gabon and Congo. These enable the marine contractor to operate a modern and versatile fleet for clients involved in development, installation, operation and maintenance in the offshore oil and gas industry and coastal infrastructure.
The company has branched into new markets from the renewable energy sector; offshore wind farm operations, marine construction, salvage operations, fish farming, cable-laying, and serving the defence industry.
Mr Dennielou added: “Jifmar is predicted to end 2021 with a €45 million turnover compared to €30 million in 2020. Since 2015, the company has enjoyed continued business growth, and it’s a trend that we continue to see.
“We are well known for working from shore, nearshore and offshore, while aiming to be a one-stop solution provider with engineering, infrastructure and planning.”
Jifmar had a hand in helping to deliver France’s first offshore floating wind turbine – a 2MW Vestas unit mounted on Ideol’s Floatgen floating platform – 12km off the coast of Le Croisic, Brittany, in 2018. Hook-up to the mooring lines was carried out by Jifmar, followed by connection to the export cable and power grid after a final series of checks.
Such opportunities to provide offshore wind services to the French market has resulted in Jifmar signing a MoU with World Marine Offshore to establish a joint venture. The new company will deliver vessels to the market and turnkey services.
Jifmar is highly focused on sustainability and reducing its carbon footprint globally, given that its vessels are presently operating in Taiwan and the Philippines, West Africa, Senegal, and across Northern Europe.
Mr Dennielou said: “As the Canopée contract with Ariane Group is for ten years, it demonstrates the kind of unique flagship project that best represents Jifmar’s efforts to reduce carbon emissions.”
The company has embarked on a project to remove engines from vessels less than 12m and equip them with electric battery power propulsion.
“We aspire to have a green fleet, especially when we look at the lifetime of a vessel. We are assessing vessels on a case by case
basis as to what we can do in switching to new technologies and minimising emissions.”
Mr Dennielou revealed Jifmar has also provided a platform to test a new type of wind technology for cargo vessel propulsion.
“It is kite technology which will be utilized to propel some vessels. We are supporting and looking at integrating this innovation for the market in general,” he added.
“Over time, we have manoeuvred into niche markets to provide a complete global solution service to clients. We are an adaptable and flexible business and bring more added value to them.”
While the pandemic impacted crew changes, the company has been highly resilient and proactive in helping to maintain their safety and security.
“We also unlocked new projects. We began operations in Mozambique and Taiwan for the first time and demonstrated our ability to maintain our flexibility under challenging circumstances,” Mr Dennielou detailed. “But the acceleration of activities, where client expectations are much higher, the immediacy of starting shorter, and reduced timeframe deliveries are just some of the challenges that we are seeing in today’s markets.”
He added: “While Jifmar is just one small piece in our bigger clients’ projects, we are still expected to reduce our carbon footprints and integrate new solutions.
“We always strive to strike a perfect balance between our engineering expertise and the skills of our seafarers. We are not a pure contractor or a pure shipowner, but a hybrid that combines everything together, and we go where the client needs us.
“We have built long-term relations with clients and shipyards, and this is through our whole-hearted commitment and trust to them.” Mr Dennielou concluded: “Our diversification has enabled us to be entirely resilient and proactive across all the industries we are active in. There are more requests from clients to come as a solution provider, with out-of-the-box thinking. For us, that is entirely natural. Engineering comes with the vessel. So we are entirely comfortable with that, and it positions us well for future industry demands.” n
Jifmar is a worldwide renowned shipowner specialised in DP multipurpose workboats. As a global leader of DP2 vessels of this kind, Sirehna has been supporting Jifmar for the last 12 years in order to ensure the best possible performance of their dynamic positioning systems for their customers.
Sirehna and Jifmar are also working together to bring innovation to the maritime world by experiencing and putting into test new sensors, operations modes and technological bricks.
“The collaboration between Sirehna and Jifmar in the last decade is a concrete proof of mutual understanding and loyalty. The expertise from both sides coming together benefits all of us; and the journey is far from over with exciting innovation and projects coming up,” said Olivier Doucy, CEO, Sirehna.
engineer of offshore heavy lifting and handling equip ment. Through strategic alliances with some of the world’s biggest and best fabricators, the company is able to offer its clients unique solutions for the toughest and most challenging scenarios. CEO and Technical Director at AXTech, Richard Myhre, spoke to Richard Hagan about what it takes to win the battle against the elements offshore.
Established by current CEO and Technical Director Richard Myhre and a partner in 2004, the decision to create AXTech AS came on the back of the lessons the pair learnt from a previous company they’d owned, which had been through a series of acquisitions. Ultimately, the two felt that they’d been left with too little decision-making power and thus decided to leave and effectively, start again. It has proven to be a shrewd move to say the least.
Today, AXTech AS is majority-owned by Mr Myhre and his business partner, while several minority shareholders (who share the pair’s vision), are also part of the ownership mix. The company is agile and designed to allow its management the flexibility to make the right decisions for its future.
“We’re now in a phase in which we’re quite ambitious about what we can do in the future, and we’re looking at what ownership structures will suit us best for future opportunities,” Mr Myhre noted. “We continue to have a dynamic approach to decisions around what is best for the company.”
That approach has led the company to a decision to focus on its engineering expertise whilst leaving the heavy lifting of fabrication to strategically selected alliance partners.
“Currently, we’re just less than 50 people working in our headquarters in Norway and then we have an additional 25 engineers spread across three facilities in Poland. These offices focus on
design work and of those, one specialises in numerical calculations. All three are fully integrated into our workflow from head office,” said Mr Myhre.
Equipment fabrication is carefully outsourced and project-managed by AXTech’s teams, as Mr Myhre explained: “Until a few months ago, we had a shareholding in a local fabrication facility, but we sold it off as we couldn’t foresee the need for any equipment within Norway. Instead, we perform fabrications through alliances in the region.”
Due to the size and weight of the equipment in the company’s portfolio, it’s more practical to have the equipment manufactured as near as possible to the quayside at which it is required or to the site at which it must be installed. This adjusted approach also suits AXTech’s green agenda, minimising transport and therefore carbon emissions, and also benefits the client by way of lower transport costs.
Project managing fabrication of the large, heavy and complex machinery designed by AXTech, requires the special management skills and industry knowledge within the company’s fabrication department.
“The first step is to understand the production facility we’ll be using for any given project, in relation to how we are designing the equipment for that project,” Mr Myhre detailed. “We try to look at how a pa r ticular design can be made to best suit that particular facility.
“Next, we look at the logistics involved in getting the machine between fabrication facilities and the end site. Then, we look at what personnel are involved and we ensure that we understand what material they’ll be using. This is all to ensure that the equipment is fabricated in the best possible way.”
AXTech has developed various methods of carrying out site surveys at its alliance fabricators.
Once these on-site checks are completed, AXTech then uses remote evaluation software to remotely test and check equip -
ment, utilising high-res on-site cameras to check any aspect of the equipment’s manufacture, at any time.
“Body cameras are even worn by production staff so that we can check, for example, exactly what the person’s hands are doing,” revealed Mr Myhre. “Finally, we use instant chat facilities with direct software connections to the production site, so we can press a button and immediately talk to the team onsite in, say, China. All of this also allows the client to be much more involved with the project no matter where they are situated on earth.”
As a designer and producer of specialist heavy-lift and heavyweight handling equipment, AXTech has a broad market of potential customers, but the opportunity that most interests the company right now is the one that exists in the booming offshore wind farm market.
“We’re progressing very well into offshore renewables,” confirmed the CEO. “Our key focus has always been heavy lifting solutions at sea, and we’ve been successful with that, but our key interest now is to look at becoming involved with those big wind turbines that must be installed and maintained.
“When there’s a need for the combination of heavy weight to be handled, and in a demanding environment, that’s where we are the most comfortable with the technology base that we have.”
The renewables market is proving to have some of its own unique challenges for a company that has traditionally been in the market for building one-off custom solutions.
“In our usual markets of oil and gas, we would move from project to project, with each being unique and requiring its own specific solutions,” said Mr Myhre. “In offshore renewables it’s different. For example, one site will need 100 turbines, and there’ll be another 100 at the next, so the logistics become
The unique demands of Axtech’s specialist winch application demanded an entirely bespoke torque limiting solution from the Wichita brand of Twiflex Limited, in the UK.
A spring applied clutch, incorporating sintered friction linings, provides high torque density with variable torque setting. Internal temperature sensors monitor slip events to optimise clutch performance.
much more demanding and challenging; you’re taking that one design and multiplying it by 100. That means that if there’s an error with that one design, it can become multiplied by 100.”
To combat the challenges, AXTech’s engineering for this market needs to be even more efficient.
“It’s a different task and mentality because obviously the risk becomes higher, and you aren’t able to tolerate errors in the same way,” he said. “You must hit the optimal design as fast and efficiently as possible, and then fabricate it competitively whilst still meeting our ‘green profile’ credentials in terms of minimising carbon emissions and long transits.”
AXTech’s main focus currently, confirmed Mr Myhre, is on the installation of these huge structures. The company is attentively working on answers to numerous questions posed by the demands associated with working in the sector.
The CEO listed a number of these questions: “How do you handle thousands of tonnes in open sea? How do you handle, guide and compensate it? A monopile weighs 3,000 tonnes; how do you safely handle that on deck? How do you lift it? How do you grab it?
“We want to look at how to handle these various big structures. We’ve got some experience with this already. We recently delivered a significant project to Belgium’s DEME in which we delivered reels for handling a vertical offshore foundation drilling machine.”
According to Mr Myhre, AXTech is excited about solving the heavy lift and handling problems of the booming offshore renewable energy market because it’s an opportunity for the company to prove its credentials to the market – despite its comparatively small size.
“We are a very small company but we believe in the skills that we have. We’ll be looking at what alliances we need to be a serious player in the market and at what investments are required to develop our tools to the fullest extent. And in general, we’ll be reviewing what infrastructure a company needs to have to be competitive in the future.”
AXTech isn’t one to shy away from a challenge. The renewables market has many, but there is one that has really grabbed the company’s attention:
“We see floating wind installations are coming – it will no longer just be bottom-fixed,” Mr Myhre predicted. “Our ambitions and aims for this particular segment of the offshore wind market is to address the technical challenges that have principally not yet been solved by the industry. For example, how do you lift and handle big objects when it’s not just the vessel moving but also the object? And how do you swap wind blades when you arrive at the turbine with a floating vessel?
“There’s a bright future for anyone who manages to ‘crack those nuts’. If we solve some of these technical challenges for floating wind energy installations, then it’ll be important for the future,” concluded Mr Myhre.
The SMS Group is a young, innovative company with a long history. As one of the UK’s leading providers of ship repair services, refits, diving and marine maintenance, the company has also established itself as a critical player for the defence industry’s service needs, and successfully operates in the dynamic cruise and ferry outfit space. Nicholas Warren and Chris Norman, Directors at The SMS Group, spoke to Richard Hagan about how the company is making waves in the UK’s marine industry and quietly building for the future.
Headquartered in Southampton, The SMS Group is one of the UK’s leading maritime maintenance, repair, refit and commercial diving service providers.
The company has a heritage dating back over 60 years to 1958. Its original founder started a small welding and marine engineering business in Kent. That business grew, and over the years, it went through a series of mergers and acquisitions until the company was rebranded as The SMS Group of today, approximately four years ago.
The SMS Group boasts facilities across eight main locations. It has three facilities that are geared towards the company’s defence sector support program, namely: Govan, in Scotland, HM Naval Base Devonport and HM Naval Base Portsmouth. Next, it has a 75m drydock with workshops and offices in Lowestoft. The company’s diving and high-speed diesel business is located in Dover as is its operation of a 3,000 tonne shiplift in Cherbourg, Northern France. Then, it has commercial ship repair hubs in both Avonmouth and Poole. Completing the list is its head office in Southampton, adjacent to the King George V drydock.
Chris Norman, Managing Director, commented: “It is this geographical reach, market spread and broad technical capability that sets us apart from others.”
Naturally, The SMS Group employs a roster of highly-trained, highly motivated specialist staff members who service the company’s various facilities and who routinely go out on emergency calls; around 50% of the group’s work involves travel to ports and harbours outside of their bases’ localities – both the workforce and service offering is fully mobile with over 40 vehicles utilised within the business.
The company has about 150 full-time employees including a senior management team of six and a general management team of 13. Impressively, around 75% of the company’s staff have been with the business for over ten years, and interestingly around half of the staff have security clearance with specific naval (also known as ‘grey ship’) experience.
The SMS Group is focused on delivering services across four main categories: defence, marine interiors and outfitting, commercial ship repair, and diving.
For its work in the defence sector, the company is generally subcontracted by large primary contractors including Babcock International and BAE Systems. The SMS Group is able to add value in various ways to these relationships, but two pertinent
areas of expertise are tendering to win fixed price packages of work to support vessels that are in-build or in refit; or alternatively, supporting shipyards and /or shipbuilders with security cleared human resources known as SQEP; suitably qualified and experienced personnel.
Thanks to its facilities inside two of the Royal Navy’s home ports, The SMS Group is also able to assist the primary contractors with newbuild related warranty works, and other additional works during and after the commissioning of new vessels. The company also works in Scotland, providing SQEP to assist directly in shipbuilding.
A particular recent highlight of The SMS Group’s defence industry participation has been its significant involvement in the Royal Navy’s commissioning of the advanced new Queen Elizabeth Class aircraft carriers. According to Nicholas Warren, Commercial Director, the project perfectly exemplifies the company’s capabilities.
“Defence is interesting. When we look at the expansion of, and national investment in, the Royal Navy, we’re excited and optimistic about the future,” he said. “You’ve got the new aircraft carriers, both wonderful ships, being managed extremely well. It has illustrated to the world the capabilities of shipbuilding in this country.”
Via its facility within HM Naval Base Devonport, The SMS Group supports Babcock International’s submarine and surface ship business. “What that means is that we have expertise in warships and submarines, and we have technical management that understands both. The resource and knowledge is transferable allowing us to move in around the country, from project-to-project,” said Mr Warren.
“That skillset allows us to perform infrastructure work too –which includes major valve replacements, the overhaul of penstocks or caissons, or even refurbishments of the actual physical naval base infrastructure. We’ve been very lucky that our expertise and resources understand the ships and the shoreside infrastructure within the bases. That has allowed us to deliver various maintenance packages in both a ship-side and shore-side environment.”
The company is committed to ongoing investment in new facilities, plant and equipment, and also additional locations, to ensure that it can keep pace with the growing demands from the defence industry.
“Our continued focus on defence will see us build additional locations in Scotland and also, potentially, move closer to the submarine sector,” Mr Warren disclosed. “Here, it will be all about the people, and ensuring that we have the right teams – colleagues with security clearance – in the right place, when we need them.”
He added: “We can foresee a capacity and a capability challenge in the defence sector. We’re entering into an incredibly busy time for the UK maritime defence sector; there are two shipyards in Scotland moving into full production, plus there’s a new fleet to be built for UK Border Force, the FSS programme and potentially a National Flagship – as well as other programmes. We want to be in a position to support those programmes; we definitely don’t want to build ships, but we do want to support those that do.”
Cruise and ferry outfit works
As we all know, the onset of the pandemic led to a shutdown of the cruise industry internationally. Fortunately, the industry is slowly recovering and getting its ships back into service. In the UK, the epicentre of cruise ship reactivations is Southampton and this has delivered a real ace for The SMS Group, as Mr Warren noted.
“We’re the only ship repairer located inside the Port of Southampton. We’re close to all of the cruise terminals and our expertise here is second-to-none,” he said. “Our welding, fabrica -
tion, pipe and mechanical teams understand larger tonnage, and the requirements onboard cruise ships, and moreover they have specific experience working on them.
We’ve also got a highly capable team working on the interior outfitting of those ships. So we’re able to support both aspects of the cruise ship business. It’s not often that you can put both of these strings to your bow; we’re unique in this sense.”
Speaking of the company’s own response to Covid-19, Mr Warren said the pandemic has not only made the business stronger, but has also reinforced the importance of the industry as a whole.
“The sector has proven to be very resilient and everybody in the industry really pulled together. Harbours had to keep trading because when all is said and done, we’re an island nation, so we upped the relevant safety protocols and we carried on.
“Basing the business around eight geographical locations means that we’d always used Teams to communicate internally, but never really with clients and suppliers. But we’ve learned to do business with those two groups remotely and it’s saved us huge travel expenses and has allowed us to actually communicate better.”
“It’s also brought us all closer together as a general management team; we’ve shared the pain and built the business back together. When lockdown came, lots of companies immediately felt fear – as we all freely admit. But it pulled us together as a team. We set our objectives and got on with it together: something that sets The SMS Group apart is the camaraderie and our ‘can do’ attitude. I’m honoured to be part of the management team – it’s a great company.”
In recent times, the company’s work in the cruise and ferry outfitting space has involved a great deal of investment in facilities, plant, equipment and personnel and those investments are delivering extremely strong results.
“Our outfit business has grown by 100% year-on-year for the last three years,” revealed Mr Warren. “We’ve made investments in premises, people and capacity and we’ve invested in storage space. I think as we move further into the outfit industry, we’d like to consider things like stand-alone premises and the ability for continuous, concurrent working. At the moment we can deliver three or four projects simultaneously, but we need to get to five or six. We need to see continuous progress in our outfit business; outfit is a big part of our future as a group.”
Commercial diving is also a core part of the company’s service offering and one that, again, is earmarked for strong growth in the future through continued investment. The company recently invested in equipment that will allow it to deploy two dive teams simultaneously, and plans are already in place to increase that to three or even four in the not too distant future.
The company’s specialised diving and subsurface engineering team are uniquely security cleared, and have created an opportunity to build a specialist service working on key national infrastructure, which is quite a big deal, as Mr Warren pointed out.
“It’s very different to working on an in-water survey or a fouled propeller/shaft line,” he noted, “You have a higher level of risk, a more challenging degree of preparation, and a high level of security clearance is often required. You must adhere to a more stringent set of rules, with a higher reporting level. It can require months of planning and a tremendous amount of patience, but that’s all part of the job and we’re happy to do it.”
The SMS Group makes use of both traditional divers in the water, and a selection of ROVs to carry out its various diving services and underwater engineering tasks.
“Deploying a man in the water requires a team of five, whereas an ROV only needs a trained pilot, so an ROV can survey very costeffectively,” Mr Warren detailed. “If we can use an ROV then we will do so; it’s definitely becoming more and more prevalent. But if it’s underwater engineering, or works such as a fouled shaft, propellor or rudder, then you need to have a person, (or persons) in the water.”
Of course, carrying out work anywhere requires getting teams and equipment to the site at which they’re required, quickly and efficiently. That’s where the company’s fleet of over 40 specialised road vehicles comes into play. The fleet consists of minibuses, mobile workshops and low-loaders based in various strategic locations.
“To be a ship repairer, you need to be able to repair ships, and that often comes with a moment’s notice,” emphasised Mr Warren.
“Our business is built around a responsive operating model and we are able to – and do – attend ships all day, even in ports that we don’t have local premises. We specialise in these emergency repairs and short-notice response calls; it’s an exciting space.”
Reflecting on the challenges of the past year or so, Mr Norman added: “2020 was undoubtedly a challenging year. That said, we easily kept our head above water and we’ve laid solid, exciting, plans for the future. These will include a focus on cruise and ferry outfit, investment in diving, our continued endeavours in defence, and staying true ourselves and our historical foundations in the commercial ship repair sector.”
Mr Norman concluded: “My sincerest thanks go to both colleagues and customers – our future success is so dependent on both. I can genuinely say that all of our colleagues within The SMS Group have been exemplary in both their commitment and commercial endeavours, and our customers have been both loyal and forthcoming. Thank you so, so much.” n
Azimuth Radio Technologies, headquartered in Cyprus, provides sales and technical support of marine electronics equipment, and services relating to maritime navigation, internet connectivity and security. Having only been established as recently as 2020, the company has flourished amidst a global pandemic. Yvonne Tsanos, Business Development Manager at Azimuth Radio Technologies, spoke to Richard Hagan about the challenges, lessons and victories the company has recorded in only a few years in business.
For some, setting up a business during a pandemic would have been a daunting prospect to say the least. For others, such as Azimuth Radio Technologies, the decision made perfect sense – and so it has proved.
“A shortfall of highly seasoned marine electronic engineers to undertake bridge communication and navigational aid services and supply of spare parts for bridge resource equipment married with the succession and sustainability of such expertise was identified,” said Yvonne Tsanos, Business Development Manager at Azimuth Radio Technologies.
“We wanted to focus on maximising navigational safety, connectivity and security, ensuring the continuous operation of vessels and minimising unplanned downtimes and exposure to threats.”
In an impressively short period of time, Azimuth Radio Technologies, based in Limassol, Cyprus, has generated a high level of customer trust and loyalty as a marine technical support services company steadfast in servicing, maintaining, inspecting, and selling marine electronic equipment to vessels worldwide. Ms Tsanos attributed this success to its affordability, flexibility, and honest, good old-fashioned service, further crediting the company’s human element for their adaptability and proactiveness in delivering those solutions.
“We were able to respond to customer enquiries and deliver friendly, efficient, cost-effective services and results to our clients,” she noted. “Our highly experienced and knowledgeable team of professionals have been drawn from across the maritime industry. Safeguarding
customer loyalty during challenging times was a milestone demonstrating that we were delivering what they sourced in terms of not only favourable pricing, quality of service and reliability but also by building on relationships.
“Despite the challenges inherent in the maritime industry, our support teams harnessed their connections and partnerships within the industry, allowing them to still deliver services remotely, regardless of the time zones in which some of the vessels were operating and global travel restrictions.”
Azimuth Radio Technologies prides itself on the boutique service it provides to its global clients and partners, with the flexibility of a 24/7 service. “No job is too
small,” Ms Tsanos remarked. “And the reality is that equipment can fail at any time, so we are available 24/7.
“Importantly, achieving approval by several classification societies and representing international brands holding a strong market share is also another reason our customers prefer Azimuth,” she added, as further proof, if it was needed, of the company’s credibility and reputation within the market.
Azimuth Radio Technologies’ technicians need to be prepared for anything and everything in terms of the equipment and brands they service, so constant training is absolutely paramount.
“Our service engineers undergo frequent, intense training for all of the brands that we represent, particularly for new equipment as it arrives on the market, but also on legacy equipment that is being phased out and replaced.”
There is added value for the client there , too. By ensuring the company’s service engineers are trained on multiple brands ’ equipment, Azimuth Radio Technologies can save the client money by becoming a single point of call for all their onboard electronics needs as well as being in a position of offering an alternative choice of reconditioned bridge navigation spares allowing a reduction in operators’ carbon footprint and OpEx.
“That’s a much better solution than bleeding a vessel’s budget dry with multiple visits from individual technicians, each representing specific brands,” said Ms Tsanos. “Integrity, transparency, attitude and ethical
best business practices formulate our success, married with being cost conscious and empathetic towards our client’s needs.
“Many clients or their vessel’s command come to us with their problems knowing that we are genuine and resultdriven. We can troubleshoot remotely; this was greatly appreciated by clients during the pandemic where we provided remote support. This and has since transpired into additional enquiries by those clients for physical attendances or spare part sales for their fleets.
Financial pressures relating to the pandemic have forced the downsizing of some service engineer departments at manufacturers, reported Ms Tsanos. That’s been good news for Azimuth Radio Technologies, filling in the gap left behind as it has become a preferred service partner.
IT products and services is an equally important aspect of what Azimuth Radio Technologies offers its clients. With video calling now a part of everyday global life, and the need for upgraded technologies onboard, seafarers have also begun wanting connectivity options with their loved ones back home.
“Video calling and internet usage is a key trend and we’re seeing a higher demand for installations to improve internet connectivity on vessels,” Ms Tsanos confirmed. “The industry is addressing this much
needed requirement. Sailors often experience isolation and disconnection from family and friends and ought to feel closer to home by way of technological opportunities.
“The ability for them to connect with and talk to friends and family back home has become one of the primary incentives for seafarers who are now keen to see this included in their packages to either enter employment or to remain with their current employers,” said Ms Tsanos. “They’ve lived through the isolation, the lockdown situations and the quarantine issues relating to Covid. So that’s made what was once considered a luxury, now a deciding factor for seafarers.
Thankfully, ship owners, she explained, are listening, and connectivity packages are becoming the norm.
“The satellite industry has also played its part, where incredible changes over the last few years have taken place in what appears to be primed for an explosion of growth through the deployment of smaller satellites where commercial customers are using them for flexibility, development speed, resilience and the associated lower costs, thus improving ship’s abilities to connect to the world.”
With improved internet access comes greater security risks and a particular issue today is ransomware, as well as progressively more sophisticated hacking attacks.
“The industry now understands that IT departments cannot be solely responsible for cybersecurity matters,” said Ms Tsanos. “They’re often not sufficiently equipped, experienced or qualified to deal with the
level of potential attacks. Ransomware, cyber threats and hacking are rising and we can assist companies with ensuring protection from these threats.”
Alongside improved internet connectivity, ship operators are generally working to improve the IT infrastructure onboard their vessels. “We’re realising the replacement of older equipment with the supply of new solutions. There’s also been a higher demand for CCTV installations and services.”
CCTV, noted Ms Tsanos, is desired not only for its usefulness as a deterrent for potential criminality but also for monitoring and gathering evidence of onboard accidents or other incidents, for later use during investigations as well as livestream monitoring of cargo operations to shore based teams.
Thanks to its ability to comprehensively meet a broad spectrum of vessel owners’ navigational, electronic and IT needs, Azimuth Radio Technologies has enjoyed impressive growth.
“We experienced 100% growth in 2021, after only operating for 10 months in 2020. We’ve also seen an 80% increase in enquiries in all areas of our operations, whether it’s for services, spare parts, IT or a combination of them,” Ms Tsanos revealed. This growth was partly fuelled by a sizeable portfolio of repeat clients.”
Not only focusing primarily on bridge navigational equipment services and supply of spare parts with annual
surveys, repairs, installations, monitoring and maintenance – the company quickly evolved its service offering to encompass IT network solutions, cybersecurity and connectivity.
On the investment front, the company has created the Multi-Art Secubox, which offers protection against unauthorised access, manipulation or disruption. Ms Tsanos said the Multi-Art Secubox allows owners or operators to act flexibly when choosing specific applications and offers a solid investment return.
“The Multi-Art Secubox is deemed as advanced technology with 4G/LTE equipment giving a connectivity range of up to 100km from the coast, is easily installed and offers multiple benefits in providing a link to the world,” she said.
The company has already ticked off a number of impressive milestones, according to Ms Tsanos, who outlined some of its achievements since the company opened its doors.
“Through our skilled team at our Hamburg office, we’re currently in the final stages of completing a ship to shore network solutions package for a fleet of vessels owned by a reputable ship management company. Meanwhile, we’re also finalising an agreement with another international organisation to include our shipboard cybersecurity solutions package within their existing cybersecurity team.
“We are also proud of the numerous bridge navigational equipment refits we’ve undertaken since opening,” she added. “We completed each of them in record time.
Projects that ordinarily would take anywhere from three to five days, were completed in less time, thus saving the ship owner significant expenses in terms of attendance.”
Looking towards the future, Azimuth Radio Technologies is optimistic. In addition to continuing to refine the comprehensive service for which it has become known and loved, the company has firm plans to expand its operations eastward from its existing locations in Cyprus and Germany.
“We’ve earmarked Singapore as the next location we’ll target as part of our expansion plans,” Ms Tsanos confirmed, adding: “Singapore is an obvious choice as an international maritime hub for the Far East.”
Azimuth Radio Technologies’ people will continue to be a strong focus too, as the company progresses, Ms Tsanos confirmed.
“Continuous professional development is so important and investing in our people is what delivers the best results. As someone once said, ‘You build your people and they will build your company’.”
She concluded with some thoughts on the company’s business ethos: “Listening to our clients’ needs and going beyond their expectations is important to us. We deliver products and services in a friendly and professional manner for an industry that never sleeps. Our integrity, transparency, attitude, our ethical business practices with our never-ending focus on delivering our clients’ needs will continue to drive us forward.” n
As a sector leader in the manufacture of propulsion systems, Portugal’s Fundilusa has set out an ambitious three-year growth plan. While reorganisation, rejuvenation and modernisation are underway, CEO Pablo Gonzalez believes the company is well on track to grow “wider and broader”. Profile by Andy Probert.
Since a group of eight colleagues founded it in 1989, propeller manufacture Fundilusa has never stopped growing and it is safe in the knowledge that its propellers are in use somewhere in the world at this moment.
Within the first decade of the 21st century, Fundilusa’s turnover increased eightfold. With an annual capacity of 900 propellers, 1800 blades and 250 hubs, caps, covers and other components, the company has succeeded in establishing a position for itself as a leader in the marine industry for a broad type of solutions.
“We don’t lose customers,” reflected CEO Pablo Gonzalez, whose father was one of Fundilusa’s pioneers. “We can lose money sometimes, but we cannot lose credibility. That enables you to maintain clients for decades and increase the client portfolio annually.”
Located in the northwest Portuguese town of Campos, close to the banks of the River Minho, Fundilusa has carved out an enviable reputation for its controllable pitch propeller (CPP) and fixed pitch propeller (FPP) systems.
Initially starting out manufacturing monoblock propellers, the company expanded and achieved significant growth as a supplier to the most critical propul -
sion companies globally, such as Schottel, Rolls-Royce (now Kongsberg Marine), ABB, MAN, CAT (now BERG Propulsion), Andritz, Siemens, Steerprop and Kawasaki, among others.
Currently employing a 200-strong workforce, the €22 million company produces FPP solutions of up to 15 tonnes in bronze alloy, with diameters up to 5.5m. The offer includes Class II, Class I and Class S types, fully CNC machined, and a capacity for stainless steel propellers.
Fundilusa also produces blades of up to eight tonnes and manufactures units in Class II, I, Class S in bronze, hubs up to nine tonnes and a variety of other components.
“Clients can suggest technical challenges, and we will rise to the challenge. As a multinational company, we employ precision technology that can reproduce any technical drawing presented by a customer with exceptional reliability,” asserted Mr Gonzalez, who joined the company in 2002.
He added: “We have a team that believes in the same objectives. They are united, and that is vital. Alone you can go very fast, but with a team, you go further.
“We have a spirit of innovation that is focused on the customer and service. We have a drive of continuous improvement, engineering control, and computer cost processes that help the flow and guarantee product quality, and quality of life for our workers and the environment .”
After a year complicated by Covid-19, Fundilusa is now undergoing significant reorganisation and “deep renovation” to help fuel a three-year strategy of continued growth.
Mr Gonzalez envisioned: “We have a target for growth of 15%, 20% and 30% per year for the next three years, with expectations that by 2025 will be a €36 million, 270-strong company.
“Central to this is investment in machinery and specialised human resources. Our objective is to grow wide to gain strategic weight, be broader for our existing clients and new ones, and expand in other markets and products. This is the natural next step of the Fundilusa DNA: to aim even higher.”
He added: “In these times of Covid, we have continued to invest, diversifying with a view to the near future, expanding our capacities by manufacturing stainless steel which is a different process from
bronze and opening up to a range of new markets such as naval.”
The plan will be to establish Fundilusa as the best option in the stainless steel and bronze markets and to adapt to the demand for clean, renewable energies, such as hydroelectric power, in which “we will soon become a world reference,” Mr Gonzalez stated.
He said the strategy would offer an exhaustive range of opportunities that enables a complete solution for the client.
“The aim is to make their life easier. We can see the order, with fewer products, but by being more specialised, focused, and complete.
“We aim to do everything from start to finish with a clear goal. So the client doesn’t have to place four orders in different companies to cast here and machine there. Fundilusa wants to be a strategic partner that sells peace of mind and trust. As in the bronze industry, we want to be considered a safe, stable and easy solution.”
Mr Gonzalez continued: “We are entirely focused on customer service and distinguish ourselves by having long-term business relationships, always looking for an opportunity to provide the best
quality and price in support of business continuity. When the customer needs our help, we are always there.
“We have many clients with up to 30 years’ collaboration as in the case of Schottel. Their problems are ours, and we are not just a supplier, but a collaborator that is one of their team. We pride ourselves on being agile and responsive.”
As a reference to its quality standards, Fundilusa is ISO 9001 and 14001 certified and is working towards its ISO 45001 certification in occupational health and safety management systems.
While challenges are focused on the fluctuating prices of metals and rising
energy costs, necessitating a long, hard look at new options to keep manufacturing costs competitive, the CEO commented:
“We would like to thank Portugal’s government for the help provided to companies that help the economy, drive exports and create employment by looking for more direct aids so we remain competitive in such a market.
“Going back in history, we also appreciate the support provided to my late father and founder of Fundilusa, Pedro Gonzalez, for all his efforts in creating this company. He offered great support
and satisfaction to the families and suppliers that have depended on us over the years.”
Mr Gonzalez said: “In terms of our suppliers and clients, they demonstrate the confidence and years of relationships we have had with them by picking up the phone through good and bad moments, and knowing over decades who was always there.
“Machines and computers cannot do that yet: someone worries about your worries. And when there is an issue,
we ensure clients receive quick and responsible communication. Transparency, honesty and responsibility make a relationship stronger.”
He concluded: “Fundilusa has a life of its own, it is magnetic, it absorbs you, I think it is my father’s energy. Undoubtedly, he is still here with us 20 years after his death. It makes us continue on as young, crazy, brave, and excited adventurers as the original pioneers did. We have an identity and an energy which we seek to continue.” n
HA-Ilarduya is proud to share industry progress, market developments and challenges with Fundilusa, as a preferred supplier of inorganic resins, catalysts and coatings specially designed to optimise the casting of ship propellers, with the highest technology and quality standards.
For further information on our products and services, please contact asier.ibarrondo@ha-group.com
Netherlands-based company CORROSION has grown into an internationally recognised leader providing creative anti-fouling and corrosion solutions for vessels, offshore wind farms, and onshore applications. These sophisticated systems are used worldwide, protecting valuable assets in the most adverse conditions.
Profile by Andy Probert.
Established in 1993, CORROSION has grown from a small unit in Moerkapelle in the Netherlands to become a global player in anti-fouling and corrosion protection, with subsidiaries in Germany, France, China and Vietnam.
Whether it is wind turbines or tankers, metal surfaces exposed to the elements are vulnerable. This can present significant economic cost in terms of replacement or repair, and significant danger in the event of catastrophic equipment failures.
CORROSION has developed internationally recognised sustainable solutions and cathodic protection. The company’s highly sophisticated ICCP and ICAF systems are utilised to protect offshore and onshore assets for the most demanding conditions.
New technologies
Consistent development led the company and its partners to create a non-chemical alternative anti-fouling method utilising UV-C light for the marine sector.
CORROSION’s Sales Manager and UV-C specialist Henk van der Lip explained the company had combined two existing technologies; UV-C light, a superb technology to prevent fouling, and pillow plate technology which provides high-efficient cooling; to create tailor-made UV-C box coolers.
UV-C technology provides complete environmental box cooler fouling protection, even with stagnant water in the box cooler sea chest. The UV-C uses underlying technology based on Philips IP to eliminate fouling growth.
UV-C coolers can be used for both retrofit and new builds. For retrofits, the UV-C cooler is designed to be backwards compatible with the existing box cooler. On new builds, the cooler is custom-designed.
“It is a proud moment for us to develop a ground-breaking system as a marine growth protection mechanism. The innovation is unlike anything on the market and fits today’s needs for sustainable solutions,” commented Mr van der Lip.
“The result is two existing and proven technologies combined in one product which helps increase operational efficiency, reduces costs and limits environmental impact.”
Ultraviolet light in its C spectrum is a green way of protecting the cooler against all types of marine growth and is highly effective in virtually all circumstances. The bulb is mounted in a quartz tube that can endure high pressure, minimising the risk of breakage.
The UV-C light breaks down the cell structure and DNA of all different types of fouling which tend to settle on the pillow plates or in their direct surroundings. As the UV-C coolers are mounted inside the sea chests, they are safe for other sea life and areas within the UV-C light range remain free of fouling.
The coolers are installed in sea chests with inlet and outlets. When a vessel sails, seawater enters the inlet grid and passes through the pillow plates. Here the cooling takes place, and heated seawater exits the sea chest from the outlet grids.
When the vessel is stationary, cooling is achieved by a natural convection flow due to the seawater close to the pillow plates
increasing in temperature. The heat transfer is completed by a controlled flow of cooling liquid through the pillow-shaped plates.
The pillow plate heat transfer technique has a higher efficiency than current tube technique, and has been used for decades across other industries.
Mr van der Lip added: “Since the innovation three years ago, we have installed units on many vessels. Our first installation is still going strong today. One client, who has taken another unit on board, has 400 vessels in their fleet, so there is plenty of potential.
“Depending on the type and size of the vessel, there can be one to 20 cooler boxes aboard. We are interested in extending it to other vessels, such as dredgers and luxury yachts, and are talking to a navy with a view to installing the solution.”
CORROSION is also a world leader in developing solutions for the wind energy sector. Its Impressed Current Cathodic Protection (ICCP) system protects various vital and valuable equipment and structures onshore and offshore.
The company is presently bolstering its presence in key offshore and wind energy sector markets with the appointments of dedicated agents to serve the UK, European, Asian and US markets at a time of rapid growth in the demand for sustainable energy.
“CORROSION is proud of its reputation as a partner with a truly global reach and local expertise,” said Bart Wessels, Chief Commercial Officer. “Through these new appointments and our unique ICCP systems, we will be able to help companies become more eco-friendly and protect vital infrastructures.”
ICCP is a protection system that consists of Mixed Metal Oxide (MMO) coated titanium anodes connected to an external power
source. This power source provides the current that leads to the electrochemical reaction required for cathodic protection.
Mr van der Lip said ICCP, as the most cost-effective, easy-tomaintain and environmentally friendly solution, presently helps protect over 2,500 offshore wind turbine foundations.
ICCP requires only a limited number of ICCP anodes and sensors to work effectively for more than 25 years – well in excess of the life of a wind turbine. As a result, the same system can continue to be used even if the offshore wind farm’s lifetime is extended.
Another advantage is that they are equipped with a standard feature to take data readings. Adjustments can be made from an offshore wind farm control centre rather than having to do so on location.
Recently, CORROSION was commissioned for 80 transition pieces to be built and assembled at Antwerp’s Smulders yard as part of the Saint-Nazaire wind farm. During this phase, the ICCP system and anodes will be installed and then be transported to France and become part of the wind farm off the coast of Saint-Nazaire.
“A typical offshore windfarm consisting of 80 monopile foundations will dissolve about 1.5 million kilograms of this aluminium alloy into the ocean over 25 years,” revealed Mr Wessels. “In addition, the carbon footprint of manufacturing these sacrificial aluminum anodes should be considered while evaluating a cathodic protection system.
“In the same application, a CORROSION ICCP system will release only 1kg of material into the ocean. Truly the ICCP system is the only green solution for corrosion protection in offshore wind energy.”
“We keep in close contact with clients through a strong agent network,” said Mr van der Lip. “We listen to them and provide data feedback to clients so they are completely aware of the solutions in action. If there is a problem, we can react quickly.”
Playing an essential part of the business is CORROSION’s unique research laboratory at Moerkapelle.
“While we have a sound reputation and proven products, we strive to pioneer in ways that go beyond theory and ideas,” he said.
“Our lab is an ideal place to test and continue our mission to bring the most sophisticated, high-quality products and services available in cathodic protection and anti-fouling technologies for the long term. The lab really differentiates us within the market. This is the place where we build on our many years of experience and expertise.”
Mr van der Lip acknowledged that 90% of CORROSION’s products are exported, with the offshore and maritime sectors claiming an equal split in business.
“We are continuing to grow, particularly in the offshore wind business, and we tend to export mainly to Europe and Asia,” he said. “We are a company with a lot of experience and good service, create products in line with the environment as a priority, such as the UV-C Cooler. Because we are highly specialised, we can offer highly detailed knowledge to clients.”
He concluded: “Our laboratory can further unlock that potential as there are still huge opportunities to maximise CORROSION’s influence within its chosen markets.”
seven seas, five oceans, one voice
subsea environmental services erma first green maritime technology hug engineering kraftpowercon
Subsea Environmental Services is an independent environmental marine company that safely removes and recycles thousands of telecommunications cables from the bottom of the world’s oceans. Co-founder John Theodoracopulos revealed how the removal of man-made material from nature is being re-purposed. Profile by Andy Probert.
Removing out-of-service (OOS) telecommunications cabling from the seabed has become a highly specialised art for Subsea Environmental Services (SES), a privately-owned New York company.
SES purchased its first coaxial cable in 2012 and commenced marine operations in 2014. Since then, the company has completed 26 missions and recovered 30,000km of submarine cable, more than any other party during this period.
That equates to more than 50,000 metric tonnes of man-made material, which has been successfully re-introduced into the world’s supply chain. This material includes ferrous metals, non-ferrous metals and plastics, all of the highest quality.
“But only a small percentage of the out-of-service telegraph, coaxial, and fibre optic cable has ever been recovered to date, and every year more systems are being laid on the seabed,” said SES co-founder and Managing Partner John Theodoracopulos.
Hence, SES has quickly evolved from a promising concept to a viable, sustainable business. As new technology develops, making older systems redundant, these OOS cables present a significant opportunity for recycling, given their constituent high-grade materials.
“The removal of obsolete cable systems from the world’s oceans is also an excellent example of environmental stewardship and demonstrates our corporate responsibility,” he added.
SES was built on the extensive experience of cabling professionals who spotted a potential gap in the market. “In the course of looking at a new project, we looked at route clearance in bringing out old cables, and we looked at what residual value they may have,” he said.
The company scaled the business up using a highly modified 55,000 DWT general-purpose vessel with a single hold containing five cable tanks to spool in and store recovered cable.
“There is no playbook here, no guidelines, so we started carefully and have retained captains, crew and winchmen, who understand the capabilities of the vessel.”
Mr Theodoracopulos said: “For every tonne of material we retrieve from the ocean floor and re-use is a tonne less of raw material being sourced and extracted to achieve the same goal. It helps offset the earth’s dwindling natural resources.
“Recycling these cables is both a viable and intelligent proposition while also demonstrating marine environmental leadership. Additional benefits include a significant reduction in CO2 output when compared to the production of similar materials from virgin feedstock.”
Re-introducing valuable, high-quality materials from redundant submarine cables also allows SES’ clients to demonstrate a smarter, responsible approach to managing their carbon footprints and green agendas.
Mr Theodoracopulos said experts are presently validating its extraction achievements to demonstrate their positive impact on the planet.
“As the company has increased its capacity, we wanted to dig deeper and find out what it all means. But we’re proud with what we have accomplished: 50,000 metric tonnes is just the start and will reap benefits to the global marine eco-system.”
He added: “90% of our work has been in the Atlantic basin and the Mediterranean over the last six years. As we acquire more assets across the planet, we want to be able to deploy more resources, but it requires the right vessel, equipment and crews.”
Depending on the location of its mission, the vessel offloads its cabling cargo across the world, including Egypt, Panama, the Netherlands, Portugal, and the Bahamas, where the cable is shipped overland to a processing facility or transferred to another ship to be taken elsewhere for recycling.
Mr Theodoracopulos, who has 30 years of experience in the marine and telecoms industries, explained that SES essentially
acquires portfolios of end-of-life cabling direct from the telecommunications companies.
SES does extensive research to identify the cabling routes and marine operations required to ensure an efficient and safe conclusion to individual projects.
“We acquire a depreciated asset and remove any potential liability. We recover it from the seabed and recycle the material ourselves, through a partnership or under contract. And then we sell the cable or the material,” he elaborated.
“As we increase our capacity, we want to get as close to our endusers as possible. We retrieve 10,000 tonnes a year of material, broken down between ferrous, non-ferrous and plastics. Almost 99% we recover is recyclable and recycled, so there is a very high yield on that material.
“We want to increase that capacity by as much as three times in the coming years and get as close to the end-users, and do away with the middle-men.”
We have built up an excellent reputation in the sector, and our clients trust us to do what we say we are going to do
Mr Theodoracopulos continued: “SES is one of only a handful of companies within this niche. There are specific cables that have certain materials and have to be disposed of in a certain way, and that’s what we do.
“When you look at popular cabling routes, they are extremely crowded, and cables often lie on top of another. In one region, we acquire cables from different eras and then remove them in reverse order to increase our yield. As we have got better at what we do, we have refined our processes.”
The key to the company’s success is consistently applying best-inclass risk management procedures, from planning and peer review through all phases of the physical cable recovery operations.
Carrying over 95% of the world’s data and voice traffic, the global submarine cable infrastructure is the keystone of our modern world economy. Maintaining its integrity is a core principle of SES.
Combining an experienced team, best-in-class technical and operational management, market-leading third party suppliers, and innovative customers allow SES to deliver focused turnkey projects on a global scale.
Recovery of OOS cable systems requires strict adherence to a core set of risk management procedures at all planning and operational levels. SES applies all applicable International Cable Protection Committee recommendations, for the recovery of OOS submarine cables, as the basis for its risk management procedures.
SES is also certified to ISO:9001 and ISO:1400, so maintaining a high degree of transparency and a responsible approach to manage cable recovery operations.
Concluding, Mr Theodoracopulos said: “We have built up an excellent reputation in the sector, and our clients trust us to do what we say we are going to do. We have kept the vessel operating throughout the pandemic, and that consistency has enabled us to demonstrate we are extremely serious in our work.”
ERMA FIRST, a leading Greek maritime-focused engineering group, has continued to evolve at pace during the pandemic by successfully transitioning to become a multiplatform solutions provider with the concerted aim to protect the environment. Having made two key acquisitions, including oneTANK, the world’s smallest ballast water treatment system, the company is now poised to launch BLUE CONNECT, an alternative management power system for vessels. By Andy Probert.
Greek maritime engineering company ERMA FIRST has gained an excellent reputation as an expert manufacturer and installer of ballast water treatment systems in the last decade. Having more than 3,000 units aboard vessels, it has been at the forefront of a fast-maturing niche market given the imposition of IMO and USCG rules on environmental protection.
While the company enjoyed a 20% uplift in BWT business in 2021, ERMA FIRST has also demonstrated its adaptability in a relatively fast-moving market.
“We completed two acquisitions, launched a new product and have other plans in the pipeline reflecting a strategy and desire to become a multi-product, multi-market player,” confirmed Managing Director and co-founder Konstantinos Stampedakis. “We are not afraid of change. We embrace it.”
Piraeus-headquartered ERMA FIRST was established in 2009 with its first generation BWTS certified in 2012 and onboarded to 50 vessels. Its second-generation FIT system was launched and installed on 2,100 ships, ranging from luxury yachts to crude oil tankers.
The company expects to see BWTS installations hit a peak of 1,000 vessel installations in 2022, compared to 800 units in 2021 and 420 installations on 320 ships in 2018.
The system was the first full flow electrolysis BWTS vendor worldwide to be granted United States Coast Guard (USCG) approval. A second USCG citation followed in 2020 for its third filter alternative by adding HYDAC filters to its range of options.
Tested in three water salinities, the FIT system offers a reliable, simple and effective solution for all types and sizes of vessels. Covering an extensive capacity range from 50 to 3,600m3/hr, FIT’s primary components are a high-end backwash filter and an electrolytic cell.
A self-cleaning automatic screen filter has a nominal filtration rate of 40 microns. It offers enormous zooplankton, phytoplankton and sediment removal, minimum pressure and uninterrupted, long-lasting operation on a small footprint element.
ERMA FIRST introduced several advancements to FIT in 2021 to aid efficient installation on larger vessels and tankers. It also launched a remote monitoring system operation for the system, with embedded artificial intelligence for data analysis collection.
While the company, which employs 200 people across Piraeus and offices in Korea and China, has continued to keep pace with BWTS demand from international clients, it also consolidated its business standing with expansion and acquisition in 2021.
Its first acquisition was Bremen, Germany-based marine water specialist RWO GmbH. RWO provides water and wastewater treatment systems for ships, ports and offshore installations and is a market leader in bilge water separation systems.
RWO’s product portfolio includes the treatment of drinking and process water, bilge oil water, ballast, wastewater, and a comprehensive range of after-sales spare parts and services. Over 16,000 ships have been equipped with RWO’s oil water separators since 1975.
Mr Stampedakis commented: “In RWO, we acquired a world leader in water treatment systems for the shipping industry with a solid customer base and a reputation for excellence and reliability. Such acquisition makes ERMA FIRST one of the biggest marine equipment suppliers when it comes to the installed basis which is in the range of 20,000 vessels.
“We have a track record of innovation with our ballast water technologies and are well known for our high-quality engineering and customer-first ethos. We are committed to building on RWO’s experience and to help take the company, its products and people to the next level of international success.”
ERMA FIRST then followed this with the acquisition of oneTANK, the world’s smallest and easiest to install ballast water treatment system. US-based oneTANK was a subsidiary of naval architecture and marine engineering firm Glosten and had developed a small scale innovative, low-cost, IMO Revised G8 Code and USCG approved compliant system.
The system can be installed in larger vessels’ aft peak tanks based on a patented mixing technology developed by the US Geological Survey. It is also suitable for workboats, tugboats, semi-submersibles, fishing vessels and superyachts.
The technology is already being adopted on ships in aft peak tanks within Overseas Shipholding Group’s tanker fleet and the dredger MV Charlock in the Netherlands.
“This is a game-changing ballast water treatment technology,” declared Mr Stampedakis. “oneTANK is compact, simple to use, and fully automated. It delivers a quick to install additional solution for after peak tanks on big ships and a stand-alone solution for small vessels.
“To win the battle against invasive marine species and effectively protect our vulnerable marine eco-systems, ballast water from internationally trading smaller vessels also needs treating in a way which is practical and economically viable. We believe we have this solution in the form of oneTANK.”
The system treats ballast water within the vessel’s ballast tank and has no filters, ultra-violet lamps or electrolytic chlorine generators. Its footprint is only 600mm x 600mm, half the size of its nearest competitor, and power consumption is similar to that of a household washing machine.
oneTANK provides a ballast water management solution that works in all water qualities and salinities. The system uses an 8.25% or 12.5% sodium hypochlorite (bleach) and 30% sodium thiosulfate solution – readily available chemicals from suppliers worldwide.
Application is practical for smaller vessels as a 20-litre container of 12.5% bleach will treat approximately 288 cbm of ballast water. For larger vessels, oneTANK can treat tanks as large as 4,000 cbm.
ERMA FIRST has since announced it would be supplying oneTANK to Damen Green Solutions, the Netherlands-based shipbuilding and engineering expert. Damen has a broad selection of BWT systems in its range, and the addition of the ERMA FIRST oneTANK will provide its clients with a solution that is small and modular.
He explained: “oneTANK is small enough to be housed in a 20ft container. This means installation is quite straightforward and, more importantly, at the end of the vessel’s operational life, it can be removed and installed on another vessel.
“The system is a game-changer for the target vessels with space limitations, struggling to comply with stringent ballast water regulations. For ERMA FIRST, it opens a completely new and exciting avenue of business opportunity and potential in the BWTS niche.”
The recent acquisitions complement the 2019 takeover by ERMA FIRST of METIS Cyberspace Technology, previously owned by Olympia Group.
METIS specialises in electronic engineering, IoT, cloud computing and artificial intelligence, offering a platform that enables shipping companies to acquire and analyse data to improve performance over a wide range of operational aspects.
The innovative METIS platform uses cloud-based virtual personal assistants that work ceaselessly to provide in-time information, diagnosis and prediction to company personnel through a conversational user interface focused on the requirements of shipping companies.
METIS’s expertise is complementary, offering an extensive added value to ERMA FIRST’s. With technology playing an increasingly critical role in every aspect of the industry, both companies recognise the need to accelerate the development of green digital solutions to ensure they remain competitive.
Mr Stampedakis revealed the company has also launched ERMA FIRST BLUE CONNECT, an alternative management power system. It is a containerised solution installed on the vessel and can be connected to shoreside electricity sources when in port, helping them reduce environmental impact.
He explained: “There are many localised regulations in ports worldwide that do not allow a vessel to burn any fossil fuels while it is in berth. Instead, the port offers a shore power connection. But to connect with an alternative power source, a vessel requires something like BLUE CONNECT that allows this connection.”
The concept of cold ironing, another definition of the alternative management power system, is not new and has been helping ships reduce their direct carbon emissions and comply with local air quality regulations. However, the increasing amount of renewably generated electricity now available on port electrical grids means that plugging into shore power really can be carbon neutral.
Every ship operator is facing the challenge of reducing their carbon footprint and increasing energy efficiency. Cold ironing offers a way of achieving this. Plugging into shore power and switching off engines also means less noise and less local particulate pollution for local port communities.
BLUE CONNECT was officially launched in November 2021 at a conference in Greece after extensive R&D trials were completed. It will initially be offered to the container, RoRo, cruise and tanker sectors.
BLUE CONNECT will provide Onshore Power Supply (OPS) systems suitable for retrofit and new-build vessels. It will be available within a container or as a stand-alone system with components installed at a convenient onboard location.
“We have received many enquiries for BLUE CONNECT, and we are hopeful that we will sign a couple of projects that will act as a pilot so the unit can perform, it can be reviewed and any design changes handled before mass production,” said Mr Stampedakis.
ERMA FIRST has also initiated R&D projects for three new products, including one for carbon capture and storage, which Mr Stampedakis described as the next big challenge facing the shipping industry.
“Challenges, such as the global supply chain issues around electrical and electronic products, and spiralling raw material cost, are being faced. But due to good planning and stocking equipment, and support of loyal suppliers, we are managing. If this situation does not resolve itself by the end of 2022, we will plan accordingly to continue to meet the high demand of the market.”
Mr Stampedakis said: “Given our financial sustainability, bringing on board two new companies and their products, and with BLUE CONNECT, we believe we will remain strong in the market.
“As for green sustainability, we are trying to measure the carbon footprints of our products in their lifecycles, trying to find ways of reducing the transportation mileage of the products, and we are also initiating a procedure of improving our packaging, either through wood or recycled materials.”
Never a company to stand still, ERMA FIRST, said Mr Stampedakis, is always looking to improve its products, making them more efficient – both cost-wise and performance-wise.
“We are committed to clients; we still manage each project uniquely with a dedicated project manager and team,” he said.
“We are not afraid of investing in new products or investing in products for the marine environment. It makes ERMA FIRST a one-stop solution for many ship owners for wastewater or water treatment onboard the vessel.
“What defines us is our can-do attitude, dedication and open relationships with clients. We will do all we can to deliver, meet their needs and find a solution to any challenges they have.”
He concluded: “We do believe when it comes to ballast water and oneTANK we can provide for every type and size of vessel. By investing in RWO, we have more than 20,000 vessels equipped with our products.
“ERMA FIRST is shifting its profile from a single-product, singlemarket company to a group of companies, with multiple products. We consider ERMA FIRST is now one of the strongest on the market, with a consistent focus on quality marine protection.”
As the marine industry continues to square up to its responsibilities on sustainability, companies such as Green Maritime Technology are only too willing to provide innovative solutions to help ship owners and operators. Focused on marine engineering and naval architecture services, GMT offers concept to installation, with Managing Director Pantelis Avlonitis asserting: “Tackling the challenges of environmentally friendly shipping operations is our mission.” Profile by Andy Probert.
Established in 2014, Green Maritime Technology was, as the title hints, set up to address a growing need to provide environmental solutions and consultancy services to ship owners.
“With our design and engineering experience, we decided to focus on providing green, as we saw a need in the sector,” commented Managing Director Pantelis Avlonitis. “Our innovative
approaches seek to improve shipping’s environmental performances and lower their operational costs.”
Grown rapidly
GMT’s services cover a wide range of engineering fields, notably 3D modelling, 3D laser scanning, design and implementation services, retrofitting feasibility and engineering studies, such as ballast
water treatment systems and scrubbers, and new build designs.
With offices in Athens, Greece, and Limassol, Cyprus, GMT has accumulated nearly 170 clients, 60% from Greece and 40% from abroad. On the project side, the almost 50-strong workforce has completed in excess of 320 projects, 560 3D scan surveys and over 600 vessel assessments.
“We have grown quite quickly since our start-up, with 2018 and 2019 notably posting growth of 40%,” reflected Mr Avlonitis. The company has continued stable growth across the pandemic, but plans to open an office in Miami, Florida, to cater to the cruise sector have been put on hold until the global industry recovers.
Notably, GMT has completed 1100 retrofit ballast water system solutions for a host of vessel owners.
“A recent industry survey estimated about 35,000 vessels have yet to be fitted
with either scrubbers or ballast water treatment systems,” reported Mr Avlonitis. “So the next two years will be hectic, and GMT is very keen to offer its services.”
GMT’s projects have been mainly focused on tankers, bulk carriers, container vessels, general cargo vessels and cruise vessels. It is expected to complete around 350 projects in 2022 compared to 200 in 2019.
“We have also developed excellent relations with two major companies; EcoSpray for their high-tech scrubber solutions, and Wärtsilä Voyage,” acknowledged Mr Avlonitis.
“When GMT began, it was more focused on the systems’ designs. But now we have expanded, and we can offer the complete installation of a BWTS. Offering an excellent combination of design, engineering, fabrication and installation means a client can come to us for the entire process.”
GMT’s teams are usually deployed onboard and carry out installations during sailing and finish within a 10 to 12 day timeframe, without impacting or interrupting the vessel’s voyage.
“Our teams have also travelled to Turkey, the Netherlands, South Korea, Portugal and the Middle East to complete the projects,” Mr Avlonitis said. “These jobs are done in collaboration with quality sub-contractors worldwide.”
He added: “We are one of the few companies that can complete onboard installations and have finalised many projects. We optimise the design to ensure a rapid and trouble-free installation of the ballast water system.”
The company is also concerned with the research and development of new technologies concerning IMO regulations on fuels, studies, assessment and design of mid-ship vessel expansion, vibration and modular analysis, resultant modification proposals and solutions in container ships, and conversions from bulk carriers to container capacities.
GMT conducts 3D scanning and modelling for component arrangement and piping of competing systems, pre-selected by the owner. A clash detection process is performed for every system to minimise the interference with existing structures and outfitting arrangements.
A detailed feasibility report is also delivered as part of the package, and after a system’s selection, an engineering study
is conducted moving forward to completing the installation process.
GMT also offers solutions for energy efficiency improvement, with the 3D design of ESDs via advanced systematic CFD calculations and modification options ranging from propeller hub cap fins, inflow improving ducts and pre-swirl stators.
“We are continuing to expand our expertise in other areas, and we hope to bring those to the fore during 2022,” added Mr Avlonitis, noting that the aim was to continue to attain double-digit growth.
“We do expect growth to continue in the next two years on the BWTS and scrubber side of the business, and from 2023 we expect more focus on the environment and emissions, something that will significantly affect the maritime industry.”
He said: “We have enjoyed 25-30% growth per year and up to 40% over the pandemic period. We carried out many investments when we started GMT, such as buying four advanced scanners.
“When we started GMT, we didn’t have any loans, so there were no problems with the banks. GMT is a €6 million turnover company and operates in a very financially-secure environment, even with the impact of Covid.”
He added: “Considering the impact of new regulations, we see growth opportunities in key areas like cold ironing, 3D printing, and solutions to comply with
EEXI and CII. We plan to achieve these through strategic partnerships with key industry stakeholders to provide solutions to our clients.”
He commented: “One focus is to continue developing collaborations with important manufacturers worldwide on new products. We are also investing in new designs and plans to bring forward patents in innovative technologies for the benefit of clients and the wider industry.”
Mr Avlonitis confirmed finding the right qualified employees remains a challenge in advancing GMT’s mission and expanding the company.
“It’s obvious you need proper engineers to expand your service profile, but it is a problem faced by many companies worldwide. We believe we have the right mentality and background to offer highquality services to clients.”
Mr Avlonitis said he is of the strong opinion that it is better to offer exceptional service and work with specific owners, than to expand services too much and have a lot of clients with the sole aim of increasing profitability.
“GMT’s position in the market is very strong with robust client relationships underpinned by open and honest communication. Because of our company structure, a client can pick up the phone and talk to anyone within the office and will get an answer to their questions immediately.
“Direct communication and a 24/7 response are important to us, but we also follow up and offer after-sales support. We don’t just walk away when a project is finished: Green Maritime Technology wants to encourage a continuous and harmonious working relationship with clients over the long-term.”
GMT, confirmed Mr Avlonitis, prides itself on the personalised services it provides.
“We don’t operate on the one solution fits all approach, and tailor services to their needs. I think this, along with a prompt reply and on time delivery, is a key to our success.”
He went further: “Irrespective of whether i t is a client or a supplier we are dealing with, the fundamentals of creating a good relationship and maintaining that over time are pretty much the same. Most importantly with all stakeholders is to make them feel we are part of the same team, and we are all working towards the same objectives and deliverables.
“With suppliers, it is important to communicate effectively, making sure they understand the scope of work and what our expectations are in meeting all deliverables on time at the agreed cost.”
At GMT, the company’s commitment to sustainability goes beyond ISO 9001 and 14001 certifications.
“ We are committed to the development of our people, both as professionals and individuals,” underlined Mr Avlonitis.
“As a service provider, we are not
directly involved with improvements in environmental performance. But we are very proactive in our mission towards helping our clients achieve better environmental performance through our engineering designs.”
Whether it is a design of BWT systems, scrubbers, or onboard installation of a BWTS, GMT’s recommendations always take into consideration the resources and carbon footprint of different solutions.
“We then work closely with our clients to convince them on the merits of more environmentally sustainable solutions,” he said, adding that, in his opinion, he can see the
maritime industry being transformed from a traditional and conservative industry into one that is willing to adopt new technologies and innovate.
“While the transformation does not come free of charge and investment is required, we see more and more clients adopting ESG strategies considering the challenges of today’s fast-developing world and emphasis on the environment.”
He concluded: “Digitalisation and decarbonisation are trends of the present and the future, and GMT, as a company, is adapting to the new reality by using solutions to help our clients achieve their strategic objectives.”
Since its establishment in 1983, Hug Engineering has been leading the path to a clean tomorrow by designing, engineering, producing, and the commissioning of custom-built exhaust emission control systems for marine, power generation and rail applications. From its high-tech headquarters in Elsau, Switzerland, near Z¨urich, the company leads a global network of offices supplying and servicing customers wherever they are in the world.
Increasingly tight emissions regulations have brought in a steady stream of new clients to the company. Lukas Cavegn, Product Line Director for Marine and Mobile, explained how Hug Engineering caters to each customer’s unique demands. Report by Richard Hagan.
Emissions and global warming are a major global concern, and will likely remain so for decades to come. As the world grapples with finding answers to the crisis, bodies such as the European Union are pushing forward with ever-tightening emissions regulations.
The automotive industry was one of the first to respond in a meaningful way, and on a commercial scale, to the need for
lower emissions. We have seen an increasingly fantastic parade of plug-in hybrid and full electric vehicles coming off factory floors, delivered sometimes in spectacular launch events and high-budget promotional videos on a and offline.
The marine industry, meanwhile, has, it is fair to say, lagged behind all this progress.
Mercifully, that is all now changing, and at a rapid pace. Increasingly strict
emissions regulations for the shipping industry are being signed and ratified and ship owners are finally realising that it is time to either adapt or sink.
Luckily for ship and yacht owners, a specialised company with highly qualified engineers is working on cutting-edge emissions reduction solutions (and associated high-tech systems) to ensure that these vessels are able to meet and exceed global legislative requirements, as well as even more stringent voluntary emission labels. That company is Hug Engineering.
Hug Engineering was established in 1983 by Hans-Thomas Hug. Shortly after that, Michael Hug, his brother, became his first employee. Initially offering general engineering, they soon identified an opportunity to become involved in not only designing but also producing at that time non-existing components for high horsepower exhaust systems. In 1988, they commissioned the first ever urea operated SCR system at a combined heat and power installation in Schaffhausen, Switzerland. A few years later in 1992, they installed their first marine exhaust system and, from there, growth came quickly.
By 2003, Hug Engineering had grown enough to open an office in Germany. That same year, Hug Engineering tackled a large government contract to supply Diesel
Particulate Filter systems (DPFs) to the Swiss Governmental Railway for 100 locomotives involved with tunnel construction.
Only two years later, in 2005, Hug Engineering got its big break into the superyacht industry when it began working with Kusch Yachts to install DPFs.
Meanwhile, to ensure that it had the resources on-hand to supply and service its growing client base worldwide, Hug Engineering founded a sales and service office in Italy in 2007, another in the United States in 2010, and in 2016 an office in the Netherlands (by buying the COdiNOx Beheer BV company).
In 2016, sails were set for even more marine activities, when the IMO TIER III emissions standard came into force for vessels sailing in emission-controlled areas, by offering reliable and high value solutions in combination with all the required certification services.
The company’s hard work and continued growth were further rewarded in 2018 when Hug Engineering was acquired by a French automotive conglomerate called Faurecia. As part of Faurecia’s Clean Mobility business group, rapid advancements in Hug Engineering’s product range were made, with a particular highlight being the first EU Stage V certification of a medium speed engine, achieved in 2020.
Less than one year later, Hug Engineering introduced its Compact SCR system, tailored to the needs of yachts below 500gt, switchable between IMO II / IMO III and
fitting in any, even extremely space constrained, engine room. This outstanding solution was enabled by the long-term inhouse development of catalytic coatings, ending in the all new high performance CCV catalyst.
Azimut|Benetti, world leader in the production of super yachts, was the first shipyard to announce an agreement with Mive Eco for the supply of exhaust systems equipped with this compact Hug Engineering SCR system.
Today, Hug Engineering employs around 250 people worldwide. All the company’s research and development, as well as most of the production, is carried out at its headquarters in Elsau, Switzerland. Its four subsidiary offices in Germany, Italy, the Netherlands and the US are sales and service hubs with project management capabilities close to the customers.
Hug Engineering prides itself on its ability to provide a comprehensive suite of exhaust treatment solutions, including products and related services that are required by clients.
Whilst competitors often only supply certain components and then lean on third parties for the remaining products and services, Hug Engineering retains every aspect of its product offering in-house. According to Lukas Cavegn, Product Line Director Marine and Mobile, that is a real selling point for the company.
“It’s very seldom in this industry to have all of the functionalities and competencies t hat we offer under one roof,” he said. “We’re a true one-stop shop, and our combination of know-how in a single service provider really sets us apart.
“If you have an issue, for example, needing to meet an emissions regulation, then we do the engineering, design and certification of the system. We then manufacture it, commission it, and once it’s installed, we carry out its full life services via our skilled service engineers. This is supported by Hug Connect, our remote digital solution bringing any of our aftertreatment systems to display, no matter if it’s a current new build or a retrofit of a long serving installation.
“Having all of this within the company allows us to provide the most efficient service thanks to short communication paths and total quality control.”
The company’s assets are the combination of highly skilled specialist staff and high-tech equipment to design, manufacture, install and service its products.
“Our people are our most important resource,” Mr Cavegn confirmed. “Thanks to them, we are able to develop everything we need and ultimately come up with the most comprehensive and efficient solution for the customer. Additionally, we have the sales teams at our global offices who keep us close to the customers and ensure that we always fully understand our client’s needs.
“These teams are working in our cutting-edge facilities,” explained Mr Cavegn. “We have substantial Computational Fluid Dynamics capabilities through Faurecia, as well as a materials lab that handles the ceramic core development for our catalytic converters. Our quality control labs have scanning electron microscopes as well as other equipment.
“Finally, we have a testing lab with small diesel and gas engines to reproduce real-life conditions and to test performance characteristics of a full system, in a scaled-down manner.”
Hug Engineering is extremely active in the superyacht industry, which itself is enjoying an unprecedented boom period that is showing no signs of slowing down. New build yachts and used yachts are being sold at record prices and within remarkably short periods of time. All of this has increased the tempo of new orders flowing into the company’s offices and required its teams to quickly adapt to the pace.
“It’s been quite a steep learning curve for us,” said Mr Cavegn. “While the increased demand in terms of the regulations, class approvals, certifications and paperwork are substantial, our big advantage is simply that we’ve done a great deal of those in the past. It means that, beyond providing our normal bouquet of services, we are also able to provide certification services and that’s been very well received by our customers.”
The company is very proud of a solution its teams developed in collaboration with the superyacht builder Lürssen, and the silencer manufacturer Niessing, in Germany The KeSS system, as it is called, is a highly integrated, extremely compact superyacht exhaust aftertreatment system that integrates the silencer.
“We saved around 40% of the space typically occupied by a system like this,” Mr Cavegn underlined. “It enables Lürssen to design a much more compact engine room.”
Hug Engineering’s speciality is designing, building and installing bespoke solutions. In addition, Mr Cavegn underlined this level of customisation in the superyacht
sector comes at the increasingly high time cost of administrative paperwork to obtain the necessary certifications.
To address this area of conflict (providing the most stringent certifications while maintaining the industry leading custom isation flexibility), Mr Cavegn confirmed the company is further modularising its solutions. This means developing a portfolio of pre-certified, core solutions that can simply be tweaked to suit various applications.
“We foresee a challenge with this in terms of satisfying the certification bodies such as Lloyds Register, because they’re not used to certifying a toolbox of functions,” he said. “With this, our aim ultimately is to be able to put systems together like Lego, using pre-certified function blocks.”
He concluded: “By doing so, we can leverage our efforts by selling higher numbers of certified core functions but still serving the low number niche with highly flexible solutions. That is why engine manufacturers have a great interest in developing their niche solutions based on our well-proved portfolio of functions which leads to low development costs and unmatched time to market.” n
Electronics manufacturing specialist KraftPowercon, based in Sweden, provides a range of power solutions that include systems to treat ballast water in commercial vessels. Despite already being one of the top suppliers for ballast water treatment solutions and the market leader in its industry across major markets including the United States and Europe, it continues to enjoy double-digit growth. Product Manager Goran Stenmark and Tommy Rochhausen, Business Unit Director – Marine, chatted to Richard Hagan about the secrets to its success in this niche industry.
With almost 100 years of history behind it, KraftPowercon is no newcomer to its business.
From its headquarters just outside Gothenburg in Sweden, and powered by a global staff roster of over 450 people, it develops and produces a range of solutions specifically geared for the transformation of electricity. Its products manage and secure electrical processes across a wide range of industries and applications such as commercial ships, nuclear plants,
renewable energy projects, and general industry.
While much can – and indeed has –been said about those other industries, Goran Stenmark, Product Manager at KraftPowercon, was keen to highlight the company’s exciting work in the marine industry specifically.
“The focus of our business unit is on the marine industry, where we generally supply solutions for powering the systems or technology sold by our OEM customers,” he said.
One of KraftPowercon’s latest innovations for the marine market is ECKraft. This air-cooled rectifier, developed especially for ballast water management systems, is a category that KraftPowercon specialises in.
“We are proud to announce that ECKraft has now been type-approved and launched to the market,” Mr Stenmark declared.
“Currently, our customers are busy with the next step of the process which is including ECKraft in their systems, after which they
will be able to start using it. We’re now at the stage where a number of new customers have already selected it as their preferred alternative, so it’s very exciting.”
Whilst confirming that the market for its products is relatively niche, the company has experienced remarkable success with the potential customers that KraftPowercon has demonstrated the product to.
“The potential market for the product is very limited, but we’ve focused on speaking
to as many potential customers as we can, and we’ve been extremely successful in terms of the number of customers who we’ve attracted,” Mr Stenmark revealed.
In the ballast water treatment industry, two of the most popular solutions are either UV treatment or electrochlorination.
KraftPowercon exclusively focuses on solutions for the latter.
“Electrochlorination (EC) involves splitting water molecules into sodium hypochlorite which we use to disinfect the ballast water,” explained Tommy Rochhausen, Business Unit Director – Marine. “In vessels with higher ballast water loads, the preferred solution tends to be EC whereas vessels dealing with lighter loads often prefer UV treatment systems. The acquisition cost of UV systems is lower but they require higher maintenance costs, so it’s a trade-off that depends on the size of the vessel and its ballasting loads.”
Mr Stenmark, meanwhile, emphasised the relative complexities of UV systems versus KraftPowercon’s more straightforward EC solution.
“UV systems require that you need to reach every single drop of the ballast water with your UV light in order to ensure that the whole volume of water is treated,” he explained. “That makes it much harder to scale up the system’s treatment volume because you end up having to add more and more UV systems in parallel, making it expensive and time-consuming. An EC system is easier to scale because the process produces the treatment chemical that you simply pour into the ballast water flow, and from there, it spreads automatically.”
In a challenging market that exists almost exclusively as a result of environmental legislation, KraftPowercon is nevertheless enjoying major success with its EC systems.
“Vessel owners are not very keen to spend a lot of money on ballast water management systems,” Mr Stenmark confirmed. “We rely on our customers’ sales efforts and we’re fortunate that their strategies are working because we’ve enjoyed a really great number of sales in the past year. We’ve had a record year in terms of revenue.”
Meanwhile, the company is seeing increasing activity in systems for hydrogen production, decarbonisation in the marine industry, semiconductor manufacture, and crystal growth.
But given the world’s increasing demand for hydrogen, particularly as a possible replacement fuel source for passenger vehicles, Mr Rochhausen explained that it’s the hydrogen market that the company is especially interested in.
“The market for hydrogen production is huge and so production of hydrogen is a big thing for us, including the use of it together with fuel cells. We think this might come into the marine market in the future as well.
“There is also major downward cost pressure,” he added. “There’s a constant race in the hydrogen industry to reduce
the cost of its production. It’s a real challenge for all of the stakeholders involved.”
The company has already begun delivering rectifier power supplies to electrolysis systems manufacturers involved with hydrogen production; its power supplies are a core component involved in the production of hydrogen gas. Trials are already underway in Sweden involving the production of green hydrogen that is powered by wind turbines or other renewable sources.
KraftPowercon has seen phenomenal sales growth in the past few years. While the group’s marine business unit has been particularly successful, the whole group has enjoyed significant growth.
“We’ve grown year-on-year by 25% since 2017,” Mr Rochhausen revealed. “We’ve
recently passed a major milestone in that we marked the delivery of our 3,000th power supply for ballast water treatment systems,” added Mr Stenmark.
As part of its aggressive growth strategy, the company is continuing to pursue new clients in the Far East. To this end, in January 2022 the company moved its South Korean team into a brand new, high-tech office in Seoul, after it outgrew its old premises in the same region. The new office
is a short 10-minute drive from Gimpo International Airport, an intentional decision to enable fast airfreight deliveries of urgent spare parts to customers anywhere in the world as well as convenient staff transport to those same sites.
Inside, the building features breathtaking views of the Han River Bridge across to nearby mountains. The offices are warmly lit and the staff operate from ergonomic, heightadjustable desks with dual-monitor displays.
The modern facility includes an outdoor garden, a well-appointed staff gym, various meeting rooms, and a bright and airy visitor lounge for casual meetings.
Supply chain chaos as a result of Covid continues to afflict companies around the world, and KraftPowercon is feeling the effects as well.
“Today, our biggest challenge is increasing material costs – they’ve really increased a lot recently,” Mr Stenmark confirmed. “We’re also experiencing a lot of delivery delays in
the supply of the components and materials we require. It’s a major difficulty right now in building our equipment. So far we’ve managed to stay on top of our production, but it’s taken a lot of hard work and money!”
With crucial implementation deadlines for ballast water treatment systems looming, Mr Rochhausen shed some light on the supply chain crunch faced by the company that is putting strain on its production.
“2022 and 2023 are the big years for ballast water treatment system retrofits, but we’re struggling to get the components and handle all of the cost increases – not only in the cost of the components themselves but also in the cost of sea and air freight.”
In conclusion, Mr Rochhausen expressed optimism that Covid numbers will be brought under control sufficiently to allow for important industry exhibitions to resume. “There are several planned for 2022 that we will certainly participate in. That’s exciting.” n
seven seas, five oceans, one voice
altamira terminal portuaria pace group port of gibraltar
A combination of infrastructure improvements, effi ciency drives and rising container traffic volumes has fuelled Altamira Terminal Portuaria’s rise to become Mexico’s fourth busiest port. With a new multi-million dollar berth extension set to boost capacity further, Terminal Director Captain Adonay Navarro Saad firmly believes the only way is up. Report by Andy Probert.
Thas been Altamira Terminal Portuaria (ATP). Tucked up in the northeast state of Tamaulipas, the country’s fourth busiest port has big plans to enable it to remain shining bright for years to come.
Handling less than 75,000 TEUs a quarter of a century ago, the terminal annually handles above 500,000 TEUs. “We manage 6.5 times more container traffic now than when we first started, but we are confident that figure could well reach 650,000 TEUs in years to come,” asserted Captain Adonay Navarro Saad, Terminal Director.
That punchy number is derived from the terminal’s plans to build a third berth at the cost of $25 million and, by sheer desire, to become the most efficient and competitive port operator in the Gulf of Mexico.
This latest commitment also reflects the port’s continued and timely improvements with infrastructure, yard and dock equipment, and high-tech solutions to deliver an efficient ecosystem. This allows cargo to be loaded /off-loaded in quick time, to be either trucked across Mexico or shipped globally.
The bigger vision to make ATP a top three national port is being backed by its parent company, Grupo Mexgal, a 100% Mexicanowned corporation. Mexgal is an independent group with long experience in international transportation and port activities.
“The total approach to customer service has driven us to constantly increase productivity rates, but never lose sight of our commitment to providing quality services,” said Capt Navarro.
In October 1995, due to the Mexican government’s privatisation of the port infrastructure, ATP obtained a concession to run the multipurpose Terminal One at the Port of Altamira and further develop container handling, dry and breakbulk cargoes. The terminal had a 300m berth, but ATP was approved to extend it by another 300m in 2007 - 08.
“That helped us offer two berths to accommodate bigger cargo volumes and arriving vessels. Doubling capacity and being able to handle vessels simultaneously was a big step for us,” he said.
In 2012, Mexican law changed again, allowing terminals to apply for an extra 350m berthing space. ATP, which operates the original 600m berth and an additional 117m berth to accommodate small ships, was granted that new extension in 2018.
LBC Logistics Solutions has been servicing Altamira Terminal Portuaria for 15 years. Our commercial relationship is strong due to the customer focus and priority we provide. We are a one-stop shop, supplying spare parts for Altamira Terminal Portuaria’s reach stackers, terminal tractors and forklifts, as well as technical support and equipment sales.
Our goal is to always exceed Altamira Terminal Portuaria’s expectations and keep growing with them organically. We appreciate the opportunity to serve them.
Works are to begin shortly on extending the original berth by 60m to an overall 660m in continual length.
“There will also be a deviation from the original line by 20 degrees, allowing us to build an additional 290m berth,” Capt Navarro revealed. “This is due to the port configuration: an unbroken 950m linear line would otherwise extend into the turning basin.”
He added: “That will allow us to have three berthing positions to efficiently attend different kinds of ships and comfortably accommodate the extra capacity in future years.”
ATP handles cargo throughput from vessels calling from northern Europe, the Mediterranean, South America and the east coast of the USA. Shipping line clients include some of the world’s most prominent, including MSC, Maersk and ZIM.
Given the steep growth experienced in the last 20 years, the terminal has also seen its workforce rise from around 100 to 1,200 employees in 2021. The terminal, which operates on a 24/7 basis, has a berth occupancy of 45%.
ATP has achieved intense productivity levels thanks to its four ship-to-shore cranes plus Panamax, and three mobile cranes, (two of which have a capacity of up to 100 tonnes each), which, in tandem, allow the handling of parts with a load of up to 200 tonnes.
With three cranes, vessel productivity is in the order of 1,500 to 2,000 movements per call, equating to 85 to 90 container moves per hour, although that figure regularly tops 100 moves an hour.
Underpinning this, ATP uses the latest version of the Navis N4 terminal system, furthering its position as a go-ahead port operator. The N4 3.7 version was launched in mid-2019.
“N4’s features enable us to optimise operations and respond swiftly to changing business requirements, keeping us one step ahead of the curve and helping us satisfy customers,” Capt Navarro remarked.
In parallel with other systems, the port also handles container cargo disbursement to trucks. In Mexico, the more common way is for a trucker to arrive with their vehicle and platform for container delivery.
“On average, we do 700 to 800 container dispersals to trucks,” added Capt Navarro. “The average turnaround time for a truck is about 25 minutes. That efficiency is achieved by ATP’s fleet of 14 rubber-tyre gantries (RTG) cranes. For cargo disbursement to trucks, we have expanded our lanes from two to nine as volume levels have risen.”
Whilst being a multi-purpose terminal, ATP’s container traffic consumes more than 93% of business activity compared to general cargo and automotive. “In the last two years, we have been more aggressive with our general cargo and believe we
will be handling close to 150,000 tonnes of general cargo once 2021’s figures are finalised. Among them, we serve a monthly service of STINNES LINE break bulk and steel cargoes”, revealed Capt Navarro.
ATP is the only terminal at the port of Altamira to handle automobile shipments for import and export. This peaked at over 300,000 automobiles in 2021, with exports mainly to the US east coast, Europe, South America and Middle Eastern markets.
Capt Navarro added: “Because Altamira is in the industrial corridor, with many exporting petrochemical and plastics manufac turers located here, we have, in the past, exported more than imported, with a 60-40 split. But today, that is closer to 50-50. That means we are handling very few empty containers, or about 10% of total volume.”
ATP’s import volumes, including components for the automotive and other industrial sectors, are predominantly distributed across Monterrey and the north-eastern parts of Mexico.
The terminal’s main competitors are others across Mexico and the Port of Houston, which lies about the same distance from Monterrey, (the region’s main industrial hub), as does Altamira.
“Altamira has become very competitive, but the biggest transportation option in and out of the terminal is still by truck rather than railroad. This is based on cost, logistics and delivery time,” he highlighted.
The construction of the new berth in 2022, an additional $5 million spend on three new RTGs, and plans to add a fifth Ship-toShore Super post-Panamax crane to serve in the next three years will help consolidate the terminal’s performance.
“These will all combine to be able to handle more significant terminal volumes,” Capt Navarro stated. “When the additional berth becomes operational, our volumes could well be above 600,000 TEUs in the next two to three years. This is also set against an average business growth rate of 7% annually.
“Everyone anticipated 2021 to be a weak year given the pandemic, but that was not the case. Freight volumes returned to what we were handling in 2019, and we expect to top that by 5%. The recovery was abnormal and not expected.
“Our goal is to ensure that we continue to offer a quality seamless service with the best equipment and people available, and not to impact a client’s own operations adversely.”
He concluded: “Whether it’s clients, importers, exporters, or with suppliers of our equipment and software infrastructure, we have always maintained long-term business relations through efficient, timely and open communication.
“We want customers to identify with our terminal and for ATP to be their best, preferred choice for all their cargo handling solutions. We are always striving to improve for them, and for the good of the terminal.” n
Through the joint effort of Pace Group – The largest transportation company in Georgia – and the US International Development Finance Corporation (DFC), the construction of a new seaport in the city of Poti has been successfully completed.
The Poti New Sea Port’s official opening ceremony was attended by Georgian Prime Minister Irakli Garibashvili, Minister of Economy and Sustainable Development Natia Turnava, US Ambassador to Georgia Kelly Degnan, members of Georgia’s Cabinet and Parliament, and representatives of the diplomatic corps and maritime industry. The guests were addressed by Irakli Garibashvili, Prime Minister of Georgia.
“One of our Government’s key goals and priorities is to shape Georgia into a regional hub tapping into our location and potential. Let me single out the engagement of our key strategic partner, the United States of America, in this project, namely US $50 million in financing allocated by the International Development Finance Corporation (DFC). This is another demonstration of Georgia being an attractive country for foreign invest -
ments; one with the largest transit and transport potential in the region,” the Prime Minister stated.
Irakli Garibashvili thanked Pace Group’s President Ioseb Dolidze and each employee of the company for successfully implementing a project of this scope, and for exhibiting remarkable social responsibility, especially in light of the pandemic, by creating hundreds of new jobs.
The Poti New Sea Port, with its value amounting to $120 million, is one of the largest among Georgia’s ongoing maritime projects. Notably, the financing allocated by the US International Development Finance Corporation is the organisation’s single largest investment into a project in the region.
“I’m delighted that the United States, through the Development Finance Corporation, has played a key role in the Pace Terminal’s construction,” US
Ambassador to Georgia Kelly Degnan said in her speech. “It is a demonstration of our continued commitment to Georgia’s prosperity and to the Georgian people.
“Georgia’s investments in becoming the safe, responsible transport partner come at an opportune time. These investments further Georgia’s ability to make global and regional connections when the world is looking for alternative routes and supply chains.”
According to Ms Degnan, this port is a key link between prosperity and security, and the United States is committed to assisting Georgia, a strategic partner, in developing port infrastructure.
“Our mutual interests are served in an environment that respects freedom of navigation, access to waterways, the rule of
law, and national sovereignty. This port is part of the physical lifeline connecting Georgia to Europe. It is also a symbol of Georgia’s continued Euro-Atlantic aspirations,” she added.
A total of $93 million has been invested in the construction of the new seaport, with large hydrotechnical facilities and modern port infrastructure built. It includes a 260m berth, fully reconstructed breakwater structures, and 5 million cbm of soil removed from the Poti New Port harbour to further increase its depth to 13m.
The investment also includes closed warehouses with a capacity of 50,000 tonnes, equipped with fully automated reloading systems manufactured in Europe, open storage areas stretching six hectares, and two new portable cranes exclusively manufactured and installed at the seaport, each with a load capacity of 100 tonnes.
The project’s subsequent expansions, an endeavour valued at an additional $30 million, involves the construction of a new
230m deep-water (13m) berth. In addition, modern port machinery and devices will be installed, such as a conveyor system and a ship-loader.
A symbol of Georgia’s imposing economic transformation
“This port symbolises Georgia’s imposing economic transformation since regaining independence in 1991. The Poti New Sea Port will create new jobs and spur economic growth, also empowering Georgia’s positions a s a strategic and transit country, linking the Caucasus and Central Asia to Europe, also bolstering trade,” Kenneth Angell, Managing Director of the US International Development Finance Corporation (DFC), emphasised in his video address.
“The Poti New Sea Port will also continue the years-long productive partnership between the United States of America and Georgia.”
The berth and new port’s infrastructure allow for serving up to 50,000 Mt cargo
capacity bulk carrier and container vessels. The port will handle bulk and break bulk cargos, as well as containers.
After the project’s finalisation, the capacity of Georgia’s unified seaport infrastructure will increase by 3.5 tonnes. These opportunities and the port’s importance are discussed by Albright Stonebridge Group’s Chair and former Secretary of State Madeleine Albright in her letter celebrating the opening of the Poti New Sea Port.
A letter written by Madeleine Albright, USA’s 64th Secretary of State, said:
“The Poti New Sea Port project offers greater economic opportunities to the residents of Poti, to Georgia, and every Black Sea and Caspian state. By transporting three million tonnes of cargo via the seaport, everyone’s a winner.
“The United States of America is convinced that every country has the right to decide its role in relations with the rest of the world. But we also know that every
country is entitled to real opportunities to trade in various markets. This instrument is part of putting to use trade and choice potential – this aspect imparting special importance to it not only from the point of view of trade and commerce, but also making a difference for all of us striving to ensure a better life for our families and countries.”
The Poti New Sea Port will give a tremendous boost to the country’s port capacity and transit potential, also offering new opportunities for redirecting new cargos to Georgia’s transport corridors.
The largest transportation company in Georgia Pace Group is the largest transportation company in Georgia, incorporating maritime agencies, brokerage, logistics, container services, berth, and terminal operator companies. The group has an annual cargo turnover of 3 million tonnes and employs over 1,000 people.
The Poti New Sea Port project offers greater economic opportunities to the residents of Poti, to Georgia, and every Black Sea and Caspian state “ “
Pace Group focuses on developing marine and transport infrastructure, and on attracting new cargos, based on modern technology.
Pace is a US-registered company established in New York, in 1992. Pace International has transported humanitarian cargos allocated by the Government of the United States of America to the Caucasus and Central Asia regions, mostly via the Poti and Batumi seaports.
In the late 1990s, Pace started transporting commercial cargo alongside humanitarian goods. Since the early 2000s, Pace – based on a long-term lease agreement – has been operating eight berths of the Poti seaport.
In 2002-2003, the company built a warehouse complex, a move making it possible to reroute the transportation of the Tajik Aluminium Plant’s primary aluminium through Georgia. Later on, after acquiring special machinery/equipment, Pace started transporting aluminium oxide, a raw material, from Poti to the plant in Tajikistan.
In 2007, Pace and Israeli company ZIM founded ZIM Georgia, enabling Pace to expand its container transportation activities.
The agreement on financing the construction of the new seaport was signed on February 4th, 2019. Construction work launched in September of 2020. n
The Port of Gibraltar, home to shipping expertise and a comprehensive range of support services, is marketing its pole position worldwide. “Our reputation as a centre of maritime excellence is one of the many reasons why the Port of Gibraltar continues to punch above its weight,” said the Minister for Business, Tourism and the Port, Vijay Daryanani. Report from Colin Chinery.
INreal estate speak, Gibraltar is hot property; a place in the sun, kerb appeal, quality of life, and a favourable fiscal climate including VAT-free status. And that ace of deal makers, location, location, location.
Centrepiece of this rocky outcrop at the southern tip of Europe, a 6.5 sqkm self-governing territory of the United Kingdom, is the Port of Gibraltar, offering an expertise and flexibility in ship management services matched by few other ports.
Of the 60,000 vessels entering the eight-mile-wide Strait of Gibraltar each year, over 9,000 call in at this strategic haven at
the Mediterranean and Atlantic shipping lane crossroads, mainly for bunkering, making Gibraltar the biggest bunker hub in the Mediterranean.
With the magnet of its prime location and daily flights to the UK from the local airport, the Port of Gibraltar provides an extensive range of other services to vessels of every size and type, including crew changes, hull cleaning, surveys, legal processes, store and spares provision.
Overseeing these operations is the Port Authority, with the strategy of building on Gibraltar’s unique geographical position and delivering best service by providing a critical link between stakeholders.
At government level, the harbour lies within the brief of the Minister for Business, Tourism and Port, Vijay Daryanani. Appointed in late-2019, his mission is driven by an aggressive marketing campaign to bring new business to the port.
“Our reputation as a centre of maritime excellence is one of many reasons why the Port of Gibraltar continues to punch above its weight when it comes to regional competition,” he said.
Gibraltar provides a service and support network that would credit many larger ports.
Cruise ships for example – a segment slowly emerging from pandemic slump – can berth alongside both sides of the cruise terminal within an hour of leaving the main shipping lanes, with a 940m quay length allowing four medium sized or two large sized vessels to berth alongside simultaneously.
Yachting facilities in Gibraltar are a major draw and include a choice of three commercial marinas and a berthing facility for superyachts at the Mid-Harbour Marina. The port is also a major crew changing hub, with the airport minutes from the cruise terminal, and entry formalities for crew streamlined and easy to use for personnel joining ships
Gibdock ship repair facilities includes three dry docks, the largest accommodating vessels up to 270m long. The shipyard also carries out work alongside or at anchor, with several companies performing underwater repairs, hull cleaning and maintenance.
Spare parts and provisions are handled by numerous shipping agents, and there are first-class medical facilities, chandleries and yacht brokerage services on hand, with comprehensive waste reception and storage facilities available for vessels needing to safely discharge offshore waste and MARPOL-prohibited substances.
Gibraltar’s outstanding professional maritime infrastructure and wide expertise were underscored during Covid-19, a global maritime crisis which saw the Port of Gibraltar remaining open and functioning.
“In 2019 we had 9,149 vessels entering our territorial waters, and in 2020 – the pandemic year – we had 9,480, an extra 300 vessels,” said Mr Daryanani.
“Not only that, but we have also managed to keep our gross tonnage statistics of vessels visiting Gibraltar’s bunkering facilities all very similar to pre-pandemic levels.”
Gibraltar is the Mediterranean’s biggest bunkering port – a ranking Mr Daryanani wants to re-enforce – with delivery typically made by barge while a vessel is at anchor in Gibraltar Bay. With all grades of marine fuel checked and supplied, deliveries can also be made alongside.
In March 2021, Shell completed its first LNG bunkering services at the Port of Gibraltar, when its chartered LNG bunker vessel Coral Methane supplied LNG to Lomonosov Prospect, an Aframax tanker operated by Sovcomflot, (Russia’s largest shipping company), one of the global leaders in the maritime transportation of hydrocarbons.
Welcoming this milestone for the port and its LNG bunkering activity, and a further step towards a greener Gibraltar, Mr Daryanani said it “further sets down a marker that the Port of Gibraltar is at the forefront of the drive for greater sustainability and improved environmental performance of the maritime industry internationally.
“It also highlights the key strengths of the port, namely our adaptability and responsiveness to the wider trends developing within the industry.”
While the pandemic demonstrated the port’s resilience and outstanding capabilities, it remains a challenge “lurking in the background,” said Mr Daryanani.
“It is not a Gibraltar issue of course, but a worldwide one. However what other jurisdictions do, or are affected by also impacts on Gibraltar.”
The other challenge – and the major one – is the terms of a postBrexit settlement, an on-going and contentious issue between the UK and Spanish governments.
Gibraltar was ceded to Britain under the 1713 Treaty of Utrecht that brought the 12-year War of the Spanish Succession to an end. But Spain’s determination to reclaim it has been far more durable, and never more so than since the UK’s exit from the EU.
Most of its 34,000 residents are British citizens, who voted almost unanimously in a 2002 referendum to remain under sole British sovereignty
In the 2016 Brexit referendum, 96% of Gibraltarians voted in favour of remaining in the EU.
Britain and Spain came to a bilateral understanding over Gibraltar in December 2020 to lay the foundations for a future agreement between London and Brussels over the fate of the strategic Rock.
But in July 2021, the then British Foreign Secretary Dominic Raab said he was “disappointed” by EU proposals for a post-Brexit deal and accused the EU of seeking “to undermine the UK’s sovereignty over Gibraltar”.
Failure to reach a satisfactory conclusion to the talks could see a ‘hard border’ appear between Gibraltar and Spain – potentially a logistical nightmare for the approximately 15,000 workers that cross the frontier every day.
“Brexit is one of the challenges,” said Mr Daryanani. “It has created uncertainty, and uncertainty is not good for business. But we are looking at factual development rather than rumour. I don’t think we will be affected, but let’s wait and see.”
He added: “I agree it will be a new era either way, whether we have a treaty or not. But at the moment we are optimistic that we will have a treaty. Discussions have started, and fingers crossed, we will get this over the line.”
In the meantime, Mr Daryanani and the Port Authority are marketing hard. With events and tradeshows now opening up post-pandemic, the port had a strong presence at the London International Shipping Week in September, and in November, The Gibraltar Port Authority, together with HM Government of Gibraltar, Gibraltar Maritime Administration, the University of Gibraltar and Petrospot collectively hosted the second edition of the biennial Maritime Week Gibraltar, promoting the thriving maritime sector to a wider international audience
“It is not easy to bring new business into Gibraltar, especially in these uncertain times, but we will keep on working on marketing Gibraltar,” said Mr Daryanani. “We are in a good place, with our strategic location, being British and operating under British law, which is a big plus. Collectively, all of these things help us in the promotion of our port.”
With its wide range of services, very competitive fuel prices and waste oil disposal, Gibraltar Port is a superyacht hub, and one Mr Daryanani is keen to expand.
“I would like to bring more superyachts to Gibraltar. It’s a very important sector and one we want to develop. Ship and yacht registration is also important for us, as are the insurance and legal sectors, and the economy in general.
“We are very competitive for the registration of vessels and yachts, and being British and governed by UK law, a perfect jurisdiction. And of course, we are strategically located at the crossroads of the Mediterranean and Atlantic.
“For me, the most important thing is to bring as much new business to Gibraltar as possible. I am very keen, and have started marketing the Port of Gibraltar aggressively.”
He concluded: “We can do so much more; providing the best possible service for our customers, enhancing our already excellent reputation in the maritime industry worldwide, and marketing Gibraltar as the best place to do business in this region.” n
seven seas, five oceans, one voice
aresa shipyard international ship repair north river boats i M
Having recently celebrated its extraordinary 60th birthday, Aresa Shipyard, in Spain, is stronger, faster, and better than ever before. With a colourful and storied history spanning leisure, commercial and naval vessels, the company is harnessing all of its skills, experience and infrastructure as it consistently delivers on the demanding needs of modern clients. Aresa Shipyard’s CEO, Oriol López, spoke to Richard Hagan about the company’s impressive line-up of high speed, high quality naval and commercial vessels.
Aresa Shipyard’s history can be traced back to 1961 when it was established by Oscar López. By all accounts, the company got off to a strong start. During the 1970s and 1980s, it established a manufacturing relationship with a major Italian shipyard. In terms of this agreement, Aresa built the yard’s models in Spain. The experience gained from that relationship provided the impetus for Aresa to subsequently design and begin producing its own range of leisure yachts. At that point in time, Aresa was a pioneer, being the only yard building yachts up to 24m in length.
The company’s next major turning point arrived in the late 1980s when it concluded a contract with the Spanish navy to supply two different coastal patrol vessels to the state, with 23 units delivered in total . The contract was an unmitigated success, but the Spanish navy ultimately shifted its procurement strategy towards much larger vessels from government shipbuilder Navantia. Nonetheless, its successful execution of that contract had solidified Aresa’s presence in the naval market. Later on, it would prove to be key to the company’s ongoing success today. Aresa began production for the commercial shipping sector in the early 1990s, before finally focusing on government projects in defence, fishing and transport from 2002 onwards for states around the world.
Today, Aresa is a leading manufacturer of modern, highly capable vessels for the defence, commercial and fishing industries.
Its beating heart is its headquarters and production facility located a short drive north of Barcelona. The impressive 25,000 sqm factory floor supports its 100m long mooring berth and three 60m long hangers. At any given time, the company employs approximately 150 staff including permanent staff and temporary contractors.
Aresa’s production strategy is built around manufacturing models that are adapted to suit its customers’ specific needs, and then supporting those models for the long term through the provision of after-sales and servicing support.
Modern naval doctrine is increasingly concerned by the threat posed by small, fast boats to naval vessels operating in shallower waters, especially along coastlines. In response, coastal governments have shown extensive interest in procuring their own small, light, fast attack and interceptor craft to meet and counter this threat.
Building very fast but capable boats sounds deceptively easy, but the truth is that it’s a real challenge requiring special expertise.
“High-speed vessels, at the lengths we specialise in, are the most difficult types to build,” Mr López added. “They must be secure but also robust enough for heavyduty use.”
Aresa has strategically positioned itself as a specialist builder within that niche. Its ability to build fast, safe, light and highly capable vessels for the world’s navies has seen it becoming the manufacturer of choice for navies in the region.
“We are really focused on small and medium-sized vessel construction. That’s what’s been coming to us in the last three projects we’ve executed,” explained Mr López.”
“This trend began emerging several years ago and it has led to a massive increase in demand from our customers for fast coastal patrol boats. Customers are looking for smaller, faster vessels with lower maintenance costs and shorter maintenance windows. Navies want faster vessels they can operate easily and get out of the harbour within minutes. We’re now focusing on delivering these very fast boats.
“For example, our last order from the Saudi Navy was for ten vessels of 17m in length capable of reaching 60 knots. Following that, we delivered four 18m vessels capable of 40 knots to the Nigerian Navy.”
Any colour as long as it’s black Naval special forces are a particularly enthusiastic customer for Aresa’s boats. Naturally, its two latest product launches are aimed directly at this important market. The first of these is the Aresa 1500 Black Falcon HighSpeed Interceptor – a fast interceptor craft designed specifically for navy seal and other special forces requirements.
The crew and passengers are safely and comfortably catered for with shock-absorbing seats by world-renowned specialist manufacturer Ullman Dynamics. Meanwhile, the boat is powered by three Yamaha 425 XTO outboards - a first for the Spanish boatbuilding industry and the first military craft in the world to receive this power package as well.
The Royal Saudi Navy has already taken delivery of ten Aresa 1500 Black Falcons and, based on the positive feedback from
the Saudi teams, more are expected to follow for other navies in the region, according to Mr López.
“The model’s manoeuvrability, stability and control at high speed really impressed the Saudi Special Forces. It’s travelling at more than 60 knots, which is impressive compared to similar models from France and the UK. This project will go down as a record for our company because of the customer’s acceptance of the project and the way the navy is promoting it in the region.”
The other new product is the Aresa 5000-4000 Peacestorm offshore patrol vessel. This substantial yet nimble craft is designed to operate effortlessly in shallower coastal waters. With an overall length of between 40m and 50m (depending on customer specifications), and a 10m beam, there’s plenty of space onboard for naval operations of various kinds. Peacestorm will be powered by 7,500hp waterjets or propellers and, thanks to its lightweight construction, is expected to reach a top speed of between 20 and 30 knots.
“We are already in negotiation with three defence customers who are interested in this model,” Mr López revealed.
Two Narwhal Rigid Inflatable Boats are carried on the aft deck for high-speed interception missions while the bridge, armoured to NIJ Level III+ is combat-ready and designed to stay in the fight.
Mr López also wished to highlight a new boat the company has sold to the Nigerian Navy: The Aresa 1800 Fighter II is an aluminium patrol vessel featuring an armoured bridge. Able to reach speeds of 40 knots, the Fighter II is an evolution of the company’s Fighter I coastal patrol vessel.
“We designed it to be easy to maintain and operate, whilst still including the latest technology like airband communications for communication with aircraft, and a vertical launching platform for the auxiliary vessel on board,” he explained. “It features two engines of 1,250hp.
The Aresa 1800 Fighter II proved to be such a hit with the Nigerian Navy that Aresa expects additional contracts for these boats from both Nigeria and other countries.
From 2004 to 2009, Aresa completed a major project for the Angolan government, manufacturing a massive fleet of 210 fishing vessels for a combined value of €84 million.
“We supplied seven different fishing vessel models and some coastal patrol vessels to protect the fishing fleet on the water. The project was a major highlight for us because it was one of the biggest of its kind ever signed in Spain,” Mr López commented.
Another project highlight came in 20132017, when the company delivered 17 military vessels to the Cameroon government. It included technical support and a logistics program spanning five years for a combined value of €36 million.
In just the last three years from 2019 to 2022, Aresa has delivered €30 million worth of projects to its clients. “We show the market what we can do using the facts of our delivered work, not just through our words,” Mr López stated emphatically.
Looking ahead, he concluded with some thoughts on the company’s future goals:
“We want to consolidate our progress in the 30m to 60m professional and defence vessel size categories. Meanwhile, we’ll continue increasing our manufacturing capabilities and capacity, through increasing the height of our main hangers and adding more powerful rolling cranes.
“Our 60 year history of success in such a challenging market is proof that we can overcome any challenges through effort, hard work and passion.” n
From a small scale crew of engineers, International Ship Repair (ISR) has become one of the biggest operators in the Gulf of Mexico, with a constant flow of domestic and international clients seeking the company’s expertise. Operating several dry docks from its Tampa shipyard, the family-run company is now planning to ramp up further and secure more vessel renovation projects. Andy Probert discovered more from Senior Vice President Hugo Ortiz.
Attentive and fast are the workforce of International Ship Repairs(ISR) when it comes to turning around variety of vessels ready for ocean life after their transformations at the Florida shipyard.
The 25-acre yard bristles with cuttingedge technology matched by quality engineering crews that have helped build ISR’s reputation for its fast-track, large steel replacement capabilities.
The company completed a 890-tonne job in just 78 days for Gulf Coast Transit – an average of more than 11 tonnes per day. Keeping ships out of the dock and moving in the water where they belong is consistently underscored as repair jobs are completed on time, on budget, and with superior craftsmanship.
Headquartered in the Port of Tampa, ISR is ideally located for vessels trading in the south-eastern US, Central America, South America and the Caribbean.
Founded by Robert Del Valle in 1973, the company began with just eight members of staff who were deployed as a sea-going engineering crew to solve repair issues as vessels sailed onwards.
George and Carl Lorton bought ISR in 1990. The brothers sparked dramatic growth by adding dry dock capabilities at the shipyard. In 1997, ISR expanded its comprehensive repair services to include conversion capabilities for the lengthening and repowering of ships.
When CEO George Lorton gained sole ownership of ISR, the company added several dry docks, including the largest floating dry dock in Florida, affording the company the largest number of operational dry docks in the state.
The main yard and seven outfitting piers now provide nearly 4,000ft of berthing space with on-site support services. Other facili -
ties offer 3,000ft for topside repair, and the shipyard can accommodate Panamax –size vessels.
Senior Vice President, Hugo Ortiz, said: “As demand from clients is to bring us larger vessels and to handle bigger projects, so ISR has grown at pace to match the need for greater capacity.”
With a staff complement reaching 200 people, investments have been consistently ploughed into new shore and floating equipment, including various cranes, such as a 275-tonne Manitowoc Crawler Crane, as well as tug boats and deck barges.
ISR has also developed highly-qualified and experienced teams to handle repair competencies from welding and pipefitting to ship fitting, painting and coating, in addition to manual and electrical services.
Three dry docks are pressed into regular service as they range in metric tonnage, with two having lift displacements of 600 and 6,000 tonnes. The biggest – dubbed ‘The
Beast’ – weighs in at 36,000 tonnes and is 257m long and 38m wide and caters up to Panamax vessel size.
Mr Ortiz added: “Because of the quality of our service and repeat business with clients that we have developed long-term relations with, we are considered as the premier leading shipyard in the Gulf of Mexico. But the market is becoming more competitive by the day.”
While some shipyards favour military contracts, ISR is firmly planted in the commercial shipping sector, both domestic and abroad, while also having completed a number of contracts for the US Coast Guard.
Mr Ortiz asserted: “We have proved to ourselves that revenue is generated from high-volume, short-stay repair projects enabling vessels to have minimal
downtime for owners. We are highly focused on fast-track renovations, repairs and conversions, and we have achieved that consistently over the decades.
“ISR has taken steps in recent years to establish more in-house services, and today our crews fully complete 80% of all contracts. This ensures efficiency and strict quality control.”
He highlighted that Tampa is blessed with satellite companies that ISR can call on to respond to handling specialist work, such as electronics, hydraulics, machinin g, and mechanical.
Surviving in the commercial market, remarked Mr Ortiz, has been one of continuous cycles with a flow of tankers, then gas carriers, container vessels, multi-purpose carriers, and then back to tankers.
“Our target has always been to grow between 7% and 10% annually, and we usually hit these targets,” he said.
The balance of domestic and international clients seeking ISR’s services changed from a 50/50 split in the early 2000s to 40:60 by the start of the 2020s.
“Because we have brokers in Germany, England, Monaco, Denmark, Greece, Singapore, and Canada, we see a rising inflow of vessels from European and Asian clients requiring all manner of repairs ISR is experienced in,” Mr Ortiz added.
“There are seasons and years that we see a majority of one type of vessel, such as tankers, and then it moves on to another, such as gas carriers. It appears to happen in cycles, but we are geared up no matter what comes through.”
For the USCG Harry Claiborne, ISR finished its core of projects, such as steering propulsion systems overhauls, tank blasting and various pipe repairs, within 45 days. The company has
also achieved significant overhauls and improvements on two 250-capacity ferries for a client in Puerto Rico.
ISR’s recent projects include handling a floatel for the energy sector, acting as a floating accommodation vessel with a capacity for 400 people; another general carrier for repairs from Singapore and a Spanish-based catamaran. Crews have also worked on repairing a support vessel dedicated to the US Coast Guard and another vessel that requires the pro pellers’ removal for an overhaul.
Looking ahead, he said: “We try to accommodate everything within our expertise and ISR is presently fully booked out for the next five months.”
While ISR remains busy, the company is acutely aware of the limitations of the channel within which it works and is in talks with local government agencies with a view to dredging operations to enable ISR to take on deeper and bigger vessels.
Mr Ortiz said: “It’s a shame that we have a big dry dock that we cannot utilise to its full potential because of the draft limitations. We hope that talks with the Port Authority and local government will be successful.
“On occasion, when we worked on some specialist vessels that were 700ft wide, we took our biggest floating dock
out to deeper water, and we were able to complete the jobs. But manoeuvring it is highly complex and requires a lot of planning, so the option to dredge deeper would be a practical solution.”
To ensure uninterrupted workflow during the pandemic, ISR adopted strict criteria and internal protocols for its staff to follow, with daily production meetings to oversee changing safety requirements.
“We have an open-door policy, and we will consider all types of repairs because anything is possible with our team. We can complete the impossible because we are highly innovative in our approach to whatever complexities we face on a project,” he added.
Material shortages, supply chain concerns, and staff shortages caused by Covid-19 remain the major challenges to the company, but it remains highly flexible to ensure vessel repairs are always completed on time and safely.
Mr Ortiz concluded: “We are well-drilled in looking after clients’ interests, and try to save them money without sacrificing on quality. We look to bring alternatives to the table, think out of the box, and see what we can achieve.
“The overriding approach has always been to achieve clients’ priorities first, and that is what has cemented our longevity and a well-earned reputation in the industry.” n
As a vendor for International Ship Repair (ISR) for over 23 years, we have a great business relationship that has helped us prosper in the Tampa Bay area. It all starts with great communication with the staff on all projects. The ISR staff helped our projects move fluidly from start to finish. Our main goal for both of us is to have a satisfied vessel owner. It is great when we see repeat customers.
For us at Q-SEA Corp, we appreciate the great partnership with ISR.
Oregon’s North River Boats is a US Pacific Northwest manufacturer enjoying tremendous demand, with orders booked through 2023 and beyond. Built on a foundation of successful diversification of pleasure and professional boats, the company is primed to reach its 50th anniversary in great health, with a dedicated team intent on leading from the front. Andy Probert caught up with Director of Sales Mike Blocher.
Whether it’s fishing, fire-fighting, force protection, or free-time enjoyment, hundreds of clients’ first choice is a North River. This Roseburg, Oregon, company continues on an unrelenting path of designing, crafting and delivering world-class vessels of purpose.
A staggering 85% of work boat trade is created through returning customers or referrals. So, it’s no surprise Director of Sales Mike Blocher has a “welcome headache” of overseeing an order book that spirals into 2024.
“2024 will be a significant year as North River Boats celebrates its 50th anniversary, and we will be announcing a new model design. Between then and now, we keep focusing on what we do best – supplying top quality products that beat expectations and ensuring customer service is nothing less than exceptional,” he commented.
Established in 1974, North River Boats began as a producer of small jet-powered sleds for use on the North Umpqua River before
moving up to create in-bound white-water jet boats. The company thrived, expanding both recreational and commercial model offerings and building upwards of 300 boats annually.
Employees are part-owners of the company CEO Brent Hutchings solely acquired the company in 2012 and, four years later, transferred 33% of that ownership into an Employee Stock Ownership Plan (ESOP), at no cost to employees.
Mr Blocher said: “The ESOP gives every qualifying team member an ownership stake in the business, which reinforces each person’s commitment to quality, operational excellence and customer service.
“Our employees not only behave like owners; they embrace our mission to enhance the lives of customers and the community by building the best boats. It also helps with employee motivation, retention and, ultimately, they have a share of the business to help in retirement.”
Diversification has been a mainstay of the company. It excels at manufacturing a range of recreational craft offered through a network of 16 US and international dealers. On its commercia l / government side, it has delivered aluminium boats for customers such as the US Navy, US Coast Guard, Hawaii Pilots Association, Army Corps of Engineers, Washington DFW, dozens of commercial customers, and state and county municipalities.
He confirmed: “We believe in diversification along several dimensions: geography, market segments, boat models and dealerships. Ultimately, it has been the key to our long-term sustainability.
“On our commercial side, we offer a more robust version of the boats we build for our recreational business. These have been used for law enforcement patrols, fire-fighting, hydrographic survey vessels, charter fishing and other workboats. We also build boats for tour operators, for whale watching in Alaska.”
He elaborated: “We pride ourselves on giving customers what they want. Around 15-20% of North River work boats are fully customised. That is underpinned by an in-house design team, and 3D modelling competencies that allow for precise router cut parts to ensure a proper fit and an excellent end product.”
The company has dedicated project managers for every commercial boat that is built. They see the boat through the entire build process, from concept to delivery and reactivation.
With a 70:30 split in favour of recreation boats, the 155-strong company predominantly builds pleasure sports fishin g /luxury boats from 18.5-37ft.
The company has a broad mix of options from small recreation fishing single outboard boats from 18-25ft lengths; its Fastpack/Hardtop category ranging from 21- 25ft; and the oceangoing Seahawk Offshore vessel from 23-37ft.
In 2019, North River Boats introduced its Offshore Voyager line. With model lengths between 33-48ft, this vessel offers exceptional comfort for extended excursions and overnight adventures on large bodies of water.
“We built a 35-footer, advanced to a 37-footer and a pair of 44s. We have three additional Voyagers on order ranging in size from 40-48ft.”
Mr Blocher reflected: “The two 44 Voyagers were big turning points for us in complexity levels. They have Quad 425 outboards, dual 600-gallon fuel tanks that are switched electrically, and the most advanced electronics package we have ever integrated. They are the most digitally complex and far surpass anything we have ever done. They were also an amazing success.
“It demonstrates what North River Boats can do in a new category. And we have since had requests to implement all these electronic complexities into smaller boats. We are continuing to push hard on diversification.”
Among the new Voyager creations is The Codfather Part II and Lucky Boy II – both built for use by private owners as Southeast
Alaska luxury sportfishing vessels. They incorporate the latest technological innovations for safety and comfort, ranging from FLIR imaging systems to the Seakeeper gyro stabilizer, Raymarine electronics suite, and Furuno WASSP and Searchlight sonars, all controlled electronically using C-Zone digital switching.
The company has also excelled in creating boats for lodges –essentially holiday resorts set in Alaska, British Columbia and other nationally protected areas of North America.
Mr Blocher explained: “We have enjoyed supplying hundreds of fishing boats to lodges. We supply single boats, or in the case of others, we have handled the complete replacement of fleets. At Waterfall Resort, in Alaska, we supplied 27 boats at Waterfall and six boats at Steamboat Bay. We have done two full fleet replacements over 25 years.
“Within the last year, Clover Bay Lodge, which started with two of our boats, grew to 16 North Rivers, including a dozen 20ft selfguided vessels and four large fishing boats. We also supply to the likes of Prince William Sound, which are big areas for our boats right now.”
The company has also invested in a new manufacturing facility at its 10-acre base, adding to its 130,000 sqft of facilities. These comprise state-of-the-art welding equipment, new modernised router tables, press brakes and shear presses, and a paint division complete with a sandblasting booth and four down-draft paint booths. The outfitting shop has nine large outfitting bays, a complete canvas and upholstery division and an extensive quality control inspection bay.
Mr Blocher added: “The newest manufacturing fabrication facility of just under 34,000 sqft was specifically designed to reflect the demands we seek as a top-class boat builder.
“We have two different areas; one for small boats and one for larger pleasure craft and commercial boats. Having everything consolidated into one compound means we have great synergies and seamless activity.”
He continued: “The new purpose-built facility, which increased our capacity and incorporated a training centre, set up the company on a 10-year growth plan. We also invested over $1 million in solar panels so that we can generate up to 85% of our electrical needs.”
Due to North River Boats’ strong brand name and devoted workforce, it remained highly productive during the pandemic, while sales growth continued on an upward trend.
“Growth expectations have reached pre-Covid levels, so we are happy with that,” he added. “The pandemic has been generally good for boat companies. We had commercial boats and contracts that we were committed to and remained optimistic as far back as March 2020.
“When June 2020 came around, our network of independent dealers had upwards of 200 units in stock for sale. But then, when people were travel-restricted and had extra money available, they decided to buy boats because they could at least get away locally and socially distance safely. That inventory level quickly reduced to below 30 units across 16 separate dealers. Pre-sold production on the pleasure side is over 60%, and recreational production backlog is now reaching to June 2023.”
On the commercial side, particularly the Voyager model, product backlog is now tailing into early 2024.
Mr Blocher said the company continued to invest in people through training and constant updates in the industry to ensure they remain cutting-edge.
“Since 2012, North River Boats has absorbed every health care increase to ensure employees are not out of pocket. We also do a lot of little things to say thank you to the employee. That includes bringing forward annual pay increases from mid-2022 to December 2021, to help employees with rising living costs and inflation pressures.
“Our people are the backbone of North River Boats, and we appreciate everything they do. We have people who have been working here for over 20 years. Because of our work culture, employee turnover is low.”
The company is currently working on a new Pursuit model , targeted for US mid-West Coast customers, and aimed as a multi-species fishing vessel ranging in length from 20-25ft.
“North River Boats is renowned for creating high-end products, and delivering customised vessels that meet the needs of the client. Our job is to build the right tool for them, and we do that very well.”
Mr Blocher concluded: “We presently have the largest backlog in recent history. With an exceptional workforce and record financial strength, North River Boats is positioned to excel in boatbuilding for the indefinite future.” n
seven seas, five oceans, one voice
rohr-idreco dredge systems vosta lmg
The merger of European dredge manufacturers Rohr of Germany and IDRECO of the Netherlands has fuelled new impetus and global expansion for ROHR-IDRECO Dredge Systems. With the recent opening of an office in the US, and new orders flowing in, CEO Fulco Vrooland Löb reflected on a whirlwind two years and detailed what lies ahead for the business. By Andy Probert.
Bringing together two former rivals in the dredging sector, ROHR-IDRECO Dredge Systems represents a united brand. Within their workforce is pooling of several decades of experience and know-how to bring the best out of the merged company.
The architect of the 2017 merger and everything that has followed since is CEO Fulco Vrooland Löb. His defining vision for the new company is clear: develop high-end 100% electric-driven zero-emission dredging systems customised to clients’ needs.
“Now as one brand, one team, a fully integrated ROHR-IDRECO has one focus: selling a comprehensive portfolio, regardless of location selling crossover,” he asserted.
The company’s product line comprises jet-suction, cutter-suction, clamshell, bucket ladder and bucket wheel dredges. Under the new company, dredgers are manufactured at the German
plant, and pumps are assembled in the Netherlands. Dredgers are optimised for mining, de-siltation, and commercial and offshore contract dredging.
Employing in excess of 80 people, the group retains offices in the Netherlands, Germany and France.
In 2020, ROHR-IDRECO opened a new office and shop in Houston, USA, where machines are built for local clients, and services and parts are offered to about 80 dredging machines still in operation in the region. The Houston office is also pushing to land new opportunities in the Canadian and Latin American market.
While the current focus for many industries has been about zero emissions and going electric – the company has been
achieving both for more than 50 years thanks to when former entities adopted electric-driven propulsion back in the 1960s.
Building on those foundations, ROHR-IDRECO has developed a series of modern-day solutions at the heart of all operational vessels. For instance, its iDredge solution drives the machines and comes in three phases: Eyes Underwater, Making Waves and iDredge For You – and all available to every vessel.
The iPump concept is the most efficient pump available for ROHR-IDRECO’s suction machines. Complete with the proprietary BoronX metallurgy for longer wear life, iPump ranges between 200mm to 1,100mm and is ideal for suction dredges, boosters, hopper dredges and other slurry applications.
Eyes Underwater is a sonar/DGPS system providing efficient material recovery. The visualisation and mapping tool can integrate with existing or active surveys, and multiple machines can be linked and displayed on a single map.
Making Waves offers automated production control, monitoring various measurements and machine conditions to control suction location, pump speed, bucket ladder speed, or clamshell cycles to maximise consistent performance.
Finally, iDredge For You focuses on support, service, and maintenance packages, including remote monitoring of the dredge by ROHR-IDRECO to assist with remote service and support, maintenance planning, and process optimisation.
Mr Vrooland said ROHR-IDRECO has also launched a new iBoat, enabling the operation to be completely electric.
Developed in cooperation with Groeneveldt Marine Construction, the iBoat support boat is designed to pair electric dredges and provide an environmentally friendly, zero-emission solution for sensitive areas. iBoat can plug into the dredge or onshore, has a 200kW battery pack, and can be equipped with a deck crane and operator cabin.
“With all these applications available, we can offer the most intelligent vessel on the market today,” he added. “We’re also planning on branching out into new industries other than dredging and mining with our pump systems.”
In late 2021, ROHR-IDRECO unveiled two new cutter suction dredge (CSD) models, the Hawk and the Falcon, to its product line-up. With a 500 mm pump, the Hawk CSD model can dredge up to 14m, while the Falcon CSD can be used for dredging up to 20m
with a 650 mm pump. These dredges are electrically driven, including the pump, cutter head and winches, with an add-on diesel generator power unit installed for when there is no access possible to the electrical grid.
On the order front, the company has delivered seven bucket ladder dredgers in a row, and produced a large cutter wheel dredger to gold mining company Mineros of Colombia.
The company has also closed a contract for a 12 cbm clamshell dredger for a repeat customer for the de-silting of a hydro dam in Austria, which is believed to be the largest dredger built to date for this type of application.
Mr Vrooland said: “We are growing as a company, both in turnover and in employees, but this is not our aim in itself. We want to remain agile and flexible, offering high-end zero-emission dredging systems tailored to clients’ needs.
“The US market is a growth market for us, especially as the newly introduced Infrastructure Bill will likely lead to many opportunities for our clients.”
While ROHR-IDRECO is emerging from the pandemic era virtually unscathed due to orders and investments not being
cancelled, it did highlight several challenges that still hamper the market.
These include North-West European governments being slow to issue new mining permits to their clients. Scouring the market for qualified personnel in the electrical field continues, and embracing the volatility and shortages in the raw materials.
Mr Vrooland said: “We will continue to focus on high-end products, very often with a significant component of customisation. We have a large team of engineers compared to other companies who stay with relatively standardised equipment.
“In maintaining good relations with our suppliers and clients, I believe in the old fashioned approach of giving a little, taking a little. We are not shopping around.”
Concluding, he added: “A lot is going on in the electrification of the dredging industry. We have been doing that for decades thanks to our roots in the mining industry and, thus, want to continue taking the lead in this development.
“Our dredgers are built to last, but we want to evolve R&D further to ensure we continue to offer the best in intelligent dredgers.” n
With nearly 150 years of experience behind it, VOSTA LMG in the Netherlands is a global specialist in dredging technology. The company produces a range of advanced and highly customisable dredging components and systems that are utilised by clients all over the world. But with increasing market volatility driving up input costs and significant changes in its customer base, how is this affecting the company? Commercial Director Gerrit Kamerman chatted to Richard Hagan.
Commercial Director, Gerrit Kamerman
Dutch dredging equipment specialist VOSTA LMG has a history dating back to 1873 when Lübecker Maschinenbau Gesellschaft (LMG) was founded in Lübeck, North Germany. Over the border in the Netherlands, in 1903 Stapel Shipyard was founded in Enkhuizen and in 1937, Vos Machine Works was established in Sliedrecht. They joined forces in 1993 and formed VOSTA.
The company was catapulted onto the global stage in the 1990s when LMG and VOSTA were bought by the Krupp organisation. Krupp went on to incorporate and integrate both companies in Germany and Holland and formed today’s VOSTA LMG. But most importantly, it exposed the two firms to Krupp’s global network of offices and agents.
At a strategic level, Krupp was intentional about developing the engineering and contracting arms of both firms, with a particular focus on the development of their own vessel designs and engineering components.
In 2012, VOSTA LMG was sold to ASL Marine Holdings in Singapore. The two had a prior working relationship, having previously collaborated on several dredgers. ASL, with its shipbuilding infrastructure, saw value in VOSTA LMG’s equipment portfolio and engineering expertise. VOSTA LMG was attracted by ASL Marine Holdings’ experience and credibility in the marine environment. The relationship was an immediate success and continues to flourish.
VOSTA LMG has two offices, both in Europe. One is located in Hoofddorp near Schiphol Airport, and the other is in the company’s historic base of Lübeck in Germany. Approximately 20 staff, mostly
engineers, operate in each office. Furthermore, the company has a workshop in Zuhai, China, with about 40 employees where the majority of its fabrication works are carried out.
VOSTA LMG’s parent company ASL also maintains shipyards in Singapore and in Batam in Indonesia. Altogether, it employs around 4,500 staff, of which about 400 are office staff and about 4,000 are shipyard staff.
“VOSTA LMG supplies the engineering and dredge systems that makes a ship a dredging vessel,” explained Mr Kamerman. “We provide equipment and services for everything from small dredging vessels up to the largest in the world.
“If you wanted to build a dredger then we have the full portfolio of products and services to help you do that. We sell our proprietary cutter head range, our own pump line and our own dredge automation systems.”
According to Mr Kamerman, the company’s three most popular products are its cutter systems, its dredge automation system, and its patented ‘F1’ multi-connector ball joint.
“Our cutter heads and teeth are easy and safe to handle because it’s a hammer-less system,” he explained. “Another reason for their popularity is because the teeth are designed to wear down in a highly efficient manner. When you remove and discard a used tooth, there is very little material left. So we offer an optimum wear rate and high cost-efficiency and that’s very popular with clients.”
VOSTA LMG’s dredge automation system is also a hit within the industry. “Our system covers the complete dredge system.
If you wanted to build a dredger then we have the full portfolio of products and services to help you do that. We sell our proprietary cutter head range, our own pump line and our own dredge automation systems “ “
It increases the complete productivity and efficiency of the dredger. We deliver all of the components. From there, the automation software controls, harmonises and orchestrates all of it for maximum uptime and efficiency.”
The company’s ‘F1’ multi-connector ball joint is a third highlight of its product portfolio. As Mr Kamerman explained, the F1 is utilised in scenarios in which dredgers employ steel pipes to move dredged material out of the dredging zone.
“A cutter suction dredge is working with much more abrasive material, using metal pipes on floaters to move the discharge out
of the work area,” he said. “The pipes consist of sections that are connected with open couplings, to allow the pipe to move with the wind, waves and tides.
“There are different kinds of ball joints on the market but the big problem is that traditionally, coupling and uncoupling sections of pipe was relatively unsafe. Workers would end up with a lot of injuries to hands and fingers and so on. Our F1 multi-connector joint automates the process of coupling and decoupling by remotely controlling it through the use of a water cylinder, removing the need for manual labour.”
Like most companies today, VOSTA LMG is grappling with market volatility, economic uncertainty caused by the pandemic and in general, the knock-on effects on global trade.
“The environment is currently very difficult; the fluctuating cost of materials, energy and transport is a real challenge for us,” Mr Kamerman remarked. “The cost of shipping a container from China to Europe is exorbitant, as are gas prices in Europe, making it difficult for us to determine prices and delivery times.
“It can also be difficult to explain to a customer why we cannot hold a price for three months, for example. Nowadays, it’s almost impossible to hold a price for longer than a month.”
Another challenge for the company is in the very nature of the work that its equipment does: “We would love to design a standard piece of equipment and just sell that, for example like building and selling aeroplanes. But soil around the globe has such different qualities and the sea conditions vary massively all over. It means that every job is unique and requires a customised solution, but ultimately that’s also what makes our work so interesting.”
Mr Kamerman believes the variable and very technical nature of the solutions that VOSTA LMG deploys for its customers is also a key ingredient in the company’s ability to attract and retain its engineering staff.
“Our engineers are pretty loyal and tend to stay with us for many years, and we have quite a number of very experienced engineers. That also kickstarts the young engineers that are joining us because they’re learning a lot from the older guys who can mentor them –they’ve got lots of stories to tell the new engineers!
“We’ve done so many projects in the past, in all kinds of countries and vessels, and solving so many problems.”
Finding those engineers is another issue, but it’s one that VOSTA LMG is addressing with the help of video conferencing tools.
“Finding people for our automation team in Lübeck is very difficult because we require a special kind of engineer. Good software engineers are already hard to find as it is. We’ve been advertising on social media and we’ve had applicants from all over the world, including India, Colombia and Saudi Arabia. Covid has made the world a very small place thanks to communication through platforms like Teams; it’s made it easy to find and interview people wherever they are based.”
According to Mr Kamerman, VOSTA LMG and indeed its clients, are not blind to the opportunities presented by the burgeoning offshore wind farm market.
“Our customers – the big dredging companies – are moving from dredging to the new energy business offshore. They’re building new vessels for wind farm installations. One of our clients recently recorded more revenue in wind energy than in dredging.
“Of course, our basis is in engineering and we’re accustomed to designing equipment on vessels, so we’ll definitely be looking at opportunities in the offshore energy market, going forward.”
With its extensive history, its expertise and its teams of committed and skilled engineers, VOSTA LMG looks set to write the next chapter of its story successfully. n
seven seas, five oceans, one voice
neptune p2p group bc service
When trouble comes knocking at sea or on land, Neptune P2P Group is the company you want to have on your side. Owned and operated by ex-British and French Special Forces operatives. Neptune P2P Group provides a range of highly specialised safety and security services to safeguard people, businesses and their assets. In an exclusive interview with Richard Hagan, Carl Sykes, co-founder and Group Managing Director, pulls back the curtains on the private security industry.
Cast your mind back to 2009. Piracy off the coast of Somalia in the Indian Ocean, is at an all-time high.
Merchant ships transiting one of the world’s busiest shipping lanes are being relentlessly threatened and attacked by armed Somali pirates in small boats. Seafarers and their ships are taken hostage, often for several months or even years at a time while criminal syndicates negotiate eye-watering ransoms with ship-owners for their release.
While the world’s naval forces scrambled to find solutions to the piracy issue and to mount a defence, Carl Sykes and his brotherin-law saw the perfect business opportunity.
Having both completed their careers in the UK’s Special Boat Service, the two men were trained and experienced in the skills necessary to provide merchant
ships with the protection services they so desperately needed. And thus it was that the early foundations for the company that would become Neptune P2P Group, were laid.
Neptune Maritime Security was formed in 2009 in the coastal town of Poole on the South Coast of England. In 2012, it relo cated its headquarters to Dubai, UAE, in order to be closer to its main areas of operations in the AMEA region.
That same year, Neptune Security Group was officially founded. Having previously operated its security teams exclusively in the maritime domain, the company would now expand its
services beyond maritime and into security risk management services, intelligence-gathering services, regional security management, and land-based protective services.
The company’s next major milestone was reached in 2016 when it merged with an industry competitor in Manchester named Port to Port. The company’s name was changed to reflect its new structure, henceforth becoming the Neptune P2P Group. In 2017 the group extended its suite of companies to include its French partners, Port2Port LPC, also owned and operated by former French Special Forces. This key strategic move enabled Neptune P2P Group to support the French and European Union Maritime Cluster as well as engage with
key French-speaking countries across North and West Africa.
With the merger complete, Neptune P2P Group continued to expand its services and operational regions as new threats to commercial shipping emerged, particularly in West Africa. However, this growth has not been without drama.
“Neptune P2P Group was one of the first companies to provide this kind of service,” said Carl Sykes, co-founder and Group Managing Director. “There was resistance to it from the shipping industry. It was the first time since the Second World War, that armed guards were used on merchant vessels. But the facts speak for themselves; not one vessel with armed guards on board has been hijacked in 12 years.”
The company employs 30 staff and around 400 contractors distributed between the HQ in Dubai and its operational support offices in the UK and France. As a primarily serviceoriented company, the calibre of its workforce is critical to the company’s success.
“Our talented and motivated people within the organisation are our biggest asset,” Mr Sykes confirmed. “We have a flat management structure and we prioritise modern management thinking. Thanks to this, we enjoy great levels of staff retention and loyalty, with many of our staff having been with us for over 10 years. We look after them and they look after us.”
Whilst the company is deliberately light on physical assets, one resource that it is especially proud of is its proprietary
Prudential Shipping is a well-recognised and reputable name in the maritime industry with expert knowledge in providing a vast portfolio of services to meet all requirements of the shipping industry.
We continue to improve our service levels meeting all international compliance standards.
Experience the difference. Come sail with us into smoother waters.
editorial mention
tracking software system, as Mr Sykes explained: “We’ve got a lot of people moving around all of the time; the system integrates with our finances, operations, resources and human assets, improving management efficiency across all aspects of our business. It means that a person who was previously handling six or seven tasks, can now handle 15 or 20, so it’s almost trebled our operational output, enables us to be lean and made us much more competitive.”
One of the company’s unique selling points is the Special Forces pedigree of its ownership and management teams. Mr Sykes and his brother-in-law, the co-founders of the business, are both drawn from the UK’s prestigious Special Boat Service – considered one of the world’s first-ever special operations units and still widely recognised as one of the best.
While Mr Sykes was understandably coy on going into any specific details of his or the other founders’ pasts, he was able to
reveal that one of the group’s co-founders was awarded a Military Cross for action in Afghanistan. Mr Sykes himself has specific expertise in hostage rescue situations, with one particular mission of note taking place during the conflict in Sierra Leone.
He was, however, quick to point out that their company requires the skills of much more than just people with Special Forces experience.
“We’re not just a team of former Special Forces. Our staff come from a variety of backgrounds including logistics and legal professions. We are an equal opportunities focused company with a good proportion of women in the team, for example, our Financial Director and Marketing Manager. You need people with different skill sets to run a successful business.”
It was clear from our conversation that the general public’s perception of risk management operatives and private security operations, thanks mainly to Hollywood, is a far cry from the reality. Most importantly,
Mr Sykes stressed, it’s not all guns and shooting. The company operates within the confines of a highly regulated, professional industry that is subject to regular audits by various stakeholders.
“We’re not mercenaries – we leave the offensive action to Armed Forces and governments. We protect people, businesses and their assets. We don’t, for example, go hunting pirates, we’re there to deter them. If we see a potentially threatening situation developing, we move away from it and avoid it.
“We are strictly regulated and there are many laws we must adhere to,” said Mr Sykes. “We’re regularly audited by our clients and government bodies. Remember, we have controlled goods like firearms and body armour travelling around the world. Departments from the UK and French governments can – and do – walk in at any time to check we are compliant with the regulations.
“We’re mission-enablers. We’re here to help people get on with their business in a safe and secure manner.”
A key sector of focus for Neptune P2P Group is the fast-growing superyacht market. These luxurious, high-tech vessels full of expensive equipment, possessions and even, potentially, the owners, make them a prime target for those with criminal intent.
In one such instance, Neptune P2P guards stationed on a superyacht as it was transiting the Gulf of Aden had to act to protect the vessel and its crew.
“Some vessels came towards us, it looked like they were coming straight at us and we had to assume they had criminal intentions. We pointed our firearms at them and as soon as we showed them we were armed, they turned away,” Mr Sykes recalled.
“Armed guards on board is an immediate response, an immediate antidote to threats at sea,” he added. “When perpetrators see firearms, 99% of the time it will deter them because the threat of retaliation is there, it’s real, and it’s right now.”
It’s not only the vessels who are at risk but also the crews. Neptune P2P Group has developed an industry-focused crew safety course to ensure that superyacht crew are safe while visiting ports and marinas around the world.
“Crews are often young university graduates or gap year type students. Some can be quite naive,” Mr Sykes noted.
“We’ve developed a training course called SAFE – Situational Awareness in Foreign Environments. We train the crew to recognise hostile threats, how they can improve their personal security and on situational, cultural and kidnap awareness. We also cover restraint techniques and day-to-day planning.”
Operating in the complex and demanding world of security, Neptune P2P Group guarantees the safety of people, assets and businesses across some of the world’s most challenging regions. Neptune P2P Group continues its fearless expansion into the world’s threat hotspots and in return, is seeing positive year-on-year growth.
In conclusion, Mr Sykes highlighted the company’s focus on continued staff development: “We constantly look at our people and how we can improve and ensure that we retain corporate knowledge. We’ve invested in our people. We believe that one well-trained and empowered staff member can do the job of a number of unmotivated, under-invested individuals.” n
When disaster strikes at sea and the lives of seafarers hang in the balance, all of a vessel’s emergency equipment must be in perfect working order and ready to go. Lives literally depend on it. BC Service, based in Italy, has a proud decades-long record of ensuring that lifesaving equipment on its clients’ ships is excellently maintained. Andrea Bruzzo, General Manager at BC Service, spoke to Richard Hagan about the business of protecting life at sea.
BCService (bcserviceinc.com) has a rich history dating as far back as 1942. Originally trading under the name Bianchi & Cecchi as a specialist lifeboat manufacturer based in Genoa, Italy, over the years that followed the company gradually evolved its product-based offering into a service-focused offering that was itself constantly adapted according to client demands on global scale.
Today, BC Service has pivoted away from lifeboat manufacturing and now offers specialised servicing of life-saving appliances (LSAs) and FFE services, through the very recent acquisition of Shipping Safety, on seagoing vessels. The equipment within those categories include things like davits the winches responsible for hoisting and lowering lifeboats the lifeboats themselves, and anything else on board relating to the vessel’s lifesaving and firefighting equipment. BC Service also supplies spare parts for the whole LSA and FFE family of equipment.
The company services client vessels worldwide thanks to its global facilities footprint. Apart from its headquarters in Miami, USA, its six main service facilities are strategically located in Algeciras, Genoa, La Spezia, Rotterdam, Shanghai, and Singapore. In addition, it has multiple local resources scattered around the world.
All seven locations boast all of the machinery and other equipment needed to carry out the company’s full shore-based service offering such as services, testing, overhauls and repair work.
Across all of its locations, the company currently employs approximately 150 staff members, the majority of which – around 100 – are specialised, highly qualified service engineers. According to Andrea Bruzzo, BC Service’s General Manager, these are far from your ordinary engineers.
“Our job is highly regulated. We have straightforward requirements from an international regulatory standpoint that govern the people we can employ as service engineers. They must have a mechanical background with two years’ experience and be trained on certain kinds of equipment before they are able to start carrying out inspections.”
In 2021, BC Service launched its brand new, state-of-the-art staff training facility near Genoa. It took six months to build and is a shining feather in the company’s hat.
“This facility is something that not many companies have,” remarked Mr Bruzzo.
Besides being able to train our personnel without relying on anyone else, it’s also a business opportunity because we can offer training services for personnel from other companies.”
The facility exists not only for training or certifying new hires, but also to ensure that BC Services’ engineers are able to practice and continuously hone their skills. After all, lives might literally depend on their ability to do their job properly and thoroughly.
“When we identify an issue, we need to be able to establish how to fix it,” stated Mr Bruzzo. “For that reason, the staff need to be at the top of their game at all times.”
BC Service is an Approved Service Provider according to Resolution 402(96) for hundreds of makes and categories of equipment, covering the majority of the ships and rigs presently in operation globally. Additionally, in 2009 the company received its ISO 9001-2008 (currently upgraded to ISO 9001:2015) and IMO and IACS Members Certifications.
“Our daily responsibility as a business is to ensure that the lifesaving equipment onboard a vessel works properly at all times –especially when an emergency happens that requires the crew to abandon the vessel,” Mr Bruzzo emphasised. “When maintenance is carried out correctly, we see LSA and FFE equipment failures occur then, rather than during an emergency when the equipment is needed most. That’s the reason that ongoing and proper maintenance is so critical.”
Potential failure points on LSA and FFE equipment are numerous and they reinforce the criticality of the work that BC Services’ engineers do on a daily basis.
“We see lifeboat release hooks that don’t open, oil on the brake pads of winches, or completely seized brakes that would prevent a lifeboat from safely getting into the water at all,” revealed Mr Bruzzo. “We’ve also seen sheaves that are bent, cutting any rope that goes into it and causing the lifeboat to fall into the water, and cracks in the fibreglass of lifeboats, allowing water in and potentially resulting in catastrophe.”
He added: “The marine environment is very aggressive. Seafarers don’t always know how to operate or maintain LSA and FFE equipment properly at sea, so our main concern is having many eyes on every job to ensure that we’re able to foresee tomorrow’s issues.”
The cruise ship industry was especially hard hit during Covid, with the world’s cruise ships sitting idle for most of 2020 and many remaining so during much of 2021. And at the time of writing, the confidence in 2022’s industry is mixed, to say the least.
This has proved challenging for BC Service, for which the cruise industry was its biggest customer. Almost overnight, its main revenue streams dried up.
“We’ve been heavily hit by Covid,” Mr Bruzzo confirmed. “Cruise operators stopped their vessels and carried out only the minimum mandatory inspection activities. Inspections were not a priority because they were just trying to survive the pandemic. There were months where we were wondering if and how we’d survive.”
Fortunately, for a company that has survived the end of World War 2, it was going to take more than a pandemic to put an end to it.
“In early 2021 we managed to stabilise the business despite low revenue. Things are improving now and the challenges of Covid have simply pushed us to embrace new ventures and new opportunities. We learnt that anything can change at a moment’s notice and that diversification is extremely important.”
In keeping with that theme, the company has very recently completed the acquisition of an FFE service provider located in Rotterdam and Algeciras, Shipping Safety (shipping-safety.com).
“The company is significantly expanding its service offering beyond simply servicing and maintaining lifeboat-related LSAs. It places us in the market as a broader safety player outside of our current work scope,” Mr Bruzzo hinted, adding that this new venture goes back to the heart of the company’s ethos of responding and adapting to client demands.
“A year and a half ago in 2020 we were worried about whether we’d survive, but now we’re adding a new chapter to our story,” he smiled.
“We sell quality,” Mr Bruzzo emphasised. “It’s a broad and generic term, but to us, it means that we carry out the job properly. Not only according to each customer’s needs but also in line with clas -
Covid has simply pushed us to embrace new ventures and new oppor tunities
sification society requirements. It refers to the quality of our suppliers and of course our personnel. So when we say quality, it’s an all-round concept.”
The company has an evaluation tool that is given to customers every time its crews board one of the client’s vessels. Based on just shy of 3,000 evaluations in 2020, BC Service’s engineers scored an 89% customer satisfaction rating. Data for 2021 is still being compiled, but the company’s goal was 91% and Mr Bruzzo said he is confident that this figure will be reached or exceeded.
BC Service has historically been well-connected in the cruise ship industry, boasting established relationships with all of the big fleet owners. With the chaos of Covid now mostly behind us, the company is looking to broaden its market and connect with vessel owners in the oil and gas industry.
“We are leaders in the cruise industry and now we want to reach out to the oil and gas industry to start establishing our services there, too,” Mr Bruzzo concluded.
With full ISO certification and detailed ISO audit trails, highly qualified and constantly retrained engineering personnel, and a global footprint able to respond to customers anywhere in the world, BC Services is ready to take on the most demanding projects wherever they may be needed. n
seven seas, five oceans, one voice
atlantic refit centre royale oceanic
Behind the glamour of owning a superyacht lies the constant maintenance work required to keep it shipshape and looking spectacular. Atlantic Refit Centre in La Rochelle on France’s west coast, offers superyacht owners and captains a truly boutique maintenance experience for their yachts. Thanks to this, the company has attracted some of the most famous yachts in the world. Owner and CEO Stéphane Marcelli spoke to Richard Hagan about the company’s ethos, achievements, and vision.
The superyacht industry is experiencing a massive boom period that shows no sign of stopping. The global market for superyachts was estimated to be worth $64.1 billion in 2020 and is expected to reach $84.7 billion by 2027. Yachts are being sold at a tempo never seen before, with some changing hands within weeks of being placed on the brokerage market.
The world has a massive appetite for superyachts and even in spite of the Covid-19 pandemic (as well as a range of other factors), it’s one that is not likely to end anytime soon.
But despite the industry’s glitzy facade, superyachts are just like any other machine. They require constant maintenance, including servicing, new parts, paint jobs and occasionally, complete refits of the interior or exterior. And when it’s time for your superyacht to head back to a yard for any of those kinds of projects, Atlantic Refit Centre is ready to carry out that work.
Stéphane Marcelli and his business partner founded Atlantic Refit Centre in 2006. With Mr Marcelli’s background in new yacht build management and with his partner’s 20-plus year career in yacht painting, the superyacht
space was an obvious target for their ambitions to create their own business.
The process of starting the company was organic, as Mr Marcelli explained: “The business began very simply. Both of us wanted to set up our own company and we felt that there was an opportunity in the yacht refit market. The port of La Rochelle wasn’t being used much at the time, which created the possibility for us to develop a great facility there.”
The company successfully negotiated for the use of the two drydocks. The bigger dock is 176m long and 22m wide, allowing the company to welcome yachts up to 140m in length.
Its first project was a 30m sailing yacht and it’s a story that the team remembers well.
“The owner brought the yacht in only for a mast replacement,” Mr Marcelli recalled. “It came out of our shipyard eight months later. We had done a full repaint, plus a full interior modification, and we’d changed the engines!” he added with a chuckle.
Since those early days in 2006 and that first hallmark project, Atlantic Refit Centre has enjoyed double-digit growth of between 10-15% every year, with the only exception
being the global recession in 2008. With the rate of growth of the global superyacht fleet and the fact that superyachts are generally very well maintained, the company expects that it will easily maintain that level of growth going forward.
“We’ve had some great projects,” smiled Mr Marcelli. “One of the most iconic was M/Y Skat when she came in for a paint job. Then in 2011, we undertook the biggest project to date for our company. We converted a 72m military frigate into an explorer superyacht. This was a huge project that took two and a half years to complete. The owner was very happy.
“Once this project was finished, we received a Boat International magazine award for ‘Best Refit Project’. This was an important milestone that also cemented our reputation in the industry for this kind of project involving converting military ships into explorer yachts. It’s an industry trend that is still important.”
In 2017, Atlantic Refit Centre welcomed an especially iconic yacht to its yard – the explorer superyacht M/Y Andromeda (then named M/Y Ulysses).
“This is the biggest yacht we’ve worked on so far. We did a full fair and paint of her hull in a record time of three and a half months.”
Another high-profile yacht client was the explorer yacht M/Y Enigma XK. This yacht –also a conversion from a military vessel – is based in Cape Town, South Africa where it takes guests to some of the far-flung corners of the world. “Since working on that yacht, we’ve had several requests for similar projects on similar vessels,” noted Mr Marcelli.
All of its work on large conversion projects has lent Atlantic Refit Centre particular expertise for this market and it’s one that the
company will be focusing on in the future, confirmed Mr Marcelli.
“We know what the right decisions and strategies are in a conversion project; it includes having the skill to select the proper vessel to convert,” he said. “Even when the client comes to us, we are able to make a critical analysis right at the beginning as to whether this is a project that we can deliver on time and to specification.”
Atlantic Refit Centre’s business strategy differs somewhat to the larger European yards who may work on up to a dozen yachts simultaneously.
“Our approach to refits and the way that we work with the client is really customised to each project,” detailed Mr Marcelli. “It’s not just a standard procedure process that you’d find in the biggest shipyards. We can’t do more than two or three projects at a time and we don’t actually want to hold many projects simultaneously. I want to stay small and take very good care of our clients.
“Our approach is to offer a very tailored level of service to our clients and to work in
very close collaboration with them. For this reason, for the projects that we do choose to take on, we want to take very good care of the client.”
But what does that level of service actually mean? Mr Marcelli was happy to elaborate.
“It starts from the beginning,” he said. “Before we sign the contract, even when we are dealing with a refit, we try to establish a very close relationship with the client in order to get all the technical information we need. This allows us to develop a detailed quote and planning programme ensuring that when we present our offer, the client can visualise how the project will run before the contract is even signed.
“Our clients know that when they request a quote from us, we go into a lot of detail with it.”
The company then sets up a comprehensive project management team to oversee every contract, with a team composition that directly reflects the desires of each client.
“We set up a custom project management team that reflects the client’s own organisation,” said Mr Marcelli, explaining that this approach ensures that the yacht’s
every need is correctly accounted for in every project.
“We want the chief engineer of the boat to speak with a chief engineer on our team. We want the chief stewardess to speak to a steward on our team, the captain to our captain, and so on,” outlined the CEO. “As a result, projects run very fluidly because it shortens the communication time between the rôle players. This is also the way I would like to be treated as a client; if the crew is happy then the owner is happy and we save time. It’s much more efficient.”
According to Mr Marcelli, sustainability and innovation are two of the biggest challenges facing the company and indeed the industry today.
“Sustainability is a growing demand from the client and it’s a trend that we need
to jump on,” he asserted. “It’s more of a challenge for newbuild yards and designers but it’s something we need to be constantly aware of too.
“Innovation is also key. In our business, that means being aware of new products and new technical solutions, and generally being up to date. We attend technical forums such as the Global Superyacht Forum every year in Amsterdam, as well as some more specific forums on subjects like painting and so on. We pay attention to these events because we need to know what’s going on and what products exist so that we can answer the client’s needs and enquiries.”
With the ongoing boom in the superyacht industry, added to Atlantic Refit Centre’s unique geographical position and its focus on delivering top-notch customer-focused service, the future of the yard looks brighter than ever.
WThe superyacht industry is in the midst of an unprecedented boom that has seen demand skyrocketing for both new and used yachts. With this demand for yachts comes a whole bouquet of associated needs, including the need for crew, refits, chartering and various other services. That’s where Royale Oceanic steps in. Shelley Dowie, Head of Yacht Management at Royale Oceanic, spoke to Richard Hagan about the company’s comprehensive range of services.
ith the Covid-19 pandemic continuing unabated, the world’s wealthiest people have increasingly seen superyachts as a means by which to escape the danger posed by crowded cities and other metropolitan areas. This, and perhaps other, more luxurious and illustrious factors, has led to them buying superyachts since early 2020 at a rate that the industry has never seen before.
Superyacht shipyards are enjoying new-build order books that are sold out years in advance, while the brokerage market for used yachts is reporting recordfast sales transactions on an almost weekly basis. Together, the superyacht industry is experiencing stratospheric revenue levels that show no sign of slowing down.
But superyachts are not islands, and running any superyacht – much like any commercial ship – requires a vast network of land-based support services. Royale Oceanic, based in Newcastle upon Tyne in the north of England, is one such provider of those services.
According to Shelley Dowie, Head of Yacht Management at Royale Oceanic, the company is not just any service provider, but one that is unique amongst its peers.
“We’re a multi-disciplinary maritime business providing a multitude of services to the yachting and wider maritime industry, including interior and exterior design, refits and new construction, project management , crew training, vessel valuations and legal services. All of the services we offer are provided by our own group of experts. The fact that we can provide all of these speciality services in-house sets us apart from our competitors.”
Establishment and facilities
Royale Oceanic was established in 2005 by its founder and current chairman, Barry Gilmour. However, Mr Gilmour’s pedigree within the industry goes much further back th rough his larger holding company, the Gilmour Group and Burness Corlett Three Quays, which has been active in the maritime industry – both yachting and in shipping – since 1952.
The Gilmour Group’s experience and knowledge in yachting and shipping, Ms Dowie remarked, have shaped Royale Oceanic today,
“Our 70-year history in both shipping and yachting sectors has given us the ability and knowledge to build a highly professional maritime company,” she said. “Our employees are our primary asset; their collective expertise, experience, knowledge and productivity allows us to attract new business and retain our existing clients, many of which we have had for many years. We place emphasis on employee contribution and engagement which helps us drive the company forward.”
Royale Oceanic employs between 30 and 50 staff members, whilst the wider groups employ several hundred. The company’s headquarters in the northern town of Newcastle upon Tyne might seem an unusual location when many similar firms are located along the country’s south coast, but according to Ms Dowie, the city provides the perfect context for the company.
“The North East is steeped in historic maritime and cultural heritage,” Ms Dowie remarked. “The shipbuilding and fishing industries were once major employers in the region and the lifeblood of many riverside and coastal communities. The River Tyne is the birthplace of the first purpose built lifeboats and the formation of what was later to become the RNLI. Consequently, there is still very good maritime infrastructure in Newcastle.”
The company has enjoyed consistent growth since its founding and has welcomed a steady stream of yachts into its management portfolio. In order to meet the refit and servicing needs of its yacht clients, Royale Oceanic’s strategy is to set up temporary offices wherever refits or other significant maintenance projects are being undertaken on its managed fleet.
“We tend to set up satellite bases as required for projects,” confirmed Ms Dowie. “For example, right now we’re about to undertake a significant refit of a 140m superyacht in Europe and for that
project, we’ll set up a satellite office in that country, near the refit yard, for the next two to three years.”
Catering to the demands of the wealthy for superyachts during the pandemic has become a lucrative but challenging undertaking for the company, explained Ms Dowie.
“A lot of the shipyards had to shut during the initial covid lockdowns, yet they already had extremely full order books. That pushed many buyers into the used market where they weren’t required to wait several years to spend quality time
on their yacht. Other people looked to the superyacht charter market for their perfect ‘Covid safe’ getaway.”
In catering to yacht buyers who are in the market for a custom-built yacht, Royale Oceanic has vast in-house expertise specially geared towards assisting these clients with finding the right shipyard and team for the project.
Royale Oceanics’ extensive range of disciplines kept the business in good stead during the pandemic.
“If the pandemic taught us one thing, it was that we are robust and adaptable” said Ms Dowie. “When travel was limited, we had to adjust to a new way of working
Wanderlust Global Services supplies any items, contractors and services a yacht may need. We are proud to have collaborated with many companies over the years, including Royal Oceanic.
The entire team at Wanderlust Global Services thanks Royal Oceanic for their ongoing custom, and we look forward to this relationship continuing for many years to come.
with our clients and suppliers. We also used the opportunity to promote our yacht valuations, expert witness and legal advice services which has expanded our client base and kept us busy with new and exciting projects”.
The global boom in technology entrepreneurs, social media millionaires and other categories involving younger wealthy people has, unsurprisingly, made its way into the superyachting world. There’s a growing shift towards younger buyers and Royale Oceanic is ready with packages and services to appeal directly to them.
“We’ve seen an increase in the younger demographic,” remarked Ms Dowie. “The younger owner brings a new demographic of yacht buyers with a completely different set of needs; most are taking a step away from the vision of opulence, and are wanting more engagement and consideration with the environment around them.”
For the next generation of owners, yachting represents excitement and adventure whilst maintaining a high l evel of comfort. Gyms, spas, outdoor and water activities, and open multifunctional spaces have become more prevalent in design, reducing restraints on guests and owners giving the freedom reflected by the explorer yacht boom.
“Younger yacht owners and guests don’t want to be tied to one place, they editorial mention
want a new experience, to go somewhere they haven’t before, creating a need for yachts with a high range but still all the size and capabilities of a luxury cruising yacht. This also brings the need to improve the efficiency of yachts and reduce their negative impact on the environment,” explained Ms Dowie.
The fact that Royale Oceanic is today equipped to cater to the demands of younger, more adventurous clientele is a testament to its ongoing commitment to stay at the cutting-edge of what its clients are really looking for.
On that note, Ms Dowie shared a story about one particularly memorable demand the company once had to accommodate.
“I once had to organise a private jet to bring some courgettes to a remote Pacific Island because the yacht owner wanted them for dinner. Clients have the same high expectations wherever they may be in the world, and it is our job to ensure their needs are met despite the logistical challenges.”
Royale Oceanic prides itself on the comprehensive suite of in-house services it is able to provide to its superyacht clients. Its staff complement includes people with vast experience and expertise drawn from across the maritime industry. Ms Dowie recalled a client who initially approached the company with a request to review a refit specification for the owner’s yacht.
“When the owner came to understand the comprehensive services we offered, our technical team was engaged to carry out a full condition survey; our valuations team carried out a full market valuation and our Royale Design company was engaged to complete design renders for a new beach club for the yacht’s refit as well as doing a complete interior design proposal.”
On the strength of the variety and quality of all of the services the company was able to provide the owner, Royale Oceanic was awarded full management
of the yacht, including the management of the refit.
“This was a huge success for us given that the relationship began with a request to provide professional advice to the client, which evolved into providing our full range of services from start to finish, culminating with us winning full management and a major refit contract,” Ms Dowie underlined.
The company maintains a strong social responsibility program, headed up by Ms Dowie’s involvement in an industry mentorship program called LEGASEA.
“The LEGASEA program is one of the ways in which we give back to the industry. The platform creates the space for yachting professionals to connect and share their knowledge while cultivating the next generation of industry leaders, both ashore and at sea. The concept is to create a robust talent pool focusing on retention and progression and ensuring talent is flowing from sea to shore. It ensures that people are hired based on their knowledge and capabilities and that they’re the right fit for a given yacht,” she concluded.
As for Royale Oceanic, having recently expanded its Newcastle team, the company is proving, time and time again, that it is most certainly the right fit for an increasing number of yacht related services. And long may that continue. n