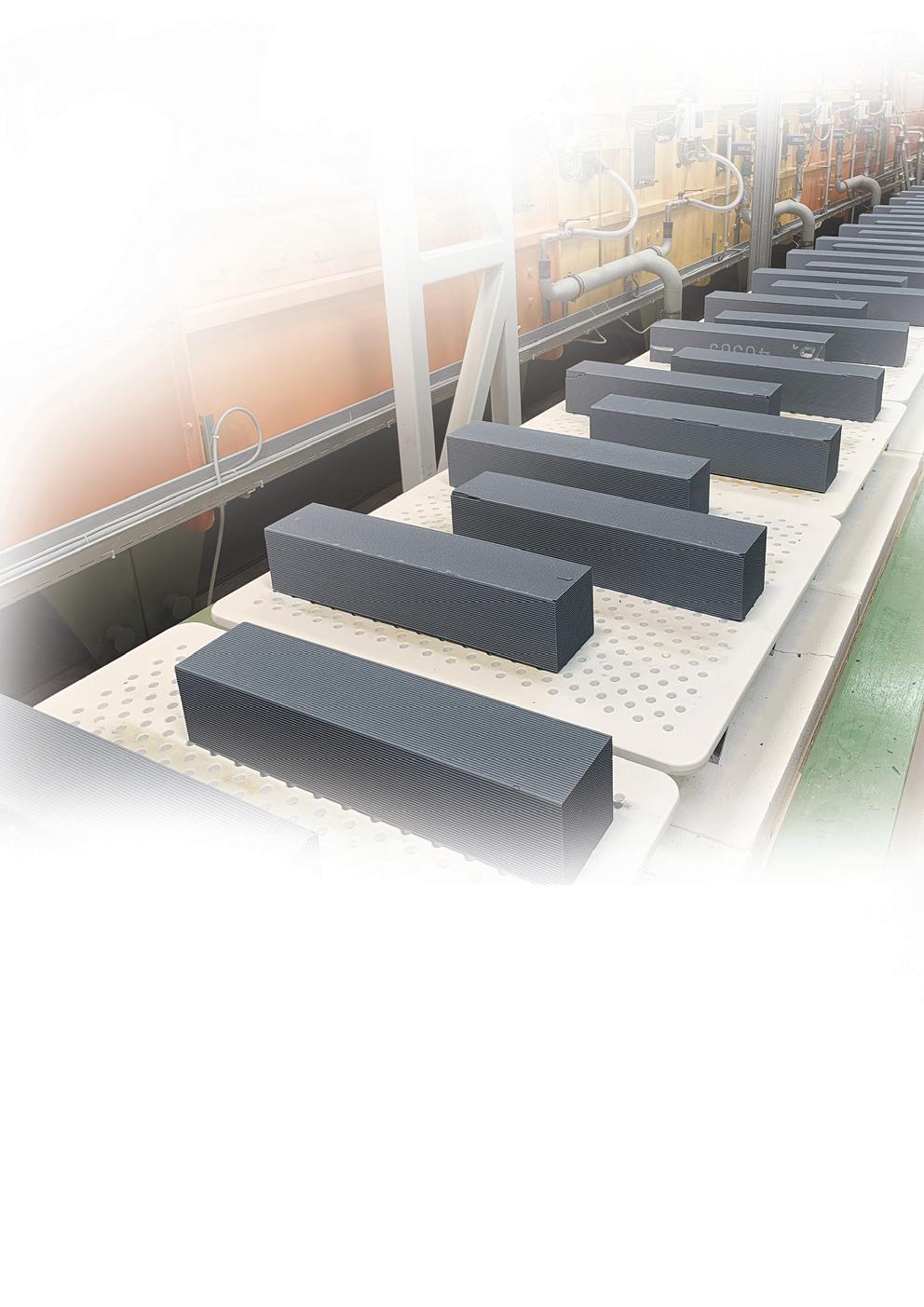
8 minute read
Paving the way for a clean tomorrow
HUG ENGINEERING I PROFILE
PAVING
Advertisement
the way
for a clean tomorrow
Since its establishment in 1983, Hug Engineering has been leading the path to a clean tomorrow by designing, engineering, producing, and the commissioning of custom-built exhaust emission control systems for marine, power generation and rail applications. From its high-tech headquarters in Elsau, Switzerland, near Z¨ urich, the company leads a global network of offices supplying and servicing customers wherever they are in the world.
Increasingly tight emissions regulations have brought in a steady stream of new clients to the company. Lukas Cavegn, Product Line Director for Marine and Mobile, explained how Hug Engineering caters to each customer’s unique demands. Report by Richard Hagan.
Emissions and global warming are a major global concern, and will likely remain so for decades to come. As the world grapples with finding answers to the crisis, bodies such as the European Union are pushing forward with ever-tightening emissions regulations.
The automotive industry was one of the first to respond in a meaningful way, and on a commercial scale, to the need for lower emissions. We have seen an increasingly fantastic parade of plug-in hybrid and full electric vehicles coming off factory floors, delivered sometimes in spectacular launch events and high-budget promotional videos on a and offline.
The marine industry, meanwhile, has, it is fair to say, lagged behind all this progress.
Mercifully, that is all now changing, and at a rapid pace. Increasingly strict emissions regulations for the shipping industry are being signed and ratified and ship owners are finally realising that it is time to either adapt or sink.
Luckily for ship and yacht owners, a specialised company with highly qualified engineers is working on cutting-edge emissions reduction solutions (and associated high-tech systems) to ensure that these vessels are able to meet and exceed global legislative requirements, as well as even more stringent voluntary emission labels. That company is Hug Engineering.
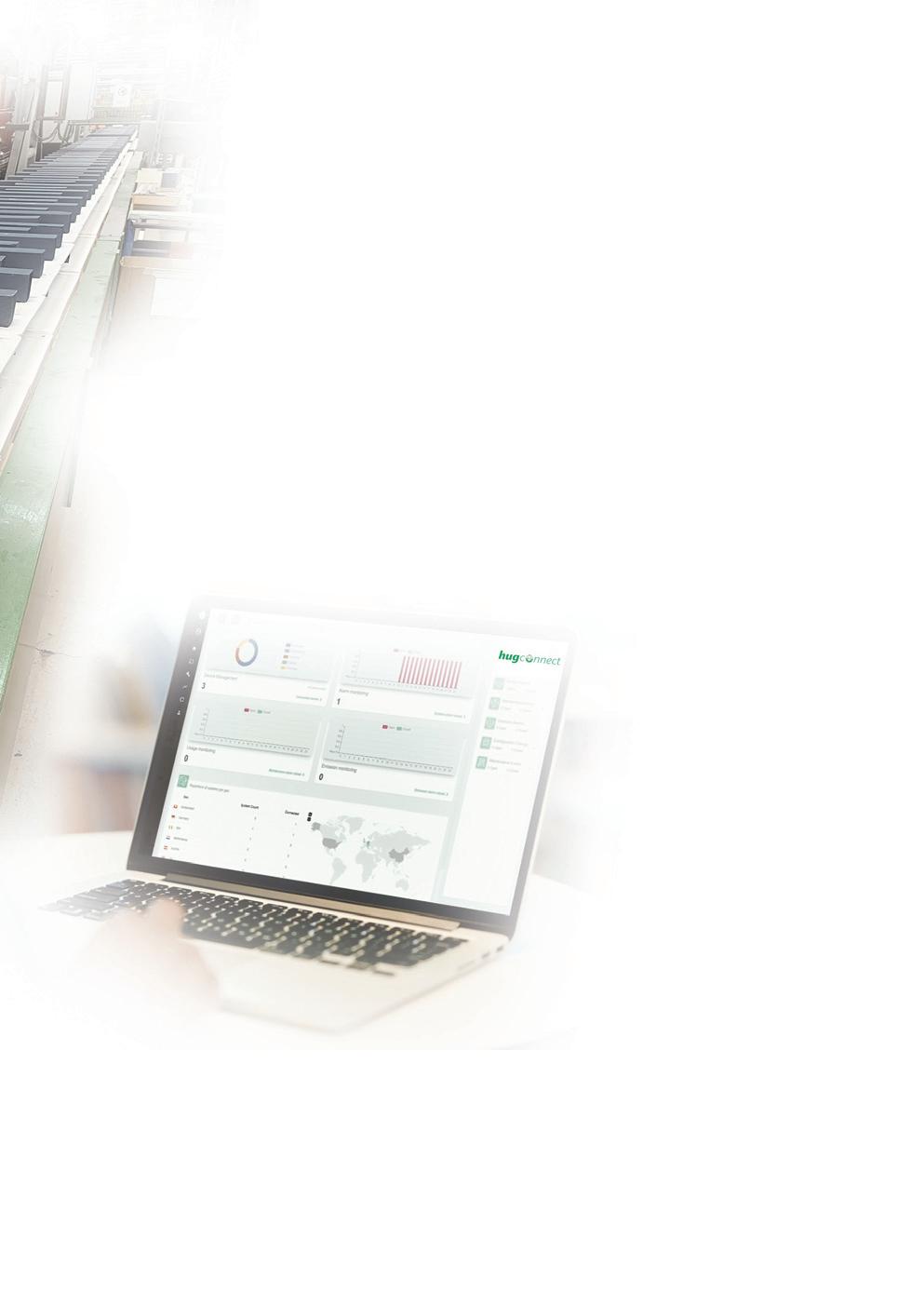
Hard work and organic growth
Hug Engineering was established in 1983 by Hans-Thomas Hug. Shortly after that, Michael Hug, his brother, became his first employee. Initially offering general engineering, they soon identified an opportunity to become involved in not only designing but also producing at that time non-existing components for high horsepower exhaust systems. In 1988, they commissioned the first ever urea operated SCR system at a combined heat and power installation in Schaffhausen, Switzerland. A few years later in 1992, they installed their first marine exhaust system and, from there, growth came quickly.
By 2003, Hug Engineering had grown enough to open an office in Germany. That same year, Hug Engineering tackled a large government contract to supply Diesel
HUG ENGINEERING I PROFILE
Particulate Filter systems (DPFs) to the Swiss Governmental Railway for 100 locomotives involved with tunnel construction.
Only two years later, in 2005, Hug Engineering got its big break into the superyacht industry when it began working with Kusch Yachts to install DPFs.
Meanwhile, to ensure that it had the resources on-hand to supply and service its growing client base worldwide, Hug Engineering founded a sales and service office in Italy in 2007, another in the United States in 2010, and in 2016 an office in the Netherlands (by buying the COdiNOx Beheer BV company).
In 2016, sails were set for even more marine activities, when the IMO TIER III emissions standard came into force for vessels sailing in emission-controlled areas, by offering reliable and high value solutions in combination with all the required certification services.
The company’s hard work and continued growth were further rewarded in 2018 when Hug Engineering was acquired by a French automotive conglomerate called Faurecia. As part of Faurecia’s Clean Mobility business group, rapid advancements in Hug Engineering’s product range were made, with a particular highlight being the first EU Stage V certification of a medium speed engine, achieved in 2020.
Less than one year later, Hug Engineering introduced its Compact SCR system, tailored to the needs of yachts below 500gt, switchable between IMO II / IMO III and fitting in any, even extremely space constrained, engine room. This outstanding solution was enabled by the long-term inhouse development of catalytic coatings, ending in the all new high performance CCV catalyst.
Azimut|Benetti, world leader in the production of super yachts, was the first shipyard to announce an agreement with Mive Eco for the supply of exhaust systems equipped with this compact Hug Engineering SCR system.
Today, Hug Engineering employs around 250 people worldwide. All the company’s research and development, as well as most of the production, is carried out at its headquarters in Elsau, Switzerland. Its four subsidiary offices in Germany, Italy, the Netherlands and the US are sales and service hubs with project management capabilities close to the customers.
Everything under one roof
Hug Engineering prides itself on its ability to provide a comprehensive suite of exhaust treatment solutions, including products and related services that are required by clients.
Whilst competitors often only supply certain components and then lean on third parties for the remaining products and services, Hug Engineering retains every aspect of its product offering in-house. According to Lukas Cavegn, Product Line Director Marine and Mobile, that is a real selling point for the company.
“It’s very seldom in this industry to have all of the functionalities and competencies that we offer under one roof,” he said. “We’re a true one-stop shop, and our combination of know-how in a single service provider really sets us apart.
“If you have an issue, for example, needing to meet an emissions regulation, then we do the engineering, design and certification of the system. We then manufacture it, commission it, and once it’s installed, we carry out its full life services via our skilled service engineers. This is supported by Hug Connect, our remote digital solution bringing any of our aftertreatment systems to display, no matter if it’s a current new build or a retrofit of a long serving installation.
“Having all of this within the company allows us to provide the most efficient service thanks to short communication paths and total quality control.”
The company’s assets are the combination of highly skilled specialist staff and high-tech equipment to design, manufacture, install and service its products.
“Our people are our most important resource,” Mr Cavegn confirmed. “Thanks to them, we are able to develop everything we need and ultimately come up with the most comprehensive and efficient solution for the customer. Additionally, we have the sales teams at our global offices who keep us close to the customers and ensure that we always fully understand our client’s needs.
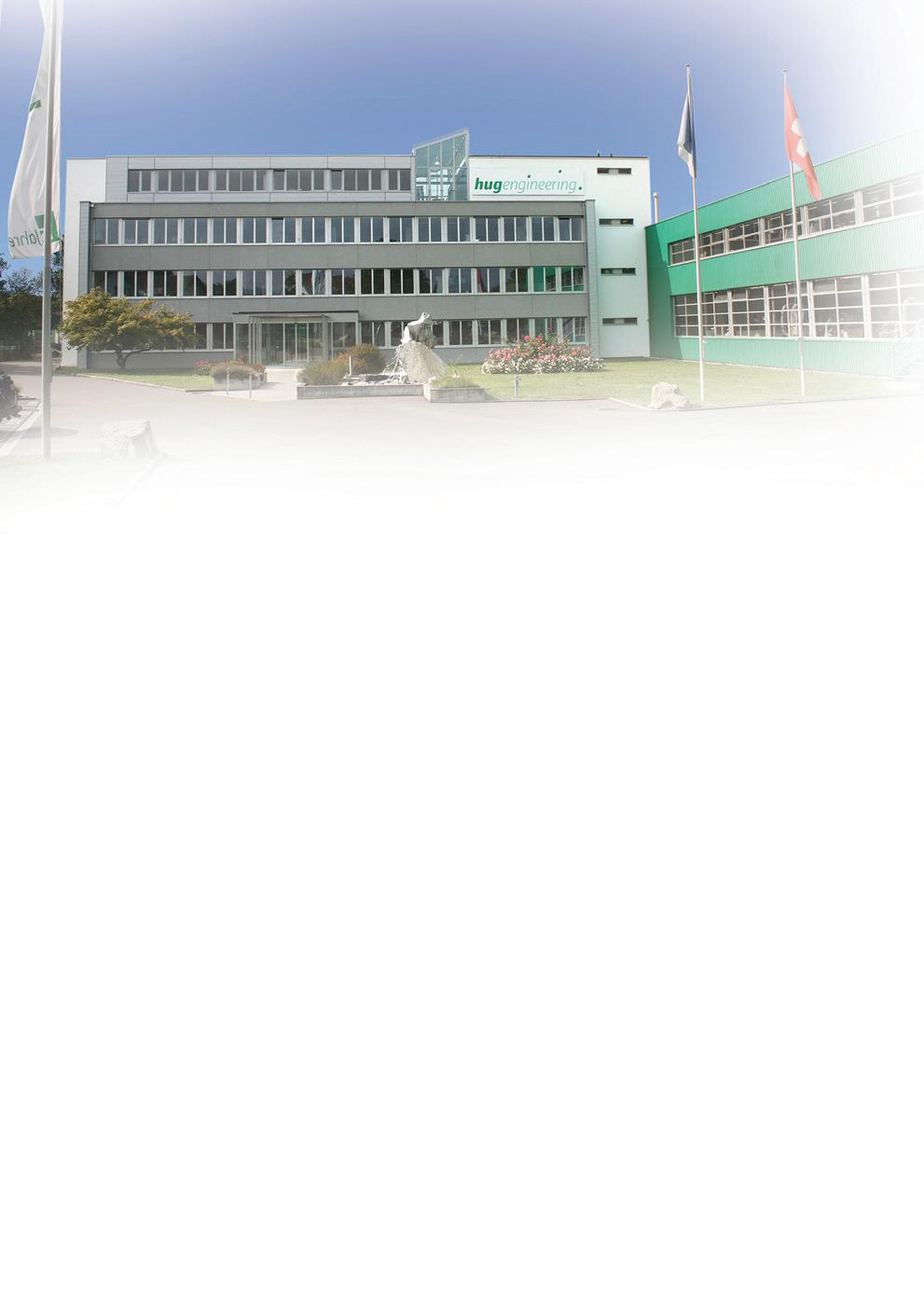
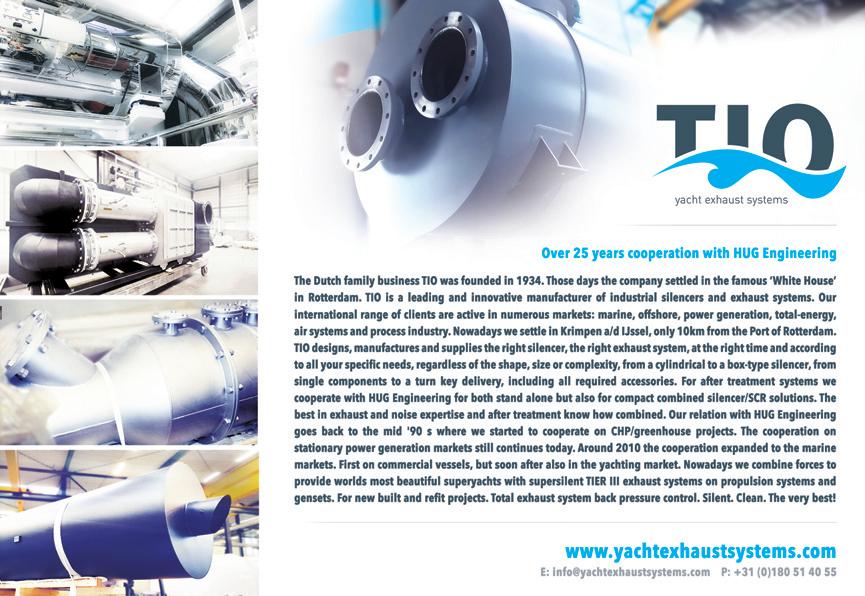
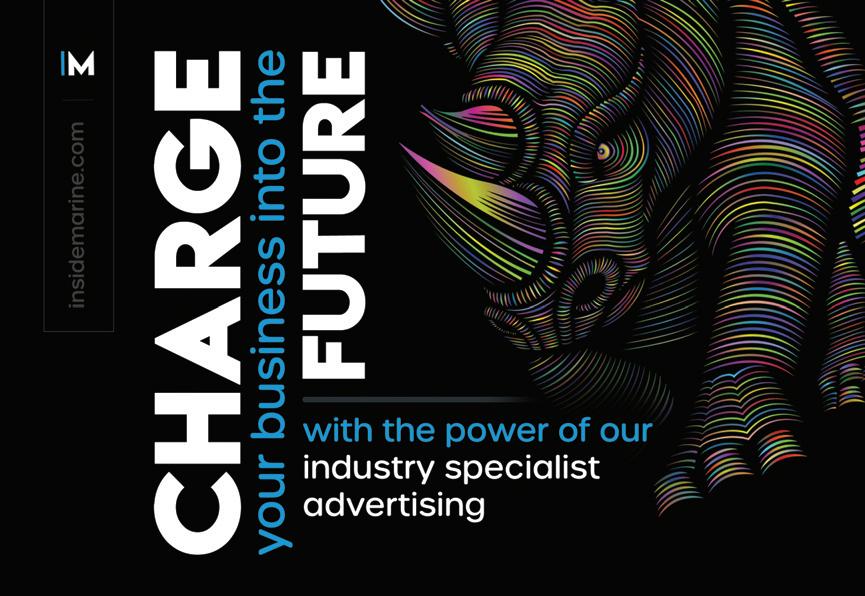
HUG ENGINEERING I PROFILE
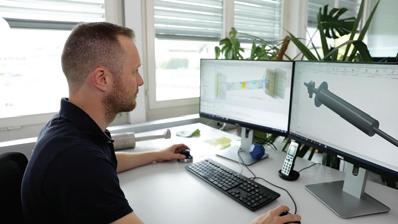
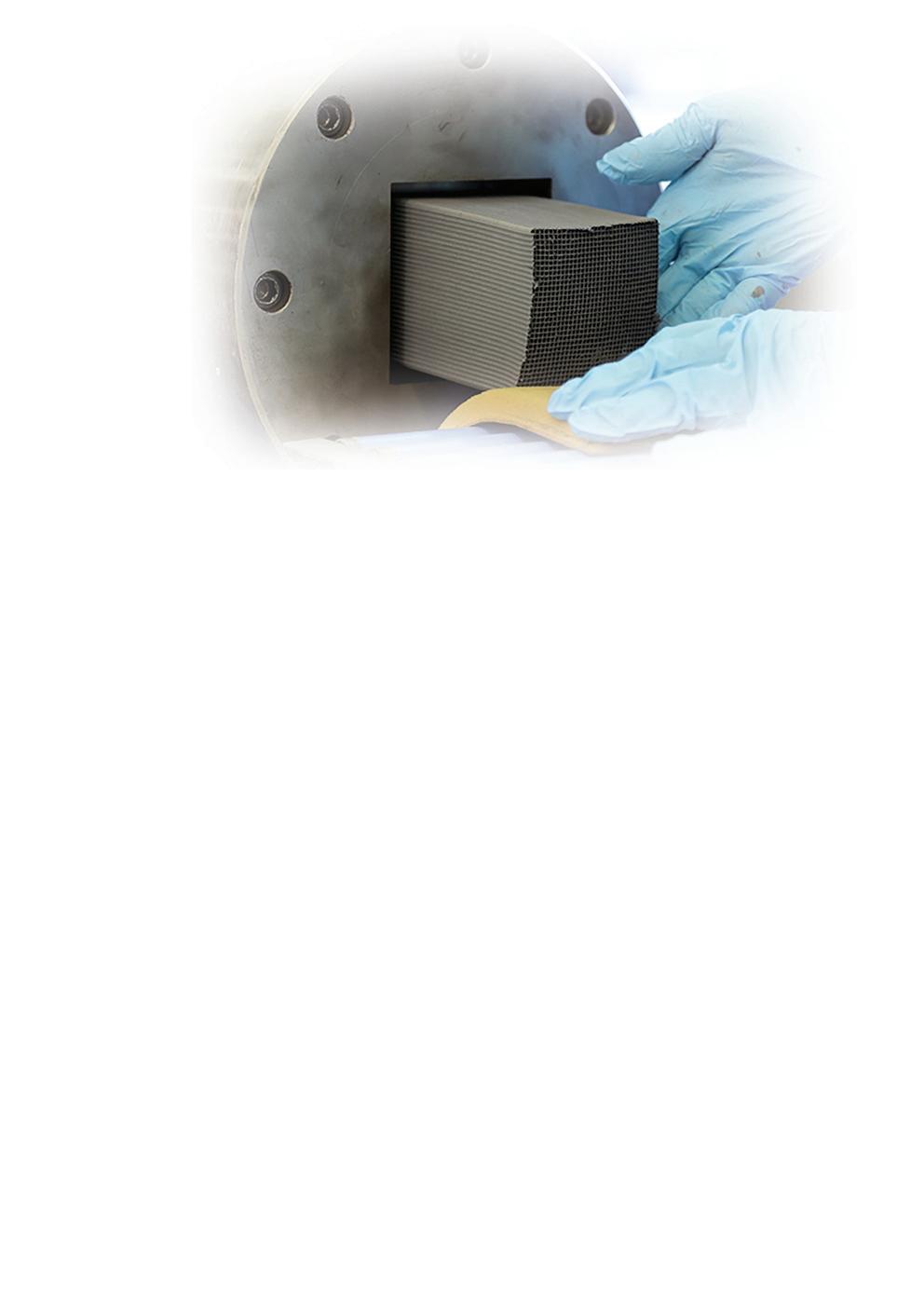
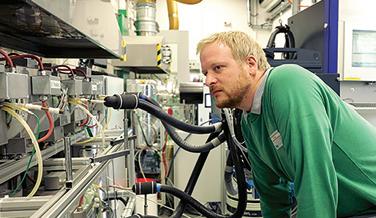
“These teams are working in our cutting-edge facilities,” explained Mr Cavegn. “We have substantial Computational Fluid Dynamics capabilities through Faurecia, as well as a materials lab that handles the ceramic core development for our catalytic converters. Our quality control labs have scanning electron microscopes as well as other equipment.
“Finally, we have a testing lab with small diesel and gas engines to reproduce real-life conditions and to test performance characteristics of a full system, in a scaled-down manner.”
Superyacht exhaust system specialist
Hug Engineering is extremely active in the superyacht industry, which itself is enjoying an unprecedented boom period that is showing no signs of slowing down. New build yachts and used yachts are being sold at record prices and within remarkably short periods of time. All of this has increased the tempo of new orders flowing into the company’s offices and required its teams to quickly adapt to the pace.
“It’s been quite a steep learning curve for us,” said Mr Cavegn. “While the increased demand in terms of the regulations, class approvals, certifications and paperwork are substantial, our big advantage is simply that we’ve done a great deal of those in the past. It means that, beyond providing our normal bouquet of services, we are also able to provide certification services and that’s been very well received by our customers.”
The company is very proud of a solution its teams developed in collaboration with the superyacht builder Lürssen, and the silencer manufacturer Niessing, in Germany. The KeSS system, as it is called, is a highly integrated, extremely compact superyacht exhaust aftertreatment system that integrates the silencer.
“We saved around 40% of the space typically occupied by a system like this,” Mr Cavegn underlined. “It enables Lürssen to design a much more compact engine room.”
Scaling regulatory challenges
Hug Engineering’s speciality is designing, building and installing bespoke solutions. In addition, Mr Cavegn underlined this level of customisation in the superyacht sector comes at the increasingly high time cost of administrative paperwork to obtain the necessary certifications.
To address this area of conflict (providing the most stringent certifications while maintaining the industry leading customisation flexibility), Mr Cavegn confirmed the company is further modularising its solutions. This means developing a portfolio of pre-certified, core solutions that can simply be tweaked to suit various applications.
“We foresee a challenge with this in terms of satisfying the certification bodies such as Lloyds Register, because they’re not used to certifying a toolbox of functions,” he said. “With this, our aim ultimately is to be able to put systems together like Lego, using pre-certified function blocks.”
He concluded: “By doing so, we can leverage our efforts by selling higher numbers of certified core functions but still serving the low number niche with highly flexible solutions. That is why engine manufacturers have a great interest in developing their niche solutions based on our well-proved portfolio of functions which leads to low development costs and unmatched time to market.” n