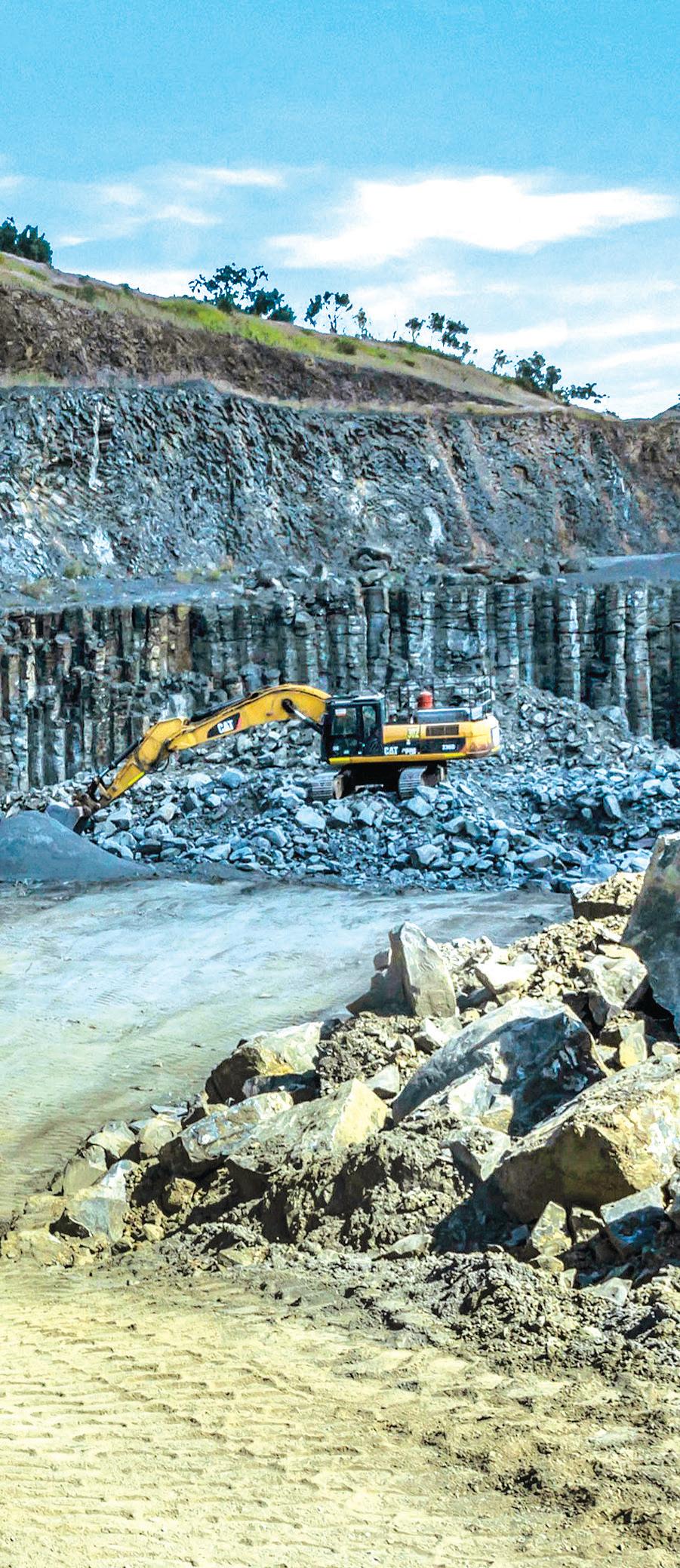
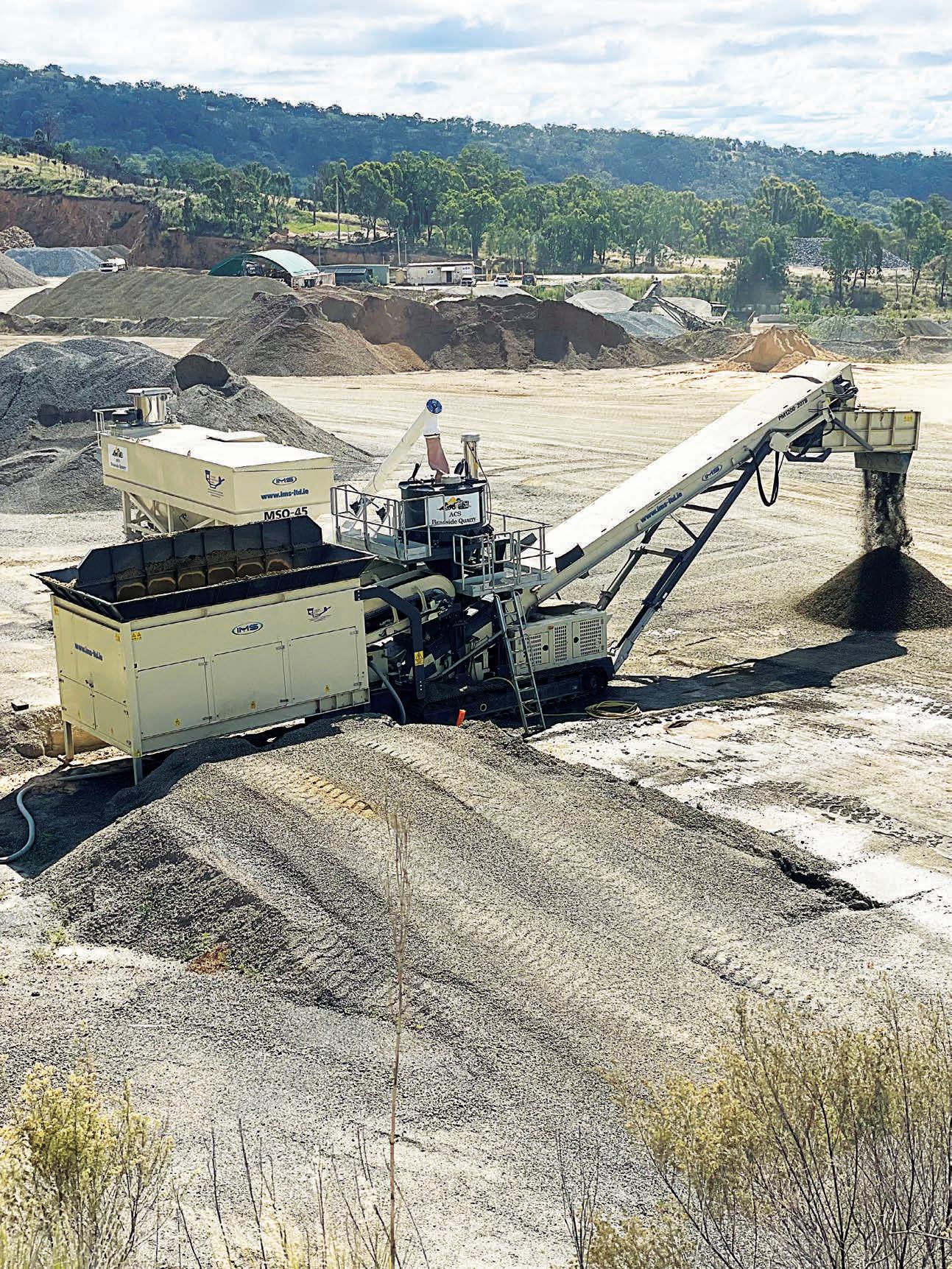
The newly designed WA475-10 features next-generation technology developed with input from customers like you to deliver improved productivity and lower fuel costs. quarry applications, this gentle giant is a unique solution for tomorrow’s challenges.
Call
Up to 30% more fuel efficient
8% more breakout force
20% more boom lift force*
North Queensland IQA legend
John Fahey opens up about quarrying and his career.
SCORPION TAKES THE STING OUT
Precisionscreen’s pugmill is turning heads with its versatility.
Details on Metso’s latest Lokolaunch with a significant equipment upgrade set to be revealed.
Quarrying industry farewells
18 DOZER DELIGHT
Newcastle Quarry Products have used the latest Liebherr Dozer.
22 MAXIMUM IMPACT
Quarry takes a look at the contractor’s best friend: Keestrack’s R3h impactor.
28 HIDDEN POWER
Volvo Productivity Services can bring quarries more insight and new capabilities to manage operations.
30 WOULD YOU LIKE TO KNOW MORE?
Caterpillar is helping quarries measure, monitor and manage their sites with VisionLink Productivity.
32 JOHN DEERE RECOGNISED
John Deere has achieved Inclusive Employer Status for the third time.
34 ERASING CARRYBACK
Failing to clean up carryback can lead to a sticky situation. Kinder Australia’s Eraser helps remove it at the source.
36 QUARRYING TO A NET-ZERO FUTURE
How quarries can use recycled product to achieve net-zero future.
40 CLOSE YET FAR
Wirtgen is using telematics to support its customers around the country before a technician even makes it to a site.
42 MAKING FILTERS SMARTER
Filter presses aren’t rocket science, but OFS has found a way to make them smart.
44 UNDERSTANDING QUARRY SCHEDULING
Steve Franklin unpacks the saying, “Better to make your mistakes on the computer than in the field.”
48 XMOR DIGS DEEPER
NEW IMS-PM1200-20TB
16
PUGMILL AND SILO OPERATING AT BRAESIDE QUARRY WARRICK QLD IMS will bring new blending equipment to Australia through its exclusive distributor Crusher Screens Sales and Hire.
EVERY MONTH
How dealers and OEMs can help utilise the XMOR Bucket. 04 FROM
Quarries have long played their part on the big screen, providing directors with the perfect site to film their TV Shows.
The British sci-fi classic, Doctor Who, is famous for sending its titular character to far-flung alien worlds, with strange alien environments that look a lot like the Winspit Quarry in Dorset. It makes sense – shooting in a quarry means you’re below the ground level, so anachronistic features like roads and buildings don’t need to be edited out in post. It also provides a plenty of angles for creative camera work.
This movie magic has led Liam Neeson on a tour of Victoria’s regional quarries, which are set to feature in his next blockbuster.
The star of the Taken franchise and Love Actually is filming Ice Road 2: Road to the Sky across Victoria and in the NantStudios at Docklands Studio. The creators have turned several quarries into action sets to recreate Nepal’s famous Road to the Sky.
According to Creative Victoria, Ice Road 2: Road to the Sky features Liam Neeson as Mike McCann on a “dramatic adventure through Nepal’s perilous mountain tops.”
But while occasionally quarrying steps into the limelight – the Hollywood life isn’t at its heart. Crushing and screening is at its core. Without it there would be no
concrete to build houses, no asphalt to build roads, or ballast for railroads.
The process is a tough one. Breaking down hard materials is an intensive job and requires equipment that can handle the worst of what the quarrying industry can throw at it. The right maintenance is important to keep machinery moving, and the Internet of Things has unlocked new ways to keep an eye on the vital process.
That’s why this edition of Quarry focuses on the crushing and screening industry, looking at some of the products, innovations and services that are involved in keeping such a vital aspect of the industry running smoothly.
Inside you will find articles that highlight the latest machinery and technology that quarries are using for crushing and screening. We speak to original equipment manufacturers, quarries, and technology providers to find out the latest happenings in the sector.
This edition also highlights some of the new technologies that are helping quarries use data to improve their operations. Companies like Caterpillar and Wirtgen have invested significant resources in ensuring the quarry managers have the right information at their fingertips.
William Arnott EditorBREAKING DOWN HARD MATERIALS IS AN INTENSIVE JOB AND REQUIRES EQUIPMENT THAT CAN HANDLE THE WORST OF WHAT THE QUARRYING INDUSTRY CAN THROW AT IT.
PERFORMANCE, PRECISION AND SUSTAINABILITY. The MOBIREX MR 130 PRO mobile impact crusher excels with outstanding performance in a diverse range of applications. With its double-deck post screening unit, the plant ensures top product quality with up to two graded end-products, while achieving impressive throughput rates of up to 600 t/h in natural stone and recycling. The all-electric E-DRIVE is not only efficient, it can also be operated with zero local emissions. Operation is intuitive thanks to SPECTIVE components. The MOBIREX MR 130 PRO – the sustainable powerhouse.
Everyone who works at a quarry deserves to get home safe after their shift. We all have a commitment and responsibility to make sure that happens.
The IQA’s mission has always been to remain as the leading provider of technical quarry training, specific quarry courses and quarry manager training for the extractive industry.
Safety is an important and integral part of this.
The IQA stresses the importance of planning training for workforce development and safety, to grow our members and ensure that the best possible safety outcomes are achieved everyday by our members. We continue to strengthen our education development pathways to support improved knowledge, skills and business outcomes for our community, regulators and stakeholders.
At the end of the day, we want our people to be as rock-solid as the material we move.
Working alongside heavy machinery has its risks. Conveyors, crushers, trucks, and more all pose potential dangers to staff on site. Knowing
how to properly minimise these risks is vital.
That’s why the IQA will continue to provide safety and health training to ensure sites of the policies and procedures to minimise the risk of injury and illness from workplace operations.
I encourage everyone to get involved, even if it’s just a refresher. The courses are designed to be accessible, and there are several webinars available for those that prefer the digital format.
The IQA has a long and proud history of bringing the extractive industry together, especially when it comes to sharing knowledge.
As always, I’d like to thank our branch members, committee members and the broader IQA community. It’s your continued support and contributions that make IQA what it is today.
Let’s all work together to grow the industry.
Duncan Harris President Institute of Quarrying AustraliaEducating and connecting people engaged with the extractive and associated industries.
The IQA’s Strategic Plan 2023 to 2026 embodies the following vision, values and strategic priorities:
Vision:
Thriving communities supported by a sustainable industry
Operational Priorities:
• Deepen industry participation
• Sustainable revenue streams
• Highly capable team
• Technological innovation
• Effective engagement
• Great governance
Strategic Priorities:
• Support industry participants with compliance and regulation
• Build a diverse and skilled industry workforce
• Foster strong industry connectivity
IQA Contacts:
Phone: 02 9484 0577
Email: admin@quarry.com.au
Deputy President
Sarah Bellman
Company Secretary
David Cowie
For all education, member and branch enquires please email: admin@quarry.com.au.
Are you finding it difficult to extract critical data from disparate systems?
Eltirus Enable brings together data from all your operational systems (including those that are paper based) and turns it into actionable information, resulting in decision making that is more predictive and less reactive. Modules include:
Prime Creative Media is Australia’s first publisher to send paper wrapped magazines at scale, in partnership with its printing and mailing supplier FSG.
Based in Bayswater, Victoria, FSG purchased the country’s first ever paper-wrapping mailing machine in January this year. Imported from UK supplier Norpak, the machine’s ability to wrap publications in paper will eliminate plastic wrapping for Quarry.
“It’s the evolution of the mailing industry to abolish the use of singleuse plastics in mailing magazines,” Michael Murphy, owner and director of FSG Mailing said. “This follows the government’s move to get disposable plastics out of our Australian systems.”
Up until this technology was in place, the only alternative option to plastics for publishers was paper envelopes. Murphy notes this was cost prohibitive for many clients, because the price of producing and printing the envelopes was high, in addition to the labour of either hand inserting magazines into the envelopes, or using very expensive equipment to insert into the envelopes and seal them. This added a significant increase to mailing costs.
Mailing houses like FSG have experimented over the years with
bioplastics, and recyclable plastics, but Murphy said the technology never quite worked out.
“We tried to use bioplastics but the settings on the machines – which use heat to seal them – make it very difficult,” he said. “Even for those companies who worked out how to mail them, it was a challenge for consumers to separate the plastics at the end of the process, or find appropriate disposal. Eventually, we saw that the only real option was paper.”
Murphy came across this technology through his supplier UK company Norpak, who previously supplied his plastic wrapping machine.
“They introduced us to the idea because they saw what was happening in the European Union with the phase out of single-used plastics,” Murphy said. “With the Australian government making similar moves towards a full phase out of single-use plastics, we think that this machine will be the catalyst to push the movement along in the mailing industry.”
Murphy notes that in Europe, where it was put into commercial use 18 months ago, it has already taken off.
“The first person to use the machine really took a leap in the dark. Now
“WITH
THE AUSTRALIAN GOVERNMENT MAKING SIMILAR MOVES TOWARDS A FULL PHASE OUT OF SINGLEUSE PLASTICS, WE THINK THAT THIS MACHINE WILL BE THE CATALYST TO PUSH THE MOVEMENT ALONG IN THE MAILING INDUSTRY.”
MICHAEL MURPHY
he has 13 of these machines, and those plastic wrapping machines are sitting there not being used – they are becoming museum pieces,” Murphy said. “That will be the future in Australia now that this machine has arrived.”
An additional environmental benefit to the machine is that because the addresses are printed directly onto the paper wrapping, it eliminates the need for flysheets – the paper that lists the addresses and is placed onto a magazine. This improves efficiency, as it limits the printing and transportation of flysheets. It also means that only a small amount of more paper is being used in with the new system, once you take into account the paper used in flysheet printing. And of course, this opens up a vast array of options in using recycled and sustainable paper products.
The only drawback, Murphy notes, is that the paper is less weather-proof. In Europe many people live in apartments instead of houses, and magazines are delivered in post boxes or through slits in doors. He said it’ll be interesting to see how the paper stands up to Australia’s climate, but confident it will work well. That being said, he notes the price of an occasional damp magazine is one worth paying to save thousands of tonnes of plastic wrapping from going to landfill every year.
Prime Creative Media COO Christine Clancy was on site at FSG in Bayswater to witness the first publications being sent out in paper-wrapping.
“It’s such an honour to watch history in the making, to see our publications make this first step in reducing single use plastics in our environment,” Clancy said.
She notes that the company has long been involved in supporting the growth of the waste management industry, through its publications Inside Waste and Waste Management Review, along with its annual Waste Awards.
“After years of reporting on the challenges of single-use plastics in the waste industry, it’s so wonderful for us to play a proactive part in it by reducing our own use,” Clancy said. “We’re fortunate to have FSG as a partner to help make this happen.”•
Dr Nicola Kimm, chief sustainability officer and Martin Harper, CEO of BirdLife international, signed the memorandum of understanding.
Heidelberg Materials has reconfirmed its environmental commitments after extending its partnership with BirdLife International.
The pair have signed a memorandum of understanding for three years to enhance biodiversity in and around the Heidelberg Material’s quarries.
“We are committed to contributing to a nature positive future, which means protecting and promoting a rich biodiversity across the areas in which we operate – both within our active quarries and during after-use”, Heidelberg Materials chief sustainability officer Dr Nicola Kimm said.
“Over the years, working with BirdLife has been instrumental in this effort. This continued partnership will now enable us to maximise our biodiversity potential and work alongside BirdLife towards our 2030 nature targets.”
More than 40 biodiversity projects have been started since the partnership first began in 2011 including Heidelberg
Materials’ sustainability strategy. The company aims for 100 per cent of its active quarries to contribute to the global goal of nature positive by 2030, with 15 per cent space for nature as well as providing education for staff.
As part of the agreement, Heidelberg Materials and BirdLife will partner on public awareness campaigns for biodiversity conservation.
“BirdLife has been delighted to work with Heidelberg Materials for more than a decade to improve wildlife across all its operations,” BirdLife International chief executive Martin Harper said.
“We need businesses to not only set high standards but also help influence positive change, which is why it has been so heartening that Heidelberg Materials continues to champion stronger laws to protect and restore nature.
“We look forward to continuing to work with and learn from each other while saving more nature together over the next three years.”•
Delta Rent operates one of the largest earthmoving equipment rental fleets of more than 450 high performance machines in Australia.
24/7 service Australia wide
Expert advice and analysis
Purpose built fleets tailored to quarry site requirements
OEM backed support, service and technicians
Late model, low hour fleet
GPS systems hardwired
deltarent.com.au
1300 793 071
Image : Heidelberg MaterialsIt is part of a potential major change for Boral, who are currently looking over a takeover bid from Seven Holding Group which was also announced this month.
It is part of a shifting trend for Deer Park in Melbourne’s north-west. While Boral is investigating potential uses for part of its quarry site, Orica sold off surplus land at its Deer Park site.
Orica completed its deal with UniSuper for $260 million for 66 hectares of surplus land, which is around half of Orica’s total surplus land holdings at Deer Park. The net profit after tax from the sale is approximately $173 million.
“The sale will not affect the ongoing operations of Orica or its tenants on the bordering industrial precinct and will allow Orica to continue to focus on its core manufacturing and customer operations at Deer Park,” Orica said in an announcement.
Boral is investigating potential development opportunities for part of its Deer Park quarry site with the aim of developing a long-term recurring income.
The proposal was revealed in the company’s 2024 half-year presentations which highlighted the 1,105-hectare site’s potential future.
Boral is working with developer Logos to identify industrial development opportunities with 450 hectares thought to be a developable area. According to reports, Boral chief executive Vik Bansal told investors the
company would be able to bank the income from the project.
“(The) underlying driver and purpose is to ideally create a longterm recurring earnings stream for Boral,” he said at the earnings presentation earlier this month.
“When it is confirmed that a site is surplus to our operations, the team shifts focus to repurposing the asset.”
The quarry site was previously identified as “state significant industrial land – future” by the Victorian government and is zoned for quarrying and industrial activities.
“The remaining surplus land at the site (stage 2) is expected to be offered to the market in the future, pending the completion of remediation activities, securing approvals from relevant authorities, and supportive market conditions.”
In announcing the deal, UniSuper indicated the site will provide modern industrial facilities in Melbourne’s west. UniSuper will work with GPT and developer HB+B Property to develop the logistics, warehousing and manufacturing site.
“This super prime parcel of industrial land further improves the quality of our diversified unlisted property portfolio and adds to our exposure to the logistics and warehousing sector following on from other recent acquisitions,” UniSuper’s senior property manager Nick Stephens said.
“The transaction highlights UniSuper’s ability to secure high-quality property investments that help our members grow their retirement savings.”•
CRH has confirmed a scheme implementation deal with materials producer AdBri, which will see them potentially take control of the company.
AdBri’s committee which looked over the proposal unanimously recommended the shareholders vote in favour of CRH’s proposal after concluding it was in their “best interests”.
Under the deal, CRH will take over the remaining 57 per cent of AdBri shares not owned by Barro Group for a cash consideration of $3.20 per share.
“We are pleased to reach this important milestone in the potential acquisition of
Adbri in partnership with the Barro family,” CRH chief executive Albert Manifold said.
“Adbri is an attractive business with highquality assets and leading market positions that complement our core competencies in cement, concrete and aggregates while creating additional opportunities for growth and development for our existing Australian business.
“We look forward to working with the Barro family over the coming years to enhance the long-term growth and performance of Adbri.”
The Barro Group nominee directors have recused themselves from the Adbri Board
and all board sub-committees, and an Independent Board Committee while the proposal was considered.
CRH’s proposal values Adbri at an equity valuation of $2.1 billion (US$1.4 billion) on a 100 per cent basis and values the approximately 53 per cent of issued share capital that the partners do not currently have an interest in and which CRH has agreed to acquire at $1.1 billion.
The proposal came to light last year as CRH announced it had partnered with Barro to potentially takeover AdBri subject to due diligence and shareholder support. •
904 P-TIER
OBSTACLE INTELLIGENCE
At 40 tons and over 30 feet long, safety comes first. By combining cameras, radar, and machine learning, obstacle intelligence gives operators eyes in the back of their head. To protect your crew, and other investments, like never before.
Komatsu has confirmed a multiyear deal with Williams Racing as a principal partner as the two brands reunite a partnership last seen in the racing team’s era of dominance.
The deal commences ahead of the 2024 Formula One World Championship season. Previously, Komatsu partnered with Williams Racing during its Constructors’ and Drivers’ Championships with Damon Hill and Jacques Villeneuve in 1996 and 1997.
“Komatsu and Williams Racing have shared values around innovation
and the development of our people,” said Komatsu Ltd president and chief executive Hiroyuki Ogawa.
“Through our partnership, we look forward to creating value together, both on and off the track. Our partnership with Williams Racing is aligned with Komatsu’s mission to create value through manufacturing and technology innovations to empower a sustainable future where people, businesses, and our planet can thrive together.”
Komatsu’s official designations with Williams Racing reflect the
“THROUGH OUR PARTNERSHIP, WE LOOK FORWARD TO CREATING VALUE TOGETHER, BOTH ON AND OFF THE TRACK.”
HIROYUKI OGAWA
Toowoomba’s Brookview Quarry has proposed a development application to the local council to ensure it can maintain a supply of “high quality” basalt supply.
Brookview Quarry is run by PK & BT Bland Rural Enterprises who applied to the Toowoomba Regional Council.
The application would keep the extraction ranges at the same levels as the existing ones but extend the quarry surface by 24 per cent to enable operators to access more material.
“The quarry will maintain the existing production rate of up to 500,000 tonnes
per annum of material suitable for a range quarry products,” the report noted.
“The proposed pit has a total volume of approximately 2.6Mm3 of a mixture of weathered and fresh basalt.”
companies’ shared focus on the longterm development of engineering, technology and new generations of talent: Official STEM and Early Careers Partner, Official Esports Partner and Official Construction Machinery Partner.
Komatsu’s logo and branding will feature prominently on the 2024 Williams Racing livery, as well as the team’s overalls and kit, during the upcoming Formula One season.
Komatsu’s Australian customers and staff will be able to see the company logo on the Formula One car at the Australian Grand Prix in Melbourne when Williams Racing and the Formula One World Championship return to the country later this year.
Williams Racing team principal James Vowles said the team was delighted to have Komatsu joining one of the most iconic Formula One teams on the grid.
“Williams Racing is delighted to be rekindling our relationship with Komatsu. We have enjoyed huge success together in the past and reuniting is a significant step in Williams Racing’s long-term mission to return to the front of the grid,” he said.
“Both Williams and Komatsu are committed to attracting and developing the best young talent in pursuit of our goals and we look forward to working together again.” •
The applicant will mainly use dozer ripping and drill and blast to extract the material. Blasting is expected to occur monthly.
The quarry will employee eight to 12 employees to carry out operations.
“The average extraction rate for the quarry is expected to be 250,000 tonnes per annum with a maximum rate of
Reports into traffic, air quality, noise impacts, site management and engineering were also submitted to the council.
500,000 tonnes per annum depending on demand,” the report stated.
Reports into traffic, air quality, noise impacts, site management and engineering were also submitted to the council last year for the application.
•
To submit new product and equipment releases, email: les.ilyefalvy@primecreative.com.au
Industry workers all know that safety is the number one priority, especially given that the job site is never the same two days in a row.
Precision construction is about total control of what you’re doing with your machine, and a way to do that is with John Deere’s obstacle intelligence system. Obstacle intelligence uses a combination of cameras, radar, and machine learning to protect anyone and anything in close proximity. And that’s better for everyone’s livelihood.
John Deere’s obstacle intelligence features rear camera monitors for the back and sides of the machine, in-cab displays put everything in front of you so blind spots are minimized, and our mirror-mounted cameras provide an extra wide field of view greater than conventional mirrors.
Obstacle intelligence is only part of the overall precision construction offering in John Deere’s construction machines, which also features grade management solutions and job site automation.
Operational intelligence helps you avoid downtime and make operational decisions based on real-time data. Machine monitoring and connected support keep you updated with machine and fleet performance, along with job progress. All to keep your business humming.
Knowing how over-grading, changes in work scope, understaffing and lack of time add up to rework. That’s why John Deere’s flexible grade-management tools are engineered to minimise rework or avoid it altogether. Boost productivity and the bottom line with grade management solutions.
The ARJES Impaktor 250 EVO, a versatile stone crusher, crushes the toughest materials, such as rubble, concrete, asphalt, and natural stones, with finesse. With features like a 2-stage crushing process, an asynchronous drive, and a powerful Volvo Penta diesel engine, this compact powerhouse ensures a uniform final product while prioritising environmental friendliness and efficiency.
The machine’s compact dimensions, low weight, and short setup times further underscore its efficiency, making it a game-changer in waste processing.
The ARJES Impaktor 250 EVO stands out as a versatile machine tailored for contractors, disposal firms, and demolition experts dealing with moderate volumes of waste.
Its dual capabilities as both a shredder and crusher make it an invaluable asset for companies aiming to enhance their existing business models by diverting waste from landfills.
The ARJES Impaktor 250 EVO can crush rubble, concrete, asphalt, and natural stones, with finesse.
They’ve learned how to mitigate and compensate for long hours, bad weather, heavy materials, and labour shortages. Whether your operator’s a greenhorn or a 40-year-veteran, job site automation ekes out efficiency in every machine in your connected fleet to make the repetitive, less repetitive.
To see and learn more about what your site could be capable of with a John Deere Machine, check out Precision Construction Technology or visit deere.com.au
The
The ARJES Impaktor 250 EVO features:
- 2-stage crushing process with special shaft geometry, secondary double jaw breaker and breaker bars
- Environmentally friendly and efficient
- Automatic reversing function protects against damage to the crushing tools
- Compact dimensions and low weight, with a total weight of approx. 15 tons allows for easy transportation
- Short set-up times, with easy access via multi-channel remote control and hydraulically lowerable chassis
For those looking to explore the possibilities in waste processing efficiency, visit triconenvironmental.com.au or call 1300 859 885.
XPower is an innovative machine concept which combines performance, fuel efficiency, robustness and comfort. With their power split driveline, XPower wheel loaders work with the greatest level of efficiency in all applications. www.liebherr.com Wheel
Crusher Screens Sales and Hire has elevated the Australian quarrying industry to the next level with the new pugmill and blenders from renowned manufacturer IMS.
Crusher Screen Sales and Hire’s exclusive partnership with Irish Manufacturing Services (IMS) will reward the Australian market with two new products to help the quarrying industry.
CSSH, the IMS Australian distributor, will distribute the IMS-BP1200-48TB and PM1200-20TB.
“The two new products from IMS bring a lot of advantages to the extractive industry,” CSSH co-owner John Andersen said.
“CSSH will be on hand to help customers who want to see how this equipment can help their operations, especially for blending materials.”
The new PM 1200-20TB pugmill is equipped with two five-metre-long feed hoppers holding 10ms each, both with separate feed hopper conveyors fitted with belt scales.
These features enable operators to blend two raw materials, liquids, or powders, at
once when the PM 1200-20TB is running at full capacity.
Quarries can add an optional vibrating hydraulic tipping grid to the feed hoppers. This feature helps remove oversized raw material and release lumps.
“This is a good option for those businesses that work in recycled materials like recycled asphalt,” Andersen said.
“By removing oversize material, businesses can have confidence in their quality control for the product and ensure they are meeting the right specifications for the job at hand.”
IMS is a Northern Ireland-based manufacturer that develops durable equipment for the extractive industries.
Since the company was founded in 2010, the company has built a portfolio of standard and bespoke equipment with a reputation for cost-effective equipment.
IMS developed the PM1200-20TB following the IMS-PM1050-16TB pugmill. CSSH, as an IMS Australian distributor, delivered over 50 IMS-PM1050-16TB pugmills into the Australian market.
Andersen said the IMS-PM1050-16TB
pugmill has been crucial to several major infrastructure projects, and the PM1200-20TB would deliver similar results.
“The options the new pugmill offers the industry are not limited to just quarry operations and the construction industry, but also in in remediation projects,” he said.
“It can also blend recycled material into road base blends on an accurate and controlled basis, ensuring the product meets specifications before leaving the quarry gate.”
Andersen said that by investing in pugmills that meet main road specifications, operators can make their operations more efficient, saving time and money.
The PM1200-20TB comes with a threemetre long pugbox to ensure a quality mix and the option of two augur designs to suit the raw material being processed.
The industry has seen recent demand for a higher percentage of blended cement and powder.
To meet the needs of the modern quarry, the PM1200-20TB can have two powder hoppers, which offer operators the ability to blend two powders.
Andersen said CSSH was able to offer mobile bulk silos from 40-100 tonnes and create a total storage and material production solution.
Using the bulk storage solution from CSSH, quarries could have one powder hopper dispensing material while the other is being refilled from the mobile silo.
Andersen said this concept could reduce slow moving products and increase sales.
IMS has equipped both feed hoppers with sensors to stop the plant before the hopper is empty and will automatically restart once refilled.
The operator maintains control of the process with a stop-and-start remote, which is linked to the pugmill.
The pugmill has Wi-Fi capabilities to connect to an iPad in a loader or site office up to 100 metres away.
“The loader operator can control the batch mix and load trucks and multiple trailers directly from the pugmill, stopping automatically after each unit has been filled to the programmed amount,” Andersen said.
“The batch report can be sent directly from the iPad to the office or client. The plant will automatically stop if the percentage is not within the programmed allowance.”
The second machine IMS is bringing down under is the IMS-BP1200-48TB electric track blender.
The IMS-BP1200-48TB is powered by a Cat C7 genset, which can be connected to the main’s power to enable quarries to run the machine cheaper than a diesel equivalent.
The blender has four 12m3 feed hoppers, which are five metres long, but the
dividing wall can be removed to create two 24m3 hoppers.
IMS has built an integrated design between the pugmill and the electric blender, that share the same feed hopper design.
“The blender can also operate with the IMS electric pugmill on skids with a 24-metre electric radial stacker,” Andersen said.
“It has the same PLC control and recording system as the Pugmills, including Wi-Fi and iPad connection.”
IMS has designed the IMS-BP1200-48TB electric track blender with a small footprint, making it portable to move around the quarry.
“The blender has a small footprint considering it has four feed hoppers and, being mobile, is ideal for moving around quarries to blend unsaleable or slow-moving products into dollars,” Andersen said.
CSSH, based in Yatala in Queensland, can provide full after sales and technical support to customers for its portfolio of IMS products.
“We stock a wide range of IMS products so if your quarry needs new equipment, we will be able to create a solution for you,” Andersen said. •
For more information, crusherscreen.com
Newcastle Quarry Products recently took ownership of the Liebherr PR 766 Litronic. The company’s quarry manager spoke with Quarry about the early benefits.
When it comes to equipment for Quarry Products Newcastle, build quality and fuel efficiency are two key factors in their buying process.
When the Newcastle team travelled to Liebherr’s Sydney facility to inspect the PR 766 dozer, Generation 8, they immediately realised they had found the right machine for their operation.
“This is the first piece of Liebherr machinery that we have purchased,” Quarry Products Newcastle quarry manager Matt Frost said.
“We were tossing up between costs and productivity, and the Liebherr was where we landed; upon seeing the dozer we immediately realised it would meet our requirements.
“The design and functionality look wellmanufactured and have high quality across the machine.”
The Newcastle business has operated out of Allandale Quarry since the late 1970s and has forged a reputation as a reliable aggregate producer. It has supplied roadbase and aggregate across the Newcastle area and construction market for nearly five decades.
Liebherr’s earthmoving and material handling team took the Newcastle operators
to a nearby Sydney site so they could see the PR 766 Litronic in action.
Liebherr told Frost and the Quarry Products Newcastle team that the fuel efficiency would deliver significant cost savings. After two months of use, the Newcastle business is already seeing the results with the Liebherr PR 766 Litronic around 10 litres an hour better than the previous machinery.
Frost estimated the machine would be used for around 1500 hours a year, equating to $30,000 of savings with the current fuel price.
Liebherr built the PR 766 G8 dozer to be able to handle a variety of heavy industry uses, from precision grading to heavy dozing. Liebherr has used advanced engine design, a proactive power adjustment feature and economy mode to help operators achieve improved fuel efficiency.
The hydrostatic drive enables the operator to maintain a constant output from the diesel engine. Avoiding speed fluctuations helps ease fuel consumption as the hydrostatic travel drive adjusts the working speed to load conditions.
According to Scott McClement, major account manager of Liebherr Australia’s earthmoving division, the constant, low engine speed, combined with commonrail fuel injection, enables optimised
cylinder management and very efficient fuel combustion.
Operators can also activate different modes on the PR 766 Litronic when they need maximum output or fuel-saving.
“Fuel efficiency is really important now with the cost of fuel, along with running costs and reliability; it is one of the major things,” Frost said.
“(For us) it has been running around 40 litres an hour, which is probably 10 litres an hour better than our old one.
“Over the life of the machine, it will make a difference.”
Liebherr built the PR 766 G8 dozer with a redesigned cabin to ensure operators had a working environment that prioritised comfort.
A fundamental feature is the insulated cabin. The pressurised cabin keeps out dust while the hydro-elastic bearing mounts absorb noise. Liebherr’s low-speed engine and on-demand cooling fan were also designed to emit lower noise emissions compared to a conventional crawler.
Frost said the cabin comfort and quietness were things his operators had noticed since getting the PR 766 Litronic.
“They’ve definitely noticed the comfort of it; it is a lot quieter than what we had, which was an older machine,” he said.
“It is quite comfortable for them to operate, so we’ve been happy with that.”
Before the Liebherr PR 766 G8 dozer arrived at Newcastle Quarry Products’ Allandale Quarry, Frost had mainly known the Liebherr brand through its work in heavy-duty mining. However, since purchasing the Liebherr machine, Frost said he would be quick to engage the international original equipment manufacturer for their next machine.
“This is our introduction to Liebherr equipment, and so far, so good; we’re looking forward to seeing how it performs and holds up long-term,” he said.
“It is pretty important to have a quick turnaround on service and parts if there is a breakdown and you need it replaced, but we haven’t had that issue yet.
“Scott and Liebherr have been very easy to deal with, and the whole process has been pretty easy.” •
The new Lokotrack EC range is advancing sustainability in the Aggregate sector by providing unparalleled reliability and performance. It features a robust design, fit-for-purpose digital tools for easier operation and maintenance, and a next-generation diesel-electric powerline for minimized operational costs and CO2 emissions.
All process functions in the Lokotrack EC range are electrically driven and automated for optimal load level performance, equipped with an integrated genset and the capability for connection to an external electricity source.
Contact metso@tuttbryant.com.au to find out more information on our Metso range today!
John Fahey made his curtain call last year as he officially retired from the quarrying industry. He tells Quarry about life, achievements, and hopes for the sector’s future.
In speaking with John Fahey, he’s remarkably modest about the results of an extensive career in Queensland’s quarrying sector.
But that would overlook a career in quarrying that spanned more than four decades, which included business success and a legacy as chairman of the Institute of Quarry Australia’s North Queensland branch.
Many within the sector consider him to have a stellar reputation and a trusted voice on issues that face the industry.
While he spent some time in construction and earthmoving after university, quarrying always managed to lure him back.
“I just wanted to be able to see the stuff on the ground; I wanted to feel the earth,” he said.
“I get great satisfaction in working with the unknown. It is the same with quarrying; every site is different, every development is different.”
Fahey has spent a vast amount of his quarrying career at the helm of BQC
The family-run business has made its reputation by serving the Burdekin, Bowen, and Whitsundays areas for major infrastructure since 1974.
Fahey said the business, a partnership of three families, had been well-served by its local community.
“We virtually grew with the industry and grew with the demand in the district and the local demand,” he said.
“We didn’t have to travel too far at all; we looked after our local market and defended it vehemently.”
While there have been significant changes in equipment and technology for the industry over that time, Fahey sees government legislation as one of the fundamental changes during his career.
“We’re pretty well regulated and very regulated as an industry; it is a matter of making sure we conform and keep up to date with all that stuff,” he said.
“That is where the Institute of Quarrying Australia (IQA) has been great in helping us
“It has been a big improvement in a lot of things; I don’t always agree with the changes and specifications, but apart from that, everything has been for the better.”
Fahey is well-placed to understand the role of the IQA within the quarrying sector.
Fahey was there for the early beginnings of the North Queensland branch, which opened in 1982. Ken Fletcher set up North Queensland as a branch rather than a subbranch, and after one meeting, Fahey was signed up as a member.
“The annual conferences were a really good affair; the wives were involved, and it was like a great big family meeting; you were able to catch up with people you hadn’t
“It was more about the camaraderie than anything, and the North Queensland branch was more of a family affair as well; it was really good.”
He also witnessed The Institute of Quarrying (Australia Division) being incorporated as the IQA and becoming the first affiliated body with the Institute of Quarrying in 1994.
At the time, Fahey was serving as the chair of the North Queensland branch and believed the change was a definitive moment.
“It meant we were able to be responsible for our own money and control it, which led to the education committee being set up and courses being launched at Box Hill,” he said.
“It gave the institute control but allowed them to go into the education, which everyone was keen on, and it went pretty seamlessly.”
Depending on who you talk to within quarrying, they may come up with a few different topics about the key issues that face the sector.
For Fahey, he sees one of the critical issues as perception.
He recounted when his daughter went to school, her teacher insinuated to her that her dad was an “environmental vandal” on account of his occupation.
“People sometimes don’t actually appreciate what is involved in quarrying; they think you just dig a hole and throw it on the back of a truck and charge a lot of money for it,” he said.
“There is a lot more involved in getting there, and I know all the community sees is a problem sometimes with dust problems or noise problems, but we’ve been lucky enough with our communities.”
Fahey and his team at BQC Quarries took it upon themselves to help change that perception by inviting the school students and teachers into the quarry.
In what became a regular occurrence, the quarry team showed students what they did and how much the local community relied on the quarry.
It remains one of Fahey’s best memories from his long career.
“The best part was some of the drawings the kids did after the tour of their interpretations of the quarry and the gear within it,” he said.
“It was a great experience being able to see all of that.”
Fahey also has a link closer to home to the North Queensland branch: his son, Lawrence, served as the North Queensland chair until recently and remains on the committee.
Lawrence also followed in his father’s footsteps in business and currently serves as the operations manager of BQC Quarries.
“As long as he thought he could handle it, I was happy for him to take the job; he has been a good chairman. It has been good for him,” Fahey said.
“He’s adapted all of his skills to the quarrying game quite quickly. I’ve been side by side with him, but he has learned incredibly quickly.
“He’s done quite well and probably brought us into the 21st century as a business and made us a lot more professional.”
Fahey announced his official retirement from the industry late last year after spending the previous year and a half transitioning with plans to travel and holiday next year.
“Even though I am retired, I think I’ll still take an interest in quarrying.” •
Quarry takes a look at the contractor’s best friend: Keestrack’s award-winning R3h impactor.
Since its introduction to the market, the Keestrack R3h impactor has taken the crushing industry by storm. The redesigned R3h has been enhanced from its predecessor, the R3. It features 30 per cent more screening surface via the screen box and 12 per cent heavier blow bars, creating greater inertia leading to more throughput and a lower cost per tonne.
The impactor’s design lends itself to various applications, including quarrying and natural rock to gravel and asphalt production, as well as brick and concrete recycling.
Ciaran Lagan, Screenmasters national sales manager, told Quarry the machine had been one of the equipment supplier’s most popular in Australia.
Screenmasters are proud of its portfolio of brands, including European manufacturer Keestrack. The Keestrack partnership was born some 20 years ago from shared values: a want to provide operators with the bestin-class equipment that is productive and cost-effective. Since Keestrack introduced the R3h impactor on the market, it has won several awards, including the German Design Prize and the Big See Award. In particular, the machine was recognised for its electric drive capability when it was announced as a prestigious Red Dot Award winner in 2018. The compact crusher, powered by a Volvo power unit and the largest rotor in its class, has a capacity of 250tph, dependent on the application.
The bottom apron on the R3h has pretensioned springs.
When foreign material like steel from recycled concrete passes to the bottom apron, the springs compress to enable the uncrushable object to pass and for the hydraulic adjustable magnet to remove the object.
“It has a heavier and larger rotor compared to the competitors, that is directly driven off the engine through a gearbox and fluid coupling, which allows it to have more inertia when crushing,” Lagan said. “This means it can crush larger feed sizes and deliver higher crushing rates, impressive for its size.”
In some instances, the Keestrack R3h’s versatility has seen operators move from a traditional jaw crusher, cone crusher and screen set-up to just one machine, the Keestrack R3h Impactor. Saving thousands on capital, transport, fuel and servicing costs.
The small footprint of Keestrack’s machine enables the end users to operate it autonomously and efficiently transport the unit from site to site, quickly and at low cost. The 30-tonne impactor does not need permits and can be transported in one piece.
Hydraulic steel pipes, sealed bearings, large access doors and ports to key components allow for easy and safe servicing, reducing downtime and costs for maintenance and replacement.
“Customers are seeing an increase in production, maintenance has been easier, and they’ve seen a decrease in fuel consumption,” Lagan said.
Keestrack uses a variable displacement pump with load-sensing hydraulics, which only uses the required amount of hydraulic power at any one time, so end users will see about 25 per cent less fuel being used. Lagan said Screenmasters customers use the Keestrack R3h impactor for everything from recycling to regular quarrying operations.
“The R3h is ideal for small to medium-sized contractors or someone who has a small quarry or recycling yard,” he said.
“Because of its onboard single deck screen, Customers can make a finished product with just one machine.”
“Those small to medium-sized contractors are working in recycling and quarrying, all sorts of applications, and they want a machine that is flexible.”
Keestrack has designed the R3h impactor with various options, including diesel/ hydraulic, diesel/electric and full electric. While the electric-drive options are more prevalent in Europe, the R3h Impactor’s fuel efficiency provides a sustainable option for the diesel drive.
According to studies on the machine, when run at its optimum parameters, the R3h has the lowest fuel consumption in its class.
Screenmasters takes pride in its aftersales support, providing expert back-up service and technical advice to keep equipment running at peak performance.
Stocking an extensive range of spare and wear parts, available for immediate delivery across three sites throughout Australia.
“It is one of our highest priorities that we focus on,” Lagan said. “It is so important to limit customers’ downtime because it costs them money.”
With good housekeeping practices, the R3h has proven to be a very reliable piece of equipment.
Issues can and do arise, 85 per cent of these issues can be sorted within acceptable timeframes, limiting costs and downtime. However, a large part of Screenmasters spare parts stock is focused on the 15 per cent of issues that rarely arise but when they do so, will prove problematic.
It is this investment, that over the last 30 years has proven invaluable to both Screenmasters and their customers.•
For more information, visit screenmasters.com.au
Volvo’s Productivity Services include everything you need to start. From operator training and smart assistance solutions, to machine confirguration and site mapping. It’s time to start doing more, and earning more. Increase your productivity in a big way.
Get the right services, and the right machine for the best solution
Productivity Services helps optimise and streamline your business operations.
Cut travel times, minimise material mixing, lower fuel consumption and reduce emissions.
Volvo productivity services generates detailed data about your production.
See how material is being moved around the job site, connecting the loader operator, site offices and trucks.
Metso is set to hold its fourth-ever Lokolaunch when it debuts the new EC range in Finland.
Quarry looks at the potential of this electric-driven equipment.
Metso will unveil the result of extensive research and development when it debuts the Lokotrack EC range later this year in Finland.
The newest addition to Metso, which marks a major shift in development for the manufacturer, will be revealed to a select group of its biggest dealers and customers in mid-May.
“It is very significant; it is a significant step change for the company,” Tutt Bryant, national business manager of crushing and screening Paul Doran, told Quarry.
“(Metso) has always been at the forefront, but this is a big step for them; it has been three years in the making.
“A company like that doesn’t sink the time and money into a project unless they think there are long-term benefits for their customers.”
The fundamental upgrade in the new Lokotrack EC range is the dieselelectric powerline.
Metso has designed the range to have all several functions powered electrically and automated to perform at optimal levels.
The 60-tonne crushing and screening range will feature a diesel engine running a generator, which will power process functions, including the belts, screens and crushing.
Metso has designed all the parts, including the wear parts, to handle 20,000 hours of maximum uptime to ensure the Lokotrack EC range stands up in all conditions.
Operators can run the machines if they have the capacity, off mainframe power, which is one of the cheapest forms of energy contractors and quarries can access.
The Lokotrack EC cone crusher has been designed to have the screen plugged into it. This enables quarries to run both units off one engine generator to improve sustainability.
“It is a lot more sustainable and better for the environment and all of those good things because the electricity has already been produced,” Doran said.
“People are starting to think about their CO2 emissions and those sorts of things and making their equipment more sustainable.
“It will make Metso Lokotrak EC owners more competitive because their sites will run at a lower cost-per-tonne than someone running a fleet of diesel-hydraulic machines.”
The equipment is part of Metso’s broader sustainability strategy, known as Planet Positive, which includes ambitious climate targets.
According to Metso, the range will meet the “evolving needs of the industry”, which is continually pushing towards greater
sustainability targets and initiatives.
Tutt Byrant, the exclusive Metso dealer for Australia, will be attending the launch of the new Lokotrack EC range. The fourth iteration of the event will be hosted at the Nokia Arena in Tampere, Finland.
Doran expects Metso, via Tutt Bryant, to bring the range to the Australian market later this year.
“I think once we start getting them in and installed and people see the value and how efficient and competitive it makes them, I think the adoption rate will go up,” he said.
“Having electric crushers and conveyors running on-site means there is less things to maintain and more time to crush.
“It means you’ll be able to put out more tonnes per day, which contractors particularly need to aim for.”
The new Lokotrak EC range is part of Metso’s strategy to bring future-focused technology to the worldwide aggregates sector.
Metso has built two key digital offerings for operators in its Metso Metrics platform and the Metso Remote IC app.
The advanced process control system in the Metso Remote IC app provides operators and quarry managers with real-time data via
a dashboard and the ability to troubleshoot through any web-enabled device.
“Metso Metrics has evolved so customers can get an amazing amount of detail, including how much they’re crushing each day and how much fuel they’re using, which enables them to refine their costing process,” Doran said.
“It will make them more competitive because they’ll have a real good handle on their outputs and costings.”
The Metso IC process control can instantly stop a feeder to prevent overloading, and the app can alert the operator instantly.
While one individual operates the process control, the app is designed so everyone on the site can see how the Lokotrack train is performing and receive alerts in case of an incident.
“For a lot of other machines, you need to wait for the feeder to run empty, stop the machine, walk out to it and make the changes you need to make,” Doran said.
“Metso’s intelligent controller app allows operators to do it all from their air-conditioned cabin without getting into the dust.”
As an authorised Metso dealer, Tutt Bryant’s team can service all of the brand’s equipment, including the new EC range, after it launches in May.
Doran said the servicing training for the new machine would be part of Metso’s product launch to ensure the customers receive after-sales support.
“There’s an ethos there for this machine that if you buy it, you are going to get an exceptional, serviceable life out of the machine,” he said.
“As part of the roll-out for this range, Metso will provide service and maintenance training on those machines.
“In time, we’ll have our own staff trained to manage the electrical side of machinery.” • For more information, visit tuttbryant.com.au
Fitted with a self-erecting onboard 40T silo using hydraulics, the Continuous Weight Mobile Pugmill can change from travel mode to fully operational within a few hours. Available with outputs of up to 400 tonnes per hour, the Rapidmix provides feed rates that are fully adjustable for the aggregate, cement and water systems.
Offering full weighing of all materials, the Rapidmix provides accuracy and accountability you can depend on.
Volvo Productivity Services can bring quarries more insight, additional opportunities for growth and new capabilities to manage operations and proactively enhance site safety and efficiency.
In discussions between contractors and heavy equipment manufacturers, the focus often centres on cutting-edge machine technologies to enhance efficiency and safety on job sites.
However, amidst the excitement over new machinery, the critical role of supporting services in optimising machine performance can sometimes be overlooked.
While high-quality machines lay the foundation, coupling them with value-added services creates a holistic solution that gives businesses a competitive edge.
“It’s not a one size fits all when it comes to productivity services; from understanding your business, your fleet, the direction of where you want to take your business and how to improve that, we can then assist in putting a plan in place to get your business there,” Andrew Minty, CJD Equipment’s product manager - site solutions, told Quarry “It’s important to understand the foundation of your business and equipment and its needs and benefits.”
Volvo Construction Equipment
recommends customers use a synergy of services with machines to deliver the best solutions. Volvo’s new services aim to
facilitate work completion and accelerate it, reduce costs, and maximise uptime.
Streamlining transport operations is crucial for cutting travel times, minimising material mixing and reducing fuel consumption and emissions. The connected map provides a real-time digital mapping of all the site’s machines, vehicles, and personnel, allowing for enhanced visibility and informed decisionmaking. This service boosts productivity and improves safety by identifying bottlenecks and optimising traffic flow.
With the Connected Map feature, all machines and vehicles can see each other, and site managers can see what the site looks like from a computer office. The Connected Maps Office Portal provides a visual overview of all machines, operators, and temporary visitors on site and allows site managers to react to the prevailing site conditions. Site managers can introduce measures such as one-way traffic or restricted zones and communicate these changes to all users instantly, helping to improve awareness, reduce accidents and increase productivity.
“Connected Maps gives insight into all the machines and your overall site view. It can be tailored to your overall needs, what you require that is visible on your site,” Minty said.
“If your focus is on reducing accidents on site, or the productivity of your equipment, looking to improve operations, or you’re looking to replace older machinery, Connected Maps helps understand the losses and gains in your site and where to improve efficiency.”
For detailed insights into production processes, Performance Indicator utilises On-Board Weighing and machine data to deliver performance metrics in real-time. With customisable dashboards, users can monitor production, fuel efficiency, and machine cycles, empowering them to make informed decisions to improve operational efficiency.
Minty said CJD helps customers understand this data to optimise their business.
“Performance indicator creates graphs, information and data to be analysed; this can be shared with operators, site managers or CEOs to understand where your losses and gains are,” he said.
“CJD Equipment can come in and help you understand what this data means and give suggestions based on the data to improve your operations.”
With the performance indicator feature, site managers can visualise their operations with clear, easy-to-create dashboards, assess whether production is on track and be forewarned of any production or operational issues; operators can take quick and appropriate action if needed. Performance indicators take the guesswork out of observing operation performance metrics so site managers can make better decisions to improve efficiency and productivity.
Speed and location are obtained from the machine’s Connected Map. Production data is captured automatically for Volvo machines with Volvo Co-Pilot and On-Board Weighing.
“Performance Indicator can also highlight if your team needs Volvo’s eco-operator training, so it can highlight what needs to be reverse-engineered to ensure your site runs as efficiently and productively as possible,” Minty said.
“This tool will enhance features of the Volvo product that you may already have, but your operators may not know about.”
Designed for overseeing larger-scale projects, Volvo Construction Equipment’s Task Manager provides visualisation tools to track project progress and manage tasks efficiently. The feature enables effective planning, ensuring timely completion of tasks and coordination among multiple stakeholders by delivering real-time updates accessible from any device.
“Task Manager is another insight program that can be tailored towards the three tiers of operation a site can have – operators,
site managers, and CEOs/owners of the business,” Minty said.
“Task Manager can track the materials and efficiencies and allows for targets to be present for people involved in the whole productivity services overview, including Connected Map.
“Task Manager allows you to set targets and goals, which could be anything from production, fuel or utilisation of the machine.”
This tool aids site managers in planning, providing foresight into project timelines to determine if they’re on schedule or facing delays. Given the interdependence of tasks on a job site, effective planning is paramount, especially when managing numerous machines and coordinating multiple companies on the same project. Task Manager proves invaluable for this user demographic, offering compatibility with machines of any brand. While operators using Volvo machines may benefit from a more
streamlined experience, those utilising other brands can access it via mobile phones.
Volvo's Connected Load Out service revolutionises the efficiency of material loading processes by facilitating seamless communication between loaders, site offices and truck drivers. By allowing truck drivers to place orders via a mobile app and coordinate loading operations, Connected Load Out optimises workflow, reduces downtime and enhances overall site organisation.
These innovative services represent Volvo’s commitment to providing cutting-edge solutions to optimise business operations. Complementing existing services like Site Simulation and Active Care empowers businesses to enhance productivity, efficiency, and safety.
“Connected Load Out is tailored for road transport operations and gives insight into how you can meet targets for your customers that require materials to be delivered on time, reduce downtimes and idling, and complement your sales techniques by capturing data you wouldn’t have previously,” Minty said.
“Both the loader and the truck on site can be assured that the correct material and weight of the material is being moved, increasing efficiency.” •
For more information, visit cjd.com.au
Caterpillar is helping quarries measure, monitor and manage their sites with VisionLink Productivity.
Improving productivity is a core part of the quarrying industry. Low productivity means low revenue, which directly impacts profitability.
To help businesses measure, monitor and manage assets to maximise jobsite efficiency, Caterpillar has developed VisionLink Productivity
VisionLink Productivity is a cloud-based platform that gathers, analyses, and summarises machine telematics and jobsite data from equipment on- and off-site, regardless of its brand.
As its name suggests, VisionLink Productivity helps improve productivity, but there’s more to this technology than that.
For site managers, owners, and operators, it’s important to understand how assets are being utilised and how operations are flowing. VisionLink Productivity delivers a deeper level of actionable insights. These allow users to manage changes and make improvements across the jobsite like lowering fleet costs, decreasing idle time, reducing fuel burn, and more.
VisionLink Productivity means businesses no longer need to manually compile data –a time-consuming process that’s far from airtight (and far from enjoyable).
DI.MA Ltd. is an Italian company that recovers waste materials and turns them into construction products.
“We produce industry-certified aggregates for use in construction. Particularly for concrete batching plants, asphalt plants, construction sites, road works and large logistics,” DI.MA chairman Paolo Ottonelli said.
Working in a very competitive market, it’s incredibly important that DI.MA has clear visibility of the costs attached to each tonne of product it sells. That’s why DI.MA became an early adopter three years ago.
VisionLink Productivity helps DI.MA know where events such as payload and dumping occur.
“It’s very important to understand where, and in which phases of the process, resources are used,” DI.MA condition monitoring and digital services developer, Andrea Bresciani said.
Using VisionLink Productivity, DI.MA
can track material movement between processing, plant and stockpiles. It can then track when and where the material is loaded onto trucks and taken to customers. Using the cost dashboard, DI.MA can also track how much it costs to do all this.
It allows the team to make the changes required to help drive down their cost per tonne.
Gian Luca Gamba, DI.MA technical director said the use of VisionLink Productivity allows the company to assess where it has leakages or inefficiencies and improve its production cycle.
“We can then make decisions based on scientific data,” Gamba said.
The VisionLink Productivity interface is easy to use despite the complex activity going on behind the screen. Businesses can now understand volumes of data at just a glance.
Michael Miller commercial Caterpillar consultant said the online tool visually represents all the data.
“You can set up simple reports to have all that information delivered straight to your inbox,” Miller said.•
John Deere Australia and New Zealand has achieved Inclusive Employer Status for the third time. Quarry finds out how the company has achieved this success.
The Diversity Council Australia (DCA) has granted John Deere Australia and New Zealand Inclusive Employer Status for the company’s commitment to its employees.
Luke Chandler, John Deere Australia and New Zealand managing director, said achieving the status for the third year in a row was a proud moment.
“Each year, this assessment has provided us with valuable insight on where to focus our efforts to ensure we offer an inclusive workplace for everyone,” he said.
“An inclusive workplace is not the result of the actions of one, but the actions of many.”
Companies can receive recognition by proving their commitment to diversity and inclusion. This includes having employees complete an in-depth survey that demonstrates the employer’s inclusion measures and produces results against national benchmarks in key areas.
John Deere is part of a select group of employers to have received the recognition three times in a row.
The company’s aftermarket team recently led an initiative at its Brisbane office to celebrate World Inclusion Day. Employees were encouraged to share their personal stories, food from their cultural backgrounds, and discuss perspectives on what inclusion means to them.
“You should feel like you can bring your true self to work every day, and John Deere really embraces that,” aftermarket marketing and communications specialist, Laura PozniakElphick said.
“While your colleagues always try to be their most professional selves, it’s important to remember they are individuals with families and lives outside work.
“Someone could be smiling on the outside but struggling on the inside, so we just need to be mindful of each other and be as kind and inclusive as possible.
“If your corporate values are rooted in diversity and inclusion, that extends to your ability to recruit the best people, which ultimately elevates your whole business.
I think there’s also a halo effect where if a company is a good corporate citizen, they’re
more likely to be offering their products and services in the best possible way.”
The DCA announced that 82 employers had gained the status as part of Inclusion of Work Week last year.
The employers range from art galleries and pharmaceutical companies to sporting bodies and machinery manufacturers like John Deere.
According to data from the DCA, workers in inclusive teams are four times more likely to provide excellent customer service, more than twice as likely to work hard and more likely to be innovative.
“We know that inclusion has significant benefits for both employers and employees. DCA’s Inclusive Employers Index is a rigorous process that reveals the state of inclusion and diversity across participating organisations,” DCA chief executive officer Lisa Annese said.
“It’s an opportunity for workplaces to show their commitment to inclusion, reflect on their achievements and identify ways to do even better.
“Recognition as an Inclusive Employer means your organisation is doing the necessary work to create a welcoming and inclusive workplace where everyone feels valued and respected.”
It may sound simple, but fostering a culture of inclusion and diversity requires work every day and a commitment from all employees.
Deere Australia and New Zealand’s diversity, equity, and inclusion journey as head of people and culture at the company.
Kelly said the journey to achieve diversity and inclusion requires time, dedication, and a holistic approach.
“It can challenge deeply held beliefs and raise difficult questions. It’s not about checkboxes or quotas, but rather it’s interwoven in everything we do and everything we want to be,” she said.
“We have taken the time and energy to expand knowledge across the company — not just talk.”
As part of its commitment to fostering this culture, John Deere has updated its policies, employee selection criteria and workplace practices. An example of this is the company’s gender-neutral parental leave and developing leadership capabilities of employees.
“As a smart industrial company, we need both diverse talent and an inclusive culture to develop this competitive advantage,” Kelly said.
“Fostering genuine, sustained diversity in the workplace takes many years and a genuine heartfelt commitment from all staff. It’s important that business leaders take charge to lead and empower other staff to follow.”
•
For more information, visit deere.com.au
Failing to clean up carryback can lead to a sticky situation. Kinder Australia’s Eraser helps remove it at the source.
When conveying material, not all of it will go where it’s supposed to. Whether it’s due to environmental reasons, or it’s just a naturally sticky substance, some quarry products get stuck to the conveyor belt.
This carryback has a habit of getting exactly where it’s not wanted – interfering with the idlers, pulleys, the nearby environment, bearings, and places where you don’t want a build-up of mess.
Tim Storer, field applications specialist at Kinder Australia, told Quarry that finding out where carryback develops on a quarry site is a question his clients always ask.
Kinder’s field applications specialists help quarries determine where the problems are occurring. They spend much of their time visiting sites to find the right solution to problems a quarry might not even know about.
“Quarry operators are busy with running their business, they don’t always have the fresh eyes to spot where the problems might be,” he said.
“That’s where we come in. We like to get out to site, seeing the good, working with the bad, and rectifying the ugly.
“There are lots of ways a site can try to eliminate carryback. Conveyor cleaners have a big job to handle, and each has their own merits on how they perform.”
be cleaned up. Not only is this losing material, but it could pose a potential safety hazard.
If it builds up on the componentry, it can reduce the efficiency of the conveyor or potentially lead to damaged components. This leads to unplanned downtime, throwing a spanner in the works of the whole operation.
Kinder’s Eraser primary conveyor belt cleaner helps quarries handle carryback before it becomes a problem. It is an industrial-grade primary series-type conveyor belt cleaner built around an industry-exclusive polyurethane tensioning system. It features a unique Safe Torque ratchet that enables easy adjustment of the reliable, spring-free Perma-Torque urethane tensioning system.
The Perma-Torque system connects to a centre torsion bar, which, unlike a springloaded system, provides uniform cleaning pressure across the entire belt.
Storer said if a conveyor belt is smooth, most cleaners will be effective. However, the heavy-duty nature of quarrying means belts start to take damage when handling the sharp, lumpy, and often abrasive materials.
“This stops cleaners from getting into the nooks and crannies on the belt, leaning to material build up,” he said.
“Most of the time, this wear point will be in the central part of the belt, which is under
Quarrying is a rough business, which is why the eraser is designed to be tough. It is corrosion resistant, fully sealed, dust proof and mounted within a heavy-duty galvanised pipe on a sturdy steel mainframe. There are no springs, hoses, cables, or shocks.
The quick release and durable engineered polyurethane blade is available in various hardness durometers to suit the primary belt cleaning application. It can also be customised to suit a quarry’s needs if required.
Storer said quarries have given positive feedback, particularly when it comes to the ease of servicing and maintenance.
“The unique tensioning system is such an easy system to work with. There are two points of engagement, and everything can be done with the same tool. The system can be tensioned or released in seconds,” he said.
“From a quarry maintenance perspective, our clients love how effective it is at keeping the belts clean and how quick and easy the system is to access. All they need to do is pop off a dust cover and release a locking pin.
“Maintenance teams love the fact it’s a single person operation that can be done in seconds.”
Kinder provides more than just the eraser for belt cleaning. It also provides other primary and secondary belt cleaners for various applications. The company has a range of brush cleaners to help clean cleated belts or belts expected to withstand heavy duty.
It can also provide V-ploughs and diagonal ploughs to help deal with carryback build-up inside conveyor belts.
Storer said the field application specialists figure out exactly what kind of solutions can help.
“We like to get up close and hands-on, liaising with our clients to find out what’s working and what’s not,” he said.
“We’re constantly listening to feedback to improve our product offering and providing support.
“If you’ve got a problem, get in touch and let us see what you’re dealing with. It’s worth it to get a fresh set of eyes to find a solution to your problems.” •
For more information, visit kinder.com.au
At the IQA, we are committed to providing educational training and workshops held both onsite and online.
Explore a snapshot of what’s coming up in 2024.
Electrical Awareness
Quarrying and associated industries often underestimate the force of electricity. There are numerous risks that need to be considered on site each day ranging from collisions, explosions, flooding and accidents involving heavy machinery. However, an often overlooked threat exists that could be the difference between injury and going home safely - the invisible danger of electricity.
Electrical incidents can have severe consequences, impacting both personnel safety and operational continuity. The IQA’s electrical awareness program ensures that every member of your team is equipped with the knowledge to identify potential electrical hazards, implement preventive measures, and respond effectively in case of emergencies.
Workshop Highlights:
Safety: Understand the essentials of electrical safety protocols tailored specifically for quarry environments.
Risk Mitigation: Identify and address potential electrical hazards before they escalate.
Operational Efficiency: Optimise your electrical infrastructure for enhanced efficiency. Discover tips and best practices for maintaining equipment, minimising downtime, and maximising productivity.
Compliance: Stay ahead of regulatory requirements. Understand industry standards and compliance measures, in line with the latest electrical safety guidelines.
Safety Management Review: Learn the process of closing the due diligence loop through a thorough safety management review.
This half-day workshop is delivered online. Visit quarry.com.au for more details.
IQA education programs may be claimable as CPD under the NSW Maintenance of Competence and QLD Practising Certificate schemes.
Quarry Roads & Onsite Vehicle Safety (1.5 hours)
Respirable Crystalline Silica Awareness (5.5 hours)
Supervising for Safety (7.5 hours)
Chain of Responsibility (3 hours)
Electrical Awareness (4 hours)
NSW
15 May
22 May
VIC
5 June
– Tomago | Learning from Disasters
– Northern Region | Supervising for Safety
– Clayton | Contractor Safety Management
For more information on Education and Training:
Please call 02 9484 0577, email: education@quarry.com.au or visit: quarry.com.au
“I was totally engaged and learnt a huge amount of information to take back to the workplace and quarry sites under my control.”
— Workshop Participant
Are quarries the key to the construction industry achieving net-zero carbon emissions by 2050? Kayasand believes so, and the secret is in the sand.
In 2022, the Australian Government legislated greenhouse gas emission reduction targets. It plans to reach net-zero emissions by 2050, as part of the global push to fight climate change.
Cement production plays an important role in this endeavour. According to Beyond Zero Emissions, an independent think tank, cement production is the world’s single biggest industrial cause of carbon pollution, amounting to about eight per cent of total global emissions.
Bram Smith, general Manager at Kayasand told Quarry that Australian quarries can help cut down on these emissions using a common byproduct in the industry – crusher dust.
“Once processed into manufactured sand, it can be widely used as a substitute for natural sand in concrete. The trouble is natural sand is becoming more difficult to access and more variable in quality,” Smith said.
“Historically, the problem with using manufactured sand in concrete is that it’s often poorly shaped, badly graded, inconsistent and often contaminated with clays and silts. As such it’s considered an inferior product to natural sand.”
“Getting it right requires precise shaping, good particle size distribution, contamination controls and quality consistency. It’s about engineering the sand not just processing it,
and the final product has many advantages over natural sand.”
“A good quality engineered sand will make stronger concrete with less cement and lower emissions than natural sand. It often outperforms natural sand in the mix.”
Kayasand’s innovative technology enables quarries to process crusher dust into a precisely engineered concrete sand.
Concrete trials have shown a cement reduction in concrete of at least 10 per cent is achievable without any impact in strength. This means substantial emissions reductions. The ability to process crusher dust into a high value product also enables quarries to better balance their inventory and minimise
waste generation and tooptimise yields, aligning with sustainable development principles and carbon reduction reporting requirements.
The United Nation’s Sustainable Development Goals requires large enterprise, regional and local government agencies to report on the sustainability of business practices and products in their supply chain.
“Using Kayasand’s V7 equipment and technology helps quarries meet this requirement,” Smith said.
“Not only that, but they add new revenue streams and help support the construction industry with high quality materials.”
Engineered sand is designed to have extremely consistent properties, allowing for more precise and optimised concrete mix designs. It leads to reduced material wastage during construction and a reduction in the overall carbon footprint of a project.
It is also often produced in quarries closer to construction sites. This reduces the need for long-distance transportation and emissions due to fuel consumption.
Smith said public concern about the environmental impact of natural sand mining is making it harder and more expensive to access natural sand resources. By using engineered sand instead of natural sand in construction projects, the growing restrictions on sand supply can be mitigated.
“The environmental and sustainability impact is even more meaningful when a quarry uses technology like Kayasand’s V7 sand plant to engineer its concrete sand. The process is dust-free, low-noise and uses no water for washing. Quarries could substantially scale back their sediment ponds and water tailings,” Smith said.
“It also helps conserve natural resources by reducing the demand for riverbed and coastal sand. Preserving these ecosystems
can help mitigate carbon emissions associated with habitat destruction and loss of carbon sinks.”
Engineered sand doesn’t just have to be about quarrying by-products and crusher dust. Kayasand technology can recycle glass and concrete back into premium concrete sand and create cement substitutes from limestone filler and slag.
Smith said quarries that sell engineered sand will be an important part of the construction industry’s push to achieving net-zero emissions.
“The environmental benefits, lower carbon footprint, consistent quality, and circular economic potential make it a viable antidote for a constrained supply chain,” he said.
“By embracing good quality engineered sand, the construction industry can build their way to a more sustainable future.”•
For more information, visit kayasand.com
Precisionscreen’s Scorpion Pugmill is an Australian-made machine designed to make operators’ lives easier.
Australia’s scorpions usually make a name for themselves in burrows, but Precisionscreen’s Scorpion Pugmill is making its name in the nation’s aggregate industry.
When asked why the company’s Scorpion Pugmill has been successful, Precisionscreen chief executive Jonny McMurtry said there was one main reason it stood out.
“It’s versatility; it can blend a variety of additives to quarry materials such as cement, activated carbon, gypsum and lime,” he said.
“There’s been a lot of interest in that sort of work across the past year for that type of stabilising and blending work.”
The Scorpion PLC Pugmill features a CAT 7.1 six-cylinder engine as well as a 10.5 cubic metre hopper, which feeds onto an independent conveyor belt separate from the hopper belt.
The Australian-designed and manufactured additive bin, complete with a rotary valve at the bottom, can accurately dose in many materials, including cement, gypsum and lime.
“The CAT 7.1 six-cylinder engine means we offer a much higher kilowatt and hydraulic power than the imported units,” McMurtry said.
One current job taking place early 2024 sees the Scorpion Pugmill being used in Bulimba blending activated carbon as part of ground stabilisation work at an old Navy base.
Precisionscreen is working with the customer to adapt the Scorpion Pugmill to match its requirements, adding a vibrating screen to help remove oversize and ensure material consistency. Jobs like this show the adaptability of the pugmill, with one of the important elements being the versatility is the Pughead.
The pughead is considerably longer than other pugmills and a huge benefit of this version is it’s discharge height for pugged material, having a 3.5m drop height. The extra height enables trucks to be loaded directly from the pughead which helps on-site efficiency and productivity.It also ensures operators avoid segregation on the belt and makes it easy to clean the main belt.
“Our Pughead is around about a metre longer than most applications or imported mobile machines, which gets a much better blend of material,” McMurtry said.
“The longer pughead allows more blending time and the material that comes out of the pughead is better mixed.”
Precisionscreen has built the Scorpion Pugmill with the operator at the forefront of it’s design and manufacturing. There is a PLC control system that allows the operator to select different product mixes with ease.
The PLC system has a new display screen which stores and saves instructions and documents for the operators such as machine and engine manuals, calibration procedures and other helpful documents to ensure the best use of the pugmill.
McMurtry said the operator has complete control of material flow by using the remote control start and stop function, which enhances the discharge process.
“The independent conveyor belt makes it easier to control and regulate the product mix,” he said.
“The PLC system and the scales can read the volume on the main conveyor belt and dose in as low as 0.5 per cent right through to 10-20 per cent if it is needed.
“The operator can pre-save different products into the PLC system to match what they need on any given day.”
Many pugmills can have a flat-bottomed floor, which can make some spots hard to inspect, clean and maintain for operators.
Precisionscreen’s Clam Shell door design changes that, using a hydraulically opening doordesign for the pughead. The clam-shell doors open up and enable the operator to
“We’ve had a lot of customers looking for bulk storage solutions and looking to consistently feed in cement or fly ash, for example, into their pugmill system,” McMurtry said.
“If they’re dealing with big batches on a daily basis, it is a cost-effective solution for bulk storage and ensuring the operation is seamless.”
Precisionscreen offers full support across its machinery, including the pugmill, which is Australian-made, and stocks spare parts and wear parts at its Brisbane factory. The company also maintains a team of technicians from Brisbane to Victoria and the Northern Territory to provide after-sales support to customers. •
As the only national quarrying publication and the official journal of the Institute of Quarrying Australia, you’ll always be up to date with the latest developments in industry news, technology and events with Quarry Magazine.
quick and easy to subscribe to our monthly print issues, our annual Suppliers Directory and our weekly eNewsletter. Don’t miss out!
Wirtgen Australia is using advanced telematics to support its crushing customers around the country before a technician even makes it to a site.
The Wirtgen Group believes in the ethos of being “close to its customers” when it comes to technical support and aftersales.
It is particularly important in Australia where crushing plants are often located in remote regions.
Nathan Friend, Wirtgen Australia product support manager for crushing and screening, told Quarry support needs to be where the machines are in metro or remote areas.
Customers often need rapid response times. Going to their site takes time, and while in transit, machines are not working how they should – potentially losing significant productivity.
Wirtgen has invested in advanced telematics to bolster its customer support in addition to its branches in Queensland, New South Wales, South Australia, Western Australia, Victoria, and New Zealand.
Friend said Wirtgen’s ability to provide remote diagnostics has been vital.
“The ability to provide remote diagnostic assistance means we have the confidence to support a remote crushing site in NSW with assessments from our Perth office,” he said.
“Our diesel electric machines can tell if there is a fault before it even becomes a fault.
“At an owner level, our systems can transmit machine information externally via email, letting the owner know if something has gone wrong, even if they’re in a different state.”
Wirtgen can aggregate data for an entire quarry site, which is then automatically linked to the machines to quickly provide a snapshot. This data can be fed back into the system to see fuel consumption on a dashboard.
This allows technicians to pre-diagnose faults before they attend the site.
Mark Drury, a product support manager at Wirtgen Australia, manages the internal diagnostics systems and helps customers use the company’s digital support platforms.
He told Quarry the company can use these technological tools to provide expert assistance through a smartphone.
“We have a platform that allows us, through the use of the Wirtgen Group Expert Assist app on smartphones or alternatively an
augmented reality headset, to communicate with personnel on site,” he said.
“Through the Expert Assist platform, we can see exactly what the operator or technician is seeing and take screenshots, circle components that need to be tested, or guide personnel onsite during troubleshooting.
“It also means that when we send a technician out to site, they can preempt the parts necessary for the job, slashing downtime.”
When it comes to spare parts, the company’s product support managers determine what will be needed in the short and long term, depending on which machines are in certain locations.
Wirtgen Australia employs a full-time data analyst to go through parts usage and determine the stocking levels, based on past data and future predictions.
Warehouse operators can also collaborate with the head office in Germany to acquire freight from facilities around the world, such as Southeast Asia.
Drury said anything that affects the cost per tonne is a big pain point for quarries, be it downtime, freight costs, or fuel consumption.
“Many of the machines in the Kleemann portfolio employ a diesel-electric drive
system technology, which is more fuel efficient,” he said.
“In addition, the Ops Centre and Spective Connect allows quarries to see any changes in fuel consumption in real time.
“Being able to see fuel consumption and plan maintenance means they can schedule downtime better.
“The scheduler might not even be on the site, they can use the telematics data to predict, based on current utilisation, when the next service will be.
“It gives sites the ability to tie maintenance at the same time, making it more effective.”
In addition to its technological offering, Wirtgen invests extensively into training for technicians and customers.
The business covers three main areas: training operators on how to best use the machine, training maintenance personnel on how to carry out preventative maintenance, and an in-depth technology and training package aimed at fitters, and electricians to diagnose faults.
Wirtgen’s internal training is vital to ensure its staff can handle the high-tech machinery they will be required to work with and fix.
Drury said because the company is a technology leader, extensive training for its support team is required.
“We’re dealing with high level technology that goes above and beyond the status quo,” he said.
Friend agreed and said the company has trainers in Germany that will fly around the
world to ensure its global staff know exactly what to do.
“For Kleemann, we’ve flown out a factory application specialist to spend about six weeks in Australia, meeting with technicians,” he said.
“They get out into the field and show people how to work with the machine. It’s a heavy investment but its worth it.”
Going forward, the company plans to continue upskilling its technicians, particularly when it comes to dual trades.
Staff members are being encouraged to take on a second apprenticeship if they show interest in electrical roles from a mechanical background.
Friend said anyone who wants to learn more is being encouraged to learn.
“Having a highly skilled team helps customers, so we’re investing a lot into our team.”•
For
Filter presses aren’t rocket science – they’re made up of a simple set of plates, cloths and a pump, but OFS has found a way to make them smart.
Filter presses are a relatively straightforward machine, generally used in quarry dewatering applications to remove fine sands and clay particles from a thickened flow stream created by washing and screening.
The filter’s plate pack, most commonly formed by recessed chamber filter plates, is arranged in a supporting structure and is compressed by a hydraulic cylinder. Filter cloth is mounted on each plate, which forms a filter chamber by the recessed body.
Slurry can then be pumped through a feed channel into the filter chamber. Solids remain on the filter cloth while the liquid departs through the drainage system of the filter plate.
Continuously feeding the press raises the solid concentration in the filter chamber and the pump head pressure, which in turn reduces the flow rate of the slurry. This is
maintained until a cake with the required solid content is formed. Finally, the filtration pressure is released, the plate pack is open, and the filter cake is discharged.
Alan Dunbar, Lincom product manager for OFS, said the process is preferable to creating a lagoon or tailing facility.
“Ultrafine material stored in tailings facilities or lagoons are highly susceptible to flood and earthquake, but the operators are also actively removing their own water storage buy ultimately filling the lagoons with material, or paying to dump wet slimes,” he told Quarry “Lagoons also need permits and may require permanent care. It’s a big area of land that you will eventually have to deal with.”
“With a filter press you can extract dry, stackable product. In many instances the filtrate and/or solids can both be reproposed.”
What elevates the OFS produce range is the integrated automation. The entire machine is
controlled by a programmable logic controller (PLC) which communicates with the range of sensors allowing individual customisation of each system.
The system uses sensors to measure pressure and flow, slurry levels and monitor safety systems which it can then use to determine when the machine should cycle.
Dunbar said “they often incorporate automated high-pressure cloth washing, which makes maintenance much easier.
“The more blind your cloths are, the less chance the filter press will work to its potential. Traditionally, washing the cloths would need to be done manually – and if you have a press with over 100 plates the idea of manual washing them all is a nightmare,” he said.
“The automatic washing is also much faster, meaning there’s less overall machine downtime and manual handling.”
Sensors can also automatically detect the capacity of the slurry tank and height of the cake pile and turn things on/off where required, allowing the machine to operate around the clock. It can also integrate with automating conveying systems if a site wants to convey or stockpile the material.
Safety systems have also been automated. If anyone attempts to interfere with the filter press while it is in operation, it will automatically shut down. It also comes with control system and guarding to Australian Standards ensure nobody can get hurt if something goes wrong.
Dunbar said the most important part of operating the filter press happens before it is even installed.
“It’s vital to find out exactly what will be filtered through the press to ensure it’s the right one for the job,” he said.
“We visit our client’s sites and work with them to get a good understanding of the operation. They’re producing a big bowl of soup with all kinds of stuff in it – and
if you don’t know what’s in the recipe, you’re in trouble.”
“The key to finding the right filter press is the testing phase. If you just buy a filter press off the shelf and cross your fingers it might work fine, or you could just end up with a machine that makes mud.”
Lincom has a scale testing lab onsite in its Narangba office, as well as a site portable testing unit. To ensure the filter press will
work with the customer’s site, the company collects samples from the customer and tests in the lab.
The Brisbane-based lab can provide detailed analysis but more importantly, a real filter press is used to run trials on customer samples.
Dunbar said the equipment is manufactured to a high-quality, German standard.
“Everyone on the design team at OFS lives and breathes filter presses – they’ve spent their whole careers working with them,” he said. “Backup and support are vital in the quarrying industry, and that starts with having a focus on analysis and education over sales techniques”.
Lincom has offices around Australia and holds OFS stock locally. That means if a press does fail, the company can provide the parts needed quickly.
The company plans to promote the OFS equipment range over the coming months, highlighting the benefits to the quarry sector.
Dunbar said the team has planned presentations with the Institute of Quarrying Australia (IQA) and will be attending several trade shows during the year.
“The OFC filter presses create very clean water that can go straight back into a wash plant and a repeatedly dry cake,” he said.
“The enhanced automation makes them more reliable, more efficient, and easy to use.”
For more information, visit lincom.com.au
• Throughput rates up to 2,500 t/h
•Used extensively in the cement, aggregate and recycling industries.
• Capable of handling material up to 3m³
•High reduction ratio.
PRIMARY IMPACT CRUSHER | HPI
• Designed for economic processing of soft, medium-hard or hard rock.
• Modular system
• Feed sizes up to 450mm
• Reliable production up 700 t/h
SECONDARY IMPACT CRUSHER | HSI
• Designed for economic tertiary crushing of hard rock.
• Modular system
• Feed sizes up to 150mm
• Reliable production up to 160 t/h
• Production of crushed stone fines and high-quality stone chippings.
TERTIARY IMPACT CRUSHER | HTI
For fullproductrange, scan QR codeor visit www.hazemag.com www.allmineral.com
A very wise person once told Steve Franklin, founder of Eltirus, “Better to make your mistakes on the computer than in the field.” So, what did he mean by that comment?
Quarry extraction planning can be a little like a three-dimensional game of chess and the people who are best at it generally have a good ability to visualise in their mind how the deposit is going to be extracted in such a way as to keep a balance of development and production material and to ensure that critical access is maintained.
These experts can visualise the sequence, run different strategies mentally and come up with an effective way forward. Unfortunately, this tends to be something they keep in their mind and don’t commit to paper. If they leave the operation, that mental plan tends to leave with them and as we progressively lose our older more experienced quarry managers, this is an increasingly important loss to any quarry business.
So, what to do? The answer in short is to build a scheduling model. But what is it and how do you put one together and then make the most of it?
SCHEDULING BASICS
When you create a scheduling model, you are working out what can be extracted and when. You need to know the geology, have a pit design, know how fast you can extract the deposit and what your targets are. From there,
the scheduling model can help you understand if what you propose is possible or not. Common questions are, can we extract the material fast enough to meet client demand? How many fleets will we need for development? When is development required? How much low-quality material do we need to dump (or sell off site etc.). All these questions (and more) can be answered through scheduling.
GEOLOGICAL INFORMATION.
First you need to know your geology. By this I mean that you need to know what type, quality, and quantity of material you have in your deposit. The best schedule in the world will be wrong to the degree that the geology is incorrect, so it is important that this step is not taken lightly. Depending on the work being done, the site may need to
do additional drilling to prove up areas of the geology that are poorly understood. Also, take the time to check geological model with site personnel to see that it aligns with their on the ground experience.
The next step is to have a well thought out, geotechnically sound pit design. This helps you to understand which parts of the deposit are going to be scheduled for extraction and how they will be accessed.
When we talk about a “sound pit design” we are talking about one that has practical haul roads and access and is designed in accordance with the site geotechnical model and any corporate guidelines. The design should be created in a three-dimensional, mining type design package, not twodimensional CAD.
With a good understand of the geology and an accurate pit design, you can create a “solid” of the material between the topography and the pit design and cut it into blocks for scheduling.
Scheduling blocks are generally the same height as the bench heights in the pit design and approximately the volume of a standard size blast. The scheduling software then interrogate the geological information and writes to each block its location, volume, tonnes and material type.
It is fairly obvious in open-pit extraction that you generally start from the top down and from an open face. Likewise, you know that you can’t extract a block before taking the
one above it. These common sense rules are important in scheduling – we call them dependencies and they help the software understand what is possible to extract at any given time.
Dependencies can be used to help set the sequence of extraction on a bench, enforce the completion of one cut-back before starting another, ensure that the walls are brought down in a geotechnically safe manner and many, many other things. As you can imagine, this can get very complicated with dependency rules, building on rules to give literally thousands of different permutations, all to ensure that access is retained, quarry safety rules are met, and extraction meets targets.
The next step in scheduling is to understand what resources (equipment) you have to extract the deposit and what their extraction rates are.
This step requires you to have a clear idea of how much material a load and haul fleet can move in a given operating scenario. For example, a fleet working in a wide-open area with good haul roads will move more material than the same fleet working on a tight, narrow bench where the trucks have to back long distances and the wheel loader loading them is struggling to maneuverer.
Taking the time to really nail down actual production rates is critical to an effective schedule. I well remember an instance many years ago where I conducted a production study to determine fleet productivity and was appalled by what I saw in the field. Imagine my surprise later when further investigation found that the performance, I saw on the day was actually thirty per cent better than their long term average performance.
Time spent working out real production rates is vital – anything else can result in wishful thinking.
The last step is to make sure that you have a good understanding of the site calendar. By this we mean, days worked, actual digging hours in a shift (or a day), downtime for maintenance, allowances for inclement weather etc. This is also the time to really understand any seasonal issues – e.g. can you actually conduct a stripping campaign in the middle of winter or not and if so at what impact on productivity?
As you can see, there are a range of factors to consider in building a schedule. You can likely also see that at any one of these steps, a lack of good data will lead to a poor outcome, so time taken to build an effective, robust model is time well spent later on.
Once the model is built, you can then run scenarios to test different ideas about how the deposit could be developed and whether your production targets can be met. This is where the real value of the work comes into play,
It is important to understand what resources (equipment) are available to extract the deposit and what their extraction rates are.
but it should be noted that it can be highly iterative work (and requires specialist mining engineering skills that are not commonplace).
For example, a schedule might result in an excellent match to sales targets for say three out of five years, but result in poor results in the other two. Likewise, you might have a situation where waste movement is too front loaded (reducing deposit NPV accordingly). An effective scheduler is often able to work through these different types of factors to “even out” a schedule and come up with the best possible result for the site.
Once an acceptable, robust schedule is built, it is vital that it is communicated with the site in such a way that they can understand and put in play. Likewise, you also have to ensure that there is a feedback loop between site and the scheduling team to communicate changes in extraction rate, sales targets, geology and geotechnical conditions. Without this communication, the model can
go out of date, lose its relevance or worse, site personnel can lose confidence in it and the value of the work.
If you go to the effort of putting a schedule in place – use it and if you find it wrong or inaccurate, don’t blame the scheduler in the first instance, take a look into the assumptions and then whether it was correctly applied in the field (and adjust accordingly).
You should also take the time to ensure that your sites have the survey equipment (e.g. GPS rover) to mark out the sequence of extraction correctly in the field and an effective, accurate site-wide drone program to be able to keep track of what has been extracted for use in updating the schedule. A good schedule can really help you understand what your stripping requirements are, how much equipment you need and when and if you can deliver on that big project you have your eye on. •
For more information, contact steve.franklin@eltirus.com
Upgraded 800i crushers with new ACS-c 5
Even the best can always get better. Upgraded 800i crushers with new ACS-c 5 are our smartest, safest and most productive yet – designed around the needs of the people who work with them to raise the bar of what a crusher can be. Combining simple yet robust mechanical design with powerful user-friendly automation, 800i crushers are true workhorses that improve your ability to process more material, more accurately and more sustainably.
Discover the upgraded 800i crusher series with new ACS-c 5 today, and see what’s possible when a crusher is designed with you in mind.
Quarry explores how dealers and original equipment manufacturers can help utilise the XMOR Bucket.
Often, clients reach out directly to ONTRAC after hearing about the XMOR Bucket, which is quickly making a name for itself in Australia’s heavy industries.
JK Williams took a slightly different approach. The NSW-based civil works company wanted a certain level of productivity from its Liebherr excavator and to find an attachment that could help it get there.
It worked closely with Liebherr area sales manager (earthmoving and material handling division) James Bond who recommended ONTRAC and the XMOR Bucket.
“We went to some of the other manufacturers, but the XMOR was able to give us the productivity without compromising the machine,” Bond told Quarry.
“Liebherr is a premium product, and we see ONTRAC as a premium product as a bucket manufacturer, so it was the right thing to pair the two together for this particular machine.
“It is one of our core values, and for us, it doesn’t come down to price; I’ll go to the bucket manufacturer and pay more if you know it will last.”
The XMOR Bucket uses SSAB’s Hardox 500 Tuf wear plates and Strenx structural steel in its durable design. The unique keel design further reduces weight and enables more structural stability. The inverted shape of the keel helps minimise ground contact and wear on the bottom of the bucket, which saves customers time on maintenance and repairs.
The bucket exchanges weight for payload while maintaining the durability and structural integrity expected from heavy industry attachments.
JK Williams is one of the bigger earthworks companies in NSW. They have come to specialise in bulk earthworks, which require durable machines and equipment that can handle a high load.
“When the bucket turned up, he didn’t really register it was the XMOR, and he asked me, ‘What’s this bucket doing here?’ and I said, ‘That’s the bucket you ordered,’ and I remember his exact words,” Bond said.
“His exact words were ‘didn’t I do well!’ and I remember that stuck out to me.”
In the case of JK Williams, which was replacing a different excavator size with its
While JK Williams has only recently taken delivery of the bucket, Bond said there were clear benefits in adding the XMOR to their Liebherr excavator.
“It gave them a bigger reach, compared to what they previously had, and maintained the capacity,” he said.
“It is an Australian-made bucket with a European design and the hardox steel as well, so there is a lot of confidence there (from our end) that it is of good quality.”
While some customers engage ONTRAC directly to see how the XMOR Bucket could help their productivity and efficiency in moving product, the Australian company also deals with original equipment manufacturers and dealers to provide a bucket solution.
Liebherr had worked previously with ONTRAC to get an XMOR Bucket into the hands of an Australian customer.
Bond worked with the team at JK Williams and ONTRAC product specialist Nick Espie to create the ideal configuration that would suit the company’s Liebherr excavator.
“I was dealing with Nick, and I was amazed by the level of detail he goes to,” Bond said.
“He took the Liebherr brochure and was able to show us the level of productivity we would get (with the XMOR bucket).
“He actually educated me as a salesperson about where we could go to, and I found him to be very engaging.”
ONTRAC values its approach to after sales
service as well. The company manufactures and holds replacement parts, called wear packs, for the XMOR Bucket and can conduct on-site inspections to ensure the bucket works as expected.
Bond told Quarry he would not hesitate to recommend ONTRAC’s XMOR bucket in the future.
“At the end of the day, that is the bit that is in the dirt and taking on most of the work,” Bond said.
“While pumps and all that can be damaged, the bucket is effectively the one which is making the money, and we know ONTRAC’s bucket will last the journey.” •
For more information, visit ontracgroup.com.au
Australia, taking a key role in all activities and particularly enjoying the opportunity to promote South Australia through the wines, fresh juice and produce at the Conferences hosted in Adelaide.
He and Betsy were regular attendees at IQA functions over many years and always added something special by their presence.
Poignantly, his casket memorabilia included his 40 years of Service Certificate, presented in 2005 at an IQA branch function and parked at the front of the church was the Foden truck that was lovingly rebuilt incorporating parts of his original truck when he was a contractor to Riverview Quarries (Highbury Quarry) in 1959.
The O’Neil family connection with quarrying in South Australia started in 1926 when Max’s grandfather “JJ’ O’Neil and his family secured a contract to provide road material for the construction of a road in the Adelaide Hills.
This marked the beginning of their involvement in an industry that would span four generations and much of Australia.
In 1931 the O’Neil family purchased a quarry in Western Australian which they called White Rock Quarries and the business evolved into Australian Blue Metal Ltd (ABML), which was publicly listed in November 1952, at its time the largest quarrying company in Australia. In 1963 the family eventually sold their shares in ABML to Readymix Concrete.
South Australia’s quarrying “family” gathered on Thursday 25th January 2024 to farewell a gentleman of the industry and the Institute, Max O’Neil.
Max was always destined to join the industry as soon as his feet were big enough for the quarry boots. He commenced in 1959 as a contractor operating his Foden truck in Adelaide. Foden trucks were an integral part of the O’Neil family’s automotive history. Max’s Uncle Les had discovered two new Fodens in an Adelaide showroom while passing through in 1939, and true to O’Neil style, both trucks were promptly purchased. Subsequently, the O’Neil family secured the Western Australian agency for Foden Trucks and eventually the New South Wales agency and were appointed the Australian factory representatives for Foden vehicles.
In 1961 Max and his brother, Gordon, were searching for their own deposit and while drilling for sand near Gawler, Max rang their father to inform him that they had found a promising deposit but unfortunately there was a lot of gravel in the sand. Lance immediately replied, “Hold on, I’ll be right there.” A lesson learnt for the brothers as the gravel made the site more valuable and they started the Gawler sand and gravel quarry under the stewardship of their father Lance.
In 1968 Max and Gordon joined forces with Ian Cocks acquiring 50 per cent of Direct Mix Concrete eventually acquiring the whole business. The two brothers established Southern Quarries Pty Ltd at Sellicks Hill in 1972 and later in 1990 Peninsula Quarries on the Yorke Peninsula. Quietly and effectively, Max and Gordon developed a business that became South Australia’s largest independent quarrying and concrete operations when they sold it to Adelaide Brighton Cement Ltd in 2015.
Max, with his brother Gordon, were innovators of the industry always challenging the convention to see if they could do it better. Many common practices, now in place, are a result of their leadership in the
industry. Max used his position tirelessly to lobby politicians and government officials how vital the quarry and transport industries are to Australia. Max was a storyteller with an amazing sense of humour and an infectious laugh. He had many anecdotes and life lessons passed down through the
family. Always the diplomat, one of Max’s favourite sayings was “Diplomacy: The ability to tell a person to go to hell, in such a way, that they look forward to the trip.”
Max’s black HSV was legendary in the industry traversing South Australia as he made his regular visits to each of his sites to check in on the team. He was immensely proud of the business and the people who worked for the family. Max’s belief in his people and the fact that he had the best products in the world were infectious. Max was a true ‘gentleman’ of the industry, and he always made the time to talk to his people, by name, from the driller to the concrete batcher. The drivers in the business were the most important salespeople in Max’s eyes, and a clean truck driven by a professional driver was not negotiable.
Max was also deeply committed to the horticultural industry and much of his spare time was spent at the family citrus property
where he took on grader duties, grading the sandy tracks around the property. In 1974 Max and Gordon partnered with the Lochert brothers, co-founding Crusta Fruit Juice, an iconic brand in South Australia.
Max was first and foremost a family man and his enduring marriage of 57 years is testament to this. After they started going out, Max would come past the News Ltd offices where Betsy was a cadet journalist at 4:30pm every Thursday and they’d do the last load together with Max’s dog, Patches, sitting between them.
Max leaves behind his widow Elizabeth (Betsy), his brother Gordon, his daughters Anna, Kate, Heidi and their families. He will be greatly missed, he has been an integral part of our Branch for longer than the living memory of the majority of our membership. He leaves an indelible mark on the Institute and the whole industry.
Thank you Max. •
NSW central west sub-branch networking dinner
On Thursday November 30, the IQA central west sub-branch gathered for its annual year-end networking dinner at Duntryleague in Orange.
Attendees seized the opportunity to exchange innovative ideas, leading to the presentation of some truly inspiring concepts.
A special thank you goes to our event sponsors, WesTrac, which has been traveling across various regions. The company recently visited the central west sub-branch, sharing insights into the latest Cat® wheel loader technologies. The presentation explored how these advancements are assisting earthmoving businesses in reaching productivity and sustainability goals.
Attendees also gained insights into WesTrac’s cutting-edge Technology Experience Centre (TXC) at its NSW head office in Tomago.
Looking ahead, we are excited to announce plans for a day trip to the WesTrac facility in mid-2024. Stay tuned for more details.
Northern NSW northern region subbranch and emergency preparedness
Late November saw people in the industry come together for an incredible day of
learning, collaboration, and emergency preparedness at the Holcim quarry in Teven.
Members and guests had the unique opportunity to connect with local rescue agencies, including fire and rescue, police rescue, volunteer rescue, and state emergency services (SES) from the Ballina and Lismore areas. The day was packed with live demonstrations of rescue scenarios relevant to the quarrying industry, fostering a forum for sharing ideas and strategies.
A massive shout-out to our event sponsors, Matt Leonard and the amazing team at Wormald Australia. Their support made this initiative possible, and their presentation shed light on their involvement in site emergency responses, offering insights on how Wormald can contribute to continuous improvement.
Special thanks to Steve Brown from the NSW Resources Regulator Emergency Management team. Steve’s engaging discussions delved into the application of the state’s emergency management plan and the crucial role the NSW Resources Regulator plays during site incidents.
A heartfelt thank you goes out to Holcim quarry manager Matt Kelly, our Young Member network coordinator, quarry supervisor Rhys O’Brien, and the entire Holcim team for their exceptional organisation of the event. Your dedication
made this day a tremendous success, providing our quarrying community with essential knowledge and fostering a stronger commitment to emergency preparedness.
After a day filled with insights and handson experiences, guests transitioned into an end-of-year networking dinner at the Cherry Street Sports Club in Ballina. The evening brought together a fantastic crowd, providing an opportunity for guests to mingle and collaborate.
Thank you goes to our event sponsor, Scope Engineering Services, and to Archie Schreiber for a captivating presentation on Scope’s specialised fixed plant solutions and Australian-made turnkey production solutions.
Special guest presenter Gareth James, executive director of NSW Reconstruction Authority, shared updates on current recovery projects and the essential civil infrastructure works in the pipeline. Wrapping up the evening, a big cheers goes to Bec and Scott at iQuarry for sponsoring a few refreshments, allowing everyone to celebrate the successes of yet another busy year.
And thanks to the Northern NSW region sub-branch for pulling together such great events, and to members, associates and all that were able to join us on the day.
Quarry spoke with Donella Cobbe, sales coordinator/pricing analyst at Hanson Australia (North Queensland), and IQA member.
What does your role involve?
I look after all the administration and background sales data for all the concrete plant and quarries from the Gold Coast all the way to Darwin, as well as assist all sales managers, concrete plant managers and quarry managers. I also manage and maintain pricing structures,
and further assist management nationally when required to improve processes based around concrete and aggregates sales, and how we drive or service the market.
How long have you been in the industry? 17 years.
What do you enjoy about your role?
Working with a wide range of people nationally, building relationships and having the opportunity to seek new challenges within the business.
What do you love the most about the quarry Industry?
I enjoy the community and seeing how much we can give back, whether it’s through charity, sharing knowledge, training, exposure to our younger generation, or many other things. It’s also really exciting to see the female presence growing in the industry compared to what it was 15 or more years ago.
Why did you join the IQA?
I was originally asked many years ago to help
organise and coordinate the annual Cairns sub-branch IQA golf day.
I enjoyed it so much that I helped organise t over the next five years and then volunteered to help with any future IQA events.
I also met my husband through the IQA.
What advice do you have for a young person looking for a career in quarrying? Take safety seriously, watch out for your colleagues, and if you enjoy what you’re doing, always put your hand up to excel and further your career.
What’s one thing – whether industry-related or not – you learned in the last month? We recently suffered a loss with a valued member of the quarry community in FNQ and it has reminded me that although work can be a priority, family comes first.
Where do you see the future of the industry?
I think it will forever be growing and improving. ’m excited to see what quarrying will look like in another 20 years’ time.
ABristol University student has unearthed a 200-million-year-old flying reptile fossil from a collection of Somerset limestone quarry fossils.
Bristol University student Mike Cawthorne has uncovered evidence of the Kuehneosaurs, which are said to be closely related to crocodilians and dinosaurs.
Cawthorne published his findings in the Proceedings of the Geologists’ Association journal. The master’s student said he initially was hoping to find a dinosaur.
“I had hoped to find some dinosaur bones or even their isolated teeth, but in fact, I found everything else but dinosaurs,” he said.
“The collections I studied had been made in the 1940s and 1950s when the quarries were still active, and palaeontologists could visit and see fresh rock faces and speak to the quarrymen.”
The Kuehneosaurs are described as being palm-sized with two variations in type. One had extensive wings, and the other had
shorter wings made of stretched skin from the Kuehneosaurs’s side rib.
It is thought that the animals fell into the quarry before water washed their bones into the limestone, which preserved them for research in the modern day.
Cawthorne was able to compare the fossils from Bristol University’s extensive collection and the Natural History Museum. German researcher Walter Kühne and Pamela L. Robinson from University College London were among those whose specimens helped the research.
Professor David Whiteside also thanked amateur fossil finder Tom Fry who worked for Bristol University in the 1940s and 1950s. Prof Whiteside noted Fry was noted for cycling to quarries to examine their histories before returning to Bristol University laden with potential fossils to research.
Bristol University’s Professor Mike Benton said Cawthorne’s research showed the area was home to diverse small reptiles feeding on the plants and insects.
“It took a lot of work identifying the fossil bones, most of which were separate and not in a skeleton,” he said.
“However, we have a lot of comparative material, and Mike Cawthorne was able to compare the isolated jaws and other bones with more complete specimens from the other sites around Bristol.
“He didn’t find any dinosaur bones, but it’s likely that they were there because we have found dinosaur bones in other locations of the same geological age around Bristol.” •
InSitu Real Estate is a boutique agency providing real estate services to the extractive industry, mining, concrete & asphalt, waste & resource management, industrial and infrastructure markets.
Our experienced team provide complete real estate transactional services across the country, priding ourselves on our deep industry knowledge and an understanding of our clients needs.
InSitu Real Estate provides a full range of real estate services including sales, leasing and royalty negotiation, transactional management and occupier advisory.
If you’d like to chat further about how InSitu Real Estate can assist you with your requirements, or to discuss our current offerings, reach out today. Providing
Todd Clark Director
Licensee in Charge
+61 (0) 424 165 077
todd@insiturealestate.com
www.insiturealestate.com
Suite 303, 17 Wurrook Circuit Caringbah, NSW 2229 InSitu Real Estate
linkedin.com/company/insitu-real-estate