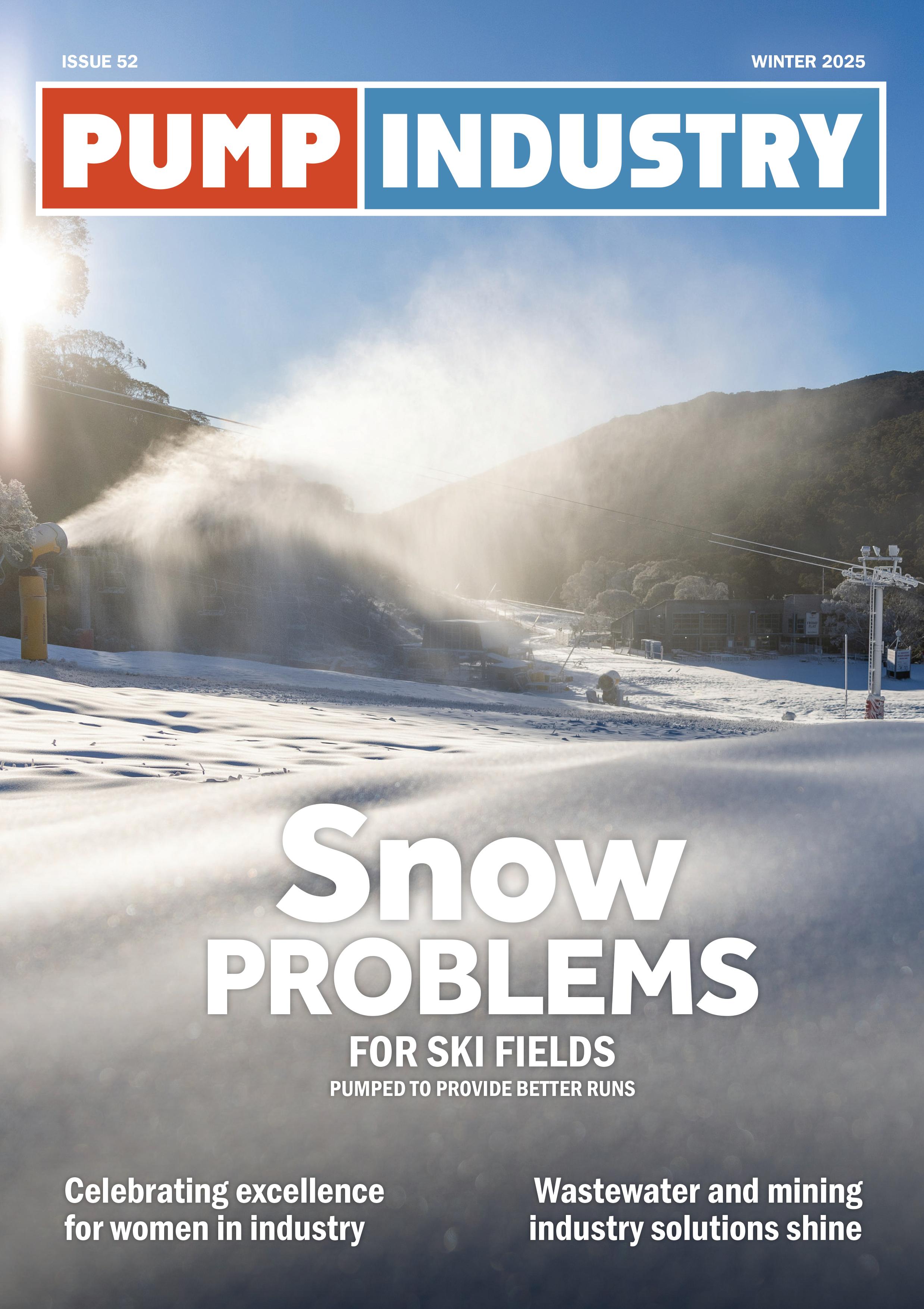
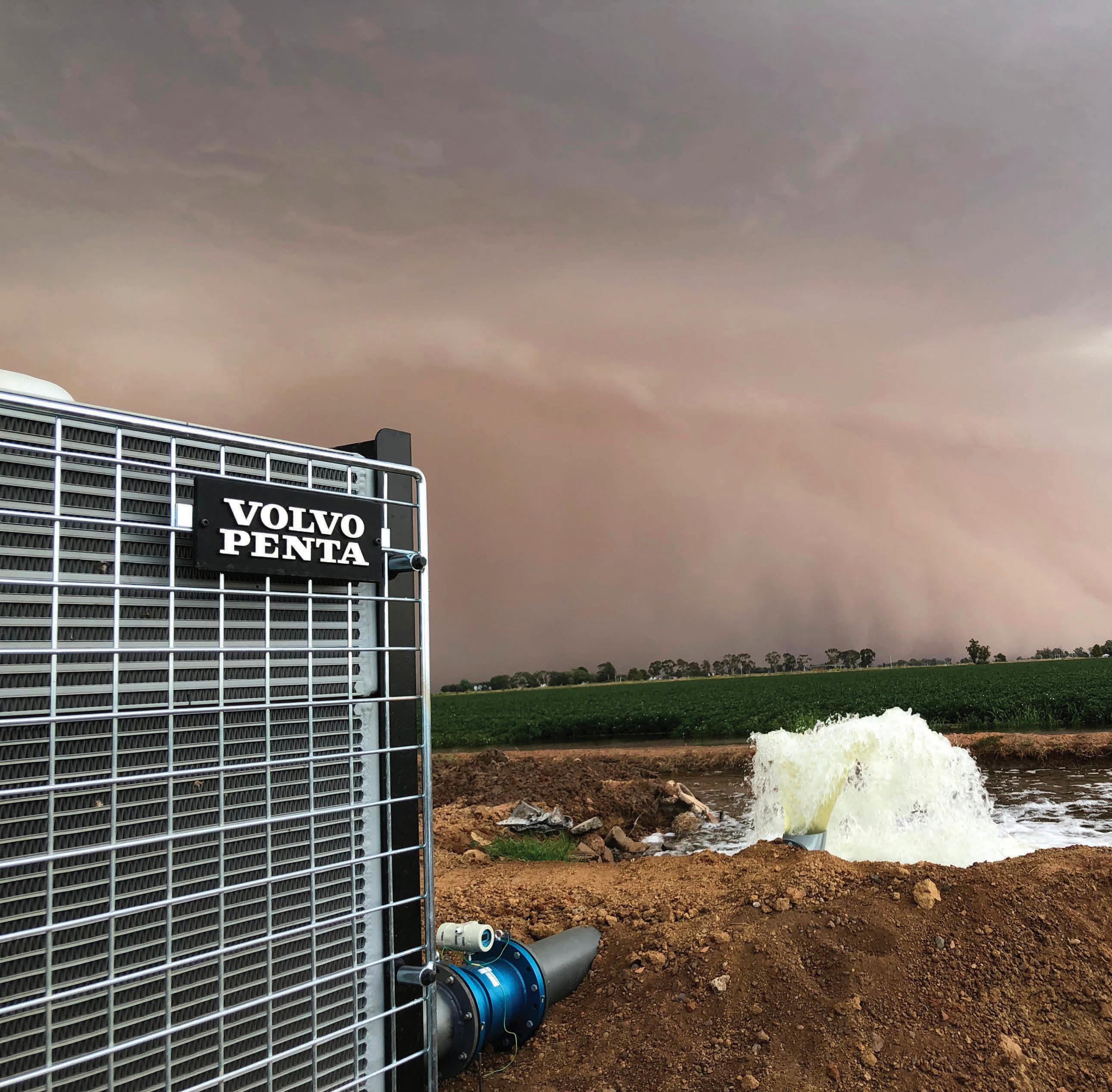
Powerful Partnership
Powerful Partnership
Engines that keep running even in the toughest conditions. Easy to install, operate and maintain. A powerful partnership you can trust all the way from the drawing board throughout the operational life of your engine. Competitively priced complete power-pack units ready for delivery Australia wide with a local support team on hand 24/7.
To find your nearest dealer visit volvopenta.com/industrial
Pump Industry Australia Incorporated
PO Box 527
YARRAWONGA VIC 3730
Phone: +61 493 975 931
secretary@pumps.org.au
www.pumps.org.au
PIA Executive Council 2025
Kylie Kinsella - President Regent Pumps
Joel Neideck – Vice President TDA Pumps
Tracey Guida – Treasurer/Secretary
Alan Rowan – Councillor
Executive O cer – Publications and Training, Life Member
Ken Kugler
Executive O cer – Standards, Life Member
Steve Bosnar – Councillor Franklin Electric/Pioneer Pumps
Michael Woolley – Councillor Tsurumi Pumps
Luke Biermann – Councillor Mechanical Seal Engineering
Tim Yakup – Councillor Regent Pumps
Alex Calodoukas – Councillor Pump Strategy
Keith Bowen – Councillor Xtron Pumps Australia
Dear PIA Members and Industry Colleagues,
Welcome to the winter edition of Pump Industry.
Winter in Australia may be milder than many other parts of the world, but a cold snap quickly reminds you that winter has arrived. We have seen extreme rainfall in New South Wales, with a month’s worth of rain falling in just one week, resulting in major � ooding. Meanwhile, Victoria, South Australia, and other states experienced cooler conditions, while all states had warmer-than-average daytime temperatures.
Since our last edition, as well as seasonal changes, there have been challenges and changes in the political environment in Australia. The federal election was held in May, with the Albanese government securing a second term. There will be changes that impact businesses moving forward as they implement their agenda and election commitments.
The re-elected government is making moves in the industrial relations space. Starting in 2027, non-compete clauses will be banned for workers earning under $175,000. This includes � xing wages and preventing sta� poaching. The government is committed to stopping the industrial umpire from altering rules regarding penalty rates for higher base pay. Several support policies will assist small businesses.
The other main event was the Reserve Bank of Australia’s (RBA) decision to cut interest rates in May. The economy is still expected to experience a weaker growth outlook, and the RBA anticipates an increase in unemployment, although this is considered low by historical standards. It brings some relief to households with further rate cuts expected later in the year.
US President Donald Trump’s tari� s have directly impacted Australian businesses. The latest information I have, as I write to you, is that the
baseline is 10 per cent on most imported goods. Steel and aluminium are being subjected to 25 per cent tari� s.
All the above matters bring about their own challenges to our economy and our businesses as we move through the next 12 months.
The committee held its most recent council meeting in May. I am pleased to announce that the committee has appointed Naomi Lincoln as the new Secretary-Treasurer. She has been in the industry for the past nine years and will be a great addition to the council.
We have also � nalised a date for our � rst training session for 2025.
This event is a partnership with the PIA, WEG, Drive Systems and Cancer Council Australia.
PIA Motor and Transmission Training
• Date: 14 August 2025
• Location: WEG Australia P/L – 14 Lakeview Drive, Scoresby, Melbourne
• Start: 8.30am – 12pm
• Morning tea provided
• Enrolment fee: Members $65.00, Non-members $75.00
We will be donating half of all proceeds to our partner, the Australian Cancer Council. There are 50 spaces available, and all booking requests can be made to secretary@pumps.org.au
A gentle reminder of our Annual AGM/ Dinner, taking place on 13 November at Crown Plaza in Melbourne. Again, all bookings can be made via our secretary.
We would also like to hear from our members who wish to purchase the Australian Pump Technical Handbook and/or Australian Pipe Friction Handbook We will make books available for purchase at our training event, or you are welcome to place an order with our secretary.
We look forward to seeing you in July.
Stay warm.
Kind regards,
Kylie Kinsella PIA, President
Scan to subscribe to Pump Industry’s weekly newsle er –delivered to your inbox every Thursday a ernoon.
Cover image: Thredbo/EVT
Published by
Chairman John Murphy
Chief Executive O� cer
Christine Clancy
Editor
Chris Edwards
Design
Jacqueline Buckmaster
Head of Design
Blake Storey
Business Development Manager
Rima Munafo
rima.munafo@primecreative.com.au +61 413 475 078
Client Success Manager
Louisa Stocks
Head O� ce
Prime Creative Media
379 Docklands Drive
Docklands Victoria 3008
P: +61 3 9690 8766
enquiries@primecreative.com.au pumpindustry.com.au
Subscriptions
P: +61 3 9690 8766
subscriptions@primecreative.com.au
Pump Industry is available by subscription from the publisher. The rights of refusal are reserved by the publisher.
6 Snowmaking pumps power Australian ski � elds PUMP NEWS
10 Optimising tailings treatment for environmental compliance and resource recovery
12 A decade of leadership in motor technology
14 Reliable pumping performance built on legacy
16 How high-� ow vertical pumps deliver reliability
18 Techtop expands VHS motor o� ering for pump applications
20 Hazardous area motors ready for pump applications
22 Tailored power, maximum e� ciency
24 Giving rotating equipment a second life
27 Uncovering the potential of industrial cooling
3 President’s welcome PUMP CURVES
50 Why NPSH Testing Sucks � nal
The publisher welcomes contributions to the magazine. All contributions must comply with the publisher’s editorial policy which follows. By providing content to the publisher, you authorise the publisher to reproduce that content either in its original form, or edited, or combined with other content in any of its publications and in any format at the publisher's discretion. COVER STORY
28 E� cient irrigation systems in Victoria
30 A trusted solution for mining applications
32 Optimising water and wastewater operations
34 Pioneering progressive cavity pump solutions in wastewater management
36 Spilling the beans on e� cient food waste handling
INDUSTRY ADVOCATES
38 Heat pumps and the path to net zero: The licensing link EVENTS
40 Recognising technical and engineering excellence across sectors
42 Western Australia thrives on pumps in mining
45 Automation in mining pumps: why AIMEX 2025 matters
48 Prospect for safer mining
PUMP HANDBOOK
52 Pump Technical Handbook: Pump Installation #3
This magazine is published by Prime Creative Media in cooperation with the Pump Industry Australia Inc. (PIA). The views contained herein are not necessarily the views of either the publisher or the PIA. Neither the publisher nor the PIA takes responsibility for any claims made by advertisers. All communication should be directed to the publisher.
Pumps Industry acknowledges Aboriginal Traditional Owners of Country throughout Australia and pays respect to their cultures and Elders past, present and emerging.
Precision-engineered for the most demanding applications, FELUWA’s MULTISAFE® technology ensures safe and efficient handling of abrasive, aggressive and toxic media – even under extreme operating conditions.
Our pumps are designed for high-pressure and high-performance requirements, delivering:
Flow rates up to 1,000 m³/h
Pressures up to 350 bar
YOUR SOLUTION FOR:
Reactor, autoclave and gasifier feeding
Concentrate and tailings transfer
Fly and bottom ash disposal
Wet oxidation
Mine dewatering
Reliable snowmaking pumps help Australian ski resorts strike a balance between performance and sustainability amid changing climates.
Thredbo’s snowmaking infrastructure ensures its facilities are always at their best for visitors.
Snowmaking has evolved from a supplementary measure to a cornerstone of operations in Australian ski resorts, driven by sophisticated pump systems that ensure consistent snow cover amid climate variability.
Australia’s alpine regions are facing increasing climate variability, characterised by shorter snow seasons and reduced natural snowfall. Ski resorts can no longer depend on consistent snowfall to attract visitors or deliver viable operating seasons. In response, snowmaking has evolved from an occasional supplement to an essential service that underpins the viability of resorts.
Behind each perfectly groomed run is a highly engineered network of pumps, pipelines, and control systems that move massive volumes of water up mountainsides and across ski � elds. From major operators such as Mt Buller and Thredbo to smaller resorts such as Corin Forest, snowmaking pumps are at the heart of keeping slopes open, safe, and skiable.
This shift has also reshaped the philosophy of snowmaking. As Mt Buller’s Snowmaking Manager, Paul Richmond, explained, “Our snowmaking system has gone from backing up natural snowfalls to being relied upon to create the base itself. It is almost a complete change.”
Australian snowmaking teams now operate with military precision, using advanced monitoring tools and highly e� cient pump systems to produce the right snow, at the right time, in the right place. The modern snowmaking pump is no longer hidden infrastructure, but an essential driver of the ski economy.
Building the snow base: Modern snowmaking in Australian ski resorts Snowmaking’s role in Australian ski resorts has undergone a signi� cant shift in recent decades. Initially viewed as an occasional supplement to natural snow, it has become mission-critical. Without reliable snowmaking, many of Australia’s ski � elds would struggle to deliver a viable season.
At Mt Buller, the history of snowmaking dates to the early 1970s, when a pilot system was tested on the Enzian run. Today, Mt. Buller operates four 300-horsepower multi-stage pumps, delivering up to 400 litres per second across 80 hectares of skiable terrain. The resort now manages 170 megalitres of water for snowmaking,
While the creation of snow may be pre y, it’s vital that everything is considered before the pumps get cranking. Image: Corin Forest
supported by more than 300 snow guns, 80 per cent of which are fully automated. Thredbo launched snowmaking in 1987. Before that, top-to-bottom skiing lasted just 20 to 30 days a season. With modern snowmaking, Thredbo now routinely achieves more than 100 days. Its � eet of more than 300 automatic guns can run up to 200 simultaneously, allowing precise snow management across the mountain.
Corin Forest represents a di� erent model. Located near Canberra, it relies entirely on snowmaking, given the region’s low natural snowfall.
“We are a snow resort where it doesn’t snow,” said owner Dane Liepins. Since 2014, Corin Forest has expanded from one leased snow gun to nine top-tier snowmakers and two snow factories capable of producing 100 tonnes of snow daily.
Switching on the snow: Decisionmaking in snowmaking operations Deciding when to activate snowmaking systems involves balancing weather conditions, operational targets, and economic considerations. Gone are the days when snowmaking was simply reactive. Today, it is a strategic process informed by weather forecasts, water availability, and visitor demand.
Mt Buller typically begins snowmaking two to three weeks ahead of the King’s Birthday long weekend, which marks the
traditional season opening. Richmond explained that the resort uses detailed weather models to plan activations.
“We start with primary slopes � rst, using both our snow guns and allweather snow factories,” he said.
At Thredbo, systems are placed on standby from early May. Test runs ensure readiness, and full-scale snowmaking commences when favourable cold snaps arrive. The resort’s supervisory control system monitors temperature, humidity, and snow depth in real time, helping to optimise when and where to make snow.
Corin Forest’s approach re� ects its status as a small business.
“It’s pure maths,” Liepins said. “We calculate the cost to make snow and how many visitors we need to justify it.”
Balancing energy demands with operational realities
Beyond managing day-to-day energy demands, resorts must also ensure their pumping systems can perform under the full range of extreme conditions their Alpine environments impose. Snowmaking is energy-intensive. Managing power demand is critical for both operational e� ciency and environmental sustainability. Resorts deploy a variety of strategies to control costs and minimise grid impacts.
Mt Buller utilises Variable Speed Drives (VSDs) on both pumps and
compressors to reduce peak demand.
“We avoid making snow after 7am whenever possible to reduce costs and grid load,” Richmond said. A large rooftop solar installation helps power the resort’s maintenance facilities year-round, contributing to its broader sustainability goals.
Thredbo operates on 100 per cent renewable electricity. Its snowmaking system consumes about three megawatts during peak operation.
“We adjust operations to � t o�peak tari� windows where possible,” Thredbo Snowmaking Manager Jonathan Batson said.
At Corin Forest, power management is an ongoing balancing act. “We can’t run everything at once,” Liepins said. “Fan guns are more e� cient, so we prioritise them. Snow factories consume a lot of energy, so we use them very strategically.”
Ensuring performance in extreme conditions
energy use, and snow output.
“We can now calculate the cost per cubic metre of snow in real time,” Richmond said.
Thredbo has seen major gains from VSD upgrades.
“We replaced older throttlecontrolled pumps with variable speed models,” Batson said. Future upgrades will focus on further optimising pump control and improving the thermal management of water.
Beyond managing energy demand on a day-to-day basis, snowmaking teams must also ensure their pump systems remain resilient across the full range of extreme conditions.
At Mt Buller, reliability starts with preventive maintenance.
“We conduct biannual vibration testing on all pumps,” Richmond said. The resort also keeps a comprehensive inventory of critical spares to minimise downtime.
Thredbo’s approach is similarly proactive.
“Proper summer preservation is critical,” Thredbo Engineering Manager Russell Nuridin said. O�-season servicing includes disassembling the pump, inspecting it, and performing performance testing.
workshops and have exchange programs with other mountains,” Richmond said. “Feedback from our teams is helping improve snowmaking technology worldwide.”
The resort also collaborates with global suppliers, in� uencing product development based on real-world Australian experience.
Water sourcing, pumping distances and handling head pressure
Of course, none of this e� ciency matters without sustainable water supplies to feed the pumps. Water sourcing is a critical element of snowmaking operations, necessitating careful management to strike a balance between operational needs and environmental responsibilities. Pumping distances and head pressure add further engineering complexity.
Mt Buller sources water from nearby creeks, springs, and rivers. Allocations are tightly controlled by GoulburnMurray Water, with pumping restricted from November to July to protect natural � ows.
Corin Forest’s small team focuses on keeping its equipment adaptable and well-maintained across all weather conditions.
“Snowmaking is inherently highpressure work, often done in the dead of night,” Liepins said.
E� ciency, sustainability, and future directions
Pump e� ciency delivers both cost savings and environmental bene� ts. With energy accounting for a large share of snowmaking expenses, even small improvements in pump performance can yield signi� cant gains.
Mt Buller has embraced advanced software to track pump performance,
Thredbo likewise values peer collaboration. “Within the local operations community, there’s great cooperation,” Nuridin said.
However, competition remains � erce among equipment providers, given the small Australian market.
“That side of the industry is very commercial,” added Batson.
This collaborative spirit ensures that Australia’s snowmaking teams remain at the forefront of global best practice. Whether through formal partnerships or casual conversations, the willingness to share knowledge strengthens the industry as a whole.
Beyond the slopes: Alternate uses of snowmaking equipment
“We often miss valuable spring rainfall because of these rules,” Richmond said.
Thredbo operates a near-closed-loop system. Water is drawn from a lake fed by the Thredbo River, then pumped to the mountain. Meltwater returns to the river.
Corin Forest enjoys a simpler hydraulic pro� le.
“We pump from a 2.5 megalitre dam just 15 metres up the hill,” Liepins said.
Collaboration across the snowmaking industry
Collaboration is a hallmark of Australia’s snowmaking community. While competition exists among equipment suppliers, operators across the resorts freely share knowledge to improve safety, e� ciency, and environmental performance.
“We all talk,” Liepins said. “It’s about sharing practical tips. The little things, like how you dry hoses, move snow guns, or maintain � ttings, can make a big di� erence.”
Informal gatherings and end-ofseason workshops foster this culture of exchange. “Every resort and team face di� erent challenges. Seeing how others solve them is incredibly valuable.”
Mt Buller embraces a similar ethos.
“We participate in international
Snowmaking infrastructure serves critical roles beyond the ski season.
Increasingly, resorts are leveraging their pump systems for asset protection and emergency response, particularly in the face of bush� re threats.
At Mt Buller, this approach is well- established.
“We install sprinklers each summer to defend lifts and buildings from bush� res,” Richmond said. The system is set up well in advance of � re season, with snowmaking pumps repurposed to drive water through rooftop and perimeter sprinklers. “It gives us an additional layer of protection, particularly for high-value assets like lift stations,” he added.
Thredbo operates within Kosciuszko National Park, one of Australia’s most sensitive natural environments. The resort uses its snowmaking system to dampen vegetation ahead of advancing � res.
“It’s an innovative application that has had a signi� cant impact,” Batson said. The ability to rapidly saturate vulnerable terrain helps slow � re fronts and protect both natural and built assets.
Corin Forest’s experience during the 2020 bush� res was a powerful example of this adaptability.
“We used our snowmaking pumps to feed irrigation sprinklers protecting our buildings,” Liepins said. “We were shooting water 40 metres into the air. It worked brilliantly.”
The success of this improvised system has led the resort to invest further in � exible connectors and hardware that can be quickly deployed in emergencies. These examples highlight the broader value of snowmaking infrastructure. Beyond enabling winter operations, wellmaintained pumps and pipelines can play a vital role in safeguarding resorts and their surrounding environments year-round.
Looking ahead: Innovations shaping the future of snowmaking
As climate patterns shift and snow windows narrow, Australian resorts are looking to innovation to sustain their snowmaking capabilities. Pump systems will continue to play a central role in this evolution.
At Thredbo, improving lance gun e� ciency and enhancing water cooling are key priorities.
“Further cooling of pumped water can signi� cantly boost snow production,” Nuridin and Batson said. This allows snow guns to operate more e� ectively at marginal temperatures, expanding the viable snowmaking window. The resort is also investing in all-weather snow factories, providing a reliable means of establishing base cover when traditional methods are not viable.
Mt Buller is pursuing multiple avenues to future-proof its operations. In addition to sourcing more � exible water supplies, the resort is investing in advanced pump controls and expanding its data analytics capabilities.
“We need to be adaptive,” Richmond said. “Improving pumping rates, e� ciency, and water sourcing is critical to the future.” The ongoing pipe replacement program, using highdurability materials, will further enhance system performance and longevity.
At Corin Forest, Liepins is closely watching material science trends.
“High-grade plastic pipe could replace steel in parts of the system,” he said. “It would save time and money on future projects.”
The resort is also exploring ways to further optimise its use of snow factories, balancing energy demands with production needs.
Across the industry, regulatory � exibility remains a shared concern.
“Snowmaking is not traditional irrigation,” Liepins said. “We are building water reservoirs in the form of snowpack, which bene�ts the environment.
Regulators are starting to understand that, but more work is needed.”
All agree the future of snowmaking in Australia will be shaped by innovation, collaboration, and a relentless drive for e� ciency. Snowmaking pumps will remain at the heart of this journey, sustaining the slopes and the communities that depend on them for years to come.
“It has gone from topping up natural snow to building the base itself,” Richmond said. “Every � ake we make supports the entire local economy, from jobs to businesses to tourism.”
then
As the by-product of mining processes, tailings are a waste stream that may contain toxic by-products or residual commodity materials. Such residual materials may become valuable in the future, depending on technological improvements and market conditions, allowing them to be reprocessed.
Optimising tailings treatment processes is critical to the economic e� ciency, environmental sustainability, and long-term safety of mining operations. As regulatory, societal, and � nancial pressures grow, mining companies are under increasing scrutiny to manage tailings more e� ectively.
It is therefore necessary to monitor the condition of tailings facilities and any leakage or runo� that may occur (for example, after heavy rain). The control of in� ows and leakage typically involves the use of a sump, which is a low-lying pit or basin designed to collect and temporarily store liquids, usually unwanted or excess water. This sump may be used to collect and pump water for reuse or to return it to the tailings
The MultiCELL product from Burket Fluid Controls
Image: Burkert Fluid Control Systems
dam. Sump levels must therefore be monitored.
Typically, mill tailings range from sand to silt-clay in particle size and can be highly aggressive substances when they come into contact with pumps, sensors, and valves used to manage them. The technology used to monitor tailings dams and sumps needs to be able to withstand the demands of the aggressive environment in which it must operate.
Bürkert’s solutions for tailings monitoring
The � ow of tailings slurries must be controlled and redirected as necessary by a valve that is una� ected by the properties of the medium. The Type 2380 bellows control valve is a high-performance, pneumatically actuated process valve featuring a polytetra� uoroethylene (PTFE) bellows that ensures complete separation between the medium and the actuator, thereby increasing service life and reliability in harsh environments, such as tailings facilities. The valve is designed for use in aggressive conditions and is easy to clean. All common port connections, up to 25 millimetres, normal pipe size 1 (DN25 / NPS 1), are supported.
Minimising control components also reduces cost and complexity. Bürkert’s Type 8619 multiCELL multifunction controller/transmitter collects data from up to six sensors, allowing for
the simultaneous measurement of temperature, pH, conductivity, and oxidation reduction potential (ORP) value in a single unit. The multi-channel transmitter can also perform a range of dosing, � ow, level, pressure and control functions. Modularity in hardware and software provides high � exibility for adapting to the application’s needs.
With full support for Modbus/TCP, PROFINET (Conformance Class B), or Ethernet/IP, the Type 8619 can be integrated into most industrial Ethernet environments, allowing important process values, such as measurement data, process diagnostics, or device status, to be easily integrated into the automation system.
Bürkert is also able to supply custom control cabinet solutions ready to interface with the tailings process. These control cabinet solutions can contain diverse components, depending on the application, combining pneumatic, electronic, and valve technology in a single unit. They can be highly complex, customised systems with control panels and functions in any suitable housing, including stainless steel.
Bürkert o� ers a broad spectrum of control cabinet solutions and technologies tailored for the application at hand, and customisable to any tailings monitoring and control application.
For more information, visit burkert.com.au
For more than 60 years, Franklin Electric Australia has been a trusted name in water solutions, supporting the nation’s essential water infrastructure across residential, agricultural, municipal, industrial, mining, commercial, and fuelling sectors.
As a subsidiary of Franklin Electric, founded in 1944 in Blu� ton, Indiana, its local operations are backed by more than 80 years of global innovation and technical excellence in water and fuel systems.
From its beginnings as a small electric motor manufacturer, Franklin Electric has evolved into a global technology leader, dedicated to moving water in the most reliable, sustainable, and e� cient manner possible. Today, that mission is re� ected in every product it engineers, and no better example exists than the high-e� ciency systems, powered by permanent magnet (PM) submersible motors.
Franklin Electric is proud to be the pioneer of permanent magnet technology in submersible motors. For more than a decade, high-e� ciency
systems have delivered proven results worldwide, achieving motor e� ciencies of up to 94 per cent. This exceptional performance doesn’t just represent engineering expertise; it translates to signi� cant energy savings, reduced environmental impact, and lower longterm operating costs for end-users.
The key to this superior e� ciency lies in the innovative design of Franklin Electric’s permanent magnet rotor, which features embedded magnets that eliminate total rotor losses, a major source of ine� ciency in traditional asynchronous motors. As the motor operates synchronously with the drive frequency, it draws fewer amps to deliver the same pump output, reducing energy consumption and mechanical stress. Additionally, the synchronous motor design generates less heat, performs more e� ciently under partial loads, and typically o� ers a longer service life.
Lighter, shorter and more e� cient than comparable asynchronous motors, Franklin’s PM motors are the ideal solution for applications where
performance, compact design and reliability are essential. And because all system components are engineered to work seamlessly together, users can count on a level of performance and dependability that sets a new standard in the industry.
To simplify commissioning and con� guration, the High E� ciency System includes an intuitive setup wizard that walks users step-by-step through the drive parameters. When paired with a variable frequency drive (VFD), users can not only optimise system performance in real time but also monitor and control operations remotely, maximising energy savings while reducing downtime and maintenance requirements.
Franklin Electric’s range of permanent magnet submersible motors is available from four to 10 inches, with � exible system con� gurations tailored to a wide variety of applications. Options include various material constructions and compatibility with solar power, further enhancing the system’s sustainability and appeal in remote or o�-grid locations.
Backed by Franklin’s long-standing reputation for quality, reliability, and local support, high-e� ciency systems empower customers to do more with less energy, maintenance, and environmental impact.
We would love for you to join us
Date: 14 August 2025, 8:00am arrival th commencing @ 8:30am
Location: 14 Lakeview Drive, Scoresby 3179
Cost: Members $65 & Non Members $75 small breakfast included ONLY 50 spots available
Contact: PIA Secretary
Email: secretary@pumps.org.au
Phone: 0422 757 898
proudly parterning with
Regent Pumps delivers consistent, high-performance pumping systems across diverse industrial sectors and challenging legacy replacements.
For more than seven decades, Regent Pumps has played a steady role across Australia’s industrial and rural landscape. From food manufacturing to irrigation and even naval defence, its pumps have delivered dependable performance across changing operational environments.
Founded in 1948, the company remains privately owned, with the third generation of the family still involved. That continuity has shaped a product line de� ned by reliability and practical engineering.
National Sales Manager Tim Yakup sees this as a core strength. “The industries we serve expect solutions that just work, even after decades in the � eld,” he said. “We’ve built our reputation by supporting those expectations, whether it means supplying a new unit or replacing one we made in the 1960s.”
Headquartered in south-east Melbourne, Regent operates a manufacturing and inventory facility in Dingley. This local presence enables rapid delivery across the country, supporting customers in both urban and remote regions where downtime can be costly.
Backward compatibility designed into every build What sets Regent Pumps apart is its
commitment to long-term support. One of the company’s de� ning features is its use of consistent dimensions across product generations. This approach allows seamless replacement of older units without the need to alter pipework or mounting systems.
“It’s not uncommon for us to receive calls from customers looking to replace a pump that’s older than some of their sta�,” Yakup said. “Because we’ve maintained the same critical dimensions, we can o� er a direct swap, even if the original pump is 40 years old.”
This strategy reduces life cycle costs for customers managing legacy infrastructure. The product range includes discharge sizes from 25 to 300 millimetres and o� ers a variety of drive types, including electric, diesel, petrol, and hydraulic.
“We’ve always aimed to be the supplier you call when others say a pump is too old or too hard to match,” Yakup said. “That’s the value of staying consistent over time.”
Evolving with industry through smart innovation
While heritage is central to Regent’s identity, the company is focused on adapting to new demands. As energy e� ciency and sustainability become key priorities, Regent is
re� ning its designs to meet higher performance expectations.
“There’s growing demand for smarter pumps that can do more with less – less power, less maintenance, less intervention,” Yakup said. “We’re integrating sensors and control systems into proven models to extend their value.”
This shift is particularly relevant for the water and wastewater sectors. Utilities are under increasing pressure to improve operational performance, reduce losses, and demonstrate environmental responsibility.
Regent aims to meet these needs by working more closely with customers to align product development with technical requirements.
A future built on legacy and trust As infrastructure operators grapple with ageing assets, uncertain supply chains, and tightening performance expectations, companies such as Regent Pumps o� er a rare combination of local expertise and longterm thinking.
From its commitment to Australian manufacturing to its customer-� rst approach to support and service, the company has demonstrated that reliability is not a marketing slogan, but a built-in feature.
“Our goal is to keep things simple for our clients,” Yakup said. “Whether it’s a brand-new installation or a pump we haven’t seen in years, we want to be the supplier they trust to get it right.”
With its legacy well-established and its future focused on innovation, Regent Pumps remains a vital partner in keeping Australia’s systems running quietly, consistently, and locally.
For more information, visit regentpumps.com.au
Steel construction.A single Carbon/ Ceramic Mechanical Seal is standard, other seals available on request or designed for application.
APPLICATIONS
Air Conditioning, Water Pressure Boosting, Heating and Cooling, Liquid transfer, Water Treatment and Supply, Effluent, Irrigation and Drainage, Petroleum Products, General Industry
PERFORMANCE
Flow rates up to 1500 litres per minute with pressures up to 150 Meters.
High-flow vertical pumps support reliable water transfer in challenging environments and demanding infrastructure projects.
When large volumes of water need to be moved reliably, and suction lift is impractical, high � ow vertical pumps are an essential solution. From irrigation and � ood control to municipal infrastructure and industrial water transfer, these pumps handle demanding � ow requirements with operational e� ciency. Selecting the right pump, engineered for long-term performance, is critical to delivering reliable water movement across diverse Australian conditions.
Selecting the right high � ow vertical pump
High � ow vertical pumps typically fall into three categories: axial � ow, mixed � ow, and vertical turbine designs. Each o� ers distinct performance characteristics.
Axial � ow pumps excel in low head, high volume scenarios, providing up to 10 metres of head with minimal energy use. They are often used in � ood control, dam operations, and river systems.
Mixed � ow pumps balance � ow and head, delivering up to 20 metres of head while maintaining strong � ow rates. They suit irrigation and infrastructure projects needing � exible solutions.
Vertical turbine pumps operate at higher heads, exceeding 15 metres and extending well beyond with multistaging. They are suited to deep well pumping, pit/river pumping, industrial water supply, and urban networks.
While higher heads can be achieved by adding stages to axial or mixed � ow designs, this adds complexity and cost. “Keeping stage count to a minimum simpli� es the design, reduces the number of parts, and improves e� ciency,” according to guidance from Sterling Pumps. Selecting the most appropriate pump ensures optimal performance and reliability.
Reducing maintenance with modern bearing technology
Historically, vertical pump designs, especially inclined and deep
installations, relied on oil-lubricated support bearings. These systems required a constant oil feed, with bearings spaced at 1.5 metre intervals. In deep installations, maintenance demand and environmental risks increased as oil entered the pumped water.
Advances in bearing technology have changed this. Water-lubricated bearings, now used in angled installation turbine/mixed � ow pumps up to 35 metres long, leverage the pumped liquid for lubrication, eliminating the need for pre-lubrication and oil supply.
This reduces maintenance and improves environmental performance, particularly for pumps drawing from rivers, dams, or municipal supplies. Adopting modern bearings extends pump life and lowers operating costs.
Engineering con� dence for Australian conditions
With many projects requiring sitespeci� c engineering, local expertise remains essential. Manufacturers such as Sterling Pumps o� er full design, manufacturing, and testing from Melbourne, ensuring that high � ow vertical pumps meet Australian standards and needs.
Collaborating with engineers during pump selection and structural analysis is particularly important for inclined or deep installations. Vibration management, structural support, and material selection all in� uence reliability. Engaging local partners who understand Australian conditions provides project teams with greater con� dence.
High � ow vertical pumps remain critical to many water systems. By selecting the right pump type, adopting modern bearing technology, and working with experienced engineers, organisations can ensure reliable, e� cient performance in demanding applications.
For more information, visit sterlingpumps.com.au
Oil & Gas, Industrial, Defence, Power, Municipal, Irrigation & Mining. Engineered and Manufactured in Melbourne
Submersible Pumps and Motors, Ballast pumps, Vertical Turbine Pumps API610 Pumps – Extensive Reference Lists Repairs, Design Upgrades, OEM spare parts and 2.5mw test facility
United Pumps support our heritage product Harland Pumps, Indeng, Johnston Pumps
Techtop Australia has launched a new range of vertical hollow sha electric motors engineered for reliability and performance in deep well and turbine pump systems. e series aims to meet the growing needs of the water, wastewater, and resource sectors.
Electric motors are the heart of pumping systems across a wide range of industries. When it comes to deep well and vertical turbine applications, few components are as critical as vertical hollow shaft (VHS) motors. Recognising this demand, Techtop Australia has expanded its VHS range to support Australian pump professionals with rugged, highperformance solutions tailored for challenging environments.
The new Techtop VHS series spans from 15 kW to 75 kW in two-pole models and from 15 kW to 300 kW in four-pole options. Designed to handle high axial loads, each unit includes a built-in non-reverse ratchet, high starting torque, and a service factor of 1.15. An enlarged oil chamber helps extend bearing life through better lubrication, while integrated thermistors and heaters ensure the motors perform reliably under varying load and temperature conditions.
A de� ning feature of Techtop’s VHS motors is their hollow shaft con� guration. Unlike conventional vertical motors that require a coupling to connect the motor to the pump shaft, the hollow shaft design allows the pump shaft to pass directly through the motor. This reduces installation time, improves alignment, and helps cut maintenance costs by reducing mechanical complexity. The result is a more streamlined installation process and less downtime in the � eld, which
is particularly valuable for remote or large-scale operations.
Vertical hollow sha motors are designed for deep well and turbine pump systems. Image:
Built for durability, the motors feature a robust insulation system that includes UL (Underwriters Laboratories)approved materials and copper wire compatible with variable voltage variable frequency (VVVF) drives. To enhance resistance to moisture and contaminants, a double vacuum pressure impregnation (VPI) process is used with non-hygroscopic epoxy varnish. Motors destined for harsh conditions such as coastal, mining, or humid areas receive additional tropicalised varnish to shield internal components from damage.
Vertical hollow shaft motors are a preferred choice in various sectors, including water and wastewater management, agriculture, pulp and paper processing, mining, and municipal infrastructure. These industries demand not only high performance but also longevity under pressure. The new VHS motors meet these expectations by striking a balance between technical excellence and practical design considerations.
Techtop’s VHS motors are already proving their value in demanding Australian environments. In regional Victoria, they are supporting deep-bore irrigation, where consistent water delivery is critical to crop viability. Mining operations in Western Australia have deployed the motors for dewatering tasks, where high axial loads and harsh
Municipalities in New South Wales have integrated them into well pump stations servicing growing townships.
In each case, the motors have simpli� ed installation and reduced maintenance overheads. These realworld applications demonstrate how the VHS range meets the practical needs of industry with reliability and minimal operational disruption.
As demand increases for water security and deeper well drilling, especially in regional and agricultural communities, motor reliability is more important than ever. Techtop’s VHS range supports sustainable infrastructure by providing energye� cient solutions that reduce the total cost of ownership over the motor’s life cycle.
Techtop’s national presence ensures timely technical support and the availability of spare parts across Australia. With branches in Melbourne, Sydney, Brisbane, Adelaide, Perth, and Auckland, the company is wellpositioned to serve a broad customer base with specialised motor solutions.
For pump professionals seeking dependable VHS motors backed by local expertise and responsive service, Techtop’s latest release o� ers a new level of assurance for critical infrastructure projects.
For more information, visit techtop.com.au
Techtop Vertical Hollow Shaft motors are designed to drive deep well turbine water pumps, mainly for irrigation.
They are the smart solution for both standard and high thrust applications.
Available from 15kW to 75kW in 2 pole, and 11kW to 300kW in 4 pole, with a service factor of 1.15.
Certified, in stock and built to last
TECO Flameproof Electric Motors are engineered for hazardous environments in mining, oil and gas, water, plus chemical processing applications. Designed to handle pumps, fans and conveyors in explosive atmospheres, all motors o� er certi� ed protection, thermal resilience, and longterm reliability.
All models are fully compliant with International Electrotechnical Commission (IECEx) and ATEX requirements, including explosion-proof (Ex d and Ex de) con� gurations, and are suitable for Zone 1 and Zone 2 areas. The range of underground miningcerti� ed models meets Group I standards, which are typically underground mines with � redamp (methane) atmospheres. In such an environment, motors must comply with IEC 60079-1 (Flameproof enclosures).
The TECO Australia Flameproof Electric Motors are designed for coal applications where � ammable gases and coal dust are present – a feature that distinguishes TECO from many imported alternatives not certi� ed for underground applications.
These motors have cast-iron housings, a high-e� ciency insulation system (rated to 155°C Class F), and are designed with a totally enclosed fan-cooled (TEFC) (IC411) con� guration. They’re engineered for continuous operation (S1 duty), where the motor runs at a constant load for a duration long enough to reach thermal equilibrium. It can run at full output in ambient temperatures up to 55°C without any derating.
This makes them ideal for pump applications in harsh Australian conditions, where high thermal performance is crucial to prevent
Ex d (Flameproof) motors are designed to contain internal explosions. Ex de (Flameproof + Increased Safety) motors combine Ex d protection with an Ex e terminal box.
The range of flameproof electric motors from TECO Australia provides enormous flexibility when used in hazardous areas. Image: TECO Australia
overheating, downtime, and loss of e� ciency.
TECO Flameproof Electric Motors are utilised in numerous critical pump systems, ranging from dewatering and slurry pumps at mine sites to chemical dosing skids, � re suppression systems, and oil transfer units in re� neries.
They are also suitable for ventilation fans, cooling towers and conveyor drives, o� ering consistent torque and stable operation even in load� uctuating conditions.
Their low vibration and noise levels help reduce mechanical stress on pump components, extending the life of seals, impellers and bearings.
One of the key advantages for customers is the ability to access local stock across Australia and New Zealand, avoiding delays.
TECO in-house ModShop can modify motors to suit speci� c site requirements. This includes rotating terminal boxes, installing anticondensation heaters, changing cable entries, or making shaft and mounting adjustments. All modi� cations are carried out in accordance with approved certi� ed procedures to ensure that compliance is maintained. This means less time lost to sourcing,
approvals, or on-site rework for original pump equipment manufacturers (OEMs), system integrators, and maintenance teams.
TECO motors are backed by technical teams that understand local standards and applications. These teams provide engineering support from selection through to commissioning.
Customers using TECO Flameproof Electric Motors bene� t from:
• Safer installations compliant with both Australian and International Ex standards
• Longer motor life through superior thermal and mechanical resilience
• Reduced downtime through local support and fast modi� cation service
• Simpli� ed wiring and installation with Ex de options
• Lower total cost of ownership attributed to e� cient, lowmaintenance operation
TECO o� ers proven, ready-to-install motor solutions backed by decades of experience and a commitment to engineering excellence in industries where reliability and safety can’t be compromised.
For more information, visit electricmotors.teco.com.au
When
it comes to industrial drive systems, e ciency
doesn’t come from a one-size-fits-all solution.
Generic, non-optimised gear motors are often the hidden culprits behind rising energy costs and underperforming equipment. This is evident across multiple sectors, including pumping, wastewater, heating, ventilation and air conditioning (HVAC), mining, and others.
Inconsistent � ow rates, excessive energy consumption, or unplanned downtime can occur when the wrong motor con� guration is chosen, quietly eroding operational performance. Whether it’s over-pumping due to a mismatch in load demands or poor pressure control in booster systems, using a generic drive solution often leads to energy waste and accelerated wear.
In wastewater, for instance, motors that aren’t speci� cally designed for continuous operation or handling varying � ow rates will experience e� ciency dips. HVAC systems often face similar issues; generic setups frequently lead to inconsistent air� ow, resulting in hot and cold spots throughout a building.
Recognising the speci� c needs of each worksite and making con� guration simple is exactly why SEW-EURODRIVE
is a leader in the gear motor space. Multiple ranges of gear units and motors have been designed with speci� c e� ciency and performance requirements for the pumping industry.
The ranges that best exemplify this dedication are the R/RX helical gear units and DRN series motors. These solutions are designed to meet the exact needs of any operation, from moving water through a treatment plant and powering conveyor systems in a mining operation to keeping critical HVAC systems running, all without compromising performance.
SEW-EURODRIVE’s R/RX helical gear units are particularly well-suited for pump-driven systems that require reliable torque and speed control. The singlestage RX series o�ers high output speeds up to 830 Nm, ideal for fast, continuous �ow applications such as booster or circulation pumps. The multi-stage R series, with its �nely stepped gear ratios reaching up to i = 289.74 (or i = 27,001 for double gear units), excels in more demanding systems, such as sludge pumps or multi-stage processing lines,
where torque consistency and durability are critical.
With 15 available sizes, these gear units strike the perfect balance between power and space e� ciency. Additionally, the modular design enables easy con� guration of units for speci� c pump applications, thereby reducing downtime and maintaining overall operating costs.
Energy e� ciency without compromise When it comes to energy e� ciency, the DRN series motors are best in class. With power ratings from 0.09 kW to 355 kW, these motors cover a wide power spectrum and meet the globally recognised e� ciency class of IE3. This
The gear ratio, or the total transmission ratio, is the angular speed of the � rst driving gear divided by the angular speed of the last driven gear of a gear train. The use of i is a convention that has been developed over many years for di� erent industries.
The range of gear motor solutions from SEW-EURODRIVE ensure that almost any industry can benefit. Image: SEW-EURODRIVE
means you can meet strict energysaving regulations without sacri� cing performance, especially in continuous operation settings.
With its S1-rated continuous duty classi�cation, the DRN motor delivers consistent output under full load conditions, making it particularly wellsuited for critical pump systems that can’t a�ord downtime or �uctuating �ow rates.
In chemical dosing and booster pump systems where � ow accuracy is critical, the DRN motors o� er inverter compatibility and integrated encoder feedback, helping operators maintain precise pressure control and avoid costly over-pumping or underdosing.
One of the standout features of the DRN series is the cost-optimised built-in encoder. Traditionally, encoders that provide speed and position feedback are mounted externally, requiring specialised shafts and brackets that add cost and complexity. SEWEURODRIVE’s approach integrates the encoder directly within the motor, eliminating the need for additional components and maintaining a compact design.
Built for � exibility and future-proo� ng
The DRN series also o� ers exceptional � exibility. With multiple pole con� gurations (2, 4, 6, or 8-pole) and support for continuous, inverter, and decentralised operation, these motors can adapt to a wide range of industrial needs.
The DRN Global Motor also meets the world’s most demanding e� ciency standards. No region-speci� c, aftermarket modi� cations will be needed when engaging with SEW- EURODRIVE.
For businesses seeking to streamline operations, lower energy costs, and minimise downtime, SEWEURODRIVE’s R/RX helical gear units and DRN series motors provide an innovative, adaptable solution. By configuring drive systems to match exact needs, businesses can achieve maximum efficiency without compromise, a critical advantage in today’s fast-paced industrial world.
For more information, visit sew-eurodrive.com.au
Replacing a part is not always the best solution. One company is providing a unique coating solution that can extend the life of pumps.
When a pump fails in a utility plant, the clock starts ticking on downtime, budget overruns, and operational headaches. But what if the solution isn’t a replacement? What if the right coating system could rewind the wear, rebuild the performance, and reset the clock?
Welcome to the world of rotating equipment rebuilds, where polymerceramic coatings transform the maintenance of asset-intensive industries. At the forefront is Chesterton’s ARC coating technology, designed to rescue, reinforce, and futureproof pumps and fans in harsh conditions.
From scrapyard to service: A new rebuild philosophy
The legacy mindset for degraded pumps or fan housings was simple: replace worn metal. However, this incurs costs, delays, and repetitive problems.
Today’s method is smarter. Coating rebuilds restore structural integrity, reclaim hydraulic e� ciency, and o� er greater resistance than the original design. It’s not just about running old assets, it’s about improving them.
Where hydraulics meet high performance
Let’s start with ARC 858. This coating isn’t just tough, it’s smart tough. Formulated to smooth internal surfaces of pumps and � ow equipment, it reduces turbulence, enhances � ow, and resists erosive wear from suspended solids or cavitation.
Maintenance teams use ARC 858 to resurface volutes, impellers, and casings, where micro-erosion a� ects performance. Operators experience immediate e� ciency improvements, achieving up to seven per cent energy savings and signi� cant extensions in mean time between failures (MTBF). In environments where reliability equals revenue, such metrics are crucial.
But what about the equipment that looks too far gone?
The ARC BX series o� ers heavy-duty rebuild composites to quickly and permanently replace lost metal. Whether volutes are corroded or fan blades eroded, BX coatings � ll, reinforce, and restore the geometry for safe operation. Rather than new parts, teams adopt a new mindset: restore and strengthen with a material that � rmly bonds and lasts longer than welded overlays or epoxy � llers.
Ready for the worst case scenario
Pumps handling abrasive slurries or aggressive chemicals often require coatings with high wear resistance. In one mining application, a tailings pump lost more than 12 millimetres of material in six months. A repair using ARC MX1, BX2, and a topcoat of ARC 855 extended the pump’s service life to more than 12 months. Repairs were minimal, with pumps returned to service within 72 hours, resulting in annual savings of approximately $13,700 per unit.
More than a � x: Engineering for reliability
ARC coatings rede� ne asset management, replacing reactive patchwork with engineered resilience. When pumps and fans utilise ARC technologies, it’s a strategic upgradetransforming worn components into high-performance assets for today’s industrial challenges.
This isn’t just a repair. It’s a redesign, with reliability in mind.
For more information, visit chesterton.com or email enquiries_apac@chesterton.com
Predict. Prevent. Perform. Stop unplanned downtime before it starts! The Chesterton Connect™ System empowers you with real-time predictive maintenance, optimising equipment performance and keeping your operations running smoothly.
Anytime, Anywhere Monitoring – Access critical pump health data straight from your smartphone, tablet, or computer with our cutting-edge IIoT technology.
Easy Setup. Instant Insights. Maximum Efficiency. Choose from preconfigured solutions tailored to your needs and take control of your equipment’s future today.
Get Started Now!
chesterton.com
chestertoncustomseal.com.au
While cooling might be one ma er for manufacturing, sustainability also comes into play. Image: Grundfos
Cooling is a critical process in industrial production, but it is o en operating ine ciently. With so much potential available, many manufacturers want to achieve higher cooling performance and control.
As the demand for industrial production grows globally, so too is the demand for cooling. In almost every industrial facility, ensuring the right temperature for machines and processes is essential to production e� ciency, reliability, and quality.
But industrial cooling is often controlled without considering the actual load. Many of these applications are operated at full capacity, leading to high operating costs since they can’t adapt to changing conditions. This means there’s currently a huge potential to optimise today’s cooling processes and ensure they’re ready for the future industrial landscape.
Furthermore, adopting advanced technologies and intelligent monitoring solutions can transform traditional cooling systems into adaptive ones. By leveraging data analytics and IoT integration, manufacturers can gain real-time insights into cooling demands and adjust operations accordingly.
This proactive approach not only enhances energy e� ciency but also extends the lifespan of cooling equipment, ultimately resulting in lower maintenance costs and increased sustainability. In this way, businesses can not only meet current demands but also position themselves advantageously for future challenges in the industrial sector.
To help industrial manufacturers realise this hidden potential, Danish company
Grundfos has several intelligent solutions as part of its Grundfos iSOLUTIONS portfolio. As one of the world’s leading pump manufacturers and solution providers, it helps industrial customers take complete control of their cooling systems, improve operational e� ciency, and achieve signi� cant savings.
With built-in pump functionalities and variable-speed controls, these intelligent solutions enable cooling systems to operate more optimally and reliably, ensuring a more effective process of cooling and heat removal in industrial production. Ultimately, this means greater energy and water savings, as well as prolonged service intervals, resulting in lower operating costs.
Variable speed control from Grundfos enables pumps to adjust their speed according to the required flow, ensuring a constant and stable cooling loop temperature. This helps reduce energy significantly. Additionally, Grundfos iSOLUTIONS allows components like control valves to be removed. With cloud-based connectivity and condition monitoring, critical system information is available to help reduce unplanned production stops.
Furthermore, Grundfos is committed to sustainability and innovation, actively seeking to reduce the environmental impact of industrial processes. By integrating advanced
data analytics and smart technology, these solutions not only optimise resource use but also contribute to a greener future for industries across Australia. With a focus on collaboration with local partners, Grundfos aims to tailor its offerings to the unique needs of the Australian market, ensuring that its customers can fully leverage the benefits of cutting-edge pumping technology.
With full control of their cooling systems, industrial companies not only have the potential to reduce energy use by up to 70 per cent, but also achieve operational expenditure savings of up to 30 per cent. It’s this kind of potential that Grundfos helped a United Kingdom packaging manufacturer realise in its cooling application as part of a retro� tting project.
Grundfos delivered an intelligent pump system solution that signi� cantly improved process operation and operating costs. The result is that the manufacturer saves 52 per cent in energy and $27,189 per year in operational expenditure.
For industrial manufacturers aiming to enhance cooling performance, reliability, operational e� ciency, and system control, Grundfos iSOLUTION o� ers a viable solution.
For more information, visit grundfos.com/au
E cient irrigation systems in Victoria are driving smarter water use with matched pump and engine packages tailored for agriculture.
In Victoria’s farming regions, water is a critical asset, both scarce and essential. As growers seek to improve productivity while cutting costs, irrigation systems powered by matched pump and engine packages are gaining traction.
A collaboration between Industrial Power Systems (Volvo Penta), Pioneer Pump (Franklin Electric), and Cobram Pumping & Irrigation is helping Victorian producers streamline operations and use water more e� ectively.
Engineered for farm performance
Volvo Penta’s industrial diesel engines are well-suited to agricultural applications due to their durability, low fuel consumption, and ease of servicing.
“Volvo Penta engines are reliable, e� cient and designed for a range of farming needs,” Mick McGee from Industrial Power Systems, distributor for Volvo Penta, said.
“They’re adaptable across irrigation systems, with features like electronic controls, advanced fuel injection and simpli� ed maintenance.”
For farmers in regional Victoria, having strong after-sales support is just as important as engine reliability.
“Our Derrimut base and dealership network across Victoria means fast access to servicing, repairs and parts,” McGee said. “When irrigation downtime isn’t an option, that support really matters.”
Pumps built to speci� cation
Pioneer Pump pairs its centrifugal pumps with Volvo Penta engines to create high-performance irrigation packages suited to varied terrain and � ow requirements.
Together, they handle high � ow rates and head pressures with con� dence, according to Zac Bosnar from Pioneer Pump.
“Our builds are tailored to duty requirements, and our team draws on over 140 years of combined experience,” he said.
Based in Sunshine West, the Australian operations are geared for fast turnaround. With 200 pump ends in stock and a large assembly area,
the company delivers custom-built systems quickly.
“We pride ourselves on � exibility – from trailers to skids, diesel sets to stainless-steel builds,” Bosnar said.
Field-tested irrigation solutions
For irrigation specialists like Cobram Pumping & Irrigation, proper system matching is crucial to achieving water e� ciency.
“When pumps and motors are selected for the right pressure and � ow, it reduces waste and energy use,” General Manager Brenton Harrison said. “That’s crucial for automated systems like centre pivots.”
Farmers upgrading their irrigation systems are looking for more than just performance; they want reliability and lower costs over time.
“We work closely with growers to assess their needs and recommend solutions that � t,” Harrison said. “It’s about long-term results, not shortterm savings.”
Volvo Penta-powered pump systems have been praised for their consistent
output, fuel e� ciency, and compact design, which makes � eld installation easier. They’ve been described as reliable in tough conditions and simple to maintain.
“The number one question we get from our clients is always around the back-up service and maintenance requirements,” Harrison said. “On-site back-up service for our clients is generally expected within 24 hours if we can’t � x it over the phone.”
A uni� ed approach to irrigation
All three companies emphasised that collaboration is the di� erence maker.
“Working together ensures every system component supports the others,” IPS said. “That means better uptime, lower running costs and better yields.”
For Cobram Pumping & Irrigation, it’s about trust in both people and products.
“Volvo Penta, Pioneer Pump and our team all bring something valuable,” they said. “When we align on goals, the farmer wins.”
For more information, visit your local dealer online.
In the demanding world of mining, where operational reliability and e ciency are vital, the choice of pumping technology can significantly impact overall performance and sustainability.
FELUWA MULTISAFE® pumps have established themselves as a benchmark for robust, energye� cient, and low-maintenance pumping solutions, particularly suited for challenging mining applications such as tailings disposal, concentrate transport, and autoclave feeding.
The management of tailings and ash is a critical task that demands durable and highly e� cient pumping systems. FELUWA MULTISAFE® pumps rise to the occasion with a design focused on reliability and sustainability. Thanks to their high e� ciency, they operate with low energy costs, directly contributing to reduced operating costs.
One of the standout features of FELUWA pumps is their double-hose diaphragm design, which ensures complete separation between the wetted parts and the drive end. This con� guration not only prevents crosscontamination but also enhances safety and prolongs the system’s longevity. Furthermore, the pumps are capable of
When it comes to solids-laden fluids, FELUWA has a solution focused on reliability and sustainability. Images: FELUWA
handling � uids with a high concentration of solids, which minimises water usage, presenting a key advantage in arid mining regions or operations aiming to lower their environmental footprint. Their exceptional wear resistance also results in shorter downtimes and less frequent maintenance interventions.
Long-distance transport of concentrates in mining operations presents unique challenges, including wear, increased energy consumption, and the requirement for consistent � ow. FELUWA’s solution excels in these scenarios, delivering energy-e� cient pumping with superior reliability. The pump’s ability to handle high solids content enables a signi� cant reduction in water consumption, an essential bene� t in modern, eco-conscious mining operations.
Managing tailings disposal is an essential part of the license conditions mining companies must follow.
hose diaphragms and valves allows for adaptation to a broad range of corrosive and abrasive media. Combined with the hermetically sealed separation of the wet and drive ends, the system ensures process safety under the most challenging conditions.
The robustness of FELUWA MULTISAFE® pumps ensures maximum availability. The wear-resistant construction signi� cantly extends service life, minimising unexpected breakdowns and optimising productivity. By reliably separating the medium from the drive end, the pump provides additional protection and durability, key in long-haul concentrate pipelines where access can be limited.
Superior autoclave feeding
Feeding autoclaves and digestors with abrasive, aggressive, and solids-laden � uids requires a pump that can withstand extreme chemical and mechanical stress. FELUWA MULTISAFE® pumps meet these demands head-on with a compact, intelligent design that reduces the number of wear parts to a minimum. This simpli� cation results in maximum system availability and easier maintenance planning.
The wide selection of materials for
FELUWA was recently chosen to supply the Autoclave Feed pumps for the Hemi Gold project, a low-cost, long-life, large-scale gold development project currently under development in Western Australia. The pumps to be provided are four TGK 200 - 3 DS 100 pumps. These are triplex (3-head), single-acting, double-hose diaphragm pumps, capable of operating up to 90 cubic metres per hour (m³/hr) at 35 Bar.
FELUWA MULTISAFE® pumps o� er a unique combination of reliability, energy e� ciency, and adaptability that makes them ideal for a range of mining applications. Whether dealing with tailings, concentrates, or autoclave feed streams, these pumps are engineered to minimise downtime, reduce environmental impact, and ensure longterm operational excellence. For mining companies striving for sustainability and performance, FELUWA delivers technology that meets and exceeds expectations.
For more information, visit feluwa.com
SEW-EURODRIVE‘s Quality Gearmotor Range
Local service and assembly backed by a global network of expertise.
Inherent to their modular design, our range of gearmotors can be individually assembled according to the required speed and torque ranges, spatial constraints, and ambient conditions. They offer a unique and finely graduated power range and the best economic prerequisites to face any drive challenge across many applications industries.
Gearmotors from SEW- E URODRIVE are broken down into the following categories:
Standard gearmotors
• Servo gearmotors
sew-eurodrive.com.au
Variable-speed gearmotors
• Stainless steel gearmotors
• Explosion-proof gearmotors
As the water and wastewater industries seek smarter solutions around energy use and sustainability, a new variable speed drive enters the space to make a di erence.
In the ever-evolving world of water and wastewater management, e� ciency, reliability, and sustainability are non-negotiable. As the industry seeks innovations and solutions to optimise energy use and process control, the WEG CFW900 Variable Speed Drive (VSD) emerges as a game changer. Designed with advanced features and intuitive control, the CFW900 is ideally suited to meet the complex demands of modern pumping applications.
The WEG CFW900 VSD delivers robust connectivity designed to meet the demanding needs of the water and wastewater industry. With native support for key industrial communication protocols like Ethernet/ IP, Modbus TCP, and PROFINET, it enables seamless integration with Supervisory Control and Data Acquisition (SCADA) systems, programmable logic controllers (PLCs), and remote telemetry units (RTUs), ensuring real-time monitoring and control of pumps, blowers, and treatment processes. With built-in support for Message Queuing Telemetry Transport (MQTT),
Having the right variable speed drive (VSD) is one important step in optimising water and wastewater treatment operations. Image: WEG
a lightweight messaging protocol optimised for IoT applications, this allows the CFW900 to securely and e� ciently transmit real-time data from � eld devices directly to cloud platforms or centralised monitoring systems, enabling more intelligent decisionmaking and remote asset management. For the water and wastewater industry, this means enhanced visibility into system performance across dispersed sites, faster response times to operational issues, and the ability to implement predictive maintenance strategies. With MQTT and IoT connectivity, the CFW900 transforms traditional drives into intelligent, networked assets – paving the way for digital transformation and smarter infrastructure.
Energy e� ciency and cost savings
One of the most signi� cant bene� ts of implementing the CFW900 in water and wastewater facilities is the energy savings it provides. Pumps account for a large portion of energy consumption in treatment plants. By running motors only at the speed required for the task, the CFW900 can reduce energy usage by up to 50 per cent compared to constantspeed operations.
Reinforcing energy e� ciency, the CFW900 is compatible with a wide range of motor technologies, including induction, permanent magnet (PM), and synchronous reluctance motors. This � exibility enables operators to select the most energy-e� cient motor for each application, thereby maximising performance while minimising power consumption.
Smart control features, such as PID (proportional-integral-derivative) control loops and sleep/wake functions, adjust pump performance based on realtime system needs. Over time, these features not only reduce operational costs but also contribute to a plant’s environmental sustainability goals.
The CFW900 o� ers predictive maintenance capabilities by continuously monitoring motor performance and drive health. Operators are alerted to issues such as bearing wear, cavitation, or seal failure before they become critical, allowing for planned interventions rather than costly emergency repairs.
The drive’s user-friendly HMI (HumanMachine Interface) and optional WEG Motor Scan and WEG DriveScan app provide real-time insights directly to smartphones or tablets, further simplifying maintenance work� ows.
As water and wastewater infrastructure continues to age and expand, the need for intelligent, e� cient, and resilient motor control solutions becomes more pressing.
The WEG CFW900 Variable Speed Drive o� ers a comprehensive solution, blending cutting-edge technology with user-centric design.
For utilities and operators seeking to boost performance, reduce costs, and future-proof their systems, the CFW900 is a strategic investment in smarter, more sustainable water management.
For more information, visit weg.net
In the ever-evolving landscape of wastewater management, e� ciency, durability, and reliability are paramount. At the forefront of this essential industry stands Roto Pumps Australia, a branch of the globally recognised Roto Pumps Ltd, renowned for its innovation in progressive cavity (PC) and twin screw pump technologies. Since establishing its presence in Australia, Roto Pumps has been instrumental in delivering high-performance solutions speci� cally engineered for the complexities of wastewater applications.
A proven legacy with a local focus Roto Pumps brings more than 50 years of global expertise in positive displacement pump manufacturing to Australia, with local operations strategically headquartered to serve the unique needs of municipal and industrial wastewater sectors. From sludge transfer to dewatering and chemical dosing, Roto’s progressive cavity pumps are trusted for their ability to handle viscous, abrasive, and shear-sensitive media – key challenges in wastewater processing.
“Our goal in Australia has always been clear,” says a spokesperson for Roto Pumps Australia. “Deliver engineered pumping solutions that reduce downtime, lower maintenance costs, and increase system e� ciency.”
Key features of Roto progressive cavity pumps
• Non-clogging design for high solid content
• Steady, pulsation-free � ow
• Low NPSHr (Net Positive Suction Head Required) – suitable for suction lift
• Compact footprint options for retro� ts
• High abrasion resistance for extended lifespan
Engineered for wastewater challenges
Roto’s progressive cavity pumps are purpose-built to tackle the toughest wastewater duties, featuring a design that provides non-pulsating � ow, low shear pumping, and precise dosing capabilities. These pumps are ideal for applications such as thickened sludge transfer, dewatering feed systems, scum and fats, oils and grease (FOG) handling, polyelectrolyte and chemical dosing, as well as digester recirculation.
The pumps feature rugged construction, high-wear-resistant components, and modular assemblies that allow for fast and economical repairs. Many models are available in vertical, hopper, and open-throat con� gurations, essential for applications with variable solid contents.
Local inventory and rapid support
One of Roto Pumps Australia’s key advantages is its local inventory and service support, which reduces lead times and enhances operational uptime for utilities and contractors. The company stocks a wide range of pump models and spare parts in Australia, ensuring quick turnaround for urgent
Progressive cavity pumps are vital for wastewater management. Image: bilanol/stock.adobe.com
replacements and refurbishments. Additionally, Roto provides custom engineering support for retro� ts, enabling plants to modernise outdated systems with minimal infrastructure modi� cations.
As Australia continues to invest in sustainable infrastructure, Roto Pumps is aligned with these objectives by o� ering energy-e� cient systems, long pump life cycles, and reduced maintenance footprints. The company’s focus on Total Cost of Ownership (TCO) appeals to municipal and industrial operators seeking long-term value in an increasingly cost-conscious market.
Looking ahead
With a robust portfolio, a proven track record, and a growing footprint in Australia, Roto Pumps is wellpositioned to remain a key partner in the wastewater industry’s pursuit of operational excellence and environmental responsibility.
For more information, visit: www.rotopumps.com.au
• Built on Maintenance in Place design platform for quick removal & maintenance of internal rotating parts.
• Equipped with Wear Compensation Stator for significantly extended stator life.
Smart air injection technology is helping Australia’s food and beverage sector reduce waste handling costs, lower emissions, and meet stringent sustainability targets.
As sustainability and coste� ciency become critical priorities for Australian food and beverage producers, SEEPEX, a global leader in progressive cavity pump technology, o� ers a transformative solution: Smart Air Injection (SAI). Designed to modernise food waste handling, SAI is a cost-e� ective, energy-e� cient and clean alternative to traditional systems, helping the industry meet evolving environmental and operational demands.
Tackling common industry challenges Food and beverage facilities across Australia face increasing pressure to reduce waste, lower energy consumption, and enhance workplace safety. Yet many still rely on outdated mechanical conveyors to transport by-products. These machines are expensive, maintenance-intensive systems that are poorly suited to modern production layouts, especially those with long distances, elevation changes, or tight space constraints.
SAI replaces these legacy systems with a compact, low-maintenance solution. Its closed piping design eliminates open handling of food waste, reducing odours, safety risks and the potential for contamination. This makes it valuable for operations where cleanliness and process integrity are essential.
Flexible transport of food waste over long distances
SAI is engineered to handle semi-solid and high-viscosity by-products such as co� ee grounds, tea leaves, and mustard husks. It combines a progressive cavity pump with controlled bursts of compressed air to transport these materials e� ciently through closed pipelines. The system reliably moves them over long distances – even around bends and up inclines –without the need for large, costly mechanical conveyors. Its low-pressure pipeline reduces installation complexity and energy use, helping food and beverage producers cut costs and minimise environmental
Strong return on investment
impact. The system also supports oilfree compressors, which are crucial for facilities that repurpose by-products, such as animal feed.
SAI delivers a strong business case for Australian manufacturers. Initial investment costs are competitive, and the system’s robust construction and low-wear parts result in long service life and reduced downtime. Combined with minimal maintenance needs, this enables a quick return on investment.
SEEPEX’s Rotor Joint Access (RJA) and Drive Joint Access (DJA) technologies enable fast and straightforward routine service. With RJA, operators can access the rotor joint by simply sliding the pump casing. There is no need to dismantle discharge pipework or stators. DJA provides quick access to the drive-side joint, enabling the fast replacement of coupling rods and mechanical seals without the need to remove hoppers. These features save time and lower operating costs.
Supporting sustainable production
In line with Australia’s growing focus on sustainable manufacturing and circular economy principles, SAI helps reduce the use of process water and cuts energy consumption compared to mechanical systems. The importance of sustainable practices in the manufacturing sector is increasing as industries strive to meet environmental goals and comply with stringent regulations.
By implementing SAI solutions, producers not only enhance their operational e� ciency but also contribute to the preservation of natural resources. For producers seeking to reduce their carbon footprint,
Pumping out crushed grapeskins is just one possible use for the SEEPEX Smart Air Injection systems. Image: Halfpoint/stock.adobe.com
SAI o� ers a compelling option. Moreover, its innovative technology is designed to seamlessly integrate into existing operations without signi� cant disruption.
In some cases, its energy e� ciency may even qualify for government or local sustainability incentives. This not only enhances economic viability but also reinforces the commitment to sustainable development, enabling businesses to remain competitive in the green economy.
Local relevance: Ideal for Australia’s food and beverage sector
Australia is well-positioned to bene� t from SAI’s capabilities due to its large geographical distances, high standards of cleanliness, and strict workplace safety regulations. The system is particularly suited for key sectors, such as plant-based food production, meat processing, and condiments manufacturing, which have experienced unprecedented growth in recent years.
“Food and beverage producers in Germany are already seeing the bene� ts of Smart Air Injection,” said Peter Vila, Managing Director of SEEPEX Australia.
“This includes specialty processors like
SEEPEX’s Easy Maintenance features RJA and DJA, which allows quick access to both joints, making routine service fast and simple. Images: SEEPEX
ready-to-drink co� ee producers, tea blenders and mustard manufacturers, who ultimately need e� cient solutions for managing waste.”
The integration of Smart Air Injection technology is expected to play a crucial role in enhancing production e� ciency and reducing waste across the food and beverage sector. As companies become more cognizant of their environmental impact, utilising advanced technologies such as SAI can help streamline operations while complying with Australia’s strict food safety standards. By embracing these innovative solutions, businesses not only maximise their pro� t margins but also contribute to a more sustainable future for the industry.
The Australian government is also incentivising investments in cleaner technologies, which will facilitate even greater adoption of systems like SAI in the food and beverage space.
A European mustard manufacturer struggling with workplace irritation caused by pungent vapours turned to SEEPEX for a solution. Its previous system failed to control mustard oil
emissions, leading to discomfort for sta� and high maintenance costs.
By installing SAI, they enclosed the transport of mustard husks in a sealed pipeline, eliminating the release of vapours into the workplace. This improvement in air quality and employee comfort was achieved while streamlining safety protocols and reducing the need for extraction systems. Operational costs dropped, and food waste was managed more e� ciently – all without compromising cleanliness or production speed.
Tailored to your process
SEEPEX specialists are available for on-site assessments in Australia to determine how SAI can be tailored to meet the individual needs of each plant.
“Smart Air Injection from SEEPEX o� ers a modern, energy-e� cient and clean alternative for handling food waste,” said Vila. “Whether the goal is to reduce costs, improve safety or enhance sustainability, SAI delivers practical bene� ts for today’s competitive food and beverage environment.”
For more information, visit seepex.com
Increased safety
Reduced costs
Longer service-life
Efficiently transport semi-solid and highly viscous food waste with lower energy consumption, minimal maintenance and enhanced safety. SEEPEX Smart Air Injection (SAI) transports by-products over long distances through a closed piping system, eliminating spillages, odors and safety risks.
YOUR BENEFITS WITH SAI FOOD WASTE
Saves energy and reduces operating costs
Easy maintenance features minimize downtime
Enclosed pipework prevents spillages and eliminates unpleasant odors
Easily transports food waste over long distances and elevation changes
Low-pressure operation ensures longer component service life
Glenn Evans from the Australian Refrigeration Council (ARC) highlights the importance of sustainability and the path to net zero via the installation of heat pumps. What does this mean for the industry?
Australia’s path to a net zero future isn’t just about ambition – it’s about action. And much of that action is already happening in our homes, through the adoption of cleaner, smarter technologies like hot water heat pump systems.
The recent federal election further underscored public backing for sustainability and climate-conscious solutions. In response, the sector is stepping up to deliver practical, scalable technologies that can accelerate our transition to net zero by 2050.
Among the most promising solutions gaining momentum is the hot water heat pump. Fast becoming a popular alternative to gas, they’re energy e� cient, climate-friendly, and increasingly backed by government incentives. But the speed of this uptake comes with a responsibility: to ensure these systems are installed safely, professionally, and in line with environmental standards.
A key detail that’s often overlooked is that many of these hot water heat pumps, such as split systems, use refrigerants, and if not properly handled, can be harmful to both people and the environment. That means installing or maintaining these units isn’t just general plumbing or mechanical work. It requires specialist knowledge and skill-set.
At the Australian Refrigeration Council (ARC), we’ve long said that working on equipment with controlled refrigerant must be treated with care, backed by formal training and licensing. That’s why the national ARCTick licence exists. This licensing framework is in place to make sure technicians working with refrigerants have the right training and credentials. Without it, there’s a risk that poor installation practices could lead to leaks, safety issues, or environmental harm.
We were pleased to see the recent announcement from the Victorian State Electricity Commission and the Victorian Government expanding their
Having properly licensed people working on hot water heat pumps is vital for their e ective use in the home. Images: Australian Refrigeration Council
all-electric housing pilot into Maroondah and the Yarra Ranges. Programs like this demonstrate strong leadership by promoting energy-e� cient homes and driving the adoption of sustainable technologies.
But as this transition accelerates, so too does the need for quali� ed professionals. Any system containing controlled refrigerants, like many heat pump units, must, by law, be installed and serviced by a licensed technician under the Ozone Protection and Synthetic Greenhouse Gas Management Act 1989. It’s not just good practice; it’s a legal requirement.
This ensures three critical things: systems are installed to a compliant standard, refrigerants are managed safely, and households are protected from the risks of substandard work.
By recognising refrigeration and air conditioning as a specialised vocation and maintaining high standards through licensing, we strengthen the
Glenn Evans, CEO of the Australian Refrigeration Council, provides his insights on the pathway to net zero.
reputation of the sector, the safety, and environmental performance of Australian homes.
The move to a net-zero economy won’t be achieved by technology alone. It will be achieved by the skilled people who bring that technology to life. Let’s make sure they have the support, training, and recognition they need to keep doing it right.
From infrastructure to manufacturing, the 2025 Women in Industry Awards showcase excellence across technical, engineering and operational sectors.
growth with lasting sector impact. This blend of performance and purpose continues to shape the evolution of Australia’s infrastructure industries.
Engineering and energy sectors spotlight strategic innovation
The 2025 awards also recognised professionals working at the cutting edge of engineering and energy, sectors that underpin many of the pump industry’s core applications. Two recipients stood out for their ability to lead across complex technical environments.
Held in Melbourne on 19 June, the 2025 Women in Industry Awards celebrated achievement, leadership, and innovation across Australia’s industrial sectors. The gala night recognised professionals who are delivering results, solving complex challenges, and driving industry forward. For the pump sector, several winners stood out for their contributions to operational excellence, infrastructure delivery, and strategic advancement across highly technical environments.
Tammy O’Connor named Woman of the Year
The night’s highest honour, Woman of the Year, was awarded to Tammy O’Connor, Managing Director of KingKira Group. Already the recipient of the Business Development Success
Award, O’Connor’s leadership has helped rede� ne operational standards in maintenance and contracting services across Western Australia.
With a background spanning on-ground operations to executive strategy, O’Connor has expanded KingKira into a respected Indigenousowned company serving major mining and infrastructure projects. Her business acumen is matched by a commitment to social procurement, particularly in creating employment pathways for Aboriginal people.
“I think it’s important that women live the industry,” O’Connor said. “I think we do things a lot di� erently, and it shows that we come from a maternal place and making all those changes.”
Her dual wins re� ect a leadership approach that combines commercial
Stacey Daniel, winner of the Excellence in Engineering award, is the Managing Director of Board Presence. Daniel has developed a reputation for her progress and advancement of the engineering leadership, innovation, careers, professional standards and skills. As a subject matter expert, she is often called upon to apply her engineering knowledge, insights and experiences for the bene� t of other engineers and the profession.
Suzanne Shipp, recognised with the Excellence in Energy award, oversees large-scale project delivery at APA Group, one of Australia’s major energy infrastructure organisations. She actively advocates for women’s advancement in the energy sector through mentoring, leadership development, creating inclusive cultures, and community engagement.
“I’m really excited to see how industry caters for women these days, and how you can have a much better balance, but not just for women, but for men, who are parents as well,” Shipp said.
“I do advocate for more engineers in board decision-making and how things happen at all sorts of levels. We must have people with technical skills around the table.”
Their contributions underscore the
importance of technical innovation in maintaining e� ciency, reliability, and long-term performance throughout the asset lifecycle.
Construction, transport, and mining professionals recognised Pumps play a crucial role in delivering water, wastewater, and transporting materials across Australia’s infrastructure networks. This year’s winners in construction, transport, and mining demonstrate the importance of sector expertise and operational leadership in delivering these outcomes.
Isolde Piet, awarded Excellence in Construction, plays a key role in the Suburban Connect alliance, part of the North East Link Program in Victoria. She is now leading the world’s � rst all-women Tunnel Boring Machine (TBM) crew, which is one of eight TBM crews that will dig the 16 kilometre twin tunnels on SRL East’s southern section between Cheltenham and Glen Waverley.
Kirryn Crossman, Principal Engineer at SMEC, was recognised with the Excellence in Transport award. Based in Queensland, Crossman has led multidisciplinary teams in delivering complex infrastructure projects, focusing on technical excellence and sustainability. She has played pivotal roles in the design and delivery of major transport infrastructure across Queensland, helping to shape safer, more sustainable, and community-focused transport systems.
“I love my job,” Piet said. “I’d love it to be extended to the whole audience, and to the women in this country. It’s an awesome, awesome industry to be part of.”
In the mining sector, Becky May Felstead received the Excellence in Mining award for her leadership in mental health programs through Strong Minds, Strong Mines. Over the past year,
she visited more than 45 mine sites and spoke to over 20,000 workers, delivering over 300 talks. Her work focuses on improving mental health, preventing suicide, and creating respectful, inclusive workplaces.
Each winner represents a di� erent facet of infrastructure excellence, whether through project delivery, asset stewardship, or workforce wellbeing.
Manufacturing and industry advocacy awards highlight system-wide impact Excellence in manufacturing and advocacy was also recognised, with winners whose work contributes to national capabilities and long-term industry resilience.
Naomi Elliott, Chief Executive O� cer of Concept Labs, received the Excellence in Manufacturing award. As Co-Founder of Suncoast Biochem, Naomi is pioneering circular manufacturing by converting agricultural waste into highperformance, clean-label ingredients using solar-powered, biotechdriven processes.
“For me, manufacturing is not just about processes,” Elliot said. “It’s about culture, a culture where women can lead con� dently, where innovation is valuesled, and where success includes impact,
not just output. I’ve seen a powerful ripple e� ect that happens when women are supported, visible and generally empowered to lead.”
Eileen Breen, of NTEX, was recognised with the Industry Advocacy Award. As President of the Waste and Recycling Industry Association NT and cofounder of NTEX, she has championed circular economy opportunities through policy advocacy, industry education, and practical demonstration. Breen has contributed to national conversations around skills shortages, inclusion, and future workforce planning – issues that directly impact pump and infrastructure businesses across Australia.
Their achievements remind us that sector advancement is not just about technical systems. It also relies on forward-thinking leadership, capacitybuilding, and policy engagement.
From strategic infrastructure projects to energy system upgrades, the 2025 Women in Industry Awards showcased excellence in action. For the pump sector and its adjacent industries, these stories highlight the importance of leadership grounded in knowledge, discipline, and collaboration. Technical strength, when paired with clear vision and practical execution, delivers results that bene� t the entire sector.
Pumps in mining are critical to e cient water use, safety, and sustainability across Western Australia’s booming resources sector.
Western Australia’s mining sector is powering forward, driven by a global demand for critical minerals and a growing emphasis on environmental responsibility. At the heart of this momentum lies an oftenunderappreciated force – pumps.
From managing groundwater and dust control to enabling smart infrastructure, pumps and pumping systems are crucial for maintaining safe, sustainable, and productive operations. As the 2025 WA Mining Conference and Exhibition approaches, attention is turning to the technologies and partnerships that will de� ne the next era of mining e� ciency.
Pumps in mining deliver safety and sustainability
Western Australia is home to some of the world’s most advanced and sustainable mining operations. According to Mines and Petroleum Minister David Michael, this is no accident.
“Western Australia’s mining sector is
recognised globally as one of the most innovative and sustainable, underpinned by strong environmental regulations and high ethical standards,” he said.
Pumping systems are central to meeting those standards. In underground mines, dewatering systems play a vital role in maintaining safe conditions.
“Dewatering pump systems are also vital for maintaining safe underground mining conditions by preventing � ooding, which is a major safety hazard,” Michael said.
Beyond safety, the industry is increasingly focused on sustainable water use. The Department of Water and Environmental Regulation (DWER) has developed Water in Mining guidelines that emphasise the e� cient use of water, particularly in arid zones. These guidelines encourage miners to reduce waste, manage extraction volumes e� ectively, and utilise high-e� ciency pumping solutions.
The ability of pumps to support water recycling and reduce reliance on fresh supplies is gaining importance.
“Pumping systems also play an essential role in reducing environmental impact by supporting water recycling systems, minimising reliance on freshwater sources, and preventing loss through leaks or ine�ciencies,” Michael said.
Smart technology and collaborative innovation
New technologies are transforming the way water is managed across remote mining operations. From smart pumps that detect leaks to autonomous systems that minimise manual labour, innovation is helping Western Australia’s resources sector meet its environmental and safety targets.
“The use of autonomous technology, smart pumps, and digitally connected pumping systems o� ers signi� cant bene� ts, including removing people from hazardous roles, improving
The address from The Hon David Michael will be a highlight of the conference for many. Image: Prime Creative Media
the e� ciency of resource discovery, extraction, and processing, and reducing waste and environmental impact,” Michael said.
The State Government has made innovation in sustainable mining a priority, backing technologies that reduce energy use and support longterm environmental performance. In this environment, pump manufacturers and suppliers can play a strategic role, not just as equipment providers, but as collaborators in designing more e� ective systems.
“The State Government encourages the mining sector to collaborate with pump manufacturers by providing feedback to improve system e� ciency, performance, and safety,” Michael said. “This collaboration will drive innovation and design improvements, helping ensure pumping systems continue to support safe and e� cient mining operations across our state.”
Local suppliers bene�t from strategic engagement Western Australia’s economic diversi� cation strategy is creating new opportunities for small and medium enterprises across the supply chain. For pump manufacturers and distributors, the State Government’s Made in WA plan o� ers a clear incentive to invest in local capability and partnerships.
“Our plan will create opportunities for small to medium-sized suppliers, including those in the pump sector, to connect with industry,” Michael said.
One such opportunity is through the Western Australia Industry Link program, which supports Regional
state.
Hosted by the Department of Jobs, Tourism, Science and Innovation (JTSI), the forums help pump businesses understand government priorities, meet prospective clients, and explore ways to align their o� erings with emerging mining needs. This kind of targeted engagement positions Western Australia as not just a mineral-rich jurisdiction but a globally competitive hub for mining innovation, engineering, and advanced manufacturing.
Future-focused skills and conference opportunities
With demand for mining and equipment services on the rise, Western Australia
is investing in its workforce. The State Government has rolled out TAFE courses and industry training programs to prepare workers for the next generation of mining jobs, many of which will rely on data, digital systems, and clean technologies.
“Collaboration between mining companies and the pump industry to build local skills, provide training, and create long-term career opportunities will be key to the sustainable growth of the mining sector,” Michael said.
The WA Mining Conference and Exhibition, scheduled for 9-10 October 2025 at the Perth Convention & Exhibition Centre, will be an ideal forum to explore these themes. The event will feature cutting-edge products, technical sessions, and panels focused on mine site e� ciency, environmental, social and governance strategies, and digital transformation. For pump professionals, it o� ers a timely opportunity to engage with mining companies seeking sustainable water solutions and reliable suppliers.
Michael said the future of the sector would depend on these collaborations, new technologies, and the people who build and support them.
“The pump industry will continue to play an important role in Western Australia’s mining sector, and its ongoing innovation will help ensure our mining operations remain environmentally responsible, sustainable, safe, and globally competitive.”
For more information, visit waminingexpo.com.au
David Michael is looking forward to the return of the WA Mining Conference and Exhibition.
Image: Western Australia Department of Mines and Petroleum
The most prestigious awards for the Australian mining and
THE ICONIC ADELAIDE OVAL WEDNESDAY, 24 SEPTEMBER
See leading technologies on display at Asia Pacific’s International Mining Exhibition. Images: Prime Creative Media
Automation is transforming pump performance and maintenance in Australia’s mining industry. Asia Pacific’s International Mining Exhibition (AIMEX) 2025 o ers pump suppliers a vital opportunity to engage with mining leaders driving this change.
Mining is one of Australia’s most demanding industrial environments, with 24/7 operations, remote sites, and extreme process conditions. Pumps are at the heart of many critical mining applications, handling dewatering, slurry transport, tailings management, and water recycling across the country’s mines. Reliability and uptime are paramount, particularly as operators seek to extract greater value from every tonne of material moved and every litre of water managed.
Today, automation is revolutionising the design, monitoring, and maintenance of pumps. The integration
of digital sensors, predictive analytics, and IoT-connected systems is driving a shift away from reactive maintenance toward proactive, data-driven strategies. This not only reduces unplanned downtime but also improves energy e� ciency, extends equipment life, and supports safer operating environments.
The growing importance of automation will be a major focus at this year’s Asia-Paci� c’s International Mining Exhibition (AIMEX) 2025, taking place from 23–25 September at the Adelaide Showgrounds. The event will bring together Australia’s largest gathering of mining suppliers, engineers, and
decision-makers, providing a vital forum for pump and automation companies to demonstrate how their technologies can support the industry’s evolving needs.
For pump manufacturers, system integrators, and technology providers, AIMEX represents a strategic opportunity to showcase solutions that help mining operators automate their critical pumping infrastructure. With mining’s shift towards centralised monitoring, remote operation, and fully digitalised asset management, pumps are a natural part of the automation conversation. Exhibitors who can demonstrate clear value in this space will be well-positioned to engage
with the sector’s key in� uencers and procurement leaders.
“Automation is reshaping the mining sector and driving new levels of e� ciency, safety, and sustainability across core systems, including traditionally manual areas like pumps and � uid management,” General Manager of Events at Prime Creative Media, Siobhan Rocks, said. “At this year’s event, we’re proud to showcase the cutting-edge technologies and integrated solutions that are pushing the boundaries of what’s possible in modern mining.
“Visitors will see � rst-hand how automation is not just a future concept; it’s actually transforming operations right now,” Rocks said.
Connecting with mining’s decisionmakers at AIMEX 2025 AIMEX 2025 o� ers more than an exhibition � oor. It provides a direct channel to the people who are shaping mining’s technology landscape. For pump and automation companies, this means the opportunity to engage with senior engineering managers, asset owners, maintenance leaders, and procurement specialists from across Australia’s mining sector.
Held for the � rst time in South Australia, AIMEX 2025 re� ects the region’s growing leadership in mining innovation. Adelaide Showgrounds will host a range of new exhibition zones designed to spotlight transformative technologies. These include the dedicated Transformative Technology zone and the Research and Development Hub, where current projects and forward-thinking strategies are actively shaping the future of the industry.
Pumps and � uid management systems are a natural � t within these themes. Mining operators are increasingly seeking to integrate pumps into their broader digital ecosystems, with an emphasis on remote condition monitoring, advanced diagnostics, and automated control. The conference program, delivered in partnership with Australian Mining magazine, will further
highlight these trends, providing pump suppliers with valuable context and networking opportunities.
For exhibitors, AIMEX represents an unmatched platform to position their technologies within mining’s strategic automation agenda. It is also an opportunity to demonstrate how pumps can contribute to broader mining goals, including decarbonisation and energy e� ciency, as well as operational resilience and workforce safety.
“AIMEX continues to be a vital platform for connection and collaboration, giving automation providers and other solution specialists, including pump suppliers, direct access to the mining leaders driving procurement and operational decisions,” Rocks said. “It’s where real conversations happen, partnerships form, and innovations �nd their way into the �eld.”
The automation opportunity for pumps in mining
Automation is no longer an aspirational goal for Australia’s miners. It is fast becoming a standard approach to achieving operational excellence.
Pumps will play a crucial role in this shift, given their critical function across mining processes and their potential for intelligent integration.
Mining operators are investing in predictive analytics, AI-based performance modelling, and advanced vibration and temperature monitoring to better manage their pump � eets. This is helping reduce unplanned outages, optimise energy use, and minimise manual inspections. Automated pump systems are also central to enabling remote and centralised operations, which are increasingly important as mines extend into more isolated locations.
For pump suppliers, this creates both challenges and opportunities. Customers expect solutions that are no longer standalone. Pumps must now integrate seamlessly with SCADA platforms, IoT dashboards, and enterprise-level asset management systems. Meeting these expectations
Thousands are expected to flock to Adelaide Showgrounds for this event.
requires not only advanced pump design but also sophisticated control, data integration, and ongoing service capability.
AIMEX 2025 will provide pump companies with a vital opportunity to showcase their capabilities to a highly targeted mining audience. It also allows them to benchmark their o� erings against emerging market needs and foster new partnerships that will drive innovation in the years ahead.
Mining operators are under increasing pressure to boost e� ciency, reduce downtime, and improve safety, which Rocks said is driving a clear shift toward automated solutions across critical infrastructure.
“From advanced pumping systems to site-wide control technologies, we’re seeing strong demand for integrated automation that delivers real operational value,” she said.
“AIMEX provides a powerful platform for suppliers to showcase these innovations directly to the decisionmakers shaping the future of mining.”
Building partnerships for a smarter mining future
Automation will continue to shape the future of mining, with pumps playing a central role in enabling more reliable, e�cient, and sustainable operations. For pump suppliers and technology providers, success will increasingly depend on their ability to deliver smart, integrated solutions that align with the broader digital strategies of the mining industry.
AIMEX 2025 provides an unrivalled platform to build these partnerships. It o� ers pump companies the chance to connect with mining’s key decisionmakers, showcase innovation, and contribute to the development of smarter, more automated mining infrastructure.
For those serious about helping mining customers navigate the challenges and opportunities of automation and reliability, AIMEX is the event that cannot be missed.
“AIMEX plays a crucial role in fostering collaboration and sparking innovation within the mining sector,” Rocks said. “By bringing together industry leaders, technology providers, and solution experts, AIMEX creates an environment where new partnerships are forged and groundbreaking ideas come to life.”
Grab your tickets before it is too late at aimex.com.au/getinvolved
Mining pumps enhance safety, performance and reliability across Australia’s harshest mine sites, supporting the innovation recognised at the Prospect Awards.
Mining is an industry where performance and safety must go hand in hand. From the iron ore hubs of the Pilbara, to the coal operations of the Bowen Basin, and the copper mines of South Australia, smart equipment and operational excellence drive success. The Australian Mining Prospect Awards celebrate these achievements, recognising the innovation, safety and e� ciency that help Australian mines perform at their best.
Now in their 21st year, the Prospect Awards honour outstanding contributions across every segment of Australia’s mining industry. Categories range from Excellence in Mine Safety,
Innovative Mining Solution, and Outstanding Mine Performance, through to sustainability, community engagement and excellence in environmental management.
For companies, teams, and individuals making a di� erence on-site, the awards are an opportunity to be recognised among industry peers and leaders. Nominations are now open, and the organisers encourage mining companies, suppliers, and professionals to submit outstanding projects and achievements.
“We strongly support the awards and the chance they o� er to celebrate innovation and excellence in mining,” said Harry Singh, National Sales
Manager at Bon� glioli Transmission Australia, which is returning as an awards sponsor in 2025. “They shine a light on work that often happens behind the scenes but has a major impact on safety and performance.”
Why celebrating innovation matters
For Bon� glioli and other industry participants, the Australian Mining Prospect Awards o� er more than recognition. They provide a platform to showcase advances that improve the performance and safety of Australia’s mining sector.
Singh said Bon� glioli’s sponsorship of the Outstanding Mine Performance Award re� ects the company’s belief in
The gear motors manufactured by Bonfiglioli represent the company’s belief in ongoing innovation and collaboration.
Images: Bonfiglioli Transmission Australia
improvement mindset that underpins Australia’s global leadership in mining.
ongoing innovation and collaboration.
“We see � rst-hand how innovation makes a di� erence on mine sites,” Singh said. “When customers improve performance or extend equipment life, it bene� ts the whole industry.”
By supporting the awards, Bon� glioli is also helping to highlight the role suppliers and engineering partners play in advancing mining outcomes.
“Collaboration across the industry is essential,” Singh said. “Solutions don’t come from one company alone. The best results come when operators, suppliers and integrators work together.”
The awards also serve a wider purpose by promoting knowledgesharing and celebrating the continuous
“Innovation in mining is often e� cient and targeted,” Singh said. “It might be an equipment redesign that improves safety, a maintenance strategy that reduces downtime or a digital solution that gives operators new insights. The Prospect Awards provide a national platform to share those ideas and inspire further progress.”
For Bon� glioli, participating in the awards reinforces its commitment to contributing to a safer and more sustainable mining industry through engineering excellence and collaborative partnerships.
Call for nominations
Nominations for the 2025 Australian Mining Prospect Awards are now open. Mining companies, suppliers and professionals are encouraged to submit entries across the wide range of categories.
Full details and nomination criteria are available at prospectawards.com.au.
“Every year, the Prospect Awards showcase stories of innovation, resilience and leadership,” Singh said.
“We encourage anyone making a positive impact in mining to get involved and share their story.”
Entering the awards is also an opportunity for companies to re� ect on their achievements and the hard work of their teams. Many past winners and � nalists report that recognition at the Prospect Awards has boosted team morale, strengthened customer relationships and created valuable new opportunities within the sector.
“The awards are not just about products or technology,” Singh said.
“They also celebrate the people and partnerships driving innovation in mining. It is about recognising the engineers, technicians, operators and project teams whose dedication underpins industry success.”
With Australia’s mining industry continuing to face new challenges and opportunities, the Prospect Awards provide a national platform to recognise achievements that make mining safer, more innovative and more sustainable, one project at a time.
For more information, visit prospectawards.com.au/get-involved
Noted Russian-American engineer Igor Karassik once said that if all the technical papers wri en about NPSH and cavitation were laid end to end, they would not reach a conclusion. In this commentary, Ron Astall focuses on NPSH testing issues.
Testing a pump to determine Net Positive Suction Head Required (NPSHr) can be problematic, particularly if the NPSHr values are low. Read on to discover why the Test Engineer might be tearing their hair in frustration.
Background
Net Positive Suction Head (NPSH) is a key parameter in a pumping system, as it represents the margin above the liquid vapour pressure. It is a measure of how close the liquid is to vaporising (or boiling). If the liquid vaporises in the pump, it causes noisy, damaging cavitation, which must be avoided to ensure a reliable installation.
NPSHa is the available Net Positive Suction Head (NPSH) in the system. NPSHr is the NPSH required by the pump to avoid cavitation. In simple terms, we need the system NPSHa to exceed the pump NPSHr.
NPSHa is typically presented as the available NPSH at the pump inlet nozzle. However, NPSHa can be calculated at any point in a piping system, as shown in Fig. 1.
Wherever the local pressure drops below the vapour pressure, cavitation, or “� ashing,” will occur. Cavitation is typically considered a pump issue, but it can also occur in piping systems, valves, and � ttings. This will severely disrupt the � ow.
In the example above, NPSHa drops alarmingly at the highest point in the system. In this example, if the highest point exceeded 12.66m above the system inlet, vaporisation (boiling) would occur. This example is a static
case without � ow. With � ow in the system, friction losses and the e� ects of bends and � ttings will create additional losses and, potentially, vapour locking at the high points.
Testing to determine Pump NPSHr
Testing is ideally performed in a closed test loop, where the loop pressure (pump inlet pressure) is progressively reduced while maintaining a constant � ow rate. For each pump inlet pressure, the NPSHa is calculated from the measured suction pressure, corrected to absolute by adding atmospheric pressure, then deducting the liquid vapour pressure, and � nally converting to head units for plotting.
When the value of NPSHa is reduced su� ciently to cause a measurable e� ect, this benchmark value is noted as the NPSHr point for that speci� c � ow rate. Conventionally, the recommendations of the Hydraulic Institute for a three per cent head drop criterion are followed, as shown in Fig. 2 below. This method is repeated to obtain NPSHr points for � ows across the pump curve, creating a complete NPSHr curve versus � ow.
This approach is generally quite straightforward when demonstrating moderate and higher NPSHr values. So, when does the poor test engineer become more frustrated than a dog trying to bury a bone on a marble � oor?
When pump NPSHr is very low
When the value of pump NPSHr to be demonstrated is low, di�culties may arise in the test loop. A typical Test loop suitable for NPSH Testing is shown in Fig. 3.
A low NPSHa value at the pump inlet indicates a low NPSHa throughout the entire test loop, extending beyond the discharge throttling valve. For a typical cold-water test, an NPSHa value of two metres or less at the pump inlet indicates that the entire loop after the throttling valve will be at a vacuum of at least -80 kilopascals (kPa), which is equivalent to an absolute pressure of less than 22 kPa.
In high velocity areas in the test loop, the pressure will be even lower due to velocity head e� ects (Bernoulli’s Theorem). This can be a particular problem at the throttling valve outlet, where the � ow is constricted. Under these circumstances, vaporisation
(cavitation) at the throttling valve is a major issue, with severe surging as vapour pockets form and collapse in turn, particularly during high-� ow pump tests. Flow control will be challenging, and in some extreme cases, � ow can be lost entirely. The associated acceleration/deceleration heads involved with � ow surging will reduce the measured pump di� erential head and e� ciency.
Another less obvious problem when the test loop is operating below atmospheric pressure is the potential for air ingress through the mechanical seals. Conventional mechanical seals are not designed to withstand vacuum conditions in the seal chamber. They can experience the opening of the seal faces or even the dislodgement of the
outer face under negative pressure. This will allow air to seep into the suction side of the pump, resulting in associated disruptions to hydraulic performance.
For these reasons, it can be di� cult to demonstrate low values of pump NPSHr during performance testing. Although frowned on by most testing standards, using a suction throttling valve ahead of the pump can be a method to maintain higher test loop pressures. Using a suction side throttling valve may transfer the surging problem to the suction side.
When pump NPSHr is extremely low
In the oil, gas, and petrochemical sectors, vertical canned pumps (Fig. 4) may be necessary to handle applications where the available Net Positive Suction
Head (NPSH) is negligible or even zero. In these circumstances, it will not be practical to demonstrate pump NPSHr in a conventional works test scenario.
Where the margin between the customer’s site NPSHa and the pump’s predicted NPSHr is signi� cant, purchaser speci� cations normally waive the NPSH testing requirement based on this margin of safety. An alternative is to test the pump without the suction can by using a temporary hard-piped suction connection.
Past test experience with the same � rst-stage impeller hydraulics in conventional above-ground con� gurations will also be a valid guide.
Conclusion
NPSH testing can be time-consuming and has associated costs. If you have plenty of NPSHa in your process compared to the NPSHr of the pump, an NPSH test is probably not warranted. If NPSHa is low, NPSH testing is undoubtedly a good idea, but be aware of the di� culties and approach it with practicality.
is third part of our installation series, covers the basis of coupling alignment and the factors a ecting misalignment.
After the pumpset has been grouted in, the foundation bolts tightened, and the suction and delivery pipework fully installed the alignment of all couplings on the pumpset must be checked and if need be, corrected.
N.B., The manufacturer does align the pumpset before dispatch, but transportation and installation can cause the alignment of the pumpset to change.
If the driver has been supplied separately from the rest of the pumpset the driver is aligned after grouting the baseplate.
It is important to note that � exible couplings permit axial movement of both pump and driver shafts and also compensates for thermal expansion. Before beginning coupling alignment ensure that the power supply is isolated from the motor.
When aligning pumpsets it is normal for the pump not to be moved, any adjustment is made to the driver. For outdoor installations make sure extreme temperature do not adversely a� ect the alignment.
Typical Couplings
Notes:
1. Normally couplings do not need to be balanced for speeds up to 3600 rpm, however care must be taken to install correctly. When running at high speed, i.e., beyond 3600 rpm balancing is recommended.
2. Pin and bush couplings are designed
to reduce shock transmission to the bearings etc., and do not compensate for misalignment very well thus should be aligned to the same accuracy as solid couplings.
When checking a couplings alignment the following errors can be expected: Errors in angularity, Fig 2.2, the axis of the shafts are not collinear and intersect in the plane of the coupling faces.
Errors in eccentricity, Fig 2.3, the shafts are parallel but not concentric.
A combination of the above, Fig 2.4 under these circumstances the axis need not be parallel, and they may or may not intersect. By separating the errors of angularity and eccentricity and measuring them independently, the extent of the combination of errors can be determined and corrected. The axial movement of the pump and drive shafts should be measured. Appropriate allowance can be made for the clearance between the coupling faces.
Factors A� ecting Misalignment:
Apart from the actual misalignment factors, there are three external factors which need to be considered when aligning couplings and these are:
Pipe strain occurs when the pipework connected to the pump places an unnecessary load on the pump � anges such that it a� ects the alignment of the pumpset. This can occur if the suction and discharge piping � anges connecting to the pump are not correctly aligned with the appropriate pump � anges and the suction and discharge pipes and valves are not adequately supported adjacent to the pump � anges.
In addition, pipe strain can also cause de� ection of the baseplate particularly when unrestrained expansion joints are used.
It is recommended that prior to checking the pumpset alignment, after the coupling has been disconnected, that the pump � ange bolts be removed.
There will be no strain on the pump if the � ange bolts slide easily in and out of the bolt holes, otherwise, it will be necessary to � x the piping either by moving it or providing better support.
After the pipe strain has been eliminated it would be expected that when the alignment is checked there will be some misalignment.
The external force most commonly found during shaft alignment is soft foot. Soft foot, e.g., a rocking four legged table has a soft foot, is the improper contact between the foot of a pump or motor and the baseplate which supports it. It may be angular or parallel, but usually a combination of both, as shown below.
The main causes of soft foot are:
• The surfaces connecting the mounting feet and baseplate are not in the same plane.
• Deformed mounting feet.
• External forces as applied by pipework and/or brackets.
• Improper shimming or dirty feet.
• To many shims under the feet, a maximum of � ve should be used.
Soft foot should be checked for and corrected before starting the alignment of a pumpset.
Feet are shown in black where signi� cant movement has been noticed.
The another factor which causes equipment to move once aligned is thermal expansion.
In the case of pumps handling hot liquids this will be a factor as the pumpset is normally aligned when the pump is cold which means that when the pump warms to its operating temperature the alignment will change.
For example – A pump operating at 150 ⁰C with a cast iron casing, a distance of 250 mm from the pump centreline to the pump feet and ambient temperature of 20 ⁰C. Basis a coe� cient of thermal expansion of 0.000010 mm/mm/⁰C, for cast iron, the thermal expansion will be: = T (Change in temperature) x L (Length of material) x C (Coe� cient of linear expansion)
= (150-20) x250 x 0.000010
= 0.325 mm
As can be seen from this example the alignment of the pumpset will be out 0.325 mm when the pump warms to its operating temperature. It is therefore essential that:
a. Allowance for thermal expansion must be made when aligning the pumpset when cold.
b. Ensure the coupling connecting the pump to the driver can accept the change in alignment, normally a spacer type coupling is the most suitable.
It should be noted that if a pump has centreline mount feet then correction for thermal expansion is not required. This article has described the need for coupling alignment and the factors a� ecting coupling misalignment our � nal chapter in this series will cover the actual process of aligning couplings.
One way to get your alignment right. Image: chaimongkol/stock.adobe.com
If your pump is misaligned, the amount of lubrication will not help you. Image: Chatchaphat/stock.adobe.com
ASIA-PACIFIC’S INTERNATIONAL MINING EXHIBITION
23-25 SEPTEMBER 2025
Adelaide Showground, South Australia
Register to attend AIMEX’s inaugural event in South Australia
SUBMERSIBLE PRODUCTS
END SUCTION PUMPS
MULTISTAGE PUMPS
BOOSTER SETS
HIGH EFFICIENCY SYSTEMS SOLAR SYSTEMS
DRIVES, CONTROL & PROTECTION