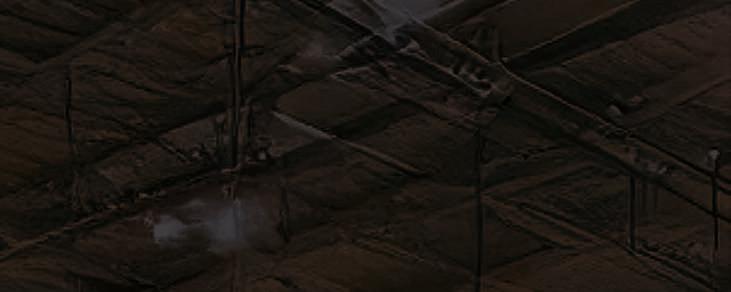
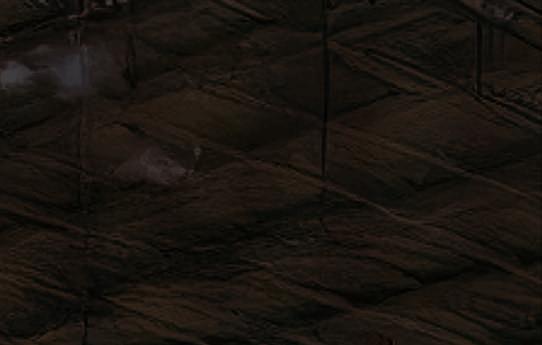
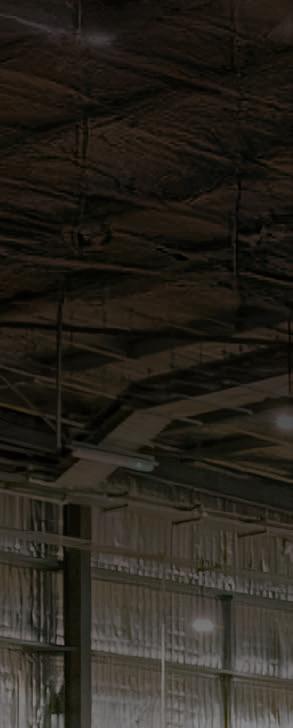
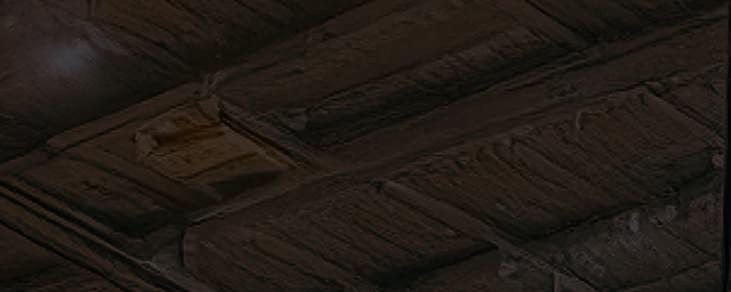
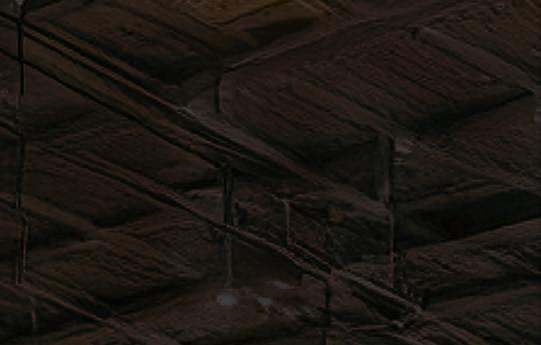

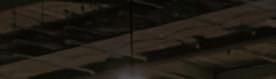
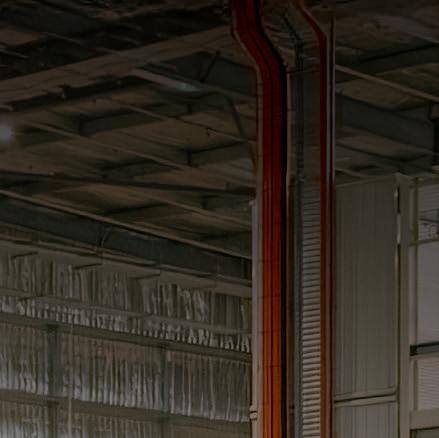
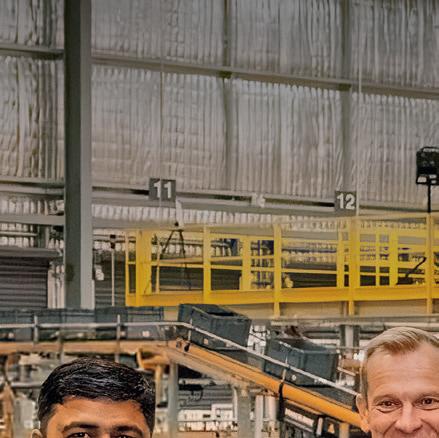


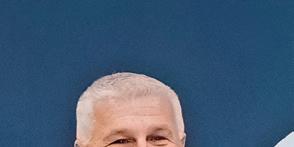

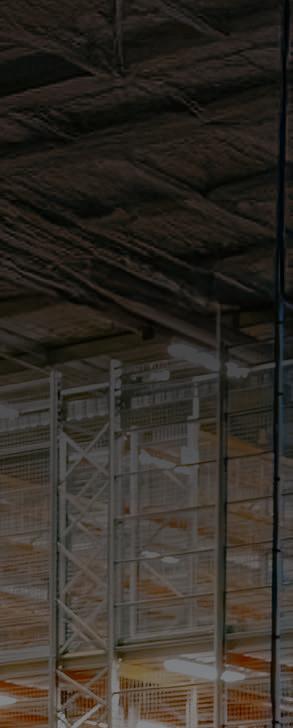
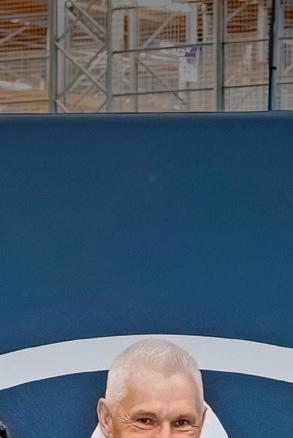
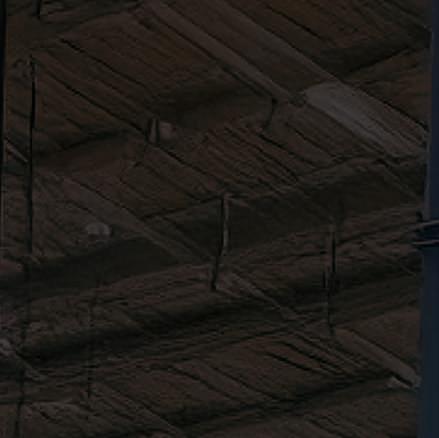
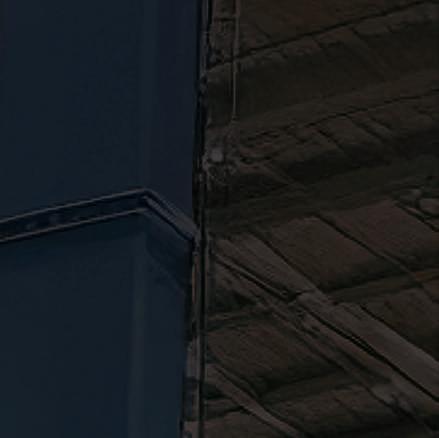

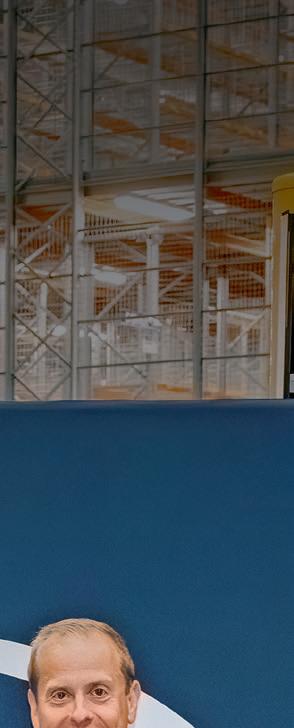
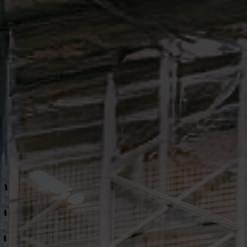
SMARTER WAREHOUSE STORAGE
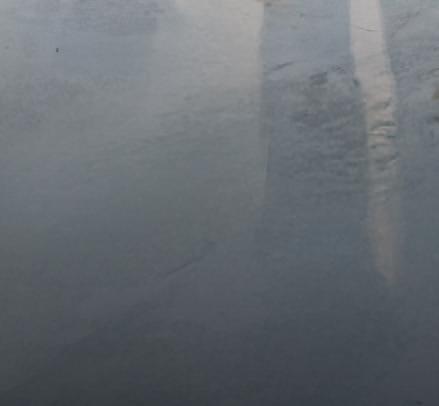

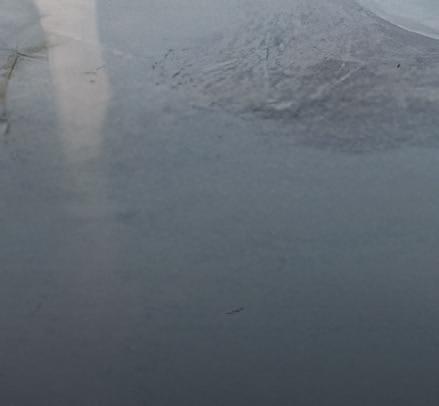
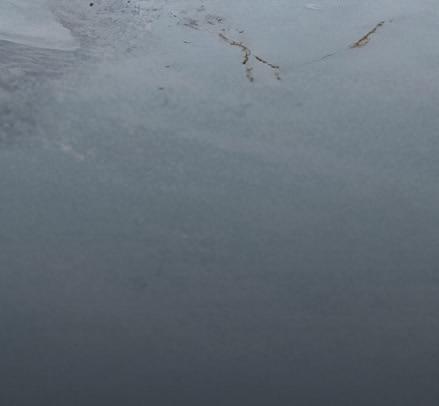
SMARTER WAREHOUSE STORAGE
Smart automation from Vanderlande reshapes parts supply and safety.
New BHD shuttle system boosts density, speed, flexibility.
STRONGER TOGETHER
Adaptalift integrates Hyster NZ into its group.
As a global leader in temperature-controlled logistics, Americold understands the importance of keeping operations moving. Partnering with the Connected Workforce Solutions (CWSTM) division at Dematic, they modernised their cold chain operations in Australia, upgrading wireless connectivity, voice-picking systems, and RF devices.
The transformation signi cantly boosted ef ciency, accuracy, and productivity. Dematic’s robust solution included meticulous planning and mapping to ensure seamless WiFi coverage and device connectivity, maintaining smooth operations, even in sub-zero conditions.
Learn more at dematic.com/americold
MHD Supply Chain Solutions is published by Prime Creative Media
379 Docklands Drive, Docklands VIC 3008
Telephone: (+61) 03 9690 8766
Website: www.primecreative.com.au
CEO: John Murphy
Chief Operating Officer: Christine Clancy
Managing Editor: Mike Wheeler
Editor: Phillip Hazell
Business Development Manager: William Jenkin
Design Production Manager: Michelle Weston
Art Director: Blake Storey
Graphic Designers: Danielle Harris, Jacqueline Buckmaster
Client Success Manager: Caitlin Pillay
FOR ADVERTISING OPTIONS
Contact: William Jenkin
william.jenkin@primecreative.com.au
SUBSCRIBE
Australian Subscription Rates (inc GST) 1yr (11 issues) for $99.00 2yrs (22 issues) for $179.00
To subscribe and to view other overseas rates visit: www.mhdsupplychain.com.au or Email: subscriptions@primecreative.com.au
ACKNOWLEDGEMENT
MHD Supply Chain Solutions magazine is recognised by the Australian Supply Chain Institute, the Chartered Institute of Logistics and Transport Australia, the Supply Chain and Logistics Association of Australia and the Singapore Logistics and Supply Chain Management Society.
Prime Creative Media. All material in MHD is copyright and no part may be reproduced or copied in any form or by any means (graphic, electronic or mechanical including information and retrieval systems) without written permission of the publisher. The Editor welcomes contributions but reserves the right to accept or reject any material. While every effort has been made to ensure the accuracy of information Prime Creative Media will not accept responsibility for errors or omissions or for any consequences arising from reliance on information published. The opinions expressed in MHD are not necessarily the opinions of, or endorsed by the publisher unless otherwise stated.
This month’s coverage reflects the changing face of Australia’s infrastructure and logistics landscape, with both public and private sectors investing in projects that will define how people and goods move across the country in the years ahead.
In South Australia, works have commenced on the Torrens to Darlington (T2D) Project, a long-anticipated development that will complete the final section of the North-South Corridor in Adelaide. Backed by a $15.4 billion investment, the project will remove 21 sets of traffic lights from a key freight and commuter route. It is expected to save up to 40 minutes of travel time during peak hour and support more than 5,000 jobs annually through to its expected completion in 2031.
Across the freight and logistics sector, companies are making bold moves to decarbonise operations and respond to changing customer expectations. Linfox has placed Australia’s largest order of batteryelectric trucks, with 30 Volvo heavy-duty electric vehicles joining its fleet. The announcement aligns with Volvo’s plan to begin EV truck production at its Wacol facility in Brisbane by 2026, reinforcing the local supply chain for zero-emissions transport.
DHL is also stepping up, establishing its Electric Vehicle Centre of Excellence in Australia. The network includes warehousing facilities in Sydney, Melbourne and Brisbane, which are equipped to handle and dispatch lithium-ion batteries safely and in line with dangerous goods regulations. These sites are integrated into a broader national transport network, supporting the country’s growing EV market.
Meanwhile, Australia Post is expanding its regional footprint, announcing six new greenfield sites across New South Wales. With parcel volumes continuing to rise in regional areas, the new facilities aim to boost capacity while incorporating solar energy, water harvesting and EV charging infrastructure.
Together, these projects show how the industry is preparing for a more efficient, connected and sustainable future. Whether it is through upgrading transport corridors, electrifying fleets or building greener last-mile networks, momentum is building behind the idea that long-term investment and innovation must go hand in hand.
At Toyota, we’re proud to be at the forefront of innovative material handling energy solutions including electric, lithium ion, hydrogen fuel cell*, and also o er our exclusive I_Site forklift telematics system helping to track and reduce energy usage. With a comprehensive range starting from pallet jacks right up to eight tonne counter-balance models, make the switch to Toyota’s electric forklifts built with quality top of mind, and that’s just part of the Toyota Forklift Advantage.
12 Vanderlande helps Toyota WA futureproof parts distribution.
23 Addverb enables smarter inhouse automation.
31 Extolla helps businesses choose supply chain software strategically.
35 Toll Healthcare strengthens quality systems and expands national cold chain logistics network.
18 Toyota Material Handling launches national Takeuchi range to expand into compact construction equipment.
27 Adaptalift Group integrates Hyster NZ.
40 BALYO cuts pallet handling costs with AGVs.
20 BHD to showcase new four-way shuttle system at CeMAT 2025.
38 PowerfleetunifiesAIsafetyacross warehouses and transport.
42 Ericsson uses private 5G to power Cypher Robotics’ autonomous drones.
45 CH Racking builds automation-ready systems to future-proof Australian warehouses.
03 Ed’s letter
06 IndustryNews
48 MegaTrans 2026
50 IndustryEvents:SupplyChainWeek
52 ASCI
54 SCLAA
57 ProductShowcase
58 People on the Move
Vanderlande collaborated with Toyota WA to implement a scalable goods-toperson warehouse automation system.
Works commence on South Australia’s $15.4 billion River Torrens to Darlington Project, which will deliver a non-stop South Road. Image: Angelov/stock.adobe.com
$15.4
Marking the start of works on the River Torrens to Darlington (T2D) Project, construction has commenced to create a non-stop South Road in South Australia (SA), saving travel time and providing job opportunities.
Funded by the Australian government, the project aims to save drivers up to 40 minutes of travel time during peak hour. The road will allow motorists to bypass 21 sets of traffic lights between River Torrens and Darlington, reducing congestion.
“This is a project that’s been long talked about – everyone knows how
important it is. Now we’re getting on with delivering it,” said Premier of SA Peter Malinauskas. “Residents in the Tonsley and Clovelly Park areas will be seeing works underway at the Southern Precinct between Tonsley Boulevard and Norrie Avenue.”
Scheduled to begin in the second half of 2026, two tunnel boring machines (TBMs) will be launched from the Southern Precinct to construct the Southern Tunnels. A third TBM will be used for the Northern Tunnels.
A bentonite plant and water treatment facility has also been constructed to produce bentonite
slurry – a wet clay used for ground stability – and to reuse water during the tunnelling process.
“The purpose-built site is where the TBMs will launch to construct the 4.5km Southern Tunnels, which will run from Clovelly Park to just south of the Glenelg Tramline in Glandore,” Malinauskas added.
The project will support 5,500 jobs per year, with close to 550 workers employed at the Southern Precinct. The T2D Alliance is committing to more than 600 jobs for apprentices and trainees, and more than 220 job opportunities for unemployed people. ■
A lineup of new Volvo electric and diesel trucks at a Linfox facility, marking the company’s order of 30 battery-electric trucks. Image: Linfox
Australian transport giant Linfox is purchasing 30 heavy-duty electric trucks from Volvo. The deal marks a step in the company’s push towards sustainable logistics.
The order comprises 29 Volvo FH Electric and one FM Electric truck, expanding on the four Volvo electric trucks already in Linfox’s fleet. Additionally, Linfox has ordered 195 Volvo FH and FM trucks with conventional drivelines.
The announcement coincides with
the upcoming start of electric truck production at Volvo’s Wacol facility in Brisbane, scheduled for 2026. This will be Volvo’s fifth electric truck production site globally, joining three in Europe and one in the United States.
“We are very proud to continue our close partnership with Linfox. The order for 30 Volvo electric trucks is proof of their trust in our company and in zero-emissions transport as a viable solution here and now,” said Roger Alm, President of Volvo Trucks.
Peter Fox AM, Executive Chairman of Linfox, said, “Linfox is excited to partner with Volvo in driving the future and leading sustainable logistics in Australia. Further electrifying our fleet sets the standard for us and our customers and the entire industry.”
Volvo Trucks has delivered more than 5,000 electric trucks to customers in 50 countries and offers eight electric models covering various transport needs. ■
At Vanderlande, we understand the complexities of warehouse management. Our flexible solutions are designed to effectively address a wide range of challenges, including:
> Growing volumes of diversified stock
> Multiple store formats
> Efficient use of space in your stores
> e-commerce
Vanderlande is a leader in food warehousing, o ering integrated automation solutions tailored to the dynamic needs of the food retail industry. Our advanced portfolio including STOREPICK, FASTPICK, and high-speed cross-dock sortation systems enables e cient handling of ambient, fresh, and chilled goods, while ensuring seamless, store-friendly deliveries.
Learn more at www.vanderlande.com/warehousing/segments/food
Australia Post has announced the development of six new greenfield sites across New South Wales (NSW). This infrastructure commitment aims to bolster capacity to support parcel volume growth and improve service across communities. The facilities will enhance service by improving operational safety and efficiency, handling between 900 and 2,200 parcels per day. The sites will be established in Tumut, Leeton, Casino, Deniliquin, Forbes and Byron Bay. With a focus on sustainability, the expansion will feature 50kW rooftop solar power generation at all sites. There will also be rainwater harvesting and EV charging capabilities.
that 82 per cent of NSW households are now shopping online,” said Australia Post general manager network development and support services, Shane Plant. “As regional areas increasingly depend on eCommerce due to fewer physical retail offerings, these purpose-built sites will enable Australia Post to meet the growing parcel demand in these regions.
“Beyond speed and efficiency, we’re focused on providing safer workplaces for our team members and building environmentally responsible infrastructure that can serve communities well unto the future.”
Details and timelines for each of the new sites are as follows:
• Leeton: Construction on the 1,105m2 site will begin in early 2026, with plans to open at the end of 2026.
• Casino: Construction on the 1,350m2 site will begin in early 2026, with plans to open at the end of 2026.
• Deniliquin: Construction on the 1,335m2 site will begin in early 2026, with plans to open at the end of 2026.
• Forbes: Construction on the 1,796m2 site will begin in early 2026, with plans to open at the end of 2026.
• Byron Bay: Construction on the 3,072m2 site will begin in mid-2026, with the site expected to open by mid-2027.
As part of this regional expansion, a brownfield site has been secured in
DP World has opened its first warehouse facility in Singapore, expanding its integrated logistics capabilities in the Asia-Pacific region.
Located in Jurong, the 17,800-squaremetre facility offers bonded and nonbonded storage, cold chain capabilities, and flexible racking systems. It is situated close to seaports and manufacturing zones and is designed to support the company’s end-to-end supply chain services.
The warehouse connects to DP World’s digital platforms, enabling customers to book, track, and manage
shipments online. According to the company, this integration will help customers respond faster to supply chain demands.
DP World stated that the Singapore warehouse would serve as a regional hub, enhancing cargo flow and warehousing operations across Southeast Asia. The facility is part of DP World’s growing footprint in the region, which includes operations in China, Thailand, Indonesia, Malaysia, and Australia.
The opening adds to DP World’s existing operations in Australia, where the company runs container terminals
in Sydney, Melbourne, Brisbane and Fremantle. The new site in Singapore is positioned to support the broader regional logistics network.
DP World has launched 100+ freight forwarding offices in the past year and is continuing to invest in end-to-end supply chain infrastructure globally. The company operates in 78 countries and handled 80 million TEUs of container throughput in 2023.
The Singapore warehouse began operations in April and is part of a series of regional investments aimed at expanding DP World’s logistics footprint in Asia. ■
Toyota WA has partnered with Vanderlande to launch a cutting-edge warehouse equipped with a scalable goods-to-person system. MHD speaks with Toyota’s Executive Director Gary Nettle and Vanderlande’s Director of Warehouse Solutions Roald de Groot about the project’s vision, execution, and early results.
When Toyota WA began exploring distribution centre automation, the team wasn’t just looking for efficiency. They were looking to futureproof their entire parts distribution strategy.
“We didn’t want to build a warehouse we’d outgrow in five years,” says Executive Director of Toyota WA’s Parts Distribution, Gary Nettle. “We wanted something we could grow into over time – and a partner who could grow with us.”
That partner was Vanderlande. Vanderlande is a global supplier
of automated logistics systems for airports, warehouses, and parcel hubs. With more than 9,000 employees worldwide, its systems are used in major airports, distribution centres, and e-commerce facilities.
In Australia, Vanderlande supports warehousing and distribution operations through technologies such as goods-to-person picking, shuttle systems, and automated sortation.
The resulting collaboration between Vanderlande and Toyota WA has seen the deployment of Vanderlande’s FASTPICK solution, an automation system tailored to Toyota’s unique operational requirements while leaving room for adaptability in a changing automotive landscape.
Like many businesses post-COVID, Toyota WA faced shifting supply chain conditions and space constraints. For Gary, automation became a necessity.
“We were dealing with wasted space and excess movement,” he explains. “And it wasn’t just about today. Electrification is changing the motor industry in unpredictable ways. We needed a system that could pivot quickly with us.”
Toyota WA began evaluating automation systems across various sectors, prioritising agility, scalability, and shared values.
“Our core goal is simple: never leave a
Toyota customer on the side of the road. We needed a partner who understood that,” says Gary.
Vanderlande, with its reputation for customer-first design and strong local presence, aligned with Toyota’s goals.
“They’re good with their people, mindful of their environmental responsibilities, and they truly listened,” Gary adds.
The FASTPICK solution stood out for its modular, scalable design and built-in redundancy – an essential factor for Toyota.
“You go into automation with nervous anticipation,” says Gary. “One of our biggest concerns was: what happens if it fails? FASTPICK gave us confidence. It’s designed to keep running even if part of it stops.”
According to Roald de Groot, Director of Warehouse Solutions at Vanderlande, FASTPICK’s redundancy is built into the architecture.
“Our shuttles can move across layers and access any tote. If a lift goes down, another can take over. The system is always thinking a step ahead,” he says.
The shuttle system can sequence orders, optimise item placement, and route inventory dynamically – making it suitable for high-volume, high-mix environments like Toyota’s.
“Each shuttle can access every lift, every aisle. That flexibility is essential
in maintaining throughput and avoiding bottlenecks,” adds Roald.
The implementation wasn’t a simple handover. From day one, Toyota WA made it clear they wanted a long-term collaboration – not just a vendor.
“We didn’t want a company to come in, install a product, and walk away,” says Gary. “We wanted someone to understand our business inside and out – and build with us.”
Over several months, the two teams worked closely, running extensive modelling, refining processes, and adapting the system to Toyota’s evolving requirements.
“There were some sleepless nights,
a few tears, and a lot of laughs,” Gary recalls. “But it was a true sense of achievement.”
“Toyota’s expectations were high – they pushed us,” Roald says. “But it made the system stronger. We designed for what their operations might look like 30 years from now.”
Both parties acknowledge that honest, open dialogue was central to success. “We had our disagreements,” Gary admits, “but we always found a solution that worked for everyone. That’s a real partnership.”
One of the key reasons Toyota selected Vanderlande was the system’s scalability and future readiness. Rather
than building around current volumes, Toyota insisted the solution be equipped for tomorrow’s needs.
“Initially we were surprised by the capacity Toyota was asking for,” Roald admits. “But they were clear – this was about the long term.”
The system’s flexibility also supports Toyota’s wider ambitions.
“We’ve built the facility and the technology to support new dealer services,” says Gary. “This isn’t just
The goods-to-person system includes multiple conveyors and lifts, designed for continuous operation.
goods-to-person system includes multiple conveyors and lifts, designed for continuous operation.
about doing what we already do more efficiently – it’s about enabling what we want to do next.”
FASTPICK also includes options for additional value-added services within the picking stations, allowing Toyota to extend capabilities over time. These include kit-building, lastminute configuration, and returns management.
“Whether it’s new product lines, evolving customer expectations, or
changing vehicle platforms, the system can adapt,” says Roald.
One of the often-overlooked challenges in automation implementation is backend integration. Toyota WA anticipated this and brought its internal IT team into the fold early on.
“We’ve got a strong IT capability internally, and they worked hand-inhand with Vanderlande’s technical
specialists,” Gary explains. “This allowed us to develop customised interfaces and real-time tracking mechanisms that give us full visibility across the system.”
According to Roald, Toyota’s IT readiness made a huge difference. “We were able to co-develop solutions that enhanced the overall system performance,” he says. “There was nothing off the shelf about this. It was a joint effort that went beyond plug-andplay.”
The collaboration allowed Toyota to build dashboards, alerts, and exception management tools specific to its operational KPIs, streamlining communication between warehouse floor activities and enterprise systems.
Although the system has only recently gone live, early feedback is promising.
“We’re still in the transition phase, but already we’re seeing significantly faster operations,” says Gary. “There’s far less movement of people, which is critical for safety and efficiency.”
One of the more unexpected changes was the noise – or lack thereof.
“Our old warehouse was full of sound – people, machines, forklifts. Now, with automation, it’s eerily quiet. It almost feels like nothing’s happening, but when you look at the data, the productivity is huge.”
Another major benefit has been training time.
“With our old systems, it took days to train someone. Now, we can have someone up and running in five to ten minutes. That’s incredible.”
The system’s accuracy has also improved. With single-item picking and automated sequencing, error rates have dropped.
“It’s a very clean handover between system and person,” says Gary.
Designed for the human element
Despite the automation, Toyota WA was adamant that ergonomics couldn’t be compromised. Vanderlande’s system includes adjustable platforms and operator-friendly interfaces to support workers in their tasks.
“Automation does the heavy lifting, but people are still essential at the end of the chain,” says Gary. “Making their jobs safer and more intuitive was a top priority.”
Vanderlande, which works with universities in the Netherlands to research ergonomic movement and long-duration workflow design, brought that knowledge into the build.
“Ergonomics is built into everything we do,” says Roald. “Because good automation supports people, not just processes.”
The design ensures that workstations minimise strain, allow for height adjustments, and streamline movement. “That’s been a huge early benefit,” says Gary. “It means our team can stay productive without fatigue.”
For Gary, the strongest endorsement is how the relationship has evolved.
“We always said we wanted a partner who could use this as a showcase –to build their presence here in WA. Vanderlande embraced that,” he says.
Toyota WA even named a viewing
platform after the company and regularly invites potential clients to tour the site.
“The more companies using this technology in WA, the better the ecosystem. We’re proud to be part of that,” Roald says.
“We’re not just implementing a system – we’re building a community around it.”
Lessons from the journey
Asked what advice he’d give others considering automation, Gary says: “Make sure the partner you choose is ready to go the distance with you. It’s not about buying tech – it’s about building something together.”
For Roald, the project has reinforced the importance of shared values.
“Toyota WA was clear about what mattered to them: reliability, service, community. That clarity shaped every decision,” he says.
With automation in place, Toyota WA is better positioned to serve its dealer network, adapt to change, and lead within Australia’s evolving logistics landscape.
As the dust settles on the project’s first phase, both companies are already looking ahead.
“The warehouse might be quiet,” says Gary, “but it’s working harder than ever.” ■
The TL8R2 track loader transfers material into the TCR50-2 crawler dumper – two machines featured in TMHA’s new Takeuchi equipment range. Images: Toyota Material Handling
TMHA expands into construction with more than 35 Takeuchi machines, supported by national sales and service networks.
Toyota Material Handling Australia (TMHA) is now the national importer and distributor of a range of more than 35 Takeuchi excavators, track loaders and crawler dumpers, giving it one of the most comprehensive lineups of compact construction equipment, backed by one of Australia’s largest sales and service operations.
The quality, durable, highperformance Takeuchi machinery joins the TMHA range of Toyota forklifts and Huski skid steer loaders and scissor lifts, providing commercial, and
government customers with a one-stop shop for their material handling and construction equipment needs.
The Takeuchi range is available through THMA’s network of 21 branches across Australia supported by 300 mobile service vehicles and more than 500 technicians and support staff.
TMHA president and CEO Steve Takacs says Toyota’s long-standing relationship with Takeuchi and the company’s parts, servicing and sales operations will deliver the very best in customer service for the construction industry.
“With this extensive new range of high-quality Takeuchi machinery, TMHA as a national importer and distributor is able to offer its customers in the construction industry a full range of products to meet their specific needs, whether that’s excavators, loaders or dumpers,” Steve says.
“But perhaps more importantly, we have the support they need with an expansive national coverage of sales outlets, large store of parts support through Toyota’s network of branches across the country, and a huge team
of highly trained technicians that are on hand to service and maintain the equipment.
“To support the launch of these new products we recently had four senior Takeuchi staff from Japan and the US come to Australia to run an extensive 10-day sales and service training for our construction teams.
“Takeuchi prides itself on the rugged reliability of its products, which combined with the legendary reliability of Toyota forklifts will continue to give our customers outstanding quality and choice, whether in the warehouse or construction site,” Steve added.
TMHA’s parent company, Toyota Industries Corporation, works closely with Takeuchi in Japan, making it a natural fit for expanding TMHA’s product offering in Australia.
TMHA’s lineup of Takeuchi excavators are available in thirteen conventional, four short tail, and three zero tail swing configurations.
The conventional excavators start with the 1865kg TB216 that offers a dig depth of 2390mm for smaller jobs through to the 15 tonne TB2150 that provides a dig depth of 5445mm for larger construction and excavation work.
All excavators feature ground level access to key daily inspection points with lockable engine and side hoods opening overhead to provide easy access for inspections and maintenance.
Triple flange track rollers, designed to reduce the potential of de-tracking when working in demanding conditions, are standard on all models while most models feature automatic load sensing two-speed travel that will step down to high torque mode for greater productivity.
Takeuchi products are known for their large spacious cabins and the excavator range is no different, providing operators with a comfortable well appointed station with multiinformation displays.
The short tail swing models are available in three lightweight configurations from 1150kg to 2670kg with dig depths between 1755mm and 2560mm, along with a heavy-duty 15,420 kg unit with a dig depth of 5.5m.
The compact short tail swing design is ideal for urban environments where space can be limited and features a wrap-around counterweight that provides excellent stability and
protection for vital engine and hydraulic components.
The smallest models in the range –TB210R and TB215R – feature retractable undercarriages that enable them to pass through a standard doorway in tight urban job sites which the operator can then expand for greater stability while working.
For job sites with space limitations, TMHA also offers the Takeuchi zero tail swing excavators that feature a patented side to side boom that enables excellent visibility when digging offset and can be stowed to allow the cab full rotation within the width of the tracks.
These models allow easy ground level access to inspection points and for engine maintenance or control valve access, they feature a tilt-forward cab.
Inside, the cabin provides exceptional operator comfort with a suspension seat, hydraulic pilot joysticks and large multi-information display.
The three zero tail swing models range from 3935kg to 8.5 tonne with dig depths from 3420mm to 4540mm.
To complement the range of excavators, Takeuchi also has five compact Track Loaders that share the same high quality, durability and performance and offer a choice of radial arm or vertical arm machines.
All models feature a tilt up operator’s station to provide access to all remote filters and hydraulic equipment for serviceability and maintenance while a heavy-duty rear swing out door enables access for daily service check points.
The three radial arm machines feature a single arm pivot point and are ideal for tough excavating and grading applications or loading and unloading flat-bed trucks.
The three radial arm models vary in engine outputs from 47.9kW to 81.8kW.
The two vertical arm machines maintain a greater centre of gravity as the load is kept closer to the machine as it is raised and are ideal for loading trucks and hoppers with high sides and provide better reach at dump height.
TMHA is launching two vertical arm Track Loaders with power outputs of 54.6kW and 81.8kW.
\All Takeuchi Track Loaders feature hydraulic pilot controls for precise control and efficiency with the spacious cab providing automotive-style features for easy intuitive use.
Rounding out the TMHA Takeuchi range is a tough, powerful and reliable crawler dumper.
Powered by a 88.4kW/410Nm Yanmar turbo diesel engine, the crawler dumper offers a spacious cabin with hydraulic joystick controls for smooth operation and a foot controlled throttle for economic and intuitive engine operations.
With a 65 degree dumping angle, 3700kg maximum loading weight, and 180 degree turning dump for sideways dumping, it is suitable for onsite construction jobs.
For more information freecall 1800 425 438 or visit www.toyotatakeuchi.com.au ■
BHD will unveil its new four-way shuttle racking system at CeMAT 2025, coinciding with a dedicated networking event aimed at showcasing its evolution and vision for the future.
BHD Storage Solutions is gearing up for a major presence at CeMAT 2025, held at the Dome in Sydney, where it will launch its new four-way shuttle racking system to the wider logistics and warehousing community.
The company’s Director and General Manager, John Harrison, said the international materials handling and logistics event will be a milestone moment for BHD, which is exhibiting the new technology for the first time.
“2025 CeMAT at the Dome in Sydney, is the launch of our four-way shuttle rack system,” John said.
The new system represents a stepchange in BHD’s product offering. While the business has previously delivered two-way shuttle systems, the four-way configuration brings added flexibility, speed, and storage density.
“It’s something that BHD has never been able to produce before,” John said. “The shuttle carts themselves
are very quick, reliable, and serviceable.”
The shuttle’s four-way movement capability allows it to travel along both axes, enabling higher throughput and greater system agility.
“It’s a cost-effective way of reducing large infrastructure investment while maximising available space,” John added.
While BHD can supply the shuttle carts with its four-way shuttle rack, John clarified that BHD is not, and does not intend to be, a systems integrator.
“We are more than happy to provide the racking solution – including the four-way shuttle – in a way that suits other integrators and their technologies,” he says. “This launch isn’t just about the shuttle; it’s about offering a racking platform that others can build into their own systems.”
Connect and collaborate
In addition to exhibiting on the show floor, BHD will also host a formal dinner event on the first evening of the trade show titled Connect and Collaborate, which John said will act as both a product launch and a celebration of the company’s journey. The function, held at the Novotel adjacent to the venue, will bring together customers, system integrators, and industry peers for a sit-down dinner and keynote address.
“The event is really about showing people what BHD is about – where we’ve come from, where we are now, and where we plan to go,” John said.
The keynote speaker for the evening will be Heenie Van Der Merwe, General Manager - Warehousing at
“We’ve partnered strongly with Komatsu over the last few years and provided them with some fantastic
solutions,” John said. “We’re keen to have Heenie share his perspective on working with us.”
The event is designed to provide a relaxed environment for attendees to network, share insights, and engage with BHD’s leadership team.
A growth journey
For BHD, this year’s CeMAT comes at a pivotal time. The company has been steadily growing its product range and capabilities, with the new shuttle system marking a leap forward in its automation-readiness.
“We see the shuttle as a foundation for more advanced, integrated solutions,” John says. “Having something like this on the floor at CeMAT is not only about selling a product – it’s about showing what we can do, where we’re headed, and how we can support the sector.”
When asked what he hoped attendees would take away from BHD’s presence at CeMAT and the Connect and Collaborate event, John was clear: “We want people to come away with a better understanding of who BHD is – not just as a product supplier, but as a service provider and solutions partner.”
The four-way shuttle will be on display at BHD’s stand throughout CeMAT, with live demonstrations expected to draw interest from integrators and facility managers alike.
BHD is encouraging early conversations during the show and welcomes inquiries from potential partners looking for dense storage, high-throughput solutions, or a pathway into smarter warehousing.
“We’re excited about where we’re going,” John said. “And we’re looking forward to sharing that with everyone at CeMAT.” ■
A view of Addverb’s automation system in action, showing blue totes travelling on conveyor systems as part of an integrated goods-to-person picking solution. Images: Addverb
Rising logistics costs and automation access are prompting firms to rethink 3PLs, with Addverb enabling smarter in-house solutions.
For years third-party logistics providers (3PLs) have supported supply chains giving companies cost-effective ways to manage warehousing, fulfilment, and distribution. In a world where quick action and growth matter, 3PLs have helped businesses stay flexible without spending big on new infrastructure. But things are changing. Higher costs, uneven service quality, and easier access to warehouse automation are making companies think hard: Should they keep outsourcing, or is it time to invest in their own automated systems?
The rising cost of outsourcing
The main selling points of 3PLs are lower capital investment, scalable operations, and logistics know-how to face challenges. Worker shortages in key markets like Australia, along with inflation and unpredictable fuel prices, have driven up operating costs for 3PLs. These costs get passed on to clients, cutting into profits and reducing the money-saving appeal that made outsourcing attractive before. Also, many companies now see that outsourcing comes with hidden costs – like less transparency, less
flexibility, and slower responses to changing needs which can outweigh its benefits. Customisation, once a bonus, has become essential in today’s fast-changing supply chains. But 3PL providers, following their own standard models often can’t offer the flexibility or integration needed to optimise operations.
The rise of in-house automation
Warehouse automation tech has gotten better making it easier for companies to manage their own supply chains. Robots that move on their own,
systems that store and grab items, and software to run warehouses have become more flexible, expandable, and affordable. Companies don’t need to spend a ton of money upfront to build high-tech facilities anymore. Now, they can start small and add more as they grow.
Ranmeet Singh, General Manager, Addverb Australia, thinks this change is part of a bigger shift in how companies see logistics.
“We see businesses in fast-paced areas like retail, groceries, and medicine focusing on seeing and moving things. They want to keep a closer eye on their stock, and automation gives them that – without the downsides that often come with letting someone else handle it.”
When it makes sense to choose a 3PL
This is not to say that the 3PL model is no longer relevant. For companies that are looking to enter new markets, manage seasonal peaks, or move at low volumes, 3PLs still remain an important intermediate solution. 3PLs take away the burden of long-term investment and offer an existing network and existing infrastructure. A small or medium size business can find this to be a useful option particularly when they have unpredictable requirements, because outsourcing 3PLs limit exposure to risk.
Some organisations deliberately focus on their core competencies –such as product innovation, customer engagement, and service – with a strong emotional component. Brand, in this context, becomes a perception, a reality, even an identity. In which case companies choose to outsource logistics to mitigate strategy distraction from supply chain issues.
In these cases, and situations, partnering with a tech led 3PL that involves automation into its operational processes may provide a double benefit. Even in this circumstance it is incumbent on businesses to conduct extensive research. Not least because automating elements of a 3PL’s operations does not automatically have a guaranteed benefit for the client unless the operational objective and data visibility requirements of the customer are met.
When In-House Automation Wins
The case for in-house automation is stronger where logistics is a strategic differentiator. For some types of companies – e-commerce, quick commerce or omnichannel retail – logistics are critical to customer experience. In these cases, speed, accuracy and inventory control determine customer experience and ultimately facilitate a competitive or logistical advantage. Funding and developing infrastructure when paired with intelligent automation can enable logistics to move from a cost centre to a competitive advantage.
For Addverb, the key is to not just automate for automation’s sake but align automation with the desired business outcomes. The software and technical solutions offered by Addverb help companies develop modular, highdensity storage systems to optimise space and throughput with minimal human assistance which is important in urban or high-rent locations where space is valuable and every square meter counts.
Aside from the initial capital and ongoing operational expenses, another way in-house automation adds value is data ownership. By owning their own fulfilment operations, companies can utilise rich datasets to make realtime decisions and predictive decisions around maintenance or customer service. This is far more difficult to achieve when you are reliant on a third-party logistics (3PL) provider’s systems and protocols.
The evidence of possible activity occurring with the conscious unbundling phenomenon is relevant in Australia, where logistics costs are amongst the highest in the world. The price of logistics activity adds to the total cost of sale of products, which departing from the 2020 pandemic years, sees a resurgence of activity in Australia due to the need to contend with Australia’s geographic location, and the changing demands affecting logistics activity given new labour constraints.
A good example is referenced by Ramneet, he says: “A number of our clients have engaged with us because they relied upon 3PLs for fulfilment services, only to find that they were: a) stuck with excessive costs to deliver or b) lacked
agility in flexibility & service delivery.
“By incrementally controlling and automating the operational delivery of their products in-house, they improved their delivery performance but also controls for inventory and order tracking.”
Ranmeet explains that logistics activity in terms of warehouse automation doesn’t have to be an all-or-nothing approach. It can start small, like picking & tracking or sorting, automation, and scale progressively.
“It’s important that our clients consider building future-ready infrastructure that grows with their needs.”
A considered approach ultimately, a business’s decision between outsourcing logistics activities in the form of third-party logistics (3PL) or in-house automation is not a binary decision, rather it is a strategic decision. Businesses need to understand their pain-points in delivering service logistically, their growth plan and their logistics’ role in the value proposition. A hybrid model is becoming more commonplace. For example, a business may be using third-party logistics for regional fulfilment but is actively trying to automate their central warehouse to efficiently handle their core SKUs and fast-moving items. This blended strategy offers the flexibility of outsourcing with the control of internal operations-an ideal middle path for many growing enterprises.
“Today, the question is not if we automate – instead it is when, where, and how,” says Ranmeet. “Companies that answer these questions wisely will not only create more effective supply chains, but they will also create future ready supply chains.”
The logistics environment is changing rapidly, caused by changing consumer expectations, labour dynamics and technology innovation. Further, while the 3PLs will continue to play a role, it is no longer the entire story. Companies that, quite simply, viewed logistics functionality as a back-office to be managed have understood the true meaning of their supply chain strategy and, automation is at the forefront of this change. ■
A New Era in Automation is Landing at CeMAT 2025. Be among the first to witness Australia’s first container-unloading robots in action. Don’t miss the logistics breakthrough everyone will be talking about.
Adaptalift Hyster forklifts are now being supported by a broader service footprint across New Zealand, following the integration of Hyster NZ into the Adaptalift Group.
Hyster NZ joins Adaptalift Group, expanding infrastructure and rebranding after 80 years in New Zealand.
Hyster New Zealand has rebranded under the Adaptalift Group following an acquisition that marks the beginning of a new chapter for the materials handling supplier as the company reaches an 80-year anniversary. The move integrates Hyster NZ into an Australian-headquartered business with a dedicated focus on forklifts, servicing, rental, and parts across Australia and New Zealand.
The change follows a strategic decision by former owner Sime Darby, which acquired the Hyster NZ business from the Gough Group in 2019.
From Adaptalift’s New Zealand leadership perspective, the goal was to ensure a unified transition. Country Manager Ryan Hosking says the process was carefully managed to bring together two well-established teams under one group identity.
“My role as Country Manager was to ensure there was a seamless integration between the two businesses – what was Hyster New Zealand and the Adaptalift Group,” Ryan says. “We’ve been very fortunate to inherit a group full of good people and strong skills. The response from the team has been overwhelmingly positive.”
As a result, Adaptalift Group entered the frame and acquired Hyster NZ, marking its formal entry into the New Zealand market. According to Shane Smith, National Sales Manager – NZ, and a former Hyster NZ employee, the
transition reflects a better strategic fit.
“Now, within the Adaptalift Group, we’re part of a dedicated materials handling business,” he says. “That’s a really good transition for us.”
Shane joined Hyster NZ in 2021 and has seen the company evolve through several structural changes.
“The Gough Group had Hyster from the beginning – dating back to 1945,” explains Shane.
“Today, in 2025 joining Adaptalift Group, we fit right in. It’s a dedicated business model that matches how we operate.”
The transition, which took place over two months, involved relocating five operational sites and onboarding approximately 110 employees. Shane noted that, despite the pace of change, efforts were made to ensure minimal disruption for existing customers.
“The main goal for us was to fully transition in a way that was seamless for the clients,” he says. “When we’re out there talking to them, the feedback we’re getting is they haven’t really seen too much of a difference in terms of transacting, and that was really key for us.”
This approach reflected a deliberate effort to prioritise team culture and communication.
“We took a people-first approach with full transparency and boots on the ground,” Ryan says. “Our Group CEO, Steve Taylor, personally visited teams across New Zealand. It’s a cultural shift – we’re not hierarchical. We know people’s names, their families,
and what’s going on in their lives. Everyone’s part of the same team.”
While the Hyster NZ brand had local recognition, the company has recently confirmed that all operations will move forward under the Adaptalift Group name.
“We’ve just announced the rebranding to Adaptalift Group,” Smith says. “Nothing official has gone out yet, but that process is already underway.”
The acquisition not only affects branding and reporting lines – it also brings a wave of investment into the New Zealand operation. Adaptalift has already begun expanding its infrastructure footprint across the country, including a new distribution centre in Christchurch to better serve the South Island.
This investment is not limited to logistics infrastructure. According to Ryan, it has also had a tangible effect on morale.
“The change has reinvigorated the team,” he says. “They’ve moved to high-quality environments and seen real investment – not just in assets, but in culture and leadership. That’s made a huge difference.”
“Previously, we only had one DC in Auckland,” Shane added. “Now we’re setting up a second DC in Christchurch. That change alone increases our ability to provide after-sales support and timely service across the country.”
Shane also highlighted the importance of parts availability and service responsiveness in the materials handling sector.
“We’re one of the few businesses actually investing into the business right now. Increasing stock holdings, increasing infrastructure – that’s a message we’re taking out to clients,” he says.
From a regional perspective, the acquisition elevates the status of the New Zealand arm within the global Hyster dealer network.
“We’re the longest-standing Hyster dealer outside of the United States,” Shane says. “And now with the Adaptalift transition, we’re also the largest dealer in the Asia Pacific region, including India and China.”
Culturally, Shane says there’s strong alignment between the former Hyster NZ team and Adaptalift.
“We’ve always presented ourselves as strong partners and we’re still committed to that,” he says. “We value long-term relationships, and it’s not just about the product – it’s what comes behind it, whether that’s servicing, parts support, or operational advice.”
The acquisition also provides new growth opportunities for the Hyster product line in New Zealand. While the brand has traditionally been associated with large container handlers and heavy equipment, Shane says the company will now look to grow its share in smaller to mid-sized forklifts and equipment.
“Historically, we’ve been strong in big trucks – container handlers and the like,” he says. “But now, with Adaptalift behind us, we’re looking to increase our presence in sectors like transport, warehousing, agriculture, and food. You’ll see more Hyster trucks in those applications.”
With shared operations and transTasman capabilities, Shane sees additional opportunities to leverage client relationships across both Australia and New Zealand.
“We’ve got touchpoints across both countries now that we can support. It puts us in a better position to work directly with clients operating in both markets.”
Looking ahead, Shane believes the acquisition marks the most important development in Hyster NZ’s recent history.
“It’s probably the most significant change we’ve had, and I think it’s certainly the right one,” he says. “It puts us in a better position with the factory and strengthens our presence in the market.”
When asked what the overarching theme of being “stronger together” means in this context, Shane pointed to benefits across multiple fronts.
“We’ll be stronger internally, stronger as a group, and stronger partners with our clients. That’s where you’ll see the difference – through the whole value chain.”
Ryan agreed, emphasising that the integration has gone beyond internal alignment to become a broader customer strategy.
“’Stronger Together’ isn’t just internal – we’re no longer two teams. We’re one Adaptalift Group,” he says. “And beyond that, it’s about partnering with our customers across New Zealand and growing with them.”
As the transition continues, the company is focused on embedding systems, consolidating operations, and delivering consistent support to customers under the new brand identity. For long-standing Hyster NZ clients, the familiar faces and technical knowledge remain – but now within a broader, better-resourced structure designed to meet future demand. ■
COMING SOON!
Perth (WA) – NEW SITE
HAZELMERE, WA 6055
•4,500 sqm
•2,200 ambient pallet
•250 cold chain pallets
•100 freezer vault pallets
Brisbane (QLD)
RICHLANDS, QLD, 4077
•4,600 sqm
•3,880 ambient pallet
•520 cold chain pallets
Adelaide (SA)
EDWARDSTOWN, SA 5039
•Ambient and cool room facilities supporting SA community
Melbourne (VIC)
MELBOURNE AIRPORT, VIC 3045
•10,000 sqm
•9,500 ambient pallet capacity
•1,173 cold chain pallets
•31 freezer vault pallets
Sydney (NSW)
EASTERN CREEK, NSW 2766
•17,600 sqm
•17,000 ambient pallet
•600 cold chain pallets
•500 freezer vault pallets
The landscape of supply chain software is crowded with acronyms – WMS, TMS, OMS, RPA – but the right choice depends on asking the right questions, not following trends. Images: Extolla
Australian businesses are rethinking supply chain software, prioritising strategy, integration, and cross-functional collaboration over hype.
Why Australia’s leading brands are changing the way they evaluate, select, test, and implement supply chain software – and what CFOs, CIOs, COOs and supply chain leaders need to know.
A decision too important to get wrong Australian supply chains are under more pressure than ever. Soaring operational costs, rising customer expectations, productivity constraints, and regulatory changes are pushing businesses to reassess how they operate – and, critically, how they use and select technology to improve supply chain performance.
Software selection has moved far beyond IT. Today, Warehouse Management Systems (WMS), Transport Management Systems (TMS), Order Management Systems (OMS), Last-Mile Delivery (LMD) and other platforms sit at the heart of customer experience, fulfilment and profitability. And yet, too many businesses still get this decision
wrong – not because the tech is poor, but because the approach to selecting it is flawed.
In a recent Extolla webinar titled “Shift Happens” available on the company’s YouTube channel, global experts reinforced what has been seen on the ground in Australia: success depends on early business-wide involvement, rigorous validation, and long-term strategic alignment - not shortlisting vendors based on sales decks or peer referrals.
The real cost of poor tech decisions
“We often see businesses come to us after choosing a system that doesn’t scale, doesn’t integrate, or doesn’t actually solve the problem they bought it for,” says Claire Bull, Director of Technology, Innovation and Sustainability at Extolla. “And the root cause is almost always the same – rushed selection, internal bias, or a lack of stakeholder input.”
The cost of a poor decision isn’t just financial. It creates operational drag, frustrates staff, and can lock businesses into long-term limitations.
In many cases, the wrong technology adds complexity – requiring manual workarounds that erode the very efficiencies software is meant to deliver.
The big shift: From software purchase to business strategy What’s changed is how Australia’s leading brands are approaching tech investments. Rather than defaulting to off-the-shelf options or chasing trending features like AI or automation, they’re taking a step back – and starting with the business.
Extolla’s approach begins by working with C-suite leaders across supply chain, finance, operations and IT to understand:
• Why a new system is needed (and whether it’s the right time)
• What success looks like across every impacted function (every function has different definitions of success)
• Which risks, gaps, or constraints exist today
• How the system needs to support future growth, compliance, and innovation
webinar panellists – “and may last longer than one!” A WMS, TMS or OMS isn’t a one-off purchase; it’s a longterm partnership. Choose accordingly.
The role of AI and automation – with caution
As discussed in Extolla’s recent webinar, one of the most overlooked steps is engaging stakeholders from across the business at the very beginning. This ensures the system meets the operational, financial, and technical needs of the company – not just the warehouse floor or IT team.
Why more than 60 per cent of tech investments fail –and how to prevent it
Businesses that get stuck in a cycle of poor technology decisions often fall into five traps:
1. Selection fatigue
Overwhelmed by options, teams choose the “least-worst” system based on the first strong pitch, internal bias, or vendor pressure.
2. Limited testing and due diligence
Believing the sales pitch without verifying. “They say there’s an API? Test it!” Too many teams accept vendor promises without verifying integration, scalability, or usability.
3. FOMO-driven decisions
Rushing to keep up with competitors or adopt AI prematurely can lead to short-sighted decisions that don’t align with business goals.
4. No clear data baseline
Without accurate operational data, businesses can’t evaluate if a solution truly fits. Metrics around receiving, picking, fulfilment, and workforce planning are essential and the first step to making a good decision.
5. Treating it like a transaction, not a relationship
“Buying supply chain software is like a marriage,” said one of the expert
AI and automation are no longer optional – they’re integral to driving speed and accuracy in warehouse performance and inventory management. But to ensure AI projects deliver, businesses should not chase these features without proper evaluation.
As our experts highlighted, AI is reshaping decision-making – but its value depends on integration, realtime data, and strategic application. A flashy demo means little if the system can’t adapt to your environment or if you lack data or the people with the skills to act and support your operational model.
The right implementation partner Choosing the right implementation partner is critical to a project’s success because they bring the expertise, structure and strategic insight needed to translate software into real business value.
A capable partner ensures your unique needs, risks, timelines and user adoption is designed into the solution. The right partnership not only reduces the risk of delays and cost overruns but also lays the foundation to ensure return on investment.
The Extolla model: Consult–Implement–Operate
That’s why Extolla takes a different approach. The company begins with deep discovery, engaging stakeholders from supply chain, IT, finance, and operations to understand success, risks, and gaps. It then guides software selection based on agnostic analysis, ensuring it aligns with your business – not just current infrastructure, but target future state.
Implementation isn’t the end. Extolla’s teams support training, go-live, optimisation, and change management to ensure long-term success – and ultimately, operational excellence.
In a recent project, Extolla supported one of Australia’s most recognisable retailers to overhaul its supply chain systems. Instead of leading with technology, the business led with strategy.
Through early stakeholder engagement and rigorous requirements analysis, Extolla helped identify a WMS and related systems that improved productivity, inventory visibility, labour efficiency, and emissions tracking. The outcome: faster fulfilment, lower costs, improved customer experience and a future-ready platform to support growth.
Why finance, IT and supply chain leaders must collaborate
This project – and dozens more like it – underscore a critical point: siloed decision-making is the enemy of successful tech investments.
• CFOs want ROI, risk mitigation, and cost visibility.
• CIOs need system compatibility, integration, and security.
• Supply chain and warehouse leads need usability, reliability, and speed. Bringing these perspectives together from the outset ensures that software doesn’t just function – it delivers real business value and return on investment.
What success looks like
Done right, technology investment in supply chains delivers:
• Real-time inventory visibility
• Increased labour productivity
• Reduced manual errors
• Better customer service
• Scalable infrastructure for growth
• Compliance and emissions reporting
• A competitive edge in uncertain markets
But these outcomes don’t come from buying the “latest and greatest” platform. They come from asking the right questions, challenging assumptions, involving the right people, and planning for the long term.
Don’t rush. Rethink. Reframe. The most successful brands don’t wait for a tech issue to blow up, they get ahead of it, they choose smarter, plan better, and leverage expert support to do so.
If you’re considering a new WMS, TMS, OMS, or supply chain system, don’t start with the tech. Start with the why. Align finance, IT and operations. Test, validate, and plan for scale. Because in supply chains – just like in marriage – the decisions you make early on shape the outcomes for years to come. ■
DRIVERLESS FORKLIFTS
FORKLIFT STRENGTH
DRIVERLESS INTELLIGENCE
80% LOWER OPERATING COST
2 out of 3 warehouses today face unreliable connectivity as a key challenge
Ericsson Private 5G meets current needs for secure, uninterrupted connectivity while enabling the future of Logistics 4.0. With impressive scalability, low and predictable latency, and fast data transfer, it eliminates Wi-Fi dead zones, makes real-time communications and inventory management seamless, and enables autonomous vehicles and robotics. Private 5G connectivity is helping industry leaders like CJ Logistics address dead zones and achieve productivity gains from day one.
Transform your warehouse operations with Ericsson Private 5G. Ericsson.com/logistics
Toll Healthcare is strengthening its quality and sustainability credentials as it expands across Australia’s healthcare logistics network.
When it comes to healthcare logistics, few things are more important than temperature control and compliance. With cold chain requirements being central to the safe and timely distribution of pharmaceuticals and medical devices, Toll Healthcare is investing in both its people and its infrastructure to stay ahead of industry needs.
Alison Tennent, recently appointed as Senior Manager, National Quality Assurance for Toll Healthcare, has entered into the role during a time of rapid change and opportunity. A pharmaceutical quality expert by trade, Alison brings experience in quality systems, GMP compliance, and consulting to her new post – and she’s
tasked with ensuring Toll’s operations remain watertight as the business scales.
“My background is mostly in pharmaceuticals manufacturing and warehousing,” she explains. “I’ve worked with major pharma companies as well as consulting firms, always in quality assurance and compliance roles. At Toll Healthcare, I have national responsibility for the quality function, including the maintenance of our GMP licences, ISO certifications, poisons licences, and the quality systems that support all of them.”
With a team of four supporting facilities across the country, Alison’s remit extends to everything from handling customer complaints to
ensuring the accuracy and rigour of preventative maintenance and training programs.
“Quality assurance isn’t just about ticking boxes,” she says. “It’s about embedding the right processes into our operations to ensure we meet our compliance obligations – and more importantly, that we meet the expectations of our customers. These aren’t just internal systems. They are core business processes.”
Meeting demand through temperature control
Toll operates behind the scenes in the healthcare supply chain, supporting pharmaceutical and biotech clients including CSL Seqirus and CSL Behring.
“We manage all their finished products and in-licensed items, and we also store raw materials in support of CSL’s manufacturing facility next door to our Melbourne Airport site,” Alison notes.
That proximity enables rapid turnaround for time-sensitive orders –a hallmark of Toll’s healthcare logistics model. The company’s core capabilities include inbound and outbound logistics, inventory control, and specialist storage for pharmaceutical and medical device products requiring strict temperature regulations.
At its Tullamarine site, the facility is divided into three separate temperature zones: ambient, chilled, and frozen. The company is also in the process of expanding its use of ultra-low temperature freezers – targeting minus 70°C – to accommodate specialised product lines.
“These zones are validated, temperature-mapped, and closely monitored in real time,” says Alison. “We’re using more modern temperature monitoring systems to gain better visibility over the performance of our fridges, freezers and cool rooms. That allows us to optimise our preventative maintenance schedules and respond quickly if there are any alarms or outof-spec risks.”
Temperature is just one part of the equation. Sustainability, particularly in packaging, is becoming a growing priority – both for Toll and its clients.
“We’re currently running a project focused on sustainable alternatives to polystyrene packaging, which are commonly used but not very environmentally friendly,” Alison says. “The goal is to identify solutions that still meet temperature control requirements but are far more sustainable. We’ll assess their feasibility and then conduct performance testing across our distribution network.”
The project is part of broader work within the group to address sustainability in its operations.
Following facility upgrades in Brisbane and Melbourne in recent years, Toll is now building a larger, more modern healthcare warehouse in Hazelmere, Western Australia.
“The new Perth facility is part of a broader strategy to expand our national footprint and support growing
Alison Tennent, Senior Manager, National Quality Assurance for Toll Healthcare.
demand,” says Alison. “It will still be TGA-licensed and GMP-compliant, but it gives us additional space and the ability to support more specialised healthcare products.”
These upgrades also coincide with system improvements designed to streamline data access and reporting, including digitised equipment tracking and quality system analytics.
“We want to be able to trend and analyse our performance data more easily so that we can continue to improve,” she explains. “Whether it’s the integrity of temperature control or the robustness of our quality systems, having real-time access helps us respond to issues faster and stay proactive.”
Building capability through training Alison is also overseeing efforts to bolster workforce capability, with new training programs, professional development, and competency-based assessments rolled out across the business.
“All of our operational and quality teams have detailed training matrices in place, and we support certification where relevant,” she says. “For example, one of my team members is completing lead auditor training this week. We also have access to Toll’s internal learning platform, and we attend conferences to stay up to date with industry developments.”
This training culture ensures Toll’s compliance practices evolve with industry standards – while also giving staff a clear pathway for professional growth.
In healthcare logistics, compliance
is critical to ensuring products reach patients safely and on time.
“Some of the products we store and distribute are going directly to hospitals or patients waiting for treatment,” Alison explains. “If something goes wrong with the logistics, it could delay that patient receiving a life-saving medicine. So, we take our quality systems extremely seriously.”
With that responsibility comes the need to future-proof the business. As Toll’s healthcare operations continue to grow, Alison is focused on ensuring quality systems scale in lockstep.
“We’ve got lots of growth opportunities, and part of my job is to make sure our processes can support that expansion,” she says. “They need to remain compliant, but also flexible enough to evolve with our clients’ needs.”
While Toll Healthcare’s team is based primarily in Australia, its success is beginning to shape the company’s global operations.
“Our Australian business is the more mature part of the healthcare network,” says Alison. “It’s got an established client base, rigorous quality systems, and a national infrastructure footprint. A lot of what we’re developing and refining here – including learnings from our team – will inform how we grow our global healthcare operations, particularly across Asia.”
Ultimately, Toll Healthcare’s Australian division is helping shape the group’s broader healthcare capabilities, particularly as expansion continues in other regions. ■
Powerfleet’s AI system helps reduce warehouse incidents by integrating real-time safety data and analytics.
Warehouse and logistics environments in Australia are under growing scrutiny following a series of incidents involving industrial machinery. In 2023, the fatality rate for machine operators and drivers reached 8.3 per 100,000 workers – higher than the 4.8 per 100,000 general population recorded for the general on-road population.
Powerfleet, a global provider of internet of things (IoT) and artificial intelligence (AI) solutions, is working to help address these safety concerns. Headquartered in the United States with operations around the world, the company develops technologies that give businesses real-time visibility and control over mobile assets such as vehicles, industrial equipment, and cargo.
As part of its focus on workplace safety, Powerfleet has created integrated systems that combine machine access control, AI-enabled cameras, and impact detection.
These tools are designed to prevent accidents involving both equipment and pedestrians – particularly in high-risk environments like warehouses
and logistics centres.
“There are serious consequences –emotional, reputational, and financial,” says Brodie von Berg, Managing Director at Powerfleet APAC. “We’ve already seen a Victorian business fined three million dollars this year over a forklift-related fatality. This isn’t an outlier. These incidents are preventable.”
Brodie says one issue is the separation between road transport and warehouse safety systems.
“A lot of operations split their safety tools between on-road transport and warehouse environments,” he says. “That’s a problem when incidents don’t respect those boundaries.”
Powerfleet’s system combines machine access control, speed monitoring, pedestrian detection, and real-time operational data into a unified interface. Brodie calls this a “single pane of glass” approach.
“We manage machine access, conduct pre-start checklists, track speed and impacts, and scan for pedestrians – then feed all of that into one system,” he says. “The value is not just in detecting incidents but in
understanding how and why they happen.”
Cameras mounted on forklifts use edge-based artificial intelligence to detect nearby pedestrians. When someone enters a predefined proximity zone, the system alerts the operator and can intervene if needed.
“As soon as someone crosses that virtual fence, it will immediately alert the operator through highly visual and audible means,” Brodie says. “It can interact with the vehicle to restrict movement much faster than a human can react.”
The system also builds behavioural profiles based on operator performance. These profiles highlight how often a driver enters close contact zones with pedestrians.
“We aggregate that data and produce profiles showing how often operators come into close contact with pedestrians,” says Brodie. “That gives us strong behavioural insights and helps organisations provide targeted coaching.”
The platform also detects impacts with infrastructure such as racking, using industry leading algorithms
An integrated AI dashboard provides warehouse operators with real-time visibility across safety, asset, and operational data –forming a “single pane of glass” to monitor and respond to incidents. Images: Powerfleet
for increased accuracy.
“There’s downtime, there are investigations, there are costs,” Brodie says. “Detecting those incidents in real time helps reduce follow-on consequences.”
Brodie says the system can be used across both small-scale and large warehouse environments.
“We support combustion vehicles, battery-powered vehicles, and integrate into existing server or cloud infrastructure,” he says. “We scope, deploy, and then hand over a login and training materials.”
He says it is not necessary to remove existing systems to install the platform.
“We’re not trying to replace everything. They don’t need to rip out their existing tools,” says Brodie.“Our goal is to bring the information together, not dictate which sensors or equipment they use.”
The system also ingests data from additional IoT sources, such as temperature monitors, asset trackers, or third-party telematics.
“Our core business model is a wide array of ingestion. We can support a tremendous amount of IoT
devices sending data in,” says Brodie. “And then we have a wide array of integrations to systems coming out.”
Deployment is managed by Powerfleet’s internal team. Brodie says the aim is to keep the process simple for the customer.
“We make the complex simple,” he says. “We’ve got an expert team that scopes and deploys the solutions so the customer just logs in, gets some training, and starts using it.”
Brodie says that Australian businesses tend to prioritise the safety features over operational efficiency.
“In the US and Europe, we see more uptake around efficiency – machine usage, optimisation, that kind of thing,” he says. “Here, businesses are more focused on reducing safety incidents.”
While he does not name specific local clients, Brodie says the platform is already used by multinational organisations globally.
“There’s a growing maturity in terms of what companies expect from their safety systems,” he says. “It’s not enough to tick a box.”
Looking ahead, Brodie says future
development will continue to focus on integrating more device types and systems.
“The future is about connecting a much broader range of IoT devices –into the thousands – and making them visible through one platform,” he says.
“We’re not trying to compete with OEMs. What we’re doing is allowing customers to integrate their equipment and see it all together.”
Powerfleet employs around 2,500 people worldwide, including a longstanding presence in Australia.
“We have an amazing local team with an operation in Australia that’s over 20 years old,” says Brodie. “We understand the localised issues and challenges, and we have the service team to deliver on it.”
While the technology continues to advance, Brodie says its effectiveness ultimately depends on how it is applied.
“Technology alone won’t solve this,” he says. “But combining clear procedures, a single pane of glass, and proper training gives operators a better chance of making it through the day safely – and going home.” ■
Autonomous pallet movers offer cost, safety, and efficiency benefits for Australian warehouses and logistics leaders. Here’s how.
REACHY working within high-bay racking to complete pallet movements in a distribution centre.
For Australian warehouse and logistics leaders, the challenges are mounting. Labour shortages, rising costs, and increasing demand for faster, more consistent throughput are squeezing margins and putting traditional warehouse models under pressure. In this environment, automation is increasingly viewed as a practical solution. This article explores how Autonomous Guided Vehicles (AGVs) can help ease these pressures –offering measurable cost benefits and long-term operational value.
The shifting landscape of Australian logistics Australia’s supply chain is operating in a complex environment. Labour costs are rising, and reliable, skilled warehouse staff are increasingly difficult to recruit and retain. In 2024, the national labour shortage rate was reported at 78 per cent. High turnover, an ageing workforce, and limited uptake of warehouse roles by younger generations continue to affect workforce availability.
Average salaries for warehouse associates range from $60,000 to $70,000 annually, with hourly rates of $24 to $34. These figures, alongside overtime, recruitment costs, and inefficiencies tied to workforce churn, contribute to rising operational expenses. Manual handling also introduces variability, human error, and safety risks.
Industrial real estate scarcity is compounding these issues. As of late 2024 and early 2025, Australia’s national industrial and logistics vacancy rate remained below 3 per cent –
among the lowest globally. This has driven up rents, with prime net face rents growing 3.4 per cent nationally in Q4 2024. Construction costs have also increased, from $750 per square metre in 2020 to $1,250 in 2024, with some multi-level sites in Sydney reaching $3,000–$3,700 per square metre.
These property and labour pressures are driving a need to improve throughput per square metre. Embracing automation, particularly through AGVs, presents one pathway to meet this demand.
To understand the value of automation, it’s useful to examine the full cost of manual pallet movement. Beyond direct wages, operations must account for superannuation, insurance, workers’ compensation, breaks, shift changes, training, absenteeism, and variation in individual productivity. These factors all contribute to a fluctuating and often unpredictable cost per pallet move. AGVs offer a more consistent and transparent cost base. Key considerations include:
• Robot cost and depreciation: The initial purchase or lease, depreciation over five to seven years, and any residual value at the end of life.
• Operational costs: Including energy use, battery lifecycle and replacement, and regular maintenance under service contracts.
• Software and connectivity: Fleet management systems, software updates, and WMS integration are generally included with transparent pricing.
reduces long-term operating costs.
Compared to rising and unpredictable manual labour expenses, AGVs can deliver lower and more consistent per-move costs. In many applications, BALYO systems have achieved operating cost reductions of up to 80 per cent compared to manual handling.
In a warehouse moving just over 1,000 pallets per day across three shifts, the traditional model would require three forklifts and eight full-time operators, rotating across shifts. With an average annual cost of $60,000 per operator and $13,000 in indirect costs (training, turnover, and minor damage), the total annual labour cost would be about $584,000. Additional pallet damage can add another $25,000 per year.
An autonomous solution using eight REACHY robots, each with 360-degree safety features and 24/7 operability, would achieve the same throughput. The combined annual cost, including maintenance, is approximately $80,000. This represents an 84 per cent reduction in operating costs, cutting hourly spend from around $58 to $9.
Beyond cost savings: the strategic advantages AGVs also bring a range of operational benefits:
• Enhanced safety: Consistent movement patterns help reduce accident risks.
• Predictable operations: Continuous uptime supports steady throughput.
• Optimised space: Narrow-aisle capability can improve storage density.
• Inventory accuracy: Reduces picking and placement errors.
• Throughput and utilisation: Pallet moves per hour and operating uptime enable accurate forecasting of performance and efficiency.
BALYO offers a pricing structure designed for transparency and longterm value. For example, the REACHY forklift is tailored for autonomous pallet handling and high-bay storage. Its operating costs are defined over its service life, inclusive of maintenance. With the ability to perform consistently across extended shifts, a single REACHY can complete a large volume of pallet moves annually. This allows for precise calculation of cost per hour and per pallet move. Factoring in end-of-life residual value further
• Scalability: Easier to expand fleet capacity than workforce headcount.
• System adaptability: BALYO’s Robotic Engineering Services team can adjust fleet logic and software as operational needs evolve.
Your partner in futureproofing logistics
For Australian operators, AGVs are increasingly becoming part of a broader strategy to manage labour challenges and maximise facility performance. With defined cost structures, operational consistency, and integration support, BALYO’s autonomous systems provide a compelling case for automation in the modern warehouse. ■
Cypher Robotics and Ericsson combine autonomous drone systems with private 5G networks to streamline inventory management. Here’s how.
four years ago in North America, where Peter King, CEO and co-founder of Cypher Robotics, was involved in developing the first 5G-enabled drone flight with Ericsson.
“From early on, we recognised the value that private 5G could bring to our industry,” Peter says. “It’s not just about connectivity – it’s about building infrastructure that lets automation scale.”
That work has since expanded into the Asia Pacific region, where Ericsson’s ANZ team, led by Ian Ross, Head of Enterprise Private Networks ANZ for Enterprise Wireless Solutions at Ericsson, is advancing the use of private 5G to support highperformance, consistent and stable enterprise-grade wireless warehouse connectivity.
“We’re working with partners like Cypher Robotics to demonstrate how dependable, high-performance 5G networks can enable digital transformation in complex environments like warehouses, and overcome the common complaints of Wi-Fi,” says Ian.
enterprise controls the network including the radio spectrum used, and they are independent and separate from public networks.”
According to Ian, this provides a key advantage over traditional wireless setups.
“You can control the coverage, bandwidth and security. No one else is on your spectrum, and only your devices can connect. That’s vital for a warehouse running 24/7 automation,” he says.
Peter agreed, stating: “With 5G, we can transmit data in real time, run analytics while the robot is in action, and interact directly with other warehouse systems. That’s not possible with patchy Wi-Fi.”
Today’s warehouses often run multiple forms of automation concurrently – drones, autonomous mobile robots (AMRs), forklifts, and people moving through the same space. Without a shared communications layer, that complexity becomes a safety risk.
“Each robot has its own system, and
resources deterministically based on the importance of the device or the application – meaning every device gets the bandwidth it needs, when it needs it.”
This reliability is essential when split-second decisions are required to avoid collisions, delays or data loss.
“It’s not just about bandwidth, it’s about timing and predictability,” Ian says.
Another benefit of private 5G is the ability to support advanced use cases beyond inventory counting. Peter says some customers want drones to inspect racking or stream footage to different software tools for analysis.
“With strong connectivity, one video feed can serve multiple purposes, in real time.”
Ian noted that this capability underpins the development of digital twins –virtual representations of physical environments used for simulation, predictive maintenance and optimisation.
“You need huge volumes of real-time
A private 5G network enables real-time connectivity and data orchestration in highthroughput warehouse environments.
Image: Anucha/stock.adobe.com
obligations without over-relying on a fluctuating labour market.
“There’s no sign that labour challenges are going away,” Peter says. “And the cost of getting inventory wrong is only increasing.”
He continued to emphasise that the solution doesn’t just benefit the bottom line.
“It improves safety, reduces turnover, and allows staff to focus on highervalue work. It’s a win for everyone.”
Ian echoed the sentiment.
“Private 5G is about giving organisations control over their environment,” he says. “When you own the network, you can customise it to suit your needs, scale with your operations, support the technology that will define the future of logistics and do it ahead of your competitors.”
As warehouses grow in complexity and automation becomes the norm, partnerships like the one between Cypher Robotics and Ericsson can point to what’s next – a warehouse environment that’s smarter, safer, and always connected. ■
Ensure every asset and operator is protected, whether theyʼre navigating city streets or handling goods inside the warehouse. Our unified safety platform brings end-to-end data together in one system. It delivers real-time alerts and actionable insights to prevent incidents and maintain compliance. Drive a zero-harm culture from the road all the way to the rack.
As warehouse operations across Australia adapt to growing demand, labour shortages, and tighter delivery windows, the need for automation-friendly infrastructure is becoming more urgent. While robotics and software often headline industry discussions, structural components like racking systems are playing a critical role in supporting the next wave of warehouse modernisation.
In this context, racking suppliers are shifting their focus from conventional static systems to solutions designed for integration with automated storage and retrieval systems (AS/RS), CTU systems, and shuttle racking technologies. These include two-way shuttle cart systems and multi-level storage frameworks that allow goods to be moved efficiently within dense storage environments.
CH Racking & Displays, a manufacturer and supplier of industrial storage systems, is among those responding to this shift. The company specialises in customised warehouse racking solutions and offers design, engineering and installation services across a range of industries including logistics, retail and manufacturing. Its product portfolio includes pallet racking; mezzanine structures and automation-ready systems built to support AS/RS, CTU systems, and shuttle racking technologies.
“Integrators need confidence that the racking they’re working with won’t become a bottleneck,” says
Zhu, General Manager at CH Racking & Displays. “At CH Racking, we engineer systems to AS4084 compliance standards where applicable and provide engineered calculations to support safety and automation alignment. We’re often brought in at the design phase to work alongside integrators, ensuring the layout can support automation hardware without later modification.”
According to Jessica, these developments go beyond just accommodating technology – they reflect a broader shift in how warehouses are being planned and executed.
“We’re seeing more businesses design their racking around future automation plans, even if implementation is staged. The ability to retrofit or integrate with automated equipment later is becoming a standard consideration at the design phase,” she says.
To support this, CH Racking regularly collaborates with system integrators from early layout concepts through to installation sequencing, ensuring minimal delays in automation commissioning and greater downstream compatibility.
Warehouses in high-density industrial zones are increasingly constrained by both footprint and floor-to-ceiling limits. As a result, improving space
utilisation is a key objective, particularly in sectors where high stock turnover demands both rapid retrieval and scalable storage.
Two-way shuttle cart systems address this by increasing pallet density while maintaining rapid accessibility. By automating pallet movement within deep lanes, these systems remove the need for wide aisles and manual forklifts in certain zones, reducing both space requirements and operational risks.
Jessica notes that this technology is useful in warehouses with variable demand cycles.
“Where throughput is high but fluctuates, automation gives operators the flexibility to scale up activity without hiring additional labour or expanding their footprint,” she says.
A growing number of warehouse managers are rethinking infrastructure investment through the lens of interoperability. This means ensuring that racking systems, material handling equipment and warehouse management software can function cohesively.
AS/RS-compatible racking must be able to accommodate vertical lifts, shuttles or robotic arms, while also supporting real-time data tracking and automated workflows. This requires planning at both the physical and digital levels, especially where automation is intended to scale over time.
“Most of our clients aren’t automating everything at once,” says Jessica. “They’re looking for ways to future-proof their racking, so it doesn’t become obsolete when other technologies are introduced.”
This modular and incremental approach is becoming more common, particularly among 3PL providers and mid-sized distributors who want to adopt automation without committing to a complete operational overhaul.
Australia’s warehousing sector continues to report difficulties attracting and retaining skilled labour. In this environment, many businesses are using automation not only to increase productivity but also to reduce reliance on manual, repetitive or highrisk tasks.
By facilitating the use of shuttle systems and automated retrieval equipment, racking infrastructure can play a role in reducing physical strain on workers and limiting humanmachine interaction in high-traffic areas.
While full automation remains out of reach for many smaller operations, partial automation supported by compatible racking offers a realistic step toward higher throughput and safer workflows.
From a strategic perspective, the integration of automation-compatible racking is being seen less as a future capability and more as a near-term competitive requirement. Businesses that fail to plan for automation risk facing disruption, particularly as customer expectations for speed and accuracy continue to grow.
Jessica confirms that CH Racking is fielding more enquiries related to automation than ever before.
“There’s a clear trend toward smarter, more adaptable warehouse infrastructure,” says Jessica. “Even businesses that haven’t yet automated are asking questions about how their current racking will fit into a future state.”
As the pace of warehouse modernisation accelerates, the conversation around racking is shifting from static storage to dynamic systems that support broader digital
Speakers exchange insights during a MEGATRANS panel session focused on emerging technologies and freight innovation. Images: Prime Creative Media
Australia’s largest logistics and supply chain trade show is set to return in 2026, uniting industry leaders around the future of sustainable freight, logistics, and transport.
Australia’s premier logistics and supply chain event, MEGATRANS, will return to Melbourne in 2026, reaffirming its role as a national platform for innovation, collaboration, and strategic growth in the sector.
Scheduled for 16-17 September 2026 at the Melbourne Convention & Exhibition Centre, MEGATRANS 2026 is expected to draw thousands of supply chain professionals, industry leaders, policymakers, and innovators from across the region and beyond.
With its ongoing theme – The Sustainable Supply Chain of the Future – the 2026 edition will showcase cutting-edge solutions across freight and logistics, warehouse operations, transport technology, infrastructure,
materials handling, and digital supply chains.
Building on the momentum of previous shows, MEGATRANS 2026 will offer a multi-channel platform designed to foster connection and knowledgesharing across the entire supply chain. The event will feature:
• Exhibition – A dynamic trade show floor spotlighting new technologies, equipment, software platforms, and integrated solutions designed to advance operational efficiency and sustainability.
• Conference – A high-level speaker program featuring government representatives, business leaders, researchers, and innovators addressing key themes including
decarbonisation, infrastructure investment, freight resilience, workforce development, and emerging technologies.
• Careers Hub – A dedicated space linking students, graduates, and job seekers with employers across the transport, logistics, and warehousing ecosystem – helping attract and retain the next generation of talent.
Siobhan Rocks, Event Director for MEGATRANS, says the return of the show is timely, as Australia’s supply chain faces growing demands around resilience, sustainability, and digital transformation.
“MEGATRANS is more than just an expo – it’s where the industry comes to connect, collaborate, and shape what’s
next,” she says. “We’re excited to welcome back exhibitors, speakers, and partners for what promises to be our biggest and most impactful event yet.”
Opportunities now open Exhibition space is now available for booking, with early registrants receiving access to premium floor locations and targeted promotional support in the lead-up to the event.
Attendees gather during MEGATRANS, exploring safety and efficiency solutions for logistics and warehouse operations.
Exhibitors will have the opportunity to engage face-to-face with a highly targeted audience of decision makers and buyers looking for solutions to their operational challenges.
Previous editions of MEGATRANS have attracted strong participation from across road, rail, ports, infrastructure, warehousing, and e-commerce. The 2026 event is expected to continue this momentum, while integrating
new focus areas including green freight corridors, automation in lastmile delivery, and circular economy practices.
Organisers encourage early expressions of interest to maximise planning, branding, and content opportunities.
To enquire about exhibiting, attending, or speaking at MEGATRANS 2026, visit: megatrans.com.au ■
Supply Chain Week 2025 focused on long-term strategies, innovation, and talent development across Australia’s logistics sector.
In its fourth year held at the ICC in Sydney, Australia, Supply Chain Week 2025 brought together executives and professionals to address the dynamic trends facing supply chains, while also showcasing innovative models and ecosystems.
The three-day event offered multiple programs for organisations looking to navigate the complexities of the supply chain system. This included streamed sessions, panel discussions, roundtables, case studies and workshops. A cocktail reception and an exclusive fine-dining dinner also provided networking opportunities. More than 400 people came together to benchmark shared challenges across the industry. With delegates from inventory, supply chain, warehousing, operations, logistics, forecasting and transport, the event featured technology-driven solutions across
sectors including FMCG; manufacturing; retail; oil, gas and mining; health and pharmaceutical; home and living; construction; utilities; and government.
A focus on long-term solutions Navigating intense weather events, industrial relations issues and global trade tensions, the event delivered a consistent message: focus on long-term solutions to overcome persistent and emerging challenges.
One of the sessions on the first day explored the future of national freight and logistics, highlighting ways to strengthen supply chains and drive economic growth. The panel encouraged bold decision-making to support the sector moving forward.
Darren McNamara, Transport for NSW’s director strategy – freight, opened the session by stressing the importance of collaboration with
government in delivering national solutions.
“Transport for NSW increasingly understands the role that we need to play in improving the collaboration with all the jurisdictions our federal counterpart’s government to really get the right outcomes for the national supply chain,” says Darren.
He says the freight logistics industry contributes around $74 billion to the NSW economy.
“It’s really important we play an increasing role in finding those national solutions,” he added.
Darren cited the development of the National Freight & Supply Chain Strategy by the Australian government as a step towards boosting productivity. While the previous approach saw jurisdictions working on nearly 250 separate initiatives, the new strategy aims to consolidate efforts into four
primary focus areas through a more collaborative model.
“If we work better with jurisdictions in our federal counterparts, we will certainly be in a much better state to achieve productivity,” says Darren.
While collaboration with government is critical, executive leader regulatory reform for the National Transport Commission, Aaron de Rozario, warned that outdated methods threaten the industry’s future workforce.
“We have massive shortage on truck drivers,” says Aaron. “A lot of workers are going to be hitting retirement age, and we are not getting young people into those industries.”
Although automation is essential for the future, Aaron observed hesitancy among organisations to embrace new technologies. He urged regulators to focus on overseeing systems rather than specific technologies to foster better decision-making and safer transport.
“Transport is an area where policy makers are traditionally very conservative,” he added. “We’ve got to regulate the system that vehicles operate in, the system that is making decisions. That is where we’re going to potentially get some of the great productivity benefits going forward.”
On the second day, director of Australasian Supply Chain Institute (ASCI) Inderjeet Virdi opened an impromptu panel to discuss the future of supply chain in the next 24 months.
Peter Bainbridge, raised concerns about
the stagnating talent pool.
“Getting young people into supply chain, to me, that’s a huge gap for us,” he says. “No matter what skill you have, there’s a role for you in supply chain and I don’t think we push that hard enough.”
Peter pointed out the absence of supply chain modules in business or commerce degrees and the general lack of awareness and interest of operations careers in school.
Massimo Giannetto, global demand and integrated business planning director at AkzoNobel, highlighted how Australasian Supply Chain Institute is addressing the talent gap.
“One of the key areas of focus is the capability development for the future,” he says.
Development programs that promote supply chain as a viable career path play a key role in building circular business models. Peter emphasised how inclusive recruitment practices are essential for the sector’s future.
“In our area of operations, we’ve got not only the United Nations, but we also have a lot of different styles of people in different ways of thinking,” he says. “I think that’s a lesson for us not to narrow down on how we recruit.
“We need to allow the opportunities in our companies to learn different things and experience different parts of the supply chain.”
Being strategic, not operational
According to Massimo, artificial
automation becomes more widespread, there’s a growing need for companies to align with long-term strategic goals.
“The operational side of most jobs right now in the supply chain will be more automated,” he says. “That was a challenge from a standpoint where we see supply chain jobs evolving in the mid to long-term. We have to be more strategic and less operational.”
He encouraged businesses to think ahead and be responsive to the fluctuating trends. This can include developing new technologies or improving communications. By creating space for long-term opportunities, there will be opportunities for a secured future.
Massimo links back to how such strategic develops will enable the next generation to succeed in the supply chain industry.
“Automation is destroying the old jobs we used to know,” he says. “The new generation should have a more strategic approach in order to succeed as a supply chain professional.”
To close the conference, director Inderjeet Virdi remarked, “Every disruption gives rise to new innovation.”
Supply Chain Week 2025 demonstrated Australia’s resilience and determination to tackle supply chain challenges through its informative sessions and open dialogue.
As new trends accelerate, businesses must adopt a forward-looking mindset that offers not only short-term
Demonstrate your ability to optimise inventory levels, improve forecasting, and master scheduling tools.
Resilience and agility are what make supply chains thrive. By earning the APICS Certified in Planning and Inventory Management (CPIM) designation, you’ll develop competencies to work across all supply chain functions
Tsuccessfully. In addition, you’ll know how to effectively manage risks and disruptions and leverage technology to streamline processes.
You can choose between self-study or joining our instructor-led course, which will begin on 26 August 2025. ■
ap the power of your supply networks to streamline processes, enhance collaboration and boost the bottom line.
Now more than ever, supply chains are essential for businesses to run, consumers to get the goods they need, and society to function. APICS Certified Supply Chain Certification (CSCP) is the playbook that helps understand and deliver this critical process.
The comprehensive program covers everything you need
to know across the global supply chain, from suppliers to customers. Earning your CSCP designation shows you have the skills to prepare for and overcome disruption, manage risk, and evaluate and implement modern supply chain technologies.
You can choose between self-study or joining our instructor-led course, which will begin on 6th August 2025. ■
Through interactive sessions, attendees examine cross-functional accountabilities and practical approaches to forecasting challenges.
ASCI’s forecasting course supports supply chain teams in applying realworld models to balance service levels with inventory efficiency. Images: ASCI
Join ASCI’s upcoming Forecasting and Demand Management 2-Day Course to improve your forecast accuracy with less forecasting effort, which will take place on 19-20 August 2024.
This workshop will provide you with a step by step approach to achieving improvements in your forecasting process, the mistakes to avoid and sure fire approaches that will reduce your forecasting effort.
Accountabilities and cross functional links will be discussed to enable you to assess the quality of your
current processes against world class checklists. Options on “where to meet the customer” will also be addressed, including the strategies associated with setting safety stocks, product offerings and a simple approach to simulating stock levels.
Classes are conducted daily, from 9 am to 5 pm Sydney Time, totaling 16 training hours. Participants will join via Zoom.
ASCI members can register for $1,950, while non-members can register for $2,350. ■
By Sue Tomic, Chair, SCLAA | Chief Strategy Officer Board Advisor
f you’ve ever worked in operations, you know the satisfying rhythm of a conveyor belt running just right –smooth, predictable, efficient. Until one thing slips. A box misaligns, a sensor misfires, and suddenly the whole system backs up.
That’s how AI is starting to feel.
What started as a fringe innovation is now stitched into everything – our inboxes, workflows, dashboards, and devices. Gmail drafts replies before we’ve thought them. Meta decides what content we care about. Copilot finishes our thoughts before we’ve had them. And in supply chain and logistics? AI is now forecasting demand, optimising routes, managing supplier risk, even screening job candidates.
It’s fast. It’s everywhere. But is it trustworthy?
This question became more urgent as AI developers themselves called for a moratorium – a moment to take stock, ask tough questions, and put a few safety measures in place before AI advanced even further into
critical systems.
But little in the way of cohesive principles and laws has eventuated so far.
We’ve seen some movement internationally – just not the kind that gives confidence.
The EU has led the charge with its Artificial Intelligence Act (AI Act): a comprehensive legal framework that regulates AI development and use within the EU, with a focus on trust, safety, and ethical considerations. It categorises AI systems based on risk and imposes mandatory requirements for developers, including those of high-risk AI. Some provisions are already in force; full enforcement is expected by 2026.
The US, on the other hand, is doing the opposite. Tucked inside the “Big Beautiful Bill” is a clause that proposes a decade-long moratorium – not on AI development, but on most state-level attempts to regulate it. In other words, it’s a green light for AI innovation with the guardrails deliberately held back.
So globally, AI regulation is disparate, with more holes than Swiss cheese.
We are at the end of the runway, and the truth is: we’re no closer to having the answers we need. There’s still no enforceable regulation. No global mandated standards. No agreed-upon principles for ethical AI use and no emergency stop button if things go off track.
The conveyor belt hasn’t stopped. In fact, it’s speeding up. And we’re still hoping nothing breaks.
Why this should concern supply chain and logistics
This industry runs on precision. We live and breathe process optimisation, predictive modelling, automation, and control. And AI promises to supercharge all of that. But it also introduces a new layer of fragility – one that hides behind an interface and speaks in probabilities, not accountabilities.
Let’s call it what it is:
• Opaque logic: We can’t trace how
many AI systems reach their conclusions. For a sector built on audit trails, security of ownership as goods and services move through the supply chain-that’s a flashing red light.
• Flawed inferences: AI doesn’t “know” context – it guesses. That’s risky in dynamic supply chain environments where nuance matters.
• Over-reliance: When something works well, we relax. But what happens when the system misfires, and no one’s watching?
Picture this: your AI tool over-predicts freight volume and you lock in too much warehousing. Or your AI-driven supplier screening tool deprioritises a trusted partner based on incomplete data. You don’t just lose efficiency - you lose trust, money, and relationships.
These aren’t hypotheticals. They’re operational risks. Financial liabilities. Reputational hazards. And they’re already happening.
This isn’t about being anti-tech. It’s about being pro-responsibility.
What needs to happen before the line breaks
No one’s saying we put the AI genie back in the bottle. But blind adoption? That’s just bad business.
If any industry knows how to manage complex systems with tight tolerances, it’s this one. We should be leading the conversation on what responsible AI actually looks like in practice. Here’s where to start:
• Sector-specific standards: One-sizefits-all frameworks won’t cut it for freight variability, port disruptions, or demand fluctuations.
• Transparency: If AI is making decisions, we deserve to know how –and where it can go wrong.
• Human oversight: AI can assist. It cannot be the final voice – especially where safety, compliance, or strategic relationships are concerned.
• Contingency protocols: What’s the playbook when AI fails? If you don’t have one, that’s your first task. AI is not inherently good or bad; it’s powerful. But power without principle?
That’s a system jam waiting to happen. As leaders in logistics and supply chain, we don’t just manage flow – we manage risk. So let’s act like it.
Let’s lead the conversation to build the right frameworks, ask the hard questions, and make sure we’re not outsourcing our judgement to an algorithm or machine that doesn’t understand the stakes.
Because when the conveyor belt breaks, it’s not the AI that wears the cost – it’s us. ■
Stay ahead of the curve in logistics, warehousing, and supply chain management. MHD Supply Chain Solutions Magazine o ers the latest trends, thought leadership, and actionable insights you need to drive your business forward.
Unlock the ideas, information, and strategies that are shaping the future of supply chain management—only available to MHD subscribers. Don’t miss out on the critical insights that can give your business the edge.
•One-year subscription: $99 for 11 issues
•Two-year subscription: $179 for 22 issues
•Auto-renew subscription: $95 per year Scan to subscribe
Contact: subscriptions@primecreative.com.au
Visit: mhdsupplychain.com.au/subscribe/
Linde Material Handling Australia is known for developing high-performance materials handling solutions, and the Linde 1251 Electric range is no exception. These counterbalance forklifts, part of the X Series released by Linde, are the first electric forklifts whose performance and durability mean they are ready for demanding applications and can serve as a genuine alternative to traditional IC trucks. Powered by a 90V lithium-ion battery, they offer clean, zero-emission operation and deliver up to 20 per cent faster lifting and lowering speeds than the industry standard. The 1251 X Series delivers reliable, compact powerhouses for warehouse operations.
Looking for a WMS that grows with your business? Meet .wms by Thomax – the cloudbased warehouse management system designed for real-time visibility, scalability, and ease of use. Whether you’re managing complex omni-channel operations or integrating with automation and robotics, .wms delivers intelligent agility without the hassle. With open API connectivity, activitybased billing, and seamless upgrades included, .wms takes the complexity out of warehousing. Trusted by major warehouses, it’s proven to boost performance fast – sometimes in just weeks. Break free from rigid systems.
The adaptable Freestanding Car Hoist from Southwell Lifts & Hoists is the ideal solution for commercial and residential needs, particularly multi-level car yards. With a robust 3,000kg capacity, this ride-on hoist offers an advantage for leased properties. Unlike permanent installations, this Australian-designed and manufactured hoist can be easily dismantled, moved, and reinstalled, making it a smart, long-term investment for businesses operating across multiple locations. Available in both 2 and 3-level configurations, it’s engineered for safety and efficiency, complying with all relevant Australian standards.
The Port Authority of New South Wales has officially appointed John McKenna as its new CEO. John, who joined the organisation in 2011 and served as Chief Customer and Commercial Officer since 2020, had been Acting CEO since December 2024. Chair David Marchant praised John’s leadership and vision, citing his deep understanding of the organisation. In response, McKenna said he was honoured to lead the team, which plays a crucial role in supporting trade, tourism, and 24/7 port operations across the state.
Ontime Delivery Solutions, has announced several new executive appointments, including the appointment of a new National People & Culture Manager, Ewa Ellis. Ewa is an executive with experience across Australian and multinational companies including the University of Melbourne, Assa Abloy Group, Telstra Super, and Target Australia. Walter Scremin, CEO of Ontime Delivery Solutions, says Ewa’s experience would be invaluable as the company continues to grow its presence nationally.
“Ewa brings a wealth of experience in HR to Ontime, and a great understanding of how the right people and culture can translate to performance,” he says. “Ewa combines professionalism with a passion for people and will be a great asset to our growing team.”
Extolla has welcomed Paul Stringleman as Senior Consultant, bringing over 25 years of global experience in high-performance automated logistics systems. Paul has delivered innovative automation solutions across retail, eCommerce and transport, including goodsto-person systems, robotic picking, and high-bay storage. Known for his technical depth, commercial acumen, and creative thinking, Paul helps clients reimagine automation to achieve measurable gains in productivity, efficiency, and scalability. At Extolla, he plays a key role in guiding clients through complex automation decisions to unlock long-term supply chain value and to rethink what’s possible.