

Appetite waning for insurers in waste industry
By Inside Waste
NATURAL DISASTERS such as floods and bushfires, as well as those caused by human action (or inaction) such as battery fires in rubbish trucks and MRFs, are on the increase. In the case of the former, these have mainly been due to an array of weather patterns blamed on climate change. In the case of the latter there has been a proliferation of lithium-ion batteries designed to drive innovative technologies that have appeared over the past decade.
What that has meant for the resource recovery sector in increased risks. This is turn leads to either an increase in insurance premiums, or insurers unwilling to issue policies due to risk factors being too high. This has a knock-on effect of investors unwilling to put monies into new facilities, which in turn affects a council or other third-party’s ability to collect and recycle resources and dispose of waste.
At a recent symposium held by


the Victorian Waste Management Association, Steve Richards, a Senior Account Manager for insurance advisory firm RSM Group, outlined some of the challenges facing the industry when it comes to insurance. He was joined by Alan Brett, Head of Commercial Underwriting at Australasia Underwriting (AU).
Richards said that RSM has tried multiple approaches to present the waste industry in different ways to make it more appealing to insurers, but the “vast majority of the insurance market doesn’t really have an appetite” for the sector.
“[That lack of appetite]is coming from the reinsurers,” he said. “It’s not something that we think will change anytime soon, however we are seeing some capacity increase. Property valuations continue to be absolutely critical and those are really based on under insurance where you get penalised for a loss. Then there is the increased cost of construction that’s come through from restrictions and pressures on the
supply chain from COVID, which we’re still recovering from.”
He said that risk management is the absolute gold standard. If a company is managing a risk, and it’s willing to demonstrate how it can be managed, then it needs to convey that to a specialist broker.
Another impact on premiums, according to Richards, is the El Nino weather pattern. It usually means warmer and drier conditions with minimal rainfall, which can lead to an increased risk of bushfires around the country. And if bushfires do start having an impact, then premiums will increase.
There is also the impact of social license. For example, if you put in a plan to get a resource recovery plant up and running, what are the risks of it being rejected by councils or town planners, or whoever has a say in whether a project can go ahead? Again, this may impact on a business’s ability to rebuild its operations due to a chance in society’s expectations.
(Continued on page 14)
By: Mike Ritchie and Conor Mackenzie, MRA Consulting Group
There is an active debate in the Australian recycling and packaging sectors about the design of our Container Deposit Schemes. The key issues include:
1. What should the rebate value be?
2. Should the schemes include wine and spirit bottles (glass) like QLD has just announced?
With the introduction of the Victorian and Tasmanian schemes we will for the first time have a national container collection arrangement.
We want to talk to the rebate value in this article. What is the right value for the rebate? It is currently 10 cents.
History
South Australia introduced its CDS scheme in 1977. It has run continuously ever since. It started with a 5c bottle return rebate, which was then increased to 10c in September 2008.
When it was introduced, the value of 5c in 1977 was about 35c today (2024) based on RBA inflation rates.
Of course, given it was a fixed 5c, its value to the person returning a bottle decreased each year due to inflation. Think of the effective rebate value as the “pulling power” or gravitational pull, of the rebate. The “pulling power” decreases over time due to inflation, until it is lifted again by regulation.
If we plot the effective rebate value in 2024 values, against the capture rate of eligible containers, we can see what sort of impact the value of the rebate has on people’s behaviour.
(Continued on page 18)

Bush fires can have a huge impact on waste industry premiums. Image: Toa55/shutterstock.com.

3-Stage Grinding Process
Provides Faster Reduction
Astec - Peterson's powerful up-turn 3-stage grinding process provides better fracturing of material and a more consistent product, giving you just the product your buyers are looking for.
The Impact Release System
Protects Your Investment
Astec - Peterson's patented Impact Release System's air bags provides uniform grinding and protection from contaminated feedstock, a feature unique to Astec - Peterson grinders.
Land clearing, mulch, compost, asphalt shingle tiles, scrap wood, biomass, green waste-we can handle it am
www.komatsuforest.com.au

The Impact Cushion System
The Second Line of Defence
Urethane cushions and shear pins help protect the mill from catastrophic damage in the event of a severe impact from contaminants in the feedstock.
Astec - Peterson offers horizontal grinders from 433-839 kW, offering grinding solutions with output at the lowest cost per ton. Visit us at www.astecindustries.com and see why we have been leading the industry for over 35 years!

2710D Horizontal Grinder

5710D Horizontal Grinder
6710D Horizontal Grinder
Largest
Chief Operating Officer
Christine Clancy christine.clancy@primecreative.com.au
Managing Editor
Mike Wheeler mike.wheeler@primecreative.com.au
Brand Manager
Chelsea Daniel chelsea.daniel@primecreative.com.au
Design Production Manager
Michelle Weston michelle.weston@primecreative.com.au
Art Director
Bea Barthelson
Client Success Manager
Glenn Delaney glenn.delaney@primecreative.com.au
Head Office
Prime Creative Pty Ltd
379 Docklands Drive
Docklands VIC 3008 Australia p: +61 3 9690 8766 enquiries@primecreative.com.au www.insidewaste.com.au
Subscriptions +61 3 9690 8766 subscriptions@primecreative.com.au
Inside Waste is available by subscription from the publisher. The rights of refusal are reserved by the publisher
Articles
All articles submitted for publication become the property of the publisher. The Editor reserves the right to adjust any article to conform with the magazine format.
Copyright
Inside Waste is owned by Prime Creative Media and published by John Murphy.
All material in Inside Waste is copyright and no part may be reproduced or copied in any form or by any means (graphic, electronic or mechanical including information and retrieval systems) without written permission of the publisher. The Editor welcomes contributions but reserves the right to accept or reject any material. While every effort has been made to ensure the accuracy of information, Prime Creative Media will not accept responsibility for errors or omissions or for any consequences arising from reliance on information published. The opinions expressed in Inside Waste are not necessarily the opinions of, or endorsed by the publisher unless otherwise stated.
Are waste facilities uninsurable?
Insurance is a necessity in the resource recovery sector, but getting coverage is getting harder. In some cases, insurers are baulking at offering any coverage. In this month’s issue, we hear from two insurance experts on what criteria insurers look at when covering infrastructure.
Why is there a reluctance to insure infrastructure in the resource recovery sector? There are a couple of glaring issues. One is the increase in unreliable weather patterns. Over the past couple of decades, the La Nina and El Nino weather phenomenon have meant there has been an increase in bushfires and floods in Australia. The other is the proliferation of lithium-ion batteries. As with any business, insurers are around to make money for their shareholders, not to be anyone’s friend. Risk is key to any decision they make. The knock-on effect of this?
Investors are reluctant to lay out capital to build new facilities.
Then there is the WorkCover aspect when it comes to the safety and health of staff. The waste/resource recovery industry has a plethora of jobs where safety is a critical aspect of the job.
Our two experts outline insurer

expectations and some of the mitigating scenarios that need to be addressed when heading into the insurance market.

edition is by Anne Prince, a doyen of the NSW resource recovery sector, who believes we are in for a rude awakening in the resource recovery targets. This will be of no surprise to anyone in the industry, but what makes Anne’s piece so compelling is the data that has been collected to show bureaucrats just how far away we are from meeting the targets. It is a comprehensive data set and is depressing reading. If anything, it might send a reality check to the public servants that make the decisions and set the targets.
Finally, the August/September issue is home to our popular Consultancy Registry. This registry has an array of consultants from around the country spruiking the different arenas in which they have expertise. As with last year, we have divided them into their different states, in the hope that this will make it easier for readers to use when it comes to researching companies that can meet their needs.
Until next time, good reading.


KIVERCO PS122 PICKING STATION
• 4 bay sorting - Recovers clean stone, wood, paper, plastics, card or other recyclable materials at the option of the operator
• Combines air separation, magnetic separation, and manual sorting in one compact unit
• Adjustable belt speed - 1200 mm wide picking belt adjustable to suit waste material and desired recovery required
• The hydraulic jack leg support offers rapid set-up and transport



Renew IT facility opens
A COLLABORATION between UNSW Sydney’s Centre for Sustainable Materials Research & Technology (SMaRT) and IT asset management company Renew IT has begun turning discarded hard plastics into 3D printer feedstock.
A UNSW-invented Plastics Filament MICROfactorie Technology module has been installed at Renew IT’s Sydney warehouse in Lane Cove, Sydney.
“Commercialising our Plastics Filament MICROfactorie Technology has taken a lot of time and effort, but it is a sustainable waste, recycling and manufacturing solution. We’re turning the hard plastics found in all modern electronic hardware but not subject to conventional recycling methods, into feedstock for a booming sector,” said UNSW SMaRT Centre founder and director, Professor Veena Sahajwalla.
“Filament is almost entirely imported to Australia and made from petrochemicals, so being able to make it locally from used plastics also reduces the environmental impacts from global freight. 3D printing is a wonderful technology enjoying rapid uptake but the tragedy is
until now 3D printing has been reliant on virgin plastics.
“These Plastics Filament MICROfactories have the potential to revolutionise 3D printer filament creation. I look forward to a time when 3D printing feedstock is sourced exclusively from recycled plastics,” she said.
UNSW Vice-President Societal Impact, Equity and Engagement, Professor Verity Firth said UNSW’s partnership with Renew IT has the potential to create genuine, large-scale change.
“The combination of Prof. Sahajwalla’s pioneering science and Renew IT’s commercial expertise and financial commitment can accelerate genuine change. This industry partnership is an exquisite example of UNSW’s commitment to societal impact,” she said.
UNSW Sydney is developing a Societal Impact Framework through which it seeks to maximise progress in environmental sustainability and resilience, social cohesion, health, and wellbeing, and economic prosperity.
“This venture addresses two wicked
issues,” said Renew IT CEO and founder James Lancaster. “Not only does it reduce virgin plastic production by creating 3D printing filament from waste items but it also stops hard plastic ending up in landfill.
“Electronic goods like televisions, computers and printers are being produced in ever-increasing numbers and often with increasingly short life-cycles, when they do reach end of life, the waste industry’s solution has been to deliver them to landfill.
“Dispatching hard plastics to landfill is
not a solution that sits easily with me. To re-purpose that plastic into a new product that’s increasingly in demand and which we can sell at a competitive price is a beautiful solution.”
If 3D printing feedstock can be competitively produced by recycling plastic, we shouldn’t be producing it with virgin materials, he said. By recovering high-quality plastics from e-waste for remanufacturing we can help organisations lower their Scope 3 emissions and boost local manufacturing.




Renew IT founder and CEO James Lancaster and UNSW SMaRT Centre founder and director Professor Veena Sahajwalla. Image: UNSW.
The Impaktor 250 evo is the perfect combination of shredder and crusher. Its compact dimensions, low weight, and quick setup times make it a game changer in waste processing efficiency.
For those interested in sustainable waste management, explore the possibilities with the ARJES Impaktor 250 evo.

E: sales@triconequipment.com.au www.triconequipment.com.au









Waste Expo offers learning opportunities for all

BSV Tyre Recycling Australia Pty Ltd Convicted and Penalised for improper Storage of Tyres at its Facility in Revesby, NSW
BSV Tyre Recycling Australia Pty Ltd (“BSV”) has been prosecuted by the Environment Protection Authority (“EPA”) for ten offences of contravening an environment protection licence (“licence”) that were committed in 2022. The prosecutions were brought because BSV stored waste tyres and waste tyre products in contravention of its licence at its facility in Revesby, NSW. The offences occurred on 30 March, 10 May, 31 May and 26 July 2022, respectively.
Since this time, however, BSV has changed ownership. The offences were committed by its previous directors. Moreover, since the change of ownership BSV has complied with the terms of the licence.
Waste tyres and waste tyre products represent a fire hazard if not stored in a proper manner. If waste tyres and waste tyre products catch alight, they are capable of causing actual harm to the environment. In this case, although no fires occurred, the offences caused potential harm to the environment. This included potential harm to air quality, nearby land and waters, human health, and property on neighbouring premises.
On 24 June 2024, the Land and Environment Court of NSW convicted BSV of ten offences of contravening an EPL and ordered BSV to:
(1) pay a monetary penalty totalling $161,200;
(2) pay the EPA’s costs in the sum of $45,000; and
(3) cause this notice to be published at its own expense.
WASTE EXPO Australia is one of the largest gatherings of waste management and resource recovery professionals in Australia.
There’s a reason for this. Behind the scenes, an advisory board brings together stakeholders from across the resource recovery, recycling, and waste industries. Together, they bring experience in a range of sectors ensuring the expo remains at the forefront of challenges and opportunities.
Michelle Mandl, general manager of communications, customer, and engagement with TOMRA Cleanaway, says evolving due to customer feedback is one factor behind Waste Expo Australia’s longevity and success.
On the advisory board for the past three years, Mandl says the expo has a strong national presence because of its curated conference program, plus an expo floor with more than 120 industry suppliers, most of who are at the cutting edge in their respective fields.
“Waste Expo Australia draws diversity from across Australia, and it affords fantastic learning and development opportunities,” Mandl said.
“Being co-located with All Energy Australia gives it another dimension for delegates to engage. That’s becoming more relevant as the renewable energy and waste sectors integrate.”
Staying relevant is vital, says Erin Ford, senior brand and marketing manager for Repurpose It. She says
board members continue to question industry trends, areas of concern, innovations, or gaps.
Case studies also play a central role in showing attendees what is, and can be, achieved within the industry.
“The expo is an area to learn and share knowledge,” Ford said. “Case studies can really step it up. They can show people the impact a company or technology is having.”
So, what does the 2024 event have in store?
Plastics, batteries, and the circular economy continue to be important.
“The number of abstracts that focused on plastics highlights that they are a huge area of concern,” Ford said.
“With single use plastics, we are trying to change embedded behaviours. We’re improving, but it’s still a big issue. And we have massive issues with batteries across all waste streams.
“The conference program will provide some insight into the challenges and what the industry is doing to address them.”
The expo has achieved 27 per cent visitor growth since the 2022 event. In 2023, more than 3500 professionals attended across the two days, putting exhibitors face-to-face with potential customers from Australia and overseas.
Attendees include local, state, and federal government, waste service providers, consultants, engineers, technology and equipment suppliers, project developers, facility managers and landfill owners/operators.
Ford said the cross-section of attendees is a drawcard, providing exhibitors with the chance to engage with people they would not normally see. She believes crowd numbers are bolstered because the expo is free to attend.
“It removes the financial barriers that could stop some people from attending,” she said. “As exhibitors, Repurpose It makes a lot of connections through the expo.
“Education is a big part of Repurpose It, and the expo gives us a chance to highlight what we do while listening to the consumer market.
“Nothing beats face-to-face business. Whether you are already in the industry, new to the market or expanding in it, Waste Expo Australia provides access to key decision-makers.”
The 2024 Waste Expo Australia, to be held at the Melbourne Convention and Exhibition Centre (MCEC) from 23-24 October, will focus on advancing toward sustainable resource recovery.
Local and international suppliers, including representatives from Ireland, Germany, France, and Japan, have confirmed their attendance. Exhibitor and sponsorship opportunities are still available.

The Australian Waste Expo has a strong national presence because of its curated conference program.

Clearing the way: Komatsu Waste Spec Dozers
Built for productivity and efficiency
The waste processing industry requires purpose-built equipment for moving highly variable materials. Komatsu creates machines and solutions designed specifically for the difficult terrain and materials involved with handling waste. Our advanced Dozers equipped with smart technology, are engineered for productivity to support your goals of a zero-harm environment.















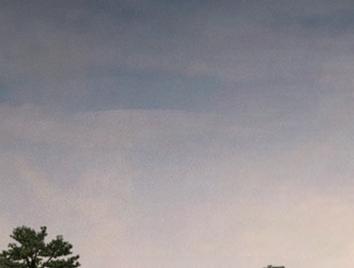




































From the CEO’s desk
The answer is product stewardship regulation







Environment Ministers will meet for the second time this year on 7 December, following the first 2018 Meeting of Environment Ministers (MEM) in April, which was in part a response to the import restrictions driven by China’s National Sword Policy and the effects this policy has had across the Australian waste and resource recovery (WARR) industry. Key decisions derived from the April MEM include:
Having just finished the 2024 ENVIRO circular economy conference in Brisbane, it struck me how loud the recurring themes were that we heard over the two days. Three in particular stood out – economics (imagine circular economy actually being about economics), regulation and leadership. All three are vital to successfully transitioning to a circular economy in 2030. However, when it largely comes to policy in this area we are severely lacking.
Early on day one, Richard Denniss presented me with a real ‘aha’ moment when he said fundamentally economics is the efficient allocation of scarce resources. After the shudder from remembering first year university economics class, I couldn’t help wondering why we do not talk more about this – and why on earth we do not act more like this in Australia. Yes, Australia is the lucky country, but our luck is not separate or distinct from the luck of the planet generally. And as Jill Riseley correctly peppered us with stats from the most recent Circularity Gap Report about the over consumption of the planet’s finite resources and the falling circularity rate of materials, frustration simply grew in the room about the lack of leadership we are seeing in Australia (despite all the rhetoric).
•Reducing waste generation, endorsing a target of 100% of Australian packaging being recyclable, compostable or reusable by 2025, and developing targets for recycled content in packaging.
• Increasing Australia’s domestic recycling capacity.
• Increasing the demand for recycled products.
• Exploring opportunities to advance waste-to-energy and waste-to-biofuels.
•Updating the 2009 Waste Strategy by year end, which will include circular economy principles.
It is time to take stock and examine what has been achieved since these decisions were announced. Now, seven (7) months may not seem like a long time, however in that time we have seen further markets close (Malaysia, Indonesia, Vietnam) and if you are an operator under continued financial stress, seven (7) months could make or break you.
As the United Nations states, some 50 per cent of global greenhouse gas emissions and 90 per cent of biodiversity loss and water stress is caused by resource extraction and processing – and as the Ellen Macarthur Foundation says up to 80 per cent of a product’s environmental impact is influenced by decisions made at the design stage. Quite simply we need to use fewer resources for longer.
How can we do that? Well, other than buying less, we can regulate more. And the most obvious and arguably effective way to do this is through product stewardship.
We all know the market will not fix itself and no matter where you sit in the supply chain, you will hear the consistent call for certainty and the need for a level playing field. To create the market conditions for the desired circular economy, we need regulation – but there appears to be complete reluctance to do this at scale.
Product stewardship means producers taking primary responsibility (including financial and operational) for minimising the environmental and human health impacts of products they put on the market, by implementing various actions across the entire product lifecycle. It provides a clear pathway for businesses and governments to operationalise circular economy objectives by designing out waste and pollution. It also helps keep products and materials circulating and restoring the environment, and let’s be clear – it must go well beyond the nebulous language that typically accompanies claims and pledges about circularity.
Following the April MEM, we have had three (3) states step in with varying degrees of financial assistance for industry (councils and operators). This should be expected considering almost all states (except Queensland and Tasmania) have access to significant waste levy income each year. On the eastern seaboard, Victoria has approximately $600 million in waste levy reserves in the Sustainability Fund and NSW raises more than $700 million per annum from the waste levy. There is certainly no lack of funds that can be reinvested into our essential industry.
Funding helps but as we know, the money goes a much longer way with Government support and leadership, as well as appropriate policy levers.
VICTORIA
Victoria has arguably been the most active and earnest in supporting the industry post-China, with two (2) relief packages announced to support the recycling industry, valued at a total of $37 million. The Victorian Government has also gone above and beyond all others states by announcing it would take a leadership role in creating market demand for recycled products.
When South Australia’s container deposit scheme began in 1977 it was one of only a handful of product stewardship schemes worldwide. By 2000, when Australia’s next major product stewardship scheme (for oil) was established, there were around 100. And there were about 400 in 2016 according to the OECD. While one Australian state was an early adopter of product stewardship, we are now being left behind globally.
SOUTH AUSTRALIA
For example, product stewardship regulations for packaging were introduced into Europe and Australia in the late 1990s. Europe was guided by the EU Packaging
Government announced a $12.4 million support package comprising $2 million of additional expenditure, $5 million additional funding for a loan scheme, together with targeted funding from the Green Industries SA budget. The Government has also offered grants for recycling infrastructure.
NEW SOUTH WALES
At first glance, New South Wales’ eye-watering $47 million recycling support package was heralded as the spark of hope industry needed. However, on closer inspection, the bulk of this package that was funded via the Waste Less, Recycle More initiative and therefore the waste levy, was not new, making it very difficult for stakeholders, including local government, to utilise the funds as they were already committed to other activities. Some of the criteria proposed by the NSW EPA also made it challenging for industry to apply to these grants. On the plus side, efforts are being made by the NSW Government to stimulate demand for recycled content through the intergovernmental agency working groups that have been established, though no tangible increase in demand or facilities have developed… Yet.
QUEENSLAND
Directive, which identified back then the growing problems of packaging waste, consumption of virgin non-renewable materials, the growing costs to government of waste management and the environmental and health impacts of hazardous components. Australia was guided by the National Environment Protection (Used Packaging Materials) Measure (NEPM). More than 25 years later, one has moved forward with a powerful new framework, and another has struggled to meet targets set.
Product stewardship shifts the economic burden of products and their impacts away from governments and the broader community to the producer and user. This increases the likelihood of genuine responsibility and investment by the private sector into activities to prevent and reduce waste, and increase lifecycle (eg design for reuse and repair), given the economic burden is placed squarely on those that benefit most from the products existence.
industry however the Queensland Government has embarked on the development of a waste management strategy underpinned by a waste disposal levy to increase recycling and recovery and create new jobs. The State will re-introduce a $70/ tonne landfill levy in March 2019. There are also strong attempts to use policy levers (levy discounts and exemptions) to incentivise the use of recycled material and make it cost competitive with virgin material. However, little has been done to establish new markets and Government has not taken the lead in the procurement of recycled material. There are grants available for resource recovery operations in Queensland although no monies have been allocated to assist in 2018. This is troubling as Queensland rolled out its Container Refund Scheme on 1 November, which will likely impact the cost and revenue models of the State’s MRFs – as we have seen most recently in NSW.
Let’s be real – without financial incentives we just are not going to get the systems shift we need, particularly when profit margins reward existing behaviour.
WESTERN AUSTRALIA
Further, following June’s Environment Ministers Meeting, it is clear there we are still tinkering and will not be getting a packaging product stewardship scheme in Australia until 2025 at the very earliest – some 27 years after the NEPM legislation. In the meantime, packaging has continued to grow with the latest APCO figures showing 6.98 million tonnes were placed on the market in 2021/22 (with 3.9 million tonnes recovered) – up from 5.45 million in 2017/18 (with 2.67 million tonnes recovered). Unless there is a financial obligation to recover the total amount and investment in the facilities and buy back, this will not shift.
The recent Planet Tracker report, The Plastic Recycling Deception, argued consumers have been made to feel responsible for low recycling rates and plastic producers have successfully passed the financial burden of dealing with its material onto others, including local councils and the WARR industry, while ignoring upstream measures to limit production, such as EPR, regulation or, for governments, taxation on production. It would be hard to argue these conclusions aren’t the case in Australia.
The Western Australian Government set up a Waste Taskforce in direct response to the China National Sword. As part of this announcement, the State Government urged all local councils to begin the utilisation of a three (3)-bin system - red for general waste, yellow for recyclables and green for organic waste - over the coming years to reduce contamination. While this taskforce is a step in the right direction, we are yet to see any tangible results from it or any funding for industry. In October, the WA Waste Authority released its draft Waste Strategy to 2030, which comprises a comprehensive and detailed roadmap towards the State’s shared vision of becoming a sustainable, low-waste, circular economy.
COMMONWEALTH
Cost must be worn where it belongs to manage the efficient use of scarce resources. This goes for soft plastics too. Unless the real cost of managing packaging is placed on the generator, with real systems shift that balances placed on market with bought from market, we will keep stumbling along for another 27 years with little progress and even more deterioration of the environment.
The argument is the same for many other product types – batteries, e-waste, paint, solar panels and the list goes on. If Australia sets a clear expectation that generators must take responsibility for the entire lifecycle of what they make, we will have a far greater circularity in Australia than the current 5.4 per cent.
Following the MEM in April, Australia now has a new Federal Environment Minister, Melissa Price, who in October reiterated to media MEM’s commitment to explore waste to energy as part of the solution to the impacts of China’s National Sword, which is troubling (EfW is not a solution to recycling). The Commonwealth has also backed the Australian Recycling Label and endorsed the National Packaging Targets developed by the Australian Packaging Covenant Organisation (APCO), which has to date, failed to incorporate industry feedback in the development of these targets. To the Commonwealth’s credit, there has been significant coordination in reviewing the National Waste Policy, with the Department of Environment bringing together industry players and States during the review process.
The updated Policy will now go before Environment Ministers on 7 December. The Commonwealth can play a key role – one that goes beyond the development of the National Waste Policy. WMAA is supportive of the Federal Government maximising the levers it has, including taxation and importation powers, to maintain a strong, sustainable waste and resource recovery industry.
Can anyone therefore please explain to me why on earth we are not moving rapidly towards a national product stewardship framework like the EU Waste Directives? Also, why are we stuck in a six-monthly cadence of Environment Ministers Meeting with very little progress towards regulation as a whole (and only tiny steps for a few products)?
AHEAD OF MEM 2
Maybe we need to go back to the start – we need leadership and regulation –sadly both appear to be currently missing in this space. When will we fix it, I am not exactly sure, but WMRR will keep fighting until we do.
Gayle Sloan, Chief Executive Officer, WMRR
There may be movement across Australia, with some states doing better than others, but the consensus is, progress is still taking way too long. It is evident that there are funds available in almost all States to assist with developing secondary manufacturing infrastructure, however the only way that this will really happen is if there is government leadership around mandating recycled content in Australia now, not later.

Unlike its neighbours, Queensland did not provide any financial support to
Voluntary schemes like the Used Packaging NEPM, under which APCO is auspiced, are not working. We have 1.6million tonnes of packaging waste in Australia, which needs to be used as an input back into packaging. Barriers to using recycled content in civil infrastructure must be identified and removed, and Government must lead in this field and prefer and purchase recycled material. A tax on virgin material should also be imposed as it is overseas. MEM must show strong leadership on this issue. Ministers have, since April, dealt directly with operators and councils that are under stress and we have a chance to create jobs and investment in Australia at a time when manufacturing is declining. Ministers have the opportunity to be leaders of today, not procrastinators – leaders of tomorrow and we are urging










NO DOWNTIME FLOORING
Appetite waning for insurers in waste industry
(Continued on from Cover)
He said one of the biggest emerging risks, which is especially pertinent to the waste industry where there is still a lot of manual labour aspects, is intercompany WorkCover recoveries. This can impact on a business, especially in a situation where WorkCover has paid out for somebody who has been injured, or on a claimable incident. WorkCover will look at who was the party that engaged the person who was injured, and who was the injured party working for at the time the incident occurred.
“And if they can recover against a third party, which is really just a separate entity to whom the injured person was employed by, then the (insurers) will go down that path,” said Richards.
He said that the easiest way to explain it is if you had one company that had two entities – let’s say RSM Waste Management, which had two subsidiaries, one that employed staff and the other that was known as RSM Trading that looked after the rest of the company’s business. The entity that employed the staff would pay the workers’ compensation premium.
However, once the bills have been paid by workers’ compensation, even if it is under the employment arm of the business, then the workers compensation insurer – depending on the circumstances – could go after the trading side of the business to recover
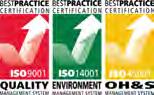
any monies it believes it is entitled.
“We’re seeing these scenarios coming through pretty thick and fast at the moment,” said Richards. “It’s got a three-fold effect on businesses. First and foremost: are your increase in WorkCover compensation premiums because claims increase?
“Second, you pay the excess, which these days starts at about $25,000 but $50,000 is becoming the norm, with even between $100-$250,000 for highrisk entities such as labour hire and transport industries.
“The third part is the policy that actually covers it, which is your public liability policy, which covers third-party bodily injury.”
Richards said from an insurance point of view, these are significant risks. RSM saw its first instance of WorkCover looking to recover monies about a year ago.
“Even though there’s a statute of limitations we had a client who was served eight or nine of these, and they’re all for incidents over the past seven years,” he said. “They’ve got an excess of $50,000 on each one and it’s coming from left field. It’s a pretty major emerging risk for us. The good news is, your public liability policy should cover it if the correct information has been disclosed.”
Unlike other insurance markets, such as a car or house, whereby incidents are covered off on (or not) pretty quickly, these longtail claims – as they are referred to within the


insurance industry – can take years to materialise after the date of loss. And, as Richards points out, they’re not something that insurers have factored into their rating but are doing so now.
AU’s Brett said that 50 per cent of his company’s gross written premiums come from the resource recovery sector. One of the most standard questions he gets almost every day is: “why is my property insurance so expensive?”
When it comes to the resource recovery industry, it is a culmination of factors. Brett said that the sector has incidents such as fires and other losses, which are significant – some would even say catastrophic – in insurance terminology.
“And the problem is globally, they are increasing in frequency,” he said. “This means that the market is reducing. Now, why is that? Well, in advanced economies across the world waste per capita is increasing. The UN Environment Agency suggests that in North America, Europe and here in Australasia, per capita waste has grown by 20 per cent in the past 20 years. And global waste is expected to double by 2050.”
He said that is great for those wanting to invest in the sector, but the increase in waste also means more combustible components entering recycling feedstock due to public negligence.
“And we’re having to underwrite that,” said Brett. “And that’s been exacerbated by China’s plastic import ban in 2018, which meant a significant amount of plastic began to be stockpiled in waste and recycling facilities, which have significant fire risks.”
He said that problem has been turbocharged by lithium-ion batteries entering the stock feed due to products such as smartphones,
smartwatches, vapes and even items such as personalised greeting cards, being discarded.
Brett provided statistics that showed in 2022 there were more than 300 fires in waste and recycling centres in North America – just under one a day. He said that was more than any other year. Data from the UK has shown that the number of fires in such facilities have doubled in the past decade.
Profit matters
When it comes to insurance of such facilities, Brett went into a deep dive as to how the insurers operate through risk selection, premium collection and claims management to create profit.
our reinsurance programs”, which impacts on profitability for their shareholders, “Or do we look to cleanse the potential volatility within those portfolios”, which many have now done. And that impacts on the resource recovery sector due to its propensity for high losses.
Brett said the Waste industry would have seen that their property options for insurance capacity greatly restricted as many insurers have decided to reduce their exposure or stop writing risks within the industry entirely.
What does that leave you with?” he asked. “Lloyd’s of London is probably the oldest insurance marketplace and have been around for over 400 years. Providing solutions for the most complex insurance challenges through a subscription model. The marketplace is made up of about 150 insurers or syndicates, which will take a small proportion of policies that could have potentially high risk.”
This means in the event of a loss, they only pay their proportion, which means that they can manage their overall profitability. Brett said the trick/skill for his company is to help those syndicates manage that volatility.
How to manage the insurance costs speak to your insurance broker and weigh up all the all options, said Brett.
“Waste and recycling facilities can be quite significant in respect to their square meterage,” he said. “Make sure that you are speaking to your broker
the waste and recycling sector, but in other sectors as well. We mandated as part of our insurance provision that unless you’ve asked us for a special dispensation, the policy states there isn’t to be any overnight charging. Also, when you do charge the forklift during work hours, make sure that the areas around forklift charging areas are free of combustible waste.”
The insurer would also expect that as part of good risk management practice, any combustible waste outside is a minimum of six metres away from the property assets that are being insured. Also be aware of unsorted stock feed as well, he said. In his experience, a lot of fires start/ spontaneously combust through direct sunlight. Then there are a facility’s electrical systems. Sometimes, as part of a policy, the insurer will ask for an annual thermographic survey. This will just test an electrical system to see if there are any heat spots that might need attending.
Finally, Brett mentioned the one item that is currently causing the most problems – lithium-ion batteries.
“There are a number of specialist recovery centres that operate just for this type of item,” he said. “But all waste and recovery sites should have a plan of what they need to do if lithium-ion batteries get into the stockfeed – a plan on how you identify and a plan of what you do in respect to storage and disposal.”
“Another impact on premiums is the El Nino weather pattern, which means warmer and drier conditions with minimal rainfall, which can lead to an increased risk of bushfires.”
Most insurers are publicly listed – meaning providing return to shareholders is the primary objective.
“And insurance is seen as a relatively stable return for shareholders,” said Brett. “A lot of pension funds will invest in the insurance sector. You pay your premiums then insurance underwriters like myself will underwrite risk, we will collect that premium, and then invest that premium. That investment minus operating costs and claims payments creates the insurer profit.”
Brett said many insurers will reinsure themselves to make sure the profit margin remains stable. However, in Australia and North America over the past five to 10 years, those reinsurance programs have dealt with a more claims due to the increased number of natural catastrophes.
He said that the insurance industry had to make a decision, which was “what do we do? Do we pay more for
about potential impact of an insurance claim on your operations. Do you have the cash flow to maintain a higher deductible? This will reduce your insurance premium.
“And from a risk management point of view, we love it when there’s a significant amount of investment in some of the new fire detection and protection technologies that are available.”
Brett said that prevention is better than the cure and went on to list some of the more hazardous situations that can arise in waste and resource recovery facilities.
Risk factors insurers don’t like Overnight electric forklift charging is a big issue.
“We see a significant number of fires emanating from overnight forklift truck charging,” he said. “Not just in
Brett said that once the risks are identified, an insurer will have a meeting and conversation about a facility’s readiness for dealing with lithium-ion batteries. He believes, the massive increase in the disposal of these type of batteries has caught both the industry and insurers off guard, which needs to be addressed collectively.
Finally, Brett touched on the insurance contract itself. He said it is important that it is read through thoroughly. His team tries to make it as simple as possible, and he makes sure that for every contract they create they have a conversation with the insurance broker/policy holder to make sure they understand their obligations and what is covered under the policy.
“Also, if you’re a tenant, make sure that you understand your property owner’s Insurance conditions, which will be set out in your tenancy agreement and may have specific requirements you need to adhere to,” he said.

The massive increase in the disposal of lithium-ion batteries has caught both the industry and insurers off guard. Image: Smile Fight/shutterstock.com.
With its multi-rotor design the Genox J-series pipe shredder easily shreds HDPE pipes of all sizes.
When combined with a Genox washing plant and Genox pelletising system, you can truly close the loop on HDPE pipes. Pipe to pellets. Pellets to pipe. This is the circular economy in action.
Genox make world-class recycling solutions, for real-world recycling applications.

Call: Email:

in 2008. It continued to decline thereafter, again due to the effect of inflation.
But we hear some of you saying –“Hold on a sec. The capture rate moves but not as much as the rebate value declines. Is the rebate value that important?”
Correct. The data does show that, but the capture data is buffered by another factor. Because MRFs also get the rebate, MRF recycling of eligible containers is included in the capture rates. So, all capture is underpinned by MRF recycling rates.
Put another way, in spite of changes to the rebate value, much of the capture would have happened anyway through
measured as the net increase in eligible container capture over and above what would have happened anyway under yellow bin and MRF collection systems.
After all, the purpose of the CDS is to capture containers that would have ended up in litter or the red bin headed to landfill. It was not designed to be a replacement for MRF recovery. The two are complimentary.
Unfortunately, many politicians talk CDS effectiveness by the total billions of containers recycled, when they should be talking about the net recovery due to the CDS alone.
It is important to note that there is a more recent argument made that CDS

Figure 1. The effect of the “pulling power” (effective rebate value in 2024 dollars) on total capture rate (%)


58 per cent of eligible containers, in the absence of a CDS.
Figure 2 provides the analysis of the rebate value against the net gain attributed to the CDS (i.e. capture from litter and red bin containers; taking out the 58 per cent that would have been recycled anyway; it is a slightly different number in different states, but the difference is consistent and shows the same effects). It shows that there is an even closer correlation of the effectiveness of the CDS system (net capture rates) with the rebate value “pulling power”. Higher rebate values
deliver higher capture rates and vice versa. Inflation erodes the rebate value over time, which reduces net capture rates.
Policy
South Australia has demonstrated that rebate value matters. Inflation erodes rebate value and with it, capture rates.
Five cents in 1977 (a 35c rebate value in 2024 values) provides the highest capture rate.
Anecdotal evidence suggests the 10c rebate is insufficient. The question is why have all new CDS schemes in Australia
adopted a 10c rebate in 2023/24?
The NSW EPA reports a 52 per cent reduction in eligible container litter with its 10c rebate. What would this be with a higher rebate value? Why stop at 52 per cent when the primary purpose of the CDS is to reduce litter? What effect would a 20c or 30c rebate have on litter?
Of course, the packaging and beverage industry is concerned about retail price rises and particularly the risk that consumers may substitute one product with a CDS container levy on its packaging, for another which has no CDS levy.
For example, swapping from bottled beer and wine, to tap water, which has no CDS levy. We think this is very unlikely. A small price increase will not get people to switch from drinking wine/beer to tap water.
We started the modern round of CDS schemes in 2017 in NSW, with the levy set at 10c. It has since reduced in value by 17 per cent. All other new schemes will have 10c rebates.
I further note that 10c rebate today is a 70 per cent discount on the starting value of the SA CDS in 1977. A 30c rebate today would go most of the way to reestablishing its “pulling power”.
If the primary purpose of the CDS is
Maximise Recovery... Reduce Landfill Costs
























An array of CDS eligible containers at a NSW landfill in 2024. Image: Ron Wainberg, MRA consulting Group.
Figure 2. Effect of the rebate on net capture (taking into account yellow bin recovery)



“Of course, the packaging and beverage industry is concerned about retail price rises and particularly the risk that consumers may substitute one product with a CDS container levy on its packaging, for another which has no CDS levy.”
to reduce litter, then 10c is achieving half of the goal (for example 52 per cent litter reduction in NSW).
A compromise position would be an immediate increase of all schemes to 20c with a “watch and wait” policy to assess the effect on net capture rate and particularly on litter reduction.
Our economy has already borne the extra costs of the CDS collection system, so we should be working the system (capital) as much as possible. That means pushing the capture rate of eligible containers in litter and red bins as high as possible. That means, at the very least, adjusting the rebates to keep up with inflation.

Waste Expo Australia is Raising the Bar in 2024
Waste Expo Australia 2024 is expected to attract over 3,000 visitors from across Australia and beyond. The free-to-attend conference program will feature keynote speakers, panel discussions, and interactive sessions led by industry experts, policymakers, and thought leaders. Topics for the event will span policy priorities, challenges, innovations, and best practices in resource management, sustainability, and the creation of a circular economy.

wasteexpoaustralia.com.au
Registration is free for all industry professionals. Scan to find out more and to register.
“We are excited to bring together the waste and recycling industry for the 2024 Waste Expo Australia. We will be raising the bar with an expanded conference program and enhanced exhibitor presence, providing an unparalleled platform for knowledge exchange and networking. We hope to spark meaningful conversations and drive positive change in the industry”.
Sherri Pearson Exhibition Manager
The rebate value matters to the CDS capture rate, it matters to litter reduction, and diversion away from the red bin. Image: Beanykin/shutterstock.com.




Invest in quality machines that are backed by a national parts and service footprint for the ultimate
From material handlers, to trommels, stackers, grinders, screens, dozers and more. Our industry specialists will create a personalised solution for your business. Onetrak, the exclusive national distributor for Fuchs, Tigercat, Anaconda, Dressta, Hidromek and Striker.


Keeping greenhouse emissions under control in landfill environs
By Inside Waste
DR. BEN DEARMAN is first and foremost an environmental pragmatist. He knows that sustainability is key for the waste and resource recovery industry moving forward. His company, Ennovo, is at the forefront of making sure landfills are managed properly with the least impact on the environment.
For seven years, Dearman and his team have knuckled down to find solutions that meet industry and community standards when it comes to landfill management. With a PhD in anaerobic digestion and a thesis titled Anaerobic Digestion of Source-Separated Food Waste Followed by Composting, you could argue he is in the driving seat when it comes to understanding how waste works in landfills.
Dearman believes a lot of landfill gas capture enterprises are driven by the amount of power and carbon credits they can generate when capturing the gas and utilising it to create power or flare. He said that while this is an important part of the process, he sees it as a byproduct of what Ennovo is doing, not the principal reason. There are also other issues, such as managing landfill gas emissions and leachate.
“We’re driven by ensuring a very high standard of environmental management is maintained,” he said. “Doing this for the greater good and the environment is important because methane is a very potent greenhouse gas. We are also aware of the role leachate has in the process and how important leachate management is, because not managing it properly can have dire impacts on both groundwater and surface water.”

Dearman said that leachate is pumped out of the landfill, where it either evaporates or is sent to a treatment plant. Once treated, it can be disposed of properly.
One of the main services offered by Ennovo is managing the pumping system. It also offers a cost-effective leachate telemetry system that allows landfill operators to know where the leachate levels are in the landfill and whether the pumps are working properly.
“The telemetry system measures the leachate levels in a landfill,” he said. “There’re strict regulations about how deep that needs to be. Normally it’s only 300mm deep. It has to be in compliance constantly. That’s the beauty of the telemetry system – it’s telling you that

the depth of the leachate in real time, so you’re constantly getting real time data.”
Once a landfill is no longer taking in feedstock, it is capped, and the amount of leachate will abate. Dearman said that in theory, once that happens, the infiltration of the stormwater – which causes the leachate – shouldn’t exceed the evaporation that occurs in that landfill cap.
“To cap it, you can put geotextile membrane over the landfill, and then you can put some soil on top and plant plants,” he said. “Alternatively, it can be a much thicker soil layer, which is called a PhytoCap. They’re quite good to use in southern parts of Australia, but not so good in the tropics because of the amount of rain that occurs.”
Dangers of Landfills
Landfill owners have an obligation to manage their landfills, even legacy ones that have been closed for some time. There is even an argument that the legacy landfills from yesteryear need more attention because they were not subject to the stringent rules that now apply.
“Any owner of a landfill has an environmental duty to manage the environmental impacts,” said Dearman. “There’re legal obligations to manage human health around these sites. In the case of landfill gas, the consequences of it going wrong are quite severe if the gas builds up and enters buildings, and nothing is done about it. People can die. The management of it is incredibly important.”
Dearman said considerations just don’t include fugitive emissions that come out of the cap and have an impact on greenhouse gases – it’s also that lateral migration of the gas; i.e that which goes through the side of the landfill. In worstcase scenarios, this can include gases travelling up into buildings, creating an explosive atmosphere.
And what landfill owners and the general public have to be aware of, said Dearman, is that there are literally thousands of these legacy landfills around Australia. A lot are low risk and will not cause issues, but there are some that need to be managed carefully. Also, a lot of these old landfills, especially those in major cities and regional towns, are covered over with soil and turned into parks or recreational facilities like sports fields and club rooms.
“You’d be surprised at how many sites we’re going around that have sporting club buildings, and we look to detect methane in them,” he said. “And quite often we get a hit.”
Solutions
Dearman said there are several ways landfills can be managed successfully without causing a lot of disruption, while making for a much safer environment. Ennovo’s solutions are varied and include innovative pinwell systems, which are small extraction wells, but capable of mitigating the lateral migration of gas. They pair it up with a Lo-Cal flare to effectively manage the low-quality gas.
Once a landfill is no longer taking in feedstock, it is capped, and the amount of leachate will abate.
Ennovo is driven to ensure a high standard of environmental management is maintained for its clients. Images: Ennovo

“That flare has the ability to combust the landfill gas with a very low concentration of methane,” he said. “This means that it can operate over a long period of time. What the flare is doing is creating a vacuum and always sucking the gases out.”
Ennovo also installs interception
trenches and biofilters around the perimeter of landfills so that, as lateral migration occurs, it can intercept any gas. The company also owns the Gasflux continuous gas analyser technology, which is used on perimeter monitoring wells that surrounds a landfill. This technology detects both gas composition
and borehole flow.
“This means if there’s a positive pressure from the gases coming out of the landfill, we quantify that, and that goes into our landfill gas risk assessment plan,” Dearman said. “This is a well-recognised process for quantifying that risk.”
Legacy
Dearman said a rule of thumb is that once a landfill stops taking waste, it needs to be managed for about 30 years, which happens in stages. He said flaring the gas might be carried out for up to 15 years. Then it’s best to move to a passive system such as cut-off trenches or monitoring. That might happen for the last 10 years, depending on how much gas is being produced.
He said that although a lot of Ennovo’s clients, including councils and large waste management companies, are up to date on leachate and landfill gas requirements when managing a site, there is expertise lacking in some areas.
“That’s why we’ve been able to do quite well because we do know how to marry those technical consulting abilities with really good design and construction capabilities,” he said.
Dearman said one of the key features of Ennovo is that the company is not only
a consultancy, but it is also a supplier and designer of landfill gas management systems.
“When we talk about a particular design, we know if you can physically construct it, build it and operate it,” he said. “We’re not just behind the desk, white collar consultants. We do the full range. We employ people, from excavator operators to people with PhDs writing reports and interrogating data.”
Dearman said that Ennovo is a technology-driven company, and he loves the whole cradle-to-the-grave approach to a project.
“The technology in this space is phenomenal in terms of the speed at which it is developing, and it’s mainly around the detection of methane from landfills,” he said. “A lot of it is coming out of the oil and gas industry, where the ability of drones, fixed-wing aircraft, and satellites can pinpoint sources of methane and also quantify methane being released from point sources – whether it’s an oil and gas field or now landfill. The onus is really on operators to make sure they’re mitigating those emissions that have significant greenhouse gas impacts. That’s where we fit into being able to provide cost-effective solutions for our clients and for the broader benefit, too.”


Once a landfill stops taking waste, it needs to be managed for about 30 years.
*F R OM C ON VE NT I ON A L PLA ST ICS


Join the sustainable revolution at your warehouse—effortlessly!


LANDFILL-BIODEGRADABLE

SUPER DURABLE

AFFORDABLE

NO SHELF LIFE ISSUES

FITS STANDARD EQUIPMENT

SOFT-PLASTICS RECYCLABLE NO MICROPLASTICS







SHOP NO W



Landfilling plastic waste will be here for a while
By Ross Headifen Ph.D
IT IS BECOMING clear that our management of plastic waste is woefully underperforming. We have set targets many years in advance for recyclability, being recycled and recycled content in new products.
However, as we approach these target dates, report after report tells us that we will not only miss the targets but miss them by significant amounts. So much so that recycling of plastics waste has changed little since the targets were set six years ago.
There are some exciting things happening for plastic waste, but their scales are still small for this discussion.
Recent articles on waste management were published citing:
l An additional 650,000 tonnes a year of waste, including plastic, paper, glass, and tyres, will flood Australia’s recycling industry when the full waste export ban comes into effect in mid-2024, according to the Library of Congress. Landfill will likely be the destination for many of the plastics, particularly film, without mechanical drivers for a circular economy.
l The CSIRO says that just a 5 per cent boost to the recycling rate per year would create many jobs and add to the GDP. It also estimates that $100 billion would be required to get recycling rates up to 20-30 per cent
l Australian Packaging Covenant Organisation (APCO) reported recycling problems are clear enough, including that the collection, sorting, and reprocessing of materials, amounting to millions of tonnes of packaging, is uneconomical. It is clear that business as usual will not cut it.
It is interesting to look at some scenarios of plastic waste and the amount that will be recycled per year for the years to come. Australia uses approximately four million tonnes of plastic per year. The consumption of plastic is forecast to grow by at least three per cent per a year, i.e. doubling by 2050 with some saying it will triple (4.2 per cent growth per annum).
To keep plastic waste out of a landfill it has to be:
1) Made part of a circular economy where the plastic waste is returned to manufacturers to make similar products from it.
2) Burned in a waste-to-energy plant, of which there are only two about to commence operations in WA.
3) Repurposed to a use where it will be lost forever, such as road base.
Currently the amount of plastic recycled is claimed to be around 15 per cent. But this included repurposing
of plastic to other end-use functions, which is not the circular economy. The amount that is recycled and returned to original plastic manufacturers is much less.
Assume for this story it is two per cent. Let’s first look at first the business-as-usual situation of recycling increasing at an aspirational five per cent per year over the previous year. Becoming more aggressive, imagine we were able to increase recycling over that of the above by a factor of five year-on-year to 20 per cent increase per year.
Here it assumes that there will always be some residual plastic waste of approximately 20 per cent that will never be recycled, and the recycling rate goes up in line with the usage rate once 80 per cent recycling is reached. This scenario has the actual recycled rate at six per cent by 2030 if we get very optimistic and spend the $100 billion to get recycling up to 20 per cent by 2030. This would require increasing the recycling rate year-on-year by 43 per cent. Given our history this would be a very difficult number to reach.
What these plots graphs (right) show is that there will be considerable blue areas for the next decade or more and still significant blue areas or plastic
“The reprocessing of some materials is uneconomical, which makes it clear that business as usual will not cut it.”





rate compared to
Experienced Practical Experts


Landfill Services
Gas collection system (GCS) design and construct
Carbon credit reporting and management
Data management and reporting
Monitoring and maintenance
Leachate system installation and servicing
Advisory and strategy
Power generator servicing and maintenance

Landfill Products
Mobile flare hire
Lo-cal flare range
High temperature flare range
Gasflux continuous gas analysers
Leachate telemetry systems
Leachate pumps and controllers
Power and heat generation systems
Latest data shows bin targets are a mess
By Inside Waste
THE SOUTHERN Sydney Regional Organisation of Councils (SSROC) has found that data is key to increasing the recovery of household waste and recycling, planning services and education programs.
SSROC has finalised its eighth, and most comprehensive yet, audit of 2,444 households, sampling 7,471 red-, yellowand green-lidded bins to help identify trends in recovery and where further education is needed. In addition, SSROC also audited 698 piles of booked and scheduled clean-up collections to better understand what households throw out and improve recovery of these materials.
SSROC has been coordinating waste audits of kerbside services for its member councils since 1999, with one of the best longitudinal household waste data sets in Australia. In the past year, 11 SSROC councils audited household bins and eight of these councils also audited bulky waste piles.
Outcomes
In the general waste bin (red-lidded bin), loose food waste is the largest individual category at 30 per cent, which is consistent with previous audits.
However, there has been a growing amount of food and liquid left in containers (12 per cent of the red bin) and thrown in the bin, some of these are recyclable containers that if emptied and
placed in the recycling bin could have been recovered.
About 11.6 per cent of general waste is material that should be in the recycling bins, 2.5 per cent is garden organics (GO) that should be in the green waste bin, and 1.2 per cent of general waste is items that should be diverted to e-waste or hazardous waste services provided. While hazardous items only make up 1.2 percent it only takes one battery in a bin to start a fire. Batteries incorrectly thrown into kerbside bins are causing on average three fires a week in NSW.
Overall, the audit showed an increase in the amount of difficult-to-recover materials placed in the red bin including contaminated paper, soft plastics (7.4 per cent), nappies (6.9 per cent) and textiles (4.6 per cent). Fourteen per cent of that 4.6 per cent is wearable clothing that could have been reused instead of thrown away.
These figures highlight the need for greater stewardship of these materials by producers.
The recycling bin mostly consists of recyclable paper (42.5 per cent) and recyclable containers (37.7 per cent), with an average of 19.7 per cent contamination although many councils have lower rates of contamination. Trends data shows that the amount of recoverable material in the recycling bin has declined with the introduction of the NSW Container Deposit Scheme and the digitisation of news, making it harder to increase recovery.

The top five contaminants in the recycling bin include:
1. Bagged material at 4.6 per cent. This includes both bagged garbage at 2.6 per cent, as well as bagged recycling 2 per cent – recycling that is placed in bags into the recycling bin but cannot be separated at the processing facility due to safety risks, so it is classed as contamination whatever the content.
2. Contaminated paper (4.6 per cent) such as wet or soiled paper or cardboard, food takeaway bags.
3. Other plastics. Mostly hard plastics that cannot be recycled, 1.2 per cent.
4. Textiles/carpet (1.2 per cent)
5. Composite materials. Mostly paper, containerised food and liquid, and plastic film all at 0.9 per cent each.
Despite decades of recycling education, we still have a long way to go to get households to place only loose recyclable containers and packaging in the recycling bin and to ensure that products sold in Australia have packaging that can easily be recycled in Australia.
The garden organics bin (green-lidded bin) has consistently been over 96 per cent acceptable vegetation and consistently had a very low contamination rate.
SSROC councils audited clean-up collections in 2014 and again last year,

yet both times the largest component of clean-up waste was furniture representing almost third of clean up piles (28.8 per cent by weight). Fifty-four per cent of this furniture was deemed suitable for reuse had the resident donated, sold or passed on the furniture instead of putting it in the clean-up collection.
The next largest components of clean up piles by weight are wood (12.2 per cent), plastic (6.7 per cent), metal (6.4 per cent), white goods and electrical (5.4 per cent), e-waste (5.3 per cent), paper and cardboard (4.7 per cent), textiles (4.5 per cent), general waste (4.5 per cent), and several smaller categories.
The state government target for household waste is a diversion of 80 per cent materials from landfill. These audits are only a sample at a point in time, yet they show that we are not halfway there with an average diversion rate of 37 per cent.
Even when some of the loose food is recovered through upcoming food and garden organics roll outs, Australia will still be a long way from this target.
“Over time, we can see that the amount of recoverable material has declined yet we have seen an increase in products on the market that cannot be easily repaired or recycled in Australia,” said Helen Sloan, SSROC CEO. “We simply cannot recycle our way out of this mess, and we will not reach diversion targets without major interventions to design waste out of products and packaging.
“If we want to progress to a circular economy, we need the Federal Government to implement tougher measures to ensure that products placed on the Australian market can be recycled and are sold in recyclable packaging.
“We also need incentives for manufacturers and brands to make their products easier to repair and provide convenient take back collections for consumers. This is important for all products but especially bulky ones like furniture, whitegoods and other electrical goods, mattresses and textiles, as these products can’t be recycled easily once placed on the kerb and create safety issues in our streets and roads.”
People are still putting wrong items in bins. Image: Sabelnikova Olga/shutterstock.com.
DELIVERING A GREENER FUTURE
Komptech CEA is a leading supplier of machinery and systems for the treatment of solid waste through mechanical and mechanical biological treatments, as well as the treatment of biomass as a renewable energy source. Komptech CEA is proud to provide innovative solutions for handling waste and biomass.
Komptech CEA’s extensive range of products cover all key processing steps in modern waste handling. At Komptech CEA the focus is always on innovative technology and solutions ensuring maximum benefit to the customer. With local representation throughout Australia and National Parts Distribution Centre Komptechg CEA has the expertise and aftersales support to confidently support your business needs.
Like to know more? why not speak to one of our team today?

SHREDDERS TROMMEL SCREENS STAR SCREENS WINDROW TURNERS

TERMINATOR
Where Function Meets Technology
A slow-running, single-shaft shredder suited to all types of waste.


CRAMBO
Less Fuel, More Power
Ideal for shredding all types of wood and green cuttings.

MULTI STAR
Screening with a Star
Makes waste wood and biomass processing highly efficient.

NEMUS
Robust and Reliable
Combining the practic proven virtues of its predecessors with new solutions for even greater performance.
TOPTURN X
The Ideal Combination of Performance and Design
With a sturdy frame, powerful hydraulics and large drum, the Topturn X is ready to handle any work situation.

HURRIKAN S
Enhancing the quality of the recyclable output.
Providing effective removal of plastic film from screen overflow.


An Inconvenient Truth

By Anne Prince
AS SOMEONE who lives by the mantra, “You can’t manage if you can’t measure”, I’ve been looking at data to inform evidence-based decisions my entire career. Data removes the subjectivity. Many of us like to think we all know the answers, but the most objective way is to let the data do the talking.
The need for robust, current data has never been more relevant to our industry, particularly as the sector moves to larger and more expensive investments with longer payback periods. The stakes have never been higher. If we get it wrong – and we have – it has lasting impacts not only on investors but also on all levels of government supporting the projects with or without financial contributions. The industry takes a collective deep breath, and we all reflect on where we went wrong.
Recently, I took some time to look at a range of our datasets to inform and frame discussions with clients and conference audiences on exactly where we currently stand are, as well as to discuss our options and opportunities for improved outcomes.
If we all believe the data doesn’t lie, then we are all in for a shock with what I’m about to reveal.
The NSW government’s NSW Waste and Sustainable Materials Strategy 2041 contains a set of interim targets, including the reduction of total waste generated per person by 10 per cent and to achieve an 80 per cent average recovery rate from all waste streams by 2030. Looking at a current kerbside bin audit data from 17 metropolitan, regional and rural councils, involving 10,000 bins from 3,500 households in 2022-23 – effectively a snapshot of the state of NSW – we see some interesting challenges emerging.
One thing that does reduce household waste generation is not where you live but what type of housing you live in. Unsurprisingly, our data consistently shows that units and
In some instances food separation exceeds 60 per cent, but data shows, overall, it is a lot less. Image: 2rogan/stock. adobe.com.
apartments generate significantly less waste. Units generate about 10 kilograms per household per week compared to single dwellings, which generate twice that amount, at 20 kilograms per week.

Data shows that units and apartments generate a lot less waste than single dwellings. Image: alexgo. photography/Shutterstock.


Units generate virtually no garden waste and half the amount of recycling. With the push to more urban consolidation and medium-density developments, we might just win the war on waste generation per capita over time from the changing mix of housing stock.
However, achieving 80 per cent recovery is entirely different. Analysing our current kerbside performance, we are achieving an average of 37 per cent with our two-, three- or four-bins systems. Looking at three future possible scenarios, which I’ve called “utopia”, “possible” and “probable”, the data tells us we have some major hurdles ahead.
Utopia scenario
Under my “utopia” scenario, the assumptions are that:
l all households have access to recycling and FOGO services;
l every household separates 100 per cent of all target materials; and
l textiles and CRC items are also separated.
In the utopia scenario, the maximum possible recovery is 66 per cent.
Possible scenario
The assumptions under my “possible” scenario are that:
l we get no improvement in current kerbside systems’ performance based on the fact that if we haven’t got all households separating recyclables and garden organics after 30 and 20 years respectively, it’s not going to happen anytime soon;
l separation of food is 60 per cent; and
l separation of textiles and CRC items is 50 per cent.
The results show the maximum recovery we will get is 49 per cent — a long way short of 80 per cent.
Probable scenario
And just when you thought things



couldn’t get any worse, under my “probable” scenario things do look worse. While we all hear fabulous stories of food separation exceeding 60 per cent, our data tells us a different story. The average food recovery across these 17 councils was 30 per cent. That means there are some high achievers with 70 per cent, but there are more low achievers getting only 15 to 20 per cent, which brings the average down to just 30 per cent as a reality.
Under my “probable” scenario the assumptions are:
l there is no improvement in current kerbside systems’ performance as discussed under the “possible” scenario;
l separation of food is 30 per cent; and
l separation of textiles and CRC items is 30 per cent.
The results show the maximum recovery we will get is 44 per cent, an
even longer way short of 80 per cent. This is 2024 and we are six years away from 2030.
While I think we might make the waste-generation reduction target, I’m convinced, and the data tells me – we have no chance of getting anywhere near 80 per cent recovery. We have to rethink. And while nothing is impossible, business as usual is not going to get us anywhere near 80 per cent. Good public policy should be constantly reviewing data and then responding with supportive research and innovation. This approach is more likely to bring us closer to our targets. We have to ask ourselves: ‘what are the implications and ramifications for sector investment and political fall-out that may follow if we fail to get even close to “utopia”?’
Anne Prince is a director of APC Waste Consultants
UTOPIA SCENARIO
POSSIBLE SCENARIO
PROBABLE SCENARIO

Leading the charge in battery collection
By Inside Waste
IN THE REALM of sustainability and environmental responsibility, Ecobatt, part of the Ecocycle Group, has a network of more than 6,500 battery collection points strategically placed across the nation. Ecobatt provides solutions for consumer convenience and round-the-clock monitored smart sensor technology, offering proper disposal options for all portable batteries. This includes Lithium-ion batteries, which require safe collection and handling processes. This is to minimise physical abuse conditions at kerbside collections because they present a high fire risk for the waste management and recycling sector. The risk of improper disposal of household batteries is a prevalent concern for the industry nationally.
Notably, nearly half of all imported portable battery chemistries are Lithium-based. Ecobatt promotes safe and sustainable end-of-life battery management practices for consumers and industry alike.
A nationwide network
The company’s battery collection points are strategically located in major supermarkets such as Coles, Woolworths, and Aldi, as well as retailers like Bunnings Warehouse, JB Hi-Fi, Mitre 10, and Big W. Ecobatt has partnered with numerous local government associations (LGAs) to establish collection points at key facilities across the country. This extensive network ensures that Australians from diverse regions have easy access to battery recycling options, mitigating the Lithium-ion
battery fire risk and environmental impact of their improper disposal.
Smart collection kiosks
Central to Ecobatt’s collection and transport network are its battery collection kiosks for household batteries. Each kiosk is fitted with a smart sensor that provides real-time 24/7 monitoring and reports on fill levels, temperature, GPS location and associated metrics.
This technology, developed in collaboration with Superfy, enables efficient management and maintenance of collection points. The sensors are set to trigger alerts when a kiosk is approaching nominated capacity or if temperature irregularities are detected, allowing for prompt and effective first line response and service calls.
A diverse range of collection solutions
Recognising that different clients have varying needs, Ecobatt provides a range of battery collection solutions. Its collection bins meet the highest safety standards, are UN certified and ADG approved. The product range includes specialist battery collection bins, and bulk battery transport containers, catering to the requirements of clients, whether they are small businesses, councils, large corporations, or the public at large.
Safe transport
Ecobatt’s commitment to safety extends to its national transport solution. All Ecobatt designated battery collection trucks and service vans are DG registered and operated by DG licensed drivers. These vehicles are
Ecobatt provides receptacles and provides a pick-up service at many retail outlets throughout Australia. Images: Ecocycle.


equipped with the latest technology, including CellBlock Fire containment systems, hand-held lithium extinguishers for adverse battery events, and in-built automated FirePro aerosol suppression systems.
Advanced battery recycling facilities
After collection, the batteries are transported to Ecobatt’s state-ofthe-art automated battery separation and recycling facility in Victoria. This facility employs the latest technology to sort and process the batteries efficiently and safely, allowing the extraction of bulk materials for reuse. It also safeguards the hazardous components. Ecobatt’s commitment to expanding its recycling capabilities is evident through strategic developments, enhancing facilities and processes nationwide.
Environmental impact and future plans
Ecobatt helps divert hazardous battery waste from landfills, reducing the environmental impact and conserving natural resources. The materials recovered through recycling can be
refined downstream to go towards producing new batteries or other products, therefore promoting a circular economy in Australia and internationally. Less waste equates to more resources for future generations.
Looking forward, Ecobatt is looking to expand its collection network and processing capabilities. The company is continuously exploring new partnerships and opportunities to increase the number of collection points and offer tailored services.
Ongoing investments in technology and collection infrastructure ensure that Ecobatt remains at the forefront of battery recycling. From handheld and portable batteries to large format energy storage and EV batteries, Ecobatt has a solution for every need. From medium and large format batteries Ecobatt aims to return the residual energy to the power grid wherever possible.

R&D and process engineering experience allows the company to develop new methods in partnership with brand owners. Large format battery importers are invited to propose their specific handling and outcome requirements and in turn get
best-in-industry results.
As the company continues to grow and innovate, Ecobatt is poised to play a pivotal role in fostering a safer, greener, more sustainable future for all Australians, delivering a positive impact on climate change with the recovery of critical resources.
Businesses like Ecobatt, along with consumers who recycle, contribute to a collective effort to protect the environment and making an informed choice towards Australian Governments’ goals to recycle 80 per cent of all waste generated in Australia onshore.
Batteries that have lithium-ion in their make-up are a fire hazard at recycling facilities.
Woolworths along with Coles and Aldi have partnered with EcoBatt to have collection points for used batteries.
Uncertainty roadblock to organics and WtE infrastructure investment
By Inside Waste
“THE LANDFILL levy needs to go up to $300 a tonne. Only very large resource recovery/waste infrastructure projects will be built if it doesn’t.”
That’s according to Hitachi Zosen Inova (HZI) Australia’s managing director, Dr. Marc Stammbach. Stammbach said the above solution is key to meeting Australia’s recycling and carbon emissions targets – and an array of other targets. There are other issues that need addressing, too, most of them ongoing, but making landfills a last resort for waste is a good start.
One of HZI’s biggest footprints in Australia is building waste-to-energy and anaerobic digestion plants. And while some people would be right in that Stammbach does have a barrow to push when it comes to getting these facilities built, he says landfill levy increases have a wider impact than being a stick to make industries that create waste comply.
“It also affects recycling, and food and green waste in particular, because we have all these food and green mandates, but a very leisurely implementation for them, and no real punishment if you don’t do it,” he said. “Also, the issue with waste levies is that some have increased – some a bit more than others. Some you can regard as just another tax grab. In essence, these state governments made it a tax and a lot

of what is collected is used it to fund other bureaucracies.”
The point being, those monies should go back into the waste industry to build infrastructure – and not just waste-toenergy plants, said Stammbach.
Some governments will point out that they have increased the levies consistently over the years, but again, Stammbach points out that increasing it within line with the consumer price index (CPI) is no real disincentive at all. Also, he said that if most state governments did have an epiphany and decided to use those CPI-increased funds to help build infrastructure, those monies wouldn’t go far.
“Construction costs in Australia have gone up more than proportionally to the CPI, probably twice,” he said. “That’s why everybody is complaining. Everything is so expensive around construction. And a big part of the construction of any facility – I’m also talking about anaerobic digestion and composting – is the civil infrastructure. That cost is what makes it hard to compete against landfills.”
Stammbach said that it’s not hard to find that – unsurprisingly – in Europe, some governments know that they need to be more proactive. In the UK, the levy is currently equivalent to AUD $200. It will increase to AUD $250 next year, in part due to the powers that be realising that there is no incentive for investors to build infrastructure and improve recycling efforts if most consumers take the cheaper option.
While there is an argument that the UK has much less land and a population more than twice that of Australia, Stammbach believes the issue goes deeper than that.
“The other thing is landfills are just net polluters. They are net producers of greenhouse gases,” he said.
Stammbach knows that there will be legacy issues with the number of landfills that are now closed but still emit greenhouse gases, and that is one reason why there needs to be incentives that encourage alternatives to landfills, especially as the outcomes are known.
“It’s absurd to keep going down that track,” he said. “That means every year we are locking in 20 years of major emissions – that’s when a landfill is very active –and another 100 years of lower activity.”
And what about landfill gas capture?
Those who specialise in such technology are doing a good job, but it’s a bit like closing the gate after the horse has bolted, according to Stammbach. He has done some analysis that shows at best about 60 per cent of greenhouse gases can be captured, which means there is still a sizable amount of methane and CO2 going into the atmosphere. He believes that there needs to be a recovery rate of about 90 percent-plus from landfill to be equivalent to a waste-to-energy in terms of environmental impact.
“Most bioenergy in this country is actually the capture of landfill gas, which historically has been okay,” he said. “However, going forward to promote it is not ideal if the various governments are going to proclaim we will be greenhouse gas neutral by 2050. That can never be, because of the waste already in landfills.”
Then there is the issue of harmonisation. If you are a local or international company looking to Australia as a place to invest long-term in resource recovery infrastructure, getting a scoping team to get its head around the various states’ legislation is almost impossible in terms of making an investment viable. Has Stammbach seen much change over the past decade regarding states getting their act together?
“We have not achieved anything,” he said. “The only harmonisation we have is the copy-and-paste approach provided by waste-to-energy regulations from Europe. That is with the exception of our basket case, New South Wales, which has outdone itself in that regard. In that state, there will need to be very difficult discussions around the licence conditions, because the regulator refuses to revise its decision (with regards to how difficult) this current framework is (to work with), which is unique in the world.”
Stammbach said the money is out there to invest in infrastructure –it’s the uncertainty that kills a project. He believes investors are looking for steady, long-term returns, but with governments often changing or amending regulations – and typically for the worse according to Stammbach – some are unwilling to take the gamble.
“For example, like we had with solid digestate from anaerobic digestion processes. The Victoria government suddenly declared it as a base of concern,

and it took quite a bit of industry lobbying to overcome that perception,” he said. “But then the regulator understood, and quickly became active, and started thinking about how it worked. They consulted more with industry, and now it’s changed. You can now bring digestate – in similar conditions as you would in Europe – to land.”
Stammbach believes he is not asking for much when it comes to regulating waste to energy, and it comes down to consistency of approach. This also includes changing the terminology of something that was once waste into a product that is no longer waste but is still be classified as such.
“We actually don’t have, in this country yet, a regulatory framework that allows you to bring a waste out of a waste regime,” he said. “They have given some exceptions, such as for paper and steel, but not bottom ash and other things. Even compost is still under the waste regulation.”
Stammbach realises that waste-toenergy facilities are a political football, especially in NSW, which as mentioned, has some archaic regulations. Both Parkes in central NSW, and Woodlawn, situated in northern NSW, have been earmarked for waste-to-energy facilities and are currently in the planning stage. The Woodlawn plant is being mooted by Veolia, while the Parkes plant is currently under review with three bids. These are from New Energy Corporation, Veolia, and a consortium of Tribe Infrastructure, Masdar Tribe Australia, Acciona Concesiones S L, John Beever (Aust), and Acciona Construction Australia. But as Stammbach points out, in the rush for politicians to secure social license from
Stammbach believes landfill levies need to go to help build infrastructure in all facets of waste, not to a state’s consolidated fund.

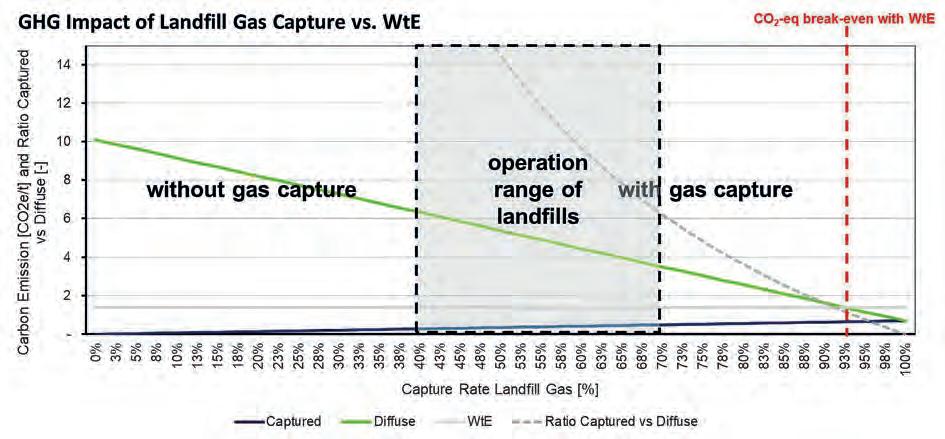
the wider community by making sure a facility is not built in suburbia, the negative impacts by placing such facilities in regional Australia might be worse.
“One air specialist already did an analysis of what it will mean to bring waste out of Sydney to Woodlawn or Parkes,” he said. “By the time waste trucks are out of the Sydney Basin, we would already have caused more pollution and human health impacts than that which might be caused by a waste-to-energy plant in the middle of Sydney. This is because the emissions coming from a waste-to-energy plant are low compared to diesel emissions – be it from a train or truck – which means they have more impact to human health than a waste-toenergy stack in built-up areas.”
Costs
As mentioned, Stammbach talked about
the landfill levy increasing in the UK from about AUD$200 to AUD$250 a tonne. He thinks that, due to construction costs in Australia, to disincentivise people from using landfills and incentivise more recycling/reusing, that a cost of about $300 a tonne would be necessary. He can’t see any state government increasing it by that much, although there is some promise from Victoria with their recently announced $40 a tonne step change, and he believes that most will stick to using the CPI as the guide. This means the highest cost to bury waste will be about $200 a tonne. And the consequences?
“A consequence is that the idea that ‘small is beautiful’ is dead,” he said, “because the unit cost of building anything small is too high. Hence, you can only build large projects. Hence projects will likely have to be at the scale of 400,000-plus tonnes to give a viable business case. And
that is in a reasonable location, and it is also subject to bottom ash recycling. And if you don’t have that, nobody will invest. Nobody will develop a project. You can quote me – projects less than 300,000 tonnes, they’re dead even if they have a licence today. They’re not going to get built.”
Even if everything falls into line, there needs to be the willingness of state governments to come to the party. Stammbach says that WA, Victoria and Queensland get things done in a responsible manner. Once again, the outlier is NSW, which has a few issues, according to Stammbach. One is that it tries to outdo everybody when it comes to ‘tough’ regulations. Another is that it is hard to get a waste-to-energy permit.
“Then there is the uncertainty around organics going to land, which has shattered the confidence of councils
and industry,” he said. “This is because they are afraid if they put food in the green organics, you have increased contamination. Suddenly the resulting compost can’t go to landfill anymore, because, for whatever reason, NSW decides to change the legislation. There is no recourse, because the way it’s structured, they can pull it from one day to the next, because it is an exemption. It’s at the prerogative of the NSW EPA.”
Stammbach is adamant that if there is a steady framework and certainty around permits and legislation, then industry and councils would probably trust this and just say, “Okay, this is unorthodox to do it like that, but so be it”.
Is getting everybody on the same page – not just the EPA and investors, but other entities too – put in the ‘too hard basket’ due to the number of entities that need to be involved to get a project over the line?
Not necessarily, said Stammbach.
“I would like to mention Switzerland,” he said. “The last big waste-to-energy plant they built was near Lucerne. It was replacing an old plant but was being relocated to a new site. There were participants from nearly 200 councils –not 20 – involved. They realised they had to do something, because when the old plant shuts down, where do they go to dispose of the waste? And if they get a new plant up and running, they will have to transport their waste further afield to existing plants, because they can’t go to landfill.
“In the end, it was accepted that they had to do something about waste, recycling and the composting, and not just talk about it for 20 years and do nothing.”
HZI’s Ultra Large WtE Boiler in Abu-Dhabi currently in the engineering phase which reached financial close on June 28, 2024. Image and graph credits: HZI.




Innovative, Sustainable Waste Management Solutions
Pure Environmental is a wholly Australian-owned company founded with the mission to transform the circular economy through advanced resource recovery. We believe in pushing boundaries and challenging norms in waste management, providing exceptional, innovative, and sustainable solutions.
year’s registry has consultancies firms offering a range of services to the wider waste community. Image : David/stock.adobe.com.


CONSULTANTS’ REGISTRY
Welcome to the 2024 Inside Waste Consultancy Directory, which is the precursor to the Inside Waste Consultants Awards that will be announced at the Waste Innovation and Recycling Awards in October in Melbourne.
In past years there have been issues with some companies not being included in the listing, which we acknowledge has not been ideal. This year, we have done our best to make sure that all of those companies that wish to be on the list have had ample time and opportunity to send in their information.
And while we believe that we have given consultants within the industry ample time and opportunity to be involved, we cannot guarantee that every company was covered. If you are a consultant who has not been listed, please get in touch so we can be sure to add you to our relevant databases for future registries.
These awards are being held at the end of the year on October 23 in Melbourne. They will take place in conjunction with the Waste Expo. The Waste Innovation and Recycling Awards are sponsored by Remondis, Veolia, Re.Group and Visy.
The Waste Innovation and Recycling Awards recognise outstanding programs and people from across the waste and resource recovery sector. Inside Waste has partnered with Waste Management Review to bring the industry these awards in 2024, and we’re looking forward to celebrating success stories from across the industry in addition to acknowledging our waste consultants.
The listing in this issue will give readers the opportunity to see
who the players are and the various consultancy they carry out.
The Registry
This year’s registry represents almost 100 consultancy firms, all offering a range of services to the wider waste community. The results of the survey have been both interesting and insightful. They vary in size from those that have less than 10 staff members to some that have more than 200.
Unsurprisingly, the three tiers of government is where a lot of work comes from, with local government at 77 per cent, being the busiest sector for consultants.
Australia is well covered in terms of the states and territories and the number of consultancies that are available for potential customers to utilise. Unsurprisingly New South Wales, Victoria and Queensland are home to majority of companies, but many are well represented in Western Australia, too. The ACT, Northern Territory and South Australia have a smattering of businesses that specialise in waste.
What is notable is that a large number of companies offer an array of services. Very few specialise in one or two aspects of the waste industry, with most choosing to spread their wisdom and knowledge throughout the industry.
The 2024 This
admin@aprince.com.au
joyanne.manning@arup.com
info@closedloop.com.au
stephen.davis@davisadvisory.com.au
info@emmconsulting.com.au
sydrec@ghd.com
sdegagny@kpmg.com.au
MW@dc8.energy cehfzambia@gmail.com
service@nationwidewaste.com.au
info@ozbincleaning.com.au
brendan.ridge@remondis.com.au
enquiries@resourcerecovery.org.au
plc.admin@ricardo.com
duane.pretorius@au.sedgwick.com
melbourne.reception@smec.com
brandoncoltonseaspan@gmail.com
hello@thewastetspot.com
engage@thinkstep-anz.com
sydney@wsp.com
Hello@4pillars.com.au
admin@aargus.net enquiries@aisit.com.au
admin@aprince.com.au
aap-sy-admin@arcadis.com
joyanne.manning@arup.com
giles@askwm.com
rowanc@atcwilliams.com.au
enquiries@atonaus.co.au enquiries@envaud.com.au bel@bcconsulting.au admin@beattyhughes.com.au
admin@bioxenvironmental.com.au
info@closedloop.com.au
Reception_Syd@cbp.com.au david.turner@maxibor.com.au
stephen.davis@davisadvisory.com.au
ecopro@rediffmail.com
info@edgeimpact.global
enquiries@edp-au.com
consulting@elephantsfoot.com.au •
info@emmconsulting.com.au
info@ennovo.com.au
sales@envirotreat.com.au
admin@ethosresources.com.au
rhofmans@expensereduction.com
henry.ongerth@fichtner.com.au
sydrec@ghd.com jo@goodforthehood.com.au
enquiries@green-connect.com.au
christian@greentecconsulting.com.au
keiran@harbak.com.au
gshapiro@honeslawyers.com.au
thomas@impactenviro.com.au
steve@ims-global.com.au
alan@insituadvisory.com stuart.clark@ipsos.com
admin@jacksonenvironment.com.au
mail@jsrs.com.au
melbourne_admin@kleinfelder.com
sdegagny@kpmg.com.au s.newey@lek.com
tracey.storm@looporganics.com.au
MW@dc8.energy
dan@methodrecycling.com
greggornall@mgbconsult.net
info@mraconsulting.com.au
info@nu-rock.com
enviro@pjra.com.au
brendan.ridge@remondis.com.au
•
•
hello@resourcehub.com.au
admin@resourceinnovations.com.au
marketing@resourcerecovery.org.au
plc.admin@ricardo.com
rm@rmcg.com.au
brophyrecycling@gmail.com
duane.pretorius@au.sedgwick.com
enquiries@senversa.com.au
clokuge@slrconsulting.com
melbourne.reception@smec.com
council@snowymonaro.nsw.gov.au hello@southlandfiltration.com.au
admin@sphereinfrastructure.com
accounts@talisconsultants.com.au
sales@tellusholdings.com
anzsales@terracycle.com
alison.leckie@strategysustainabilityco.com.au
care@theafa.asn.au
louise@plasticcollective.co
hello@thewastenotspot.com
engage@thinkstep-anz.com
adelaide@tonkin.com.au
australia@tonkintaylor.com.au
sales@triconequipment.com.au brisbane@trinityconsultants.com
hello@utl-utilities.com.au reception.pyr@veolia.com •
memberservices@wcra.com.au
Steven Molino
contact@wpsas.com.au
info@zenergyaustralia.com.au
info@zephyrenviro.com
admin@ethosresources.com.au
sydrec@ghd.com
christian@greentecconsulting.com.au
sdegagny@kpmg.com.au
plan@masterplan.com.au
digestor MW@dc8.energy business@ntex.com.au
brendan.ridge@remondis.com.au
duane.pretorius@au.sedgwick.com
clokuge@slrconsulting.com
melbourne.reception@smec.com
sales@tellusholdings.com
hello@thewastenotspot.com
Maree.Marshall@wsp.com
admin@aargus.net
gr.act.group@gmail.com
info@advisorypartner.com.au
aap-sy-admin@arcadis.com
joyanne.manning@arup.com
rowanc@atcwilliams.com.au
enquiries@atonaus.co.au
std.aton.info@gmail.com enquiries@envaud.com.au
enquiries@envaud.com.au
admin@bioxenvironmental.com.au
bnpauspty@gmail.com
peandjm@gmail.com
info@closedloop.com.au
info@closedloop.com.au
stephen.davis@davisadvisory.com.au
consulting@elephantsfoot.com.au
consulting@elephantsfoot.com.au •
info@emmconsulting.com.au
info@ennovo.com.au
admin@ethosresources.com.au
rhofmans@expensereduction.com
sydrec@ghd.com
admin@greentecconsulting.com.au alex.stengl@gympie.qld.gov.au
keiran@harbak.com.au info@hrl.com.au
info@hrl.com.au info@hydroterra.com.au
admin@itn.com.au
alan@insituadvisory.com stuart.clark@ipsos.com
melbourne_admin@kleinfelder.com
sdegagny@kpmg.com.au
plan@masterplan.com.au
MW@dc8.energy
robert@milnelegal.com.au
info@mraconsulting.com.au
mail@mraenvironmental.com.au
service@nationwidewaste.com.au
contact@nomorebutts.org
sales@oleology.com.au
info@ozbincleaning.com.au
admin@phronis.com.au
martin@radicleag.com.au
lholt@ramboll.com mail@ratio.com.au sales@rawmetalcorp.com
brendan.ridge@remondis.com.au
admin@resourceinnovations.com.au
marketing@resourcerecovery.org.au
gavin@reuseandrecycle.com.au
plc.admin@ricardo.com
duane.pretorius@au.sedgwick.com
enquiries@senversa.com.au
clokuge@slrconsulting.com
melbourne.reception@smec.com hello@southlandfiltration.com.au
admin@sphereinfrastructure.com
cara@sustainablemindset.com.au
waste.enquiries@talisconsultants.com.au
sales@tellusholdings.com
care@theafa.asn.au
hello@thewastenotspot.com
adelaide@tonkin.com.au
australia@tonkintaylor.com.au
sales@triconequipment.com.au brisbane@trinityconsultants.com
hello@utl-utilities.com.au
Maree.Marshall@wsp.com
joyanne.manning@arup.com enquiries@envaud.com.au
enquiries@envaud.com.au
info@circular-vision.com
info@closedloop.com.au
enquiries@ehs-support.com
info@emmconsulting.com.au
info@ennovo.com.au
jayantk@enproenvirotech.com
info@envirorisk.com.au
•
duane.pretorius@au.sedgwick.com
enquiries@senversa.com.au
clokuge@slrconsulting.com
melbourne.reception@smec.com
Maree.Marshall@wsp.com
info@zephyrenviro.com
admin@aprince.com.au
rowanc@atcwilliams.com.au
enquiries@envaud.com.au
stephen.davis@davisadvisory.com.au
sydrec@ghd.com
sdegagny@kpmg.com.au
service@nationwidewaste.com.au
lholt@ramboll.com mail@ratio.com.au
brendan.ridge@remondis.com.au
plc.admin@ricardo.com
rm@rmcg.com.au
duane.pretorius@au.sedgwick.com
melbourne.reception@smec.com hello@southlandfiltration.com.au
admin@talisconsultants.com.au
hello@thewastenotspot.com
Maree.Marshall@wsp.com
gr.act.group@gmail.com
info@adilam.com.au
aus.consulting@anvarta.com
admin@arcenvironmental.com.au
aap-sy-admin@arcadis.com
joyanne.manning@arup.com
rowanc@atcwilliams.com.au enquiries@envaud.com.au
admin@automatedenvironmental.com
info@beconsult.com.au
admin@bioxenvironmental.com.au
blue@blueenvironment.com.au
info@cenvp.org
matt@circularfutures.com.au
admin@craus.com.au
info@closedloop.com.au
consult@coasteco.com.au
info@curriecommunications.com.au
admin@dartmouthconsulting.com.au
stephen.davis@davisadvisory.com.au
savings@energyconservation.com.au
accounts.payable@ecsustainable.com
enquiries@edp-au.com
enquiries@ehs-support.com
consulting@elephantsfoot.com.au
info@emmconsulting.com.au
info@ennovo.com.au
trevor@infrasolutions.com.au
alan@insituadvisory.com stuart.clark@ipsos.com
info@jvaengineering.com.au
melbourne_admin@kleinfelder.com
sdegagny@kpmg.com.au
Remediation admin@landserv.com.au
info@leighdesign.com.au s.newey@lek.com
info@ozbincleaning.com.au
enviro@pjra.com.au
admin@phronis.com.au
paul@randellenvironmental.com.au mail@ratio.com.au mail@ratio.com.au
brendan.ridge@remondis.com.au
ims-sales@remondis.com.au
hello@resourcehub.com.au
plc.admin@ricardo.com
rm@rmcg.com.au
rtrevaskis@hotmail.com •
duane.pretorius@au.sedgwick.com
enquiries@senversa.com.au
aaron@sleenvironmental.com.au
clokuge@slrconsulting.com
melbourne.reception@smec.com hello@southlandfiltration.com.au
admin@sphereinfrastructure.com
info@spm.com.au
info@spm.com.au
admin@talisconsultants.com.au
tandemsolutions4@gmail.com
sales@tellusholdings.com
care@theafa.asn.au •
hello@thewastenotspot.com
engage@thinkstep-anz.com
adelaide@tonkin.com.au
australia@tonkintaylor.com.au
sales@triconequipment.com.au
hellowastepac@gmail.com •
Maree.Marshall@wsp.com
info@zephyrenviro.com
giles@askwm.com
rowanc@atcwilliams.com.au
enquiries@envaud.com.au
bellsurveyingservices@gmail.com •
info@circularseed.com.au
info@closedloop.com.au
info@coterra.com.au
enquiries@ehs-support.com
info@emmconsulting.com.au
rhofmans@expensereduction.com
sydrec@ghd.com
christian@greentecconsulting.com.au
alan.hoskins2@gmail.com stuart.clark@ipsos.com
sdegagny@kpmg.com.au
jill@lethleanfireandenvironment.com.au
MW@dc8.energy
info@mraconsulting.com.au
service@nationwidewaste.com.au
sales@oleology.com.au
lholt@ramboll.com rarevoyage@bigpond.com
brendan.ridge@remondis.com.au
ims-sales@remondis.com.au
plc.admin@ricardo.com
enquiries@senversa.com.au
clokuge@slrconsulting.com
melbourne.reception@smec.com
sales@tellusholdings.com
hello@thewastenotspot.com
marcus.tso@veolia.com
Maree.Marshall@wsp.com
Organics at forefront of circular economy
By John McKew
THE AUSTRALIAN Organics Recycling Association (AORA) 2024 Annual Conference concluded at Sea World Resort Conference Centre on the Gold Coast on Friday 7 June. The threeday event, themed Collaboration for Success - Securing our Industry’s Future, brought together key stakeholders from Australia’s organics recycling industry (business, government, and academia) to discuss the importance of working together to secure the future of our industry. Strong foundations for collaboration were established between all parties, focusing on navigating regulatory landscapes, identifying priority issues, and exploring investment avenues for the industries sustainable growth.
The first AORA conference was held in 2013 in Sydney and is now run annually, rotating the location around Australia. After the success of the conference in Melbourne in 2023, the challenge was for Queensland was to go one better and that was achieved. The 2024 conference was the largest and most successful for the Association so far. Highlights included: l The 2024 AORA Annual Conference kicked off with the sixth Equipment Demonstration Day, allowing attendees to see shredders, screens, grinders, loaders, excavators, and more in operation. Participants had the opportunity to compare different models, engage with suppliers,
and necessary materials for the day.
l Thirty-five exhibitors showcased their equipment and services at the trade display. The exhibition was the centre piece for the conference breaks, allowing delegates on each day the opportunity to investigate the latest in industry innovation.
l A speaker program including keynote addresses from:
Prof Sally Brown, University of Washington (USA). Compost is the Environmental Equivalent of Duct Tape was the title of Brown’s speech. Among other information, she stated that compost can effectively hold the planet together. Pretty much anything you need done, you can do either by composting or by using compost. There is methane avoidance when food scraps are taken from the landfill to the pile. For soils, it enriches soil carbon and is the most effective tool for both soil carbon storage and restoring soil health.

Steve Nicholson, Eniver farm and agricultural agronomy consultant (NSW). His presentation discussed why his company started using organics, its results achieved so far, its failures and successes, the problems encountered, and strategies the company used to overcome them. Additionally, it explored the significance of organics in a soil carbon program and its role in the future.
A total of 304 individuals attended the conference, with attendees travelling from across Australia and the world.
economy transition. With almost half of the country’s waste streams constituting organic material, an effective circular economy will be elusive without a sustainable, and effective organics recycling industry.
2. The critical importance of soil and soil health continues to emerge, and organics have a critical role to play in achieving this. Aside from the importance of diversion from landfill and the benefits of this to help mitigate the impacts of climate change, organics will increasingly become important to improving our soils through improved carbon storage, improving water holding

challenging issue, especially in securing the much-needed future investment and confidence in the Australian organics recycling industry, is the lack of harmonisation of regulations across the Australian states/territories. The current review of the AS4454 standards (composts, soil conditioners and mulches) is well supported by the industry through the consultation phase of the review but concerns exist that the revised standard will lack the acceptance and adoption of states and territory regulators, potentially resulting in an impotent outcome.
4. Effective collaboration is a key ingredient to the future of the industry. As I noted during my welcome address on the Thursday morning, the room was full of passionate and committed industry participants, all willing to share their knowledge and to be part of the solutions to secure the industry’s future, but we can’t do it alone. AORA would like to acknowledge the generous support of all of its sponsors and partners in helping to achieve the success on the 2024 Annual Conference with a special thanks to the Queensland Government for being our Government Partner in 2024. Thank you to all of our speakers for generously sharing their knowledge and insights and a big thank you to all attendees – AORA recognises your commitment to be part of our conference and for that we are grateful.

John McKew is the National Executive Officer for AORA
AROA executive officer John McKew giving an address at the association’s 2024 conference. Image: AORA.
There was an array of live equipment demonstrations at the event. Image: AORA.
WASTE INNOVATION & RECYCLING AWARDS
Recognising excellence across the waste and resource recovery sector. Sponsorship opportunities are now available for 2024.
www.wasteawards.com.au





One-stop-shop for commercial composting needs

By Inside Waste
ONE OF THE BIGGEST bugbears when processing organics is trying to separate contaminants from the material that can be composted. One of the main culprits is plastic material. States and territories have strict criteria as to what constitutes compostable material. Therefore, it’s important to make sure that the separation plant and equipment being used are up for the task.
Deon Cope is a brand leader for Komptech, a company that specialises in plant and machinery that can meet an organic processing facility’s needs.
“With a lot of councils and governments mandating FOGO (food organics/green organics) be collected, contamination is an issue,” said Cope. “Most commercial composters are looking to get a better separation of their light plastics so they can get a better-quality product. They can use our Topturn machines to turn the windrows, Nemus drum screens are then used to separate out different size fractions, while the Hurrikan S is used to separate light plastics.”
Crambo 5200 Shredder
This direct low-speed dual-shaft shredder is designed for the first step in composting. Using such a machine at the front end of the process creates a product
with a greater surface area, which in turn helps with better aeration and porosity in a windrow. It also makes the removal of contaminants easier.
Other key features of the machine include the easy handling of contaminants such as rocks and metals; the ability to keep contaminants at a large enough size that they can be removed at a later stage; and allowing for an increase in airflow in the windrow, which assists with more consistent decomposition.
The machine has a throughput of up to 80 tonnes an hour, a CAT C13 engine, and a large feeding area with a flap-and-fold system for filling the hopper.
Topturn X5000 and X63 turners
Both turners have a place in the role of composting. Which machine is suitable depends on the area and pad size that needs turning, and the volume of material that needs composting.
A good turner will create tall, peaked windrows that will lead to successful composting. Such a windrow will allow for the right amount of porosity and pile structure to increase temperatures, minimise odours and reduce composting times.
The X5000 has the capability to create a windrow width of 5m and height of 2.2m. It has a sturdy frame, powerful hydraulics, and a big drum. The cabin

The X63 unit comes with a 390HP engine, and the ability to create windrows with a width of up to 6m and height of 2.8m. It also has a cooling system that works under heavy loads and high outside temperatures. Like the X5000 it has a large, comfortable cabin and hydraulically extendible platforms. It also has available an array of extras upon request.
Nemus 2700
Wheel Starscreen
The Nemus 2700 combines solutions and innovative details and comes with a large, steep walled hopper.
Its screen drum has an improved material feed compared to other

harmonised with its diesel-hydraulic drive.
Screening compost helps ensure a high quality, uniform product, which is why the choice of trommel or star screen is important. Drum screens like the Nemus 2700, are built for heavy, abrasive materials often found in topsoil.
Star screens create flexibility and are easily adjusted to account for the output of various particle sizes.
The Nemus 2700 model comes with a hopper volume of 5m³, a filling length of 4m and filling height of 2.85m. It can handle throughputs of up to 170m³ an hour.
Hurrikan S Wind Sifter
Designed for the end of the composting process, the Hurrikan S is suitable for removing plastic film from screen overflow. The designers of the machine have developed a patented pressure-suction process that gives the unit its separation efficiency of up to 95 per cent.
It has an electric drive of all components that provides an array of control possibilities coupled with top efficiency.
It has a loading width of 1.6m and a loading height of up to 2.25m. Its throughput can be as much as 60m³ an hour.
The Nemus 2700 can handle throughputs of up to 170m³ an hour. Images: Komptech.
The X63 unit has the ability to create windrows with a width of up to 6m.
The Hurrikan S utilises pressure-suction process that gives the unit a separation efficiency of up to 95 per cent.
Cat loaders deliver cutting-edge features
By Inside Waste
BUILDING on the D3 series compact track loader’s success, the next generation Cat 255 and 265 compact track loaders are a ground-up redesign of the previous series, improving on the features of the previous models. These next generation models have improved engine performance, lift and tilt performance, stability, operator comfort and technology.
“We kept the DNA of the D3 series while reimagining the possibilities of loader performance using voice of customer feedback to lead the way,” Trevor Chase, product application specialist for Caterpillar. “Both next generation models leverage the many benefits offered by the vertical lift design. The new Cat 255 replaces the 259D3, while the 265 replaces both the 279D3 and 289D3 machines.”
All loaders are identified by the ending model number 5. The simplified nomenclature uses the middle number to represent machine size with larger numbers designating larger machines.
A new performance standard
The 255 and 265 loaders are powered by Cat C2.8T and Cat C2.8TA engines respectively, which offer 74.3 hp (55.4 kW). The new engines maintain horsepower across a wide RPM range and have torque increases of 13 per cent for the 255 and 43 per cent for the 265. A redesigned engine compartment mounts the engine and cooling package lower into the frame for improved stability, giving the operator confidence in handling heavy loads and throughout all aspects of the work cycles.
The new 255 loader delivers classleading lift height, and compared to the 259D3, delivers 36 per cent more tilt breakout, 26 per cent higher lift breakout force and a 24 per cent increase in rated operating capacity (ROC). Height to the B-pin for the 265, compared to the 289D3, increases by 7.6 in (193 mm), resulting in a maximum lift height of 11 ft (3.35 m) for easier truck loading.
The 265 also delivers 19 per cent higher tilt breakout force and 22 per cent higher lift breakout force.
Standard hydraulic system pressure is increased to 3,500 psi (24130 kPa). New for these next generation machines, the closed-centre auxiliary hydraulic system allows the 255 and 265 to operate all Cat Smart Attachments, including the Cat
Dozer Blade, with the standard auxiliary hydraulics provided.
For machines equipped with Standard Flow, both models are shipped from the factory outfitted as “High Flow ready”.
The High Flow functionality is easily activated via a new software-enabled attachment (SEA), permitting on-machine or remote activation of increased hydraulic flow to 30 gpm (113 l/min) at the standard system pressure. The High Flow XPS factory option increases auxiliary hydraulic system pressure to 4061 psi (28000 kPa) for both models, while also increasing the hydraulic flow to 30 gal/min (113 l/min) for the 255 and 34 gal/min (129 l/min) for the 265. The 255, equipped with the High Flow XPS option, offers customers auxiliary hydraulic performance not previously available in a mid-size chassis machine.
Reengineering of lower machine components results in a stronger and stiffer undercarriage for improved machine stability and less pitching when filling the bucket with material. Its torsion suspension undercarriage delivers better operator comfort, track wear and material retention, plus the stiffer design results in smoother graded surfaces. The 255 loader offers a new 12.6-in (320-mm) bar-tread narrow track option.
Improved operator’s office
Both loaders feature a larger cab design with 22 per cent more overall volume and
26 per cent additional foot space. With a 2.75-in (70-mm) increased interior width, the new cab expands footwell-to-ceiling height by 1.8 in (46 mm), and allows for an additional 1.5 in (40 mm) of hip room and 1.1 in (28 mm) more width between the joysticks for improved operator comfort.
A range of new mechanical and airride suspension seat options are available for the loaders, including a high-comfort seat that is both ventilated and heated. New auto temperature control plus vent outlet positioning above the operator helps the new HVAC system to cool the cab’s interior.
Next generation loaders are equipped with either a 5-in (127-mm) standard LCD monitor or an 8-in (203-mm) advanced touchscreen monitor, depending on the technology package selected. Like the D3 series’ advanced display, the standard monitor features Bluetooth connectivity and supports functionality for rearview camera feed, creep, job clock, maintenance reminders and 32 languages. The touchscreen monitor provides a higher level of control over standard monitor functionality, delivers advanced radio control, and supports the multicamera 270-degree option and 32 language choices. The joysticks provide integrated control of the touchscreen monitor so all machine function control and adjustments can be made without the operator removing their hands from the controls.
Featuring a low entry point, entering and exiting the 255 and 265 loaders is much easier. The redesign allows the operator to open the cab door without the lift arms being fully lowered to the frame stops. A simplified two-step door removal process allows operators to remove it without tools.
Visibility is improved via the lower engine mounting, a 59 per cent larger rear window and bigger top window that provides a 15 per cent increase in viewable area.
Advanced technologies
These loaders deliver the next level of integrating machines with technology. Both the standard and advanced monitors offer the ability to run Cat Smart Attachments, such as the dozer and grader blades and backhoe. These attachments are tied into the joysticks, and the machine automatically recognises the type of attachment and the required joystick pattern for controlling it.
The available Cat Product Link Elite system tracks machine hours, location, asset utilisation, provides fault code details and delivers advanced monitoring and machine health, which is remotely accessible via VisionLink. In addition, Product Link Elite provides remote flash and troubleshooting capabilities and quickly enables the remote activation of the SEA High Flow feature.

These next generation track loader models have improved engine performance, lift and tilt performance and operator comfort. Image: Caterpillar.
Smart
Fuchs meets needs of busy recycler

By Inside Waste
KARL ALFARO is the owner of Top Dollar Metal Recyclers, offering an innovative approach to scrap metal recycling. Its NSW location at Miller Road in Villawood, Sydney provides competitive rates and prompt service for cars or trucks.
Top Dollar’s certified weighbridge is designed to handle trucks of all sizes, including semi-trailers. With separate entry and exit points on different streets, it guarantees minimal wait times. On average, customers spend less than 10 minutes on site. Payments are instantly processed through the “osko” banking system, ensuring that the funds are in their customers account by the time their vehicle leaves the premises.
Top Dollar has been operating in the scrap business for 20 years, with the company initially focused on non-ferrous products before transitioning into the steel market in 2005. For 16 years it was located on Fairfield Road before relocating to its current site. Initially, the company used tracked excavators to load semi-trailers for domestic use.
On-site, a range of machines are utilised for processing the scrap metal from demolition projects. These include excavators, shears, shear balers, and a processing plant. The machinery is used to sort the metal and remove any nonmetallic contaminants and prepare for
further shredding, cutting or compressing in preparation for loading the scrap metal to send to its final destination.
In more recent years Top Dollar had decided to export its steel, but encountered challenges when they realised its existing equipment, mainly excavators and grabs, were not suitable for the task. While these machines were effective for loading open semis for local transportation by grabbing materials of various sizes and compacting them, different equipment was needed for loading containers bound for overseas shipment.
After conducting research and seeking advice on the most efficient way to load containers for overseas shipping, it acquired a second-hand Fuchs MHL350, which proved to be a game-changer, significantly improving the process.
Packing 24-foot containers with steel was streamlined by positioning the container upright, allowing for precise material placement with minimal space wastage around the steel. The Fuchs machine facilitated easier access during the process. Alfaro highlighted that the Fuchs machines are also easy to repair, and not as prone to dipper arm breakages, which had been an issue in the past.
Over time, as the business grew, another machine was needed. Once again Top Dollar completed its due diligence and researched other brands. However
it was happy with the Fuchs machine in relation to durability and precision, so went ahead with another Fuch.
It opted for a smaller model, downsizing from a MHL350 to a MHL331 due to limited space.
“Our team puts the equipment through its paces, as this industry can be quite demanding on machinery and the Fuchs definitely holds up,” said Alfaro.
The MHL331 is known for its comfort, exceptional visibility, and pre-start access. At Top Dollar, operators frequently use the same machine, which encourages a feeling of responsibility towards maintenance and overall machine care. They find this model to be
local dealer for Fuchs is
Alfaro likes the ongoing support and services that continue to grow with Onetrak’s expansion. Top Dollar is happy with Onetrak’s staff and its responsiveness to servicing and repairs. During Onetrak field technician Dan Mills’ recent visit, Karl noted that he accurately diagnosed an issue, estimated the repair time correctly, and even offered some additional tips. His personable nature and extra advice were appreciated.
“As the equipment ages, reliable backup support becomes increasingly vital,” said Alfaro.
As the business continues to grow Top Dollar is looking at a third machine, most


The
Onetrak.
Fuchs excavators are known for their comfort, visibility, and convenient pre-start access.
Images: Onetrak.
Fuchs machines are easy to repair and not as prone to dipper arm breakages.


Taking the guesswork out of disposal costs
By Inside Waste
SPACE CAN BE at a premium at back of dock, so having fit-for-purpose waste handling equipment that makes life easy for employees is a good start.
Wastech Double-Decker compactors are designed to compact multiple waste streams in areas where there is limited access.
The equipment has two stacked compactors, allowing simultaneous handling of multiple waste types, which is why it is ideal for facilities that want to fully utilise limited footprint, and also have the ability to sort an array of waste.
It is uniquely fabricated to fit into single footprint loading docks. It offers versatile loading options, including hand- or bin-lifter loading, and it is suitable for both dock and ground-level operations.
“As well as allowing you to double stack products, it comes with a remote control,” said Wastech business development manager Greg Scott. “Its throughput is also great, whether it’s a high volume of cardboard, or it’s a higher volume of general waste, Wastech can design the working space to suit the site’s needs in a limited amount of space.
The compactors are a hardworking piece of machinery and, as a rule, according to Scott, have a packing ratio of about three-to-one with very low running cost.
Wastech can customise the setup to match specific waste management needs and volume. Each compactor is emptied only when full, reducing unnecessary transport costs.
The lower unit container is 12-15m³ in size, while the upper container can be between 19, 23m³ and 35m³.
Smartweigh
Then there is Wastech’s Smartweigh system, which is turning out to be popular among the waste industry, not least because it gets rid of uncertainty around how much waste is being disposed of by customers.
It comes with an integrated screen where all relevant
bin capacity. It will even provide troubleshooting tips when needed.
Designed to cater for bins from 120L to 1100L, the Smartweigh system can come equipped with a Wastech compactor or be retrofitted to any existing unit.
Wastech sees the system as doing away with an ambiguity about how much waste is being disposed of,
“Smartweigh allows owners to distribute compactor collection costs between users and monitor usage.”
information is displayed including the status of the Smartweigh, the weight of waste being disposed of, and the ID of the user.
Another feature is that the compactor operations are monitored through the same screen, showing compactor
with accuracy being the paramount feature.
“It provides accurate, comprehensive data on each individual disposal,” said Scott. “It allows equipment owners to distribute compactor collection costs between users and monitor usage.”
The compactors are a hardworking piece of machinery and have a packing ratio of about three to one. Image: Wastech.
Permanent Deep Field and Electromagnetic Scrap Drums
More: Using our sophisticated design software and unique magnetic circuits, Eriez provides permanent and electromagnetic scrap drums with deeper magnetic fields to reclaim ferrous materials in automotive shredder residue (ASR), materials recovery facilities (MRF), municipal solid waste (MSW), scrap metal yards, wood waste, slag, incinerator bottom ash, foundry sand and minerals processing applications.
Permanent
Deep Field Magnetic Drums
This design uses permanent magnets and bucking poles to project a deep magnetic field capable of removing ferrous from distances of up to 15 inches (380 mm). The permanent scrap drums are ideal for applications with limited or unstable electrical power.
Electromagnetic Scrap Drums
The All Electro Agitator type utilizes a deep field rectangular core pickup magnet to reach out and grasp the ferrous, and a second rectangular-core agitator magnet to flip or agitate the ferrous, cleaning it of contaminants such as loose mud, paper, fluff and trash. Eriez also builds a non-agitating transfer design that uses a deep field radial pickup magnet and pole shoes to convey or transfer the ferrous around the drum shell to the discharge area.
Eriez Suspended Electromagnets
Company: Eriez
Name: Jonathan Schulberg, Business Development Manager –Heavy Industry, Eriez-Australia

Phone Number: +61-3-8401-7400
Email: jschulberg@eriez.com
More: The Suspended Electromagnet provides tramp metal collection from conveyed materials. The electromagnet is typically mounted or suspended over a conveyor belt to remove large pieces of tramp metal that represent a hazard to downstream crushers, mills, pulverisers and grinders. Suspended electromagnets also remove sharp metal that can damage or tear expensive conveyor belts, especially at transfer points. Product purity is enhanced with the separation power of the suspended electromagnet.
Features & Benefits:
• Exclusive oil expansion tank prevents condensation and protects against hot spots to extend coil life
• Aluminum or copper coils use Nomex insulation and fiberglass spacers to prevent shorts
• Five-year warranty on coil assembly
• Adjustable oil expansion tank design for any installation angle is mounted with slotted brackets, allowing the user to rotate the tank so the moisture drain is always on the low side
• Lift lugs now include two side-by-side holes to allow for simultaneous hoisting and installation of the suspension gear
• 23 magnet sizes, 69 standard models and hundreds of special designs available for unique applications Special options, including:
- CSA approved designs for both manual and self cleaning units
Vermeer HG6000TX Horizontal Grinder
Gross horsepower: 755 hp (563 kW)
Length: 11.4m (transport, without dolly)
Width: 2.8m (transport, without dolly)
Height: 3.8m (transport, without dolly)
Weight: 36,287 kg
Make and model: CAT C18 T4/STAGE IVB (Engine Option 1)
More: The Vermeer chip drum offers customers versatility and consistency, allowing you to use one grinder to process both wood waste and biomass. Increase productivity thanks to the exclusive Vermeer SmartGrind system, which automatically controls grinding speed based on engine rpm levels. Top-loading screens are designed to give operators easy access.
Name: Vermeer Australia
Phone number: 1300 VERMEER (837 633)
Website: vermeeraustralia.com.au
Email: enquiries@vermeeraustralia.com.au
- Upgraded coil design for elevations greater than 3,000 feet above sea level
- High fire point coolants
- Zero speed switches
- Dust covers
- Pulley guards and controls
- Permanent extensions and monitoring devices
- Force-cooled units available for high temperature applications
Company: Eriez
Name: Jonathan Schulberg, Business Development
Manager – Heavy Industry, Eriez-Australia
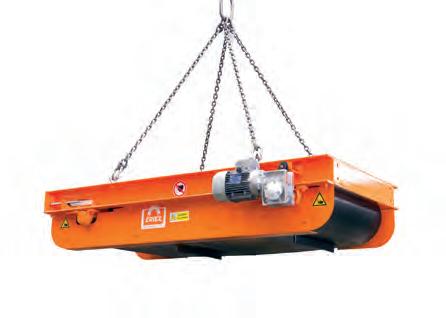
Phone Number: +61-3-8401-7400
Email: jschulberg@eriez.com

ERIEZ

really enjoyed that job, very rewarding and a great way to establish connections in the industry. Sometimes I go back to old landfills to see how they are going.”
This job helped Wright in his subsequent roles because, when he’s dealing with contractors, he’s done what they’ve done. He’s had to pull pumps out of wells, install equipment, author reports and deal with clients. After Eurofins Scientific he went to Resolve Environmental, a growing environmental consultancy. Resolve is a consultancy that specialises in assisting petroleum and waste management clients to meet their environmental obligations. The role involved fieldwork, sampling, laboratory analysis and report writing and allowed Wright to further expand his knowledge of landfill facilities. And it was through Resolve’s client Cleanaway that he got his current position as landfill manager.
At Resolve, he completed environmental monitoring for a large number of clients in Victoria. Landfills, quarries, petroleum, and property development were our major clients. Within that role, Wright would complete groundwater, landfill gas sampling, analyse the data and provide conclusions and recommendations to clients.
Saving the world one day at a time
By Inside Waste
DANIEL WRIGHT initially wanted to follow in his father’s footsteps, who was an accountant for Macquarie Bank, so he started a double degree in economics and science. Then he had an epiphany.
“I came to an early conclusion that anything in economics, I could learn through practice,” he said. “What I really wanted to do was spend three years diving deep into chemistry and get a deeper understanding of our molecular world. So, I swapped out of the double degree into a degree in advanced science (chemistry).”
Back then, Wright, who now manages the Kemps Creek Landfill at Cleanaway’s Resource Recovery Park, wanted to learn how things worked; how to break things apart and how to build them back together. He got involved early on in a research project into solar cells using indigenous plants. It involved grinding up the plants and using them as part of the
makeup of solar cells. Wright loved the idea that he could use plants and nature to make the world a better place.
Having seen first-hand the difference like-minded people can achieve when it comes to making a healthier environment, he knew what he wanted to do for the rest of his life, but it was how to do it that became the problem. When he graduated, he found that there were not many openings in the areas he was keen to develop his skills.
“I couldn’t get a job when I graduated,” he said. “It was a tough, hard thing to face. I applied for almost every engineering, science and finance graduate program - mining companies, CSIRO, the four major banks – nothing.”
Then he managed to get a position with medical supply company Livingstone International as a quality assurance officer. The role involved testing and approving medical equipment before release to hospitals and surgeries around Australia, such as
syringes, needles, gloves, and monitoring equipment.
While Wright knew he wanted to do more with the environment than the role offered, it did teach him about the importance of quality assurance and quality control – two essential skills that are needed in his current role.
The following year Wright took a year off to travel Europe and the USA before returning to Sydney. His next move would see him go down to Melbourne to work for multi-national environmental analytical laboratory company Eurofins Scientific. This role allowed him to put his chemistry degree to the test. After a year into the job, he finally saw a hint of what was to come in terms of his career.
“I joined their Groundwater Sampling Team as a field technician, and I started sampling groundwater/surface water from a few landfill and petroleum sites around Victoria.
“From Sale to Wangaratta, almost every landfill in Victoria,” he said. “I
Wright found the role very rewarding, as it “required a mix of fieldwork and office-work and allowed me to expand my technical skills in data analysis and report writing”.
Wright managed to get an in-depth knowledge of how landfills work and the engineering controls in place that protect our environment once waste is disposed permanently to the earth. But as we know, landfill management has come a long way, and Wright learnt how important it is to design, construct and operate landfills properly.
While at Resolve, Wright was seconded to Suez for four months, then a three-month secondment at Cleanaway followed. At the end of the secondment with Cleanaway Wright felt compelled to join the company, where he could use his analytical and technical experience to work on landfill projects.
In March 2021, Wright relocated to Sydney to work with Cleanaway’s engineering team led by Barry Griffin, head of engineering - landfill and remediation. Wright hit the ground running working on an infrastructure project at Cleanaway’s Erskine Park Landfill site, a Mechanically Stabilised Earth (MSE) Wall to increase airspace and provide an additional three years of operational life. The project endured the 2021/2022 floods and the second wave of COVID-19. That award-winning project finished in 2022. This in turn freed Wright up to take up his current role. Wright leads a team of 25. A big part of his role is to build and develop
Dan Wright at the Kemp’s Creek Landfill. Images: Cleanaway.
the team so that they can become the best of the best in terms of landfill operations.
“We have a vision to become a flagship site within Cleanaway and a benchmark of what good looks like in our industry,” he said. “We’re not there yet, but every day we are getting closer, and the team is fully committed to the journey. I am incredibly proud to represent our site.”
What does a typical week look like?
“We are really big on getting everyone to attend the morning toolbox at 7am, so all days start with a group toolbox at the Operations Office. It’s a great opportunity to get a feel for the day ahead and tackle problems early on,” he said.
On Monday’s Wright starts with payroll, followed by a performance report on how the previous week.
“The report contains the usual KPIs of any landfill – safety, environment, tonnes in, density achieved, leachate treated, landfill gas extracted and a number of others,” he said. “It articulates what we are doing to improve site safety and drills deeper into any incidents, near misses – hopefully both of those are zero – and serves to spotlight how many HSE conversations we had with our team. I’ve found having face-to-face conversations (HSE or otherwise) at the morning toolbox, the most effective way of building good site culture”.
Part of Wright’s job is to look at the landfill’s gas performance; how much gas is being extracted from the waste cell each week. That gas is distributed to a pair of 1.4MW generators that allows Cleanaway to generate renewable electricity, which makes its way back into the grid.
A myriad of other tasks takes up Wright’s week – anything from scoping out future leachate treatment technologies to managing the sites landfill gas extraction system. There is always something happening, and Wright wouldn’t have it any other way. And what are some of the key issues facing the industry?
Flock is an opportunity worth looking into, he said. For the uninitiated, flock is shredded car parts. He said it is a relatively homogenous waste containing assorted plastics, sponges, insulation and other materials unable to be recycled from cars that have reached end of life.
“Of all the waste streams I see every day it’s about 20 per cent of what we get,” he said. “While most components of cars are recycled, the flock is the remaining material that currently can’t be. It’d be worth exploring government initiatives that promote a beneficial
reuse of this material”.

He also wants to work closely with the NSW EPA when completing major projects and to further improve the current operational purpose deductions (OPDs) process. He believes that Cleanaway’s landfill assets are contributing to continuous improvement within the industry, always looking for the next opportunity to do more. Therefore, companies like Cleanaway and the EPA must work hand-in-hand to make sure landfills have positive long-lasting effects for our communities and the environment.
“The more we work together and think of it as a joint venture – not a Cleanaway way of doing things or an EPA way of doing things – then that would be beneficial to everyone,” he said. “We have very strong internal regulations because our CEO and executive team demand it, and consequentially have developed a good relationship with the NSW EPA”.
Bringing the private sector & NSW EPA closer together would be the final piece of the puzzle in achieving big things for the NSW waste sector.
“I am a firm believer that our waste
industry needs greater recognition for what we do for society. Our industry is not a collection of isolated businesses working for the short term, but instead is a network of assets and operations that together, form the essential service that is waste. We are a service that is required for seven days of the week and at Cleanaway we have demonstrated our commitment to acting beyond today and working towards a more sustainable future together. I look at what the industry has achieved over the past 10 years, and it makes me excited for the next 10 to come.”
Wright’s day is never dull as he has a plethora of duties to carry out.
Breaking cover
Hello Sir
It’s been interesting times down under as government-mandated deadlines hover over the horizon. Industry wonks and insiders aren’t even bothering to hedge their bets; they’re all saying that the deadlines will not be met.
Why is this? I don’t even know where to begin. It’s like a Penrose Staircase – everyone is going round and round in circles, and they don’t really know why. I exaggerate slightly; it’s not completely true. Those at the coalface of industry know why, but those who make the decisions have no idea. However, they do know when the next election cycle will come around. They know how to work a crowd. Pity they don’t know how to work an industry.
I don’t think I blather on about the reasons . Okay, I’ll mention a few. There is no harmonisation
between the states, unrealistic goals, and a lack of infrastructure. More importantly, companies are unwilling to invest in facilities due to a whole raft of reasons that I won’t go into now (with the exception of one; see below). I believe that I could write this letter to you two years from now, and I wouldn’t have to change one word for it to still be true.
Now for that exception: insurance coverage. By golly, I remember when I went to get my life insurance and told the broker my occupation, he almost choked on his tie. There must be a similar reaction CEOs are getting in the waste industry when getting insurance premium quotes and being told that 1) they’ll get no coverage unless a whole lot of expensive remedies are carried out on their premises, or 2) they’ll get no coverage at all.
Having spoken to a broker or two recently about several different types of insurance (it’s amazing –ahem – how much my life insurance premiums will go down if you ever decide to put me behind a desk instead of out in the field, Sir), and the considerations that are made when getting a quote – they’re called ‘mitigating circumstances’. There is an array of these circumstances, depending on the situation. It’s like trying to navigate a minefield – one wrong step and you’re in big trouble.
You want an example? My two friends say that it is not advisable to charge your electric forklift overnight. Do that, and an insurer will either hike your premium markedly or, more likely, not give you a policy at all.
Apparently, throughout the world, there has been a big increase
in such fires, not just in waste facilities, but in an array of other industries’ buildings.
Insurers know that lithiumion batteries are here to stay for the immediate future, so they are factored in when putting together risk factors.
And remember, this is only one aspect taken into consideration by an insurer. Think of all the other risks that abound within the industry. It’s a risk assessment that would make even Q sweat.
I’d like to end on a more positive note by wishing the country the best in its efforts to reach the many recycling and reuse targets being set. But I can’t. Because it’s not going to happen. The funny thing is, the remedies are not that hard to come by, but apparently backbones are.
JB
“Apparently, throughout the world, there has been a big increase in such fires, not just in waste facilities, but in an array of other industries’ buildings. Insurers know that lithium-ion batteries are here to stay for the immediate future, so they are factored in when putting together risk factors.”







So Does Perth.

Our solutions are based on efficient and environmentally sound in-house technology, and cover the entire life cycle of an Energy-from-Waste facility. Our proven technologies have been part of more than 700 plants worldwide. As a global leader in energy from waste we are proud to be able to say: We deliver. Check our references. Waste is our Energy www.hz-inova.com
Oslo, Norway Dublin, Ireland
London, United Kingdom
Rockingham, Australia




