opportunity ambition
More than a pay cheque –Mel Morrison shares how Komatsu is reshaping what it means to work in construction and heavy machinery.
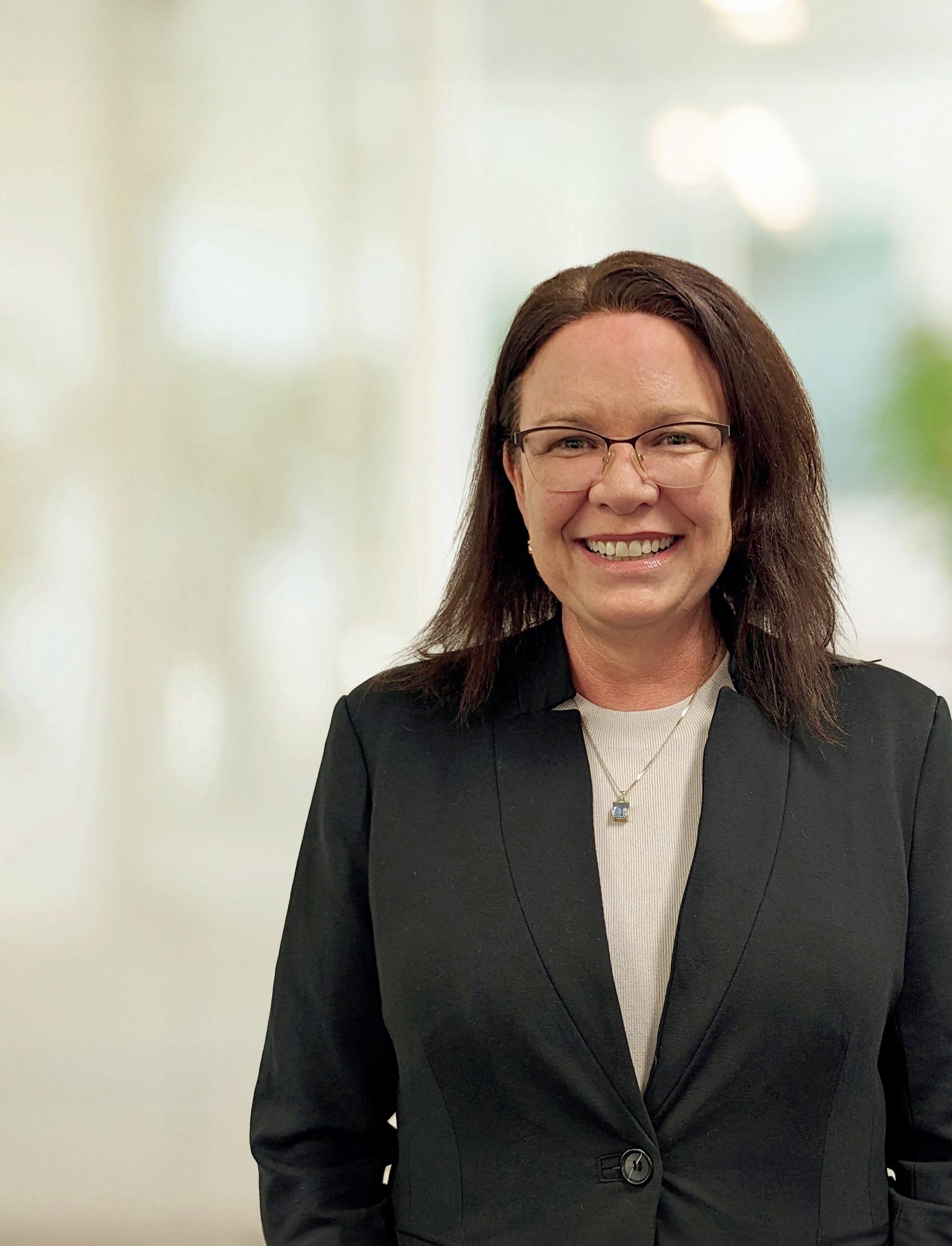
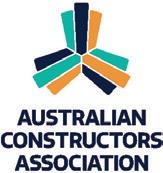
Serrated Flanged Class 12.9 Bolt and Class 12 Nut

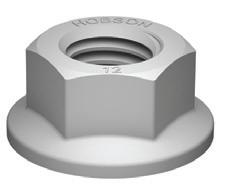
ZINC FLAKE Coating
Features
D-LOK® bolts are designed for applications where there is constant vibration. They are fatigue resistant and reusable with no decrease in performance.
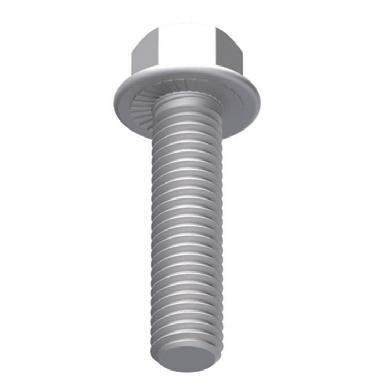
» Flanged — no additional washer required
» Serrated — to lock and clamp the connection
» Environmentally friendly






Serrations LOCK and clamp the connection.

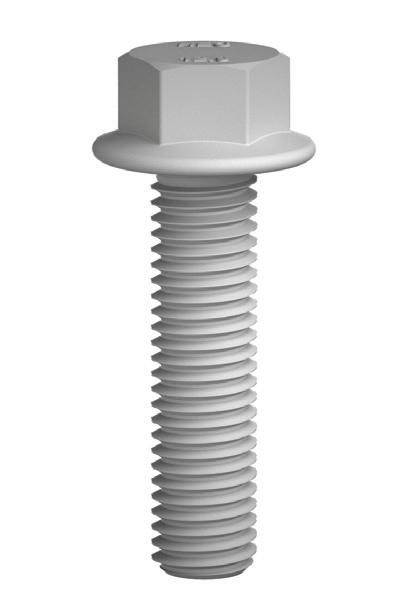
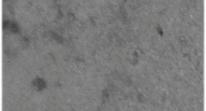





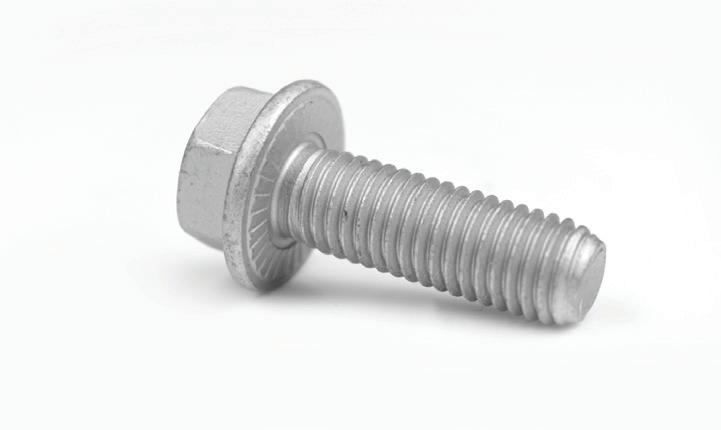
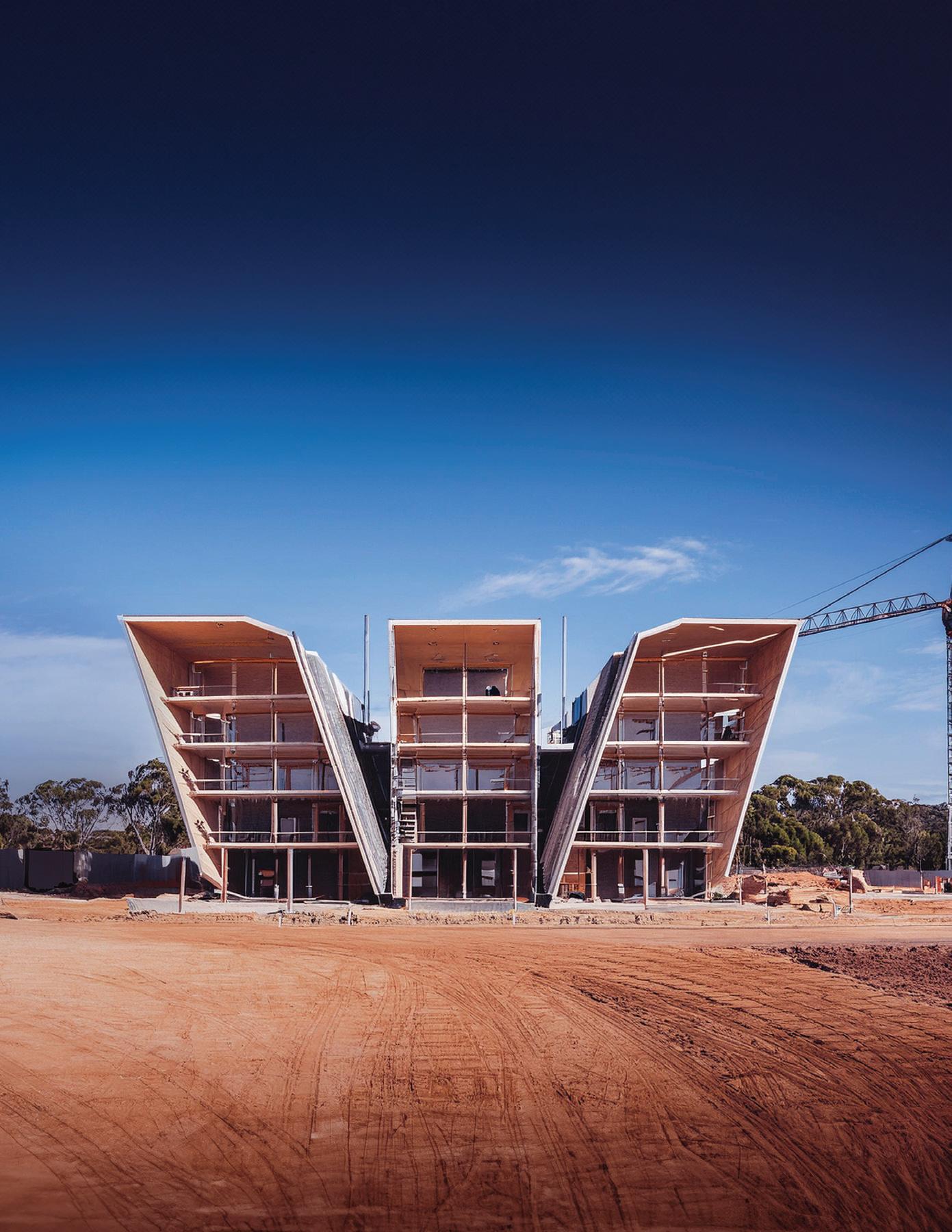

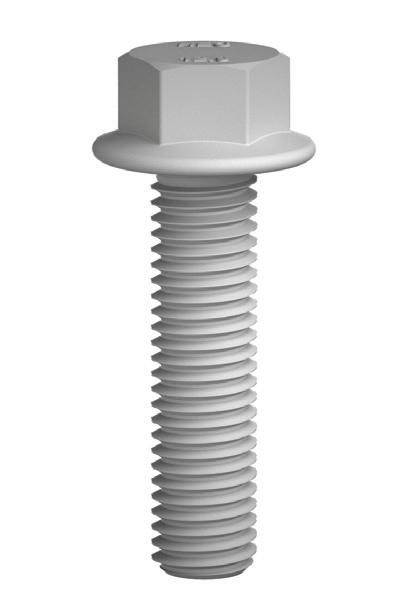
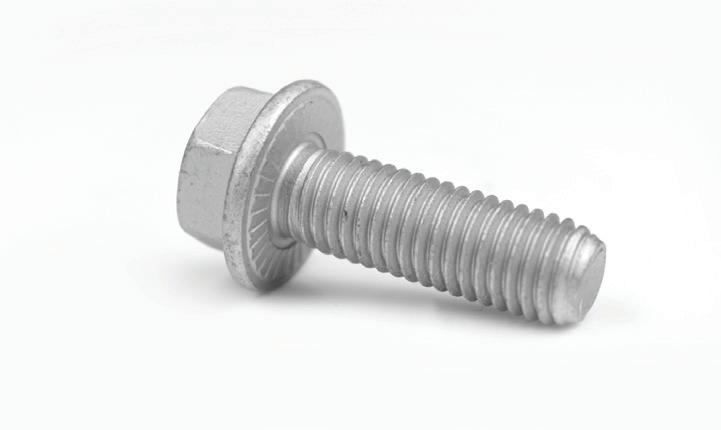

REGULAR

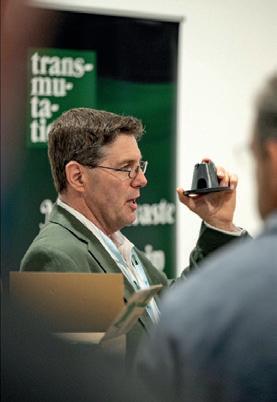
Komatsu creates a culture that champions professional growth and personal wellbeing, redefining careers in construction and heavy machinery.
46 Jagoda Grigorean: From law to landmark projects
From a law classroom to leading commercial teams on global infrastructure builds, discover how Jagoda Grigorean’s career defies convention.
48 Jordyn Allan: Wiring a bright future
Jordyn Allan shares how a chance conversation in a fastfood dining room led her from restaurant management to electrical work on a major Sydney tunnelling project. ASSOCIATIONS
52 Uccello rising
The National Precast Concrete Association Australia presents the Pagewood Centro Uccello project, a precast concrete development in New South Wales.
54 Redefining industry success
The National Association of Women in Construction aims to create a more equitable industry by fostering cultural change.
56 Creating safe and supportive spaces
NexGen showcases how programs like BESIX Watpac’s Lean In Circles are changing the game for women in construction.
57 More than just the biggest and best
The Australian Constructors Association gears up to announce this year’s Australian Construction Achievement Award winner.
58 Honouring the achievements of apprentices
Empowered Women in Trades recognises and celebrates apprentices across Australia. OPINION
50 Smart leadership: Connecting to a strong support system
Dr Gretchen Gagel illustrates the power of leadership rooted in collaboration with mentors, sponsors, coaches and allies.
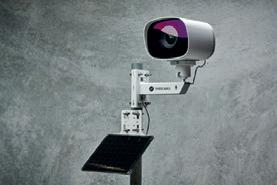
EVENTS

Civil Contractors Federation Victoria takes the spotlight as an Association Partner at Converge 2025.
FOCUS
A coat above
Hobson Engineering addresses the challenge of hydrogen embrittlement in fasteners using zinc flake coatings. 22 Strength in service
Backing its fleet of machinery, Jacon Equipment spotlights the support and training it provides to keep construction projects running smoothly.
Taking on the big recycling challenges
Transmutation proves that even the hardest-to-recycle construction materials can find a second life.
28
Embracing the benefits of light gauge steel
Discover how light gauge steel framing made from TRUECORE steel accelerated the construction of the Sunkids Childcare Centre.
Linking the quality lifecycle
Visibuild explores how connecting every phase of construction simplifies quality, empowers teams, and transforms insights into real progress.
Digging deep
McConnell Dowell discusses how refined trenchless techniques are advancing project delivery in the water sector.
38 Maximising ROI at every stage of construction
Timescapes explains how timelapse cameras and job site analytics provide a practical gateway to digital innovation in construction.
42 A lifeline for skilled labour
IMMIGATE assists businesses in accessing overseas talent to bridge the skills gap in construction.
High-rise, high-tech
KONE highlights how its high-rise elevator systems are designed for the next generation of skyscrapers, featuring lighter materials and smarter technology.
From the editorial team
Forging ahead
Construction is pushing past the limits of today, forging a future where innovation, ambition and bold ideas set the foundations for what comes next.
Today’s construction industry is no longer solely about deadlines and budgets. It’s about daring to build differently, reimagining possibilities and shaping the world in meaningful ways.
Sustainability, diversity and innovation have become the blueprints for progress, not just fleeting trends. In this edition, we spotlight the visionaries turning tomorrow’s challenges into today’s breakthroughs, creating a lasting legacy.
One pressing challenge is the ongoing skills shortage, driven by an ageing workforce, evolving employee expectations and a lack of new talent. While this issue won’t resolve overnight, one construction equipment manufacturer is setting a new standard by fostering professional growth and prioritising employee wellbeing.
A specialist immigration agency is also playing a crucial role, helping businesses navigate red tape to secure skilled workers through employer-sponsored migration – a practical solution to keep operations thriving.
On the sustainability front, a plastic recycling company is demonstrating how even the most challenging construction waste can be repurposed, paving the way for a circular economy within the sector and beyond.
Efficiency is another cornerstone of sustainability. A software company is showcasing how timelapse cameras and job site analytics can uncover inefficiencies, refine designs and enhance decision-making – improving project outcomes across the board.
An elevator manufacturer is delivering systems for both new developments and modernisation projects, designed to improve building efficiency and help move people, buildings and cities into the future.
Meanwhile, a childcare centre project in Queensland highlights the potential of light gauge steel framing. By minimising on-site waste, cutting costs and enabling efficient delivery, this project exemplifies how smart material choices can benefit both the environment and the bottom line.
We also share exciting news for Converge 2025, the only Australian-owned major event showcasing the latest tools and technology in municipal works, civil and commercial construction.
What unites these stories is innovation – the driving force behind the next era of growth for Australian construction.
Inside Construction is dedicated to supporting the individuals and organisations shaping the industry’s future. Through these stories, we aim to spark fresh ideas and inspire new possibilities for continued progress.


Chief Executive Officer John Murphy
Chief Operating Officer Christine Clancy
Managing Editor Mike Wheeler mike.wheeler@primecreative.com.au
Editor
Ashley Grogan ashley.grogan@primecreative.com.au
Sales Director
Brad Buchanan bradley.buchanan@primecreative.com.au
Design Caterina Zappia
Head of Design Blake Storey blake.storey@primecreative.com.au
Business Development Manager
Nhung Nguyen nhung.nguyen@primecreative.com.au p: +61 0412 845 608
Client Success Manager Louisa Stocks louisa.stocks@primecreative.com.au
Cover image credit Komatsu
Head Office
Prime Creative Pty Ltd 379 Docklands Drive, Docklands, Victoria 3008 Australia p: +61 3 9690 8766 enquiries@primecreative.com.au www.insideconstruction.com.au
Subscriptions
+61 3 9690 8766 subscriptions@primecreative.com.au
Inside Construction is available by subscription from the publisher. The rights of refusal are reserved by the publisher
Articles
All articles submitted for publication become the property of the publisher. The Editor reserves the right to adjust any article to conform with the magazine format.
Copyright
Inside Construction is owned by Prime Creative Media and published by John Murphy. All material in Inside Construction is copyright and no part may be reproduced or copied in any form or by any means (graphic, electronic or mechanical including information and retrieval systems) without written permission of the publisher. The Editor welcomes contributions but reserves the right to accept or reject any material. While every effort has been made to ensure the accuracy of information, Prime Creative Media will not accept responsibility for errors or omissions or for any consequences arising from reliance on information published. The opinions expressed in Inside Construction are not necessarily the opinions of, or endorsed by the publisher unless otherwise stated.


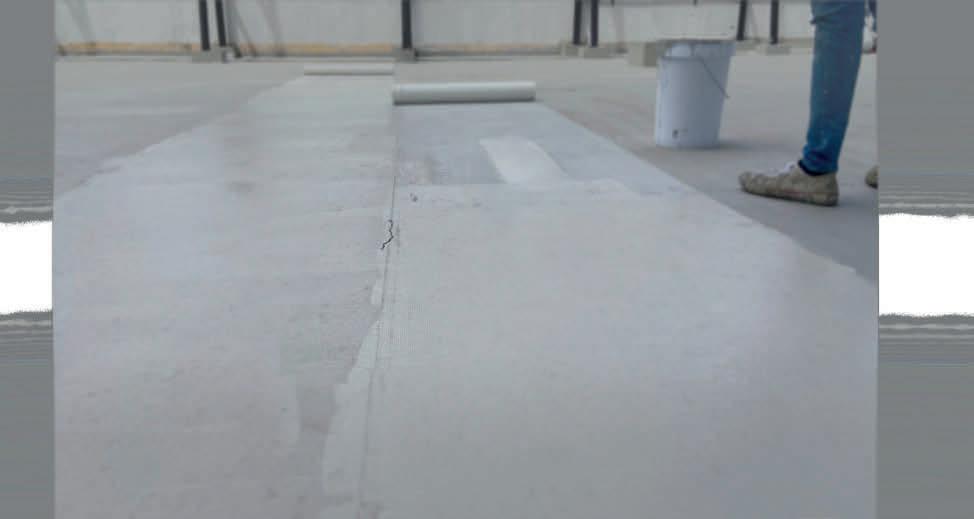
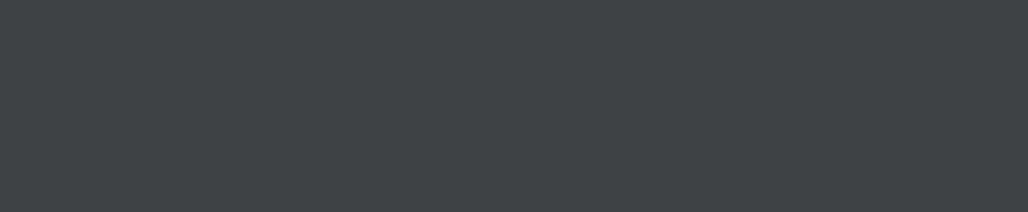

Project Picks
Project Picks
A defence facility, regional hospital and convention centre – this month’s featured projects showcase the diverse expertise of Australia’s major contractors.
Eurobodalla Regional Hospital, New
South Wales
Contractor: Multiplex
Current value: $300 million
Details: The Eurobodalla Regional Hospital will offer expanded and improved health services on the New South Wales South Coast, enhancing access to high-quality healthcare for the local community. Multiplex will build a new emergency department, an intensive care unit, surgical and operating theatres, and a day-stay surgical unit spread across three clinical levels within approximately 20,500 square metres. Additionally, it will provide a new access road and a hospital car park area.
Status: Work is underway on the structure, with the first ground floor slab recently completed. The initial slabs will form the future lower ground floor of the hospital, which will house the first paediatric department in the region and a modern maternity unit. Construction of a new roundabout on Princes Highway will commence in the coming months, with the project expected to be completed by late 2026.
Initiatives: To assist with excavating the high-strength rock encountered onsite, the team has adopted a methodology in which the rock is line-drilled, grout is then added, reacting to impose pressure and fracture the rock, creating a seam that allows for excavation.
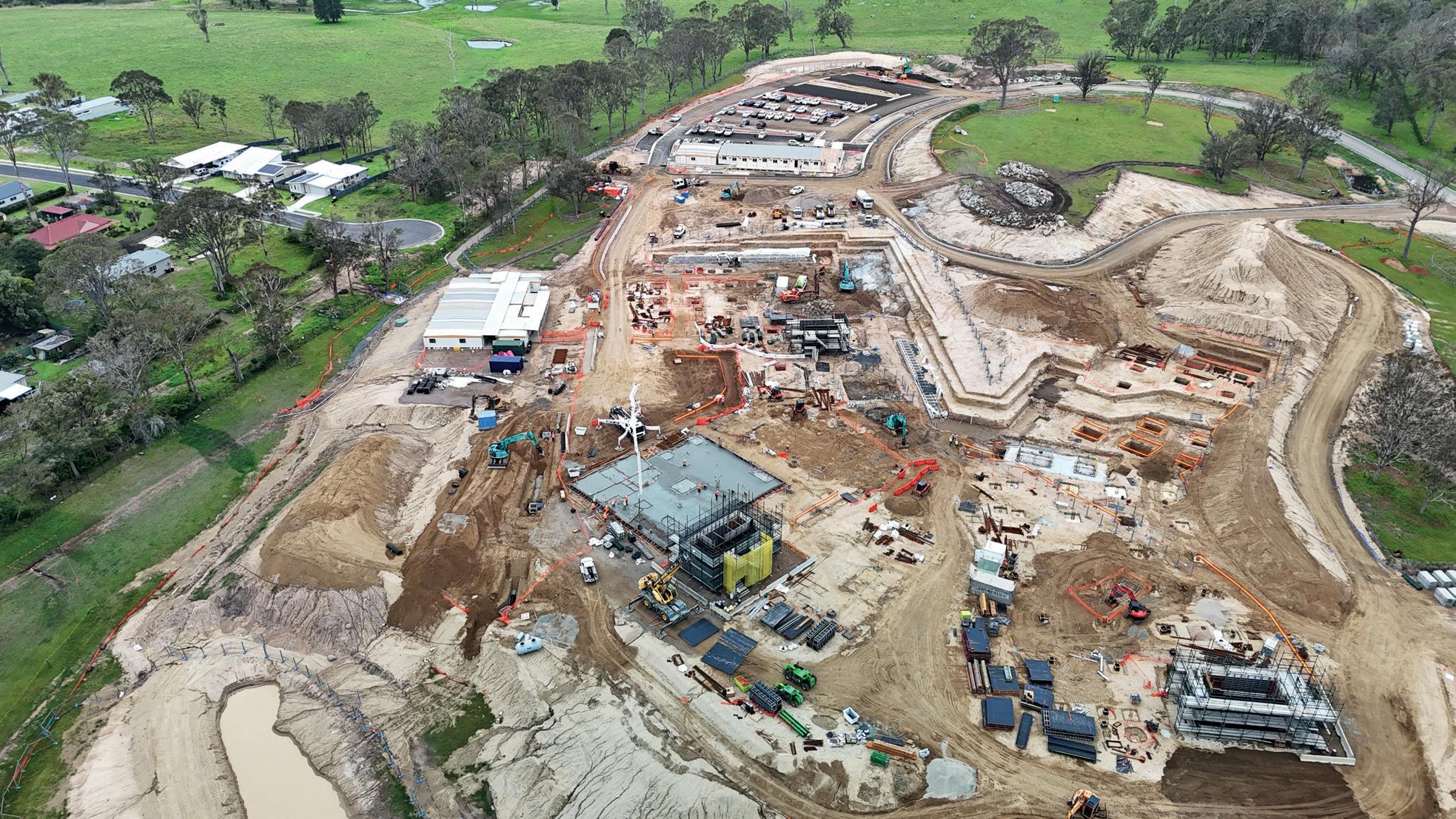
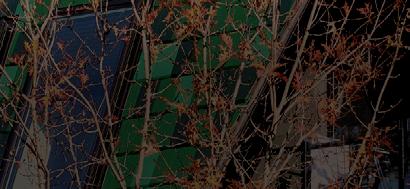
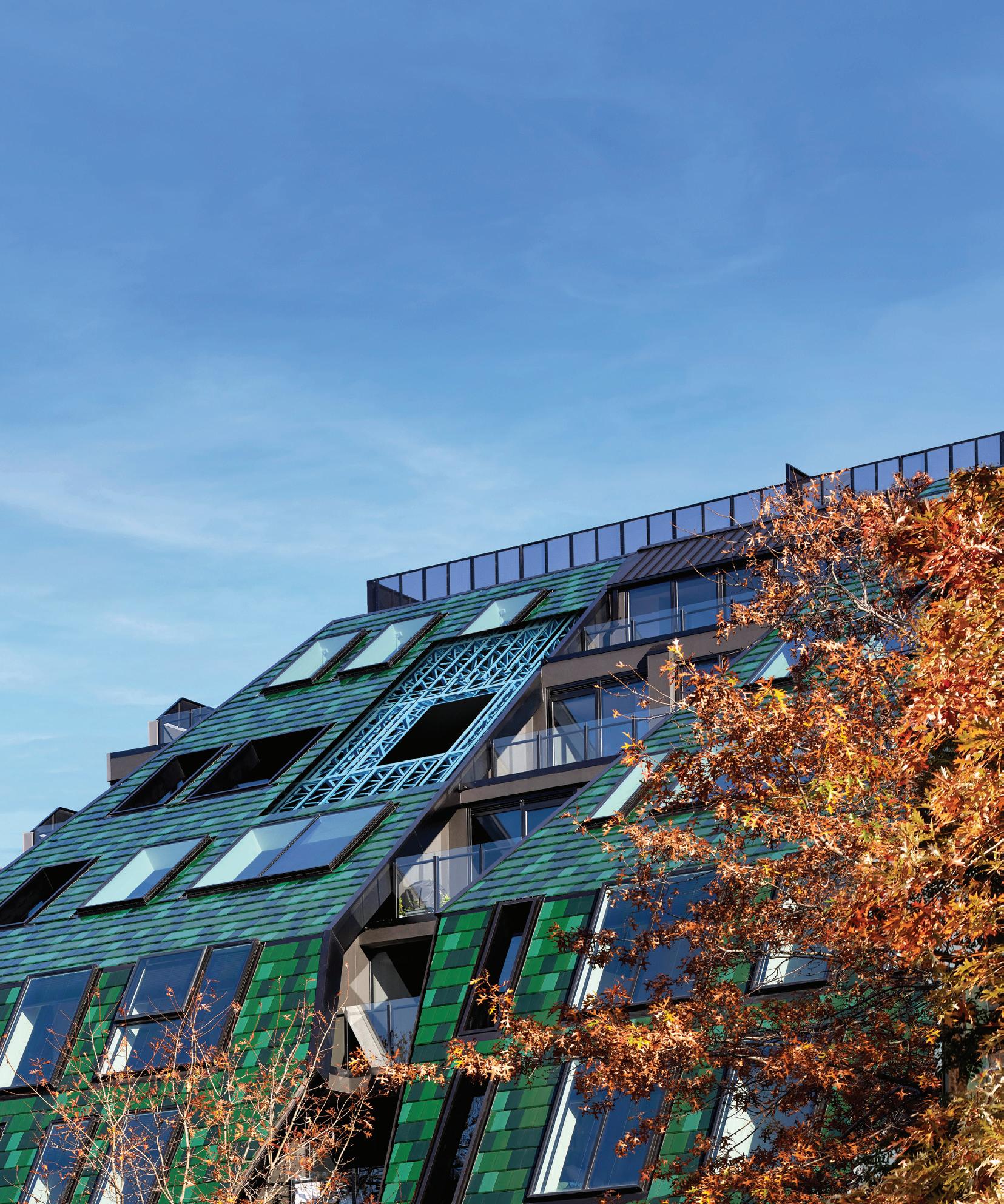
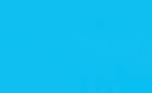
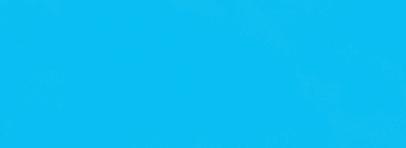

A stunning facade, seamlessly supported by TRUECORE® steel.
Inspired by its surroundings, this striking facade delivers more than harmony with its natural setting. Lightweight yet strong, TRUECORE® steel was the material of choice for the facade’s structure.
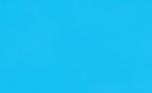
Fabricated to fine tolerances, the framing made from TRUECORE® steel structurally supports the large windows and mottled green roof tiles, while cleverly accommodating the flashings required for water management. The framing that seamlessly supports this beautiful facade was the winner of the 2022 Australian Steel Institute’s Innovative Cold Form Steel Building Award. Visit truecore.com.au to learn more.

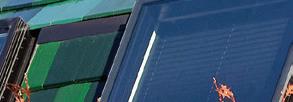

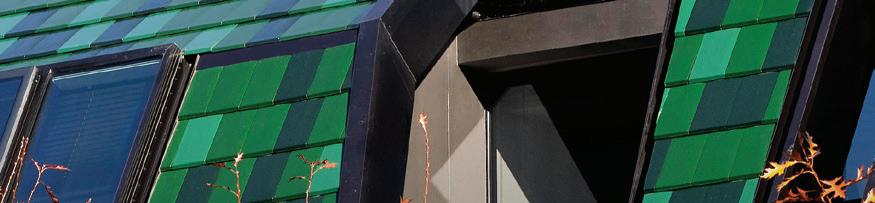
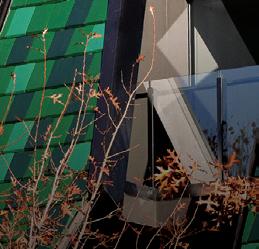
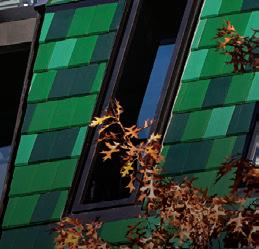

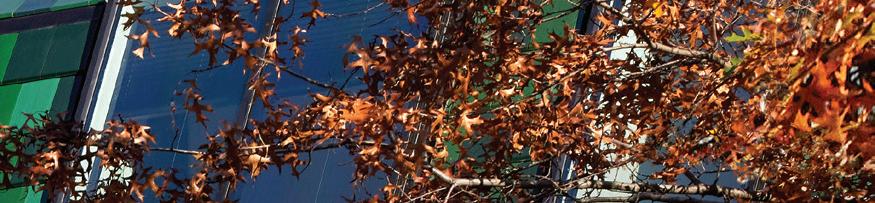
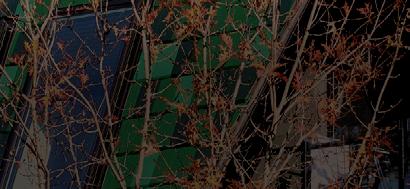
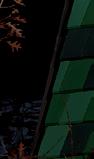
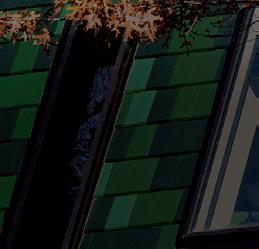
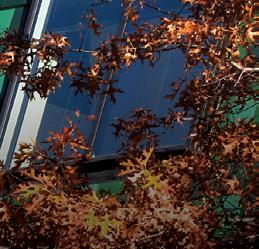

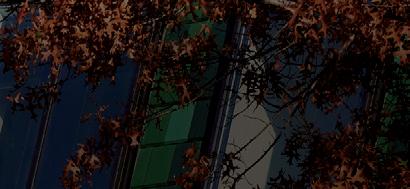

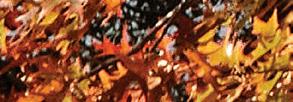

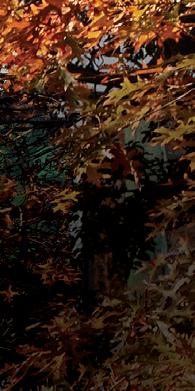
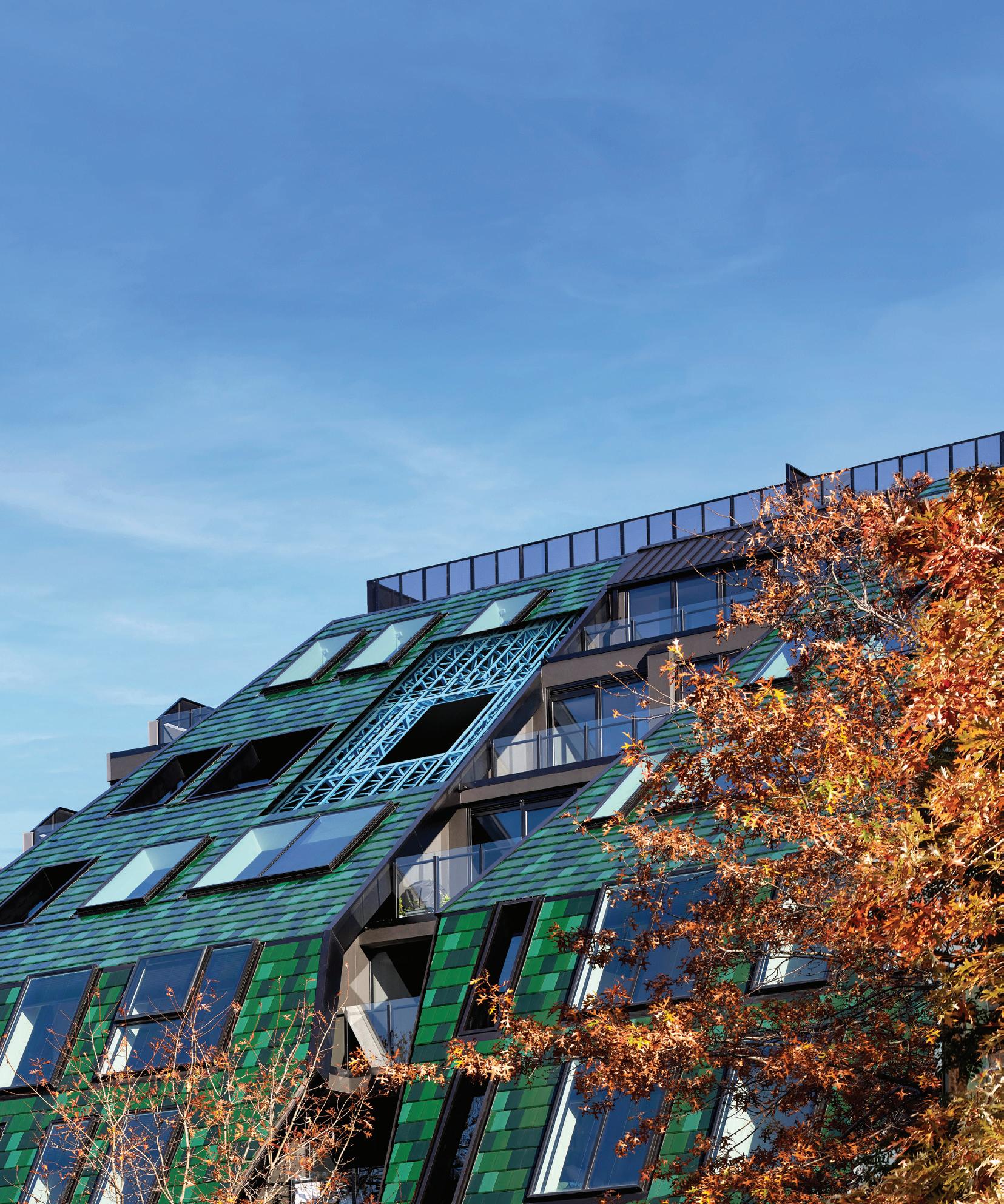
Project Picks
The Deep Maintenance and Modification Facility is progressing, with key structures now in place.
(Image: BESIX Watpac)

Nyaal Banyul Geelong Convention and Event Centre, Victoria
Contractor: Built
Current value: $449 million
Details: The Nyaal Banyul Geelong Convention and Event Centre, located on the Geelong waterfront, is one of the largest developments in regional Victoria. The 1.6-hectare project will include a purpose-built convention and exhibition space, incorporating a 1,000-seat venue, two large exhibition spaces, conference facilities and flexible event spaces. The precinct will also be home to retail spaces for food and beverage, a public plaza, and the city’s largest hotel. This architectural landmark will be a climate-positive, world-class events space, while also setting a gold standard for social procurement in government-led projects. More than 1,450 jobs will be supported during construction, and hundreds of new jobs will be created once the precinct is open for the Geelong community in 2026. Nyaal Banyul is the centrepiece of the Geelong City Deal, a $676 million collaboration between the Australian and Victorian Governments and the City of Greater Geelong. The consortium comprises Plenary Group as sponsor and investor, Built as builder, BGIS as facilities management services contractor, and Woods Bagot as designer and architect.
Status: The team recently celebrated the precinct’s topping-out, marking the 200-room Crowne Plaza Geelong reaching its highest point and a major milestone for the city’s newest tourism asset.
Deep Maintenance and Modification Facility, South Australia
BESIX Watpac
Current value: $200 million
n 2024, BESIX Watpac was appointed as the design and construction contractor to deliver one of the largest construction projects ever undertaken by Renewal SA, the South Australian Government’s urban development agency. Located adjacent to the Royal Australian Air Force (RAAF) Edinburgh base in northern Adelaide, the Deep Maintenance and Modification Facility (DMMF) is designed to accommodate the long-term maintenance and modification requirements for the Australian Defence Force’s fleet of Boeing 737-variant military aircraft. The facility includes a 240-metre-long, 60-metre-wide, 25-metre-high four-bay hangar with warehouses and workshops. he team has made progress over the past few months, recently completing the structural steel for two of the four hangars. Roofing activities commenced on the workshop before the end of 2024 and have now extended to the hangars. Precast works are also underway onsite, with installations for the first and second hangars now complete. Other progress includes commencing works at the adjacent Defence RAAF Base, with tie-in activities for the live runway also underway. Displacement works have been carried out, with line marking completed outside regular hours to facilitate runway shortening. This enables BESIX Watpac’s civil team to work both parallel to and on the active runway during operational hours.
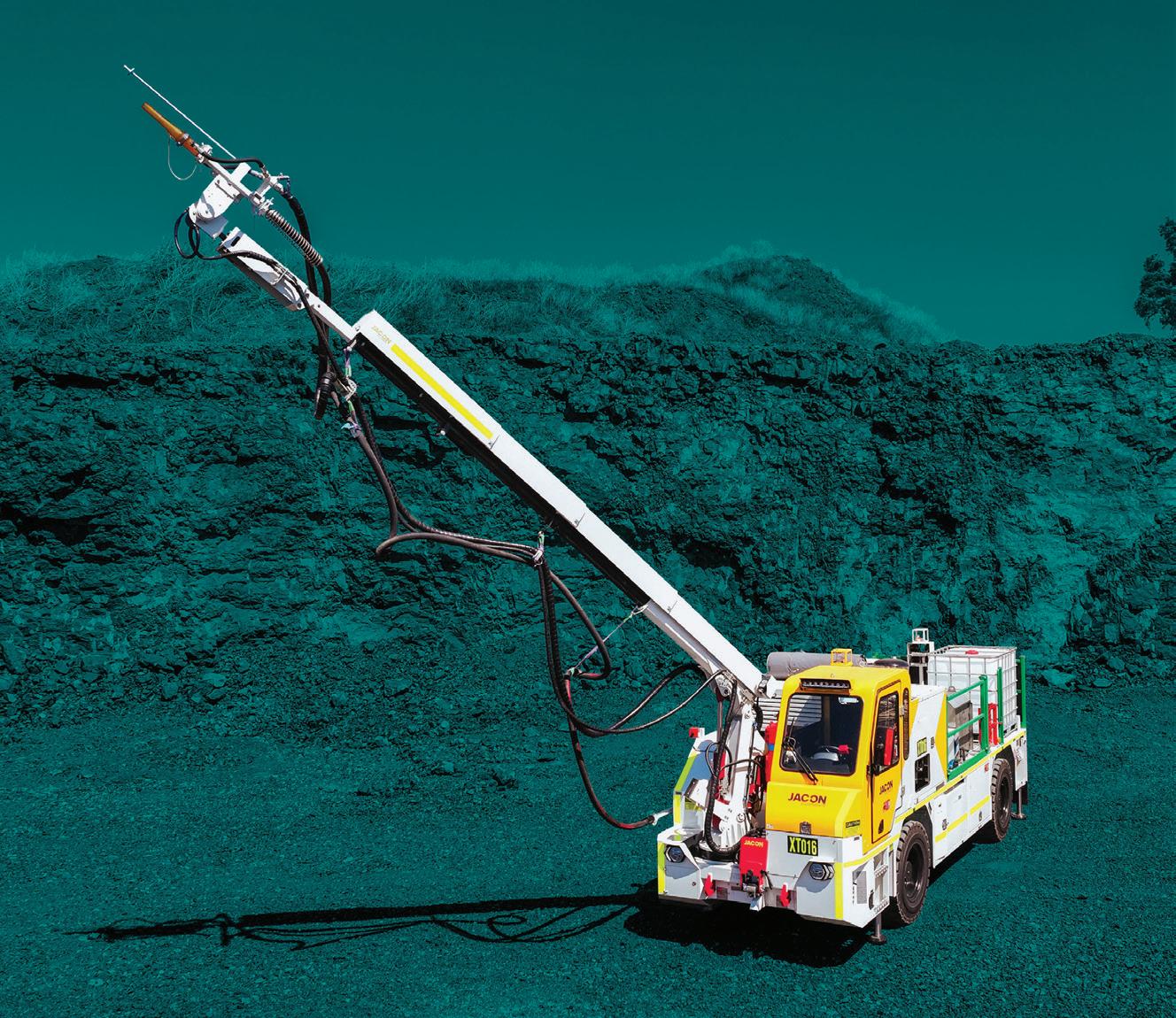
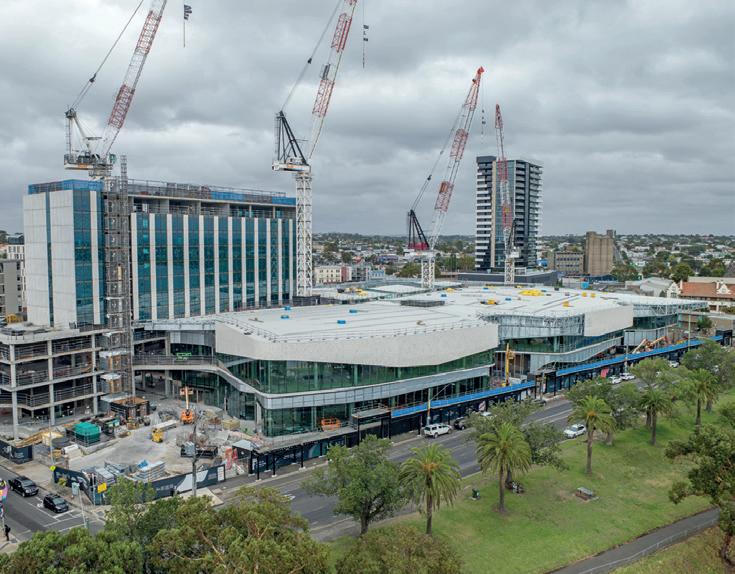
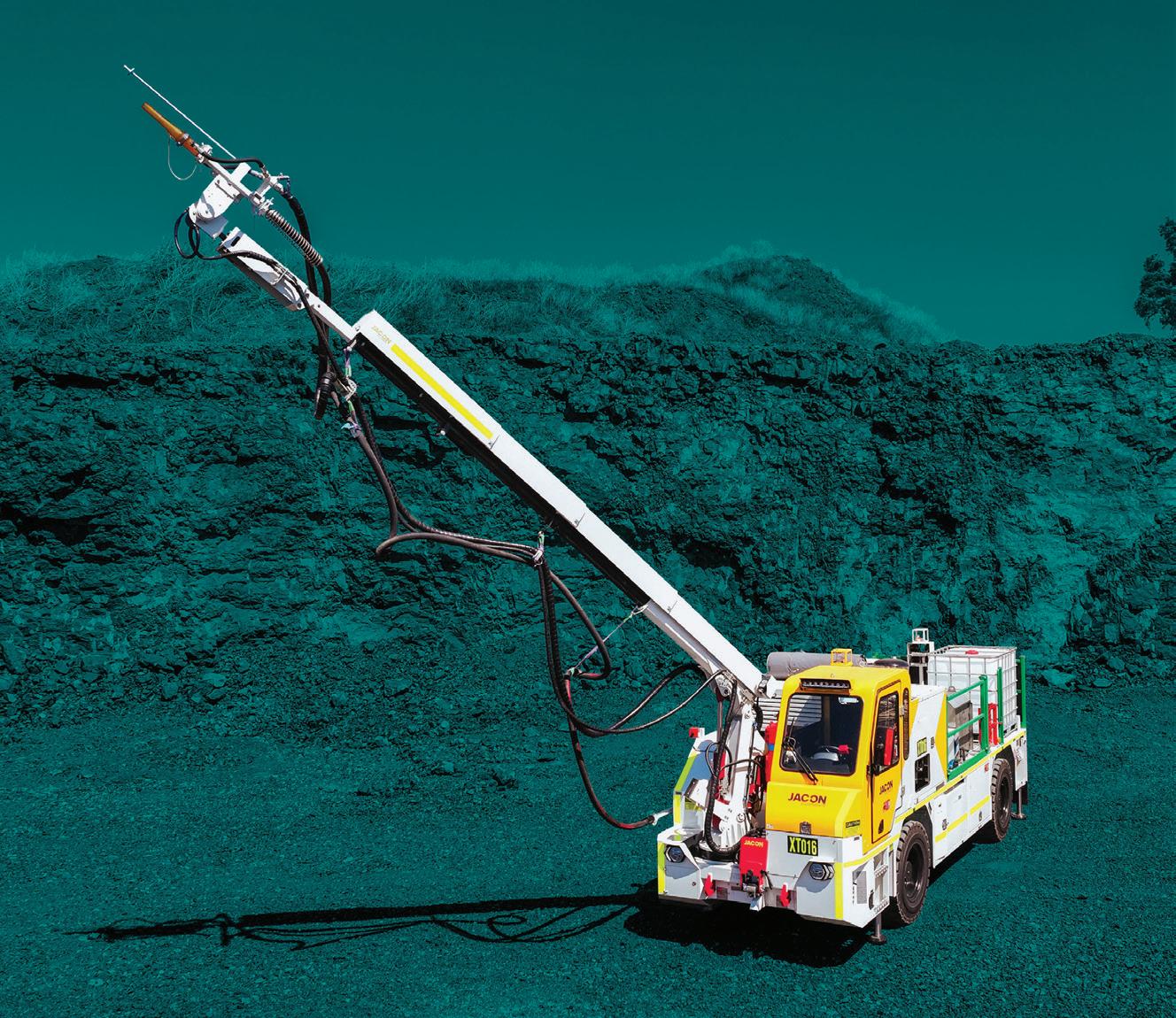
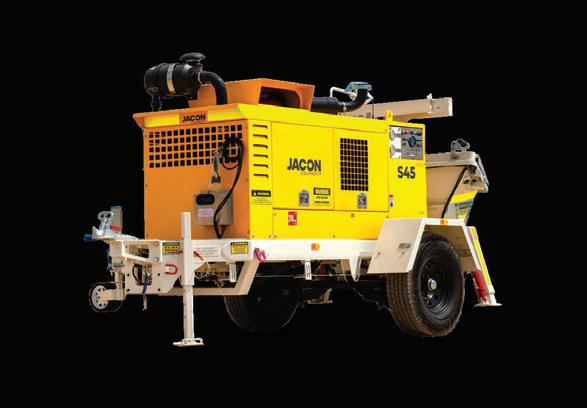
Where ambition meets opportunity

Supporting ambitions and building careers –Komatsu’s commitment to its employees goes beyond a pay cheque.
With the construction industry balancing an ageing workforce and shifting employee expectations, Komatsu is focused on attracting, retaining and inspiring top talent. By creating a culture that champions professional growth and personal wellbeing, the company is reshaping what it means to work in construction and heavy machinery.
A workplace that cares
Over the past couple of years, Komatsu has taken a deliberate approach to employee attraction and retention, responding to a competitive job market with initiatives that align with what employees truly value. One of the most impactful changes has been the evolution of its Families at Komatsu policy, ensuring benefits are more inclusive.
Mel Morrison, executive general manager – people and culture at Komatsu, says these changes were designed to support all employees.
“With over 80 per cent of our workforce being male, we recognised the need for inclusive policies rather than focusing solely on one group, such as women in our business,” says Morrison. “We benchmarked our parental leave policies against industry standards, assessed whether our offering benefited our entire workforce, and found room for improvement.”
Komatsu increased primary carers’ leave from 12 to 16 weeks at full pay – applicable to all primary carers, including fathers and blended families. Recognising that most secondary carers in its workforce are
fathers, the company extended secondary carers’ leave from one to four weeks.
Support doesn’t stop there. Komatsu strengthened its domestic violence support, offering 10 days of fully paid leave, financial assistance, a private mobile phone and financial assistance to help impacted employees establish security. Compassionate leave provisions for miscarriage further highlight the company’s commitment to inclusivity and care.
Expanding its employee assistance program through TELUS Health, Komatsu ensures employees and their families have access to professional support whenever needed.
“This service isn’t just about work-related challenges – it extends to personal matters like health crises, life transitions and financial concerns,” says Morrison. “It’s a safety net that provides mental health and general support beyond the workplace.”
Flexibility at every level
As workplace expectations evolve, Komatsu has adapted with a 60/40 office-flex policy, allowing office-based employees to work remotely 40 per cent of the time. But flexibility isn’t just for those at desks.
“We have also introduced flexible shift options for frontline employees, which we are particularly proud of. Employees can choose traditional Monday-to-Friday schedules or lifestyle rosters, such as working seven days on and seven days off,” says Morrison.
“This has been well received, as many employees prioritise work-life balance. Offering flexibility to all employees, not just office staff, is a key part of our strategy.”
Careers with a clear direction
Career development remains central to Komatsu’s approach, with its structured My Career framework providing employees with a clear view of growth and progression opportunities. Featuring 12 defined career paths, the initiative outlines necessary skills, proficiency levels and associated roles.
“We actively promote internal vacancies and introduced a system where employees can share their career aspirations and development goals,” says Morrison. “This has transformed how we approach internal mobility, allowing us to align vacancies with employee ambitions.”
Komatsu’s global footprint also creates international career opportunities, while its apprenticeship program – hiring 70 to 80 apprentices annually – offers pathways for both technical and office-based employees to expand their expertise.
Passing the torch
With a well-established approach to career development and flexibility, Komatsu also prioritises knowledge transfer as experienced professionals move toward retirement. Mentorship occurs both formally
“We put inclusion at the heart of our thinking and have a multi‑faceted approach to diversity –generational, gender and cultural.”
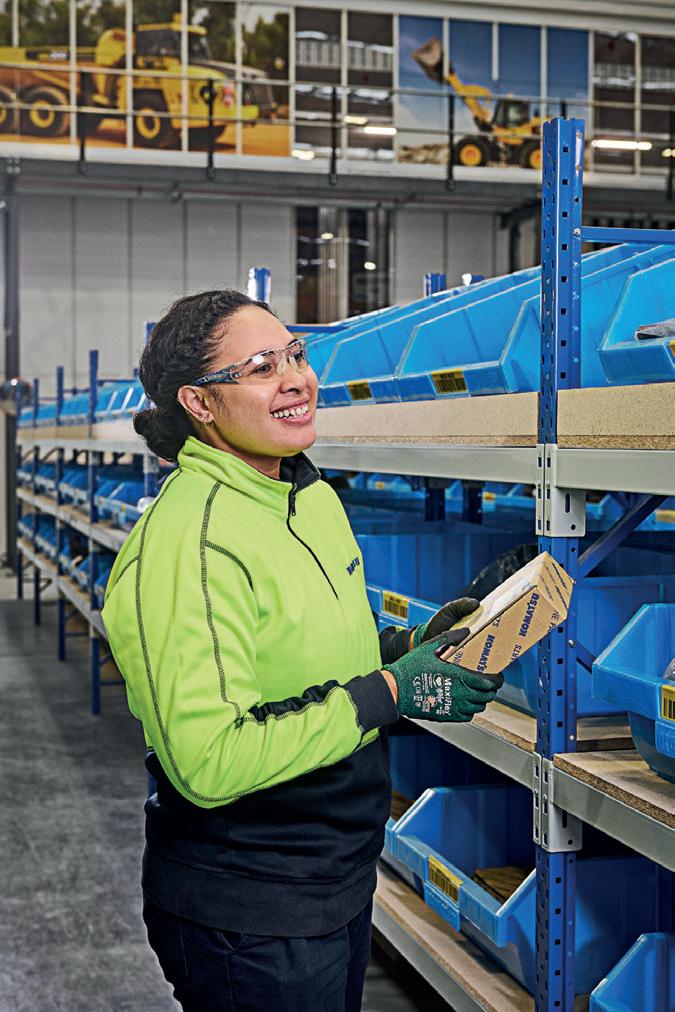
Komatsu’s structured My Career framework provides employees with a clear view of growth and progression opportunities.
Construction careers
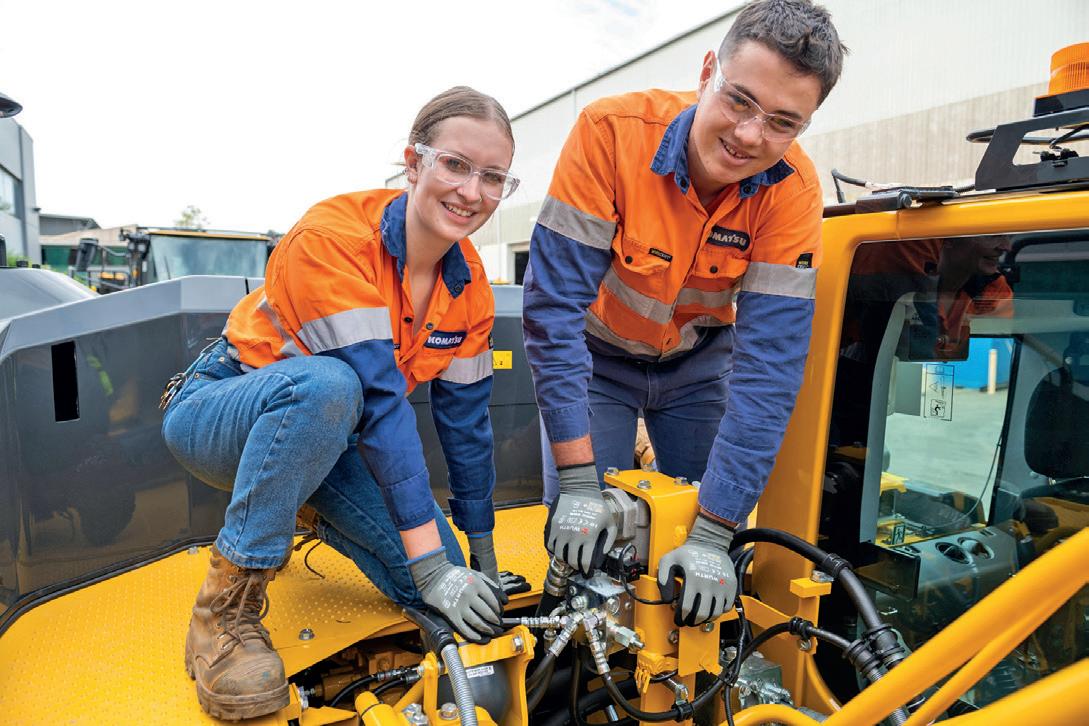
planning and flexible work considerations to help employees phase into retirement.”
Engaging future talent
Attracting younger talent requires fresh thinking, and Komatsu’s partnership with Williams Racing has helped build interest in the brand.
“The Williams F1 partnership has sparked interest among those drawn to innovation and cutting-edge technology,” says Morrison. “Younger generations seek flexibility, a supportive environment and accelerated career growth. They’re also drawn to strong brands and competitive employment conditions.”
“Respect is fundamental. We work closely with our leaders to ensure they foster open and constructive conversations within their teams,” says Morrison. “Despite being a large organisation, Komatsu has retained a close-k nit, relationship-driven culture.”
Having worked across multiple organisations, Morrison finds Komatsu’s culture to be unique.
“Komatsu has a community/family feel, built on long-standing relationships, strong values, and a genuine passion for our products and customers. There is a real sense of belonging, which we must continue to nurture as our workforce changes,” she says.
Future-proofing careers
“Despite being a large organisation, Komatsu has retained a close‑knit, relationship driven culture.”
To meet these expectations, Komatsu has implemented a multi-faceted inclusion and diversity strategy that considers generational differences, gender diversity and cultural representation.
“Inclusion and diversity at Komatsu are continually evolving. Hiring diverse talent isn’t enough. It’s the workplace experience that shapes whether people remain and thrive,” says Morrison. “We put inclusion at the heart of our thinking and have a multi-faceted approach to diversity – generational, gender and cultural.”
Culture
as the cornerstone
A strong workplace culture is the foundation of Komatsu’s strategy. Respect, inclusivity
Komatsu’s people and culture strategies are woven into its broader business objectives, with ongoing refinement ensuring workplace culture and talent management remain priorities.
“As we navigate workforce challenges –including an ageing workforce, generational shifts and new technology – our strategy remains focused on building the right capabilities,” says Morrison. “Artificial intelligence, data analytics and emerging technology will shape our workforce needs, and we’re preparing by upskilling our employees and attracting the right talent.”
With a long-term vision, Komatsu continues to evolve as a workplace where careers thrive and employees feel valued.
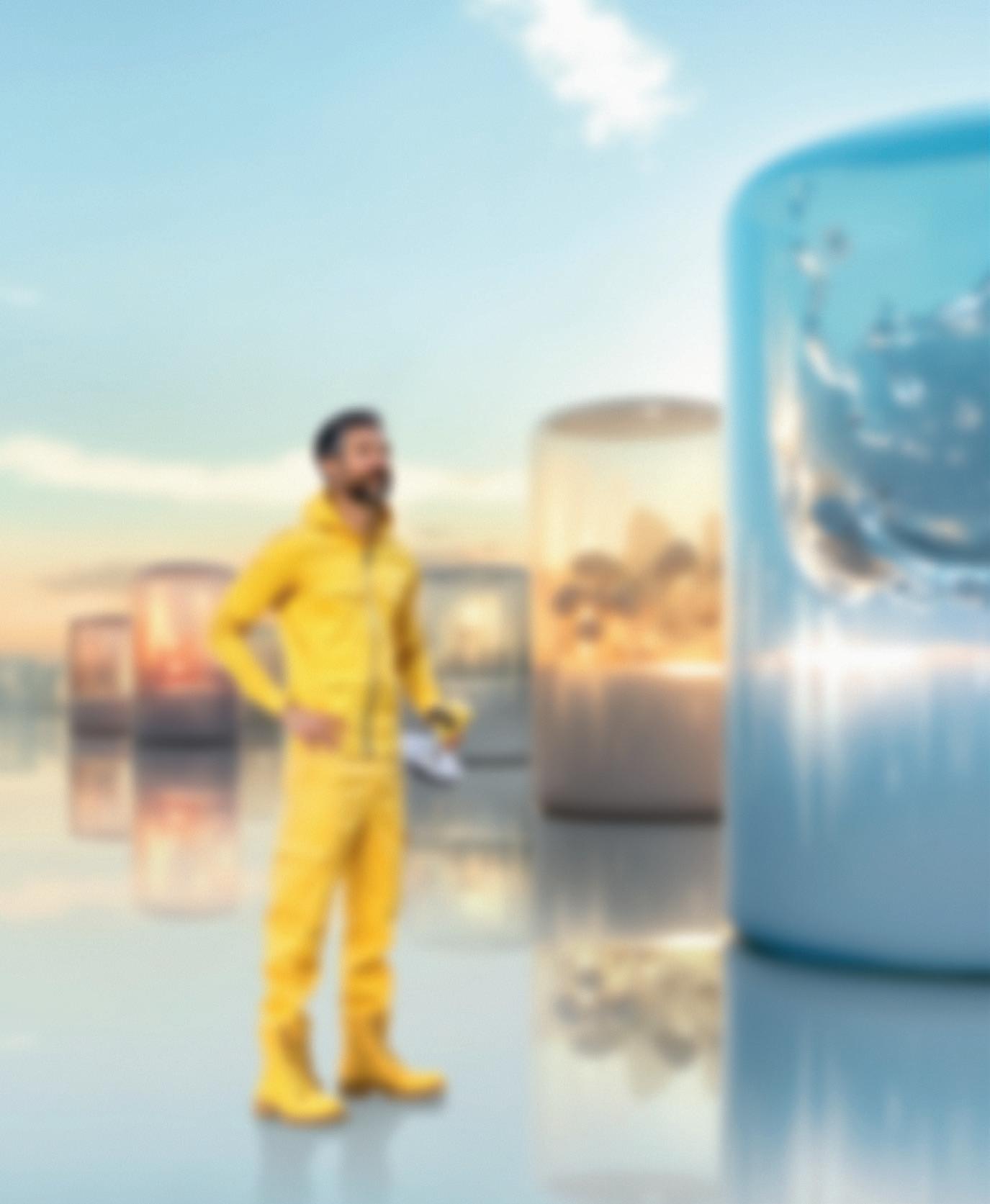
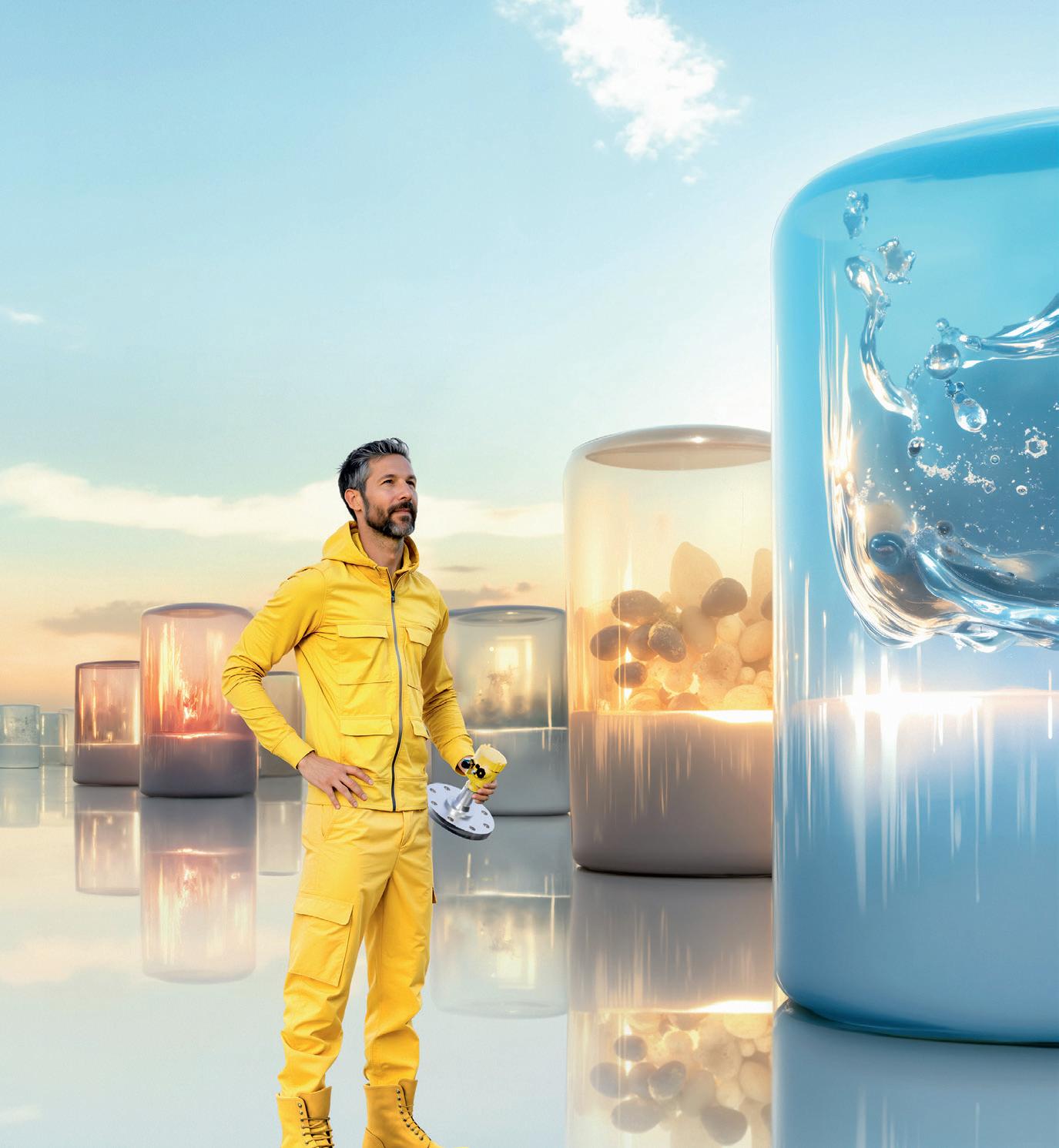
Our answer: Yes! What was the question?
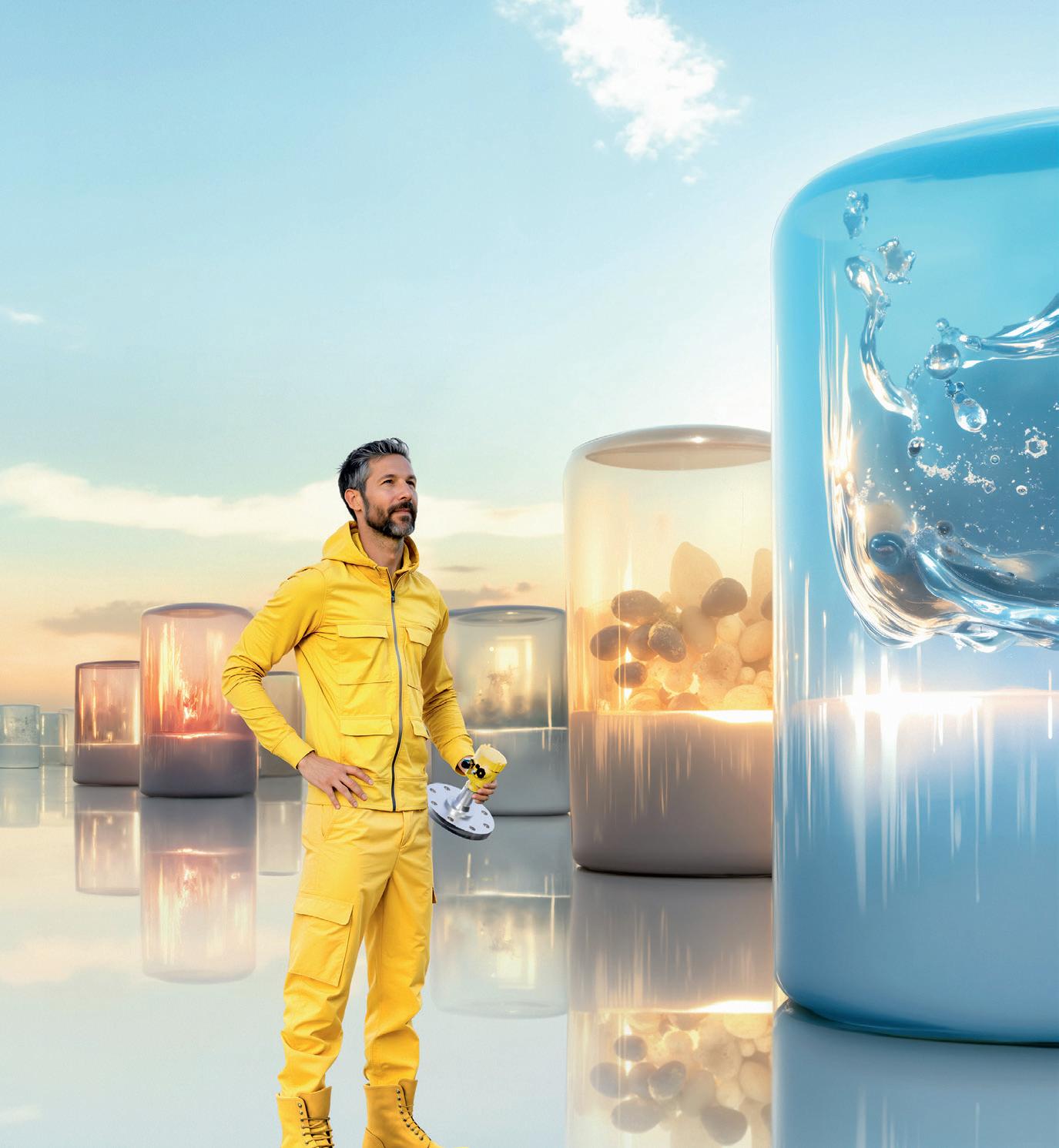
When your measurement is crucial, VEGA is the right choice. Our level and pressure measurement technology is not just state of the art – it sets the industry standard. With clear vision, technical expertise and strong innovation, we always have the right answer. No matter what the question is.
Everything is possible. With VEGA.
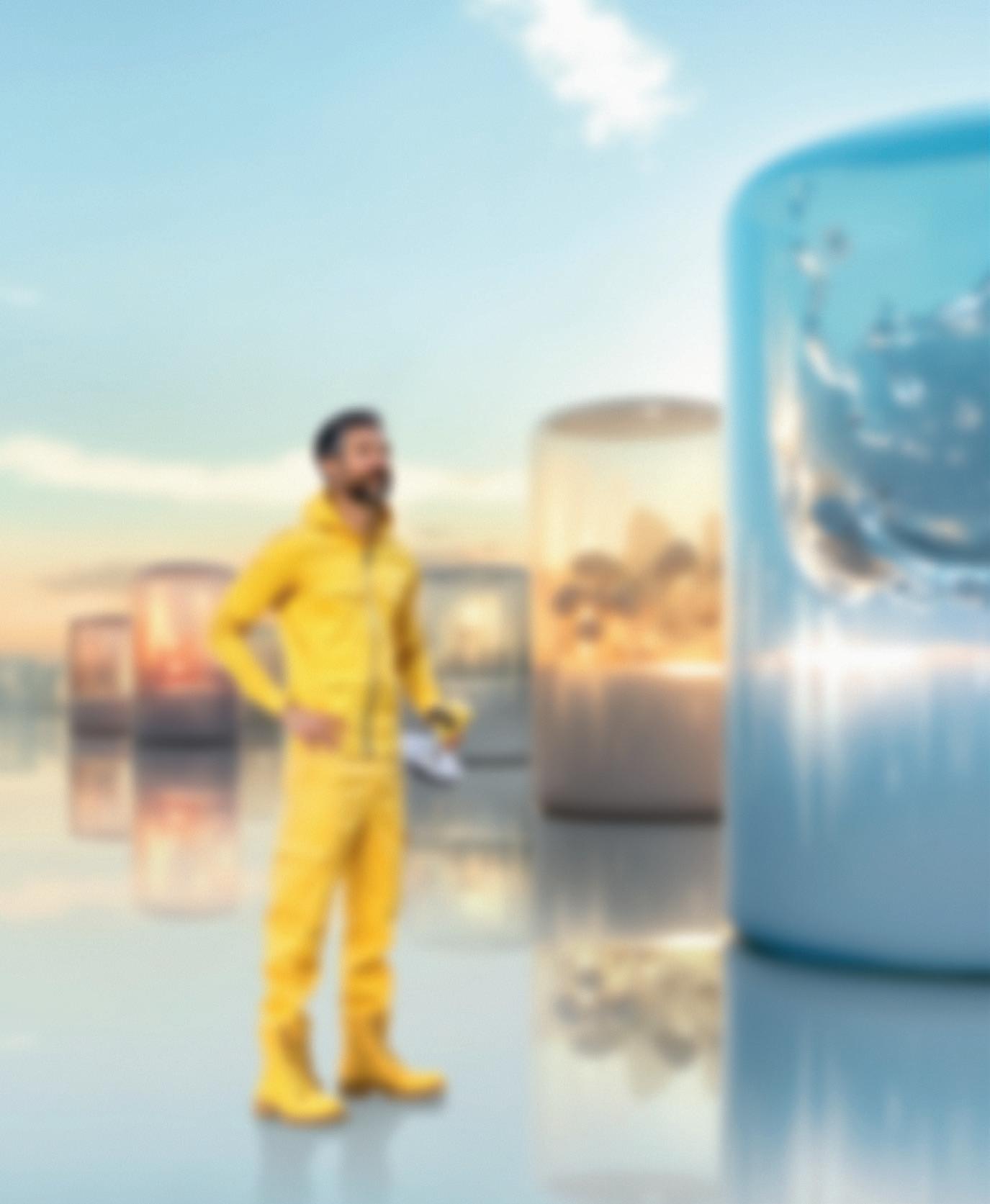
Smart buildings
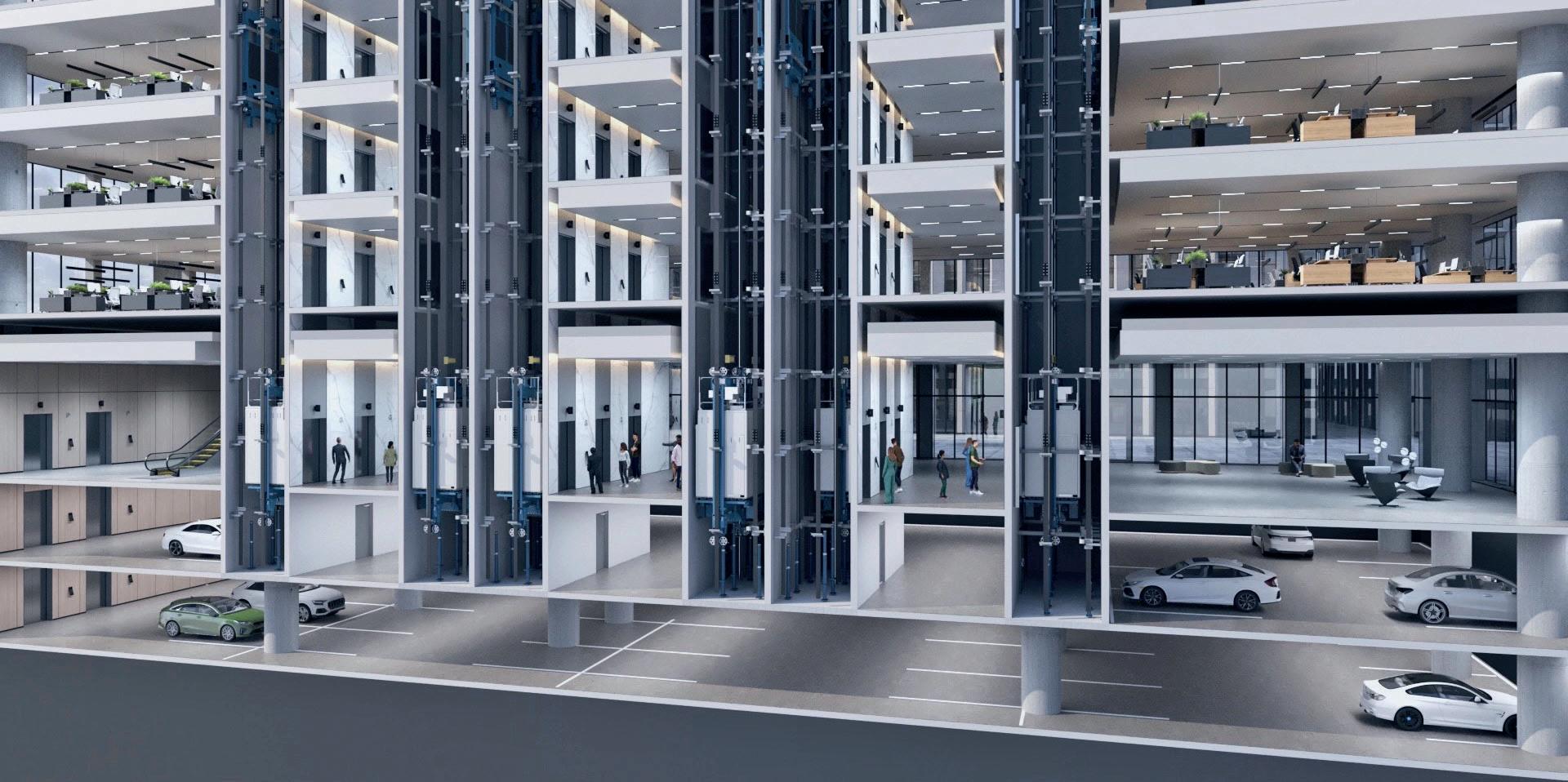
High-rise, high-tech
Lighter materials, smarter technology and stronger performance – KONE’s high-rise elevator systems are built for the next generation of skyscrapers.
Australia’s skyline is reaching new heights.
In Sydney, Melbourne and Brisbane, towers are rising fast, reshaping cityscapes and demanding infrastructure that keeps pace. In this vertical race, elevator systems are more than just a convenience – they are essential to functionality, efficiency and sustainability. For buildings designed to stand for decades, elevators must be built for the long haul. KONE has engineered its High-Rise MiniSpace DX system to meet this challenge, optimising space, reducing lifecycle costs and improving energy efficiency. With lightweight hoisting technology and a new precision control system, it ensures smooth operation and minimal service interruptions – an advantage for both new developments and modernisation projects.
KONE’s high-rise solutions enhance both new developments and modernisation projects. (Images: KONE Australia)
A key innovation behind these advancements is UltraRope, a carbon-fibre hoisting solution replacing traditional steel ropes. Weighing 80 per cent less than steel, UltraRope reduces strain on elevator systems, enabling a more compact setup while maintaining speed and safety. Originally developed for mega-towers reaching 1,000 metres in height, it has also proven valuable in high-rises as low as 70 to 80 metres, where efficiency is equally critical.
“Because UltraRope is significantly lighter, we can downsize motor room machinery and optimise shaft dimensions. We have also integrated a new control system that provides much more precise lift positioning within the shaft,” says Robert Haig, head of major projects at KONE.
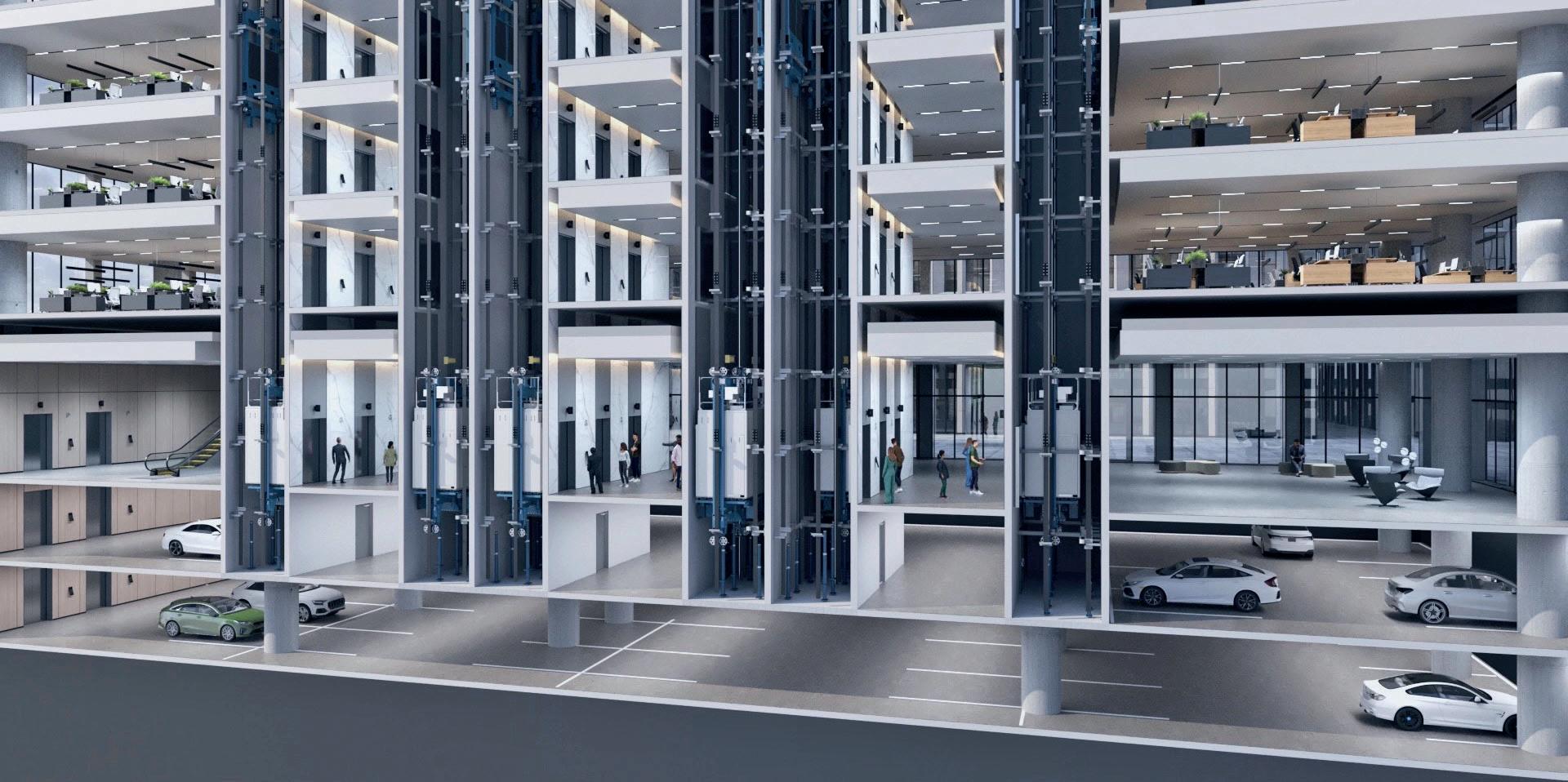
“Together, these advancements allow us to optimise vertical space in new construction, reducing headroom at the top of the shaft, pit depth at the bottom and the height of the machine room. The result is substantial cost savings in both construction and excavation.”
Reducing pit depth also simplifies compliance. Under Australian and international lift codes, pits exceeding certain depths require access doors instead of ladders, adding complexity and cost. The High-Rise MiniSpace DX can eliminate this requirement, streamlining construction. Likewise, lower headroom and machine room height allow for more usable space within planning constraints.
“In some cases, this allows for an additional floor to be accommodated within the building while still complying with planning regulations,” says Haig.
Historically, taller buildings required deeper lift pits, as faster lifts demanded greater clearance. This increased construction costs, particularly where excavation was required.
For modernisation projects, where existing shaft dimensions are fixed, the system can enhance lift speed, improving passenger flow and reducing wait times.
“UltraRope, along with the improved positioning system, plays a key role in reducing critical dimensions within the lift shaft,” says Haig. “We have worked with customers in Australia modernising their buildings to improve capacity. Our approach delivers distinct advantages: first, reducing lift downtime; second, increasing speeds to
cut travel times. The result is an improved experience for building occupants.”
In one project, KONE doubled the lift speed within existing constraints. Each modernisation project is assessed individually, as shaft dimensions and designs vary, but in this case, sufficient pit depth, headroom and machine room height allowed KONE to increase speed from 5 to 10 metres per second.
“Each project is assessed case by case. Many customers come to us when their lift systems near the end of their operational life,” says Haig.
“Traditionally, modernisation focused on like-for-like replacements with some upgrades to meet code requirements, improve safety and integrate new technologies. Now, we are seeing a shift. By increasing lift capacity and reducing energy consumption, we can enhance building efficiency.”
For example, instead of a floor being occupied at a density of one person per 12 square metres, KONE’s solutions may enable occupancy at one per 10 square metres, allowing building owners to lease office spaces at a higher density and maximise commercial potential.
“You do not have to follow the same traditional approach,” says Haig.
“With new technology, we can help rethink strategy and achieve greater efficiency with existing assets.”
Sustainability is another driving force behind KONE’s high-rise solutions. A lift’s energy consumption largely depends on the weight of its moving components – the counterweight, lift car and ropes.
“With new technology, we can help rethink strategy and achieve greater efficiency with existing assets.”
Optimised for city growth, KONE’s Next-Gen technology enhances space efficiency and sustainability, allowing for more rentable space.
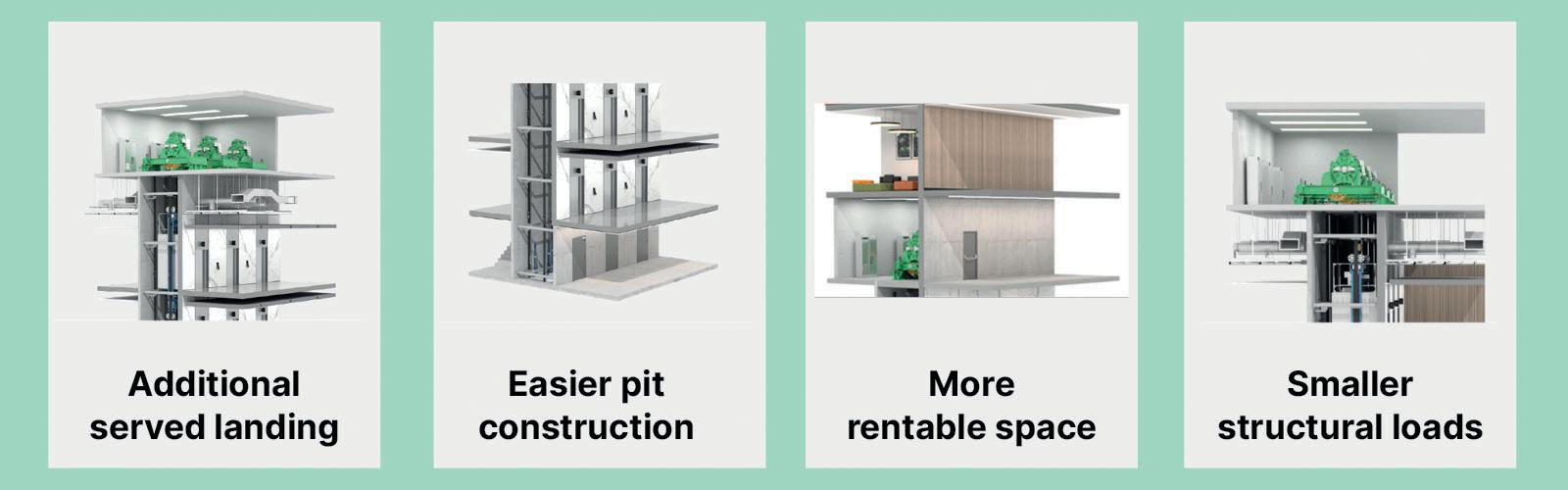
FEATURE
Smart buildings
The KONE UltraRope is lighter, stronger and designed to improve lift performance while reducing energy consumption.
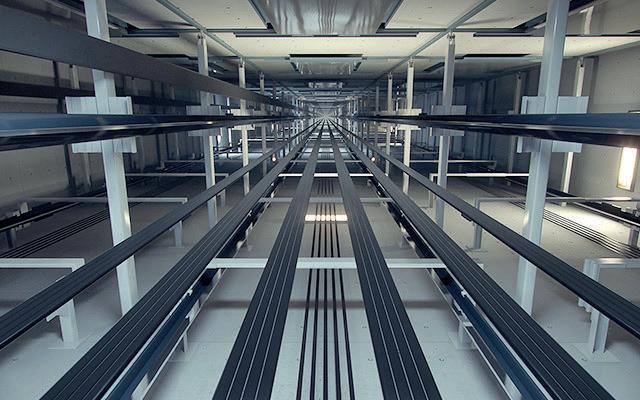
“Since UltraRope is 80 per cent lighter than steel ropes, the total weight being moved is reduced,” says Haig. “This translates to lower energy consumption per journey.”
Steel ropes typically need replacing every four to five years, generating material waste. UltraRope, certified to last 15 years without replacement, minimises waste and reduces environmental impact. For new builds, the High-Rise MiniSpace DX’s lower energy consumption, smaller motors and extended lifespan contribute to better Green Star and NABERS ratings by improving efficiency and reducing material use.
“Many of the same benefits apply to modernisation projects,” says Haig. “In one case, our high-rise technology contributed to a half-star improvement in an existing building’s NABERS rating, highlighting its impact on sustainability.”
“In a high-rise office tower with 18 lifts, each would be out of service for about two days every four to five years for re-roping. While that may not seem significant for one lift, the cumulative downtime is substantial,” says Haig. “By eliminating frequent replacements, UltraRope ensures higher uptime throughout a building’s lifecycle.”
Fewer rope replacements also mean fewer manual handling risks for technicians. Being much lighter than steel, UltraRope reduces the physical strain of installation and does not require lubrication, eliminating the use of oils and chemicals typically needed for steel ropes. This contributes to a cleaner, safer working environment.
As buildings grow taller and cities become denser, elevator systems are evolving to be faster, smarter and more efficient.
“We can now fit faster lifts into smaller footprints and, in some cases, reduce the number of lifts needed in a group, as they can travel faster within the required dimensions,” says Haig.
“This brings greater efficiency through reduced rope replacements, optimised spatial requirements and improved control systems.
“Maintenance is becoming smarter, lifts are getting more intelligent, and we are doing more with less.”
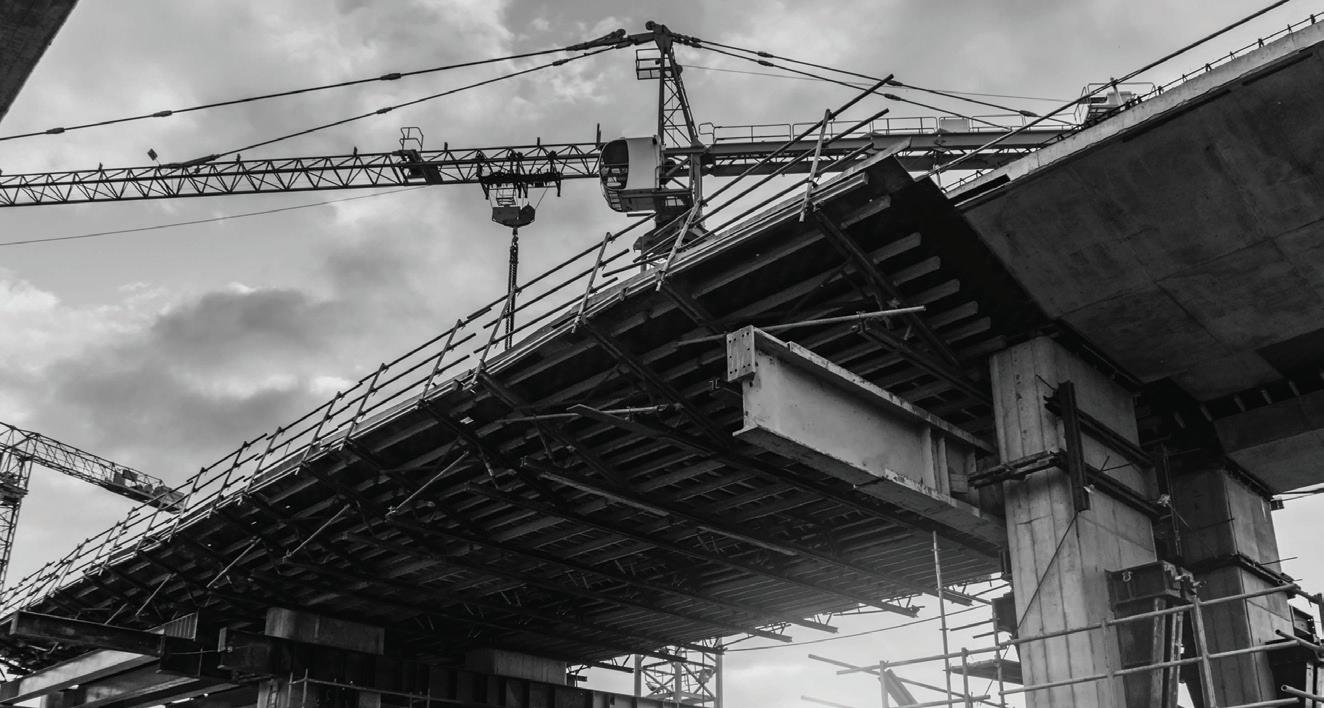
“Maintenance is becoming smarter, lifts are getting more intelligent, and we are doing more with less.”
Maintenance is another area where UltraRope offers an advantage. Replacing steel ropes is labour-intensive and disrupts lift availability.
From developers and contractors to building managers and occupants, KONE’s high-r ise elevator systems are designed to move people – and buildings – into the future.
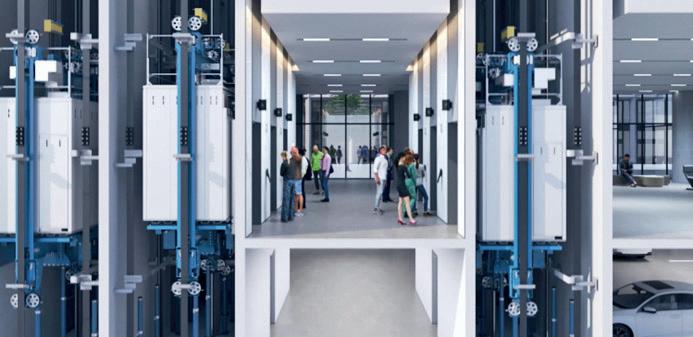
KONE’s high-rise solutions optimise space and efficiency, adapting to evolving city landscapes.
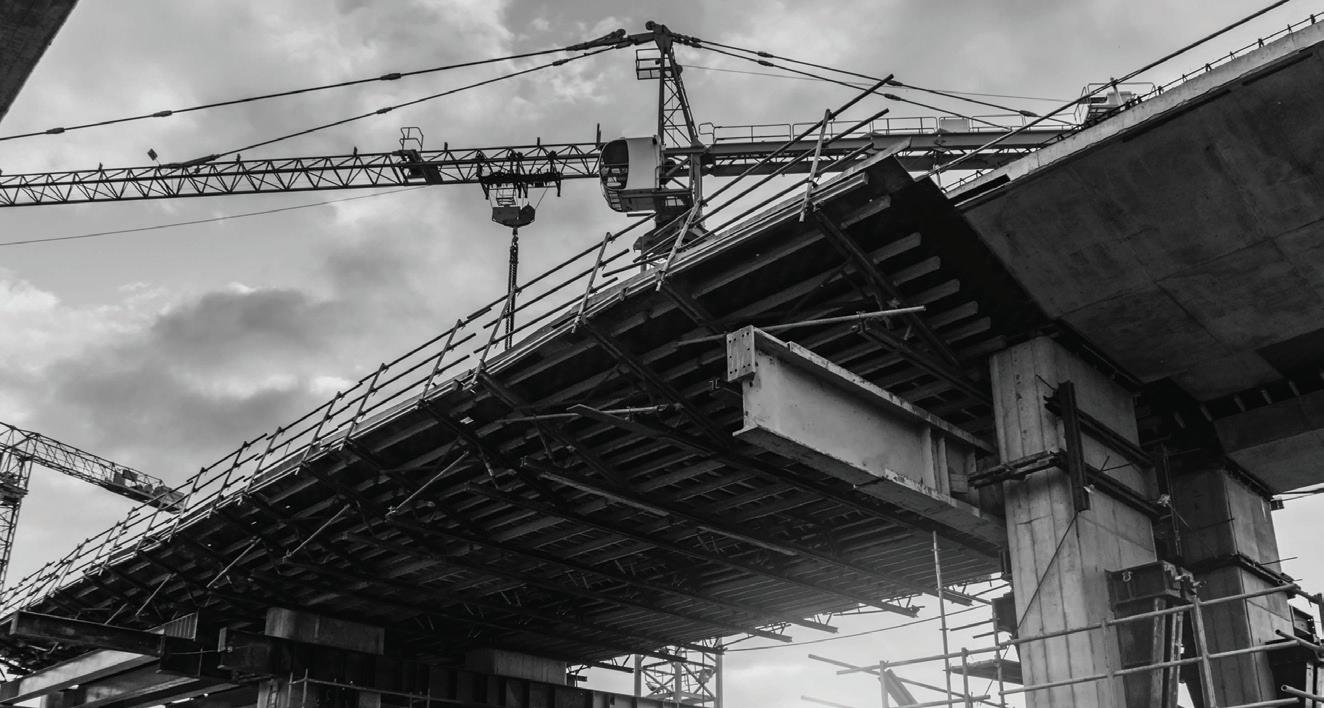
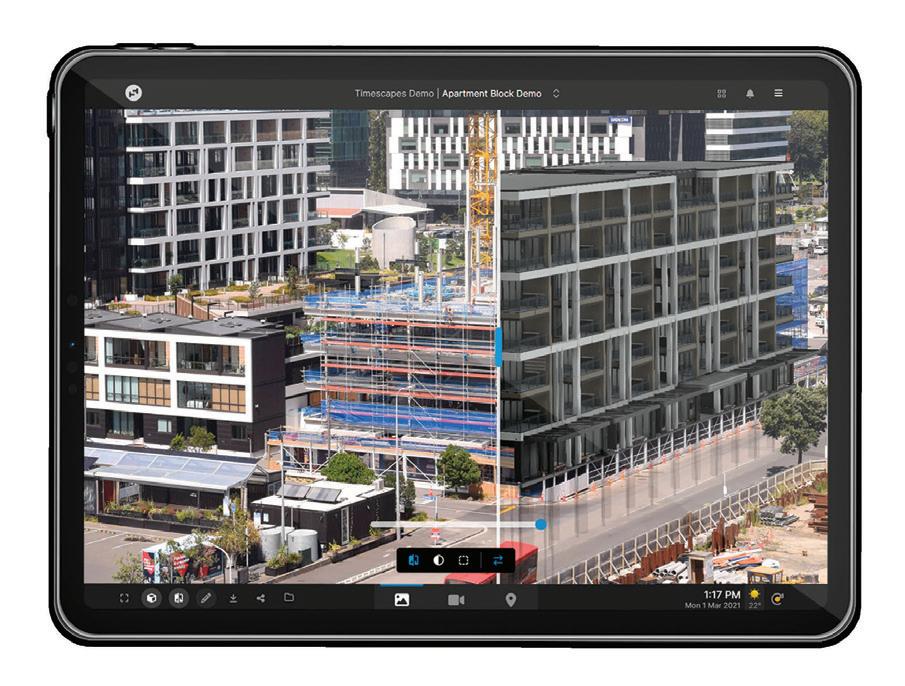
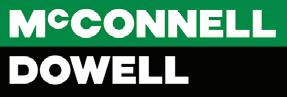

Construction hardware
A coat above
Hydrogen embrittlement presents a risk to fasteners in construction, but Hobson Engineering is tackling the challenge with zinc flake coatings.
For decades, the engineers and specialists at Hobson Engineering have been at the forefront of fastener technology, helping the industry navigate risks and best practices. As Australia increases its use of high-tensile steels, the company is raising awareness of hydrogen embrittlement – a hidden threat that can lead to sudden failures – and how zinc flake coatings offer a reliable solution.
Hydrogen embrittlement is a critical failure mechanism in high-tensile steels, occurring when specific conditions align. For embrittlement to take place, three factors must be present: high steel hardness, a high tensile load, and exposure to hydrogen. High-tensile fasteners, particularly those at Property Class (PC) 10.9 and above, are most vulnerable. The risk increases with higher tensile load on the fastener and when hydrogen is introduced into the metal.
Hydrogen exposure often happens during coating processes. Electroplated zinc carries
acid cleaning is involved. Once a fastener under load becomes embrittled, failure can occur without warning.
Gavin McPherson, lead engineer at Hobson Engineering, explains that hydrogen embrittlement can occur in two ways: internally during manufacturing or externally from environmental exposure.
“Internal hydrogen embrittlement arises from processes such as electroplating, where hydrogen is introduced during manufacturing,” says McPherson.
“Environmental hydrogen embrittlement results from external sources, such as certain chemicals used onsite near the fastener. While both are uncommon, they are important considerations in failure analysis.”
When a fastener fails unexpectedly, hydrogen embrittlement is often one of the first suspects. It can affect bolts, casehardened screws, and other high-strength components, usually within 24 hours of being
“As Australia transitions to greater use of high-tensile steels, the risks associated with hydrogen embrittlement become more pressing.”
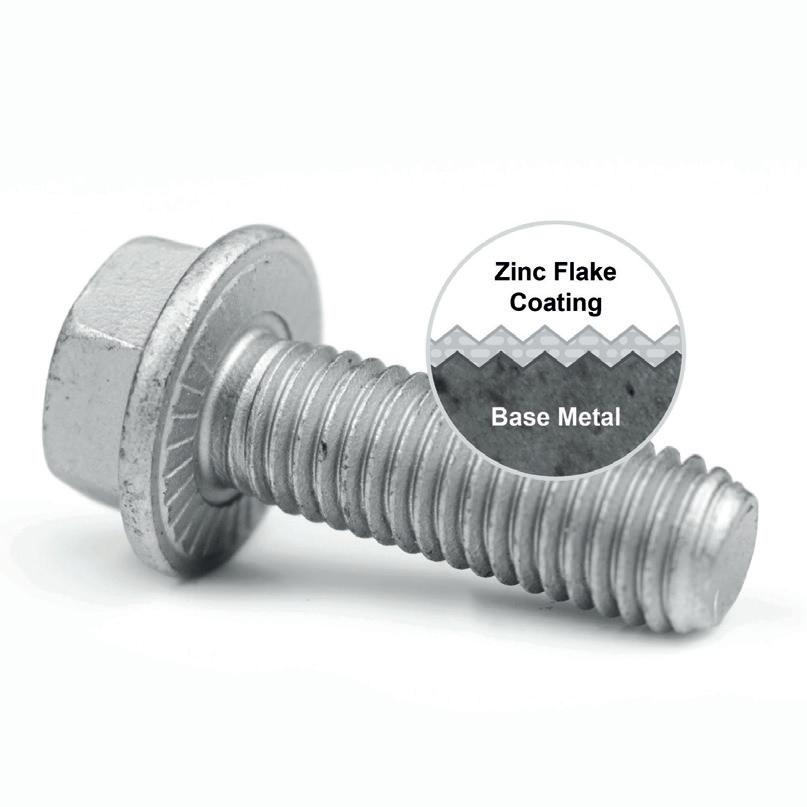
As demand for high‑performance fasteners grows, zinc flake coating is set to strengthen structural integrity in construction. (Images: Hobson Engineering)
Zinc flake coating enhances durability while preventing hydrogen embrittlement.
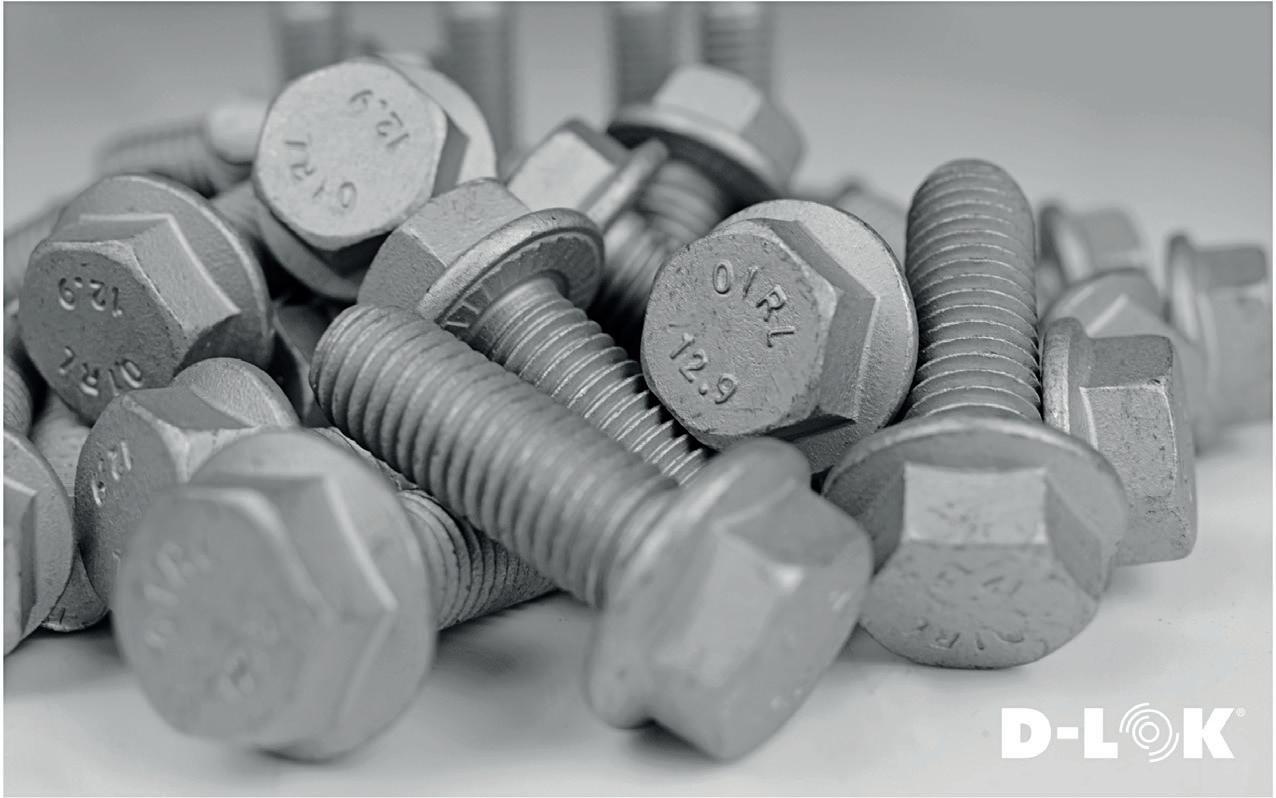
associated with hydrogen embrittlement become more pressing,” says McPherson.
“In the structural bolt market, PC 8.8 bolts – particularly our K0 range – are widely used. These bolts have a hardness below the critical threshold, removing the risk of hydrogen embrittlement. However, the use of PC 10.9 structural bolts is increasing, and these are at risk of susceptibility to hydrogen embrittlement.”
To mitigate risk, Hobson Engineering sources its PC 10.9 structural bolts from a trusted fastener manufacturer in limited factories. These bolts are hot-dip galvanised, providing a more controlled and reliable option. While it is possible to source
hot-d ip galvanised PC 10.9 structural bolts, the increased control over forming, heat treatment, coating and testing is cost-prohibitive, and any oversight puts the entire manufacturing run at risk. For this reason, zinc flake carries a much lower risk of non-conforming products being put into the market. Another way that engineers can design out the risk is by using high-tensile stainless steel, such as Bumax, which has no coating.
Socket screws, traditionally zinc-plated or electroplated, require additional safeguards. Manufacturers manage embrittlement risk through controlled processing, including a baking procedure that allows trapped
“Zinc flake coatings perform comparably to hot-dip galvanising, but with added benefits.”
Construction hardware FOCUS
Zinc flake coating provides strong corrosion protection among its many benefits.
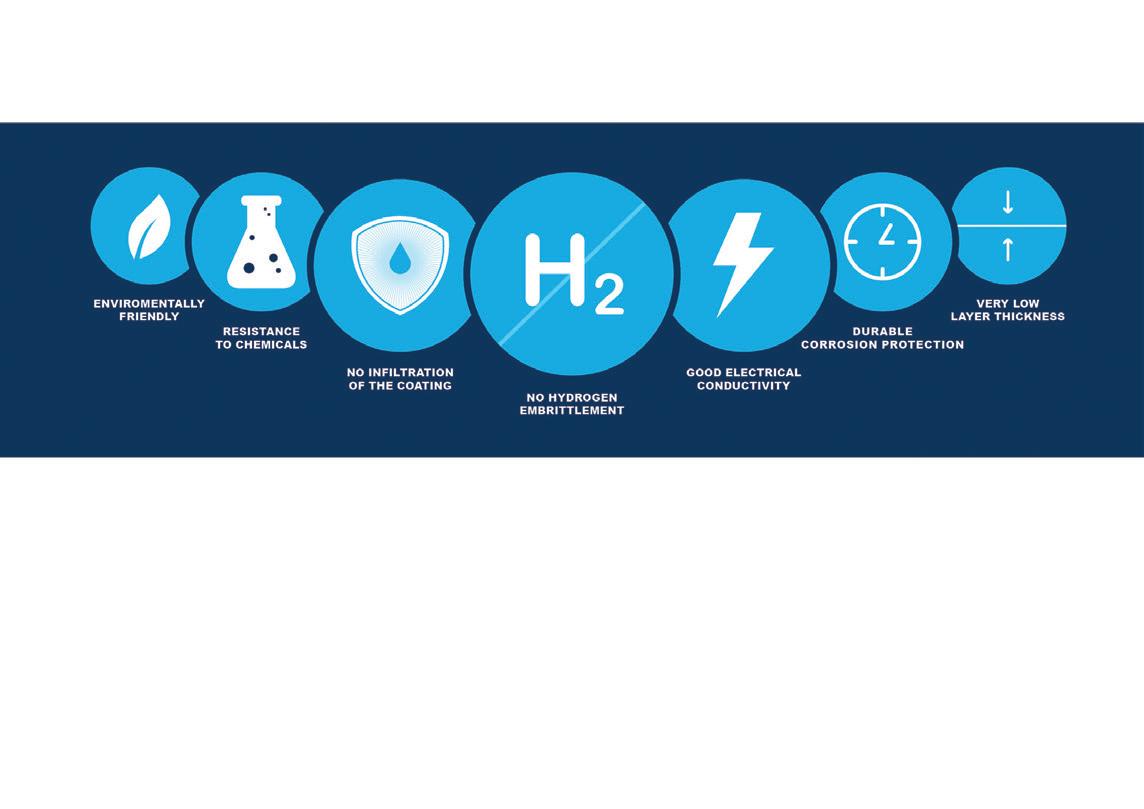
some time and are similar to ZAM coating, a blend of zinc, aluminium and magnesium used on cold-formed steel.”
electroplating or acid-based treatments, this process eliminates the primary sources of hydrogen exposure, reducing embrittlement risk. As a result, it allows for the use of high-tensile fasteners in demanding applications without compromising reliability.
“Zinc flake coatings have been in use for some time and are similar to ZAM coating, a blend of zinc, aluminium and magnesium used on cold-formed steel. This combination provides superior corrosion protection compared to zinc alone,” explains McPherson.
“The aluminium protects the steel while also providing cathodic protection, a key function of coatings. Zinc flake coatings perform comparably to hot-dip galvanising, but with added benefits. For high-tensile fasteners, I would recommend zinc flake coatings over hot-dip galvanising.”
Zinc flake coatings come at a higher cost than standard hot-dip galvanising, but McPherson believes the investment
durability in demanding environments, though gaining traction in the industry remains a challenge.
“We offer a range of coatings, including zinc flake,” he says. “We also use Ruspert, a ceramic coating, on some anchors and screws, as well as e-coating, an electronically applied epoxy coating that performs well without relying on cathodic protection.”
While hot-dip galvanising has long been the industry standard due to its durability, zinc flake coatings provide an alternative where hydrogen embrittlement is a concern.
As awareness of the risks grows, and the demand for high-performance fasteners increases, zinc flake coatings are set to play a greater role in securing the integrity of structures across the construction industry.
For more information or tailored advice on zinc flake coating solutions, contact the Hobson Engineering team.
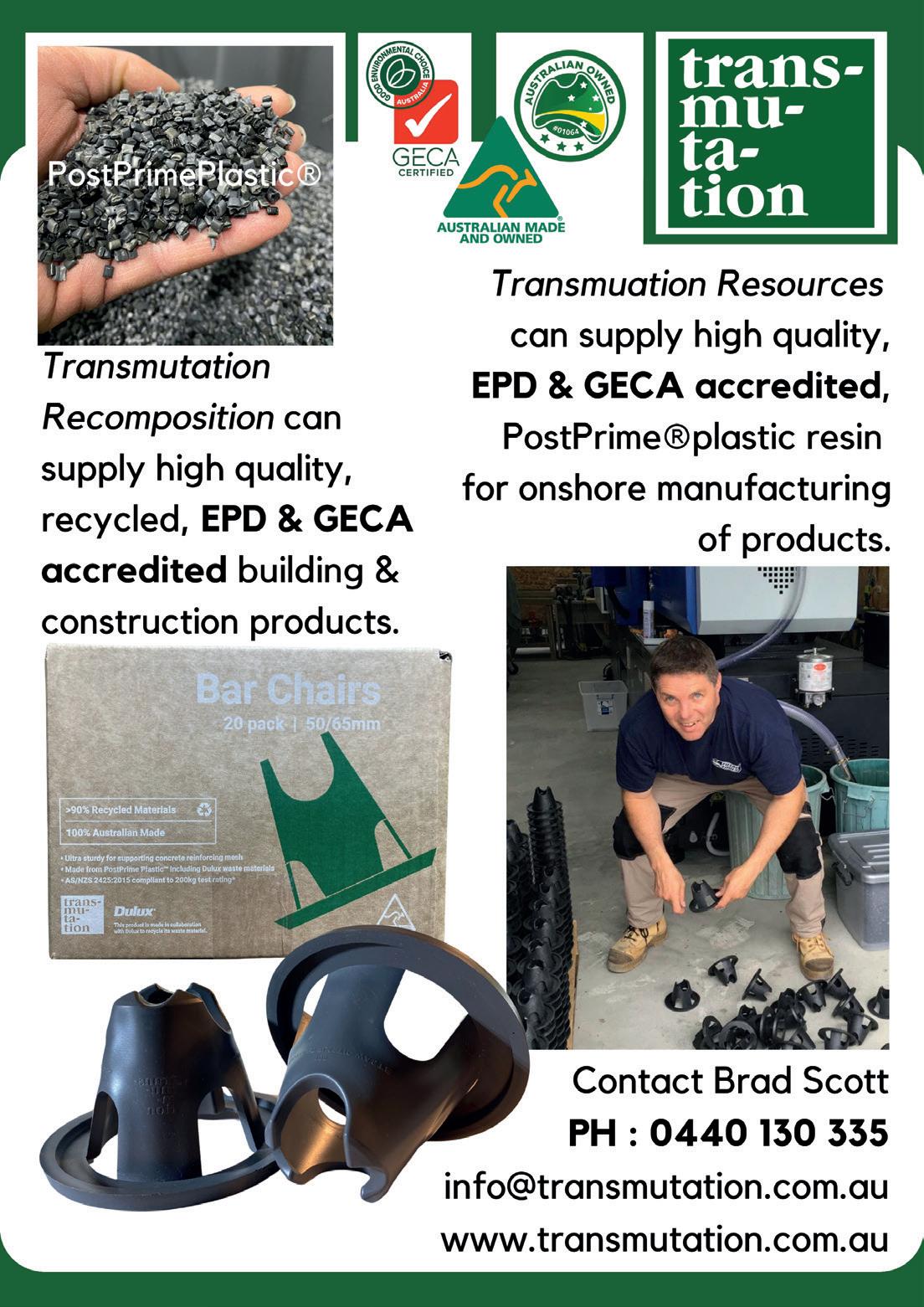
Construction equipment
Strength in service
Backing its fleet of machinery, Jacon Equipment provides the support and training that keep construction projects running smoothly and downtime at bay.
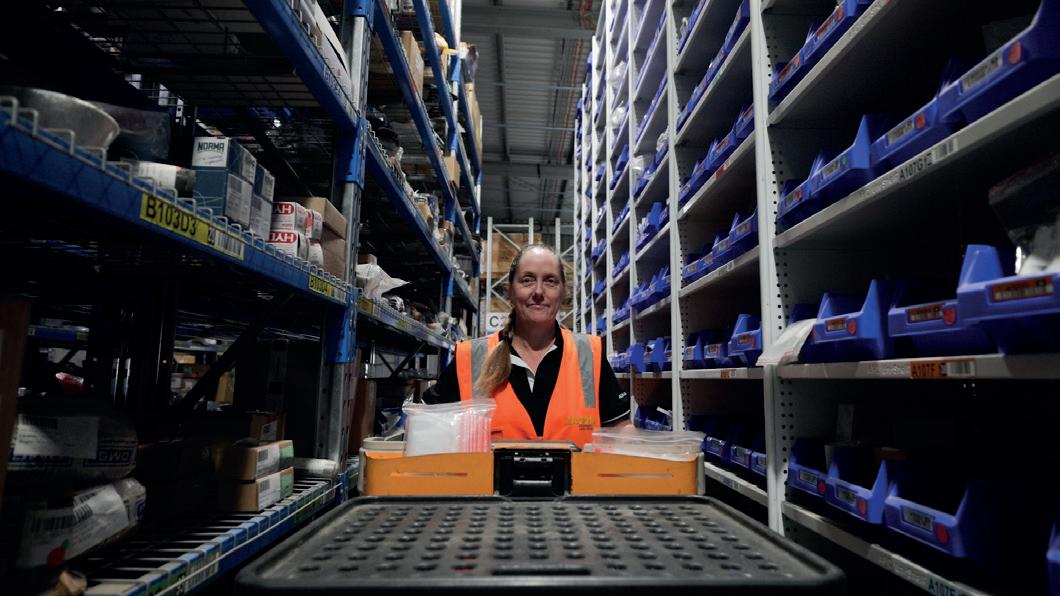
A machine is only as strong as the support behind it. At Jacon Equipment, after-sales service is built into the foundation of every sale. With rapid-response maintenance, a finely tuned spare parts network and operatorfocused training, Jacon ensures its equipment delivers long after it leaves the warehouse.
“We have heavily invested in our distribution network and grown our inventory.”
Downtime derails progress, and Jacon is in the business of keeping projects on track. Darryl Simms, product specialist and business development manager at Jacon, says the company’s proactive approach ensures customers have what they need, when they need it.
“Providing customers with all the relevant contacts in our organisation, including afterhours support, gives them peace of mind and helps immensely,” says Simms. “Checking in with customers during and after each sale is key to ensuring their success.”
After-sales support is a threefold strategy: maintenance, spare parts and technical assistance. With technicians stationed in Sydney, Brisbane, Melbourne, Newcastle and Perth, expertise is never far away.
The company’s growing distribution network spans Brisbane, Sydney and Perth, extending further into Indonesia, Vietnam and South Africa. This ensures a steady flow of critical spare parts wherever they are needed. Pankaj Parbhakar, APAC supply chain manager at Jacon, highlights the importance of this reach.
“We have heavily invested in our distribution network and grown our inventory. As our customer base grows, we will continue to expand our distribution network, whether directly or through dealers,” says Parbhakar.
“With our hubs and spoke model, customer needs are carefully assessed. Critical and recommended spare parts are stocked to support the machine population in the region. In 2025, we achieved another milestone by starting to provide 24/7 support for machinedown and emergency spare parts requests.”
A refined service approach
From the warehouse to the worksite, Jacon is committed to its customers’ needs. With rapid-response service centres and
mobile teams, professional maintenance is always within reach.
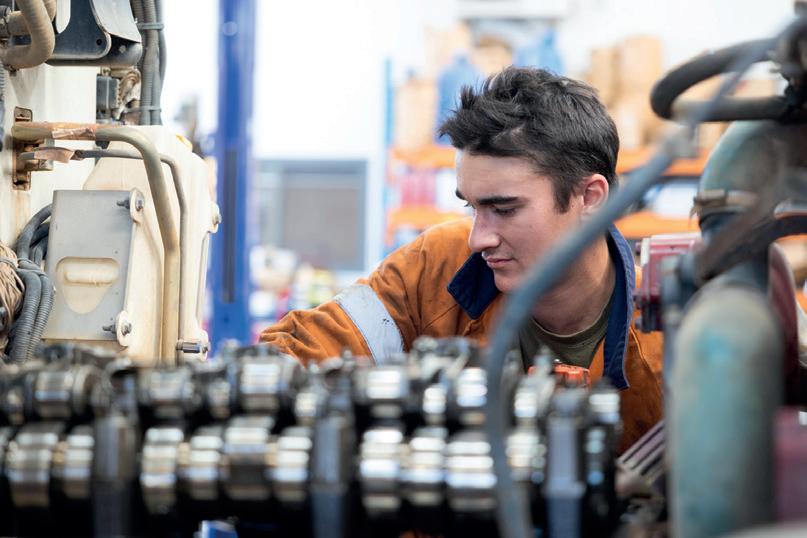
“Jacon’s main warehouse in Brisbane and satellite warehouses in Perth and Sydney allow for quick access to parts and support,” says Karatas. “Our strategically placed teams ensure timely responses to customer needs, reducing downtime on construction sites.”
Support also means customisation. When a client needed a machine modification to improve operator comfort, Jacon’s head engineer flew from Vietnam to Perth, coordinating with a subcontractor to complete the job in six business days.
Construction sites do not run on a nineto-five schedule, and neither does Jacon. A dedicated after-hours service keeps trained support staff on call for urgent issues.
“When a machine is down, customers need immediate solutions,” says Parbhakar. “That’s why we implemented an after-hours, on-call service based on direct customer feedback. Regular interactions help us refine our approach and build stronger relationships.”
Training for peak performance
Training is another pillar of Jacon’s support, ensuring operators are confident and competent with their equipment. Many technical issues can be solved with a phone call or video chat, while complex problems prompt an in-person visit from Jacon’s specialists.
“Naturally, we do not expect operators to know how to properly maintain the equipment to reduce downtime and repair costs,” says Karatas. “However, the civil industry is increasingly pushing operators to stay engaged with maintenance processes and basic fault-finding.”
In one instance, an operator suspected a faulty throttle position sensor. With Jacon’s guidance, the real issue – damaged wiring – was identified, saving time and unnecessary repairs. “While it sounds simple, identifying the root cause can be challenging.
cause analysis, which is where our technical team come to the rescue and guide them through the process,” says Karatas.
“In this case, with our help, the operator successfully identified the issue and advised the inhouse maintenance team to replace the damaged wiring.”
Jacon’s training ensures operators maximise their equipment’s potential. Every purchase includes product familiarisation training, covering everything from basic operation to safety features.
Among its offerings is EFNARC training, a specialised certification for shotcrete nozzle operators. Leander Venter, Africa sales director at Jacon, explains that this training combines real-world techniques with virtual reality (VR) technology, allowing trainees to refine their skills in a risk-free environment.
“Those who successfully complete the assessment earn the prestigious EFNARC Nozzle Operator Certificate, an internationally recognised credential that opens doors to exciting opportunities worldwide,” says Venter.
Venter notes that the VR platform eliminates material waste and time constraints, allowing operators to train as much as needed without onsite limitations.
Jacon ensures its own team is highly trained, maintaining a strong level of expertise within the industry.
“Our technicians hold Certificate IV Training qualifications,” says Karatas. “For new hires, Jacon requires completion of Certificate IV Training by the end of their probation period, ensuring consistent expertise across the board.”
By keeping spare parts stocked, technicians on hand and training readily available, Jacon Equipment keeps construction projects moving. Every call answered, every operator trained and every machine working – because strong support builds a stronger industry.
“Our strategically placed teams ensure timely responses to customer needs, reducing downtime on construction sites.”
“Jacon’s main warehouse in Brisbane and satellite warehouses in Perth and Sydney allow for quick access to parts and support.”
Recycling
Taking on the big recycling challenges
From a humble shed in South Australia to the frontlines of construction waste innovation, Transmutation is proving that even the hardest-to-recycle materials can find a second life.
Construction remains one of the world’s biggest waste-producing industries, but Australia’s approach is shifting. Companies like Transmutation are proving that discarded materials hold untapped value, driving new solutions for a more sustainable future.
In 2022–23, Australia generated an estimated 26.8 million tonnes of building and demolition waste, according to the National Waste and Resource Recovery Report 2024. Tackling this challenge takes bold ideas and unconventional thinking – qualities that define Transmutation and its founder, Brad Scott.
A journey of reinvention
Scott spent three decades in heavy logistics across waterfront, road and rail transport before shifting to consultancy, where he turned around struggling projects under immense pressure. But the relentless cycle of high-stakes decision-making took its toll. Then, the unexpected happened.
“With our kids grown up, my wife proposed selling our house in Brisbane, storing nothing and travelling Australia with no fixed plan. It caught me off guard, but I embraced it,” says Scott.
The couple hit the road, picking up temporary jobs along the way. They managed motels in Victoria, ran an outback pub in Queensland, and worked in hotels in South Australia. Scott enjoyed the nomadic life, but after 18 months, his wife was ready to settle.
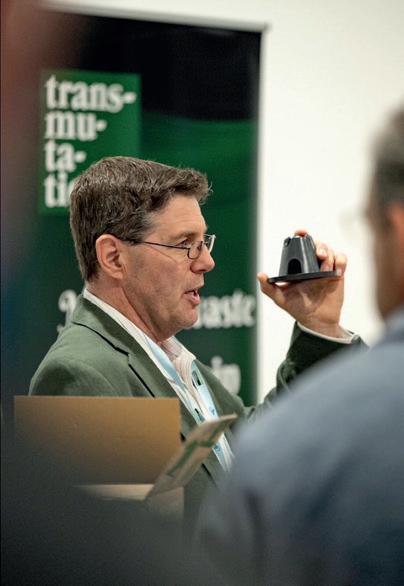
“Today, Transmutation manufactures bar chairs for the construction industry using PostPrime Plastic, with several new products in the pipeline.”
“She made me a deal: we would find a place we both liked, she would take a full-time job, and we would buy an empty shed where I could figure out my next step,” he says.
It was in that shed in Robe, South Australia, where the foundation was laid for what Transmutation has become today – a business challenging the status quo in recycling and manufacturing.
A business with purpose
When Scott told his wife he wanted to turn the shed into a business, they considered how best to use his skills. He had a chemistry degree – one he had never fully utilised – but now saw an opportunity to bring it into play.
“Recycling and environmental issues have always been important to me,” says Scott. “Why would you trash the planet if you can do something about it?”
That mindset led him to plastic recycling. While researching, he discovered the Precious Plastic movement – an initiative that provided open-source plans for small-scale recycling machines. The idea struck a chord. Scott saw not just a business opportunity, but a way to educate and inspire.
“Recycling is notoriously difficult to make profitable, so we structured the business carefully,” he says. “We set up a small shop selling wholesale and retail homewares, featuring work from other makers, while also doing some manufacturing ourselves. The manufacturing side was more about education – showing people how easy it can be to recycle in a small space.”
It started as a modest venture, but within a year, demand outpaced expectations.
Scaling up
Transmutation quickly gained traction, but its breakthrough came when the Aussie Bread Tags for Wheelchairs charity approached Scott. They had been collecting bread tags nationwide but had no way to recycle them in Australia. Scott devised a solution, shifting the
recycling process from South Africa – where the charity was originally established – to a local facility.
Then came an unexpected call from Country Road Australia. Sceptical at first, Scott hung up, assuming it was a prank. The clothing retailer called back. That partnership propelled Transmutation into the national spotlight, proving that high-quality, recycled homewares could command commercial interest.
Another chance encounter led to an even bigger leap. An executive from architectural paint brand Dulux, visiting Robe, walked into Transmutation’s store and mentioned a persistent industry problem – powder coating waste, an ultrafine thermoset plastic that had long been considered unrecyclable.
Cracking the construction waste code Thermoset plastics do not melt; they burn, making traditional recycling impossible. On top of that, powder coating waste is so fine that it clogs conventional recycling systems.
“No one had found a solution,” says Scott. “But I did – in the back shed.”
After two years of development, Transmutation pioneered PostPrime Plastic, a new thermoplastic blend that repurposes powder coating waste, agricultural waste and other recycled materials. It functions like polypropylene but is uniquely its own.
“Today, Transmutation manufactures bar chairs for the construction industry using PostPrime Plastic, with several new products in the pipeline,” says Scott.
“In 2025, we have four major projects across different sectors. One of them, which we call ‘Tier One,’ involves supplying recycled products specifically for Tier 1 construction companies. We have one product on the market, with four or five expected by year’s end.”
The company has also secured a supply deal for the Western Sydney International Airport project and is experimenting with incorporating e-waste and soft plastics into a masonry-like building material.
“Our growth is exciting, and more companies see us as problem-solvers, turning hard-to-recycle wastes into viable products,” says Scott.

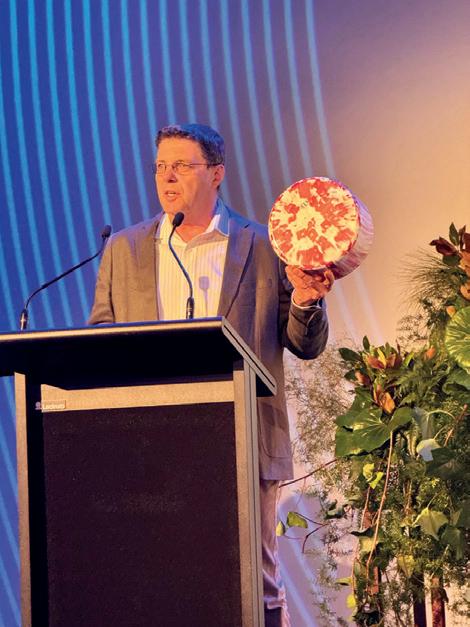
Transmutation’s 5065mm bar chairs are environmentally accredited and made from PostPrime plastic derived from waste powder coating and agricultural waste.
want to be at the forefront of ESG and the circular economy.”
Transmutation’s co-founder and chief polisher, Narelle Scott, hand polishes the bread tag products before they are presented in the factory shop.
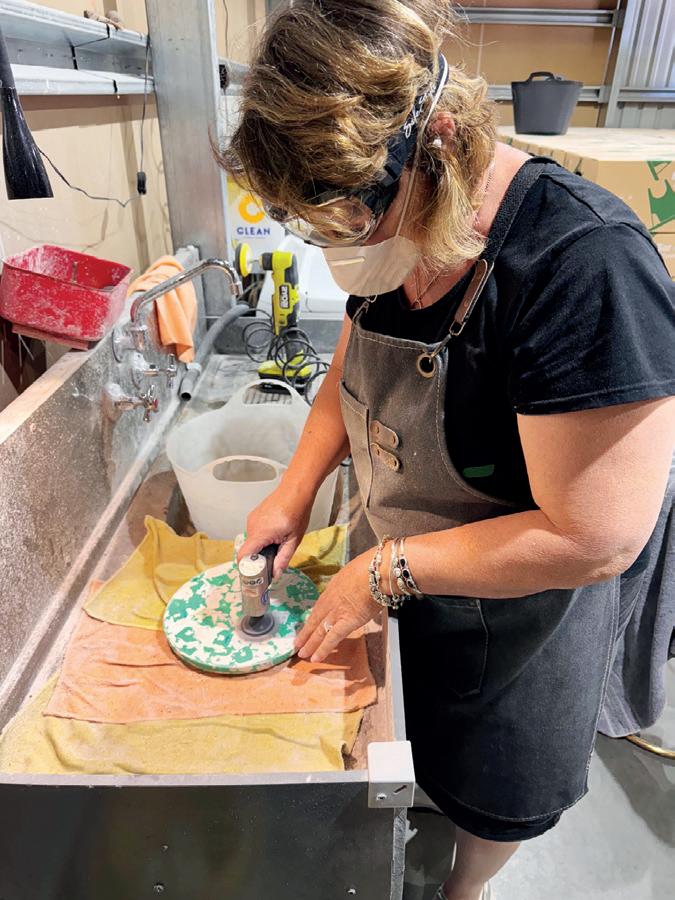
and charitable partnerships,” says Scott. “Our ESG strategy covers environmental impact, governance through product traceability via QR codes, and social contributions, ensuring transparency and accountability.”
“That reinforced that we are on the right track – our position, timing and direction in the market,” says Scott.
“There are often assumptions and prejudices that come with being a small business based in regional South Australia. If you’re a Tier 1 builder, you’re probably not thinking of sourcing first-class building materials from Robe.
“This kind of recognition helps break through those barriers. It reinforces that while we are a small factory in regional South Australia, we’re also a provider of first-class building materials at scale.”
Breaking boundaries
As green building standards tighten and industries demand smarter sustainability solutions, Transmutation is ready to lead.
“Construction is ahead of the curve when it comes to ESG,” says Scott. “That is why we are focused on it – because it is where real change is happening. But other industries will follow, and we will be ready.”
For a sector long plagued by ‘impossibleto-recycle’ waste streams, Transmutation represents a new frontier. With ingenuity and problem-solving at its core, the company is proving that even the most challenging construction wastes can be repurposed.
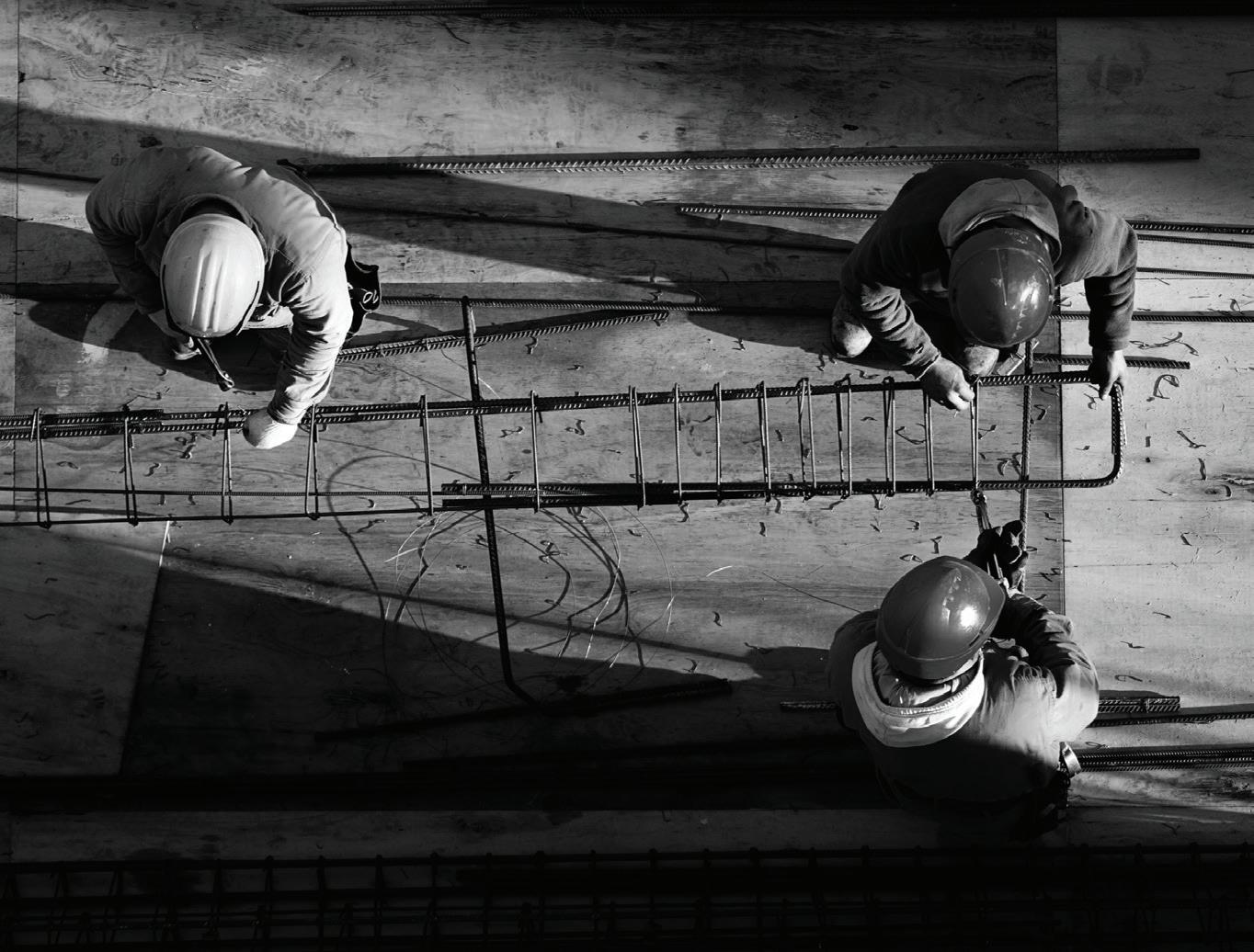
“No one had found a solution. But I did – in the back shed.”
Unlike most small businesses, Transmutation has pursued international certifications, including ISO, GECA and United Nations Global Compact membership, positioning itself alongside major corporations in the circular economy.
The company aims to disrupt the typical client-supplier relationship in favour of a more collaborative approach.
“Ultimately, we want to be at the forefront of ESG and the circular economy. We see ourselves as experts in this space, even as a small business. Some might call it ambitious, but we see ourselves as part of the big picture in the circular economy.”
Recognition has followed. In 2024, Transmutation won the National Embracing Innovation Award at the Telstra Best of Business Awards – further proof that its approach is breaking barriers.
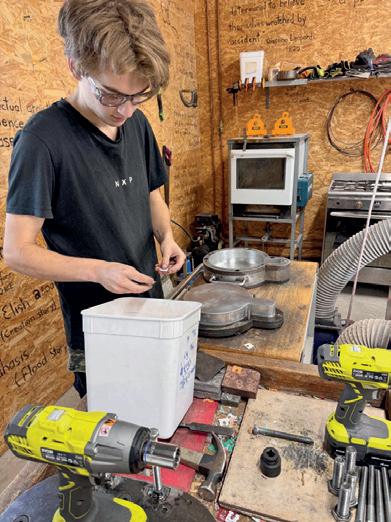
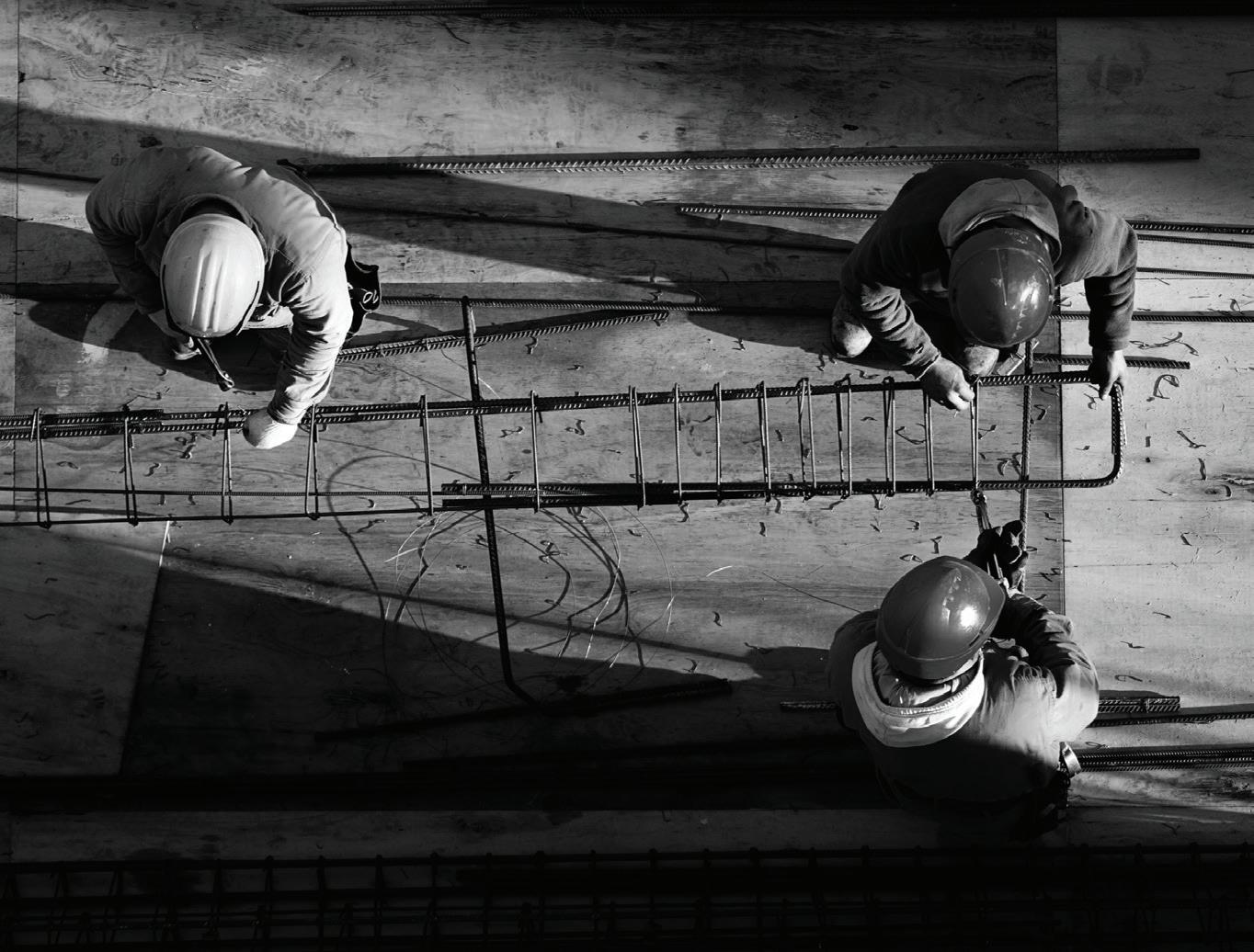
A LIFELINE FOR SKILLED LABOUR
A new and more simplified sponsored work visa program to hire overseas workers
Australia’s construction industry is facing a critical skills shortage, but IMMIGATE is helping businesses access overseas talent to bridge the gap.
On the 7th of December 2024, the Department of Home Affairs updated its employer-sponsored visa program, now called the 482 Skills in Demand (SID) Visa, making it easier for companies to recruit global talent.
This presents an excellent opportunity for the industry to take advantage of these new policies.
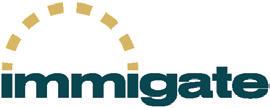
Construction materials
Embracing the benefits of light gauge steel
An engineered, light gauge steel framing solution expedited the construction of this distinctive Queensland childcare centre, delivering time and cost savings.
Project
Sunkids Childcare Centre
Location
Mermaid Waters, Queensland
Principal Steel
Product
24 tonnes of light gauge steel framing made from TRUECORE® steel
Builder
9 Constructions
Steel fabricator
Australian Framing Solutions
Architect
Realspace Creative
Photography
Australian Framing Solutions
Sunkids Childcare Centres have a holistic approach to early childhood education, where parents are honoured as the ‘first teachers’, early childhood professionals are the ‘second teachers’, and the physical environment is the ‘third teacher’, providing a safe space where children are allowed to learn, play, grow and explore.
With this core philosophy in mind, architect Hooman Jaffar from Realspace Creative had a clear objective when designing the facility. He set out to create a space with a sense of gathering and community where families and staff could come together in a shared environment to support and encourage early childhood development.
This design vision would be physically represented by two sweeping curves, which Jaffar said take their cues from human notions of embrace and nurturing. These curved structures would house the centre’s learning areas, activity rooms, amenities and encircle the central courtyard’s global village, a playscape that would introduce ‘the world’ to these young, curious minds.
The centre was initially designed to be constructed with concrete blocks as the predominant walling material and a suspended concrete slab for the roof. However, when Riaz Rezvani from 9 Constructions suggested an alternative, Realspace Creative and the client were keen to explore other options.
using light gauge steel (LGS) framing made
from TRUECORE steel and believed there was an opportunity to incorporate prefabricated LGS frames in the build without compromising the design and still maintain the building’s thermal, acoustic and structural integrity.
Using prefabricated LGS framing also helped minimise on-site waste and create a safer work environment. Framing was delivered to the site in packages, which reduced worksite congestion and supported the planned delivery and installation schedule.
A collaborative team was then formed with Australian Framing Solutions (AFS), which provided engineering and design expertise using its 3D modelling software. This led to the development of a prefabricated solution that delivered tangible benefits to the project, including an increase in floor area due to the smaller footprint offered by LGS framing.
Additionally, by modelling the centre in 3D, Sunkids early childhood professionals were able to assess and contribute to the design of the open-plan, interactive spaces, ensuring the childcare centre was designed to support and meet the needs of its young clients and centre staff.
“By using prefabricated LGS framing made
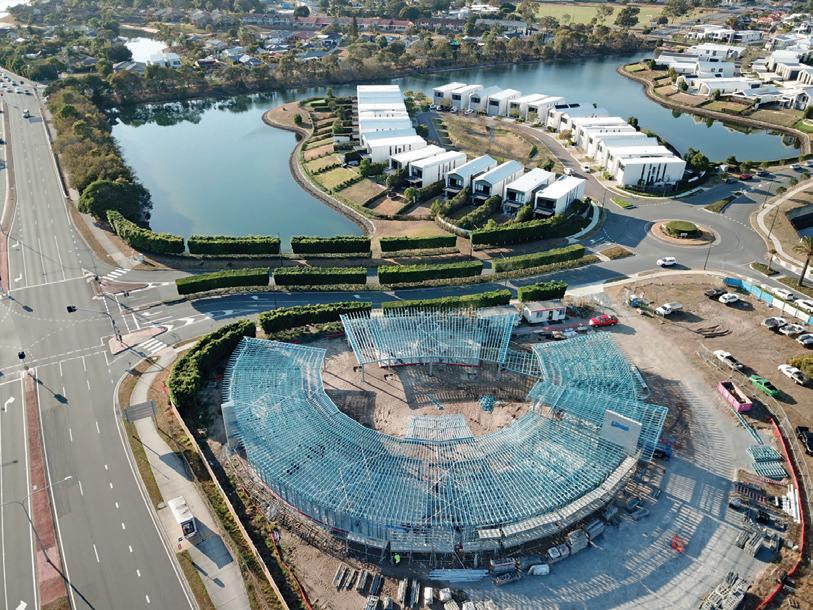
TRUECORE steel was specified for the framework of the childcare centre and, incidentally, the adjacent townhouse development.

As an end-to-end design, engineering, manufacturing and installation company, AFS was an integral partner in the development and construction of this project. It ensured design challenges were turned into design solutions, while maintaining the building’s architectural intent.
The most notable of these design challenges was related to the complexity of the circular roof structure. AFS’s solution featured more than 300 individually engineered roof trusses, uniquely fabricated to deliver the roof’s striking shape and structural integrity. Each custom-made truss was around 14 metres long, spanning the width of the building, and had to be precisely positioned using mobile site cranes. The correct placement of these trusses was crucial to the project’s timeline and only made possible because of AFS’s detailed 3D modelling, precision manufacturing, thorough site plans and clearly marked frames and trusses.
These trusses provide the supporting framework for the specialised, tapered, standing seam roof profile used on the project. The Fielders Freeform profile was selected and roll-formed onsite. Fielders Mobile Mill expedited the installation process by tapering each roof sheet in a continuous length to
eliminate joins and align with the complex, concave geometry of the roof.
Another challenge that needed to be resolved related to the massive shade sails covering the central courtyard. AFS needed to overcome the lateral forces these sails would generate, particularly during high wind periods. AFS’s engineered solution included a customised connection that allowed all lateral forces to be transferred back to the structural steel posts without impacting the adjacent lightweight steel framing structure.
“Undoubtedly, this has been one of the most exciting early learning centre projects we have ever participated in,” says Jake Gundry, managing director of AFS.
“Collaboration was key to this success: AFS worked closely with the architect, builder, engineers, and other stakeholders to effectively problem-solve throughout the project.”
Sunkids Mermaid Waters was designed and built as part of a new precinct called ‘The Lanes,’ featuring a topography with an expansive waterways system synonymous with Gold Coast living. This environment contributed to TRUECORE steel being specified for the framework of the childcare centre and, incidentally, the adjacent townhouse development.
TRUECORE steel is durable and resilient, with BlueScope’s metallic coating, incorporating Activate technology, to provide enhanced corrosion resistance. (Images: Australian Framing Solutions)
“Undoubtedly, this has been one of the most exciting early learning centre projects we have ever participated in.”
Linking the quality lifecycle
Visibuild is built for the real world – connecting every phase of construction to simplify quality, empower teams and turn insights into real progress.
“Visibuild now allows people to get faster snapshots of recurring errors, problematic contractors and elements of their management system that are inefficient.”
Quality issues in construction often stem from the earliest project stages, yet many builds fail to address them until problems arise onsite – if they are addressed at all. This disconnect leads to costly rework, shrinking profit margins and inefficiencies that persist across multiple projects. Visibuild is changing this by integrating quality management throughout a project’s lifecycle, ensuring data‑driven improvements from planning to post‑completion. Its solution is designed with simplicity in mind, making adoption quick and practical for real world projects.
Quality begins before construction
The foundation of a high performing project is set long before ground is broken. Planning, design and pre construction decisions shape the build, yet these stages are often disconnected from what follows, particularly in quality management. As Damien Quinn, co founder and CEO of Visibuild, explains,
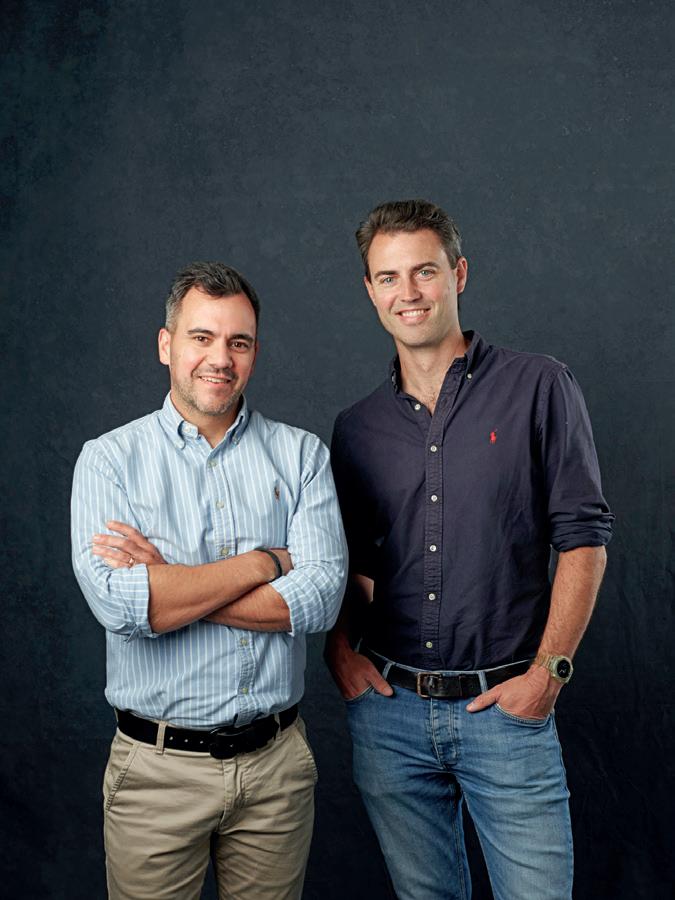
UK not for profit the Get It Right Initiative states that up to an 18 per cent cost improvement is built into a project if everything is done right from the start. However, an additional 3 to 5 per cent is typically lost after completion. These inefficiencies narrow profit margins, with commercial construction profit margins estimated to be below 2 per cent. The rectification and maintenance of projects containing latent defects often drive margins negative when viewed across the post completion horizon.
“A huge portion of margin erosion stems from construction errors; however, this doesn’t even account for the lost opportunity of error contingency that is baked into projects from the beginning – meaning the opportunity for improvement is immense,” says Ryan Treweek, co founder and CRO at Visibuild.
Breaking the costly cycle
Project costs are often estimated using subcontractor rates based on previous projects, with adjustments for inflation and material costs. However, these rates frequently carry the weight of past mistakes, perpetuating inefficiencies from one project to the next.
“Construction businesses love the notion of lessons learned being applied to future projects, but too often, the lessons aren’t realised and communicated fast enough and they’re not done using meaningful data,” says Treweek. “Visibuild now allows people to get faster snapshots of recurring errors, problematic contractors and elements of their management system that are inefficient.”
By optimising planning and design, teams can prevent errors before they happen, documenting challenges along the way. This proactive approach not only reduces mistakes but also establishes a framework for continuous improvement, ensuring lessons from past projects inform future builds.
“It’s one thing to acknowledge spending $10 million on defects last year, but there may be another $50 million in untapped potential simply by managing projects differently from the outset,” says Treweek.

A connected approach
These problems are not new, and they can feel too big to solve easily; however, the response is surprisingly easy to implement. It does not require a dedicated taskforce or additional resources, but small tweaks to how projects are managed. Using a tool like Visibuild can be a force multiplier in solving these challenges.
Traditionally, three key systems govern construction projects: quality management, defects and handover management, and post‑completion or asset management. However, these systems often operate in isolation.
“The asset management phase begins after completion and extends through the defects liability and warranty period,” says Quinn. “Yet, issues identified in this phase rarely make their way back to the teams responsible for quality management at the start.”
This results in three separate repositories of valuable information that don’t communicate with each other. The ideal process, Quinn argues, would link pre construction, quality management, completion, commissioning and defect management into one seamless system. It would also extend into post completion processes such as asset and warranty management.
Visibuild’s platform is designed to close these gaps, ensuring improvements go beyond minor refinements.
“If past defects are simply compared to new defects without addressing their root causes, the same problems will persist. Similarly, warranty claims are often handled in isolation. Instead of feeding that information back into the early stages of a project, issues are managed reactively rather than proactively prevented,” says Quinn.
“Visibuild’s approach creates a continuous improvement loop, embedding quality management into the entire project lifecycle.”
Expanding the vision
While eliminating all defects in such a complex industry is impossible, reducing recurring problems through data d riven insights offers an opportunity. The post completion phase is a critical period where long term performance is measured, and ongoing issues are identified. Integrating post completion and legacy management into the quality lifecycle captures warranty claims, maintenance challenges and user feedback in a centralised way.
Visibuild is already streamlining pre construction, construction and defect management, with its influence extending into warranty phases. Now, the company is developing a dedicated asset management module to further enhance post completion processes. This new feature will integrate external sources of information – from tenants, buyers, government bodies and building owners – into one simplified and centralised system.
“If past defects are simply compared to new defects without addressing their root causes, the same problems will persist.”
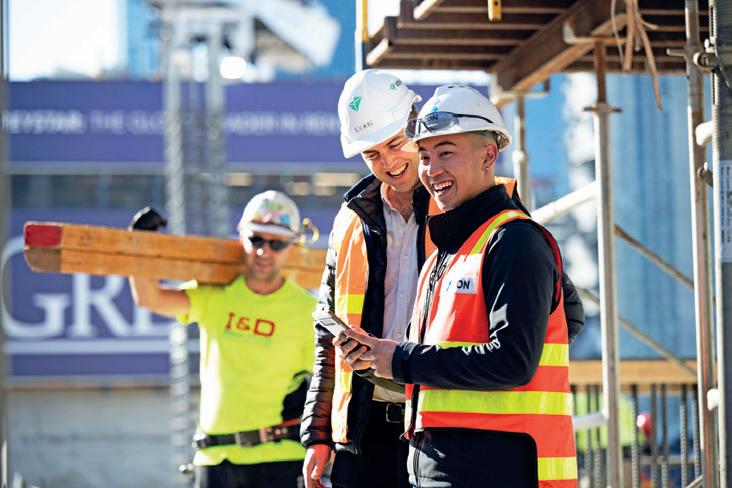
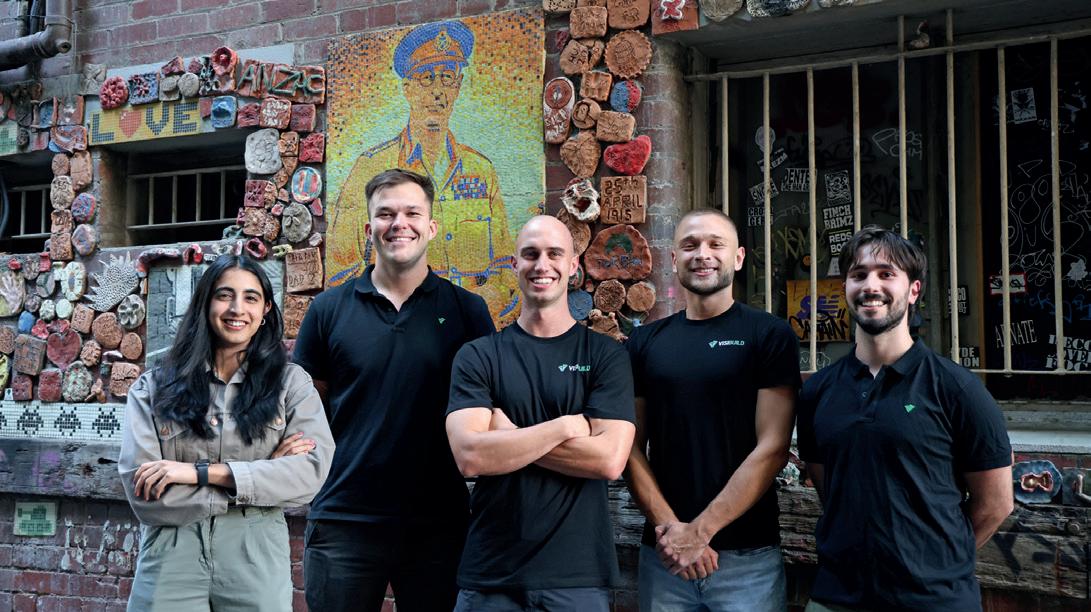
“Right now, this information comes in through phone calls and emails,” says Quinn. “We want to capture all post completion warranty issues in one place, creating a single source of truth.”
During the handover stage, the focus isn’t merely on transferring control from builders to owners – it’s about establishing a lasting legacy. A detailed handover process provides all stakeholders, from facility managers to future maintenance teams, with a complete history of the project. This transparency allows teams to pinpoint recurring issues, schedule timely interventions, and integrate lessons learned into future project planning.
Quinn. The first step was identifying the problem. The next was developing a solution that brought everyone in.
“We focused on quality first because it’s such a critical piece of the puzzle. But we designed the system knowing it had to address multiple challenges simultaneously,” says Quinn. “That’s why we didn’t just build another tick box system – we built something that could change the culture of quality, a real‑world solution that is deliberately simple, enabling teams to implement change without feeling overwhelmed.”
“We want to capture all post‑completion warranty issues in one place, creating a single source of truth.”
The platform’s intuitive design ensures that the handover process remains simple and hassle‑free, allowing stakeholders to concentrate on building rather than managing bureaucratic overhead.
“Our approach extends the quality management process well beyond project completion,” says Treweek.
“By linking post completion insights, warranty data and handover documentation with early‑stage planning, we create a continuous improvement loop that benefits every phase of construction.”
By capturing and analysing data from the warranty period and legacy management stages, Visibuild aims to help prevent future errors and streamlines asset management. This integrated process not only enhances the overall quality of a build but also ensures that valuable insights are consistently fed back into new projects, paving the way for smarter, safer and more efficient construction practices.
Building a quality-first culture
Before Visibuild, no single tool connected all these lifecycle processes in one system, says
The opportunity lies in engaging more team members early on. Once a project is set up in Visibuild and can be tracked, quality becomes visible, and its impact becomes tangible. This comprehensive approach extends beyond site work to program monitoring, off site procurement and precast production, increasing transparency and reducing inefficiencies.
“Many senior project leaders have traditionally turned a blind eye to quality,” says Quinn. “They collect statistics, include them in reports, and move on. But without real t ime visibility, they miss the opportunity to step in and make improvements before it’s too late.”
Visibuild brings quality full circle, giving construction teams the tools to build smarter, reduce risks, and deliver projects with confidence. With a comprehensive approach that spans from initial planning to post completion legacy management, Visibuild ensures that quality is maintained throughout the entire lifecycle – paving the way for a more efficient and forward t hinking future in construction.
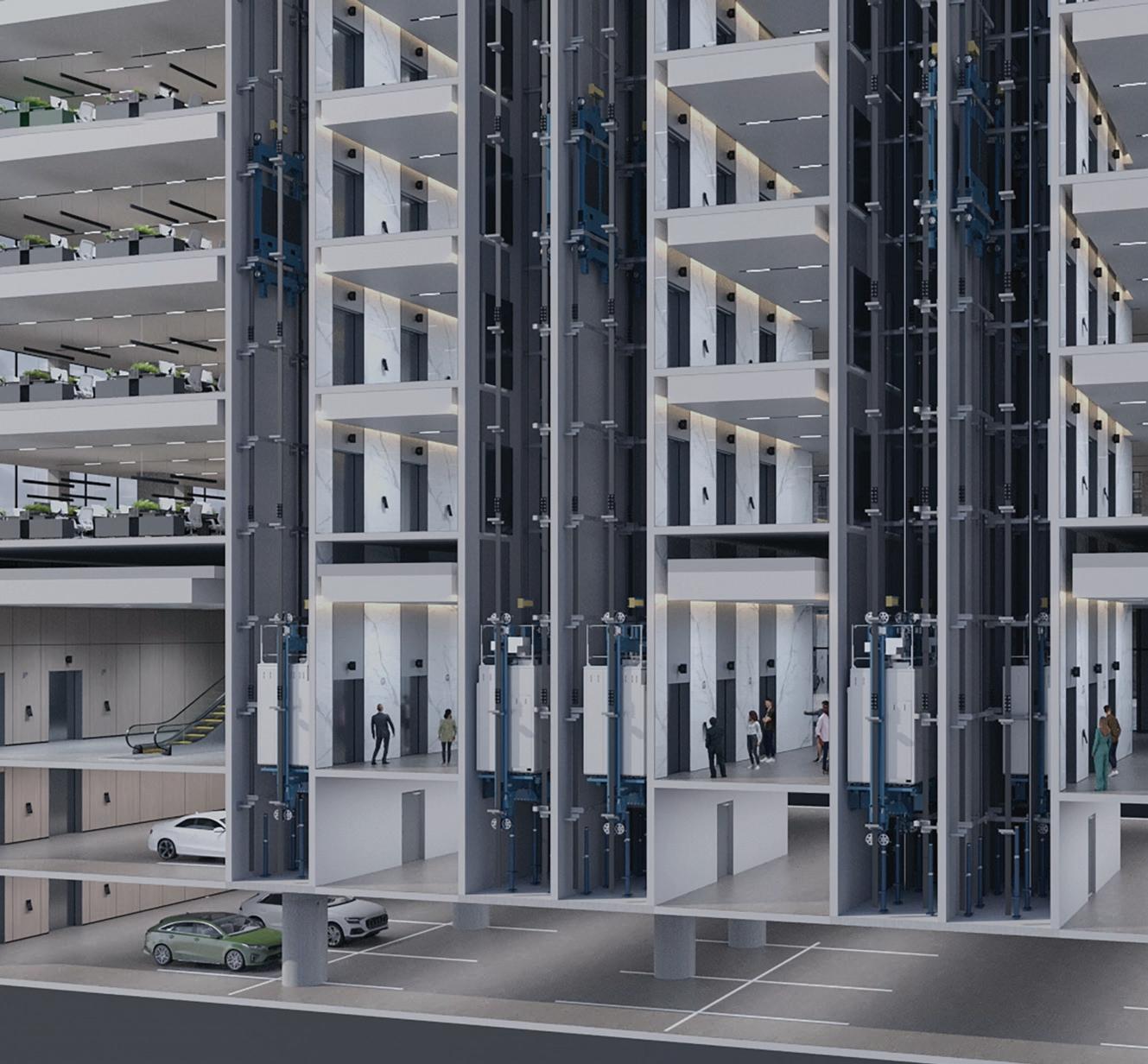
Is your building ready for the future?
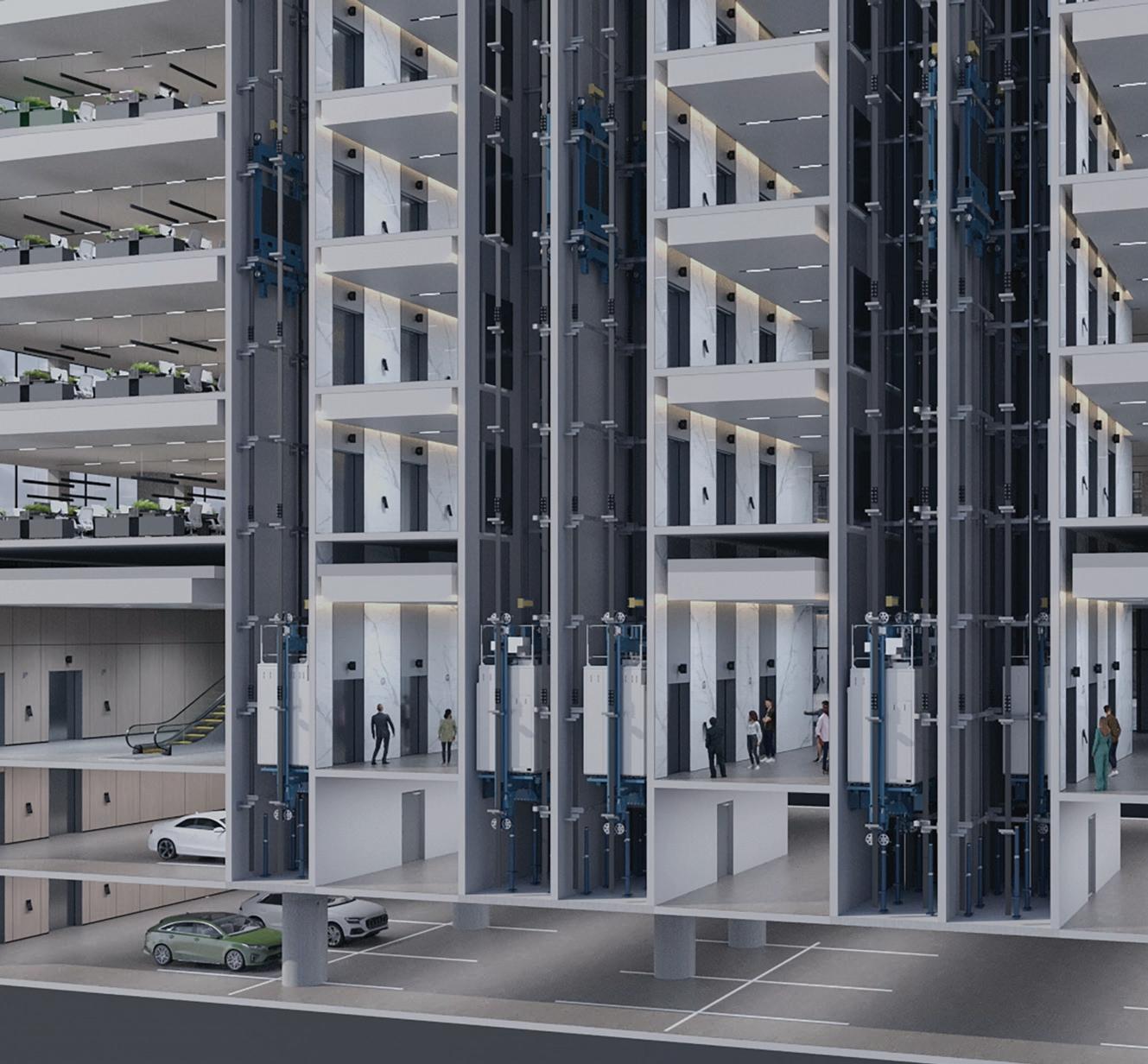
Built-in connectivity for smart upgrades
KONE UltraRope for energy efficiency
Smaller machine room and reduced shaft for better space efficiency
KONE’s Next-Generation High-Rise Solutions deliver cutting-edge technology that optimises space, boosts efficiency and reduces emissions –ideal for new high rise builds.
Destination Control System for smoother movement
Transform your building with KONE – your trusted partner for smarter, more sustainable high-rise elevators.
Water infrastructure
Digging deep
Combining a rich engineering legacy with refined trenchless techniques, McConnell Dowell continues to advance project delivery in the water sector.

Since its inception in 1961, McConnell Dowell has had a hunger for technically complex work – it is part of its DNA. This mindset has taken the ‘Creative Construction’ company across Australia, Southeast Asia and beyond, establishing it as a leader in the water sector.
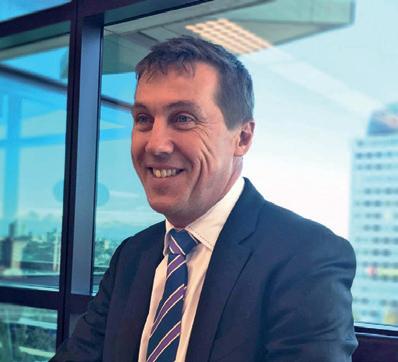
Dr James Glastonbury, chief engineering and innovation officer
(Images: McConnell Dowell)
Water infrastructure remains integral to McConnell Dowell’s long-term strategy. With water security and water quality among the world’s most pressing challenges, the company is committed to delivering smarter, more sustainable solutions across the water and wastewater cycle. As industry demands evolve, so too does McConnell Dowell’s approach.
Dr James Glastonbury, chief engineering and innovation officer at the company, highlights how regulatory shifts and technological advancements are shaping McConnell Dowell’s work.
“We’re increasingly seeing positive regulatory changes in various jurisdictions setting improved wastewater discharge requirements and firmer environmental protections,” says Glastonbury. “Technology is a major lever in our response to this evolving landscape. We are continuously assessing and
Army Bay Ocean Outfall project –Introduced to New Zealand by McConnell Dowell, Direct Pipe, enables the installation of large-diameter pipelines over large distances with greater accuracy than traditional trenchless techniques.
integrating new advancements to improve water sector outcomes.”
Balancing innovation with experience, McConnell Dowell draws on decades of expertise while embracing new thinking where it adds value – whether through smarter, more efficient, safer or higher-quality solutions. Trenchless technology is a prime example, particularly in densely populated or environmentally sensitive areas.
“In many cases, traditional construction methods can cause significant disruption to roads, community assets and parklands,” says Glastonbury. “While conventional methods remain an option in urban settings, technology-enabled solutions can help reduce that community impact.”
McConnell Dowell’s expertise in trenchless methods is particularly evident in New Zealand, where the company has built a strong reputation in complex water transmission and treatment projects.
Daniel Patten, McConnell Dowell’s GM engineering – New Zealand and Pacific, notes that tightening environmental regulations have driven changes, particularly around seabed and foreshore excavation.
“Where we once relied on staged excavations with large temporary works, we have transitioned to trenchless crossings,” says Patten. “As the technology has advanced, we have embraced deeper and longer crossings to meet evolving requirements.”
Patten has been involved in many of these New Zealand water projects over his 22 years with the company. One standout example is the Army Bay Ocean Outfall project in Auckland. Engaged by Watercare Services, McConnell Dowell designed and constructed a new wastewater outfall, upgraded an existing pump station and built a new ultraviolet disinfection facility – all while working within a conservation area.
With most construction occurring within a pest-free conservation zone and the need to avoid disrupting plant operations, the project team introduced Direct Pipe. This method, combining micro-tunnelling and horizontal directional drilling, allowed for long pipe installations in a single drive well below the surface, minimising environmental impact. The team not only pioneered its use within the company but also set a new Direct Pipe tunnelling world record, reaching 1,985 metres for the land section of the pipeline.
Building on this success, McConnell Dowell has since worked with Watercare to complete
the Snells Algies wastewater pipe and outfall project, further extending the tunnel length and establishing a new world record of 2,021 metres.
More recently, the company completed Watercare’s Warkworth to Snells Transfer Pipeline, where trenchless technology provided a more efficient and less disruptive alternative to a conventional dig-and-lay approach along a challenging route.
“This project was more of a cross-country tunnelling effort. The original plan involved a pipeline installation along a difficult, winding road – the only viable access route to Snells and Algies Beach. The road presented geotechnical challenges, including a high risk of slips,” says Patten.
“Instead, we proposed a cross-country tunnelling solution that eliminated almost all disruption, minimised the impact on landowners and delivered significant cost savings. Not only did this reduce construction costs, but it also lowered operational expenses by eliminating one of three pump stations and deferring another.”
As trenchless technologies in the water and wastewater sector continue to advance, McConnell Dowell is not just an early adopter but often a first adopter, setting new industry benchmarks.

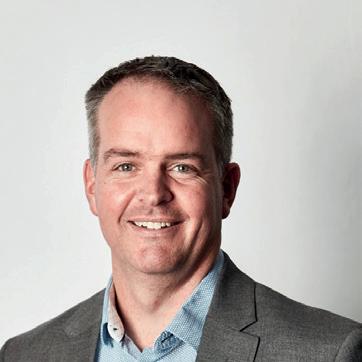
“Implicit in the projects we have delivered in the water sector is a powerful cycle of learning, refinement and optimisation.”
Water infrastructure

Aura
“These three factors – safety, sustainability and constructability –are the key forces driving us to innovate.”
“Implicit in the projects we have delivered in the water sector is a powerful cycle of learning, refinement and optimisation. I think of it as a flywheel of continuous improvement,” says Glastonbury.
“Just like in sport, where teams analyse games to refine their performance, we take lessons from each project and apply them to the next. That level of precision is visible onsite – it is tangible, and it is what makes this work exciting.”
For the company, three key drivers shape its approach to innovation. Safety remains paramount, influencing both design and construction processes.
Sustainability is another focus, with efforts to improve efficiency – such as exploring ways to directly install product pipes rather than using carrier pipes, reducing tunnel size and material duplication.
Constructability is the third driver. While McConnell Dowell is not a consultancy, it often provides constructability input to clients tackling complex challenges.
“A stormwater catchment prone to flooding in a highly urbanised area may require an innovative solution to efficiently redirect water,” says Patten. “As new technologies emerge, addressing these challenges becomes more feasible. These three factors – safety, sustainability and constructability – are the key forces driving us to innovate.”
While technical expertise plays a crucial role, McConnell Dowell’s ability to self-perform has
also strengthened its position in the market. “We own or lease our tunnelling machines and deliver projects with our own engineers, technicians and labour,” says Patten. “This hands-on approach has allowed us to refine our capabilities and push the boundaries of trenchless technology.”
That expertise is now informing projects beyond New Zealand. As similar opportunities arise in Australia, McConnell Dowell’s New Zealand operations are sharing their knowledge across the business, fostering strong collaboration between teams in both countries.
“The expertise in New Zealand is helping our Australian colleagues tackle similar opportunities, where that experience, technology and key partnerships can be applied to the local market,” says Glastonbury.
“Knowledge-sharing requires constant nurturing, but we are adept at connecting the right experts with the right teams – both internally and with our clients – across our business footprint.”
Trenchless methods have gained traction in New Zealand due to environmental and water control legislation, and a similar shift is now underway in Australia.
“In some of Australia’s most urbanised areas, there is limited community support for disruptive construction methods such as digging up roads, parklands or national parks – for good reason,” says Glastonbury.
“Trenchless technology offers a viable alternative, and we are actively engaging with water agencies to explore its potential –particularly for urban areas where much of the major water conveyance infrastructure is reaching the end of its service life.
“There are opportunities for asset renewals and the replacement of key water infrastructure using trenchless methods. Shore crossing projects are another area where we see potential in the Australian market. Overall, there is growing relevance and increasing interest in these technologies.”
With urbanisation on the rise and greater demand for efficient water and wastewater infrastructure in Australia, McConnell Dowell is well positioned to drive the next wave of innovation – delivering solutions that balance technical excellence with environmental and community considerations.
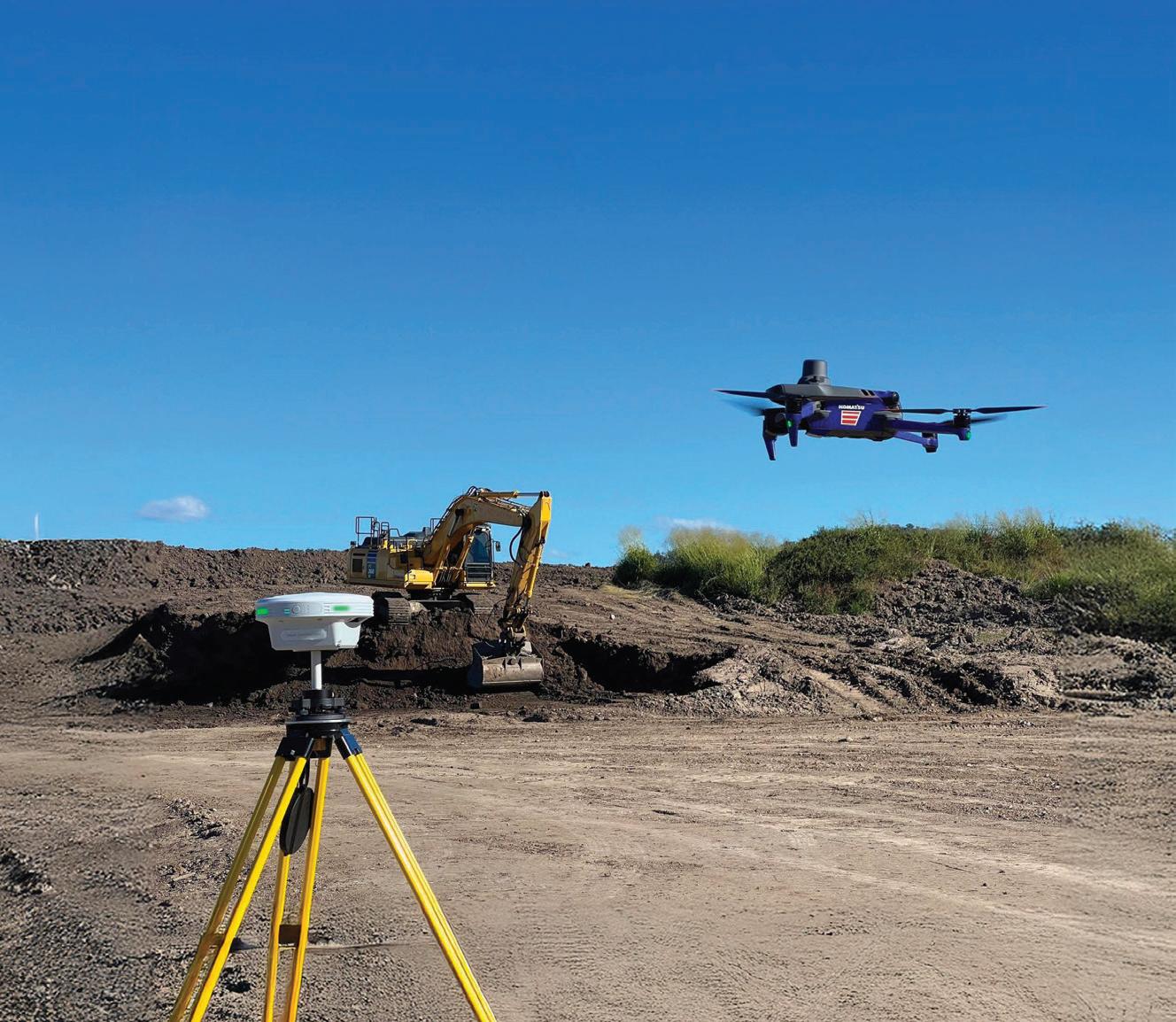
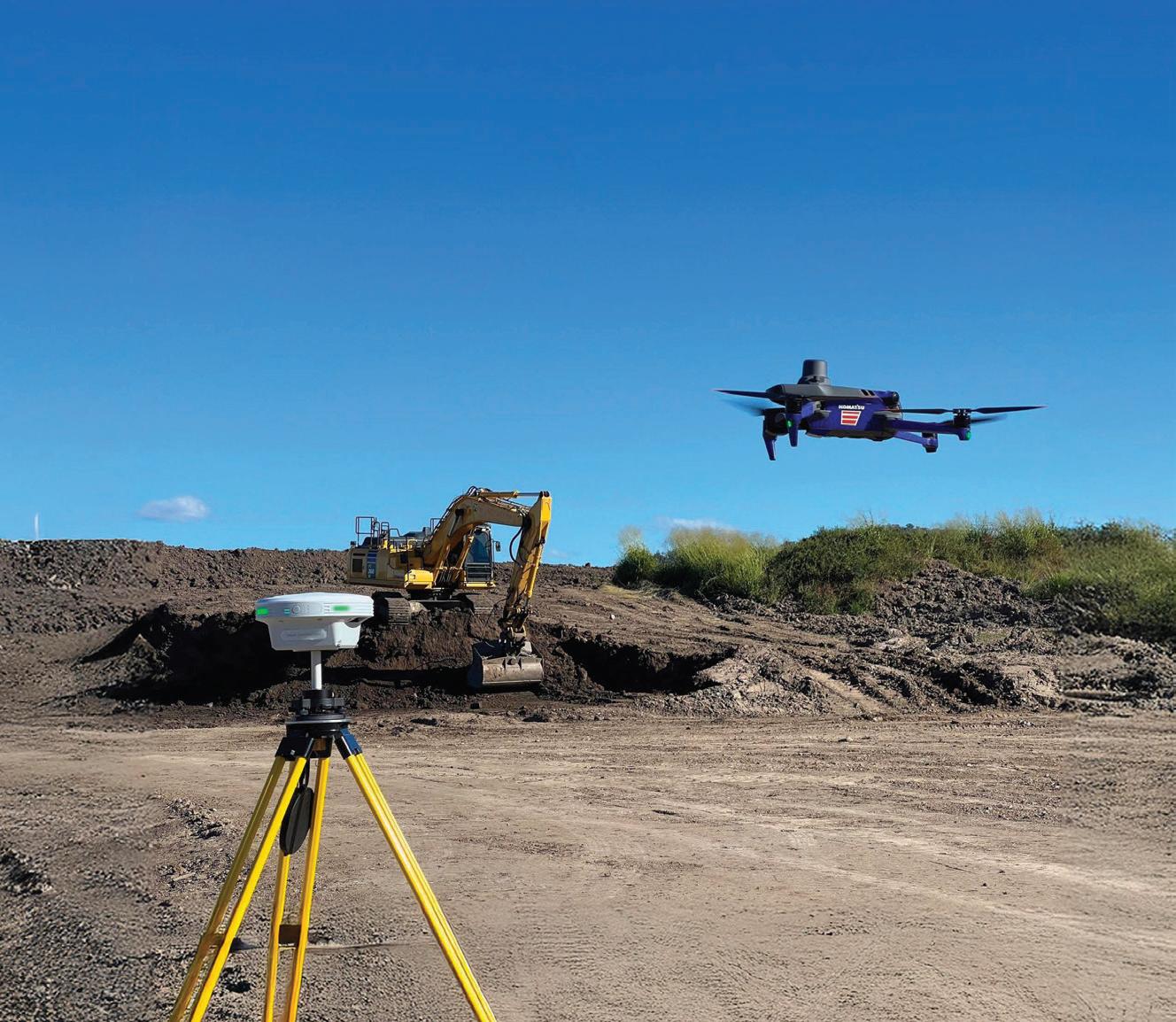
Maximising ROI at every stage of construction
Timelapse cameras and job site analytics offer a practical gateway to digital innovation in construction.
“People
don’t often think of timelapse and pre-construction together, but investing in a solution like Timescapes can yield cost savings in all phases of a project.”
Convincing a project team to invest in new technology on a construction site is no easy task. The stakes are high, time and budgets are limited, and the inherent risks of rolling out something unfamiliar can feel overwhelming. Many project owners and managers hesitate, fearing disruptions, steep learning curves or the potential for wasted funds if the solution doesn’t deliver tangible results. In fact, 55 per cent of construction leaders in Deloitte’s 2025 Engineering and Construction Industry Outlook said their main barrier to leveraging new technologies like artificial intelligence is identifying the right use cases.
Yet, tools like timelapse cameras and job site analytics provide an approachable, impactful entry point to digital innovation. While the investment may seem like a gamble, the results – streamlined efficiency, enhanced communication and reduced disputes –consistently prove their value.
These technologies can provide a measurable return on investment (ROI) at every stage of a construction project, from pre-construction planning to post-completion marketing.
Through real-world examples and proven strategies, Josh King, solutions consulting
director at Timescapes, showcases how industry leaders implement timelapse solutions and deliver results that drive long-term success.
Setting the foundation for success
Before construction begins, timelapse cameras and job site analytics can play a role in site preparation and planning.
At the design stage, architects, engineers and construction teams can use high-resolution images and timelapse footage from previous projects to gain a deeper understanding of how they were executed, allowing them to anticipate challenges, refine their designs and make more informed decisions.
Similarly, estimators and schedulers can identify trends and patterns in historical data to better understand how specific challenges were handled, how long certain phases of the project took to complete, and where efficiencies or delays occurred.
“People don’t often think of timelapse and pre-construction together, but investing in a solution like Timescapes can yield cost savings in all phases of a project. With data from previous projects, project teams can build more accurate budgets and schedules, so

Timescapes’ small form cameras have a rugged custom enclosure to withstand harsh construction environments. The onboard cellular connectivity, internal battery and solar panel remove the need for an external, wired power source. (Images: Timescapes)

there is less need for large contingencies and a lower risk of budget overruns,” says King.
“Improving cost estimation accuracy by just 1 per cent on a $30 million project could save a head contractor more than $200,000.
“Similarly, enhancing schedule estimation accuracy by 1 per cent on a two-year project could prevent up to seven days of delays and over $100,000 in costs. Customers leveraging a robust visual progress monitoring solution like Timescapes across their projects can start realising a measurable ROI before construction even begins.”
Stronger collaboration and fewer risks
Once construction is underway, timelapse cameras and job site analytics transform how teams collaborate and respond to challenges. With real-time visual data, project owners and managers can maintain constant oversight, ensuring timelines are met, resources are optimised, and risks are minimised.
Overseeing site preparation – Real-time oversight of site preparation activities – from clearing and grading to initial logistics and setup – is critical to ensuring a smooth start to any project. Timelapse and job site analytics help head contractors improve planning and coordination, reducing errors and minimising the risk of delays. The detailed visual record they provide offers stakeholders a view of site readiness, supporting seamless progress into the next phases of construction.
Enabling remote site management –The ability of any project team member to continuously monitor site activity remotely is key. This includes project directors overseeing multiple sites from afar as well as on-site team members at large sites who need to understand where to focus their attention on walk-throughs. Timelapse and job site analytics enable this, allowing teams to detect and address inefficiencies early, keeping projects on track and within budget.
Enhancing collaboration and productivity – Timelapse and job site analytics platforms like Timescapes integrate with tools like building information modelling (BIM) and project management software, offering precision in tracking progress and maintaining alignment with project specifications. By sharing key images to project management platforms or overlaying real-time visual data with BIM models, teams can identify discrepancies, optimise resource allocation and keep all stakeholders aligned. This transparency fosters better collaboration among head contractors, subcontractors and owners, reducing misunderstandings and minimising errors or rework.
Improving communications – Effective communication with stakeholders – trade partners, owners, developers and investors –is crucial to the success of any construction project and to the reputation of the head contractor. High-resolution timelapse videos enable stakeholders to visually monitor project
Head contractors can add context to project images and timelapse footage with actionable job site analytics, as well as optimise the efficiency of heavy equipment and quantify the impact of weather and site conditions on project schedules.
“Improving cost estimation accuracy by just 1 per cent on a $30 million project could save a head contractor more than $200,000.”
FOCUS
Construction technology
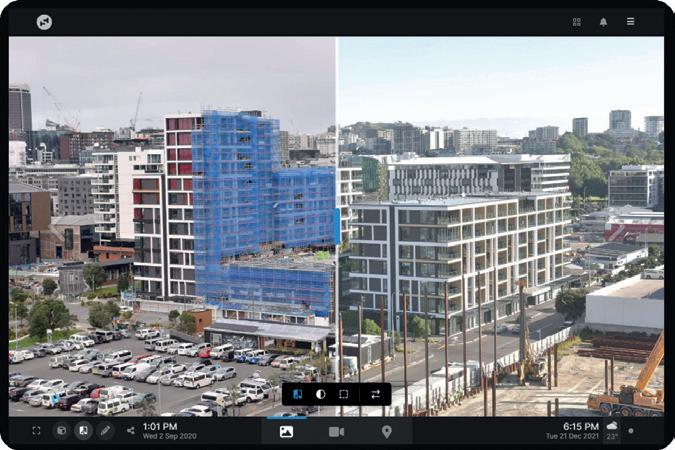
Timescapes provides instant moment‑to‑moment awareness of project status, with the ability to compare progress between timepoints.
Head contractors can compare 3D BIM design models to the current state of the project to identify deviations early and avoid rework.
progress remotely, eliminating the need for frequent on-site visits while fostering trust and confidence in the project’s trajectory.
Ensuring health and safety compliance –
Visual data captured by timelapse and job site analytics platforms helps identify potential safety hazards and enforce health and safety protocols. For instance, project managers can use this data to track compliance, review safety incidents and implement corrective measures promptly. Additionally, leveraging captured images in safety training promotes a culture of zero harm and lowers the likelihood of accidents.
ROI of timelapse and job site analytics –
Timelapse and job site analytics platforms can improve productivity, safety and collaboration.
“Real-time visibility in Timescapes reduces the time project managers and owners spend on site visits and reviewing emails,
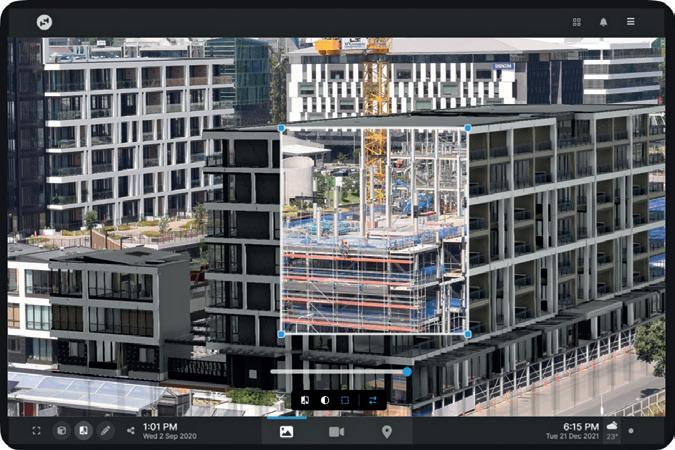
logs and reports, enabling them to focus on higher-value activities,” says King.
By promoting a strong safety culture, a timelapse solution helps minimise the risks of incidents or project shutdowns.
Additionally, its transparency fosters collaboration and dispute resolution, helping to avoid delays and disputes that could add 2 per cent to project costs and extend timelines by over 5 per cent.
Unlocking value beyond the build
Timelapse technology delivers ongoing value, even after project completion, enhancing marketing efforts, improving training programs and safeguarding against liability issues.
“Our customers use our high-resolution timelapses to create compelling marketing content that showcases their work without spending a fortune on production costs.
Traditional video production can cost upwards of $10,000, but with Timescapes, customers can download a high-quality, branded timelapse video at no cost,” says King.
“For those who want a bit more, we offer a professional timelapse production for as low as $1,500 – a major savings.”
These visual success stories help win new business while strengthening trust and transparency with stakeholders.
“Even beyond the build, our customers benefit from having a complete visual record of the construction process,” says King. “It can be invaluable for resolving any disputes or insurance claims that may come up.”
The proactive documentation provided by a timelapse and job site analytics platform can protect against soaring legal and insurance costs, while reinforcing a commitment to quality and compliance.
Driving the future of construction
Timelapse technology and job site analytics provide practical value throughout the construction process, helping to improve project outcomes and deliver ROI.
Visit www.timescapes.co to learn how Timescapes empowers project teams to improve efficiency, enhance collaboration and minimise risk – all while staying on time and within budget.
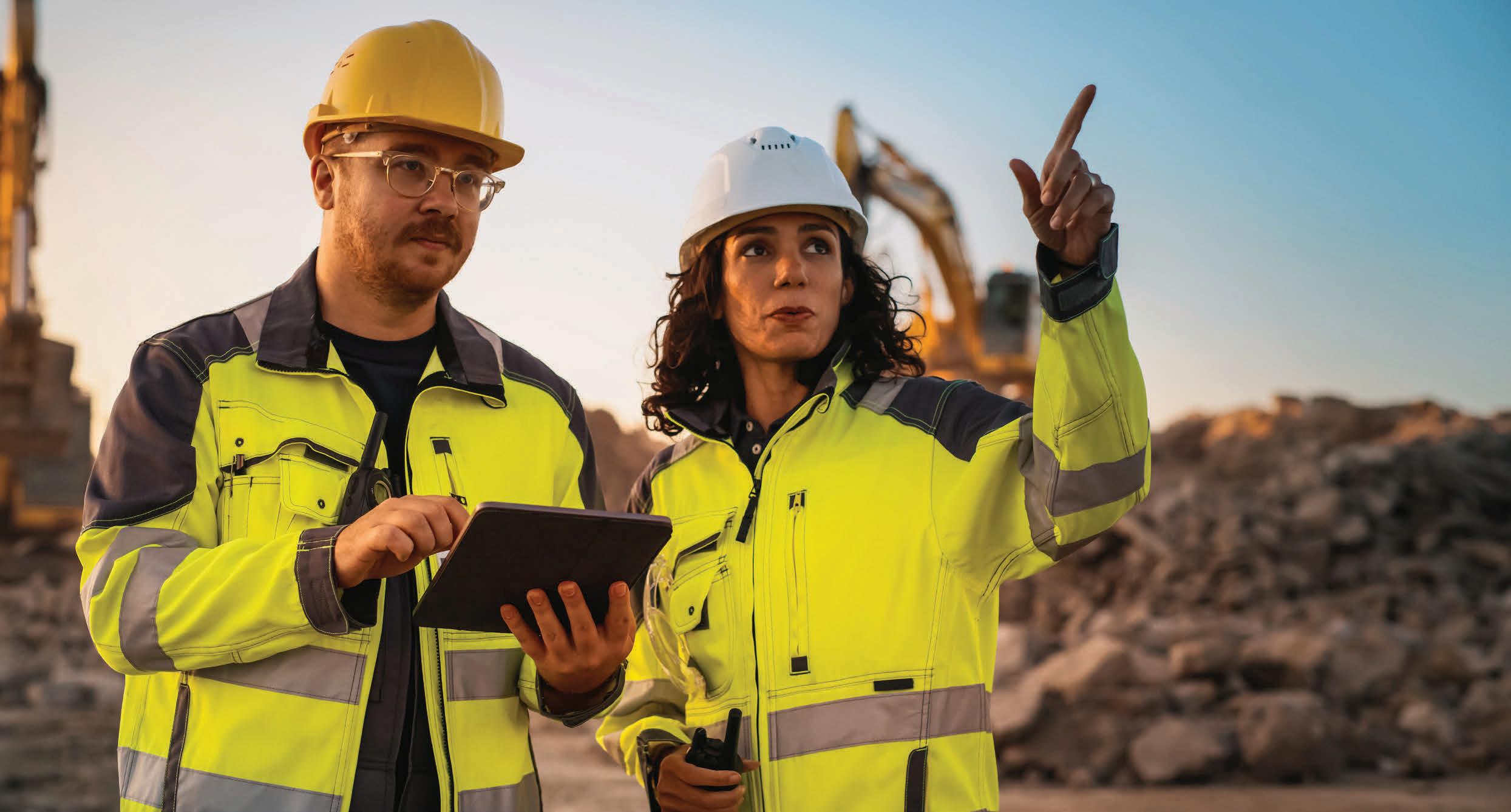
Building Australia’s Future – together.
Over the next 10 years, the Australian Government is investing more than $120 billion in infrastructure development. Will you be a part of it?
LEARN MORE
17–18 SEPTEMBER 2025
Melbourne Convention & Exhibition Centre
Find out how you can take part in Australia’s premiere event for the municipal works, commercial and civil construction industries. convergeexpo.com.au
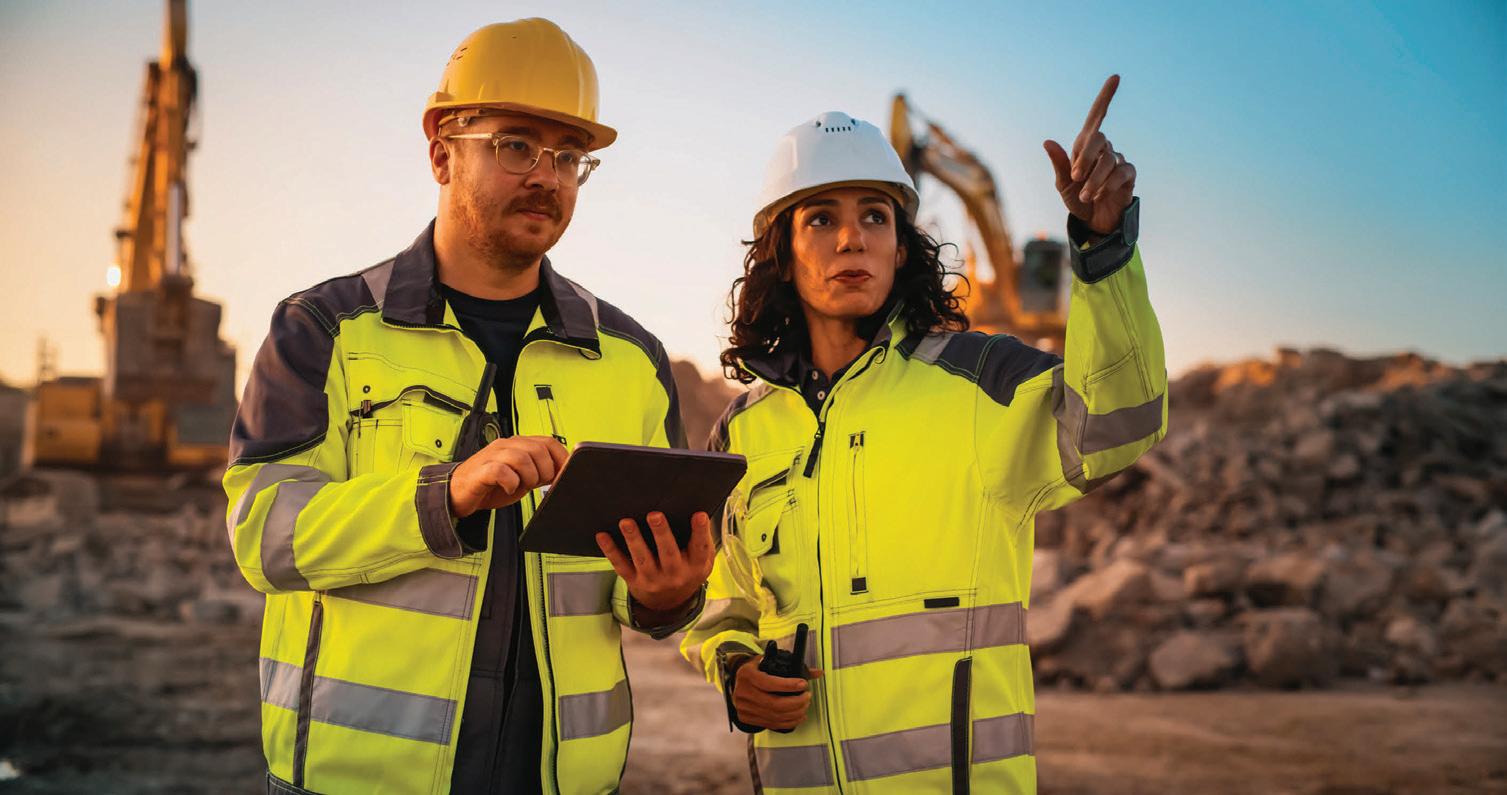



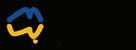

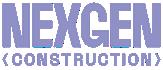
A lifeline for skilled labour
Australia’s construction industry is facing a critical skills shortage, but IMMIGATE is helping businesses access overseas talent to bridge the gap.
A shortage of skilled workers is delaying construction projects and increasing costs across Australia. Traditional recruitment methods – whether local hiring or labour hire – are failing to keep up. But an oftenoverlooked solution is already available: employer-sponsored work visas.
The construction skills shortage is driven by several factors. Intense competition within the industry makes it difficult for construction and engineering firms to attract and retain talent. Inadequate investment in training programs and apprenticeships has left too few new workers entering the industry to replace those retiring. Additionally, businesses often struggle to access skilled workers from overseas due to a lack of guidance and support in navigating migration pathways.
IMMIGATE, a specialist immigration agency, is helping construction businesses cut through red tape and secure the workforce they need to sustain and grow their operations.
Expanding access to skilled workers
On 7 December 2024, the Department of Home Affairs (DOHA) introduced updates to its employer-sponsored visa program, now known as the 482 Skills in Demand (SID) Visa.
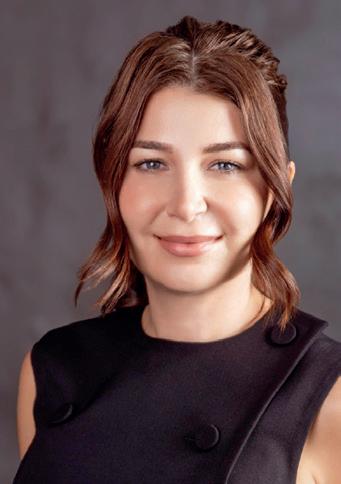
These changes make it easier for businesses to tap into global talent.
Diana Faraj, principal migration agent at IMMIGATE, says the revised program brings welcome improvements.
“DOHA has introduced a consolidated list of eligible occupations known as the Core Skills Occupation List (CSOL), which includes a wide range of construction and engineering professions and introduces new roles such as building associates, trade technicians, other draftspersons, bricklayers and others,” says Faraj.
“The SID Visa also simplifies the application process for both migrants and employers, particularly for those nominated for highsalary roles (above $135,000) through the Specialist Skills Stream.
“The work experience requirement for nominated workers has been decreased from two years to one year, marking a positive change, particularly for recent graduates.
“Additionally, the SID Visa offers a straightforward pathway for sponsored workers to obtain permanent residency, presenting an appealing opportunity for overseas workers to work in Australia.”
The introduction of the new legislative changes marks a milestone in Australia’s

The Company-Specific Labour Agreement allows businesses to negotiate tailored agreements with the Australian Government. (Image: khwanchai/stock.adobe.com)
The Department of Home Affairs has introduced updates to its employersponsored visa program, now known as the 482 Skills in Demand Visa.
(Image: krumanop/stock.adobe.com)

skilled immigration policy. It expands immigration pathways to include more construction and engineering occupations, while also providing a more flexible and efficient route for employer-sponsored visas.
“For the industry, this is an opportune moment to leverage the benefits of these policy changes and start considering accessing overseas talent,” says Faraj.
For businesses needing immediate access to skilled specialists, the 400 Temporary Work (Short Stay Specialist) Visa offers an alternative. Designed for urgent short-term contracts or projects, it allows companies to bring in overseas workers for up to six months – without an English test or the usual sponsorship obligations.
“Once onshore, employers have the option to decide whether to extend a worker’s stay through the 482 SID Visa program,” says Faraj. “The average processing time for this visa is around four weeks, and its costs are generally lower than those of other sponsored visa programs.”
Beyond these visa programs, many construction companies overlook an important alternative: the Labour Agreement migration program, namely the CompanySpecific Labour Agreement. This initiative allows businesses to negotiate tailored agreements with the Australian Government to address workforce shortages in specific roles that may not be covered under standard visa sponsorships.
“Despite its potential benefits, only around 40 Australian construction companies have access to such agreements,” says Faraj.
“By securing a Labour Agreement, businesses can fill critical skill gaps with overseas talent when local hiring proves challenging. It also provides greater
flexibility in employment conditions and broadens recruitment options.”
For construction firms facing workforce shortages, the program represents a strategic solution.
“While many migration agencies can outline available sponsorships, few truly understand the key prerequisites of these agreements. Even fewer have our level of experience in successfully negotiating and administering them,” says Faraj.
Guidance through the process
With 18 years of experience in employersponsored migration, IMMIGATE has helped construction businesses of all sizes navigate Australia’s complex visa system. Faraj, who founded the agency in 2008, is committed to making the process as simple and transparent as possible.
“ IMMIGATE offers a personalised service that allows clients to engage in a non-traditional approach to client relationships,” says Faraj.
“Our focus is on building meaningful connections and understanding the unique needs of each client, rather than adhering to standard practices.
“We enjoy simplifying the immigration process for our clients, providing them with clear and easy-to-understand information instead of overwhelming them with complex legal jargon.”
As workforce shortages persist, employersponsored migration is a practical solution – and IMMIGATE is helping businesses make it happen.
To learn more about how IMMIGATE can assist with navigating the immigration process, visit immigate.com.au
“While many migration agencies can outline available sponsorships, few truly understand the key prerequisites of these agreements.”
“IMMIGATE offers a personalised service that allows clients to engage in a non-traditional approach to client relationships.”
Converge 2025
An opportunity to ‘converge’
Uniting civil construction, Civil Contractors Federation Victoria drives the conversation at Converge 2025.
“You can’t have homes, energy and utilities without the enabling infrastructure that helps bring it all online.”
Sustainable civil infrastructure, such as roads and bridges, connects communities and provides the foundations for cities, towns and suburbs.
(Image: KRUTOPIMAGES/ stock.adobe.com)
Since 1943, Civil Contractors Federation
Victoria (CCF Victoria) has laid the groundwork for Victoria’s civil construction sector, ensuring every foundational effort is recognised. Now, stepping into the spotlight as an Association Partner at Converge 2025, the organisation is ready to cement civil construction’s role in shaping Australia’s future.
Converge, a premier municipal works, civil and commercial construction event, has found a natural ally in CCF Victoria. Both rally around the mission of strengthening the industry –building connections, facilitating knowledge sharing and influencing the policy landscape.
“For some time now, Australia’s civil construction industry has been mostly overlooked in public policy debates and developments around topics including housing and the renewable energy transition,” says CCF Victoria CEO Lisa Kinross.
Kinross points to housing development as a prime example of civil construction’s often unrecognised impact.
“You cannot have housing without the enabling infrastructure that needs to go in first: this includes subdividing and clearing lots, constructing essential road networks for
residential and connecting infrastructure and ensuring vital utilities such as water, electricity and sewage are in place,” she says.
For CCF Victoria, Converge 2025 represents a chance to change the narrative.
“It looked like an exciting new opportunity for us to reset the ledger and get civil firmly front and centre in the minds of policymakers and other decisionmakers, among other key stakeholder audiences,” she adds.
As the peak body for Victoria’s civil contractors, CCF Victoria represents 460 member businesses and employs 45,000 professionals who deliver close to $22 billion in public and private infrastructure each year. Alongside strong advocacy, the organisation paves the way in skills development through specialised training and apprenticeships, equipping the workforce for Victoria’s evolving infrastructure needs.
This mission aligns with Converge 2025’s agenda – gathering industry leaders to tackle pressing challenges. With infrastructure budgets under tight strain, Kinross views the event as a timely stage to champion industry-led solutions.
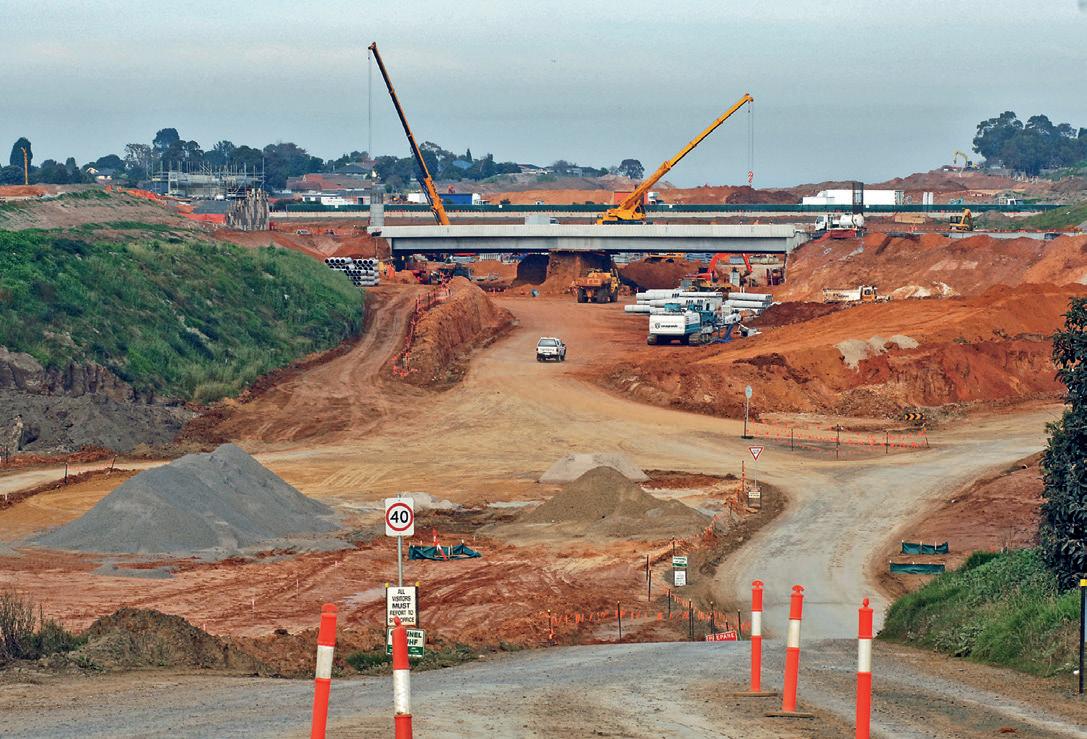
“Converge 2025 can be a catalyst for positive change, enabling our industry to influence policy settings that support governments at all three levels to achieve their infrastructure objectives,” she says.
CCF Victoria’s participation at Converge is part of a broader effort to amplify civil construction’s voice.
“The work our highly skilled contractor members do is all around creating safe and connected communities by building sustainable civil infrastructure for current and future generations,” says Kinross.
“By actively and collaboratively engaging with government and industry partners on major projects and ongoing infrastructure maintenance, we can achieve common goals of building vibrant, liveable cities, suburbs and communities in all parts of the state.”
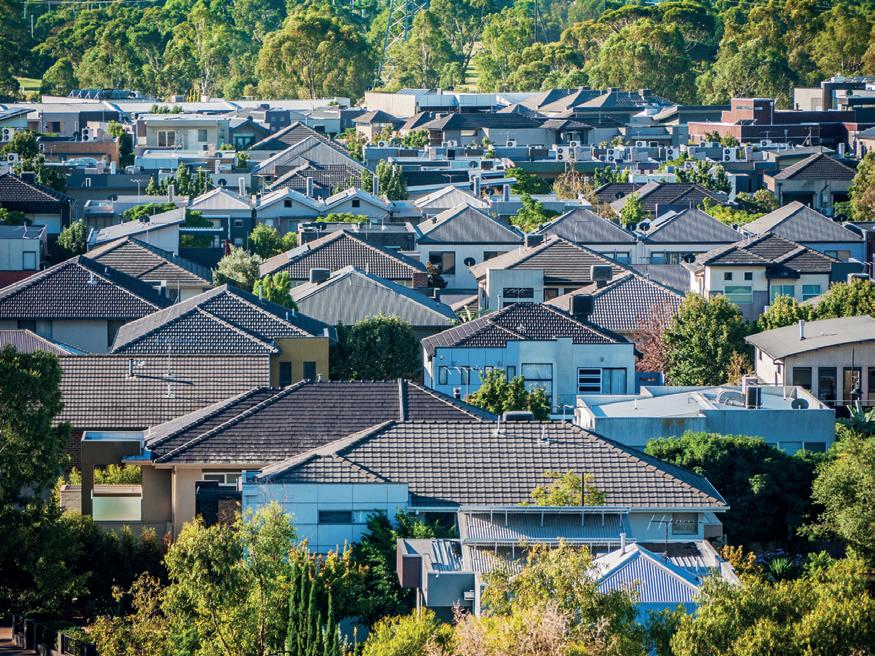
At Converge 2025, CCF Victoria aims to raise awareness among decision-makers –particularly in government – about the pivotal role of civil contractors, and to unify the industry’s voice.
“CCF Victoria is pleased to be reactivating the Victorian Civil Construction Industry Alliance (VCCIA), an initiative we founded 20 years ago to strengthen the sector through a diverse group of niche interest groups, member associations and peak bodies,” says Kinross.
“We are equally pleased to see several alliance members – AustStab, Municipal Works Australia and Australian Flexible Pavement Association – also supporting Converge 2025 as Association Partners.”
While indispensable, the civil construction industry faces mounting pressures. As Kinross explains, “Despite many reasons to be excited and hopeful for the future of civil construction, our industry continues to face significant headwinds, particularly in Victoria, with a contracting state budget that forecasts reduced spending on infrastructure, in a bid to rein in soaring public debt. Add to that ongoing issues around workforce shortages, continuing cuts to skills training and apprenticeships funding delivered by independent RTOs, complex IR issues, and a volatile and polarising political and policy climate, it’s possible to appreciate the work we still have to do.”
At Converge 2025, CCF Victoria’s message is clear: construction priorities cannot be
planned and delivered in isolation. “The government needs to understand it is falling increasingly short of its current targets for homes and will ultimately fail in this endeavour unless it prioritises civil construction and the enabling infrastructure that contractors deliver,” says Kinross.
“For any contractor, large or small, and every project engineer or LGA procurement professional with a stake in construction infrastructure, this is our opportunity to ‘converge’, to unite and demonstrate how our industry can deliver national priorities such as housing and energy.
“You can’t have homes, energy and utilities without the enabling infrastructure that helps bring it all online.”
Key themes at Converge 2025 will include the role of enabling infrastructure in government policy, avenues for civil contractors to adjust to shifting national priorities, the value of industry alliances in linking civil and vertical construction, and strategies for achieving sustainable infrastructure delivery while keeping public debt in check. The future landscape of Victoria’s civil construction sector will also be a central topic of discussion.
With the civil construction industry at a crossroads, CCF Victoria is ready to make its voice heard – championing the sector’s role in building the future – at Converge 2025.
To learn more about how you can get involved in Converge 2025, visit convergeexpo.com.au
“The government needs to understand it is falling increasingly short of its current targets for homes and will ultimately fail in this endeavour unless it prioritises civil construction and the enabling infrastructure that contractors deliver.”
Jagoda Grigorean: From law to landmark projects
From a law classroom to leading commercial teams on global infrastructure builds, Jagoda Grigorean’s career defies convention.
“I have always worked with great people, and that is one of the best aspects of construction –onsite, there is a strong sense of camaraderie.”
While at law school, Jagoda Grigorean developed a keen interest in the complexities of the commercial law framework, which ultimately led her to explore opportunities in the construction industry. Drawn to the high stakes of major infrastructure projects, she traded legal briefs for contract negotiations and tunnel-boring machines (TBMs). Her career, spanning continents, has been shaped by adaptability, ambition and the ability to thrive in unfamiliar territory.
While her legal background was the starting point, an opportunity at Linklaters, an international law firm, ignited her interest in construction law, setting her on a new professional path.
“I found the work fascinating and wanted to gain more experience,” says Grigorean.
Interested in understanding more about work on large-scale infrastructure, she pursued opportunities in Qatar, where major projects were taking shape and an infrastructure construction boom was occurring. She explored opportunities at Al Faisal Holding and then Gas Exporting Countries Forum (GECF). From there, she moved into infrastructure construction, joining QDVC (a VINCI Construction Grands Projets subsidiary in Qatar), a major player in global infrastructure.
Starting as a junior member within the legal support function at the company, which provided support to projects being delivered by QDVC at the time, such as Doha Metro, Lusail Underground Car Parks Project, New Orbital Highway Project II and Lusail Light Railway Transit Systems, she quickly found herself involved in contract management – visiting sites and assisting her senior team members with contractual support to the site teams.
“I assisted with contractual tender reviews and analysis, the development of commercial toolkits for the site teams, and helped project operations with ad hoc designated tasks – including letters, contract reviews and claims,” she says. “Through these experiences, I developed a greater interest in contract management than in the legal support function.”
Her career took a new direction when her manager supported her in exploring contract management. She then undertook
various specialised training to transition into her desired role.
Her next move kept her in Qatar but expanded her expertise. A former colleague at QDVC recommended her for a role on the Inner Doha Re-sewerage Implementation Strategy – Northern Package (IDRIS MTS01) and Inner Doha Re-sewerage Implementation Strategy – Southern Package (IDRIS MTS03), a tunnelling initiative for sewer systems using TBMs, being delivered by Bouygues.
“Eventually, I was responsible for procurement, upstream and downstream contract management, across two packages, MTS01 and MTS03,” she says.
“My time at IDRIS (MTS01 & MTS03) with Bouygues TP was the turning point in my career. The exposure and responsibility I gained, along with the involvement in complex commercial matters – some of which may happen only once in a lifetime for a contract manager – were invaluable.”
This role led to a recommendation for a position in Australia on the Metro Tunnel Project in Melbourne as part of the Cross Yara Partnership D&C Joint Venture (CYP), where she relocated in 2019. Initially assisting the legal and commercial teams with some commercial matters at play, she soon took on the role of commercial manager – upstream. In this role, she also supported the design team at the encouragement of her manager. Her experience with the design team was valuable because it provided more perspective on other issues key to an infrastructure project and helped create a broader understanding she now uses when considering project commercial matters.
As the project neared completion, she sought a new challenge and joined the Spark North East Link Project with the joint venture Spark D&C (Spark), which is delivering the central package, in 2023. She took on the role of commercial manager, employed by GS Engineering and Construction, and was promoted in 2024 to senior commercial manager, overseeing the successful delivery of critical components of the project. Her role involves overseeing the commercial governance function across the project and managing commercial activities for site operations at multiple key sites, including Bulleen, Manningham, Surface Works,
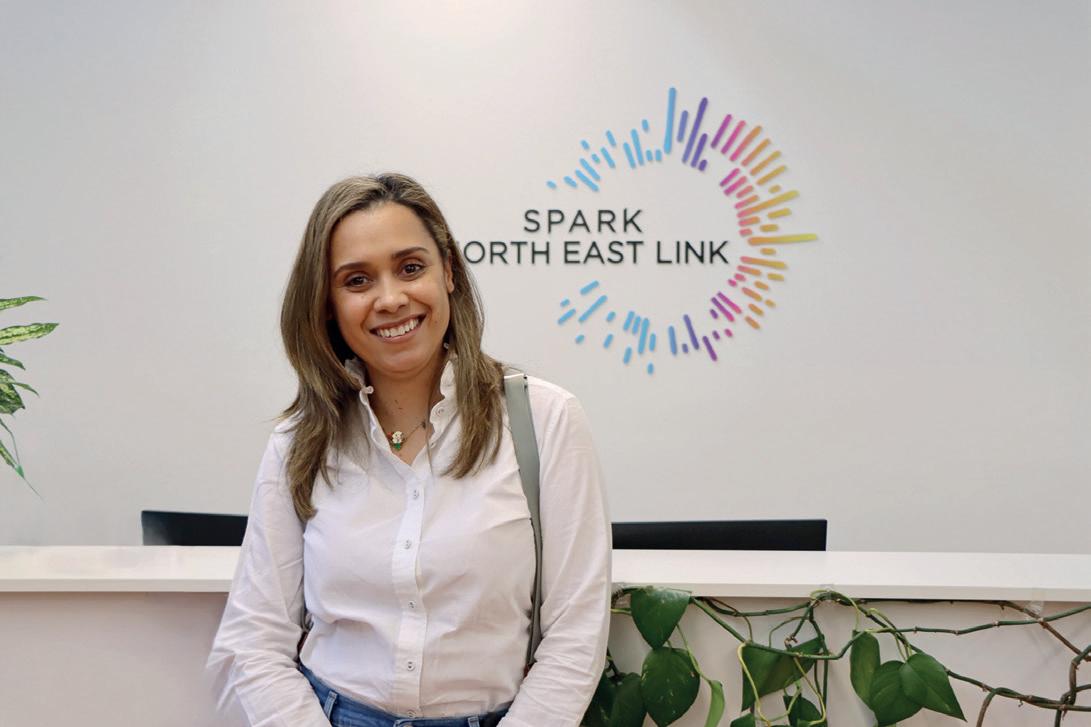
Tunnelling, and Benalla Precast Factory.
In her current project, Grigorean has led the procurement and commercial activities essential for the successful execution of key milestones. These include diaphragm wall operations at Bulleen and Manningham, temporary road diversions, the delivery of TBMs via super loads, and the assembly and timely launch of the TBMs.
“I have been very fortunate at Spark. The culture is great, and given the scale of the project, there are vast opportunities to learn and grow,” says Grigorean. “The strong support and encouragement from our leaders are huge motivators.”
Grigorean credits her success to managers and mentors who challenged her, supported her growth and placed their trust in her. Even in regions where women on construction sites were rare, she found teams that valued her contributions.
“I have always worked with great people, and that is one of the best aspects of construction – onsite, there is a strong sense of camaraderie. Everyone looks out for each other, ensuring both safety and success,” she says.
Grigorean thrives in commercial management because of its dynamic nature and the camaraderie she experiences onsite. She moves between sites, working both on paper and in the field, ensuring that every decision is grounded in practical understanding. “If there is a commercial issue I prefer to visit the site, discuss it with
the construction team, see the works in question, and gain real insights,” she says. “My work has also taken me to different countries, exposed me to diverse cultures, and allowed me to collaborate with people from various backgrounds.”
Her role on the North East Link project involves overseeing procurement and contracts administration, ensuring financial management aligns with project needs. She focuses on clear communication between stakeholders, believing that alignment between delivery, commercial, finance, subcontractors and client leads to risk mitigation and successful project delivery. By being present onsite and approachable, Grigorean has built strong relationships with all stakeholders, ensuring their concerns are heard and addressed.
“At the end of the day, I oversee commercial matters, but I cannot do my job without the construction team’s input,” she says. “We work together, complementing each other’s skills to deliver the final product.”
With every project, Grigorean sharpens her expertise and expands her influence. One day, she aims to take on the role of commercial director on a mega infrastructure project and then within a Tier 1 construction company, shaping both the strategy and execution at the highest level to allow the commercial teams to hit the ground running.
“That is a goal I would truly love to achieve,” she says, and given her track record, it seems inevitable.
“My work has also taken me to different countries, exposed me to diverse cultures, and allowed me to collaborate with people from various backgrounds.”
Jordyn Allan: Wiring a bright future
A chance conversation in a fast-food dining room led Jordyn Allan from restaurant management to electrical work on a major Sydney tunnelling project.

Raised in a family with roots in the building trades, Jordyn Allan’s interest in hands‑on work developed early. With her mother constructing homes during pregnancy and her grandfather and uncle operating a construction business, practical skills and craftsmanship were always part of her environment.
“There is a real sense of satisfaction in stepping back and thinking, ‘I did that’.”
Although Allan once considered careers in teaching and childcare, her aptitude for practical work became evident when, in her mid teens, she began repairing her own car and undertaking household projects. These early experiences steered her toward a career that aligned with her longstanding familiarity with construction.
Initially joining the family business, and later embarking on a carpentry apprenticeship with another firm, Allan faced financial challenges that required her to reassess her career path.
“I was renting my own place, and my sister was living with me. I wasn’t earning enough to cover rent and support both of us, so I started working at McDonald’s to help financially, where I eventually advanced into management,” says Allan.
Then, a chance conversation in the restaurant dining room opened a new door. A customer mentioned that the Gamuda Laing O’Rourke Consortium (GLC) was hiring through a pre employment program specifically for women. Intrigued by the opportunity, Allan applied, and within weeks, she relocated from Goulburn to Sydney to join GLC on the Sydney Metro West – Western Tunnelling Package.
As one of 15 participants in Sydney Metro’s pre employment all female program, delivered by GLC in partnership with Empowered Women in Trades and the Health & Safety Advisory Service, Allan engaged in a two week training designed to build foundational knowledge in civil construction at the Tunnelling & Infrastructure Academy.
“I built so many connections with people I never expected to,” she says. “I arrived on this big site, and everyone was friendly, open and willing to have a conversation.”
While many of her peers pursued a Certificate III in Civil Construction following the program, Allan opted to advance her career with a Certificate III in Electrotechnology.
“Now that I’m working towards my Cert III
Apprenticeship, it’s incredible to understand how everything works and see it in action,” she says. “Being able to say that I installed or worked on something and then watch it come to life has been rewarding.”
On the Sydney Metro West – Western Tunnelling Package, Allan has gained experience in the delivery of major tunnelling works. Working on a rotating shift schedule – two weeks of 12 hour day shifts followed by two weeks of night shifts – she addresses electrical breakdowns in machinery, lighting systems and power networks, in addition to managing surface level electrical installations and troubleshooting issues.
“I love that it is both mentally and physically challenging because I am constantly thinking about what I am doing, putting it all into place, and then testing and verifying my work to ensure it is done correctly,” says Allan. “There is a real sense of satisfaction in stepping back and thinking, ‘I did that’.”
Allan credits both the collaborative environments at GLC and that onsite for her professional growth.
“Although my team members have been working in construction for longer, they have welcomed me in,” she says. “We joke around and communicate like good friends, which makes the experience even better.”
In just one and a half years with GLC, Allan has celebrated several milestones –including completing her first year at TAFE and receiving the National Association of Women in Construction’s Transport for NSW Tradesperson Scholarship in 2024.
“Seeing my own progress and gaining confidence in my expertise has been rewarding,” she says. “Mentoring a work experience student recently was an unexpected responsibility that underscored my development on the job.”
Despite initial apprehensions about entering a traditionally male dominated industry, Allan has found that a focus on delivering quality work is key.
“Rather than feeling the need to prove myself, I concentrate on consistently doing my best. At the end of the day, you want to be able to step back and know you gave it everything you could,” she says. “That mindset really helped me. Rather than thinking that I have to prove myself because I am not
as strong as someone else, I shifted my focus to just doing the work.”
From Sydney Metro’s pre employment program to ongoing support from GLC’s workforce development team and her apprenticeship, Allan’s career has given her stability, boosted her confidence and eased financial pressures.
“The support from everyone has been incredible – it feels like I have my own little family here in Sydney. The support from the team has been there every step of the way,” she says. “They did not just train us for two weeks and then leave us to figure things out on our own. They have consistently checked in and made sure we are doing okay.”
As she refines her technical expertise and takes on greater responsibility, Allan is determined to complete her apprenticeship and establish herself in the industry. She envisions building a strong reputation and progressing into leadership roles while continuing to explore different opportunities.
“I would also like to try fly i n, fly out work at some point, just to gain that experience and say I have done it,” says Allan. “Overall, I want to experience different areas of the industry and give everything a go.”
It is rare for a construction career to begin in a fast food dining room, but for Allan, that unexpected encounter proved to be the turning point that led her back to her true passion. Through the Women Who Work in Tunnelling Pre Employment Program, she has steadily progressed, setting her sights on a future as an industry leader.
“Seeing my own progress and gaining confidence in my expertise has been rewarding.”

Smart leadership: Connecting to a strong support system
Leadership isn’t a solo pursuit; it thrives in collaboration, with mentors, sponsors, coaches and allies playing key roles in driving success.
“You need to be challenged. You need people with different ideas, with different thought processes.”

In last month’s edition of Inside Construction, I shared my viewpoint that leadership starts with you and is grounded in your personal values and purpose in life. This edition’s feature theme of “Smart Buildings: Innovations for a connected and efficient tomorrow” reminded me of the next important step in leadership – how smart you are in connecting with what I call ‘Team Gretchen,’ your support network of brilliant people that enable your success. People are surprised to learn that I have four mentors, a coach and sponsors at this stage of my career. I am not done learning, and I certainly continue to benefit from support.
Anna Meares, Australian short-track Olympian and Chef de Mission of the Australian Olympic Team, and Greatness Podcast host Dr Gretchen Gagel, 2020: “I can’t do it on my own. Even though I’m an individual athlete, it takes a great team of people who are all experts in their field. They dedicate their life to being an expert in areas such as nutrition, strength and conditioning, mechanics, biomechanics, science, sports science, statisticians, coaches, tacticians, skill acquisition specialists, media, analysis, management, administration staff. I can’t be an expert in each of these fields and who fills each role is critical to not just the team’s success but the outcome for me as an athlete. Each person is like a spoke, and you need spokes that pull from opposite sides of the hub to make that wheel function at its best capacity. You need to be challenged. You need people with different ideas, with different thought processes.”
My book, Building Women Leaders: A Blueprint for Women Thriving in Construction, devotes a great deal of time to what this support network looks like and how to build it for both women and men. Here are what I believe to be the key elements of having a world-class support network:
1. Mentors – Mentors can be either formal –someone you are working with on a regular basis over time – or informal – someone you go to as needed for advice. These people share their wisdom and emotional support, and there is no correct number of mentors. Finding them entails asking yourself, “What advice would be most helpful to me – in
either my business career or my personal life?” These people ask great questions that prompt reflection and revelation. At times, they provide specific expertise that cause you to grow as a leader.
As Maddie Gosser, human resource OpX program manager for Baker Construction, shares, “Mentors have been a huge part of my entire career; a sounding board. They are there when I don’t have the lived experience, and they help me navigate the challenges. They are cheerleaders. If I mess up, I can ask, ‘How do I fix this?’ They are my own board of directors.”
2. Sponsors – Sponsors differ from mentors in that they are typically from within your organisation and advocate on your behalf to help you achieve your career aspirations. I say “typically” because my sponsors today are advocating for me as a board member and are therefore outside of my organisation. Sponsors offer you advice on how to navigate the political landscape of your organisation and what skills and exposure you may need to gain to take that next important career step. When selecting a sponsor, think of someone one, two or maybe three or four levels above you who has the emotional capacity and political clout to assist you. You might approach them by saying something like, “I am happy at XYZ company, and envision myself five years from now in XYZ role. I think you are someone who might be able to help me understand how to achieve that goal. Would it be possible for us to meet occasionally to discuss how I might develop into this role?”
3. Coaches – Coaches are similar to mentors, except they are paid for their advice and often follow a structured approach. The critical aspect of successful coaching arrangements is that the person being coached understands what they want out of the coaching relationship, and that the coach is someone they trust and admire for the advice they can provide. One of the greatest gifts of my life was my formal coaching relationship with the noted author and academic Edgar Schein before his passing.
David Goldsmith, co-founder of the International Coaching Federation, and
Mentors can be formal, working with you regularly, or informal, offering advice as needed. (Image: Dragana Gordic/stock. adobe.com)

Greatness Podcast host Dr Gretchen Gagel, 2023: “Who is going to coach you fearlessly and be able to say, ‘Hey, Gretchen, I think your idea here isn’t going to work,’ or ‘You said you were going to do this for the last three sessions, and you haven’t done it.’ An internal person may not feel they have the safety to be able to have that conversation. I think the outside person also brings a range of perspectives from all the people they’re working with, as they’re often working with a variety of leaders from a variety of organisations.”
4. Allies – I believe that allyship is often overlooked but is incredibly important. I did not achieve what I did in the construction industry without allies, most of them male, as there were few women peers early in my career. Allyship means speaking up for someone when you see them being marginalised, cheering for someone and giving them encouragement. Early in my career at FMI in the US, contractors would, at times, ask that a woman not be sent to work with them on their strategic plan or project execution strategies. My boss Lou’s response? “You will need to go find another consulting firm because Gretchen is an important member of our team.” That is allyship.
Great leaders understand that leadership is not a solo sport. Great leaders engage in meaningful, trusting relationships with a variety of people who support their efforts and experience their gratitude for that support. I encourage each of you to set aside time to think about your “team” of supporters and the categories above that would benefit from additional effort on your part. Not only are these relationships helpful, but they can also be deeply meaningful and fun.
Dr Gretchen Gagel, GAICD, is the former chair of Brinkman Construction (US) and a member of the Risk Committee for GHD Engineering, the National Academy of Construction (US), the Construction Industry Culture Taskforce (AUS), and the Associated General Contractor (AGC) of America National Diversity and Inclusion Committee. Gretchen is passionate about leading change in the construction industry and developing our future leaders. You can hear more from Gretchen on her Spotify podcast, Greatness and her book, Building Women Leaders: A Blueprint for Women Thriving in Construction, is available for pre-order on Amazon. Find out more at gretchengagel.com
“Great leaders understand that leadership is not a solo sport.”
National Precast Concrete Association Australia
Uccello rising
The Pagewood Centro Uccello project represents a landmark precast concrete development within the Pagewood Centro master-planned community, the first of its kind in Australia.
Master Precaster
Advanced Precast
Precast staining ECOTONE
Developer and builder Meriton Group
Architect Woods Bagot

The ambitious Pagewood Centro Uccello project features two iconic towers, each rising 20 levels and standing as the tallest structures in Pagewood and Eastgardens. Bookended by parks, the precast towers overlook a new retail precinct, which will serve as the ‘town centre’, offering a mix of specialty stores, a supermarket and an openair laneway filled with restaurants and outdoor dining. Designed by award-winning architect Woods Bagot, it will be a residential oasis that integrates with its surroundings, including golf courses, beaches and universities.
Precast elements and design features National Precast Master Precaster Advanced Precast supplied an array of precast elements for the project, including walls, columns, hobs and cores, all of which enhanced the

while delivering a high-quality aesthetic. Among the features of the precast elements are 562 wall panels and 605 spandrel panels, which have been directly connected to the structural slab for stability and durability, both during construction and throughout the building’s life.
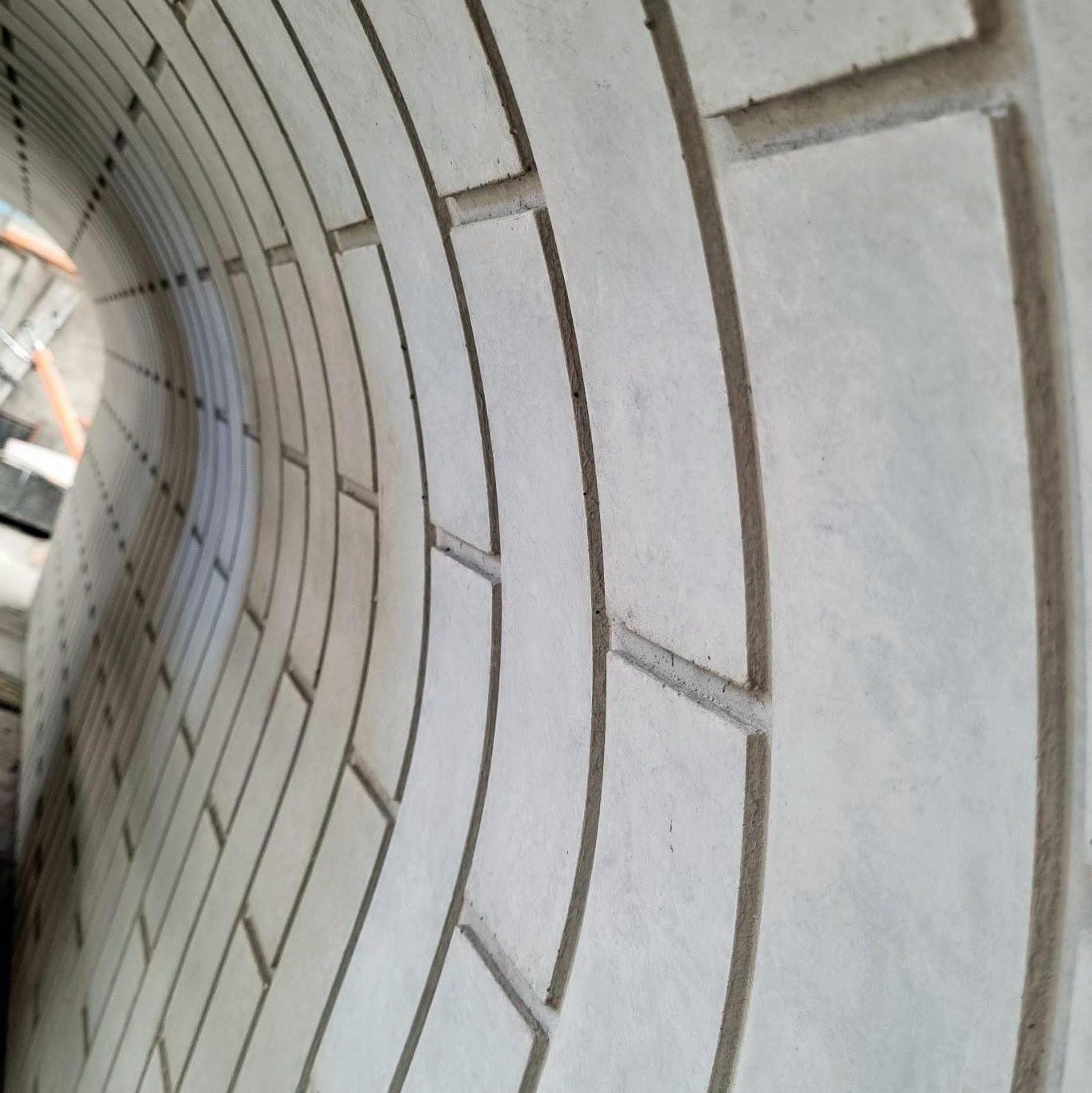
shapes with special rebates. The blend of bold, gold lines and dark window finishes adds a contemporary flair to the overall architectural vision.
The company first applied a colourfast and durable aqueous mineral silicate emulsion stain to the formliner-moulded grey concrete (which preserves natural surfaces while providing the desired colour), followed by another equally durable aqueous emulsion stain in a specified pale finish. To protect against water ingress and enhance durability, a high-performance, high-solids barrier sealer was applied.
Efficient construction and time savings
Utilising precast methodology for the project’s brick-patterned panels facilitated easy installation, quick construction, reduced labour costs and mitigated site disruptions –an improved outcome compared to traditional brick construction.
landscape, fostering a vibrant community atmosphere while promoting sustainable urban living. With its strategic location adjacent to Westfield Eastgardens and in proximity to transport routes, Uccello will become a central hub for residents and visitors alike.
The project is a testament to innovative architectural design and the effective use of precast technology. Streamlining construction processes to speed timelines and enhance site safety has saved costs and delivered a durable and low-maintenance result, paving the way and setting a benchmark for future developments within the master-planned community.
As the precast towers rise above Eastgardens, they signify a new era of residential living, embodying the spirit of modern urban development, while enhancing the local community’s quality of life.
“Designed by award-winning architect Woods Bagot, it will be a residential oasis that integrates with its surroundings, including golf courses, beaches and universities.”
ASSOCIATIONS
The National Association of Women in Construction
Redefining industry success
The National Association of Women in Construction is working to create a more equitable industry by fostering cultural change.
“We simply cannot deliver the pipeline of construction projects in housing, infrastructure and energy without people –lots of them.”
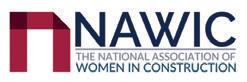
By Cathryn Greville, CEO
of the National Association of Women in Construction.
We are on the cusp of a cultural shift in Australian construction, one that sees workplaces accommodate the respective needs of all workers, regardless of their background.
We’re moving toward a future where businesses and the community capitalise on the myriad benefits that equitable and inclusive environments bring, such as improved financial returns, greater innovation, a positive reputation, achievement of work health and safety imperatives, better compliance and ways of working, reduced workforce shortages and lower risk.
This change is long overdue. While great inroads have been made by dedicated and forward-thinking leaders and organisations across the many market segments impacted by construction work, the uptake hasn’t been widespread enough. Many organisations lack maturity in diagnosing issues in their own backyard and need assistance in designing and implementing appropriate fixes.
These are issues ripe for the picking, and we can shift the dial by focusing on culture – by which I mean the behaviours and attitudes that are accepted, justified and promoted in and around construction sites and the various services and activities that support them.
Unlocking potential through people Any culture change comes back to people. And people are at the heart of what makes construction tick.
We simply cannot deliver the pipeline of construction projects in housing, infrastructure and energy without people – lots of them. At no other time has it been more critical to attract, retain and advance our people than during this period of massive skills and talent shortages.
The industry needs more than 400,000 new workers over the next five years. Yet, a staggering 110,000 workers leave each year through attrition. The full talent pool remains largely untapped, with women making up only 12.4 per cent of the workforce and just 3.4 per cent of trades roles. Meanwhile, the industry is struggling to attract enough young people to build the talent pipeline and offset the reality that
a quarter of the workforce is over 55, with many nearing retirement.
We know that increasingly, workers are viewing workplaces and prospective workplaces with a cultural lens. Young people want to work for organisations serious about equity. Across the board, people stay in positive environments that meet their needs.
Too many women face microaggressions – the small acts that make people feel less welcome, less valued, or less safe – and this is having a macro impact on businesses and the sector. On its own, a single act may seem little. But when we add up all the microaggressions women face over time, the impact is not so little. In fact, our Not So Little Things research study found that 88 per cent of respondents had experienced microaggressions in the sector, 41 per cent of aggressors are supervisors or managers, and another 38 per cent are clients or customers. Having experienced microaggressions, a lack of opportunity, a lack of flexibility and/or poor work culture, 8 per cent of women had left the industry entirely.
We can no longer hold tight to old ways of working that are outdated and serve no purpose in our modern workforce.
Flexibility, safety in all its guises, accounting for health and wellbeing, incorporating the needs of parents, those with disabilities, neurodivergence, actively taking steps to close the gender pay gap, demonstrating inclusive leadership and holding businesses and individuals accountable – all must become part of the usual way of working. This is what our current and future workforce is telling us they need and want.
The focus must be on building a sector that people – of all genders, races, ages, strengths and abilities – choose to join and stay. A fair, inclusive and respectful culture underpins our success. We simply cannot deliver for the nation without it.
Driving cultural change
The National Association of Women in Construction (NAWIC) is leading this cultural change movement to achieve an equitable construction industry for all.
NAWIC has been at the forefront of driving positive changes to enable and benefit women and underrepresented groups to
have successful careers in construction for 30 years. We take a multi-faceted and multi-disciplinary approach – working to support members, build community, deliver education and development opportunities, celebrate achievements and advocate for change.
We understand the issues impacting women, including the reasons for their low representation, poor experiences, and the failure to meet the needs of the sector. All our work is designed to enable women to join, stay and thrive in construction.
Indeed, we have numerous examples of women in the industry who exemplify what success looks like. We also have examples of committed leaders and organisations doing great things to improve the sector for women.
In 2025, our focus is on:
1. Supporting our members: Continuing to provide support for members, who consist of both individuals and organisations in various roles and market segments of construction. NAWIC membership is open to all, and 11 per cent of our membership identifies as male.
2. Changing the industry: Looking at the environment, designing and implementing targeted, evidence-based initiatives, and ultimately driving fair, inclusive and respectful workplaces.
What does industry success look like?
The ultimate success would be a sector of choice for people seeking a meaningful career – one that is welcoming to all, regardless of background, and recognises the benefits that diverse perspectives and experiences bring to both the decision-making table and the work of an organisation.
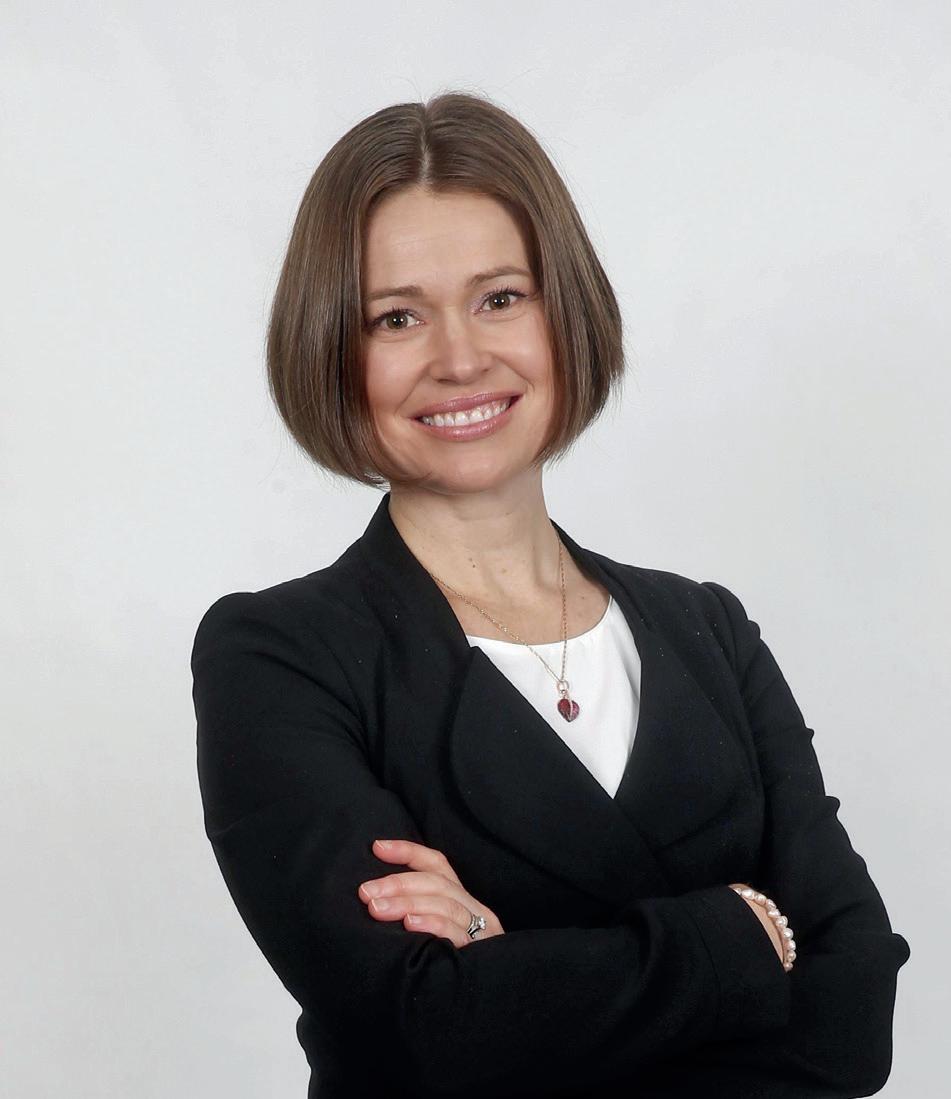
It would be one where everyone can play their part in building and maintaining the very places and spaces in which we all live, work and play.
It would be one characterised by fairness, inclusion and respect in construction and the built environment.
It’s well and truly time. Let’s work together to create the industry that we all want, where everyone can thrive.
Join us in the cultural change movement and help us amplify our impact.
NAWIC is the peak membership body for women working in the construction industry and supporting sectors across the built environment. A national notfor-profit association dedicated to the attraction, development and retention of women in the construction industry, NAWIC has local chapters in every state and territory and forms part of a global NAWIC network. NAWIC connects likeminded people focused on driving gender equity. You can find out more about NAWIC through its social media channels @nawicau or on the NAWIC website, nawic.com.au
Creating safe and supportive spaces
Programs like BESIX Watpac’s Lean In Circles are changing the game for women in construction.
“Research shows that diverse teams make better decisions, are more innovative, and perform better overall.”
The construction industry is changing. Slowly but surely, more women are stepping into leadership roles, and proving that construction is for everyone. But while progress is being made, one of the biggest challenges isn’t just getting women into the industry; it’s keeping them here and ensuring they thrive.
That’s why programs like BESIX Watpac’s Lean In Circles matter. They’re not just another corporate initiative; they’re real, practical spaces where women can connect, share experiences, and build confidence in an industry where they’re often the minority. And it seems to be working.
Launched nationally in 2023 after a successful pilot in New South Wales, Lean In Circles are small, peer-to-peer mentoring groups designed to give women a safe and supportive space to develop their skills. They’re about having a network of people who ‘get it’, who understand the unique challenges women face in construction and can offer guidance, support and a good dose of reality.
The feedback has been positive, and because of that, BESIX Watpac has embedded the program across the company, with workshops already completed in 2024 and the next one locked in for March 2025 across Australia and New Zealand. It’s a big step forward, proving that when companies actively invest in their people, the whole industry benefits.

By Lauren Fahey, executive director at NexGen. (Image: NexGen)

Diversity is about making the industry stronger. Research shows that diverse teams make better decisions, are more innovative, and perform better overall. When we bring different perspectives to the table, we challenge outdated ways of thinking and find smarter, more efficient ways to build our cities and infrastructure.
Yet, the construction industry still struggles with attracting and retaining women, with female representation hovering at just 13 per cent in Australia. That’s not just a gender issue; it’s a workforce issue.
If we don’t bring more people into construction, we’ll be facing even bigger skill shortages in the coming years. Programs like Lean In Circles are a proven way to ensure that women not only enter the industry but stay, grow and lead.
BESIX Watpac is leading by example, and other companies should take note. Its success with Lean In Circles shows that creating a more inclusive industry isn’t just possible, it’s essential.
At NexGen, we’re committed to getting more young people into construction, but that’s only half the battle. Once they’re in, we need to make sure they feel supported, valued and have opportunities to grow. It is also up to the industry to keep them in. How can other businesses learn from this?
• Create structured support networks –Don’t just talk about diversity; actively create spaces where underrepresented employees can connect and grow. Lean In Circles provide a model that any company can adapt.
• Encourage mentorship and sponsorship – Women in construction need strong mentors and sponsors who will advocate for their growth and help them access leadership opportunities.
• Make inclusion part of company culture – Diversity efforts shouldn’t be ‘extra’ initiatives; they should be embedded into company culture, leadership training and recruitment strategies.
• Celebrate and showcase talent – Seeing women in leadership roles inspires the next generation. Companies should highlight success stories, promote role models, and actively encourage more women into leadership pathways. Programs like Lean In Circles prove that workplace culture can change when companies step up and create spaces where people feel like they belong. BESIX Watpac is leading the way, but there’s still room for more businesses to step up and take action. The future of construction depends on attracting and retaining a diverse workforce. When we invest in people, we invest in the future of the industry, and that’s a win for everyone.
To build a stronger, more diverse construction industry, businesses must step up and take action. NexGen works with industry partners to connect young people and job seekers with real opportunities, provide pathways into construction and create programs that drive change. Partners of NexGen inspire the next generation, support diversity, and shape the future of construction. Contact NexGen at hello@nex-gen.au or visit www.nex-gen.au to learn more.
More than just the biggest and best
The countdown is on to crown this year’s Australian Construction Achievement Award winner.
Size and complexity often take centre stage in construction. But the Australian Construction Achievement Award (ACAA) is different. It’s not just about the biggest project – it’s about industry transformation. Winning is about setting new benchmarks for how construction should be done. The award highlights companies that prioritise people, sustainability and innovation, showing what the future of construction should look like.
Presented by the Australian Constructors Association and Engineers Australia, the ACAA has been celebrating industry achievements for 28 years. Last year’s winner, the Rookwood Weir Project, stood out not only for its innovative fish lock and the world’s first turtle passage design but also for the strong collaboration within the alliance (Sunwater, GHD, ACCIONA and McCosker Contracting). The project exceeded its training targets and Indigenous employment goals. By embracing sustainable practices and new technology, it set a benchmark for environmental responsibility and innovation.
The ACAA has a rigorous judging process. This year’s panel, chaired by Tanya Cox and including Duncan Gibb, Elizabeth Taylor and Dr Charles Macdonald, follows a three-stage
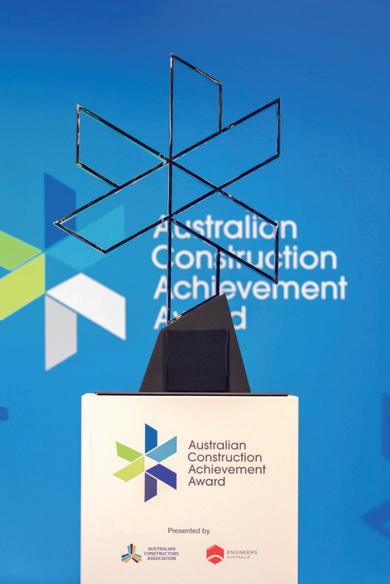
evaluation process. Entries begin with an initial project submission, after which shortlisted finalists advance to the next stage. Finalists then submit detailed reports and host site tours, where judges engage directly with project teams and clients to assess the projects.
Value for money outcomes make up 40 per cent of the judging criteria. Entrants must demonstrate expertise in delivering complex projects while maximising social and economic benefits. Judges assess risk management, time, cost and quality optimisation, and commitment to local suppliers, including social and Indigenous enterprises. Long-term community benefits also play a crucial role.
Capacity, capability and skills development account for 30 per cent of the assessment.
Judges look for projects that lift workforce skills and drive productivity improvements. Entrants promote innovation, adopt digital technologies that reduce whole-of-life asset costs and invest in training initiatives that equip workers with essential skills. Meeting or exceeding targets for female participation, Indigenous employment and social inclusion is also key.
Positive workplace culture makes up the final 30 per cent. Winning projects prioritise worker wellbeing by promoting a safe, inclusive and flexible environment. Judges consider efforts to promote diversity, encourage collaboration across all stakeholders, and implement initiatives that minimise environmental impact and drive sustainability.
The winner of the 2025 ACAA will be announced at a black-tie dinner on 6 August in Brisbane. This event will be held alongside Foundations and Frontiers (FF25), a forum dedicated to tackling the industry’s biggest challenges and opportunities. Bringing both events together reinforces a shared commitment to shaping the future of construction.
“It’s not just about the biggest project – it’s about industry transformation.”
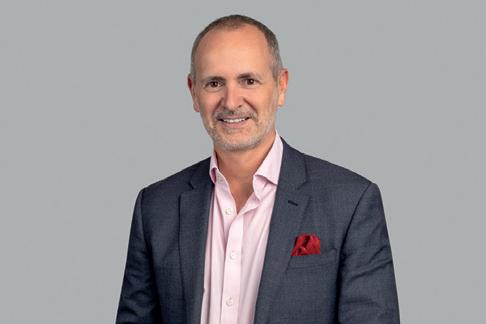
The finalists will showcase the best of Australian construction. When the winner is announced, it won’t be about the biggest or most ambitious project. It will be about celebrating the company leading the way in making construction better for everyone.
Find out more at acaa.net.au
By Jon Davies, CEO of
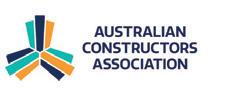
Empowered Women in Trades
Honouring the achievements of apprentices
The Empowered Women in Trades team recently celebrated National Apprentice Week Australia, recognising and celebrating apprentices across the country.
“Clea knew from a young age that she wanted to follow in her dad’s footsteps and become a carpenter, and this was only made clearer after completing woodwork at school.”
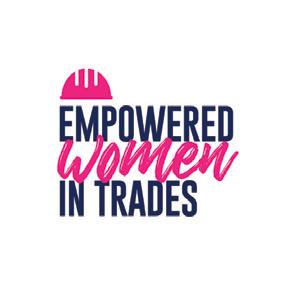
in Trades.
Apprentices are our future, and the team enjoyed showing them how grateful and appreciative we are for all they do for trades. Most of the apprentices didn’t know there was such a thing as National Apprentice Week and were surprised to be celebrated. We heard some incredible stories of their achievements, defining moments and wins they had along the way. We also heard about the challenges and the stories of resilience –apprenticeships aren’t easy.
Our team went out with the crew from APM Apprenticeships to Swinburne TAFE, Box Hill Institute, Skillinvest, and Builders Academy, celebrating apprentices with donut drops and morning tea. We spoke to carpenters, plumbers, electricians, and even some students completing their studies as part of their school experience.
The highlight of the week was the celebration of seven female apprentices who are out there doing what they love and doing it incredibly well. These trailblazers are setting the standard and serving as role models for anyone considering undertaking an apprenticeship.
First up, we had Jasmine, a plumbing apprentice from Reed Plumbing and Drainage Solutions. Jas loves being a plumber but didn’t always have the confidence to back herself. Jas had some great advice for anyone struggling with confidence: build a strong village around you of friends and family and allow them to be your confidence, lifting you up until you have the belief to lift yourself up.
We celebrated Ana, a first-year fabrication apprentice who is also a mum of four, a student, and a women-in-trades advocate with the AMWU. Ana is the first to recognise that taking on an apprenticeship has been a big challenge, and her plate is very full trying to juggle her commitments. But Ana’s advice is this: you can make anything work if you really want to.
Jenna was up next, a fourth-year electrical apprentice who is about to graduate.
Jenna loves her job and couldn’t speak more highly of how incredibly supportive everyone she has interacted with onsite has been throughout her journey. Jenna was a career changer who has found her calling. Good culture onsite makes such a big difference to everyone.
Our fourth apprentice was Clea, a fourth-year carpentry apprentice with Lizad Building and Development. Clea knew from a young age that she wanted to follow in her dad’s footsteps and become a carpenter, and this was only made clearer after completing woodwork at school. You cannot be what you cannot see – a shining example of how important role models are.
Sam, a furniture maker in Victoria, has recently finished her apprenticeship and could not be happier to be qualified in her trade. Sam went from not knowing what she wanted to do and trying lots of things to now holding a qualification and loving her job. Sam highlights the importance of work experience and gaining exposure to different careers, which allows people to find the right apprenticeship for them.
The sixth apprentice was Shae, a thirdyear boilermaker apprentice. Shae started a Nutrition Science degree but quickly realised that wasn’t where she was meant to be and would rather be welding metal. A highlight of her apprenticeship is being out and about and seeing things she has made, and being able to tell people – ‘I made that’. Wrapping up our apprentices for National Apprentice Week Australia 2025 was Courtney, a third-year electrical apprentice. Courtney has been a regular at our Empowered Women in Trades (EWIT) schools programs, sharing her incredible knowledge and passion for her trade.
Courtney credits a great environment at both her workplaces, Beal Electrical and TAFE, Box Hill Institute, as a big part of her success. It takes a village.
If you want to know more about these amazing apprentices, you can check out their videos on the EWIT YouTube channel. Thank you to our apprentices for sharing their journeys with us and inspiring future apprentices.
A big thank you to our wonderful partners and EWIT alliance members APM Apprenticeships, DeWalt, Anthem Workwear and Steel Blue for getting behind the celebrations and supporting the apprentices with some incredible prizes. Finally, to all the apprentices out there: we celebrate you. You are doing an amazing job, and our future is in great hands.
BEST IN BUSINESS BANKING
Supporting businesses large and small with award-winning customer service.
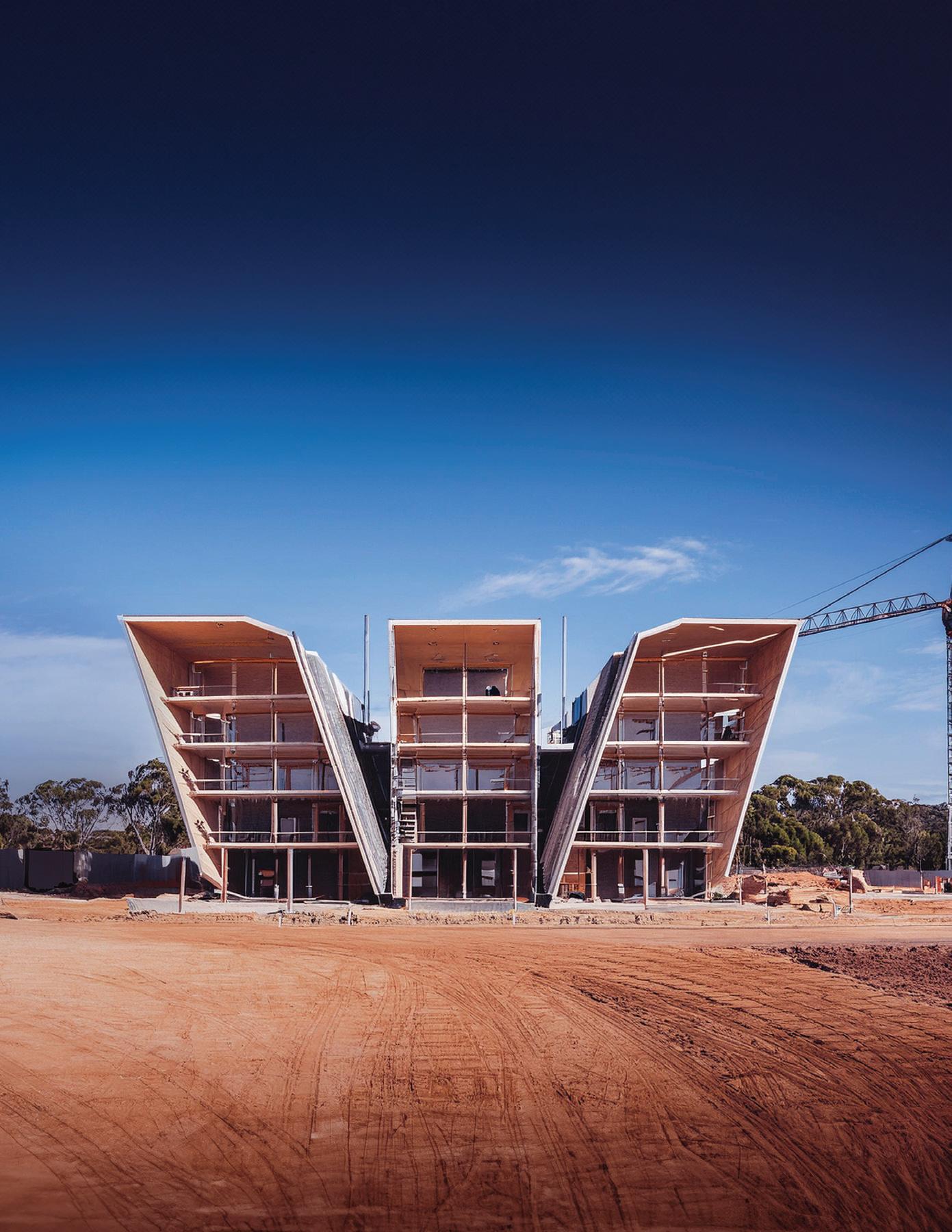
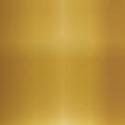

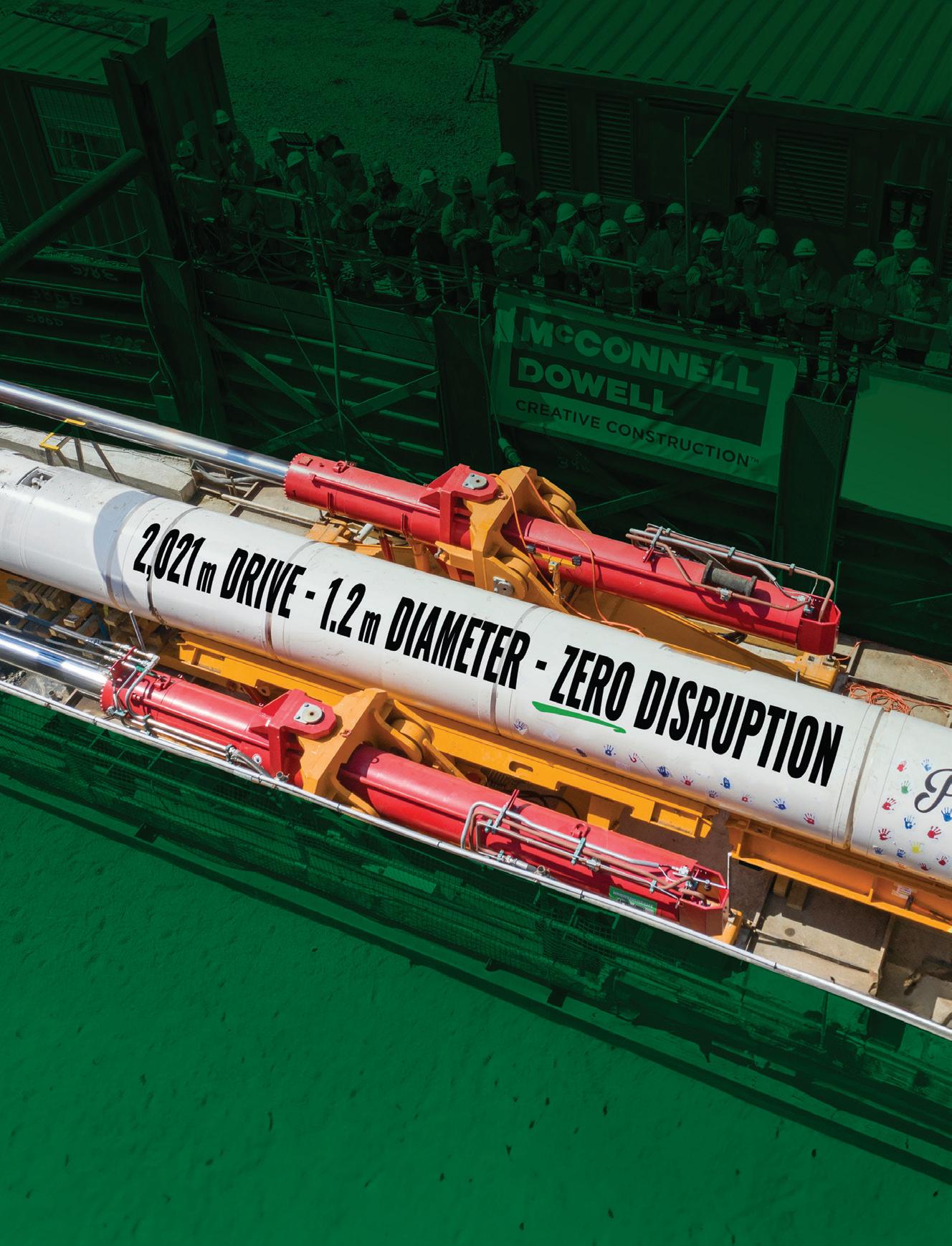
