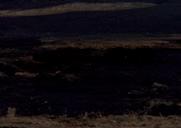
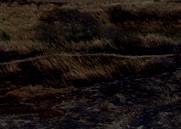
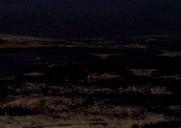
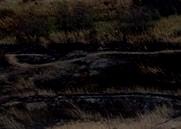

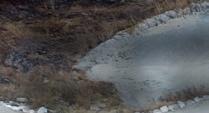
Compact, powerful and versatile: Introducing the MOBISCREEN MSS 502 EVO mobile coarse screening plant. Its compact size, low transport weight and impressive feed capacity of up to 350 tonnes per hour ensure that this versatile machine can be used flexibly and quickly for even the most heavy-duty applications in natural stone and recycling. The compact MSS 502 EVO, with its advanced ergonomics, was designed for exceptional operability. It can also be operated electrically thanks to its optional dual-power drive. The MOBISCREEN MSS 502 EVO: the (small) multi-talented powerhouse.
www.wirtgen-group.com/mss-502-evo-kleemann
Eskay Crushers has grown to be one of the flagship quarries in South Africa.
Carlisle TyrFil o ers an innovative solution to keep operations flat-free.
All
Examining
Manufacturers and suppliers are eyeing a positive future in Southeast Asia’s
CheckProof CEO Håkan Holmgren discusses the company’s rise from a small Swedish start-up business and its recent expansion to the US.
A look at how alternative fuels are influencing the quarrying and aggregates sectors.
Electric innovation continues in the crushing and screening sector as manufacturers capitalise on demand.
Technology has never been more important in quarrying and aggregates.
32
Non-genuine, counterfeit or fake parts can place operations at considerable risk
34 INTERVIEW
Talking to Grete Aspelund, head of NCC Industry
Eskay Crushers is setting the bar high in compliance, health and safety, and environmental management. Image: Eskay Crushers
Next-generation
Recycled
2-3 JULY 2025 THE STANLEY HOTEL
PORT MORESBY, PAPUA NEW GUINEA
Tickets now available for the premier event helping PNG and Australia’s industrial, mining and resources industries forge connections, network and do business.
Don’t miss your chance to connect with key players and industry leaders. Tickets are selling fast – secure yours now.
HEAD OFFICE
Prime Global Publishing Capitol Square 4–6 Church Street Epsom, KT 17 4NR
EDITOR
Guy Woodford +44 (0) 7879 408 069 guy.woodford@primeglobalpublishing.com
ASSISTANT EDITOR
Adam Daunt adam.daunt@primeglobalpublishing.com
BUSINESS DEVELOPMENT MANAGER
Les Ilyefalvy +61 423 177 966 les.ilyefalvy@primeglobalpublishing.com
CHIEF EXECUTIVE OFFICER
John Murphy
CHIEF OPERATING OFFICER
Christine Clancy GROUP MANAGING EDITOR
Paul Hayes
CLIENT SUCCESS MANAGER
Janine Clements +61 432 574 669 janine.clements@primeglobalpublishing.com
ART DIRECTOR Michelle Weston COVER IMAGE CREDITS Eskay Crushers CheckProof Sedelnikovsky Plant Metso
SUBSCRIPTIONS subscriptions@primeglobalpublishing.com
No part of this publication may be reproduced in any form whatsoever without the express written permission of the publisher. Contributors are encouraged to express their personal and professional opinions in this publication, and accordingly views expressed herein are not necessarily the views of Prime Global Publishing. From time to time statements and claims are made by the manufacturers and their representatives in respect of their products and services. Whilst reasonable steps are taken to check their accuracy at the time of going to press, the publisher cannot be held liable for their validity and accuracy.
IPUBLISHED BY Prime Global Publishing
AGGREGATES BUSINESS USPS: is published six times a year.
PRINT: ISSN 2051-5766
ONLINE: ISSN 2057-3405
PRINTED BY: Warners (Midlands) PLC
have spent many years reporting on the vital work of the Global Cement and Concrete Association (GCCA) and its company and association members. GCCA members account for 80 per cent of the global cement industry volume outside of China, and include some key Chinese manufacturers. It is a true global industry advocate and champion.
The GCCA’s innovative industry agenda took another major step forward in April when the Association launched Low Carbon Ratings (LCR) for Cement and Concrete. This rst-of-its-kind transparent global rating system will enable cement and concrete to be identi ed based on their carbon footprints.
The ratings system is designed to help customers prioritise sustainability when selecting construction materials. It uses a clear and intuitive AA to G scale.
Inspired by well-known appraising schemes such as the EU’s Energy Performance Certi cates and the US Home Energy Rating System, the LCR offers a simple, transparent and adaptable tool that helps builders, architects, governments, planners, and consumers around the world make more informed and sustainable choices.
“Cement and concrete are the foundations of modern life – from the buildings we live and work in to the roads we travel and the infrastructure that supports clean water and green energy,” GCCA chief executive of cer Thomas Guillot said. “As global demand for sustainable construction grows, the need for greater transparency around the carbon footprint of construction materials is more critical than ever.
“Our Low Carbon Ratings system supports more sustainable procurement practices and will empower the entire value chain to accelerate decarbonisation.”
The GCCA-devised ratings system, designed to be easily recognisable, comes with a simple visual graphic that clearly indicates a product’s rating. The carbon rating system for cement and concrete provides consistency and comparability. Countries can adopt the global ratings as they are or adapt them if local carbon accounting differs from global norms.
“This is a huge step forward towards harmonising global de nitions for low-emission cement and concrete in support of decarbonisation,” United Nations Industrial Development Organization energy systems and decarbonisation unit chief Riccardo Savigliano said.
“With notable construction projects already demonstrating the use of lower-carbon cement and concrete, the GCCA emphasises that the industry is making important progress. The association stresses that the launch of this global rating system marks another milestone on the road to greater sustainability.”
Bouygues Bâtiment International decarbonisation and sustainable design expert Marlène Dance said she fully endorses the new LCR system. “We believe a globally consistent carbon rating system – adopted by all countries and used by all concrete suppliers – would be a gamechanger,” she said.
“We see great value in a simple, user-friendly tool, tailored for construction teams. It will help empower our site crews to better understand and manage the carbon footprint of the concrete they use.”
Guillot said the GCCA is eager to see the industry’s response to the organisation’s latest initiative.
“With this rating system in place, governments, policymakers and the private sector can now prioritise lower-carbon cement and concrete in the procurement process, which will in turn further stimulate the industry’s focus on decarbonising these essential building materials,” he said.
“We will closely follow industry customers’ response to the GCCA-led LCR ratings for cement and concrete. It captures the welcome and critically important sustainability zeitgeist evident in the cement and concrete industry.
“Cement manufacturing accounts for about eight per cent of the world’s global CO2 emissions. However, introducing these LCR ratings and many other green industry initiatives highlights a critically important global industry that is hard at work getting its emissions down while maintaining outstanding nal product quality.” GW guy.woodford@primeglobalpublishing.com
Almost 20 years ago, CDE, one of the leading suppliers of wet processing solutions for the natural minerals processing and waste recycling sectors, secured a landmark contract to design and engineer one of the world’s largest sand washing plants – a 1200-tonne-per-hour solution for Qatar Primary Materials Company (QPMC).
Fast-forward two decades, and QPMC’s original capital expenditure investment continues to lead the region in total capacity. Seventy million tonnes of sand have been washed, and fresh upgrades are afoot to ensure the plant delivers maximum productivity for years to come.
Comprising four operating lines, each processing up to 300 tonnes per hour, the plant uses an elevated platform that enables a continuous ow of inbound trucks to feed the hopper directly.
Each line runs in unison and consists of a series of 7x2m coarse rinsing screens, CDE’s patented EvoWash sand washing system, a network of stockpile conveyors, and water management systems, including CDE’s AquaCycle thickener and a high-capacity lter press.
Together, they process up to 12,000 tonnes per hour and produce up to 24,000 tonnes of washed and graded sand per day, presenting a unique challenge for the after-sales team, according to CDE customer care manager Sena Biswas.
“A plant of this sheer scale requires an always-on approach to maintenance,” he said. “It’s a bit like the analogy of painting the Golden Gate Bridge; it’s a continuous process.
“QPMC is also one of the three biggest local suppliers of construction materials in what is a fast-developing region, so proactive, preventative and
After two decades, QPMC’s original investment continues to lead the region in total capacity.
responsive on-the-ground support is paramount.
QPMC supports Qatar’s construction sector by providing essential materials and logistics services.
From Mesaieed Port (GBT), QPMC offers stevedoring facilities for both aggregate and non-aggregate importers and storage solutions.
Cemex EMEA (Europe, Middle East, Africa) has celebrated some of its most outstanding regional projects at its Global Research & Development (GRD) Center in Bruegg, Switzerland, under the theme, ‘Shaping the future together’.
Among the highlighted developments were the latest regional winners of the Cemex Building Awards (CBA) international edition, a major competition celebrated since 1991. An external jury selected these projects based on their exceptional innovation and commitment to sustainability.
The regional winners recognised at the GRD event:
•Multi-Family Housing Category: 3rd place – “La Pigna” (Montenegro)
•Public Space Category: 2nd place – “Smetanova lávka (Czech Republic) Collective
•Buildings Category: 1st place – “Gampa a Sféra Pardubice” (Czech Republic); 3rd place – “One Za’abeel” (United Arab Emirates)
•Infrastructure Category: 2nd place – “New Dirout Group of Regulators – Finished Sections” (Egypt)
The international competition featured 43 nalist projects from 17 countries, judged by a panel of renowned architects and engineers from different parts of the world.
In addition, special regional recognitions were given to projects demonstrating exceptional contributions to sustainable development through innovative use of Cemex materials:
•Annenhöfe (Germany)
•A33 Yecla-Caudete (Spain)
•Pierre Fabre Foundation –Lavaur (France)
•One Oval Square (United Kingdom)
• Świnoujście Tunnel (Poland)
Representatives from each awarded project attended the event, along with Cemex EMEA’s new regional president José Antonio Cabrera, and Brandon Clifford, a well-known architect and MIT associate professor of architecture.
Clifford attended the event as a valued Cemex collaborator, highlighting the ongoing partnership in developing innovative projects addressing sustainable construction.
Participants experienced an exclusive guided tour of Cemex’s research and development laboratory led by global vice president of research and development Davide Zampini.
The tour included an engaging hands-on workshop demonstrating
As a key supplier of primary construction materials, QPMC provides washed sand, dune sand, gabbro and limestone to meet the industry’s demands. In line with its commitment to sustainability, QPMC also processes construction, demolition, and excavation waste, producing high-quality recycled aggregates.
Cemex’s latest innovations in concrete technology.
“It was a privilege to welcome some of the leading talents of the region’s construction industry to the GRD Center, following their deserved recognition in our Building Awards,” Zampini said.
“Concrete performed a crucial role in their winning projects, and will continue to do so in the outstanding developments of the years to come. Collaborating with the visionaries of our industry will enable us to build better, smarter and more ef ciently, meeting the everchanging needs of the world around us.”
The ceremony concluded with awards and special recognitions, reinforcing Cemex’s dedication, alongside its partners, to building a more sustainable and innovative future for generations to come.
of materials, including aggregate stone, crusher sand, roadstone and ballast. AfriSam senior engineer for the Western Cape Desmond Jacobs said this investment aligns with the company’s long-term capital strategy.
Key features such as its hydraulic Hydroset system and Automatic Setting Regulation (ASRi) system, which enhance performance and streamline maintenance, drove the decision to install the Sandvik CH430. The Hydroset system enables precise automated closedside setting adjustments, while the ASRi system continuously monitors and optimises crusher performance.
“Our initial assessments showed a dramatic reduction in oversize material being sent for secondary crushing,” he said. “This allows us to optimise throughput and potentially eliminate redundant processing steps in the future.”
A crucial factor in selecting the Sandvik CH430 was its compact footprint, which closely matched the previous crusher.
“As a brown elds project, we had to work within existing site constraints,” Jacobs said. “Matching the footprint was essential as we had limited time for installation and could not accommodate extensive structural modi cations.”
AfriSam has enhanced its Rheebok Quarry operation by installing a high-capacity Sandvik CH430 cone crusher from Sandvik Rock Processing. The upgrade ensures reliable, safe production with reduced maintenance and a lower carbon footprint.
Located near Malmesbury in South Africa’s Western Cape, the granite quarry produces a range
“We appreciate how the Sandvik CH430 minimises operator intervention allowing real-time adjustments to the closed-side setting,” Jacobs said. “This improves product size consistency and quality. The system also tracks key parameters like temperature and pressure, enabling proactive maintenance and reducing unexpected breakdowns.”
Jacobs said that the new unit has already demonstrated its impact on product quality by reducing oversized material in the feed stream.
South Africa-based Tru-Trac Rollers unveiled a new belt scale system at bauma 2025, o ering operators insights into longterm data.
Tru-Trac Rollers showcased its intelligent belt scale system, which features an integrated artificial intelligence (AI)-driven continuous calibration checking and realtime load cell monitoring with traditional belt scales. This next-generation solution goes beyond measuring tonnes per hour (tph) to deliver advanced conveyor belt monitoring.
Integrating seamlessly with the awardwinning Rip Prevent+ system, which Tru-Trac debuted to its African customers at Electra Mining Africa 2024, this innovation leverages AI to detect anomalies or rip events on all conveyor belt types including steel cord, pipe and fabric belts.
“This intelligent belt scale sets a new standard Tru-Trac bulk materials handling,” division sales manager Tinus Ludik said.
“It is not just technologically advanced but also user-friendly, providing unprecedented data that conventional belt scales simply don’t o er.”
Sandvik Rock Processing business line manager for crushing solutions PC Kruger said the Sandvik Plant Designer platform, which helped optimise the model selection process. The energyef cient crusher, powered by a 132kW motor, aligns with AfriSam’s speci cation, contributing to lower energy costs and reduced emissions.
With a local of ce and warehouse in Cape Town, Sandvik Rock Processing ensures AfriSam receives prompt technical support, spare parts and plant audits whenever required.
Cemex’s EMEA business has a new regional president. José Antonio Cabrera has been heading up all of Cemex’s operations in Europe, the Middle East and Africa since April 1. Cabrera began his career at Cemex in 2000 and has since been appointed to various positions in strategic planning, operations, and trade. Through these positions, he has supported Cemex operations and contributed to the company’s growth in global regions.
For the past six years, Cabrera has been general director of Cemex Cluster Caribe (Dominican Republic and Puerto Rico). In his new role as President of Cemex EMEA, he will continue the work begun by previous president Sergio Menéndez to prioritise our strategic priorities; fostering a safe and healthy work environment for all employees and contractors; placing customer centricity at the forefront to enhance customer satisfaction; and focusing on challenging decarbonisation goals to reduce emissions across the value chain. Furthermore, Cabrera will champion innovation, leveraging Cemex’s knowledge and resources to achieve breakthrough advancements towards carbon-neutrality while supporting financial growth by advancing the sustainability agenda through smart financial strategies and maintaining the region’s strategic position as a key part of the business portfolio.
Business across Russia’s aggregates sector remains relatively strong, though headwinds in the construction industry could impact demand.
Demand for Russian aggregates has remained relatively healthy despite international economic sanctions and the country’s complex business environment. The country’s roadbuilding and construction sectors have historically represented a 700-million-tonnesplus-a-year production market, making it the biggest customer for aggregates.
While the current situation in Russia’s roadbuilding sector remains generally stable, the same cannot be said for the nation’s construction industry, particularly the housing construction segment. Three years after the beginning of the Russia–Ukraine war, it has been unable to adapt to changed market realities.
Russia’s construction industry was hit by the October 21 2024 decision by the Russian Central Bank to increase the country’s key interest rate by 200 basis points to a recordhigh 21 per cent, an attempt by the nancial regulator to stop the ever-rising in ation caused by a rapidly expanding militaryindustrial complex.
The sizeable increase deepened an existing construction sector crisis leading to a large reduction in lower-cost, mass housing construction, historically accounting for most national construction activities. Russia’s construction industry misfortune spread to the country’s mortgage industry, which for the entire 2024 dropped by 35 per cent.
On July 1 2024, the Russian Government cancelled two large-scale and popular preferential mortgage programs: one offering mortgages with an eight per cent interest rate for housing under construction and another offering family mortgages with a six per cent interest rate.
DOM.RF, a Russian nancial institution for housing development, recently tipped the volume of new Russian housing construction projects to drop to 38 per cent in 2025.
Housebuilding in Russia is currently regulated by the Housing and Urban Environment state program, whose budget is expected to be cut. Most local analysts predict this will lead to a drop in the production and consumption of aggregates, along with other construction materials, as early as the second half of 2025.
The 2023–24 period was relatively good for Russian aggregates commerce, the spokesperson or Russian Minister of Industry and Trade and the state of cial responsible for developing the national aggregates sector Anton Alikhanov recently said.
According to a recent report titled ‘Analysis of the Market of Aggregates Construction Materials in Russia’ from research agency BusinesStat, Russian aggregates sales in 2023 were up year-onyear by 4.5 per cent, from 586 cubic metres to 612 million. However, stagnation in 2024
may create concerns for expansion plans.
On the production side, Russia’s overall aggregate production dipped by 3.7 per cent in 2023. While of cial results for 2024 have not yet been published, analysts expect aggregate production to have declined by a further 5–6 per cent.
Russia’s major aggregate companies include JSC LSR Basic Materials, JSC First Aggregates Company, JSC Bashkiravtodor, JSC Kiembaevsky Mining and Processing Plant Orenburg Minerals, and JSC Sibagropromstroy.
LSR Basic Materials has become a leading player in the north-west Russia aggregates market and has impressive further expansion plans. According to the company, it remains the largest producer of crushed stone in St. Petersburg.
LSR plans to accelerate its investment activities this year following the launch of a sand quarry at the Brusova Gora-2 deposit. The quarry is located in the Tosnensky district of St. Petersburg, with material processed via the dry excavated method. Its expected annual output is 17,760 cubic metres of sand.
LSR’s capacities are estimated at more than seven million cubic metres of crushed stone and more than eight million cubic metres of sand annually. However, the company plans to increase these gures further in the coming years by expanding existing agship quarries and mines and opening new sites.
LSR’s Granit-Kuznechnoye production complex, located in the Priozersk district of the St. Petersburg region, consists of three granite quarries and ve crushing and sorting plants that produce over 4.2 million cubic metres of crushed stone of various fractions annually.
Another important company asset is the largest sand quarry in north-west Russia – the Manushkino quarry, which is situated in the Vsevolozhsk district of the Leningrad region. It annually produces over 2.5 million cubic metres of washed sand via hydromechanised extraction from under water in an arti cial reservoir. LSR has exciting plans to develop this site in the next few years.
Moscow-based First Aggregates Company (Pervaya Nerydnay Company), another major player in the Russian aggregates sector, has eye-catching development plans from now until 2029, aligning with its corporate growth strategy. The plans include the further expansion of production capacities and the widespread introduction of new operation technologies.
First Aggregates Company is also keen to explore export markets for its diverse product portfolio. The business has a current annual
production capacity of around 10 million cubic metres. Production is carried out at 17 crushed stone plants, with the largest being Angasol, Beslan and Gavrilovsky.
The planned increase of the company’s aggregate production output has not yet been disclosed.
Some Russian business analysts expect that the ever-rising prices for aggregates in the domestic market may prevent the sector’s further development. According to of cial data from the Russian state statistics service Rosstat, the growth of prices for most aggregates in the country was 15–25 per cent in 2024. At the same time, the overall growth of prices for the past four years was 70 per cent.
Still, according to data of some independent analysts, the real growth of prices was signi cantly higher (by 2–2.5 times, compared to the beginning of 2022).
Most Russian aggregates producers are wary of making sales forecasts for the next 12 months, as much will depend on the level of demand from major consuming industries.
There are big hopes for the possible improvement of relations between Russia
and the US and the possible lifting of at least part of the sanctions.
As peace talks are ongoing, most Russian business analysts hope to ease banking sanctions, the most painful sanctions for the national aggregates sector, as they seriously complicate most foreign activities and collaborations with local players. In addition, many aggregate producers are alarmed by their depleted workforce.
“The most serious pressure is from the labour market,” head of JSC Levoberezhny Sand Quarry Georgy Chukhrov said.
“On the one hand, there is an expectation of high salaries [in the last two years, an alternative has appeared to earn big money through military service under contract or at defence enterprises].
“On the other hand, there is a shortage of people, including due to Russia’s demographics, the consequences of which are catching up with us.
“As a result, a ‘bubble’ is growing, with salaries growing at an accelerated rate. The ght for personnel is reaching a new level, and the economy does not have time to develop quickly enough. Also, not enough worker training is being done.” AB
Southeast Asia is a key construction materials market.
Manufacturers and suppliers are eyeing a positive future in Southeast Asia’s key quarrying and aggregates market.
There has been some interest in how the Southeast Asia market will continue to grow in the coming years.
Market research rm Arizton has tipped the construction equipment market to grow by more than four per cent in compound annual growth rate.
The latest analysis from the advisory and market intelligence specialist comes from its strategic assessment and forecast of market trends from 2024 to 2029. The report estimates the Southeast Asia construction equipment market’s revenue to be US$ 9.1 billion by 2029, with the market
volume increasing from 74,025 units in 2023 to 97,452 by 2029. Any notable rise in construction equipment sales usually goes hand-in-hand with a noteworthy increase in aggregates and linked building materials demand.
Arizton pointed to a series of regional government initiatives that would support the growing demand for construction equipment.
“The government across the Southeast Asian region is investing in redeveloping infrastructure projects, including expanding ports, railway lines, roadways and highways. The surge in infrastructure development
projects is expected to drive the Southeast Asia construction equipment market during the forecast period,” Arizton wrote.
“Furthermore, Southeast Asia, with four countries in the top 10 for construction machinery exports [Indonesia, India, Vietnam, Thailand], is seeing signi cant growth fuelled by initiatives like the ‘Belt and Road Initiative’ and the ‘Regional Comprehensive Economic Partnership [RCEP] Agreement.”
The data indicates that earthmoving equipment underpins much of the construction equipment market in the region. Excavators had the largest
Volvo CE excavators are popular in Southeast Asia.
share. Similar to other global markets, another emerging trend is a rise in interest in compact and electric construction equipment.
“The electric equipment market in the Southeast Asia construction equipment market is anticipated to be driven by factors like government initiatives, growing demand for eco-friendly construction projects, and the trend toward industrialisation,” Arizton wrote.
“However, a signi cant challenge is the substantial cost of electric construction machinery, which might impede industry growth. However, to align with the global net-zero emission target, the companies are focusing on capitalising on lithium-ion battery technology in electric excavators and other products to reduce their carbon footprint.”
Volvo’s next generation
Volvo Construction Equipment (CE) believes there is a strong future in Southeast Asia, and is “optimistic” about trends in the region.
“Volvo CE continues to engage closely with customers across Southeast Asia and sees a mixed but cautiously optimistic sentiment across the region,” Volvo CE head
of productivity and retail development for the region Ramarajan Rangarajan said.
“In the construction sector, there is continued hopefulness driven by government-led urbanisation and infrastructure initiatives. Countries across the region, including Indonesia, Vietnam, the Philippines and Thailand, are advancing large-scale projects in transport, energy, and housing, which continue to stimulate equipment demand.
“Looking ahead, the strong momentum observed in Q1 2025 is expected to level out over the year, resulting in overall demand comparable to 2024, demonstrating both stability and resilience in the face of global headwinds.”
The company marked a major milestone earlier this year as it launched its nextgeneration products, including excavators, wheeled loaders, articulated haulers and compactors. Volvo CE also expanded its connected services portfolio, which includes Volvo ActiveCare, Co-Pilot, and Proactive Monitoring Systems.
“Excavators remain the primary demand driver in the region, serving a broad spectrum of applications from urban construction to rural development,” Rangarajan said.
“Volvo CE’s machines are particularly well-suited to meet the unique challenges
of the region’s diverse terrain and applications. Moreover, sustainability is gaining traction in customer purchasing criteria.
“Customers are increasingly evaluating both product ef ciency and the sustainability of site operations. Volvo CE’s offerings, with their lower emissions, fuel-saving technologies and lifecycle support, are well-positioned to meet this shift in expectations.”
Rangarajan cited strategic investment in key industrial sectors and infrastructure projects as strong reasons for optimism in the region.
“Southeast Asia is an important growth engine for Volvo CE, and its relevance will only increase in the years ahead. Rapid urbanisation, sustained population growth, and strategic government investment in infrastructure and mining are creating fertile ground for construction equipment demand,” he said.
“With regional economies showing strong fundamentals and an appetite for technological modernisation, Volvo CE sees a signi cant opportunity to expand its footprint.
“The company is committed to being a trusted partner in Southeast Asia’s development journey, offering innovative products, smart services and a brand experience rooted in reliability, performance, and sustainability.”
EvoQuip has con rmed Nguyen Vinh Holding as its new authorised distributor in Vietnam.
Nguyen Vinh Holding has maintained a long-standing presence in the Vietnamese construction and quarrying sectors. The company possesses industry expertise, a strong network, and a customer-centric approach that underpins its business.
EvoQuip business development manager Paul O’Hagan said the partnership will
enhance the company’s presence in Southeast Asia.
“Vietnam is a key growth market for us, and working with an experienced and reputable company like Nguyen Vinh will enable us to serve local customers and deliver tailored solutions for their crushing and screening needs,” he said.
Under the agreement, Nguyen Vinh Holding will provide Vietnamese customers with sales, service and spare parts for the EvoQuip range of compact crushing and screening equipment. This will support EvoQuip’s ambitions to grow in the Vietnamese construction, demolition and recycling industries.
“We are proud to represent EvoQuip in Vietnam. EvoQuip is one of the leaders in the compact crushing and screening industry, and backed by their global reputation for quality and support, we will have the opportunity to offer this to the Vietnamese market,” Nguyen Vinh Holding sales executive Xuan Hoang said.
“We look forward to working together to deliver exceptional solutions to our customers.”
New name and vision
Cemex Philippines is no more after the company’s new ownership gained approval for a new name, Concreat Holdings.
Cemex announced last year its decision to divest its operations in the Philippines as
part of its “portfolio rebalancing strategy”. Cemex completed the agreement with DACON Corporation, DMCI Holdings Inc. and Semirara Mining & Power Corporation.
“Proceeds from this divestment are expected to be used to fund the company’s bolt-on investment growth strategy in its key markets, reduce debt, and for other corporate purposes,” Cemex said in a statement about the agreement.
Fast forward to this year, and a new era is apparent as DMCI Holdings discussed its plans for the newly minted Concreat Holdings. Concreat president and chief executive of cer Herbert M. Consunji provided an update in the president’s report for the annual general meeting in May.
“It brings together two strong foundations: CHP’s national footprint in cement, and DMCI’s broad capabilities across construction, real estate, energy, mining, water services and logistics,” he told shareholders. “Together, we form a powerful combination – aligned not just in operations but in vision, values, and long-term goals. And while the short term may be challenging, we remain focused – and cautiously optimistic about the future.”
Consunji pointed to the Government’s commitment to investment in the Philippines, with a current commitment of at least ve per cent of GDP towards infrastructure spending. He also indicated that the estimated housing backlog, expected to reach 10 million units by 2028, presented an opportunity.
“We recognise that 2025 will bring continued pressures to the industry. The cement business is highly competitive, and global challenges – from trade tensions to recession risks and geopolitical uncertainty – can weigh down costs, pricing, and demand,” he said. “But these headwinds are not new to DMCI. We have a long and proven history of navigating complex market cycles with scal discipline, determination and a strong work ethic.
“And, if there is one thing our experience has taught us, it is this: what matters most is not the dif culty of the environment but how we respond to it.”
The new leadership has already instituted change within the organisation. The rst step included expanding its solid cement plant with a new 1.5 million-tonne line, which became operational in April.
Ordinary Portland cement has also been reintroduced into Concreat’s product line to support large-scale construction projects. The company has also increased its alternative fuel consumption to bolster its sustainability and cost-ef ciency across its operations.
“We recognise that these steps, while timely and impactful, will not change the fortunes of CHP overnight. Turning around a company takes time, discipline, and consistency,” Consunji said.
“But we are con dent that the steps we are taking today are steering CHP toward strength, ef ciency and long-term competitiveness.” AB
completely eliminates at tires. Compared to other No Flat products such as
From humble beginnings, Eskay Crushers has grown to be one of the flagship quarries in South Africa and is setting a high bar in terms of productivity and compliance.
Located in Piet Retief, a small town in South Africa’s Mpumalanga province, Eskay Crushers was founded some 60 years ago by Bob Hawker. It initially produced a meagre 6m³ of aggregate per week. Robert and Phillip Hawker, the sons of the late founder, took over the business from their father in the early 1970s, building it up to its current status.
Eskay Crushers managing director John Davis told Aggregates Business how, in the founding days, a construction contractor, the only client at the time, would come to fetch a single 6m³ truck load of material every Monday.
Over the years, the business has gradually grown to become the formidable quarry operation it is today. This is despite the fact it is located in a very small town with very limited and cyclical construction activity.
One of the de ning moments in the quarry’s history, Davis said, was when it clinched a contract to supply material for the construction of a major railway line within its vicinity. In fact, that contract funded the construction of the current
South Africa.
processing plant back in 1982. Over the years, the plant has been upgraded to improve production and ef ciency.
The major talking point, however, is how Eskay Crushers is setting the bar high in terms of compliance, not only in health and safety but also in environmental management.
Having placed second in the 2023 ISHE Audit, a stringent annual health and safety audit conducted by surface mining association, ASPASA, Eskay Crushers demonstrated its commitment to continuous improvement by clinching the top independent performer in the 2024 ISHE Audit.
The quarry has also been named the top independent performer in the online Environmental Audit for two years running (2023 and 2024), highlighting its commitment to environmental management on site.
Davis himself received the auditor’s award for Outstanding Environmental Commitment in 2023, recognising his efforts in advancing environmental compliance.
Eskay Crushers was awarded the top independent performer in the 2024 ISHE Audit.
For Davis, however, compliance is not about scores and awards; it is about creating a safe working environment that allows every worker to return home to their family unharmed every day. Equally, environmental management is not just about creating a favourable environmental pro le, but about building a legacy for the next generation.
“I commend ASPASA for its efforts in helping us with our compliance management. Under the association’s guidance, the industry has upped its game in terms of compliance,” Davis said. “For me, however, our efforts over the years are not about scoring a high mark in the audit; it is more about ensuring continuous improvement. Every year, we recognise our shortcomings and try to improve on that.
“Our achievements in recent years are a culmination of these small, continual improvements.”
Eskay Crushers is setting the bar high in terms of compliance, health and safety, and environmental management.
While the operation is passing the test with ying colours, Davis said that compliance by its very nature is not without challenges.
Compliance can be expensive, especially for a small operation like Eskay Crushers. All operations, irrespective of size and operating pro le, must adhere to a variety of rules and principles. Having to operate on the same playing eld as the bigger players and the mainstream mines with a bigger purse can be challenging, but it has to be done.
“Although we are doing it according to the law book, I believe there could be better ways to make safety easier to implement,” Davis said. “However, I understand why the regulator makes it complicated to comply; the overarching intent is to ensure that we create a safe working environment to achieve the industry’s quest for zero harm.”
Central to Eskay Crushers’ safety and environmental excellence is a team that shares a common goal and has embraced the need to work safely all the time and to be environmentally compliant.
“We promote a team ethic across our operation. We treat each other with dignity and respect, which is key for us in pulling together towards a common goal,” Davis said.
“Without the team, we would not be able to achieve what we have achieved.
Continuous improvement is the name of the game for Eskay Crushers, which is important in helping the team identify weaknesses, improve processes and enhance innovation and ef ciency, while maximising employee engagement. In addition, competence within the team is critical.
Competencies can help employees identify areas for improvement and advance all areas of the business.
To ensure a competent workforce on site, management at Eskay Crushers places a high value on continuous on-thejob training for its 26 workers and a few contractors on site. Davis said continuous training helps employees improve their skills and knowledge, which can lead to higher performance levels. The quarry also makes
use of knowledgeable consultants, who ll some of the crucial knowledge gaps and form an integral part of the Eskay Crushers team.
Davis said the company’s unrelenting focus on proper documentation is a parameter that sounds basic but is one of the true cornerstones of good compliance practices.
“One of the major initiatives we are busy with on the health and safety side is trying to bring our work in line with the written procedures, or vice versa,” he said.
“In many cases, operations end up with procedures that state one thing and people doing it in a different way.”
On the environmental side of things, one of the focus areas has been alien vegetation control, which is continual by its nature. Controlling alien vegetation in mines and quarries is important because invasive plants can threaten biodiversity, water resources and the environment.
The other focus area is water management and, in particular, stormwater control, which, due to the quarry being on a slope that starts right at the top of the operation and ends in the Mkhondo River, is of vital importance. Waste management and rehabilitation of disturbed areas are other key focus areas of the environmental management plan.
Community relations is another big focus area for Eskay Crushers. The quarry strives to forge close relationships with its immediate neighbours and works hard to implement its social and labour plans. Davis said this is no easy feat, but remains work in progress.
Eskay Crushers mines and processes a competent granite rock. One of the key challenges is the complex geology – the rock is a granite-quartzite mixture with many intrusions, which makes it dif cult to blast.
Unlike a dolerite rock, which turns out to be blocky and fragments well during blasts, the type of rock at Eskay Crushers has weathered top layers and complex jointing sets, which lead to loss of energy during blasts, resulting in poorer fragmentation, characterised by big boulders.
Eskay Crushers prides itself on safety and environmental excellence.
One of the interventions in recent times has been the appointment of a blasting contractor who brings a wealth of knowledge to blast effectively in the face of the challenging geology.
“In addition, we have adjusted the size of the burden to hole diameter ratio, spacing to burden ratio, stemming length to burden ratio, and ultimately the charge/powder factor, which is the relationship between the explosive and the rock mass. These all have a big effect on the level of fragmentation,” Davis said.
The challenge is to get the right balance between these blasting techniques and some of the recent blasting requirements from the regulator to ensure safety. For quarries, one of the biggest challenges is their proximity to communities and existing infrastructure. In line with the requirements of South Africa’s Regulation 4.16(2) of the Mining Health and Safety Act’s Explosives Regulations of 2018, quarries need to acquire a licence to blast within 500m of structures.
“We have recently done a Code of Practice for minimum standards on ground vibration, noise, airblast and yrock near surface structures and communities,” Davis said.
“To some extent, we nd these requirements to be counterproductive to good fragmentation. There is almost a trade-off between fragmentation and health and safety, and the latter has to win. We are continuously netuning our blasting parameters to ensure that we can still achieve good fragmentation while meeting these requirements.”
Eskay Crushers operates a very complicated plant. The secondary and tertiary parts of the plant alone have a total of ve crushers, ve screens and 24 conveyor belts. This allows the team to produce a range of products with ease.
The quarry generally produces various sizes of washed roadstone – 7mm, 10mm, 14mm and 20mm. This is complemented by normal concrete stone in various sizes – 20mm, 26mm and 37mm. In addition, the operation produces different sizes of crusher run such as G1, G2, G4, G5 and G7, as well as handstone for gabion baskets and ballast for railway lines.
On average, the quarry currently produces about 8000 tonnes per month (tpm), which can be pushed up to about 30,000tpm when demand is high.
Having initially been installed in 1982, the plant has bene ted from major upgrades in recent times. For example, the team installed a Trio 12x52 granulator secondary crusher in recent years, as well as an Osborn SBS 38H gyro tertiary crusher. A new vertical shaft impact from Techroq has just been installed to improve the shape and quality of the product.
The quarry is also currently busy with the installation of a new primary crusher, an Astec 3042, which replaces the old Astec (previously Osborn) 2536, which was installed in 1982. Davis said the durability, simplicity and resilience of the Astec offering, which has served the company well for over 40 years with no issues, was a highlight.
“As a result of these plant upgrades and ne-tuning of the existing plant set-up, we have been able to increase our plant production capacity from 100tph to 150tph,” Davis said. “With the addition of a new primary crusher, we expect to ramp up to 200tph. The idea is to increase our tonnes per hour, which allows us to work the same hours but produce more.
“Apart from increased productivity, this offers the bene t of reduced input costs related to wear and tear and electrical costs.” AB
Carlisle TyrFil o ers an innovative solution for the quarrying and aggregates industry to enhance environmental practices and minimise downtime.
The quarrying and aggregates industry is undergoing a shift towards greater sustainability.
One such move is the disposal of off-the-road (OTR) tyres, which are predominantly used in heavy industries, including quarrying, aggregates, mining and construction.
In years past, some industries would have stored at OTR tyres on-site or taken them to land lls. However, in some regions, that practice is outlawed, with regulators seeking a more environmentally friendly solution.
This created a window of opportunity that has been seized by an innovative manufacturer, Carlisle TyrFil, that makes and distributes the TyrFil atproo ng product and whose founders were the pioneers in developing the technology decades ago.
TyrFil was created as a response to tackle a common pain point in many heavy industrial businesses and environments: at tyres.
Flat tyres can appear innocuous at rst glance but, as anyone who has experienced unexpected equipment failures will know, they can be costly in terms of both time and money.
TyrFil improves on traditional tyre technology by effectively “ atproo ng” heavy construction equipment. This improvement can lead to a reduction in unplanned downtime and associated improvements in worker safety and environmental footprint.
“TyrFil offers a compelling alternative to conventional pneumatic tyres. TyrFil atproo ng technology is revolutionising construction site operations by ensuring more uptime, extending tyre life, increasing safety for workers, and supporting environmentally conscious business practices,” the company said.
Heavy industrial workplaces are lled with potential tyre hazards, including sharp debris, nails, glass and ferrous metals, which can all easily puncture traditional tyre technology.
TyrFil technology eliminates the risk of at tyres, allowing businesses to continue their essential work by replacing the tyre air with an innovative, durable polyurethane ll that cures into a solid elastomer core.
“This puncture-proof system enables construction vehicles to keep moving without the constant worry of tyre-related downtime,” the company said.
“Whether operating on rugged terrains or navigating debris-laden work areas, equipment out tted with TyrFil can maintain consistent performance, keeping projects on track.”
“TyrFil offers far more than just atproo ng – it’s an innovation designed to elevate the entire performance, safety, and longevity of your eet.”
Additional bene ts By protecting construction equipment against punctures, companies gain a host of bene ts that underpin the productivity and ef ciency of their business.
The TyrFil product can lead to reduced or eliminated downtime. The TyrFil solution means tyres stay operational in hazardous environments. Worksites in the quarrying environment present a rugged terrain for OTR tyres, but the TyrFil product enables the tyres to continue operating and avoid unplanned downtime, which can impact project deadlines.
TyrFil can also support reduced wear and tear on machinery. The quarrying environment can be especially harsh on any equipment, particularly heavy construction equipment. The properties of TyrFil enable lled-pneumatic OTR tyres to have reduced wear and tear, as it absorbs the shocks of the operating environment.
Operating heavy machinery for daily tasks can take a toll on operators. The working environment may cause operators to experience “solid shock,” which is triggered by the rough and jolting ride. The shock-absorbing properties of the polyurethane- lled pneumatics in TyrFil can reduce solid shock and, in some cases, prevent it from occurring.
“Tyre ll, known in the industry as foam ll, is a shock-absorbing, atproo ng alternative to solid tyres, which helps to prevent the harmful effects of solid shock and its unwanted companion – whole-body vibration,” Carlisle TyrFil said.
“Tyre ll is a polyurethane liquid that is pumped into pneumatic tyres to replace
the air with a resilient, synthetic elastomer core that eliminates at tyres and provides a smoother and safer ride.
“Recent testing con rmed that polyurethane- lled pneumatics transfer signi cantly less G-force than solid aperture tyres.
“The testing measurably validated that TyrFil, Carlisle’s branded ‘foam ll’ product, offers better shock absorption and a more comfortable, safer ride – something that should be imperative to OTR operators concerned with protecting their people and their equipment.”
The polyurethane ll in TyrFil can be reclaimed and reused, unlike the technology in solid tyres. This means business can reduce their land ll material and reduce operational costs while also supporting their environmental objectives by limiting land ll overcrowding.
“Choosing TyrFil is about more than just atproo ng. It’s about investing in a smarter, safer, and more sustainable future for your equipment and team,” the company said.
“TyrFil offers unparalleled bene ts that go far beyond tyre technology.
TyrFil transforms the way industries like construction, mining and agriculture approach tyre technology.” AB
Aggregates Business sat down with CheckProof chief executive o cer Håkan Holmgren to learn about the Swedish-based company’s exciting growth plans.
Håkan Holmgren’s face lights up as he talks about working at Rimbo Jord, his father Nisse’s quarrying business in Rimbo, north of Stockholm.
“I started at the age of 12 or 13, helping after school to repair wheeled loaders, excavators and screening equipment,” Holmgren told Aggregates Business
“Dad founded the company in the 1960s. It had around 45 employees and two quarries full of crushers, washing plants, trucks and all the other regular machines. I did everything – working evenings, running crushers, running washing plants.
“I eventually became the business’s CEO [chief executive of cer], and in 2009 we got a big new permit spanning over 105 more hectares of our Ledinge quarry. This allowed us to process a much higher volume of aggregate material.
“In 2011, Jehander [now Heidelberg Materials Ballast Sweden], a subsidiary of Heidelberg Materials, acquired our company.”
Shortly after acquiring Rimbo Jord, Holmgren joined Heidelberg Materials Northern Europe’s production performance team as a process development and project manager.
“The team went around lots of Heidelberg Materials Northern Europe quarries and other sites, reviewing how they operated, including their approach to maintenance, health and safety, quality and environment,” he said.
During Holmgren’s time at Heidelberg, he got to do site visits in the UK and Belgium.
“From working within and eventually running a family quarrying company, I knew all the issues around product [European] construction equipment marking, quality control, and people not doing the maintenance they should,” he said. “After starting work at Heidelberg Materials Northern Europe, I soon realised they faced the same challenges. Too many routine tasks were done on pen and paper and not carried out ef ciently.”
Being part of the production performance team gave Holmgren access to priceless quarrying process information, partly through the business’s aggregates academy and aggregates handbook. He trained his Swedish colleagues at Heidelberg Materials Ballast Sweden on compact Swedish versions of the aggregates academy.
“It [Heidelberg Materials Northern Europe] was an awesome place to work with great colleagues,” Holmgren said.
In 2014, one of Holmgren’s childhood friends, Jonas Pålgård, married into his wife’s family’s ship-loading company, where he worked in IT support. Pålgård’s dad was also a quarry foreman at Rimbo Jord, so the wider Holmgren and Pålgård families were also close.
“Jonas did much of his work on paper, such as safety checks and fuel consumption logging. It never worked well,” Holmgren said. “Jonas thought having an app that acted as a checklist and advisor for his work would be a good idea.
“We then started discussing the idea, and that’s pretty much how CheckProof started. Jonas had also previously worked as an art director, and we sat down over several evenings and weekends and began designing an app.
“After nalising some work projects, I resigned from Heidelberg Materials Northern Europe at the end of 2014. In 2015, Jonas and I started designing the rst CheckProof [software] codes, and we released the rst version of CheckProof in May of that year. We started working quite closely with Heidelberg Materials Ballast Sweden and Pålgård and Söner Kran.”
CheckProof provides a mobile- rst platform that simpli es maintenance management and health, safety, environment and quality processes. Combining intuitive technology with actionable insights, CheckProof helps companies in the construction materials sector and heavy industries follow routines, mitigate risks, minimise costs, and enhance safety.
“Around 2017, we realised that we needed to scale the CheckProof offer so there weren’t just two or three people working on it,” Holmgren said.
“We then searched for capital to enable us to run the business at scale. We secured investment, started to take on more customers, and developed the app to make it available in different languages.
“We now have around 350 customers in 38 countries. This includes major building materials companies, like Cemex and Heidelberg Materials, which use the system in multiple countries, and small and medium enterprises, including contract crushing companies with 15 to 20 employees. We have built a system that should solve all the operational pain points around maintenance, health and safety, environmental protection, et cetera, on one platform.
“We currently have over 40 employees based in our head of ce in Sweden, Germany and the UK. We are also recruiting in France, redeploying two employees to North America, and hiring six more people to work in that market. The US is huge. Texas alone is bigger than Sweden.”
CheckProof’s recruitment drive and business scale-up are largely funded by a summer 2024 investment from Viking Venture, a leading Nordic business-tobusiness software investor renowned for its
backing of fast-growing scale-up companies in the Nordics.
“Granitor Growth Management, another of our key investors, has a base in Indonesia, and we are building a CheckProof development team there. It means that later this year we will pass 50 employees,” Holmgren said.
Holmgren announced CheckProof’s of cial opening of its rst US of ce during a press conference in March at AGG1/World of Asphalt 2025 in St. Louis, Missouri. The news of the US of ce in Houston, Texas, came alongside con rmation that the Swedish company has registered its new US subsidiary, CheckProof US Inc.
“Opening a US of ce brings us closer to our customers, providing dedicated support in their time zone while expanding our presence in this key market,” Holmgren said.
“To accelerate growth, we’re hiring four sales executives and two customer success managers and relocating two key members from our UK team. This ensures we offer hands-on expertise and service to our growing customer base. Our goal is to provide digital solutions that optimise operations and drive continuous improvement.”
The aggregates industry, characterised by heavy machinery, complex operations, high safety risks, and navigating sustainability challenges, can signi cantly bene t from digital tools. Holmgren said paper-based processes are time-consuming and prone to errors, often leading to costly inef ciencies, resource strain, and overlooked risks.
Digitalisation and solutions like CheckProof address these challenges by streamlining data collection, automating insights, and enabling game-changing predictive maintenance to enhance operational ef ciency and ensure equipment reliability and workplace safety.
At CheckProof, telematics and integrations are central to enhancing operational ef ciency in the aggregate industry.
The platform connects to telematics systems across various machines and vehicles, regardless of brand. This integration enables seamless access to vital data such as fuel consumption, geographic location, idle time, error codes, and CO2 emissions.
CheckProof can then merge the machine data with frontline employee reports. This holistic approach allows businesses to proactively address deviations, monitor performance trends, and ensure compliance with maintenance routines – all from a single platform.
In addition, CheckProof offers integrations with original equipment manufacturer (OEM) industry leaders and third-party providers, offering vibration and temperature sensors and belt-weigher software. This helps users harness real-time insights and automate maintenance work ows, bringing the concept of a truly connected plant to life.
This approach transforms raw telematics data into actionable insights, driving operational improvements and creating smarter, more connected plants and sites.
CheckProof content specialist Anju Khanna Saggi is on the Aggregates Business call with Holmgren. She said the company uses a direct sales approach with salespeople recruited from the quarrying industry, giving them an instant connection with potential customers and a better understanding of their needs.
“Check Proof has a very open leadership style, and that same spirit of openness is seen in how the company works with customers to get things done,” she said.
Holmgren agreed with Saggi’s comments and said CheckProof’s success is rooted
in collaboration. By working closely with clients, the company re nes its platform based on real-world challenges and opportunities. This collaborative ethos fosters long-term partnerships, drives innovation, and ensures the platform remains indispensable to its users.
“When you start with CheckProof, you buy the software. You get assigned a customer success manager to help you work the system at the required scale. It’s taking things step by step, and there are system add-ons you can pay to have, depending on the scale at which you want CheckProof to work,” Holmgren said. “When you look at the work of a quarry manager, for example, they are on-site with responsibility for everything: plant operation and maintenance, walkaround inspections, site health and safety, implementing environmental best practices, and lots more.
“I remember being on a quarry site after a big crusher failed. A €50 air lter hadn’t been changed, so dust had entered the crusher’s oil tank, leading to a €55,000 repair bill and lost production time. The site team said, ‘Oh, we missed that’. Those things can happen continuously in the industry.”
CheckProof can assist with quarry employees’ regular routines, alerting them to technical issues and any checks and maintenance needed at timed intervals.
“It creates, in effect, a ‘My task’ list –showing everything that needs to be done on-site that day,” he said. “The success of CheckProof is based on how much you utilise it. We have multiple quarrying customer success stories. We have seen a 33 per cent reduction in yearly maintenance cost per tonne with the full use of CheckProof.
“In other instances, we have seen daily output increase up to 75 per cent on a site when they utilise CheckProof to drive behaviour change to improve operations. We are continuously working to develop the software to create even more value for our customers.”
Holmgren said CheckProof its focused on achieving its 2025 priorities.
“We are focused on expanding our sales team in North America,” Holmgren said.
“We will showcase CheckProof and highlight some new features of the software.”
Quarrying has long been a conservative industry, with many of its experienced professionals resistant to change.
A key part of Holmgren and his CheckProof colleagues’ mission is to persuade quarry operators to invest in the Software as a Service solution.
“It’s about showing the value of CheckProof, which includes demonstrating how easy it is to communicate with colleagues through the platform app, log an issue with a case number, comment on how it is being progressed, tagging particular colleagues, and then solving it. You don’t need a WhatsApp group,” Holmgren said.
“It’s about how you encourage the change to a digital approach.
“We had one client, an older man in his 60s, who told us he was ne with pen and paper and didn’t need any digital system. Six months later, he was standing on a stage at an internal company meeting, telling his colleagues how the CheckProof app could give him this and that and that he loved it.”
Holmgren said quarry operators can enjoy sustainability gains from using CheckProof.
“If you can make your equipment eet last longer by using our software, that’s good for your sustainability,” he said. “The eet optimisation you can get from using CheckProof, such as reduced machine idle time, is also a big sustainability gain.
“With our system, you can put all the telematics from your machine eet into it and can see an instant leaderboard in the app
showing which machine has the highest or lowest idle time. When we did a pilot study, we saw a 25 per cent reduction in eet idling. If you have a big machine eet, the reduced idle hours easily equates to replacing one less machine per year.”
In 2024, CheckProof was selected as a key vendor at the AggNexus Digital Innovation Conference at the University of Texas, Austin campus, highlighting its position as a leader in digital transformation for the aggregates sector.
On the event’s second day, Holmgren participated in a panel discussion on ‘Challenges and opportunities in digitalisation for the industry’.
During the hour-long session, Stockpile Reports developer David Boardman described data as “truly the new oil”, adding that capital expenditures for harvesting data will grow by an “order of magnitude”.
“AggNexus was inspiring. Seeing all the different digital solutions for the quarrying industry was great,” Holmgren said.
“There is huge potential to stage this event in other world regions, such as Europe.”
Holmgren said he has found the journey with CheckProof in the global quarrying marketplace to be an especially rewarding one.
“Once you start something, there is no turning back. You have to succeed, and you need that mentality ,” he said.
“We are clear on how to solve a problem in the [quarrying and wider construction materials] industry, and we want to keep going and make real changes for both the frontline workers and management.
“What drives me is receiving or hearing positive customer feedback. I remember early in the business when a colleague discovered a comment by our customer, Cemex UK in a LinkedIn post, describing CheckProof as a ‘game-changer’.
“It was incredibly rewarding.” AB
This year’s bauma exhibition in Munich saw several leading o -highway equipment names showcase eye-catching alternative-fuel-powered machines and concepts.
Agroundbreaking all-electric line-up from Volvo Construction Equipment (Volvo CE) pushed the boundaries of innovation at bauma 2025 in Munich, Germany, in April.
“This zero-emission line-up is a marker of our commitment to drive change,” Volvo CE president Melker Jernberg said. “Together with our pioneering service, solutions and updated portfolio of conventional machine variants, we show that we stand alongside our customers to support them across every stage of their journey.
“We show that we are committed to our ambitions, not just because we can but because it is the right thing to do.”
The star of the all-electric platform was the “game-changing reveal” of the A30 Electric articulated hauler, representing the rst in a key industrial segment for Volvo CE and the world’s rst serial-produced batterypowered solution of its size class.
It will be available to rent, alongside the larger A40 Electric, for select customers in select European markets in 2026, ensuring quarrying, mining and construction customers can now match high productivity with a more sustainable operation.
Volvo CE also showcased at bauma 2025 its conventional combustion engine options available to customers for all zero-emission models on display. These are designed to deliver claimed industryleading fuel ef ciency, with up to 15 per cent
improvements and exceptional productivity. This multi-technology approach ensures that Volvo CE provides versatile solutions for various customer requirements, wherever they are in their transformation journey.
Perkins’ growing portfolio has welcomed the addition of a new battery-electric power unit technical demonstrator, shown for the rst time at bauma 2025. Shown in a pipe fusion machine, the plug-and-play battery-electric power unit is designed to enable off-highway original equipment manufacturers (OEMs) to transition seamlessly from diesel to a batteryelectric powertrain.
“We’re actively helping customers navigate the shift in power system requirements, with a range of advanced power systems including electric, dieselelectric and alternative fuel compatible engines,” Perkins vice president of global sales, marketing, service and parts Jaz Gill said.
“When it comes to the innovative fully integrated battery-electric power unit, it can be ‘dropped in’ to a machine to replace a diesel engine.
"The system consists of a Perkins battery, inverters, motors and on-board chargers – all packaged up into a compact drop-in system to support seamless transition from diesel to electric for our customers looking to make that move.”
The Perkins battery-electric power unit has been tested in a McElroy TracStar 900i pipe fusion machine as a commercial demonstrator, with the battery-electric power unit replacing a 3.6L 904 Series diesel engine. The power unit’s compact design enabled the seamless transition from diesel engine to electric, with the power unit tting within the same chassis space and having the same mechanical connection and electrical interface points as the 3.6L diesel engine power unit it replaced.
“This is a fully integrated battery drop-in solution, reducing the need for OEMs to invest in costly engineering and design projects and allowing them to electrify their machinery quickly and cost-effectively, without sacri cing performance,” Gill said.
“I’d encourage anyone considering the move towards electri cation to come and talk to us about this drop-in solution, which can deliver a faster return on investment, while providing the owner–operator with a low-maintenance, cost-effective power solution.”
Hybrid power versatility
Project Coeus was showcased at bauma 2025. It saw Perkins partner with e-powertrain specialists Equipmake and Loughborough University’s Wolfson School of Mechanical, Electrical, and Manufacturing Engineering to develop an innovative, advanced con gurable-fuel drop-in hybrid power unit that can directly replace a diesel engine. The four fuels selected for inclusion in Project Coeus – ethanol, methanol,
bio-methane, and hydrogen – all have one characteristic: they are spark-ignited fuels, creating the project’s common con gurable combustion platform.
The rst phase of the project involves developing a 180–280-kilowatt (kW) hybrid power system.
This system will deliver a robust and trusted fuel-con gurable plug-and-play solution that produces consistent power performance regardless of the fuel type, ensuring long-term exibility for the user.
In addition to Project Coeus, Perkins highlighted what it has learned about diesel-electric hybrids and full electric applications. A diesel–electric hybrid demonstrator machine has been optimised to improve ef ciency without compromising performance.
In another project, Perkins has fully electri ed a technology demonstrator machine with a Perkins Li-ion battery.
John Deere Power Systems (JDPS) and KREISEL Electric (KREISEL) are developing battery and charging solutions to bring battery-powered equipment to key off-highway markets including construction, quarrying, mining, and material handling. At bauma 2025, attendees explored the latest advancements in battery technology, including the KBE.59.750M battery pack, estimated to be in production in 2026. The KBE.59.750M and all KREISEL batteries
feature Dynamic Performance Management, which uses patented cell immersion cooling technology and advanced software systems. This technology is engineered to optimise daily performance at extreme temperatures while meeting or exceeding industry safety standards.
Designed to prioritise energy density, runtime and seamless integration with off-highway machinery, KREISEL batteries feature a exible, modular architecture. Highperformance, high-durability batteries allow John Deere to provide all-electric vehicles and powertrains to off-highway equipment customers across equipment segments and applications. The serial production KBP63 battery pack was also displayed at bauma in the outdoor Wirtgen booth.
John Deere recognises that building a robust charging ecosystem is crucial to adopting battery-powered construction equipment. To effectively support the transition to electric-powered off-highway machinery, John Deere is committed to providing charging solutions that are as
versatile and adaptable as their job sites. This means developing stationary and mobile charging options with varying power outputs and charge times that can be scaled. With KREISEL, JDPS is pursuing charging solutions to serve off-road electric construction vehicles where typical grid infrastructure is unavailable or insuf cient.
JDPS showcased a concept mobile charging solution powered by KREISEL battery technology at the Wirtgen booth. This concept demonstrates the company’s focus on developing exible charging options that can be easily deployed wherever needed.
In addition to the mobile concept unit, the serial production CHIMERO stationary charger from KREISEL was displayed on the Wirtgen booth. The CHIMERO offers highpowered DC fast charging for locations with lower grid connections.
With mobile and stationary options, John Deere aims to provide its customers with the infrastructure they need to integrate electric-powered equipment into their operations seamlessly.
Hyundai Construction Equipment (Hyundai CE) had its HW155H hydrogen fuel-cellpowered wheeled excavator concept working on the demonstration area throughout this year’s bauma exhibition. The pre-production machine, rst seen as a static exhibit at the last bauma in 2022, demonstrated to customers how hydrogen could contribute to future carbon-free operation on construction sites across Europe.
A hydrogen fuel cell uses a chemical reaction between hydrogen carried on board and oxygen in the atmosphere to generate electricity. The only emission is water vapour. The fuel cell delivers power on demand to drive the machine, either through electric motors or via electrically driven hydraulic pumps.
The project to develop a fuel cell for the HW155H has been a cooperation between Hyundai CE and Hyundai Motor Company, which has a range of powertrain solutions available in the passenger car and utility vehicle markets.
Two cells have been designed, creating 30kW and 50kW of power, with the HW155H using a combination of fuel cells to provide 70–100kW of power. These fuel cells would suit a range of machines, including the 15-tonne wheeled excavator, forklift trucks and emergency generators.
The HW155H is a 15-tonne wheeled excavator that combines on-road and off-road capabilities, making it ideal for hydrogen power. The machine uses the fuel cell to power an electric motor, which then drives the hydraulic system. The hydrogen storage on-board has the capacity to allow a full eight hours of operation, with refuelling taking between 10–20 minutes.
Hyundai CE said hydrogen is a safe fuel, with an auto-ignition temperature higher than petrol or diesel. As it is 14 times lighter than air, hydrogen also disperses harmlessly into the atmosphere. Hyundai has developed a world- rst, innovative low-pressure hydrogen storage solution that offers high-density storage for extended operating autonomy.
Hydrogen diggers on UK roads
JCB has hailed the UK Government decision to change the law to allow hydrogen diggers to drive on UK roads.
Minister for the Future of Roads Lilian Greenwood signed a statutory instrument allowing hydrogen-fuelled construction and agricultural machinery to use the public highway from 29 April 2025.
JCB Chairman Anthony Bamford, who instigated a £100 million project to develop a hydrogen combustion engine to power JCB’s machines, called the news “historic”.
Lord Bamford’s reaction came as a hydrogen-powered JCB digger was driven around London’s roads to mark the momentous announcement, calling in at the Department for Transport on April 29 to meet Greenwood.
JCB has invested more than £100 million to produce a range of super-ef cient zero-emission hydrogen engines. This pioneering project at JCB’s engine plant in Derbyshire has been personally driven by Bamford, who challenged the company’s engineers to make a major breakthrough in the use of hydrogen as a fuel in a combustion engine.
JCB has been operating prototype hydrogen-powered Loadall telescopic handlers, backhoe loaders and generators on sites near Birmingham, and is now testing a range of equipment in partnership with rental companies and leading contractors across the UK.
“The JCB team has done amazing work to develop a hydrogen combustion engine. It has already been given resounding
backing from our customers who have been evaluating the technology; they say it is simple to use and performs as well as diesel counterparts,” Bamford said.
“We are delighted that the Government has now endorsed the use of hydrogen in machinery. There has been a lot of work to get to this point. It is truly a historic day for JCB and a milestone moment for the use of hydrogen as a zero-carbon fuel in the construction and agricultural machinery industries. We now have the legislation that allows hydrogen powered machines to drive on the road between sites and between farms.”
Greenwood signed the statutory instrument in early April to pave the way for an amendment to the Road Vehicles (Construction and Use) Regulations 1986
to enable the road use of hydrogen-fuelled non-road mobile machinery.
The change in legislation has come into force. Other hydrogen powered vehicles, including cars, buses and trucks were already permitted by law to use UK roads, but hydrogen-fuelled construction and agricultural machinery could not – until the amendment.
“We’re supporting the UK’s Plan for Change by working closely with brilliant British companies like JCB to harness the opportunities of the net-zero transition, driving innovation and creating jobs to put money in the pockets of hardworking people and secure our future,” Greenwood said. AB
Electric innovation continues at pace in the crushing and screening sector as manufacturers capitalise on growing consumer demand.
Sandvik Mobile Crushing and Screening has unveiled its latest innovation in tracked cone crushers, the QH443E.
Sandvik designed the new tracked cone crusher for crushing and screening operators transitioning to “greener” operations.
The release of the new unit completes Sandvik’s rollout of the electric train, which includes the UJ443E fully electric jaw crusher, the QE342E hybrid scalper, and the QA452E hybrid triple-deck Doublescreen. Sandvik began the rollout with the QE342e and the QA452e in 2022, and the UJ443E launched in 2023.
Sandvik Mobile Crushing and Screening division president Manny Moloney said the QH443E is Sandvik’s agship Q-Range electric-driven cone plant.
“This is just the beginning of our commitment to develop solutions that improve the productivity, safety, and sustainability of our customers’ operations,” he said.
“With its advanced capabilities, this technology is particularly well-suited for heavy-duty applications, including large quarries and mining operations, where maximising uptime and reducing environmental impact are critical.”
The QH443E combines electric drives and track mobility on a single platform. This hybrid unit bridges the gap between tracked mobile, wheeled portable, and stationary plants.
Sandvik has updated the tracked platform with a diesel/electric generatorbased drivetrain.
The QH443E is equipped with a suite of technological features that allow operators and quarry managers to make informed decisions. These include the Optik automation system and My Fleet remote monitoring. The centrepiece of Sandvik’s latest machine is the CH440 Hydrocone crusher, which features advanced settings, including the Hydroset CSS regulation and protection system.
The Hydroset CSS uses Constant Liner Performance (CLP) to track liner wear and optimise production throughout the machine.
Customers can choose between multiple chambers and settings to suit various applications. The choice enables quarry operators to ne-tune the QH443E to extract the most from their application.
These features make the QH443E viable for secondary or tertiary crushing in the quarrying or aggregates sectors. It can also work in an electric train with the aforementioned Sandvik equipment.
According to Sandvik, the fully electric track drives also reduce hydraulic oil usage by up to 91 per cent. The electric drives and the hybrid “e” drive of the QA452e Doublescreen allow the operator to run the train from the most economical energy source.
“Sandvik Mobiles has always been at the forefront of innovation, and completing the development of our tracked electric train marks a signi cant step towards a more sustainable and cost-effective future for the crushing and screening industry,” Maloney said.
Finlay’s future focus
Finlay has taken a major step in its manufacturing by unveiling the Finlay 883+ Electric Scalper.
The new unit is an addition to the 883+ model, which is designed to work as a primary or secondary screening application within quarry, sand, gravel or construction and demolition waste applications.
Finlay has equipped the 883+ Electric Scalper with a redesigned feeder, which includes hydraulic folding and locking extensions and the ability to rear-feed material. The hopper has been upgraded with wear-resistant steel and different hopper linings.
The 883+ Electric Scalper can be operated using mains power, including grid electricity, or a genset, which enables customers to reduce operating costs and operate in a lower-noise environment. The electric drive system operates the feeder, screen box and conveyors, which can help customers reduce their carbon footprint.
Finlay’s business line director Matt Dickson said the upgrades came about after receiving feedback from the Terex Materials Processing brand’s customers and distributors.
“As our agship model, the 883+ has always set the standard for performance and versatility,” he said. “The 883+ Electric Scalper represents a forwardthinking solution for businesses looking to reduce their environmental impact, while continuing to bene t from the superior performance and exibility that Finlay equipment is renowned for.”
Six of the best Metso has of cially launched the sixth model of its Nordberg HPe crusher series in another range expansion.
The Nordberg HP450e is the latest model in the HPe series, which debuted in 2023 and has grown substantially in the past two years. The range now includes solutions across the production process, encompassing secondary, tertiary and quaternary crushing.
The market response has been positive, with more than 200 units sold globally, while older HP models have been retro tted with the HPe upgrade kits.
According to Metso, the Nordberg HP450e crusher delivers enhanced performance due to its redesigned, ef cient crushing chamber. It has more head motion, 13 per cent more power, and 20 per cent more force than previous models.
The HPe series also makes it an environmentally friendly option, as it does not require a backing material. The six HPe crusher models have 10 different chamber pro les and advanced simulation software. They can be con gured for various applications, including wheelmounted Nordwheeler setups, modular Nordplant installations, and track-mounted Lokotrack units.
"With the latest addition of the Nordberg HPe crusher series, we are able to offer customers the ideal balance of power and ef ciency for their speci c crushing needs,” Metso’s Aggregates business area product manager of HP Cones Ilkka Somero said.
Metso has debuted the Nordberg HP450e crusher.
“The HP450e, as a mid-range unit, is designed for customers who require reliable, high-capacity crushing without excessive energy consumption. With this unit, we have further improved its application exibility so that customers get the maximum production and yield of wanted end products.”
Metso shared how its stationary screens are con rmed to meet the safety standards set by the European Union (EU), including the EU standard (EN 1009-1:2020).
The EU standard (EN 1009-1:2020) refers to the safety requirements and veri cation required when designing and constructing screening machinery for quarrying, recycling, and processing minerals and by-products.
The EU standard sets the minimum distance requirements for the intermediate space between screens, which Metso said is met by most of its stationary screening range.
According to Metso central region screen business line vice president Adrian Wood, the manufacturer has a role in ensuring a safe working environment.
“Good equipment design should create safe working and operating conditions. Our stationary screens not only meet but exceed current safety requirements set by the European Union,” he said.
“This easy access is critical as screen maintenance and inspection interventions are frequent, with not only regular weekly and monthly routine-based condition checks but potentially regular replacement of screen panels which must be carried out safely whilst still aiming for the shortest possible maintenance downtime.”
Oceania expansion
McCloskey has con rmed Rokbro Material Processing Equipment has joined as its latest New Zealand dealer.
Under the agreement, Rokbro will represent McCloskey’s full line of crushers, screeners and stackers.
“We are excited to be joining the McCloskey network and to bring their
top-tier equipment to New Zealand,” Rokbro Material Processing Equipment director Dane Fitzpatrick said. “The reputation of McCloskey in the industry is second to none, and we are eager to represent their products, which will empower our customers to optimise productivity and performance.”
The announcement will expand McCloskey International’s presence in the New Zealand market and for its existing customers in the country.
“We are thrilled to partner with Rokbro Material Processing Equipment,” McCloskey International’s sales and marketing director Anthony Bouvie said.
“Their reputation for excellence and deep understanding of the local market make them the ideal partner to represent our brand in New Zealand. Together, we are committed to offering high-quality products and outstanding after-sales support to help our customers achieve success in their operations.” AB
Caterpillar has signed an agreement with Luminar.
The role of technology in the quarrying and aggregates industry has never been more important, especially when it comes to hauling and transport.
Technology has caused many major advancements in the quarrying and aggregates sector, with several recent examples underlining their potential.
Attendees to bauma 2025 in Munich, Germany, saw what was said to be the world’s rst serial-produced battery-electric articulated haulers for their size class.
Volvo Construction Equipment (Volvo CE) unveiled the A30 Electric and A40 Electric, marking a signi cant milestone for the manufacturer.
Volvo CE said the zero-emission models can be combined with conventional combustion engine options to support customers transitioning to more sustainable fuel sources.
“This zero-emission line-up is a marker of our commitment to drive change,” Volvo CE president Melker Jernberg said.
“Together with our pioneering service, solutions and updated portfolio of conventional machine variants, we show that we stand alongside our customers to support them across every stage of their journey.”
The A30 Electric and A40 Electric will be available for rent for select customers in select European markets in 2026.
Volvo CE has complemented the launch of its new zero-emission line-up with several service solutions, including a new load ticket tool and two new services, site operations and site optimisation.
The load ticket tool is designed to streamline invoicing. The site operations service is a brand-agnostic eet monitoring tool, with the site optimisation tool functioning as an advisory service for customers to enhance their operations.
These solutions were showcased at Volvo CE’s interactive Solutions Bar at bauma 2025.
“Our industry’s transformation may be slower than we would like, but our commitment remains strong as we continue to invest in building a better world for all – as demonstrated by our pioneering 100 per cent zero-emission line-up at the recent bauma show,” Jernberg said.
Caterpillar’s collaboration Technology improvements are creating a range of improvements in the hauling space, not just limited to electric-drive equipment.
Caterpillar recently announced a collaboration with Luminar, which will see LiDAR (light detection and ranging) technology in its next-generation autonomous solutions, including the Cat Command for hauling. The Cat Command is designed for quarry and aggregates operations.
The rst development in this collaboration will see a Cat off-highway truck feature two Iris LiDAR with a unique integration system designed exclusively for Caterpillar.
LiDAR supports navigation and obstacle detection in autonomous machines. The technology uses light as a pulsed laser to continuously scan the surrounding environment and provide high-precision measurements of the shape and size of nearby objects.
“We are proud to collaborate with Luminar on our next-generation autonomous solution,” Caterpillar chief technology of cer Jaime Mineart said. “We’ve invested in autonomy and automation for more than 30 years, and we’ve seen how it adds value for our customers in terms of safety, productivity and ef ciency.”
Luminar chief executive of cer and founder Austin Russell said the partnership marks an important milestone for the company.
“[It] has the opportunity to be a spearhead for the next industrial revolution of automation,” he said.
“Now that Luminar has successfully executed for automotive series production, we’re able to branch out to adjacent markets with a shared mission. Together, we look forward to saving lives and enhancing pro tability for Cat customers around the world with industry-leading capabilities.”
Komatsu unveils new dump truck
Komatsu Europe has revealed the HD605-10 rigid dump truck as the latest addition to its customer hauling line-up. The company has designed the HD605-10 to be a workhorse in the quarrying and aggregates sectors.
The rigid dump truck features a 610 kW Stage V engine with three selectable modes, including economy, economy light, and power, so operators can adapt to suit their applications. Also included is a new cooling system and a lightweight body option to deliver fuel ef ciency and reduced operating costs for customers.
The HD605-10 includes a strengthened transmission, torque converter, main frame, differentials, and nal drive components to operate in a quarry’s harsh environment. Operators can also use the new features, including hill start assist and cruise control, to make the operation easier.
The HD605-10 rigid dump truck was demonstrated for bauma 2025 attendees in April, when the trade show took place in Munich, Germany.
Komatsu Europe product manager Juuso Ahola said the HD605-10 rigid dump truck is the perfect partner for the WA700-8.
“Our development teams have prioritised customer needs to deliver a machine that not only builds on the reliability of its predecessor but also introduces signi cant performance enhancements,” he said.
“These enhancements include increased power, weight reductions, expanded load capacity up to 64 tonnes with 43 m³ body, improved durability, enhanced visibility systems, and reduced fuel consumption.” AB
Komatsu’s HD605-10 rigid dump truck can pair with the WA700-8.
Non-genuine, counterfeit or fake parts can place operations at considerable risk.
Genuine parts for crushers and screens are an essential part of the promise that original equipment manufacturers (OEMs) make to the market – to keep their customers’ projects pro table and their businesses sustainable.
On the other side of the coin, however, are the risks that non-genuine, counterfeit or fake parts place on operations, according to Metso distributor Pilot Crushtec sales and marketing director Francois Marais.
“OEMs like Metso spend decades developing and supporting technologies that provide customers with reliable and high-performance solutions for crushing and screening,” Marais said.
Genuine large parts like gears help to ensure optimal performance, reliability and minimal downtime.
“However, this work is quickly undone when non-OEM parts are installed in our equipment, supposedly to save a few rand in maintenance costs.”
Marais said the performance and reliability of Metso’s equipment is based on its proven design and precision engineering. This includes the various components and wear parts that must be replaced from time to time. Copied parts from other sources do not carry this technical heritage, undermining performance and reliability.
Metso vice president for aftermarket distribution management Merja Tyyni said it also impacts the value of the relationship that OEMs work so hard to build with their customers.
“Our customer relationships focus on the whole process of delivering value to their operations,” Tyyni said. “We pay attention to the end-product value, where we can supply not only the appropriate capital equipment but also the follow-up troubleshooting, repairs and overall technical advice.”
The quality of these solutions and services is based on years of research, development and testing, as well as continuous investment in the necessary technical infrastructure and capability to respond quickly to customer needs. However, all these efforts are compromised when customers place non-OEM parts into their machines, as the quality chain is only as strong as its weakest link.
Metso head of aftermarket for Europe, Middle East, Africa and Central Asia Karima Dargaud said that OEMs have in-depth knowledge of their equipment that allows customers to achieve results that are optimal and predictable.
“Our OEM spares are an essential aspect of the support we provide, so that customers can reliably meet their production targets and avoid costly penalties,” Dargaud said.
“Customers build their reputations on this consistent performance, by producing the right results safely, on time and within budget. Using non-OEM spares only puts this reputation at risk, as machines then become unreliable.”
The OEM pitman is designed for optimal performance and reduced wear in every crushing operation.
OEMs like Metso design and manufacture their own spare parts to help ensure customers achieve optimal results.
The extreme forces and speeds that are often involved in heavy machinery mean there are also safety considerations for not using the speci ed parts in crushers and screens. Metso wear parts have been designed and manufactured with specialised material and hardening techniques, for instance, to ensure safety and performance.
“Fake parts will compromise worker safety, as there are normally a number of people in close proximity to this equipment who could be affected by a failure,” Marais said.
“A business that buys and ts pirate parts runs the risk of sending a negative message to its operators – that saving money is more important than the safety of crews on site.” AB
Headquartered in Sweden, Nordic Construction Company is geared for sustainability-minded growth despite many market challenges.
According to the Swedish Transport Administration, it is estimated that the country’s building and construction market has a turnover of approximately SEK 750 billion (€68.06 billion).
But it is not immune to current-day pressures. A recent Business Wire report found that Swedish construction industry output declined in real terms by about 6.1 per cent in 2024. Higher construction materials costs, rising energy prices, and a wider economic downturn affected building activity
with fewer building permits and the persisting weakness in the country’s residential sector. Such headwinds have led to delays or the cancellation of some of the country’s biggest construction projects
Sweden, the largest nation in the Nordic region, has several strong construction-sector players, many of whom combine their building activities with the production of construction materials.
One such leading business is the Nordic Construction Company (NCC).
NCC’s origins go back to 1890, when Axel Johnson, a well-known Swedish businessman, established Nordstjernan – the North Star, which later became one of the leading Nordic shipping companies.
The NCC Group was legally formed on January 1 1989, when two companies – JCC and ABV – united. In 2024, NCC had sales of about SEK 62 billion (€5.62 billion).
The Nasdaq Stockholm-listed Group has around 11,800 employees and builds residential properties, industrial facilities, public buildings, roads, civil engineering structures, and other types of infrastructure. NCC also sells aggregates, asphalt, and other construction materials, ful ls paving contracts and has a commercial property development division.
Grete Aspelund is head of NCC Industry, NCC’s subsidiary, which focuses on producing stone materials and asphalt, foundation work, and asphalt paving.
She told Aggregates Business that NCC’s construction materials production business is important because it allows the group to offer a comprehensive package for Sweden’s major infrastructure projects and the wider construction industry in the country and other Nordic states.
According to Aspelund, NCC’s stone and asphalt business, also known as the NCC Industry business area, develops, produces and sells stone materials and asphalt products for construction and infrastructure projects in Sweden, Norway, Denmark, and Finland. The business accounts for approximately 20 per cent of NCC’s sales. NCC Industry produced and sold 5.1 million tonnes of asphalt and 25.6 million tonnes of aggregates in 2024.
NCC has about 50 asphalt plants and 200 quarries and stone material sites in the Nordics and offers aggregates, asphalt production, paving services, ooding prevention products, asphalt with a lower CO2 footprint, and different stone products.
“We do environmental product declarations [EPD] and also work to ensure biodiversity in the areas where we are active – during application, operation, and part of the rehabilitation,” she said.
Due to the Nordic states’ serious climate goals and requirements for reducing their
carbon footprints, NCC pays close attention to sustainability issues.
Aspelund said NCC would continue transitioning its operations to be even more sustainable. This will comply with more rigorous Swedish Government sustainabilitybased legislation around using raw materials and lower-carbon-emitting equipment coming into force in 2035. NCC is also looking to be a climate-neutral business by 2045.
“Demands from customers, authorities and legislation require a continuous adaptation and development of our offering and also to be a driver in establishing recognition of the importance of both primary and secondary aggregates in developing sustainable societies,” Aspelund said.
NCC is working with customers, suppliers, and other stakeholders to develop new building materials using virgin, recycled, and mixed materials to cater to an evergrowing demand for circular-economy-based products. Some of these products will likely help meet the higher demand for building materials for huge onshore and offshore projects in Northern Europe and the Baltic region.
NCC has introduced several circulareconomy-based building materials in recent years, including NCC crushed concrete and NCC machine sand.
The crushed concrete can replace virgin materials such as natural gravel, rock and sand in various building works. Using NCC crushed concrete and other recycled crushed concrete is a cost-effective way of protecting natural resources. Its production starts with the company gathering demolition concrete, which is checked and sorted based on composition and properties. It is then manufactured according to applicable standards and technical speci cations based on the intended use area, with a CE mark obtained where required.
compactors working at Denmark’s Great Belt Bridge (Storebæltsbroen).
NCC machine sand (MCC Maskinsand) can replace natural sand or gravel in concrete production, asphalt production, sports and recreational infrastructure, and civil engineering projects. It is also suitable for tackling slippery roads, cable sand, and sealing layer applications.
Aspelund said climate change affects all of society and fully supports the construction industry’s efforts to minimise and counter its impact. As a prominent aggregate producer, she is keen for NCC to play an important role in works focused on, among other applications, coastal erosion control, coastal and riverbank protection, and road reconstruction.
“We have a portfolio of solutions to offer to various stakeholders, both as preventive solutions and solutions to manage and restore [eg NCC armour stone], both within our Nordic countries and through export to countries in Northern Europe,” she said.
Regarding NCC’s approach to sustainability in its stone materials and asphalt production, Aspelund said it is working to eliminate greenhouse gas emissions from its entire value chain, while simultaneously increasing energy ef ciency. The company currently works in several areas of its stone and asphalt production to reduce emissions; for example, electri cation of mobile stone crushers, which will deliver extensive energy ef ciency gains, electri ed transport in all countries, energy converting asphalt plants to run on biofuel, developing asphalt products with a lower climate
impact (eg focusing on biofuel, mixing in recycled asphalt and lower temperatures) and replacing fossil bitumen with bio-based binders in the asphalt.
Aspelund said NCC actively uses digitalisation and automation solutions in its stone materials and asphalt production, and realises the importance of arti cial intelligence (AI) technologies.
“We have a structured approach to reducing the impact of our operations by continuously improving production ef ciency and striving to give more than we take from nature,” she said.
“This is done by implementing digital tools to improve ef ciency in our production plants. When we nd an identi ed need, we implement new technologies, like AI.”
Aspelund said that by collecting extensive production data and input from company machine operators, NCC management gains valuable insights into various aspects of group operations. This detects inef ciencies, optimises resource usage, and enhances overall production ef ciency.
“Through continuous monitoring and analysis, we can make data-informed decisions to improve our production ef ciency and achieve our sustainability goals,” she said. “The collected data provides a comprehensive view of the production environment, empowering our team to implement targeted improvements and drive sustainable change throughout our operations.”
NCC can provide customers with Environmental Product Declarations (EPDs) documenting the environmental performance of its products in a transparent, objective and standardised way.
Aspelund said EPDs make it easier for NCC customers to calculate and meet their environmental goals. By actively engaging in lifecycle analyses and EPDs, the company can observe how its production and resource ef ciency improvements improve its climate impact.
NCC has also achieved “signi cant” progress in electrifying its production, according to Aspelund. This is partly re ected in all of its stationary crushing plants being electri ed, and the fact purchase agreements for renewable electricity have been signed in all Nordic countries.
Furthermore, all of NCC’s mobile crushing units are now diesel-electric hybrids. Aspelund said that while there can be issues around accessing enough electric power from local grids to run a complete NCC electric-powered machine eet, there has been a sizeable increase in NCC mobile plant production now powered by grid electricity. During 2024, 36 per cent of the group’s mobile plant production was powered by renewable electricity.
NCC Industry uses AI technology to detect large boulders in customer trucks. Until recently, identifying boulders (large stone blocks) in truckloads of excavated rocks has always been challenging for the group. The boulders reduce ef ciency and pro tability, as they incur additional handling costs since they must be manually sorted and broken into smaller pieces before they can be put in the crusher.
NCC Industry’s AI solution, based on Microsoft’s AI service in the eld of computer vision, analyses photographs of truckloads to predict the likelihood of boulders being present. A customer can be invoiced for the additional costs if a boulder is identi ed.
NCC has a long-term development strategy extending beyond the next decade. In February 2025, Aspelund played a central role in the wider group’s strategic review of the NCC Industry business area. The review evaluated various strategic options, including a possible divestment. The purpose was to review the best way to develop the business area going forward and to increase shareholder value in NCC.
Aspelund said NCC Industry has a leading market position and has developed a strong product and services portfolio, offering many further growth opportunities. It has signi cantly increased its pro tability by focusing on operational discipline and customers’ needs.
As a leading company in the Nordics, NCC Industry has already taken a prominent position in asphalt with a lower carbon footprint. AB
12-month partners get priority on the best branding opportunities.
Aggregates Business is a go-to source for up-to-date news and views on the European, American, Asian, African and Middle Eastern aggregates and building materials sectors. Our wide-ranging features line-up includes in-depth articles on the latest crushing and screening, loading and hauling machines.
A rich variety of next-generation o -highway machine engines has created considerable industry interest and excitement.
Cummins’ next-generation X15 Off-Highway engine platform was a big draw at bauma 2025 in Munich, Germany.
The latest addition to the US-headquartered company’s off-highway line-up is part of the Cummins Higher Ef ciency, Lower Emissions, Multiple Fuels (HELM) fuel-agnostic engine platform. It promises original equipment manufacturers (OEMs) and end users a list of advancements over its predecessor, powering large-scale construction and industrial equipment such as wheeled loaders, cranes, excavators, air compressors, and more.
Telematics, lower fuel consumption, easier maintenance, and long life to overhaul are all bene ts new Cummins X15 customers should count on to improve their bottom line, according to the company.
“We’ve introduced a simpli ed clean sheet design that offers numerous bene ts for our OEM partners and end users adopting the next-gen X15 off-highway,” Cummins vice president of engine business engineering Jonathon White said.
“Customers will see powerful performance and higher ef ciency now in a lighter, smaller package, all while maintaining the steadfast durability Cummins has long been known for in construction applications.”
According to Cummins, the latest off-highway X15 delivers up to 10 per cent better fuel economy than the prior X15 model, with comparable ratings and duty cycles. The X15’s high-ef ciency fuel injection provides precise fuelling and combustion control at ultra-high pressures. Together with the newly optimised HE550 Wastegate turbocharger, the system offers excellent transient response and altitude capability, built with new upgraded materials for durable and reliable performance.
Alongside improvements in fuel ef ciency, the next-generation X15 also promises cost savings related to routine maintenance.
New adopters can expect up to 1000hour service intervals from the X15, according to Cummins, which means less overall maintenance is required. Coupled with an improved design, whereby its fuel lter and oil drain now share the same
replacement interval, common service items can occur simultaneously, which results in less downtime and improved maintenance planning for eets.
The X15 now also offers a maintenance-free breather and has no exhaust gas recirculation system, which will collectively cut down on maintenance costs for new customers. In addition, the new platform has been designed to provide a long life to overhaul, resulting in potentially more productivity and a stronger return on investment.
Capabilities to support remote monitoring and diagnostics, together with over-the-air (OTA) software updates, make maintaining engine health a less costly pursuit through the next-gen X15’s telematics features.
Jobsite service professionals can take advantage of priority-ranked real-time alerts and be paired with Cummins engineering recommendations on how and when to service potential issues before they progress. When Cummins releases new engine calibrations, the X15 OTA programming capabilities allow for secure software updates using cellular connectivity.
Both digital technologies help reduce the need and cost for technician dispatches and unnecessary service stops, while ensuring more timely and accurate diagnostic reports and up-to-date engine calibrations. These digital capabilities require a compatible OEM gateway and a participating telematics service provider.
In addition to lower total operating costs, the next-generation X15 will be more easily installed into machine equipment.
With more than 20 ratings that range 298–522kW and peak torque up to 3200Nm, off-highway OEMs upgrading their offerings with Cummins’ next generation X15 will be
able to deliver higher power and torque to customers with less weight and a smaller package size that resembles a 13L engine.
The X15 has many OEM integration options and application features, designed for easier installation and service. Modular component design further simpli es the integration process for off-highway equipment manufacturers, providing added exibility to reach key connection points while reducing the number of components by 30 per cent in critical systems such as cooling and lubrication.
Meanwhile, the ex-module aftertreatment with a new mixer design simpli es the installation, offering various installation con gurations to meet the needs of different applications better. The elimination of the exhaust gas recirculation system (EGR) reduces the cooling system requirements for machines.
The new X15 is also available without after-treatment to support varying regulations across countries, simplifying integration across different regions.
“As the world’s largest independent diesel engine manufacturer, our volume allows us to invest in new and innovative technologies to meet future requirements and emissions,” Cummins vice president of engine business global off-highway markets Marina Savelli said.
The bauma showcase included, among other platforms, the award-winning Cat C13D and a new high-power C3.6 delivering 106kW.
“In turn, we can bring exciting innovations to the market and help power our OEM partners’ success well into the future.”
Fuel-agnostic engine platform
Cummins is developing various solutions, including three new clean-sheet engine platforms designed to meet future emissions and CO2 norms.
The B, L and X engine platforms will be compatible with a variety of current and future low- and zero-carbon fuels, including natural gas, clean diesel, and hydrogen.
This means it’s possible to integrate these solutions, including the X15, into OEM equipment with limited proliferation by deploying Cummins HELM platforms. These platforms leverage common base engine hardware and unique fuel or air handling solutions to operate on varying fuel sources.
The ability to select different fuel types without requiring signi cant changes to the machine equipment makes X15 integration even more noteworthy. Customers who use Cummins HELM platforms can choose to power with clean diesel or biofuels today and move to a lower emissions alternative, like hydrogen, in the future.
Powered up
Caterpillar Industrial Power Systems
showcased a range of optimised, fuelexible engines, integrated advanced power technologies and services solutions at bauma 2025. The theme, ‘A journey to a lowercarbon future’, highlighted Caterpillar’s ongoing commitment to sustainably powering a better world.
The 13L Cat C13D diesel engine platform is designed to achieve best-in-class power density, torque and fuel ef ciency for optimising the performance of heavy-duty off-highway applications. Engineered to Caterpillar’s standards for reliability and productivity, the inline, six-cylinder Cat C13D engine platform will offer eight power ratings from 340–515kW with up to 3200Nm of peak torque. Engine-mounted after-treatment and cooling packs will also be available from the factory to reduce installation and validation costs.
The C13D will meet the emissions standards of highly regulated markets, such as EU Stage V, US EPA Tier 4 Final, China Nonroad Stage IV, Korea Stage V, and Japan 2014, with models available for less regulated markets.
By supplying more power and torque available from Caterpillar’s current 13-, 15- and single-turbo 18L engine platforms, the C13D platform provides an opportunity for OEMs to downsize the engine and simplify design, assembly, and supply chain requirements across multiple applications. This consolidation can also reduce maintenance, parts and technical training complexity for end users.
The Cat C13D, which goes into production in 2026, is designed for use in a wide range of off-highway equipment, including rock crushers, screeners and grinders; trenchers; agriculture tractors, harvesters and self-propelled sprayers; woodchippers; material-handling equipment; and large industrial pumps.
“Off-highway OEMs and equipment owners face a rapidly evolving business environment that demands improved worksite productivity and reduced operating costs while addressing increasingly stringent emissions standards,” Caterpillar Industrial Power Systems senior vice president Steve Ferguson said.
L–R: The Cat 13L C13D engine is designed to achieve best-in-class power density, torque and fuel e ciency; the Cat C3.6 delivers 106kW of power and addresses customer needs for more power from a compact package.
“Internal combustion engines are the prevailing workhorses on most jobsites around the world, which is why we’ve invested in the next-generation Cat C13D diesel engine platform to address their challenges.”
The engine platform offers up to a 20 per cent increase in power and up to 25 per cent more low-speed torque over the previous generation of Cat engines in its power class. It is designed to perform at altitudes of up to 12,000ft, which is twice as high as legacy Cat engines, and in extreme ambient temperatures as high as 60 °c (140°f) and as low as -40°c (-40°f) with aids.
Extended service intervals – 1000 hours oil and fuel lter – will reduce operating costs and downtime. By modularising and eliminating components, its architecture is space-protected to accommodate con guration adjustments anticipated for future tiers of emission standards in the US and EU without relocating customer connection points.
The Cat C13D engine platform can be powered by renewable liquid fuels such as 100 per cent hydrotreated vegetable oil (HVO), up to B20 for models with aftertreatment and B100 for models without after-treatment. The machine’s core architecture is designed to support future development for alternative fuels such as natural gas and hydrogen.
In late-2024, Caterpillar started work on an advanced hydrogen–hybrid project,
leveraging the versatile new C13D engine platform. The three-year program will develop a transient-capable system for off-highway applications, demonstrating how state-of-the-art control systems and electric-hybrid components can help hydrogen-fuelled engines match traditional diesel engines’ power density and transient performance.
The 100kW Cat C3.6 engine platform has seen a six per cent power boost over its predecessor and is designed to address customers’ needs for more power in a compact package.
To enable customers to extend the lifecycle of their engine across their eets, Caterpillar Industrial Power Systems also exhibited at bauma 2025 a range of exible parts and services solutions to support each stage of the engine lifecycle, including extended service contracts, customer value agreements, parts, repair options and its global dealer network.
904 Series diesel engine. Its compact design enabled the seamless transition from diesel engine to electric, with the power unit tting within the same chassis space and having the same mechanical connection
An interactive simulator promoted the importance of condition monitoring for proactive diagnostics and a right- rst-time x to reduce downtime.
The Caterpillar Industrial Power Systems’ stand also featured an eye-catching deconstructed Cat C7 Reman engine, including Cat remanufactured parts and end-of-life parts, also known as ‘core’. The display showed the contrast between core and Cat Reman parts to highlight the remanufacturing processes in Caterpillar facilities.
Cat Reman products help OEMs extend their machine’s lifecycle, reduce waste, and keep the engine running strong. Fully assembled and ready to run, Cat Reman complete engines are dynamometer-tested and tuned for like-new performance and fuel ef ciency.
With an extensive offering from simple components to overhaul kits to complete engines, Cat Reman enables customers to reduce downtime, quickly get back into operation and bene t from like-new performance on the toughest jobs.
Available in 2026 and showcased at bauma 2025, the Perkins 2600 Series engine platform is designed to meet the demands of construction and many other off-road, heavyduty applications.
According to Perkins, the 13L diesel engine platform achieves power density, torque, fuel ef ciency and productivity. Industrial open power units con gured with engine-mounted after-treatment and cooling packs will also reduce installation and validation costs for OEMs.
The 2600 Series will meet the emissions standards of highly regulated territories. Its engine platform also enables the use of renewable fuels like HVO.
The Perkins stand also featured the new 106kW variant of the 904 Series platform. With a six per cent power uplift from the
Perkins said its 2600 Series achieves best-in-class power density, torque, fuel e ciency and productivity.
100kW model and a three per cent increase in torque, the new offering is ideally suited to applications that need more power in a compact package. The standard offering also comes with electro-magnetic apical treatment (EMAT) to minimise installation costs.
The Perkins 904J-E36TA has been tted with a new 12-plate oil cooler to improve the engine’s durability and reliability, while high-ef ciency fuel lters improve altitude capability. The engine meets EU Stage V, US EPA Tier 4 Final, and Japan 2014 emissions standards. It can also run on a range of fuels, subject to the fuel meeting Perkins’ speci cations, including 100 per cent HVO1.
“Perkins continues to invest in and optimise its established internal combustion engine platforms to make them even more ef cient and fuel exible,” Perkins vice president, global sales, marketing, service and parts Jaz Gill said.
“OEMs want the exibility to use multiple fuels without sacri cing power, reliability or ease of integration. The new 2600 Series and higher power 904 Series deliver high ef ciency with ease of integration, helping our customers achieve their objectives without a full re-design of their machine.”
Perkins’ growing advanced power portfolio has welcomed the addition of a new battery-electric power unit technical demonstrator, shown for the rst time at bauma 2025. Shown in a pipe fusion machine, the plug-and-play battery electric power unit is designed to enable off-highway OEMs to transition seamlessly from diesel to a battery-electric powertrain.
The Perkins battery electric power unit has been tested in a McElroy TracStar 900i pipe fusion machine as a commercial demonstrator, with the unit replacing a 3.6L
Given today’s customers operate in a fast-paced world where cost-effective engine management and operational ef ciency are an absolute necessity, Perkins has developed a comprehensive connectivity and conditionmonitoring solution to meet customers’ requirements and deliver measurable bene ts to OEMs and operators.
the space measurable operators. engine
from monitoring and insights that are sent to the
A telematics data sharing application programming interface (API), is available for OEMs to share engine data from pre-existing telematics systems, supporting equipment owners with enriched advanced analytics from the engine, supported by condition monitoring and insights that are sent to the customer’s engine support ecosystem.
“Seamlessly linking to customers’ equipment, Perkins connectivity solutions improve operational control,” Gill said.
“Whether monitoring performance or optimising ef ciency, the real-time insights and proactive support available from the Perkins distribution network help to minimise downtime through faster service response times and an increased rst-time x rate, as well as signi cantly reduced costs.
“The importance of protecting your engine investment for a lifetime is a key message at bauma, with an interactive display on the bene ts of register, maintain, extend and replace. Together, these four actions optimise engine performance throughout its entire life cycle,” Gill said.
“This approach enables our customers to prevent downtime and reduce the total cost of engine ownership, all while ensuring their worksites run ef ciently and effectively.”
Volvo Penta shifts with customer demands
Volvo Penta has streamlined its dealer network, focusing on stronger and highly specialised partners in response to shifting customer demands and the increasing complexity of industrial equipment.
“Our customers don’t just need an engine supplier – they need a long-term service partner who understands the challenges of their industry,” Volvo Penta industrial head of global service market Björn Säljö said.
“By re ning our dealer network, we’re ensuring that every partner has the technical expertise, nancial strength, and investment capacity to provide world-class service and adapt to the future of power solutions.”
The strategy furthers the specialisation of Volvo Penta’s dealer network across the broader service ecosystem, which includes OEMs and their retail channels. Volvo Penta aims to secure seamless support from traditional diesel power to emerging electri cation and data-driven services by aligning expertise and capabilities across these key partners.
Volvo Penta said it is moving towards a “service-driven ecosystem”. At bauma
2025, the company highlighted how service contracts now support engine sales, such as performance-based service agreements that optimise uptime and reduce operating costs, subscription models for predictive maintenance and remote monitoring, and bundled solutions covering a holistic service ecosystem to maximise equipment ef ciency.
“Our customers increasingly prioritise operational ef ciency and long-term value over one-time purchases,” Volvo Penta industrial service market manager for Central Europe Judith Karl said.
“Our service-and-performance- rst approach aims to integrate predictive analytics and connectivity to enhance uptime, optimise costs, and ensure that businesses stay competitive.”
Volvo Penta brings the strength of its industrial expertise to construction equipment. The company leverages extensive experience in ports, mining and material handling and ensures that eets bene t from the same high-reliability service standards used in the most demanding industrial sectors.
At the core of Volvo Penta’s service transformation is connectivity, driven by advancements in Internet of Things (IoT), digital twins, and real-time eet analytics. These technologies enable real-time engine monitoring to help minimise downtime and optimise maintenance costs.
By integrating data-driven insights into service contracts, Volvo Penta can help enhance long-term operational value and performance. This approach supports modular contracts for electri ed equipment, off-highway productivity solutions, and engine services designed to boost ef ciency and cut emissions.
Guided by its ‘Made to Move You‘ tagline, Volvo Penta aims to drive its future of industrial services with dynamic partnerships that power ef ciency, reliability, and longterm customer success.
A new era in power
At bauma 2025, John Deere Power Systems (JDPS) embraced “a new era in power”, according to John Deere director of global marketing and sales Nick Block.
“This means developing technologies that not only meet today’s needs but also anticipate the challenges our industry will face in the years to come,” he said.
“We believe the future of power is not de ned by a single solution but by a range of options that allow our customers to choose the best t for their operations.”
The JDPS show line-up included the Next Generation engines – the JD4, JD14 and JD18. These platforms are built from a cleansheet design and engineered to power the construction industry, now and in the future. Designed for lasting performance, these engines deliver impressive power density, optimised fuel ef ciency, and streamlined serviceability; all critical features for working on today’s rugged jobsites.
JDPS also continues to improve its current offerings. Attendees of bauma 2025 learnt that the JD9 engine provides more power than the John Deere PSS 9L engine and offers streamlined integration,
making it ideal for a wide range of construction applications.
The optimised JD9 builds on the proven performance of the existing 9L engine to offer lower complexity and installation costs while maintaining the renowned John Deere quality and reliability.
Whether with purpose-built engines for a range of construction needs or optimised versions of trusted models, JDPS is dedicated to providing its customers with reliable, powerful, and ef cient solutions for the future of construction. JDPS offers customers comprehensive after-market solutions designed to keep equipment running strong.
At bauma, JDPS showcased its robust service network, which includes more than 9000 service locations worldwide with skilled engine experts ready to assist.
Attendees also learnt about the John Deere Lifecycle Service Solution, a complete service package that includes engine maintenance plans, PowerGard Protection Plan, and John Deere Connected Support. These solutions provide customers with the tools and support they need to proactively manage maintenance and optimise the performance of their John Deere engine. AB
With recycled materials becoming increasingly important in the construction materials sector, manufacturers are meeting this need through new machines and innovations.
Recycled material usage in infrastructure projects is only set to increase due to an expanded push from outside and within the construction materials sector to become more environmentally friendly.
BP Mitchell is an established name in London’s construction materials space. From its headquarters in Hertfordshire, north of London, the producer processes mixed construction and asphalt waste for various uses.
Construction and demolition waste, or asphalt waste, can present a unique challenge for a construction materials provider and differ in its production cycle from virgin rock.
BP Mitchell operates a large wash plant where recycled materials can be cleaned for further processing and a Ciber asphalt plant for its asphalt-related products.
When it comes to crushing and screening equipment, the Hat eld-based company turns to one name: Kleemann.
“Our goal is to produce recycled material of the highest quality possible. To achieve this, we invest in high-quality, cutting-edge machinery,” BP Mitchell managing director Brendan Mitchell said.
“What impresses us time and again about the Kleemann plants is their innovative features and outstanding ease of use. Our people nd the machines very easy to handle. Everything can be adjusted and operated intuitively and conveniently.”
BP Mitchell recently purchased a new MOBIREX MR 100i NEO mobile impact crusher for its operations.
This recent addition expands the company’s existing Kleemann eet, which includes four MOBICAT jaw crushers, two MOBISCREEN coarse material screening plants, and a MOBIBELT mobile stacker.
BP Mitchell’s plant in Hat eld produces material for road substructures (Type 1, less than 40mm grain size) and provides further processing for the washed plant. It also recycles asphalt grains smaller than 20mm for the Ciber asphalt plant.
The MOBIREX MR 100i NEO was selected because it can handle sticky materials and mixed feed materials.
The crusher’s features, including the automatic crushing cap adjustment, enable it to handle this varied load of materials with ease.
This means the MR 100i NEO can easily switch between washing plant feeding and processing recycled asphalt (RAP).
“The crushing gap adjustment can be operated at the push of a button – de nitely a highlight in this machine class,” Mitchell said. Kleemann designed the MOBIREX MR 100i NEO to handle a high production load while also requiring low-fuel consumption. The balance can be tricky to strike, but BP Mitchell has noticed the new Kleemann machine only consumes 11L of fuel per hour while producing up to 60 tonnes per hour of 0–20mm grain size.
“The advice and service we receive are rst-class,” Mitchell said. “We know that we can rely on the on-site technicians, and that gives us real peace of mind.”
success
Due to the signi cant demand for recycled construction materials, some manufacturers are beginning to specialise in equipment for the sector.
Screencore’s international distributor network has supported a growing list of producers of recycled construction materials. This group of dealers and distributors has provided Screencore equipment to the US, French, UK, Australian, and South African markets.
Screencore offers a range of solutions, including tracked jaw crushers, Trident scalper-screens, Orbiter trommels and radial stockpilers to customers working in the sector.
The company can also develop a bespoke selection of stationary recycling plants based around its Orbiter trommel range, which works alongside Screencore’s stockpilers and scalpers.
“The Screencore product range was developed to meet the needs of the modern contractor and materials handling operation. We have set out to build the highest standards of equipment that helps people in the eld be more pro table, ef cient and effective in what they do,” Screencore director Ciarán Ryan said.
“We have also incorporated environmental ef ciency into our processes to minimise customers’ carbon footprint. All this has meant that working with our distributors
Screencore o ers a range of solutions for recycled construction materials.
has seen Screencore equipment adopted on numerous projects, turning construction waste into reusable and/or resaleable products.”
The ScreencoreXJ is a machine crusher with a dual-power 1000x650mm jaw crusher. The crusher is fed demolished or excavated materials by an excavator or loading shovel before crushing to -100mm.
Any ferrous metals, such as rebar or wire, are easily removed for resale or recycling by the overband magnet on the XJ crusher’s discharge conveyor before being fed into the Trident 124 scalper/screener.
The Screencore XJ Dual-Power Crusher is easily transportable due to its lightweight, allowing contractors and rental eets to move it with ease. The combination of the Screencore XJ Dual-Power Crusher and Trident 124 scalper/screener can be set up in less than 30 minutes.
“Screencore will custom-design conveyors, stockpilers and feeders to meet application requirements,” Ryan said.
“Our designs are renowned for their quality and ease of assembly, arriving in neatly packed containers and speci ed to over-deliver on throughput expectations.
“We also supply a range of air separation systems for stationary and mobile plants.
“Screencore has gained much experience using electric power from various sources. Main electricity has proved to be an ideal power source, delivering a cost-effective and environmentally ef cient solution.
“Through this power source, or the dual-power solution, precision processing of materials is accomplished without producing the emissions that would be of concern, and at the same time, at a low [operating] cost.” AB
Hyundai’s HX230e is a 25-tonne machine powered by a 420kWh battery pack.
A vibrant quarrying-suited loader market is giving buyers many new, highly innovative, and sustainability-minded models in which to invest.
Hitachi Construction Machinery (Europe) (HCME) has unveiled Hitachi’s vision for the future of construction equipment with its pioneering excavator concept: LANDCROS One. HCME said this innovative machine development “represents a fundamental shift in how machinery interacts with operators, job sites, and the broader construction ecosystem”.
Launched at bauma 2025 in Munich, Germany, LANDCROS One brings HCME’s forward-looking vision to life through design collaboration with Granstudio, an automotive and mobility design studio.
“LANDCROS One showcases Hitachi’s vision of a safer, smarter and more sustainable future, blending groundbreaking AI [arti cial intelligence], gami ed ergonomics, autonomous and remote operations capabilities,” HCME president and chief executive of cer Francesco Quaranta said. “We’re proud to lead the next wave of innovation, empowering the next-generation
workforce and rede ning possibilities in the construction machinery industry.”
The concept introduces what HCME calls a “phygital” approach – the seamless integration of “physical” controls and “digital” interfaces to create an intuitive operator environment.
The innovative design features a modular cab with intuitive ergonomics, speci cally engineered to appeal to the next-generation workforce through gamifying operations and AI-assisted interfaces.
HCME’s LANDCROS One is said to be based on four transformative innovation pillars:
The concept’s integrated AI and automation systems fundamentally change the operator experience by handling routine tasks and providing intelligent assistance during complex operations.
The functional design integrates cameras, sensors and advanced digital assist systems co-developed with strategic partners.
With combined onboard and offboard landscape scanning capabilities, including drone technology, HCME called LANDCROS One a “cornerstone in creating a comprehensive construction ecosystem”.
This intelligent support system reduces operator fatigue, increases productivity, and helps address the industry’s ongoing labour shortage by making advanced equipment more appealing to newer operators.
LANDCROS One features advanced connectivity and remote operation capabilities. The machine can be controlled from virtually anywhere, enabling true 24–7 operation through different time zones and allowing (specialised) operators to work across multiple sites without physical relocation.
These capabilities maximise equipment utilisation and enhance safety by removing operators from remote, dif cult and hazardous environments while maintaining precise control over operations.
Recognising the diverse needs of today’s construction workforce, the excavator offers three distinct operation modes:
• Manual Mode provides complete control for operators supported by AI for standard or complex tasks, reducing fatigue and increasing productivity
• Autonomous Mode is triggered by operator instructions for repetitive and predicted tasks
• Remote Mode enables full operation from any location, 24–7, providing exibility with operator availability worldwide
Adaptive power systems for every jobsite
Environmental responsibility meets operational exibility with the concept’s propulsion system available in three distinct power modes: electric, combustion and hydrogen.
“At Granstudio, we are proud to have partnered with Hitachi to bring to life a revolutionary concept excavator that rede nes the future of construction equipment,” Granstudio founder and creative director Lowie Vermeersch said.
“By blending our expertise in design and innovation with Hitachi’s engineering excellence, we have created a vision that pushes the boundaries of ef ciency, sustainability, and user experience.”
This concept demonstrates how HCME’s engineering and design expertise can challenge conventional approaches to construction equipment. The result is machinery that is more powerful and ef cient, intuitive, adaptable, and connected.
“LANDCROS One is more than just a machine. It’s our commitment to deliver solutions beyond machinery in a new construction ecosystem,” Quaranta said.
“We’re building a smarter tomorrow together with our strategic partners and customers.”
Komatsu’s operator-centric excavators
Komatsu Europe has unveiled the all-new PC220LC-12 and PC220LCi-12 excavators.
With these premium machines, Komatsu said it has successfully uni ed “striking aesthetics,
intuitive ergonomics, extreme fuel ef ciency, ultra-low emissions, effortless performance, revolutionary levels of digitalisation, and comprehensive safety measures into a single, truly exceptional operator-centric package”.
These state-of-the-art machines result from Komatsu’s long-standing commitment to innovation and excellence. The company said the new machines are engineered to set a new benchmark for performance, ef ciency, operator comfort and digitalisation across the construction industry, to deliver “extraordinary customer value”.
“Our approach to the next generation PC220LC and PC220LCi excavators was completely in line with our philosophy of creating value together,” Komatsu Europe product manager Paul Dickinson said.
“We visited numerous customers’ jobsites, listened to their needs, and brought those requirements back to our innovation and technical centres.
“Concepts were born, checked with customers, re ned, checked again, and by continually listening and innovating, we now come to market with a product bursting with customer value.”
The PC220LC/LCi-12 is built on an all-new, powerful 129kw high-torque Komatsu next-generation engine paired
Komatsu’s PC220LCi-12 o ers unique iMC 3.0 features.
with the new high-ef ciency electronically controlled hydraulic system. This translates to an 18 per cent reduction in average fuel consumption, saving customers approximately 2.1L per hour compared to the previous model. This means lower operating costs and a reduced environmental footprint with minimal CO2 emissions per tonne of material moved.
The new hydraulic system, combined with large-class hydraulic cylinders and highcapacity hydraulic pumps, delivers a seven per cent increase in arm and bucket forces allowing for easier digging and material movement, reducing tonne costs.
The advanced hydraulic system translates to sharp re exes and zero-lag response to the operators’ input, creating an intuitive connection where the machine and driver become one, Komatsu said.
Furthermore, the all-new P+ mode increases productivity by 18 per cent and fuel ef ciency by 20 per cent, offering substantial cost savings, improved output, and an uncompromised return on investment.
Beyond ease of operation, Komatsu said the all-new cabin design takes operator comfort to an “unprecedented” level.
A signi cantly larger cab with 30 per cent more legroom and an all-new premium seat option ensures operators can comfortably work. Fifty per cent increase in lower righthand side visibility, overhead cooling vents, joystick steering as standard, and numerous storage spaces further contribute to a pleasurable working environment.
Advanced operator assist technology complements these physical improvements. A high-de nition eight-inch touch-panel monitor provides intuitive control and easy information access. Moreover, the machine features ultra-versatile, programmable, super-ergonomic electronic control levers and fully customisable hydraulic settings that
allow operators to tailor the machine to their speci c needs.
Thanks to the operator ID system, which stores up to 50 pro les, operators are recognised via electronic key or typed ID, and their personalised settings are automatically loaded.
In addition, advanced technologies, including an integrated payload metre, integrated 2D machine control designed for simple depth and slope grading, and a 2D virtual safety wall, are provided as standard on PC220LC-12.
Built on Komatsu’s more than 10 years of experience in factory-integrated intelligent Machine Control (iMC), the PC220LCi-12 offers unique iMC 3.0 features.
Compatible with tiltrotator, iMC 3.0 offers advanced features such as 3D boundary control and automated steer-to-line. Advancing towards autonomous operation, iMC 3.0 introduces auto swing, enabling semi-automatic truck loading. Features such as swing-to-line and travel-along-line functionalities further simplify trenching operations for operators of any skill level.
The new 10-inch iMC 3.0 monitor, with intuitive 3D graphics, is a leading driver assist system.
With Smart Construction Remote as standard, customers can seamlessly transfer design les remotely and troubleshoot by taking over the screen, eliminating unnecessary site visits.
The PC220LCi-12 features an advanced payload meter, optimising loads and preventing overloading. Connecting with the optional Smart Construction Fleet allows automatic transmission of truck information to the excavator, so no manual input is necessary.
PC220LC-12 owners can access these features via a factory-made upgrade. This comprehensive kit provides a straightforward pathway to integrate the full suite of iMC 3.0 features so the investment remains future-proof.
“We pioneered fully factory-integrated machine control on excavators back in 2014. Those more than 10 years of constant development, deep experience of learning from customers, and fully supporting them on the jobsite to get the best out of this type of technology has led to these truly unique assist features we see on iMC 3.0,” Komatsu Europe product manager Rob Macintyre said.
The PC220LC/LCi-12 has many advanced safety features, including a 360° KomVision system, an optional human-detection system and rollover avoidance indicator for absolute situational awareness and accident prevention.
Komatsu excavators have long been synonymous with exceptional durability. With the Dash 12 generation, Komatsu presents an even more robust machine that offers durability and resilience, regardless of application. This is made possible by implementing heavy-duty strengthened work equipment, including a new reinforced heavy-duty boom, arm, upper structure, and a new track frame design.
The PC220LC/LCi-12 also features low-cost maintenance with extended service intervals. Engine oil changes are required every 1000 hours, double the previous 500 hours.
The hydraulic oil lter replacement interval has tripled to 3000 hours, and DPF cleaning is scheduled every 8000 hours.
Building on Komatsu’s commitment to customer satisfaction and longterm performance, the PC220LC/LCi-12
is supported by the Komatsu Care programme, so every customer can enjoy absolute peace of mind throughout the lifecycle of their machines.
The PC220LC/LCi-12 made its highly anticipated international debut at bauma 2025. Visitors witnessed the machine’s capabilities rst-hand through dynamic, live outdoor demonstrations, while a static indoor exhibit allowed people to jump in the operator cab and check out the machine’s most innovative features.
The presentation at bauma 2025 was the rst opportunity for a global audience to experience the PC220LC/LCi-12 outside of Japan.
Cat 395 FS on show Caterpillar chose bauma 2025 to unveil the Cat 395 Front Shovel Large Excavator, the company’s rst new front shovel con guration in 15 years.
Designed to meet the exacting needs and expectations of quarrying and mining customers, this new model fully takes advantage of standard next-generation features, such as fuel economy and low maintenance costs, while further improving Caterpillar’s world-class levels of operator comfort and control.
“The 395 FS has an of cial target launch of October 2025,” Caterpillar senior product and sales consultant Vincent Migeotte said.
“But there’s no better place than bauma to showcase the pre-production model and have potential customers see it in the metal. We’re excited to have the 395 FS join the Large Excavator line-up.”
Migeotte said three primary objectives were at the top of the design wish list for the 395 FS: robust digging and breakout force, lightning-quick loading cycles, and rigorous bucket full.
“Customers repeatedly told us that they need a machine that not only offers peak performance but that can operate consistently at those peak levels,” he said.
“That’s borne out in the 395 FS with a maximum ground level digging force up to truck height, matched by a powerful breakout force at the bucket cutting edge that promises superior material penetration and optimal bucket ll factors.
“And of course, that’s complemented by bucket capability. Here’s a machine that’s compatible with bucket volumes up to 6.5m3, or maximum material density of up to 1.85t/m3. That offers operators a big boost in productivity.”
Caterpillar’s values of durability, reliability and serviceability are woven through the design of the 395 FS, evident in features such as the reinforced, extra-durable undercarriage and additional cylinder guards, plus long-life fuel and hydraulic oil lters to reduce costs and downtime.
There’s also the assurance conveyed by all next-generation models sharing common parts, backed up by Cat dealers’ far-reaching customer service and celebrated product support.
Operator-oriented in-cab controls are easily accessible, enhancing material penetration, fast loading, and smooth oor clean-up. Inside, the cab features an ergonomic seat, a touchscreen display, climate control, noise insulation, and vibration reduction, all contributing to a more comfortable and ef cient operating experience.
“Of course, a machine only delivers its best performance when it works in harmony with its operator, which is why we’ve paid so much attention to operator optimisation through next generation developments,” Migeotte said.
“The 395 FS has been engineered with a parallelogram-type front linkage, coupled with a master cylinder that allows the operator to extract the machine’s maximum capability. By keeping the bucket parallel to the ground, the operator can optimise penetration, loading, sorting and breaking, and complete a smooth oor clean-up when the hard work’s over.
“Building the 395 FS around the nextgeneration cab, we’ve also tted a xed riser which allows the operator to see above the side of the truck body while loading. Premium work task visibility helps increase both productivity and worksite safety.”
Develon transparent bucket Develon, formerly Doosan Construction Equipment, has introduced the Transparent Bucket 2.0 (TB2.0) system, an advanced safety and visibility system for the company’s wheeled loaders. Designed to eliminate blind spots, TB2.0 improves both operator safety and jobsite ef ciency.
Traditional wheeled loaders create blind spots in front of the machine due to the raised bucket, posing serious safety risks. The Develon Transparent Bucket solves this problem by using high-tech front-mounted cameras to create a real-time see-through effect on the cab monitor. This gives the operator a clear view of the obstructed area, ensuring greater awareness and precision when handling materials such as aggregates, sand and soil.
Building on the success of the previous version of the system, TB2.0 introduces AI-powered Object Detection and Object Recognition to provide enhanced safety and real-time hazard alerts.
AI-powered Object Detection identi es objects – including people – within 10m and immediately alerts the operator with a red triangular warning on the monitor. With Object Recognition, the system learns the position of the bucket and automatically adjusts the composite image to match the movement of the bucket, ensuring accurate real-time visualisation.
TB2.0 integrates two cameras mounted on the cab and front frame to create a seamless, curved projection composite image of the space in front of the bucket. This helps to ensure the display dynamically adjusts as the loader moves, maintaining a clear, uninterrupted view for the operator.
As part of TB2.0, Develon has improved the warning system with colour-coded alerts that instantly communicate the level of danger to the operator:
•Red ashing border – if an object is detected within the bucket’s transparency zone, the monitor ashes bold red to indicate immediate danger
•Yellow ashing border – if an object is detected outside of the visibility zone, the monitor will ash thick yellow, signalling a potential hazard
These instant, intuitive alerts help operators make quick, informed decisions to prevent accidents and improve work ow safety. While it forms an intelligent additional safety solution that dramatically improves visibility and safety, Develon said it remains a complementary tool and operators should always visually inspect their surroundings and not rely on the system alone.
LiuGong battery-electric expertise
LiuGong showcased its expertise in batteryelectric vehicle technology at bauma 2025, highlighting more than a decade of development and real-world application. Among its comprehensive line-up were the 975F excavator and the 890T wheeled loader.
As the agship model of the T-Series, the 890T has undergone over 20,000 hours of rigorous testing, ensuring exceptional reliability and ef ciency. With a load capacity of 10.5 tonnes and a 5.4m³ bucket, it offers enhanced fuel ef ciency, increased operator comfort, and total maintenance access, making it the ideal choice for demanding mining and quarrying applications.
A heavy-duty 75-tonne class excavator, the 975F has been tailored to the needs of European customers, offering durability, ef ciency and operator comfort. It features LiuGong’s latest F-Series cab, which enhances visibility and control and makes it an industry powerhouse in demolition and quarrying applications.
Hyundai concept meets reality
Hyundai Construction Equipment (Hyundai CE) demonstrated a concept full-size electric crawler excavator at bauma 2025. The HX230e is a 25-tonne machine powered by a 420kWh battery pack, which will provide up to eight hours of operating autonomy between charging stops.
An optional 503kWh battery will extend potential working time. The excavator has a regular AC charging input and a rapid CCS2 DC charging capability, allowing quick battery recharging to deliver maximum productivity.
The charge powers an electric e-pump, which drives the excavator’s hydraulic system. In addition, it has an e-swing slew motor, an e-thermal management system, and an auto sleep setting to maximise operation ef ciency. The excavator boasts a full electronic hydraulic control system, allowing the operator to customise each hydraulic function to match the task and increase ef ciency.
The HX230e offers performance similar to a conventional diesel-powered machine of the same weight, but with zero emissions at the tailpipe and a lower operating noise level. This will become increasingly important as major cities worldwide impose increasingly stringent emissions regulations on off-highway equipment over the coming years.
Hyundai CE said many contractors and equipment rental businesses are already calling on manufacturers to offer diesel power alternatives for their machinery.
The company is committed to building a sustainable construction site through its rapidly expanding electri ed and hydrogenpowered machinery line. The HX230e is expected to reach production by the end of 2027.
Hyundai CE also unveiled the rst two models in the Next Generation of crawler excavators as part of its bauma 2025 showcase.
Hyundai’s award-winning DX08 diesel engine powers the 36-tonne HX360L and 40-tonne HX400L and features many new technologies to make operation easier and safer and boost customer productivity.
The six-cylinder Hyundai DX08 engine is a clean-sheet design that develops up to 254kW and a powerful 1460Nm of torque. A two-stage turbocharger contributes to a 23 per cent higher power output than previous engines. The EU Stage V/Tier 4F engine is constructed of high-strength materials, with wear resistance to all major drivetrain components.
The result is improved performance and economy, with lower operating costs.
The engines boast an eight per cent fuel ef ciency gain over older designs. Oil lter and engine oil change intervals have been extended to 1000 hours of operation, reducing cost and cutting downtime. The engine meets EU Stage V emissions regulations without needing costly exhaust gas recirculation (EGR), and diesel particulate lter (DPF) cleaning intervals are extended up to 8000 hours.
The Next Generation cab delivers a new level of operator comfort and control. Premium leather seating is available, with heating and cooling functions. Two 12.8-inch high-de nition monitors are on offer, and the electro-hydraulic lever and pedal controls allow the operator to set the response and speed of each individual hydraulic function to suit their own preference.
Hyundai’s popular Advanced Around View Monitoring (AAVM) has been upgraded to Smart Around View Monitoring (SAVM). The new machines boast six cameras, including three embedded into the counterweight, in place of the previous four-camera system. With the help of AI, the system automatically detects human presence within the operating area, with images shown on the large monitors in the cab.
Wide-opening access panels provide easy service and maintenance, with engine oil
and fuel lter intervals extended from 500 to 1000 hours. Coolant changes are set at 6000 hours, and DPF ash cleaning is at 8000 hours, reducing downtime and boosting productivity. The machines have a reversible cooling fan, making removing debris from the cooling radiators on dusty jobsites easier.
CASE introduces 421G
CASE Construction Equipment is lling the gap between its compact and medium wheeled loaders with the launch of the 421G. With an operating weight of 8970kg, the machine has been designed to work with a 1.5m³ standard bucket or a 1.7m³ lightmaterial bucket.
Powered by a 3.6L Fiat Powertrain Technologies (FPT) turbocharged diesel engine, the 421G boasts a rated power of 72kW and a peak power of 84kW at 200rpm –backed by a strong 453Nm of torque.
The engine utilises FPT’s proven SCR-T after-treatment system to minimise emissions. The machine is equipped as standard with an ECO operating mode and cruise control to reduce fuel consumption and emissions.
The EU Stage V engine drives through a two-speed ‘shift-on- y’ hydrostatic transmission that seamlessly transitions between the two drive ranges. The transmission delivers a 40km/h maximum speed, with a 20km/h speed limiter as an option. It has a creep setting as standard. The heavy-duty axles have a standard limited-slip differential front and rear and an optional 100 per cent differential lock.
Though working within compact overall dimensions, the 421G has a straight tipping load with a standard bucket of 6500kg and a full-turn tipping load of 5500kg. When equipped with pallet forks, that full-turn tipping load is 4200kg. Payload with forks is a competitive 3360kg, and the lift arms have a hinge pin height on 17.5 R25 tyres of 3707mm. With a bucket, the breakout force is 7161kg. The machine has standard boom and bucket setting modes and a boom oat. AB
JULY 2025
2–3
PNG Industrial and Mining Resources Exhibition and Conference
Location: Port Moresby, Papua New Guinea
Organiser: Prime Creative Media
Tel: +61 466 602 893
30–31
IQA 2025 NSW Safety and Health Conference
Location: Hunter Valley, Australia
Organisers: Institute of Quarrying Australia
Tel: +61 2 9484 0577
SEPTEMBER 2025
23–25
Asia-Pacific’s International Mining Exhibition
Location: Adelaide, Australia
Organiser: Prime Creative Media
Tel: +61 3 9690 8766
16–19
NSSGA Legislative and Policy Forum 2025
Location: Washington, D.C. US
Organiser: National Stone, Sand and Gravel Association (NSSGA)
Tel: +1 (703) 525 8788
OCTOBER 2025
14–15
BULKEX 2025
Location: Warwickshire, UK
Organiser: Materials Handling Engineers Association
Tel: +44 1257 412635
2026
3–7
CONEXPO CON/AGG
Location: Las Vegas, US
Producer: Association of Equipment Manufacturers
Tel: +1 (866) 236 0442
JUNE 2026
23–25
Hillhead 2026
Location: Buxton, UK
Organiser: The QMJ Group
Tel: +44 (0) 115 945 4367
To fully enhance the performance of your rigid haul truck, choose EARTHMAX SR 468. Its unique tread design with special tread compounds makes it perfect for hard, rocky and tough mining conditions, while its tread lug blocks with circumferential grooves and intertwined blocks ensures effective heat dissipation.
EARTHMAX SR 468 is developed using BKT’s cutting-edge technology to carry heavy loads, deliver longer service life and provide resistance to rock cuts and punctures.
For info: europe@bkt-tires.com
ASIA-PACIFIC’S INTERNATIONAL MINING EXHIBITION
23-25 SEPTEMBER 2025
Adelaide Showground, South Australia
Register to attend AIMEX’s inaugural event in South Australia