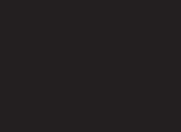
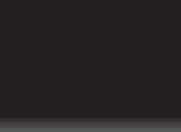
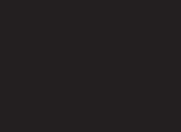
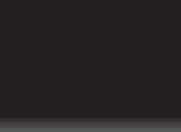
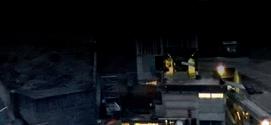
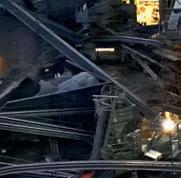
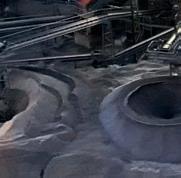
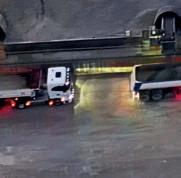
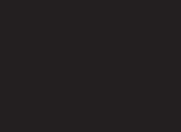
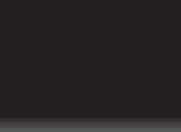
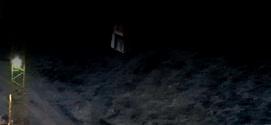
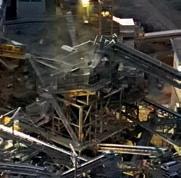
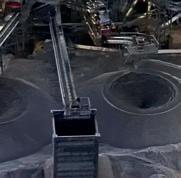
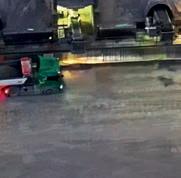
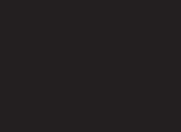
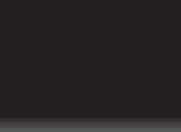

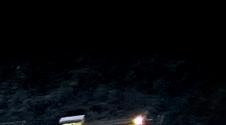
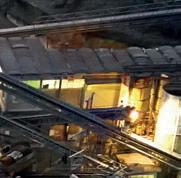
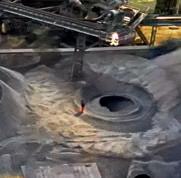
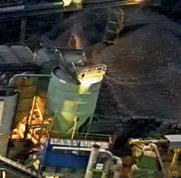
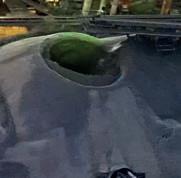
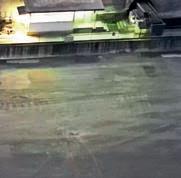
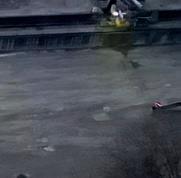
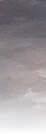
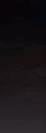
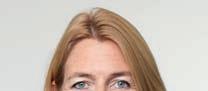
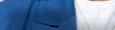
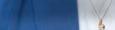

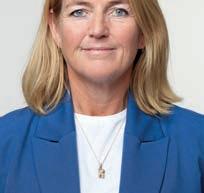
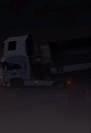






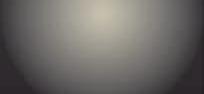




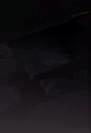







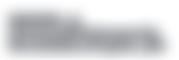












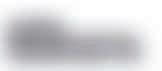
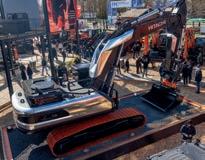

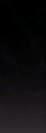


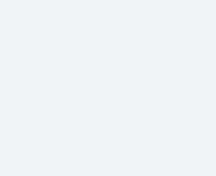
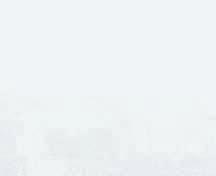
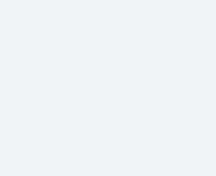
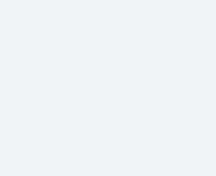
Compact, powerful and versatile: Introducing the MOBISCREEN MSS 502 EVO mobile coarse screening plant. Its compact size, low transport weight and impressive feed capacity of up to 350 tonnes per hour ensure that this versatile machine can be used flexibly and quickly for even the most heavy-duty applications in natural stone and recycling. The compact MSS 502 EVO, with its advanced ergonomics, was designed for exceptional operability. It can also be operated electrically thanks to its optional dual-power drive. The MOBISCREEN MSS 502 EVO: the (small) multi-talented powerhouse.
www.wirtgen-group.com/mss-502-evo-kleemann
“We
A
The
and updates from Aggregates Europe – UEPG. 50
All the key events in the quarrying and aggregates world.
An in-depth look at how Cat’s longtime Italian dealer CGT and Cave Pegogna work together.
Heidelberg Materials forges ahead with its decarbonisation initiatives.
CheckProof CEO Håkan Holmgren discusses the company’s rise from a small Swedish start-up business and its recent expansion to the US. 24
Cat’s long-time Italian dealer CGT and Cave Pegogna have a special relationship. Image: Cave Pedogna
A look at how alternative fuels are influencing the quarrying and aggregates sectors. 28
Electric innovation continues in the crushing and screening sector as manufacturers capitalise on demand. 30
Technology has never been more important in the quarrying and aggregates industry.
32
Non-genuine, counterfeit or fake parts can place operations at considerable risk.
Next-generation
HEAD OFFICE
Prime Global Publishing Capitol Square 4–6 Church Street Epsom, KT 17 4NR
EDITOR
Guy Woodford +44 (0) 7879 408 069 guy.woodford@primeglobalpublishing.com
ASSISTANT EDITOR
Adam Daunt adam.daunt@primeglobalpublishing.com
BUSINESS DEVELOPMENT MANAGER
Les Ilyefalvy +61 423 177 966 les.ilyefalvy@primeglobalpublishing.com
CHIEF EXECUTIVE OFFICER
John Murphy
CHIEF OPERATING OFFICER
Christine Clancy
GROUP MANAGING EDITOR
Paul Hayes
CLIENT SUCCESS MANAGER
Janine Clements +61 432 574 669 janine.clements@primeglobalpublishing.com
ART DIRECTOR Michelle Weston
COVER IMAGE CREDITS Cave Pedogna Hitachi Cummins Nordic Construction Company
SUBSCRIPTIONS subscriptions@primeglobalpublishing.com
No part of this publication may be reproduced in any form whatsoever without the express written permission of the publisher. Contributors are encouraged to express their personal and professional opinions in this publication, and accordingly views expressed herein are not necessarily the views of Prime Global Publishing. From time to time statements and claims are made by the manufacturers and their representatives in respect of their products and services. Whilst reasonable steps are taken to check their accuracy at the time of going to press, the publisher cannot be held liable for their validity and accuracy.
PUBLISHED BY
Prime Global Publishing
AGGREGATES BUSINESS USPS: is published six times a year.
PRINT: ISSN 2051-5766
ONLINE: ISSN 2057-3405
PRINTED BY: Warners (Midlands) PLC
A great industry and
really enjoyed April’s bauma 2025, the world’s biggest exhibition for construction, quarrying, mining, and recycling equipment. There was so much new product and linked technology showcased and so much interesting discussion on the key off-highway machine topics of sustainability, digitalisation, machine automation, and how advances in arti cial intelligence (AI) are enhancing original equipment manufacturers’ (OEMs) products and services offer to customers while simultaneously empowering industry professionals to make more informed business decisions.
I was among around 600,000 visitors from more than 200 countries enjoying the surprisingly warm early spring sunshine while taking in the eye-catching OEM stands and demonstrations at the Messe München Exhibition Centre.
Over the next few issues of ABE, you will be able to read about everything I saw and heard. The Aggregates Business website will also be regularly updated with bauma 2025 content.
Attending major shows like bauma provides the opportunity to spend valuable time with many work colleagues and friends in one place. In between many, many press conferences, stand visits, and enjoyable working breakfasts or evening dos, the latter either on OEM or trade association show stands or, in the Wirtgen Group’s case, chatting over a relaxing and delicious Bavarian dinner in central Munich, I also had several chance encounters with longstanding industry pals, such as Smiley Monroe chief marketing of cer and sustainability lead Tim Monroe.
I have known Tim for many years and always enjoy our wide-ranging conversations, either when visiting the supplier of highquality endless conveyor belts, cut rubber and plastic parts for the materials processing equipment manufacturing sector’s headquarters in Lisburn, Northern Ireland, or at industry trade shows worldwide.
After a general chat about our thoughts on this year’s bauma and the health of the off-highway equipment market, we talked about a non-work subject close to our hearts: football – speci cally his love of Arsenal Football Club and mine of another London team, Crystal Palace. I was delighted that he liked my longheld idea of developing a football stadium-based version of the famous board game Monopoly. I have admired and reported on Smiley Monroe’s big growth journey over the past decade, regarding product sales, rising revenue, and strong sustainability-minded business practices. However, to fully get to know an OEM, you must know its people. So here’s to more random conversations, Tim.
Walking around the bauma showground, the atmosphere was upbeat. It was heartening to hear from many OEM contacts that unit sales had been agreed upon during the show, with other dealer–customer meetings indicating a strong likelihood of future sales and enhanced eet servicing agreements being nalised.
There was a fair bit of talk about the US’s April announcement of protective trade tariffs affecting nearly all goods imported into the country. Most conversations on this were of the “Let’s wait and see what happens next” kind.
Many felt it was too early to assess how the rapidly evolving US trade tariffs landscape would impact the global off-highway equipment industry over the next few years. Focusing on the European off-highway equipment market, there was a largely optimistic mood among my industry sources.
One notable customer trend touched on during my bauma 2025 conversations and in chats with OEMs and their dealer representatives before the big showpiece event was the big rise in remanufactured plant business. It was a hot topic at Caterpillar’s pre-bauma event in Spain in February, and you can read more about what I learned on this subject from Caterpillar and other leading OEMs in forthcoming editions GW guy.woodford@primeglobalpublishing.com
Water is a shared and nite resource, increasingly vulnerable to the pressures of climate change and variable in its impact, as seen in increasing droughts or oods. For the European aggregates industry, water is indispensable and carefully managed, an operational necessity handled with deep environmental responsibility.
In May, Aggregates Europe – UEPG participated in the European Commission’s Strategic Coordination Group for the Common Implementation Strategy of the Water Framework Directive (WFD), engaging in discussions on the ongoing review of this legislation and contributing to the shaping of the EU’s forthcoming Water Resilience Initiative.
As one of Europe’s largest extractive sectors by volume, aggregates operations require certain access to water supply (groundwater and surface) for various technical processes, including dewatering, washing, and dust suppression. At the same time, as a sector aware of supply variability, the industry
plays a proactive role in protecting water quality, ensuring ef cient use, and contributing to long-term water resilience. Aggregates Europe – UEPG’s contributions are captured in the recently published Water Management Guidance, highlighting the tangible and scalable practices already in Europe, from closed-loop water systems that minimise abstraction to restoration efforts that return extracted areas to wetland ecosystems of high ecological value.
The industry’s relationship with water is not passive. Many quarries, through carefully designed operations and supported by legally compliant restoration plans, can support groundwater recharge and natural water retention. Those measures can go beyond the usual provision of biodiversity services after extraction. They can be directly addressed to mitigate the real impacts of climate change, adding value to the sector’s activity. After extraction, sites often become reservoirs, ponds or habitats supporting biodiversity, ood
control and recreation. These outcomes are not incidental – they result from sustained investment, innovation, and compliance with strict environmental standards. Water is not discharged indiscriminately but managed through sedimentation basins, ltration systems, and regular monitoring, all aimed at maintaining or improving the water status required by national and European legislation. At the EU level, this is compliant under the WFD and the operative River Basin Management Plans (RBMPs).
The aggregates industry continues to face regulatory and administrative challenges under the current implementation of the WFD. The Joint Position Paper by Aggregates Europe and its partners in the non-energy extractive industries (NEEIP) expresses concern over the legal uncertainty surrounding Articles 4(5) to 4(7) of the Directive, which de ne exemptions and allow for time extensions or less stringent objectives. These provisions are often interpreted inconsistently, leading to delays
and complications in permitting. There is a need for harmonised guidance that recognises the role of sustainable extraction and enables operators to work within a predictable regulatory framework.
Similarly, as the EU prepares its wide policy reference document under the name of “Water Resilience Initiative”, the aggregates sector calls for a balanced and sciencebased approach that supports environmental protection and critical industries. Water resilience cannot be achieved solely through restriction; it must also be fostered through cooperation, datasharing, and investment in integrated land and water use strategies. With its extensive experience in site-level water management and landscape restoration, the aggregates industry is well-positioned to partner in this effort.
Through its contributions, Aggregates Europe – UEPG af rms that the path to a water-resilient Europe must include those who manage water daily. AB
Designed with a unique combination of power and intelligence the TA 230 features market leading technology, an innovative weighing system, automatic traction control, hill start assist, not to mention the superior cabin design to leave your operator feeling good. Simply put, a perfect mix of agility with outstanding performance.
It’s a Liebherr. Job done.
Sales and growth opportunities remain on o er in the UK and Irish building materials and quarrying machinery markets.
The UK Government is being urged by a key industry advocate to support the quarrying and aggregates sector through proactive policy changes.
The suggestion follows the release of new data from the Minerals Product Association (MPA) that shows a mixed outlook for the sector in key areas. The MPA believes new policies could enhance this outlook
According to the MPA’s latest sales volume survey, demand for heavy-side materials in Great Britain weakened at the start of this year.
Sales of ready-mixed concrete and asphalt fell by 6.3 per cent in the rst quarter of 2025 compared to the previous quarter, while primary aggregates (crushed rock and sand and gravel) recorded an increase of 0.5 per cent.
Mortar sales provided a bright spot, rising for a fourth consecutive quarter, by 3.8 per cent, and signalling potentially improving housebuilding activity.
The latest results re ect challenges facing the construction sector and its supply chain, including economic growth, cost pressures, planning delays and project cancellations, all of which continue to affect con dence in investing in new projects.
Demand for ready-mixed concrete, a material used in all types of construction, has fallen to around three million cubic metres per quarter, its lowest level in 60 years.
Infrastructure markets present a mixed picture. Major projects such as HS2, Hinkley Point C and Sizewell C, alongside several offshore wind projects underway, continue to support demand for construction mineral products, particularly aggregates and readymixed concrete.
This strength is somewhat offset by a road sector weakness. Asphalt sales in the rst quarter of 2025 were the lowest since 2013 (outside of the pandemic period), impacted by the cancellation or delay of key strategic road schemes and continuing nancial constraints on local authority maintenance budgets.
Overall, broader infrastructure activity remains patchy, with delays and cost pressures continuing to challenge project delivery across the public and private sectors.
Housebuilding activity shows some signs of recovery. Mortar sales have risen for four consecutive quarters, suggesting a slow but steady improvement in housebuilding activity. However, the housing market recovery remains sensitive to household con dence and borrowing conditions, with mortgage rates and increased economic
uncertainty since last autumn continuing to weigh on affordability and buyer sentiment.
The MPA’s latest market forecast, published in February, predicts modest overall growth across mineral products markets in 2025, supported by major infrastructure projects and a hoped-for pick-up in housebuilding in the year’s second half. The outlook is contingent on supportive domestic policy action and a more stable economic and policy environment.
“Construction cannot happen without a secure supply of mineral products, yet domestic production faces mounting pressures from both home and abroad,” MPA executive chair Chris Leese said.
“Without a clear commitment to supporting UK industry through competitive energy costs, better planning, and a public procurement policy that prioritises domestically produced mineral products like cement and concrete, the risk is that essential mineral extraction and products manufacturing capacity will be lost, just when the country needs it most.
“Government must act now to strengthen the foundations of growth and support an industry that supplies the essential materials underpinning the UK’s ambition to build and grow the economy.”
Questions have also emerged in the global economy. US trade tariffs have resulted in uncertainty, which is expected to impact UK growth prospects, construction activity and prospects for the supply chain.
While the largely domestic mineral products sector is resilient to direct trade exposure, there are risks that cement imports, already representing nearly a third of the UK market, could rise further as materials originally set for the US seek new markets.
Global trade disruptions, reduced investor con dence, and renewed in ationary pressures are compounding existing headwinds for construction and mineral products markets. The pipeline of construction projects is likely to remain on hold for longer, delaying progress in the housing market, large commercial and industrial construction, and infrastructure. At the same time, the potential for a more cautious approach to interest rate cuts risks undermining the housing recovery, which has underpinned recent gains in mortar sales MPA director of economic affairs Aurelie Delannoy said the gures are affected by economic uncertainty.
“While there are early signs of improvement in housebuilding, the broader construction pipeline remains fragile,” she said. “New global risks, particularly the potential impact of US trade tariffs, add further pressures when the UK urgently needs a resilient and competitive domestic supply chain to support the Government’s green growth ambitions.”
The MPA has suggested the UK Government could act to strengthen the resilience of domestic mineral products production, including supporting energy cost competitiveness, industrial decarbonisation, planning reform, and public procurement policies that support the nation’s industries.
truck transports quarried materials at Coldstones Quarry in the Yorkshire
northern England.
A pair of Cat 320D3 hydraulic excavators at work.
Such action would help to underpin the mineral products sector’s critical role in enabling economic growth, housing delivery and national infrastructure ambitions.
Finning UK and Ireland is the two countries’ largest Caterpillar equipment dealer.
Speaking to Aggregates Business, Finning UK and Ireland extraction and infrastructure manager Mick Knight said demand for quarrying and heavy construction equipment in the UK and Ireland has remained positive since 2023.
“There are multiple factors in uencing the current level of demand. This includes a natural cycle of machine replacement, whereby customers are looking to replace ageing assets with some of the latest machines, which will help them increase productivity and lower emissions,” Knight said. “Tailored nance solutions have allowed customers access to this new equipment, allowing them to invest capital in other areas as opposed to mobile plant equipment.
“The industry has recently seen a slow-down in new infrastructure projects; however, there is between £700 billion and £900 billion currently forecasted to be spent on infrastructure capital investment in the UK from 2025 to 2030 across eight sectors. This is between 2.1 and 2.7 times the amount spent between 2020–2025. On this basis the aggregates market remains cautiously optimistic on output for the next 12–18 months, with a strong pipeline of work that re ects the UK Government’s commitment to kickstarting economic growth.
“It also re ects the formation of the new National Infrastructure and Service Transformation Authority [NISTA], which will support the implementation of the Government’s 10-year infrastructure strategy.
“In addition, the UK Government is streamlining the planning process for key strategic projects by removing speci c steps and regulations, aiming to speed up infrastructure delivery and potentially reduce costs.”
Knight said Finning UK and Ireland sees a trend in customers insourcing operations at their larger and strategically important quarries.
“This also re ects an increased focus on upskilling workforces to enhance operational capabilities with the aim of improving ef ciency, reducing costs and carbon emissions. UK infrastructure project owners [end clients] are devising roadmaps for decarbonisation as the UK moves to achieve 2050 net-zero goals, with interim dates differing by customer,” he said,
“There will be an increased target in CO2 reporting in all phases of construction, including the extraction and handling of raw materials, as well as added scrutiny in procurement, with mandates for low-carbon construction and incentives in contracts to eliminate the most carbon-intensive concrete products.”
Re ecting the focus on sustainability, Knight said there is increasing demand for Caterpillar rebuild machines that typically save customers 20–30 per cent of the cost of new machines, allowing capital expenditure to go further whilst enhancing sustainability.
Knight said the CAT XE range of wheeled loaders is also extremely popular and is becoming the preferred option over conventional powershift models when purchasing new machines. These units are said to deliver increased fuel ef ciency of up to 35 per cent and up to 10 per cent more productivity, and have lower maintenance costs.
“At Finning, we have multiple strategic initiatives in place to help customers address key operating challenges in the quarrying and heavy construction sectors,” Knight said.
“We focus on driving operational best practices, including employing site optimisation studies to right-size eets based on current and future production targets.
“We work with customers to develop a deep understanding of production plant and site restrictions and make informed suggestions to improve site set-ups. Our data-driven insights also help customers focus on speci c targets and KPIs
[key performance indicators], such as tonnes of material moved per litre and driving down cost per tonne of material produced while eliminating waste.
“To enhance productivity, sustainability and cost ef ciencies for our customers, we can provide a host of digital tools, such as VisionLink, a cloud-based telemetry platform that monitors asset performance, including idle time and machine health.
“These insights can pinpoint issues with the operating techniques and quickly identify other machine-related issues on sites. The platform links the operator, machine and site, providing real-time reports on on-site operations, and monitors other factors such as fuel burn rates and carbon emissions. In addition, Finning and Caterpillar also have the expertise to assist with scoping and managing the charging or electric infrastructure ecosystem.”
Knight said adopting best practices to link machines, operators and sites is critical to successfully transitioning new technologies and solutions.
“Our certi ed training programmes [MPQC accreditation] help develop operator competencies, including our proprietary Eco-Drive training designed speci cally for machine operators, and Advanced Eco-Drive training for site supervisors to develop operational awareness and ef ciency,” he said,
Irish market forecasts
The Irish Concrete Federation (ICF) is the national representative organisation for the Irish aggregates and concrete products industries. It has 74 members and associate members operating at around 300 locations throughout Ireland. The membership includes publicly listed and family-owned businesses.
ICF chief executive of cer Gerry Farrell told Aggregates Business there is hope for the market to replicate 2024 levels in Ireland.
“Last year’s demand for construction materials was slightly disappointing, and we are still unsure where this year is going to go. We are hoping that the market will maintain last year’s level at least, but given the current uncertainty, we are not predicting any signi cant growth,” he said.
Farrell said that several key factors contributed to the Irish building materials market.
“If you look at the big sectors that our members sell products into, despite strong growth in indicative housing commencements last year, housing completions actually fell 10 per cent,” he said.
“This was largely due to a fall in apartment construction linked to a rise in interest rates and a perceived lack of return on investment for international investors, mainly due to regulatory constraints in Ireland.
“There has been some discussion of removing rental caps to encourage investment in new apartment construction, but the government has made no decisions.
“The signi cant rise in the cost of building materials, energy and labour is another key factor that has slowed down investment. The
construction of one-off houses and housing schemes has remained steady. There is a lack of major infrastructure projects like major road works or projects similar to the new National Children’s Hospital, a huge project in recent years for some of our members based in Dublin.
“Much of our commercial and industrial construction projects have been linked to Ireland’s high presence of US pharmaceutical and IT rms, whose building plans seem to be on hold due to the lack of clarity in the global economy. However, we are hopeful of some increase in domestic agriculture-related building activity, which should help boost demand for materials.”
Farrell said that Irish exports of precast concrete to the UK have remained consistent over the past year.
“Those exports have grown signi cantly since the 2008 [global] economic crash to a value of up to €200 million from only approximately 15 industry companies with the support of Enterprise Ireland and other state agencies,” he said. “The new Everton FC stadium recently won an industry award, recognising Irish companies that export products or services off the island of Ireland, re ecting the continued emphasis on export for Irish construction.
Farrell said Ireland does not currently have a signi cant recycled aggregates market like the UK.
“We don’t have the volume of construction and demolition waste materials to generate a substantial recycled aggregates business,” he said.
“We estimate that a maximum of ve per cent of the total volume of aggregate sales in Ireland is available for recycling from construction and demolition waste.
“In addition, while a welcome rst step, the national end-of-waste criteria for recycled aggregates produced from waste concrete, published just over 12 months ago by the Environmental Protection Agency [EPA], are very restrictive. Recycled aggregates, for example, cannot be used in structural concrete.”
Farrell provided insights into the ICF’s plans to publish an Irish version of the Future Homes Hub’s (FHH) report on ‘Embodied and Whole Life Carbon of Future Homes Standard Options’ for the UK this year.
“We will also be publishing a report before the summer based on our analysis of the planning system for quarries in Ireland over the last eight years,” he said.
“Our research has shown that the planning system replenishes a little over half of the aggregates used annually, so in effect we use almost double what we replenish nationally. This is not sustainable.
“There is an urgent need for a national policy statement by the Irish Government to facilitate the long-term sustainable supply of essential aggregate materials. The policy statement should explicitly recognise that aggregates are a strategic national resource, essential for the future development of Ireland and fundamental to meeting societal needs.
“This policy statement should be further implemented in regional and local planning policies to provide planning authorities with a clear government position on consenting sustainable development of long-term aggregate supply.”
The recently published FHH report presented whole-life carbon data for three different types of construction, testing two homes with walls made from concrete blocks and one using timber.
The MPA welcomed the FHH report and said the ndings challenge common assumptions about building materials. For example, FHH research shows that the whole-life carbon for a new mid-terrace house ranges from 571–584kg CO2e/m2 across the various construction speci cations, a two per cent difference between timber and concrete.
The report concluded that the different speci cations “have broadly similar upfront and whole-life embodied carbon impacts” and there is “no silver bullet solution when it comes to reducing the embodied carbon of new homes”.
The MPA said many other advantages of concrete, such as re resistance, durability, longevity, thermal mass and a resilient, local supply chain, and advancements in low-carbon concrete, make it a superior choice for building sustainably.
The Future Homes Hub was established to facilitate collaboration within and beyond the new homes sector to help meet climate and environmental challenges. The FHH report is a resource for homebuilders and designers navigating the path to net zero.
Malcolm Construction goes big on Cat Finning UK and Ireland has supplied £1.1 million of Cat machinery to Malcolm
Construction, one of Scotland's largest construction and contracting companies.
Malcolm Construction, a division of the Malcolm Group, has invested in two Cat 745 three-axle articulated trucks and one Cat 352 excavator from Finning UK and Ireland, the world’s largest dealer of Cat equipment, parts and after-market services. This purchase comes as part of the company’s continued investment in heavy machinery to further enhance the ef ciency at its Loanhead Quarry.
The productivity, ef ciency and nancial bene ts of the Cat 745 articulated trucks and the Cat 352 excavator were key to the investment.
To showcase the advantages of these machines, Finning provided the company with a demonstration Cat 745 for a week, and the bene ts were immediately clear.
“Being able to demo the Cat 745 for a week was invaluable in validating the numerous bene ts of this machine,” Loanhead managing director Euan Malcolm said.
“Thanks to integrated VisionLink technology, we were able to see the actual fuel burn gures of the machine, which came in at an average of 73.2L daily, and 586L total for the week – an impressive gure given the load and rigorous application.
“With the machine’s higher payload capacity of up to 41 tonnes, you might expect higher average fuel burn, but we found the opposite. The machine’s Eco Mode undeniably helped to optimise our operating
costs over the week, at no detriment to the performance of the machine.
“Our machines endure the most demanding applications, which means durability, versatility and stability are a high priority when we are investing in new equipment.
“The Cat 352 excavator is already proving it is just as ef cient as our other Cat machines, and just as robust, handling large tools and heavy loads with ease.”
New appointment for HD Hyundai CE UK and Ireland
HD Hyundai Construction Equipment (CE) Europe has appointed Anthony Hogben as its regional sales manager for the UK and Ireland.
An experienced construction equipment engineer, Hogben brings many years of sales and distribution experience, most recently as a regional sales manager for Manitou UK.
Hogben was originally trained as an engineer at TH White, a construction and agricultural machinery specialist in southwest England.
Making the decision to move into machinery sales, he has developed his career across the industry, working with a wide range of equipment in varied sectors.
Hogben has been meeting with HD Hyundai CE’s dealers across the UK and Ireland since starting with the company in late-2024.
Hogben’s appointment highlights HD Hyundai CE Europe’s commitment to strengthening customer relationships and further expanding the UK and Ireland distribution network.
Hogben said he is focused on strengthening the supply of new equipment and ensuring that customers continue receiving market-leading levels of parts and service supply.
“I’m looking forward to working with partners across the network and building relationships with all our dealers and customers,” he said.
“It is a really exciting time to be joining the company, as HD Hyundai Construction Equipment Europe has a wide range of new and updated equipment coming to the market this year, starting at the bauma exhibition in April.
“We have a real opportunity to build the company’s presence in the UK and Ireland markets.”
Liebherr GB makes its mark in UK Liebherr Great Britain (Liebherr GB) is a prominent name in the UK quarrying machinery market.
Liebherr GB national business development manager Chris McGee said several factors have been in uencing unit demand in the market.
“Demand has remained constant over the past two to three years,” he told Aggregates Business
“We did see a slight drop off in 2024, [but] early indications show demand returning to pre-COVID levels.
“Market uncertainty, in ation and political factors such as tariffs and wage increases play their role.
“Large ongoing infrastructure projects such as HS2 and Hinkley Point C protect material demand. Demand is likely to increase slightly [over the next 12–18 months], with end users looking to lower their carbon footprint by replacing their ageing eets with new, more economical
products such as battery electric and CVT drivelines [X Power].”
McGee said machine rebuilds and overhauls have increased over the past few years, with end users seeking ways to reduce costs and lower their carbon footprints.
“Fleet management and an increased focus on utilisation and fuel consumption quickly highlight problematic machines,” he said.
“Our new platform, MyLiebherr, gives customers one portal for all services, from telematics to machine documents and share parts.
“New technologies such as the batteryelectric L507E are available today, and
the prototype H2 hydrogen-powered and autonomous wheeled loader is in its testing phase.”
Liebherr Rental national rental sales manager Gareth Blythin said rental of off-highway equipment in the UK has seen a notable uptick in recent years.
“Liebherr Rental has seen an increase in demand over the last two to three years, especially for wheeled loaders, which are up around 15 per cent,” he said.
“Customers are looking for more fuelef cient machines, especially since the introduction of white diesel.
“This has provided more rental opportunities for a couple of reasons: with customers running more ageing eets, there are more breakdowns and hence the requirement for stop-gap machines. The same applies to companies replacing machines; a rental is often used as a stopgap until the new machine arrives.”
Blythin said that Liebherr GB is helping customers address its key challenges in quarrying and heavy construction.
“From a money-saving perspective, Liebherr wheeled loaders are particularly fuel ef cient thanks to the dual drive technology,” he said
“Liebherr rental carries a large range of machines with dump trucks, excavators, and wheeled loaders all built to work in the quarrying or aggregates industries and available with full spec and additional safety features [eg rear personnel detection on the wheeled loaders].
“Rental terms also offer exibility, with both short- and long-term hires available in the UK.” AB
A successful family-owned-and-run limestone quarrying business in Tuscany continues to see big productivity and e ciency gains from its extensive Caterpillar machine fleet after entering its sixth decade of working with Cat’s longtime Italian dealer CGT.
The happy faces of Cave Pedogna co-founder Vittorio Lumini and long-standing CGT technician Stefano Bastianoni make it clear the two are very comfortable with each other. The 88-year-old Lumini’s arm is around Bastianoni’s shoulder as he playfully points his walking stick towards the photographer on the 2025 Cave Pedogna calendar photoshoot.
In his seventies, Bastianoni has worked with Cave Pedogna’s Caterpillar eet for many years. His close working relationship with Lumini is a great example of the partnership between Caterpillar, CGT and the quarrying business that Lumini jointly owns with Massimo Del Debbio and the wider Del Debbio family.
Bastianoni spoke about the longtime partnership during a visit to Cave Pedogna by Aggregates Business
“I’ve been a technician for 50 years, 30 of which I’ve spent at CGT, and for the past 15 years I’ve been speci cally dedicated to Cave Pedogna. Over time, we’ve built a strong relationship of trust,” he said.
“CGT has always shown maximum commitment to the customer, and I’ve personally responded even at night or on weekends when necessary. Today, thanks to the connectivity of the new machines, the service has evolved and most of the time we can plan interventions, arriving at the quarry with a clear idea of what needs to be done.”
Cave Pedogna turned 50 in 2023, and during Aggregates Business’s visit in early May, commemorative memorabilia, including a special plaque from CGT, were on display in the company’s central meeting room. Also displayed were many miniature versions of Caterpillar machine models purchased from CGT over many years.
Before moving to its current quarry home, a 30-minute drive north of Lucca, Cave Pedogna used excavators to extract Calcare limestone from the nearby Serchio River,
crushing it into nal-grade product at a site neighbouring the notable regional waterway.
“The company moved to this quarry in the 1970s as we wanted to increase production and process bigger rocks,” Lumini said.
Lumini’s rst Caterpillar machine was a D8 dozer, followed by a D9 dozer. Lumini and some colleagues visited Caterpillar’s Malaga Demonstration and Learning Centre (MDLC) in 1988 to see potential new machines for Cave Pedogna being demonstrated. This led to the company purchasing a Cat D11 dozer, Cat 990 and Cat 992 wheeled loaders, and a Cat 775 rigid dump truck for its quarry set-up.
Fast-forward to 2025, and Cave Pedogna has an eet of 19 Caterpillar machines. In early May, Cave Pedogna was awaiting the delivery of a new Cat 775 rigid dump truck.
The current eet comprises one Cat 992, one Cat 988K, one Cat 980M, and one Cat 980H (wheeled loaders), one Cat 374, one Cat 325F, one Cat 365, one Cat 301.7 CR, and one Cat 318C (excavators), one Cat 745, one Cat 740 and one Cat D300E (articulated dump trucks), two Cat 777D and one Cat 775D (rigid dump trucks), one Cat 226D3 skid steer, two Cat D11R and one Cat D7R (dozers).
Lumini told Aggregates Business why Cave Pedogna has been buying Caterpillar machines for more than four decades.
“We have a lot of Caterpillar machines and continue to buy them because of their quality and reliability, and the strong partnership we have with CGT,” he said. “We believe in partnering with just one equipment supplier, so we can count on working with the same people and have access to reliable product servicing and support.”
Downloading machine data and accessing it via Cat VisionLink, CGT produces monthly eet operation reports for Cave Pedogna. These reports can identify any production issues to be addressed and suggest new ways to boost equipment productivity and ef ciency further.
Cave Pedogna has Caterpillar Diamond Plus Customer Value Agreements (CVAs) offering three years of full maintenance and repair for each covered machine. This includes Genuine Cat Parts delivered to site when needed, Cat Condition Monitoring via Remote Flash, Cat S.O.S Fluid Analysis, Cat Inspect, and Cat Preventive Maintenance. Under Cave Pedogna’s Cat CVAs, CGT technicians must repair any machine
within four days, or a replacement machine will be supplied.
Cave Pedogna also has an extended warranty of three years or 4000 hours on the new Cat 992, and Bastianoni is a near-daily on-site presence as the company’s dedicated CGT technician.
Bastianoni assembled Cave Pedogna’s new Cat 992, which was delivered to the quarry in March. Last year, Cave Pedogna turned to CGT for a certi ed rebuild of the engine on its Cat D7 dozer, prolonging the reliable machine’s working life.
“In 2024, CGT celebrated 90 years of history, while Cave Pedogna marked its 50th anniversary in 2023. Our two companies have shared a strong and enduring relationship built on mutual trust,” CGT sales director Marco Villa said.
“In addition to the reliability of Caterpillar products, Cave Pedogna relies on CGT for the quality of its after-sales service, which keeps its machines ef cient and productive. They can count on our preventive maintenance contracts and the constant presence of a highly experienced technician who provides dedicated support.
“Moreover, Cave Pedogna has always been able to count on the support of the CGT branches in Livorno, Florence and Arezzo, and over time, a strong connection has grown with our people there.
“Over the years, Cave Pedogna has also turned to CGT for other solutions, such as the purchase of used equipment, rental services, and tailored nancing options. We can proudly say that we are not just suppliers but true partners.”
During the Aggregates Business visit, Lumini is keen to learn more about how Caterpillar and CGT compete with Chinese original equipment manufacturers (OEMs), some of which have notably enhanced their Italian market presence in recent years.
Peter-Valentin Sauter, a Caterpillar quarry machine specialist also on the visit to Cave Pedogna, addressed the question.
“We work to deliver machines that offer the lowest cost per tonne, and with Cat CGT,
you have the highest quality support of any dealer,” he said.
Cave Pedogna works two quarry faces, the highest of which is 530m above sea level, producing up to 7000m³ of Calcare limestone products daily in a ve-day-a-week operation. The company produces 500,000m³ of product annually, down from one million cubic metres in the 1990s. Material product sizes range from 120mm down to 0–4mm.
The in-house team blasts around once a week after an Epiroc drill rig is used to prepare the blasting holes. A Cat D11 dozer pushes blasted material near the quarry wall
down one level. The material gets loaded by Cat 992 wheeled loaders into a Cat 777D rigid dump truck for transporting to and feeding a primary jaw crusher for initial processing. Other material lying further away from the wall is loaded by Cat 374 and Cat 365B excavators into Cat 740 and Cat 745 articulated dump trucks for transport to and feeding the primary jaw crusher.
The material then passes through secondary cone crushers and screens before being processed in a wash plant and discharged onto a conveyor for stockpiling. Around 200 road trucks are lled daily to transport quarried products to customers.
Cave Pedogna’s customers are located within an 80km radius of the quarry, including the Del Debbio construction company and Prefabbricati LP, another Lumini company, as well as road construction and highway maintenance contractors, and asphalt producers.
Breaking off from working a Cat 374 excavator at Cave Pedogna’s highest quarry face, Livio Bechelli told Aggregates Business about his experience with the excavator.
“It’s a one-year-old excavator and very comfortable in the cabin,” he said.
“The controls are very easy to use, and the machine is very responsive. I move around 3000m³ of limestone a day with the Cat 374.
“The more power I have, the better for my work, and this machine is very powerful.”
In another part of Cave Pedogna’s quarry, Cat 992 operator Massimo Luschini has time for a few words while waiting for an empty Cat articulated dump truck to arrive and be loaded with another batch of limestone to transport to the site’s primary jaw crusher.
“Its fuel consumption is 30–40 per cent less than the Cat 992G,” he said. “It’s also faster and has a more powerful engine.
“The cabin is 100 per cent more comfortable, and I also like that daily uid checks can now be done at ground level and from one part of the machine.”
Luschini’s Cat 992 is one of the rst in Italy to be tted with the new Cat Operator Coaching Technology for Wheeled Loaders. This system that monitors operator technique, detects speci c coaching opportunities during truck loading, and provides corresponding tips for the operator through the display in the cab. They can review the data and watch video tutorials while in a safe state on a secondary display, then improve by following the tips.
There are currently 21 tips available on the Cat 992. A 250-hour free trial is available through SEA activation before any subscription is required.
“It is a good system, particularly for less experienced operators. A message comes up if you have not done a process point correctly. It shows what you have done and explains how you should do it,” Luschini said.
As Aggregates Business returns to Cave Pedogna’s HQ of ces at the end of our tour, a wheeled loader is parked in a company warehouse. It won’t be long until the quarrying business’s new Cat 775 arrives, and the image of CGT’s Stefano Bastianoni getting it ready for work, with Vittorio Lumini playfully waving his stick again while stopping by to see his close business colleague and dear friend at work, is clear. AB
Heidelberg Materials has unveiled two major announcements as the company continues to pursue decarbonisation strategies.
Decarbonisation has become the name of the game for Heidelberg Materials as it continues to pursue a strong agenda. The major construction materials provider recently announced a Memorandum of Understanding (MoU) with Arup to pursue decarbonisation of the “built environment”.
Under the agreement, the two organisations will explore the feasibility and capability of deploying carbon capture and storage (CCS)-enabled cement and concrete through production and supply.
It builds on an earlier partnership between Heidelberg Materials and Arup announced in November 2024. As part of that collaboration, the two organisations examined the bene ts and technical complexities of carboncaptured cements and concrete.
Heidelberg Materials chief sustainability and new technologies of cer Dr Katharina Beumelburg said she was excited to work more with Arup.
“Decarbonising our industry is an urgent and monumental task and can only be achieved in close collaboration between the most important players,” she said. “Our know-how and pioneering role in CCUS [carbon capture, utilisation, and storage], combined with Arup’s techno-economic and strategic expertise when it comes to reducing emissions in the global built environment create a perfect t. We’re excited to join forces and make a real difference together.”
The two organisations will conduct research and technical opportunities of deployment opportunities for CCS to decarbonise cement and concrete products.
Arup chief sustainable development of cer Dame Jo da Silva said this technology will play a key role in heavy industrial industries.
“The global built environment is a signi cant contributor to climate change and action is needed now to decarbonise critical building materials production,” she said.
“Carbon capture and storage technologies will play an important role in reducing emissions from hard-to-abate industries, including cement and concrete. Heidelberg Materials’ rst-mover investment in industrial-scale carbon capture at its Brevik facility in Norway is a notable step forward.”
Heidelberg Materials’ partnership announcement with Arup comes as the company gets set to make its CCS facility in Norway operational.
At the time of writing, the Brevik CCS facility in Norway was set to become operational in June which, according to Heidelberg Materials, will make it the “ rst CCS plant in operation at scale within the global cement industry”.
The facility will provide storage capabilities as well as the ability for Heidelberg Materials to supply its carbon-captured cement and concrete, evoZero. It reached a major milestone with the achievement of mechanical completion in late-2024.
The project is part of the Norwegian government’s Longship initiative and will capture 400,000 tonnes of CO2 annually. Once captured, it will be transported by ship to an onshore terminal on the Norwegian west coast, and then the lique ed CO2 will be
sent via pipeline to a storage site beneath the North Sea for permanent storage.
The current cement plant includes the carbon-capture facility integrated into the set-up, accomplished through 1.2 million hours of technical work by an on-site team of up to 400 employees and external partners.
“We are very proud of this important achievement, which positions us as a leader in the global transition to a net zero economy,” Heidelberg Materials chief technology of cer Axel Conrads said.
“The project’s progress towards the start of the Brevik CCS plant is a testament to our engineering expertise and to the close collaboration between the project team in Brevik, the experts in our global Competence Center Cement, and our trusted partners for this rst-of-its-kind application.
“With most modern training tools, we have laid the foundation for the next crucial step of commissioning the new equipment. We are looking forward to launching the plant into full operation.”
The Brevik project has spawned multiple other CCS projects around the world that use the lessons learned by Heidelberg Materials with many visitors travelling to see the Norwegian facility.
“The Brevik CCS project is a landmark achievement for Heidelberg Materials. As part of the Norwegian Longship program, it demonstrates not only cutting-edge technology but also the strength of the industrial–governmental partnership model,” Heidelberg Materials Northern Europe general manager Giv Brantenberg said.
“Ultimately, our customers across Europe will be empowered to lead the way and build a more sustainable future by incorporating our evoZero carbon-captured cement and concrete into their projects.” AB
Aggregates Business sat down with CheckProof chief executive o cer Håkan Holmgren to learn about the Swedish-based company’s exciting growth plans.
Håkan Holmgren’s face lights up as he talks about working at Rimbo Jord, his father Nisse’s quarrying business in Rimbo, north of Stockholm.
“I started at the age of 12 or 13, helping after school to repair wheeled loaders, excavators and screening equipment,” Holmgren told Aggregates Business
“Dad founded the company in the 1960s. It had around 45 employees and two quarries full of crushers, washing plants, trucks and all the other regular machines. I did everything – working evenings, running crushers, running washing plants.
“I eventually became the business’s CEO [chief executive of cer], and in 2009 we got a big new permit spanning over 105 more hectares of our Ledinge quarry. This allowed us to process a much higher volume of aggregate material.
“In 2011, Jehander [now Heidelberg Materials Ballast Sweden], a subsidiary of Heidelberg Materials, acquired our company.”
Shortly after acquiring Rimbo Jord, Holmgren joined Heidelberg Materials Northern Europe’s production performance team as a process development and project manager.
“The team went around lots of Heidelberg Materials Northern Europe quarries and other sites, reviewing how they operated, including their approach to maintenance, health and safety, quality and environment,” he said.
During Holmgren’s time at Heidelberg, he got to do site visits in the UK and Belgium.
“From working within and eventually running a family quarrying company, I knew all the issues around product [European] construction equipment marking, quality control, and people not doing the maintenance they should,” he said. “After starting work at Heidelberg Materials Northern Europe, I soon realised they faced the same challenges. Too many routine tasks were done on pen and paper and not carried out ef ciently.”
Being part of the production performance team gave Holmgren access to priceless quarrying process information, partly through the business’s aggregates academy and aggregates handbook. He trained his Swedish colleagues at Heidelberg Materials Ballast Sweden on compact Swedish versions of the aggregates academy.
“It [Heidelberg Materials Northern Europe] was an awesome place to work with great colleagues,” Holmgren said.
In 2014, one of Holmgren’s childhood friends, Jonas Pålgård, married into his wife’s family’s ship-loading company, where he worked in IT support. Pålgård’s dad was also a quarry foreman at Rimbo Jord, so the wider Holmgren and Pålgård families were also close.
“Jonas did much of his work on paper, such as safety checks and fuel consumption logging. It never worked well,” Holmgren said. “Jonas thought having an app that acted as a checklist and advisor for his work would be a good idea.
“We then started discussing the idea, and that’s pretty much how CheckProof started. Jonas had also previously worked as an art director, and we sat down over several evenings and weekends and began designing an app.
“After nalising some work projects, I resigned from Heidelberg Materials Northern Europe at the end of 2014. In 2015, Jonas and I started designing the rst CheckProof [software] codes, and we released the rst version of CheckProof in May of that year. We started working quite closely with Heidelberg Materials Ballast Sweden and Pålgård and Söner Kran.”
CheckProof provides a mobile- rst platform that simpli es maintenance management and health, safety, environment and quality processes. Combining intuitive technology with actionable insights, CheckProof helps companies in the construction materials sector and heavy industries follow routines, mitigate risks, minimise costs, and enhance safety.
“Around 2017, we realised that we needed to scale the CheckProof offer so there weren’t just two or three people working on it,” Holmgren said.
“We then searched for capital to enable us to run the business at scale. We secured investment, started to take on more customers, and developed the app to make it available in different languages.
“We now have around 350 customers in 38 countries. This includes major building materials companies, like Cemex and Heidelberg Materials, which use the system in multiple countries, and small and medium enterprises, including contract crushing companies with 15 to 20 employees. We have built a system that should solve all the operational pain points around maintenance, health and safety, environmental protection, et cetera, on one platform.
“We currently have over 40 employees based in our head of ce in Sweden, Germany and the UK. We are also recruiting in France, redeploying two employees to North America, and hiring six more people to work in that market. The US is huge. Texas alone is bigger than Sweden.”
CheckProof’s recruitment drive and business scale-up are largely funded by a summer 2024 investment from Viking Venture, a leading Nordic business-tobusiness software investor renowned for its
backing of fast-growing scale-up companies in the Nordics.
“Granitor Growth Management, another of our key investors, has a base in Indonesia, and we are building a CheckProof development team there. It means that later this year we will pass 50 employees,” Holmgren said.
Holmgren announced CheckProof’s of cial opening of its rst US of ce during a press conference in March at AGG1/World of Asphalt 2025 in St. Louis, Missouri. The news of the US of ce in Houston, Texas, came alongside con rmation that the Swedish company has registered its new US subsidiary, CheckProof US Inc.
“Opening a US of ce brings us closer to our customers, providing dedicated support in their time zone while expanding our presence in this key market,” Holmgren said.
“To accelerate growth, we’re hiring four sales executives and two customer success managers and relocating two key members from our UK team. This ensures we offer hands-on expertise and service to our growing customer base. Our goal is to provide digital solutions that optimise operations and drive continuous improvement.”
The aggregates industry, characterised by heavy machinery, complex operations, high safety risks, and navigating sustainability challenges, can signi cantly bene t from digital tools. Holmgren said paper-based processes are time-consuming and prone to errors, often leading to costly inef ciencies, resource strain, and overlooked risks.
Digitalisation and solutions like CheckProof address these challenges by streamlining data collection, automating insights, and enabling game-changing predictive maintenance to enhance operational ef ciency and ensure equipment reliability and workplace safety.
At CheckProof, telematics and integrations are central to enhancing operational ef ciency in the aggregate industry.
The platform connects to telematics systems across various machines and vehicles, regardless of brand. This integration enables seamless access to vital data such as fuel consumption, geographic location, idle time, error codes, and CO2 emissions.
CheckProof can then merge the machine data with frontline employee reports. This holistic approach allows businesses to proactively address deviations, monitor performance trends, and ensure compliance with maintenance routines – all from a single platform.
In addition, CheckProof offers integrations with original equipment manufacturer (OEM) industry leaders and third-party providers, offering vibration and temperature sensors and belt-weigher software. This helps users harness real-time insights and automate maintenance work ows, bringing the concept of a truly connected plant to life.
This approach transforms raw telematics data into actionable insights, driving operational improvements and creating smarter, more connected plants and sites.
CheckProof content specialist Anju Khanna Saggi is on the Aggregates Business call with Holmgren. She said the company uses a direct sales approach with salespeople recruited from the quarrying industry, giving them an instant connection with potential customers and a better understanding of their needs.
“Check Proof has a very open leadership style, and that same spirit of openness is seen in how the company works with customers to get things done,” she said.
Holmgren agreed with Saggi’s comments and said CheckProof’s success is rooted
in collaboration. By working closely with clients, the company re nes its platform based on real-world challenges and opportunities. This collaborative ethos fosters long-term partnerships, drives innovation, and ensures the platform remains indispensable to its users.
“When you start with CheckProof, you buy the software. You get assigned a customer success manager to help you work the system at the required scale. It’s taking things step by step, and there are system add-ons you can pay to have, depending on the scale at which you want CheckProof to work,” Holmgren said. “When you look at the work of a quarry manager, for example, they are on-site with responsibility for everything: plant operation and maintenance, walkaround inspections, site health and safety, implementing environmental best practices, and lots more.
“I remember being on a quarry site after a big crusher failed. A €50 air lter hadn’t been changed, so dust had entered the crusher’s oil tank, leading to a €55,000 repair bill and lost production time. The site team said, ‘Oh, we missed that’. Those things can happen continuously in the industry.”
CheckProof can assist with quarry employees’ regular routines, alerting them to technical issues and any checks and maintenance needed at timed intervals.
“It creates, in effect, a ‘My task’ list –showing everything that needs to be done on-site that day,” he said. “The success of CheckProof is based on how much you utilise it. We have multiple quarrying customer success stories. We have seen a 33 per cent reduction in yearly maintenance cost per tonne with the full use of CheckProof.
“In other instances, we have seen daily output increase up to 75 per cent on a site when they utilise CheckProof to drive behaviour change to improve operations. We are continuously working to develop the software to create even more value for our customers.”
Holmgren said CheckProof its focused on achieving its 2025 priorities.
“We are focused on expanding our sales team in North America,” Holmgren said.
“We will showcase CheckProof and highlight some new features of the software.”
Quarrying has long been a conservative industry, with many of its experienced professionals resistant to change.
A key part of Holmgren and his CheckProof colleagues’ mission is to persuade quarry operators to invest in the Software as a Service solution.
“It’s about showing the value of CheckProof, which includes demonstrating how easy it is to communicate with colleagues through the platform app, log an issue with a case number, comment on how it is being progressed, tagging particular colleagues, and then solving it. You don’t need a WhatsApp group,” Holmgren said.
“It’s about how you encourage the change to a digital approach.
“We had one client, an older man in his 60s, who told us he was ne with pen and paper and didn’t need any digital system. Six months later, he was standing on a stage at an internal company meeting, telling his colleagues how the CheckProof app could give him this and that and that he loved it.”
Holmgren said quarry operators can enjoy sustainability gains from using CheckProof.
“If you can make your equipment eet last longer by using our software, that’s good for your sustainability,” he said. “The eet optimisation you can get from using CheckProof, such as reduced machine idle time, is also a big sustainability gain.
“With our system, you can put all the telematics from your machine eet into it and can see an instant leaderboard in the app
showing which machine has the highest or lowest idle time. When we did a pilot study, we saw a 25 per cent reduction in eet idling. If you have a big machine eet, the reduced idle hours easily equates to replacing one less machine per year.”
In 2024, CheckProof was selected as a key vendor at the AggNexus Digital Innovation Conference at the University of Texas, Austin campus, highlighting its position as a leader in digital transformation for the aggregates sector.
On the event’s second day, Holmgren participated in a panel discussion on ‘Challenges and opportunities in digitalisation for the industry’.
During the hour-long session, Stockpile Reports developer David Boardman described data as “truly the new oil”, adding that capital expenditures for harvesting data will grow by an “order of magnitude”.
“AggNexus was inspiring. Seeing all the different digital solutions for the quarrying industry was great,” Holmgren said.
“There is huge potential to stage this event in other world regions, such as Europe.”
Holmgren said he has found the journey with CheckProof in the global quarrying marketplace to be an especially rewarding one.
“Once you start something, there is no turning back. You have to succeed, and you need that mentality ,” he said.
“We are clear on how to solve a problem in the [quarrying and wider construction materials] industry, and we want to keep going and make real changes for both the frontline workers and management.
“What drives me is receiving or hearing positive customer feedback. I remember early in the business when a colleague discovered a comment by our customer, Cemex UK in a LinkedIn post, describing CheckProof as a ‘game-changer’.
“It was incredibly rewarding.” AB
This year’s bauma exhibition in Munich saw several leading o -highway equipment names showcase eye-catching alternative-fuel-powered machines and concepts.
Agroundbreaking all-electric line-up from Volvo Construction Equipment (Volvo CE) pushed the boundaries of innovation at bauma 2025 in Munich, Germany, in April.
“This zero-emission line-up is a marker of our commitment to drive change,” Volvo CE president Melker Jernberg said. “Together with our pioneering service, solutions and updated portfolio of conventional machine variants, we show that we stand alongside our customers to support them across every stage of their journey.
“We show that we are committed to our ambitions, not just because we can but because it is the right thing to do.”
The star of the all-electric platform was the “game-changing reveal” of the A30 Electric articulated hauler, representing the rst in a key industrial segment for Volvo CE and the world’s rst serial-produced batterypowered solution of its size class.
It will be available to rent, alongside the larger A40 Electric, for select customers in select European markets in 2026, ensuring quarrying, mining and construction customers can now match high productivity with a more sustainable operation.
Volvo CE also showcased at bauma 2025 its conventional combustion engine options available to customers for all zero-emission models on display. These are designed to deliver claimed industryleading fuel ef ciency, with up to 15 per cent
improvements and exceptional productivity. This multi-technology approach ensures that Volvo CE provides versatile solutions for various customer requirements, wherever they are in their transformation journey.
Perkins’ growing portfolio has welcomed the addition of a new battery-electric power unit technical demonstrator, shown for the rst time at bauma 2025. Shown in a pipe fusion machine, the plug-and-play battery-electric power unit is designed to enable off-highway original equipment manufacturers (OEMs) to transition seamlessly from diesel to a batteryelectric powertrain.
“We’re actively helping customers navigate the shift in power system requirements, with a range of advanced power systems including electric, dieselelectric and alternative fuel compatible engines,” Perkins vice president of global sales, marketing, service and parts Jaz Gill said.
“When it comes to the innovative fully integrated battery-electric power unit, it can be ‘dropped in’ to a machine to replace a diesel engine.
"The system consists of a Perkins battery, inverters, motors and on-board chargers – all packaged up into a compact drop-in system to support seamless transition from diesel to electric for our customers looking to make that move.”
The Perkins battery-electric power unit has been tested in a McElroy TracStar 900i pipe fusion machine as a commercial demonstrator, with the battery-electric power unit replacing a 3.6L 904 Series diesel engine. The power unit’s compact design enabled the seamless transition from diesel engine to electric, with the power unit tting within the same chassis space and having the same mechanical connection and electrical interface points as the 3.6L diesel engine power unit it replaced.
“This is a fully integrated battery drop-in solution, reducing the need for OEMs to invest in costly engineering and design projects and allowing them to electrify their machinery quickly and cost-effectively, without sacri cing performance,” Gill said.
“I’d encourage anyone considering the move towards electri cation to come and talk to us about this drop-in solution, which can deliver a faster return on investment, while providing the owner–operator with a low-maintenance, cost-effective power solution.”
Hybrid power versatility
Project Coeus was showcased at bauma 2025. It saw Perkins partner with e-powertrain specialists Equipmake and Loughborough University’s Wolfson School of Mechanical, Electrical, and Manufacturing Engineering to develop an innovative, advanced con gurable-fuel drop-in hybrid power unit that can directly replace a diesel engine. The four fuels selected for inclusion in Project Coeus – ethanol, methanol,
bio-methane, and hydrogen – all have one characteristic: they are spark-ignited fuels, creating the project’s common con gurable combustion platform.
The rst phase of the project involves developing a 180–280-kilowatt (kW) hybrid power system.
This system will deliver a robust and trusted fuel-con gurable plug-and-play solution that produces consistent power performance regardless of the fuel type, ensuring long-term exibility for the user.
In addition to Project Coeus, Perkins highlighted what it has learned about diesel-electric hybrids and full electric applications. A diesel–electric hybrid demonstrator machine has been optimised to improve ef ciency without compromising performance.
In another project, Perkins has fully electri ed a technology demonstrator machine with a Perkins Li-ion battery.
John Deere Power Systems (JDPS) and KREISEL Electric (KREISEL) are developing battery and charging solutions to bring battery-powered equipment to key off-highway markets including construction, quarrying, mining, and material handling. At bauma 2025, attendees explored the latest advancements in battery technology, including the KBE.59.750M battery pack, estimated to be in production in 2026. The KBE.59.750M and all KREISEL batteries
feature Dynamic Performance Management, which uses patented cell immersion cooling technology and advanced software systems. This technology is engineered to optimise daily performance at extreme temperatures while meeting or exceeding industry safety standards.
Designed to prioritise energy density, runtime and seamless integration with off-highway machinery, KREISEL batteries feature a exible, modular architecture. Highperformance, high-durability batteries allow John Deere to provide all-electric vehicles and powertrains to off-highway equipment customers across equipment segments and applications. The serial production KBP63 battery pack was also displayed at bauma in the outdoor Wirtgen booth.
John Deere recognises that building a robust charging ecosystem is crucial to adopting battery-powered construction equipment. To effectively support the transition to electric-powered off-highway machinery, John Deere is committed to providing charging solutions that are as
versatile and adaptable as their job sites. This means developing stationary and mobile charging options with varying power outputs and charge times that can be scaled. With KREISEL, JDPS is pursuing charging solutions to serve off-road electric construction vehicles where typical grid infrastructure is unavailable or insuf cient.
JDPS showcased a concept mobile charging solution powered by KREISEL battery technology at the Wirtgen booth. This concept demonstrates the company’s focus on developing exible charging options that can be easily deployed wherever needed.
In addition to the mobile concept unit, the serial production CHIMERO stationary charger from KREISEL was displayed on the Wirtgen booth. The CHIMERO offers highpowered DC fast charging for locations with lower grid connections.
With mobile and stationary options, John Deere aims to provide its customers with the infrastructure they need to integrate electric-powered equipment into their operations seamlessly.
Hyundai Construction Equipment (Hyundai CE) had its HW155H hydrogen fuel-cellpowered wheeled excavator concept working on the demonstration area throughout this year’s bauma exhibition. The pre-production machine, rst seen as a static exhibit at the last bauma in 2022, demonstrated to customers how hydrogen could contribute to future carbon-free operation on construction sites across Europe.
A hydrogen fuel cell uses a chemical reaction between hydrogen carried on board and oxygen in the atmosphere to generate electricity. The only emission is water vapour. The fuel cell delivers power on demand to drive the machine, either through electric motors or via electrically driven hydraulic pumps.
The project to develop a fuel cell for the HW155H has been a cooperation between Hyundai CE and Hyundai Motor Company, which has a range of powertrain solutions available in the passenger car and utility vehicle markets.
Two cells have been designed, creating 30kW and 50kW of power, with the HW155H using a combination of fuel cells to provide 70–100kW of power. These fuel cells would suit a range of machines, including the 15-tonne wheeled excavator, forklift trucks and emergency generators.
The HW155H is a 15-tonne wheeled excavator that combines on-road and off-road capabilities, making it ideal for hydrogen power. The machine uses the fuel cell to power an electric motor, which then drives the hydraulic system. The hydrogen storage on-board has the capacity to allow a full eight hours of operation, with refuelling taking between 10–20 minutes.
Hyundai CE said hydrogen is a safe fuel, with an auto-ignition temperature higher than petrol or diesel. As it is 14 times lighter than air, hydrogen also disperses harmlessly into the atmosphere. Hyundai has developed a world- rst, innovative low-pressure hydrogen storage solution that offers high-density storage for extended operating autonomy.
Hydrogen diggers on UK roads
JCB has hailed the UK Government decision to change the law to allow hydrogen diggers to drive on UK roads.
Minister for the Future of Roads Lilian Greenwood signed a statutory instrument allowing hydrogen-fuelled construction and agricultural machinery to use the public highway from 29 April 2025.
JCB Chairman Anthony Bamford, who instigated a £100 million project to develop a hydrogen combustion engine to power JCB’s machines, called the news “historic”.
Lord Bamford’s reaction came as a hydrogen-powered JCB digger was driven around London’s roads to mark the momentous announcement, calling in at the Department for Transport on April 29 to meet Greenwood.
JCB has invested more than £100 million to produce a range of super-ef cient zero-emission hydrogen engines. This pioneering project at JCB’s engine plant in Derbyshire has been personally driven by Bamford, who challenged the company’s engineers to make a major breakthrough in the use of hydrogen as a fuel in a combustion engine.
JCB has been operating prototype hydrogen-powered Loadall telescopic handlers, backhoe loaders and generators on sites near Birmingham, and is now testing a range of equipment in partnership with rental companies and leading contractors across the UK.
“The JCB team has done amazing work to develop a hydrogen combustion engine. It has already been given resounding
backing from our customers who have been evaluating the technology; they say it is simple to use and performs as well as diesel counterparts,” Bamford said.
“We are delighted that the Government has now endorsed the use of hydrogen in machinery. There has been a lot of work to get to this point. It is truly a historic day for JCB and a milestone moment for the use of hydrogen as a zero-carbon fuel in the construction and agricultural machinery industries. We now have the legislation that allows hydrogen powered machines to drive on the road between sites and between farms.”
Greenwood signed the statutory instrument in early April to pave the way for an amendment to the Road Vehicles (Construction and Use) Regulations 1986
to enable the road use of hydrogen-fuelled non-road mobile machinery.
The change in legislation has come into force. Other hydrogen powered vehicles, including cars, buses and trucks were already permitted by law to use UK roads, but hydrogen-fuelled construction and agricultural machinery could not – until the amendment.
“We’re supporting the UK’s Plan for Change by working closely with brilliant British companies like JCB to harness the opportunities of the net-zero transition, driving innovation and creating jobs to put money in the pockets of hardworking people and secure our future,” Greenwood said. AB
Electric innovation continues at pace in the crushing and screening sector as manufacturers capitalise on growing consumer demand.
Sandvik Mobile Crushing and Screening has unveiled its latest innovation in tracked cone crushers, the QH443E.
Sandvik designed the new tracked cone crusher for crushing and screening operators transitioning to “greener” operations.
The release of the new unit completes Sandvik’s rollout of the electric train, which includes the UJ443E fully electric jaw crusher, the QE342E hybrid scalper, and the QA452E hybrid triple-deck Doublescreen. Sandvik began the rollout with the QE342e and the QA452e in 2022, and the UJ443E launched in 2023.
Sandvik Mobile Crushing and Screening division president Manny Moloney said the QH443E is Sandvik’s agship Q-Range electric-driven cone plant.
“This is just the beginning of our commitment to develop solutions that improve the productivity, safety, and sustainability of our customers’ operations,” he said.
“With its advanced capabilities, this technology is particularly well-suited for heavy-duty applications, including large quarries and mining operations, where maximising uptime and reducing environmental impact are critical.”
The QH443E combines electric drives and track mobility on a single platform. This hybrid unit bridges the gap between tracked mobile, wheeled portable, and stationary plants.
Sandvik has updated the tracked platform with a diesel/electric generatorbased drivetrain.
The QH443E is equipped with a suite of technological features that allow operators and quarry managers to make informed decisions. These include the Optik automation system and My Fleet remote monitoring. The centrepiece of Sandvik’s latest machine is the CH440 Hydrocone crusher, which features advanced settings, including the Hydroset CSS regulation and protection system.
The Hydroset CSS uses Constant Liner Performance (CLP) to track liner wear and optimise production throughout the machine.
Customers can choose between multiple chambers and settings to suit various applications. The choice enables quarry operators to ne-tune the QH443E to extract the most from their application.
These features make the QH443E viable for secondary or tertiary crushing in the quarrying or aggregates sectors. It can also work in an electric train with the aforementioned Sandvik equipment.
According to Sandvik, the fully electric track drives also reduce hydraulic oil usage by up to 91 per cent. The electric drives and the hybrid “e” drive of the QA452e Doublescreen allow the operator to run the train from the most economical energy source.
“Sandvik Mobiles has always been at the forefront of innovation, and completing the development of our tracked electric train marks a signi cant step towards a more sustainable and cost-effective future for the crushing and screening industry,” Maloney said.
Finlay’s future focus
Finlay has taken a major step in its manufacturing by unveiling the Finlay 883+ Electric Scalper.
The new unit is an addition to the 883+ model, which is designed to work as a primary or secondary screening application within quarry, sand, gravel or construction and demolition waste applications.
Finlay has equipped the 883+ Electric Scalper with a redesigned feeder, which includes hydraulic folding and locking extensions and the ability to rear-feed material. The hopper has been upgraded with wear-resistant steel and different hopper linings.
The 883+ Electric Scalper can be operated using mains power, including grid electricity, or a genset, which enables customers to reduce operating costs and operate in a lower-noise environment. The electric drive system operates the feeder, screen box and conveyors, which can help customers reduce their carbon footprint.
Finlay’s business line director Matt Dickson said the upgrades came about after receiving feedback from the Terex Materials Processing brand’s customers and distributors.
“As our agship model, the 883+ has always set the standard for performance and versatility,” he said. “The 883+ Electric Scalper represents a forwardthinking solution for businesses looking to reduce their environmental impact, while continuing to bene t from the superior performance and exibility that Finlay equipment is renowned for.”
Six of the best Metso has of cially launched the sixth model of its Nordberg HPe crusher series in another range expansion.
The Nordberg HP450e is the latest model in the HPe series, which debuted in 2023 and has grown substantially in the past two years. The range now includes solutions across the production process, encompassing secondary, tertiary and quaternary crushing.
The market response has been positive, with more than 200 units sold globally, while older HP models have been retro tted with the HPe upgrade kits.
According to Metso, the Nordberg HP450e crusher delivers enhanced performance due to its redesigned, ef cient crushing chamber. It has more head motion, 13 per cent more power, and 20 per cent more force than previous models.
The HPe series also makes it an environmentally friendly option, as it does not require a backing material. The six HPe crusher models have 10 different chamber pro les and advanced simulation software. They can be con gured for various applications, including wheelmounted Nordwheeler setups, modular Nordplant installations, and track-mounted Lokotrack units.
"With the latest addition of the Nordberg HPe crusher series, we are able to offer customers the ideal balance of power and ef ciency for their speci c crushing needs,” Metso’s Aggregates business area product manager of HP Cones Ilkka Somero said.
Metso has debuted the Nordberg HP450e crusher.
“The HP450e, as a mid-range unit, is designed for customers who require reliable, high-capacity crushing without excessive energy consumption. With this unit, we have further improved its application exibility so that customers get the maximum production and yield of wanted end products.”
Metso shared how its stationary screens are con rmed to meet the safety standards set by the European Union (EU), including the EU standard (EN 1009-1:2020).
The EU standard (EN 1009-1:2020) refers to the safety requirements and veri cation required when designing and constructing screening machinery for quarrying, recycling, and processing minerals and by-products.
The EU standard sets the minimum distance requirements for the intermediate space between screens, which Metso said is met by most of its stationary screening range.
According to Metso central region screen business line vice president Adrian Wood, the manufacturer has a role in ensuring a safe working environment.
“Good equipment design should create safe working and operating conditions. Our stationary screens not only meet but exceed current safety requirements set by the European Union,” he said.
“This easy access is critical as screen maintenance and inspection interventions are frequent, with not only regular weekly and monthly routine-based condition checks but potentially regular replacement of screen panels which must be carried out safely whilst still aiming for the shortest possible maintenance downtime.”
Oceania expansion
McCloskey has con rmed Rokbro Material Processing Equipment has joined as its latest New Zealand dealer.
Under the agreement, Rokbro will represent McCloskey’s full line of crushers, screeners and stackers.
“We are excited to be joining the McCloskey network and to bring their
top-tier equipment to New Zealand,” Rokbro Material Processing Equipment director Dane Fitzpatrick said. “The reputation of McCloskey in the industry is second to none, and we are eager to represent their products, which will empower our customers to optimise productivity and performance.”
The announcement will expand McCloskey International’s presence in the New Zealand market and for its existing customers in the country.
“We are thrilled to partner with Rokbro Material Processing Equipment,” McCloskey International’s sales and marketing director Anthony Bouvie said.
“Their reputation for excellence and deep understanding of the local market make them the ideal partner to represent our brand in New Zealand. Together, we are committed to offering high-quality products and outstanding after-sales support to help our customers achieve success in their operations.” AB
Caterpillar has signed an agreement with Luminar.
The role of technology in the quarrying and aggregates industry has never been more important, especially when it comes to hauling and transport.
Technology has caused many major advancements in the quarrying and aggregates sector, with several recent examples underlining their potential.
Attendees to bauma 2025 in Munich, Germany, saw what was said to be the world’s rst serial-produced battery-electric articulated haulers for their size class.
Volvo Construction Equipment (Volvo CE) unveiled the A30 Electric and A40 Electric, marking a signi cant milestone for the manufacturer.
Volvo CE said the zero-emission models can be combined with conventional combustion engine options to support customers transitioning to more sustainable fuel sources.
“This zero-emission line-up is a marker of our commitment to drive change,” Volvo CE president Melker Jernberg said.
“Together with our pioneering service, solutions and updated portfolio of conventional machine variants, we show that we stand alongside our customers to support them across every stage of their journey.”
The A30 Electric and A40 Electric will be available for rent for select customers in select European markets in 2026.
Volvo CE has complemented the launch of its new zero-emission line-up with several service solutions, including a new load ticket tool and two new services, site operations and site optimisation.
The load ticket tool is designed to streamline invoicing. The site operations service is a brand-agnostic eet monitoring tool, with the site optimisation tool functioning as an advisory service for customers to enhance their operations.
These solutions were showcased at Volvo CE’s interactive Solutions Bar at bauma 2025.
“Our industry’s transformation may be slower than we would like, but our commitment remains strong as we continue to invest in building a better world for all – as demonstrated by our pioneering 100 per cent zero-emission line-up at the recent bauma show,” Jernberg said.
Caterpillar’s collaboration Technology improvements are creating a range of improvements in the hauling space, not just limited to electric-drive equipment.
Caterpillar recently announced a collaboration with Luminar, which will see LiDAR (light detection and ranging) technology in its next-generation autonomous solutions, including the Cat Command for hauling. The Cat Command is designed for quarry and aggregates operations.
The rst development in this collaboration will see a Cat off-highway truck feature two Iris LiDAR with a unique integration system designed exclusively for Caterpillar.
LiDAR supports navigation and obstacle detection in autonomous machines. The technology uses light as a pulsed laser to continuously scan the surrounding environment and provide high-precision measurements of the shape and size of nearby objects.
“We are proud to collaborate with Luminar on our next-generation autonomous solution,” Caterpillar chief technology of cer Jaime Mineart said. “We’ve invested in autonomy and automation for more than 30 years, and we’ve seen how it adds value for our customers in terms of safety, productivity and ef ciency.”
Luminar chief executive of cer and founder Austin Russell said the partnership marks an important milestone for the company.
“[It] has the opportunity to be a spearhead for the next industrial revolution of automation,” he said.
“Now that Luminar has successfully executed for automotive series production, we’re able to branch out to adjacent markets with a shared mission. Together, we look forward to saving lives and enhancing pro tability for Cat customers around the world with industry-leading capabilities.”
Komatsu unveils new dump truck
Komatsu Europe has revealed the HD605-10 rigid dump truck as the latest addition to its customer hauling line-up. The company has designed the HD605-10 to be a workhorse in the quarrying and aggregates sectors.
The rigid dump truck features a 610 kW Stage V engine with three selectable modes, including economy, economy light, and power, so operators can adapt to suit their applications. Also included is a new cooling system and a lightweight body option to deliver fuel ef ciency and reduced operating costs for customers.
The HD605-10 includes a strengthened transmission, torque converter, main frame, differentials, and nal drive components to operate in a quarry’s harsh environment. Operators can also use the new features, including hill start assist and cruise control, to make the operation easier.
The HD605-10 rigid dump truck was demonstrated for bauma 2025 attendees in April, when the trade show took place in Munich, Germany.
Komatsu Europe product manager Juuso Ahola said the HD605-10 rigid dump truck is the perfect partner for the WA700-8.
“Our development teams have prioritised customer needs to deliver a machine that not only builds on the reliability of its predecessor but also introduces signi cant performance enhancements,” he said.
“These enhancements include increased power, weight reductions, expanded load capacity up to 64 tonnes with 43 m³ body, improved durability, enhanced visibility systems, and reduced fuel consumption.” AB
Komatsu’s HD605-10 rigid dump truck can pair with the WA700-8.
Non-genuine, counterfeit or fake parts can place operations at considerable risk.
Genuine parts for crushers and screens are an essential part of the promise that original equipment manufacturers (OEMs) make to the market – to keep their customers’ projects pro table and their businesses sustainable.
On the other side of the coin, however, are the risks that non-genuine, counterfeit or fake parts place on operations, according to Metso distributor Pilot Crushtec sales and marketing director Francois Marais.
“OEMs like Metso spend decades developing and supporting technologies that provide customers with reliable and high-performance solutions for crushing and screening,” Marais said.
Genuine large parts like gears help to ensure optimal performance, reliability and minimal downtime.
“However, this work is quickly undone when non-OEM parts are installed in our equipment, supposedly to save a few rand in maintenance costs.”
Marais said the performance and reliability of Metso’s equipment is based on its proven design and precision engineering. This includes the various components and wear parts that must be replaced from time to time. Copied parts from other sources do not carry this technical heritage, undermining performance and reliability.
Metso vice president for aftermarket distribution management Merja Tyyni said it also impacts the value of the relationship that OEMs work so hard to build with their customers.
“Our customer relationships focus on the whole process of delivering value to their operations,” Tyyni said. “We pay attention to the end-product value, where we can supply not only the appropriate capital equipment but also the follow-up troubleshooting, repairs and overall technical advice.”
The quality of these solutions and services is based on years of research, development and testing, as well as continuous investment in the necessary technical infrastructure and capability to respond quickly to customer needs. However, all these efforts are compromised when customers place non-OEM parts into their machines, as the quality chain is only as strong as its weakest link.
Metso head of aftermarket for Europe, Middle East, Africa and Central Asia Karima Dargaud said that OEMs have in-depth knowledge of their equipment that allows customers to achieve results that are optimal and predictable.
“Our OEM spares are an essential aspect of the support we provide, so that customers can reliably meet their production targets and avoid costly penalties,” Dargaud said.
“Customers build their reputations on this consistent performance, by producing the right results safely, on time and within budget. Using non-OEM spares only puts this reputation at risk, as machines then become unreliable.”
The OEM pitman is designed for optimal performance and reduced wear in every crushing operation.
OEMs like Metso design and manufacture their own spare parts to help ensure customers achieve optimal results.
The extreme forces and speeds that are often involved in heavy machinery mean there are also safety considerations for not using the speci ed parts in crushers and screens. Metso wear parts have been designed and manufactured with specialised material and hardening techniques, for instance, to ensure safety and performance.
“Fake parts will compromise worker safety, as there are normally a number of people in close proximity to this equipment who could be affected by a failure,” Marais said.
“A business that buys and ts pirate parts runs the risk of sending a negative message to its operators – that saving money is more important than the safety of crews on site.” AB
Headquartered in Sweden, Nordic Construction Company is geared for sustainability-minded growth despite many market challenges.
According to the Swedish Transport Administration, it is estimated that the country’s building and construction market has a turnover of approximately SEK 750 billion (€68.06 billion).
But it is not immune to current-day pressures. A recent Business Wire report found that Swedish construction industry output declined in real terms by about 6.1 per cent in 2024. Higher construction materials costs, rising energy prices, and a wider economic downturn affected building activity
with fewer building permits and the persisting weakness in the country’s residential sector. Such headwinds have led to delays or the cancellation of some of the country’s biggest construction projects
Sweden, the largest nation in the Nordic region, has several strong construction-sector players, many of whom combine their building activities with the production of construction materials.
One such leading business is the Nordic Construction Company (NCC).
NCC’s origins go back to 1890, when Axel Johnson, a well-known Swedish businessman, established Nordstjernan – the North Star, which later became one of the leading Nordic shipping companies.
The NCC Group was legally formed on January 1 1989, when two companies – JCC and ABV – united. In 2024, NCC had sales of about SEK 62 billion (€5.62 billion).
The Nasdaq Stockholm-listed Group has around 11,800 employees and builds residential properties, industrial facilities, public buildings, roads, civil engineering structures, and other types of infrastructure. NCC also sells aggregates, asphalt, and other construction materials, ful ls paving contracts and has a commercial property development division.
Grete Aspelund is head of NCC Industry, NCC’s subsidiary, which focuses on producing stone materials and asphalt, foundation work, and asphalt paving.
She told Aggregates Business that NCC’s construction materials production business is important because it allows the group to offer a comprehensive package for Sweden’s major infrastructure projects and the wider construction industry in the country and other Nordic states.
According to Aspelund, NCC’s stone and asphalt business, also known as the NCC Industry business area, develops, produces and sells stone materials and asphalt products for construction and infrastructure projects in Sweden, Norway, Denmark, and Finland. The business accounts for approximately 20 per cent of NCC’s sales. NCC Industry produced and sold 5.1 million tonnes of asphalt and 25.6 million tonnes of aggregates in 2024.
NCC has about 50 asphalt plants and 200 quarries and stone material sites in the Nordics and offers aggregates, asphalt production, paving services, ooding prevention products, asphalt with a lower CO2 footprint, and different stone products.
“We do environmental product declarations [EPD] and also work to ensure biodiversity in the areas where we are active – during application, operation, and part of the rehabilitation,” she said.
Due to the Nordic states’ serious climate goals and requirements for reducing their
carbon footprints, NCC pays close attention to sustainability issues.
Aspelund said NCC would continue transitioning its operations to be even more sustainable. This will comply with more rigorous Swedish Government sustainabilitybased legislation around using raw materials and lower-carbon-emitting equipment coming into force in 2035. NCC is also looking to be a climate-neutral business by 2045.
“Demands from customers, authorities and legislation require a continuous adaptation and development of our offering and also to be a driver in establishing recognition of the importance of both primary and secondary aggregates in developing sustainable societies,” Aspelund said.
NCC is working with customers, suppliers, and other stakeholders to develop new building materials using virgin, recycled, and mixed materials to cater to an evergrowing demand for circular-economy-based products. Some of these products will likely help meet the higher demand for building materials for huge onshore and offshore projects in Northern Europe and the Baltic region.
NCC has introduced several circulareconomy-based building materials in recent years, including NCC crushed concrete and NCC machine sand.
The crushed concrete can replace virgin materials such as natural gravel, rock and sand in various building works. Using NCC crushed concrete and other recycled crushed concrete is a cost-effective way of protecting natural resources. Its production starts with the company gathering demolition concrete, which is checked and sorted based on composition and properties. It is then manufactured according to applicable standards and technical speci cations based on the intended use area, with a CE mark obtained where required.
compactors working at Denmark’s Great Belt Bridge (Storebæltsbroen).
NCC machine sand (MCC Maskinsand) can replace natural sand or gravel in concrete production, asphalt production, sports and recreational infrastructure, and civil engineering projects. It is also suitable for tackling slippery roads, cable sand, and sealing layer applications.
Aspelund said climate change affects all of society and fully supports the construction industry’s efforts to minimise and counter its impact. As a prominent aggregate producer, she is keen for NCC to play an important role in works focused on, among other applications, coastal erosion control, coastal and riverbank protection, and road reconstruction.
“We have a portfolio of solutions to offer to various stakeholders, both as preventive solutions and solutions to manage and restore [eg NCC armour stone], both within our Nordic countries and through export to countries in Northern Europe,” she said.
Regarding NCC’s approach to sustainability in its stone materials and asphalt production, Aspelund said it is working to eliminate greenhouse gas emissions from its entire value chain, while simultaneously increasing energy ef ciency. The company currently works in several areas of its stone and asphalt production to reduce emissions; for example, electri cation of mobile stone crushers, which will deliver extensive energy ef ciency gains, electri ed transport in all countries, energy converting asphalt plants to run on biofuel, developing asphalt products with a lower climate
impact (eg focusing on biofuel, mixing in recycled asphalt and lower temperatures) and replacing fossil bitumen with bio-based binders in the asphalt.
Aspelund said NCC actively uses digitalisation and automation solutions in its stone materials and asphalt production, and realises the importance of arti cial intelligence (AI) technologies.
“We have a structured approach to reducing the impact of our operations by continuously improving production ef ciency and striving to give more than we take from nature,” she said.
“This is done by implementing digital tools to improve ef ciency in our production plants. When we nd an identi ed need, we implement new technologies, like AI.”
Aspelund said that by collecting extensive production data and input from company machine operators, NCC management gains valuable insights into various aspects of group operations. This detects inef ciencies, optimises resource usage, and enhances overall production ef ciency.
“Through continuous monitoring and analysis, we can make data-informed decisions to improve our production ef ciency and achieve our sustainability goals,” she said. “The collected data provides a comprehensive view of the production environment, empowering our team to implement targeted improvements and drive sustainable change throughout our operations.”
NCC can provide customers with Environmental Product Declarations (EPDs) documenting the environmental performance of its products in a transparent, objective and standardised way.
Aspelund said EPDs make it easier for NCC customers to calculate and meet their environmental goals. By actively engaging in lifecycle analyses and EPDs, the company can observe how its production and resource ef ciency improvements improve its climate impact.
NCC has also achieved “signi cant” progress in electrifying its production, according to Aspelund. This is partly re ected in all of its stationary crushing plants being electri ed, and the fact purchase agreements for renewable electricity have been signed in all Nordic countries.
Furthermore, all of NCC’s mobile crushing units are now diesel-electric hybrids. Aspelund said that while there can be issues around accessing enough electric power from local grids to run a complete NCC electric-powered machine eet, there has been a sizeable increase in NCC mobile plant production now powered by grid electricity. During 2024, 36 per cent of the group’s mobile plant production was powered by renewable electricity.
NCC Industry uses AI technology to detect large boulders in customer trucks. Until recently, identifying boulders (large stone blocks) in truckloads of excavated rocks has always been challenging for the group. The boulders reduce ef ciency and pro tability, as they incur additional handling costs since they must be manually sorted and broken into smaller pieces before they can be put in the crusher.
NCC Industry’s AI solution, based on Microsoft’s AI service in the eld of computer vision, analyses photographs of truckloads to predict the likelihood of boulders being present. A customer can be invoiced for the additional costs if a boulder is identi ed.
NCC has a long-term development strategy extending beyond the next decade. In February 2025, Aspelund played a central role in the wider group’s strategic review of the NCC Industry business area. The review evaluated various strategic options, including a possible divestment. The purpose was to review the best way to develop the business area going forward and to increase shareholder value in NCC.
Aspelund said NCC Industry has a leading market position and has developed a strong product and services portfolio, offering many further growth opportunities. It has signi cantly increased its pro tability by focusing on operational discipline and customers’ needs.
As a leading company in the Nordics, NCC Industry has already taken a prominent position in asphalt with a lower carbon footprint. AB
12-month partners get priority on the best branding opportunities.
Aggregates Business is a go-to source for up-to-date news and views on the European, American, Asian, African and Middle Eastern aggregates and building materials sectors. Our wide-ranging features line-up includes in-depth articles on the latest crushing and screening, loading and hauling machines.
A rich variety of next-generation o -highway machine engines has created considerable industry interest and excitement.
Cummins’ next-generation X15 Off-Highway engine platform was a big draw at bauma 2025 in Munich, Germany.
The latest addition to the US-headquartered company’s off-highway line-up is part of the Cummins Higher Ef ciency, Lower Emissions, Multiple Fuels (HELM) fuel-agnostic engine platform. It promises original equipment manufacturers (OEMs) and end users a list of advancements over its predecessor, powering large-scale construction and industrial equipment such as wheeled loaders, cranes, excavators, air compressors, and more.
Telematics, lower fuel consumption, easier maintenance, and long life to overhaul are all bene ts new Cummins X15 customers should count on to improve their bottom line, according to the company.
“We’ve introduced a simpli ed clean sheet design that offers numerous bene ts for our OEM partners and end users adopting the next-gen X15 off-highway,” Cummins vice president of engine business engineering Jonathon White said.
“Customers will see powerful performance and higher ef ciency now in a lighter, smaller package, all while maintaining the steadfast durability Cummins has long been known for in construction applications.”
According to Cummins, the latest off-highway X15 delivers up to 10 per cent better fuel economy than the prior X15 model, with comparable ratings and duty cycles. The X15’s high-ef ciency fuel injection provides precise fuelling and combustion control at ultra-high pressures. Together with the newly optimised HE550 Wastegate turbocharger, the system offers excellent transient response and altitude capability, built with new upgraded materials for durable and reliable performance.
Alongside improvements in fuel ef ciency, the next-generation X15 also promises cost savings related to routine maintenance.
New adopters can expect up to 1000hour service intervals from the X15, according to Cummins, which means less overall maintenance is required. Coupled with an improved design, whereby its fuel lter and oil drain now share the same
replacement interval, common service items can occur simultaneously, which results in less downtime and improved maintenance planning for eets.
The X15 now also offers a maintenance-free breather and has no exhaust gas recirculation system, which will collectively cut down on maintenance costs for new customers. In addition, the new platform has been designed to provide a long life to overhaul, resulting in potentially more productivity and a stronger return on investment.
Capabilities to support remote monitoring and diagnostics, together with over-the-air (OTA) software updates, make maintaining engine health a less costly pursuit through the next-gen X15’s telematics features.
Jobsite service professionals can take advantage of priority-ranked real-time alerts and be paired with Cummins engineering recommendations on how and when to service potential issues before they progress. When Cummins releases new engine calibrations, the X15 OTA programming capabilities allow for secure software updates using cellular connectivity.
Both digital technologies help reduce the need and cost for technician dispatches and unnecessary service stops, while ensuring more timely and accurate diagnostic reports and up-to-date engine calibrations. These digital capabilities require a compatible OEM gateway and a participating telematics service provider.
In addition to lower total operating costs, the next-generation X15 will be more easily installed into machine equipment.
With more than 20 ratings that range 298–522kW and peak torque up to 3200Nm, off-highway OEMs upgrading their offerings with Cummins’ next generation X15 will be
able to deliver higher power and torque to customers with less weight and a smaller package size that resembles a 13L engine.
The X15 has many OEM integration options and application features, designed for easier installation and service. Modular component design further simpli es the integration process for off-highway equipment manufacturers, providing added exibility to reach key connection points while reducing the number of components by 30 per cent in critical systems such as cooling and lubrication.
Meanwhile, the ex-module aftertreatment with a new mixer design simpli es the installation, offering various installation con gurations to meet the needs of different applications better. The elimination of the exhaust gas recirculation system (EGR) reduces the cooling system requirements for machines.
The new X15 is also available without after-treatment to support varying regulations across countries, simplifying integration across different regions.
“As the world’s largest independent diesel engine manufacturer, our volume allows us to invest in new and innovative technologies to meet future requirements and emissions,” Cummins vice president of engine business global off-highway markets Marina Savelli said.
The bauma showcase included, among other platforms, the award-winning Cat C13D and a new high-power C3.6 delivering 106kW.
“In turn, we can bring exciting innovations to the market and help power our OEM partners’ success well into the future.”
Fuel-agnostic engine platform
Cummins is developing various solutions, including three new clean-sheet engine platforms designed to meet future emissions and CO2 norms.
The B, L and X engine platforms will be compatible with a variety of current and future low- and zero-carbon fuels, including natural gas, clean diesel, and hydrogen.
This means it’s possible to integrate these solutions, including the X15, into OEM equipment with limited proliferation by deploying Cummins HELM platforms. These platforms leverage common base engine hardware and unique fuel or air handling solutions to operate on varying fuel sources.
The ability to select different fuel types without requiring signi cant changes to the machine equipment makes X15 integration even more noteworthy. Customers who use Cummins HELM platforms can choose to power with clean diesel or biofuels today and move to a lower emissions alternative, like hydrogen, in the future.
Powered up
Caterpillar Industrial Power Systems
showcased a range of optimised, fuelexible engines, integrated advanced power technologies and services solutions at bauma 2025. The theme, ‘A journey to a lowercarbon future’, highlighted Caterpillar’s ongoing commitment to sustainably powering a better world.
The 13L Cat C13D diesel engine platform is designed to achieve best-in-class power density, torque and fuel ef ciency for optimising the performance of heavy-duty off-highway applications. Engineered to Caterpillar’s standards for reliability and productivity, the inline, six-cylinder Cat C13D engine platform will offer eight power ratings from 340–515kW with up to 3200Nm of peak torque. Engine-mounted after-treatment and cooling packs will also be available from the factory to reduce installation and validation costs.
The C13D will meet the emissions standards of highly regulated markets, such as EU Stage V, US EPA Tier 4 Final, China Nonroad Stage IV, Korea Stage V, and Japan 2014, with models available for less regulated markets.
By supplying more power and torque available from Caterpillar’s current 13-, 15- and single-turbo 18L engine platforms, the C13D platform provides an opportunity for OEMs to downsize the engine and simplify design, assembly, and supply chain requirements across multiple applications. This consolidation can also reduce maintenance, parts and technical training complexity for end users.
The Cat C13D, which goes into production in 2026, is designed for use in a wide range of off-highway equipment, including rock crushers, screeners and grinders; trenchers; agriculture tractors, harvesters and self-propelled sprayers; woodchippers; material-handling equipment; and large industrial pumps.
“Off-highway OEMs and equipment owners face a rapidly evolving business environment that demands improved worksite productivity and reduced operating costs while addressing increasingly stringent emissions standards,” Caterpillar Industrial Power Systems senior vice president Steve Ferguson said.
L–R: The Cat 13L C13D engine is designed to achieve best-in-class power density, torque and fuel e ciency; the Cat C3.6 delivers 106kW of power and addresses customer needs for more power from a compact package.
“Internal combustion engines are the prevailing workhorses on most jobsites around the world, which is why we’ve invested in the next-generation Cat C13D diesel engine platform to address their challenges.”
The engine platform offers up to a 20 per cent increase in power and up to 25 per cent more low-speed torque over the previous generation of Cat engines in its power class. It is designed to perform at altitudes of up to 12,000ft, which is twice as high as legacy Cat engines, and in extreme ambient temperatures as high as 60 °c (140°f) and as low as -40°c (-40°f) with aids.
Extended service intervals – 1000 hours oil and fuel lter – will reduce operating costs and downtime. By modularising and eliminating components, its architecture is space-protected to accommodate con guration adjustments anticipated for future tiers of emission standards in the US and EU without relocating customer connection points.
The Cat C13D engine platform can be powered by renewable liquid fuels such as 100 per cent hydrotreated vegetable oil (HVO), up to B20 for models with aftertreatment and B100 for models without after-treatment. The machine’s core architecture is designed to support future development for alternative fuels such as natural gas and hydrogen.
In late-2024, Caterpillar started work on an advanced hydrogen–hybrid project,
leveraging the versatile new C13D engine platform. The three-year program will develop a transient-capable system for off-highway applications, demonstrating how state-of-the-art control systems and electric-hybrid components can help hydrogen-fuelled engines match traditional diesel engines’ power density and transient performance.
The 100kW Cat C3.6 engine platform has seen a six per cent power boost over its predecessor and is designed to address customers’ needs for more power in a compact package.
To enable customers to extend the lifecycle of their engine across their eets, Caterpillar Industrial Power Systems also exhibited at bauma 2025 a range of exible parts and services solutions to support each stage of the engine lifecycle, including extended service contracts, customer value agreements, parts, repair options and its global dealer network.
904 Series diesel engine. Its compact design enabled the seamless transition from diesel engine to electric, with the power unit tting within the same chassis space and having the same mechanical connection
An interactive simulator promoted the importance of condition monitoring for proactive diagnostics and a right- rst-time x to reduce downtime.
The Caterpillar Industrial Power Systems’ stand also featured an eye-catching deconstructed Cat C7 Reman engine, including Cat remanufactured parts and end-of-life parts, also known as ‘core’. The display showed the contrast between core and Cat Reman parts to highlight the remanufacturing processes in Caterpillar facilities.
Cat Reman products help OEMs extend their machine’s lifecycle, reduce waste, and keep the engine running strong. Fully assembled and ready to run, Cat Reman complete engines are dynamometer-tested and tuned for like-new performance and fuel ef ciency.
With an extensive offering from simple components to overhaul kits to complete engines, Cat Reman enables customers to reduce downtime, quickly get back into operation and bene t from like-new performance on the toughest jobs.
Available in 2026 and showcased at bauma 2025, the Perkins 2600 Series engine platform is designed to meet the demands of construction and many other off-road, heavyduty applications.
According to Perkins, the 13L diesel engine platform achieves power density, torque, fuel ef ciency and productivity. Industrial open power units con gured with engine-mounted after-treatment and cooling packs will also reduce installation and validation costs for OEMs.
The 2600 Series will meet the emissions standards of highly regulated territories. Its engine platform also enables the use of renewable fuels like HVO.
The Perkins stand also featured the new 106kW variant of the 904 Series platform. With a six per cent power uplift from the
Perkins said its 2600 Series achieves best-in-class power density, torque, fuel e ciency and productivity.
100kW model and a three per cent increase in torque, the new offering is ideally suited to applications that need more power in a compact package. The standard offering also comes with electro-magnetic apical treatment (EMAT) to minimise installation costs.
The Perkins 904J-E36TA has been tted with a new 12-plate oil cooler to improve the engine’s durability and reliability, while high-ef ciency fuel lters improve altitude capability. The engine meets EU Stage V, US EPA Tier 4 Final, and Japan 2014 emissions standards. It can also run on a range of fuels, subject to the fuel meeting Perkins’ speci cations, including 100 per cent HVO1.
“Perkins continues to invest in and optimise its established internal combustion engine platforms to make them even more ef cient and fuel exible,” Perkins vice president, global sales, marketing, service and parts Jaz Gill said.
“OEMs want the exibility to use multiple fuels without sacri cing power, reliability or ease of integration. The new 2600 Series and higher power 904 Series deliver high ef ciency with ease of integration, helping our customers achieve their objectives without a full re-design of their machine.”
Perkins’ growing advanced power portfolio has welcomed the addition of a new battery-electric power unit technical demonstrator, shown for the rst time at bauma 2025. Shown in a pipe fusion machine, the plug-and-play battery electric power unit is designed to enable off-highway OEMs to transition seamlessly from diesel to a battery-electric powertrain.
The Perkins battery electric power unit has been tested in a McElroy TracStar 900i pipe fusion machine as a commercial demonstrator, with the unit replacing a 3.6L
Given today’s customers operate in a fast-paced world where cost-effective engine management and operational ef ciency are an absolute necessity, Perkins has developed a comprehensive connectivity and conditionmonitoring solution to meet customers’ requirements and deliver measurable bene ts to OEMs and operators.
the space measurable operators. engine
from monitoring and insights that are sent to the
A telematics data sharing application programming interface (API), is available for OEMs to share engine data from pre-existing telematics systems, supporting equipment owners with enriched advanced analytics from the engine, supported by condition monitoring and insights that are sent to the customer’s engine support ecosystem.
“Seamlessly linking to customers’ equipment, Perkins connectivity solutions improve operational control,” Gill said.
“Whether monitoring performance or optimising ef ciency, the real-time insights and proactive support available from the Perkins distribution network help to minimise downtime through faster service response times and an increased rst-time x rate, as well as signi cantly reduced costs.
“The importance of protecting your engine investment for a lifetime is a key message at bauma, with an interactive display on the bene ts of register, maintain, extend and replace. Together, these four actions optimise engine performance throughout its entire life cycle,” Gill said.
“This approach enables our customers to prevent downtime and reduce the total cost of engine ownership, all while ensuring their worksites run ef ciently and effectively.”
Volvo Penta shifts with customer demands
Volvo Penta has streamlined its dealer network, focusing on stronger and highly specialised partners in response to shifting customer demands and the increasing complexity of industrial equipment.
“Our customers don’t just need an engine supplier – they need a long-term service partner who understands the challenges of their industry,” Volvo Penta industrial head of global service market Björn Säljö said.
“By re ning our dealer network, we’re ensuring that every partner has the technical expertise, nancial strength, and investment capacity to provide world-class service and adapt to the future of power solutions.”
The strategy furthers the specialisation of Volvo Penta’s dealer network across the broader service ecosystem, which includes OEMs and their retail channels. Volvo Penta aims to secure seamless support from traditional diesel power to emerging electri cation and data-driven services by aligning expertise and capabilities across these key partners.
Volvo Penta said it is moving towards a “service-driven ecosystem”. At bauma
2025, the company highlighted how service contracts now support engine sales, such as performance-based service agreements that optimise uptime and reduce operating costs, subscription models for predictive maintenance and remote monitoring, and bundled solutions covering a holistic service ecosystem to maximise equipment ef ciency.
“Our customers increasingly prioritise operational ef ciency and long-term value over one-time purchases,” Volvo Penta industrial service market manager for Central Europe Judith Karl said.
“Our service-and-performance- rst approach aims to integrate predictive analytics and connectivity to enhance uptime, optimise costs, and ensure that businesses stay competitive.”
Volvo Penta brings the strength of its industrial expertise to construction equipment. The company leverages extensive experience in ports, mining and material handling and ensures that eets bene t from the same high-reliability service standards used in the most demanding industrial sectors.
At the core of Volvo Penta’s service transformation is connectivity, driven by advancements in Internet of Things (IoT), digital twins, and real-time eet analytics. These technologies enable real-time engine monitoring to help minimise downtime and optimise maintenance costs.
By integrating data-driven insights into service contracts, Volvo Penta can help enhance long-term operational value and performance. This approach supports modular contracts for electri ed equipment, off-highway productivity solutions, and engine services designed to boost ef ciency and cut emissions.
Guided by its ‘Made to Move You‘ tagline, Volvo Penta aims to drive its future of industrial services with dynamic partnerships that power ef ciency, reliability, and longterm customer success.
A new era in power
At bauma 2025, John Deere Power Systems (JDPS) embraced “a new era in power”, according to John Deere director of global marketing and sales Nick Block.
“This means developing technologies that not only meet today’s needs but also anticipate the challenges our industry will face in the years to come,” he said.
“We believe the future of power is not de ned by a single solution but by a range of options that allow our customers to choose the best t for their operations.”
The JDPS show line-up included the Next Generation engines – the JD4, JD14 and JD18. These platforms are built from a cleansheet design and engineered to power the construction industry, now and in the future. Designed for lasting performance, these engines deliver impressive power density, optimised fuel ef ciency, and streamlined serviceability; all critical features for working on today’s rugged jobsites.
JDPS also continues to improve its current offerings. Attendees of bauma 2025 learnt that the JD9 engine provides more power than the John Deere PSS 9L engine and offers streamlined integration,
making it ideal for a wide range of construction applications.
The optimised JD9 builds on the proven performance of the existing 9L engine to offer lower complexity and installation costs while maintaining the renowned John Deere quality and reliability.
Whether with purpose-built engines for a range of construction needs or optimised versions of trusted models, JDPS is dedicated to providing its customers with reliable, powerful, and ef cient solutions for the future of construction. JDPS offers customers comprehensive after-market solutions designed to keep equipment running strong.
At bauma, JDPS showcased its robust service network, which includes more than 9000 service locations worldwide with skilled engine experts ready to assist.
Attendees also learnt about the John Deere Lifecycle Service Solution, a complete service package that includes engine maintenance plans, PowerGard Protection Plan, and John Deere Connected Support. These solutions provide customers with the tools and support they need to proactively manage maintenance and optimise the performance of their John Deere engine. AB
With recycled materials becoming increasingly important in the construction materials sector, manufacturers are meeting this need through new machines and innovations.
Recycled material usage in infrastructure projects is only set to increase due to an expanded push from outside and within the construction materials sector to become more environmentally friendly.
BP Mitchell is an established name in London’s construction materials space. From its headquarters in Hertfordshire, north of London, the producer processes mixed construction and asphalt waste for various uses.
Construction and demolition waste, or asphalt waste, can present a unique challenge for a construction materials provider and differ in its production cycle from virgin rock.
BP Mitchell operates a large wash plant where recycled materials can be cleaned for further processing and a Ciber asphalt plant for its asphalt-related products.
When it comes to crushing and screening equipment, the Hat eld-based company turns to one name: Kleemann.
“Our goal is to produce recycled material of the highest quality possible. To achieve this, we invest in high-quality, cutting-edge machinery,” BP Mitchell managing director Brendan Mitchell said.
“What impresses us time and again about the Kleemann plants is their innovative features and outstanding ease of use. Our people nd the machines very easy to handle. Everything can be adjusted and operated intuitively and conveniently.”
BP Mitchell recently purchased a new MOBIREX MR 100i NEO mobile impact crusher for its operations.
This recent addition expands the company’s existing Kleemann eet, which includes four MOBICAT jaw crushers, two MOBISCREEN coarse material screening plants, and a MOBIBELT mobile stacker.
BP Mitchell’s plant in Hat eld produces material for road substructures (Type 1, less than 40mm grain size) and provides further processing for the washed plant. It also recycles asphalt grains smaller than 20mm for the Ciber asphalt plant.
The MOBIREX MR 100i NEO was selected because it can handle sticky materials and mixed feed materials.
The crusher’s features, including the automatic crushing cap adjustment, enable it to handle this varied load of materials with ease.
This means the MR 100i NEO can easily switch between washing plant feeding and processing recycled asphalt (RAP).
“The crushing gap adjustment can be operated at the push of a button – de nitely a highlight in this machine class,” Mitchell said. Kleemann designed the MOBIREX MR 100i NEO to handle a high production load while also requiring low-fuel consumption. The balance can be tricky to strike, but BP Mitchell has noticed the new Kleemann machine only consumes 11L of fuel per hour while producing up to 60 tonnes per hour of 0–20mm grain size.
“The advice and service we receive are rst-class,” Mitchell said. “We know that we can rely on the on-site technicians, and that gives us real peace of mind.”
success
Due to the signi cant demand for recycled construction materials, some manufacturers are beginning to specialise in equipment for the sector.
Screencore’s international distributor network has supported a growing list of producers of recycled construction materials. This group of dealers and distributors has provided Screencore equipment to the US, French, UK, Australian, and South African markets.
Screencore offers a range of solutions, including tracked jaw crushers, Trident scalper-screens, Orbiter trommels and radial stockpilers to customers working in the sector.
The company can also develop a bespoke selection of stationary recycling plants based around its Orbiter trommel range, which works alongside Screencore’s stockpilers and scalpers.
“The Screencore product range was developed to meet the needs of the modern contractor and materials handling operation. We have set out to build the highest standards of equipment that helps people in the eld be more pro table, ef cient and effective in what they do,” Screencore director Ciarán Ryan said.
“We have also incorporated environmental ef ciency into our processes to minimise customers’ carbon footprint. All this has meant that working with our distributors
Screencore o ers a range of solutions for recycled construction materials.
has seen Screencore equipment adopted on numerous projects, turning construction waste into reusable and/or resaleable products.”
The ScreencoreXJ is a machine crusher with a dual-power 1000x650mm jaw crusher. The crusher is fed demolished or excavated materials by an excavator or loading shovel before crushing to -100mm.
Any ferrous metals, such as rebar or wire, are easily removed for resale or recycling by the overband magnet on the XJ crusher’s discharge conveyor before being fed into the Trident 124 scalper/screener.
The Screencore XJ Dual-Power Crusher is easily transportable due to its lightweight, allowing contractors and rental eets to move it with ease. The combination of the Screencore XJ Dual-Power Crusher and Trident 124 scalper/screener can be set up in less than 30 minutes.
“Screencore will custom-design conveyors, stockpilers and feeders to meet application requirements,” Ryan said.
“Our designs are renowned for their quality and ease of assembly, arriving in neatly packed containers and speci ed to over-deliver on throughput expectations.
“We also supply a range of air separation systems for stationary and mobile plants.
“Screencore has gained much experience using electric power from various sources. Main electricity has proved to be an ideal power source, delivering a cost-effective and environmentally ef cient solution.
“Through this power source, or the dual-power solution, precision processing of materials is accomplished without producing the emissions that would be of concern, and at the same time, at a low [operating] cost.” AB
Hyundai’s HX230e is a 25-tonne machine powered by a 420kWh battery pack.
A vibrant quarrying-suited loader market is giving buyers many new, highly innovative, and sustainability-minded models in which to invest.
Hitachi Construction Machinery (Europe) (HCME) has unveiled Hitachi’s vision for the future of construction equipment with its pioneering excavator concept: LANDCROS One. HCME said this innovative machine development “represents a fundamental shift in how machinery interacts with operators, job sites, and the broader construction ecosystem”.
Launched at bauma 2025 in Munich, Germany, LANDCROS One brings HCME’s forward-looking vision to life through design collaboration with Granstudio, an automotive and mobility design studio.
“LANDCROS One showcases Hitachi’s vision of a safer, smarter and more sustainable future, blending groundbreaking AI [arti cial intelligence], gami ed ergonomics, autonomous and remote operations capabilities,” HCME president and chief executive of cer Francesco Quaranta said. “We’re proud to lead the next wave of innovation, empowering the next-generation
workforce and rede ning possibilities in the construction machinery industry.”
The concept introduces what HCME calls a “phygital” approach – the seamless integration of “physical” controls and “digital” interfaces to create an intuitive operator environment.
The innovative design features a modular cab with intuitive ergonomics, speci cally engineered to appeal to the next-generation workforce through gamifying operations and AI-assisted interfaces.
HCME’s LANDCROS One is said to be based on four transformative innovation pillars:
The concept’s integrated AI and automation systems fundamentally change the operator experience by handling routine tasks and providing intelligent assistance during complex operations.
The functional design integrates cameras, sensors and advanced digital assist systems co-developed with strategic partners.
With combined onboard and offboard landscape scanning capabilities, including drone technology, HCME called LANDCROS One a “cornerstone in creating a comprehensive construction ecosystem”.
This intelligent support system reduces operator fatigue, increases productivity, and helps address the industry’s ongoing labour shortage by making advanced equipment more appealing to newer operators.
LANDCROS One features advanced connectivity and remote operation capabilities. The machine can be controlled from virtually anywhere, enabling true 24–7 operation through different time zones and allowing (specialised) operators to work across multiple sites without physical relocation.
These capabilities maximise equipment utilisation and enhance safety by removing operators from remote, dif cult and hazardous environments while maintaining precise control over operations.
Recognising the diverse needs of today’s construction workforce, the excavator offers three distinct operation modes:
• Manual Mode provides complete control for operators supported by AI for standard or complex tasks, reducing fatigue and increasing productivity
• Autonomous Mode is triggered by operator instructions for repetitive and predicted tasks
• Remote Mode enables full operation from any location, 24–7, providing exibility with operator availability worldwide
Adaptive power systems for every jobsite
Environmental responsibility meets operational exibility with the concept’s propulsion system available in three distinct power modes: electric, combustion and hydrogen.
“At Granstudio, we are proud to have partnered with Hitachi to bring to life a revolutionary concept excavator that rede nes the future of construction equipment,” Granstudio founder and creative director Lowie Vermeersch said.
“By blending our expertise in design and innovation with Hitachi’s engineering excellence, we have created a vision that pushes the boundaries of ef ciency, sustainability, and user experience.”
This concept demonstrates how HCME’s engineering and design expertise can challenge conventional approaches to construction equipment. The result is machinery that is more powerful and ef cient, intuitive, adaptable, and connected.
“LANDCROS One is more than just a machine. It’s our commitment to deliver solutions beyond machinery in a new construction ecosystem,” Quaranta said.
“We’re building a smarter tomorrow together with our strategic partners and customers.”
Komatsu’s operator-centric excavators
Komatsu Europe has unveiled the all-new PC220LC-12 and PC220LCi-12 excavators.
With these premium machines, Komatsu said it has successfully uni ed “striking aesthetics,
intuitive ergonomics, extreme fuel ef ciency, ultra-low emissions, effortless performance, revolutionary levels of digitalisation, and comprehensive safety measures into a single, truly exceptional operator-centric package”.
These state-of-the-art machines result from Komatsu’s long-standing commitment to innovation and excellence. The company said the new machines are engineered to set a new benchmark for performance, ef ciency, operator comfort and digitalisation across the construction industry, to deliver “extraordinary customer value”.
“Our approach to the next generation PC220LC and PC220LCi excavators was completely in line with our philosophy of creating value together,” Komatsu Europe product manager Paul Dickinson said.
“We visited numerous customers’ jobsites, listened to their needs, and brought those requirements back to our innovation and technical centres.
“Concepts were born, checked with customers, re ned, checked again, and by continually listening and innovating, we now come to market with a product bursting with customer value.”
The PC220LC/LCi-12 is built on an all-new, powerful 129kw high-torque Komatsu next-generation engine paired
Komatsu’s PC220LCi-12 o ers unique iMC 3.0 features.
with the new high-ef ciency electronically controlled hydraulic system. This translates to an 18 per cent reduction in average fuel consumption, saving customers approximately 2.1L per hour compared to the previous model. This means lower operating costs and a reduced environmental footprint with minimal CO2 emissions per tonne of material moved.
The new hydraulic system, combined with large-class hydraulic cylinders and highcapacity hydraulic pumps, delivers a seven per cent increase in arm and bucket forces allowing for easier digging and material movement, reducing tonne costs.
The advanced hydraulic system translates to sharp re exes and zero-lag response to the operators’ input, creating an intuitive connection where the machine and driver become one, Komatsu said.
Furthermore, the all-new P+ mode increases productivity by 18 per cent and fuel ef ciency by 20 per cent, offering substantial cost savings, improved output, and an uncompromised return on investment.
Beyond ease of operation, Komatsu said the all-new cabin design takes operator comfort to an “unprecedented” level.
A signi cantly larger cab with 30 per cent more legroom and an all-new premium seat option ensures operators can comfortably work. Fifty per cent increase in lower righthand side visibility, overhead cooling vents, joystick steering as standard, and numerous storage spaces further contribute to a pleasurable working environment.
Advanced operator assist technology complements these physical improvements. A high-de nition eight-inch touch-panel monitor provides intuitive control and easy information access. Moreover, the machine features ultra-versatile, programmable, super-ergonomic electronic control levers and fully customisable hydraulic settings that
allow operators to tailor the machine to their speci c needs.
Thanks to the operator ID system, which stores up to 50 pro les, operators are recognised via electronic key or typed ID, and their personalised settings are automatically loaded.
In addition, advanced technologies, including an integrated payload metre, integrated 2D machine control designed for simple depth and slope grading, and a 2D virtual safety wall, are provided as standard on PC220LC-12.
Built on Komatsu’s more than 10 years of experience in factory-integrated intelligent Machine Control (iMC), the PC220LCi-12 offers unique iMC 3.0 features.
Compatible with tiltrotator, iMC 3.0 offers advanced features such as 3D boundary control and automated steer-to-line. Advancing towards autonomous operation, iMC 3.0 introduces auto swing, enabling semi-automatic truck loading. Features such as swing-to-line and travel-along-line functionalities further simplify trenching operations for operators of any skill level.
The new 10-inch iMC 3.0 monitor, with intuitive 3D graphics, is a leading driver assist system.
With Smart Construction Remote as standard, customers can seamlessly transfer design les remotely and troubleshoot by taking over the screen, eliminating unnecessary site visits.
The PC220LCi-12 features an advanced payload meter, optimising loads and preventing overloading. Connecting with the optional Smart Construction Fleet allows automatic transmission of truck information to the excavator, so no manual input is necessary.
PC220LC-12 owners can access these features via a factory-made upgrade. This comprehensive kit provides a straightforward pathway to integrate the full suite of iMC 3.0 features so the investment remains future-proof.
“We pioneered fully factory-integrated machine control on excavators back in 2014. Those more than 10 years of constant development, deep experience of learning from customers, and fully supporting them on the jobsite to get the best out of this type of technology has led to these truly unique assist features we see on iMC 3.0,” Komatsu Europe product manager Rob Macintyre said.
The PC220LC/LCi-12 has many advanced safety features, including a 360° KomVision system, an optional human-detection system and rollover avoidance indicator for absolute situational awareness and accident prevention.
Komatsu excavators have long been synonymous with exceptional durability. With the Dash 12 generation, Komatsu presents an even more robust machine that offers durability and resilience, regardless of application. This is made possible by implementing heavy-duty strengthened work equipment, including a new reinforced heavy-duty boom, arm, upper structure, and a new track frame design.
The PC220LC/LCi-12 also features low-cost maintenance with extended service intervals. Engine oil changes are required every 1000 hours, double the previous 500 hours.
The hydraulic oil lter replacement interval has tripled to 3000 hours, and DPF cleaning is scheduled every 8000 hours.
Building on Komatsu’s commitment to customer satisfaction and longterm performance, the PC220LC/LCi-12
is supported by the Komatsu Care programme, so every customer can enjoy absolute peace of mind throughout the lifecycle of their machines.
The PC220LC/LCi-12 made its highly anticipated international debut at bauma 2025. Visitors witnessed the machine’s capabilities rst-hand through dynamic, live outdoor demonstrations, while a static indoor exhibit allowed people to jump in the operator cab and check out the machine’s most innovative features.
The presentation at bauma 2025 was the rst opportunity for a global audience to experience the PC220LC/LCi-12 outside of Japan.
Cat 395 FS on show Caterpillar chose bauma 2025 to unveil the Cat 395 Front Shovel Large Excavator, the company’s rst new front shovel con guration in 15 years.
Designed to meet the exacting needs and expectations of quarrying and mining customers, this new model fully takes advantage of standard next-generation features, such as fuel economy and low maintenance costs, while further improving Caterpillar’s world-class levels of operator comfort and control.
“The 395 FS has an of cial target launch of October 2025,” Caterpillar senior product and sales consultant Vincent Migeotte said.
“But there’s no better place than bauma to showcase the pre-production model and have potential customers see it in the metal. We’re excited to have the 395 FS join the Large Excavator line-up.”
Migeotte said three primary objectives were at the top of the design wish list for the 395 FS: robust digging and breakout force, lightning-quick loading cycles, and rigorous bucket full.
“Customers repeatedly told us that they need a machine that not only offers peak performance but that can operate consistently at those peak levels,” he said.
“That’s borne out in the 395 FS with a maximum ground level digging force up to truck height, matched by a powerful breakout force at the bucket cutting edge that promises superior material penetration and optimal bucket ll factors.
“And of course, that’s complemented by bucket capability. Here’s a machine that’s compatible with bucket volumes up to 6.5m3, or maximum material density of up to 1.85t/m3. That offers operators a big boost in productivity.”
Caterpillar’s values of durability, reliability and serviceability are woven through the design of the 395 FS, evident in features such as the reinforced, extra-durable undercarriage and additional cylinder guards, plus long-life fuel and hydraulic oil lters to reduce costs and downtime.
There’s also the assurance conveyed by all next-generation models sharing common parts, backed up by Cat dealers’ far-reaching customer service and celebrated product support.
Operator-oriented in-cab controls are easily accessible, enhancing material penetration, fast loading, and smooth oor clean-up. Inside, the cab features an ergonomic seat, a touchscreen display, climate control, noise insulation, and vibration reduction, all contributing to a more comfortable and ef cient operating experience.
“Of course, a machine only delivers its best performance when it works in harmony with its operator, which is why we’ve paid so much attention to operator optimisation through next generation developments,” Migeotte said.
“The 395 FS has been engineered with a parallelogram-type front linkage, coupled with a master cylinder that allows the operator to extract the machine’s maximum capability. By keeping the bucket parallel to the ground, the operator can optimise penetration, loading, sorting and breaking, and complete a smooth oor clean-up when the hard work’s over.
“Building the 395 FS around the nextgeneration cab, we’ve also tted a xed riser which allows the operator to see above the side of the truck body while loading. Premium work task visibility helps increase both productivity and worksite safety.”
Develon transparent bucket Develon, formerly Doosan Construction Equipment, has introduced the Transparent Bucket 2.0 (TB2.0) system, an advanced safety and visibility system for the company’s wheeled loaders. Designed to eliminate blind spots, TB2.0 improves both operator safety and jobsite ef ciency.
Traditional wheeled loaders create blind spots in front of the machine due to the raised bucket, posing serious safety risks. The Develon Transparent Bucket solves this problem by using high-tech front-mounted cameras to create a real-time see-through effect on the cab monitor. This gives the operator a clear view of the obstructed area, ensuring greater awareness and precision when handling materials such as aggregates, sand and soil.
Building on the success of the previous version of the system, TB2.0 introduces AI-powered Object Detection and Object Recognition to provide enhanced safety and real-time hazard alerts.
AI-powered Object Detection identi es objects – including people – within 10m and immediately alerts the operator with a red triangular warning on the monitor. With Object Recognition, the system learns the position of the bucket and automatically adjusts the composite image to match the movement of the bucket, ensuring accurate real-time visualisation.
TB2.0 integrates two cameras mounted on the cab and front frame to create a seamless, curved projection composite image of the space in front of the bucket. This helps to ensure the display dynamically adjusts as the loader moves, maintaining a clear, uninterrupted view for the operator.
As part of TB2.0, Develon has improved the warning system with colour-coded alerts that instantly communicate the level of danger to the operator:
•Red ashing border – if an object is detected within the bucket’s transparency zone, the monitor ashes bold red to indicate immediate danger
•Yellow ashing border – if an object is detected outside of the visibility zone, the monitor will ash thick yellow, signalling a potential hazard
These instant, intuitive alerts help operators make quick, informed decisions to prevent accidents and improve work ow safety. While it forms an intelligent additional safety solution that dramatically improves visibility and safety, Develon said it remains a complementary tool and operators should always visually inspect their surroundings and not rely on the system alone.
LiuGong battery-electric expertise
LiuGong showcased its expertise in batteryelectric vehicle technology at bauma 2025, highlighting more than a decade of development and real-world application. Among its comprehensive line-up were the 975F excavator and the 890T wheeled loader.
As the agship model of the T-Series, the 890T has undergone over 20,000 hours of rigorous testing, ensuring exceptional reliability and ef ciency. With a load capacity of 10.5 tonnes and a 5.4m³ bucket, it offers enhanced fuel ef ciency, increased operator comfort, and total maintenance access, making it the ideal choice for demanding mining and quarrying applications.
A heavy-duty 75-tonne class excavator, the 975F has been tailored to the needs of European customers, offering durability, ef ciency and operator comfort. It features LiuGong’s latest F-Series cab, which enhances visibility and control and makes it an industry powerhouse in demolition and quarrying applications.
Hyundai concept meets reality
Hyundai Construction Equipment (Hyundai CE) demonstrated a concept full-size electric crawler excavator at bauma 2025. The HX230e is a 25-tonne machine powered by a 420kWh battery pack, which will provide up to eight hours of operating autonomy between charging stops.
An optional 503kWh battery will extend potential working time. The excavator has a regular AC charging input and a rapid CCS2 DC charging capability, allowing quick battery recharging to deliver maximum productivity.
The charge powers an electric e-pump, which drives the excavator’s hydraulic system. In addition, it has an e-swing slew motor, an e-thermal management system, and an auto sleep setting to maximise operation ef ciency. The excavator boasts a full electronic hydraulic control system, allowing the operator to customise each hydraulic function to match the task and increase ef ciency.
The HX230e offers performance similar to a conventional diesel-powered machine of the same weight, but with zero emissions at the tailpipe and a lower operating noise level. This will become increasingly important as major cities worldwide impose increasingly stringent emissions regulations on off-highway equipment over the coming years.
Hyundai CE said many contractors and equipment rental businesses are already calling on manufacturers to offer diesel power alternatives for their machinery.
The company is committed to building a sustainable construction site through its rapidly expanding electri ed and hydrogenpowered machinery line. The HX230e is expected to reach production by the end of 2027.
Hyundai CE also unveiled the rst two models in the Next Generation of crawler excavators as part of its bauma 2025 showcase.
Hyundai’s award-winning DX08 diesel engine powers the 36-tonne HX360L and 40-tonne HX400L and features many new technologies to make operation easier and safer and boost customer productivity.
The six-cylinder Hyundai DX08 engine is a clean-sheet design that develops up to 254kW and a powerful 1460Nm of torque. A two-stage turbocharger contributes to a 23 per cent higher power output than previous engines. The EU Stage V/Tier 4F engine is constructed of high-strength materials, with wear resistance to all major drivetrain components.
The result is improved performance and economy, with lower operating costs.
The engines boast an eight per cent fuel ef ciency gain over older designs. Oil lter and engine oil change intervals have been extended to 1000 hours of operation, reducing cost and cutting downtime. The engine meets EU Stage V emissions regulations without needing costly exhaust gas recirculation (EGR), and diesel particulate lter (DPF) cleaning intervals are extended up to 8000 hours.
The Next Generation cab delivers a new level of operator comfort and control. Premium leather seating is available, with heating and cooling functions. Two 12.8-inch high-de nition monitors are on offer, and the electro-hydraulic lever and pedal controls allow the operator to set the response and speed of each individual hydraulic function to suit their own preference.
Hyundai’s popular Advanced Around View Monitoring (AAVM) has been upgraded to Smart Around View Monitoring (SAVM). The new machines boast six cameras, including three embedded into the counterweight, in place of the previous four-camera system. With the help of AI, the system automatically detects human presence within the operating area, with images shown on the large monitors in the cab.
Wide-opening access panels provide easy service and maintenance, with engine oil
and fuel lter intervals extended from 500 to 1000 hours. Coolant changes are set at 6000 hours, and DPF ash cleaning is at 8000 hours, reducing downtime and boosting productivity. The machines have a reversible cooling fan, making removing debris from the cooling radiators on dusty jobsites easier.
CASE introduces 421G
CASE Construction Equipment is lling the gap between its compact and medium wheeled loaders with the launch of the 421G. With an operating weight of 8970kg, the machine has been designed to work with a 1.5m³ standard bucket or a 1.7m³ lightmaterial bucket.
Powered by a 3.6L Fiat Powertrain Technologies (FPT) turbocharged diesel engine, the 421G boasts a rated power of 72kW and a peak power of 84kW at 200rpm –backed by a strong 453Nm of torque.
The engine utilises FPT’s proven SCR-T after-treatment system to minimise emissions. The machine is equipped as standard with an ECO operating mode and cruise control to reduce fuel consumption and emissions.
The EU Stage V engine drives through a two-speed ‘shift-on- y’ hydrostatic transmission that seamlessly transitions between the two drive ranges. The transmission delivers a 40km/h maximum speed, with a 20km/h speed limiter as an option. It has a creep setting as standard. The heavy-duty axles have a standard limited-slip differential front and rear and an optional 100 per cent differential lock.
Though working within compact overall dimensions, the 421G has a straight tipping load with a standard bucket of 6500kg and a full-turn tipping load of 5500kg. When equipped with pallet forks, that full-turn tipping load is 4200kg. Payload with forks is a competitive 3360kg, and the lift arms have a hinge pin height on 17.5 R25 tyres of 3707mm. With a bucket, the breakout force is 7161kg. The machine has standard boom and bucket setting modes and a boom oat. AB
JULY 2025
2–3
PNG Industrial and Mining Resources Exhibition and Conference
Location: Port Moresby, Papua New Guinea
Organiser: Prime Creative Media
Tel: +61 466 602 893
30–31
IQA 2025 NSW Safety and Health Conference
Location: Hunter Valley, Australia
Organisers: Institute of Quarrying Australia
Tel: +61 2 9484 0577
SEPTEMBER 2025
23–25
Asia-Pacific’s International Mining Exhibition
Location: Adelaide, Australia
Organiser: Prime Creative Media
Tel: +61 3 9690 8766
16–19
NSSGA Legislative and Policy Forum 2025
Location: Washington, D.C. US
Organiser: National Stone, Sand and Gravel Association (NSSGA)
Tel: +1 (703) 525 8788
OCTOBER 2025
14–15
BULKEX 2025
Location: Warwickshire, UK
Organiser: Materials Handling Engineers Association
Tel: +44 1257 412635
2026
3–7
CONEXPO CON/AGG
Location: Las Vegas, US
Producer: Association of Equipment Manufacturers
Tel: +1 (866) 236 0442
JUNE 2026
23–25
Hillhead 2026
Location: Buxton, UK
Organiser: The QMJ Group
Tel: +44 (0) 115 945 4367
To fully enhance the performance of your rigid haul truck, choose EARTHMAX SR 468. Its unique tread design with special tread compounds makes it perfect for hard, rocky and tough mining conditions, while its tread lug blocks with circumferential grooves and intertwined blocks ensures effective heat dissipation.
EARTHMAX SR 468 is developed using BKT’s cutting-edge technology to carry heavy loads, deliver longer service life and provide resistance to rock cuts and punctures.
For info: europe@bkt-tires.com
No matter the task at hand, we’ve always got your back. At ROKBAK, our haulers are built to take on the toughest jobs, so you can power through any obstacle. Designed to last, we take pride in the reliability of our machines, and so do our customers. ROKBAK haulers have become the spine to thousands of businesses around the world, delivering results day in, day out.