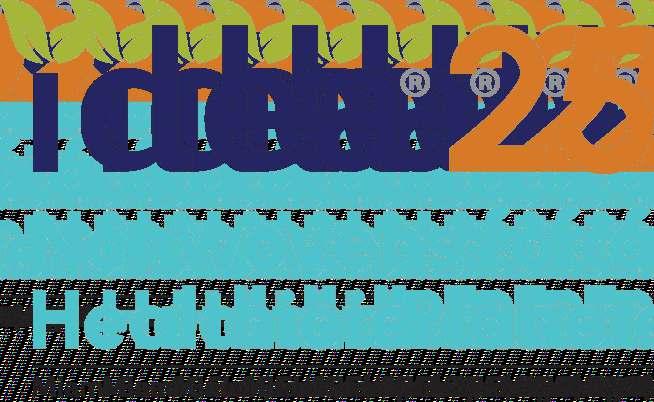
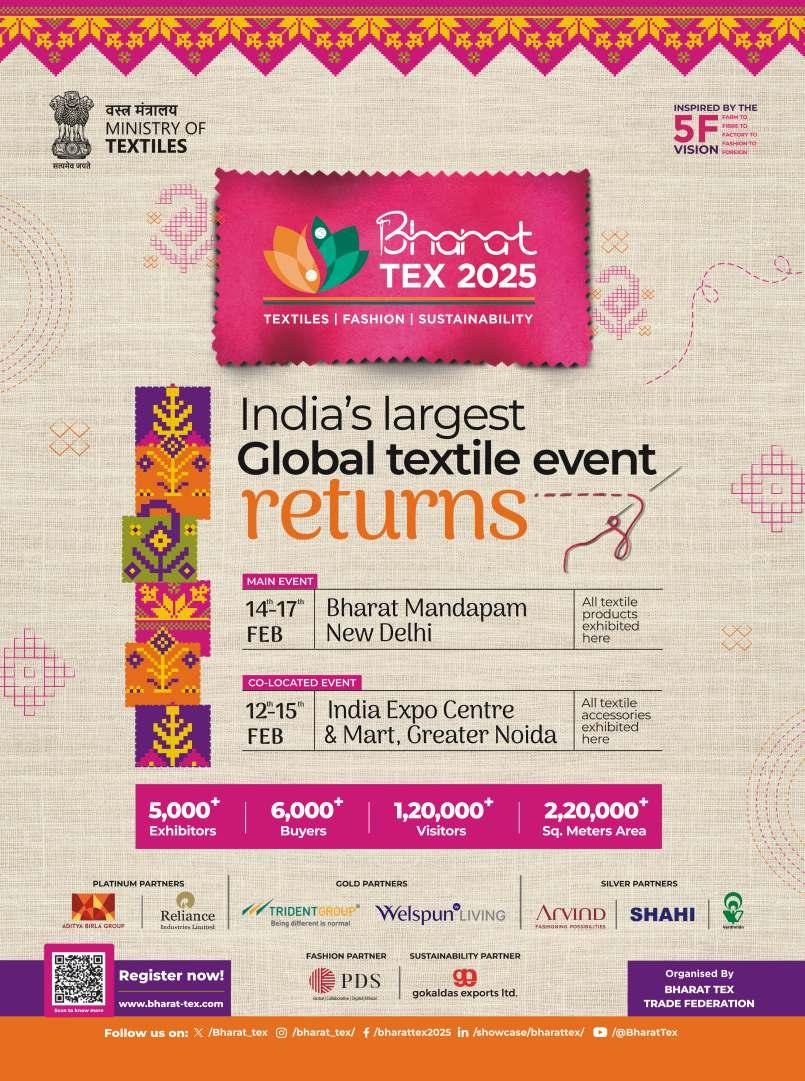
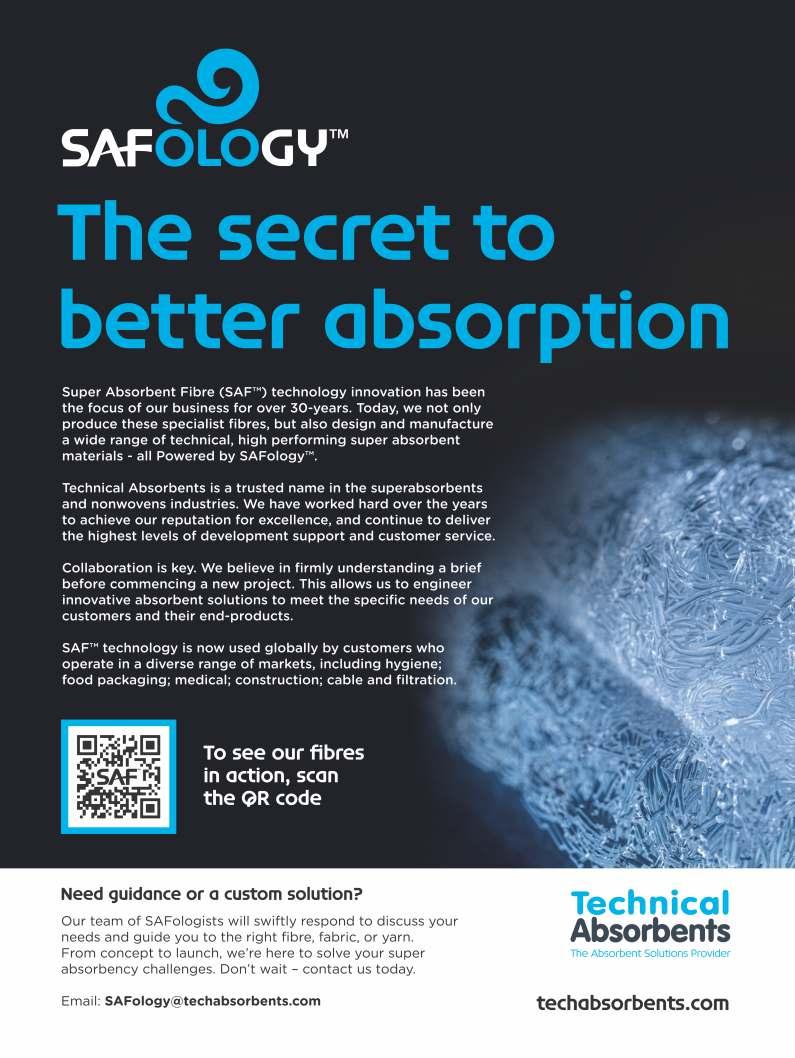

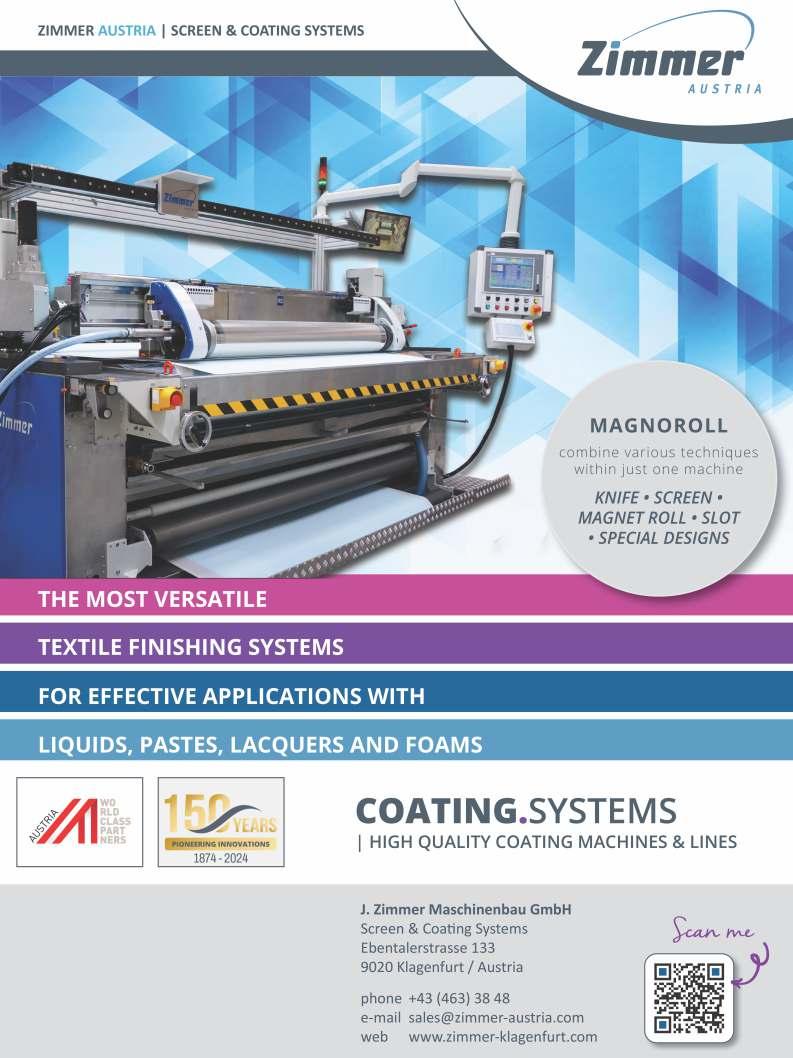



Uğurteks is pleased to offer an exclusive selection of second-hand dyeing and nishing machinery from industry-leading brands such as Benninger, Galvanin, and Monforts. These machines have been an integral part of our production process, consistently delivering outstanding results in fabric dyeing and nishing.
Benninger Machinery: Renowned for precision and reliability, perfect for efcient and highquality dyeing processes.
Galvanin Machines: Ideal for achieving vibrant colors and exceptional dye uniformity, trusted by textile manufacturers worldwide.
Monforts Equipment: Known for advanced nishing capabilities, ensuring superior fabric quality and durability.
All machines have been meticulously maintained by our expert technical team, using only original spare parts to ensure peak performance. This is a unique opportunity to acquire premium European machinery at competitive prices, ideal for scaling or enhancing your textile operations.
Detailed specications, images, and pricing information are available upon request. Don’t miss out on this chance to invest in high-performance machinery tailored to your business needs.
Details of machines will be shared upon Request
Contact Us Today
Mr. Alper Yakuppur ayakuppur@ugurteks.com.tr
Editorial
IDEA2025:PioneeringtheFutureofNonwovens withInnovation,Sustainability,andSmartFibers!
EmtecElectronicEmbarksonaBoldExpansioninNorthAmerica
RevolutionizingSleep:DevanChemicalsUnveilsGroundbreakingSleepTightTechnology
BigC:RedefiningRelaxationwithSustainabilityandInnovation
PioneeringSustainability:OerlikonBarmagandEvonik JoinForcesforaCircularPlasticsEconomy
TechtextilandTexprocess2026:PioneeringMarket OpportunitiesinaDynamicTextileLandscape
FocusonDTYsolutions
Full-Care®6550:TheGame-ChangingAdhesivefor ActiveWomen–Secure,Comfortable,andResidue-Free!
GTTES2025:IgnitingGlobalInnovation&SustainableGrowthinTextiles
editor-in-chief
Prakashkinny
contributor
ThomasChang circulation
PamelaJones administration
JoePereira accounts
RameshJain
photography
TonyFernandes
RetailPrice:Rs.100.00
InsideIndia
Annualsubscription:Rs.400.00
OutsideIndia
AnnualSubscription:US$30.00
editorial office
TECHNICALTEXTILESINNOVATION
House No. 157, Satpala, Bhandra Lee
Post:Agashi, Tal: Vasai
Dist: Palghar (401 301)
State: Maharashtra, INDIA
Mobile: +91-7798189485/09892723562
Email:info@timesinternational.in prakashkinny@yahoo.com techtexin@gmail.com
www.timesinternational.in
JAPAN
KatsuhiroIshii
MediaRepresentative ACEMEDIASERVICEINC.
12-6,4-chome,Nishiiko,Adachi-ku, Tokyo121-0824Japan
Tel:81-3-5691-3335Fax:81-3-5691-3336 amskatsu@dream.com
TAIWAN,R.O.C
Kenlychang
BUILDWELLINTERNATIONALENT.,CO.,LTD.
HeadOffice:No.120,Huludun2ndSt., FongyuanCity, TaichungCounty42086,Taiwan,R.O.C
Tel:886-4-25123015Fax:886-4-25122372
E-mailaddress:buildwel@ms23.hinet.net
India,Pakistan,Bangladesh,Srilanka,Vietnam,Indonesia,Thailand, China,HongKong,USA,Germany,Spain,Italy,U.K.&France
India's
$309
India's technicaltextileindustry is on a remarkable growth trajectory, emerging as the fifth-largest market globally. Valued at $29 billion in FY2024, the sector is set to soar to $309 billion by 2047, driven by innovation, policy support, and rising exports.
Akey contributor to this expansion is governmentbacked initiatives such as the National Technical Textiles Mission (NTTM) and the Production Linked Incentive (PLI) Scheme, both fostering R&D, infrastructure, and investment. The PM MITRA Scheme has further boosted production efficiency with seven integrated textile parks, strengtheningIndia'sglobalcompetitiveness.
Despite rapid growth, challenges persist. Low domesticpenetration(5-10%vs.30-70%globally), dependency on imported machinery, and limited awareness about advanced applications hinder progress However, advancements in nanotechnology, smart textiles, and sustainable manufacturing are positioning India as a future leaderinthisdomain.
AsexportsofIndutechandPacktechproductssurge, investment in automation and fiber innovation will be crucial. With strategic planning and sustained efforts,India'stechnicaltextilesindustryisontrack toredefineglobalstandards,fuelingitsambitionto bea$309billionpowerhouseby2047.
IDEA 2025 is set to redefine the landscape of nonwovensandengineeredfabrics,solidifyingits status as the world's premier platform for innovations in fibers, raw materials, machinery, and sustainable solutions. As the industry acceleratestowardsustainability,automation,and performance-driven materials, IDEA 2025 is expected to spotlight groundbreaking advancements that will shape the next era of nonwovens.
This report outlines the projected themes, innovations, and expectations for IDEA 2025 basedonemergingindustrytrends.
1.SustainabilityattheCoreofIDEA2025
Sustainability will take center stage at IDEA 2025, with industry leaders focusing on environmentally responsible manufacturing processesandmaterials.
1.1.Bio-BasedandRecycledFibers
Manufacturers will unveil a new generation of biodegradable nonwovens, particularly PLA (polylactic acid), bamboo, hemp, and lyocellbasedfibers.
Closed-loop recycling systems will gain
prominence, ensuring fibers like polypropylene (PP) and polyethylene (PE) remain within the productioncycle,minimizingwaste.
Water-basedandchemical-freeprocessingwillbe at the forefront, reducing environmental impact withoutcompromisingperformance.
Industry-wide efforts will focus on achieving zero-waste production, incorporating fiber recoveryandrecyclablehygieneproducts. Compostable nonwoven materials for wipes and personal care will enter the mainstream, catering to rising consumer demand for sustainable hygienesolutions.
Brandswillemphasizelife-cycleanalysis(LCA) metrics,demonstratingreal-timecarbonfootprint reductionsacrossthesupplychain.
IDEA 2025 will serve as the launchpad for the next generation of nonwoven fibers, offering unparalleled strength, durability, and multifunctionality.
Nanofiber-infused nonwovens will dominate, providing ultra-thin yet high-strength materials formedicalandfiltrationapplications.
Smart fibers with embedded sensors will enable real-time tracking of temperature, pressure, and even microbial contamination, revolutionizing healthcareandindustrialapplications.
Self-healing and adaptive fibers will emerge, leveraging nanotechnology to repair minor tears andenhancelongevity.
2.2.
Next-generation absorbent cores will redefine hygiene and medical textiles, with ultra-thin yet high-absorbencylayers.
Superhydrophobic and antimicrobial fibers will provide added protection for medical PPE, filtration,andindustrialworkwear
Fire-resistantandthermallyinsulatednonwovens will see increased applications in automotive, aerospace,anddefense.
3. Machinery & Automation: The Digital RevolutioninNonwovens
IDEA 2025 will highlight advancements in Industry 4.0, driving efficiency, precision, and sustainabilityinnonwovenmanufacturing.
3.1.AI-PoweredManufacturing
AI-driven quality control systems will ensure near-zerodefects,reducingmaterialwaste.
Digitaltwintechnologywillallowmanufacturers to simulate production runs before real-world application,optimizingefficiency.
Automated material handling and robotic assembly lines will become standard in highvolumenonwovenproductionfacilities.
3.2.
Waterless dyeing and chemical-free finishing techniques will become mainstream, reducing pollutionandresourceconsumption. Low-energy spunlace and meltblown processes will offer enhanced fiber bonding without excessiveheatapplication.
Solar-powered and carbon-neutral production plants will gain prominence, aligning with corporatesustainabilitycommitments.
Withglobaldemandfornonwovensatanall-time high, IDEA 2025 will witness a surge in participation from industry leaders, startups, and researchinstitutions.
Asia-Pacificwilldominatethegrowthtrajectory, particularly in medical textiles, filtration, and industrialapplications.
North America and Europe will focus on highperformance and sustainability-driven nonwovens, leveraging innovation and policydrivenincentives.
Emerging markets in Africa and Latin America will present new opportunities for nonwovenbasedinfrastructureandhygienesolutions.
Cross-industry collaborations between chemical
companies, machinery manufacturers, and nonwovenproducerswillfuelR&Dinvestments.
The rise of hybrid nonwoven composites, combiningnaturalandsyntheticfibers,willdrive superiorproductperformance.
Global alliances will push for unified regulatory standards, ensuring consistent quality and sustainabilitybenchmarksacrossmarkets.
IDEA2025 will mark a new era for nonwovens, fibers, and engineered fabrics, bringing together cutting-edge innovation, sustainability, and digitaltransformation.FromsmartfibersandAIpowered manufacturing to circular economy solutions, the event will define the future of nonwovens.
With industry giants, startups, and policymakers coming together, IDEA2025 will be a milestone event,shapingtheglobalroadmapfornonwoven textilesandsustainablefibersolutions.
Emtec Electronic GmbH, a German leader in innovative testing solutions, is making a significant leap forward in its North American business strategy, encompassing the USA and Canada. Starting January 1, 2025, the company will engage directly with manufacturers and converters in the paper, nonwoven, and textile industries, as well as their suppliers, ensuring a more flexible and responsive presence in the region.
Foryears,emtecElectronicoperatedindirectlyin North America Now, with direct sales, the company aims to strengthen customer relationships and deliver faster, more tailored support.ThisnewchapteralsowelcomesMr.Eric Haagen as the dedicated sales representative for NorthAmerica, offering a direct point of contact forinquiriesandcollaborationopportunities.
Emtec Electronic expresses deep gratitude to its former sales and service partner, Industrial
Physics Inc. (formerlyTechnidyne Corporation), for their longstanding partnership, which concludedattheendof2024.
Founded in Leipzig, Germany, in 1995, emtec Electronic has been a trusted global provider of cutting-edge testing solutions, particularly in the pulp and paper industry. Since 2015, it has successfully expanded its expertise to the nonwoven and textile sectors. Renowned for its commitmenttoquality,intuitiveinnovations,and exceptional customer service, emtec remains steadfastinitsmissiontoempowerindustrieswith state-of-the-arttestingsolutions.
Thisboldstepreinforcesemtec'svisiontoconnect more deeply with North American businesses, fostering growth, innovation, and excellence acrosstheindustriesitserves.
Devan Chemicals, a global pioneer in sustainable textile innovations, has introduced an extraordinary advancement in sleep-enhancing technology at Heimtextil 2025. Their "Devan SleepTight"technologypromisesatransformative impact on sleep quality, combining sustainability withinnovativescience.
TheInnovation:
Inspiredbythe"BeautySleep"trend,thiscuttingedge technology utilizes an active ingredient derivedfromupcycledAustralianTeaTreeoil.The dual-action mechanism works via inhalation and skin contact to boost melatonin, enhance antioxidant activity, and promote skin regeneration. The result? Healthier, rejuvenated skinandanoverallrevitalizedlookeachmorning.
TechnologyinAction:
The product utilizes +97% biobased microcapsules that release active ingredients throughfriction.Thecapsulesbreakuponcontact, releasing volatile components that are inhaled, whileotherelementsareabsorbedbytheskin.This eco-friendly approach aligns perfectly with Devan's commitment to sustainable and biodegradable solutions, certified under OECD guidelines.
ClinicalValidation:
Arigorous clinical trial with 33 participants aged 18-60validatedtheefficacyofDevanSleepTight. Over 30 days, participants reported notable
improvements in sleep quality, reduced disturbances,enhanceddaytimefunctionality,and overall well-being.These findings underscore the product'spotentialtoredefinesleepexperiences.
CollaborationsandMarketLaunch:
The product debuted at Heimtextil 2025 in Frankfurt,showcasingpartnershipswithesteemed beddingandsleepwearmanufacturerslikeCrispim Abreu, Lameirinho, and Naturtex. These collaborations ensure the technology reaches markets by Q2 2025, offering manufacturers and consumersarevolutionarysleepexperience.
IndustryImpact:
“Devan Sleep Tight sets a new standard in sleeppromotingtextiles,”saysMarleenVanderAuwera, BU Leader of Devan's Health & Wellness Division The technology underscores Devan's dedication to innovation, sustainability, and wellbeing.
Conclusion:
DevanChemicals'SleepTighttechnologyismore thanaproduct;itisasolutionredefiningself-care andholisticwellness.Withitsinnovativefeatures and robust market entry, it exemplifies the potential of sustainable science in improving everydaylives.
ContactInformation:
For further details, visit http://www.devan.net/ or emailinfo@devan-be.com.
Chemnitz,theEuropeanCapitalofCulture2025, issettingnewbenchmarksforsustainabledesign and innovation with its eye-catching “Big C” street furniture. Developed as part of the city's vibrant cultural program, which includes over 1,000eventsand150projectsunderthetheme“C the Unseen,” the “Big C” stands as a symbol of creativityandenvironmentalresponsibility
This unique C-shaped seating prototype was conceived by the “Lightweight Construction in Civil Engineering” research team at Chemnitz UniversityofTechnology.Followingitsdebut,20 units will be installed across the city, offering citizensandvisitorsasustainablespacetounwind amidstthefestivities.
The “Big C” uses innovative materials and processes that marry aesthetics with ecoconsciousness.Itsconcretestructureisreinforced with carbon warp knitted fabric featuring weft insertion, enabling a lightweight, robust, and environmentallyfriendlydesign.Producedusing KARL MAYER's advanced RS MSUS-G/HG warp knitting machine and its successor, the WEFTTRONIC® II G, the textile reinforcement reducesconcreteusagebyupto80%
of KARL MAYER proudly states, “The Big C demonstrates the versatility of our warp knitting technology and reflects our commitment to sustainableinnovation.”
ASmallerCarbonFootprint
Unlike traditional reinforcements, textile structures resist corrosion, eliminating the need for a thick concrete cover. Additionally, CO2reducedcement,recyclablecorrugatedcardboard
formwork,and3Dconcreteprintingcontributeto the project's minimal environmental impact. Ergonomically designed wooden slats enhance seating comfort, ensuring a functional yet ecofriendlysolution..
KARLMAYER'sWEFTTRONIC®IIGisatthe
heart of this innovation, delivering high-quality textile reinforcements at speeds of up to 1,600 min ¹ . Its flexibility, low maintenance, and efficiency make it ideal for producing technical fabricstailoredtotheBigC'srequirements.
The “Big C” is more than street furniture – it's a statementofsustainableurbandesign,combining cutting-edge technology with environmental responsibility to leave a lasting impression in
JochenAdler,CTO,andGeorgStausberg,CEO,bothOerlikonManmadeFibersSolutions,Dr MaxPreisenberger,HeadofCatalystsatEvonik,LukasAdamek,HeadofStrategy&Business Development Oerlikon Manmade Fibers Solutions, and Dr Gerd Löhden, SVPR&D Smart MaterialsEvonikattheofficialfoundingofthenewpartnershipbetweenOerlikonBarmagand Evonik
OerlikonBarmagandEvonikhaveembarkedona strategic partnership to revolutionize the circular economy in the plastics industry by advancing chemicalrecyclingofPolyethyleneTerephthalate
(PET) waste. This collaboration aims to deliver cutting-edge technologies for efficient depolymerization and purification, integrated with robust repolymerization processes and tailoredEPCbusinessmodels.
Oerlikon Barmag, a global leader in polymer processing machinery for chemical fibers and packaging materials, brings its deep-rooted expertiseandextensivemarketaccessthroughthe Oerlikon Manmade Fibers Solutions network. Evonik, a pioneer in specialty chemicals, leverages its innovative catalytic processes and commitmenttosustainabilitytocomplementthis partnership.
Together,theseindustryleadersaimtotransform how PET waste is managed, addressing contamination challenges and providing highquality recycled PET for diverse applications. Thispartnershipsignifiesapivotalstepforwardin reducing reliance on virgin plastics and minimizingenvironmentalimpact.
With plans to commercialize their chemical recycling technology by the end of the decade, Oerlikon Barmag and Evonik are fostering collaboration across the ecosystem, inviting participation from feedstock suppliers, technologyinnovators,andglobalpartners.Their goal is to create a scalable, sustainable, and integrated solution that seamlessly fits into existingPETproductionprocesses.
Thejointlydevelopedrecyclingtechnologyoffers numerous benefits, including efficiency, costeffectiveness, and scalability By addressing mixed and heavily contaminated PET waste often destined for landfills or
incineration the technology will enable a significantreductioninplasticwasteandsupport asustainablecirculareconomy.
“This partnership with Evonik allows us to drive innovationinPETrecyclingandestablishastrong market position as a total solution provider,” stated Georg Stausberg, CEO of Oerlikon ManmadeFibersSolutions.“Together,weaimto advance the next generation of sustainability withintheplasticsindustry.”
Evonik's Head of Catalysts, Max Preisenberger, added, “Our innovative chemical technologies and catalytic processes will complement mechanical recycling, enabling high-quality recyclate from challenging PET waste streams. Thispartnershipisakeystepinachievingatruly circulareconomy.”
ThecollaborationseekstoenablePETproducers and processors worldwide to adopt sustainable practices, reducing environmental impact while achieving high fossil-like recyclate quality. By scaling their technology, Oerlikon Barmag and Evonikareempoweringtheindustrytoembracea sustainablefuture.
With this partnership, Oerlikon Barmag and Evonik are charting a transformative course for the plastics industry, creating a foundation for a circular economy that tackles global challenges andensuresamoresustainabletomorrow
As the textile and apparel industries navigate a rapidly evolving global market, Techtextil and Texprocess 2026 stand as the premier platforms drivinginnovation,collaboration,andgrowth.Set totakeplacefromApril21-24,2026,inFrankfurt amMain,theseleadingtradefairsareunveilinga restructured hall layout, new product areas, and expanded content formats, providing exhibitors and attendees with unprecedented opportunities to forge international business relationships, access expert knowledge, and engage with the nextgenerationofindustryprofessionals.
The textile and apparel sectors face mounting challenges, from fluctuating energy costs and shifting consumer behaviors to economic
uncertainties and investment hesitancy. In response, Techtextil and Texprocess 2026 are strategically positioning themselves as catalysts for change. By offering cutting-edge solutions, facilitating global partnerships, and highlighting emerging technologies, these fairs are equipping businesseswiththetoolstheyneedtothriveinan increasinglycompetitivelandscape.
'New technologies and innovative materials hold immensepotentialforthefuture.AtTechtextiland Texprocess, we are committed to helping companies realize this potential, fostering new business partnerships, and expanding market access on an international scale,' says Olaf Schmidt, Vice President Textiles & Textile TechnologiesatMesseFrankfurt.
The 2026 edition of Techtextil and Texprocess introduces a refined hall configuration designed to maximize synergies and improve visitor experience.Keyadjustmentsinclude:
· Texprocess in Hall 8.0 – Now situated near 'Textile Production Technologies' in Hall 12.0 and 'Performance Apparel Textiles' in Hall 9.0, ensuring seamless connectivity between manufacturingandapplication.
· Performance Apparel Textiles in Hall 9.0 – Highlighting functional and highperformance fabrics used in aerospace, firefighting,andsportswear
· NaturePerformanceZoneinHall9.1–Focusing on the rising demand for sustainable naturalfiber-basedmaterials.
· NewTextileChemicals&DyesSegment – Positioned alongside 'Fibres & Yarns' and 'Performance Apparel Textiles' to enhance collaborationandinnovationintextilechemistry.
Texprocess 2026 sets new benchmarks in digitalization, automation, and artificial intelligence(AI)fortextileandflexiblematerials processing.Attendeeswillgainfirsthandinsights into advanced sewing technology, CAD/CAM solutions,andrevolutionaryfinishingtechniques, as digital and automated processes redefine the futureoftextilemanufacturing.
'In a rapidly changing market, Texprocess provides companies with a crucial platform to showcase pioneering technologies and position themselves internationally,' emphasizes Elgar Straub, Managing Director of VDMA Textile Care,Fabrics,andLeatherTechnologies.
Recognizing the importance of fresh ideas and
emerging talent, Techtextil and Texprocess 2026 placeastrongemphasisonengagingstartupsand young professionals. Dedicated platforms will spotlightbreakthroughinnovations,enablingnew players to connect with established industry leaders,fosteringdynamiccollaborationsthatwill shapethefutureoftextilesandapparel.
Sustainability remains a driving force behind industry advancements, and Techtextil 2026 continues to spearhead progress in eco-friendly solutions. With the integration of the EU Green Deal and the rise of conscious consumerism, sustainable materials, textile recycling, and environmentally responsible manufacturing processeswillbeattheforefrontofdiscussions.
Astandoutfeature,the'PerformanceApparelson Stage' showcase, will provide an immersive experience where visitors can explore end-use applications of functional textiles in safety gear, activewear,andhigh-performanceapparel.
With 72% of Techtextil visitors also engaging with Texprocess in 2024, the synergy between thesetwofairshasproveninstrumentalindriving industry-wide innovation and collaboration. In 2026, this interconnected approach will further strengthen business networks, enhance crosssector integration, and open new pathways for growth in textiles, technical fabrics, and apparel technologies.
As the textile industry braces for transformative changes,TechtextilandTexprocess2026emerge astheultimatedestinationsforbusinessesseeking to embrace innovation, sustainability, and international market expansion Early-bird exhibitor registration is open until March 12, 2025—secure your place now and be part of the futureoftextilesandapparel!
Morethan300participantslistenedattentivelythroughoutthedayandwereimpressed bythetechnologysolutionspresentedbytheOerlikonexperts.
Oerlikon Manmade Fibers Solutions recently hosted its highly anticipated Innovation and Technology Day at the Deltin Hotel in Daman by end of January 2025. The event attracted over 300 participants, including industry experts, partners, and stakeholders, who gathered to explore the latest advancements and trends in the manmade fibers industry in India.
TheInnovationandTechnologyDaycommenced with a warm welcome and introduction by Wolfgang Ernst, Chief Sales Officer (CSO) at Oerlikon Manmade Fibers Solutions, and Debabrata Ghosh, Head of Sales at Oerlikon Textile India. They provided an overview of the Indian market and its challenges. “The Indian textile industry, particularly the chemical fiber sector, is experiencing significant growth and transformation. This development is driven by increasing production capacities, strategic
investments, and a shift in global consumption patterns”, said Ghosh. India's production of manmade fibers (MMF) is robust, with annual outputs of 4.8 million tons of Polyester Filament Yarn (PFY), 1.7 million tons of Polyester Staple Fiber (PSF), 0.7 million tons of viscose, 0.2 million tons of Polyamide 6 (PA 6), and 25 thousandtonsofacrylic.Additionally,thecountry boasts substantial capacities for PET bottles and films,growingatratesof7%and15%perannum, respectively. The Indian market is witnessing significant expansions in PTA (Purified TerephthalicAcid) capacity, with major projects underway by Indian Oil Corporation, GAIL, MCPI, Reliance Industries, and the AdaniIndoramajointventure.Theseexpansionsareset to increase the PTA capacity from the current 6.296milliontonstoover14milliontonsby2030.
Market Dynamics and strategic investments “The global consumption landscape is shifting
ExpertsfromOerlikonBarmag,OerlikonNeumagandOerlikonNonwoven,aswellasfrom BBEngineering,Luwa,IGH/IGAandThemapresentedthelatesttechnologydevelopmentsin thefieldofmanmadefibersproductiontoover300participants.
towardsIndiaandemergingAsia,drivenbyrising incomes and changing demographics. By 2050, India and emergingAsia are expected to account for 30% of global consumption at purchasingpower parity (PPP), up from 12% in 1997. This shiftunderscoresthegrowingimportanceofthese regionsintheglobaleconomiclandscape”,Ghosh continuous. Significant investments are being made to enhance production capacities and integrate advanced technologies.Indian Oil Corporation, in a joint venture with MCPI, is establishing a 900 TPD continuous polymerization unit in Odisha, supported by substantial government subsidies. Similarly, the
Adani Group, in partnership with Indorama, is enteringthepetrochemicalsectorwitha$3billion PTAplantinMaharashtra.
Despite the positive outlook, the industry faces challenges such as ensuring cost efficiency, scalability, and the seamless integration of new technologies into existing production processes. However,thesectorisoptimisticaboutimproving profitability, driven by favorable supply-demand dynamics and strategicinvestments.“TheIndian textile and chemical fiber industry is poised for significant growth, supported by strategic investments,capacityexpansions,andafavorable global consumption shift. These developments
positionIndiaasakeyplayerintheglobaltextile market, driving towards a sustainable and prosperousfuture”,saidErnst.
After the introduction about the current market situation, the event continued with numerous technicalpresentationsinwhichOerlikonandits partners presented their technological and solution expertise along the textile value productionchain“FromMelttoYarn,Fibersand Nonwovens”.
“To spin an excellent yarn, you need the prefect melt”,saidModeratorAndréWissenberg,Headof Marketing, Corporate Communications, and Public Affairs at Oerlikon Manmade Fibers Solutions. How this can be produced using extrusion or continuous polycondensation technology was demonstrated by the keynote speakersSvenStreiber,RegionalSalesDirectorat Oerlikon Barmag, Deepak Lokre, Head of Engineering at Oerlikon Textile India, and Matthias Schmitz, Head of Engineering RecyclingTechnologyatBBEngineering(BBE).
The second session focused on Oerlikons technology partner for manmade fiber spinning mills Presentations covered topics such as enhancing manmade fiber production with innovative air engineering, automatic handling solutions and quality inspections, as well as air texturizing solutions. Notable speakers included Praveen Kumar Singh, Managing Director of LuwaIndia,andLucaLacitignola,SalesDirector at Irico Gualchierani Handling (IGH), Simone Ducceschi, Sales & Project Manager at Thema Systems, as well as Ralf Morgenroth, Head of EngineeringTextileMachineryatBBE.
The third session delved into solutions for producing the perfect fibers and yarns, with a focusonOerlikonBarmagPOY/DTY,FDY,IDY technologies as well as Oerlikon Neumag BCF and staple fiber line plants. Presentations were delivered by Philip Jungbecker, Head of R&D, andGuidoDresen,RegionalSalesDirector,both at Oerlikon Barmag, as well Chetan Bhagat, General Manager Sales, and Sameer Mehrotra,
General Manager Service at Oerlikon Textile India. Ralf Morgenroth added further insights of the compact spinning solution VarioFil from BBE.
The fourth session highlighted environmentally friendly recycling solutions, featuring insights from Sven Streiber and Sudipto Mandal, Sales andMarketingManageratOerlikonTextileIndia, andagainMatthiasSchmitz,BBE.Theyprovided a detailed portfolio overview in the field of mechanical and chemical recycling. The new partnership between Oerlikon Barmag and Evonik was also presented to the audience. Finally, this was followed by a session on customer services and digital solutions, where Michael Ruebenhagen, Head of Global Service Sales and Ivan Gallo, Digital Solutions, both at Oerlikon Manmade Fibers Solutions discussed current upgrade and retrofit options, the Digital Academy, and the future of digitalization in manmadefiberspinningmills.SharedKulkarnie, GeneralManagerServiceSales&Workshops,as well as Chandru Gurbaxani, Digital Solutions, performedtogetherwiththeirGermancolleagues.
The event concluded with closing remarks again from Wolfgang Ernst, who provided a global market overview and outlook for 2025. Final remarks were given by Atul Vaidya, Managing Director of Oerlikon Textile India. Finaly the event ended with a gala evening with more than 500participantsfeaturingafashionshow,music, dancing, and excellent food, supported by DecathlonandGardenVareli.
The Oerlikon Manmade Fibers Solutions
Innovation and Technology Day 2025 was a resounding success, fostering collaboration and knowledge sharing among industry leaders and setting the stage for future advancements in the manmade fibers sector Participants had the opportunitytonetworkduringtheevent,engaging with experts from Oerlikon, Luwa, IGA/IGH, Thema,andBBEatvariousmarketplaces.
EgyStitch&TexExpo2025:OerlikonManmadeFibersSolutions setsthetoneintheEgyptianmarket
TheeAFKBigVmulti-spindletexturingmachineispartofOerlikonBarmag'sefficient solutionformanufacturinghigh-quality,high-tenacityyarns.
WithaclearfocusontheneedsoftheEgyptian market, Oerlikon Manmade Fibers Solutions willbepresentingitselfattheEgyStitch&Tex Expo 2025 in Cairo from February 20 to 23, 2025. At the booth of Oerlikon agent ATAG Ltd.TradingExport&ImportinHall1,Booth 1A12, experts from Oerlikon Barmag and fromBBEngineering(BBE)willbeexplaining the comprehensive product and service portfolio.
ThecomprehensiveDTYsolutionsfromOerlikon Manmade Fibers Solutions are the focus of the tradeshowappearance:
DTY yarns – uncompromising quality and maximumflexibility
Clothing, home textiles, automotive – there are countlessapplicationsfortexturedyarns.Forthe efficient and sustainable production of high-
qualitytexturedyarnsmadeofdifferentpolymers, from polyester and polyamide to polypropylene, PLAandPTT,OerlikonBarmagprovidesawide range of different DTY machine configurations. With sophisticated components, expertise and proventechnology,themodularDTYmachines–whether manual or automatic – produce textured yarnsforexcellentdownstreamprocessing,while keepingOPEXcoststoaminimum.
Increasing demand for fancy yarns "But the demand for textiles with special properties, irregularities and a special look and feel is also becoming more and more important," explains JilaliLakraa,RegionalSalesDirectoratOerlikon Barmag."Forsuchfabrics,so-calledfancyyarns are required that deviate from the standard, e.g. cotton-like DTY, linen-like DTY or wool-like DTY Effect yarns include a very wide range of yarntypesthataremanufacturedusingavarietyof
TheJeTexairtexturingmachinefromBBEngineeringensuresbothgentleyarntreatmentwithreliable texturingeffectsandefficientproduction.
methods and additional components," he continues With its high-quality and flexible technology, detailed knowledge of the yarn path and the necessary parameter settings, Oerlikon Barmagistheidealpartnerforthesuccessfuland flexible production and continuous development ofthesespecialtyyarns.
Extended product range for the manufacture ofcarpetyarns
The knowledge of all relevant technologies in manmadefiberspinningallowsOerlikonBarmag, astheonlymanufacturerworldwide,toextendits range of services for the production of carpet yarns. The system concept based on a POY and texturizing process is designed for a carpet and home textile product area that requires particularlysoftandbulkypolyesterthreadswith BCF-like properties. The aim here is to produce yarnswithatiterofupto1300dtexandtypically over1000filaments.Typicalproductsinclude,for example, 1300dtex f1152 or 660dtex f1152 and 990dtex f768. The machine concept consists of the familiar WINGS HD POY winder and the eAFKBig-Vtexturingmachine.
VarioFil® – flexible compact spinning system forcountlessapplicationsandspecialties Whethercarpetsorupholsteryfabrics,fashionor sportswear,orseatbeltsorairbags–awiderange of products is no challenge for the VarioFil® systemfromBBE.Thiscompactturnkeyspinning system is also ideal for producers who manufacture small batch sizes or specialized products.Itissimilarlyflexiblewhenprocessing variouspolymers,regardlessofwhetheritisPET, PP,PA6andPA6.6orPBT.
Customized conversion packages enable quick adaptation of the system to constantly changing market demands. In combination with Oerlikon Barmag texturing machines, a wide range of end products can be covered. This ranges from standard textile yarns to textured yarns with propertiessimilartoBCF.
Furthermore,withtheVarioFil®R+itispossible to recycle and process PET bottle granulate and PET waste, which is produced during start-up, directlybackintoPOY Thesustainablemachine concept allows for high product flexibility,
includingthemanufacturingofspun-dyedyarn.
JeTex® air texturing enables a broad and flexibleproductportfolio
And for BB Engineering, it does not stop with yarn spinning: the Oerlikon Barmag subsidiary also offers a solution for texturing – with a flexibility similar to VarioFil®. The JeTex air texturing system perfectly complements the OerlikonBarmagDTYsystem,thusenablingthe customer to expand its product portfolio to includehigh-qualityATYbasedonPOYandFDY for a wide range of textile and industrial applications.Thecoreelementofthesystemisthe texturing box developed by BB Engineering, which, in addition to many other state-of-the-art componentsfromOerlikonBarmag,ensuresboth gentle yarn treatment with reliable texturing effects and production efficiency in terms of OPEX,handlingandspeed.
Particularlysmart:JeTex®isnotonlyavailableas a closed system, but also as a conversion variant forexistingOerlikonBarmagDTYsystems.This allows customers to expand or convert their product portfolio to ATY in a cost-saving and comparativelyshorttime.
VersatilePETrecyclingsolutionswithVacuFil andVisco+
"Fromwastetovalue"–that'swhatBBE'sVacuFil PET recycling system does It is specially designed for high-quality processing of textile waste. The technology is unique and based on decadesofexperienceinextrusion,filtrationand spinning: it combines gentle large-area filtration with targeted IV regulation for consistently excellentrPETmeltquality,comparabletovirgin material.Awide range of input materials can be processed: in addition to the usual bottle flakes, VacuFil is particularly suitable for production wastefromspinningmills,fromstart-uplumpsto yarn and fabrics, and can also handle postconsumer waste. The patented key component
Visco+, a liquid-state polycondensation, quickly and reliably removes volatile impurities and automatically regulates the IV There are also various options for further processing the recycledmelt.Themeltcanbeaddedtothemain melt flow, processed into chips via a pelletizing processorfeddirectlybackintothespinningmill. TheVacuFilrecyclingsystemcanthusbeflexibly and modularly customized to the customer's requirements.
With Oerlikon Barmag's Lifecycle Management, chemical fiber producers can maintain and improvethefutureviabilityoftheirmachinesand systems. Pragmatic solutions for increasing and safeguarding productivity, including opening up new markets, enable profitable business over the entire service life of the machines.As a partner, OerlikonBarmagoffersleadingtechnologiesand services for long-term competitiveness – from upgrades and modernizations to preventive maintenance and repairs with original parts. The originalpartpackagesareexplicitlydesignedfor thedemandinguseofthesystemsforwhichthey areintended.Duetotheirhigh-qualitystandards, they have a significantly longer service life than other spare parts This avoids unplanned production downtimes and saves money in the end.
Upgrade solutions are based on the existing machineplatforms,regardlessofwhethertheyare
Ÿ technology upgrades to expand the product rangeandincreasecompetitiveness,
Ÿ process upgrades to improve throughput and yarnproperties,
Ÿ component upgrades to improve life expectancy,easeofuseandcostsavings,or
Ÿ softwareupgrades.
®Full-Care 6550:
H.B.FullerUnveilsaRevolutionforActiveWomen: Full-Care®6550SecureFixPositioningAdhesive Empowering Movement with Confidence
H.B. Fuller (NYSE: FUL) is excited to announce the launch of Full-Care® 6550 SecureFix, a revolutionarypositioningadhesivedesignedforthe dynamic needs of active women. This innovative product promises to redefine the standards of comfort and reliability in feminine hygiene products.
AboutFull-Care®6550SecureFix:
Womenhavelongfacedchallengeswithpantyliners, from dealing with daily discharge and odor to protecting their underwear during workouts or unexpectedperiodevents.Thetraditionaladhesives used in pantyliners often fail to secure fixation duringphysicalactivities,leadingtodiscomfortand a lack of protection when it's most needed Recognizing these challenges, H B Fuller has developed Full-Care® 6550 SecureFix to address andovercometheseobstacles,ensuringthatwomen can remain active and confident without compromise.
In today's fast-paced world, active women demand solutionsthatcankeepupwiththeirlifestyle.They seek products that offer secure fixation, without compromising on comfort or performance Recognizing this need, H.B. Fuller has developed Full-Care®6550SecureFix,deliveringunparalleled performanceinsecuringpantyliners.
KeyBenefitsforActiveUsers:
Reliable Adhesion: Sticks to cotton or microfiber evenwithminimalmountingpressure,ensuringthe linerremainssecurethroughouttheday
EnhancedPerformance:Growsinadhesionstrength to cotton or microfiber as the textile becomes wet, providingpeaceofmindduringworkoutsorhumid days.
Residue-Free Removal: Easily removes from textiles without leaving any residue, preserving the qualityandcomfortoftheuser'sfavoriteunderwear.
Consumer Study: Performance of Full-Care®
At H.B. Fuller, we understand that real-world performance is crucial for evaluating product success.TovalidatetheeffectivenessofFull-Care® 6550SecureFixcomparedtoindustrystandards,we conducted an initial consumer study with 24 active women This study assessed the adhesive's performance under high-moisture conditions, such asduringworkouts.
KeyFindings:
· 71%ofparticipantsreportedthatFull-Care®6550 had better adhesion during active use compared to theindustrystandard.
· 100% of participants confirmed that Full-Care® 6550 did not leave any adhesive residue on undergarmentsafterremoval.
· 67%ofpeoplewouldbuyalinerwithFull-Care® 6550positioningadhesiveagain.
These results demonstrate that Full-Care® 6550 SecureFix provides superior adhesion in highmoisture environments, ensuring that products stay inplaceduringexercise,withoutleavingbehindany residue - a common challenge with standard adhesives.
Full-Care® 6550 SecureFix is more than just an adhesive;it'sacommitmenttoempoweringwomen to lead active lifestyles without compromise. By addressing the challenges of moisture and movement, Full-Care® 6550 ensures that women can stay focused on their activities, not their femininehygieneproducts.
H.B.Fullerisproudtobringthisinnovativesolution to market, reinforcing our dedication to improving productsandlivesthroughadhesivetechnology We believe Full-Care® 6550 SecureFix will set a new benchmark in the feminine hygiene industry, offering both manufacturers and consumers a productthattrulystickstoitspromises.
The Indian International Textile Machinery ExhibitionsSociety(IndiaITMESociety)yetanother timeispoisedtotakethetextileindustrybystormwith the third edition of the Global Textile Technology & Engineering Show (GTTES 2025), a landmark event forthetextileindustryfromthe21stto23rdFebruary 2025 at the Bombay Exhibition Centre, Goregaon (East), Mumbai, India.This event by the India ITME Societypromisestobeaglobalplatformforthetextile industry and engineering sector across the world showcasingthelatestadvancements,innovations,and opportunities with the aim to redefine global textile innovation.
Talkingaboutthisevent,MrKetanSanghvi,Chairman and members of the steering committee of India International Textile Machinery Exhibitions said, “GTTES 2025 is a transformative event, aimed to be responsivetothechangingneedsoftheglobaltextile andmachineryindustry Beyondyarnandfibers,itwill cover state-of-the-art advancements in weaving, processing, finishing, garments, knitting, and technical textiles with eco-friendly practices and sustainable growth. The event will witness extensive participation with top exhibitors coming up with innovative solutions, product launches, and precious networking opportunities. It is to be a part of India's textile ecosystem, which would help the nation achieveitsvisionofbecomingagloballeaderintextile technologyandengineeringby2047.”
GTTES 2025 marks an important journey for India's Textile Industry, the third edition of GTTES is set to elevate the Indian Textile Ecosystem by bringing together175exhibitorsacrosseightmajorcategories. With special emphasis on advanced weaving, machinery, sustainable processing solutions, digital printing, and knitting technologies, are featuring 42 exhibitors in weaving and 38 in processing alone. The Indian textile market is poised on a growth trajectory toward US$ 350 billion by 2030, while textileexportsareexpectedtoreachUS$100billion. GTTES will take center stage to drive technological innovation to help achieve this vision in 2025. The eventwillbeashowstopper,asgreentechnologiesand sustainable solutions are going to be the biggest
highlights of this event, making GTTES the hub for advancedtextiletechnologies.
Leading suppliers of textile technologies from countriesincludingGermany,Switzerland,andChina shall ensure that GTTES 2025 is an outright worldlevel event. Over 27 countries such as Australia, Bangladesh, China, Germany, the US among others will also be represented during the event which is estimatedtoattractmorethan25,000professionals.As part of it, B2B meetings involving international delegationsfromSriLanka,Ghana,andEthiopiashall aim at further cementing trade collaboration with India.
Don't miss the chance to witness the groundbreaking innovations and valuable partnerships that will shape thefutureofthetextileindustry
GTTES2025isthekeyplatformforproductlaunches fromtopindustryplayersinthecountryin2025.Inthe WeavingSegment,LaxmiShuttlelessLoomsPvtLtd, Riser Import and Export PVT LTD, Sumaria Global SalesLLP,OmCorporationwilllaunchnewproduct. In Digital Print Segment ColorJet India Limited will launch new product and in processing we have CaruNatex,NationalElectricalEngineeringCompanywill announcenewproducts.Insparepartsforspinningwe haveSamruddhiEngineering,willlaunchinnovation. Ingersoll-Rand (India) Limited will also use GTTES as launch for their product and services. These Innovation and new technologies make GTTES most important exhibition to visit by the textile industry looking for the latest in the market. There also will exclusive investment promotion program by the Chhattisgarh Government to highlight the opportunities in the state. It will not only be a trade exhibition but an energizer to fuel the Indian Textile Industrytowardtheworldmarket.
Theexhibitionissettostartfrom21stto23rdFebruary 2025,atBombayExhibitionCentreinMumbai,India, whether you are a manufacturer, distributor, investor, or industry professional, GTTES 2025 is the place to be.
PicturedattheMonfortsATC(lefttoright)areArchoma'sGlobalMarketSegmentSyntheticsExpert MarkDohmanandTechnicalSegmentManagerforCoatingDirkGrafen,MonfortsTechnologistSaskia Kuhlen,RickStanford,MichaelSchuhmannandHansGerhardWroblowski.
Monforts has completed the installation of a Baldwin TexCoat™ G4 digital spray unit at its Advanced Technology Center (ATC) in Mönchengladbach, Germany
It has been successfully integrated into one of the two full-size Montex stenter lines at the ATC and is now available for full customer trials, especially for making full use of the latest advanced sustainable finishing chemistriessuppliedbyArchroma.
BW Converting's TexCoat G4 enables softeners, antimicrobials,durablewaterrepellents,flameretardants and many other water-based chemicals to be precisely applied to textile surfaces, and in combination with industry-leading Montex stenters can reduce water, chemistry and energy consumption by up to 50% comparedtotraditionalpadapplicationprocesses.
Monforts is providing vital support to dyeing and finishing manufacturers in their development projects, successfully boosting the quality and performance of many new finished products while at the same time maximisingproductivityandresourceutilisation
“OurATChousestwofullMontexstenterfinishinglines engineered to accommodate an extremely diverse range of processes, in addition to a Thermex range for the continuous dyeing of denim and other woven fabrics, a fullcolorkitchenandanumberoflab-scalesystemsfor smaller batch trials,” says Monforts Head of Sales for South-East Asia Hans Wroblowski. “It enables our
customerstotesttheirowntextilesandtechnicalfabrics under fully confidential, real production conditions and usingtheresultsfromthesetrialswearealsoabletomake recommendationsforimprovingmanyfabricfinishes.
“The new TexCoat installation will make an important contributiontowhatwecanachieveandweareexcitedto beworkingtogetherwithArchromaandBaldwintobring furthertransformativechangetothedyeingandfinishing space.”
“This partnership is already creating a buzz in the industryandwehaveseveraltextilemanufacturerslining up to take advantage of running production trials at the ATC,” adds Rick Stanford, vice-president of global business development for textiles at BW Converting.
“Together we are in a position as never before to accelerate the pace of transformative change in the dyeingandfinishingspacethatwillresultinsignificantly lower energy, chemicals and water consumption with increasedproductivityandhigherquality.”
“With the extension of our long-standing partnership with Baldwin – now including the processing expertise and knowhow of Monforts – the development of new concepts for chemical functionalisation and coloration will be taken a step further,” says Michael Schuhmann, GlobalMarketSegmentManagerforTechnicalTextiles atArchromaTextile Effects. “Additionally, we can now demonstrate potential savings and performance levels under actual industrial conditions, providing mill partnerswithclearproofofefficiencywithoutdisrupting theirproduction.”