
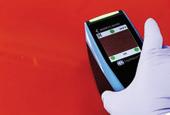
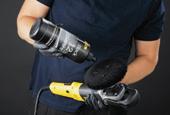
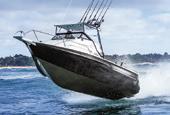
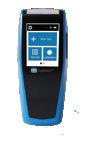
With all the hi-tech, cordless de-nibbing and polishing tools and accessories packed into a handy carry case, the MIRKA Systainer is all about simplicity, convenience and productivity. Featuring advanced Li-ion batteries, the trio of MIRKA tools deliver powerful performance to use wherever you like. Compact, fast and effective, the MIRKA Systainer is a box full of solutions that save you valuable time on everyday jobs.
PPG Australia McNaughton Road Clayton South, VIC, 3168
PPG New Zealand
5 Vestey Drive Mount Wellington, 1060 0800 320 320
Editor-In-Chief Paul Galea
Published for and on behalf of PPG Industries Pty Limited by
Kisschasey Creative Pty Ltd
Unit 113, 91 Murphy St. Richmond, Victoria, 3121 Telephone (03) 9421 3311
Australia Head Office
Locked Bag 888, Clayton South, Victoria 3169. McNaughton Road, Clayton, Victoria, Australia, 3168 Telephone: 13 24 24 www.ppgrefinish.com.au
New Zealand Head Office 5 Vestey Drive, Mt Wellington, Auckland, New Zealand. Toll Free Telephone: 0800 320 320 Victoria 104-106 Woodlands Drive, Braeside, 3195 Telephone (03) 8586 0000
New South Wales 10 Peter Brock Drive, Eastern Creek, 2766 Telephone (02) 9854 6600 Queensland 18 Breene Place, Morningside, 4170 Telephone (07) 3823 8000
South Australia 97-105 Bedford Street, Gillman, 5013 Telephone (08) 8346 6870 Tasmania 136 Invermay Rd, Invermay, 7248 Telephone 1300 305 699
Western Australia Unit 2/6 Colin Jamieson Drive, Welshpool, 6106 Telephone (08) 9256 3920
paradigm shift Two remarkable technologies change colour matching forever!
A father and son team sharing a passion for perfection
Over 25 years of operation, Perkins Engineering masterminded and built a catalogue of 49 Supercars and 198 race engines. Jack Perkins has now taken on the mammoth task of restoring and maintaining this family business legacy for future generations.
Finished in its radiant, earthy green colour, with sharp, clean graphics and matt black accented components, SATA’s latest special edition, the SATAjet X 5500 FUTURE foresees a greener, more connected world. As well as putting the focus on sustainability, the high-quality anodised finish features a globe shape, made up of interconnecting circuits, to represent the technology that is connecting people and enabling the globalised world of the future.
As a manufacturer, SATA is keen to play its part, including having a consistent focus
on resources conservation and waste avoidance. For example, SATA produces a portion of its electricity from its own photo-voltaic system and has reduced waste volume by around 20% in the last five years.
The special edition SATAjet X 5500 FUTURE is available in HVLP and RP technologies, in various nozzle sizes and in non-digital format or the hugely popular SATA DIGITAL® version. As a strictly limited edition, it’s sure to sell out quickly so contact your authorised SATA distributor to reserve yours now. R
Created by PPG’s local technical team, the new Delfleet Evolution Setup Guide is all about giving technicians a quick reference source regarding the application process. Developed using extensive testing in a wide variety of conditions, the quick and easy reference tool provides a clear set of easy-to-follow guidelines, suggestions and tips, including recommended fan, fluid and pressure settings for a variety of application situations.
The Delfleet Evolution Setup Guide is designed to be printed out and mounted in the paint area where it’s perfect for helping to maximise performance, reduce material usage and produce a consistent result every time. Available to users free of charge, getting your own Delfleet Evolution Setup Guide is as simply as
contacting your PPG Territory Manager, your PPG Training Manager or PPG’s Customer Service Hotline 13 24 24 (Aust) or 0800 320 320 (NZ). R
Paint and colour play a dynamic role in bringing dreams to life for all who visit the world’s most magical destinations at Disney Parks, Experiences and Products. Now, thanks to a multi-year parks alliance agreement, PPG has been recognised as the Official Paint of Walt Disney World® Resort and Disneyland® Resort, as well as the Official Paints, Finishes and Coatings Provider of Walt Disney World® Resort and Disneyland® Resort. Along with the pop of colour it adds to the façade of some of the
most-famed streets in Florida and California, PPG paints and coatings also provide a protective layer to surfaces where guests eat, play, stay and relax, according to Doug Wagner, Vice President, Engineering Services, at Walt Disney World® Resort. “PPG paints are known for exceptional quality and they colour some of our signature immersive experiences which delight our guests as they make unforgettable memories with friends and families while visiting us.” R
How cool is the promotional material for the upcoming Adelaide Auto Expo?
For its posters, banners and stubbie holder, event organisers have chosen two of last year’s showstopping PPG painted vehicles – and why not! Pride of place is Brenton Dalwood’s ’35 Ford Coupe, complete with a gob-smacking PPG paintjob, which collected a stack of awards at the 2021 event, including ‘Elite Best Paint’ and ‘1st Elite’. Also taking centre stage is the one-of-a-kind ‘PPG Juicy Orange’ paintwork, of Joe Esposito’s ultra-tough ’68 Chevy Camaro, that took several highprofile awards, including ‘Runner-up Elite’.
It’s not just you! When challenged by a situation, it’s easy to fall into the trap of thinking it’s just happening to you or your business or your industry. It should be obvious to us all now that the skill shortage our industry has suffered from for many years, has now risen to new heights. And guess what, it’s not just you, it’s not just in your state and not even just in your country. This is a global industry problem that continues to worsen.
This is why, for several years now, PPG has been focused on automation and the de-skilling of processes. We have invested heavily in developing technologies that will help our customers be less reliant on rare skillsets. Those skills can then be utilised where they are needed most. As these exclusive PPG technologies rollout, we are already seeing customers making the shift.
On page 14 you can read about how Repairhub New Zealand is employing non-technical people and training them to smoothly operate the PPG MOONWALK® automated dispensing machines.
The key result is more time for painters to devote to skilled tasks. I can foresee the same scenario playing out with the launch of PPG’s game-changing VISUALIZID™ and DIGIMATCH™ technologies (page 6). They work so well together and are so intuitive to use, it raises the question amongst switched on collision centre owners – do I really need the skills of an increasingly scarce paint technician to perform this task? Once they get to know and trust these technologies, I’m confident we will see another shift in mindset. R
Adelaide Auto Expo 2022 runs from Friday night 18th November to all-day Saturday 19th November. Be sure to visit the huge onsite PPG stand, have a chat about your latest project and get expert advice about the PPG products that can help it really stand out from the crowd. R
Forget physical sprayout cards –PPG’s incredible new DIGIMATCH spectro and VISUALIZID 3D visualisation software take colour matching into a whole new dimension.
Looked at individually, the exclusive new DigiMatch spectrophotometer and VisualizID 3D visualisation software are remarkable innovations in their own right. However, when you put them together, the performance of these PPG developed technologies delivers a game changing capability to the colour matching process. In fact, they are so quick, precise and intuitive to use, it actually brings into question whether traditional colour matching tasks need to be carried out by a specialised tradesperson. Arriving hot on the heels of PPG's ground-breaking MOONWALK® automated dispensing technology, these two advanced colour matching tools are the latest components of the PPG LINQ end-to-end digital ecosystem which continues to rollout clever technologies that will change collision centre operations forever.
process, a painter produces a sprayout card of their selected colour formulation and then checks it against the vehicle. To get a little extra certainty they move the vehicle outside to make a comparison in natural light. After that, they call another tradesperson over to get their opinion and it can go on and on. Although the painters are not deliberately wasting time, it can be a time-consuming, drawn-out process. This is where
camera gathering data from six imaging angles, PPG’s exclusive new DigiMatch spectrophotometer instantly sets an all-new benchmark. Despite its sophisticated technology, its compact, ergonomic design makes it very easy to use – even with one hand – and its intuitive touchscreen means it’s quick to navigate through the process of taking readings. As with any spectrophotometer, an essential part of taking any reading is to go through the best practice surface preparation process (contact your PPG Territory Manager for details)
perfect partner for VisualizID. Thanks to its ability to take readings from six angles of reflectance, along with six camera angles, DigiMatch is able to capture an extraordinary amount of data about the vehicle colour being measured. In particular, the camera angles provide crucial texture information about pigment particle size, etc – something that is simply not available with lesser spectros. That detailed information is seamlessly transferred to the VisualizID ® XI via WiFi or
• Large storage capacity of around 160 jobs
• Docking station to charge and store the device dust free
Refinish painters tend to be ‘visual people’ who are skilled at identifying subtle differences between colours in order to
sprayout cards to 3D digital sprayout cards. Where a physical sprayout card is a representation of the chosen colour formulation which is then checked against the target colour (usually the vehicle), VisualizID is exactly the same, except in an electronic 3D rendering that is depicted on a computer screen. A typical sprayout card process consumes around 25 to 30 minutes of colour matching time or more and, sometimes, a job can require more than one sprayout. Thanks to its next generation approach, VisualizID eliminates these steps and replaces them with a super-quick, on screen, 3D digital sprayout of any chosen colour from PPG’s massive colour database. Just like a regular sprayout card, this on-screen version of a colour can be easily compared to a spectro-generated depiction of the target vehicle’s colour, including the ability to look at them from different angles and with different light sources. Best of all, you can choose the correct job colour without using a single drop of tinter!
PPG has been building expertise in the digital colour matching space for many years. For example, the clever algorithms developed by the PPG colour team, have been working in the background to enable features, such as the current ‘match rating’ system. With the launch of DigiMatch and VisualizID, these proprietary mathematical algorithms have taken another giant leap forward. As a result of this impressive behind the scenes work, VisualizID is able to generate a clear image of every
Seamless compatibility with PaintManager XI and perfect partner for VisualizID
VisualizID – your 3D digital sprayout
single ENVIROBASE® High Performance waterborne basecoat colour formula available in the vast PPG database.
From the third quarter of 2022, the VisualizID 3D visualisation software will be incorporated into the PaintManager XI software system. The combination of DigiMatch and VisualizID will then be available for customers to use via a very reasonably priced subscription model. Although quite similar to a conventional colour matching process, this new-age method brings a sophisticated digital element, very much in tune with the high-tech collision centre of the future.
As with the conventional colour matching process, the DigiMatch spectro is used to take a number of readings of the target vehicle’s paintwork, before the data is downloaded to PaintManager XI. At this point, the manufacturer’s colour code for the vehicle is required in order to conduct a search. As it does currently, the search brings up the closest colour formulations (within that colour code) and gives a match rating for each one, along with how closely it compares in terms of effect coarseness. Instead of the technician choosing one or more of these formulations to sprayout
and compare against the vehicle, the VisualizID colour matching system lets you move straight onto comparing the spectro reading with any formula from PPG’s extensive colour database associated with the manufacturer’s colour code for the target vehicle.
On one side of the screen, the VisualizID 3D visualisation software will display a digital representation of the target vehicle colour, created by the PPG colour science team using a clever algorithm. Then, by simply clicking on any of the colour formulation results from the VisualizID search, a technician can put a digital sprayout right next to the target vehicle colour and make comparisons as if they were holding a conventional sprayout card against the vehicle.
To provide extra confidence when making colour formulation choices, technicians have a wide variety of options when conducting a comparison, including:
View – When comparing the two images next to each other on screen, technicians can toggle between ‘blend view’ or ‘edge view’. Blend view runs a thin line between the two images which is great for representing how the colours compare in a refinish blend situation. Alternatively, edge view removes the dividing Iine and places the two colour immediately adjacent to each other, as would happen in an edge-to-edge refinish method.
Angle – As with conventional colour matching, the VisualizID colour matching system gives the option to assess the ‘flash’, ‘flop’ and ‘face’ of the colours in order to compare the colour travel. In each case, the colour images are illuminated as if they were by a sunlight source.
Rotate and zoom – When conducting a comparison, the VisualizID 3D visualisation software’s display images can be easily rotated to any desired viewing direction.
At the same time, the direction of the light source can be moved around the images to see different effects. For a closer look, it’s simple to zoom right into the images to help pick up small details and potentially subtle differences. There is even an option, called ‘light booth’, which mimics what you would see if the vehicle is in a light booth, illuminated by specialised colour matching lights.
Rather than detract from a painter’s skillset, VisualizID 3D visualisation software actually enhances it. Extensive trials conducted across Europe, the US and locally, have shown that the VisualizID colour matching system actually provides more information in more versatile formats. This empowers painters by expanding their options, rather than reducing their colour matching skills. Although it’s a major shift in thinking, it’s simply a matter of learning to trust the technology just as we have in other areas of our life or even when spectros first arrived as a colour matching tool. At the end of the day, this is a process that fits perfectly with the next generation refinish paint shop.
Given how easy DigiMatch and VisualizID make the colour matching process, does it need to be performed by a qualified painter? With the skill shortage continuing to get worse, these two PPG technologies could help make a difference. PPG trials have already shown that a well-trained person from outside the trade is perfectly capable of following a best practice process to take an accurate DigiMatch spectro reading, before going through the various checks to choose the best colour formulation match with VisualizID. Afterwards, they could even precisely mix the formulation using MoonWalk. That way, painters are left to do what they do best – paint!
The saying goes ‘the apple doesn’t fall far from the tree’ and that certainly seems true for Andy Minas and his son, James. In his early teens, Andy was bitten hard by the hot rod and custom car bug and now James has followed suit with a passion for older cars rivalling his father. After completing Year 12, Andy began studying electrical engineering but it only lasted 12 months before his car-crush took over. He took up an apprenticeship at a Darlinghurst, Sydney, shop that carried out lots of restoration work, while also doing a sideline in building hot rods for mates and doing touch up jobs in a home workshop.
As things got busier, he leased a number of workshops, each one bigger than the last, before custom building the current home of Andy’s Restorations to suit the workload. Located in the Sydney suburb of Kurnell, it’s where James also fell in love with cars, even building his own ’32 Roadster in his spare time. When James decided to join the business in 2009,
For over 40 years, Andy Minas has set a gold standard for custom and restoration work – now his son, James, is adding his passion and drive to the thriving business.there were no half measures – after first completing a panel beating apprenticeship, he returned to do spray painting and then
each of them and is more than capable of dealing with customers.”
Despite a shared passion for what they do, Andy is quick to point out it’s still a business which has to hit all the regular productivity markers to ensure it’s profitable.
“Just like a big collision shop, we have a schedule of work that has to be done in order to meet our targets. It’s not just about making a reasonable profit for the work we do, it’s also about paying for the latest equipment that helps us be efficient.
We have a good fabrication area, two hoists and two spray booths – thanks to Low Bake, one of them has an airbag floor so there is no need for an external ramp.”
Throughout his decades in the industry, Andy says he has learnt to embrace a steady stream of new techniques and technologies in order to work smarter.
“Some changes are simple. For example, in the ’70s we only had small tools to block
Now we have blocking tools that are two or three-foot-long so you can get the car laser straight.
Computers have made a big difference, too. Using the right program, we can design a job on screen and then show the customer a rendering of the finished job, including the colour, to make sure they are happy with it before we start. I have also learnt to work more efficiently by first standing back to think about the best way to go about the job. Rather than rush in, it’s better to engineer the job by looking and coming up with a plan of attack from start to finish.”
“Another big change is the technology and materials for going from bare metal through to clearcoat. We have been with PPG since 1974 so I have used
all the different technologies from Duco and Dulon onwards. Nowadays, we use the latest PPG technology – ENVIROBASE® High Performance waterborne basecoat –along with VIBRANCE COLLECTION® primers and clearcoat which are perfectly suited to the type of work we do. As well as supporting us with technical information, the PPG team also provides us with recommended settings for our SATA spray guns so we get absolutely consistent results.”
For many years, Andy’s Restos supplemented its regular work with collision work on modern prestige cars and the odd classic car. However, after the COVID pandemic, it was decided to restructure, says James.
“Unless you have the latest technology and the team is setup to do late model cars, it’s often not worth it financially so we have stopped doing collision work. At one time, we had a nine-person team but now we have trimmed it down to four, including Dad and I.”
Not willing to rest on his laurels, Andy has continued to invest in the business, including some recent innovations to make Andy’s Restos even more of a focal point for enthusiasts.
“A few years back, we visited a huge one-day hot rod show in Yokohama, Japan, to educate ourselves on ways to run our show. We struck up a good relationship
with the organiser who also owns the MOONEYES brand worldwide.
He reckoned we needed a meeting point in Sydney where hot rod enthusiast could hang out but the cost of a venue was so expensive. Instead, we added a double mezzanine floor at our workshop and fitted it out with a ’50s ‘Kool Kulture’ diner and a shop with lots of MOONEYES products and other cool stuff.
At the moment it’s open on Saturdays and Sundays but, once it’s licensed, we will probably do Friday, Saturday and Sunday nights.”
Over the last 20 years or so, Andy estimates the market for custom cars, street machines, hot rods and restorations has grown by around 400 percent. Today, customers come from across the country and from all walks of life.
“The success of this business is all to do with our customers – they keep coming back! One of our biggest is from Melbourne and we have built nine cars for him.”
Owners: Andy & Donna Minas
Staff: Four
PPG Product: Envirobase
High Performance Territory Manager: Michael Drury
“And it doesn’t matter how much money they are spending – here, you get treated the same and we don’t compromise on quality. For example, we might be building a nice street car for a customer but there are no shortcuts and we still use all the right products and processes. The price begins to rise when you add time consuming things, like tighter panel gaps, fine details and show car paint jobs. We have built award winning show cars but you don’t want to do too many because it’s stressful and it burns you out chasing perfection.”
At 63 years of age, Andy has no intention of ever retiring but, with James managing day-to-day operations, it gives him and wife, Donna, the opportunity get out and about doing what they really enjoy – meeting people. Plans are in place to use a large enclosed car trailer to travel to all the major Australian automotive shows and introduce people to the Kool Kulture and MOONEYES brands. At the same time, Andy’s Restos will continue to be a leader in the local industry, says James.
“Dad has done a huge amount for the local industry over the years and whatever I know, he has taught me. However, if we want the industry to continue, we need to continue to reinvest – not just in technology but also in upskilling people. We want Andy’s Restos to be the place where we can nurture the next generation of custom / hot rod fabricators and painters.” R
The latest PPG training course covers off on a crucial but sometimes underrated step in the refinish process –polishing / detailing – and it comes I-CAR Australia approved.
For decades, PPG has committed to supporting the local collision repair industry with specialised training programs which provide valuable upskilling opportunities that help members meet the challenges of constantly evolving technology and techniques. Today, the region wide PPG training team is able to offer a wide variety of courses, particularly for those working in the modern paint shop environment. Indeed, there is a PPG course to cover every step in the process, from product application and SMART repairs, through to effective colour matching and dealing with the latest tricky OEM finishes.
Driven by demand from the industry, an all-new course has recently joined the list and it’s aimed squarely at those performing the polishing or detailing role. Although it might seem relatively straightforward, it’s an area that offers extensive opportunities to boost productivity and the quality of the end finish, according to Terry Noble, PPG Refinish Business Support Specialist.
“The polishing or detailing role is one that doesn’t really have a formal qualification so we were getting collision repairers asking us for a course that gave their staff a standardised, best practice process. From there, we formalised a course syllabise and teaching modules, as well as a post-course
can earn I-CAR points. This is a step-by-step polishing course that is all about refining the art of polishing and detailing. As a result, it focuses on everything from de-nibbing through to rectifying paint defects, as well as effective polishing, particularly for dark colours and more difficult colours. Because the modern polishing process is also about being efficient, we take advantage of a variety of MIRKA products, including the latest battery powered tools that help target the job, along with next generation polishing compounds that get the job done quickly and effectively.
Course content even
By following the process, users can look forward to a predictable, repeatable process every time.”
Courses are generally held at one of PPG’s training centres spread across the region, thus ensuring all the facilities are on hand and there are no distractions. Best of all, participants not only leave with extra skills, they can also be allocated points to earn or maintain I-CAR Gold™ status or Platinum Individual™ status.
R
Despite its outstanding success following the initial MoonWalk launch in Europe, the PPG regional team felt it was important to thoroughly evaluate this advanced automated dispensing system under local conditions to ensure all the benefits of precision, speed and waste minimisation flowed through to local collision repairs.
Having followed the progress of MoonWalk in European industry publications for some time, Gary Geeves, Executive Manager Repairhub New Zealand, was keen to put the ground breaking technology through its paces. “I contacted the local PPG team, saying I wanted to take a look at MoonWalk as soon as it
arrived and that resulted in a visit to PPG’s NSW Training Centre. We put MoonWalk through every test we could think of, including really messing with it by pushing it to the limit. After that, we chose colour formulations that would be really difficult for a human to mix accurately and then asked MoonWalk to mix them in tiny volumes – it did it! MoonWalk passed with flying colours and Repairhub New Zealand agreed to be part of the local trial program.”
With Repairhub NZ sites processing 80 to 100
trial, says Gary.
“One of the big motivations was colour accuracy. Using humans to mix colours, particularly if they have lots of tinters or tiny tinter amounts, opens up the possibility of human error. For example, you might select exactly the right colour match formulation on PAINTMANAGER® XI but, through human error when mixing, you make ‘another version’ of it. Research has shown that,
After acing an exhaustive trial at Repairhub New Zealand, PPG’s new MOONWALK® technology is ready for Kiwi repairers up and down the country to take advantage.
even in a good quality bodyshop, the human error rate when mixing can be as high as 50% and that can often lead to rework.
The only job you get paid for is the job you do once so accuracy is important. MoonWalk is accurate to 0.01 of a gram and it’s consistent. Now we make the colour and it’s the colour that was selected. Because MoonWalk’s colour accuracy is so good, we can actually paint less of the car. Generally, it’s good enough to do an edge-to-edge repair, on say a bumper, rather than having to blend into all the adjacent panels.”
Another factor that was highlighted by the trial was MoonWalk’s sustainability credentials. Because all the tinter containers are mounted upside down in the machine, the tinter inside drains down to the point where all the material is used, says Gary. “I must admit, I was sceptical about the claim that MoonWalk uses up all the tinter in each container. When we installed the first machine, I told the person mixing the colours that as soon as the first container empties, I want you to cut it open, take a photo and send it to me. It was absolutely 100% used up!”
“Once we saw MoonWalk in action, we realised we didn’t need a tradesperson to be mixing colours. As a result, we have brought new people into the industry, fully trained them to operate MoonWalk, and they now have a journey in the industry. Most body shops use a highly skilled person to mix colours whereas we don’t need to anymore. As a result, our painters can get on with more skilled tasks.”
“I can’t speak highly enough about MoonWalk and I am really glad that Repairhub NZ lead the way with the trial process. We have well and truly proven the technology, to the point where we are installing MoonWalk in the mixing room at each Repairhub site in New Zealand. We know we are using less paint and we know we are having less rework due to the colour accuracy. Obviously, there is also the efficiency. While MoonWalk is mixing a colour, the operator can be off
doing another productive task. As a result, we gain some more time during the day. Everyone who has used MoonWalk has quickly taken to the technology. At Repairhub NZ we now have three robots – a car wash robot, gas-fired infrared robots and MoonWalk – and it’s all part of our continual search for technologies that help to keep our people busy but less stressed. We are certainly sold on the benefits of MoonWalk and we anticipate that our return on investment will be quite quick.”
With new MoonWalk units arriving in both New Zealand and Australia, now is the time to put your name on one. Simply contact your PPG Territory Manager or the PPG Customer Service Hotline (NZ 0800 320 320 or Aust 13 24 24) to express your interest or to join the list to have a MoonWalk installed and start enjoying the many benefits.
R
“Thanks to Perkins Engineering, I have been involved in quite a lot of facets of a race team business. I have done time in the subassembly department, as well as in the engine shop, on wheels and tyres and directly on the cars. Back in 2011, Dad had sold the Perkins Engineering race team to Kelly Racing and I was at a loose end so he asked me to help pack up the team’s old Moorabbin Airport facility where it had been since 1993. As it became more common knowledge that the business was disappearing, the owners of Perkins Engineering cars got a little concerned that they would not have a support avenue to service their cars and engines.”
In 35 years, Jack Perkins has never missed a Bathurst 1000. In fact, he was just months old when he first visited ‘The Mountain’. After that, the annual pilgrimages were either to support the racing efforts of his father, Larry, or later to carve his own piece of Mount Panorama history – 2022 will be his
When Perkins Engineering kicked off in 1985, it had one full time employee, no race cars, no engines and no sponsors. What it did have was Larry Perkins’ determination to apply sound engineering principles in order to build consistently competitive machinery. When an off-the-shelf part was not up to scratch, Perkins Engineering became legendary for using outside-the-square thinking to come up with a better solution. Today, around 3500 technical drawings of components are part of the team’s inventory.
In a labour of love, Jack Perkins has taken on the task of keeping Perkins Engineering’s extensive treasure-trove of racing history alive for future generations to enjoy.
For example, the first step for the 1997 car restoration was to check over the mechanicals. We found the engine oil filter was full of metal and the gearbox and differential magnets were covered in metal particles. That meant pulling out the engine, gearbox and diff to get them serviced. Another example is the 1993 car (chassis 17) and the 1994 car (chassis 19) we are restoring. They are both VP Commodores but, in their lifetime, they were upgraded to VR / VS specification which meant having to go back and find all the original components.”
Unlike a typical road car which tends to retain all its major and minor components
over its lifetime, race car components are regularly swapped out for replacements. To ensure authenticity, Jack quickly realised the importance of picking a point in time to restore to. It also inspired a level of attention to detail equal to that of his father.
“The first car we started back in 2012 was chassis 41 from 2003. It was the only car that Dad retained ownership of and it happened to be his last Bathurst car.
We decided it would be restored as it sat on the Bathurst grid on Sunday morning with fresh bodywork, engine, etc. It meant finding the correct engine which was fitted at that moment in time – number 184 – and then the correct gearbox and so on and so on. If I had used, say, engine number 175 instead, it would be a replica, not a restoration.”
“The story of its steering wheel was a unique one, too. During final Saturday practice, Dad made heavy contact with the wall at ‘The Cutting’ which did a lot of damage to the right front corner and also bent the steering wheel. Perkins Engineering didn’t have a spare in the truck so Dick Johnson Racing kindly provided us with a replacement steering wheel. That was great for the race but, subsequently, it was removed and fitted to another car so I had to set about finding that exact steering wheel to make the restoration authentic.”
Information for a 20- to 30-year-old race car tends to be pretty thin on the ground. As a result, Jack has had to scrounge up any references he can find and even call on people power. “I rely massively on photos from back in the day, as well as documentation, to help prove that the engine number, the seat style, the steering wheel, etc. is correct. I knew I was not going to be able to do it on my own so I set up a Perkins Engineering Facebook page – we are up to about 35,000 ‘friends’ who are 100% race fans. When I needed to find a specific part for one of these old cars, Facebook provided a noticeboard system where I could reach out to so many people who were willing to support the program.”
“The Perkins Engineering restoration program has allowed us to continue the partnership with PPG which goes right back to the early days. For the 2003 car, PPG still had the colours on file but it was a different prospect for the ’93 and ’94 cars because the paint technology and codes from back then didn’t carry over. Manny Grillo (ANZ Colour Auditor) and the PPG Clayton Colour Lab team were great to deal with. I actually found an original door which I was able to borrow and take to PPG to get matched. Manny was able to cross reference against some old codes and create a modern formula to match. We don’t use any body filler in the cars – like back in the day, it’s all tapped into shape to minimise weight. As well as the cars, we have restored nearly 50 wheels and, again, Manny was able to formulate the exact white which actually has a blue tint in it. We are very proud of our relationship with PPG and they have provided great passion and support.”
fter chasing his childhood dream all the way to the Supercars grid, Jack’s progress was hit by frustrating and potentially life-threatening health issues. First, he was diagnosed with Type 1 Diabetes – also call juvenile diabetes, it’s an autoimmune condition that has no cure. Thanks to evolving technology, he was able to manage the condition and return to racing before suffering a stroke at just 29 years old. Fortunately, he made a full recovery and was able to return to racing. Since then, Jack has volunteered his time to work with a number of diabetes charities, as well as the Stroke Foundation, to tell his story and raise much needed awareness and funding.
During the COVID pandemic, Jack says he was looking for a way to remain connected with fans so he created a dedicated YouTube channel for Perkins Engineering. Today, there is a growing list of interesting and informative videos that cover many aspects of the race car builds and include cameo
A lot of people ask Jack why it takes so long to complete a restoration but he is quick to point out that it’s important not to rush. After starting the 2003 car in 2012, it took until 2020 to complete, however during that time he was also heavily involved in racing duties and had other customer jobs on the go. Jack says he prides himself on the attention to detail and that takes time.
Rather than have a favourite, Jack reckons he likes all of the team’s 49 cars for different reasons because each has its own individual story. For example, the 1993 Bathurst winning car is the last time a Holden race car won at Mount Panorama, powered by a Holden engine – since then it has been done with Chevrolet-derived engines. For Jack, continuing the Perkins Engineering name has been a labour of love.
“Looking back, it’s just a great family automotive business success story. Perkins Engineering
was about making race cars but they had to be competitive, reliable and successful in order to be able to sell them to pay for it all. The legacy I am most proud of is continuing the family business my Dad set up which put us through school and got us to the stage where we are in life. I look at my two-year-old daughter and I realise her generation will need to be educated on the racing heroes, such as Dad, Dick Johnson, Peter Brock and Allan Moffat. We are restoring the Perkins Engineering legacy and celebrating it because it’s a story that has to be told.” R
Like it or not, colour variation on plastic parts is a fact of life. However, how it’s dealt with can be the difference between a happy, satisfied customer and a frosty reception.
When someone purchases a new vehicle, the thought of colour variation between different components is the furthest thing from their mind. After all, it has a fresh factory finish so it must all match, right? Unfortunately, as many in the collision repair sector are well aware, perceived colour variation can be a major bugbear, even today.
The widespread arrival of large, painted plastic parts was a real windfall for vehicle designers because it brought far more as a slight mismatch of colour between a bumper and the adjacent body panels. The culprit can be found in various areas of the OEM production process where it’s not uncommon for plastic components to painted in different ways to the metal parts:
• Using different paint technology, i.e. waterborne versus solvent-borne.
• Using different application methods.
• In totally different manufacturing locations and then brought together for assembly.
• Using a different spectral grey primer colour
This is the most crucial step. By researching and understanding why apparent colour variations happen from the OEM factory, you will be in the best position to help vehicle owners understand the phenomena. Owners tend not to notice any colour variations until an accident puts the focus directly on an area. This is why it’s super important to cover off on the issue with the owner before repairs commence. When the vehicle is checked in or arrives for an estimate, use this opportunity to have a discussion with the owner. Look at the vehicle together, point out any existing colour variations and explain why they happen. The common owner response is, ‘I never noticed that’. It’s here that you can explain the challenges this presents to refinish painters but that your team has the skills, products and processes to either return the vehicle to the factory appearance or even slightly better it. With everyone on the same page, it should make for a much smoother vehicle pick up after the repair.
When choosing a refinish process, there are a variety of factors that can help contribute to achieving a factory finish or better.
• Hitting the target. A key advantage of managing customer expectations is that your painters then have a target. Instead of aiming for perfection, which might not be achievable, they can target the best match possible. For example, this might mean simplifying the refinish process – and reducing the job cost – by just painting the replacement bumper, rather than blending into the adjacent panels.
• Polish up your spectro reading. As with any repair, it’s crucial to properly prepare and polish the places where spectro readings are
going to be taken in order to bring out the true depth of colour and ensure the most precise data is recorded. If you don’t, spectroing is a waste of time because it won’t be accurate. The recommended method is to use MIRKA Polarshine F05 compound and a black pad. For paintwork in reasonable condition, it takes around 30 seconds to polish and, if it’s a little faded or scratched, you are talking 60 seconds so there is no excuse.
• Spray gun setup. This is another crucial step. To provide refinish technicians with all the tools they need, PPG’s local team has carried out in-depth research on all-important spray gun setup, as well as the most effective application tips and techniques. These recommendations not only make the job easier for technicians, they actually help them mimic the OEM paint
process which produced the colour in the first place. Ask you PPG Territory Manager for printouts of the step-by-step process which can be mounted on the wall for easy reference.
• Avoid a black mark. Never be tempted to paint straight over a new black plastic part. As well as consuming a lot more material and application time, it provides insufficient adhesion to the substrate. And, in the end, the black underneath will still grin through to affect the overall colour match.
• Prime, even when pre-primed. When a new plastic part comes pre-primed, don’t take the shortcut of simply rubbing it and painting over the top. Applying a quality Wet-On-Wet primer gives two advantages – it allows the right spectral grey groundcoat shade to be applied and it ensures there is a solid foundation and adhesion between the substrate and the basecoat.
R
• Spectral grey groundcoat. One of the keys to achieving the target match is to use the correct spectral grey groundcoat shade underneath. Because most modern OEM colours tend to be transparent, the groundcoat actually forms a crucial part of the overall topcoat colour. It also cuts your cost by reducing topcoat material usage and application time. PPG’s industry leading, PAINTMANAGER® XI software includes a recommended spectral grey groundcoat shade for every topcoat colour on the database.
One of the many fallouts from the global pandemic is the lack of opportunity for the PPG team to deliver on its wide range of training content. However, with restrictions now easing, this is the moment to make up for lost time and take advantage of the upskilling opportunities that PPG offers as part of its support package to customers, says Alan Gibbons, PPG New Zealand Training Manager.
I am sure painters haven’t forgotten how to paint over the past couple of years but there are always new technologies and techniques coming to the market which can help make their life easier and produce a better result in a faster time and getting a heads-up on that is something they have been missing out on. Even throughout COVID, the region wide PPG training team has been updating and refining our training syllabus to include the very latest best practices. That makes ‘now’ the best time to sign up for one – or even two or three! – of our wide range of training courses which cover off on pretty much any process you can think of in the refinish paint shop. At the moment, the three most popular would be ENVIROBASE® High Performance application, DELFLEET® High Solids and Colour Adjustment but there are plenty of others to choose from. Depending on your needs, you might prefer effective SMART repairs
(including UV8080 UV Cured Primer Surfacer), ‘effective sanding’ using MIRKA tools and abrasives or ‘best practice polishing’ with MIRKA’s state-of-the-art products. And these courses are not one-size-fits-all – I can tune the course content to the needs of the people involved to ensure they get the very most from their time.
Not long prior to the arrival of COVID, our Auckland Training Centre, at 5 Vesty Drive in Auckland, came in for a major update. The aim wasn’t just to provide all the space and features required to meet our training needs, it was also about giving people a training environment that mimics what you would find in a modern, high productivity workshop. It starts with a new car spray booth that has plenty of room for a training group. Next door we have two large mixing rooms that have a big, double sided mixing
As we emerge from pandemic restrictions, an updated PPG New Zealand training centre is ready and raring to get back to its role
bench and dedicated spaces for each of PPG’s paint systems.
For the prepping process, there is a double prep bay complete with sanding stations and a dual infrared and UV curing head mounted on an extendable arm. With it, we can show people exactly what distance it needs to be away from the job for safe, fast curing. Next up is a consumables room fully kitted out with SATA, MIRKA and Startline products. To make training as realistic as possible, we have also benefited from some fantastic donated parts, including a Toyota bodyshell, a Ford Ranger bodyshell, some Toyota HiAce panels and two fibreglass truck fronts.
As well as the opportunity to sharpen and finetune a technician’s skillset, PPG training courses have the added bonus of contributing I-CAR New Zealand points. We are finding that many people are motivated to do training for this reason. Given that we are providing solutions to help people in their day-to-day role, if they are also after I-CAR points, that is a win / win.
While PPG does deliver some training for certain customers in-house, there are big advantages in doing it off-site in a PPG training centre. In-house at a collision repairer, technicians find it hard to get into learning mode because they tend to get caught up with the process of getting jobs out the door.
In the training centre, everyone is much more tuned into the training message. It’s also easy to stop and discuss particular areas of the process to reinforce key points and allow them to sink in. Lastly, regardless of their experience level, people typically have a lot of questions during the course. I encourage that but you need to have time to answer those questions.
To give owners / managers a better understanding of how the course went, I have implemented a feedback process. As a result, I’m able to give them a brief overview of the training, along with some of the key points the group covered off on, as well as how the technicians participated and learnt from the course content. I think it reinforces the value of the training and the enjoyment technicians get from building on their skillset.
As well as Vesty Drive in Auckland, I also conduct training in Wellington and on the South Island. To enquire about upcoming courses, contact your territory manager or distributor who can provide you with a list of available courses and dates and guide you through the process of booking a spot. R
At first glance, the McDonalds business model might appear to have nothing in common with modern collision repairs. However, it does and it’s all about achieving a predictable end result. Walk into a McDonalds Restaurant anywhere across the region, or indeed the world, and you can purchase a burger that is essentially the same. The key factor is to have Standard Operating Procedures (SOPs) or standardised processes which are fully understood by the staff who use them and are then followed from start to finish.
Despite the obvious differences with repairing a vehicle, they are both process driven and getting it right lays the all important groundwork for how a business operates with consistency and efficiency. Currently, the PPG team is seeing various MSOs put a lot of effort into getting the
correct standardised processes, along with compliance strategies, in place because they understand the importance.
Often, owners will have the shop’s processes locked up in their head. Not only are they inconvenient to access, the verbal instructions for these processes are then
open to interpretation. To be effective, collision centre processes need to be in writing, easily accessible and fully agreed to and understood by the people meant to use them. It sounds relatively simple and it can be but it takes effort and attention to detail in order to put all the pieces in place. This is where the region-wide MVP Business Solutions team works with individual repairers to help them create, implement, refine and monitor SOPs. As well as tapping into the resources of the local PPG Technical team who have developed standardised processes for the paint shop and surface finishing, the MVP Business Solutions team has a set of best practice processes to cover virtually every collision centre process you can think of. Because every repairer is different, the team work with each owner and their staff to fine-tune the processes to suit their individual needs. Best of all, it’s available as part of the support package that comes with using PPG products – you just need to ask.
One of the keys to achieving long term collision centre performance is to implement a set of standardised processes, follow them to the letter and hit ‘repeat’, says Greg Tunks, PPG MVP Business Solutions Manager ANZ.
Even if you have definite ideas for each and every process, it pays to get input from your team. Get them involved by explaining what you want to achieve and the steps, equipment and products involved. Whether it’s the process for greeting each customer, the way parts are ordered and received or the way detailing is done prior to returning the vehicle to the customer, ask the appropriate team members what they think. They will appreciate it and, because they are dealing with these situations on a daily basis, they often have excellent ideas that can help build better processes for the business. Not only that, giving them an understanding of what each process is meant to achieve and keeping them involved, is a great way to get team buy-in so that they take ownership and ensure process compliance.
When it comes to standardised processes, one of the key elements is to ensure the necessary information is effectively delivered to the end users. The aim of standardised processes is to streamline operations so information locked in an owner’s head or stuck in a file on a shelf doesn’t help anyone.
As well as being written down in detailed form in an easily referenced SOP folder, everyone involved needs to be properly trained so they recognise why it’s being done this way and what the benefits are. With a clear understanding, staff tend to take ownership of the individual processes and are happy to comply. Process charts are a great way to consistently reinforce the message. Being highly visual, they can be mounted in the appropriate areas to provide a handy reference and reminder. What’s more, when a new staff member joins, standardised processes make it much easier to induct them into the business and quickly get them up to speed.
What we can guarantee is that, because collision repairs are done by humans and not robots, things will go wrong. However, having standardised processes in place makes it easy to work backwards, step-by-step, to determine where the fault is. If you think about the McDonalds model –their processes allow them to produce a totally predictable result, with the same burger appearance, taste, etc, everywhere you go. When something goes wrong, it’s because someone has stepped outside the process. With a little determination, any collision centre can do the same thing. It might seem a little daunting but your MVP Business Solutions Manager will be happy to guide you through the development and implementation process. Then, once SOPs are in place and being followed, all that is needed is a little finetuning as new products and techniques arrive.
The drive to offer something back to the trade he enjoyed so much saw Nigel take up a series of industry support roles starting in the early 2000s. Recently, he took that passion to an all-new level when he became MVP Business Solutions Manager New Zealand. This sees him work closely with collision repair business owners up and down the country to help them become more successful.
Nigel’s biggest early influence was his father who owned a standalone panel shop where he would help out after school and on holidays. When an associated paint shop offered Nigel a spray-painting apprenticeship, he jumped at the opportunity. Having gathered plenty of experience in the trade, he joined PPG as a Territory Manager in 2004 and went on to become a long serving member of the PPG New Zealand team. Recently, he was thrilled to utilise his skills and knowledge and throw himself into his new role.
“Often, collision centre owners have come up from being a tradesperson so part of our role is to coach them to think more like a business person. Nowadays, a key focus of the MVP Business Solutions program is about making improvements to productivity by using best practice processes from start to finish. This drives increased shop throughput which, in turn, drives the financial performance.
Favourite hobbies /pastimes? Boating, fishing and diving
Favourite food? Vietnamese and seafood
Favourite drink? Gin and tonic
Favourite music / band? Eagles or Dire Straits
Favourite car / motorcycle? My ’65 Cadillac Convertible
Favourite holiday destination? Anywhere in Europe where it’s warm in our winter
One of the biggest challenges is getting total buy in from everyone at the collision centre. However, when you work closely with a customer, supply all the solutions to suit their specific needs and see the results flow in terms of improved cycle-time and profitability, it gives you a real buzz. The other great thing is the strong relationships you form while working together. Overtime, they build into real friendships which is really important to me.”
MIRKA continues to raise the bar for effective tools with the launch of a pneumatic belt sander that comes with innovative design, powerful performance and clever features.
Having established an outstanding reputation for using outside the square thinking to develop tools that are more reliable and efficient, MIRKA is showing no signs of slowing down. The latest tool to join the range, the MIRKA Pneumatic Belt Sander, has been finetuned to a variety of everyday tasks in the panel beating workshop. Available in either
attention to detail means all the adjustments, such as setting the speed and the angle and changing the belt, are hassle-free,
For example, smooth speed control
operate regulator that requires no tools and an intelligently designed tension arm mechanism takes belt changing from a chore to a breeze. Setting the angle of the arm is also very straightforward thanks to the hex key needed for arm adjustments being cleverly integrated into the tool handle where it’s
the innovative design also prioritises the health and comfort of the operator and their co-workers. For example, the rubber-coated handle makes the MIRKA Pneumatic Belt Sander comfortable to hold and prevents
and low noise level makes it a dream to
To further boost performance, MIRKA has also launched a selection of Mirkon Belts to fit the MIRKA Pneumatic Belt Sander. Available in P40, P60 and P80 grits, these tough and durable belts are perfectly suited to the aggressive machine
capable of taking plenty of
The polishing procedure is one of those areas in the modern repair process where speed and efficiency have become crucial in order to return the vehicle to the customer in prime condition while also maximising profitability. Thanks to its market leading Polarshine range, it’s an area MIRKA has devoted a lot of time to perfecting and the latest updates bring a variety of worthwhile improvements in performance, efficiency and end result.
This newly formulated, coarse, fast cutting polishing compound was developed to help save time,
This water-based and silicone-free polishing compound offers a one-step solution for the removal of scratches from P2000 or finer (depending on the surface and polishing pad) to really bring the underlaying colour to life. It has been formulated to deliver a perfect balance between speed of cut versus the effective removal of surface imperfections, such as de-nibbing and sanding scratches, to avoid haze and hologram issues.
For extra convenience, it comes in a black compound for tackling darker colours and a white compound for lighter colours. Both colours also come in 1L and 250ml.
Note: As part of this latest upgrade, Polarshine 12 replaces the existing Polarshine 15 Polishing Compound.
Made from a reticulated foam that has an excellent balance of elasticity and softness, this new pad features a waffle shape with an optimised pattern for improved cutting performance, reduced surface temperature during polishing and long-lasting durability.
The Black Waffle Foam Polishing Pad is especially well suited to polishing darker colours in combination with Polarshine 12 Black Polishing Compound. R
yet still achieve a deep gloss finish. It has been particularly targeted at hard surfaces and coatings – especially within the marine sector, as well as for automotive ultra-high solid coatings – and is ideal for use in both production and restoration type processes. In contrast to compounds that simply fill scratches, Polarshine 45 actually removes deep sanding scratches and finer imperfections, quickly and permanently. It comes in 1L and 250ml bottles.
Note: As part of this latest upgrade, Polarshine 45 replaces the existing Polarshine 35 Polishing Compound.
t’s ironic that sunlight is brilliant for showing off vehicle paint colours, yet it’s also the key culprit behind paint degradation. Although there are a few other contributing factors, it’s exposure to sunlight that does the real damage, says Scott Mandragona, Technical Manager at PPG Clayton.
Of the sunlight that reaches the earth, it’s actually the Ultra Violet (UV) spectrum that attacks paintwork. Paint resins are made up of long chains of chemicals and when they are hit by UV rays, the chemical bonds within the resin are slowly broken apart. When you start to see ‘chalking’, it’s an outside sign that the resins are breaking down and, eventually, the result is loss of gloss and, ultimately, coatings failure. Paint film is also affected by free radicals, humidity and dirt and grime. If you don’t ever wash your car, the dirt and grime combined with UV will just accelerate the degradation.
It’s fair to say that our local product development team spends a lot of time ensuring we cover off on durability.
It’s particularly important in Australia where we record some of the highest UV readings in the world. Durability starts with getting the choice of the resin and the pigment correct. Resin development is a key area where PPG is an established global leader, particularly in terms of durability. When it comes to pigments, although there is a vast range of choices available, we would only ever consider using the very top tier in refinish products. Because they need to thoroughly prove themselves, a pigment that is developed today can take many years before it’s considered to be a safe, viable choice in the refinish space. Often, the pigments used in refinish are driven by the pigments chosen by vehicle OEMs who tend to be equally fussy about durability. All this explains why the pigments used are a significant contributor to the cost of a refinish paint product.
In order to prove the durability of a paint product, it essentially needs to endure and survive the worst of conditions it’s likely to face in the real world. For a key proportion of this, PPG uses independent test sites which are chosen for the amount of sunshine they receive and the different types of weather conditions they are exposed to. Although the internationally recognised benchmark location for outdoor exposure testing is Q-Lab Florida, in the southern United States, we have found that the Australian site, in Townsville, offers an even tougher challenge. Whether we are testing a potential new
Sunlight kills paintwork but that is where paint chemists come in. Only by carefully selecting ingredients and testing to the max, can they deliver long-term durability.
product or a production batch of an existing product, we will paint test panels and send them to the test site. Basically, the panels remain fixed to a framework, out in the open for years on end and are checked at set intervals. For comparison, we have sent exactly the same paint samples to both Q-Lab Florida and the Allunga Exposure Laboratory in Townsville. The results showed that the northern Australia site is around 30 to 40 percent more severe on paint than Florida! This is also an indication of why we have seen competitors bring paint products to Australia which work perfectly well overseas but fail miserably here. We also have a number of machines here in the PPG Clayton lab that allow us to perform accelerated testing.
For example, one of our machines alternates between hitting the panel with four hours of constant UV, followed by four hours of water spray. Using this method, it’s possible to condense around three years of exposure testing into just a
few months. While that is fine for quickly screening a formulation, it’s no substitute for outdoor exposure testing. Another crucial test subjects the panel to 100% humidity. If there are any tiny weaknesses, the moisture tends to work its way between the layers to degrade the coating.
Combined with the resin and the pigment, the final weapon in the paint chemist’s arsenal is an additive call ‘UV absorbers’. Added to the coatings package, it absorbs some of the UV light hitting the paint film, thus giving increased durability. This is why UV absorbers have become an integral part of PPG’s product development and finetuning for the local market, particularly when it comes to clearcoats. For example, we have had products that originated in Europe where we have had to add double the amount of UV absorbers in order to get the required performance for Australian conditions. The other thing to understand is that UV absorbers have a certain lifespan –as they absorb UV energy and protect the resin and pigment, they also break down.
There are no shortcuts when it comes to product development and testing and the fact we have the expertise and resource to do it here in Australia is a real benefit to the local market.
It’s a scenario that could play out pretty much anywhere around Australia’s approximately 34,000km of coastline. You have had an epic day of fishing at your favourite offshore reef but, when it’s time to head home, Mother Nature starts throwing her weight around. With the wind rising and the wave height growing by the second, it has the potential to be the stuff of boating nightmares. From the very beginning, this is exactly what Bar Crusher Boats were designed for, according to co-founder, Peter Cleland.
When the going gets rough, Bar Crusher Boats are the fisherman’s friend, delivering stability, a super-smooth ride and long-lasting performance, along with killer looks!
“Back in late 1999, my brother Warren and myself felt there was an opportunity to offer a better engineered, better built boat to the Australian trailer boat market. We were recreational fishermen who grew up using a pressed sheet aluminium tinny-style boat so we knew the shortcoming of that product. They tend to be hard riding boats and typically not built to handle rougher conditions. In contrast, our target audience has always been passionate fisher-people and the whole Bar Crusher essence is about giving them a boat they can use to confidently head offshore in rougher conditions and still feel safe and secure as they enjoy some adventures on the water.”
Bar Crusher Boats incorporate a range of design innovations, including a crucial element that is key to delivering on the brand promise. “Although we didn’t invent it, we were able to refine, bring to market and promote the benefits of a key water ballast technology, we call ‘Quickflow®’. Running along the length of the keel there is a cavity which is open at the transom. When the boat stops, water floods in to reduce buoyancy and make it more stable at rest. This lets us build more ‘V’ into the hull with our Waveslicer® design and that allows it to cut through rougher conditions. It gives a nice
combination of a stable fishing platform, yet with enough ‘V’ to create a smoother ride.”
In the early days, Peter and Warren literally dipped their toe in the water by working with another small business which allowed them to test their concept and gave the business a kickstart. This laid the groundwork for Bar Crusher to set the standard for a ‘plate boat’. Each boat is fabricated from heavier than standard aluminium plates which are formed into the shapes required and then further reinforced with a robust, Rigideck® engineered subfloor structure and a welded in floor.
After grabbing the market’s attention in its first year, the Bar Crusher team continued to step things up in terms of models, options and finish. Having gone through four factories in its pursuit of more production capacity, Bar Crusher Boats are now manufactured at a neat, spacious and well laid out facility in the Melbourne suburb of Dandenong South. Although Bar Crusher is proudly made in Australia, that does bring challenges in terms of containing manufacturing costs in order to ensure a competitively priced product. The answer has been to tailor and refine every step, says Production Manager, Glen Kostiuk.
“Traditionally, a boat builder will have a fabricator working on one boat until it’s complete but we have chosen a more efficient and consistent system. While it’s not a true production line, what we have done is break the system down into standardised pieces of work and this helps us maintain efficiencies and quality. For example, although we manufacture a range of sizes
from 5.35 metres to 7.8 metres, the front and the back are the same right across the board. On top of this, we have just a few different cabin variations, along with a range of standardised options for customers to choose from. As a result, the process for building the boats is very similar, regardless of the size.”
There are a number of key skillsets required on the production floor, including welding, fabrication and painting. Like other industries, it can be a challenge to find the right people in a tight labour market, according to Glen. “Most of our skilled staff are actually trained ‘on the job’. Generally, we employ for attitude and the ability to fit into our culture. If we think a person has the potential to be a Bar Crusher person, we will train them. To give us greater flexibility, there is also a lot of cross training on the production floor which means we have multi-skilled people who can switch to different roles, as required.”
While the on-water performance of Bar Crusher Boats is the stuff of boating folklore, what really grabs attention on or off water is the paint finish. Over the years, customers
have demanded a higher and higher level of finish and a close partnership with PPG has helped to consistently exceed expectations, says Glen. Today, Bar Crusher uses a range of products from PPG’s Commercial Performance Coatings brand, including 625 Polythane – an ultratough, two-pack polyurethane topcoat that delivers exceptional durability, along with premium gloss and colour retention.
“From the early days, the PPG team has been heavily involved in the paint process we use and is constantly exploring ways to help us do it quicker, better and smarter. It’s not just about buying a pot of paint. It’s a combination of great products, great service and great technical support – all the things any long-term partnership relies on. Being Australian made, we are also keen to source locally made products which includes PPG’s Commercial Performance Coatings range. Every Bar Crusher Boat is painted and customers have a range of standard colour options to choose from. We have gone through a period where a lot of customers chose jet black but we are now starting to see more primary colours come back. All of our paintjobs are done from a bare metal finish – we don’t use any fillers anywhere in the process. It’s a real credit to our paint team and the PPG products that they achieve such flat, smooth and glossy results day-in, day-out.”
The most popular Bar Crusher models tend to be the middle sizes because they tick a lot of boxes in terms of being easy to tow, easy to store, good fuel economy and reasonable purchase price. Indeed, hitting the target market has been a Bar Crusher strength from day one, says Peter Cleland. “We have spent a lot of time listening to what Australian fishermen want in their boat and we are very much tuned into that market. We recognised early on that the overall customer experience was paramount, so we have introduced features, such as a custom-designed trailer for each boat and the innovative Bar Catch® system that allows for single-handed launch and retrieval. As we evolve the Bar Crusher product range and increase capacity, we will continue listening and being responsive to those needs.”
Despite a worrying drop in demand when the COVID pandemic hit, Bar Crusher sales quickly picked up to the point where they are now riding the crest of a wave, says Peter. “We are now very, very busy, with a long order pipeline. In a little over 20 years, our vision for offering the market a better boat has taken Bar Crusher from nowhere to one of the most recognised and respected brands in the aluminium boat space.” R
Thanks to an unrivalled combination of exceptional speed, superb colour accuracy, no-fuss ease of use and effortless blending and mottle control, this is simply the best refinish technology on the market. Backed by a range of primers and clearcoats featuring advanced low-VOC technology, it’s the eco-friendly choice which really delivers on outright speed. With everything a modern, fast-paced collision centre needs to slash cycle-time while boosting productivity and profitability, Envirobase® High Performance is engineered for excellence!
This advanced, 3D digital colour visualisation tool smoothly interfaces with the next-generation PPG DigiMatch™ camera-equipped spectrophotometer to totally transform the user experience of selecting the best colour match formulation from PPG’s extensive library.
PPG’s high tech DigiMatch spectrophotometer features a digital colour camera to significantly boost performance. The camera’s six imaging angles combine with six reflective angles to provide additional texture information to help quickly and precisely retrieve the correct formula match.