PERI scope
In Focus
Building bridges on a major dualling project in Wales
A465 Heads of the Valleys, Wales
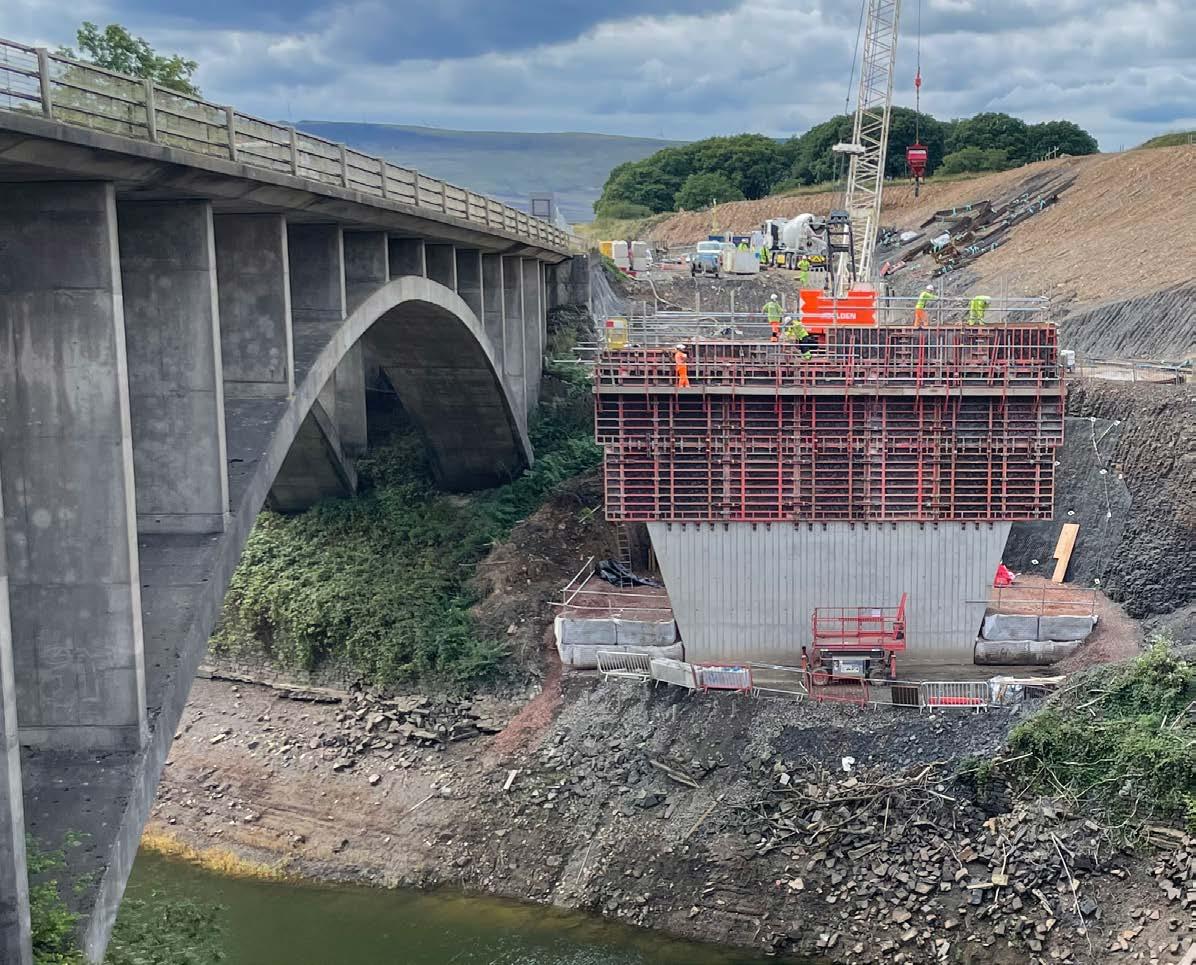
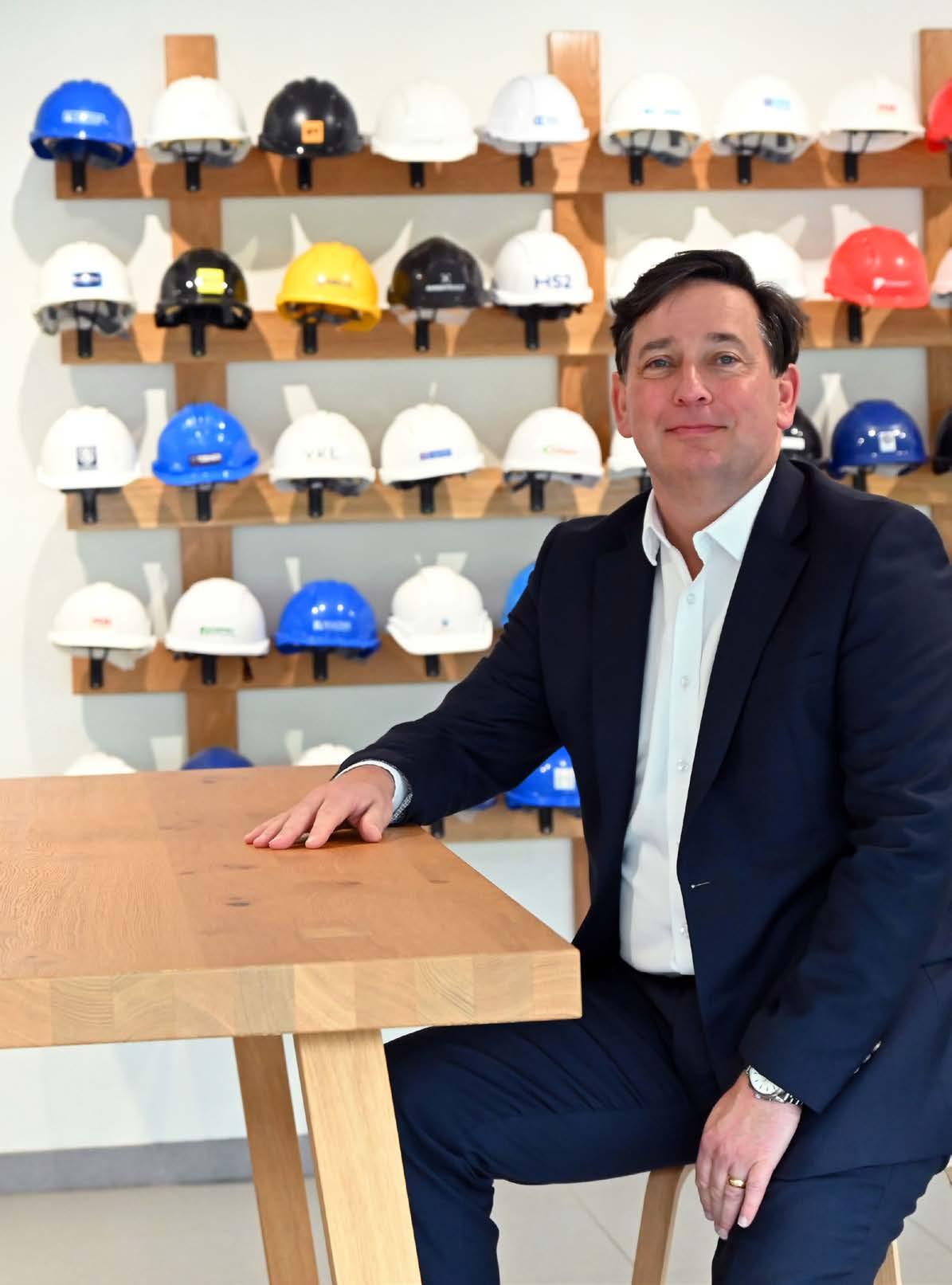
In Focus
Building bridges on a major dualling project in Wales
A465 Heads of the Valleys, Wales
I’m delighted to present to you the latest issue of PERIscope and my first as the Managing Director of PERI UK. As you may already know, Alasdair stepped down from the business in April this year after a successful 10-year long tenure with PERI.
I joined PERI in May, and I’ve had an insightful few months getting to know the business, including my visits to near and far offices to meet our employees in person. I’m immensely proud of our people, products and services, and have seen very early on just how hard our teams work to make construction faster, safer and more efficient for everyone.
I’ve also had the pleasure of meeting some of our customers, visiting project sites all over the UK and understanding how we can better support you moving forward. If we haven’t met just yet, I’m sure the opportunity will arise in the near future.
Throughout my career I have specialised in formwork and concrete, working as a contractor and supplier, so I’m well-acquainted with the challenges the industry faces. I’m looking forward to working with my team to continue delivering high quality across our products and services. Of course, we always want to do better. We value your feedback and are committed to improving your experience with PERI.
As we all know, there are inconsistencies in the market at present – from developers reassessing project start dates to demand for infrastructure schemes increasing. But these market characteristics are no surprise considering the political turbulence and economic predictions from a year ago.
We continue to be both proactive and reactive, adapting to market needs and demonstrating our position as a leader in the industry through new product ranges across our core construction sectors.
This year, we’ve introduced our ALPHAKIT and VST heavy-duty shoring systems to provide high-load support for major infrastructure schemes like HS2.
To complement our existing formwork offering and help you construct faster, we now stock a competitive range of construction accessories through our partnership with DYWIDAG. Products like DYWIDAG form ties, Starter Packs – Continuity Strips and Speed Edge formwork are already proving a success on project sites across the UK.
We’ve also made changes to our customer portal. The latest version of myPERI will make processes such as tracking and returning equipment on site simpler through any device. I recommend signing up if you haven’t already and seeing how it can make managing your project with PERI easier.
In this issue, we share some of our recent project stories, each one involving different requirements and challenges. You’ll get to see how we’re helping to deliver Manchester’s first cylindrical high-rise and how we continue to be associated with a major dualling project in Wales.
Editor PERI Ltd.
Formwork
Scaffolding Engineering
Market Harborough Road
Clifton upon Dunsmore Rugby CV23 0AN
United Kingdom
Responsible PERI UK
Editor-in-chief
Jinal Kansara
Editing and graphics
Dekany Design
Photos
Simon Turner
Darren Powell
Amber Toogood
Neil Terry Design & Print
Copyright
The photos used in this brochure feature certain situations at particular moments on various construction sites. Additional images, e.g. regarding safety and anchor details, cannot always be considered as conclusive or final. These are subject to the risk assessment carried out by the contractor.
© PERI GmbH
Charles Stratford discusses the benefits of system scaffolding on remedial projects
9 Façade access for a geometrically challenging building
Payne Road, London
10 Building bridges on a major dualling project in Wales
A465 Heads of the Valleys, Wales
12 Going full circle on Manchester‘s first cylindrical high-rise
Three60, Manchester
14 News
Charles Stratford, Business Development Manager for PERI UP Scaffolding, highlights the importance of utilising system scaffolding to speed up remedial work on high-rises and reduce the disruption caused to residents occupying these buildings.
Following the Grenfell Tower tragedy in 2017, the UK Government addressed the fire safety risks caused by unsafe cladding on high-rise buildings. It has since introduced the most significant building safety reforms in 40 years. The Building Safety Act, which was granted Royal Assent in April 2022, has been a catalyst for major changes in building construction and remedial works.
Since the surge of recladding work in the UK, temporary access has been in high demand. Growing pressure to hand these projects over quickly means the speed of installation and removal of temporary access is important to all contractors involved. The speed at which these projects are completed is equally important to the residents occupying the buildings, as their lives are often disrupted due to the work being carried out.
With a significant number of high-rise buildings yet to be fully remediated and further potentially unsafe buildings to be assessed, it’s crucial that we provide the right temporary access systems on these projects to shorten programmes and minimise disruption in the future.
To replace cladding, contractors need access to the façade. In most cases, this requires working at height and at multiple levels simultaneously, making scaffolding the ideal solution. This type of access system enables different trades to carry out tasks at the same time, speeding up the entire process. Additionally, scaffolds are less likely to be affected by high winds as they are not typically weather-dependent.
Mast climbers on the other hand offer less protection from the elements, which could mean work is delayed until weather conditions are more favourable. The longer a project is delayed, the costlier it becomes. Another cost to factor in is the power source required for mast climbers to work, which varies depending on the size of the system.
Although motorised systems like this have their advantages and can be a good solution for modern facades, they are not always practical when removing EPS cladding systems found on older buildings. This is because EPS cladding comprises lightweight polystyrene insulation which breaks apart during the removal process and is difficult to
contain in windy conditions if the access system is not enclosed properly. This type of cladding is thought to be just as prevalent in the UK as the ACM cladding system used on Grenfell Tower.
In many cases, mast climbers are limited at lower heights, which suggests that they work best when used in conjunction with scaffolding, as the latter can provide access around the base and the lower floors, offering protection to the public while works continue above.
Cladding removal poses a risk of falling objects and debris if the temporary access system is not contained properly. To prevent this risk when using scaffolding, protective sheeting such as Monarflex can be wrapped around the structure.
Although protective sheeting for scaffolding provides a safer working environment for contractors, it raises the issue of an entire building being covered for a long period of time, often obstructing windows in the process. While this has been the norm for recladding projects, residents are continually disrupted by poor exposure to natural light in their living environment.
Research shows that poor exposure to natural light for prolonged periods can have an impact on mental health and wellbeing. According to UCLA Health (2022), being in an environment with low levels of natural light can result in ‘poor sleep, low mood and depression’.
In the worst cases, cladding remediation on a high-rise building above 18 metres high can take up to two years. Programme extensions and delays like this can be caused by the complexity of the project, labour shortages, means of access and the cost and availability of materials required.
Timber boards, often used for traditional tube and fit scaffolding, is one material which has been affected by economic changes in recent years, with high demand and fewer imports causing price increases and project delays.
In addition to price volatility and supply shortages, the use of timber for façade applications such as recladding seems illogical as it’s a combustible material. Surely using non-combustible materials around buildings that pose a fire risk should be a priority?
We know scaffolding plays a vital role in critical remediation work. With the scope of this work widening as more buildings are assessed, it’s important to work with smarter systems to minimise the cost and duration of remedial works, while improving the safety and wellbeing of all involved.
Innovative and modular scaffold systems offer many benefits, such as shorter programme times, reduced preliminary costs, flexible arrangements, minimal components, and a reduced risk of falling objects, slips, trips and falls.
System scaffolding encourages best working practices such as early engagement and planning to ensure build sequences are economical and practical. From basing out correctly to minimising the impact on residents at each lift, everything is considered prior to the build. Proper planning thus ensures faster build times and promotes faster removal of scaffolding, presenting a multitude of options to suit the main contractor’s programme.
For instance, PERI UP, like most other system scaffolds, has built-in steel locking decks instead of traditional timber boards which lock into position instantly. No additional components are required for installation. Other safety components, like the advanced guardrail on the PERI UP Easy façade system, enables the next level to be constructed from the working platform below. With integrated safety features like this, we can prevent the need to implement proprietary equipment such as Scaff Steps, resulting in minimal effort and time required to erect the next scaffolding lift.
The common perception is that system scaffolding lacks the flexibility that conventional scaffolding offers. However, system scaffolds have evolved significantly over the years, with standard solutions being equally capable of accommodating complex geometries such as stepped façade elevations and curved building façades.
When comparing the speed of system scaffolds to conventional scaffolding, it’s also worth considering the weight of the material and the number of components being handled manually. Typically, system scaffolding components are lighter. With fewer and lighter components, coupled with advanced build technologies such as built-in advanced guardrail systems (AGS), there is potential for scaffolders to erect more square metres a day.
This was the case on The Link – a residential high-rise building in London requiring façade access for remedial works. It was predicted that access installation would take 16 weeks using traditional scaffolding methods. With the PERI UP Easy system, it was completed in just four weeks, reducing installation time by 75%.
It is also important to note that system scaffolding is made of noncombustible components like steel –a safer alternative to using timber on recladding projects.
System scaffolding can support the long-term projection for cladding remediation. With the right planning and training, scaffolding and cladding contractors can save time, labour, and prelim costs, while reducing the impact on residents.
After the Grenfell tragedy and the anxiety surrounding the recladding industry, the importance of making the process as smooth and fast as possible is greater than ever.
If you have any questions on this topic or would like to use system scaffolding for your project, you can contact Charles Stratford at: charles.stratford@peri.ltd.uk or info@peri.ltd.uk
References:
Gov.UK ‘The Building Safety Act’ (July 25, 2022). Available at https://www.gov.uk/guidance/ the-building-safety-act
BBC News Online, ‘Residents of Ipswich flat say cladding repairs affecting health’ (July 22, 2021). Available at https://www. bbc.co.uk/news/uk-englandsuffolk-57916147
UCLA Health, ‘Being in natural light improves mood, increases happiness’ (March 25, 2022). Available at: https://www. uclahealth.org/news/being-innatural-light-improves-moodincreases-happiness
Essex-based scaffolding contractor PDC Scaffolding has embarked on its biggest project using PERI’s scaffolding system, PERI UP Flex. The project, known as Payne Road, is a geometrically challenging recladding scheme in East London.
PDC Scaffolding required a façade access system that could be adapted to the building’s geometry, which becomes more irregular as it grows in height.
The solution was to wrap scaffolding around the building. This consisted of 221 tonnes of PERI UP Flex scaffolding, providing perimeter access to all 16 storeys to facilitate cladding replacement.
Principal scaffolding designer, PSD Prime Scaffold and Structural Designs Ltd, worked with PERI’s design team throughout the planning phase. Collaborating with the scaffolding supplier early on in the project enabled PSD to get an understanding of the system’s specifications and capabilities, making the installation process on site smoother.
Paul Casey, Managing Director of PDC Scaffolding, explained how flexible system components benefitted the project:
“The reason we’ve used the PERI UP system is because it’s the most versatile system out there. The different deck sizes available in the PERI UP range have been beneficial as we’ve been able to install a deck arrangement that accommodates the shape of the building. In addition to the decks, using components like the console brackets meant that we could get around every part of the building safely, covering all the gaps.”
“This has been a challenging project given the awkward shape of the building. There are different angles, terraces, and vertical shafts. Nothing is at a right angle. The scaffolding arrangement had to be designed to the absolute millimetre to make it work.
PERI UP Flex is ideal for this type of project as the system lends itself to odd shapes. It’s also perfect for cladding projects because the lack of bracing gives the contractor unrestricted access around the scaffold to carry out the work.”
Construction on the A465 Heads of the Valleys project has been ongoing since the early 2000s, with the final sections, section 5 and 6, due for completion in 2025. Work is being carried out to expand the route from Neath Port to Monmouthshire into a dual carriageway, which will improve traffic flow and make travelling from south-east to south-west Wales more accessible and safer. As the final sections of the project are underway, we wanted to reflect on our involvement across the project.
Sections 5 and 6
This phase comprised a mix of insitu and precast construction. Over thirty bridges are being built for the final section. Finishes across these structures range from a basic to fluted to a brick effect finish at the Jones Street site which was achieved using a reckli liner and TRIO formwork.
For the abutments, our design team looked at how the formwork panels could be tied together without compromising the finish. The solution involved installing ties and walers from the back of the panels to minimise the visual impact on the concrete surface.
Along with the finish, the rate of rise and access requirements for pouring and installation were factors that determined the temporary works design for the tallest abutment which is 14 metres high. Larger formwork ties and additional walers were used to withstand a pressure of 80kN per sq m and achieve the 3-metre an hour pour rate.
Accessibility on bridge projects can often be challenging. Heads of the Valleys is no different, with many of the project’s piers and abutments situated in inaccessible areas.
The piers supporting the Nant-hir bridge are a prime example of this type of challenge, as the bridge crosses over the Nant Hir Reservoir. Adding to the complexity is the splayed shape of the piers which have been formed with TRIO to support the pour sequence and height.
As the piers were poured in two segments, using a panel system made it easier to extend the formwork without making changes to the fluting. Given the confined space on site, this would have been challenging to build with a traditional system as climbing platforms would be required to support the weight of the formwork.
Access across site
Multiple access requirements were fulfilled with PERI UP scaffolding. For
the abutments, TVC required access from the ground up to facilitate the installation of steel reinforcement followed by formwork. The scaffolding was designed to serve both parts of this process with minimal adaptations required.
Typically, scaffolding towers at this height would be tied into permanent structures. In this case, lack of permanent structures meant the scaffolding had to be self-supporting with bracing and buttresses incorporated into the design for stability.
Access scaffolding has also been instrumental in prefabrication work. The PERI UP system was used to facilitate the build of reinforcement cages in a different location on site before they were repositioned in situ by crane.
Scaffolding has also facilitated the construction of the Taf Fawr bridge deck, with a 30m-high PERI UP 75 stair tower erected to provide an access point for Tecozam’s traveller system. A smaller staircase will connect the traveller to the main platform to support pouring operations.
JANUARY 2023
SECTION 5 & 6: Dowlais Top to Hirwaun
JULY 2013
SECTION 3: Brynmawr to Tredegar
Section 3
Between 2013 to 2015, improvements were made to a 7.8km stretch of the road between Brynmawr junction and Tredegar, also known as phase 3 of the Heads of the Valleys project. This phase involved upgrading the existing three-lane road to a dual carriageway, including a 3km surfaced cycleway.
We supplied our VARIOKIT parapet track and carriage to four bridges, which were made from a mix of steel and concrete. For access to the parapet track, we supplied our PERI UP scaffolding.
Three60 is one of the newest high rises making its way into Manchester’s skyline. On completion, it will stand 51 storeys tall and comprise over 400 apartments. Renaker is delivering the project as part of the wider Great Jackson Street development scheme.
“By working closely with PERI when we were designing the screens and specifying our exact needs on site, we were able to come to quick and easy solutions.”
Tom McDonnell Renaker | Project EngineerConstructing at such heights meant there was a requirement to transport material up the building efficiently, as well as the need for perimeter protection to shield the working levels from the wind and leading edges.
Early involvement on the project meant that we could align our temporary works offer with Renaker’s programme seamlessly. This enabled our team to keep up with the construction pace and accommodate the building’s facetted structure.
Our Lightweight Protection Screens (LPS) were installed over four floors. In addition to deflecting wind loads as the building grew in height, the design of these screens had to account for other demands, such as cycle time, access to the slab edge and avoid potential clashes with columns.
We used a double-rail platform screen for this requirement, which offered a working platform between the slab edge and screens. The platforms provided access to prefix bolt boxes for cladding installation.
To accelerate screen installation, we preassembled the masts offsite. Each section was then connected on site with drift pins before being tied to the structure.
The low weight of the screens along with hydraulic lifting saved Renaker time, as the team were able to cycle two screens simultaneously.
When designing the screen solution and slab shoe layout, we had to take the position of the columns around the slab edge into account to avoid clashes.
With the assistance of 3D visualisations, we were able to declash prior to erecting the screens. Having visibility of this information early in the programme meant that the site team could tie the screen design in with other temporary works elements such as the propping and falsework, ensuring all systems worked cooperatively.
Integrating an efficient transportation system into the programme was crucial as this enabled material and operatives to move quickly between the working levels. As well as providing safe access at height, it enabled the crane to be released for other tasks on site.
assembled in a day
2
cycled in 15 minutes
Adrian Robinson Renaker | Contracts Manager“The process of cycling the screens was really easy. We could cycle two screens at once, which is a big advantage as it saved us a lot of time and helped us to push the project along.”
We’re pleased to announce that the new version of myPERI is here. myPERI is an exclusive digital portal for our customers where you can find all your PERI project information in one place, from technical documents to rental and sales invoices.
The portal has been upgraded with new features to help you better manage your project from the moment you place an order with us to the moment you’re ready to close off the project.
New customers: If you haven’t already, register for access by clicking or scanning the link below. Your Sales Engineer is on hand to answer any questions about the portal and to help you get started.
What can you do with the latest update?
• See all PERI stock that’s on your site, so you can manage stock levels with confidence
Existing customers: You can log into the portal with your email address by following this link:
• Get Assembly and Instructions for Use guides at your fingertips
• Arrange returns online at your convenience
If you have any queries relating to your myPERI account please contact us at myPERI@peri.ltd.uk