PERI scope
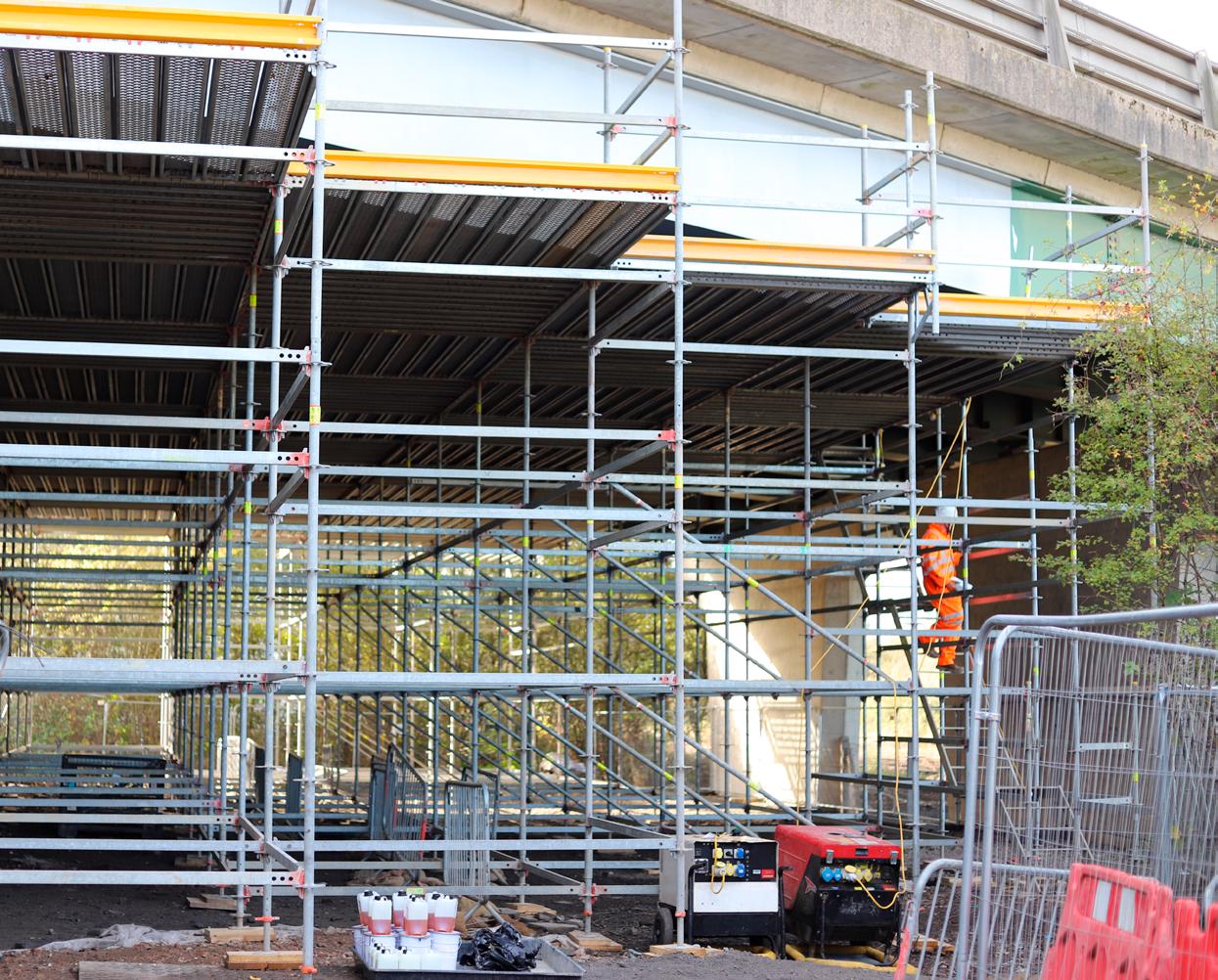
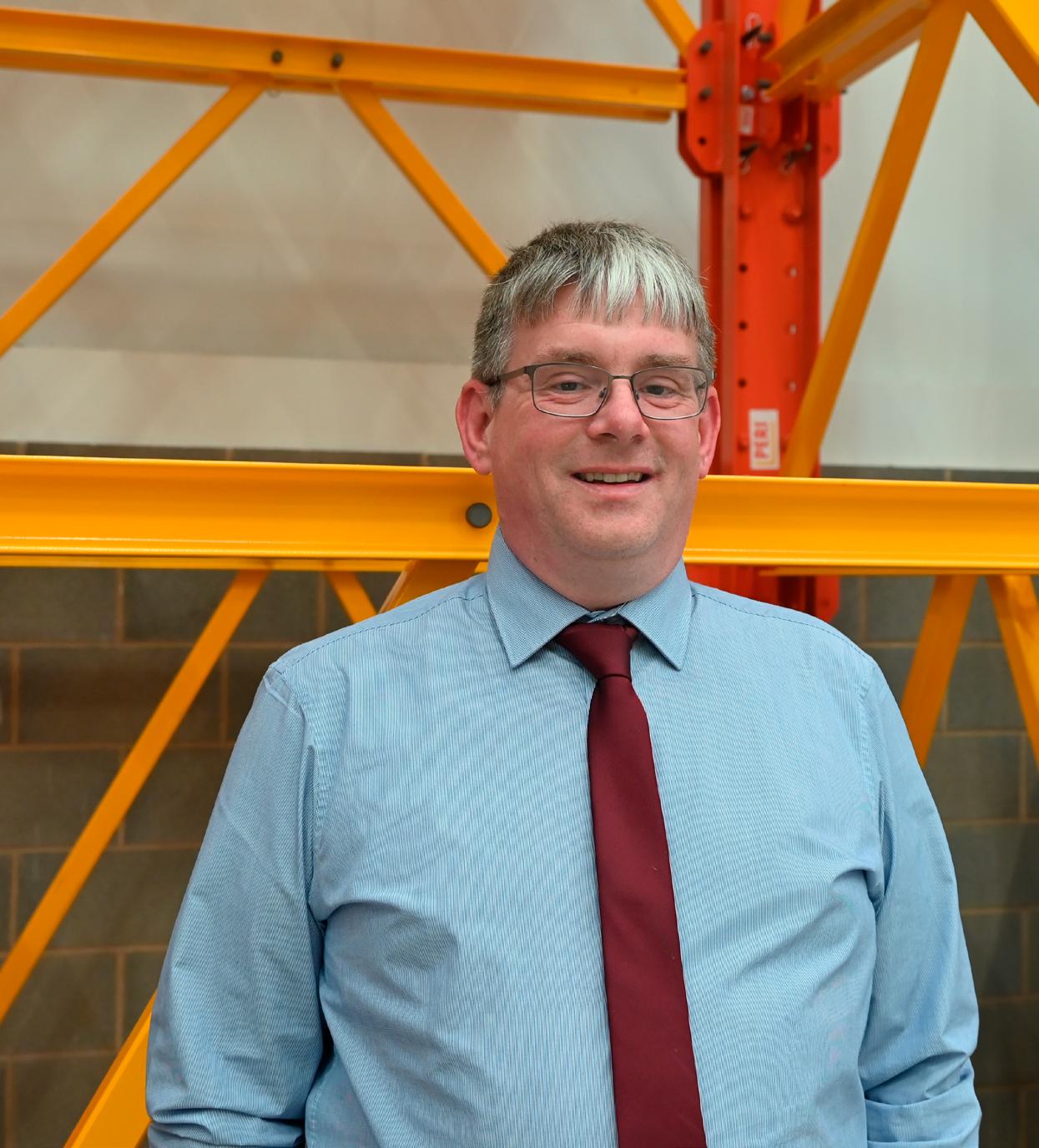

Welcome to the latest issue of PERIscope.
Inside this issue, you will find out how our VTC tunnel carriage helps to make tunnelling more efficient, proven by case studies of projects from around the world.
Alongside formwork, we’re also contributing to the success of infrastructure projects with our permanent stop end solution, BECOSTOP. On HS2’s Bromford Tunnel site, our solution significantly improved on-site efficiency when forming day joints, enabling full continuity of reinforcement and benefiting the programme time. It also contributed to cost savings for our customer compared to other systems by eliminating expensive fixing systems and providing a full temporary works solution using materials commonl y used on site.
We’re also supporting the demands of high-rise construction as concrete cores are progressing at pace with the utilisation of hydraulic climbing operations and safe and adaptable access solutions.
Although they may be considered supplementary, our construction accessories are essential to every project we undertake. From ensuring reinforcement continuity for stronger construction joints to using tie bars that secure formwork shutters high above ground, the importance of choosing genuine, reputable products over lower-quality alternatives should not be underestimated.
I’m pleased to share that our range of construction accessories continues to expand under the System Plus concept, with additional products guaranteed to add value to your projects. This year, we’ve introduced three new products as well as reviewing our existing portfolio to offer only the best quality and value for our customers.
In recent months, we’ve designed bespoke FERBOX units to provide reinforcement continuity on a high-rise project in Manchester, enabling our customer to make a 16% saving on materials. We also supported a mixed-use project in London with BECOSTOP, enabling a faster pour rate for the ground slab and saving valuable space on site.
Demonstrating how these products drive value across modern construction sites is important. Time, costs and efficiency are factors that influence many of the decisions we make. With our complimentary CPD sessions, we give our customers an insight into the benefits and proper application of the products within our construction accessories range.
We’ve delivered several exclusive lunch-and-learn sessions, with more scheduled over the coming months. It’s fantastic to see the positive impact these sessions are having on our customers and their success across the infrastructure, commercial, and resid ential sectors.
If you would like further information about our CPD sessions or want to arrange a lunch and learn for your team at your site, please get in touch with me at Neale.beardsley@peri.ltd.uk.
We hope you enjoy this issue.
Neale Beardsley UK Construction Accessories Manager PERI UK
Editor PERI Ltd.
Formwork
Scaffolding Engineering
Market Harborough Road
Clifton upon Dunsmore
Rugby CV23 0AN United Kingdom
Responsible PERI UK
Editor-in-chief
Jinal Kansara
Editing and graphics
Dekany Design
Photos Jessica Harding
Neil Terry Design & Print
Copyright
The photos used in this brochure feature certain situations at particular moments on various construction sites. Additional images, e.g. regarding safety and anchor details, cannot always be considered as conclusive or final. These are subject to the risk assessment carried out by the contractor.
© PERI GmbH
8
UK Construction Accessories Manager, Neale Beardsley, covers the importance of working with genuine highquality formwork components.
Michigan Avenue, Manchester
Some of the smallest components are often the most important, especially when it comes to formwork. One of these is the tie bar or form tie. Without threading tie bars through the formwork prior to concreting, there would be nothing to prevent the pressure and weight of the concrete from pushing the formwork apart. Despite its importance, the quality of these components is often overlooked.
Depending on the size and in particular the height of the finished structure, as well as the concrete’s consistency and rate of rise, there will be more bars, more closely spaced near the bottom of the pour, where the pressure will be at its highest. To cope with the calculated pressures, these bars are available in a range of diameters and safe working load limits, with those available from PERI including a 2x safety factor.
For those new to temporary works, tie bars and accompanying wing nuts may look like interchangeable components.
However, only tie bars and supplementary wing nuts, bolts, and other components designed to work together—such as those we specify—will provide the riskfree solution that every contractor seeks. Unfortunately, many of these types of components have become commoditised over time, making it easy to obtain parts that may not have been tested or that are incompatible because they come from different systems or suppliers.
The parts being used could be coming in from countries that don’t prioritise traceability. Additionally, there is no reassuring CE marking or similar, because these parts haven’t been manufactured to a harmonised standard. If the system fails, it becomes difficult to hold suppliers accountable or demand compensation.
Using non-traceable components can also harm the credibility and reputation of contractors, as clients may question the overall quality and safety of the project.
It has to be a responsible supplier and a reliable system, or else there’s zero traceability or accountability.
Not all components are the same, not all will do the same job and when specifying components to deliver a riskfree pour, buying the cheapest is rarely the best approach.
For use with PERI formwork, we specify DYWIDAG bars, due to their high-quality and enduring reliability, along with the appropriate DYWIDAG nuts, connectors, waler plates, bolts, etc.
Due to its extensive use, the name DYWIDAG has become synonymous with any version of the threaded tie bar and regardless of where this component is manufactured, many contractors do not recognise the difference – or the risks of mixing and matching components, branded or otherwise.
When the bar and the wing nuts holding it in place are specified to withstand 90kN of force during the pour, opting for cheaper, weaker alternatives that withstand only 70-75kN risks component failure, potentially leading to serious issues on site.
These cheap, de-rated wing nuts often fail and the sound of weak poorly fitting nuts slipping over threads will be familiar to any site worker.
The failure of even a single de-rated wing nut will immediately increase pressure on adjacent ties, causing the formwork to bulge or at worst, collapse.
This will have several consequences, the most important being the potential health and safety implications for every site operative and the public at ground level. When formwork buckles due to wing nut failure, any scaffolding in place could be damaged too, with serious consequences for any workers using it at the time.
In addition to compromising safety, this will also impact you financially. Whether you own or have rented the formwork, the costs to repair or replace any damaged equipment due to wing nut failure can be expensive. Disposing of or recycling any unusable concrete will further increase costs.
We recognise the need to reduce costs whenever possible on site, but making marginal savings by using cheaper, weaker equipment ties is not the right approach and will end up being more costly in the long run. The equipment ties we specify in our formwork designs are the gold standard. When it comes to project efficiency and site safety, these should be the only components used to retain high-quality formwork and concrete.
As we all know, rework isn’t just costly – it affects productivity too. Clean-up operations and repeating the process with new formwork and fresh concrete can significantly delay construction schedules—all of which you can prevent by choosing high-quality components.
The initial risk of not purchasing the correct system to the proper specification or of combining components from different systems is compounded when these individual components (such as bars, wing nuts, waler plates, etc.) are reused multiple times without checking for damage or wear and tear.
We specify equipment ties with big safety margins for a reason, but when cheaper, lower-quality rusty bars and wing nuts with little thread left in them, are used repeatedly on site, the potential for failure increases each time.
Hydraulic climbing systems are increasingly being adopted on sites outside London, as contractors respond to the rapid growth of mid- to high-rise construction projects further north and seek ways to accelerate programmes without depending on traditional crane operations.
One such project utilising hydraulic operations is Michigan Avenue in Manchester, where our RCS CL hydraulic climbing system is cycling formwork shutters and platforms on Tower 2.
All elements of the substructure and superstructure on the newest phase of the Media City development are being delivered by concrete frame contractor Heyrod Construction.
Heyrod’s use of our hydraulically powered RCS system played a critical role in forming the concrete core of the 35-storey tower, which houses three lift shafts, three smoke risers, a stairwell, and two lobbies across all levels.
A key challenge and the driver behind hydraulic operations on this site is the high demand for the tower crane, as it supports numerous construction activities simultaneously. By incorporating the RCS CL system, the site team were able to accelerate core construction ahead of the rest of the building. This allowed other elements of the supporting frame and permanent access to progress swiftly, leading to the timely handover of the lower floors and contributing to overall project efficiency, with the team now three days ahead of schedule.
By significantly reducing reliance on the tower crane, the project team has been able to reallocate crane operations to other essential tasks, allowing various activities to run concurrently.
For internal access to the live work areas within the core, Heyrod installed our PERI UP Flex Stair 75, a compact in-line stair tower. The site team praised the system for its easy installation and how well it adapted to the limited space inside the core.
Beyond formwork and scaffolding, we also collaborated closely with Heyrod Construction to address the challenge of achieving seamless continuity between concrete pours. PERI designed and supplied customised FERBOX continuity strips for the suspended reinforced concrete (RC) and post-tensioned (PT) slabs to align with the structural design provided by WSP. The careful design of the FERBOX units is vital for preventing water and concrete ingress, which can otherwise compromise the structural integrity and long-term performance of the building.
Stewart Burns
Assistant Project Manager
Heyrod Construction Ltd
“We have a well-established relationship with PERI, and in our opinion, they are the market leaders when it comes to formwork. Any opportunity to reduce hook time was always going to be a huge benefit for us and the programme. With hydraulic climbing, we have been able to progress the core at a faster rate and cycling the formwork has been a smoother process.”
Through early engagement with clients and main contractors, we are tackling tunnelling challenges, striving for carbon neutrality and automation by reducing human intervention across our solutions. Our design engineers combine custom and standard components to reduce programme times, material and labour costs and most importantly, deliver safer working environments for end users.
Much of the machinery and materials used in infrastructure projects are typically single-use, resulting in significant waste.
With sustainability increasingly becoming a focus across the construction industry as the UK races to reduce greenhouse gas emissions to net zero by 2050, minimising material waste at every opportunity is crucial.
The UK Green Building Council (UKGBC) reports that the built environment is directly responsible for 25% of the UK’s carbon emissions1 with the infrastructure sector contributing 6%. Construction work contributes to around 50 million tonnes of these emissions in addition to producing over 60% of waste in the UK. 2
Choosing the right temporary works when forming tunnels can help make
a difference, and the higher the degree of flexibility, the greater the chances of success. The VARIOKIT VTC tunnel carriage is a tunnel forming system made of standard, rentable components from our VARIOKIT Engineering Construction Kit.
With telescopic props, the same VTC carriage can be adjusted to suit changes in cross-section height, ensuring project continuity and preventing additional material requirements.
Bespoke carriage configurations can be created using the 125mm incremental grid of core components, precisely matching the specific diameter and shape requirements of each tunnel while minimising material usage. Once a project is complete, these core components can be dismantled and repurposed for new projects with different specifications.
During the construction of the Place de Martyrs Metro Station in Algeria, an international team of experts from PERI developed an adaptable VTC tunnel carriage designed to accommodate the station’s varying arch widths, ranging from 23 metres in the central section to 16.5 metres at the northern and southern ends. This innovative approach allowed both cross sections to be constructed cost-effectively, utilising the same components and formwork segments throughout.
1 UK Green Building Council (UKGBC), Net Zero Whole Life Carbon Roadmap Technical Report (November 2021)
2 Department for Environment, Food and Rural Affairs, UK statistics on waste (March 2020)
Automating aspects of a construction project to reduce human intervention is a significant advantage for contractors, as labour remains one of the highest costs on any site—a trend that shows no sign of slowing due to the ongoing skills shortage.
The VTC tunnel carriage can be powered entirely via hydraulics, from shuttering and striking the tunnel walls and soffits to repositioning the carriage, so no additional machinery is required.
Such hydraulic operations were integrated with the VTC carriage designed to shutter and strike the soffits and interior walls in tandem on the Werrington Grade Separation scheme in Cambridgeshire in the UK. The combination of the pour sequence and speed of the system contributed to shorter cycle times, ultimately saving 10 days per segment.
Throughout infrastructure projects, multiple operations occur simultaneously. Optimising space for site traffic – a prerequisite for mined tunnels, tunnelling machinery and material, as well as accommodating structural changes is vital but can be tricky logistically.
To construct the concrete elements of the Marieholm Tunnel in Sweden, PERI engineers engaged early in the planning phase, enabling them to collaborate with the client to develop a cost-effective, comprehensive solution. The design was an optimal combination of standard systems with project-specific formwork, ensuring efficient on-site operations.
The advantage of using the VARIOKIT solution was its high degree of flexibility combined with a low weight, which meant that the slab formwork carriage was relatively light, weighing around 75 tonnes. Thanks to the VTC’s modular design, the carriage could easily be divided longitudinally. This approach was highly beneficial for the final removal of the formwork, as the carriage was divided into six separate units, allowing for easy removal from the 18m-deep dry dock despite its spatial limitations.
Proactive repair work is underway to maintain the A180 Gilbey Road Bridge in North East Lincolnshire, helping to prevent the need for extensive repairs and potentially complete closure of the route in the future.
The work includes steel beam refurbishment and bearing replacement between the bridge deck and the piers and abutments – essential for transferring the dead load of the structure and live load from the traffic flowing above.
IE Access was appointed to deliver full temporary access to the underside of the bridge to enable the repair work. The scaffolding and access contractor chose to use our PERI UP Flex system across all five spans. For one of the spans, the team had to accommodate a river and a public walkway. This required an access solution that was highly adaptable while minimising the number of components to ensure a safer and more efficient working environment.
With the river, walkway, and bridge each running in a different direction,
careful coordination in the pre-planning phase was essential. Close collaboration between VSL’s temporary works team, IE Access, and our project team ensured the proposed scaffolding solution was both efficient and well-integrated with the site’s unique layout.
Speed and efficiency were key drivers in selecting PERI UP Flex for this project, especially when considering the obstacles on site. Once the scaffolding had been based out on the railway sleepers, it was easy to adjust and align the system with the river’s course — stepping it in and out as needed.
Another requirement during the project was to maintain public access under the bridge, which was achieved by creating a tunnel structure with PERI UP, protecting pedestrians from the repair work above.
The system’s standardised, wide bay sizes and minimal components eliminated the safety risks associated with traditional scaffolding when working in proximity to the public, such as smaller components and fixings potentially falling from the scaffold during installation. In addition to safer working, PERI UP also accelerated the build as fewer components reduced fastening operations and manual handling between scaffolders.
Adaptability was crucial even after the structure was erected, as IE Access had to make adjustments to meet VSL’s revised leg load requirements on the pavement. The PERI UP system demonstrated the flexibility of our modular scaffolding, allowing for quick and easy adaptions to the existing birdcage structure.
Charlie Wheeler Managing Director – IE Access
“Minimal standard components from the PERI UP range made work easier for our scaffolders. We didn’t have to manage numerous small parts and fittings or worry about safety while working above the public walkway. It also minimised material handling during construction.”
The scaffolding enclosure system that’s been shortlisted for an NASC award
PERI UP Cladding is the latest system in our scaffolding range. The enclosure system is designed to offer protection to scaffolders, building contractors and the public while work is being carried out on PERI UP scaffolds across façade and industrial projects. It combines all the benefits of existing enclosure systems with superior functionality, making it the ultimate safety enclosure system on the market.
For scaffolders, our product addresses the top ten needs for customer satisfaction, which ranges from environmental protection to one standard panel that is built for purpose. The system provides an additional safety barrier to prevent the risk of falls, which is crucial when working at height.
How does it differ from existing systems?
Our system features overlapping cladding elements which ensures no gap is left uncovered. PERI UP Cladding also offers scaffolders protection from inclement weather, enabling them to continue working in the event of severe wind, rain and snow conditions. Although sealed off from external elements, the translucent panels allow natural light to flood in, reducing the need for electricity during daylight hours.
PERI UP Cladding’s sustainable credentials are even greater when considering the system’s versatility and use for various applications. In addition to using the panels as a protection system, our customers have maximised the
system’s potential by utilising panels for temporary roofing structures or hoarding around building sites.
We’re thrilled that it’s been shortlisted for the NASC Product of the Year award. We’re also excited to exhibit at Scaffex24, where we’ll have the chance to connect with industry professionals and, of course, find out if we’ve won!
It’s been one year since we installed photovoltaic (PV) panels across our sites in Rugby, Glasgow and Brentwood and we’re pleased with the results so far. By the end of the first full year in operation, we generated a total of 742 MWh (megawatt-hours) of energy, demonstrating the impact of solar technology in meeting today’s sustainability requirements.
Since our 1-year milestone, our energy production figures have surpassed 1,000 MWh, equivalent to 1 gigawatt of energy.
Environmental Impact
We’ve also seen the positive impact our efforts are having on the environment, as we’ve successfully reduced our carbon dioxide (CO₂) emissions by 200,000 kg
The bespoke continuity system
FERBOX is a reinforcement continuity system, designed to maintain structural continuity across construction joints in reinforced concrete structures.
Available in standard and bespoke sizes. Get in touch at ukconstructionaccessories@peri.ltd.uk
Save 70% on your next training course with us!
We’re part of CITB’s Employer Networks initiative, which will fund 70% of any training course you sign up for with us.
1 gigawatt = 350 Houses
200,000 kg CO 2 = 12,000 Trees
Terry Hall | Field Services Manager, PERI UK
“We are on a mission to make formwork training compulsory across the construction industry. Joining forces with CITB and being part of the Employer Networks initiative widens our reach and will enable us to demonstrate the importance of proper, regulated training to more contractors. We hope to see more employers in the industry at our Brentwood training facility as they make the most of the funding offered by CITB.”
“The site engineer wanted to make adjustments to the leg loads on the pavement after the scaffolding was installed. Thanks to the flexibility of the PERI UP system, we were able to modify the structure with ease.”
Charlie Wheeler | Managing Director – IE Access
PERI UP Flex for
versatility