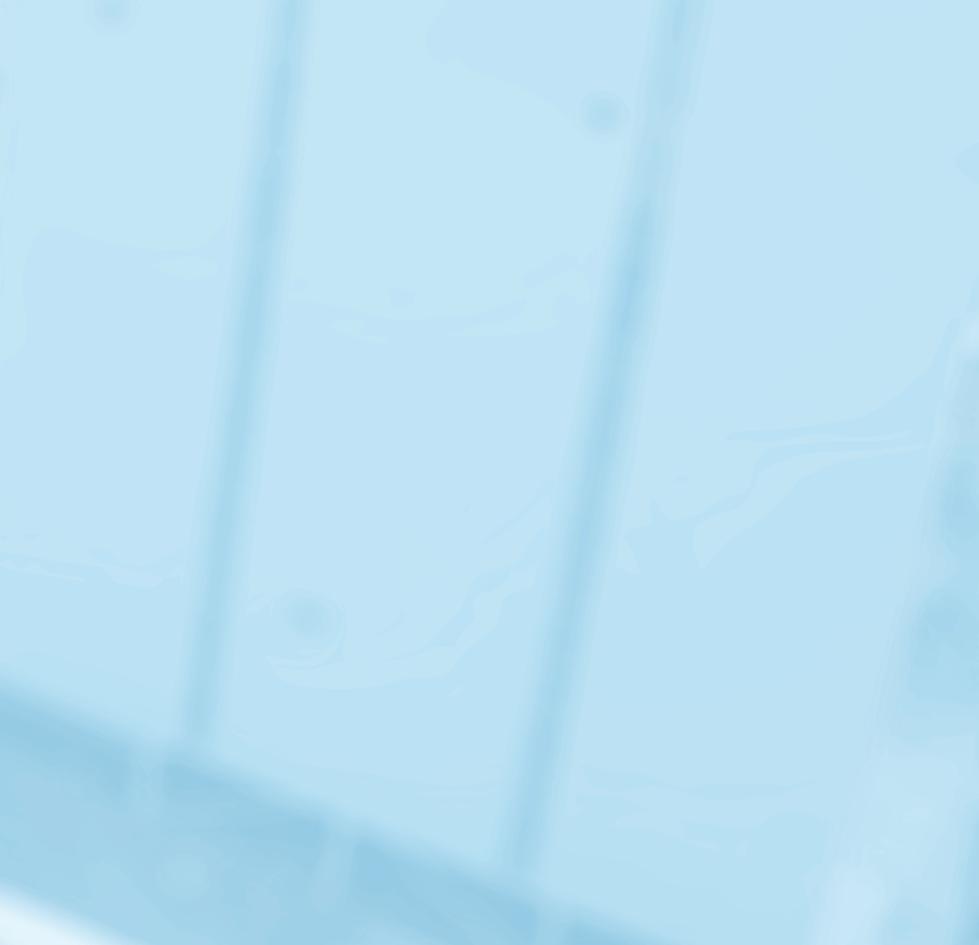
12 minute read
Fast. Fair. Flexible.
Focus on precision: InterSep
InterSep enables you to separate a wide variety of raw materials in a highly energy-efficient manner, while remaining flexible and compact. With the upgrade of the new high-performance separator of the latest generation, InterCem has the right product for every specific application. A low bypass rate ensures the highest possible separation efficiency. Whether as a single component or in a complete plant.
Contact us: InterCem professionals will also find the right solution for your requirement.
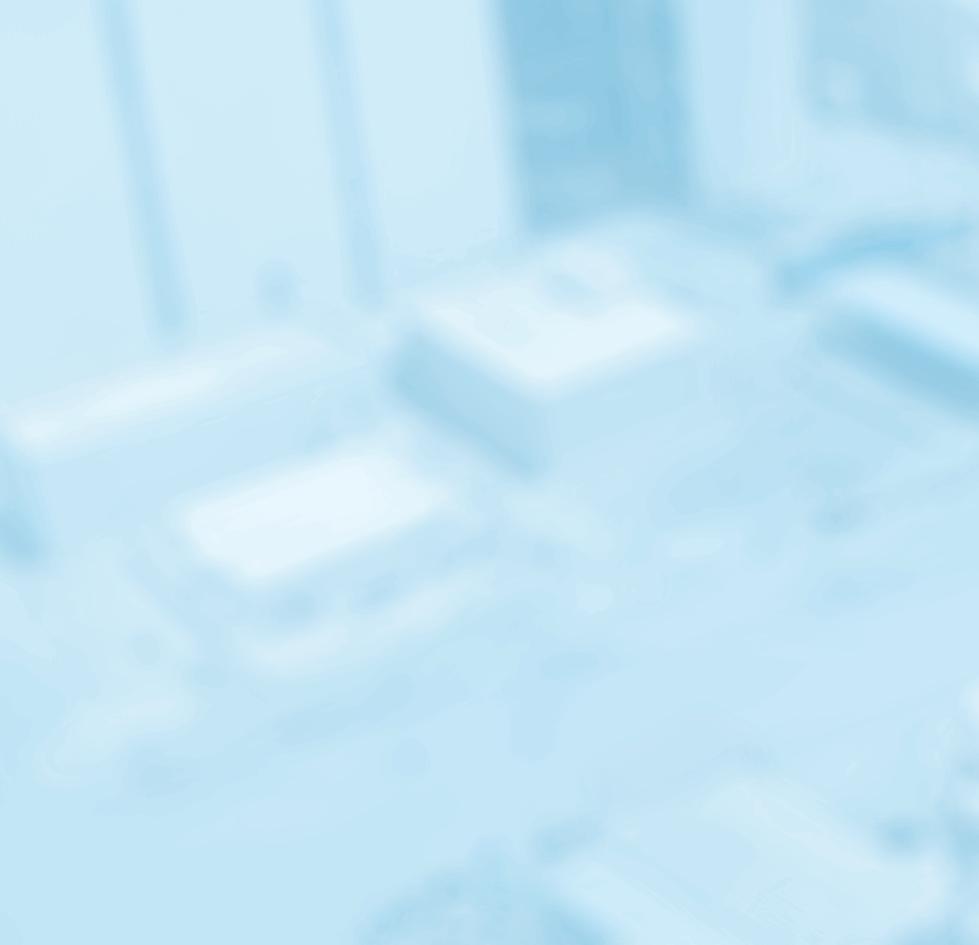
BLENDSCAN Advantages
Increased profits
Max Tschurtschenthaler, ABB, and Joonas Rauramo, Coolbrook, discuss how a pioneering project aimed at replacing fossil fuels with renewable electricity has the potential to slash carbon emissions from cement production and help meet customer demand for CO2-free products.
The global cement sector, like so many other energy-intensive industries that produce materials vital to modern life, finds itself at a crossroads. On the one hand, the production of cement, the second-most consumed material in the world after water, is expected to increase worldwide through the mid-century. 1
On the other hand, the industry is responsible for 7 – 8% of global carbon dioxide (CO 2) emissions, 2 even more than aviation. Cement production is notoriously difficult to decarbonise due to the high temperatures required in the kiln and the emissions produced by the calcination of limestone. According to the International Energy Agency (IEA), the direct CO 2 intensity of cement production increased by about 1.5% per year in 2015 – 21; 3% annual declines to 2030 are required to meet the IEA’s ‘Net Zero Emissions by 2050 Scenario’. 3
Solutions such as reducing the clinker-to-cement ratio (by including a greater uptake of blended cements) and deploying innovative technologies such as electric kilns, carbon capture and storage (CCS), and clinker made from alternative raw materials, must therefore be more of a priority, says the IEA.
A new technology
Now for the good news.
First, throughout the industry, ABB sees that more and more companies are focusing investment on reducing emissions to protect their licence to operate. At the recent COP27 climate conference in Egypt, concrete and cement producers joined the First Movers Coalition, a collection of 50+ companies committed to decarbonising seven highly polluting industrial sectors. These first movers pledged to purchase at least 10% near zero carbon cement and concrete by 2030. 4
Second is technology innovation, specifically a joint project involving ABB and the Finnish company Coolbrook to advance technology that helps decarbonise the chemicals, cement, and steel industries, which are collectively responsible for 70%, or six billion tpy, of industrial CO 2 emissions. 5
The solution combines Coolbrook’s RotoDynamic technology (which replaces fossil fuels with renewable electricity), with ABB’s motors, power electronics, and process automation for optimised energy efficiency and operational processes.
By developing and scaling up RotoDynamic technology for use in emission-heavy industries such as cement manufacture, Coolbrook and ABB aim to cut carbon emissions annually by up to 2.4 billion t. 6
Achieving higher temperatures using electrification
During cement production, the chemical process, whereby limestone is heated and combined with various components to produce clinker, 7 is responsible for around 60% of CO 2 emissions, while the remainder (around 40%) is released during the combustion of fuels to activate the chemical process.
At present, heavy industry uses polluting fossil fuels for this process because electric heaters are not capable of heating gases to the extremely high temperatures required – up to 1700˚C. In traditional electric heaters, the electric current is directed through resistive material to produce heat, which limits the achievable temperature to 500 – 600˚C.
Coolbrook’s RotoDynamic Heater (RDH) has the potential to reach temperature levels of 1700˚C without burning fossil fuels, enabling it to replace fossil-fired furnaces and kilns with electric heating during the production of cement, steel, iron, and chemicals. The key differentiator here is that the RDH solution is essentially a turbo machine that increases the temperature internally within the gas. The gas is first heated to supersonic velocity and then slowed down very quickly in a diffuser, which converts electric energy to kinetic energy, and then the kinetic energy to thermal energy. By performing this acceleration/deceleration process multiple times, it is possible to achieve significantly higher temperatures compared with existing electric heater solutions.
Unlike existing electric heating technologies, the RDH is a turbo machine, meaning it is compact and can be retrofitted easily in almost any type of brownfield industrial processing facility, including cement plants, where it can be used in multiple applications, such as the pre-heating of feedstocks and heat provision to the pre-calciner, where the majority of the fuel is used. Ultimately, the aim is to replace the burner in the main kiln with the electrification unit, where temperatures reach in excess of 1700˚C.
Energy efficiency and emissions
The efficiency of the electricity to heat process in the RDH unit is extremely high – as much as 95% – which minimises the energy lost from excess heat generation. The other benefit, of course, is that there is no combustion, meaning the factory does not have to burn any fuel, thus reducing or even eliminating sulfur oxide, nitrogen oxide, and particle emissions from the manufacturing process.
As mentioned earlier, the majority of emissions from cement production, around 60%, come from the chemical process, whereby the limestone is split into calcium oxide and CO 2. Burning fuels typically involves having a high amount of nitrogen in the flue gas and a relatively low CO 2 content, which – in terms of decarbonising the entire system – makes it more difficult to capture the CO 2. With electrification it is possible to increase the share of CO 2 in the flue gas, making it easier to capture in the long term, and so not only directly reduces CO 2 emissions by as much as 40% but also makes it easier to eliminate the remaining 60% from chemical reactions.
As also touched upon at the outset, reducing the carbon footprint of hard-to-abate sectors like cement not only requires investment in specific technologies but also the need to look at decarbonisation from a wider perspective, including the integration of clean energy into emissions-heavy processes.
Coolbrook’s RDH solution, for example, generates heat using renewable energy, which typically means domestic energy sources. Not having to import fuels is an increasingly important consideration in many countries and industries, bypassing supply chain and logistics issues, and reducing OPEX.
Recent research by KPMG estimates that the potential reduction in emissions offered Coolbrook’s Rotodynamic Heater and Rotodynamic Reactor technologies (in both cement and other key industries) is more than two billion t of CO 2 annually, equivalent to around 7% of manmade CO 2 emissions, or roughly 30% of all industrial CO 2 emissions. The target of the RDH project is therefore to help replace the combustion of industrial fossil fuels on a global scale.
Testing of the RDH technology began at Coolbrook’s pilot facility in the Netherlands in December 2022, and is ongoing, with the immediate aim of demonstrating the current rotating unit’s ability to heat air to 1000˚C.
Motors, drives, and asset performance management
The RDH solution is based on Coolbrook’s RotoDynamic technology, which uses electrification powered by renewable energy to eliminate 100% of the CO 2 emissions created in the steam cracking process, the first and most polluting step in the production of plastic.
In January 2022, ABB and Coolbrook signed a memorandum of understanding (MoU) to advance the development and scaling-up of the RDH technology. The standardised and modular solution covers the RDH package, electric motor and drive, automation, safety, power distribution, instrumentation and analysers, condition monitoring, and full digitalisation, offering chemical producers multiple benefits, including increased operational yields, lower OPEX, easier maintenance, and reduced capital costs. 8
It quickly became clear that the RotoDynamic technology also offered potential for decarbonising cement industry processes. The RDH solution also benefits from an industrial-scale electric motor and variable speed drives to run the rotating component, as well as ABB’s automation, electrification, and digitalisation solutions for preventative maintenance, monitoring, control, and plant integration.
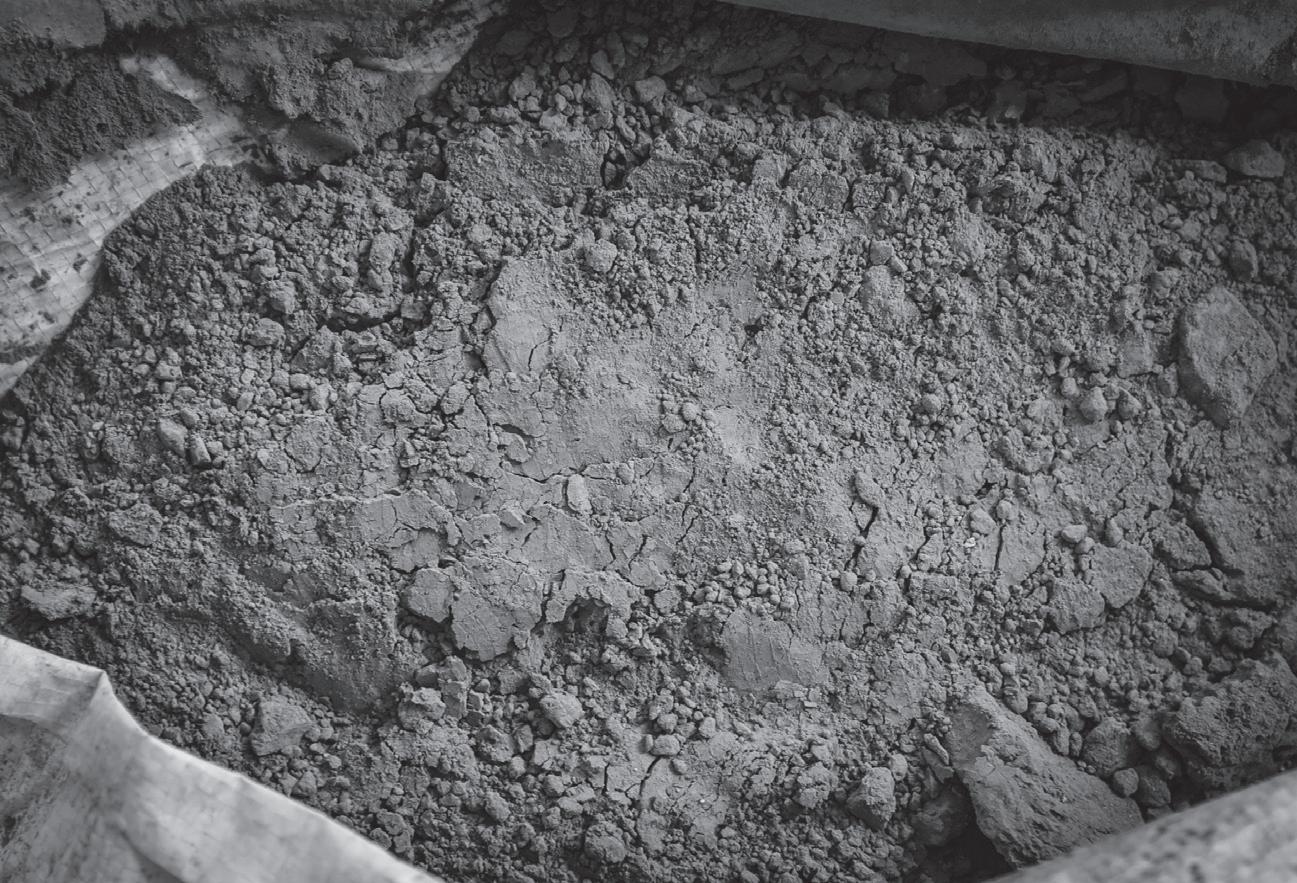
The RDH is a type of turbine; the quicker it runs, the more heat it generates. It is critical therefore that the speed is controlled so that the temperature remains stable throughout the entire cement production process. For this, ABB is supplying variable speed drives, as well as motors that can be adapted to the size and application of each RDH unit, in addition to a control system that can be seamlessly integrated into that of the existing cement plant and provide advanced data analytics.
Preventing unscheduled downtime using asset performance management tools is also of major importance to optimise production and quality control. ABB’s motor and drive solutions for the RDH are connected to monitoring equipment that continually assesses their performance and alerts the operator to potential failures, facilitating predictive maintenance and maximising asset life.
Not costing the Earth
COP27 saw a significant shift within the heavy industries, and the cement sector in particular, to prioritise investment in decarbonisation solutions that reduce their environmental footprint and future-proof operations. In many countries – India, for example, where there is already interest in the ABB/Coolbrook RDH solution – ABB are also seeing a push to develop domestic wind, solar, and hydropower capacity with the aims of reducing reliance on fossil fuels and promoting energy independence.
This forward-looking strategy prioritises long-term reductions in CO 2 emissions over short-term cost savings; in other words, ABB believes that customers are willing to pay an initial premium for electrification solutions that satisfy environmental targets and customer demand for CO 2-free products.
The construction industry is the perfect example of this. Concrete constitutes only a fraction of the overall cost of the building; however, the overall carbon footprint of that building is much more important. A recent study revealed that even if cement became 70% more expensive, say, the price of a building would only increase by about 3%, which is nothing compared with the cost of a failure to comply with environmental regulations and protecting both construction and cement companies’ operating licences.
In conclusion, pre-engineered and pre-fabricated electrification technologies such as the one being pioneered by ABB and
Coolbrook constitute a potential step change in the decarbonisation of heavy industries, replacing the burning of polluting fossil fuels with renewable electricity for the cleaner, safer, and more efficient production of essential materials such as concrete, and enabling manufacturers to hit emissions targets, protect their licence to operate, and meet increased customer demand for ‘green’ cement.
References
1. ‘Concrete is Worse for the Environment Than Flying. Why Aren’t More People Talking About It?’, Inside Climate news, 2022 – https://insideclimatenews. org/todaysclimate/concrete-is-worse-for-the-climatethan-flying-why-arent-more-people-talking-about-it.
2. ‘Cement makers across world pledge large cut in emissions by 2030’, The Guardian, 2021 – https://www. theguardian.com/business/2021/ oct/12/cement-makers-acrossworld-pledge-large-cut-inemissions-by-2030-co2-netzero-2050#:~:text=The%20 industry%20is%20 responsible%20for,and%20 concrete%20release%20CO2.
3. ‘Cement’, International Energy Agency, 2022 – https:// www.iea.org/reports/cement.
4. ‘First Movers Coalition backs deal for low-carbon concrete and cement at COP27’, World Economic Forum, 2022 – https://www.weforum.org/ agenda/2022/11/first-moverscoalition-cop27-concretecemenet-industry.
5, 6. ‘Coolbrook and ABB expand partnership with investment to accelerate decarbonisation of heavy industries’, ABB, 2022 – https:// new.abb.com/news/detail/96352/ coolbrook-and-abb-expandpartnership-with-investment-toaccelerate-decarbonization-ofheavy-industries.
7. ‘Best ways to cut carbon emissions from the cement industry explored’, Imperial College London, 2021 – https://www. imperial.ac.uk/news/221654/ best-ways-carbon-emissions-fromcement/
8. ‘ABB and Coolbrook collaborate to reduce emissions in petrochemical market’, Coolbrook, 2022 – https://coolbrook.com/ news/2022/coolbrook-abb
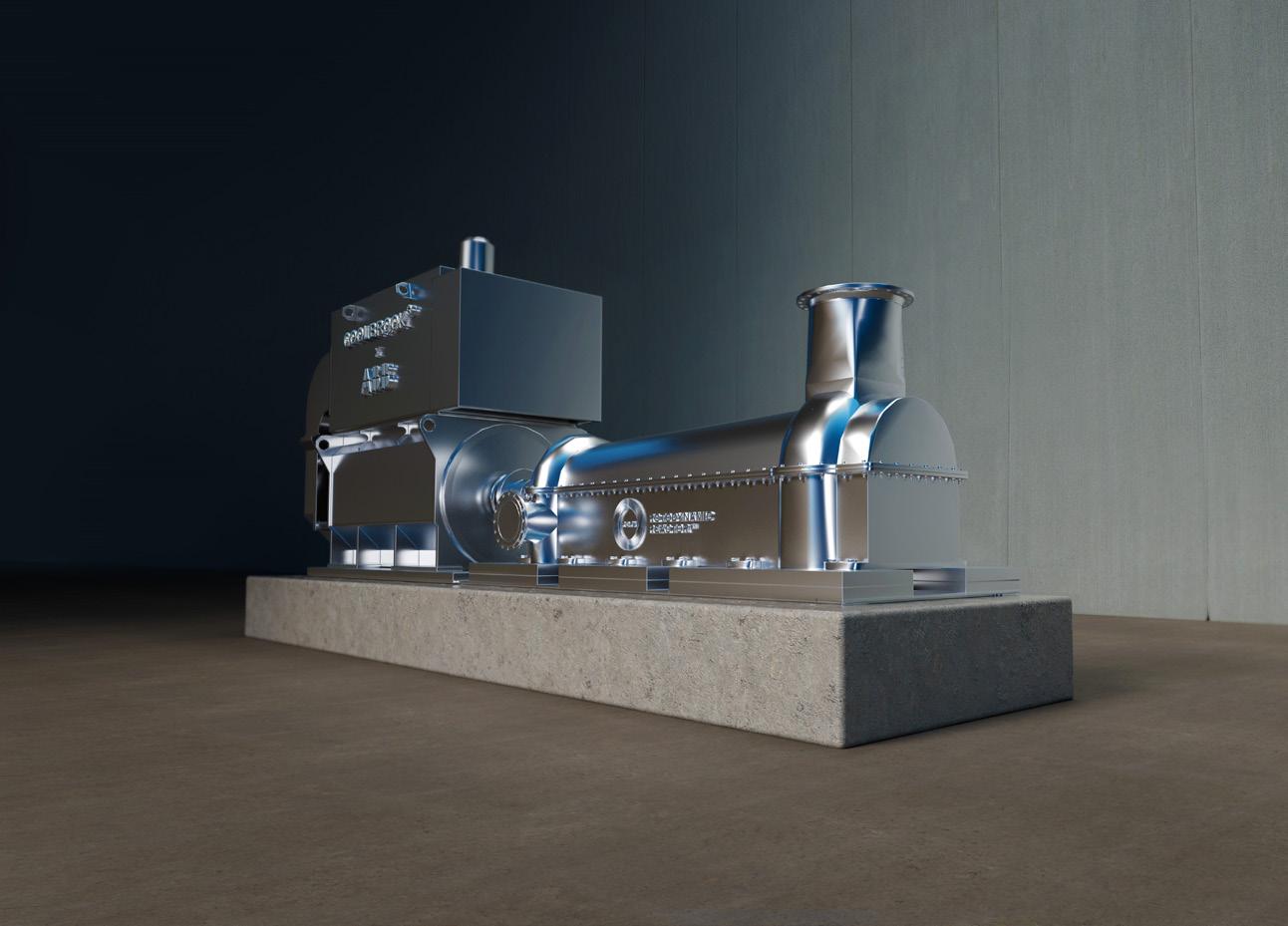

Carmen Kaiser Brügmann, Rigaku, discusses the process of determining
Customer support in the cement industry is very important. When civil engineers make concrete, it is imperative from the perspective of quality that they get the support on the mix design and the final concrete that is produced.
Investigating the finished product is also necessary if there is a customer query on the quality of the concrete made onsite. The concrete made onsite must also be validated for the mix design used.
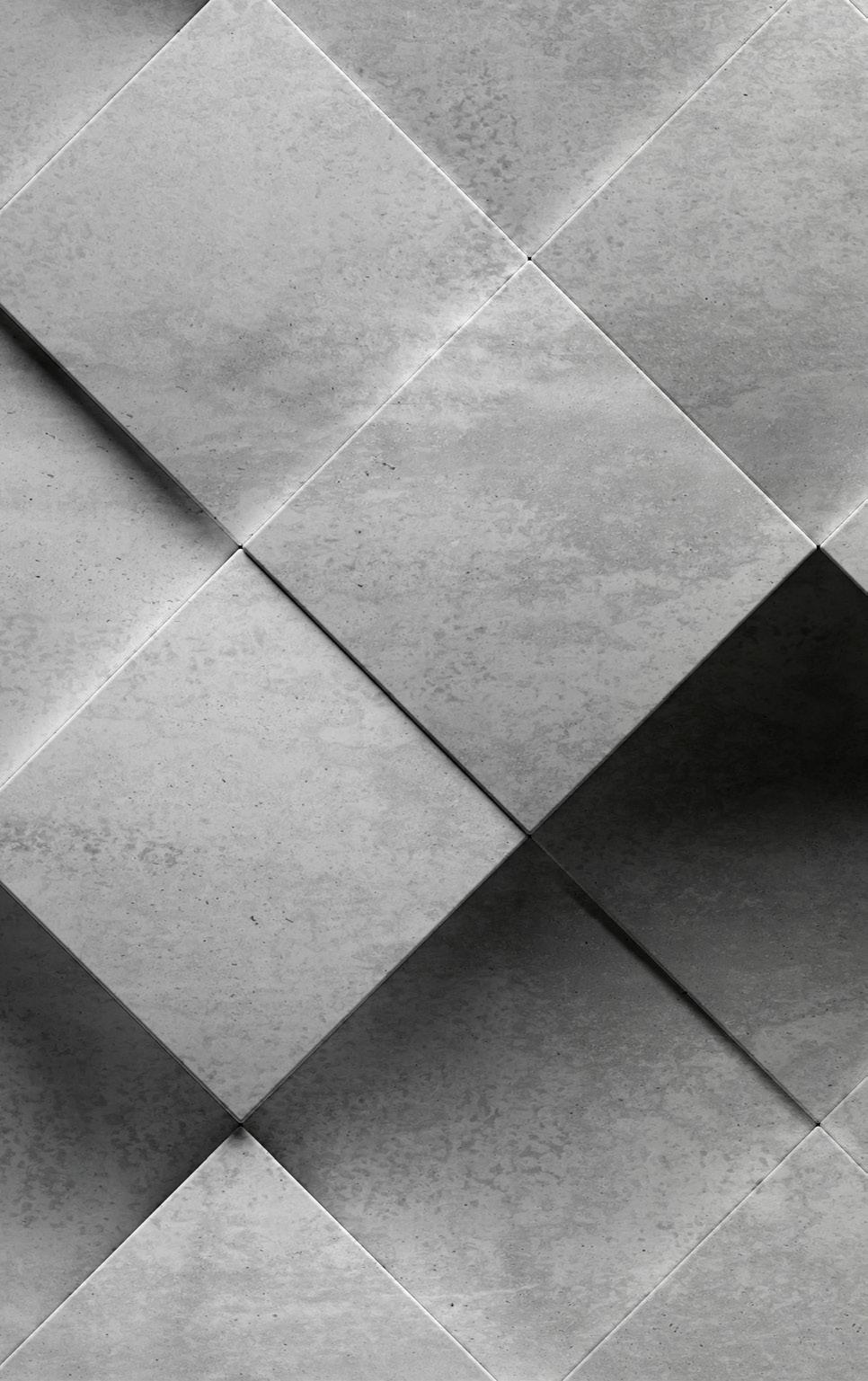
The method presented in this article resolves a complex mixture into its constituents. It is well suited to the examination of concrete products and blends of cement and materials such as slags, fly ashes, and pozzolana. The solution requires the use of a software program called Original Multiple Mix Resolution, which solves simultaneous equations.

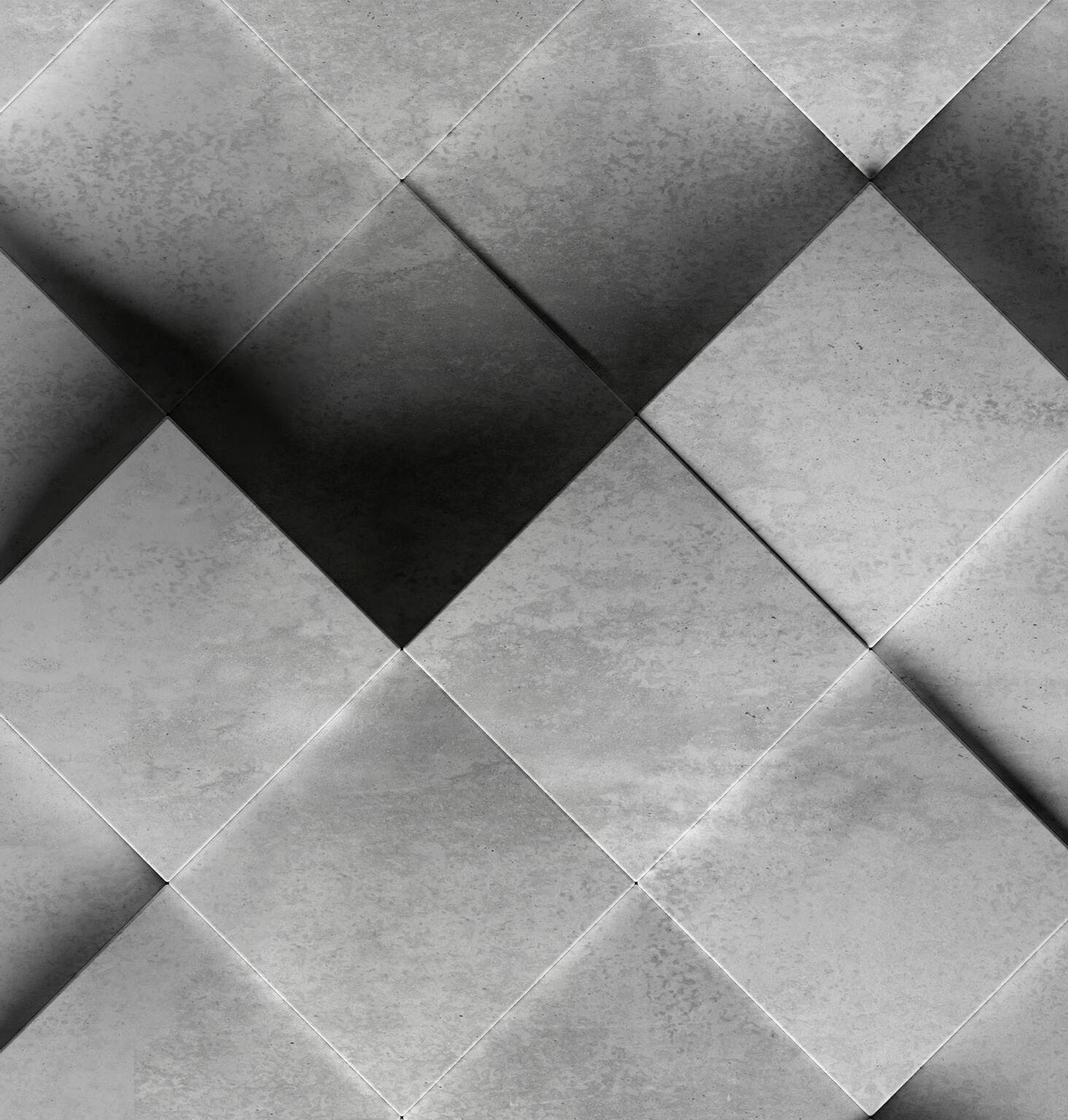
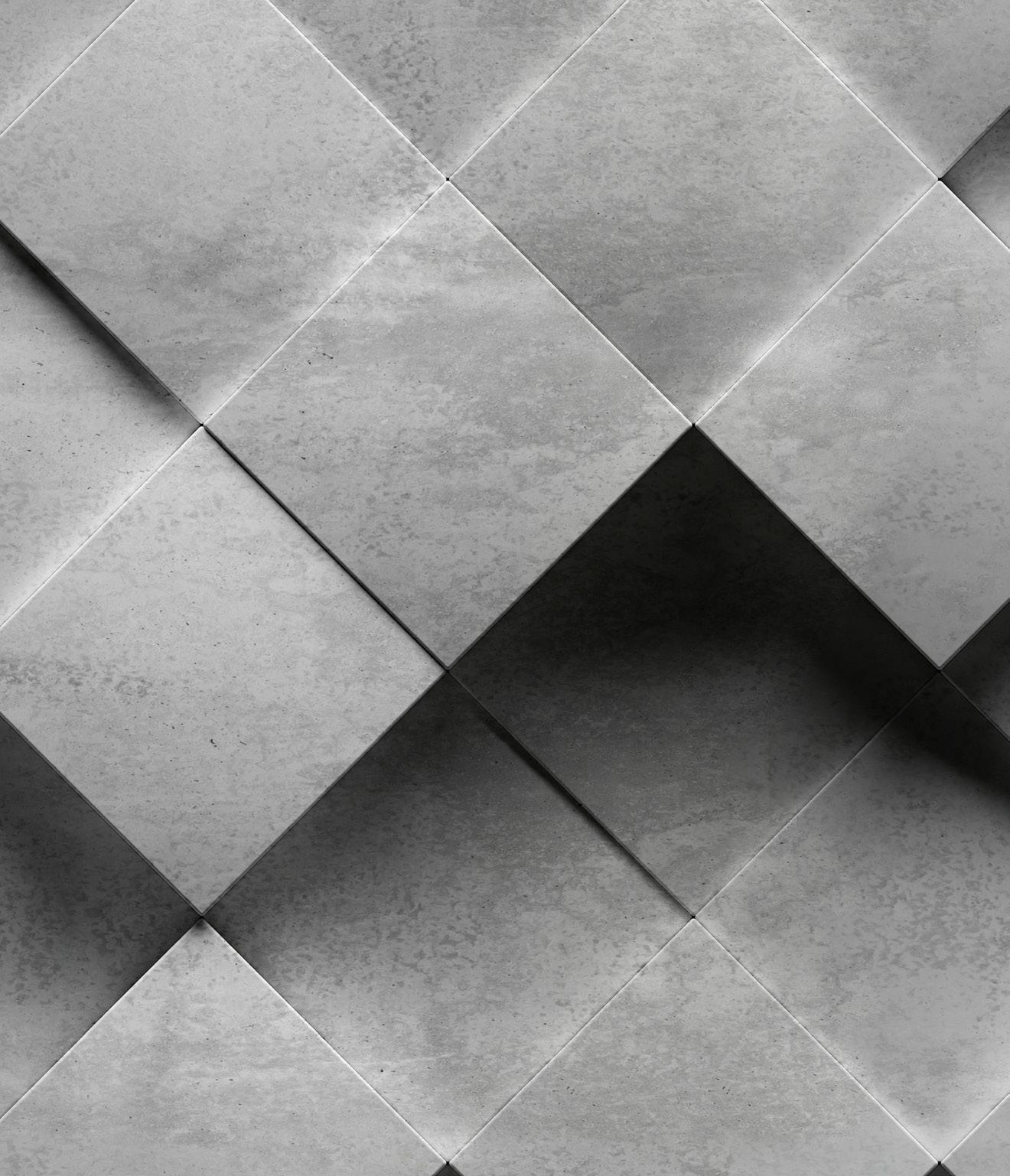
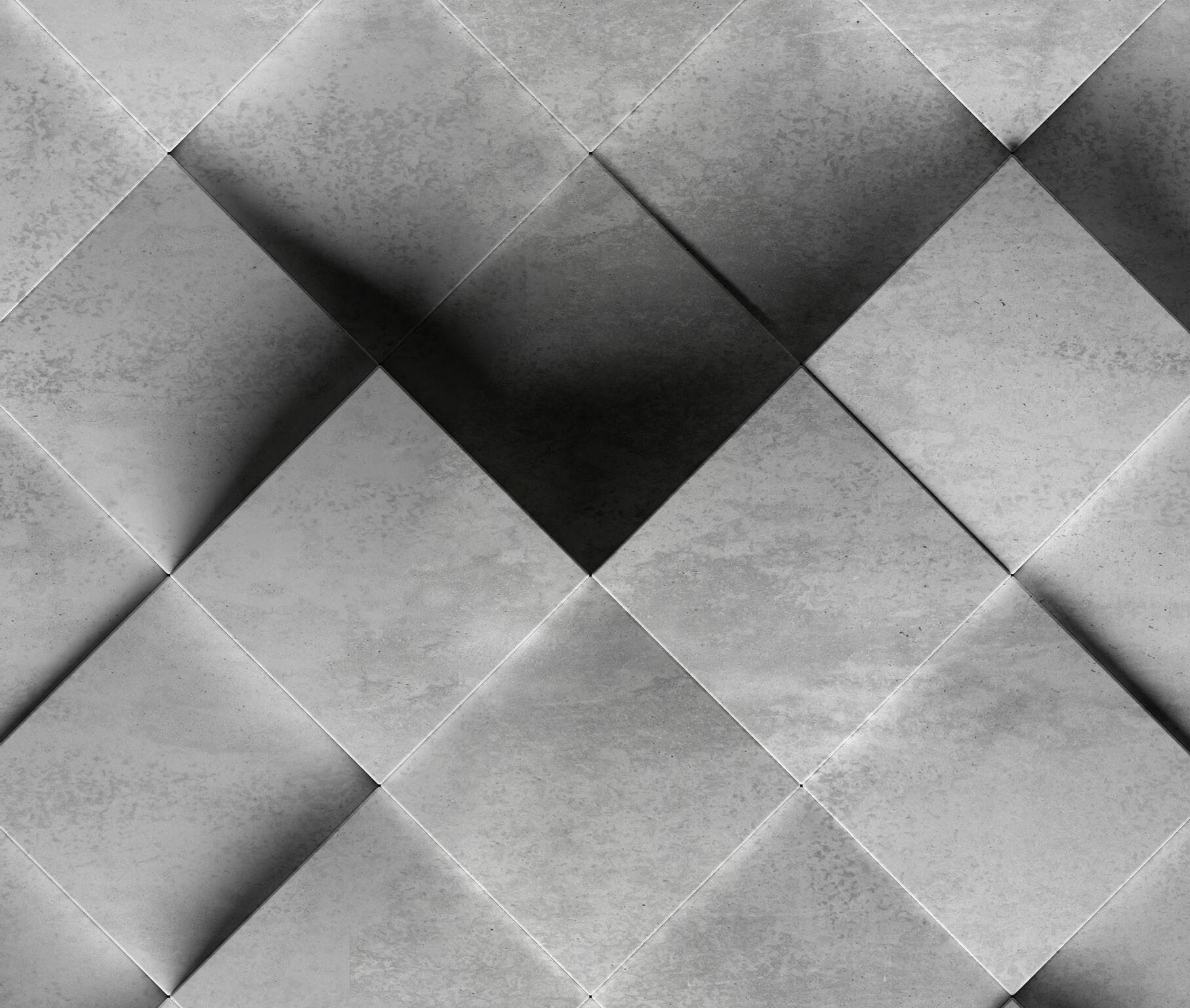
The method requires high-quality analysis of all the constituents and for the constituents. Superior solutions are derived by the selection of a smaller analyte set. The chemist in the laboratory is aided by a verification option in the program as to which analytes will give the best solution. Analysis of the constituents and mix is obtained by the XRF fusion method. The calibration method on the ZSX Primus IV was set up using Certified Reference Standards with a suitable range of the 12 oxides.

Introduction
Quality is an imperative and integral part of the production of durable and sustainable concrete. Quality Assurance (QA) is the activity of providing the evidence needed to establish confidence that quality-related activities are being performed effectively. Planned or systematic actions are necessary to provide adequate confidence that a product or service will satisfy given requirements for quality. QA consists of the steps taken to assure the quality of the laboratory output.
For an analytical result to be fit for its intended purpose, it must be sufficiently reliable that any decision based on it can be taken with confidence. Thus, the performance of the method must be validated and the uncertainty of the result, at a given level of confidence, estimated. Uncertainty should be evaluated and quoted in a way that is widely recognised, internally consistent, and easy to interpret. Most of the information required to evaluate uncertainty can be obtained during the validation of the method.
Instrument
The ZSX Primus IV wavelength dispersive X-ray fluorescence (WDXRF) spectrometer, with tube-above configuration (a safe solution for powder samples), is a floor-standing spectrometer, which has the advantage of a high spectral resolution and high sensitivity for light elements. The instrument is designed to provide reliable analysis results and its flexibility provides multipurpose availability to a wide range of applications. It has an elemental range from beryllium (Be) to curium (Cm).
Configuration summary f 4 kW Rh tube with 30 µm Be window. f Tube-above geometry. f Dual-detector configuration with scintillation counter (SC) and proportional counter (PC). f 48-position sample changer. f 10-position analysing crystal changer standard (LiF200, RX26, GeH, and PETH). f 5 diaphragms. f 5 primary beam filters (Ni400, Ni40, Al125, Al25 and Be30). f 3 collimation slits (S2, S4, S8).
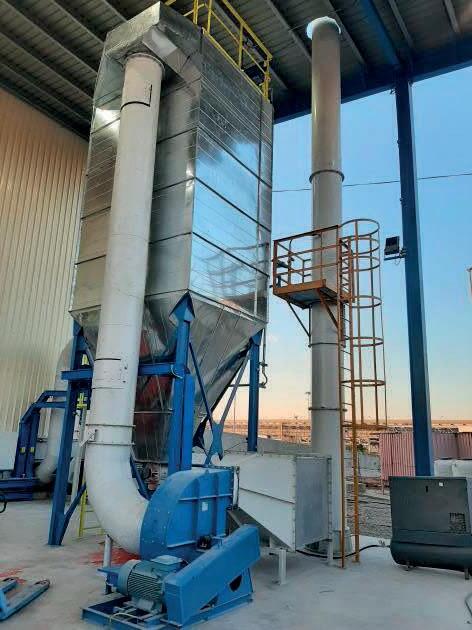
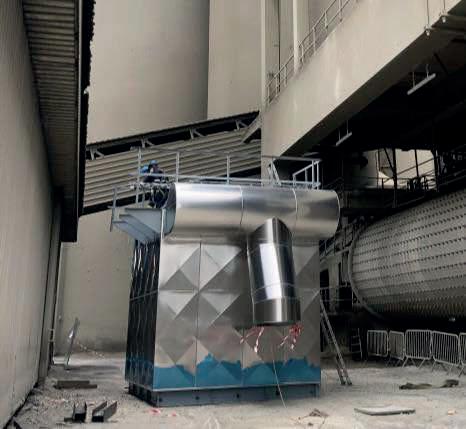
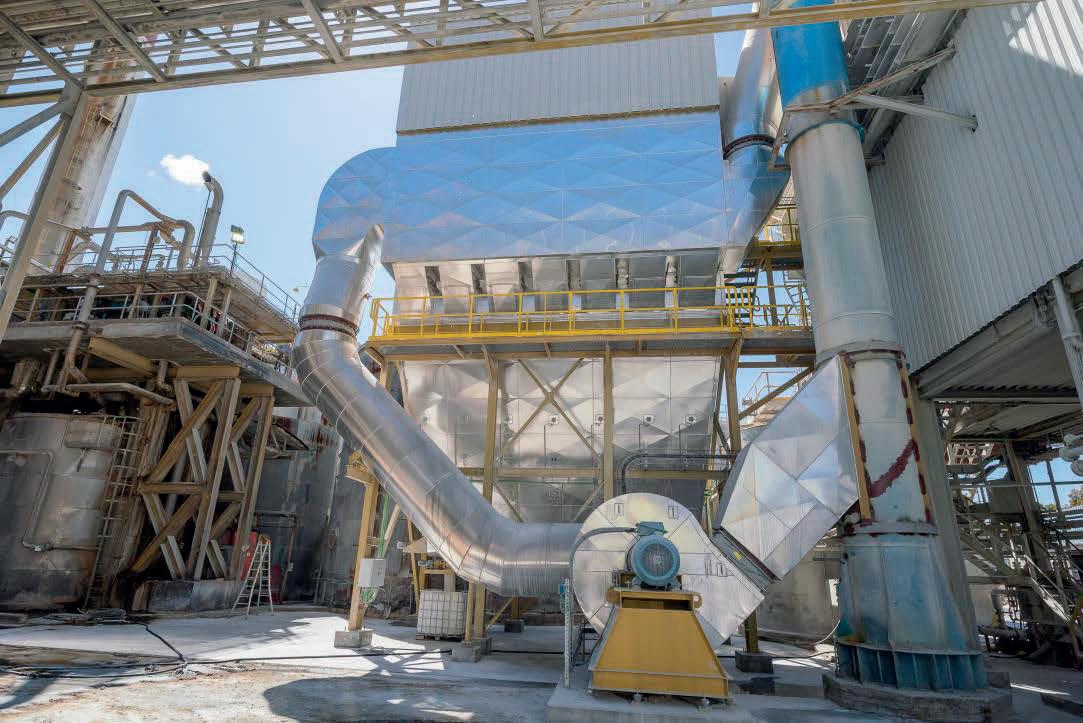
Features and benefits f The thin (30 µm) Be window on the X-ray tube results in a 40% increase in intensity, which is especially beneficial for light element detection, resulting in lower limit of detection. f High sensitivity enables short measurement times and low detection limits. f The tube-above system ensures the long-term usage of the X-ray tube. With no dust on the thin Be window, the loss of intensity is reduced, thus offering enhanced reliability and durability. Accidental contamination of the goniometer or inadvertent damage to the X-ray tube is minimised. f Automatic central wire cleaning mechanism, controlled by users via software, results in reduced service costs, improved resolution on the F-PC detector, and better light element detection with less variation. f Dual-vacuum system is safe and fast, and results in higher sample throughput. f Various algorithm correction models are available, which provides automatic overlap correction without the need for additional standards. f Automatic quantitative method setup, with all measuring conditions chosen based on the elements, concentration range, and sample type. f Built-in expertise – method development made fast and easy.
Method
It is important to ensure that the sampling quality matches that of the analysis. Onsite, mix materials are notoriously inhomogeneous and care must be taken to ensure that a sufficiently large sample is taken to minimise these effects.
Treatment of the concrete cubes or cores f When concrete cubes or cores are received, a photo must be taken of the cubes/cores on a white background. f The cubes/cores are then cut into four pieces and opposite sides are taken for the chemical analysis. f The other opposite sides are taken for physical separation. f The different sides are photographed again using a white background. f The sides for chemical analysis are dried as per the material type and prepared as per the massive sample reduction, splitting, pulverisation, and fine milling. This will ensure a representative sample is obtained for the XRF fusion of the materials.
Physical separation
f The cube/core for physical separation is dried at 110˚C overnight.
f The sample is cooled and weighed.
f The sample is then placed in a cold furnace and the temperature is slowly raised to 600˚C. The sample is kept at this temperature overnight.
f The sample is then removed carefully and submerged in a bath of cold water. A hammer is used to break up the concrete.
f The stones (13 and 26 mm) are then physically separated and cleaned using the hammer.
f The stones are screened to separate the 13 mm and the 26 mm stones.
f The stones are dried at 110˚C overnight, then cooled and weighed.
f The stones are expressed as a percentage of the total concrete cube.
f The stones are used in the calculation of the components.
Often, a concrete cube contains a 13 mm stone, 26 mm stone, and crusher sand that all have the same chemical analysis. In this case, the average of the 13 mm stone, 26 mm stone, and crusher sand is used in the calculation, thus giving a combined result. Then, physical separation is used to differentiate the 13 mm stone, 26 mm stone, and the crusher sand.
If the stones cannot be cleaned properly, wash them in a 10% dilute HCl solution. Wash the stones thoroughly afterwards with water and dry them to a constant mass. After the physical separation, the stone can be prepared for chemical analysis.
The chemical analysis of the physically separated stone should be compared to that of the stone supplied by the customer.
Procedure for analysis
f Dry and reduce the individual materials to analytical samples as described in the massive sample reduction.