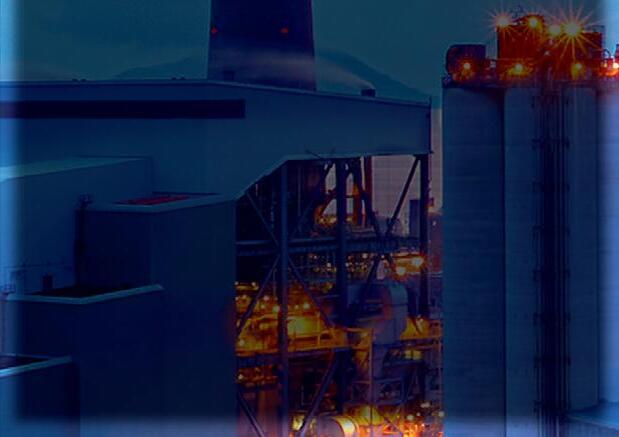
5 minute read
WE MOVE INDUSTRIES
HEKO offers the whole range of chains, rollers, sprockets and scrapers for reclaimers.
HEKO products are proven in thousands of bucket elevators and conveyors, worldwide.
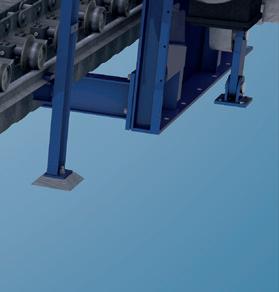
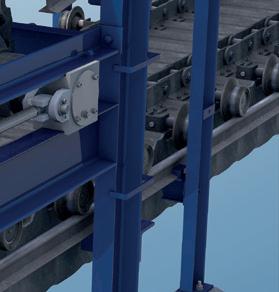
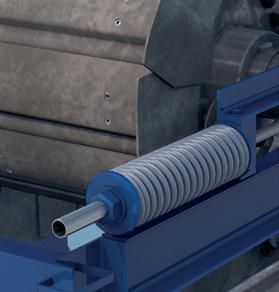

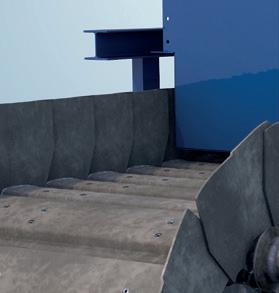
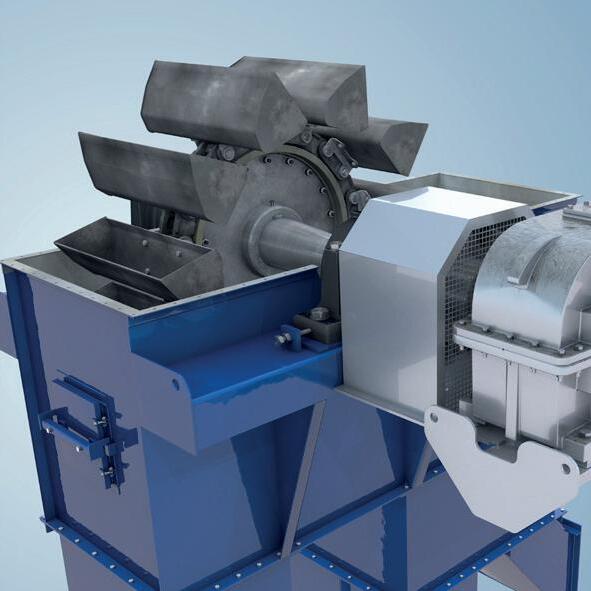
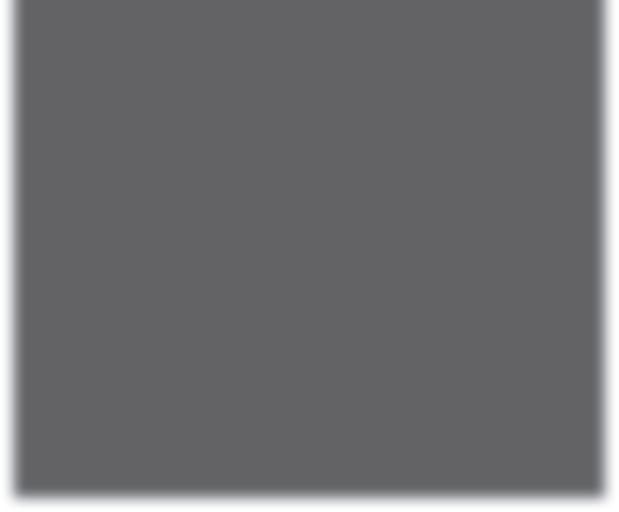
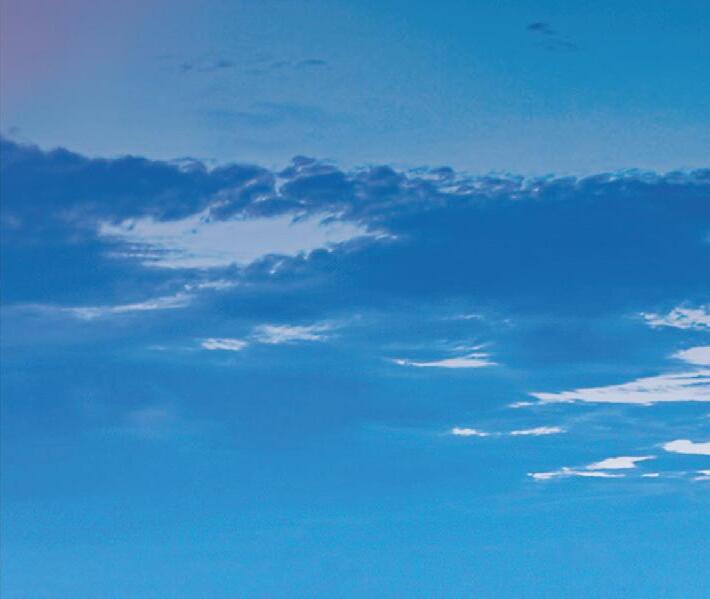
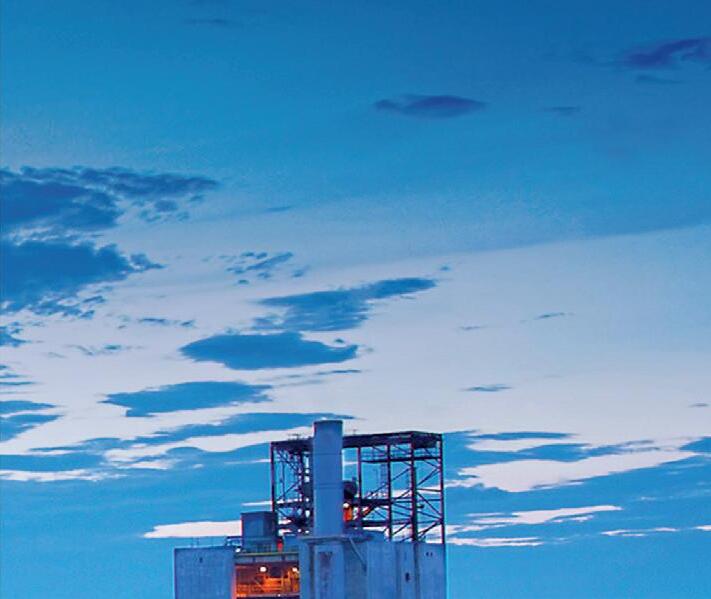
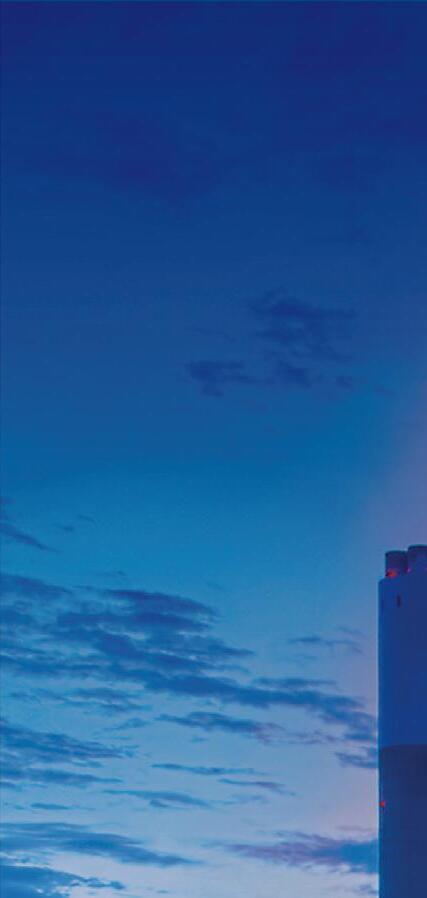
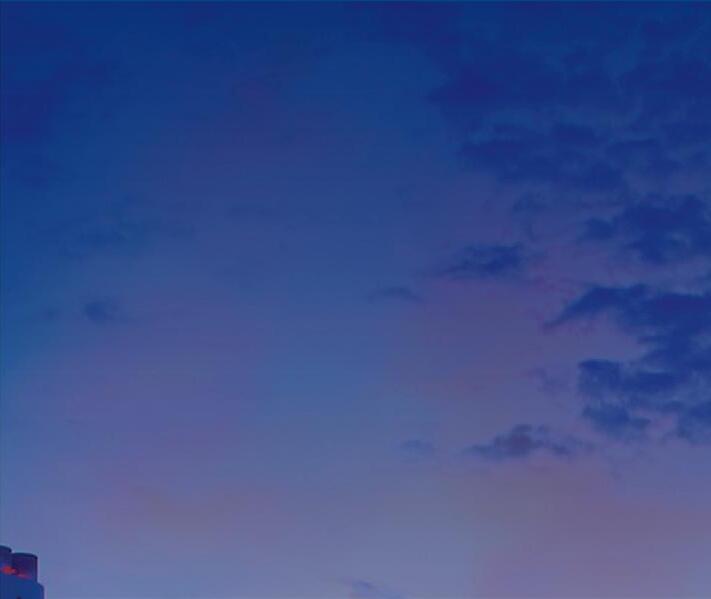
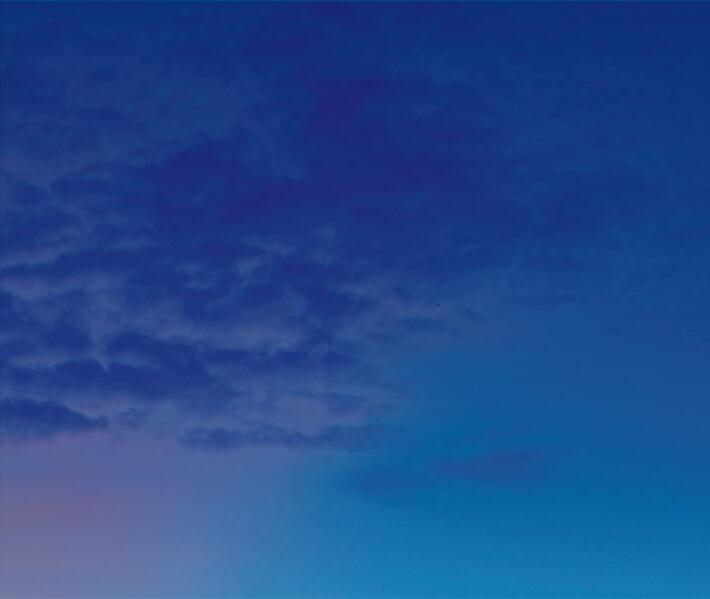
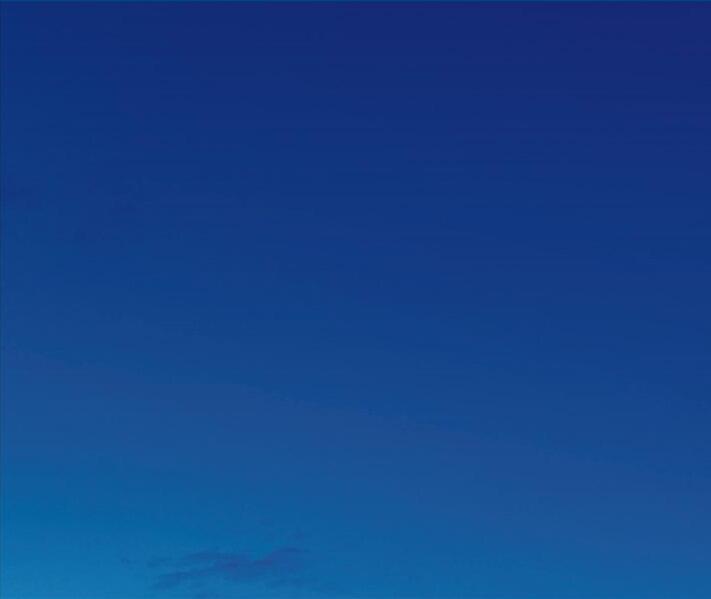
Our components for the cement industry: central chains, link chains, reclaimer chains, sprockets, bucket elevators and clinker conveyors.
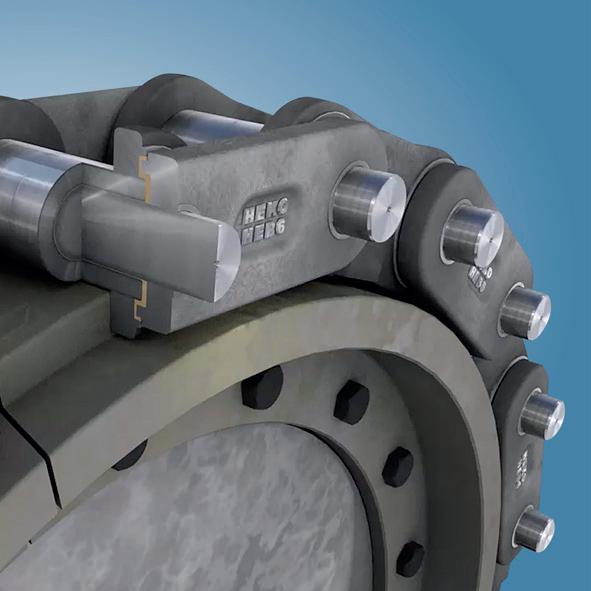
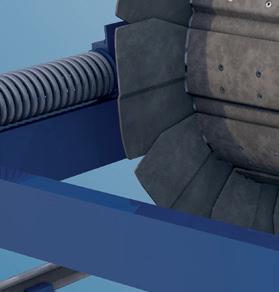
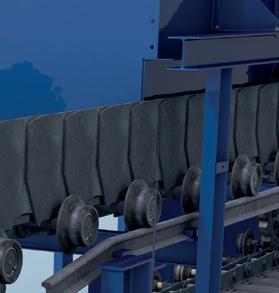
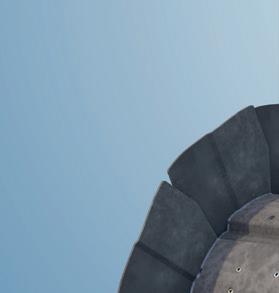
MORE THAN
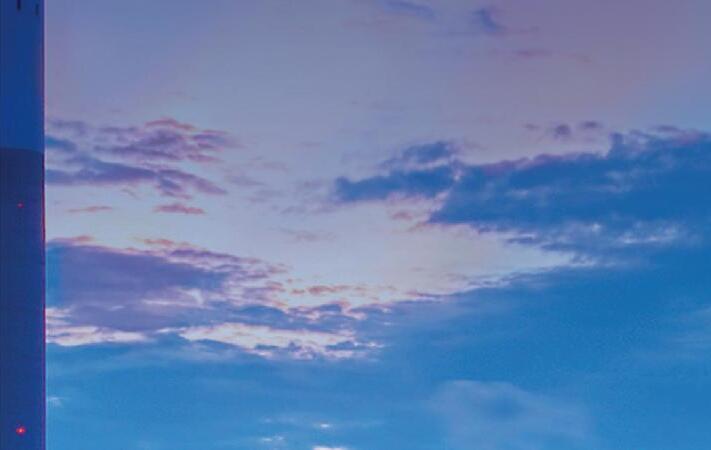
Controlled by a 3-stage system that can be adjusted by a hand-held remote, the first stage is highly effective on moderate days for airborne and surface coverage. It uses a 25 hp/30 000 ft3/min. (849.5 m3/min.) fan and misting ring to deliver fine atomised mist over a wide area. For windy days, stage two features a pressurised stream delivered by the central nozzle. On high wind days, operators can utilise the fan, misting ring and centre nozzle for maximum coverage.
The versatility and coverage area are extended with the customisable 359˚ horizontal oscillation range and 0 – 50˚ vertical throw angle. Using the hand-held remote, the operator can raise the spray angle to reach extended heights, directing the 250 ft (76 m) spray.
Mounted on a heavy-duty roadworthy trailer, the unit can be placed by a pickup truck, skid steer, or lift truck wherever dust suppression is needed. After the initial setup, the cannon requires no labour to operate. The remote control has a 1000 ft (305 m) range, so operators using heavy machineries like front loaders and reclaimers can control the settings without leaving the cab.
Dust control at the quarry
It is common for cement producers to operate a limestone quarry. Since it is the very beginning of the material supply chain and is the most prominent ingredient, dust mitigation should begin there. Open area mining is perhaps the most exposed to wind conditions, thus properly controlling dust at the point of emission as it is extracted and loaded for transport is important.
Pointing the cannon with the wind toward the general area where emissions originate will fill the area with droplets and control fugitive dust. By limiting the oscillation range, the maximum volume of mist is directed at the source of the dust, ensuring particulates are addressed quickly before they can travel.
Dust cannons for outdoor storage piles
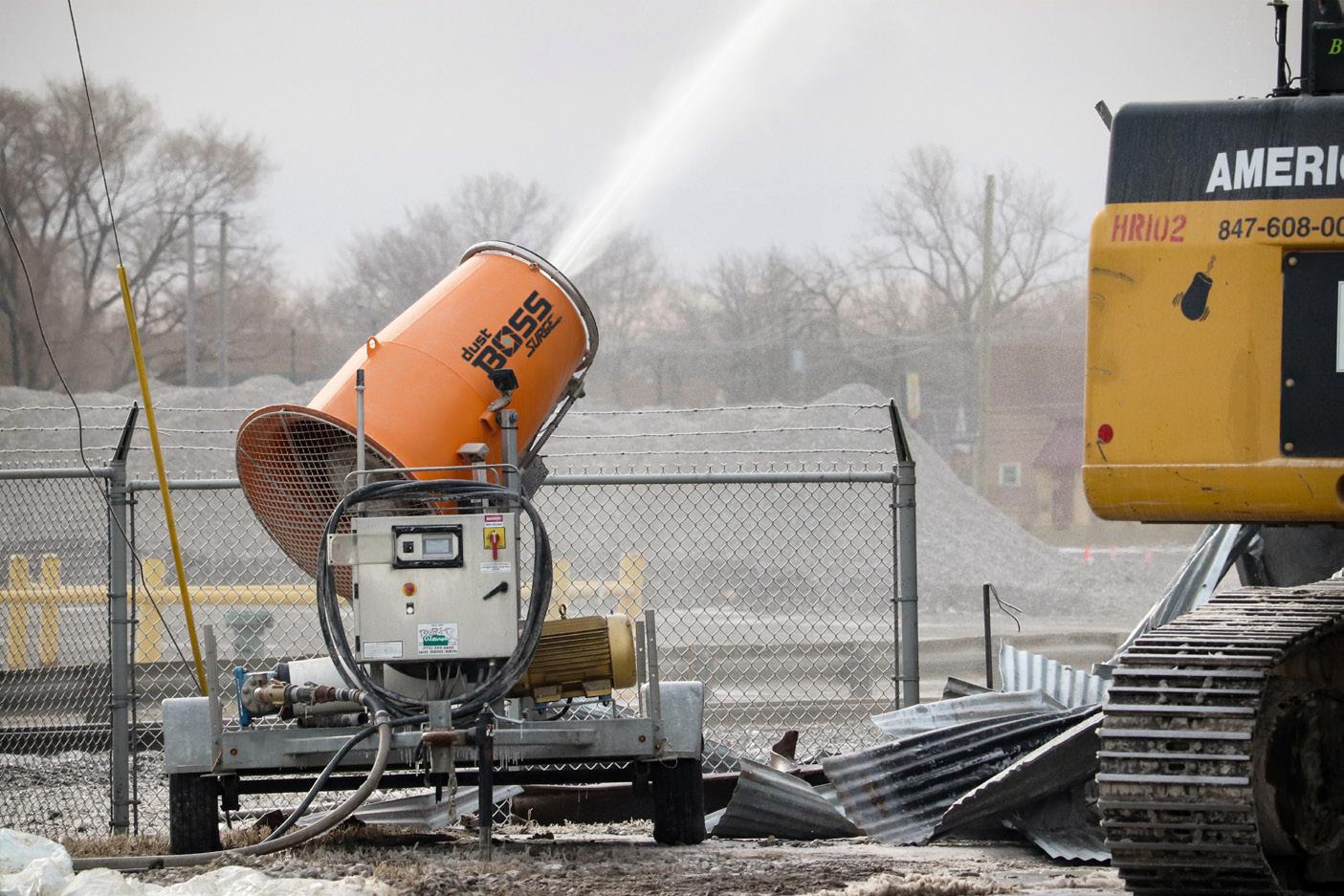
Outdoor storage piles require surface suppression in case of wind, as well as airborne suppression when the material is disrupted during the loading and moving process. A versatile machine that offers both surface and airborne control will be able to adjust water volumes, oscillation and water stream to changing conditions using the remote control or touchpad system.
For designated outdoor storage areas, operators should consider a tower mounted air cannon arrangement. With storage piles placed alongside natural wind barriers
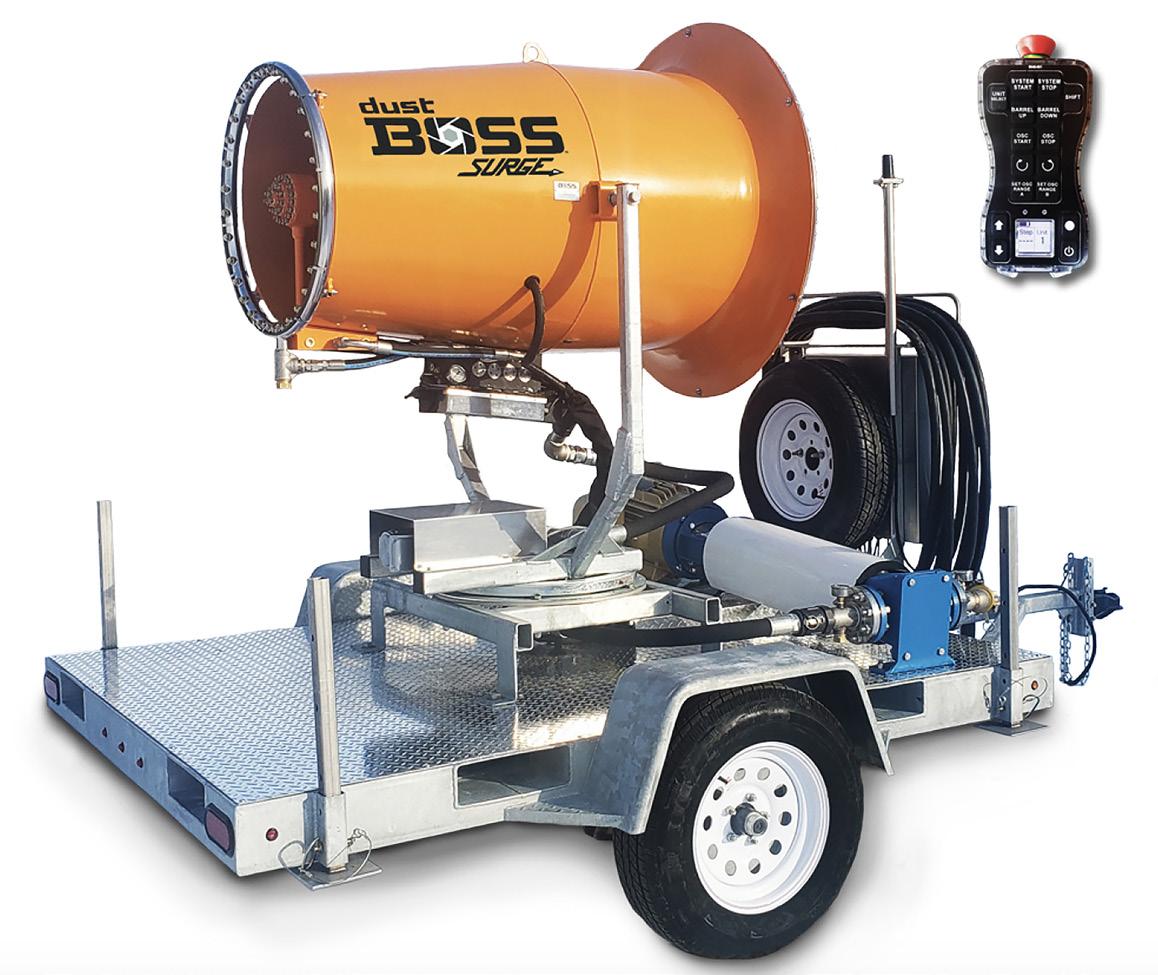
(trees, structures, hills, etc.), tower-mounted cannons can attack dust from above, ensuring the optimum coverage angle for surface and airborne treatment. Tower-mounted units might also expand the coverage area in some instances.
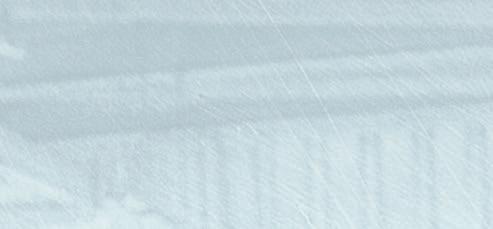
Dust cannons for indoor storage piles
Domes or massive storage sheds with tripper conveyors and reclaimers can contain a tremendous amount of dust. Although workers are generally protected within a sealed cab, material discharge, conveying, and other material disruptions can raise dust levels above the regulated thresholds, potentially exposing unprotected workers and creating a violation. Workers outside open bay doors may also be inadvertently exposed.
A dust cannon with 359˚ oscillation that is strategically placed in the centre of the area provides enough coverage to raise the humidity in the area and mitigate airborne dust. Stationary misting rings or nozzles can also be placed at the discharge of tripper conveyors or transfer chutes to create a curtain of fine droplets around the discharge stream. Cannons can even be mounted in the rafters of a storage enclosure to ensure the entire area receives full coverage.

Mist cannons at crushers and transfer points
Beyond the tripper conveyor, fixed transfer points such as the crusher, preheater tower and clinker conveyor can generate a disproportionate amount of dust. Studies of different cement production operations have found that the highest dust exposure for workers in cement manufacturing is in the crusher area. 3 Transfer points high up in towers can be exposed to higher wind conditions that change minute by minute and can carry dust emissions long distances. Leaving the cooling area, clinker can still be >200˚F (>93.3˚C). The convective heat rises, carrying fine dust particles (<PM 10) with it, further contributing to the volume of emissions. 4
Dust cannons can be positioned at each of these points to mitigate fugitive dust and, in some cases, help cool the heated material further. Plants require a crusher to reduce the size of material for proper flow through each stage, but the demanding high-volume cement environment often exceeds the capabilities of dust control systems on most crushers. Misting cannons can be placed out of the way and offer a wider coverage area than standard crusher dust control systems. This also applies to conveyor transfer points that are not enclosed and may have problems with fugitive dust.
Atomised mist and air circulation in high heat areas
Maintenance work can be unpleasant in some areas of the cement plant, especially the highest heat areas such as on the preheater tower, near the kiln, around the clinker cooling area, and in the clinker barn/storage area. Industrial dust control cannons have been successfully adapted to improve high heat conditions and circulation in the aluminium die casting industry for years. 5 For maintenance projects occurring near high heat sources, a cannon mounted on a skid or trailer can be moved and positioned to improve working conditions and safety, possibly extending the amount of time work can be conducted in the area.
There are two main elements that cool the area: f The fine mist droplets evaporate on contact with the heat, cooling down the immediate area. Raising the humidity level of the area also supports the body’s natural temperature regulation. f The high-powered fan guides the heated air away from the work area. Redirecting the heat radiating from a surface allows work in areas that may have previously only accommodated limited activity.
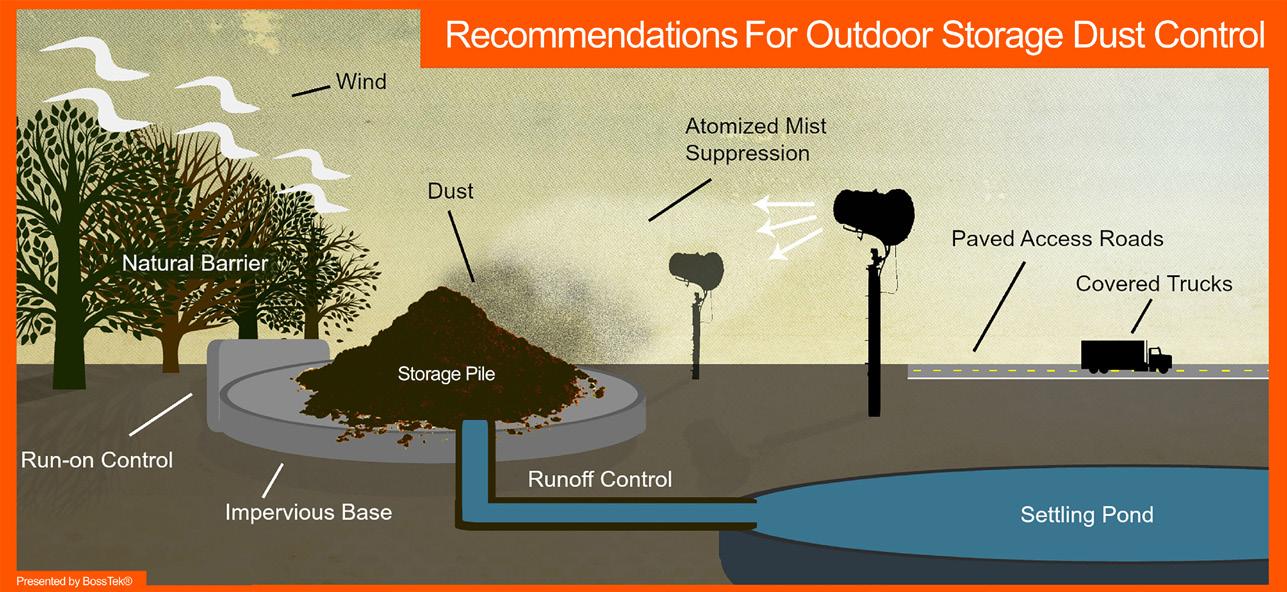
Conclusion
The journey of dusty limestone and other materials through the cement manufacturing process could find the cargo encountering dust control misting cannons several times. With fine atomised mist, the material remains relatively dry, while the dust is still suppressed. The versatility allows misting cannons to be located in fixed positions where dust is most prevalent, and mobile cannons can be moved and positioned for specific duties or changes in weather conditions.
OSHA rules regarding dust generated by cement producers are only getting stricter, and the industry must seek ways to mitigate dust in the most economical ways possible. By reviewing applicable uses for industrial mist cannons, operators improve air quality and worker safety, reducing the chance of a violation. Mist cannons can improve working conditions in some of the most unpleasant parts of the plant, while reducing the amount of cleanup, labour, and fouled equipment associated with fugitive dust emissions.
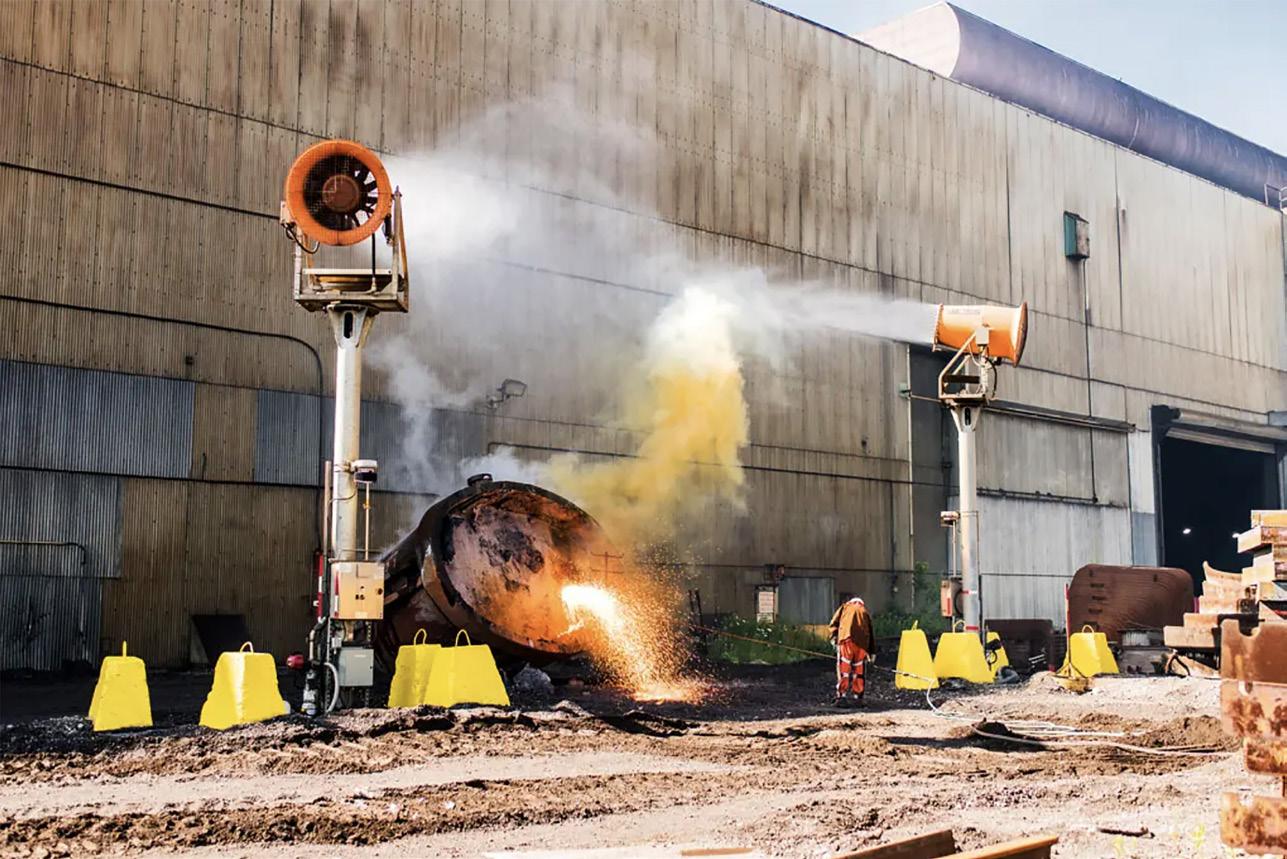
References
1. Engineering ToolBox, Particle Size, 2005 – https://www. engineeringtoolbox.com/particlesizes-d_934.html
2. VAN DER DOES, M., KNIPPERTZ, P., ZSCHENDERLEIN, P., et al, ‘The mysterious longrange transport of giant mineral dust particles’, Science Advances 4(12), 2018 – https://www.ncbi.nlm. nih.gov/pmc/articles/PMC6291315/
3. CIOBANU, C., ISTRATE, I. A., et al. ‘Dust Emission Monitoring in Cement Plant Mills: A Case Study in Romania’, International Journal of Environmental Research and Public Health 18, 2021 – https:// www.ncbi.nlm.nih.gov/pmc/articles/ PMC8431024/
4. ‘How Weather Affects Air Quality. University Corporation for Atmospheric Research’, 2020 – https://scied.ucar. edu/learning-zone/air-quality/howweather-affects-air-quality
5. ‘How To Create Positive Air Flow In Large Roof-Vented Facilities. Manufacturing Net’, 2017 – https:// www.manufacturing.net/safety/ article/13194808/how-to-createpositive-air-flow-in-large-roofventedfacilities