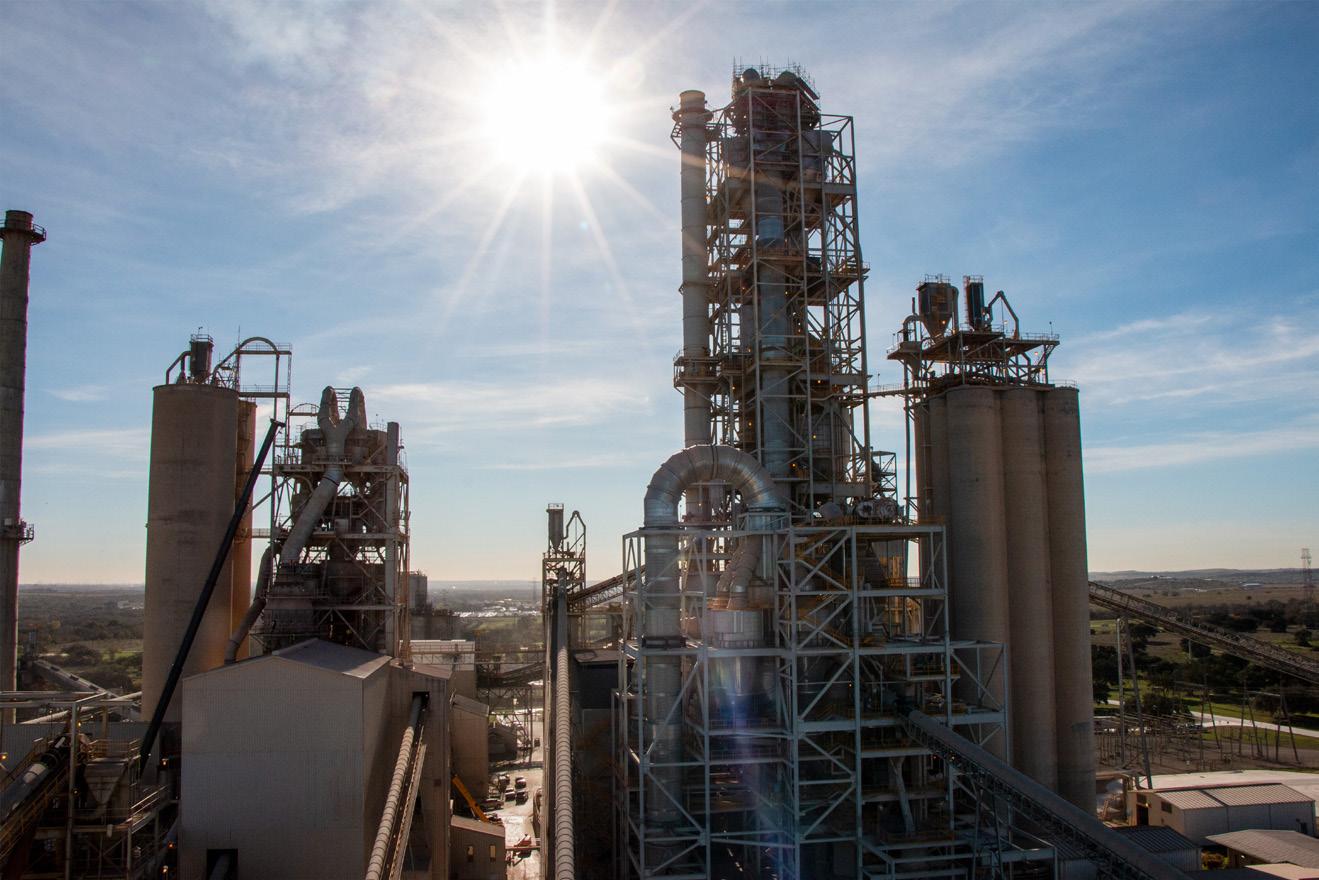
2 minute read
BLOWING AWAY CEMENT’S DUST PROBLEM
placed, can improve air quality around stockpiles, transfer points, and loading areas. New developments in nozzle technology have made them extremely effective, even in high-wind conditions. Operators that own mobile units are discovering that the fan-driven misting technology is also effective in improving conditions during maintenance in high-heat environments.
Causes of dust in cement production
Crystalline silica, commonly found in limestone, can be smaller than 10 µm (microns in width) – the size of pollen – making it invisible to the naked eye and able to travel long distances. When inhaled, it is small enough to avoid the body’s natural defenses and penetrate deep into the lungs, and over time can cause serious chronic health issues for workers.
Wind is likely the greatest cause of dust that operators contend with. Even relatively slow atmospheric currents can pick up a particulate as small as 200 µm – roughly the width of a human hair – and transport it several miles. 1,2
To mitigate the effects of wind, it is common to see cement plants with storage domes, clinker barns, conveyor covers, and sealed transfer points, particularly in towers.
Material disruption also releases fugitive dust. Whether it is caused by a front loader or simply a conveyor belt bouncing on an idler, every time the material moves there is a chance it will shed particulates. The force of the disruption, the size of the particulate, and the moisture content are the major factors in the volume and travel distance of dust emissions.
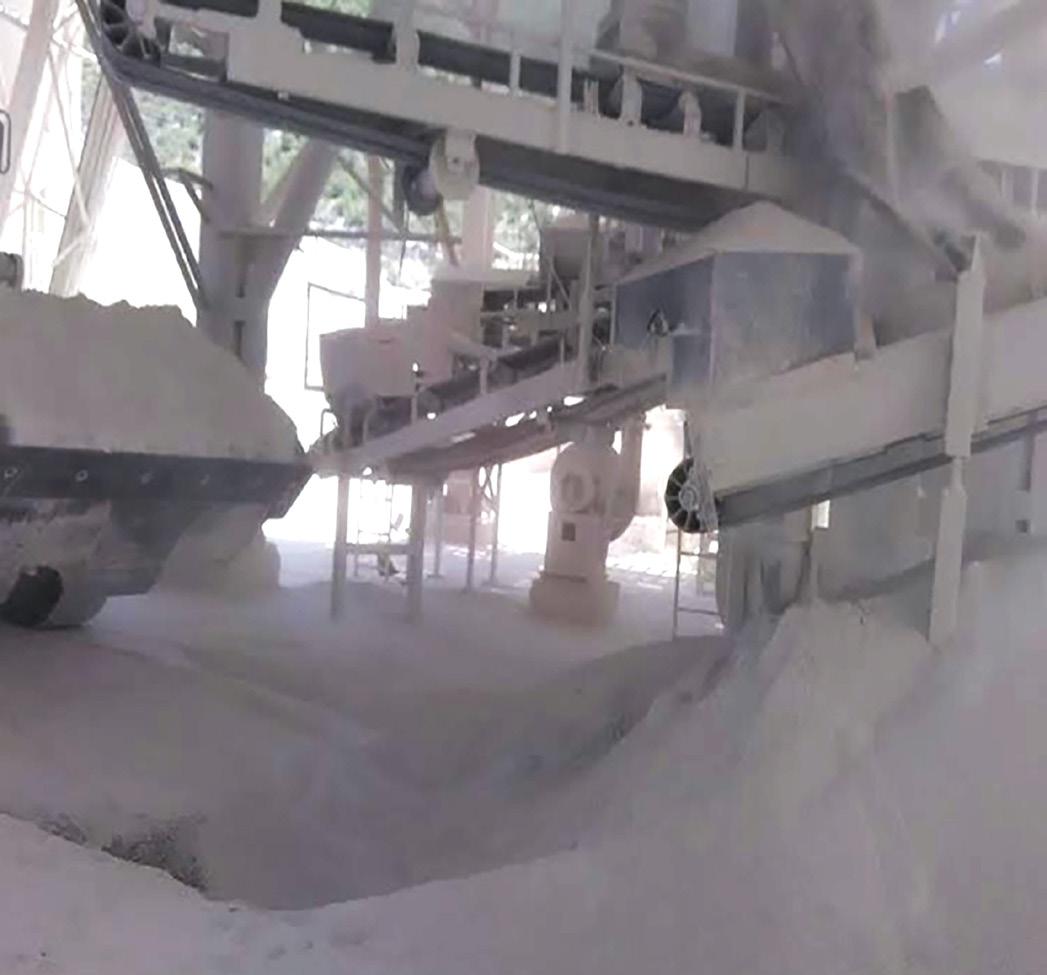
Atomised mist innovations for changing conditions
Cement plant operators can assign workers to hose down material for surface suppression, creating a damp outer layer, but the material underneath will still emit airborne dust once it is exposed. No matter where in the operation this method is employed, hosing down material increases labour costs and does not control the inevitable airborne emissions. Large droplets from hoses range in size from 200 µm to 1000 µm. At this size, the droplets create a slipstream effect causing the tiny dust particles to get caught in the droplet’s air current and move around it rather than suppress it.
In contrast, atomised mist delivers surface suppression with no labour and is the only technology that can also suppress dust once it has become airborne. The key factor is the small droplet size: atomised mist cannons introduce millions of tiny droplets into the area, ranging between 50 µm and 200 µm in size, roughly the same as the dust particles. The smaller droplets travel on ambient air currents with the dust, collide with the particles, and pull them to the ground. But the small size also makes the droplets vulnerable to changing wind conditions. BossTek, the manufacturer of DustBoss® Mist Cannons, has designed a new model that can adapt to changing conditions without manual labour, no matter where the machine is being employed.
The DB-60 Surge has a heavy-duty barrel body with a powerful industrial fan at its rear, misting ring in front and a central high-pressure spray nozzle with the reach and force of a hose. The pressurised spray resists wind shear and even uses the force of the wind to further fragment and carry the droplets, enhancing its dust suppression capabilities. Fed by a standard 1 – ½ in. (38 mm) hose with a cam-and-groove quick disconnect coupling, the booster pump delivers as much as 500 PSI (27.5 bar) of water pressure to the centre nozzle, with an output of only 37 – 100 gal./min. (140 – 378 l/min.). In contrast, a hose or sprinkler has an output of between 75 – 500 gal./min. (283 – 1892 l/min.), causing standing water, substantially more runoff and increasing water costs.