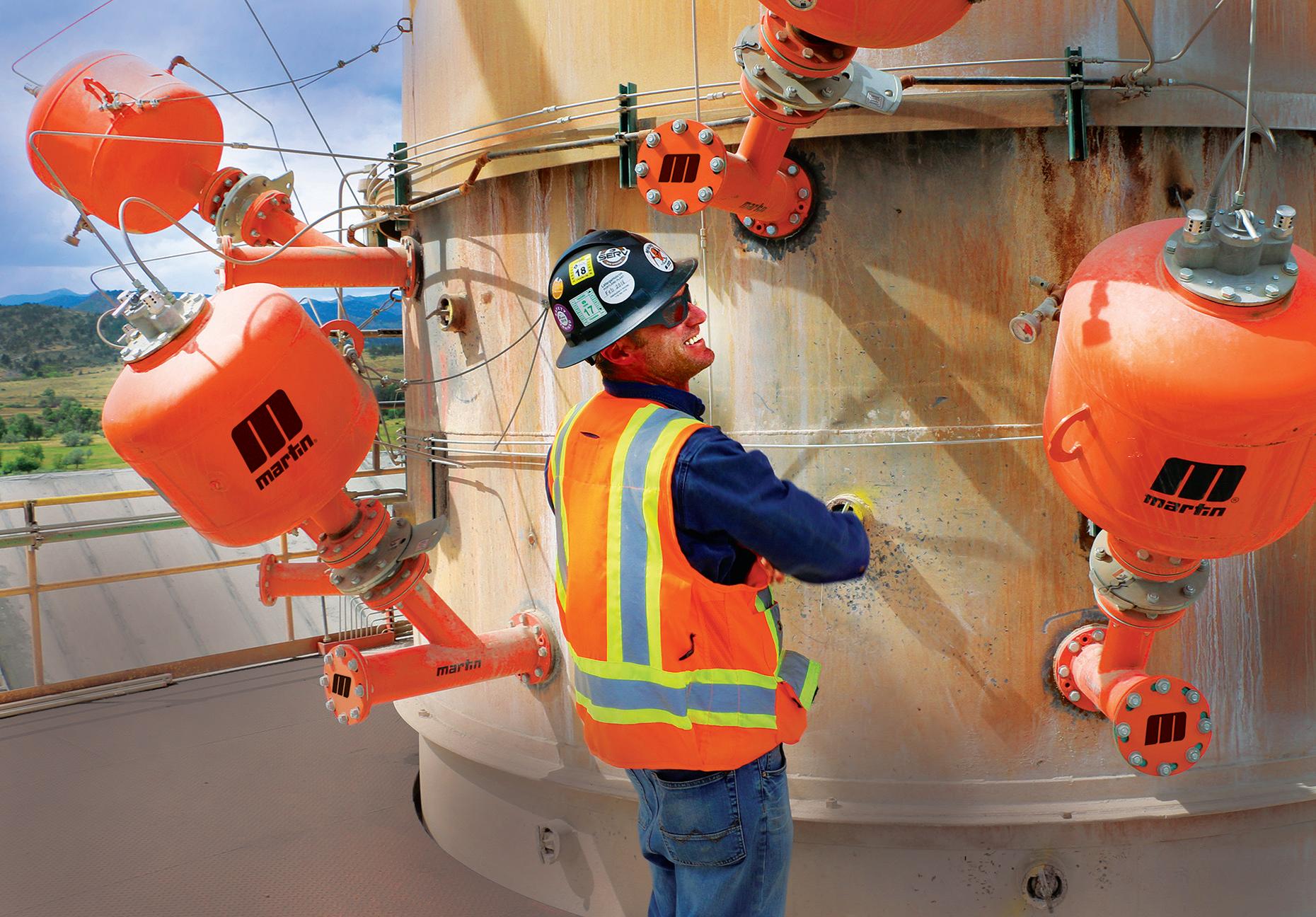
7 minute read
Sorting out the standards
Katie Wills, Cemfree, explores the changes that need to be made to construction industry standards to support the widespread use of AACMs
There is no denying the versatility of cement. Yet with growing concerns over its impact on CO2e emissions, the construction industry should now be looking for more eco-friendly options.
Pioneering technologies that promise to decrease the construction industry’s carbon footprint are already in progress, such as carbon capture, usage, and storage (CCUS). Whilst these future technologies are pioneering, they are still in their infancy and any benefit is unlikely to be realised for many years, and will require huge amounts of capital investment.
The alkali-activated cementitious materials (AACMs) family of cement alternatives provide a solution to the challenges the industry faces. These products represent an ultra low-carbon option for construction, and critically, they are available right now.
Slow-moving industry standards currently stand in the way of widespread AACM adoption, leaving a largely untapped potential.
What can be done to change this?
Laying the environmental foundations
Tough and adaptable, concrete is a construction all-rounder that has been widely used for hundreds of years. Due to its flexibility in the building process and broad range of applications, concrete made with traditional cement has long been the go-to material for construction projects around the globe, forming the literal foundations of the built environment.
However, cement, the key active ingredient in concrete, comes at a high environmental cost, and its carbon footprint does not sit well alongside the industry’s decarbonisation goals.
Concrete’s environmental impact
The accessibility, usability, and affordability of cement have made it a vital material for building society’s infrastructure, but cement’s environmental impact is dramatic: f Each year, 4.5 billion t of ordinary Portland cement (OPC) is produced globally.1 f On a global scale, cement manufacturing has a huge carbon footprint, responsible for around 4 – 8% of the world’s CO2e emissions.2 f To produce 1 t of OPC, approximately 2.5 t of fuel and raw materials are consumed, with almost 1.35 billion t of CO2e annually released into the environment from OPC production. f Next to water, concrete is the second most-consumed substance on earth.3
The construction industry has set ambitious decarbonisation targets.4 The Mineral Products Association (MPA) aims to reduce the emissions from cement manufacturing by 16% by 2050, championing carbon capture, usage and storage (CCUS), despite its commercial rollout remaining far in the distance.5
In the meantime, use of AACMs and ultra low-carbon concretes can play a key part in the construction industry’s aim to achieve net zero and tackle its large carbon footprint. This goal sits alongside the UK’s ‘Build Back Greener’ initiative that seeks to decarbonise all areas of the UK economy, and its industrial decarbonisation strategy, which aims to reduce carbon emissions by at least 90% by 2050.
The industry increasingly understands it needs to act now to achieve these targets.
As Jan Theulen, Group Director of Alternative Sources at HeidelbergCement points out in Building Magazine’s 2021 article, ‘What are we going to do about concrete?’: “2050 is tomorrow.”
Cement will undoubtedly remain part of the construction mix, but eco-friendly alternatives can help support demanding construction projects while simultaneously supporting the industry’s collective global sustainability aims.
Understanding AACMs
AACMs are created at room temperature by combining an alkaline solution (the formula activator) and a crystalline aluminosilicate material (the precursor). The resulting products, such as Cemfree, have a significant ecological advantage over traditional Portland cement.
AACMs are an alternative binder to traditional Portland cement and can be used in a wide range of concretes and concrete products.
As the conversation around concrete increasingly trends towards carbon neutrality and carbon reduction, AACMs are not only practical, but they also offer a preferable carbon footprint.
So why are they not being used more often?
Moving past the AACM roadblocks
Despite a growing eco-consciousness in construction and their proven usability, uptake of AACMs has been slow.
Hesitancy to adopt AACMs is primarily due to the minimum level of ordinary Portland cement (OPC) that is mandated within the relevant standard for concrete manufacture. The British Standards are respected and prescribed, leaving few opportunities for using alternatives that do not fit within them.
Many engineers are risk-averse and use the available standards and data to help them make a decision about which materials to use on a build. This often leads to the use of OPC even when other, tried and tested ultra low-carbon materials would be equally well-suited to the project.
Challenging and adapting standards to include AACMs has become an important issue in construction, with both an environmental and economic impact.
The cost of OPC is liable to rise as carbon taxation comes into effect, and as The Organisation for Economic Co-operation and Development stresses:
“Companies that are able to integrate climate risks and impacts within their business are better able to meet investor and consumer expectations, mitigate reputational damage, increase competitiveness, and protect their bottom line.”
Challenging existing standards
For concrete formulas to qualify for the BS EN 8500, they must contain at least 5% ordinary Portland cement. Since AACMs are created without OPC, this leaves products such as Cemfree unable to fit into any category.
These prescriptive standards around clinker content are currently blocking the innovative solutions that could bring the industry in line with a more sustainable construction future. Yet thanks to innovations in both the products and standards themselves, this could all be set to change.
A performance-based standard
While the current standards present a roadblock to innovation, it is sometimes possible to navigate around the obstacles and use AACMs in a building project.
Instead of working to the British Standards, construction companies can instead use performance-based standards as the guiding principle when selecting which materials to work with. This is a dynamic solution until industry standards have caught up with demand and changing ideas about sustainable construction.
A relevant performancebased standard is the PAS8820:2016: f The PAS has been used for a number of years, and is regarded as pre-standard to the full British Standard. f It provides a valuable blueprint for teams aiming to incorporate carbon-reducing alternatives into their project.
There are further standards such as BS EN 998-2 Mortar and the BS EN 771-3 Blocks (Precast) which are performance-based standards that do not require a percentage of clinker as per the BS 8500. Instead, these are based on being fully compliant to the standards.
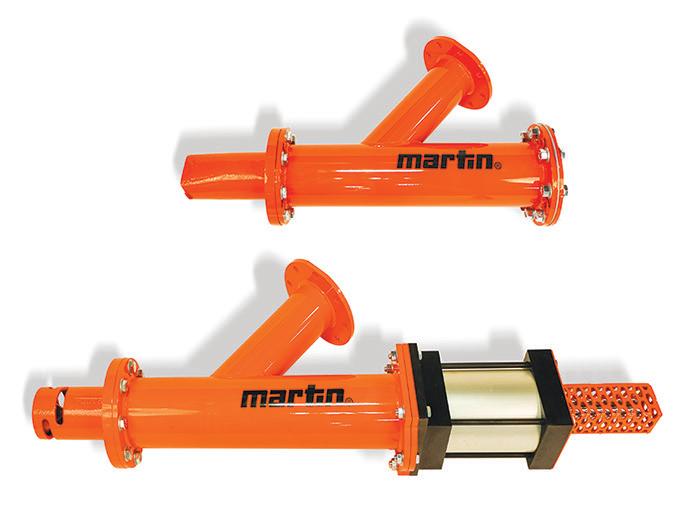
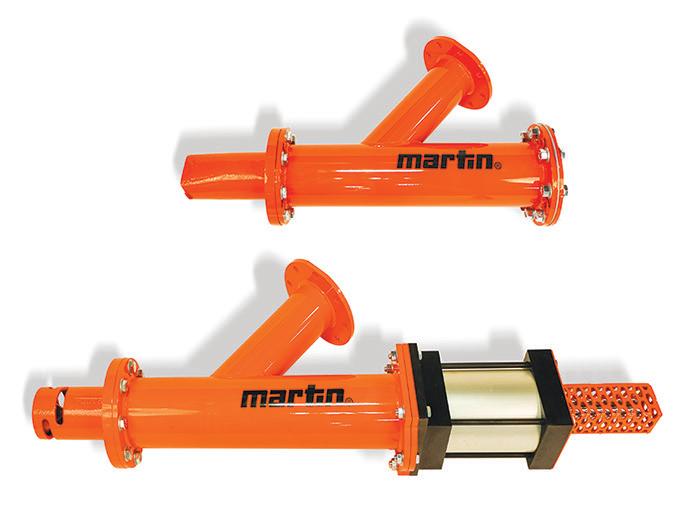
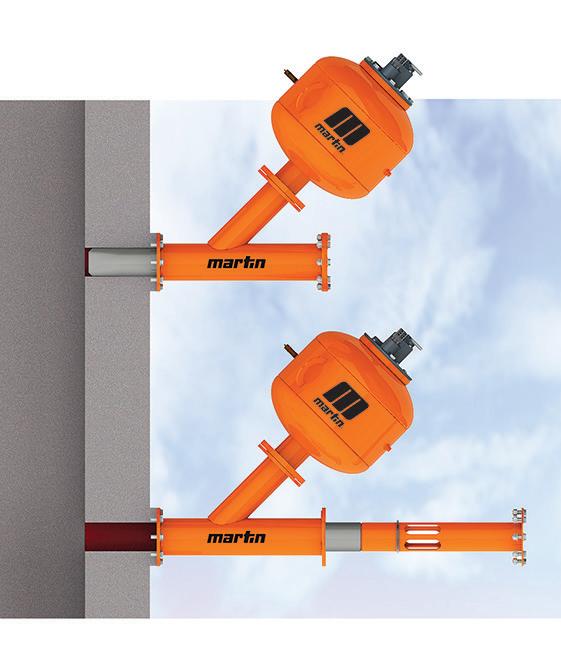
The technology around construction is constantly evolving – but waiting for innovations like CCUS to become accessible and affordable will prevent the industry from facing its net zero goals straight away. Meanwhile, AACMs are a viable and highly-effective solution.
Changing the landscape for AACMs
Companies developing AACM materials have been working closely with other organisations, encouraging changes to the British Standards.
One such organisation is A3CM. This newly-formed body is dedicated to spreading the word about AACM products and pushing for change. A3CM seeks to build a community of like-minded people in the building sector, helping to raise awareness about how AACMs can transform the built environment for the better.
Another organisation that is working to drive change is the Green Construction Board, a consulting forum that works to fuel innovation and sustainable growth within the construction, design, and property industries. The board has been vocal about the concrete challenge, encouraging best practices for concrete consumption and manufacture while supporting cleaner, carbon-neutral alternatives.
Cemfree is one of the companies leading the shift towards the development and application of ultra low-carbon options. The product marks a major milestone in concrete technology, and can help reduce embodied CO2e by as much as 80%.
A real-world solution
One way to reduce carbon emissions in construction projects, is to use less OPC in concrete. While standards dictate a minimum clinker content, some applications allow the performance-based standard to apply and make room for the use of AACMs and alternative technologies.
AACMs are proven to work well in a variety of contexts. Cemfree was used in construction work for Network Rail in 2020, with 300 m3 of continuous pour supporting a new step-free access at Chatham station.
This marked the first use of Cemfree on the UK rail network, and the choice to use an AACM rather than an OPC product saved around 62 t of carbon –comparable to 230 000 miles in a diesel car.
Ongoing AACM research
There have been many projects that reinforce and research the application of AACMs in construction. For example, Cemfree has partnered with Innovate UK, which are now undertaking a 2-year exploration of novel concrete formulations that replace OPC with AACMs. Known as low-carbon concrete in aggressive ground (LOCOWAG), the study has been carrying out a mixture of laboratory tests and site pilots to showcase the benefits of these products.
Cemfree, alongside many other organisations, must continue to work with standards bodies to break down standards-related barriers to AACMs in construction.
Where to go from here
Until British Standards are adapted to suit AACM use, the construction industry is locked in a vicious cycle, having identified a growing problem but remaining powerless to make full use of the available and effective solutions.
Now is the ideal time to develop new industry-wide guidance and standards that support innovation and sustainability. By exploring the cement alternatives already on the market, the industry can work towards cleaner, greener construction that works in harmony with the environment.
There are numerous effective, ultra low-carbon materials available that work alongside cement to support the built environment. AACM products can help reduce CO2e emissions, but standards-related barriers currently prevent their use in most building projects across the UK.
While cement will never be replaced, engineers should challenge the industry, and reduce embodied carbon across their building projects.
Instead of waiting for the technology of the future, it is time to approach construction with a new focus on sustainable products, using ultra low-carbon cement alternatives.
About the author
Katie Wills is a Business Development Manager at Cemfree. She has over 11 years’ experience within the construction industry having worked for both a Masonry sub-contractor and a manufacturer of premium steel products. In these roles Katie worked across a vast range of construction projects, working with Tier 1s, Frame Contractors, Architects, and Engineers, playing a significant role in creating and sustaining new and existing relationships with key clients, working with relevant disciplines in breaking specifications, and having an in-depth understanding of the clients and contractor’s desires. During this time, she also gained her BA (Hons) in Leadership & Professional Development.
Katie now uses this wealth of knowledge and experience in her role at Cemfree as Business Development Manager, predominantly focusing on Cemfree mortar and blocks, including Project Management, establishing a route to market and premium product sales. Since joining the group in 2021, she has also gained her Tech ICT qualification.
References
1. ‘The Cement Industry, One of the World’s Largest CO2 Emitters, Pledges to Cut Greenhouse Gases ‘, Yale School of the Environment, 2018 – https://e360.yale.edu/digest/ the-cement-industry-one-of-the-worlds-largest-co2-emitterspledges-to-cut-greenhouse-gases?msclkid=44d08603c66b1 1eca3f206b64ae474c8
2. ‘Making Concrete Change: Innovation in Low-carbon Cement and Concrete‘, Chatham House Report, 2018 – https://www.chathamhouse.org/sites/default/files/ publications/2018-06-13-making-concrete-change-cementlehne-preston-final.pdf
3. WATTS. J., ‘Concrete: the most destructive material on Earth’, The Guardian, 2019 – https://www.theguardian.com/ cities/2019/feb/25/concrete-the-most-destructive-materialon-earth
4. LANE. T., ‘Concrete: the most destructive material on Earth’, The Building Boardroom, 2020 – https://www. building.co.uk/focus/countdown-to-zero-how-can-the-ukmeet-its-2050-carbon-targets/5109420.article
5. SALAU. M., and GARDNER. A., ‘The Race To Net Zero; How Construction Is Modernising Their Materials And Construction Methods Ahead Of 2050’, Beale & Co, 2021 – https://beale-law.com/article/the-race-to-net-zero-howconstruction-is-modernising-their-materials-and-constructionmethods-ahead-of-2050/