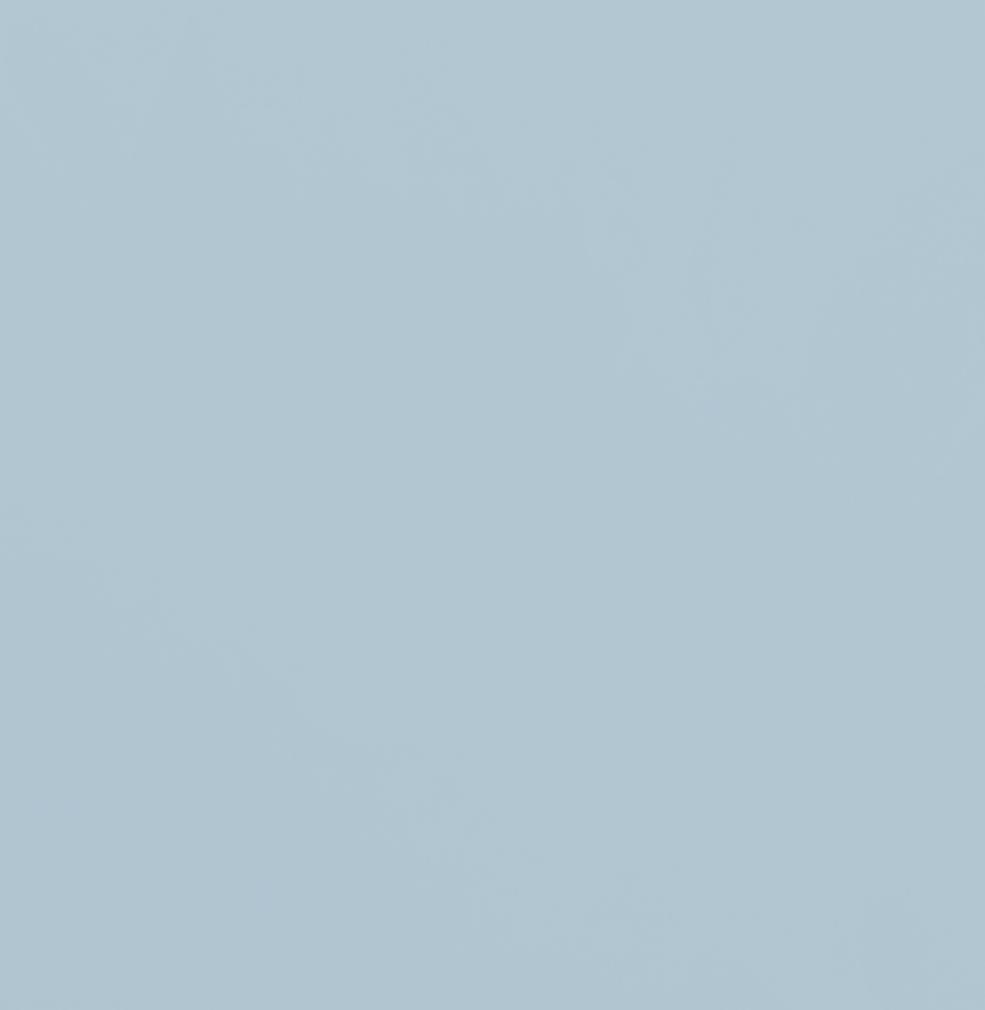
6 minute read
Preventing Production Stoppages
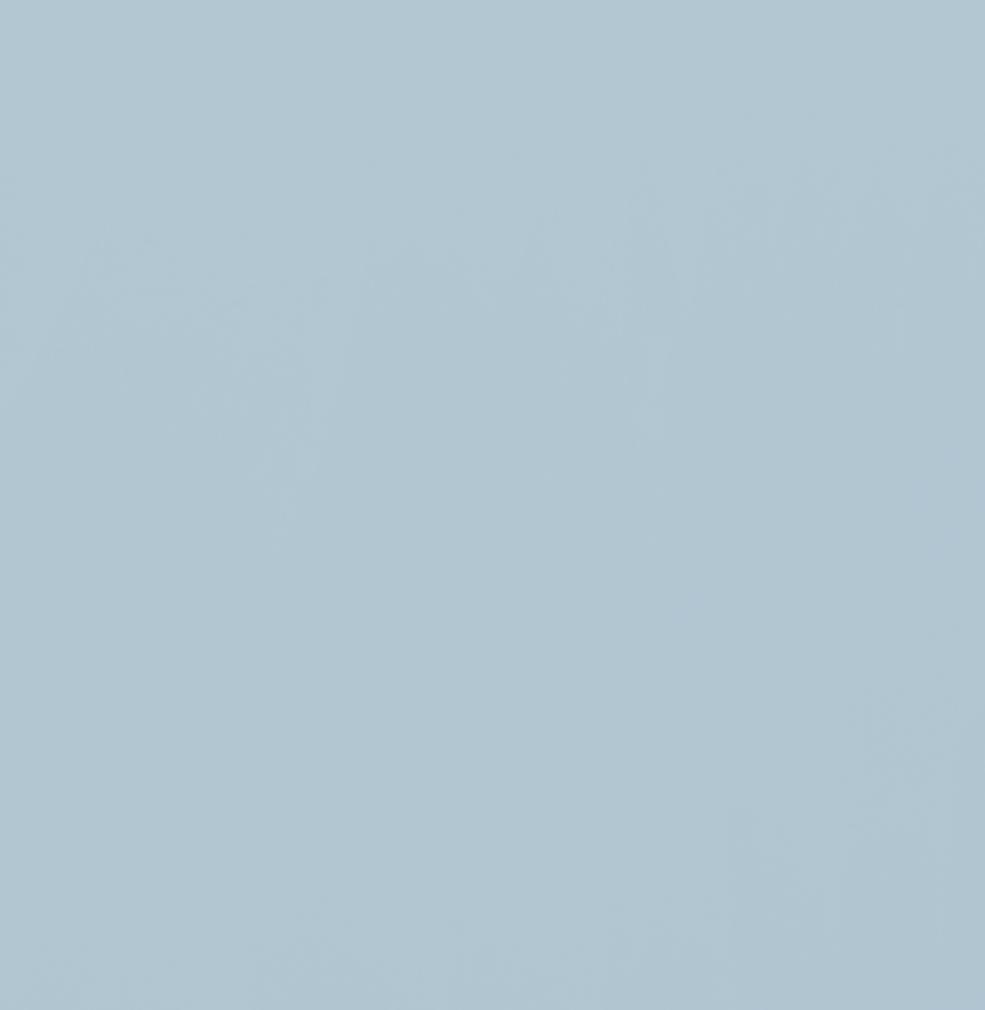

Benoit Pluchon, Standard Industrie Singapore, discusses how product stoppages due to material build-up can be prevented.
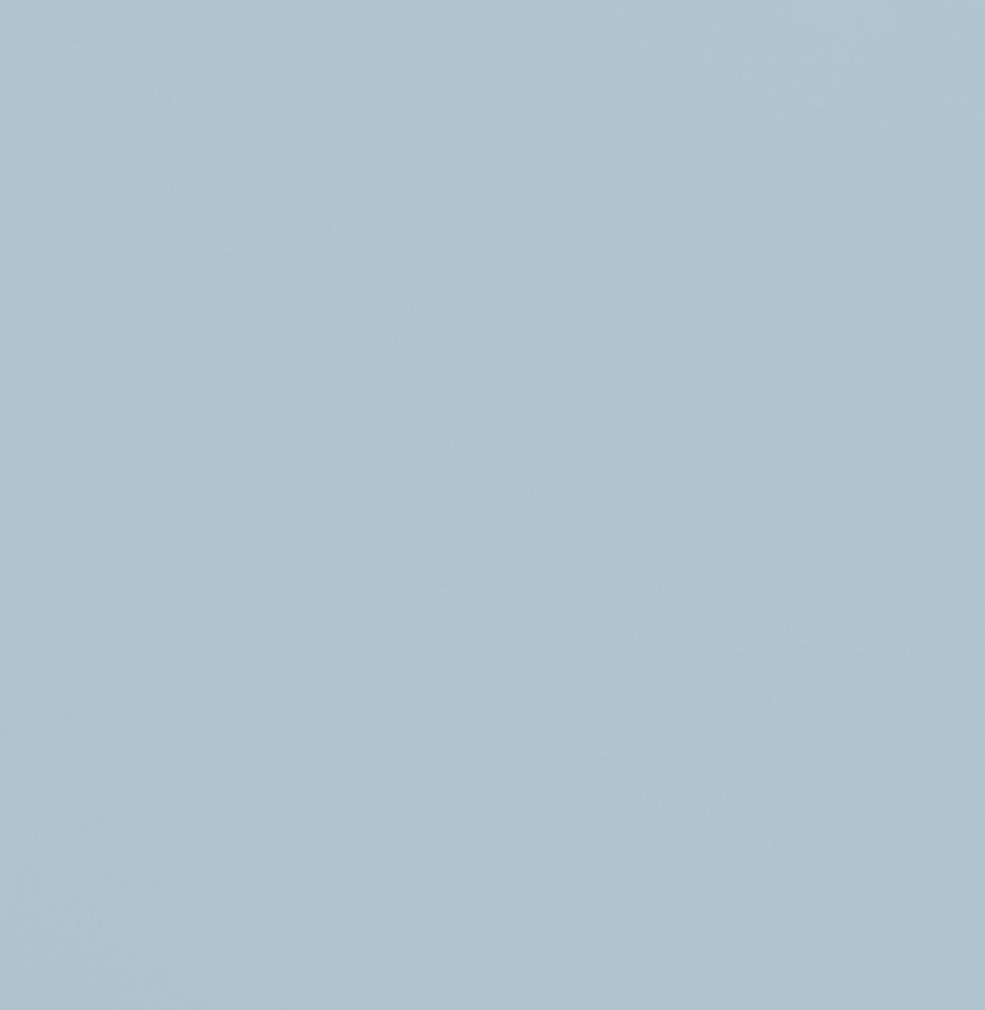
Material build-ups in the production process often lead to reduced plant productivity and higher cleaning costs, as well as increased safety risks to maintenance staff. Such issues can be avoided by undertaking measures, including blockage and build-up removal and silo and hopper cleaning.
Having developed expertise in both these areas, Standard Industrie International has helped a number of plants across the world improve their productivity; reduce cleaning
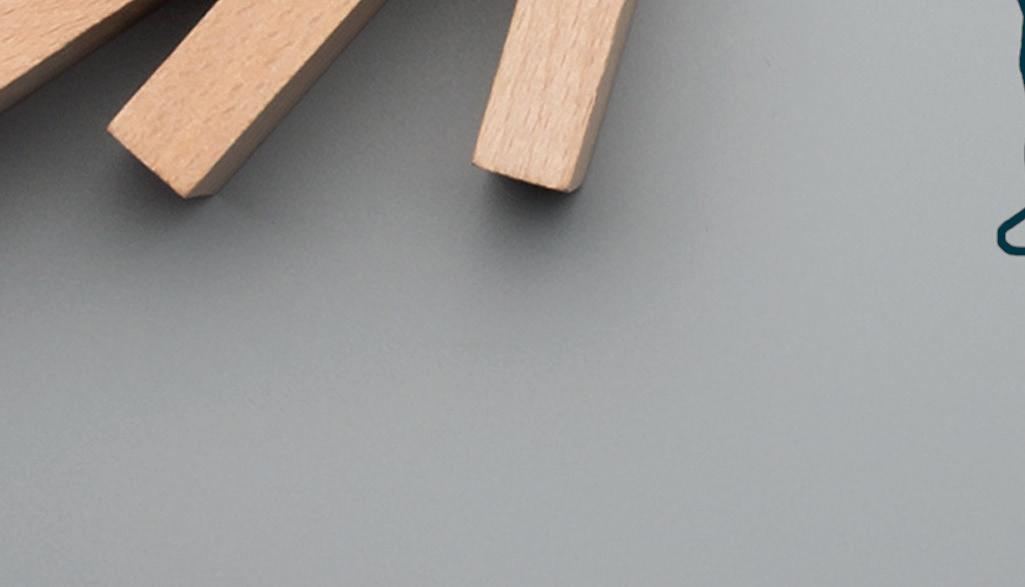
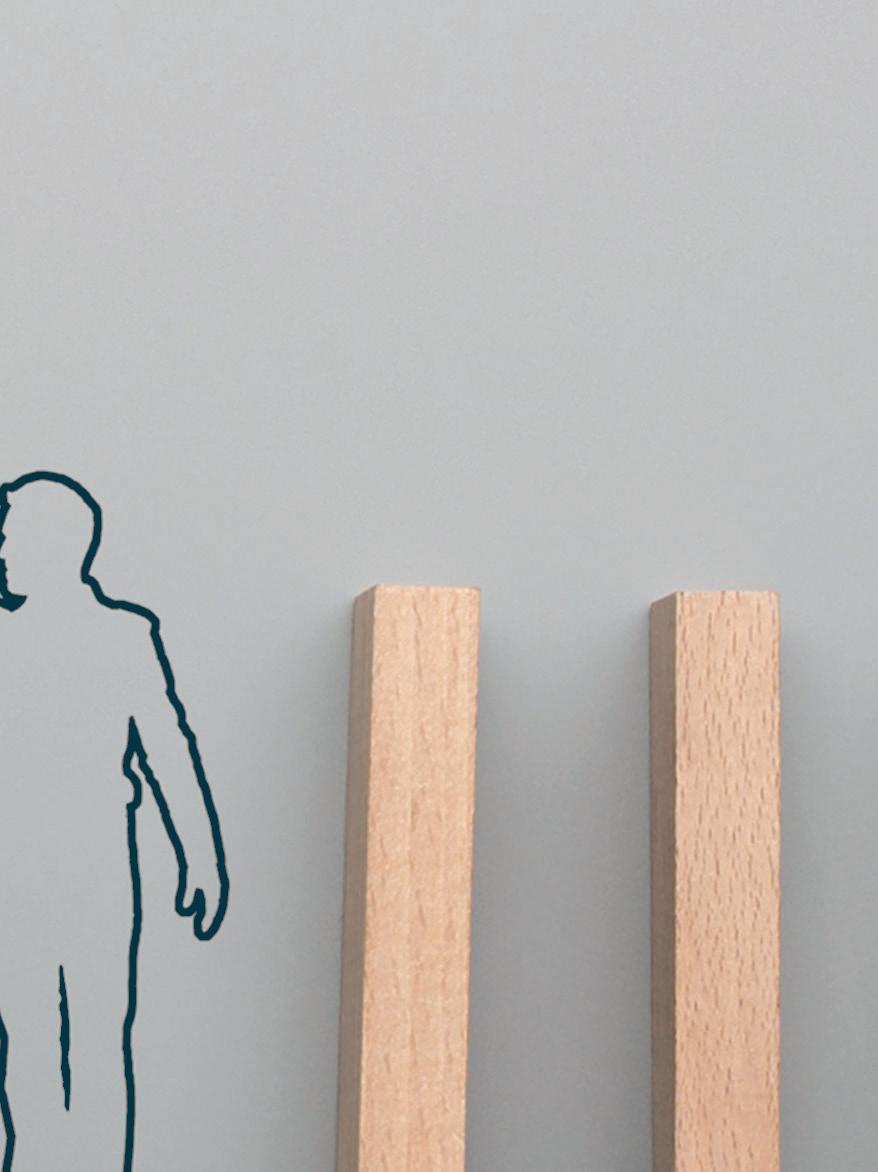
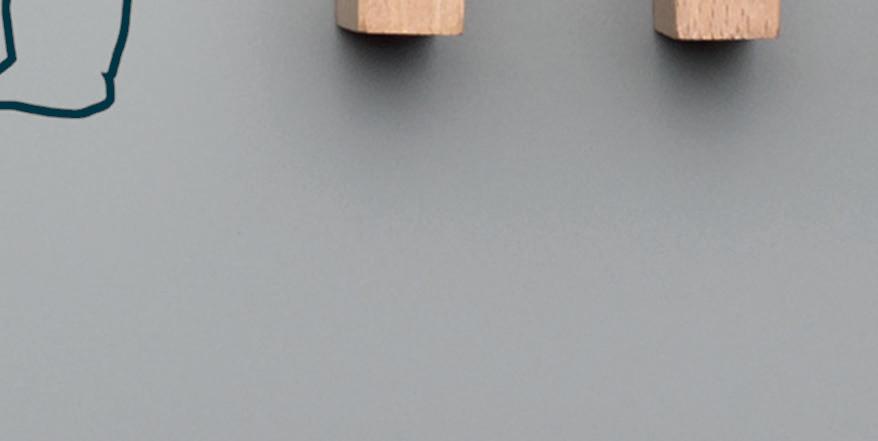
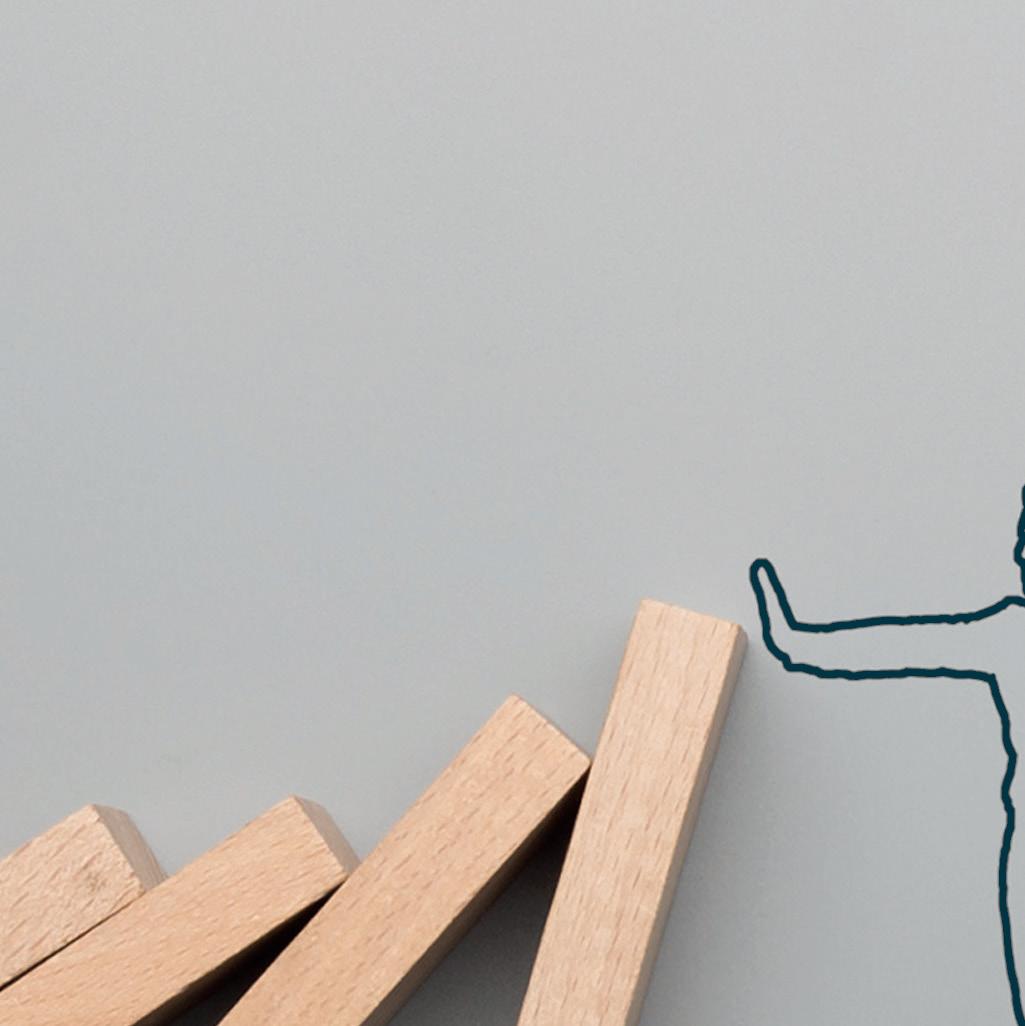
costs and lower accident risks.
Since 1978, the company has been a leading group in the engineering and manufacturing of industrial equipment specialised in the handling, storage, and transportation of bulk materials. Its solutions help improve production performance and efficiency, reduce maintenance costs and risks, and ensure a safer working environment.
Among these solutions is the AIRCHOC® air cannon which, placed on silos or hoppers, acts preventively on the material inside to prevent it from clogging, as a result of regular shots. It is an economical solution that uses air only when the shots are activated. With a wide range (tank capacity from 4 – 400 l), this solution is suitable for many sectors interacting with bulk cargo, including sectors handling coal.
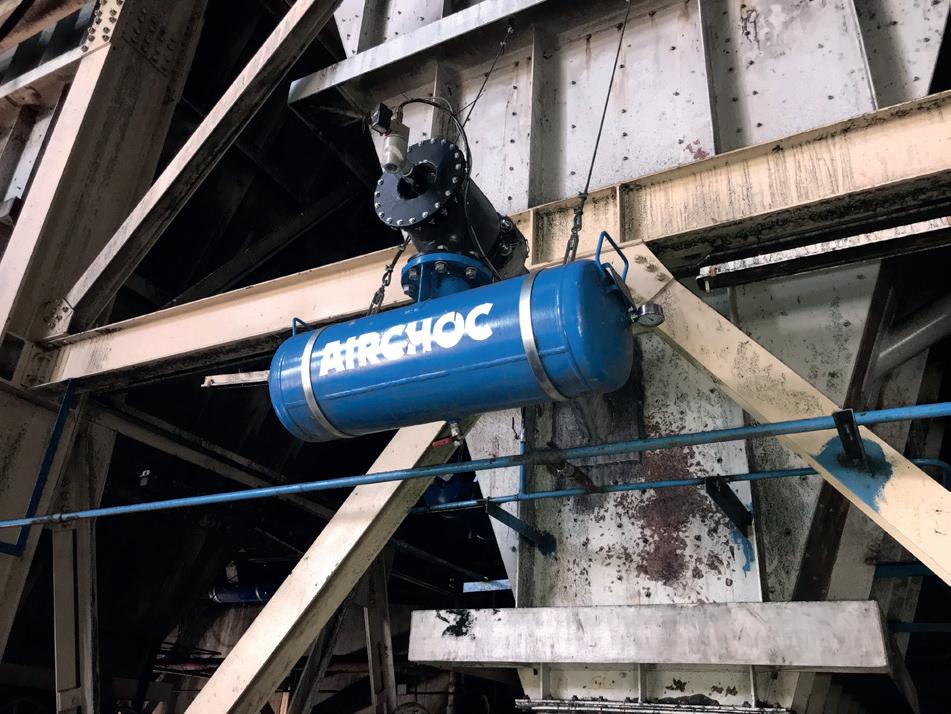
Figure 1. Airchoc ACC3SDX dn 150 mm 100 l – ATEX zone 20.
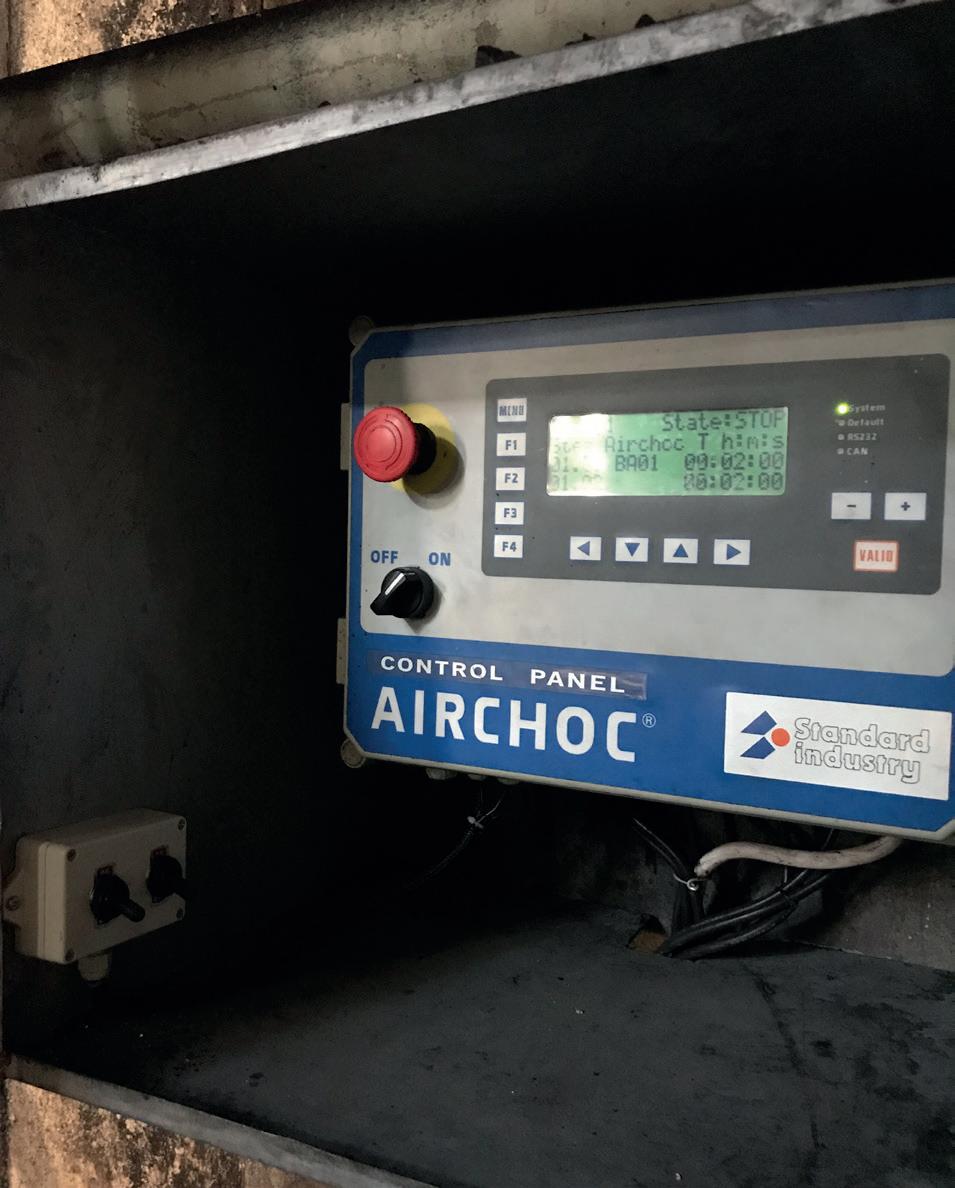
Figure 2. Control panel COFS8230 with special switch (on/off) and electrical operated release device ATEX ELESDA1322.
Case study: Indonesia
The problem
A frequently encountered problem was the blockage of two coal bunkers during the rainy season when the humidity level is very high.
Temporary solution
The client implemented the following solutions: The operators attempted to unblock the coal bunkers by using hammers and metal bars to hit the hopper at the accumulation place. Installing liners on the inside to reduce the fixation of coal on the walls.
Solution
After the problem continued to persist, four AIRCHOC ATEX devices were installed on each of the two hoppers to solve the clogging problem (Figure 1). An ATEX version was chosen in order to avoid explosion risks.
A switch was also installed for each hopper at the customer’s request in order to manually start the Airchoc operations 4 – 5 times a day, sequenced by a control panel (Figure 2). This frequency of shots ensures efficient and constant cleaning of the air pipes. An air filter on each hopper was also installed to neutralise fine carbon dust. This prevents them from being deposited on the AIRCHOC mechanism and preserves air quality.
Results
The customer was satisfied with the result of the installation of the air cannons, as they allowed them to cease the ‘manual’ unclogging of these two hoppers during the rainy season.
AIRCHOC is thus used in many other applications. It is regularly installed on raw material storage units (sand, powders, flours, grains, wood chips, peat, straw, mulch, etc.) all around the world, and can also be found at the end of the process on fly ash or lime silos.
The company’s technical teams study the clogging factors, the behaviour of the clogged product, the inclinations of the storage unit, the productivity issues, etc. This complete diagnosis allows for the establishment of an optimal installation recommendation according to the environment of use (various risks, high heat zone, corrosiveness, type of fuels burnt). The recommended solution will also consider the need for precise orientation of the shot, the number of shots, the diameter of the blow pipe according to the available pressure, the volume of the tank, and the blow pipe length.
Silo cleaning service and safety
In case the plant faces reduced collection capacity, the use of the pneumatic GIRONET, proposed by the company will help to clean the silos and allow for the restoration of the full storage capacity.
The articulated arm of the GIRONET rotates at 360˚ and eliminates the rat holing problems.
This solution meets stringent safety standards – it avoids having any human presence inside silos, therefore enabling an increase in the capacity of collection, which in turns helps to avoid supply disruptions.
The GIRONET is effective on any type of blockage, product or storage unit, and can be used without stopping production. In addition, declogging with the POWERNET will solve bridging problems through the safe breaking down of the clogged material to help it flow more freely. The POWERNET is used before the GIRONET when the storage unit is completely blocked.
Case Study: Bavarian power station
As an example relating to the silo cleaning activity, Standard Industrie recently carried out an intervention in a coal power station located in Bavaria. This plant contacted Standard Industrie to perform a complete cleaning of its five coal storage hoppers. The purpose of the operation was to make the hoppers safe for scaffolding and work.
The cleaning technique used was the ATEX GIRONET. Build ups, as well as bridging piling up in three of a range of five coal hoppers, were reducing the flow of coal to the boiler. To compensate for the reduction in storage capacity, it was necessary to operate with continuous discharge; this seriously affected the boiler capacity and production plans. One of the main reasons the plant decided to appoint Standard Industrie for the cleaning of the three silos was the safety factor offered by the Gironet solution – i.e. it meant no human intervention was necessary inside the silo. Cleaning operations are performed from the top of the silo, without putting people at risk inside the silo (Figure 3).
Moreover, Standard Industrie offered an Atex solution in the form of its ATEX GIRONET using brass chains.
No real adaptations of the hoppers needed to be made, as the cleaning GIRONET operators installed the GIRONET on existing 500 x 500 mm openings. The existing hoppers could easily support the weight of one person and the equipment. Air pressure was available so everything was here to do the job quickly and safely. After five days of interventions, the three hoppers had been cleaned, and a total of 10 t of material was extracted. The customer can now resume operation of the boiler with less risks of up and downs.
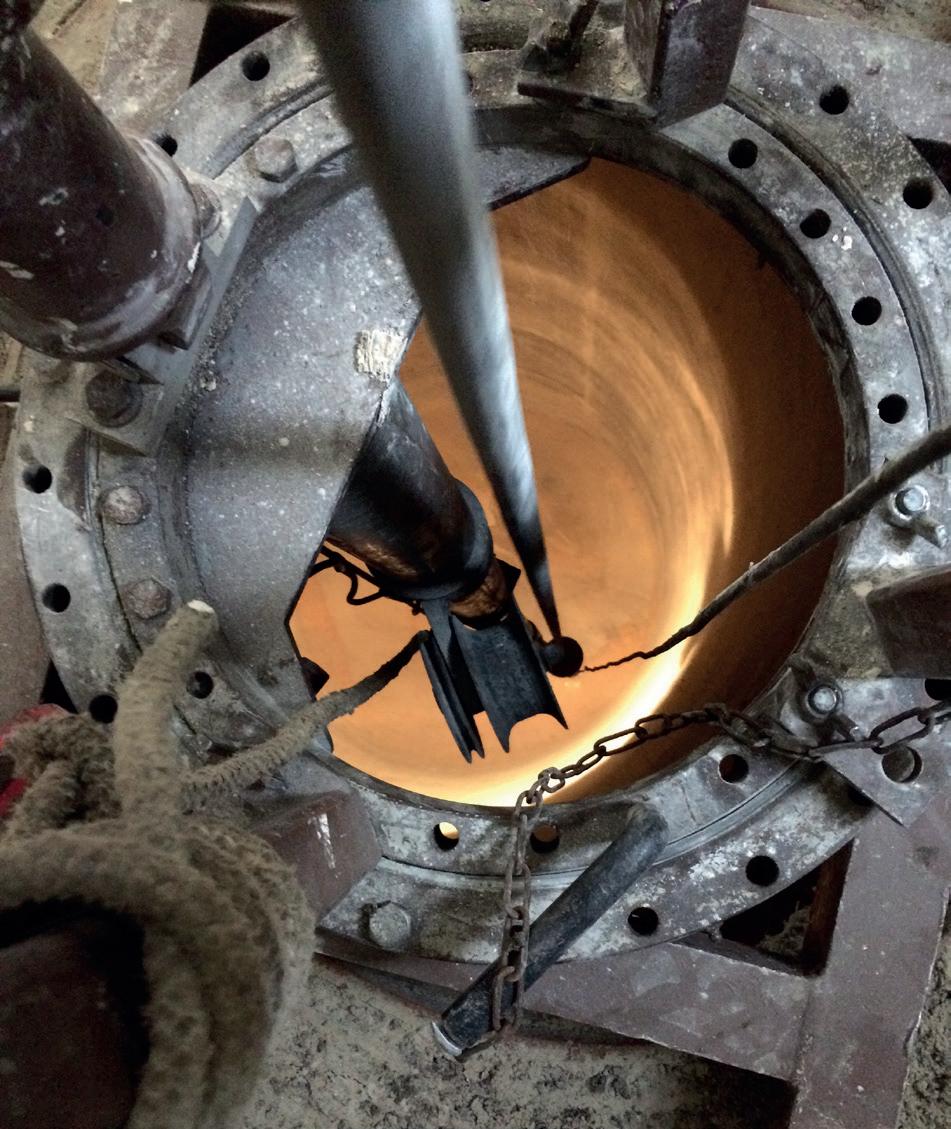
Figure 3. The Gironet, placed on top of the silo, for safe cleaning. Case study: South African power station
In another power station in South Africa, the GIRONET was implemented to clean the coal build up all around the extraction.
The 7 m rotating and articulated robust arm goes through the hole and gets attached to a mast which is fixed on to the structure of the bunker making the whole unit safe and secure.
Results
No personnel inside the bunker means there is no risk of fatal accidents. All sections of the 36 coal bunkers can be cleaned to maintain the delivery of coal to the boilers. This solution benefits the performance of the power station globally.
Conclusion
Over the years, many industries have successfully replaced manual cleaning with an air cannon. Manual cleaning unnecessarily requires qualified personnel and high levels of supervision; moreover, extra safe measures have to be taken and sometimes may lead to unplanned shutdown, which involves loss of production. This type of human intervention is both difficult and dangerous, and can cause serious or even fatal accidents. In addition, the advantages it offers include: effective declogging of the structure without interrupting the production process; elimination of the risk of feed restrictions, blockages and production downtime, proportionally to the installed equipment; increased safety of the principle; and a fast return on investment.