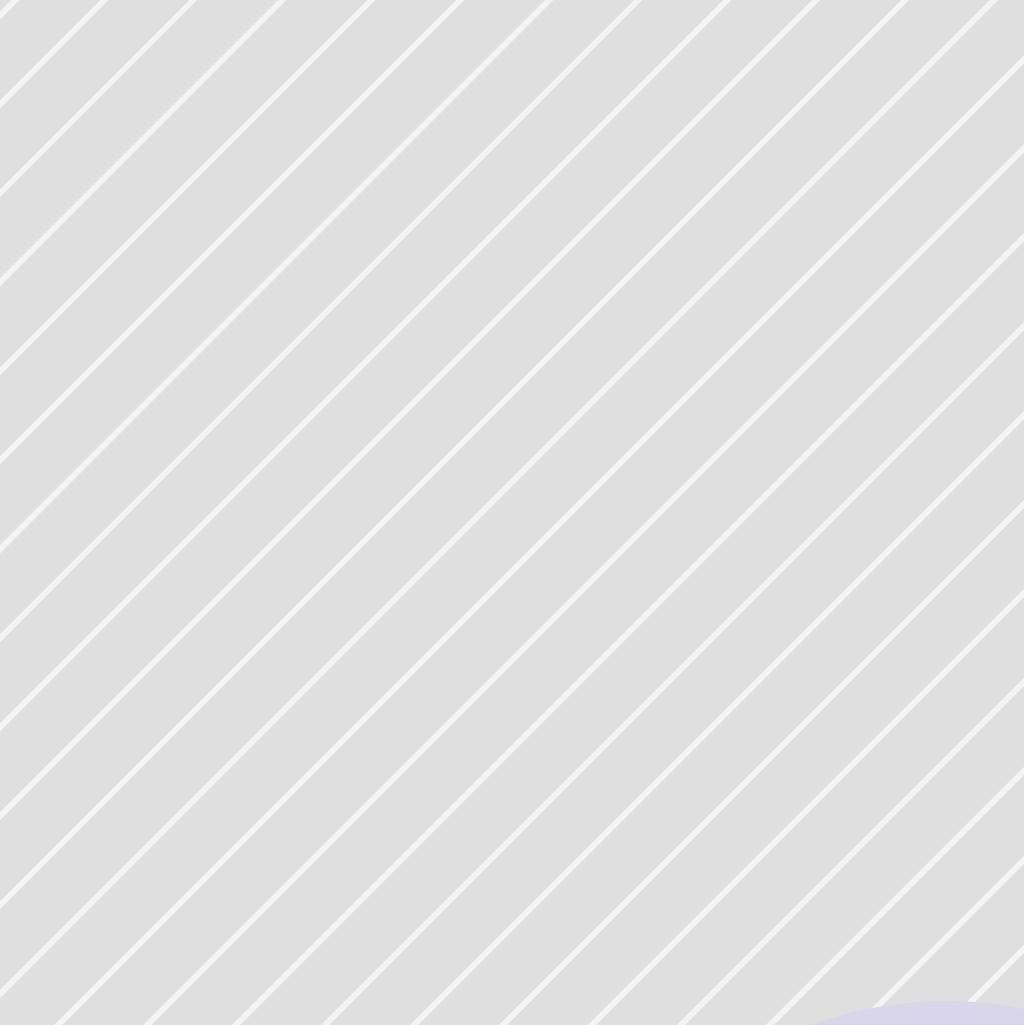
6 minute read
Unlocking Load And Haul Effi ciencies
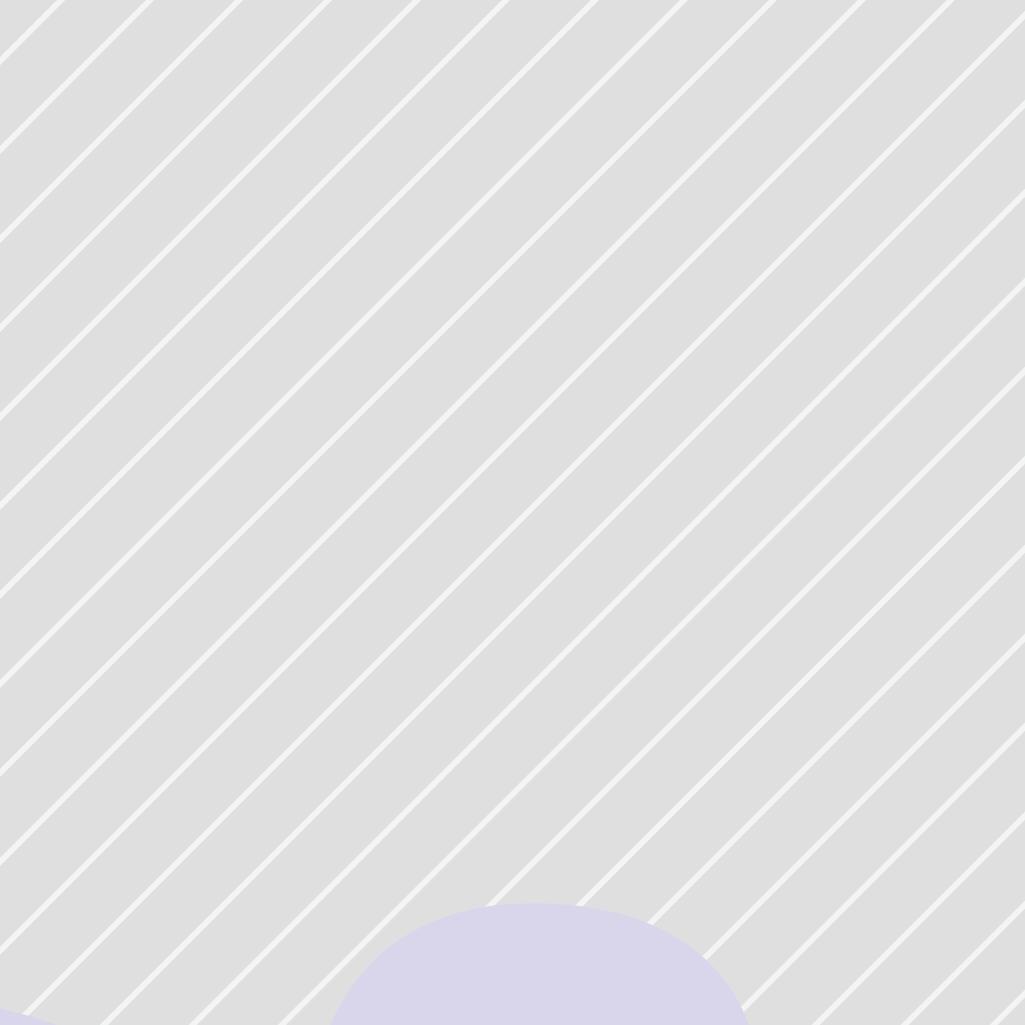


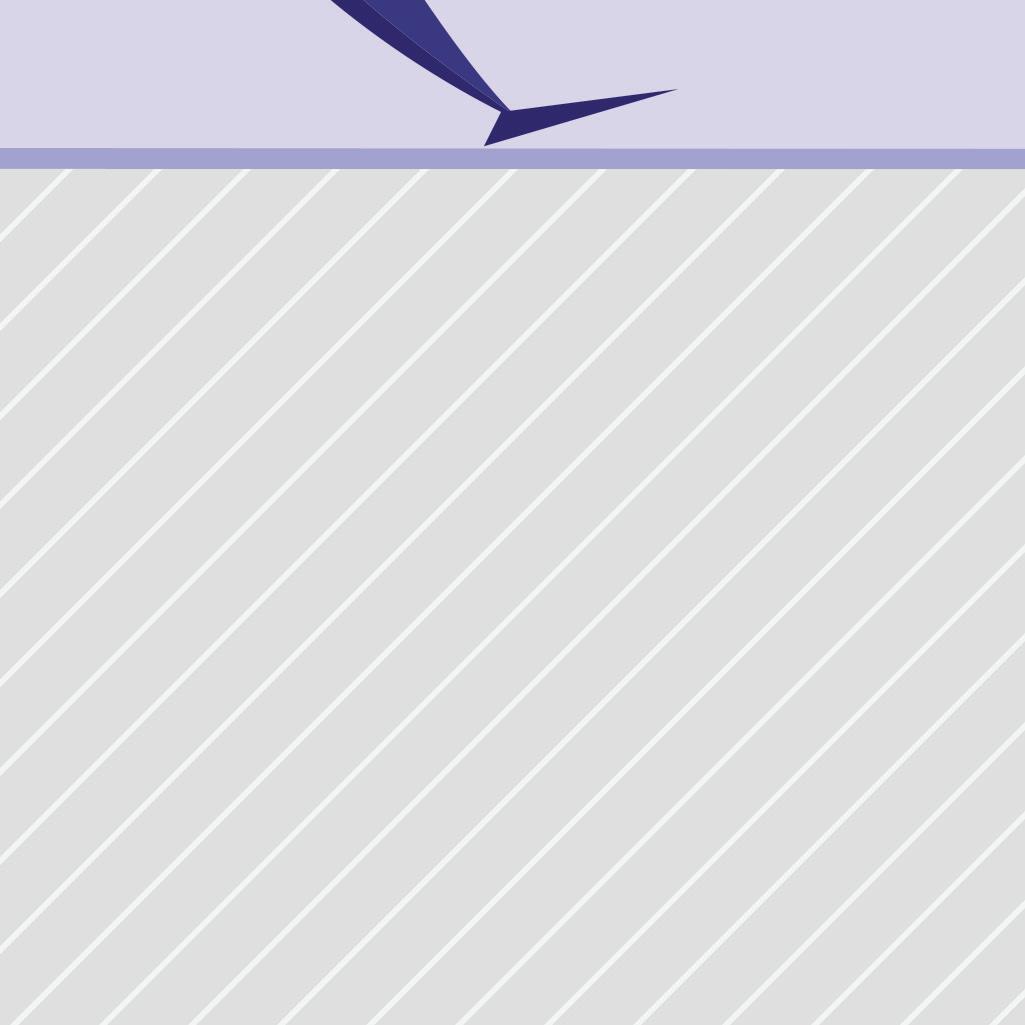
As the coal industry continues to deal with fluctuating coal prices, it is critical to improve operational eff iciencies in order to maintain profitability goals. A tighter integration and smarter analysis of the big data now available can be a strong contributor here – especially in load and haul process route optimisation, payload compliance, and fleet uptime and longevity.
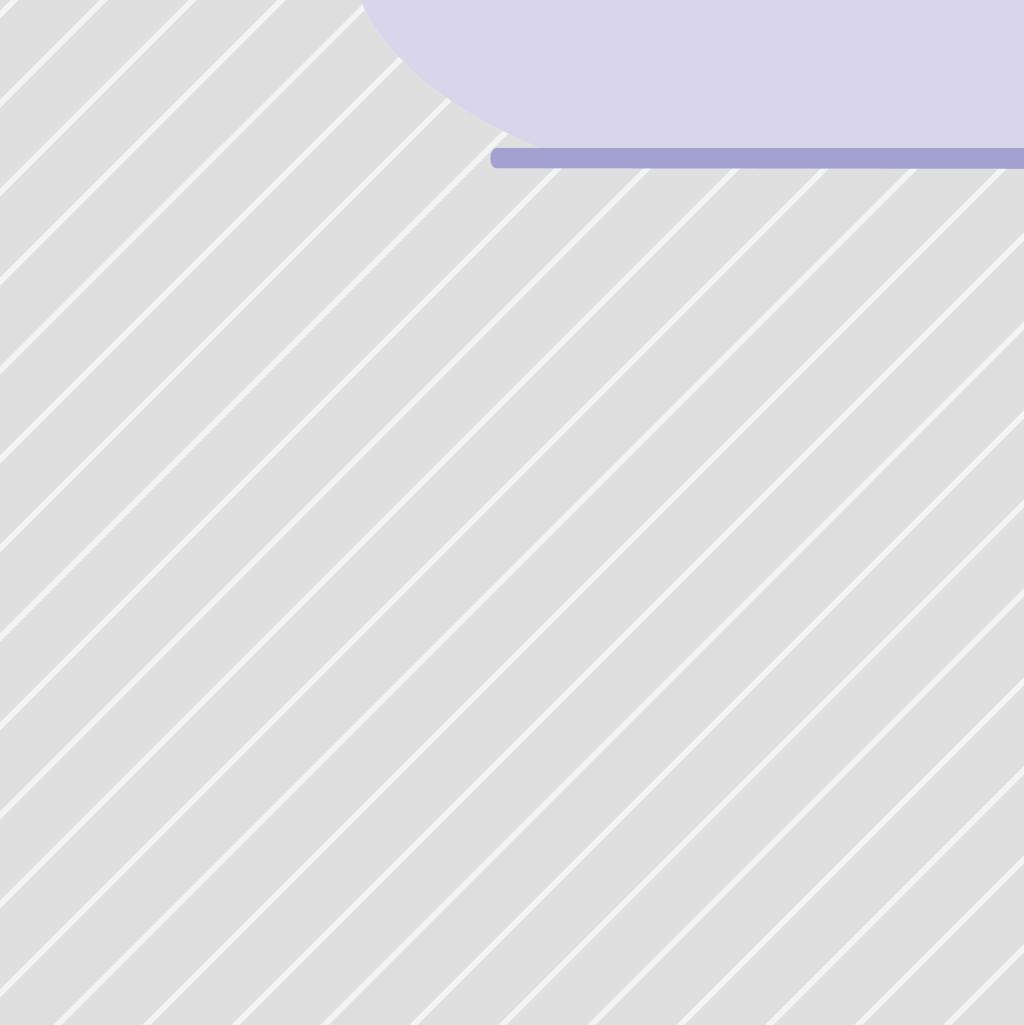
Data solutions
Traditionally, mining companies have looked to a combination of on-board control systems and original equipment manufacturer (OEM)-agnostic technologies, in order to assist in improving individual load and haul tasks. Onboard control systems provide critical data, such as machine health and payload. And, OEM-agnostic technologies off er real-time information for payload optimisation, machine guidance, fleet management, and a range of other tasks.
While each control system or technology can provide value on its own, it is the integration of these onboard control systems and OEM-agnostic systems that empower valuable insights for faster and more-informed decisions. Mines that push ahead in this area can expect significant benefits, such as: Consistent operations with increased safety. Optimised dispatching and real-time decision-making. A next-level competitive advantage with cost savings and reduced cycle times. Optimisation across the load and haul process. Maximisation of the entire value chain.
OEMs, such as Komatsu, are focused on creating, connecting, and transforming data and systems to better manage the ever-increasing complexity of mining operations. In partnering with their customers, Komatsu provides expertise and integrated solutions that can
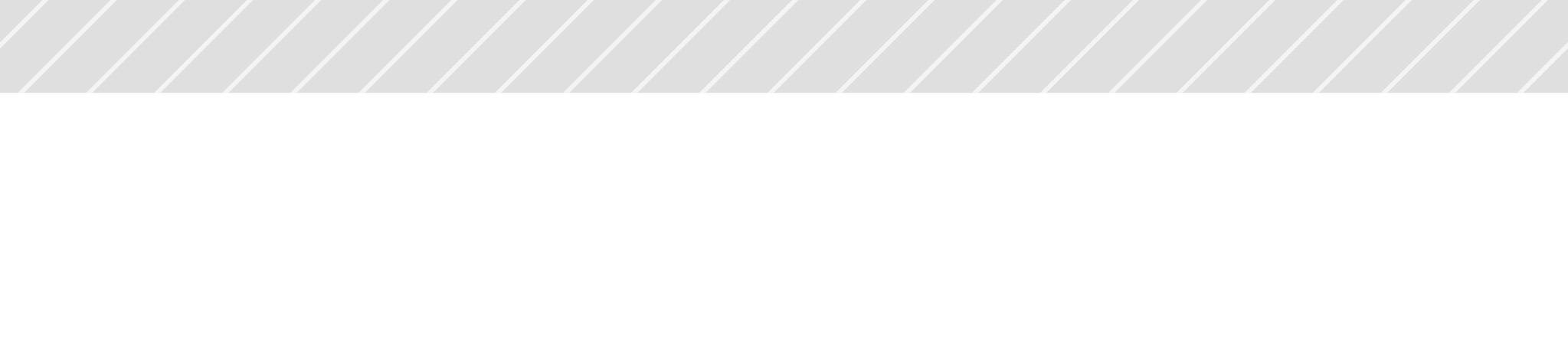

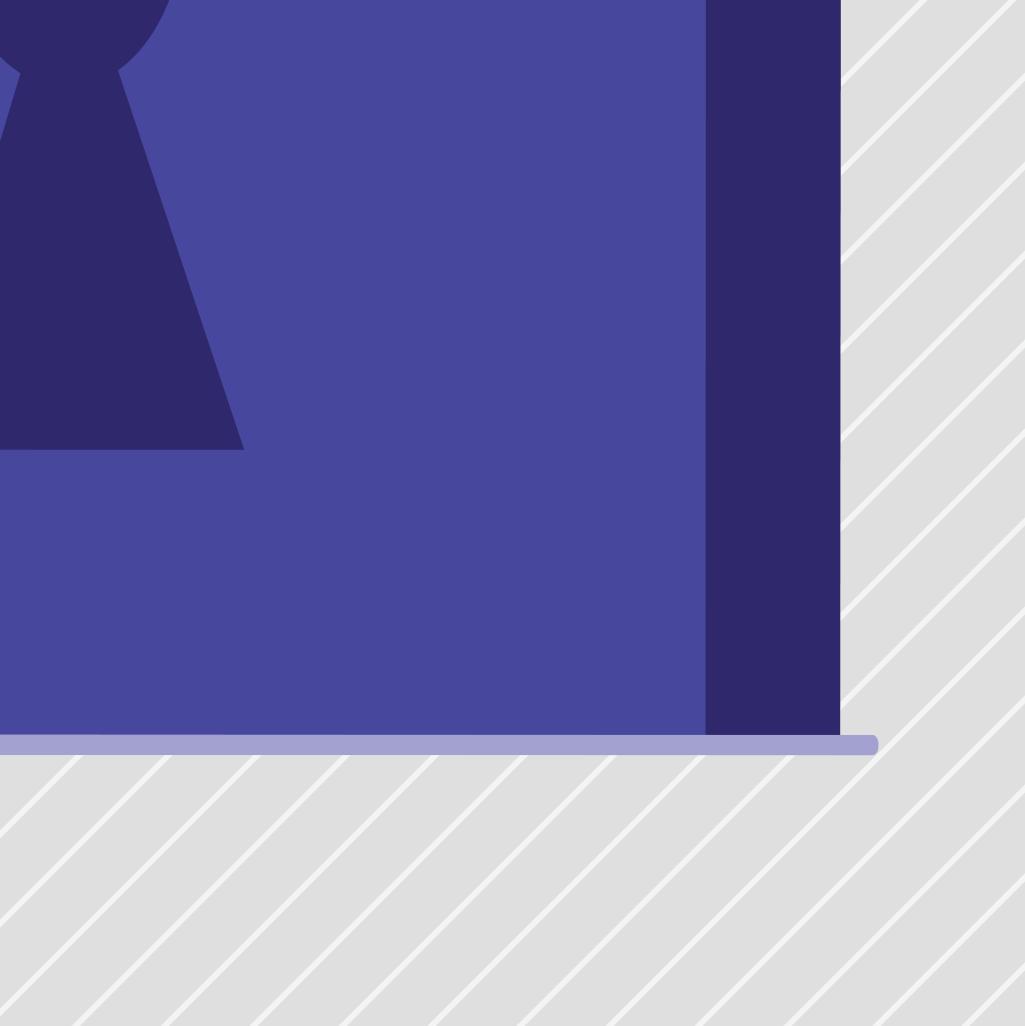
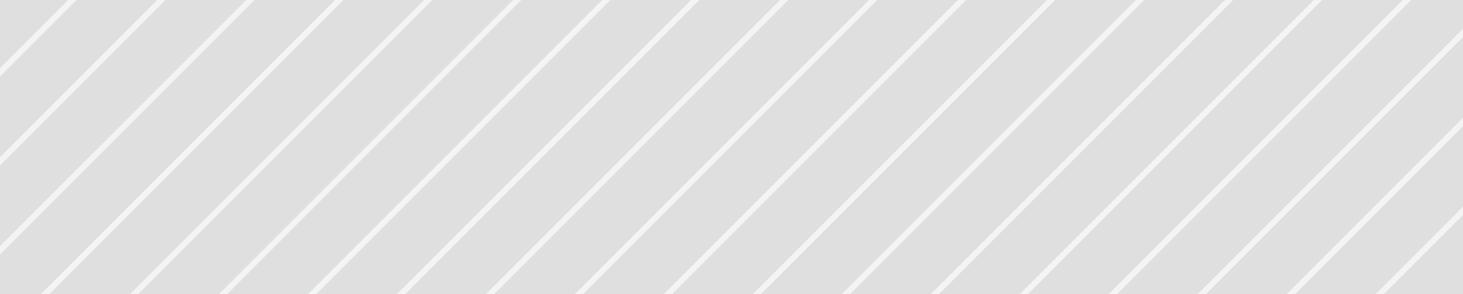
Simon van Wegen, Komatsu, USA, outlines how to unlock load and haul eff iciencies by better integrating and analysing data.
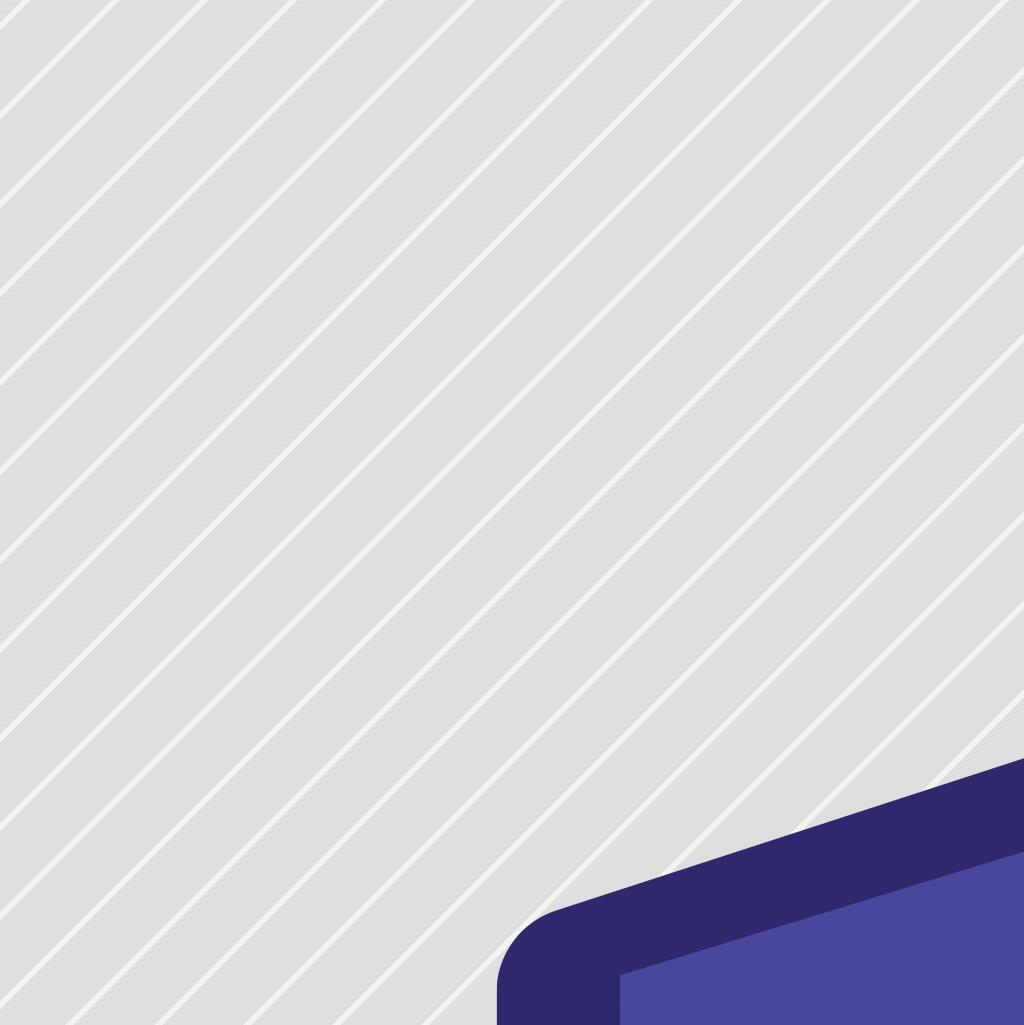
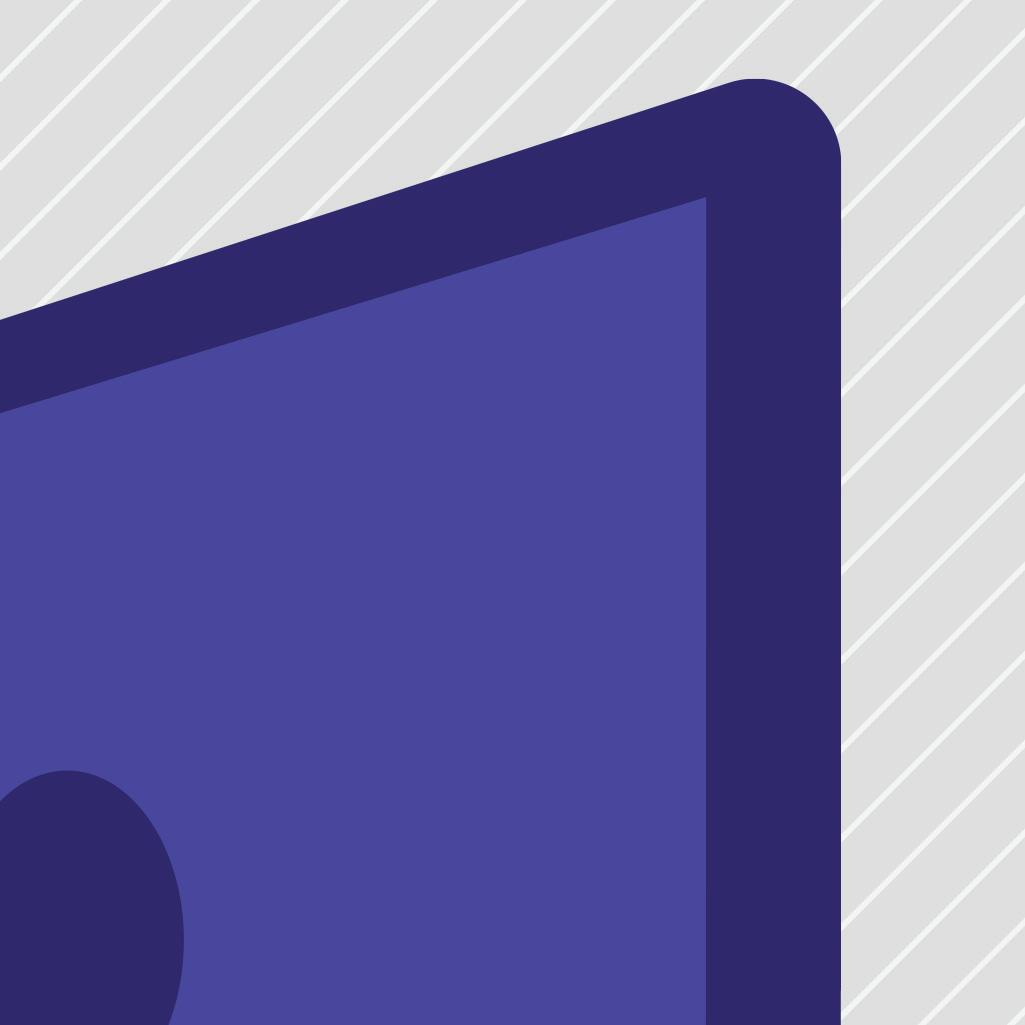
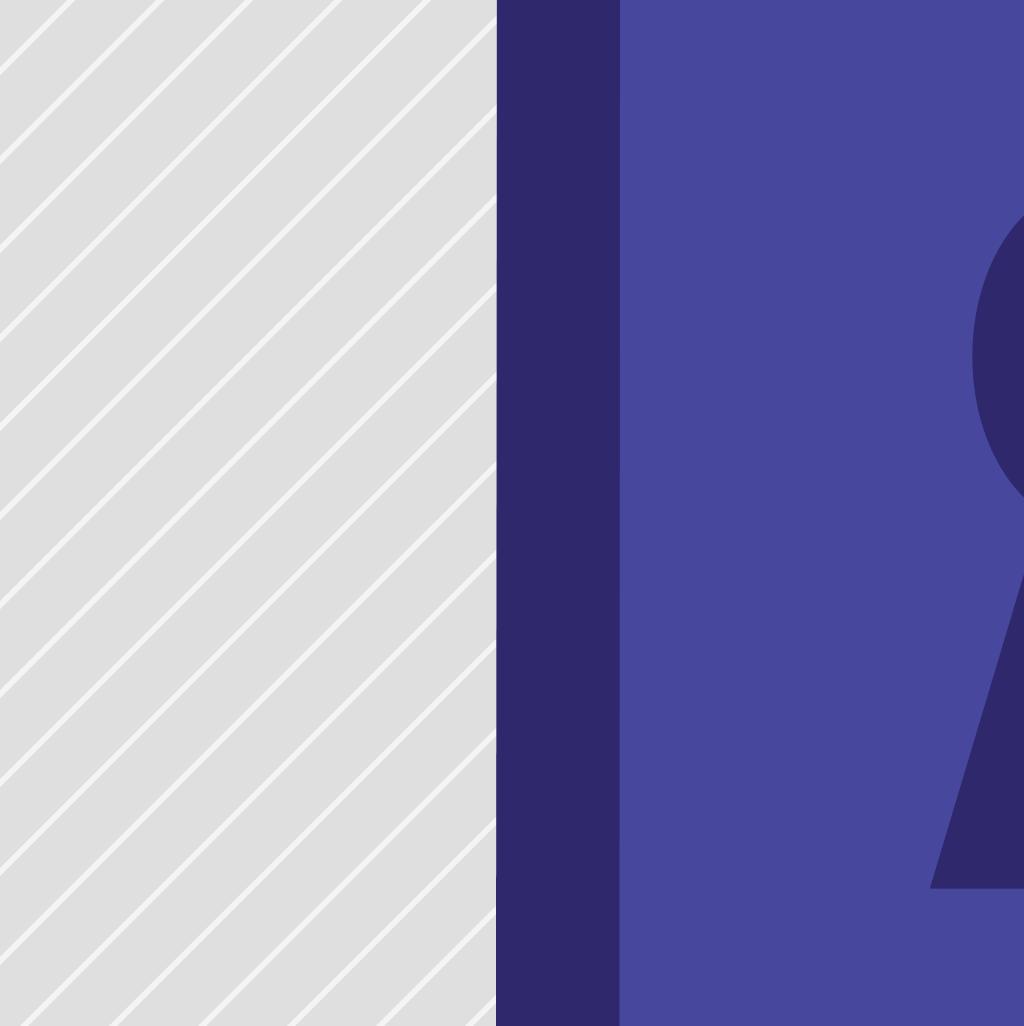
do just that. The company’s smart mining approach is designed to accommodate any mining operation regardless of equipment, technology, or data maturity.
Centred around the load and haul process, these data solutions services focus on boosting productivity, increasing eff iciency, while remaining focused on safety.
With a range of holistic solutions that translate data into insights using connected cloud and edge data, these insights identify patterns and actions to continuously improve the load and haul process, as well as the entire value chain.
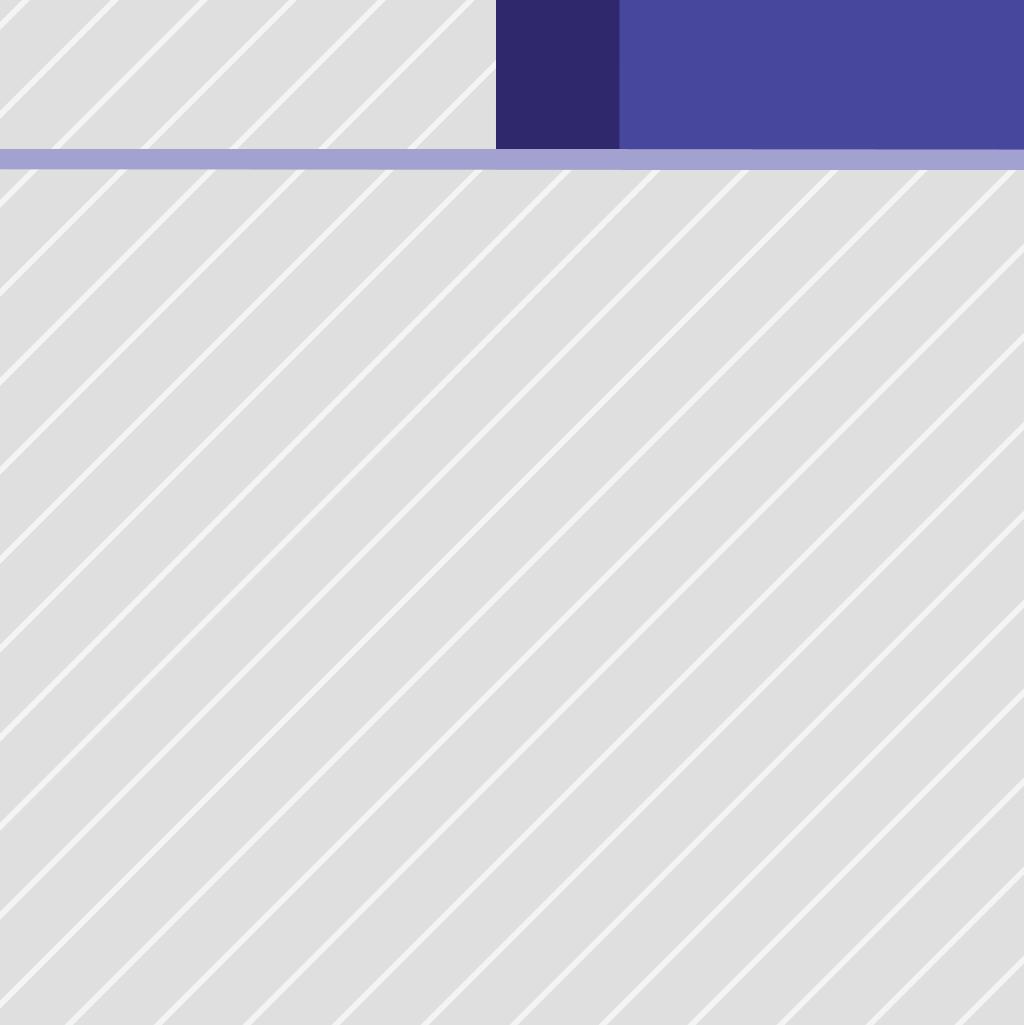
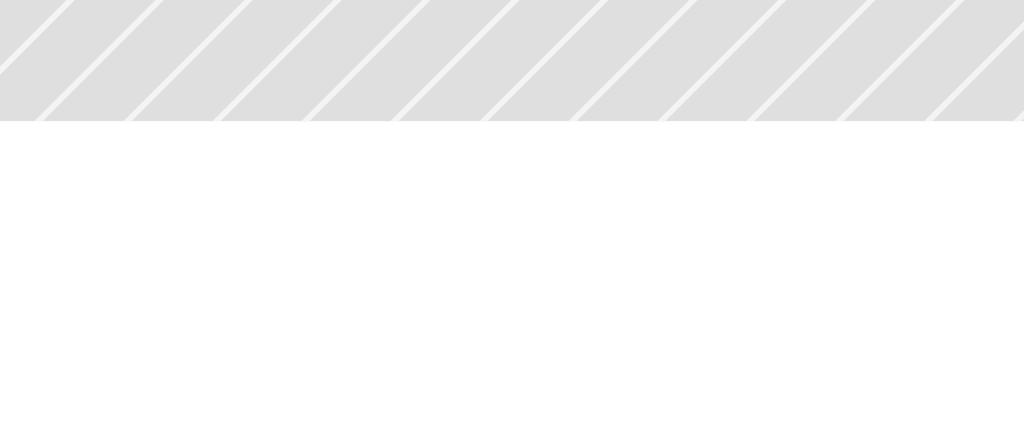
Load up on payload results
Both underloading and overloading haul trucks can negatively impact the production of mining operations: an underloaded truck reduces eff iciency and productivity, while an overloaded truck can create higher maintenance costs. In order to avoid both scenarios, operators require real-time payload information.
Komatsu’s Integrated Payload Management solution leverages a mine’s existing equipment and technology to deliver just that. Integrating all payload systems across all makes of equipment provides a comprehensive view for operators, and empowers full collaboration between personnel using truck and shovel payload management systems.
An example of the optimised payload process shows the on-board truck payload system communicating the target payload information through the fleet management system to the shovel operator (Figure 1). The shovel operator then loads the truck to its optimal target load, adjusting for any carryback.
An Australian coal mine has benefited from the Integrated Payload Management solution with the help of local Komatsu experts. Working collaboratively with the operations team to integrate their existing on-board controls systems and OEM-agnostic technologies, the mine was able to improve payload accuracy by 5%.
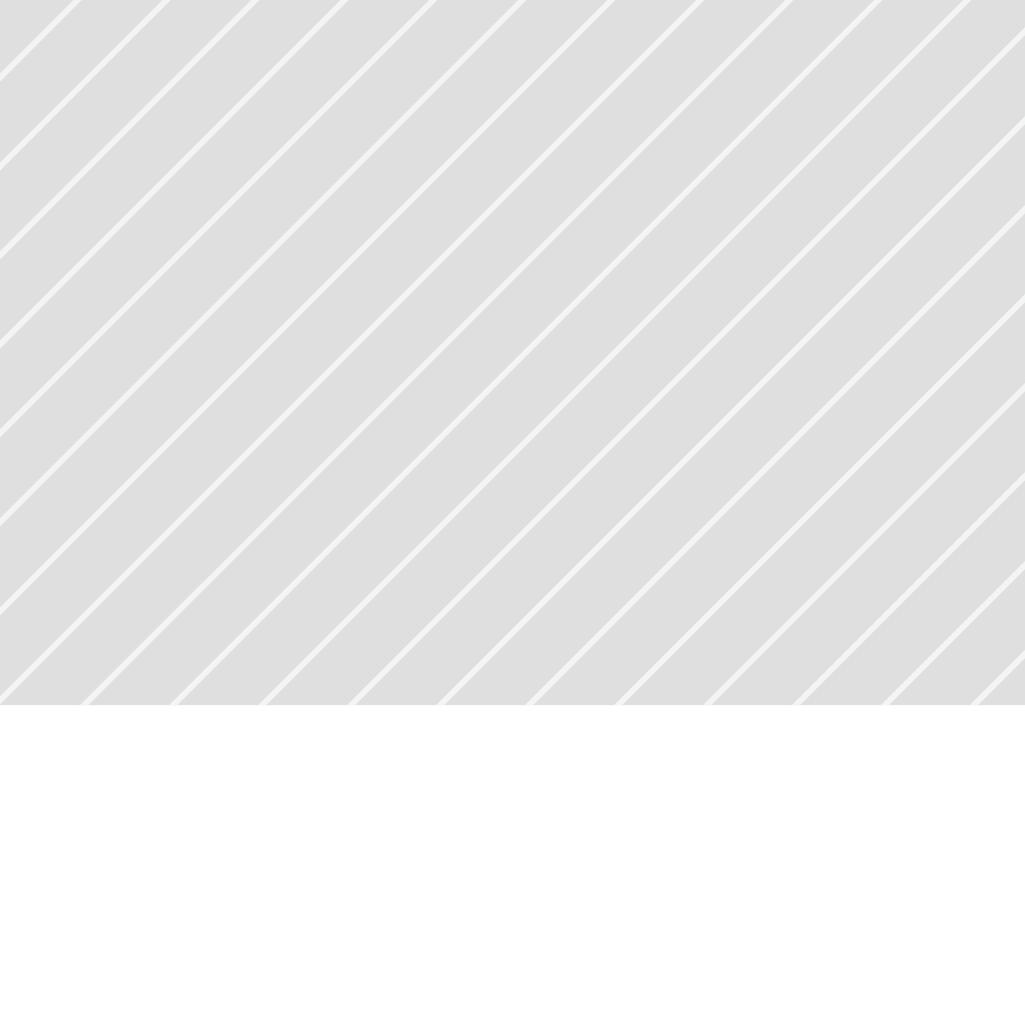
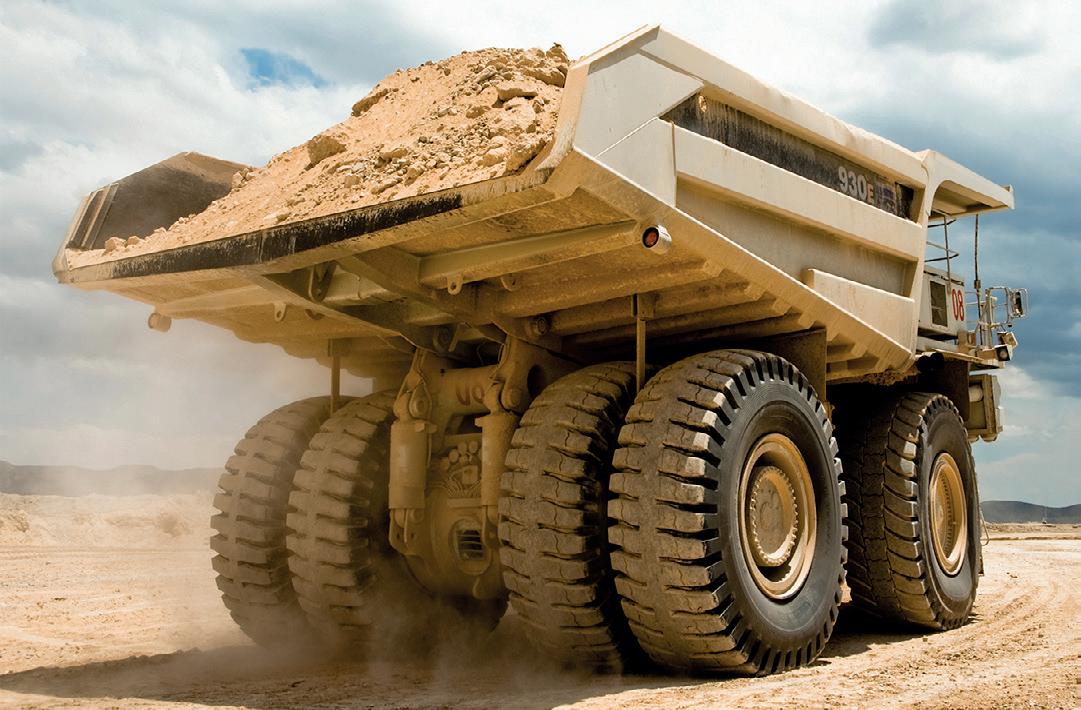
Phase 2: implementation
Once the assessment is completed, the recommendations are implemented, such as route modifications and operator training.
Phase 3: sustainable results
It is important to be able to Figure 1. Visual representation of the optimised payload management process through the integration of on-board and OEM-agnostic technologies. continuously test and improve. So, Komatsu’s team creates a digital simulation of the road network and compares the set targets and baseline performance metrics against the real-time data. If reality does not match the plan, the mine is alerted so corrective actions can be taken. Mines using truck cycle optimisation are seeing results. Komatsu and partner customers have achieved up to 23% improvement in truck cycle times.
Shift from reactive to proactive
Tuning the truck haulage cycle
Ensuring that the load and haul process is not a bottleneck in the value chain is essential. Eliminating issues such as poor road conditions, traffic congestion, speed restrictions, long route layouts, and inconsistent operator practice can help to reduce cycle times, accelerate productivity, and reduce light-vehicle interaction for additional safety (Figure 2).
Komatsu’s truck cycle optimisation solution enables mines to make more informed decisions to achieve excellent haul cycle rates and safety. By utilising data in digital simulation and scenario assessments, mines can continuously refine haul and vehicle routes to reduce haulage cycle times, move more material, and reduce equipment interactions. Komatsu can help establish key performance indicators (KPIs) for truck speed and continuously monitor results against baseline targets to ensure optimisation is ongoing.
Further optimising the efficiency of loading and hauling is not enough if haulage equipment is unreliable. To address this, Komatsu has a focused remote health monitoring (RHM) solution. Figure 2. Utilising data in digital simulation and scenario assessments, The RHM programme creates a more integrated mines can continuously refine haul routes to reduce haulage cycle asset health management ecosystem, giving times, move more material, and reduce equipment interactions. mines a more comprehensive picture of their operations. It combines real-time data insight, OEM equipment knowledge specialists, and cloud-hosted big data analytics. With RHM, Komatsu and mines track critical machine and production data and then use it to prevent unplanned downtime and better prepare for planned downtime by monitoring machine health. In some cases, it could be machine data alone identifying an imminent issue or a deviation in production performance. Because the monitoring is remote, operations benefit from Komatsu expertise on site or at the factory or service centre. With RHM, the integration of multiple data sources and systems, such as MineCare and Komtrax Plus, helps customers minimise downtime with proactive and real-time alarms. Operations using Komatsu RHM have seen machine availability increase by more than 5%, and mean time between failures increasing by more than 150%.
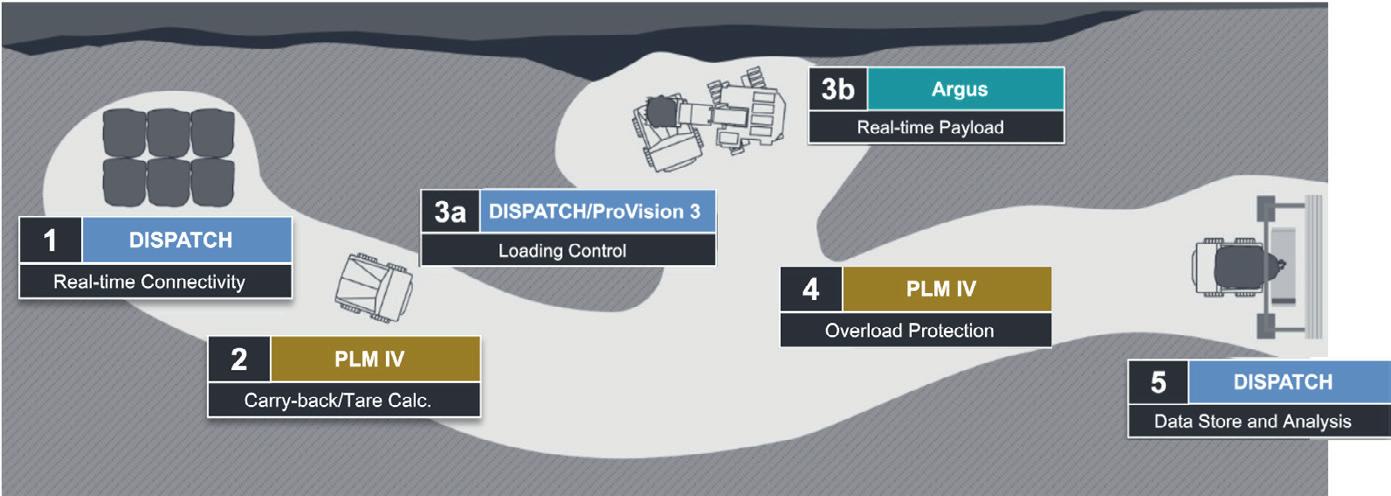
Implementing truck cycle optimisation
Phase 1: assessment
Includes simulation and evaluation of a mine’s baseline performance targets and metrics to quantify areas for opportunity. Komatsu mining teams work with mine personnel to develop an action plan to optimise the road network.
Creating value together
Each solution plays an integral part in further optimising the load and haul process. While many mining companies own mining assets with on-board controls and OEM-agnostic technologies, companies, such as Komatsu, are working with customers to maximise the value of their systems through integration and innovation.