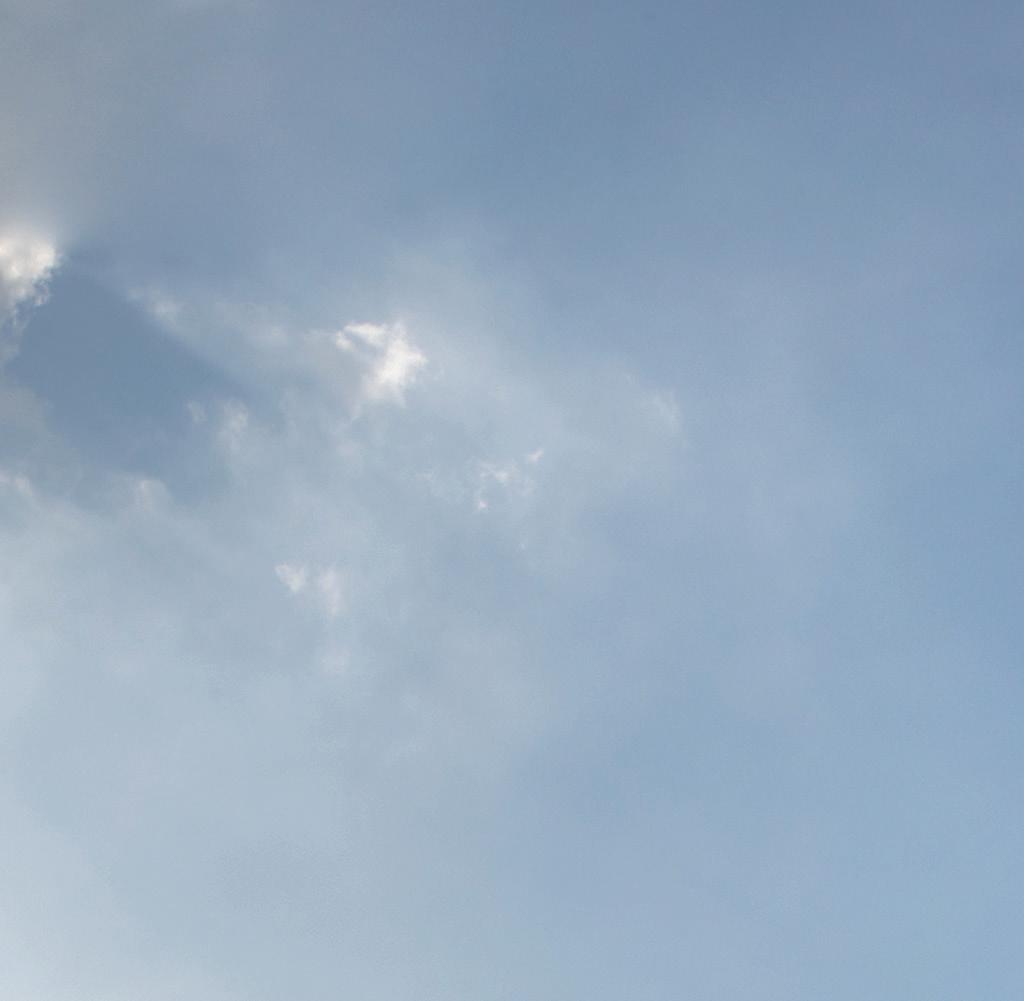
9 minute read
Surface Mining For Cleaner Coal
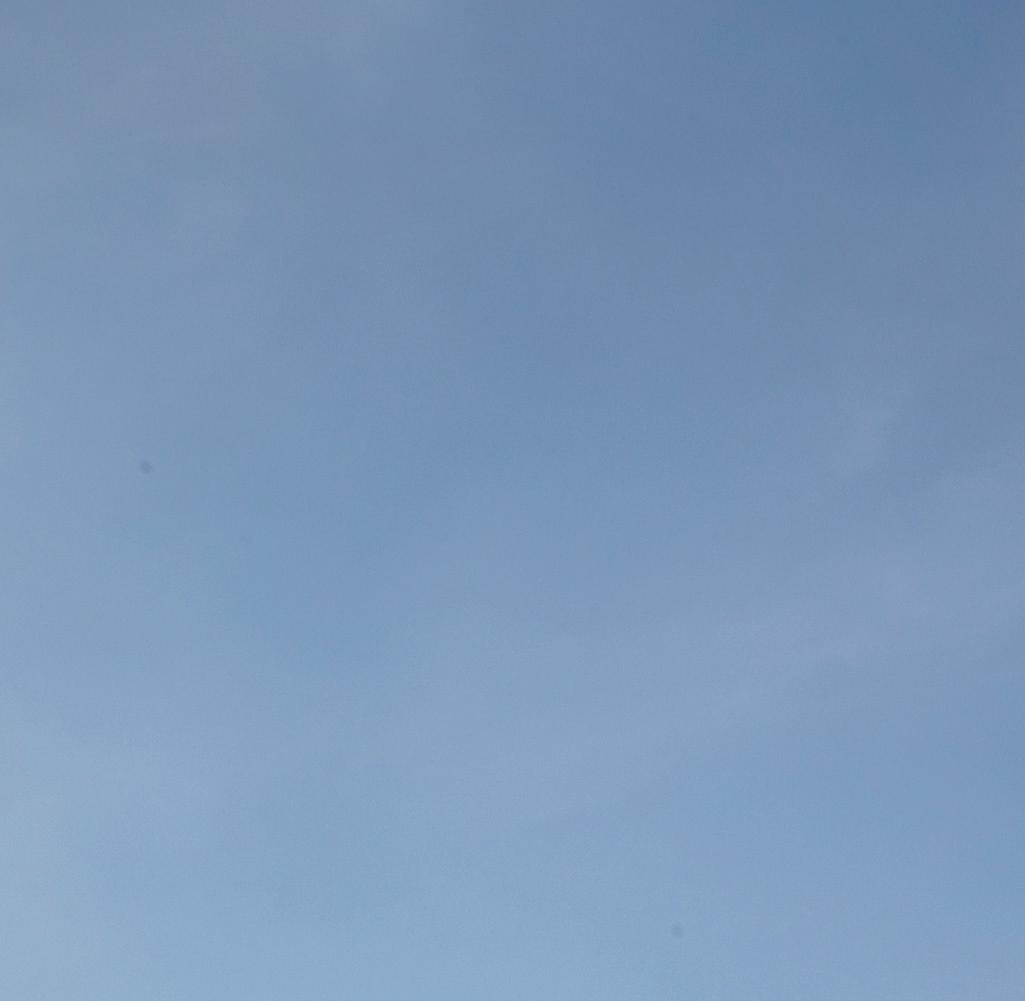
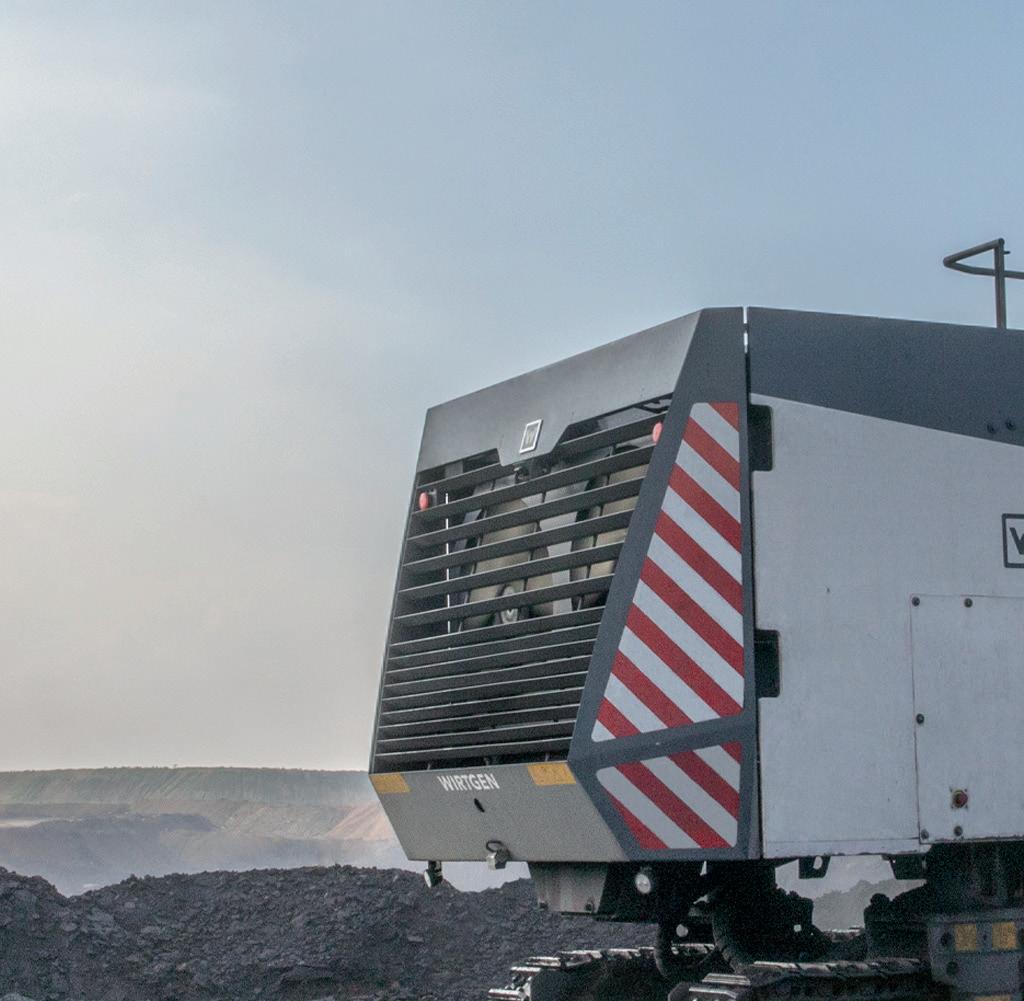
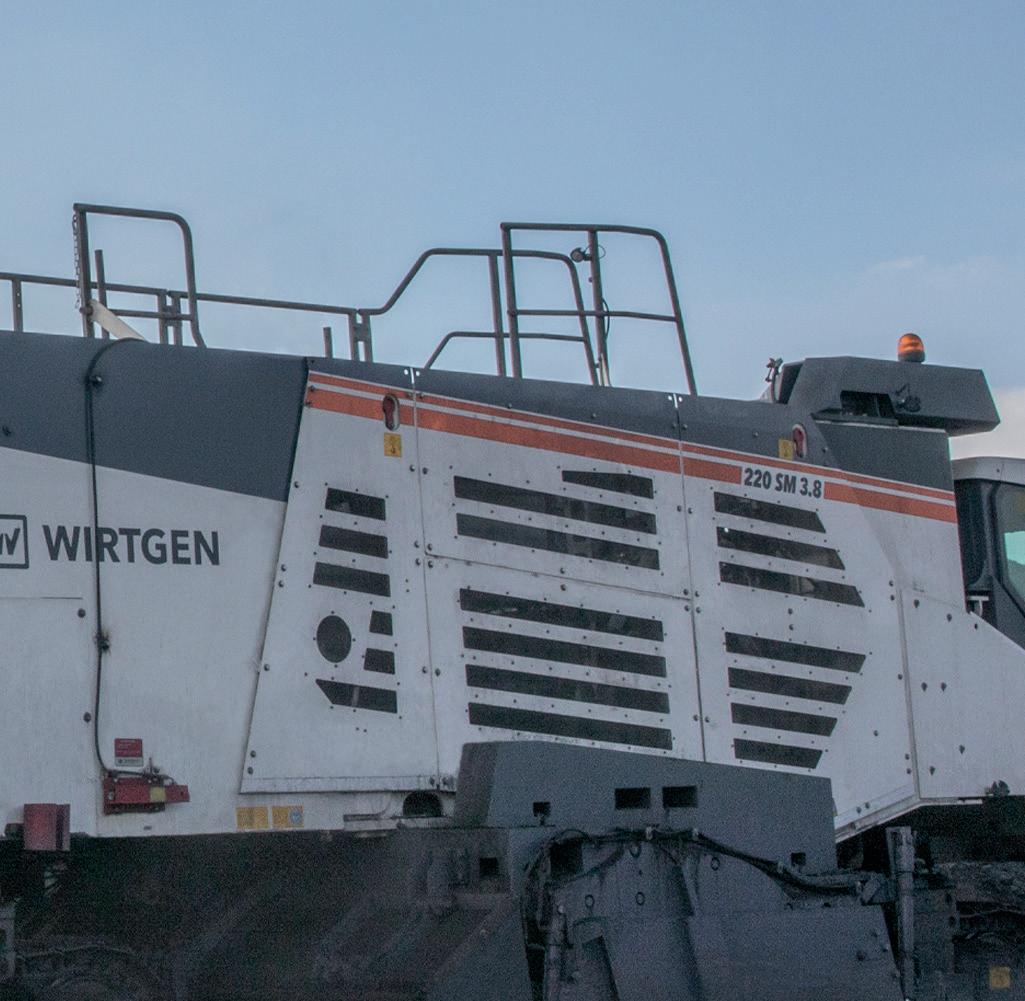


Dr Erik Zimmermann, Wirtgen GmbH, Germany, provides insight into how surface miners can help coal operations become more environmentally responsible.

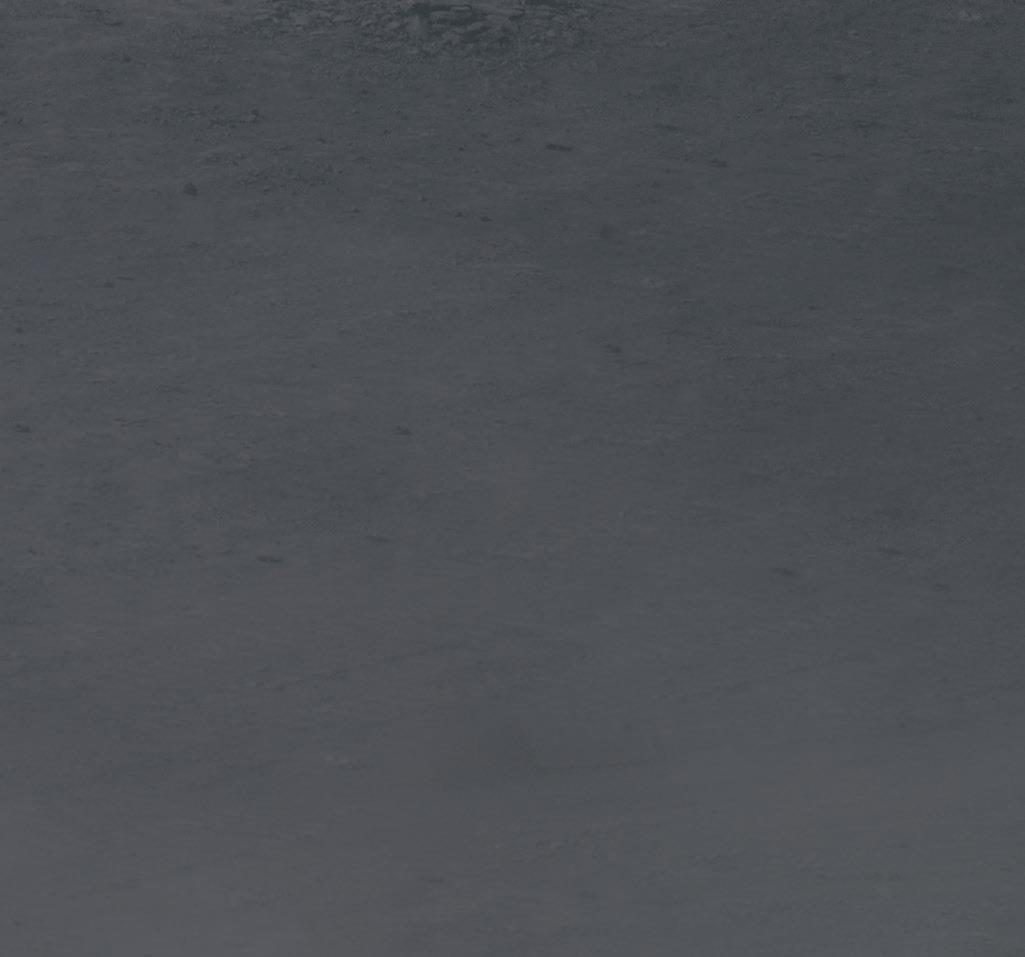
Today, more than ever before, industrial processes pivot on sustainability and environmentally compatible technologies. The prioritisation of these aspects is also becoming increasingly important in opencast coal mining.
Conventional mining methods for the extraction of primary resources include, for example, ‘rip-and-stack’ and ‘drill-and-blast’. Here, too, mining companies are making every eff ort to achieve environmental compatibility. In particular, they have already consistently reduced the exhaust gas emissions of the machines deployed and the environmental eff ects of blasting. Despite these successes, the fulfillment of the intended objectives is becoming increasingly diff icult.
A simple and economically viable way of reducing the exhaust gas emissions of the machine fleets deployed is to simply mine the same volume of materials with fewer machines. This lowers the specific fuel consumption per tonne of material mined.
The environmental eff ects of blasting can be minimised by reducing the explosive energy released
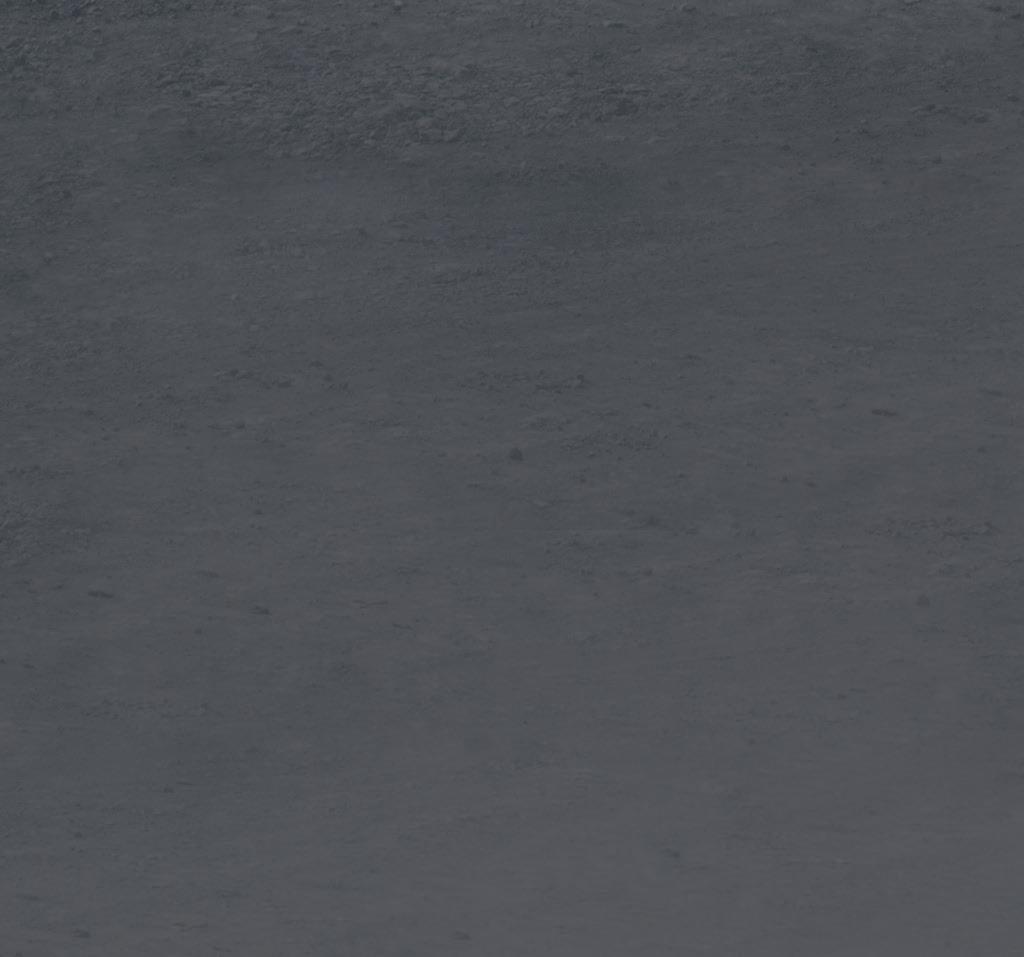
in the blasting process to a minimum, and keeping the number of blasting operations as small as possible.
Benefits of surface miners
This is precisely where surface miners can help bring significant advantages. As the first step in the process chain, they can play a decisive role in the realisation of more efficient, safer, and more environmentally friendly opencast mining of primary resources. They selectively mine coal – as well as other raw materials, such as: limestone, salt, bauxite, iron ore, and gypsum – with an absolute minimum of interburden. This results in products with a high degree of purity that can be loaded from the surface miner’s belt conveyor system directly into transport vehicles, or stockpiled for loading at a later stage of the mining operation. The use of surface miners can effectively eliminate the need for drilling and blasting.
In comparison to conventional equipment, a further advantage is that the machines can also be used in urban environments. The mining process produces level surfaces that serve as stable roadways and facilitate fast and safe transport of material. Another contrast to conventional equipment is that there is also a considerable reduction of environmental impact in the form of vibration, dust and noise, and a simultaneous improvement of safety at opencast mines.
Selective mining of pay minerals
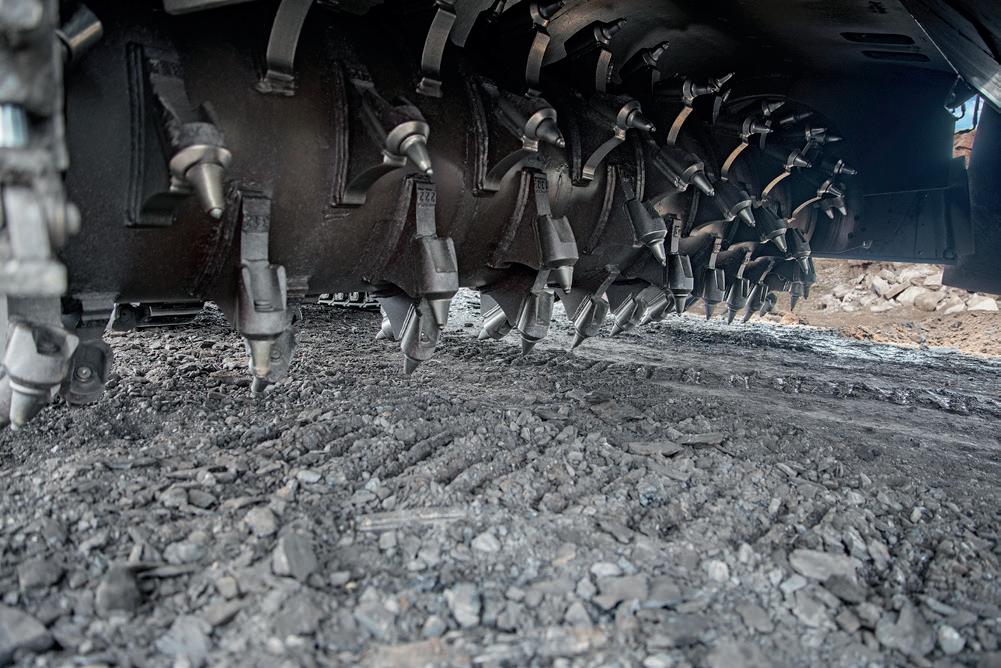
Figure 1. Cutting drum of a 220 SM 3.8 for coal mining. As the surface miner moves forward, a cutting drum fitted with numerous picks rotates against the direction of travel (up-cut method), cutting layers of material from the rock formations and crushing it in the drum housing. Depending on the method selected, there are now two different loading options. For example, in the ‘cut-to-ground’ method, the mined material is deposited directly behind the machine for loading into transport vehicles by wheeled loaders at a later stage of the mining operation. The second option is direct loading into transport vehicles by means of the machine’s belt conveyor. Here, the primary conveyor receives the material from the drum housing and transports it to the rear of the machine, where it is then transferred to the slewing and height-adjustable discharge conveyor. The discharge conveyor either loads the material directly into transport vehicles (direct loading), or discharges it alongside the surface miner (side casting). The discharge height can be adjusted to the height of the transport vehicles. An automatic levelling system ensures that the machine maintains the exact cutting depth, allowing even thin seams or layers to be selectively mined with maximum precision.
The use of surface miners, such as those offered by Wirtgen, is accompanied by the following characteristic process benefits:

Selective mining
Figure 2. Comparison: amount of equipment.
Figure 3. Surface miner operating principle. Thin seams interspersed with intermediate rock layers can be mined precisely and economically. Surface miners ensure high-quality run-of-mine material by adjusting the cutting depth in millimetre precision. Higher quality of the mined material. Better stripping ratio due to reduced dilution. Increased processing plant recovery.
Blast-free-mining
Environmentally friendly mining – due to no vibration and fly rock, reduced dust, fumes, and noise.
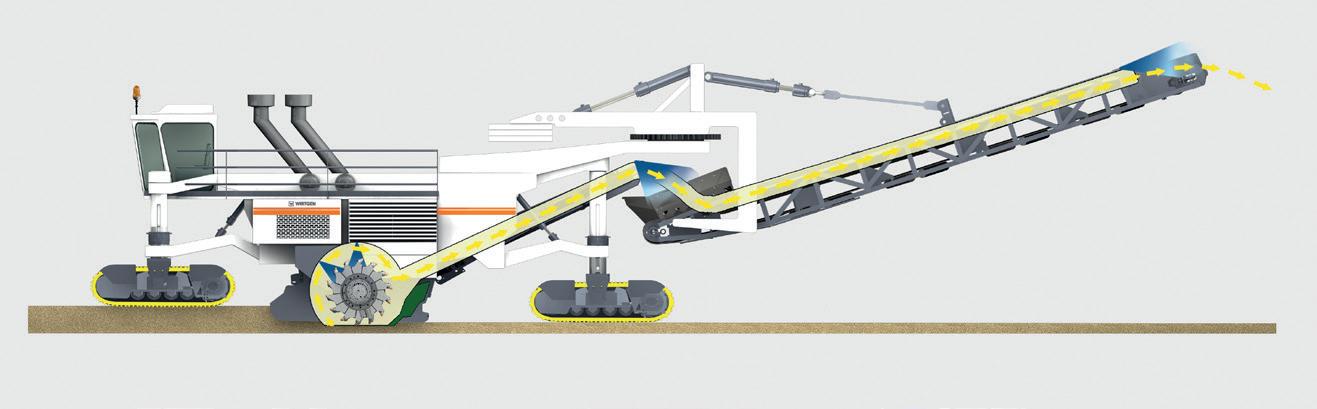
Better drainage, with less water seepage into floor. Easier slope reclamation. Improved safety due to no usage, handling, or storage of explosives. Effective mining close to residential areas, public roads, or pipelines is possible. Reduced amount of work for permission and documentation of explosives. Improved slope stability, and thus less rock fall. No oversize rock handling caused by poor blasting. Higher pit availability – due to no production delays and stoppages caused by blasting.
Cut, crush, and load in a single operation
Streamlining the mining operation. Simplification of production planning. Simplification of administration and maintenance. Higher pit availability – due to reduced time losses in-between mining steps. Reduced number of mobile equipment and thus lower emissions and operating costs – due to reduced maintenance, health and safety equipment, personnel, and fuel. Lower mining unit costs (US$/t). Potentially saving the primary crushing stage.
Reduced haulage costs
Creation of smooth and levelled surfaces. Smaller on-highway trucks can be used. Reduced haul road maintenance. Smooth surfaces allow for faster haulage. Less wear and tear on truck tyres. Smooth and consistent loading operation. Less wear and tear on truck bodies, frame, suspension, and tyres. Loading consistent to design payload.
Maximum reserve extraction
Improved deposit exploitation, improved stripping ratio, and increased reserve base due to: Increased slope stability and higher slope angle. Buffer/safety zones can be mined additionally. Additionally mined thin seams.
In addition to blasting operations, the most significant environmental effects of opencast mining are due to the use of a whole variety of different machines. Reducing the number of machines deployed leads to lower carbon dioxide (CO2) emissions. Studies and tests have been conducted at a number of opencast coal mining sites over a period of several years. Comparisons with conventional opencast mining show that the use of surface miners is accompanied by a significant reduction
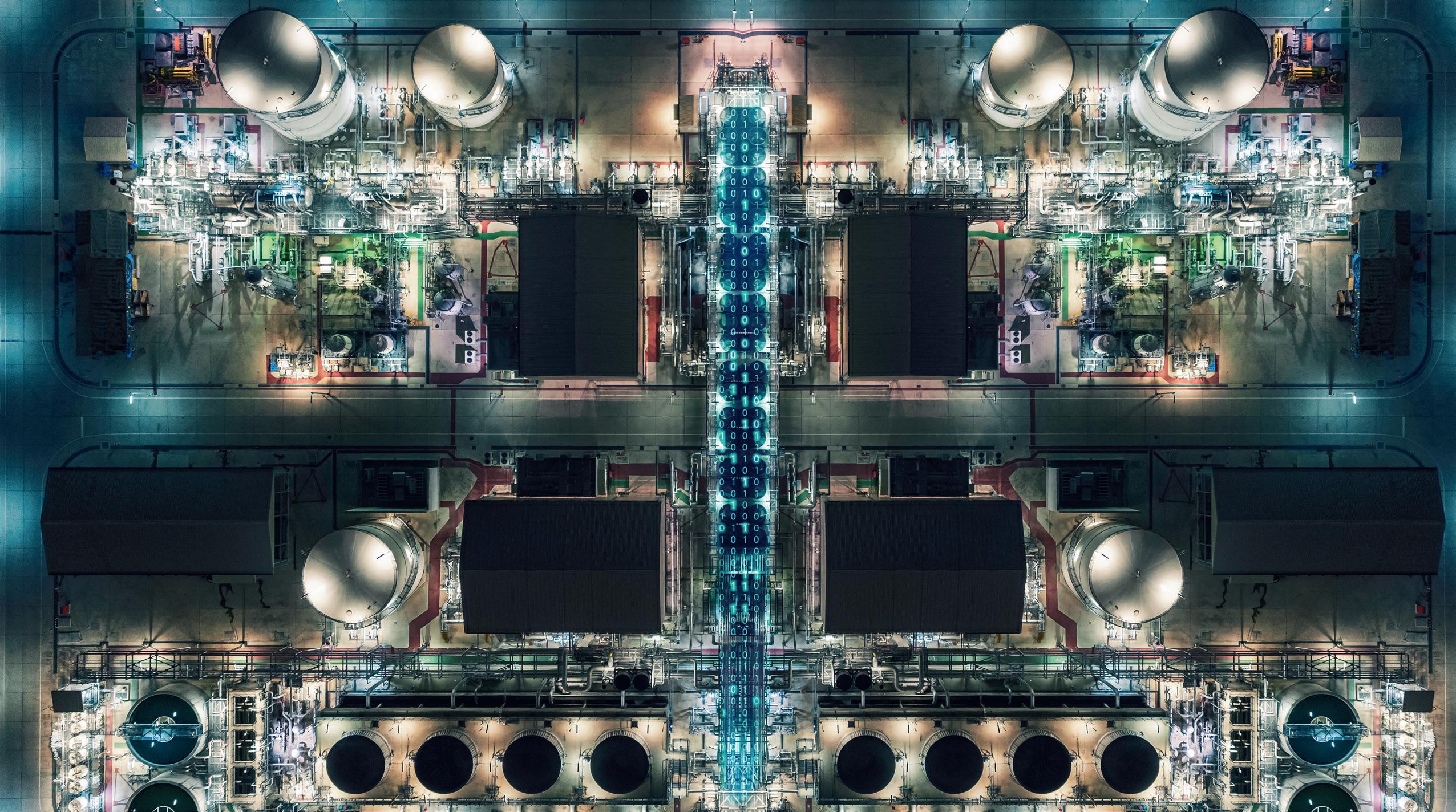
in the amount of equipment usually required. They can cut, crush, and load materials in a single operation and, in some cases, can even eliminate the need of the primary crushing stage.
On average, a Wirtgen 4200 SM, for example, can reduce the number of machines otherwise required for conventional mining by 65%. At the mines in question, the average fuel consumption of the machine fleets was reduced by around 50% and, in some cases, the resulting fuel savings were even more significant.
In view of this, the use of surface miners is a relatively simple solution for reducing CO2 emissions and achieving emission reduction targets while maintaining the same production rate.
Surface miners in use around the globe
In the course of time, more than 600 Wirtgen Surface Miners have been deployed in a wide range of mining scenarios. Of these, almost 200 are used for coal mining.
Case study: Talcher, India
Bhubaneswari Coal Mines Ltd (BCML) has been mining coal near the town of Talcher in the Indian state of Odisha since the 1990s. Mining operations at the Bhubaneswari coal mine are conducted 24 hours a day to constantly supply the nearby coal-fired power stations with the fuel they need for generating electricity. The opencast mine has an output of 25 million tpy of coal with an unconfined compressive strength of up to 35 MPa.
The use of surface miners eliminates the need for drilling and blasting, as well as offering further advantages. It increases the safety in the opencast mine by eliminating the need for storing and handling explosives; improved slope stability and a lower incidence of rockfalls also contribute to greater safety. Surface miner technology also allows for uninterrupted mining, as the mine no longer needs to be closed while blasting is in progress. In addition, it eliminates the time and effort required for obtaining blasting permits and the laborious documentation this entails. In Talcher, the coal is mined using the windrowing method, which means that the machine can work continuously without having to wait for transport vehicles.
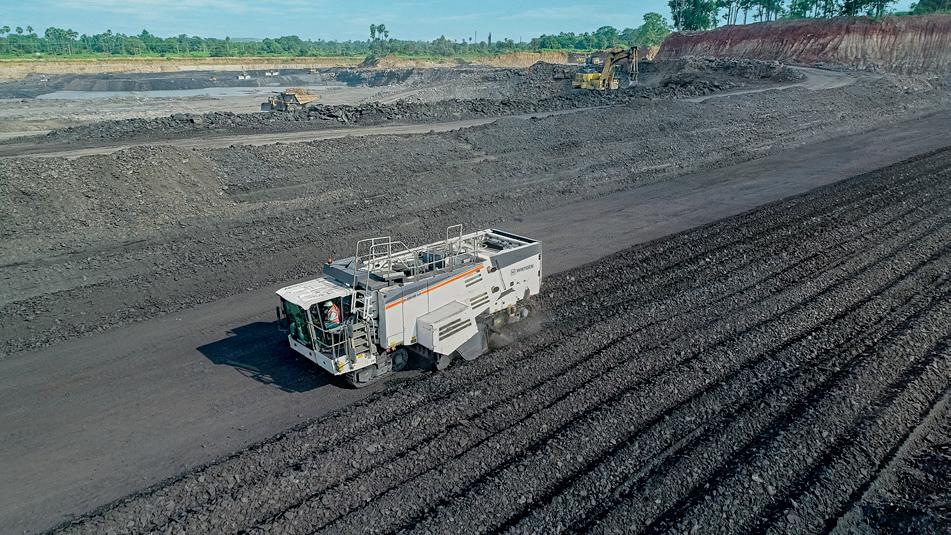
Figure 4. When working in windrowing mode, the cut material is deposited directly behind the machine.
Figure 5. Direct loading onto trucks is usually the most economical method if the material is to be transported over distances of more than approximately 250 m. Case study: Farmington, USA
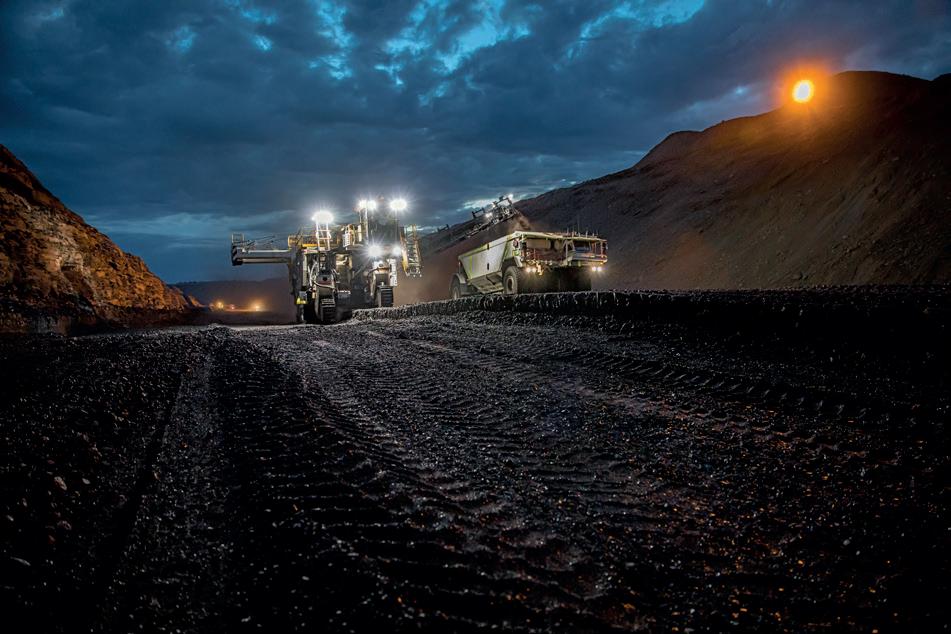
In Farmington, a 4200 SMi Surface Miner has replaced the three mining machines previously used at the mine and enables a noticeable reduction of noise, dust, and exhaust gas emissions. In contrast to the crawler dozers and wheeled loaders, which created considerable amounts of dust, the dust generated by the surface miner in the cutting process is captured and bound by an integrated water spray system. A comparative analysis of the two mining methods also reveals that the fuel consumption when working with surface miners is approximately 80% lower than it was with the previously used method. The lower number of machines deployed at the mine also has a positive effect on risk management, as fewer machines mitigate the risk of accidents in the mine.
In Farmington, the surface miner mines up to 2300 tph of coal and, in addition to the positive aspects mentioned above, reduces the overall mining costs per tonne by 60%.
Conclusion
Surface miners, such as the Wirtgen Surface Miner portfolio, can help offer solutions for every application. For example, the company’s portfolio all have the central drum design in common, where the cutting drum unit is located centrally under the machine, resulting in optimum weight distribution. As a result, the machine’s weight force can be used optimally for the cutting process. No other concept offers comparable results when mining rock with a rotating cutting drum.
Surface miners are used for mining coal and a wide variety of raw materials. Whether small quantities in small opencast mines in confined spaces, continuous operation in large opencast mines with several machines, or for routing work and large infrastructure projects, a surface miner can help operations reduce exhaust gas emissions and make coal mining more environmentally responsible.