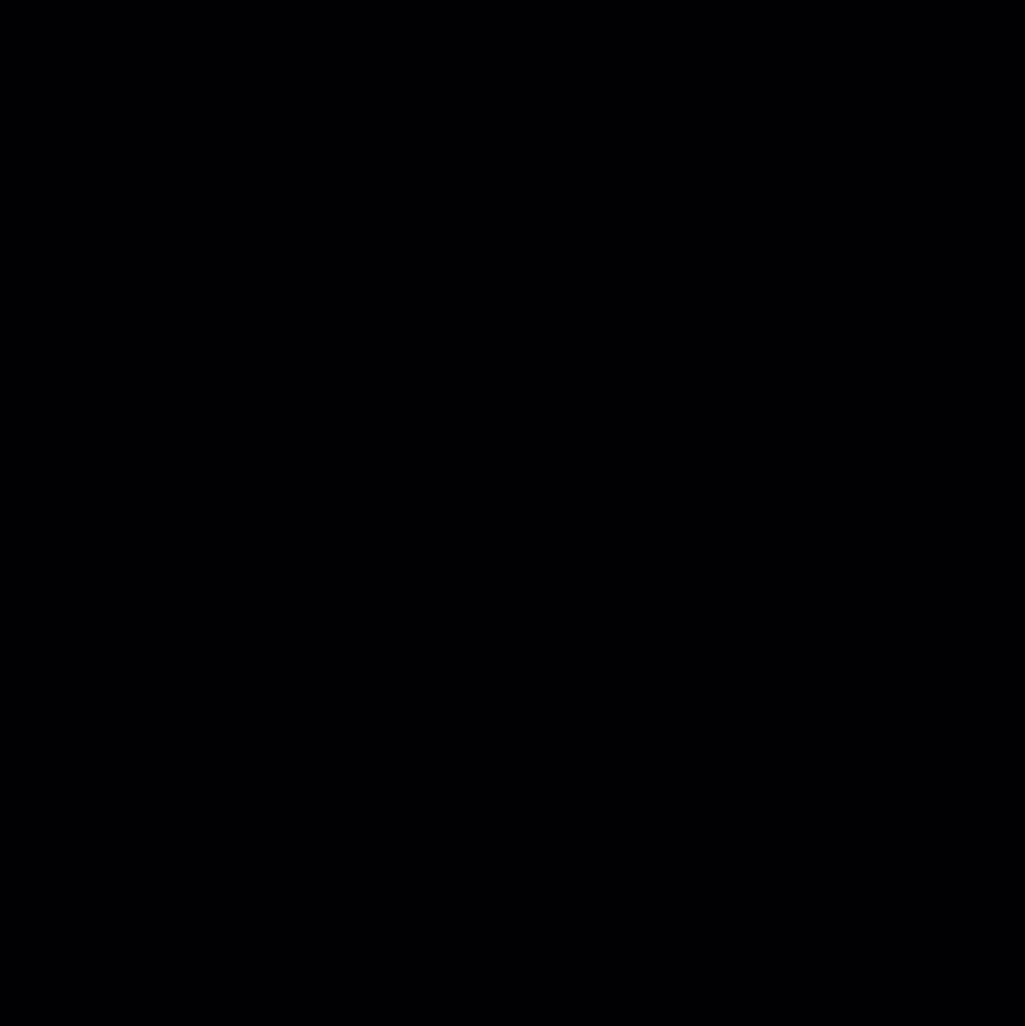
7 minute read
Developing Shotcrete Solutions
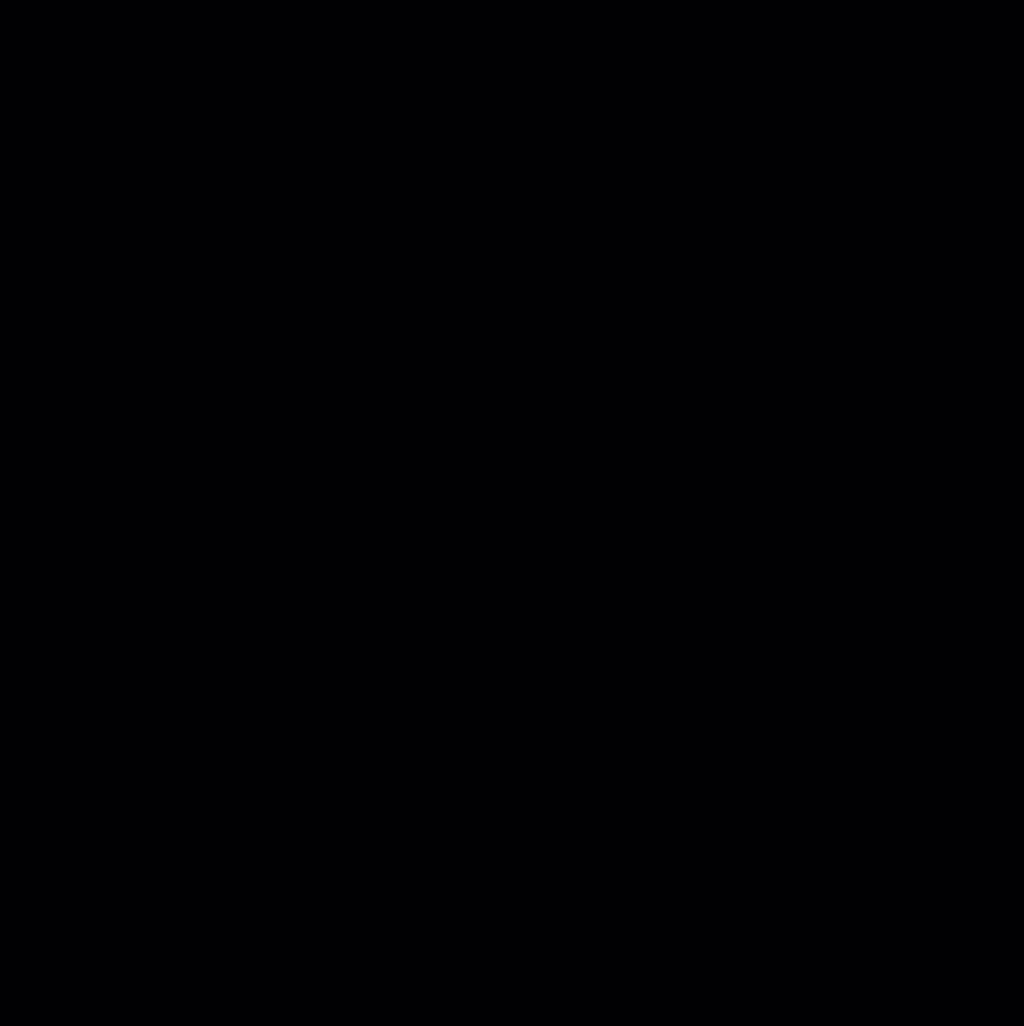
Donald O Connor and Bryce Nhlapho, Minova, explain how recent developments in shotcrete solutions have helped provide secondary support to mining operations across the globe.
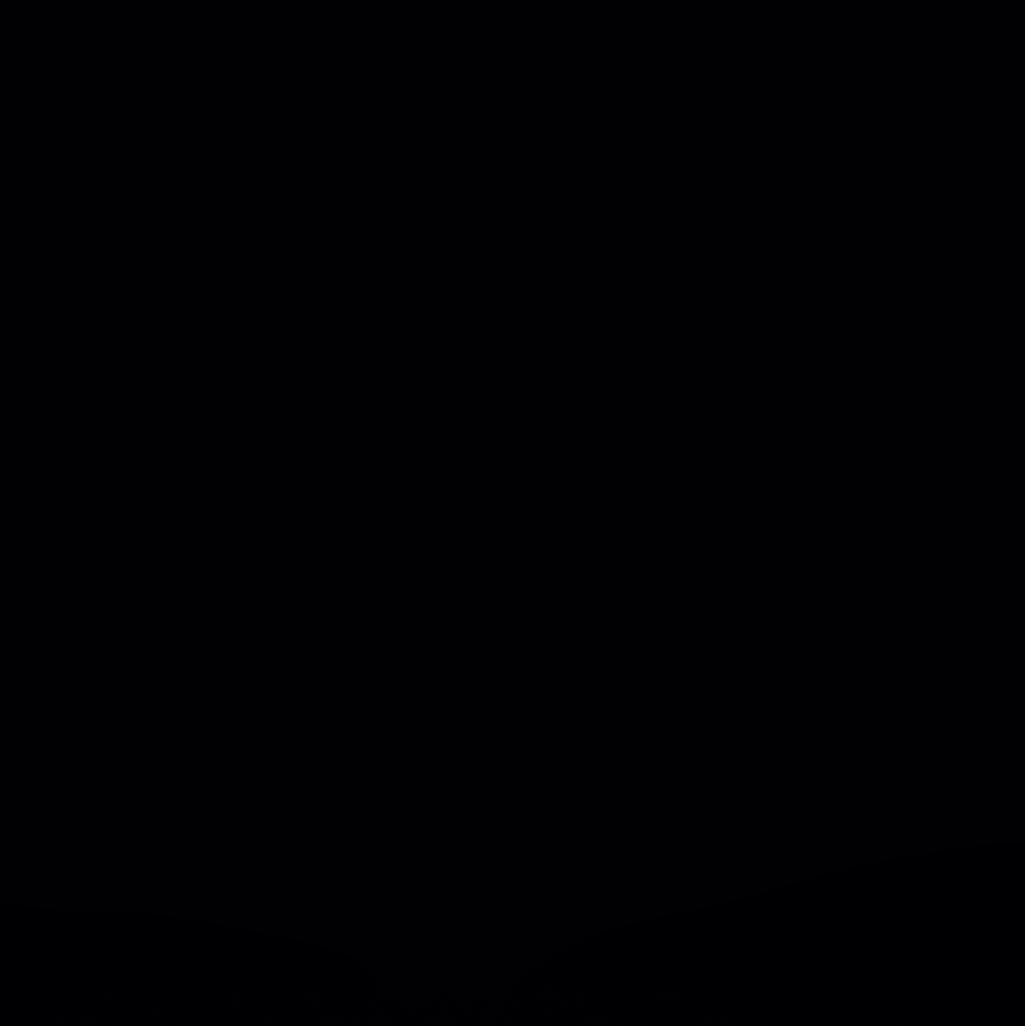
Globally, the mining industry faces relentless pressure to simultaneously improve safety and productivity. Nimbleness in adopting new technologies is a key to facing that challenge.
In recent years, Minova has developed several shotcrete solutions that are used across the globe to provide secondary support to mining operations.
Its recent innovation, TekCrete Fast M, is an ultra-fast, high-strength shotcrete that is sprayed onto the rock requiring support. Originally developed to stabilise earthquake or bomb-damaged buildings to allow rescuers to enter safely, the product has been adapted for use in mining by the addition of dust-reducing agents to minimise dust when spraying underground. It is supplied as a dry powder that is sprayed using a dry shotcrete pump.
Consistent with its original time-critical mission, TekCrete Fast M has fast strength development and high ultimate strength. Within 15 minutes, compressive strength reaches 1000 psi (6.9 MPa)
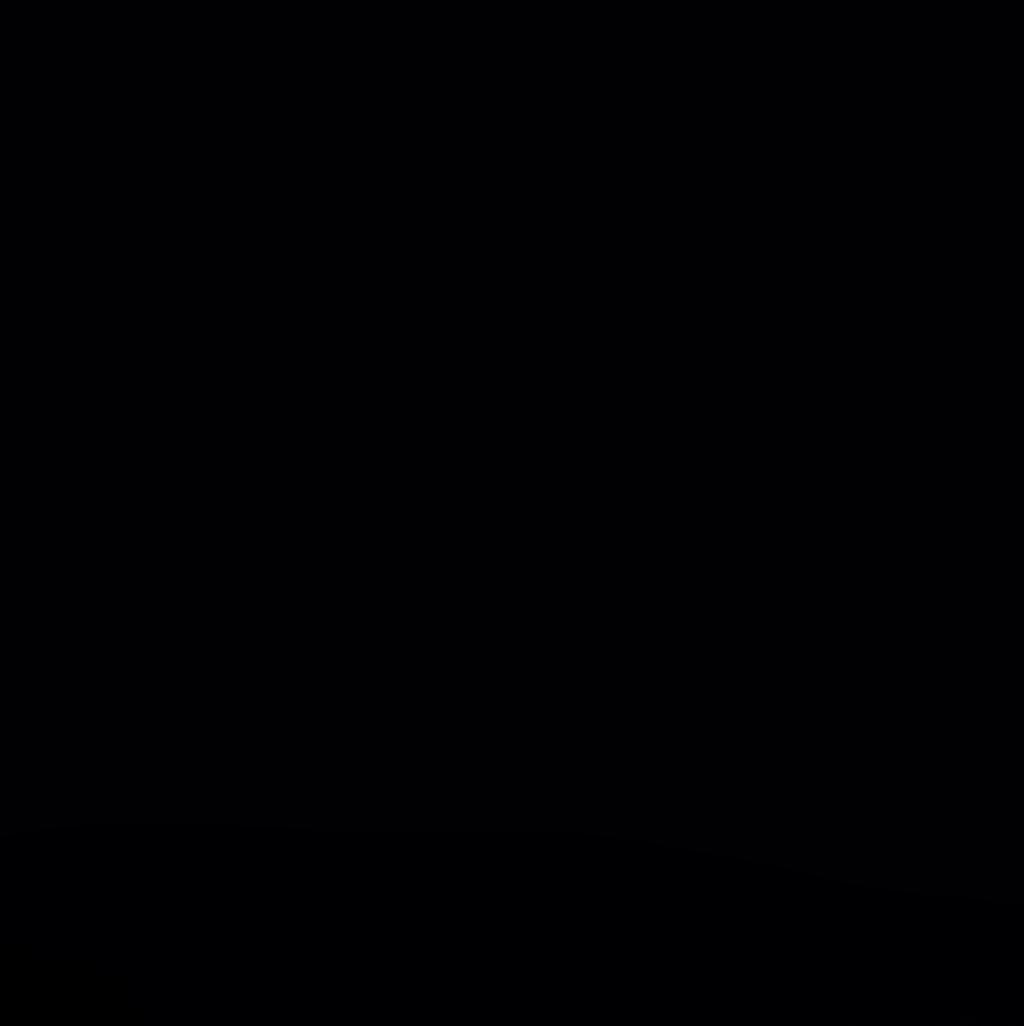
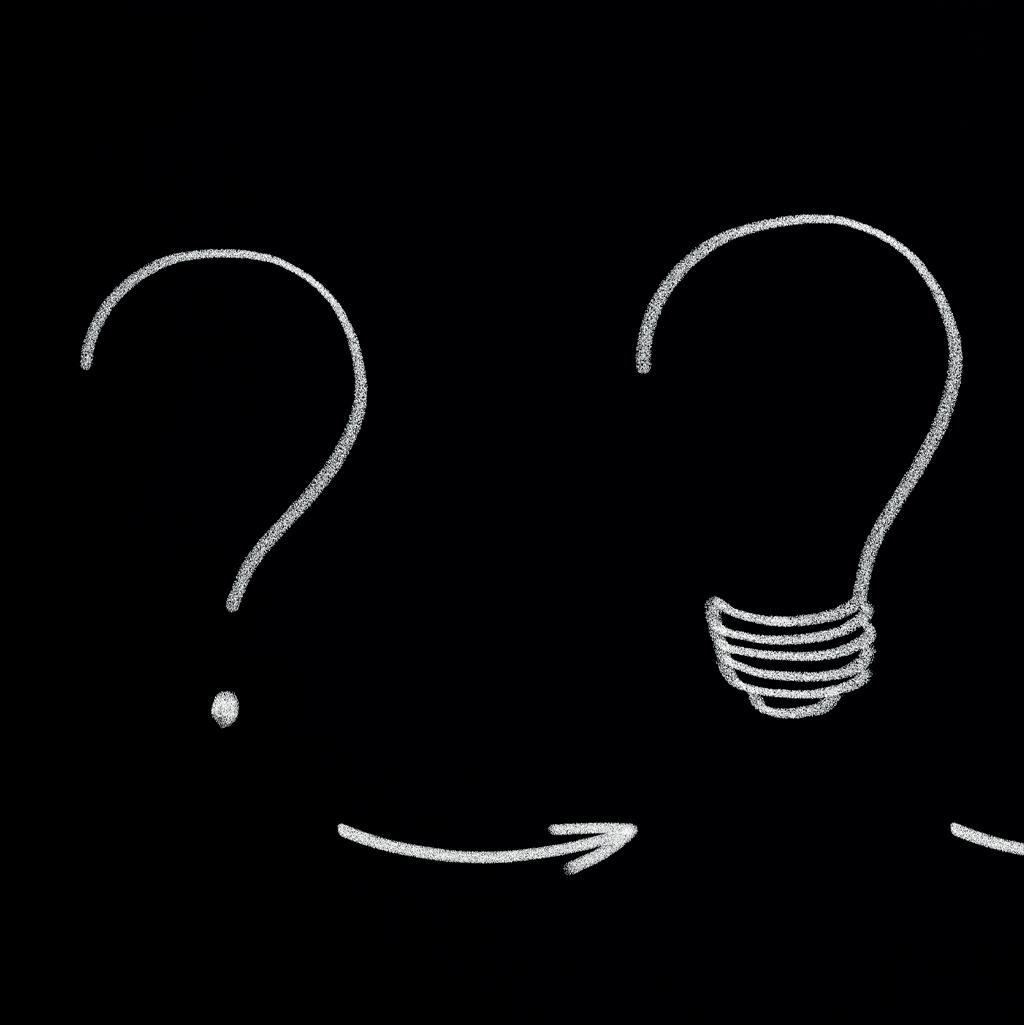
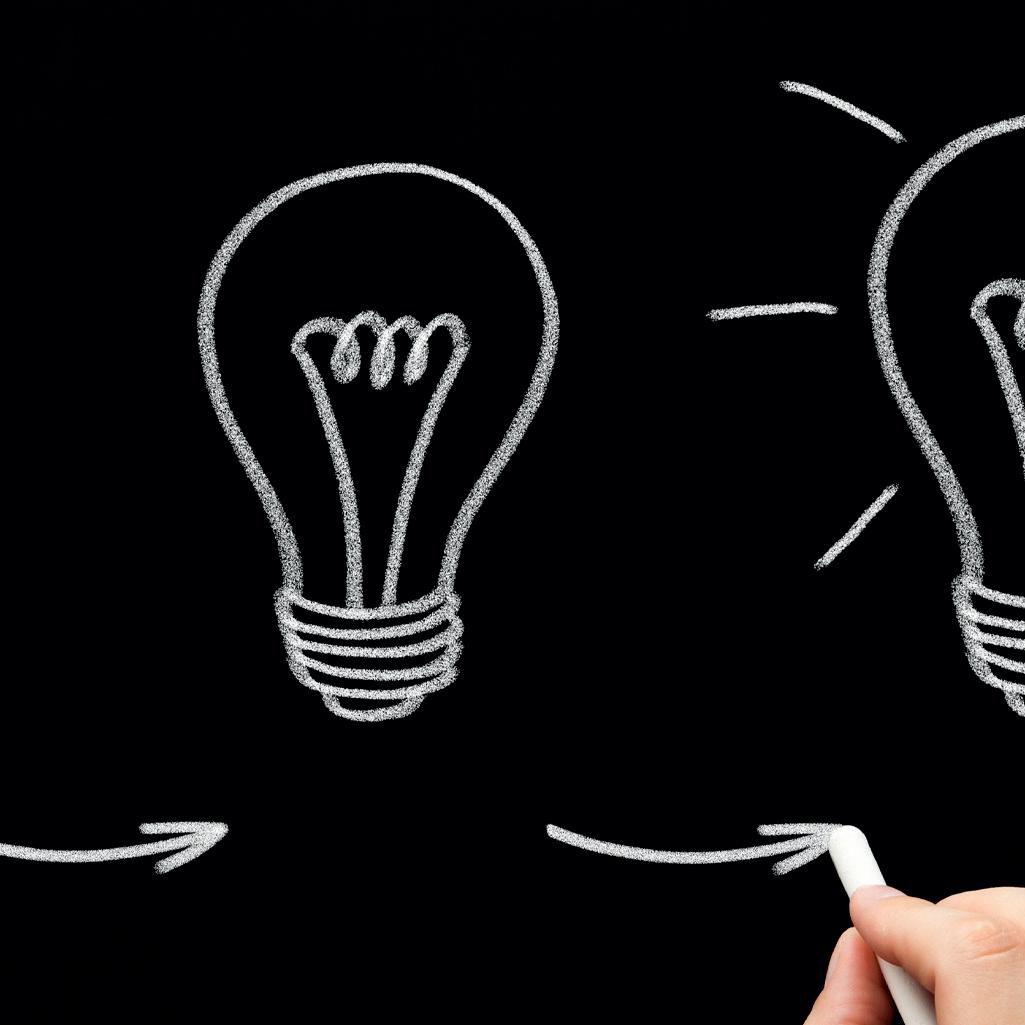
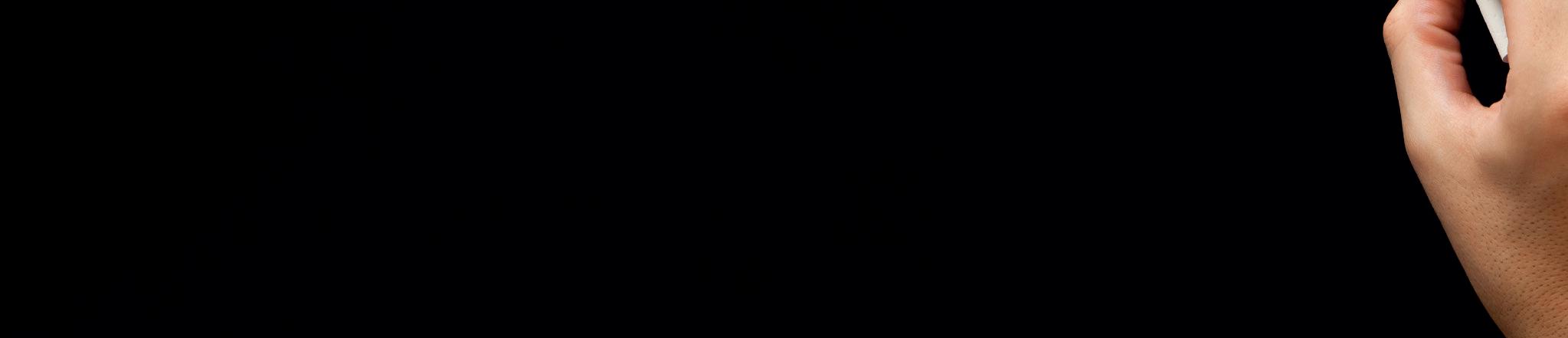
and final strength exceeds 6700 psi (46 MPa). The high strength means that a much thinner coating is needed – typically only 12 – 15 mm. This reduces the volume of material required and provides rapid area coverage. In contrast, even one hour after spraying, conventional shotcrete shows essentially zero strength, and final strength seldom reaches even 28 MPa – meaning it requires a much thicker application.
Case study: Africa
TekCrete Fast M was recently used by the Minova Africa team, who were requested to develop a rock-reinforcing solution as part of the rehabilitation of a main conveyor drive at a coal mine in Mpumalanga, South Africa. The project was a great success, and was completed ahead of the eight-month planned schedule, with no injuries occurring during its duration.
Project scope
The strata in the immediate roof of a main conveyor belt line passing through an old mined-out area of a coal storage facility was deteriorating and required rehabilitation. The worsening condition of the roof posed a high risk to employees working in the vicinity of the belt. Additionally, there was the risk of damage to the belt, due to falls of ground. Scaling of the side walls and the old roof support posed major hazards. The roof had to be first stabilised before new permanent resin bolt support was installed, as the operators were exposed to hazardous and unpredictable conditions.
The project required a system to immediately stabilise the rock, providing protection to the rehabilitation crews, and to build sufficient enough strength so that it was part of the permanent reinforcement of the roof strata. Minova identified the rapid-setting, fast coverage rate, and high ultimate strength of TekCrete Fast M as the core of its solution.
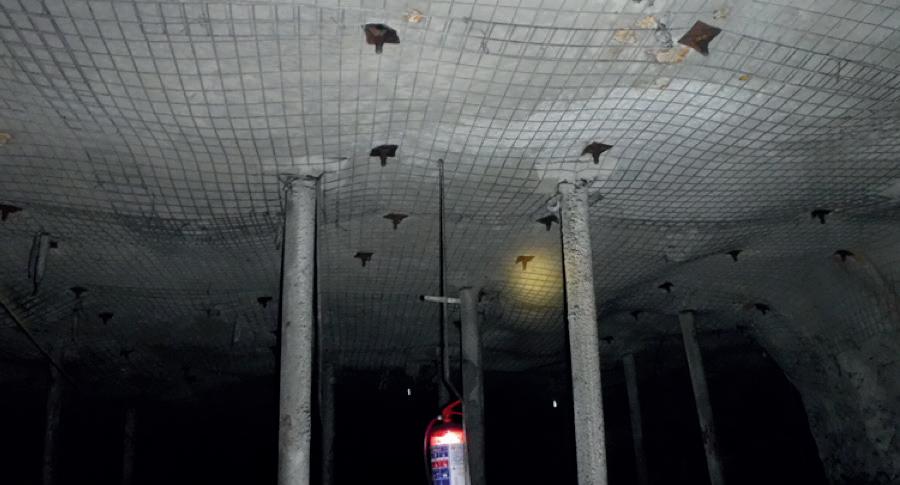
Figure 1. Mining roof post application with Tekcrete Fast M.
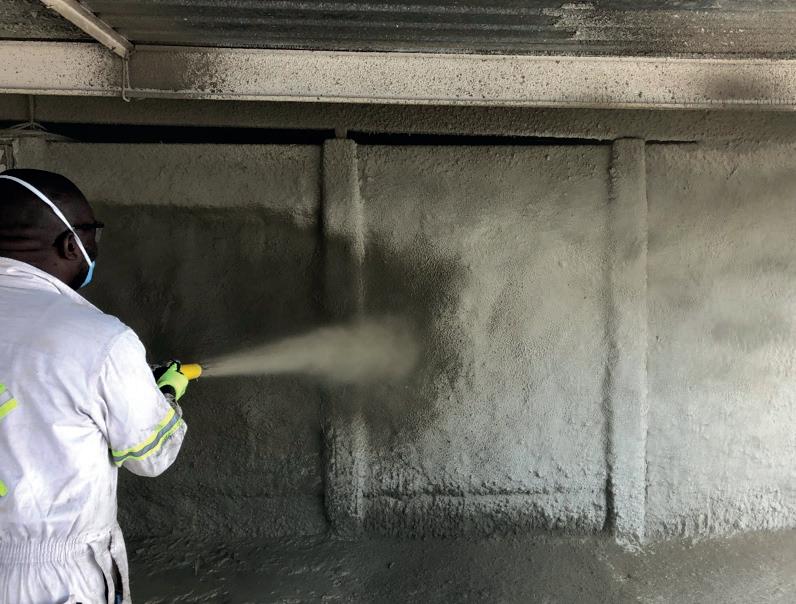
Figure 2. TekCrete Fast M application at Minova Africa’s testing facility. The solution
Minova supported the customer with product training and its expertise in the application of TekCrete Fast M, built up in previous local and international projects. The project also included the erection of scaffolding over the conveyor belt to spray TekCrete Fast M.
The fast setting of the product required the development of new methods for on-site quality control. The strength of conventional shotcrete is measured by spraying the material into cube moulds, that are then taken to a specialist laboratory on surface for compressive testing. This inevitably introduces a delay between spraying and testing, sometimes of several hours or as long as days.
This method was too slow to produce meaningful data on the hardening of TekCrete Fast M, where the strength increase takes place within the first few hours. An in-situ test method was found, using the depth of penetration and pull-out resistance of a nail fired into the sprayed material, to give a strength index that was correlated to laboratory-measured compressive strength.
TekCrete Fast M acted as a critical barrier between high-risk roof conditions and the people, enabling them to safely and systematically re-support the length of the belt. The belt drive was refurbished and provides a long-term solution to safely transport coal.
This was not the first time that the company had worked with the same customer to provide a solution that delivered immediate and tangible benefits to the mining operations. Some years ago, the customer was grappling with resin bolting cycle times that were constraining mining rates. Minova proposed using a faster-setting resin capsule. After months of laboratory development and site testing, they delivered a decrease of 15 seconds per bolt, which highly increased the efficiency of the mine.
The additional time gained by speeding up rock bolting with resin capsules, allowed the customer to gain an extra month’s bolting time in each year. This enabled bolting to catch up with mining rates and even allowed the customer to consider additional bolting operations, such as reinforcing the coal ribs
with glass-fibre reinforced plastic (GFRP) bolts.
Challenges
One of the challenges faced was the need to reduce the cost of the nuts, which was as high as the GFRP bolts. The company has re-evaluated its supply chain to provide savings to its customer and deliver a substantially more cost-effective product without detriment to its performance.
Minova Africa’s focus was to provide a one stop shop solution to their customer. With streamlined supply chain, the mine could then focus on the operations element. Thanks to the securing of the continuous supply of products, the customer was given peace of mind and allowed them to focus on their daily tasks.
Conclusion
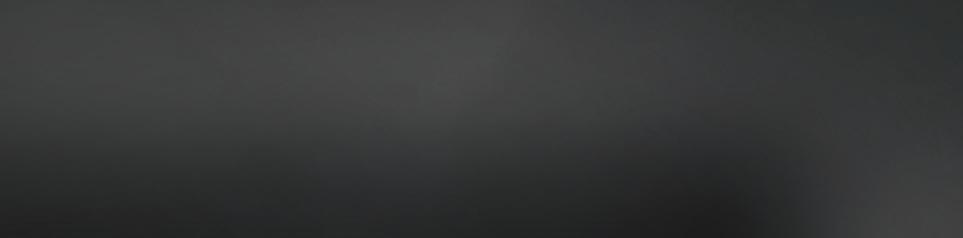
The confluence of deep expertise in materials science and understanding of the needs of mining has resulted in a stream of solutions that are providing immediate and real benefits to mining opetrations .
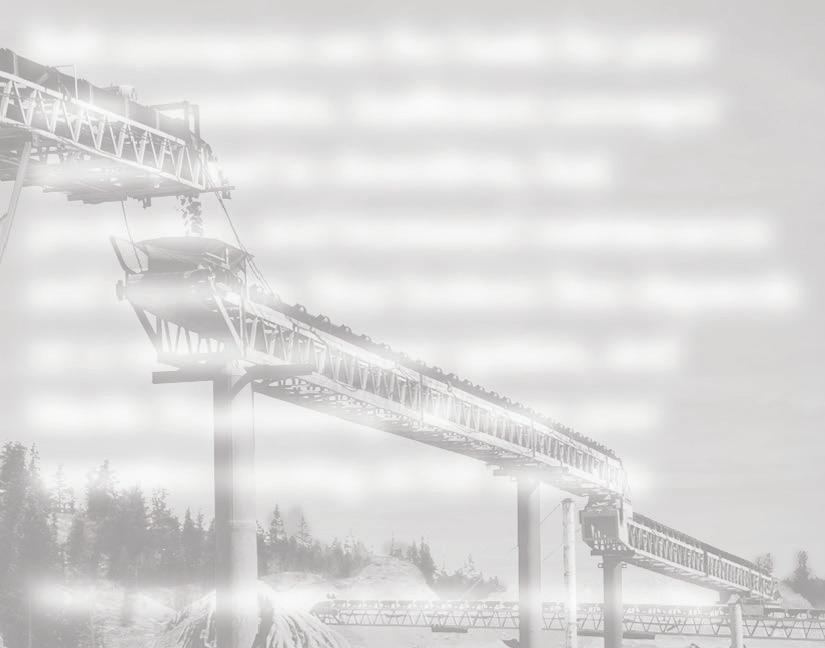
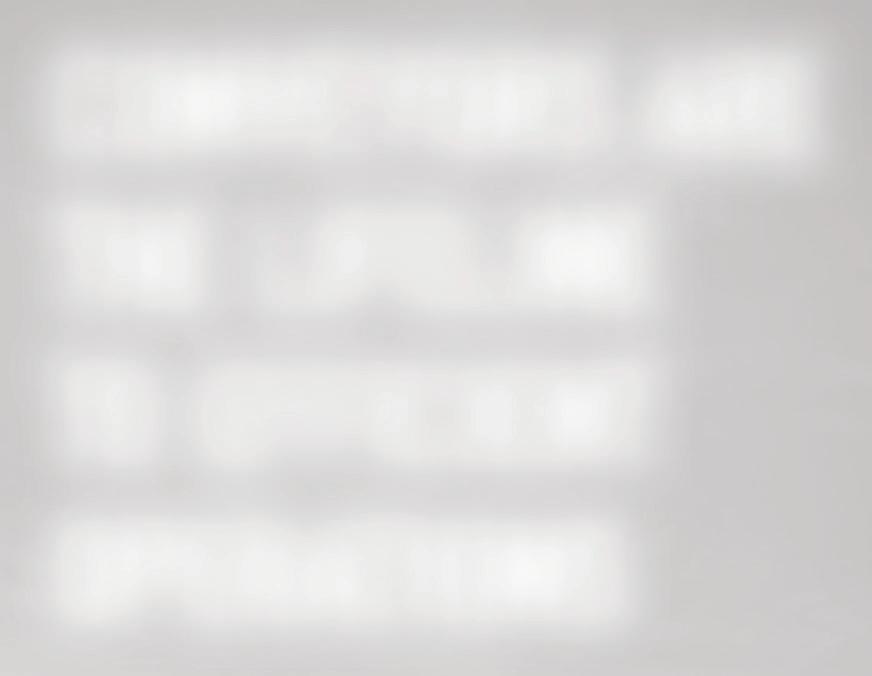
The results
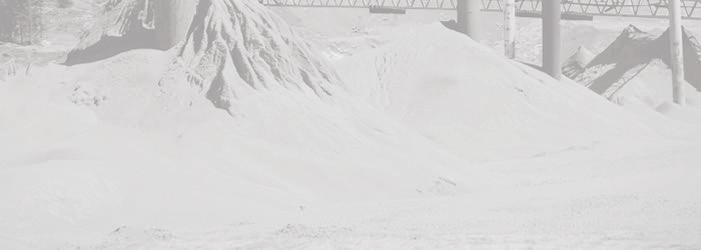
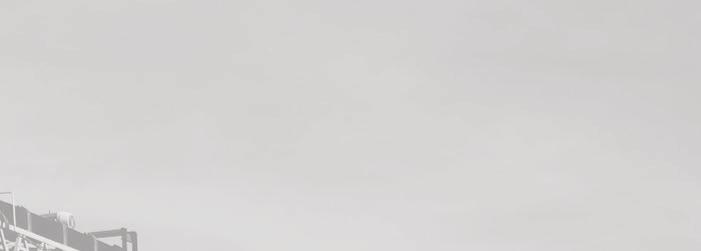

TekCrete Fast M is now regularly used on a variety of underground and opencast coal mines throughout Africa. The product is supported by field technical service advisors who help to plan the project and provide ongoing support such as training, quality assurance for the users.
With the help of Minova’s sister company, GroundProbe, the application of sprayed cement has become easier and more efficient. GroundProbe has developed specialist laser scanning hardware and software to estimate the quantity of TekCrete Fast M required for a particular application. The system also provides continuous monitoring of the thickness during the project. This provides the customer with peace of mind that the design thickness is being correctly applied without over application. This in turn helps to keep the cost close to budget and minimises product waste.
The company is working on further improving the product by developing a full portfolio of coatings that are based on this technology. The future uses will include structural concrete repair and trowel-on application for smaller tasks. This will enable users to benefit from the unique properties of the material without having to purchase or hire full scale application equipment.
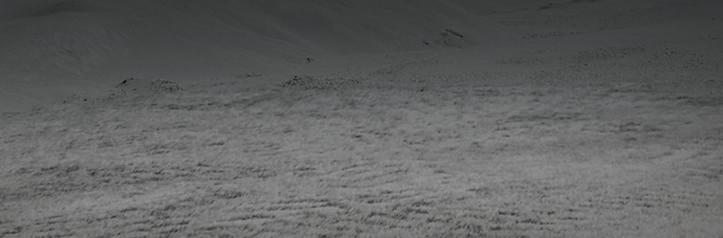
CONVEYORS ARE THE LIFELINE TO EFFICIENT OPERATIONS
Belt conveyors are the basis for your entire operation. Ineffi cient conveyor systems lead to downtime, lost production, and increased maintenance and expenses. Your bottom line depends on a reliable conveyor system, and Martin Engineering will keep your operation running at full capacity.
Visit our website to learn more today.
martin-eng.com
® Registered trademark of Martin Engineering Company in the US and other select locations. © 2021 Martin Engineering Company. Additional information can be obtained at www.martin-eng.com/trademarks and www.martin-eng.com/patents