
10 minute read
Underestimating The Missing Link Of Longwall Automation
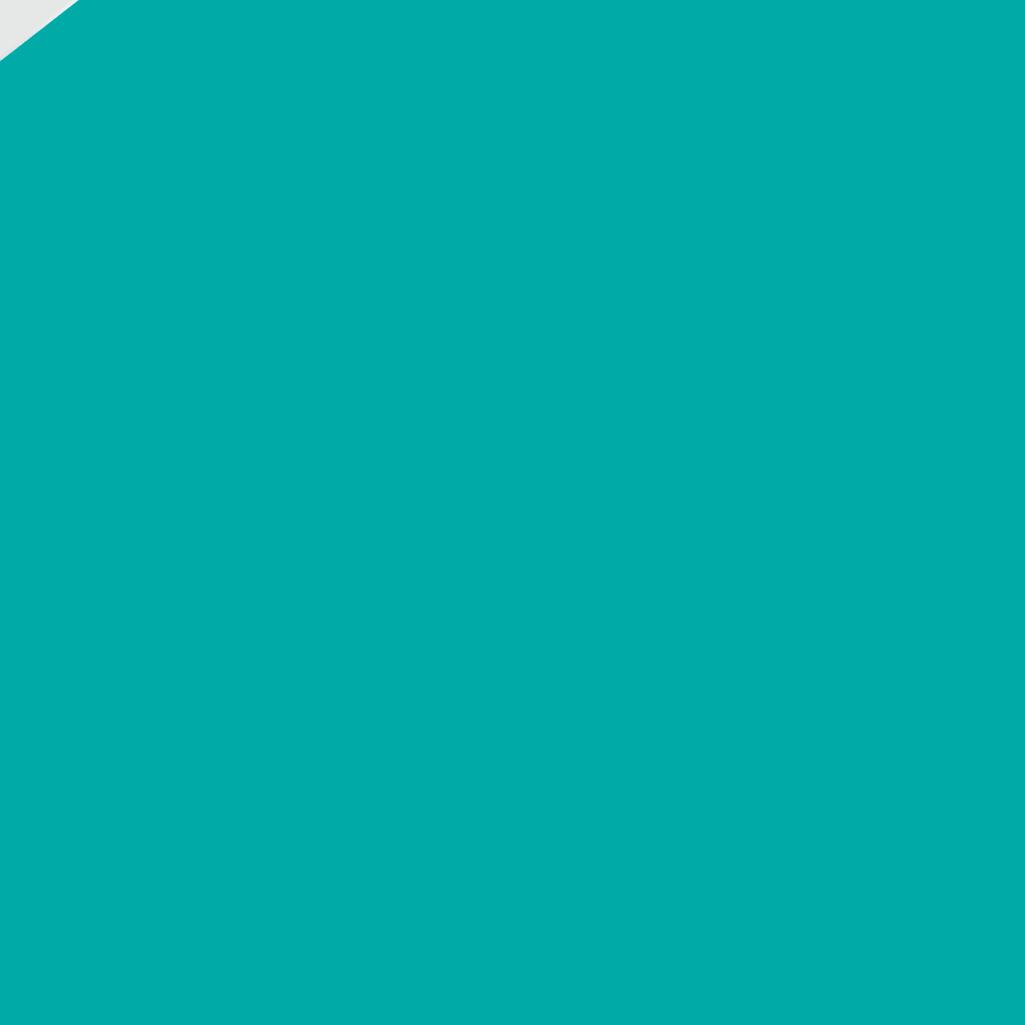
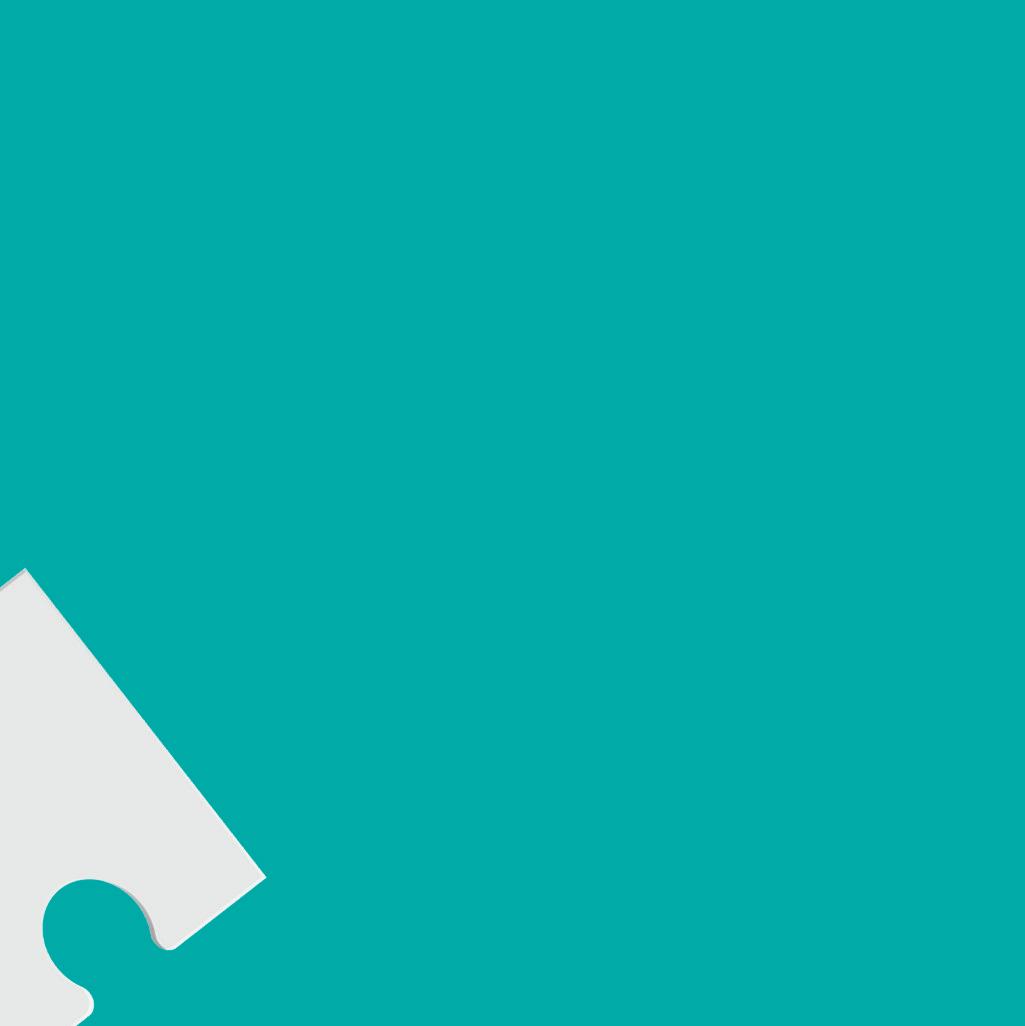
Karol Bartodziej, FAMUR, Poland, considers the importance of automated face advancing units when trying to achieve longwall automation.
For many years, achieving longwall automation has been a goal of mine authorities and machinery manufacturers. Nowadays, the number of longwalls mined with the use of an electrohydraulic control system for powered roof supports is relatively high, and shearers that can automatically perform one or more cuts are also increasingly popular.
However, the use of an electrohydraulic control system for powered roof support is not enough to make a longwall unmanned. In fact, there is an element of the longwall system that is not being addressed at all.
Overcoming the beam stage loader
Automated face advancing
While the longwall face can progress on its own due to electrohydraulic control of the machines, the beam stage loader (BSL) remains in its static position and must be moved manually by the operator. As an example, one of the solutions to this problem is FAMUR’s UPZP-1200 automated face advancing unit. It has two cylinders and the construction of the belt conveyor’s turning section allows the BSL to be pulled up synchronously to the machines working the longwall.
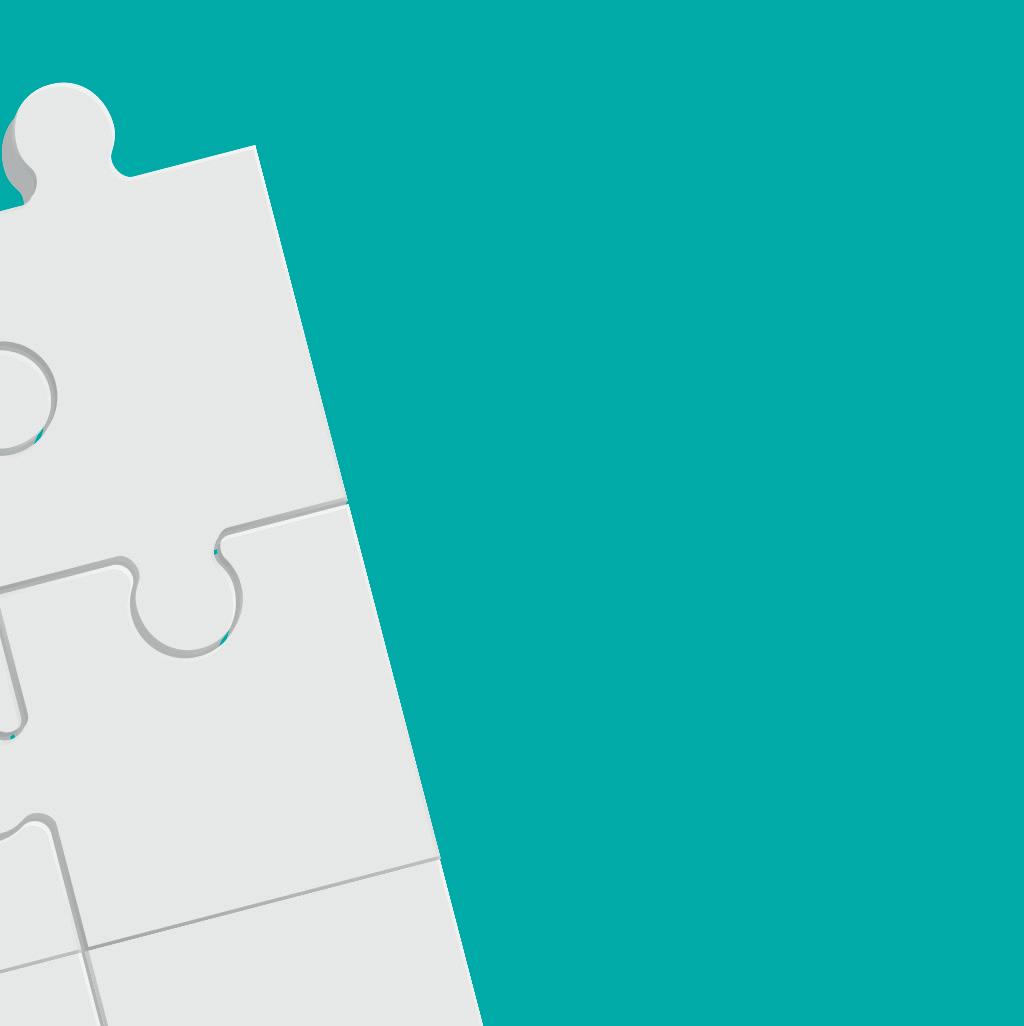
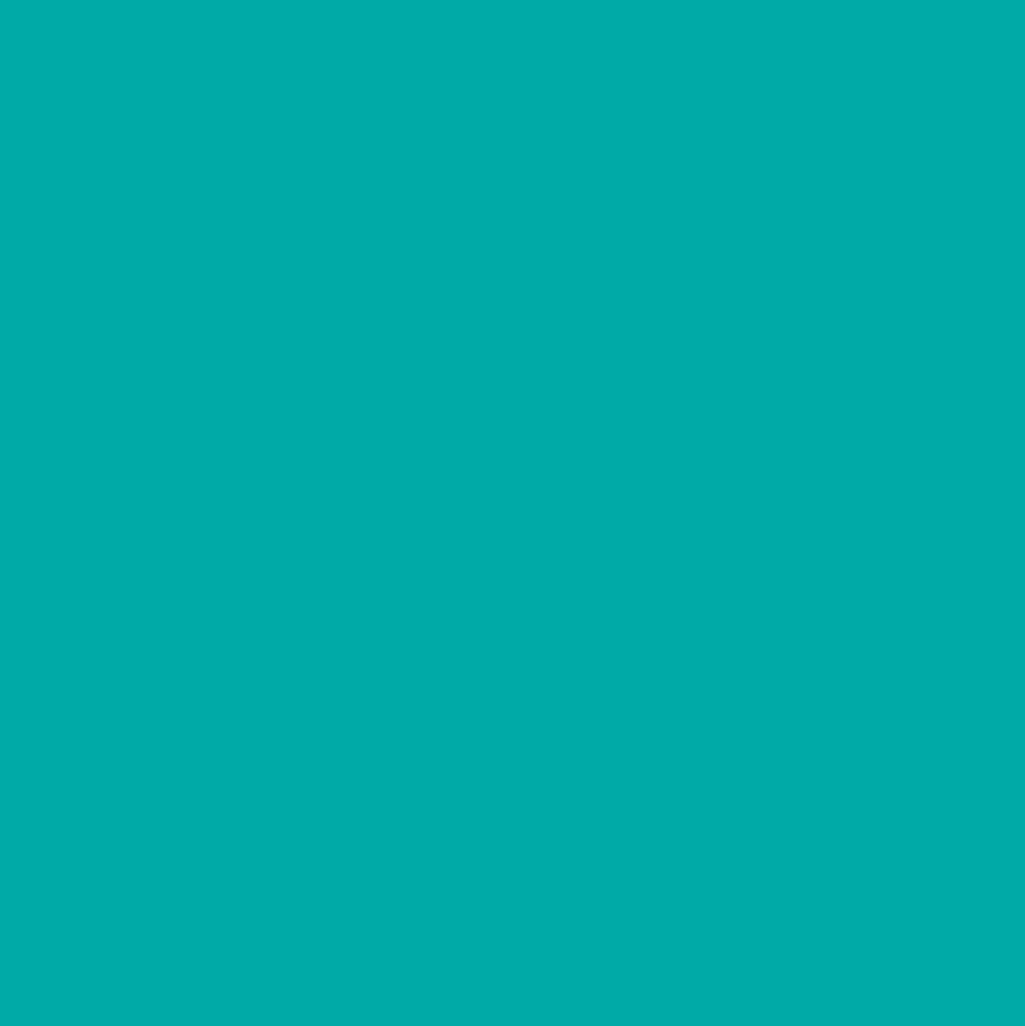

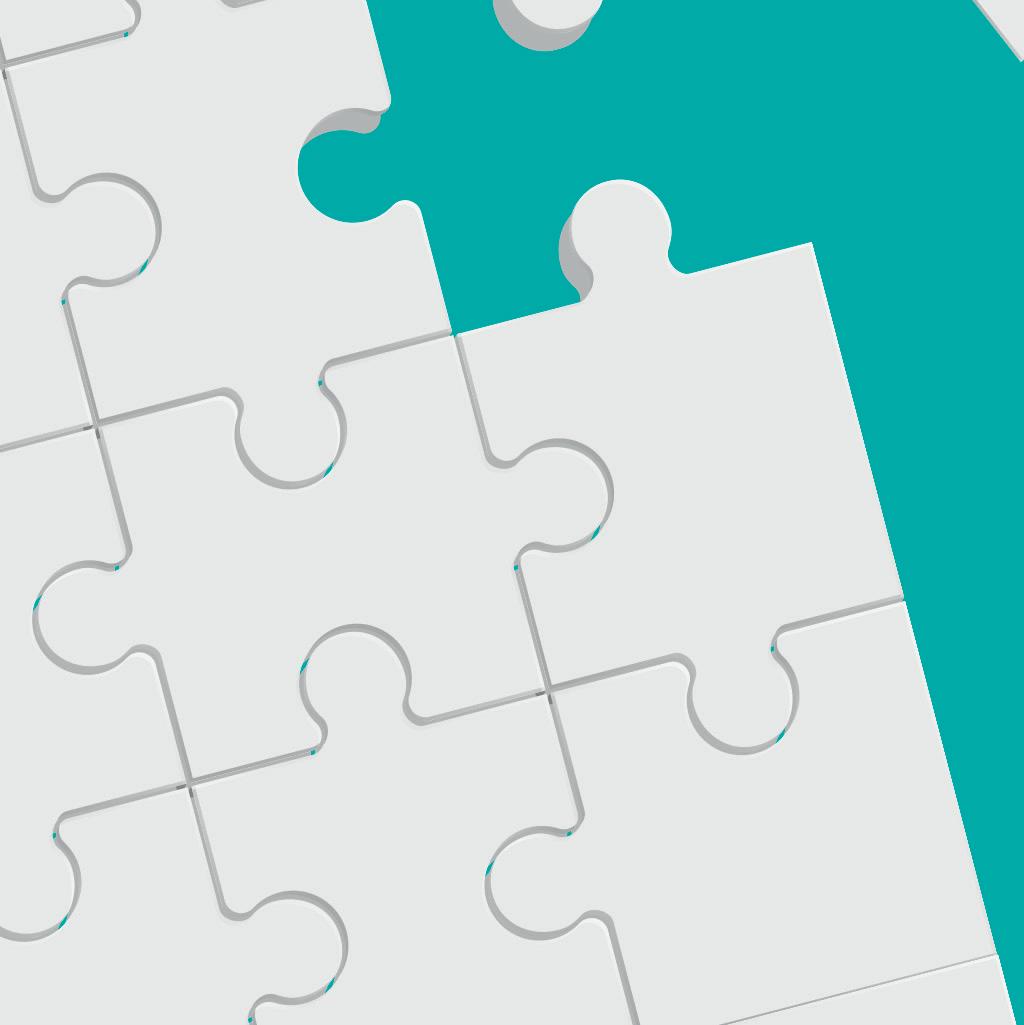
The key role is played by the unit’s control algorithm, which interacts with the control system of machines by detecting their status and the length of the extended shifter cylinder pushing out the armoured face conveyor (AFC) adjacent to the BSL in real time. In case the face advancing unit is unable to perform an automatic movement, it alerts the operator of the need for them to take control and sends a signal to the control system for powered roof supports to stop performing an automatic repositioning cycle, so that the operator can remove the problem.
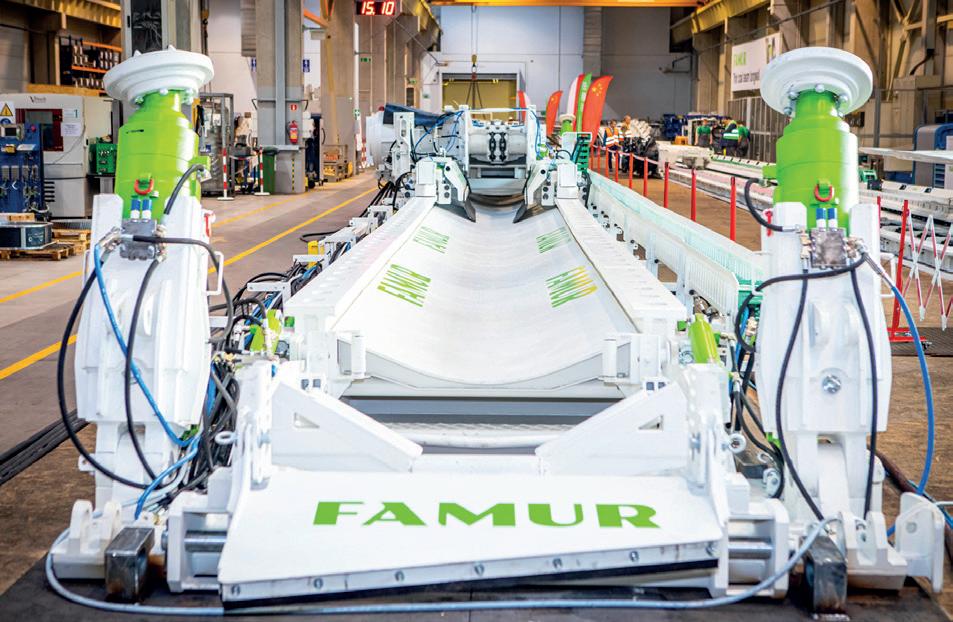
Figure 1. UPZP-1200 overlapping station – conveyor belt return part, and vertical stabilising cylinders.
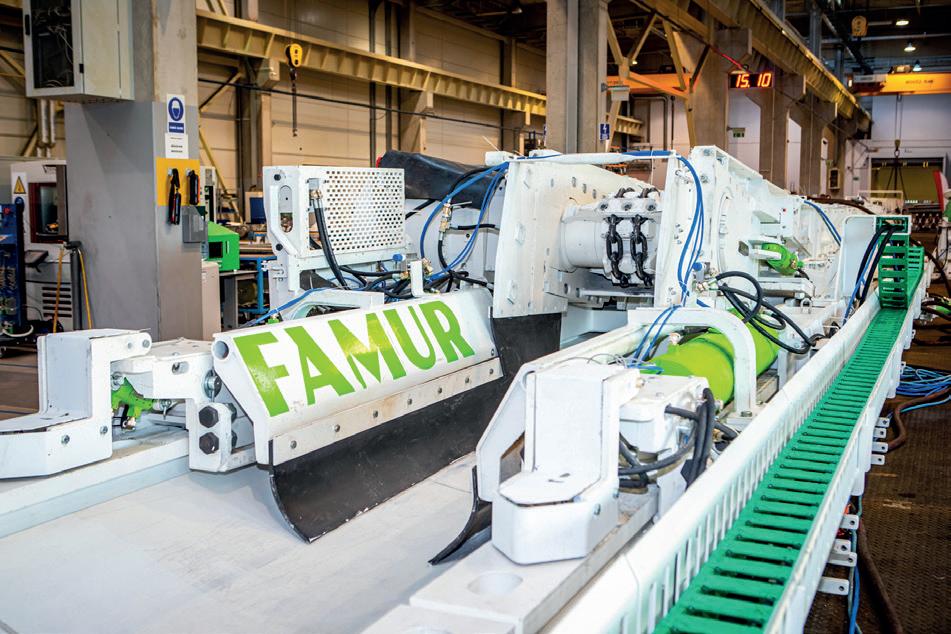
Figure 2. UPZP-1200 – station feed cylinders, and a BSL discharge part.

Figure 3. UPZP-1200 – flexible part of a BSL entering the belt return (lower) part. The ‘master-slave’ mode
The unit control system operates in a ‘master-slave’ mode, where the unit is controlled by the control system of the longwall powered roof support, subjecting itself to its operation cycle. As a result, there is no need to interfere with the control system of powered roof support; only the standard information that such systems exchange with SCADA visualisation systems is used. This means that the use of products, such as the UPZP-1200 unit, is possible without involving the programming team of the roof support control system’s manufacturer.
The system can operate as a ‘slave’ element for the central control system. The prepared communication interface enables the visualisation of its operating and alarming states, as well as the possibility of controlling the UPZP-1200 unit.
If, on the other hand, the user wishes to implement the UPZP-1200 unit as a system that is not linked to the central SCADA, a computer with FAMUR’s SmartMine application will be provided, where the user can supervise the operation of the system.
Mechanical structure
Another element of the UPZP-1200 unit is its mechanical structure. Due to the mechanical solutions, the automation system is as simple as possible. The design effectively prevents stalls of the BSL during progression cycles and enables operation even when the BSL is subjected to bends in each axis.
The overlapping station has a number of features facilitating automation, e.g. the passage of cables and hoses between the lower and upper part of the unit through a cable gland, which makes them self-guiding to prevent damages during operation. In addition, the latching holes, against which the cylinders are locked are designed in such a way to be self-cleaning, in order to prevent the accumulation of excavated material, which helps to ensure that the system is self-operating.
The length of the unit together with the BSL is selected according to the daily progress of mining – e.g. in the Shigetai mine, the conveyor allowed for 20 m of adjustment in automatic mode. Due to this configuration, manual intervention in the system to move the belt return (lower) part of the unit takes place only once a day during maintenance shift.
The operation of the cylinders is supported by a set of proximity sensors detecting the point when the cylinders can lock against the lower part of the unit and detecting irregularities in locking, e.g. due to clogging of the latching holes with excavated material. If the system detects an anomaly, it attempts to reposition the cylinders and if it cannot lock them properly, it signals the operator of the problem and enters manual control mode.
Radio remote control
An additional feature of the UPZP-1200 unit is the operation of each cylinder in manual mode using a radio remote control. This significantly increases safety
in relation to standard overlapping stations, where the operator controls the operation cycle by switching hydraulic valves mounted on the station itself. In such a configuration, the station’s movement can pose a danger to the operator. Operation using radio remote control allows the operator to freely choose their position so that they can work safely.
The operation cycle of the UPZP-1200 unit starts with the stable expansion of the cylinders stabilising the return (lower) part of the unit in relation to the floor, roof, and walls. As a result, the return part of the unit is a stable track needed for the process of pulling up the discharge (upper) part of the unit. The turning section is equipped with guides with a series of holes which the bolts of the feed cylinder pins enter, pulling up the discharge section of the unit. The feed cylinders start their operation cycle from the maximal spreading of the cylinders. Due to a set of sensors, the system detects holes against which the cylinder can interlock. Aft er stable locking against the belt return part (lower) of the UPZP-1200, the system is ready to pull up the BSL. When the roof supports in the longwall start to push the AFC conveyor, the UPZP-1200 receives information about this activity and pulls the BSL forward, adjusting the pulling rate to the rate of AFC movement. Upon completing this operation, the system re-extends the cylinders and interlocks them to be ready for the next cut of the machine.
Case study: China
Due to its versatility, the UPZP-1200 unit control system can be configured to work with any electrohydraulic control system for powered roof support. For example, during the implementation of this unit at the Chinese Shigetai mine in the Shanxi province, the unit cooperated with machines controlled by the system of the Chinese company, HNDZ, where the exchange of information between them took place in the Modbus protocol. The native transmission protocols in the system are Modbus, OPC and MQTT, but the control system architecture is versatile enough to cooperate with most of the contemporary communication protocols. Both the communication protocol and the interface are matched for a specific installation.
The implementation of the UPZP-1200 overlapping station at the Shigetai mine was very unusual. Commissioning of the unit took place in 2Q20, during the period of the worldwide COVID-19 outbreak. Due to air traff ic blockages and the inability to obtain visas to China for FAMUR service representatives, the implementation of this system had to take place without their presence on site. Timing and synchronisation of operation between HNDZ systems and the FAMUR overlapping station were done remotely.
The installation of this unit at the Shegetai mine was also unusual for another reason. The UPZP-1200 unit had to cooperate with a longwall system with a rather unusual mining method. In the place of a standard roadheader with two long arms, a Heilong’s (Mikrus’s) GUŁ-500 cutting and loading head was used. This system has a non-standard operation cycle – when the
Cincinnati Dual Sprocket Conveyor Chains are proven to be better than other mining chains. Tons better, in fact. Tests confirm our chains deliver 20 percent more strength . The result is greater durability, maximum availability and a trouble-free service life. That’s how we deliver the lowest cost per ton. For 90 years, Cincinnati has proven to be THE STRONGEST LINK .
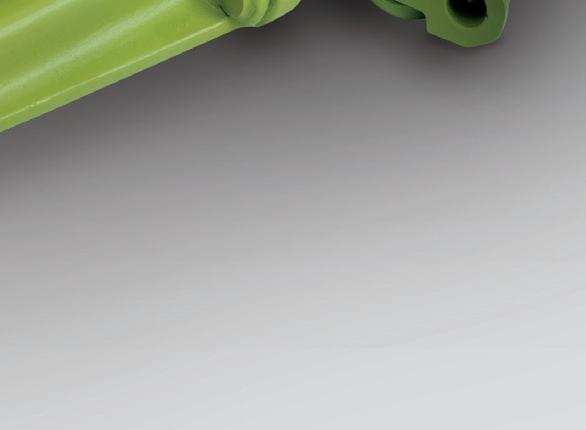


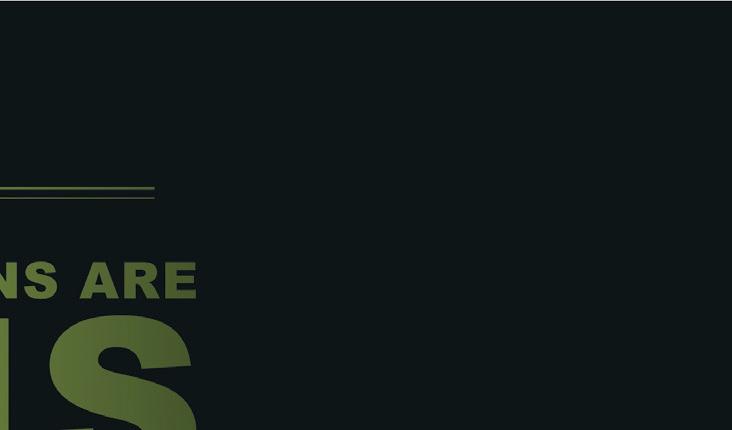
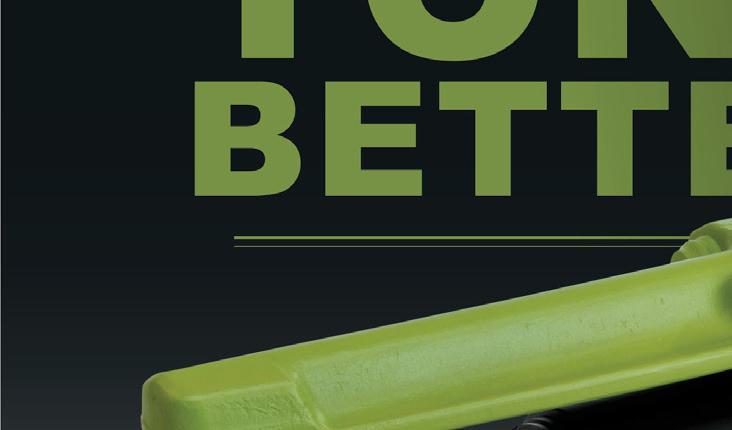
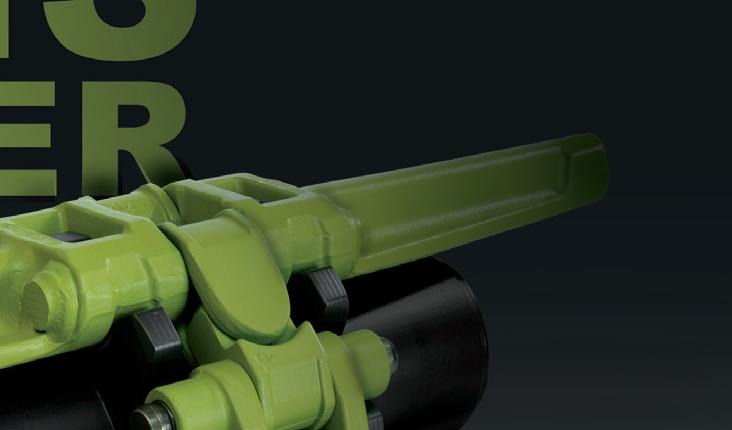
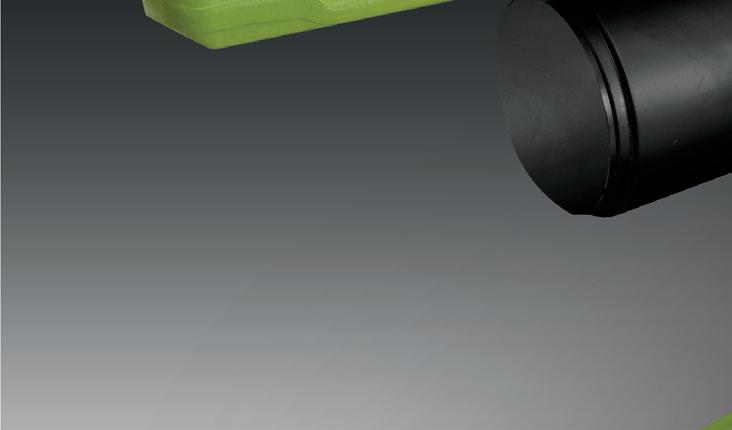
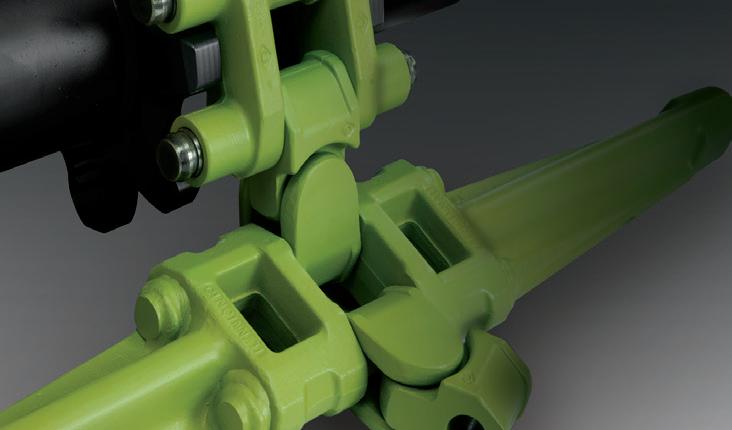
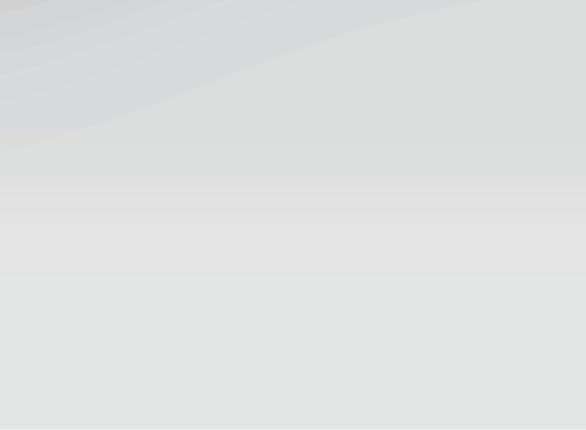
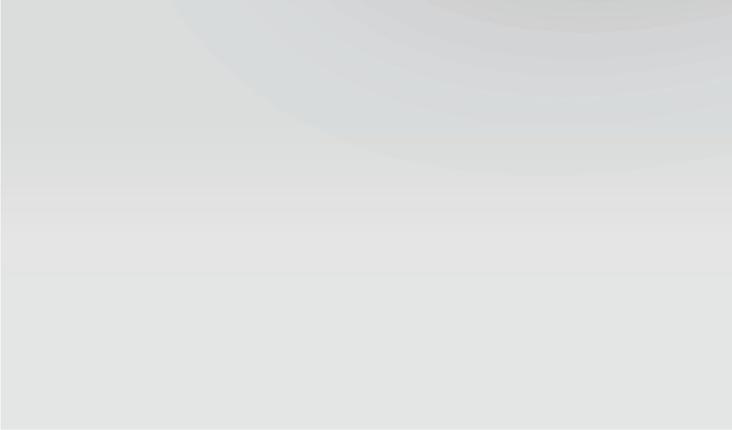
cutting and loading head arrives at the end of the longwall it almost completely gets into the main gate or rail gate gallery, after which the GUŁ-500 makes a full step forward into a coal face, and then starts the next cut. Therefore, the control algorithm of UPZP-1200 unit had to take into account the additional factor of the frontal sumping of GUŁ-500’s head and react appropriately to anomalies in this process, so as not to interrupt automatic operation.
As the GUŁ-500 head goes almost entirely into the main gate, the AFC also is abnormally long and goes deeply into the side galleries. Therefore, the BSL is located virtually at the very opposite face to the longwall. Due to the ergonomics of longwall operation, the belt conveyor receiving the excavated material is on the other hand located at the opposite side of the transportation tunnel. In order to solve this problem, the BSL had to be designed in such a way that its standard layout is snake-shaped, passing from one side of the transportation tunnel to the opposite side. In spite of this unusual design, the UPZP-1200 and the BSL enable an automatic progression cycle in line with the operation cycle mining the longwall. GUŁ-500 is a machine designed for thin coal seams with thicknesses from 1.2 m. Anyone who has worked on such a low longwall, or at least had to walk through it on their knees, knows how difficult and dangerous such conditions are for human labour. Therefore, it is not surprising that, in order to minimise the presence of people in the mining area, such longwalls are much more frequently subject to automated mining than higher longwalls.
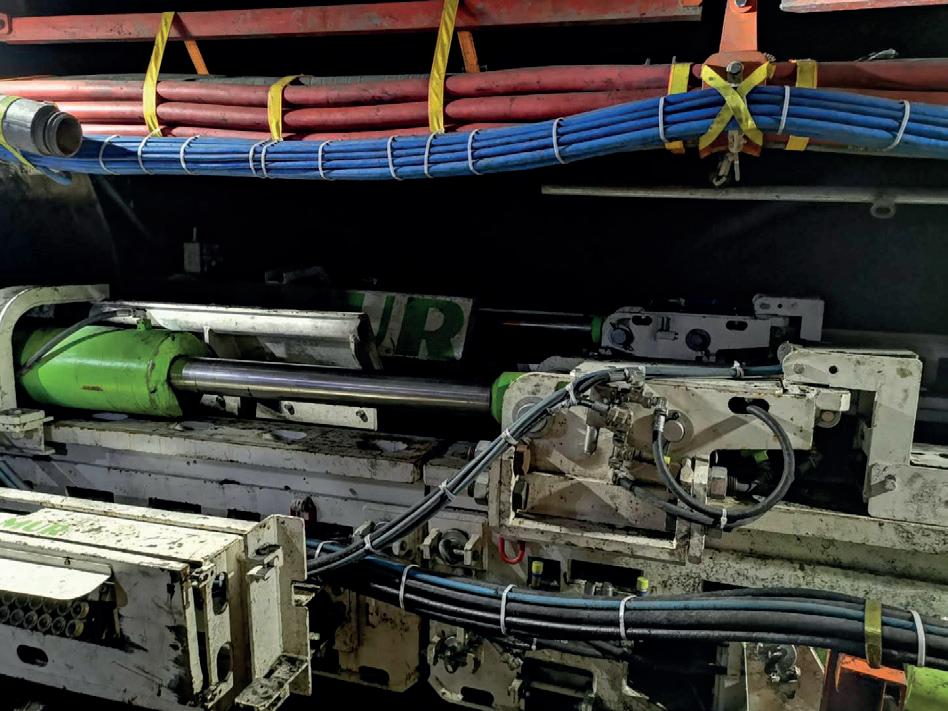
Figure 4. UPZP-1200 – feed cylinders interlocked against the belt return (lower) part.
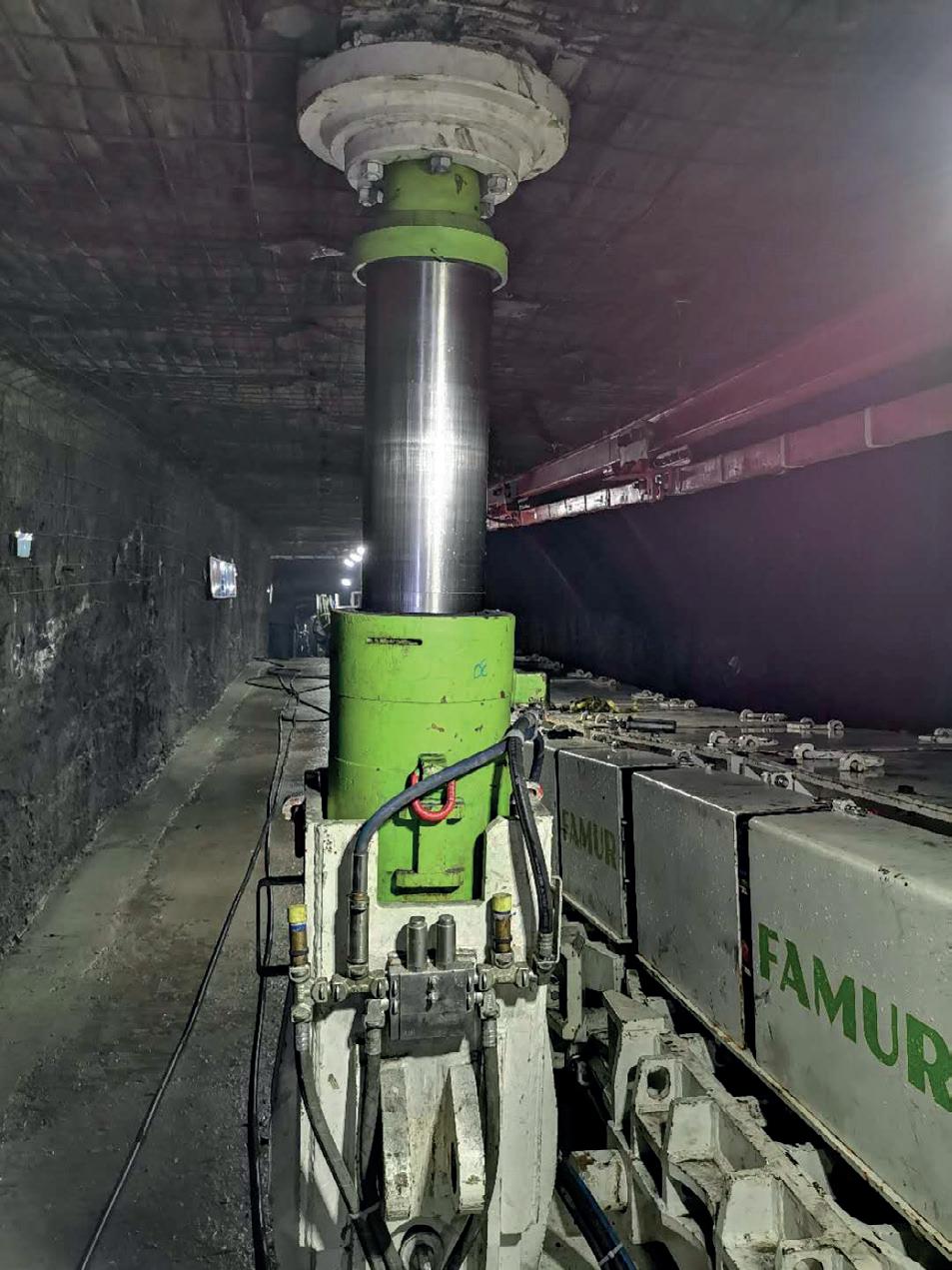
Figure 5. Vertical stabilising cylinder extended against the floor and ceiling, in the maingate tunnel.
Conclusion
The development of technology in the field of mining automation could be compared to the development of many items; it has already been forgotten that a lot of these items did not appear suddenly as a finished product, but are the result of gradual evolution in a given field.
Take, for example, smartphones. First, all the component technologies had to emerge, such as the development of a way to produce electronic components, then a specific design of radio transmitters, a charging system, a display or even a specific user interface, which are now taken for granted and cannot imagine that someone could have designed it differently. Therefore, history has repeatedly shown that the inventions that are used today were very rarely the work of a single author, and were most often a series of relatively small innovations that, when put together, produce the desired end result.
This is also the case with longwall automation. The aforementioned electrohydraulic control system for powered roof supports, or shearers capable of cutting automatically, are all significant milestones on the road to full longwall automation. Just as a smartphone would not be such an indispensable product if not for the development of touchscreens, one cannot afford to have missing links in mining technology, which would cause that the final effect of longwall automation is lost because it has to be supported by manual work.
Although it will probably take a few more years to see the autonomous operation, it must be stated with certainty that, as the numerous geological challenges are a separate area of problems waiting to be solved and hindering the automatic operation of the machines themselves, the use of automatic overlapping stations, such as the UPZP-1200, is one of those necessary milestones required for unmanned mining.