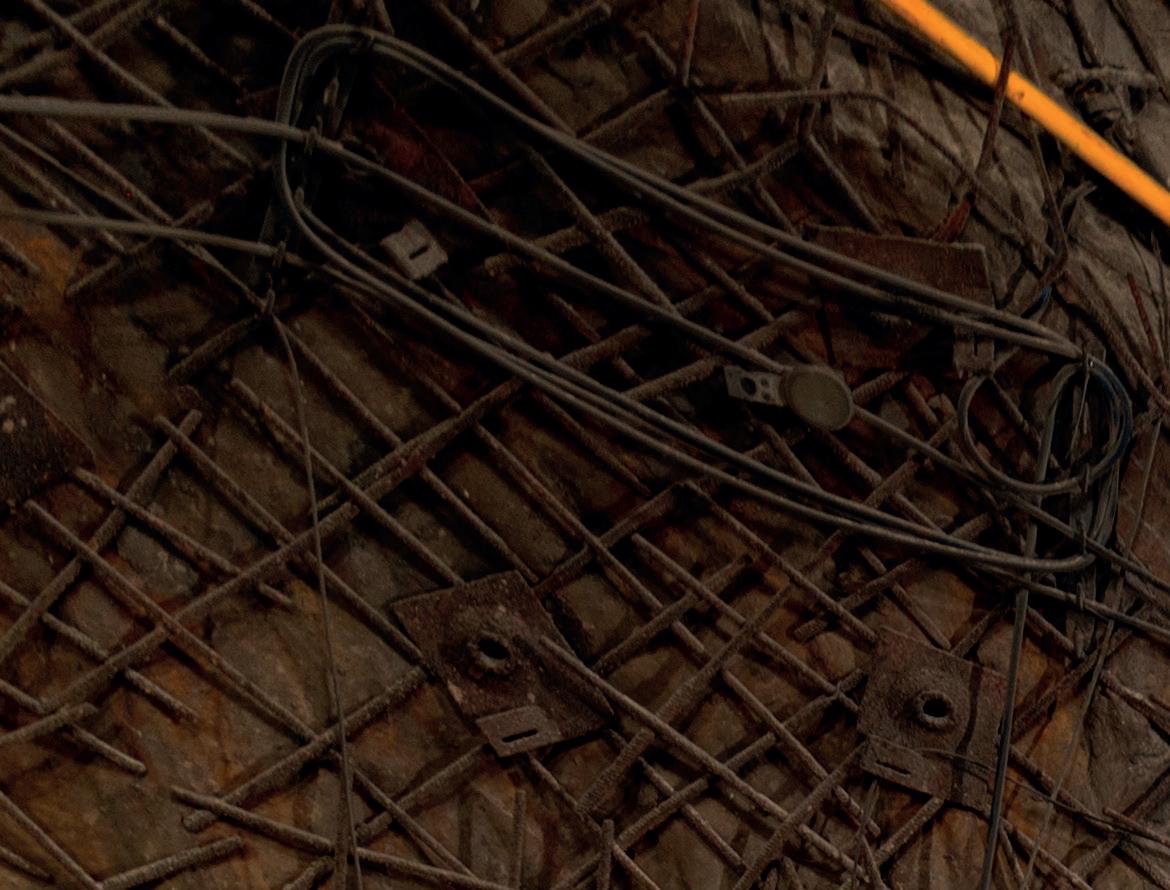
11 minute read
Driving Effi ciency In Underground Mining

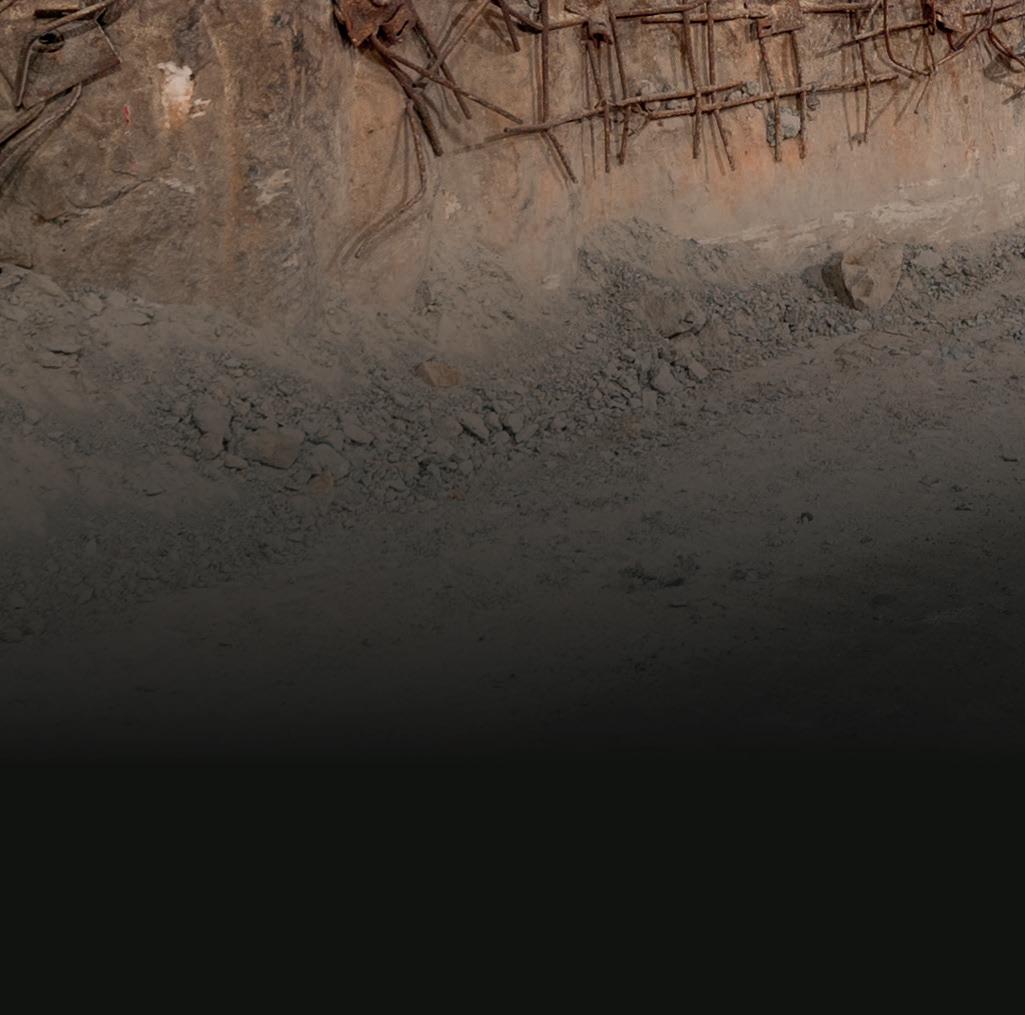

underground mining
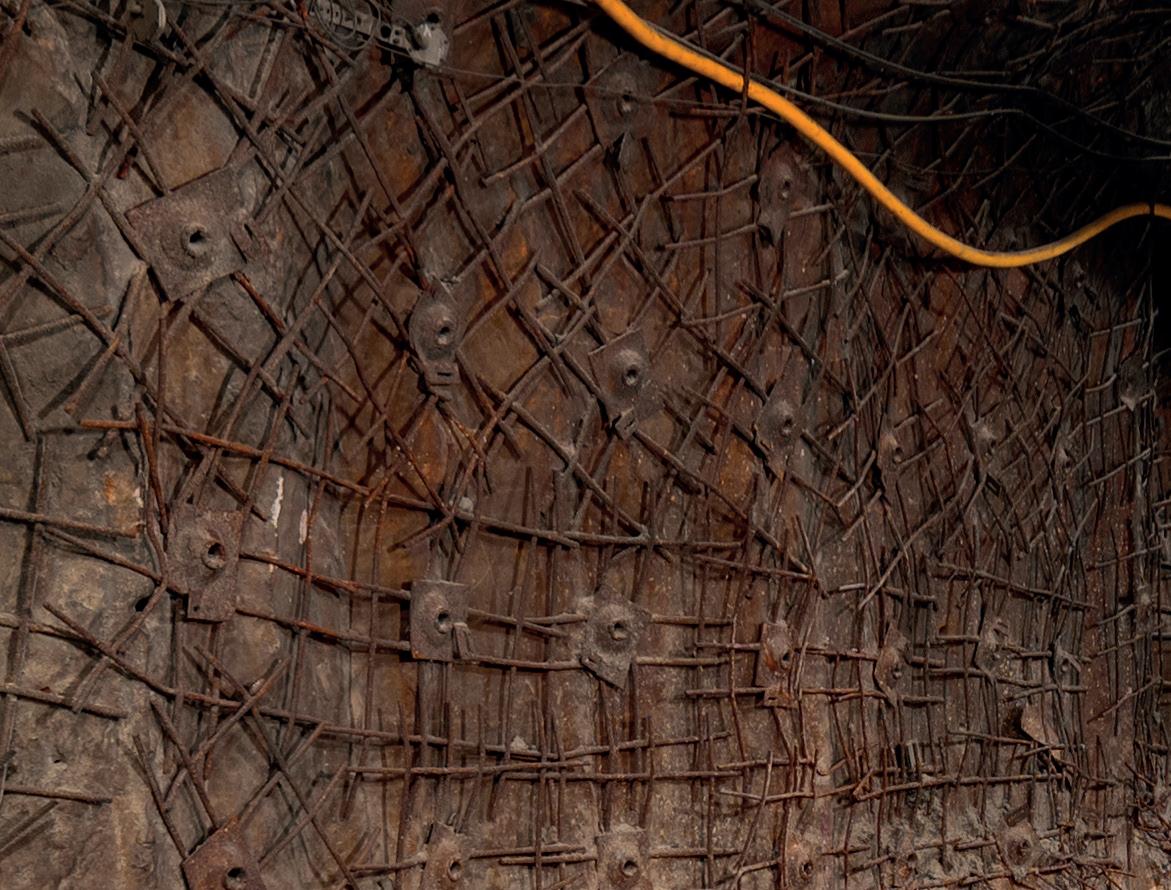
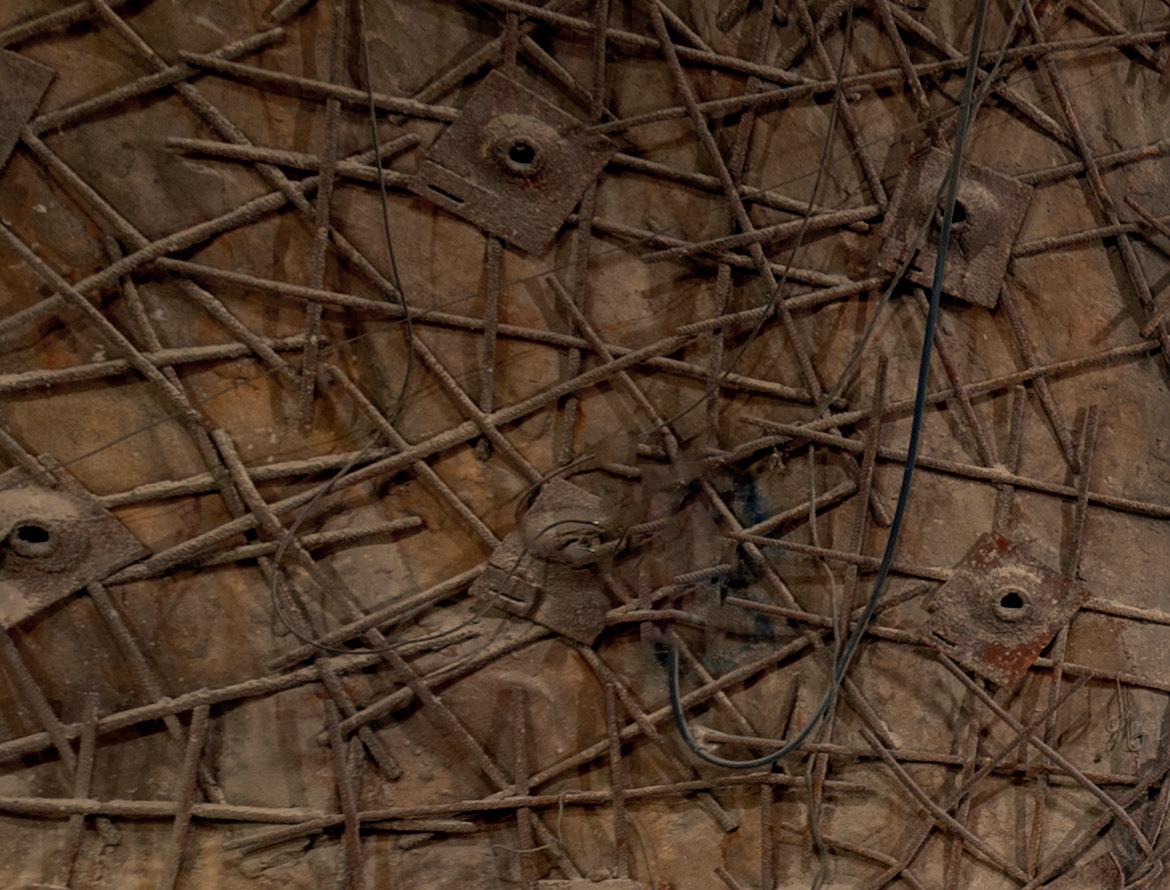
Andreas Westphalen, Caterpillar, Germany, explores how high-torque drive systems can off er increased eff iciency and reliability in underground mining.
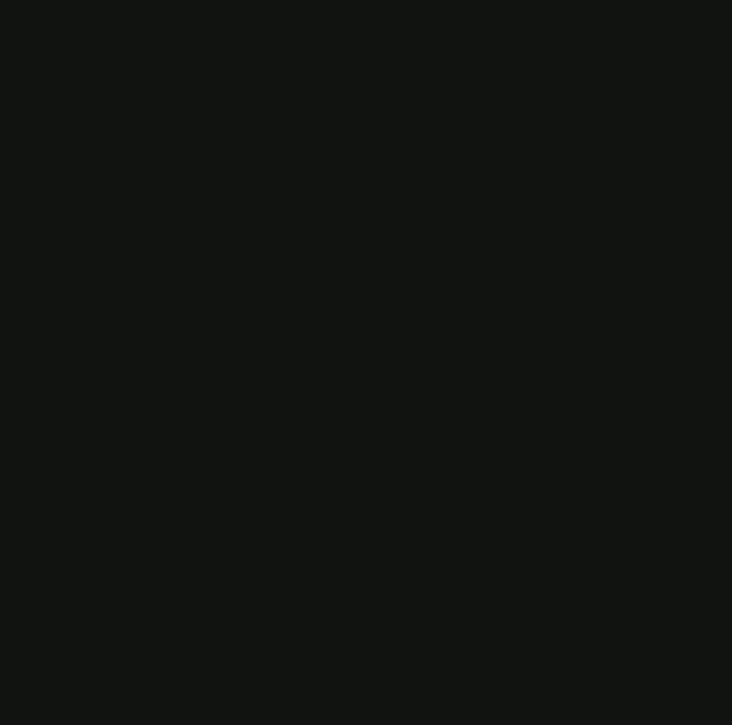
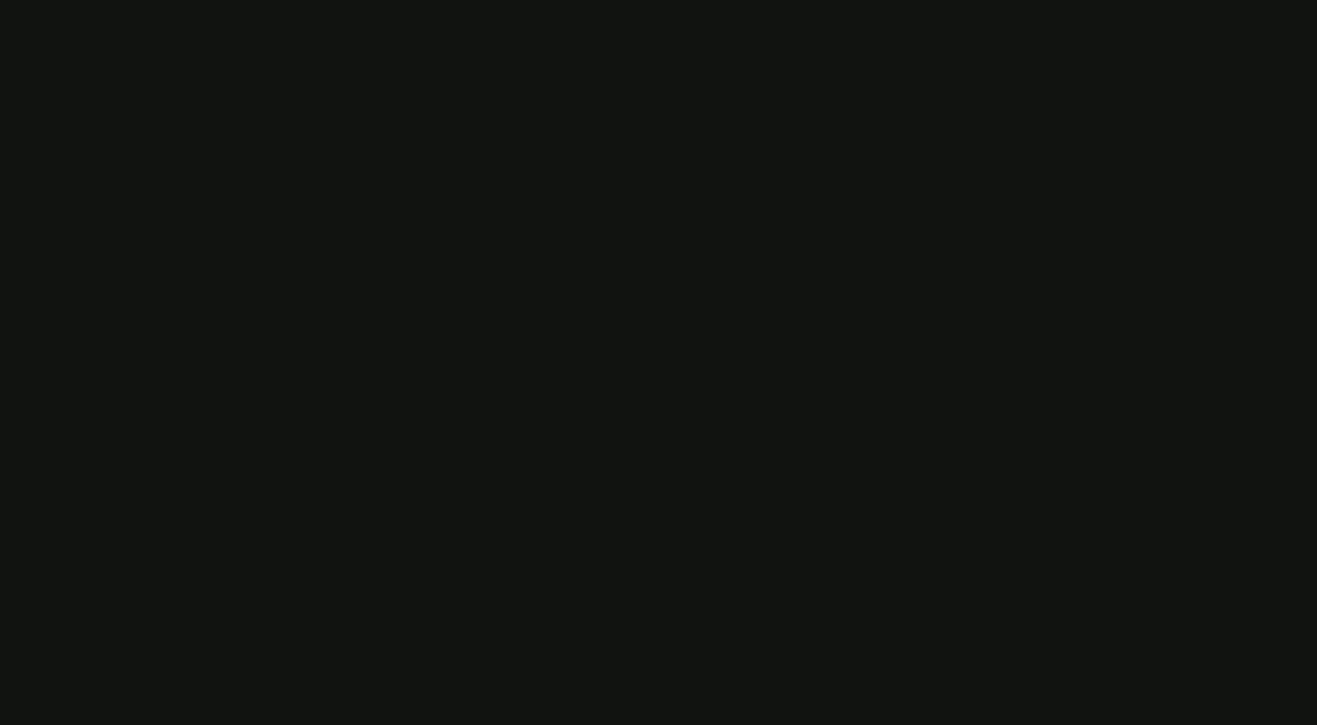
Underground mining places high demands on the reliability, efficiency, and capacity of the machinery. The economic development toward higher operating performance drives technological progress.
When coal is extracted in longwall mining, a chain scraper conveyor transports the raw material extracted by the mining machine to the end of the longwall. Conventionally, the drive is implemented at both ends of the chain scraper conveyor by means of two-pole squirrel cage asynchronous motors that include reduction gears.
Cat face conveyors with controlled start transmission (CST) technology have established themselves on the market. Equipped with a slip clutch, the CST gearbox allows for the load-free motor start-up and heavy-load start of the conveyor using the motor stalling torque, as well as the load sharing required for distributed drives by targeted use of the slip clutch.
Currently, Caterpillar is developing a modular system of high-torque drives (HTD): permanent magnet excited synchronous machines (PMSM) of different outputs – from 300 – 1600 kW – supplied

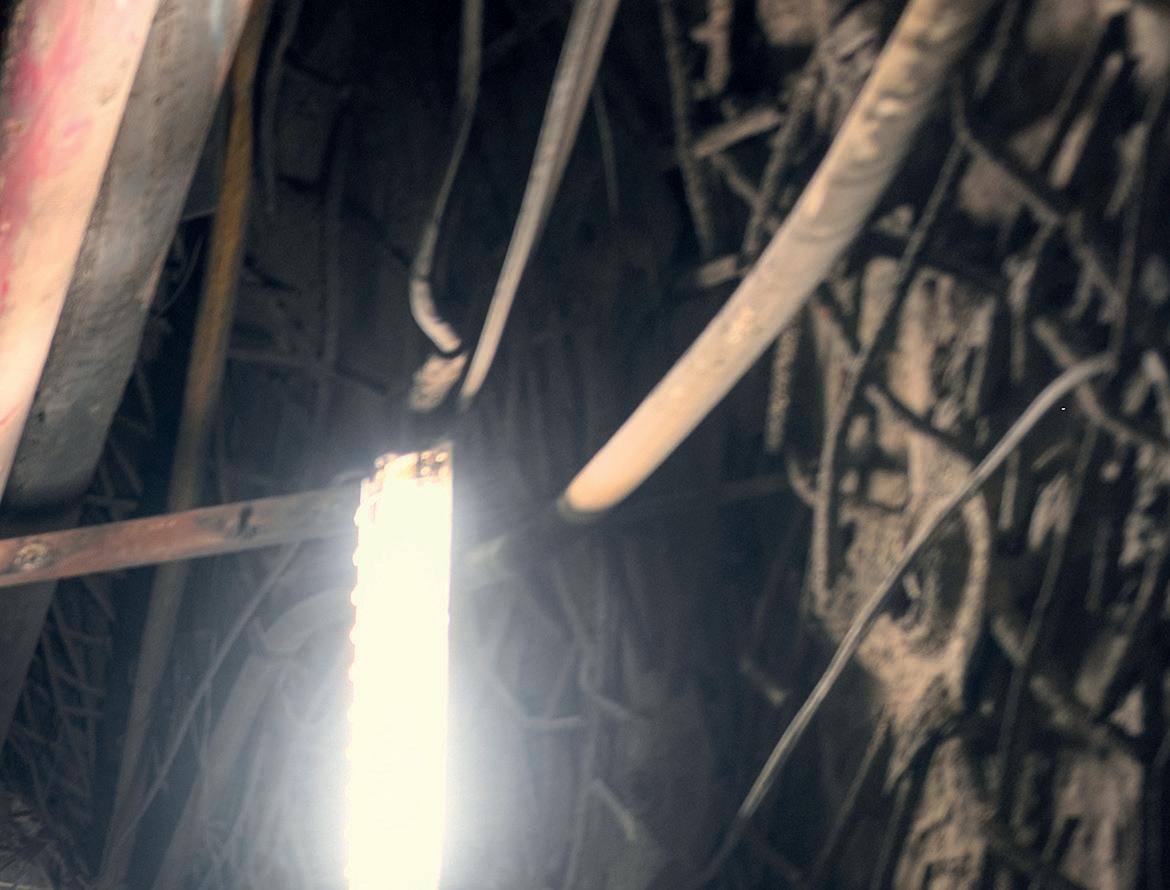
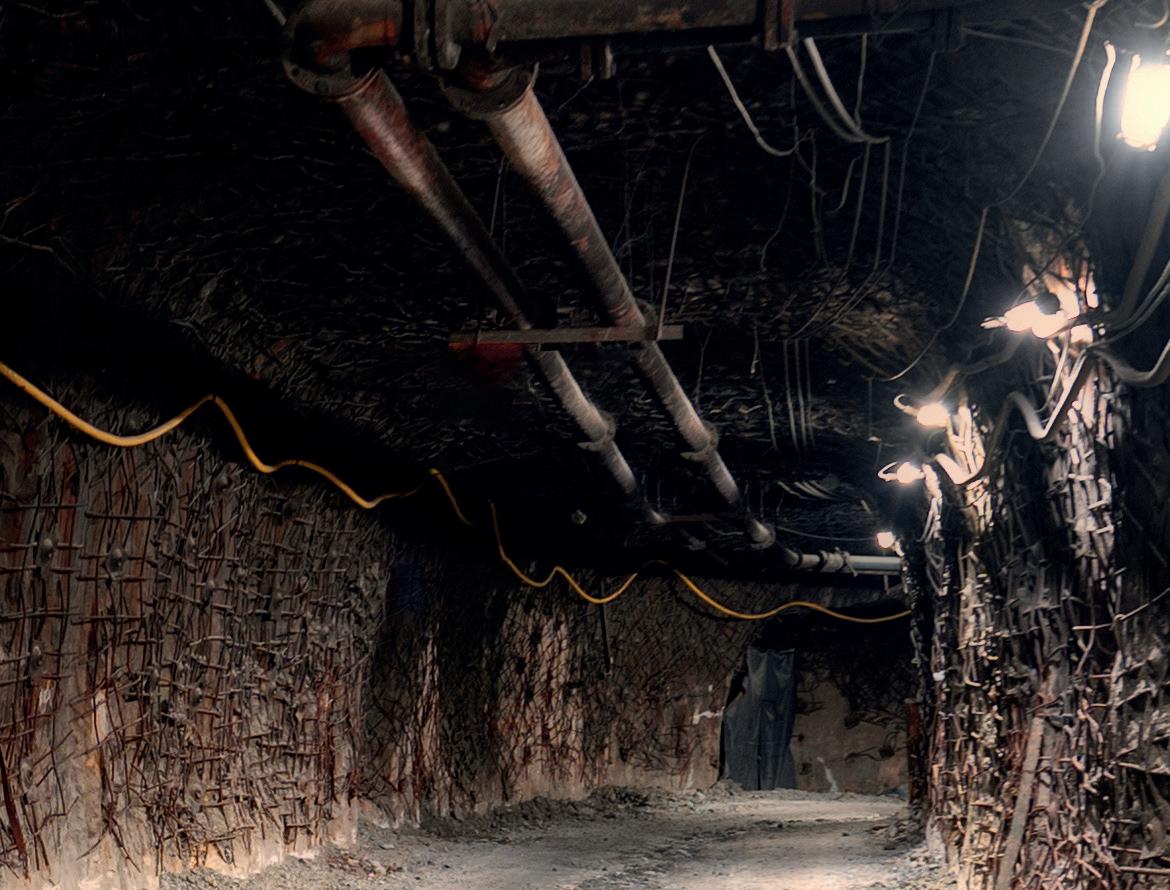
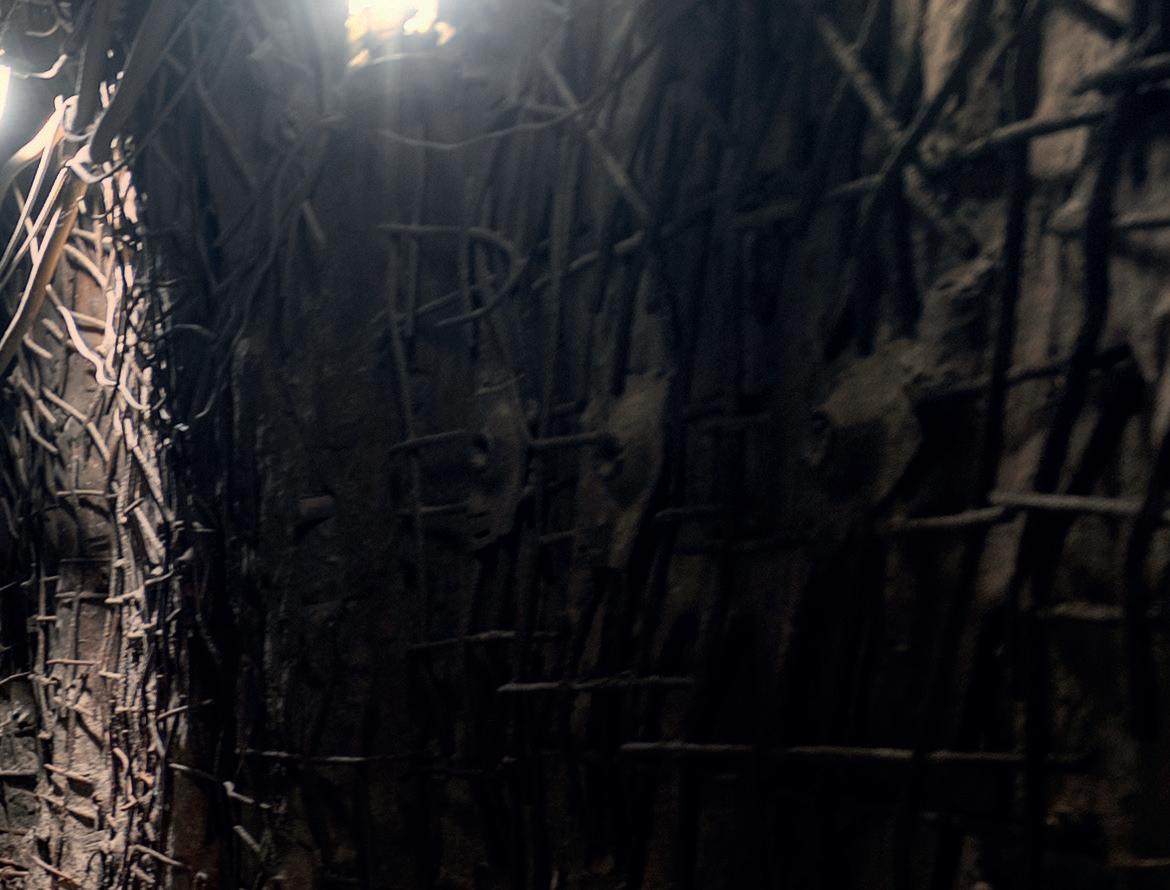
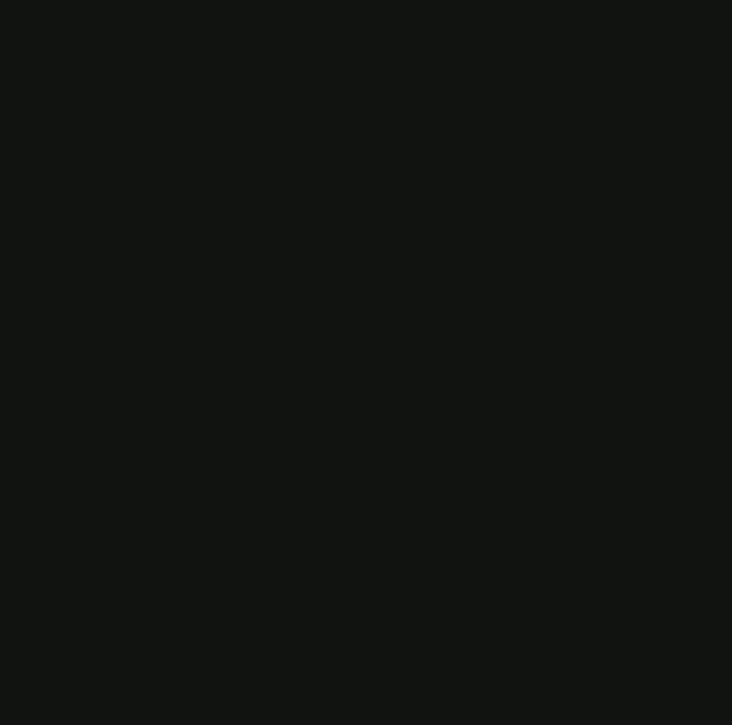
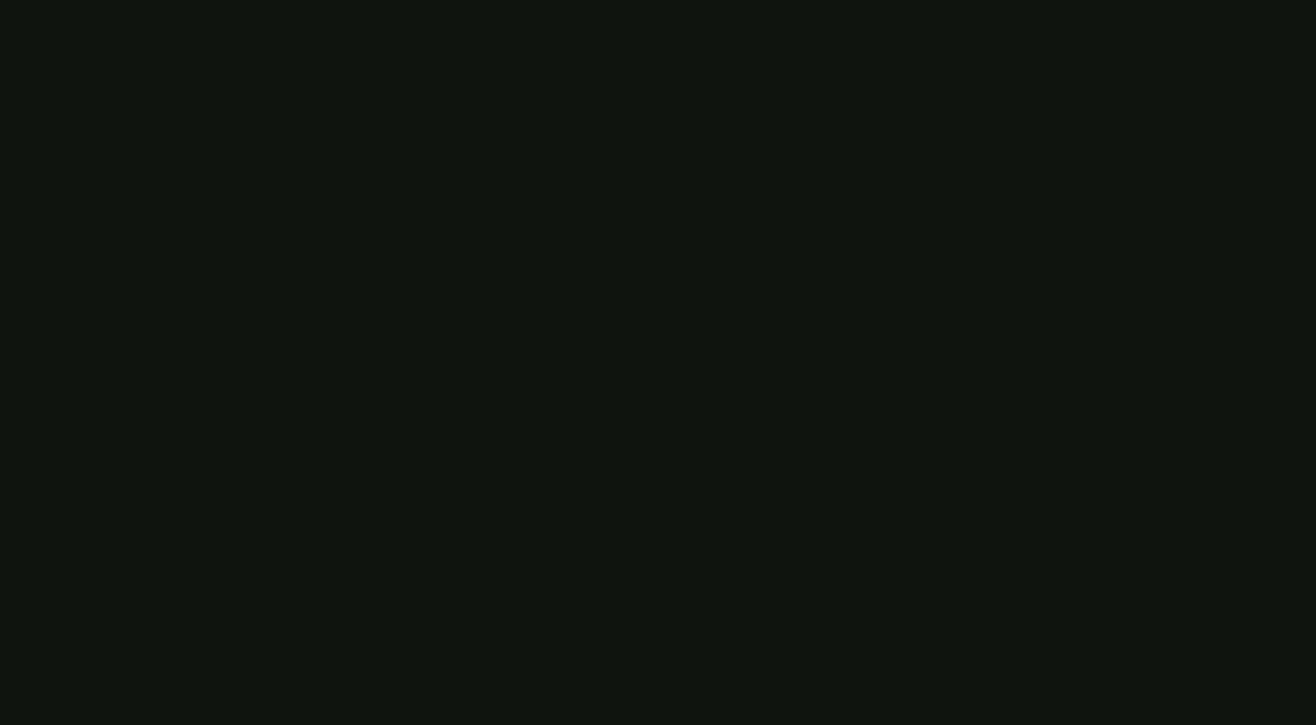
by medium-voltage converters. The HTD system is characterised by high efficiency, high-rated torque ranging from 9000 – 70 000 Nm, and significantly reduced rated speeds of 300 – 600 rpm. Its modular design allows the new technology to be used underground for other drive applications beyond face conveyors.
HTD system technology offers new degrees of freedom and opens new possibilities for the raw materials industry. Due to the slower speed and modified gear ratio, the moment of inertia visible on the gear output shaft is reduced by a factor of eight. As a result, system damage from conveyor blockages will be less severe or virtually non-existent.
Another advantage from this new technology: instead of using only the narrow working area of the asynchronous machine between the stalling point and the synchronous point, the HTD system provides a complete torque-speed map by using frequency inverters.
Depending on the selection, the new drive system offers precise control over torque or speed. This precision enables smoother starting and
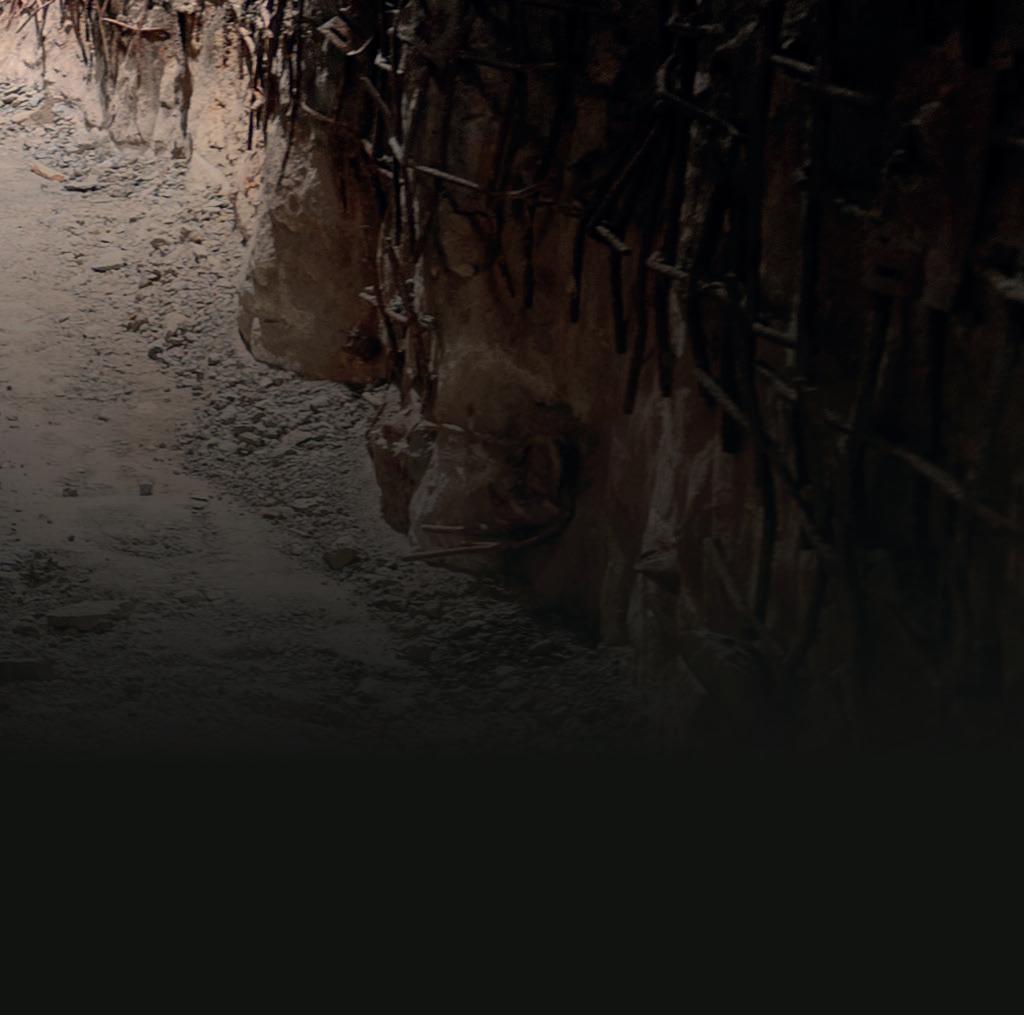
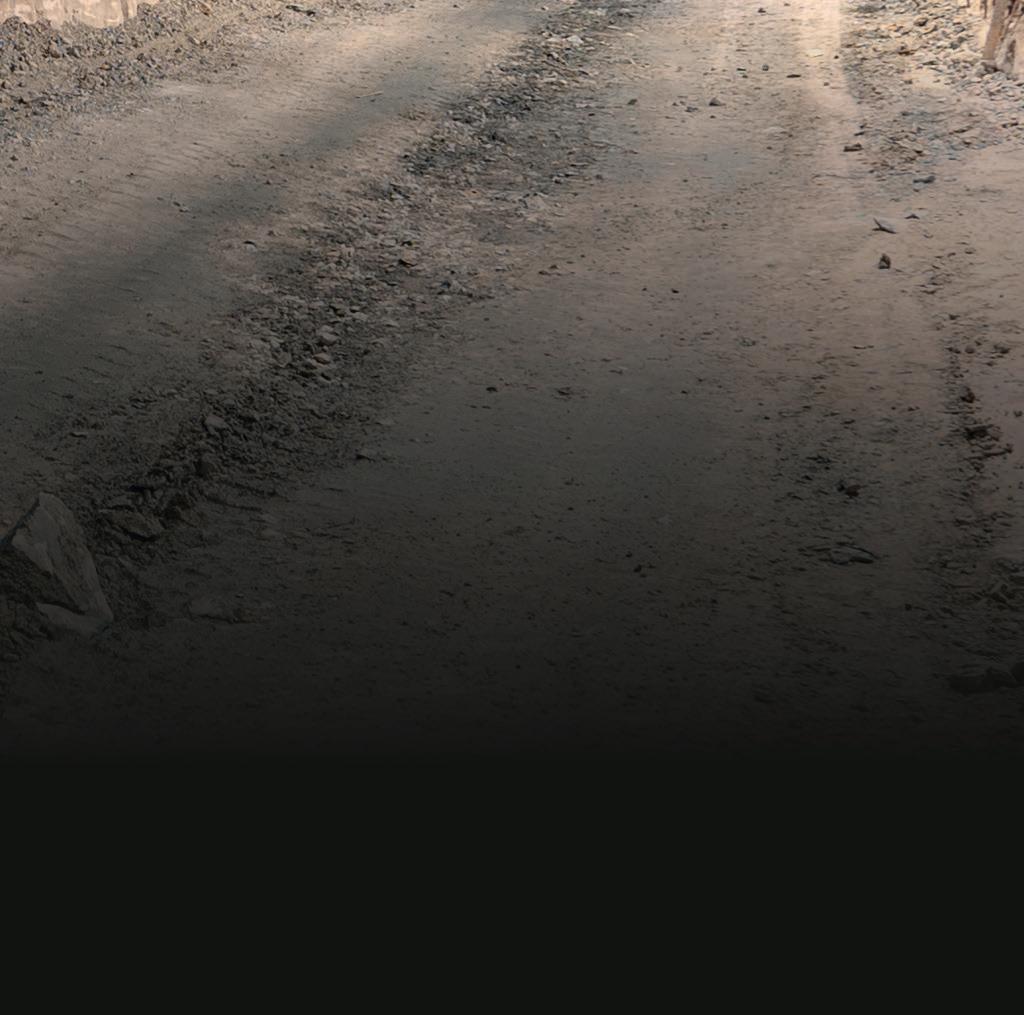
braking processes, targeted speed ramps, rapid intervention in the event of a fault, improved load sharing between the head and tail gates, creep, and reverse travel. The conveying rate can be optimally adapted to the production rate, and necessary speed adjustments can be made when encountering difficult geological conditions to avoid damage to the system.
In general, the HTD system is more efficient and reliable than conventional drive technology. It offers lower energy consumption and less cooling capacity, plus system component wear is reduced due to a simpler gearbox with fewer rotating parts.
Conveyor start-up
The start-up process of a chain scraper conveyor is a special event due to the process, but it must be carried out safely and reliably. A classic distinction is made between a smooth and a heavy-load start-up. The smooth start-up serves to protect the system and increases the service life. The aim is to introduce the force into the chain in a controlled manner without peaks and fluctuations during acceleration.
In the case of a heavy-load start-up with fully loaded or even overloaded conveyors, however, the drive must be able to provide the maximum possible and permissible chain tractive force.
The qualitative load curve shown in Figure 1a shows the required torque over the motor speed that is passed through during start-up until the nominal speed is reached. When the conveyor is started, three components act on the chain force and thus on the motor torque: The mass of the chain as a dead load on one side and the load as a payload on the other lead to a friction force directed against the movement, which must be overcome (sliding friction). After a prolonged standstill, residual loads can bake into the conveyor and lead to a greatly increased static friction. The force required to accelerate the masses to be moved.
Conventionally, underground asynchronous machines are used as conveyor drives. They have established themselves as an efficient, reliable, and safe drive variant. However, in terms of its characteristics, the load torque is higher than the pull-up torque of the motor (Figure 1b) to manage the task at hand.
For this reason, an additional technical system component is required for a heavy-load start. Cat conveyors are equipped with CST technology for this purpose. A slip clutch in the gearbox separates the motor from the load, so that the motor can run up freely to the nominal speed at the beginning. When the coupling closes, the motor comes into contact with the load, and the heavy-load conveyor start can be carried out with the help of the available stalling torque of the motor. There is a compromise for the system – a longer start-up time. To protect the electrical power network, the motors of the chain scraper conveyor start in stages. Prior to the conveyor starting, the CST coupling’s hydraulic components are then prefilled, and the couplings are closed in a time-based way and coordinated with each other to keep the slack chain accumulation low, among other things. Only then does the conveyor start. Another issue with conventional technology is that motor currents rise sharply when a stalling torque is used. On the one hand, high motor currents are only allowed for three seconds for operational reasons, so the conveyor must have broken away by then. On the other hand, a voltage drop occurs in weak electrical networks, causing the effectively available torque to drop. The high reduction ratio of
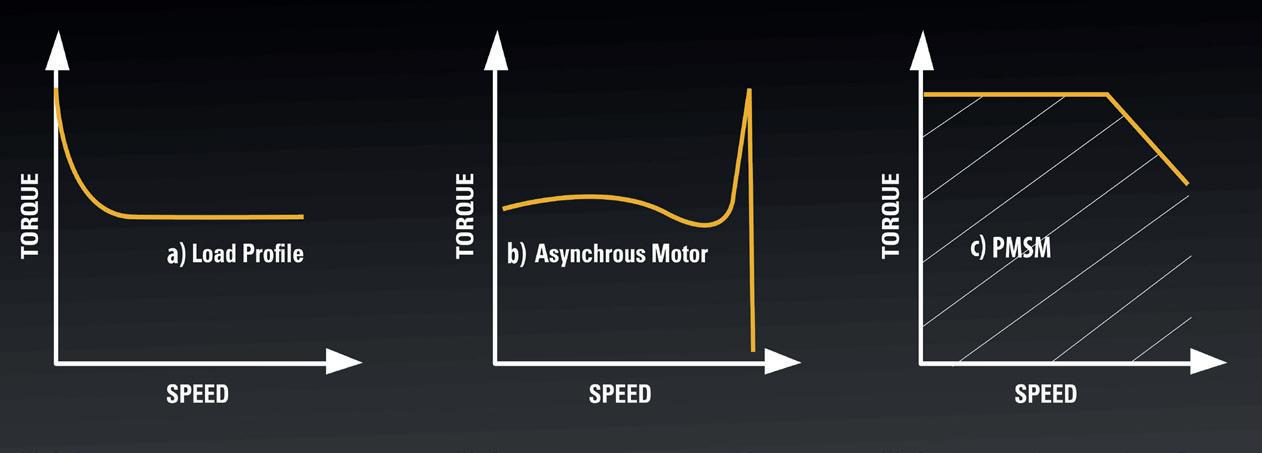
Figure 1. a) Load characteristics of a chain scraper conveyor; b) Torque-speed characteristic of an asynchronous motor; and c) Torque-speed characteristic diagram of a PMSM. Figure 2. The torque curve of a CST drive (blue), as well as the speed (green), during the heavy-load start of a conveyor (simulation). The torque builds up at the output because of the timed closing of the CST coupling. If it exceeds the breakaway torque, the conveyor accelerates to operating speed within a short amount of time.
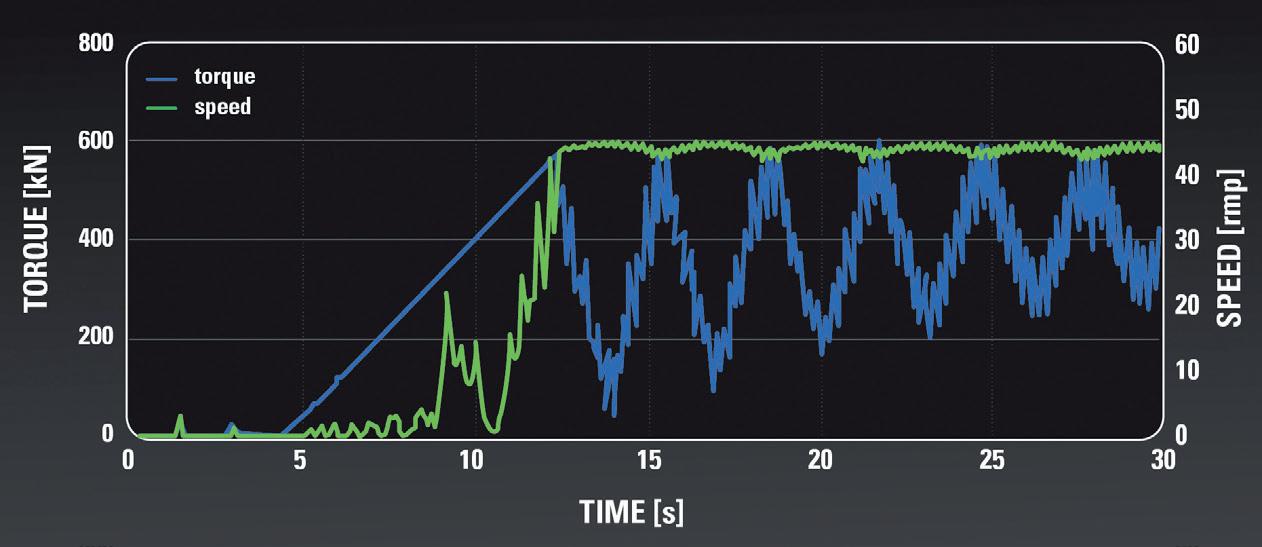
the gearbox (typically 33:1), the rapidly rotating masses, and the high moments of inertia related to the load require measures to protect the system components in the event of a fault, such as a blockage.
Figure 2 shows a torque time curve and CST drive speed during a heavy-load start, which was obtained with the digital twin of a chain scraper conveyor. The breakaway of the conveyor is based on a torque ramp. The actual acceleration phase is quite short and lasts approximately three seconds. The chain is locally stretched to different degrees and accelerated to operating speed. In the initial phase, significant torque fluctuations occur, which decay over time.
HTD systems
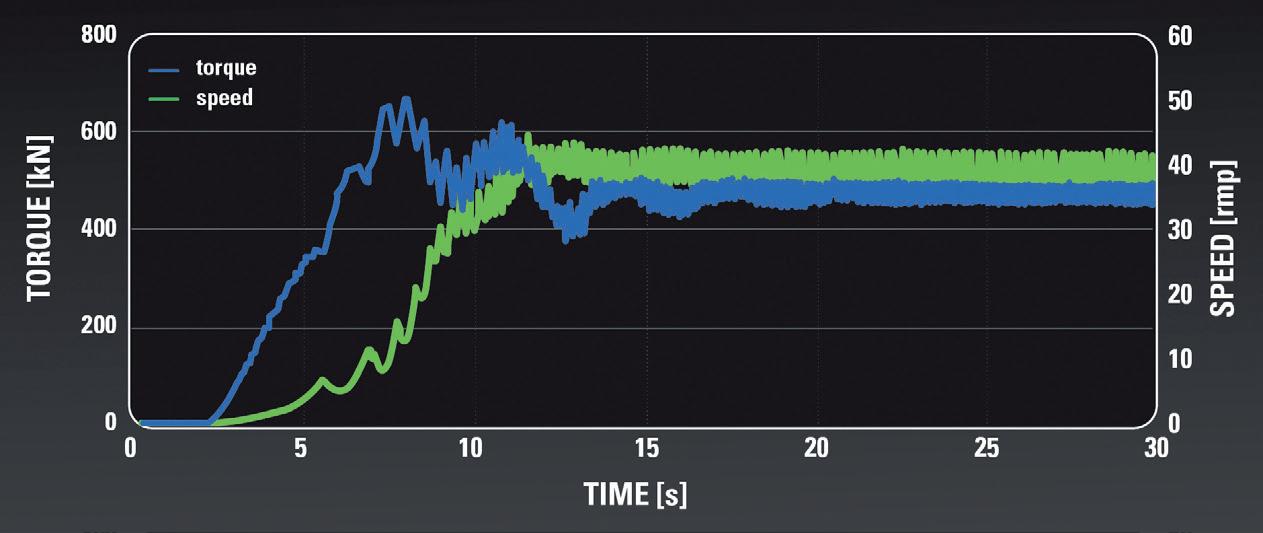
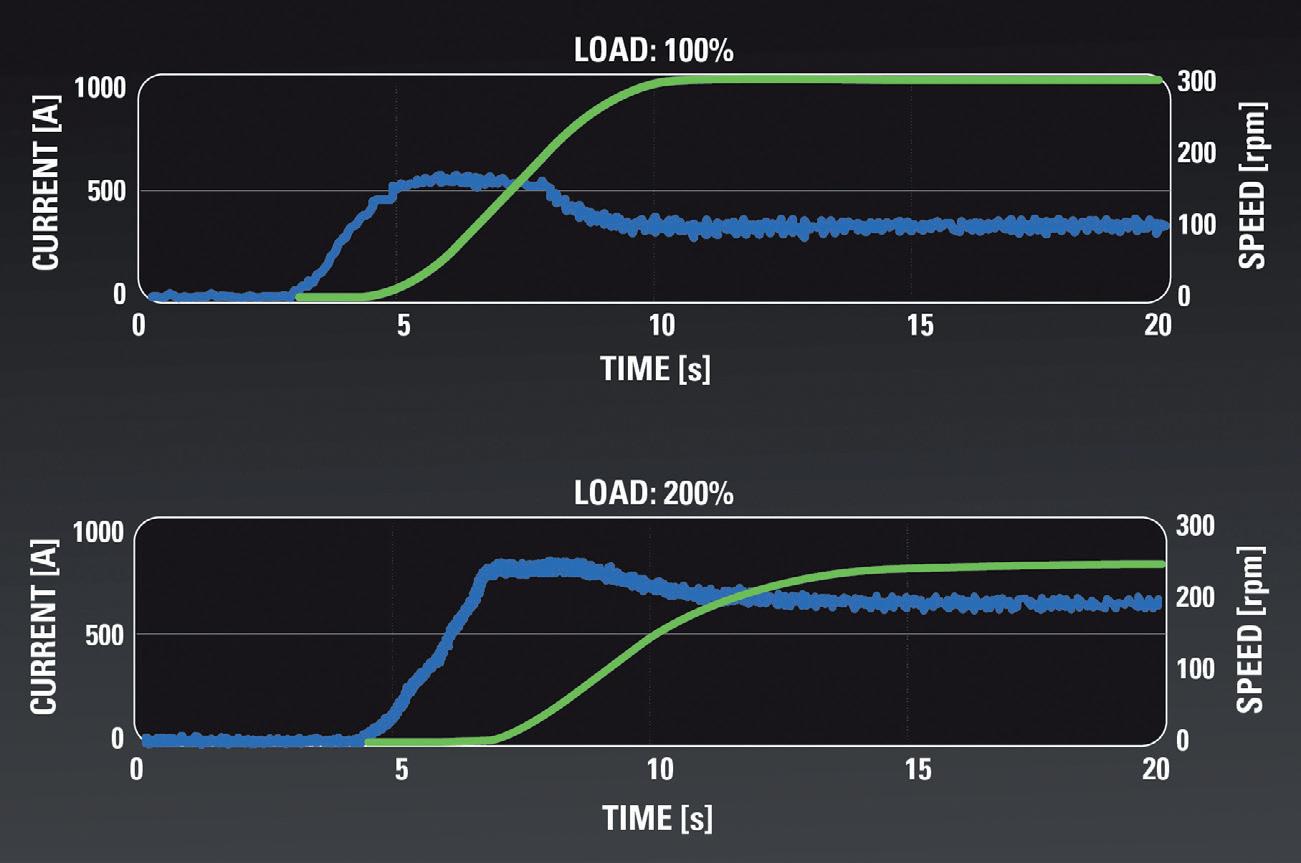
The Cat HTD system (Figure 3) consists of a PMSM with slow rotation compared to an asynchronous machine, a medium-voltage converter, and a gearbox with a much smaller reduction ratio, typically 6:1. The reduced mass moment of inertia is considerably smaller by a factor of eight than of the CST drive, eliminating the need for design measures to protect components in the event of a fault.
Compared to the asynchronous motor, the availability of a torque-speed map (Figure 1c) through an inverter drive offers a significant advantage. For a start, the load does not have to be separated from the motor, and the necessary torque is available from zero speed. To obtain an optimum ratio of torque to current, the reluctance torque of the machine is used.
The HTD system masters the handled load profile without further difficulties (the load profile and the PMSM characteristic in Figure 1). In the heavy-load start shown in Figure 4, the simulated torque and speed obtained are plotted over time. In contrast to the CST technique, the start-up is speed-controlled. The controlled acceleration phase over the selected 10 seconds runs more smoothly regarding the torque behaviour; the amplitude of the initial torque oscillation due to the breakaway has decayed significantly, becoming both smaller and faster. The heavy-load start does not differ qualitatively from a smooth start-up, something that cannot be achieved through conventional technology. Figure 5 compares a smooth start-up with a heavy-load start, as recorded on a motor test bench. In both cases, the measurement data of the speed and motor current (as a measure of torque) show a smooth acceleration process to the Figure 3. High-torque drive Cat HTD4100.
Figure 4. The torque curve of a HTD (blue), as well as the speed (green), during the simulated heavy-load start of a conveyor. When the speed is specified, the torque required for acceleration is built up. The gradient of the speed ramp determines the time until the operating speed is reached. Figure 5. Measurement data for the starting behaviour of a HTD against a load of 100% (top) or 200% (bottom); the motor current (blue) is shown as a measure of the torque and the speed (green). Regardless of the size of the load, there is a smooth acceleration process.
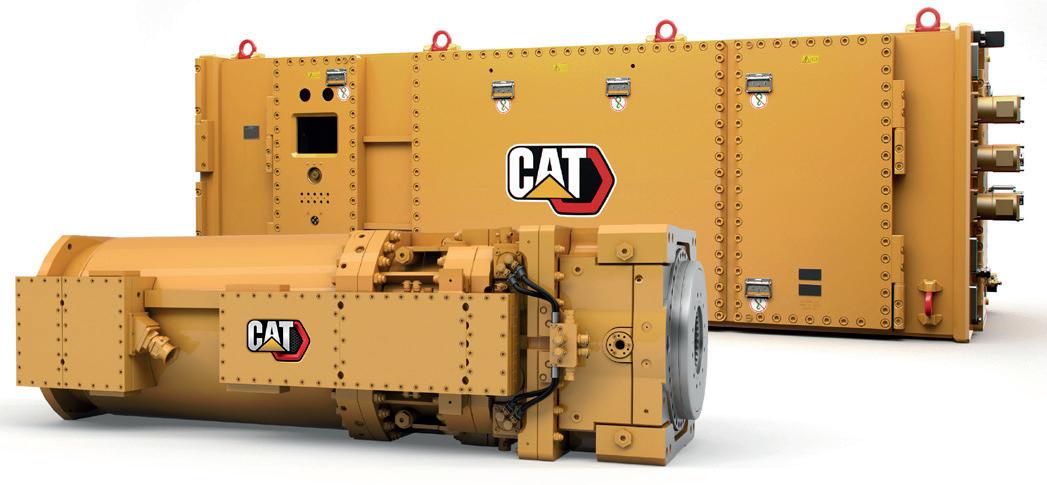
maximum permissible operating speed due to the load. With this behaviour, the HTD system exceeds the previous catalogue of requirements for conveyor drives, because the previous technology cannot reconcile a reduction of the load peaks and chain force oscillations with the introduction of the maximum possible and permissible chain force.
Conveyor blockage
Although unlikely, hard blockage occurrences do happen in the field. In such a case, the individual components of the conveyor are strongly stressed, especially if the blockage occurs close to the drive. If a face conveyor is equipped with a cross frame, this represents a potential source for such a blockage.
With CST technology, the moments of inertia of the motor and gearbox drive line components are clearly dominant overall in comparison to the rest (Figure 6). In the case of a hard blockage, large dynamic forces act on the weakest link – the conveyor chain. The safety equipment must therefore be designed to prevent chain breakage as far as possible. Otherwise, production downtime will occur, resulting in high costs for the plant operator.
With CST technology, the coupling is opened after a blockage is detected, and the motors are switched off. The separation of the drive line from the chain prevents the fast-rotating drive masses from damaging the chain. The simulation with the digital twin (Figure 7 – blue curve) shows that the introduced force is limited to approximately 4000 kN. However, a single chain strand cannot be prevented from being torn (breaking force 2800 kN) in an extreme case with an asymmetric twin inboard chain strand. A symmetrical double chain strand can withstand the peak force without damage.
However, this is not the case with a conveyor drive with a fast-rotating asynchronous motor, frequency inverter, and rigid gearbox (VFD) without additional safety equipment (Figure 7 – green curve). There, the dynamic forces caused by the rotating masses break through and destroy the entire chain assembly. The HTD technology, which has a similar structure in principle but significantly lower moments of inertia in the drive line, offers better protection than other drive technologies, since the peak force remains below the critical limit for a single chain strand (Figure 7 – red curve).
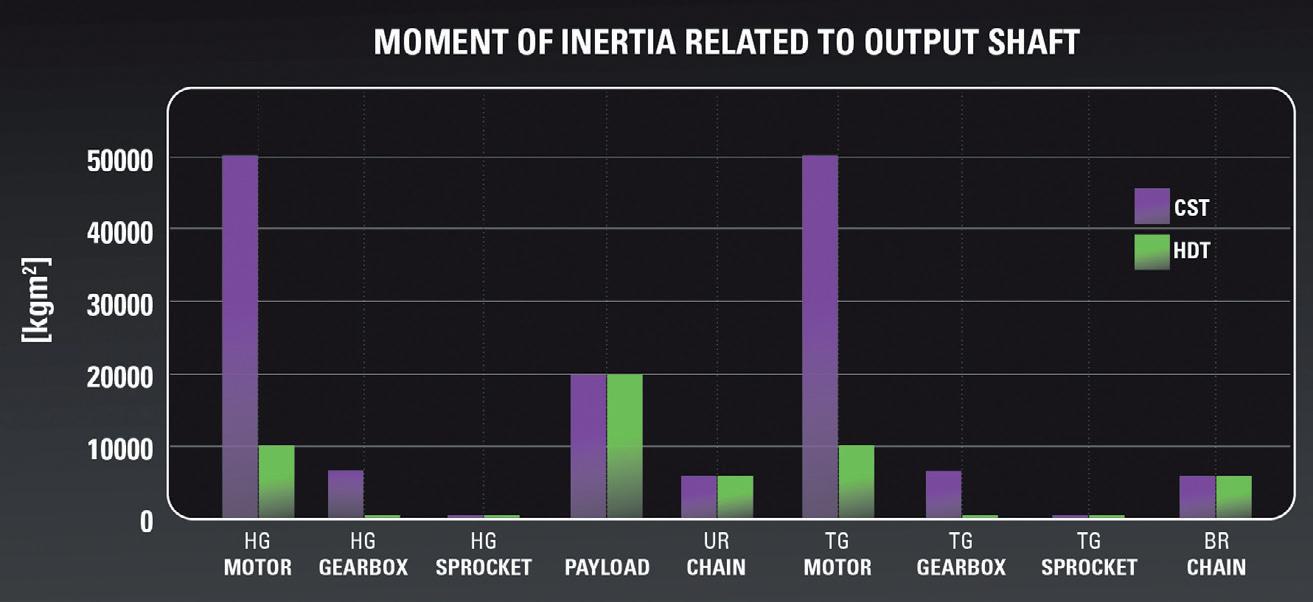
Figure 6. Comparison of the moments of inertia related to the output shaft of the individual conveyor components for CST and HTD technology (HG: head gate, TG: tail gate, UR: upper run, BR: bottom run). In comparison, CST technology is clearly Summary dominated by the moments of inertia of the motor and gearbox. In the case of a HTD drive systems offer the blockage, they can have a negative effect on the other components. most advantages when system and component properties are prepared: smooth start-up even with heavy loads, overload and blockage protection, precise load sharing, creep mode, and reverse travel. In addition, the HTD drive offers great potential regarding its reliability and availability with fewer rotating parts, no overload coupling, constant condition monitoring, less wear, and lower maintenance costs. It also offers productivity advantages over its service life through lower Figure 7. Chain forces during a hard blockage for different drive systems (simulation). With VFD technology, the force peak triggered by the blockage exceeds the breaking force of the twin inboard chain assembly. The slip clutch of the CST technology significantly limits the peak force. The HTD technology is characterised by the fact that energy consumption, and total cost advantages over the life cycle through lower total cost the force peak remains below the chain breaking force in the considered blockage case. of ownership.
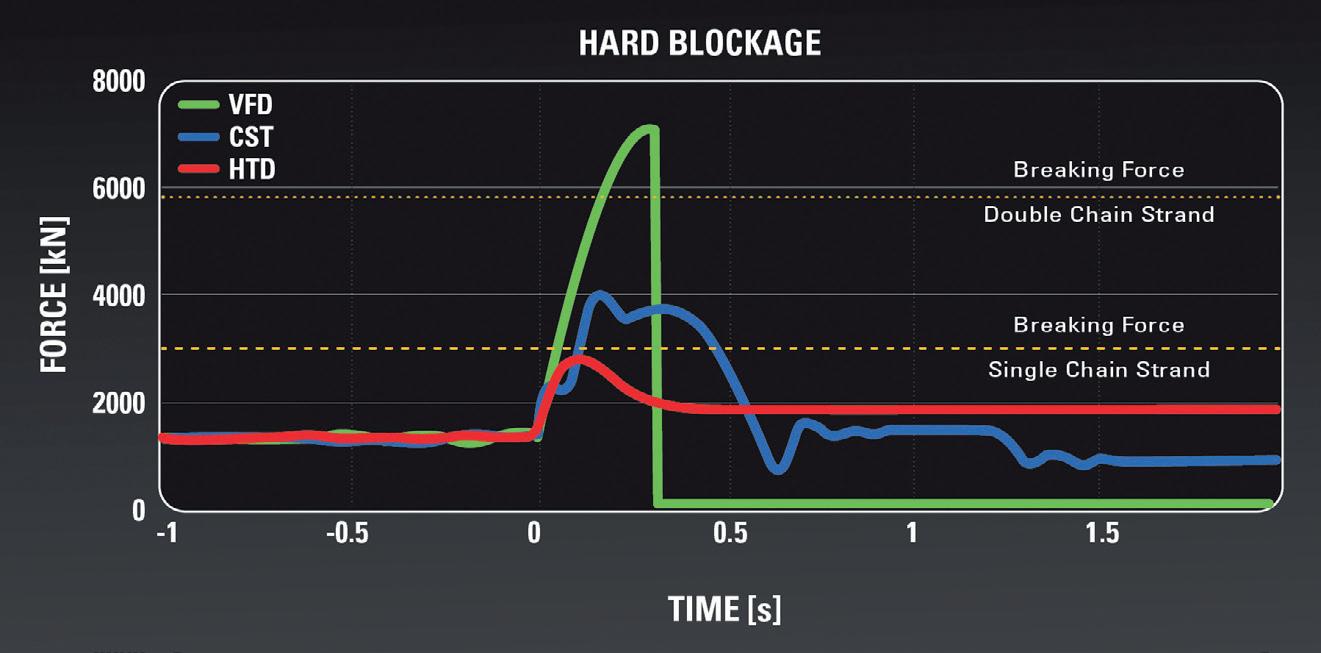