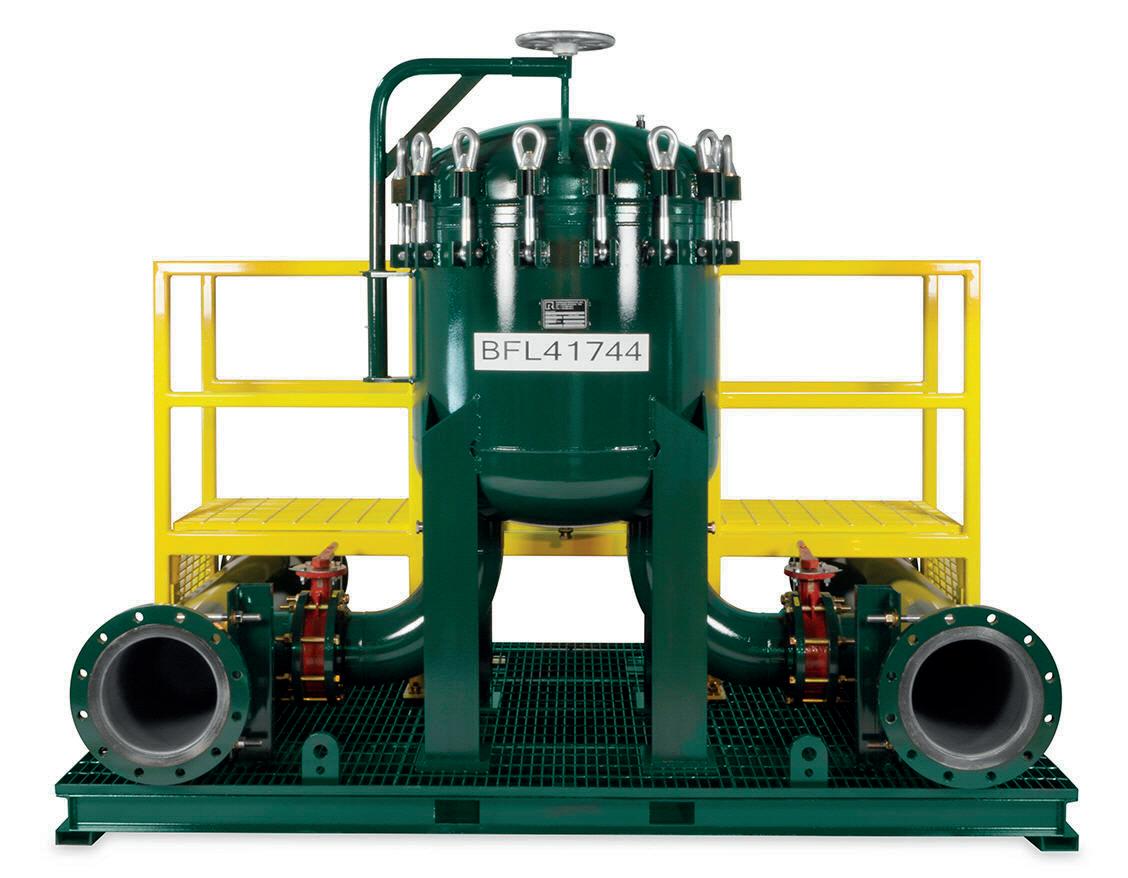
6 minute read
Can electric pull its weight?
operations, and the added disposal costs are factored in, this turns out to be an expensive choice.
Even with all of the advances in filtration technology, many facilities continue to make purchases based on the assumption that they are saving money by buying the least expensive filter product. What is often overlooked is the added costs that may be incurred whilst making this choice. Customers should be supplied with informative filtration information ahead of a purchase in order to assess the benefits of working with a knowledgeable supplier who can also provide technical support on many levels.
To form the basis of a strategy and ensure that everyone is on the same page regarding CAPEX and OPEX expectations, it can be helpful to ask buyers and users what they consider to be the most important feature(s) of their filtration requirements. This might include some or all of the following: n Efficiency of the product (nominal, absolute, high efficiency). n Price. n Dirt capacity (lower operational servicing). n Availability (inventory-logistics). n Any special features deemed important. n Technical support.
Figure 3. A gas conditioning filtration skid.
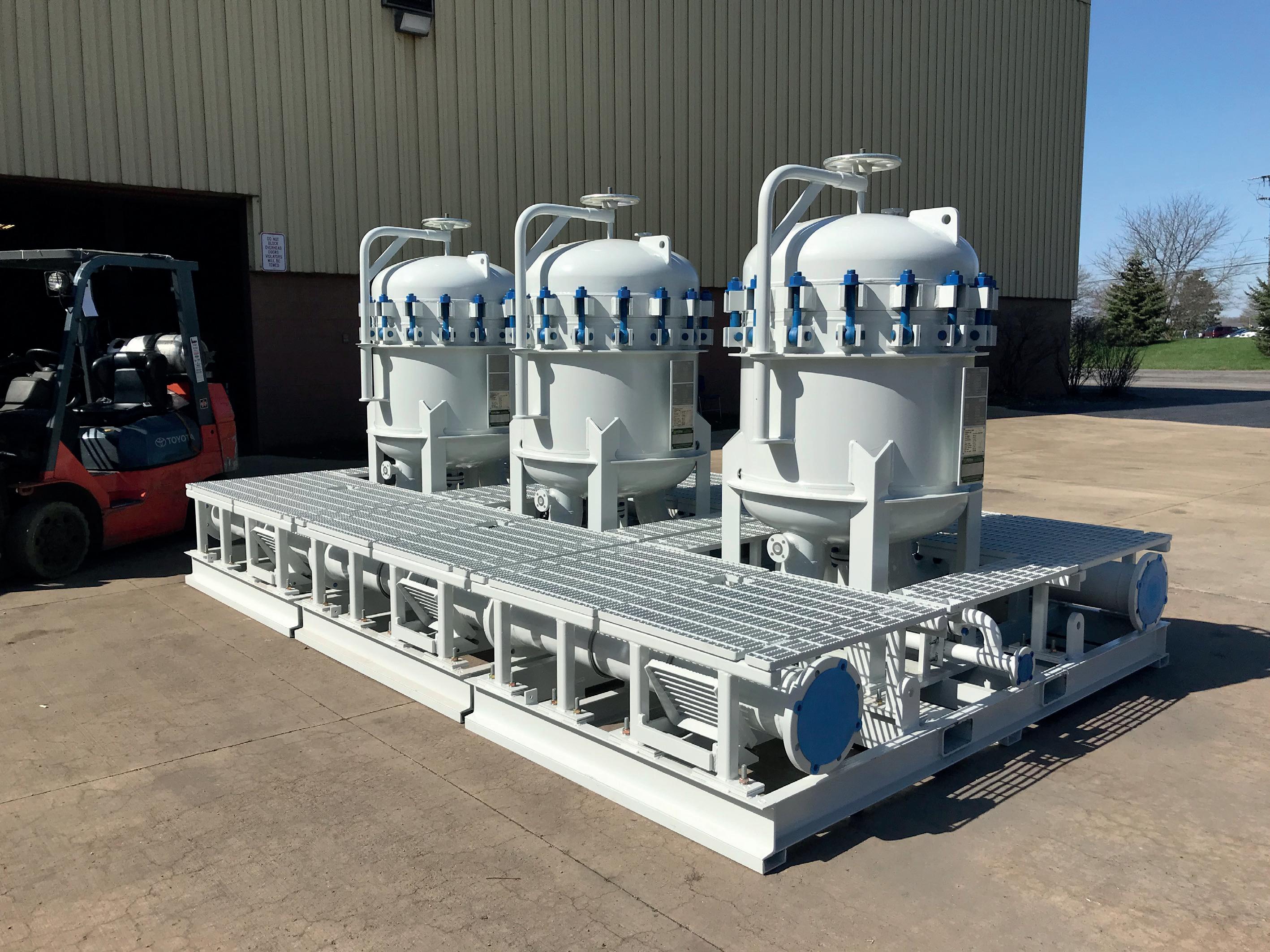
Figure 4. PS Filter’s multi-plex filtration package.
Common mistakes
Three common filtration mistakes that can cost operations are as follows: n Choosing the wrong efficiency filter to meet performance criteria. n Buying the cheapest filter thinking it will save money. n Not having all of the filter performance information documented to ensure it will be operationally suitable.
Questions to ask
Three simple questions to ask when choosing a filter are: n Does the filter have the dirt capacity required to be operationally feasible? n Does the filter have the performance efficiency required for a particular process? n Is the filter designed to meet desired flow requirements so that it will be cost-effective?
The consumable filter business is an area for improvement, and the market is growing as companies strive to increase oil and gas production targets as environmentally-consciously and cost-effectively as possible. Companies need to ensure that their target customers have a positive experience, and it is important to demonstrate authenticity in order to offer value in all products and services. Building success in this market will provide added references and case histories that can be used to expand into the upstream, midstream and downstream oil and gas market, and present opportunities for company growth.
There are thousands of companies in the supply chain. Unless these companies can find ways to add value to the end user, they will be faced with difficulties. Some of the current trends in oil and gas supply chain management include:1 n Increasing supply chain responsiveness. n Forming strategic partnerships – successful and trusting relationships with top-performing suppliers. n Operations demand management – match demand to available capacity. n Supply chain process integration – when supply chain participants work towards a common goal.
Even though the market is very concentrated, with lots of buyers and sellers, there is still room for a new entrant who can bring fresh ideas and process innovations to the table to improve the bottom line of its customers.
Conclusion
In Alberta, there are over 600 active gas processing plants that recover natural gas liquid mix or specification product, 11 fractionation plants that separate out natural gas liquid mix streams into specification products, and eight straddle plants.
No matter what area of energy production, filtration is of paramount importance to ensure production is optimised and operational costs are kept within budget forecasts. Producers need to work with suppliers who have a proven project track record and the experience to understand the intricacies of each process application.
Reference
1. ‘Plants and facilities’, Alberta Energy Regulator, (June 2021), https:// www.aer.ca/providing-information/data-and-reports/statistical-reports/ st98/pipelines-and-other-infrastructure/plants-and-facilities
Decarbonisation efforts worldwide have accelerated the shift from fossil fuels to renewables. One way many industrial organisations can embrace this is by changing process heater systems from fuel-burning to electric. Dennis Long and Roly Juliano, Watlow, USA, detail why.
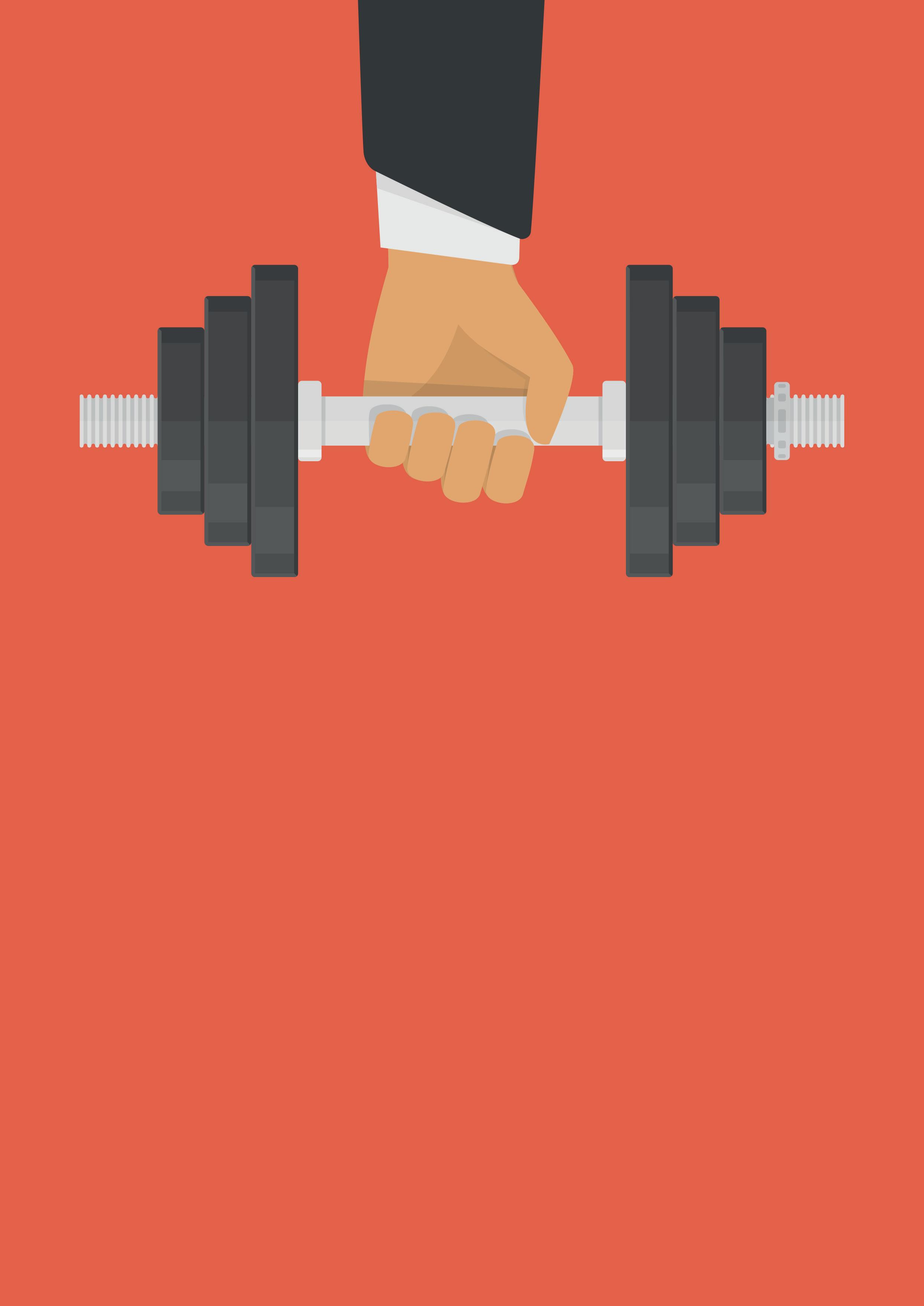
There is a sea-change occurring when it comes to process heating. Pressures to electrify all industrial processes are increasing, from governments, non-profits and business leaders alike. However, the transition from gas to electric process heating is not as simple as flicking a switch. This article illustrates, in broad brush strokes, how that transition can occur (and why it should happen sooner rather than later).
The market pull toward electrification and decarbonisation
According to the US Environmental Protection Agency (EPA), a substantial portion of global greenhouse gas (GHG) emissions (21% as of 2010) comes from industrial sources burning fossil fuels. Much of this energy is burned onsite for energy and heating needs. In fact, the US Department of Energy’s (DOE) Energy Information
Table 1. Reduction in cable size and number of branch circuits Administration estimates that the industrial (7.5 MW heater example) sector uses approximately 24 quadrillion Btu/yr MW Voltage of heat, or roughly one-third of the country’s supply (AC) delivered energy supply. Process heating applications alone account for 36% of total delivered energy consumption within the manufacturing sector. Thus, there is increasing pressure to decarbonise and electrify, where possible. This pressure has resulted in the following measures: n In 2015, the historic Paris Agreement was signed, with countries agreeing to curb the increase in global average temperature well below 2°C, and pursuing efforts to limit the temperature increase to 1.5°C. That same year, the Deep Decarbonization Pathways Project (DDPP) suggested fuel switching as a key part of any strategy to reduce carbon emissions. n In 2017, the DOE published a report analysing US energy use and GHG emissions in scenarios where there is widespread electrification and solar power decarbonisation. n In 2018, the Bank of England released a statement stating that the financial sector has been “too slow in divesting investments into fossil fuels” and warned that assets could become useless. Two years later, BlackRock leads several firms that have begun divesting themselves of companies that are not addressing climate change. n After years of protests, 17 000 Dutch citizens sued Royal Dutch Shell in 2019. In May 2021, a Dutch court ruled that the company must dramatically reduce its carbon emissions by 45% compared to 2019 levels. As a result of these pressures, industry has been accelerating the pace of decarbonisation. In a recent survey, Watlow found that over 90% of respondents in the oil and gas industry have developed, or are in the process of developing, a long-term strategy to reach sustainable, low-carbon site statuses.
Phase Total amperage Branch circuits required
Connection cables required
7.5 690 3 6275 131 393 7.5 4160 USA 3 1040 21 63 7.5 6900 IEC 3 627 13 39
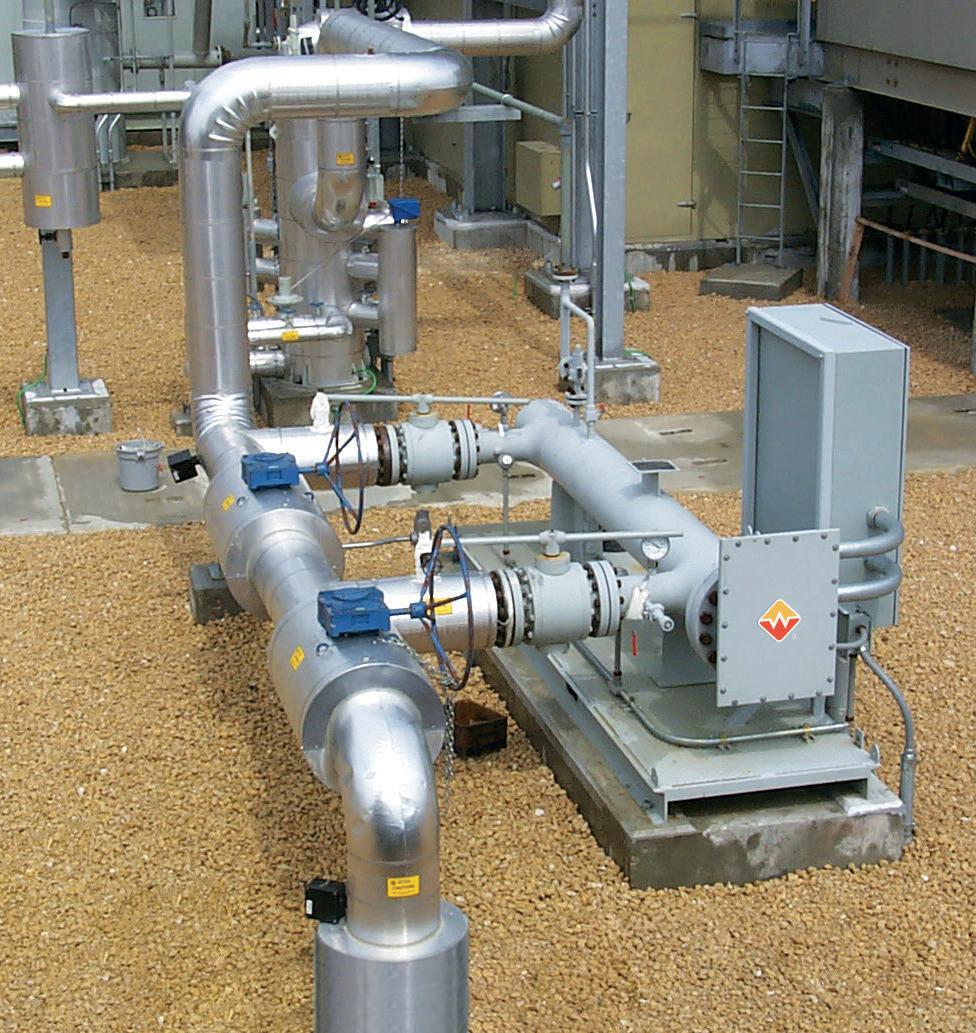
Figure 1. Fuel gas heater for a gas turbine.
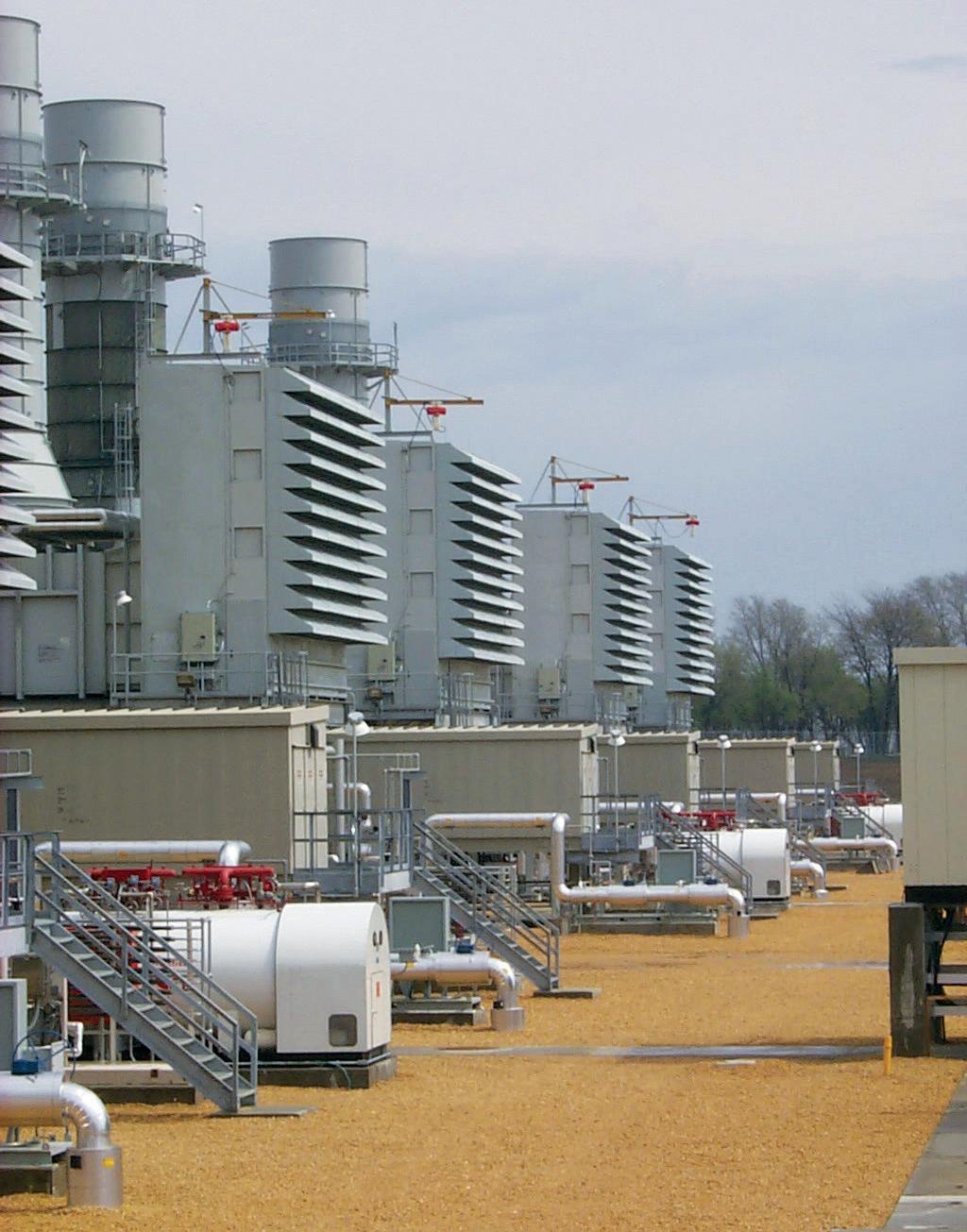
Figure 2. Gas turbine energy station.
The electrification of heat
Electrification of processes – and more specifically, process heating – is one of the key strategies for addressing climate change concerns in oil and gas. This requires shifting to electric heat exchangers in several applications. These electric heaters do not burn fossil fuels and can be powered via renewable energy sources.
Electric heat exchangers are no stranger to oil and gas operations. Historically, however, they have only been used in applications with a nameplate under 1 MW (for example, glycol reboiler heaters, knock-out drum heaters, seawater heaters, fuel gas heaters and preheaters, lubrication oil and seal gas heaters, etc). Gas-fired process heaters are still used in several ways, since the Btu requirements for some of these processes can only be met by electric heaters with a much higher wattage. Some examples include: n Feed/product exchanger (2 MW). n Dehydration inlet preheater (3 MW). n Heater treater (4 MW). n Molecular sieve regen (6 MW). n Waste gas heater (6 MW). n Once-through steam generator (20 MW). n Crude oil heater (28 MW).