
6 minute read
Out with the old
Figure 3. Seamless cooperation between process and operation experts and machine learning specialists is the key to success in an implementation project for a digital operator assistant. A typical project starts with a workshop where the potential and benefits of a digital operator assistant are identified.
NAPCON Phenomena Indicator, are the latest additions to the company’s product portfolio. Both are based on machine learning and AI. These products are an example of how data analysts and machine learning experts have entered the oil refining and petrochemical industry, which until recently has made slow progress when it comes to AI and machine learning.
The products work in real time and use the same data, but from the operator’s perspective they are two completely different products. Where Advisor predicts how the process will behave up to six hours ahead, Phenomena Indicator usually predicts just one variable, mostly for which there is no hard or correct information that can be measured in traditional terms.
Complex problems require complex solutions
A typical example of the need for a soft sensor is when a product must meet a particular quality requirement, but can only do so with expensive additives. If more additives are used than are needed, it is just a waste of money. However, with traditional measuring methods it is difficult to continuously estimate certain phenomena during the process because of the many factors affecting the production line. One factor is that the crude oil may come from different batches. As such, the recipe for a certain product can vary hugely at short notice, which is why a phenomena indicator using the same data as the digital assistant is needed.
The term ‘soft sensor’ is nothing new in the process industry, but until recently, it has not been based on machine learning. The big difference is that the machine learning model makes it possible to estimate much more complicated things than before. Therefore, an AI-driven soft sensor enables the continuous adjustment of the process so that the product meets the specification, but does not overdo it. Ecologically, this is also the soundest solution because the process uses just the amount of energy needed and no more. Additionally, it is also possible to use cheaper raw materials, as
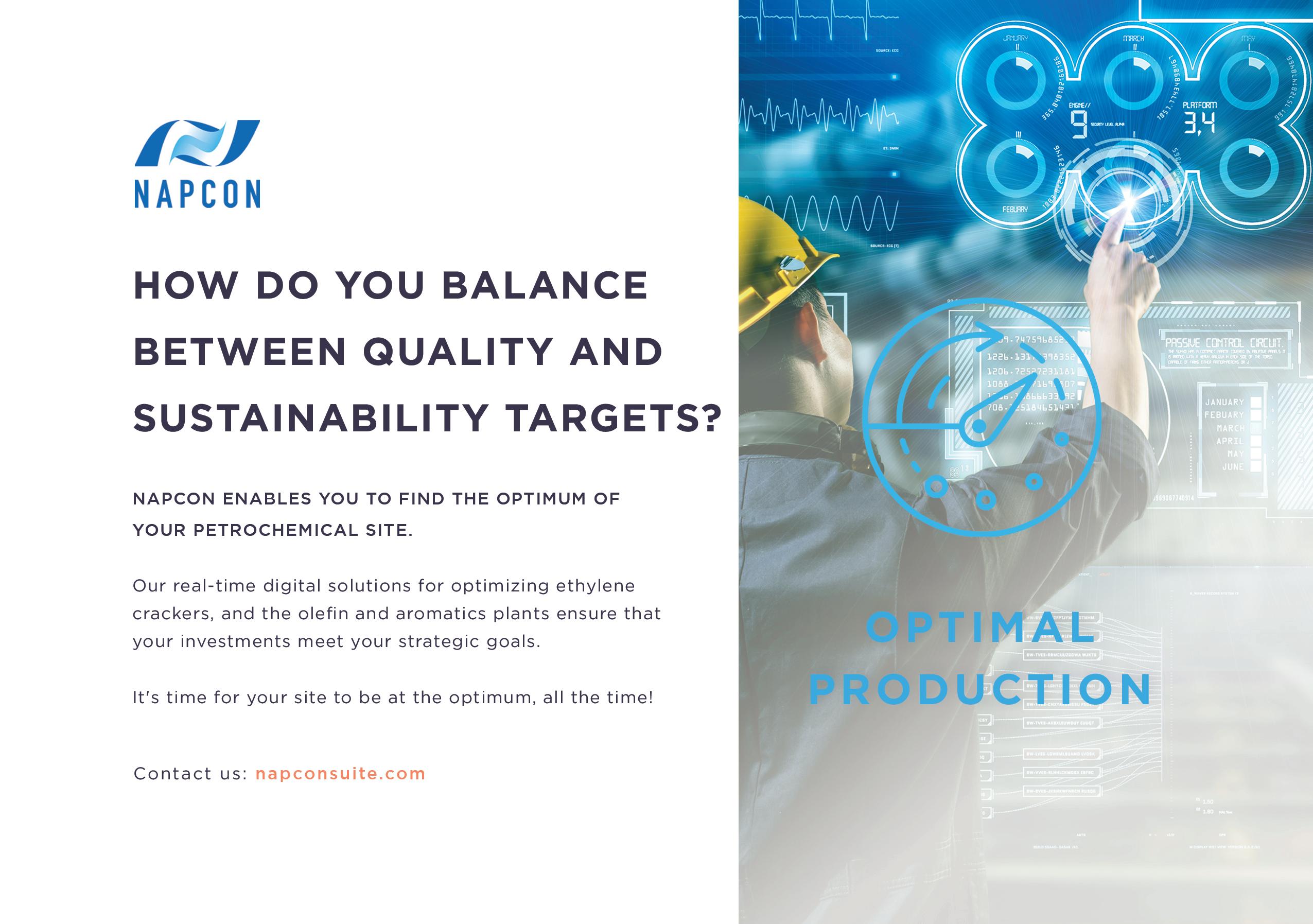
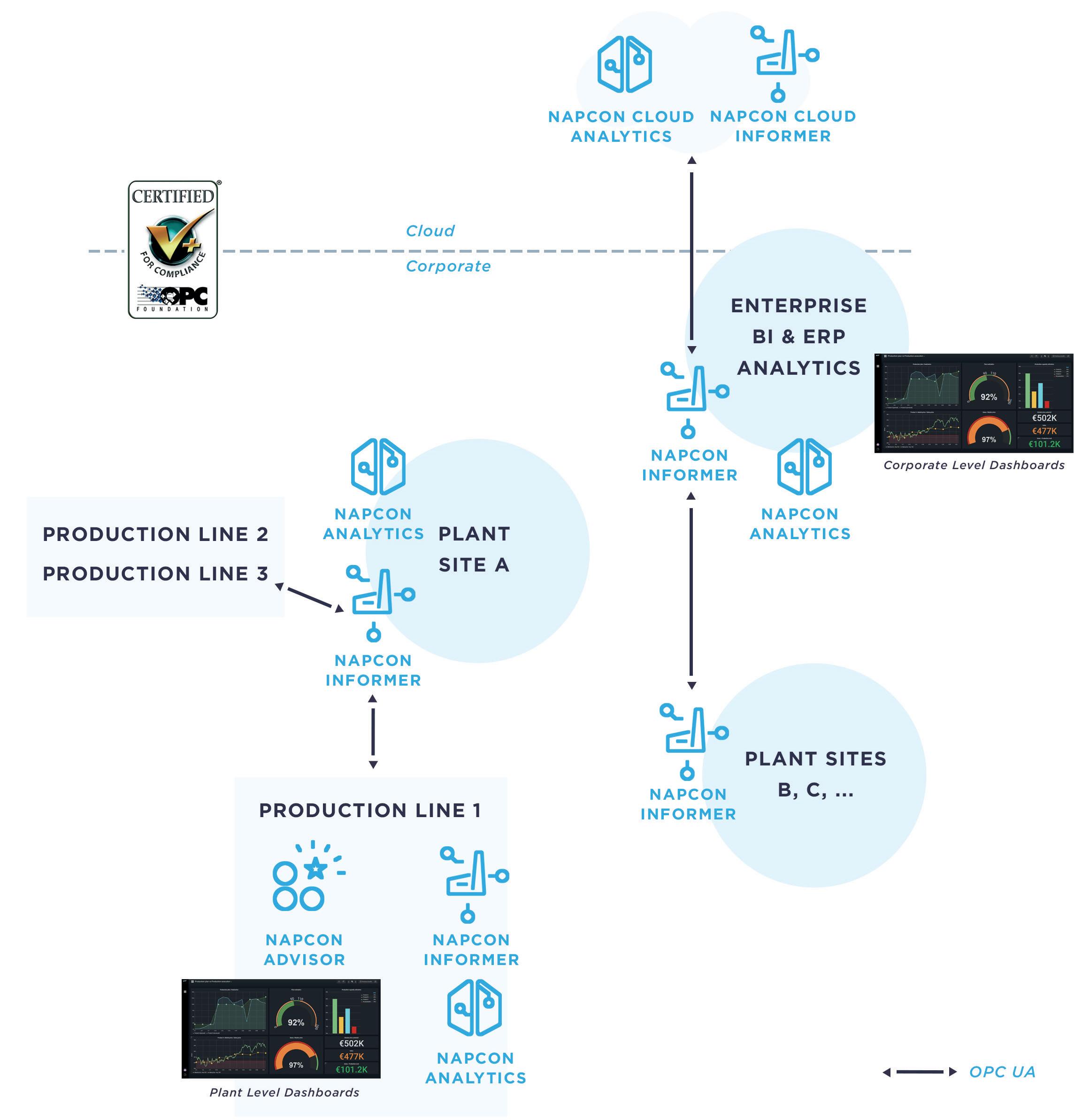
Figure 4. Digital operator assistants are a means to increase situational awareness. There are other important data analytics applications, such as dashboards and other visualisations, that can be implemented on various levels – production line, site and enterprise. operators have better control over the process.
With a digital advisor and an AI-driven soft sensor rendering the forecasting of what will happen within a few hours possible – as well as the analysis of what happens in the process under different conditions – oil refineries can make big strides. As huge amounts of data are collected every day at a chemical processing plant, man power is unable to keep up with this volume of information, but a digital assistant can continuously suggest effective means of optimisation.
The value of digital assistance
Many of the experienced operators in the process industry will soon retire and be substituted with younger operators that lack the same experience but who are born into the digital world. This means that a digital assistant can secure competence and support new operators. With the help of a digital assistant, which constantly analyses the process and makes forecasts based on the readings, it is significantly easier for inexperienced operators to run a plant under varying circumstances.
Need a reprint?

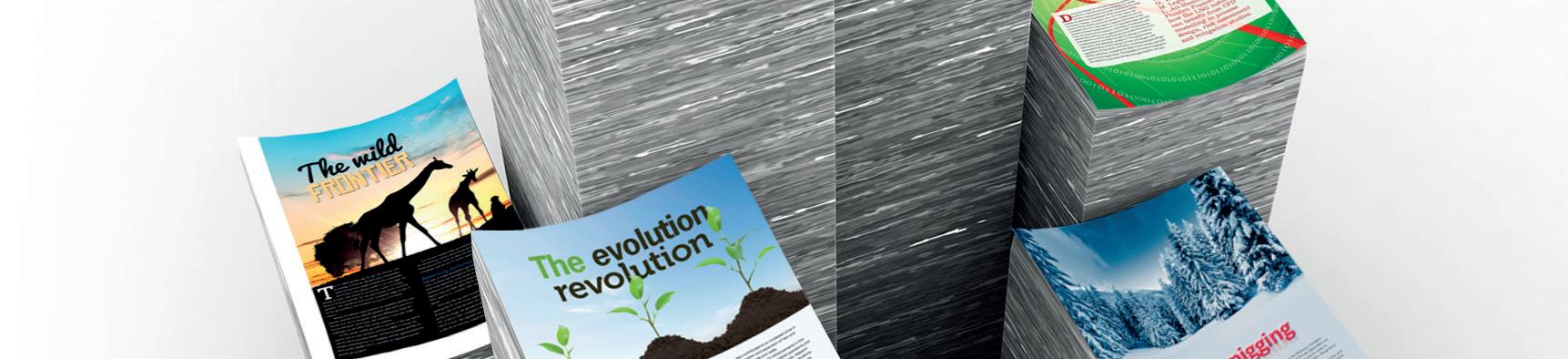
We can tailor to your requirements, produce 1 - 12 page formats, print colour or mono and more
Phil Millette, Honeywell Process Solutions, UK, discusses how timely technology upgrades extended the life of critical assets at Petroleum Development Oman’s government gas plant.
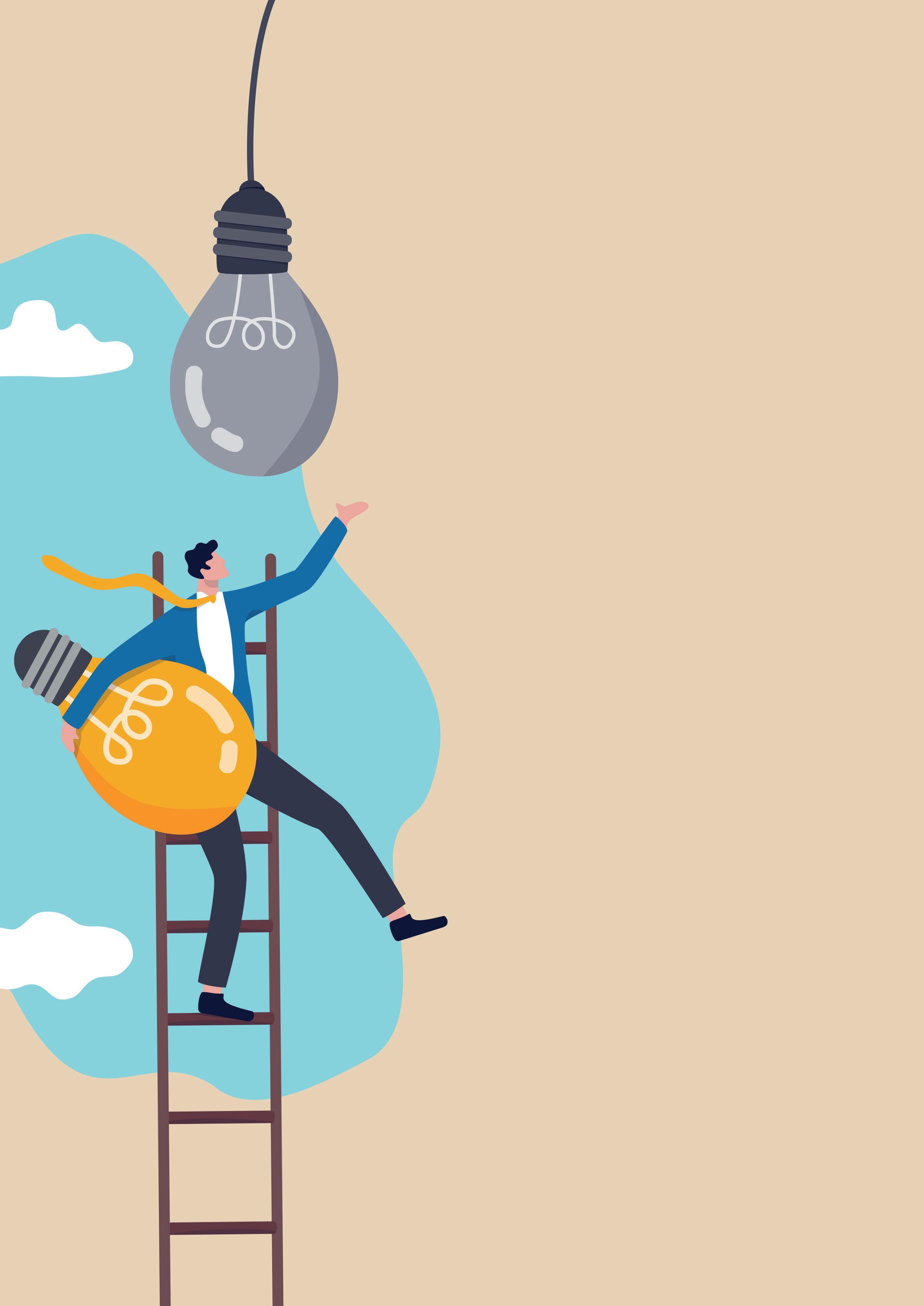
As a major oil and gas industry operator, Petroleum Development Oman (PDO) required a proven solution to upgrade existing process automation systems (PAS) and other automation assets, without the risk of costly downtime or the loss of valuable intellectual property.
Background
PDO is the leading exploration and production company in the Sultanate of Oman. The company delivers the majority of the country’s crude oil production and natural gas supply. It is jointly owned by the government of Oman, Royal Dutch Shell, Total and Partex. PDO’s first economic oil find was made in 1962, and the first oil consignment was exported in 1967. Its government gas plant (GGP) was established in 1978 in northern Oman. The facility has been the main gas operation for the Sultanate of Oman, finding gas fields and developing them into producing assets on behalf of the government.
GGP was originally constructed by PDO at its Yibal field to process as much as 2 million m3/d of gas, most of it to be delivered to the Al Ghubrah Power and Desalination Plant in Muscat via a 20 in. pipeline. Since then, the demand for gas in Oman has increased at a steady pace, calling for PDO to progressively expand the GGP, as well as the pipelines and associated pressure-limiting and valve stations of its gas transportation system.
Moreover, there was a need to upgrade the PAS to the latest technology to meet the life cycle demands.
Challenges
Gas processing facilities strive to optimise production throughput and minimise downtime and operational costs, while maintaining safe operation. To meet these objectives, their automation systems and related technology assets must meet stringent process control requirements, and be both reliable and scalable.
As with other major petroleum industry organisations, PDO has a critical need to address the following: n Reduce the risk of unplanned downtime. n Increase the efficiency and reliability of processes. n Ensure consistent gas quality. n Achieve greater throughput with existing equipment.
At the GGP facility, engineers sought to optimise the footprint of various control system components, including controllers and cabinets. They also wanted to upgrade all legacy Honeywell High-Performance Process Managers (HPMs) to Experion® PKS C300 controllers and enhance the capacity of the plant’s fault-tolerant Ethernet network infrastructure.
Over the years, the GGP facility had progressed from a TDC 3000 control system with Advanced Process Managers to the TotalPlantTM Solution platform with C200s and FailSafe Controllers (FSCs®), then to Experion PKS with C300 controllers, and finally to the Enhanced High-Performance Process Manager and Enhanced Universal Control Network solutions. In 2019, the GGP upgraded all of its FSCs to the new Safety Manager (SM) system.
Due to the increasing gas demand in Oman, PDO sought more sustainable operations and a better process control environment at the GGP facility. The specific goals for technology upgrades were to improve operational efficiency while retaining valuable intellectual property and enhancing life cycle planning.
However, the company’s project team faced several engineering, planning and execution challenges in undertaking technology upgrades. The duration of an operational shutdown for the modernisation tasks was critical. Engineering work for outdated auxiliary control room assets would prove to be complicated. Moving operator workstations and transitioning networks to a new standard would also be difficult. Wiring and loop checks for thousands of control loops would present significant risks.
In addition to the above, an overarching challenge for the entire GGP upgrade project was the limitation of resources imposed by the COVID-19 pandemic.
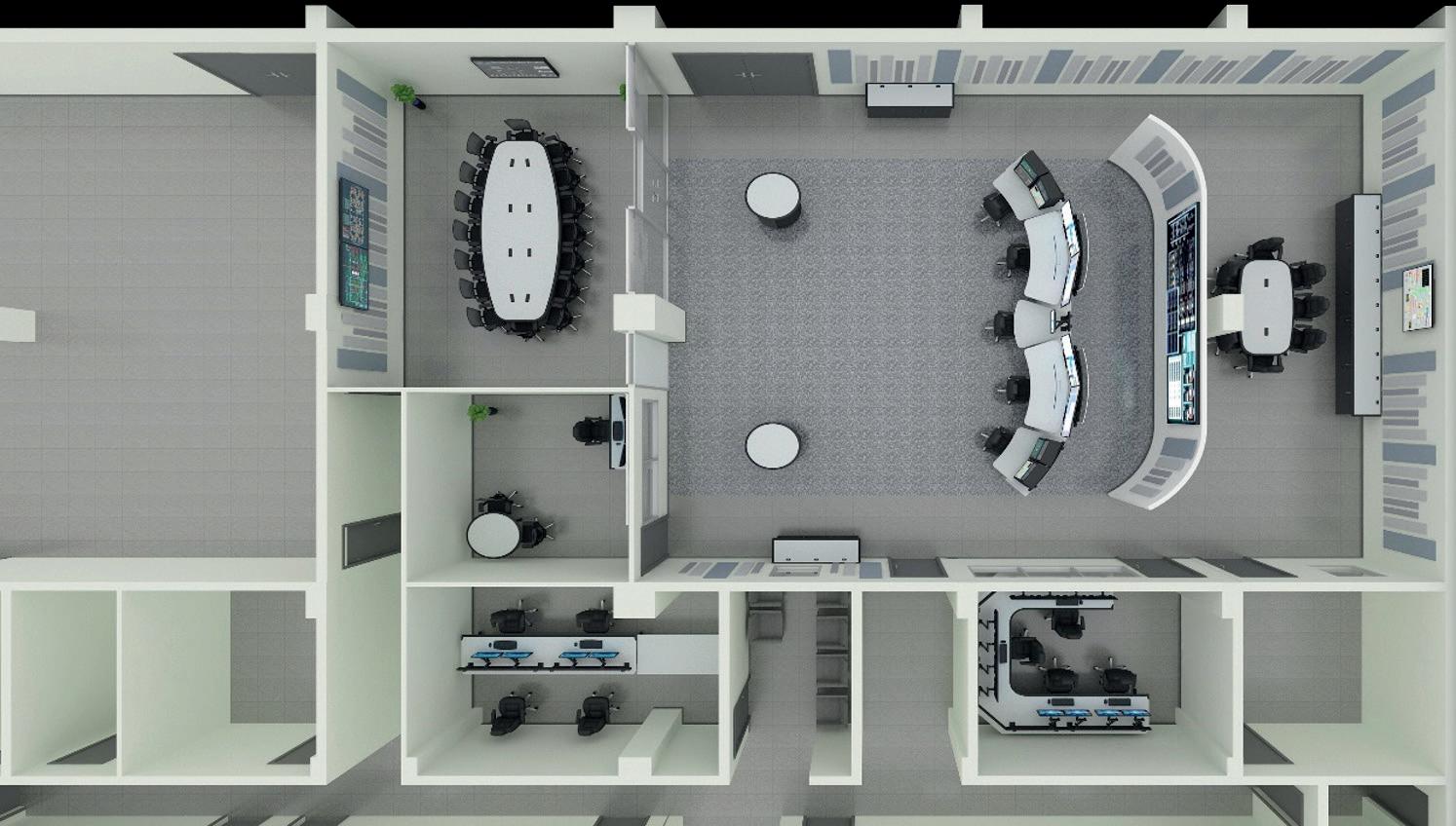
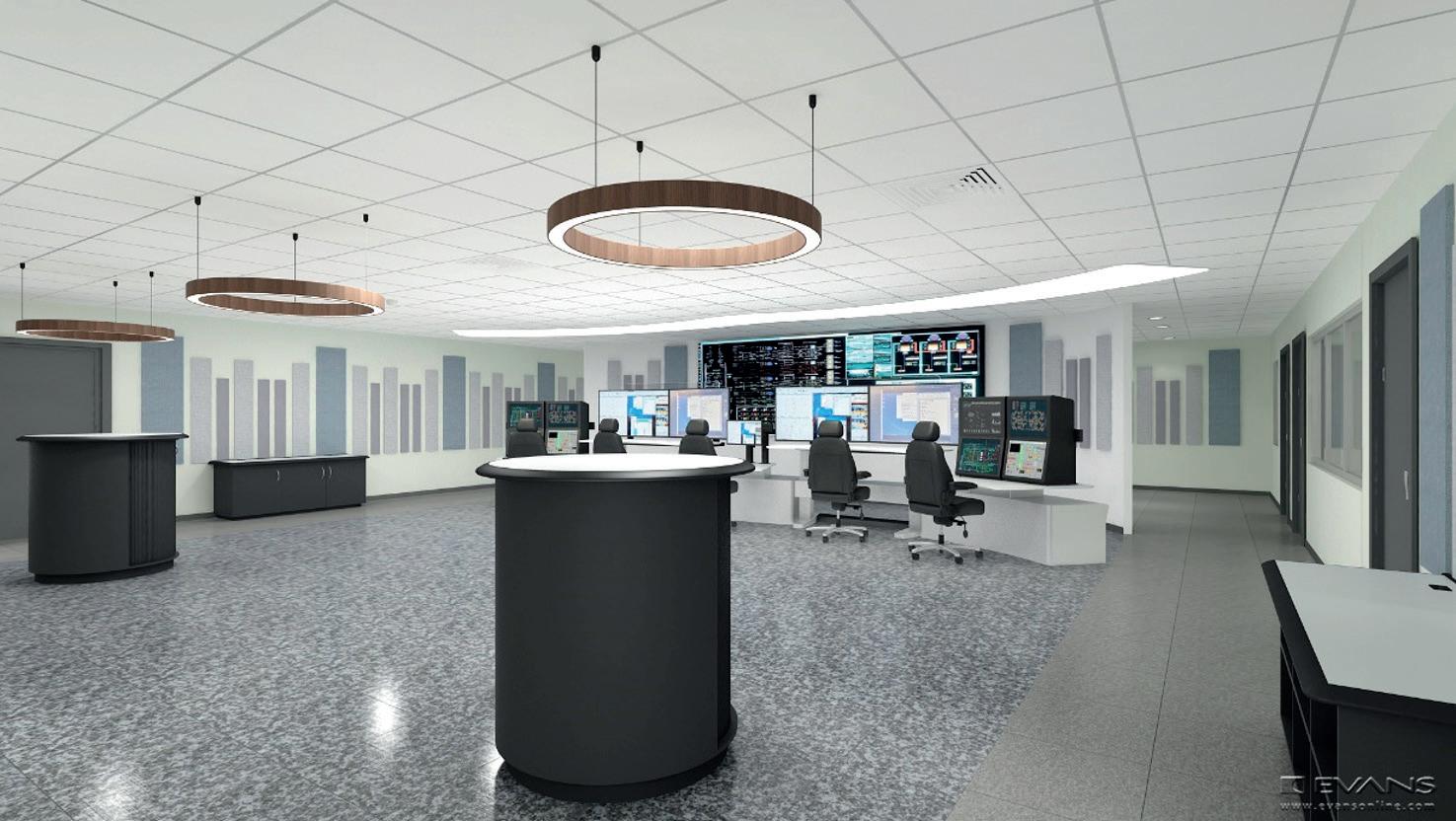
Solution
Figure 1. Design of an ICR.
Figure 2. PDO’s upgraded system architecture. PDO developed a technology rejuvenation strategy to improve the GGP’s ability to operate at higher availability and efficiency levels. This far-reaching project addressed numerous production assets across the company’s large gas processing operation. Based on the findings from a baseline assessment; fire, gas dispersion and explosion assessment; and quantitative risk assessment, PDO decided to relocate the GGP’s central control building (CCB) and auxiliary buildings to a safer location, away from the facility’s existing export line. The plan was to build a new integrated control room (ICR)
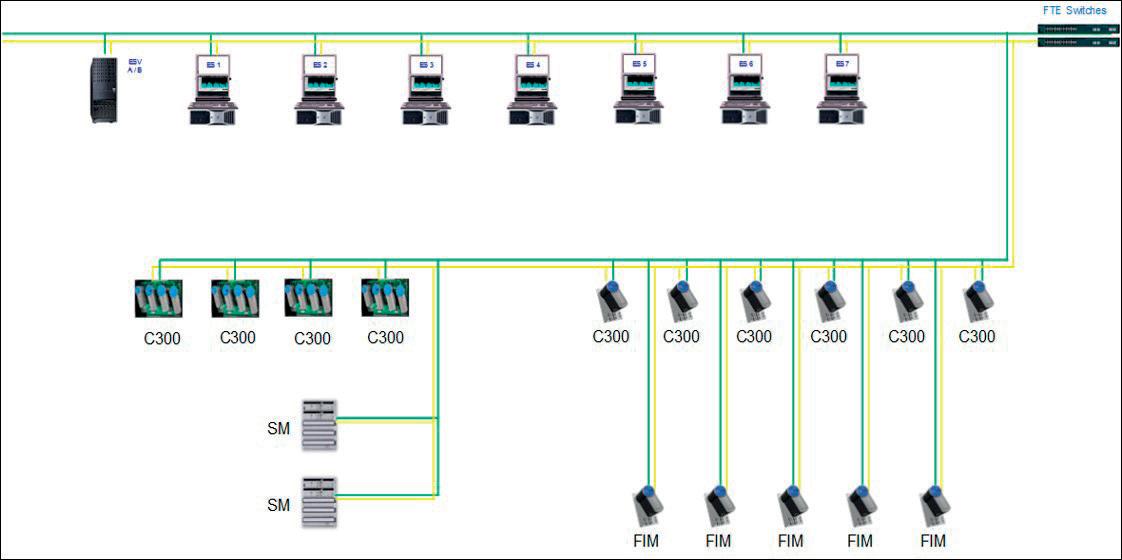