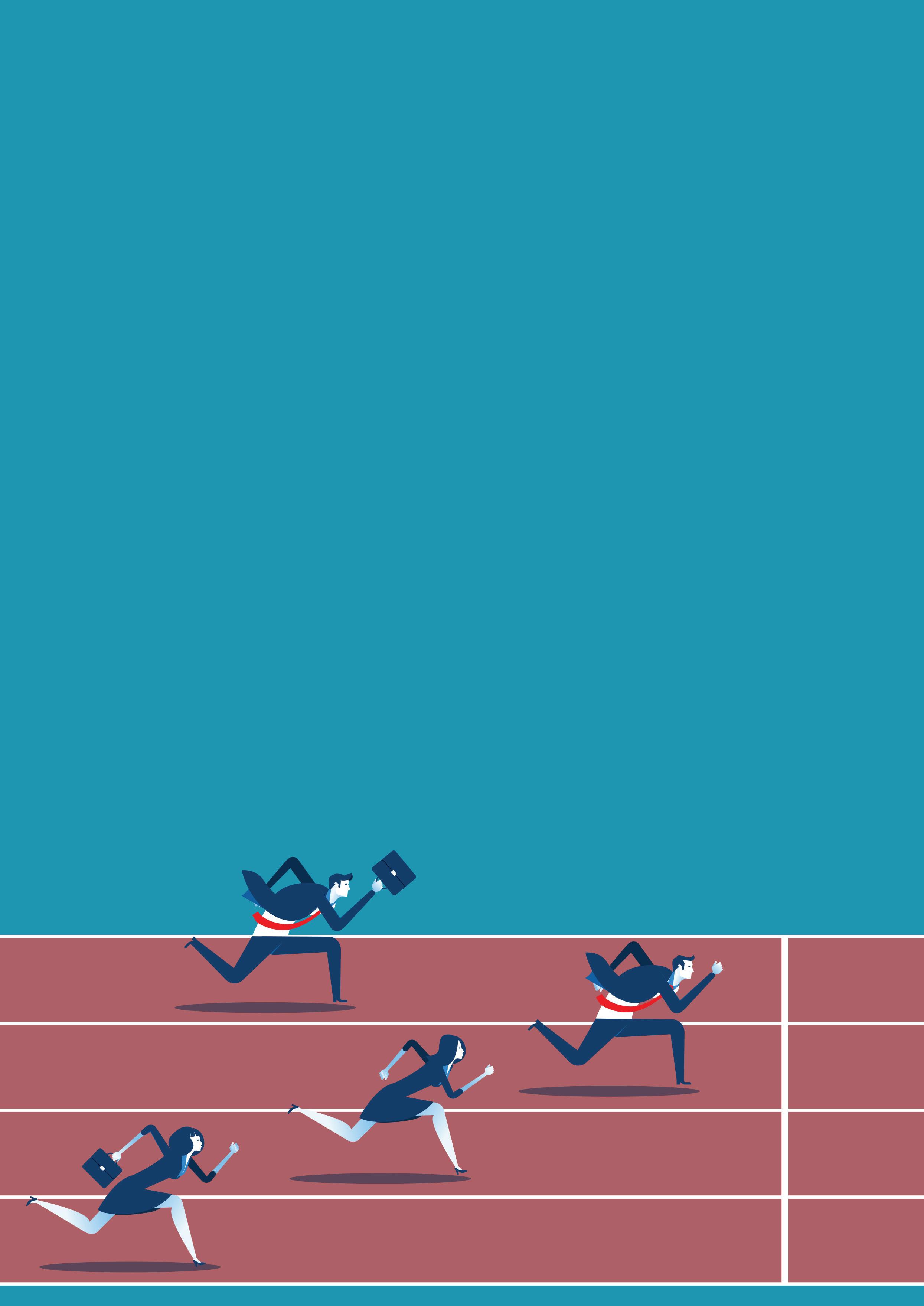
3 minute read
A race to the bottom
Neil Richards, PS Filter, Canada, explains why buying the cheapest product is not always the best solution.
The constraints and pressure placed on producers to reduce costs in order to maintain profitability in the face of slumping revenues is enormous in the energy sector. This is nothing new when it comes to up and down cycles of commodity products such as oil and gas, but in today’s environment, there are indiscriminate cost-cutting measures that will have severe ramifications, costing operators dearly. Whilst this article will specifically address filtration-separation, there are many other areas with indiscriminate cost cutting that are also impacting production and operations in detrimental ways that have yet to be addressed.
It is unrealistic and impractical – from both a functional and safety standpoint – that the cheapest possible product will always be the most suitable.
Filtration specifications are put in place for a reason and not following them will lead to various issues, such as: n Amine foaming – an excessive amount of chemicals to control because of poor effluent filtration quality. n Increased operator exposure to hazardous hydrogen sulfide (H2S) – excessive sour service maintenance and filter changes. n Water flood/water disposal/formation damage/plugging – resulting in lost production. n Excessive maintenance of rotating equipment as passing contaminants downstream causes erosion, wear and plugging issues for equipment such as pumps, contactor tray towers, heat exchangers and carbon beds. n The environmental impact of high disposal costs (of thousands of dollars) due to inefficient filters that are underperforming. This can be avoided with the right technology in place.
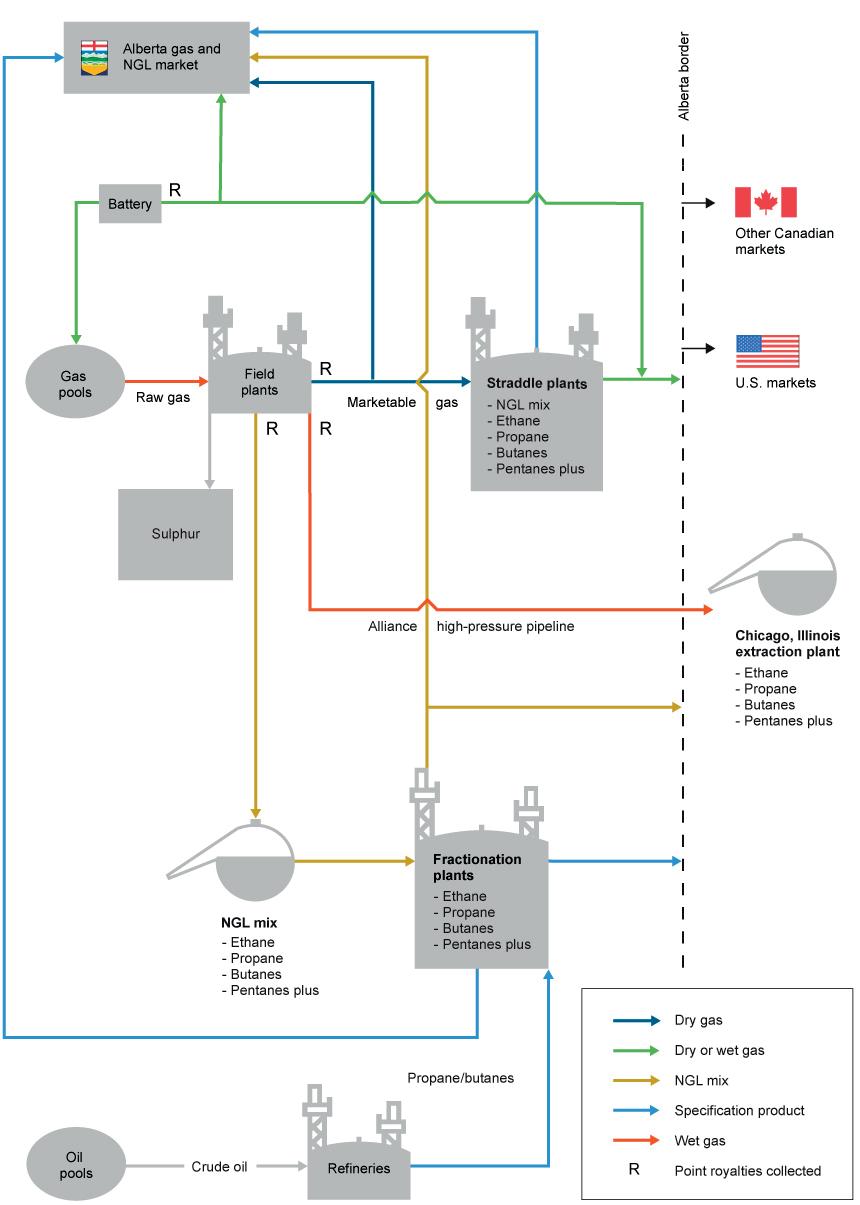
Figure 1. Schematic of Alberta NGL flow.
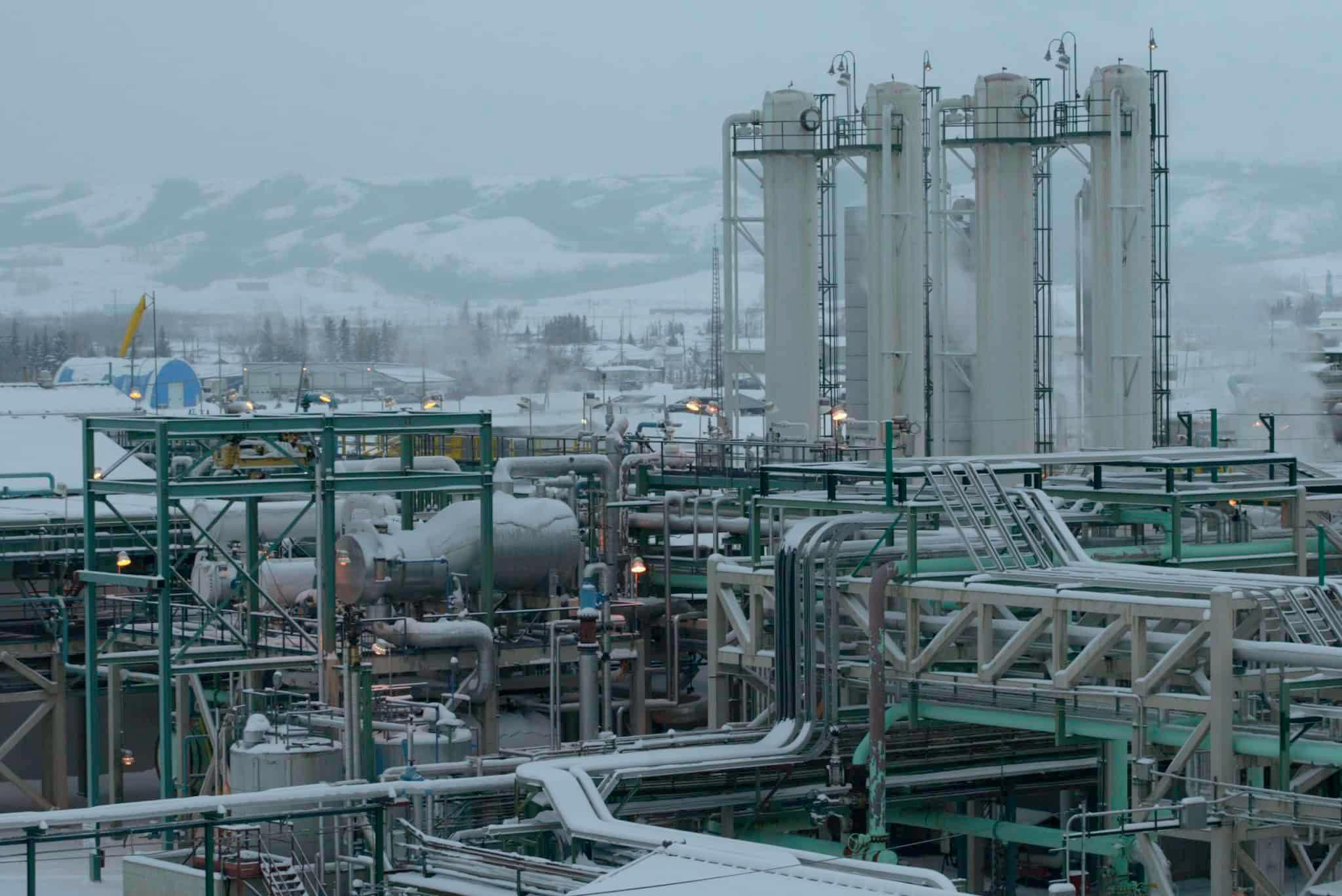
Figure 2. A gas processing plant where PS Filter tested its filtration systems.
Filtration needs to be addressed as a systems approach. There is not one solution that fits all – what may work in one process may need to be fine-tuned to work effectively in another situation. Buying the cheapest and least effective product is not a viable answer to reducing overall costs, and this is where the expertise of a trusted partner is required. PS Filter has over 32 years’ experience working on various filtration applications in the energy sector, and works with its customers to understand their process application requirements to ensure a positive solution.
Hundreds of millions of dollars are spent each year in Alberta, Canada, alone on consumable filtration for oil and gas processing operations. An estimate based on the company’s sales volume in this sector would be a total market in the range of US$200 million+ (based on the company’s market share, which it estimates at 5% [US$1 million] consumable filter sales yearly). There is enormous growth potential. With the right strategy of using customer investigation to better understand their needs, suppliers can work to provide true value in this area.
The market consists of many procurement types, from company head offices to various field offices at plant facilities, and they all have purchasing power based on their individual budgets. Each group may be influenced by technical specifications from engineering or operations input, or they may be free to make purchases based on their own criteria and past vendor experiences. Operator input weighs heavily on filter products that may or may not be chosen, and it is imperative to understand what influences decisions in order to ensure the provision of a product that effectively meets or exceeds requirements.
Based on industry knowledge and experience, companies must work together with buyers and users to educate them to provide a technically-superior product that will improve filtration systems and lower total filtration costs. This is done by first providing a minimum viable product (MVP) to gain trust, followed by the introduction of upgraded pleated medias that can provide longer intervals between servicing, and fewer filter disposal costs. On the surface, a less expensive commodity type product may appear to offer cost savings, but when increased operational costs, lower performance affecting downstream