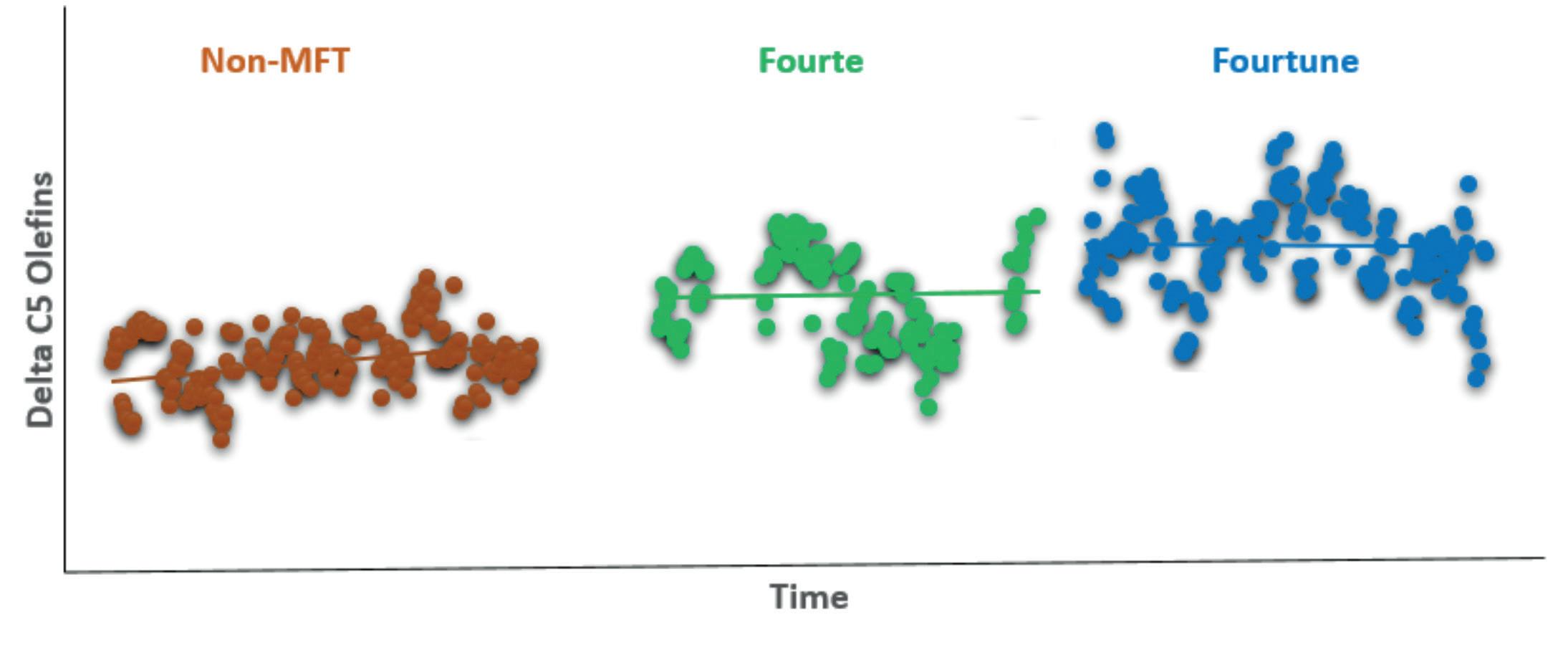
11 minute read
Keeping things flexible
Figure 4. Operation data analysis with regression analysis model on Delta C5= (actual - predict) for unit 1.
Table 1. Regression modelling results for MFT catalyst transitions in MPC units
Unit Catalyst Delta C5= (wt%)
1 Fourte 0.24
1 Fourtune 0.53
2 Fourte 0.55
3 Fourte 0.33
4 Fourtune 0.10
5 Fourte 0.50
Table 2. KBC kinetic modelling results for MFT catalyst transitions in MPC unit 1
Catalyst Non-MFT Fourte Fourtune
Delta C5= (vol%) Base +0.19 +0.36 Gasoline (vol%) Base -1.35 -0.19
analytical expertise. These testing capabilities are part of the company’s Refining Analytical and Development (RAD) facility located adjacent to the Catlettsburg refinery in Kentucky, US. MPC’s testing philosophy is to run lab units with commercially-collected materials and adjust the pilot plant operating parameters to generate lab yields that match the commercial units. By minimising offsets between the lab and commercial units, a high degree of confidence can be placed in the measured results. The testing results are used within an FCC process model (KBC’s FCC-SIM) to determine expected yields and optimised unit conditions for each catalyst candidate. Pilot unit results have been validated with post-audits of unit data from numerous commercial catalyst changes.
Another important part of the catalyst selection philosophy is the close working relationship that the company establishes with each of the participating FCC catalyst suppliers. This collaboration is needed to select catalyst candidates formulated to have the highest likelihood of success, and to ultimately support the commercial FCC application for the selected catalyst. MPC strives to understand the technology behind the catalyst formulations so that the technology advantages for a given catalyst can be recognised in the test results. A consistent thread between catalyst design, intended performance, and the test results ensures that final catalyst selection is correct for the operating FCC unit.
Testing results
Figures 2 and 3 show Circulating Riser Unit (CRU) testing results for back-to-back commercial trials from BASF’s non-MFT incumbent catalyst to the Fourte and Fourtune MFT catalysts in an MPC unit 1. MFT catalysts were qualified based on CRU testing results carried out at MPC for lab-deactivated fresh catalysts. As shown is Figure 2, MFT catalysts Fourte and Fourtune demonstrated increased C5 olefins compared to the non-MFT catalyst. Ultimately, the refinery performed commercial trials with both Fourte and Fourtune formulations. In the post-audit study carried out at an MPC facility, equilibrium catalysts were drawn from the unit during each catalyst trial at close to the full catalyst turnover in the unit. These catalysts were then tested in CRU to evaluate C5 olefin production. As shown in Figure 3, the results clearly demonstrated that BASF’s Fourte and Fourtune MFT catalysts delivered increased C5 olefin yields compared to the non-MFT catalyst.
To further validate the results obtained in the circulating riser evaluations, the companies examined unit 1 operating data (Figure 4). Multivariable regression analysis was employed to determine olefin yield deltas observed in the FCC unit. The strongest operating variables found to impact C5 olefin yield shifts include riser outlet temperature, equilibrium catalyst activity, feed API, unit conversion, and ZSM-5 zeolite crystal content of the circulating inventory. The regression results showed that C5 olefin yields increased by an average of over 0.24 wt% for Fourte and 0.53 wt% for Fourtune.
Similarly, regression analyses of several MPC units where MFT catalysts were employed were carried out. In each case, it was observed that C5 olefin gain with the catalyst transitions to MFT catalysts (Table 1). Furthermore, heat-balanced KBC FCC-SIM modelling studies were carried out based on MPC CRU testing results for unit 1, with non-MFT, Fourte and Fourtune. The modelling results at optimised conditions showed a C5 olefin increase for MFT catalysts in both optimised cases (Table 2).
Conclusion
In summary, the benefits that MFT-based catalysts provide with respect to delivering profitability through butylene maximisation and octane enhancement can be further magnified for refineries that have the capability to alkylate C5 olefins or otherwise profitably handle additional C5 olefin products. Both Fourte and Fourtune delivered enhanced C5 olefin production to further increase FCC profitability in a number of MPC’s units.
References
1. NIELSEN, R., ‘Refinery C5s Utilization’, IHS Markit, Report No. 254, (November 2004). 2. LARSEN, N., CLARK, T., CLOUGH MASTRY, M., and DE SILVA, N.,
‘Boosting profitability with butylenes’, Hydrocarbon Engineering, (June 2020), pp. 43 – 46. 3. LARSEN, N., CLARK, T., DE SILVA, N., YANG, Y., and NEUMAN, D.,
‘Boosting profitability with butylenes to propylene ratio’,
Hydrocarbon Engineering, (September 2020), pp. 53 - 58. 4. LEE, J., HONG, U. G., HWANG, S., YOUN, M. H., and
SIONG, K., ‘Catalytic cracking of C5 raffinate to light olefins over phosphorous modified microporous and mesoporous ZSM-5’,
Journal of Nanoscience and Nanotechnology, (November 2013), pp. 7504 - 7510.
Jitendra Chellani, KBC (A Yokogawa Company), and Hans Lidman, Nynas, outline how to improve margins through feedstock flexibility.
The cost of feedstock has a significant impact on revenue and, therefore, the profitability of a refinery and petrochemicals complex. The quality of different feeds governs the overall yields and thus the gross product worth. With feedstock flexibility, these facilities can process diverse feeds from different sources and at different prices. In the dynamic market, the availability and price of feedstocks swing continuously. In addition, crack spreads and product demand have an impact on feed selection. With this, it is evident that being able to know what and how to process a range of feedstocks can improve operating margins. Pacesetters are equipped with precise tools, methodologies and resources to process the best possible feedstocks for their assets. These practices are essential in the existing dynamic market in which various parameters change continuously.
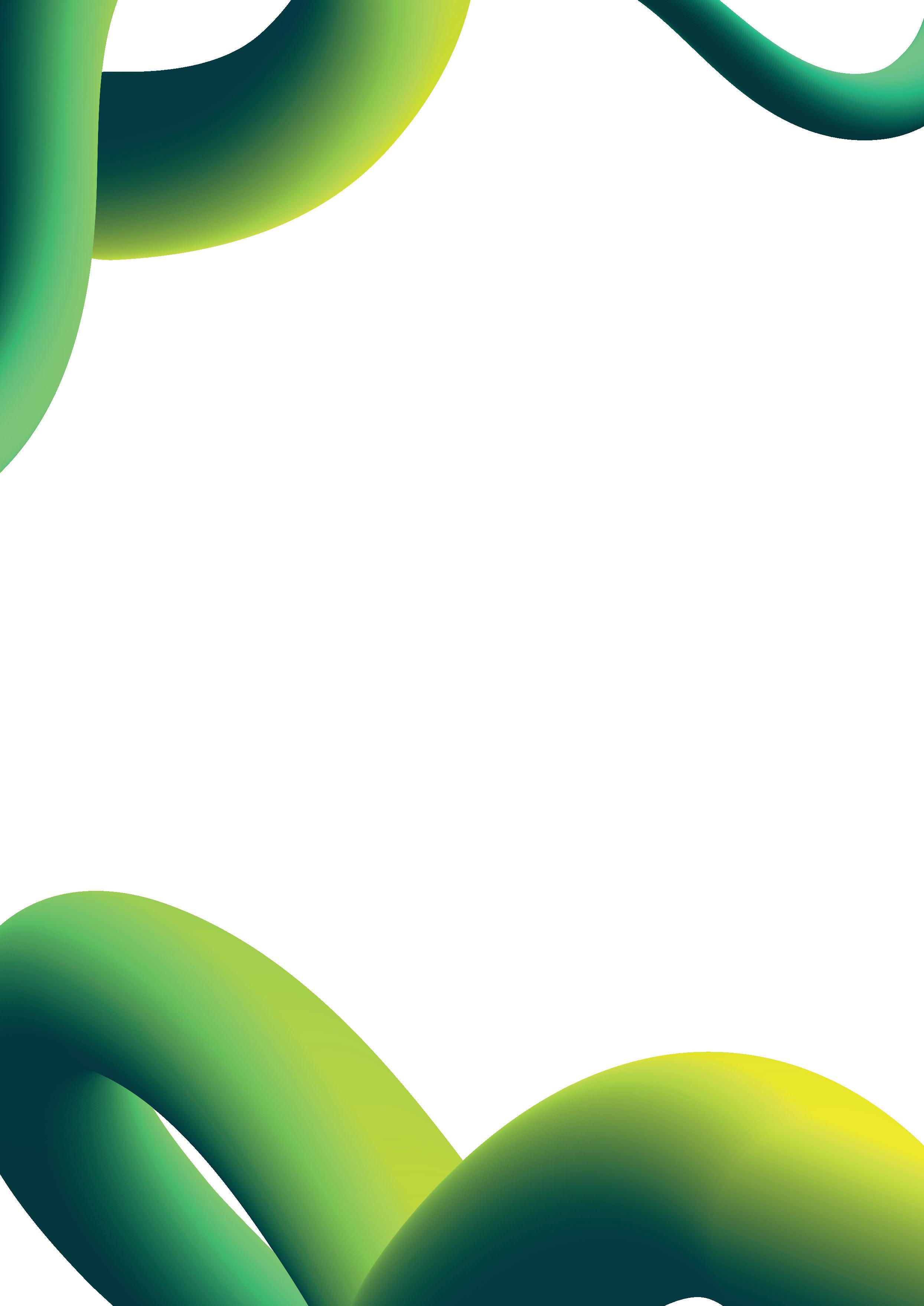
Constraints for feedstock flexibility
Though feedstock flexibility is preferred by most refinery and petrochemical complexes, various constraints impose restrictions on changing feed quality. Some of these constraints are imposed by the logistics and location of the complex. Configuration of the complex, operating limits, and unit design also determine the feedstock quality range.
Logistics
Coastal facilities usually have higher degrees of freedom with regard to feedstock flexibility than those that are landlocked. For a coastal complex, the flexibility is determined by the available infrastructure e.g. port facilities, capacity, and the number of tanks. Availability of storage tanks and the set-up for blending different crudes may also restrict the number and types of crudes that can be processed.
The logistics of importing crude through the terminal, infrastructure for transferring crude to the processing units, and product dispatch can be major constraints for the operator. For landlocked facilities, further constraints to feed flexibility are associated with the feed and product pipelines or truck facilities.
Configuration
The overall configuration of the refinery and petrochemicals complex decides the feasibility and economics of processing different feedstocks. The design of the crude unit limits the maximum volume of impurities in the fresh feed, whereas the design of downstream process units restricts the qualities of products from the crude unit. The operating constraints of individual process units and equipment also limit the quality and quantity of feed that can be processed in the complex.
Figure 1. The feasibility of processing new feedstock.
Apart from the operating constraints, the economics of processing new feedstocks should be attractive. Bottom-of-the-barrel technologies are required to upgrade the heavy crudes, and an integrated refinery/petrochemicals complex can upgrade naphtha in the lighter crudes.
Integrated operation
Though the integrated operation of the upstream facility with the refinery, and the refinery with the petrochemical complex, is beneficial, in most cases it eliminates feedstock flexibility. A refinery that is designed to operate with specific types of local crudes without logistics for importing new feeds may not be beneficial throughout the life cycle of the assets. If the price of the local crudes increases or its quality changes, processing imported feedstock and exporting local crudes can be positive for both the refinery and the upstream facility. A similar philosophy is applicable for a petrochemicals complex as well. Rather than processing heavy naphtha from the refinery in a steam cracker, it can be sold to the aromatics complex, and light naphtha can be imported for the cracking. These changes will increase freight costs and the complexity of logistics, but have been found to be economically-attractive in several cases.
The feasibility of processing different feedstocks requires techno-economic analysis of various parameters. The methodology for assessing the feasibility of processing new feedstock is shown in Figure 1. If the logistics allow for processing of new feedstocks, a holistic view of the overall complex is required ahead of analysing individual process units and equipment.
A linear programming (LP) model provides an excellent solution for this problem, as various parameters, including the percentage of new crude in the crude basket, are estimated by the model. The optimisation includes constraints such as unit capacities, product demand, and specifications. This step ensures that the processing of new feedstock in the complex is economically-attractive.
Validation of the LP solution can be performed using refinery-wide flowsheets. These flowsheets include reactors which are simulated using non-linear first principles kinetics or equilibrium equations. The fractionation is simplified to represent individual sections in the column rather than each tray. The refinery-wide flowsheets can ensure that the major constraints in the unit including qualities of the downstream units will not be violated with the new feed. The flowsheets can also help to identifiy probable bottlenecks that require further analysis. This analysis is usually carried out using rigorous standalone models of the individual units.
The rigorous models of the units can identify bottlenecks for primary and secondary equipment. This analysis is generally not required for all process units and equipment – the focus area is identified using results from the refinery-wide flowsheets. The first step in this evaluation is to focus on primary equipment, including reactors and distillation columns. Flooding analysis of the columns may be required with an increase in the unit capacity or with a significant shift in the yield of specific products. A qualifying analysis of secondary equipment i.e. heaters, compressors, pumps, etc. is performed to ascertain violations of any operating limits before performing the rigorous calculations.
The refinery-wide flowsheets and standalone models ensure that the unit operating conditions will be within the safe operating envelope. In addition to this, these models estimate the operating targets which are required for a substantial shift in the unit operation.
After assessing the feasibility of processing new feedstock, its relative ranking is required. This is to ensure that the right feedstock is purchased when all feasible feeds are available to the traders. These feedstocks may be purchased using
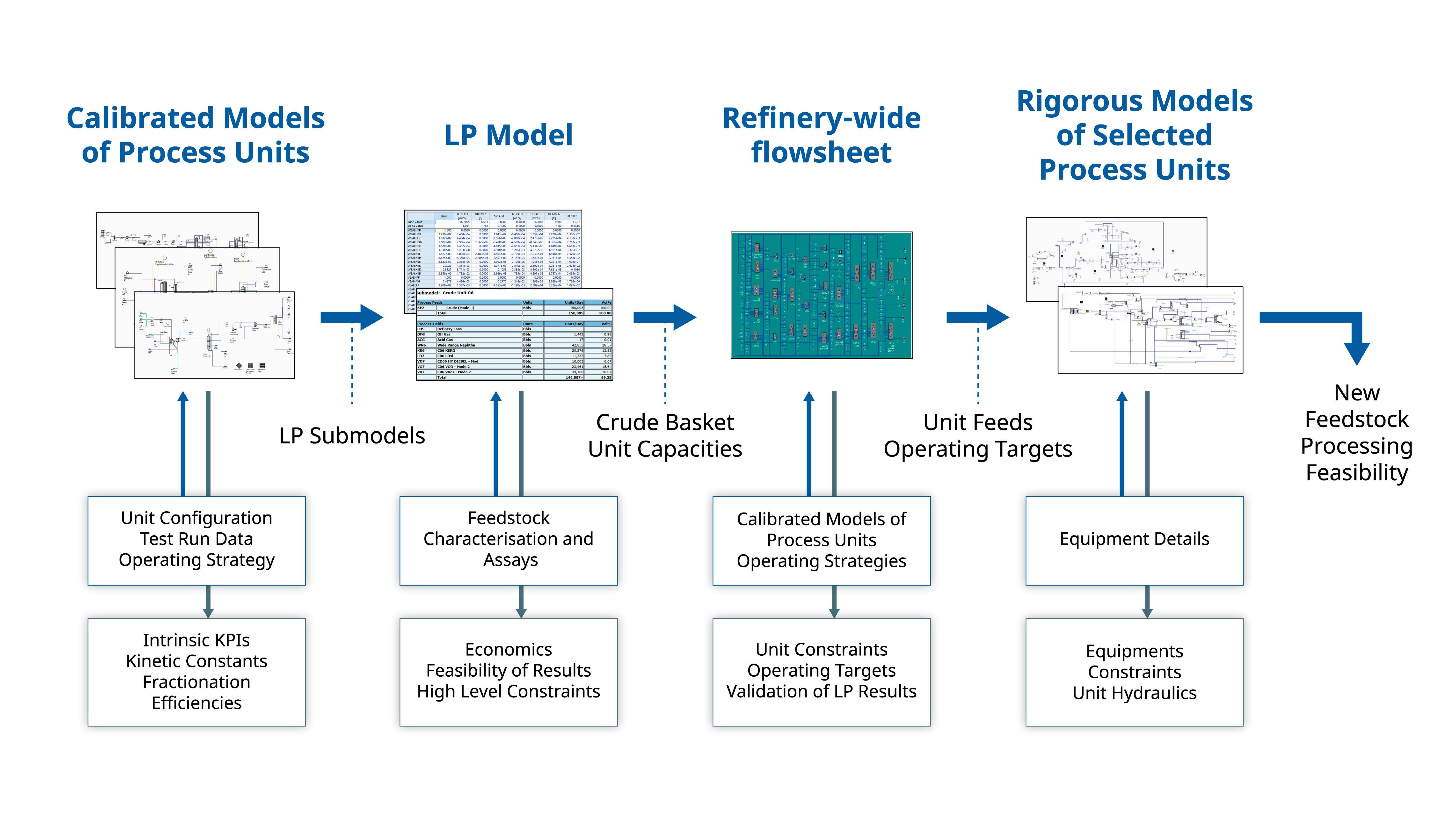
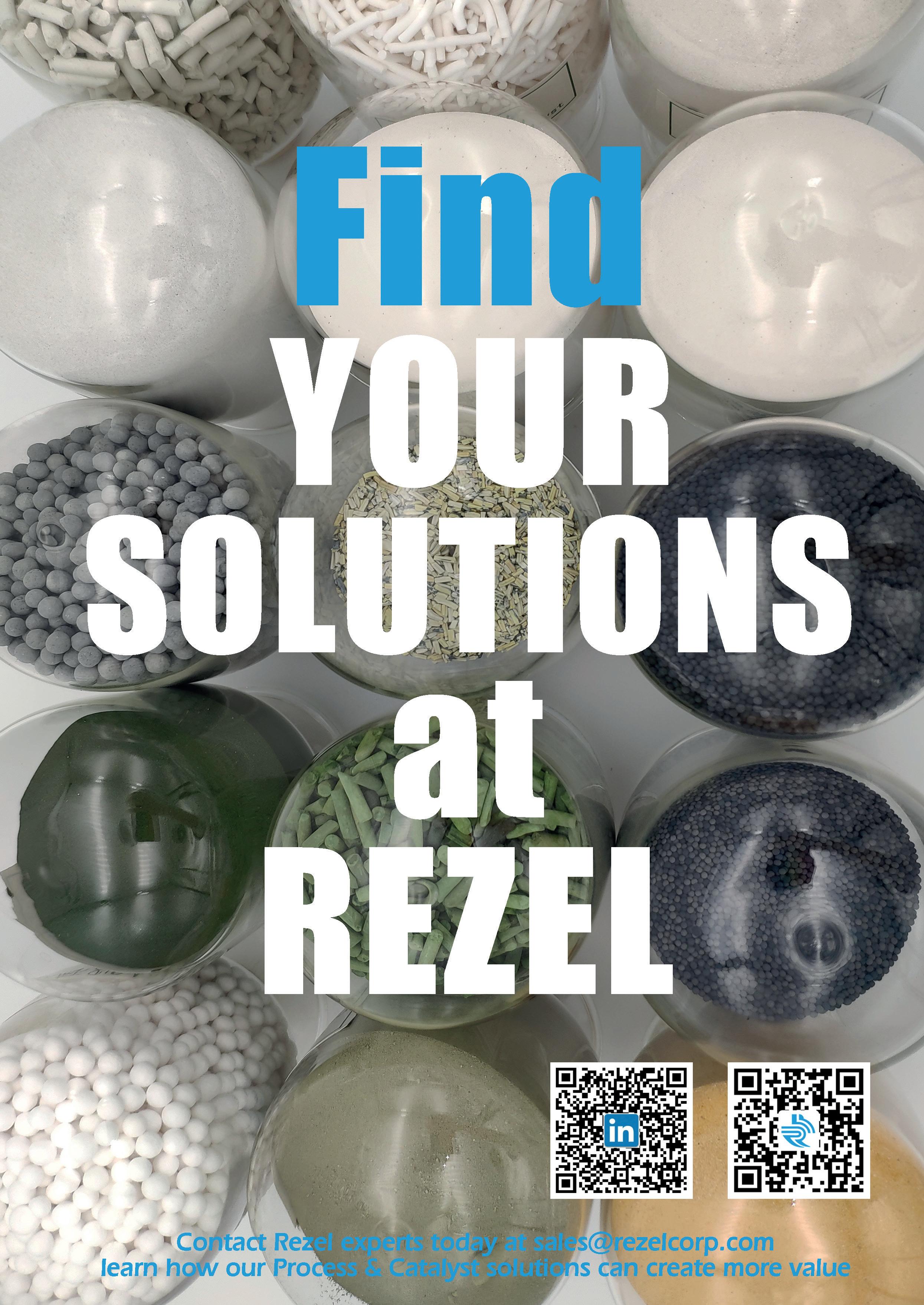
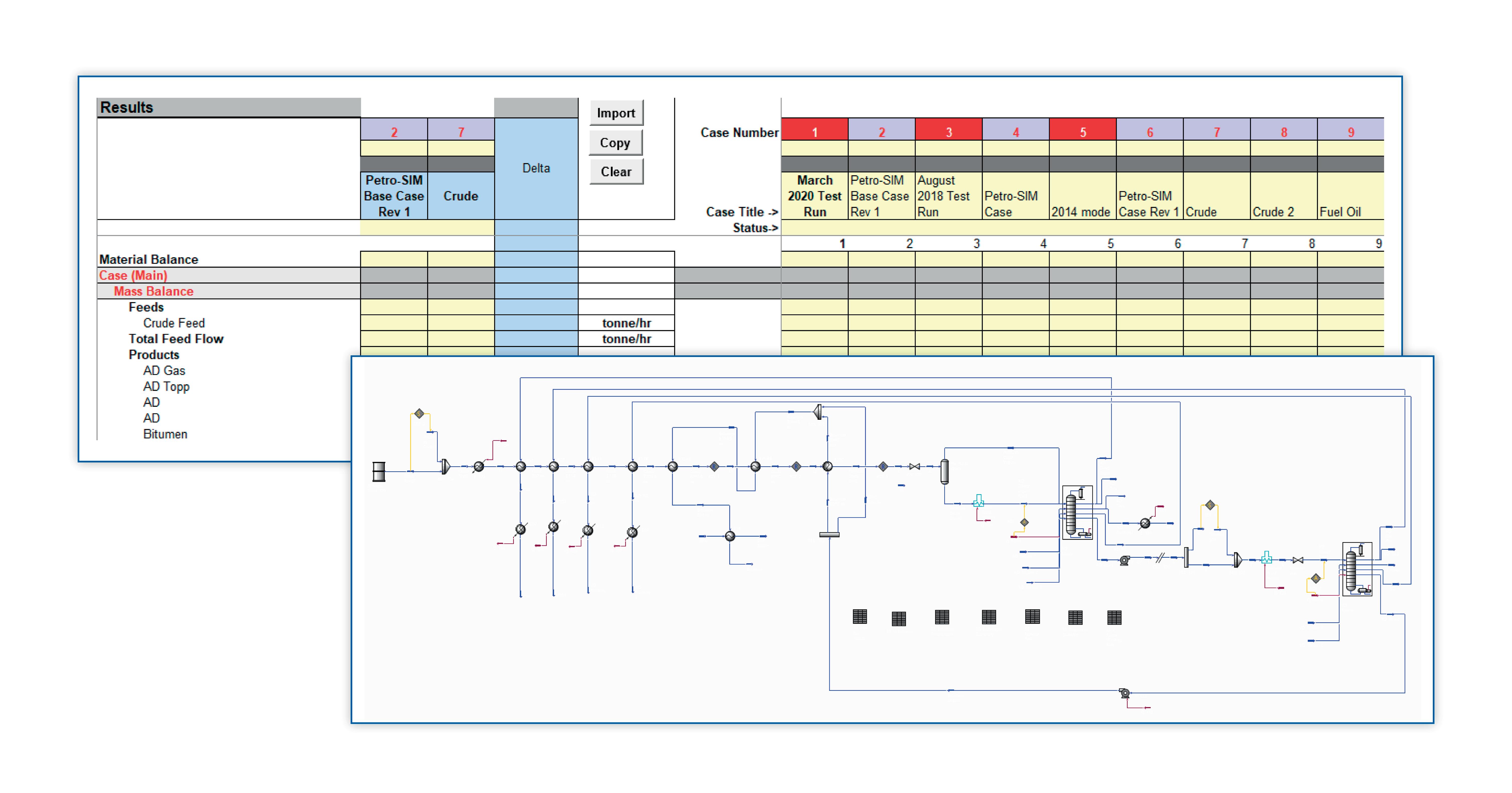
Figure 2. A Petro-SIM simulation and Excel workbook for the case study.
long-term contracts or on a spot basis. As such, the relative ranking and incremental values of the feedstocks should be available to traders.
The relative ranking of feedstocks is usually performed using complex-wide tools i.e. LP or refinery-wide flowsheets. For a crude basket, a fixed percentage of crude is replaced with new feedstock to understand the impact on the margins. Based on the shift in the margins, incremental values and the breakeven price of the new feedstock are estimated.
Case study
Nynas specialises in the production of naphthenic oils and bitumen which are produced from its various refineries in Europe. In close collaboration with its customers, the company has developed products for various applications.
The company was interested in processing different feedstocks at one of its refineries. The purpose of processing these feedstocks was to improve the yield and quality of the high-value products from the refinery. KBC and Nynas worked together to assess the feasibility of processing various feedstocks.
To understand the operating constraints of the existing assets, a roundtable discussion was conducted. The operating strategy and key bottlenecks observed to date were discussed during this meeting, and operating data for various feeds was analysed. Product yields, properties, and feed assays were also analysed to form a representative operation.
To estimate intrinsic key performance indicators (KPIs) and bottlenecks, the Petro-SIM® model for the operating assets was developed. Results from the simulation were compared with the operating data to improve confidence in the model results. Some of the KPIs estimated by the model provided insights into equipment that are difficult to measure and monitor using just raw data. Along with the model, an Excel® workbook was automatically generated to contain all of the results from the model in a user-friendly tool in order to compare various cases. Figure 2 shows a snapshot of the Petro-SIM model and Excel workbook.
The list of probable feedstocks was populated based on discussions with various stakeholders. Rather than performing rigorous analysis for all feedstocks, a preliminary assessment was performed to eliminate similar feedstocks.
A rigorous assessment, which included an adequacy check of major equipment, was performed for the selected feeds. The simulation model was utilised to identify the key bottlenecks for various feeds. New feedstocks were defined using detailed information in the form of assays, and improved product qualities were targeted in the model. To manage some of the operating constraints, operating targets were adjusted within the operating envelope.
The Petro-SIM simulation was able to identify the feasibility of processing some of the feedstocks and bottlenecks for the rest of the feedstocks with the targeted product qualities. The bottlenecks of primary and secondary equipment were identified using the simulation. Various recommendations were made to eliminate these bottlenecks. These recommendations are in the form of a roadmap that includes various options for the equipment that will constrain the processing of new feedstocks.
Conclusion
Feedstock flexibility is an essential mechanism for profit improvement of a refinery and/or petrochemicals complex. The feasibility of processing new feedstock depends on the economics and various constraints. An LP model is required to understand the economics of processing different feedstocks and to identify high-level constraints. The results from the LP model should be validated using the integrated complex-wide flowsheet. Petro-SIM flowsheets and rigorous models not only validate the results but also identify constraints at the unit and equipment levels. These models can also estimate the operating targets for new feedstocks.