Work Health, Safety & Environment (WHSE)
Group Minimum Standards for Compliance and Risk Reduction
July 2024
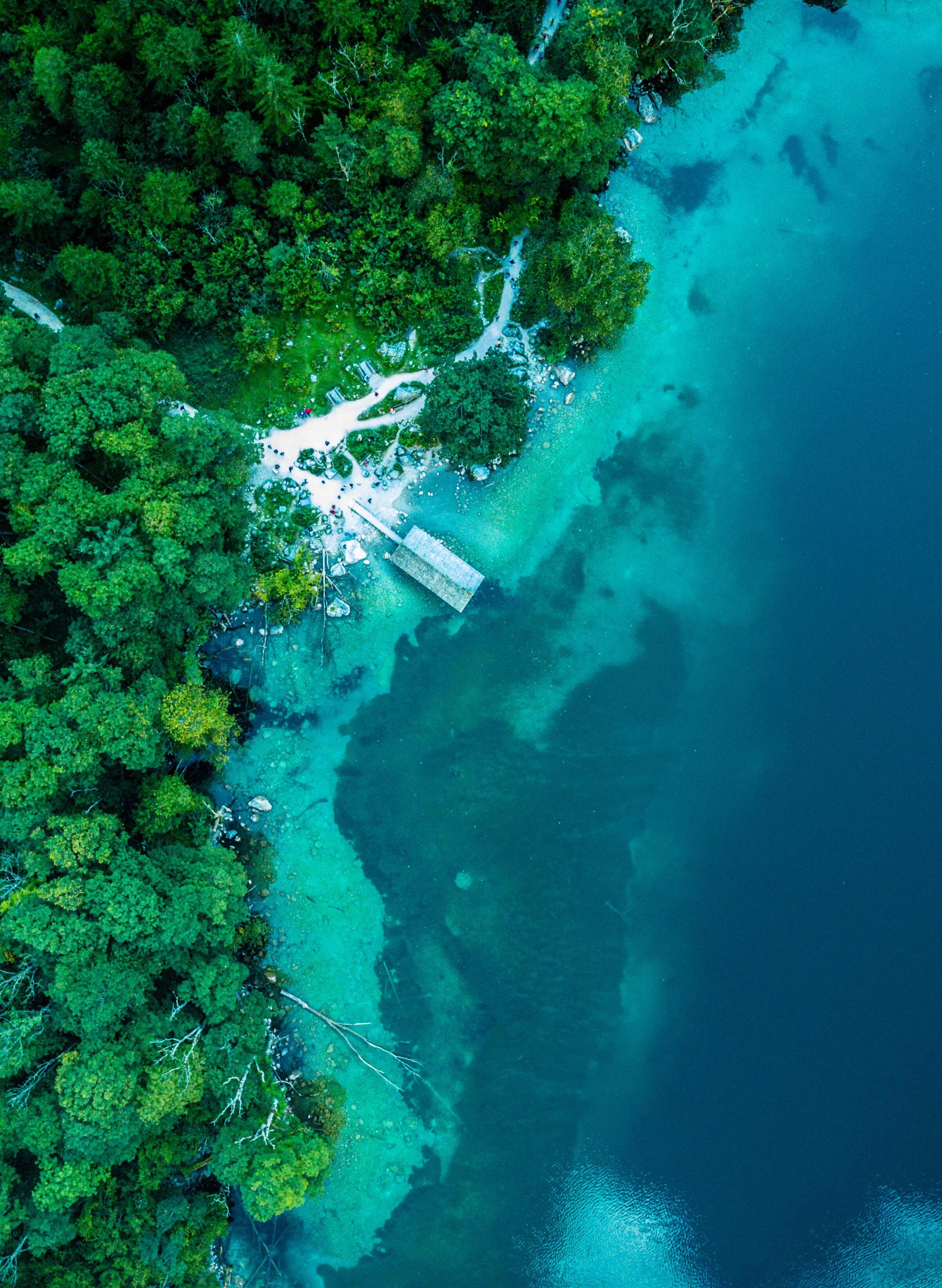
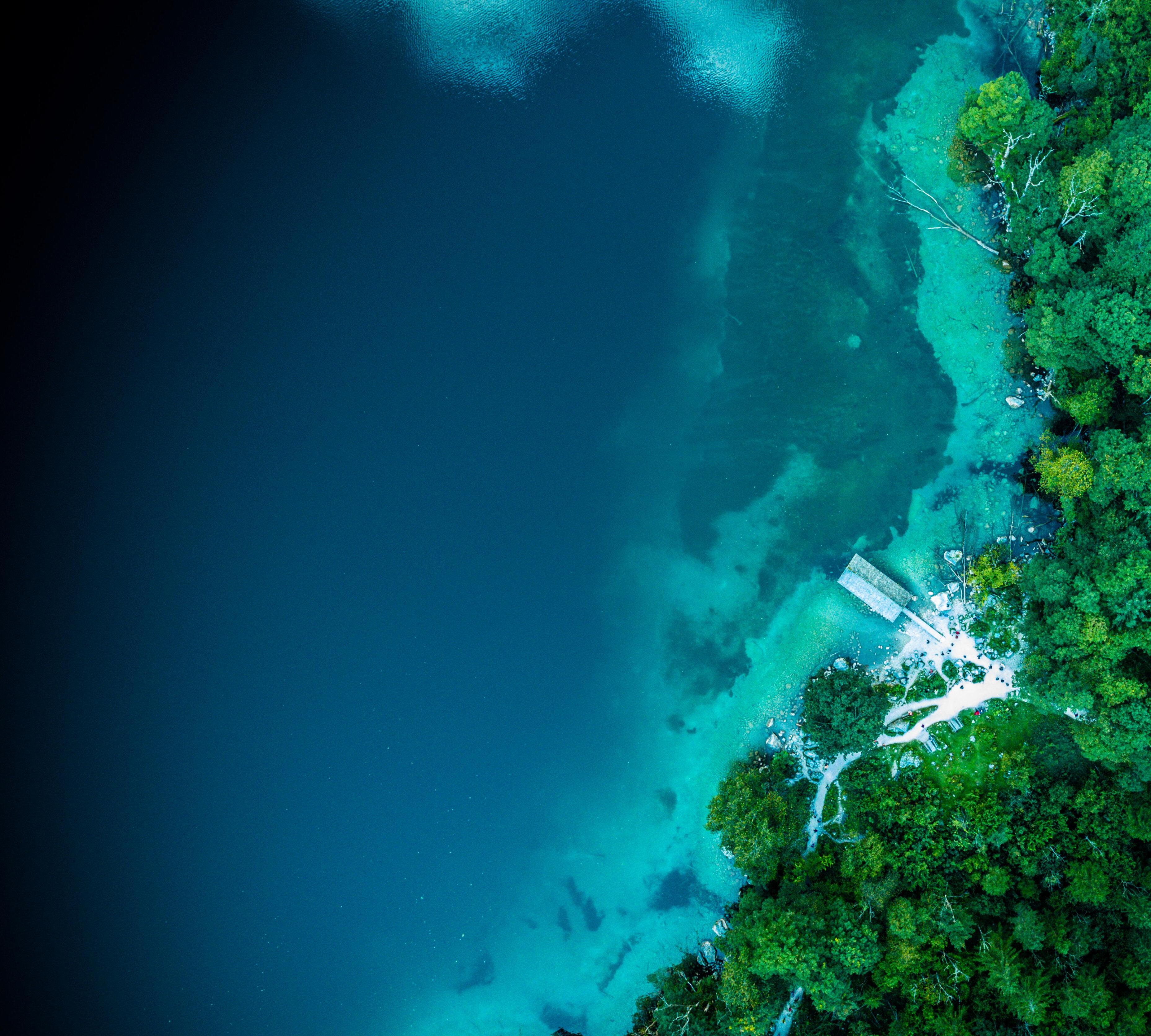
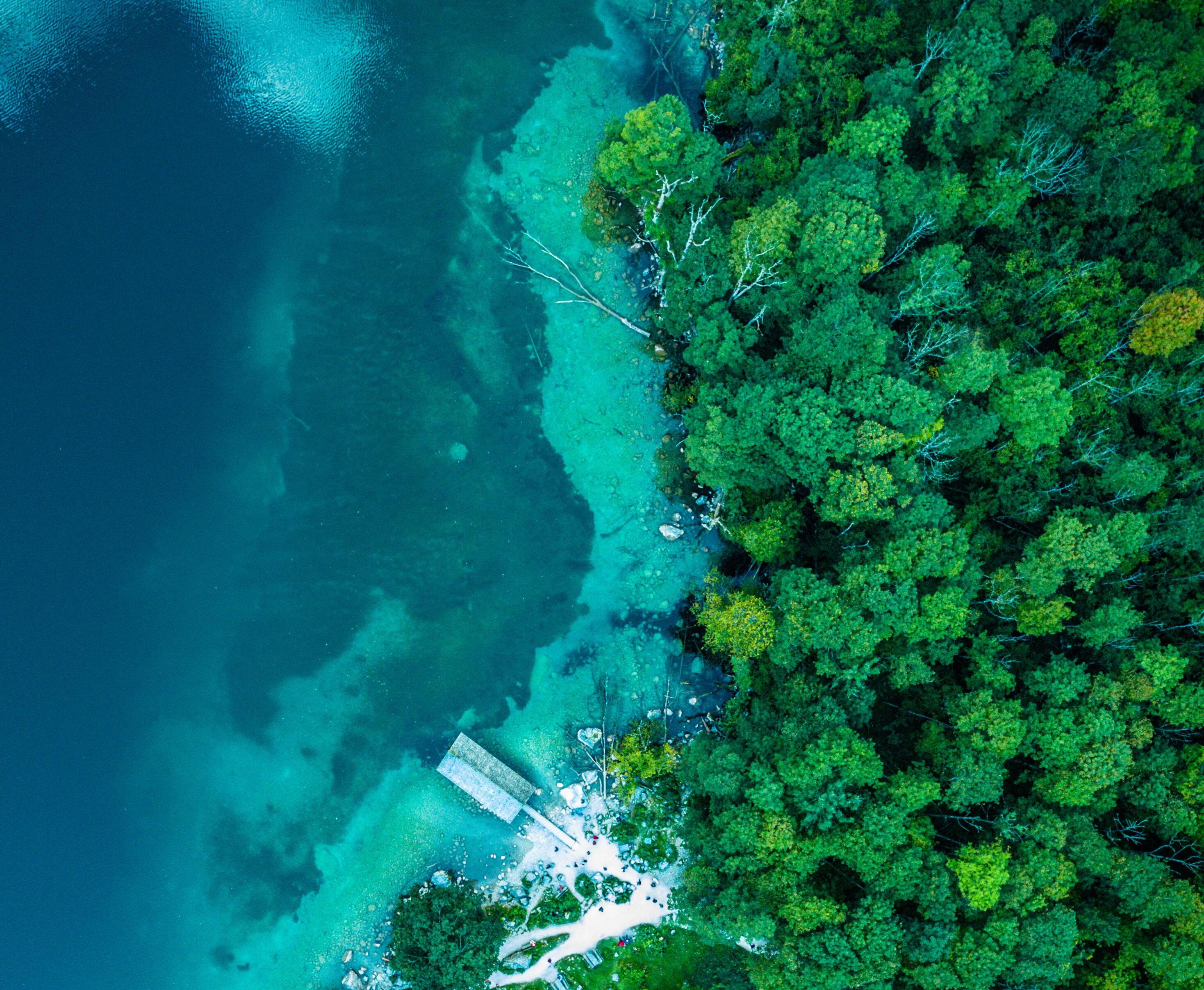
Group Minimum Standards for Compliance and Risk Reduction
July 2024
The WHSE Group Standards are a set of mandatory, minimum WHSE requirements that apply to all Company operations. The minimum requirements aim to ensure legal compliance and reduce risk.
A risk is critical when the consequence is nonrecoverable. If control is lost, the critical risks could result in fatal or serious injury or illness to people, major property damage, and a major impact on the environment.
Non-immediately life-threatening Risks, that won’t cause major property damage and won’t cause a major impact on the environment but are still important and demand attention due to their potential to cause harm. Significant risks need to be prioritised for proactive measures and controls.
Adhering to WHSE rules set down by the regulatory bodies and legislators. The Pact Group must comply with the WHSE laws and regulations that apply in each state or country in which we operate.
They apply to all employees, contractors, labour-hire workers, and visitors.
By embedding The WHSE Group Standards and Risk Controls, the standards will remain high across our operations, and critical risks that could cause fatal or serious injury will be managed.
Each WHSE topic is presented in the following way:
Expectation
Group Standards
A high-level statement describing what Pact expects
A list of mandatory, and minimum requirements
Resources A link to additional resources, support information and guidance material
• Provide appropriate resources to ensure the WHSE Group Standards and Critical Risk Controls can be embedded across The Company
• Understand and embed the WHSE Group Standards and Critical Risk Controls at their sites.
• Plan all work to comply with the WHSE Group Standards and Critical Risk Controls
• Support Managers and workers to understand and embed the WHSE Group Standards and Critical Risk Controls
• Coordinate assurance activities to verify the effective implementation of the WHSE Group Standards and Critical Risk Controls
• Actively participate in programs aimed at embedding the WHSE Group Standards and Critical Risk Controls
• Comply with applicable WHSE Group Standards and Critical Risk Controls
Throughout this booklet QR codes have been placed alongside standards and can be scanned with a mobile device. The link will take you to a website that contains additional information about that topic. The online resource library that supports extended learning about the topics covered in this booklet will continue to expand into the future.
Chemicals Storage & Handling
Confined Space Entry (CSE)
Cranes and Lifting Equipment
Electrical Safety
Fire
Fixed Plant and Equipment
Hazardous Energy – Isolation and Lock Out Tag Out (LOTO)
Health & Wellbeing
Mobile Plant
Prevention of Falls
Stormwater Management
Contractor Engagement
Hand Tools
Hot Work
Manual Handling and Ergonomics
Air Quality
Asbestos Management
Assessment and Improvement
Bulk Material Handling
Chain of Responsibility (CoR)
- Heavy Vehicle Operations
Consultation, Communication, and
Issue Resolution
Cooling Towers
Driving
Drugs and Alcohol
Emergency Response
Materials Handling and Storage
Permit Systems
Solid and Liquid Waste Management
Fatigue Management
Hazard Identification, Risk Assessment and Control
Induction (WHSE) and Site Orientation
Injury Management
Land Management
Personal Protective Equipment (PPE)
Public Safety
Reporting, Investigation and Learning
Workplace and Health Monitoring
Workplace Inspections
Expectation Understand and manage the specific risks associated with chemical storage and handling on-site. Includes Hazardous and non-hazardous Chemicals, Substances, Dangerous Goods and Hazardous Waste. Includes occupational exposures to such materials.
Includes the storage, transfer, handling, and disposal of these materials e.g., manual, road, mobile equipment, crane, or rail
Group Standards
• A risk assessment is completed for hazardous chemicals before purchase.
• All chemicals on site and quantities are recorded in ChemWatch.
• All chemicals are stored in areas fit for purpose including secondary containment.
• All chemicals are stored away from ignition sources.
• All chemical storage incompatibilities are identified and managed.
• SDSs for all chemicals are made available to employees in the local language
• Chemical storage areas and containers (including decanted chemicals) are labelled in line with the Globally Harmonized System of Classification (GHS)
• PPE requirements for each chemical are, at a minimum, as per the safety data sheet and risk assessment.
• Training and Competency Assessments are completed by people storing or handling chemicals.
• Spill kits are available and maintained where chemicals are stored.
• All chemicals no longer used or past their expiry date are disposed of appropriately
Resources Hazardous Chemical Handling (sharepoint.com)
Expectation WHSE risks associated with confined space entry are managed
Group Standards
• Ensure Confined Space training documentation is available for all identified CS personnel (including the permit issuer) and the personnel completing the CS entry work must be medically fit for this type of work.
• A job-specific rescue plan is developed, and the workgroup has reviewed it and checked all rescue equipment before entering.
• The atmosphere in the confined space is tested before entry and continuously monitored during work.
• All energy sources present are appropriately isolated before entering the confined space.
• The assigned and trained permit issuer will ensure the CSE entry permit contains all required information and is always available during works
Resources Permit to Work (sharepoint.com)
Expectation
Group Standards
Loads will be lifted & secured with suitable equipment in a controlled manner. Cranes and Lifting equipment include all cranes, hoists, and associated equipment attachments such as chains, slings, carabiners, and shackles.
• All cranes and lifting equipment will be inspected and assessed as being safe before use (at least once per shift when used)
• Use of and maintenance will be completed as per the manufacturer’s specification.
• All cranes that have been modified have the manufactures approval and have the proper certification (as per legislative requirements)
• All persons operating cranes and lifting equipment are trained and dependent on the equipment and type of lifting being completed to be licensed (as per legislative requirements)
• A Job Safety Analysis (or other risk assessment and containment process e.g. Take 5) is completed for any task where there is no documented procedure.
• Loads must not be lifted or suspended over people; appropriate demarcation and exclusion zones must be enforced.
• All cranes must have an annual inspection completed by an accredited person and associated lifting equipment every quarter.
• All cranes and lifting equipment must have a major inspection completed by a competent person in alignment with the manufacturer’s recommendations, legislative requirements, and/ or every ten years (whichever is the most frequent inspection requirement)
Resources Cranes & Lifting Equipment (sharepoint.com)
Expectation Controls are designed to prevent electrocution, fire, and explosion from uncontrolled electrical energy.
Group Standards
• Work on any equipment 24 volts and over must only be carried out by an authorised electrical worker (i.e., electricians, installers, instrument technicians, communication technicians) working under their required competencies and relevant licences in accordance with electrical and safety regulations.
• Live electrical work is prohibited, unless it can be proved that there are no other options or ways to identify either, the electrical fault or to be able to test the equipment.
• Where there is any risk of contact with live electrical wires/ exposed busbars i.e. in machine control cabinets and switchboards/ distribution boards or other electrical circuits. A completed arc flash study along with the documented Risk Assessment/Safe Work Method (SWMS) must be completed to determine the arc flash boundary, the suitable controls and PPE requirements.
• When working on or near live equipment, barriers shall be installed to prevent inadvertent contact and if working on live distribution/ switchboards with exposed busbars. the requirements and controls from a completed Arc Flash Study/Risk Assessment are implemented also to protect other people in the area.
• Live electrical circuits are identified and isolated wherever possible, before penetrating surfaces (walls, flooring, and roofing).
Continued in next page
Group Standards
• Even temporary electrical work must be installed, tested, and certified by a qualified person in accordance with the applicable electrical standard.
• When working near Overhead Live Equipment (OHLE) regulated safe working distances/exclusion zones are identified and maintained.
• All electrical equipment (including test leads) must be inspected for damage before use.
• All temporary electrical leads must be protected from water immersion and damage.
• All portable electrical equipment must be tested and tagged.
• All non-portable electrical equipment not protected by Residual Current Devices must be regularly inspected and tested (at a minimum mechanical/physical damage or loose wires) by a competent person in accordance with Original Equipment Manufacturers (OEM) requirements or at least every 3 years.
• Residual Current Devices are required for:
- High-risk fixed electrical equipment/installations.
- All tools connected to power circuits.
• Electrical cabinets and distribution boards must be fully sealed with no holes in the cabinet exterior and no gaps in the front of the switch panel exposing live electrical circuits inside. This equipment should be locked and have restricted access to authorised people only.
• Electrical distribution boards to be Thermo imaged annually, and all hazards identified are rectified.
Resources Electrical Safety (sharepoint.com)
Expectation Fire includes all incidents that involve a flame that was not purposefully ignited by an individual for work purposes.
Group Standards
• In some countries/states buildings must have an Annual Fire Safety Statement (or equivalent) completed by a qualified person (refer to your WHSE divisional manager if you are unsure if this is relevant to your area).
• Thermal imaging is completed at a minimum every two years on electrical panels, cabinets, and distribution boards.
• Housekeeping and maintenance of machinery must consider fire risk and controls.
• Emergency planning and response procedures must be in place
Resources Fire (sharepoint.com)
Expectation
Group Standards
Controls are implemented to ensure energy is controlled during work. Fixed Plant and Equipment includes all secured machinery, but also includes all powered and non-powered tools.
• A Pact Group isolation standard and procedure is in place and followed.
• All persons will be trained, and competency assessed (tailored, as appropriate, by role) in isolation procedures.
• Isolation procedures are always followed when accessing machinery.
Continued in next page
Group Standards
• Each site must have a machine guarding audit completed by a suitably qualified person, within the last three years.
• All very high and high machine guarding audit findings will result in the machine being isolated until an acceptable risk reduction is achieved.
• Machine guarding audit finding action plans will be in place and will be prioritised by risk.
• All new and reconditioned/relocated fixed plant and equipment comply with relevant AS/NZS standards (including maintenance and inspections)
• All hoses that have been identified to be high pressure are checked annually by a suitably qualified person - including, the age/condition of the hoses and based on the pressure and location of the hoses (exposed hoses near people working), determines whether they require to be whip checked or covered.
• A Job Safety Analysis (or other risk assessment and control process, e.g. Take 5) is completed for any task where there is no documented procedure
Resources Plant and Equipment (sharepoint.com)
Expectation
Group Standards
Potentially hazardous energy sources are identified and isolated to prevent uncontrolled release.
• Machine/task-specific procedures are developed to identify the specific steps necessary for isolating hazardous energy.
• All hazardous energy sources for each piece of equipment have been identified/documented and made available at the equipment for employee reference.
• Information made available to all employees on what processes/ tasks require energy isolation to be completed and what energy sources are to be isolated for that specific process/task.
• All new and existing equipment and systems with a hazardous energy source must have lockable isolation points labelled with a unique identifier.
• LOTO equipment must be made available to all employees and only these trained and approved employees can use it. Suitable equipment can include (padlocks, valve cover locks, electrical locks etc).
• All energy isolations and de-isolations are completed by a competent person.
• Physical isolation, de-isolation and any isolation changes are communicated to affected workers and stakeholders.
• Prior to working on isolated equipment/systems:
- All hazardous energy sources are identified, de-energised and physically isolated prior to working on equipment/systems
- Testing must be completed to verify that the correct services, plant, or equipmentare de-energised.
- All employees/contractors must place their personal danger tag and lock on theisolation point or group isolation device (lock box).
Continued in next page
Group Standards
• The removal of an individual’s LOTO equipment must only be completed by that individual or if the individual is not on site. By the site manager with written approval (can be a text message) from the individual.
• If the individual is not able to be contacted - the LOTO equipment can only be removed after an investigation including a documented/managed safety test/validation with sign-off by the site manager before the equipment is handed over for production purposes.
Resources Hazardous Energy – Isolation and Lock Out Tag Out (LOTO) (sharepoint.com)
Expectation Health and Wellbeing include all occupational physical and psychological factors with the potential to affect health (such as but not limited to workplace conditions, and fatigue) and well-being (such as workplace harassment, bullying, job demands, abuse, stresses, and post-traumatic stress). It also includes personal health factors (such as cancer, cardiovascular disease, diabetes, drugs, and alcohol) and wellness factors (such as anxiety, depression, and sleep disorders) which have the potential to impair a person’s ability to work safely or increase the risk of injury at work.
Group Standards
• A Pact Group Health and Wellbeing procedure is in place.
• Each business will understand psychosocial hazards, identify, and have a plan in place with regular review.
• Each site must deliver health and wellbeing training as directed by the Group Wellbeing team.
• Health and wellbeing initiatives will be implemented in consultation with the Wellbeing team.
Resources Health and Wellbeing (sharepoint.com)
Expectation Mobile plant will be operated safely. Mobile Plant includes all movable machinery such as forklifts, side lifters, elevated work platforms, trucks, oversized vehicles and so on.
Group Standards
• A traffic management risk assessment and plan has been completed at each site.
• Engineering controls (as a minimum) are implemented in all “very high and high” risk areas.
• All persons operating mobile plant are licensed (as per legislative requirements)
• Training and competency assessment is completed for all persons operating mobile plant annually and externally every 3 years.
• A pre-start check is completed once per shift for each item of mobile plant. The mobile plant must be assessed as being safe prior to use.
• A seatbelt, interlocked to the ignition, is worn on all forklifts, side lifters and trucks.
• Audible reversing devices are installed on all mobile plant.
• Fall prevention and fall arrest equipment will be utilised (as per legislative requirements) in all elevated work platforms.
Continued in next page
Group Standards
• A three-metre separation between the operating mobile plant and pedestrians is always maintained, (joint accountability) unless separated by a protective barrier.
• If mobile plant and pedestrians are within 3m, then tynes must be down (where present), handbrake on and ignition off
• Speed is limited to 10km/hr indoors and 15km/h outdoors.
• Maintenance is completed as per manufacturer’s specification
Resources Mobile Plant (sharepoint.com)
Expectation Prevent all falls when working at height. Falls include incidents related to working at heights, working from trucks, EWP, falling objects, falling through surfaces and slips, trips, and collapses.
Group Standards
• Fall prevention or fall arrest systems are in place and are used for work >2m
• A fall-arrest system must only be used if it is not reasonably practicable to use higher-level controls or if higher-level controls might not be fully effective in preventing a fall on their own.
• All equipment used for fall arrest should be designed, manufactured, selected and used in compliance with the standards
• Fall prevention and fall arrest systems are periodically inspected and maintained by an external provider.
• Fall prevention and fall arrest systems are inspected before each use.
• A Job Safety Analysis (or other risk assessment and containment process, e.g. Take 5) is undertaken before working at a height.
• All persons working at heights will be trained, and competency assessed in working at heights.
• Ladders should only be used as a means of access and/or egress unless they are approved, ‘step platform’ ladders.
• Scaffolds must comply with standards, be installed by a licenced scaffolder, and be regularly inspected.
• EWP selection is correct for the task e.g. boom lift, scissor lift. EWP must comply with standards.
Resources Working at Heights (sharepoint.com)
Expectation Sites understand potential waterway contaminants, regularly maintain stormwater drains and are prepared to respond to spills.
Group Standards
• Only clean rainwater is to be discharged through the site’s stormwater infrastructure.
• Stormwater drains must be always kept free of any obstruction.
• Solid and liquid chemicals and liquid wastes generated by site activities must be stored in a manner where spills cannot easily enter stormwater drains or any other waterway (i.e., secondary containment).
• Secondary containment of bulk wastewater storage tanks must include level alarms that notify employees on and offsite once triggered.
Continued in next page
Group Standards
• Drains at risk from solid contaminants such as resin beads, litter, and debris, must be protected using an appropriate drain guard (i.e., drain meshing, filter socks etc).
• Drain guards must be inspected and cleaned frequently and replaced once damaged or ineffective.
• Redundant machinery must be stored in a manner whereby leaks or residues are captured and prevented from entering stormwater drains.
• The discharge points to waterways or stormwater within the site boundaries, and the receiving body of water after discharge should be marked on a site plan.
• Spill kits must be placed in areas of potential chemical spillage and regularly maintained.
• Workers must be trained in spill response and be familiar with the location of spill response equipment.
Resources Stormwater Management (sharepoint.com)
Expectation Processes are in place to facilitate the selection and engagement of contractors considering relevant WHSE requirements
Group Standards
• Contractors have the relevant skills, experience, and qualifications for the work to be undertaken.
• Contractors are inducted and receive information about sitespecific hazards before starting work.
• Contractors must provide the relevant JSEAs/SWMMs/licences and insurances, particularly for all high-risk work completed.
• Contractors are appropriately supervised when on site.
• Contractor performance is monitored and reviewed
Resources Contractor Engagement (sharepoint.com)
Expectation
Group Standards
Hand Tools include all tools that are powered by hand rather than a motor. Categories of hand tools include wrenches, pliers, cutters, files, striking tools, struck or hammered tools, screwdrivers, vices, clamps, snips, saws, drills, and knives.
• All handheld tool usage is approved for the work about to be conducted, (the right tool for the right job) by the tool user completing the task
• All Hand Tools will be inspected and assessed as being safe, before each use by the tool user completing the task.
• Processes that require the use of “homemade hand tools” shall be Risk Accessed by each site to determine if they can be engineered out of the process. If not, safer and more permanent hand tools are to be provided for the task.
• A Job Safety Analysis (or other risk assessment and containment process e.g. Take 5 which includes correct personal protective equipment) is completed for any task, where there is no documented procedure.
• Training and competency assessment covering - “what is acceptable tool condition and how to use them correctly” has been completed for all persons using hand tools
Resources Workshop and Hand Tool Safety (sharepoint.com)
Expectation
Group Standards
The potential for fire and explosion is controlled when performing hot work. Hot work includes, but is not limited to welding, metal grinding, thermal and oxygen cutting, and flame heating.
• All hot work is conducted in a designated hot work area.
• When hot work is conducted outside a designated hot work area, a hot work permit is completed
Resources Permit to Work (sharepoint.com)
Expectation
Group Standards
Manual Handling and Ergonomics includes any manual task, such as lifting, but also includes office/workstation ergonomics and the use of handheld tools.
• Each site will identify its top ten manual handling tasks, will risk assess each task and will have a risk reduction plan in place for each task in line with the hierarchy of controls.
• A Job Safety Analysis (or other risk assessment and control process) is completed for any task where there is no documented procedure.
• All manual handling or ergonomic incidents, near misses and impacts (no matter how minor) will be immediately reported to the site supervisor and recorded in the incident database.
Resources Manual Handling (sharepoint.com)
Expectation
Group Standards
Material Handling and Storage includes all items stored and handled, such as items on racking (e.g., moulds; chemicals; bins) or trucks, falling material or material blocking fire exits.
• Equipment used for the storage and handling of materials and products is of appropriate design and rating for its duty.
• Equipment used for the storage and handling of materials and products will have its maximum load rating clearly displayed.
• Storage equipment is inspected periodically and repaired/ maintained to be able to perform at the design rating.
• All items stored and handled are secured to prevent shift/collapse and falling objects.
• Products are stored in designated areas separate from walkways, work areas, and emergency exits
Resources Materials Handling and Storage (sharepoint.com)
Expectation
Group Standards
High-risk activities are identified and appropriately managed as part of work initiation, scheduling, planning and execution
• High-risk activities requiring permits are identified
• Controls needed to allow safe execution of high-risk work are documented on the permit and effectively implemented. Continued in next page
Group Standards
• Only Properly trained individuals in hazard identification, assessment, and control can issue Permits to Work (training must include the type of high-risk permits that are in Pact’s safety programme).
Resources Permit to Work (sharepoint.com)
Expectation Waste generated and stored on site is managed and disposed of in accordance with environmental legislation and minimal waste is sent to landfill by implementing effective recycling systems.
Group Standards
• All waste streams generated on site must be identified and the disposal method after collection known.
• Waste bins are available for all waste streams and appropriately labelled.
• Waste bins are stored in appropriate locations, to optimise usage.
• Waste bins should have a lid to prevent waste from falling out and entering the environment.
• Waste bins without lids must be stored undercover, to prevent rainwater from entering and leaching contaminates.
• Waste bins containing liquids or resin pallets must be completely sealed to prevent waste from escaping.
• Controlled/regulated waste must not be disposed to landfill.
• Controlled/regulated waste must be disposed of via a licensed contractor.
• Waste transport certificates are required for the collection and transport of controlled/regulated waste.
• Liquid wastes, including wastewater generated on-site, must be collected, and removed by an external contractor or treated and released to sewer (under agreement with local authorities)
Resources Waste (sharepoint.com)
Expectation All emissions made to the air are identified and appropriately controlled to limit the impact on human health and the environment.
Group Standards
• The substance being released, and the corresponding emission quantity is known for all emissions to air.
• All emissions into the air are appropriately controlled to limit the impact on human health and the environment.
• Ensure that any substances released into the air do not exceed the threshold for regulatory reporting or necessitate continuous monitoring.
• Ensure enclosed areas are free of excessive odour.
• If dust or odour is generated, it does not extend beyond the boundary of the site.
Resources Air Quality (sharepoint.com)
Expectation Asbestos and Asbestos Containing Materials (ACM) are identified and appropriately managed. This includes buildings, structures, plants, machinery, and natural assets that contain or are suspected of containing, Asbestos or ACM.
Group Standards Where asbestos is present on site:
• Maintain a site asbestos register and plan.
• Prepare, maintain, and review an asbestos management plan and communicate it to affected workers.
• Label asbestos-containing material.
• Control asbestos using the four risk control options - Removal, Encapsulation, Enclosure or Administration
• Only use appropriately licenced asbestos removalists and ensure they dispose of asbestos appropriately
Resources Asbestos Management (sharepoint.com)
Expectation WHSE performance is assessed, and action is taken to continuously improve
Group Standards
• Implementation of Group Minimum Standards for Compliance and Risk Reduction are assessed periodically by competent people.
• Assessment findings and actions are reported to the appropriate level of leadership.
• Preventive action is taken to mitigate potential risk.
• Corrective action is taken for existing systemic risks to prevent recurrence ALARP.
• The effectiveness of the Pact’s WHSE system is evaluated through a formal, periodic management review
Resources Assessment and Improvement (sharepoint.com)
Expectation Material delivered to the site in bulk is controlled in a way that has minimum impact on health, safety and the environment.
Group Standards
• All bulk material storage silos/tanks must be controlled in a way that ensures the material can exit and enter without spillage. This includes installing socks (or other devices) on pipes to capture overflow.
• Bulk material unloading zones must be within a secondary containment area
• A permanent spill control station must be maintained within a short distance of bulk material unloading areas.
• Material spills during unloading must be cleaned up immediately.
• Drivers delivering bulk material must not leave the site until they inspect the unloading area and confirm that no spill has occurred.
Continued in next page
Group Standards
• Any spills must be immediately reported to the workplace manager, who must then contact the delivery company.
• Any waste from the unloading process is to be placed in sealed bins that have a lid.
• Ensure that inspection and maintenance schedules recommended by the manufacturer are kept, or a schedule is developed by a competent person where necessary.
Resources Bulk Material Handling (sharepoint.com)
Expectation All parties who influence, direct or control vehicle transport operations over 4.5t GVM comply with CoR obligations.
Group Standards
• Transport activities, including loading and unloading vehicles, are done safely.
• Controls are implemented to meet CoR obligations.
• Operational activities do not require or encourage a driver to, Exceed the speed limits, exceed regulated driving hours, fail to meet the minimum rest requirements, Drive while impaired by fatigue.
• Contractors and suppliers using heavy vehicles must have appropriate systems in place to meet their CoR obligations
Resources Chain of Responsibility (sharepoint.com)
Expectation Consultative and communication arrangements are established at all sites.
Group Standards
• Mechanisms are established to communicate and consult with workers and other stakeholders about WHSE matters.
• Issue resolution processes have been established
Resources Communication, Consultation and Issue Resolution (sharepoint.com)
Expectation WHSE risks associated with cooling towers are managed
Group Standards
• A maintenance program is established for all cooling towers and completed by an accredited contractor/employee.
• Cooling towers are registered and licenced with the relevant local authority (where applicable)
• Biocide and anti-corrosion chemicals used to dose cooling towers are stored in a covered and bunded area.
• Liquid waste must not drain directly to stormwater.
• Liquid waste must be collected and removed by an external contractor or treated and released to the sewer (under agreement with local authorities)
Resources Cooling Towers (sharepoint.com)
Expectation WHSE risks associated with driving are managed
Group Standards
• Only drive vehicles you are licenced to drive.
• Never drive if you are fatigued, distracted, or affected by drugs or alcohol.
• Always wear a seatbelt
• Obey road rules and speed limits.
• Secure loads correctly
• Watch out for wildlife.
• Park in designated parking areas
• Ensure your vehicle is maintained in accordance with the manufacturer’s requirements
Resources Driving (sharepoint.com)
Expectation Workers are physically and mentally prepared to carry out their tasks.
Group Standards
• People presenting for work must not be adversely affected by; illegal, prescribed, or ‘over the counter’ medication and other drugs.
• People presenting for work must have a zero blood alcohol reading.
• Notify your manager/supervisor if you believe you may not be physically or emotionally fit for work.
• Do not come to work when unwell.
• Employees and contractors must present for any random or ‘for cause’ drug and alcohol testing programs
Resources Drugs and Alcohol (sharepoint.com)
Expectation Processes are in place to identify potential emergencies and their impacts, including those associated with activities in the vicinity of a Pact workplace
Group Standards
• Emergency Response Plans are developed in consultation with stakeholders to cover potential emergency scenarios.
• Emergency Response Plans are periodically reviewed and updated to reflect changes in the workplace.
• An Emergency Control Organisation is established, and people are trained for their roles.
• Emergency Response Plans are tested (at least annually) in consultation with stakeholders.
• Records are maintained of evacuation drills and exercises including improvement opportunities
Resources Emergency Response (sharepoint.com)
Expectation Fatigue-related risks are identified, assessed, and managed in the workplace
Group Standards
• Managers and Supervisors are aware of and adhere to fatigue minimisation measures, such as work hour limits, task durations, shift schedules and rosters, call-out and overtime arrangements.
• Managers and Supervisors make team members aware of the health risks associated with fatigue.
• Managers and Supervisors manage team members showing signs of fatigue to give them enough time to rest and recover.
• Team members present for work suitably rested and able to work safely.
• Team members advise their supervisor/manager if they are unfit to commence or continue work
Resources Fatigue Management (sharepoint.com)
Expectation
Group Standards
Hazards are identified and reported, risks assessed, and appropriate controls implemented
• The identification and reporting of hazards is encouraged.
• Formal risk assessment processes occur as part of work initiation, scheduling, planning and execution.
• Controls are implemented following the hierarchy of control.
• Control effectiveness is periodically reviewed.
• People are trained, where necessary, in the hazard identification, risk assessment and control process.
Resources Hazard Identification Risk Assessment and Controls (HIRAC) (sharepoint.com)
Expectation All people are inducted and oriented to safely perform their tasks or activities.
Group Standards
• Workers, contractors, and labour hire employees to complete inductions prior to starting to work on site.
• Site specific orientations complement inductions and will be completed by managers/supervisors/hosts.
• Visitors follow sign-in/sign-out requirements and reasonable directions from their host
Resources Induction (sharepoint.com)
Expectation Injured workers are supported in returning to work following a workplace injury
Group Standards
• Early intervention programs are implemented in consultation with the Group Wellbeing and Recovery Team.
• Recovery coaches are available to support workers’ recovery at work.
• Discomfort/Injury/Illness reporting process is followed.
• Precautionary duties are identified and communicated for each site.
Resources Injury Management (sharepoint.com)
Expectation The risk of land pollution is always controlled
Group Standards
• Storage of equipment, chemicals or any materials is not permitted on unsealed land.
• Discharge of any liquid or solid substance onto unsealed land is not permitted and must be immediately reported to site management, Pact’s WHSE Team and the land then remediated.
• Staining of sealed surfaces due to any chemical spills must be cleaned, and the surface restored to pre-spill condition.
Resources Land Management (sharepoint.com)
Expectation
Group Standards
Workers are protected from contact, impact, or harm.
• Minimum PPE requirements are established and communicated for each site.
• Tasks requiring specific PPE are identified and the appropriate PPE is provided.
• Training in the use, storage, cleaning, and maintenance of PPE is provided where necessary.
• PPE is checked for damage and is fitted properly before use.
• A stock of replacement PPE is kept on-site and a process is in place to make it available to all employees.
Resources Personal Protective Equipment (sharepoint.com)
Expectation We plan and act in the interests of public safety, in the same way we do for employees.
Group Standards
• Public safety is considered at the interface of our works and the community.
• Public safety incidents are treated in the same manner as those involving employees.
• The potential impact on the public is considered while planning for emergency response.
• The use of administrative controls is avoided wherever possible when managing the public safety interface.
Resources Public Safety (sharepoint.com)
Expectation Hazards, near misses and incidents, are reported and where possible, lessons learned and communicated
Group Standards
• WHSE hazards, near misses and incidents, are reported to site management and Pact’s WHSE Professionals
• Notifiable incidents are reported to relevant external agencies, the General Manager, and the Divisional WHSE Manager.
• Significant incidents and injuries are reviewed to learn.
• WHSE statistics are analysed and communicated across the organisation
Resources Incident Reporting and Investigation (sharepoint.com)
Expectation
Group Standards
Workplace and health monitoring programs are in place to support employees’ health, hygiene, and wellbeing
• Systems are in place for the identification of hazards and occupational health exposures associated with the work environment.
• Health and hygiene surveillance programs are established where necessary considering the statutory requirements as a minimum.
Resources Workplace and Health Monitoring (sharepoint.com)
Expectation Regular inspections of the workplace are conducted by a range of people to ensure risk controls are in place and working
Group Standards
• Workplace Inspections are scheduled to cover all areas of the site in a 12-month period.
• Workplace Inspection checklists are used to provide useful prompts and promote consistency.
• Managers, Supervisors, HSRs, WHSE advisors and workers participate in workplace inspections.
• Records of workplace inspections are kept.
• Corrective actions are created for items that could not be immediately fixed
Resources Workplace Inspections (sharepoint.com)