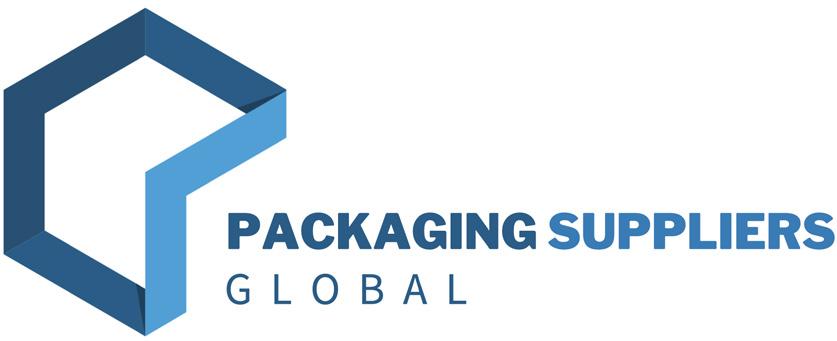
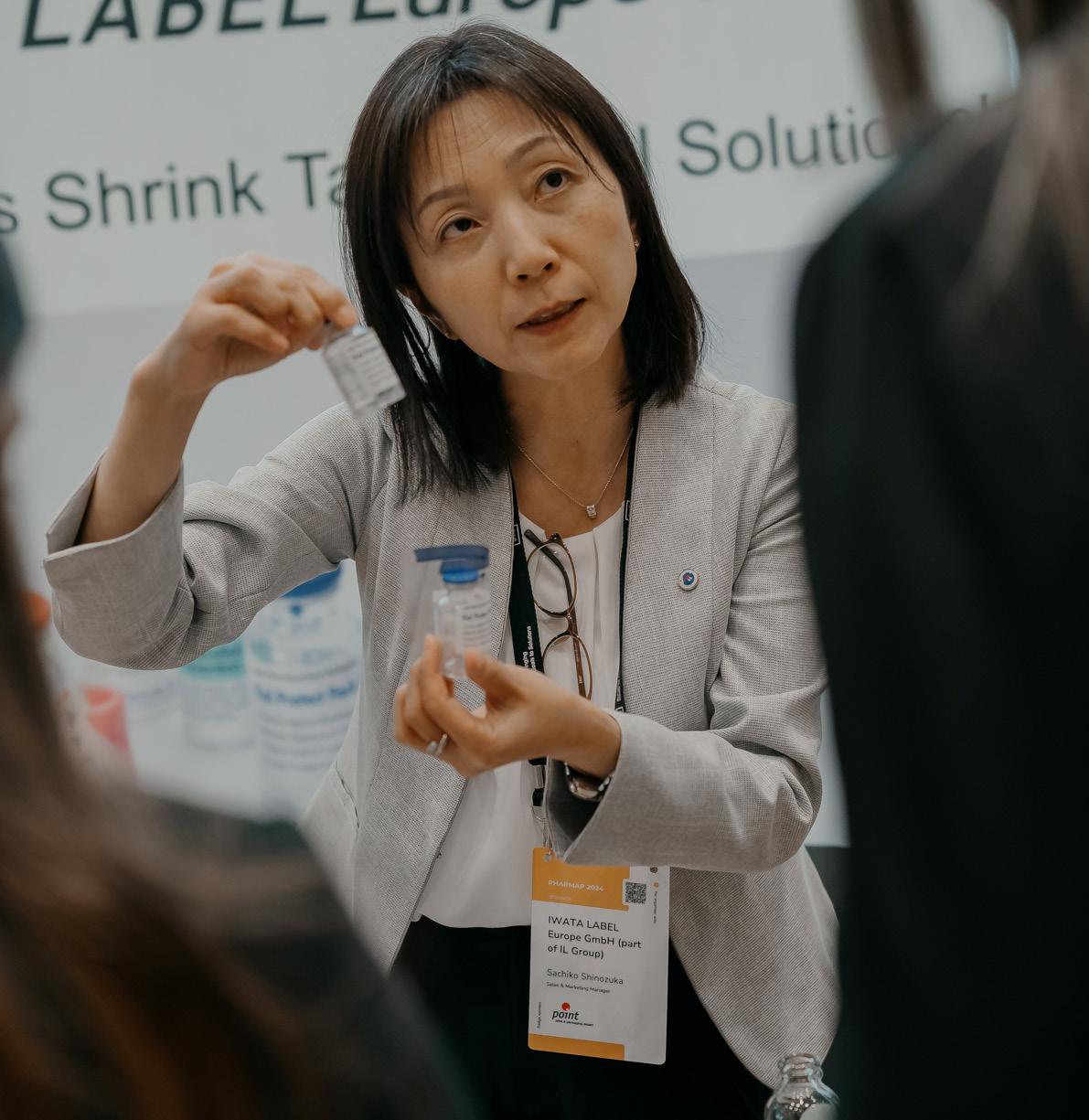

• Green pills and smart packaging: Solving pharma’s challenges
• Ton’s take: How to ensure safety and efficiency in pharma co-packing
• Anti-counterfeiting, sustainable primary and secondary packaging & much more!
Welcome to our second edition of 2025 – a pharmaceutical packaging special.
This issue is dedicated to the world of pharma, where precision, safety and innovation must go hand in hand. Our spotlight feature delves into PHARMAP 2025 – where industry leaders gather to share ideas, insights, and solutions for the sector’s most pressing challenges.
Inside, you’ll find expert perspectives on anticounterfeiting technologies, child-resistant packaging, and the growing demand for sustainable primary and secondary materials. In this edition, ‘Ton’s take’ explores how co-packing in pharma can be optimised for both safety and efficiency.
From supply chain traceability to circular solutions, this issue is packed with strategies and innovations shaping the future of pharmaceutical packaging.
Happy reading!
w: packagingsuppliers global.com
e: info@packaging suppliersglobal.com
5
PHARMAP 2025: Green pills and smart packaging: Solving pharma’s challenges
Ton’s take: How to ensure safety and efficiency in pharma co-packing
Adelphi: How one Radiopharmacy’s need led to 28 years of NHS supply
From good to better: How we re-engineered the child-resistant Wallet Box by Gianni Linssen
The feather effect: How nature is transforming thermal packaging
41
t: +44 (0)117 318 4321 8 13 20 23
System thinking: The untold story of sustainability in primary pharma packaging 5 8 13 20 23 41
The pharmaceutical industry is at a crossroads, facing increasing pressure from environmental regulations, technological advancements and intensifying competition. Companies strive to reduce costs while ensuring quality, efficiency and sustainability in manufacturing and packaging.
Difficult questions arise for pharmaceutical companies: how could they optimise costs without compromising quality? What role does digitalisation play in streamlining production? How can sustainability goals be achieved without disrupting operations?
These challenges are too complex for any single organisation to tackle alone. Collaboration is essential for overcoming the obstacles of the market, and that is the key mission of the Pharmaceutical Manufacturing and Packaging Congress (PHARMAP) 2025.
One of the most pressing concerns for pharmaceutical companies is balancing cost reduction with high-quality production. Outsourcing and contract manufacturing are
emerging as strategic solutions to optimise expenses. Recognising the significance of the approach, PHARMAP 2025 features a session on this topic.
One of the Congress’s speakers is Hichem Chougui, Business Development at Spa Pharma Invest. He presents strategies for optimising pharma partnerships through efficient supply chains and strategic proximity:
“We are dedicated to reshaping the pharmaceutical landscape by aligning with the highest standards, offering both cost efficiency and compliance with global regulatory frameworks.
Affordable labour costs and energy resources enable the provision of competitive manufacturing solutions.”
Other participants in this discussion are Allpack Group AG, KAESER Kompressoren SE, Onesource Specialty Pharma Ltd, and Bayer. The delegates present their insight about potentials in the compressed air syste, outsourcing and external partnerships for CMC development, combination drug delivery systems and more.
Sustainability is another critical challenge for the pharmaceutical sector, which accounts for approximately 4.5% of global greenhouse gas emissions. With growing awareness of environmental impact, experts are exploring bio-based and recyclable materials to reduce reliance on traditional plastics.
PHARMAP 2025 dedicates significant attention to green initiatives, including a roundtable discussion featuring Bayer, Merck, SÜDPACK Medica AG
and others. Topics cover blister materials, polypropylene-based packaging for oral solid doses, supply chain decarbonisation and green synthesis design.
Moreover, Maja Diebig-Lorenz, Head of Sustainability and Innovation at INVITE GmbH, shares insights into sustainable pharmaceutical packaging:
“Our research addresses this challenge by developing monoblister solutions that offer the necessary high-barrier properties while achieving a high level of recyclability. This involves analysing the barrier requirements of various pharmaceutical products, evaluating existing monomaterial blister foils and exploring emerging technologies in the field.”
The focus on practical solutions extends to an exhibition zone of the Congress, where delegates can explore cutting-edge technologies and services from over 50 contractors. Among them, POLIROM Packaging Srl, Druckerei Bauer GmbH, LEIPA Georg Leinfelder GmbH and others showcase secondary
packaging solutions designed to meet sustainability goals.
The rapid digital transformation of the pharmaceutical sector is making it easier to address main challenges. As the industry moves towards Pharma 4.0, the adoption of Artificial Intelligence and smart systems is accelerating. Computer vision is being used to inspect products for defects, ensuring highquality output, while robotics and automation streamline repetitive tasks, enhancing precision and reducing human error. These advancements significantly shorten time-to-market for new medications.
To address this issue, PHARMAP 2025 emphasises specialised sessions on innovative packaging solutions with key topics covering:
• providing patient information on packaging and package leaflets in Europe;
• sustainable flexible packaging solutions for the pharmaceutical market;
• transitioning from paper to digital leaflets;
• enhancing semi-automated equipment with robotic systems.
Karel van der Waarde from Lucerne University of Applied Sciences and Arts highlights the importance of regulatory changes in packaging during this session:
“Packaging and package inserts will need to change substantially to adhere to EU laws. Not only will the materials and dimensions change, but also the approach to informing people about their medicines. Despite the good intentions of everyone involved, people struggle to use medicines. Errors, poor adherence, high waste, substantial costs and unsatisfactory results are common.”
Experts from Graphic Packaging International, UNICEF, Roche Ecuador S.A., Lucerne University of Applied Sciences and Arts, LEIPA Georg Leinfelder GmbH and INVITE GmbH also join the session to present their visions of the issue.
As regulatory demands tighten and environmental concerns grow, companies must adopt innovative strategies to remain competitive. Outsourcing, smart manufacturing and sustainable packaging are no longer optional but essential components of a forward-thinking pharmaceutical strategy.
Understanding the importance of changes, the Pharmaceutical Manufacturing and Packaging Congress always strives to craft a business programme full of relevant discussion and practical solutions.
Brett Marshall, Vice President of Zuellig Pharma, underlined the relevance of PHARMAP’s agenda:
“It’s always a good opportunity when you get manufacturing and packaging specialists together to talk about the issues that are affecting the industry.”
Since 2021, PHARMAP has welcomed over 1,000 delegates from leading pharmaceutical
companies, CMOs, CDMOs and service providers to establish business connections. This year, the Congress reached an important landmark – its 5th anniversary. To celebrate the occasion, PHARMAP is having a special edition of a Gala Dinner with a grand lottery
With its dynamic programme and expert-led discussions, PHARMAP 2025 is set to be a key venue for industry leaders who are looking for advanced packaging solutions and manufacturing technologies.
Join PHARMAP 2025 in Berlin on 13-14 April to engage in discussions defining the next era of the pharmaceutical industry: https://pharmap-congress. com
Dear Packaging Suppliers
Global reader,
This is my first contribution for PSG of this year. A lot has changed since I wrote my last ‘Ton’s take’, not only in global politics, but also in packaging. Last year, the PPWR came into place in the EU and some member states started with
the so called Eco-Modulation. For those who missed this, this is basically a system where recyclable materials are taxed lower than non-recyclable materials. Obviously there are lots of nuances to be taken into consideration, including the lack of available recycling infrastructure, but at least the ‘powers that be’ took this very important step to incentivise the usage of optimised packaging materials. Money talks, as some tend to put it bluntly.
As this edition of PSG is dedicated to pharmaceutical packaging, I had a close look at my ‘Ton’s take’ of last year about pharma. Where last year I focused on the challenges of
using sustainable packaging for the pharma industry, this time, I’d like to focus on the challenges of optimising the actual contract manufacturing and packing process of pharmaceuticals.
I spoke with 2 industry leaders, who supply their products into the contract manufacturing and packing industry. Adelphi Manufacturing supplies flexible, scalable filling machinery, ideal for pharmaceutical Contract Manufacturing Organisations (CMOs) and Nulogy provides specialised software for complex supply-chain industries, such as pharmaceuticals.
Let’s start with the hardware and hear from the machine
people first. I talked with Rachel Birrell-Gray, Associate Director of Marketing at Adelphi Manufacturing. Adelphi Manufacturing is part of the highly regarded Adelphi Group of Companies, a multi awardwinning UK manufacturer and supplier of packing machinery and equipment, whose 4 divisions have a high focus on equipment for pharmaceutical contract manufacturing and packing.
Ton: “Rachel, what would you say are the most prevalent challenges which pharmaceutical CMO customers discuss, when consulting with Adelphi about machinery options?”
Rachel: “Worn down from wearing too many hats; weighted with worries about the implications of geo-political instabilities; or followed home after-hours by emails coming direct to your phone… Contract Manufacturers globally are reporting that the pressures/ demands on their time have never been higher.
We also understand that loyalty is a rare commodity in today’s world, where moving between suppliers can feel as simple as flicking a switch. Scarily, contract manufacturing partners themselves can even be seen as dispensable and interchangeable!
At Adelphi we always advocate for creating mutually valuable supply partnerships, rather than jumping between suppliers. These longer-term relationships provide valuable dependability for pharmaceutical CMOs – to help eliminate uncertainties, mitigate risks, and control what is possible to control.”
Ton: “So, you’re talking about added value for CMOs. How do you believe machinery and equipment suppliers can add value for pharmaceutical CMO’s, and how can this drive results?”
Rachel: “As well as enhancing
business stability for CMOs, long-term supplier partnerships can drive value in many other ways.
At Adelphi these can include accepting orders for the year and holding stock to ensure quick fulfillment, as well as working together on optimised delivery times and terms. These can prevent long wait times, which can halt your operations and strain your stakeholder relationships.
Working with suppliers who understand and meet your procedural standards will also reduce the likelihood of administrative headaches such as non-conformances later down the line, as well as contributing to a positive impression for your customers, ultimately supporting you to win new contracts.”
Ton: “Rachel, in an earlier conversation you spoke about shared values, as a way that CMOs’ suppliers can add value. What do you mean by that?”
Rachel: “Proactively sharing the company values which underpin your service offering, and which you expect from your strategic suppliers, can help you avoid getting into price wars with other CMO’s – the quality of your values represents an additional layer of investment value for your customers.
For example, if you value quality, look for a supplier with a strong code of conduct, to ensure that both their team and their downstream network will meet your high expectations.
If you have sustainability goals to meet, a supplier who has been externally recognised for their sustainability efforts and impact, e.g.: through Certification or Awards, is a great place to start.”
Ton: “Within the world of pharma contract manufacturing and packing, production hygiene and
flexibility are paramount. How do you approach these two critical points, when it comes to investing in new equipment?”
Rachel: “At Adelphi we’ve created what we call the ‘Response’ range of flexible filling machinery, since it was created in response to customer requests! These are especially designed to give CMO’s a competitive advantage, including when you consider filling accuracy and precision. In pharmaceutical manufacturing accuracy levels of ±0.5% or better, to ensure consistent dosing and regulatory compliance are the standard, but Adelphi commits to ±0.25%.
Hygienic & GMP-compliant design of your equipment should be applied to machine parts, which will come in contact with your product. Ideally your supplier should be able to provide X-Ray analysis and Surface Finish certification for this critical material, to guarantee quality.
Flexibility and Versatility makes for smart investment solutions, meaning that filling machinery should be able to fill many or all of your containers types (including vials, syringes, ampoules, bottles, tubes and more), as well as all of your different product viscosities, from gels to liquids to creams and suspensions. We call this invest once and invest right!
Rachel Birrell-Gray, Associate Director of Marketing at Adelphi Manufacturing
The thorough cleaning and sterilising processes required in the pharmaceutical industry can be extremely time consuming, negatively affecting your profitability potential. A filling machine which is simple to disassemble for cleaning can therefore reduce downtime between production batches, increasing your efficiency.
Last but not least, let’s not forget regulatory compliance and safety features. You should ask your suppliers about their compliance with FDA, EU GMP and ISO standards, as well as integrated validation support. Ask for references from other pharmaceutical CMO’s: an ideal partner will be happy to share this with you.”
Ton: “So Rachel, if I understand you correctly, you’re saying that the quality and longevity of both equipment and relationships should not be taken for granted?”
Rachel: “Yes, understanding the long-term benefits can prevent false-economy and should not be underestimated indeed.”
Ton: “I agree that a long-term approach in a competitive market pays off. Thanks for the insights Rachel.”
As you all know, the keyword in the industry is digitalisation and this also applies to contract manufacturing and packing, especially when handling pharmaceuticals. For this topic, I reached out to Josephine Coombe, Chief Commercial Officer at Nulogy Europe and a well-known person in the European packaging and distribution industry.
Ton: “Josephine, thanks for taking the time out of your busy schedule and talk with me. How does digitalisation enhance collaboration between pharmaceutical brands and their external supply chain partners?”
Josephine: “In the pharmaceutical and life sciences sectors, maintaining high-quality standards while managing increasingly intricate supply chains is paramount. As reliance on third-party contract packing and contract development and manufacturing
organisations (CDMO) continues to grow, so too does the need for better ways to collaborate with these partners. Nulogy’s cloud-based platform is purpose-built to address these challenges, empowering pharmaceutical brands to gain better visibility into and improve collaboration with their external supply networks.”
Ton: “In what ways does this optimise operational workflows and resource management?”
Josephine: “Pharmaceutical supply chains are inherently intricate, involving multiple stakeholders such as Contract Development and Manufacturing Organisations (CDMOs), co-packers, raw material suppliers, and brand owners. Efficient collaboration between these partners is essential to ensure smooth production processes, accurate forecasting, and adherence to regulatory standards and quality requirements. Thus, visibility and data sharing across external networks is paramount to avoid inefficiencies, misalignment, and operational delays. Our multi-enterprise collaboration platform mitigates such
challenges by offering a unified digital space where partners can work together in a singlepoint-of-truth environment. The Supplier Collaboration Solution synchronises brands and their external partners to optimise order coordination and materials and capacity management across the external supply chain. By providing full visibility into capacity, order status, inventory levels, and timelines, this approach enables faster decision-making, improved response times, and market agility.”
Ton: “Why is real-time collaboration crucial for improving decision-making and responsiveness in the pharmaceutical supply chain?”
Josephine: “While the pharmaceutical sector already operates within a data-driven and highly regulated environment, the increasing demand for speed and flexibility requires agile systems that can scale with the business. Our Shop Floor Solution complements this by providing real-time operational insights and streamlining workflows tailored to contract manufacturers and co-packers
in the pharmaceutical space. This enables enhanced control over production, inventory, and labour and allows third party outsourcers to be more responsive to customer demands and market fluctuations. One key feature of this solution is the Production Scheduling module, which optimises complex scheduling variables such as order priority, materials availability, line constraints, and workforce allocation. This allows companies to improve On-Time In-Full (OTIF) delivery performance, reduce bottlenecks, and ensure smooth operations even when demand or circumstances shift unexpectedly. With this added layer of flexibility, pharmaceutical companies can respond faster to changes in the market, ensuring that customers’ needs are met without compromising on product quality.”
Ton: “How does Nulogy help pharmaceutical companies and their CMO’s scale operations and adapt to evolving market demands?”
Josephine: “As the pharmaceutical industry continues to evolve, scalability becomes a key factor in staying competitive. Traditional systems often struggle to keep pace with increasing product portfolios, new geographic markets, and shifting regulatory requirements. Our platform is designed to help pharmaceutical manufacturers and their outsourced copackers scale efficiently and effectively. By providing realtime insights into production and predictive analytics, the platform allows organisations to optimise asset utilisation and enhance cost-effectiveness. Given the projected compound annual growth rate (CAGR) of 10.2% for contract packaging services between 2020 and 2030, the ability to scale operations in line with market demand is critical. With our platform, pharmaceutical companies gain the agility
they need to adapt to an everchanging landscape while ensuring that their external partners remain aligned and responsive to evolving needs.”
Ton: “Thanks, Josephine for the helpful information.”
I hope that this little deepdive into the processes for pharmaceutical contract manufacturing and packing has given you some better understanding. Also, I hope that you’ll agree with me that in order for our European pharmaceutical supply chain to stay competitive, investing in the right hardware and software is key. If you have any comments or suggestions, please feel free to contact me through my regular mail address ton@tkpackagingconsulting. com or find me on LinkedIn
See you at the next edition of Packaging Suppliers Global!
As it happens, I’ll be at the upcoming PHARMAP event in Berlin (April 14-15) and it would be nice to meet some of you there and discuss how we could all best cooperate to create value!
2797 0086
®
Anoxos sterile nitrogen filled vials are supplied internally clean, sterile, and particle-free – ready to use
The current radiopharmacy at NHS Greater Glasgow and Clyde was opened in 1990 . It is an NHS manufacturing site producing small-volume injectable radiopharmaceutical patient doses. These doses are used in Nuclear Medicine for the purpose of diagnostic scans and therapeutic treatments. The radiopharmacy serves on average 30,000 patients per year.
Most doses produced here use Technetium-99m, a radionuclide
agent which is added to tracers that will accumulate in various parts of the body (e.g. bone, liver, kidney, thyroid), to indicate the presence of cancerous cells and other forms of disease, such as poor kidney or liver function, or inflammation.
Technetium 99m solution is eluted from a generator and this solution is used to reconstitute kits containing the required tracer. These kits are then sub-dispensed into individual patient doses in 10ml sterile nitrogen filled vials.
This West Glasgow Hospital was instrumental in helping Adelphi to develop the Anoxos® vial, which has since become a staple in NHS radiopharmacies and nuclear medicine departments across the UK.
In this article we explore what the Anoxos range of vials is, how it came into being and why it remains the trusted dosing container for radiopharmaceuticals across the NHS.
Almost 30 years ago the Head of Radiopharmacy at Greater Glasgow and Clyde approached Adelphi and asked if we could produce an internally sterile vial, for the purpose of holding doses of radiopharmaceuticals.
Adelphi Managing Director, Gavin Crauford Taylor remembers the project well:
“Greater Glasgow and Clyde needed a sealed 10ml vial which was guaranteed internally sterile. As the Technetium products used in radiopharmacies are sensitive to oxidation, it also needed a sterile nitrogen fill to counteract the negative effects of oxygen.
“Whilst we hadn’t produced something to this specification before, we were keen to help and certain we had the right contacts to make it happen”
The Adelphi team set about finding the ideal contract manufacturing partner for the project. It needed to be a facility that was used to processing vials for injectable use, with stringent
monitoring of sterility and able to commit to a strict validated process.
Once our trusted European manufacturer was in place, development could begin. Months of process testing and validation ensued, and in 1997 the Anoxos sterile nitrogen filled vial was born.
We asked current Head of Radiopharmacy, Kay Pollock, what the primary goal had been when selecting a packaging partner for this project:
“It was my predecessor who was involved in developing the Anoxos vials. At the time it was important we could be certain of good, reliable service and a consistently high-quality product. For example, any changes to packaging specifications need to be risk assessed for potential effects on our products, and then stability work might need to be carried out, so consistency of specification and reliability of supply was critical. This is something we felt we could rely on Adelphi for.”
Adelphi’s Regulatory Compliance Manager, Lorna Finch explains:
“Anoxos specifications are controlled and registered in our CE and UKCA Technical Documentation. These specifications have not changed for our Anoxos stock range since 1997.
“If changes ever are required, for example to comply with new regulations, these would be strictly controlled under our change control procedure and would include full revalidation.”
So, what is it that makes Anoxos the perfect product for the job?
Anoxos vials are internally clean and sterile and particle free, which is vitally important for all injectable products, but especially for those given intravenously to patients who may be immunocompromised and particularly vulnerable to infection.
“The Anoxos Vial provides an inert, bacteria-free
environment for our products. We have great confidence in its reliability for our sensitive radiopharmaceutical formulations.” says Kay.
“Additionally, the MDR certification gives us the assurance that the vials meet the standard required. We manufacture our doses under a licence from the MHRA (The Medicines and Healthcare products Regulatory Agency) so this is essential for us”.
Many of the Technetium products used in Nuclear Medicine are susceptible to oxidation. For this reason, Anoxos vials were developed with a nitrogen fill. This inert nitrogen atmosphere aids stability by limiting oxidation, while a slight vacuum allows for successful filling of the sealed vials using a needle through the stopper.
Crauford Taylor
“When European law changed in relation to medical devices, it presented a number of new challenges. The new Medical Device Regulations mandated requirements far beyond those of the MDD. With MDR we are responsible for the entire life cycle of the product. Our responsibilities have expanded to include, among others: increased General Safety and Performance Requirements, clinical evaluation, and data collection relating to customer usage. To meet these challenges, we have invested in intensive staff training and additional team members.”
Asked why Adelphi chose to make the significant investment in time and resource to keep the Anoxos range on the market, Gavin says:
“Although it would undoubtedly have been easier not to, we couldn’t in good conscience allow a product which is relied upon so widely for cancer screening to be removed from the market. I see it as a moral obligation, and Anoxos is a product worth investing in!”.
The Anoxos vial has been a trusted storage and patient delivery device at Glasgow for 28 years and is now supplied regularly to more than 60 NHS sites across the UK.
Our sterile nitrogen filled vials were first protected by the guidelines of the Medical Device Directive (MDD) in 2006, highlighting our commitment to the highest standards of quality and safety.
The Directive has more recently been superseded by the EU Medical Device Regulations (MDR), now with more stringent requirements which are enforceable by EU law. It is a requirement that all medical device manufacturers obtain MDR certification by December 2027, or their product be removed from the market. We are proud to confirm our Anoxos range is both EU MDR and UK MDR certified (complete with the associated CE and UKCA markings), and we can continue to ensure a safe, consistent, and secure supply of sterile vials to our customers in the UK and abroad.
View and download our Medical Device Regulations certificates here
Outside of radiopharmacy, we have seen customers using Anoxos for alternative applications including for clinical trials, and for drug preparations such as mixing, dilution and reconstitution, which require a clean and sterile container.
Our customer base continues to grow outside of the UK too, and we now supply Anoxos vials to over 30 countries worldwide. We are excited to see where else Anoxos takes us in the future, and we’ll be sure to keep you updated every step of the way.
Would you like to know more about Anoxos internally sterile nitrogen filled vials? Contact our friendly team with any questions or to request a quote: sales@adelphi-hp.com
Please note, Adelphi can produce bespoke Anoxos vials to customer specifications on request!
See us at Pharmatag 2025!
Come discover the full Syntegon RTU offer, and get an exclusive sneak preview of our most advanced fill-finish innovation to date, at Pharmatag 2025.
By Klaus Ullherr, Senior Product Manager, Syntegon Technology
Special and often personalized medications have led to a revolution in pharmaceutical manufacturing: while highspeed, high-throughput lines used to be in greatest demand, more and more pharmaceutical companies are now investing in the development and commercialization of smallvolume medicines, which have very different production and filling requirements.
The increasing prevalence of advanced therapy medicinal products (ATMPs), such as cell and gene therapies and
bioengineered tissue products, shows that the industry is specializing steadily. These drugs are not manufactured on huge lines. Instead, the focus is on what is commonly known as small batch production. Following the FDA’s “Guidance for Industry, ANDAs: Stability Testing of Drug Substances and Products, Questions and Answers”, small batches consist of at least ten percent of the proposed maximum commercial batch size, or less than 15,000 to 60,000 containers based on fill volumes. The batch size shrinks to a few thousand containers for
parenterals used in clinical trials. For highly specialized treatments such as autologous cell therapy, batches are even smaller.
The growing number of cell and gene therapies in the development phase underlines the importance of ATMPs. Conventional high-speed machines can no longer meet the requirements of these new products. But how to produce these small or even very small
batches economically? What must a line do to satisfy both pharmaceutical companies and patients? Flexibility is at the top of the list of requirements.
A wide variety of products must be filled into different container sizes and types such as vials, syringes, or cartridges. Singleuse technologies are particularly popular for handling and processing these biotech drugs in a flexible manner since they eliminate the effort and costs involved in cleaning validation. Another criterion for flexibility is the reduced number of format parts, which obviates the need for lengthy format changes. In addition, these very small quantities require maximum product yield or low rejects. In a nutshell, any product loss must be avoided.
Human intervention is still the main reason for contaminated pharmaceuticals. Automation is essential to reduce or eliminate these interventions. For example, as far back as 2004, the FDA required that “the design of equipment used in aseptic processing should limit the number and complexity of aseptic interventions by personnel.” In addition, the FDA states that “automation of other process steps, including the use of technologies such as robotics, can further reduce risk to the product.” In the long run, aseptic filling will evolve from human-
centered to fully automated production with the use of appropriate technologies.
This change is already in full swing. For example, if containers within the isolator are conveyed to the filling station and on to the crimping station by a robotic arm, the risk of contamination is reduced manifold. Robots can also decrease the number of format parts and eliminate any glass-to-glass contact. Newly developed systems, such as Syntegon’s Versynta FFP (Flexible Filling Platform), also feature a laminar flow-optimized design to make sure that the air flow can reach the containers and flow around them without obstruction. One hundred percent in-process control (IPC) during the filling process reduces product loss to a minimum and ensures that almost every milliliter of the high-quality product is filled.
Following the small batch principle described above, the process goes even further – in a numerically downward way. While a modular small batch system such as the Versynta FFP still handles up to 3,600 vials, syringes, or cartridges per hour, its little sister processes a mere 120 to 500 containers per hour. The highly flexible, fully automated Versynta microBatch production cell fills and seals the smallest batches in different containers. Batch changes
are possible in only two hours. Syringes, cartridges, and vials made of glass or plastic can be filled with virtually no product loss.
The dimensions of the machine are just as small as its output. With a length of barely 3.5 meters, a width of around two meters, and a height of three meters, the machine can easily be integrated into existing production environments. The isolator cell itself measures just 1.6 x 1.5 meters. It houses tub opening, the filling station including one hundred percent in-process control, and the combined stoppering and crimping station. Thanks to the integrated air treatment system, hardly any interfaces to the building or technical ceiling installations are required. The new development sets new standards, particularly in terms of automation. The gloveless isolator with integrated air treatment significantly reduces the risk of contamination by eliminating manual intervention on the part of the operating personnel. The microBatch set-up meets the highest sterility requirements as specified by Annex 1. Steam-
sterilized parts are fed via port systems and installed by the robot.
The latest developments in the field of small and micro batches pay tribute to another trend. The market for ready-to-use (RTU) containers has been growing rapidly for years. This is not surprising, as pharmaceutical manufacturing companies benefit from simpler processing procedures, reduced total
cost of ownership, and greater flexibility. RTU containers are the preferred choice for small batch production, and their number is growing steadily. According to recent reports, the market for RTU vials alone is expected to grow by 14.5 percent over the next ten years.
In addition to vials, pre-sterilized cartridges are also becoming increasingly popular. First and foremost, however, RTU syringes paved the way for other pre-sterilized containers as early as the 1980s. In fact, the advantages of smaller batches of RTU containers are enormous. Bulk syringes, for example, are supplied non-sterile. Since they are not stable standing, they require complex handling in the machine and filling process. Syringes also require siliconization, which involves a special, format-dependent process. The latter depends on the way the syringes are filled. Biotechnologically produced drugs, for example, require a particularly low level of siliconization.
The advantages of RTU containers become particularly clear in the process steps described above. Although they are currently still quite cost-intensive, they save pharmaceutical manufacturers a great deal of time, space, and money. Numerous steps, such
as cleaning, siliconization, and sterilization of components, are outsourced to the packaging suppliers of RTU containers. They have the expertise and make sure that all processes are qualified and validated according to current global requirements and that containers are delivered with a certified endotoxin, germ, and particle concentration. In the case of pre-sterilized syringe systems, this also includes the required siliconization process.
The demand for high-priced ATMPs and the variety of RTU packaging materials are rising steadily – as are the requirements for new equipment for small and very small batch sizes. The latter should not only be flexible in the processing of the packaging materials; appropriate machines must also meet the trends in terms of automation and the least possible human intervention. In the best-case scenario, primary packaging material and machine manufacturers work closely together to develop new solutions. Systems that ensure flawless processing for pharmaceutical manufacturers and the highest level of product safety for patients can only be developed if both partners not only react to trends but proactively shape them together from the outset.
w: syntegon.com Connect with our experts
Discover the insights you need – simply click the links below!
• VIDEO: Highlights of Versynta microBatch
• DOWNLOAD: RTU filling machines portfolio
By Gianni Linssen, Business Development, Ecobliss Pharmaceutical Packaging
Innovation doesn’t stop. Not when you’re serious about making something better
A year ago, we launched the Locked4Kids Wallet Box, the first fully paper-based, childresistant wallet for blister packs. It was a game-changer: smart design, tough as hell for kids to open, 100% recyclable, and yet, senior-friendly.
But here’s the thing about progress: the moment you stop improving, you start falling behind.
So, we went back to work. And today? We’re launching the next version of the Wallet Box. Thinner. Smarter. More efficient. Same security, but built to be produced easier, shipped better, and used smoother.
What changed? Everything that needed to change.
Why go further? Wasn’t the first Wallet Box already good?
Yes. It was good. But good doesn’t mean done.
The first version was proof of concept, a fully paper wallet that could pass the toughest child-resistance tests. But when you launch something new, reality hits fast. Suddenly, you see how it could be better.
Here’s what we learned from version 1.0:
• It was effective, but bulkier than we wanted. More material than needed.
• It worked, but some seniors found the threestep lock a bit much.
• Production was efficient, but we saw ways to make it even faster.
Bottom line? The first Wallet Box did its job. But if you don’t find ways to improve, you’re just waiting for someone else to do it first.
So, what’s actually different?
We took everything that worked, stripped away what didn’t, and made it leaner, smoother, and better.
1. A sleeker, more efficient design:
• Less material: Thinner box, but still just as strong.
• Refined structure: Keeps its shape without extra layers.
• Universal fit for blisters: Works with 95% of blister variants.
The first version was effective, but it had extra layers to ensure it was strong enough. We figured out a better way to build it, so now it’s just as solid, without the bulk.
The result? Less waste, easier storage, better handling.
2. Smarter locking mechanism: from three steps to two:
The original Wallet Box had a push, hold, and slide system. Worked perfectly to keep kids out, but some seniors found it a bit too much. So, we simplified it:
• Now, it’s just two push points.
• Still (almost) impossible for kids.
• But even easier for adults
Less effort, same security
3. Faster, more scalable production:
Here’s something most people don’t think about: how you make something is just as important as what you make
The new Wallet Box isn’t just a better product, it’s a better process.
• Fewer components: Easier to assemble.
• Smarter cuts and folds: Faster production.
• Lower material use: Less cost, less waste.
This means faster production, higher output, and better pricing.
And that’s a huge win for pharmaceutical companies.
beyond just a buzzword
Look, every company loves to talk about sustainability. But the real question is: what are you actually doing?
From the start, the Wallet Box was designed to be 100% paperbased and recyclable. But we didn’t stop there.
Here’s how the new version goes even further:
• Less material: Lower carbon footprint.
• Optimized production: Less energy use.
• Maintains full recyclability: No compromise on ecofriendliness.
Sustainability isn’t just a checkbox. It’s built into everything we do.
Child resistance meets real-world usability
A child-resistant package is worthless if adults struggle with it. That’s why we made usability a priority from day one.
Child-resistant. Seniorfriendly. And tested to prove it.
We put the new design through extensive real-world testing, focusing on:
• Ease of use for seniors: 100% success rate in senior testing.
• Security against children: Fully certified, again.
It’s all about the balance: Too easy? Kids can open it. Too hard? Adults get frustrated. Just right? That’s what we built.
The new Wallet Box hits that sweet spot.
Where we go from here:
• More sizes: Three certified already
• More efficiency: Every production run gets better.
• More innovation: The goal? Keep pushing until we come as close to perfection as possible.
Because the second you stop improving, you start falling behind.
Let’s discuss your specialty packaging needs. Connect with me on LinkedIn and let’s explore the possibilities!
The world’s first thermal packaging solution made from recycled feathers
In the healthcare and pharmaceutical sectors, a variety of critical medicines and vaccines rely on being maintained at precisely regulated temperatures to remain safe and effective. Thermal packaging solutions protect such shipments from changes in temperature during transport, however traditionally they are made from synthetic materials.
As the demand for more sustainable solutions grows, PluumoPlus bridges that gap
by harnessing feathers as nature’s best insulator to deliver robust temperature-controlled performance while helping protect the planet.
Driven by the rise of nextgeneration treatments and personalised medicine, temperature-sensitive products now occupy a growing share
of pharmaceutical pipelines. Therapies such as cell and gene treatments often require ultracold conditions (below -70°C), and vaccines can require chilled between 2 to 8 °C storage. Stability at ambient temperatures of between 15 to 25°C is also important for medication such as emollients. At the same time, smaller, individualised doses must reach patients without temperature excursions, increasing the demand for temperature-controlled packaging. These factors
greatly expand the scope and complexity of supply chain logistics, forcing manufacturers and logistics partners to seek reliable, scalable solutions.
While temperature control is essential, it also presents formidable sustainability hurdles. Maintaining conditions often relies on plastics like EPS foam, which can remain in landfills for centuries and is made from non-renewable petroleum resources. Tight safety regulations and product integrity concerns leave little room for experimentation, and many available “green” packaging alternatives struggle to match the performance standards that safe healthcare distribution demands. As a result, the sector has been slow to retire legacy packaging. Approximately 70% of global consumers are willing to pay more for sustainable packaging and similarly, a demand for a more environmentally friendly packaging is also rising in the pharmaceutical sector, with more patients and consumers considering sustainability factors when choosing products.
Created in response to these challenges, PluumoPlus is the world’s first thermal packaging solution made using recycled feathers. These feathers are sourced from post-consumer items such clothing and bedding, before being meticulously cleaned, sanitised and processed under strict quality controls to form an input material for PluumoPlus’ patented high-performance insulation panels. These panels are placed inside a shipping container and paired with the required coolants to form a complete thermal packaging solution. The PluumoPlus insulation is also designed to be
biodegradable. By transforming what could have been waste into high-performance insulation, PluumoPlus embraces the circular economy, whereby linear consumption (take, make, throw away) is replaced with more sustainable practices.
Feathers have long been prized as nature’s best insulator. Evolved over millions of years, they are composed of hollow keratin fibres to form intricate interlocking structures that are highly effective at trapping air which is a key factor for their ability to insulate. Still, trapped air is very good at preventing heat transfer. This can be scientifically determined using measurements of thermal conductivity (the intrinsic rate at which heat can flow through any given material). Feathers 15% lower thermal conductivity than standard EPS foam, meaning that they are a superior thermal insulator. This enhanced performance can translate into a variety of benefits for shipments, such as requiring fewer coolants, increasing product payload capacity or extending the duration of temperature-control. As well as these advantages, PluumoPlus is price comparable to EPS, making the switch economical as well as ecological. Together this innovative feather-based
thermal packaging solution can drive reductions in cost and your carbon footprint all at the same time.
Designed around rigorous life sciences standards, PluumoPlus integrates smoothly into existing temperature-controlled supply chain systems to deliver exceptional thermal protection for shipments. Tested under challenging ISTA 7D temperature profiles, the PluumoPlus 2-8°C solution can provide temperature control for over 72 hours, while the dry ice solutions can provide over 120 hours below -20°C. This goes above and beyond what has been previously
possible with EPS alternatives in the market, unlocking new opportunities as feather-based insulation delivers reliable protection without the burden of single-use plastics.
Ongoing R&D efforts at PluumoPlus are aimed at expanding performance profiles and product sizes. Through constant innovation, we remain committed to enabling costeffective, planet-positive solutions in healthcare and pharmaceutical supply chain logistics—where reliable product integrity goes hand in hand with genuine ecological stewardship. PluumoPlus is more than a single product—it’s part of a wider mission to rethink what is possible with natural materials. By partnering with logistics providers and pharma companies, our goal is to empower the global cold chain to adopt greener practices without sacrificing performance or patient safety.
t: +44 (0) 7775 816944 e: info@pluumoplus.com w: pluumoplus.com
Combination pack with pen: Sealable paper pouches have the advantage of low weight, significant CO2 savings and recyclability © Faller Packaging
Can medicines and medical devices be sold in paper pouches? This works well with groceries, and it could also be a sustainable solution in the pharmaceutical and healthcare industries. Faller Packaging has now developed paper pouches that could be an alternative to folding cartons.
Nikolaus Reichenbach, Director of Strategic Development at Faller Packaging, has a trained eye when it comes to sustainable packaging. His expertise also
serves him well when he shops for groceries. As an environmentalist he gladly opts for items that are sold in paper bags. At work he is also concerned with packaging, but here the focus is on folding cartons. Reichenbach and his colleagues have been discussing possible uses for paper pouches as packaging for medicines. The idea drew attention at Faller Packaging and has taken a long trip through the company’s product innovation process.
The innovation team first looked for a suitable paper pouch material. Then it carried out printing tests and perfected the finishing process with machine manufacturer Gerhard Schubert. Faller’s employees were on hand for this purpose with trays, pens and blister packs. Using the test machine, they packed the items in prototypes of the printed paper pouches. The primary aim of these tests was to make sure that the pouches complied with industry standards for conventional secondary packaging in terms of durability and functionality.
The results confirmed that the process was feasible, and cooperation with the material and manufacturing experts went well. “The way is now clear for developing a biodegradable, sealable and sustainable paper package for medicines,” says Marketing Manager Sarina Diebold. “And the best thing is that we can use it for a variety of applications while also complying with product protection standards.” Faller Packaging is planning to carry out additional production tests with Schubert in the future.
Paper pouches have a number of convincing advantages. Their
Paper pouches provide a good example of how the product innovation process (PIP) works:
• At the start, the task to be handled was discussed in detail by those involved in the project. Here the focus was on the market and target group. The aim was to gain a thorough understanding of the dynamics and challenges involved.
• Then material experts were consulted in order to choose the paper that was best suited to meet the needs of the pharmaceutical and healthcare industry.
• Next, three different pouch prototypes were manufactured: one for a tray and pen, one for two blister packs, and one for a pen only.
• Then, in order to verify the planned CO2 reduction, Faller Packaging commissioned a life cycle assessment (LCA) in which the three prototypes were compared with a folding carton. The result was convincing: the pouch with a pen generated 90 percent less CO2.
• The final test looked at feasibility. Manufacturing the pouches by machine was not a problem. The important question was their stability in transport. When properly packed in a larger carton, the pouches showed hardly and signs of damage.
low weight reduces the volume required for storage, transport and waste. Users can save up to 90 percent in CO2 emissions and optimise their carbon footprint, as confirmed by an independent life cycle assessment. Various kinds of paper, with and without additional coatings, are available. The pouches are sealable and manufactured to show if they have already been opened. This makes the use of other features such as tamper-evident labels unnecessary. They are recyclable and can be disposed of with waste paper after use.
Nikolaus Reichenbach’s highly promising idea of using paper pouches for packaging medicines will be implemented step by step by the innovation team. The next step will be to meet with pharmacists and users of secondary packaging in order to discuss applications. Their feedback will play a key role in the agile product innovation process (PIP). Faller Packaging wants to ensure through direct dialog that the new packaging
solutions satisfy the market’s requirements and offer genuine added value.
The environmentally friendly paper pouches are not yet being used on the market for pharmaceuticals and healthcare products. But this could soon change. “We’re open for talks. Interested parties are invited to get in touch with us to learn more about paper pouches and share their views with us,” says Sarina Diebold. “Our goal is to help companies achieve their sustainability goals. They should see this innovation as an opportunity.”
Packaging expert Nikolaus Reichenbach is delighted by the success of the feasibility study. Now customer feedback is important. If the packaging process and distribution also get a positive assessment, it won’t be long before the first medicines in paper pouches appear on the market.
Feedback on paper pouches can be submitted at https:// www.faller-packaging.com/ en/innovations-and-solutions/ paper-pouches
By Timo Kollmann, Managing Director, Hugo Beck
In today’s pharmaceutical landscape, packaging plays a pivotal role that extends well beyond mere containing products.
Quality, safety, and compliance are paramount as medications and medical devices move from manufacturing lines to healthcare facilities and, ultimately, to patients. Against this backdrop, packaging machine technology has advanced significantly to meet stringent requirements for hygiene, protection, and sustainability.
The pharmaceutical packaging imperative
Pharmaceutical products must consistently meet high standards for sterility and integrity. Each dose, vial or device must be sealed against contaminants, while also preserving active ingredients from potential degradation caused by moisture, oxygen or light. At the same time, the industry is under constant regulatory scrutiny, with requirements ranging from Good Manufacturing Practice (GMP) guidelines
to international standards on labelling and traceability. The need for absolute reliability has driven manufacturers to adopt smart packaging lines capable of validating each step in the packaging process.
Moreover, pharmaceutical companies are increasingly focusing on sustainability. Patients, healthcare professionals and regulatory bodies are calling for eco-friendly materials that minimise environmental impact while maintaining product safety. Balancing these dual needs
– protective performance and reduced resource usage – has become a key concern.
The demand for automation in pharmaceutical packaging continues to rise, with robotic systems and integrated handling solutions playing a pivotal role. Custom-designed machines are essential to meet industry requirements such as cleanroom hygiene, documentation, safety, and traceability. As the industry increasingly seeks comprehensive solutions, the need for end-to-end support is growing. This includes providing full validation and qualification services, ensuring that manufacturers receive a complete, streamlined service from a single provider.
In addition, advanced packaging machines address the industry’s need for airtight seals, tamper evidence and compliance with strict hygiene standards. Highspeed capabilities also help pharmaceutical manufacturers meet market demand efficiently. Flexible designs enable swift changeovers between different product sizes or formats, crucial for facilities that handle multiple product lines. Machines that support both film and paperbased materials allow companies to experiment with greener solutions without compromising the integrity of the package.
While advanced packaging solutions benefit multiple industries, Hugo Beck’s systems are particularly well-suited for the pharmaceutical and medical technology sector, where efficiency, precision and compliance are critical. Designed for high-speed production –ranging from 3,000 to 18,000 cycles per hour – these machines ensure consistent packaging quality without sacrificing accuracy. Many of Hugo Beck’s
packaging systems are highly customised to meet specific industry requirements, offering solutions such as flowpacks, shrink packs and poly bags as primary and secondary packaging. This flexibility allows pharmaceutical manufacturers to select the ideal packaging for different products, ensuring maximum protection and reliability. Additionally, the combination of airtight, highbarrier packaging and the ability to accommodate various product sizes and bundle configurations, makes Hugo Beck’s flowpack machines particularly well-suited for pharmaceutical applications.
Hugo Beck’s machines support a range of packaging materials, including composite and barrier films of varying thicknesses, polypropylene and polyethylene monomaterials, and Tyvek®. Furthermore, our flowpack machines enable a transition to paper-based packaging with a minimal sealable coating, ensuring recyclability without compromising packaging integrity. Additional features such as modified atmosphere packaging (MAP), automatic film-changing devices, and leaflet insertion systems further enhance customisation options.
Sustainability, while increasingly important, presents unique challenges in the pharmaceutical packaging sector. Unlike industries where film packaging may be more readily reduced and eliminated or substituted for paper the protection and integrity required for pharmaceutical products often necessitate specific packaging materials. Nonetheless, Hugo Beck has long used resourcesaving machine technology aimed at minimising packaging material. We advise customers to use recyclable packaging films that are as thin and lightweight as possible to reduce the overall environmental impact or to switch to recyclable paper where possible.
For more insight into Hugo Beck, we invite visitors to our Open House events on May 7 - 8 and 14 - 15, 2025, at our headquarters in Dettingen/Erms, Germany. As part of our 70thanniversary celebrations, these events will feature live demonstrations of our packaging solutions, industry expert lectures, along with opportunities to explore our showroom and production areas.
For more details on Hugo Beck’s 70th Anniversary Open Houses and to register attendance, visit: https:// www.hugobeck.com/en/ company/newsroom/ events/open-houses-2025
HUGO BECK is a world leading specialist in horizontal film packaging machines, flowpack and paper packaging machines as well as automation solutions with the range of 3,000 to 18,000 cycleper-hour. Our comprehensive machine range handles flowpacks, bags and shrink packs, as both primary and secondary packaging. HUGO BECK machines are used worldwide across many different sectors, including pharmaceutical & medical technology, confectionery, e-commerce, household goods, wood & long parts.
In developing innovative machine technology we aim to make packaging as resource-efficient as possible. From extremely tight packaging that minimizes the use of film and paper to flexible machine solutions, which allow the production of film and paper packaging on just one machine or pure paper packaging machinery – we have all sustainability needs covered.
State-of-the-art, in-house project planning and manufacturing processes ensure we can react to virtually all our customers’ needs.
n High-grade customized installations
n Validation and qualification services, GMP certification
n S afe and hygienic, airtight and high-barrier packaging
n Meeting clean room specifications
n Track & Trace capability
n Minimal film and paper use across the packaging process
n Automatic adaptation of the shipping bag size to varying product dimensions in length and width
n Optimized user-friendliness and accessibility
n High quality, extremely tight packaging with minimum use of resources
n Maximum machine uptime
n High packaging speeds of up to 18,000 cycles/h
n Wide range of packaging types and films processed
Cleaning is mere child’s play
• World‘s first completely closed pallet box
• Rib-free construction for ideal hygiene
• Smooth interior walls with large radii
• Extremely easy to clean
www.craemer.com
Find out more and request a quote:
Hygiene is a crucial factor in technical and logistical processes involving pharmaceutical and chemical products. Craemer, pioneer in plastics processing, has developed the new HB3, a pallet box entirely made of PE: hygienic, robust, ideal for this sector.
Particularly demanding requirements and strict laws apply when it comes to processing chemical and pharmaceutical products. This also applies to transport and storage of these products.
In the process industry for chemical engineering, process technology and biotechnology, base materials and finished products are subject to high safety requirements covering the entire production environment. Due to the sensitivity of these products, all relevant hygiene regulations must be complied with in both, technical and intralogistical processes. In this context, plastic load carriers make a decisive contribution – the HB3 pallet box from Craemer enhances the safety of products and processes.
Craemer Group has acquired extensive know-how and draws from decades of experience. The family-run company with headquarters in Germany has been processing plastics since 1958. Hygienic, durable, sturdy, versatile, maintenancefree, reliable – these are the characteristics of today’s portfolio of products made of high-quality, single-grade, foodsafe and recyclable polyethylene (PE). Particularly suitable for the chemical and pharmaceutical industries: the HB3, specially designed as a hygiene box (HB).
With this development, the specialist in plastics offers a world innovation: HB3 is the first and only completely closed pallet box on the market with welded runners. The HB3 box in industrial size (outer dimensions, l x w x h: 1200 x 1000 x 790 millimetres) consists of two one-piece injection-moulded elements: the box body as the top part and the pallet with three welded runners as the bottom part.
Another special feature: A patented weld seam geometry for joining both plastic elements ensures maximum impact resistance and break strength; the weld seam is contour-milled and therefore almost invisible.
The HB3 box, with a tare weight of approx. 43.5 kilograms (without reinforcement profiles), can carry a volume of max. 620 litres and withstand a stacking load of 5000 kilograms and a payload of 900 kilogramms. The box is extremely rigid thanks to the welding of top and bottom part. Three additional metal reinforcement profiles (available as an option) permit a further increase of bending stiffness.
Construction and design of the box body ensure optimum hygiene. According to the manufacturer, the completely closed pallet box has excellent cleaning properties and has no nooks or crannies in which bacteria may settle. The seamless design, the smooth inner walls and the welded runners allow easy emptying, cleaning and drying. The almost invisible contour-milled welding seam, the clean and clear lines, the minimal ribbing and the rounded shape also contribute to this.
The special shape, combined with excellent tipping properties, ensures easier emptying. The design of the new hygiene box has neither any cavities nor ribs and provides reliable protection against contamination or water ingress. This makes the HB3 box perfect for hygienic applications and clean rooms in the chemical and pharmaceutical industries.
Sensitive contents are protected during all (intra-)logistical processes. The double-walled design of the side walls above the entry openings provides increased impact protection against forklift tines, while the reduced entry height ensures smooth movement and storage in automated high-rack systems. Like all Craemer load carriers, the HB3 runs smoothly on all standard conveyor elements, chain and roller conveyors –thanks to the robust, welded runners with high dimensional stability.
The HB3 is optionally available with two closed drain ports. The integrated 1-inch and 2-inch thread and a drill mark make it easier to open the drains at a later stage, if required. The box has a circumferential stacking step in the top and bottom rim (Euro stacking system), which makes it compatible with a
wide range of other boxes. A custom-fit end lid is available as an optional feature. With or without lid, the hygiene box can be stacked three units high. It can be equipped with RFID transponders to permit seamless tracking.
Further quality features of the hygiene box: It can withstand temperatures of -30 to +40 degrees Celsius, briefly up to +90 degrees, runs smoothly, is maintenance-free, remains dimensionally stable even during intensive use – and is therefore durable and sustainable. In addition, printing fields offer space for an individual logo, lettering or numbering; studded fields can be used for temporary stickers.
Founded in 1912, the Germanybased Craemer Group, a specialist in metal forming, plastics processing and toolmaking, is currently managed by the fifth generation. In 2023, the world’s leading manufacturer of plastic (intra-)logistics solutions with four European production sites and approx. 1100 employees achieved a total operating performance of 355 million Euros.
t: +49 5245 43-0 e: info@craemer.com w: www.craemer.com
Downloadable resources
Further technical information is available – simply click the links below to download the datasheets:
• HB3 Standard
• HB3 with three reinforcement profiles
WiseSorbent Technology has been at the forefront of moisture control solutions for over two decades, providing reliable desiccants and innovative packaging solutions to industries worldwide. With a strong presence across Asia, Europe, and the Americas, WiseSorbent continuously pioneers sustainable and efficient adsorption technologies to meet the evolving demands of pharmaceutical, food, healthcare, and industrial applications.
Driven by a commitment to environmental responsibility, WiseSorbent has established multiple manufacturing facilities and R&D centers, focusing on cutting-edge solutions that enhance product stability and extend shelf life. The company’s expertise lies in moisture control, odor removal, and oxygen absorption, ensuring the quality and stability of products across various industries, while providing safer and more reliable storage and packaging solutions.
Introducing ink-free & glue-free desiccants: A breakthrough in sustainable packaging
In response to increasing global sustainability requirements, WiseSorbent has developed an innovative desiccant solution that eliminates the use of ink and glue in its packaging. This groundbreaking advancement addresses the environmental concerns associated with
traditional desiccant packaging, which often relies on chemicalbased printing and bonding agents.
The new Ink-free & Glue-free Desiccants offer several key benefits:
• Eco-friendly design: By removing ink and glue from the packaging process, WiseSorbent reduces chemical waste and minimizes the potential for contamination in sensitive applications such as pharmaceuticals and food storage.
• Enhanced product safety: Traditional ink and adhesives may introduce unwanted substances into packaging environments. WiseSorbent’s new desiccant formulation ensures a cleaner, safer, and more reliable solution for moisture control.
• Sustainable manufacturing: The production process is optimized to reduce resource consumption and lower carbon emissions, aligning with global sustainability goals.
• Certified for food safety: The Ink-free & Glue-free Desiccants have received European food contact safety certification, ensuring compliance with stringent regulations for use in food packaging applications.
WiseSorbent’s Ink-free & Gluefree Desiccants are designed to meet the stringent regulatory requirements of industries that demand the highest reliability and safety standards. The company’s advanced adsorption technology ensures optimal performance in applications such as:
• Pharmaceutical and healthcare packaging: Protecting medicines and medical devices from moisture-related degradation.
• Food preservation: Maintaining freshness and preventing spoilage in packaged goods.
• High-tech and industrial use: Ensuring stability in electronics, precision instruments, and other moisture-sensitive equipment.
As a global leader in adsorption solutions, WiseSorbent continues to invest in research and development, aiming to redefine industry standards for sustainability and efficiency. The introduction of ink-free, glue-free desiccants marks a significant step toward a cleaner, more responsible future in packaging technology.
By combining innovation with environmental consciousness, WiseSorbent remains dedicated to providing high-performance solutions that not only protect products but also contribute to a more sustainable world.
In the professional personal care and pharmaceutical industries, efficiency, sustainability, and hygiene are critical factors in product packaging. JOMA’s Creme Dispenser Pump has been meticulously engineered to address these needs, delivering a revolutionary solution that minimises waste, reduces costs, and enhances user satisfaction.
Traditional dispensers can leave behind up to 25% of the product, resulting in significant waste and lost revenue. JOMA’s innovative dispenser pump eliminates this problem with a vacuum-based system that ensures zero residual content. Every drop is used,
maximising product value and reducing inefficiencies.
With adjustable dispensing settings of 3ml, 5ml, and 7ml, the pump provides precise control for a wide range of applications, from professional skincare creams and pharmaceutical ointments to high-viscosity gels. This versatility ensures optimal dosing for both consumers and
professionals, cutting down on waste and boosting cost efficiency.
JOMA’s dispenser pump integrates seamlessly with refill packs, offering businesses an opportunity to drastically reduce packaging expenses. By switching to a refillable system, companies can achieve up to 42% savings in carbon emissions, aligning their operations with sustainability goals. This ecofriendly approach is ideal for organisations committed to reducing their environmental footprint while maintaining product performance.
Dispensing thick, viscous products has long been a challenge for conventional pumps, often leading to frustration and product waste. JOMA’s dispenser pump is specifically designed to handle these formulations with ease. It delivers smooth, consistent dispensing from the first pump to the last, ensuring professionals in personal care and pharmaceutical fields can rely on it for their most demanding products.
Hygiene and product integrity are non-negotiable in professional settings. JOMA’s dispenser pump features a self-closing cap that prevents contamination and ensures product freshness. Additionally, its double originality protection safeguards the integrity of the product, offering peace of mind for users in healthcare and personal care environments.
JOMA’s dispenser pump has already delivered outstanding results across various sectors.
Here are some key highlights from recent applications:
• Enhanced efficiency: The pump dispenses up to six times more product per stroke at its highest setting compared to standard pumps.
• Reduced waste: Its advanced vacuum system ensures nearly 100% of the product is used, leaving no wasted residue.
• Fast and reliable dispensing: While many competitor pumps require up to 21 strokes for initial use, JOMA’s pump operates smoothly after just a few.
These features make JOMA’s dispenser pump an ideal choice for organisations looking to improve efficiency, cut costs, and deliver a superior user experience.
t: +43 2236 33633
e: Paul.Weissenstein@ jomapackaging.com w: jomapackaging.com
EXPLORE JOMA’s range of high-viscosity dispensers in multiple sizes and find the perfect fit for your product!
In fast-paced industries, every step matters. Our latest conveyor delivers smooth handling for packaged goods, from cartons to cases, with improved throughput and optimized space utilization.
Its advanced design offers exceptional flexibility, energy-efficient performance, and effortless installation—keeping your warehouse and distribution operations moving faster, smarter, and seamlessly.
PIONEERING THE FUTURE OF MATERIAL HANDLING
Get in touch with our experts for personalized insights and more details on how MCP PLAY can enhance your business.
By Agnieszka van Batavia, Constantia Flexibles
In the discourse around sustainable packaging, the focus often narrows to recyclability and end-of-life considerations. While these aspects are crucial, they represent only a fraction of the complexities inherent in achieving truly sustainable packaging solutions, particularly in the pharmaceutical industry.
This article explores the broader perspective necessary for sustainable innovation in
pharma packaging, emphasizing the need for system thinking to navigate the multifaceted challenges and align with ambitious sustainability strategies.
Pharma companies face an array of challenges that extend beyond recycling. Upcoming
legal requirements, stringent greenhouse gas (GHG) emissions reduction targets, and the demand for high technical performance complicate the landscape. The European Union’s Packaging and Packaging Waste Regulations (PPWR), for instance, mandates significant recycling and waste reduction targets that pharma companies must meet. Simultaneously, they must ensure their packaging maintains the safety and efficacy of their products.
System thinking offers a fresh and comprehensive approach to tackling the complexities of sustainable packaging by looking at the entire packaging ecosystem and how each part of the packaging lifecycle interconnects. This method examines the intricate interactions between different packaging elements, covering aspects like functionality, legal requirements, circular compatibility, and environmental impact. It emphasizes recognizing relationships between components (interconnectedness), combining them to create a sustainable system (synthesis), and seeing how their interactions lead to new behaviours (emergence). It also involves understanding the ripple effects of changes (feedback loops), addressing root causes instead of symptoms (causality), and mapping out the entire lifecycle to spot improvement opportunities (system mapping). By embracing these six basic principles of system thinking, pharma companies can innovate and develop sustainable packaging solutions that are both resilient and adaptable to future challenges.
Sustainable packaging development integrates functionality, legal requirements, circular compatibility, and environmental impact. This holistic approach ensures that packaging serves its purpose while minimizing negative impacts on people and the planet. A key element is the Lifecycle Assessment (LCA), which is a scientific methodology used to quantify the environmental impacts of packaging throughout its lifecycle. Robust lifecycle assessment calculations could be complex and often time consuming, however the
methodology provides a blueprint for designing pragmatic impact mitigation strategies aimed and efficient management of the resources (energy and raw materials) and elimination of losses to the systems in the form of waste and emissions.
From a system perspective recycling should not be defined as a waste disposal practice. It must be regarded as manufacturing process of secondary resources. Shifting the focus from the end to the beginning of the cycle requires redefined priorities.
Simply using technically recyclable materials does not ensure that packaging is effectively recyclable, and the resources remain within the loop. Optimal compatibility with the system in which the packed product functions, depends not only on adherence to designfor-recycling guidelines but is also influenced by geographical location and the infrastructure available for sorting and collecting materials. Effective material recovery of pharma packaging faces additional challenges such as material incompatibility, contamination risks, and the small size of packaging components. Overcoming these challenges necessitate innovations like mono-material packaging and advancements in sorting and recycling technologies. At the same time a question arises - is compliance with consumer goods packaging system the most beneficial strategy for pharmaceutical industry or should we be looking into tailored circular solutions that account for the specific characteristic of pharmaceutical packaging system?
It is crucial to look beyond immediate solutions and adopt a long-term perspective. System thinking enables pharma companies to create packaging solutions that are not only compliant with current
regulations but also adaptable to future changes in legislation and technology. To develop sustainable packaging solutions, pharma companies should integrate system thinking principles to address the entire lifecycle of the product, leverage lifecycle assessments to identify environmental impacts and opportunities for improvement, continuously embrace new technologies and materials that reduce environmental footprints and enhance recyclability, and collaborate across the value chain with suppliers, regulators, and other stakeholders to create a sustainable packaging ecosystem.
One of the very few examples of medicine packaging designed in accordance with system thinking principles are a PVC-free cold forming aluminium blisters with
complex plastics enhanced material recovery, reduced air pollution and contributed to better machinability on the blister forming lines, while maintain the protective barrier and patient experience.
Innovations like inert anodes and green electricity further decrease the environmental
environment while enhancing corporate responsibility and consumer trust.
In conclusion, while recyclability and end-of-life considerations are vital, they are just a part of a larger sustainability narrative. Applying system thinking to pharma packaging innovation unravels complexities and
The fully automated Parcel Pack system, a packaging solution developed by Lantech, produces trays in letterbox format. E-commerce retailers and fulfilment service providers benefit from this efficient parcel logistics system.
The TE Parcel Tray Erector machine and the LA Parcel lid applicator machine produce up to 1,000 perfectly rectangular corrugated cardboard letterbox
packages per hour. These compact systems are easy to integrate into the shipping departments of e-commerce or fulfilment services.
The small footprint TE Parcel Tray Erector and LA Parcel Lid Applicator are designed for efficient space saving and ease of use. With its fully enclosed design, the combination
maximises security and minimises exposure to external elements. The ergonomically designed tray magazine makes tray replenishment and handling easy.
With an impressive speed of 1,000 trays and lids per hour, these machines offer fast and reliable production performance. It’s simple and precise
adjustments make it possible to quickly achieve the desired settings, increasing productivity and reducing the risk of errors. In addition, its unique design allows tray sizes to be changed in just 5 easy steps. This makes it easy to adapt to different production needs.
With the TE Parcel and LA Parcel, Lantech says companies can optimise their production processes while meeting the highest standards of quality and efficiency. Both machines are also available separately.
Parcel machine features:
• Sturdy, letter-sized packaging saves on shipping costs
• The cushioning effect of corrugated protects against product damage
• No padding required inside
the parcel
• Small size optimises truck loading
• Reduces CO2 emissions
• Does not require the recipient to be present for delivery
Since the Parcel Pack introduction last year the machine combination has been embraced by the pharmaceutical industry. The ability to change tray heights from a minimum of 160x115x20mm to a maximum of 400x300x100mm in just 5 easy steps certainly contributes to that as well as the protection against product damage.
Contact our Sales Team to learn more: euromarketing@ lantech.com
Packaging machinery manufacturer Lantech is a global leader in Stretch wrapping machines and robust, efficient case and tray handling machines. The familyowned company, founded in 1972, designs, builds and services packaging machines, conveyor modules and other complementary systems. Machines are built in the Netherlands (Malden) and the USA (Louisville KY) with additional offices in Australia and China. The European office in Malden (the Netherlands) designs and assembles case and tray handling machines. With more than 200 employees and a strong network of partners, sales and service within Europe are organised from there.
www.lantech.com
With three decades of expertise in the industry, Paramount Packaging Systems, the leading supplier of Fuji flow wrapping solutions for pharmaceuticals and medical devices, is driving groundbreaking advancements that enhance regulatory compliance, sustainability, operational efficiency and cost savings within the sector.
Paramount Packaging Systems is at the cutting edge of technological innovation, offering stateof-the-art Fuji flow wrapping machines that meet the rigorous standards of the pharmaceutical industry. These machines are recognised for their reliability, safety and flexibility, ensuring they deliver exceptional performance while adhering to strict industry regulations.
Fuji’s advanced wrappers, distributed by Paramount Packaging Systems, are designed with stainlesssteel construction to ensure optimal hygiene levels and feature superior temperature
control, four-level security on the HMI, active directory option, batch records output and full servo motor control, all while being fully validatable.
The FW3400B high-speed box motion wrapper exemplifies this innovation, capable of producing hermetically-sealed packs at a remarkable rate of up to 400 packs per minute. The machine includes an Automated Feeder, Auto Film Splicer for seamless film roll changeovers, and a cantilevered frame that facilitates quick and easy cleaning, saving valuable time for businesses.
The diverse range of Fuji wrappers, available through Paramount Packaging Systems, can be tailored to
meet specific product and customer requirements. Notably, the Alpha 8 series features Induction Heaters for fin seals, which consume 30% less energy compared to standard mould heaters, while providing enhanced temperature control for consistently sealed packs.
Additionally, Fuji’s Box Motion and Inverted Box Motion sealing systems deliver high-quality seals essential for Hermetic and Modified Atmosphere Packs. These systems incorporate temperature pre-boost technology and intelligent temperature control to
maintain precise temperatures, reducing maintenance needs and downtime while facilitating efficient product changeovers with minimal operator intervention.
Paramount Packaging Systems is dedicated to sustainability, leveraging technological advancements to offer clients cost-effective solutions that minimise environmental impact. Fuji’s horizontal flow wrapping machines are compatible
with mono-layer, eco-friendly recyclable and compostable films, and can be supplied with Ultrasonic sealing technology that further reduces energy consumption, film usage and material costs.
Built using renewable energy, Fuji machines are manufactured in a state-of-the-art facility that supports global environmental conservation efforts. Paramount Packaging Systems remains committed to delivering innovative, sustainable solutions that address operational challenges and help businesses save money.
For more information about sustainable and innovative packaging solutions, contact Paramount Packaging Systems on 01252 815 252 or fuji@ paramount-packaging.co.uk
• Operator friendly to use
• Compatible with recyclable, biodegradable and compostable films
• Gas tight packs for M.A.P
• Simple and fast product changeovers
• Minimal maintenance required / low cost to run
• Unique Fuji IH centre sealers, maintenance-free, 20% more e cient than traditional mould heaters with better sealing speed and integrity
• Patented Fuji Box Motion - fastest hermetic end sealing in the world
• All relevant and necessary validation documentation can be prepared and compiled using Fuji’s in-house team
Spiral Conveyors need less floor space than conventional incline conveyors and are faster and more reliable than any elevator or lift.
Royal APOLLO Group is a world leader in Vertical Transport Systems, providing tailored solutions to clients globally from our strategically located facilities across Europe, Asia, and the United States. Our core products include Spiral Conveyors and Bucket Elevators, designed to optimize material handling and streamline logistics across various industries.
VTS France APOLLO VTS Mexico
VTS Germany
APOLLO VTS Italy
Contact
discover
VTS India APOLLO VTS Thailand APOLLO VTS Spain
APOLLO VTS China
The PPMA Show is the largest process packaging machinery exhibition in the 23 - 25 September 2025, NEC, Birmin
23 - 25 September, Nuremberg, Germany
FACHPACK is the leading European trade fair for processes, technology and trends in the packaging industry
15 - 17 July 2025, Las Vegas
Cosmopack North America, part of Cosmoprof, is the premier event in the Americas fully dedicated to the entire beauty supply chain.
13 - 15 May 2025 at Bilbao Exhibiti
PICK&PACK combines the Europe Logistics Summit and the National 4 0 Congress
07 - 08 May 2025 at CBS Arena, Coventry, UK
gham, UK
sing and UK
Automation UK is the UK’s leading industrial show for automation, robotics and vision.
03 - 04 September 2025, Manchester, UK
UKPackaging Expo 2025 is your gateway to the latest packaging trends in innovation, sustainability, and business solutions
ion Centre
ean Packaging
14 - 15 April 2025, Berlin, Germany
In 2025, Pharmaceutical Manufacturing & Packaging Congress celebrates the 5th Anniversary