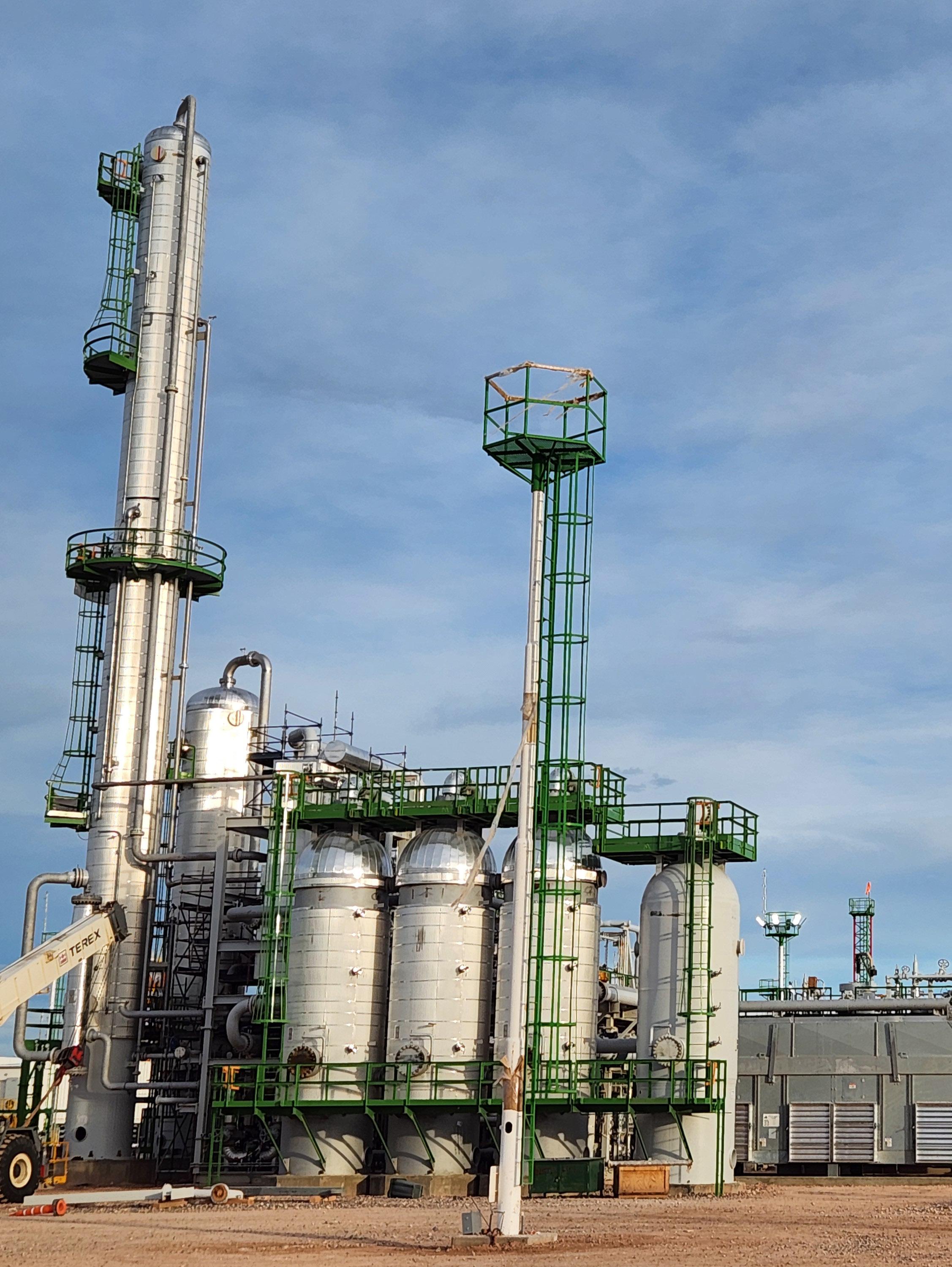
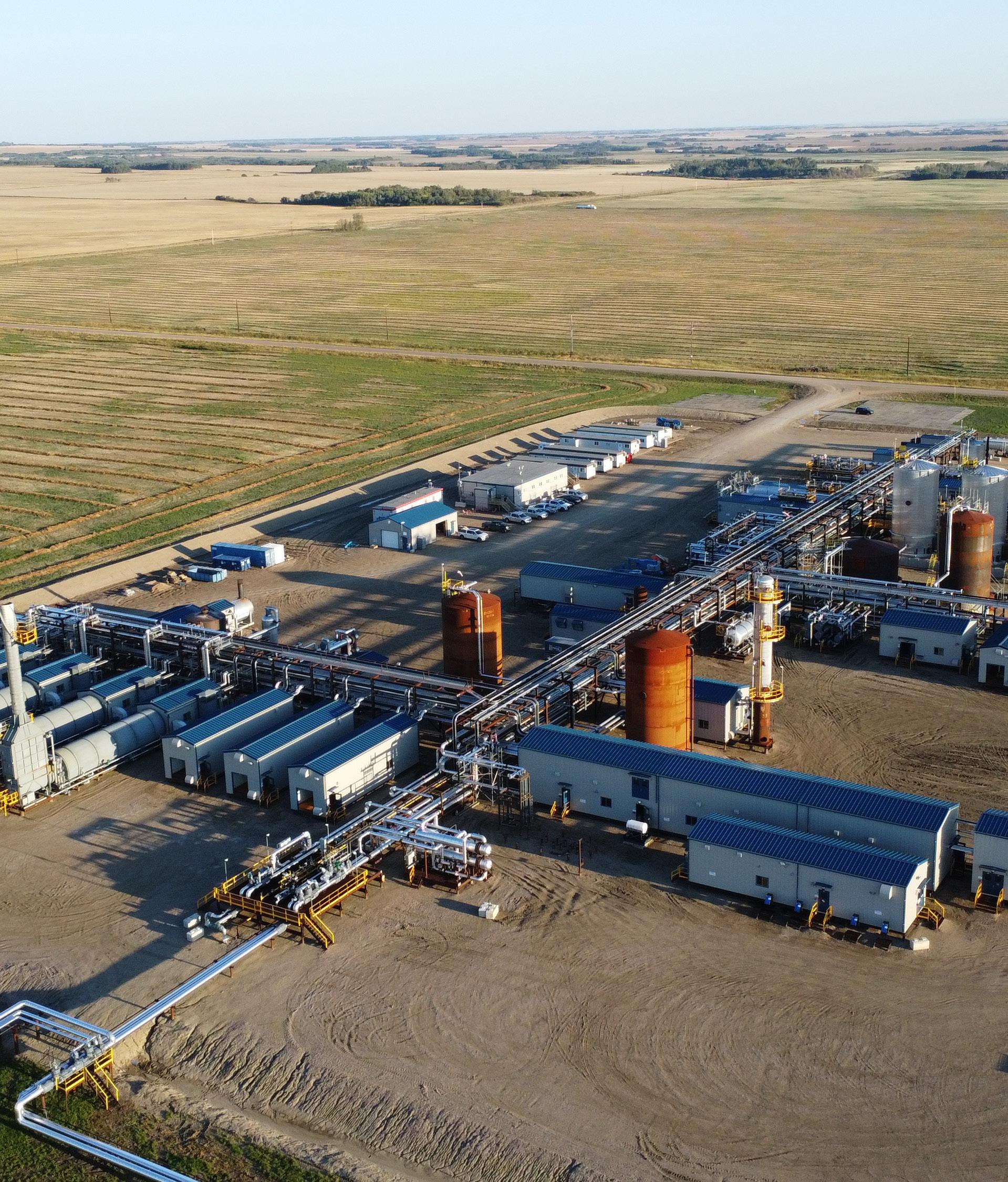
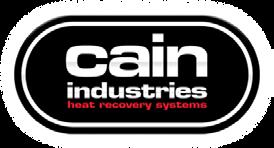
Canada’s current midstream oil and gas sector presents an equally challenging and dynamic environment, playing a crucial role in transporting and processing hydrocarbons for upstream production and downstream distribution processes. Although the industry has faced numerous challenges including evolving regulatory frameworks,
environmental considerations, and the need for technological innovation, these also present opportunities for market players to offer innovative solutions that enhance efficiency and sustainability in energy processing. This is particularly the case for Propak Systems Ltd. (Propak), a Canadian-owned company specializing in the design, engineering, fabrication, and
construction of energy processing facilities and equipment.
The company excels in offering products and services tailored to the needs of the energy processing sector, supporting projects from initial conception through detailed engineering and design to construction, commissioning, and start-up activities.
“Canada’s energy sector is known
Over the last 50 years, Propak Systems Ltd. has grown to become a leading engineering and fabrication services provider. Jim Hanson, Managing Director of Technical Sales, talks us through the company’s vast range of state-of-the-art facilities and turnkey solutions
Writer: Lucy Pilgrim | Project Manager: Ben Weaver
around the world for its efficiency, innovation, and high safety standards. At Propak, we’re proud to be part of that story, and we bring the innovation and quality that we’ve learned here at home to the products and services we deliver to customers globally,” opens Jim Hanson, Managing Director of Technical Sales.
The company’s expertise spans gas processing, gas compression,
enhanced oil recovery – including extensive experience in delivering thermal oil central processing facilities and associated well pads – heat recovery, and steam generation and power systems, including systems designed to minimize carbon dioxide (CO2) emissions.
Moreover, maintaining a high degree of quality is an imperative component of Propak’s activities
across the full life cycle of a project.
“We are creating a culture of quality to instill value into all aspects of our operations.”
Propak currently employs 1,500 staff across major manufacturing facilities in Airdrie, Alberta and Cambridge, Ontario, alongside a range of service facilities further across Canada and the US.
Since its inception in 1976, Propak has built a reputation for outstanding client service, integrity, and reliability.
In the last half a century, the company has cultivated a signature ability to design and construct both large turnkey processing facilities and individual processing units on modular, shippable skid-mounted packages, distinguishing the company from its competitors.
“Our unique integration of engineering and fabrication capabilities combine to create maximum customer value through bespoke design solutions, reduced capital costs, reliable project execution, and industry-leading product performance,” Hanson prides.
In addition, Propak’s modular expertise, standardized designs, and integrated engineering, fabrication, and construction capacities grant it the ability to accelerate its schedules to completion on a fast-track basis.
Such unparalleled expertise unlocks an international operational network for the company, which supplies energy processing facilities to businesses in more than 40 countries, working in every continent except Antarctica.
Propak’s exceptional experience and focus on the modularization of facilities has also allowed it to minimize field labor requirements, thereby enabling customers to deploy
modern, high-quality equipment to meet their processing needs in areas of the world where specialized labor is constrained.
“We are experts in designing equipment to be transportable from our facilities to anywhere a truck can go. We’ve even shipped facilities via barges to sites where no roads existed,” Hanson reveals.
Such success wouldn’t be realized without Propak’s extensive worldwide
“OUR UNIQUE INTEGRATION OF ENGINEERING AND FABRICATION CAPABILITIES COMBINE TO CREATE MAXIMUM CUSTOMER VALUE
THROUGH BESPOKE DESIGN SOLUTIONS, REDUCED CAPITAL COSTS, RELIABLE PROJECT EXECUTION, AND INDUSTRY-LEADING PRODUCT PERFORMANCE”
– JIM HANSON, MANAGING DIRECTOR OF TECHNICAL SALES, PROPAK SYSTEMS LTD.
network of partners and suppliers that support its operations and are foundational to its success.
“We rely heavily on the relationships we have with our suppliers to ensure we can provide the high-quality, cost competitive, and timely delivery of products to customers. Our company is made stronger by leveraging the strengths of our suppliers and partners.”
A noteworthy example of this is Propak’s role as the authorized distributor for Ariel Corporation (Ariel) gas compressors, which allows the company to benefit from Ariel’s market-leading expertise while bringing its own strengths to the market.
Propak boasts a vast range of projects across the US, Canada, and internationally that establish its track
record of engineering achievements and outstanding product performance.
The company has built hundreds of gas processing and compressor facilities around the world, including multiple Modularized Gas Compressor Stations in North Dakota.
One notable example, situated on the Bakken Formation, saw Propak supply eight modular compressor packages to pressurize and transport raw gas via a downstream pipeline.
The specifications of the modular compressors included 2,200 horsepower (hp), electric drive, fourstage reciprocating compressors, designed to efficiently compress gas. The station was supplied complete with all interconnecting piping, piperacks, and necessary auxiliary and utility systems.
The packages were purposefully designed for easy transportation within tight shipping constraints and
simple on-site reassembly. Moreover, thanks to a standard packaged design, the gas compressors were developed in a staged approach, granting the company the ability to fit additional compressor units as the station’s capacity increased.
Propak expertly engineered and designed the compressor modules to the client’s requirements and provided reassembly, start-up, and commissioning support on-site.
The compressor package design has subsequently been duplicated and installed at multiple different locations, emphasizing its repeatable modularity.
Elsewhere, the company boasts the provision of world-class cryogenic turbo-expander plants. An exemplary facility was constructed in Northeast British Columbia, where Propak provided detailed engineering and design, procurement, and fabrication services.
The facility was designed to process 200 million standard cubic feet per day (MMSCFD) of raw natural gas in order to meet pipeline specifications and efficiently extract and fractionate ethane, propane, and butane, alongside other natural gas liquids.
The plant involved the employment of Propak’s design strategy for facility modularization, which allowed for the trial fitting of modules prior to shipping. The modules were then staged and shipped in close coordination with field construction operations, thus providing efficient execution and improvements to the project schedule.
The project scope called for engineering, design, procurement,
and fabrication services, as well as start-up support, which were all provided on a lump-sum basis.
Based on the successful completion of the project, the client returned to Propak for a second, pre-planned identical facility.
Propak’s journey is marked by the strategic expansion of its manufacturing facilities across Canada, first sparked by the
company’s expansion to Airdrie in 1978, having outgrown its initial smallscale fabrication workshop.
This expansion facilitated the establishment of the company’s second building at a time when the city’s population was approximately 1,000 people.
“The Airdrie facility, which once housed the entire company, now operates as our primary pressure vessel manufacturing facility,” Hanson highlights.
“THROUGH THE DELIVERY OF PRODUCTS THAT IMPROVE EFFICIENCY AND REDUCE EMISSIONS, WE ARE ABLE TO SUPPORT OUR CLIENTS IN THEIR SUSTAINABILITY
– JIM HANSON, MANAGING DIRECTOR OF TECHNICAL SALES, PROPAK SYSTEMS LTD.
• Gas processing – Complete turnkey facilities and modular units used for natural gas processing. These include:
• Modular cryogenic processing facilities
• Amine-based gas sweetening facilities
• Turnkey gas compression stations for gathering Propak’s pipeline applications
• Mechanical refrigeration facilities
• Triethylene glycol gas dehydrators
• Molecular sieves
• Helium recovery facilities
• Enhanced oil recovery and heavy oil processing
– Modular thermal heavy oil central processing facilities, processing up to 20,000 barrels per day, per train. This is conducted in standardized modular well pad facilities for all types of lift mechanisms.
• Gas compression and power – Modular gas compressors and power generation units designed to reduce project schedules and installation costs. The company packages compressors and power generation units from 200 to 10,000 hp.
• Heat recovery and steam generation – Propak IST markets HRSGs for power generation and
cogeneration industries as well as gas-fired OTSGs for enhanced oil recovery applications.
• Energy systems – Propak’s Energy Systems business unit supports clientele in the execution of projects related to emerging technologies and sustainability initiatives.
Its products and services include the design, evaluation, and provision of carbon capture utilization and storage facilities and hydrogen production facilities, alongside novel technology and sustainable energy scale-up feasibility studies.
• Construction services – Domestic and international field construction and construction management services are provided through Propak’s whollyowned subsidiary, Process Plant Constructors Ltd. (PPCL).
The subsidiary’s expertise includes civil and earthworks, foundation installations, equipment setting and installation, full mechanical construction services, electrical and instrumentation services, and insulation installation.
PPCL’s projects include gas compressor stations, heavy oil treatment facilities, and gas processing and treatment facilities.
Proudly serving the energy industry since 2010, Leading Manufacturing Group (LMG) is your premier choice for steel manufacturing services. With hundreds of years of combined experience in manufacturing, coating, painting, insulation, and quality control, we bring unmatched expertise to every project.
Founded by Lee Gottschlich in 2010, LMG has an extensive history in the industry. Our fabrication facilities are designed to optimize the fabrication process.
Whether it’s Steel Storage Tanks, Pressure Vessels, Pressure Piping, or Tank Accessories look no further than LMG.
We offer a wide range of steel storage tanks, designed to meet the diverse needs of various
applications. Our tanks, made from stainless, duplex, and carbon steel, are engineered for durability and reliability, ensuring optimal performance in even the most demanding environments.
Our Quality Management System (QMS), controlled indoor environment and rigorous inspection processes ensure that every tank meets the highest standards. Our certifications include API, ASME, and CSA, with in-house API-653 and NACE inspectors overseeing quality control.
In addition to shop fabricated work, we also offer field tank fabrication and a full spectrum of field modification services. Our services include detailed inspections by our in-house API-653 and NACE certified inspectors.
Working with LMG offers numerous advantages designed to ensure the highest quality and efficiency. Our experienced team brings expertise and dedication to every project, guaranteeing exceptional results. We utilize advanced technologies and industry best practices to deliver precise and reliable services.
Our commitment to safety and environmental responsibility means that all our work adheres to the strictest standards, minimizing risks and protecting your investment. Partnering with LMG means benefiting from our unparalleled customer service, swift response times, and a track record of excellence.
Proudly serving Western Canada and the Northern United States since 2010, Leading Manufacturing Group (LMG) is your premier choice for steel manufacturing services. At LMG, we specialize in fabricating high-quality steel storage tanks, pressure equipment, and structural components which are all designed for various industrial applications. Our equipment is engineered for durability, safety, and performance, ensuring they meet the rigorous demands of the oil, gas, and mining industries. LMG has state-of-the-art facilities in Nisku (Edmonton), Battleford, SK, Vermillion, AB and a dedicated sales office in Calgary. LMG is committed to excellence in quality, engineering, and safety, backed by a robust set of certifications and memberships.
Located at 505 East Lake Boulevard, the facility houses specialized equipment to produce pressure vessels including a plasma cutting table, large steel profiler capable of cutting and beveling steel up to six inches in thickness, and numerous submerged arc welding machines.
The pressure vessel shop also regularly fabricates vessels in excess of three inches thick and up to 500,000 pounds.
Typical pressure vessels produced by the facility include:
• Two and three-phase separators
• Knockout drums
• Distillation columns, including demethanizers, de-ethanizers, depropanizers, debutanizers, stabilizers, amine contractors, and regenerators
• Filter housings
• Molecular sieves
• Mercury removal units
• Water treatment vessels
• Well test separators
“PROPAK REFLECTS THE COMBINED TALENT, EXPERIENCE, DEDICATION, AND DILIGENCE OF OUR STAFF.
INNOVATION IS ENCOURAGED AND NO IDEA IS DISMISSED WITHOUT CAREFUL CONSIDERATION”
– JIM HANSON, MANAGING DIRECTOR OF TECHNICAL SALES, PROPAK SYSTEMS LTD.
The facility’s heat exchanger shop, meanwhile, manufactures and assembles shell and tube heat exchangers built to meet Tubular Exchanger Manufacturers Association (TEMA) Class C and R standards and includes milling equipment used to fabricate heat exchanger tube sheets.
Propak additionally has a number of locations in Airdrie, including the structural shop where the company fabricates structural steel skids, modular pipe racks, and miscellaneous steel structures.
Elsewhere, in the panel shop, Propak manufactures electrical and control panels. Here, the company can complete many types of explosion-proof and general-purpose custom panels that are certified to international standards. These panel types include programmable logic controllers (PLCs), remote input/output (I/O), distributed control system (DCS), DCS marshalling, compressor, communication, supervisory control and data acquisition (SCADA), lighting contactor, heat trace control, amongst others.
AXH air-coolers unparalleled level of experience and technical expertise throughout the entire organization, coupled with the largest manufacturing facility in the industry, enables us to offer a complete range of air-cooler models and types to fit any standard or custom application. We have the capacity to design, supply and duplicate virtually any replacement section or cooler and can respond to fully support the reapplication of existing coolers.
Most notable, however, is the 404 shop, Propak’s largest fabrication and assembly facility which is fully equipped to assemble large process and compression modules.
The facility includes numerous overhead cranes, semi-automatic welding machines, a profiler used to cut and bevel pipes, a large carbon steel pipe spooling shop, a stainless steel pipe fabrication shop, a hydrostatic testing facility, an enclosed sand blasting bay, and two paint shops.
“In addition to the painting capacity, we are also able to apply internal pipe coatings in this facility. Most impressive is its main shop, which has large work areas that enable the assembly of our process and compression modules,” Hanson adds.
Elsewhere, on Veterans Boulevard, Propak’s 925 facility houses the company’s Enhanced Oil Recovery, Energy Systems, and Power and
Steam Systems engineering teams. Its attached shop is equipped for pressure vessel manufacturing, OnceThrough Steam Generator (OTSG) fabrication and process module assembly.
The facility contains a fullyequipped engine cylinder head remanufacturing shop and spare parts warehouse which maintains approximately $10 million worth of inventory.
“It also contains our controls simulation room, which allows for full software acceptance testing activities to be completed prior to automation systems being deployed to the field.” he informs us.
In 2018, Propak acquired the assets of Innovative Steam Technologies (IST), including its intellectual property and facility in Cambridge, Ontario becoming a key division of the
company.
Located at 549 Conestoga Road, the Propak IST facility includes office areas for engineering operations and a 100,000-square-foot manufacturing space for OTSGs used in heat recovery applications. The Cambridge facility also houses two tube-finning lines utilizing a proprietary brazing process.
“This process increases the quality of bonding between the fins and tubes, enabling higher performance than more traditional finning methods,” Hanson insights.
Propak IST adds significant value to the power generation and energy industries as a unique provider of Heat Recovery Steam Generators (HRSGs).
The division is therefore strategically positioned to provide improved energy efficient solutions to support the ongoing global energy transition.
FlareTech Overview:
FlareTech is a family-run business based in Stettler, Alberta, established in 2009, with over 40 years of experience. The company operates a 25,000 sqft manufacturing facility, fully equipped with welding bays, overhead cranes, CNC automation, and plasma cutting capabilities. Their 20-acre storage yard supports operations and laydown.
Turn-Key Services:
FlareTech offers end-to-end solutions including flare system sizing and design, fabrication, installation, commissioning, inspections (UAV & hands-on), routine maintenance, shop repairs, stock flare availability, and rental units.
Flare Systems and Structural Design:
Their systems include utility, assisted (air, gas, low-pressure), sonic, Variable Slot Sonic, combination flares, Mobile flare trailers, Vent, Flue Gas, and Exhaust Stacks. They specialize in guy-wire-supported and self-supported flare stacks.
Ignition Systems and Monitoring:
FlareTech provides retractable pilot systems, fuel gas manifolds, and electronic spark ignitors (ESI). Their monitoring and ignition systems feature PLC-based control panels, duplex thermocouples, HMI displays, solar backup, and Modbus communication for seamless operations.
Enclosed Combustion Solutions:
They offer vapor combustion units, enclosed ground flares, and Thermal Oxidizers designed for temperature-controlled combustion, natural/forced draft systems, and refractory lining to maintain combustion efficiency.
FlareTech provides 24/7 service for retrofit projects, bolt-up & torquing, erection, guy wire tensioning, and flare tip replacements. Their teams include B-Pressure welders, High Angle Technicians, and they use UAV drones for inspections on Flare Tips and Internals, along with cleaning, including new drone pressure washing technology.
The company integrates knock-out drums, flame arrestors, detonation arrestors, variable frequency drive (VFD) blower systems, aircraft warning lights, beacons, obstruction lights, and flow meters into designs. They conduct Flare & Knockout Sizing, dispersion modeling, wind load analysis, skid and pile design, FEA, proximity planning. We are also designing and building enclosed combustion units.
In summary, FlareTech is an industry leader in flare system design, manufacturing, installation, and maintenance, delivering comprehensive solutions for oil, gas, and energy operations with a commitment to efficiency and safety.
The FlareTech Detonation Arrestor is a revolutionary design in detonation safety technology. FlareTech has created a Detonation Arrestor that is lighter in weight, has a lower pressure drop, high continuous endurance burn rating, and a lower cost than competitors’. The design of the FlareTech Detonation Arrestor stops the sonic flame front, defusing the initial forces before it reaches the flame quenching element.
Guy Cassidy - Cell: (403) 742-2212 | guy@flaretechinc.com
Scott Phillips - Cell: (403) 510-9898 | Scottp@flaretechinc.com www.flaretechinc.com
“Propak’s IST division has the expertise to provide the most efficient heat recovery and utilization solutions for our clients’ power needs.”
Additionally, its patented SQ-90 rifled tube technology provides an industry-leading solution for steam generation and enhanced oil recovery applications, delivering the highestquality steam for enhanced oil recovery applications.
“Propak IST is your solution for heat recovery and steam generation, done a better way,” Hanson excites.
The company also provides parts and maintenance services through Propak Energy Services, which equally addresses customers’ needs in an expert and highly efficient manner.
The division operates product support, service, and parts facilities throughout Western Canada and the US with locations in Airdrie, Grande Prairie, Medicine Hat, Lloydminster, and Red Deer (Alberta); Fort St John (British Columbia); and Kindersley, Weyburn, and Swift Current (Saskatchewan).
The company similarly has facilities in the US, including Williston, North Dakota and Casper, Wyoming.
“Propak Energy Services’ personnel are supported by our engineering and automation capabilities and staff, which differentiate us from other service companies,” he points out.
Propak’s staff are the core of the company’s success, as its team members are empowered to employ their professional and technical skills to continuously improve product offerings.
“Propak reflects the combined talent, experience, dedication, and diligence of our staff. Innovation is encouraged and no idea is dismissed without careful consideration,” urges Hanson.
Staff are recognized through a variety of means, including annual service awards. The company’s manufacturing personnel specifically are rewarded with numerous safety accolades and afforded the opportunity for career development by gaining skills through in-house training programs.
Propak similarly supports the development of new tradespeople by setting up apprenticeships in cooperation with local technical education institutions.
Moreover, the company values its staff by continuously exploring how it can foster a better culture where its employees are passionate about engineering and manufacturing quality rather than simply obeying the rules of a project.
In order to deeply embed quality within its culture, Propak adheres to four key pillars – leadership emphasis, message and communication clarity, encouragement of peer involvement, and employee ownership of quality improvement.
Regarding the former, the company’s management team
www.qualitytube.com
We are Canada’s leading stocking distributor and project partner specializing in tubing products for the heat exchanger, boiler, condenser, and air cooler markets. In addition to bare tubing, we bring a series of valueadded products and partnerships through our in-house facilities and extensive international supply chains. We focus on Canada only, with crane-serviced warehouses located in Calgary, Alberta and Ancaster, Ontario.
From day one, Propak Systems has been a valued partner. We cherish this relationship and look forward to building on our partnership and supporting them for years to come.
purchaseorders@qualitytube.com | cpotter@qualitytube.com
• 1976 – Incorporated on 1st October.
• 1976 – Opened for business in Calgary with a staff base of 15.
• 1978 – A new workshop and office was constructed in Airdrie to handle growing business demand.
• 1979 – Awarded a major Canadian gas plant project.
• 1981 – Executed its first major gas processing plant construction project in the US near Vernal, Utah.
• 1984 – Opened a sales office in Denver, Colorado to enhance business growth in the country.
• 1986 – Awarded and executed its first turnkey project outside North America for the Barbados National Oil Company.
• 1990 – Awarded a contract to build the first liquefied petroleum gas (LPG) recovery plant for Petrobras, a Brazilian energy company, in the Amazon. Propak subsequently fabricated two major expansions at the plant location in 1996 and 2003/04.
• 1995 – Opened an office in Buenos Aires to enhance business growth in South America.
• 1995/96 – Awarded major projects in Argentina, Poland, and New Zealand, which were all successfully executed. The company also continued to expand its product lines, such as aerial coolers.
• 1997 – Commenced the design and manufacturing of directfired process heaters.
• 1999 – Opened a sales and service office in Beijing, China.
• 2004 – Completed and put into operation the first liquefied natural gas (LNG) plant equipped with a methane liquification unit.
• 2005 – Opened its PPCL subsidiary.
• 2006 – Number of staff across all divisions exceeded 750.
• 2009 – Created a fully modular steam-assisted gravity draining (SAGD) well pad design.
• 2013 – Developed the engineering for a fully modular SAGD central processing facility.
• 2016 – Worked in partnership with IST to design and modularize an OTSG for use in enhanced oil recovery projects.
• 2018 – Acquired the assets of IST.
• 2024 – Awarded the contract for the supply of HRSGs to power a large data center in Ireland.
instils a culture of quality by engaging with all disciplines throughout every stage of the project.
Moreover, Propak’s integrated organizational structure allows fabrication, construction, and field service personnel to be involved across all project stages, from initial reviews through to closeout sessions where teams reflect on the lessons learnt on a project, thereby fostering continuous improvement.
Quality is further interwoven into the business with message and communication clarity.
“Open, transparent, and clear communication is essential for spreading the message about quality. Propak utilizes a variety of channels to communicate the importance of quality to employees across all levels and departments of the organization,” Hanson emphasizes.
The company additionally greatly focuses on encouraging peer involvement as it relies heavily on the engagement of its workforce to advance many quality aspects.
From developing new internal process standards to delivering detailed questions to engineering teams and suggesting design improvements, employees across the company are encouraged to engage.
Finally, employee ownership of quality improvement resides as a key component in its mission to maintain quality throughout the organization.
“Propak’s culture of quality requires employees to apply their skills and make decisions to foster an environment of continuous quality improvement.”
Propak considers sustainability, environmental impact, and quality in the development of all its projects and are key parts of its product design process.
“Through the delivery of products that improve efficiency and reduce
Congratulations on reaching this incredible milestone! For half a century, Propak Systems has demonstrated excellence, innovation, and a lasting commitment to quality, service, and community. Your journey is a testament to strong leadership, dedicated employees, and a vision that continues to inspire.
Totran values our long-term relationship with Propak and we are grateful for the partnership we have developed over the past 20 years. Everyone at Totran Transportation Services is wishing Propak Systems continued success and growth for many more years to come!
Head Office: 403-723-0025 | Conroe TX: 713-450-4700 info@totran.ca | totransales@totran.ca | www.totran.ca
emissions, we are able to support our clients in their sustainability initiatives,” Hanson insights.
More specifically, the company focuses on efficiency, modularization, emissions control, produced water recycling, process heat integration, noise control, and spill and leak prevention and control when developing products.
Propak’s Energy Systems business unit was specifically formed to provide sustainable solutions to clients seeking to reduce their emissions and minimize the environmental impact of their activities and business endeavors.
Propak IST likewise delivers on strong environmental commitments, particularly its patented SQ90™ OTSG technology. The equipment’s industry-leading design produces 90 percent quality steam which provides a number of key benefits when compared to typical industry standards.
For instance, the SQ90™ OTSG reduces fuel consumption and the blowdown rate while maintaining the same dry steam flow as competitors, resulting in less greenhouse gas emissions during operation.
Additionally, due to the lowered feedwater flow rate, the technology utilizes less pumping energy while also decreasing the amount of chemicals used in the process.
On the manufacturing front, Propak partners with a local metal recycling company to send carbon and stainless steel, aluminum, wire, and other materials to be recycled, processed, and returned to the market.
“Last year, we recycled just over three million pounds (lbs) of steel product, diverting it from landfills,” Hanson closes.
Propak also possesses an on-site cardboard baler that is used to compress the cardboard boxes its abundance of materials arrive in. As such, the company can collect,
bale, and palletize large amounts of cardboard before having it sent to a processing facility.
In 2024, Propak recycled approximately 60,000 lbs of cardboard, as well as recycling soft plastics – such as pallet wrap and bags – separately from its landfill waste facility.
As one of Canada’s largest manufacturers of energy processing equipment, the company will continue to create maximum customer value through fit-for-purpose design solutions, reduced capital costs, reliable project execution, and industry-leading product performance, cementing its enviable position.
Tel: 403-912-7000 sales@propaksystems.com www.propaksystems.com www.otsg.com